-
0 items in quote
No products in the Quote Basket.
Fully Sintered (Metal Bond) Diamond & CBN, Wafering Blades
SMART CUT® Fully Sintered (Metal Bond) diamond wafering blades are fully sintered from OD to ID of the blade. Meaning they have diamonds completely impregnated through the blade. Unlike standard diamond & cbn wafering blades with steel core and diamond section. Instead of having a steel core and small diamond bond edge (usually 1/8″/3.2mm). The diamond edge is all the way through the blade, from its Outside Diameter to Inside Diameter of the blade. You can use until the entire Outside Diameter of the blade is consumed.
DESCRIPTION
SPECIFICATIONS
FREQUENTLY ASKED QUESTIONS
INDUSTRIES USED IN
ACCESSORIES
USAGE RECOMMENDATION
DESCRIPTION
These types of blades may last as much as 3 to 4 standard blades with steel core put together. Since the entire blade is diamond and same thickness from OD to ID (with no thinner steel core to flex, warp, or loose its flatness). The fully sintered (metal bond) blades is more rigid. Providing minimum heat generation and stress to material being cut. This allows for thinner kerf thicknesses that would not be normally possible with wafering blades made with steel core, longer blade life, better cut quality and more rigidity. These are an excellent choice for sectioning large variety of ultra-hard and brittle materials, delicate samples, crystals, teeth, bones, composites, metals, and much more.
SPECIFICATIONS
Tab Contant
FREQUENTLY ASKED QUESTIONS
SMART CUT™ blades are fully sintered from the Outside Diameter (OD) to Inside Diameter (ID), meaning they have diamonds impregnated throughout the entire blade, unlike the conventional blades which have a steel core and a diamond edge. This construction allows for enhanced performance and longer blade life.
These blades offer a range of advantages:
⦁ Longer lifespan
⦁ Enhanced stability and rigidity
⦁ Consistent cutting performance
⦁ Better heat resistance
⦁ Ideal for sectioning hard and brittle materials
⦁ Reduced blade flex
⦁ Thinner kerf thickness than steel core blades
A SMART CUT™ blade may last as long as 3 to 4 standard steel core blades combined due to its fully sintered diamond composition.
They’re perfect for sectioning a wide range of materials, including fragile crystals, ultra-hard ceramics, brittle materials, teeth, bones, composites, metals, and much more
Yes! Discounts are available when purchasing in larger quantities. For example, the price per blade decreases when buying two or three at a time.
Kerf thickness refers to the width of the cut a blade makes. A thinner kerf means less material is removed, which can be crucial for precision cuts or when working with expensive materials.
Yes, the blades come in different abrasive types like Diamond (Fine or Medium) and CBN (Medium). The grit size determines the coarseness of the blade, affecting the finish and speed of the cut.
Absolutely! Since the blade is fully sintered, you can use it until the entire Outside Diameter of the blade is consumed.
CBN stands for Cubic Boron Nitride, a synthetic abrasive second only to diamond in terms of hardness. It’s particularly effective for cutting metals.
“Fully sintered” means that the blade is manufactured in a way where the diamonds are impregnated throughout the entire matrix of the blade, from the outside diameter (OD) to the inside diameter (ID), as opposed to just on the edge.
The unique construction of SMART CUT™ blades provides more rigidity, reducing friction during cutting, which, in turn, minimizes heat generation. This ensures the material being cut doesn’t get damaged due to excessive heat.
Due to their fully sintered design, the blades continuously expose new diamond grits as they wear, maintaining their sharpness. Therefore, there’s typically no need for external sharpening.
The arbor size refers to the diameter of the hole in the center of the blade. It’s essential to match the arbor size of the blade with the spindle of your cutting equipment to ensure compatibility and secure fitting.
Always follow standard safety procedures when using wafering blades. This includes wearing appropriate protective gear, such as safety glasses, gloves, and ensuring the equipment is in good working condition. Also, avoid forcing the blade through the material, which can lead to blade damage or breakage.
Store the blades in a cool, dry place away from direct sunlight. It’s recommended to keep them in their original packaging to protect them from dust and potential damage.
The choice of blade depends on the material you are cutting, the required precision, and the desired finish.
Yes, SMART CUT™ blades can cut metals, especially when using the CBN (Cubic Boron Nitride) variant, which is well-suited for cutting hard metals.
Regularly inspect the blade for wear or damage. Clean it after use to remove any debris and avoid storing it in locations where it could be exposed to corrosive elements. Proper maintenance ensures optimal performance and longevity.
Due to their thin kerf and uniform diamond distribution, SMART CUT™ blades provide precise cuts, making them ideal for delicate samples where minimal material loss is crucial.
While SMART CUT™ blades provide clean and precise cuts, achieving a mirror finish may require further polishing or finishing processes depending on the material.
The fully sintered design of SMART CUT™ blades offers enhanced rigidity, reducing the risk of warping, especially when compared to blades with steel cores.
Yes, SMART CUT™ blades are versatile and can be used on multi-material samples. However, it’s essential to consider the hardness and properties of each material to ensure the best results.
The listed sizes are the most we keep in stock. We can manufacture almost any blade specification, diameter, inside diameter, kerf thickness grit size or abrasive type
Since the blade is fully sintered with diamonds from the OD to ID, the lifespan is typically longer than standard blades. The blade can be used until its entire Outside Diameter is consumed. Regular inspection will help gauge its remaining life.
The blades are designed for durability and longevity, reducing the need for frequent replacements.
While many blades benefit from a break-in period to ensure even diamond exposure, the fully sintered design of SMART CUT™ blades typically means they’re ready to perform optimally right out of the box.
The ideal cutting speed can vary based on the material being cut and the specific blade type. These blades can be used on both low and high speed saws. Minimum recommended rpm’s is 100 and max rpm’s 12,500. Optimal rpm’s will be based on material properties, shape, and preferred cut quality and surface finish.
Thanks to the fully sintered design, as the blade wears, new diamond particles get exposed, ensuring consistent cutting performance throughout its life.
INDUSTRIES USED IN
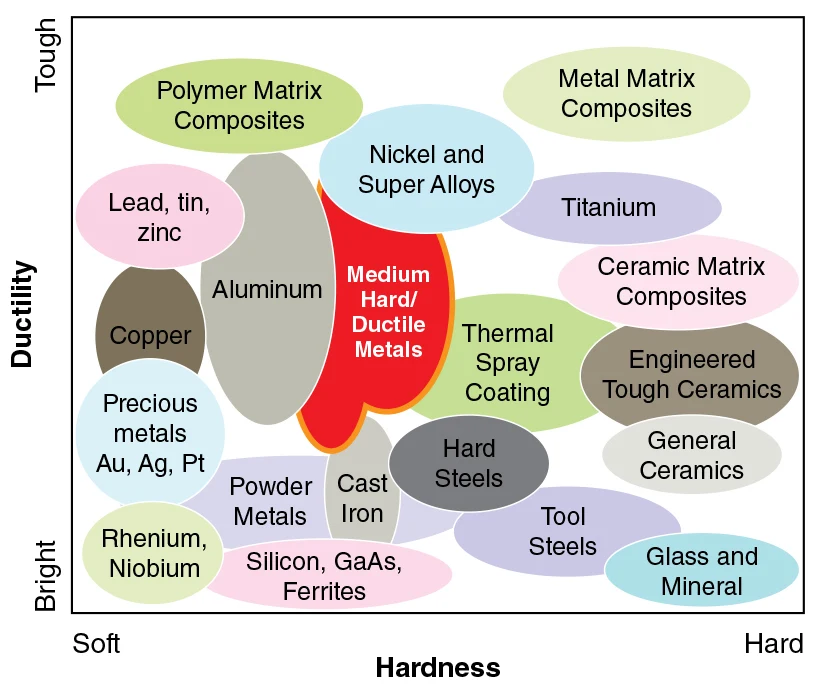

INDUSTRIES USED IN:
- Advanced Ceramics
- Composites
- Glass
- Geology
- Quartz
- Materials Research
- Medical Devices
- Metallography
- Photonics / Optics
- Semiconductor
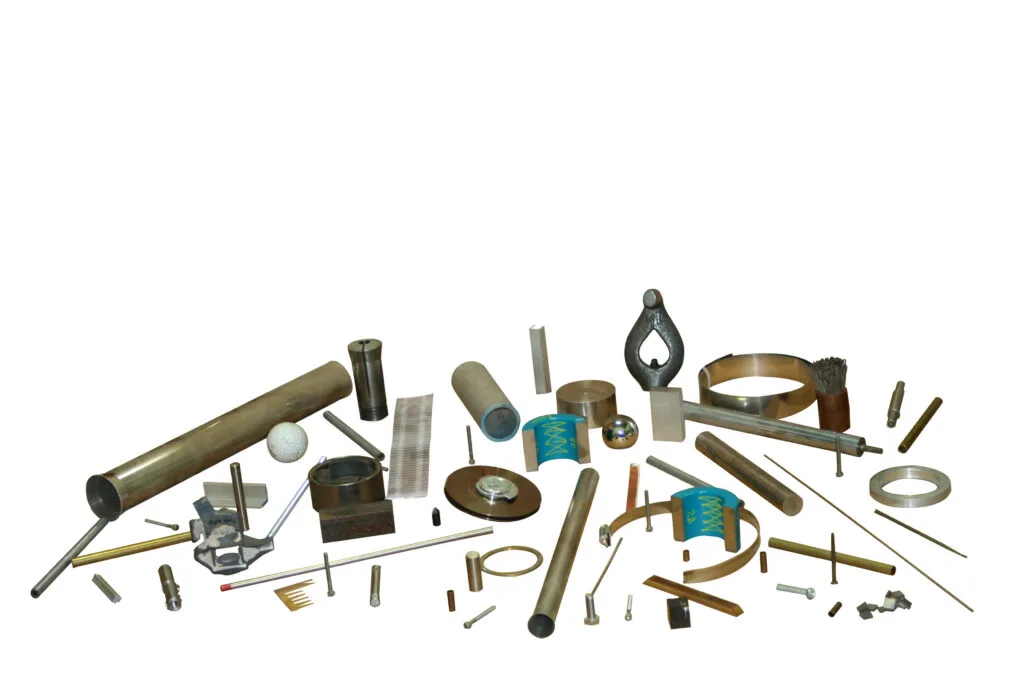
Ferrous & Non-Ferrous Metals:
- Plain Carbon Steels
- Electronic Packages
- Stainless Steels Plastics
- Tool Steels Fasteners
- Aluminum Refractories
- Copper Base Alloys Integrated Circuits
- Magnesium Thermal Spray Coatings
- Titanium Metal Matrix Composites
- Biomedical Wafers
- Petrographic
- PCB.s Ceramics
ACCESSORIES
Customer matched zone “Locations not covered by your other zones”
“SMART CUT® DIAMOND WAFERING BLADES SINTERED (METAL BOND)” has been added to your cart. View cart
Showing 1 – -1 of 13 results Showing all 13 results Showing the single result No results found
Sort by Price low to high
Filters Sort results
Reset Apply
Image | Name | COMPATIBILITY WITH DRILL SERIES | Price | Quantity | Add to cart |
---|---|---|---|---|---|
Recommended for use in Diamond Tools 150 Grit Size (mesh… | $15.39 | Max: Min: 1 Step: 1 | |||
Recommended for coarser grits found in segment wheels, core drills… | $15.99 | Max: Min: 1 Step: 1 | |||
5/8″-11″ thread. Fits into drill press chuck. Shank adapter threads… | $22.46 | Max: Min: 1 Step: 1 | |||
5/8″-11″ thread. Fits into drill press chuck. Shank adapter threads… | $26.72 | Max: Min: 1 Step: 1 | |||
SMART CUT® General Materials Formula Synthetic Water Soluble Coolant | $34.81 | Max: Min: 1 Step: 1 | |||
Recommended for use in Diamond Tools 150 Grit Size (mesh… | $39.47 | Max: Min: 1 Step: 1 | |||
Recommended for coarser grits found in segment wheels, core drills… | $39.47 | Max: Min: 1 Step: 1 | |||
SMART CUT® General Materials Formula Synthetic Water Soluble Coolant | $99.81 | Max: Min: 1 Step: 1 | |||
105DE, 135DB, 115DM, 125DM, 130DMN, 140DM (up to 1-5/8″ OD) | $154.87 | Max: Min: 1 Step: 1 | |||
105DE, 135DB, 115DM, 125DM, 130DMN, 140DM (up to 1-5/8″ OD) | $154.87 | Max: Min: 1 Step: 1 | |||
105DE, 135DB, 115DM, 125DM, 130DMN, 140DM (up to 1-5/8″ OD) | $235.00 | Max: Min: 1 Step: 1 | |||
SMART CUT® General Materials Formula Synthetic Water Soluble Coolant | $317.41 | Max: Min: 1 Step: 1 | |||
SMART CUT® General Materials Formula Synthetic Water Soluble Coolant | $1,745.00 | Max: Min: 1 Step: 1 |
USAGE RECOMMENDATION
Diamond & CBN Wafering Blade Articles
02
Jun
How to Properly Use Precision Diamond & CBN Blades
The diamond blade itself is only a small factor in your cutting operation. Successful diamond sawing is both an art & science. Requiring proper use and understanding of the right: RPM’s, Coolants, Equipment, Dressing Devices, Accessories…
02
Jun
Precision & Ultra Thin Diamond Blade Guide
Diamond and CBN blades are available in an extensive array of varieties, each differing in bond types, manufacturing methods, and design specifics. Ultra Thin & High Precision Diamond Blades are particularly versatile, applicable…
02
Jun
Troubleshooting Diamond Sawing Problems
Having issues with your diamond cutting operation? This Illustrated Guide can help. Learn the most common problems most people have in using diamond cutting blades. How to resolve them and avoid them in…
02
Jun
How to Improve & Optimize Your Diamond Sawing Operation
There are numerous variables that affect the performance of diamond and CBN cutting blades. Understanding these variables will help end users select the right diamond blade specifications for their applications and optimize their…
02
Jun
Evaluating & Comparing Diamond Blades
Share this Article with Friend or Colleague
Proper testing procedures and methodologies must be set up and used to obtain accurate as well as repeatable testing results. This article will discuss several simple procedures which…
02
Jun
Selecting Right Wafering Blade for your application
Cross Sectioning is the first and most important step in the sample preparation process. Getting the best results involves obtaining a smooth surface finish, minimum chipping, material deformation, without sacrificing cutting speed. Today, most laboratories, work with dozens…
02
Jun
Wafering Blade Usage Recommendations
The wafering/sectioning blade itself is only a small factor in your sectioning operation. Successful wafering/sectioning operation is both an art & science. Requiring proper use and understanding of selecting the right diamond wafering/sectioning…
02
Jun
Wafering Blade Case Studies
Step by step guide on how to properly use and care for your diamond drills. Selecting the right diamond drill/diamond drill bit parameters, often involves a trial and error process. Many which can be avoided…
22
Apr
Diamond & CBN Wafering Blade Performance Metrics
When evaluating Diamond & CBN wafering blades, especially for metallography and sample preparation, it is critical to consider a set of key evaluation criteria and performance metrics. These factors help determine the effectiveness of a…
24
Apr
Understanding & Comparing Diamond & CBN Wafering Blades
Share this Article with Friend or Colleague
Diamond wafering blades are designed for sectioning a large variety of materials and sample types. In order to identify the best diamond wafering blade for your specific material/application,…
25
Apr
Diamond & CBN Wafering Blade Guide
Share this Article with Friend or Colleague
All you need to know about wafering blades (understanding variables & specifications)
This guide is designed to help you navigate the various variables and possibilities associated with diamond wafering…
31
Jul
Top 5 Diamond & CBN Cutting Blade Performance Metrics
Share this Article with Friend or Colleague
When evaluating diamond and cubic boron nitride (CBN) cutting blades, it’s crucial to consider key performance metrics and criteria. Different applications have varying goals, making it…
01
Aug
Diamond & CBN Cutting Blade Performance Metrics that you Should Know
Share this Article with Friend or Colleague
When evaluating diamond and cubic boron nitride (CBN) cutting blades, it’s crucial to consider key performance metrics and criteria. Different applications have varying goals, making it important to…
02
Aug
Total Cost of Ownership & Why its Important
Share this Article with Friend or Colleague
Diamond and CBN cutting blades are available in a myriad of specifications, with virtually limitless options. The industry is saturated with numerous manufacturers, each professing to offer the…
19
Aug
Understanding & Calculating Return on Investment for Diamond & CBN Blades
The term “ROI” (Return On Investment) is frequently mentioned across various industries, often with different interpretations depending on the context. However, few take the time to thoroughly understand what ROI truly represents and its specific…
09
Sep
Understanding Tradeoffs – Searching for Perfect Diamond Drill & Tool
Choosing the right diamond drill or tool can significantly impact efficiency, cost, and quality. However, this is not a simple and clear-cut process. Selecting the optimal drill or tool involves navigating a complex landscape of…
Examples of cutting times for Sectioning of Specific Materials 0.25″ (6.4mm) diameter rod. Using various cutting speeds.
Material |
Blade Type |
Diamond Concentration |
Speed (RPM’s) |
Load (grams) |
Estimated Cutting Time |
---|---|---|---|---|---|
Hot Pressed Silicon Nitride Si3N4 |
Series 20LCU |
Low |
4,000 |
800 |
0:30 |
Boron Carbide B4C |
Series 20LCU |
Low |
3,500 |
700 |
0:15 |
Sapphire Al203 |
Series 15LCU |
Low |
1,500 |
300 |
0:40 |
Chromium Doped Sapphire Al203 |
Series 15LCU |
Low |
500 |
500 |
0:20 |
Partially stabilized Zirconia ZrO2 |
Series 15LCu |
Low |
2,500 |
500 |
0:38 |
Silicon Carbide, SiC |
Series 15LCU |
Low |
2,500 |
500 |
0:16 |
Case Hardened Steel |
Series 15HCU |
High |
2,500 |
500 |
0:16 |
Grey Cast Iron |
Series 15HCU |
High |
2,500 |
500 |
0:25 |
Titanium Alloy |
Series 15HCU |
High |
2,500 |
500 |
0:32 |
Zinc Alloy |
Series 15HCU |
High |
2,500 |
800 |
0:15 |
Tungsten Carbide 6% cobalt binder, wC |
Series 15HCU |
High |
4,500 |
900 |
0:15 |
Tungsten Carbide 25% cobalt binder, WC |
Series 15HCU |
High |
1,500 |
300 |
1:55 |
High Purity fused silica SiO2 |
Series 15HCU |
High |
2,500 |
500 |
0:40 |
Extruded Alumina, Al203 |
Series 15HCU |
High |
3,000 |
600 |
0:40 |
Aluminum Nitride AIN |
Series 15HCU |
High |
1,500 |
300 |
0:30 |
Nickel Zinc Ferrite |
Series 15HCU |
High |
1,500 |
300 |
0:30 |
Manganese Zinc Ferrite |
Series 15HCU |
High |
Content |
5,000 |
0:30 |
Yttrium aluminum garnet, YAG |
Series 15HCU |
High |
3,000 |
Content |
1:15 |
8 micron graphite fiber reinforced zirconium diboride/molybenum disilicide composite |
Series 15HCU |
Low |
2,500 |
300 |
0:20 |
White Cast Iron |
Series Metacut CBN |
High |
2,500 |
700 |
|
Thermal Spray Coatings |
Series 15HCU |
High |
3,000 |
700 |
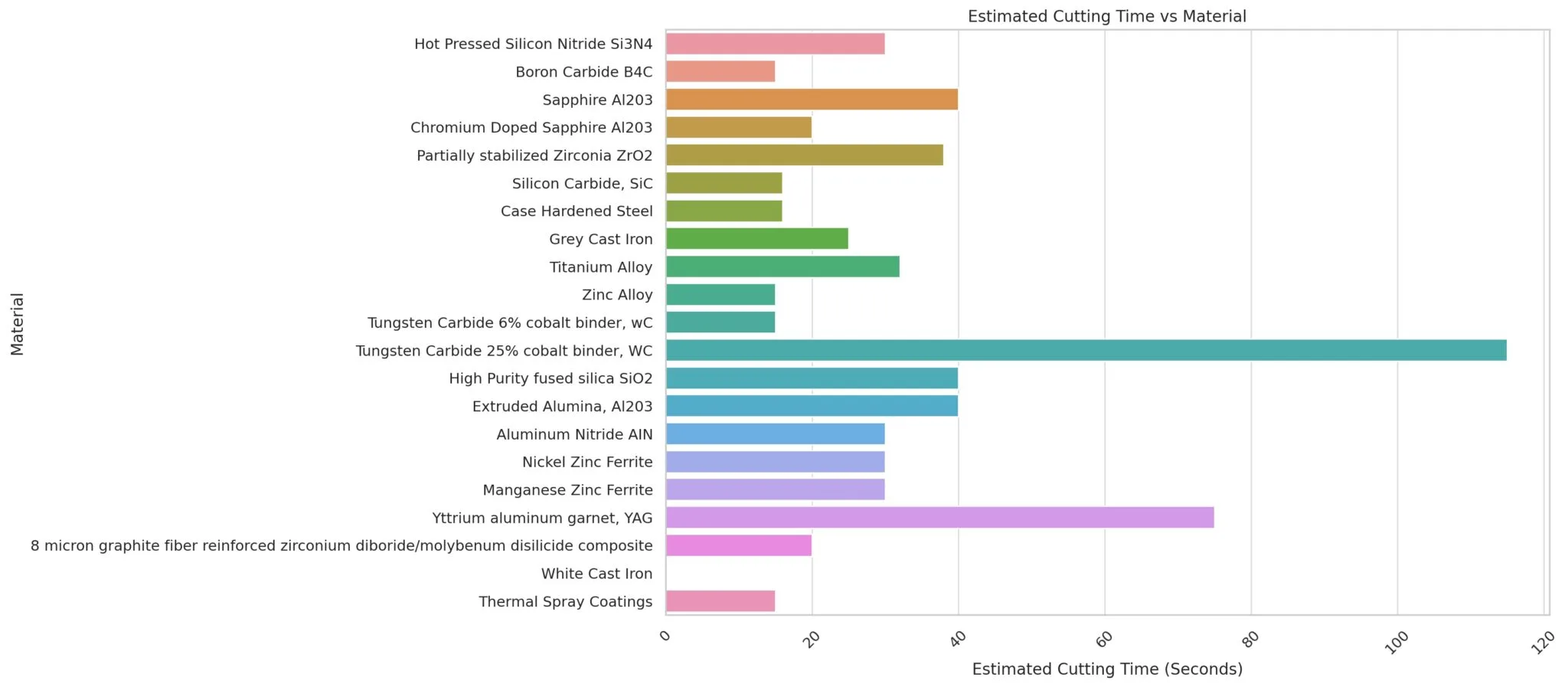
Advantages
- Longer Life: Fully sintered blades tend to have a longer lifespan than resin-bonded or steel core blades. This is because the diamonds are embedded throughout the entire blade matrix, not just at the edge.
- More Stable and Rigid: The uniform composition of a fully sintered blade offers better stability and rigidity than blades with a steel core. This can result in straighter cuts with fewer deviations.
- Wear Uniformity: As a fully sintered blade wears, new diamond grits are continually exposed, maintaining cutting performance over the life of the blade.
- Heat Resistance: Metal bonded blades generally possess better heat resistance compared to resin-bonded or steel core blades.
- Sectioning Hard and Brittle Materials: Fully sintered blades are often chosen for sectioning hard and brittle materials because they maintain their edge and shape over prolonged usage.
- Reduced Blade Flex: Since they're made entirely of the sintered material, these blades have less flex, which can be essential when precision and sectioning accuracy are crucial.
- Thinnest Possible Kerf thickness – that would not be possible with steel core
Showing 1 – -1 of 9 results Showing all 9 results Showing the single result No results found
Sort by Price low to high
Filters Sort results
Reset Apply
Image | Item No | Outside Diameter | Kerf Thickness | Arbor Size / Inside Diameter | Abrasive Type / Grit Size | Price | Quantity | Add to cart |
---|---|---|---|---|---|---|---|---|
3" (76.2mm) | .006" (0.15mm) | 1/2" (12.7mm) | Diamond / Fine | $165.00 2 pcs - $160.00 ea ⋅ 3 pcs - $155.00 ea | Max: Min: 1 Step: 1 | |||
3" (76.2mm) | .006" (0.15mm) | 1/2" (12.7mm) | Diamond / Fine | $165.00 2 pcs - $160.00 ea ⋅ 3 pcs - $155.00 ea | Max: Min: 1 Step: 1 | |||
3" (76.2mm) | .004” (0.10mm) | 1/2" (12.7mm) | Diamond / Fine | $185.00 2 pcs - $160.00 ea ⋅ 3 pcs - $155.00 ea | Max: Min: 1 Step: 1 | |||
3" (76.2mm) | .006" (0.15mm) | 1/2" (12.7mm) | CBN / Medium | $185.00 2 pcs - $180.00 ea ⋅ 3 pcs - $175.00 ea | Max: Min: 1 Step: 1 | |||
3" (76.2mm) | .006" (0.15mm) | 5/8” (15.87mm) | Diamond / Fine | $185.00 2 pcs - $180.00 ea ⋅ 3 pcs - $175.00 ea | Max: Min: 1 Step: 1 | |||
4" (101.6mm) | .006" (0.15mm) | 1/2" (12.7mm) | Diamond / Medium | $185.00 2 pcs - $180.00 ea ⋅ 3 pcs - $175.00 ea | Max: Min: 1 Step: 1 | |||
4" (101.6mm) | .008” (0.20mm) | 1/2" (12.7mm) | Diamond / Medium | $185.00 2 pcs - $180.00 ea ⋅ 3 pcs - $175.00 ea | Max: Min: 1 Step: 1 | |||
4" (101.6mm) | .010” (0.25mm) | 1/2" (12.7mm) | Diamond / Medium | $185.00 2 pcs - $180.00 ea ⋅ 3 pcs - $175.00 ea | Max: Min: 1 Step: 1 | |||
4" (101.6mm) | .013" (0.33mm) | 1/2" (12.7mm) | Diamond / Fine | $185.00 2 pcs - $180.00 ea ⋅ 3 pcs - $175.00 ea | Max: Min: 1 Step: 1 |
3030604,3030605,3030402,3030608,3030408,3030405,3030406,3030407,3030404,
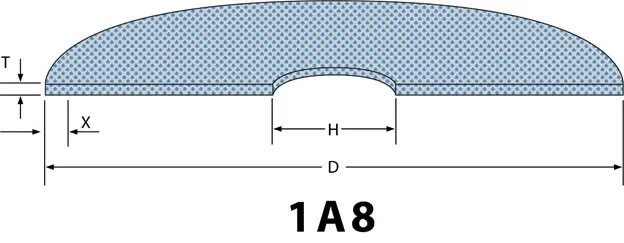
About Sintered (Metal Bond)
Sintered (Metal Bond) diamond tools have multiple layers of diamonds impregnated inside the metal matrix. Diamonds are furnaces sintered in a matrix made of iron, cobalt, nickel, bronze, copper, tungsten, alloys of these powders or other metals in various combinations. Metal bonded diamond tools are “impregnated” with diamonds. This means that selected diamonds are mixed and sintered with specific metal alloys to achieve the best cutting performance possible on any materials such as sapphire, advanced ceramics, optics, glass, granite, tile and etc. The metal bond surrounding the diamonds must wear away to continuously keep re-exposing the diamonds for the diamond tool to continue cutting. Sintered (metal bonded) diamond tools are recommended for machining hard materials from 45 to 75 on rockwell scale (5 to 9.5 on mohe’s scale of hardness).
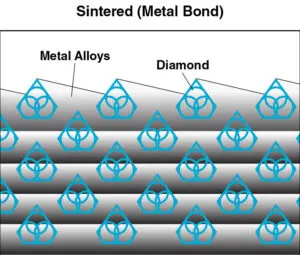
SMART CUT® Difference
How SMART CUT® Diamond & CBN Wafering Blades are Different in comparison to other Wafering blades.
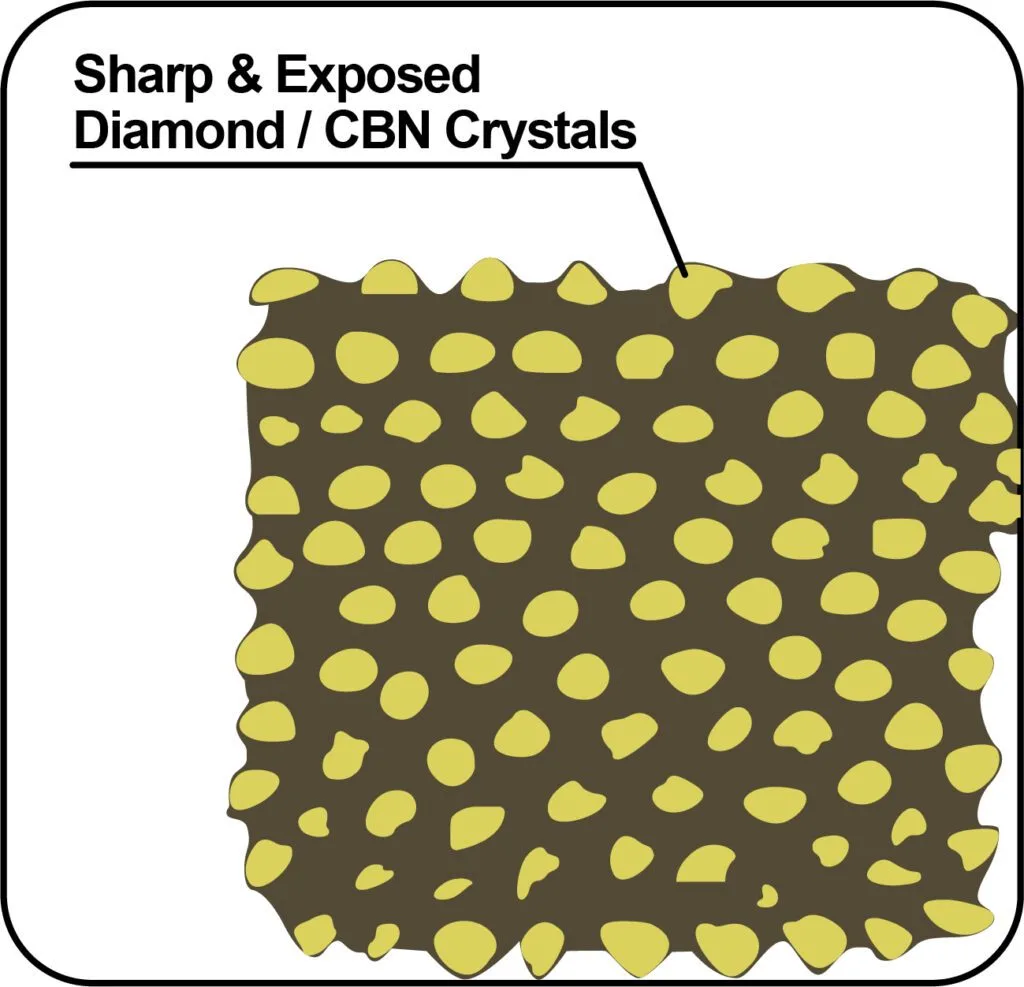
No Glazing
Diamond & CBN tools with SMART CUT® technology require minimum dressing, the bond renews itself.
Faster Drilling Action
Diamond drills made utilizing SMART CUT® technology are much more aggressive than your conventional drills. They can drill faster, while still leaving behind a smooth finish free of material deformation.
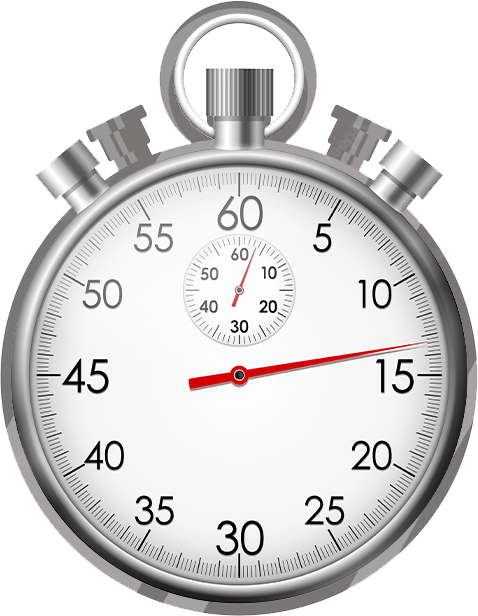
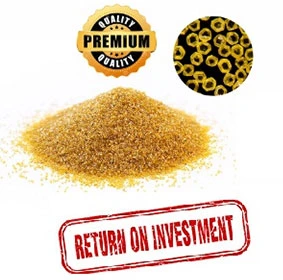
Manufactured Using The Highest Quality Raw Materials
Only the highest quality synthetic diamonds and raw materials are used in the manufacturing process. The highest quality standards and product consistency is maintained, using sophisticated inspection and measurement equipment.
Best Performance & Value on the Market
SMART CUT® Multi Layered Electroplated Diamond Drills are the best investment you can make! Although they may cost more than electroplated (nickel bond), Diamond Drills. They will more than pay for themselves in terms of overall performance and provide best Return on Investment.
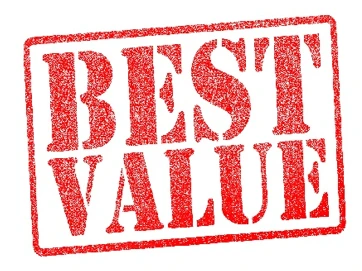
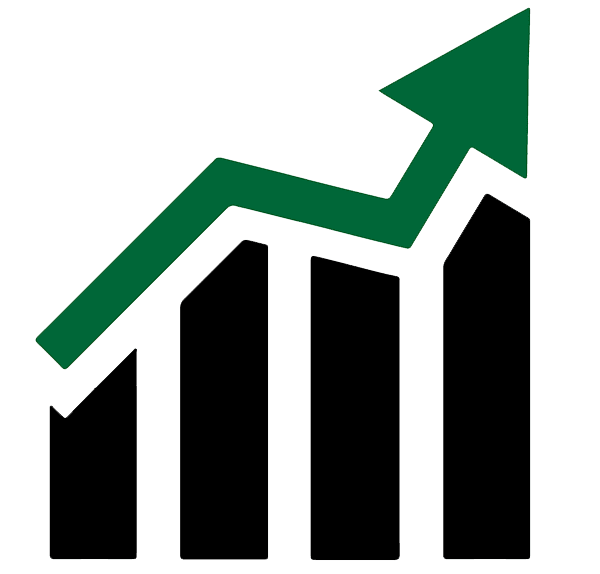
Longer Life
In most cases tools manufactured utilizing SMART CUT® technology, will outlast other conventional nickel bonded diamond & CBN drills. SMART CUT® diamond & CBN tools are more sturdy than tools manufactured with conventional technologies. They are capable to retain their form and bond configuration all the way through the tools life.
More Consistent Performance
SMART CUT® Multi Layered Electroplated Diamond Drills have three diamond layers impregnated inside the bond matrix. Unlike Many Other drill Types, they wear evenly, and are known for their consistency. You will get consistent cutting speed, and overall consistent performance, with minimum amount of dressing even on the hardest to cut materials
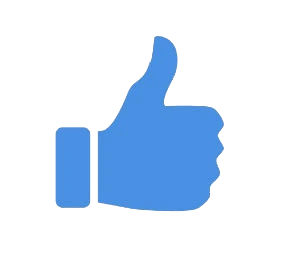
Its what you cant see that makes all the Difference
How SMART CUT® Bond Works?
Step 1
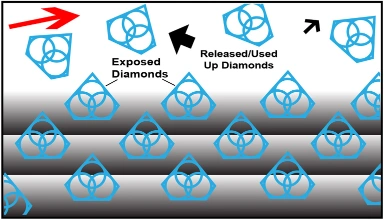
Sharpest And Finest Quality Diamonds
The newly exposed diamonds don’t effect diamonds already working on the material. Unlike many other diamond bonds, diamonds in a SMART CUT® Bond remains sharp and grow sharper with each cut, prolonging product life and consistent performance.
Step 2
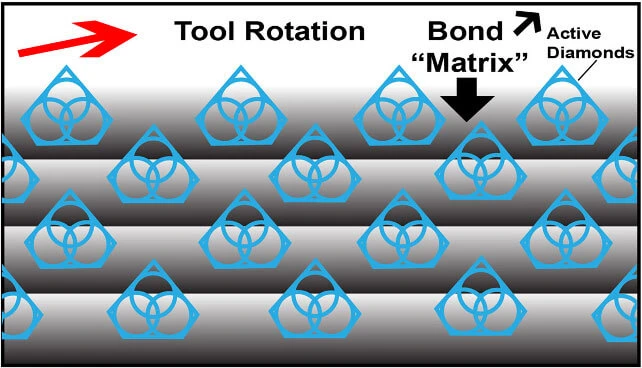
Diamonds or CBN Crystals
Diamonds or CBN Crystals are activated only at the exposed layer. As Bond Matrix layer begin to wear out, diamonds in a new Bond Matrix layer are immediately activated, substituting the already used up diamond layer. The SMART CUT® Diamond Hybrid Bond makes sure every diamond is in the right place and at the right time, working where you need it most.
Step 3
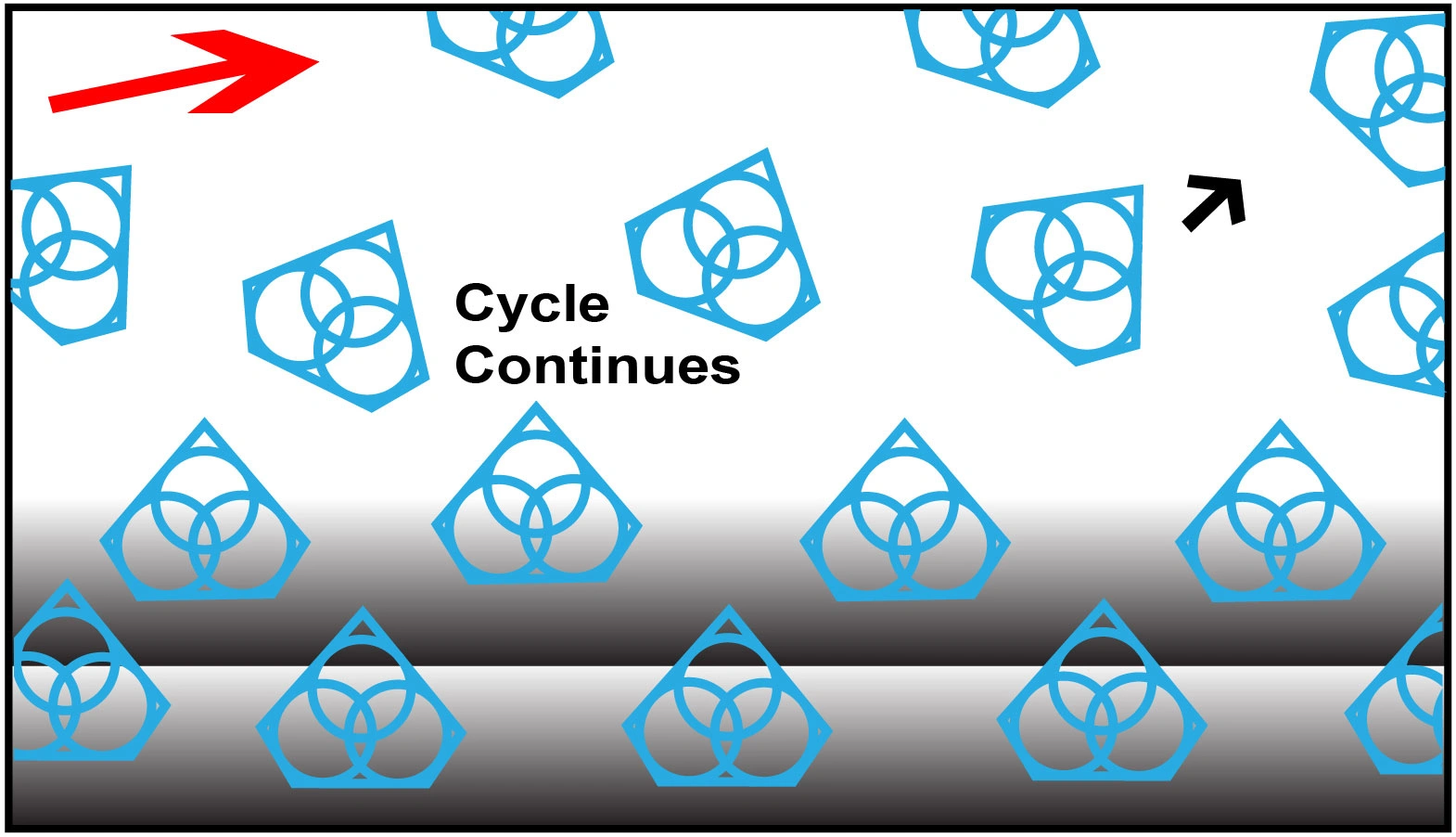
Advanced Formulated Open Diamond Bond Design
This advanced formulated open diamond bond design insures minimal chipping, fast cut, constant speed of cut, minimal cutting noise, and most important of all, consistent performance.
Diamond & CBN Wheel
Selection Variables
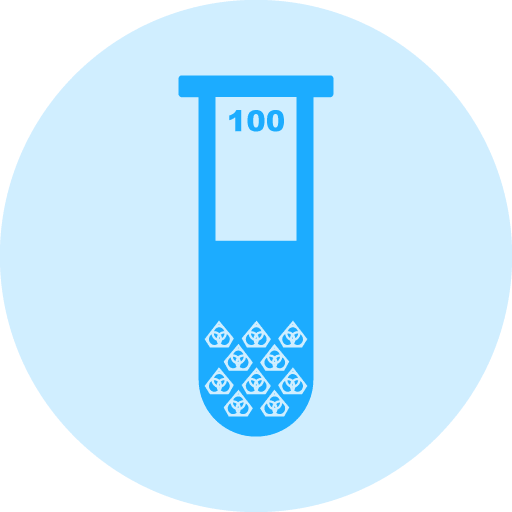
Diamond Concentration
Wafering blade thickness typically ranges from .006” to .040” (1mm). Thinner and thicker wafering blade are available, frequently from stock upon request. Kef thickness typically increases with blade diameter (in proportion to diameter of the blade). Kerf is the amount of material removed from the material/sample due to the thickness of blade passing though the material/sample. Blade thickness is important for users requiring most minimal amount of material loss during sectioning. For example if the user requires precision position of the cutting plane relative to the detail on the sample (IC circuit for example), a thinner and smaller diameter blade would be best for this application. Blades ranging from 3” to 5” (75mm to 125mm) in diameter and thickness .006” to .015” (0.2mm to 0.4mm) would be bet suited for this purpose. There are large variety of factors that will contribute to optimal blade thickness for your material/application Including your desired cutting speed, load/feed rate, material diameter, thickness, hardness, density, and shape. As well as skill & experience of the operator. Thicker wafering blades are more stiff and can whistand higher loads/feed rates. Another advantage of thicker kerf blades is they are more forgiving to operator error and abuse. Thicker kerf blade are recommended for use in environment where large number of individuals will be sharing and using same equipment. Perfect for less experienced and novice saw operators, such as in University laboratory.
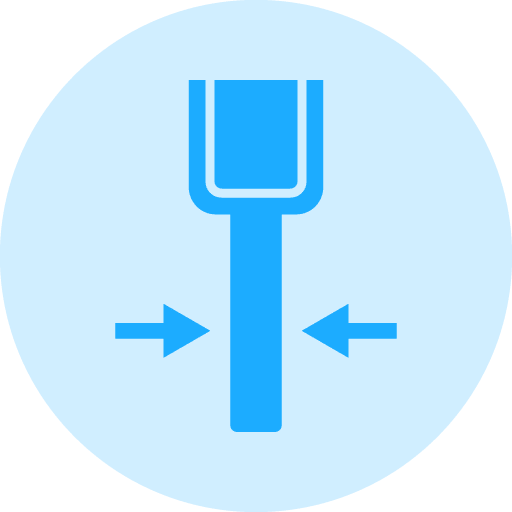
Blade Thickness :
The thickness of diamond and CBN (Cubic Boron Nitride) grinding wheels varies widely to suit different applications and material processing needs. For precision grinding tasks, wheels are typically thinner, ranging from about 0.5 mm to 10 mm, allowing for meticulous and detailed material removal. Cut-off wheels, used primarily for slicing through materials, tend to be even thinner, with thicknesses from 0.1 mm to 3 mm to facilitate precise cuts. Conversely, surface and tool grinding wheels, which are used for more extensive surface grinding, generally have thicknesses from 3 mm to 40 mm. For heavy-duty grinding operations involving large workpieces or substantial material removal, wheel thickness can be significantly greater, often from 10 mm up to 100 mm or more.
The thickness of a diamond or CBN grinding wheel directly impacts its grinding performance. Thicker wheels facilitate higher material removal rates, making them suitable for heavy-duty grinding tasks but tend to generate more heat and require more power. Thinner wheels excel in precision grinding tasks due to their ability to produce finer finishes and more detailed work. They also dissipate heat more effectively, minimizing thermal damage to both the wheel and the workpiece.
Stability increases with wheel thickness; thicker wheels resist bending under pressure, thereby enhancing their lifespan and ensuring consistent performance. However, they may require multiple dressings over their lifespan to maintain effectiveness. Thinner wheels, while more flexible for precision work, wear out quicker as they contain less material for dressing.
.
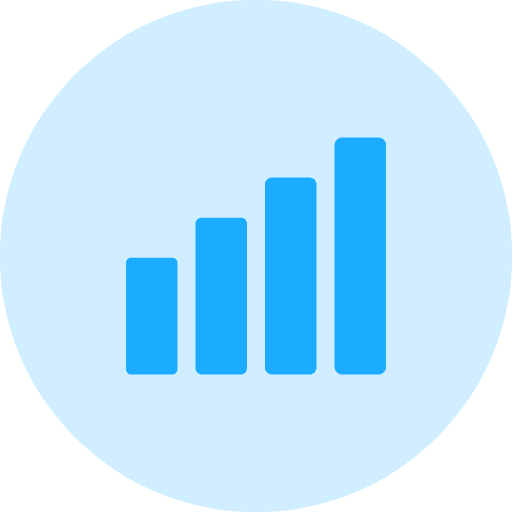
Feed Rates
Load/Feed Rate applied to wafering blades typically vary from 10-1000 grams. Generally, harder specimens are cut at higher loads and speeds (e.g. ceramics and minerals) and more brittle specimens are cut at lower loads and speeds (e.g. electronic silicon substrates). The Speeds/RPM’s you are using, shape/geometry of the specimen, and how the specimen is being clamped/hold in place will affect the load that can be used for your application.
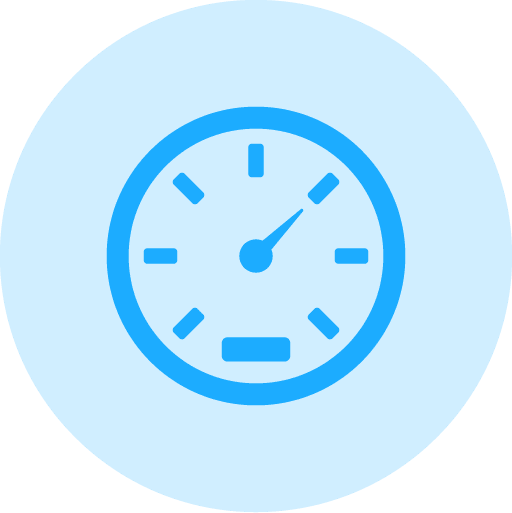
Blade Speeds/RPM’s :
The RPM (Revolutions Per Minute) of diamond and CBN grinding wheels plays a key role in determining grinding performance. Harder materials like ceramics and hardened steel typically require lower RPMs to prevent overheating and excessive wear, while softer materials can be ground at higher RPMs. Larger wheels, due to their size, should run at lower speeds compared to smaller wheels, which can handle higher RPMs.
For fine precision and smooth surface finishes, lower RPMs are ideal, providing better control and reducing the risk of surface damage. Higher RPMs can be used for faster material removal but require careful attention to heat generation and wheel wear. Excessive RPMs can cause overheating, damaging both the wheel and the workpiece, particularly with heat-sensitive materials.
In general, diamond and CBN wheels operate effectively within a range of 3,000 to 6,000 RPM, depending on the material and wheel size. Adhering to optimal RPMs ensures efficient grinding, longer wheel life, and better overall results.
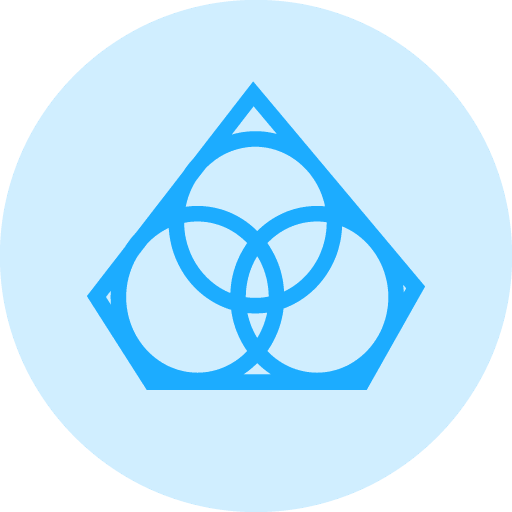
Diamond Particle/Grit size
In diamond and CBN grinding wheels, the particle or grit size profoundly influences several aspects of the wheel's performance. Coarser grits enable faster material removal rates due to their aggressive cutting action, which is beneficial for increasing productivity in scenarios where high grinding speeds are necessary. Conversely, finer grit sizes produce a smoother finish, as the smaller particles make less aggressive cuts, reducing surface roughness. This is crucial for applications that demand a high-quality finish.
The amount of chipping during grinding is also impacted by the grit size. Finer grits typically result in less chipping, making them suitable for grinding brittle materials or when precise, clean edges are essential. However, coarser grits might cause more significant damage to the material’s microstructure because of their aggressive nature, which could be problematic in precision engineering applications where the integrity of the material is critical.
Selecting the appropriate grit size is vital for optimizing both the material removal rates and the quality of the finished surfaces. Coarse grits are preferred for rapid material removal when finish quality is less critical, while finer grits are ideal for achieving high-quality finishes and minimizing damage, particularly in delicate or precise grinding tasks.
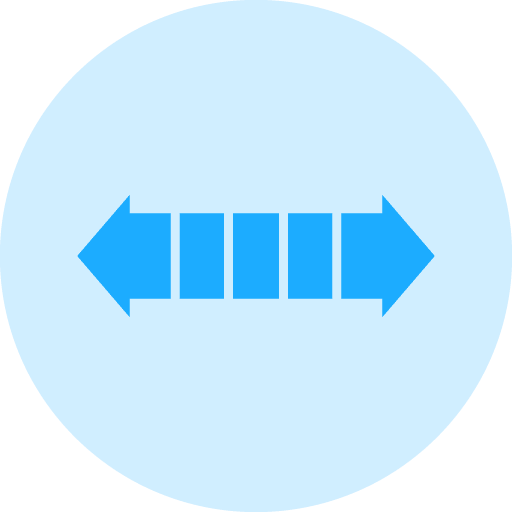
Bond Hardness
Ability of the bond matrix to hold diamonds. As the hardness of the bond is increased, its diamond retention capabilities increase as well. However the trade off is slower cutting speed. Life of the diamond blade is usually increased with hardness of its bond matrix. Bonds are designated on their scale of hardness from Soft, Medium, and Hard. There are dozens of variations and classification schemes based on bond degree of hardness or softness. Using diamond blades with optimum bond hardness for your application is important to successful precision diamond sawing operation. Bond matrix that is too soft for the material being cut will release diamond particles faster than needed, resulting in faster wear and shorter diamond blade life. On other hand bond matrix that is too hard will result in much slower cutting speeds and require constant dressing to expose the next diamond layer. As rule of thumb, harder materials such as sapphire and alumina generally require a softer bond. Whereas softer and more brittle materials require a harder bond.
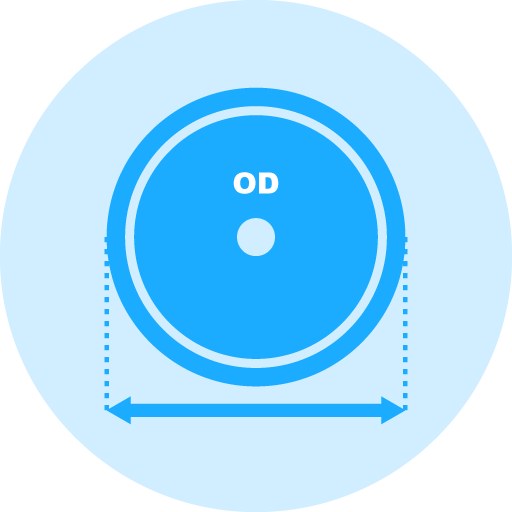
Blade Outside Diameter
Typically wafering blade diameters range form 3” (75mm) to 8” (200mm). Wafering blade diameter should be selected based on material diameter and thickness being cut. Smaller diameter wafering blades are thinner than the larger diameter blades and are more prone to bending and warping. Although large diameter blades are thicker, they are typically used for cutting larger and heavier samples at higher loads and speeds than smaller blades.
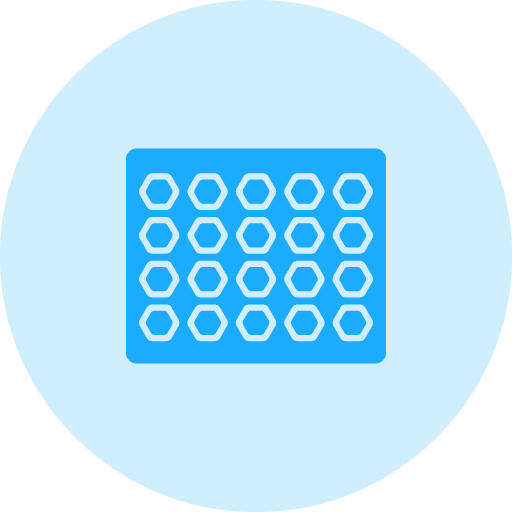
Bond Type :
Metal bonding offers long life and durability, while resin bonding creates less heat, provides better surface finish and is well suited for cutting hard, delicate or brittle materials.
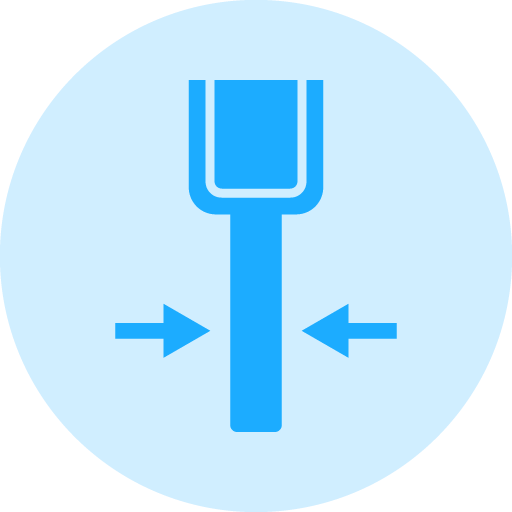
Blade Thickness :
Wafering blade thickness typically ranges from .006” to .040” (1mm). Thinner and thicker wafering blade are available, frequently from stock upon request. Kef thickness typically increases with blade diameter (in proportion to diameter of the blade). Kerf is the amount of material removed from the material/sample due to the thickness of blade passing though the material/sample. Blade thickness is important for users requiring most minimal amount of material loss during sectioning. For example if the user requires precision position of the cutting plane relative to the detail on the sample (IC circuit for example), a thinner and smaller diameter blade would be best for this application. Blades ranging from 3” to 5” (75mm to 125mm) in diameter and thickness .006” to .015” (0.2mm to 0.4mm) would be bet suited for this purpose. There are large variety of factors that will contribute to optimal blade thickness for your material/application Including your desired cutting speed, load/feed rate, material diameter, thickness, hardness, density, and shape. As well as skill & experience of the operator. Thicker wafering blades are more stiff and can whistand higher loads/feed rates. Another advantage of thicker kerf blades is they are more forgiving to operator error and abuse. Thicker kerf blade are recommended for use in environment where large number of individuals will be sharing and using same equipment. Perfect for less experienced and novice saw operators, such as in University laboratory.
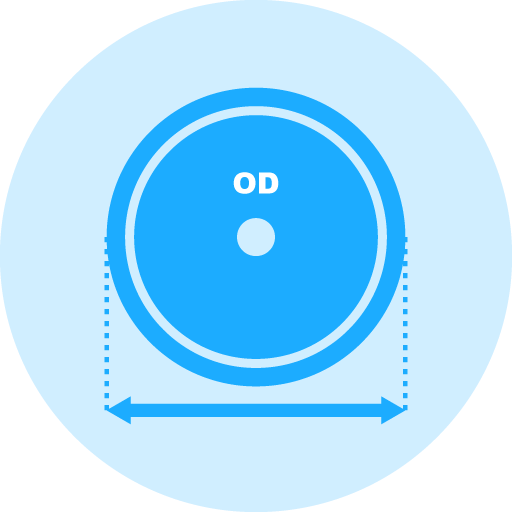
Blade Outside Diameter :
Typically wafering blade diameters range form 3” (75mm) to 8” (200mm). Wafering blade diameter should be selected based on material diameter and thickness being cut. Smaller diameter wafering blades are thinner than the larger diameter blades and are more prone to bending and warping. Although large diameter blades are thicker, they are typically used for cutting larger and heavier samples at higher loads and speeds than smaller blades.
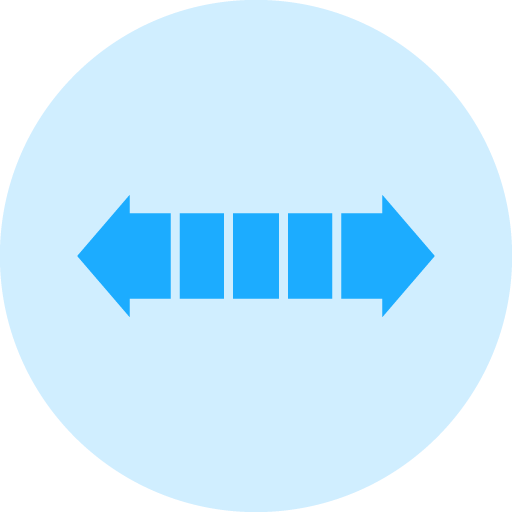
Bond Hardness :
Ability of the bond matrix to hold diamonds. As the hardness of the bond is increased, its diamond retention capabilities increase as well. However the trade off is slower cutting speed. Life of the diamond blade is usually increased with hardness of its bond matrix. Bonds are designated on their scale of hardness from Soft, Medium, and Hard. There are dozens of variations and classification schemes based on bond degree of hardness or softness. Using diamond blades with optimum bond hardness for your application is important to successful precision diamond sawing operation. Bond matrix that is too soft for the material being cut will release diamond particles faster than needed, resulting in faster wear and shorter diamond blade life. On other hand bond matrix that is too hard will result in much slower cutting speeds and require constant dressing to expose the next diamond layer. As rule of thumb, harder materials such as sapphire and alumina generally require a softer bond. Whereas softer and more brittle materials require a harder bond.
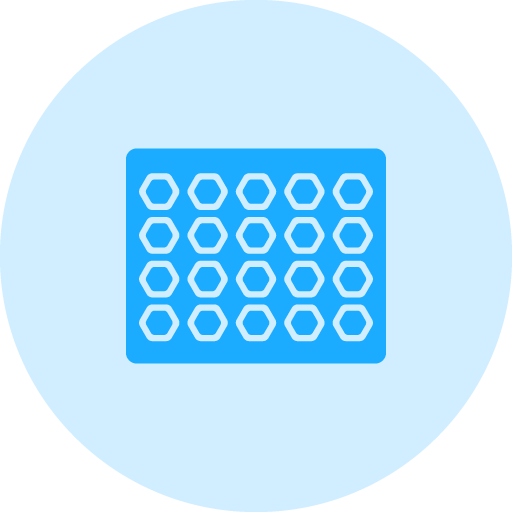
Bond Type :
Metal bonding offers long life and durability, while resin bonding creates less heat, provides better surface finish and is well suited for cutting hard, delicate or brittle materials.
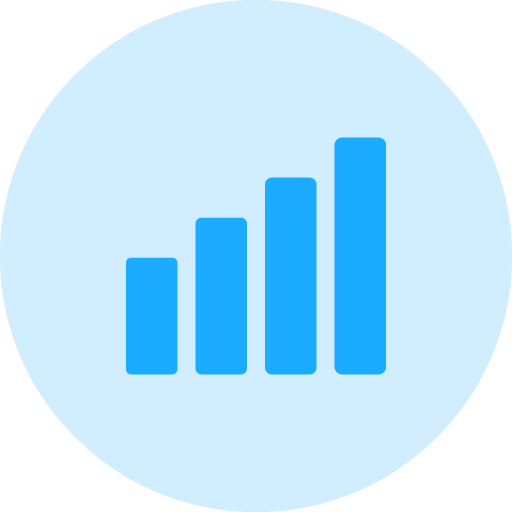
Feed Rates :
Load/Feed Rate applied to wafering blades typically vary from 10-1000 grams. Generally, harder specimens are cut at higher loads and speeds (e.g. ceramics and minerals) and more brittle specimens are cut at lower loads and speeds (e.g. electronic silicon substrates). The Speeds/RPM’s you are using, shape/geometry of the specimen, and how the specimen is being clamped/hold in place will affect the load that can be used for your application.
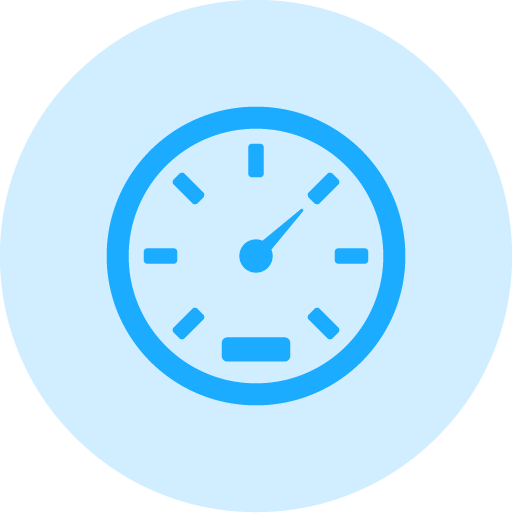
Blade Speeds/RPM’s :
Most wafering blades are used between 50 to 6,000 RPM’s Typically harder and more denser materials such as Silicon Carbide, are cut at higher RPM’s/speeds Where more brittle materials such as silicon wafers and gallium arsenide are cutting at lower RPM’s. Low Speed saws RPM’s are typically limited from 0 to 600 RPM’s. Where high speed saws offer much large variety of cutting speeds from 0 to 6,000 RPM’s.

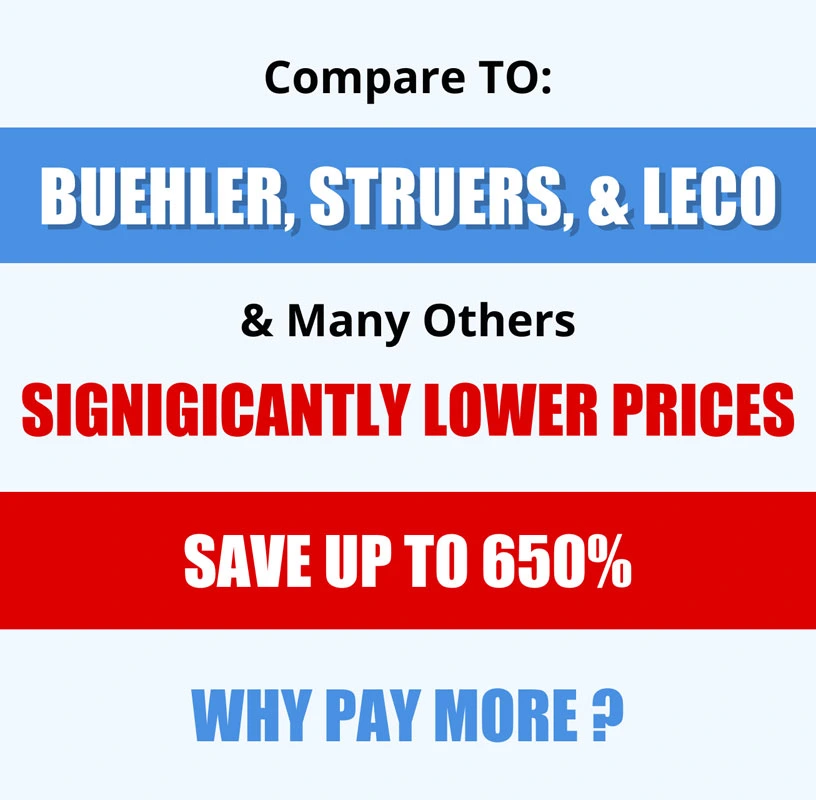
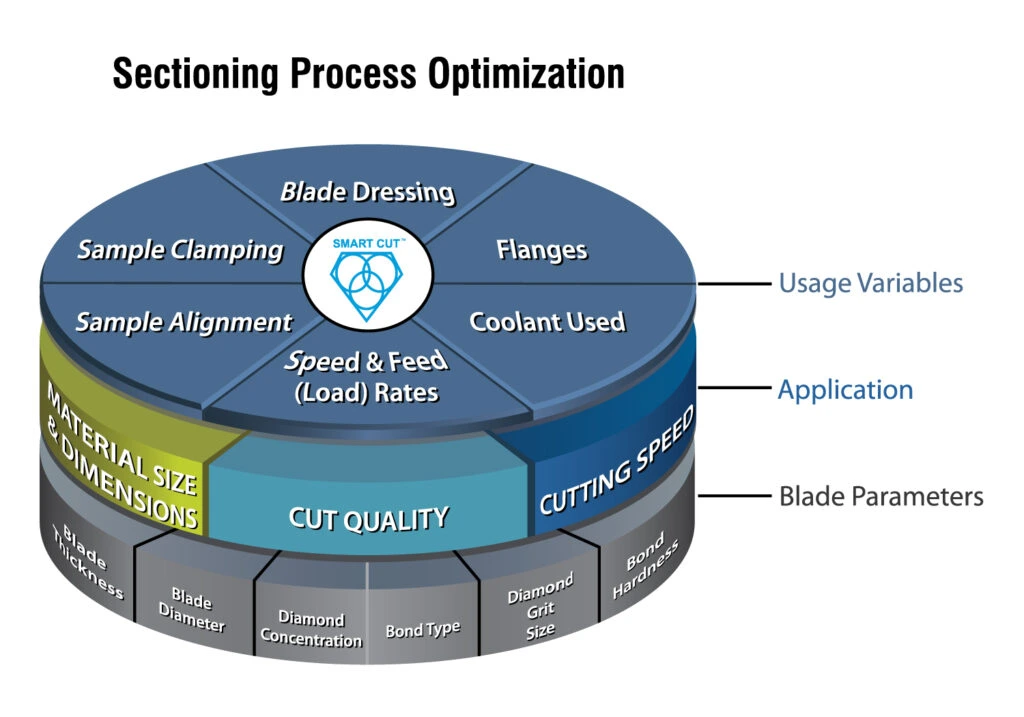
Why Choose Us?
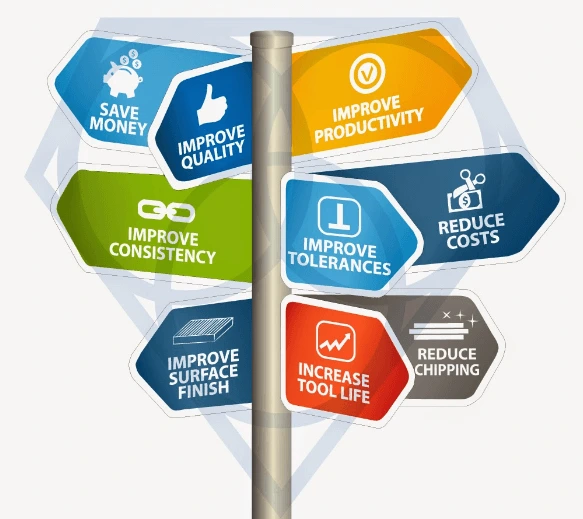
- Unmatched Selection For Many Applications
- Unmatched Technical Support & Expertise
- Superior Quality & Consistency
- Super Technology & innovation
- Immediate Worldwide Delivery
- American Based Manufacturer
-
Custom
Manufacturing - Better Value manufacturer Direct Price
Why Work With Us?
Read More
We produce diamond consumables for some of the leading world OEM manufacturers. We offer Manufacturers Direct Prices
We have the largest variety of diamond & cbn wafering blades available in stock. As well as large inventory of diamond & abrasive consumables. We also custom manufacture diamond and cbn tools, consumables and machines to better fit customer specific needs. Just about any tools & consumables can be designed and manufactured per client drawing or specificrtion
WE ARE A PARTNER IN YOUR SUCCESS
Our proprietory diamond chemistory , precision , manufacturing metods , quality control methods allow us to control and regulate the dozens of variables to that affect consumable life , quality , and consistency.
The more you understand about what we can do for you the better our partnership will be. Here you will find most comprehensive source of information and optimizing and improving your cutting , drilling , grinding and polishing on the web. find everything you ever wanted to know about diamond tools.
AMERICAN MANUFACTURER
"ONE OF THE MOST EXPERIENCED COMPANIES IN THE INDUSTRY"
Save Money Save up to 650%
COMPARE TO: BUEHLER , STRUERS , LECO & MANY OTHERS
Large Inventory & Custom Manufacturing
Umatched Technical Support
Developing close ties with our customers is the foundation of our business. At the core of
our company is a team of world class engineers, knowledgeable customer service personnel here to serve you. Whether is designing or manufacturing a special solution. We will go out of our way to optimizing your process to ultimate level of efficiency
Superior Quality & Consistency
EXPECT MORE FROM YOUR TOOLS
Comprehensive Source Of Information For Sample Preparation
Advanced Technology
As one of the few remaining independent U.S.Diamond Tool & machine builders. We have the experience & tradition to help you remain at frontier of technology Our experience has been further enhanced by acquiring assets and processes from some of the oldest American tool
manufacturers, along with their decades of experience and R& D. This has positioned us as one of the most experienced companies in the industry .Depend on us to bring you technology of tomorrow today.
Experience Makes All The Differences
Over the years we have worked with some of the leading Fortune 500 companies , thousands of universities , government and private research labs , and small organisations. We have made thousands of custom tools , built custom machines , work-holding fixtures , etc for hundreds of applications. Many of our staff members have been working in their respective fields for over 50 years and have gained a wealth of knowledge over the years
Let Us Help You
Related Products
SMART CUT® DIAMOND WAFERING BLADES SINTERED (METAL BOND)
$0.00
SMART CUT® CBN WAFERING BLADES SINTERED (METAL BOND)
SMART CUT® Ultra Thin Abrasive Cut off Blades
SMART CUT Series Ultra Thin Abrasive Blades are designed to provide high quality sectioning results with no burning and minimal surface deformation. This can reduce the amount of grinding & polishing required later in the preparation process. Our blades are Formulated for fast sectioning with minimum kerf loss. They Provide for cool cutting action & Minimize the structural damage to the sample/material.
The thin kerf is designed to save money by reducing kerf loss. This is especially important when cutting very expensive materials, or when kerf loss represents a significant portion of the original material cost.
Used On: All Low & High Speed Wafering Saws, Sectioning Saws, Such as Buehler, Struers, Leco, & many others.
SMART CUT® Series 3000R Resin Bond, Diamond Cut Off Blade
Resin Bond Diamond Cut off blades (Fine Size Diamond) for use on manual tile saws
SMART CUT® Series 3000R are the highest quality & most commonly used Resin Bond Diamond Cut off Blades / Cut Off Wheels available today. Finer Diamond Grit Size, and Slightly Higher Diamond Content then the SMART CUT Series 2000R blades. They are used for cutting very thin wall tubing, more fragile material, that need best surface finish possible to achieve. Cutting speed would be slower then the 2000R series. These blades cut more slowly due to their finer grit size, which provides less aggressive material removal. They are better suited for precision tasks where cut quality is prioritized over speed. The finer grit results in a much smoother surface finish with minimal chipping, making them ideal when a high-quality, clean cut is needed, especially for delicate materials The resin bond diamond cut off blades / cut off wheels excel in delivering superior cut quality compared to other diamond cutting blade, making them ideal for applications where cut quality and surface finish is highly important. They are designed to operate at higher speeds to minimize heat generation and improve surface finishes.SMART CUT® Series 400 Wafering Blade, Resin Bond
Resin Bond Diamond Wafering Blades for use on Precision & Laboratory type Cut off Saws
SMART CUT® Series 400 are Designed for Precision, Chip Free cutting of wide variety of materials These are very thin kerf blades and are very delicate. Must be used on high precision specialized laboratory cutting saws (not tile saws, trim saws, etc) The diamond section can be easily broken if the material moves while cutting, blade is dropped, material is feed to fast into the blade, material is not fed consistently straight into the blade (shifts position) etc. Diamond Size is Medium providing faster cutting speed, while still providing surface quality unmatched by 95% of other blades.SMART CUT 105N Diamond, Nickel Bond Wafering Blades INTERRUPTED RIM
SMART CUT™ Series 105N more freer cutting & aggressive than continuous rim nickel bond wafering blades. Best Suited for cutting larger variety of micro-electronics packages, pcb boards, plastics, composites, soft and precious metals, fish and human bones, graphite, GRP, FR4. Core steel with memory. Always snaps back to its original shape no matter how much bent.
Standard arbor size inside diameter is ½” (12.7mm) (* we can modify arbor size of any blade to anything you want same day for a small additional fee, if needed)
SMART CUT® Series 100N Wafering Blade, Nickel Bond
NICKEL BOND, DIAMOND CONTINUOUS RIM
SMART CUT® Series 100N will provide finer cut quality than interrupted rim nickel bond wafering blades. Best suited for cutting soft and fragile crystals, silicon wafers & substrates, fiberglass, glass fibers. made with stainless steel core Standard arbor size inside diameter is ½” (12.7mm) (* we can modify arbor size of any blade to anything you want same day for a small additional fee, if needed) Nickel Bond Diamond Cut off blades Blades usually have a single layer of diamonds, held by a tough durable nickel alloy. diamond particles to protrude from the bond matrix, providing a free, faster cutting action with minimum heat generation.Diamond, Nickel Bond Cut Off Blades for Laboratory & Other Saws
SMART CUT® Fully Sintered (Metal Bond) Diamond & CBN, Wafering Blades
SMART CUT® Fully Sintered (Metal Bond) diamond wafering blades are fully sintered from OD to ID of the blade. Meaning they have diamonds completely impregnated through the blade. Unlike standard diamond & cbn wafering blades with steel core and diamond section. Instead of having a steel core and small diamond bond edge (usually 1/8"/3.2mm). The diamond edge is all the way through the blade, from its Outside Diameter to Inside Diameter of the blade. You can use until the entire Outside Diameter of the blade is consumed.
Recently Viewed Products
ARE YOU USING RIGHT TOOLS
FOR YOUR APPLICATION?
LET US
HELP YOU
HAVING ISSUES WITH
YOUR CURRENT TOOLS?
Knowledge Center
02
Jun
Select right Diamond Blade for your application
Selecting the right parameters for your Precision & Ultra Thin Diamond Blade can be a very time consuming, trial & error frustrating process. The guide below has been designed to help you better understand...
02
Jun
How to Properly Use Precision Diamond & CBN Blades
The diamond blade itself is only a small factor in your cutting operation. Successful diamond sawing is both an art & science. Requiring proper use and understanding of the right: RPM's, Coolants, Equipment, Dressing Devices, Accessories...
02
Jun
Precision & Ultra Thin Diamond Blade Guide
Diamond and CBN blades are available in an extensive array of varieties, each differing in bond types, manufacturing methods, and design specifics. Ultra Thin & High Precision Diamond Blades are particularly versatile, applicable...
02
Jun
Troubleshooting Diamond Sawing Problems
Having issues with your diamond cutting operation? This Illustrated Guide can help. Learn the most common problems most people have in using diamond cutting blades. How to resolve them and avoid them in...
02
Jun
How to Improve & Optimize Your Diamond Sawing Operation
There are numerous variables that affect the performance of diamond and CBN cutting blades. Understanding these variables will help end users select the right diamond blade specifications for their applications and optimize their...
02
Jun
Evaluating & Comparing Diamond Blades
Share this Article with Friend or Colleague
Proper testing procedures and methodologies must be set up and used to obtain accurate as well as repeatable testing results. This article will discuss several simple procedures which...
02
Jun
Selecting Right Wafering Blade for your application
Cross Sectioning is the first and most important step in the sample preparation process. Getting the best results involves obtaining a smooth surface finish, minimum chipping, material deformation, without sacrificing cutting speed. Today, most laboratories, work with dozens...
02
Jun
Wafering Blade Usage Recommendations
The wafering/sectioning blade itself is only a small factor in your sectioning operation. Successful wafering/sectioning operation is both an art & science. Requiring proper use and understanding of selecting the right diamond wafering/sectioning...
02
Jun
Wafering Blade Case Studies
Step by step guide on how to properly use and care for your diamond drills. Selecting the right diamond drill/diamond drill bit parameters, often involves a trial and error process. Many which can be avoided...
22
Apr
Diamond & CBN Wafering Blade Performance Metrics
When evaluating Diamond & CBN wafering blades, especially for metallography and sample preparation, it is critical to consider a set of key evaluation criteria and performance metrics. These factors help determine the effectiveness of a...
24
Apr
Understanding & Comparing Diamond & CBN Wafering Blades
Share this Article with Friend or Colleague
Diamond wafering blades are designed for sectioning a large variety of materials and sample types. In order to identify the best diamond wafering blade for your specific material/application,...
25
Apr
Diamond & CBN Wafering Blade Guide
Share this Article with Friend or Colleague
All you need to know about wafering blades (understanding variables & specifications)
This guide is designed to help you navigate the various variables and possibilities associated with diamond wafering...
31
Jul
Top 5 Diamond & CBN Cutting Blade Performance Metrics
Share this Article with Friend or Colleague
When evaluating diamond and cubic boron nitride (CBN) cutting blades, it's crucial to consider key performance metrics and criteria. Different applications have varying goals, making it...
01
Aug
Diamond & CBN Cutting Blade Performance Metrics that you Should Know
Share this Article with Friend or Colleague
When evaluating diamond and cubic boron nitride (CBN) cutting blades, it's crucial to consider key performance metrics and criteria. Different applications have varying goals, making it important to...
02
Aug
Total Cost of Ownership & Why its Important
Share this Article with Friend or Colleague
Diamond and CBN cutting blades are available in a myriad of specifications, with virtually limitless options. The industry is saturated with numerous manufacturers, each professing to offer the...
19
Aug
Understanding & Calculating Return on Investment for Diamond & CBN Blades
The term "ROI" (Return On Investment) is frequently mentioned across various industries, often with different interpretations depending on the context. However, few take the time to thoroughly understand what ROI truly represents and its specific...
09
Sep
Understanding Tradeoffs – Searching for Perfect Diamond Drill & Tool
Choosing the right diamond drill or tool can significantly impact efficiency, cost, and quality. However, this is not a simple and clear-cut process. Selecting the optimal drill or tool involves navigating a complex landscape of...
- Unmatched Selection For Many Applications
- Superior Quality & Consistency
- Immediate Worldwide Delivery
- Technical Support & Expertise
- American Based Manufacturer
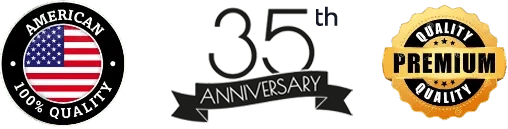

- Different Product
- Different Technology
- Different Company
- Expect MORE from your tools
Let Us HELP You!
Subscribe To Our Newsletter
Signup for email offers, updates, and more
Contact Us
- 25205 & 25201 Avenue Tibbits Valencia CA 91355 USA
-
Phone : (661) 257-2288
FAX : (661) 257 -3833 - lel@ukam.com
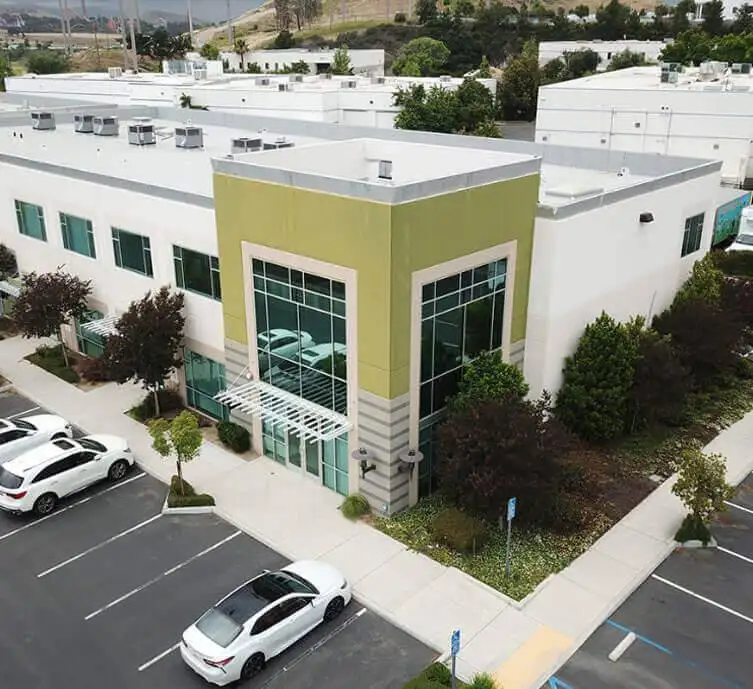
UKAM Industrial Superhard Tools is a U.S. High Technology, Specialty Diamond Tool & Equipment manufacturer. We specialize in producing ultra thin, high precision cutting blades, precision cutting machines diamond drills, diamond micro tools, standard & custom advanced industrial diamond tools and consumables.
- 25205 & 25201 Avenue Tibbits Valencia CA 91355 USA
-
Phone : (661) 257-2288
FAX : (661) 257 -3833 - lel@ukam.com
- 25205 & 25201 Avenue Tibbits Valencia CA 91355 USA
-
Phone : (661) 257-2288
FAX : (661) 257 -3833 - lel@ukam.com
DIAMOND TOOLS BY BOND
EQUIPMENT
KNOWLEDGE CENTER
OUR PRODUCTS
COMPANY
CUSTOMER SERVICE
Shipping Methods


Safe & Secure Payments

© Copyright 1990-2025. UKAM Industrial Superhard Tools – Terms of Use