There are numerous variables that affect the performance of diamond and CBN cutting blades. Understanding these variables will help end users select the right diamond blade specifications for their applications and optimize their cutting operations to achieve the highest level of efficiency. The objective of this article is to demonstrate that each variable in the diamond sawing process is just one component of a larger system. Altering one component or variable alone cannot create efficiency; it is only when all components of the system work together that the desired results can be achieved.
Similar to a mathematical equation, one incorrectly selected variable or component can negatively impact all other properly selected variables, rendering the entire diamond sawing system inefficient. Many end users approach their diamond sawing applications uninformed or misled, leading to errors during the setup phase and the skipping of critical steps. When problems arise, most rush to treat the symptoms rather than addressing the root cause. This frustration often leads them to incorrectly attribute their issues to the diamond cutting blade being used.
For example, what some customers consider a serious problem may be resolved by something as simple as adjusting the pressure or direction of the coolant flow. Solutions can also be as straightforward as changing the mounting method, RPMs, or educating the customer on the need to dress the blade. Selecting the right combination of variables for a specific material or application is both an art and a science, often taking years to master.
Share this Article with Friend or Colleague
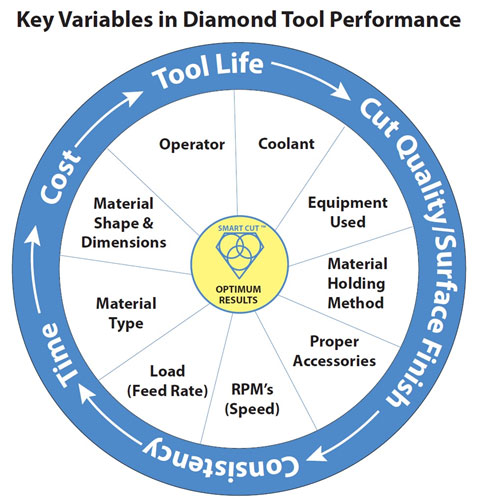
Errors are made in the set up phase and critical steps are skipped. When problems do surface, most rush to treat a symptom rather than the cause. Frustration leads them attribute their problems to diamond cutting blade being used. What some customers refer to as serious problem for example, may be resolved by something as simple as changing pressure or direction of coolant flow. The solution can be as easy as changing mounting method, RPM’s, or educating customer about need to dress blade. Selecting the right combination of these variables for a specific material / application is both an art and science that often takes years to master. Information presented in this article is not based on R & D, but primarily on many years of process optimization experience.
DIAMOND BLADE SELECTION – (Selecting the Right Diamond Blade for your Application)
Each diamond blade application exhibits similar characteristics, whether its in specification or performance. Below is a list of the most important characteristics/parameters obtained from years of experience.
BASIC APPLICATION PARAMETERS
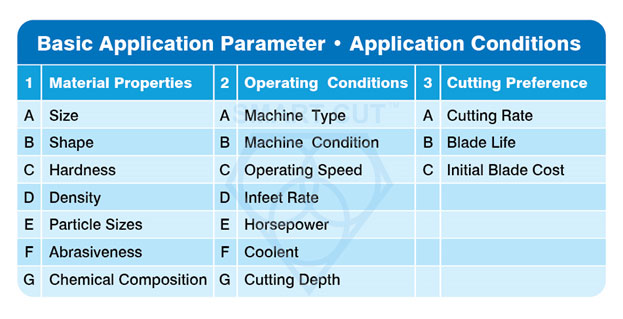
Diamond Blade Properties
1. Diamonds
-
Grit Size
-
Origin
-
Type
-
Shape
-
Grade
-
Quality
-
Coating
-
Friability
-
Hardness
2. Bond Type & Composition
-
Type
-
Density
-
Hardness
-
Concentration
-
Tensile Strength
-
Kerf Angle
3. Metal Core
-
Thickness
-
Tensioning
-
Gullet Design
-
Grade
-
Hardness
These parameters will play a major role in diamond blade performance. For the diamond blade manufacturer to recommend the right blade for your application. It is critical that the customer provide as much application information as possible. The first step in this process is to consider the properties of the material to be cut and to match diamond blade properties to this material. Table 2 shows a general matching of three basic blade properties to three basic material properties.
Common non metallic materials cut with diamond blades vary from hard, dense products like high alumina to loosely bonded, highly abrasive products like concrete block. No attempt is made to list specific diamond mesh sizes, concentrations or bond hardness to cut these materials. This information is to be used just as a guide in selecting diamond blade specifications.
Table 2 indicates that hard metal bonds are selected for highly abrasive material. Although physical prosperities are of primary importance in selecting blade properties, chemical properties can also play an important part. With refractory materials, for instance a high alumina content usually indicates that the material will be dense and hard requiring softer bond types and finder diamond mesh sizes.
Matching Basic Blade Properties to Material Properties
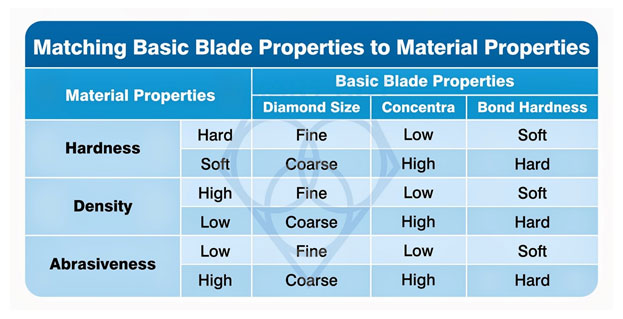
The second step in the blade selection process is to consider the effects of operating conditions on the diamond blade. Table 3 shows these anticipated effects.
An operating condition which causes a diamond blade to have shorter life and a faster cutting rate is said to make the blade act softer.
A blade with longer life and slower cutting rate is harder acting blade (harder cutting action). Having tentatively selected a combination of blade materials from the material properties guidelines in Table 2 a change in diamond blade materials is made if there is a specific operation condition which will affect diamond blade hardness as shown on Table 3.
Effect of Operating Conditions on Blade Actions
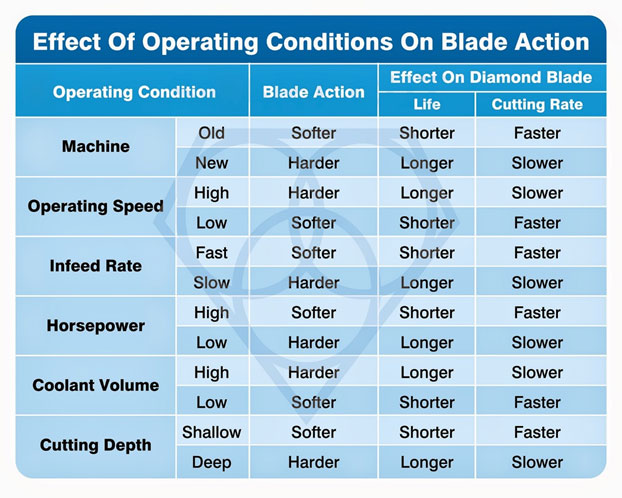
The third and final step in the blade selection process is the consideration of the customers stated blade preference, if any. Cutting rate (speed) and blade life are the primary measurements most customers are concerned with. Usually high cutting speeds reduce labor costs and high blade life reduces blade costs. There is an inverse relationship between blade life and cutting rate. as blade life increases, cutting rate deceases. The most common customer preference is for a diamond blade which will provide both longer life and a faster cutting speed. It is the job of the diamond
blade manufacturer to evaluate which is more important to the customer, blade life or cutting speed and then to adjust blade specification selection accordingly
If blade cost is the most important customer consideration
Initial cost of a diamond blade is primarily dependent on diamond content (concentration). A popular misconception among end users is that diamond content (concentration) and performance are directly proportional. However this is not the cause. In practice, there is an optimum number of diamond particles of a specific diamond mesh size in a specific bond which will produce optimum performance for a specific application. On many applications lower cutting costs are obtained user lower rather than higher diamond concentrations which, in some cases will not cut at all. For this purpose the customer should be concerned with performance, not diamonds.
What application parameters are the most significant in making application decisions? In general, the most important factor is the type of material being cut. Manufacturers recommended stock specifications have been developed to cut specific materials under average operating conditions where no specific customer preference has been expressed.
For example soft diamond bond, with coarse diamond size and high diamond grade has been found to provide optimum performance on most alumina cutting applications.
This specification was developed as a result of many laboratory and field tests of various diamond blade specifications cutting same material. However when this specification does not provide optimum performance, specifications changes are made following the general guidelines presented in Table 2 and Table 3.
OPTIMIZING BLADE PERFORMANCE
For a any set of application conditions there is a combination of diamonds and bond which will produce optimum diamond blade performance. Finding that combinations depends on
- the customers knowledge and ability to communicate initial application conditions, blade performance results and operating conditions changes
- application engineers knowledge and ability to interpret those results and take appropriate action.
Except on most common applications, a successful initial blade tests is rare. In many cases it may take several attempts and adjustments on both part of customer and diamond blade manufacturer to come to optimum solution.
APPLICATION RULES
Blade performance is adjusted by changing blade materials, but it can also be adjusted by changing operating conditions. Information presented in Table 2 and Table 3 implies certain application rules. Table 4 summarizes these rules showing the effect of changing either blade materials or operating conditions, holding all other variable constant.
- Increasing diamond concentration causes a blade to act harder because there are more diamond particles in contact with the material which reduces the unit pressure per diamond particle and the grain penetration depth.
- Increase diamond mesh size cause softer blade action because the fewer diamond particles are subjected to higher unit pressures.
- Increased bond hardness’s make a blade act harder because of increased diamond holding capacity and abrasion resistance.
- Increase machine operating speeds (RPM’S) make a blade act harder because each diamond particle is in contact with the material being cut for a shorter time period reducing grain penetration and removing less material per diamond particle per blade revolution.
- Increased infeed rates cause a blade to act softer because the increased unit pressure causes each diamond particle to do more work per blade revolution. Some diamond particles may be prematurely pulled out of the blade because of increased pressure.
- Increased horsepower causes a blade to break down faster because of premature pull out of diamond particles caused by higher cutting pressures. Stated another way, higher horsepower applications allow the use of harder bonds with hold the diamond particles longer because dull diamond particles cut better at highrather than at low horsepower ratings.
- An increased coolant volume aids cutting swarf removal which reduces the amount of wear on the bond making the blade act harder
- Increased blade cutting depths cause a blade to act harder because the increased contact area reduces the pressure per unit particle and the grain penetration depth
These are the few important rules which guide the diamond blade manufacturer and customer in changing blade elements or operating conditions to optimize blade performance
APPLICATION RULES
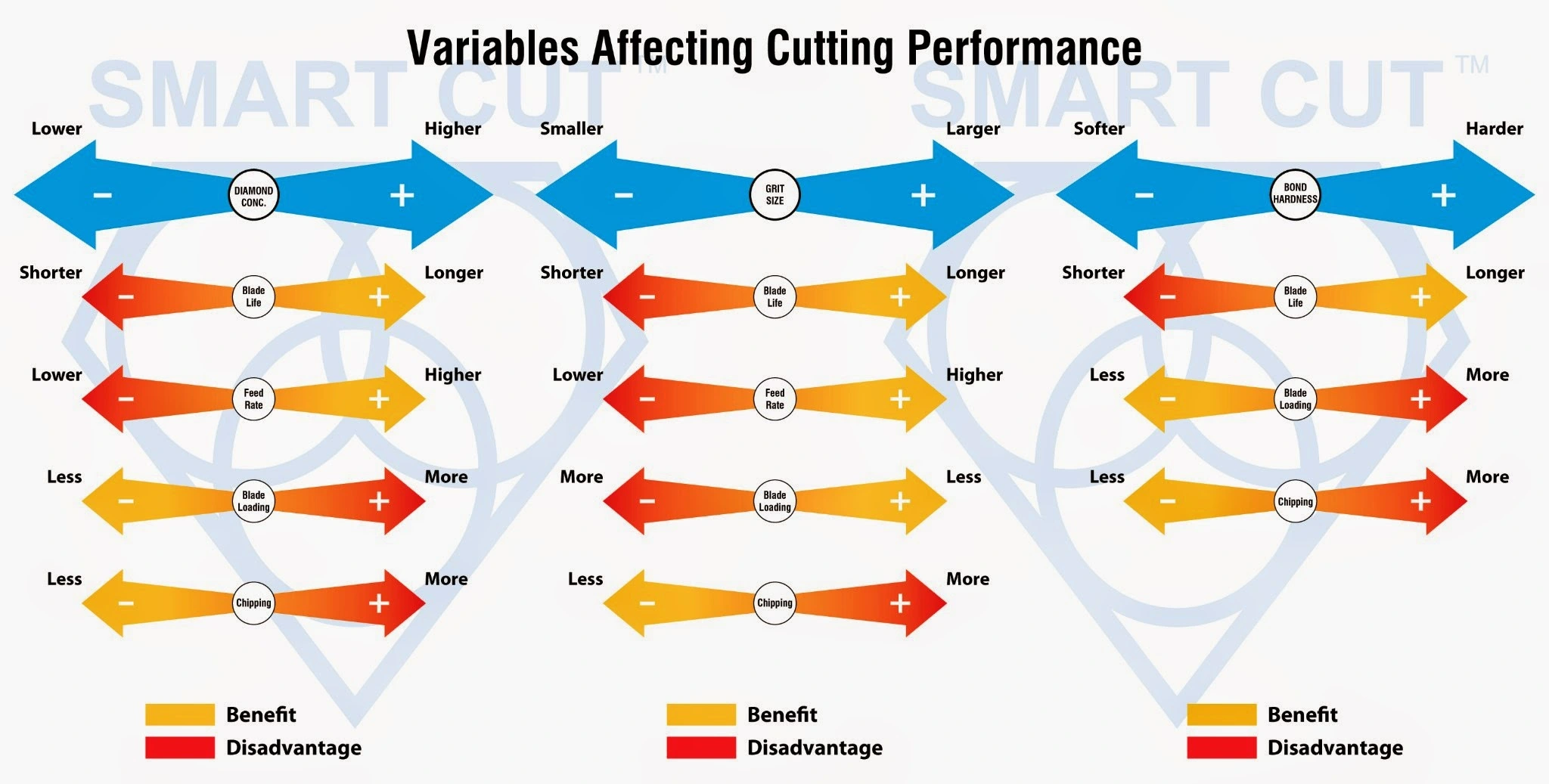
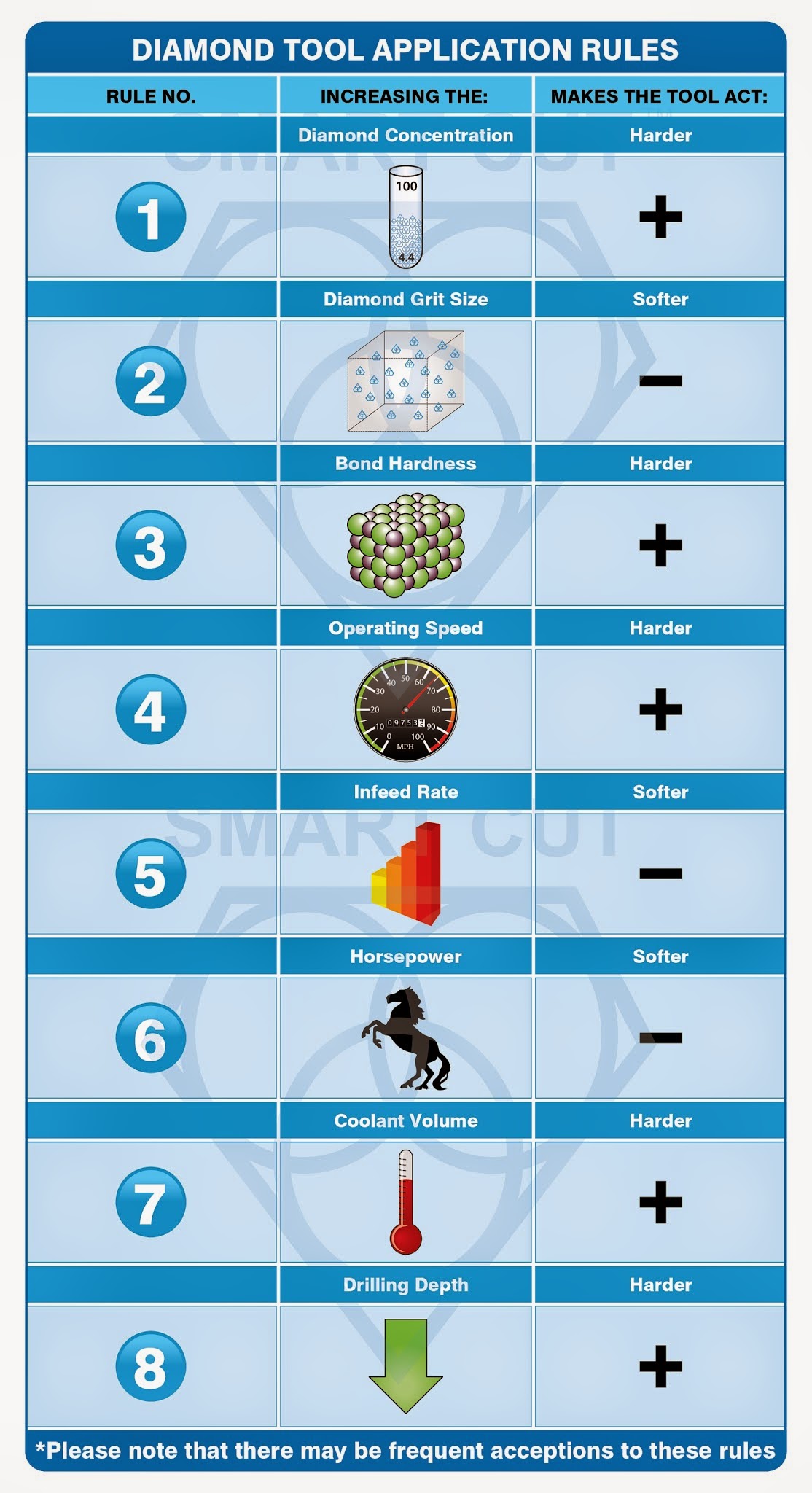
Nevertheless there are frequently exceptions. For example beyond optimum point O, blade life decreases with increased concentration. This may occur because the harder acting blades require dressing to maintain a satisfactory cutting action, or increased infeed pressures may have to be used to maintain satisfactory cutting rates.
Increased diamond size beyond optimum point O cause a blade to act harder because the coarser particles do not penetrate a very hard material. There is a complex relationship between the number of diamond particles in a blade and the contact area of a single diamond particle. For example a change from 20/30 mesh diamond to 30/40 mesh diamond at the same concentration level provides approximately three times as many diamond particles but reduces the individual particle contact area by approximately one third. It is common to expect harder bonds to produce longer blade life.
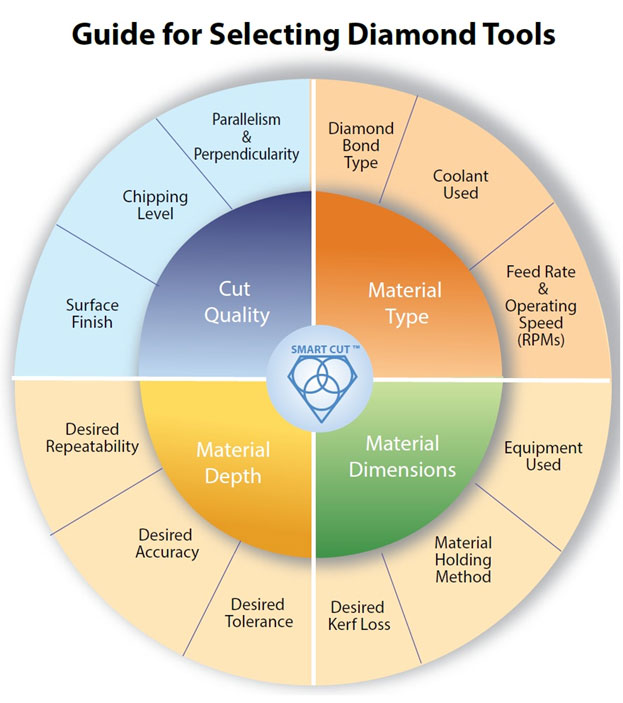
One theory that supports the contradiction beyond optimum point O is that harder bonds are more brittle and start to break away rather than wear away, This causes shorter blade life
Other changes in diamond blade materials or operating conditions which make a blade act harder will produce similar effects. Contradictions beyond optimum hardness’s can be explained with similar theories. The accuracy of these theories is not important when considering the blade selection process.
VARIATION
Variation is a critical factor which further complicates the blade selection process. Some degree of variation is fairly common and is to be expected involving most aspects of diamond blade usage, raw material composition, operating conditions and etc.
Some sources of variation diamond blade applications:
1. Diamond Blade
Diamonds
-
Origin
-
Friability
-
Hardness
-
Internal Structure
-
Processing
-
Sizing
-
Ovalizing
-
Tabling
-
Sorting
-
Grinding
Powdered Metal
-
Particle Sizes
-
Particle Size Distribution
-
Physical Properties
-
Chemical Properties
-
Flow Rate
Processing
-
Weighing
-
Mixing
-
Pressing Pressure
-
Processing Temperatures
-
Finished Dimensions
-
Tensioning
-
Core Quality
-
Hardness
1. Machine Operating Condition
Machine
-
Speed
-
Feed
-
Horsepower
-
Type
-
Power Source
-
Condition
-
Coolant Volume
Operator
-
Skill
-
Temperament
-
Objectivity
Purchaser
-
Flexibility
-
Communicativeness
2. Material Being Cut (Raw Materials)
-
Particle Sizes
-
Particle Size Distribution
-
Grog Size & Type
-
Chemical Composition
Processing
-
Weighing
-
Pressing
-
Firing
-
Kiln Location
Final Product
-
Tensile Strength
-
Chemical Composition
-
Refractoriness
-
Abrasiveness
-
Hardness
-
Density
-
Permeability
Many factors can affect each of the variables listed above and methods used to control and minimize these variations. Manufacturer of diamond blades goes to great length to control the quality of the diamonds and powders used and to control the processing conditions which affect the performance of the finished product.
By the same taken raw material manufacturers that supply material that is cut by diamond blades also have formable quality control standards to minimize process and manufacturing variation. Unfortunately the cut ability of these materials is seldom taken into consideration in initial raw material design and process control when designing original product. Refractory products for example are closely controlled for properties such as thermal conductivity, spalling and refractoriness, but cut ability (hardness and abrasiveness) is not specifically controlled. Operating conditions are typically under poorer control than either material properties or diamond blade properties. For instance, the objectivity of the saw operator and the communicativeness of the purchaser are major sources of variations that have important effect on blade performance.
Typically the diamond blade manufacturing processes are in far better control than other factors of the application environment in which those diamond blades perform.
AFFECTS OF PRODUCT, PROCESS AND APPLICATION VARIABLES ON DIAMOND BLADE PERFORMANCE
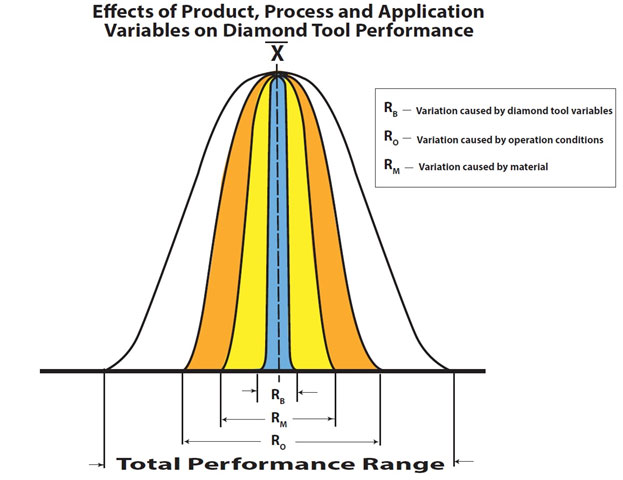
This normal variation curve represents a hypothetical population of blade performance results on the a specific application. The curve represented by range Rb depicts the relative amount of variation caused by diamond product variables. Curve represented by range RM accounts for the amount of variation cause by variables in the material being cut.
The range Ro represents the variation in performance results due to variations in operation conditions. The goal in this case is not to relieve the blade manufacturer of the all responsibility of application variations, but it does express the experience of diamond blade manufacturers.
One of the most difficult tasks an application engineer faces is solving application problems that are cause by variation. For example, in cutting one material typical blade life is average of 500 cuts per blade is considered normal.
Figure 1 presents another frequency distribution curve showing the average and range of performance on this specific hypothetical application
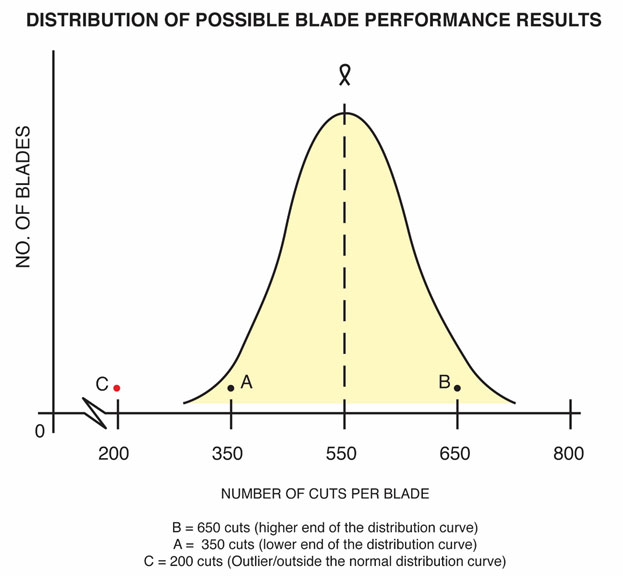
Blade represented by point A performed 350 cuts. The user of this blade is not happy and may request a credit. However what the end user should realize is that blade life they have experienced is not out of the ordinary and still falls within the normal distribution curve. When using this particular diamond blade the user was affected by all variables discussed above. Therefore, credit is not really warranted (despite what the customer may feel).
This problem occurs frequently and it is the diamond blade manufacturers application engineers task to explain to the disappointed end user that the 350 cut performance level, although low is normal. In these situations, note that blade performance represented by point B is rarely mentioned.
On other hand if a blade provided only 200 cuts as shown in point C, this would be outside the normal distribution curve. There could be more than one explanation to attribute to this poor blade performance. In statistics this performance would be attributed to assignable cause. Finding and assigning cause and correcting the problem behind this poor performance is a challenging task. Most customers logically conclude that there is something wrong with this diamond blade. However, this is not always the case.
In this situation it is very important of the customer (end user) and blade manufacturer (supplier) to face these circumstances with an open mind in order to resolve the problem. Both blade manufacturer and user can dramatically benefit by working together to resolve problem, instead of approaching it as advisories.
The end users lack of cooperation with blade manufacturer or supplier will be costly to the end user. Important information will be lost unless the end user communicates complete blade application information to manufacturer.
The manufacturer can assist the end user by providing important recommendations in changing operation conditions or usage parameters. And in some cases provide different blade specification that will more closely and better match customers application parameters.
It’s important for the customer to understand that manufacturers do not rule out diamond blade variability as cause of poor diamond blade performance. Its just very rare. Most diamond blade manufacturers maintain elaborate records documenting diamond blade manufacturing and quality control process at every stage.
Each batch and blade produced is frequently assigned as serial number. Every processes underwent in diamond blade manufacturing process can be reexamined and traced to each individual blade.
This information is frequently inspected when looking into validity of customer poor blade performance claims.
Most customers when experiencing poor blade performance or variation frequently assume the tool used (diamond blade) is at fault. Rarely do these users consider material variations or changes in operating conditions as a factor behind these problems.
DESIGNING BLADE TESTS
Rarely does the first blade specification recommended by diamond blade manufacturer provide optimized level of performance desired by customer. Even if by chance the first blade specification tested hits the target, subsequent blades would not perform to most optimized level of performance. This is why results of one blade test are not particularly valid. It is recommended that several blades of same specification by used to establish a average and a range of performance results before adjusting a specification of optimum results.
It is therefore in customers best interest to sample as many blade specifications and their variations as possible to establish a precedent (performance benchmark) from which they can measure all other blades.
In constructing field tests, the end user should attempt to control operating conditions and material specifications as much as possible to minimize diamond blade performance variation. For this reason laboratory tests utilize statistical methods such as random or multiple blade deigns to minimize the affects all variables that may cause variation, except for those being specifically evaluated.
Here are some of the methods used to control and minimize variation in laboratory testing environment
-
when possible, use automatic cutting equipment which operates at a constant surface speed, infeed pressure and power consumption. If using a human operation becomes necessary, specific amperage levels should be selected and operators cutting technique closely monitored to make sure physical movements are as consistent as possible.
-
material being cut is consistent and carefully controlled. We recommend purchasing large lot of material to represent a total range of variation in cutting properties of that specific material. Doing so will minimize effect of piece to piece variation, when selecting individual pieces at random. In order to minimize material hardness variation, we recommend selecting different places of material and cutting at each different location.
-
when evaluation one or several variables such as diamond mesh size, bond hardness, concentration, andetc in same test, select specific blade specification combination at random. By selecting random sequent in which only a few cuts are made with each combination of variables and then another random sequence selected. This is important to minimize variation cause by factors such as operator fatigue, weather conditions, power sources variations and machine condition changes.
PREDICTING DIAMOND BLADE PERFORMANCE RESULTS
Frequently customers ask the manufacturer to make certain predictions about diamond blade performance.
Questions such as “How many cuts will this blade make?” are frequently asked. Unfortunately, there is not real answer to this question. Because it takes a considerable amount of time and patience to explain all of possible variations behind diamond blade performance.
Why can performance results be more accurately predicted?
One customer may achieve certain blade life or chipping level on specific application. While another customer may experience longer or shorter life on exact same material and application. Even though operating condition and materials appear to be relative same. Any estimate from blade manufacturer may be interpreted by customer as a commitment or statement of performance guarantee. This is unrealistic and discourages for objective testing, the results of which will benefit both customer and manufacturer. Find out more: Evaluating & Comparing Diamond Blades >>>
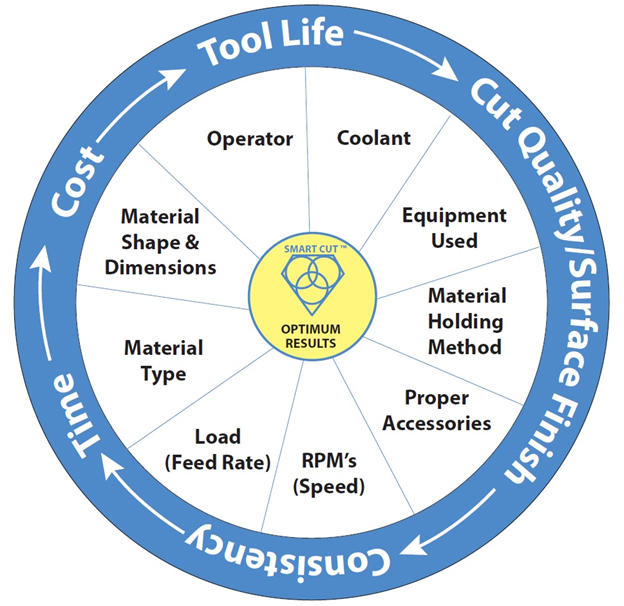
The information presented in this article is based not on research and development alone, but primarily on many years of process optimization experience. By understanding and optimizing each variable, end users can achieve superior performance and efficiency in their diamond sawing operations.
To optimize your diamond sawing operation, it is essential to understand and consider various application parameters and conditions. The table below outlines the key factors to take into account:
Basic Application Parameters and Conditions
Material Properties |
Operating Conditions |
Cutting Preferences |
---|---|---|
1. Size |
1. Machine Type |
1. Cutting Rate |
2. Shape |
2. Machine Condition |
2. Blade Life |
3. Hardness |
3. Operating Speed |
3. Initial Blade Cost |
4. Density |
4. Infeed Rate |
4. Surface Finish Quality |
5. Particle Sizes |
5. Horsepower |
5. Tolerances and Precision |
6. Abrasiveness |
6. Coolant |
6. Cutting Noise Levels |
7. Chemical Composition |
7. Cutting Depth |
7. Environmental Impact |
8. Thermal Conductivity |
8. Vibration Control |
8. Operator Safety |
9. Brittleness |
9. Blade Mounting Method |
9. Material Waste Minimization |
10. Electrical Conductivity |
10. Cutting Environment (Wet/Dry) |
10. Ease of Blade Maintenance |
11. Toughness |
11. Material Clamping Method |
11. Cycle Time |
12. Heat Generation and Management |
||
13. Flexibility and Versatility |
||
14. Automation and Integration |
||
15. Cost per Cut |
Material Properties:
1 Size: The dimensions of the material being cut, including length, width, and thickness.
2 Shape: The geometric shape of the material, whether it is a flat sheet, cylinder, or complex shape.
3 Hardness: The resistance of the material to deformation or scratching, often measured on the Mohs scale.
4 Density: The mass per unit volume of the material, which affects cutting resistance and blade wear.
5 Particle Sizes: The size distribution of particles within the material, relevant for composite or granular materials.
6 Abrasiveness: The tendency of the material to wear down the cutting blade through friction.
7 Chemical Composition: The elemental makeup of the material, which can influence the choice of blade and cutting conditions.
8 Thermal Conductivity: The material’s ability to conduct heat, which affects cooling requirements.
9 Brittleness: The material’s tendency to fracture or break under stress, influencing cutting speed and blade choice.
10 lectrical Conductivity: The material’s ability to conduct electricity, which may affect certain cutting methods.
11 Toughness: The material's ability to absorb energy and plastically deform without fracturing, impacting the cutting strategy.
Operating Conditions:
-
Machine Type: The specific type of cutting machine being used, such as a precision saw, high-speed saw, or manual saw.
-
Machine Condition: The maintenance and operational status of the machine, ensuring it is in good working order.
-
Operating Speed: The rotational speed of the blade, measured in RPM (revolutions per minute).
-
Infeed Rate: The speed at which the material is fed into the blade, affecting the cutting rate and quality.
-
Horsepower: The power output of the machine's motor, which influences cutting efficiency and capability.
-
Coolant: The type and flow rate of coolant used to reduce heat and remove debris from the cutting area.
-
Cutting Depth: The depth to which the blade penetrates the material in a single pass.
-
Vibration Control: Measures to minimize vibrations during cutting to ensure precision and blade longevity.
-
Blade Mounting Method: The technique used to secure the blade in the machine, impacting stability and cut quality.
-
Cutting Environment (Wet/Dry): Whether the cutting process is performed wet (with coolant) or dry, which affects heat generation and debris management.
Material Clamping Method: How the material is held in place during cutting to ensure stability and accuracy.
Cutting Preferences:
-
Cutting Rate: The desired speed at which the material is cut, balancing between efficiency and quality.
-
Blade Life: The expected durability of the blade before it needs replacement, influencing overall cost and downtime.
-
Initial Blade Cost: The upfront cost of purchasing the blade, which needs to be balanced with performance and longevity.
-
Surface Finish Quality: The desired smoothness or roughness of the cut surface, which affects the need for additional finishing processes.
-
Tolerances and Precision: The acceptable level of dimensional accuracy and precision in the cuts, crucial for applications requiring tight tolerances.
-
Cutting Noise Levels: Acceptable noise levels during cutting operations, important for maintaining a comfortable and safe working environment, especially in noise-sensitive areas.
-
Environmental Impact: Consideration of the ecological footprint of the cutting process, including the disposal of coolants and other waste products, as well as energy consumption.
-
Operator Safety: Measures to ensure the safety of the operator, such as the use of blade guards, proper training, and adherence to safety protocols.
-
Material Waste Minimization: Strategies to reduce the amount of material waste generated during the cutting process, which can help in cost savings and environmental sustainability.
-
Ease of Blade Maintenance: The ease with which the blade can be maintained, cleaned, and dressed, impacting downtime and operational efficiency.
-
Cycle Time: The total time required to complete a cutting cycle, including both setup and actual cutting time, which affects overall productivity.
-
Heat Generation and Management: The amount of heat generated during cutting and methods to manage it to prevent damage to both the blade and the material.
-
Flexibility and Versatility: The ability of the blade to handle a variety of materials and cutting conditions, providing operational flexibility.
-
Automation and Integration: Compatibility with automated systems and the ability to integrate the cutting process into existing production workflows for enhanced efficiency.
Cost per Cut: The overall cost efficiency measured as the cost incurred per cut, taking into account the blade life, cutting rate, and other operational costs.
Assess Material Properties
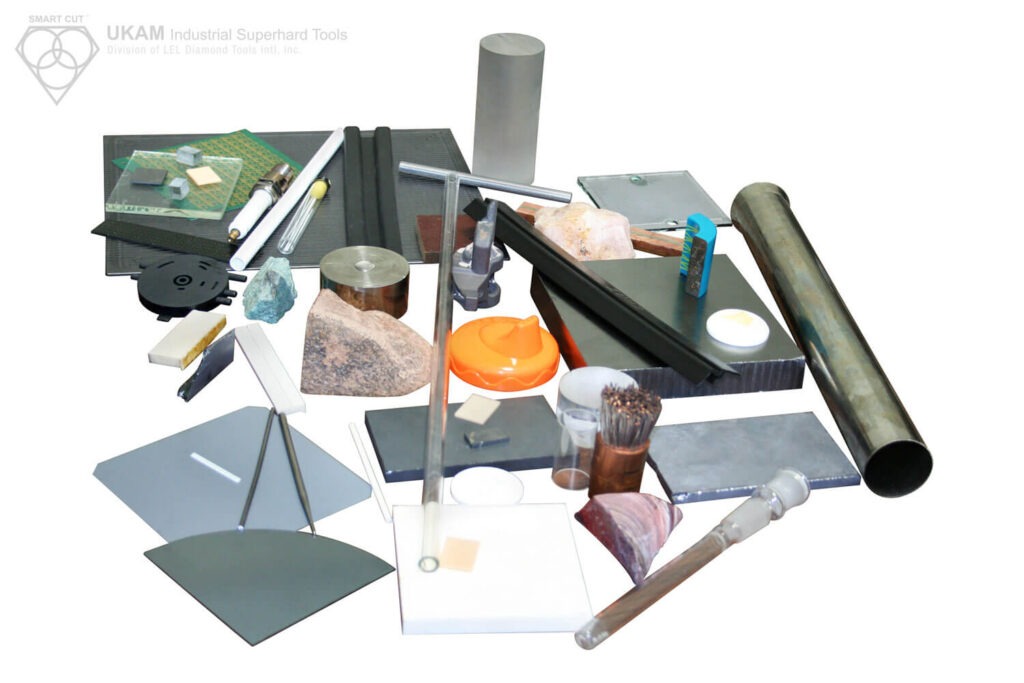
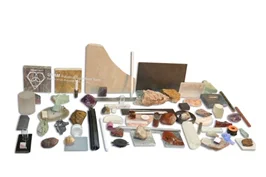
Understanding the material you will be cutting is the foundational step in optimizing your diamond sawing operation. The properties of the material directly influence the choice of diamond & cbn blade specifications, cutting parameters, and overall process efficiency. Below are the key material properties to assess:
A. Material Size
The size of the material refers to its overall dimensions, including length, width, and thickness. Accurate measurements of these dimensions are crucial as they determine the type and size of the blade needed for effective cutting. For larger materials, blades with a greater diameter and cutting depth capacity are often required. These high-durability blades ensure that the material can be cut efficiently and effectively without compromising on the quality of the cut. Conversely, smaller materials necessitate the use of precision blades that offer fine control and accuracy. These blades are designed to handle intricate cuts with high precision, ensuring that the smaller dimensions of the material are not damaged or inaccurately cut.
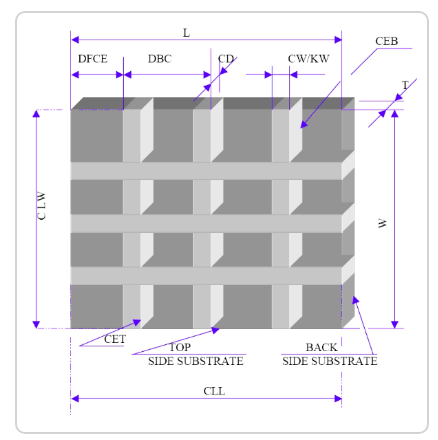
In addition to the general considerations for size, it's important to understand the specific requirements of different sizes of materials. For example, large materials might not only need larger blades but also robust machines with higher horsepower to manage the increased load. The cutting speed and feed rate must also be adjusted accordingly to handle the larger size without causing undue stress on the blade or the material. On the other hand, smaller materials, while requiring precision blades, also benefit from higher RPMs and more controlled infeed rates to achieve the delicate and accurate cuts needed for small dimensions.
Understanding the implications of material size also involves considering the setup and support for the material during the cutting process. Larger materials may require additional supports and clamping methods to ensure stability during cutting, preventing vibrations and movement that could affect the cut quality. Smaller materials, while easier to handle, require precise clamping methods that do not damage the material but provide sufficient stability for accurate cutting.
For large materials, selecting high-durability blades with larger diameters ensures the blade can withstand the increased load and provide effective cutting depth. For small materials, using precision blades that offer fine control and accuracy is essential for achieving intricate cuts with high precision. The machine setup, including horsepower, RPM, and infeed rates, must be tailored to accommodate the specific size of the material, ensuring stability and cut quality.
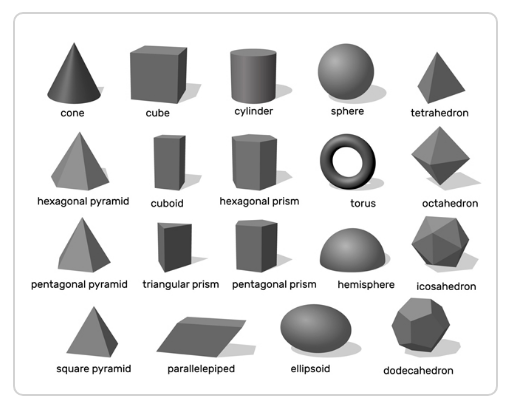
B. Material Shape
The shape of the material is a critical factor in the diamond sawing process, as it can range from simple geometric forms to complex and irregular profiles. Understanding the shape of the material is essential for selecting the appropriate blade that can navigate through the material effectively without causing damage or inaccuracies.
For simple shapes, such as straight lines, squares, or circles, standard blades are typically sufficient. These blades are designed to handle straightforward cuts with ease, providing consistent performance and good cut quality. The simplicity of the shape allows for a more predictable and manageable cutting process, reducing the likelihood of errors and ensuring efficient material removal.
In contrast, complex or irregular shapes present unique challenges that require specialized solutions. Materials with intricate designs, curves, or non-uniform profiles may necessitate custom blade profiles or specialized blades specifically designed for intricate cuts. These blades are engineered to handle the nuances of complex shapes, ensuring precision and minimizing the risk of damaging the material. Custom blades can be tailored to the specific requirements of the shape, providing the necessary control and accuracy for high-quality cuts.
When dealing with complex shapes, it is also important to consider the cutting strategy and machine settings. Precision cutting machines with advanced control systems can significantly improve the accuracy and quality of cuts for irregular shapes. Features such as CNC (Computer Numerical Control) technology allow for precise movement and positioning of the blade, ensuring that even the most intricate shapes can be cut accurately.
Additionally, the material's shape can impact the setup and clamping methods used during the cutting process. Simple shapes often require minimal setup and standard clamping techniques to hold the material securely in place. However, complex shapes may need specialized fixtures or supports to ensure stability during cutting. Proper clamping is crucial to prevent movement or vibrations that could compromise the cut quality and lead to material damage.
For simple shapes, standard blades are generally sufficient, handling straightforward cuts with ease and ensuring consistent performance. For complex or irregular shapes, custom blade profiles or specialized blades designed for intricate cuts are necessary to achieve precise and high-quality results. The cutting strategy, machine settings, and clamping methods must be carefully considered to accommodate the specific requirements of the shape, ensuring effective and accurate cutting without damaging the material.
C. Material Hardness
Material hardness is a critical factor in blade selection and plays a significant role in determining the appropriate blade specifications. Hardness is typically measured using the Mohs scale or more precise methods such as Vickers or Knoop hardness tests. These measurements provide insight into the material’s resistance to deformation or scratching, which directly influences the type of blade needed for effective cutting.
Understanding Hardness Measurements:
-
Mohs Scale: This scale ranks materials based on their ability to scratch or be scratched by other substances. It ranges from 1 (talc) to 10 (diamond), with higher numbers indicating harder materials.
-
Vickers/Knoop Hardness Tests: These tests provide more detailed measurements of a material's hardness by assessing the size of an indentation left by a specific force applied through a diamond indenter. The results are expressed in terms of hardness numbers, which are used to determine the material's resistance to deformation.
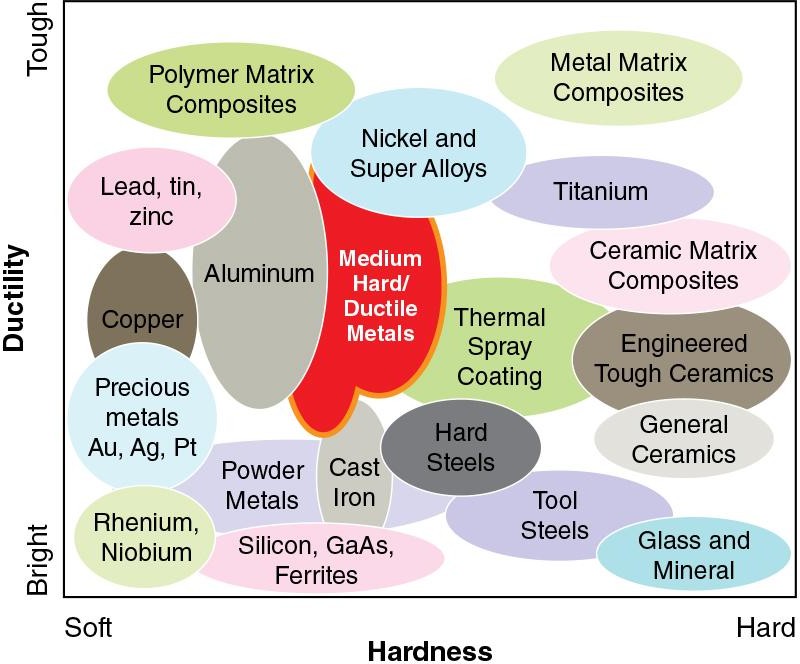
Hard Materials: Hard materials such as ceramics, metals, and gemstones present significant cutting challenges due to their high resistance to abrasion and deformation. To effectively cut these materials, blades with a high diamond concentration are required. Diamonds are the hardest known material and can efficiently cut through hard substances. Additionally, the bonding matrix that holds the diamonds in place must be exceptionally durable to withstand the increased cutting resistance and prevent premature wear of the blade.
For instance, when cutting ceramics or hard metals, the blade must maintain sharpness and integrity over extended periods. Therefore, a tough bonding matrix, such as a metal bond, is often used to ensure that the diamonds remain securely embedded and continue to cut effectively. These blades are designed to handle the high stress and heat generated during the cutting process, ensuring precise and efficient material removal.
Soft Materials: In contrast, soft materials such as plastics, rubber, and softer metals do not require the same level of cutting intensity. Blades with a lower diamond concentration are often sufficient for these materials. The reduced hardness of the material means that the cutting force required is significantly lower, and the blade does not need to be as robust.
For soft materials, a softer bonding matrix can be used. This type of bond allows for a quicker exposure of new diamonds as the old ones wear down, maintaining the blade’s cutting efficiency without excessive wear. Resin bonds are commonly used for softer materials, providing the necessary flexibility and wear rate to handle the material without causing damage or excessive blade wear.
D. Material Density
The density of a material is a crucial factor in the cutting process as it significantly affects the rate of material removal and the stress exerted on the blade. Density, typically measured in grams per cubic centimeter (g/cm³) or kilograms per cubic meter (kg/m³), represents the mass per unit volume of the material. This property influences how the material interacts with the blade during cutting, impacting both the efficiency of the cut and the wear on the blade.
High-Density Materials: High-density materials, such as certain metals, ceramics, and composite materials, pose a greater challenge during the cutting process due to their substantial mass and compact structure. These materials require robust, high-performance blades capable of handling the increased load and resistance. The blades must be designed to withstand the higher forces involved in cutting dense materials without deforming or wearing out prematurely.
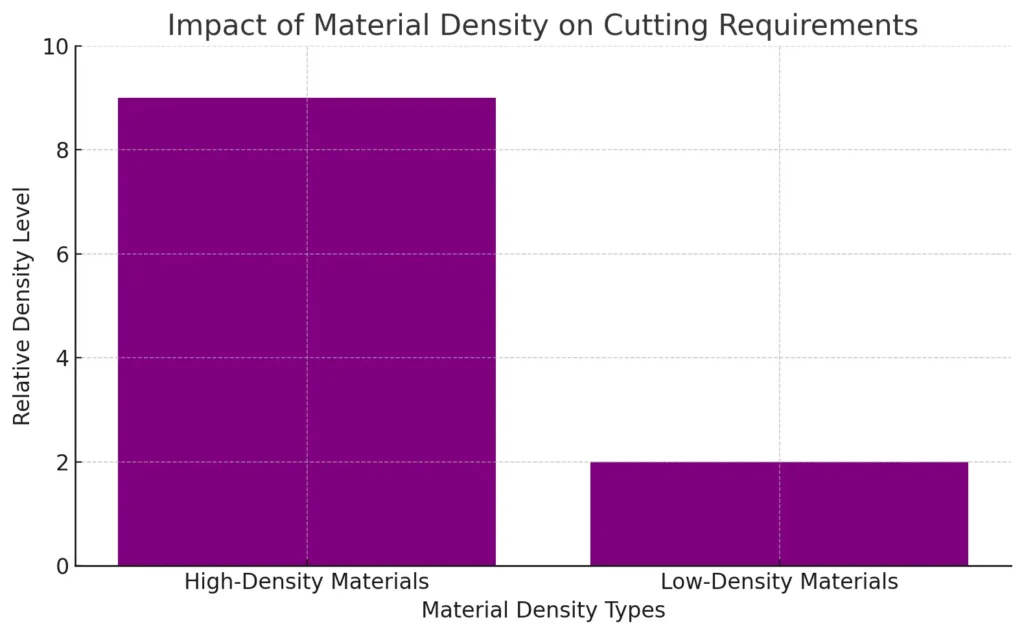
To effectively cut high-density materials, blades with a higher concentration of diamonds and a durable bonding matrix are essential. The increased diamond concentration provides the necessary cutting power, while the tough bond, often a metal or hybrid bond, ensures that the diamonds remain securely in place and resist the stresses encountered during cutting. Additionally, these blades must be able to dissipate heat effectively to prevent overheating, which can lead to blade failure and poor cut quality.
Low-Density Materials: Low-density materials, such as plastics, foams, and some softer metals, are easier to cut due to their lower mass and less compact structure. These materials do not require the same level of cutting force, allowing standard blades to be used effectively. The focus when cutting low-density materials is often on speed and efficiency rather than the robustness of the blade.
Standard blades with a lower diamond concentration and a softer bond, such as a resin bond, are suitable for cutting low-density materials. These blades can achieve high cutting speeds and remove material quickly without excessive wear. The softer bond allows for rapid exposure of new diamonds, maintaining the blade's cutting efficiency over time.
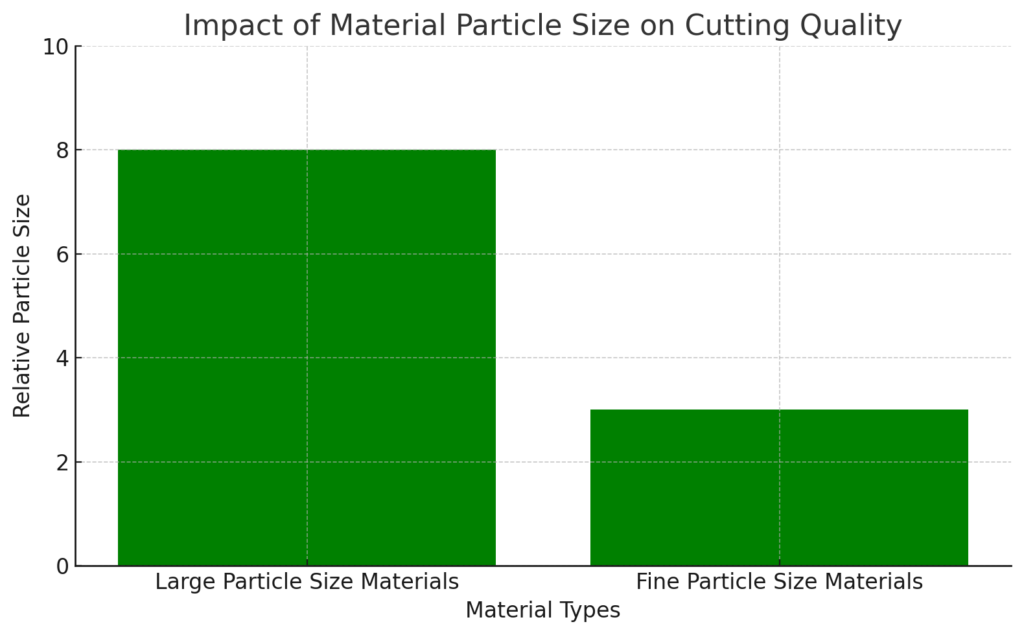
E. Material Particle Sizes
The size of the particles within a material is a critical factor that influences both the surface finish and the overall cutting quality. Particle size refers to the dimensions of the individual grains or components that make up the material. These sizes can vary significantly and are typically measured in micrometers (µm). The particle size affects how the material interacts with the cutting blade and can dictate the type of blade needed to achieve the desired cut quality and surface finish.
Materials with larger particle sizes can result in a rougher cut surface. This is because the larger particles create more significant disruptions along the cutting path, leading to an uneven finish. To effectively cut materials with large particle sizes, blades need to be designed to manage these particles, which often involves using blades with larger diamond grits. The larger grits can better handle the roughness and irregularities caused by big particles, ensuring the blade can cut through efficiently without being prematurely worn down.
Conversely, materials with fine particle sizes typically produce smoother cut surfaces. The smaller particles create fewer disruptions along the cutting path, allowing for a finer finish. Precision blades with finer diamond grits are essential for cutting materials with fine particle sizes. These blades can make cleaner cuts and provide high-quality surface finishes, which are often required in applications where precision and aesthetics are crucial.
F. Material Abrasiveness
The abrasiveness of a material is a critical factor that affects the longevity and performance of cutting blades. Abrasiveness refers to the material's tendency to wear down or erode the cutting edge of the blade through friction and mechanical interaction. Materials that are highly abrasive can cause rapid blade wear, leading to frequent blade replacements and increased operational costs if the wrong type of blade is selected. Therefore, understanding the abrasiveness of the material and choosing blades with appropriate wear-resistant properties is essential for efficient and cost-effective cutting operations.
High Abrasiveness: Materials such as reinforced composites, concrete, fiberglass, and certain ceramics are considered highly abrasive. These materials contain hard, gritty particles that can quickly wear down the blade's cutting edge. To effectively cut highly abrasive materials, blades with advanced wear-resistant properties are required.
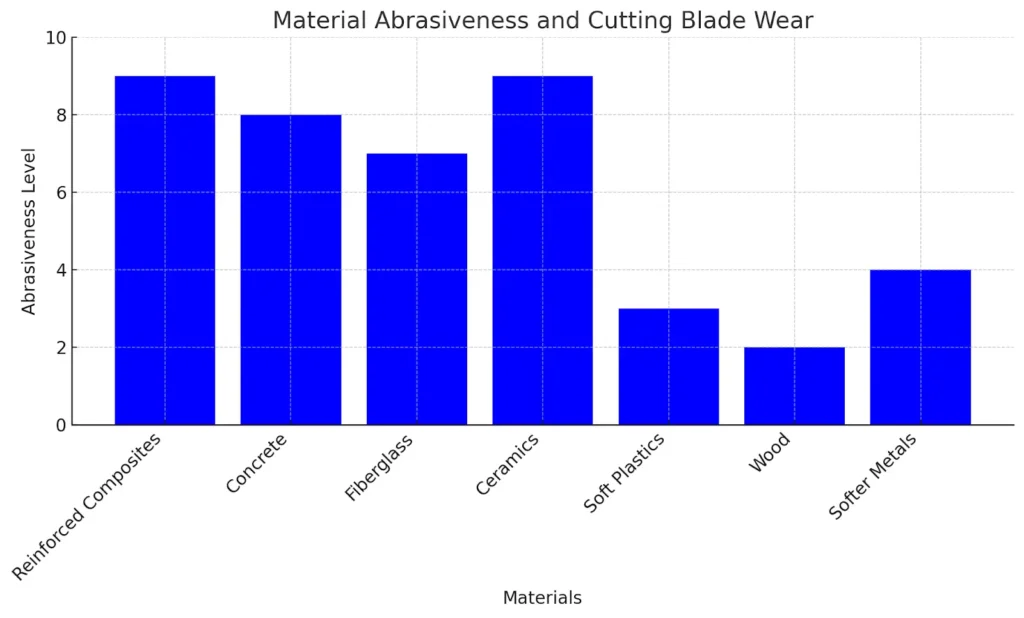
Blades for highly abrasive materials often incorporate a metal bond, which is tougher and more durable compared to other bond types. The high diamond concentration and the use of superior quality diamonds ensure that the blade maintains its sharpness and cutting efficiency over an extended period, even when subjected to the abrasive nature of the material. Additionally, the design of these blades may include features such as segmented rims or specific gullet configurations to improve debris removal and cooling, further enhancing their wear resistance.
Low Abrasiveness: Materials such as soft plastics, wood, and some softer metals exhibit low abrasiveness. These materials are less likely to cause significant wear on the cutting blade, allowing for the use of standard blades with moderate wear resistance. Blades for low abrasive materials typically have a lower diamond concentration and use softer bonding matrices, such as resin bonds, which provide sufficient durability for the task while being cost-effective.
Standard blades for low abrasive materials focus on maintaining a balance between cutting efficiency and blade longevity. Since these materials do not exert as much wear on the blade, there is less need for the advanced wear-resistant properties required for highly abrasive materials. This allows for faster cutting speeds and higher productivity, as the blade can maintain its performance over longer cutting cycles without the need for frequent maintenance or replacement.
G. Material Chemical Composition
The chemical composition of the material is a crucial factor that can significantly affect the interaction between the cutting blade and the material being cut. The presence of certain chemicals in the material can lead to reactions with the blade's bond, potentially causing degradation, corrosion, or reduced performance. Understanding the chemical makeup of the material is essential for selecting blades with bond materials that are compatible and resistant to any adverse chemical reactions.
Materials with reactive chemicals can interact negatively with the bonding matrix of the blade. These interactions can weaken the bond, causing the diamonds to dislodge prematurely and reducing the overall efficiency and lifespan of the blade. For instance, materials containing acids, alkalis, or other corrosive substances can corrode metal bonds, while certain polymers or composites might react with resin bonds, leading to bond breakdown and compromised cutting performance.
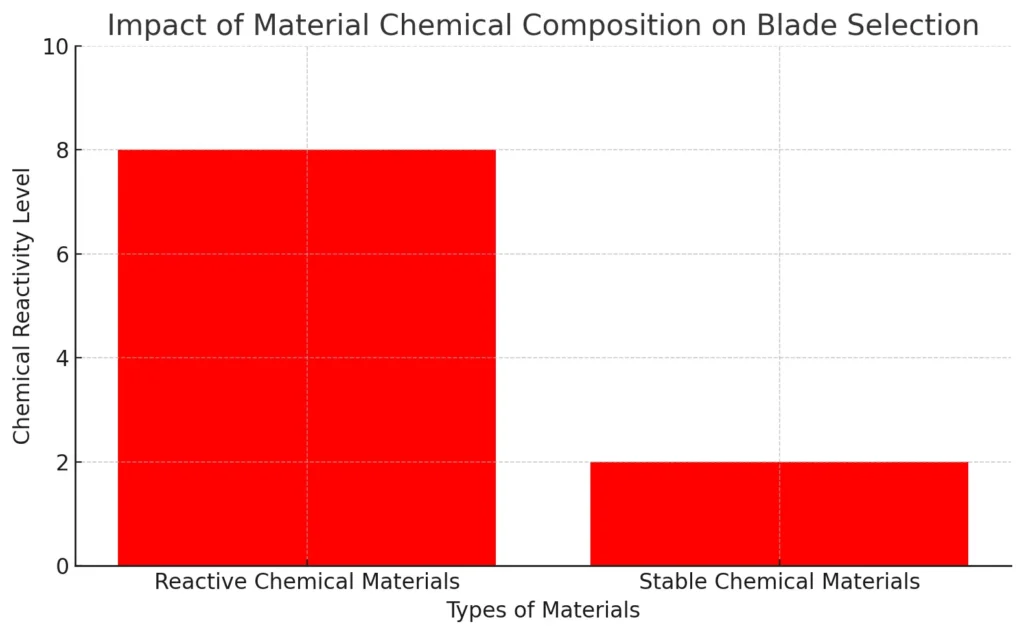
To mitigate these issues, it is important to select blades with chemically resistant bonds when working with reactive chemicals. Chemically resistant bonds are designed to withstand corrosive environments and prevent degradation. These bonds may include specialized coatings or formulations that protect the bond from chemical attack, ensuring the blade maintains its integrity and cutting performance over time.
In contrast, materials with stable chemicals do not pose the same risk of adverse reactions with the blade's bond. Standard blade bonds, whether metal or resin, are typically sufficient for cutting non-reactive materials. These bonds provide reliable performance without the need for additional chemical resistance, allowing for efficient cutting and long blade life.
2. Evaluate Operating Conditions
Evaluating and optimizing the operating conditions of your diamond sawing operation is crucial for achieving the desired cutting performance and efficiency. By examining the machine type, condition, and specific operating parameters, you can ensure that the cutting process is both effective and reliable. Here are the key factors to consider:
A. Machine Type
The type of machine used in the cutting operation plays a significant role in determining the appropriate blade and cutting parameters. Different machines are designed for specific types of cuts and materials.
-
Precision Saws: Ideal for intricate cuts and high-precision applications.
-
High-Speed Saws: Suitable for rapid cutting of hard materials.
-
Manual Saws:Used for smaller, less complex cuts.
-
Automatic Saws: Provide consistent and repeatable cuts for high-volume production.
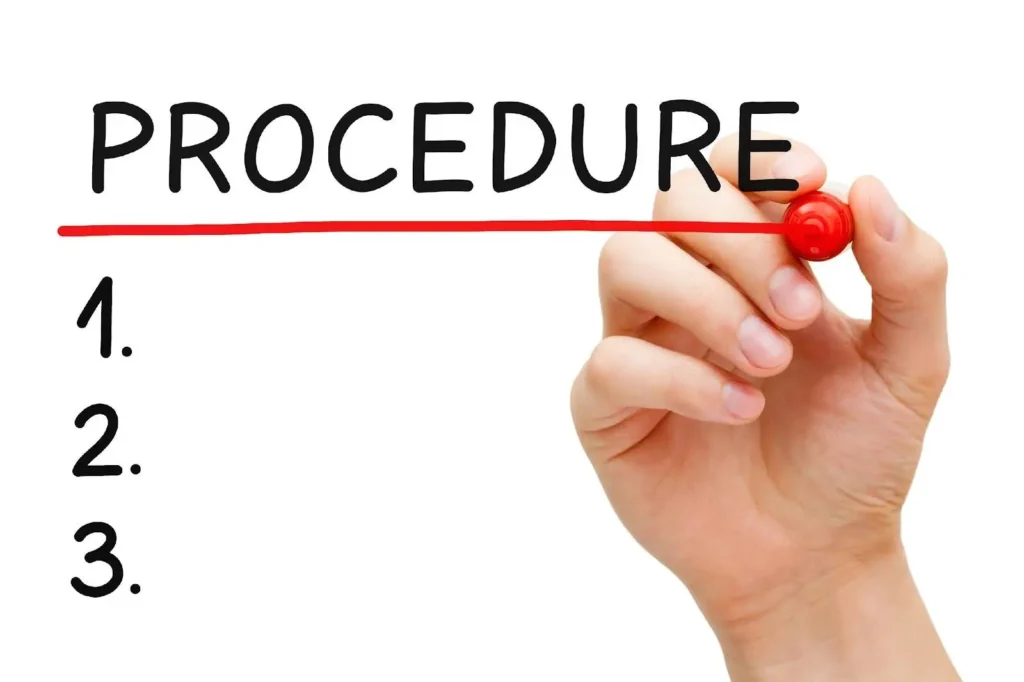
B. Machine Condition
The condition of the machine directly impacts the cutting performance. Regular maintenance and inspection are essential to ensure the machine operates efficiently.
-
Maintenance:Regularly check for wear and tear, and replace worn-out parts.
-
Alignment Ensure the machine is properly aligned to avoid inaccurate cuts.
-
VibrationMinimize machine vibration to prevent blade damage and ensure smooth cutting.
C. Operating Speed
Operating speed, measured in revolutions per minute (RPM), is a critical factor that affects the cutting efficiency and blade life. The optimal speed varies based on the material and blade type.
-
High-Speed Operation:Regularly check for wear and tear, and replace worn-out parts.
-
Low-Speed Operation: Better for softer materials and precision cuts, extending blade life.
D. Infeed Rate
The infeed rate, or the speed at which the material is fed into the blade, needs to be carefully controlled to achieve the desired cut quality and prevent blade damage.
-
High Infeed Rate:Increases cutting speed but can lead to poor cut quality and higher blade wear.
-
Low Infeed Rate:Provides better cut quality and reduces blade wear, suitable for precision applications.
E. Cutting Depth
Adjusting the cutting depth according to the material properties ensures efficient material removal and prolongs blade life.
-
Deep Cuts:Require blades with greater durability and robust bond systems.
-
Shallow Cuts: Suitable for thin or delicate materials, reducing the risk of damage.
F. Horsepower
The machine's horsepower must be adequate to handle the material and blade type. Insufficient power can lead to stalling and poor cut quality.
-
High Horsepower:Necessary for cutting hard or dense materials.
-
Low Horsepower: Sufficient for softer materials and small-scale operations.
Determine Cutting Preferences
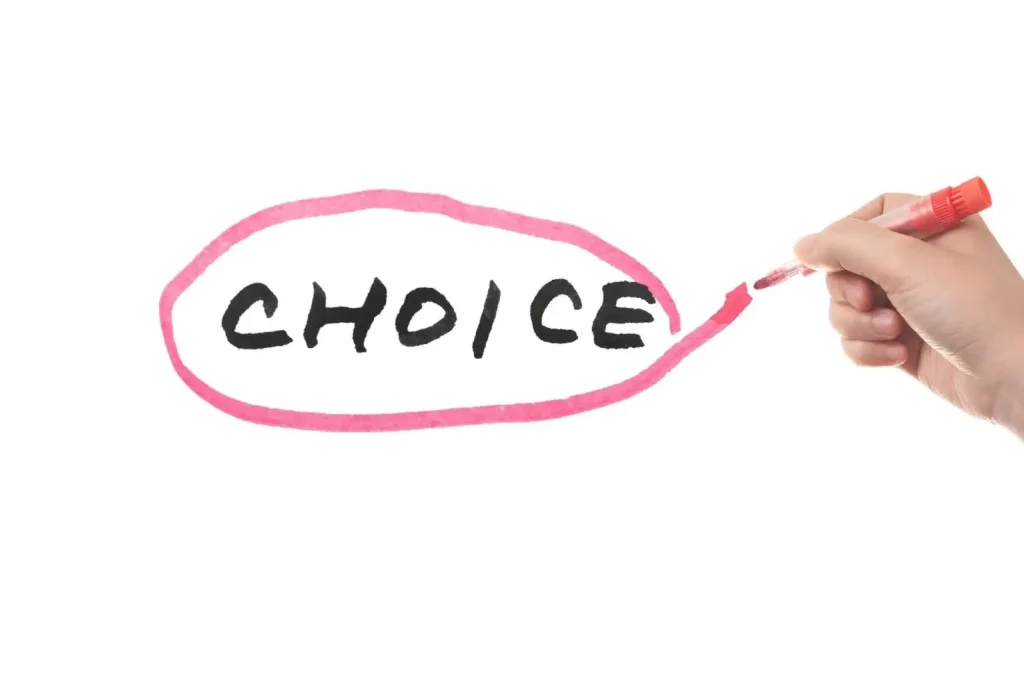
Determining your cutting preferences is a crucial step in optimizing your diamond sawing operation. By clearly defining your cutting goals, you can select the most appropriate blade and set the optimal cutting parameters to achieve the desired results. Here are some additional articles that can help with this
Here are the primary factors to consider:
A. Cutting Rate
The cutting rate, or speed at which the material is cut, is a key performance metric that impacts productivity and efficiency. Determining the ideal cutting rate involves balancing the need for speed with the quality of the cut and the longevity of the blade.
-
High Cutting Rate:Prioritizing a high cutting rate is suitable for applications where productivity is paramount. This often involves using blades with aggressive cutting action but may lead to increased blade wear and reduced cut quality.
-
Moderate Cutting Rate: Balancing speed and quality is essential for many applications. This approach ensures reasonable productivity while maintaining acceptable cut quality and blade life.
-
Low Cutting Rate:A slower cutting rate is often necessary for precision applications where cut quality and surface finish are critical. This reduces blade wear and ensures high-quality cuts but may decrease overall productivity.
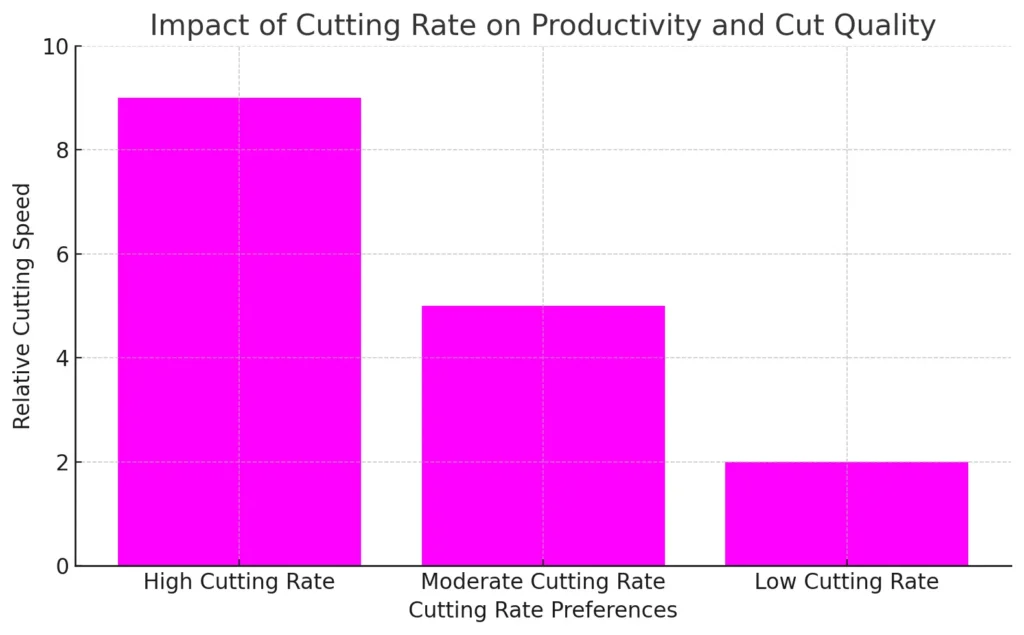
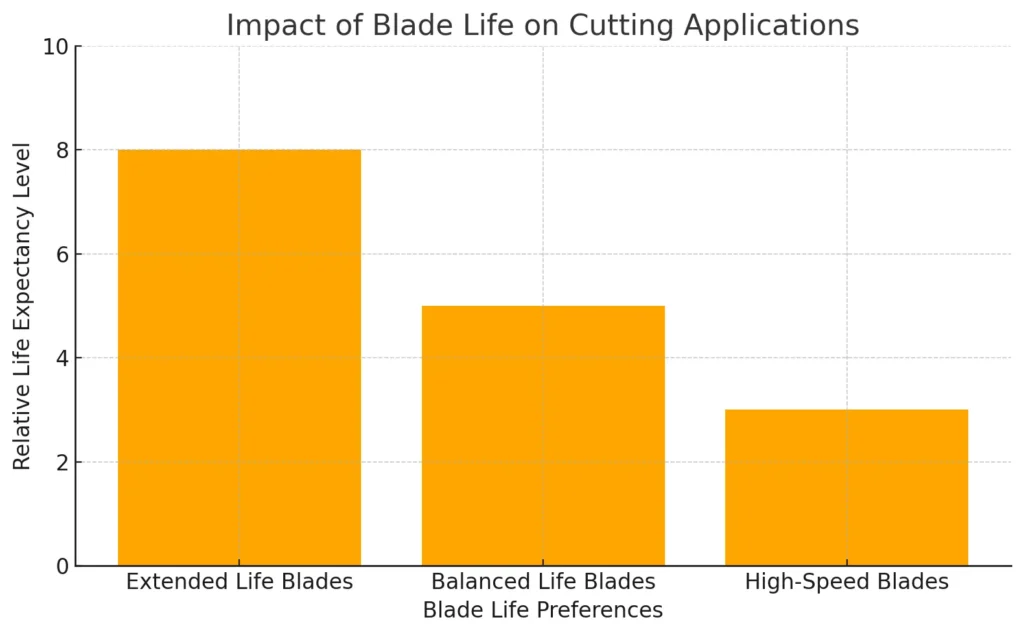
B. Blade Life
Diamond & CBN Blade life, or the durability of the blade, is another crucial factor that impacts the cost-effectiveness and consistency of the cutting process. Longer blade life reduces downtime and blade replacement costs but may require a trade-off with cutting speed. Blades designed for extended life are ideal for applications where minimizing downtime and replacement costs is essential.
These blades may have a slower cutting rate but provide consistent performance over a longer period. A balanced approach, where blade life is sufficient for regular use without compromising too much on cutting speed, is suitable for most general-purpose cutting applications. In scenarios where maximum cutting speed is required, blades may wear out more quickly. This is acceptable for short-term projects or when cutting soft materials where blade replacement costs are lower.
C. Initial Blade Cost
The initial cost of the blade is an important consideration, especially when working within budget constraints. Balancing initial cost with performance and longevity ensures cost-effective operations. High-quality blades with superior performance and longevity often come with a higher initial cost.
These are suitable for critical applications where precision and durability are essential. Diamond & CBN Blades that offer a good balance between cost and performance are ideal for many standard applications, providing reliable performance without excessive upfront investment. Economical blades are suitable for short-term projects or less demanding applications. While they may have a shorter lifespan and reduced performance, they help keep initial expenses low. Find out more: Diamond & CBN Blade Total Cost of Ownership >>>
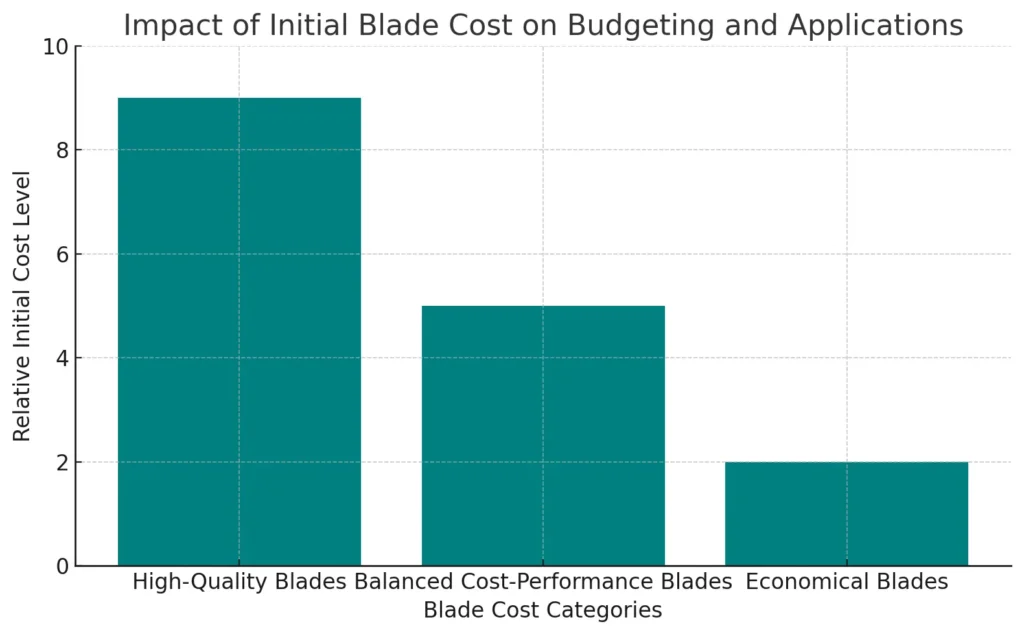
Diamond and CBN Blade Properties
Category |
Property |
Description |
---|---|---|
1. Diamonds and CBN |
Grit Size |
Size of the diamond or CBN particles used in the blade |
Origin |
Source of the particles (natural or synthetic) |
|
Type |
Monocrystalline, polycrystalline, cubic boron nitride (CBN) |
|
Shape |
Cubic, irregular, etc. |
|
Grade |
Overall quality and purity of the particles |
|
Quality |
Level of defects and inclusions |
|
Coating |
Surface treatment (e.g., nickel or titanium coating) |
|
Friability |
Tendency of the particles to fracture |
|
Hardness |
Hardness of the particles (Mohs scale or Vickers/Knoop) |
|
Thermal Stability |
Ability to withstand high temperatures |
|
Toughness |
Resistance to impact and chipping |
|
2. Bond Type & Composition |
Type |
Metal, resin, hybrid, etc. |
Density |
Density of the bonding material |
|
Hardness |
Hardness of the bonding material |
|
Concentration |
Amount of diamonds or CBN within the bond |
|
Tensile Strength |
Strength of the bond to withstand cutting stresses |
|
Kerf Angle |
Angle of the cut created by the blade |
|
Wear Resistance |
Ability to withstand wear and maintain cutting edge |
|
Chemical Resistance |
Resistance to degradation by chemicals |
|
Thermal Conductivity |
Ability to dissipate heat generated during cutting |
|
Flexibility |
Ability to absorb stress and maintain structural integrity |
|
3. Metal Core |
Thickness |
Thickness of the metal core |
Tensioning |
Method of tensioning to ensure stability |
|
Gullet Design |
Design of the spaces between segments for debris removal |
|
Grade |
Quality of the metal used in the core |
|
Hardness |
Hardness of the metal core |
|
Thermal Stability |
Ability to withstand high temperatures |
|
Vibration Dampening |
Ability to reduce vibrations during cutting |
|
Corrosion Resistance |
Resistance to rust and corrosion | |
Flexibility |
Ability to absorb stress and maintain structural integrity |
1. Diamonds or CBN Particles
A. Grit Size
The grit size of the diamond or cbn particles, determines the surface finish and cutting efficiency. Finer grits produce smoother finishes, while coarser grits are used for faster cutting of harder materials.
-
Fine Grit:deal for precision cutting and smooth surface finishes.
-
Coarse Grit:Suitable for rapid material removal and cutting harder materials.
B. Origin
The origin of the diamonds (natural vs. synthetic) can influence their properties.
-
Natural Diamonds:Generally harder but more variable in quality.
-
Synthetic Diamonds: More consistent in quality and tailored for specific applications.
C. Type
Different types of diamonds are used depending on the application.
-
Monocrystalline Diamonds:Single crystal structure, offering durability and consistency.
-
Polycrystalline Diamonds: Multiple crystal structures, providing high wear resistance and toughness.
D. Shape
The shape of the diamond particles affects cutting efficiency and blade life.
-
Cubic:Provides sharp cutting edges and efficient material removal.
-
Irregular Offers multiple cutting points, enhancing cutting efficiency.
E. Grade
The grade of the diamonds refers to their overall quality, including purity and defect levels.
-
High-Grade:Few impurities and defects, ensuring superior cutting performance.
-
Low-Grade: More impurities and defects, suitable for less demanding applications.
F. Quality
The overall quality of the diamonds used in the blade impacts its performance and lifespan.
-
Premium Quality:Long-lasting and high-performance, suitable for critical applications.
-
Standard Quality: Adequate for general-purpose cutting tasks.
G. Coating
Diamonds can be coated to enhance their properties, such as bonding strength and thermal stability.
-
Nickel Coating:Improves diamond retention in the bond.
-
Titanium Coating: Enhances thermal stability and wear resistance.
H. Friability
Friability refers to the diamond’s tendency to fracture. Controlled friability ensures self-sharpening of the blade.
-
High Friability:Self-sharpens but wears out faster.
-
Low Friability: Lasts longer but may require frequent dressing.
I. Hardness
The hardness of the diamonds determines their ability to cut through materials.
-
Higher Hardness: Suitable for cutting hard materials.
-
Lower Hardness: Used for softer materials.
2. Bond Type & Composition
The bond holds the diamond or cbn particles in place and wears away to expose new diamond cutting edges. Its properties are critical to blade performance.
A. Type
The bond type varies depending on the application and material.
- Metal Bond (Sintered): Durable and wear-resistant, suitable for hard materials.
- Resin Bond: Provides a smoother finish, ideal for delicate materials.
- Hybrid Bond: Combines properties of metal and resin bonds for versatile performance.
- Nickel Bond - A medium hardness bond that offers a balance between durability and flexibility
- Braised Bond - strong, durable bond that holds abrasive grains securely, ideal for aggressive cutting and rapid stock removal
B. Density
The density of the bond affects the blade’s cutting ability and wear rate.
-
High Density:Provides greater support for diamonds, extending blade life.
-
Low Density: Wears away quickly, exposing new diamonds faster.
C. Hardness
The bond’s hardness must match the material being cut.
-
Hard Bond:Used for soft, abrasive materials to minimize bond wear.
-
Soft Bond:Suitable for hard materials to ensure efficient diamond exposure.
D. Concentration
The concentration of diamonds or cbn particles within the bond impacts cutting efficiency.
-
High Concentration: Increases cutting speed and longevity.
-
Low Concentration: Reduces cost but may wear out faster.
E. Tensile Strength
The bond’s tensile strength ensures it can withstand cutting stresses without breaking.
-
High Tensile Strength: Suitable for high-stress applications.
-
Moderate Tensile Strength: Adequate for general-purpose cutting.
F. Kerf Angle
The angle of the kerf (cut created by the blade) affects the quality and efficiency of the cut.
-
Narrow Kerf:Reduces material waste and requires less power.
-
Wide Kerf: Suitable for thicker materials but increases material waste.
3. Metal Core
The metal core provides the structural backbone of the blade, affecting its stability and performance.
A. Thickness
The thickness of the core influences the blade’s stability and cutting performance.
-
Thicker Core:Provides stability and reduces blade flexing.
-
Thinner Core: Allows for finer cuts and is less resistant to flexing.
B. Tensioning
Tensioning ensures the blade runs true and reduces wobbling.
-
Proper Tensioning:Essential for maintaining blade stability and cut quality.
-
Improper Tensioning: Leads to blade wobble and poor cutting performance.
C. Gullet Design
The gullets (spaces between the segments) are designed to remove debris and reduce heat.
-
Large Gullets:Improve debris removal and cooling but may reduce blade stability.
-
Small Gullets: Increase stability but may require more frequent cleaning.
D. Grade
The grade of the metal core affects its durability and performance.
-
High-Grade Steel:Offers superior strength and longevity.
-
Standard-Grade Steel: Suitable for less demanding applications.
E. Hardness
The hardness of the metal core ensures it can withstand the rigors of cutting.
-
High Hardness:Provides better stability and longer life.
-
Moderate Hardness: Adequate for general-purpose cutting.
Understanding and Selecting Diamond Blade Specifications
The parameters outlined will play a major role in determining diamond blade performance. For a diamond blade manufacturer to recommend the right blade for your application, it is critical that the customer provides as much application information as possible. The first step in this process is to consider the properties of the material to be cut and to match the diamond blade properties to this material. The table below illustrates a general matching of three basic blade properties to three basic material properties.
Common non-metallic materials cut with diamond blades vary widely, from hard, dense products like high alumina to loosely bonded, highly abrasive products like concrete blocks. While this guide does not list specific diamond mesh sizes, concentrations, or bond hardness required to cut these materials, it serves as a general framework for selecting Diamond & CBN blade specifications.
For instance, Table 2 indicates that hard metal bonds are selected for highly abrasive materials. Although physical properties are of primary importance in selecting blade properties, chemical properties can also play an important part. With refractory materials, for example, a high alumina content usually indicates that the material will be dense and hard, necessitating the use of softer bond types and finer diamond mesh sizes.
Material Properties |
Blade Properties |
---|---|
High Abrasiveness |
Hard metal bonds |
High Density and Hardness |
Softer bonds and finer diamond mesh sizes |
Low Density and Softness |
Standard bonds and coarser diamond mesh sizes |
This information should be used as a guide to help in selecting the appropriate diamond blade specifications for various materials. By providing detailed application information, you can ensure that the diamond blade manufacturer can recommend the most suitable blade for your specific needs.
Matching Basic Blade Properties to Material Properties
The second step in the blade selection process is to consider the effects of operating conditions on the diamond or cbn blade. The table below shows these anticipated effects.
An operating condition that causes a diamond or cbn blade to have a shorter life and a faster cutting rate is said to make the blade act softer. Conversely, a blade with a longer life and a slower cutting rate is considered to have a harder cutting action.
After tentatively selecting a combination of blade materials based on the material properties guidelines in Table 2, adjustments to the diamond blade materials can be made if specific operating conditions affect the blade's hardness.
Material Properties Affect on Diamond & CBN Blade Speciation
Material Properties |
Basic Blade Properties |
Diamond Size |
Concentration |
Hardness |
---|---|---|---|---|
Hardness |
Hard |
Fine |
Low |
Soft |
Soft |
Coarse |
High |
Hard |
|
Density |
High |
Fine |
Low |
Soft |
Low |
Coarse |
High |
Hard |
|
Abrasiveness |
Low |
Fine |
Low |
Soft |
High |
Coarse |
High |
Hard |
Effects of Operating Conditions on Diamond Blade
Operating Condition |
Effect on Blade Life |
Effect on Cutting Rate |
Blade Action |
---|---|---|---|
High Speed |
Shorter |
Faster |
Softer |
Low Speed |
Longer |
Slower |
Harder |
High Feed Rate |
Shorter |
Faster |
Softer |
Low Feed Rate |
Longer |
Slower |
Harder |
Inadequate Coolant Flow |
Shorter |
Faster |
Softer |
Adequate Coolant Flow |
Longer |
Slower |
Harder |
High Pressure |
Shorter |
Faster |
Softer |
Low Pressure |
Longer |
Slower |
Harder |
When specific operating conditions are known to impact blade hardness, adjustments should be made accordingly. This ensures optimal performance and efficiency of the diamond or cbn blade in your specific application. By understanding and incorporating both material properties and operating conditions, users can achieve superior cutting results and extend the life of their diamond or cbn blades.
Effects of Various Operating Conditions on Blade Action
Operating Condition |
Blade Action |
Effect on Diamond Blade Life |
Cutting Rate |
---|---|---|---|
Machine |
|||
Old |
Softer |
Shorter |
Faster |
New |
Harder |
Longer |
Slower |
Operating Speed |
|||
High |
Harder |
Longer |
Slower |
Low |
Softer |
Shorter |
Faster |
Infeed Rate |
|||
Fast |
Softer |
Shorter |
Faster |
Slow |
Harder |
Longer |
Slower |
Horsepower |
|||
High |
Harder |
Longer |
Slower |
Low |
Softer |
Shorter |
Faster |
Coolant Volume |
|||
High |
Harder |
Longer |
Slower |
Low |
Softer |
Shorter |
Faster |
Cutting Depth |
|||
Shallow |
Softer |
Shorter |
Faster |
Deep |
Harder |
Longer |
Slower |
Machine Age:
-
Old Machines:Tend to produce a softer blade action, leading to a shorter blade life but a faster cutting rate. This might be due to wear and tear reducing the machine’s efficiency in maintaining optimal blade stability.
-
New Machines: Generally offer harder blade action, promoting longer blade life but at a slower cutting rate. This can be attributed to better precision and stability in newer machines.
Operating Speed:
-
High Speed:Results in harder blade action which extends the life of the blade but decreases the cutting rate due to the increased heat and potential for blade wear.
-
Low Speed: Causes softer blade action, reducing blade life but increasing the cutting rate because of the reduced heat generation and mechanical stress.
Infeed Rate:
-
Fast:Softens the blade action, shortens the life but increases the cutting rate. This could be due to the increased mechanical load causing quicker wear.
-
Slow: Hardens the blade action, which prolongs the life of the blade and decreases the cutting rate, likely due to less stress on the blade per unit of time.
Horsepower:
-
High: Provides a harder blade action, lengthening blade life and reducing the cutting rate. Higher horsepower might stabilize the blade and reduce the blade’s exposure to mechanical stresses per cut.
-
Low: Leads to softer blade action, shorter blade life, and a faster cutting rate, likely because the blade isn’t driven as forcefully.
Coolant Volume:
-
High:Harder blade action, longer blade life, and slower cutting rates. This may be because ample coolant reduces overheating and wear.
-
Low: Softer blade action, shorter blade life, and faster cutting rates, possibly due to less effective cooling and lubrication.
Cutting Depth:
-
Shallow: Results in softer blade action, shorter blade life, and faster cutting rates. Shallow cuts reduce mechanical stress per cut.
-
Deep Causes harder blade action, which extends blade life and reduces cutting rates, likely due to increased stability and effective use of the blade's cutting edge.
The third and final step in selecting a blade is to consider any specific preferences the customer may have stated, focusing primarily on cutting rate (speed) and blade life—key metrics of concern for most users. Typically, higher cutting speeds can lower labor costs, while extended blade life can reduce the cost of the blades themselves.
There exists an inverse relationship between these two factors: as blade life increases, the cutting rate typically decreases. Commonly, customers prefer a diamond blade that offers both longer life and faster cutting speeds. It is the responsibility of the diamond blade manufacturer to determine which aspect—blade life or cutting speed—is more crucial to the customer and to tailor the blade specifications accordingly.
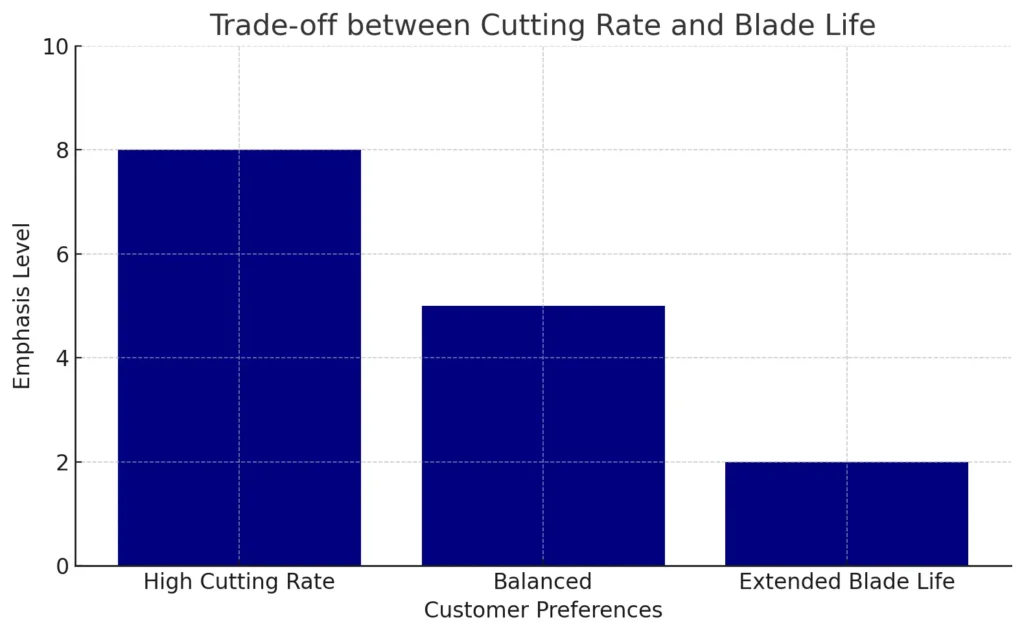
If diamond or cbn blade cost is the primary concern for the customer, it is important to note that the initial cost of a diamond blade is primarily influenced by the diamond content (concentration). Contrary to popular belief among end users, higher diamond concentration does not necessarily equate to better performance. In fact, for many applications, optimal performance is achieved with a lower concentration of diamonds, as excessively high concentrations can sometimes lead to ineffective cutting. Therefore, customers should prioritize performance over mere diamond content.
When deciding on application parameters, the most crucial factor is typically the type of material to be cut. Manufacturers' recommended stock specifications are designed to efficiently cut specific materials under average operating conditions when no particular customer preference has been specified.
For instance, a soft diamond bond with a coarse diamond grit size and high diamond grade is generally optimal for cutting most alumina applications. This specification is derived from extensive laboratory and field testing of various diamond blade specifications on the same material. If this specification does not yield optimal performance, adjustments are made following the general guidelines as outlined in Table 2 and Table 3. These adjustments are based on a comprehensive understanding of material properties and cutting requirements to ensure the best possible outcome.
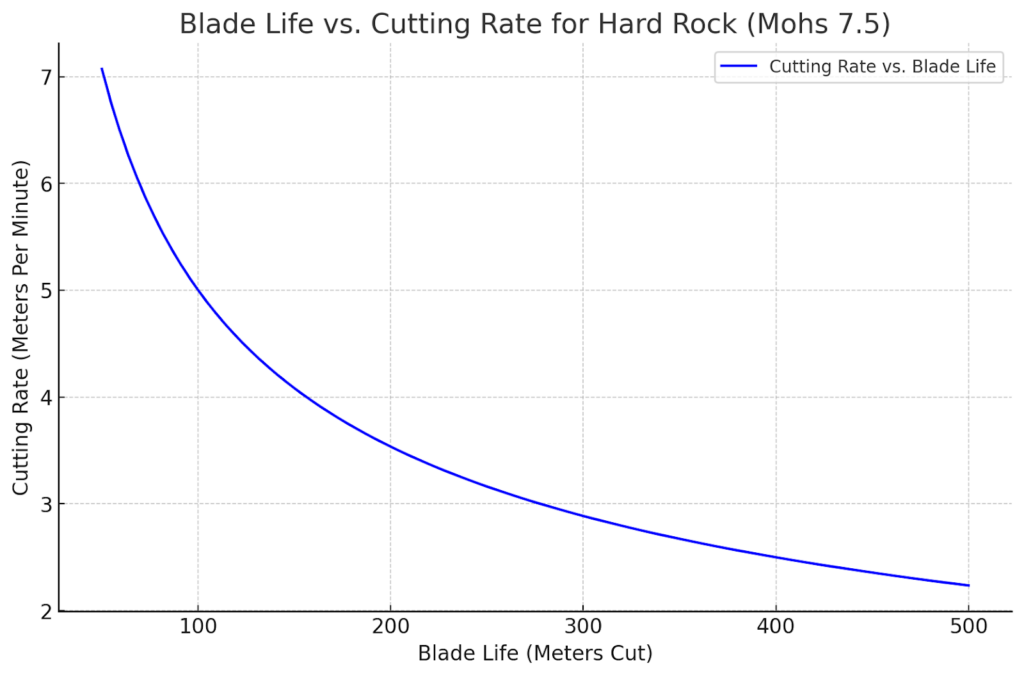
relationship between blade life and cutting rate for cutting hard rock with a Mohs hardness of about 7.5, using a 10-inch diameter blade. As illustrated, as blade life increases (measured in meters cut), the cutting rate (in meters per minute) decreases. This visualization helps underscore the trade-off between maximizing blade longevity and achieving higher cutting speeds, which is crucial for optimizing operational efficiency and cost-effectiveness in such demanding cutting applications.
Optimizing Blade & CBN Performance Process
Achieving optimal performance from a diamond & cbn blade involves identifying the precise combination of diamond properties and bonding material that best suits specific application conditions. The success of this optimization process hinges on several key factors:
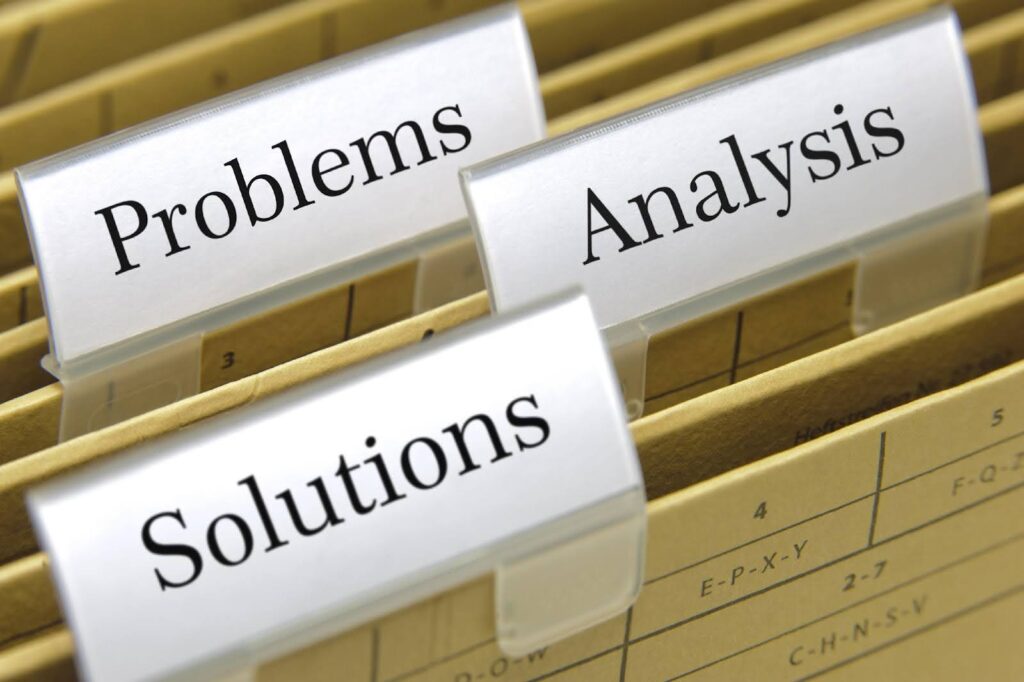
-
Customer Input: The effectiveness of the optimization process largely depends on the customer's knowledge and their ability to accurately convey initial application conditions and blade performance results, as well as any changes in operating conditions. Clear communication from the customer provides the essential data needed to make informed adjustments.
-
Application Engineer Expertise: The application engineer's role is critical in interpreting the data provided by the customer. Their expertise in understanding the nuances of blade performance under various conditions allows them to make calculated adjustments to the blade's specifications. This includes selecting the appropriate type and concentration of diamonds and the bond matrix to maximize the blade's effectiveness.
-
Iterative Testing and Adjustment: Unlike most common applications where initial blade tests may occasionally lead to immediate success, achieving optimal blade performance in specialized or challenging conditions typically requires a series of iterative tests. These tests are collaborative efforts between the customer and the blade manufacturer, involving continuous feedback and modifications. It is not uncommon for several attempts and adjustments to be necessary before arriving at the optimal solution. This iterative process is crucial because it allows for fine-tuning the blade's properties based on real-world performance feedback, ensuring the blade is tailored to the specific needs of the application.
-
Customization for Unique Applications: For applications that are less common or more demanding, the need for a customized approach becomes even more significant. Each unique application may require a specific type of diamond, diamond concentration, and bonding matrix that differs from general or widely-used configurations. The customization process must be dynamic and responsive to the subtle variations in material properties and cutting conditions encountered.
Continuous Improvement: Even after an optimal blade configuration is determined, the pursuit of excellence in blade performance does not stop. Ongoing improvements and refinements are essential as new materials and technologies become available, or as operating conditions evolve. This continuous improvement cycle ensures that blade performance remains at the forefront of industry standards and customer expectations.
Application Guidelines for Optimizing Blade Performance
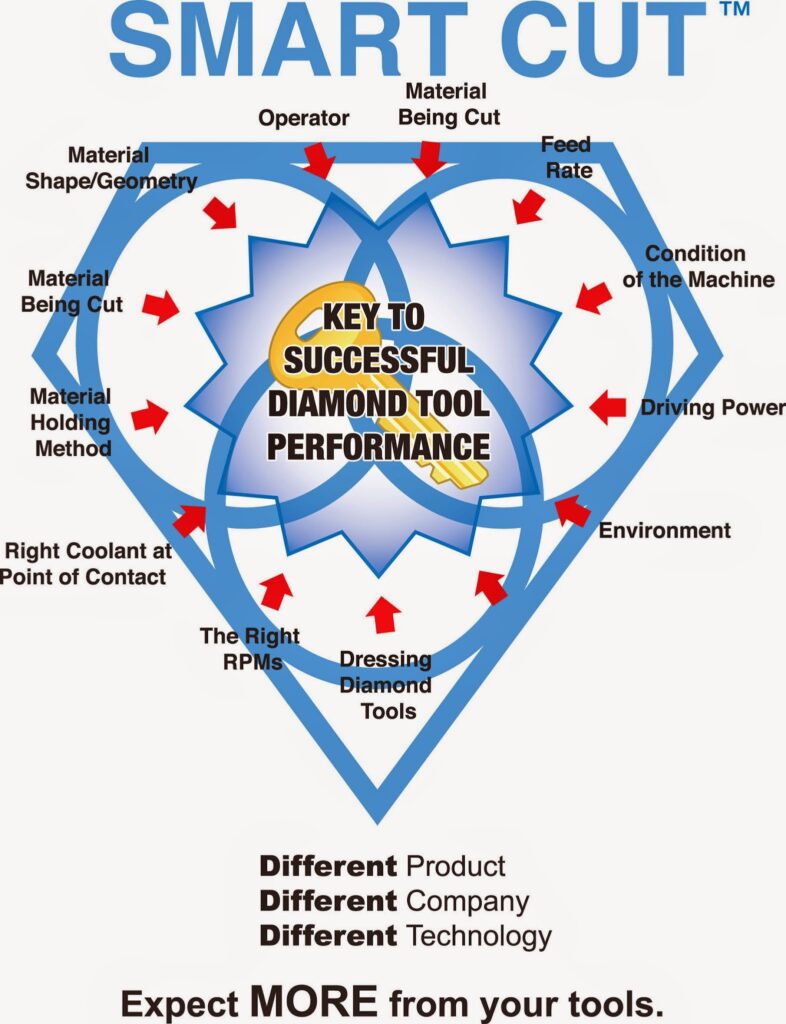
The performance of diamond blades can be modified not only by altering the materials of the blade but also by adjusting the operating conditions. The insights derived from Tables 2 and 3 suggest specific application rules, which are succinctly summarized in Table 4. This table demonstrates the effects of changing either blade materials or operating conditions while keeping other variables constant.
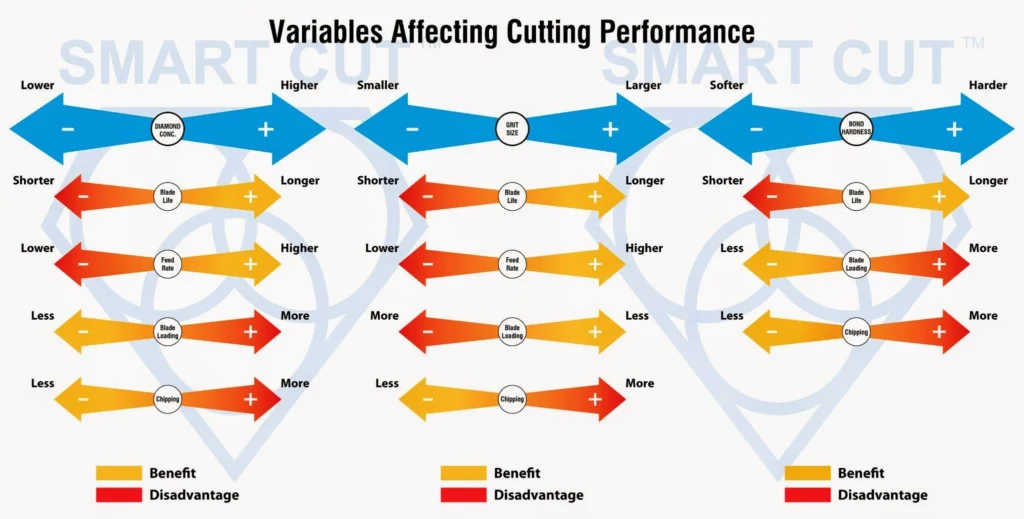
-
Increasing Diamond Concentration: When the concentration of diamonds is increased, the blade tends to act harder. This is because more diamond particles are in contact with the material being cut, which reduces the unit pressure on each diamond particle and decreases the grain penetration depth.
-
Increasing Diamond Mesh Size: Larger diamond mesh sizes result in softer blade action. This occurs because there are fewer diamond particles, each subjected to higher unit pressures, affecting the depth and efficiency of material penetration.
-
Increasing Bond Hardness: Harder bonds make a blade act harder due to improved diamond retention and increased abrasion resistance. This allows the blade to maintain its cutting edge longer, enhancing durability.
-
Increasing Machine Operating Speeds (RPMs): Higher RPMs result in a harder blade action as each diamond particle spends less time in contact with the material per revolution. This reduces grain penetration and the amount of material removed per diamond particle, enhancing the blade's efficiency.
-
Increasing Infeed Rates: Higher infeed rates soften the blade action because the increased pressure per unit area forces each diamond particle to perform more work per revolution. This can lead to premature loss of diamond particles from the blade due to the heightened pressure.
-
Increasing Horsepower: Higher horsepower can cause the blade to wear down more quickly due to the premature pull-out of diamond particles under increased cutting pressures. Conversely, higher horsepower settings can benefit from harder bonds, which retain dull diamond particles more effectively, allowing them to perform better under high stress.
-
Increasing Coolant Volume: More coolant facilitates better removal of cutting swarf, which in turn reduces wear on the bond. This makes the blade act harder by minimizing the mechanical stress on each particle and enhancing overall blade longevity.
-
Increasing Cutting Depth: Deeper cuts make a blade act harder as the increased contact area spreads the pressure more evenly across each particle, reducing the penetration depth per grain and enhancing the blade's effective action.
-
Blade Geometry and Configuration: The shape and thickness of the blade also play critical roles in performance. For example, a thinner blade can reduce the load on the blade during cutting, potentially increasing speed but might be more susceptible to wear and breakage. Conversely, a thicker blade offers greater durability but may reduce cutting speed.
-
Environmental Conditions: Ambient temperature and humidity can affect the cutting performance. For instance, high humidity can impact the effectiveness of the cooling system, potentially causing the blade to overheat and wear faster. Adjusting environmental conditions or compensating for them in blade choice and operation settings is crucial.
-
Material Properties: The specific characteristics of the material being cut, such as hardness, abrasiveness, and brittleness, directly influence blade selection. Different materials require different diamond sizes, concentrations, and bond strengths to optimize cutting efficiency and minimize blade wear.
-
Operator Skill and Technique: The expertise of the operator can significantly affect blade performance. Proper techniques in handling, cutting speed, and feed rates can reduce blade stress and extend its life. Training operators to understand and implement best practices is essential for maximizing blade effectiveness.
Maintenance and Handling: Regular maintenance of both the blade and cutting equipment ensures optimal performance. This includes routine inspections for wear and damage, proper cleaning of blades, and ensuring that equipment is calibrated and functioning correctly. Proper storage and handling of blades are also vital to prevent premature wear or damage.
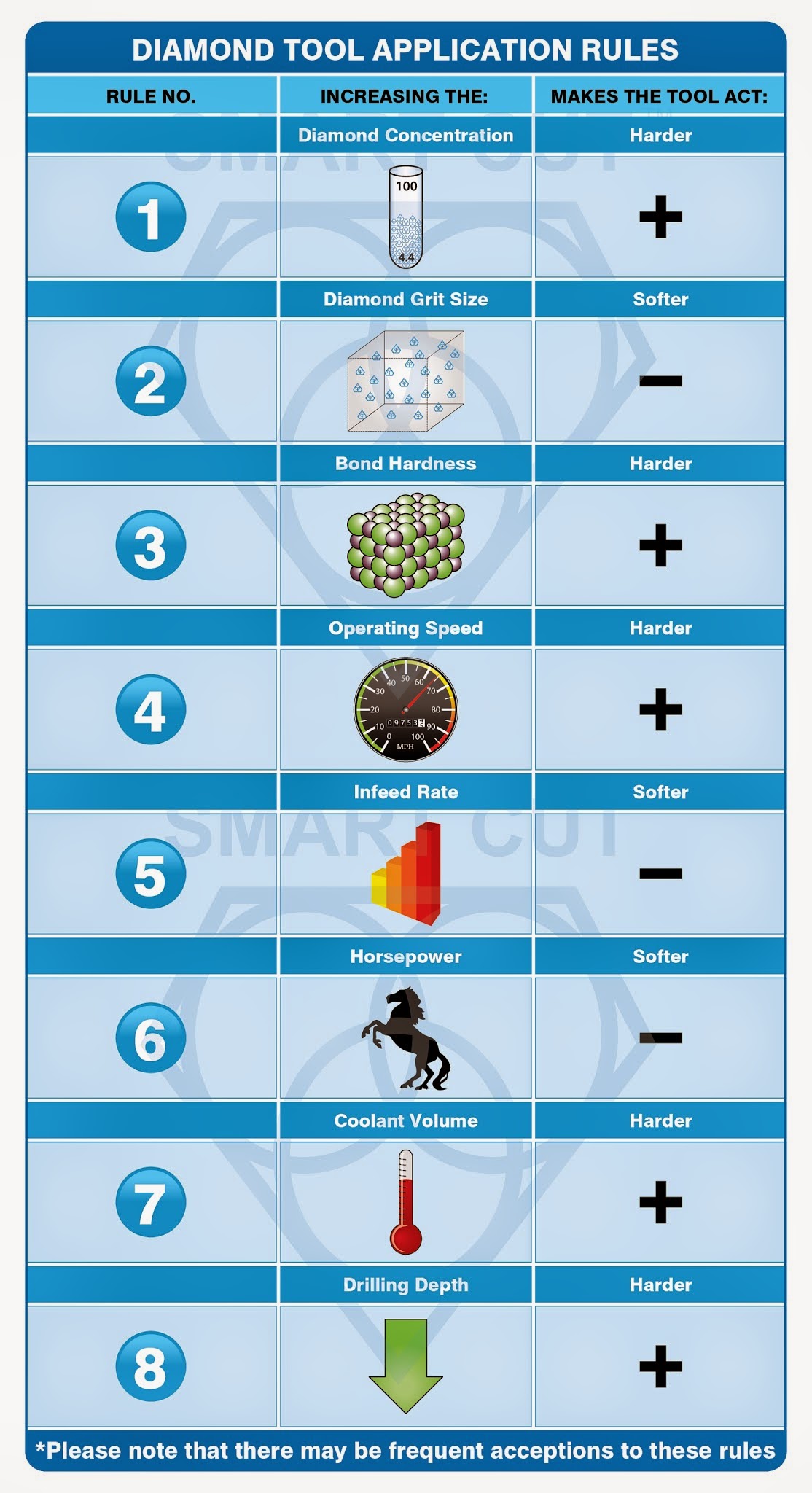
Exploring Exceptions in Blade Performance Beyond Optimal Settings
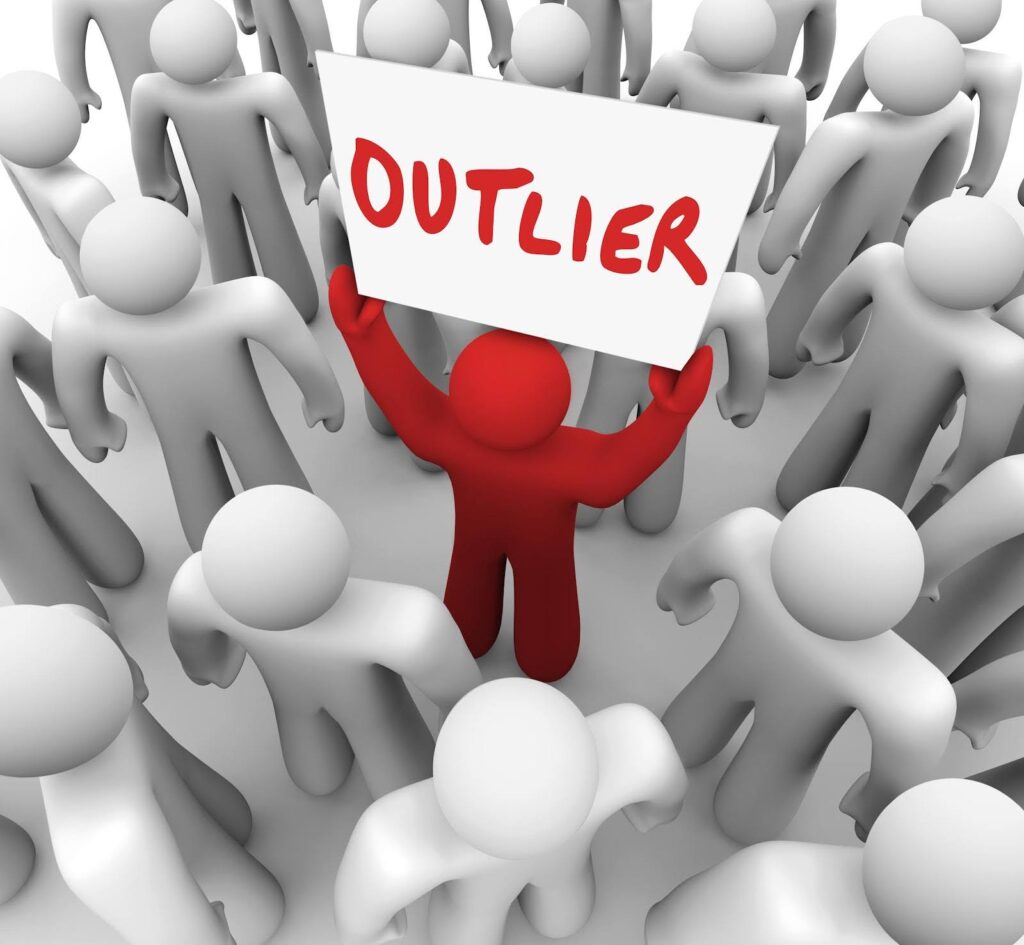
While general guidelines significantly help in optimizing blade performance, there are often exceptions that require a deeper understanding of the dynamics involved. Particularly beyond the optimal point, designated as point O, blade behavior can exhibit counterintuitive results that merit careful examination.
Decrease in Blade Life at Higher Diamond Concentrations
Beyond point O, an increase in diamond concentration doesn't always equate to better performance. Higher diamond concentrations can lead the blade to act harder, which might necessitate additional interventions such as blade dressing to maintain effective cutting action. This is due to the blades becoming too "glazed" or smooth, reducing their ability to cut efficiently without additional surface texturing.
At the same time, maintaining satisfactory cutting rates might require increased infeed pressures. This adjustment can lead to accelerated wear and tear on the blade because the increased pressure can cause premature breakdown of the bonding matrix holding the diamonds.
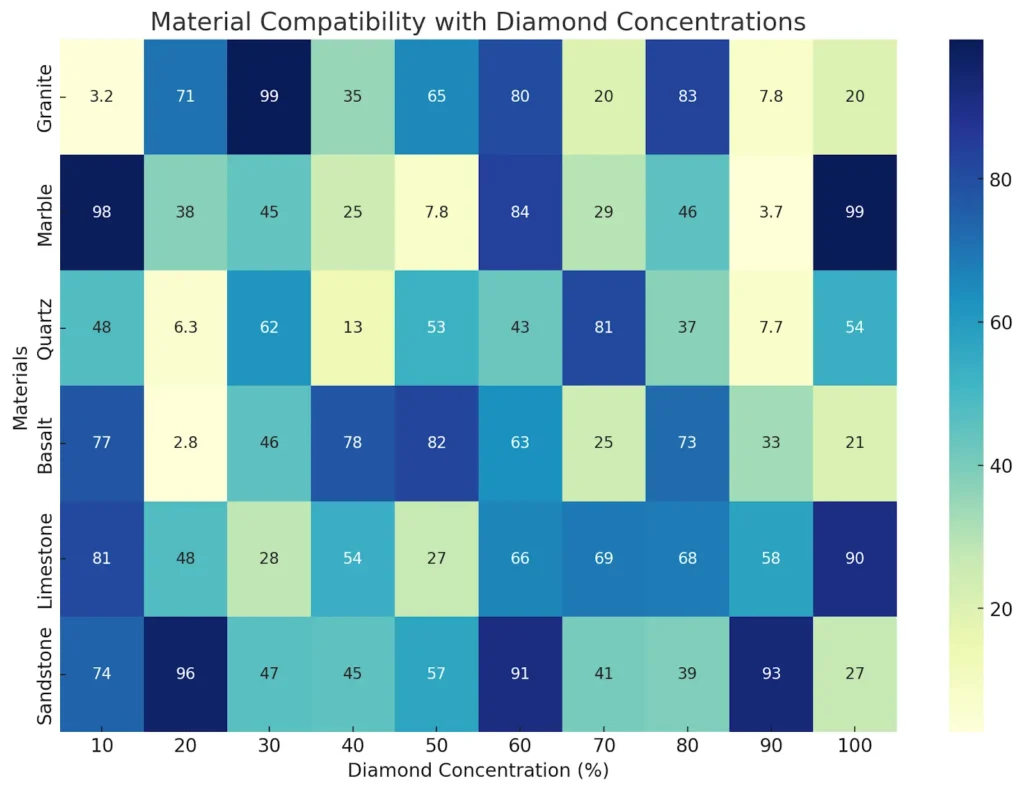
The numbers inside the squares of the heat map represent the efficiency or wear rate of diamond blades when cutting different materials at various diamond concentrations. These values are expressed in arbitrary units for illustration purposes in this example. Here's what they signify:
-
Higher Values: Indicate better efficiency or lower wear rate. This means the blade performs more effectively at these diamond concentrations for the specified material, resulting in less wear and tear on the blade, potentially extending its life and improving its cutting speed.
-
Lower Values: Suggest less efficiency or higher wear rate. Blades with these specifications may not perform as well, requiring more frequent replacements or adjustments due to faster wear
The color gradient also aids in visualization: lighter colors (towards green in this case) suggest higher efficiency or lower wear rates, while darker colors (towards blue) indicate less efficiency. This visual representation allows quick identification of the most effective combinations of material and diamond concentration, optimizing blade selection for specific cutting tasks.
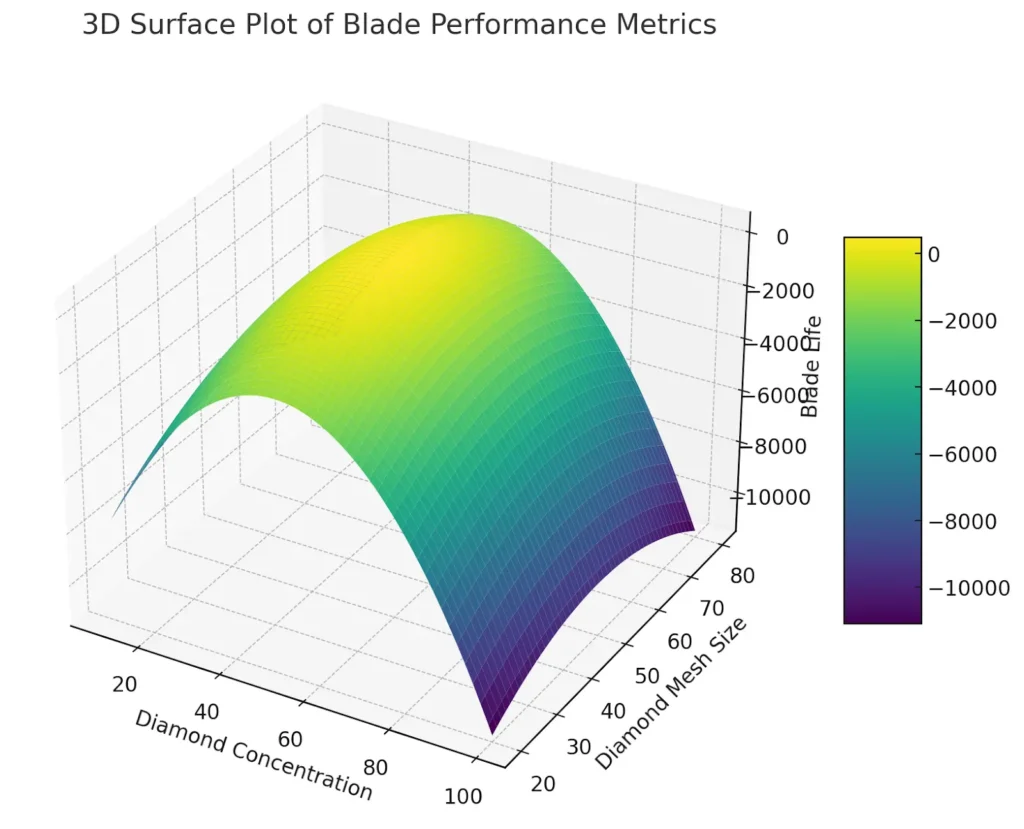
Impact of Increased Diamond Size
Increasing the size of the diamond or cbn particles beyond the optimum point can also lead the blade to behave differently. Coarser diamond particles may not penetrate very hard materials effectively, leading to less efficient cutting action. The relationship between the number of diamond particles and the contact area of a single diamond particle adds another layer of complexity. For example, shifting from a 20/30 mesh diamond to a 30/40 mesh at the same concentration level results in roughly three times as many diamond particles, yet the individual contact area per particle is reduced by about a third. This alteration affects how the diamond interacts with the material being cut, often necessitating harder bonds to maintain blade integrity and extend life.
3D surface plot illustrating how blade life varies with changes in diamond concentration and mesh size. This visualization shows the peak performance at an optimal point, with performance declining as you move away from this optimal region in terms of both concentration and mesh size. The color gradient aids in identifying areas of higher and lower blade life, clearly depicting how different combinations affect performance, and highlighting the decline in blade life beyond the optimal point O.
3D surface plot illustrating how cutting speed varies with changes in diamond concentration and diamond or cbn mesh size. This plot uses a color gradient to indicate areas of higher and lower cutting speeds, with the pattern showing that cutting speed increases as you move away from the optimal point for blade life. The visualization clearly highlights the trade-offs between achieving optimal blade life and maximizing cutting speed, depending on the diamond properties used.
The Role of Bond Hardness
The theory that harder bonds might lead to shorter blade life beyond point O is rooted in the material properties of the bond itself. Harder bonds tend to be more brittle and may start to chip or break away rather than wearing down evenly. This brittleness can unexpectedly reduce the lifespan of the blade, contrary to the typical expectation that harder bonds enhance durability.
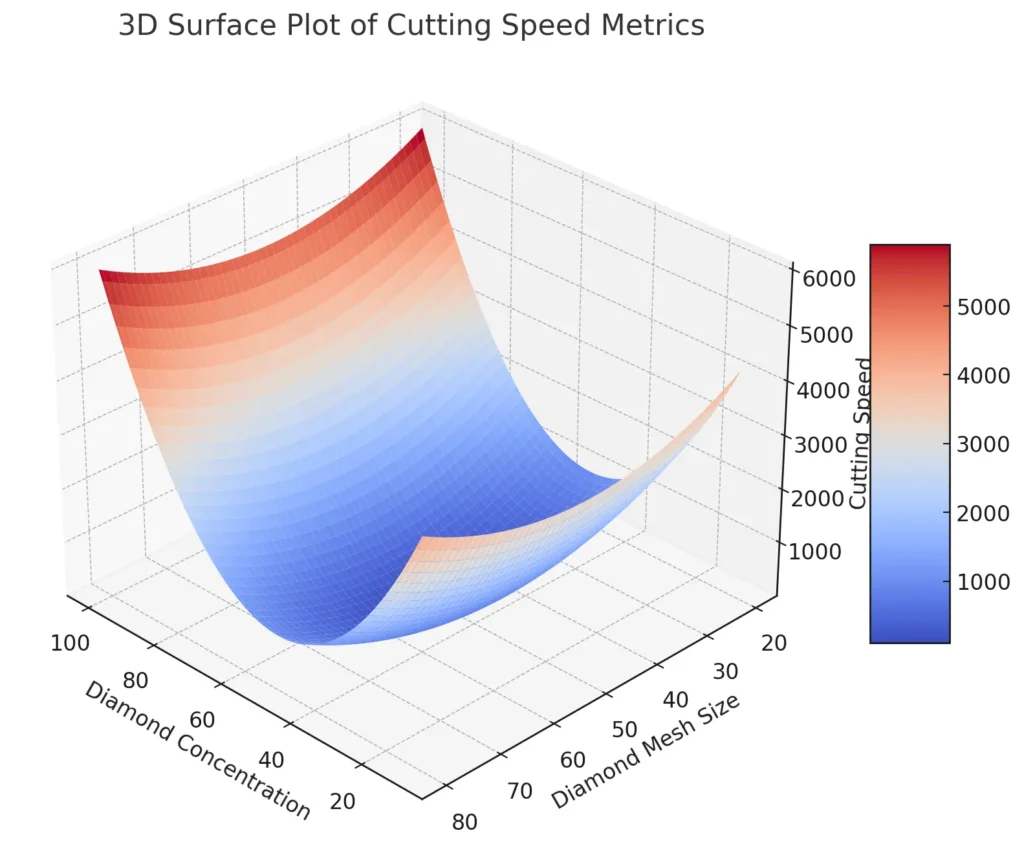
General Exceptions in Blade Behavior
Changes in blade materials or operating conditions that cause a blade to act harder can lead to similar unexpected effects. Contradictions beyond optimum hardness levels can be analyzed using similar theories, which help to explain these anomalies. Understanding these contradictions is essential, even if the exact theoretical accuracy may not always be critical for practical blade selection processes.
Understanding Variations in Diamond Blade Applications
Variation plays a critical role in the complexity of selecting and using diamond blades. Inherent variations across numerous factors can significantly impact blade performance and operational efficiency. While some degree of variation is expected in virtually all aspects of diamond & cbn blade usage—from raw material composition to operating conditions—it’s essential to recognize and manage these differences to optimize blade selection and performance.
Sources of Variation in Diamond Blade Applications
1. Diamond Blade
Diamonds
-
Origin
-
Friability
-
Hardness
-
Internal Structure
-
Processing
-
Sizing
-
Ovalizing
-
Tabling
-
Sorting
-
Grinding
Powdered Metal
-
Particle Sizes
-
Particle Size Distribution
-
Physical Properties
-
Chemical Properties
-
Flow Rate
Processing
-
Weighing
-
Mixing
-
Pressing Pressure
-
Processing Temperatures
-
Finished Dimensions
-
Tensioning
-
Core Quality
-
Hardness
Table 1: Diamond Blade Characteristics
Category |
Details |
---|---|
Diamonds |
Origin, Friability, Hardness, Internal Structure, Processing |
Processing |
Sizing, Ovalizing, Tabling, Sorting, Grinding |
Powdered Metal |
Particle Sizes, Size Distribution, Physical & Chemical Properties, Flow Rate |
Manufacturing Process |
Weighing, Mixing, Pressing Pressure, Processing Temperatures, Finished Dimensions, Tensioning, Core Quality |
1. Machine Operating Condition
Machine
-
Speed
-
Feed
-
Horsepower
-
Type
-
Power Source
-
Condition
-
Coolant Volume
Operator
-
Skill
-
Temperament
-
Objectivity
Purchaser
-
Flexibility
-
Communicativeness
Table 2: Machine Operating Conditions
Category |
Details |
---|---|
Machine |
Speed, Feed, Horsepower, Type, Power Source, Condition |
Coolant |
Volume |
Operator |
Skill, Temperament, Objectivity |
Purchaser |
Flexibility, Communicativeness |
2. Material Being Cut (Raw Materials)
-
Particle Sizes
-
Particle Size Distribution
-
Grog Size & Type
-
Chemical Composition
Processing
-
Weighing
-
Pressing
-
Firing
-
Kiln Location
Final Product
-
Tensile Strength
-
Chemical Composition
-
Refractoriness
-
Abrasiveness
-
Hardness
-
Density
-
Permeability
Table 3: Material Being Cut (Raw Materials)
Category |
Details |
---|---|
Physical Properties |
Particle Sizes, Particle Size Distribution, Grog Size & Type, Tensile Strength, Density, Permeability |
Chemical Properties |
Composition, Refractoriness, Abrasiveness, Hardness |
Processing |
Weighing, Pressing, Firing, Kiln Location |
Final Product Specifications |
Thermal Conductivity, Spalling, Refractoriness, Abrasiveness, Hardness |
These tables categorize the various sources of variation that can influence the performance of diamond & cbn blades, helping to highlight where adjustments or more stringent controls might be necessary to optimize blade selection and use.
Numerous factors affect the variables related to diamond & cbn blade performance, and controlling these variations is crucial for consistent results. Diamond blade manufacturers invest heavily in ensuring the quality of diamonds and powders and in maintaining precise processing conditions to ensure optimal performance of the finished products.
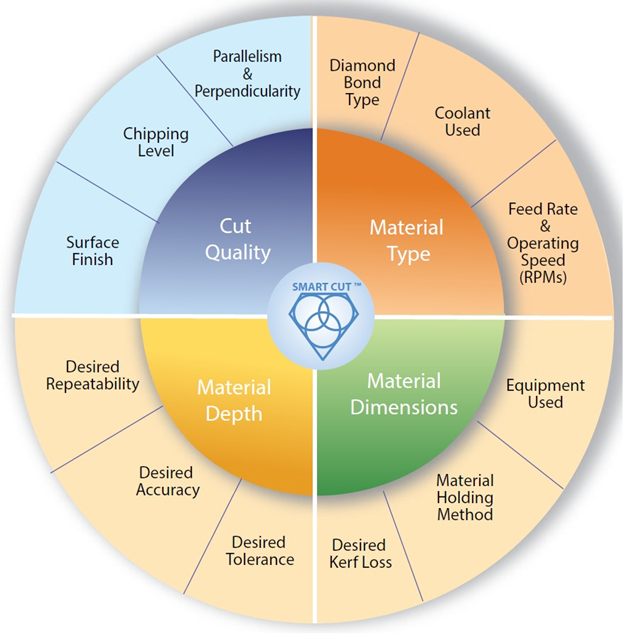
Similarly, suppliers of the materials cut by these blades maintain strict quality control standards. However, the cutability of these materials, particularly their hardness and abrasiveness, is often overlooked during the design and process control phases. For instance, while refractory products are closely monitored for properties such as thermal conductivity and refractoriness, their cutability is not typically controlled, which can impact blade selection and performance.
Operational conditions often have less stringent controls than material or blade properties. Factors such as the operator's skill and the purchaser's communicativeness can introduce significant variability, affecting everything from blade efficiency to lifespan. Despite these challenges, the manufacturing processes of diamond blades are generally under tighter control than the application environments in which the blades are used.
To reduce variations and improve blade performance, it is crucial for both manufacturers and users to focus on enhanced material design to include cutability as a key criterion, develop comprehensive training programs for operators, and establish robust feedback mechanisms between all parties involved. This comprehensive approach can help ensure the reliability and effectiveness of diamond cutting tools in diverse operational settings.
Typically the diamond blade manufacturing processes are in far better control than other factors of the application environment in which those diamond blades perform.
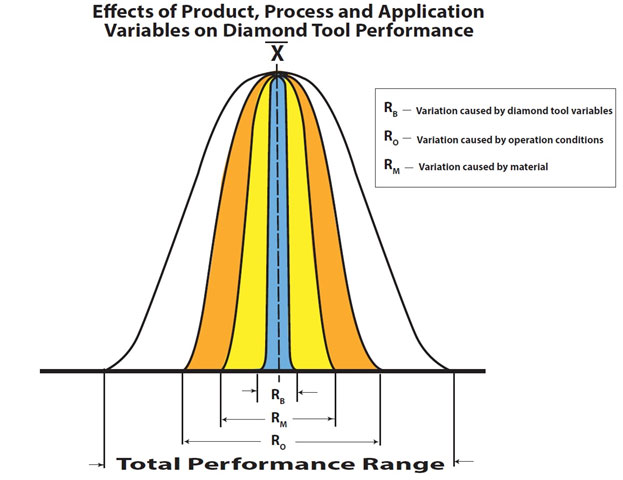
Effects of Product, Process, and Application Variables on Diamond Blade Performance
This normal variation curve represents a hypothetical population of blade performance results for a specific application. The curve depicted by range Rb illustrates the variation caused by diamond product variables, while the curve represented by range RM reflects the variation due to the material being cut. Range Ro captures the variation in performance resulting from differences in operating conditions. While this does not absolve the blade manufacturer of all responsibility for application variations, it reflects the common experience of those in the industry.
One of the more challenging tasks for an application engineer is addressing application problems caused by these variations. For instance, in a scenario where cutting a particular material, an average blade life of 500 cuts per blade is normal.
Figure 1 shows another frequency distribution curve, highlighting the average and range of performance for this hypothetical application. A blade represented by point A, which performed 350 cuts, might lead to dissatisfaction and a request for credit from the user. However, it's important for the user to understand that this blade life, while on the lower end, still falls within the normal distribution curve and is influenced by all the aforementioned variables. Thus, a credit might not be justified despite the user's feelings.
This type of issue is common, and it falls upon the diamond blade manufacturer's application engineers to explain to disappointed users that a 350 cut performance, although not ideal, is within the expected range. In these discussions, it's rare to hear about performances like those represented by point B, which are more satisfactory.
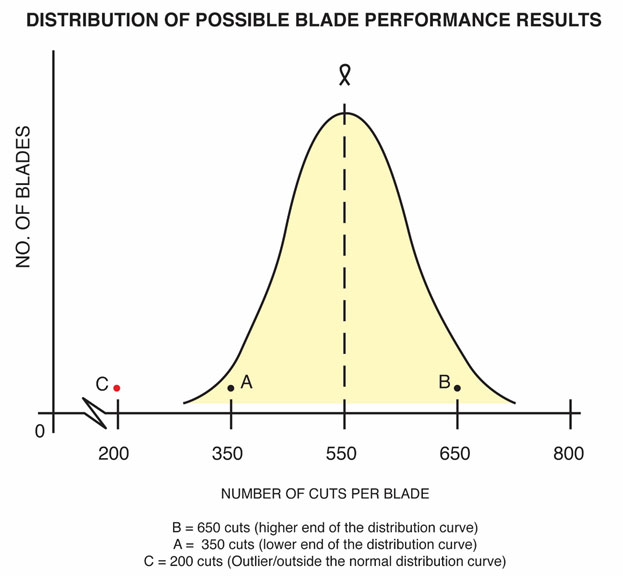
Conversely, a blade that only manages 200 cuts, as shown at point C, would fall outside the normal distribution curve. This unusually poor performance could be due to a number of factors and, in statistical terms, is attributed to an assignable cause. Determining and addressing the cause behind such performance is a complex challenge. While it's logical for customers to suspect a defect in the blade, the issue might not always be straightforward.

Here is a bell curve chart illustrating the distribution of possible blade performance results. This chart shows a normal distribution of the number of cuts per blade, with points A, B, and C marked to indicate specific performance instances:
-
Point A (350 cuts): Represents blade performance at the lower end of the distribution curve.
-
Point B (650 cuts): Represents a higher-end performance within the normal range.
-
Point C (200 cuts): An outlier, indicating performance that falls outside the normal distribution curve.
This visual representation helps in understanding the spread of performance results and how specific data points relate to the general population of blade performance
Here is the box plot that illustrates the distribution of blade performance based on the number of cuts per blade. This visualization provides a clear overview of the data, highlighting:
- The outlier at 200 cuts, indicating a performance that is significantly lower than typical.
- The lower quartile at 350 cuts, showing where the bottom 25% of the data falls.
- The median at 550 cuts, indicating the middle point of the data.
- The upper quartile at 650 cuts, representing the top 25% of performances.
- The maximum performance observed at 800 cuts, which does not have any outliers beyond this point.
This graph can help users understand the typical performance range and variability they may expect from diamond blades under different conditions and usage scenarios.
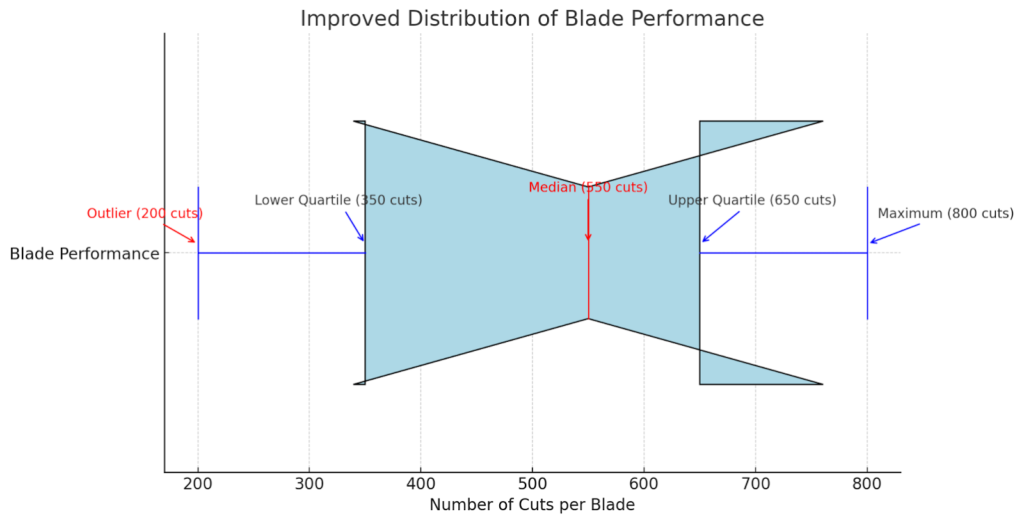
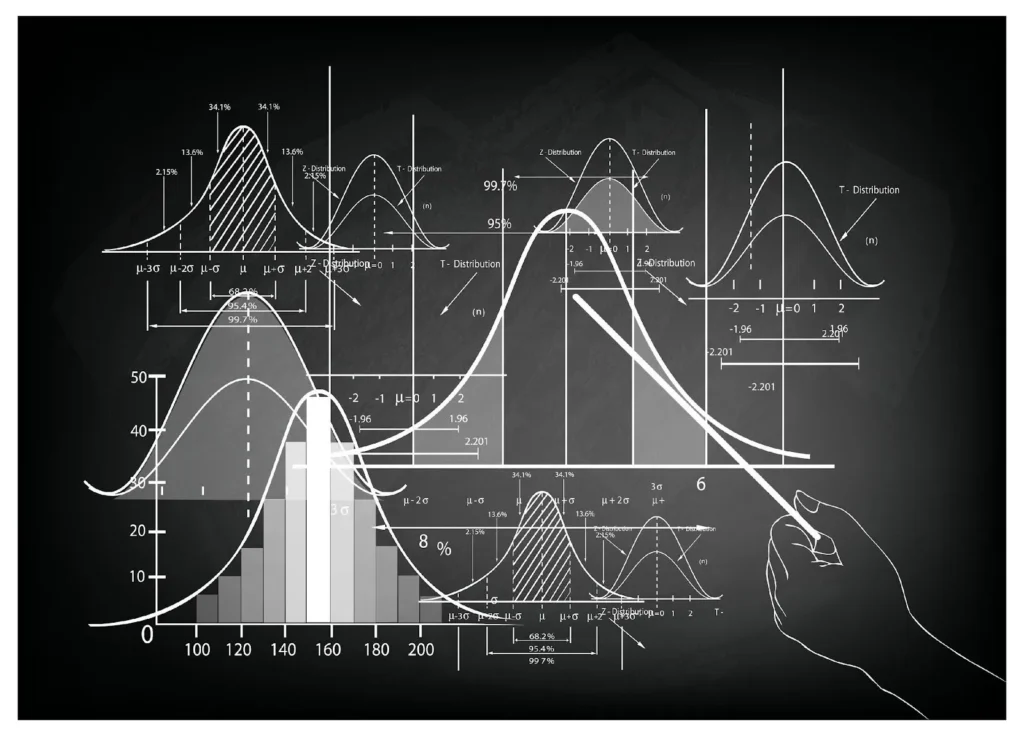
Analyzing Variation in Performance – Cooperating Between User & Blade Manufacturer
In situations where blade performance is suboptimal, it is crucial for both the customer (end user) and the blade manufacturer (supplier) to approach the issue with an open mind to effectively resolve the problem. Collaborative efforts between the blade manufacturer and the user can lead to significant benefits, rather than viewing the relationship as adversarial.
A lack of cooperation from the end user can be costly, as vital information may be lost if they do not communicate complete blade application details to the manufacturer. On the other hand, the manufacturer can aid the end user by offering crucial recommendations for adjusting operating conditions or usage parameters. In some cases, they may even provide a different blade specification that better aligns with the customer's application needs.
It’s important for customers to understand that while manufacturers acknowledge the possibility of diamond & cbn blade variability as a cause of poor performance, such instances are very rare. Diamond blade manufacturers typically maintain extensive records documenting each stage of the manufacturing and quality control processes.
Each batch and individual blade is often assigned a serial number, allowing every step in the manufacturing process to be reviewed and traced back to each blade. This detailed information is crucial when investigating the validity of claims regarding poor blade performance.
When experiencing poor performance or variability, customers often assume that the diamond blade is at fault. However, they rarely consider variations in the materials being cut or changes in operating conditions as potential underlying factors. This oversight can lead to misdiagnosed issues and unresolved problems, highlighting the importance of considering all variables in the cutting environment.
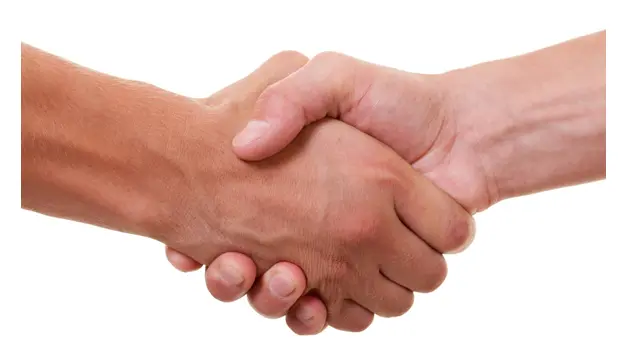

Designing Diamond & CBN Blade Testing Methodology
The process of identifying an optimally performing diamond blade is rarely straightforward. Initial specifications provided by manufacturers often do not achieve the peak performance customers expect. Even when the first tested blade specification seems effective, subsequent blades typically fail to maintain this level of optimized performance. This indicates that the results from a single blade test are generally insufficient for making definitive conclusions.
To truly determine the most effective blade specifications, it is crucial for customers to conduct extensive testing with multiple blades of the same specification. This approach allows them to establish a robust performance baseline, which includes both an average and a range of possible outcomes. With this data in hand, adjustments to the blade specifications can be precisely tailored to achieve optimal results.
Customers are encouraged to test as many blade specifications and variations as possible. This extensive sampling is crucial for establishing a clear performance benchmark, setting a standard that all future blades are measured against. This rigorous testing regime enables customers to pinpoint which blade specifications consistently yield the best results.
Laboratory testing offers a more controlled environment where statistical methods are critical. Techniques such as randomized trials or the use of multiple blade designs help isolate the impact of specific variables. These methods effectively minimize the influence of confounding variables, focusing exclusively on those aspects under evaluation.
When conducting field tests, controlling external variables is vital to minimize variations that could skew the performance data. It’s important to standardize operating conditions and material specifications as much as possible. This ensures that any performance differences are attributed to the blade's characteristics, rather than external influences.
When establishing a robust testing regimen for diamond & cbn blades, several considerations can enhance the process and outcomes. An incremental testing approach, where one variable is altered at a time, allows for a clear identification of how each change impacts performance. This method ensures each variable's effect is understood in isolation before combining them, helping to refine blade specifications more precisely.
With advancements in computational power, it’s now possible to simulate diamond blade performances under various conditions before physical tests are conducted. This can save substantial time and resources by identifying promising blade specifications early in the testing process. Incorporating feedback from operators who use the blades daily provides invaluable insights that laboratory tests might overlook. This regular feedback on blade performance can reveal practical challenges and preferences not apparent in controlled environments.
As materials science progresses, testing on new materials such composite materials or reinforced polymers or new generation nano materials requires adjustments in methodologies to account for their unique properties. Additionally, with increasing awareness of environmental impacts, evaluating the sustainability of diamond blades is crucial. This includes assessing the lifecycle impact and exploring recyclable or less environmentally damaging materials and processes.
Finally, expanding performance metrics to include economic and operational efficiency metrics offers a more holistic view of blade performance. Metrics like cost-per-cut, downtime due to blade changes, and operational delays provide a broader perspective on what makes a blade specification successful in practical terms.
To effectively control and minimize variation in the laboratory testing environment for diamond blades, it's essential to implement standardized and rigorous methods:
-
Using automatic cutting equipment is highly recommended whenever possible. This equipment should maintain constant surface speed, infeed pressure, and power consumption to ensure uniformity in test conditions. If manual operation is necessary, it is crucial to set specific amperage levels and monitor the operator's cutting technique closely. This ensures that physical movements remain as consistent as possible, reducing variability introduced by human error.
-
The consistency of the material being cut is also vital. To control for variability in material properties, it is advisable to purchase a large lot of the material, representing the total range of variation in cutting properties. This approach minimizes the effects of piece-to-piece variation. To further control for material hardness variation, it is recommended to select different places on the material and perform cuts at each location.
-
When evaluating variables such as diamond mesh size, bond hardness, concentration, etc., in the same test, it is beneficial to adopt a random selection strategy for the blade specification combinations. Implementing a random sequence where only a few cuts are made with each combination before selecting another random sequence helps minimize variation caused by external factors. These factors include operator fatigue, weather conditions, variations in power sources, and changes in machine condition.
Find Out More: How To Properly Test, Compare, & Evaluate Diamond & CBN Blades
Predicting Diamond & CBN Blade Performance
Predicting the performance of diamond & cbn blades is a common request from customers to manufacturers. They often ask questions like, “How many cuts will this blade make?” Unfortunately, providing a definitive answer is challenging due to the myriad of variables that influence blade performance.
The complexity arises because diamond & cbn blade performance can vary significantly even under seemingly similar conditions. For instance, one customer might achieve a certain blade life or experience minimal chipping on a specific application, while another might see a markedly different performance on the same material and application. This variability can occur even if the operating conditions and materials used appear to be the same.
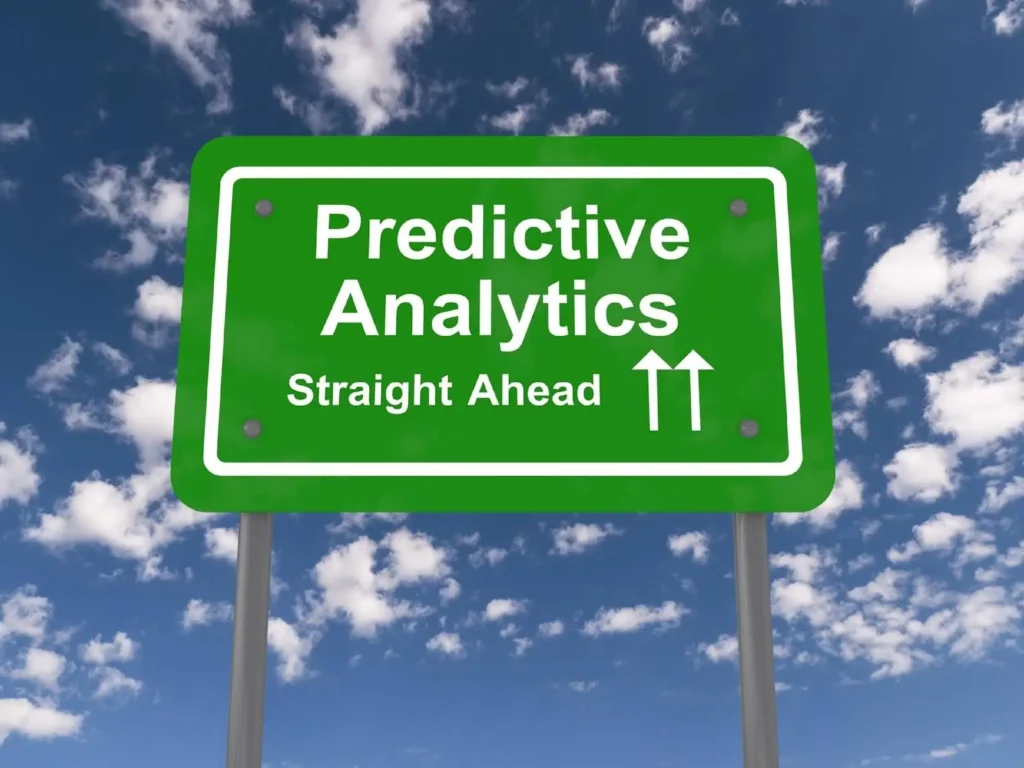
Accurately predicting blade performance is complicated because any estimation given by the manufacturer might be perceived by the customer as a performance guarantee. This perception can set unrealistic expectations and hinder objective testing, which is crucial for both the customer's and manufacturer's benefit.
- Detailed Usage Parameters: Manufacturers can improve prediction accuracy by gathering comprehensive data on how the blade is used, including machine type, cutting speed, feed rate, and the cooling method employed. This information helps in tailoring predictions more closely to specific user conditions.
- Historical Data Analysis: Analyzing historical performance data from a wide range of users and conditions can help manufacturers identify patterns and predict outcomes more reliably. Advanced data analytics and machine learning models can be used to analyze this data, providing insights that help refine performance estimates.
- Standardized Testing Protocols: Developing and using standardized testing protocols that simulate a range of realistic conditions can also aid in making more accurate predictions. These tests can help establish baseline performance metrics that can be adjusted based on specific customer usage scenarios.
- Continuous Feedback Loop: Establishing a continuous feedback loop with customers to gather real-time data on blade performance can also enhance predictive accuracy. This ongoing dialogue allows manufacturers to update their predictions based on the latest data, improving reliability over time.
- Customized Predictive Tools: Creating customized predictive tools or software that customers can use to input their specific usage parameters to get performance estimates might also be beneficial. These tools can use data from both lab tests and real-world user feedback to provide more personalized predictions.
Find Out More >>>
Top 5 Diamond & CBN Cutting Blade Performance Metrics
Diamond & CBN Cutting Blade Performance Metrics that you Should Know
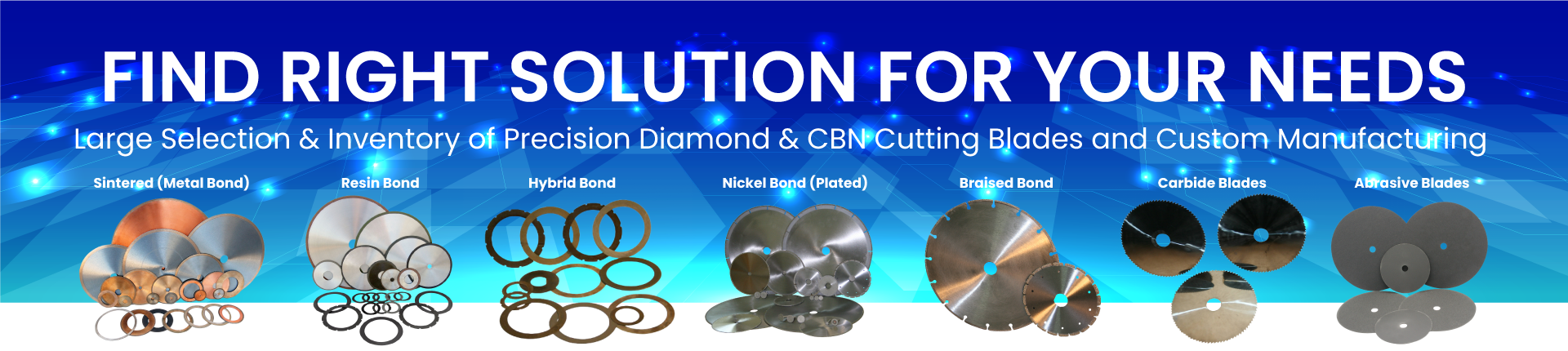
ARE YOU USING RIGHT DIAMOND & CBN BLADES
FOR YOUR APPLICATION?
LET US
HELP YOU
HAVING ISSUES WITH
YOUR CURRENT DIAMOND & CBN BLADES?
Knowledge Center
Select right Diamond Blade for your application
How to Properly Use Precision Diamond & CBN Blades
Precision & Ultra Thin Diamond Blade Guide
Evaluating & Comparing Diamond Blades
Top 5 Diamond & CBN Cutting Blade Performance Metrics
Diamond & CBN Cutting Blade Performance Metrics that you Should Know
Total Cost of Ownership & Why its Important
Understanding Tradeoffs- Searching for Perfect Diamond & CBN Blade
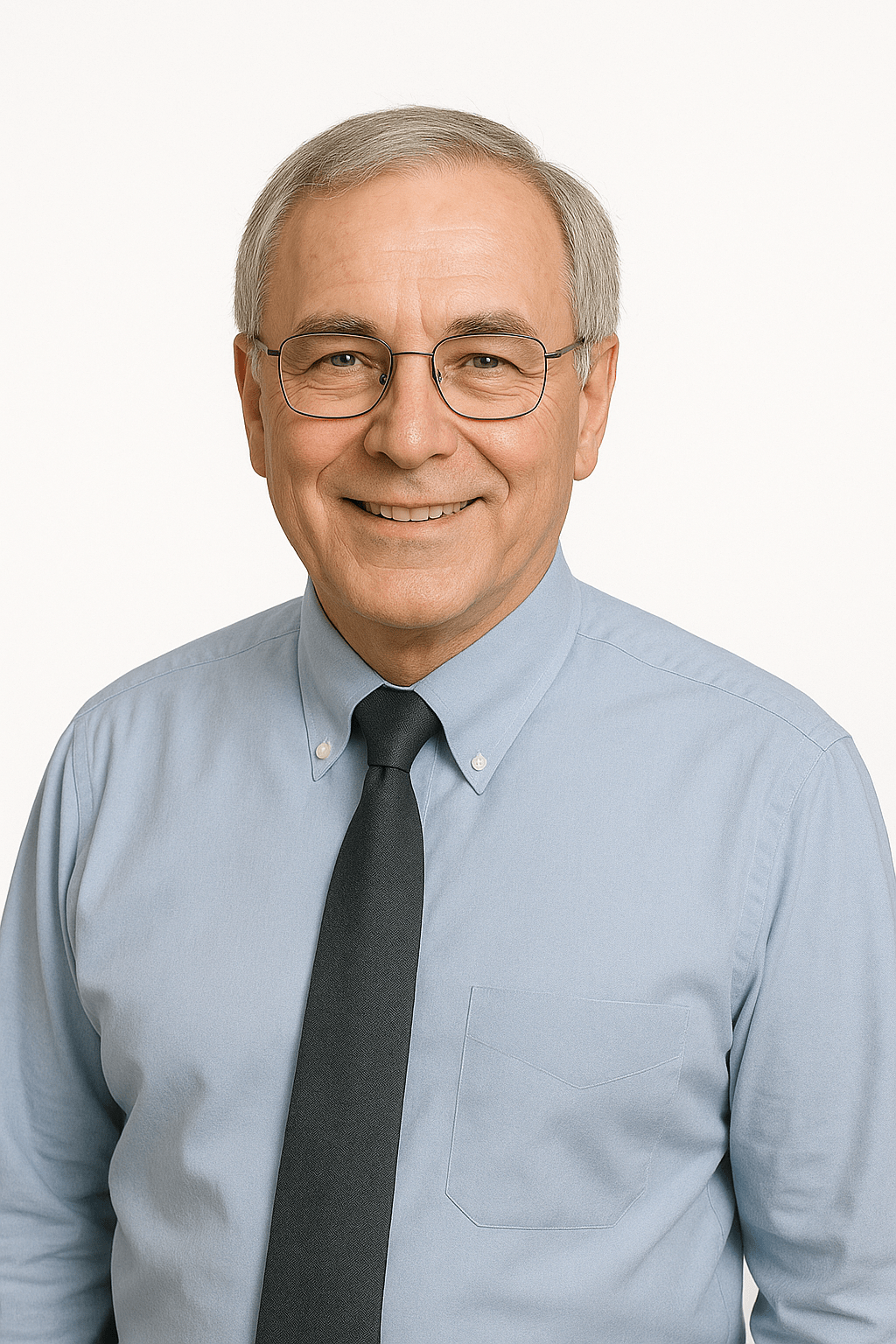
Alexander Schneider is a senior applications engineer and leading authority in the industrial diamond tooling industry, with over 35 years of hands-on experience in the development, application, and optimization of ultra-thin and high-precision diamond blades, diamond core drills, and diamond and CBN grinding wheels. His work spans a wide range of advanced materials including ceramics, glass, composites, semiconductors, and high-performance metals.
Throughout his career, he has collaborated with leading R&D institutions, national laboratories, and high-tech manufacturing companies across Europe, North America, and Asia, providing technical expertise and tailored solutions for demanding cutting and surface preparation applications.
Mr. Schneider has played a pivotal role in advancing precision cutting, sectioning, dicing, and grinding technologies used in research, production, and failure analysis. He is widely respected for his ability to optimize tool design and cutting parameters to meet exacting industry standards—balancing factors such as cut quality, blade life, material integrity, and process consistency.
As an author, Mr. Schneider is known for delivering practical, application-focused insights that translate complex technical challenges into clear, actionable strategies. His articles and technical guides serve as trusted resources for engineers, researchers, and manufacturers seeking to improve precision, reduce process variability, and enhance tool performance in critical applications.
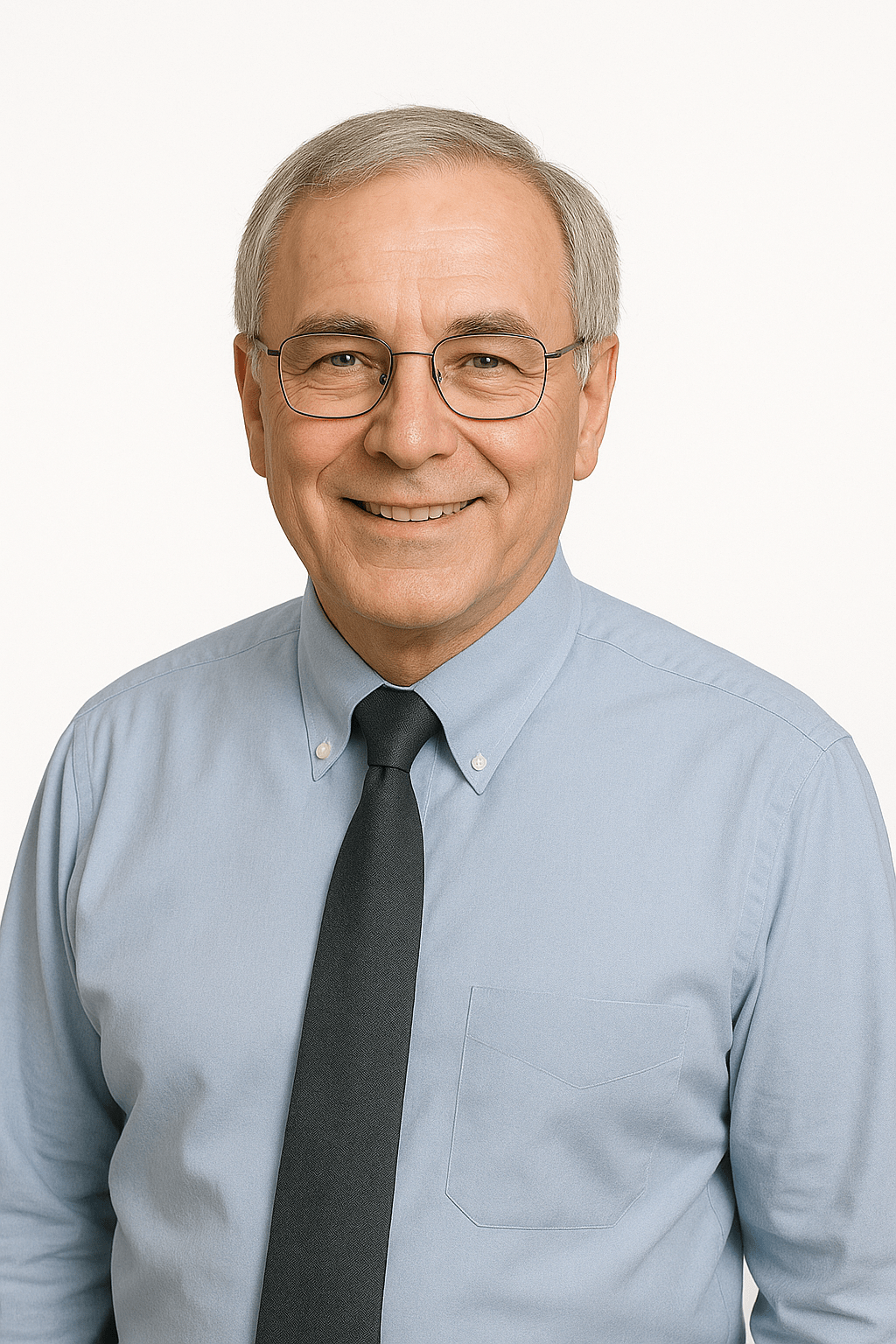
Alexander Schneider is a senior applications engineer and leading authority in the industrial diamond tooling industry, with over 35 years of hands-on experience in the development, application, and optimization of ultra-thin and high-precision diamond blades, diamond core drills, and diamond and CBN grinding wheels. His work spans a wide range of advanced materials including ceramics, glass, composites, semiconductors, and high-performance metals.
Throughout his career, he has collaborated with leading R&D institutions, national laboratories, and high-tech manufacturing companies across Europe, North America, and Asia, providing technical expertise and tailored solutions for demanding cutting and surface preparation applications.
Mr. Schneider has played a pivotal role in advancing precision cutting, sectioning, dicing, and grinding technologies used in research, production, and failure analysis. He is widely respected for his ability to optimize tool design and cutting parameters to meet exacting industry standards—balancing factors such as cut quality, blade life, material integrity, and process consistency.
As an author, Mr. Schneider is known for delivering practical, application-focused insights that translate complex technical challenges into clear, actionable strategies. His articles and technical guides serve as trusted resources for engineers, researchers, and manufacturers seeking to improve precision, reduce process variability, and enhance tool performance in critical applications.