Choosing the right diamond drill or tool can significantly impact efficiency, cost, and quality. However, this is not a simple and clear-cut process. Selecting the optimal drill or tool involves navigating a complex landscape of trade-offs, where factors such as drilling speed, surface finish, drill longevity, and cost must be carefully balanced. This article explores the critical performance trade-offs associated with diamond drills & tools, providing insights to help you make informed decisions that align with your specific drilling requirements and operational goals. Understanding these trade-offs is essential for optimizing your processes, enhancing productivity, and achieving superior results in your drilling applications.
Share this Article with Friend or Colleague
Table Showing Interrelationship & Tradeoffs of Different Diamond Drill Variables
Variables Compared |
Importance |
Interrelationships and Trade-offs |
---|---|---|
Drilling Speed vs. Surface Finish |
Drilling speed affects how quickly a drill penetrates material but can impact the quality of the finish. |
Higher speeds can decrease surface quality due to increased heat and vibration, requiring a balance to achieve optimal results. |
Quality / Longevity vs. Price |
Higher quality and longer-lasting drills cost more but provide better long-term value. |
Investing in high-quality drills reduces long-term costs by decreasing replacement frequency and improving performance. |
Drilling Speed vs. Drill Life |
Higher drilling speeds can reduce drill life due to increased wear and tear. |
A balance must be found between speed and drill durability to optimize both productivity and cost-effectiveness. |
Surface Finish vs. Drill Price |
The price of the drill can influence the achievable surface finish. |
Higher-priced drills often yield a finer finish due to better materials and technology, but at an increased cost. |
Drilling Speed vs. Drill Price |
Faster drilling speeds may require more expensive drills capable of handling higher stresses. |
Drills designed for high speeds typically cost more due to advanced materials and engineering, impacting the overall budget. |
Surface Finish vs. Drill Life |
The pursuit of an excellent surface finish can affect how long a drill lasts. |
Drills that offer finer finishes may wear out quicker, especially if not matched properly with the material and drilling parameters. |
Quality & Drill Life vs. Price |
The better the quality and the longer the life expectancy of a drill, the higher the price. |
Investing in higher-quality drills that last longer can be cost-effective over time, despite a higher initial price. |
Feed Rate vs. Drill Life |
The speed at which material is fed to the drill impacts how quickly the drill wears out. |
Higher feed rates generally increase drill wear, reducing lifespan, while lower rates extend life but may reduce efficiency. |
Feed Rate vs. Drilling Speed |
Feed rate and drilling speed together determine the drilling efficiency and drill stress. |
Optimal synchronization of feed rate and drilling speed is essential to maximize efficiency and minimize drill wear. |
Drilling Speed vs. Surface Finish
Drilling speed plays a crucial role in how quickly a diamond drill or tool can penetrate a material. However, higher speeds often result in increased heat and vibration, which can adversely affect the surface finish. Achieving the right balance between drilling speed and surface finish requires careful consideration of the material properties and the specific requirements of the application.
Drilling speed, measured in revolutions per minute (RPM), is a critical factor that influences both the efficiency of material penetration and the quality of the surface finish in diamond drilling operations. A higher drilling speed enhances productivity by reducing the time required to penetrate the material. However, it also leads to increased frictional heat at the contact surface, potentially causing thermal damage to both the drill bit and the workpiece. This can result in microcracks, deformation, or changes in material properties. Additionally, higher speeds increase the likelihood of vibrations, which can induce irregularities in the hole walls and lead to a degraded surface finish. Rapid speeds can also accelerate the wear rate of the diamond drill, reducing its lifespan and effectiveness over time.
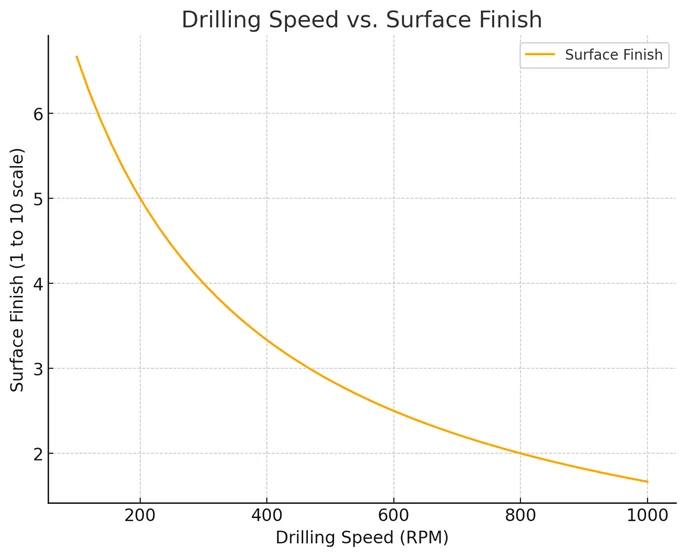
Conversely, lower drilling speeds are often usually recommended for when a high-quality surface finish and chipping level is important. These slower speeds minimize the heat produced during drilling, thereby preventing damage from overheating. They also improve drilling accuracy, as reduced vibration allows the drill to maintain better contact with the material, ensuring more higher level of precision, accuracy and repeatability and a smoother finish. Furthermore, less wear on the diamond drill means a longer operational lifespan and reduced diamond drill & tool costs.
Selecting the right drilling speed must also consider the material being drilled and diameter of the diamond drill or tool used. Harder materials such as ceramics, hardened steels, and certain gemstones often require slower speeds to minimize the risk of chipping or cracking. Softer materials might allow for higher speeds without as significant a risk to surface quality, though heat generation must still be managed.
The required drilling speed often depends on the specific demands of the application. Industries like semiconductor and medical devices, where high level of accuracy and repeatability is necessary, may necessitate lower speeds to ensure the integrity and functionality of the drilled parts. In contrast, applications where speed is more critical than finish, such as in some construction or stone operations, might favor higher speeds to maximize throughput.
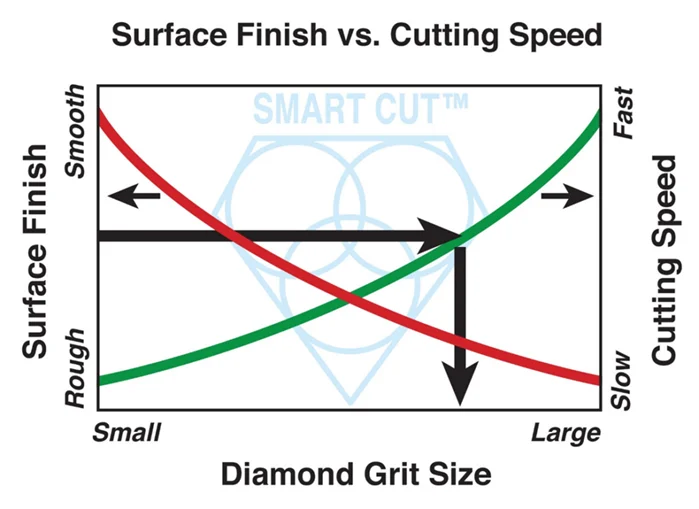
Achieving the optimal balance requires conducting sample tests with different speeds to observe the impact on both drilling efficiency and surface finish.
Consulting with tooling experts and engineers to select the best speed settings based on the material and application requirements is also essential. Regularly checking the condition of both the drill bit and the workpiece to adjust speeds proactively before quality issues arise is crucial for maintaining optimal performance and outcomes.
Quality / Longevity vs. Price
Investing in high-quality diamond drills involves higher upfront costs but can offer substantial long-term benefits. These drills are produced using higher quality materials and cutting-edge technologies that not only enhance their performance but also increase their durability. Such diamond drills and tools are wear out less frequently, thereby reducing the frequency of replacements and minimizing downtime, which is crucial in maintaining continuous use.
While the initial purchase price of high-quality diamond drills & tools may be higher, the overall cost of ownership tends to be lower. With increased lifespan, these diamond drills & tools don't need to be replaced as frequently, which means fewer interruptions in production and less money spent on new equipment over time. The improved longevity of the drills & tools translates to a lower cost per use, making them a better value and cost-effective option in the long run and best return on investment.
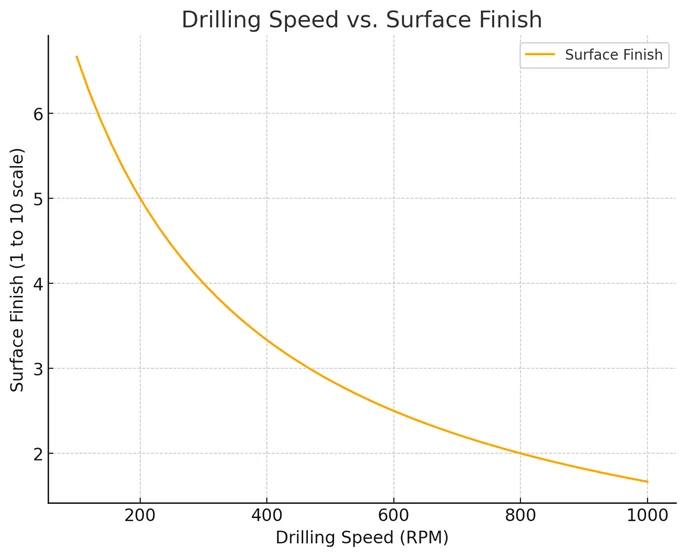
The operational efficiency and consistency of using high quality diamond drills and tools is also improved. These drills maintain optimal speeds and accuracy, allowing most jobs to be completed faster and with higher level of quality and consistency. This boost in productivity is especially beneficial in across all industries and specially in applications where they are for production of high value parts such as in precision optics, semiconductor, aerospace, and related applications.
Additionally, higher-quality diamond drills and contribute to safer working environments. They are less likely to break or malfunction, which reduces the risk of accidents. Their design and construction also minimizes the generation of debris and waste materials. Higher quality diamond drills can greatly improve a company's reputation by ensuring that products are consistently made with high accuracy and reliability.
Drilling Speed vs. Drill Life
The relationship between drilling speed and drill life is crucial for efficient drilling operations. Operating diamond drills & tools at high speeds increases friction and heat, which accelerates wear and tear on the diamond section of the drill or tool, thereby shortening their lifespan. This higher rate of wear leads to more frequent diamond drill and tool changes, increasing operational costs and downtime. High-speed drilling may also compromise the integrity of the material by introducing thermal stress and potential structural weaknesses.
Conversely, lower drilling speeds generate less friction and heat, leading to less wear on the diamond drill and extending its life. This reduction in wear decreases the frequency of replacement needs and lowers long-term costs. However, the drawback is that lower speeds can reduce overall productivity, which might not be suitable in high-volume or time-sensitive production environments.
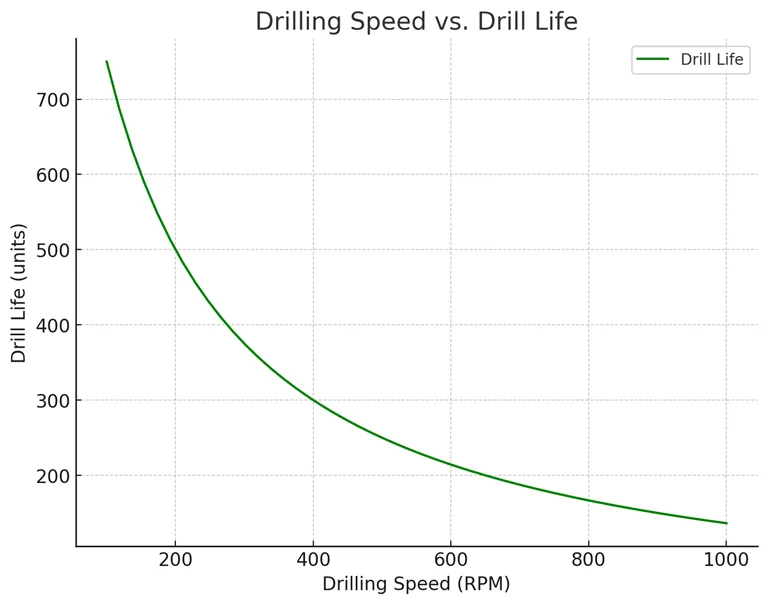
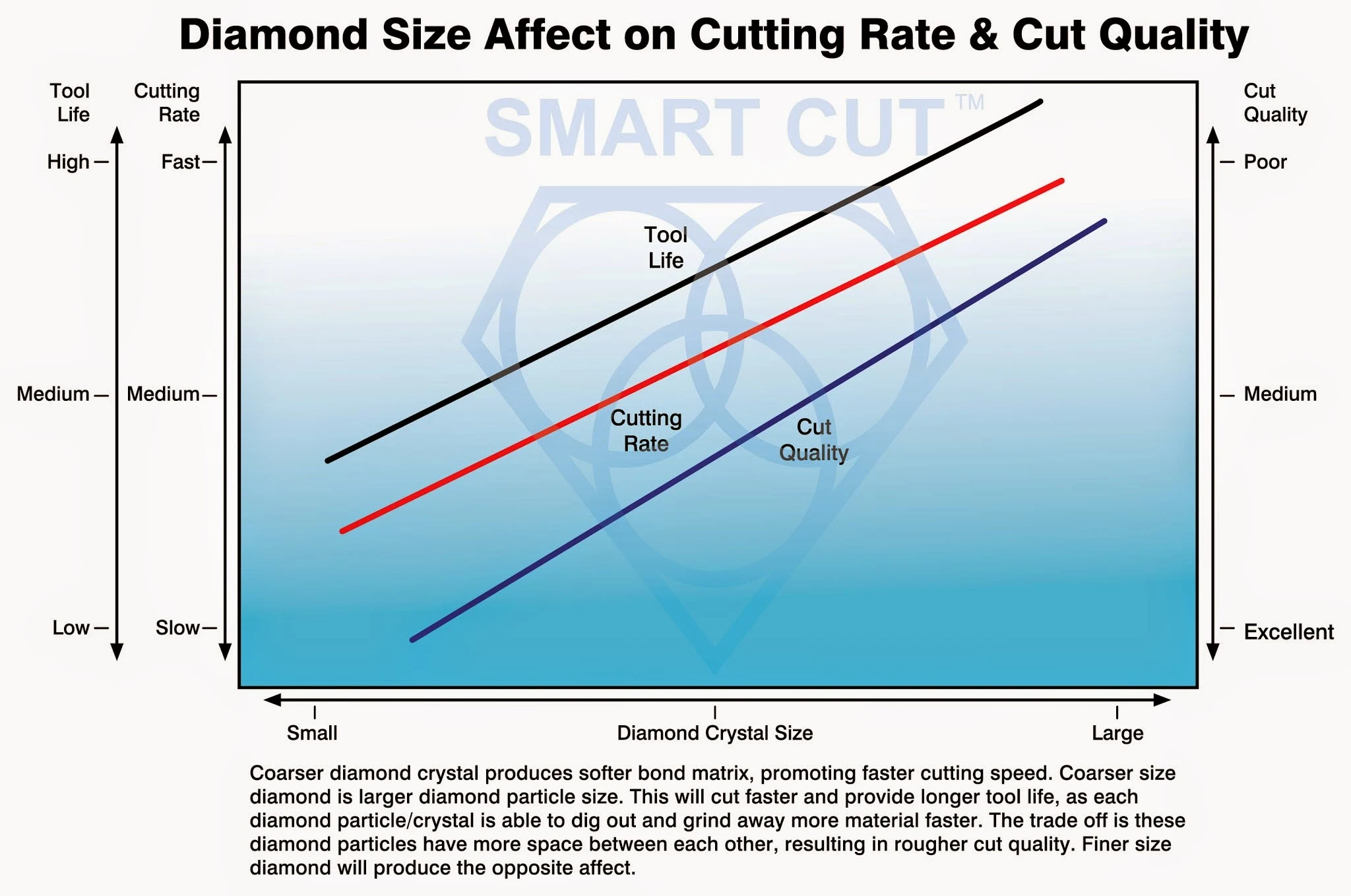
Finding the optimal drilling speed that balances efficiency and longevity is a challenge. This optimal speed varies depending on several factors, including the hardness of the material being drilled, the type of drilling equipment and diamond drill or tool being used, and the client requirements. Operators can improve diamond drill or tool life while maintaining satisfactory productivity by selecting the right diamond drills or tools for the application, using appropriate coolants to manage heat, performing regular maintenance such as dressing to ensure peak efficiency, and conducting tests to determine the most effective speeds for specific materials and drills.
Surface Finish vs. Drill Price
The relationship between the surface finish that a diamond drill can achieve and its price is a significant consideration for businesses deciding on the right tools for their operations. Diamond drills, known for their hardness and precision, vary in price based on the quality of the materials and technology used in their construction.
Higher-priced diamond drills are usually made with higher quality industrial diamonds and advanced bonding technologies that enhance their cutting capabilities. This allows them to produce exceptionally smooth and precise finishes on a variety of materials, from tough metals to delicate ceramics and composites. The superior finish is crucial in high-stakes applications such as in aerospace, medical devices, and precision engineering, where even minor surface irregularities can lead to failures or underperformance of the final product.
These higher quality diamond core drills, while more expensive, provide significant value in reducing the need for secondary finishing processes. By delivering a higher-quality initial finish, they help save on additional grinding or polishing steps, which can be costly and time-consuming. This makes the investment in higher cost diamond drill worthwhile for industries where precision and performance is important
On the other hand, for applications where the demands for surface finish are less critical, more economically priced drills may be adequate. These drills are capable of achieving acceptable finishes for general construction, basic fabrication, or when the final product will undergo additional finishing regardless of the initial drilling quality. In such cases, opting for a less expensive drill can be a cost-effective decision, as the slight compromise in finish quality does not impede the functionality of the end product.
Ultimately, the choice between high-end and more economical diamond drills should be guided by a thorough assessment of the specific application needs and the expected return on investment.
Drilling Speed vs. Drill Price
Drills designed for higher speeds are usually more expensive due to the advanced materials and engineering required to handle the increased stresses. When selecting drills for high-speed operations, it's essential to weigh the benefits of increased productivity against the higher costs. For some applications, the investment in high-speed capable drills can significantly enhance operational efficiency and justify the additional expense.
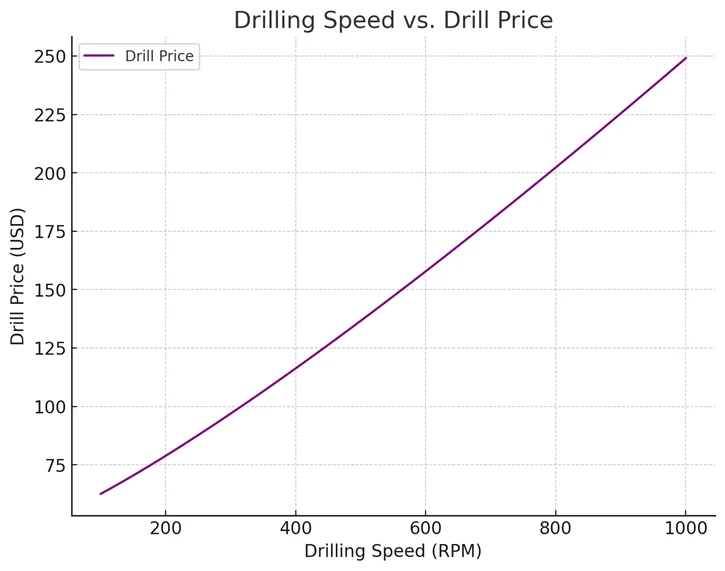
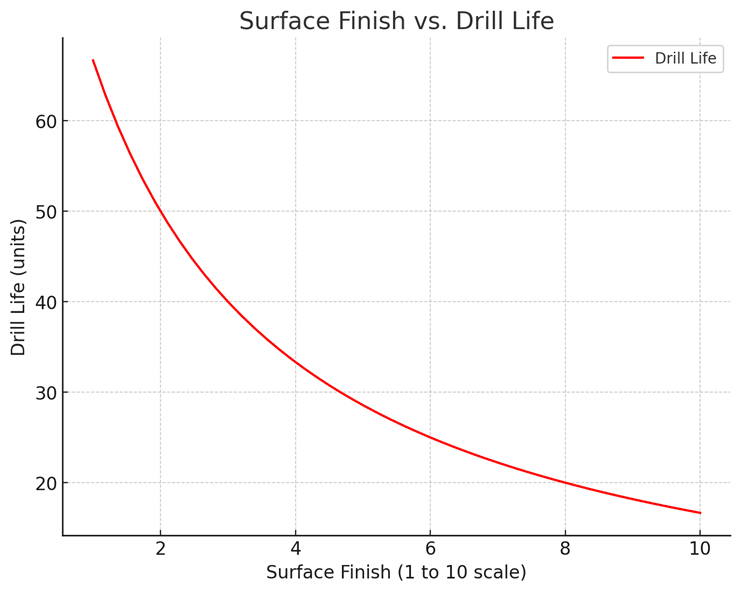
Surface Finish vs. Drill Life
Achieving an excellent surface finish often necessitates the use of drills that wear out more quickly. This trade-off requires careful matching of drill specifications with material properties and the desired outcome. For applications where surface finish is important, it may be necessary to accept shorter drill life and plan for more frequent replacements. Conversely, if drill life is a priority, compromising slightly on surface finish might be acceptable.
Quality & Drill Life vs. Price
The correlation between drill quality, life expectancy, and price is straightforward. Higher-quality drills that offer extended life come at a premium cost. This trade-off is crucial for applications where drill longevity and consistent performance are vital. The higher initial investment in quality drills can lead to lower overall costs by reducing downtime and the frequency of replacements, making it a cost-effective choice in the long run.
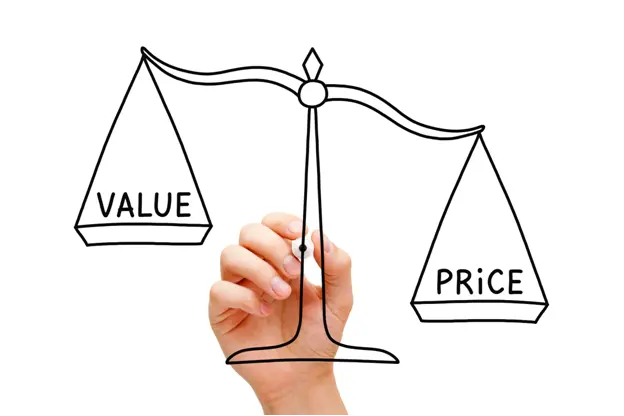
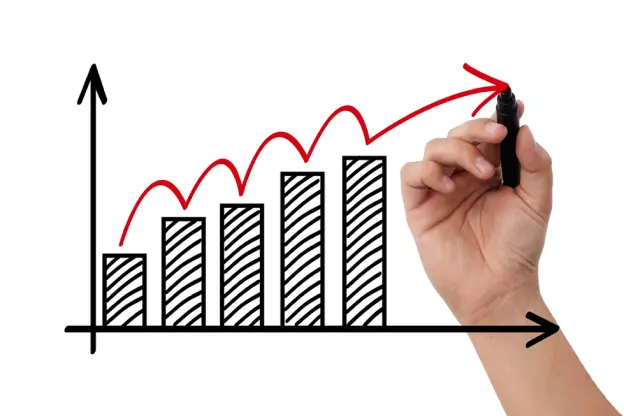
Feed Rate vs. Drill Life
The feed rate, or the speed at which material is introduced to the drill, directly impacts drill wear. Higher feed rates can accelerate wear, reducing drill life, while lower feed rates can extend drill life but may slow down the process. Balancing feed rate with diamond drill life is essential to ensure efficient and cost-effective operations. Optimizing feed rates can help maximize drill lifespan without significantly compromising productivity.
When materials are introduced to diamond core drills at higher feed rates, the drills experience increased stress and greater impact forces. This heightened load accelerates wear and can lead to faster degradation of the diamond edges. Additionally, elevated feed rates tend to generate excessive heat, which can result in material chipping or breakage, especially if the drill or the setup is not optimized for such speeds.
On the other hand, operating at lower feed rates places less stress on the diamond core drill, potentially extending its operational life. This more controlled drilling approach reduces heat generation and lessens the risk of drill overload, thereby preserving the integrity of the diamond cutting edges. However, overly slow feed rates may lead to underutilization of the drill's capabilities, decreasing productivity and increasing the time and cost per operation.
Finding the optimal balance in feed rate is crucial for maximizing drill life while maintaining efficiency. It requires a thoughtful evaluation of the drill's performance limits, the material's properties, and the specific requirements of the drilling task. For example, harder materials may necessitate slower feed rates to minimize wear on the diamond segments, whereas softer materials can often be drilled at faster rates without significantly impacting drill longevity.
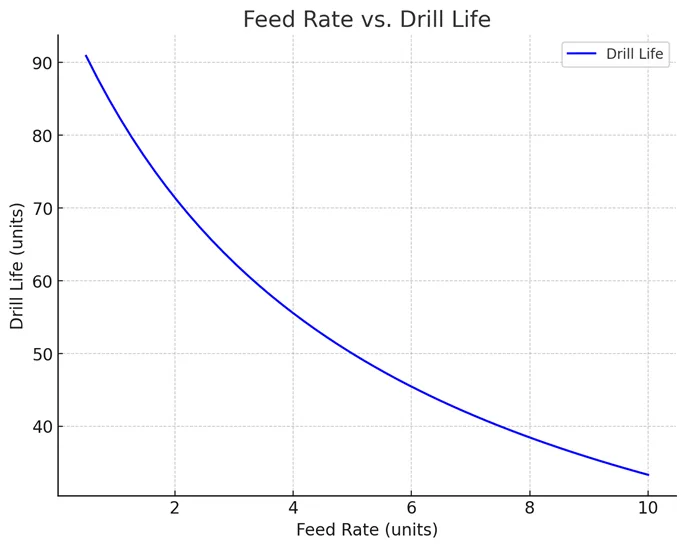
Feed Rate vs. Drilling Speed
Feed rate, or the speed at which the drill advances into the material, directly influences the volume of material removed per pass and the stress placed on the drill. Higher feed rates can accelerate material removal but also increase mechanical stress on the diamond segments, leading to faster wear and potential degradation. Additionally, high feed rates can cause excessive heat buildup and mechanical stress, resulting in chipping or cracking, particularly in brittle materials like ceramics or glass.
Drilling speed, which refers to the rotational speed of the core drill, plays a significant role in how effectively the tool penetrates the material. Higher drilling speeds can enhance productivity by reducing the time required for each hole, but they also introduce heat and thermal stress, which can shorten drill life due to wear on the diamond segments.
Striking the right balance between these two factors is critical. If the feed rate is too high in relation to the drilling speed, the drill may experience excessive stress, leading to premature wear or even failure. Conversely, if the drilling speed is too high for the chosen feed rate, the tool may fail to remove material efficiently, potentially glazing over or overheating, compromising both the cut quality and drill lifespan.
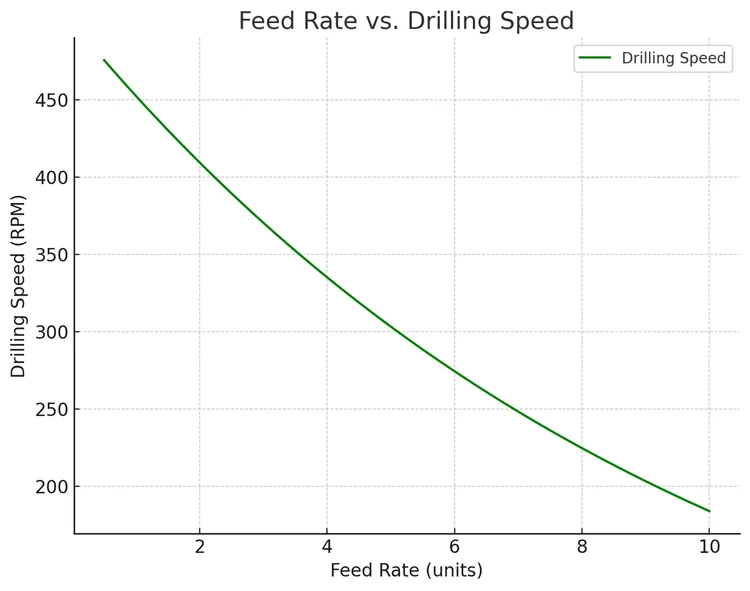
Synchronizing feed rate and drilling speed is crucial for achieving high drilling efficiency and increasing diamond drill life.
Achieving the optimal balance depends on several factors, including the material hardness, the type of diamond core drill in use, and the desired outcome of the operation. Softer materials may allow for higher feed rates and speeds without significantly impacting tool life, while harder materials often require more moderate settings to protect the drill and maintain a smooth finish.
Proper coordination of feed rate and drilling speed improves overall productivity by ensuring efficient material removal with minimal passes and adjustments. This not only saves time but also extends drill life by minimizing stress, reducing the frequency of replacements, and lowering operational costs. Additionally, optimal settings result in better surface finish, reducing the need for secondary finishing processes.
Operators should start with manufacturer guidelines but also perform their own tests to determine the best parameters for specific applications. Regular monitoring of the drilling process—especially for signs of wear, such as chipping, noise changes, or increased vibrations—can indicate when adjustments are necessary.
While finding the right settings may require some initial effort, the long-term benefits include reduced tool costs, lower downtime, and overall cost savings. This careful management enhances both drilling efficiency and the quality of results, leading to significant improvements in productivity and operational cost-effectiveness.
ARE YOU USING RIGHT TOOLS
FOR YOUR APPLICATION?
LET US
HELP YOU
HAVING ISSUES WITH
YOUR CURRENT TOOLS?
ARE YOU USING RIGHT DIAMOND CORE DRILLS & TOOLS
FOR YOUR APPLICATION?
LET US
HELP YOU
HAVING ISSUES WITH
YOUR CURRENT DIAMOND CORE DRILLS & TOOLS?
Knowledge Center
Select right Diamond Drill for your application
How to Properly Use Precision Diamond Drills
Diamond Drills Guide
Diamond Tools Guide – Selecting Right Drills & Tools for your application
Optimizing your Diamond Drilling Operation
Micro Drilling Guide
Selecting Right Drilling Equipment for your Application. What you features & functionality you should look for?
Diamond Core Drill & Drill Trouble Shooting Guide
Understanding & Calculating Return on Investment for Diamond Core Drills & Other Tools
Understanding Tradeoffs – Searching for Perfect Diamond Drill & Tool
Why Use Diamond Drills?
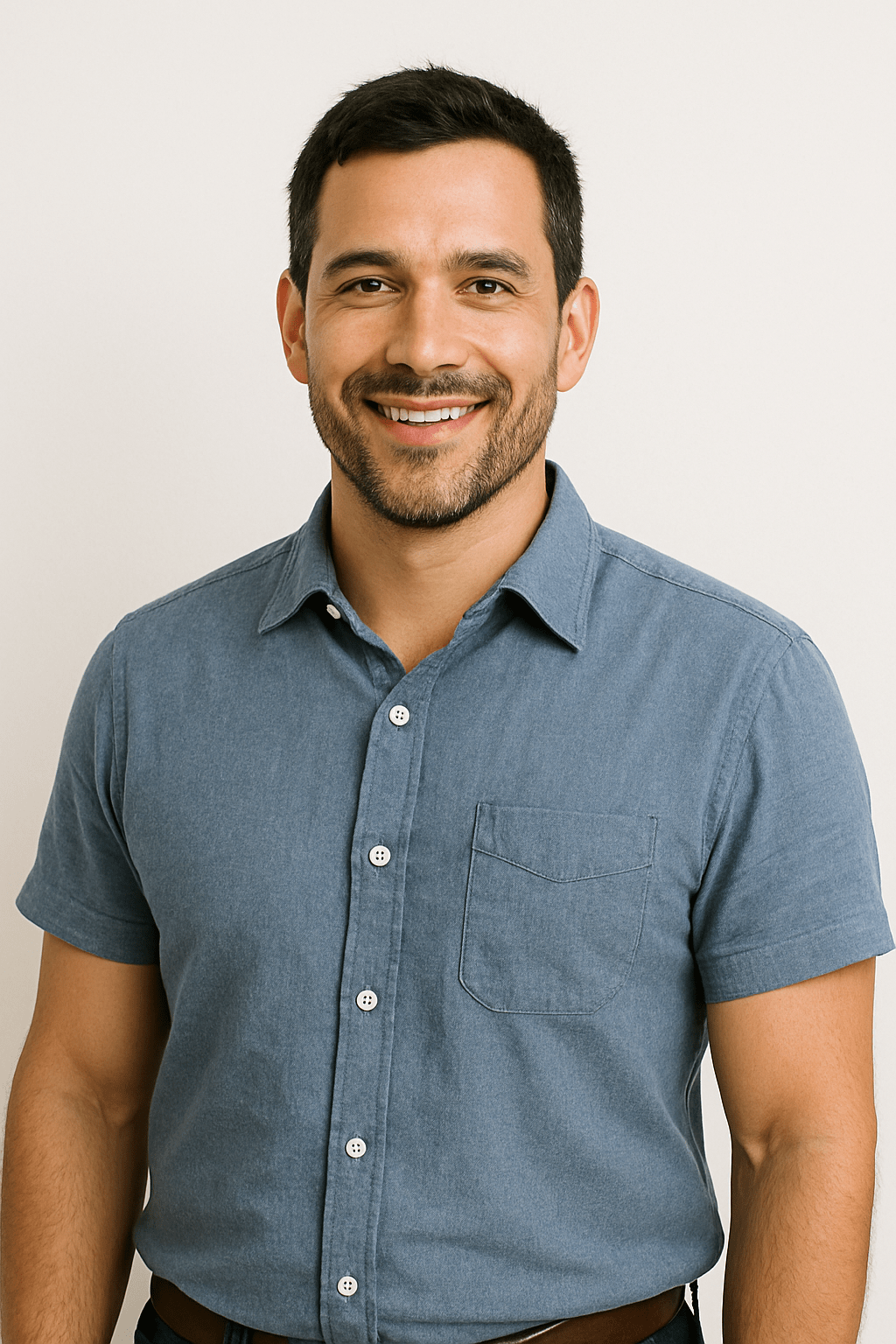
Carlos Sanchez is a senior technical specialist and field applications trainer with more than 17 years of experience in the use and optimization of industrial diamond tools, including ultra-thin diamond blades, core drills, and CBN grinding wheels. With a foundation in industrial engineering and technical operations, Mr. Sanchez has worked extensively with manufacturers and laboratories around the world, providing hands-on support and practical training for a wide range of cutting, grinding, and sample preparation applications.
Fluent in both English and Spanish, Carlos is known for his ability to translate complex tooling concepts into clear, actionable procedures for engineers, technicians, and production staff. His approach emphasizes real-world process improvement, tool longevity, and operator education—ensuring clients get the most out of their diamond tooling investments.
As an author, Mr. Sanchez shares field-tested insights on tool performance optimization, defect prevention, training methodologies, and troubleshooting common cutting issues.
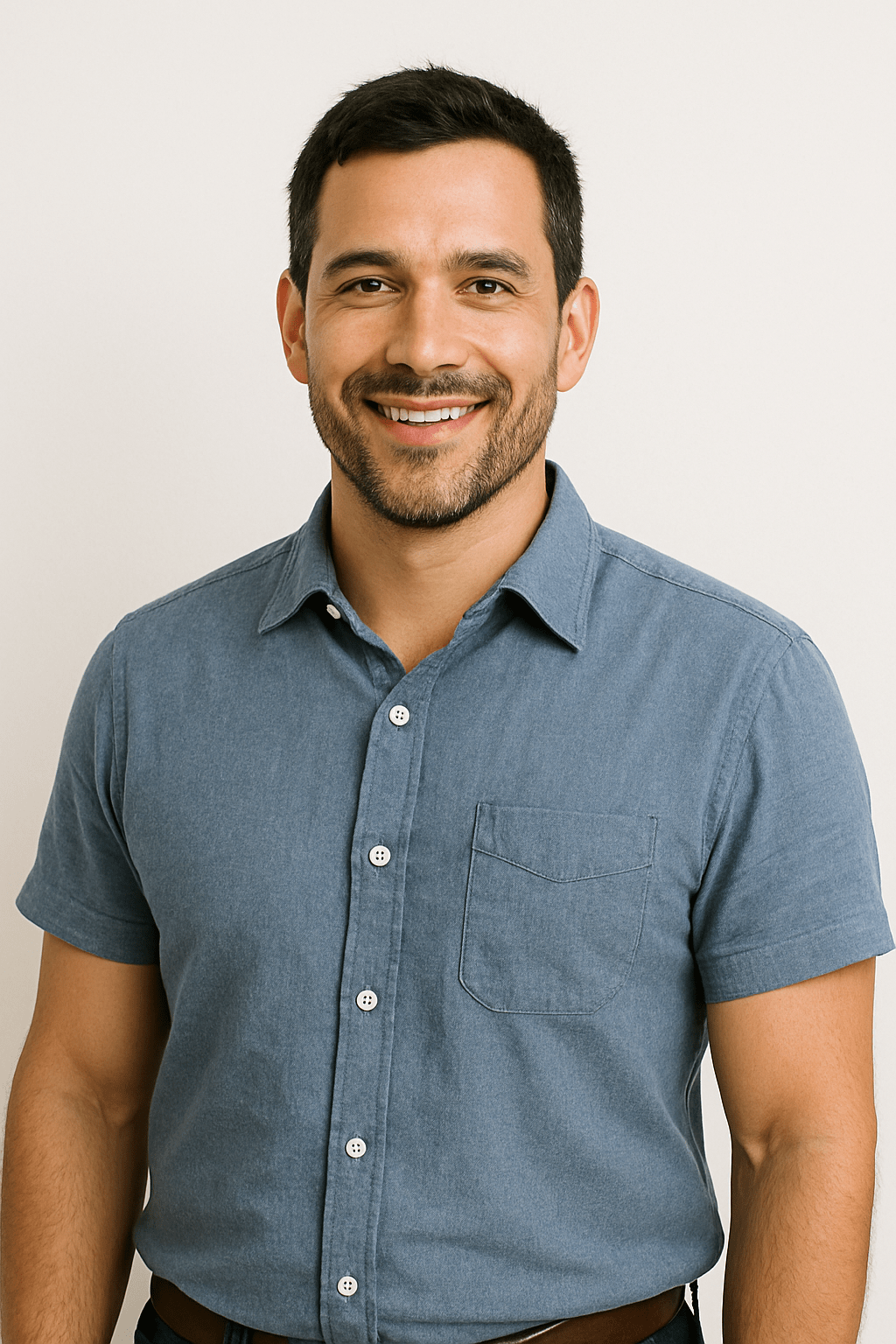
Carlos Sanchez is a senior technical specialist and field applications trainer with more than 17 years of experience in the use and optimization of industrial diamond tools, including ultra-thin diamond blades, core drills, and CBN grinding wheels. With a foundation in industrial engineering and technical operations, Mr. Sanchez has worked extensively with manufacturers and laboratories around the world, providing hands-on support and practical training for a wide range of cutting, grinding, and sample preparation applications.
Fluent in both English and Spanish, Carlos is known for his ability to translate complex tooling concepts into clear, actionable procedures for engineers, technicians, and production staff. His approach emphasizes real-world process improvement, tool longevity, and operator education—ensuring clients get the most out of their diamond tooling investments.
As an author, Mr. Sanchez shares field-tested insights on tool performance optimization, defect prevention, training methodologies, and troubleshooting common cutting issues.