-
0 items in quote
No products in the Quote Basket.
Resin Bond Diamond Discs
Resin Bond Discs are designed removal of material/sample scratches, chips. high spots, & as well as pre-polishing on a larger variety of materials. Using a propriety technique, a high concentration of premium diamond is loaded onto each disc to provide an extremely aggressive grinding rate yet leaves an exceptionally smooth surface finish. Each disc is color coded to easily determine the diamond size of the disc. These resin bond diamond discs are guaranteed to out-perform many cloth polishing discs using loose conventional abrasive or diamond compound/slurry finishing systems. Depending on the application and process these discs on average will last for 100-200 parts/samples & maintain consistent level of performance. These are perfect for hard materials such as metals, ceramics, refractories, cement, geological rocks, glass, optics, composites, and many other materials 35 and up Rockwell C scale of hardness. All discs come with a 3M pressure-sensitive adhesive backing that bonds to backing plates, or with magnetic backing to attach to steel plates. Must be used with coolant. Not recommended for heavy stock material removal
DESCRIPTION
SPECIFICATIONS
FREQUENTLY ASKED QUESTIONS
INDUSTRIES USED IN
ACCESSORIES
USAGE RECOMMENDATION
DESCRIPTION
Each disc is color coded to easily determine the diamond size of the disc. These resin bond diamond discs are guaranteed to out-perform many cloth polishing discs using loose conventional abrasive or diamond compound/slurry finishing systems. Depending on the application and process these discs on average will last for 100-200 parts/samples & maintain consistent level of performance. These are perfect for hard materials such as metals, ceramics, refractories, cement, geological rocks, glass, optics, composites, and many other materials 35 and up Rockwell C scale of hardness. All discs come with a 3M pressure-sensitive adhesive backing that bonds to backing plates, or with magnetic backing to attach to steel plates. Must be used with coolant. Not recommended for heavy stock material removal
SPECIFICATIONS
Tab Content
FREQUENTLY ASKED QUESTIONS
They are primarily used for the removal of material/sample scratches, chips, high spots, and for pre-polishing on a vast variety of materials. These discs provide an aggressive grinding rate, yet leave a smooth surface finish.
Each disc is color-coded for easy identification of diamond size.
Depending on the application and process, these discs on average will last for 100-200 parts/samples while maintaining a consistent level of performance.
They are perfect for hard materials such as metals, ceramics, refractories, cement, geological rocks, glass, optics, composites, and many other materials with a hardness of 35 and up on the Rockwell C scale.
The discs come with either a 3M pressure-sensitive adhesive backing that bonds to backing plates or a magnetic backing to attach to steel plates.
They must be used with coolant. It’s not recommended for heavy stock material removal.
These discs offer a greener option because they require no conventional free abrasive or diamond slurry disposal.
The life of resin bond diamond discs is approximately 1/4 to 1/3 that of metal bond diamond discs.
No, all discs come with either a PSA (pressure-sensitive adhesive) or magnetic backing to ensure proper attachment and functionality.
Yes, we offer these discs in different sizes such as 8″ OD, 10″ OD, and 12″ OD with both PSA backing and magnetic backing.
The color code is a quick reference for the diamond size of the disc. It’s essential to select the appropriate size based on your specific requirements.
The magnetic backing discs are generally priced higher than the PSA backing discs. Prices vary based on the size and micron/mesh size.
These discs out-perform many cloth polishing discs and offer several advantages like faster polishing time, less heat generation, minimal material deformation, reduced chance of contamination, better economic value, and being environmentally friendly.
Yes, compatibility numbers for these brands are provided for each disc to ensure easy matching and purchasing.
Resin Bond Diamond Discs are designed for the removal of material/sample scratches, chips, high spots, and for pre-polishing on a vast array of materials. They are not recommended for heavy stock material removal.
Our Resin Bond Diamond Discs have a high concentration of premium diamond, ensuring an aggressive grinding rate and an exceptionally smooth finish. They are guaranteed to out-perform many cloth polishing discs that use conventional abrasive or diamond compound/slurry finishing systems.
On average, depending on the application and process, these discs will last for 100-200 parts/samples and maintain a consistent performance level throughout.
Yes, these discs are ideal for hard materials such as metals, ceramics, refractories, cement, geological rocks, glass, optics, composites, and any other materials that have a Rockwell C scale of hardness of 35 and up.
All our discs come with a 3M pressure-sensitive adhesive backing (PSA) or with a magnetic backing. The PSA bonds to backing plates, while the magnetic backing attaches to steel plates.
The discs must be used with a coolant to ensure effective and safe operation.
The color-coding system on each disc allows users to easily determine the diamond size of the disc.
Some of the key advantages include faster polishing time, reduced heat generation, minimal material deformation, reduced chance of contamination, and being environmentally friendly as they require no conventional free abrasive or diamond slurry disposal.
The MICRON SIZE and MESH SIZE are indicators of the granularity and coarseness of the diamond particles on the disc. A lower micron/mesh size denotes finer granularity, while a higher number indicates coarser granularity.
Generally, the Magnetic backing discs are priced slightly higher than their PSA counterparts. The exact difference can vary based on the size and specifications of the disc.
While resin bond diamond discs offer many advantages, they tend to wear out faster than metal bond diamond discs due to the softer nature of the resin bonding material.
Please contact our customer support or sales team for custom requests. We aim to cater to specific requirements whenever possible.
Yes, each disc size and type has a recommended RPM range to ensure optimal performance and longevity. Please refer to the product manual or specification sheet for this information. Always ensure the RPM does not exceed the maximum limit to prevent damage or risk.
Store discs in a cool, dry place away from direct sunlight. It’s also essential to ensure they are free from any residual abrasive material or contaminants before storing to prevent damage or reduced efficacy.
Yes, our Resin Bond Diamond Discs are versatile and compatible with both manual and automatic machines. Ensure you’re using the disc within the machine’s specifications.
If you observe a significant drop in performance, uneven surface finishes, or visual wear and tear on the disc’s surface, it might be time for a replacement.
The ideal pressure varies based on the material being polished and the specific disc. Generally, maintaining a medium pressure is recommended. Too much pressure might cause the disc to wear out faster and could lead to sample deformation.
Our Resin Bond Diamond Discs are designed primarily for wet grinding and polishing to ensure effective material removal and cooling. Using them dry might decrease their lifespan and compromise the quality of the finish.
We often provide sample discs for potential customers to test in their applications. Please contact our sales team to inquire about sample availability and conditions.
Always wear appropriate personal protective equipment, including safety glasses, gloves, and a lab coat or apron. Ensure the machine is in good working condition, and the workspace is clean. Also, always make sure the discs are securely attached to the machine to prevent them from coming off during operation.
After each use, clean the discs with a soft brush or cloth to remove any abrasive residues. Using a mild detergent and water can help in removing stubborn residues. Always allow the disc to dry completely before storage.
Yes, we offer discounts for bulk or volume orders. Please get in touch with our sales team for detailed information on discounts and offers.
As long as the disc’s size and specifications match the machine’s requirements, there shouldn’t be any compatibility issues. However, always refer to your machine’s manual and our product specifications to ensure proper compatibility.
While our Resin Bond Diamond Discs are versatile, they might not be suitable for certain extremely hard or abrasive materials which can cause excessive wear. It’s always recommended to consult the product specifications or our technical support for guidance on specific materials.
Excessive heat can soften the resin bond, leading to faster wear or deformation of the disc. High humidity can affect the adhesive properties and might lead to the diamond particles being stripped from the disc. Always ensure the discs are used in environments with controlled temperature and humidity for optimal performance.
No, once the discs have worn past their usable lifespan, they cannot be refurbished or resurfaced. They should be replaced to ensure consistent and quality results.
Our Resin Bond Diamond Discs are designed with a unique bonding system that ensures a consistent distribution of diamond particles. This leads to a uniform removal rate, long lifespan, and exceptional finishes on a wide range of materials.
Yes, there’s a potential risk. To minimize cross-contamination, it’s recommended to thoroughly clean the sample, holder, and the machine between switching grit sizes. Also, consider using dedicated discs for certain sensitive applications.
We have a range of standard sizes and grits, but we understand that certain applications might require customization. Please contact our sales or technical team to discuss any specific requirements you might have.
Yes, we offer a limited warranty against manufacturing defects. Details of the warranty, including duration and terms, can be found in the product documentation or by contacting our customer service.
Used discs should be treated as industrial waste. Ensure they’re disposed of in accordance with local regulations and guidelines. Avoid discarding them in regular trash to prevent potential environmental hazards.
Yes, we offer online tutorials, manuals, and can also arrange in-person training sessions for bulk purchasers or institutions. Our technical support team is always available to assist with any queries.
Resin bond diamond discs are generally more flexible and can deliver smoother finishes, especially on softer materials. Metal bond discs, on the other hand, are more durable and suitable for harder materials but might not provide as smooth a finish.
In resin bond diamond discs, the diamond particles are embedded within a resin matrix. During the manufacturing process, the resin, which is in a liquid or semi-liquid state, is mixed with the diamond particles. As the resin solidifies, it holds the diamond particles firmly in place.
Discs should be stored flat, away from direct sunlight, and in a cool, dry place. Avoid stacking them with different grits facing each other to prevent contamination.
For best results and longer disc life, it’s recommended to use them wet. Using them dry might generate excessive heat and can wear out the disc faster. Some discs are designed specifically for wet use, so always check the manufacturer’s guidelines.
Yes. Always wear safety glasses and a dust mask, especially if operating dry (though wet operation is recommended). Ensure your workspace is well-ventilated and that there’s no risk of slipping if water is used.
The lifespan largely depends on the usage intensity, material being processed, and adherence to recommended operating guidelines. With proper care, a typical disc can last for several months to a year under regular use. However, heavily abrasive materials might reduce the disc’s lifespan.
While you can use them for both applications, it’s advisable to use different grit sizes. Coarser grits are suitable for rough grinding, while finer grits will deliver a polished finish.
Discs can be cleaned using warm water and a mild detergent. Use a soft brush to gently scrub the surface, then rinse thoroughly and allow to air dry. Ensure no abrasive particles remain on the disc as they can affect subsequent uses.
Reduced efficiency, visible wear on the disc surface, or uneven grinding patterns are signs that the disc might be nearing the end of its life.
The RPM can influence the grinding speed and finish quality. Too high an RPM might cause excessive heat, while too low an RPM can lead to suboptimal results. Always follow the manufacturer’s recommendations for optimal RPM settings.
While they can be used on a variety of machines, ensure that the machine’s specifications align with the disc’s requirements for optimal performance and safety.
Consistent pressure, maintaining the recommended RPM, and regularly checking the disc for wear are key factors. Also, using a consistent water flow when operating wet can aid in achieving a uniform finish.
Generally, once the diamond particles wear out, the disc cannot be re-sharpened. However, occasional dressing (a process to expose new diamond particles) can be done using a diamond dressing tool, extending the disc’s life.
The color often corresponds to the grit size or a specific manufacturer’s branding. It helps users quickly identify the grit size or disc type.
Some manufacturers recommend a brief break-in period to ensure optimal performance. This might involve using the disc at a reduced pressure initially or for a shorter duration.
Extreme temperature changes can potentially affect the resin’s integrity. It’s best to store and use the discs in a stable environment and avoid drastic temperature fluctuations.
Absolutely. Many professionals use a sequence of discs with progressively finer grits to achieve a polished finish in stages.
Glazing occurs when the spaces between diamond particles get clogged, reducing the disc’s cutting ability. You can combat this by dressing the disc or occasionally using it on a rougher surface to open up the diamond grit.
When used wet, ensure that the water runoff is collected and treated if it contains potentially harmful residues. Additionally, always dispose of worn-out discs in accordance with local waste disposal regulations.
Yes, many resin bond diamond discs are compatible with handheld machines, but always check the disc’s specifications and the machine’s compatibility.
Lifespan can vary based on usage, material type, and disc quality. With proper care, some discs can last for several months or longer, while others might wear out after just a few uses on harder materials.
: Regular maintenance, ensuring even pressure during use, and preventing overheating can extend a disc’s lifespan. Proper storage when not in use is also essential.
While the resin is designed to handle friction, excessive heat due to prolonged use without cooling or using it on materials it’s not designed for can cause the resin to soften or degrade.
Regular maintenance, ensuring even pressure during use, and preventing overheating can extend a disc’s lifespan. Proper storage when not in use is also essential.
While the resin is designed to handle friction, excessive heat due to prolonged use without cooling or using it on materials it’s not designed for can cause the resin to soften or degrade.
Always wear safety goggles, gloves, and protective clothing. If operating wet, consider anti-slip footwear. Using a dust mask is also advisable, especially when working dry, to prevent inhalation of fine particles.
Some discs are designed for both wet and dry use, but always refer to the manufacturer’s guidelines. Switching between the two can affect the disc’s performance and longevity.
Mild soap and water with a soft brush can be effective. Ensure the disc is thoroughly dried before storing or using again.
Many resin bond diamond discs are compatible with automated machinery. However, always ensure that the disc’s specifications match the machine’s requirements.
Various industry standards might apply, depending on the region or specific application. Always choose discs from reputable manufacturers who adhere to recognized quality and safety standards.
Brand reputation can indicate quality, research & development, and consistency in performance. However, some generic or lesser-known brands might also offer high-quality discs. Always review product specifications, user reviews, and performance data before making a purchase.
Metal bond discs tend to be more durable and long-lasting than resin bond discs, especially when cutting or grinding harder materials. However, resin bond discs might offer smoother finishes in certain applications.
Overloading the disc with pressure, using the disc on inappropriate materials, not allowing proper cooling, and not regularly checking for wear are some common mistakes.
Generally, once the diamond particles on a resin bond disc are worn down, they cannot be re-sharpened. It’s usually more economical and effective to replace the disc.
Some manufacturers may use eco-friendly resins or production methods. It’s essential to check with individual manufacturers about their sustainability initiatives and eco-friendly product options.
Store in a cool, dry place away from direct sunlight. Ensure discs are clean and dry before storage, and avoid stacking them in a way that might cause warping or damage.
Stop using the disc immediately. A wobble can indicate warping, improper mounting, or other damage. Ensure the disc is mounted correctly and check for any visible damage. If the problem persists, consider replacing the disc.
Regularly inspecting the disc after every use is recommended. Check for visible wear, cracks, or any other damage that might affect performance or safety.
Recycling options may vary depending on the disc’s composition and local recycling facilities. Some components, like the diamond particles, may not be recyclable, while others, like certain resins, might be. Always check with the manufacturer or local waste management for proper disposal.
A finer grit results in smoother finishes but might be slower in material removal. Coarser grits remove material more quickly but can leave a rougher finish.
INDUSTRIES USED IN
Tab Content
ACCESSORIES
Tab Content
USAGE RECOMMENDATION
Tab Content
Advantages of Resin Bond Diamond Discs
- Faster Polishing Time
- Less Heat Generation
- Less Material Pull out
- Minimum Material Deformation
- Less Chance of Contamination
- Better Value & More Economic
- Greener for the environment
- Requires no conventional free abrasive or diamond slurry disposal
- Utilizing a dense synthetic felt substrate, diamonds are resin bonded to the pad using a phenolic type resin.
- Lfe of resin bond diamond discs is 1/4 to 1/3" of metal bond diamond discs
Resin Bond Diamond Discs have diamonds locked into a multi-level resin material. Utilizing a dense synthetic felt substrate, diamonds are resin bonded to the pad using a phenolic-type resin.
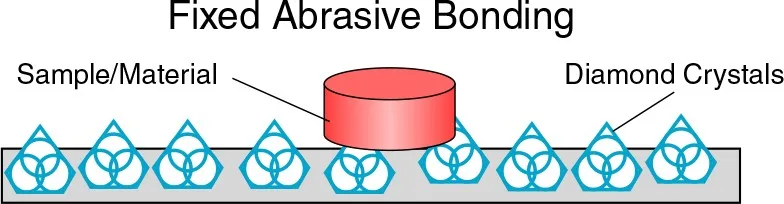
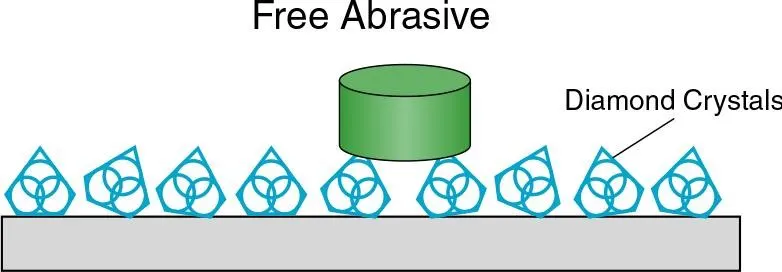
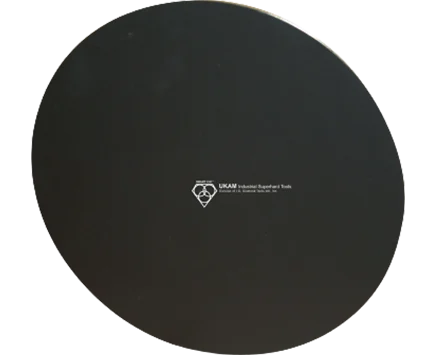
Magnetic Backing
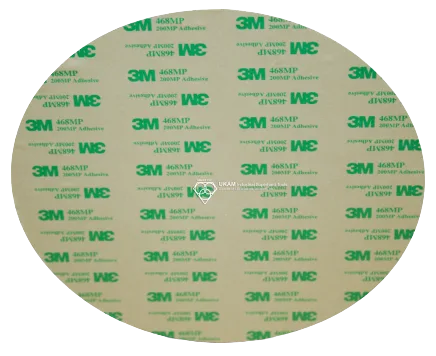
PSA Adhesive Backing
Resin Bond Discs are designed removal of material/sample scratches, chips. high spots, & as well as pre-polishing on a larger variety of materials. Using a propriety technique, a high concentration of premium diamond is loaded onto each disc to provide an extremely aggressive grinding rate yet leaves an exceptionally smooth surface finish. Each disc is color coded to easily determine the diamond size of the disc. These resin bond diamond discs are guaranteed to out-perform many cloth polishing discs using loose conventional abrasive or diamond compound/slurry finishing systems. Depending on the application and process these discs on average will last for 100-200 parts/samples & maintain consistent level of performance. These are perfect for hard materials such as metals, ceramics, refractories, cement, geological rocks, glass, optics, composites, and many other materials 35 and up Rockwell C scale of hardness. All discs come with a 3M pressure-sensitive adhesive backing that bonds to backing plates, or with magnetic backing to attach to steel plates. Must be used with coolant. Not recommended for heavy stock material removal
8" OD Resin Bond Diamond Discs - PSA backing
Showing 1 – -1 of 15 results Showing all 15 results Showing the single result No results found
Sort by Price low to high
Filters Sort results
Reset Apply
Image | MICRON SIZE | MESH SIZE | COLOR | BUEHLER NO. | STRUERS NO. | LECO NO. | UKAM NO (PSA BACKING) | Price | Quantity | Add to cart |
---|---|---|---|---|---|---|---|---|---|---|
240 | 60 | 6140478 | $85.00 | Max: Min: 1 Step: 1 | ||||||
165 | 100 | Black | 4080-0098 | 6140479 | $85.00 | Max: Min: 1 Step: 1 | ||||
125 | 120 | 415108 | 4080-0091 | 6140480 | $85.00 | Max: Min: 1 Step: 1 | ||||
75 | 180 | 413508 | 6140481 | $85.00 | Max: Min: 1 Step: 1 | |||||
70 | 220 | Purple | 415208 | 4080-0094 | 6140482 | $85.00 | Max: Min: 1 Step: 1 | |||
55 | 325 | Brown | 413608 | 6140483 | $85.00 | Max: Min: 1 Step: 1 | ||||
45 | 400 | 415308 | 6140484 | $85.00 | Max: Min: 1 Step: 1 | |||||
35 | 413708 | 6140485 | $85.00 | Max: Min: 1 Step: 1 | ||||||
30 | 600 | Red | 415408 | 408-0060 4080-0109 | 6140486 | $85.00 | Max: Min: 1 Step: 1 | |||
1200 | Blue | 413808 | 4080-0105 | 6140487 | $85.00 | Max: Min: 1 Step: 1 | ||||
9 | 1800 | 415608 | 408-0061 | 6140488 | $85.00 | Max: Min: 1 Step: 1 | ||||
8 | 6140489 | $85.00 | Max: Min: 1 Step: 1 | |||||||
6 | 3000 | Orange | 6140490 | $85.00 | Max: Min: 1 Step: 1 | |||||
3 | 8000 | Yellow | 6140491 | $85.00 | Max: Min: 1 Step: 1 | |||||
0.5 | 50000 | 415908 | 6140492 | $85.00 | Max: Min: 1 Step: 1 |
Resin Bond Diamond Discs 8" OD - Magnetic backing
Showing 1 – -1 of 15 results Showing all 15 results Showing the single result No results found
Sort by Price low to high
Filters Sort results
Reset Apply
IMAGE | MICRON SIZE | MESH SIZE | BUEHLER NO. | STRUERS NO. | LECO NO. | UKAM NO (PSA BACKING) | PRICE | QUANTITY | Add to cart |
---|---|---|---|---|---|---|---|---|---|
6140493 | $98.50 | Max: Min: 1 Step: 1 | |||||||
165 | 100 | 4080-0098 | 6140494 | $98.50 | Max: Min: 1 Step: 1 | ||||
125 | 120 | 415108 | 4080-0091 | 6140495 | $98.50 | Max: Min: 1 Step: 1 | |||
75 | 180 | 413508 | 6140496 | $98.50 | Max: Min: 1 Step: 1 | ||||
70 | 415208 | 4080-0094 | 6140497 | $98.50 | Max: Min: 1 Step: 1 | ||||
55 | 413608 | 6140498 | $98.50 | Max: Min: 1 Step: 1 | |||||
45 | 400 | 415308 | 6140499 | $98.50 | Max: Min: 1 Step: 1 | ||||
35 | 413708 | $98.50 | Max: Min: 1 Step: 1 | ||||||
30 | 600 | 413708 | 408-0060 4080-0109 | 6140501 | $98.50 | Max: Min: 1 Step: 1 | |||
15 | 1200 | 413808 | 6140502 | $98.50 | Max: Min: 1 Step: 1 | ||||
9 | 1800 | 415608 | 408-0061 | 6140503 | $98.50 | Max: Min: 1 Step: 1 | |||
8 | 6140504 | $98.50 | Max: Min: 1 Step: 1 | ||||||
6 | 3000 | 6140505 | $98.50 | Max: Min: 1 Step: 1 | |||||
3 | 8000 | 6140506 | $98.50 | Max: Min: 1 Step: 1 | |||||
0.5 | 50000 | 415908 | 6140507 | $98.50 | Max: Min: 1 Step: 1 |
Resin Bond Diamond Discs 10" OD - PSA backing
Showing 1 – -1 of 15 results Showing all 15 results Showing the single result No results found
Sort by Price low to high
Filters Sort results
Reset Apply
IMAGE | MICRON SIZE | MESH SIZE | COLOR | BUEHLER NO. | STRUERS NO. | LECO NO. | UKAM NO (PSA BACKING) | PRICE | QUANTITY | Add to cart |
---|---|---|---|---|---|---|---|---|---|---|
240 | 60 | 413310 | 6140508 | $98.50 | Max: Min: 1 Step: 1 | |||||
165 | 100 | 415010 | 6140509 | $98.50 | Max: Min: 1 Step: 1 | |||||
125 | 120 | 415010 | 6140510 | $98.50 | Max: Min: 1 Step: 1 | |||||
75 | 180 | 6140511 | $98.50 | Max: Min: 1 Step: 1 | ||||||
70 | 220 | 415210 | 6140512 | $98.50 | Max: Min: 1 Step: 1 | |||||
55 | 325 | 413610 | $98.50 | Max: Min: 1 Step: 1 | ||||||
45 | 400 | 415310 | 6140514 | $98.50 | Max: Min: 1 Step: 1 | |||||
35 | 413710 | 6140515 | $98.50 | Max: Min: 1 Step: 1 | ||||||
30 | 600 | 415410 | 6140516 | $98.50 | Max: Min: 1 Step: 1 | |||||
15 | 1200 | 415510 | $98.50 | Max: Min: 1 Step: 1 | ||||||
9 | 1800 | 415610 | 6140478 | $98.50 | Max: Min: 1 Step: 1 | |||||
8 | 6140519 | $98.50 | Max: Min: 1 Step: 1 | |||||||
6 | 3000 | 415710 | 6140520 | $98.50 | Max: Min: 1 Step: 1 | |||||
3 | 8000 | 415810 | 6140521 | $98.50 | Max: Min: 1 Step: 1 | |||||
0.5 | 50000 | 415910 | 6140522 | $98.50 | Max: Min: 1 Step: 1 |
Resin Bond Diamond Discs 10" OD - Magnetic backing
Showing 1 – -1 of 15 results Showing all 15 results Showing the single result No results found
Sort by Price low to high
Filters Sort results
Reset Apply
IMAGE | MICRON SIZE | MESH SIZE | BUEHLER NO. | STRUERS NO. | LECO NO. | UKAM NO (PSA BACKING) | PRICE | QUANTITY | Add to cart |
---|---|---|---|---|---|---|---|---|---|
240 | 60 | 413310 | 6140523 | $98.50 | Max: Min: 1 Step: 1 | ||||
165 | 100 | 415010 | 6140524 | $125.00 | Max: Min: 1 Step: 1 | ||||
125 | 120 | 415110 | 6140525 | $125.00 | Max: Min: 1 Step: 1 | ||||
75 | 180 | 6140526 | $125.00 | Max: Min: 1 Step: 1 | |||||
70 | 415210 | 6140527 | $125.00 | Max: Min: 1 Step: 1 | |||||
55 | 413610 | 6140528 | $125.00 | Max: Min: 1 Step: 1 | |||||
45 | 400 | 415310 | 6140529 | $125.00 | Max: Min: 1 Step: 1 | ||||
35 | 413710 | 6140530 | $125.00 | Max: Min: 1 Step: 1 | |||||
30 | 600 | 415410 | 6140531 | $125.00 | Max: Min: 1 Step: 1 | ||||
15 | 1200 | 415510 | 6140532 | $125.00 | Max: Min: 1 Step: 1 | ||||
9 | 1800 | 415610 | 6140533 | $125.00 | Max: Min: 1 Step: 1 | ||||
8 | 6140534 | $125.00 | Max: Min: 1 Step: 1 | ||||||
6 | 3000 | 415710 | 6140535 | $125.00 | Max: Min: 1 Step: 1 | ||||
3 | 8000 | 415810 | 6140536 | $125.00 | Max: Min: 1 Step: 1 | ||||
0.5 | 50000 | 415910 | 6140537 | $125.00 | Max: Min: 1 Step: 1 |
Resin Bond Diamond Discs 12" OD - PSA backing
Showing 1 – -1 of 15 results Showing all 15 results Showing the single result No results found
Sort by Price low to high
Filters Sort results
Reset Apply
IMAGE | MICRON SIZE | MESH SIZE | BUEHLER NO. | STRUERS NO. | LECO NO. | UKAM NO (PSA BACKING) | PRICE | QUANTITY | Add to cart |
---|---|---|---|---|---|---|---|---|---|
240 | 60 | 6140538 | 6140538 | $125.00 | Max: Min: 1 Step: 1 | ||||
165 | 100 | 6140539 | 6140539 | $125.00 | Max: Min: 1 Step: 1 | ||||
125 | 120 | 6140540 | 6140540 | $125.00 | Max: Min: 1 Step: 1 | ||||
75 | 180 | 6140541 | 6140541 | $125.00 | Max: Min: 1 Step: 1 | ||||
70 | 6140542 | 6140542 | $125.00 | Max: Min: 1 Step: 1 | |||||
55 | 6140543 | 6140543 | $125.00 | Max: Min: 1 Step: 1 | |||||
45 | 400 | 6140544 | 6140544 | $125.00 | Max: Min: 1 Step: 1 | ||||
30 | 6140545 | 6140545 | $125.00 | Max: Min: 1 Step: 1 | |||||
30 | 600 | 6140546 | 6140546 | $125.00 | Max: Min: 1 Step: 1 | ||||
15 | 1200 | 6140547 | 6140547 | $125.00 | Max: Min: 1 Step: 1 | ||||
9 | 1800 | 415612 | 6140548 | $125.00 | Max: Min: 1 Step: 1 | ||||
8 | 413912 | 6140549 | $125.00 | Max: Min: 1 Step: 1 | |||||
6 | 3000 | 415712 | 6140550 | $125.00 | Max: Min: 1 Step: 1 | ||||
3 | 8000 | 415812 | 6140551 | $125.00 | Max: Min: 1 Step: 1 | ||||
0.5 | 50000 | 415912 | 6140479 ⋅ 6140552 | $125.00 | Max: Min: 1 Step: 1 |
Resin Bond Diamond Discs 12" OD - Magnetic backing
Showing 1 – -1 of 15 results Showing all 15 results Showing the single result No results found
Sort by Price low to high
Filters Sort results
Reset Apply
Image | MICRON SIZE | MESH SIZE | BUEHLER NO. | STRUERS NO. | LECO NO. | UKAM NO (PSA BACKING) | Price | Quantity | Add to cart |
---|---|---|---|---|---|---|---|---|---|
240 | 60 | 413312 | $140.00 | Max: Min: 1 Step: 1 | |||||
165 | 100 | 415012 | $140.00 | Max: Min: 1 Step: 1 | |||||
125 | 120 | 415112 | $140.00 | Max: Min: 1 Step: 1 | |||||
75 | 180 | 6140556 | 6140556 | $140.00 | Max: Min: 1 Step: 1 | ||||
70 | 220 | 6140557 | 6140557 | $140.00 | Max: Min: 1 Step: 1 | ||||
55 | 270 | 6140558 | $140.00 | Max: Min: 1 Step: 1 | |||||
45 | 320 | 6140559 | 6140559 | $140.00 | Max: Min: 1 Step: 1 | ||||
35 | 400 | 6140560 | 6140560 | $140.00 | Max: Min: 1 Step: 1 | ||||
30 | 500 | 6140561 | 6140561 | $140.00 | Max: Min: 1 Step: 1 | ||||
15 | 600 | 6140562 | 6140562 | $140.00 | Max: Min: 1 Step: 1 | ||||
9 | 820 | 6140563 | 6140563 | $140.00 | Max: Min: 1 Step: 1 | ||||
8 | 900 | 6140564 | 6140564 | $140.00 | Max: Min: 1 Step: 1 | ||||
6 | 1100 | 6140565 | 6140565 | $140.00 | Max: Min: 1 Step: 1 | ||||
3 | 3000 | 6140566 | 6140566 | $140.00 | Max: Min: 1 Step: 1 | ||||
0.5 | 50000 | 6140567 | 6140567 | $140.00 | Max: Min: 1 Step: 1 |
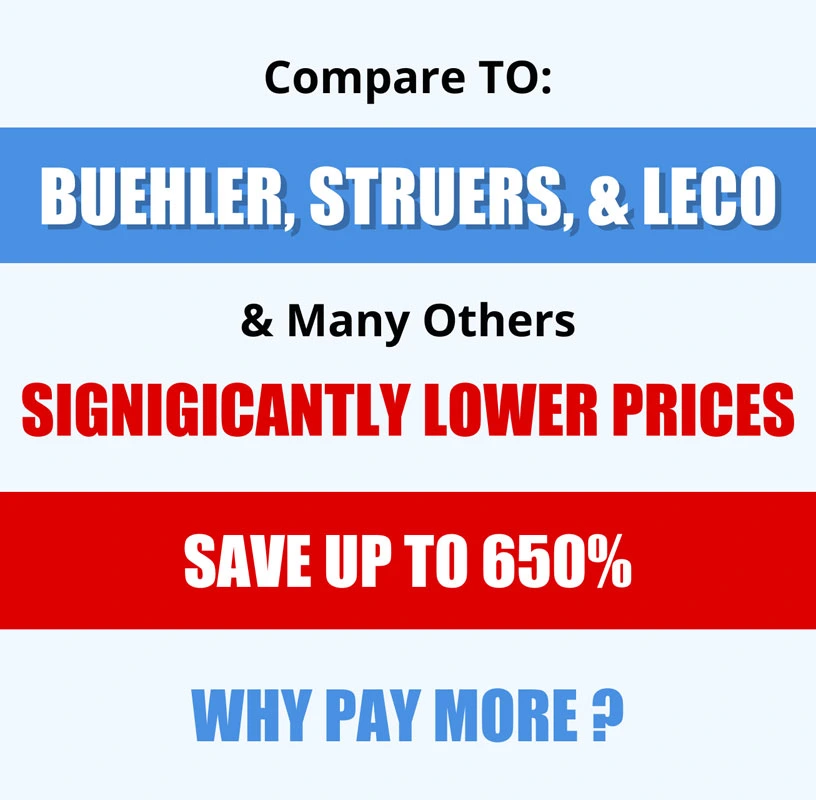
Why Choose Us?
- Unmatched Selection For Many Applications
- Unmatched Technical Support & Expertise
- Superior Quality & Consistency
- Super Technology & innovation
- Immediate Worldwide Delivery
- American Based Manufacturer
-
Custom
Manufacturing - Better Value manufacturer Direct Price
Contact Us for FREE Quote & Recommendation
Why Work With Us?
Read More
We produce diamond consumables for some of the leading world OEM manufacturers. We offer Manufacturers Direct Prices
We have the largest variety of diamond & cbn wafering blades available in stock. As well as large inventory of diamond & abrasive consumables. We also custom manufacture diamond and cbn tools, consumables and machines to better fit customer specific needs. Just about any tools & consumables can be designed and manufactured per client drawing or specificrtion
WE ARE A PARTNER IN YOUR SUCCESS
Our proprietory diamond chemistory , precision , manufacturing metods , quality control methods allow us to control and regulate the dozens of variables to that affect consumable life , quality , and consistency.
The more you understand about what we can do for you the better our partnership will be. Here you will find most comprehensive source of information and optimizing and improving your cutting , drilling , grinding and polishing on the web. find everything you ever wanted to know about diamond tools.
AMERICAN MANUFACTURER
"ONE OF THE MOST EXPERIENCED COMPANIES IN THE INDUSTRY"
Save Money Save up to 650%
COMPARE TO: BUEHLER , STRUERS , LECO & MANY OTHERS
Large Inventory & Custom Manufacturing
Umatched Technical Support
Developing close ties with our customers is the foundation of our business. At the core of
our company is a team of world class engineers, knowledgeable customer service personnel here to serve you. Whether is designing or manufacturing a special solution. We will go out of our way to optimizing your process to ultimate level of efficiency
Superior Quality & Consistency
EXPECT MORE FROM YOUR TOOLS
Comprehensive Source Of Information For Sample Preparation
Advanced Technology
As one of the few remaining independent U.S.Diamond Tool & machine builders. We have the experience & tradition to help you remain at frontier of technology Our experience has been further enhanced by acquiring assets and processes from some of the oldest American tool
manufacturers, along with their decades of experience and R& D. This has positioned us as one of the most experienced companies in the industry .Depend on us to bring you technology of tomorrow today.
Experience Makes All The Differences
Over the years we have worked with some of the leading Fortune 500 companies , thousands of universities , government and private research labs , and small organisations. We have made thousands of custom tools , built custom machines , work-holding fixtures , etc for hundreds of applications. Many of our staff members have been working in their respective fields for over 50 years and have gained a wealth of knowledge over the years
Let Us Help You
Related Products
SMART CUT® Resin Bond Diamond Discs for Grinding & Polishing Machines
SMART CUT® Metal Bond Diamond Discs for Large Grinding / Polishing Machines
SMART CUT® Resin Bond Diamond Polishing Discs
DIAMOND LAPS
UKAM Industrial Superhard Tools manufactures & offers a large variety of diamond laps & polishing discs. Below you will find information, specifications & prices on all laps & polishing discs we offer for this application. Contact us for volume pricing. We can also produce any custom diamond wheel per your specification. Contact us Today for Free Quote!
Recently Viewed Products
ARE YOU USING RIGHT Diamond Discs
FOR YOUR APPLICATION?
LET US
HELP YOU
HAVING ISSUES WITH
YOUR CURRENT Diamond Discs?
Knowledge Center
02
Jun
Diamond vs CBN (cubic boron nitride) Tools
Cubic Boron Nitride (CBN) is a synthetic material that is renowned for its exceptional hardness and high thermal stability. It is composed of boron and nitrogen atoms arranged in a crystal lattice structure, similar to...
02
Jun
Discover the Right Diamond Powder for Your Application: Choosing Between Monocrystalline and Polycrystalline Diamonds
Which to use for your application?
Diamond shape plays a significant role in the effectiveness of polishing solutions, affecting both the polishing rate and the quality of the final finish. Understanding the differences between monocrystalline and...
02
Jun
Comparing Two Different Cutting Methods (Low Speed Saw vs. Wire Saw)
Share this Article with Friend or Colleague
For metallography, sample preparation, materials research and working with large variety of materials, selecting the optimal cutting technology is crucial for achieving high-quality results across various materials and applications....
11
Jun
Selecting the Right Diamond Suspension for your Application – Monocrystalline or Polycrystalline?
Choosing the correct diamond suspension, whether monocrystalline or polycrystalline, significantly impacts the quality and efficiency of the polishing and material removal processes. Understanding the properties and applications of both types of suspensions can help you...
17
Jun
Improve Sample Quality & Optimize your Polishing Operating for Metallography & Sample Preparation
Polishing is important step in metallography & sample preparation for revealing the true microstructure of materials, including grain boundaries, phases, and inclusions, which provide insights into material properties and history. This guide is designed to...
26
Jun
Optimize your Grinding Operation for Metallography & Sample Preparation
Share this Article with Friend or Colleague
Grinding is a fundamental mechanical process in metallography that involves removing material from a specimen using hard, abrasive particles. This process is essential for preparing specimens for microscopic...
08
Jul
Low Speed Saw Case Studies
Share this Article with Friend or Colleague
Introduction
In the realm of precision cutting, the SMART CUT® 6005 Low Speed Diamond Saw stands out for its capability to handle a variety of materials with high...
11
Sep
What is the difference between Lapping, Grinding, & Polishing
Some of the major differences include the type and diamond mesh size of diamond discs used, type and size of abrasives used and their holding method. Other factors include RPM’s (speed) used and pressure applied...
30
Jan
Select the Right Silicon Carbide Paper Discs for Metallography Sample Preparation
Selecting the right silicon carbide paper for metallographic sample preparation is important for achieving accurate and reliable results in material analysis. The grinding and polishing process plays a fundamental role in preparing specimens for microscopic...
30
Jan
Upgrading Metallography Grinding with Silicon Carbide Paper
This guide covers the best practices for using silicon carbide paper in metallography. It includes tips on proper grit progression, optimizing pressure and speed settings, preventing common issues, and extending the life of the abrasive....
- Unmatched Selection For Many Applications
- Superior Quality & Consistency
- Immediate Worldwide Delivery
- Technical Support & Expertise
- American Based Manufacturer
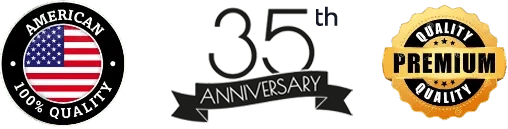

- Different Product
- Different Technology
- Different Company
- Expect MORE from your tools
Let Us HELP You!
Subscribe To Our Newsletter
Signup for email offers, updates, and more
Contact Us
- 25205 & 25201 Avenue Tibbits Valencia CA 91355 USA
-
Phone : (661) 257-2288
FAX : (661) 257 -3833 - lel@ukam.com
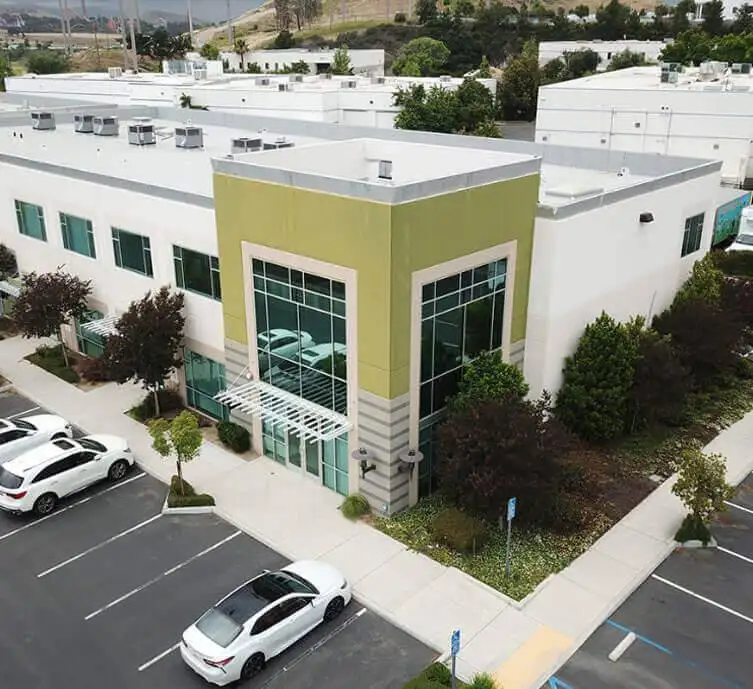
UKAM Industrial Superhard Tools is a U.S. High Technology, Specialty Diamond Tool & Equipment manufacturer. We specialize in producing ultra thin, high precision cutting blades, precision cutting machines diamond drills, diamond micro tools, standard & custom advanced industrial diamond tools and consumables.
- 25205 & 25201 Avenue Tibbits Valencia CA 91355 USA
-
Phone : (661) 257-2288
FAX : (661) 257 -3833 - lel@ukam.com
- 25205 & 25201 Avenue Tibbits Valencia CA 91355 USA
-
Phone : (661) 257-2288
FAX : (661) 257 -3833 - lel@ukam.com
DIAMOND TOOLS BY BOND
EQUIPMENT
KNOWLEDGE CENTER
OUR PRODUCTS
COMPANY
CUSTOMER SERVICE
Shipping Methods


Safe & Secure Payments

© Copyright 1990-2025. UKAM Industrial Superhard Tools – Terms of Use