-
0 items in quote
No products in the Quote Basket.
SMART CUT® Resin Bond Diamond Polishing Discs
SMART CUT® Resin Bond Diamond Discs are designed for fine and coarse grinding/polishing of high hardness materials such as metals, ceramics, refractories, cement, geological rocks, glass, optics, composites, and many other materials 35 and up Rockwell C scale of hardness
DESCRIPTION
SPECIFICATIONS
INDUSTRIES USED IN
FAQ
ACCESSORIES
USAGE RECOMENDATION
DESCRIPTION
Only the highest quality diamonds and raw material is used in manufacturing process. The highest quality standards and consistency are maintained using sophisticated measurement and inspection equipment. Please inquire, we will be happy to accommodate your specific needs.
SPECIFICATIONS
- Diamond Grit sizes: 100 mesh to 100,000 mesh
- Colors: Black to Pink
- Backing Type: Psa adhesive, Magnetic, no backing, Velcro
- Outside Diameter: 6” to 30”
- Inside Diameter: no hole, ½”, 5/8”, ¾”, 1.0” or any hole
INDUSTRIES USED IN
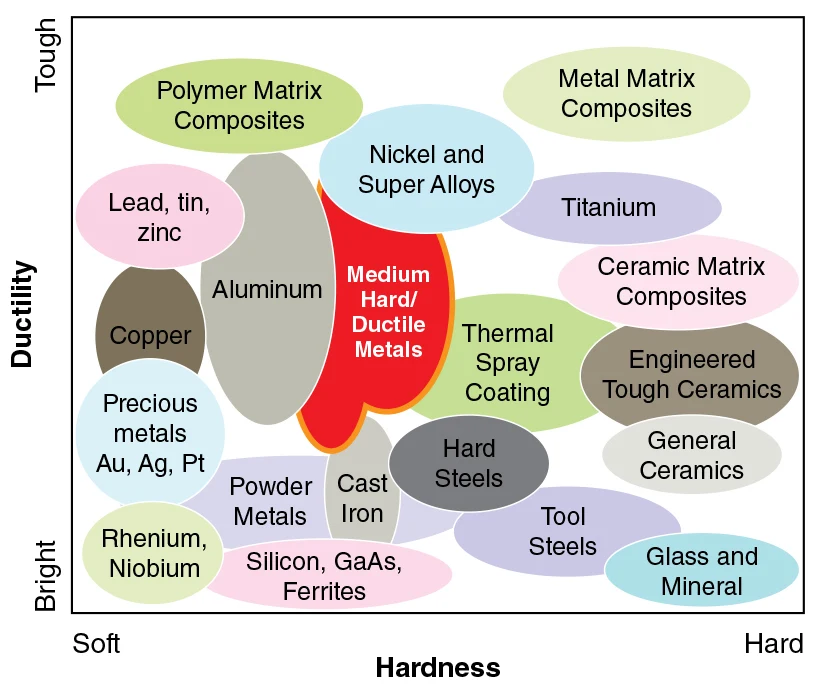

INDUSTRIES USED IN:
- Advanced Ceramics
- Composites
- Glass
- Geology
- Quartz
- Materials Research
- Medical Devices
- Metallography
- Photonics / Optics
- Semiconductor
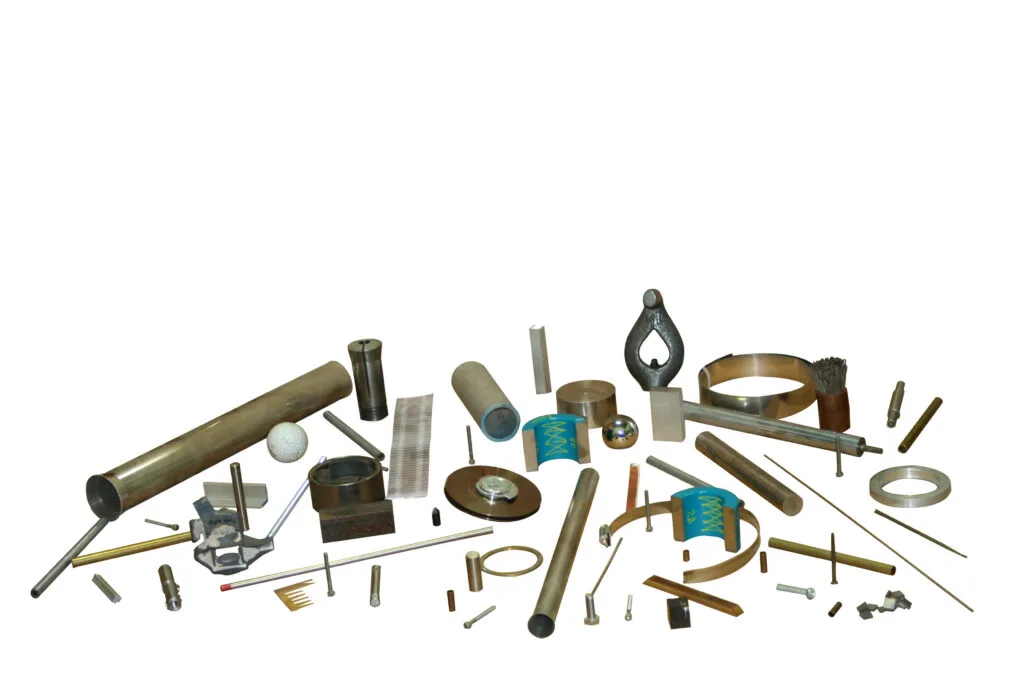
Ferrous & Non-Ferrous Metals:
- Plain Carbon Steels
- Electronic Packages
- Stainless Steels Plastics
- Tool Steels Fasteners
- Aluminum Refractories
- Copper Base Alloys Integrated Circuits
- Magnesium Thermal Spray Coatings
- Titanium Metal Matrix Composites
- Biomedical Wafers
- Petrographic
- PCB.s Ceramics
FAQ
SMART CUT Diamond Discs are designed for materials with a hardness of 35 Rockwell C scale and higher. This includes metals, ceramics, refractories, cement, geological rocks, glass, optics, composites, and many others. The key is selecting the right diamond mesh size and disc type for your specific material.
The diamond mesh size or grit size determines the aggressiveness of the disc. Coarse grits (e.g., 40) are suitable for rapid material removal, while finer grits (e.g., 200 or 1 micron) are ideal for achieving a polished surface. Consider the material’s hardness and the desired finish when selecting grit size.
Yes, SMART CUT Diamond Discs are versatile and can be used for both grinding and polishing. However, you may need to change to a finer grit disc for polishing after the initial grinding stages for optimal results.
The backing type determines how the disc attaches to your grinding or polishing equipment. Choose the backing that is compatible with your machine setup. Magnetic and adhesive PSA are common choices, but velcro and no backing options are available for specific needs.
- Start with Proper Cleaning: Ensure your workpiece is clean and free from debris before grinding or polishing to prevent contamination and scratches.
- Use Adequate Lubrication: Depending on your material and disc, use water, oil, or a compatible lubricant to cool and lubricate the grinding process.
- Apply Even Pressure: Maintain consistent pressure on the workpiece to avoid uneven wear on the disc and achieve uniform results.
- Progressive Grit Sequence: Begin with a coarser grit disc for material removal and gradually switch to finer grits for polishing. This progressive sequence minimizes surface imperfections.
- Monitor Disc Wear: Regularly inspect the disc for wear and replace it when necessary to maintain consistent performance.
- Work Safely: Always follow safety guidelines and wear appropriate protective gear, including safety glasses and gloves, when using diamond discs.
Yes, SMART CUT offers customization options. You can request specific inside diameter (ID) hole sizes, no hole configurations, and even discuss unique requirements with our team. We’re here to accommodate your specific needs.
To extend the lifespan of your discs, follow proper usage and maintenance guidelines. Avoid excessive pressure, use the correct lubrication, and periodically inspect the disc for wear. Replacing discs when they show signs of wear ensures consistent performance and longevity.
Yes, SMART CUT Resin Bond Diamond Discs are compatible with a wide variety of lapping, grinding, and polishing machines. Ensure you select the right disc size and backing type that matches your specific equipment for seamless operation.
Feel free to reach out to our expert team at SMART CUT. We’re here to assist you in selecting the right discs, providing usage recommendations, and answering any questions you may have to optimize your grinding and polishing process.
Yes, SMART CUT Diamond Discs are versatile and can be used for both wet and dry applications. Wet grinding and polishing can help control heat and reduce dust, while dry methods offer convenience. Choose the method that best suits your material and workspace conditions.
Safety is paramount. Always wear appropriate protective gear, including safety glasses, gloves, and respiratory protection if needed. Ensure that your workspace is well-ventilated, and follow safety guidelines for your specific equipment and material.
Monitor the surface finish closely. When the surface starts to exhibit a smoother, more polished appearance and the desired level of material removal is achieved, it’s time to switch to a finer grit disc for the final polishing stages.
Absolutely. SMART CUT Diamond Discs are known for their precision and consistency. They can be used for applications requiring tight tolerances, such as optics, electronics, and precision machining. Select the appropriate grit size and follow recommended procedures for achieving precision results.
Store SMART CUT Diamond Discs in a dry and clean environment to prevent contamination. Inspect them regularly for damage or wear and replace them as needed to maintain quality and safety. Follow proper cleaning procedures and lubrication recommendations during use.
Can these discs be used for curved or irregular surfaces, or are they best suited for flat surfaces?
SMART CUT Diamond Discs are versatile and can be used on both flat and curved surfaces. However, extra care may be needed to maintain even pressure and achieve consistent results on irregular shapes. Consider the disc size and backing type for the best performance on curved surfaces.
SMART CUT Diamond Discs provide longer lifespan, faster material removal, and superior surface finish compared to traditional abrasive discs. They also reduce the risk of overheating and material deformation, making them a preferred choice for high-precision applications.
Yes, SMART CUT Diamond Discs are suitable for projects of all sizes. They are used in small-scale workshops, laboratories, as well as large industrial operations. Choose the appropriate disc size and grit for your specific project and machinery.
Yes, SMART CUT Diamond Discs are well-suited for precision machining of extremely hard materials like sapphire, tungsten carbide, and other super-hard alloys. Selecting the appropriate grit size and following recommended procedures is crucial for achieving accurate and consistent results in such applications.
- Use the appropriate grit size for each stage of your process to minimize unnecessary wear.
- Maintain a consistent and moderate pressure on the workpiece to avoid excessive stress on the disc.
- Ensure proper lubrication or coolant flow to dissipate heat and prevent overheating.
- Periodically check the disc for any signs of uneven wear, damage, or clogging and replace it as needed.
- Store your diamond discs in a clean, dry environment to prevent contamination.
Yes, SMART CUT Diamond Discs can be used for edge grinding and beveling applications. Careful control of the angle and pressure is necessary to achieve the desired edge profile. Additionally, you may need to transition to finer grit discs for edge polishing.
The recommended RPM settings depend on the disc diameter, machine type, and material being worked on. Consult the manufacturer’s guidelines for your specific machine and adapt the RPM accordingly for safe and efficient operation with SMART CUT Diamond Discs.
Can these diamond discs be used for restoration or repair of optical components and glass artifacts?
Yes, SMART CUT Diamond Discs are suitable for restoration and repair of optical components, glass artifacts, and delicate surfaces. They provide the precision required for such applications and can be used to remove scratches and imperfections before final polishing.
While SMART CUT Diamond Discs can be used for both wet and dry applications, it’s essential to consider the compatibility of the disc and material with your chosen method. Some materials may yield better results with wet grinding and polishing, while others may perform well in dry conditions. Always prioritize safety and effectiveness when selecting the method.
SMART CUT Diamond Discs are typically designed for single-use due to the wear and degradation of the diamond abrasive during operation. Attempting to recondition or resurface them may not yield satisfactory results, and it’s generally more cost-effective to replace the disc when it shows signs of wear.
Absolutely. SMART CUT Diamond Discs are compatible with a wide range of equipment, including both manual and automated systems. Whether you’re operating a handheld grinder or an automated CNC machine, you can adapt SMART CUT Diamond Discs to suit your needs.
Yes, SMART CUT Diamond Discs are capable of high-precision micro-machining and intricate detailing. By selecting finer grit sizes and carefully controlling pressure and speed, you can achieve intricate and precise results, making them suitable for applications like microelectronics and precision optics.
SMART CUT Diamond Discs excel in a wide range of applications, including but not limited to material research, semiconductor manufacturing, metallography, geological sample preparation, precision optics, and aerospace component fabrication. Their versatility and precision make them a top choice across various industries.
Yes, SMART CUT Diamond Discs are suitable for both large, thick workpieces and smaller, thinner samples. By selecting the appropriate disc size and grit, you can effectively process workpieces of varying sizes and thicknesses while maintaining quality and efficiency.
The lifespan of a SMART CUT Diamond Disc depends on several factors, including the material being processed, the grit size, and the operating conditions. Typically, they have a long lifespan due to their high-quality diamond abrasives. To maximize longevity, follow proper usage guidelines, maintain consistent pressure, and replace the disc when it shows signs of wear.
Achieving a mirror-like finish on glass or optics requires careful progression through finer grit sizes and meticulous attention to detail. Start with a coarse grit for material removal and gradually transition to finer grits. Additionally, use a polishing compound or slurry designed for glass or optics to achieve the desired mirror finish.
Yes, SMART CUT Diamond Discs can be used for non-traditional applications like artistic glass shaping or sculpting. Their precision and versatility make them suitable for creating intricate and artistic designs in glass and similar materials.
Proper alignment and centering are crucial for achieving consistent results. Follow the equipment manufacturer’s guidelines for mounting and aligning discs. Ensure that the disc is securely attached and runs true to the equipment’s axis to prevent vibrations and uneven wear.
While SMART CUT Diamond Discs are primarily designed for grinding and polishing, they can be used for precision cutting, especially when combined with appropriate cutting fluid and equipment. However, for dedicated cutting applications, specialized diamond cutting discs or blades may be more suitable.
Proper disposal of used SMART CUT Diamond Discs should follow local regulations and guidelines for the disposal of abrasive materials. In some cases, used diamond discs may be considered hazardous waste due to the diamond abrasives. Consult with local authorities or waste management services for guidance on safe disposal practices.
Yes, SMART CUT Diamond Discs can be used for polishing natural stone surfaces like granite or marble countertops. Select the appropriate grit sizes and follow a progression from coarse to fine grits for effective polishing. Be sure to use a compatible stone polishing compound or slurry for the best results.
SMART CUT Diamond Discs are commonly used for preparing samples for microscopy and material analysis. Their precision and consistency make them an excellent choice for producing thin sections and polished surfaces suitable for detailed examination and analysis.
SMART CUT Diamond Discs can be used with both portable hand-held grinders and polishers as well as stationary machines. Their versatility allows for adaptability to various equipment types, making them suitable for a wide range of applications and setups.
SMART CUT Diamond Discs typically do not require dressing or conditioning before use. They are precision-manufactured to provide consistent performance out of the box. However, if you encounter any irregularities or inconsistencies, consult the manufacturer’s guidelines for specific recommendations on conditioning or truing the disc.
SMART CUT Diamond Discs are not typically used for faceting gemstones, as faceting requires specialized lapidary equipment and diamond laps. However, they can be used for other lapidary applications, such as shaping and polishing cabochons or flat surfaces on minerals and gemstones.
SMART CUT Diamond Discs are designed to maintain their flatness and shape with proper use. Avoid applying excessive pressure and use proper lubrication or coolant to dissipate heat and prevent overheating, which can lead to disc deformation. Regularly inspect the disc for any signs of wear or uneven wear patterns.
SMART CUT Diamond Discs can be used for beveling edges on glass and other materials. To achieve consistent bevels, set the angle and depth on your grinding or polishing equipment to match your desired bevel profile. Begin with a coarser grit disc for material removal, then gradually switch to finer grits for smoother bevels. Maintain a consistent feed rate and pressure to ensure uniform results.
Yes, SMART CUT Diamond Discs are suitable for applications involving composite materials like carbon fiber and fiberglass. Choose the appropriate grit size for your specific composite material, and follow recommended procedures to achieve precise cutting, grinding, and polishing results.
SMART CUT Diamond Discs are commonly used for thinning and sectioning semiconductor wafers. To thin a wafer, start with a coarser grit disc for material removal, then switch to finer grits for polishing. Be sure to use proper cooling and lubrication to prevent heat buildup, which can damage the wafer. Follow industry-specific guidelines for semiconductor thinning processes.
Cleaning SMART CUT Diamond Discs is essential to prevent cross-contamination between materials. Use a compatible cleaning solution or solvent, such as acetone or isopropyl alcohol, to remove residue. Gently scrub the disc surface with a soft brush or cloth, taking care not to damage the diamond abrasive. Rinse thoroughly with clean water and allow the disc to dry completely before reuse.
SMART CUT Diamond Discs are suitable for precision grinding and polishing of ceramics used in dental and medical applications. Select the appropriate grit size and follow recommended procedures to achieve the desired surface finish and precision required for dental crowns, orthopedic implants, and similar applications.
To control the removal rate with SMART CUT Diamond Discs, consider the following:
- Adjust the grit size: Coarser grits remove material more quickly, while finer grits offer finer control.
- Control pressure and feed rate: Adjust the pressure and feed rate to regulate the material removal rate.
- Monitor material thickness: Measure the material thickness during the process to ensure you achieve the desired level of removal.
Yes, SMART CUT Diamond Discs can be used for polishing hardened steel and achieving a mirror-like finish on precision components. Start with a coarse grit disc for material removal, then progressively switch to finer grits for polishing. Proper lubrication and consistent pressure are essential for obtaining a mirror finish on hardened steel.
To select the ideal SMART CUT Diamond Disc for your project, consider factors such as material hardness, desired finish, and equipment type. Consult the manufacturer’s guidelines, which often provide recommendations and guides for disc selection based on material and application. If in doubt, you can reach out to our experts for personalized guidance.
Achieving flatness and parallelism in precision components with SMART CUT Diamond Discs involves:
- Using a precision machine with proper alignment and control.
- Choosing the appropriate grit sizes and a progressive sequence for material removal and polishing.
- Ensuring consistent pressure and feed rate during the process.
- Regularly inspecting the workpiece to monitor progress and adjust as needed.
SMART CUT Diamond Discs can be used for high-temperature applications to some extent, but it’s essential to manage heat effectively. Proper cooling and lubrication are crucial to prevent overheating and damage to the diamond abrasive. Use cooling systems compatible with your equipment for such applications.
Yes, SMART CUT Diamond Discs can be used for precision surface finishing of 3D-printed parts made from various materials. Select the appropriate grit size and follow recommended procedures to achieve the desired surface finish and dimensional accuracy on 3D-printed components.
When working with brittle materials like ceramics or glass, take the following precautions:
- Use a gentle touch and minimal pressure to reduce the risk of cracking.
- Maintain proper cooling and lubrication to dissipate heat and prevent thermal stress.
- Consider using a finer grit disc for smoother material removal, which reduces the risk of chipping.
- Handle workpieces with care to avoid accidental damage during the process.
SMART CUT Diamond Discs can be used for contour grinding and polishing on irregularly shaped workpieces. To achieve uniform results, focus on the following techniques:
- Maintain a consistent angle and pressure relative to the contour’s shape.
- Use slow and controlled movements to prevent uneven wear.
- Progress through a sequence of grit sizes, starting with coarser grits for material removal and transitioning to finer grits for polishing.
- Adapt your technique to the specific contours and shapes of the workpiece for even coverage.
SMART CUT Diamond Discs can be suitable for applications requiring sub-micron level precision, such as semiconductor manufacturing and nanotechnology research. To achieve such precision, select the finest available grit size and follow meticulous procedures for material removal and polishing. Additionally, ensure your equipment is capable of sub-micron level control.
Yes, SMART CUT Diamond Discs can be used for restoration and conservation work on historical artifacts and sculptures made of stone or other materials. They are valuable tools for removing damage, corrosion, or unwanted layers while preserving the original material. Follow best practices for restoration and consult with conservation experts when working on valuable or culturally significant items.
When transitioning from one grit size to another with SMART CUT Diamond Discs, consider the following:
- Ensure that the workpiece is thoroughly cleaned and free from residue from the previous grit.
- Adjust the machine settings and feed rate if needed to match the new grit’s characteristics.
- Start with the coarsest grit size in the sequence and progressively move to finer grits.
- Pay attention to the material removal rate and adjust pressure and speed accordingly for optimal results.
SMART CUT Diamond Discs can be used for applications involving ferrous metals like stainless steel or hardened steel alloys. However, consider using specialized diamond discs designed for ferrous materials to achieve the best results, as these materials can be more abrasive and wear down diamond abrasives more quickly.
Achieving sharp edges and precise corners with SMART CUT Diamond Discs involves careful control and technique:
- Use smaller disc sizes or diamond tools specifically designed for edge work.
- Pay close attention to the angle and pressure applied to the workpiece near edges and corners.
- Transition to finer grits as you approach the desired sharpness.
- Consider using additional tools or techniques, such as hand polishing, for fine detailing on corners and edges.
SMART CUT Diamond Discs can be used for removing old coatings or paint layers from various surfaces. To do this effectively and safely:
- Use an appropriate grit size based on the coating or paint material.
- Ensure proper ventilation and wear protective gear to minimize exposure to dust and fumes.
- Use a suitable dust collection system or wet method to control dust and contaminants.
- Be cautious when removing lead-based paint or hazardous coatings, and follow environmental regulations and safety guidelines.
Yes, SMART CUT Diamond Discs are commonly used for sample preparation in metallurgy and material science. They are suitable for cutting and grinding metallographic specimens. Select the appropriate disc size and grit for your specific metallurgical samples and follow recommended procedures for precise and consistent results.
To achieve perfectly flat and parallel surfaces on large workpieces with SMART CUT Diamond Discs:
- Ensure the workpiece and machine are properly aligned and leveled.
- Choose a disc size that adequately covers the workpiece.
- Use a progressive sequence of grit sizes, starting with coarser grits for material removal.
- Employ a cross-grinding pattern to maintain flatness.
- Regularly check for flatness and parallelism using precision measurement tools.
Yes, SMART CUT Diamond Discs can be used for precision grinding and polishing of semiconductor silicon wafers for the electronics industry. They are suitable for achieving the flatness and surface finish required for semiconductor manufacturing. Follow industry-specific guidelines and procedures for silicon wafer processing.
Yes, SMART CUT Diamond Discs are compatible with automated robotic systems for high-throughput manufacturing or testing applications. They can be integrated into automated setups for consistent and efficient material processing. Ensure proper equipment compatibility and programming for robotic operation.
SMART CUT Diamond Discs can be used for shaping and profiling natural stone surfaces like granite or marble in architectural and sculptural applications. Select the appropriate disc size, profile, and grit for your specific stone shaping needs. Proper technique and equipment setup are essential for achieving precise and artistic results.
When working with heat-sensitive materials using SMART CUT Diamond Discs:
Use a fine grit size to minimize heat generation.
Employ water-based cooling or lubrication to control temperature.
Monitor the workpiece and disc temperature to prevent overheating.
Minimize dwell time on the material to reduce heat exposure.
SMART CUT Diamond Discs can be used for achieving precise dimensions and tolerances in precision machining applications. To maintain dimensional accuracy:
- Use the appropriate grit size for material removal and precision finishing.
- Control pressure, feed rate, and machine settings for accuracy.
- Periodically check and measure the workpiece dimensions to ensure they meet the desired tolerances.
- Inspect the SMART CUT Diamond Disc for wear or irregularities that may affect precision.
SMART CUT Diamond Discs can be used for restoration and conservation work on delicate artifacts made of materials like porcelain, ceramic, or glass. Their precision and versatility make them suitable for removing damage, restoring intricate details, and achieving the desired finish on delicate surfaces. Handle artifacts with care to avoid accidental damage during the restoration process.
Yes, SMART CUT Diamond Discs can be used for grinding and polishing advanced engineering ceramics like silicon nitride or alumina, commonly used in aerospace and high-tech industries. Their precision and consistency make them suitable for achieving the required surface finish and dimensional accuracy on these materials.
SMART CUT Diamond Discs can be employed for precision thinning and sectioning of semiconductor packages and components. Key considerations include:
- Selecting an appropriate disc size and grit for the semiconductor material.
- Using proper cooling and lubrication to prevent heat-related damage.
- Employing precise equipment with control over thickness and parallelism.
- Following industry standards and guidelines for semiconductor thinning and sectioning.
SMART CUT Diamond Discs can be used for polishing optical lenses, mirrors, or prisms to achieve optical-grade surfaces. Techniques include:
- Starting with coarser grits for material removal and progressing to finer grits for polishing.
- Using optical-grade polishing compounds or slurries.
- Employing controlled pressure, speed, and fluid management to minimize surface imperfections.
- Inspecting the optical surfaces for clarity and precision at each stage of the process.
Yes, SMART CUT Diamond Discs can be used for precision finishing of ceramic or metal injection-molded (MIM) components used in industries like automotive and medical devices. They provide the required precision and surface finish for such applications. Follow recommended procedures for achieving the desired results on MIM components.
To achieve extremely smooth and mirror-like surfaces on semiconductor wafers using SMART CUT Diamond Discs for final polishing:
- Use the finest grit size available.
- Ensure precise machine control and alignment.
- Apply a high-quality semiconductor polishing slurry.
- Use proper cooling and lubrication.
- Monitor the surface finish closely and inspect with optical measurement tools for desired results.
SMART CUT Diamond Discs can be used for precision sharpening and honing of cutting tools like carbide inserts or high-speed steel (HSS) tools. They offer the precision required for achieving sharp cutting edges. Select the appropriate grit size and follow recommended procedures for tool sharpening.
Yes, SMART CUT Diamond Discs are compatible with various types of grinding and polishing equipment, including both single and double-sided machines. They are versatile and can be adapted to different equipment configurations, making them suitable for a wide range of applications.
SMART CUT Diamond Discs can be used for grinding and polishing composite materials used in the aerospace industry, including carbon fiber-reinforced composites and composite panels. Proper grit selection and technique are essential for achieving the desired results on these materials while preserving their structural integrity.
Yes, SMART CUT Diamond Discs can be used for precision finishing of optical components with complex shapes, including aspheric or freeform lenses. Their versatility and precision make them suitable for achieving the required surface profiles and optical quality on such components. Careful control of pressure, speed, and fluid management is essential for optimal results.
To use SMART CUT Diamond Discs for removing burrs and sharp edges from metal or plastic parts in manufacturing processes:
- Select a disc with an appropriate grit size for the material and burr size.
- Set up the equipment with controlled pressure and feed rate.
- Gently deburr the edges by moving the part against the disc at the desired angle.
- Inspect the part for the removal of burrs and sharp edges and make adjustments as needed.
Yes, SMART CUT Diamond Discs can be employed for precision machining of ceramics and composites used in the dental industry for restorations and prosthetics. They provide the necessary precision and surface finish for dental applications. Follow recommended procedures for dental material processing.
Safety precautions for using SMART CUT Diamond Discs in industrial settings include:
- Wearing appropriate personal protective equipment (PPE) such as safety glasses, gloves, and respiratory protection if necessary.
- Ensuring proper ventilation to control dust and fumes.
- Using dust collection or wet methods to minimize airborne particles.
- Following manufacturer guidelines for equipment operation and maintenance.
- Monitoring and controlling equipment settings to prevent accidents.
- Providing training and awareness to personnel regarding the safe use of diamond discs.
SMART CUT Diamond Discs can be used for surface modification or texturing of materials to enhance adhesion or optical properties. By selecting the appropriate grit size and texture pattern, you can achieve desired surface characteristics for specific applications. Proper technique and control are crucial for achieving consistent results.
SMART CUT Diamond Discs can be utilized for deburring and edge rounding of metal components in industries like automotive and aerospace manufacturing. They are effective tools for removing sharp edges and achieving smoother, safer edges on metal parts. Follow recommended procedures and safety guidelines for edge rounding applications.
Yes, SMART CUT Diamond Discs can be used for precision lapping and polishing of optical flats and prisms used in interferometry and optical testing. They are well-suited for achieving the flatness and surface quality required for precise optical measurements. Follow recommended procedures and monitor the optical quality during the process.
SMART CUT Diamond Discs are available in various thicknesses to suit different applications. Typical thicknesses can range from a few millimeters to several millimeters. Custom thicknesses may also be available upon request to meet specific application requirements.
SMART CUT Diamond Discs can be used for precision machining of materials with high thermal conductivity, such as copper or aluminum. However, consider using specialized diamond discs designed for non-ferrous metals to achieve the best results, as these materials can be abrasive and may require specific diamond characteristics.
The recommended RPMs for SMART CUT Resin Bond Diamond Discs typically vary depending on the disc’s diameter and the specific material being processed. As a general guideline, start with a lower RPM setting and gradually increase it while monitoring the material removal rate and the disc’s performance. Consult the manufacturer’s guidelines and equipment specifications for precise RPM recommendations based on your application.
It is essential to use an appropriate coolant or lubrication when using SMART CUT Resin Bond Diamond Discs. Water-based coolants are commonly used because they dissipate heat effectively, prevent thermal damage to the diamond abrasive, and help flush away debris and swarf. Using the right coolant ensures a longer disc lifespan, improved material removal, and better surface finish. Always follow manufacturer recommendations for coolant selection and application.
The amount of pressure applied when using SMART CUT Resin Bond Diamond Discs depends on various factors, including material hardness, disc grit size, and the desired material removal rate. As a general guideline, start with light to moderate pressure and gradually increase it as needed while monitoring the disc’s performance. Excessive pressure can lead to premature wear and reduced disc life, so it’s crucial to find the right balance. Follow manufacturer guidelines and recommendations for specific pressure ranges based on your application.
SMART CUT Resin Bond Diamond Discs are typically designed to rotate in a clockwise direction. The rotation direction matters because it affects the cutting or grinding action and the quality of the finished surface. Ensure that the disc is mounted on your equipment in the correct orientation as specified by the manufacturer. Using the correct rotation direction helps achieve optimal results and extends disc life.
Dressing SMART CUT Resin Bond Diamond Discs is essential for maintaining their performance and longevity. Dressing involves removing glazing, worn abrasive particles, and debris from the disc’s surface to expose fresh diamond abrasives. You can dress the disc using a dressing stick or a diamond dressing tool. The frequency of dressing depends on the specific application and the disc’s condition. Regularly inspect the disc and dress it when you notice reduced cutting or grinding efficiency, uneven wear, or surface imperfections.
Cleaning SMART CUT Resin Bond Diamond Discs is crucial to prevent cross-contamination between different materials and maintain consistent performance. To clean the disc, follow these steps:
- Remove the disc from the equipment.
- Use a compatible cleaning solution or solvent, such as acetone or isopropyl alcohol.
- Gently scrub the disc surface with a soft brush or cloth to remove residue.
- Rinse the disc thoroughly with clean water.
- Allow the disc to dry completely before reuse.
Proper cleaning ensures that the disc remains free from contaminants and maintains its cutting or grinding efficiency. It also helps prevent material transfer between different workpieces, which is particularly important in applications where cleanliness is critical.
For specific recommendations on RPMs, coolants, pressure, rotation direction, dressing, and cleaning tailored to your application and material, consult the manufacturer’s guidelines or reach out to their technical support team for expert assistance.
Yes, SMART CUT Resin Bond Diamond Discs can be used with variable-speed equipment. Adjusting the RPM during operation can help optimize the cutting or grinding process. Here’s how to do it:
- Start with a lower RPM setting.
- Gradually increase the RPM while monitoring material removal and disc performance.
- Pay attention to the sound of the operation; a high-pitched whine may indicate excessive RPM.
- Adjust the RPM to achieve the desired material removal rate and surface finish.
- Refer to the manufacturer’s recommendations for RPM ranges based on disc diameter and material type.
It is advisable to avoid using coolants or lubricants that are incompatible with the materials being processed or that can adversely affect the disc’s resin bond. Some materials and applications may require specialized coolants or lubricants, so consult the manufacturer’s guidelines for compatibility and recommendations. Avoid using coolants or lubricants containing corrosive or abrasive substances that can damage the disc or compromise the quality of the workpiece.
Yes, it is possible to apply too much pressure when using SMART CUT Resin Bond Diamond Discs, and doing so can have adverse consequences. Excessive pressure can lead to:
- Premature wear and reduced disc lifespan.
- Increased heat generation, which may cause thermal damage to the diamond abrasive and the workpiece.
- Poor surface finish and the risk of material deformation.
- Higher energy consumption and potential equipment strain. To avoid these issues, start with light to moderate pressure and gradually increase it as needed while monitoring the disc’s performance. Follow manufacturer recommendations for specific pressure ranges based on your application.
SMART CUT Resin Bond Diamond Discs are typically designed to rotate in a clockwise direction. The rotation direction is essential because it can affect the cutting or grinding action and the quality of the finished surface. Using the correct rotation direction specified by the manufacturer helps achieve optimal results. While some applications may tolerate counterclockwise rotation, it’s generally recommended to follow the manufacturer’s guidelines to ensure consistent performance and extend disc life.
Signs that indicate SMART CUT Resin Bond Diamond Discs may need dressing include:
- Reduced cutting or grinding efficiency.
- Uneven wear patterns on the disc’s surface.
- Surface imperfections on the workpiece.
- Glazing or clogging of the diamond abrasive. Dressing should be performed as needed based on these signs. There is no fixed schedule for dressing, as it depends on the specific application, material, and disc condition. Regularly inspect the disc during operation, and when you observe any of these signs, initiate the dressing process to restore the disc’s cutting or grinding efficiency.
Failing to properly clean SMART CUT Resin Bond Diamond Discs after use can have several consequences:
- Cross-contamination between different materials, leading to compromised results and quality issues.
- Residue buildup on the disc’s surface, reducing cutting or grinding efficiency.
- Increased friction and heat generation, potentially damaging the diamond abrasive and the workpiece.
- Reduced disc lifespan due to abrasive particles and contaminants embedded in the disc. Improper cleaning can negatively impact subsequent operations by affecting the quality, accuracy, and efficiency of the work. To avoid these issues, always follow the recommended cleaning procedure, ensuring the disc is thoroughly cleaned and dried before reuse.
SMART CUT Resin Bond Diamond Discs can be used with ultrasonic or vibratory equipment for precision grinding and polishing. When using these setups, consider the following special considerations:
- Ensure compatibility between the disc and the equipment to avoid excessive vibration or stress.
- Pay attention to the frequency and amplitude settings to optimize the grinding or polishing action.
- Use the appropriate coolant delivery system to maintain consistent lubrication.
- Monitor the condition of the disc closely, as ultrasonic or vibratory equipment can introduce unique wear patterns.
While water-based coolants are commonly recommended for use with SMART CUT Resin Bond Diamond Discs, alternative cooling methods like air cooling or mist cooling can be used in certain applications. Here are some considerations:
- Air cooling may be suitable for dry grinding applications with reduced heat generation.
- Mist cooling can provide localized cooling, but it’s important to control mist delivery to prevent excessive moisture or residue buildup on the disc.
- Ensure that the cooling method you choose is compatible with the material being processed and does not compromise disc performance.
- Monitor disc temperature and performance when using alternative cooling methods to ensure effective heat control.
Pressure recommendations for SMART CUT Resin Bond Diamond Discs can vary depending on material hardness, grit size, and specific application requirements. While a universal pressure setting may work in some cases, it’s generally advisable to adjust the pressure based on the material and application. Light to moderate pressure is often recommended as a starting point and can be gradually increased as needed. Consult the manufacturer’s guidelines for pressure recommendations tailored to your specific material and application.
SMART CUT Resin Bond Diamond Discs are typically designed for clockwise rotation, as specified by the manufacturer. Reverse rotation is generally not recommended unless explicitly stated in the manufacturer’s guidelines. While there may be specific situations where reverse rotation could be advantageous, it’s important to consult with the manufacturer or technical support to ensure that it won’t compromise disc performance or safety.
Dressing SMART CUT Resin Bond Diamond Discs involves removing glazing, worn abrasive particles, and debris to maintain their cutting or grinding performance. Best practices for dressing include:
- Using a diamond dressing tool or dressing stick compatible with resin bond discs.
- Dressing the disc while it is stationary to avoid damage.
- Applying light pressure and making several passes to achieve uniform dressing.
- Dressing as needed based on signs of reduced efficiency or uneven wear. The dressing frequency can indeed vary based on the material type, as some materials generate more swarf or glazing than others. Regularly inspect the disc during operation and dress it as soon as you notice signs of reduced performance.
Failing to dress SMART CUT Resin Bond Diamond Discs regularly can have several consequences:
- Reduced cutting or grinding efficiency due to glazing and worn abrasive particles.
- Uneven wear patterns on the disc’s surface, leading to inconsistent results.
- Surface imperfections on the workpiece caused by uneven abrasion.
- Longer processing times and increased energy consumption. Improper dressing can negatively impact the quality, accuracy, and efficiency of the work. To avoid these issues, maintain a regular dressing schedule based on the specific application and material type.
Specific cleaning agents or solvents recommended for cleaning SMART CUT Resin Bond Diamond Discs can include acetone, isopropyl alcohol, or compatible cleaning solutions. It’s important to use chemicals that are safe for the disc’s resin bond and diamond abrasive. Exercise caution when handling cleaning agents, and follow safety guidelines and regulations regarding their use and disposal. Avoid using harsh chemicals that may damage the disc or pose health and environmental risks.
ACCESSORIES
Showing 1 – -1 of 16 results Showing all 16 results Showing the single result No results found
Sort by Name A – Z
Filters Sort results
Reset Apply
Image | Item No. | Description | Price | Quantity | Add to cart |
---|---|---|---|---|---|
Color: 5/8″-11″ thread. Fits into drill press chuck. Shank adapter threads into 5/8″-11″ female thread of diamond drill. Can be used with any other tool with 5/8″-11″ thread. | $26.72 | Max: Min: 1 Step: 1 | |||
Color: 5/8″-11″ thread. Fits into drill press chuck. Shank adapter threads into 5/8″-11″ female thread of diamond drill. Can be used with any other tool with 5/8″-11″ thread. | $22.46 | Max: Min: 1 Step: 1 | |||
1 Gallon Blue SMART CUT® General Materials Formula Synthetic Water Soluble Coolant | $99.81 | Max: Min: 1 Step: 1 | |||
1 Quart Blue SMART CUT® General Materials Formula Synthetic Water Soluble Coolant | $34.81 | Max: Min: 1 Step: 1 | |||
5 Gallons Blue SMART CUT® General Materials Formula Synthetic Water Soluble Coolant | $317.41 | Max: Min: 1 Step: 1 | |||
55 Gallons Blue SMART CUT® General Materials Formula Synthetic Water Soluble Coolant | $1,745.00 | Max: Min: 1 Step: 1 | |||
1/2″ x 1/2″ x 6.0″ White Recommended for coarser grits found in segment wheels, core drills, or Blanchard grinding. Excellent performance on 120 grit tools. | $8.65 | Max: Min: 1 Step: 1 | |||
1.0″ x 1.0″ x 6.0″ White Recommended for coarser grits found in segment wheels, core drills, or Blanchard grinding. Excellent performance on 120 grit tools. | $15.99 | Max: Min: 1 Step: 1 | |||
1/2″ x 1/2″ x 6.0″ White For use on diamond tools 150 to 220 Grit Size. | $8.65 | Max: Min: 1 Step: 1 | |||
1.0″ x 1.0″ x 6.0″ Black Recommended for use in Diamond Tools 150 Grit Size (mesh size) or finer. | $15.39 | Max: Min: 1 Step: 1 | |||
2.0″ x 2.0″ x 6.0″ Black Recommended for use in Diamond Tools 150 Grit Size (mesh size) or finer. | $39.47 | Max: Min: 1 Step: 1 | |||
1.0″ x 1.0″ x 6.0″ Black Recommended for coarser grits found in segment wheels, core drills, or Blanchard grinding. Excellent performance on 120 grit tools. | $15.99 | Max: Min: 1 Step: 1 | |||
2.0″ x 2.0″ x 6.0″ Black Recommended for coarser grits found in segment wheels, core drills, or Blanchard grinding. Excellent performance on 120 grit tools. | $39.47 | Max: Min: 1 Step: 1 | |||
$154.87 | Max: Min: 1 Step: 1 | ||||
$154.87 | Max: Min: 1 Step: 1 | ||||
$235.00 | Max: Min: 1 Step: 1 |
USAGE RECOMENDATION
- Safety Precautions:
- Prioritize safety by wearing appropriate personal protective equipment (PPE), including safety glasses, gloves, and respiratory protection if necessary.
- Ensure proper ventilation to control dust and fumes generated during operation.
- Equipment Setup:
- Use a compatible grinding or polishing machine equipped with the appropriate spindle or tool holder.
- Confirm that the machine is in good working condition, with properly aligned and balanced components.
- Disc Selection:
- Choose the right SMART CUT Resin Bond Diamond Disc based on your application’s specific requirements, including disc diameter, grit size, and profile.
- Refer to the manufacturer’s guidelines for disc selection tailored to your material and application.
- RPM (Revolutions Per Minute):
- Determine the recommended RPM range for your SMART CUT Resin Bond Diamond Disc based on its diameter and the material being processed.
- Start at the lower end of the recommended RPM range and gradually increase the speed while monitoring performance.
- Coolant/Lubrication:
- Use an appropriate coolant or lubrication system to control temperature, flush away debris, and extend disc life.
- Water-based coolants are commonly recommended; consult the manufacturer’s guidelines for specific recommendations.
- Mist cooling or air cooling can be considered for dry grinding applications, but ensure proper control and monitoring to prevent overheating.
- Pressure:
- Apply the appropriate amount of pressure based on the material type, disc grit size, and desired material removal rate.
- Start with light to moderate pressure and adjust as needed during the operation.
- Avoid excessive pressure, which can lead to premature wear and reduced disc life.
- Rotation Direction:
- SMART CUT Resin Bond Diamond Discs are typically designed for clockwise rotation. Ensure the disc is mounted correctly as specified by the manufacturer.
- Dressing:
- Regularly dress the disc to remove glazing, worn abrasive particles, and debris from the disc’s surface.
- Use a diamond dressing tool or dressing stick compatible with resin bond discs.
- Dress the disc while it is stationary to prevent damage.
- Follow manufacturer recommendations for dressing frequency based on your application.
- Cleaning:
- After use, remove the disc from the machine.
- Clean the disc using a compatible cleaning solution or solvent, such as acetone or isopropyl alcohol.
- Gently scrub the disc surface with a soft brush or cloth to remove residue.
- Rinse the disc thoroughly with clean water.
- Allow the disc to dry completely before storage.
- Inspection and Maintenance:
- Regularly inspect the disc for signs of wear, damage, or uneven wear patterns.
- Check for disc flatness and alignment.
- Inspect the disc mounting system for secure attachment.
- Maintain proper machine alignment and balance.
- Material Handling:
- Handle delicate or brittle materials with care to avoid accidental damage during loading, unloading, or operation.
- Secure workpieces firmly to prevent movement or vibration during grinding or polishing.
- Documentation and Record-Keeping:
- Maintain records of disc usage, including RPM settings, coolant types, pressure levels, and dressing frequency.
- Document any issues or anomalies observed during operation.
- Material Compatibility:
- Confirm that the material you intend to grind or polish is compatible with resin bond diamond discs. Some materials may require specialized diamond discs designed for their unique properties.
- Workpiece Fixturing:
- Ensure that workpieces are securely fixtured or held in place to prevent movement or vibration during the grinding or polishing process. Unwanted vibrations can impact surface quality.
- Pre-Grinding Steps:
- For materials with significant surface imperfections or roughness, consider initial pre-grinding or lapping steps using coarser grit SMART CUT Diamond Discs before moving to finer grits for polishing.
- Material Cleaning:
- Before grinding or polishing, ensure that the material surface is clean and free from contaminants, oils, or residues. Cleaning the workpiece can prevent disc contamination and maintain consistent results.
- Coolant Management:
- Continuously monitor coolant levels and quality during operation. Maintain a consistent and adequate coolant flow to prevent overheating and maintain consistent lubrication.
- Quality Control:
- Periodically inspect the quality of the ground or polished surfaces using appropriate measurement tools or inspection equipment. This ensures that the desired surface finish and dimensional accuracy are achieved.
- Grit Progression:
- Follow a systematic grit progression sequence, starting with coarser grits for material removal and gradually progressing to finer grits for polishing. This helps achieve the desired surface finish.
- Material Surface Preparation:
- Before using SMART CUT Resin Bond Diamond Discs, ensure that the material surface is properly prepared. This may involve cutting, sawing, or shaping the material to the desired dimensions to minimize material removal during grinding and polishing.
- Surface Cleaning During Operation:
- Periodically clean the surface being worked on during grinding and polishing to remove loose abrasive particles and debris. This practice helps maintain consistent material removal rates and surface finish quality.
- Material Hardness Consideration:
- Be aware of the hardness of the material you are working with and select the appropriate SMART CUT Resin Bond Diamond Disc with a grit size and concentration suited to that hardness. Harder materials may require finer grit sizes.
- Material Handling Techniques:
- Develop proper material handling techniques to avoid introducing scratches, dents, or other defects to the workpiece during loading, unloading, or positioning. Use soft materials or protective covers if needed.
- Tool Balancing:
- Ensure that the grinding or polishing tool is balanced correctly on the machine spindle. Imbalanced tools can lead to uneven wear and vibration, affecting the quality of the finished surface.
- Monitoring Disc Wear:
- Regularly inspect the condition of the SMART CUT Resin Bond Diamond Disc during operation. If you notice uneven wear, glazing, or decreased performance, consider dressing or replacing the disc as needed.
- Material Fixturing Alternatives:
- For complex or irregularly shaped workpieces, explore custom fixturing or holding solutions that provide stability and prevent movement during grinding and polishing.
Advantages
- Flexible Resin Bonded Diamond Disc.
- High Concentration of Diamond Mixed in Resin.
- Magnetic Backing
- Fast Grinding
- Removes Chips and Scratches
- Replaces Cork / Pumice
- Needs Only Water for Coolant
- Center Hole or No Hole
- Long Lasting
- Takes place of Cork with Pumice
Features
- Universal Application: SMART CUT® Resin Bond discs are engineered to tackle a wide array of materials, including metals, ceramics, refractories, cement, geological rocks, glass, optics, composites, and more. No matter the material, our diamond discs deliver outstanding results.including lapping, grinding, and polishing. Their versatility and quality make them suitable for use in research, manufacturing, construction, and many other fields.
- Highest Quality Diamond Particles: We use only the highest quality diamonds and raw materials in our manufacturing process. This commitment to excellence ensures that our discs provide consistent, reliable performance with exceptional longevity.
- Rigorous Quality Control: Maintaining the highest quality standards is paramount to us. Our manufacturing process incorporates sophisticated measurement and inspection equipment, guaranteeing the utmost precision and uniformity in every disc we produce.
- Custom Manufacturing: We understand that each project has its unique requirements. SMART CUT® Resin Bond Diamond Discs can be customized to accommodate your specific needs, including inside diameter (ID) hole size or no hole, diamond mesh size/grit sizes from coarse (40 grit) to ultra-fine (1 micron), and a variety of backing options such as magnetic, adhesive PSA, no backing, or velcro.
- Wide Range of Sizes:SMART CUT® Resin Bond Discs are available in diameters ranging from 6 inches to an impressive 30 inches (150mm to 762mm). This versatility allows you to select the perfect size for your machinery and application.
- Versatile Mounting Options: Whether you prefer magnetic, adhesive PSA, no backing, or velcro, our discs can be configured to your specific machine setup. This adaptability ensures ease of use with your existing equipment.
- Improved Efficiency: SMART CUT® Resin Bond discs are designed for both fine and coarse grinding/polishing, eliminating the need for multiple discs or tools. This streamlines your workflow and increases efficiency, saving you valuable time and effort.
- Improve Surface Finish: Achieve superior surface finishes with SMART CUT® Resin Bond Diamond Discs. Their precision and uniformity ensure that your workpiece will exhibit a mirror-like finish, enhancing both aesthetics and functionality.
- Reduced Material Waste: The exceptional material removal capabilities of these discs minimize waste during the grinding and polishing process. This not only saves materials but also reduces the overall cost of your projects.
- Long Life: Thanks to the use of high-quality diamonds and raw materials, SMART CUT® Resin Bond Diamond Discs exhibit exceptional durability. This longevity means fewer replacements, reducing downtime and maintenance costs.
6130500, 6130900, 6131800, 6132300, 6690500, 6690900, 6691800, 6692300, 6130100, 6130220, 6130325, 6130600, 6131200, 6133000, 6138000, 6140900, 6141800, 6142300, 6150500, 6150900, 6151800, 6152300, 6710500, 6710900, 6711800, , 6712300, 6700500, 6700900, 6701800, 6702300, 6140100, 6140220, 6140325, 6140600, 6141200, 6143000, 6148000, 6160500, 6160900, 6161800, 6162300, 6170500, 6170900, 6171800, 6172300, 6180500, 6180900, 6181800, 6182300, 6190500, 6190900, 6191800, 6192300, 6200500, 6200900, 6201800, 6202300, 6140500
Showing 1 – 57 of 57 results Showing all 57 results Showing the single result No results found
Sort by Price low to high
Filters Sort results
Reset Apply
Image | Item No | Outside Diameter | Backing Type | Inside Diameter | Mesh/Color | Quantity | Get Quote |
---|---|---|---|---|---|---|---|
6" (152.4mm) | Adhesive Backing | No Hole | 500/Blue | Max: Min: 1 Step: 1 | |||
6" (152.4mm) | Adhesive Backing | No Hole | 900/Brown | Max: Min: 1 Step: 1 | |||
6" (152.4mm) | Adhesive Backing | No Hole | 1800/Red | Max: Min: 1 Step: 1 | |||
6" (152.4mm) | Adhesive Backing | No Hole | 2300/Green | Max: Min: 1 Step: 1 | |||
6" (152.4mm) | Magnetic Backing | No Hole | 500/Blue | Max: Min: 1 Step: 1 | |||
6" (152.4mm) | Magnetic Backing | No Hole | 900/Brown | Max: Min: 1 Step: 1 | |||
6" (152.4mm) | Magnetic Backing | No Hole | 1800/Red | Max: Min: 1 Step: 1 | |||
6" (152.4mm) | Magnetic Backing | No Hole | 2300/Green | Max: Min: 1 Step: 1 | |||
6" (152.4mm) | Adhesive Backing | No Hole | 100/Black | Max: Min: 1 Step: 1 | |||
6" (152.4mm) | Adhesive Backing | No Hole | 220/Purple | Max: Min: 1 Step: 1 | |||
6" (152.4mm) | Adhesive Backing | No Hole | 325/Brown | Max: Min: 1 Step: 1 | |||
6" (152.4mm) | Adhesive Backing | No Hole | 600/Red | Max: Min: 1 Step: 1 | |||
6" (152.4mm) | Adhesive Backing | No Hole | 1200/Blue | Max: Min: 1 Step: 1 | |||
6" (152.4mm) | Adhesive Backing | No Hole | 3000/Orange | Max: Min: 1 Step: 1 | |||
6" (152.4mm) | Adhesive Backing | No Hole | 8000/Yellow | Max: Min: 1 Step: 1 | |||
8" (200mm) | Adhesive Backing | No Hole | 900/Brown | Max: Min: 1 Step: 1 | |||
8" (200mm) | Adhesive Backing | No Hole | 1800/Red | Max: Min: 1 Step: 1 | |||
8" (200mm) | Adhesive Backing | No Hole | 2300/Green | Max: Min: 1 Step: 1 | |||
8" (200mm) | Adhesive Backing | With Hole (1/2") | 500/Blue | Max: Min: 1 Step: 1 | |||
8" (200mm) | Adhesive Backing | With Hole (1/2") | 900/Brown | Max: Min: 1 Step: 1 | |||
8" (200mm) | Adhesive Backing | With Hole (1/2") | 1800/Red | Max: Min: 1 Step: 1 | |||
8" (200mm) | Adhesive Backing | With Hole (1/2") | 2300/Green | Max: Min: 1 Step: 1 | |||
8" (200mm) | Magnetic Backing | No Hole | 500/Blue | Max: Min: 1 Step: 1 | |||
8" (200mm) | Magnetic Backing | No Hole | 900/Brown | Max: Min: 1 Step: 1 | |||
8" (200mm) | Magnetic Backing | No Hole | 1800/Red | Max: Min: 1 Step: 1 | |||
8" (200mm) | Magnetic Backing | No Hole | 2300/Green | Max: Min: 1 Step: 1 | |||
8" (200mm) | Magnetic Backing | With Hole (1/2") | 500/Blue | Max: Min: 1 Step: 1 | |||
8" (200mm) | Magnetic Backing | With Hole (1/2") | 900/Brown | Max: Min: 1 Step: 1 | |||
8" (200mm) | Magnetic Backing | With Hole (1/2") | 1800/Red | Max: Min: 1 Step: 1 | |||
8" (200mm) | Magnetic Backing | With Hole (1/2") | 2300/Green | Max: Min: 1 Step: 1 | |||
8" (200mm) | Adhesive Backing | No Hole | 100/Black | Max: Min: 1 Step: 1 | |||
8" (200mm) | Adhesive Backing | No Hole | 220/Purple | Max: Min: 1 Step: 1 | |||
8" (200mm) | Adhesive Backing | No Hole | 325/Brown | Max: Min: 1 Step: 1 | |||
8" (200mm) | Adhesive Backing | No Hole | 600/Red | Max: Min: 1 Step: 1 | |||
8" (200mm) | Adhesive Backing | No Hole | 1200/Blue | Max: Min: 1 Step: 1 | |||
8" (200mm) | Adhesive Backing | No Hole | 3000/Orange | Max: Min: 1 Step: 1 | |||
8" (200mm) | Adhesive Backing | No Hole | 8000/Yellow | Max: Min: 1 Step: 1 | |||
12" (304.8mm) | Magnetic Backing | With Hole (1") | 500/Blue | Max: Min: 1 Step: 1 | |||
12" (304.8mm) | Magnetic Backing | With Hole (1") | 900/Brown | Max: Min: 1 Step: 1 | |||
12" (304.8mm) | Magnetic Backing | With Hole (1") | 1800/Red | Max: Min: 1 Step: 1 | |||
12" (304.8mm) | Magnetic Backing | With Hole (1") | 2300/Green | Max: Min: 1 Step: 1 | |||
16" (406.4mm) | Magnetic Backing | With Hole (1") | 500/Blue | Max: Min: 1 Step: 1 | |||
16" (406.4mm) | Magnetic Backing | With Hole (1") | 900/Brown | Max: Min: 1 Step: 1 | |||
16" (406.4mm) | Magnetic Backing | With Hole (1") | 1800/Red | Max: Min: 1 Step: 1 | |||
16" (406.4mm) | Magnetic Backing | With Hole (1") | 2300/Green | Max: Min: 1 Step: 1 | |||
18" (457.2mm) | Magnetic Backing | With Hole (1") | 500/Blue | Max: Min: 1 Step: 1 | |||
18" (457.2mm) | Magnetic Backing | With Hole (1") | 900/Brown | Max: Min: 1 Step: 1 | |||
18" (457.2mm) | Magnetic Backing | With Hole (1") | 1800/Red | Max: Min: 1 Step: 1 | |||
18" (457.2mm) | Magnetic Backing | With Hole (1") | 2300/Green | Max: Min: 1 Step: 1 | |||
24" (609.6mm) | Magnetic Backing | With Hole (1") | 500/Blue | Max: Min: 1 Step: 1 | |||
24" (609.6mm) | Magnetic Backing | With Hole (1") | 900/Brown | Max: Min: 1 Step: 1 | |||
24" (609.6mm) | Magnetic Backing | With Hole (1") | 1800/Red | Max: Min: 1 Step: 1 | |||
24" (609.6mm) | Magnetic Backing | With Hole (1") | 2300/Green | Max: Min: 1 Step: 1 | |||
29.5" (749.3mm) | Magnetic Backing | With Hole (1") | 500/Blue | Max: Min: 1 Step: 1 | |||
29.5" (749.3mm) | Magnetic Backing | With Hole (1") | 900/Brown | Max: Min: 1 Step: 1 | |||
29.5" (749.3mm) | Magnetic Backing | With Hole (1") | 1800/Red | Max: Min: 1 Step: 1 | |||
29.5" (749.3mm) | Magnetic Backing | With Hole (1") | 2300/Green | Max: Min: 1 Step: 1 |
SMART CUT® Resin Bond Diamond Discs are used for large variety of applications, industries, lapping, grinding & polishing machines. Diamond Discs are available from 6" to 30" (150mm to 762mm) in Diameter. Diamond discs can be produced with any inside diameter (ID) hole size or no hole. Diamond mesh size/grit sizes available from as coarse as 40 grit to fine as 1 micron. Diamond Discs can be placed on either magnetic or adhesive PSA backing, no backing, and velcro.
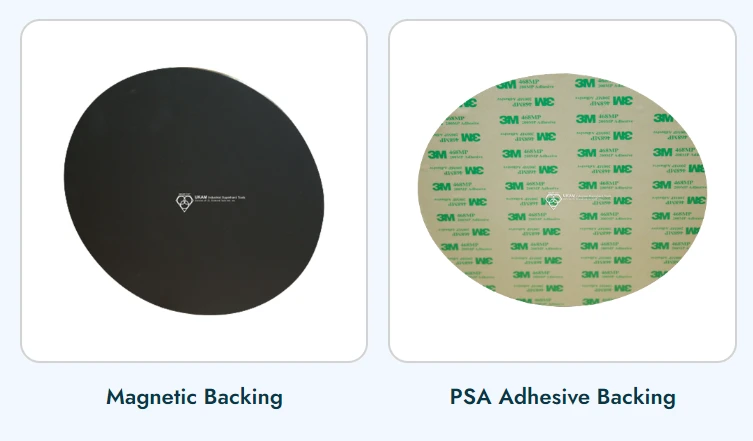
How SMART CUT® Bond Works?
Step 1
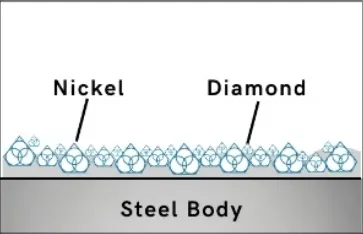
Sharpest And Finest Quality Diamonds
Diamonds or CBN Crystals are activated only at the exposed layer. As Bond Matrix layer begin to wear out, diamonds in a new Bond Matrix layer are immediately activated, substituting the already used up diamond layer. The SMART CUT® Bond Diamond Bond makes sure every diamond is in the right place. and at the right time, working where you need it most.
Step 2
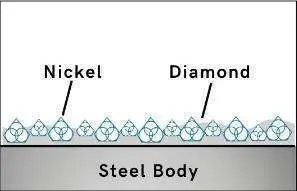
Diamonds or CBN Crystals
The newly exposed diamonds don’t effect diamonds already working on the material. Unlike many other diamond bonds, diamonds in a SMART CUT® remains sharp and grow sharper with each cut, prolonging product life and consistent performance.
Step 3
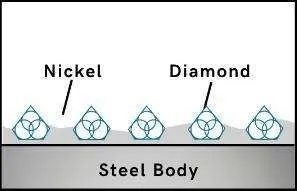
Advanced Formulated Open Diamond Bond Design
This advanced formulated open diamond bond design insures minimal chipping, fast
cut, constant speed of cut, minimal cutting noise, and most important of all, consistent performance.
About Nickel Bond (Electroplated) Tools
Electroplated (nickel bond) diamond products usually have a single layer of diamonds, held by a tough durable nickel alloy. Nickel is frequently used as a base for plating diamond. Because of its excellent strength, toughness and flexibility during the plating process. Electroplated diamond products are able to retain their original shape and dimensions thought their working life. Unlike sintered (meal bond) or resin bond diamond products, where diamond particles are buried in bond and held together by metal or resin binder deep inside.
Electroplating allows diamond particles to protrude from the bond matrix, providing a free, faster cutting action with minimum heat generation.
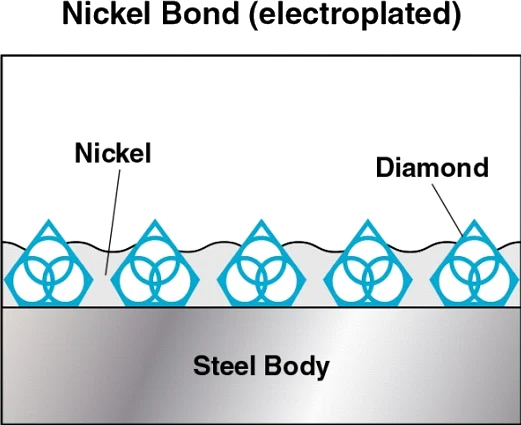
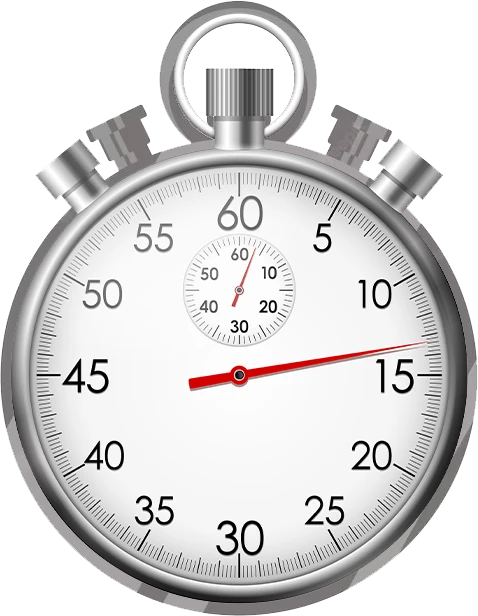
Faster & Freer Action
Diamond drills made utilizing SMART CUT® technology are much more aggressive than your conventional Tools. They can cut faster, while still leaving behind a smooth finish free of material deformation.
Longer Life
In most cases tools manufactured utilizing SMART CUT® technology, will outlast other conventional nickel bonded diamond CBN drills. SMART CUT® diamond CBN tools are more sturdy than tools manufactured with conventional technologies. They are capable to retain their form and bond configuration all the way through the tools life.
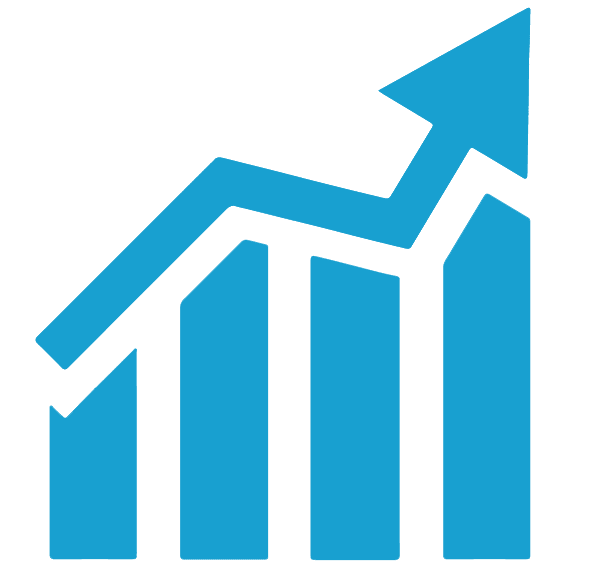
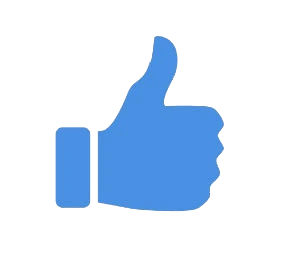
More Consistent Performance
SMART CUT® Multi Layered Electroplated diamond cutting blade three diamond layers impregnated inside the bond matrix. Unlike Many Other blade Types, they wear evenly, and are known for their consistency. You will get consistent cutting speed, and overall consistent performance, with minimum amount of dressing even on the hardest to cut materials
Manufactured Using The Highest Quality Raw Materials
Only the highest quality synthetic diamonds and raw materials are used in the manufacturing process. The highest quality standards and product consistency is maintained, using sophisticated inspection and measurement equipment.
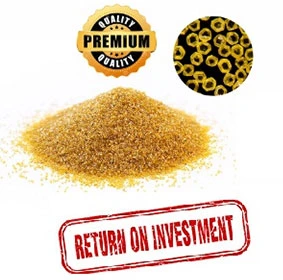
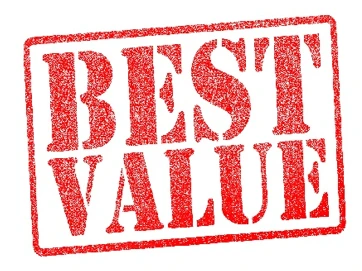
Best Performance & Value on the Market
SMART CUT® Multi Layered Electroplated Diamond Drills are the best investment you can make! Although they may cost more than electroplated (nickel bond), Diamond Drills. They will more than pay for themselves in terms of overall performance and provide best Return on Investment.
Why Choose Us?
Optimize your application to ultimate level of efficiency
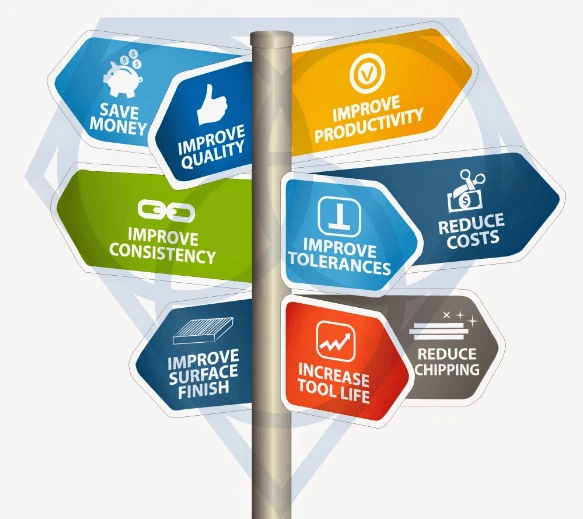
- Unmatched Selection For Many Applications
- Unmatched Technical Support & Expertise
- Superior Quality & Consistency
- Super Technology & innovation
- Immediate Worldwide Delivery
- American Based Manufacturer
-
Custom
Manufacturing - Better Value manufacturer Direct Price
Why Work With Us?
Read More
We produce diamond consumables for some of the leading world OEM manufacturers. We offer Manufacturers Direct Prices
We have the largest variety of diamond & cbn wafering blades available in stock. As well as large inventory of diamond & abrasive consumables. We also custom manufacture diamond and cbn tools, consumables and machines to better fit customer specific needs. Just about any tools & consumables can be designed and manufactured per client drawing or specificrtion
WE ARE A PARTNER IN YOUR SUCCESS
Our proprietory diamond chemistory , precision , manufacturing metods , quality control methods allow us to control and regulate the dozens of variables to that affect consumable life , quality , and consistency.
The more you understand about what we can do for you the better our partnership will be. Here you will find most comprehensive source of information and optimizing and improving your cutting , drilling , grinding and polishing on the web. find everything you ever wanted to know about diamond tools.
AMERICAN MANUFACTURER
"ONE OF THE MOST EXPERIENCED COMPANIES IN THE INDUSTRY"
Save Money Save up to 650%
COMPARE TO: BUEHLER , STRUERS , LECO & MANY OTHERS
Large Inventory & Custom Manufacturing
Umatched Technical Support
Developing close ties with our customers is the foundation of our business. At the core of
our company is a team of world class engineers, knowledgeable customer service personnel here to serve you. Whether is designing or manufacturing a special solution. We will go out of our way to optimizing your process to ultimate level of efficiency
Superior Quality & Consistency
EXPECT MORE FROM YOUR TOOLS
Comprehensive Source Of Information For Sample Preparation
Advanced Technology
As one of the few remaining independent U.S.Diamond Tool & machine builders. We have the experience & tradition to help you remain at frontier of technology Our experience has been further enhanced by acquiring assets and processes from some of the oldest American tool
manufacturers, along with their decades of experience and R& D. This has positioned us as one of the most experienced companies in the industry .Depend on us to bring you technology of tomorrow today.
Experience Makes All The Differences
Over the years we have worked with some of the leading Fortune 500 companies , thousands of universities , government and private research labs , and small organisations. We have made thousands of custom tools , built custom machines , work-holding fixtures , etc for hundreds of applications. Many of our staff members have been working in their respective fields for over 50 years and have gained a wealth of knowledge over the years
Let Us Help You
Related Products
SMART CUT® Resin Bond Diamond Discs for Grinding & Polishing Machines
SMART CUT® Metal Bond Diamond Discs for Large Grinding / Polishing Machines
Resin Bond Diamond Discs
Resin Bond Discs are designed removal of material/sample scratches, chips. high spots, & as well as pre-polishing on a larger variety of materials. Using a propriety technique, a high concentration of premium diamond is loaded onto each disc to provide an extremely aggressive grinding rate yet leaves an exceptionally smooth surface finish. Each disc is color coded to easily determine the diamond size of the disc. These resin bond diamond discs are guaranteed to out-perform many cloth polishing discs using loose conventional abrasive or diamond compound/slurry finishing systems. Depending on the application and process these discs on average will last for 100-200 parts/samples & maintain consistent level of performance. These are perfect for hard materials such as metals, ceramics, refractories, cement, geological rocks, glass, optics, composites, and many other materials 35 and up Rockwell C scale of hardness. All discs come with a 3M pressure-sensitive adhesive backing that bonds to backing plates, or with magnetic backing to attach to steel plates. Must be used with coolant. Not recommended for heavy stock material removal
DIAMOND LAPS
UKAM Industrial Superhard Tools manufactures & offers a large variety of diamond laps & polishing discs. Below you will find information, specifications & prices on all laps & polishing discs we offer for this application. Contact us for volume pricing. We can also produce any custom diamond wheel per your specification. Contact us Today for Free Quote!
Recently Viewed Products

ARE YOU USING RIGHT TOOLS
FOR YOUR APPLICATION?
LET US
HELP YOU
HAVING ISSUES WITH
YOUR CURRENT TOOLS?
Knowledge Center
02
Jun
How to properly use Diamond Tools
UKAM Industrial Superhard Tools manufactures precision diamond tools for a large variety of applications, materials, and industries.
Share this Article with Friend or Colleague
Metal Bonded Diamond Tools are “impregnated” with diamonds. This means that selected...
02
Jun
Why use diamond
Diamond is the hardest material known to man kind. When used on diamond/tools, diamond grinds away material on micro (nano) level. Due to its hardness Diamond will work all types of materials from...
02
Jun
Selecting Right Wafering Blade for your application
Cross Sectioning is the first and most important step in the sample preparation process. Getting the best results involves obtaining a smooth surface finish, minimum chipping, material deformation, without sacrificing cutting speed. Today, most laboratories, work with dozens...
02
Jun
Wafering Blade Usage Recommendations
The wafering/sectioning blade itself is only a small factor in your sectioning operation. Successful wafering/sectioning operation is both an art & science. Requiring proper use and understanding of selecting the right diamond wafering/sectioning...
02
Jun
Wafering Blade Case Studies
Step by step guide on how to properly use and care for your diamond drills. Selecting the right diamond drill/diamond drill bit parameters, often involves a trial and error process. Many which can be avoided...
- Unmatched Selection For Many Applications
- Superior Quality & Consistency
- Immediate Worldwide Delivery
- Technical Support & Expertise
- American Based Manufacturer
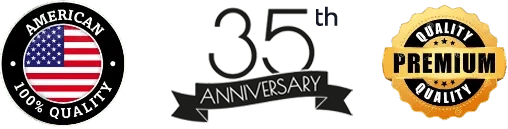

- Different Product
- Different Technology
- Different Company
- Expect MORE from your tools
Let Us HELP You!
Subscribe To Our Newsletter
Signup for email offers, updates, and more
Contact Us
- 25205 & 25201 Avenue Tibbits Valencia CA 91355 USA
-
Phone : (661) 257-2288
FAX : (661) 257 -3833 - lel@ukam.com
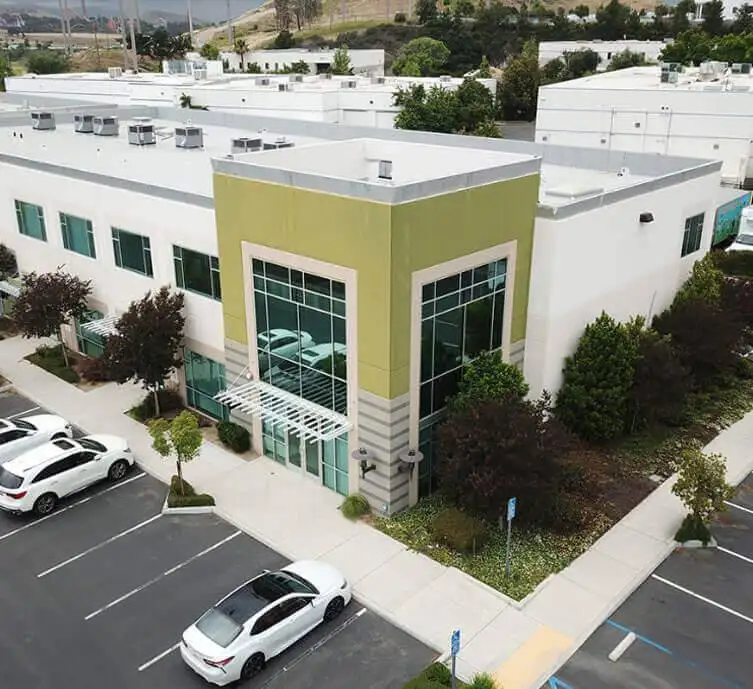
UKAM Industrial Superhard Tools is a U.S. High Technology, Specialty Diamond Tool & Equipment manufacturer. We specialize in producing ultra thin, high precision cutting blades, precision cutting machines diamond drills, diamond micro tools, standard & custom advanced industrial diamond tools and consumables.
- 25205 & 25201 Avenue Tibbits Valencia CA 91355 USA
-
Phone : (661) 257-2288
FAX : (661) 257 -3833 - lel@ukam.com
- 25205 & 25201 Avenue Tibbits Valencia CA 91355 USA
-
Phone : (661) 257-2288
FAX : (661) 257 -3833 - lel@ukam.com
DIAMOND TOOLS BY BOND
EQUIPMENT
KNOWLEDGE CENTER
OUR PRODUCTS
COMPANY
CUSTOMER SERVICE
Shipping Methods


Safe & Secure Payments

© Copyright 1990-2025. UKAM Industrial Superhard Tools – Terms of Use