This guide covers the best practices for using silicon carbide paper in metallography. It includes tips on proper grit progression, optimizing pressure and speed settings, preventing common issues, and extending the life of the abrasive. The article will take you through each step, from selecting the right silicon carbide paper to its disposal, while also troubleshooting some of the most frequent problems. Whether you're in a research lab or an industrial environment, adhering to these guidelines will enhance grinding performance, preserve sample integrity, and guarantee high-quality metallographic results.
1. Select the Right Silicon Carbide Paper Specification for your machine & application
Silicon carbide paper used for metallography and sample preparation is available in various specifications, including different diameters, backing types, thicknesses, and options for wet or dry applications. It's essential to first ensure that the silicon carbide paper is compatible with your polishing equipment for effective use. Determine if the paper is intended for manual hand-polishing or machine-operated polishers, as this will influence your choice of paper, adhesive, and grit. Always check the manufacturer's recommendations for abrasive papers to achieve optimal performance with your polishing equipment. Additionally, consider the type of adhesive required; some papers feature pressure-sensitive adhesives for easy application and removal, which is perfect for automatic polishers that need quick changes between grits. Others may require a more permanent adhesive for longer-term use. Lastly, make sure that the size and shape of the silicon carbide paper fit your equipment to avoid issues like poor attachment, uneven wear, and potential damage.
2. Prepare to Set up
Environment Setup
Setting up the right environment is fundamental for successful use of silicon carbide paper. The area where the polishing or grinding is to take place must be kept clean and free from contaminants. This is especially important when working with high-purity materials or in applications that demand a high degree of precision. Any dust, debris, or residual material from previous operations could impact the abrasive effectiveness of the silicon carbide paper and potentially contaminate the sample, leading to inaccurate results. Having controlled environment will help ensure the integrity of both the abrasive paper and the material being processed, which is important for achieving consistent results.
Check your Grinding / Polishing Machine
Before starting the polishing process, it is important to carefully check all equipment. This includes making sure all devices are clean, working correctly, and properly set up. This step is important for both manual and automated systems, as accuracy and consistency rely on the equipment working within set limits. Proper setup ensures the equipment will work as it should, giving steady pressure, speed, and movement, which are key for getting the right surface finish. Also, checking that the equipment is clean helps avoid mixing different materials or types of silicon carbide paper, which can change the surface quality of the sample being prepared.
3. Mounting and Installation
Properly Attach Silicon Carbide Disc
Achieving proper adhesion of the silicon carbide paper to the platen or holder is critical for effective polishing or grinding. The paper needs to be tightly fixed to avoid moving during use, as this can change how evenly material is removed and might lead to poor finishing or damage to the item. To do this, it's important to use glues made for abrasive papers. These glues should keep the paper steady during the polishing but also let you easily take off and replace the paper without leaving any mess that could spoil the base or the new sheet. Depending on the setup, this might mean using spray glues, sticky-backings, or magnetic systems that match the needs of the polishing tools and materials.
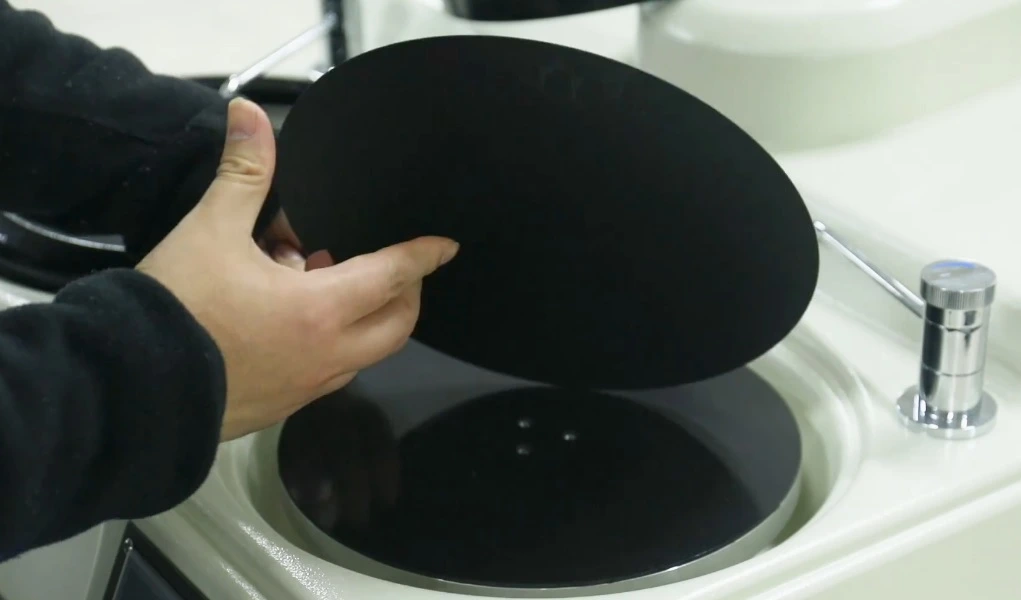
Insure & Check for Flatness
The next important step is to ensure that the silicon carbide paper is laid down in its utmost flattest state on the mounting surface. Any flatness deviations, in the form of wrinkles, folds, or air bubbles trapped underneath the paper, would cause uneven contact with the sample. This unevenness can lead to inconsistent material removal rates, scratch patterns that are difficult to polish out, or sometimes even physical damage to the fragile samples in their processing. To promote as much flatness as possible, the paper should be carefully laid on the platen from one edge and smoothed along the length of the paper toward the opposite edge in order to prevent the entrapment of air. For larger sheets and stiffer backings, a roller or some other device may be useful to apply uniform pressure so as to fully adhere the paper across the entire surface.
4. Polishing Process
Starting to Use
The initial set of conditions must be established in a manner that enables effective and efficient material removal. Select the grit size of the silicon carbide paper according to the present condition of the sample's surface. In cases where the surface shows wide roughness or is markedly imperfect, performance will be better when coarser grit is selected from the very beginning to allow for the fast reduction of high spots and smoothing of rough areas without undue wear on finer grits, which are not designed for heavy material removal. Progressive fine-gritting should occur as the surface becomes smooth enough to the desired finish.
Wet vs Dry Grinding
When preparing metallographic samples, the choice between wet or dry grinding with silicon carbide discs plays a crucial role in the quality of the analysis and the preservation of the sample's integrity. Each method offers distinct advantages and potential downsides. Wet grinding utilizes water as a coolant, which is beneficial as it helps prevent overheating of both the disc and the sample, thereby avoiding alterations to the material's properties or damage to its microstructure.
Moreover, water aids in binding the dust generated during grinding, which reduces airborne particles that could pose health risks and maintain cleanliness in the lab. Typically, wet grinding yields a smoother surface since the water minimizes friction and cools the surface, leading to fewer scratches and defects. However, it does require extra setup for water feeds and entails more cleanup due to the formation of slurry.
Additionally, if certain materials are not dried properly, there is a risk of corrosion or rust, and the grinding equipment may need more frequent maintenance due to constant exposure to water. Conversely, dry grinding is often faster and more straightforward, as it eliminates the need for water feeds and extensive cleanup, making it ideal for situations where time is of the essence.
The absence of water also means there’s no risk of rust on the equipment or samples, which is crucial for materials prone to oxidation. However, this method does have its drawbacks, such as increased airborne dust, which can be a health hazard and requires proper ventilation. Furthermore, without the cooling effect of water, there is a greater chance of overheating the sample, which can impact its microstructure and lead to more wear on the grinding disc. Dry grinding may also produce a rougher finish due to heightened friction and heat, particularly with harder materials.
The decision to use wet or dry grinding typically hinges on the specific needs of the material analysis and the characteristics of the sample being prepared. Wet grinding might be the better choice for heat-sensitive materials or those that produce a lot of dust, even though it requires more setup. On the other hand, for quick tasks or materials that don't react well to water, dry grinding could be more suitable. Recognizing these factors is essential for selecting the appropriate method to achieve effective material preparation and reliable results.
Table comparing the characteristics of wet and dry grinding with silicon carbide discs
Attribute |
Wet Grinding |
Dry Grinding |
---|---|---|
Cooling Effect |
Prevents overheating, keeps the sample cool |
None, higher risk of overheating |
Dust Management |
Water binds dust, reducing airborne particles |
Increased airborne dust, requires ventilation |
Surface Finish |
Produces a smoother surface, minimizing defects |
Potentially rougher due to increased friction and heat |
Setup and Cleanup |
Requires setup for water feeds, more extensive cleanup |
Minimal setup and cleanup required |
Risk of Corrosion |
Possible if not dried properly |
No risk of rust or corrosion |
Equipment Maintenance |
May require more frequent due to water exposure |
Less frequent, no water exposure |
Operational Speed |
Can be slower due to setup and cleanup |
Faster as no water setup is needed |
Risk of Overheating |
Low due to cooling effect |
Higher due to lack of cooling |
Suitability for Quick Jobs |
Less suitable due to preparation and cleanup demands |
More suitable for quick tasks |
Water or Coolant Application
In wet polishing, the application of water or a suitable coolant is essential to maintain the quality of both the sample and the abrasive. Evenly distributing a coolant across the surface of the silicon carbide paper helps in several ways: it reduces heat generation during polishing, which can alter the physical properties of the sample; it prevents premature dulling of the abrasive grains; and it helps remove swarf and debris, which can cause additional scratches and surface defects. The type of coolant may vary depending on the material being polished and environmental or safety considerations.
Pressure and Speed
Adjusting the pressure and speed during the polishing process is critical to achieving optimal results. The amount of pressure applied should be enough to facilitate effective abrasion but not so high that it causes excessive wear or damage to the silicon carbide paper and the sample. Similarly, the speed of the polishing tool should be set to a level that allows for efficient material removal without generating excessive heat. High speeds, combined with too much pressure, can lead to thermal damage to both the sample and the abrasive paper. Each material may require different settings, which should be determined based on experimental results or established guidelines.
Table comparing recommended speed and pressure settings for different material types in metallography, along with specific considerations for each:
Material Type |
Recommended Speed |
Recommended Pressure |
Considerations |
---|---|---|---|
Soft Materials (Aluminum, Copper) |
Lower speeds |
Lighter pressure |
Avoid excessive removal and deformation |
Hard Materials (Steel, Hardened Alloys) |
Moderate to high speeds |
Higher pressure |
Ensure sufficient abrasive action |
Brittle Materials (Ceramics, Glass) |
Moderate speeds |
Light to moderate pressure |
Prevent chipping or cracking |
Composite Materials |
Adjust based on hardest component |
Varying pressure |
Handle different components effectively |
Ultra-Precise Finishing (Optical Materials) |
Lower to moderate speeds |
Very light pressure |
Achieve ultra-high precision and control |
Polishing Motion
The motion used during polishing affects the uniformity of the material removal and the final finish of the sample. Consistent and controlled motions, such as circular or figure-eight patterns, are recommended as they ensure that all areas of the sample are evenly abraded. This uniformity is crucial for preventing localized over-polishing or under-polishing, which can lead to artifacts in the sample analysis. The specific polishing motion may need to be adjusted depending on the shape of the sample and the type of material to account for any unique physical properties or desired outcomes.
5. Progression and Transition
Ensuring a proper grit progression during grinding is key to achieving a smooth, defect-free surface on your sample. Start with coarser grits to eliminate large imperfections and progressively transition to finer grits to refine the surface. This systematic approach prevents deep scratches from remaining while ensuring particles from earlier stages are efficiently removed. Skipping intermediate grit sizes may seem time-saving but often leads to uneven finishes, forcing repeated corrections later.
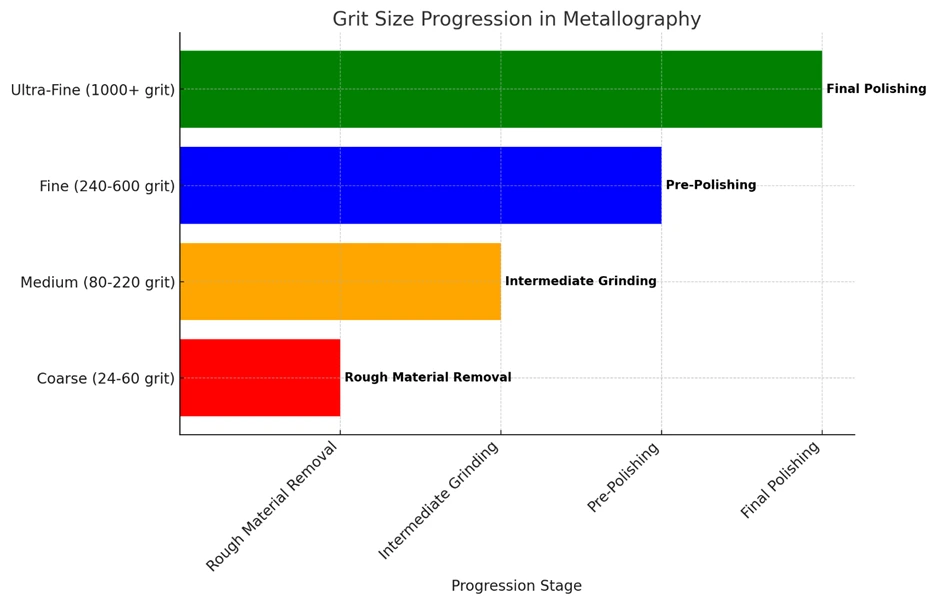
-
Coarse (24-60 grit): Ideal for removing large surface irregularities or significant rough areas.
-
Medium (80-220 grit): Refines the surface by addressing marks from the coarse grit and preparing it for finer polishing.
-
Fine (240-600 grit): Prepares the sample for final polishing by leaving an almost flawless surface.
Cleaning Between Stages
After each grit stage, thoroughly clean both the sample and equipment to avoid cross-contamination. Particles from coarser grits can interfere with finer polishing, causing unexpected scratches. Use clean water or an appropriate cleaning solution to wash off particles and inspect for residue. For maximum preservation of results, regularly flush your workspace and polishing tools.
6. Post-Polishing Care
Inspection
Once polishing is complete, inspect the sample under bright light or a microscope. Look for uniformity in the finish, ensuring there are no scratches or defects visible. If imperfections appear, revisit the prior polishing stages or adjust your equipment settings for improved control.
Cleaning
To ensure the sample retains its polished qualities, clean it meticulously. Use non-reactive cleaning agents or distilled water to prevent reactions with the material. Similarly, clean the polishing equipment thoroughly to remove any leftover residues that might affect subsequent projects. Regular maintenance also ensures long-term equipment performance.
7. Maintenance and Storage
Abrasive Care
Proper care of silicon carbide paper is crucial for extending its usability and maintaining its effectiveness. After use, if the paper is intended for reuse, it should be cleaned gently to remove any accumulated debris and residues. This can be done using a soft brush or a clean, dry cloth to brush away particles without damaging the abrasive surface. For more thorough cleaning, a mild solvent or water may be used, depending on the type of backing and adhesive. Once cleaned, the paper should be allowed to dry completely before storage.
In terms of storage, silicon carbide paper should be kept either flat or gently rolled. Avoid folding the paper, as this can create creases that compromise its flatness and lead to uneven polishing results in future uses. If rolling the paper for storage, use a wide diameter roll to prevent kinking and ensure the paper remains smooth.
Storage Conditions
The environment in which silicon carbide paper is stored can significantly affect its longevity and performance. To preserve the adhesive and abrasive properties of the paper, store it in a cool, dry place. Exposure to high humidity can cause the backing to warp or the adhesive to weaken, leading to detachment of the abrasive grains. Similarly, high temperatures can soften the adhesive, potentially causing it to become tacky or to degrade prematurely.
It's also advisable to keep the paper away from direct sunlight. UV light can degrade some adhesives and backing materials, reducing the overall lifespan of the abrasive paper. Storing the paper in an environment-controlled room or cabinet is ideal to prevent such damage and ensure the paper maintains its effectiveness for as long as possible.
8. Disposal
Proper disposal of used silicon carbide paper is essential for minimizing its environmental impact. Users must adhere to local environmental regulations specific to their area when disposing of used abrasive materials. These regulations often categorize waste into different types, such as hazardous or non-hazardous, and dictate specific disposal methods and designated facilities for each category.
Before considering disposal, explore any available recycling options. Some components of silicon carbide paper, particularly the backing material, may be recyclable depending on their composition. Local waste management services can provide information on whether they offer recycling programs for abrasive materials and the requirements for participation. Recycling used abrasives can significantly reduce waste and contribute to resource conservation.
Additionally, users should seek ways to minimize the environmental impact of their activities. This can be achieved by extending the life of silicon carbide paper through proper usage and maintenance, thereby reducing the frequency of its replacement. Choosing abrasive products that feature recyclable or biodegradable components can also help. When purchasing new abrasives, opting for products manufactured through environmentally friendly practices can further support.
9. Trouble shooting Guide
Issue |
Symptom |
Possible Causes |
Solutions |
---|---|---|---|
Excessive Wear on the Disc |
Disc wears out faster than expected. |
Reduce pressure, check speed, use correct grit size. |
Reduce pressure, check speed, use correct grit size. |
Inadequate Material Removal |
Disc does not remove material efficiently. |
Too low speed or insufficient pressure; grit size too fine. |
Increase speed, adjust pressure, switch to a coarser grit. |
Poor Surface Finish |
Finished surface is not as smooth or even as expected. |
Worn-out disc; incorrect grit progression. |
Replace disc, ensure proper grit progression. |
Disc Slippage or Misalignment |
Disc slips or does not stay properly aligned during operation. |
Improper installation; worn or damaged backing pad. |
Check installation, secure disc, replace backing pad if worn. |
Excessive Heat Generation |
Disc and/or material becomes too hot during grinding. |
Too high speed or excessive pressure; insufficient coolant. |
Reduce speed and pressure, ensure adequate coolant flow. |
Noise and Vibration |
Excessive noise or vibration during operation. |
Unbalanced disc or machine; loose parts or improper assembly. |
Check balance of disc, tighten any loose components. |
Uneven Wear of the Disc |
The disc shows uneven wear patterns. |
Improper loading or uneven distribution of the sample on the disc; unbalanced equipment or misalignment. |
Ensure even loading and distribution of the sample; check and calibrate equipment regularly. |
Clogging of the Disc |
The disc becomes clogged with debris, reducing its effectiveness. |
Grinding of particularly soft or ductile materials; insufficient coolant flow. |
Use a disc with a more open structure or coarser grit; increase coolant flow. |
Discoloration of Material |
The material being polished shows discoloration. |
Excessive heat during grinding; contamination from previous materials. |
Adjust speed and pressure to reduce heat; clean the disc thoroughly after each use. |
Surface Scratching |
Unexpected scratches appear on the sample surface. |
Using a disc that is too coarse for the application; debris trapped under the disc. |
Switch to a finer grit appropriate for the polishing stage; ensure the disc and sample are clean before use. |
Reduced Grinding Efficiency |
The disc no longer grinds effectively. |
Disc is glazed or loaded with material; inappropriate grit for the material hardness. |
Clean the disc to remove build-up; choose the correct grit size for the material being processed. |
Vibration During Use |
The machine vibrates excessively during operation. |
Disc is unbalanced; machine components are loose or worn. |
Balance the disc properly; inspect and tighten or replace worn machine components. |
Increased Operational Noise |
Noise levels are higher than usual during grinding. |
Bearings are worn out; debris or misalignment causing increased friction. |
Check and replace bearings if necessary; clean and realign the disc setup. |
Heat Marks on Material |
Discoloration due to heat on the material surface. |
Excessive speed or pressure; insufficient cooling during grinding. |
Reduce speed and pressure; ensure adequate coolant flow during operation. |
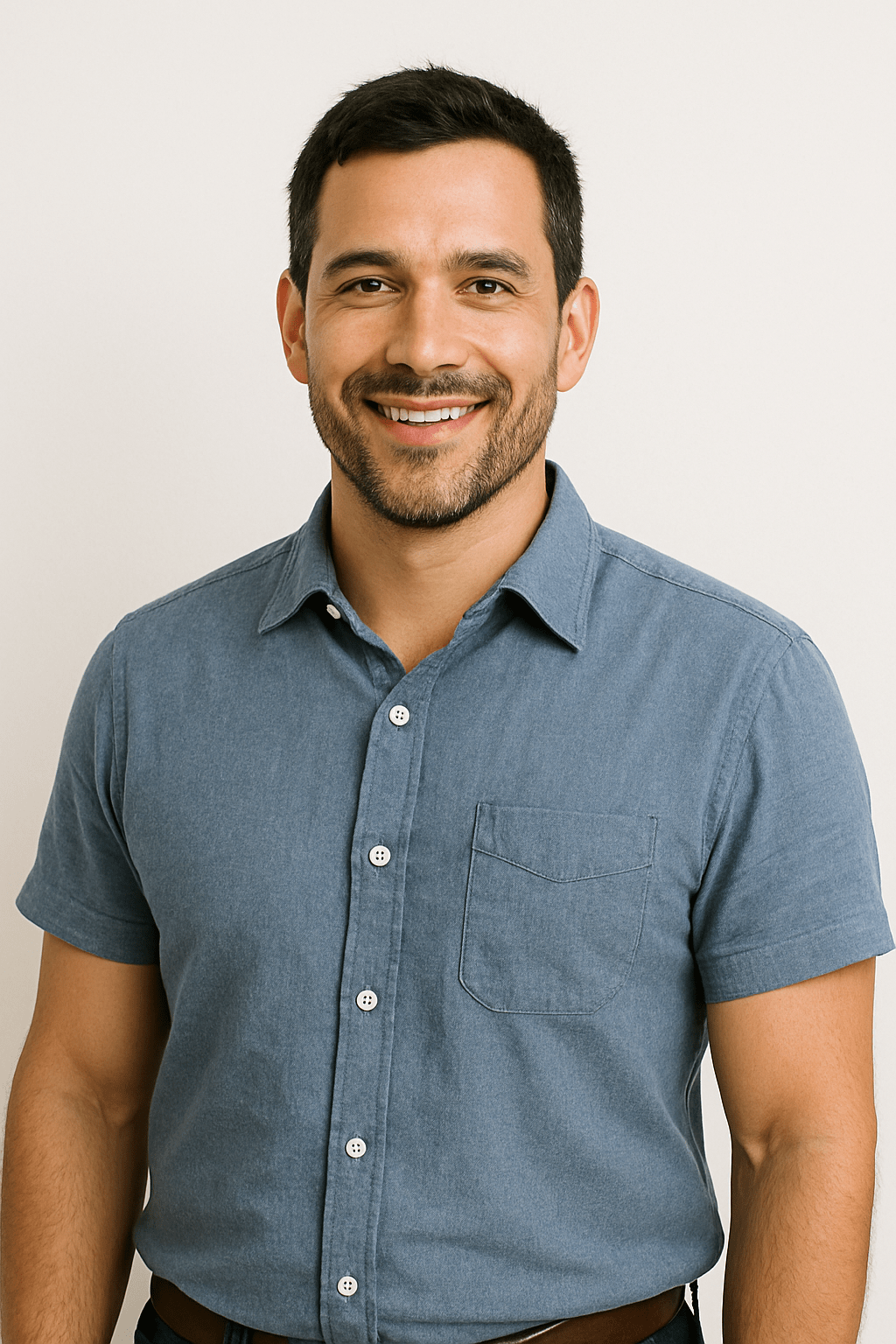
Carlos Sanchez is a senior technical specialist and field applications trainer with more than 17 years of experience in the use and optimization of industrial diamond tools, including ultra-thin diamond blades, core drills, and CBN grinding wheels. With a foundation in industrial engineering and technical operations, Mr. Sanchez has worked extensively with manufacturers and laboratories around the world, providing hands-on support and practical training for a wide range of cutting, grinding, and sample preparation applications.
Fluent in both English and Spanish, Carlos is known for his ability to translate complex tooling concepts into clear, actionable procedures for engineers, technicians, and production staff. His approach emphasizes real-world process improvement, tool longevity, and operator education—ensuring clients get the most out of their diamond tooling investments.
As an author, Mr. Sanchez shares field-tested insights on tool performance optimization, defect prevention, training methodologies, and troubleshooting common cutting issues.
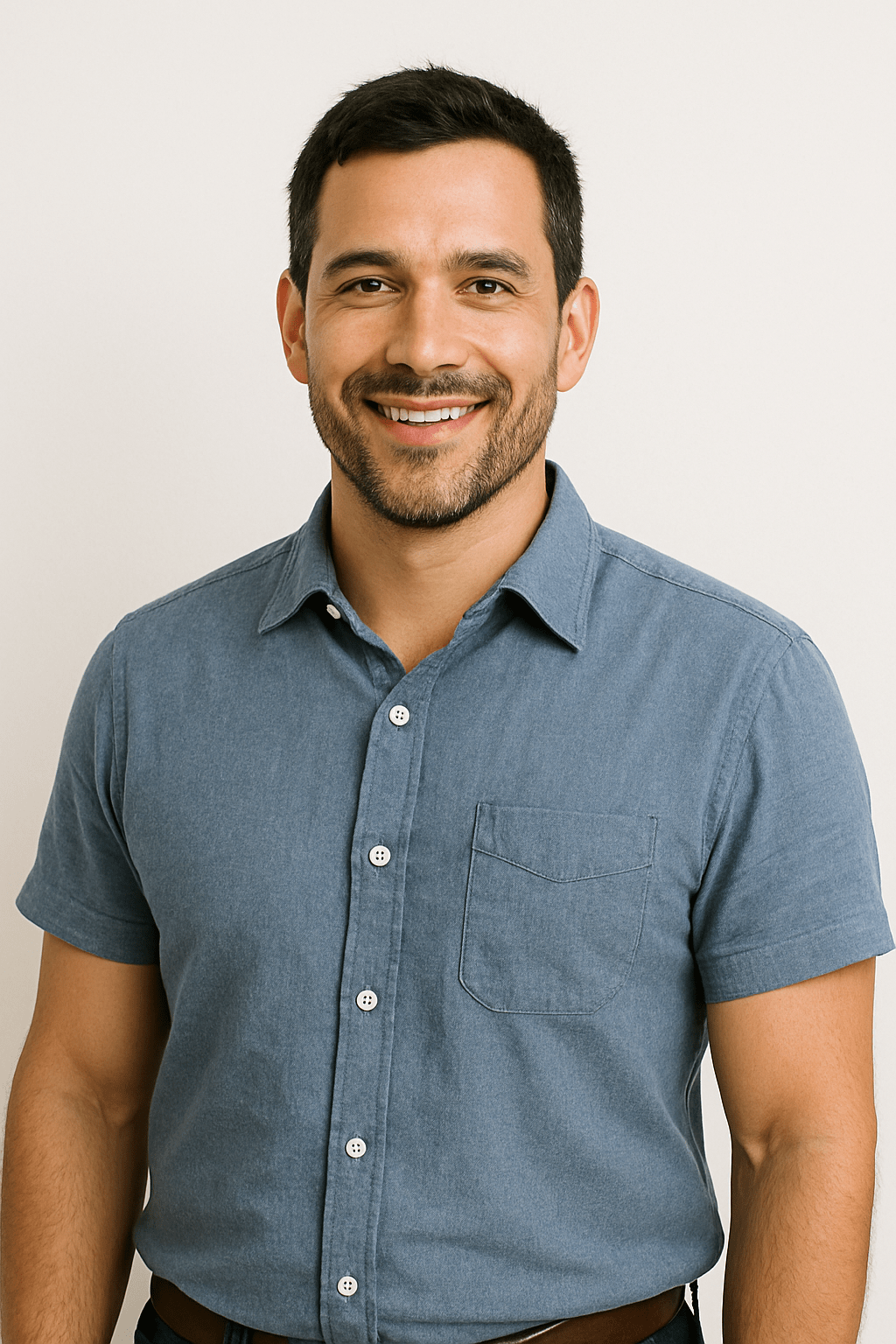
Carlos Sanchez is a senior technical specialist and field applications trainer with more than 17 years of experience in the use and optimization of industrial diamond tools, including ultra-thin diamond blades, core drills, and CBN grinding wheels. With a foundation in industrial engineering and technical operations, Mr. Sanchez has worked extensively with manufacturers and laboratories around the world, providing hands-on support and practical training for a wide range of cutting, grinding, and sample preparation applications.
Fluent in both English and Spanish, Carlos is known for his ability to translate complex tooling concepts into clear, actionable procedures for engineers, technicians, and production staff. His approach emphasizes real-world process improvement, tool longevity, and operator education—ensuring clients get the most out of their diamond tooling investments.
As an author, Mr. Sanchez shares field-tested insights on tool performance optimization, defect prevention, training methodologies, and troubleshooting common cutting issues.