Some of the major differences include the type and diamond mesh size of diamond discs used, type and size of abrasives used and their holding method. Other factors include RPM’s (speed) used and pressure applied to material workpiece.
Lapping, grinding, and polishing are all finishing processes used in various manufacturing sectors to improve the surface finish, dimensional accuracy, or mechanical properties of a workpiece. Lapping, Grinding, & Polishing processes are very similar. Each process serves distinct purposes and employs different methods to achieve specific results, making them indispensable in manufacturing and material processing. Understanding the differences between these processes is essential for selecting the appropriate technique for a given application, ensuring optimal performance, and achieving high-quality finishes.
Main differences lie on the end users objectives. Such as removing a certain amount of material or removing scratches and micro cracks caused by prior machining operations. Usually the same machine can be used for all three operations.
Some of the major differences include the type and diamond mesh size of diamond discs used, type and size of abrasives used and their holding method. Other factors include RPM’s (speed) used and pressure applied to material workpiece.
Another important difference between lapping and more finer polishing is the composition of diamond disc backing plate. Typically cast iron is used as a backing plate for lapping. Backing plates made from aluminum, bronze, or composites are more frequently used for polishing.
Lapping is primarily used to improve form accuracy and achieve a high degree of flatness on a workpiece. This slow material removal process involves fine abrasives suspended in a slurry, which reduces surface roughness and ensures precise dimensional tolerances. Grinding, on the other hand, focuses on removing large amounts of material quickly to shape the workpiece and enhance its surface finish. Utilizing coarse and fine abrasives, grinding is a fast process that generates significant heat, requiring effective cooling methods. Polishing, the final stage of precision finishing, aims to smooth out surfaces and achieve a mirror-like, highly reflective finish. By using very fine abrasives, polishing removes minimal material, eliminating surface imperfections and providing superior surface quality. Each of these processes—lapping, grinding, and polishing—plays a vital role in the production of high-precision components across industries such as aerospace, optics, medical devices, and semiconductors.
Here is a table that compares the lapping, grinding, and polishing processes:
Feature/Aspect |
Lapping |
Grinding |
Polishing |
---|---|---|---|
Primary Purpose |
Improve form accuracy and flatness |
Remove large amounts of material, shape, and finish |
Smooth out surface, improve finish, remove defects |
Material Removal |
Very slow, typically a few microns |
High, removes significant amounts of material |
Very minimal, just enough to eliminate imperfections |
Abrasive Type |
Fine abrasives in slurry (aluminum oxide, silicon carbide, diamond) |
Coarse and fine abrasives (aluminum oxide, silicon carbide, zirconia alumina) |
Very fine abrasives (aluminum oxide, silicon carbide, diamond, cerium oxide) |
Surface Finish |
Reduces surface roughness but primary focus on flatness |
Improves surface finish, primary focus on shape |
Achieves the best surface finish, focuses on smoothness and clarity |
Form Accuracy |
High, intended for precise dimensional tolerances |
Moderate to high, depends on grinding precision |
Low, less emphasis on form accuracy, more on surface quality |
Speed |
Slow |
High |
Medium |
Heat Generation |
Low, due to low speeds |
High, significant heat due to high speeds |
Medium, can cause thermal damage if not controlled |
Common Abrasives |
Aluminum oxide, silicon carbide, diamond |
Aluminum oxide, silicon carbide, zirconia alumina |
Aluminum oxide, silicon carbide, diamond, cerium oxide, colloidal silica |
Applications |
Semiconductor wafers, optics, precision engineering |
Metalworking, automotive, aerospace |
Optics, medical devices, jewelry, semiconductors |
Challenges |
Consistent process control, abrasive selection |
Material cracking, heat generation, tool wear |
Surface contamination, heat generation, tool wear, achieving uniformity |
Equipment |
Lapping plates, lapping machines |
Grinding machines, abrasive wheels or belts |
Polishing pads, wheels, belts, automated polishing machines |
Cooling/Lubrication |
Often uses slurry as a lubricant |
Uses coolants or lubricants to manage heat |
Uses polishing compounds and sometimes cooling fluids |
Typical Industries |
Semiconductor, optics, aerospace |
Metalworking, automotive, aerospace |
Jewelry, medical devices, semiconductor, optics |
Surface Characteristics |
Flat, smooth, slightly textured |
Variable, depends on grinding precision and abrasives |
Mirror-like, highly reflective, smooth |
Cost |
Moderate to high due to precision |
Variable, can be low to high depending on equipment and abrasives |
Moderate to high, especially with advanced polishing compounds |
Environmental Considerations |
Slurry disposal, abrasive waste |
Coolant disposal, abrasive wear particles |
Polishing compound disposal, potential chemical use |
Automation Potential |
Moderate to high |
High, especially with CNC grinding machines |
High, with automated polishing systems |
Skill Level Required |
High, for precision and consistency |
Moderate to high, depending on complexity |
High, especially for achieving uniform, high-quality finishes |
Process Monitoring |
Essential for maintaining flatness and precision |
Important for preventing defects and ensuring quality |
Crucial for achieving and maintaining surface quality |
Typical Surface Roughness (Ra) |
0.01-0.1 µm |
0.1-1.0 µm |
0.01-0.1 µm |
End Products |
Highly flat and smooth surfaces, precision components |
Shaped and semi-finished components |
Finished components with high aesthetic and functional quality |
Lapping Process
Lapping and polishing are precision finishing processes which involve different mechanical arrangements. The goal is to improve surface finish and achieve high degree of flatness. Lapping is a slow material removal operation. Though lapping tends to decrease the original surface roughness, it main purpose is to remove material and modify the shape. Lapping is used primarily to improve form accuracy rather than to reduce surface roughness. Polishing on the other hand deals with material surface finish and plays little attention to form accuracy. Lapping and polishing are used for many materials such as glass, ceramic, plastic, metals and their alloys, sintered materials, stellite, ferrite, copper, iron, steel and etc. The relative speeds in lapping and polishing are much lower than in grinding. Consequently the concentration of energy in the contact area is much lower than in grinding. The amount of material removed during lapping process is usually only few microns. . Lapping involves the use of loose abrasive particles suspended in a liquid or carried on a lapping plate. These abrasives create a fine cutting action that removes material from the workpiece surface, leading to a more uniform and controlled shape.
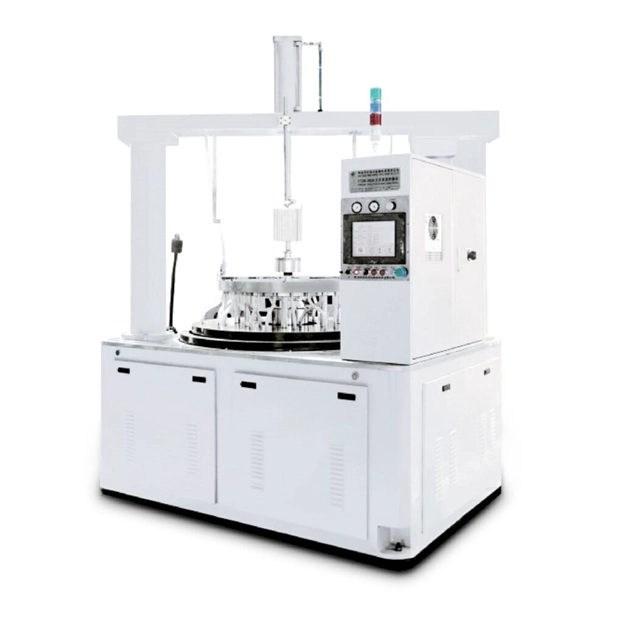
Key Characteristics of Lapping:
-
Material Removal: Lapping removes material at a very slow rate, typically only a few microns. This precision is ideal for achieving specific dimensional tolerances and flatness.
-
Surface Roughness: While lapping tends to decrease the original surface roughness, its main purpose is to modify the shape and improve form accuracy.
-
Low Energy Concentration: The relative speeds in lapping are much lower compared to grinding. Consequently, the energy concentration in the contact area is significantly lower, reducing the risk of thermal damage to the workpiece.
-
Applications: Lapping is used for a wide range of materials, including glass, ceramic, plastic, metals and their alloys, sintered materials, stellite, ferrite, copper, iron, and steel. Its versatility makes it an essential process in various industries such as semiconductor manufacturing, optical components production, and precision engineering.
Grinding Process
Grinding is a critical process in manufacturing and material processing, used to remove significant amounts of material to achieve the desired shape, finish, or sharpness of a part. This process is distinguished by its ability to handle a variety of materials, including metals, ceramics, plastics, and composites. Grinding is typically performed at high speeds using abrasive wheels or belts to achieve the desired outcomes efficiently and accurately.
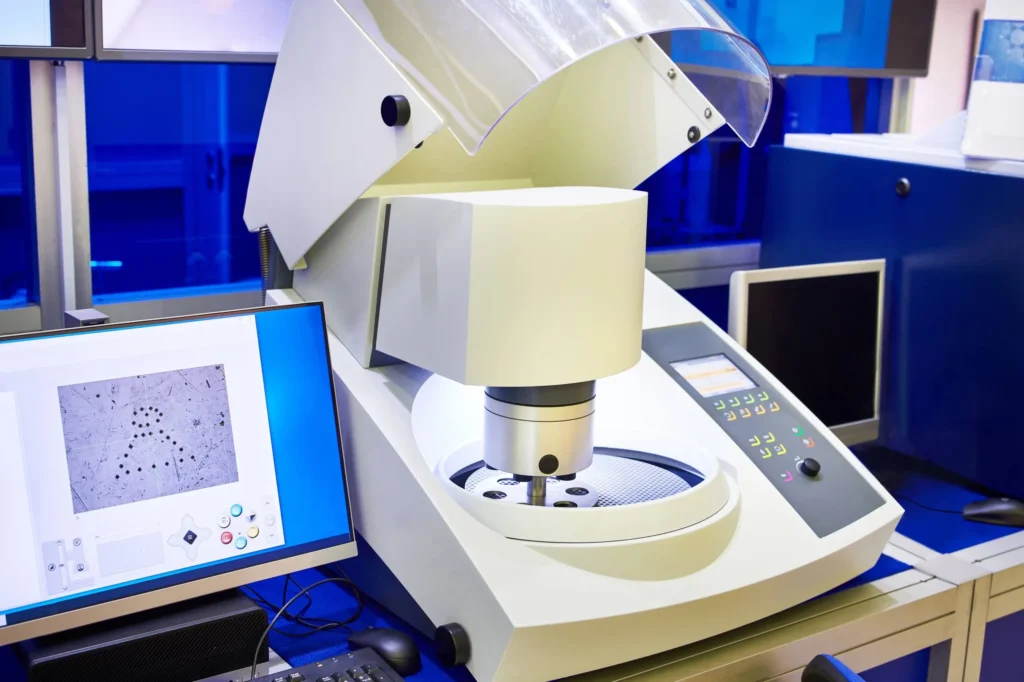
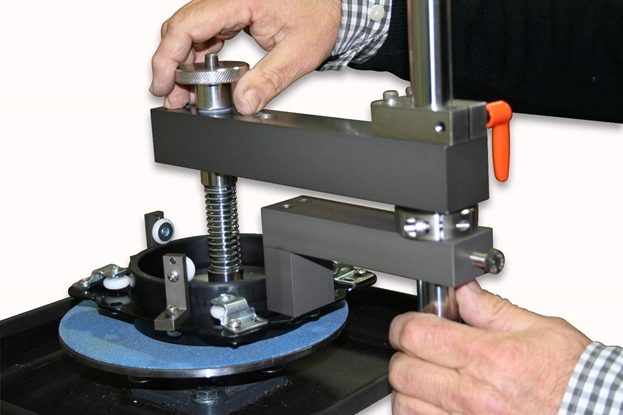
Rough Grinding
Rough grinding is the preliminary stage of the grinding process, intended to remove substantial irregularities, defects, or scratches from the workpiece. This step is crucial for preparing the material for further refinement and achieving the basic shape and dimensions needed for subsequent processes. In rough grinding, a high material removal rate is achieved through the use of coarser grits of abrasive materials, which makes it particularly suitable for quickly eliminating large volumes of material. Common abrasive materials used in rough grinding include aluminum oxide, silicon carbide, and zirconia alumina, all of which are effective in cutting through tough materials and addressing significant surface irregularities.
During the rough grinding process, the workpiece is securely fixed in place, and the appropriate abrasive wheel or belt is selected based on the material and the desired outcome. The abrasive tool is then applied to the workpiece at high speeds, removing considerable amounts of material and smoothing out major surface defects. After rough grinding, the workpiece is carefully inspected for any remaining significant defects to ensure it is adequately prepared for the next stage of grinding or finishing.
Fine Grinding
Following rough grinding, fine grinding is employed to further refine the surface and remove the scratches and marks left by the initial rough grinding process. Fine grinding is essential for achieving the final desired surface finish and precision, using finer abrasives to smooth the surface and achieve a higher level of detail and finish. This step is crucial in applications requiring a high degree of surface finish and precision, such as the production of precision components, tooling, and dies.
In fine grinding, finer abrasives such as fine-grit aluminum oxide, silicon carbide, or diamond are chosen based on the material and the desired surface finish. The process begins with cleaning and preparing the workpiece, ensuring that any loose particles or contaminants from the rough grinding process are removed. The fine abrasive wheel or belt is then applied to the workpiece at controlled speeds and pressures to achieve the desired surface finish and precision. After fine grinding, the workpiece is thoroughly inspected to ensure it meets the required specifications and surface finish. Any remaining imperfections are addressed through additional fine grinding or polishing.
Challenges in the Grinding Process
The grinding process, while highly effective, presents several challenges that must be managed to achieve optimal results:
Material Cracking and Chipping: Grinding can induce stresses in the material, leading to cracking or chipping, particularly in brittle materials like ceramics and some hard metals. Proper selection of grinding parameters and abrasives is crucial to mitigate these issues.
Heat Generation: Grinding generates significant heat due to friction between the abrasive and the workpiece. Excessive heat can cause thermal damage, material deformation, and changes in material properties. To manage heat generation, cooling fluids or lubricants are often used during the grinding process. These cooling agents help to dissipate heat, reduce friction, and prevent thermal damage to the workpiece.
Surface Burns: High temperatures during grinding can lead to surface burns, which affect the surface integrity and aesthetic appearance of the workpiece. Proper cooling and the use of appropriate grinding techniques can minimize this risk, ensuring the workpiece maintains its intended properties and appearance.
Tool Wear: Abrasive wheels and belts can wear out quickly, especially during rough grinding. Regular monitoring and replacement of grinding tools are essential to maintain consistent performance and quality. Worn tools can lead to uneven material removal, poor surface finish, and decreased precision.
Vibration and Stability: Vibration during grinding can lead to poor surface finish and reduced precision. Ensuring the stability of the grinding setup and using vibration-damping techniques are crucial for achieving better results. Proper machine maintenance and the use of stable fixtures can help minimize vibration and improve the overall quality of the grinding process.
Polishing Process
Polishing is a surface finishing process designed to smooth out and enhance the quality of a material's surface. Its primary goal is to remove or reduce the visibility of grinding or lapping lines, scratches, and other surface defects, thereby decreasing the surface roughness. This process focuses on achieving the best possible surface finish with minimal emphasis on shape and form accuracy. Additionally, polishing helps remove damage such as microcracks, voids, and inclusions caused by previous machining operations like cutting and grinding. The amount of material removed during polishing is typically very small, just enough to eliminate scratches and imperfections.
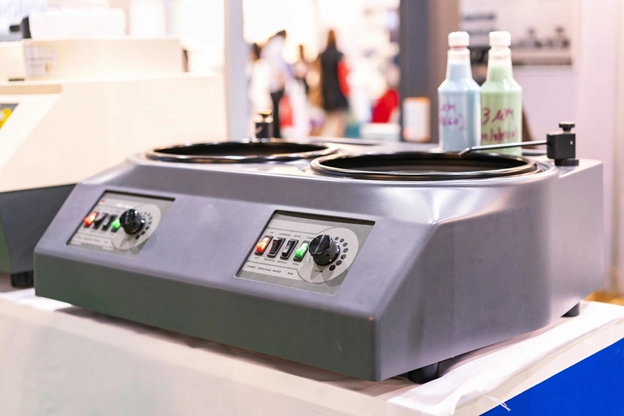
Mechanics of Polishing
Polishing involves using fine abrasives and polishing compounds to achieve a smooth and reflective surface. The process can be done manually or with automated polishing machines, depending on the requirements and complexity of the workpiece. The abrasives used in polishing are much finer than those used in grinding or lapping, allowing for a high degree of surface refinement.
Polishing Materials and Abrasives
The choice of polishing materials and abrasives depends on the type of workpiece material and the desired surface finish. Common polishing abrasives include aluminum oxide, silicon carbide, diamond, cerium oxide, and colloidal silica. Each of these abrasives is suited for specific materials and applications, offering different balances between cutting action and surface finish.
Polishing Methods
Polishing can be performed using various methods, each suited for different materials and applications. Mechanical polishing involves using polishing pads, wheels, or belts coated with fine abrasives, with the workpiece moved against the abrasive surface in a controlled manner. Electrochemical polishing combines mechanical action with electrochemical reactions to remove material and achieve a smooth surface, particularly effective for metals. Chemical-mechanical polishing (CMP), commonly used in semiconductor manufacturing, combines chemical reactions with mechanical abrasion to polish the surface, ensuring a high degree of planarity and smoothness.
Applications of Polishing
Polishing is used in a wide range of industries and applications where surface finish and appearance are critical. In aerospace and automotive industries, it achieves high-quality finishes on engine components, turbine blades, and structural parts, reducing friction, improving aerodynamic performance, and enhancing aesthetic appeal. In optics and photonics, polishing is essential for producing lenses, mirrors, and other optical components, ensuring minimal light scattering and optimal performance. In the medical field, polishing ensures that implants, surgical instruments, and other devices have smooth, biocompatible surfaces, reducing infection risks and improving performance. Semiconductor manufacturing relies on polishing for achieving the flatness and smoothness required for photolithography and other processes, with CMP being commonly used. In the jewelry industry, polishing is crucial for achieving the desired luster and finish on precious metals and gemstones, enhancing their visual appeal and value.
Challenges in the Polishing Process
Polishing, while effective, presents several challenges that must be managed to achieve the best results. Surface contamination can affect the final finish, necessitating proper cleaning and preparation of the workpiece before and after polishing. Achieving a consistent and uniform finish across the entire workpiece can be challenging, especially for complex shapes, requiring careful control of polishing parameters and techniques. Polishing generates heat due to friction between the abrasive and the workpiece, which can cause thermal damage or warping, particularly in sensitive materials; appropriate cooling methods and controlled polishing speeds can help manage this heat generation. Polishing tools and abrasives can wear out over time, affecting the consistency of the finish, necessitating regular monitoring and replacement of polishing tools. Vibration during polishing can lead to poor surface finish and reduced precision, so ensuring the stability of the polishing setup and using vibration-damping techniques is crucial.
Loose Diamond & Abrasives Consumables Used
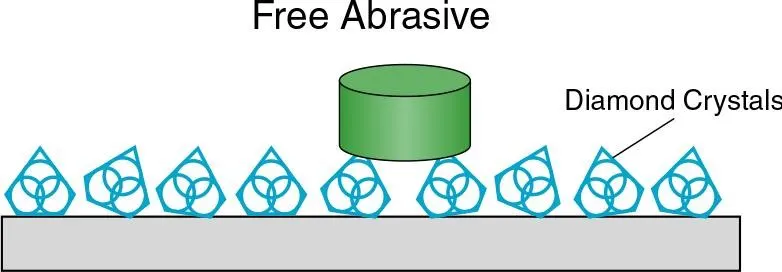
There is a large variety of abrasives than can be used for lapping, grinding, & polishing. Below is a description of various lapping, grinding, and polishing media/powders that is typically used for most lapping, grinding, and polishing operations.
Diamond & Abrasive Consumables Used in Lapping, Grinding, and Polishing
The choice of abrasive materials is crucial for the effectiveness and efficiency of lapping, grinding, and polishing operations. Different abrasives are suited to different materials and applications, depending on factors such as hardness, material removal rate, surface finish requirements, and the nature of the workpiece. Below is a detailed description of various lapping, grinding, and polishing media and powders typically used in these processes.
Diamond
-
Properties: Diamond is the hardest material known to mankind, offering unparalleled cutting efficiency and durability.
-
Applications: Diamond abrasives are typically used for ultra-hard materials and tungsten carbide. They are embedded in discs or used in slurry form to cut fast and produce a fine finish. Due to its extreme hardness, diamond is ideal for applications requiring precise, high-quality finishes on very hard materials.
-
Common Uses: Diamond abrasives are used in the precision machining of hard ceramics, gemstones, glass, and advanced composites. They are also used for grinding and lapping operations where high precision and smooth finishes are required.
Cubic Boron Nitride (CBN)
-
Properties: CBN is the second hardest material after diamond, with excellent thermal and chemical stability, making it suitable for high-speed grinding applications.
-
Applications: CBN is typically used for lapping and grinding ferrous metals, including 52100 bearing steel, cast iron, tool steel, stellite, super alloys, and occasionally ceramics. Its superior hardness and resistance to heat make it ideal for high-precision applications on tough materials.
-
Common Uses: CBN abrasives are used in tool and die manufacturing, automotive component production, and aerospace applications, where maintaining tight tolerances and achieving high surface quality on hard metals are critical.
Aluminum Oxide
-
Properties: Aluminum oxide is a versatile abrasive known for its hardness, toughness, and low cost.
-
Applications: It is used for general lapping, grinding, and polishing with low surface roughness. Aluminum oxide is typically employed for high tensile strength materials, rough lapping operations, hardened gears, ball bearing grooves, and lapping operations where pressure can be exerted to break down the crystals.
-
Common Uses: Aluminum oxide is widely used in metalworking, including the production of automotive components, aerospace parts, and general machinery. It is also used in the preparation of surfaces for further finishing processes.
Silicon Carbide
-
Properties: Silicon carbide is known for its high hardness, sharp edges, and fast cutting ability.
-
Applications: It is used for fast stock removal for both hard and soft materials. Silicon carbide is typically employed for rough lapping and grinding operations, forged or hardened gears, valves, tool room work, and general maintenance where a fine polish is not essential.
-
Common Uses: Silicon carbide abrasives are used in grinding operations involving cast iron, non-ferrous metals, and composites. They are also used in the preparation of surfaces for coating or bonding.
Boron Carbide
-
Properties: Boron carbide is extremely hard, almost as hard as diamond, with high wear resistance.
-
Applications: It is used for lapping and grinding hard materials such as ceramics, carbide, and other hard substances.
-
Common Uses: Boron carbide abrasives are used in applications requiring the machining of very hard materials, such as in the production of ceramic components, advanced composites, and certain metal alloys.
Calcined Alumina
-
Properties: Calcined alumina is produced by heating aluminum oxide, resulting in a material with controlled crystal structure and properties.
-
Applications: It is used for polishing metals, optics, silicon wafers, and other semiconductor materials. Calcined alumina offers high purity and uniform particle size, making it suitable for fine finishing operations.
-
Common Uses: Calcined alumina is used in the final polishing stages of precision optics, semiconductor wafers, and metal components requiring a high degree of surface smoothness.
Unfused Alumina
-
Properties: Unfused alumina, also known as hydrate-calcined alumina, is relatively soft and used for polishing. Its flat, plate-like crystals distribute pressure evenly, minimizing the risk of deep scratches.
-
Applications: Unfused alumina is recommended for lapping and polishing harder materials (Rockwell C 45-63). The disc-shaped particles provide a shaving action rather than a rolling or gouging action, leading to a smoother finish.
-
Common Uses: Unfused alumina is used in the lapping and polishing of hardened steels, precision tools, and certain ceramics, where maintaining a high-quality surface finish is essential.
Zirconia Alumina
-
Properties: Zirconia alumina is a tough, durable abrasive material with self-sharpening properties. It offers a high degree of strength and longevity.
-
Applications: Ideal for high-pressure grinding and cutting operations, zirconia alumina is commonly used for grinding metals, especially stainless steel and other ferrous alloys.
-
Common Uses: Zirconia alumina abrasives are used in heavy-duty applications such as metal fabrication, foundry work, and tool sharpening.
Cerium Oxide
-
Properties: Cerium oxide is a rare earth metal abrasive known for its ability to polish glass and achieve a high-quality finish.
-
Applications: Used extensively in the optics industry, cerium oxide is perfect for polishing glass, crystals, and optical components.
-
Common Uses: Cerium oxide is commonly used in the final polishing stages of lenses, mirrors, and other glass products to achieve a clear and reflective surface.
Garnet
-
Properties: Garnet is a natural abrasive with moderate hardness and sharp edges, making it suitable for a variety of applications.
-
Applications: It is used for blasting, waterjet cutting, and polishing applications where a moderate finish is required.
-
Common Uses: Garnet abrasives are used in woodworking, surface preparation before painting, and in waterjet cutting systems for cutting metals and other materials.
Silicon Nitride
-
Properties: Silicon nitride is a high-strength ceramic abrasive known for its thermal stability and resistance to wear.
-
Applications: Suitable for high-precision grinding and polishing of ceramics, silicon wafers, and other semiconductor materials.
-
Common Uses: Silicon nitride abrasives are used in the semiconductor industry for wafer thinning, in the production of advanced ceramics, and in applications requiring high-temperature stability.
Colloidal Silica
-
Properties: Colloidal silica consists of fine silica particles suspended in a liquid, providing a high level of precision in polishing.
-
Applications: Used for chemical-mechanical polishing (CMP) in semiconductor manufacturing, colloidal silica is essential for achieving extremely smooth surfaces.
-
Common Uses: Colloidal silica is widely used in the semiconductor industry for polishing silicon wafers and in the production of optical components requiring a pristine surface finish.
Chromium Oxide
-
Properties: Chromium oxide is a green, fine abrasive known for its ability to produce a high gloss finish.
-
Applications: Primarily used for polishing metals, especially stainless steel and other ferrous alloys, as well as in buffing compounds.
-
Common Uses: Chromium oxide abrasives are used in metal finishing, tool sharpening, and in the production of mirrors and reflective surfaces.
Comparison table that includes all the abrasive materials mentioned, their properties, applications, common uses, and suitability for lapping, grinding, and polishing.
Abrasive Material |
Properties |
Applications |
Common Uses |
Lapping |
Grinding |
Polishing |
---|---|---|---|---|---|---|
Diamond |
Hardest known material, excellent cutting efficiency |
Ultra-hard materials, tungsten carbide |
Precision machining of hard ceramics, gemstones, glass, advanced composites |
Yes |
Yes |
Yes |
Cubic Boron Nitride (CBN) |
Second hardest material, high thermal and chemical stability |
Ferrous metals, including bearing steel, cast iron, tool steel, stellite, super alloys, ceramics |
Tool and die manufacturing, automotive components, aerospace applications |
Yes |
Yes |
Yes |
Aluminum Oxide |
Hard, tough, low cost |
General lapping, grinding, and polishing of high tensile strength materials |
Metalworking, automotive components, aerospace parts, general machinery |
Yes |
Yes |
Yes |
Silicon Carbide |
High hardness, sharp edges, fast cutting ability |
Fast stock removal for both hard and soft materials |
Grinding cast iron, non-ferrous metals, composites, surface preparation |
Yes |
Yes |
No |
Boron Carbide |
Extremely hard, high wear resistance |
Lapping and grinding hard materials |
Ceramic components, advanced composites, certain metal alloys |
Yes |
Yes |
No |
Calcined Alumina |
High purity, uniform particle size |
Polishing metals, optics, silicon wafers, semiconductor materials |
Precision optics, semiconductor wafers, metal components |
No |
No |
Yes |
Unfused Alumina |
Relatively soft, flat crystals, even pressure distribution |
Lapping and polishing harder materials (Rockwell C 45-63) |
Hardened steels, precision tools, certain ceramics |
Yes |
No |
Yes |
Zirconia Alumina |
Tough, durable, self-sharpening |
High-pressure grinding and cutting of metals |
Metal fabrication, foundry work, tool sharpening |
No |
Yes |
No |
Cerium Oxide |
Effective for glass polishing |
Polishing glass and optical components |
Lenses, mirrors, glass products |
No |
No |
Yes |
Garnet |
Moderate hardness, sharp edges |
Blasting, waterjet cutting, polishing |
Woodworking, surface preparation, waterjet cutting |
No |
Yes |
Yes |
Silicon Nitride |
High-strength ceramic, thermal stability |
High-precision grinding and polishing of ceramics, silicon wafers |
Semiconductor industry, advanced ceramics production |
Yes |
Yes |
Yes |
Colloidal Silica |
Fine silica particles, high precision |
Chemical-mechanical polishing (CMP) in semiconductor manufacturing |
Polishing silicon wafers, optical components |
No |
No |
Yes |
Chromium Oxide |
Fine, green abrasive, high gloss finish |
Polishing metals, especially stainless steel |
Metal finishing, tool sharpening, mirrors |
No |
No |
Yes |
Comparison table of lapping, grinding, and polishing processes, focusing on equipment used, RPMs, cycle times, abrasive or diamond consumables, and methodologies:
Feature/Aspect |
Lapping |
Grinding |
Polishing |
---|---|---|---|
Equipment Used |
Lapping plates, lapping machines, slurry systems |
Grinding machines, abrasive wheels or belts |
Polishing pads, wheels, belts, automated polishing machines |
Typical RPMs |
10-200 RPM (depending on material and plate size) |
1,000-10,000 RPM (depending on the operation) |
100-5,000 RPM (depending on the material and desired finish) |
Cycle Times |
Hours to days (for high precision and flatness) |
Minutes to hours (depending on material and amount of removal) |
Minutes to hours (depending on the desired surface quality and material) |
Abrasive/Diamond Consumables |
Fine abrasives in slurry (Aluminum Oxide, Silicon Carbide, Diamond) |
Coarse and fine abrasives (Aluminum Oxide, Silicon Carbide, Zirconia Alumina, Diamond) |
Very fine abrasives (Aluminum Oxide, Silicon Carbide, Diamond, Cerium Oxide, Colloidal Silica) |
Methodologies |
- Preparation: Clean and secure workpiece. - Abrasive Selection: Choose appropriate slurry. - Lapping: Apply slurry to plate, move workpiece in controlled manner. - Post-Lapping: Clean workpiece. |
- Preparation: Secure workpiece, select abrasive wheel or belt. - Grinding: High-speed material removal with abrasive wheel or belt. - Cooling: Use coolants to manage heat. - Post-Grinding: Inspect and clean workpiece. |
- Preparation: Clean and secure workpiece. - Abrasive Selection: Choose appropriate fine abrasive. - Polishing: Apply abrasive to pad/wheel, move workpiece at controlled speeds. - Post-Polishing: Clean and inspect workpiece. |
Type of Diamond Consumables |
Loose diamond slurry, diamond paste, fixed diamond discs |
Fixed diamond wheels, diamond-impregnated belts |
Loose diamond slurry, diamond paste, diamond-impregnated pads or wheels |
Form of Diamond Abrasive |
- Loose: Diamond slurry, diamond paste - Fixed: Diamond discs, diamond films |
- Fixed: Diamond wheels, diamond-impregnated belts, diamond-coated tools |
- Loose: Diamond slurry, diamond paste - Fixed: Diamond-impregnated pads, diamond-coated wheels |
Abrasive Size (Grit) |
Range from very fine (0.1 µm) to coarse (45 µm) |
Range from fine (4 µm) to coarse (150 µm) |
Range from very fine (0.1 µm) to fine (6 µm) |
Material Removal Rate |
Low to moderate |
High |
Very low |
Surface Finish |
Moderate to high |
Moderate to high |
Very high, mirror-like finish |
Typical Applications |
Precision flatness and dimensional control, semiconductor wafers, optics, advanced ceramics |
Heavy material removal, shaping, tool grinding, metalworking |
Final surface finishing, optics, semiconductor wafers, fine jewelry |
Advantages |
- Provides high precision and flatness - Can achieve excellent form accuracy - Suitable for a wide range of materials |
- High efficiency in material removal - Long-lasting abrasive - Suitable for hard materials |
- Achieves superior surface finish - Ideal for delicate materials - Can be used for both intermediate and final polishing |
Disadvantages |
- Slower material removal compared to grinding - Requires careful control of slurry concentration and distribution |
- Can generate significant heat - Requires effective cooling - More expensive consumables |
- Slow material removal rate - Requires meticulous cleaning to prevent contamination |
Diamond consumables used in lapping, grinding, and polishing, including both fixed and loose diamond abrasives:
Both fixed and loose diamond abrasives play crucial roles in lapping, grinding, and polishing processes. Fixed diamond abrasives, such as diamond grinding wheels, belts, tools, pads, discs, and films, are essential for heavy-duty and high-efficiency applications, providing consistent performance and durability. Loose diamond abrasives, including diamond slurry and paste, are ideal for achieving high precision and superior surface finishes, especially in applications requiring meticulous control over material removal and surface quality. Understanding the specific properties and suitable applications of each type of diamond abrasive helps manufacturers select the most appropriate consumables for their precision finishing operations, ensuring optimal results and high-quality outcomes.
Comparison of Fixed and Loose Diamond Abrasives
Feature/Aspect |
Fixed Diamond Abrasives |
Loose Diamond Abrasives |
---|---|---|
Form |
Diamond grinding wheels, belts, tools, pads, discs, films |
Diamond slurry, diamond paste |
Applications |
Heavy-duty grinding, shaping, precision polishing |
Precision lapping, localized polishing |
Material Removal Rate |
Moderate to high |
Low to moderate |
Surface Finish |
Moderate to high |
High to very high |
Typical Uses |
Metalworking, tool grinding, aerospace, automotive |
Semiconductor wafers, optics, advanced ceramics |
Grit Size Range (Microns) |
0.1 µm to 150 µm |
0.1 µm to 45 µm |
Advantages |
Long-lasting, consistent performance, suitable for hard materials |
High precision, excellent surface finish, adaptable to different processes |
Disadvantages |
Higher initial cost, requires specific equipment |
Requires careful handling and preparation, potential for uneven distribution |
ARE YOU USING RIGHT TOOLS
FOR YOUR APPLICATION?
LET US
HELP YOU
HAVING ISSUES WITH
YOUR CURRENT TOOLS?
Knowledge Center
How to Selecting Right Diamond Tools for your application
How to properly use Diamond Tools
Why use diamond
Diamond vs CBN (cubic boron nitride) Tools
What is Diamond Mesh Size and how to select best one for your application
What is Diamond Concentration and which to use for your application
Diamond Tool Coolants Why, How, When & Where to Use
Get to Know the Diamond Tool Bond Types and Which to use for your application
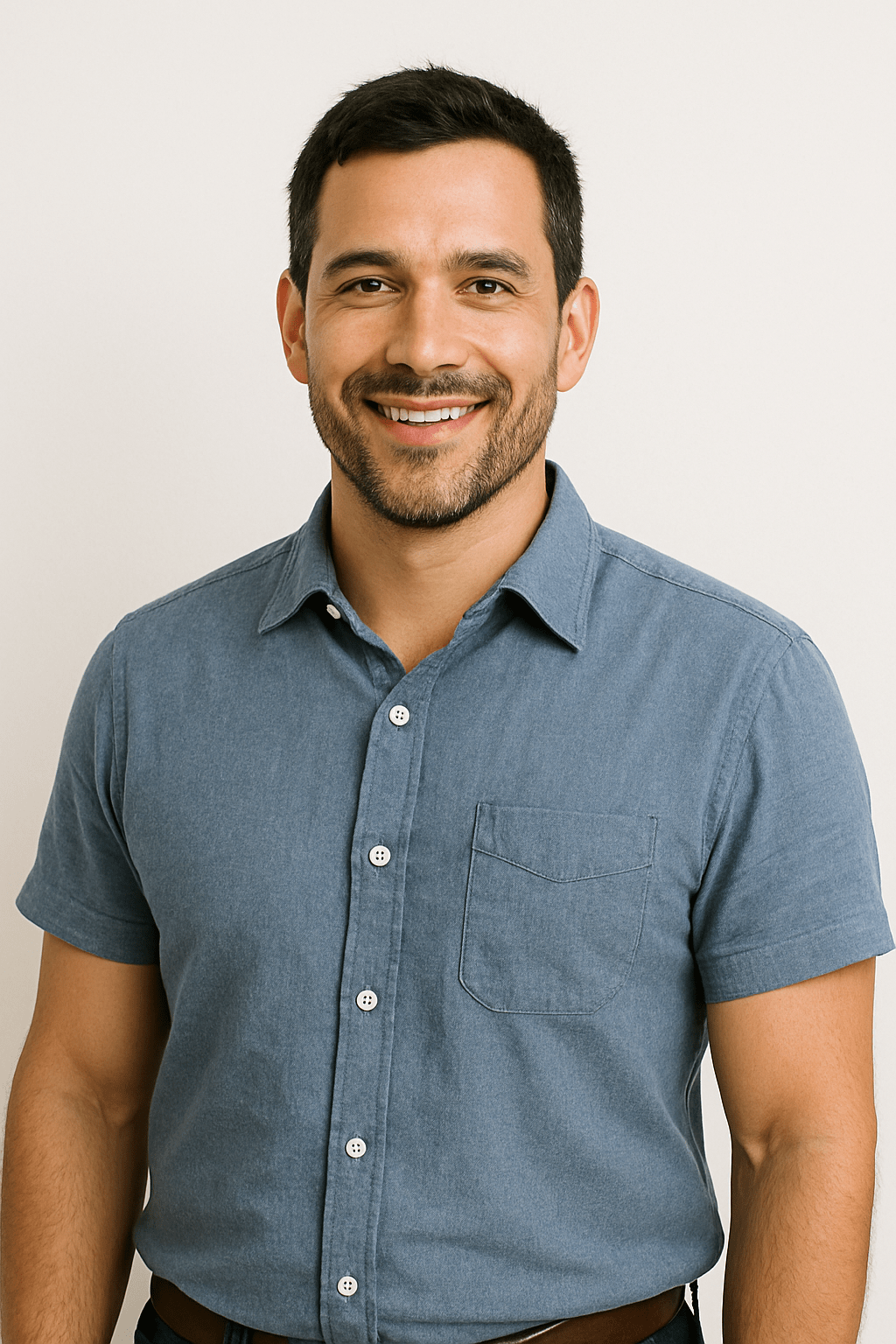
Carlos Sanchez is a senior technical specialist and field applications trainer with more than 17 years of experience in the use and optimization of industrial diamond tools, including ultra-thin diamond blades, core drills, and CBN grinding wheels. With a foundation in industrial engineering and technical operations, Mr. Sanchez has worked extensively with manufacturers and laboratories around the world, providing hands-on support and practical training for a wide range of cutting, grinding, and sample preparation applications.
Fluent in both English and Spanish, Carlos is known for his ability to translate complex tooling concepts into clear, actionable procedures for engineers, technicians, and production staff. His approach emphasizes real-world process improvement, tool longevity, and operator education—ensuring clients get the most out of their diamond tooling investments.
As an author, Mr. Sanchez shares field-tested insights on tool performance optimization, defect prevention, training methodologies, and troubleshooting common cutting issues.
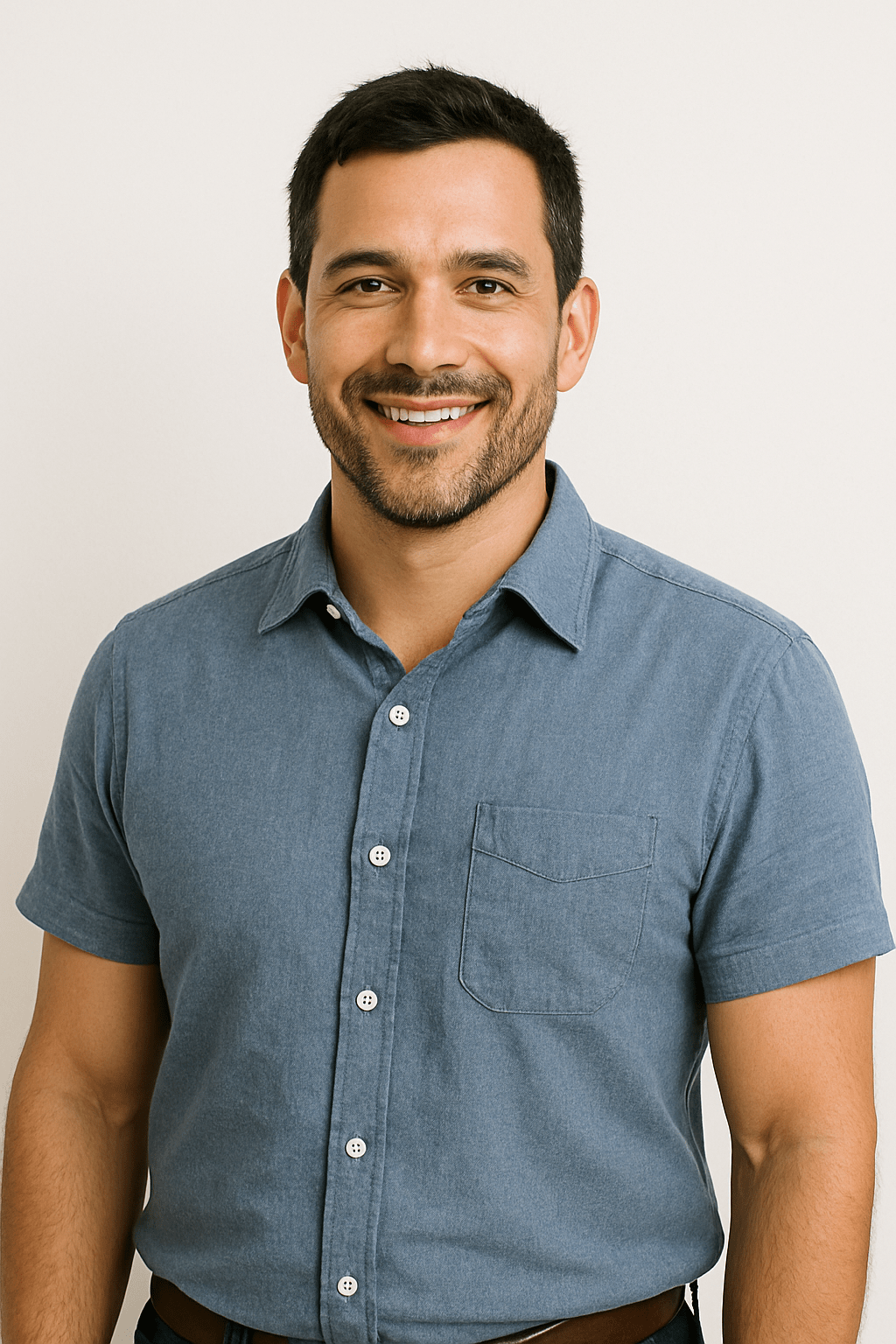
Carlos Sanchez is a senior technical specialist and field applications trainer with more than 17 years of experience in the use and optimization of industrial diamond tools, including ultra-thin diamond blades, core drills, and CBN grinding wheels. With a foundation in industrial engineering and technical operations, Mr. Sanchez has worked extensively with manufacturers and laboratories around the world, providing hands-on support and practical training for a wide range of cutting, grinding, and sample preparation applications.
Fluent in both English and Spanish, Carlos is known for his ability to translate complex tooling concepts into clear, actionable procedures for engineers, technicians, and production staff. His approach emphasizes real-world process improvement, tool longevity, and operator education—ensuring clients get the most out of their diamond tooling investments.
As an author, Mr. Sanchez shares field-tested insights on tool performance optimization, defect prevention, training methodologies, and troubleshooting common cutting issues.