Table of Contents
ToggleCutting glass is a delicate process that requires the right set up, technique and process to avoid cracks, chips, or fractures. The inherent brittleness and hardness of glass make it challenging to work with, requiring specialized diamond cutting blades, equipment, rpm’s, coolant, and cutting methods. Whether cutting for architectural purposes, artistic endeavors, or industrial applications, the process with which glass is cut directly impacts the final product’s structural integrity, aesthetic appeal, and overall performance.
Share this Article with Friend or Colleague
Diamond cutting blades have long been used for cutting large variety of glass such as soda lime and borosilicate glass, optical glass such as fused silica and bk7, quartz and pyrex. The material can be of almost any thickness, dimension, and shape.
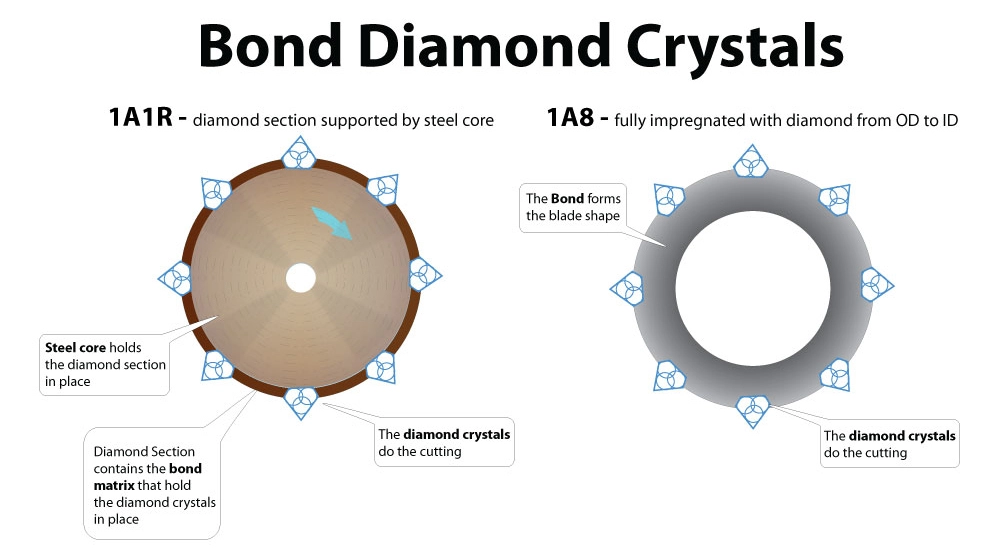
Diamond cutting blades are embedded with industrial diamonds, which offer unparalleled hardness and sharpness, ensuring clean, faster and freer cutting action with minimum chipping. The structure of the diamond blade allows for minimal chipping while providing high durability and cutting efficiency. Diamond blades reduce the risk of glass cracking under pressure, as the cutting process is smoother and more controlled compared to traditional blades such as abrasive or carbide.
Selecting of the Right Blade for Different Glass Cutting Applications
Choosing the right diamond cutting blade for glass depends on large variety of factors. Each application, whether it's architectural, automotive, or artistic, has unique demands that influence the blade selection process:
Factor |
Description |
Considerations for Glass Cutting |
---|---|---|
Type of Glass |
Different types of glass, such as float glass, tempered glass, or laminated glass, require specific blade properties to ensure a precise cut without damaging the material. |
Each glass type has varying hardness and brittleness, requiring tailored blade designs for optimal performance. |
Glass Dimensions and Shape |
The size, thickness, and shape (e.g., flat, curved, irregular) of the glass material influence the cutting process and blade choice. |
Larger or thicker glass may require thicker blades, while intricate shapes and thinner glass need finer blades for precision. Complex shapes may require slower cutting speeds and finer diamond grit. |
Blade Size and Thickness |
The size and thickness of the diamond blade should match the material’s dimensions and thickness to prevent excessive material loss or blade wear. |
Larger, thicker blades are suited for thicker glass, while thinner blades are required for delicate or thinner glass. |
Blade Bond Type |
The bond type holds the diamonds in place and affects cutting performance. Soft bonds are suited for hard materials like glass. |
A softer bond ensures diamonds stay exposed when cutting hard materials like glass, preventing premature wear. |
Diamond Grit Size |
Refers to the size of the diamond particles embedded in the blade. Finer grit sizes are used for smoother cuts, while coarser grit sizes are more aggressive. |
Finer grits (e.g., 400-600 mesh) are ideal for precise, chip-free cutting in thin, delicate glass. Coarser grits (e.g., 100-200 mesh) are suitable for faster cuts in thicker, harder glass. |
Diamond Concentration |
Represents the amount of diamond material present in the blade. Higher concentrations increase cutting efficiency and blade lifespan. |
High diamond concentrations (e.g., 100%) are needed for thick, tough glass, while lower concentrations (e.g., 50%) can be used for thin, delicate glass. |
Diamond Bond Hardness |
Indicates how hard or soft the bond holding the diamonds is. Softer bonds wear faster, allowing new diamonds to be exposed, while harder bonds last longer. |
For glass, a softer bond is typically preferred to expose new diamonds quickly as the glass wears down the blade. Harder bonds may be used for extended blade life in less demanding applications. |
Cutting Speed (RPM) |
The correct rotational speed of the blade is crucial for smooth, clean cuts. Improper speeds can cause overheating and glass damage. |
Higher RPMs work well for precise, fast cutting, while lower RPMs are better for fragile, thin glass. |
Coolant and Lubrication |
Coolants prevent overheating, reduce friction, and extend blade life while maintaining cut quality. |
Essential for glass cutting to avoid thermal shock, blade overheating, and to achieve smoother finishes. |
Desired Cut Quality |
The surface finish, chipping levels, and cut quality required depend on the glass's final application. |
High-precision applications may need ultra-fine blades and lower feed rates to minimize chipping and roughness. |
Type of Cutting Equipment |
The machine or equipment used for cutting (e.g., wet saws, CNC machines, manual cutters) influences the blade type and settings. |
Automated machines like CNC ensure precision, while manual cutters require specific blade sizes and feed rates for accuracy. Equipment compatibility with coolant systems and blade speed settings is also crucial. |
Glass Properties and Material Characteristics
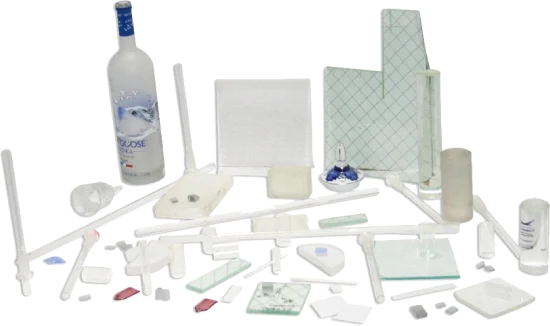
Table that includes the characteristics, common uses, and the challenges encountered when cutting each type of glass using a diamond blade:
Glass Type |
Performance |
Common Uses |
Properties |
Strength |
Challenges When Cutting with Diamond Blades |
Brittleness |
Hardness |
Thermal Conductivity/Heat Sensitivity |
---|---|---|---|---|---|---|---|---|
Soda Lime Glass |
Excellent |
Windows, containers, everyday products |
Good chemical resistance, thermal stability |
Acceptable for non-structural applications |
Tends to crack easily due to thermal expansion. Careful control of feed rates and cooling is needed to prevent overheating. |
High |
Medium |
Medium (Prone to thermal shock) |
Float Glass
|
Excellent |
Building windows, mirrors, glass doors |
Flat, uniform thickness, good optical clarity |
Acceptable, can be tempered or laminated for strength |
Thinness makes it prone to edge chipping. Adequate coolant and precise cutting speeds are crucial to avoid micro-cracking. |
High |
Medium |
Medium (Heats up quickly) |
Tempered Glass |
Excellent for safety |
Car windows, shower doors, public spaces |
Shatters into blunt pieces for safety |
Excellent, but cannot be cut post-tempering |
Cannot be cut after tempering. Attempts to cut can cause it to shatter immediately. Pre-tempered glass must be precisely cut. |
High |
Medium |
Medium (Sensitive to heat build-up) |
Laminated Glass |
Excellent for soundproofing |
Car windshields, skylights |
Superior sound insulation, UV protection |
Strong, impact-resistant |
Cutting through the plastic interlayer can result in uneven cuts or melting. Requires a specialized blade and slower cutting speed. |
Medium |
Medium |
Low (Plastic interlayer complicates cooling) |
Borosilicate Glass (Pyrex) |
Excellent thermal resistance |
Cookware, laboratory glassware |
Withstands extreme temperatures |
Good impact resistance |
Susceptible to thermal shock during cutting. Proper coolant flow is necessary to prevent cracking due to rapid temperature changes. |
High |
High |
Low (Prone to thermal shock) |
Low-E Glass |
Excellent for energy efficiency |
Energy-efficient windows |
Reflects infrared, reduces heat transfer |
Acceptable |
The reflective coating can wear down diamond blades faster. Precision is required to avoid damaging the coating during cutting. |
Medium |
Medium |
Medium (Sensitive to heat) |
Insulated Glass (IGU) |
Excellent for insulation |
Windows and doors with thermal insulation |
Reduces heat transfer, improves energy efficiency |
Strong, often used with tempered glass |
Multiple layers complicate cutting. Each pane may respond differently to the blade, requiring precision and careful cooling to avoid delamination. |
High |
Medium |
Low (Multiple layers need careful cooling) |
Patterned Glass
|
Excellent for privacy |
Decorative windows, doors |
Textured, allows light diffusion |
Acceptable |
Textures can cause uneven cuts or lead to blade wear. Specialized blades may be needed to handle the surface irregularities. |
High |
Medium |
Medium |
Quartz Glass (Fused Silica) |
Excellent thermal resistance |
Optics, semiconductor industry |
Withstands extreme heat, excellent optical clarity |
Good, but can crack under heavy mechanical stress |
Brittle and prone to cracking. Requires slow cutting speeds and optimal cooling to manage heat buildup and avoid surface stress. |
Very High |
Very High |
Low (Highly prone to thermal shock) |
Toughened Glass |
Excellent for safety |
High-stress environments like building facades |
Impact and temperature resistant |
Excellent, stronger than standard glass |
Like tempered glass, it shatters upon cutting. Must be cut before toughening or use pre-cut sizes. |
High |
Medium |
Medium (Heats up quickly) |
Fire-Rated Glass |
Excellent for fire resistance |
Fire doors, walls, and windows |
Resists flames and high heat for extended periods |
Adequate for normal use, strong under heat exposure |
Special coatings or layers can complicate cutting. High heat during cutting may reduce fire resistance properties. |
High |
Medium |
Medium (Sensitive to heat) |
Frosted Glass |
Excellent for privacy |
Bathroom windows, office partitions |
Diffuses light, blocks visibility |
Acceptable |
Frosted surfaces can wear blades more quickly and result in uneven edges. Diamond blade should be finely tuned for precision. |
High |
Medium |
Medium |
Tinted Glass |
Excellent for solar control |
Windows in buildings and vehicles |
Reduces heat and glare |
Acceptable |
The tinting layer can interfere with smooth cuts. Requires careful speed and cooling control to maintain an even edge and avoid chipping. |
Medium |
Medium |
Medium |
Acid-Etched Glass |
Excellent for aesthetics |
Decorative windows, doors |
Smooth, translucent finish |
Similar to float glass |
The acid-etched surface is prone to micro-cracks during cutting. Diamond blade wear can increase if the etching is deep. |
High |
Medium |
Medium |
Annealed Glass |
Excellent in basic applications |
Windows, doors, picture frames |
Shatters into large shards, untreated after forming |
Acceptable |
More prone to chipping and cracking during cutting compared to tempered glass. Requires slower speeds to minimize breakage. |
High |
Medium |
Medium |
Lead Glass (Crystal) |
Excellent for optical clarity |
High-quality glassware, chandeliers |
High refractive index, brilliant sparkle |
Acceptable, but softer and prone to scratching |
The softer nature of lead glass causes it to wear diamond blades faster. Chipping is common unless the blade is well-calibrated. |
Medium |
Low |
Medium |
Optical Glass |
Excellent for precision optics |
Lenses, prisms, cameras, microscopes |
Exceptional clarity, controlled light transmission |
Strong, varies based on specific application |
Extreme precision required. High-quality blades with fine grit are necessary to avoid optical distortions or scratches on the surface. |
High |
High |
Medium |
Fused Silica/Quartz Glass |
Excellent for high temperatures |
Optics, laboratory equipment, high-temperature uses |
Withstands extreme heat, low thermal expansion |
Strong, heat-resistant but prone to mechanical stress |
Brittle and challenging to cut. Needs slow feed rates, precise RPM control, and excellent cooling to prevent thermal stress and cracking. |
Very High |
Very High |
Low (Very prone to thermal shock) |
Smart Glass (Electrochromic) |
Excellent for dynamic privacy |
Privacy windows, skylights, energy-efficient buildings |
Changes opacity with electrical current |
Acceptable, mainly used for privacy |
Cutting may damage the electrical layers, leading to functionality issues. Requires highly specialized cutting equipment to avoid internal damage. |
Medium |
Medium |
Medium (Electrical layers can overheat) |
Bulletproof Glass |
Excellent for impact resistance |
Armored vehicles, security windows |
Laminated layers of glass and polycarbonate for strength |
Strong, multi-layered and thick |
The laminated structure makes it challenging to cut, and multiple passes may be required. Delamination can occur if not cut at the correct speed and pressure. |
Medium |
High |
Low (Interlayers complicate cooling) |
Photovoltaic (Solar) Glass |
Excellent for energy generation |
Building facades, solar panels |
Converts sunlight into electricity |
Similar to structural glass, mainly used for solar |
Requires precision to avoid damaging embedded solar cells. Blade wear increases due to glass thickness and embedded elements. |
Medium |
High |
Medium (Sensitive to heat) |
Reflective Glass |
Excellent for solar control |
Building facades, energy-efficient windows |
Reflects solar radiation, reduces heat gain |
Acceptable, used primarily for energy efficiency |
Reflective coating can wear down diamond blades faster. Cutting must be precise to avoid damaging the reflective surface, and adequate cooling is necessary. |
Medium |
Medium |
Medium (Coating heats up quickly) |
Switchable Privacy Glass |
Excellent for dynamic privacy |
Office partitions, high-end residential windows |
Switches between transparent and opaque states |
Acceptable for privacy applications |
Cutting can damage the internal layers that control opacity. Special care and tools are needed to maintain functionality after cutting. |
Medium |
Medium |
Medium (Electrical layers heat up) |
Self-Cleaning Glass |
Excellent for low-maintenance uses |
Skylights, high-rise windows, hard-to-reach places |
Coating that breaks down dirt and organic matter |
Acceptable for most architectural uses |
The self-cleaning coating is delicate and can wear down blades more quickly. Careful handling and precision cutting are necessary to preserve the coating’s effectiveness. |
Medium |
Medium |
Medium (Coating sensitive to heat) |
Soundproof Glass |
Excellent for noise reduction |
Windows and partitions in noisy environments |
Laminated with acoustic interlayers |
Strong, often multi-layered for sound insulation |
Multi-layered structure complicates cutting, requiring precision and control. Delamination is a risk if not cut with the correct settings. |
Medium |
Medium |
Low (Interlayers complicate cooling) |
Antireflective Glass |
Excellent for optical clarity |
Display cases, camera lenses, solar panels |
Reduces glare, enhances light transmission |
Adequate for typical optical applications |
Antireflective coatings can cause uneven wear on the blade. Precision is key to avoid damaging the coating during cutting. |
Medium |
Medium |
Medium (Coating heats up) |
Gorilla Glass |
Excellent for scratch resistance |
Smartphones, tablets, portable electronics |
Lightweight, thin, scratch-resistant |
Strong for handheld electronics, high impact resistance |
Tough to cut due to its chemical strengthening. Requires special high-quality diamond blades and slow feed rates to avoid micro-fractures. |
Medium |
High |
Low (Very heat-sensitive) |
Dragontrail Glass |
Excellent for impact resistance |
Smartphones, consumer electronics |
Similar to Gorilla Glass, durable, and lightweight |
Strong, high scratch and impact resistance |
Similar to Gorilla Glass, cutting is difficult due to its toughness. Precision blades and cooling are necessary to prevent stress cracks. |
Medium |
High |
Low (Prone to heat build-up) |
Chromatic Glass |
Excellent for dynamic light control |
Architectural applications, tint-changing windows |
Adjusts opacity or color in response to light or temperature |
Acceptable, mainly used for tint control |
Changing opacity layers are delicate and can be easily damaged during cutting. Precision cutting and proper equipment are essential to maintain functionality. |
Medium |
Medium |
Medium (Sensitive to heat) |
Ceramic Glass |
Excellent for heat resistance |
Stovetops, fireplaces, high-temperature environments |
Withstands high heat without cracking |
Strong under thermal stress, prone to brittleness |
Brittle and prone to cracking if cut too quickly. Slower feed rates and higher precision are required to prevent thermal stress during cutting. |
High |
High |
Low (Resistant to thermal expansion) |
Stained Glass |
Excellent for decorative purposes |
Church windows, artistic installations |
Colored with metallic salts, used for intricate designs |
Acceptable for low-stress environments |
The brittle nature of stained glass makes it susceptible to cracking during intricate cuts. Special thin blades are needed for detailed designs, and slow cutting speeds reduce stress. |
High |
Medium |
Medium (Heats up quickly) |
Art Glass |
Excellent for artistic expression |
Sculptures, decorative panels |
Unique patterns, colors, and textures |
Acceptable for decorative purposes |
Variations in thickness and texture can lead to uneven cuts. Fine diamond blades and careful control of speed and feed rates are necessary for cutting intricate shapes in art glass. |
High |
Medium |
Medium (Heats up quickly) |
Glass Assemblies |
Excellent for multi-pane applications |
Insulated glass units, complex window assemblies |
Combines the benefits of multiple glass types |
Strong, layered for specific performance needs |
Multiple layers require precision in cutting. Each layer may behave differently under the blade, increasing complexity and risk of delamination. |
Medium |
Medium |
Low (Multiple layers need cooling) |
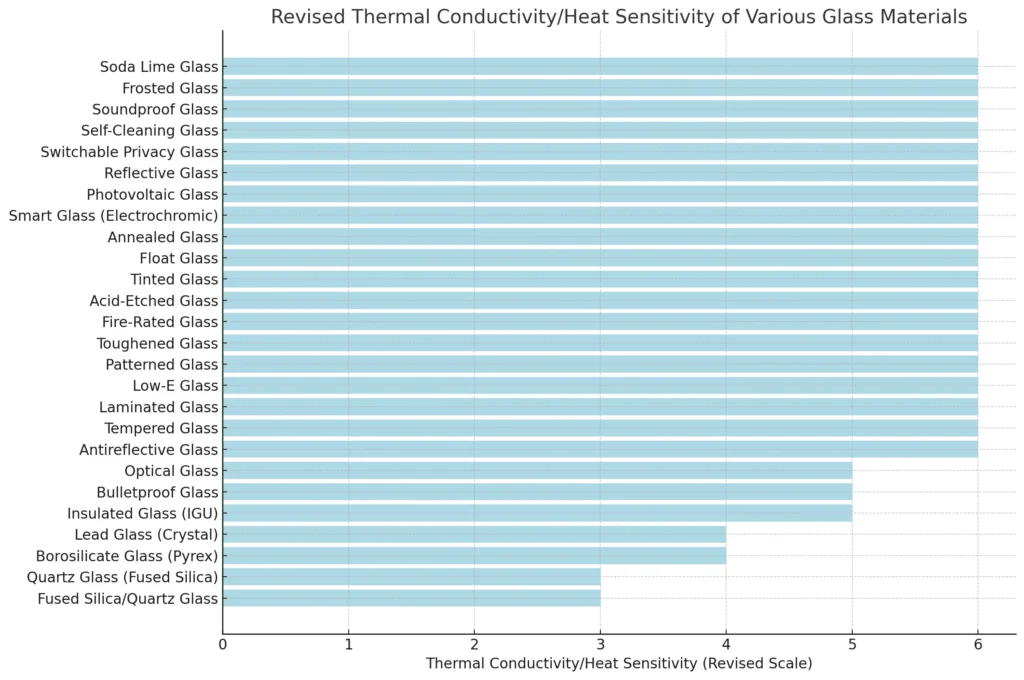
Thermal Conductivity/Heat Sensitivity of Various Glass Materials," visualizes the thermal properties of different glass materials on a scale of 1 to 6, where lower values indicate lower thermal conductivity and higher heat sensitivity. This scale is crucial for understanding how glass materials behave when subjected to the heat generated during cutting processes. The heat sensitivity of the material influences the selection of diamond blades, cutting equipment, coolant systems, and the overall process control. Glass materials typically have low thermal conductivity, meaning they heat up quickly during cutting, which can lead to thermal stress, cracking, and warping. Proper cooling is essential to control the heat generated by the diamond blade. If not managed properly, materials like borosilicate, quartz, and laminated glass can crack due to heat buildup. Effective coolant flow and cutting speed adjustments are crucial to avoid thermal damage and ensure smooth, defect-free cuts.
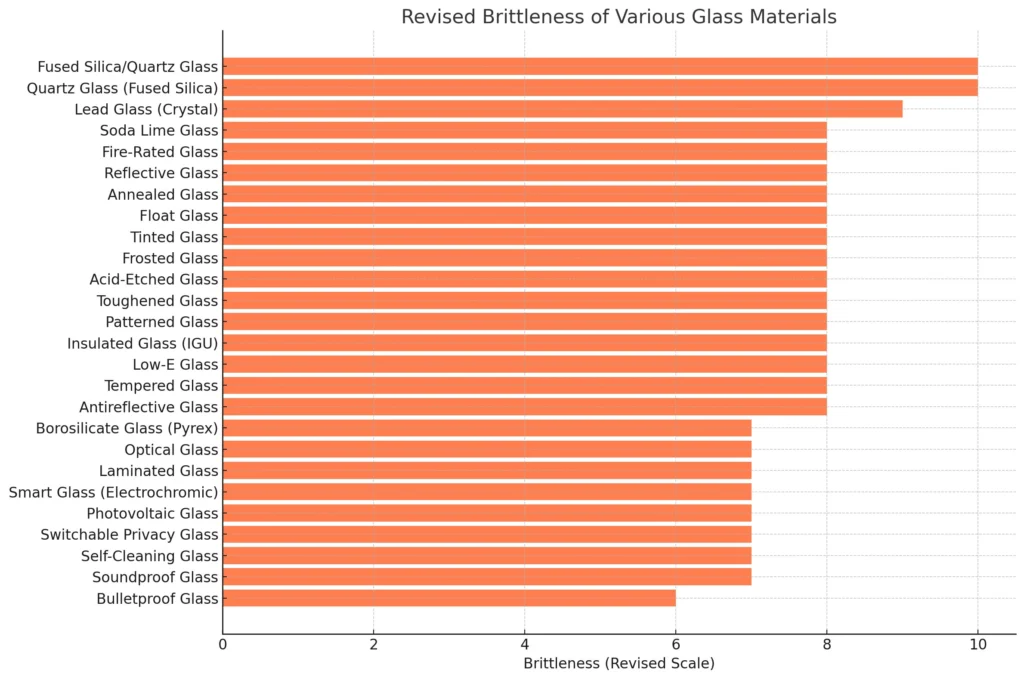
This chart, titled " Brittleness of Various Glass Materials," visually represents the relative brittleness of different types of glass materials on a scale from 1 to 10. It helps in understanding how fragile each material is under stress, particularly when subject to cutting with diamond blades. The brittleness scale is critical for determining the appropriate cutting tools, equipment, and processes, especially for glass applications where cracking, chipping, or shattering is a concern. Glass is inherently brittle, and this property affects nearly every glass type. Brittle materials are prone to cracking, chipping, and shattering under stress, making it essential to use diamond blades with appropriate feed rates, speeds, and cooling to minimize damage. Managing the material's brittleness is critical for achieving clean, smooth cuts without breaking the glass, especially with more delicate or high-value glass types like optical glass, quartz, and borosilicate glass.
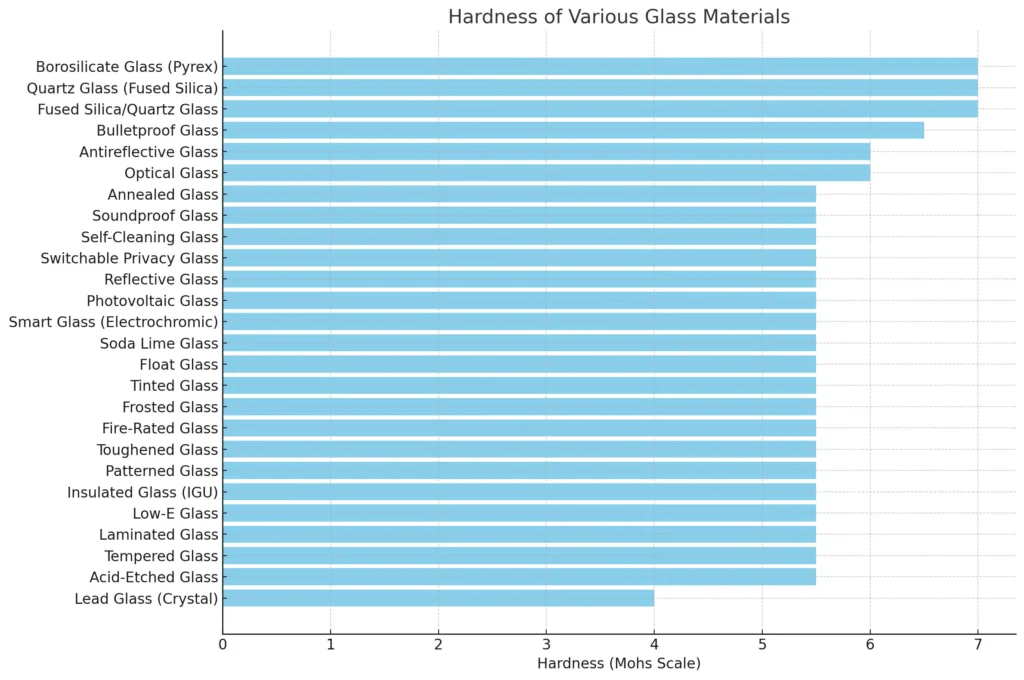
Hardness of Various Glass Materials," visualizes the hardness of different glass materials using the Mohs hardness scale. The hardness of a material indicates its resistance to scratching, wear, and abrasion, making it a crucial factor in determining the type of diamond blade, cutting technique, and speed needed to achieve clean and precise cuts. Glass hardness determines the durability of the blade and the cutting speed. Harder glass materials require more durable diamond blades and slower cutting speeds to avoid premature blade wear and ensure clean cuts. For example, fused silica (quartz) and borosilicate glass are harder than soda-lime glass, requiring tougher diamond blades and more precise control. Hardness affects the efficiency of the cut and the lifespan of the blade.
Examples of Popular Glass Cutting Applications
float glass is one of the most widely used glass types in applications such as windows, mirrors, and architectural panels. Its smooth surface, coupled with its cost-effectiveness, makes it a preferred choice in both residential and commercial settings. Typically, float glass has a thickness ranging from 3 to 12 mm, with thinner glass (3 to 6 mm) being used in standard windows, while thicker variants (10 to 12 mm) are used in architectural applications or areas that require enhanced durability.
Borosilicate glass is recognized for its remarkable resistance to heat and chemicals, making it ideal for use in laboratory equipment, cookware, and industrial environments. This type of glass can withstand extreme temperatures and exposure to harsh chemicals without compromising its structural integrity. Borosilicate glass varies in thickness from 10 to 50 mm, with thicker versions often used in high-stress environments like laboratories and thinner ones found in everyday cookware.
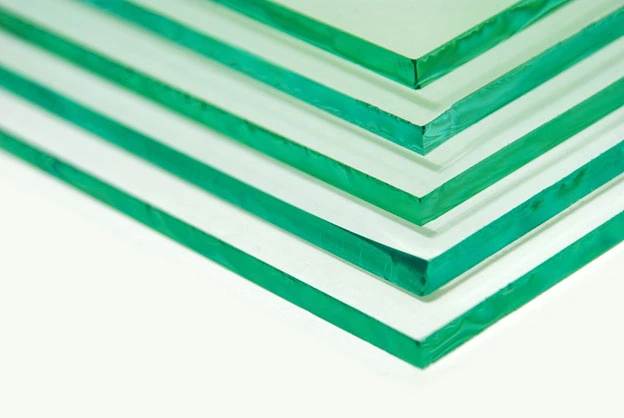
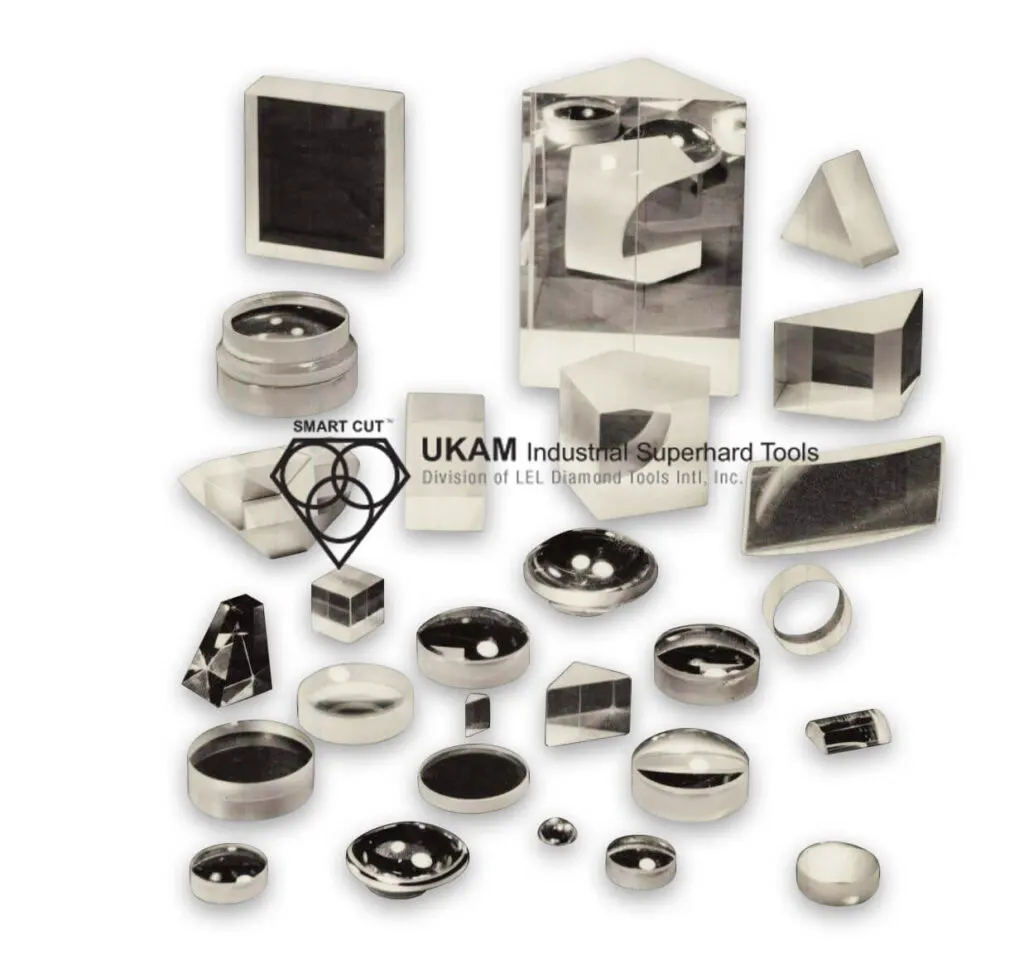
Tempered glass, known for its safety features, is extensively used in both automotive and architectural applications. Through thermal or chemical treatments, tempered glass becomes much stronger than standard glass, making it suitable for areas where safety is a concern, such as building facades and shower enclosures. Unlike regular glass, tempered glass shatters into small, blunt pieces when broken, reducing the risk of injury. Its thickness typically ranges from 5 to 25 mm, depending on whether it is used in automotive windows or large architectural panels.
Fused silica, also known as quartz glass, is a high-purity material prized for its thermal resistance, chemical stability, and optical clarity. These characteristics make it a go-to material in industries like semiconductors, optics, and aerospace, where precision is critical. Fused silica is commonly found in thicknesses ranging from 1 to 20 mm, with thinner glass often used in optical components and thicker glass in high-temperature industrial applications.
Leaded glass, often referred to as crystal glass, contains lead oxide, giving it a signature brilliance and weight. Primarily used for decorative purposes, this type of glass is found in luxury glassware, chandeliers, ornaments, and artistic designs. Its refractive properties make it ideal for creating intricate, elegant pieces. While leaded glass is typically thinner than other types of glass, its thickness generally ranges up to about 10 mm, depending on the application.
Material Shape and Dimensions
When cutting glass, the shape and dimensions of the material play a significant role in determining the type of diamond blade and cutting method used.
Flat panels are one of the most common forms of glass used in various applications, such as windows, doors, and large architectural panels. These panels range in size from small sections of about 5 cm² to larger sheets, often measuring up to 3 x 2 meters.
Cutting flat glass panels is a challenging process across industries like architecture, automotive, solar, and electronic displays, with each requiring specialized tools and techniques.
In the architectural industry, large panels for windows and facades, sometimes as big as 3 x 2 meters, require high precision. Maintaining straight, smooth cuts over such long distances is difficult. Any minor deviation can result in uneven edges or cracks, affecting both the structural and aesthetic integrity of the glass. Automated cutting systems with high-precision diamond blades are essential, and proper support and handling, using equipment like vacuum lifts, are required to prevent stress points or sagging that could damage the panels. Cooling systems are also critical to prevent thermal stress that could lead to cracks, especially in thick or coated glass.
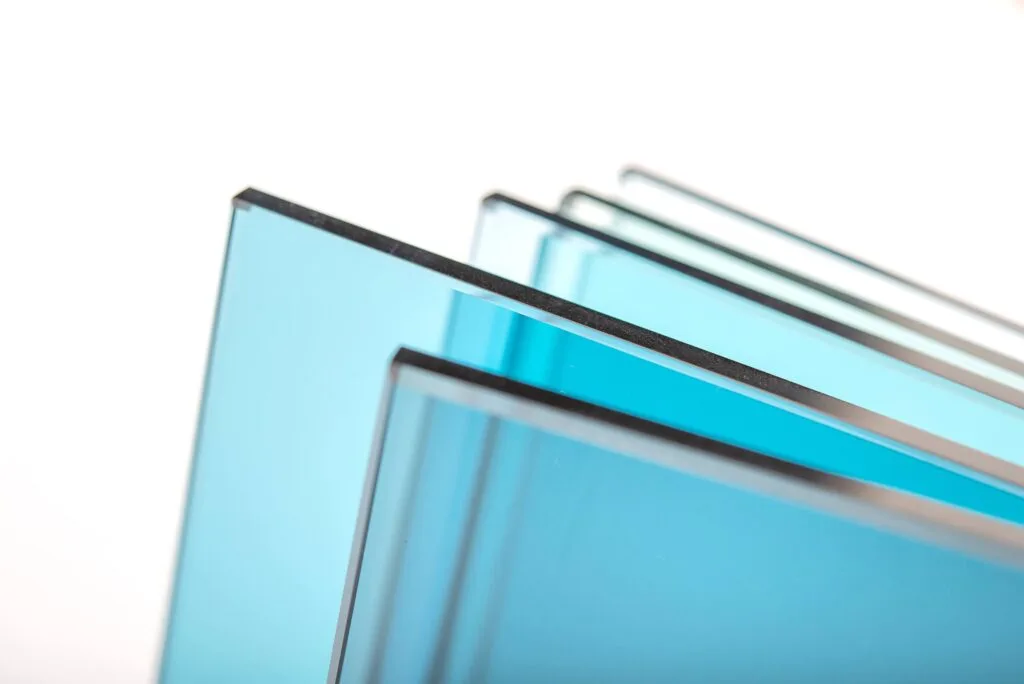
In the automotive industry, cutting laminated glass for windshields and tempered glass for windows involves additional complexities. Laminated glass, with its plastic interlayer, requires precision to ensure smooth cuts through both the glass and plastic. Managing heat buildup is crucial, as thermal stress can lead to cracks in tempered glass, especially on curved surfaces. Cooling systems, specialized diamond blades, and precise cutting speeds help meet safety standards while preventing defects.
The solar industry faces its own challenges, particularly when cutting large glass panels for solar cells. These panels are typically made of low-iron glass to maximize light transmission, but cutting must be precise to avoid micro-cracks that could compromise the efficiency of the solar cells. As with architectural glass, managing thermal stress through effective cooling systems is essential to prevent damage during the cutting process.
In electronic displays, such as those used in smartphones, tablets, and televisions, the glass is often thin and extremely delicate. Cutting these panels requires high precision to avoid chipping, which could affect both the functionality and appearance of the final product. Fine-grit diamond blades and careful control of cutting pressure and speed are critical for smooth, chip-free edges. Since these glass panels are so fragile, proper handling throughout the process is essential to prevent cracks or breakage.
Across these industries, managing thermal stress, ensuring precision, and handling large or delicate glass panels properly are the key challenges that require the right combination of diamond blades, cutting equipment, and cooling systems.
Tubes and cylinders (Hollow Glass Materials) represent another important category of glass shapes, commonly used in lighting applications and scientific instruments. These cylindrical glass pieces come in a wide range of diameters, from as small as 5 mm for delicate components to larger sizes reaching up to 500 mm. Cutting cylindrical glass requires specialized equipment that can make precise cuts without compromising the material's integrity, as the curved surface can complicate the cutting process.
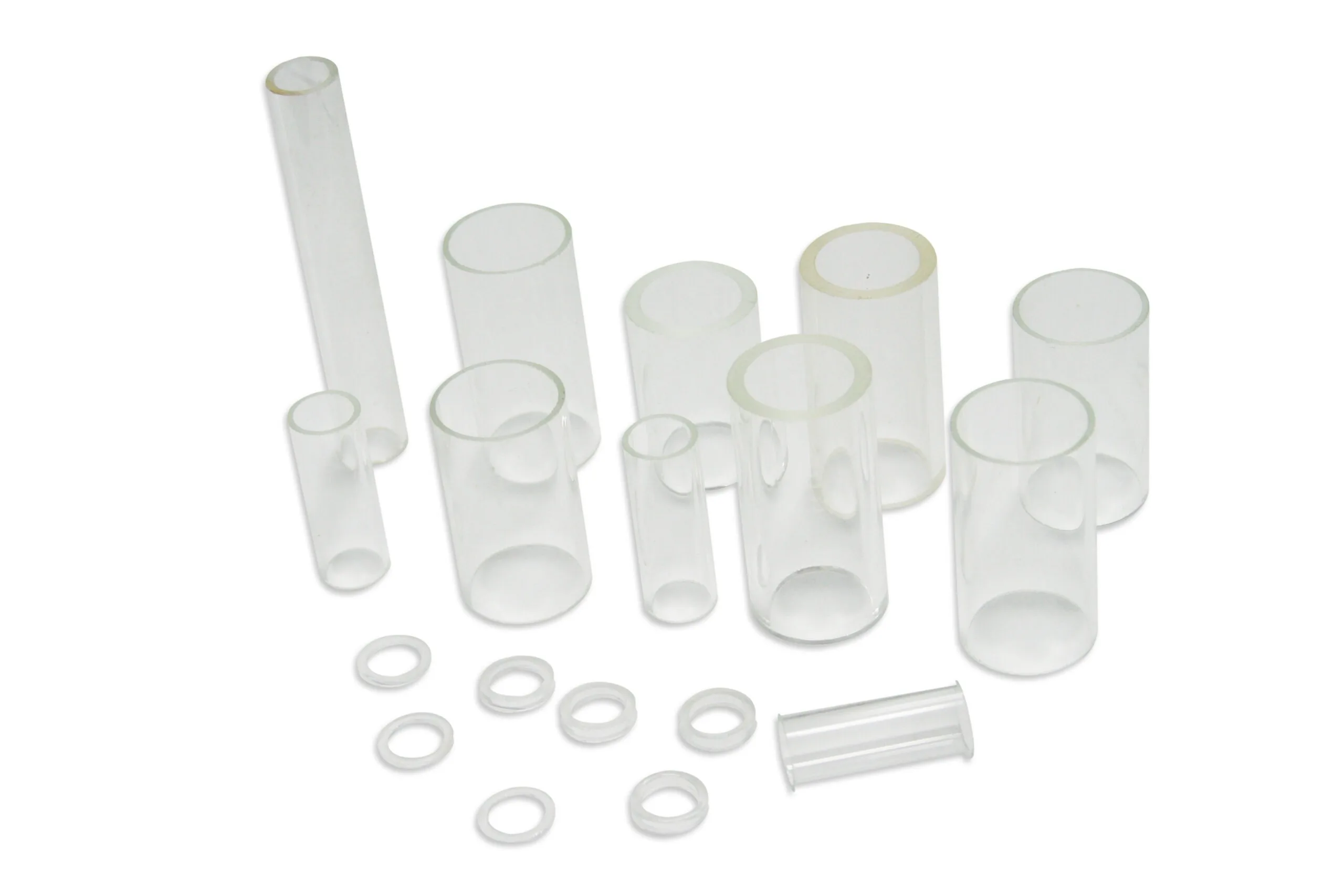
Challenges Cutting Hollow Glass Materials
1. Variable Wall Thickness
2. Internal Stress
3. Fragility and Risk of Collapse
4. Control of Cutting Dynamics
Cutting hollow glass materials presents several challenges that must be carefully managed to avoid damage and ensure precision. One significant issue is the variable wall thickness often found in hollow glass items. This inconsistency can lead to uneven pressure distribution during the cutting process, greatly increasing the risk of cracking or breaking the material. Such variations require precise adjustments and careful monitoring to maintain stability and integrity throughout the cutting operation.
Another challenge lies in the internal stress inherent in mechanically blown or molded hollow glass. These stresses, built up during the manufacturing process, can be unpredictably released when the glass is cut. This release can result in unexpected cracks or breaks, making it essential to understand and anticipate the internal stress patterns of the glass to mitigate potential damage.
The inherent fragility and risk of collapse associated with hollow glass further complicate the cutting process.
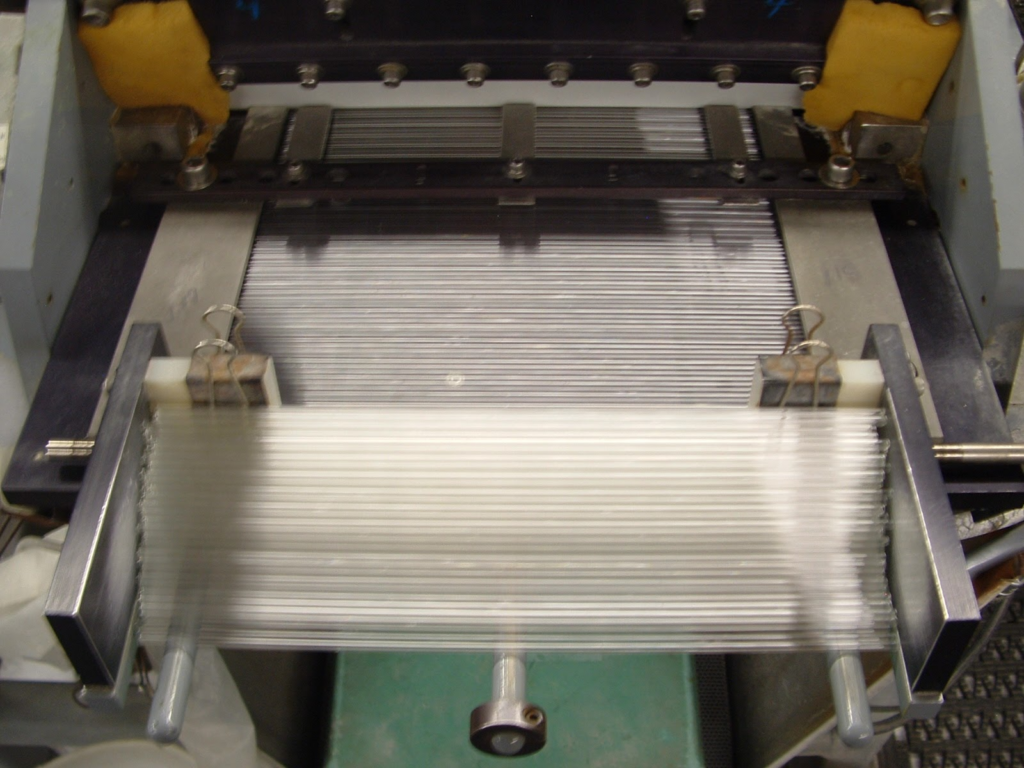
The hollow structure, by its nature, is more susceptible to collapsing under pressure, especially if the cutting process is not meticulously controlled. Managing this fragility requires an expert approach to pressure application and support during cutting to prevent collapse.
Control of cutting dynamics is another critical aspect when dealing with hollow glass. Achieving a consistent cutting speed, minimizing vibration, and ensuring proper blade engagement are significantly more challenging with hollow glass compared to solid materials. The lower structural integrity of hollow glass demands a higher level of precision and careful calibration of cutting equipment to avoid introducing stress that could lead to fractures.
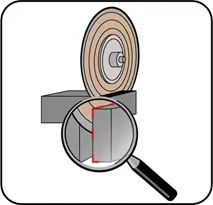
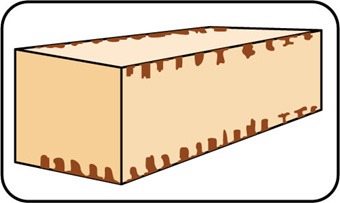
Chipping is another prevalent issue when cutting hollow glass. The brittle nature of glass makes it susceptible to chipping, especially along the cut edges. This can result in a rough finish, which may not only be aesthetically displeasing but could also compromise the structural integrity of the glass. Using the correct blade type and ensuring that the cutting speed and feed rate are optimized can help minimize chipping and produce smoother edges.
A rough finish is often the result of improper cutting techniques or equipment settings. Achieving a smooth finish on hollow glass requires fine-tuning the cutting parameters and using high-quality, precision diamond blades designed for glass. The right coolant can also play a crucial role in reducing friction and heat, which can contribute to a finer finish.

Material cracking is a critical concern due to the brittleness and internal stress of hollow glass. Cracking can occur if the cutting process generates excessive heat or if the glass is subjected to sudden impacts or vibrations. Controlling the temperature, using adequate lubrication, and employing a slow, steady cutting motion are essential practices to prevent cracking.
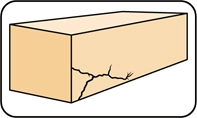
Curved or three-dimensional glass shapes are increasingly prevalent in custom artistic projects and advanced optical applications. These forms vary widely in size and complexity, with each project requiring a highly customized cutting approach. The unique curvature and contours of 3D glass pieces make it essential to use diamond blades designed for flexibility and precision, as even slight inaccuracies can lead to imperfections or unwanted breakage.
Cutting curved or three-dimensional glass shapes comes with several challenges, especially as these materials are used in custom artistic projects and advanced optical applications. One of the main difficulties is maintaining precision on curved surfaces. The irregular angles and depths make it difficult to achieve smooth cuts, as even small inaccuracies can lead to imperfections or structural issues. Standard diamond blades are often not flexible enough for these contours, so specialized blades are necessary to follow the curvature without damaging the glass.
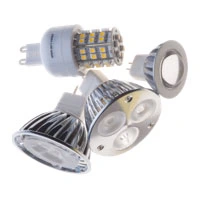
Another challenge is avoiding stress concentrations that can lead to breakage. The curves and contours of the glass can create points where stress builds up during cutting, increasing the risk of cracks. This issue is particularly problematic with thin, delicate glass. To prevent damage, cutting needs to be done slowly and with precision, using fine-grit diamond blades that minimize pressure. In many cases, multiple passes are required to gradually remove material without causing stress.
Another challenge is avoiding stress concentrations that can lead to breakage. The curves and contours of the glass can create points where stress builds up during cutting, increasing the risk of cracks. This issue is particularly problematic with thin, delicate glass. To prevent damage, cutting needs to be done slowly and with precision, using fine-grit diamond blades that minimize pressure. In many cases, multiple passes are required to gradually remove material without causing stress.
Managing thermal stress is another concern, as the uneven thickness and geometry of 3D glass surfaces can result in unpredictable heat distribution. Excessive heat buildup can lead to cracking or warping, especially in more delicate areas. Effective cooling systems, such as water sprays or liquid coolants, are essential to maintain consistent temperatures across the surface and prevent thermal damage.
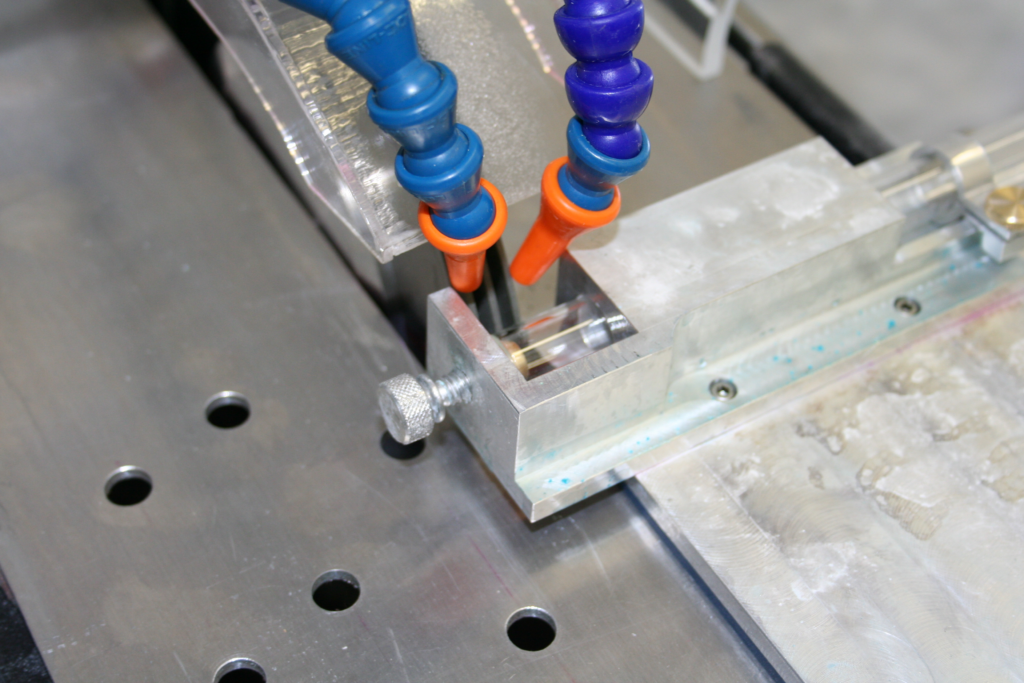
Handling and supporting irregular glass shapes during cutting is also more complicated than working with flat panels. The unique contours require specialized support systems to keep the glass stable and prevent unwanted movement. Proper handling is crucial to avoid uneven cuts or breakage, and custom fixtures or automated handling systems are often needed. After cutting, the edges of curved glass also require careful polishing and grinding to smooth out any imperfections, which is difficult due to the varied surface angles. This post-cut treatment must be performed with precision to ensure the edges are flawless and the shape remains intact.
Small precision components made of glass are frequently used in electronics, optics, and micro-engineered parts. These components often require ultra-thin, highly accurate cuts, as the sizes involved can be incredibly small. In such cases, diamond cutting blades designed for micro-fine work are essential to achieve the necessary precision without damaging the delicate material.
Cutting small precision components made of glass, often used in electronics, optics, and micro-engineered parts, presents several key challenges. One of the primary difficulties is achieving the ultra-thin, highly accurate cuts required for such small components. The precision needed in these cases leaves little room for error, and any deviation can result in unusable parts. To ensure accuracy, diamond cutting blades designed specifically for micro-fine work must be used. These blades allow for extremely fine cuts without causing undue stress on the glass, but they also need to be handled with care to avoid even minor imperfections.
Another challenge is preventing damage to the delicate material. Since these glass components are often very small and fragile, the risk of cracks, chips, or fractures is high. Using the wrong cutting speed or blade pressure can easily cause the material to break. Therefore, it's crucial to control the cutting parameters very closely, ensuring that the blade moves slowly and precisely, with minimal pressure applied to the glass.
Handling and stabilizing these small components during cutting is another significant challenge. Due to their size, these parts are more difficult to hold in place, which can lead to movement during the cutting process. Even the slightest shift can affect the precision of the cut or cause damage to the material. Specialized fixtures or mounts are often necessary to keep the glass stable throughout the cutting process.
Lastly, managing heat buildup is particularly important when working with small, thin glass components. Even slight temperature increases during cutting can lead to thermal stress, which can cause the material to crack or deform. Cooling systems, such as liquid coolants or air jets, are essential to dissipate heat and protect the glass from thermal damage.
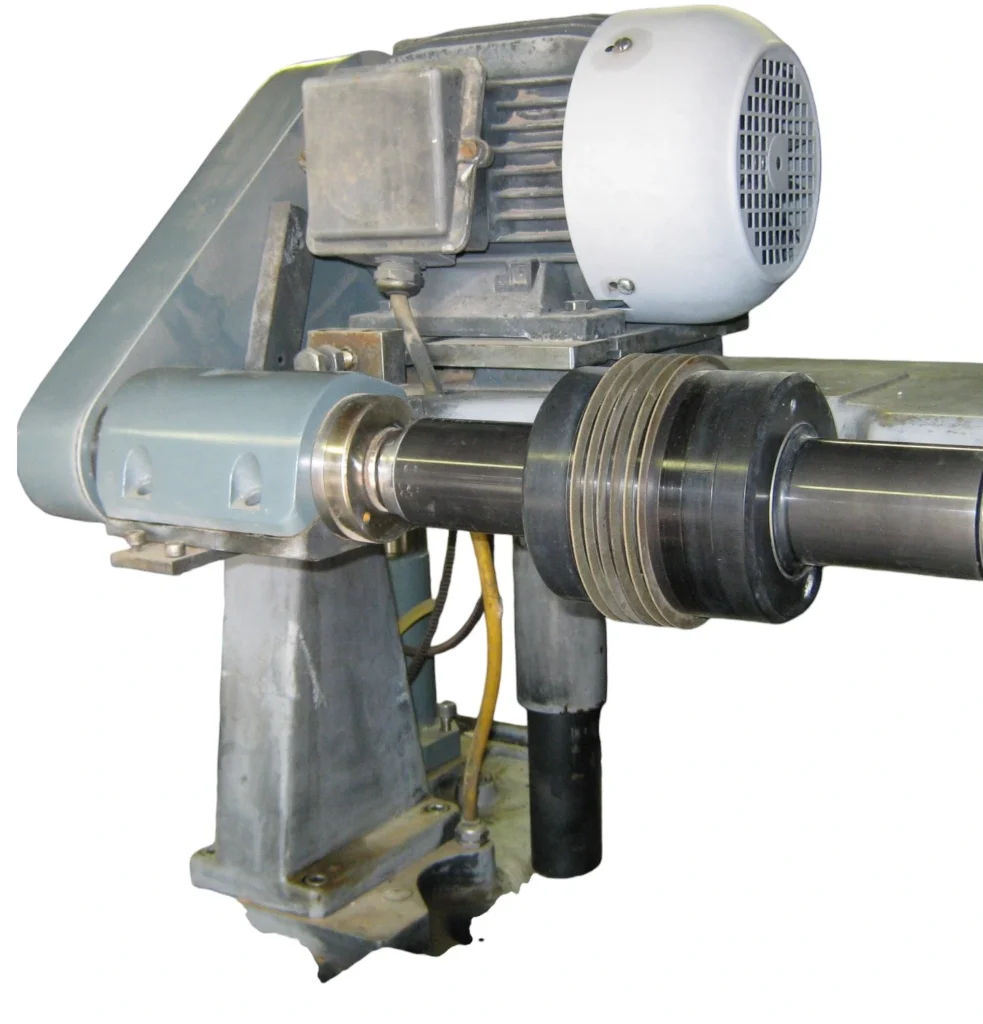
Cutting Machine Used for Cutting Glass
The type of cutting machine used for glass cutting plays a pivotal role in determining the efficiency, precision, accuracy, and quality of the cut. Depending on the application, material dimensions, and required cut accuracy, different machines are selected to best meet the specific cutting needs. Each type of saw is suited for different applications, depending on the complexity of the cut and the nature of the glass.
For cutting glass materials different cutting methods are used depending on the movement of the blade and the material, each tailored to the specific needs of the application.
One common approach involves a stationary diamond blade while the material is pushed into it. This is typically done on machines with sliding or moving tables, allowing the operator to guide the glass into the blade. This method is frequently used for cutting flat panels or hollow glass tubing, where precise control over the feed rate is needed to ensure clean, smooth cuts without damaging the material.
Another widely used method involves keeping the glass material stationary while the blade moves. In this case, the blade, usually mounted on an overhead arm or pivot, is lowered onto the glass to make the cut. This technique is ideal for short, precise cuts, especially when working with smaller components like glass rods or tubes. By keeping the material fixed in place, the risk of movement or misalignment during the cut is minimized, ensuring accuracy.
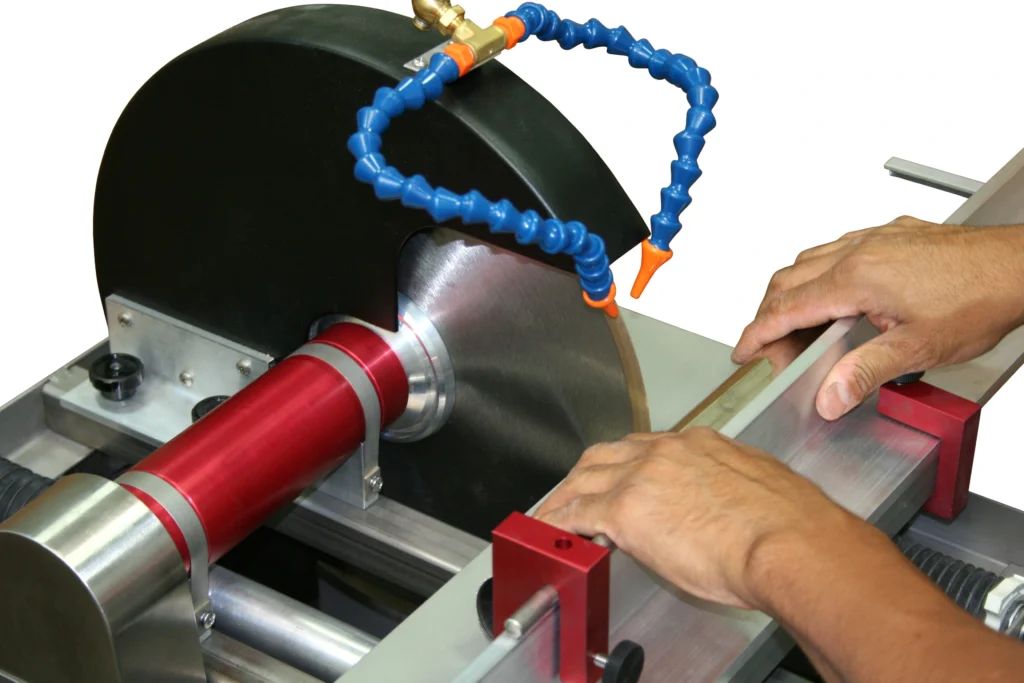
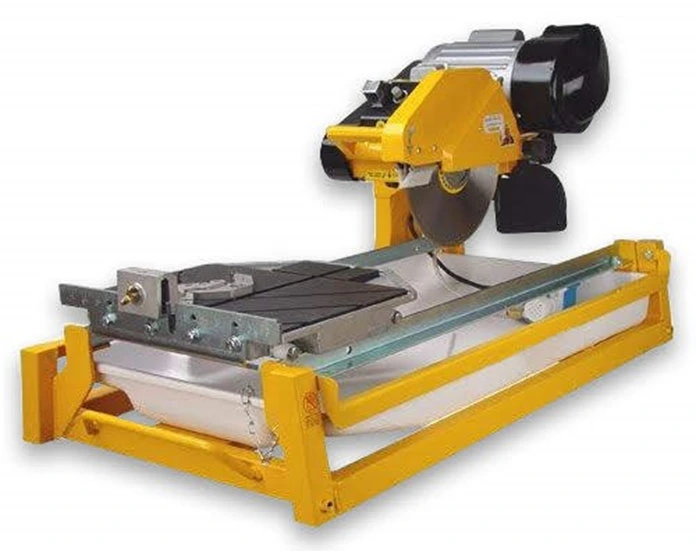
For more complex or intricate cutting tasks, machines are often used where both the blade and the material move. This is common in CNC-controlled glass cutting machines, where the process is fully automated. The blade and material are simultaneously positioned and adjusted, allowing for extremely precise cuts on intricate designs or multi-dimensional glass shapes.
Another method involves continuously feeding the glass material past a rotating diamond blade. In this setup, the glass moves automatically, typically via a conveyor system, while the blade remains fixed in position. This method is highly efficient for high-volume production runs, where uniform pieces of glass, such as panels or tubes, need to be cut quickly and consistently. Each of these methods offers distinct advantages depending on the glass shape, size, and precision required for the specific cutting task.
Tile saws are a popular choice for glass cutting due to their simplicity and accessibility. Originally designed for ceramic and stone tiles, these saws can be fitted with diamond blades to cut through glass. A key feature of tile saws is the water-cooled cutting system, which sprays water on the blade and glass to reduce heat buildup and prevent cracks. In this method, the blade remains stationary while the glass is pushed into it. This makes tile saws ideal for straightforward cuts on flat glass sheets, tiles, or small, simple shapes, though they are less suited for intricate designs or curved cuts due to their limited flexibility.
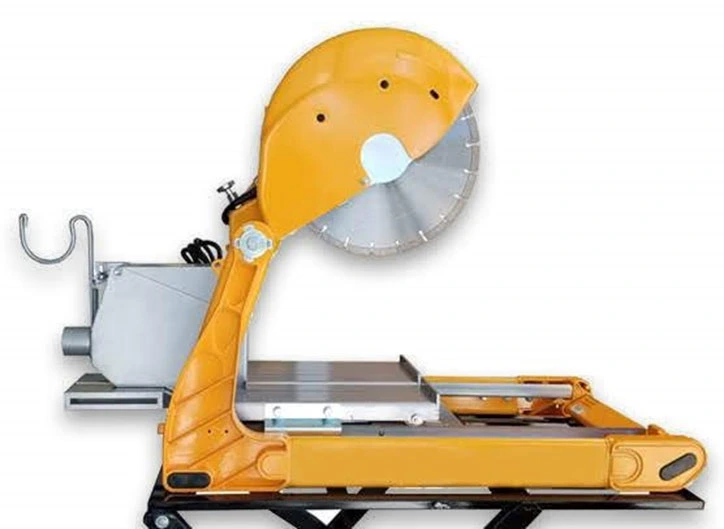
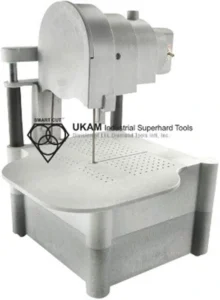
Masonry saws, typically used for hard materials like stone or bricks, can also be adapted for cutting thicker glass panels when equipped with diamond blades. These saws are larger and more powerful than tile saws, making them effective for cutting through thicker, more robust glass like laminated or safety glass. As with tile saws, the glass is pushed into the stationary blade, and water cooling helps manage heat and minimize blade wear. Masonry saws are particularly useful for larger-scale projects that involve stronger glass but may be too bulky or overpowered for thinner or more delicate glass, requiring careful control to avoid damage.
Band saws offer greater flexibility in cutting glass due to their unique blade design, which consists of a continuous loop that rotates around wheels. This allows for curved or intricate cuts, making band saws an excellent choice for more complex designs. Unlike tile and masonry saws, band saws allow for multi-directional cutting, which is especially useful for artistic or decorative glass pieces. They provide smoother cuts with less chipping or breakage but require more maintenance and operator skill to maintain precision.
Ring saws, also known as ring cutters, provide even more flexibility and precision, especially for intricate or detailed cuts. With a diamond blade shaped like a ring that rotates in 360 degrees, ring saws allow the operator to cut in any direction without needing to reposition the material. This makes them ideal for cutting complex shapes, rounded forms, and internal cuts, making them particularly useful for artistic glass cutting projects like stained glass. Ring saws are more expensive and require a higher skill level to operate effectively, but they offer unmatched control for highly detailed work.
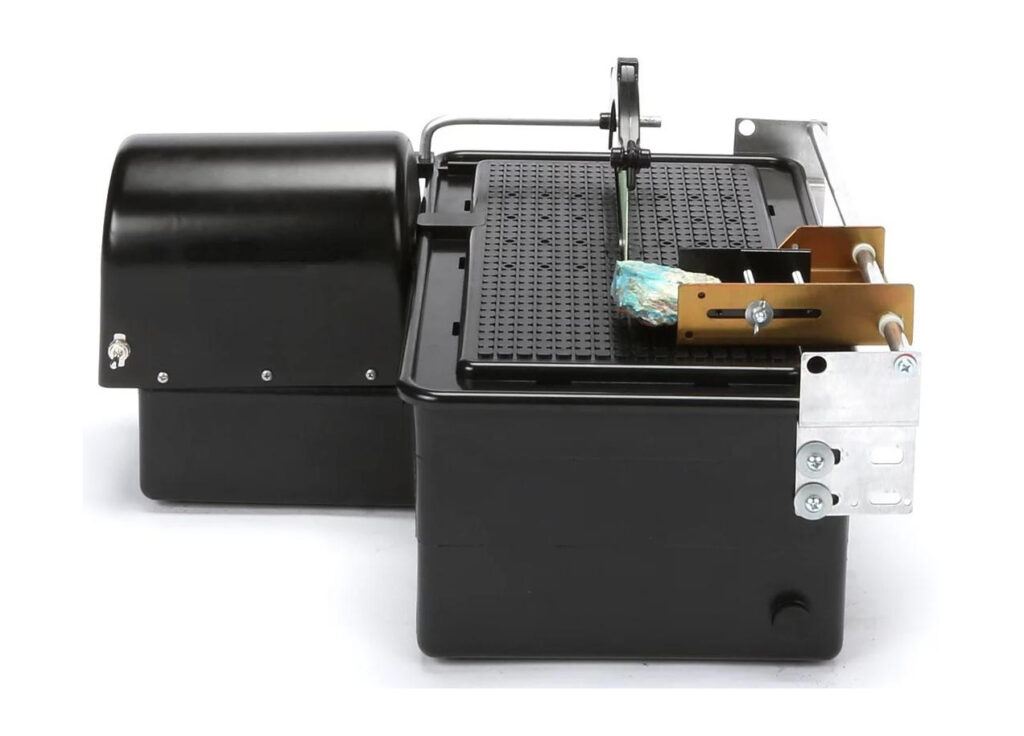
Trim saws work similarly to tile saws, with a stationary blade mounted on a platform, and the material is pushed into the blade for cutting. They are typically water-cooled to prevent heat buildup, which can cause thermal stress in the glass. The fine diamond blades used in trim saws provide high precision, making them excellent for tasks that require tight control, such as cutting small glass components, detailed artistic pieces, or trimming edges on pre-cut glass. Their small size allows for a high degree of maneuverability, which is crucial when working with fragile or thin glass materials. One of the advantages of using trim saws is their ability to make clean, precise cuts without chipping, especially along the edges of the glass. This makes them particularly useful for fine-tuning and finishing tasks, where achieving a smooth edge is crucial for the final product. They are also commonly used in tasks that involve adjusting or reshaping glass pieces rather than making long, continuous cuts.
Precision Cutting Saws for Glass Tubing and Rod
Precision cutting of glass tubing and rods requires specialized equipment that can handle the fragility and complexity of these materials while achieving clean, accurate cuts. The cutting process varies based on the type of saw used, ranging from simple manual saws to fully automated systems. Each type of saw offers different levels of precision, efficiency, and control, making them suitable for a range of applications from small-scale to high-volume production.
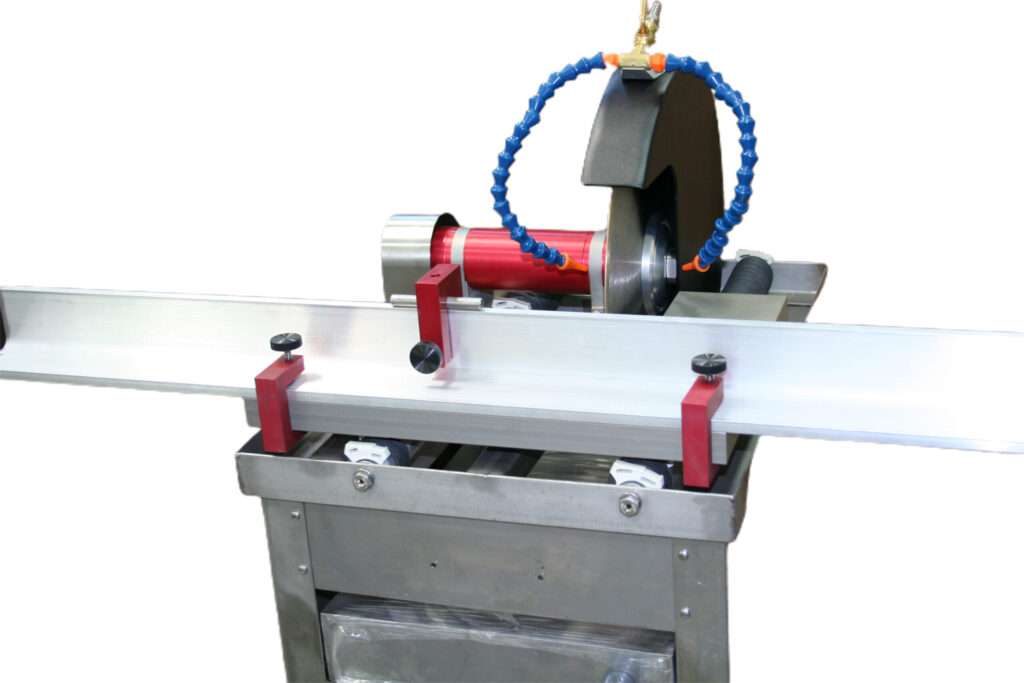
Manual Precision Cutting Saws
Manual cutting saws are the most basic and cost-effective option for cutting glass tubing and rods. These saws typically use diamond-edged blades, which are ideal for cutting through glass without causing excessive chipping or cracking. In a manual setup, the operator is responsible for feeding the material into the blade and controlling the cutting speed and pressure.
Manual saws are ideal for small-scale or artistic projects where flexibility and control are needed. They allow the operator to make precise adjustments throughout the cutting process, making them a good option for cutting shorter lengths of glass tubing or rods. However, because the process is entirely operator-driven, manual saws can be slower and less efficient for large-scale or high-volume production. Care must also be taken to avoid breakage, as manual cutting requires constant attention to the material’s fragility.
Semi-Automatic Precision Cutting Saws
Semi-automatic saws provide a higher level of precision and control than manual saws while still requiring some operator input. In this setup, the glass tubing or rod is manually loaded into the saw, but the cutting process is more controlled. The saw may be equipped with automated feed systems that push the material into the blade at a consistent speed, reducing the risk of operator error and ensuring smoother, more consistent cuts.
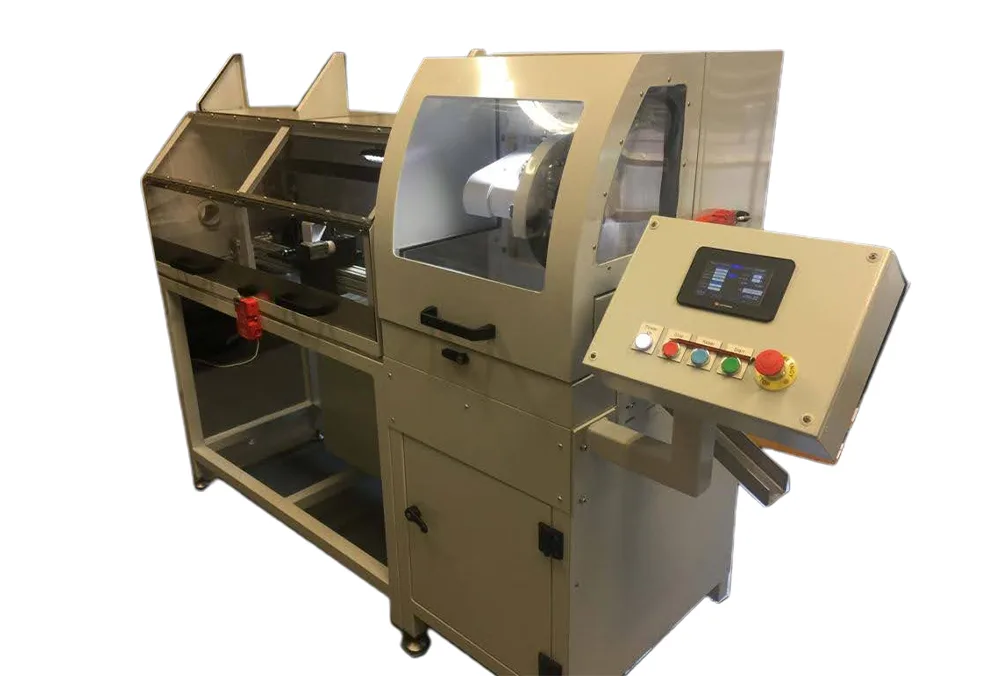
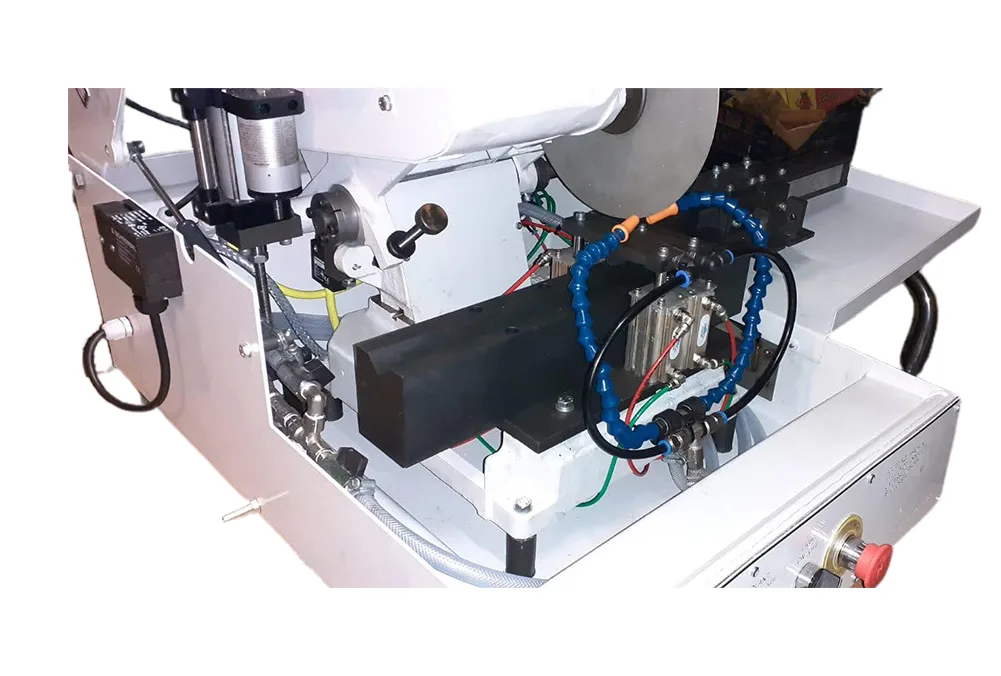
Semi-automatic saws are typically equipped with fine diamond blades and cooling systems to prevent heat buildup, which can cause stress fractures in the glass. These machines are ideal for mid-level production where higher accuracy and repeatability are required but full automation isn’t necessary. They are often used in industries that need precision cuts without the complexity or expense of fully automatic systems.
Fully Automatic Precision Cutting Saws
Fully automatic precision cutting saws are designed for high-volume, highly accurate cutting of glass tubing and rods. These machines are fully automated, meaning that the entire process—from loading the material to making the cuts—is controlled by the machine, requiring minimal operator intervention. Automatic saws use CNC (Computer Numerical Control) technology to ensure precise, repeatable cuts with tight tolerances.

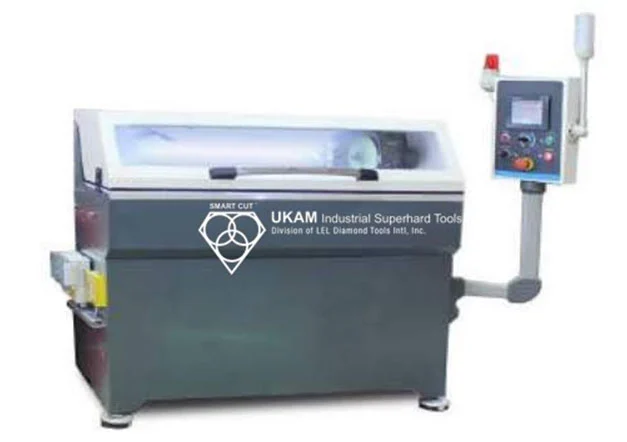
In an automatic saw, the glass tubing or rod is typically loaded onto a conveyor system or into a holding fixture. The machine is programmed to cut the material into specific lengths, and the process is carried out with precise control over the cutting speed, blade feed, and cooling system. This level of automation is particularly useful in industries like pharmaceuticals, optics, and electronics, where the glass components must meet strict dimensional requirements.
Automatic saws are highly efficient and can cut large quantities of glass tubing or rods with minimal downtime. They also significantly reduce the risk of human error, as the machine controls all aspects of the cutting process. However, these systems are more expensive and may require skilled operators to set up and maintain the equipment.
Gang Saws for Glass Tubing and Rods
Gang saws represent the highest level of production efficiency for cutting glass tubing and rods. These saws are designed to make multiple cuts simultaneously, dramatically increasing throughput in high-volume production environments. A gang saw typically consists of multiple diamond blades arranged in parallel, allowing the machine to cut several pieces of tubing or rod at once. This setup is ideal for industries that need to produce large quantities of identical glass components in a short amount of time.
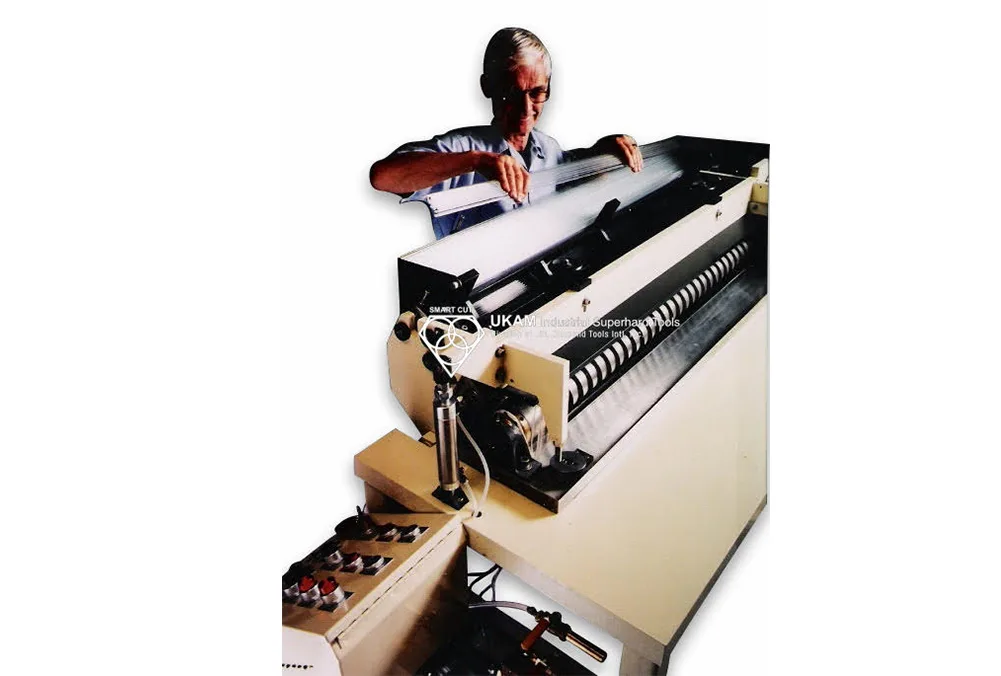
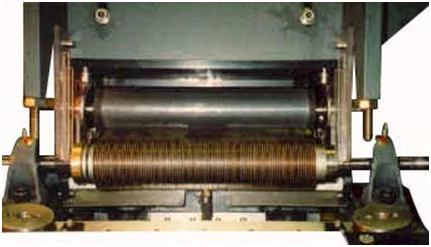
In a gang saw, the glass tubing or rod is fed through the saw in a continuous process, with each blade making its cut at precise intervals. Like fully automatic saws, gang saws are often equipped with CNC controls to ensure accuracy and repeatability. They are also designed with advanced cooling systems to manage the heat generated by multiple blades cutting simultaneously.
Gang saws are particularly useful for cutting large batches of glass tubing or rods for applications like laboratory glassware, medical devices, and industrial components. While these machines offer unparalleled efficiency, they are also the most expensive and complex option, requiring specialized setup and maintenance.
Precision Cutting of Flat Glass Materials
The precision cutting of flat glass materials varies significantly depending on the size, thickness, and intended application of the glass. From small, thin wafers and substrates used in electronics and optics to larger glass panels used in architectural applications, the type of cutting saw and technique plays a critical role in achieving clean, accurate cuts. Selecting the right machine, whether manual, semi-automatic, or fully automated, depends on the scale of the project and the desired precision.
Cutting Small and Thin Glass Wafers and Substrates
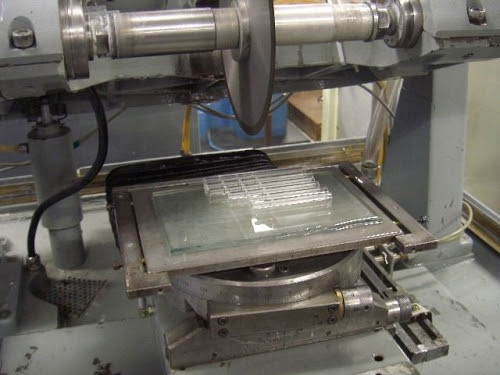
When working with small, thin glass wafers or substrates, such as those used in the electronics, semiconductor, and optics industries, precision is paramount. These materials are often fragile, requiring high accuracy with minimal chipping, cracking, or thermal stress.
For such applications, manual precision saws with fine diamond blades are commonly used for small batches or specialized cuts. These saws allow for careful control by the operator, making them suitable for cutting smaller pieces with tight tolerances. However, manual saws can be slow and less efficient for larger batches, making them ideal for research and development, prototyping, or laboratory environments.
For higher precision and increased efficiency, semi-automatic saws are used. These saws automate parts of the cutting process, such as material feeding and speed control, while still allowing the operator to adjust for precision.
Semi-automatic machines are useful for cutting small wafers or substrates that need to meet specific dimensional requirements, as the machine helps eliminate human error and maintains consistent pressure and cutting speed. These saws are commonly found in laboratories that require both flexibility and precision.
For even greater accuracy and higher throughput, fully automatic precision saws are employed. These machines use advanced CNC (Computer Numerical Control) systems to achieve highly repeatable, error-free cuts, making them ideal for cutting small substrates in mass production. In fully automatic saws, the glass wafer or substrate is placed in the machine, and the entire cutting process is controlled automatically. These machines are essential in industries such as semiconductors or photonics, where exact precision and minimal material loss are critical.
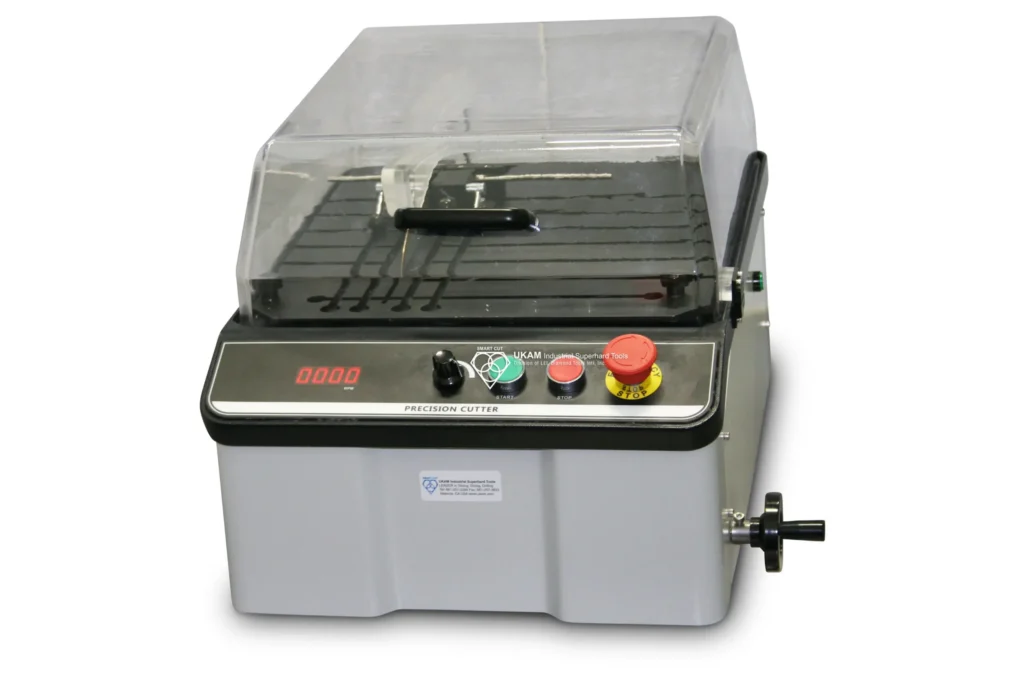
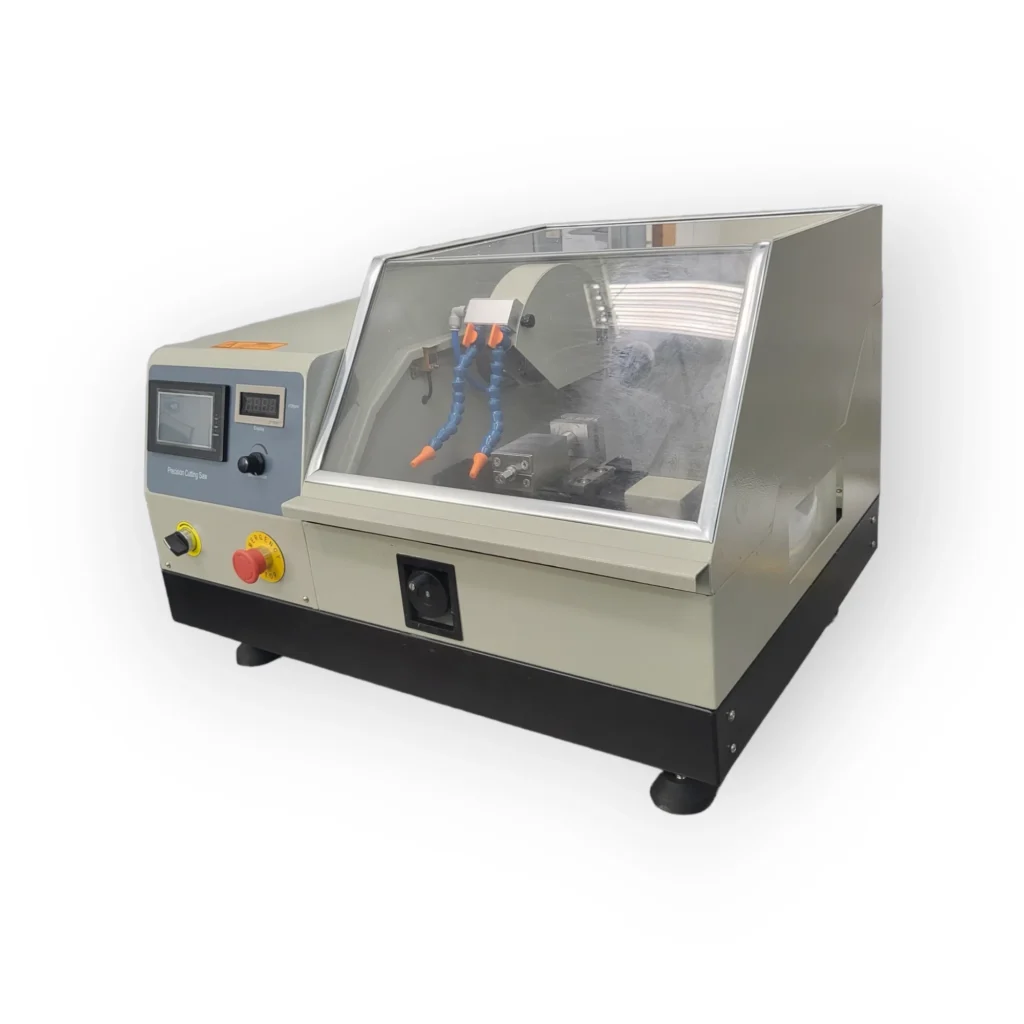
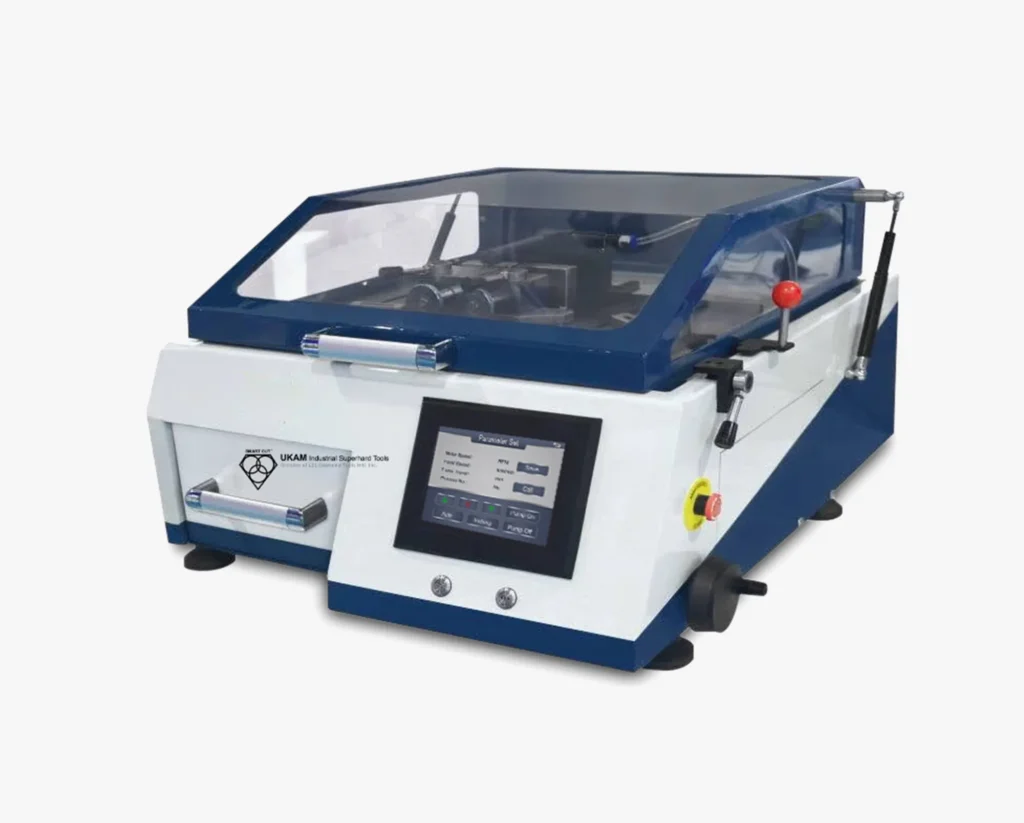
Cutting Large Glass Panels
At the other end of the spectrum are large glass panels, often used in architectural applications such as windows, doors, or facade cladding. Cutting large glass panels presents different challenges, such as managing the weight and size of the material, maintaining straight, clean cuts over long distances, and preventing thermal stress or cracking.
For smaller projects, manual cutting saws can still be used, particularly in scenarios where the glass panel needs custom trimming or specialized cuts. These manual saws are usually equipped with larger diamond blades and water-cooling systems to prevent heat buildup during cutting. However, due to the size of the material, handling and supporting the glass manually can be difficult, making manual cutting more labor-intensive and less suitable for large-scale work.
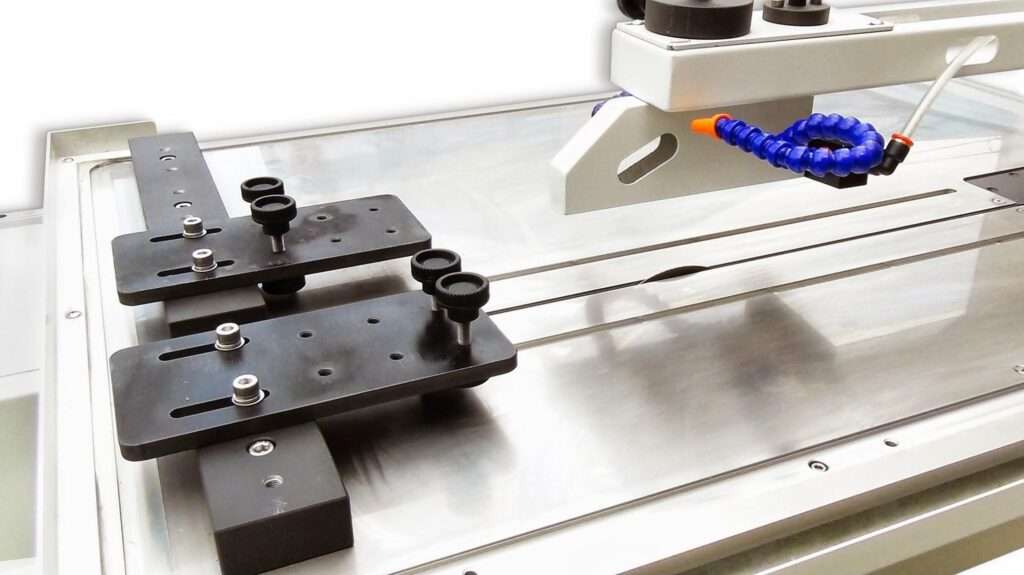
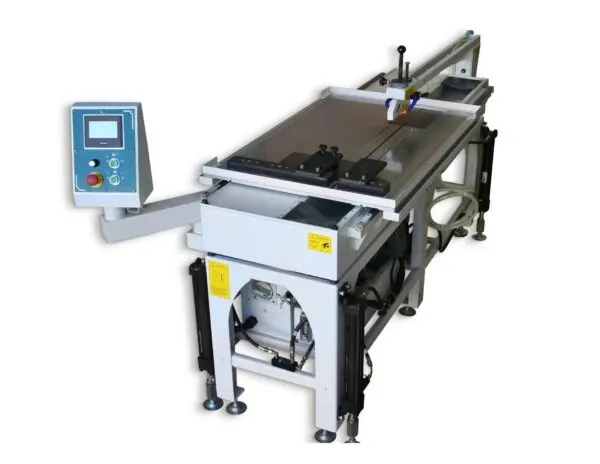
In semi-automatic systems, the glass panel is typically loaded onto a sliding table or roller system that feeds the material into the blade. The operator can control aspects like blade speed and feed rate while the machine ensures stability and precision. These saws are commonly used for cutting medium-sized panels and are ideal for laboratories or small-scale production where customization is required, but efficiency is also a concern.
For large-scale or high-precision cutting of extensive glass panels, fully automatic saws are essential. These machines often feature CNC controls to program and execute precise cuts, even on very large glass panels. The glass is loaded into the machine and securely held in place, while the automatic system controls the entire cutting process. These machines are equipped with water-cooling systems to manage heat, as well as advanced blade positioning technologies to ensure the cuts are perfectly straight and smooth over large areas. Fully automatic saws are typically found in industrial settings where large quantities of glass panels must be cut with high precision.
Large cutting machines, designed specifically to handle oversized panels, can accommodate glass sheets measuring up to several meters in length and width. These machines feature powerful, durable diamond blades and automated systems that can handle the weight and size of the panels without compromising precision. Equipped with advanced cooling and feed mechanisms, these machines are used in high-volume production environments, such as factories that produce glass for construction or automotive applications.
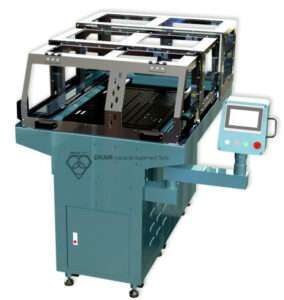
RPM’s For Cutting Glass
When cutting glass with diamond blades, selecting the appropriate RPM (revolutions per minute) is critical for achieving smooth cuts and preventing material damage. The RPM must be carefully matched to the glass thickness, shape complexity, and blade diameter to ensure optimal performance.
For thick glass ranging from 10 to 50 mm, a lower RPM range is recommended. Operating at 1,500 to 3,000 RPM helps prevent the blade from overheating, which is essential when working with thicker materials that generate more friction during the cutting process. Running at lower speeds reduces the risk of thermal stress on both the blade and the glass, ensuring cleaner cuts without cracking or chipping.
In contrast, thin glass (1 to 5 mm) requires higher RPMs for smoother and faster cuts. When working with thinner glass, the cutting process demands less force, allowing the blade to run at higher speeds—typically between 5,000 and 15,000 RPM. These higher speeds provide the necessary precision and efficiency to create clean edges without the risk of breakage, which can be a concern at slower speeds for thin materials.
When dealing with complex shapes and curves, such as in artistic or high-precision optical applications, variable RPMs are necessary to achieve the required level of precision. RPMs typically range from 2,000 to 6,000, depending on the complexity of the shape and the degree of control needed. Lower speeds may be necessary for intricate cuts, while higher speeds may be applied to broader, simpler curves.
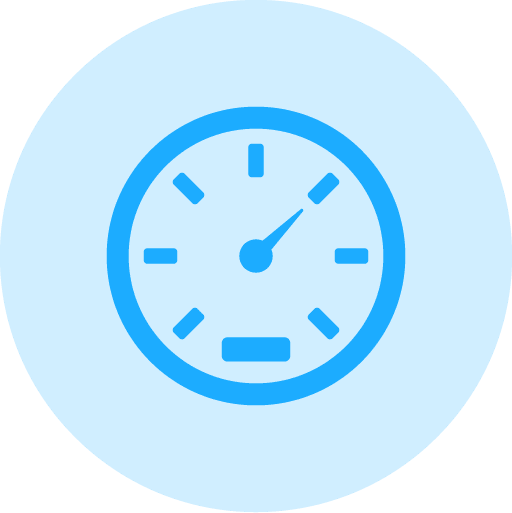
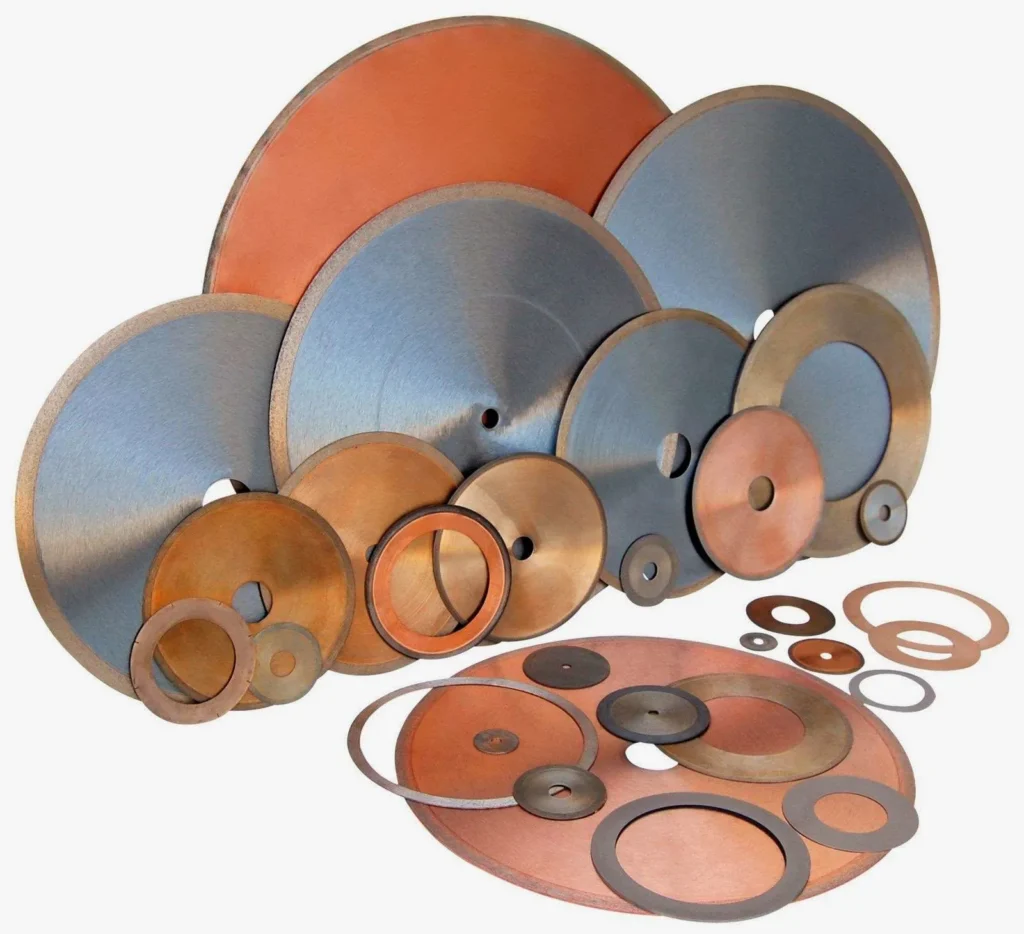
Another essential factor is matching RPM with blade diameter. Larger blades, which are commonly used for cutting thicker glass, must operate at lower RPMs to maintain control and avoid excessive friction. Conversely, smaller blades, which are more suitable for thin glass or detailed work, can handle higher RPMs. The relationship between blade size and RPM is important in preventing overheating and ensuring the longevity of the blade while achieving the best cutting results.
RPMs are also influenced by the type of diamond bond used. For example, resin bond diamond cut-off blades typically operate at much higher RPMs compared to their sintered (metal bond) counterparts. This is particularly true when cutting softer or more fragile materials like glass, where resin bond blades offer a smoother cut and can withstand the high speeds required to minimize chipping or fracturing.
In addition to bond type, other important variables affecting the optimal RPMs include the diameter of the blade, kerf thickness, diamond grit size, and diamond concentration. Larger diameter blades typically require lower RPMs to maintain cutting precision, while smaller diameter blades can operate at higher speeds, providing greater efficiency in cutting applications such as glass. The kerf thickness also plays a critical role; thinner kerf blades reduce cutting resistance, allowing for smoother operation at higher speeds, which is crucial when working with delicate glass materials to avoid excessive heat buildup or stress cracks.
The diamond grit size and concentration further refine the RPM selection. Finer grits are typically preferred for glass cutting, as they produce a smoother finish and reduce the risk of chipping. A higher concentration of diamonds on the blade can increase the blade's cutting efficiency, which, combined with the right RPM, ensures optimal performance for precision cutting of glass in various shapes and thicknesses.
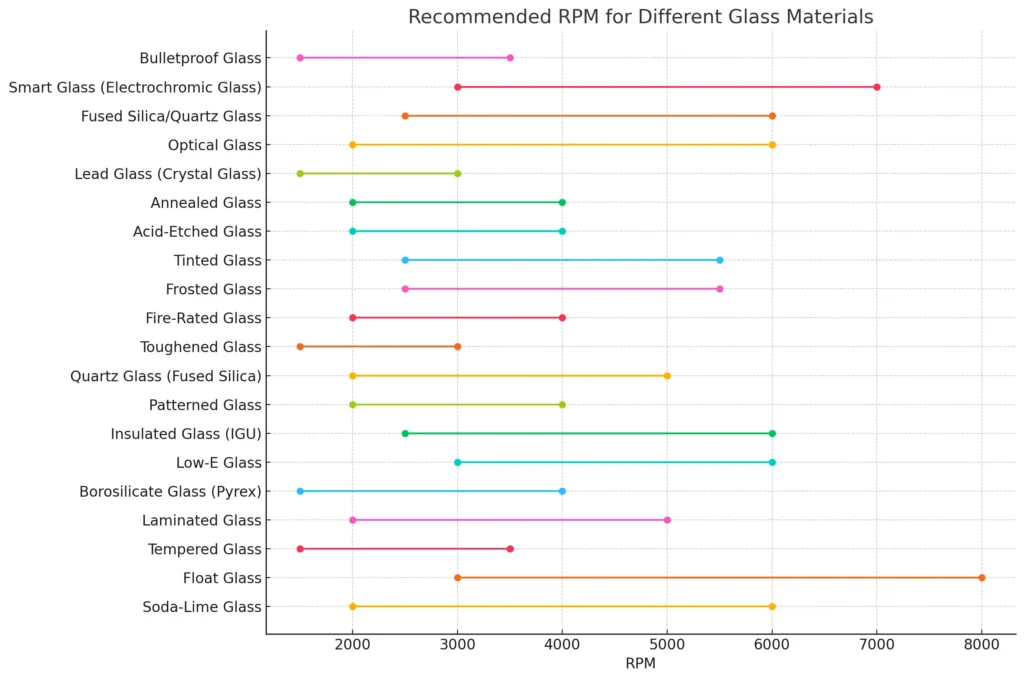
Recommended RPM range for cutting various types of glass materials using diamond blades:
Material Type |
Recommended RPM Range |
---|---|
Soda-Lime Glass |
2,000 – 6,000 RPM |
Float Glass |
3,000 – 8,000 RPM |
Tempered Glass |
1,500 – 3,500 RPM |
Laminated Glass |
2,000 – 5,000 RPM |
Borosilicate Glass (Pyrex) |
1,500 – 4,000 RPM |
Low-E Glass |
3,000 – 6,000 RPM |
Insulated Glass (IGU) |
2,500 – 6,000 RPM |
Patterned Glass |
2,000 – 4,000 RPM |
Quartz Glass (Fused Silica) |
2,000 – 5,000 RPM |
Toughened Glass |
1,500 – 3,000 RPM |
Fire-Rated Glass |
2,000 – 4,000 RPM |
Frosted Glass |
2,500 – 5,500 RPM |
Tinted Glass |
2,500 – 5,500 RPM |
Acid-Etched Glass |
2,000 – 4,000 RPM |
Annealed Glass |
2,000 – 4,000 RPM |
Lead Glass (Crystal Glass) |
1,500 – 3,000 RPM |
Optical Glass |
2,000 – 6,000 RPM |
Fused Silica/Quartz Glass |
2,500 – 6,000 RPM |
Smart Glass (Electrochromic Glass) |
3,000 – 7,000 RPM |
Bulletproof Glass |
1,500 – 3,500 RPM |
Coolants
Coolants play an essential role in glass cutting processes, particularly when using diamond cutting blades, as they help control heat buildup and prevent damage to both the glass and the blade. The choice of coolant and its proper application directly impact cutting quality, blade longevity, and the overall efficiency of the operation.
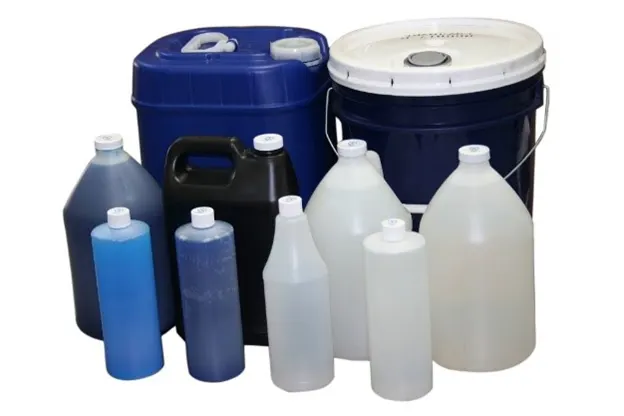
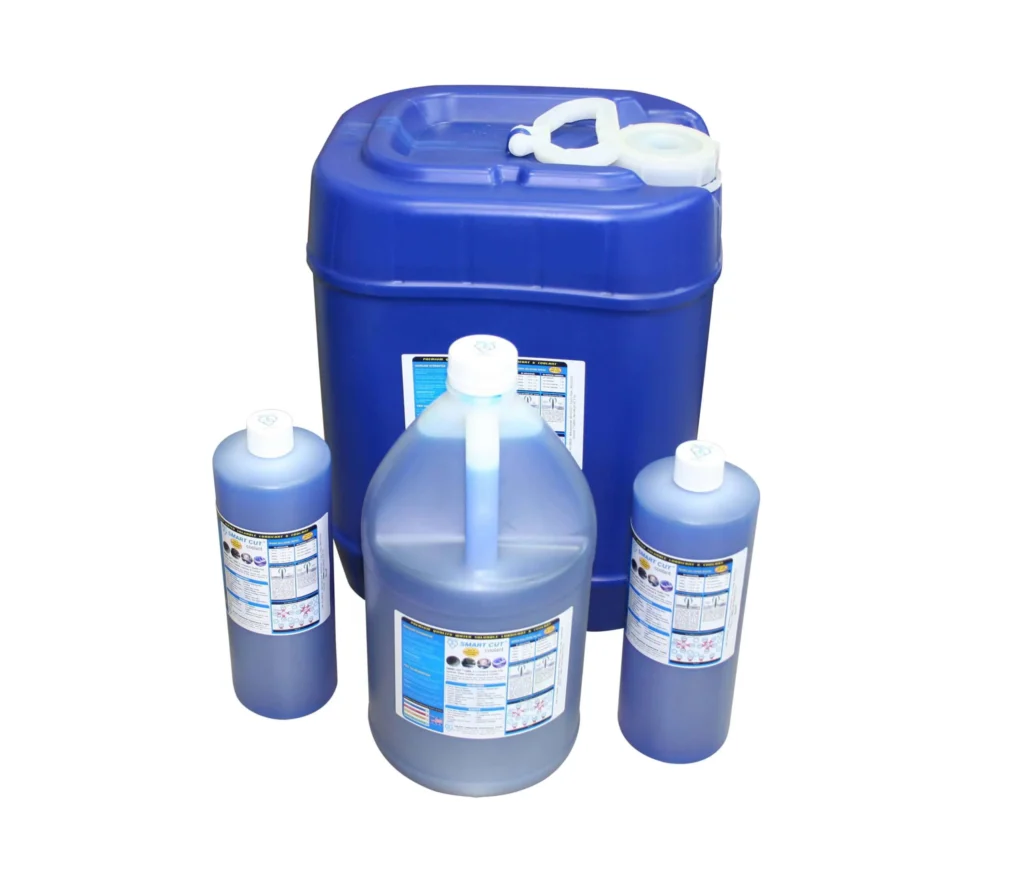
Water-based coolants are the most commonly used cooling method for glass cutting. They are suitable for most glass cutting applications due to their ability to effectively reduce heat generated during the process. Water-based coolants help keep both the blade and the glass material at an optimal temperature, reducing the risk of thermal stress, warping, or cracking. Their wide applicability makes them the standard choice for cutting standard float glass, tempered glass, and similar materials.
For cutting high-purity glass materials, such as quartz or silica, the choice of coolant is crucial to avoid contamination and preserve the integrity of the material, especially in sensitive applications like semiconductors and optics. water-based coolants—often deionized and combined with specific additives—are preferred. These coolants effectively manage heat and flush debris while minimizing the risk of contamination. In applications where avoiding chemical reactions is critical, water-based coolants offer a clean, efficient solution that helps maintain the material’s purity without introducing unwanted residues.
In certain advanced applications, special coolant additives are required to meet the stringent quality demands. These additives are often introduced to water- or oil-based coolants to prevent contamination and enhance surface quality during the cutting process. Industries like aerospace, medical technology, and precision optics may rely on such additives to achieve ultra-smooth finishes, as they help minimize microscopic chipping and improve the overall cleanliness of the cut surface.
The coolant flow rate is also critical in glass cutting, particularly when working with thick glass. Ensuring a sufficient and consistent flow of coolant is essential to prevent localized heat buildup, which can cause cracking or thermal shock, especially in thicker glass materials. For such applications, an optimized coolant flow rate ensures uniform heat distribution, enabling smooth and controlled cuts without causing stress to the glass.
Selecting the Right Diamond Cutting Blade for Cutting Glass
Selecting the appropriate diamond cutting blade for glass cutting is crucial to achieving the desired cut quality, preventing damage to the material, and ensuring efficient cutting operations. The blade selection process is influenced by several factors, including material diameter, thickness, RPM, coolant type, and feed rate.
Here is a guide based on different glass thicknesses and material characteristics:
Thin Glass (1–5 mm) When cutting thin glass, which includes materials like float glass, continuous rim blades are recommended for their precision and ability to deliver clean cuts with minimal chipping. An ultra-thin continuous rim blade, which minimizes the kerf width, is ideal for such applications. The recommended RPM range for thin glass is between 5,000 and 10,000 RPM, providing the necessary speed for a smooth cutting process. To maintain the integrity of the thin glass and prevent thermal stress, water-based coolants are preferred. Feed rates should be set between 0.5 to 1.5 mm per second to allow for controlled cutting without causing stress fractures. This setup results in minimal chipping and smooth edges, ensuring high-quality cuts.
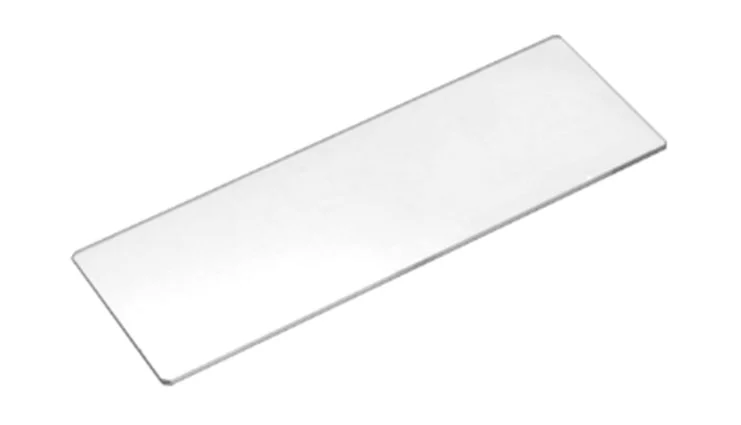
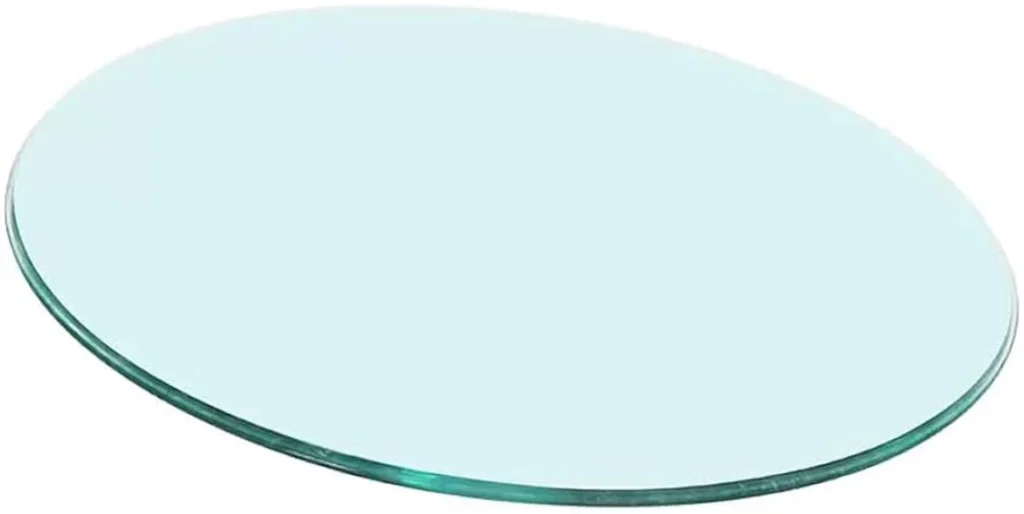
Medium-Thickness Glass (5–20 mm) For medium-thickness glass, both continuous rim and segmented blades can be used depending on the specific requirements of the application. Continuous rim blades are suitable for smooth cuts, while segmented blades provide better cooling and are ideal for higher feed rates. The recommended RPM range for cutting medium-thickness glass is 2,000 to 5,000 RPM. Water-based coolants are still suitable for most applications, but oil-based coolants may be preferred when cutting high-purity glass such as quartz or borosilicate. Feed rates should be set between 1.0 to 2.0 mm per second to ensure efficient cutting while minimizing wear on the blade. The cut quality is typically smooth, with slight chipping tolerance acceptable for some applications.
Thick Glass (20+ mm) Thick glass materials, such as tempered or borosilicate glass, require more robust blades. Segmented rim or slotted diamond cut off blades are recommended due to their strength, durability, and ability to dissipate heat effectively during the cutting process. These blades are built to handle the demands of cutting through thicker materials without overheating or warping. The RPM range for cutting thick glass should be between 1,500 and 3,500 RPM, as lower speeds help prevent thermal buildup and excessive wear on the blade. Oil-based coolants or specialized coolant additives are essential for managing heat, especially when cutting thicker, high-purity glass. The recommended feed rate is between 1.0 to 2.5 mm per second, allowing for a controlled and gradual cutting process. While some roughness in the edges is acceptable for thicker glass, particularly for applications like borosilicate and tempered glass, proper blade selection ensures that the cuts remain accurate and free from significant defects.
Guide to Selecting the Right Diamond Cutting Blade
Different glass shapes require specific cutting techniques and blade selections to ensure optimal results. Whether cutting flat panels, tubes, or more complex curved forms, choosing the right diamond blade and coolant system is essential for maintaining cut precision and preventing damage.
Flat Panels
Flat glass panels, such as those used for windows, doors, and architectural applications, are typically cut with continuous rim blades. These blades are designed to deliver smooth, clean edges with minimal chipping. Since flat glass allows for straightforward cutting operations, continuous rim blades maintain the necessary contact and precision across the material's surface. To manage heat buildup and provide consistent cooling, water-based coolants with high flow rates are recommended. This coolant system ensures the blade remains cool, reducing wear and improving cut quality without compromising the glass.
Tubes and Cylinders
Cutting cylindrical or tubular glass, such as those used in lighting or scientific instruments, presents a unique set of challenges due to the curved surface. The choice of blade depends on the diameter of the tube or cylinder. Thin continuous rim blades are suitable for smaller diameters, as they provide precise cuts with minimal surface disruption. For larger diameter tubes, segmented rim blades offer enhanced cooling capabilities and prevent the blade from binding as it passes through the material. Water soluble coolants are preferred for tube and cylinder cutting as they reduce surface tension and provide better lubrication on the curved surfaces. This helps to minimize friction and ensures smoother cuts without distorting the shape.
Complex/Curved Shapes
For intricate or custom-designed glass shapes, such as those found in artistic projects or advanced optical applications, thin continuous rim blades are the best choice. These blades provide the flexibility and precision required to navigate the curves and contours of complex shapes. Because such materials are highly susceptible to stress fractures, the use of high-pressure water coolants with specialized additives is essential. This combination helps to avoid overheating and reduces the stress placed on the glass during the cutting process. The additives in the coolant further enhance surface quality and ensure that even the most intricate cuts maintain structural integrity.
Type of Diamond Cutting Blades – Edge Type
Selecting the appropriate diamond cutting blade is essential for achieving the best results when working with different types of glass. The blade type should be matched to the glass's thickness, fragility, surface finish and required chipping level to ensure clean cuts, minimal chipping, and maximum efficiency. Below is an overview of the most commonly used types of diamond cutting blades for various glass cutting applications:
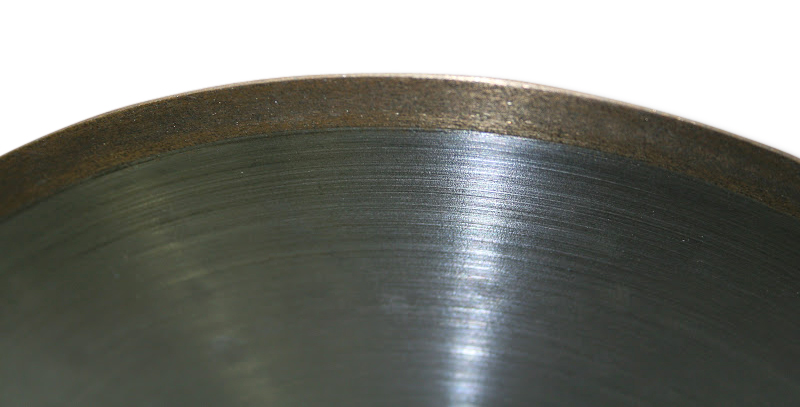
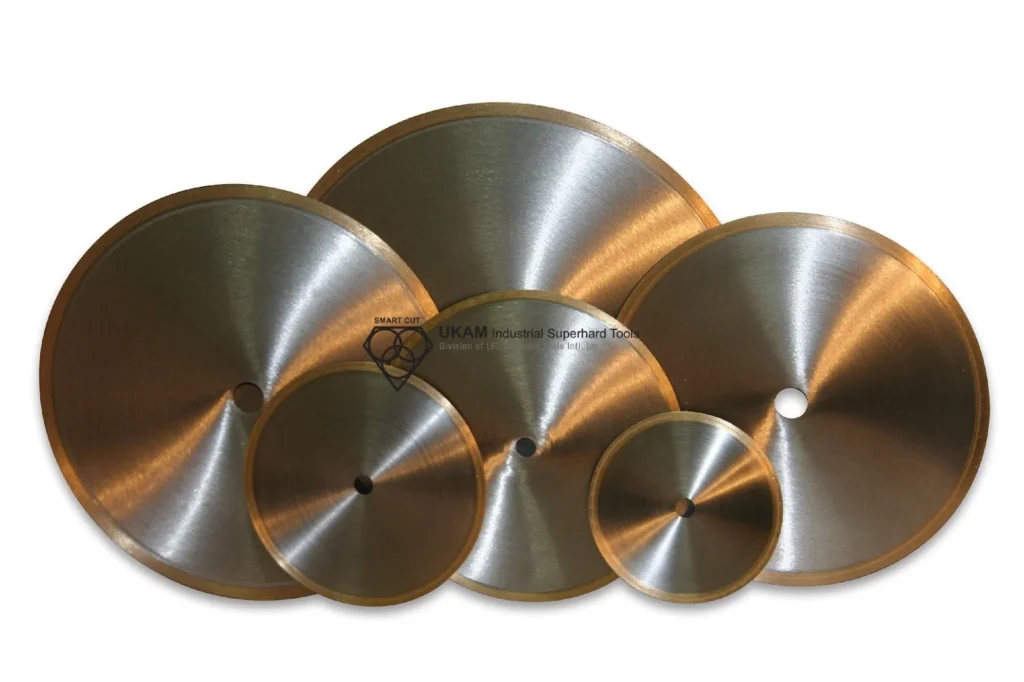
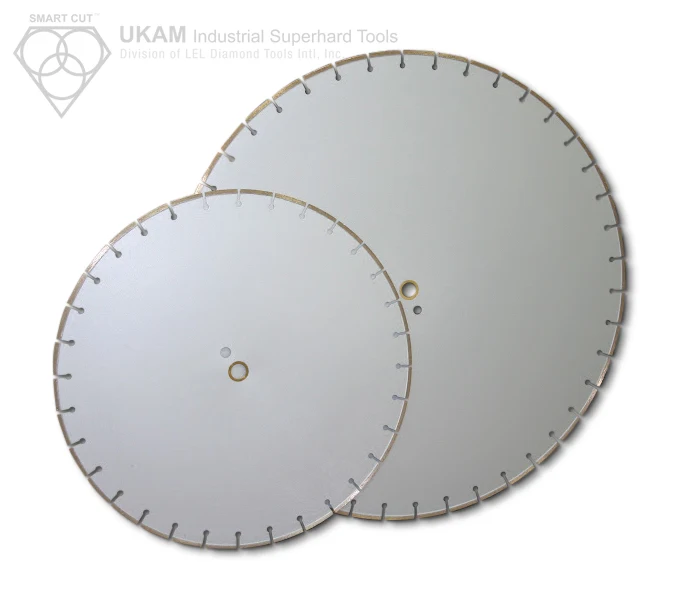
Continuous Rim Blades - Continuous rim blades are ideal for cutting thin and fragile glass that requires a smooth, clean edge. These blades have a continuous band of diamonds along the edge, which ensures that the glass is cut without interruption. This design minimizes the risk of chipping, making continuous rim blades perfect for thin materials like float glass, standard window glass, and glass panels used in electronics. The consistent contact with the glass ensures high precision and minimal material loss, especially in delicate applications. Continuous rim diamond cutting blades for glass are available in different bond types such as sintered (metal bond) and resin bond. And many different diamond grit sizes from 80 to 320 mesh, and low to high diamond concentration.
Segmented Rim Blades - Segmented rim blades are designed for thicker, tougher glass, such as borosilicate, tempered glass, and laminated glass. These blades feature segments separated by gullets (gaps), which allow better airflow and cooling during cutting. This helps reduce the risk of overheating, particularly when cutting thick glass, which generates more friction.
Segmented rim blades are well-suited for high-volume or heavy-duty applications where durability and speed are important. While they may produce slightly more chipping than continuous rim blades, they are ideal for more robust glass types that can tolerate a rougher edge finish.
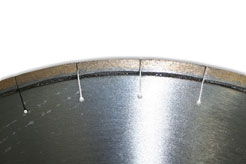
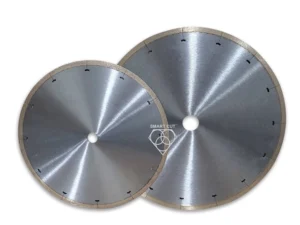
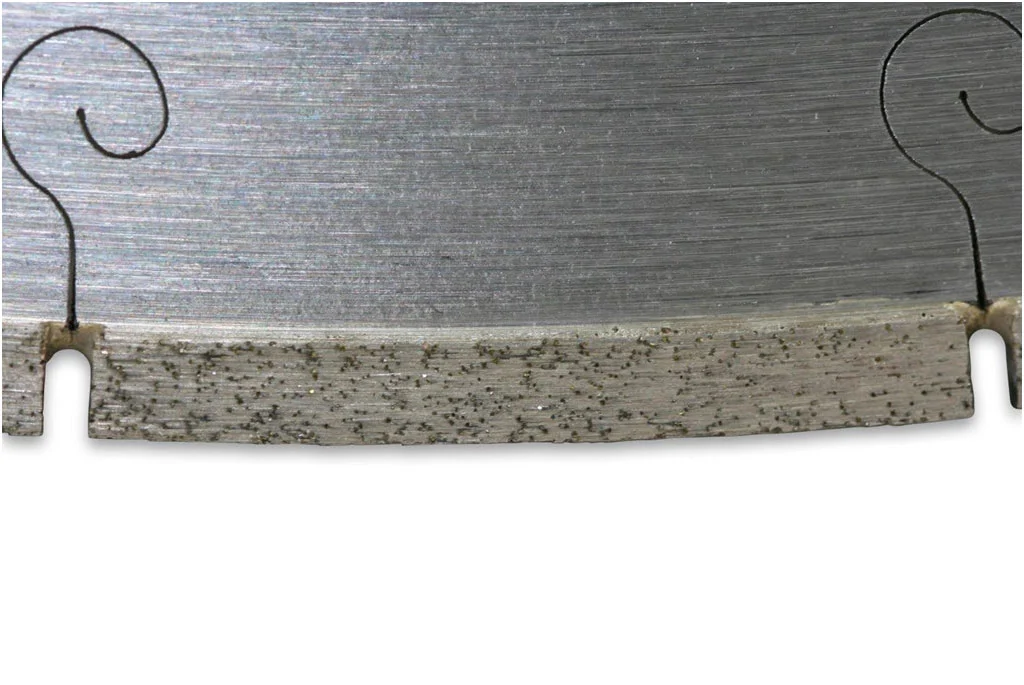
Slotted diamond blades - are another important option for glass cutting, particularly when working with materials that require efficient cooling and debris removal during the cutting process. These blades feature small slots or notches along the rim, which help improve airflow and coolant penetration, effectively dissipating heat and flushing away glass particles. This design makes slotted diamond blades well-suited for cutting thicker, heat-sensitive glass, such as laminated or tempered glass, where overheating can lead to stress fractures or warping.
The slots also reduce the overall blade weight, allowing for faster cutting speeds without sacrificing precision. While slotted blades may create slightly more chipping than continuous rim blades, they provide a balance between cutting speed and edge quality.
The design is particularly beneficial in applications where rapid, efficient cuts are needed, such as in industrial production or large-scale glass fabrication, where faster and freer cutting is more preferred over minimizing chipping. Additionally, slotted diamond blades are commonly used in scenarios where maintaining a cool cutting environment is crucial for preserving both blade life and the integrity of the glass material.
Ultra-Thin Diamond Blades - Ultra-thin diamond blades are used for high-precision cuts on small or intricate glass components, often in electronics, optics, or fine glassware. These blades, typically ranging in thickness from 0.1 to 0.3 mm, allow for extremely delicate cutting with minimal material loss. Ultra-thin blades are essential when working with glass pieces that demand tight tolerances and mirror-like finishes. They are often used in situations where even the slightest chipping or roughness would compromise the glass's functionality or appearance.
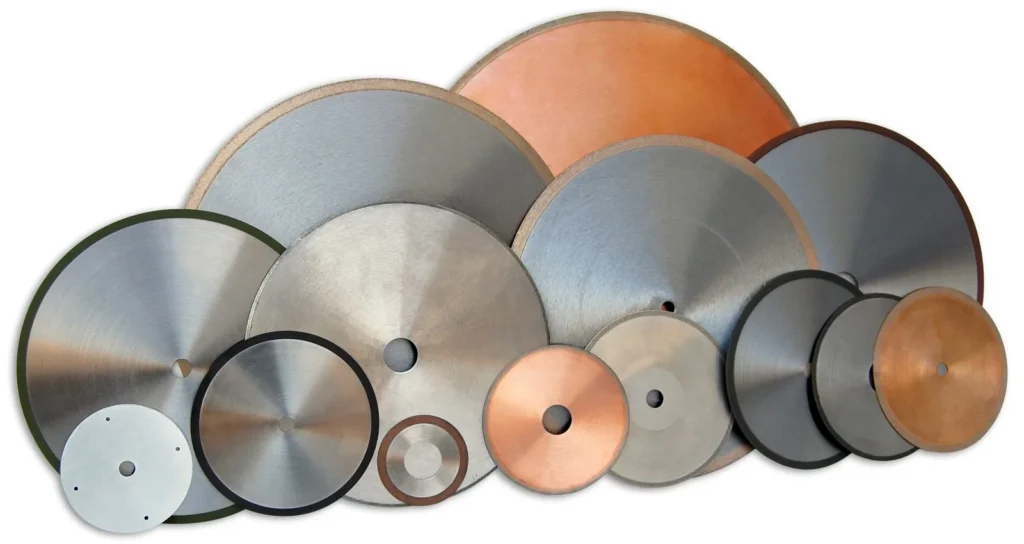
Type of Diamond Cutting Blades – Bond Type
SINTERED (MEAL BOND) DIAMOND BLADES
Sintered (metal bonded) diamond blades are engineered through a process that embeds diamonds within a metal matrix, composed of metals like iron, cobalt, nickel, bronze, copper, tungsten, or their alloys. This integration is achieved by mixing diamonds with selected metal alloys and then compacting this mixture under precise conditions, where temperature, pressure, heating rate, and holding time are carefully controlled according to the matrix composition. The design intent is to create a blade that excels in cutting performance, particularly for a variety of glass materials including flat, optical, and specialized glass types.
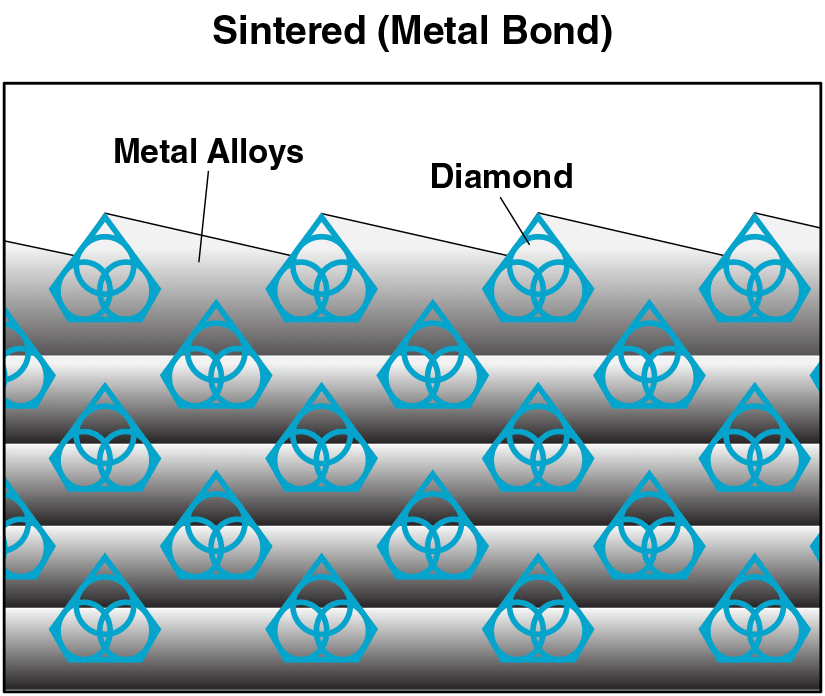
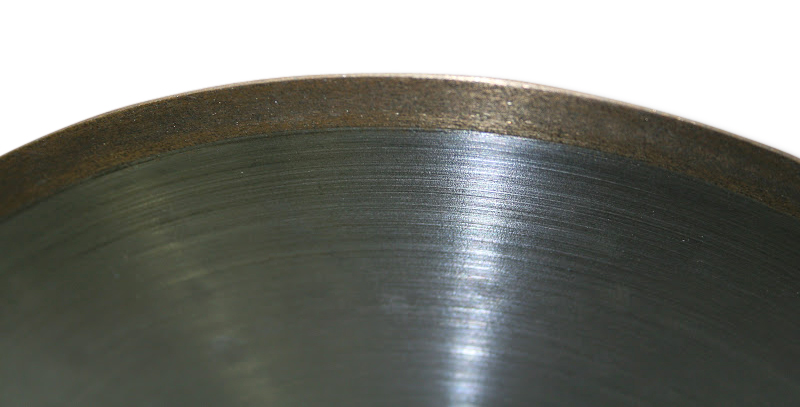
These metal bonded blades are notable for their durability. The matrix is designed to wear away gradually, consistently exposing fresh diamonds for cutting, which ensures the blade remains effective over an extended period. This attribute makes metal bonded diamond blades superior in terms of longevity and consistency when compared to other blade types, such as resin bond and electroplated (nickel bond) blades, which might wear down more quickly or unevenly.
The gradual wear of the metal matrix also means that these blades typically require lower cutting speeds. This slower cutting speed is advantageous when working with glass, as it reduces the risk of chipping and cracking, ensuring a cleaner cut. It's particularly beneficial when handling brittle materials like glass, as it allows for precise cuts without placing undue stress on the material.
Sintered diamond blades are highly recommended for cutting a diverse range of glass materials, from robust borosilicate glass used in laboratory settings to delicate stained glass used in artistic applications. Their ability to deliver precise cuts with minimal chipping is critical in industries where dimensional accuracy and edge quality are paramount. The metal bond’s wear resistance and secure diamond retention further enhance their suitability for complex glass cutting tasks, providing high cutting efficiency and optimal yield.
Metal Bond Blades are more durable and better suited for high-volume cutting. These blades are designed to cut through thicker or harder glass, such as tempered or borosilicate, where strength and longevity are important. While they may generate more heat, they provide superior blade life and are cost-effective for large-scale or industrial glass-cutting operations.
Diamond Grit Sizes & Concentrations Used for Sintered (metal bond) diamond cutting blades for Cutting Glass Materials
For cutting glass sintered (metal bond) diamond cutting blades are used between 80 to 320 mesh, in large variety of concentrations ranging from 25 to 100 con.
Coarser diamond grit sizes (SMART CUT 310M) between 80 to 120 mesh usually used for cutting flat soda lime and borosilicate and other art glass types. Coarser diamond grit sizes, typically ranging from 80 to 120 mesh, are commonly used for cutting thicker and more robust glass types such as flat soda lime, borosilicate, and various forms of art glass. These coarser grits are favored for their aggressive cutting capability, which allows for faster material removal, making them ideal for initial cuts and bulk material processing.
The larger diamond particles in coarser grits can remove more material per pass, which is particularly valuable in high-volume production settings where rapid removal is crucial. This aggressive cutting action not only reduces the time required for initial cuts but also ensures that the blade can penetrate tough materials like flat soda lime and borosilicate glass efficiently without excessive wear, enhancing both durability and longevity of the cutting tools.
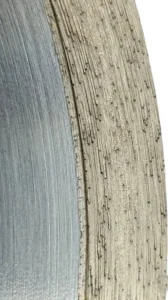
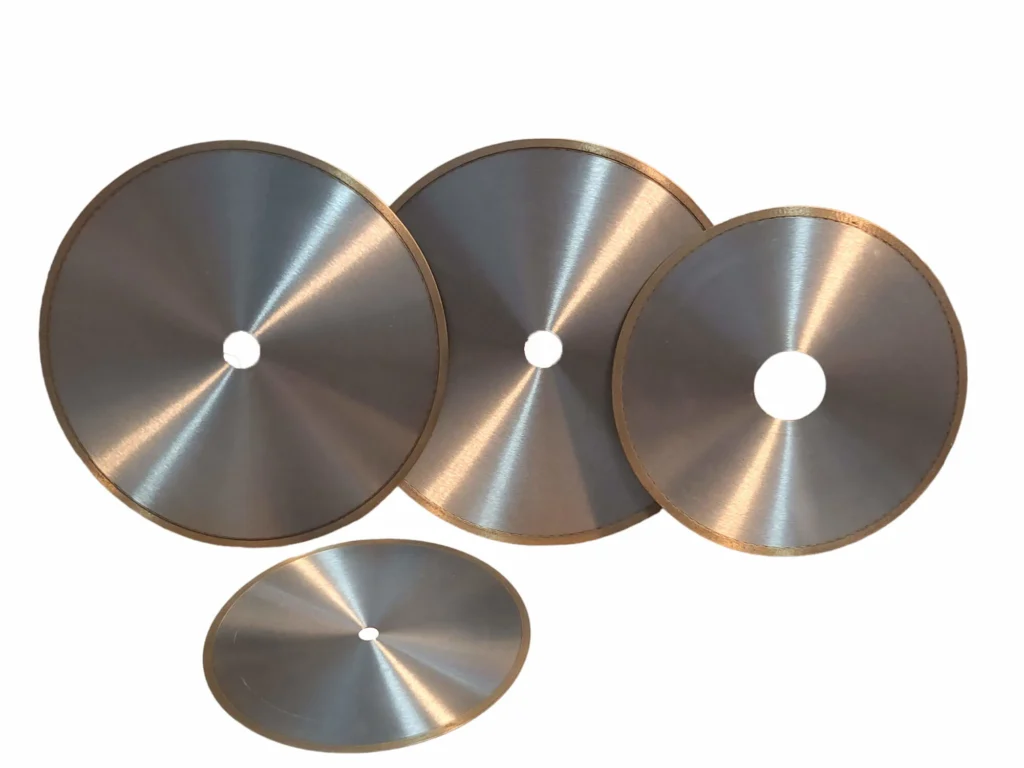
In the realm of art glass, known for its aesthetic qualities and varied textures, coarser grits provide the necessary power to shape and trim quickly. This facilitates creative design processes without compromising the material’s integrity, allowing artists and fabricators to adjust shapes and sizes effectively during crafting.
Despite their aggressive nature, coarser grits can sometimes produce less heat per unit area of cut compared to finer grits when used appropriately. This is because the larger particles remove material quickly, spending less time in contact with any one point on the cutting surface, thus potentially reducing heat buildup that could lead to thermal stress and cracking in sensitive glass types.
Using coarser grits can also be cost-effective, particularly when rough cuts are required. These blades tend to be less expensive than finer grit blades and offer a more economical choice for projects where a perfect surface finish is not the primary concern.
When employing coarser diamond grits for cutting, it's crucial to adjust the cutting speed and coolant flow to suit the specific type of glass being cut. For instance, while flat soda lime glass may tolerate faster cutting speeds, borosilicate glass, with its thermal resistance, might require more moderate speeds to minimize the risk of thermal shock. Similarly, in art glass processing, careful handling is essential to maintain the aesthetic attributes of the glass while efficiently performing cuts.
Medium diamond grit sizes (SMART CUT 455M)between 140 to 200 mesh for cutting large variety of more fragile glass materials. When cutting a wide range of fragile glass materials, selecting the appropriate diamond grit size is crucial for balancing cutting efficiency, surface finish, and material integrity. Medium diamond grit sizes, specifically in the range of 140 to 200 mesh, are particularly effective for diverse applications such as Soda Lime Glass, Quartz Glass, and Technical Glass 1737F. This grit size offers a harmonious balance between cutting speed and precision, allowing for a smoother finish that is critical for materials prone to chipping or cracking.
Using medium grit sizes results in cleaner edges with minimal chipping, which is vital in applications like Optics, Photonics, and Electronic Glass where edge integrity and surface smoothness are paramount.
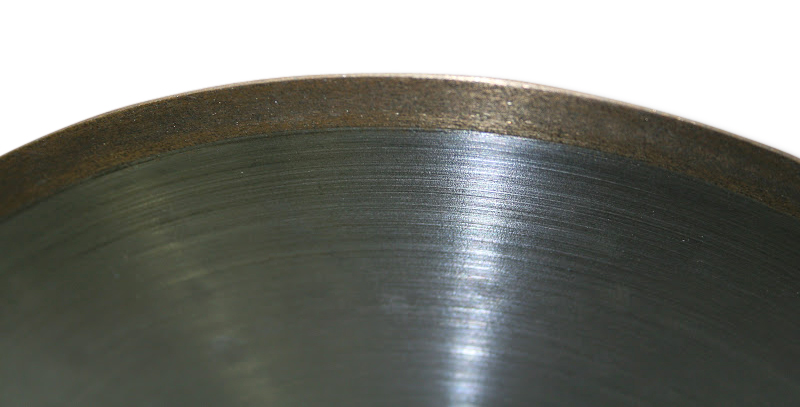
This smoother surface reduces the need for extensive secondary finishing processes, saving both time and resources. The versatility of this grit range means it can handle everything from harder materials like Quartz and Ceramic Glass to softer types like Soda Lime Glass, providing sufficient cutting aggression while being gentle enough to prevent material damage.
Furthermore, medium grit diamonds generate less heat compared to coarser grits, which is crucial in preventing thermal stress and cracking in fragile glass materials. This is especially important when cutting materials with varying thermal expansion properties, such as Borosilicate Glass or Fused Silica.
For intricate cutting patterns required in Stained Glass and Art Glass, which demand high fidelity to design without compromising structural integrity, medium grit size allows for detailed and delicate cuts. In industrial applications like Flat Glass and Automotive Glass, where both speed and finish quality are necessary, medium grit sizes streamline the process by combining efficiency with quality.
Resin Bond Diamond Cutting Blades
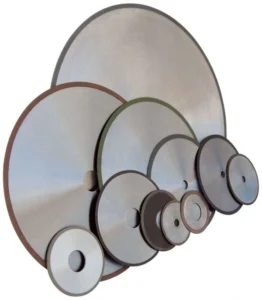
Resin Bond Diamond Cutting Blades - Resin bond is the softest of all bond types and is commonly used in applications requiring a smooth surface finish. These blades are formed through a process involving high pressure and high temperature. Resin bond diamond cut-off wheels and blades are primarily used for cutting ultra-hard and tough metals. The key advantage of resin bond blades lies in their ability to wear faster, which allows diamond particles to break out of the bond matrix more quickly, exposing fresh, sharp diamonds. This self-sharpening feature, due to the faster bond wear, makes resin bond diamond blades an excellent choice for cutting a wide range of materials, including glass.
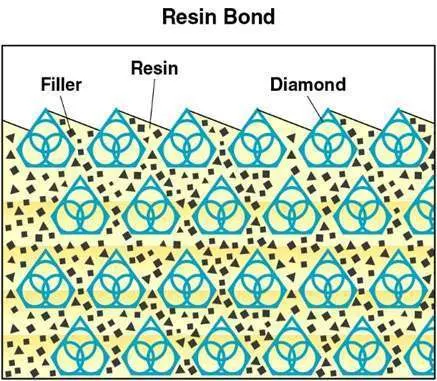
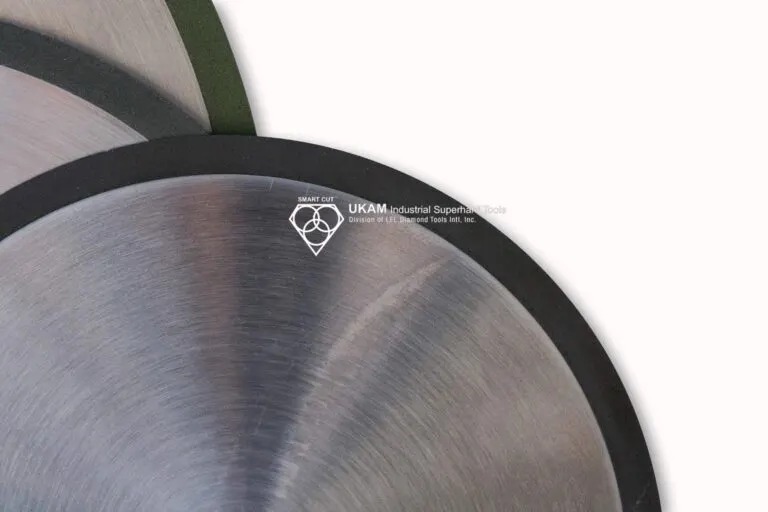
Manufactured using phenolic resin as the binder, diamond abrasive as the cutting medium, and ceramic and other advanced components as filler, resin bond diamond cutting blades are produced with an advanced molding process. They are available in a wide variety of shapes, diamond sizes, concentrations, and bond hardness levels. Resin Bond Blades are softer and generate less heat during cutting, making them better suited for cutting brittle glass types, such as thin or fragile glass panels. Also these are most preferred for cutting glass tubing,, rods and hollow types of glass. The reduced heat minimizes the risk of cracking or stress fractures, making resin bond blades an excellent choice for low-heat cutting applications. The suface finish and chipping level provided by these blades do not require any secondary finishing operation such as fire polishing.
Resin bond diamond blades offer superior cut quality compared to any other type of diamond blade. They are especially recommended for applications where cut quality and surface finish are critical. When compared to sintered (metal bond) blades, resin bond blades deliver significantly better cut quality than even the finest metal bond blades. However, they must be operated at higher speeds for optimal performance.
Resin bond diamond cutting blade for cutting glass materials are usually available from 100 to 220 mesh in low to high diamond concentration.
Coarser Diamond Grit Size resin bond diamond cutting blades are usually 100 to 140 mesh (SMART CUT® Series 2000R) and are usually used for cutting soda lime and borosilicate glass tubing, and optical glass such as fused silica or bk7. Resin bond diamond cutting blades with coarser grit sizes, typically ranging from 100 to 140 mesh, are specifically designed for cutting a variety of glass materials, including soda lime and borosilicate glass tubing, as well as optical glass like fused silica or BK7. These blades are chosen for their ability to combine efficient material removal with minimal chipping, crucial for maintaining the integrity of the glass during cutting processes.
The resin bond matrix in these blades allows for a smoother interaction between the blade and the glass material. This is because the resin material can absorb some of the cutting stresses, reducing the incidence of cracks and chips.
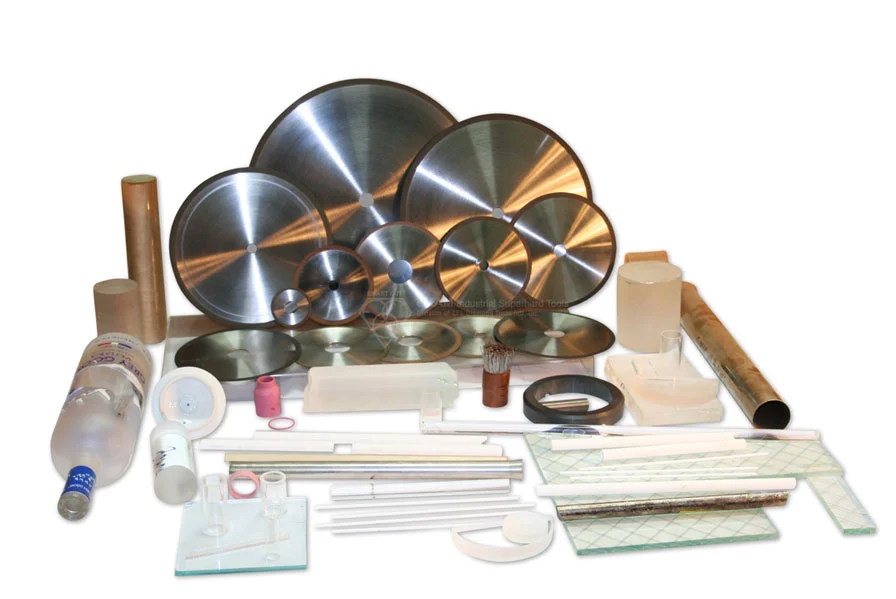
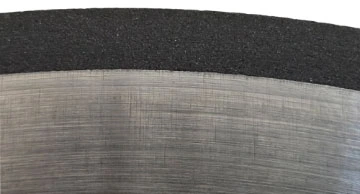
This feature makes these blades particularly well-suited for cutting delicate optical glass, where precision and surface finish are critical. The softer bond matrix also facilitates a smoother cut, making it ideal for applications requiring high-quality finishes.
In addition to their primary applications in cutting tubing and optical materials, these coarser grit resin bond blades are also effective for initial rough cuts in more complex glass fabrications. They can handle the necessary depth and speed required for segmenting large blocks of glass without causing thermal stress or structural weaknesses.
Medium to Fine diamond grit size resin bond diamond cutting blades Medium to fine diamond grit size resin bond diamond cutting blades (SMART CUT® Series 3000R) are specifically engineered for applications that require high-quality finishes and precision, such as cutting Pyrex and quartz tubing, particularly when dealing with very thin-walled and fragile materials. These blades feature diamond particles ranging from 180 to 600 mesh embedded in a resin matrix, making them ideal for achieving a smooth and precise cut.
Medium to fine grit blades are particularly effective in providing superior surface finishes crucial for applications like laboratory glassware made from Pyrex or optical components from quartz, where any surface imperfections can affect the integrity and functionality of the final product. The finer grit allows for cleaner cuts with minimal chipping, important for preserving the structural integrity of fragile materials or thin-walled tubing.
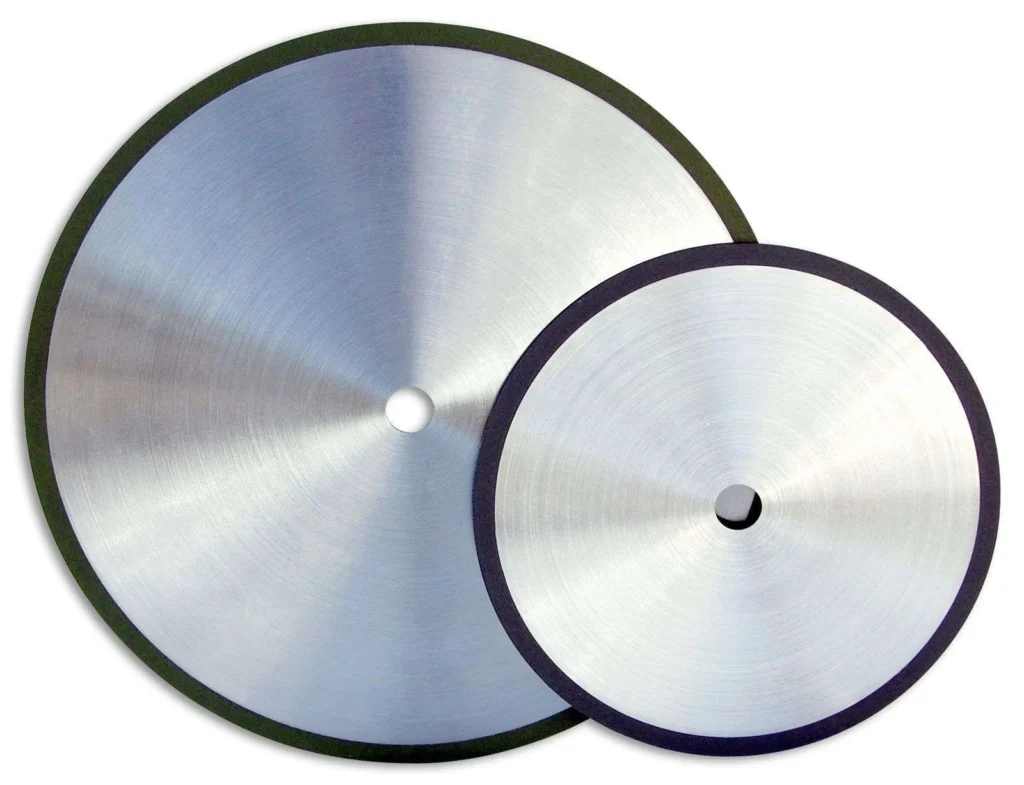
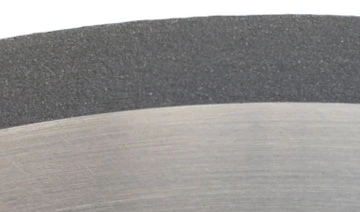
These blades also offer enhanced precision, essential when working with high-value or critical components where the accuracy of cuts ensures that the dimensions and tolerances required for specific applications are strictly adhered to. Optimized for delicate operations, the resin bond and fine grit combination provide a balance between cutting speed and minimizing thermal and mechanical stresses that could lead to material damage.
Although these blades operate at a slower speed compared to coarser grit blades, the trade-off results in better control over the cutting process, contributing to the overall quality of the cut by reducing potential for errors and unwanted material removal. Beyond glass, these blades are also suitable for cutting other brittle materials such as certain ceramics and minerals, making them a valuable tool in various industrial, research, and artistic settings.
ELECTROPLATED (NICKEL BOND) DIAMOND BLADES
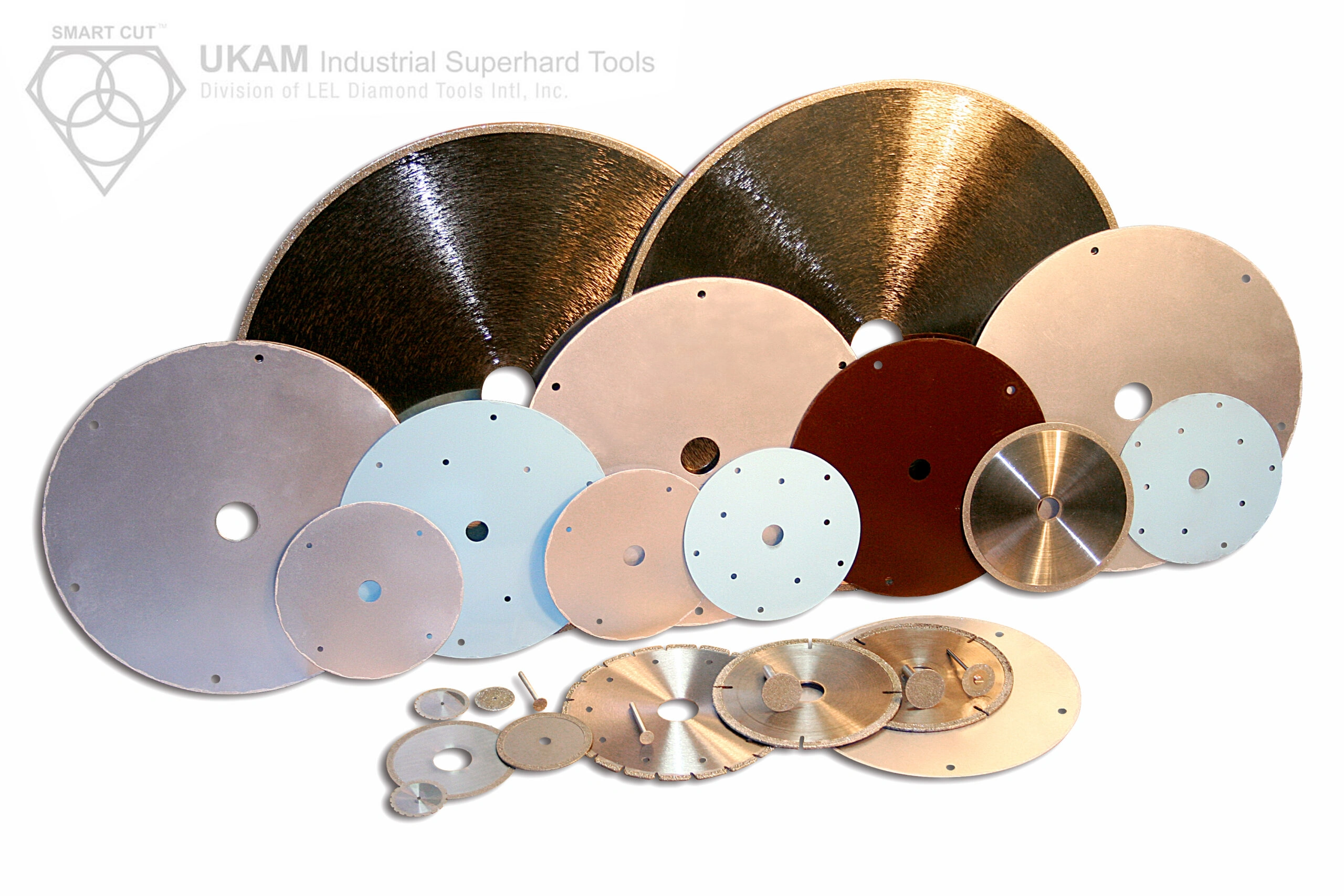
Electroplated Diamond Blades Electroplated diamond blades are distinguished by their high diamond concentration, which provides a fast and free cutting action with minimal heat generation. This makes them particularly effective for cutting glass materials where quick material removal is desired without excessive thermal stress that could lead to cracking or other damage. The diamonds in these blades are bonded directly onto the blade's surface, allowing for fast cutting since more diamond particles are exposed during the cutting process.
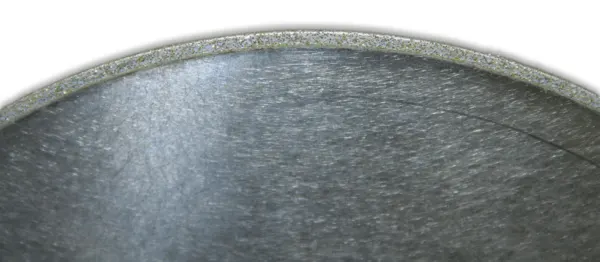
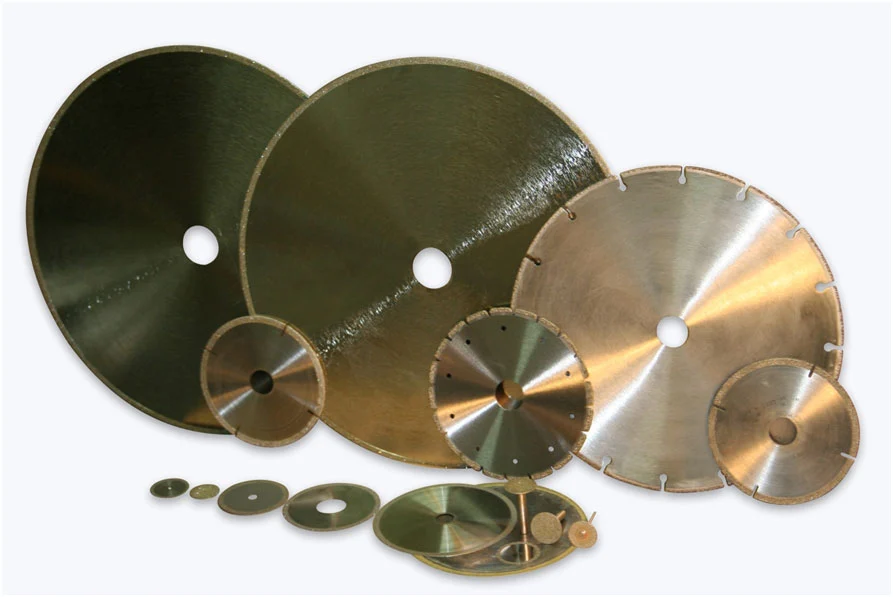
Electroplated diamond blades generally have a shorter lifespan compared to metal bond, resin bond, or hybrid bond blades. Despite this, they are the least expensive type of diamond blades available, making them an economical option for smaller jobs or initial cutting operations. Their cost-effectiveness and performance characteristics make them an attractive choice for those new to glass cutting or for projects where budget constraints are significant.
One of the notable advantages of electroplated diamond blades is their suitability for dry cutting. This feature is particularly valuable in situations where the use of coolant is impractical or impossible. Dry cutting is beneficial not only for certain types of glass but also for a variety of other materials, including very soft, ductile, and gummy substances. Electroplated blades excel in applications requiring quick, clean cuts without the mess or complication of wet cutting systems.
In addition to glass, electroplated diamond blades are frequently used for cutting thermosetting plastics, GRP, pre-sintered and pre-fired (green) materials, electro carbons, graphite, soft ferrites, and farinaceous products. They are also adept at handling unusual cutting tasks such as slicing through deep-frozen fish, bones, and printed circuit boards (PCBs), where their ability to cut quickly and cleanly without coolant makes them indispensable.
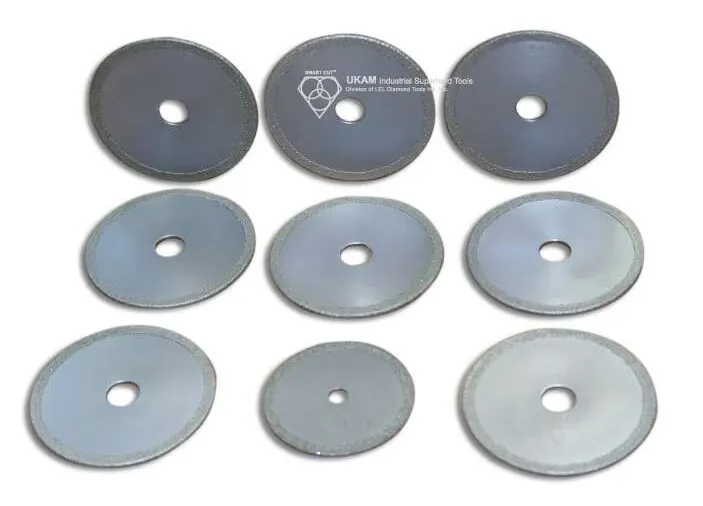
For glass cutting, electroplated blades are particularly suitable for handling delicate tasks where precision and minimal chipping are crucial. They can efficiently cut through various types of glass, including stained glass, decorative glass panels, and even reinforced glass, depending on the specific requirements of the project. The ability to operate without coolant also allows for greater flexibility in workshop setups and mobile work scenarios, where setting up a wet cutting system might be challenging.
Braised Bond Diamond Cutting Blades
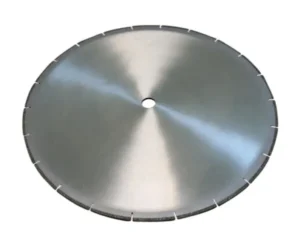
Brazed diamond blades are crafted using a specialized process that creates a strong fusion between the diamonds and the metal bond, distinguishing them significantly from electroplated (nickel bond) diamond tools. Unlike electroplating, brazing involves a high-temperature vacuum oven process where a single layer of diamond crystals is bonded to the steel body with a high level of diamond exposure. This method ensures a robust and durable bond that is ideal for intensive cutting operations.
Brazed diamond blades offer several benefits including faster cutting speeds and the capability for dry cutting, making them a preferred choice in environments where managing slurry or wet setups is impractical. However, these blades typically produce a rougher edge quality due to their high level of diamond exposure and aggressive cutting nature, which prioritizes speed and efficiency over smoothness.
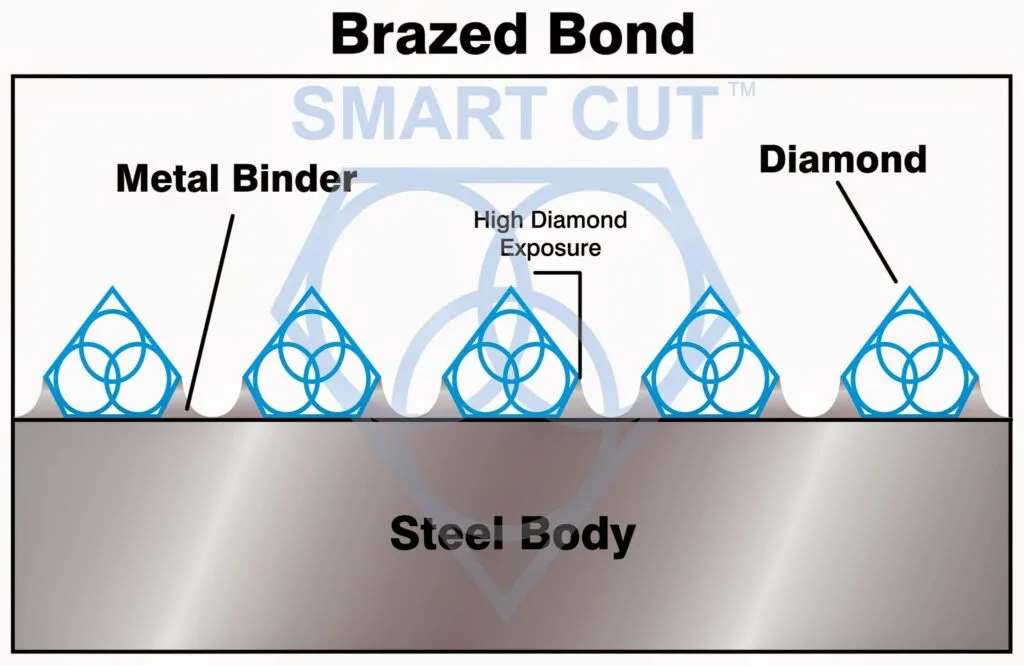
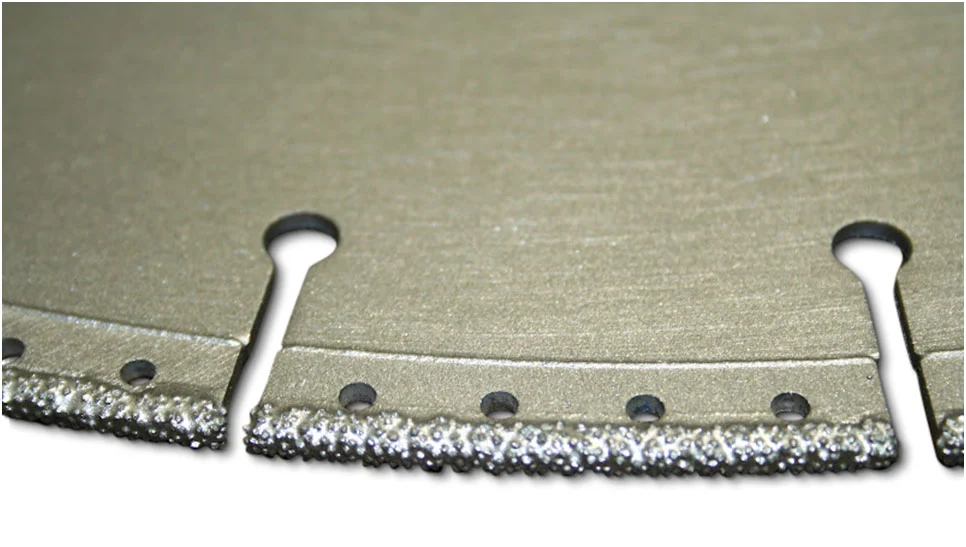
The faster cutting speed of brazed diamond blades is particularly valuable in settings where time efficiency is critical and the volume of material to be processed is high. For glass cutting, this means cuts can be completed more quickly, but it may require additional steps to finish or smooth the edges. The ability to operate without water or coolant is beneficial for quick setup and cleanup, reducing overall project times and facilitating easier handling of materials.
Despite these advantages, the rougher edge quality can be a drawback, especially in applications requiring a high degree of finish, such as decorative glass or precision optics. The rough edges might necessitate secondary processing, such as grinding or polishing, to achieve the desired finish. Therefore, brazed diamond blades are well-suited for initial rough cuts or when cutting less critical pieces where edge smoothness is not the primary concern. They are ideal for bulk and rough processing tasks in construction and demolition, rough shaping in art or craft projects, or where further finishing processes will follow.
Diamond Bond Type Recommendations for Cutting Glass
When evaluating the suitability of diamond bond types for cutting glass, it's important to understand what different performance levels such as excellent, good, acceptable, and not used indicate in practical terms. Each of these categories reflects how well a particular bond type performs in terms of cutting efficiency, precision, durability, and overall suitability for glass cutting applications.
-
Excellent: Best performance and longevity.
-
Good: Decent performance; effectively usable.
-
Acceptable: Marginal performance; can be used if necessary.
-
Not Used: Generally unsuitable for this material.
Glass Material |
Sintered (Metal Bond) |
Resin Bond |
Nickel Bond (Plated) |
Brazed Bond |
---|---|---|---|---|
Soda Lime Glass |
Excellent |
Good |
Good |
Acceptable |
Float Glass |
Excellent |
Good |
Good |
Acceptable |
Tempered Glass |
Excellent |
Not Used |
Good |
Acceptable |
Laminated Glass |
Excellent |
Not Used |
Good |
Acceptable |
Borosilicate Glass (Pyrex) |
Excellent |
Good |
Good |
Acceptable |
Low-E Glass |
Excellent |
Not Used |
Good |
Acceptable |
Insulated Glass (IGU) |
Excellent |
Not Used |
Good |
Acceptable |
Patterned Glass |
Excellent |
Not Used |
Good |
Acceptable |
Quartz Glass (Fused Silica) |
Good |
Excellent |
Good |
Acceptable |
Toughened Glass |
Excellent |
Not Used |
Good |
Acceptable |
Fire-Rated Glass |
Excellent |
Not Used |
Good |
Acceptable |
Frosted Glass |
Excellent |
Good |
Good |
Acceptable |
Tinted Glass |
Excellent |
Good |
Good |
Acceptable |
Acid-Etched Glass |
Excellent |
Good |
Good |
Acceptable |
Annealed Glass |
Excellent |
Good |
Good |
Acceptable |
Lead Glass (Crystal Glass) |
Excellent |
Good |
Good |
Acceptable |
Optical Glass |
Good |
Excellent |
Good |
Acceptable |
Fused Silica/Quartz Glass |
Good |
Excellent |
Good |
Acceptable |
Smart Glass (Electrochromic Glass) |
Excellent |
Not Used |
Good |
Acceptable |
Bulletproof Glass |
Excellent |
Not Used |
Good |
Acceptable |
Photovoltaic (Solar) Glass |
Excellent |
Not Used |
Good |
Acceptable |
Reflective Glass |
Excellent |
Not Used |
Good |
Acceptable |
Switchable Privacy Glass |
Excellent |
Not Used |
Good |
Acceptable |
Self-Cleaning Glass |
Excellent |
Not Used |
Good |
Acceptable |
Soundproof Glass |
Excellent |
Not Used |
Good |
Acceptable |
Antireflective Glass |
Good |
Excellent |
Good |
Acceptable |
Gorilla Glass |
Good |
Excellent |
Good |
Acceptable |
Dragontrail Glass |
Good |
Excellent |
Good |
Acceptable |
Chromatic Glass |
Excellent |
Not Used |
Good |
Acceptable |
Ceramic Glass |
Excellent |
Good |
Good |
Acceptable |
Stained Glass |
Good |
Excellent |
Good |
Acceptable |
Art Glass |
Good |
Excellent |
Good |
Acceptable |
Glass Assemblies |
Excellent |
Not Used |
Good |
Acceptable |
Fused Silica/Fused Quartz |
Good |
Excellent |
Good |
Acceptable |
Automotive Glass |
Excellent |
Not Used |
Good |
Acceptable |
Flat Glass |
Excellent |
Not Used |
Good |
Acceptable |
1737F Glass |
Excellent |
Not Used |
Good |
Acceptable |
B270/Crown Glass |
Good |
Excellent |
Good |
Acceptable |
Hollow Glass |
Excellent |
Not Used |
Good |
Acceptable |
Excellent: A diamond bond rated as excellent for cutting glass offers the highest level of performance in terms of both cutting precision and blade longevity. This bond type is ideally suited for cutting glass efficiently and with minimal chipping, while also maintaining the sharpness and durability of the blade over long periods of use. Excellent performance typically means that the bond type can handle a wide variety of glass types—whether thin, thick, delicate, or hard—without significant wear on the blade or excessive stress on the glass.
Blades with excellent bond types:
-
Provide the cleanest cuts, with smooth edges and little to no chipping.
-
Have a long service life, which is especially beneficial in high-volume cutting operations.
-
Are well-suited for high-precision tasks where both the quality of the cut and the durability of the blade are critical.
-
Perform optimally across different types of glass, including thick architectural glass, laminated glass, and delicate substrates.
Good: A bond type rated as good is highly functional and performs well in most glass-cutting applications, though it may not provide the same longevity or exceptional performance as the top-rated bond types. Good bond types are reliable for cutting a variety of glass materials and deliver clean, smooth cuts with moderate chipping. While these blades may wear faster than those rated as excellent, they are still effective for regular use in medium-precision applications.
Blades with good bond types
-
Deliver adequate precision and produce mostly clean edges, though some minor chipping may occur.
-
Offer a reasonable lifespan, making them suitable for consistent use, though they may need to be replaced sooner than blades with excellent-rated bonds.
-
Work well in environments where cutting speed and efficiency are important, but where absolute perfection in edge quality isn't necessary.
-
Are suitable for cutting a variety of glass types, but may not be ideal for cutting very thick or ultra-delicate glass over long periods.
Acceptable: A bond type rated as acceptable offers marginal performance and is typically used when no better options are available. These bond types can get the job done but may result in more chipping, rougher edges, and faster wear on the blade. While acceptable bond types can still cut glass, they are not ideal for high-precision tasks or where a perfect finish is required. In many cases, blades with this rating are used as backups or in situations where precision is not the top priority.
Blades with acceptable bond types:
-
May produce rougher cuts with more visible chipping, requiring post-cut processing such as polishing.
-
Have a shorter lifespan, meaning they need to be replaced more frequently.
-
Are suitable for low-precision applications, where surface finish and edge quality are less critical.
-
Should be used for temporary or non-critical tasks, such as basic glass cutting that doesn't demand high precision or when cutting thicker, more robust glass materials.
Not Used: A bond type rated as not used indicates that the bond is generally unsuitable for cutting glass. These bond types may result in excessive chipping, blade wear, or even damage to the glass. Using a bond type that falls into this category can compromise the quality of the cut and may lead to blade failure or even breakage of the glass. Not used bonds are usually designed for cutting other materials such as metals, stone, or ceramics, and do not have the necessary properties to handle the specific demands of glass cutting.
Blades with not used bond types:
-
Are likely to produce poor-quality cuts with excessive chipping and damage to the glass surface.
-
Can result in blade wear or failure much faster than acceptable, good, or excellent-rated bonds.
-
Should be avoided for glass cutting as they do not meet the required standards for precision or finish quality.
-
Are typically formulated for materials other than glass, such as metal or harder industrial materials, making them inappropriate for delicate, brittle glass surfaces.
Find out more: Selecting Right Blade for your application
Feed Rates for Cutting Glass
Feed rates refer to the speed at which the glass is advanced towards the cutting blade during the cutting process. Proper feed rate management is essential to ensure clean, accurate cuts while minimizing the risk of cracking, chipping, or overheating the glass. The feed rate varies depending on the thickness and toughness of the glass, as well as whether the cutting process is automated or manual.
Optimal Feed Rates for Thin Glass (1–5 mm) - When cutting thin glass, such as float or architectural glass with a thickness between 1 and 5 mm, the feed rate must be carefully controlled to prevent cracking and excessive chipping. The recommended feed rate is typically between 0.5 and 1.5 mm per second. This slower feed rate ensures that the cutting process is gentle enough to maintain the integrity of the thin glass, allowing the blade to gradually cut through the material without exerting too much pressure. Thin glass is more prone to stress fractures if pushed too quickly, so maintaining a lower feed rate is crucial to achieving smooth cuts with minimal damage.
Feed Rates for Thick Glass (10+ mm) - For thicker glass, such as tempered glass, laminated glass, or borosilicate with a thickness of 10 mm or more, a higher feed rate is typically used, ranging from 1.0 to 2.5 mm per second.
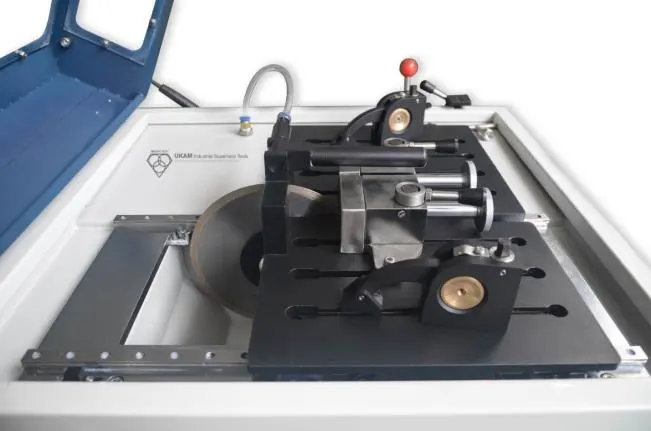
The specific feed rate depends on the glass's toughness and the blade's RPM. Thicker glass can handle a slightly faster feed rate without the same risk of cracking as thinner materials, but careful attention must still be paid to the blade's performance and the material's resistance. As the material gets thicker, the feed rate must balance cutting speed with the risk of overheating the blade, ensuring smooth, efficient cuts without compromising the glass quality.
Automatic vs. Manual Feed - When comparing automatic and manual feed systems, automatic feeds generally provide more consistent results. Automatic feed systems apply constant and even pressure to the glass, which reduces the risk of human error, such as uneven pressure that can lead to breakage or imperfect cuts. Automation helps maintain a consistent feed rate, especially when cutting thick or fragile glass materials, resulting in cleaner and more precise cuts. On the other hand, manual feed systems depend on the operator’s skill and can introduce variability in pressure and speed, which increases the risk of errors such as cracking or uneven cuts.
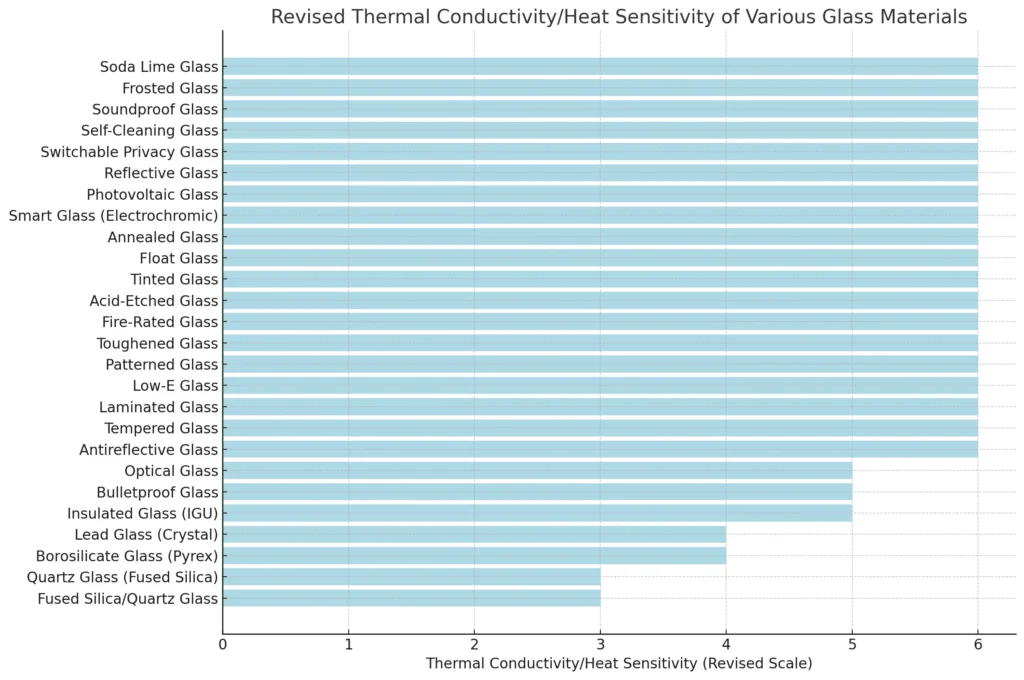
Table listing the recommended feed rates for cutting various glass materials with diamond blades:
Material Type |
Recommended Feed Rate (mm/sec) |
---|---|
Thin Glass (1–5 mm)
|
0.5 – 1.5 mm/sec |
Standard Float Glass
|
0.5 – 1.5 mm/sec |
Tempered Glass
|
1.0 – 2.0 mm/sec |
Laminated Glass
|
1.0 – 2.0 mm/sec |
Borosilicate Glass (Pyrex)
|
1.0 – 2.5 mm/sec |
Low-E Glass
|
1.0 – 2.0 mm/sec |
Insulated Glass (IGU)
|
1.0 – 2.5 mm/sec |
Patterned Glass
|
1.0 – 2.0 mm/sec |
Quartz Glass (Fused Silica)
|
0.8 – 2.0 mm/sec |
Optical Glass
|
0.5 – 1.5 mm/sec |
Lead Glass (Crystal Glass)
|
0.5 – 1.5 mm/sec |
Fire-Rated Glass
|
1.0 – 2.0 mm/sec |
Frosted Glass
|
0.8 – 1.5 mm/sec |
Tinted Glass
|
1.0 – 2.0 mm/sec |
Acid-Etched Glass
|
1.0 – 2.0 mm/sec |
Thick Glass (10+ mm)
|
1.0 – 2.5 mm/sec |
Smart Glass (Electrochromic Glass)
|
1.0 – 2.0 mm/sec |
Bulletproof Glass
|
1.0 – 2.5 mm/sec |
Wired Glass
|
1.0 – 2.0 mm/sec |
Fused Silica/Quartz Glass
|
0.8 – 2.0 mm/sec |
Desired Surface Finish Quality and Chipping Level
Achieving the desired surface finish and controlling chipping levels are critical considerations when cutting glass with diamond blades. The final surface quality is influenced by several factors, including the type of glass, the cutting method, and the type of blade in use. Balancing precision and efficiency is key to ensuring that the cut meets the required specifications for its intended application, whether it's for aesthetic purposes, functional needs, or both.
The condition and type of diamond blade used are fundamental in determining the surface finish. Continuous rim blades are designed to provide smoother, cleaner cuts with minimal chipping, making them ideal for applications where a fine surface finish is essential, such as in optics or decorative glass. In contrast, segmented rim blades are more aggressive and are often used when speed and efficiency are prioritized over surface smoothness. However, they may leave a rougher finish and cause minor chipping, which may be acceptable for industrial applications. Ensuring that the blade is in good condition is crucial; worn or dull blades can significantly affect the quality of the cut, leading to increased chipping and rough edges.
Other factors that impact the surface finish and chipping include the rotational speed of the blade, the feed rate of the material, and the cooling system. The RPM (revolutions per minute) of the blade must be properly adjusted depending on the thickness and type of glass. Thin or delicate glass benefits from higher RPMs, as this reduces the chance of chipping by making smoother, finer cuts. Conversely, thicker glass requires slower RPMs to manage the additional stress and heat generated during cutting. The feed rate also plays an essential role; pushing the material too quickly into the blade can result in excessive chipping or even cracking, while feeding it too slowly can cause the glass to overheat, leading to thermal stress and surface imperfections.
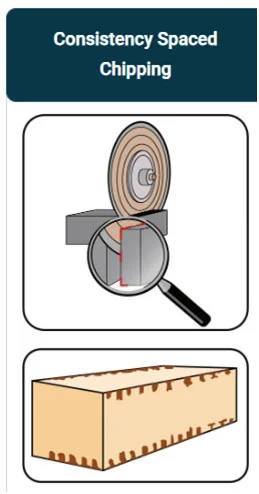
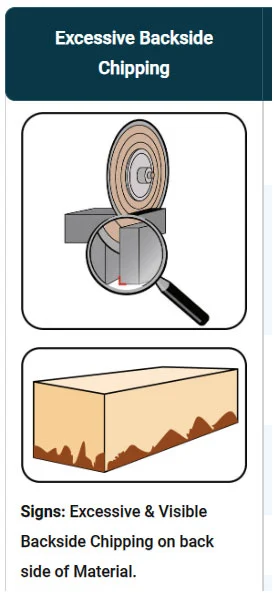
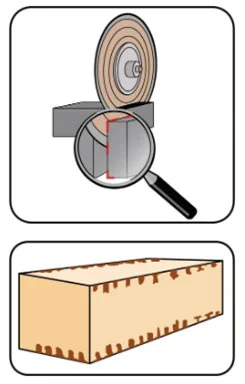
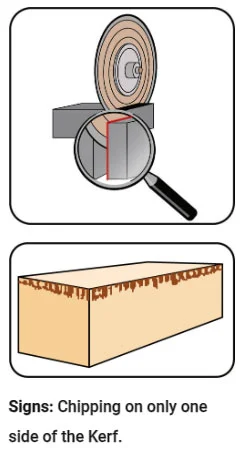
The use of coolant is vital in maintaining a consistent cutting temperature and reducing friction between the blade and the glass. Coolant serves as both a temperature regulator and a lubricant, preventing excessive heat buildup, which can degrade the cut quality and increase chipping. It ensures that the blade stays sharp longer, allowing for smoother cuts and reducing the likelihood of imperfections.
The desired surface finish quality and allowable chipping level are critical considerations when selecting the appropriate diamond cutting blade and optimizing cutting conditions. Different types of glass, depending on their application, require varying levels of precision in terms of finish and chipping tolerance.
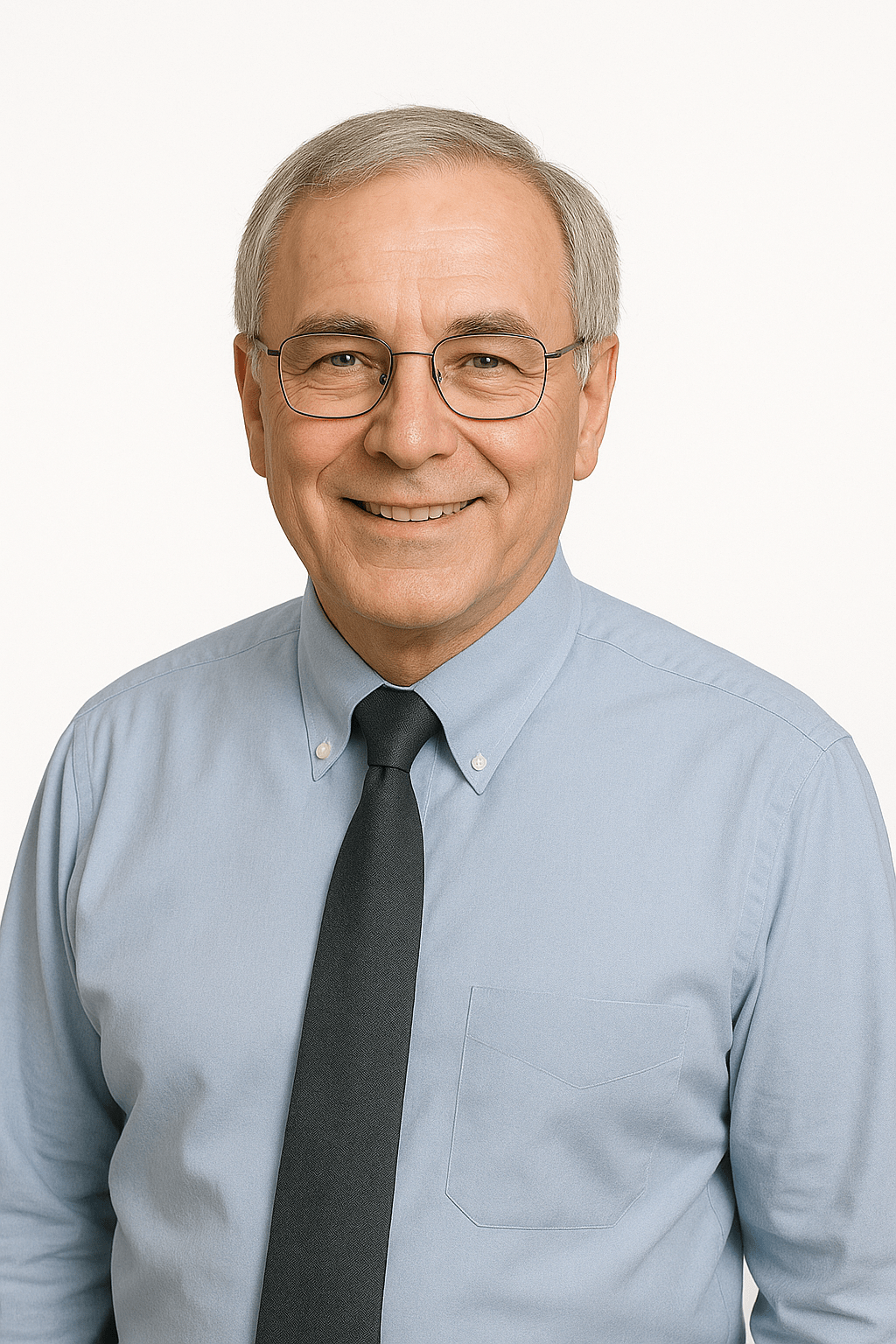
Alexander Schneider is a senior applications engineer and leading authority in the industrial diamond tooling industry, with over 35 years of hands-on experience in the development, application, and optimization of ultra-thin and high-precision diamond blades, diamond core drills, and diamond and CBN grinding wheels. His work spans a wide range of advanced materials including ceramics, glass, composites, semiconductors, and high-performance metals.
Throughout his career, he has collaborated with leading R&D institutions, national laboratories, and high-tech manufacturing companies across Europe, North America, and Asia, providing technical expertise and tailored solutions for demanding cutting and surface preparation applications.
Mr. Schneider has played a pivotal role in advancing precision cutting, sectioning, dicing, and grinding technologies used in research, production, and failure analysis. He is widely respected for his ability to optimize tool design and cutting parameters to meet exacting industry standards—balancing factors such as cut quality, blade life, material integrity, and process consistency.
As an author, Mr. Schneider is known for delivering practical, application-focused insights that translate complex technical challenges into clear, actionable strategies. His articles and technical guides serve as trusted resources for engineers, researchers, and manufacturers seeking to improve precision, reduce process variability, and enhance tool performance in critical applications.

ARE YOU USING RIGHT DIAMOND & CBN BLADES
FOR YOUR APPLICATION?
LET US
HELP YOU
HAVING ISSUES WITH
YOUR CURRENT DIAMOND & CBN BLADES?
Knowledge Center
Select right Diamond Blade for your application
How to Properly Use Precision Diamond & CBN Blades
Precision & Ultra Thin Diamond Blade Guide
How to Improve & Optimize Your Diamond Sawing Operation
Evaluating & Comparing Diamond Blades
Top 5 Diamond & CBN Cutting Blade Performance Metrics
Diamond & CBN Cutting Blade Performance Metrics that you Should Know
Total Cost of Ownership & Why its Important
Understanding Tradeoffs- Searching for Perfect Diamond & CBN Blade
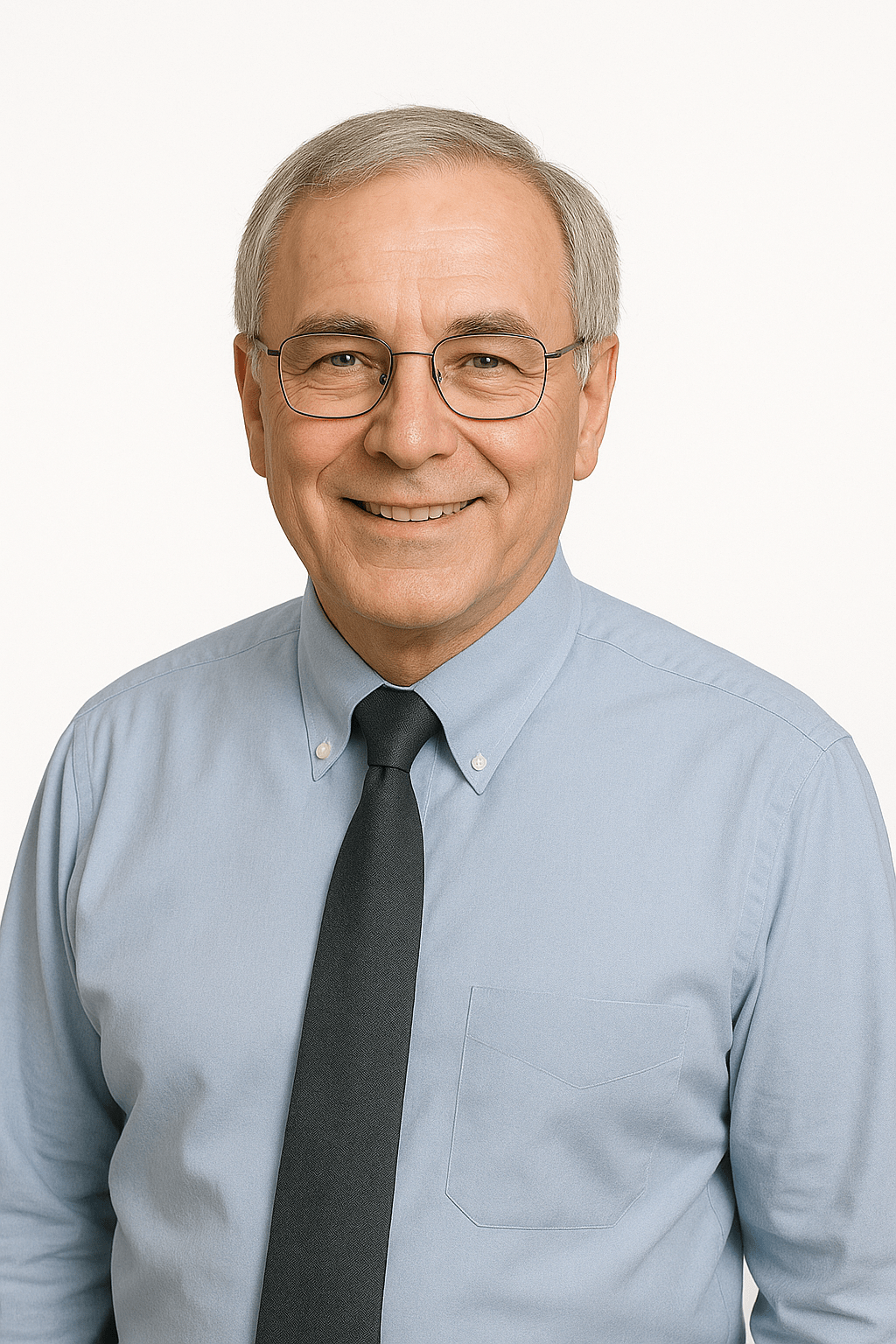
Alexander Schneider is a senior applications engineer and leading authority in the industrial diamond tooling industry, with over 35 years of hands-on experience in the development, application, and optimization of ultra-thin and high-precision diamond blades, diamond core drills, and diamond and CBN grinding wheels. His work spans a wide range of advanced materials including ceramics, glass, composites, semiconductors, and high-performance metals.
Throughout his career, he has collaborated with leading R&D institutions, national laboratories, and high-tech manufacturing companies across Europe, North America, and Asia, providing technical expertise and tailored solutions for demanding cutting and surface preparation applications.
Mr. Schneider has played a pivotal role in advancing precision cutting, sectioning, dicing, and grinding technologies used in research, production, and failure analysis. He is widely respected for his ability to optimize tool design and cutting parameters to meet exacting industry standards—balancing factors such as cut quality, blade life, material integrity, and process consistency.
As an author, Mr. Schneider is known for delivering practical, application-focused insights that translate complex technical challenges into clear, actionable strategies. His articles and technical guides serve as trusted resources for engineers, researchers, and manufacturers seeking to improve precision, reduce process variability, and enhance tool performance in critical applications.