Table of Contents
ToggleSelecting the right diamond dicing blade & parameters for your material/application can be a very time consuming, trial & error frustrating process. The guide below has been designed to help you better understand the most important diamond blade variables, which will play a major role in performance, cutting speed, and surface finish of your dicing blade
Share this Article with Friend or Colleague
SELECTING RIGHT DIAMOND DICING BLADE FOR YOUR APPLICATION
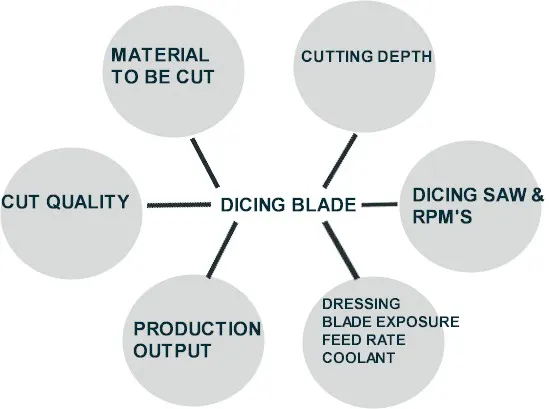
The following variable should be considered in selecting the right dicing blade for your application:
-
Type of material to be cut
-
Depth of required cuts
-
Cut quality needed
-
Equipment Used & its Speed/RPM’s Used
-
Production output required
These parameters will play a major role in determining and/or limiting the blade bond/binder to use, blade thickness and diamond particle/abrasive size. Additional factors to be considered is blade dressing, blade exposure, feed rate, spindle speed, and supply of adequate amount of coolant in dicing zone.
When choosing the best dicing blade specification for your application, we recommend remaining objective as possible and considering all parameters discussed in this article. For most dicing blade users, blade life and cut quality is typically the most important criteria in selecting the right dicing blade for their needs. However, other factors such as consistency, unit cost, lead time/availability, technical support may have just as much priority, if not more importance in the decision making process.
When observing dicing blade consistency, we recommend considering the dicing blades Yield. Average blade that can be measured. Such as number of packages or wafers cut, linear feet or meters cut. For example, if a particular vendors dicing blade can cut up to twenty five thousand cuts, however at eighteen thousand cuts inconsistency surfaces, the yields deviate. Yield deviation negatively affects production and quality control. At the same time as dicing blades become more inconsistent, dicing saw operators must monitor the process more closely and make necessary parameter changes. These parameter changes may extend dicing blade life back to twenty five thousand cuts. However, the extra time spend adjusting could have been better utilized monitoring other machines and/or operations.
Unit cost should be directly correlated to dicing blade life in linear millimeters. For example if blade X cost eighteen thousand dollars as an example. And cuts hundred thousand of linear millimeters, then cost is $ .00018 USD per linear millimeter. On the other hand if dicing blade Y costs twenty two thousand dollars, however cuts one hundred fifty thousand linear millimeters. Actual cost is $ .00016 USD per linear millimeter. As you can see the higher cost blade is more economical to use. At first glance the Y dicing blade appears to cost four dollars more than blade X. When dicing blade yield has be evaluated, dicing blade Y saves you more money, as well as reduces operator involvement in blade change and set up time.
MATERIAL TO BE CUT
Materials you are planning to cut will have a large impact in the types of diamond dicing blade you can use. If you are dicing ultra hard and brittle materials such as alumina or sapphire, it is generally recommended that you use a soft bond, thin kerf dicing blades such as Resin Bond. However, if you are cutting softer materials, material minimum thickness such as substrates and wafers. Nickel bond diamond dicing blade may be the best solution
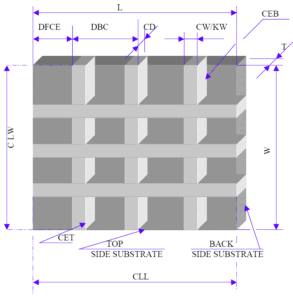
Material Hardness – hard & brittle materials require a softer Dicing Bond Matrix, to cut faster and freer. While softer and abrasive materials require a harder bond blade bond matrix, to last longer. Harder bond matrixes hold diamond in place for very long time, providing longer blade life. This requires use of very hard diamond particles in order for the dicing blade to maintain its sharp edges for long periods of time. Material Hardness is defined as the materials capability to resist deformation. All materials are classified by their scale of hardness. Material hardness is measured by many different hardness scales such as Mohs, Vickers, Knoop and other scales of hardness.
Material Thickness – will determine blade diameter, thickness, blade exposure ratio, dicing blade bond type, diamond size and concentration to use.
Depth of Cut - To optimize a blade's capability in cutting, always take into account the thickness of the blade, and the exposure needed to reach the required depth. Eg: .050" thick Alumina Substrate should not be cut with .0040" mil. thick blade because it is too thin of a blade for such a deep cut, it will result in deflection.
DICING PROCESS
Dicing process is used in a large variety of industries and applications.
Singulation - dicing process used in semiconductor industry. Where diamond dicing blade is used for die and package separation.
Scribing – process when cutting is not completely through the material. Final separation is done by breaking. Dicing process is also used for cutting very hard and brittle materials partially or completely through wide range of materials such as ceramics, optical glass, composites and many other materials. Dicing creates almost perfect edges, scribing allows much higher cutting speeds. Blade life is typically 2 to 4 times higher in scribing operation.
HOW DICING BLADES WORK
Simply, the diamond dicing blade is a cutting tool which has exposed diamond particles captured in a bond matrix each with a small cutting edge. Diamond particles are hold together with a binder such as resin bond, sintered (metal bond) or nickel bond (electroplated). The number of cutting edges which is determined by the number of diamonds (or concentration) make up the structure of the diamond blade, along with its matrix, (metal or nickel bond). The size of the diamond particle in the blade will have a direct result in on surface finish quality and material surface finish the blade leaves behind. The thickness of the blade (diamond particle plus matrix) will determine the width of the cut. Therefore, blade selection along with feed rate, cutting speed, and depth of cut will ultimately determine the blades success. Each diamond particles grinds away material on micro level. As the diamond crystal/particles breaks or shatters an new sharp point is formed, hence continuing the process until the blade is worn out. Blade performance is determined by bond/binders ability to retain diamond particles/crystals and release and orient their sharpest point/edge at right time and place when needed.
Why use Diamond or CBN?
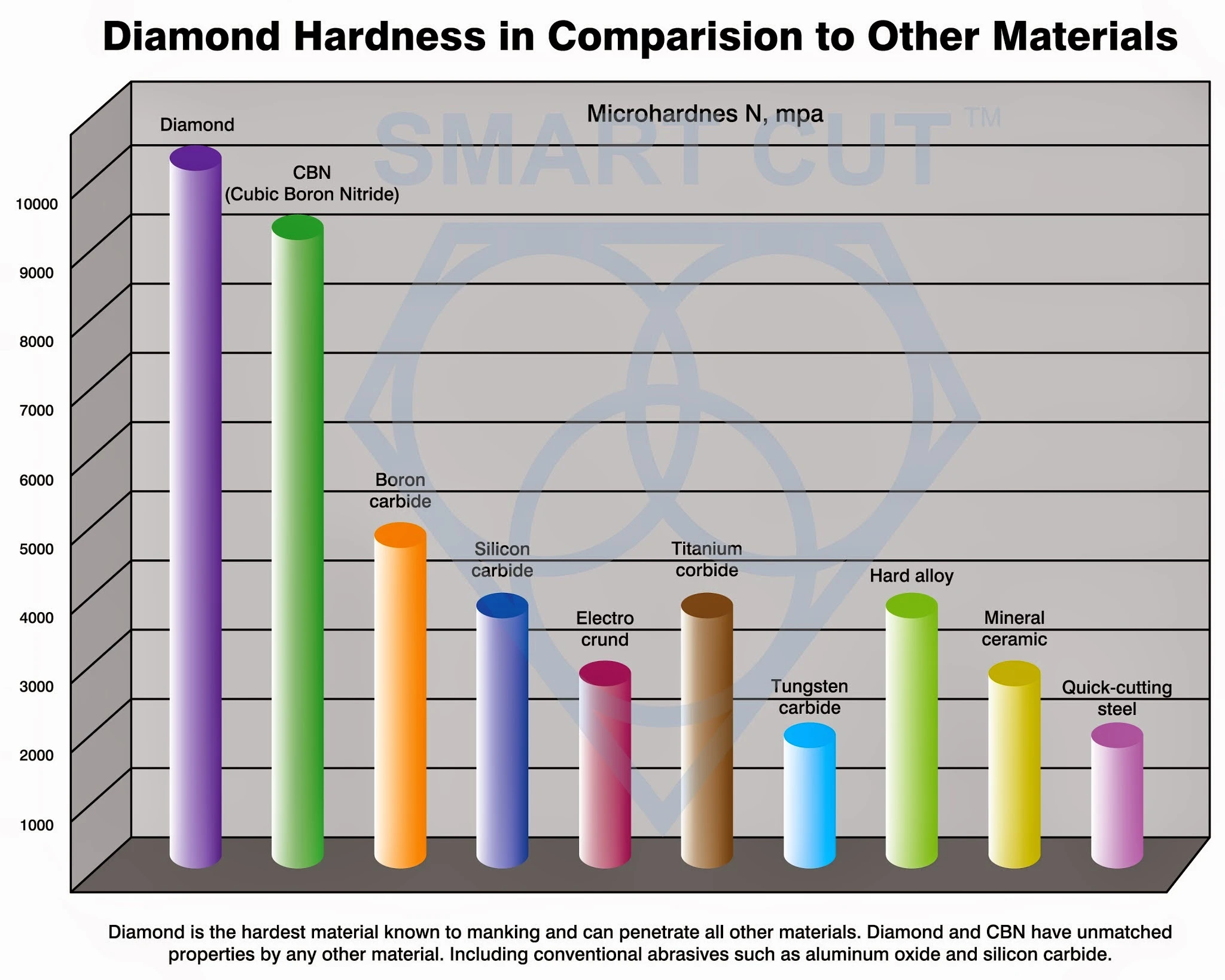
Diamond is the hardest material known to man kind. When used in dicing blades, diamond grinds away material on micro (nano) level. Due to its hardness Diamond will work all types of materials from hardness of 40 on Rockwell scale and up. Diamond Blades will machine hardest material, including those materials that other conventional types of abrasives, carbide and high speed steel will not. Diamond Blades will cut faster, produce smoothes surface finish quality, provide consistent performance, & yield (cost per part) possible. Diamond hardness, wear resistance and high natural strength are unchallenged among conventional abrasives.
DICING BLADE TYPES
Hubbed Diamond Dicing blades – dicing blade is already mounted on hub, comes ready to use. Once the blade is used, it is disposed. Typically these type of blades are use din applications requiring minimal blade vibration, such as cutting silicon & germanium wafers.
Hubless Diamond dicing blade – dicing blade is placed on flange/assembly. The flange assembly. The same assembly is used all the time. Typically applications that use hubless type of diamond dicing blades where effecting cooling of blade during cutting process is very important to obtain maximum results. For some applications such as cutting silicon wafers, hubbed dicing blades offer the greatest blade life, require minimum set up time, and provide better consistency. Hubless dicing blades are more sensitive to foreign particles such a s slurry accrued from cutting wafers. Careful attention to detail should be taken in order to clean the inner and outer flanges when mounting these blades.
Hubbed diamond dicing blades have the following Advantages:
Easier blade handling for the operator
Blade is plated on very accurate aluminum hub, it is stiffer. Hence producing better cut quality. This can bee seen in the kerf having straight cross section and longitudinal cut through the street being straight and parallel to the street.
Fewer vibration on the blade during cutting, due to increase blade stiffness. Many operators note the cut/kerf is cleaner and there is less chipping
Hubbed type dicing blades are pre dressed, hence requiring very simple and shore dressing procedure.
Hubless dicing blades advantages
Can be re used with smaller flanges
All the operator to utilize and experiment with different flange types best suited for their application
High cooling flange are available, allowing water directly onto the blade. This provides better blade and substrate cooling, resulting in better cut quality and longer blade life.
DICING BLADE BOND TYPES |
RESIN |
SINTERED (METAL BOND) |
HYBRID BONDTM |
NICKEL BOND (HUBLESS) |
NICKEL BOND (HUBBED) |
---|---|---|---|---|---|
|
|
|
|
|
|
DICING BLADE APPLICATIONS |
|
|
|
|
|
Dicing Blade Characteristics |
Resin Bond dicing blade are typically more forgiving. self dressing, and freer cutting. Excellent choice for Ultra Hard & Brittle Materials. Recommended for applications where cut quality and surface finish is very important. |
Sintered (metal bond) Dicing blades have excellent form holding & corner characteristics, provide very long life, high level of consistency. Recommended for users requiring very straight cuts and larger blade |
You will find all the advantages of cutting speed and fine finish that you have come to expect in a resin bond, and long life, consistency, aggressiveness, durability, and excellent performance on you look for in a metal bond. |
Nickel Bond dicing blades are available with and without hubs. Capable of maintaining excellent form & sharpness. Widely used for cutting wafers and thin substrates. Nickel Bond dicing blades provide minimum level of chipping on wide variety materials. |
Nickel Bond Hubbed dicing blades are typically used for dicing silicon and III-V materials. Creates very thin kerfs, <50 microns. Providing excellent cut quality with low wear rate |
DICING BLADE BONDS |
|
|
|
|
|
Abrasive (Diamond/CBN) Sizes |
3 to 151 micron |
3 to 126 micron |
3 to 151 micron |
3 to 70 micron |
2 to 50 micron |
Abrasive (Diamond/CBN) Types |
Coated & Uncoated Synthetic Diamond or CBN |
Natural Diamond, Coated & |
Coated & Uncoated Synthetic Diamond or CBN |
Natural & Synthetic Diamond |
Natural & Synthetic Diamond |
Abrasive Concentration |
25 to 200 con |
25 to 200 con |
25 to 200 con |
100 to 250 con |
100 to 250 con |
Minimum Dicing Blade Thickness |
.003" (.076mm) |
.004" (0.101mm) |
.004" (0.101mm) |
0003" (0.0076mm) |
.0003" (0.0076mm) |
SINTERED (METAL BOND) DICING BLADES
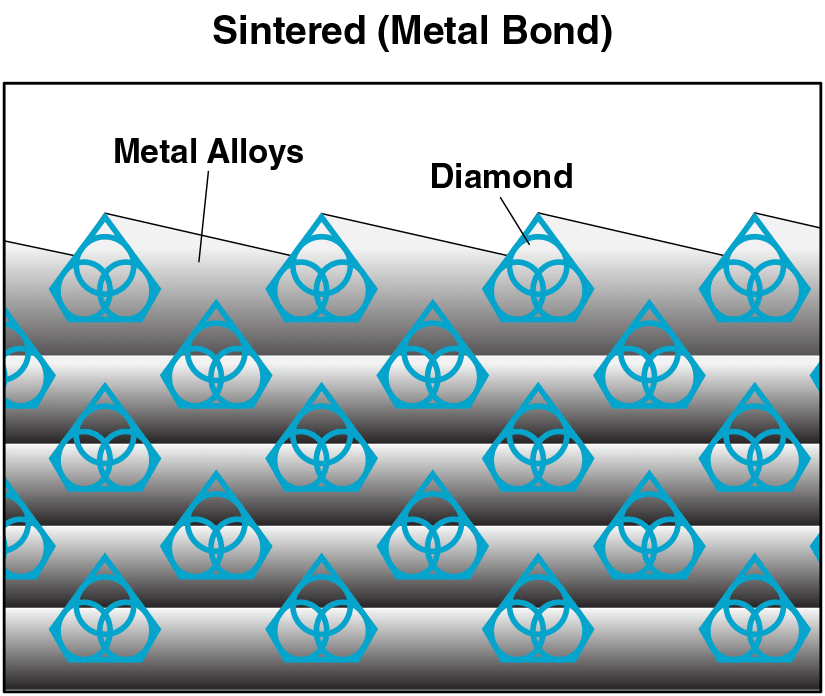
Sintered (Metal bonded) dicing blades diamonds sintered and multiple layers of diamonds impregnated inside the metal matrix. Diamonds are furnaces sintered in a matrix made of iron, cobalt, nickel, bronze, copper, tungsten, alloys of these powders or other metals in various combinations. Metal Bonded Dicing Blades are “impregnated” with diamonds. The compacted materials are then hot pressed or sintered to full density. Heating rate, applied pressure, sintering temperature and holding time, are all controlled according to the matrix composition. This means that selected diamonds are mixed and sintered with specific metal alloys to achieve the best cutting performance possible on any large variety of material. The metal bond surrounding the diamonds must wear away to continuously keep re-exposing the diamonds for the diamond tool to continue cutting.
Sintered (metal bonded) dicing blades are recommended for cutting wide variety of materials from 45 to 75 on Rockwell Scale (5 to 9.5 on mohs scale of hardness). It is more wear resistant and holds diamond well in place, usually producing the highest yield/cutting ratio. As a general rule of thumb, Metal Bond (sintered) diamond dicing blades longer than other dicing blades such as resin bond and electroplated (nickel bond) blades. |
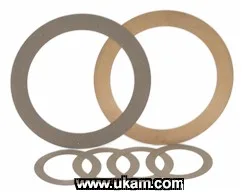
They wear evenly, and are known for their long life & consistency. Metal bond matrix does not protrude diamonds very high and hence usually requires lower cutting speeds than electroplated (nickel bond) and resin bond blades. In many dicing applications sintered (metal bond) dicing blades are used in applications which are not super hard or super brittle and with minimum tendency to produce chips or cracks.
RESIN BOND DIAMOND DICING BLADES
Advantages:
Cuts almost any material
Clan cuts on hard and brittle material
Any blade thickness is available .003” and up
Minimum dressing required
Wide variety of bond matrixes and specifications available
Low cost
Disadvantages
Fast/High Blade Wear
Edge geometry is lost faster than with other types of dicing blades
Requires use of lower spindle speed (RPM)
Minimum blade thickness .003”
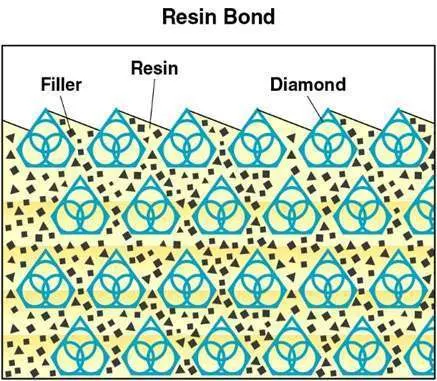
Resin bond dicing blades are made with high temperature phenolic resin, diamond particles, ceramic filler and often additional additives. Resin Bond is the softest of all the bonds, frequently used in applications that require a smooth surface. This type of dicing blade is used on majority of ultra hard & brittle materials. Resin bond dicing blades allow the bond matrix to wear faster, and allow for diamond particles/crystals to break out of their matrix faster, so that new sharp diamond particles become exposed. This self sharpening characteristic of resin bond dicing blades, based on faster bond wear out is what make this blade choice in almost half of all dicing application. Typical Resin Bond Diamond Blades last less than Sintered (Metal Bond) diamond blades, but more than electroplated (nickel bond) diamond blades. finish and minimum amount of chipping.
Some disadvantages of resin bond dicing blades is resin bond must remain very fragile in order to expose new diamonds. Resin bond is the softest of the all the dicing bond matrixes. For this reason, strong and high quality diamonds cannot be used in a resin bond. High quality diamonds are harder than a resin bond matrix, and would soon disintegrate the bond that keeps them in place. This brings about the need for frequent blade dressing, causing the cut to loose its roundness or form. |
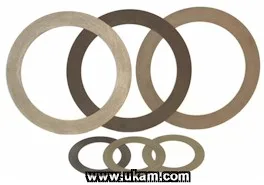
Another disadvantage of Resin bond is its high wear rate, lack of stiffness, and thickness limitation. Resin bond can cut hard & brittle materials fast, but will provide much shorter life. Thinnest blades that can be produced in resin bond is .004". Many of the resin bond dicing blade weaknesses and limitation have been resolved by utilizing different phenolic resin types, mixtures, fillers, and molding techniques in our New Generation Extended wear resin bond and Hybrid bond dicing blades. Hence increasing their field or use in greater amount of applications.
NICKEL BOND DIAMOND DICING BLADES
Advantages:
Very low blade wear
Maintains good edge geometry
Excellent on applications requiring high accuracy
Ultra thin blade thickness are available such .0006” (0.018mm)
Disadvantages
Blade thickness is limited to .020” (0.5mm)
Longer blade dressing process
Higher blade cost
Cannot be used on ultra hard & brittle materials
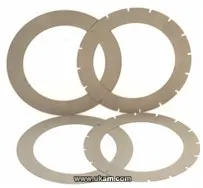
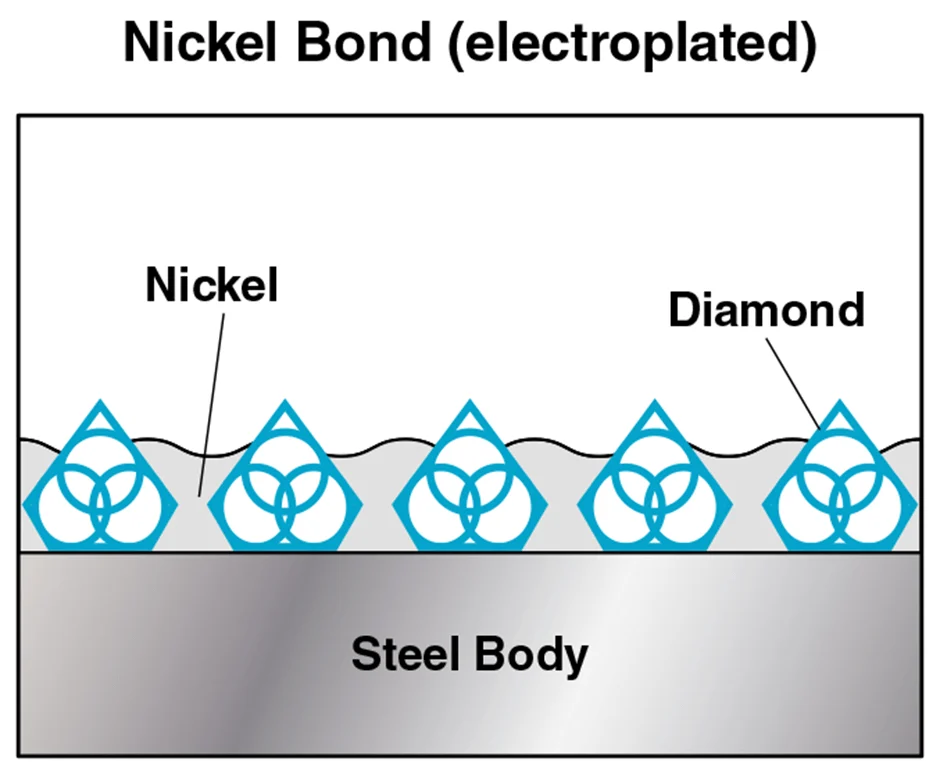
Nickel Bond Dicing Blades have a high diamond concentration and give a freer, faster cutting action with minimum heat generation. Diamonds have higher protrusion ratio, staying on the surface of the cut allowing for fast material removal. Electroplated Diamond Blades last less than metal bond, resin bond, hybrid bond blades and are the least expensive diamond blades available. Silicon wafer dicing is usually done with the plated diamond blade (hubbed or hubbless) which has proven most effective for this application. The Kerfs are typically in the 1-3 mil. range using a nominal spindle speed of 30,000 RPM with feed rates as high as 8 inch per sec.
RECOMMENDED DIAMOND SIZES FOR DIFFERENT MATERIALS & APPLICATIONS
Material |
Nickel |
Metal Bond |
Resin Bond |
---|---|---|---|
This guide is designed to help you select the best diamond mesh size for your material / application |
|
|
|
Alumina |
53 microns |
||
Ferrite |
3-6 microns |
2-4 microns, 3-6 microns |
9 microns |
Glass |
45 microns |
||
Garnet |
35 microns |
||
Barium Titanate |
17 microns |
9 microns |
|
Kovar |
53 microns |
||
Quartz |
30 microns |
||
Silicon |
3-6 microns |
53 microns |
|
Germanium |
3-6 microns |
53 microns |
|
GaAs |
1-2 microns, 2-3 microns, 3-6 microns |
53 microns |
|
Sapphire |
53-63 microns, 45 microns |
||
Ruby |
53 microns |
||
Titanium Carbide |
17 and 30 microns |
10 microns, 17 microns |
53 microns |
Piezoelectric (PZT) |
3-6 microns, 4-8 microns, 10 microns |
||
Lead Telluride |
3-6 microns |
||
Alumina Nitride |
88 microns, 105 microns |
||
P.C. Boards |
30 microns, 50 microns |
30 microns, 50 microns |
|
FR4 |
30 microns, 50 microns |
30 microns, 50 microns |
|
Bithmuth Telluride |
17 microns, 30 microns |
45 microns |
|
Galum Phosphite |
3-6 microns |
9 microns |
|
Green Ceramic |
17 micron and 30 micron |
Dicing Blades & Cutting Speeds
The RPM’s of the machine spindle should be noted when selecting the right dicing blade specification of your application.
Dicing saw spindle diameter
Blade outside diameter
Blade thickness
Blade bond types such as resin bond, nickel bond or metal bond
Material being cut
Spindle Speed/RPM - The RPM of your dicing saw should be variable, ranging from 10,000 to 40,000 RPM. When using standard dicing blades such as 2" 3" 4" diameter for example, blade the best spindle speed is usually determined by the hardness of your material and the depth of your cut. Diamond may break (fracture) at very high speeds, and fall out at very slow speeds. An optimum surface speed / RPM's must be selected to balance out the two disadvantages. Diamond Blade life will usually increase at slower cutting speeds. However the increase in labor costs, utilities costs, depreciation of equipment and other overhead expenses. Will usually offset the saving of diamond blade life and other consumables. Cutting Speed & Surface Finish Quality is often the most important consideration when selecting the right diamond blade for your application. The operator mush choose a balance between life of the blades and their cutting rate. Diamond has a higher impact strength than the material being machined. During the dicing operation, the diamond ruptures the material by impact. Each diamond is able to transfer the electrical power from your cutting machine, into momentum that breaks the material on nano / micro level.
By increasing power on your dicing saw, your diamond blade RPM's and surface speed will increase as well. Hence, each diamond will chip off a smaller amount of material, reducing its impact force on material being machined. And reducing cutting resistance. In theory, by increasing surface speed / RPM's, each diamond should receive a smaller impact force. However, because impact is supported by a smaller volume, the impact force with this low volume is actually increased. There is a higher probability that the diamond particles will break or shatter. Hence, cutting materials at very low surface speeds, creates a large impact force between diamond and material being machined. Although the diamond may not break, the risk that the diamond will be pulled out of diamond blade and causing premature failure of the blade increases.
Dicing Blade General Speed Guidelines and Recommendations
2” diameter machine spindle. For cutting silicon substrates with nickel type dicing blades. Recommended RPM’s range from 30 to 35 KRPM (max speed: 40 KRPM). in most cases for 4” OD nickel bond dicing blades. Maximum RPM’s are 30 KRPM for resin bond diamond dicing blades 4” OD, maximum RPM depends on blade thickness
up to .015” thickness – 16 KRPM max
.015” to 0.025” thickness – 14 KRPM
.025” to .035” thickness – 12 KRPM
over .035” thickness – 10 KRPM
Speed range recommendations for typical applications when using 4" OD dicing blades
Application |
Blade Type |
Cutting Speed Range |
---|---|---|
TIC, land definition |
Nickel Bond |
12 to 14 KRPM |
TIC, cutting through |
Nickel |
12 to 15 KRPM |
Silicon |
Nickel Bond |
18 to 20 KRPM |
Hard Alumna |
Resin Bond |
14 KRPM |
Green Ceramic, wet |
Nickel Bond |
12 to 16 KRPM |
Green Ceramic, Dry |
Nicekl Bond & Carbide Blades |
10 KRPM (16 KRPM for carbide blades) |
Sapphire S.O.S |
Resin Bond |
12 to 14 KRPM |
Quartz |
Resin Bond |
12 to 14 KRPM |
Ferrites |
Nickel Bond & Resin Bond |
14 to 18 KRPM (nickel) 10 to 14 KRPM (resin) |
Glass |
Resin Bond |
12 to 14 KRPM |
DIAMOND / ABRASIVE SELECTION
Diamond is universally recognized as the hardest substance known to man. Diamond is recommended for machining hard & brittle materials, optics, semiconductor packages, advanced materials, composites, ferrous & non ferrous metallic materials from 40 on Rockwell scale and up. Diamond crystals can be synthetically grown in a wide variety of qualities, shapes and sizes. Diamond is grown with smooth crystal faces in a cubo-octahedral shape and the color is typically from light yellow to medium yellow-green. Diamond is also grown to a specific toughness, which generally increases as the crystal size decreases.
Synthetic (Men Made) Diamonds - Most frequently used for most diamond blade manufacturing including sintered (metal bond), resin bond, electroplating (nickel bond). Synthetic diamond is more consistent in particle shape, hardness, and density. Synthetic diamond has replaced natural diamond in most dicing blades applications because of its superior consistency and ability to tailor-make the diamond for the specific application.
Cubic Boron Nitride (CBN) - often used for machining materials with high metallic content.
Materials recommended for cutting with CBN:
-
Alloy steels (45-68 RC)
-
Carbon tool steels (45-68 RC)
-
Die steel (45-68 RC)
-
High speed steel (45-68 RC)
-
Chilled cast iron
-
Ni Hard
-
Forged steel
-
Meehanite iron
-
Moly chrome steel rolls
-
Inconel 600
-
Rene
-
Incoloy
-
Monel
-
Stellite
-
Colmonoy
-
Waspoloy
The ability of a diamond to withstand an impact load is typically referred to as diamond impact strength. Other diamond-related factors, such as crystal shape, size, inclusions and the distribution of these crystal properties, play a role in the impact strength as well. Impact strength can be measured and is commonly referred to as Toughness Index (TI). In addition, crystals are also subjected to very high temperatures during manufacturing and sometimes during the cutting process. Thermal Toughness Index (TTI) is the measure of the ability of a diamond crystal to withstand thermal cycling. Subjecting the diamond crystals to high temperature, allowing them to return to room temperature, and then measuring the change in toughness makes this measurement useful to a diamond tool manufacturer.
The manufacturer must select the right diamond based on previous experience or input from the operator in the field. This decision is based, in part, on the tool's design, bond properties, material to be cut and machine power. These factors must be balanced by the selection of diamond grade and concentration that will provide the operator with optimum performance at a suitable cost.
DICING BLADE VARIABLES
BOND HARDNESS – Ability of the bond matrix to hold diamonds. As the hardness of the bond is increased, its diamond retention capabilities increase as well. However the trade off is slower cutting speed. Life of the diamond blade is usually increased with hardness of its bond matrix. Bonds are designated on their scale of hardness from Soft, Medium, and Hard. There are dozens of variations and classification schemes based on bond degree of hardness or softness. Using diamond dicing blades with optimum bond hardness for your application is important to successful dicing operation. Bond matrix that is too soft for the material being cut will release diamond particles faster than needed, resulting in faster wear and shorter diamond blade life. On other hand bond matrix that is too hard will result in much slower cutting speeds and require constant dressing to expose the next diamond layer. As rule of thumb, harder materials such as sapphire and alumina generally require a softer bond. Whereas softer and more brittle materials require a harder bond.
it is very important to use blades of proper bond hardness for your dicing application. For example if dicing blade you are using has too soft of a bond hardness, diamond particles/crystals will be pulled out or fall out prematurely. Hence causing blade failure and loading. On the other hand using very hard bond dicing blade (blade that retains its diamond particles beyond their useful life) may cause burning in the material cutting zone and glazing of blades diamond section. Diamond particle size inside dicing blades bond matrix will also affect blades hardness. Lower diamond concentration will create a softer and more brittle bond. Where high diamond concentration would create more harder bond type.
DIAMOND GRIT SIZE (Mesh Size) – grit size (mesh size) is generally selected depending on the speed you wish to operate the cut and surface finish of your material. According to U.S. Standards, mesh designates the approximate number of sieve meshes per inch. High Mesh Sizes mean fine grits, and low numbers indicate coarse grits. Diamond Mesh Size plays a major role in determining the surface finish quality, smoothness, level of chipping you will obtain, and material microstructure damage you will obtain. Finer mesh size diamonds such as 20 microns are much smaller in size than coarser diamond particles. And will give you a very smooth surface finish, with minimal amount of chipping on edges. These mesh sizes are usually used for fine cutting of a full rage of materials such as: LiNbO3, YVO4, GaAs, and optical materials. Courser diamond particles are much larger in diameter and are frequently used fast cutting / material removal on more harder materials such as silicon carbide, zirconia, Al2O3, and other advanced ceramics and high metallic content materials. Which do not require a very fine surface finish. A full range of diamond Mesh Sizes is utilized for precision diamond sawing operations ranging from as coarse as 120microns to as fine as 0.5 micron
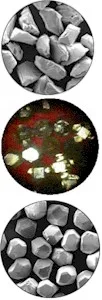
The diamond mesh size in a dicing blade also directly relates to the number of crystals per carat and the free cutting capability of the dicing blade. The smaller the mesh size, the larger the diamond crystals, while larger mesh size means smaller diamond. A 30/40 Mesh blocky diamond has about 660 crystals per carat, while a 40/50 Mesh diamond will have 1,700 crystals per carat. Specifying the proper mesh size is the job of the dicing blade manufacturer. Producing the right number of cutting points can maximize dicing blade life and minimize the machine power requirements. As an example, a dicing blade manufacturer may choose to use a finer mesh size to increase the number of cutting crystals on a low concentration blade, which improves dicing blade life and power requirements.
Diamond Mesh size does have considerable effect on cutting speed. Coarse Diamonds are larger than finer diamonds and will remove more material than finer diamond particles. This means that coarse diamond dicing blades are more aggressive for material removal than the finer size diamond dicing blades and will cut faster. However, the tradeoff is increase in material micro damage. If you are cutting fragile, more delicate materials then finer mesh size diamond dicing blades are recommended. Diamond mesh size (grit size) should provide maximum removal rate at minimal acceptable finish.
Typically finder size diamond particles require more horsepower than finer size diamond particles, as well as provide more heat buildup. A good rule to follow when selecting the right diamond size for your dicing blade is to use the largest diamond size possible for particular dicing blade thickness. And decrease the diamond size until desired surface finish quality is obtained.
DIAMOND CONCENTRATION - The proportion, and distribution of diamond abrasive particles, also known as concentration. has an effect on overall cutting performance and price of precision diamond blades. Diamond concentration, commonly referred to as CON, is a measure of the amount of diamond contained in a diamond section of drill based upon volume. Diamond concentration is usually defined as: Concentration 100 = 4.4 ct per cm layer volume (mesh size + bond). Based on this definition a concentration of 100 means that the diamond proportion is 25% by volume of diamond layer, assuming at diamond density is 3.52 g/cm3 and 1 ct = 0.2g. Nominal diamond concentration in precision diamond blades range from 0.5 ct/cm3 to 6 ct/cm3. This means diamond concentrations are available from 8 to 135). Selecting the Right Diamond Concentration can be critical in optimizing your dicing operation. Selecting Optimum Diamond Concentration for your application will depend on a large number of factors, such as:
-
Material Being Cut
-
Bond Type and Hardness
-
Diamond Mesh Size
-
Cutting Speeds
-
Coolants being used
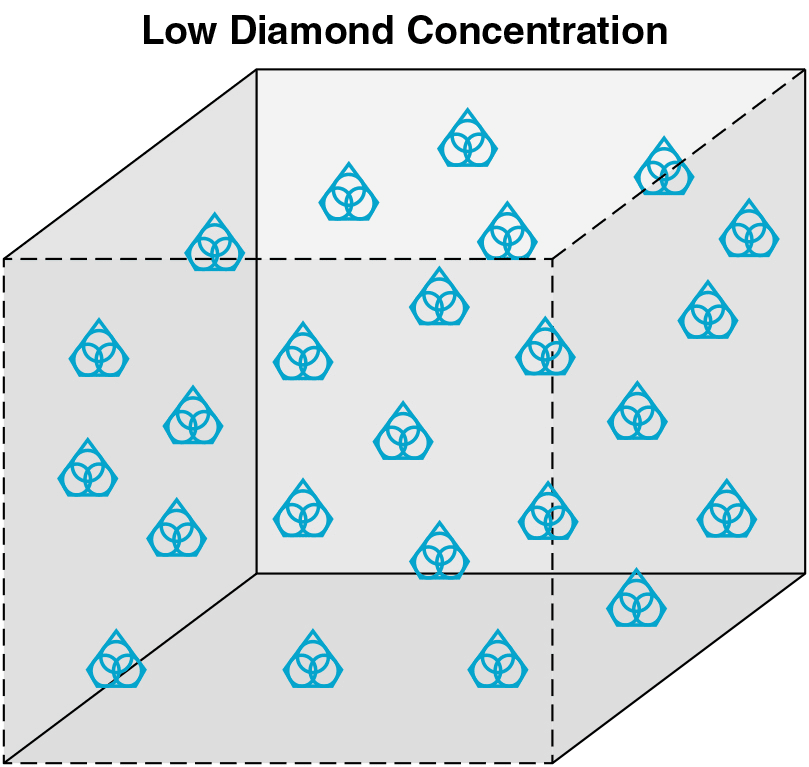
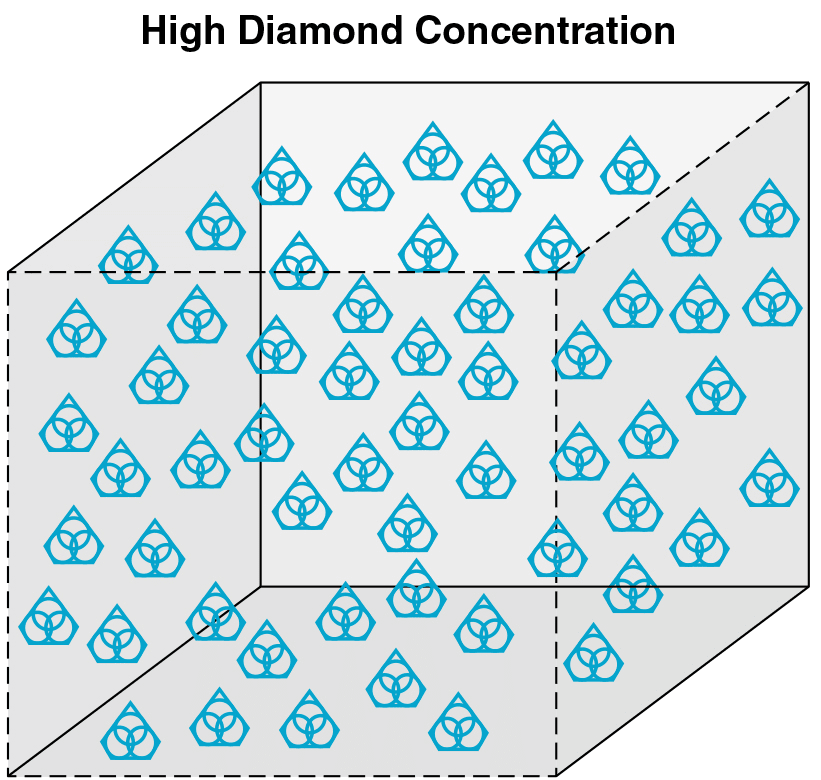
Diamond Concentration will play a major role in determining the life and cutting speed of your dicing blade.
High Diamond Concentration
Higher diamond concentration causes the blade to act harder and wear slower. Hence, higher diamond concentration is recommended and usually used for cutting softer and more abrasive types of materials. However, the trade off is significantly slower cutting speed. Since there is higher density of diamond particles in bond matrix, there is not enough space for the debris and fine powder created during dicing process to escape. Blade overloading is often a result of selecting improper diamond concentration.
Low Diamond Concentration
Low diamond concentration dicing blade is softer and faster wearing blade, creating better cut quality and surface finish. Low diamond concentration is often recommended and widely used for cutting ultra hard and brittle materials. Lower diamond concentration has larger spacing between diamond particles and can accept more fine powder debris generated from dicing. This typically creaster faster and more freer cutting blades, leas loasing and better surface finish quality. Lower diamond concentration dicing blades will however wear out faster than their high concentration counterparts.
Diamond Concentration is usually determined by the the slowest cutting speed that is acceptable for a specific application. Optimum performance can be achieved when the diamond tool manufacturer utilizes their experience and analytical capabilities to balance diamond concentration and other factors to achieve optimum performance for the tool operator. UKAM Industrial Superhard Tools has the experience & applications laboratory to help you select all the right diamond blade variables for your unique application.
Diamond Concentration & CBN (cubic boron nitride) blades
For CBN (cubic boron nitride) concentration is defined by volume. For example V120 = 12% by volume, V180 = 18% by volume.
SLOTTED DICING BLADES
Slotted dicing allow for better coolant circulation and chip clearance in the cut. This provides for an improved washing action of kef, reducing abrasive action of the slurry which is otherwise confined to the cutting edge area. Of even greater importance is the reduction of heat because an lager percentage of the coolant is carried to the point of contact. Excess heat will shorten the life of the blade and may cause permanent damage to the. Slots help by eliminating continuous contact between blade and material, hence proving improved coolant fro both blade and material being cut. As a blade diameter and cutting depth increase, the advantage of slotted dicing blade design over continuous rim dicing blades is apparent.
Nickel bond slotted/serrated dicing blades are standard product. Slots/serrations are also available for both resin bond and metal bond diamond dicing blades.
Advantages of Slotted/Serrated Blades
Less contact between edge and material, this provides less loading during cutting
Better cooling characteristics, serrations/slots allow heat to dissipate
Disadvantages
Kerf width is not accurate as with regular continuous rim dicing blades.
Some vibration will be present with using slotted dicing blades
Dicing Blade life
Dicing blade life is determined by large variety of factors such as
-
Bond type
-
Diamond mesh size
-
Diamond concentration
-
Bond hardness
-
Cutting speed/RPM’s
-
Material thickness, hardness and density
It is possible to tailor dicing blade hardness to provide optimum performance under specific combinations of variables indicated above. When determining the parameters above, a good rule to remember: higher blade lifer, the lower its wear rate and shorter smaller self sharpening effect. Self sharpening is correlated to blade wear. Dicing blade wear typically causes a reduction in OD of dicing blade. Although it is not possible to accurate predict dicing blade wear. Some characteristics that can assist you are:
Nickel Bond Dicing Blades
6 to 8 micron / 100m – pure Si (scribing)
25 – 30 microns / 100m – Si + Adhesion + Tape (dicing)
Resin Bond Dicing Blades
70 to 100 micron / 10m Glass
250 to 400 micron / 10mm Al203 (99.6% alumina)
DICING SOLUTIONS FOR PACKAGE SINGULATION
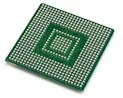
BGA (Ball-Grid Array)
Common Materials - FR4 and epoxy mold compound.
Typical Concerns:
-
Cut quality
-
chipping
-
burrs
-
slivers
-
protrusions
-
race shorts
-
Blade life
Dicing Blade Recommendation:
-
SMART CUT HYBRID BOND or sintered (metal bond) series
-
Diamond size: 30 - 55 microns
-
Blade Thickness: .008” - .014”
Dicing Process Recommendations:
-
Feed rate: 50-250 mm/sec
-
Spindle speed: 20-40 krpm depending on blade O.D.
-
Multi panel mounting on UV tape
-
Minimal dressing so as not to create a large radius on the blade edge
QFN (Quad Flat No Lead)

Typical Concerns:
-
Chipping
-
Burrs
-
Lead smearing
-
Melting
Dicing Blade Recommendation:
-
SMART CUT HYBRID BOND or sintered (metal bond) series
-
Diamond grit size: 45 - 88 microns
-
Thickness: .008” - .020”
Dicing Process Recommendations:
-
Feed rate: Half Etched substrates 30-75 mm/sec, Full Copper substrates 15-30 mm/sec
-
Spindle speed: 22-35 krpm depending on blade O.D.
-
Multi panel mounting on UV tape
-
Override process over one substrate to reach final feed rate
LED (Light-Emitting Diode)

Typical Concerns:
-
Copper burrs
-
End of blade life due to limited exposure
-
Throughput (maximize UPH)
Dicing Blade Recommendation:
-
SMART CUT HYBRID BOND or Nickel Bond series
-
Diamond size: 10,13 & 17 microns
-
Thickness: .003” - .008”
Dicing Process Recommendations:
-
Feed rate: 80-150 mm/sec
-
Spindle speed: 25-30 krpm
-
Multi panel mounting on UV tape
CMOS (Complementary Metal-Oxide Semiconductor)

DWDM (Dense Wavelength Division Mulitplexing) Filters

Typical Concerns:
-
Top-side and back-side chipping
-
Cut perpendicularity
-
Kerf side surface finish
Dicing Blade Recommendation:
-
SMART CUT series Resin, HYBRID, & Sintered (metal bond) blades
-
Diamond size: 30 - 45 microns (resin) and 7 - 15 microns (sintered)
-
Thickness: .006" - .012”
Dicing Process Recommendations:
-
Feed rate: 4 - 20 mm/sec
-
Spindle speed: 20 - 30 krpm (2") 10 - 15 krpm (4")
-
Dicing synthetic water soluble coolants may reduce chipping and improve surface finish
HDD (Hard Disk Drive)

Typical Concerns:
-
High Mechanical (internal) stress
-
burrs
-
large kerf width
-
lack of accuracy
Dicing Process Recommendations:
The MR head substrate is made of ferromagnetic ceramic material, which has an extremely hard wear resistance and excellent magnetic properties. a typical MR substrate is AlTiC. Substrate thickness typically ranges from 200 to 300 microns. Substrates for HDD read heads require machining after being sintered into bars or sheets. Than they have to be diced into very small unit with very high precision tolerances.
Semiconductor Wafer

Typical Concerns:
-
Top-side and back-side chipping
-
Cracking
-
Wafer contamination due to ESD issues and poor cleaning
Dicing Blade Recommendation:
-
SMART CUT Nickel Bond or HYBRID series
-
Diamond size: 4 - 6 microns
-
Thickness: .0008” - .0016”
Dicing Process Recommendations:
-
Feed rate: 25 - 75 mm/sec
-
Spindle speed: 30 - 50 krpm
-
Mounting: Blue or UV tape
-
Cooling type: DI water with and without additives
-
Carbon dioxide bubbler is optional
Silicon & GaAs are the two most common materials used for semiconductor wafers. Wafers are typically available in sizes up to 12" in diameter, with 6" and 8" most popular. Typical thicknesses are between 100 - 650 microns.
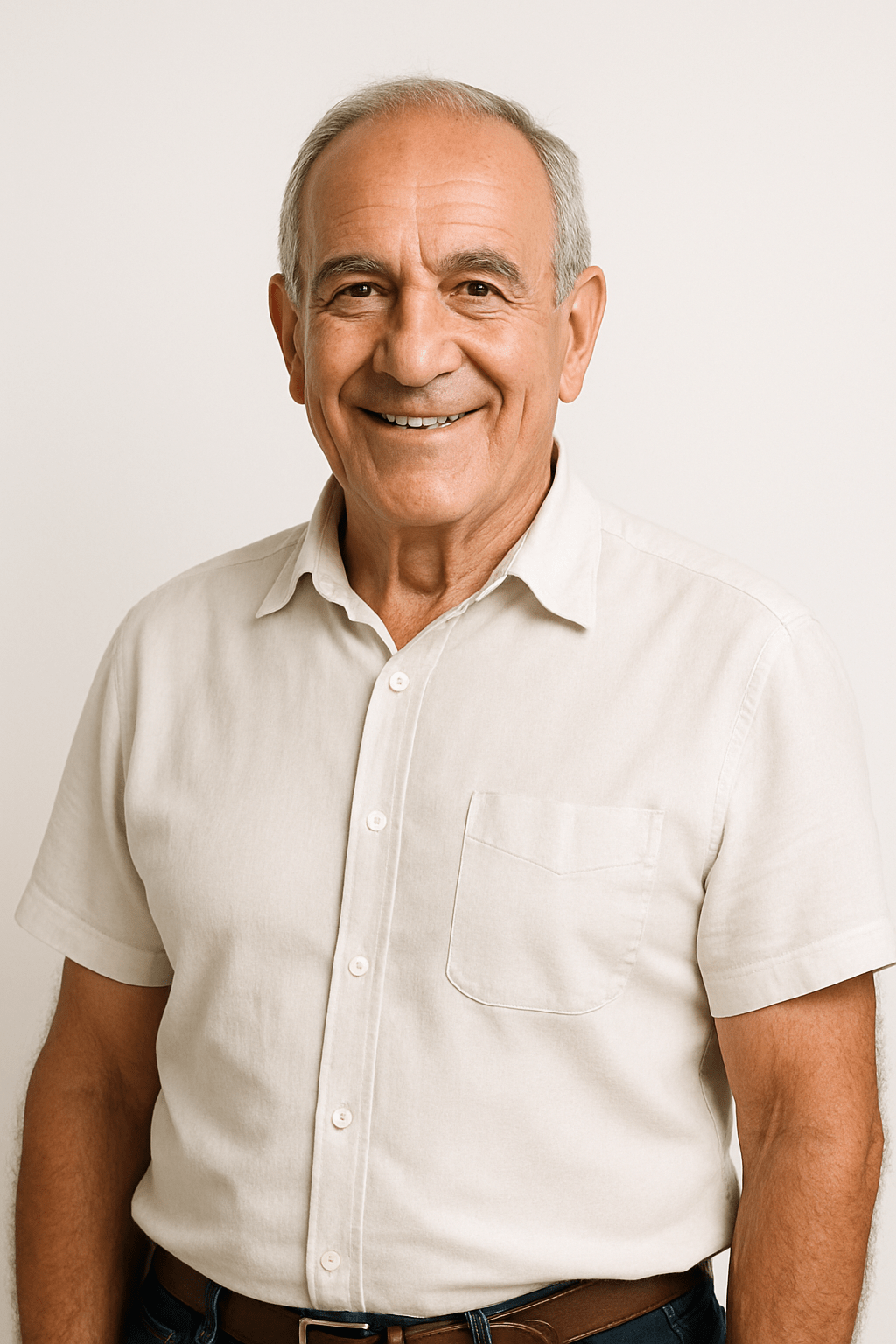
Leon Meyer is a veteran manufacturing engineer and technical consultant with over 50 years of experience in the development, implementation, and troubleshooting of industrial diamond tooling systems. Having spent his career at the intersection of tool design, precision manufacturing, and production engineering, Mr. Meyer is widely regarded as one of the most experienced voices in the application of ultra-thin diamond blades, sintered core drills, and CBN grinding wheels across heavy industry, advanced materials, and research sectors.
Known for his pragmatic, no-nonsense approach, Leon has advised manufacturers across the United States, Europe, and East Asia—helping streamline cutting processes, extend tool life, and solve complex issues related to material breakage, chipping, and tolerance drift. His expertise has directly contributed to improved production efficiency in industries ranging from aerospace alloys and technical ceramics to optics, composites, and high-nickel superalloys.
As an author, Mr. Meyer brings a lifetime of field knowledge to his writing, with a focus on real-world problem solving, cost-performance optimization, and tool reliability under demanding conditions.
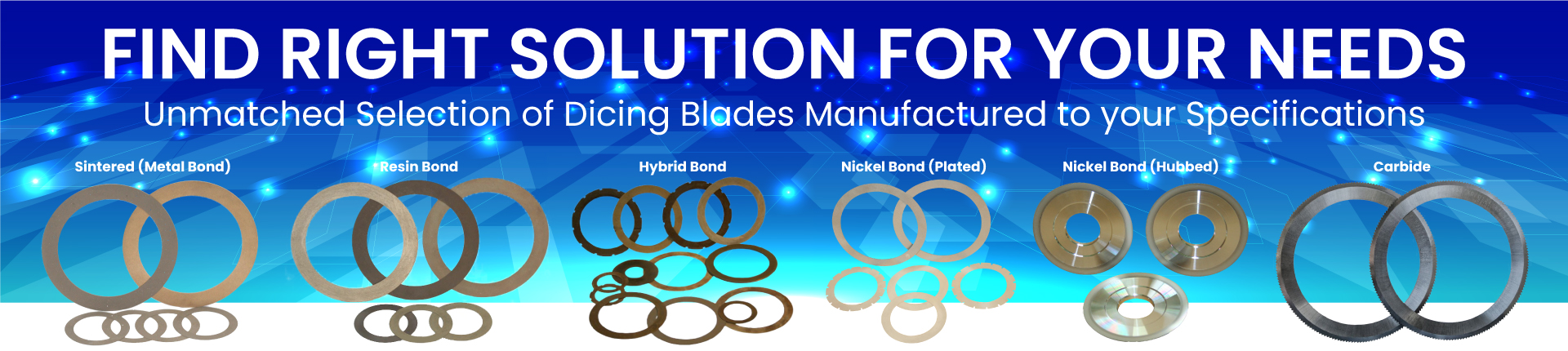
ARE YOU USING RIGHT DICING BLADES
FOR YOUR APPLICATION?
LET US
HELP YOU
HAVING ISSUES WITH
YOUR CURRENT DICING BLADES?
Select right Diamond Dicing Blade for your application
Dicing Blade Operations Recommendations
Optimizing Dicing Blade Performance
Trouble Shooting Dicing Problems
Application Recommendations
Dicing Blade Case Studies
Optimizing QFN Package Dicing Process Using SMART CUT® Dicing Blades
How to Selecting Right Diamond Tools for your application
How to properly use Diamond Tools
Why use diamond
What is Diamond Mesh Size and how to select best one for your application
What is Diamond Concentration and which to use for your application
Diamond Tool Coolants Why, How, When & Where to Use
Diamond vs CBN (cubic boron nitride) Tools
Get to Know the Diamond Tool Bond Types and Which to use for your application
Choosing The Correct Diamond Bond Type
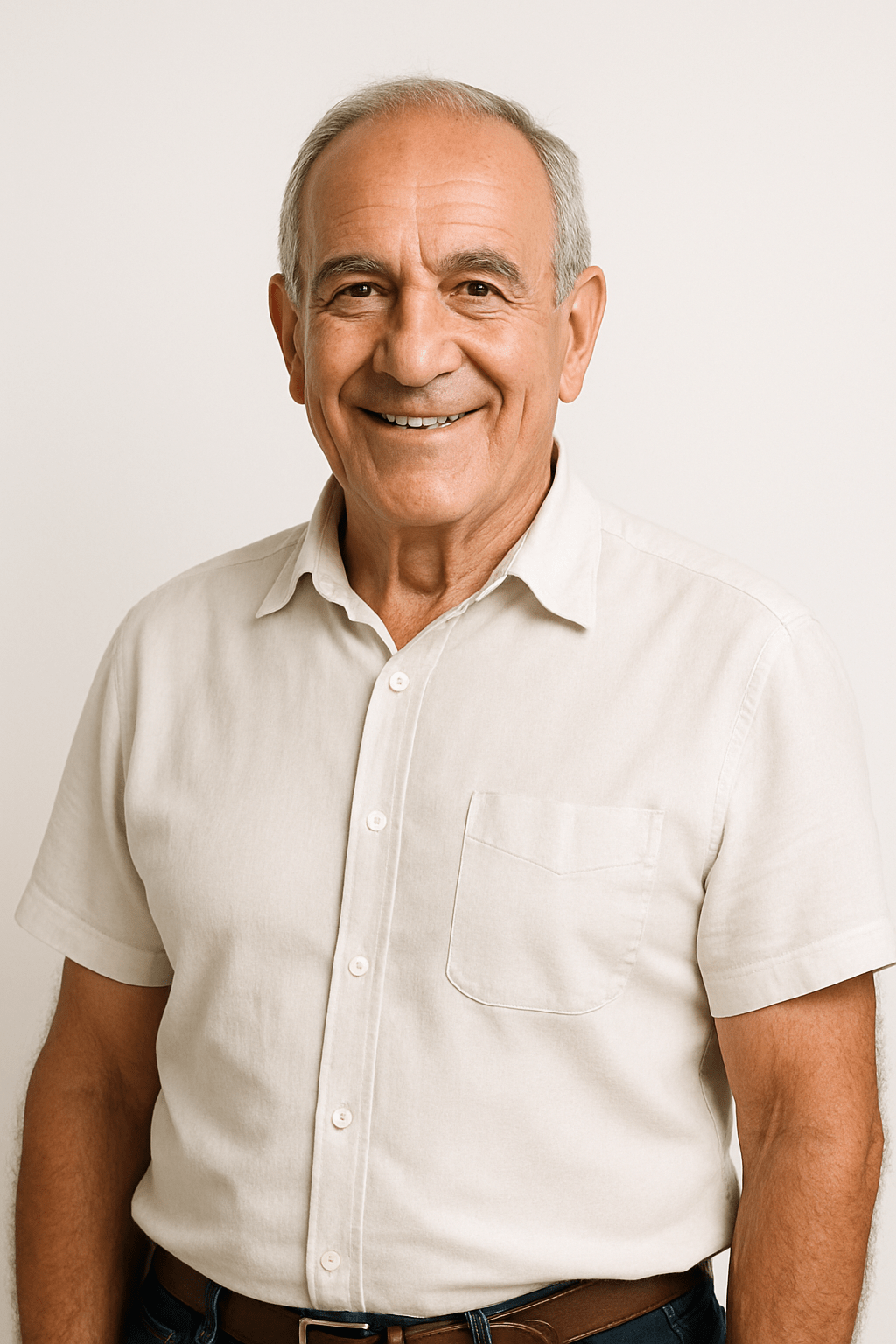
Leon Meyer is a veteran manufacturing engineer and technical consultant with over 50 years of experience in the development, implementation, and troubleshooting of industrial diamond tooling systems. Having spent his career at the intersection of tool design, precision manufacturing, and production engineering, Mr. Meyer is widely regarded as one of the most experienced voices in the application of ultra-thin diamond blades, sintered core drills, and CBN grinding wheels across heavy industry, advanced materials, and research sectors.
Known for his pragmatic, no-nonsense approach, Leon has advised manufacturers across the United States, Europe, and East Asia—helping streamline cutting processes, extend tool life, and solve complex issues related to material breakage, chipping, and tolerance drift. His expertise has directly contributed to improved production efficiency in industries ranging from aerospace alloys and technical ceramics to optics, composites, and high-nickel superalloys.
As an author, Mr. Meyer brings a lifetime of field knowledge to his writing, with a focus on real-world problem solving, cost-performance optimization, and tool reliability under demanding conditions.