Table of Contents
ToggleDiamond concentration is measured based on the volume of diamond within a section of the tool. It is typically defined as Concentration 100, which equates to 4.4 carats per cubic centimeter of the diamond layer (including mesh size and bond). This means that a concentration of 100 corresponds to a diamond proportion of 25% by volume of the diamond layer, given that diamond density is 3.52 g/cm³ and 1 carat equals 0.2 grams. In precision diamond and CBN tools, nominal diamond concentrations range from 0.5 carats per cubic centimeter to 6 carats per cubic centimeter, translating to concentrations from 8 to 135.
Share this Article with Friend or Colleague
The life of a diamond or cbn tool is largely determined by the amount of diamond crystal within the bond matrix, a metric known as “diamond concentration.” A higher diamond concentration typically extends the tool's lifespan, but it can also result in slower cutting speeds. Diamond concentration, often abbreviated as CON, represents the proportion and distribution of diamond abrasive particles in the tool, influencing overall cutting performance and cost.
Choosing the right diamond concentration is crucial for optimizing precision diamond sawing operations. The optimal concentration for a given application depends on several factors, including the material being processed, the desired cutting speed, and the tool’s expected wear rate. Understanding and selecting the appropriate diamond concentration can significantly enhance tool performance and efficiency, ensuring the best balance between tool longevity and cutting speed for specific industrial applications.
Diamond concentration significantly influences the lifespan and cutting speed of diamond and CBN tools. A higher diamond concentration is typically recommended for cutting softer and more abrasive materials, as it enhances tool life. However, this comes with the trade-off of a notably slower cutting speed. Conversely, a lower diamond concentration is preferred for ultra-hard and brittle materials, allowing for faster cutting speeds.
The appropriate diamond concentration is usually determined based on the slowest cutting speed that is acceptable for a given application. Achieving optimal performance involves the diamond tool manufacturer leveraging their expertise and analytical capabilities to balance diamond concentration with other relevant factors. This ensures that the tool operator attains the best possible performance, combining durability and efficiency tailored to the specific requirements of the task.
Various factors interconnect to influence the selection of optimum diamond concentration for your application:
Factor |
Influence on Diamond Concentration |
Interconnected Variables |
---|---|---|
Material Hardness |
Harder materials require higher diamond concentrations for effective cutting or grinding. |
Tool Bond Type, Tool Wear Rates |
Cutting/Grinding Speed |
Higher speeds may need higher concentrations to maintain tool efficiency and lifespan. |
Cooling and Lubrication, Tool Wear Rates |
Surface Finish |
Finer surface finishes may require lower concentrations to achieve smoother results. |
Tool Geometry, Application Type |
Tool Bond Type |
Softer bonds may necessitate different concentrations as they release diamonds more quickly, affecting tool performance. |
Material Hardness, Tool Wear Rates |
Tool Geometry |
Certain shapes may distribute stress differently, impacting the required diamond concentration. |
Surface Finish, Application Type |
Application Type |
Cutting, grinding, drilling, or polishing applications each have unique demands on diamond concentration. |
Surface Finish, Tool Geometry |
Workpiece Size/Thickness |
Larger or thicker pieces might need higher concentrations for effective material removal. |
Tool Wear Rates, Cutting/Grinding Speed |
Tool Wear Rates |
Expected wear rates guide the concentration selection to balance tool longevity and cutting efficiency. |
Material Hardness, Cutting/Grinding Speed |
Cost Considerations |
Higher concentrations increase tool cost, so balancing cost with performance is crucial. |
Material Hardness, Tool Wear Rates |
Cooling and Lubrication |
Effective cooling enhances tool performance and lifespan, potentially allowing for adjustments in diamond concentration. |
Cutting/Grinding Speed, Tool Wear Rates |
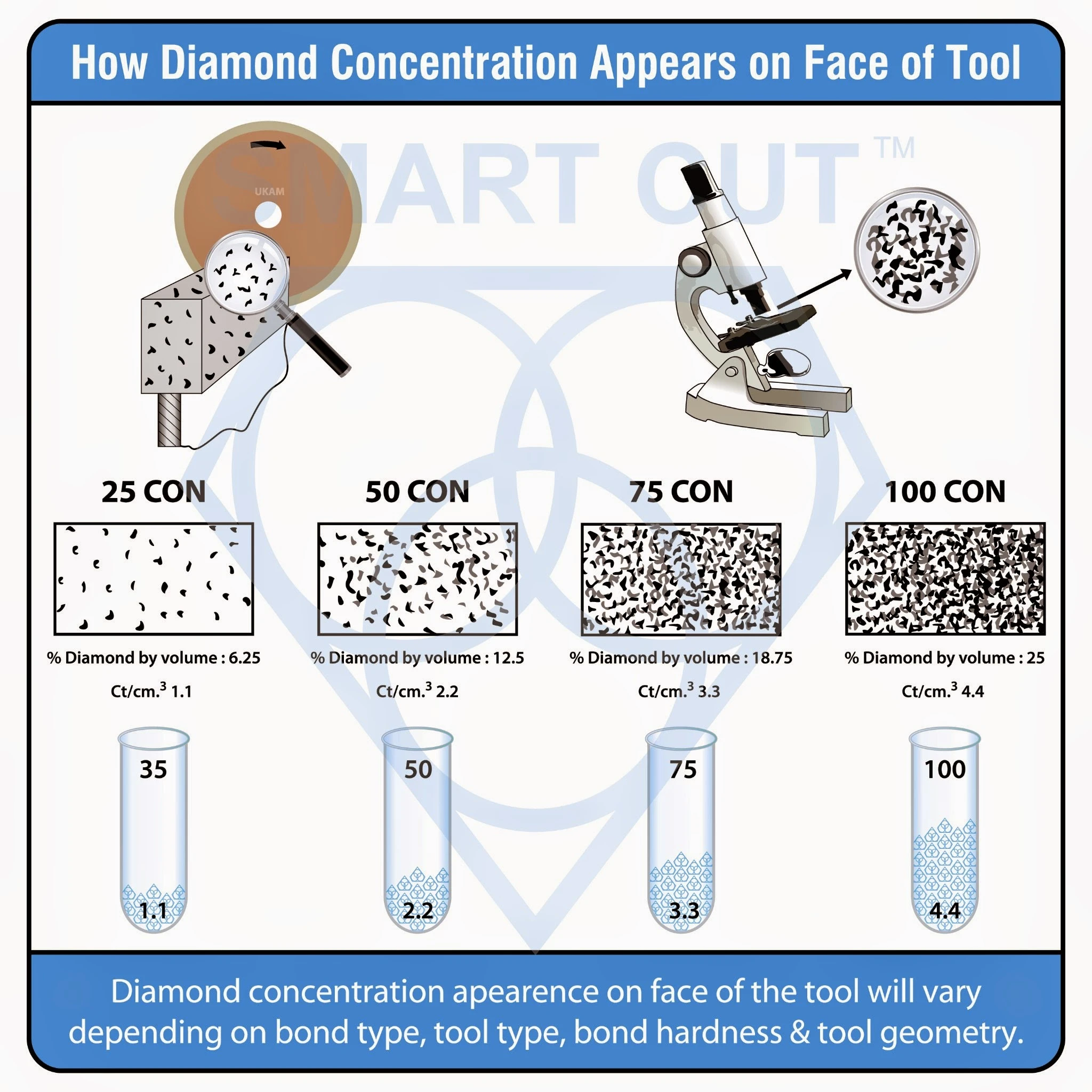
The illustration provides a detailed visual representation of how diamond concentration appears on the face of a diamond tool, commonly used in cutting or grinding applications. The concentrations are categorized into four levels: 25 CON, 50 CON, 75 CON, and 100 CON. For 25 CON, the diamond concentration is 6.25% by volume, with a carat per cubic centimeter (Ct/cm³) measurement of 1.1. This level shows a sparse distribution of diamond particles. In contrast, 50 CON has a 12.5% diamond concentration by volume and a Ct/cm³ of 2.2, exhibiting a moderate distribution of diamond particles that is more frequent than 25 CON.
Moving to 75 CON, the diamond concentration increases to 18.75% by volume, with a Ct/cm³ of 3.3, resulting in a dense distribution of diamond particles. The highest concentration, 100 CON, has a 25% diamond concentration by volume and a Ct/cm³ of 4.4, displaying a very dense distribution of diamond particles that cover most of the tool's surface. The images under each concentration level show the microscopic view of how densely the diamond particles are distributed on the tool surface.
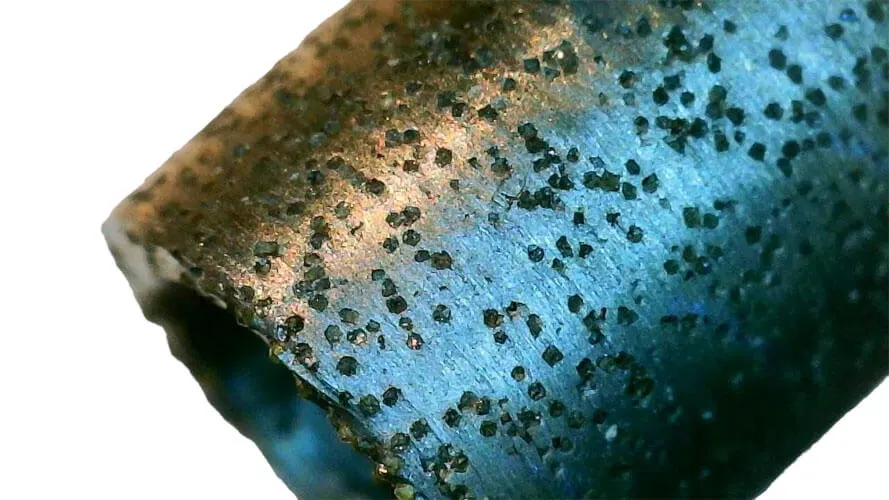
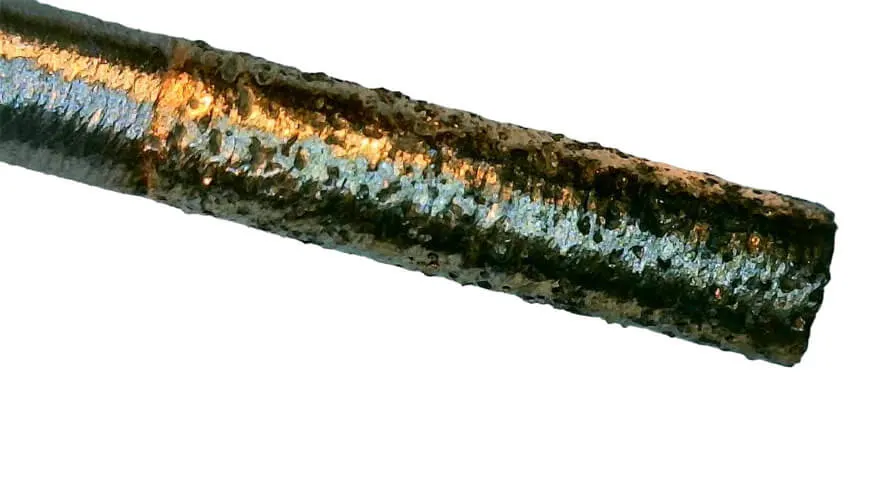
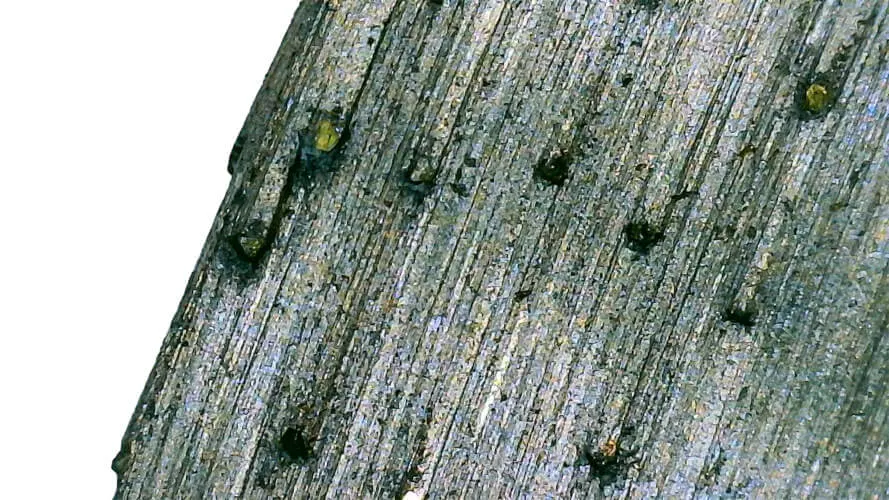
Additionally, the appearance of diamond concentration on the face of the tool will vary depending on factors such as bond type, tool type, bond hardness, and tool geometry. Bond type and hardness significantly affect how the diamonds are held in the tool matrix, influencing the tool’s performance and lifespan. Lower concentrations like 25 CON and 50 CON are suitable for softer materials or applications requiring less aggressive cutting or grinding. These typically result in less wear on the tool but may require more time to complete the task.
In contrast, higher concentrations like 75 CON and 100 CON are ideal for harder materials or applications demanding more aggressive material removal. These tools have a higher cutting efficiency but may wear out faster due to the greater density of diamonds. Specifically, 25 CON and 50 CON are best for applications like polishing or finishing where fine, controlled material removal is needed. Meanwhile, 75 CON and 100 CON are suitable for heavy-duty cutting, grinding, or drilling in hard materials like ceramics, glass, and hard metals.
What is the Difference between High & Low Diamond / CBN Concentration?
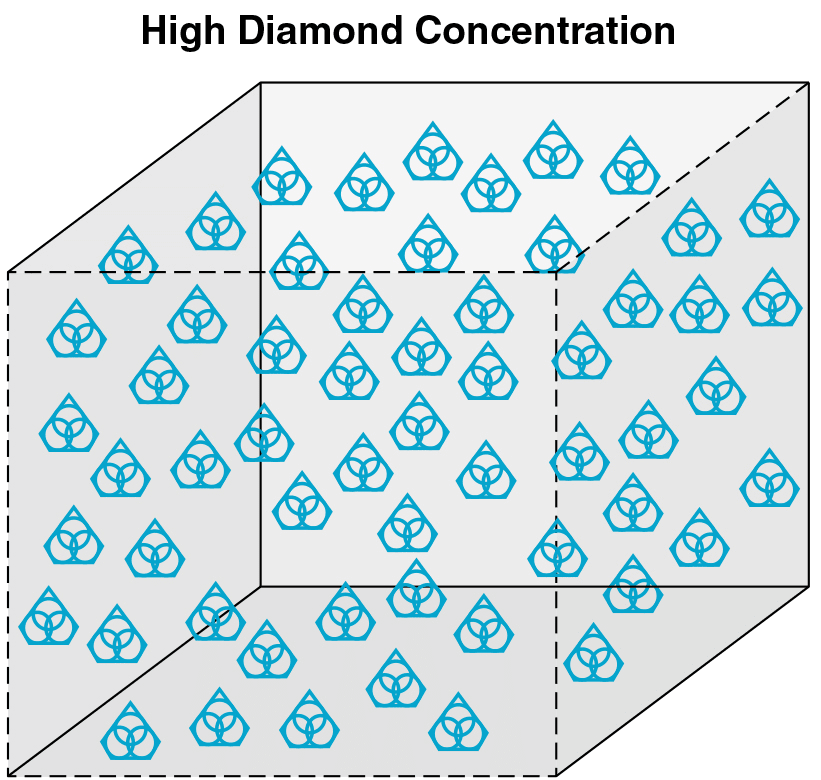
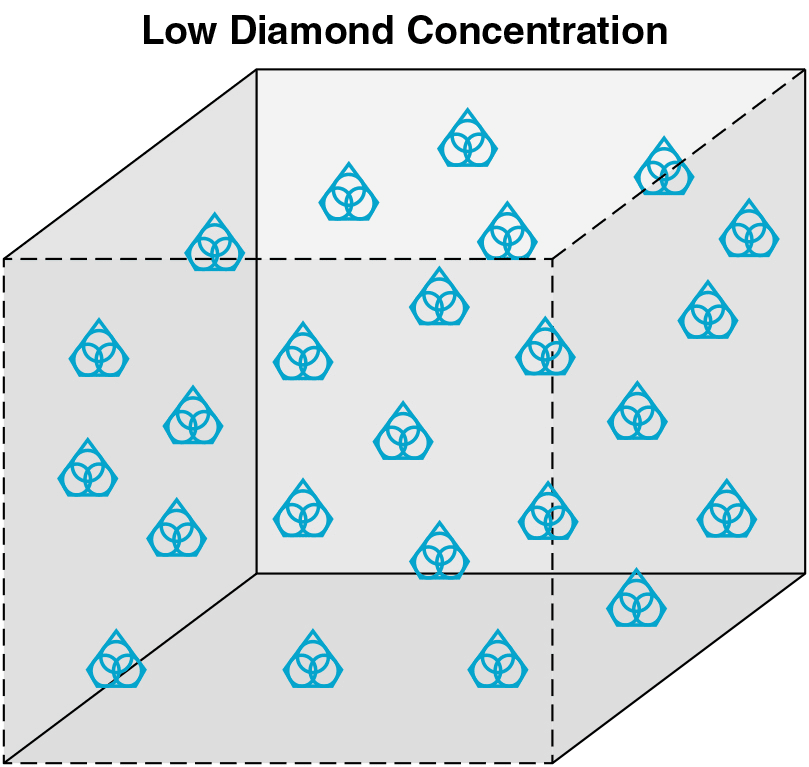
The chart effectively demonstrates how the diamond concentration percentage correlates with the actual amount of diamond material (in carats) present in a specific volume. This is crucial for applications requiring precise diamond tool specifications, ensuring the right concentration is selected for optimal performance based on the material being cut or polished.
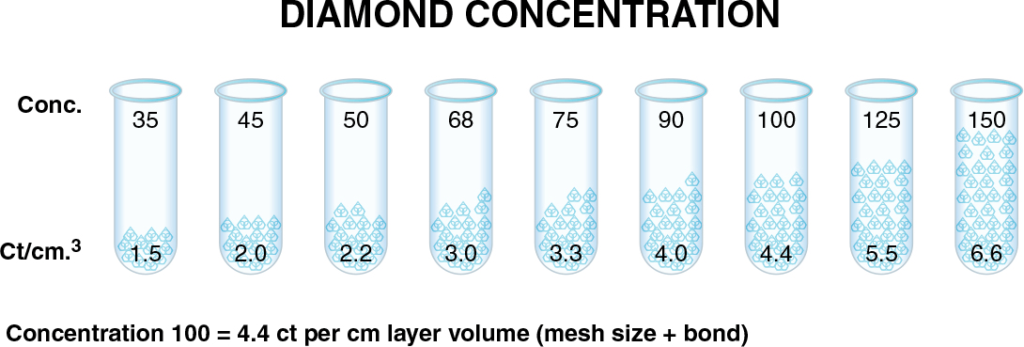
How to Select the Right Diamond or CBN Concentration for your Application
Differences between high diamond concentration and low diamond concentration, including recommendations for their use and the reasoning behind each choice:
Aspect |
High Diamond Concentration |
Low Diamond Concentration |
---|---|---|
Definition |
High proportion of diamond particles in the tool’s matrix |
Low proportion of diamond particles in the tool’s matrix |
Typical Applications |
Cutting softer and more abrasive materials |
Cutting ultra-hard and brittle materials |
Material Examples |
Soft stones, asphalt, limestone, and softer metals |
Hard ceramics, glass, tungsten carbide, and hardened steels |
Tool Life |
Longer tool life due to more cutting edges |
Shorter tool life compared to high concentration |
Cutting Speed |
Slower cutting speed due to higher resistance |
Faster cutting speed due to less resistance |
Heat Management |
Better heat distribution and management |
Requires efficient cooling to prevent overheating |
Wear Rate |
Lower wear rate due to distributed load |
Higher wear rate, more frequent diamond exposure |
Cost |
Higher cost due to more diamond material |
Lower cost, uses less diamond material |
Performance Efficiency |
Suitable for prolonged use on abrasive materials |
Suitable for precise, fast cuts on hard, brittle materials |
Surface Finish Quality |
Produces smoother surface finishes |
May produce coarser finishes, but faster material removal |
Bond Type Compatibility |
Typically used with softer bonds |
Typically used with harder bonds |
Recommended Use |
For applications requiring durability and extended tool life |
For applications requiring speed and precision |
Trade-Offs |
Higher cost, slower speed |
Shorter life, potential for higher wear |
Selection Criteria |
Chosen when extended tool life and heat management are critical |
Chosen when cutting speed and precision are paramount |
Comparing High & Low Diamond / CBN Concentration
Advantages and disadvantages of high and low diamond concentrations:
Concentration Level |
Advantages |
Disadvantages |
---|---|---|
High Diamond Concentration |
Extended Tool Life: More diamonds provide numerous cutting edges, reducing wear. Enhanced Heat Management: Improved ability to dissipate heat. Finer Surface Finish: Achieves smoother finishes on materials. Increased Durability: Ideal for abrasive and long-duration applications. |
Higher Cost: Increased diamond content raises the price of the tool. Reduced Cutting Speed: Greater resistance due to higher diamond density. Complex Manufacturing Process: Requires advanced techniques, increasing production complexity. |
Low Diamond Concentration |
Cost-Effective: Fewer diamonds lower the material cost. Increased Cutting Speed: Less resistance allows for quicker material removal. Precision Cutting: Suitable for hard, brittle materials needing fine cuts. Effective for Hard Materials: Ideal for ultra-hard materials like ceramics and glass. |
Reduced Tool Longevity: Fewer cutting edges lead to quicker wear Higher Wear Rate: More frequent exposure of diamonds. Requires Efficient Cooling: Needs effective heat management to prevent overheating. Potential for Coarser Finishes: May result in rougher surface finishes on some materials. |
When to Use High Diamond Concentration vs. Low Diamond Concentration in Diamond Tools
Selecting the right diamond concentration is crucial for optimizing the performance and efficiency of diamond tools in various industrial applications. The choice between high and low diamond concentrations depends on the specific requirements of the task, including material properties, desired cutting speed, tool longevity, and overall cost considerations.
High Diamond Concentration
High diamond concentration tools contain a greater volume of diamond particles within the bond matrix. This increased density of diamonds provides several advantages, making them ideal for specific applications. They offer extended tool life as the abundance of diamond particles provides more cutting edges, which distribute wear more evenly across the tool. This is particularly beneficial for prolonged use in demanding environments. Additionally, high diamond concentration improves the tool’s ability to dissipate heat generated during cutting or grinding, especially useful when working with softer, more abrasive materials like asphalt, limestone, and softer metals. These tools also produce finer surface finishes, ideal for applications where surface quality is critical, such as in the production of optical components or fine polishing tasks. Lastly, they are more durable and can withstand the rigors of cutting or grinding highly abrasive materials, reducing the frequency of tool replacements and downtime.
When to Use High Diamond Concentration: Use high diamond concentration for cutting or grinding softer, abrasive materials, in applications requiring long tool life and durability, for tasks needing superior heat management, and in projects where a smooth surface finish is essential.
Low Diamond Concentration
Low diamond concentration tools have fewer diamond particles in the bond matrix, offering distinct advantages for different types of applications. With fewer diamonds used, these tools are generally more economical, making them a cost-effective choice for less demanding applications. The reduced density of diamond particles results in less resistance, allowing for quicker material removal. This makes low concentration tools ideal for applications where speed is a priority. Low diamond concentration is well-suited for cutting ultra-hard, brittle materials like ceramics, glass, and tungsten carbide. The lower concentration allows for precise, controlled cuts, minimizing the risk of material damage. These tools are effective for ultra-hard materials, providing the necessary sharpness and cutting efficiency without excessive wear.
When to Use Low Diamond Concentration: Low diamond concentration should be used when cutting ultra-hard, brittle materials, in applications requiring fast cutting speeds, for tasks where cost-effectiveness is a priority, and in situations needing precise, controlled cuts.
How to Select the Right Diamond or CBN Concentration for your Application
Selecting the optimum diamond concentration for your application will depend on a variety of factors, such as:
Material Hardness:
Material hardness significantly influences the choice of diamond concentration in cutting and grinding tools. Harder materials, such as ceramics, glass, gemstones, and high-strength alloys, exhibit greater resistance to abrasion and cutting forces. This resistance necessitates a higher concentration of diamond abrasives to effectively penetrate and remove material. Higher diamond concentration provides more cutting points, increasing the tool’s effectiveness in cutting through tough, resilient materials. This distribution of the cutting load across the tool’s surface reduces wear on individual diamonds and enhances the overall tool life.
Conversely, softer materials, like softer metals, plastics, and composites, require less abrasive force for effective material removal. A lower diamond concentration ensures that the tool is not excessively aggressive, which could lead to rapid material removal, potential damage to the workpiece, or unnecessary wear on the tool.
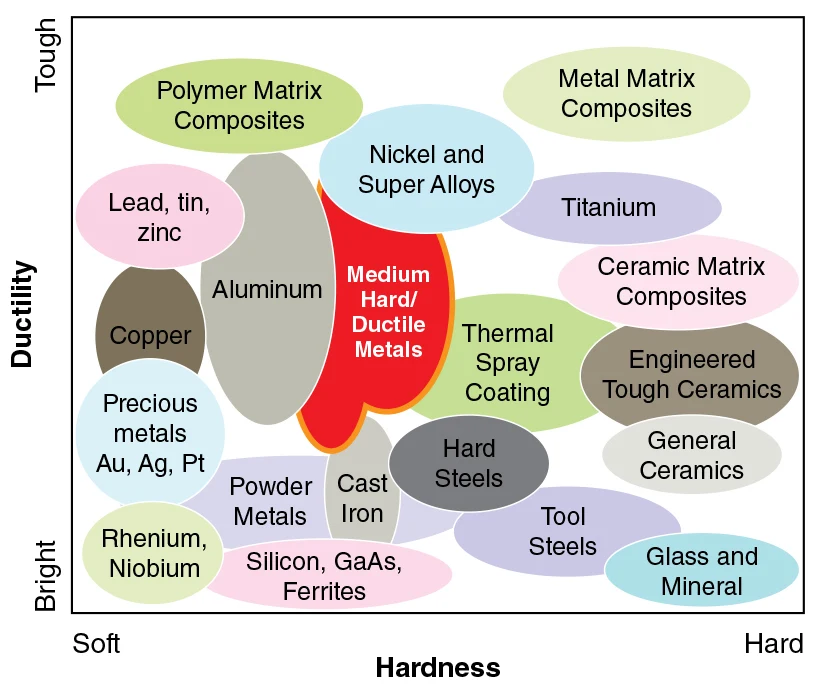
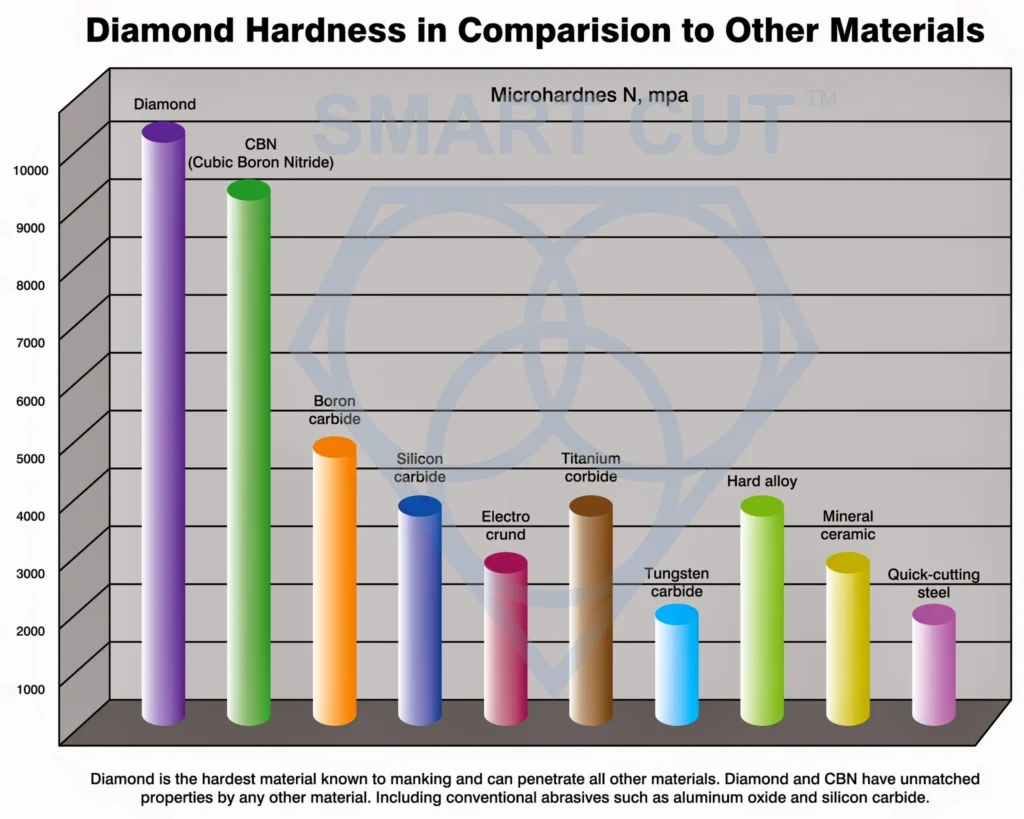
Materials are often rated on the Mohs hardness scale, ranging from 1 (talc) to 10 (diamond). For instance, materials like silicon carbide, tungsten carbide, and hardened steel are at the higher end of this scale, indicating significant hardness. Tools designed for these harder materials often feature a harder bond matrix that holds the diamonds more securely, preventing premature loss of diamond particles under high stress. Higher diamond concentrations support the creation of more aggressive cutting edges, essential for penetrating hard materials.
Cutting or grinding hard materials generates significant heat, and tools with higher diamond concentrations help distribute this heat more effectively, reducing the risk of thermal damage to both the tool and the workpiece. Adequate cooling systems are essential when working with hard materials to prevent overheating and maintain tool performance. While tools with higher diamond concentrations are typically more expensive, they offer superior performance and longevity when cutting hard materials, justifying the investment through improved efficiency and reduced downtime.
For specific applications like cutting silicon wafers, high diamond concentration blades are used to achieve precise, clean cuts necessary for semiconductor manufacturing. Similarly, grinding carbide tools involves high diamond concentration grinding wheels to shape and finish carbide tools, ensuring durability and precision.
Material hardness is a decisive factor in selecting the appropriate diamond concentration for cutting and grinding tools. For harder materials, higher diamond concentrations are essential to achieve efficient cutting and grinding, ensuring tool effectiveness and longevity. For softer materials, lower diamond concentrations are sufficient, providing a balance between performance and tool wear. Understanding the interplay between material hardness and diamond concentration is crucial for optimizing tool selection and achieving desired outcomes in various industrial applications.
Find out more about usage recommendations for different materials>>>
Cutting or Grinding Speed:
The speed at which cutting or grinding operations are performed significantly influences the selection of the appropriate diamond concentration for a tool. The desired speed impacts the tool's efficiency, material removal rate, heat generation, and overall tool life.
At higher cutting or grinding speeds, there is increased friction, leading to more heat generation at the tool-workpiece interface. Tools need to withstand this elevated heat to prevent degradation or failure. A higher diamond concentration helps distribute the heat more evenly across the tool surface, reducing localized overheating and extending tool life. Additionally, higher speeds enhance the material removal rate, necessitating more cutting points (diamonds) to maintain efficiency. Higher diamond concentration provides additional cutting edges, ensuring effective material removal and reducing the risk of tool clogging or glazing. Furthermore, more diamonds in contact with the material enhance cutting efficiency by reducing the load on individual diamonds, which minimizes wear on each diamond and improves tool durability and performance. Higher speeds often require a harder bonding matrix to secure the diamonds against centrifugal forces and the stresses of high-speed operation. The combination of higher diamond concentration and a harder bond ensures the tool maintains its integrity and cutting capability at elevated speeds.
In contrast, lower cutting or grinding speeds generate less friction and heat. Tools can operate with a lower diamond concentration without risking overheating or thermal damage, as heat buildup is less significant. Reduced speeds decrease the material removal rate, which can be efficiently managed with fewer diamonds. A lower diamond concentration is adequate, as there is less demand for multiple cutting points to handle the material removal. Fewer diamonds in contact with the material result in a smoother cutting or grinding action, which can be beneficial for achieving finer surface finishes and reducing tool wear. Softer bonds may be sufficient at lower speeds, as the mechanical stresses are reduced. Lower diamond concentration tools with softer bonds can effectively handle the reduced operational stresses.
In practical applications, high-speed cutting or grinding is often required in industries such as aerospace and automotive, where machining hard metals and composites is common. In these cases, tools with high diamond concentrations and harder bonds are preferred to withstand the demands of high-speed operations. Conversely, low-speed cutting or grinding is typically used in precision finishing operations, such as polishing or grinding delicate components in the optics or electronics industry. For these applications, tools with lower diamond concentrations and softer bonds are suitable, providing control and fine surface finishes.
The illustration demonstrates the relationship between cutting speed, cutting ratio, and diamond concentration in diamond cutting tools, highlighting how these factors interact under different conditions.
The horizontal axis shows diamond concentration, ranging from low to high, while the vertical axis on the left represents cutting speed from slow to fast. The vertical axis on the right indicates the cutting ratio, ranging from low to high. The red curve illustrates how cutting speed varies with diamond concentration, showing that as diamond concentration increases, cutting speed decreases. This suggests that higher diamond concentration may lead to slower cutting speeds. Conversely, the green curve depicts the relationship between cutting ratio and diamond concentration, indicating that as diamond concentration increases, the cutting ratio also increases. This implies that a higher diamond concentration results in a more efficient material removal process.
At the point where the two curves intersect, there is an optimal balance between cutting speed and cutting ratio for a specific diamond concentration. This intersection is critical for determining the most efficient operational settings for diamond cutting tools.
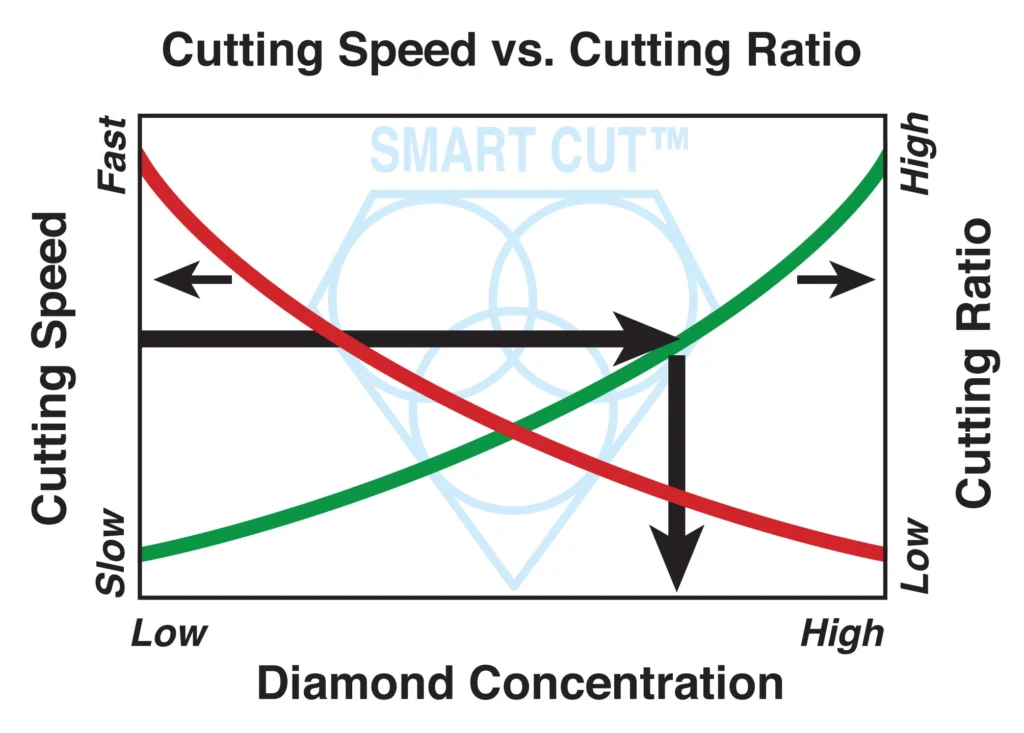
The arrows on the illustration further clarify these trends, with the left arrow on the red curve showing a decrease in cutting speed as diamond concentration increases, and the right arrow on the green curve indicating an increase in cutting ratio with higher diamond concentration. The vertical arrows illustrate the overall trend of changes in cutting speed and cutting ratio relative to diamond concentration.
For practical use, a low diamond concentration results in higher cutting speeds but lower cutting ratios, making it suitable for applications that require faster cutting where cutting efficiency is less critical. On the other hand, a high diamond concentration leads to lower cutting speeds but higher cutting ratios, ideal for applications where cutting efficiency and precision are essential, even if the process is slower.
In terms of practical considerations, the choice of diamond concentration should align with the material being cut and the specific requirements of the application, balancing speed and efficiency. Higher diamond concentration can enhance tool life and performance, especially in demanding applications, by increasing the cutting ratio. This illustration serves as a useful guide for selecting the appropriate diamond concentration in diamond cutting tools, helping to optimize the balance between cutting speed and cutting ratio to achieve desired performance outcomes in various industrial applications.
Find out more about diamond & cbn tools recommended rpm’s>>>
Cutting/Grinding Speed |
High Diamond Concentration |
Low Diamond Concentration |
---|---|---|
High Speed |
- May lead to slower cutting speeds due to higher resistance. - Effective heat management with more diamonds distributing heat. - Suitable for precision cutting where tool longevity is critical. |
- Enables faster cutting speeds due to lower resistance. - Requires efficient cooling to manage heat. - Ideal for applications needing quick material removal. |
Low Speed |
- Provides consistent cutting performance with reduced heat generation. - Prolonged tool life due to even wear distribution. - Suitable for detailed finishing tasks. |
- Maintains high cutting efficiency with minimal heat issues. - Less aggressive, allowing for precise control. - Effective for delicate or brittle materials. |
Surface Finish Requirements:
The desired surface finish quality is crucial in selecting the appropriate diamond concentration for a cutting or grinding tool. Surface finish refers to the texture and smoothness of a material's surface after processing, quantified by parameters such as roughness, waviness, and lay.
For achieving finer surface finishes, tools typically require a less aggressive cutting action. Lower diamond concentrations provide fewer abrasive points in contact with the material, resulting in a smoother and more controlled removal process. With fewer diamonds, the cutting edges are less pronounced, reducing the likelihood of deep scratches or gouges on the material surface, leading to a finer finish and better surface quality. Tools designed for finer finishes often use softer bonding matrices that allow diamonds to wear and expose fresh, sharp edges gradually. This gradual exposure ensures consistent cutting action without excessive aggressiveness, which is essential for achieving smooth surface finishes. Applications requiring fine finishes include polishing optical lenses, finishing medical devices, and preparing semiconductor wafers, where tools with lower diamond concentrations and finer grit sizes are preferred to produce delicate and smooth finishes.
In contrast, for applications where a coarser finish is acceptable or desired, higher diamond concentrations are beneficial. They provide more abrasive points, leading to faster material removal and a rougher surface texture. The increased number of cutting edges from higher diamond concentrations facilitates aggressive material removal, suitable for tasks that do not require a high degree of surface smoothness. Harder bonding matrices are used to retain diamonds more firmly, allowing for sustained cutting action in rough finishing processes. These matrices prevent rapid diamond wear and loss, maintaining the tool's effectiveness for coarse grinding or cutting operations. Applications requiring coarse finishes include rough grinding of construction materials, initial shaping of hard metals, and deburring operations, where tools with higher diamond concentrations and coarser grit sizes provide the necessary abrasiveness for efficient roughing tasks.
Balancing surface finish and material removal involves controlling abrasiveness to achieve the desired surface finish while maintaining efficient material removal rates. Selecting the appropriate diamond concentration requires considering the trade-off between smoothness and cutting speed, with lower concentrations favoring smoothness and higher concentrations enhancing cutting speed and material removal. Tools with lower diamond concentrations tend to wear more slowly in fine finishing applications, maintaining consistent surface quality over longer periods.
Practical considerations include tool geometry and design, which play a significant role in determining the achievable surface finish. Tools designed for fine finishes often feature specific geometries that enhance control and reduce vibration, contributing to smoother surface outcomes. Additionally, operational parameters such as feed rate, cutting speed, and coolant application affect the surface finish. Adjusting these parameters in conjunction with selecting the appropriate diamond concentration helps achieve the desired surface quality.
Surface Finish Quality |
High Diamond Concentration |
Low Diamond Concentration |
---|---|---|
Smooth Finish |
- Provides finer finishes due to more cutting edges - Ideal for applications requiring high surface quality - Reduces surface irregularities and ensures consistency. |
- Achieves smooth finishes on hard, brittle materials with precision - Requires efficient cooling to avoid overheating - Suitable for delicate finishing tasks. |
Coarse Finish |
- May produce smoother finishes even on abrasive materials - Maintains consistent performance in high-wear applications - Effective for applications needing durability and precision. |
- Typically results in rougher finishes due to fewer cutting edges - Allows for rapid material removal - Effective for initial rough cutting or grinding. |
Diamond & CBN Tool Bond Type:
The relationship between diamond & cbn tool bond type and diamond concentration is crucial in optimizing tool performance for various cutting and grinding applications. Here’s a detailed explanation of how these elements interconnect:
Softer Bonds and Diamond Concentration:
Softer bonds are designed to wear away more quickly, which facilitates the release of diamond particles as they become dull. This characteristic is critical for maintaining sharp cutting edges throughout the tool's lifespan. Due to the rapid wear of the bond, diamonds are exposed and released more frequently. Consequently, tools with softer bonds typically require higher diamond concentrations to ensure a continuous supply of fresh cutting edges. The higher concentration compensates for the quicker loss of diamonds, maintaining the tool’s cutting efficiency and effectiveness.
In applications where a consistent sharpness is essential, such as in finishing or polishing softer materials, the frequent renewal of diamonds provided by softer bonds is advantageous. These applications benefit from the softer bond’s ability to maintain a steady cutting performance, even though the tool itself may wear down faster. Therefore, higher diamond concentrations are necessary to sustain the tool's functionality over its operational life.
Harder Bonds and Diamond Concentration:
Harder bonds are more durable and wear-resistant, holding diamond particles more securely for extended periods. This slower rate of bond wear means that diamonds are not released as frequently, which is beneficial for cutting or grinding harder materials. Consequently, tools with harder bonds can operate effectively with lower diamond concentrations. The durability of harder bonds enhances the tool's lifespan, making them suitable for heavy-duty applications where maintaining the tool's structural integrity is critical.
For tasks involving high mechanical stresses or elevated temperatures, such as machining hard metals, ceramics, or composites, harder bonds are ideal because they withstand such conditions without significant degradation. Since the bond retains diamonds longer, fewer diamonds are needed, allowing for lower concentrations while still achieving effective material removal and tool longevity.
Balancing Bond Type and Diamond Concentration:
The interplay between bond type and diamond concentration is essential for achieving the desired tool performance. Softer bonds necessitate higher diamond concentrations to offset the rapid release and wear of diamonds, ensuring continuous cutting sharpness and efficiency. Conversely, harder bonds, with their secure retention of diamonds, allow for lower concentrations, enhancing tool durability and performance in demanding applications.
Diamond & CBN Tool Geometry:
Diamond & CBN Tool geometry, including the shape, size, and design of a cutting or grinding tool, plays a significant role in determining the optimal diamond concentration. The distribution of stress, heat, and wear across the tool's surface varies with different geometries, affecting performance and durability.
For tools with complex geometries, such as segmented blades or wheels with intricate patterns, the cutting forces and stresses are distributed unevenly across the surface. These designs often concentrate stress in specific areas, which requires higher diamond concentrations to ensure sufficient abrasive action and tool durability in high-stress zones. By having more diamonds in these areas, the tool can effectively handle the increased load, reducing the likelihood of localized wear or failure. Additionally, tools with complex geometries often generate more heat due to the concentration of cutting forces.
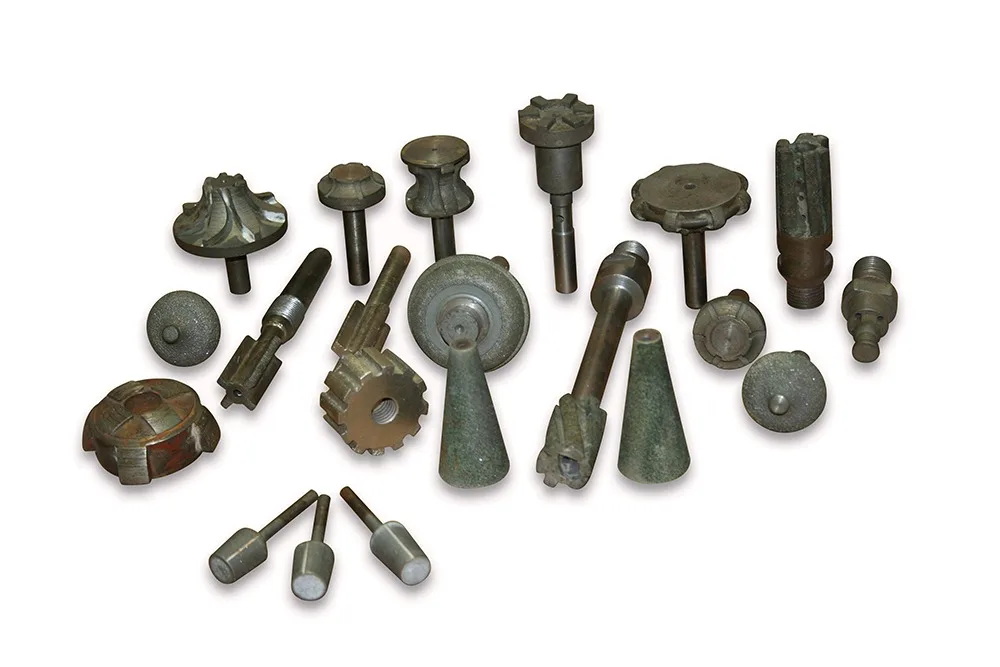
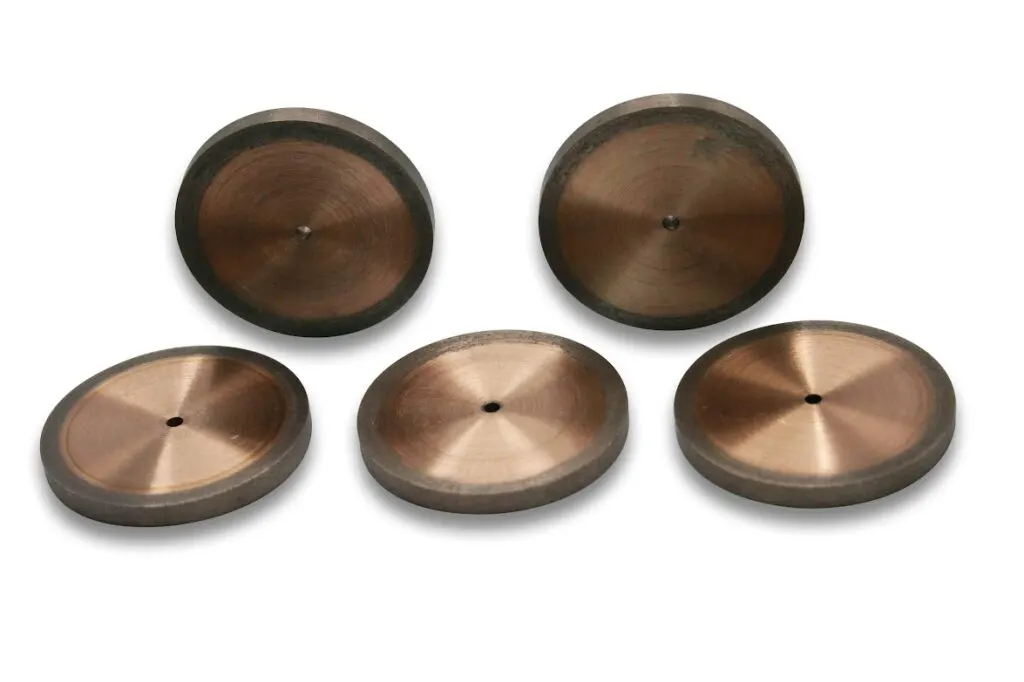
Higher diamond concentrations help dissipate this heat more effectively, preventing thermal damage to the tool and the workpiece. The increased number of diamonds provides additional cutting edges, spreading the heat over a larger area, enhancing cooling, and reducing the risk of overheating. Complex geometries are designed to enhance material removal efficiency by maximizing the contact area and cutting edges. Higher diamond concentrations ensure that the tool maintains its cutting performance and efficiency, even under heavy loads, which is particularly important in applications requiring aggressive material removal.
In contrast, tools with simpler geometries, such as continuous rim blades or straight grinding wheels, tend to distribute stress more uniformly across the surface. This even distribution allows for lower diamond concentrations while still achieving effective cutting or grinding. The uniform stress reduces the need for additional diamonds, as the load is spread evenly across the tool, minimizing localized wear and extending tool life.
Simple geometries typically generate less heat because the cutting forces are more evenly distributed, allowing lower diamond concentrations to manage heat effectively, with less risk of thermal damage.
These tools can maintain their performance with fewer diamonds, as the reduced heat generation lowers the demand for extensive cooling. Tools with simpler geometries are often used in applications requiring controlled material removal and finer finishes. Lower diamond concentrations help achieve smooth and precise cuts or grinds, enhancing the quality of the surface finish, making these tools ideal for tasks where precision is more critical than aggressive material removal.
Specific applications highlight the importance of geometry and diamond concentration. Segmented blades, with gaps or segments that enhance cooling and reduce friction, typically require higher diamond concentrations to maintain cutting performance. These blades are used in cutting concrete, masonry, and other hard materials, where efficient heat dissipation and durability are essential. Continuous rim blades, with a smooth, continuous cutting edge, provide a uniform cutting action and can operate with lower diamond concentrations due to their even stress distribution. They are ideal for cutting tiles, ceramics, and other brittle materials, where a smooth cut is desired. Cup wheels, with a cup-shaped design that concentrates cutting forces on the edge, need higher diamond concentrations to handle the concentrated stress and ensure efficient grinding. They are commonly used in surface grinding and finishing applications, where maintaining sharp cutting edges is crucial. Flat grinding wheels, with a flat, circular design, distribute cutting forces evenly, and lower diamond concentrations are adequate for maintaining performance. These wheels are suitable for general-purpose grinding and shaping of metals and other materials.
Application Type:
The type of application—cutting, grinding, drilling, or polishing—significantly influences the choice of diamond concentration in tools. Each application places distinct demands on the tool, affecting its design, performance requirements, and optimal diamond concentration.
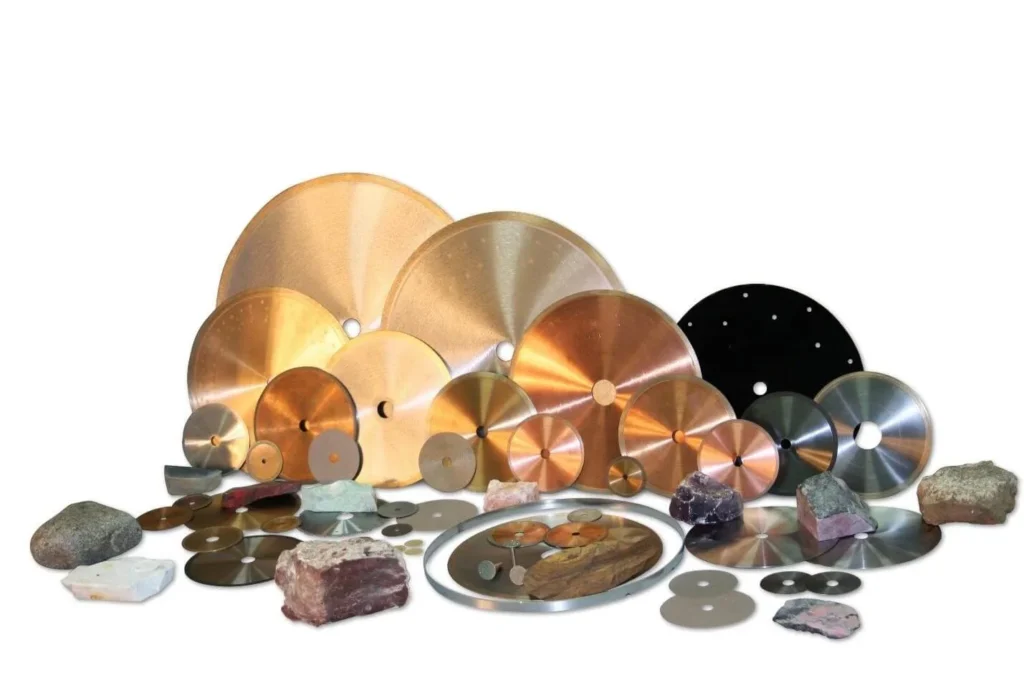
Cutting applications involve slicing through materials to achieve a specific shape or dimension. These applications typically require tools with higher diamond concentrations to ensure efficient cutting performance and to handle the high stresses encountered during the process. The higher concentration provides more cutting edges, enhancing the tool's ability to penetrate and slice through hard materials, such as metals, ceramics, and composites. For instance, diamond saw blades used in cutting granite or reinforced concrete need a high diamond concentration to maintain sharpness and cutting efficiency over extended periods.
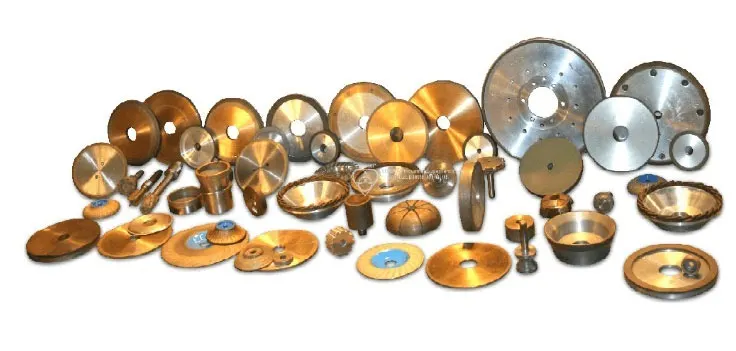
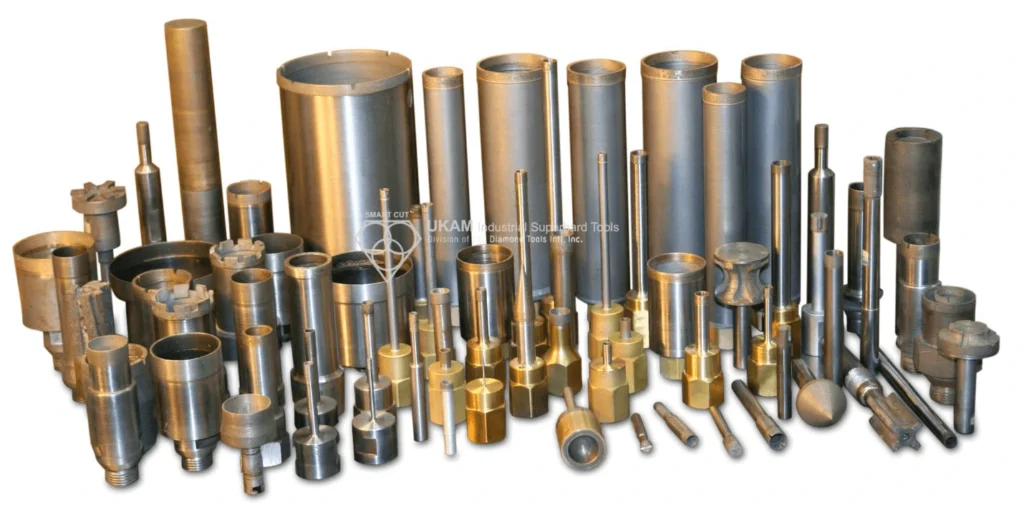
Grinding applications involve the removal of material from a workpiece's surface to achieve a desired shape, finish, or dimensional accuracy. Grinding tools may vary in their diamond concentration depending on the hardness of the material and the desired surface finish. For rough grinding, where material removal rate is prioritized over surface finish, higher diamond concentrations are preferred to enhance cutting efficiency and tool durability. Conversely, for fine grinding, where a smoother finish is required, lower diamond concentrations are often used to reduce the aggressiveness of the tool, preventing deep scratches and ensuring a finer surface texture.
Drilling applications involve creating holes or cavities in materials. Diamond concentration in drilling tools, such as diamond core drills, must balance between maintaining cutting efficiency and managing heat generation. Higher diamond concentrations are often necessary for drilling hard materials like stone, glass, or reinforced concrete, as they provide sufficient cutting points to penetrate the material effectively. The increased number of diamonds also helps distribute the cutting load and heat, reducing the risk of tool overheating and wear. However, in softer materials, lower diamond concentrations may be adequate, providing enough cutting action without excessive tool wear.
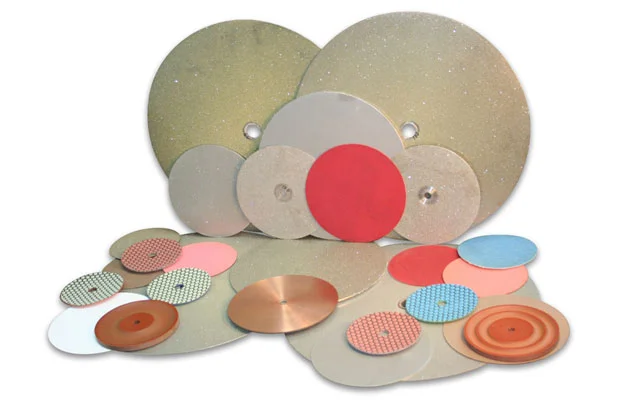
Polishing applications aim to achieve a high-quality, smooth surface finish on a workpiece. Tools used for polishing typically have lower diamond concentrations to ensure a gentle abrasive action that minimizes surface damage and produces a fine finish. The lower concentration allows for a controlled, smooth removal of material, essential for applications requiring high precision and aesthetic quality, such as polishing optical lenses, gemstones, or delicate electronic components. The reduced number of diamonds also helps prevent excessive heat buildup, which can be detrimental to the surface quality of the polished material.
Material Size and Thickness and Shape:
The size, thickness, and shape of the material being processed are critical factors in determining the optimal diamond concentration for cutting, grinding, drilling, or polishing tools. These factors influence the tool’s performance, the efficiency of material removal, and the overall effectiveness of the processing operation.
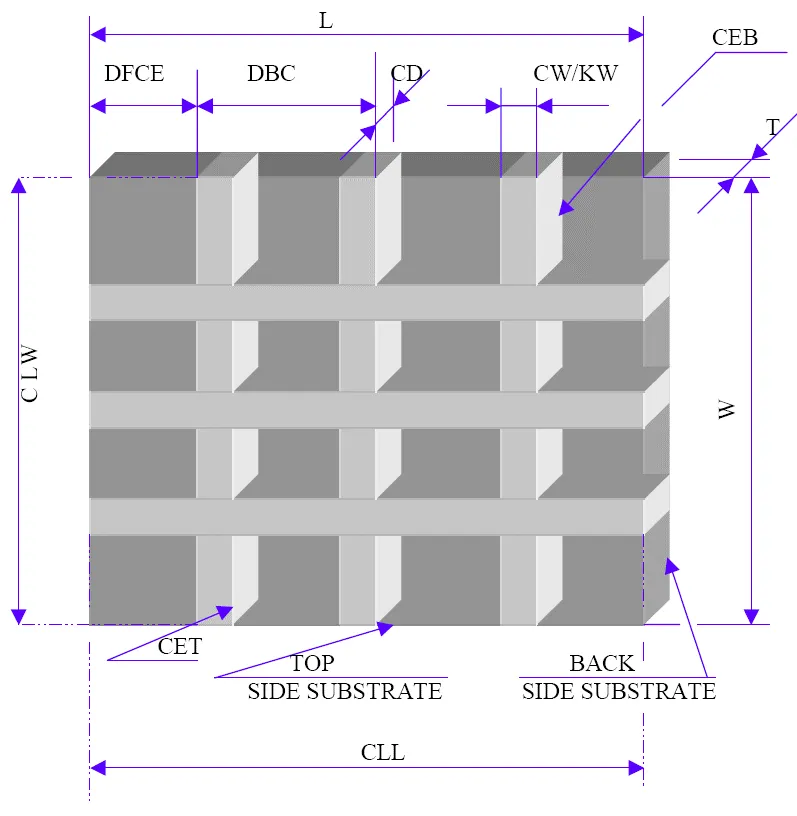
Larger or Thicker Materials:
When working with larger or thicker materials, higher diamond concentrations are often necessary. The primary reason for this is the increased volume of material that needs to be removed, which requires more cutting points to maintain efficiency and effectiveness. Higher diamond concentrations provide a greater number of abrasive edges, which helps distribute the cutting forces more evenly across the tool’s surface. This distribution reduces the likelihood of localized wear or damage, enhancing the tool’s durability and performance. For instance, in applications like cutting thick slabs of granite or concrete, diamond saw blades with higher concentrations are essential to ensure a smooth and efficient cutting process. The increased number of diamonds helps maintain the tool’s sharpness and cutting ability over prolonged use, preventing premature tool wear and ensuring consistent performance.
Heat Management:
Processing larger or thicker materials generates more heat due to the increased friction and prolonged contact between the tool and the material. Higher diamond concentrations help in dissipating this heat more effectively, reducing the risk of thermal damage to both the tool and the material. The additional diamonds provide more cutting edges, spreading the heat over a larger area and enhancing cooling efficiency. This is particularly important in applications like drilling deep holes or grinding large surfaces, where effective heat management is crucial to prevent tool failure and maintain material integrity.
Material Shape:
The shape of the material also influences the choice of diamond concentration. Irregularly shaped materials or those with complex geometries may present challenges in terms of stress distribution and cutting dynamics. Higher diamond concentrations can help address these challenges by providing more abrasive points to handle the varied cutting angles and stress points. This is especially useful in applications like shaping or contouring hard materials, where maintaining consistent cutting performance across different surfaces and angles is essential. For example, in shaping intricate ceramic components or sculpting stone, tools with higher diamond concentrations ensure that the cutting edges remain effective, even when dealing with complex shapes and varying material thicknesses.
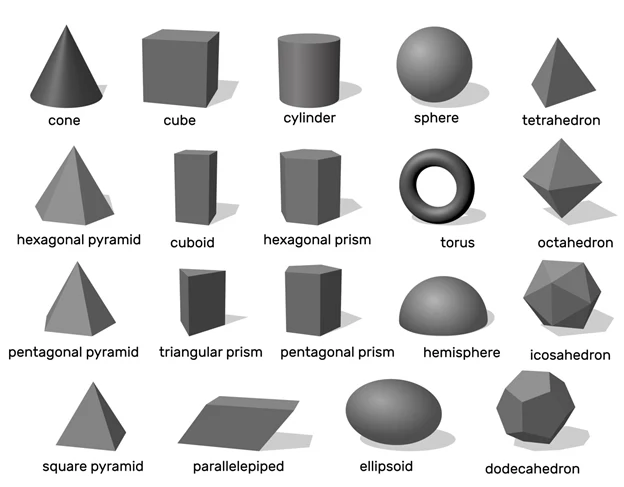
Uniform Stress Distribution:
For materials with uniform shapes and consistent thicknesses, the stress distribution across the tool’s surface is more even. In such cases, lower diamond concentrations may be sufficient to achieve effective material removal without excessive wear. The even distribution of cutting forces reduces the need for additional diamonds, allowing the tool to perform efficiently with fewer abrasive edges. This is particularly relevant in applications like cutting or grinding uniform metal sheets or flat surfaces, where maintaining a steady cutting action is key to achieving a smooth finish and consistent material removal.
Tool Geometry and Design Considerations:
The tool’s design must also be optimized to handle the specific size, thickness, and shape of the material. For larger or thicker materials, tools with robust designs and higher diamond concentrations are preferred to withstand the increased cutting forces and ensure long tool life. Conversely, for smaller or thinner materials, tools with finer designs and lower diamond concentrations can provide the precision and control needed for delicate operations. In applications such as precision grinding of thin glass panels or delicate electronic components, tools with lower diamond concentrations offer the necessary finesse and reduce the risk of damaging the material.
Balancing Performance and Tool Life:
Selecting the appropriate diamond concentration involves balancing the need for efficient material removal with the goal of maximizing tool life. Higher diamond concentrations enhance cutting efficiency and tool durability for larger or thicker materials, but they may increase the tool’s cost. Lower concentrations may suffice for smaller or thinner materials, offering a cost-effective solution while maintaining adequate performance. Understanding the specific demands of the material’s size, thickness, and shape allows for the selection of diamond tools that deliver optimal performance, efficiency, and longevity across various industrial applications.
Diamond & CBN Tool Wear Rates:
Understanding the expected wear rate of a tool is essential in selecting the appropriate diamond concentration to achieve a balance between tool longevity and cutting efficiency. Tool wear rates are influenced by several factors, including the material being processed, operational parameters, and the specific application. Managing these factors effectively can enhance tool performance and extend its useful life.
Material hardness and abrasiveness play a significant role in determining tool wear rates. Harder and more abrasive materials, such as ceramics, hard metals, and composites, typically cause higher wear rates on diamond tools. The constant contact with hard particles leads to faster degradation of the cutting edges. To counteract this, tools used for such materials often require higher diamond concentrations. The increased number of diamonds provides more cutting points, distributing the wear more evenly and reducing the stress on individual diamonds. This distribution helps maintain cutting efficiency and prolongs tool life despite the harsh conditions.
Operational parameters such as cutting speed, feed rate, and depth of cut significantly impact tool wear rates. Higher cutting speeds and feed rates increase friction and heat generation, accelerating tool wear. Selecting the right diamond concentration can help manage these effects. Higher diamond concentrations are often needed to withstand the increased stresses and maintain effective material removal rates. Additionally, optimizing operational parameters to match the tool’s capabilities can further mitigate wear and enhance performance.
Different applications, such as cutting, grinding, drilling, or polishing, impose varying demands on the tool, affecting its wear rate. Cutting and drilling often involve higher forces and deeper material penetration, leading to increased wear, while grinding and polishing may involve more surface contact and friction. For applications with higher wear rates, such as deep drilling or heavy-duty cutting, tools with higher diamond concentrations are necessary to ensure durability and maintain efficiency. Conversely, for applications like fine grinding or polishing, lower diamond concentrations can be sufficient, balancing wear and performance while achieving the desired surface finish.
Choosing the appropriate bond type is also crucial in managing tool wear rates. The bond type that holds the diamond particles in place significantly influences tool wear rates. Softer bonds wear more quickly, releasing diamonds and exposing new cutting edges, which can be beneficial for maintaining sharpness but may result in faster overall tool wear. For applications with high wear rates, harder bonds are preferred as they provide better retention of diamonds, reducing the frequency of diamond release and enhancing tool longevity. Matching the bond type with the diamond concentration helps optimize tool performance for specific wear conditions.
Higher diamond concentrations provide more abrasive points, reducing the load on each diamond and spreading the wear across a larger surface area. This distribution helps maintain cutting efficiency and extends tool life. Conversely, lower diamond concentrations may be adequate for less demanding applications, where the wear rates are lower, and the need for extensive abrasive points is reduced. This approach can help lower costs while still achieving satisfactory performance.
Effective cooling and lubrication are crucial in managing tool wear rates, especially in high-speed or high-friction applications. Adequate cooling reduces heat buildup, which can degrade both the tool and the workpiece. Ensuring proper lubrication minimizes friction and wear, enhancing the tool’s performance and extending its lifespan. This is particularly important in applications involving hard or abrasive materials, where heat and friction are significant concerns.
Regular maintenance and monitoring of tool condition can help identify wear patterns and optimize diamond concentration and operational parameters accordingly. This proactive approach ensures that tools are used within their optimal performance range, reducing unexpected wear and improving overall efficiency. Implementing a maintenance schedule that includes inspection, cleaning, and adjustment of operational settings can significantly enhance tool longevity and performance.
Balancing cost and efficiency is crucial when selecting diamond concentrations. Higher diamond concentrations generally increase tool costs, but they also enhance durability and cutting efficiency, especially in high-wear applications. Balancing the initial investment with the expected performance benefits is crucial in optimizing tool selection. For less demanding applications, lower diamond concentrations can offer a cost-effective solution while still meeting performance requirements, providing a balanced approach to tool wear management and efficiency.
Cooling and Lubrication:
The availability and type of cooling or lubrication used during cutting, grinding, drilling, or polishing processes significantly influence the choice of diamond concentration in tools. Effective cooling and lubrication are critical for enhancing tool performance, extending lifespan, and ensuring efficient material removal.
Cooling and lubrication play essential roles in managing the heat generated during material processing. The friction between the tool and the workpiece produces heat, which can affect the tool's efficiency and durability. Effective cooling helps dissipate this heat, preventing thermal damage to both the tool and the workpiece. Lubrication reduces friction, which not only minimizes heat generation but also reduces wear and tear on the tool, enhancing its lifespan.
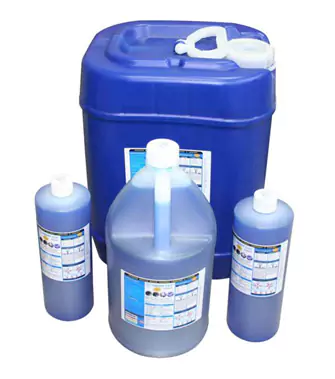
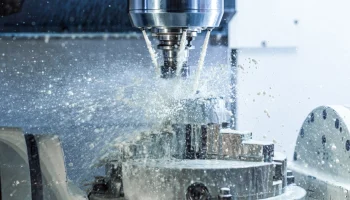
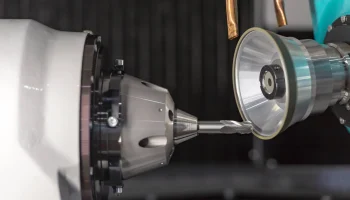
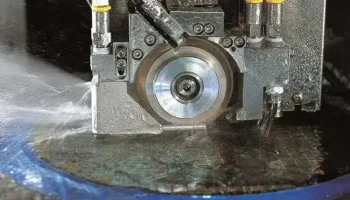
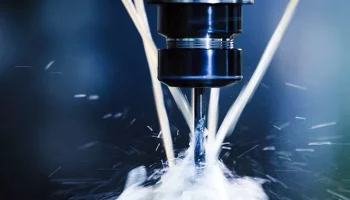
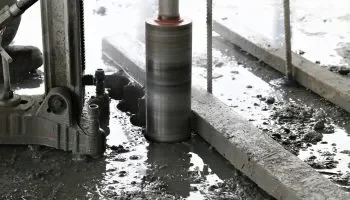
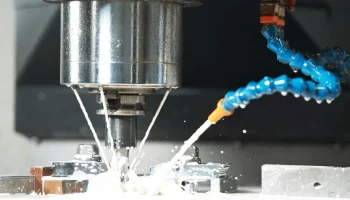
Flood cooling involves a continuous and abundant flow of coolant over the tool and workpiece. This method is highly effective in managing heat and is often used in applications involving high cutting speeds and heavy material removal. In processes with flood cooling, higher diamond concentrations can be utilized. The continuous cooling prevents overheating, allowing the tool to maintain its cutting efficiency and durability. The higher diamond concentration provides more cutting edges, which, in combination with effective cooling, ensures consistent performance and prolonged tool life. Mist cooling uses a fine spray of coolant, combining cooling and lubrication effects. It is suitable for applications where excessive coolant use is undesirable, such as in environments where water use needs to be minimized.
With mist cooling, a moderate diamond concentration is often appropriate. The cooling effect, although less intense than flood cooling, still helps manage heat effectively. The lubrication provided by the mist also reduces friction, allowing the tool to perform efficiently without excessive diamond concentration. Dry cooling relies on ambient air or forced air to cool the tool and workpiece. This method is less effective in heat dissipation compared to liquid coolants and is generally used for applications with lower heat generation. In dry cooling scenarios, lower diamond concentrations are typically preferred. The reduced cooling capability necessitates a more conservative approach to diamond concentration to prevent overheating and excessive tool wear. Lower concentrations help maintain manageable temperatures and reduce the risk of thermal damage.
Oil-based lubricants provide excellent lubrication and some cooling effects. They form a lubricating film that reduces friction between the tool and the workpiece, minimizing heat generation and wear. When using oil-based lubricants, a higher diamond concentration can be advantageous. The lubrication reduces friction effectively, allowing the tool to handle increased diamond density without excessive heat buildup. This combination enhances cutting efficiency and tool longevity, especially in demanding applications. Water-based lubricants offer good cooling properties and moderate lubrication. They are often used in applications where effective heat dissipation is crucial.
With water-based lubricants, a balanced diamond concentration is usually optimal. The cooling effect of water helps manage heat, while the lubrication reduces friction, supporting efficient cutting or grinding. This balance ensures that the tool performs well without the need for extremely high diamond concentrations. Synthetic lubricants are designed to provide specific cooling and lubrication properties, tailored to the requirements of different applications. They can offer superior performance in terms of reducing friction and managing heat. Using synthetic lubricants allows for a versatile approach to diamond concentration. Depending on the lubricant’s properties, tools can be optimized with either higher or lower diamond concentrations to match the desired balance of cooling and lubrication.
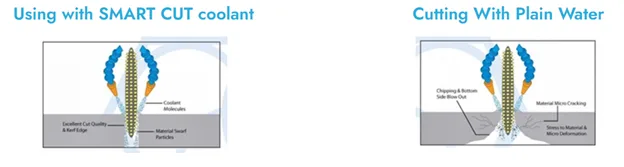
The choice of cooling and lubrication methods directly influences the selection of diamond concentration. Effective cooling systems, such as flood cooling or mist cooling, enable the use of higher diamond concentrations by effectively managing heat and preventing thermal damage. This allows the tool to maintain its cutting or grinding efficiency and extend its lifespan. Conversely, in scenarios with limited cooling, such as dry cooling, lower diamond concentrations are preferred to mitigate the risk of overheating and excessive tool wear. Lubrication also plays a critical role in tool performance. Oil-based and synthetic lubricants, with their superior friction-reducing properties, support higher diamond concentrations by minimizing heat generation and wear. Water-based lubricants, with their strong cooling effects, balance the need for effective cooling and lubrication, making them suitable for moderate diamond concentrations.
The choice of cooling and lubrication methods should be tailored to the specific requirements of the application. For high-speed, high-load operations, robust cooling and lubrication systems are essential to support higher diamond concentrations and ensure tool durability. For precision applications, where heat generation is lower and surface finish is critical, moderate cooling and lubrication can suffice, allowing for balanced diamond concentrations that ensure smooth, controlled cutting or grinding. Effective cooling and lubrication enhance operational efficiency by maintaining optimal tool temperatures and reducing wear. This minimizes downtime for tool changes and maintenance, improving overall productivity. By selecting the appropriate diamond concentration in conjunction with effective cooling and lubrication, you can achieve a balance between cutting efficiency, tool longevity, and operational cost-effectiveness. The choice of cooling and lubrication methods should also consider environmental impact and workplace safety. Water-based and synthetic lubricants may offer eco-friendly and safer alternatives to oil-based options, influencing the selection of diamond concentrations to match these sustainable practices.
Find out more about proper use of coolants for diamond & cbn tools >>>
Cost Considerations:
Cost considerations are a critical aspect of selecting the appropriate diamond concentration for cutting, grinding, drilling, or polishing tools. Higher diamond concentrations generally increase the cost of the tool due to the higher amount of diamond material required. Therefore, balancing cost with performance needs is essential to ensure economic efficiency while meeting the operational demands of the application.
Diamonds can be one of the higher cost components in the manufacturing of diamond & cbn tools. Higher concentrations require more diamonds, directly increasing the material costs. This increase is reflected in the overall price of the tool. The quality of diamonds used also affects the cost. High-quality diamonds with better cutting or grinding properties are more expensive, further raising the cost of tools with higher diamond concentrations.
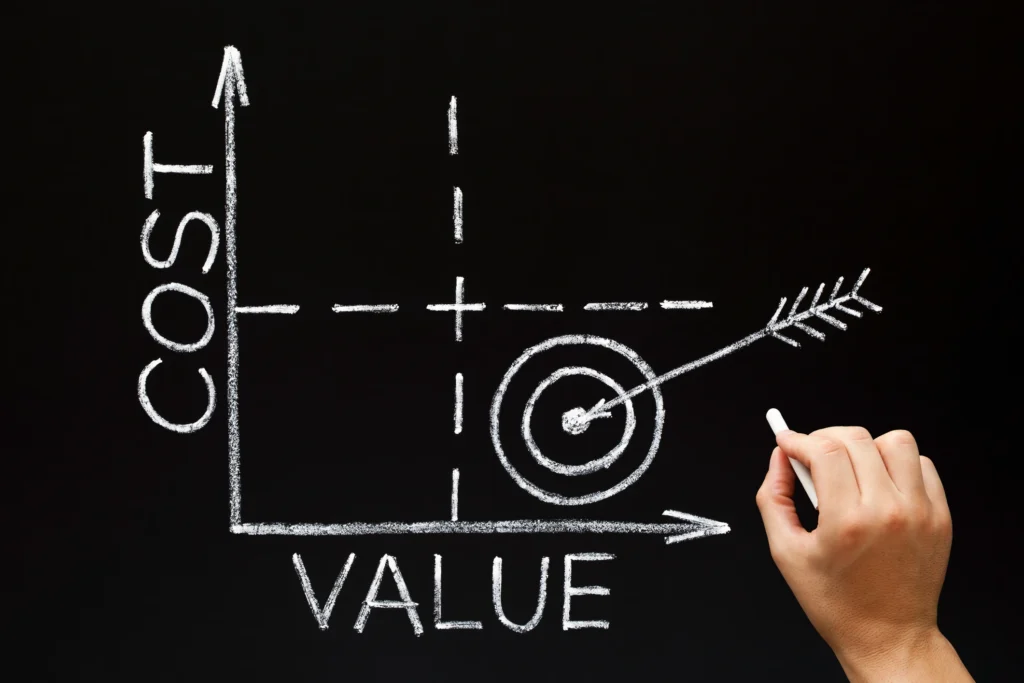
Diamond & CBN Tools with higher diamond concentrations often involve more complex manufacturing processes to ensure uniform diamond distribution and optimal bonding. This complexity can increase production costs. Advanced technologies and precise engineering are required to produce tools with high diamond densities, adding to the manufacturing expenses.
The specific requirements of the application play a crucial role in determining the optimal diamond concentration. For high-demand applications, such as cutting or grinding hard materials, the benefits of higher diamond concentrations often justify the increased cost due to enhanced performance and durability. For less demanding applications, lower diamond concentrations can provide sufficient performance at a reduced cost, offering a cost-effective solution.
Higher diamond concentrations generally enhance tool longevity and cutting efficiency by providing more cutting edges and distributing wear more evenly. This can reduce the frequency of tool replacements and maintenance, potentially offsetting the initial higher cost. In applications where tool longevity is critical, investing in tools with higher diamond concentrations can result in long-term cost savings through reduced downtime and lower replacement rates.
Diamond & CBN Tools with higher diamond concentrations often (but now always) perform better in terms of cutting speed and material removal rate, leading to increased productivity and lower operational costs. This performance boost can justify the higher initial investment. Efficient tools reduce labor costs and energy consumption, contributing to overall cost savings in the production process.
Higher diamond concentrations can improve the quality and precision of cuts or finishes, which is essential in industries where high-quality output is critical, such as electronics, aerospace, and medical device manufacturing. The added cost may be justified by the superior product quality and reduced need for rework.
Conducting a cost-benefit analysis helps in evaluating the trade-offs between tool cost and performance benefits. This analysis considers factors such as tool lifespan, operational efficiency, product quality, and maintenance requirements. By comparing the total cost of ownership for tools with different diamond concentrations, manufacturers can make informed decisions that balance upfront costs with long-term benefits.
Customizing diamond concentration based on specific application needs allows for optimization of both cost and performance. Tailoring the concentration to match the material hardness, cutting speed, and desired finish ensures that the tool is neither over-specified nor under-specified, maximizing cost-efficiency. Collaboration with tool manufacturers to develop application-specific tools can lead to optimized solutions that meet performance requirements while controlling costs.
Market conditions and budget constraints also influence the choice of diamond concentration. Manufacturers must balance the need for high-performance tools with the available budget, seeking solutions that offer the best value for money. In competitive markets, cost-effective tools with adequate performance may provide a competitive advantage, allowing manufacturers to offer high-quality products at lower prices.
Evaluating the return on investment for tools with different diamond concentrations helps in understanding the long-term financial impact. Tools with higher initial costs but longer lifespans and better performance may offer a higher ROI compared to cheaper tools with shorter lifespans. Investing in high-quality, high-concentration diamond tools can lead to improved profitability through enhanced efficiency, reduced downtime, and higher product quality.
Higher diamond concentrations may lead to more sustainable tool usage by reducing the frequency of replacements and waste. This sustainability aspect can contribute to cost savings and align with environmental goals. Efficient use of resources through optimized diamond concentrations supports sustainable manufacturing practices, balancing economic and environmental considerations.
How Diamond Concentration Affects Diamond & CBN Tool Life, Cutting Speed, & Surface Finish
The illustration provided demonstrates the relationship between diamond concentration in a cutting tool and its impact on tool life, cutting speed, cut quality, and dressing frequency. Here’s a detailed breakdown of each component illustrated:

Key Components of the Diagram
1. Diamond Concentration
-
X-Axis (Low to High): Represents the amount of diamond particles embedded in the bond matrix of the tool.
2. Tool Life:
-
Y-Axis on the Left (Low to High): Indicates the longevity of the tool.
-
Curve Behavior: As diamond concentration increases, the tool life also increases, reaching a peak before slightly declining.
3. Cutting Speed (Cutting Rate):
-
Y-Axis on the Left (Slow to Fast): Represents how quickly the tool can cut through material.
-
Curve Behavior: Higher diamond concentration generally reduces cutting speed because the bond matrix becomes harder, slowing the cutting process.
4. Cut Quality
-
Y-Axis on the Right (Poor to Excellent): Indicates the fineness and smoothness of the cut produced by the tool.
-
Curve Behavior: As diamond concentration increases, cut quality improves, reaching an optimal point before potentially declining.
5. Dressing Frequency
-
Y-Axis on the Right (High to Low): Refers to how often the tool needs to be dressed to maintain its cutting efficiency.
-
Curve Behavior: Higher diamond concentration results in lower dressing frequency, as the tool maintains its cutting edge for longer periods.
Detailed Interpretation
High Diamond Concentration
-
Tool Life: Longer due to a harder bond matrix that wears out more slowly.
-
Cutting Speed: Slower because the denser matrix offers more resistance to cutting.
-
Cut Quality: Finer due to more closely packed diamond particles, leading to smoother cuts.
-
Dressing Frequency: Lower as the tool retains its sharpness longer, reducing the need for frequent maintenance.
Low Diamond Concentration
-
Tool Life: Shorter as the bond matrix wears out faster.
-
Cutting Speed: Faster since the tool can cut through material more quickly with less resistance.
-
Cut Quality: Poorer due to fewer diamond particles, resulting in rougher cuts.
-
Dressing Frequency: Higher as the tool needs frequent dressing to maintain efficiency.
Relationship Between Diamond Concentration and Diamond Grit Size
The relationship between diamond grit size and diamond concentration is integral to the performance and efficiency of diamond tools. Both parameters influence the tool’s cutting or grinding characteristics, and their interplay determines the tool’s suitability for specific applications.
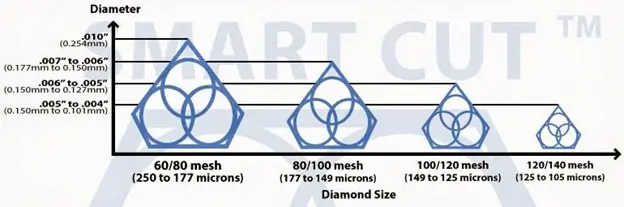
Diamond grit size refers to the size of the diamond particles used in the tool, typically measured in mesh size. Finer grits have higher mesh numbers, indicating smaller particles, while coarser grits have lower mesh numbers, indicating larger particles. Diamond concentration indicates the proportion of diamond particles within the bond matrix of the tool, usually expressed as a percentage or carats per cubic centimeter (ct/cm³).
Tools with larger diamond particles and high concentration are effective for aggressive material removal, rough cuts, and applications requiring high cutting efficiency. The larger particles create deeper cuts and grooves, while the high concentration ensures ample cutting edges to maintain performance. Conversely, tools with smaller diamond particles and low concentration are suited for fine finishing and polishing tasks. The smaller particles produce a smoother surface finish, and the lower concentration reduces the tool’s aggressiveness, preventing surface damage.
Regarding tool wear and longevity, a combination of coarse grit size and low concentration is often used for rapid material removal where tool longevity is less critical. The larger particles provide aggressive cutting action, while the lower concentration minimizes the cost and can be adequate for short-term use. On the other hand, tools with fine grits and high concentration are ideal for precision applications where tool wear needs to be minimized. The high concentration supports prolonged tool life by providing numerous cutting edges, while the fine grit ensures detailed and precise material removal.
In terms of heat management and load distribution, coarse grit size and high concentration help in effective heat management and load distribution during heavy-duty cutting or grinding. The larger particles and high density of diamonds spread the cutting load and heat over a larger area, reducing the risk of localized overheating. Fine grit size and low concentration are suitable for delicate operations where minimal heat generation and fine control are essential. The small particle size reduces friction and heat, while the lower concentration ensures gentle material removal.
Application-specific considerations show that coarse grit size and high concentration are commonly used in industries like construction and stone processing, where rapid material removal and durability are required. In contrast, fine grit size and low concentration are preferred in applications such as electronics, optics, and precision engineering, where surface quality and precision are paramount.
Relationship Between Diamond Concentration and Diamond Bond Type
The relationship between diamond concentration and diamond bond type is crucial in determining the performance and suitability of diamond tools for various applications. Each bond type interacts differently with diamond concentration, affecting the tool’s durability, cutting efficiency, heat management, and overall effectiveness.
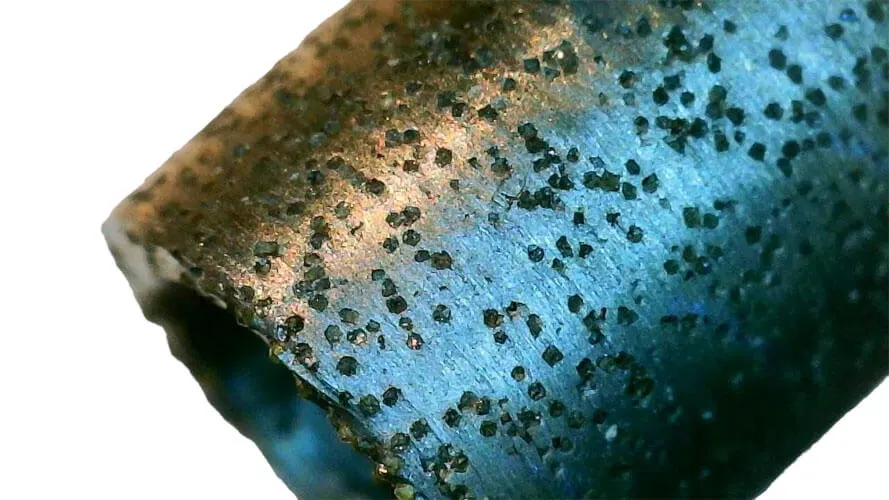
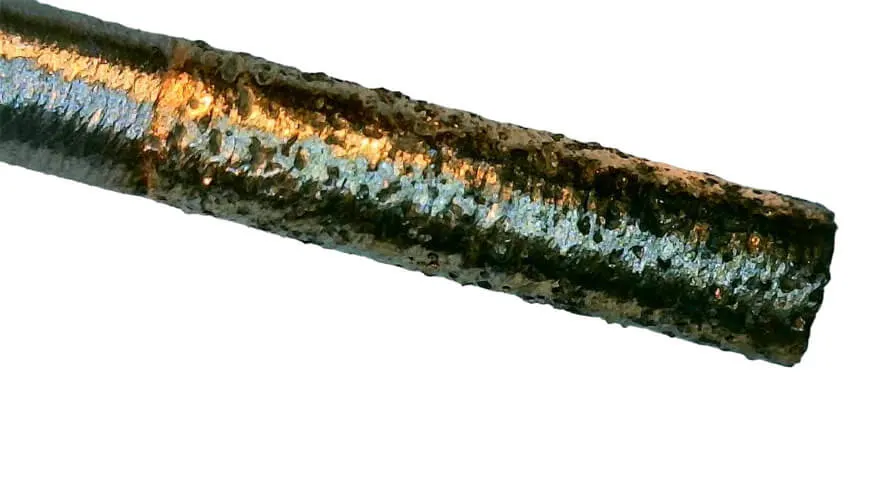
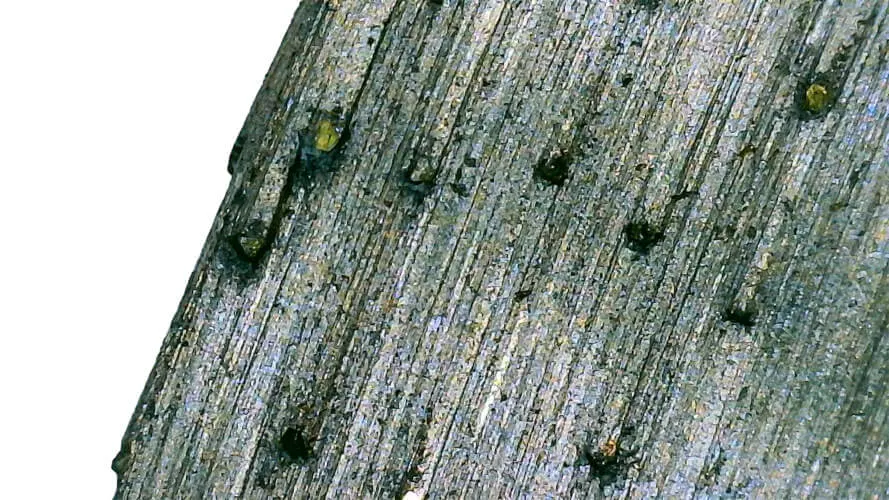
Sintered or metal bonds are created by fusing metal powders with diamond particles under high pressure and temperature. This type of bond is known for its durability and ability to hold diamonds firmly in place. Metal bonds can support high diamond concentrations due to their strong binding properties. This combination is ideal for heavy-duty applications, such as cutting hard and abrasive materials like stone, concrete, and ceramics. The high diamond density and robust bond ensure long tool life and effective heat management. While metal bonds can handle lower concentrations, they are less common in light-duty tasks due to their inherently strong bonding characteristics.
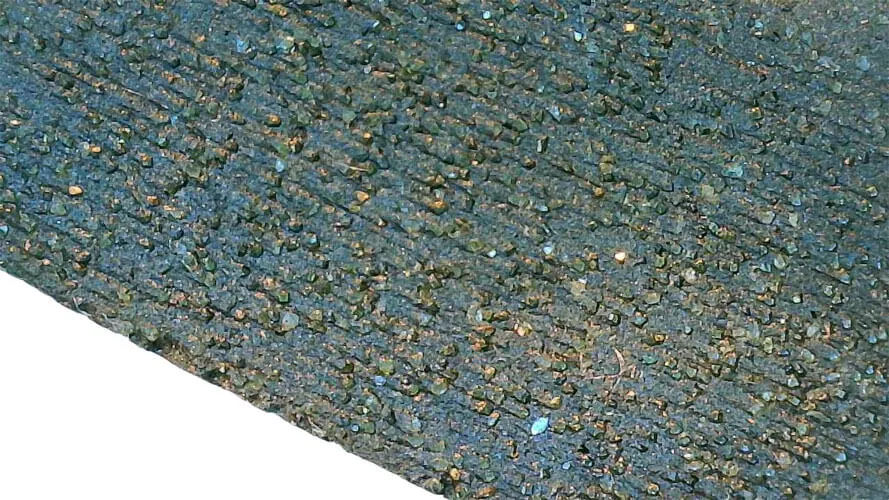
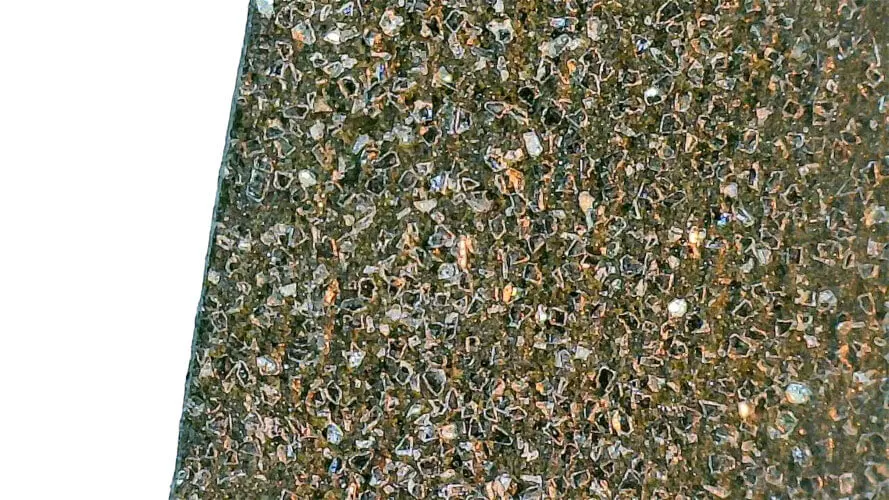
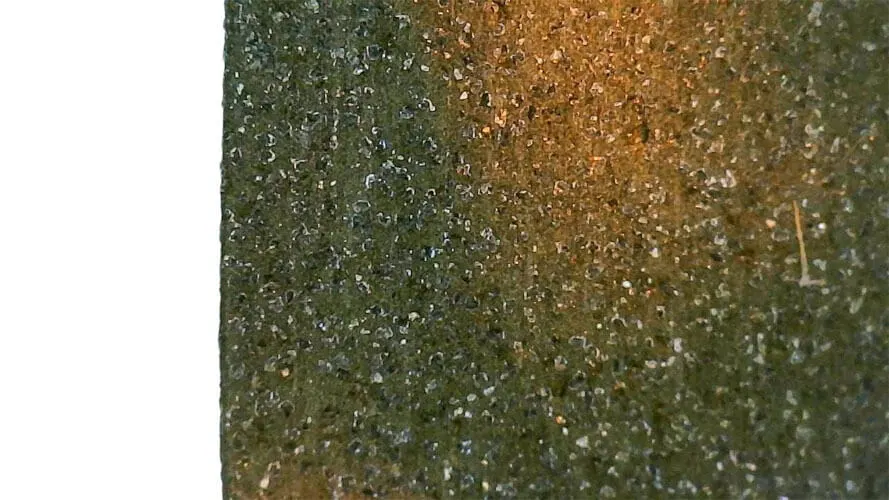
Resin bonds use synthetic resins to hold diamond particles, offering flexibility and ease of manufacture. They are commonly used for grinding and polishing applications. High diamond concentrations are used for applications needing fine finishes and detailed work, such as grinding and polishing hard metals and ceramics. The combination of high diamond concentration and resin bond provides a smooth surface finish and precise control. Low diamond concentrations are ideal for applications involving softer materials or where a balance between cost and performance is desired. The flexibility of the resin bond accommodates the reduced diamond density while maintaining adequate cutting efficiency.
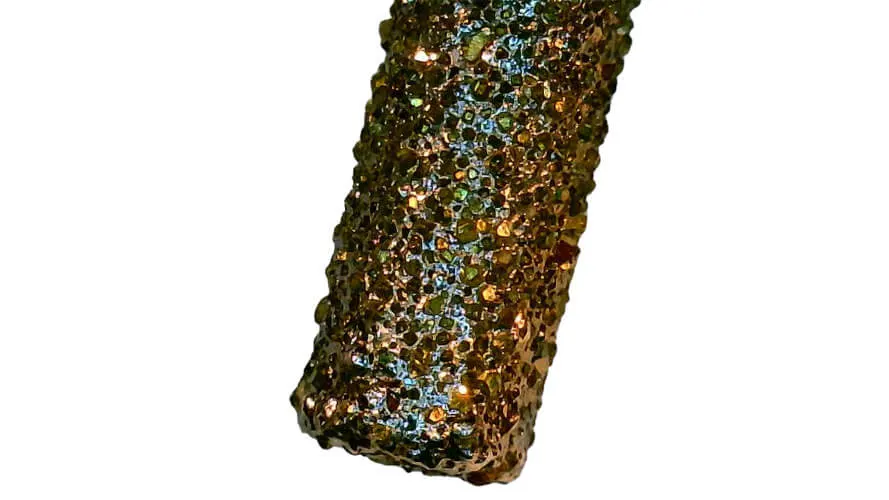
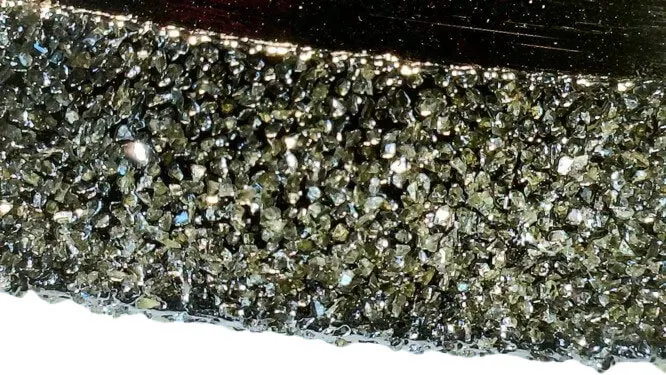
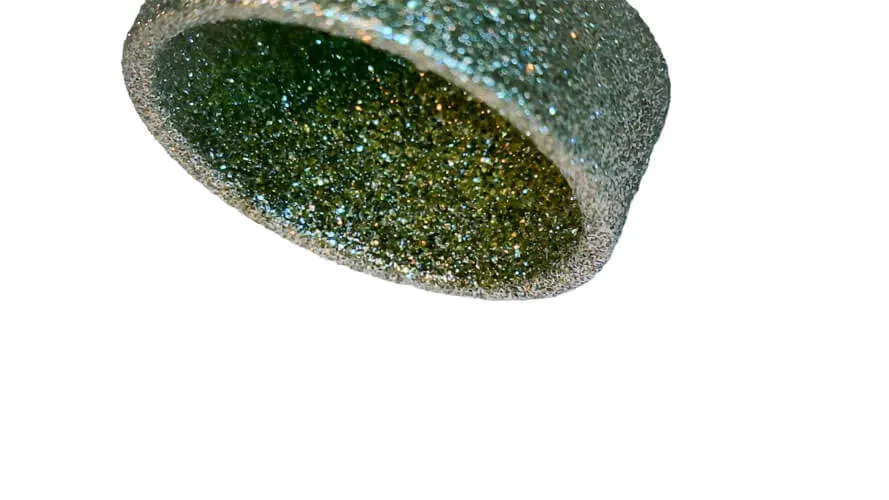
Nickel bonds are created by electroplating a nickel layer onto the tool surface, embedding the diamond particles. Nickel bonds can maintain high diamond concentrations, which is beneficial for applications requiring robust cutting action and high precision, such as in electronic component manufacturing and fine grinding. Low diamond concentrations are suitable for applications that require precision without aggressive cutting, such as light grinding or finishing. The electroplating process allows for precise control over diamond placement, making it effective even with lower concentrations.
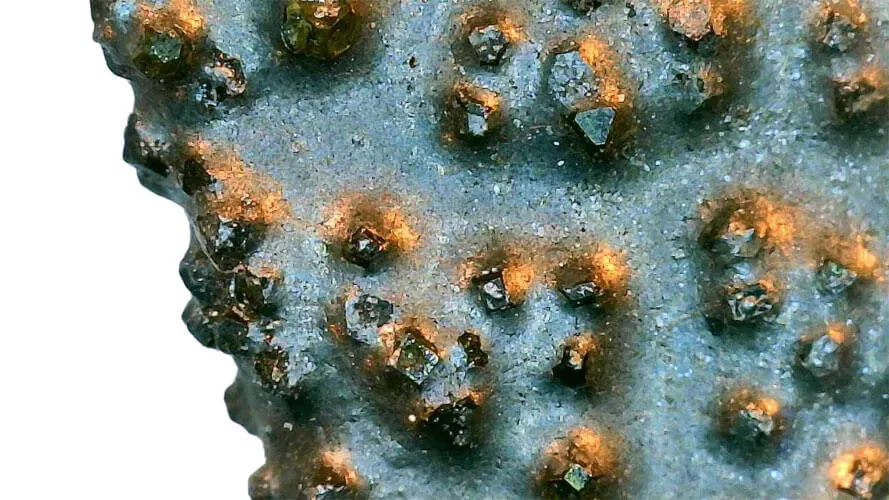
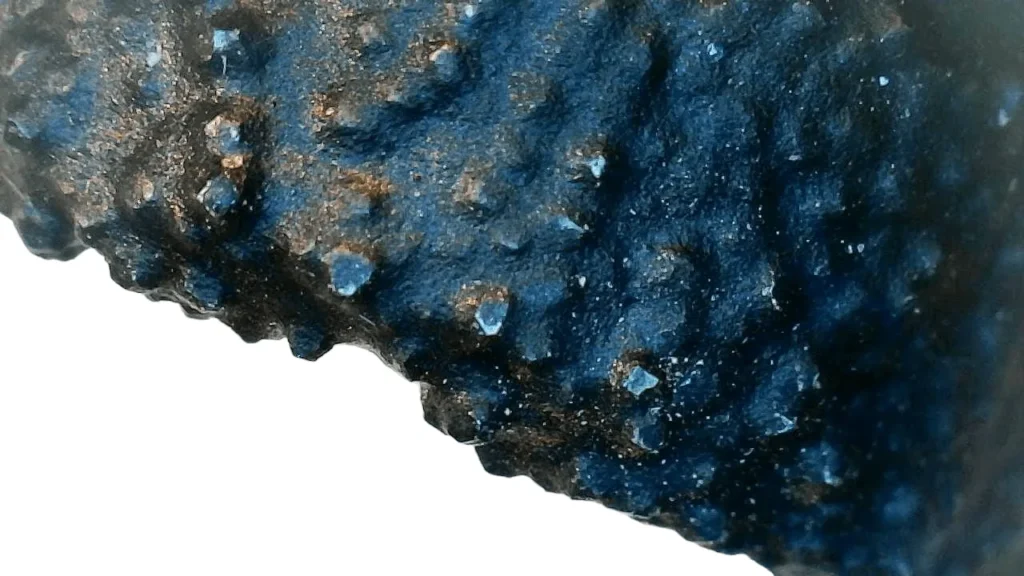
Brazed bonds use a brazing process to attach diamond particles directly to the tool surface, creating a strong bond. This bond type is effective for applications needing robust and durable cutting tools, such as cutting and drilling hard materials. The brazed bond’s strength supports high diamond densities, ensuring prolonged tool life and cutting efficiency. Lower diamond concentrations are less common in brazed bonds due to the nature of the bonding process, which is optimized for high diamond density and strong adhesion.
Vitrified bonds use ceramic materials to hold diamond particles, providing rigidity and high thermal stability. High diamond concentrations are suitable for high-precision grinding applications, such as in the automotive and aerospace industries. The vitrified bond’s rigidity supports high diamond concentrations, offering excellent wear resistance and precise material removal. Low diamond concentrations are useful for applications requiring fine control and surface finish, where excessive cutting power is unnecessary. The vitrified bond’s stability ensures consistent performance even with lower diamond densities.
Hybrid bonds combine elements of resin and metal bonds to leverage the benefits of both. High diamond concentrations are ideal for applications needing a balance of durability and flexibility, such as precision cutting and grinding. The hybrid bond can accommodate high diamond concentrations, providing robust performance and extended tool life. Lower diamond concentrations are suitable for applications requiring versatility and cost-effectiveness, allowing for efficient material removal with moderate diamond density.
Find out more about selecting the right diamond & cbn bond type for your application>>>
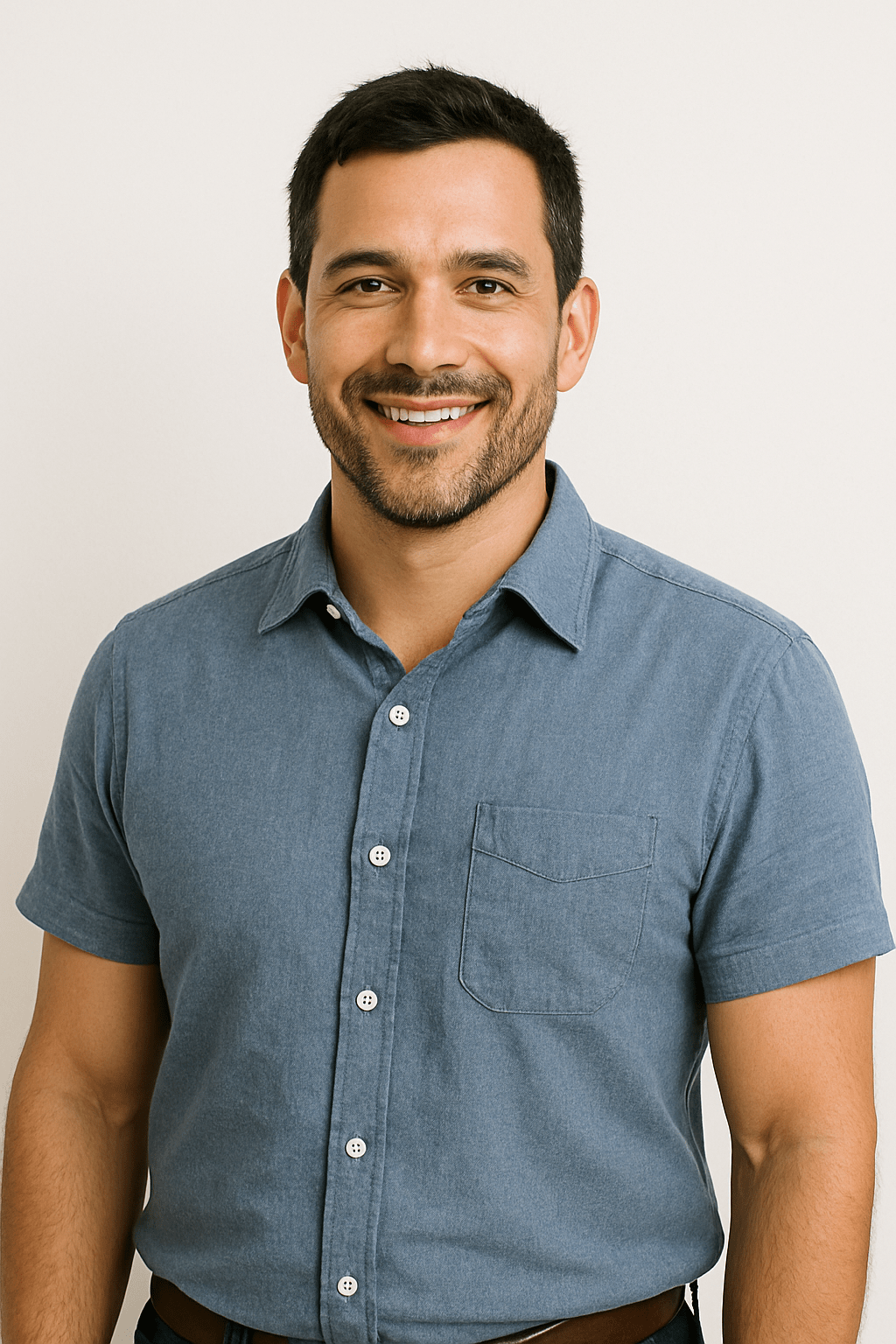
Carlos Sanchez is a senior technical specialist and field applications trainer with more than 17 years of experience in the use and optimization of industrial diamond tools, including ultra-thin diamond blades, core drills, and CBN grinding wheels. With a foundation in industrial engineering and technical operations, Mr. Sanchez has worked extensively with manufacturers and laboratories around the world, providing hands-on support and practical training for a wide range of cutting, grinding, and sample preparation applications.
Fluent in both English and Spanish, Carlos is known for his ability to translate complex tooling concepts into clear, actionable procedures for engineers, technicians, and production staff. His approach emphasizes real-world process improvement, tool longevity, and operator education—ensuring clients get the most out of their diamond tooling investments.
As an author, Mr. Sanchez shares field-tested insights on tool performance optimization, defect prevention, training methodologies, and troubleshooting common cutting issues.
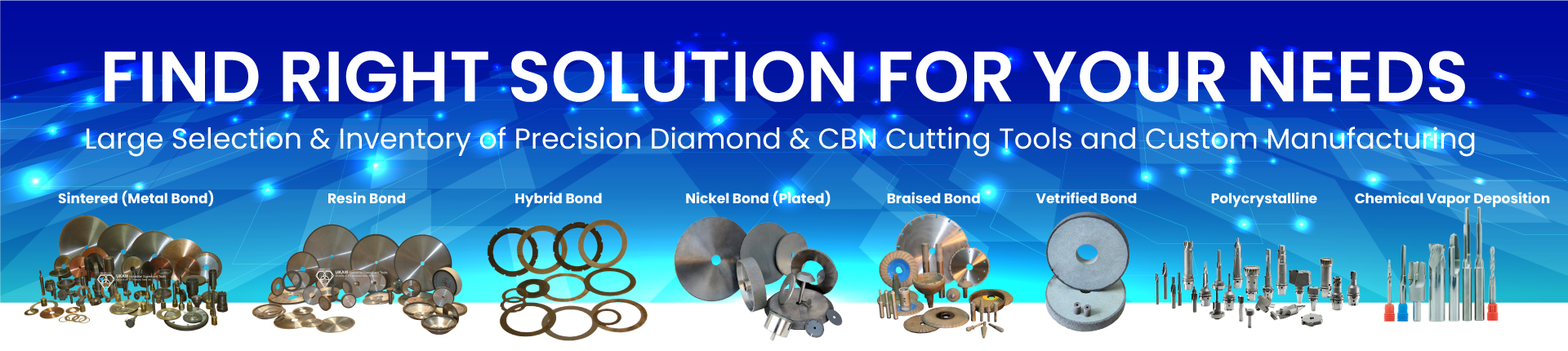
ARE YOU USING RIGHT TOOLS
FOR YOUR APPLICATION?
LET US
HELP YOU
HAVING ISSUES WITH
YOUR CURRENT TOOLS?
Knowledge Center
How to Selecting Right Diamond Tools for your application
How to properly use Diamond Tools
Why use diamond
Diamond vs CBN (cubic boron nitride) Tools
What is Diamond Mesh Size and how to select best one for your application
What is Diamond Concentration and which to use for your application
Diamond Tool Coolants Why, How, When & Where to Use
Choosing The Correct Diamond Bond Type
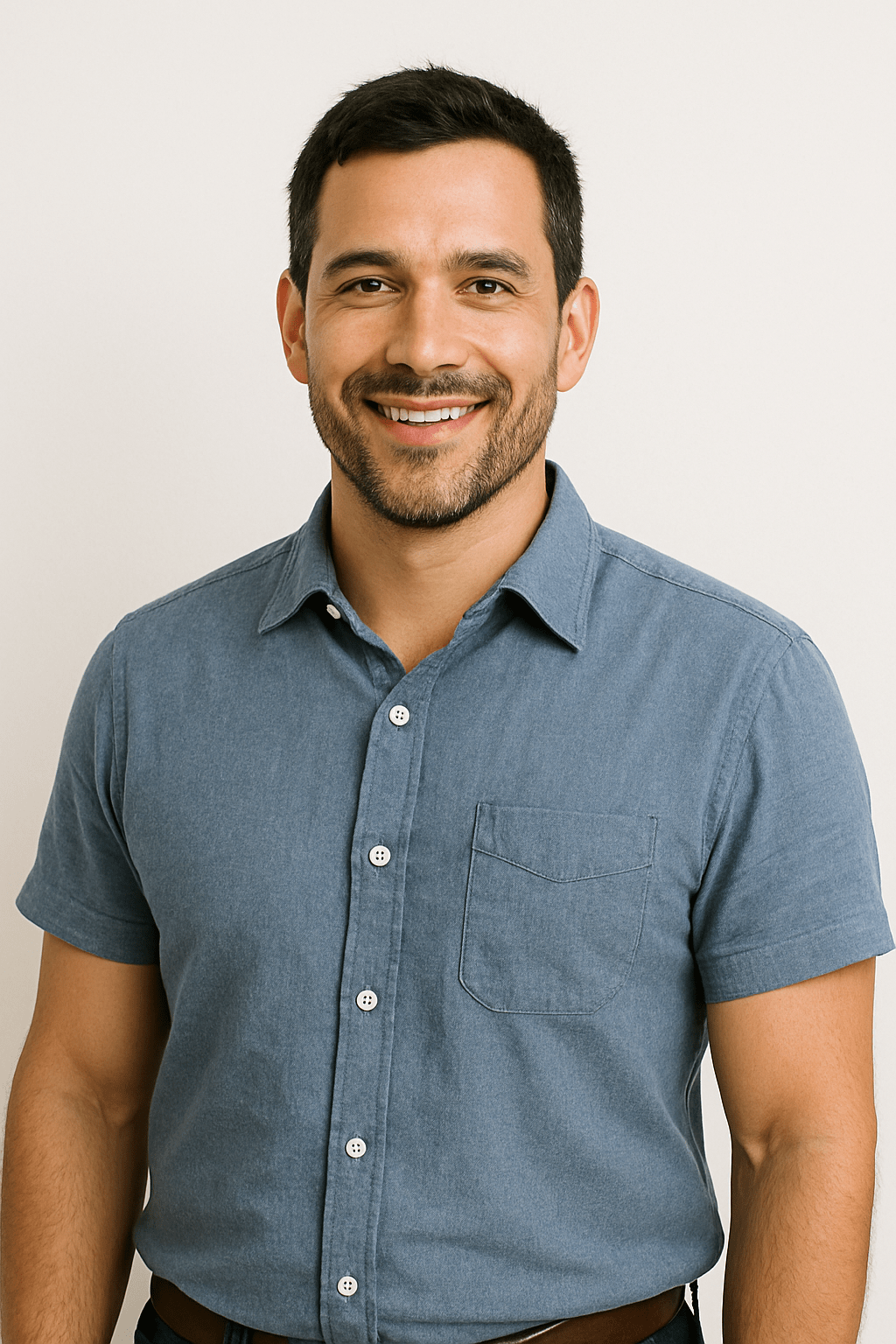
Carlos Sanchez is a senior technical specialist and field applications trainer with more than 17 years of experience in the use and optimization of industrial diamond tools, including ultra-thin diamond blades, core drills, and CBN grinding wheels. With a foundation in industrial engineering and technical operations, Mr. Sanchez has worked extensively with manufacturers and laboratories around the world, providing hands-on support and practical training for a wide range of cutting, grinding, and sample preparation applications.
Fluent in both English and Spanish, Carlos is known for his ability to translate complex tooling concepts into clear, actionable procedures for engineers, technicians, and production staff. His approach emphasizes real-world process improvement, tool longevity, and operator education—ensuring clients get the most out of their diamond tooling investments.
As an author, Mr. Sanchez shares field-tested insights on tool performance optimization, defect prevention, training methodologies, and troubleshooting common cutting issues.