-
0 items in quote
No products in the Quote Basket.
NEW GENERATION AND TECHNOLOGY
SINTERED (METAL BOND)
SMART CUT® Series (SCM)
Diamond & CBN Dicing Blades
SMART CUT® Series (SCM) Sintered (Metal Bond) Diamond CBN Dicing Blades are designed to provide some the best return on investment (ROI) in dicing application. They provide superior longevity, accuracy, and consistency across a wide range of applications. Engineered using advanced SMART CUT® technology, these blades are among the thinnest, most durable, and highest-performing dicing solutions available today. Their sintered metal bond structure ensures a self-renewing sharpness, delivering consistently clean and precise cuts over extended periods.
The Metal Bond Hubless Blade formulation features a specially developed sintered metal bond matrix that securely holds and retains diamond grains, enhancing blade durability and cutting efficiency. Unlike standard formulations, these blades have lower wear resistance, helping to reduce defects such as slanted-kerf and edge chipping, ensuring high-quality, straight cuts. Their high rigidity is equal to or surpasses that of electroformed blades, preventing wavy cutting and improving processing speed, stability, and cutting consistency. This makes them particularly well-suited for applications requiring long blade exposure and ultra-precise results.
Manufactured through high-pressure sintering, these blades are composed of multiple layers of high-quality diamond particles embedded within a metal matrix consisting of iron, cobalt, nickel, bronze, copper, tungsten, and other metal alloys.
This structure ensures excellent wear resistance and cutting efficiency, making them ideal for cutting hard, brittle, and high-precision materials such as BGA, soft alumina, TiC, LTCC, ferrite, silicon wafers, glass, piezoelectric ceramics, quartz, optical materials, and semiconductor components. The controlled sintering process optimizes the balance between cutting speed, blade longevity, and wear resistance, ensuring a consistent cutting performance throughout the blade’s lifecycle.
With their high rigidity and minimal blade wear, SMART CUT® SCM Sintered (Metal Bond) Dicing Blades ensure stable, highly precise cutting with minimal material deformation and contamination. They are designed to withstand high cutting loads while maintaining edge integrity, making them an excellent choice for applications where accuracy, durability, and efficiency are critical. The self-sharpening mechanism of these blades allows for continuous diamond exposure, preventing glazing and reducing the need for frequent blade replacements.
SMART CUT® SCM dicing blades offer a wide selection of blade thicknesses, ranging from 80 µm to 1500 µm, accommodating both ultra-thin and heavy-duty cutting requirements. Additionally, they provide customizable diamond grit sizes from 2 µm to 70 µm, ensuring the optimal balance between cutting speed, material removal rate, and surface finish quality. These blades are also available with serrated edges and various edge shapes, enhancing their ability to cut specific materials with greater efficiency and precision.
By integrating advanced rigidity, self-sharpening properties, and optimized bond formulations, SMART CUT® SCM Sintered (Metal Bond) Dicing Blades deliver exceptional performance across industries including electronics, semiconductor manufacturing, ceramics, and optics. Their prolonged lifespan, superior rigidity, and optimized diamond concentration make them the preferred choice for precision cutting applications where minimizing blade change frequency, improving cut quality, and enhancing overall process efficiency are essential.
Compare to any other Sintered (Metal Bond) Dicing Blade
- Outside Diameter (D): 2” (50mm) to 6” (154mm)
Blade Thickness Range
- Thickness (TE): 80 µm to 1500 µm
- Ultra-Thin Blades: Down to 45µm available for high-precision applications
- Standard Thickness Tolerances: ±0.002” (higher tolerances available upon request)
Inside Diameter (Arbor Hole)
- Standard Sizes: 40mm
- Custom Inside Diameters: Available to fit specific dicing saws or mounting requirements
Diamond Grit Sizes
SMART CUT® Sintered Metal Bond Dicing Blades are available in a broad range of diamond grit sizes, enabling users to balance cutting speed, surface finish, and blade longevity:
- Diamond Grit Size Range: 2µm to 70µm
- Fine Grits (2µm - 15µm): Recommended for ultra-precise applications requiring a superior surface finish and minimal chipping
- Medium Grits (30µm - 54µm): Best for general-purpose cutting of brittle and dense materials
- Coarse Grits (D76 - D126): Ideal for aggressive material removal and faster cutting rates
Diamond Concentration
The diamond concentration is precisely controlled to optimize blade performance based on the material being cut. Higher concentrations extend blade life, while lower concentrations improve free-cutting action.
- High Concentration: Used for cutting hard, dense materials like fiberglass (FGS), tungsten carbide (TGC), QFN packages, tool steels, Inconel, and Monel
- Low Concentration: Recommended for brittle and fragile materials such as optical glass, ceramics, lithium niobate (LiNbO₃), sapphire, quartz, and silicon carbide (SiC)
Bond Hardness Designation System
SMART CUT® sintered metal bond dicing blades come in multiple bond hardness formulations to match specific applications:
- Hard Bonds (VVVHB, VVHB, VHBH, HBH, HBM): Best suited for aggressive cutting applications requiring long blade life and high wear resistance
- Medium Bonds (SBL, MHBL, MHBM): Balanced formulation for controlled wear and stable cutting performance
- Soft Bonds (VVVSB, VVSB, VSB): Ideal for fast cutting, reduced heat generation, and minimal material deformation
Edge Profiles and Serration Options
To enhance performance in specific cutting applications, SMART CUT® offers a variety of serrated and edge profile options:
- Straight Edge: Provides smooth, clean cuts for materials with minimal chipping concerns
- Serrated Edge: Increases coolant flow and debris removal, reducing heat buildup and improving cut quality
- Custom Edge Geometries: Available upon request for specialized applications
Tolerance Standards
SMART CUT® dicing blades are manufactured to extremely tight tolerances, ensuring high precision and repeatability:
- Outside Diameter Tolerance: ±0.002”
- Blade Thickness Tolerance: ±5µm to ±15µm (depending on thickness and application)
- Runout: ≤ 0.001” (≤ 25µm) for high-precision applications
Material Compatibility & Applications
SMART CUT® Sintered (Metal Bond) Dicing Blades are engineered for precision cutting of hard, brittle, and composite materials in industries such as electronics, semiconductor packaging, ceramics, optics, and advanced materials research.
These blades excel in cutting:
- Semiconductors & Electronics: BGA, CSP, MLCC, QFN, silicon wafers, thin-film disk drive heads, aluminum titanium carbide
- Ceramics & Hard Materials: LTCC, zirconia (ZrO₂), aluminum nitride (AlN), boron carbide (B₄C), titanium diboride (TiB₂)
- Optical & Photonics: Optical glass, photonics glass, sapphire, ruby, lithium niobate, lithium tantalate
- Superalloys & Metals: Tungsten carbide, hardened steels, high-speed tool steels, die steels, Inconel, Monel, Wasapalloy
- Other Specialty Materials: Fiberglass (FGS), quartz, silicon carbide (SiC), Barium Titanate (BTI), Bi12Si22, ZnSe
SMART CUT® Sintered (Metal Bond) Dicing Blades are used for high-precision cutting, dicing, slotting, and grooving of hard, brittle, and composite materials such as semiconductors, ceramics, optical glass, quartz, sapphire, silicon carbide (SiC), and superalloys. They are commonly used in electronics, semiconductor packaging, optical components, and advanced materials processing.
Unlike resin or electroplated blades, sintered metal bond blades have multiple layers of diamond particles embedded in a durable metal matrix, ensuring continuous diamond exposure and self-renewing sharpness. This results in longer blade life, better wear resistance, and enhanced precision, making them ideal for applications requiring consistent performance over extended cutting cycles.
SMART CUT® sintered dicing blades are available in a range of diameters:
⦁ Standard diameters: 2” (50mm) to 6 (154mm)
⦁ Custom diameters: Available upon request
⦁ Thickness range: 80 µm to 1500 µm
⦁ Ultra-thin options: Down to 45µm for high-precision applications
⦁ Standard thickness tolerances: ±0.002” (tighter tolerances available upon request)
SMART CUT® sintered dicing blades come in a wide range of diamond grit sizes to optimize cutting performance:
⦁ Grit size range: 2 µm to 70 µm
⦁ Common sizes: D126, D107, D91, D76, D54, D46, 45µm, 30µm, 15µm, 9µm, 6µm
⦁ Fine grit (2µm – 15µm): For ultra-precise cuts with minimal chipping
⦁ Medium grit (30µm – 54µm): For general-purpose cutting
⦁ Coarse grit (D76 – D126): For faster cutting speeds and high material removal rates
SMART CUT® dicing blades are available in different bond hardness formulations to match specific applications:
⦁ Hard Bonds (VVVHB, VVHB, VHBH, HBH, HBM): Ideal for hard materials requiring long blade life and high wear resistance
⦁ Medium Bonds (SBL, MHBL, MHBM): Balanced wear resistance for versatile cutting applications
⦁ Soft Bonds (VVVSB, VVSB, VSB): Designed for fast, free-cutting action with reduced heat buildup
Diamond concentration is carefully controlled based on material type and cutting requirements:
⦁ High Concentration: Used for abrasive and dense materials like fiberglass, tungsten carbide, tool steels, and superalloys
⦁ Low Concentration: Ideal for fragile, brittle materials such as ceramics, silicon, sapphire, lithium niobate, and photonics glass
⦁ Standard arbor hole sizes: 40mm
⦁ Custom inside diameters: Available upon request
⦁ Straight edge: Smooth cutting for minimal chipping applications
⦁ Serrated edge: Enhances coolant flow and debris removal for better cutting efficiency
⦁ Custom edge geometries: Available for specialized applications
⦁ Harder bonds (HBH, HBM) last longer but cut at a slightly slower rate due to increased wear resistance.
⦁ Softer bonds (VSB, VVSB) cut faster but wear more quickly, requiring more frequent blade replacements.
⦁ Medium bonds (MHBM, MHBL) offer a balance between cutting speed and longevity.
These blades are widely used in industries that require precision cutting, including:
⦁ Semiconductors & Electronics: BGA, CSP, MLCC, QFN, thin-film disk drive heads, aluminum titanium carbide
⦁ Ceramics & Advanced Materials: LTCC, zirconia (ZrO₂), aluminum nitride (AlN), boron carbide (B₄C), titanium diboride (TiB₂)
⦁ Optical & Photonics: Optical glass, sapphire, lithium niobate (LiNbO₃), lithium tantalate (LiTaO₃)
⦁ Superalloys & Hard Metals: Tungsten carbide, hardened steels, Inconel, Monel, Wasapalloy, tool steels
⦁ Other Specialty Materials: Fiberglass, quartz, silicon carbide, barium titanate, Bi12Si22, ZnSe
Selecting the correct SMART CUT® dicing blade depends on several factors, including:
⦁ Material type (hardness, density, brittleness)
⦁ Cutting speed and precision requirements
⦁ Surface finish expectations
⦁ Desired blade life and maintenance schedule
⦁ Blade thickness and diamond concentration
If you are unsure which blade is best for your application, our team can help you determine the optimal specification based on your cutting parameters.
Yes! We offer custom blade diameters, thicknesses, bond formulations, diamond concentrations, edge profiles, and arbor hole sizes to meet your specific cutting needs.
The lifespan depends on:
⦁ Material type and hardness
⦁ Diamond grit size and concentration
⦁ Cutting speed and feed rate
⦁ Coolant use and cutting conditions
Compared to resin bond and electroplated dicing blades, sintered metal bond blades offer significantly longer life due to their multiple layers of embedded diamond particles.
SMART CUT® Sintered (Metal Bond) Dicing Blades are compatible with most precision dicing saws used in semiconductor, optics, and ceramics industries. If you have specific mounting or machine compatibility concerns, we can provide customized blade configurations.
You can contact us directly with your material type, cutting requirements, and preferred blade specifications, and we will recommend the best option for your needs. We also offer custom blade configurations upon request.
Choosing the right blade thickness depends on material type, cutting precision, and blade stability:
⦁ Thin blades (80µm – 200µm): Ideal for precision applications with minimal kerf loss and ultra-fine cuts.
⦁ Medium blades (250µm – 750µm): Suitable for general-purpose cutting where both precision and durability are needed.
⦁ Thick blades (800µm – 1500µm): Used for deep cuts, tough materials, or increased blade exposure requirements.
⦁ Low concentration → Faster cutting speeds, less heat generation, better for brittle materials.
⦁ Medium concentration → Balanced performance for a wide range of materials.
⦁ High concentration → Longer blade life, best for hard, dense materials like tungsten carbide and superalloys.
Blade exposure refers to how much of the blade is extending beyond the mounting flanges:
⦁ Low exposure → More stability, better control, and reduced vibration.
⦁ High exposure → Deeper cutting capability but may require adjustments in feed rate and coolant application to prevent blade flexing.
⦁ Too high RPM → Increased heat, risk of material burning or cracking.
⦁ Too low RPM → Slower cuts, increased blade wear due to inefficient diamond exposure.
⦁ Optimized RPM → Clean, smooth cuts with minimal stress on the blade and material.
⦁ Ensure correct RPM and feed rate settings based on material hardness.
⦁ Use proper blade mounting techniques to prevent misalignment.
⦁ Avoid excessive blade exposure beyond the flanges.
⦁ Maintain adequate coolant flow to reduce thermal stress.
⦁ Deionized water → Common for semiconductor and optical applications, prevents contamination.
⦁ Water-soluble coolants → Reduce friction and extend blade life.
⦁ Low-foaming coolants → Improve process stability, particularly in high-speed cutting.
⦁ Insufficient coolant application → Ensure proper coolant flow rate and distribution.
⦁ Improper feed rate → Adjust to prevent overheating.
⦁ Glazed blade → Dressing the blade may be required to restore cutting efficiency.
⦁ Use a fine-grit dressing stick to remove bond material buildup and expose fresh diamonds.
⦁ Dress blades periodically to maintain optimal cutting speed and prevent glazing.
⦁ Avoid over-dressing, as this can reduce blade life.
No. These blades require coolant for effective operation. Dry cutting will cause excessive heat buildup, rapid wear, and material damage.
⦁ Running the blade at incorrect RPM → Reduces performance and increases wear.
⦁ Improper blade mounting → Causes deflection and imprecise cuts.
⦁ Ignoring coolant flow → Leads to overheating and premature blade failure.
⦁ Not dressing the blade when needed → Results in glazing and reduced cutting efficiency.
Excessive machine vibration can cause:
⦁ Blade deflection → Reduces cutting accuracy.
⦁ Inconsistent kerf width → Leads to uneven cuts.
⦁ Premature wear → Blade life decreases due to erratic cutting forces.
To prevent this, ensure the dicing saw is properly calibrated and stabilized.
Yes. Custom edge geometries such as serrated edges, segmented rims, or special notches can be provided for improved coolant flow, heat dissipation, and material removal efficiency.
⦁ Vacuum chucks → Provide stable, high-precision cutting for thin materials.
⦁ Wax mounting → Used for delicate substrates, reduces vibration.
⦁ Mechanical clamping → Works for larger, rigid materials but may introduce stress.
A blade should be replaced when:
⦁ Cutting speed significantly decreases despite proper feed rates.
⦁ Chipping or microcracks appear on the material surface.
⦁ Dressing no longer restores performance.
⦁ Blade edge shows excessive wear or deformation.
Yes, SMART CUT® sintered dicing blades are compatible with robotic wafer dicing, CNC precision cutting, and automated dicing equipment used in semiconductor, optical, and ceramic industries.
⦁ Use consistent cutting parameters (RPM, feed rate, coolant).
⦁ Regularly inspect and replace worn blades.
⦁ Calibrate dicing equipment to maintain precision.
⦁ Optimize blade thickness and diamond grit size based on production needs.
⦁ Store in a dry, controlled environment to prevent oxidation.
⦁ Keep blades in original protective cases to avoid accidental chipping.
⦁ Avoid stacking or direct contact between blades to prevent damage.
SMART CUT® sintered dicing blades are used in:
⦁ Semiconductor Fabrication → Wafer dicing, MEMS, IC packaging (BGA, QFN, CSP).
⦁ Optical & Photonics → Sapphire, quartz, optical glass cutting.
⦁ Advanced Ceramics → LTCC, zirconia, alumina, boron carbide.
⦁ Electronics Manufacturing → PCB, MLCC, thin-film disk drive components.
⦁ Superalloy Processing → Tungsten carbide, Inconel, tool steels.
Yes. SMART CUT® provides custom blade configurations, including:
⦁ Specific bond hardness and diamond concentrations.
⦁ Custom diameters, thicknesses, and arbor sizes.
⦁ Serrated, notched, or segmented edge profiles.
Contact us with details about your material type, cutting requirements, and machine specifications, and our technical team will recommend the best blade for your needs.
Feed rate should be optimized based on:
⦁ Material hardness – Harder materials require slower feed rates.
⦁ Blade thickness – Thinner blades work better with moderate to slower feed rates.
⦁ Coolant efficiency – Poor coolant flow may require reducing the feed rate to prevent overheating.
⦁ Chipping sensitivity – Lower feed rates help reduce microcracking on fragile materials.
Yes, but deep cutting requires:
⦁ Increased blade thickness and rigidity to prevent deflection.
⦁ High diamond concentration to improve longevity.
⦁ Serrated or segmented blades to enhance debris removal and coolant flow.
⦁ Lower feed rates to reduce stress on the blade and material.
Excessive spindle vibration can:
⦁ Reduce cut accuracy and increase kerf width variation.
⦁ Cause premature blade wear and breakage.
⦁ Increase material chipping and microcracks.
⦁ Reduce coolant effectiveness by disrupting flow patterns.
To minimize vibration, ensure the spindle is balanced, clean, and properly maintained.
⦁ Standard precision flanges – Suitable for most cutting applications.
⦁ Large-diameter flanges – Recommended for ultra-thin and high-precision blades to improve blade stability.
⦁ Custom-balanced flanges – Can help minimize spindle vibration and improve performance in sensitive applications.
⦁ Thinner kerf blades (≤100µm): Reduce material loss, ideal for high-value materials.
⦁ Medium kerf blades (100µm – 300µm): Balance between material yield and blade stability.
⦁ Thicker kerf blades (>300µm): More durable but reduce material efficiency.
Selecting the right kerf width is essential for maximizing yield while maintaining cutting stability.
⦁ Straight-edge blades – Provide clean cuts with minimal chipping.
⦁ Serrated-edge blades – Improve coolant retention and heat dissipation, reducing cutting stress.
⦁ Notched blades – Help reduce friction and improve cutting speed.
⦁ Discoloration or burn marks on the material.
⦁ Increased blade glazing, requiring more force to cut.
⦁ Material warping or increased chipping.
⦁ Rapid blade wear.
To prevent overheating, optimize coolant flow, adjust feed rates, and ensure correct RPM settings.
The arbor hole must match the machine’s spindle precisely.
⦁ Too large: Causes misalignment and vibration, leading to uneven cuts.
⦁ Too small: Can cause excessive blade stress and improper mounting.
⦁ Properly fitted arbor holes ensure stable, accurate, and vibration-free operation.
Regular maintenance includes:
⦁ Checking and calibrating spindle alignment to ensure precision.
⦁ Cleaning and inspecting flanges for wear or debris buildup.
⦁ Replacing worn coolant nozzles to maintain proper fluid flow.
⦁ Ensuring proper machine vibration damping to avoid cut irregularities.
Yes, step-cutting (cutting in multiple passes) is possible and is recommended for hard or thick materials to reduce blade stress.
⦁ Use moderate feed rates to avoid excessive force.
⦁ Ensure coolant reaches the blade consistently to prevent overheating.
⦁ Choose appropriate blade exposure to balance cut depth with stability.
⦁ Low coolant pressure → Poor heat dissipation, increased blade wear.
⦁ High coolant pressure → Improved cooling but may cause material deflection in fragile materials.
⦁ Optimized coolant pressure ensures consistent chip removal, cooling, and cutting efficiency.
⦁ Choose balanced bond hardness to handle different material properties.
⦁ Use moderate diamond concentration for controlled cutting.
⦁ Adjust feed rate and coolant flow based on the most sensitive material being cut.
⦁ Sintered Blades → Longer lifespan, multiple diamond layers, self-sharpening mechanism, better for tough materials.
⦁ Electroplated Blades → Single-layer diamonds, faster initial cutting but shorter lifespan.
Sintered blades are preferred for high-precision, high-durability applications.
⦁ Check for glazing – Dress the blade if needed.
⦁ Ensure correct RPM and feed rate – Adjust to improve efficiency.
⦁ Increase coolant flow – Helps keep diamonds exposed and reduces heat.
Replace the blade if worn – Continuous use of a dull blade increases chipping and process instability.
The maximum depth depends on blade thickness and material hardness.
⦁ Thin blades (≤100µm): Up to 2mm depth per pass.
⦁ Medium blades (100µm – 500µm): Up to 5mm depth per pass.
Thicker blades (>500µm): Can cut deeper but may require step-cutting to maintain quality.
⦁ Sintered Metal Bond → Longer life, superior rigidity, better form retention, ideal for hard materials.
⦁ Resin Bond → Smoother cuts on softer materials, faster initial cutting, shorter lifespan.
Sintered blades outperform resin bond blades in demanding, high-precision applications.
For multi-layered ceramics, composites, or bonded structures:
⦁ Start with lower feed rates to prevent delamination.
⦁ Use progressive step-cutting to maintain structural integrity.
⦁ Ensure coolant penetrates between layers to avoid overheating and uneven cutting.
Yes. SMART CUT® sintered blades can complement laser-assisted dicing by handling final separation cuts, improving edge quality, and reducing stress fractures in sensitive materials.
⦁ Use clean gloves to avoid contamination.
⦁ Store in original packaging to prevent warping or edge damage.
⦁ Avoid excessive force when mounting, as ultra-thin blades are more fragile.
Yes, we offer OEM private labeling, batch tracking, and custom laser-etched branding for bulk orders.
⦁ Frequent dressing ensures the blade remains sharp and prevents glazing.
⦁ Over-dressing may reduce blade life by prematurely exposing too many diamonds.
⦁ Recommended Approach: Dress only when performance declines (e.g., slower cutting speed, increased chipping, or excessive heat buildup).
Yes, these blades are compatible with ultrasonic-assisted dicing systems, which enhance cutting efficiency for brittle, high-precision materials like sapphire and ceramics by reducing cutting forces and minimizing chipping.
⦁ Humidity & Temperature: Excess moisture can lead to bond degradation; temperature fluctuations may cause material expansion, affecting cut precision.
⦁ Airborne Contaminants: Dust and debris can clog blade surfaces, reducing efficiency.
⦁ Vibration & Airflow: Unstable environments can disrupt spindle balance, impacting cut quality.
⦁ Blade misalignment or wobble → Check spindle and flange alignment.
⦁ Inconsistent feed rate → Optimize feed rate for material and blade thickness.
⦁ Vibration in the dicing machine → Inspect for mechanical wear or misbalanced blades.
- Improper coolant application → Ensure even coolant distribution.
⦁ Low-viscosity coolants improve chip removal and cooling efficiency.
⦁ High-viscosity coolants may reduce splashing and improve lubrication but could trap debris.
⦁ Electrostatic-sensitive applications require specialized low-foaming coolants.
⦁ Outside diameter tolerance: ±0.002” (higher precision upon request).
⦁ Blade thickness tolerance: ±5µm to ±15µm depending on application.
⦁ Runout tolerance: ≤ 0.001” for high-precision applications.
⦁ Higher SFPM (Surface Feet Per Minute): Faster cuts but increased wear.
⦁ Lower SFPM: More controlled cuts, but slower cutting speed.
Optimal SFPM varies based on material type and blade specification.
Yes, but special considerations must be taken:
⦁ Ensure no excessive heat buildup due to limited cooling options.
⦁ Use dry-cut optimized variants if coolant cannot be used.
No. These blades rely on continuous diamond exposure as the bond wears down. If the blade is dull, it is time for replacement.
⦁ Synthetic diamonds offer uniform size and predictable performance.
⦁ Natural diamonds may provide better toughness but with inconsistent grit shape.
SMART CUT® exclusively uses precision-graded synthetic diamonds for maximum control over cutting efficiency.
⦁ Ensure blade mounting is secure and properly aligned.
⦁ Verify correct spindle RPM and feed rate settings.
⦁ Inspect for uneven wear or bond breakdown.
⦁ Check machine vibration levels—loose parts or worn-out bearings can cause skipping.
Yes, we offer ESD-safe dicing blades for applications where electrostatic discharge is a concern, such as semiconductor and photonics glass cutting.
Yes. Submerged dicing reduces heat buildup, improves debris removal, and minimizes chipping for ultra-precise applications.
⦁ Metal Bond → Long life, high wear resistance, best for hard, brittle materials.
⦁ Vitrified Bond → Faster cutting speeds, better for softer materials requiring minimal heat generation.
Materials like ceramics, quartz, and optical glass expand with temperature changes. To prevent thermal damage:
⦁ Use a finer grit size to reduce cutting stress.
⦁ Optimize coolant flow to control heat buildup.
⦁ Choose a bond hardness that balances wear resistance with cutting precision.
⦁ Blade thickness – Thinner blades are more prone to flexing.
⦁ Feed rate – Too aggressive a feed rate can cause bending.
⦁ Machine stability – Improper spindle calibration increases deflection.
⦁ Material hardness – Harder materials require higher blade rigidity.
Yes, these blades are ideal for grooving and partial-depth cuts, provided that:
⦁ The feed rate and blade exposure are properly adjusted.
⦁ The material is adequately supported to prevent breakage.
⦁ Coolant flow is directed to avoid chip accumulation.
Yes, SMART CUT® offers coatings that:
⦁ Reduce friction and extend blade life.
⦁ Minimize electrostatic charge in sensitive applications.
⦁ Enhance wear resistance for aggressive cutting applications.
⦁ Run the blade at a moderate feed rate for the first few cuts.
⦁ Ensure coolant flow is optimal to prevent overheating.
Gradually increase the cutting speed as the blade settles into the process.
Yes, but selecting the correct diamond grit size, bond hardness, and concentration is critical to avoid layer separation or delamination.
⦁ Use precision flanges to maintain alignment.
⦁ Avoid over-tightening to prevent warping.
⦁ Ensure machine vibration is minimal to maintain straight cuts.
⦁ Flat-edge blades – Uniform cutting, smooth finishes.
⦁ Serrated blades – Higher removal rates, better coolant flow.
Segmented blades – Reduced heat buildup, better for deep cuts.
A narrow kerf increases material efficiency but requires higher blade precision.
A wider kerf provides better coolant flow and chip evacuation but increases material loss.
Yes, provided that the blade bond and diamond concentration are selected to withstand extreme temperature variations.
02
Jun
Dicing Blade Operations Recommendations
Share this Article with Friend or Colleague
Selecting the right dicing blade parameters often involves a trial and error process, many aspects of which can be mitigated through experience and a deep understanding of how...
02
Jun
Optimizing Dicing Blade Performance
There are many variables that affect dicing blade performance. Each variable of the dicing process is only of the many components of a larger dicing system (equation). Changing one component or variable of...
02
Jun
Trouble Shooting Dicing Problems
Guide on most common dicing problems and how to resolve them
Share this Article with Friend or Colleague
ARE YOU USING RIGHT TOOLS
FOR YOUR APPLICATION?
LET USHELP YOU
CONTACT US
HAVING ISSUES WITH
YOUR CURRENT TOOLS?
What...
02
Jun
Application Recommendations
See what blade specifications we recommend to use for different applications, along with rpm's and feed rated
Share this Article with Friend or Colleague
ARE YOU USING RIGHT TOOLS
FOR YOUR APPLICATION?
LET USHELP...
Case Study: Dicing Blade for for BGA
- Blade Type: SMART CUT® Series (SCM) Sintered (Metal Bond) Dicing Blade
- Model: SMART CUT® Series (SC1M)
- Blade Size: 56 D × 0.1 T × 40 H
- Machine Model: DISCO DAD3350
- Application: BGA (Ball Grid Array)
- Material: High-Density, Environmentally Friendly PCB (Printed Circuit Board)
Blade Specifications & Performance Comparison
Parameter |
SMART CUT® Blade |
Competitor Blade |
---|---|---|
Blade Size |
56 D × 0.1 T × 40 H |
56 D × 0.1 T × 40 H |
Diamond Grit Size |
4-6 µm |
4-6 µm |
Diamond Concentration |
100 |
100 |
Bond Type |
Metal Bond |
Metal Bond |
Spindle Speed |
30,000 RPM |
30,000 RPM |
Feed Rate |
100 mm/s |
100 mm/s |
Dimensional Accuracy |
±18 µm | ±20 µm |
Blade Lifespan |
6,200 meters (24% longer) |
5,000 meters |
Cutting Depth |
0.6 mm |
0.6 mm |
Burr Size |
<14 µm (Superior finish) |
<20 µm (More post-processing required) |
Key Benefits of SMART CUT® Blade
- 24% Longer Lifespan: Extends blade usage, reducing tool changes and cutting costs.
- Higher Precision: ±18 µm accuracy, reducing material waste and improving process consistency.
- Superior Surface Finish: Burr size <14 µm, minimizing post-processing time and improving final product quality.
- Consistent Performance: Maintains the same spindle speed, feed rate, and cutting depth, proving that SMART CUT®
Series (SC1M) outperforms the competition in longevity and cut quality under identical conditions.
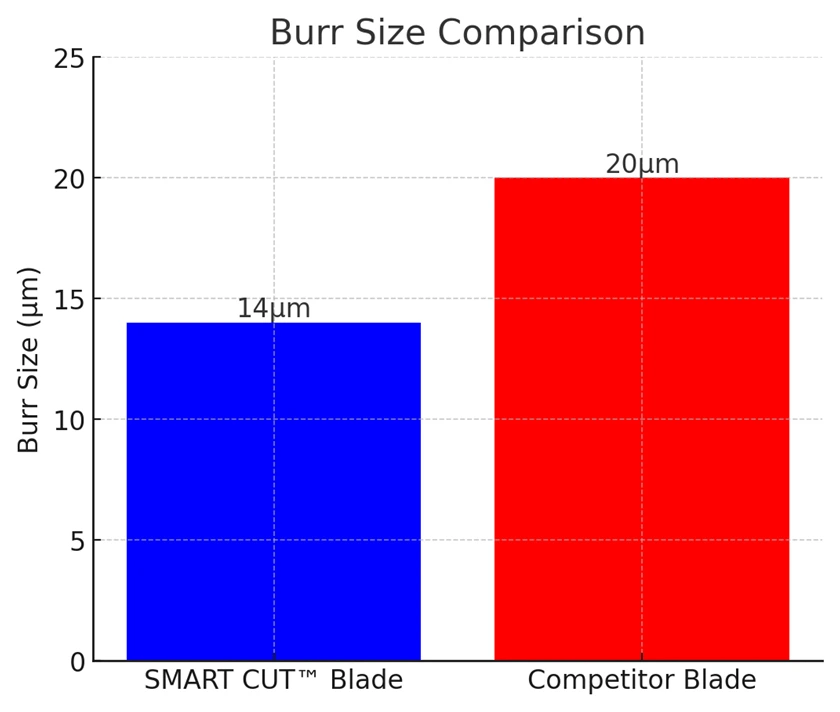
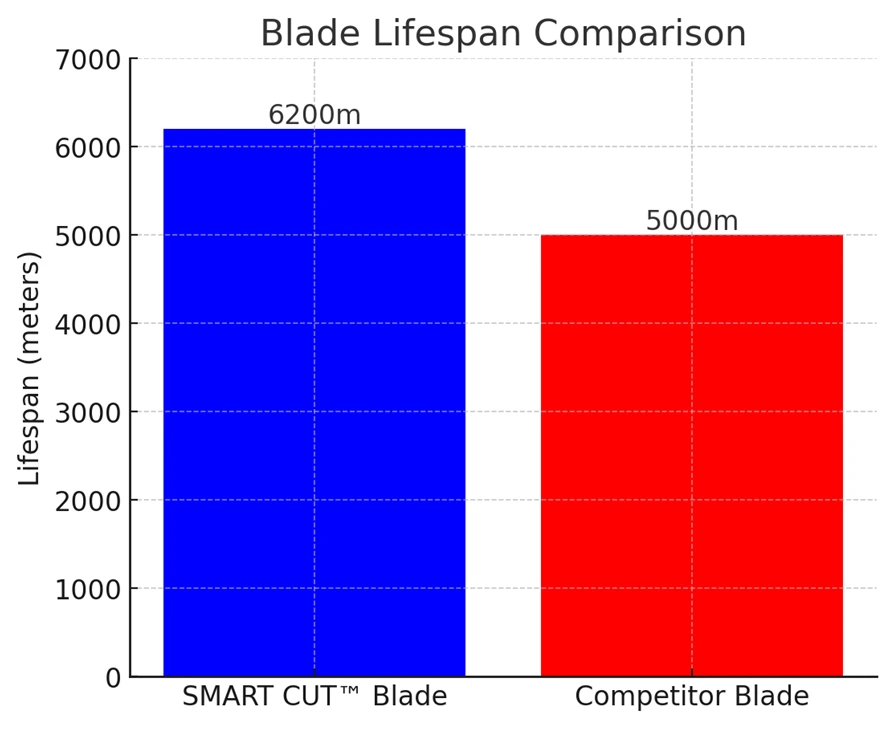
Case Study: Dicing Blade for AlN Substrate (LED Packaging)
Blade Specification:
- Blade Type: SMART CUT® Series (SCM) Sintered (Metal Bond) Dicing Blade
- Model: SMART CUT® Series (SC1M)
- Blade Size: 56 D × 0.2 T × 40 H
- Material: Silica Gel + Aluminum Nitride
Performance Comparison: SMART CUT® Series (SCM) vs. Competitor Blade
Performance Metric |
SMART CUT® Blade |
Competitor Blade |
---|---|---|
Chipping (µm) |
<48 µm (Superior edge quality) |
62-75 µm (Higher chipping) |
Blade Life (Lines Processed) |
2,100 lines (More than 2× longer lifespan) |
950 lines |
Current Value (A) |
2.4 – 2.5 A |
2.3 – 2.5 A |
Key Benefits of SMART CUT® Series (SC1M) Blade
- Minimizes chipping to <48 µm, ensuring cleaner cuts and reducing post-processing.
- More than doubles blade life, processing 2,100 lines vs. 950 lines with the competitor blade.
- Enhanced wear resistance, reducing overall cost per cut and machine downtime.
- Optimized cutting performance for Aluminum Nitride (AlN) substrates in LED packaging applications.
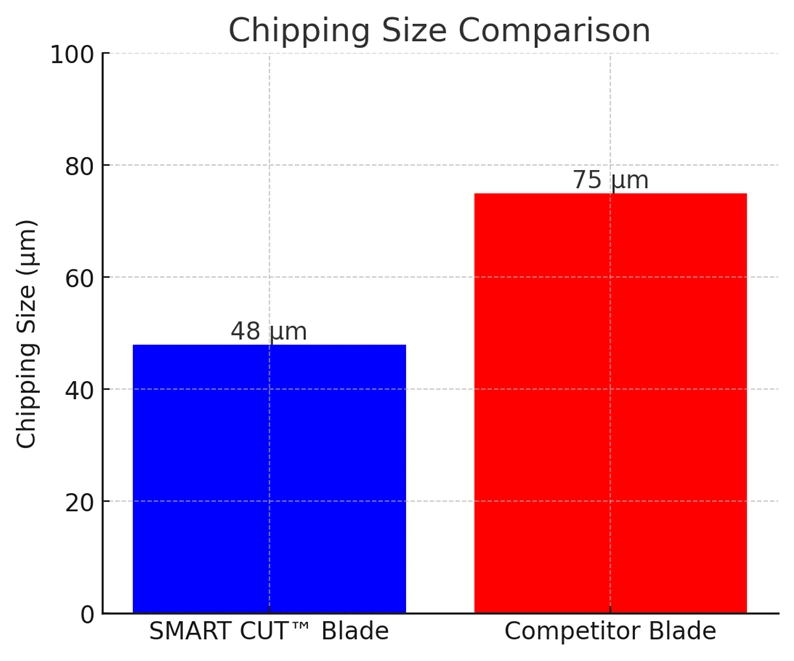
Case Study: Dicing Blade for MLCC (Passive Components Packaging)
Blade Specification:
- Blade Type: SMART CUT® Series (SCM) Sintered (Metal Bond) Dicing Blade Model: SMART CUT® Series (SC1M)
- Blade Size: 54mm D × 0.127mm TH × 40H
Performance Comparison: SMART CUT® Series (SCM) vs. Competitor Blade
Performance Metric |
SMART CUT® Blade |
Competitor Blade |
---|---|---|
Chipping (µm) |
<22 µm (Superior edge quality) |
>28 µm (Higher chipping) |
Blade Life (Meters Cut) |
8,300 m (Longer-lasting performance) |
7,000 m |
Current Value (A) |
2.3 – 2.5 A |
2.4 – 2.7 A |
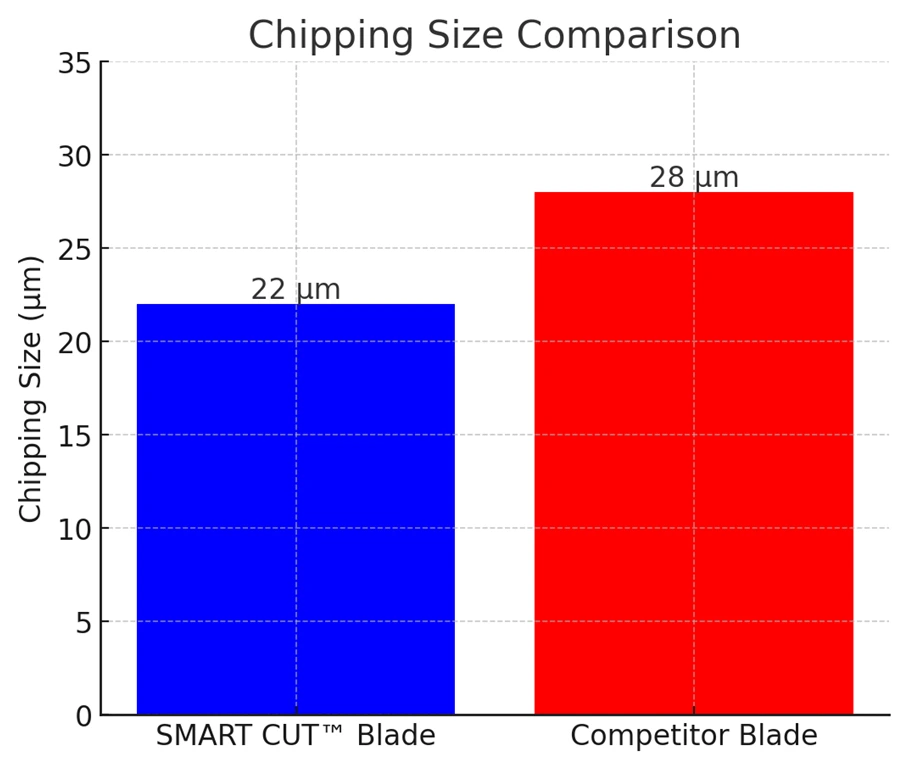
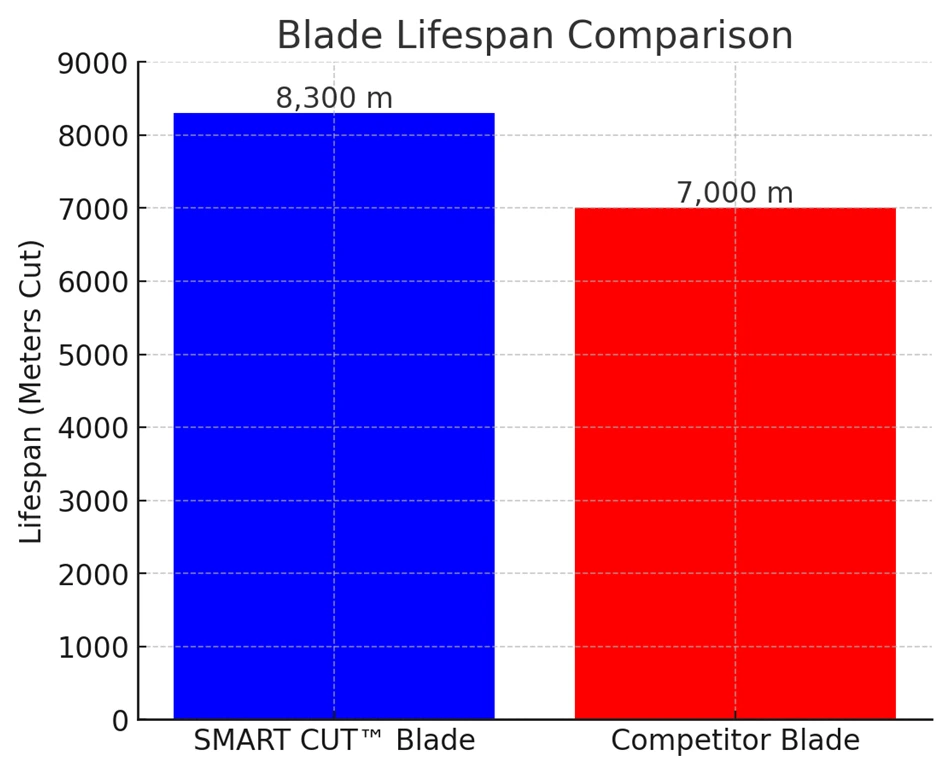
Key Benefits of SMART CUT® Series (SC1M) Blade
- Minimizes chipping to <22 µm, providing superior edge quality.
- Extends blade life to 8,300 meters, lasting longer than the competition.
- More stable cutting performance, operating at lower current values (2.3-2.5 A).
- Optimized for MLCC and passive component packaging, ensuring precision, speed, and cost-efficiency.
Case Study: High-Precision Dicing of Silicon Nitride (Si₃N₄) Using SMART CUT™ Diamond Blades
Application Overview
- Material: Silicon Nitride (Si₃N₄)
- Machine Spindle Speed: 25,000 RPM
- Feed Rate: 8 mm/sec
- Blade Type: SMART CUT® Series (SCM) Sintered (Metal Bond) Dicing Blade Model: SMART CUT® Series (SC4M)
- Blade Size: 54mm D × 0.2mm T × 40H
Blade Specifications & Performance Comparison
Performance Metric |
SMART CUT™ Blade |
Competitor Blade |
---|---|---|
Blade Type |
Metal Bond Diamond Blade |
Metal Bond Diamond Blade |
Blade Size |
56D × 0.2T × 40H |
56D × 0.2T × 40H |
Diamond Grit Size |
6–10 µm (Optimized for Si₃N₄) |
8–12 µm |
Diamond Concentration |
100 (High-density diamond) |
75 (Lower concentration) |
Blade Lifespan |
5,000 meters (30% longer) |
3,800 meters |
Chipping Size |
≤12 µm (Superior edge quality) |
≤22 µm (Higher chipping) |
Cutting Speed Stability |
Highly stable, maintains precision |
Prone to performance loss over time |
Key Advantages of SMART CUT® Series (SC4M) Blade
- 30% Longer Blade Life → Processes 5,000 meters vs. 3,800 meters, reducing blade changes.
- Minimized Chipping → Produces ≤12 µm chipping, ensuring high-precision cuts with minimal post-processing.
- Higher Diamond Concentration → Provides better wear resistance and more consistent cutting performance.
- Optimized Diamond Grit Size → Achieves a cleaner surface finish while maintaining high cutting speeds.
Features
- Advanced Sintered Metal Bond Matrix
- Large Variety of Bond Matrixes for all Applications
- Superior Rigidity & Form Holding
- Wide Range of Diamond Grit
- Customizable Bond Hardness
- Optimized Diamond Concentration
- Minimal Chipping & Smooth Surface Finish
- Serrated & Custom Edge Profiles Available
- Compatible with Most Precision Dicing Equipment
- Works on a Wide Range of Materials
- Less wear/higher blade life
- Highly accurate blade dimensions
- Minimal Chipping of Critical Edges
- Less wear/higher blade life
Benefits
- Increase Blade Life
- Reduce Chipping
- Reduce Blade Wear
- Increase Process Consistency
- Maintain Consistent Cutting Speed
- Reduce Blade Change & Mounting Cost
- Reduce Cost
- Lower Operating Costs
- Higher Cutting Efficiency
- Improved Cut Quality
- Versatile Application
- Better Material Yield
- Precision and Reliability
Advantages
- Extended Blade Life
- Superior Cutting Precision
- Consistent Performance
- Reduced Chipping & Surface Damage.
- Higher Wear Resistance –
- Customizable for Any Application
- Efficient Coolant Retention
- Compatible with Most Dicing Machines
- Cost-Effective
- Excellent Return on Investment
- Maximum Cutting Performance
- No Glazing
- Faster Cutting Action
- Improved surface finish quality
- Better coolant retention
- No Material Deformation
- No Contamination
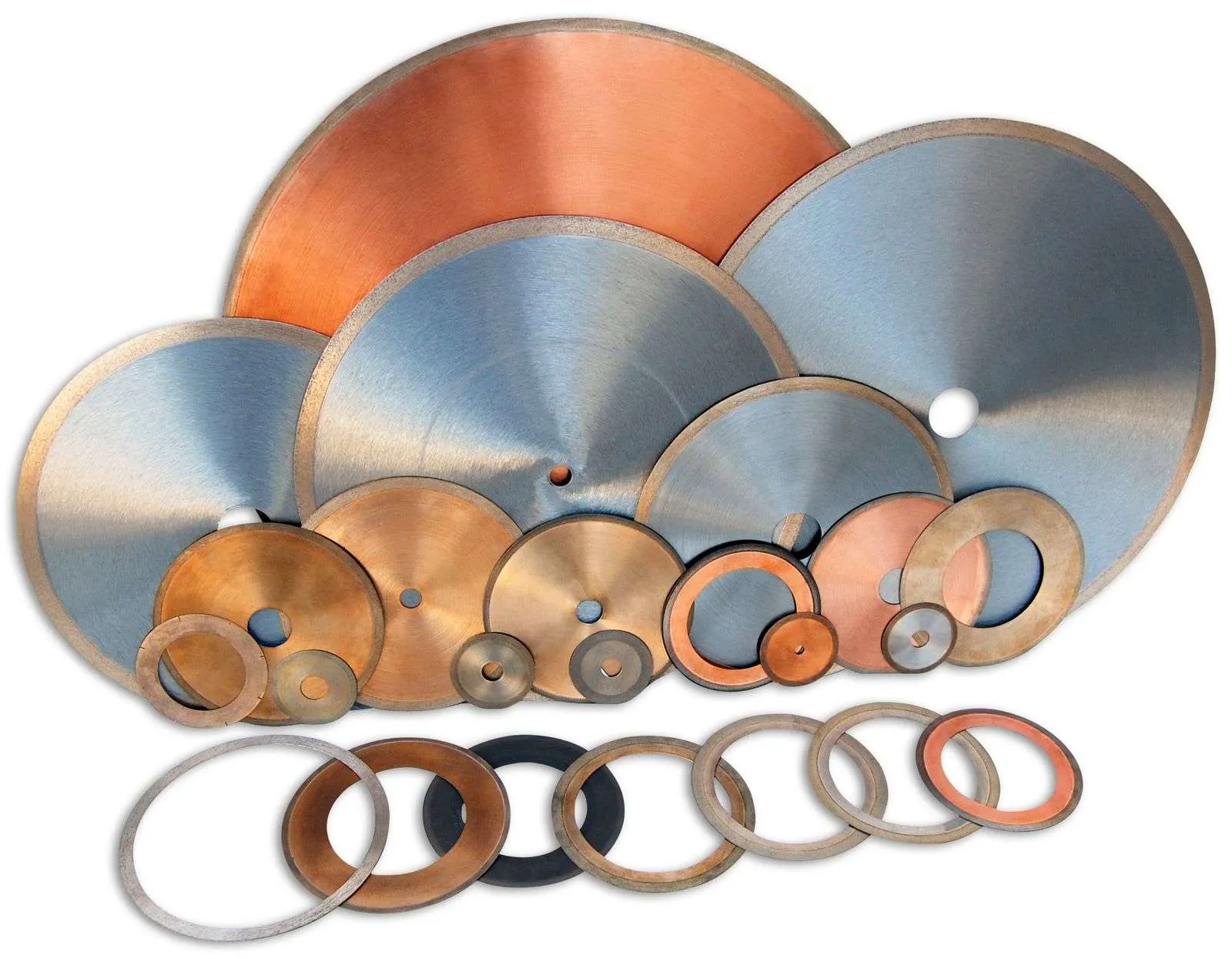
SMART CUT® Sintered Metal Bond Dicing / Slicing Blades with a Steel Core
SMART CUT® Sintered metal bond dicing / slicing blades with a steel core offer exceptional strength and rigidity, making them well-suited for high-precision applications. The combination of the sintered metal bond and the steel core provides added durability, ensuring that the blade maintains its form during demanding cutting operations. These blades are perfect for deep or aggressive cutting, grooving, and slicing of a variety of materials, both delicate and tough. The added rigidity minimizes blade deflection, which is critical for maintaining consistent performance and protecting the workpiece from damage.
The reduced deflection helps lower operational costs by decreasing the likelihood of material defects and reducing the need for frequent blade replacements. These blades are available in diamond, CBN, and custom grit formulations, offering versatility to meet a wide range of cutting requirements.
The blade sizing and shape are highly customizable to suit specific applications, ensuring optimal performance across different materials and cutting conditions.
One of the key benefits of SMART CUT® sintered metal bond blades with a steel core is their extended lifespan. This design allows for longer periods of use, improving productivity and reducing downtime. Additionally, the blades can be equipped with or without water slots, depending on the cooling and lubrication requirements of the application. The edge design/radius can abrasive edge be customized enabling precise control over the depth, width, and shape of the cut.
Advantages:
- High Strength and Rigidity
- Extended Blade Life
- Minimal Deflection
- Ideal for Deep or Aggressive Cutting
- Available in Various Grit Formulas
- Highly Customizable
- Improved Precision
- Versatility in Applications
- Resistant to Wear
- Low Vibration
Why Work With Us?
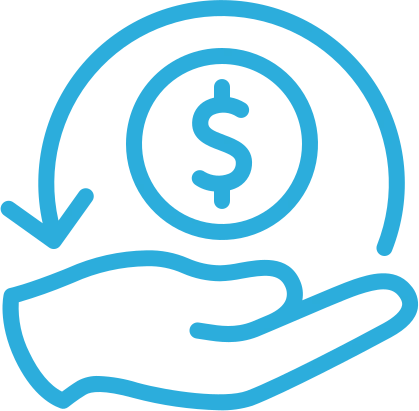
Best Return
on Investment
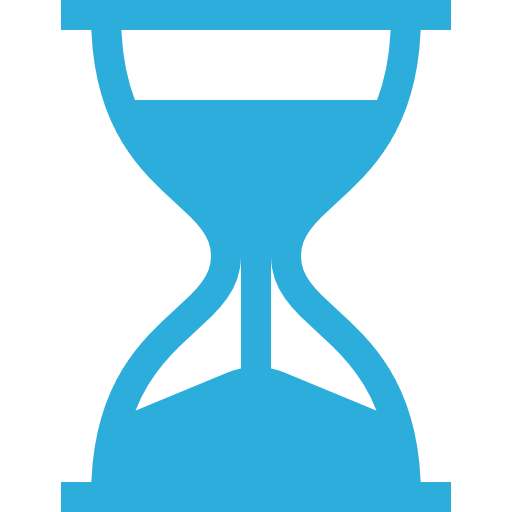
Attractive Cost of
Ownership
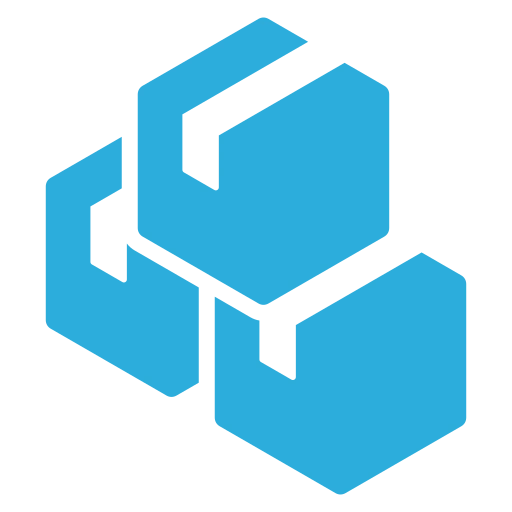
Thousands of Diamond & CBN Blades in stock
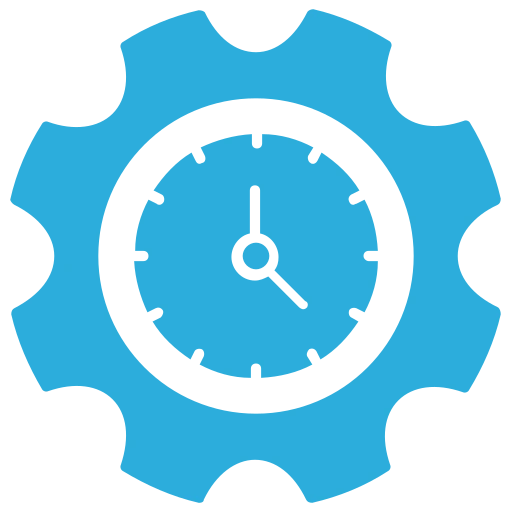
Custom Manufacturer with Fast Lead times
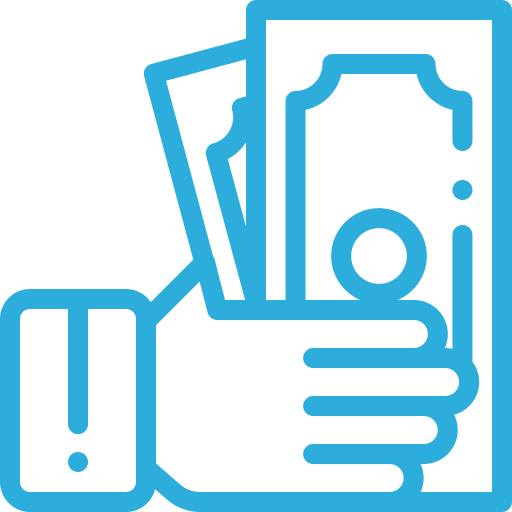
Unmatched
Prices in North America
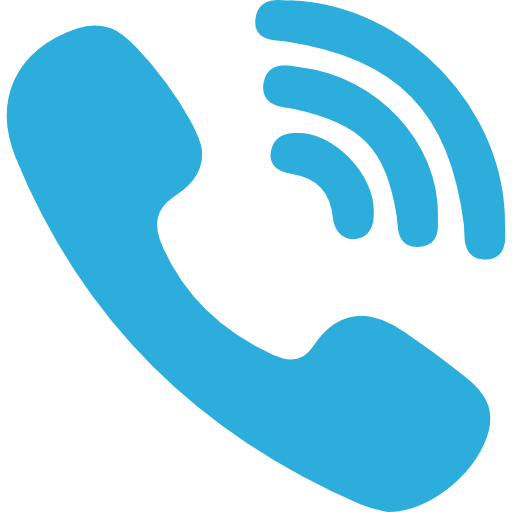
Unmatched Experience & Technical Support
Different Technology
SMART CUT® technology
Manufactured utilizing SMART CUT® technology, each diamond works like a small horse. Diamonds come in contact with the material in the right place and at the right time, working where you need them most. You get the maximum use out of diamond and bond.
Diamonds are oriented inside metal matrix, so that every diamond is better able to participate in cutting action.
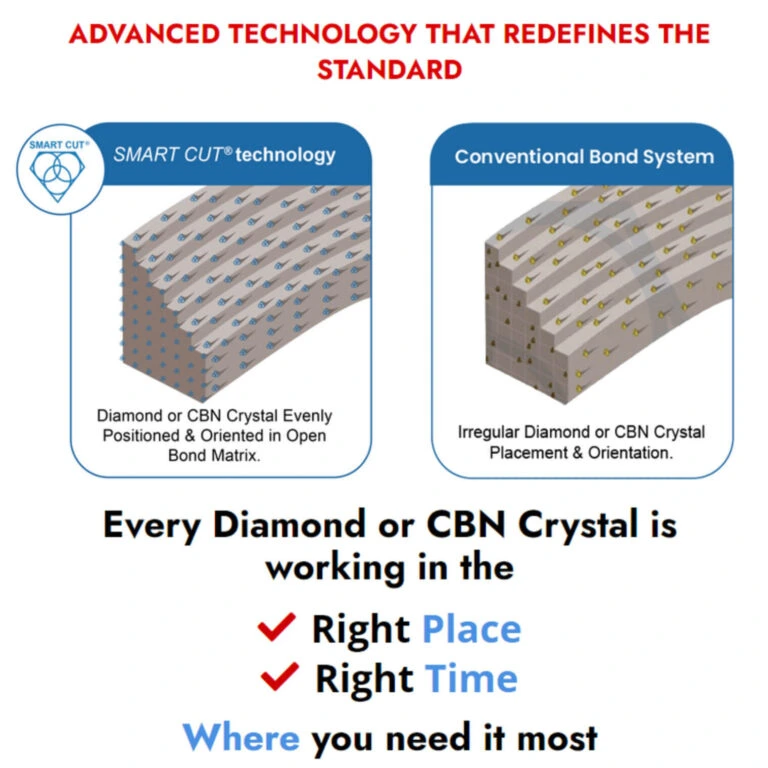
How SMART CUT® Bond Works?
Step 1
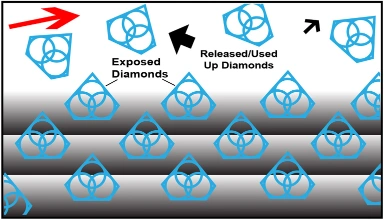
Sharpest And Finest Quality Diamonds
The newly exposed diamonds don’t effect diamonds already working on the material. Unlike many other diamond bonds, diamonds in a SMART CUT® Bond remains sharp and grow sharper with each cut, prolonging product life and consistent performance.
Step 2
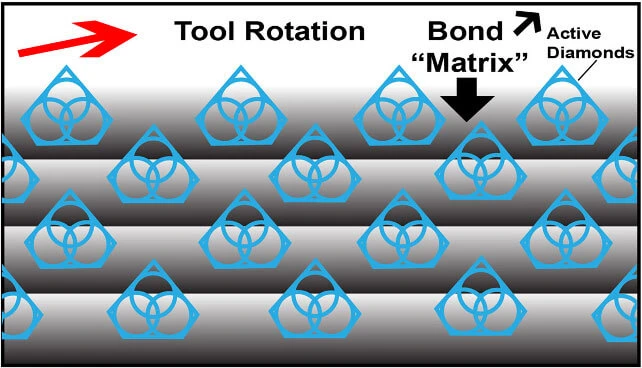
Diamonds or CBN Crystals
Diamonds or CBN Crystals are activated only at the exposed layer. As Bond Matrix layer begin to wear out, diamonds in a new Bond Matrix layer are immediately activated, substituting the already used up diamond layer. The SMART CUT® Diamond Hybrid Bond makes sure every diamond is in the right place and at the right time, working where you need it most.
Step 3
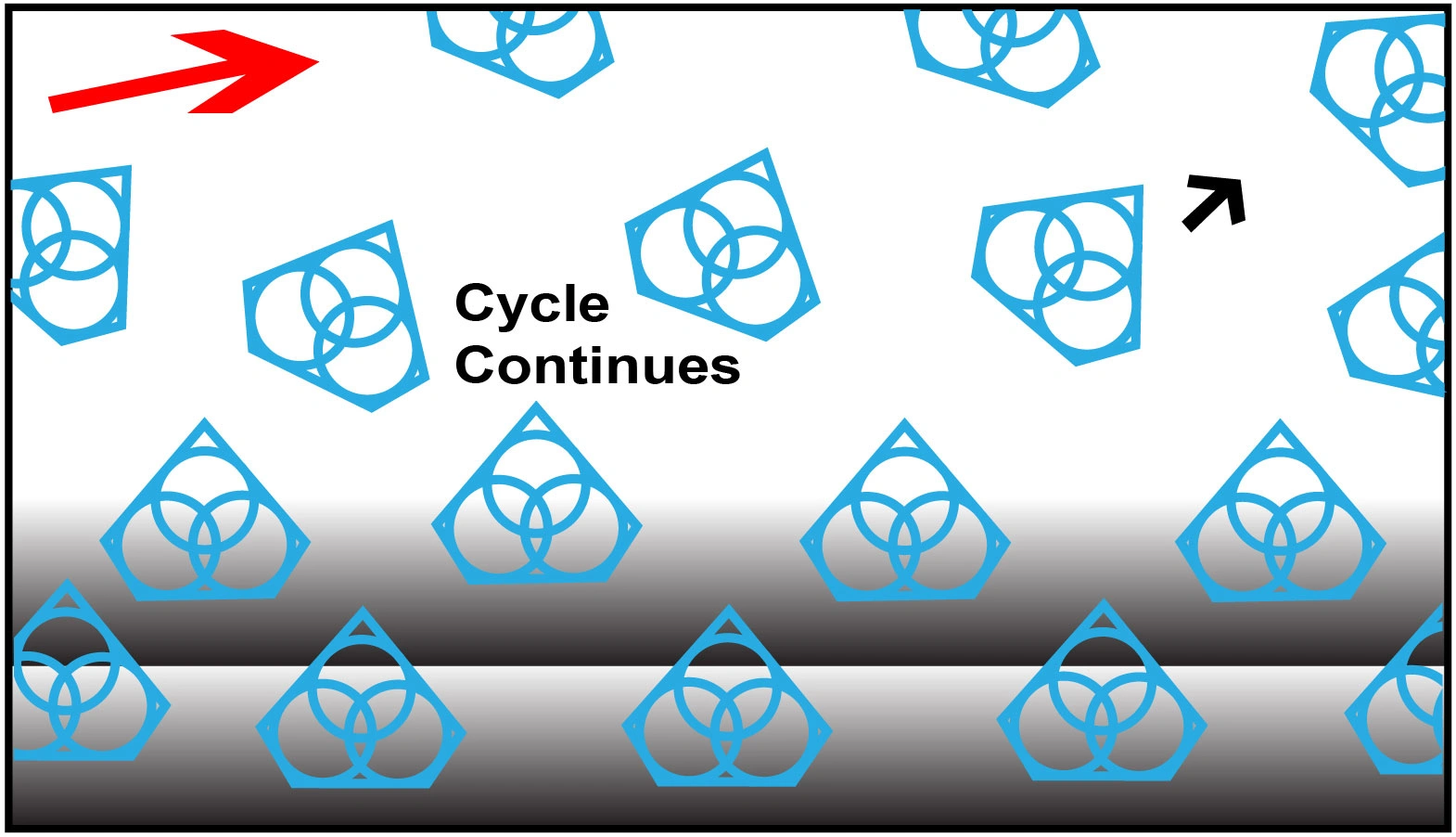
Advanced Formulated Open Diamond Bond Design
This advanced formulated open diamond bond design insures minimal chipping, fast cut, constant speed of cut, minimal cutting noise, and most important of all, consistent performance.
About Sintered (Metal Bond)
Sintered (Metal bonded) diamond blades diamonds sintered and multiple layers of diamonds impregnated inside the metal matrix. Diamonds are furnaces sintered in a matrix made of iron, cobalt, nickel, bronze, copper, tungsten, alloys of these powders or other metals in various combinations. Metal Bonded Dicing Blades are “impregnated” with diamonds. The compacted materials are then hot pressed or sintered to full density. Heating rate, applied pressure, sintering temperature and holding time, are all controlled according to the matrix composition. This means that selected diamonds are mixed and sintered with specific metal alloys to achieve the best cutting performance possible on any large variety of material. The metal bond surrounding the diamonds must wear away to continuously keep re-exposing the diamonds for the diamond tool to continue cutting.
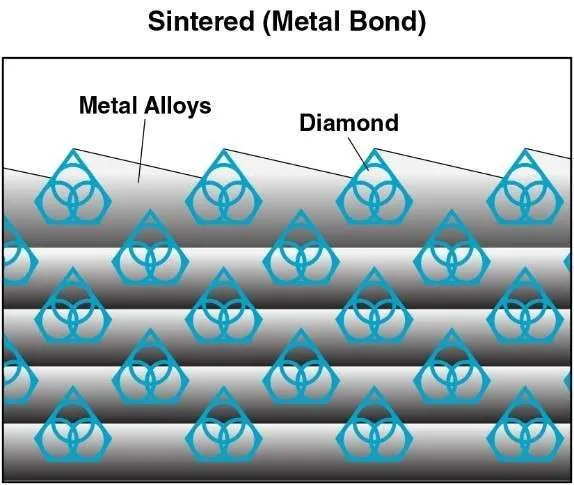
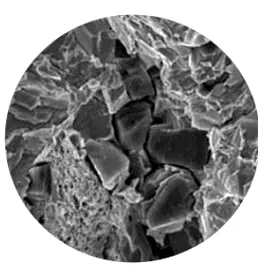
Sintered (metal bonded) dicing blades are recommended for cutting wide variety of materials from 45 to 75 on Rockwell Scale (5 to 9.5 on mohs scale of hardness). It is more wear resistant and holds diamond well in place, usually producing the highest yield/cutting ratio.
As a general rule of thumb, Metal Bond (sintered) diamond dicing blades longer than other diamond bond blades such as resin bond and electroplated (nickel bond) blades.
They wear evenly, and are known for their long life & consistency. Metal bond matrix does not protrude diamonds very high and hence usually requires lower cutting speeds than electroplated (nickel bond) and resin bond blades. In many dicing applications sintered (metal bond) dicing blades are used in applications which are not super hard or super brittle and with minimum tendency to produce chips or cracks.
Compare to any other Sintered (Metal Bond) Dicing Blade.
START SAVING TIME & MONEY TODAY!
Contact us for Free Quote & application recommendation.
We will work with you to determine your needs, and recommend the right parameters for your specific material/application. If you are not using SMART CUT® Sintered (Metal Bond) SCM series, you are loosing money & missing out on incredible performance.
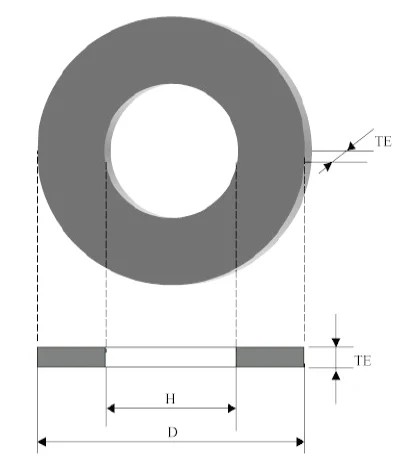
SMART CUT® Series SCM
SINTERED (METAL BOND) Specifications
Size designation: D x TE x H, where: D-Outside Blade Diameter, TE –Blade Thickness, H- Blade Inside Diameter.
Note: Our standard Tolerance on Outside Diameter for all blades is +/-.002”, tolerance. Higher tolerances are available upon request
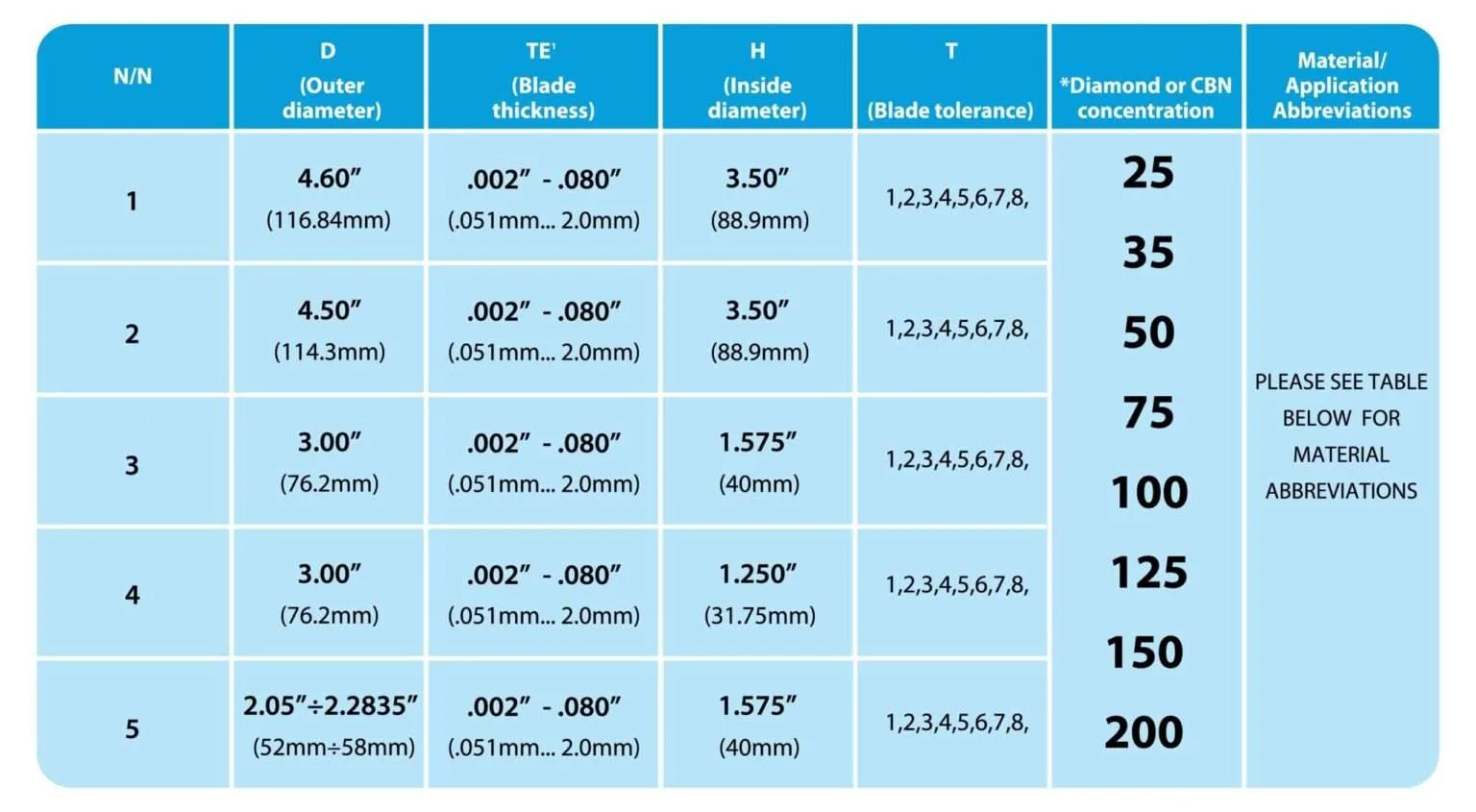
Material / Application |
Material Abbreviation |
SMART CUT™ Blade Series |
Diamond Particle Size |
Bond Hardness |
Diamond Concentration |
---|---|---|---|---|---|
FIBERGLASS |
FGS |
SC1M |
D126, D107, D91, D76, D54, D46 |
VVVHB, VVHB, VHBH, HBH, HBM |
HIGH CONCENTRATION |
CARBON |
CN |
SC1M |
D91, D76, D54, D46, 45µm, 30µm , 15µm |
VVVSB, VVSB, VSB |
LOW CONCENTRATION |
CERAMICS |
FRP, CS |
SC1M |
D54, D46, 45µm, 30µm, 15µm |
SBL, MHBL, MHBM |
LOW CONCENTRATION |
CARBIDE TGC |
CE |
SC1M |
D91, D76, D54. |
VVHB, VHBH, HBH, HBM |
HIGH CONCENTRATION |
QUARTZ |
QZ |
SC1M |
D54, D46, 45µm, 30µm, 15µm |
SBL, MHBL, MHBM |
LOW CONCENTRATION |
OPTICAL GLASS |
OG |
SC1M |
D54, D46, 45µm, 30µm, 15µm |
SBL, MHBL, MHBM |
LOW CONCENTRATION |
PHOTONICS GLASS |
PG |
SC1M |
D54, D46, 45µm, 30µm, 15µm |
SBL, MHBL, MHBM |
LOW CONCENTRATION |
MULTI-LAYER CERAMIC CAPACITORS |
BGA CSP MLCC |
SC1M |
30µm, 15µm, 9µm, 6µm, 45µm |
SBL, MHBL, MHBM |
LOW CONCENTRATION |
THIN FILM DISK DRIVE HEADS, ALUMINUM TITANIUM CARBIDE |
PZT; TFDDH |
SC1M |
D54, D46, 45µm, 30µm, 15µm |
SBL, MHBL, MHBM |
LOW CONCENTRATION |
SAPPHIRE, AL2O3 +Fe +Ti |
SE |
SC6M |
D54, D46, 45µm, 30µm, 15µm |
SBL, MHBL, MHBM |
LOW CONCENTRATION |
RUBY AL2O3 + Cr |
RY |
SC1M |
D91, D76, D54, D46, 45µm, 30µm , 15µm |
VVVSB, VVSB, VSB |
LOW CONCENTRATION |
LITHIUM NIOBITE LiNbO3 |
LN |
SC1M |
30µm, 15µm, 9µm, 6µm, 45µm |
SBL, MHBL, MHBM |
LOW CONCENTRATION |
LITHIUM TANTILATE LiTaO3 |
LT |
SC1M |
30µm, 15µm, 9µm, 6µm, 45µm |
SBL, MHBL, MHBM |
LOW CONCENTRATION |
ALUMINA (HYBRID SUBSTRATES AND CERAMICS PACKAGES |
AL |
SC1M |
D91, D76, D54, D46, 45µm, 30µm , 15µm |
VVVSB, VVSB, VSB |
LOW CONCENTRATION |
QFN, COPPER + EPOXY MOLDING |
QFN |
SC1M |
D126, D107, D91, D76, D54, D46 |
VVVHB, VVHB, VHBH, HBH, HBM |
HIGH CONCENTRATION |
ALUMINUM NITRIDE |
ALN |
SC1M |
D91, D76, D54, D46, 45µm, 30µm , 15µm |
VVVSB, VVSB, VSB |
LOW CONCENTRATION |
ZIRCONIA (ZrO2) |
ZA |
SC1M |
D54, D46, 45µm, 30µm, 15µm |
SBL, MHBL, MHBM |
LOW CONCENTRATION |
BORON CARBIDE (B4C) |
BC |
SC1M |
D91, D76, D54, D46, 45µm, 30µm , 15µm |
VVVSB, VVSB, VSB |
LOW CONCENTRATION |
TITANIUM DIBORIDE (TiB2) |
TD |
SC1M |
D91, D76, D54, D46, 45µm, 30µm , 15µm |
VVVSB, VVSB, VSB |
LOW CONCENTRATION |
GLASS + SiO2 |
GSi |
SC6H |
30µm, 15µm, 9µm, 6µm, 45µm |
SBL, MHBL, MHBM |
LOW CONCENTRATION |
SILICON |
Si |
SC1M |
D54, D46, 45µm, 30µm, 15µm |
SBL, MHBL, MHBM |
LOW CONCENTRATION |
SILICON-CARBIDE SiC |
SC |
SC1M |
D91, D76, D54, D46, 45µm, 30µm , 15µm |
VVVSB, VVSB, VSB |
LOW CONCENTRATION |
ZINK-SELENIDE ZnSe |
ZS |
SC1M |
D91, D76, D54, D46, 45µm, 30µm , 15µm |
VVVSB, VVSB, VSB |
LOW CONCENTRATION |
BARIUM-TITINATE |
BTI |
SC1M |
D91, D76, D54, D46, 45µm, 30µm , 15µm |
VVVSB, VVSB, VSB |
LOW CONCENTRATION |
BISMUTH-SILICATE Bi12Si22 |
BS |
SC1M |
D91, D76, D54, D46, 45µm, 30µm , 15µm |
VVVSB, VVSB, VSB |
LOW CONCENTRATION |
BISMUTH-TELLURIDE |
BTE |
SC1M |
D91, D76, D54, D46, 45µm, 30µm , 15µm |
VVVSB, VVSB, VSB |
LOW CONCENTRATION |
GGGNaGd (W04)2 |
G2 |
SC1M |
D91, D76, D54, D46, 45µm, 30µm , 15µm |
VVVSB, VVSB, VSB |
LOW CONCENTRATION |
GARNET |
G |
SC4H |
D91, D76, D54, D46, 45µm, 30µm , 15µm |
VVVSB, VVSB, VSB |
LOW CONCENTRATION |
KOVAR NiFeCo |
K |
SC4M |
30µm, 15µm, 9µm, 6µm, 45µm |
SBL, MHBL, MHBM |
LOW CONCENTRATION |
SILICON NITRIDE Si3N4 |
SN |
SC4M |
D91, D76, D54, D46, 45µm, 30µm , 15µm |
VVVSB, VVSB, VSB |
LOW CONCENTRATION |
STONE |
SE |
SC5M |
D107, D91, D76. |
VVHB, VHBH, HBH, HBM |
HIGH CONCENTRATION |
NON-FERROUS ABRASION RESISTANT MATERIALS |
NFARS |
SC6M |
D107, D91, D76. |
VVHB, VHBH, HBH, HBM |
HIGH CONCENTRATION |
HIGH SPEED TOOL STEELS |
HSTS |
SC3M |
B126, B107, B91, B76, B54, B46 |
VVVHB, VVHB, VHBH, HBH, HBM |
HIGH CONCENTRATION |
DIE STEELS |
DS |
SC3M |
B126, B107, B91, B76, B54, B46 |
VVVHB, VVHB, VHBH, HBH, HBM |
HIGH CONCENTRATION |
HARDENED CARBON STEEL |
HCS |
SC3M |
B126, B107, B91, B76, B54, B46 |
VVVHB, VVHB, VHBH, HBH, HBM |
HIGH CONCENTRATION |
INCONEL |
IL |
SC3M |
B126, B107, B91, B76, B54, B46 |
VVVHB, VVHB, VHBH, HBH, HBM |
HIGH CONCENTRATION |
MONEL |
ML |
SC3M |
B126, B107, B91, B76, B54, B46 |
VVVHB, VVHB, VHBH, HBH, HBM |
HIGH CONCENTRATION |
RENE |
RE |
SC3M |
B126, B107, B91, B76, B54, B46 |
VVVHB, VVHB, VHBH, HBH, HBM |
HIGH CONCENTRATION |
WASPALLOY |
WY |
SC3M |
B126, B107, B91, B76, B54, B46 |
VVVHB, VVHB, VHBH, HBH, HBM |
HIGH CONCENTRATION |
HARD FERROUS SUPERALLOYS |
HFS |
SC3M |
B126, B107, B91, B76, B54, B46 |
VVVHB, VVHB, VHBH, HBH, HBM |
HIGH CONCENTRATION |
** Letter Abbreviations: D-FOR DIAMOND, B -FOR CBN.
**** If Material or Application is not listed in the chart above, please inquire. We can provide proper blade specification for just about any type of material/application.
Material / Application
Material Abbreviation
SMART CUT™ Blade Series
Diamond Particle Size
Bond Hardness
Diamond Concentration
FIBERGLASS
FGS
SC1M
D126, D107, D91, D76, D54, D46
VVVHB, VVHB, VHBH, HBH, HBM
HIGH CONCENTRATION
CARBON
CN
SC1M
D91, D76, D54, D46, 45µm, 30µm , 15µm
VVVSB, VVSB, VSB
LOW CONCENTRATION
CERAMICS
FRP, CS
SC1M
D54, D46, 45µm, 30µm, 15µm
SBL, MHBL, MHBM
LOW CONCENTRATION
CARBIDE TGC
CE
SC1M
D91, D76, D54.
VVHB, VHBH, HBH, HBM
HIGH CONCENTRATION
QUARTZ
QZ
SC1M
D54, D46, 45µm, 30µm, 15µm
SBL, MHBL, MHBM
LOW CONCENTRATION
OPTICAL GLASS
OG
SC1M
D54, D46, 45µm, 30µm, 15µm
SBL, MHBL, MHBM
LOW CONCENTRATION
PHOTONICS GLASS
PG
SC1M
D54, D46, 45µm, 30µm, 15µm
SBL, MHBL, MHBM
LOW CONCENTRATION
MULTI-LAYER CERAMIC CAPACITORS
BGA CSP MLCC
SC1M
30µm, 15µm, 9µm, 6µm, 45µm
SBL, MHBL, MHBM
LOW CONCENTRATION
THIN FILM DISK DRIVE HEADS, ALUMINUM TITANIUM CARBIDE
PZT; TFDDH
SC1M
D54, D46, 45µm, 30µm, 15µm
SBL, MHBL, MHBM
LOW CONCENTRATION
SAPPHIRE, AL2O3 +Fe +Ti
SE
SC6M
D54, D46, 45µm, 30µm, 15µm
SBL, MHBL, MHBM
LOW CONCENTRATION
RUBY AL2O3 + Cr
RY
SC1M
D91, D76, D54, D46, 45µm, 30µm , 15µm
VVVSB, VVSB, VSB
LOW CONCENTRATION
LITHIUM NIOBITE LiNbO3
LN
SC1M
30µm, 15µm, 9µm, 6µm, 45µm
SBL, MHBL, MHBM
LOW CONCENTRATION
LITHIUM TANTILATE LiTaO3
LT
SC1M
30µm, 15µm, 9µm, 6µm, 45µm
SBL, MHBL, MHBM
LOW CONCENTRATION
ALUMINA (HYBRID SUBSTRATES AND CERAMICS PACKAGES
AL
SC1M
D91, D76, D54, D46, 45µm, 30µm , 15µm
VVVSB, VVSB, VSB
LOW CONCENTRATION
QFN, COPPER + EPOXY MOLDING
QFN
SC1M
D126, D107, D91, D76, D54, D46
VVVHB, VVHB, VHBH, HBH, HBM
HIGH CONCENTRATION
ALUMINUM NITRIDE
ALN
SC1M
D91, D76, D54, D46, 45µm, 30µm , 15µm
VVVSB, VVSB, VSB
LOW CONCENTRATION
ZIRCONIA (ZrO2)
ZA
SC1M
D54, D46, 45µm, 30µm, 15µm
SBL, MHBL, MHBM
LOW CONCENTRATION
BORON CARBIDE (B4C)
BC
SC1M
D91, D76, D54, D46, 45µm, 30µm , 15µm
VVVSB, VVSB, VSB
LOW CONCENTRATION
TITANIUM DIBORIDE (TiB2)
TD
SC1M
D91, D76, D54, D46, 45µm, 30µm , 15µm
VVVSB, VVSB, VSB
LOW CONCENTRATION
GLASS + SiO2
GSi
SC6H
30µm, 15µm, 9µm, 6µm, 45µm
SBL, MHBL, MHBM
LOW CONCENTRATION
SILICON
Si
SC1M
D54, D46, 45µm, 30µm, 15µm
SBL, MHBL, MHBM
LOW CONCENTRATION
SILICON-CARBIDE SiC
SC
SC1M
D91, D76, D54, D46, 45µm, 30µm , 15µm
VVVSB, VVSB, VSB
LOW CONCENTRATION
ZINK-SELENIDE ZnSe
ZS
SC1M
D91, D76, D54, D46, 45µm, 30µm , 15µm
VVVSB, VVSB, VSB
LOW CONCENTRATION
BARIUM-TITINATE
BTI
SC1M
D91, D76, D54, D46, 45µm, 30µm , 15µm
VVVSB, VVSB, VSB
LOW CONCENTRATION
BISMUTH-SILICATE Bi12Si22
BS
SC1M
D91, D76, D54, D46, 45µm, 30µm , 15µm
VVVSB, VVSB, VSB
LOW CONCENTRATION
BISMUTH-TELLURIDE
BTE
SC1M
D91, D76, D54, D46, 45µm, 30µm , 15µm
VVVSB, VVSB, VSB
LOW CONCENTRATION
GGGNaGd (W04)2
G2
SC1M
D91, D76, D54, D46, 45µm, 30µm , 15µm
VVVSB, VVSB, VSB
LOW CONCENTRATION
GARNET
G
SC4H
D91, D76, D54, D46, 45µm, 30µm , 15µm
VVVSB, VVSB, VSB
LOW CONCENTRATION
KOVAR NiFeCo
K
SC4M
30µm, 15µm, 9µm, 6µm, 45µm
SBL, MHBL, MHBM
LOW CONCENTRATION
SILICON NITRIDE Si3N4
SN
SC4M
D91, D76, D54, D46, 45µm, 30µm , 15µm
VVVSB, VVSB, VSB
LOW CONCENTRATION
STONE
SE
SC5M
D107, D91, D76.
VVHB, VHBH, HBH, HBM
HIGH CONCENTRATION
NON-FERROUS ABRASION RESISTANT MATERIALS
NFARS
SC6M
D107, D91, D76.
VVHB, VHBH, HBH, HBM
HIGH CONCENTRATION
HIGH SPEED TOOL STEELS
HSTS
SC3M
B126, B107, B91, B76, B54, B46
VVVHB, VVHB, VHBH, HBH, HBM
HIGH CONCENTRATION
DIE STEELS
DS
SC3M
B126, B107, B91, B76, B54, B46
VVVHB, VVHB, VHBH, HBH, HBM
HIGH CONCENTRATION
HARDENED CARBON STEEL
HCS
SC3M
B126, B107, B91, B76, B54, B46
VVVHB, VVHB, VHBH, HBH, HBM
HIGH CONCENTRATION
INCONEL
IL
SC3M
B126, B107, B91, B76, B54, B46
VVVHB, VVHB, VHBH, HBH, HBM
HIGH CONCENTRATION
MONEL
ML
SC3M
B126, B107, B91, B76, B54, B46
VVVHB, VVHB, VHBH, HBH, HBM
HIGH CONCENTRATION
RENE
RE
SC3M
B126, B107, B91, B76, B54, B46
VVVHB, VVHB, VHBH, HBH, HBM
HIGH CONCENTRATION
WASPALLOY
WY
SC3M
B126, B107, B91, B76, B54, B46
VVVHB, VVHB, VHBH, HBH, HBM
HIGH CONCENTRATION
HARD FERROUS SUPERALLOYS
HFS
SC3M
B126, B107, B91, B76, B54, B46
VVVHB, VVHB, VHBH, HBH, HBM
HIGH CONCENTRATION
** Letter Abbreviations: D-FOR DIAMOND, B -FOR CBN.
**** If Material or Application is not listed in the chart above, please inquire. We can provide proper blade specification for just about any type of material/application.
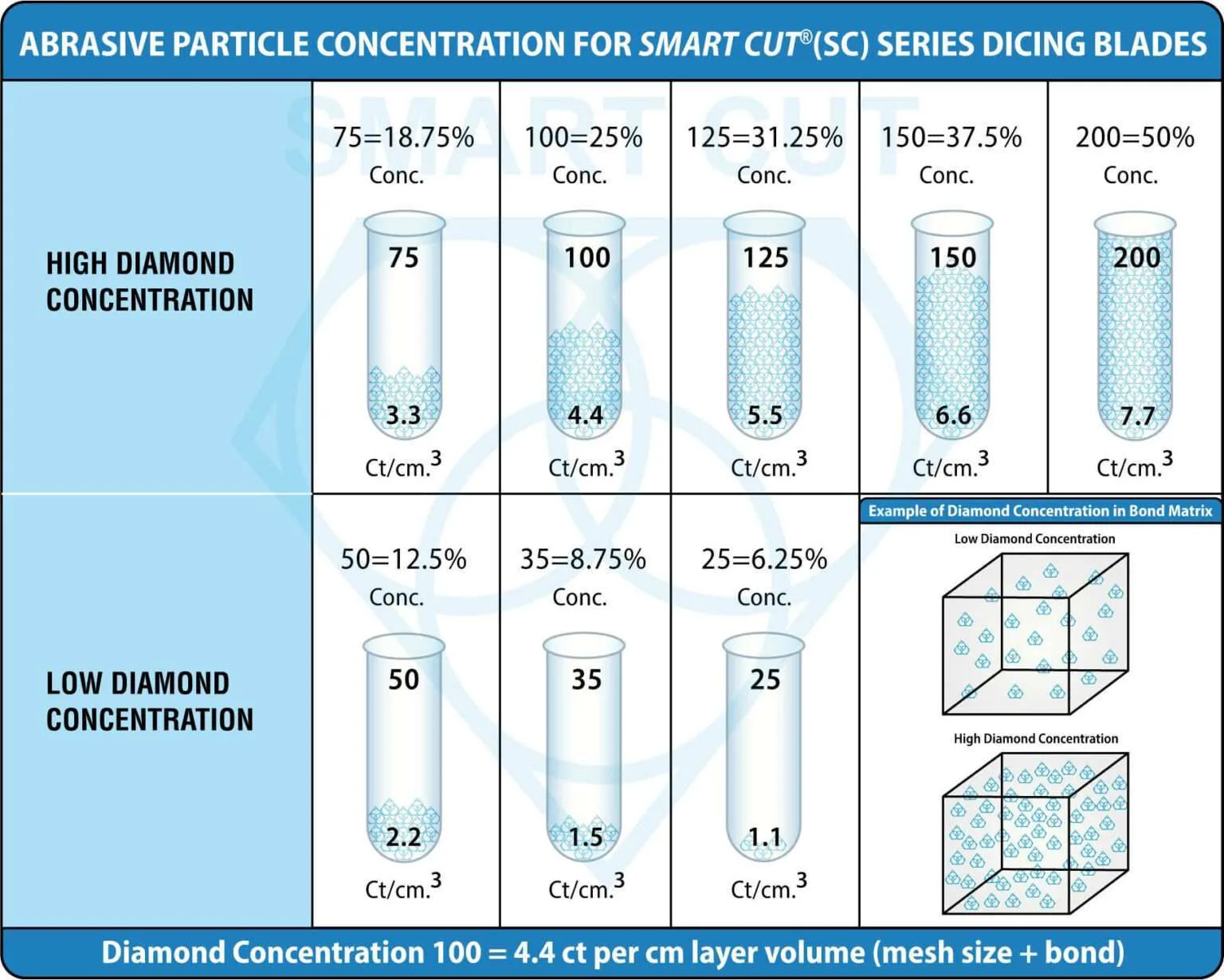
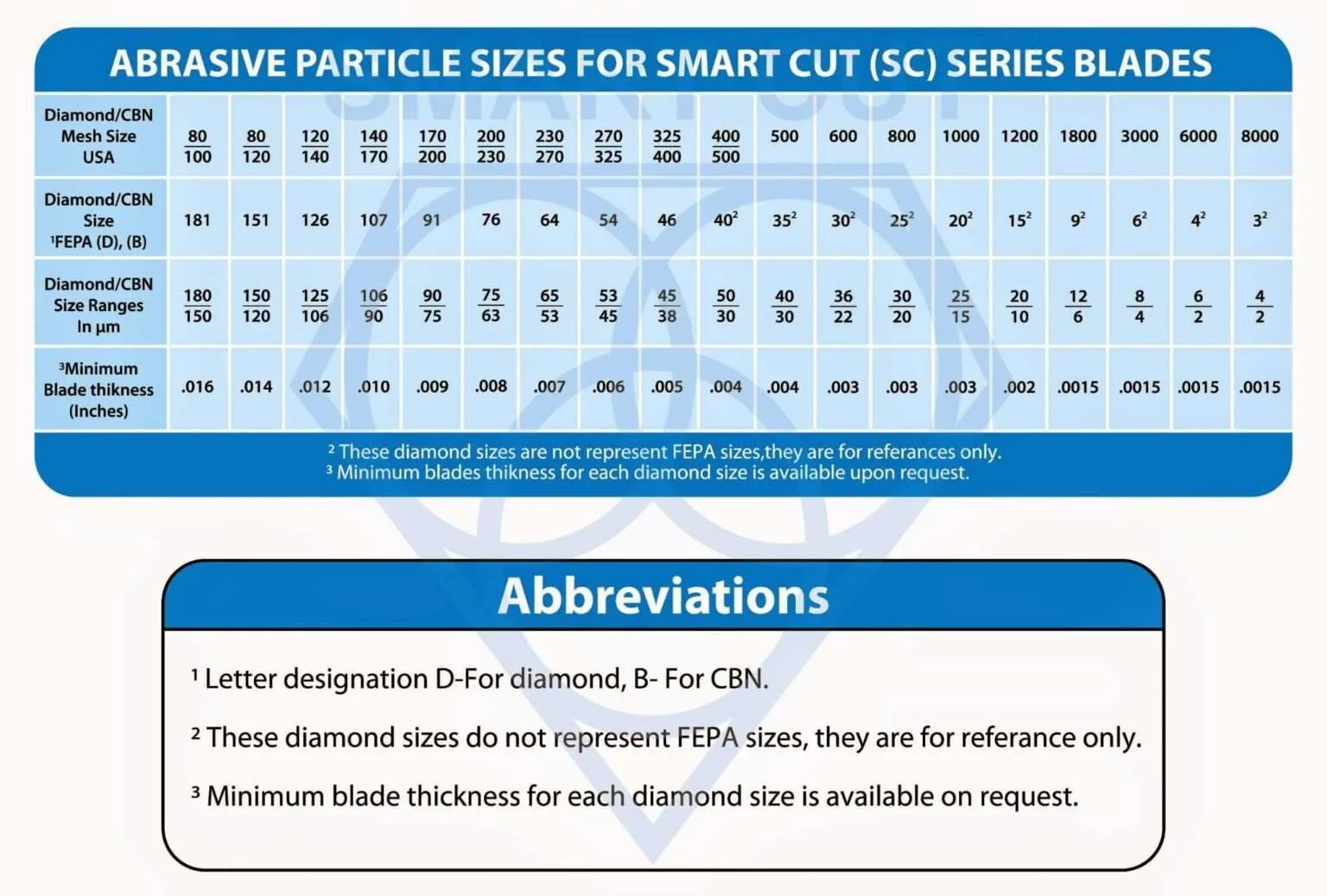
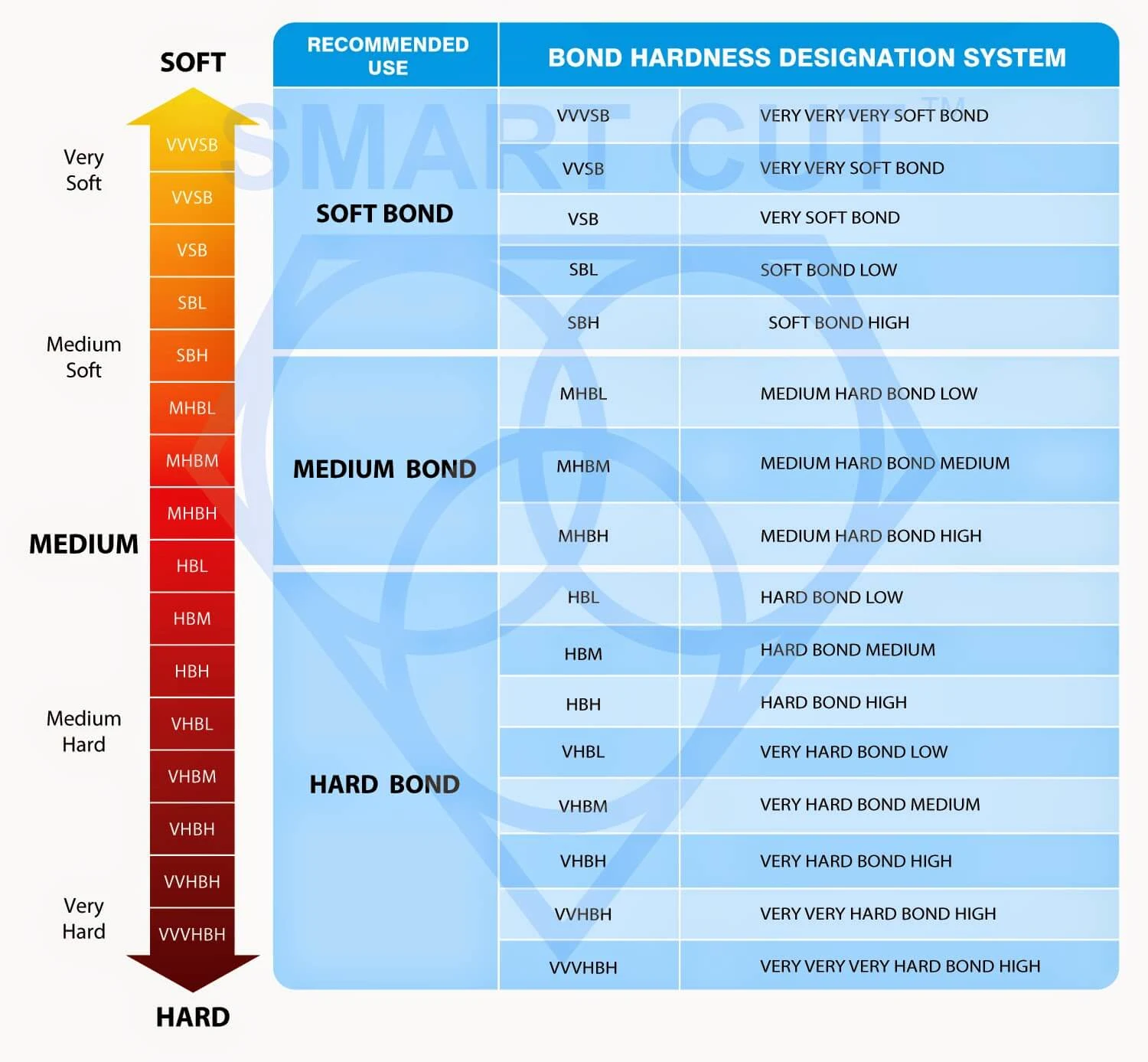
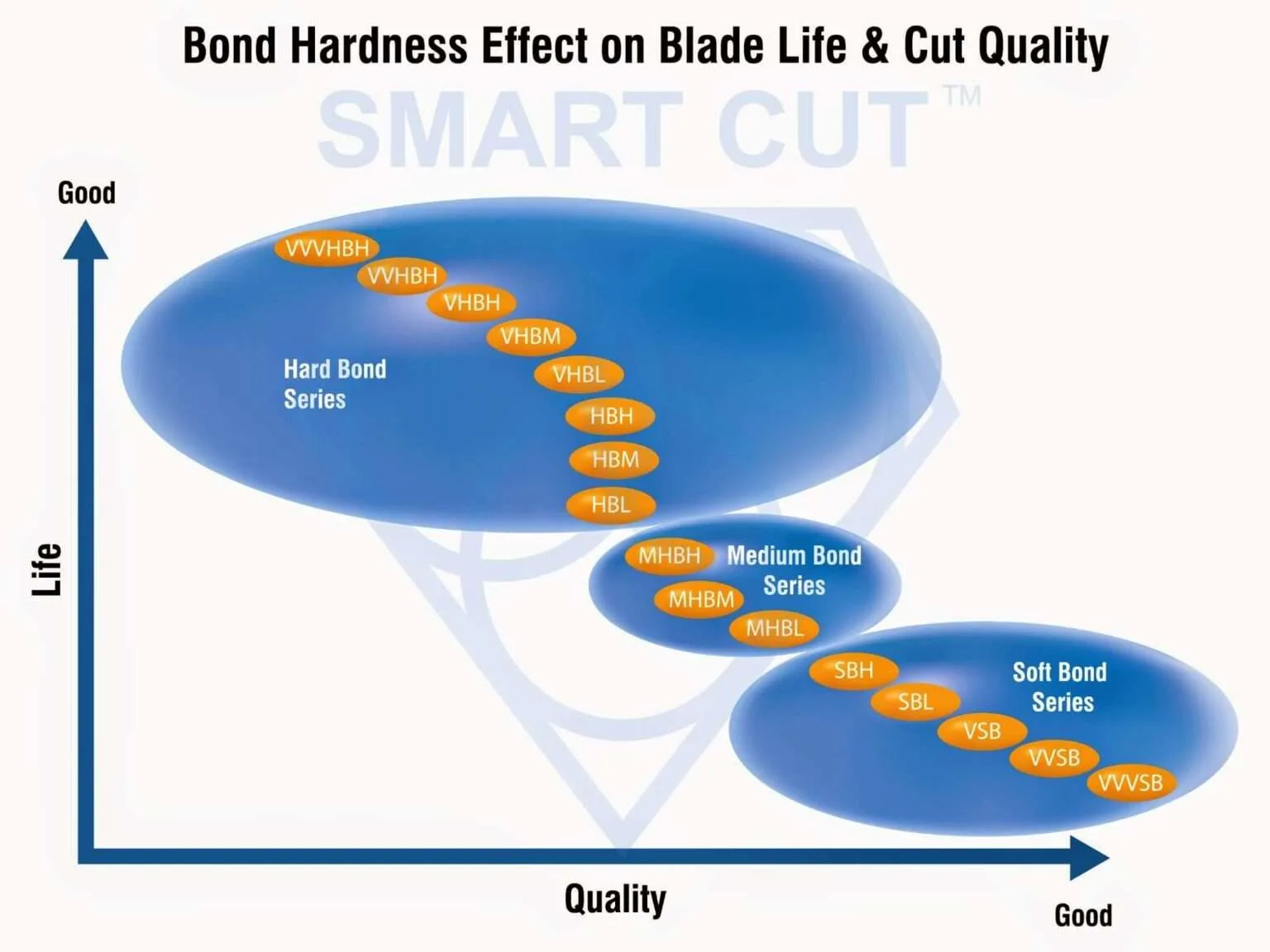
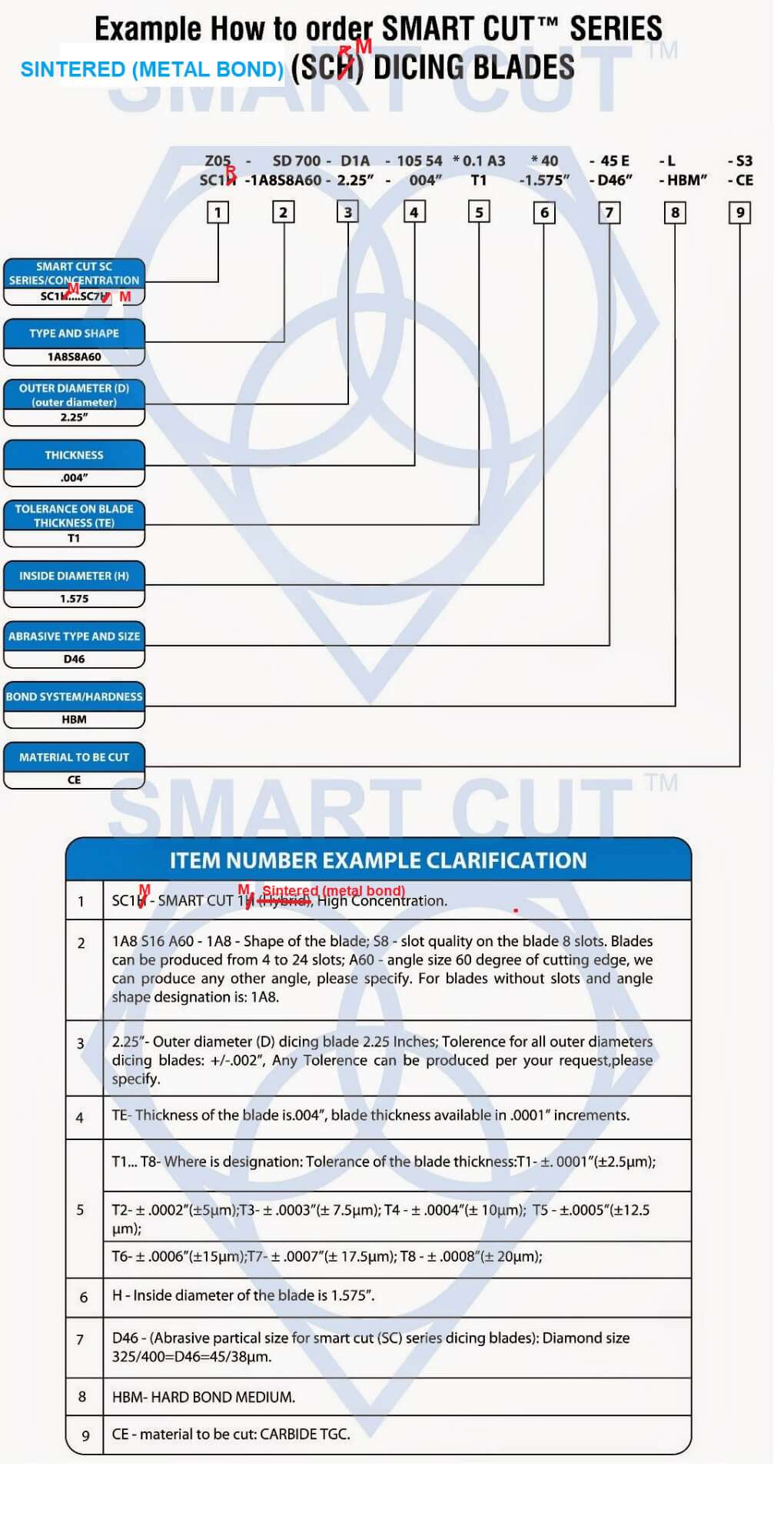
Example How to Order SMART CUT® Series (SCM) Dicing Blades
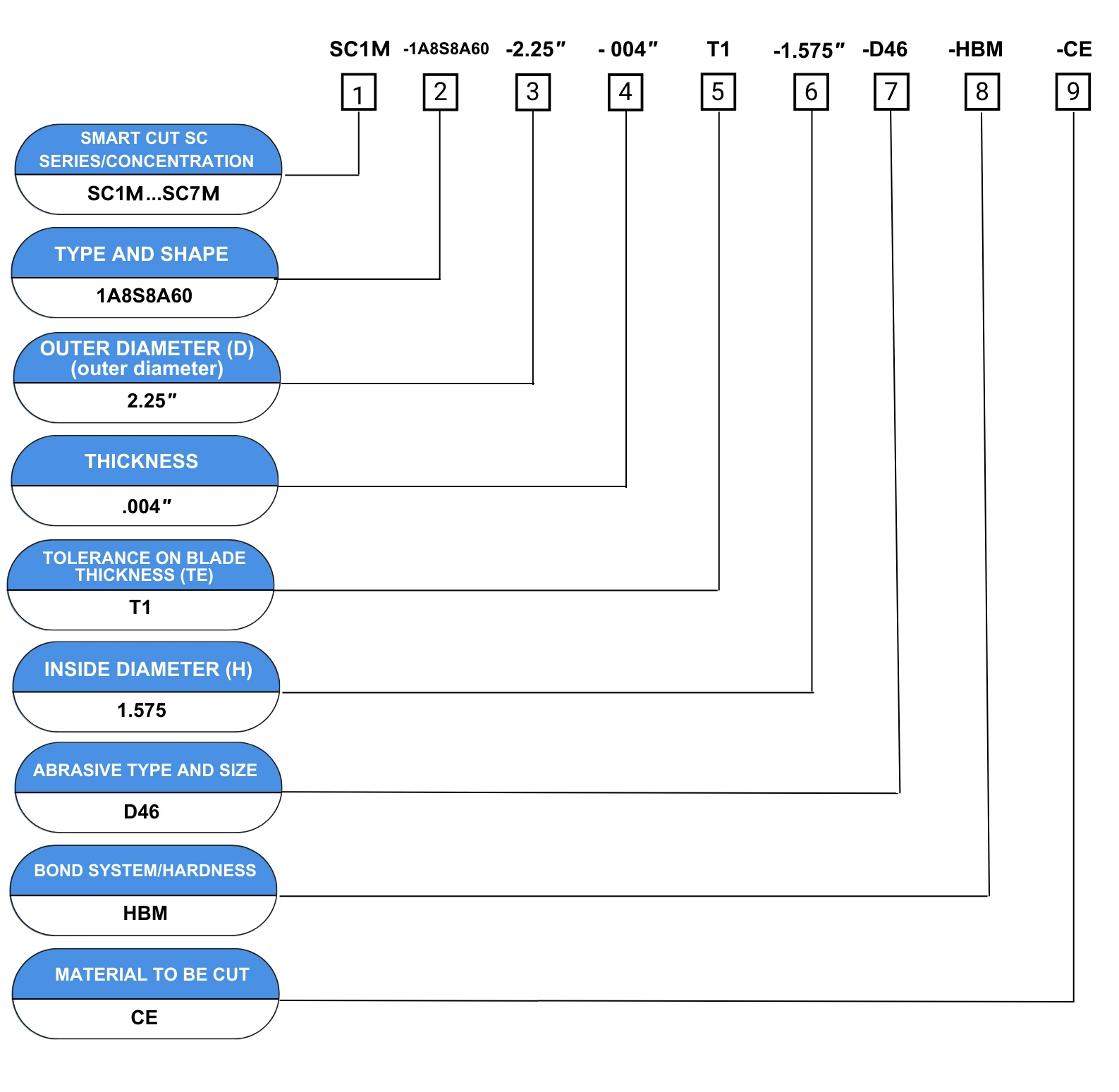
Item Number Example Explanation
# |
Specification |
Description |
---|---|---|
1 |
SC1M |
SMART CUT® (sintered, metal bond), High Concentration |
2 |
1A8 S16 A60 - 1A8 |
Blade shape: S8 (slot quality: 8 slots). Blades can be produced from 4 to 24 slots. A60: 60-degree cutting edge. Other angles are available by request. For blades without slots and angles, shape designation is 1A8. |
3 |
2.25" - Outer Diameter (D) |
Dicing blade outer diameter: 2.25 inches. Tolerance for all outer diameters: +/- .002" (custom tolerance available upon request). |
4 |
TE - Thickness of Blade |
Blade thickness: 0.004". Available in increments of .0001". |
5 |
T1 - T8 (Tolerance of Blade Thickness) |
Tolerances: T1: +.0001" (+2.5µm), T2: +.0002" (+5µm), T3: +.0003" (+7.5µm), T4: +.0004" (+10µm), T5: +.0005" (+12.5µm), T6: +.0006" (+15µm), T7: +.0007" (+17.5µm), T8: +.0008" (+20µm). |
6 |
H - Inside Diameter of the Blade |
Inside diameter: 1.575 inches. |
7 |
D46 (Abrasive Particle Size) |
Diamond size for SMART CUT® (SC) series dicing blades: 325/400 = D46 = 45/38µm. |
8 |
HBM |
Hard Bond Medium |
9 |
CE |
material to be cut: CARBIDE TGC |
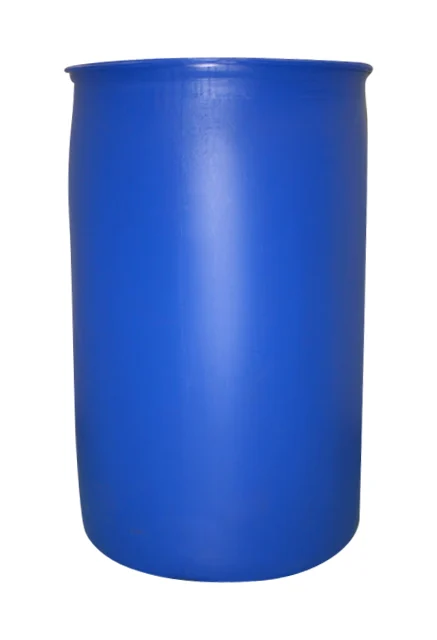
SMART CUT® XP Dicing Fluid, Coolant, & Surfactant
Available in 4 Different Formulas to Fit Most Dicing Applications
XP-1 is a general-purpose dicing fluid within the SMART CUT® range, designed to reduce debris, improve tool life, and prevent corrosion, while ensuring smooth cutting and protecting sensitive materials from ESD.
XP-2 enhances lubrication for demanding applications, offering superior cutting speeds, tool longevity, and advanced cleaning capabilities for tough materials like SiC and sapphire.
XP-3 is ideal for high-pressure systems, offering consistent cooling performance without foam buildup.
XP-4 specifically protects electrostatic-sensitive components by eliminating ESD, reducing defects, and extending tool life during the dicing process.
Related Products
Hybrid Bond Dicing Blades
Nickel Bond Hubbed Dicing Blades
Resin Bond Dicing Blade
SMART CUT® Water Soluble Dicing Coolant
SMART CUT® XP Water Soluble Dicing Coolant added to deionized (DI) water reduces surface tension flowing from saws injection system and is carried directly of dicing blade.
This reduces material thermal stress, edge damage, and internal cracking, assuring long-term integrity of material being processed. Since SMART CUT® XP Dicing Coolant is a coolant and lubricant, and Surfactant both the dicing blade and substrate / wafer / package benefit.
SMART CUT® XP Dicing Coolant/Lubricant is a specially formulated low-foaming dicing and sawing coolant/lubricant designed for precision applications involving wafers with integrated circuits, MEMS devices, and IC packaging. This aqueous-based synthetic formulation enhances the dicing process by ensuring superior cleanliness of the die or package after dicing while preventing corrosion and oxidation on exposed metals. It eliminates electrostatic discharge, which can be generated during the rotation of the dicing blade, protecting delicate components from damage.
Tungsten Carbide Dicing Blades
Why Work With Us?
Comprehensive Source Of Information On Dicing Blades
We understand that your success depends on select the right dicing blade, and optimizing your dicing parameters to best fit your applications/needs. The more you understand about what we can do for you, the better our partnership will be. On our website you will find the Most Comprehensive Source of Information on Everything you wanted to know about diamond dicing blades & industrial diamond tools.
Large Inventory & Custom Manufacturing
Largest Inventory of Precision & Ultra Thin Diamond Dicing Blades in the U.S. Available in different sizes, thickness, arbor sizes, diamond concentrations, diamond mesh sizes, and bond hardness's.
Experience Makes All The Difference
"ONE OF THE MOST EXPERIENCED COMPANIES IN THE INDUSTRY"
Over the years we have enjoyed working with all types if clients, regardless of size. Proprietary dicing blade chemistry, precision manufacturing methods, modern quality control methods, allow us to control and regulate the dozens of variables that affect blade life, quality of cut, surface finish. Reducing and often eliminating additional steps often required after cutting.
Umatched Technical Support
We Are a Partner In Your Success
Developing close ties with our customers is the foundation of our business. At the core of
our company is a team of world class engineers, knowledgeable customer service personnel here to serve you. Whether is designing or manufacturing a special solution. We will go out of our way to optimizing your process to ultimate level of efficiency.
Advanced
Technology
American Manufacturer As one of the few remaining independent U.S.Diamond Tool & machine builders. We have the experience & tradition to help you remain at frontier of technology Our experience has been further enhanced by acquiring assets and processes from some of the oldest American tool manufacturers, along with their decades of experience and R& D. This has positioned us as one of the most experienced companies in the industry.
Superior Quality &
Consistency
Our unique bond formulations, tool designs, stringent requirements, and utilization of exceptionally high-quality diamonds and raw materials ensure top-notch products that adhere to strict ISO 9000 standards.
Our proprietary technology allow us to control and regulate the dozens of variable that affect toolife, quality, & consistency
Expect More From Your Tools
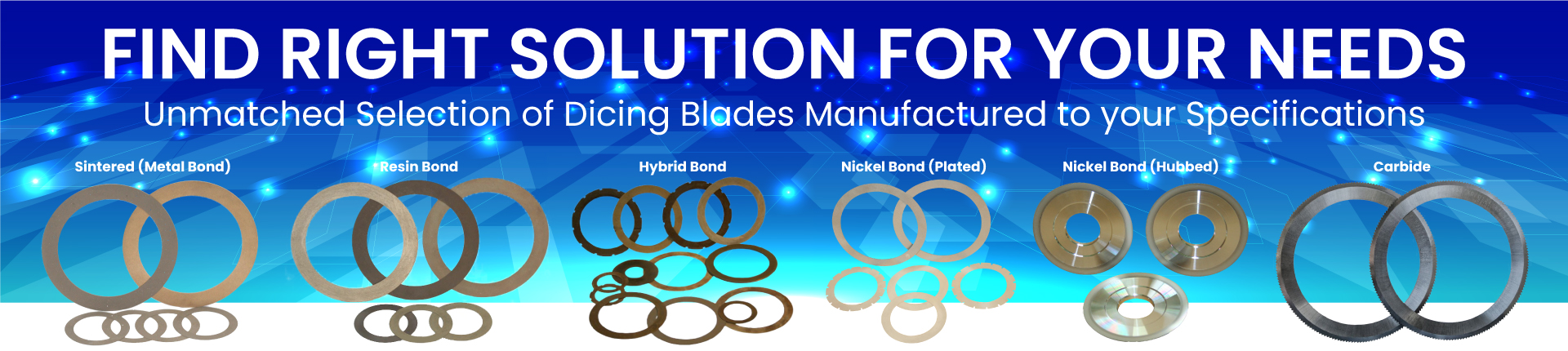
ARE YOU USING RIGHT DICING BLADES
FOR YOUR APPLICATION?
LET US
HELP YOU
HAVING ISSUES WITH
YOUR CURRENT DICING BLADES?
01
Jun
Select right Diamond Dicing Blade for your application
Selecting the right diamond dicing blade & parameters for your material/application can be a very time consuming, trial & error frustrating process. The guide below has been designed to help you better understand the most important...
02
Jun
Dicing Blade Operations Recommendations
Share this Article with Friend or Colleague
Selecting the right dicing blade parameters often involves a trial and error process, many aspects of which can be mitigated through experience and a deep understanding of how...
02
Jun
Optimizing Dicing Blade Performance
There are many variables that affect dicing blade performance. Each variable of the dicing process is only of the many components of a larger dicing system (equation). Changing one component or variable of...
02
Jun
Trouble Shooting Dicing Problems
Guide on most common dicing problems and how to resolve them
Share this Article with Friend or Colleague
ARE YOU USING RIGHT TOOLS
FOR YOUR APPLICATION?
LET USHELP YOU
CONTACT US
HAVING ISSUES WITH
YOUR CURRENT TOOLS?
What...
02
Jun
Application Recommendations
See what blade specifications we recommend to use for different applications, along with rpm's and feed rated
Share this Article with Friend or Colleague
ARE YOU USING RIGHT TOOLS
FOR YOUR APPLICATION?
LET USHELP...
02
Jun
Dicing Blade Case Studies
This article provides important guidelines for optimizing the dicing process in semiconductor packaging, focusing on package singulation for various technologies such as BGA, QFN, LED, CMOS, and wafer substrates. It covers key variables such as...
01
Jun
Optimizing QFN Package Dicing Process Using SMART CUT® Dicing Blades
Share this Article with Friend or Colleague
Dicing QFN packages presents several challenges due to the composition of materials and the precision required for clean, defect-free cuts. These challenges arise from the multi-layered structure of...
27
Aug
Selecting the Right Wafer Dicing Saw Practical Guide
Selecting the proper wafer dicing saw is a important decision for manufacturers, researchers, and engineers working with large variety of materials. Whether processing silicon wafers in microelectronics, ceramics in materials science, or glass substrates in...
02
Jun
How to Selecting Right Diamond Tools for your application
Selecting the appropriate Diamond & CBN Tool specification is a crucial aspect of achieving your objectives. Opting for the ideal specification not only yields optimal results but also ensures the best return on investment. Conversely,...
02
Jun
How to properly use Diamond Tools
UKAM Industrial Superhard Tools manufactures precision diamond tools for a large variety of applications, materials, and industries.
Share this Article with Friend or Colleague
Metal Bonded Diamond Tools are “impregnated” with diamonds. This means that selected...
02
Jun
Why use diamond
Diamond is the hardest material known to man kind. When used on diamond/tools, diamond grinds away material on micro (nano) level. Due to its hardness Diamond will work all types of materials from...
02
Jun
What is Diamond Mesh Size and how to select best one for your application
Diamond grit size can be defined as the size of the diamond particles used in the bond matrix. The larger the diamond particles (grit size) the faster the tool will cut.
Share this Article with Friend or...
02
Jun
What is Diamond Concentration and which to use for your application
Diamond concentration is measured based on the volume of diamond within a section of the tool. It is typically defined as Concentration 100, which equates to 4.4 carats per cubic centimeter of the diamond layer...
02
Jun
Diamond Tool Coolants Why, How, When & Where to Use
Coolant is one of the most overlooked variables in the overall diamond or cbn tool machining process. Effective and proper use of coolant and recalculating coolant system will pay off in terms of improved surface...
02
Jun
Diamond vs CBN (cubic boron nitride) Tools
Cubic Boron Nitride (CBN) is a synthetic material that is renowned for its exceptional hardness and high thermal stability. It is composed of boron and nitrogen atoms arranged in a crystal lattice structure, similar to...
17
May
Choosing The Correct Diamond Bond Type
Selecting the appropriate diamond bond type for specific applications is crucial for several reasons. Diamond bond type directly affects the tool's performance, efficiency, and longevity. Different bond types determine how well a tool can withstand...
- Unmatched Selection For Many Applications
- Superior Quality & Consistency
- Immediate Worldwide Delivery
- Technical Support & Expertise
- American Based Manufacturer
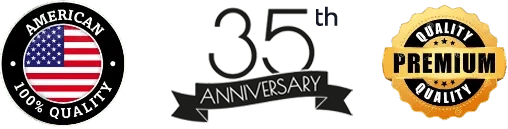

- Different Product
- Different Technology
- Different Company
- Expect MORE from your tools
Let Us HELP You!
Subscribe To Our Newsletter
Signup for email offers, updates, and more
Contact Us
- 25205 & 25201 Avenue Tibbits Valencia CA 91355 USA
-
Phone : (661) 257-2288
FAX : (661) 257 -3833 - lel@ukam.com
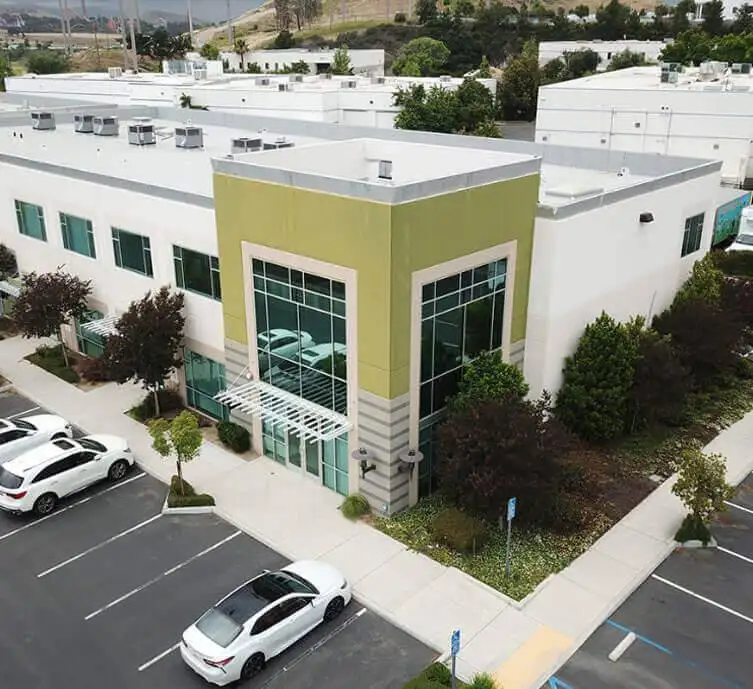
UKAM Industrial Superhard Tools is a U.S. High Technology, Specialty Diamond Tool & Equipment manufacturer. We specialize in producing ultra thin, high precision cutting blades, precision cutting machines diamond drills, diamond micro tools, standard & custom advanced industrial diamond tools and consumables.
- 25205 & 25201 Avenue Tibbits Valencia CA 91355 USA
-
Phone : (661) 257-2288
FAX : (661) 257 -3833 - lel@ukam.com
- 25205 & 25201 Avenue Tibbits Valencia CA 91355 USA
-
Phone : (661) 257-2288
FAX : (661) 257 -3833 - lel@ukam.com
DIAMOND TOOLS BY BOND
EQUIPMENT
KNOWLEDGE CENTER
OUR PRODUCTS
COMPANY
CUSTOMER SERVICE
Shipping Methods


Safe & Secure Payments

© Copyright 1990-2025. UKAM Industrial Superhard Tools – Terms of Use