-
0 items in quote
No products in the Quote Basket.
SMART CUT® 1800
Precision Saw
For this reason SMART CUT™ 1800 is well suited for cutting larger and longer sample coupons such as PCB Boards, FR4 composite panels, ceramic substrates, electronic packages, plate material, composites, optical or flat glass pieces, ultra hard material tiles, and other glass, carbon fiber, honeycomb, and many other materials. That are too big to fit cut with other high precision saws
DESCRIPTION
SPECIFICATIONS
ADVANTAGES
INDUSTRIES USED IN
FAQ
ACCESSORIES
OPERATING MANUALS
DESCRIPTION
VERY HIGH PRECISION CUTTING SAW FOR MANUAL CUTTING OF PANNELS
High Precision Cutting Machine for precise cutting of Composite Panels, Coupons, and test specimens. The machine allows high precision cutting of very large and long composite test specimens to accuracy
of 25 microns. Material is clamped to the steel table which glides toward
the blade on high precision linear rails. Machine is equipped with HMI tough screen control that allows the operator to control the Speed, Start & stop the motor. As well as control the machine height position up and down through hydraulic movement. Coolant is filtered and recirculated in fully enclosed tank that comes with machine
SPECIFICATIONS
- Cutting Capacity:8mm to 30mm
- Material Dimensions Accommodates:750mm x 600mm x30mm
- Blade Diameter:6″ (150mm) to 8″ (200mm)
- Blade Feed Method:Horizontal Movement
- Rotation Speed:0 to 2,000 RPM
- Automatic Feed:
- Cutting Stroke:750mm
- Clamping Vice:
- Table Dimensions:760mm x730mm
- Motor Power:370w
- Arbor Size:1″ (25.4mm)
ADVANTAGES
- Super High Precision Cutting to 25 micron accuracy
- Larges Surface Area in its Class
- Cut of Very Large & Long Panels up to 750mm L
- Variable Speed from Low to High to accommodate all Material Types
- HMI touch screen controls all function of Machine
- Adjustable Height Position using hydraulics
- Accommodates super thin materials and thick materials up to 30mm
- Super Smooth Surface Finish
- Largest selection of blades from .009″ to .080 kerf thickness
- Recirculation Coolant System
INDUSTRIES USED IN
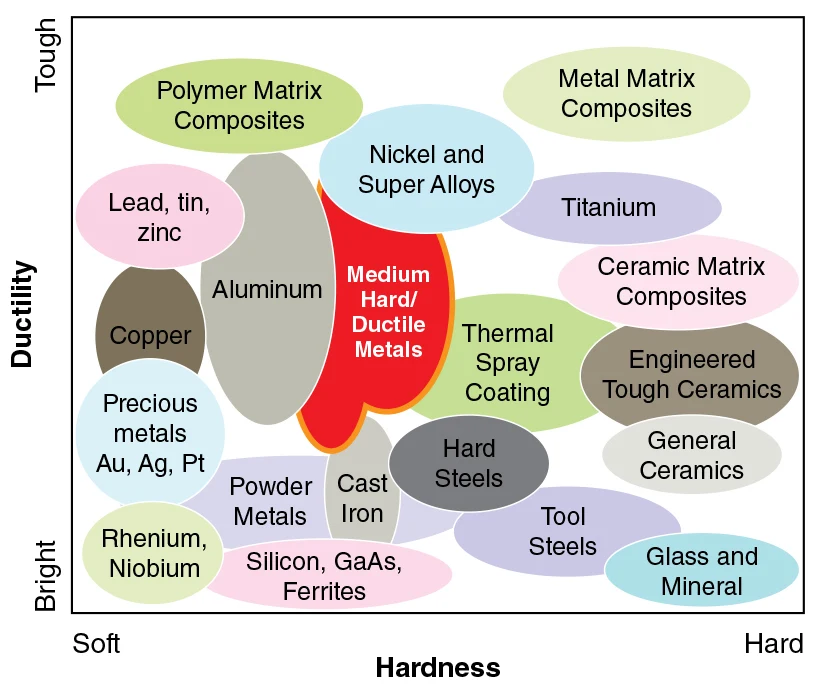

INDUSTRIES USED IN:
- Advanced Ceramics
- Composites
- Glass
- Geology
- Quartz
- Materials Research
- Medical Devices
- Metallography
- Photonics / Optics
- Semiconductor
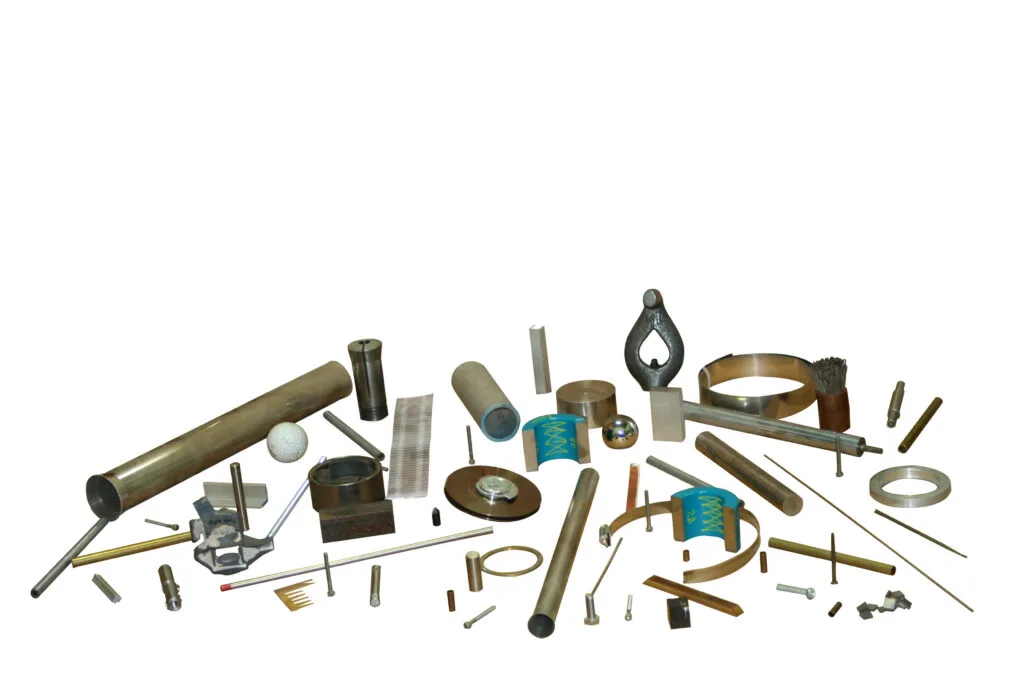
Ferrous & Non-Ferrous Metals:
- Plain Carbon Steels
- Electronic Packages
- Stainless Steels Plastics
- Tool Steels Fasteners
- Aluminum Refractories
- Copper Base Alloys Integrated Circuits
- Magnesium Thermal Spray Coatings
- Titanium Metal Matrix Composites
- Biomedical Wafers
- Petrographic
- PCB.s Ceramics
FAQ
The SMART CUT™ 1800 is designed for very high precision manual cutting of large and long panels such as PCB Boards, FR4 composite panels, ceramic substrates, electronic packages, and many other materials.
The saw is well-suited for materials like PCB Boards, FR4 composite panels, ceramic substrates, electronic packages, plate material, composites, optical or flat glass pieces, ultra-hard material tiles, glass, carbon fiber, honeycomb, and many other materials too large for other high precision saws.
It has the largest work surface area in its class, measuring 750mm x 600mm, making it ideal for manual sectioning of oversize samples. Its precision allows for cutting to 25 micron accuracy.
The operator pushes the cutting table, which glides towards the rotating blades using high precision linear rails. An HMI touch screen controls all functions of the machine.
The cutting capacity ranges from 8mm to 30mm.
It can handle material dimensions of up to 750mm x 600mm x30mm.
Yes, it has a fully enclosed recirculating coolant system designed for high flow rates and minimal debris build-up.
The saw features easy-to-use quick clamps that allow for the fixturing of just about any panel in less than 30 seconds. The holding fixture ensures the material is held accurately in place without causing any stress or deformation.
The saw accommodates blade diameters ranging from 6″ (150mm) to 8″ (200mm) and a selection of blades from .009″ to .080 kerf thickness.
Yes, the rotation speed is variable from 0 to 2,000 RPM, accommodating a variety of material types.
Yes, the height position is adjustable using hydraulics.
Its super high precision and ability to cut very large and long panels make it ideal for preparing test coupons from a variety of materials with utmost accuracy.
The HMI touch screen offers intuitive control over the machine’s functions, allowing operators to easily adjust settings like speed, start & stop the motor, and control the machine height position.
The horizontal blade feed method allows for accurate, consistent cuts, especially for larger and longer sample coupons that need precision.
Absolutely. It can accommodate super thin materials and thick materials up to 30mm.
The recirculation coolant system helps in maintaining the blade’s temperature, ensuring longevity and consistent cutting performance. It also helps prevent debris buildup, leading to cleaner cuts.
The saw is powered by a 370w motor, ensuring efficient and powerful cutting capabilities.
The table dimensions are 760mm x 730mm. This larger work surface area facilitates manual sectioning of oversized samples, allowing for greater flexibility and versatility in cutting projects.
The clamping vice ensures that the material is securely held in place during the cutting process, eliminating any movement that could result in inaccurate or uneven cuts.
The built-in recirculating coolant system effectively manages the blade’s temperature, reducing the risk of overheating even at high RPMs.
The hydraulic movement offers smooth and precise adjustments for height positioning, ensuring the blade is at the optimal height for each specific cutting task.
A 25-micron accuracy means that the cuts are incredibly precise, essential for tasks requiring high precision, such as creating test coupons or handling delicate materials.
The cutting stroke is 750mm, allowing for the sectioning of long panels or materials with ease.
The fully enclosed design ensures that debris and coolant are contained, reducing potential hazards. Additionally, the HMI touch screen offers control over the machine’s functions, ensuring safe operations.
With the easy-to-use quick clamps, fixturing of just about any panel can be done in less than 30 seconds.
Like all precision equipment, periodic maintenance is recommended to ensure longevity and optimal performance. It’s advisable to check the coolant system, blades, and moving parts regularly.
While the blade’s durability depends on the materials being cut and the frequency of use, it is designed for prolonged use with various materials. Regular inspections and replacements as needed will ensure consistent cutting performance.
We provide operating manual and training videos. As well as support over phone and video chat. Onsite training and support is available for additional fee
Yes, the SMART CUT™ 1800 is designed to handle both laboratory and industrial applications, especially given its capacity to handle larger and longer materials with precision.
Yes all parts are available from stock
The machine is constructed using robust materials, including steel for the table, ensuring durability and stability during the cutting process.
The machine’s design, combined with its high-precision linear rails and stable construction, minimizes vibrations, ensuring clean and accurate cuts.
While the SMART CUT™ 1800 is designed for manual operation, its features and consistency could potentially be integrated into specific automated workflows with the right setup.
The fully enclosed design and recirculating coolant system work in tandem to manage and minimize dust and debris during cutting, ensuring a cleaner workspace and better cut quality.
The primary design is for straight precision cuts. For angled cuts, additional attachments or equipment might be required.
Operators should always wear safety glasses, avoid loose clothing, ensure materials are securely clamped, and be familiar with the machine’s operations. Regularly checking the equipment for any signs of wear or damage is also essential.
The 370w motor provides a balance between power and energy efficiency. However, actual energy consumption might vary based on usage patterns.
With proper maintenance and regular inspections, the SMART CUT™ 1800 is designed for long-term use in both laboratory and industrial settings.
It’s advisable to operate the machine in a clean, dry environment free from excessive dust or moisture to ensure precision and longevity.
It’s recommended to use the manufacturer-approved coolant to prevent any damage to the machine and ensure optimal performance.
The frequency of coolant replacement depends on usage. Regularly checking for contamination and clarity will help determine when it’s time for a change.
Precision equipment typically incorporates safety features, including overload protection. Refer to the product manual for detailed safety specifications.
While it’s possible, using blades specifically designed or recommended for the SMART CUT™ 1800 ensures optimal performance and safety.
The user manual will provide a step-by-step guide for calibration. Regular calibration ensures consistent precision.
Precision equipment is typically shipped securely to prevent any damage.
The SMART CUT™ 1800 boasts a larger work surface and high precision. It’s recommended to compare specifications, user reviews, and costs with other models to make an informed decision.
Yes financing through third part equipment leasing / financing companies is avaialble
Used coolant should be disposed of following local environmental regulations and guidelines. Some suppliers or local agencies might offer disposal services or guidance.
Depending on the design, certain components might be upgradable.
Noise levels vary based on materials and cutting speed. However, precision equipment like this is designed to minimize noise where possible. Exact decibel levels can be found in the product specifications.
ACCESSORIES
OPERATING MANUALS
Download Operating Manuals
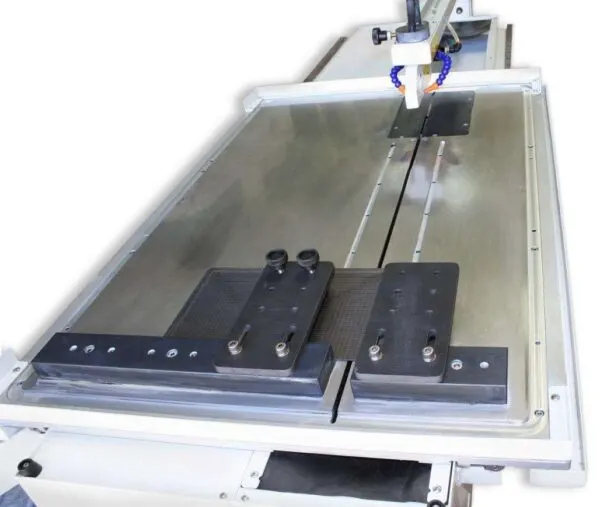
Larger Work Surface Area For Cutting Longer Samples
SMART CUT™ 1800 has largest work surface area than any other saw in its class. The cutting table measures 750mm x 600mm. This much larger work area then normally available on high precision saw and provides an excellent solution to manual sectioning of oversize samples.
For this reason SMART CUT™ 1800 is well suited for cutting larger and longer sample coupons such as PCB Boards, FR4 composite panels, ceramic substrates, electronic packages, plate material, composites, optical or flat glass pieces, ultra hard material tiles, and other glass, carbon fiber, honeycomb, and many other materials. That are too big to fit cut with other high precision saws
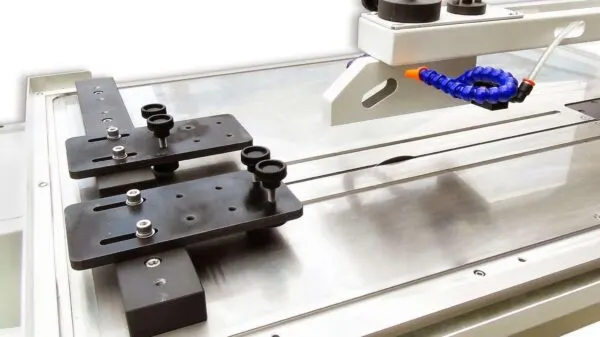
Easy to use quick clamps allow fixturing of just about any panel in less then 30 seconds. The holding fixture makes sure the material is hold accurately in place without causing any stress or deformation to the material
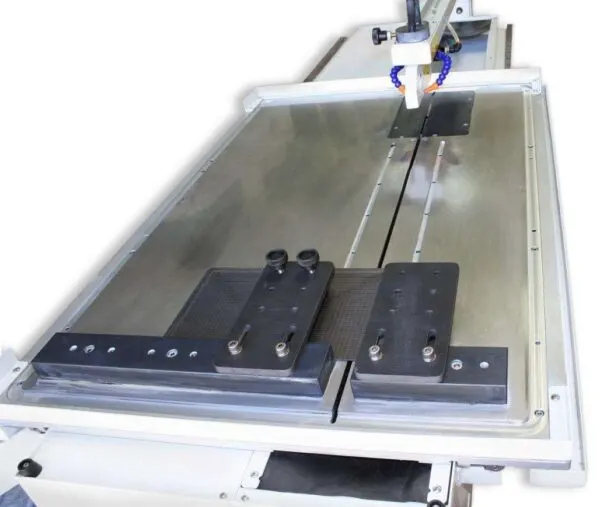
SMART CUT™ 1800 has largest work surface area than any other saw in its class. The cutting table measures 750mm x 600mm. This much larger work area then normally available on high precision saw and provides an excellent solution to manual sectioning of oversize samples.
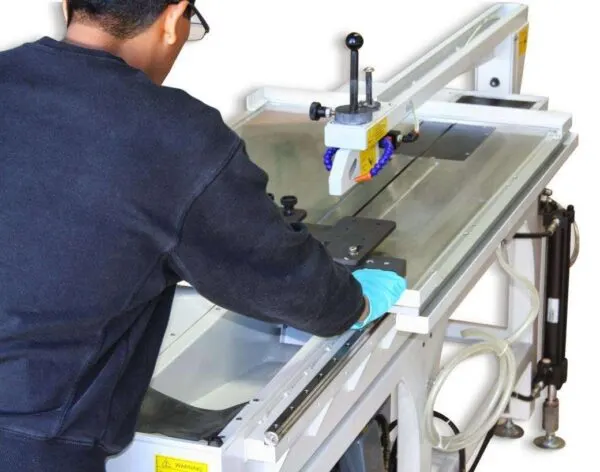
the operator pushes the cutting table, which glides towards the rotating blades using high precision linear rails back and forward.
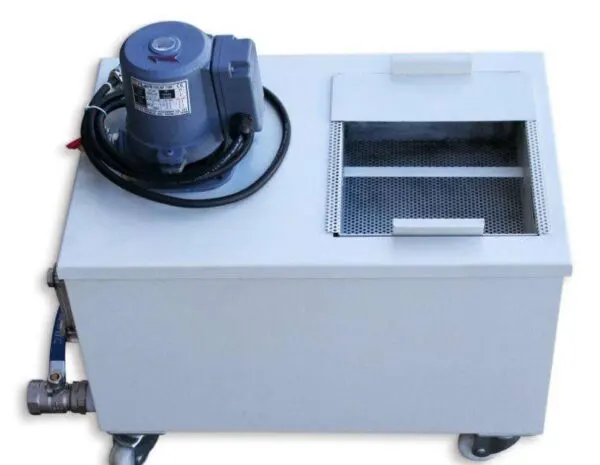
fully enclosed recalculating coolant system for high flow rates and minimal debris build up
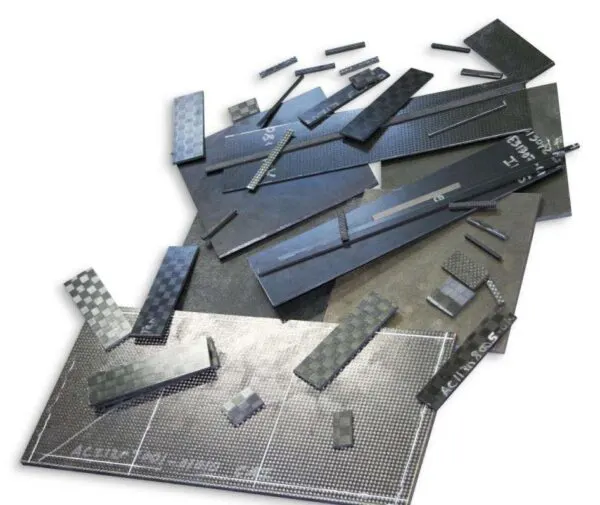
Precision Cutting Saw For Test Cupon Preperation
SMART CUT® COOLANTS
Your choice of one (1) quart of SMART CUT™ Water Soluble Coolant or Mineral Oil is included with machine. SMART CUT™ Water Soluble Coolant Reduces material thermal stress, edge damage, and internal cracking, increases blade life, provides better cut quality, preserves material micro structure
Hence, assuring long-term integrity of material being sectioned. Since SMART CUT coolant is both a coolant and lubricant, both the wafering blade and material benefit. Mix ratio is 1:20 (1 part coolant, 20 parts water) on very hard and dense materials and 1:40 (1 part coolant, 40 parts water) on softer materials. Depending on mix ratio 1 quart will produce 5.7 to 9 gallons of coolant when mixed with water. As a coolant, SMART CUT KOOL reduces heat caused by friction. As a lubricant, SMART CUT KOOL lowers friction and surface tension, which increases swarf dispersion.
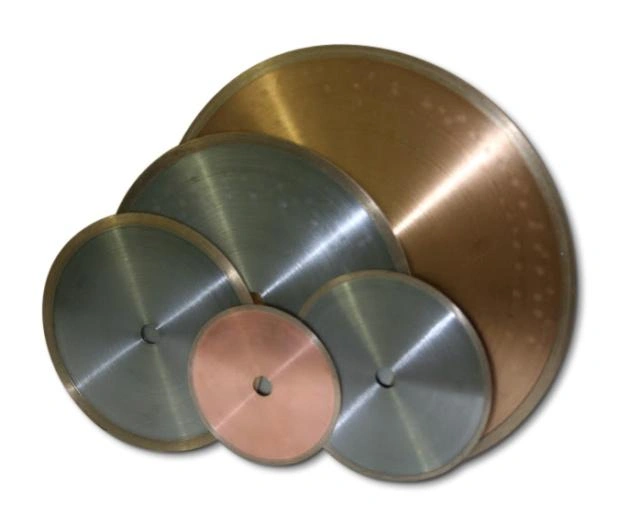

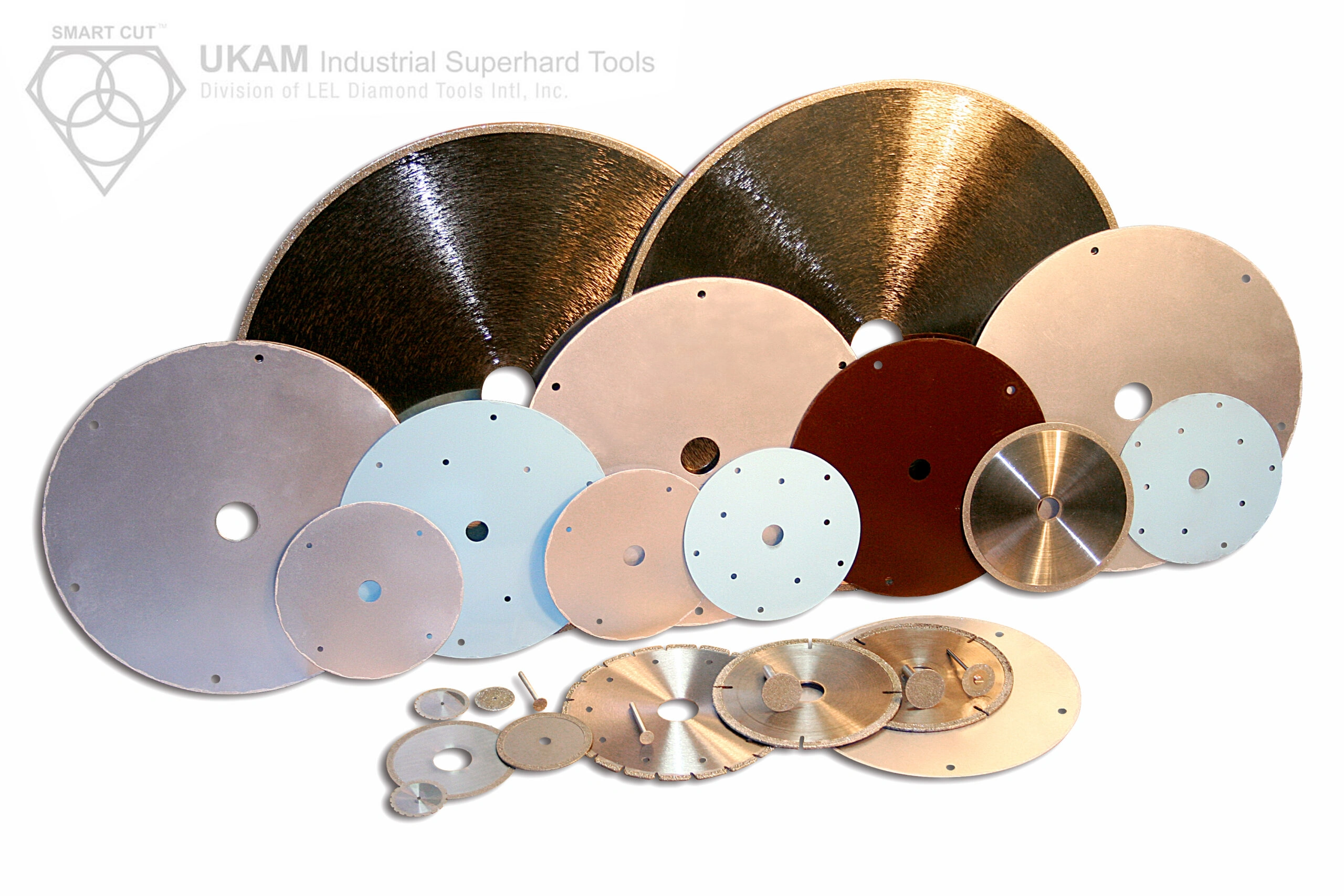
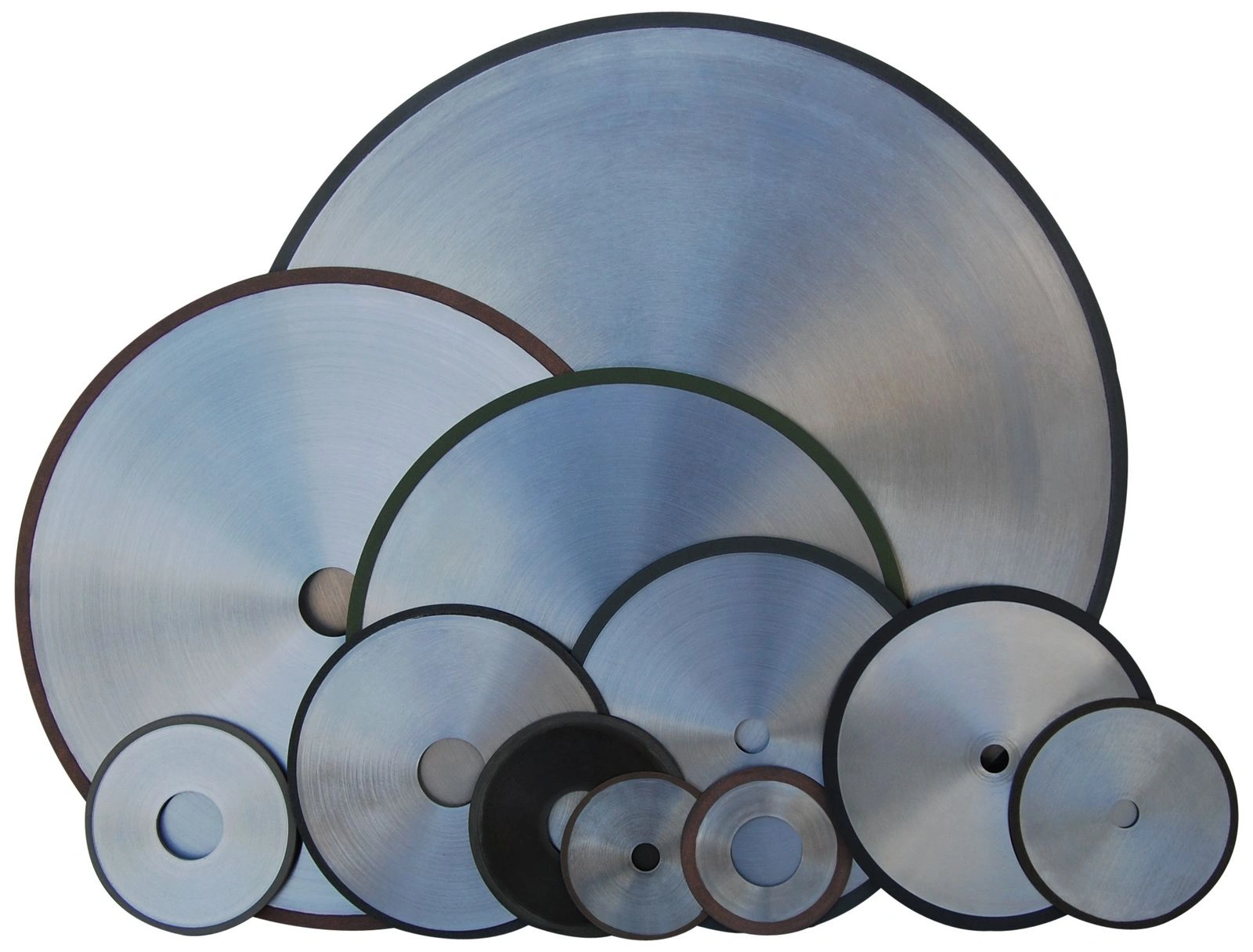
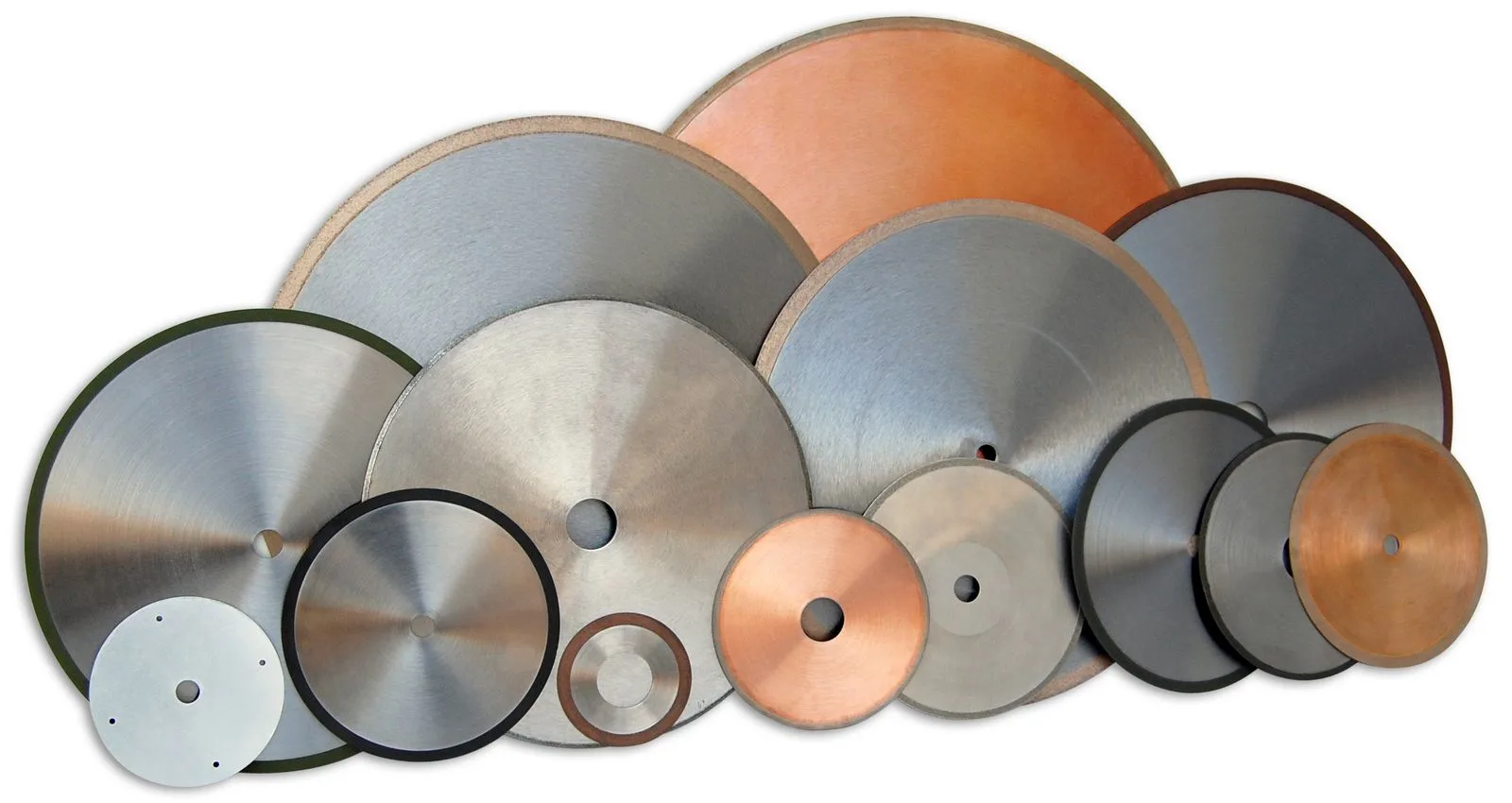
LARGEST SELECTING OF DIAMOND & CBN WAFERING BLADES AVAIALBLE
one (1) diamond wafering blade any specification is included FREE OF CHARGE with purchase of any machine (any specification). we have almost unlimited number of diamond & CBN wafering blade specifications in stock available for immediate delivery. Available in different sizes, thickness, arbor sizes, diamond concentrations, diamond mesh sizes, and bond hardness’s. With several thousand unique blade specification in stock not listed on our standard stock program. This insures you will receive the best blade specification possible for your specific application.
THE RIGHT DRESSING STICK FOR YOUR APPLICATION
One (1) dressing stick is included with the purchase of any machine free of charge. The dressing stick we supply is similar to the diamond size of the wafering blade you have chosen (or we recommended) for your application. Wafering Blades must be diamonds particles/crystals exposed properly through frequent dressing. Otherwise, the diamond tool will glaze over. They will begin to tear rather than grind which is very destructive. Tearing caused from unexposed diamonds creates friction. This causes uneven wear and/or heat cracks in the wafering blade and/or material being cut. Resulting in premature blade wear, blade tensioning problems, and will eventually destroy the blade. The more frequently the blade is dressed the freer and cooler it will cut with lot more consistency.
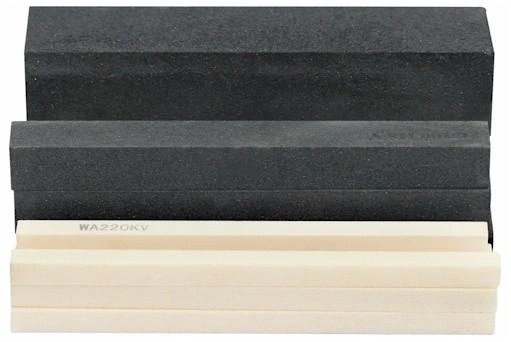
Related Products
SMART CUT® 1600 SAW
SMART CUT® 1805 – Precision Saw
Recently Viewed Products
ARE YOU USING METALLOGRAPHY SECTIONING SAWS
FOR YOUR APPLICATION?
LET US
HELP YOU
HAVING ISSUES WITH
YOUR METALLOGRAPHY SECTIONING SAWS?
Knowledge Center
02
Jun
Diamond Wire Advantages & Application
Diamond Wire saws provide the most accurate cutting with the least amount of material deformation and chipping of material.
Share this Article with Friend or Colleague
HOW DIAMOND WIRE WORKS
Today diamond wire sawing is preferred by...
02
Jun
Troubleshooting Diamond Sawing Problems
Having issues with your diamond cutting operation? This Illustrated Guide can help. Learn the most common problems most people have in using diamond cutting blades. How to resolve them and avoid them in...
02
Jun
How to Improve & Optimize Your Diamond Sawing Operation
There are numerous variables that affect the performance of diamond and CBN cutting blades. Understanding these variables will help end users select the right diamond blade specifications for their applications and optimize their...
02
Jun
Evaluating & Comparing Diamond Blades
Share this Article with Friend or Colleague
Proper testing procedures and methodologies must be set up and used to obtain accurate as well as repeatable testing results. This article will discuss several simple procedures which...
02
Jun
Selecting Right Wafering Blade for your application
Cross Sectioning is the first and most important step in the sample preparation process. Getting the best results involves obtaining a smooth surface finish, minimum chipping, material deformation, without sacrificing cutting speed. Today, most laboratories, work with dozens...
02
Jun
Wafering Blade Usage Recommendations
The wafering/sectioning blade itself is only a small factor in your sectioning operation. Successful wafering/sectioning operation is both an art & science. Requiring proper use and understanding of selecting the right diamond wafering/sectioning...
02
Jun
Wafering Blade Case Studies
Step by step guide on how to properly use and care for your diamond drills. Selecting the right diamond drill/diamond drill bit parameters, often involves a trial and error process. Many which can be avoided...
22
Apr
Diamond & CBN Wafering Blade Performance Metrics
When evaluating Diamond & CBN wafering blades, especially for metallography and sample preparation, it is critical to consider a set of key evaluation criteria and performance metrics. These factors help determine the effectiveness of a...
24
Apr
Understanding & Comparing Diamond & CBN Wafering Blades
Share this Article with Friend or Colleague
Diamond wafering blades are designed for sectioning a large variety of materials and sample types. In order to identify the best diamond wafering blade for your specific material/application,...
25
Apr
Diamond & CBN Wafering Blade Guide
Share this Article with Friend or Colleague
All you need to know about wafering blades (understanding variables & specifications)
This guide is designed to help you navigate the various variables and possibilities associated with diamond wafering...
08
Jul
Low Speed Saw Case Studies
Share this Article with Friend or Colleague
Introduction
In the realm of precision cutting, the SMART CUT® 6005 Low Speed Diamond Saw stands out for its capability to handle a variety of materials with high...
31
Jul
Top 5 Diamond & CBN Cutting Blade Performance Metrics
Share this Article with Friend or Colleague
When evaluating diamond and cubic boron nitride (CBN) cutting blades, it's crucial to consider key performance metrics and criteria. Different applications have varying goals, making it...
01
Aug
Diamond & CBN Cutting Blade Performance Metrics that you Should Know
Share this Article with Friend or Colleague
When evaluating diamond and cubic boron nitride (CBN) cutting blades, it's crucial to consider key performance metrics and criteria. Different applications have varying goals, making it important to...
02
Aug
Total Cost of Ownership & Why its Important
Share this Article with Friend or Colleague
Diamond and CBN cutting blades are available in a myriad of specifications, with virtually limitless options. The industry is saturated with numerous manufacturers, each professing to offer the...
04
Aug
Diamond Wire vs band saw blades and circular blades
Diamond wire, band saw blades, and circular blades are all cutting tools used in various industries for different purposes. Each tool has its advantages and applications
For cutting ultra hard...
05
Aug
Understanding Tradeoffs- Searching for Perfect Diamond & CBN Blade
Share this Article with Friend or Colleague
Choosing the right blade diamond or cbn blade can significantly impact efficiency, cost, and quality. However, this is not simple and clear cut process. Selecting the optimal blade...
19
Aug
Understanding & Calculating Return on Investment for Diamond & CBN Blades
The term "ROI" (Return On Investment) is frequently mentioned across various industries, often with different interpretations depending on the context. However, few take the time to thoroughly understand what ROI truly represents and its specific...
- Unmatched Selection For Many Applications
- Superior Quality & Consistency
- Immediate Worldwide Delivery
- Technical Support & Expertise
- American Based Manufacturer
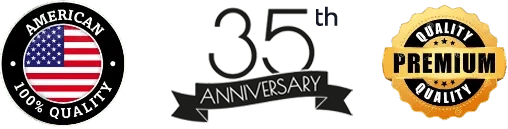

- Different Product
- Different Technology
- Different Company
- Expect MORE from your tools
Let Us HELP You!
Subscribe To Our Newsletter
Signup for email offers, updates, and more
Contact Us
- 25205 & 25201 Avenue Tibbits Valencia CA 91355 USA
-
Phone : (661) 257-2288
FAX : (661) 257 -3833 - lel@ukam.com
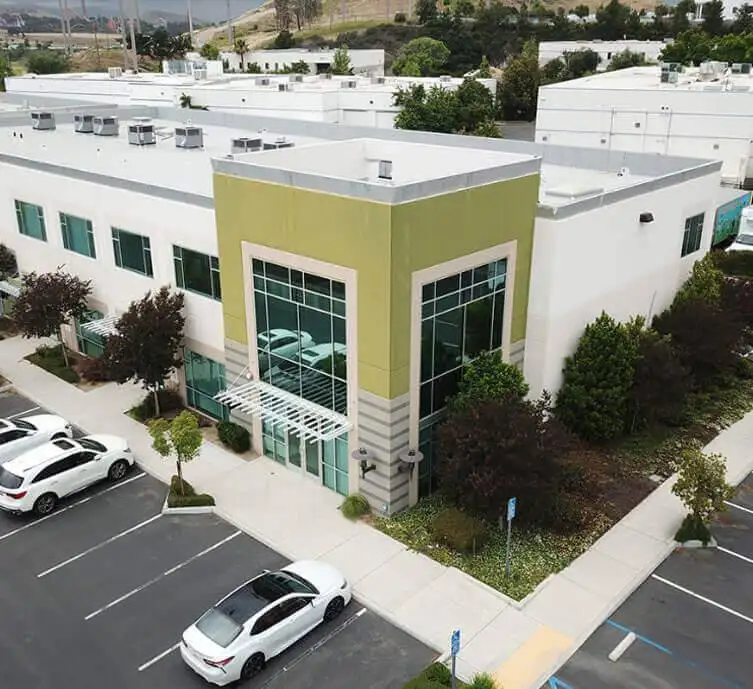
UKAM Industrial Superhard Tools is a U.S. High Technology, Specialty Diamond Tool & Equipment manufacturer. We specialize in producing ultra thin, high precision cutting blades, precision cutting machines diamond drills, diamond micro tools, standard & custom advanced industrial diamond tools and consumables.
- 25205 & 25201 Avenue Tibbits Valencia CA 91355 USA
-
Phone : (661) 257-2288
FAX : (661) 257 -3833 - lel@ukam.com
- 25205 & 25201 Avenue Tibbits Valencia CA 91355 USA
-
Phone : (661) 257-2288
FAX : (661) 257 -3833 - lel@ukam.com
DIAMOND TOOLS BY BOND
EQUIPMENT
KNOWLEDGE CENTER
OUR PRODUCTS
COMPANY
CUSTOMER SERVICE
Shipping Methods


Safe & Secure Payments

© Copyright 1990-2025. UKAM Industrial Superhard Tools – Terms of Use