-
0 items in quote
No products in the Quote Basket.
NEW GENERATION AND TECHNOLOGY
Nickel Bond Hubbed Dicing Blades
SMART CUT® Series SCNH
SMART CUT® Nickel Bond Hubbed Dicing Blades are the preferred choice for semiconductor component manufacturing, offering ultra-thin precision cutting with exceptional stability. Designed for dicing narrow wafers with impeccable accuracy, these blades utilize a nickel electroplated bond combined with larger diamond grit, ensuring an extended lifespan and consistently high-quality performance.
Engineered for maximum customization, SMART CUT® Nickel Bond Hubbed Dicing Blades are available in a wide range of stocked variations.
DESCRIPTION
SPECIFICATIONS
FREQUENTLY ASKED QUESTIONS
ACCESSORIES
USAGE RECOMMENDATION
CASE STUDIES
DESCRIPTION
Each blade consists of a precisely manufactured hub, designed for optimum cooling efficiency, and carries an electrodeposited nickel alloy layer embedded with diamond grains. The etched aluminum support is removed during manufacturing, leaving a free-standing nickel-diamond matrix that determines cut depth based on the exposed diamond rim.
UKAM Industrial Superhard Tools’ proprietary manufacturing process ensures precise control over diamond grit size, concentration, and nickel bond hardness, optimizing these variables to produce hubbed dicing blades that offer unmatched cut quality, superior blade life, and high throughput efficiency. These blades are highly versatile and perform exceptionally well in a wide range of applications, including silicon wafer dicing, brittle III-V compound materials such as gallium arsenide and indium phosphide, PZT ceramics, tantalates, aluminas, and silica-filled plastics for chip-scale package singulation.
SMART CUT® Nickel Bond Hubbed Dicing Blades feature a robust structure that enhances durability and provides superior cut quality with minimal chipping. They create ultra-thin kerfs, often less than 50 microns, enabling precision cutting while maintaining tight kerf width control. Their improved diamond exposure reduces the need for frequent dressing, allowing for more efficient and consistent cutting performance. These blades are designed to handle high exposure-to-width ratios and support advanced dicing techniques such as bevel and step cutting. A wide range of grit sizes and bond types is available to accommodate different application requirements.
This results in excellent cut quality with a low wear rate, reducing waste and improving productivity. The combination of an ultra-thin diamond blade and a precision aluminum hub provides stable cutting results while improving overall operation efficiency. These blades are particularly well suited for dicing silicon and III-V semiconductor materials.
SPECIFICATIONS
- Outside Diameter Range: 2” (50 mm) to 2.5” (65 mm)
- Inside Diameter (Arbor Hole): 3/4” (19.05 mm) standard
- Diamond Grit Size Range: #5000 to #1500
- Diamond Concentration Range: Low, Medium, High (50 to 130 con)
- Bond Hardness: Soft, Medium, Hard
- Exposure Range (μm): 380, 510, 640, 760, 890, 1020, 1150, 1270
- Kerf Width (μm): 380-510, 510-640, 640-760, 760-890, 890-1020, 1020-1150, 1150-1270, 1270-1400
- Angles/Radiuses: Custom beveled or radius edge configurations available for specialized applications
Tolerances:
- Inside Diameter Tolerance: +0.008 mm / +0.003 mm
- Outside Diameter Tolerance: +0.100 mm / +0.000 mm
- Blade Thickness Tolerance: ±5 μm
- Kerf Width Tolerance: ±10 μm
- Runout (Flatness) Tolerance: ≤5 μm
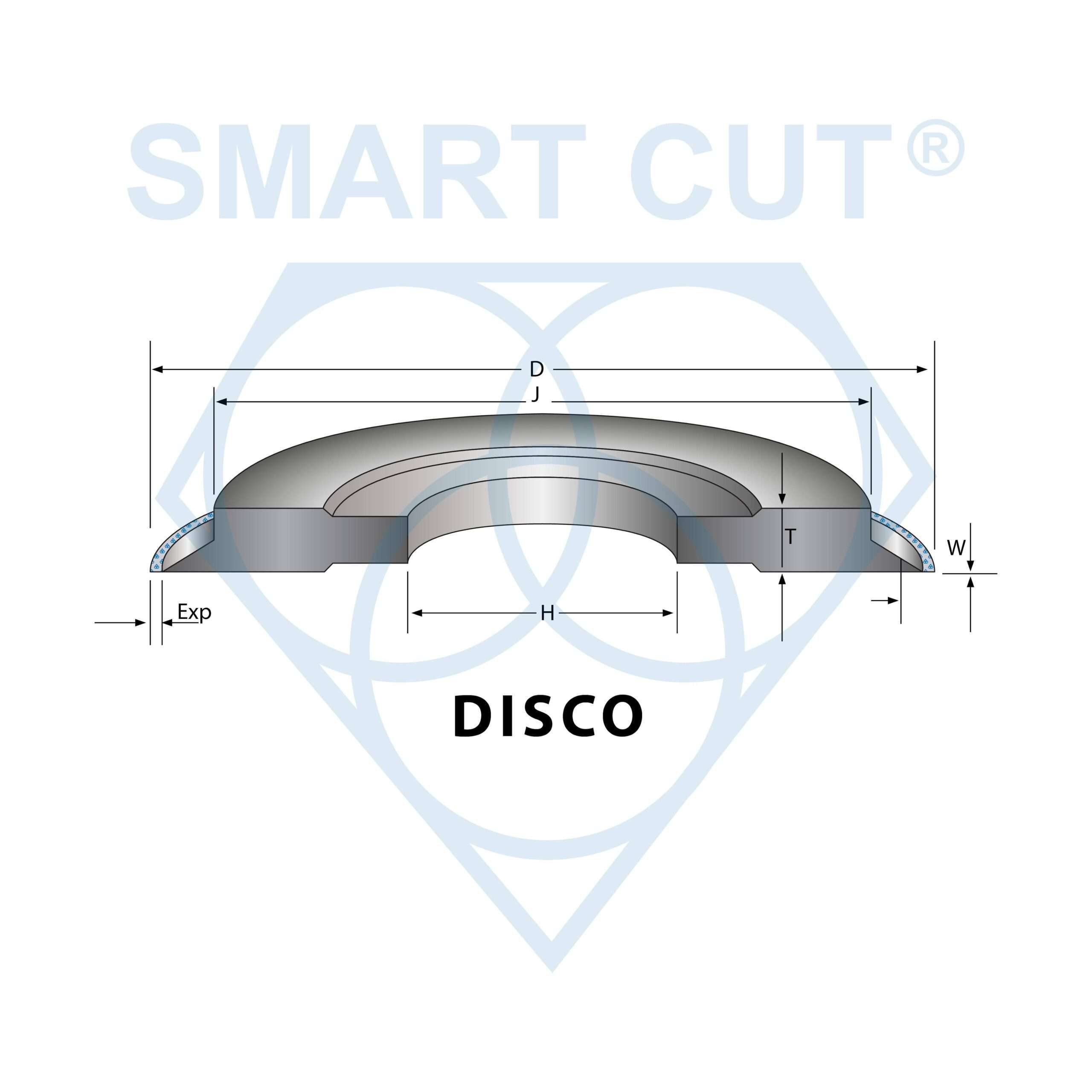
FREQUENTLY ASKED QUESTIONS
Nickel Bond Hubbed Dicing Blades are advantageous for cutting hard and brittle materials like ceramics and glass with precision and minimal chipping.
These blades can cut a variety of materials including ceramics, glass, silicon, and other hard and brittle materials.
Blades come in various sizes and thicknesses to accommodate different cutting requirements. Consult the manufacturer for specific options.
Lifespan depends on factors like the material being cut, cutting speed, and maintenance. Proper use and regular maintenance can extend the blade’s life.
Use recommended cutting speeds and feed rates for the material being cut. Regular maintenance and cleaning are crucial.
Always wear appropriate safety gear such as gloves and eye protection, and follow the manufacturer’s safety guidelines.
Compatibility depends on the blade model and machine specifications. Consult the manufacturer for details.
Regular cleaning and maintenance are important to extend the blade’s life. Specific guidelines should be obtained from the manufacturer.
A well-designed hub ensures balance and stability during cutting, contributing to a precise and smooth cut.
Some blades can be re-sharpened, while others need to be replaced when dull. Check with the manufacturer for specific guidance.
Radius options:
0.5mm to 5mm, with custom options available.
Angle options:
45°, 90°, and other specific angles as per customer requirements.
0.5mm to 5mm, with custom options available.
Angle options:
45°, 90°, and other specific angles as per customer requirements.
This will depend on blade diameter, kerf thickness and specification. However as general rule of thumb maximum blade exposure is usually around half of the blade’s diameter
Minimum blade thickness depends on blade diameter and exposure. Blades can have kerf thicknesses as low as 10 to 15 microns (0.01 to 0.015 mm), although thinner kerfs may be possible depending on the specific application requirements
diamond grit size for these types of blades can range from very fine to coarse, with typical grit sizes ranging from 0.5 to 50 microns. This depends on diameter and kerf thickness and exposure of the blade. The appropriate grit size depends on the material being cut and the desired cut quality
tolerances can range from ±1 micron to ±5 microns or more. These tolerances are dependent on factors such as the blade’s thickness, the diamond grit size, and the manufacturing process.
The cost varies depending on the specific blade such as blade diameter, kerf thickens, exposure and tolerances, but for reference purposes Nickel Bond Hubbed Dicing Blades cost less the most other diamond dicing blade types.
Minimum order quantity depends on specification and is usually 5 to 10 pcs
Lead time is usually 4 to 5 weeks
Yes, we can produce custom specifications per your requirements
Lead times vary by manufacturer and availability. It’s best to consult the manufacturer or distributor for specific information.
There may be some shipping restrictions or precautions due to the sharpness of the blades. Consult the manufacturer or shipping company for details.
There may be some shipping restrictions or precautions due to the sharpness of the blades. Consult the manufacturer or shipping company for details.
yes we can provide coatings for this purpose to enhance performance or extend lifespan.
Nickel Bond Hubbed Dicing Blades offer a balance between the precision and smoothness of a resin bond blade however the life span is much shorter then sintered (metal bond) and hybrid bond dicing blades
The recommended RPM varies based on the specific blade and material being cut. Its usually much higher the for other dicing blades types.
Store blades in a cool, dry place and protect them from physical damage.
Yes, these blades are suitable for cutting a variety of hard and brittle materials, including glass and ceramics.
What kind of quality control measures are in place during the manufacturing process of these blades?
we have strict quality control measures in place, including inspections and testing, to ensure the blades meet the required specifications and standards.
The nickel bond provides a good balance of precision and durability, making it suitable for cutting a wide variety of materials
The blades are designed to handle a range of cutting speeds, but the optimal speed will depend on the material being cut and other factors. Do not exceed maximum cutting speeds.
The environmental impacts are generally low, but it is important to dispose of used blades properly and follow any relevant regulations.
Consult local regulations
The blade’s diameter can affect the maximum cutting depth and the surface speed of the blade, which can in turn affect the cutting performance.
The thickness of the blade can affect the width of the cut (kerf) and the surface finish. Thinner blades typically provide a finer cut, but may be less durable than thicker blades.
Regular cleaning to remove debris, proper storage to prevent damage.
While primarily designed for cutting hard and brittle materials, these blades can sometimes be used for cutting certain types of plastics or soft metals.
Consider factors such as the material being cut, required precision, and machine compatibility. Consult our technical support team for advice.
Common causes of blade failure include incorrect use, excessive wear, and lack of maintenance. Following our recommendations and guidelines and regular maintenance can help prevent failure.
optimal blade speed will vary depending on the material being cut. Factors to consider include the hardness and abrasiveness of the material, as well as the desired cut quality. As a general guideline, harder materials may require lower speeds, while softer materials may be cut at higher speeds. Additionally, finer diamond grit sizes typically require higher speeds. It is essential to consult the manufacturer’s guidelines or a technical expert to determine the most suitable blade speed for your specific application. Always conduct test cuts and adjust the speed as necessary to achieve the desired results.
The hub affects the blade’s balance and stability, which can in turn impact performance and longevity. A well-designed hub can help ensure optimal performance.
The edge design affects the sharpness and durability of the blade, which in turn affects the cutting performance. A well-designed edge provides a precise and smooth cut.
Yes, these blades are typically compatible with automated dicing machines. These can be used on most common dicing saws on market today such as Disco and many others
Common problems include blade misalignment, incorrect cutting speed, and lack of maintenance. Please read our illustrated trouble shooting guide for support.
Proper coolant flow can help dissipate heat, reduce friction, and remove debris, thereby enhancing blade performance and longevity.
The diameter affects the maximum cutting depth and the surface speed of the blade. Larger diameters may allow for deeper cuts, but also require higher rotational speeds.
When cutting brittle or fragile materials, it is important to use lower feed rates and cutting speeds to prevent chipping or cracking.
How do these blades compare in terms of cost-effectiveness compared to other types of dicing blades?
Nickel Bond Hubbed Dicing Blades offer a good balance of cost and performance, providing a durable and precise cutting solution for wide variety of materials. They usually cost less the most other dicing blade types
Make sure the blade is installed in the correct orientation, with the cutting edge facing the correct direction. Use appropriate safety gear such as gloves and eye protection.Before starting the cutting process, run a test to verify that the blade is installed correctly and the machine is functioning properly.
The suitability depends on the specific blade and the type of coating or film. Consult our technical support team for recommendation
please read our illustrated trouble shooting guide and contact our technical support.
Can these blades be used in manual dicing machines, or are they only suitable for automated systems?
The compatibility depends on the specific blade and machine. This will depend on rpm’s, coolant set up, and machine design and your requirements.
Yes, blade alignment is crucial for achieving a precise cut. Use precision instruments such as dial indicators or laser alignment tools to measure and adjust the blade alignment accurately. Check Alignment Regularly: Regularly check the blade alignment during the cutting process, especially after changing the blade or adjusting any machine settings. Adjust as Necessary: If any misalignment is detected, make the necessary adjustments. Conduct Test Cuts: After adjusting the alignment, conduct test cuts to verify that the blade is properly aligned and producing the desired results.
The blades are designed to handle a range of materials, but the performance may vary based on the abrasiveness of the material.
The nickel bond helps to dissipate heat, thereby preventing overheating and potential damage to both the blade and the material being cut.
Common signs of wear include reduced cutting performance, visible blade damage, or irregularities in the cut surface. Replace the blade when these signs are evident.
Harder and more abrasive materials typically wear down the blade faster, reducing its lifespan.
Blade geometry, including edge design and thickness, affects the sharpness, durability, and cutting performance of the blade.
A hubbed design provides better support and stability during cutting, enhancing performance and reducing the risk of blade damage or misalignment.
The blade’s speed must be properly matched to the material being cut to achieve the best cut quality. Incorrect speeds can result in chipping, cracking, or poor surface finish.
Common causes include improper use, excessive force, or hitting hard inclusions in the material. Prevent chipping or breakage by following our recommendations and using proper cutting techniques.
A sharper edge provides a cleaner, more precise cut, while a dull edge can result in a rough surface finish and potential material damage.
ACCESSORIES
USAGE RECOMMENDATION
02
Jun
Dicing Blade Operations Recommendations
Share this Article with Friend or Colleague
Selecting the right dicing blade parameters often involves a trial and error process, many aspects of which can be mitigated through experience and a deep understanding of how…
02
Jun
Optimizing Dicing Blade Performance
There are many variables that affect dicing blade performance. Each variable of the dicing process is only of the many components of a larger dicing system (equation). Changing one component or variable of…
02
Jun
Trouble Shooting Dicing Problems
Guide on most common dicing problems and how to resolve them
Share this Article with Friend or Colleague
ARE YOU USING RIGHT TOOLS
FOR YOUR APPLICATION?
LET USHELP YOU
CONTACT US
HAVING ISSUES WITH
YOUR CURRENT TOOLS?
Knowledge…
02
Jun
Application Recommendations
See what blade specifications we recommend to use for different applications, along with rpm’s and feed rated
Share this Article with Friend or Colleague
ARE YOU USING RIGHT TOOLS
FOR YOUR APPLICATION?
LET USHELP…
Recommended Dressing Process
SMART CUT™ series Nickel Bond Hubbed diamond dicing blades are pre-dressed at the time of manufacturing. Dressing is the final step of the SMART CUT™ series Nickel Bond Hubbed dicing blades manufacturing process. This process levels the abrasive/diamond particle surface by removing extended diamond and plating protrusions. Pre-dressing is done in a way to best fit your anticipating dicing requirements/application.
However, we still recommend dressing the blade prior to use on your own dicing equipment. Doing so will help you achieve optimum blade roundness and eliminate pulsating peaks of grinding pressure, and prepare the blade for the needed cutting depth. Many users gradually break in their nickel bond hubed dicing blades by first making few trial cuts in order to verify acceptable performance/cut quality and proper alignment of optics and coolant on their saw. Consequently, they start cutting material at slow speed and gradually increase the speed and feed rate step by step towards their required feed rate.
Dressing Recommendations
- 6 cuts at 10 mm / s
- 6 cuts at 25 mm / s
- 6 cuts at 30 mm / s
- 6 cuts at 35 mm / s
- 6 cuts at 40 mm / s
- 6 cuts at 45 mm / s
- 6 cuts at 50 mm / s
- 6 cuts at 55 mm / s
- 6 cuts at 60 mm / s
- 6 cuts at 65 mm / s
- 6 cuts at 70 mm / s
- 6 cuts at 75 mm / s
100 Total cuts on 4″ (100mm) wafer
- Blades are individually packaged in clear plastic cases
- Each dicing blade box holds 4 individually packaged blades
- Typically minimum order is 4 pcs (this applies to samples as well). Unless the specifications is very popular.
CASE STUDIES
Tab Content
Features:
- Ultra-thin precision cutting for semiconductor applications
- Nickel electroplated bond with larger diamond grit for longer blade life
- Customizable options
- Optimized hub design for superior cooling efficiency
- Free-standing nickel-diamond matrix for precise cut depth control
- Excellent cut quality with minimal chipping
- Ultra-thin kerfs (<50 microns) for high-precision dicing
- Improved diamond exposure reduces the need for frequent dressing
- Handles high exposure-to-width ratios for stable cutting
- Supports advanced dicing techniques like bevel and step cutting
- Available in various grit sizes and bond types for different applications
- Ideal for silicon, III-V compounds, PZT ceramics, and more
- Ultra-thin kerfs (<50 microns) for high-precision dicing
Advantages
- Maximum cutting performance
- No glazing
- Faster cutting action
- Improved surface finish quality
- Better coolant retention
- No Material Deformation
- No Contamination
Benefits
- Increase Blade Life
- Reduce Chipping
- Reduce Blade Wear
- Increase Process Consistency
- Increase Blade Life
- Reduce Chipping
- Reduce Blade Wear
Why Work With Us?
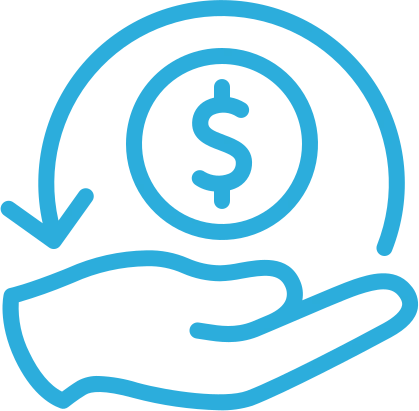
Best Return
on Investment
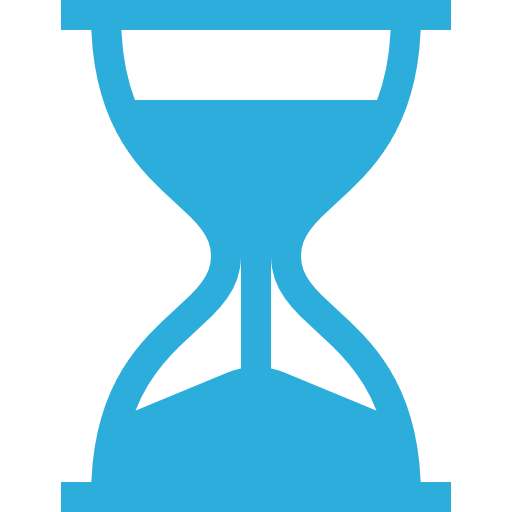
Attractive Cost of
Ownership
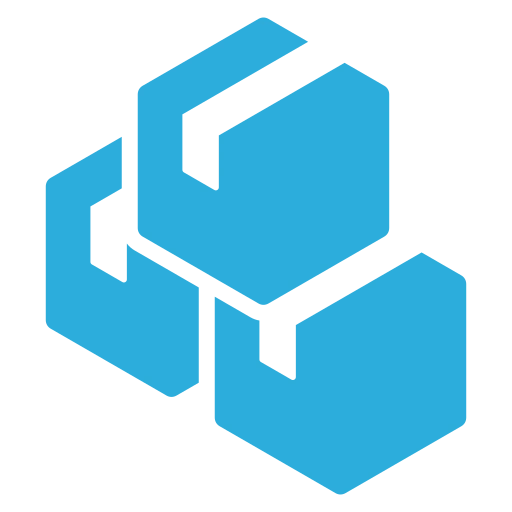
Thousands of Diamond & CBN Blades in stock
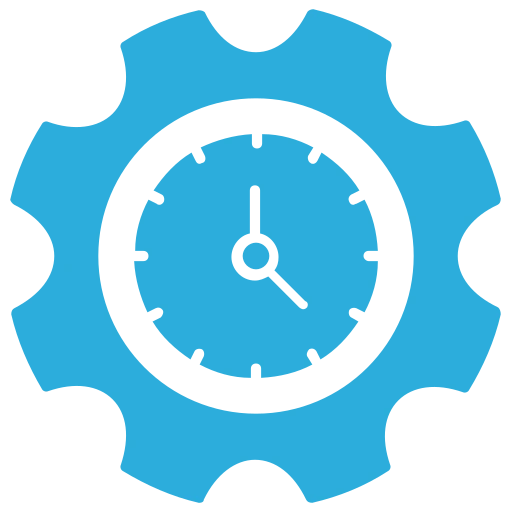
Custom Manufacturer with Fast Lead times
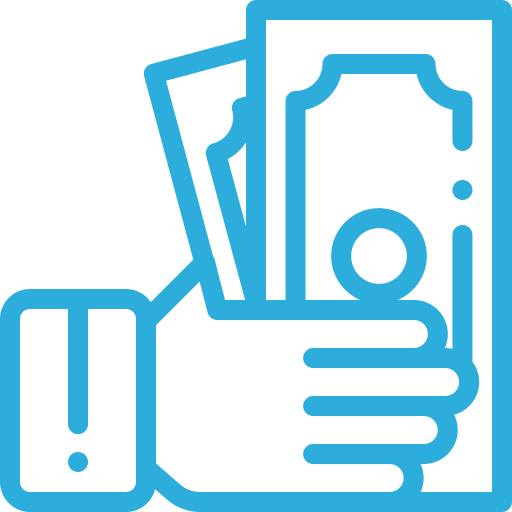
Unmatched
Prices in North America
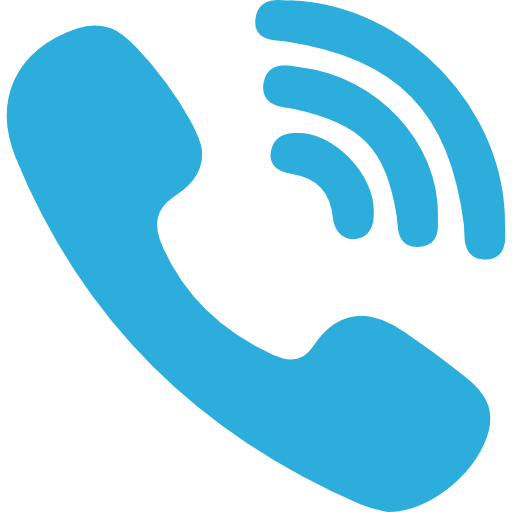
Unmatched Experience & Technical Support
SMART CUT® Series SCNH
Specifications Available
Exposure (microns) |
380 |
510 |
640 |
760 |
890 |
1020 |
1150 |
1270 |
||||
---|---|---|---|---|---|---|---|---|---|---|---|---|
Thickness (μm) |
Tolerance Range (μm) |
380-510 |
510-640 |
640-760 |
760-890 |
890-1020 |
1020-1150 |
1150-1270 |
1270-1400 |
Grit Size |
Concentration |
Bond Hardness |
20 |
16-20 |
20 x 380 |
20 x 510 |
5000 |
50 |
S |
||||||
25 |
21-25 |
25 x 380 |
25 x 510 |
25 x 640 |
4500 |
50 |
S |
|||||
30 |
26-30 |
30 x 380 |
30 x 510 |
30 x 640 |
30 x 760 |
30 x 890 |
4000 |
70 |
M |
|||
35 |
31-35 |
35 x 380 |
35 x 510 |
35 x 640 |
35 x 760 |
35 x 890 |
35 x 1020 |
3500 |
70 |
M |
||
40 |
36-40 |
40 x 380 |
40 x 510 |
40 x 640 |
40 x 760 |
40 x 890 |
40 x 1020 |
40 x 1150 |
3000 |
90 |
M |
|
50 |
41-50 |
50 x 380 |
50 x 510 |
50 x 640 |
50 x 760 |
50 x 890 |
50 x 1020 |
50 x 1150 |
50 x 1270 |
2500 |
90 |
M |
60 |
51-60 |
60 x 510 |
60 x 640 |
60 x 760 |
60 x 890 |
60 x 1020 |
60 x 1150 |
60 x 1270 |
2000 |
110 |
H |
|
70 |
61-70 |
70 x 510 |
70 x 640 |
70 x 760 |
70 x 890 |
70 x 1020 |
70 x 1150 |
70 x 1270 |
1800 |
110 |
H |
|
80 |
71-80 |
80 x 760 |
80 x 890 |
80 x 1020 |
80 x 1150 |
80 x 1270 |
1700 |
130 |
H |
|||
90 |
81-90 |
90 x 1020 |
90 x 1150 |
90 x 1270 |
1500 |
130 |
H |
Recommended Applications & Diamond Sizes
Material |
Application |
2/4 |
4/6 |
8/12 |
10/15 |
15/25 |
30/40 |
40/60 |
---|---|---|---|---|---|---|---|---|
GaS |
Opto, LED |
X |
||||||
InP |
Opto |
X |
||||||
Si,Ge |
Discrete |
X |
X |
|||||
Si |
IC |
X |
||||||
PZT |
Sensor |
X |
X |
|||||
SiC |
Discrete |
X |
||||||
MLCC |
MLCC |
X |
||||||
CSP |
CSP |
X |
X |
|||||
μ-BGA |
μ-BGA |
X |
X |
X |
||||
FR4 |
PCB |
X |
||||||
LiNbO₃ |
SAW |
X |
||||||
Cu |
Metallic L/F |
X |
||||||
Epoxy |
Mold Compound |
X |
X |
X |
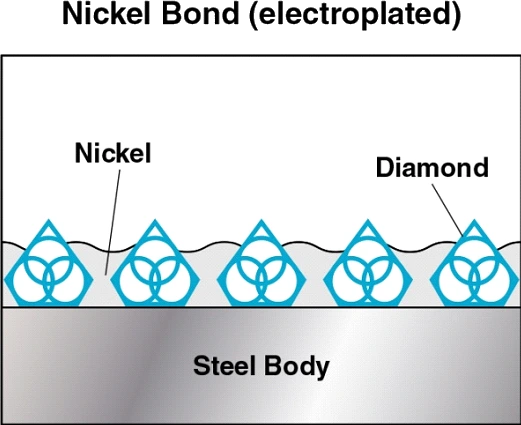
About Nickel Bond (Electroplated) Tools
Electroplated (nickel bond) diamond products usually have a single layer of diamonds, held by a tough durable nickel alloy. Nickel is frequently used as a base for plating diamond. Because of its excellent strength, toughness and flexibility during the plating process. Electroplated diamond products are able to retain their original shape and dimensions thought their working life. Unlike sintered (meal bond) or resin bond diamond products, where diamond particles are buried in bond and held together by metal or resin binder deep inside.
Electroplating allows diamond particles to protrude from the bond matrix, providing a free, faster cutting action with minimum heat generation.
SMART CUT™ Series Nickel Bond Hubbed diamond dicing blades consist of a precisely made hub, shaped for optimum cooling results. The hub carries an electrodeposited layer of proprietary nickel alloys and diamond grains. When the supporting aluminum is etched back, a free standing nickel diamond matrix remains. The length of this free standing (exposed) diamond rim determines how deep the blade can cut. Please see formula below for more information.
UKAM Industrial Superhard Tools proprietary blade manufacturing processes, which allow precise control of diamond grit size, diamond concentration, and nickel bond hardness, are used to optimize these variables and produce hub blades that offer unparalleled cut quality, blade life and throughput.SMART CUT™ Series Nickel Bond Hubbed diamond dicing blades provide excellent performance on large variety of applications ranging from silicon dicing, very brittle III-V compound materials, PZT ceramics, tantalates, aluminas, to silica filled plastics for chip scale package singulation.
Manufactured utilizing SMART CUT™ technology, each diamond works like a small horse. Diamonds come in contact with the material in the right place and at the right time, working where you need them most. You get the maximum use out of diamond and bond.
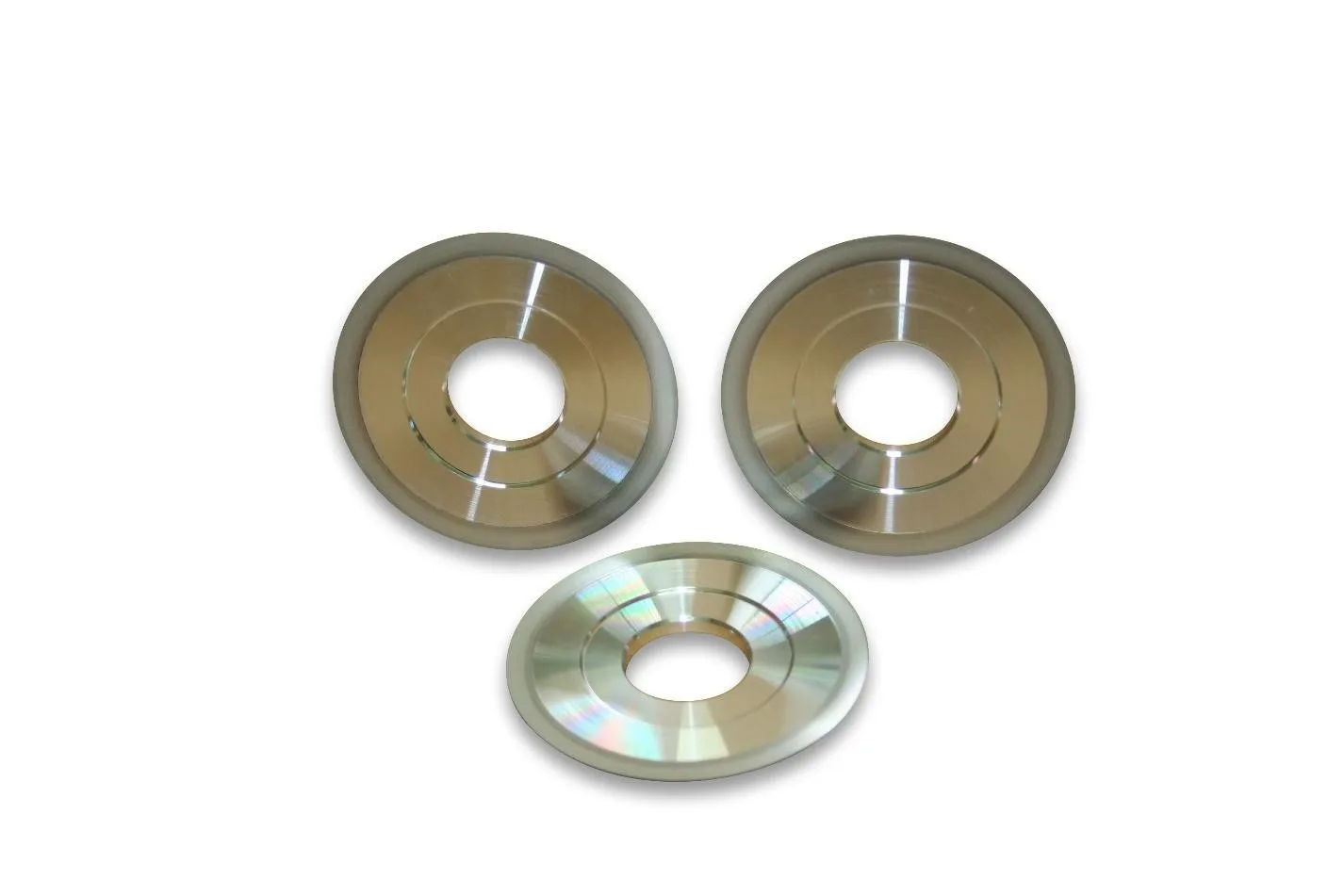
Nickel Bond Diamond Dicing Blade
Blade Thickness
Diamond Concentration is still a factor in determining the life and cutting speed of your Diamond Blade. Higher diamond concentration is recommended and usually used for cutting softer and more abrasive types of materials. However, the trade off is slower cutting speed. Low diamond concentration is recommended and widely used for cutting harder materials
Blade Exposure
Blade exposure is the minimum dimensions of the nickel rim to protrude over the aluminum hub. Selecting the proper blade exposure is function of total cut depth. Due to the self sharpening nature of the nickel bond diamond matrix, this dimension will be reduced during operation by wear. Blade exposure to be selected by cutting into substrate is
E1 = CS + SG + BW
for cutting through a substrate into a sporting dicing tape, the amount of cutting into the tape must be added to the above formula:
E2 = CT + CS + SG + BW
Typical dimensions are
CS = Cutting Substrate depth = Cut depth or material thickness
SG = Safety Gap between alu-Hub and substrate
BW = Amount of Blade to be worn (used up) during
For Example: Exposure for a 600 micron substrate cutting into tape is 30 + 600 + 130 + 200 = 960 microns. Recommended maximum blade exposure is about 25 x blade thickens for soft nickel alloy bond and 35 x blade thickness for hard nickel alloy bond.
Nickel Bond Hardness
Bond hardness determines how fast the nickel bond dicing blade will protrude/release its sharpest point of diamond particles in order to maintain consistent cut quality. Smoothness of diamond abrasive particles of the substrate, without considering diamond grit size is influenced by the stability of the bond binder. As the diamond particles become dull during usage, the speed and force required for their release from bond matrix. depends on strength they are bonded with. Hard nickel alloys firmly hold diamonds in place. They typically wear less and hence have little self sharpening. Softer nickel alloys on the other hand release dull diamond easily. And more frequently expose continuously sharp diamond particles. For this reason they are more self sharpening. SMART CUT™ series Nickel Bond Hubbed diamond dicing blades are available in soft or hard nickel alloys depending on customers dicing objective of clean cut quality vs. long blade life.
Diamond Mesh Size
Nickel hardness and size of diamond particles plays a major role in determining cut quality, feed rate, RPM's, blade life, and overall performance. Finer diamond particles produce very smooth cut quality, along with minimum kerf less, and most minimal amount of chipping. Smaller diamond particles are release from bond faster, exposing new sharp diamond particles and maintaining excellent cut quality. The trade off is lower blade life and much slower cutting speeds. Since smaller/finer diamond particles remove less material, they require higher spindle speeds and slower feed rates. Finer diamond particle nickel bond dicing blades, also tend to load up (clogging diamond particles cavities with material residue being cut). Coarser size (larger) diamond particles provides much higher feed rates. Coarser diamond nickel bond dicing blades provide longer life and exhibit very little tendency to load up. The trade off more chipping, greater kerf loss, and rougher cut quality. SMART CUT™ series Nickel Bond Hubbed diamond dicing blades are available in large variety of diamond particle sizes, please see table below for more information.
Long Exposure
SMART CUT® Difference
How SMART CUT® Dicing Blades are Different in comparison to other dicing blades.
Faster
Cutting Action
SMART CUT® technology enhances nickel bond hubbed dicing blades, delivering faster cutting speeds without sacrificing cut quality. The advanced bond ensures minimal wear, leaving a smooth finish and reducing material deformation.
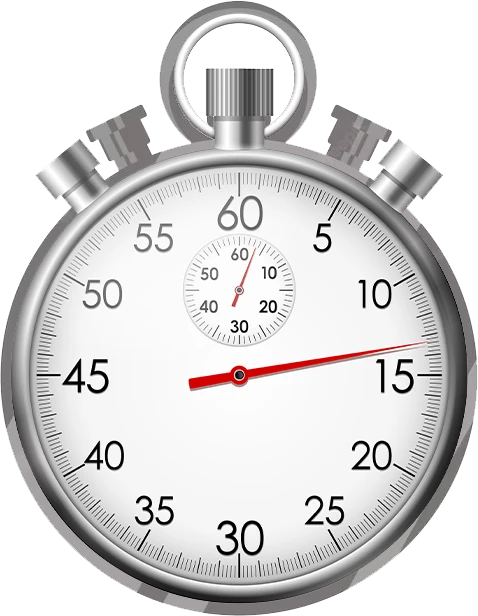
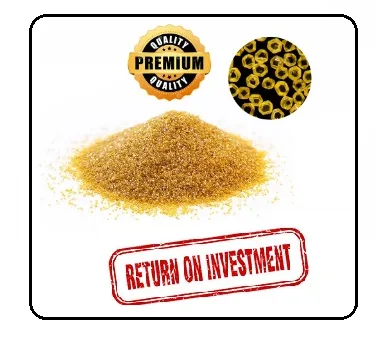
Manufactured Using
The Highest Quality Raw Materials
Only the highest quality synthetic diamonds and raw materials are used in the manufacturing process. The highest quality standards and product consistency is maintained, using sophisticated inspection and measurement equipment.
Best
Performance & Value on the Market
SMART CUT® Nickel Bond Hubbed Diamond Dicing Blades deliver superior performance and value when compared to similar products. While the initial cost may be comparable or slightly higher than other nickel bond blades, their longer lifespan and greater cutting efficiency result in a lower cost per cut, offering significant savings in both time and money over the long term.
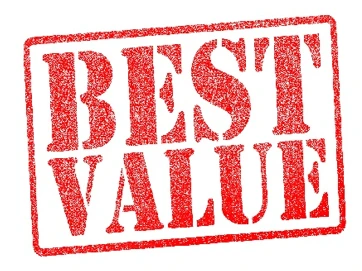
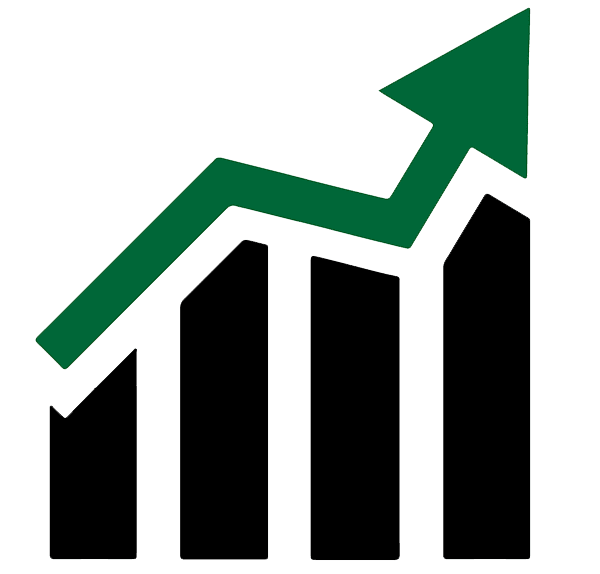
Longer
Life
SMART CUT® Nickel Bond Hubbed Diamond Dicing Blades deliver superior longevity over standard nickel bond hubbed blades. The advanced bond structure increases resistance to wear, allowing the blade to maintain cutting performance over a longer period, reducing downtime, and improving overall efficiency.
More
Consistent Performance
SMART CUT® Nickel Bond Hubbed Diamond Dicing Blades are engineered for uniform wear, ensuring a stable cutting edge & diamond exposure for the duration of the blade’s life. This consistency provides reliable cutting speed and performance across a range of challenging materials, reducing the need for frequent dressing and improving overall productivity.

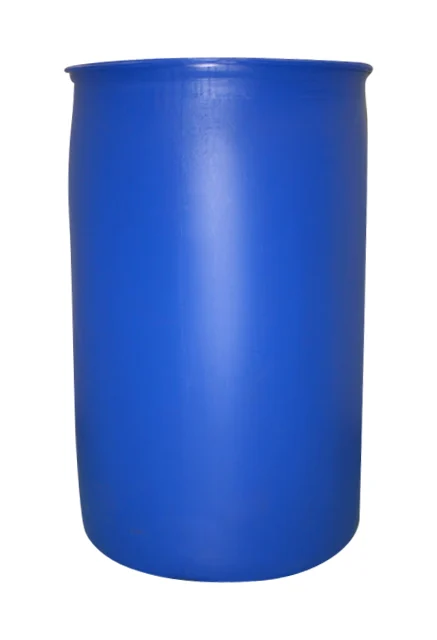
SMART CUT® XP Dicing Fluid, Coolant, & Surfactant
Available in 4 Different Formulas to Fit Most Dicing Applications
XP-1 is a general-purpose dicing fluid within the SMART CUT® range, designed to reduce debris, improve tool life, and prevent corrosion, while ensuring smooth cutting and protecting sensitive materials from ESD.
XP-2 enhances lubrication for demanding applications, offering superior cutting speeds, tool longevity, and advanced cleaning capabilities for tough materials like SiC and sapphire.
XP-3 is ideal for high-pressure systems, offering consistent cooling performance without foam buildup.
XP-4 specifically protects electrostatic-sensitive components by eliminating ESD, reducing defects, and extending tool life during the dicing process.
Why Work With Us?
Comprehensive Source Of Information On Dicing Blades
We understand that your success depends on select the right dicing blade, and optimizing your dicing parameters to best fit your applications/needs. The more you understand about what we can do for you, the better our partnership will be. On our website you will find the Most Comprehensive Source of Information on Everything you wanted to know about diamond dicing blades & industrial diamond tools.
Large Inventory & Custom Manufacturing
Largest Inventory of Precision & Ultra Thin Diamond Dicing Blades in the U.S. Available in different sizes, thickness, arbor sizes, diamond concentrations, diamond mesh sizes, and bond hardness's.
Experience Makes All The Difference
"ONE OF THE MOST EXPERIENCED COMPANIES IN THE INDUSTRY"
Over the years we have enjoyed working with all types if clients, regardless of size. Proprietary dicing blade chemistry, precision manufacturing methods, modern quality control methods, allow us to control and regulate the dozens of variables that affect blade life, quality of cut, surface finish. Reducing and often eliminating additional steps often required after cutting.
Umatched Technical Support
We Are a Partner In Your Success
Developing close ties with our customers is the foundation of our business. At the core of
our company is a team of world class engineers, knowledgeable customer service personnel here to serve you. Whether is designing or manufacturing a special solution. We will go out of our way to optimizing your process to ultimate level of efficiency.
Advanced
Technology
American Manufacturer As one of the few remaining independent U.S.Diamond Tool & machine builders. We have the experience & tradition to help you remain at frontier of technology Our experience has been further enhanced by acquiring assets and processes from some of the oldest American tool manufacturers, along with their decades of experience and R& D. This has positioned us as one of the most experienced companies in the industry.
Superior Quality &
Consistency
Our unique bond formulations, tool designs, stringent requirements, and utilization of exceptionally high-quality diamonds and raw materials ensure top-notch products that adhere to strict ISO 9000 standards.
Our proprietary technology allow us to control and regulate the dozens of variable that affect toolife, quality, & consistency
Expect More From Your Tools
Related Products
Resin Bond Dicing Blade
Sintered (Metal Bond) Diamond & Cbn Dicing Blades
Sintered (metal bonded) diamond tools have multiple layers of diamonds impregnated inside the metal matrix. Diamonds are furnaces sintered in a matrix made of iron, cobalt, nickel, bronze, copper, tungsten, alloys of these powders or other metals in various combinations. Metal bonded diamond tools are impregnated” with diamonds.
Tungsten Carbide Dicing Blades
Hybrid Bond Dicing Blades
Nickel Bond Dicing Blades
SMART CUT® Nickel Bond Hubless Dicing Blades are designed to provide exceptional precision, longevity, and consistency for cutting a wide range of materials. Engineered with a high diamond concentration and advanced Nickel bond matrix, these blades deliver efficient cutting performance with minimal heat generation. Their ability to maintain excellent form retention and diamond exposure makes them ideal for applications requiring high accuracy, such as wafer dicing, thin substrate cutting, and microelectronics fabrication.
The Nickel binder used in these blades is specifically developed to offer a hard bond for soft materials, ensuring longer blade life and reduced wear rates. This unique combination of bond structure and abrasive composition allows for faster cutting while minimizing chipping, making it an optimal choice for materials such as printed circuit boards (PCB), silicon, and ball grid array (BGA) components. By maintaining sharp diamond exposure throughout the cutting process, these blades enhance material removal efficiency while ensuring a stable and controlled cut.
Recently Viewed Products
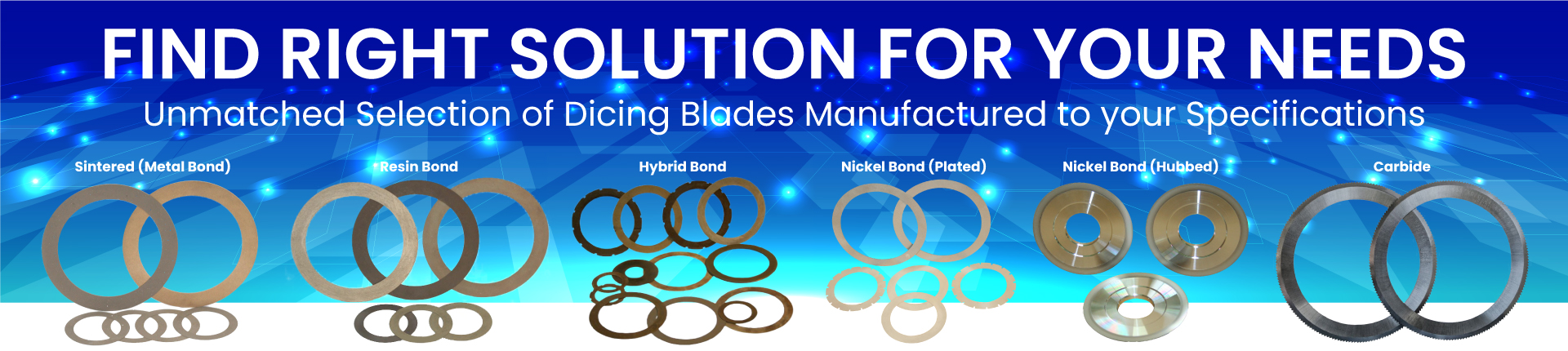
ARE YOU USING RIGHT DICING BLADES
FOR YOUR APPLICATION?
LET US
HELP YOU
HAVING ISSUES WITH
YOUR CURRENT DICING BLADES?
01
Jun
Select right Diamond Dicing Blade for your application
Selecting the right diamond dicing blade & parameters for your material/application can be a very time consuming, trial & error frustrating process. The guide below has been designed to help you better understand the most important...
02
Jun
Dicing Blade Operations Recommendations
Share this Article with Friend or Colleague
Selecting the right dicing blade parameters often involves a trial and error process, many aspects of which can be mitigated through experience and a deep understanding of how...
02
Jun
Optimizing Dicing Blade Performance
There are many variables that affect dicing blade performance. Each variable of the dicing process is only of the many components of a larger dicing system (equation). Changing one component or variable of...
02
Jun
Trouble Shooting Dicing Problems
Guide on most common dicing problems and how to resolve them
Share this Article with Friend or Colleague
ARE YOU USING RIGHT TOOLS
FOR YOUR APPLICATION?
LET USHELP YOU
CONTACT US
HAVING ISSUES WITH
YOUR CURRENT TOOLS?
Knowledge...
02
Jun
Application Recommendations
See what blade specifications we recommend to use for different applications, along with rpm's and feed rated
Share this Article with Friend or Colleague
ARE YOU USING RIGHT TOOLS
FOR YOUR APPLICATION?
LET USHELP...
02
Jun
Dicing Blade Case Studies
This article provides important guidelines for optimizing the dicing process in semiconductor packaging, focusing on package singulation for various technologies such as BGA, QFN, LED, CMOS, and wafer substrates. It covers key variables such as...
01
Jun
Optimizing QFN Package Dicing Process Using SMART CUT® Dicing Blades
Share this Article with Friend or Colleague
Dicing QFN packages presents several challenges due to the composition of materials and the precision required for clean, defect-free cuts. These challenges arise from the multi-layered structure of...
02
Jun
How to Selecting Right Diamond Tools for your application
Selecting the appropriate Diamond & CBN Tool specification is a crucial aspect of achieving your objectives. Opting for the ideal specification not only yields optimal results but also ensures the best return on investment. Conversely,...
02
Jun
How to properly use Diamond Tools
UKAM Industrial Superhard Tools manufactures precision diamond tools for a large variety of applications, materials, and industries.
Share this Article with Friend or Colleague
Metal Bonded Diamond Tools are “impregnated” with diamonds. This means that selected diamonds...
02
Jun
Why use diamond
Diamond is the hardest material known to man kind. When used on diamond/tools, diamond grinds away material on micro (nano) level. Due to its hardness Diamond will work all types of materials from...
02
Jun
What is Diamond Mesh Size and how to select best one for your application
Diamond grit size can be defined as the size of the diamond particles used in the bond matrix. The larger the diamond particles (grit size) the faster the tool will cut.
Share this Article with Friend or...
02
Jun
What is Diamond Concentration and which to use for your application
Diamond concentration is measured based on the volume of diamond within a section of the tool. It is typically defined as Concentration 100, which equates to 4.4 carats per cubic centimeter of the diamond layer...
02
Jun
Diamond Tool Coolants Why, How, When & Where to Use
Coolant is one of the most overlooked variables in the overall diamond or cbn tool machining process. Effective and proper use of coolant and recalculating coolant system will pay off in terms of improved surface...
02
Jun
Diamond vs CBN (cubic boron nitride) Tools
Cubic Boron Nitride (CBN) is a synthetic material that is renowned for its exceptional hardness and high thermal stability. It is composed of boron and nitrogen atoms arranged in a crystal lattice structure, similar to...
17
May
Get to Know the Diamond Tool Bond Types and Which to use for your application
Selecting the appropriate diamond bond type for specific applications is crucial for several reasons. Diamond bond type directly affects the tool's performance, efficiency, and longevity. Different bond types determine how well a tool can withstand...
09
Oct
How to Properly Use Diamond Carving Points
Diamond carving points are essential tools for anyone working with hard materials like glass, stone, and metals. These tools help with detailed tasks like engraving and finishing, providing good control and helping you work efficiently....
- Unmatched Selection For Many Applications
- Superior Quality & Consistency
- Immediate Worldwide Delivery
- Technical Support & Expertise
- American Based Manufacturer
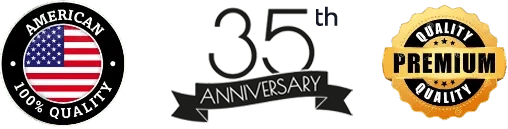

- Different Product
- Different Technology
- Different Company
- Expect MORE from your tools
Let Us HELP You!
Subscribe To Our Newsletter
Signup for email offers, updates, and more
Contact Us
- 25205 & 25201 Avenue Tibbits Valencia CA 91355 USA
-
Phone : (661) 257-2288
FAX : (661) 257 -3833 - lel@ukam.com
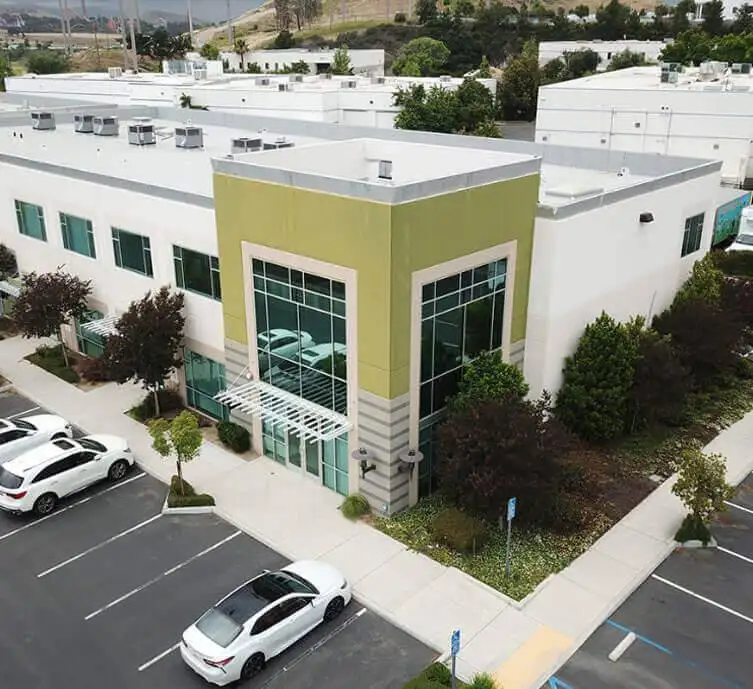
UKAM Industrial Superhard Tools is a U.S. High Technology, Specialty Diamond Tool & Equipment manufacturer. We specialize in producing ultra thin & high precision cutting blades and precision cutting machines diamond drills, diamond micro tools, standard & custom advanced industrial diamond tools and consumables.
- 25205 & 25201 Avenue Tibbits Valencia CA 91355 USA
-
Phone : (661) 257-2288
FAX : (661) 257 -3833 - lel@ukam.com
- 25205 & 25201 Avenue Tibbits Valencia CA 91355 USA
-
Phone : (661) 257-2288
FAX : (661) 257 -3833 - lel@ukam.com
DIAMOND TOOLS BY BOND
EQUIPMENT
KNOWLEDGE CENTER
OUR PRODUCTS
COMPANY
CUSTOMER SERVICE
Shipping Methods


Safe & Secure Payments

© Copyright 1990-2025. UKAM Industrial Superhard Tools – Terms of Use