-
0 items in quote
No products in the Quote Basket.
SMART CUT® 6009
LOW SPEED SAW
SMART CUT® 6009 Low Speed Precision Saw is an affordable state-of-the-art solution designed for precise sectioning of various materials, including high-value and fragile components, with unparalleled accuracy. Engineered for reliability and ease of use, this saw features an impressive cutting capacity of up to 2 inches (50mm) and supports diamond & cbn wafering blades 4” (101mm) to 6” (154mm) in diameter with a 1/2-inch arbor. Its variable speed range, adjustable from 50 to 700 RPM (with optional configuration 50 to 1,500 RPM’s) ensures optimal performance across a variety of applications.
DESCRIPTION
SPECIFICATIONS
ADVANTAGES
INDUSTRIES USED IN
FAQ
OPERATING MANUALS
ACCESSORIES
DESCRIPTION
At the heart of the SMART CUT® 6009 is its touch panel interfaceinterface, allowing operators to easily control the cutting process. The integrated micrometer cross-feed adjustment, with a range of 0-25 mm and an accuracy of 0.01 mm, provides precise positioning for consistent results. Additionally, the saw comes equipped with an automatic cut-off switch, ensuring safety and precision by automatically stopping the process once the cut is complete.
The gravity-feed weight system allows for controlled cutting pressure, ensuring smooth operation even with delicate materials. The clear safety splash guard offers maximum visibility and operator protection, enhancing usability and compliance with safety standards.
Compact and robust, the SMART CUT® 6009 is ideal for research and development, as well as advanced material preparation applications. Its thoughtful design and innovative features make it an indispensable tool for achieving high-precision cuts while maintaining ease of operation and user safety. It’s straight forward design allows the operator to concentrate on sectioning samples, not operating the machine.
SPECIFICATIONS
- Electric power:50W,220V/110V
- Spindle speed: 0~700 r/min
- Positioning accuracy: 0.01mm
- Wafering Blade Diameters Used: 4” (101mm), 5” (17mm), 6” (154mm)
- Micrometer Cross Feed: 0-25mm
- Dimension: 350mm (14” ) ×350mm (14”) ×200mm (8”)
- Weight: 18Kg (40 lbs)
ADVANTAGES
- Precise Cutting Performance: The combination of variable speed control and micrometer cross-feed adjustment ensures unparalleled accuracy for cutting delicate and hard materials.
- Versatility: Supports a range of applications with a cutting capacity of up to 2 inches and compatibility with cut-off wheels up to 6 inches (154mm) in diameter. Ideal for advanced materials, crystals, ceramics, and fragile components.
- Ease of Use: The PLC touch screen provides an intuitive interface for easy operation, allowing users to customize and monitor cutting processes efficiently.
- Consistent Results: The gravity-feed weight system ensures uniform cutting pressure, delivering smooth and even cuts without manual intervention.
- Enhanced Safety: Features an automatic cut-off switch and clear safety splash guard, ensuring a secure working environment and protecting operators from coolant spray and debris.
- Durability and Reliability: Constructed with a robust aluminum base and stainless steel components, offering long-lasting performance even in demanding environments.
INDUSTRIES USED IN
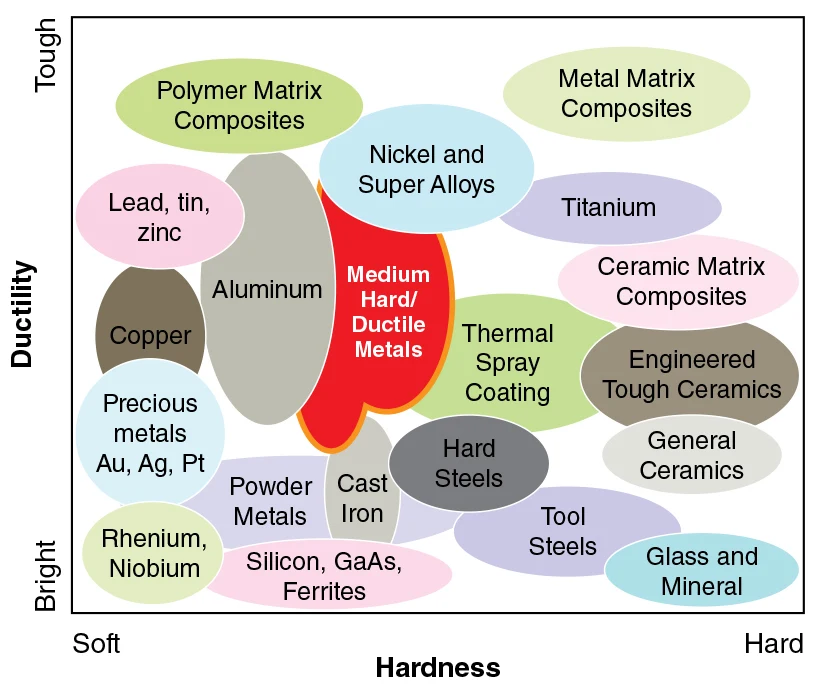

INDUSTRIES USED IN:
- Advanced Ceramics
- Composites
- Glass
- Geology
- Quartz
- Materials Research
- Medical Devices
- Metallography
- Photonics / Optics
- Semiconductor
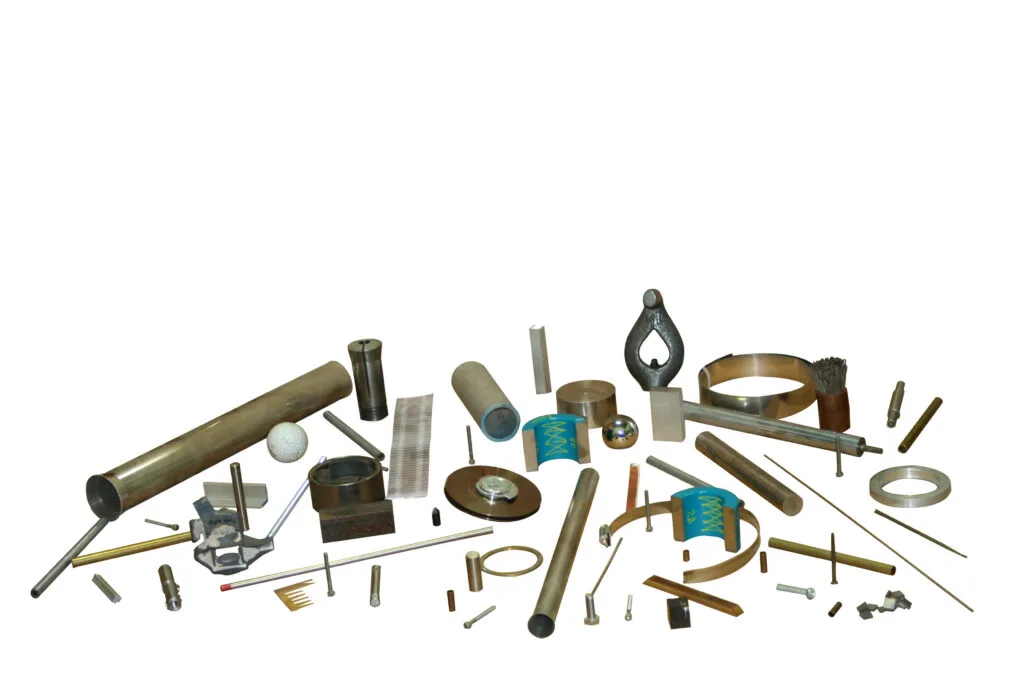
Ferrous & Non-Ferrous Metals:
- Plain Carbon Steels
- Electronic Packages
- Stainless Steels Plastics
- Tool Steels Fasteners
- Aluminum Refractories
- Copper Base Alloys Integrated Circuits
- Magnesium Thermal Spray Coatings
- Titanium Metal Matrix Composites
- Biomedical Wafers
- Petrographic
- PCB.s Ceramics
FAQ
Tab Content
OPERATING MANUALS
Tab Content
ACCESSORIES
Tab Content
Features
- Cutting capacity up to 2 inches.
- Supports cut-off wheels up to 6" (154mm) in diameter with a 1/2-inch arbor.
- Variable speed control ranging from 60 to 700 RPM for precise cutting.
- Gravity-feed weight system for consistent cutting pressure.
- Touch panel interface for easy control.
- Micrometer cross-feed adjustment with a range of 0-25 mm and accuracy of 0.01 mm.
- Automatic cut-off switch for safety and precision.
- Clear safety splash guard for operator visibility and protection.
- Durable aluminum base and stainless steel construction for long-term reliability.
- Compact, lightweight design suitable for labs and workshops.
- Includes versatile accessories such as Single Saddle Vice, Double Saddle Vice, Universal Single Saddle Vice, Bar/Tube Chuck
SMART CUT® Coolants
Your choice of one (1) quart of SMART CUT® Water Soluble Coolant or Mineral Oil is included with machine. SMART CUT® Water Soluble Coolant Reduces material thermal stress, edge damage, and internal cracking, increases blade life, provides better cut quality, preserves material micro structure
Hence, assuring long-term integrity of material being sectioned. Since SMART CUT coolant is both a coolant and lubricant, both the wafering blade and material benefit. Mix ratio is 1:20 (1 part coolant, 20 parts water) on very hard and dense materials and 1:40 (1 part coolant, 40 parts water) on softer materials. Depending on mix ratio 1 quart will produce 5.7 to 9 gallons of coolant when mixed with water. As a coolant, SMART CUT KOOL reduces heat caused by friction. As a lubricant, SMART CUT KOOL lowers friction and surface tension, which increases swarf dispersion.
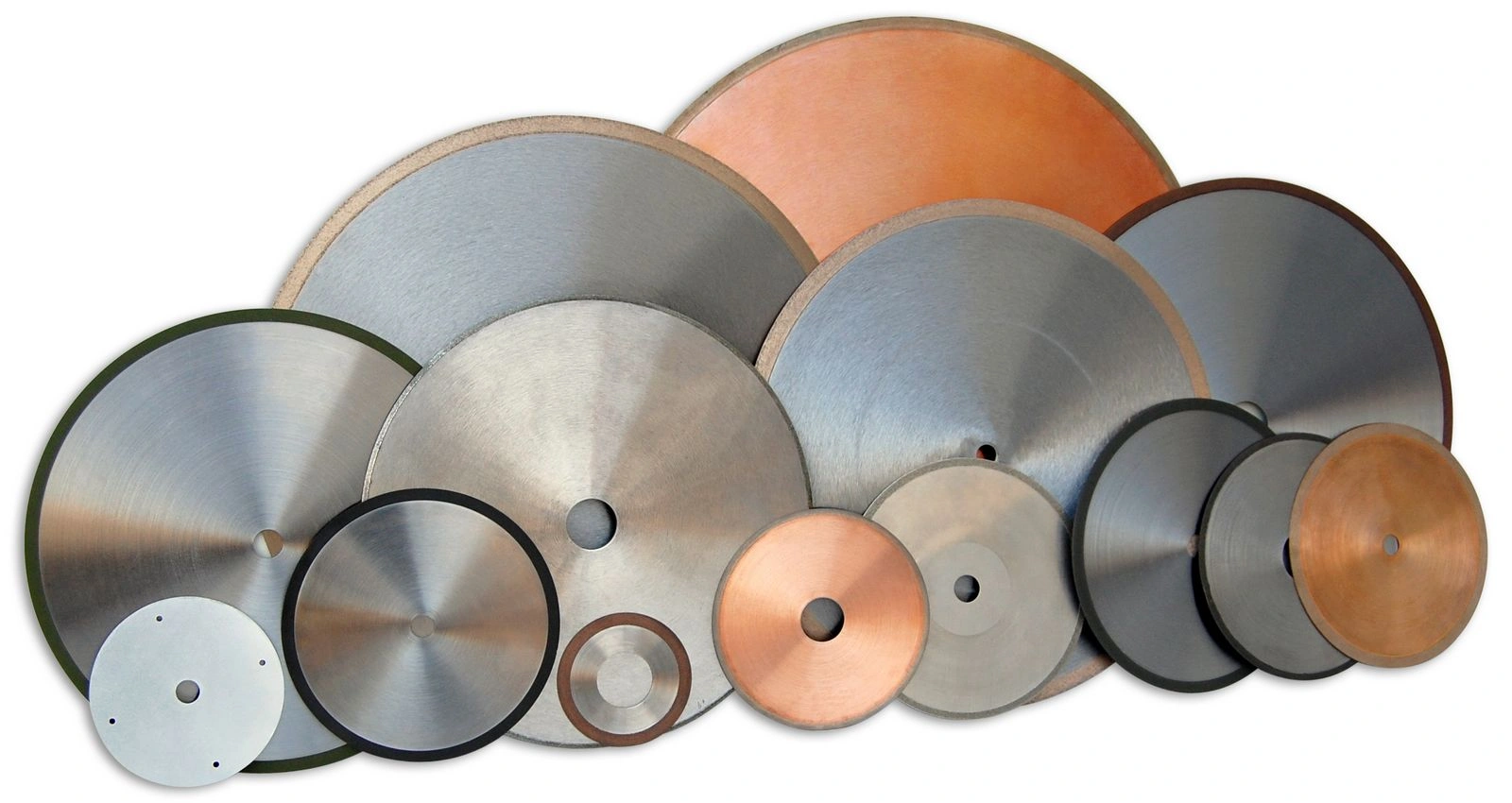
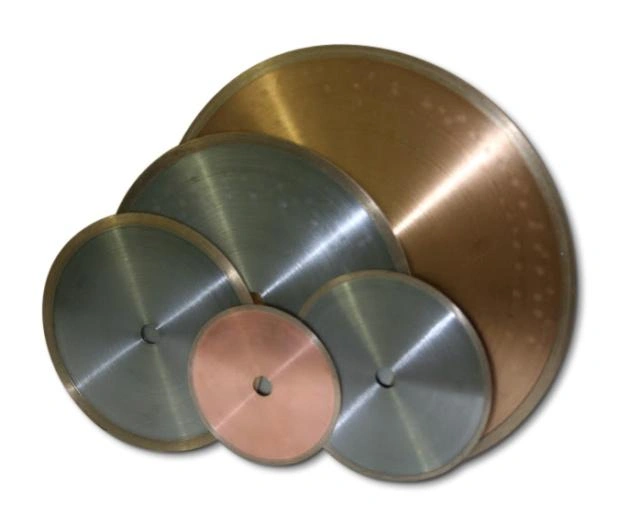

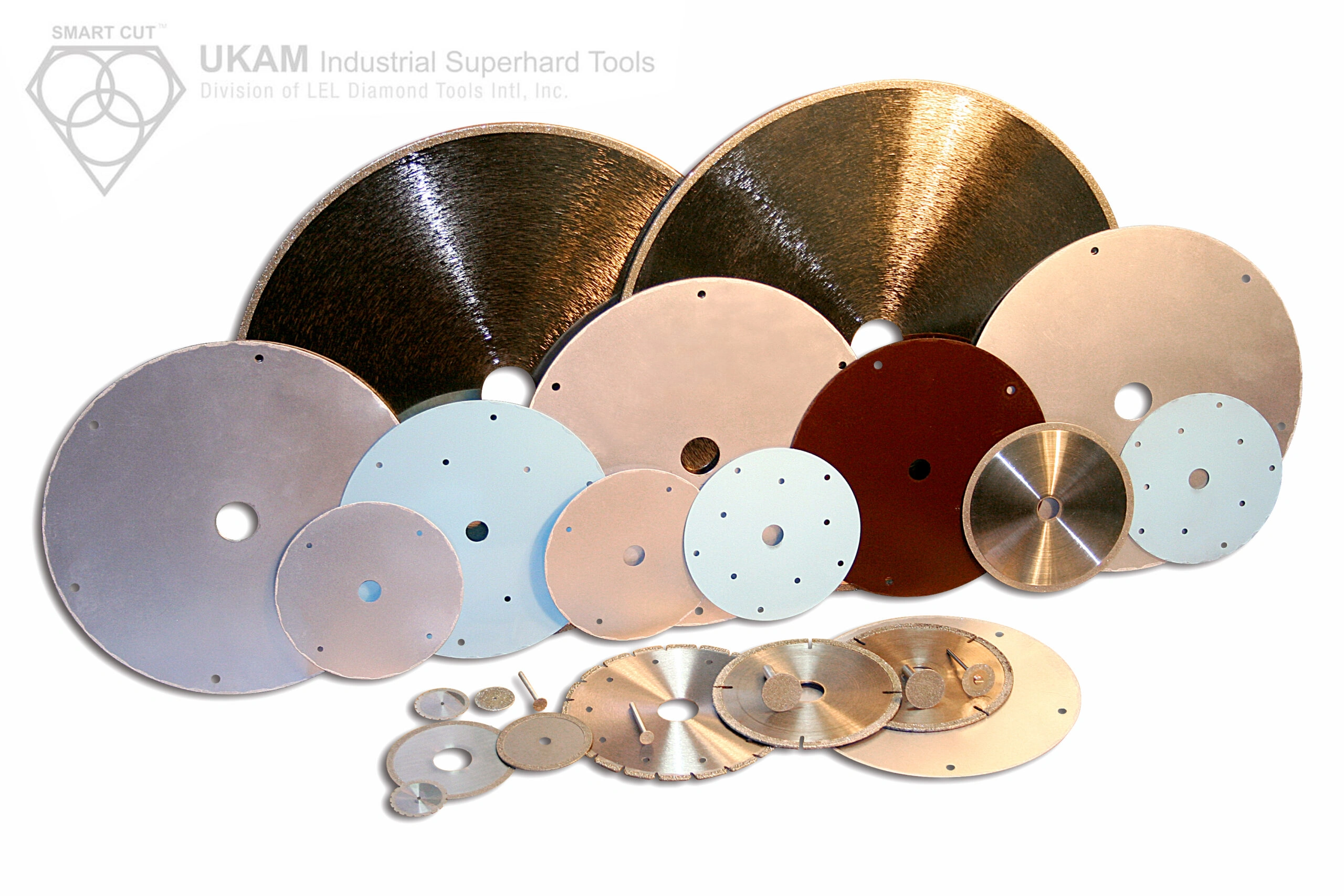
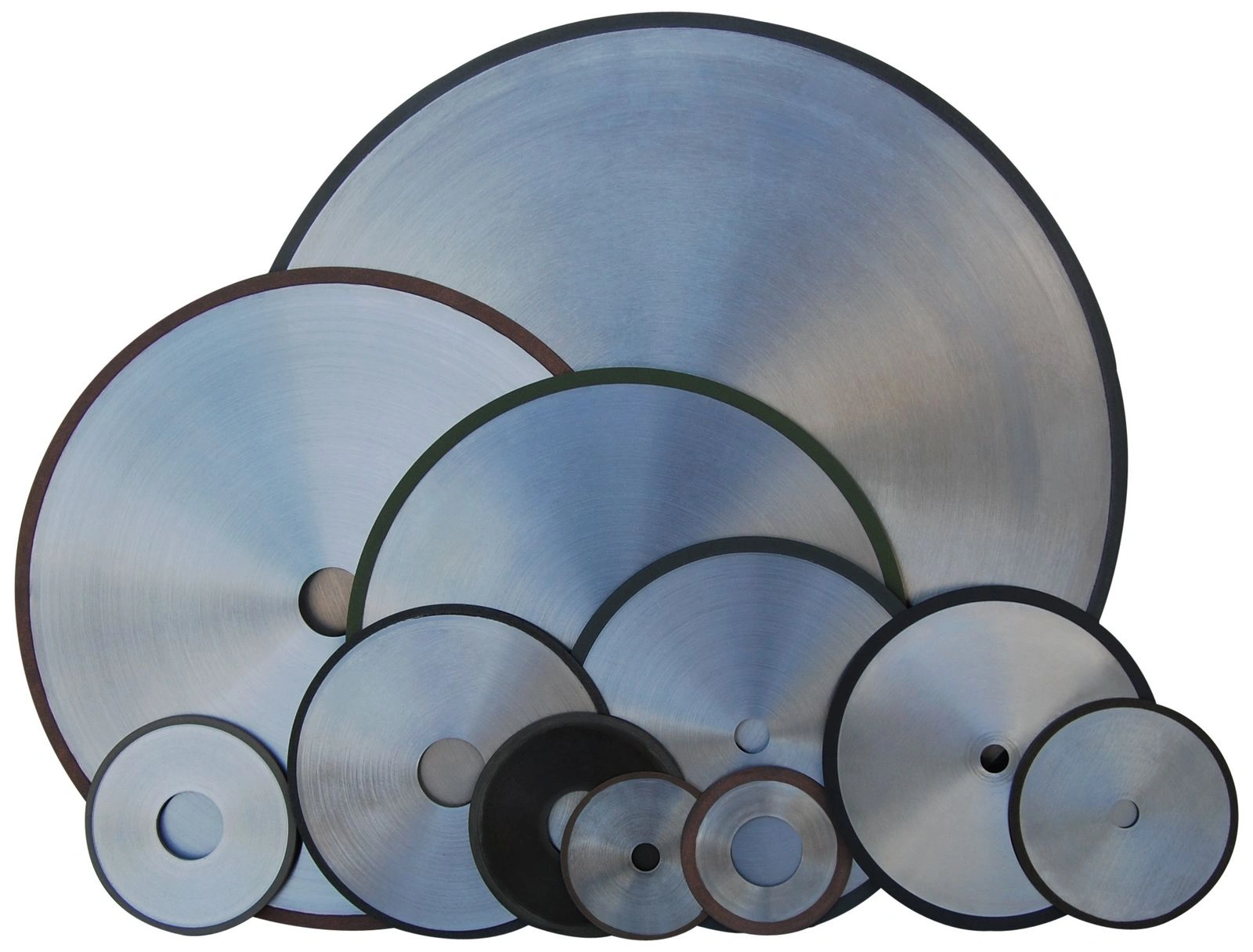
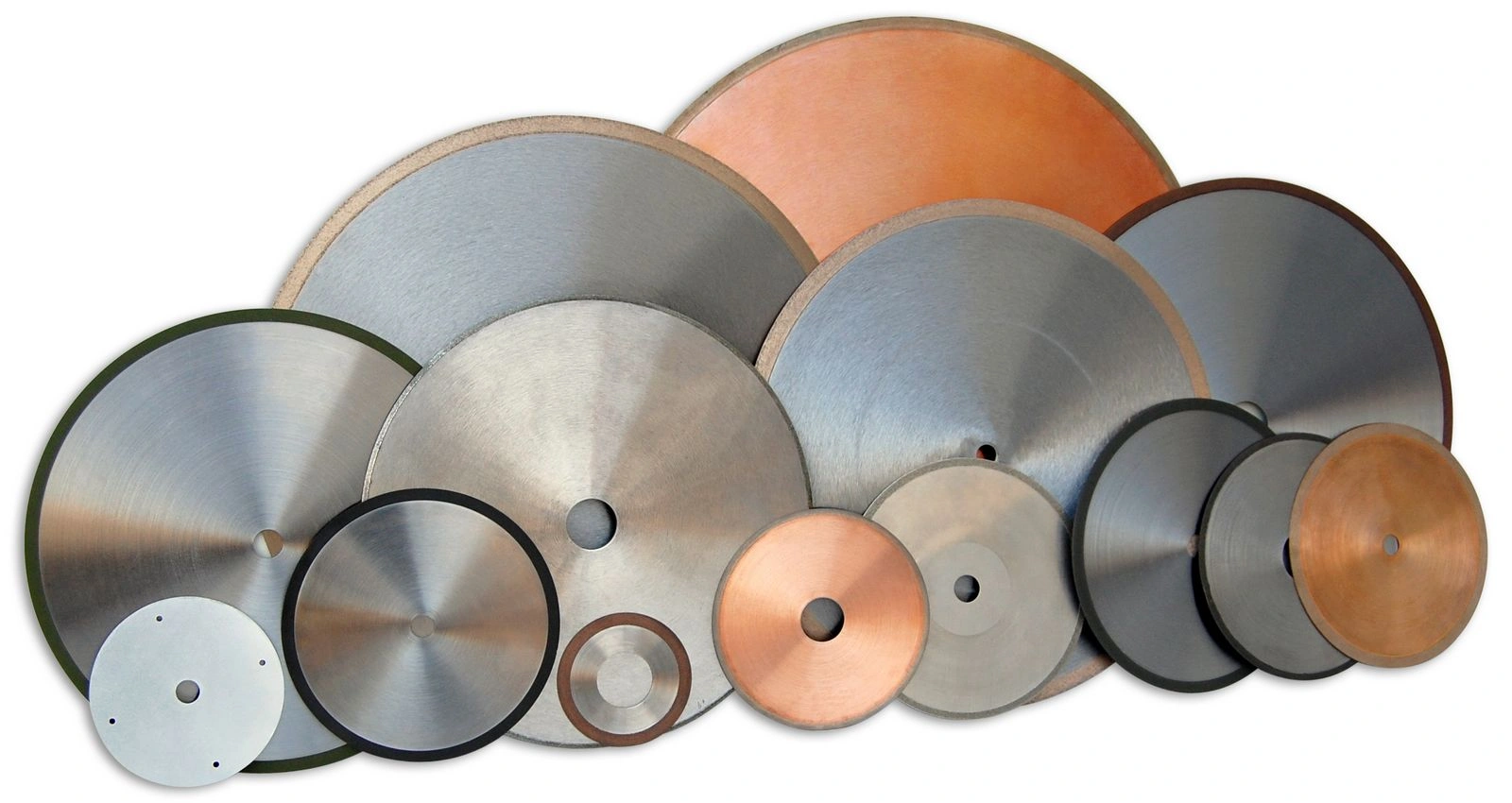
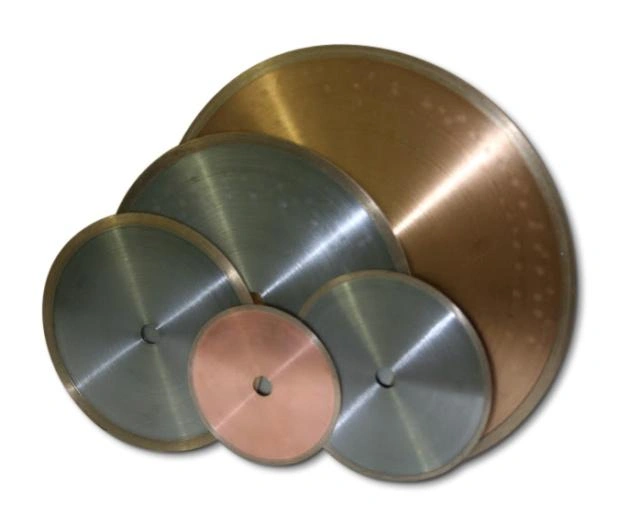
Largest Selecting Of Diamond & Cbn Wafering Blades Available
one (1) diamond wafering blade any specification is included FREE OF CHARGE with purchase of any machine (any specification). we have almost unlimited number of diamond & CBN wafering blade specifications in stock available for immediate delivery. Available in different sizes, thickness, arbor sizes, diamond concentrations, diamond mesh sizes, and bond hardness’s. With several thousand unique blade specification in stock not listed on our standard stock program. This insures you will receive the best blade specification possible for your specific application.
The Right Dressing Stick For Your Application
One (1) dressing stick is included with the purchase of any machine free of charge. The dressing stick we supply is similar to the diamond size of the wafering blade you have chosen (or we recommended) for your application. Wafering Blades must be diamonds particles/crystals exposed properly through frequent dressing. Otherwise, the diamond tool will glaze over. They will begin to tear rather than grind which is very destructive. Tearing caused from unexposed diamonds creates friction. This causes uneven wear and/or heat cracks in the wafering blade and/or material being cut. Resulting in premature blade wear, blade tensioning problems, and will eventually destroy the blade. The more frequently the blade is dressed the freer and cooler it will cut with lot more consistency.
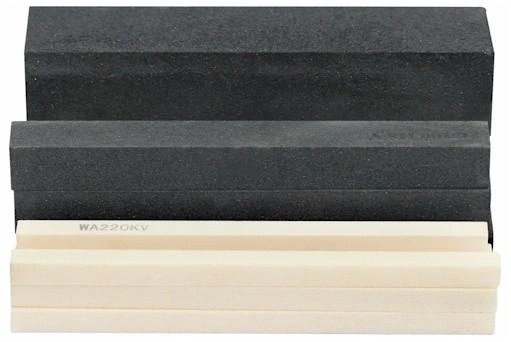
Related Products
SMART CUT® 4005 – Low Speed Saw
SMART CUT® 6005 – Low Speed Saw
SMART CUT® 6010 – Sectioning Saw
SMART CUT® 6035 – PRECISION CUTTING SAW
SMART CUT® 6040 – PRECISION CUTTING SAW
Recently Viewed Products
ARE YOU USING METALLOGRAPHY SECTIONING SAWS
FOR YOUR APPLICATION?
LET US
HELP YOU
HAVING ISSUES WITH
YOUR METALLOGRAPHY SECTIONING SAWS?
Knowledge Center
02
Jun
Diamond Wire Advantages & Application
Diamond Wire saws provide the most accurate cutting with the least amount of material deformation and chipping of material.
HOW DIAMOND WIRE WORKS
Today diamond wire sawing is preferred by majority...
02
Jun
Troubleshooting Diamond Sawing Problems
Having issues with your diamond cutting operation? This Illustrated Guide can help. Learn the most common problems most people have in using diamond cutting blades. How to resolve them and avoid them in...
02
Jun
How to Improve & Optimize Your Diamond Sawing Operation
There are numerous variables that affect the performance of diamond and CBN cutting blades. Understanding these variables will help end users select the right diamond blade specifications for their applications and optimize their...
02
Jun
Evaluating & Comparing Diamond Blades
Proper testing procedures and methodologies must be set up and used to obtain accurate as well as repeatable testing results. This article will discuss several simple procedures which...
02
Jun
Selecting Right Wafering Blade for your application
Cross Sectioning is the first and most important step in the sample preparation process. Getting the best results involves obtaining a smooth surface finish, minimum chipping, material deformation, without sacrificing cutting speed. Today, most laboratories, work with dozens...
02
Jun
Wafering Blade Usage Recommendations
The wafering/sectioning blade itself is only a small factor in your sectioning operation. Successful wafering/sectioning operation is both an art & science. Requiring proper use and understanding of selecting the right diamond wafering/sectioning...
02
Jun
Wafering Blade Case Studies
Step by step guide on how to properly use and care for your diamond drills. Selecting the right diamond drill/diamond drill bit parameters, often involves a trial and error process. Many which can be avoided...
22
Apr
Diamond & CBN Wafering Blade Performance Metrics
When evaluating Diamond & CBN wafering blades, especially for metallography and sample preparation, it is critical to consider a set of key evaluation criteria and performance metrics. These factors help determine the effectiveness of a...
24
Apr
Understanding & Comparing Diamond & CBN Wafering Blades
Diamond wafering blades are designed for sectioning a large variety of materials and sample types. In order to identify the best diamond wafering blade for your specific material/application, we...
25
Apr
Diamond & CBN Wafering Blade Guide
All you need to know about wafering blades (understanding variables & specifications)
This guide is designed to help you navigate the various variables and possibilities associated with diamond wafering blades,...
08
Jul
Low Speed Saw Case Studies
Introduction
In the realm of precision cutting, the SMART CUT® 6005 Low Speed Diamond Saw stands out for its capability to handle a variety of materials with high accuracy. To...
31
Jul
Top 5 Diamond & CBN Cutting Blade Performance Metrics
When evaluating diamond and cubic boron nitride (CBN) cutting blades, it's crucial to consider key performance metrics and criteria. Different applications have varying goals, making it important...
01
Aug
Diamond & CBN Cutting Blade Performance Metrics that you Should Know
When evaluating diamond and cubic boron nitride (CBN) cutting blades, it's crucial to consider key performance metrics and criteria. Different applications have varying goals, making it important to understand...
02
Aug
Total Cost of Ownership & Why its Important
Diamond and CBN cutting blades are available in a myriad of specifications, with virtually limitless options. The industry is saturated with numerous manufacturers, each professing to offer the...
04
Aug
Diamond Wire vs band saw blades and circular blades
Diamond wire, band saw blades, and circular blades are all cutting tools used in various industries for different purposes. Each tool has its advantages and applications
For cutting ultra hard...
05
Aug
Understanding Tradeoffs- Searching for Perfect Diamond & CBN Blade
Choosing the right blade diamond or cbn blade can significantly impact efficiency, cost, and quality. However, this is not simple and clear cut process. Selecting the optimal blade...
19
Aug
Understanding & Calculating Return on Investment for Diamond & CBN Blades
The term "ROI" (Return On Investment) is frequently mentioned across various industries, often with different interpretations depending on the context. However, few take the time to thoroughly understand what ROI truly represents and its specific...