-
0 items in quote
No products in the Quote Basket.
NEW GENERATION AND TECHNOLOGY
Tungsten Carbide Dicing Blades
SMART CUT® Series
Tungsten Carbide Slitting / Dicing Blades
SMART CUT® Tungsten Carbide Dicing Blades are expertly crafted for high-precision slitting and cutting applications across various industries. Designed to handle challenging materials with ease, these blades offer exceptional durability and consistent performance. They are ideal for slitting magnetic tape, metal foils, P.E.T., polyester, sheet rubber, fine gauge steel, film, abrasive materials, and paper products, providing clean, precise cuts even in the most demanding applications.
Available in sizes ranging from 40mm to 203mm (8") in diameter, with customizable inside diameters from 0.375” (9.52mm) to 4” (100mm), SMART CUT® Tungsten Carbide Dicing Blades meet the exacting requirements of slitting and dicing tasks.
DESCRIPTION
SPECIFICATIONS
FREQUENTLY ASKED QUESTIONS
ACCESSORIES
USAGE RECOMMENDATION
CASE STUDIES
DESCRIPTION
With tight tolerances maintained within ±0.0005 mm (0.000020″) for thickness, flatness, and parallelism, these blades ensure exceptional cutting accuracy and superior consistency.
These blades feature kerf thicknesses ranging from 0.05mm to 0.20mm, with the option for custom thicknesses. The tooth count varies between 40 to 200 teeth, depending on the specific application, while the tooth spacing (pitch) ranges from 0.2mm to 1mm, offering both fine and coarse pitches. The tooth configurations include flat, serrated, alternate top bevel (ATB), and variable tooth pitch, and coatings such as diamond, TiN (Titanium Nitride), and TiC (Titanium Carbide) are available for enhanced performance.
SMART CUT® Tungsten Carbide Dicing Blades are designed to be used with all popular slicing, dicing, and slitting saws, ensuring compatibility with a wide range of equipment.
These blades are suitable for a variety of applications, including cutting green ceramics, Printed Circuit Board (PCB) substrates, fiberglass, laminates, Molded Lead Frame Packages (MLP), and Quad Flat No-leads (QFN). They are also ideal for slitting graphite, plastics, rubber, wood, and MDF, as well as carbon fiber, aluminum foils, copper, brass sheets, stainless steel, resin, titanium alloy, and both low and medium carbon steel.
SPECIFICATIONS
- Outside Diameter: 40mm to 203mm (8″)
- Inside Diameter: 0.375” (9.52mm) to 4” (100mm)
- Kerf Thickness: 0.05mm to 0.20mm (custom options available)
- Tooth Count: 40 to 200 teeth (depending on application)
- Teeth Spacing (Pitch): 0.2mm to 1mm (fine to coarse pitch)
- Tooth Configuration: Flat, serrated, alternate top bevel (ATB), variable tooth pitch
- Tooth Coating: Diamond, TiN (Titanium Nitride), TiC (Titanium Carbide)
- Thickness Tolerance: ±0.0005 mm (0.000020″)
- Flatness & Parallelism: ±0.0005 mm (0.000020″)
- Equipment Used On: All popular slicing, dicing, and slitting saws
FREQUENTLY ASKED QUESTIONS
Tungsten carbide dicing blades are precision cutting tools designed for high-accuracy slitting and cutting applications in various industries. Unlike diamond blades, which use embedded diamonds to grind through materials, tungsten carbide blades feature finely crafted teeth that slice through workpieces. This design allows them to cut through a wide range of materials, particularly composite materials and delicate substrates like PCBs, fiberglass, and ceramics.
SMART CUT Tungsten Carbide Dicing Blades are designed for cutting a wide range of materials, including:
⦁ Green ceramics
⦁ Printed Circuit Board (PCB) substrates
⦁ Fiberglass
⦁ Laminates
⦁ Molded Lead Frame Packages (MLP) / Quad Flat No-leads (QFN)
⦁ Graphite
⦁ Plastics
⦁ Rubber
⦁ Carbon Fiber
⦁ Wood and MDF
⦁ Aluminum and Copper Foils
⦁ Brass Sheets
⦁ Stainless Steel
⦁ Titanium alloys
⦁ Low and medium carbon steel
The optimal RPM range for SMART CUT Tungsten Carbide Dicing Blades typically falls between 500 to 800 RPM, depending on the material being cut and the application. For example, cutting QFN packages yields the best results at these speeds with a feed rate of approximately 100mm/sec, ensuring superior cut quality with minimal burrs and spearing.
The lifespan of Tungsten Carbide Dicing Blades depends on several factors, including the material being cut and the operating parameters. On average, a tungsten carbide blade may last for approximately 200 meters of cutting before needing replacement. While they are effective for many applications, they may require more frequent replacement compared to diamond blades.
SMART CUT Tungsten Carbide Dicing Blades are designed primarily for slow-speed cutting machines that operate at below 1,000 RPM. If used on high-speed machines designed for diamond blades, the teeth on the tungsten carbide blades may experience excessive wear and thermal stress, potentially causing immediate damage.
When selecting the right blade, consider the following factors:
⦁ Material type and thickness
⦁ Desired cutting speed and surface finish
⦁ Blade diameter and inside diameter for compatibility with your equipment
⦁ Tooth configuration and pitch for precise cuts or faster material removal
⦁ Blade longevity and frequency of replacement
SMART CUT Tungsten Carbide Dicing Blades are made using a sintering process that involves mixing carbide powders with metallic binders, typically cobalt, and then subjecting the mixture to hot isostatic pressing (HIP). This process eliminates internal porosities and improves the mechanical properties of the blade, enhancing both its hardness and wear resistance. The fine-grain structure ensures a sharp edge and superior cutting performance, even under demanding conditions.
Yes, SMART CUT Tungsten Carbide Dicing Blades can be customized to meet specific requirements. Customizations can include adjustments to the blade diameter, inner diameter, kerf thickness, tooth configuration, and coatings based on your cutting needs.
To maintain optimal performance and extend the life of your SMART CUT Tungsten Carbide Dicing Blades, it is essential to operate them within the recommended RPM and feed rate parameters. Regularly check for signs of wear and replace the blade when necessary. Additionally, ensure that the cutting machine is properly aligned and maintained to reduce undue strain on the blade.
Yes, Tungsten Carbide Dicing Blades are best suited for low-speed cutting machines with rotational speeds below 1,000 RPM. Using them at high speeds, such as those common in standard diamond blade saws, can lead to rapid wear and thermal damage to the teeth. For optimal performance, it’s important to monitor the machine’s settings and ensure the blade is not subjected to excessive heat buildup. Maintaining a consistent feed rate is also essential to achieve the best cutting results while minimizing wear.
The key difference lies in the cutting mechanism. Diamond blades use embedded diamonds to grind through materials, whereas Tungsten Carbide blades rely on finely crafted teeth that slice through materials. Tungsten Carbide blades are ideal for slower cutting speeds and are more suitable for materials that do not require the extreme precision or high-speed cutting provided by diamond blades. While diamond blades tend to have a longer life due to the hardness of diamonds, Tungsten Carbide blades are more cost-effective for specific applications that do not demand diamond-level precision.
Tungsten Carbide Dicing Blades are extremely durable and capable of cutting tough materials like carbon fiber, fiberglass, aluminum, and stainless steel. However, compared to diamond blades, they may not be as efficient for extremely hard materials like certain ceramics or gemstones. For materials that require ultra-precise cuts or extensive wear resistance, diamond blades may be more suitable. Tungsten carbide blades are designed for medium to high-density materials, making them ideal for composite materials, printed circuit boards (PCBs), and laminated products.
To maximize the lifespan of Tungsten Carbide Dicing Blades, always operate them within the recommended RPM and feed rate ranges for the material being cut. Avoid high-speed cutting, which can cause thermal stress and premature wear. Additionally, proper cooling with a suitable coolant is crucial, especially when cutting materials that generate significant heat. Regularly inspect the blade for signs of wear, and replace it when necessary to maintain cutting accuracy.
Tungsten Carbide Dicing Blades generally cannot be sharpened in the traditional sense. However, they can sometimes be reconditioned by a professional service, which may involve rebalancing or cleaning the blade. It is important to note that Tungsten Carbide blades wear down over time, particularly after extensive use, and will eventually require replacement. Regular maintenance and careful operation will help to extend their useful life before they need to be replaced.
Choosing the right Tungsten Carbide Dicing Blade depends on several factors, including:
⦁ Material Type: Consider the hardness and abrasiveness of the material being cut.
⦁ Blade Size: Ensure the diameter and inside diameter match the requirements of your equipment.
⦁ Tooth Configuration: Choose from flat, serrated, alternate top bevel (ATB), or variable tooth pitch based on whether you need smooth cuts or faster material removal.
⦁ Cutting Speed and Feed Rate: Match the blade to the appropriate RPM and feed rate for optimal performance.
⦁ Cut Quality: If a high-quality surface finish is required, a blade with more teeth and finer spacing may be needed.
Consulting with a knowledgeable supplier or expert in Tungsten Carbide Dicing Blades can help ensure you select the best blade for your specific needs.
SMART CUT Tungsten Carbide Dicing Blades are commonly used in industries that require high-precision cuts for delicate materials. Some of the most common applications include:
⦁ Microelectronics: Cutting PCB substrates and molded lead frame packages (MLP/QFN)
⦁ Composite Materials: Cutting fiberglass, carbon fiber, and laminates
⦁ Ceramics: Precision cutting of green ceramics for R&D or manufacturing
⦁ Automotive and Aerospace: Slitting metal foils, plastics, and sheet rubber
⦁ Packaging and Manufacturing: Cutting paper products and thin materials
These blades excel in applications where slower cutting speeds are acceptable and where precision and clean cuts are paramount.
The recommended feed rate for SMART CUT Tungsten Carbide Dicing Blades varies depending on the material and desired cut quality. For example, when cutting delicate materials like QFN packages, the feed rate is typically around 100mm/sec at speeds between 500 to 800 RPM. This ensures the blade can maintain a clean cut with minimal burrs. For faster cutting of softer materials, a higher feed rate may be used, but care should be taken to avoid overheating and excessive wear.
SMART CUT Tungsten Carbide Dicing Blades are designed to be compatible with a wide range of slicing, dicing, and slitting saws that operate at slower rotational speeds (typically under 1,000 RPM). They are optimized for machines that can handle precision cutting, and using them on machines designed for high-speed diamond blades may lead to faster wear. Be sure to check that the machine’s RPM and feed rates match the specifications for the best results.
Tungsten Carbide offers several key advantages:
⦁ Cost-Effectiveness: Compared to diamond blades, Tungsten Carbide blades are more affordable while still providing high precision.
⦁ Versatility: Tungsten Carbide blades can handle a variety of materials like metals, plastics, ceramics, and composites, making them suitable for a broad range of industries.
⦁ Durability: Tungsten Carbide is known for its hardness and ability to maintain a sharp edge, though it does have a shorter lifespan than diamond blades in some applications.
⦁ Precision: The finely crafted teeth of Tungsten Carbide blades provide smooth, accurate cuts, especially for applications that do not require the extreme precision of diamond tools.
To ensure the best performance, it is essential to:
⦁ Monitor RPM: Use the blade within the optimal speed range, typically between 500 to 800 RPM, depending on the material.
⦁ Maintain a consistent feed rate: This prevents overheating and ensures that the teeth are not over-stressed, which can lead to premature wear.
⦁ Use the appropriate coolant: For materials that generate significant heat during cutting, apply a suitable coolant to reduce friction and heat buildup.
⦁ Regularly inspect the blade: Check for signs of wear or damage, especially after extended use. Replace the blade when it shows significant wear to maintain cut quality.
To optimize cutting efficiency, it’s essential to fine-tune the cutting parameters based on the material being processed. Here are a few tips:
⦁ Adjust feed rates: For materials like fiberglass or plastic, moderate feed rates help avoid material chipping and improve surface finish.
⦁ Utilize proper tooth configurations: For clean, precise cuts in hard materials like metals, use blades with a higher tooth count and a finer tooth pitch. For rougher cuts in softer materials, fewer teeth and coarser pitch will allow for faster cuts.
⦁ Monitor the cutting environment: Make sure that the cutting environment is clean, and use proper cooling techniques to ensure that the blade operates efficiently and without excessive heat buildup.
While Tungsten Carbide Dicing Blades are excellent for many applications, there are some challenges to consider:
⦁ Blade Wear: Tungsten Carbide blades are subject to wear over time, especially when cutting harder materials. The blades may need to be replaced more frequently than diamond blades, particularly in high-volume applications.
⦁ Heat Generation: The blades generate heat during cutting, especially at higher feed rates or speeds. It’s important to manage heat effectively with appropriate coolant and by using lower RPMs to prevent damage to the blade.
⦁ Material Compatibility: Tungsten Carbide blades are ideal for medium-density and composite materials but may not perform as efficiently on ultra-hard materials like sapphire or certain ceramics. In these cases, a diamond blade may be more appropriate.
SMART CUT Tungsten Carbide Dicing Blades offer a unique combination of performance characteristics:
⦁ Precision and Versatility: While standard carbide tools are often used for rough cutting, Tungsten Carbide Dicing Blades are designed for high-precision applications, making them versatile for both fine and general-purpose cutting.
⦁ Superior Hardness: The hardness of Tungsten Carbide allows these blades to maintain sharpness for longer periods compared to many other cutting tools, though they still require maintenance and replacement.
⦁ More Adaptable Design: Tungsten Carbide Dicing Blades feature finely crafted teeth and customizable configurations, making them suitable for a wider range of cutting tasks, especially in industries like microelectronics and PCB manufacturing.
Yes, SMART CUT Tungsten Carbide Dicing Blades are well-suited for high-volume production environments, particularly in industries such as microelectronics, automotive, and aerospace. These blades offer efficient material removal, and while their lifespan may be shorter than diamond blades, they provide a cost-effective solution for specific applications. Frequent blade replacement may be necessary in very high-volume environments, but their superior cutting speed and precision ensure they remain an excellent choice for many production lines.
There are several indicators that it’s time to replace a Tungsten Carbide Dicing Blade:
⦁ Reduced Cutting Performance: If the blade no longer provides a clean, precise cut or begins to produce more burrs or rough edges, it may be time for a replacement.
⦁ Visible Wear: Inspect the teeth for signs of significant wear or damage. If the teeth appear chipped, cracked, or overly rounded, the blade should be replaced.
⦁ Excessive Heat Generation: If the blade is overheating more than usual or requiring more cooling to maintain performance, it may be a sign of wear that needs replacement.
⦁ Increased Vibration: A worn-out blade can cause vibrations during cutting, leading to reduced accuracy and surface finish quality.
The price of SMART CUT Tungsten Carbide Dicing Blades varies depending on several factors such as blade size, tooth count, configuration, and coating. Custom blades, specific dimensions, or special coatings like diamond or TiN can influence the price.
Yes, SMART CUT Tungsten Carbide Dicing Blades can be custom-made to suit specific cutting requirements. Customization options include adjusting the blade’s diameter, inside diameter, tooth configuration, kerf thickness, and coating. These custom blades are often requested for unique applications where standard sizes may not be suitable, ensuring the blade perfectly matches the equipment and material being processed.
Tungsten Carbide Dicing Blades are widely used across several industries, including:
⦁ Microelectronics: For cutting PCB substrates, lead frame packages, and other delicate electronic components.
⦁ Automotive: Ideal for slitting metal foils, plastics, and sheet rubber used in automotive manufacturing.
⦁ Aerospace: Cutting advanced composite materials like carbon fiber, fiberglass, and laminated products.
⦁ Packaging: For slitting paper products, film, and other packaging materials.
⦁ Medical: Used in precision cutting applications for medical device manufacturing and other sensitive components.
⦁ Manufacturing: Commonly used for slitting and cutting composite materials and engineered plastics.
These industries rely on Tungsten Carbide Dicing Blades for their precision, durability, and ability to handle a wide variety of materials.
Yes, SMART CUT Tungsten Carbide Dicing Blades can be used for wet cutting, which involves using a coolant to reduce friction and heat generation during the cutting process. Wet cutting is particularly beneficial when working with materials that tend to generate high temperatures during cutting. The use of coolant also helps to maintain the blade’s performance by preventing excessive wear and prolonging its lifespan. However, it’s essential to use the correct type of coolant for each material and cutting application to ensure optimal results.
The maximum thickness of material that can be cut depends on the specific blade’s diameter, tooth configuration, and cutting parameters. However, in general, SMART CUT Tungsten Carbide Dicing Blades are suitable for cutting materials with thicknesses ranging from thin substrates to materials as thick as several millimeters. For thicker materials, slower cutting speeds and optimized feed rates should be used to prevent blade wear and ensure clean cuts.
Yes, SMART CUT Tungsten Carbide Dicing Blades can be coated with several specialized materials to enhance their performance:
⦁ Diamond Coating: Improves hardness, wear resistance, and cutting performance, making it ideal for very hard materials.
⦁ Titanium Nitride (TiN): Provides an additional layer of hardness, reduces friction, and improves tool life.
⦁ Titanium Carbide (TiC): Increases wear resistance, particularly useful for cutting abrasive materials. These coatings can be applied based on the application requirements, helping to extend blade life and improve cutting quality.
For cutting composite materials such as fiberglass, carbon fiber, or laminated products, serrated or alternate top bevel (ATB) tooth configurations are often the best choices. These configurations help to reduce the risk of material splintering and ensure smooth, precise cuts. Additionally, finer tooth pitches are ideal for these materials as they minimize the tendency for the material to chip or fracture during cutting.
The tooth angle plays a crucial role in the cutting performance of Tungsten Carbide Dicing Blades:
⦁ Positive Tooth Angles: These angles are more aggressive and are suitable for cutting softer materials at higher feed rates. They can remove material faster, making them ideal for rough cutting or when cutting non-ferrous materials like plastics and softer metals.
⦁ Negative Tooth Angles: These angles are typically used for cutting harder materials, such as metals and ceramics. They provide smoother cuts, greater wear resistance, and a longer tool life, making them more suitable for high-precision tasks.
Tooth pitch, or the spacing between teeth, affects the cutting performance in several ways:
⦁ Fine Pitch: A smaller pitch (closer teeth) provides finer cuts and is ideal for brittle or hard materials where chip removal and surface finish are critical. However, fine-pitch blades may require slower feed rates to avoid overheating.
⦁ Coarse Pitch: A wider pitch (fewer teeth) allows for faster cutting speeds and higher feed rates, which is beneficial for softer materials. However, the cuts tend to be rougher, and there may be more material tearing or splintering.
Proper storage of SMART CUT Tungsten Carbide Dicing Blades is crucial to ensuring their longevity and performance. Blades should be stored in a clean, dry environment, away from moisture or chemicals that could cause corrosion. It is recommended to store the blades in protective cases or covers to prevent physical damage or accidental impacts. Additionally, keep the blades away from direct sunlight and high-temperature environments, as excessive heat may cause damage to the blade material or coatings.
Yes, SMART CUT Tungsten Carbide Dicing Blades can be used for dry cutting; however, it is essential to operate within the blade’s specified feed rates and RPMs to prevent excessive heat buildup. Dry cutting may not be suitable for materials that generate significant heat during cutting, such as metals or composites, as this can lead to premature wear or damage to the blade. For such materials, wet cutting is recommended to ensure optimal performance and blade longevity.
Choosing the right number of teeth depends on the material being cut and the desired cutting speed:
⦁ More Teeth: Higher tooth counts provide smoother cuts, ideal for precision applications, such as cutting hard plastics or metals, where surface finish is important. However, these blades operate best at slower feed rates to avoid overheating.
⦁ Fewer Teeth: Blades with fewer teeth are suitable for faster material removal and cutting softer materials, like rubber or low-density composites, but the cuts may be rougher.
SMART CUT Tungsten Carbide Dicing Blades are compatible with a wide range of slicing, dicing, and slitting saws, but they are specifically designed for machines operating at lower rotational speeds (below 1,000 RPM). Machines designed for diamond blades that operate at higher speeds may not be suitable for Tungsten Carbide blades, as this could lead to excessive wear and reduced performance. Always ensure that the machine’s RPM and feed rate are within the recommended specifications for optimal results.
ACCESSORIES
USAGE RECOMMENDATION
02
Jun
Dicing Blade Operations Recommendations
Share this Article with Friend or Colleague
Selecting the right dicing blade parameters often involves a trial and error process, many aspects of which can be mitigated through experience and a deep understanding of how…
02
Jun
Optimizing Dicing Blade Performance
There are many variables that affect dicing blade performance. Each variable of the dicing process is only of the many components of a larger dicing system (equation). Changing one component or variable of…
02
Jun
Trouble Shooting Dicing Problems
Guide on most common dicing problems and how to resolve them
Share this Article with Friend or Colleague
ARE YOU USING RIGHT TOOLS
FOR YOUR APPLICATION?
LET USHELP YOU
CONTACT US
HAVING ISSUES WITH
YOUR CURRENT TOOLS?
What…
02
Jun
Application Recommendations
See what blade specifications we recommend to use for different applications, along with rpm’s and feed rated
Share this Article with Friend or Colleague
ARE YOU USING RIGHT TOOLS
FOR YOUR APPLICATION?
LET USHELP…
CASE STUDIES
Tab Content
Why Work With Us?
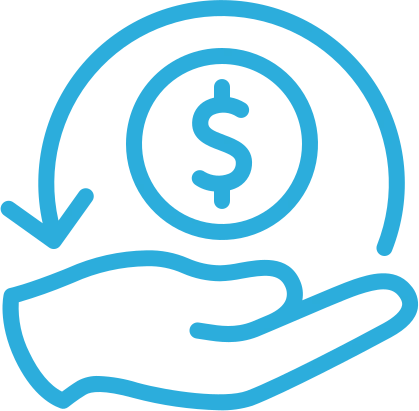
Best Return
on Investment
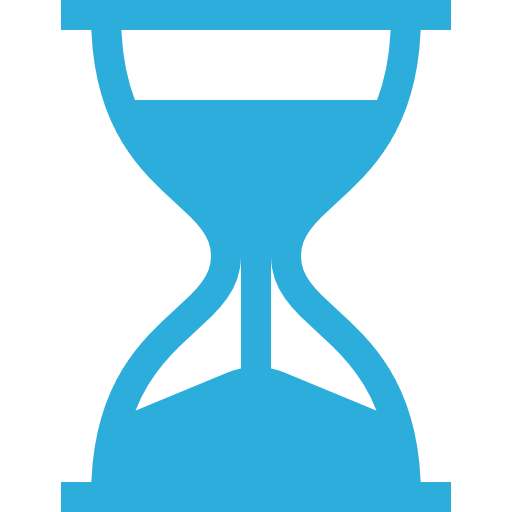
Attractive Cost of
Ownership
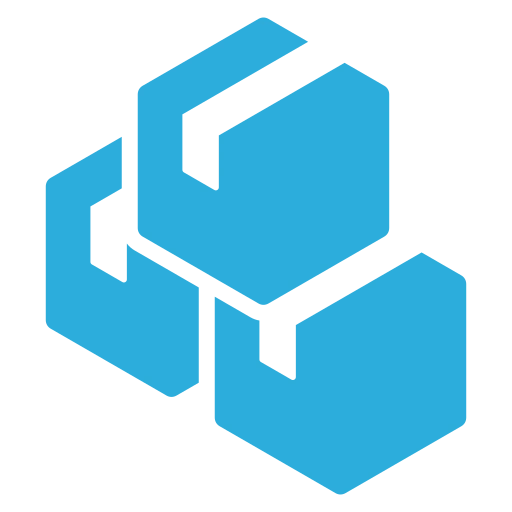
Thousands of Diamond & CBN Blades in stock
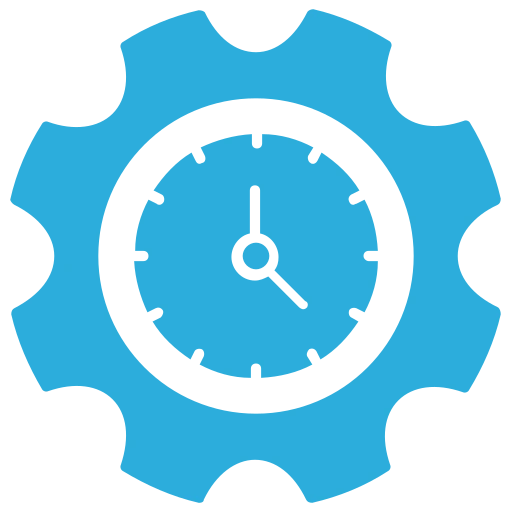
Custom Manufacturer with Fast Lead times
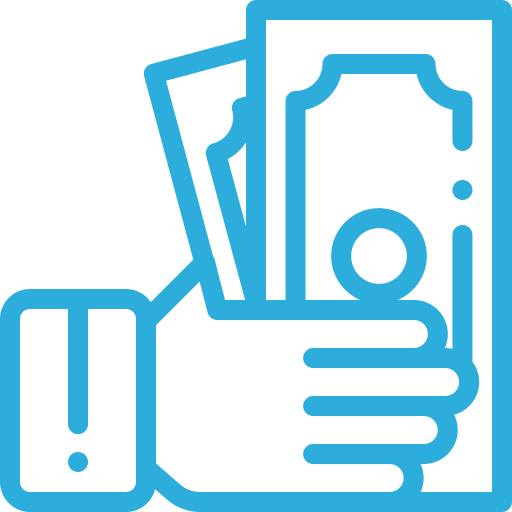
Unmatched
Prices in North America
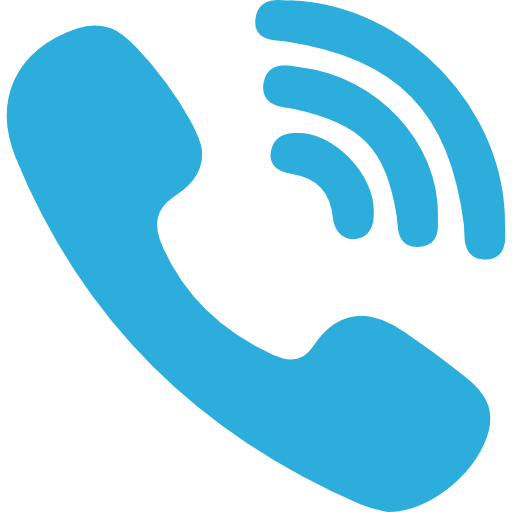
Unmatched Experience & Technical Support
What are Tungsten Carbide Slicing & Dicing Blades
Tungsten carbide dicing or slitting blades bear some resemblance to diamond cutting blades in terms of their outer diameter (OD), thickness (TH), and inner diameter (ID). However, a significant distinction lies in their cutting mechanism. Unlike diamond blades that use embedded diamonds to grind through materials, tungsten carbide blades are equipped with teeth that slice through the workpiece. This fundamental difference in design affects both their applications and operational parameters.
Design and Operation
These blades are particularly suited for slow-speed cutting machines, typically operating at rotational speeds below 1,000 RPM. The design of tungsten carbide blades incorporates finely crafted teeth, which are essential for the precise cutting of delicate materials. When operated at high speeds, as is common with standard dicing saws designed for diamond blades, the teeth on tungsten carbide blades can suffer immediate damage due to excessive wear and thermal stress.
Application:
-
Green ceramics
-
Printed Circuit Board (PCB) substrates
-
Fiberglass
-
Laminates
-
Molded Lead Frame Packages (MLP)/Quad Flat No-leads (QFN)
-
Graphite
-
Plastics
-
Rubber
-
Wood and MDF
-
Carbon Fiber
-
Aluminum Foils
-
Copper and Brass Sheets
-
Copper
-
Aluminum
-
Stainless steel
-
Resin
-
Titanium alloy
-
Low carbon steel
-
Medium carbon steel
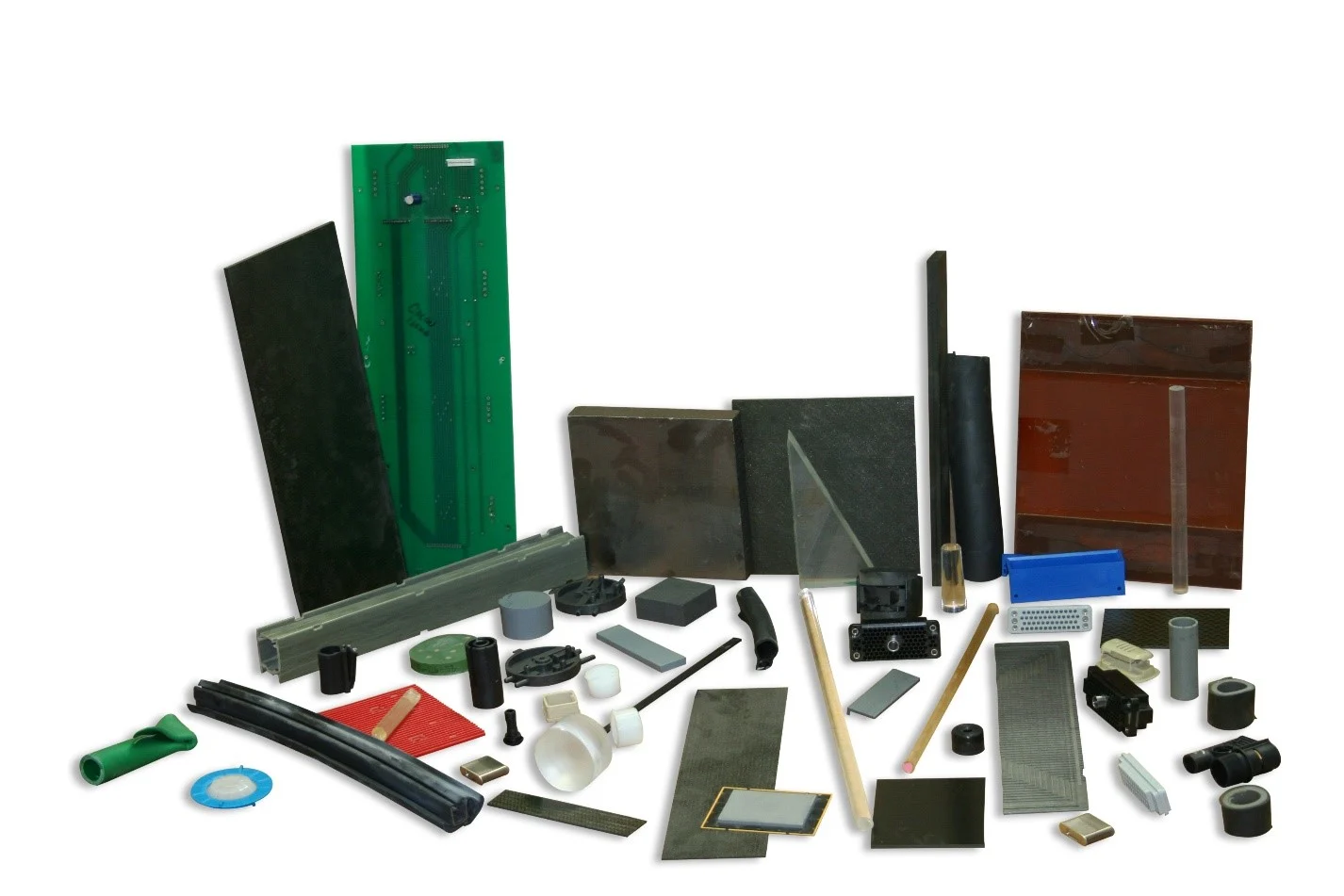
Features:
-
Precision Cutting for clean, accurate cuts.
-
Durable Tungsten Carbide construction for extended blade life.
-
Customizable Sizes (40mm to 203mm diameter, 0.375” to 4” inside diameter).
-
Optimal Performance Range (500 to 800 RPM).
-
Multiple Tooth Configurations: flat, serrated, ATB, variable tooth pitch.
-
Precision Tolerances: ±0.0005 mm (0.000020").
-
Versatile Applications: Suitable for various materials like ceramics, PCB substrates, metals, and composites.
-
Coating Options: Diamond, TiN, TiC for enhanced performance.
-
Higher Feed Rate for increased productivity.
-
Cost-Effective compared to diamond blades.
-
Reduced Cutting Time with efficient chip clearance.
-
Improved Blade Life with careful use.
-
Fine Grain Structure for sharpness and wear resistance.
-
Customizable for Specific Applications based on cutting needs.
-
High-Quality Surface Finish with minimal burr formation.
Advantages:
-
High Precision
-
Durability
-
Versatility
-
Customizable
-
Cost-Effective
-
Improved Productivity
-
Superior Surface Finish
-
Longer Tool Life
-
Enhanced Cutting Efficiency
-
Better Heat Resistance
Optimal Performance Parameters
The optimal performance of tungsten carbide blades is achieved within specific operational parameters. For example, cutting QFN packages yields the best results at speeds ranging from 500 to 800 RPM, with a feed rate of approximately 100mm/sec. At these settings, the blades can provide superior cut quality with minimal burrs and spearing—a critical requirement in precision applications. This controlled operation also contributes to a high-quality surface finish on the cut edges.
Advantages and Trade-offs
A significant advantage of using tungsten carbide blades is their ability to maintain a high feed rate, which enhances productivity. However, this comes at the cost of reduced blade life. In typical applications, a tungsten carbide blade might last for approximately 200 meters of cutting, which is less than some other types of blades might offer under similar conditions. Thus, while these blades are effective for specific applications, they may require more frequent replacement compared to their diamond counterparts.
How They are Made
There are several variations of tungsten carbide blades, each tailored to meet specific cutting demands. Some blades feature thinner profiles, enhancing precision and reducing material waste, which is particularly advantageous in fine machining applications. However, a common choice in the microelectronics sector is the WC (tungsten carbide) saw blades. These blades are preferred due to their exceptional hardness and ability to produce clean, precise cuts in delicate electronic components.
The manufacturing process of these blades is a sophisticated operation that begins with the sintering of carbide powders mixed with metallic binders, typically cobalt, to form a solid, durable matrix. A critical technique employed in this process is the HIP (hot isostatic pressing). During HIP, the blade blanks are subjected to simultaneous high pressure and temperature, which eliminates internal porosities and significantly improves the mechanical properties of the tungsten carbide.
The HIP process not only increases the blade's toughness, evident in its enhanced transverse rupture strength (TRS), but also optimizes the balance between hardness and wear resistance—two attributes that are typically difficult to optimize simultaneously. The use of ultra-fine carbide powders is a key factor in this optimization. These powders create a more homogenous and dense material structure, allowing the blades to achieve superior hardness without compromising their toughness.
This fine-grained structure of the sintered material does more than enhance mechanical properties; it also impacts the blade's cutting performance. Blades with a finer grain size can maintain a sharper edge and exhibit better wear resistance, enabling them to maintain performance over longer periods and through more demanding cutting tasks. Additionally, these blades can be engineered with specific grain orientations to further enhance cutting efficiency and durability, making them highly suitable for a variety of applications beyond PCB fabrication, including the cutting of composite materials and ceramics.
Blade Geometry
The design of tungsten carbide saw blades is a critical aspect that significantly impacts their performance and application effectiveness. Three key elements define the blade geometry: the teeth's shape, their number, and the surface finish of the blade.
The geometry of the teeth on a tungsten carbide blade encompasses several parameters, including the tooth profile, pitch (the distance between the teeth), and the tooth angle. Each aspect is engineered to suit specific materials and cutting requirements. For instance:
-
Tooth Profile: Flat-top teeth are ideal for cutting fibrous materials, while alternate top bevel (ATB) teeth are better for precise, clean cuts in solid materials such as metals or hardwoods.
-
Tooth Pitch: Finer tooth pitches are used for cutting harder, more brittle materials to reduce the material's tendency to chip. In contrast, a coarser pitch is effective for softer materials, allowing faster feed rates and quicker cuts.
-
Tooth Angle: Positive angles are aggressive and cut more quickly, suitable for softer materials. Negative angles are typically used for cutting harder materials, offering smoother cuts and greater wear resistance.
Number of Teeth
The number of teeth on a blade directly affects the cut's finish and the blade's feed speed. More teeth lead to smoother cuts but require a slower feed rate to avoid overheating and premature wear. Conversely, blades with fewer teeth remove material faster, beneficial for rough cuts where finish is not the primary concern.
-
More Teeth: Blades with a higher tooth count produce finer, smoother cuts and are preferable for precision work where a clean finish is important. These blades are ideal for cutting harder or more brittle materials like metals or hard plastics, where minimizing chipping and splintering is crucial. However, because each tooth removes less material, these blades operate best at slower feed rates and can generate more heat due to increased friction.
-
Fewer Teeth: Blades with fewer teeth are designed for faster cutting speeds. They remove more material with each pass, which makes them suitable for rough cuts in softer materials or when speed is more important than the finish. The downside is that the cuts are generally rougher and there can be more tear-out or splintering, especially in brittle materials.
Spacing Between the Teeth
The spacing, or pitch, between the teeth affects how quickly and efficiently a blade can cut through material and manage waste and heat:
-
Tight Spacing: Close spacing between the teeth is advantageous for creating smooth, fine cuts. This arrangement is beneficial when working with metals or other materials where precision is paramount. The downside is that tightly spaced teeth can lead to quicker accumulation of heat and might require more frequent cooling pauses or slower feed rates to mitigate the heat buildup.
-
Wide Spacing: Blades with teeth widely spaced apart can clear more material per cut and are typically used for faster cutting in softer or non-abrasive materials. The wider spacing facilitates better chip ejection, reducing the risk of clogging and allowing for higher feed rates. However, the broader spacing usually results in a rougher cut surface.
Application Specific Design
The ideal number and spacing of teeth on a blade depend heavily on the specific application, including the type of material being cut and the desired outcome of the cut (e.g., surface finish, speed, heat management).
Surface Finish
The surface finish of the blade, particularly in the gullet (the space between the teeth), influences chip removal and heat dissipation. A smoother finish in these areas can enhance the saw's ability to expel chips efficiently, reducing the risk of clogging and overheating, which in turn prolongs the blade's operational life. Advanced coating technologies such as titanium nitride (TiN) or diamond-like carbon (DLC) can be applied to improve surface hardness and reduce friction, further enhancing cutting efficiency and the durability of the blade.
Blade Diameter
The diameter of the blade not only determines the maximum depth of cut but also affects the blade's stiffness and cutting performance. Larger diameters provide deeper cuts but require more power from the saw, which can influence the choice of blade based on the available equipment. The stiffness of a larger diameter blade can also reduce vibration during cutting, improving cut accuracy and smoothness.
Tungsten Carbide saw blades come in various diameters, typically ranging from 50mm (2") to 152mm (6"), with the majority having a diameter of 114.3mm (4.5"). The available blade thicknesses start from as thin as 0.127mm (.005") and can be thicker, depending on the blade's application. Thinner blades, while more delicate and prone to breaking, are necessary for specific precision cutting tasks. The blade's longevity and performance are highly dependent on the quality of the WC (tungsten carbide) material, the finish of the teeth, and the blade's overall design. Maintaining a sharp edge is crucial, and specific angles in the blade geometry, such as a subtle side release angle on both sides of the blade, optimize the blade's cutting ability and longevity. This side release angle, typically less than 1°, ensures minimal blade deflection and maximized cutting accuracy throughout the blade's life.
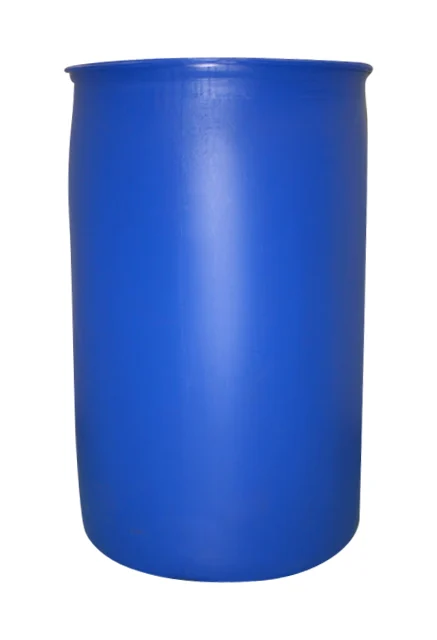
SMART CUT® XP Dicing Fluid, Coolant, & Surfactant
Available in 4 Different Formulas to Fit Most Dicing Applications
XP-1 is a general-purpose dicing fluid within the SMART CUT® range, designed to reduce debris, improve tool life, and prevent corrosion, while ensuring smooth cutting and protecting sensitive materials from ESD.
XP-2 enhances lubrication for demanding applications, offering superior cutting speeds, tool longevity, and advanced cleaning capabilities for tough materials like SiC and sapphire.
XP-3 is ideal for high-pressure systems, offering consistent cooling performance without foam buildup.
XP-4 specifically protects electrostatic-sensitive components by eliminating ESD, reducing defects, and extending tool life during the dicing process.
Why Work With Us?
Comprehensive Source Of Information On Dicing Blades
We understand that your success depends on select the right dicing blade, and optimizing your dicing parameters to best fit your applications/needs. The more you understand about what we can do for you, the better our partnership will be. On our website you will find the Most Comprehensive Source of Information on Everything you wanted to know about diamond dicing blades & industrial diamond tools.
Large Inventory & Custom Manufacturing
Largest Inventory of Precision & Ultra Thin Diamond Dicing Blades in the U.S. Available in different sizes, thickness, arbor sizes, diamond concentrations, diamond mesh sizes, and bond hardness's.
Experience Makes All The Difference
"ONE OF THE MOST EXPERIENCED COMPANIES IN THE INDUSTRY"
Over the years we have enjoyed working with all types if clients, regardless of size. Proprietary dicing blade chemistry, precision manufacturing methods, modern quality control methods, allow us to control and regulate the dozens of variables that affect blade life, quality of cut, surface finish. Reducing and often eliminating additional steps often required after cutting.
Umatched Technical Support
We Are a Partner In Your Success
Developing close ties with our customers is the foundation of our business. At the core of
our company is a team of world class engineers, knowledgeable customer service personnel here to serve you. Whether is designing or manufacturing a special solution. We will go out of our way to optimizing your process to ultimate level of efficiency.
Advanced
Technology
American Manufacturer As one of the few remaining independent U.S.Diamond Tool & machine builders. We have the experience & tradition to help you remain at frontier of technology Our experience has been further enhanced by acquiring assets and processes from some of the oldest American tool manufacturers, along with their decades of experience and R& D. This has positioned us as one of the most experienced companies in the industry.
Superior Quality &
Consistency
Our unique bond formulations, tool designs, stringent requirements, and utilization of exceptionally high-quality diamonds and raw materials ensure top-notch products that adhere to strict ISO 9000 standards.
Our proprietary technology allow us to control and regulate the dozens of variable that affect toolife, quality, & consistency
Expect More From Your Tools
Related Products
Resin Bond Dicing Blade
Nickel Bond Hubbed Dicing Blades
Nickel Bond Dicing Blades
SMART CUT® Nickel Bond Hubless Dicing Blades are designed to provide exceptional precision, longevity, and consistency for cutting a wide range of materials. Engineered with a high diamond concentration and advanced Nickel bond matrix, these blades deliver efficient cutting performance with minimal heat generation. Their ability to maintain excellent form retention and diamond exposure makes them ideal for applications requiring high accuracy, such as wafer dicing, thin substrate cutting, and microelectronics fabrication.
The Nickel binder used in these blades is specifically developed to offer a hard bond for soft materials, ensuring longer blade life and reduced wear rates. This unique combination of bond structure and abrasive composition allows for faster cutting while minimizing chipping, making it an optimal choice for materials such as printed circuit boards (PCB), silicon, and ball grid array (BGA) components. By maintaining sharp diamond exposure throughout the cutting process, these blades enhance material removal efficiency while ensuring a stable and controlled cut.
SMART CUT® Water Soluble Dicing Coolant
SMART CUT® XP Water Soluble Dicing Coolant added to deionized (DI) water reduces surface tension flowing from saws injection system and is carried directly of dicing blade.
This reduces material thermal stress, edge damage, and internal cracking, assuring long-term integrity of material being processed. Since SMART CUT® XP Dicing Coolant is a coolant and lubricant, and Surfactant both the dicing blade and substrate / wafer / package benefit.
SMART CUT® XP Dicing Coolant/Lubricant is a specially formulated low-foaming dicing and sawing coolant/lubricant designed for precision applications involving wafers with integrated circuits, MEMS devices, and IC packaging. This aqueous-based synthetic formulation enhances the dicing process by ensuring superior cleanliness of the die or package after dicing while preventing corrosion and oxidation on exposed metals. It eliminates electrostatic discharge, which can be generated during the rotation of the dicing blade, protecting delicate components from damage.
Sintered (Metal Bond) Diamond & Cbn Dicing Blades
Sintered (metal bonded) diamond tools have multiple layers of diamonds impregnated inside the metal matrix. Diamonds are furnaces sintered in a matrix made of iron, cobalt, nickel, bronze, copper, tungsten, alloys of these powders or other metals in various combinations. Metal bonded diamond tools are impregnated” with diamonds.
Recently Viewed Products
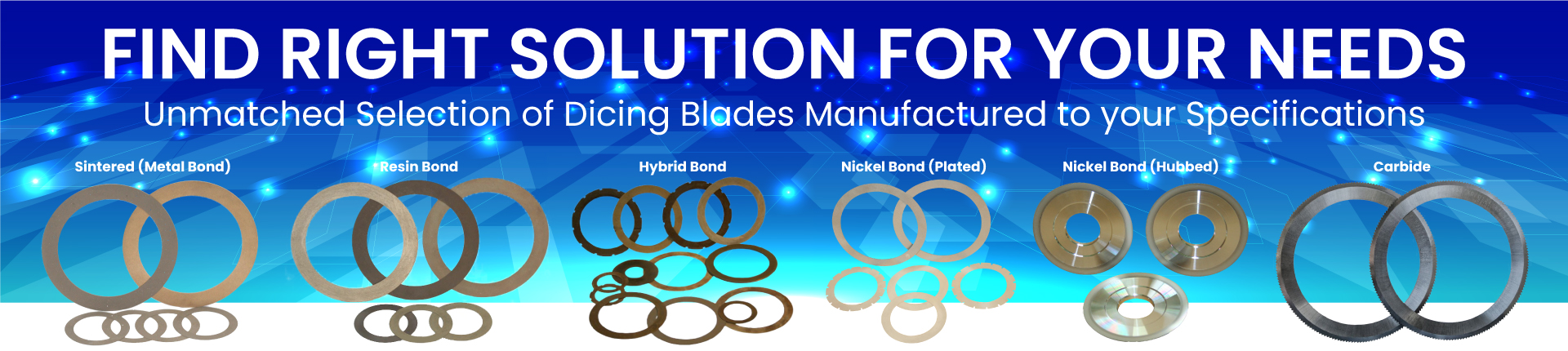
ARE YOU USING RIGHT DICING BLADES
FOR YOUR APPLICATION?
LET US
HELP YOU
HAVING ISSUES WITH
YOUR CURRENT DICING BLADES?
01
Jun
Select right Diamond Dicing Blade for your application
Selecting the right diamond dicing blade & parameters for your material/application can be a very time consuming, trial & error frustrating process. The guide below has been designed to help you better understand the most important...
02
Jun
Dicing Blade Operations Recommendations
Share this Article with Friend or Colleague
Selecting the right dicing blade parameters often involves a trial and error process, many aspects of which can be mitigated through experience and a deep understanding of how...
02
Jun
Optimizing Dicing Blade Performance
There are many variables that affect dicing blade performance. Each variable of the dicing process is only of the many components of a larger dicing system (equation). Changing one component or variable of...
02
Jun
Trouble Shooting Dicing Problems
Guide on most common dicing problems and how to resolve them
Share this Article with Friend or Colleague
ARE YOU USING RIGHT TOOLS
FOR YOUR APPLICATION?
LET USHELP YOU
CONTACT US
HAVING ISSUES WITH
YOUR CURRENT TOOLS?
What...
02
Jun
Application Recommendations
See what blade specifications we recommend to use for different applications, along with rpm's and feed rated
Share this Article with Friend or Colleague
ARE YOU USING RIGHT TOOLS
FOR YOUR APPLICATION?
LET USHELP...
02
Jun
Dicing Blade Case Studies
This article provides important guidelines for optimizing the dicing process in semiconductor packaging, focusing on package singulation for various technologies such as BGA, QFN, LED, CMOS, and wafer substrates. It covers key variables such as...
01
Jun
Optimizing QFN Package Dicing Process Using SMART CUT® Dicing Blades
Share this Article with Friend or Colleague
Dicing QFN packages presents several challenges due to the composition of materials and the precision required for clean, defect-free cuts. These challenges arise from the multi-layered structure of...
02
Jun
How to Selecting Right Diamond Tools for your application
Selecting the appropriate Diamond & CBN Tool specification is a crucial aspect of achieving your objectives. Opting for the ideal specification not only yields optimal results but also ensures the best return on investment. Conversely,...
02
Jun
How to properly use Diamond Tools
UKAM Industrial Superhard Tools manufactures precision diamond tools for a large variety of applications, materials, and industries.
Share this Article with Friend or Colleague
Metal Bonded Diamond Tools are “impregnated” with diamonds. This means that selected...
02
Jun
Why use diamond
Diamond is the hardest material known to man kind. When used on diamond/tools, diamond grinds away material on micro (nano) level. Due to its hardness Diamond will work all types of materials from...
02
Jun
What is Diamond Mesh Size and how to select best one for your application
Diamond grit size can be defined as the size of the diamond particles used in the bond matrix. The larger the diamond particles (grit size) the faster the tool will cut.
Share this Article with Friend or...
02
Jun
What is Diamond Concentration and which to use for your application
Diamond concentration is measured based on the volume of diamond within a section of the tool. It is typically defined as Concentration 100, which equates to 4.4 carats per cubic centimeter of the diamond layer...
02
Jun
Diamond Tool Coolants Why, How, When & Where to Use
Coolant is one of the most overlooked variables in the overall diamond or cbn tool machining process. Effective and proper use of coolant and recalculating coolant system will pay off in terms of improved surface...
02
Jun
Diamond vs CBN (cubic boron nitride) Tools
Cubic Boron Nitride (CBN) is a synthetic material that is renowned for its exceptional hardness and high thermal stability. It is composed of boron and nitrogen atoms arranged in a crystal lattice structure, similar to...
18
Jul
Get to Know the Diamond Tool Bond Types and Which to use for your application
The indication of this premature loss of diamond is deep pocket left behind. The presence of many pockets means the diamond is wasted without being used. Each diamond must protrude high to cut fast with...
17
May
Get to Know the Diamond Tool Bond Types and Which to use for your application
Selecting the appropriate diamond bond type for specific applications is crucial for several reasons. Diamond bond type directly affects the tool's performance, efficiency, and longevity. Different bond types determine how well a tool can withstand...
- Unmatched Selection For Many Applications
- Superior Quality & Consistency
- Immediate Worldwide Delivery
- Technical Support & Expertise
- American Based Manufacturer
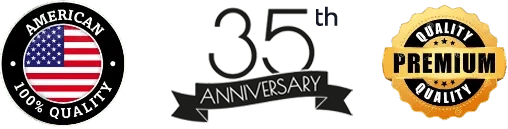

- Different Product
- Different Technology
- Different Company
- Expect MORE from your tools
Let Us HELP You!
Subscribe To Our Newsletter
Signup for email offers, updates, and more
Contact Us
- 25205 & 25201 Avenue Tibbits Valencia CA 91355 USA
-
Phone : (661) 257-2288
FAX : (661) 257 -3833 - lel@ukam.com
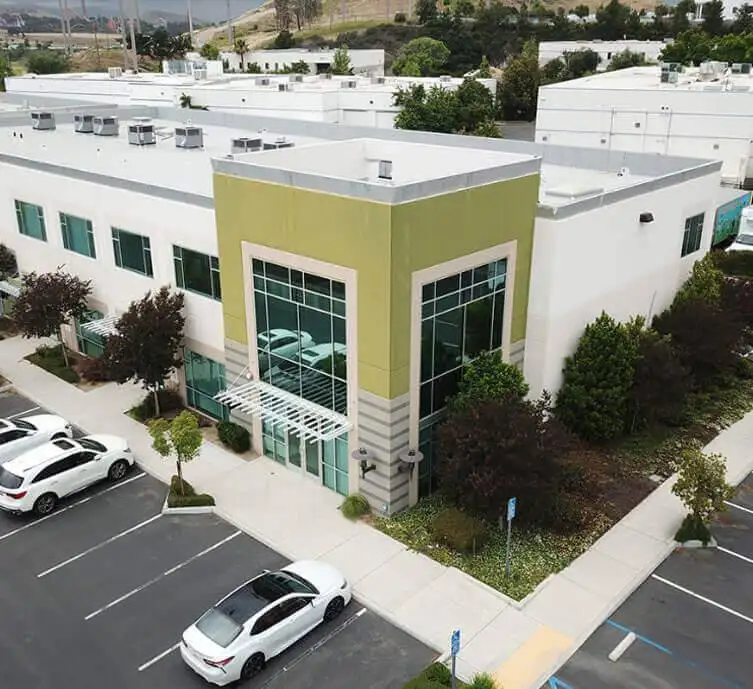
UKAM Industrial Superhard Tools is a U.S. High Technology, Specialty Diamond Tool & Equipment manufacturer. We specialize in producing ultra thin, high precision cutting blades, precision cutting machines diamond drills, diamond micro tools, standard & custom advanced industrial diamond tools and consumables.
- 25205 & 25201 Avenue Tibbits Valencia CA 91355 USA
-
Phone : (661) 257-2288
FAX : (661) 257 -3833 - lel@ukam.com
- 25205 & 25201 Avenue Tibbits Valencia CA 91355 USA
-
Phone : (661) 257-2288
FAX : (661) 257 -3833 - lel@ukam.com
DIAMOND TOOLS BY BOND
EQUIPMENT
KNOWLEDGE CENTER
OUR PRODUCTS
COMPANY
CUSTOMER SERVICE
Shipping Methods


Safe & Secure Payments

© Copyright 1990-2025. UKAM Industrial Superhard Tools – Terms of Use