-
0 items in quote
No products in the Quote Basket.
SMART CUT® 6012
Diamond Wire Saw (Lab)
SMART CUT® 6012 Miniature/Lab Precision wire saw is designed to provide a very smooth cutting for almost all kinds of materials, especially for very fragile crystals and substrates such as SrTiO3, YVO4, and GaAs etc. SMART CUT® 6012 by using either a diamond impregnated or a plain wire blade with abrasive slurry. It is an ideal saw for your needs of cutting valuable delicate and fragile crystals. It is a very helpful for your R&D and laboratory applications.
DESCRIPTION
SPECIFICATIONS
ADVANTAGES
INDUSTRIES USED IN
FAQ
ACCESSORIES
OPERATING MANUALS
DESCRIPTION
SMART CUT® 6012 has sample holder to hold samples of any shape. The sample stage can rotate at 360 degree horizontally and at 30 degree vertically. wire blade tension is adjustable to provide most accurate cutting capability.
Diamond Wire Saw offers the most gentle mechanical method for cutting virtually any material. It is most useful for cutting fragile crystals, substrates with delicate layers or any material that would be damaged when using a diamond cut off saw or any other cutting method.
SPECIFICATIONS
- Stage Travel Distance: Maximum 50.8 mm (2 inches)
- Stage Features: 360-degree horizontal rotation and 30-degree vertical tilt
- Arm Adjustment: Counterbalanced arm for fine cutting adjustments
- Micrometer Mechanism: Cross-feed mechanism for precise sample positioning
- Micrometer Head: 2-inch digital micrometer, accuracy of +/- 0.005 mm (5 microns)
- Sample Stage Size: 80 x 51 mm
- Wire Traveling Speed: 0-3 m/sec
- Rotation Speed: 50-900 rpm
- Diamond Wire Specifications: One-piece loop type, 840 mm long, 0.3 mm diameter, diamond-coated
- Included Accessories: Diamond Blade Dressing Stone for wire maintenance
- Cutting Thickness: Capable of cutting up to 50 mm
- Power Supply: Selectable A/C 110V or 220V
- Package Dimensions: 43″ x 23″ x 30″
- Shipping Weight: 120 lbs
- Warranty: One year limited, excluding cutting wire
ADVANTAGES
- Precision Cutting: The saw is designed for ultra-precision cutting, featuring a 2-inch digital micrometer head that ensures traveling position accuracy within +/- 0.005 mm (5 microns). This high level of precision is crucial for applications requiring meticulous material processing.
- Adjustable Speed and Rotation: With wire traveling speeds ranging from 0 to 3 meters per second and a rotate speed capability between 50 and 900 rpm, the SMART CUT® 6012 allows for optimal adjustment according to the specific requirements of the material being cut. This versatility ensures that the user can achieve the best possible cutting results without damaging the material.
- Advanced Stage Features: The stage of the SMART CUT® 6012 can rotate 360 degrees horizontally and tilt 30 degrees vertically, providing exceptional flexibility in sample positioning. This feature is particularly useful for complex cutting tasks involving irregularly shaped or unusually oriented materials.
- Enhanced Safety and Control: The counterbalanced arm and precise cross-feed mechanism facilitate fine adjustments during cutting, enhancing both the safety and the control over the cutting process. This is particularly important when working with fragile or expensive materials where every micron counts.
- Diamond Wire and Maintenance Tools: The machine uses a high-quality, diamond-coated wire, ideal for cutting a wide range of materials. Additionally, it includes a Diamond Blade Dressing Stone, which helps maintain the sharpness and longevity of the wire, reducing the need for frequent replacements and ensuring continuous high performance.
- Robust Design and Build: The robust construction of the SMART CUT® 6012 ensures durability and reliability in demanding laboratory environments. Its design includes waterproof features that meet the IP54 standard, protecting the machine from water and dust ingress.
- Versatility in Applications: This wire saw is capable of handling various materials, from fragile crystals to robust substrates, making it suitable for a wide range of scientific and industrial applications. Whether for semiconductor manufacturing, crystallography, or advanced material research, the SMART CUT® 6012 is an invaluable tool.
- Ease of Use and Setup: The selectable AC power supply (110V or 220V) and comprehensive controls make it easy to integrate and use the saw in various laboratory settings around the world. Its compact dimensions and weight are thoughtfully balanced to optimize lab space without sacrificing capability.
- Minimal Material Loss: The precision and adjustability of the SMART CUT® 6012 lead to minimal material loss during cutting. This is crucial for research and development environments where the samples are often rare or expensive, and maximizing material usage is essential.
- Adaptability to Various Materials: The versatility of the SMART CUT® 6012 extends to its ability to cut a broad range of materials with varying degrees of hardness and brittleness. This makes it a preferred choice for labs dealing with diverse research subjects, from metals and ceramics to biologically-derived materials.
- Enhanced User Safety: The design of the SMART CUT® 6012 incorporates several features that enhance user safety, including a controlled cutting environment that reduces the risk of accidents. The precision mechanics also minimize the chance of unexpected movements that could lead to injuries.
- Environmental Considerations: With features that include a low power consumption and the efficient use of cutting materials such as the diamond wire, the SMART CUT® 6012 is aligned with environmental sustainability goals. It reduces waste and energy usage, which is increasingly important in research and industrial applications focused on eco-efficiency.
- Cost-Effectiveness: Despite its advanced features, the SMART CUT® 6012 is designed to be cost-effective in the long run. The durability of the components, such as the diamond-coated wire and the robust mechanical structure, extends the life of the machine, reducing the total cost of ownership. Furthermore, the maintenance tools provided, like the Diamond Blade Dressing Stone, help maintain the machine’s performance without frequent professional servicing.
- Ease of Maintenance: The design of the SMART CUT® 6012 allows for easy access to all parts that might require maintenance or replacement, thereby reducing downtime and maintaining productivity. Regular maintenance tasks can be performed in-house, thanks to the intuitive design and the detailed operation manual provided.
INDUSTRIES USED IN
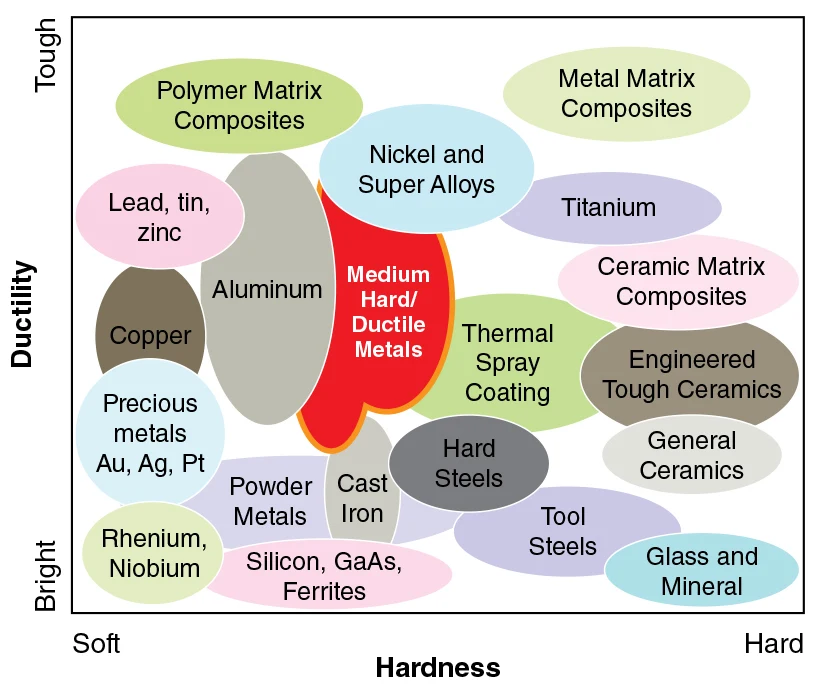

INDUSTRIES USED IN:
- Advanced Ceramics
- Composites
- Glass
- Geology
- Quartz
- Materials Research
- Medical Devices
- Metallography
- Photonics / Optics
- Semiconductor
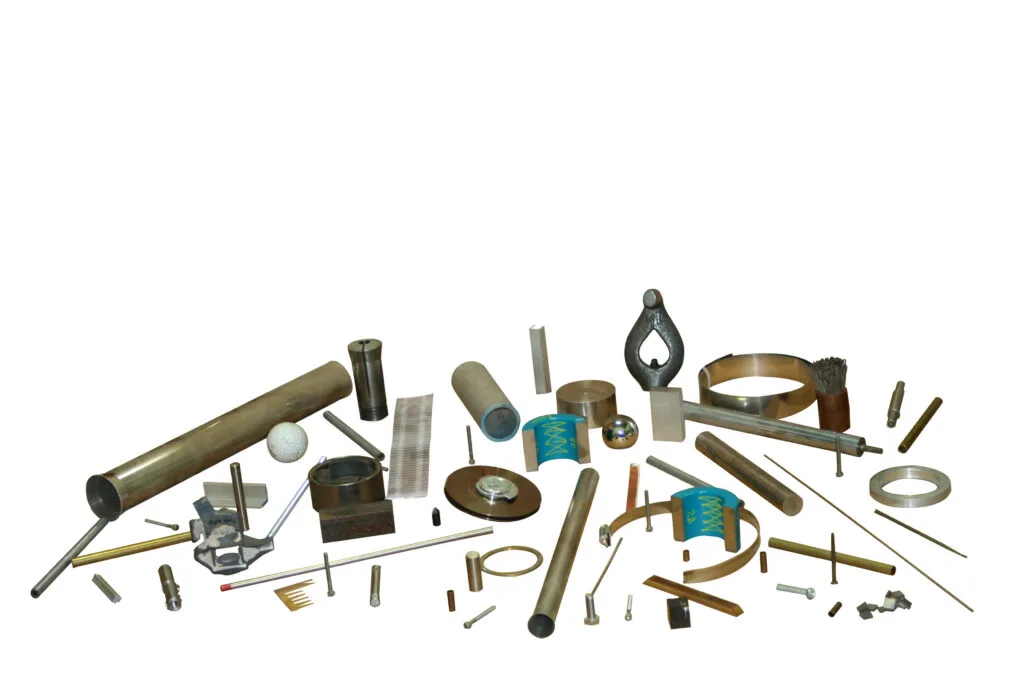
Ferrous & Non-Ferrous Metals:
- Plain Carbon Steels
- Electronic Packages
- Stainless Steels Plastics
- Tool Steels Fasteners
- Aluminum Refractories
- Copper Base Alloys Integrated Circuits
- Magnesium Thermal Spray Coatings
- Titanium Metal Matrix Composites
- Biomedical Wafers
- Petrographic
- PCB.s Ceramics
FAQ
The SMART CUT® 6012 is designed primarily for cutting delicate and fragile crystals and substrates, making it ideal for R&D and laboratory applications.
Yes, while it is optimized for fragile crystals and substrates, it can provide smooth cutting for almost all kinds of materials.
3. What types of wire blades does the saw support?
The saw can utilize either a diamond impregnated wire blade or a plain wire blade with abrasive slurry.
The SMART CUT® 6012 comes with a sample holder that can hold samples of any shape, ensuring stability during the cutting process.
Yes, the sample stage can rotate 360 degrees horizontally and 30 degrees vertically.
The wire blade tension is adjustable to provide optimal cutting accuracy. Refer to the user manual for specific adjustment instructions.
Diamond Wire Sawing is the gentlest mechanical method, ensuring minimal damage to delicate materials, making it suitable for fragile crystals or substrates with delicate layers.
The sample can be attached to a holder provided with the saw. Details and best practices are available in the user manual.
The appropriate load can be adjusted using the counterbalancing weight. The mechanical downstop can be set to ensure the wire blade doesn’t exert excessive force on the sample.
The machine comes with a micrometer that aids in the precise positioning of the sample relative to the wire blade.
As the arm is lowered and the wire rotates, you’ll feel a gentle resistance when the blade contacts the sample. This tactile feedback helps prevent forceful contact that might damage the material.
Always wear safety glasses, ensure the work area is clean, and be careful not to apply excessive force when lowering the arm. Make sure to read the safety guidelines in the user manual before operating.
Yes, both diamond impregnated and plain wire blades can be purchased from the manufacturer or authorized dealers.
While designed primarily for manual operation, specific integration into automated workflows may be possible with the right setup. It’s best to consult the manufacturer for such custom solutions.
The lifespan of the wire blade depends on usage frequency and the materials being cut. Regular inspection will help determine when it’s time for a replacement.
Manufacturers typically provide training sessions, guides, or manuals for users. Contact the supplier for more details on training opportunities.
Regular checks of the wire blade, tensioning system, and moving parts are essential. The user manual will provide a detailed maintenance schedule and best practices.
The saw is designed for precision cutting, especially for delicate samples. While it can handle extended use, it’s essential to monitor the machine and ensure it doesn’t overheat or stress the wire blade.
Using a damp cloth or soft brush, gently clean any debris or residual slurry from the machine. Ensure the wire blade is clean and free from any particles. For more intensive cleaning, consult the user manual.
To ensure precise cuts and longevity of the equipment, it’s best to operate in a clean, dry environment free from excessive dust or humidity.
While the saw is compatible with various abrasive slurries, using one recommended by the manufacturer can ensure optimal cutting results.
Specific power supply requirements will be detailed in the product’s technical specifications, which can be found in the user manual or product documentation.
Precision saws like the SMART CUT® 6012 are designed to minimize heat buildup. Still, it’s always good to give the machine periodic breaks during extended cutting sessions.
The rotation speed of the wire blade is typically fixed for optimal performance. If adjustable speeds are a feature, this will be mentioned in the product specifications.
Depending on the manufacturer’s offerings, there may be additional attachments or upgrades available. It’s advisable to check with the supplier or manufacturer for available options.
The maximum cutting thickness would be detailed in the product’s technical specifications. Ensure the material being cut falls within the recommended parameters to achieve the best results.
The manufacturer or supplier typically provides after-sales service. It’s recommended to contact them directly regarding any servicing or repairs.
Safety is a priority in the design of such equipment. Features might include safety locks, emergency stop buttons, or protective guards. Consult the user manual for detailed safety guidelines and features.
The wire blade’s durability depends on the materials being cut and usage frequency. However, when used appropriately and maintained well, the diamond impregnated wire blade is designed to offer an extended service life.
While the SMART CUT® 6012 is versatile, there might be certain materials it’s not optimized for. Always refer to the user manual for a list of recommended and non-recommended materials.
The SMART CUT® 6012 stands out due to its precision and capability to cut fragile materials. Specific comparisons would depend on the other models in question, but features like the 360-degree rotating sample stage give it a competitive edge.
With proper maintenance and usage, the SMART CUT® 6012 is built for longevity. The exact lifespan can vary based on usage frequency and the types of materials cut.
Absolutely. The SMART CUT® 6012 is ideal for R&D and laboratory applications, making it suitable for educational environments where precision is paramount.
Regular calibration ensures consistent and precise cuts. The frequency can vary based on usage, but a general recommendation is to calibrate it periodically, especially after extensive use.
Machine is fully assembled and ready to use out of the box
While the machine is user-friendly, it’s essential to understand its functions and safety protocols. Training, either through the manufacturer or in-house experts, is recommended.
The primary operation of the SMART CUT® 6012 is mechanical.
Disposal practices should adhere to local regulations and environmental guidelines. Check with local waste management authorities on how to dispose of used abrasive slurry.
Safety goggles, lab coats, and gloves are standard safety gear. Depending on the material being cut, additional precautions might be necessary.
We have replacement parts available
With proper use and maintenance, the risk is minimal. However, regularly inspect the blade for any signs of wear or warping.
While designed primarily for lab and R&D applications, its suitability for industrial use would depend on the specific requirements of the task.
The machine is optimized for cutting fragile materials, ensuring minimal damage and offering precise, smooth cuts, even for very thin samples.
While designed for precision and stability, its size and weight would determine its portability. It’s best to check the user manual or product specifications for details on the machine’s weight and dimensions.
The frequency of blade replacement depends on the types of materials being cut and the frequency of use. Regular inspection for signs of wear or damage can guide replacement decisions.
It’s advisable to use wire blades recommended by the manufacturer to ensure optimal performance and safety. Using third-party components might affect the machine’s performance and could void any warranties.
Most laboratory equipment is designed to work with standard electrical outlets, but always refer to the user manual for any specific electrical requirements or recommendations.
Signs like inconsistent cuts, excessive vibration, or unusual machine noises can indicate that wire tension needs adjustment. The user manual will provide guidance on this aspect.
Regular cleaning, blade inspections, tension checks, and lubrication of moving parts (if required) are essential. The user manual will provide a detailed maintenance schedule and steps.
While the machine is primarily mechanical, you should refer to the manufacturer’s documentation or contact them directly to know if any advanced control features are available.
It’s ideal for the machine to operate in a controlled environment without extreme temperature fluctuations. The product specifications or user manual might provide detailed environmental recommendations.
The SMART CUT® 6012 is designed to handle abrasive slurries and cut various materials. However, regular cleaning and maintenance are crucial to protect it from prolonged exposure to corrosive substances.
Financing or leasing options are available
The precision design and gentle mechanical cutting method of the machine ensure minimal sample loss and high-quality cuts, especially for fragile materials.
Yes, most precision equipment like the SMART CUT® 6012 comes with a user manual that outlines safety protocols and guidelines. Always follow these recommendations for safe operation.
The machine is designed for optimal performance without overheating, but users should ensure that it’s operated within the recommended time limits and settings. Additionally, the equipment might have built-in safety features to prevent overheating.
Wire blades and perhaps some other components might be considered consumables. The frequency of replacement would depend on usage.
The machine’s design focuses on precision, but automation capabilities would depend on its features. Refer to the user manual for detailed operation guidelines.
The user manual will typically provide troubleshooting steps for common issues like jams or blockages. It’s essential always to follow safety protocols when addressing such problems.
ACCESSORIES
OPERATING MANUALS
Download Operating Manuals
Features
- Versatile Cutting Options: The saw operates with either a diamond-impregnated or a plain wire blade alongside an abrasive slurry, enhancing its cutting capabilities across various materials.
- Adjustable Orientation: It features a sample stage that can rotate 360 degrees horizontally and tilt 30 degrees vertically, accommodating samples of any shape and size.
- Precision Engineering: The wire blade tension is adjustable, ensuring the most accurate cuts. Additionally, a counterbalanced arm and a micrometer cross-feed mechanism allow for fine adjustments, making it ideal for handling even the most sensitive materials.
- Digital Micrometer Head: Equipped with a 2" digital micrometer head that provides exceptional travel position accuracy of +/- 0.003 mm (3 microns). It also offers instant inch/millimeter conversion and reads to 0.001 mm with 0.005 mm accuracy.
- Enhanced Mobility and Flexibility: Features a wire traveling speed of 0-5 mm/sec and a maximum cutting thickness of up to 50 mm, accommodating a broad range of research needs.
- User-Friendly Design: The sample stage measures 80 x 51 mm, providing ample space for various sample sizes. The saw also includes a stage traveling distance feature with a maximum of 50.8 mm (2 inches), incorporating both a 360-degree rotating and 30-degree tilt stage for optimal positioning.
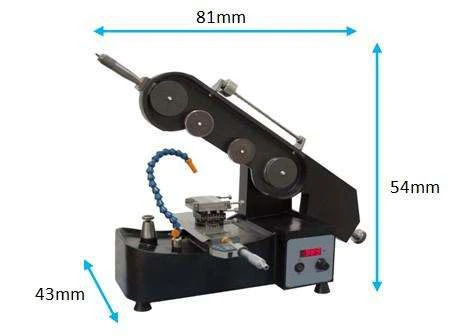
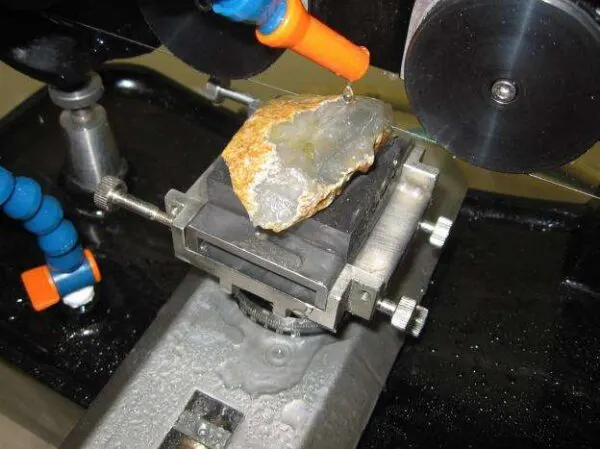
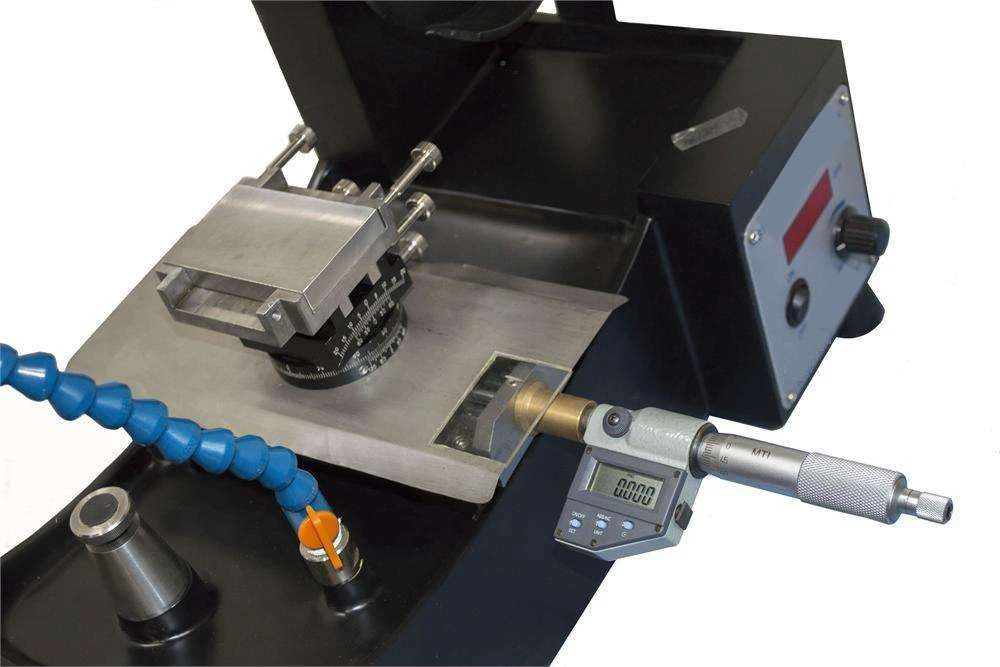
A sample is mounted to a sample holder and attached to a work table on the base of the saw. An appropriate load is applied by adjusting the counterbalancing weight and the mechanical downstop is set. The sample is then positioned in any starting position relative to the wire blade and then a micrometer is used for precise sample positioning. With the wire rotating, the arm is gently lowered until the wire blade touches the sample.
Standard Package (Include With Each Machine)
Picture |
Item No. |
Standard items included on package |
Quantity |
---|---|---|---|
|
8000011 |
SMART CUT® 6012 – Diamond Wire Saw (Lab) |
1 pcs |
|
8000012 |
2″ Rotatable and tilt-able Sample Holder |
1 pcs |
|
8000013 |
Digital Micrometer Head 2″ Travel 0.005 mm accuracy |
1 pcs |
|
8000014 |
Cross Vise for Holding Sample |
1 pcs |
![]() |
8000015 |
840 mm long, 0.35 mm dia. Diamond Loop Wire |
1 pcs |
![]() |
8000016 |
Driving Belt |
1 pcs |
|
8000017 |
Wax Bulk |
1 pcs |
|
8000018 |
Graphite Block |
1 pcs |
|
8000019 |
Screw Driver |
1 pcs |
|
8000020 |
Fuse |
1 pcs |
|
8000021 |
AC Power Cord |
1 pcs |
|
8000022 |
Operation Manual |
1 pcs |
|
8000023 |
Hoses |
1 pcs |
![]() |
SMARTC1G |
SMART CUT® General Materials Formula Synthetic Water Soluble Coolant – 1 Quart |
1 pcs |
Picture |
Item No. |
OPTIONAL Items at Additional Cost |
Quantity |
---|---|---|---|
![]() |
8000024 |
Coolant Circulating Pump |
1 pcs |
![]() |
8000025 |
Heavy Duty Coolant Circulating Tank with Pump, 4 L |
1 pcs |
SMART CUT® COOLANTS
Your choice of one (1) quart of SMART CUT™ Water Soluble Coolant or Mineral Oil is included with machine. SMART CUT™ Water Soluble Coolant Reduces material thermal stress, edge damage, and internal cracking, increases blade life, provides better cut quality, preserves material micro structure
Hence, assuring long-term integrity of material being sectioned. Since SMART CUT coolant is both a coolant and lubricant, both the wafering blade and material benefit. Mix ratio is 1:20 (1 part coolant, 20 parts water) on very hard and dense materials and 1:40 (1 part coolant, 40 parts water) on softer materials. Depending on mix ratio 1 quart will produce 5.7 to 9 gallons of coolant when mixed with water. As a coolant, SMART CUT KOOL reduces heat caused by friction. As a lubricant, SMART CUT KOOL lowers friction and surface tension, which increases swarf dispersion.
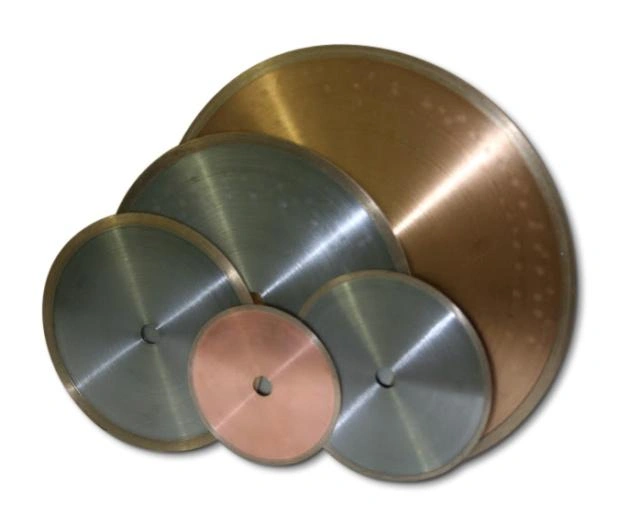

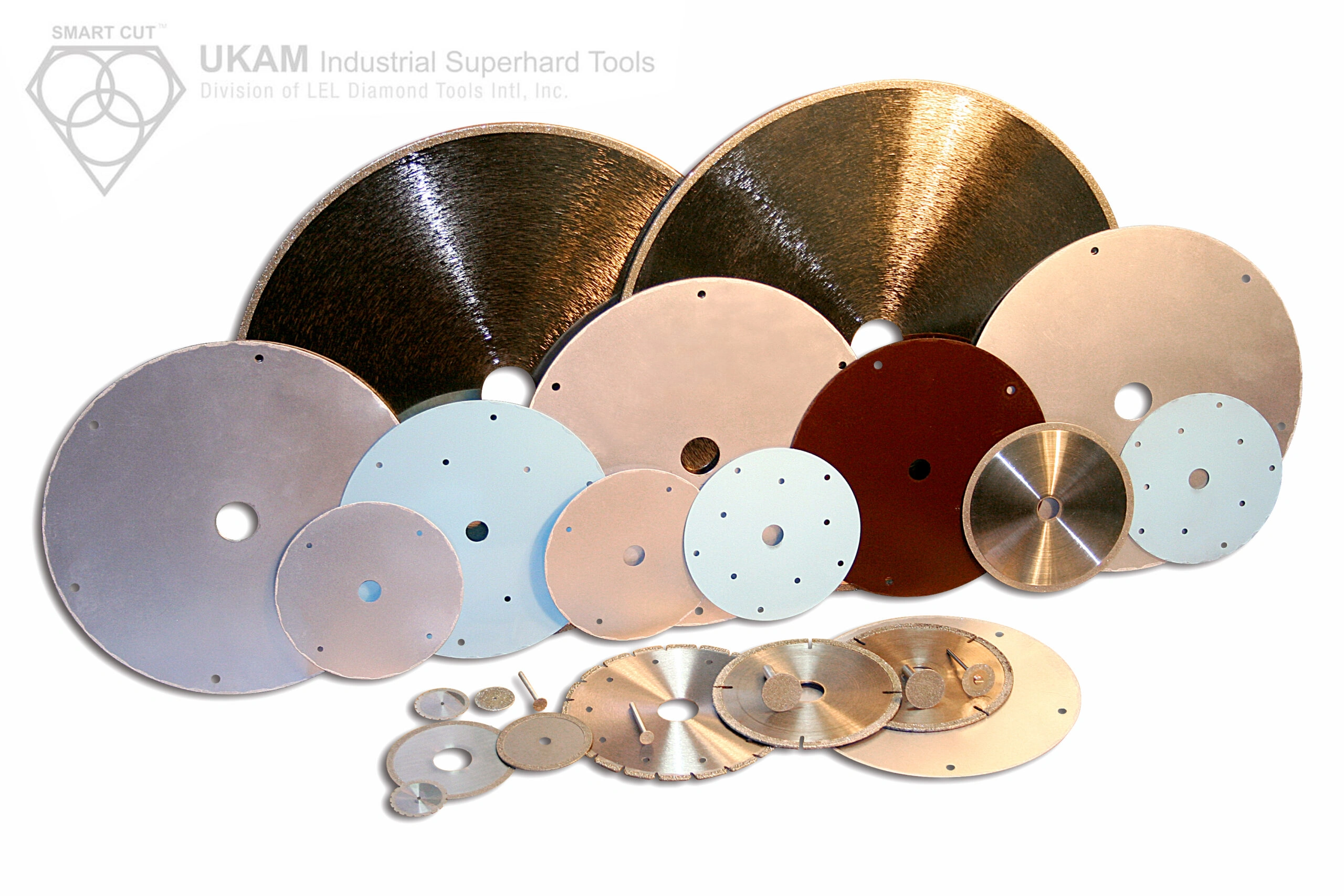
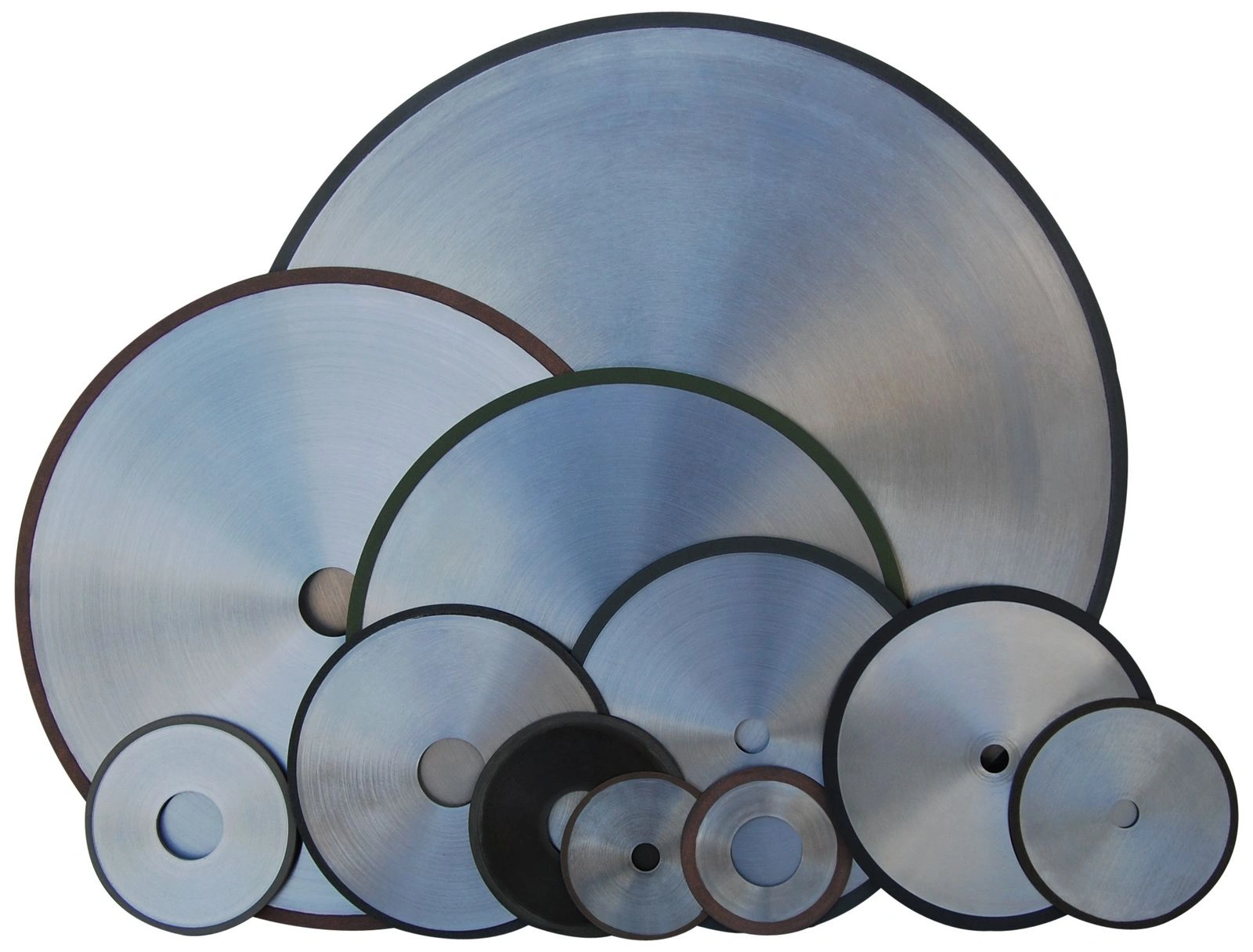
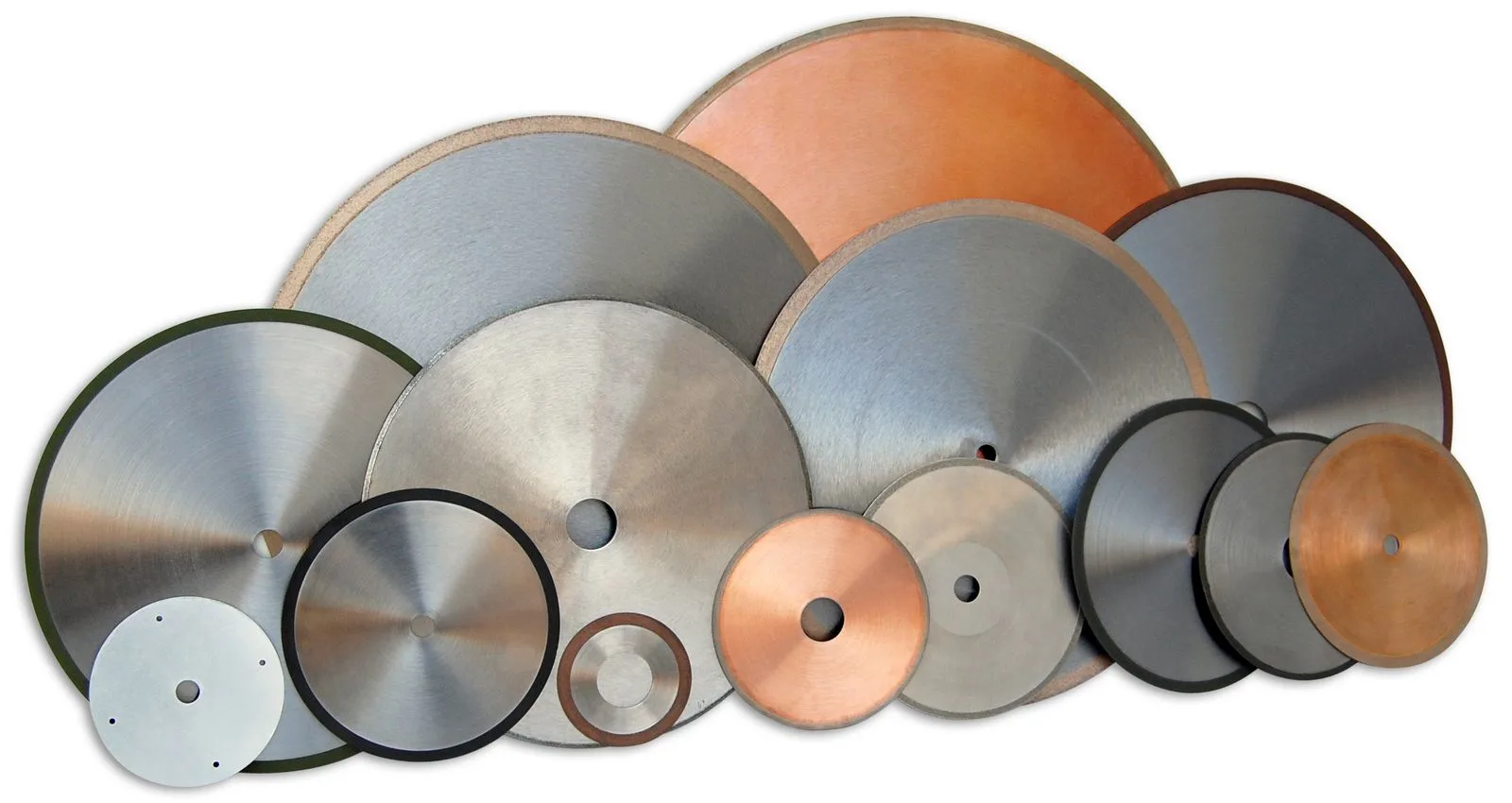
LARGEST SELECTING OF DIAMOND &
CBN WAFERING BLADES AVAIALBLE
one (1) diamond wafering blade any specification is included FREE OF CHARGE with purchase of any machine (any specification). we have almost unlimited number of diamond & CBN wafering blade specifications in stock available for immediate delivery. Available in different sizes, thickness, arbor sizes, diamond concentrations, diamond mesh sizes, and bond hardness’s. With several thousand unique blade specification in stock not listed on our standard stock program. This insures you will receive the best blade specification possible for your specific application.
THE RIGHT DRESSING STICK FOR YOUR APPLICATION
One (1) dressing stick is included with the purchase of any machine free of charge. The dressing stick we supply is similar to the diamond size of the wafering blade you have chosen (or we recommended) for your application. Wafering Blades must be diamonds particles/crystals exposed properly through frequent dressing. Otherwise, the diamond tool will glaze over. They will begin to tear rather than grind which is very destructive. Tearing caused from unexposed diamonds creates friction. This causes uneven wear and/or heat cracks in the wafering blade and/or material being cut. Resulting in premature blade wear, blade tensioning problems, and will eventually destroy the blade. The more frequently the blade is dressed the freer and cooler it will cut with lot more consistency.
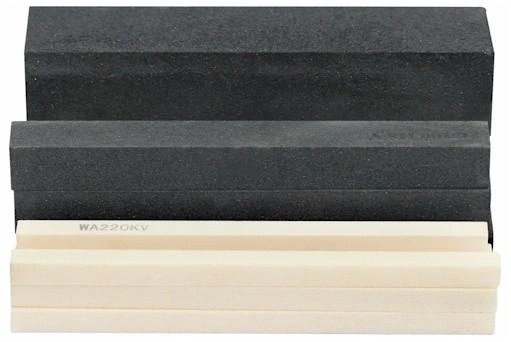
Related Products
SMART CUT® – DIAMOND DICING / SLICING SAW
SMART CUT® 6035 Diamond Wire Saw
Recently Viewed Products
ARE YOU USING METALLOGRAPHY SECTIONING SAWS
FOR YOUR APPLICATION?
LET US
HELP YOU
HAVING ISSUES WITH
YOUR METALLOGRAPHY SECTIONING SAWS?
Knowledge Center
02
Jun
Diamond Wire Advantages & Application
Diamond Wire saws provide the most accurate cutting with the least amount of material deformation and chipping of material.
Share this Article with Friend or Colleague
HOW DIAMOND WIRE WORKS
Today diamond wire sawing is preferred by...
02
Jun
Troubleshooting Diamond Sawing Problems
Having issues with your diamond cutting operation? This Illustrated Guide can help. Learn the most common problems most people have in using diamond cutting blades. How to resolve them and avoid them in...
02
Jun
How to Improve & Optimize Your Diamond Sawing Operation
There are numerous variables that affect the performance of diamond and CBN cutting blades. Understanding these variables will help end users select the right diamond blade specifications for their applications and optimize their...
02
Jun
Evaluating & Comparing Diamond Blades
Share this Article with Friend or Colleague
Proper testing procedures and methodologies must be set up and used to obtain accurate as well as repeatable testing results. This article will discuss several simple procedures which...
02
Jun
Selecting Right Wafering Blade for your application
Cross Sectioning is the first and most important step in the sample preparation process. Getting the best results involves obtaining a smooth surface finish, minimum chipping, material deformation, without sacrificing cutting speed. Today, most laboratories, work with dozens...
02
Jun
Wafering Blade Usage Recommendations
The wafering/sectioning blade itself is only a small factor in your sectioning operation. Successful wafering/sectioning operation is both an art & science. Requiring proper use and understanding of selecting the right diamond wafering/sectioning...
02
Jun
Wafering Blade Case Studies
Step by step guide on how to properly use and care for your diamond drills. Selecting the right diamond drill/diamond drill bit parameters, often involves a trial and error process. Many which can be avoided...
22
Apr
Diamond & CBN Wafering Blade Performance Metrics
When evaluating Diamond & CBN wafering blades, especially for metallography and sample preparation, it is critical to consider a set of key evaluation criteria and performance metrics. These factors help determine the effectiveness of a...
24
Apr
Understanding & Comparing Diamond & CBN Wafering Blades
Share this Article with Friend or Colleague
Diamond wafering blades are designed for sectioning a large variety of materials and sample types. In order to identify the best diamond wafering blade for your specific material/application,...
25
Apr
Diamond & CBN Wafering Blade Guide
Share this Article with Friend or Colleague
All you need to know about wafering blades (understanding variables & specifications)
This guide is designed to help you navigate the various variables and possibilities associated with diamond wafering...
08
Jul
Low Speed Saw Case Studies
Share this Article with Friend or Colleague
Introduction
In the realm of precision cutting, the SMART CUT® 6005 Low Speed Diamond Saw stands out for its capability to handle a variety of materials with high...
31
Jul
Top 5 Diamond & CBN Cutting Blade Performance Metrics
Share this Article with Friend or Colleague
When evaluating diamond and cubic boron nitride (CBN) cutting blades, it's crucial to consider key performance metrics and criteria. Different applications have varying goals, making it...
01
Aug
Diamond & CBN Cutting Blade Performance Metrics that you Should Know
Share this Article with Friend or Colleague
When evaluating diamond and cubic boron nitride (CBN) cutting blades, it's crucial to consider key performance metrics and criteria. Different applications have varying goals, making it important to...
02
Aug
Total Cost of Ownership & Why its Important
Share this Article with Friend or Colleague
Diamond and CBN cutting blades are available in a myriad of specifications, with virtually limitless options. The industry is saturated with numerous manufacturers, each professing to offer the...
04
Aug
Diamond Wire vs band saw blades and circular blades
Diamond wire, band saw blades, and circular blades are all cutting tools used in various industries for different purposes. Each tool has its advantages and applications
For cutting ultra hard...
05
Aug
Understanding Tradeoffs- Searching for Perfect Diamond & CBN Blade
Share this Article with Friend or Colleague
Choosing the right blade diamond or cbn blade can significantly impact efficiency, cost, and quality. However, this is not simple and clear cut process. Selecting the optimal blade...
19
Aug
Understanding & Calculating Return on Investment for Diamond & CBN Blades
The term "ROI" (Return On Investment) is frequently mentioned across various industries, often with different interpretations depending on the context. However, few take the time to thoroughly understand what ROI truly represents and its specific...
- Unmatched Selection For Many Applications
- Superior Quality & Consistency
- Immediate Worldwide Delivery
- Technical Support & Expertise
- American Based Manufacturer
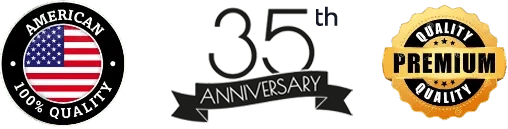

- Different Product
- Different Technology
- Different Company
- Expect MORE from your tools
Let Us HELP You!
Subscribe To Our Newsletter
Signup for email offers, updates, and more
Contact Us
- 25205 & 25201 Avenue Tibbits Valencia CA 91355 USA
-
Phone : (661) 257-2288
FAX : (661) 257 -3833 - lel@ukam.com
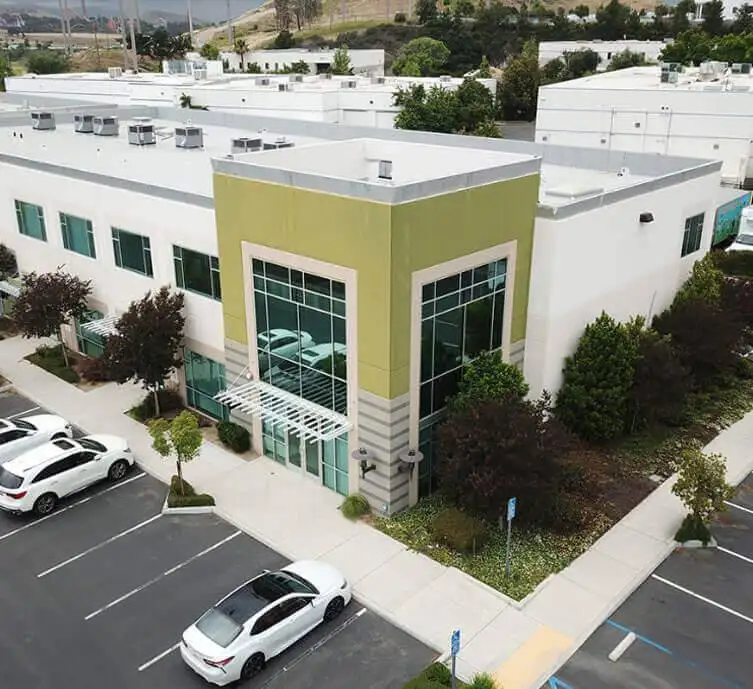
UKAM Industrial Superhard Tools is a U.S. High Technology, Specialty Diamond Tool & Equipment manufacturer. We specialize in producing ultra thin, high precision cutting blades, precision cutting machines diamond drills, diamond micro tools, standard & custom advanced industrial diamond tools and consumables.
- 25205 & 25201 Avenue Tibbits Valencia CA 91355 USA
-
Phone : (661) 257-2288
FAX : (661) 257 -3833 - lel@ukam.com
- 25205 & 25201 Avenue Tibbits Valencia CA 91355 USA
-
Phone : (661) 257-2288
FAX : (661) 257 -3833 - lel@ukam.com
DIAMOND TOOLS BY BOND
EQUIPMENT
KNOWLEDGE CENTER
OUR PRODUCTS
COMPANY
CUSTOMER SERVICE
Shipping Methods


Safe & Secure Payments

© Copyright 1990-2025. UKAM Industrial Superhard Tools – Terms of Use