-
0 items in quote
No products in the Quote Basket.
SMART CUT® 1805
Precision Saw
SMART CUT 1805 is well suited for cutting sample coupons such as PCB Boards, FR4 composite panels, ceramic substrates, electronic packages, plate material, composites, optics or flat glass pieces, ultra hard material tiles and other glass, carbon fiber, honeycomb, and many other materials. That are too large to fit on other high precision cutting machines.
Easy to use quick clamps allow fixturing of just about any material in less then 30 seconds. The holding fixture makes sure the material is hold accurately in place without causing any stress or deformation to material.
DESCRIPTION
SPECIFICATIONS
ADVANTAGES
INDUSTRIES USED IN
FAQ
ACCESSORIES
OPERATING MANUALS
DESCRIPTION
Manual & Fully Automatic Function
High Precision Cutting Machine for precise cutting of Composite Panels, Coupons and test specimens. The machine allows high precision cutting of large and long composite test specimens to accuracy up to 25 microns.
Material is clamped to steel table which glides towards the rotating blade on high precision linear rails automatically or manually.
Machine is equipped with HMI touch screen control that allows the operator to control the speed, feed rate, start & stop the motor and control all other functions of the machine. The coolant is filtered and recalculated in fully enclosed thank that comes with machine
SPECIFICATIONS
- Motor power : 370W
- Cutting capacity table : 600mmx550mm
- Cut off blade : Max. 200mm(8″)
- Feed rate : 0~150 mm/min (Min:25)
- Feeding method Auto : Button control, automatic home point return after cutting
- Feeding method Manual : Button control
- Rotational speed : 0~2000RPM
- Cutting depth : 550mm
- Vise : Fasten vise
- Cooling : 1/4 HP
- Water capacity tank : 17L
- Machine size (WxDxH) :1150mmx1800mmx1350mm
- Weight :
- Power supply : 10 AC220V
- Optional vise : Special vises can be ordered
ADVANTAGES
Super High Precision Cutting to 25 micron accuracy
Larges Surface Area in its Class
Cut of Very Large & Long Panels up to 750mm L
Variable Speed from Low to High to accommodate all Material Types
HMI touch screen controls all function of Machine
Adjustable Height Position using hydraulics
Accommodates super thin materials and thick materials up to 30mm
Super Smooth Surface Finish
Largest selection of blades from .009″ to .080 kerf thickness
Recirculation Coolant System
INDUSTRIES USED IN
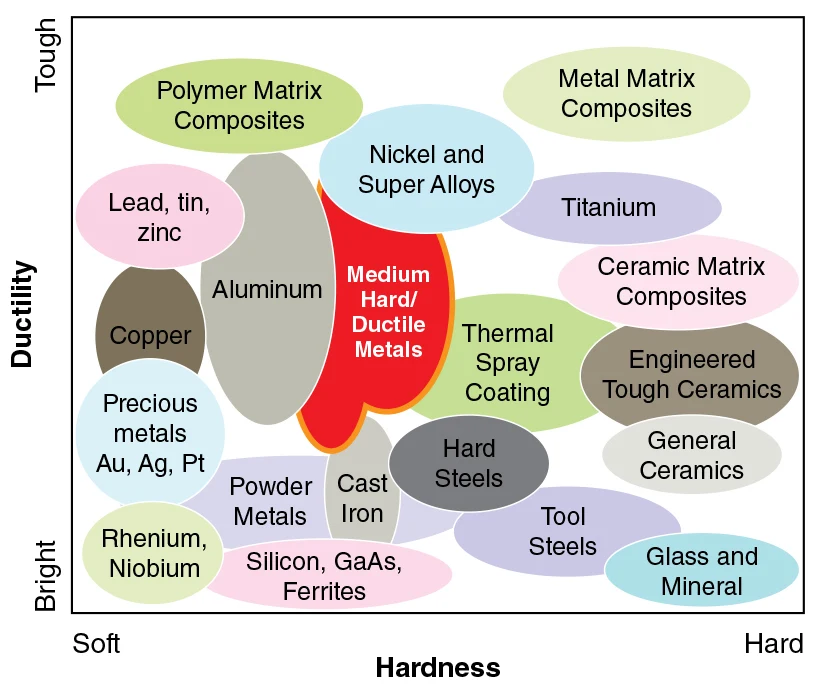

INDUSTRIES USED IN:
- Advanced Ceramics
- Composites
- Glass
- Geology
- Quartz
- Materials Research
- Medical Devices
- Metallography
- Photonics / Optics
- Semiconductor
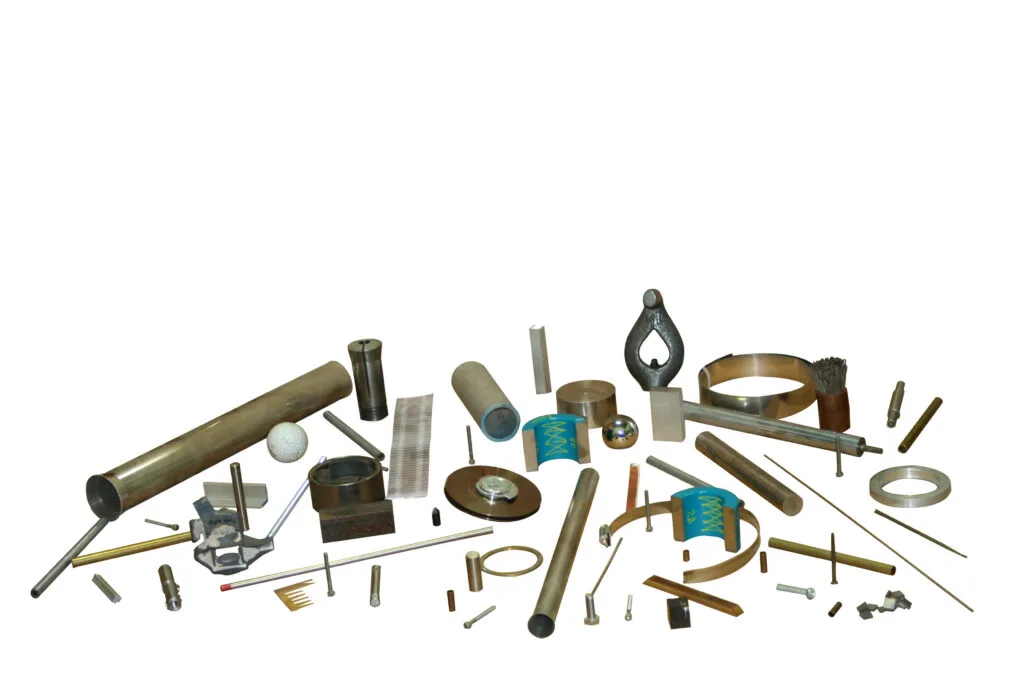
Ferrous & Non-Ferrous Metals:
- Plain Carbon Steels
- Electronic Packages
- Stainless Steels Plastics
- Tool Steels Fasteners
- Aluminum Refractories
- Copper Base Alloys Integrated Circuits
- Magnesium Thermal Spray Coatings
- Titanium Metal Matrix Composites
- Biomedical Wafers
- Petrographic
- PCB.s Ceramics
FAQ
The SMART CUT 1805 is specialized for cutting sample coupons from materials such as PCB Boards, FR4 panels, ceramic substrates, and much more, especially those too large for other precision cutting machines.
It can cut materials like PCB Boards, FR4 composite panels, ceramics, electronic packages, optics, flat glass, ultra-hard tiles, carbon fiber, honeycomb, and many other materials.
With the easy-to-use quick clamps, materials can be fixed in less than 30 seconds.
It ensures the material is held accurately in place without causing any stress or deformation.
The SMART CUT 1805 offers super high precision cutting up to 25-micron accuracy.
It can cut very large and long panels up to 750mm in length.
The variable speed, ranging from low to high, can be adjusted to accommodate all types of materials.
The machine can be operated both manually and automatically. An HMI touch screen controls all functions, from speed and feed rate to motor functions.
Yes, its height can be adjusted using hydraulics.
The machine can handle super thin materials to thicker ones up to 30mm.
It supports a wide selection of blades, ranging from .009″ to .080 kerf thickness.
It comes with a recirculation coolant system, ensuring the blade remains cool and the cuts are clean.
Yes, special vises can be ordered as per the requirements.
The machine’s design and features ensure a super smooth surface finish on the cut material.
The coolant is filtered and recirculated in a fully enclosed tank that comes with the machine, ensuring efficient cooling.
While it boasts an intuitive HMI touch screen control, training is recommended to get the best out of the machine and ensure safety.
Among its features, it offers the largest surface area in its class, variable speeds, and super high precision cutting, making it stand out.
The adjustable height allows for precise positioning of the material, accommodating various thicknesses and ensuring optimal cuts every time.
While specific materials aren’t mentioned in the provided details, the saw accommodates a variety of blades from .009″ to .080 kerf thickness, suitable for diverse cutting needs.
Yes, the saw’s variable speed feature and diverse blade selection allow it to cut through both soft and ultra-hard materials with precision.
The recirculation coolant system continuously cycles and filters the coolant to keep the blade temperature stable, preventing overheating and ensuring smooth cuts.
Like all machines, regular maintenance ensures optimal performance. It’s advisable to check the coolant levels, clean filters, and monitor the system for any anomalies.
The machine’s design includes safety measures like the enclosed coolant system and clamps that hold materials securely, preventing slips or dislodgment during operation.
The HMI touch screen simplifies machine operation, allowing users to adjust settings, control speeds, and monitor processes in real-time.
Yes, the SMART CUT® 1805 is designed to handle industrial-grade cutting, especially for materials too large for other precision cutting machines.
Absolutely. The machine’s feed rate can be adjusted between 0~150 mm/min to cater to the material’s hardness and the desired precision.
After a cut, the automatic home point return ensures that the blade returns to its starting position, making it ready for the next cutting process and reducing manual intervention.
Given its versatility, industries dealing with PCB boards, optics, composites, and other similar materials will find the SMART CUT® 1805 especially beneficial.
While the provided information doesn’t specify, it’s always recommended to install precision equipment in a stable environment, free from excessive dust, humidity, and temperature fluctuations.
While not explicitly mentioned, manufacturers typically provide replacement parts for their machines. You’d need to contact them directly for specifics.
The fasten vise securely holds materials in place, ensuring they don’t move during cutting. This stability results in more accurate and consistent cuts.
Given its manual and fully automatic functions, SMART CUT® 1805 can be integrated into various workflows. However, specifics would depend on the assembly line’s requirements.
Regularly checking and maintaining the coolant is crucial. Depending on usage, a periodic change is recommended, but always refer to the manufacturer’s guidelines.
The machine promises a super smooth surface finish, ensuring minimal post-cut processing for many materials.
A 25-micron accuracy ensures extremely precise cuts, crucial for industries where minute discrepancies can affect product quality or functionality.
Choosing the right blade depends on material hardness and desired cut precision.
Always ensure the machine is turned off and unplugged during blade changes. Wear protective gloves, and follow the user manual’s guidelines for safe blade replacement.
Routine cleaning, especially of the cutting chamber and coolant system, is advisable. For specific cleaning guidelines, consult the operating manual.
Different materials require different cutting speeds. A broad RPM range ensures versatility in accommodating various materials and achieving the desired cut quality.
The machine’s design, including the quick clamps and holding fixture, minimizes stress and deformation risks, ensuring material integrity.
The machine runs on a 370W motor. While its exact energy consumption isn’t specified, it’s designed for industrial use, balancing performance and energy efficiency.
ACCESSORIES
OPERATING MANUALS
Download Operating Manuals
Features:
- Ideal for Cutting a Variety of Materials: Suitable for cutting PCB boards, FR4 composite panels, ceramic substrates, electronic packages, composite materials, optics, glass, carbon fiber, honeycomb, ultra-hard material tiles, and more.
- Quick Clamping System: Easy-to-use quick clamps that enable fixturing of materials in under 30 seconds.
- Stress-Free Material Holding: Holding fixture ensures materials are held securely without causing stress or deformation.
- Manual & Fully Automatic Functions: Offers both manual and automatic cutting modes for flexibility.
- High Precision Cutting: Accuracy up to 25 microns for cutting composite panels, coupons, and test specimens.
- Large Cutting Capacity: Cutting table size of 600mm x 550mm; accommodates large and long panels up to 750mm in length.
- Adjustable Feeding Methods: Automatic or manual feeding with button control.
- HMI Touch Screen Control: Provides easy access to speed, feed rate, start/stop motor, and other machine functions.
- Variable Speed: Speed range from 0–2000 RPM, adjustable for different material types.
- Precision Feed Rate: Feed rate range from 0 to 150 mm/min, with a minimum of 25 mm/min.
- Hydraulic Adjustable Height: Allows adjustable cutting height for different material thicknesses.
- Versatile Blade Selection: Offers a wide range of blade kerf thicknesses from 0.009" to 0.080".
- Smooth Surface Finish: Delivers super smooth cutting results.
- Recirculating Coolant System: Equipped with a coolant system (1/4 HP) with a 17L water capacity tank.
- Precision Vise: Fasten vise with an optional special vise for more precise cutting.
- Ease of Use: The user-friendly design and intuitive HMI touch screen make it easy to control and operate the machine, even for operators with minimal training.
- High Cutting Depth: Capable of cutting materials up to 550mm in depth, making it suitable for thicker substrates and composite materials.
- Stable and Accurate Material Clamping: The steel table ensures secure clamping of materials, preventing any shifts or deformation during the cutting process.
- Automatic Home Point Return: After cutting, the automatic home point return feature ensures the system resets accurately for the next operation.
- Versatile Cutting Capabilities: With the ability to cut both ultra-thin and thick materials (up to 30mm), the machine provides flexibility for a wide range of applications.
- Compact Design for Larger Surface Area: The machine provides a large cutting surface area for its class, enhancing its capability to handle larger material sizes.
- Efficient Coolant Filtration: The recirculating coolant system keeps the cutting process cool and prevents overheating, while ensuring that the coolant is filtered and recalculated for longer machine life.
- Heavy Duty Motor: Equipped with a 370W motor, offering reliable power for continuous operation and consistent cutting performance.
- Extended Material Capacity: The maximum cut-off blade size of 200mm (8 inches) allows for cutting larger material samples.
- Quick Adjustments for Custom Applications: Adjustable height and feeding methods (manual or automatic) offer flexibility for different material types and cutting needs.
- Fast & Efficient Operation: The combination of automatic feed and fast-clamping system significantly reduces setup time and increases productivity.
- Low Maintenance: The enclosed coolant tank and recirculating system contribute to a lower need for maintenance, ensuring consistent performance.
- Reliable Cutting Precision: Able to handle large and long specimens with high precision, ensuring quality cuts with minimal variation.
- Optional Accessories: The option to order special vises and other accessories allows for customization to meet specific project requirements.
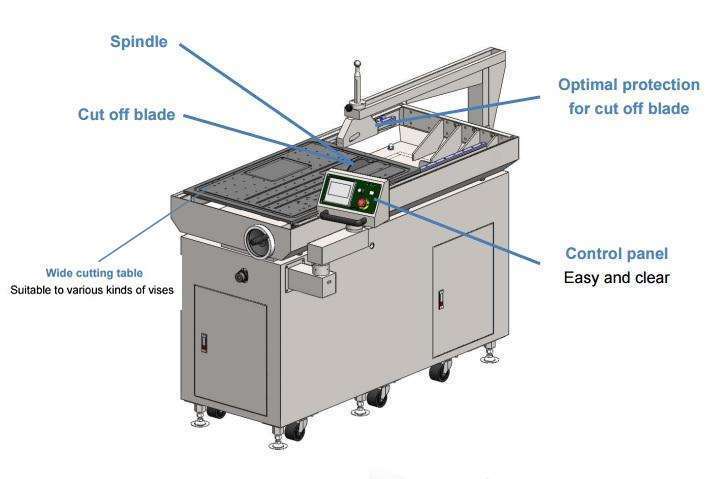
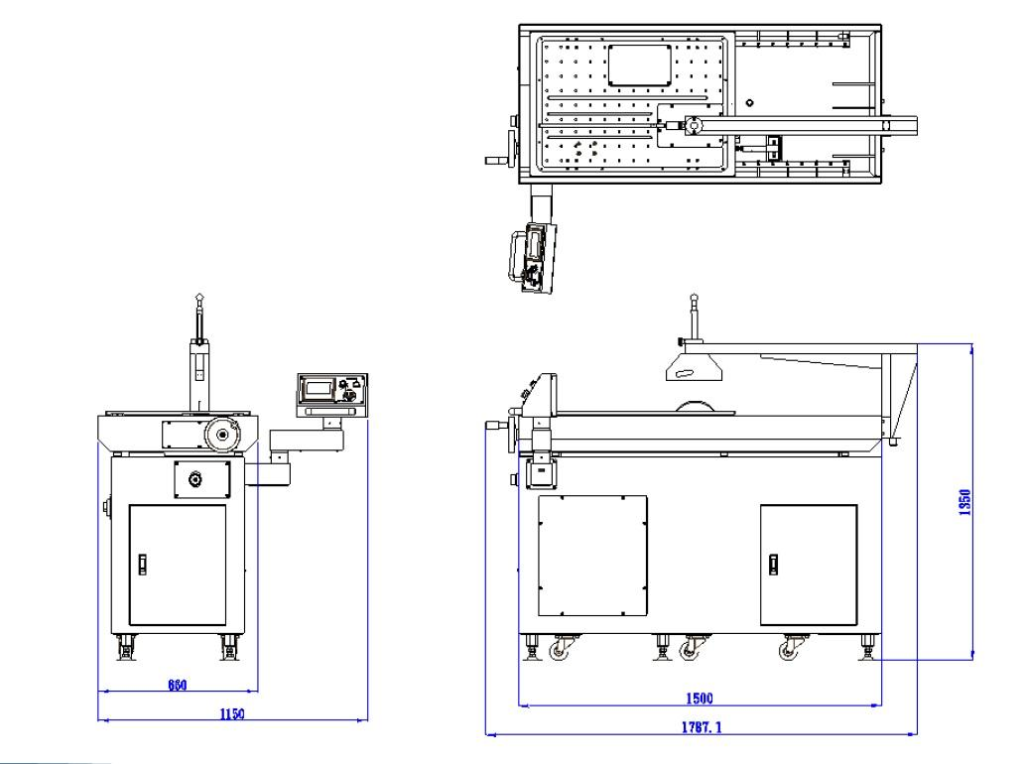
SMART CUT® COOLANTS
Your choice of one (1) quart of SMART CUT™ Water Soluble Coolant or Mineral Oil is included with machine. SMART CUT™ Water Soluble Coolant Reduces material thermal stress, edge damage, and internal cracking, increases blade life, provides better cut quality, preserves material micro structure
Hence, assuring long-term integrity of material being sectioned. Since SMART CUT coolant is both a coolant and lubricant, both the wafering blade and material benefit. Mix ratio is 1:20 (1 part coolant, 20 parts water) on very hard and dense materials and 1:40 (1 part coolant, 40 parts water) on softer materials. Depending on mix ratio 1 quart will produce 5.7 to 9 gallons of coolant when mixed with water. As a coolant, SMART CUT KOOL reduces heat caused by friction. As a lubricant, SMART CUT KOOL lowers friction and surface tension, which increases swarf dispersion.
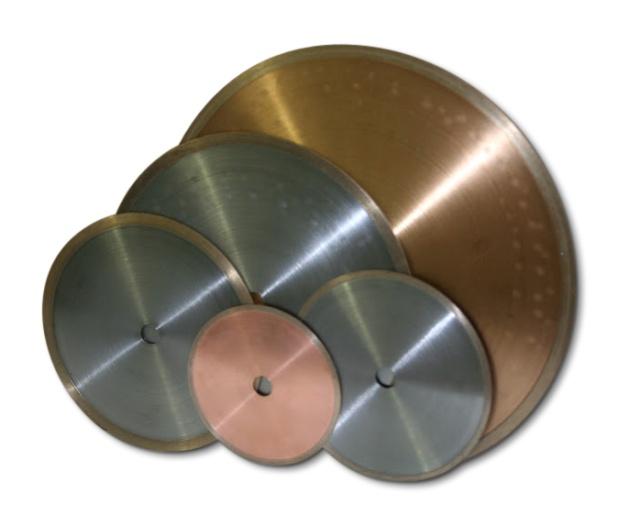
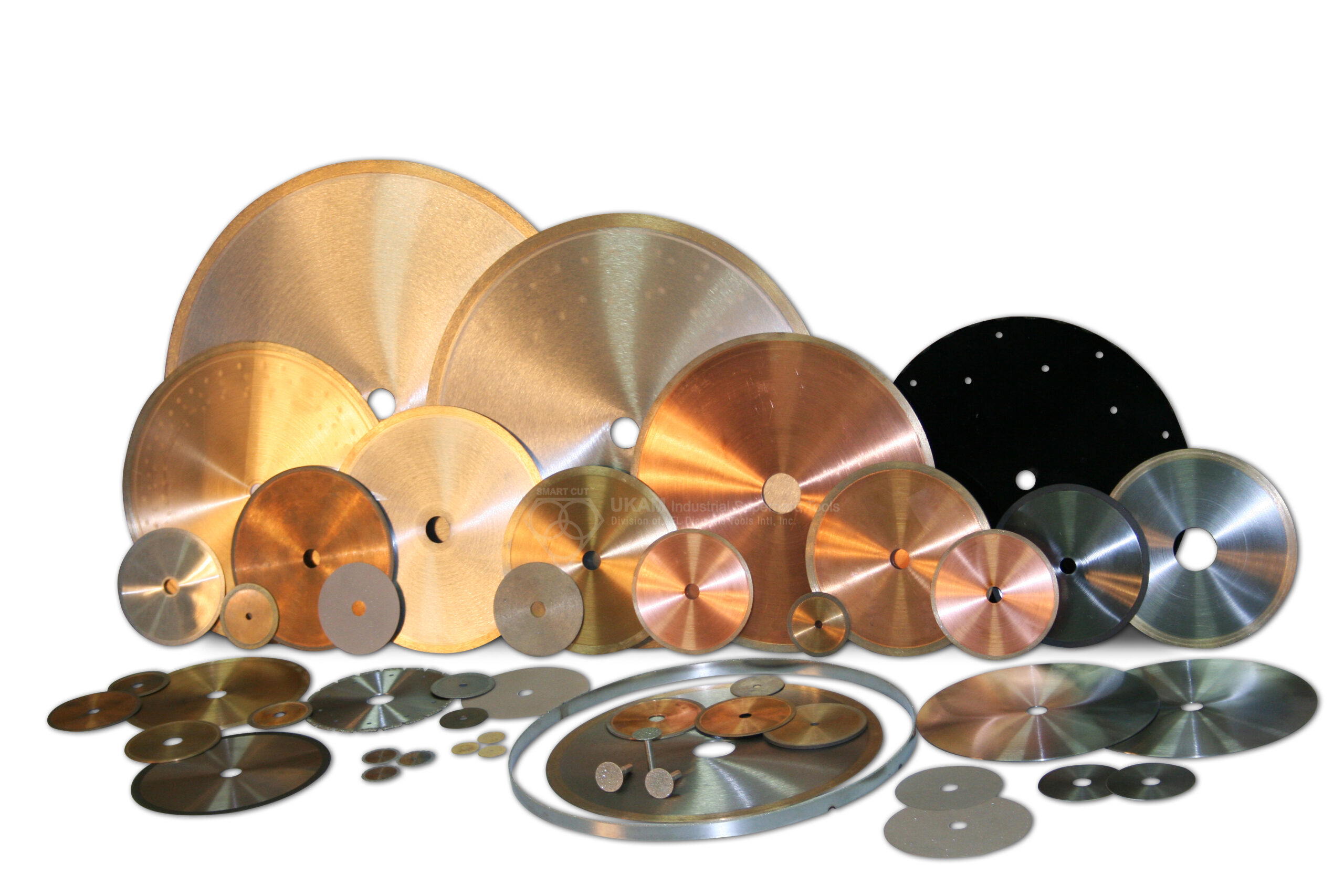
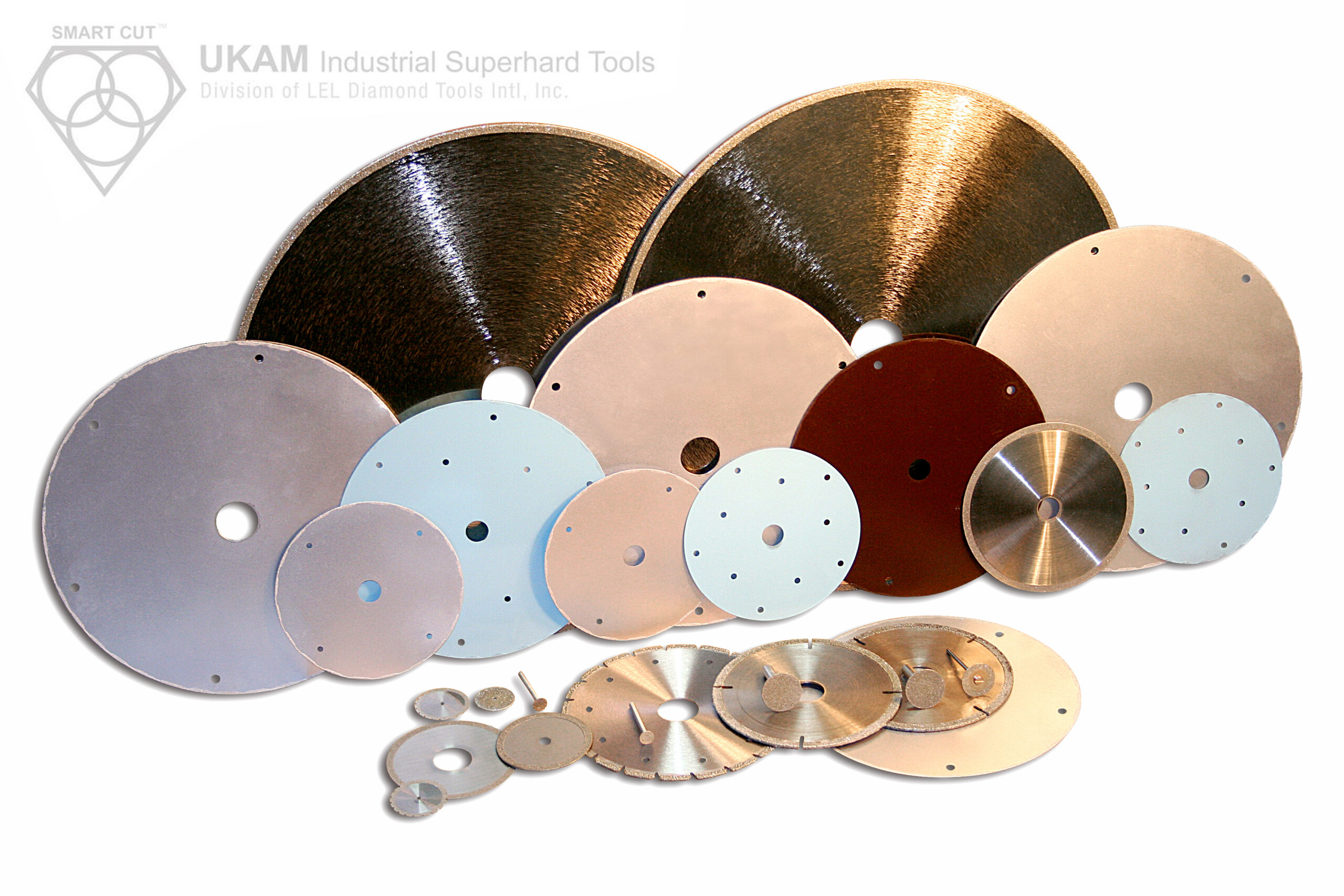
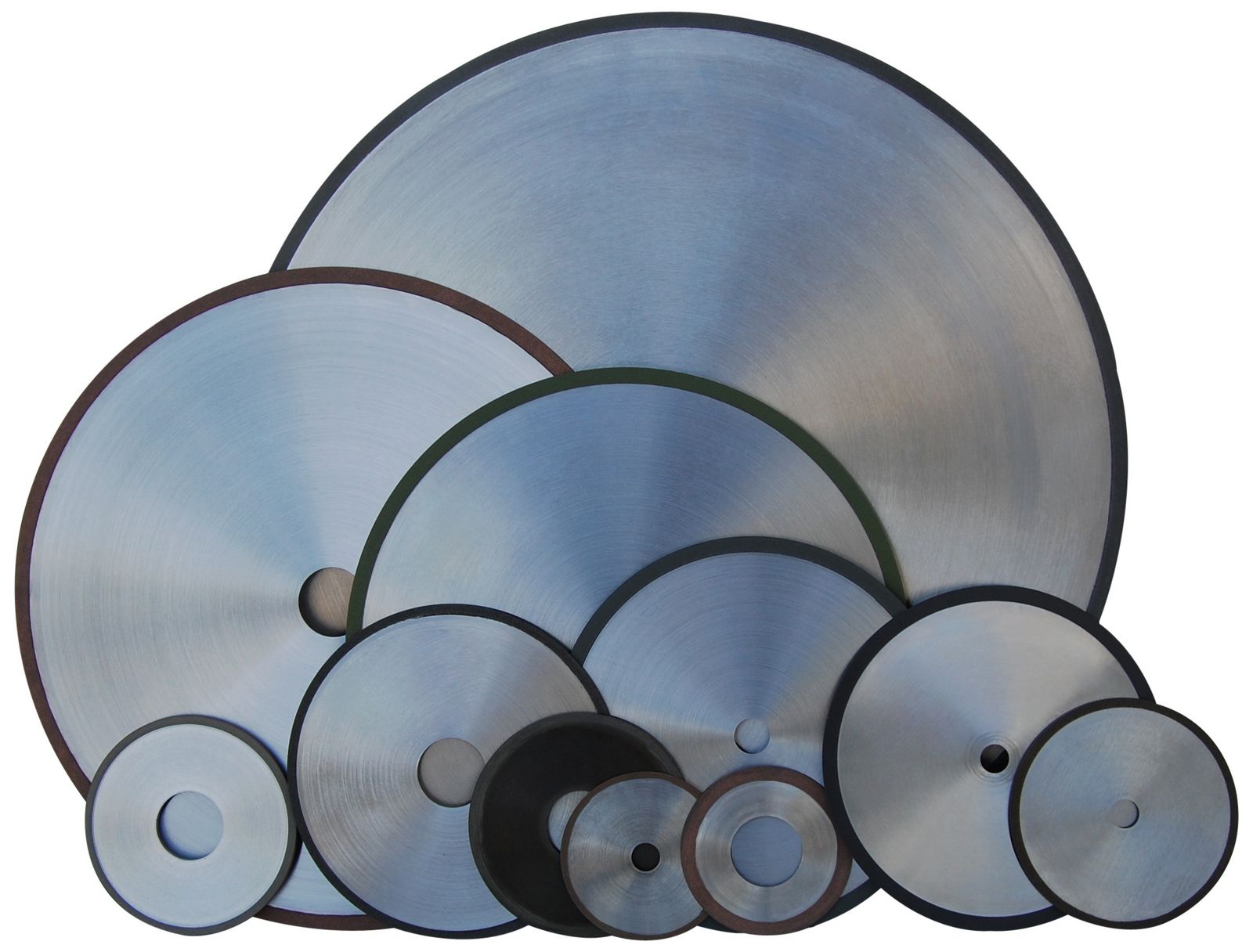
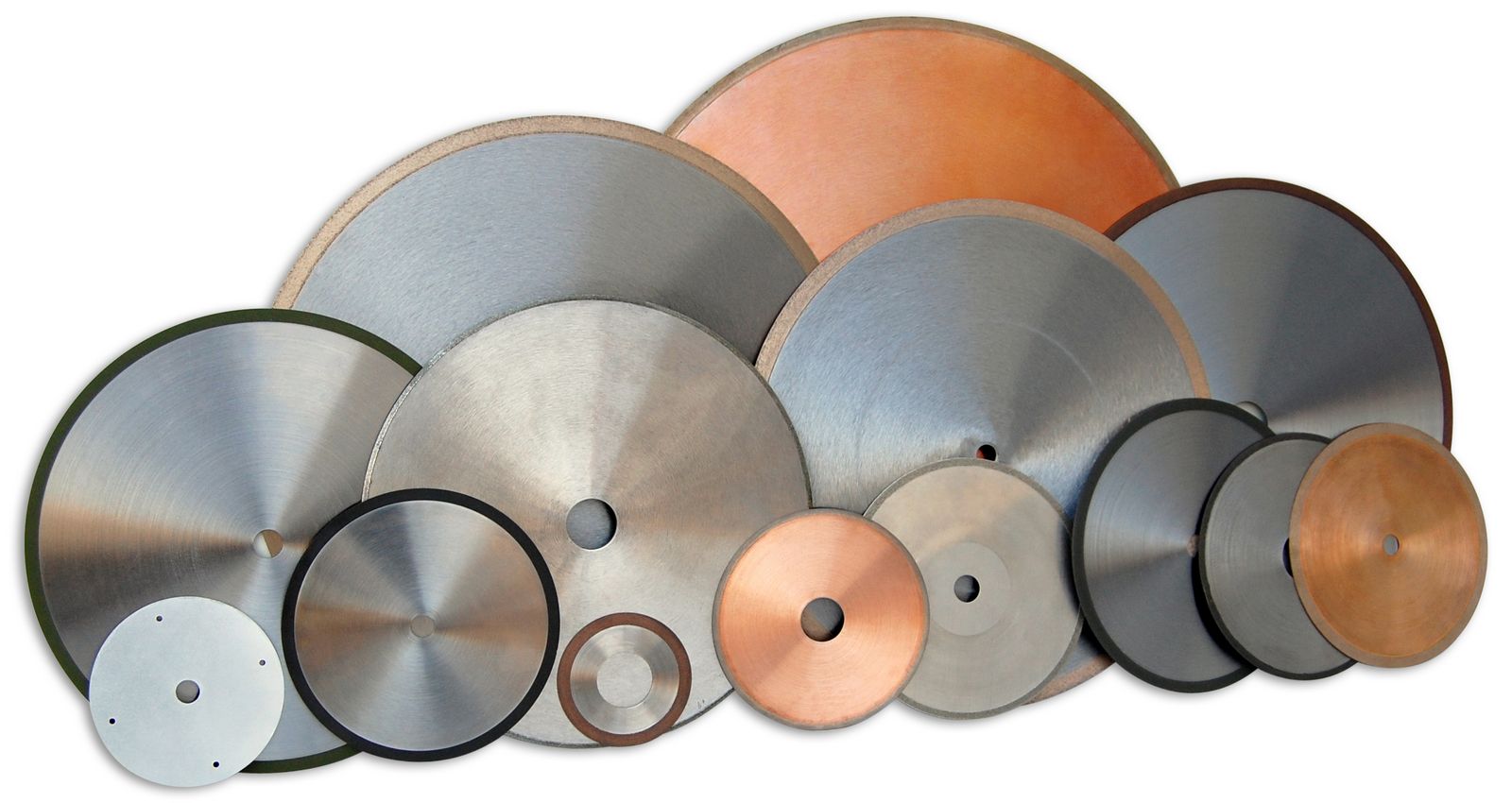
LARGEST SELECTING OF DIAMOND &
CBN WAFERING BLADES AVAIALBLE
one (1) diamond wafering blade any specification is included FREE OF CHARGE with purchase of any machine (any specification). we have almost unlimited number of diamond & CBN wafering blade specifications in stock available for immediate delivery. Available in different sizes, thickness, arbor sizes, diamond concentrations, diamond mesh sizes, and bond hardness’s. With several thousand unique blade specification in stock not listed on our standard stock program. This insures you will receive the best blade specification possible for your specific application.
THE RIGHT DRESSING STICK FOR YOUR APPLICATION
One (1) dressing stick is included with the purchase of any machine free of charge. The dressing stick we supply is similar to the diamond size of the wafering blade you have chosen (or we recommended) for your application. Wafering Blades must be diamonds particles/crystals exposed properly through frequent dressing. Otherwise, the diamond tool will glaze over. They will begin to tear rather than grind which is very destructive. Tearing caused from unexposed diamonds creates friction. This causes uneven wear and/or heat cracks in the wafering blade and/or material being cut. Resulting in premature blade wear, blade tensioning problems, and will eventually destroy the blade. The more frequently the blade is dressed the freer and cooler it will cut with lot more consistency.
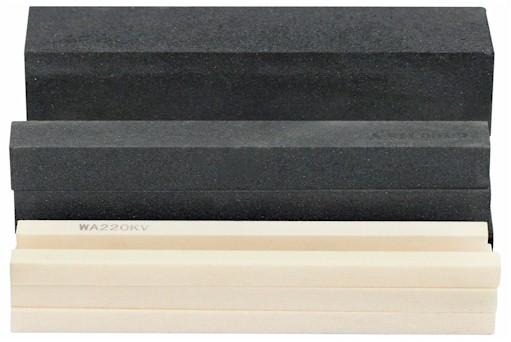
Related Products
SMART CUT® 1600 SAW
SMART CUT® 1800 – Precision Saw
Recently Viewed Products
ARE YOU USING METALLOGRAPHY SECTIONING SAWS
FOR YOUR APPLICATION?
LET US
HELP YOU
HAVING ISSUES WITH
YOUR METALLOGRAPHY SECTIONING SAWS?
Knowledge Center
02
Jun
Diamond Wire Advantages & Application
Diamond Wire saws provide the most accurate cutting with the least amount of material deformation and chipping of material.
Share this Article with Friend or Colleague
HOW DIAMOND WIRE WORKS
Today diamond wire sawing is preferred by majority...
02
Jun
Troubleshooting Diamond Sawing Problems
Having issues with your diamond cutting operation? This Illustrated Guide can help. Learn the most common problems most people have in using diamond cutting blades. How to resolve them and avoid them in...
02
Jun
How to Improve & Optimize Your Diamond Sawing Operation
There are numerous variables that affect the performance of diamond and CBN cutting blades. Understanding these variables will help end users select the right diamond blade specifications for their applications and optimize their...
02
Jun
Evaluating & Comparing Diamond Blades
Share this Article with Friend or Colleague
Proper testing procedures and methodologies must be set up and used to obtain accurate as well as repeatable testing results. This article will discuss several simple procedures which...
02
Jun
Selecting Right Wafering Blade for your application
Cross Sectioning is the first and most important step in the sample preparation process. Getting the best results involves obtaining a smooth surface finish, minimum chipping, material deformation, without sacrificing cutting speed. Today, most laboratories, work with dozens...
02
Jun
Wafering Blade Usage Recommendations
The wafering/sectioning blade itself is only a small factor in your sectioning operation. Successful wafering/sectioning operation is both an art & science. Requiring proper use and understanding of selecting the right diamond wafering/sectioning...
02
Jun
Wafering Blade Case Studies
Step by step guide on how to properly use and care for your diamond drills. Selecting the right diamond drill/diamond drill bit parameters, often involves a trial and error process. Many which can be avoided...
22
Apr
Diamond & CBN Wafering Blade Performance Metrics
When evaluating Diamond & CBN wafering blades, especially for metallography and sample preparation, it is critical to consider a set of key evaluation criteria and performance metrics. These factors help determine the effectiveness of a...
24
Apr
Understanding & Comparing Diamond & CBN Wafering Blades
Share this Article with Friend or Colleague
Diamond wafering blades are designed for sectioning a large variety of materials and sample types. In order to identify the best diamond wafering blade for your specific material/application, we...
25
Apr
Diamond & CBN Wafering Blade Guide
Share this Article with Friend or Colleague
All you need to know about wafering blades (understanding variables & specifications)
This guide is designed to help you navigate the various variables and possibilities associated with diamond wafering blades,...
08
Jul
Low Speed Saw Case Studies
Share this Article with Friend or Colleague
Introduction
In the realm of precision cutting, the SMART CUT® 6005 Low Speed Diamond Saw stands out for its capability to handle a variety of materials with high accuracy. To...
31
Jul
Top 5 Diamond & CBN Cutting Blade Performance Metrics
Share this Article with Friend or Colleague
When evaluating diamond and cubic boron nitride (CBN) cutting blades, it's crucial to consider key performance metrics and criteria. Different applications have varying goals, making it important...
01
Aug
Diamond & CBN Cutting Blade Performance Metrics that you Should Know
Share this Article with Friend or Colleague
When evaluating diamond and cubic boron nitride (CBN) cutting blades, it's crucial to consider key performance metrics and criteria. Different applications have varying goals, making it important to understand...
02
Aug
Total Cost of Ownership & Why its Important
Share this Article with Friend or Colleague
Diamond and CBN cutting blades are available in a myriad of specifications, with virtually limitless options. The industry is saturated with numerous manufacturers, each professing to offer the...
04
Aug
Diamond Wire vs band saw blades and circular blades
Diamond wire, band saw blades, and circular blades are all cutting tools used in various industries for different purposes. Each tool has its advantages and applications
For cutting ultra hard...
05
Aug
Understanding Tradeoffs- Searching for Perfect Diamond & CBN Blade
Share this Article with Friend or Colleague
Choosing the right blade diamond or cbn blade can significantly impact efficiency, cost, and quality. However, this is not simple and clear cut process. Selecting the optimal blade...
19
Aug
Understanding & Calculating Return on Investment for Diamond & CBN Blades
The term "ROI" (Return On Investment) is frequently mentioned across various industries, often with different interpretations depending on the context. However, few take the time to thoroughly understand what ROI truly represents and its specific...
- Unmatched Selection For Many Applications
- Superior Quality & Consistency
- Immediate Worldwide Delivery
- Technical Support & Expertise
- American Based Manufacturer
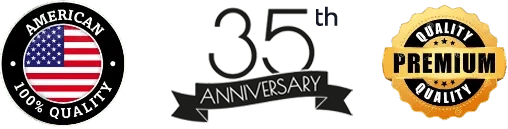

- Different Product
- Different Technology
- Different Company
- Expect MORE from your tools
Let Us HELP You!
Subscribe To Our Newsletter
Signup for email offers, updates, and more
Contact Us
- 25205 & 25201 Avenue Tibbits Valencia CA 91355 USA
-
Phone : (661) 257-2288
FAX : (661) 257 -3833 - lel@ukam.com
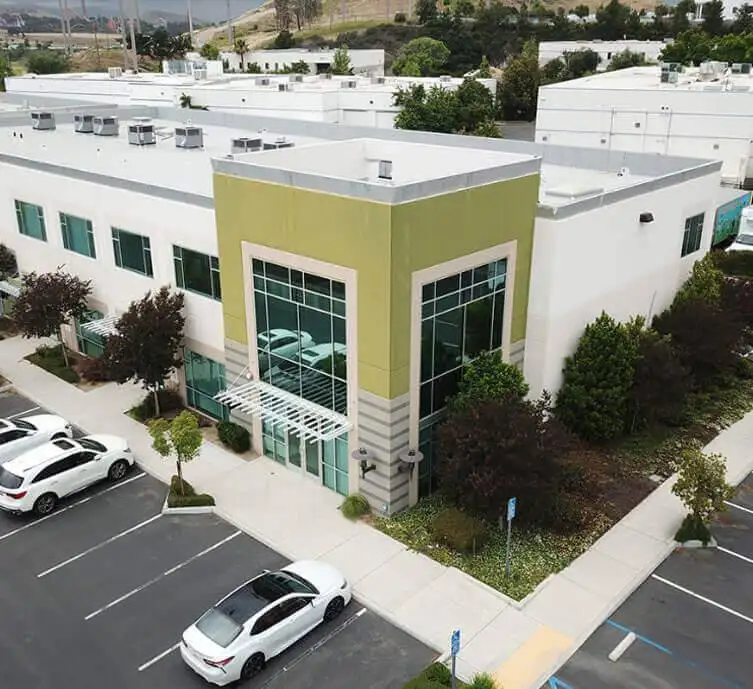
UKAM Industrial Superhard Tools is a U.S. High Technology, Specialty Diamond Tool & Equipment manufacturer. We specialize in producing ultra thin & high precision cutting blades and precision cutting machines diamond drills, diamond micro tools, standard & custom advanced industrial diamond tools and consumables.
- 25205 & 25201 Avenue Tibbits Valencia CA 91355 USA
-
Phone : (661) 257-2288
FAX : (661) 257 -3833 - lel@ukam.com
- 25205 & 25201 Avenue Tibbits Valencia CA 91355 USA
-
Phone : (661) 257-2288
FAX : (661) 257 -3833 - lel@ukam.com
DIAMOND TOOLS BY BOND
EQUIPMENT
KNOWLEDGE CENTER
OUR PRODUCTS
COMPANY
CUSTOMER SERVICE
Shipping Methods


Safe & Secure Payments

© Copyright 1990-2025. UKAM Industrial Superhard Tools – Terms of Use