-
0 items in quote
No products in the Quote Basket.
SMART CUT® 005DME MCDU Diamond Micro Drills
SMART CUT® 005DME diamond micro drills are produced using electroplated (nickel bond) galvanic plating process. These tools can be used for drilling and machining large variety of materials such as Precision Optics, Silicon Carbide, Boron Nitride, Boron Carbide, Alumina Ceramics, Silicon, Sapphire & Yag, Glass, Quartz, & Pyrex Tubing & Many Other Applications.
Small diameter below .020” (0.5mm) are made using diamond plating (galvanic) method, where the diamond crystals are deposited evening on the tip evenly over time. The steel body using is usually high speed steel ranging in hardness from 40 to 50 Rockwell scale C. Precision tolerances are maintain on diameter.
DESCRIPTION
SPECIFICATION
FREQUENTLY ASKED QUESTIONS
INDUSTRIES USED IN
ACCESSORIES
USAGE RECOMMENDATION
DESCRIPTION
Diamond sizes used range form 6 microns to 120 microns. Head length made in proportion to diameter of the tool. Usually it cannot exceed 15 times the diameter of the tool. Diamond grit size used in in proportion to diameter of the drill tip and can range form 3 to 70 microns. shank size is .040” (1mm).
Height of diamond coating can be adjusted to fit your particular requirements. Standard configuration of standard stock diamond micro tools is flat end cylinder but the angle and radius can also be customized if needed. diamond micro drills are used at high speeds ranging from 150,000 to 35,000 RPM’s. The smaller the diameter the tool the higher the recommended speed for optimal performance. The drills may work at lower rpm’s with significantly shorter drill life and possible drill breakage. We recommend using with our SMART CUT water soluble coolant for optimal results.
SPECIFICATION
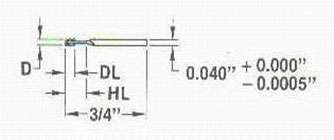
Bond Type: Nickel Bond (Plated) Multi Layered
Edge Type: Flat End Cylinder
Diamond Grit Size: Medium to Very Fine (each size has different diamond size)
Transition Angle Yes
Shank Diameter: .040” (1.0”)
Overall Length: 3/4″ (19.05mm)
Minimum Operating Speed: 30,000
Maximum Operating Speed: 150,000.
Always drill with a coolant and use submerged-pressure sensitive feed.
Recommended Coolant: water, for ultra hard materials best results will be achieved with mineral oil or synthetic water soluble coolant.
FREQUENTLY ASKED QUESTIONS
SMART CUT 005DME diamond micro drills are precision tools made using an electroplated (nickel bond) galvanic plating process. They are designed for drilling and machining a wide range of materials, including Precision Optics, Silicon Carbide, Boron Nitride, Boron Carbide, Alumina Ceramics, Silicon, Sapphire & Yag, Glass, Quartz, & Pyrex Tubing, and many others.
Micro drills with diameters below 0.020” (0.5mm) are created using a diamond plating (galvanic) method, ensuring even deposition of diamond crystals on the tip over time. The steel body is typically high-speed steel with a hardness ranging from 40 to 50 Rockwell scale C. Precision tolerances are maintained on the diameter, and the diamond sizes used range from 6 microns to 120 microns. The head length is proportional to the tool’s diameter and usually does not exceed 15 times the diameter.
These micro drills are suitable for a wide range of materials, including Alumina, Glass, Quartz, Ruby, Sapphire, Yag, Silicon, Fused Quartz, Bk7, and many others.
Diamond is the hardest material known to man, making it ideal for drilling materials harder than 35 Rockwell scale C. Diamond micro drills provide faster drilling of hard materials, a smoother surface finish, and consistent performance. They preserve material microstructures, drill greater depths, and offer excellent cost per part value.
These micro drills come in various sizes, from 0.006″ (.152mm) to 0.015″ (.381mm) in diameter, with corresponding diamond heights and head lengths. Standard stock diamond micro tools have a flat-end cylinder configuration, but custom angles and radii can be accommodated if needed.
- High-quality diamond crystals and materials
- Consistent manufacturing process
- Maximum diamond particle exposure
- Preservation of true material microstructure
- Excellent return on investment
- Custom manufacturing options
- Longer tool life
- Less chipping and material stress
- Faster and freer cutting action
- Smoother surface finish
- Reduced heat generation
Variables that influence diamond micro drill specifications include the steel body composition, diamond or CBN particle sizes used, head lengths, recommended RPMs, shank diameter, and recommended coolants. Optimal RPMs depend on various factors such as cut quality, drill depth, material properties, and more.
Yes, yes can produce custom diamond and CBN micro drills and tools according to your specifications or drawings. Customization options include diameter, head geometry, head length, drill lengths, shank diameters, and diamond or CBN sizes.
Typically, the minimum order quantity for custom diamond micro drills is 10 pieces, with a lead time of 4 to 6 weeks. Please inquire for specific details.
chemical vapor deposition micro drills and tools are usually made from tungsten carbide with very thin coating. The crystalline diamond slowly grows on the surface forming a continuous coating of up to 20 microns in thickness. The micro drills and tools are usually used on softer and gummy materials such as machining graphite, hard carbon, green ceramic, carbon fiber, reinforced polymers, fiberglass, plastics, wood laminates, non ferrous metals. while these can be used on harder materials same as our SMART CUT 005DME Diamond Micro Drills, the life span would be lot shorter. Also the minimum RPM’s are lot higher for our SMART CUT 005DME Diamond Micro Drills then chemical vapor deposition micro drills & tools.
Diamond grit size used is in proportion to the diameter to the tool and varies between 70 to 3 microns.
SMART CUT 005DME Diamond Micro Drills are produced under the highest quality standards, including a controlled galvanic plating process and a clean room environment. The steel bodies are machined with precision tolerances, and quality control measures are in place at all stages of manufacturing. This ensures consistent product quality for demanding applications.
Only the highest quality raw materials are used in the manufacturing process to ensure the best possible diamond drill life, quality of cut, and surface finish.
SMART CUT diamond and CBN micro drills are designed to operate at high speeds, ranging from 150,000 to 35,000 RPMs. It’s important to note that smaller diameter tools require higher recommended speeds for optimal performance. Operating at lower RPMs may result in shorter drill life and possible drill breakage. The optimum RPM can vary depending on factors such as cut quality, drill depth, material hardness, density, shape, and porosity. Please consult our technical support team or engineering department for guidance on the best RPM settings for your specific application.
The shank size for these micro drills is typically either 1/8” (3.2mm) or .040” (1mm) to fit most collets. The shank diameter is designed to be in proportion to the diameter of the drill/tool. Smaller diameter micro drills/tools, ranging from .001” to .015”, will have a shank diameter of .040” (1mm), while larger diameter micro drills/tools, ranging from .016” to .040”, will have a shank diameter of 1/8” (3.2mm). If you require different shank diameters, they can be made upon request.
Yes, we recommend using our SMART CUT water-soluble coolant for optimal results. Using the proper coolant type at the right velocity and angle at the drilling zone will improve the life and performance of your tool while helping to reduce drill breakage.
Yes, SMART CUT Diamond Micro Drills are suitable for various industries and applications, including Nano Technology, MEMS (Micro-Electro-Mechanical Systems), Materials Research, and more. Our customers range from leading Fortune 500 companies to universities, military organizations, space flight agencies, laboratories, advanced material fabricating facilities, and small machine shops.
SMART CUT 005DME Diamond Micro Drills are produced under highly controlled conditions in a galvanic plating process and a clean room environment. The steel bodies are machined with very high precision tolerances, and experienced engineers and chemists continuously monitor and control all material input and output at all manufacturing stages. The use of world-class quality control, inspection, and measurement equipment ensures product consistency for use in demanding and sensitive applications.
SMART CUT Diamond Micro Drills offer unmatched performance on a wide spectrum of materials. With a focus on quality, precision manufacturing, and custom capabilities, they are designed to provide longer tool life, reduced chipping, faster and smoother cutting action, and consistent performance. The use of high-quality diamond crystals and materials ensures the best possible results for your drilling needs.
Absolutely, SMART CUT Diamond Micro Drills are an excellent choice for research and development projects, allowing you to drill and machine a variety of materials with precision and consistency. If you have specific research requirements, our custom manufacturing capabilities can tailor the tools to your needs.
Diamond micro drills offer several advantages over conventional options. They can drill harder materials faster, maintain a smoother surface finish, preserve the microstructure of the material being drilled, handle greater depths, provide consistent performance, and yield a better cost per part. They are especially effective for materials harder than 35 Rockwell scale C.
Yes, SMART CUT Diamond Micro Drills are suitable for drilling extremely small holes, with diameters as low as 0.006″ (.152mm). The ability to customize the tool’s diameter, head geometry, and head length makes them versatile for a wide range of applications, including those requiring tiny, precision holes.
Yes, these micro drills are well-suited for high-precision applications, including those in the electronics industry. Their ability to provide consistent performance, smooth surface finishes, and the option for custom manufacturing makes them valuable tools for precision work in various industries.
Yes, SMART CUT Diamond Micro Drills are designed to minimize chipping and cracking when drilling brittle materials. Their high-quality diamond crystals and precise manufacturing help reduce material stress and produce clean, high-quality holes in such materials.
Yes, we offer technical support to help you select the right micro drill for your specific application. Our team can assist you in determining the optimal drill size, RPM settings, and coolant recommendations to achieve the best results in your drilling projects.
When using these micro drills, it’s essential to follow standard safety precautions associated with high-speed drilling tools. This includes wearing appropriate personal protective equipment, ensuring proper ventilation, and following recommended RPMs and coolant usage guidelines to prevent overheating and maximize tool life.
To request a quote or place an order, please contact our sales team or customer service department. They will guide you through the ordering process, provide pricing information, and assist with any customization requirements you may have.
SMART CUT Diamond Micro Drills are not typically designed for re-sharpening or re-coating due to their precision manufacturing and the specialized electroplated diamond coating process. It is generally more cost-effective to replace them with new drills when they become worn or dull.
To ensure the longevity and performance of SMART CUT Diamond Micro Drills, store them in a clean and dry environment, away from moisture and extreme temperatures. It’s advisable to keep them in their original packaging or a suitable storage container to prevent any damage or contamination.
Yes, these micro drills are compatible with automated machining systems and CNC machines, making them suitable for precision drilling in various manufacturing processes. Their consistent performance and customizability make them valuable tools for automated applications.
SMART CUT Diamond Micro Drills have found applications in a wide range of industries, including aerospace, medical devices, electronics, optics, automotive, semiconductor manufacturing, and more. Their ability to drill and machine hard and brittle materials efficiently has made them indispensable in these fields.
For the best results when using SMART CUT Diamond Micro Drills, consider the following tips:
- Follow the recommended RPM settings for your drill size and material.
- Use the recommended SMART CUT water-soluble coolant for optimal performance.
- Ensure proper ventilation and wear appropriate personal protective equipment.
- Consult with our technical support team for guidance on specific applications.
Yes, SMART CUT Diamond Micro Drills are well-suited for drilling fragile materials like glass and ceramics. Their precise manufacturing and diamond crystal composition help reduce the risk of damage, chipping, or cracking in these materials.
When using SMART CUT Diamond Micro Drills for high-precision optics applications, it’s essential to ensure a clean and controlled environment to prevent contamination. Additionally, follow recommended RPM settings and coolant usage to achieve the desired surface finish and accuracy.
Yes, SMART CUT Diamond Micro Drills can be used with both handheld and machine-driven drilling equipment, offering versatility in various drilling setups and applications.
Absolutely, these micro drills are suitable for both prototyping and small-scale production runs. Their custom manufacturing capabilities allow for tailored solutions, making them ideal for specialized projects and limited production quantities.
We can provide educational resources and training materials on the use of SMART CUT Diamond Micro Drills upon request. If you or your team require specific training or guidance, please let us know, and we will do our best to assist you.
To extend the life of SMART CUT Diamond Micro Drills, always handle them with care to avoid damage. Keep them clean and free from contaminants. When not in use, store them in a suitable container to protect their delicate tips. Regularly inspect the drills for signs of wear and replace them when necessary.
SMART CUT Diamond Micro Drills can be used for applications requiring deep holes, but the depth achievable depends on several factors, including the material being drilled, the drill size, and the RPM settings. For applications with very deep holes, consult with our technical support team to determine the best approach and tool specifications.
SMART CUT Diamond Micro Drills stand out in the market due to their high-quality diamond crystals, precision manufacturing, customizability, and consistent performance. Our commitment to meeting the needs of various industries and applications has made SMART CUT a trusted choice among professionals.
The manufacturing process of SMART CUT Diamond Micro Drills is conducted in a clean room environment, which helps control and minimize environmental contamination. The use of water-soluble coolants also contributes to a more environmentally friendly process compared to some oil-based alternatives.
Yes, SMART CUT Diamond Micro Drills are well-suited for precision micro-machining applications in industries such as aerospace and medical device manufacturing. Their ability to provide consistent performance and drill hard materials efficiently makes them valuable tools for achieving tight tolerances and high-quality results.
SMART CUT Diamond Micro Drills have been successfully used in industries such as:
- Aerospace: For drilling precision holes in aircraft components.
- Electronics: For micro-machining of electronic components.
- Optics: For drilling holes in optical lenses and components.
- Medical Devices: In the production of medical instruments and implants.
- Semiconductor Manufacturing: In the fabrication of microelectronics.
- Materials Research: For drilling and sampling materials in research labs.
Yes, SMART CUT Diamond Micro Drills can be customized to create holes with complex geometries, including angled or radiused holes. Custom head geometries can be tailored to meet your specific drilling requirements.
The expected lifespan of SMART CUT Diamond Micro Drills can vary depending on factors such as the material being drilled, the drilling conditions, and the drill size. Generally, they offer longer tool life compared to conventional micro drills like carbide or high-speed steel. For specific tool life estimates, please consult with our technical support team, as they can provide guidance based on your application.
SMART CUT Diamond Micro Drills are typically replaced when they become worn or dull, as they are not designed for reconditioning or re-gritting due to their specialized electroplated diamond coating process.
Yes, safety data sheets (SDS) and product safety information are available for SMART CUT Diamond Micro Drills and their associated coolants. These documents provide important safety and handling information. Please request SDS or safety information from our customer service team when needed.
Yes, SMART CUT Diamond Micro Drills can be used for drilling composites or layered materials with varying hardness. Their ability to drill hard materials efficiently allows them to handle the challenges posed by layered materials effectively.
Lead times for standard SMART CUT Diamond Micro Drills may vary based on factors such as availability and order volume. Typically, orders are processed and shipped in a reasonable timeframe. For specific lead time estimates or expedited orders, please contact our sales team for assistance.
Yes, SMART CUT Diamond Micro Drills are suitable for drilling advanced ceramics such as zirconia and alumina. Their precision and hardness make them effective tools for machining these challenging materials.
In high-precision microfluidics or MEMS applications, it’s essential to ensure the cleanliness and precision of the drilling process. Follow recommended RPM settings and use the provided SMART CUT water-soluble coolant to achieve the required accuracy and surface finish. Consult with our technical support team to tailor the tool specifications to your specific microfluidics or MEMS requirements.
SMART CUT Diamond Micro Drills are primarily designed for drilling hard and brittle materials. While they can be used on materials like copper and aluminum, it’s important to consider factors like tool wear and heat generation, as these materials have high thermal conductivity. Consult with our technical support team for guidance on using these drills with copper or aluminum.
Used SMART CUT Diamond Micro Drills should be disposed of following local regulations and guidelines for handling industrial tools. Ensure that any hazardous waste, such as used coolant, is disposed of in accordance with environmental regulations.
Yes, SMART CUT Diamond Micro Drills can be used for drilling holes in composite materials like CFRP. Their ability to provide clean and precise holes makes them valuable tools for working with composite materials.
The maximum drill depth achievable with SMART CUT Diamond Micro Drills depends on various factors, including the material being drilled, the drill size, and the RPM settings. While they can handle relatively deep holes, consult with our technical support team to determine the specific depth limitations for your application.
The recommended feed rate for drilling operations with SMART CUT Diamond Micro Drills can vary based on the specific material and drilling conditions. For optimal results, it’s advisable to consult with our technical support team to determine the appropriate feed rate for your application.
Yes, SMART CUT Diamond Micro Drills are well-suited for micromachining applications that involve intricate patterns or small features. Their precision and customizability allow for the creation of intricate designs and small details with high accuracy.
To ensure consistency in tool specifications when reordering SMART CUT Diamond Micro Drills, it’s recommended to provide the same specifications or part numbers as in your previous orders. Our sales team can assist you in reordering the exact tools you need to maintain consistency in your drilling operations.
SMART CUT Diamond Micro Drills can be used for drilling materials with varying degrees of hardness within the same workpiece. However, it’s important to adjust drilling parameters and tool specifications to account for the different material properties to achieve optimal results.
Yes, SMART CUT Diamond Micro Drills are suitable for creating small holes in precision watchmaking and jewelry manufacturing applications. Their precision and ability to drill hard materials make them valuable tools in crafting intricate and precise components.
When using SMART CUT Diamond Micro Drills in high-temperature environments or for drilling heat-resistant materials, it’s essential to ensure proper cooling using the recommended SMART CUT water-soluble coolant. Adequate cooling helps maintain drill performance and prolongs tool life in such conditions.
Yes, SMART CUT Diamond Micro Drills are commonly used in scientific research and laboratory applications for drilling holes in brittle materials. Their precision and ability to minimize material stress make them valuable tools in various research settings.
SMART CUT Diamond Micro Drills can provide minimal tool runout and high concentricity when used in precision drilling applications. Proper tool selection and setup, along with adherence to recommended RPM settings, can help achieve these requirements.
SMART CUT Diamond Micro Drills are suitable for drilling applications involving highly abrasive materials like composite laminates or fiberglass. Their diamond crystals are well-equipped to handle abrasive materials efficiently.
The primary benefit of using electroplated (nickel bond) galvanic plating in the production of SMART CUT Diamond Micro Drills is the even and precise distribution of diamond crystals on the drill tip. This process ensures consistent performance and allows for the creation of high-quality holes with minimal chipping and smooth finishes.
SMART CUT Diamond Micro Drills can be customized to drill holes with specific angles or tapers as needed for your application. Custom head geometries can be designed to achieve the desired hole shape or angle.
Between uses, it’s advisable to inspect SMART CUT Diamond Micro Drills for any signs of wear or damage. Store them in a clean and dry environment to prevent contamination or corrosion. Avoid dropping or mishandling the drills to protect their delicate tips.
Yes, SMART CUT Diamond Micro Drills can be used for drilling highly dense and non-porous materials like sapphire or ruby. Their diamond crystals are capable of efficiently drilling through these hard materials while maintaining precision.
SMART CUT Diamond Micro Drills are advantageous for applications requiring extremely small hole diameters below 0.020″ (0.5mm) due to their ability to provide precise and consistent drilling at such small scales. Their customization options also allow for tailored solutions to meet specific requirements.
Yes, SMART CUT Diamond Micro Drills are available in various packaging options to suit your needs. You can purchase them individually, in sets, or in bulk quantities, depending on your requirements and preferences.
Yes, SMART CUT Diamond Micro Drills are suitable for drilling extremely precise and small holes required for microfluidic devices and lab-on-a-chip applications. Their precision and ability to create clean, small holes make them valuable tools in microfabrication.
SMART CUT Diamond Micro Drills can be used for drilling holes in hard-to-reach or confined spaces within a workpiece. Their small diameters and customizability allow for drilling in tight spaces and complex geometries.
SMART CUT Diamond Micro Drills can be used for drilling holes with high aspect ratios, but the achievable aspect ratio depends on factors such as the material, drill size, and drilling conditions. Consult with our technical support team for guidance on achieving high aspect ratio holes for your specific application.
Yes, SMART CUT Diamond Micro Drills can be used for creating blind holes in materials where the hole does not go through the entire material thickness. The drilling depth can be customized to meet your specific requirements.
To maintain consistent tool performance during long drilling operations or extended tool usage, it’s important to monitor tool wear and replace the drill when signs of wear become noticeable. Using the recommended coolant and adhering to recommended RPM settings can also help extend tool life and maintain performance.
Yes, SMART CUT Diamond Micro Drills can be used for precision applications in the automotive industry, including drilling engine components, fuel injectors, and other high-precision parts. Their ability to drill hard materials with precision makes them valuable in automotive manufacturing.
SMART CUT Diamond Micro Drills are suitable for drilling holes in brittle materials like ceramic tiles or porcelain. Their ability to minimize chipping and provide clean holes makes them useful tools in applications involving such materials.
Yes, SMART CUT Diamond Micro Drills can be used for creating holes in jewelry-making applications involving gemstones and precious metals. Their precision and ability to work with hard materials make them valuable tools in jewelry fabrication.
SMART CUT Diamond Micro Drills can be used for creating small holes in dental implants or prosthetic devices. Their precision and ability to work with hard materials make them suitable for dental applications.
Yes, SMART CUT Diamond Micro Drills are suitable for drilling holes in silicon wafers and semiconductor materials. Their precision and ability to work with hard and brittle materials make them valuable in semiconductor manufacturing and microelectronics applications.
SMART CUT Diamond Micro Drills can be used for drilling high-density printed circuit boards (PCBs) with precision and accuracy. Their ability to create clean and small holes is advantageous in PCB manufacturing and electronics assembly.
When using SMART CUT Diamond Micro Drills with automated robotic systems or CNC machines for high-throughput drilling applications, ensure that the equipment is properly calibrated and that tool changes are performed efficiently. Monitoring tool wear and replacing drills as needed will help maintain consistent performance in high-throughput scenarios.
Yes, SMART CUT Diamond Micro Drills can be used for drilling holes in medical implants made of materials like titanium or stainless steel. Their precision and ability to work with hard metals make them valuable tools in medical device manufacturing.
SMART CUT Diamond Micro Drills are suitable for drilling holes in glass substrates used in the display industry and electronics applications. Their precision and ability to create clean holes in brittle materials are advantageous in these industries.
Yes, SMART CUT Diamond Micro Drills can be used for applications involving microneedles or microfluidic channels in the medical field. Their precision and ability to create small and precise features make them valuable in medical device manufacturing and research.
SMART CUT Diamond Micro Drills are suitable for applications in the aerospace industry that require drilling holes in composite materials used for aircraft components. Their ability to handle abrasive and hard materials efficiently is valuable in aerospace manufacturing.
Yes, SMART CUT Diamond Micro Drills can be used for drilling holes in ceramic substrates used in electronic packaging applications. Their precision and ability to work with hard and brittle ceramics make them valuable in the electronics industry.
Yes, SMART CUT Diamond Micro Drills can be manufactured with non-standard or custom shank sizes upon request to meet specific application requirements. Customization options are available to tailor the drills to your needs.
SMART CUT Diamond Micro Drills can be used for drilling holes in advanced materials used in renewable energy applications, including solar panels and fuel cells. Their precision and ability to work with a wide range of materials make them valuable tools in renewable energy manufacturing.
INDUSTRIES USED IN
Composites
Gem Stones
Sapphire
Silicon
Glass Materials
Lapidary
Stone
Advanced Ceramics
Photonics
ACCESSORIES
Showing 1 – -1 of 16 results Showing all 16 results Showing the single result No results found
Sort by Name A – Z
Filters Sort results
Reset Apply
Image | Item No. | Description | Price | Quantity | Add to cart |
---|---|---|---|---|---|
Color: 5/8″-11″ thread. Fits into drill press chuck. Shank adapter threads into 5/8″-11″ female thread of diamond drill. Can be used with any other tool with 5/8″-11″ thread. | $26.72 | Max: Min: 1 Step: 1 | |||
Color: 5/8″-11″ thread. Fits into drill press chuck. Shank adapter threads into 5/8″-11″ female thread of diamond drill. Can be used with any other tool with 5/8″-11″ thread. | $22.46 | Max: Min: 1 Step: 1 | |||
1 Gallon Blue SMART CUT® General Materials Formula Synthetic Water Soluble Coolant | $99.81 | Max: Min: 1 Step: 1 | |||
1 Quart Blue SMART CUT® General Materials Formula Synthetic Water Soluble Coolant | $34.81 | Max: Min: 1 Step: 1 | |||
5 Gallons Blue SMART CUT® General Materials Formula Synthetic Water Soluble Coolant | $317.41 | Max: Min: 1 Step: 1 | |||
55 Gallons Blue SMART CUT® General Materials Formula Synthetic Water Soluble Coolant | $1,745.00 | Max: Min: 1 Step: 1 | |||
1/2″ x 1/2″ x 6.0″ White Recommended for coarser grits found in segment wheels, core drills, or Blanchard grinding. Excellent performance on 120 grit tools. | $8.65 | Max: Min: 1 Step: 1 | |||
1.0″ x 1.0″ x 6.0″ White Recommended for coarser grits found in segment wheels, core drills, or Blanchard grinding. Excellent performance on 120 grit tools. | $15.99 | Max: Min: 1 Step: 1 | |||
1/2″ x 1/2″ x 6.0″ White For use on diamond tools 150 to 220 Grit Size. | $8.65 | Max: Min: 1 Step: 1 | |||
1.0″ x 1.0″ x 6.0″ Black Recommended for use in Diamond Tools 150 Grit Size (mesh size) or finer. | $15.39 | Max: Min: 1 Step: 1 | |||
2.0″ x 2.0″ x 6.0″ Black Recommended for use in Diamond Tools 150 Grit Size (mesh size) or finer. | $39.47 | Max: Min: 1 Step: 1 | |||
1.0″ x 1.0″ x 6.0″ Black Recommended for coarser grits found in segment wheels, core drills, or Blanchard grinding. Excellent performance on 120 grit tools. | $15.99 | Max: Min: 1 Step: 1 | |||
2.0″ x 2.0″ x 6.0″ Black Recommended for coarser grits found in segment wheels, core drills, or Blanchard grinding. Excellent performance on 120 grit tools. | $39.47 | Max: Min: 1 Step: 1 | |||
$154.87 | Max: Min: 1 Step: 1 | ||||
$154.87 | Max: Min: 1 Step: 1 | ||||
$235.00 | Max: Min: 1 Step: 1 |
USAGE RECOMMENDATION
02
Jun
How to Properly Use Precision Diamond Drills
Step by step guide on how to properly use and care for your diamond drills. Selecting the right diamond drill/diamond drill bit parameters, often involves a trial and error process. Many which can be avoided…
02
Jun
Diamond Drills Guide
Diamond are used across large variety of industries and applications. This guide explores the wide range of diamond drill types, including hollow core drills designed for removing a cylindrical core, non-core formation drills that grind…
02
Jun
Diamond Tools Guide – Selecting Right Drills & Tools for your application
These tools are used for many different industries grinding and shaping material into different forms, expanding exiting inside diameters, grinding, finishing and polishing existing material. Grinding different angles and radius, creating cavities of various forms,…
02
Jun
Optimizing your Diamond Drilling Operation
There are numerous factors that influence the performance of diamond drills. Understanding these factors helps users select the appropriate diamond drill specifications for their specific applications, optimizing drilling operations to achieve maximum efficiency….
02
Jun
Micro Drilling Guide
Share this Article with Friend or Colleague
In order for you to get the most out of your diamond micro drill or carbide / high speed steel micro drill, we strongly urge you to read…
03
May
Diamond Core Drill & Drill Trouble Shooting Guide
Learn the most common problems most people have in using diamond drills. How to resolve them and avoid them in first place
Troubleshooting Drilling Problems
Having issues with your diamond drilling operation? This Illustrated Guide…
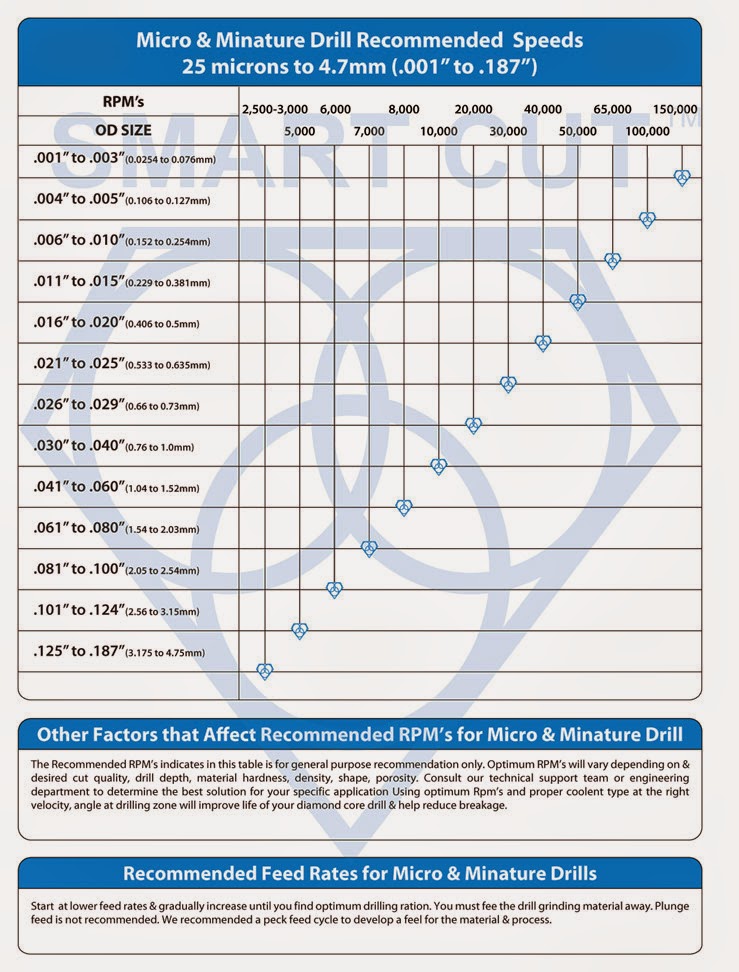
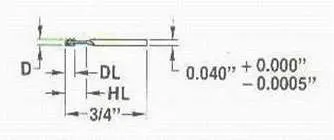
Equipment Used on:
- High Speed Drill Press
- Mounted Hand Piece Drill (such as: Foredom & Dremel),
- High Speed Air Spindles
Advantages
- Longer Life
- Less Chipping
- Faster & Freer cutting action
- Less Material Stress
- Consistent Performance
- Smoother Surface Finish
- Less Heat Generation
Application (Materials Used on)
SMART CUT® Series Micro Diamond Drills provide the most excellent performance large spectrum of ultra hard, brittle, and dense materials such as:
- Alumina
- Glass
- Quartz
- Ruby
- Sapphire
- Yag
- Silicon
- Fused Quartz
- Bk7
- Many Other Materials
Features
- High Quality Diamond Crystals & Materials
- High Quality & Consistent Manufacturing Process
- Maximum Diamond Particle (Grit) Exposure
- Preserves True Material Micro Structure
- Excellent Value (return on investment)
- High Quality & Consistent Manufacturing Process
- High diamond exposure
- Overall 10+ sizes available from stock
- Custom Manufacturing (almost any diameter, shape, head length)
Showing 1 – -1 of 9 results Showing all 9 results Showing the single result No results found
Sort by Name A - Z
Filters Sort results
Reset Apply
image | New Item No. | Old Item No. | Diameter (D) | Diamond Height (DL) | Head Length (HL) | Total Length | price | Quantity | Add To Cart |
---|---|---|---|---|---|---|---|---|---|
2010007 | MCDU7 | 0.007" (.117mm) | Entire Head | 0.028 (0.71mm) | .687” (17.47mm) | $69.71 3 pcs - $67.80 ea 6 pcs - $64.50 ea 10 pcs - $62.31 ea | Max: Min: 1 Step: 1 | ||
2010008 | MCDU8 | 0.008" (.203mm) | Entire Head | 0.050" (1.27mm) | .687” (17.47mm) | $57.82 3-5 pcs - $53.97 ea 6-8 pcs - $51.34 ea 9-12 pcs - $49.86 ea 12-15 pcs - $47.36 ea 16-20 pcs - $45.87 ea 21-30 pcs - $43.12 ea | Max: Min: 1 Step: 1 | ||
2010009 | MCDU9 | 0.009" (.228mm) | Entire Head | 0.060" (1.524mm) | .687” (17.47mm) | $57.82 3-5 pcs - $53.97 ea 6-8 pcs - $51.34 ea 9-12 pcs - $49.86 ea 12-15 pcs - $47.36 ea 16-20 pcs - $45.87 ea 21-30 pcs - $43.12 ea | Max: Min: 1 Step: 1 | ||
2010010 | MCDU10 | 0.010" (.254mm) | Entire Head | 0.049" | .687” (17.47mm) | $57.82 3-5 pcs - $53.97 ea 6-8 pcs - $51.34 ea 9-12 pcs - $49.86 ea 12-15 pcs - $47.36 ea 16-20 pcs - $45.87 ea 21-30 pcs - $43.12 ea | Max: Min: 1 Step: 1 | ||
2010011 | MCDU11 | 0.011" (.279mm) | Entire Head | 0.080" (2.032mm) | .687” (17.47mm) | $57.82 3-5 pcs - $53.97 ea 6-8 pcs - $51.34 ea 9-12 pcs - $49.86 ea 12-15 pcs - $47.36 ea 16-20 pcs - $45.87 ea 21-30 pcs - $43.12 ea | Max: Min: 1 Step: 1 | ||
2010012 | MCDU12 | 0.012" (.304mm) | Entire Head | 0.080" (2.032mm) | .687” (17.47mm) | $57.82 3-5 pcs - $53.97 ea 6-8 pcs - $51.34 ea 9-12 pcs - $49.86 ea 12-15 pcs - $47.36 ea 16-20 pcs - $45.87 ea 21-30 pcs - $43.12 ea | Max: Min: 1 Step: 1 | ||
2010013 | MCDU13 | 0.013" (.330mm) | Entire Head | 0.090" (2.286mm) | .687” (17.47mm) | $57.82 3-5 pcs - $53.97 ea 6-8 pcs - $51.34 ea 9-12 pcs - $49.86 ea 12-15 pcs - $47.36 ea 16-20 pcs - $45.87 ea 21-30 pcs - $43.12 ea | Max: Min: 1 Step: 1 | ||
2010014 | MCDU14 | 0.014" (.335mm) | Entire Head | 3/32" (2.381mm) | .687” (17.47mm) | $57.82 3-5 pcs - $53.97 ea 6-8 pcs - $51.34 ea 9-12 pcs - $49.86 ea 12-15 pcs - $47.36 ea 16-20 pcs - $45.87 ea 21-30 pcs - $43.12 ea | Max: Min: 1 Step: 1 | ||
2010015 | MCDU15 | 0.015" (.381mm) | Entire Head | 3/32" (2.381mm) | .687” (17.47mm) | $57.82 6-8 pcs - $51.34 ea 9-12 pcs - $49.86 ea 12-15 pcs - $47.36 ea 16-20 pcs - $45.87 ea 21-30 pcs - $43.12 ea | Max: Min: 1 Step: 1 |
2010006,2010007,2010008,2010009,2010010,2010011,2010012,2010013,2010014,2010015,
High Quality & Consistent
Manufacturing Process/Quality Control
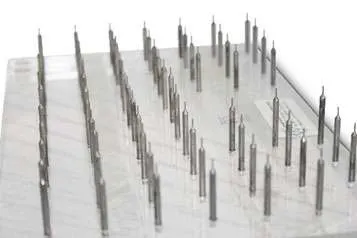
SMART CUT™ Series 005DME & 010DME electroplated diamond core drills are products in highly controlled, galvanic plating process & clean room environment under the Highest Quality Standards to Mil Specs. Steel bodies are machined to very high precision tolerances from M2 or M42 hardened steel on Swiss Screw Machines Highly Experienced Engineers and chemists constantly monitor and control all material input & output at all stages of manufacturing process. Utilizing world class quality control, inspection, and measurement equipment. Insuring product consistency for use in demanding & sensitive applications. This process allows the tools to be produced with very tight tolerances, and optimize kerf shape, geometry, diamond size, and bond hardness to fit your particular application/requirements
Insuring product consistency for use in demanding & sensitive applications such Nano Technology, MEMS, Materials Research, and etc. Customers include some of the Leading Fortune 500 companies, Universities, Military, Space Flight Organizations, Laboratories, Advanced Material Fabricating Facilities to small machine shops.
UKAM Industrial Superhard Tools experience, precision manufacturing, modern quality control methods, allow us to control and regulate dozens of variables that affect diamond drill life, quality of cut, surface finish
Highest Quality
Diamond Crystals & Raw Materials
Only the highest quality raw materials are used in manufacturing process.
Our experience, precision manufacturing, modern quality control methods, allow us to control and regulate dozens of variables that affect diamond drill life, quality of cut, surface finish.
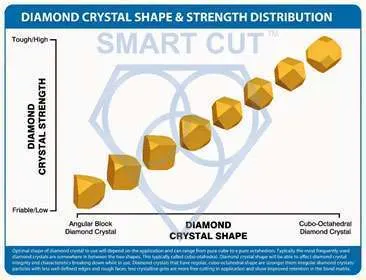
SMART CUT® Difference
How SMART CUT® Diamond Micro Drills are Different in comparison to other Micro Drills.
Faster Drilling Action
Diamond drills made utilizing SMART CUT® technology are much more aggressive than your conventional drills. They can drill faster, while still leaving behind a smooth finish free of material deformation.
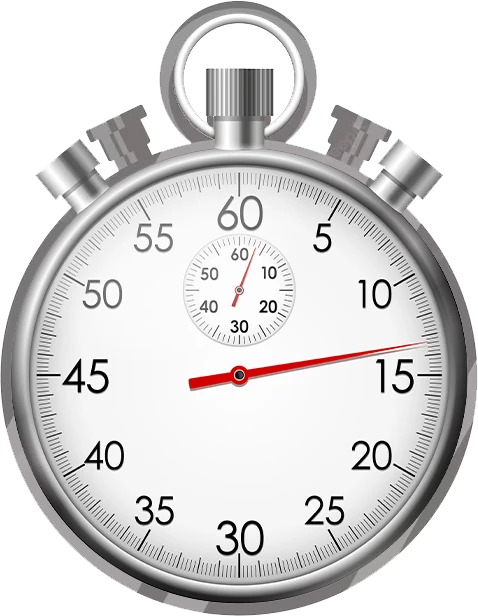
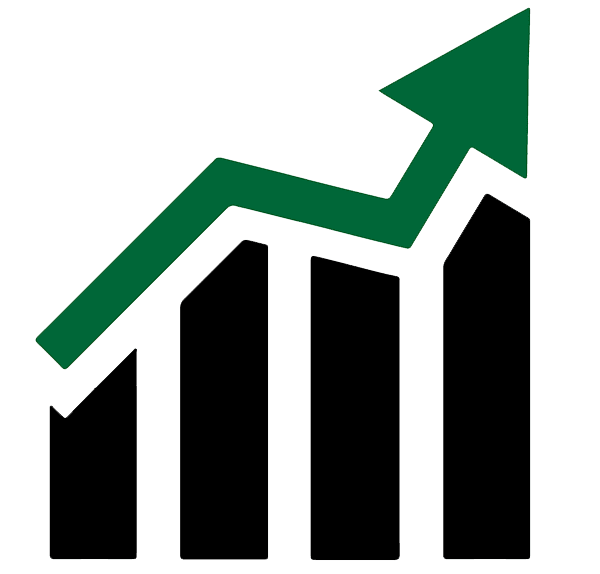
Longer Life
In most cases tools manufactured utilizing SMART CUT® technology, will outlast other conventional nickel bonded diamond & CBN drills. SMART CUT® diamond & CBN tools are more sturdy than tools manufactured with conventional technologies. They are capable to retain their form and bond configuration all the way through the tools life.
More Consistent Performance
SMART CUT® Multi Layered Electroplated Diamond Drills have three diamond layers impregnated inside the bond matrix. Unlike Many Other drill Types, they wear evenly, and are known for their consistency. You will get consistent cutting speed, and overall consistent performance, with minimum amount of dressing even on the hardest to cut materials
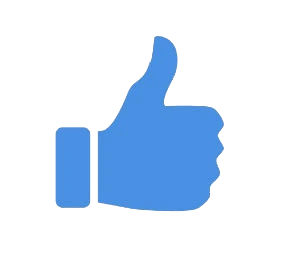
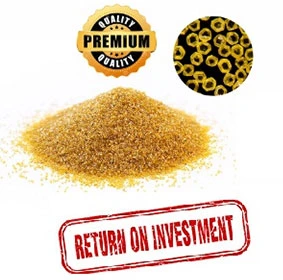
Manufactured Using The Highest Quality Raw Materials
Only the highest quality synthetic diamonds and raw materials are used in the manufacturing process. The highest quality standards and product consistency is maintained, using sophisticated inspection and measurement equipment.
Best Performance & Value on the Market
SMART CUT® Multi Layered Electroplated Diamond Drills are the best investment you can make! Although they may cost more than electroplated (nickel bond), Diamond Drills. They will more than pay for themselves in terms of overall performance and provide best Return on Investment.
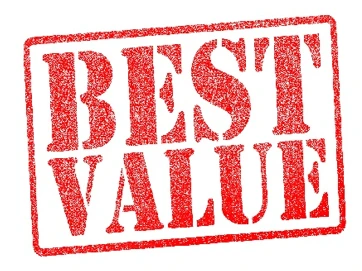
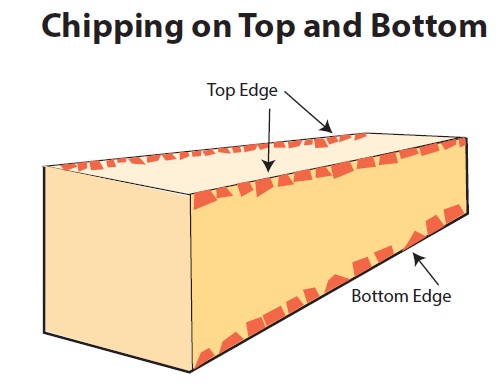
Minimize Chipping & Improve Surface Finish
SMART CUT® Multi Layered Electroplated Diamond Drills have diamonds oriented and evenly distributed in a bond matrix. Providing faster, freer cutting action with minimum heat generation. This translates in improved surface finish and minimum chipping.
About Nickel Bond (Electroplated) Tools
Electroplated (Nickel Bond) diamond products usually have a single layer of diamonds, held by a tough durable nickel alloy. Nickel is frequently used as a base for plating diamond. Because of its excellent strength, toughness and flexibility during the plating process. Electroplated diamond products are able to retain their original shape and dimensions thought their working life. Unlike sintered (meal bond) or resin bond diamond products, where diamond particles are buried in bond and held together by metal or resin binder deep inside. Electroplating allows diamond particles to protrude from the bond matrix, providing a free, faster cutting action with minimum heat generation.
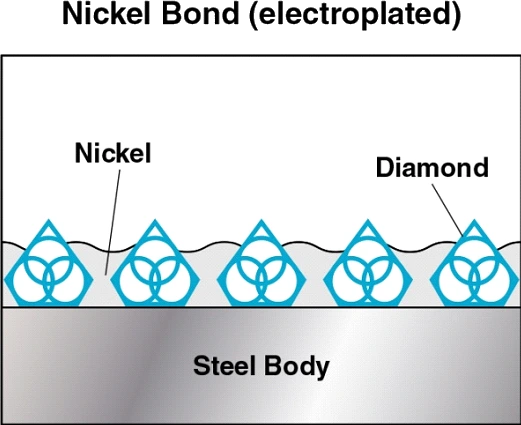
Electroplated Diamond Products Manufactured by UKAM Industrial are Multi Layered. They have 3 layers of diamonds, not just 1 layer of diamonds like conventional electroplated diamond tools.
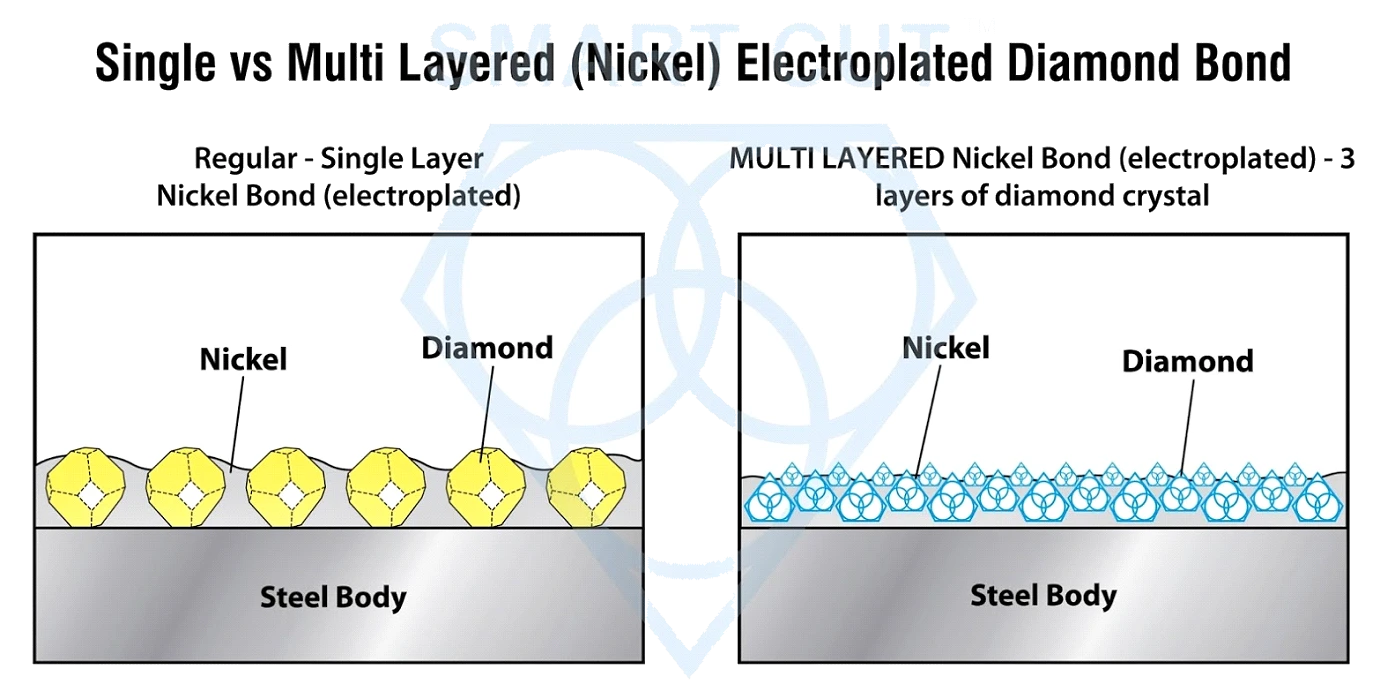
Multi Layered Electroplated Diamond & CBN Coatings
they have several layers of diamonds, held by a tough durable nickel alloy. Providing high diamond concentration, better diamond crystal retention and maximum diamond particle (grit) exposure/protrusion ratio. This provides freer, faster cutting action with minimum heat generation. Advantages of this type of technology include: longer tool life, more uniformity in performance, less stress to material being worked on, minimum material deformation, and better preservation of true material micro structure. This is specially important for more delicate, sensitive applications such as: glass, crystals, silicon wafers, carbon composites, sapphire, etc.
Its what you cant see that makes all the Difference
How SMART CUT® Bond Works?
Step 1
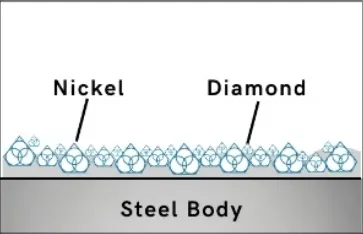
Sharpest And Finest Quality Diamonds
Diamonds or CBN Crystals are activated only at the exposed layer. As Bond Matrix layer begin to wear out, diamonds in a new Bond Matrix layer are immediately activated, substituting the already used up diamond layer. The SMART CUT® Bond Diamond Bond makes sure every diamond is in the right place. and at the right time, working where you need it most.
Step 2
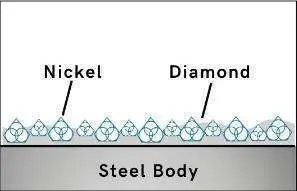
Diamonds or CBN Crystals
The newly exposed diamonds don’t effect diamonds already working on the material. Unlike many other diamond bonds, diamonds in a SMART CUT® remains sharp and grow sharper with each cut, prolonging product life and consistent performance.
Step 3
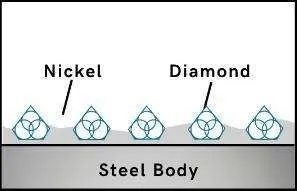
Advanced Formulated Open Diamond Bond Design
This advanced formulated open diamond bond design insures minimal chipping, fast
cut, constant speed of cut, minimal cutting noise, and most important of all, consistent performance.
Variables that Influence
Diamond Micro Drill Specification
Steel Body Composition
The steel body using is usually high speed steel ranging in hardness from 40 to 50 Rockwell scale C. Standard configuration of standard stock diamond micro tools is flat end cylinder but the angle and radius can also be customized if needed.
Diamond / CBN Particle Sizes Used
Diamond sizes used range form 6 microns to 120 microns. Diamond grit size used is in proportion to diameter of the drill tip and can range form 3 to 70 microns.
Head Lengths
Head length made in proportion to diameter of the tool. Usually it cannot exceed 15 times the diameter of the tool.
Recommended RPM’s
diamond & CBN micro drills are used at high speeds ranging from 150,000 to 35,000 RPM’s. The smaller the diameter the tool the higher the recommended speed for optimal performance. The drills may work at lower rpm’s with significantly shorter drill life and possible drill breakage. Optimum RPM's will vary depending on desired cut quality, drill depth, material hardness, density, shape & porosity. Please consult our technical support team or engineering department to determine the best solution or your specific application.
Shank Diameter
shank size is usually 1/8” (3.2mm) or .040” (1mm) to fit most collets. The shank diameter is designed to be in proportion to diameter of the drill/tool. Very small diamond & cbn micro drills .001” to .015” will have shank diameter of .040” (1mm). Larger diameter micro drills .016” to .040” will have shank diameter of 1/8” (3.2mm). Smaller diameter micro drills/tools can be produced with 1/8” (3.2mm) shank and larger micro drills/tools can be made with .040” (1mm) shank. Other shank diameters can be made upon request.
Recommend Coolants
We recommend using with our SMART CUT water soluble coolant for optimal results. using proper coolant type at the right velocity, angle at drilling zone will improve the life & performance of your tool and help reduce drill breakage.
Diamond & CBN Micro Drills / Tools
Custom Manufacturing Capabilities
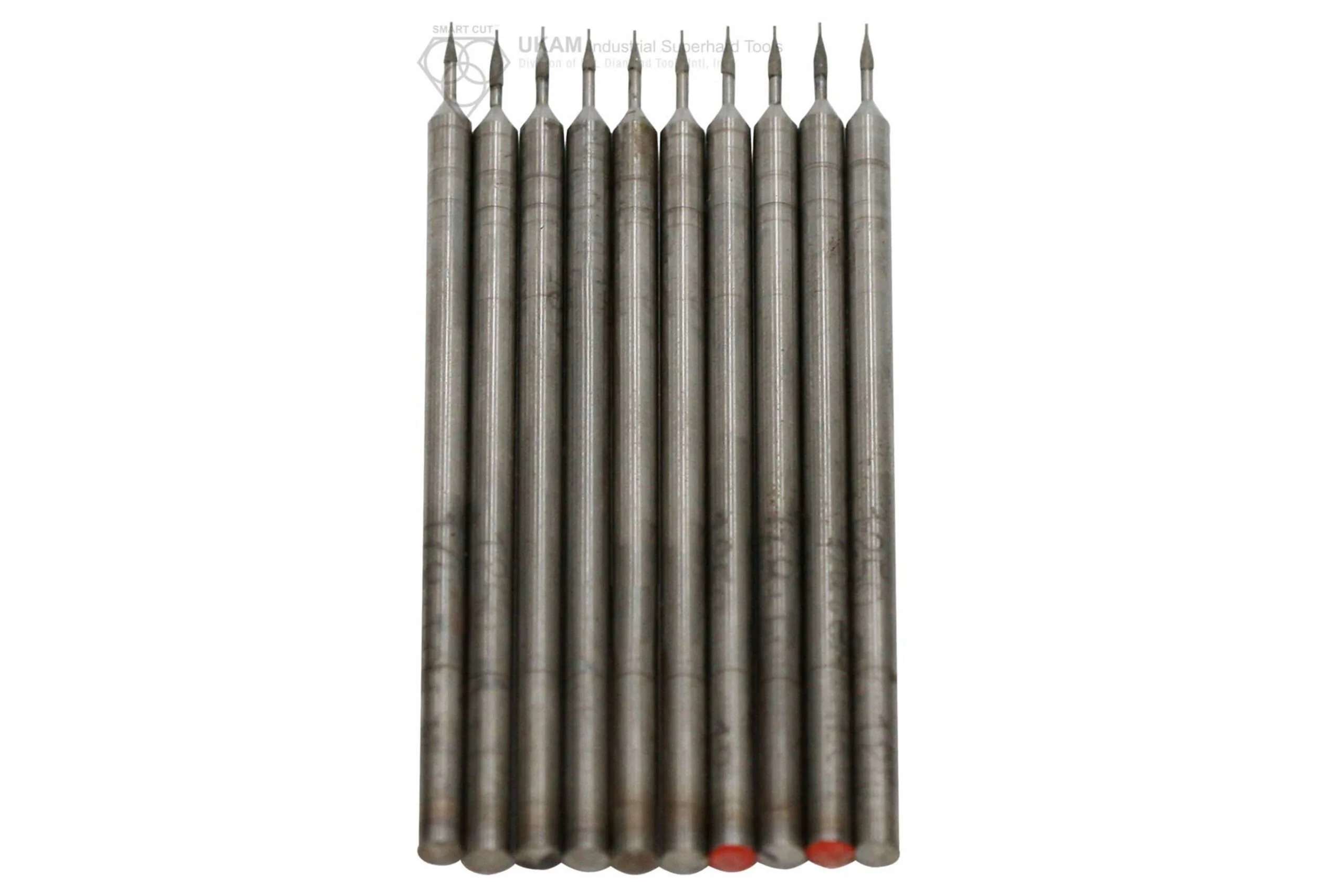
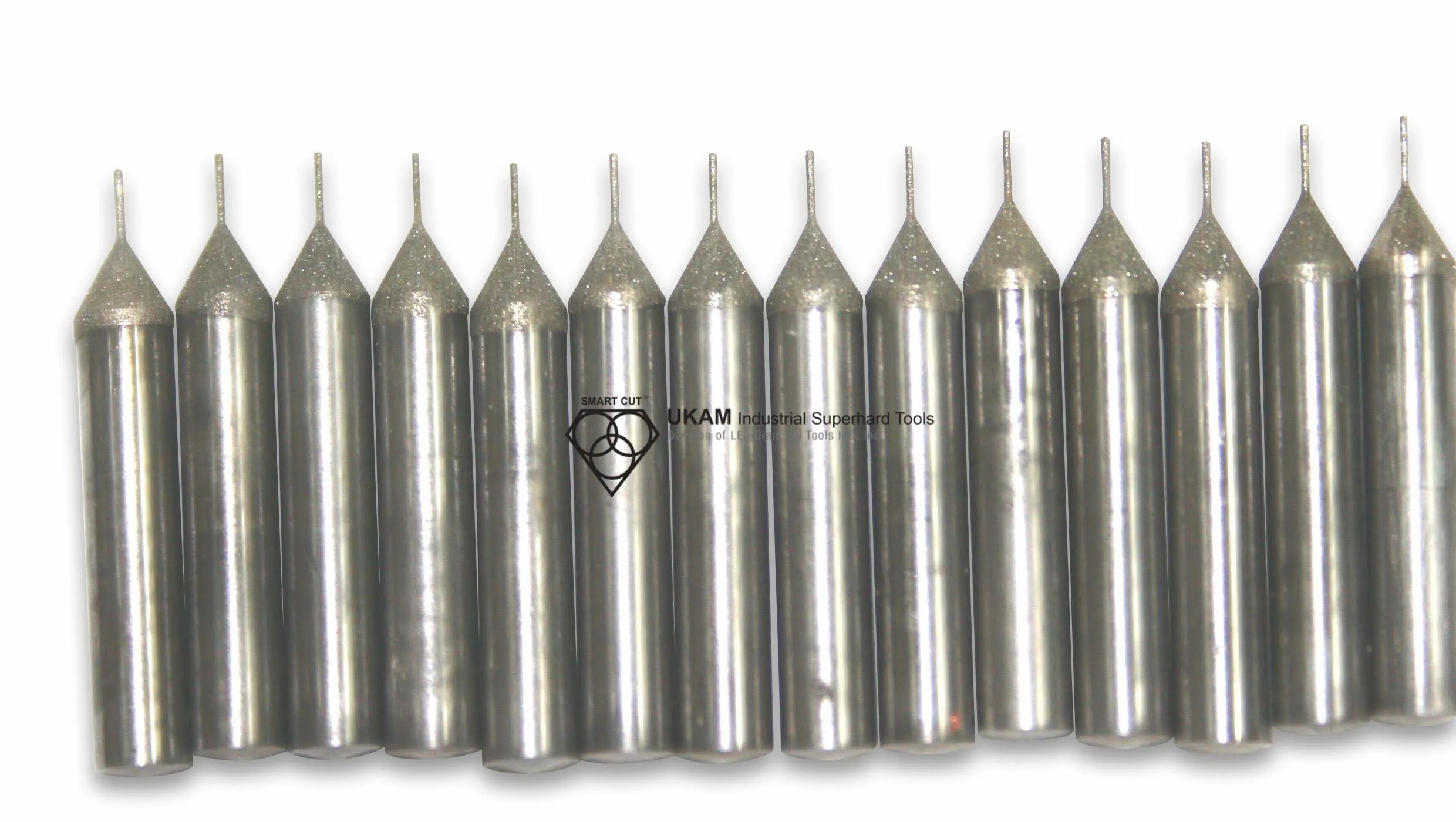
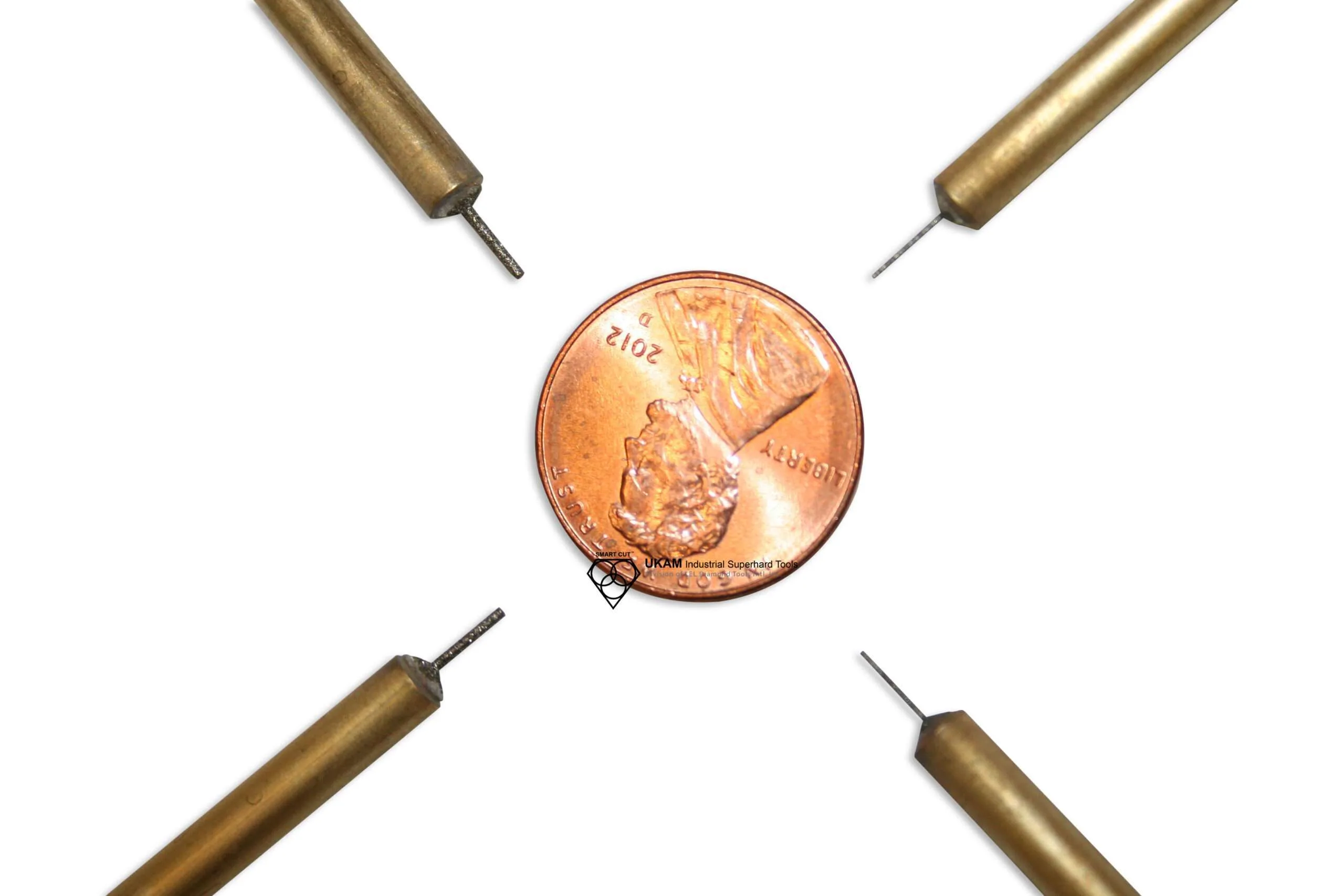
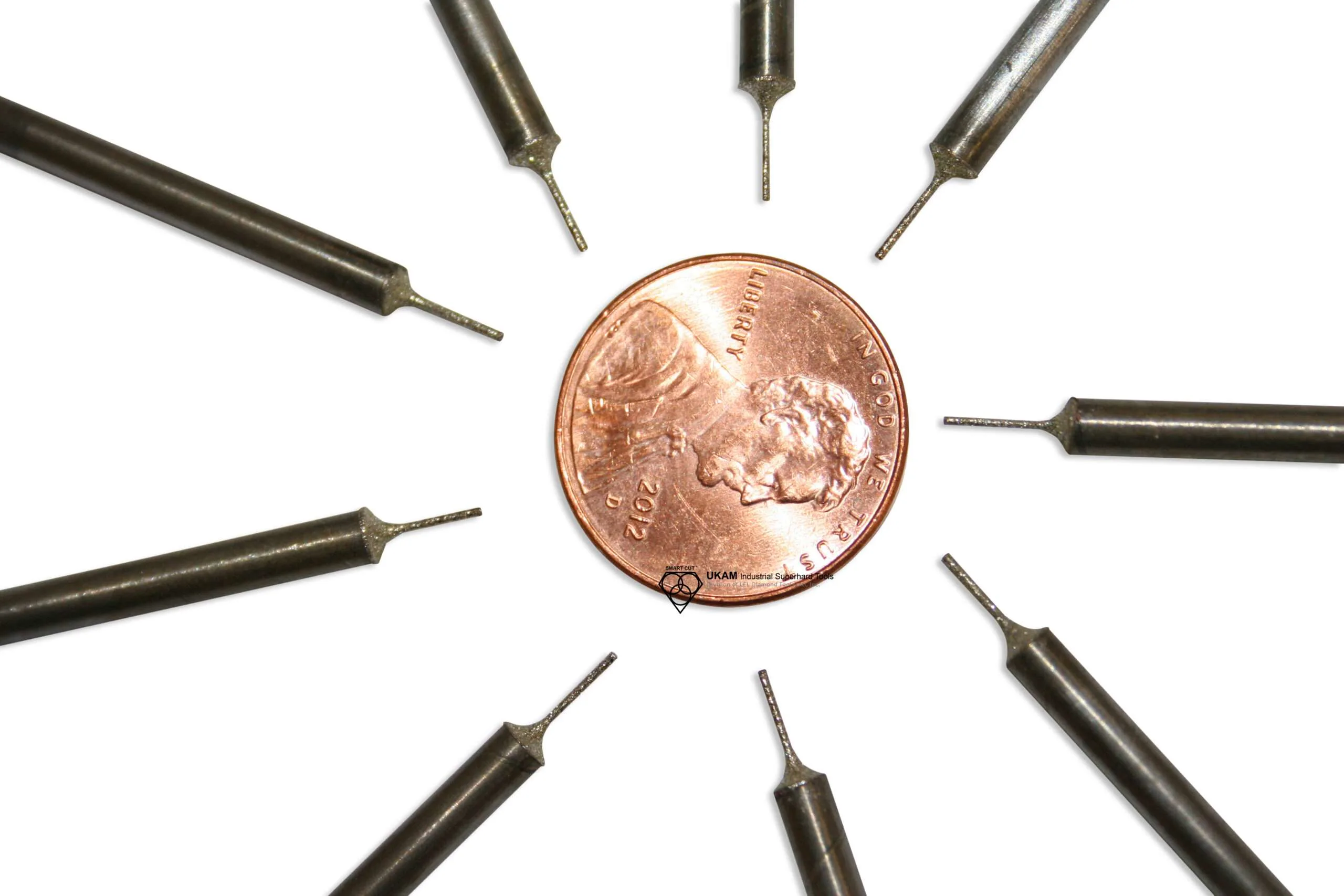
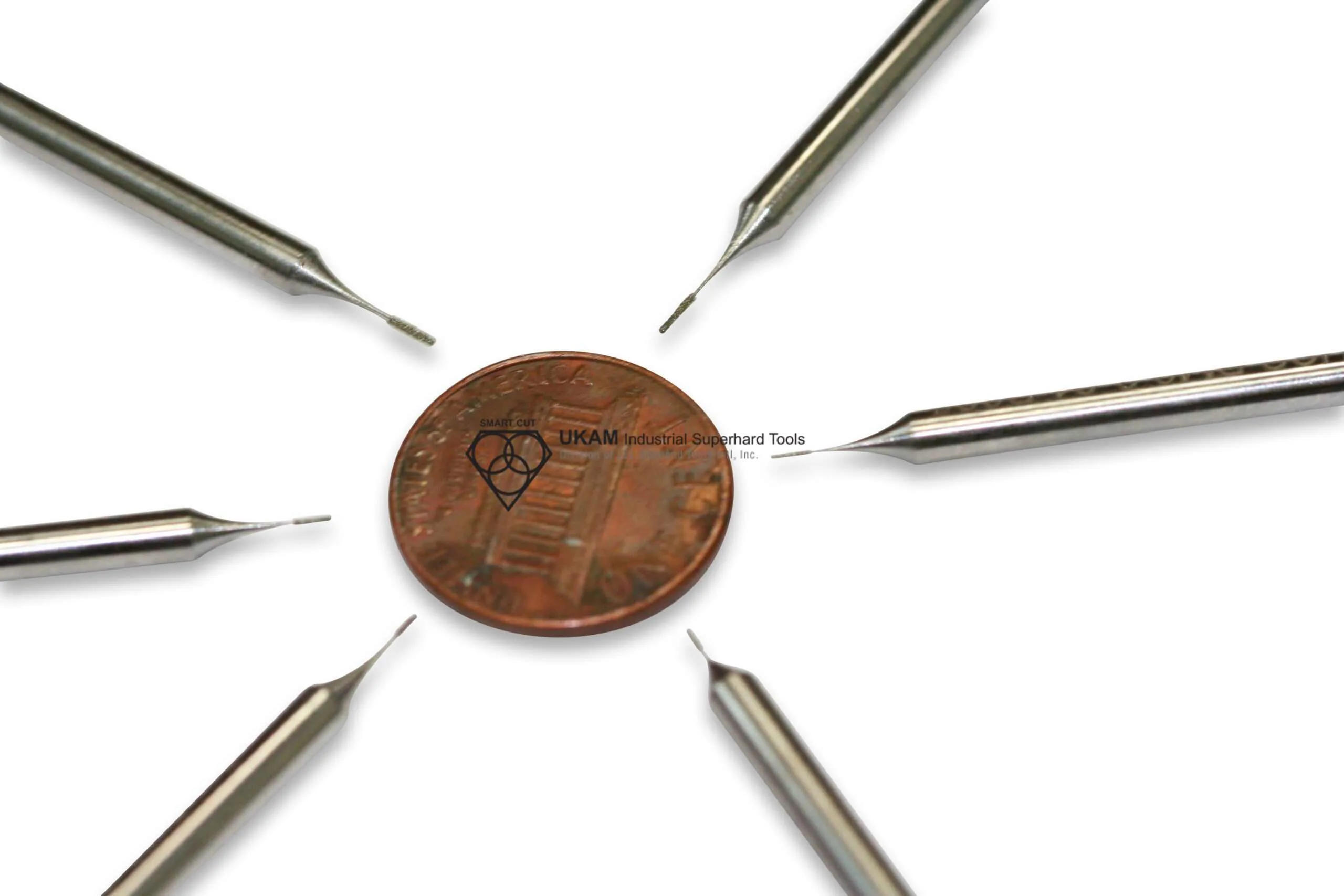
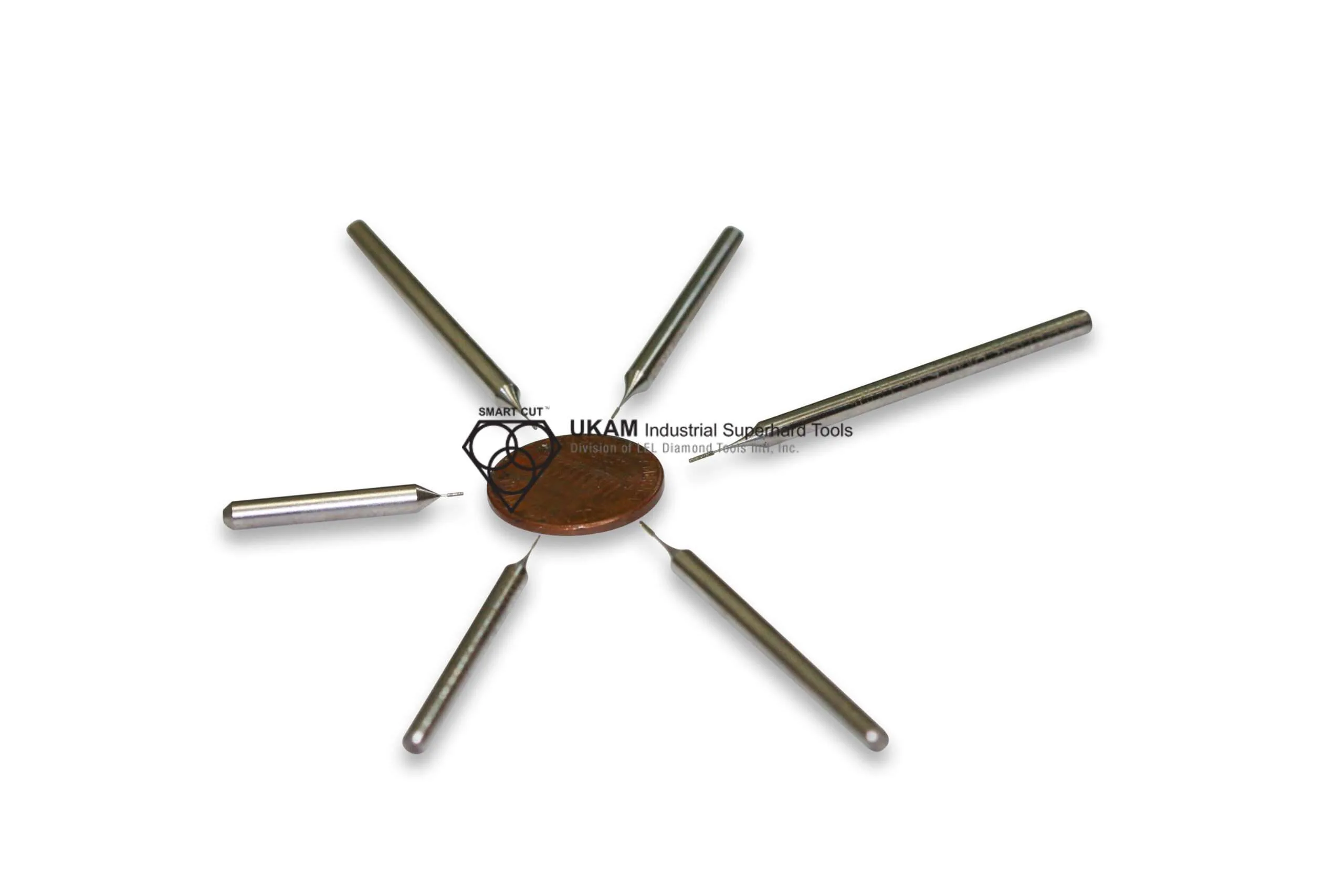
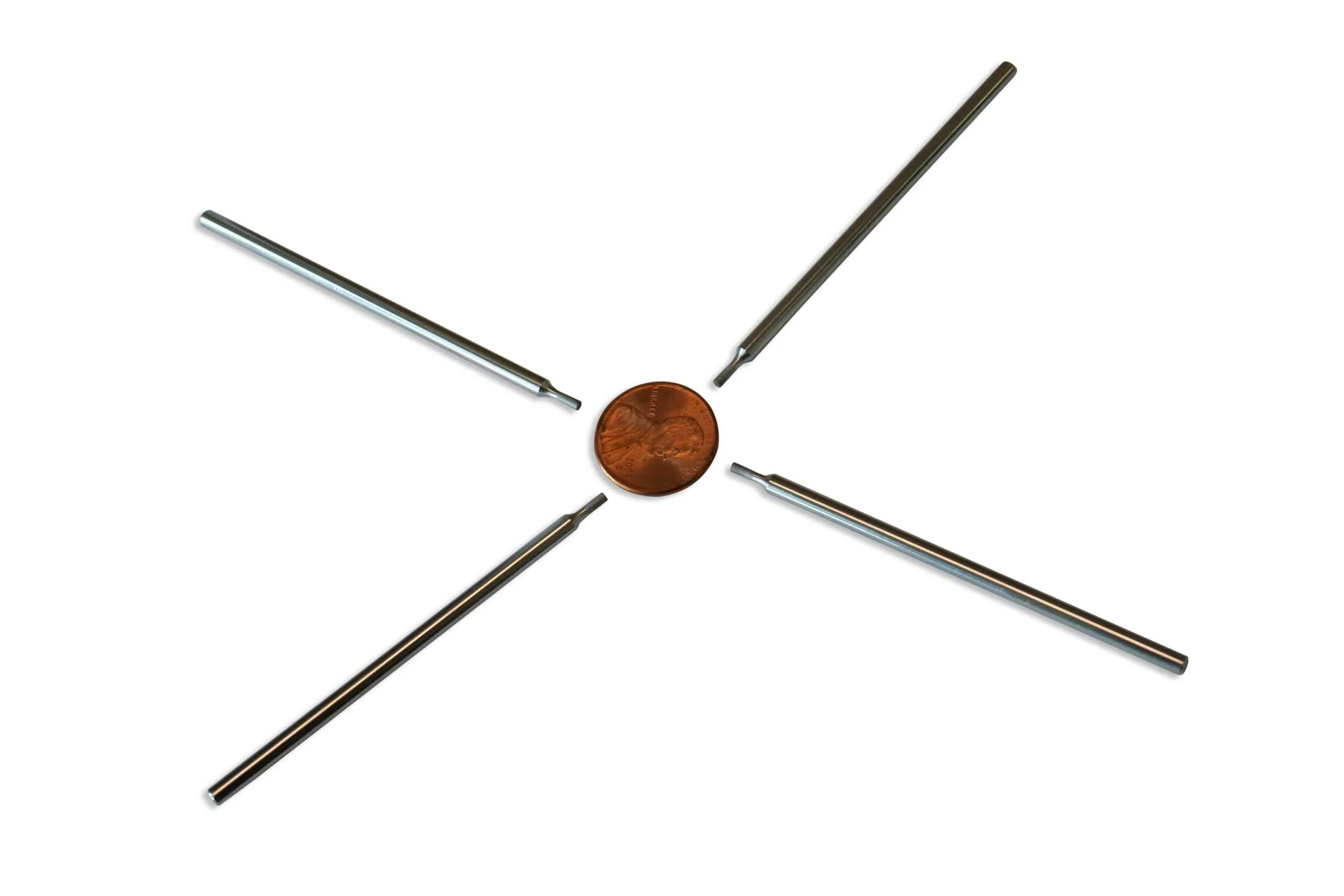
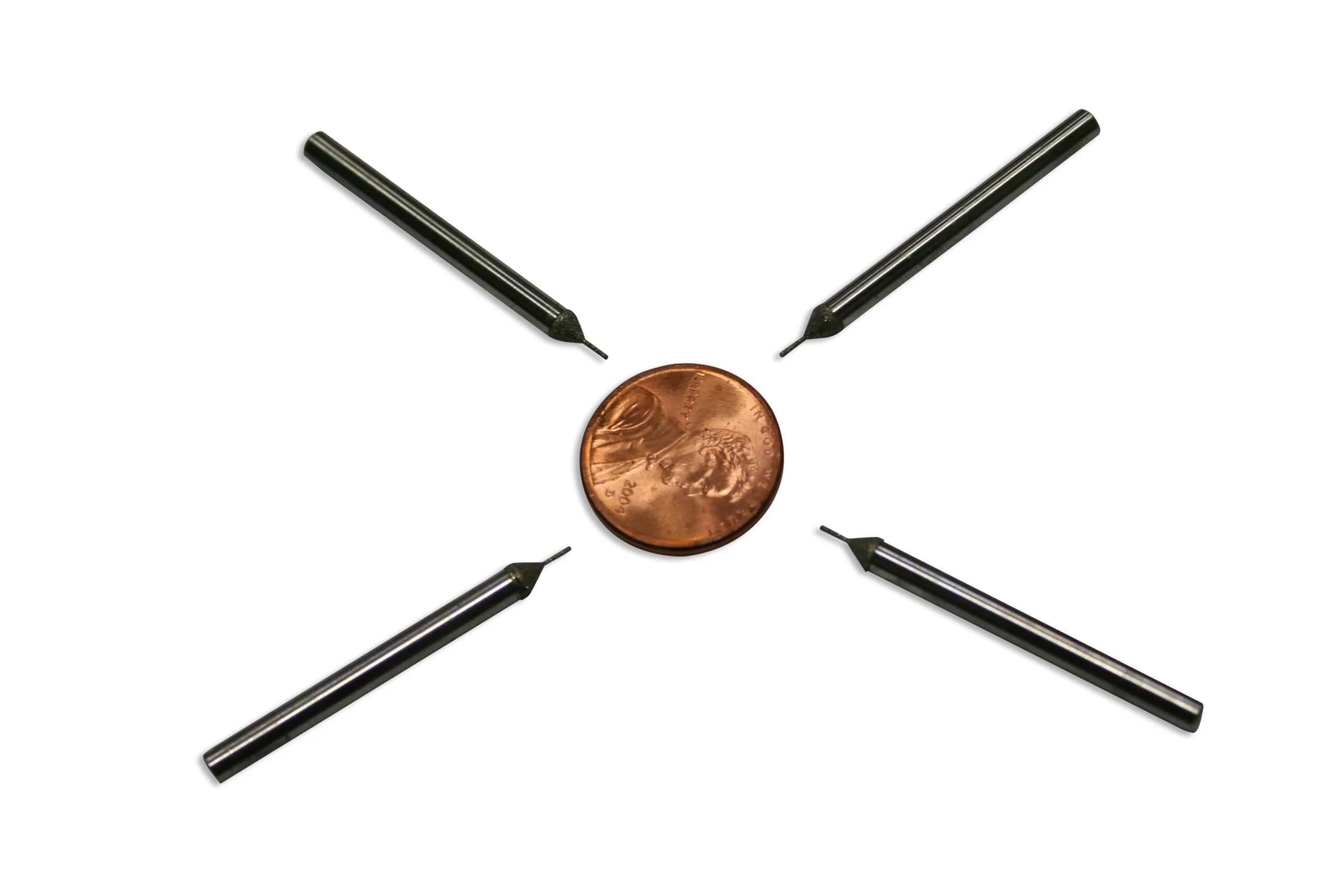
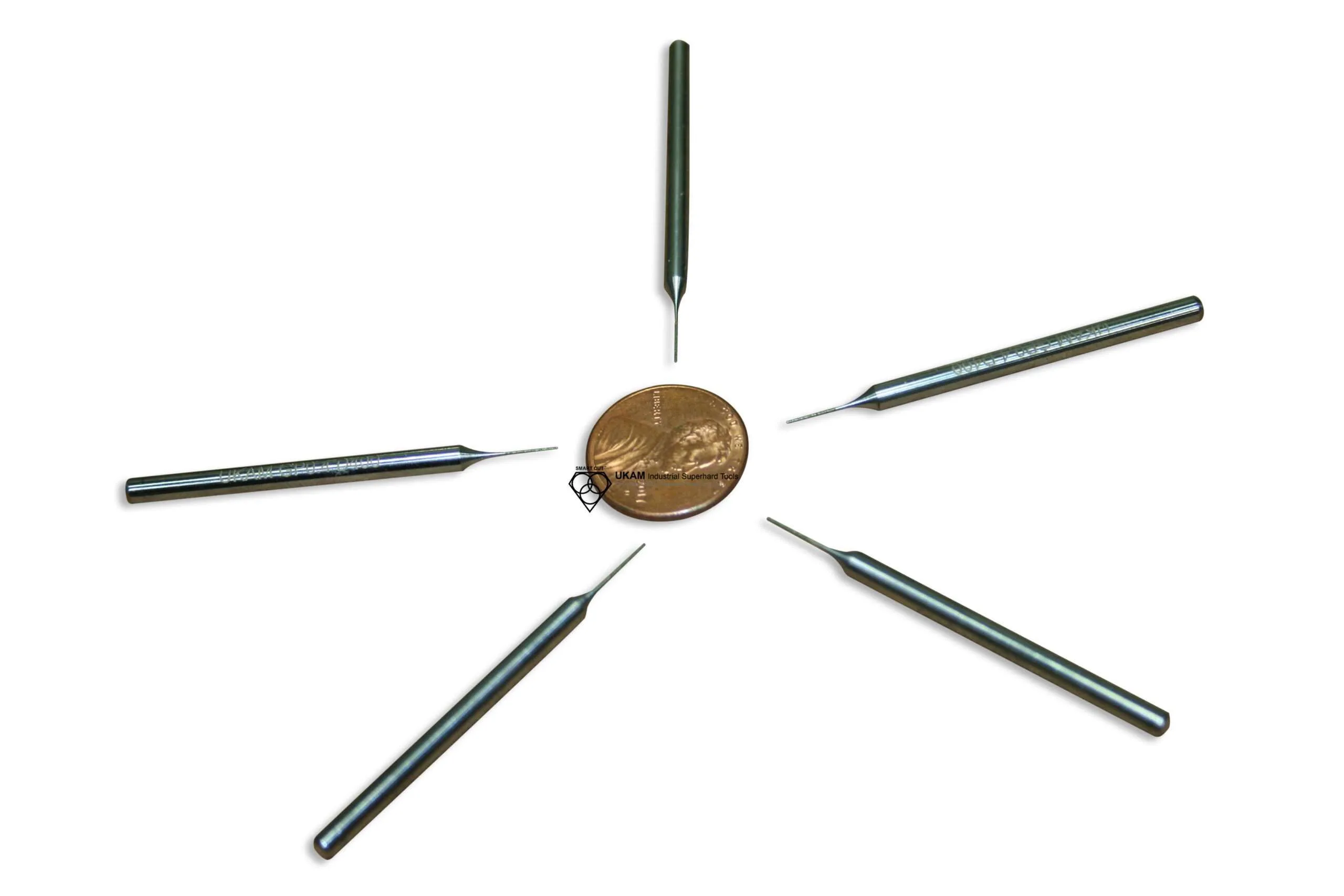

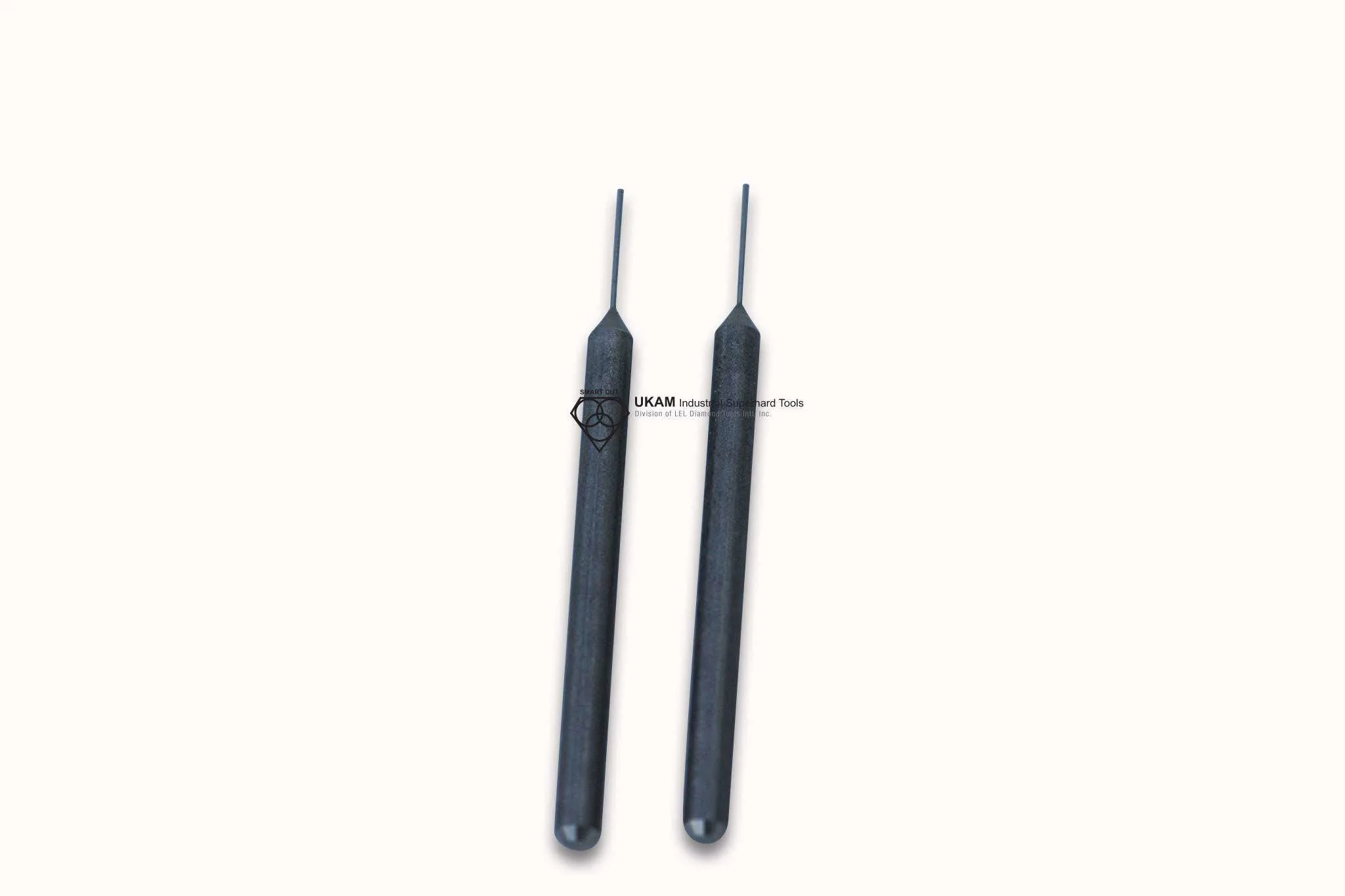
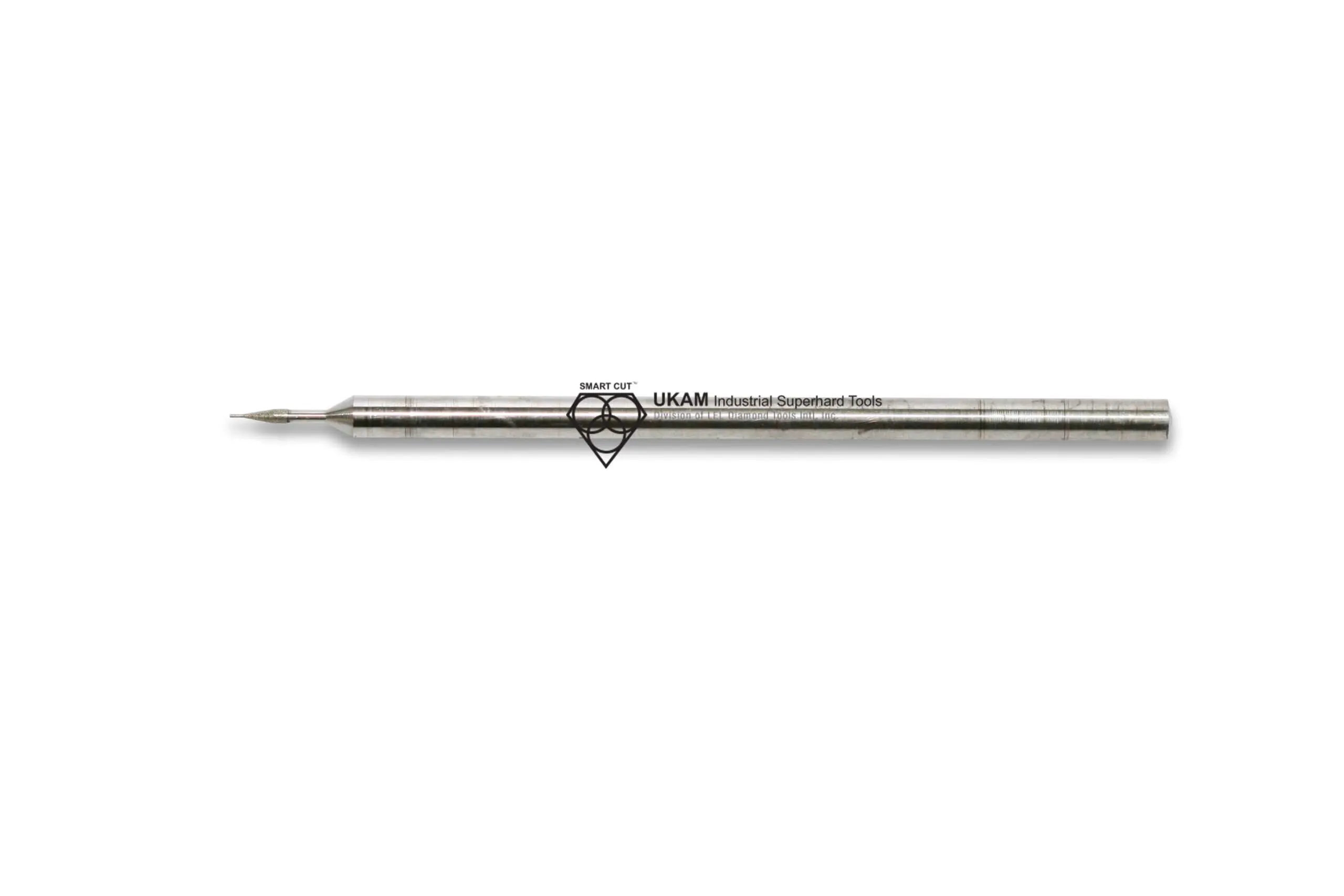
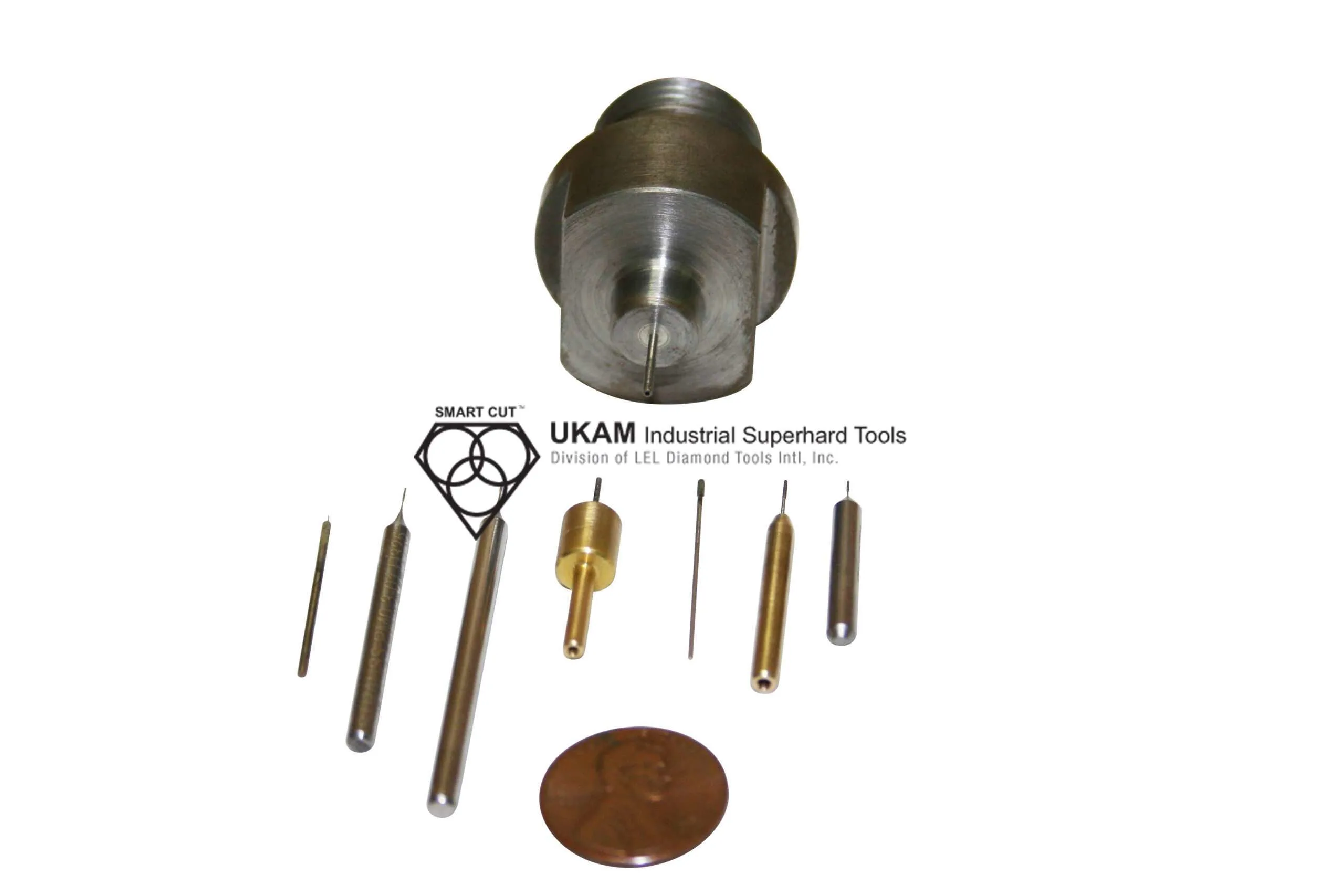
In addition to the standard SMART CUT® series Diamond Micro Drills typically available from stock. We can produce large variety of custom diamond & cbn micro drills and tools per your specification or drawing
- Almost any diameter
- Head geometry (anygle/radius)
- Head length in proportion to diameter of the tool
- Custom drill lengths
- Custom shank diameters
- Almost any diamond or cbn size in proportion to diameter of the tool
Typically minimum order would be 10 ps and lead time 4 to 6 weeks.
Related Products
SMART CUT® Micro & Miniature Core Drills
SMART CUT® Micro & Miniature Diamond Core Drills
SMART CUT® 010DME (SMCDU)
SMART CUT® 010DME diamond micro drills are produced using electroplated (nickel bond) galvanic plating process. These tools can be used for drilling and machining large variety of materials such as Precision Optics, Silicon Carbide, Boron Nitride, Boron Carbide, Alumina Ceramics, Silicon, Sapphire & Yag, Glass, Quartz, & Pyrex Tubing & Many Other Applications.
Small diameter below .020” (0.5mm) are made using diamond plating (galvanic) method, where the diamond crystals are deposited evening on the tip evenly over time.
The steel body using is usually high speed steel ranging in hardness from 40 to 50 Rockwell scale C. Precision tolerances are maintain on diameter. Diamond sizes used range form 6 microns to 120 microns. Head length made in proportion to diameter of the tool. Usually it cannot exceed 15 times the diameter of the tool. Diamond grit size used in in proportion to diameter of the drill tip and can range form 3 to 70 microns. shank size is usually 1/8” (3.2mm) or .040” (1mm).
CVD Micro Drills
Micro Drills
SMART CUT® CVD diamond micro drills are used for drilling micro holes in large variety of hard and brittle materials such as sapphire, high density ceramics, micro-circuit substrates, glass, silicon, various wafers, substrates, tubes etc We offer large variety of standard stock & custom micro drills from 0.05mm diameter to 6mm. with 3mm and 3.2mm shanks, and various heald lengths from 0.5mm and up, and flute specifications.PCD (Polycrystalline) Micro Drills
Diamond Micro Drills
SMART CUT® PCD (Polycrystalline Diamond Micro Drills) are available starting 0.4mm diameter with various head length and shank diameters in 3mm and 3.2mm Micro PCD drills are used in the semiconductor industry for monocrystalline applications such as cleaning and inspection jigs.SMART CUT® Diamond & CBN Micro Drills, Sintered (Metal Bond)
Carbide Micro Drills
SMART CUT® 005DME MCDU
SMART CUT® 005DME diamond micro drills are produced using electroplated (nickel bond) galvanic plating process. These tools can be used for drilling and machining large variety of materials such as Precision Optics, Silicon Carbide, Boron Nitride, Boron Carbide, Alumina Ceramics, Silicon, Sapphire & Yag, Glass, Quartz, & Pyrex Tubing & Many Other Applications.
Small diameter below .020” (0.5mm) are made using diamond plating (galvanic) method, where the diamond crystals are deposited evening on the tip evenly over time. The steel body using is usually high speed steel ranging in hardness from 40 to 50 Rockwell scale C. Precision tolerances are maintain on diameter.
Recently Viewed Products
ARE YOU USING RIGHT DIAMOND CORE DRILLS & TOOLS
FOR YOUR APPLICATION?
LET US
HELP YOU
HAVING ISSUES WITH
YOUR CURRENT DIAMOND CORE DRILLS & TOOLS?
Knowledge Center
02
Jun
Select right Diamond Drill for your application
Learn important diamond drill methodology. understand diamond drill specifications and their differences Selecting the right Diamond Drills/Bits for your application is key to obtaining desired diamond drilling results. Using the Right Diamond Drill will...
02
Jun
How to Properly Use Precision Diamond Drills
Step by step guide on how to properly use and care for your diamond drills. Selecting the right diamond drill/diamond drill bit parameters, often involves a trial and error process. Many which can be avoided...
02
Jun
Diamond Drills Guide
Diamond are used across large variety of industries and applications. This guide explores the wide range of diamond drill types, including hollow core drills designed for removing a cylindrical core, non-core formation drills that grind...
02
Jun
Diamond Tools Guide – Selecting Right Drills & Tools for your application
These tools are used for many different industries grinding and shaping material into different forms, expanding exiting inside diameters, grinding, finishing and polishing existing material. Grinding different angles and radius, creating cavities of various forms,...
02
Jun
Optimizing your Diamond Drilling Operation
There are numerous factors that influence the performance of diamond drills. Understanding these factors helps users select the appropriate diamond drill specifications for their specific applications, optimizing drilling operations to achieve maximum efficiency....
02
Jun
Micro Drilling Guide
Share this Article with Friend or Colleague
In order for you to get the most out of your diamond micro drill or carbide / high speed steel micro drill, we strongly urge you to read...
02
Jun
Selecting Right Drilling Equipment for your Application. What you features & functionality you should look for?
Share this Article with Friend or Colleague
There are hundreds or even thousands of different drilling equipment options. Selecting the right equipment for a specific application involves carefully considering several variables and attributes of the...
03
May
Diamond Core Drill & Drill Trouble Shooting Guide
Learn the most common problems most people have in using diamond drills. How to resolve them and avoid them in first place
https://ukam.com/wp-content/uploads/2024/07/diamond-drill-troublehsooting-guide.mp4
Troubleshooting Drilling Problems
Having issues with your diamond drilling operation? This Illustrated Guide...
09
Sep
Understanding & Calculating Return on Investment for Diamond Core Drills & Other Tools
The term "ROI" (Return On Investment) is widely used across industries, often interpreted differently depending on the context. However, few truly understand what ROI represents and its specific implications, particularly in the context of diamond...
09
Sep
Understanding Tradeoffs – Searching for Perfect Diamond Drill & Tool
Choosing the right diamond drill or tool can significantly impact efficiency, cost, and quality. However, this is not a simple and clear-cut process. Selecting the optimal drill or tool involves navigating a complex landscape of...
19
Sep
Why Use Diamond Drills?
Diamond, known as the hardest material on Earth, enables diamond drills and tools to grind away material at a micro (nano) scale. This extreme hardness allows diamond tools to effectively work on materials with a...
- Unmatched Selection For Many Applications
- Superior Quality & Consistency
- Immediate Worldwide Delivery
- Technical Support & Expertise
- American Based Manufacturer
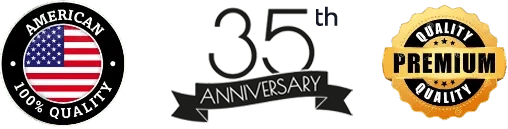

- Different Product
- Different Technology
- Different Company
- Expect MORE from your tools
Let Us HELP You!
Subscribe To Our Newsletter
Signup for email offers, updates, and more
Contact Us
- 25205 & 25201 Avenue Tibbits Valencia CA 91355 USA
-
Phone : (661) 257-2288
FAX : (661) 257 -3833 - lel@ukam.com
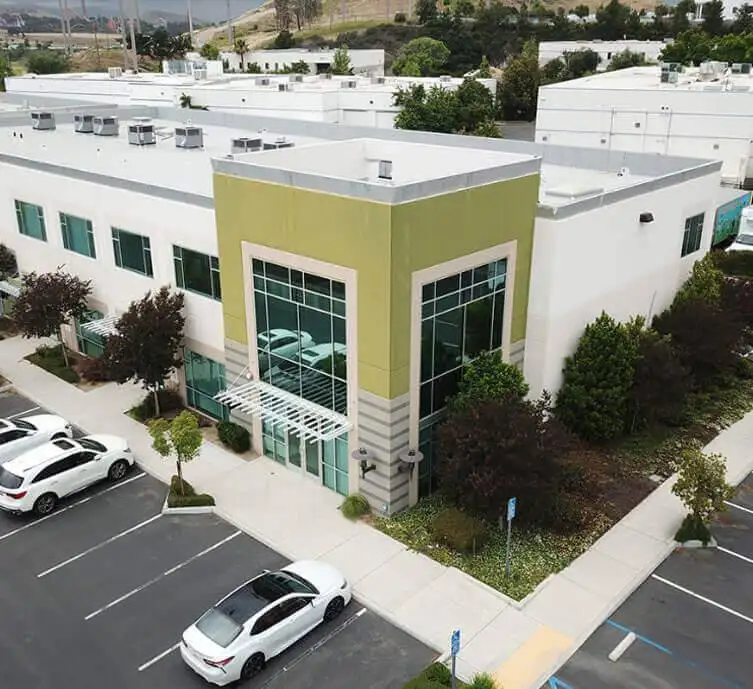
UKAM Industrial Superhard Tools is a U.S. High Technology, Specialty Diamond Tool & Equipment manufacturer. We specialize in producing ultra thin, high precision cutting blades, precision cutting machines diamond drills, diamond micro tools, standard & custom advanced industrial diamond tools and consumables.
- 25205 & 25201 Avenue Tibbits Valencia CA 91355 USA
-
Phone : (661) 257-2288
FAX : (661) 257 -3833 - lel@ukam.com
- 25205 & 25201 Avenue Tibbits Valencia CA 91355 USA
-
Phone : (661) 257-2288
FAX : (661) 257 -3833 - lel@ukam.com
DIAMOND TOOLS BY BOND
EQUIPMENT
KNOWLEDGE CENTER
OUR PRODUCTS
COMPANY
CUSTOMER SERVICE
Shipping Methods


Safe & Secure Payments

© Copyright 1990-2025. UKAM Industrial Superhard Tools – Terms of Use