In order for you to get the most out of your diamond micro drill or carbide / high speed steel micro drill, we strongly urge you to read and follow these instructions and suggestions. Doing so will help you save money and time. These suggestions and recommendations have come from years of experience in research, development and manufacturing of diamond micro drills. As well as years of personal experience, micro drilling service, process development and observations of diamond micro drills users like you. The diamond micro drills itself is only a small factor in your drilling operation. Successful diamond micro drilling is both an art & science. Requiring proper use and understanding of selecting the right diamond micro for your material / application.
When drilling very small, deep holes, there are three main goals: accuracy, hole quality and productivity. In this process, having the right equipment/machine and an optimum micro drill and drilling parameters for your application are components for success.
Selecting the micro drill and drilling parameters, often involves a trial and error process. Many which can be avoided through experience and understanding of how to use these parameter for your specific application. What works for one application, may not work for another. While there is no real substitute for experience, even new micro drill users can quickly become proficient by learning and applying some basic principles of micro drilling.
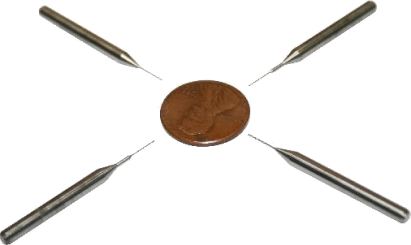
Carbide drills are made by combining tungsten particles with carbon and cobalt under high pressure and heat. This could be likened to a concrete post made up of sand and using cement as a binder. A carbide drill does not get dull because of wear like a steel drill does. It gets dull because the cobalt gets warm and it cannot hold the tungsten particles on the very fine cutting edges. Tungsten is a very hard metal and does not in itself experience much wear.
During the actual drill stroke when the drill is removing material, some of the generated heat is taken away by the chips. After the hole is completed, it is absolutely necessary to remove the drill from the hole as soon as possible. Sitting in the hole at thousands of revolutions per minute generates heat that can only go into the drill bit.
This is damaging to the binding strength of the cobalt, and as a result, some of the tungsten particles are released from the cutting edges of the drill. As this blunting proceeds, each succeeding drill stroke adds more heat to the drill. When the cobalt reaches a certain level of warmth, it deteriorates very quickly and can result in a broken drill if not changed immediately.
SELECTING RIGHT MICRO DRILL FOR YOUR APPLICATION
The micro drill is perhaps the most important factor in any drilling process. Even if all the other segments of the drilling operation are perfect, the outcome would be less than optimum if a damaged or improper micro drill is used. Micro drills are designed with three basic needs in mind. The micro drill needs to be rigid to address the critical aspect of registration through the hole and to ensure straight holes, from top to bottom through the stack. It also needs strength to withstand the forces generated during drilling and finally, it must be maintained to provide a sharp cutting edge over the life of the tool.
In order to achieve proper feed and table speed, many variables have to be taken into account, that’s why the tool parameters are never perfect. Every drill room has a different opinion when it comes to the importance of bit life, hole quality, drill wander and hit rate.
Optimum feed and speeds for small hole production greatly depend on the drilling machine’s performance and micro drill design. Based on the experience of experts and on the results of many tests, some parameters are well known.
Micro Drills Head Length/Flute Length

Choosing the proper diamond micro drill head length or carbide micro drill flute length is a very important step, equal in importance to selecting the correct feed and speed. If a micro drill with head length or flute long is to long. Potential problems that can surface include: unnecessary drill breakage due to the reduced micro drill strength of an extended head length/flute length; accuracy problems due to the micro drills tendency to wander more because of the added length; and reduced productivity due to reduced feed rates to compensate for the first two problems.
On the other hand is micro drills with too short head length/flute length is used. The trade off and possible problems include: incomplete drilling due to the micro drill being too short to completely drill through the material; and poor hole wall quality due to the bit overheating and its inability to remove chips from the hole.
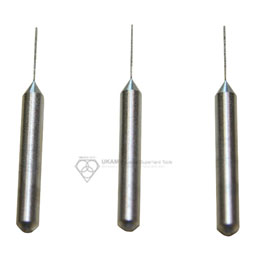
Drill breakage can also be caused by the bit snagging on the chips that haven’t been removed. The overall flute length should be the thickness of the material to be drilled plus 20% for chip clearance at the top of the stack
COOLANT MAINTENANCE & OPTIMIZATION
Coolant supply position and pressure is critical to optimize drill life, minimize chipping, and maintain consistent and acceptable surface finish quality.
Coolant serves many functions in diamond micro operation:
-
Cools drill diamond section and material being drilled
-
Provides lubrication to minimize friction between drill and material
-
Washes out and removes powder residue and swarf from drilling process
Coolant should be pointed at drill tip and point of with material. The dual nozzle system provides two separate streams of coolant into drilling zone at angle of diamond tip of drill. Each stream will cool one side of the drill. The nozzles should be as close as possible to the point where the drill enters the material. Coolant flow should blast with high velocity into the drill to improve removing debris. Typically most drill premature wear out, tip breakage of failure is a result is a result of improper drilling speeds and coolant amount or flow applied at drilling zone. By correctly position the coolant stream in front of the drill, the coolant will flow on top of the material. In addition,
coolant will be drawn into the hole
Coolant is one of the most overlooked variables in the micro drilling process. Effective and proper use of coolant and recalculating coolant system will pay off in terms of improved surface finish quality, increased drill life and more consistent drilling results. Coolant does more than just cool the drill and material, it other more important roles include: lubrication, flush away swarf particles generated while drilling. For most effective use of coolant the quality of water being used, coolant concentration, and maintenance of the coolant tank makes a difference. Different geographic areas have different water harnesses. Water containing less than six grains of dissolved minerals per gallon is considered soft water, water containing more then seventeen grains per gallon is considered hard. The best coolant water to use in a coolant system is chemically pure water, which is free of all dissolved solids. Chemically pure water and reverse osmosis. Reverse osmosis is the method most recommended by coolant manufacturers, however not always available. Deionized water offers much improvement over available city water.
Water in the tank can evaporate and remaining water can become harder. Hard water affects coolant capabilities in many ways decreased capability to the rust inhibitor, increased foaming, formation of a sticky residue, and increased bacteria counts Coolant concentration should be controlled and maintained to ensure.
the coolant is being used at optimum efficiency. Too little coolant in the tank will lead to corrosion and rancidity, while too high of a concentration can also cause foaming. Maintenance of the recirculating tank is also critical to coolant performance. Cleaning he tank is a dirty job, but if done often enough and thoroughly, it can increase the performance of your sectioning saw. Keeping he coolant tank clean will ensure that you are getting the most form your coolant, keeping corrosion and bacterial growth a bay while providing the necessary coolant, lubrication and protection of your blades and material.
RECIRCULATING COOLANT SYSTEMS
Recirculating systems in the past have been used very infrequently in most ultra hard and brittle material machining applications
Recalculating coolant systems, require filtering to remove the swarf particles created during cutting process. These coolants systems typically use either cartridge, centrifugal, or cascade. Which process to use will depend on your application. Excessive amount of swarf particles mixed in coolant will slow heat transfer of coolant and may cause surface damage to material being drilled. Coolant system must be constantly controlled and monitored in order to insure process consistencyCoolant temperature will also have an affect on drill life and surface finish quality. Typically coolant temperatures of 50 degrees F (10 degrees Celsius) will provide best results. White coolant temperatures above 80 degrees F (27 C) should be avoided. Refrigeration of the coolant system can be used with most coolant systems and will provide best results.
Minimize Drill & Material Overheating
Frictional heat produced at the working face of diamond tip must be disposed immediately. Otherwise the diamond become rapidly damaged by oxidation and graphitization. Excessive heat generated while drilling will also damage the metal matrix holding the diamonds in place.
Insure Drilling Consistency
Debris generated while drilling should be removed as soon as they are produced. When this drilling debris is not removed rapidly, diamond wear increases through abrasion caused by the presence of excessive coarse stone fragments.
Reduce Friction between material and drill
Water/coolant also penetrates the micro-cracks which are generated upon impact of material and diamond drill. Under ideal conditions, the material will absorb water/coolant, hence becoming completely saturated with water/coolant. In this state the material is weaker and more easily drillable.
The coolant surface tension also plays an important part in the drilling operation. Usually the lower the surface tension, the easier it is for the coolant to enter the microcracks. Coolant with a lower surface tension also wets the diamonds more easily. Most users find that by lowering the surface tension of their coolant, resulted in better cooling (wetting) of their diamond, and more effective overall cooling. Lower surface tension also improves material debris lubrication, promoting efficient removal.
MATERIAL MOUNTING / HOLDING METHOD
Material mounting, properly securing material in place is one of the first and most important steps in the micro process. The function of the material mounting / holding method is to keep the sample/material firmly in place, preventing it from moving. For this reason, it is very important to use the right mounting media for your specific application/requirements. There is large variety of mounting methods available to best suit each micro drilling application. Selecting the right material holding method will play a major role in optimizing your micro drilling application to ultimate level of efficiency.
When material is to be drilled partially (not all the way through). The mounting method to use is of little importance. However when drilling all the way through the material there will be many variable in play that need to be controlled in order to achieve best results.
Material holding method will depend on your beginning material dimensions, desired drill depth, and material properties (hardness, brittleness, shape/geometry). Your goal should be to have good and uniform contact between material and holding method (such as clamp/fixture, wax, or tape). Material should lie flat, without presence of any air bubbles, dust or dirt particles between material and its mounting.
MECHANICAL CLAMPING/FIXTURING
Mechanical clamping is typically used when geometry of material being mounted is unevenly shaped, that other mounting methods cannot be used. This method also offers number of advantages for more standardize/flat materials in ease of use, loading, and unloading. Some challenges of material chucks and holding fixtures is occasional chipping and material blow out at exit of hole. The problem is the backside of material does not have firm support at drilling zone, therefore creating higher chipping rate when diamond micro drill head exits the hole. When material is hold in chuck/clamping fixture it should not move while being drilled. Any movement of material can damage or break the diamond micro drill or material itself. At the same time the sample time the micro drilling machine operator must take precaution to not over tighten material. Doing so may possibly damage the chuck/holding fixture or material itself. Some of the more brittle materials such in the glass and refractory families can fracture if over tightened in chuck/holding fixture. Where the harder and more denser materials such as silicon carbide may cause dents in the chuck if excessive force is applied. Dents or nicks in the chuck will affect the materials drilled in same chuck causing damage and possible cracks.
Holding Fixture / Chuck Padding
Padding can help prevent damage of material hold inside chuck and the chuck itself. Padding serves many functions including: protecting material, protecting chuck/material holding fixture, avoids material shifting when pressure is being applied, buffers from damaged/nicked areas of the chuck/material holding fixture..
TAPE MOUNTING
Tape is most common and frequently used mounting methods for thin material substrates and wafers with material thickness under 1 mm. Tapes are preferred for thin and brittle materials because of their ease of use, ease of handling. Large variety of tapes are available today. Low strength, medium strength, and high strength tapes Mounting is done manually or utilizing wafer mounting systems.
Tapes are available with different adhesives with what is called “tackiness characteristics”. Adhesion characteristics of the most common tapes are 215-315 fr/25 mm. Tape thickness varies depending on application and material/substrate being. For example for drilling silicon wafers tape thickness of .010” (0.25mm) is typically used, where for thick alumina substrates tape thickness of .080 (2.03mm) is implemented
Determining which tape to use for your application, sometimes may involve some trial and error.
For example the length of time the material or wafer will stay in contact with the mounting tape before and after drilling will determine whether to use medium or high strength tapes.
Wafer/material thickness is another consideration when selecting the right mounting adhesive. Very thin dies work well with waxes and medium strength tapes. Whereas, thicker wafers work better with medium to high strength tapes.
drilling too deep into the mounting media will cause the drill to “load”. Minimize the depth in which the drill touches the mounting media. It is recommended to drill no more thane twenty five microns into the media. drilling too deep into the media will cause premature tool failure. The drill can also agglomerate with the cutting media, resulting in chipping.
Double sided adhesive Tape
Double-back adhesive tape has been used for many years to hold thin parts during surface grinding. This material mounting method can be effective, only when horizontal shear forces are light. The geometry and composition of many materials however, limits the use of tape during many micro drilling operations. Another set back to using double sided tape, is the time needed to remove it and possibility of losing material flatness/rigidity to very thin parts and substrates. .
WAX/GLUE MOUNTING TO MEDIA
-
Improved holding characteristics, specially when drilling thin material substrates/wafers
-
No lip effect – capability to drill much deeper into the base material. This typically results in better surface finish quality, specially on backside of material.
-
Substrates not perfectly flat can be mounted. The wax/glue compensates by filling in the gaps
-
Different hardness base media can be used to control drill wear and simultaneously dress the drill. Common base media used is glass or ceramic.
Wax mounting is typically used for mounting very thin and brittle materials. There is a large variety of waxes that can be used for this purpose. These are typically available in lumps, molded bricks, flakes, chips and powders. Wax provides best adhesion of material to supporting substrate. Allowing deep drilling into substrate. This frequently eliminates cracks at the bottom of material. Also wax expands as it fills in the gaps of a non flat substrate. Providing best adhesion of material, equates in superior surface finish quality and consistency.
Some disadvantages of wax mounting is that is a relatively messy process. Specially taking off the material and cleaning it afterwards.
Waxes have various characteristics that make the best suited for specific applications than others. This depends on their melting point, flash point, specific gravity, structure, hardness, brittleness, flexible and elastic characteristics.
Colleting devices
During the last 2 to 3 years there has been ever increasing variety of fixtures being offered for holding micro and minature parts. Among the increasing variety of holding these very small parts. Collets are the simplest and cheapest way to hold microparts. Standard 1C collets with diameters down to 0.010" are off ered. The 5C collets on the market are almost as small, but there are fewer standard sizes to choose from.
MICRO DRILLING EQUIPMENT
Micro drilling requires us of proper drilling equipment and faster drilling speeds designed to meet the requirements of micro hole challenges. Conventional drilling machines and drilling methods do not provide the right combination of speeds (RPM’s), accuracy, feed rates and holding methods necessary for diamond micro drilling of very small diameter holes.
Use of conventional drilling equipment and methods such as large CNC machines causes high micro drill and tool breakage rates. Frequently the blame is in correctly assigned to operator error, nature of small tools or incorrect machining parameters. The reality is that it’s due to the force of a conventional machine’s heavy spindle and it’s inability to reach the high RPM speeds required for diamond particles on drill to effectively grinding away material and remove material chips and debris from hole cavity. Smaller drills/tools require higher spindle speeds/RPM’s than larger and more conventional size drills/tools. In order to avoid drill/tool breakage and obtain more consistent results. High-frequency spindles with speed ranges higher to 60,000 RPM are recommended for optimal performance.
Many changes have been made to drilling equipment in the last few years. The principal areas where attention has been directed are:
-
Spindle speed
-
Spindle collet run-out
-
Pressure foot
-
Axes positioning and stability
Since abandoning ball bearing spindles, where the maximum speed was 80,000 RPM, the performance
of air-bearing spindles has greatly helped the micro drilling process, and today, spindles running at more than 250,000 RPM are available.
HIGH SPEED AIR SPINDLES
Air spindles rotate the micro drill as accurately as possible, with respect to both speed and geometric uniformity, in order to drill the required hole as productively and as precisely as possible. Allowing for very low friction, high stiffness and low geometric runout. High speed air spidles provide the maximum performance performance for majority of micro drilling applications. In air spindle the drill itself is rotating at high speeds and is the only member which is stroking up and down. Because of the extremely small weight of the drill, it can be retracted from the drilled hole in 5 to 10 milliseconds. This allows only a small amount of heat to be generated and conducted into the drill.High speed air spindles
Mechanical and air bearing spindles have certain inherent disadvantages. One is that they use the motor core to turn the drill. This means that the motor core must turn at the same RPM as the desired drill speed. Mechanical bearings lose their effectiveness at relatively low speeds. Air bearings allow much higher speeds, but still have limitations. Motor cores are heavy, resulting in having to strike a balance between ideal speed and the tendency for the large mass to become unstable or come apart at high speeds. A solution to this is to reduce the mass and diameter of the motor core, essentially miniaturizing the standard air bearing design. As the mass and diameter reduce, however, so does the effective torque. This reduces the ability to drive larger diameter drills, often resulting in stalling or a complete inability to drill larger holes when required.
Some manufacturers have gone so far as to provide special, reduced diameter drill bits which are non-standard to the rest of the industry. Air bearings also require cooling. The very air cushion which provides the low friction bearing surface is also an excellent insulator. Heat generated by the motor core is insulated from the surrounding material, which might otherwise conduct it away. Water cooling systems are often used to assist in heat dissipation, creating bulky connections and heat exchanger maintenance.
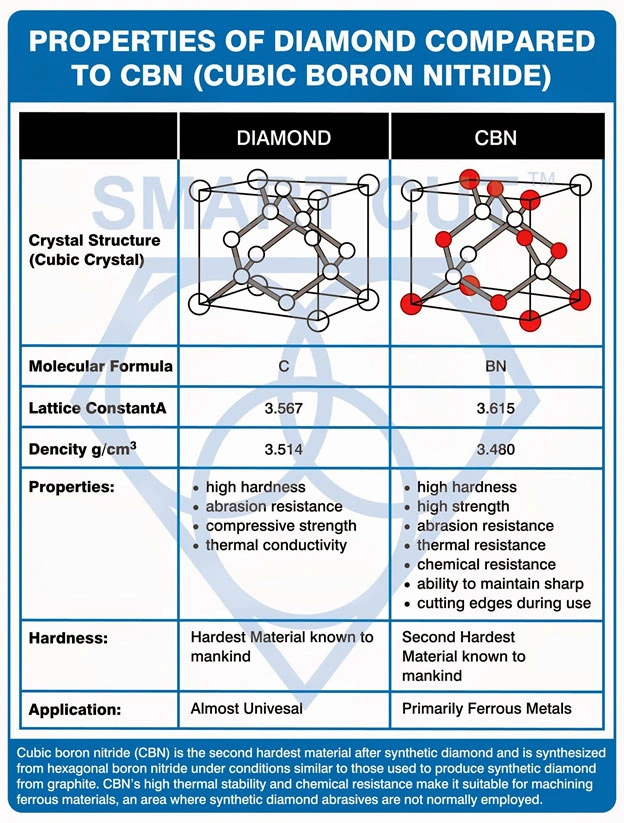
OPTIMAL MICRO DRILL DRILLING SPEEDS / RPM’S
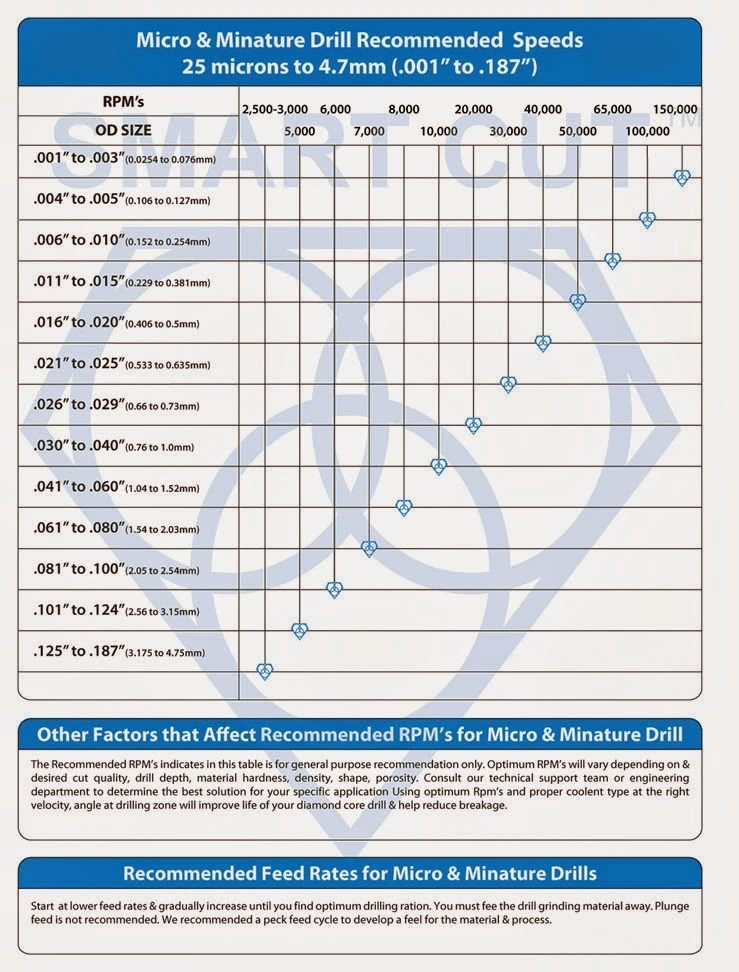
Drills - Metric
Low Carbon Steel
50 80
30 45
46 68
Low Carbon Steel
25 60
29 46
25 60
High Carbon Steel
20 50
12 35
14 40
16 46
18 53
21 61
High Carbon Steel
15 35
10 25
12 29
13 33
15 38
17 44
10 25
7 15
8 17
9 20
11 23
12 26
Stainless Steel
Ferritic + Austenitic, Ferritic, Martensitic
23 53
5 25
6 29
7 33
8 38
9 44
Stainless
Austenitic
15 40
5 20
6 23
7 26
8 30
9 35
Precipitation Hardened
25 65
5 15
6 17
7 20
8 23
9 26
Nickel Alloys
Nickel, Unalloyed
15 40
10 15
12 17
13 20
15 23
17 26
Ni/Co
Nickel Alloys Nimonic 75, Monel 400
>150<240
10 30
10 15
12 17
13 20
15 23
17 26
Nickel Alloys Nimonic 80, Inconel 718
9 25
5 10
6 12
7 13
8 15
9 17
Titanium
Nickel, Unalloyed
<200
25 56
7 25
8 29
9 33
11 38
12 44
Ti
Titanium Alloy, Cast
<270
7 25
7 25
8 29
9 33
11 38
12 44
Titanium Alloys
>270 ≤350
7 25
7 25
8 29
9 33
11 38
12 44
Cast Iron
Soft Gray Cast, Ferritic
<150
30 80
20 50
23 58
26 66
30 76
35 87
Cast Iron
Soft Gray Cast, Pearlitic
>150 <260
30 80
20 50
23 58
26 66
30 76
35 87
Nodular Graphite, Malleable Cast Iron
>150 <320
25 65
20 50
23 58
26 66
30 76
35 87
Aluminum
Al, MG, Unalloyed
100kg
200 350
20 50
29 58
33 66
38 76
44 87
Alu
Al Alloys, Si>5%
150kg
150 300
45 60
52 69
60 79
68 91
79 105
Al Alloys, Si>5% <10%
120kg
100 200
45 60
52 69
60 79
68 91
79 105
Copper - Brass Alloys
Copper Alloys, Wrought
100 225
25 40
29 46
33 53
38 61
44 70
Copper Alloy
Brass, Bronze
100 225
30 60
35 69
40 79
46 91
52 105
High Strength Bronze
50 125
25 50
29 58
33 66
38 76
44 87
Plastics
Duroplastics
Plastics
Thermoplastics
150 150
50 250
58 288
66 331
76 380
87 337
Fiber-reinforced syntheticse
To maximize the life of your diamond micro drill and minimize material damage, it is important to run your drills at the proper drill speed and pressure. Recommended RPM’s for diamond micro drills range from 65,000 to 350,000. Drilling speeds are typically determined by diameter of diamond micro drill, drill depth, and material properties. Using optimal RPM’s for your application will help increase drill life and reduce drill wreckage. Different material have different requirements for drilling speed. Material hardness, density, will affect both spindle speed and therefore surface finish quality.
The high spindle speed provides many advantages in diamond and carbide micro drilling process (specially for diamond and CBN). Higher RPM’s significantly drill life, reduce the forces between the tool and the material. High-speed/low-force spindles and drilling equipment produce less heat, reduce drill/tool deflection, and allows drilling and milling of smaller holes and thinner walled workpieces. This translates in superior surface and edge quality, higher accuracy, minimal material deformation and micro cracks. As well as by-product (of low force), easier workholding — since modular vacuum tables can be employed for quick setup and job changeover (particularly with thin flat substrates).
Diamond micro drills can be used at lower than 65,000 RPM’s. However, drill life will be much shorter and depending on micro drill diameter, there would be much higher change for drill wreckage. Lower RPM’s will cause softer drilling action, where each diamond particles grind out larger portion of material. Higher spindle RPM’s will do the opposite. Each diamond particle will grinds away a small portion of material, creating harder drilling action. A good rule of thum to remember: for soft, abrasive materials, RPM should increase. For hard, dense materials, RPM should decrease. It is generally recommended that you use a drill as fast as it will drill freely.
For carbide and high speed steel micro drills, the recommended RPM’s are different. Exotic ferrous metals covering all of the high strength steels including stainless steel, the best rule to follow is to start at a low rpm such as 1,000 and gradually increase the speed as a "feel" is developed for the proper feed rate to maintain a continuous chip structure. . For the more exotic ferrous metals covering all of the high strength steels including stainless steel, the best rule to follow is to start at a low rpm such as 1,000 and gradually increase the speed as a "feel" is developed for the proper feed rate to maintain a continuous chip structure. drilling of plastics and printed circuit boards can generally be accomplished in the higher ranges of speeds between 10,000 and 20,000 rpm.
DRILLING FEED RATE
Feed rate should be determined by diamond micro drill diameter, head length, your desired surface finish quality, material hardness, density, geometry, and thickness. Since goal of majority of diamond micro drilling operations is to introduce most minimal amount of /material deformation and preserve true material microstructure. The diamond micro drill head should slowly penetrate into the material so it does not lead off. Excessive pressure can cause the diamond micro drill head to fracture or snap. As well as create unwanted material burning, smearing, cracks, and deformation.
Best practice to follow would be to start by applying light to medium pressure. Gradually feeding the drill into material, until it begins to drill at its own speed. If you can see dark “burn” marks around the diamond section, the drilling speed you are using is too fast or you are applying too much pressure. Feed rate should never be so great that drill slows down. For this reason great care and caution should be taken when increasing feed rate. When drilling completely through a material and the hole is near completion, reduce slightly the fee rate/pressure on your drill considerably. Doing so will reduce chipping sample/material as you exit the hole.
SUBMERGED PRESSURE
Using frequent up and down motion when drilling will help propel coolant deeper into the hole being drilled. It is highly recommended that drilling should be done in even intervals. Drilling for about 5 seconds, lift diamond drill up from drilling zone to let it cool in air and diamond and coolant reach further into the drilling zone. Following this technique will reduce premature and uneven diamond drill wear and avoid diamond drill/bit wreckage.
MAXIMUM DRILL DEPTH
Maximum drill depth of diamond micro drills is typically limited to 25 times the diameter of the drill head. Exceeding the maximum head length would create very high change of drill wreckage. For Carbide and High speed steel micro drills, maximum head lengths for micro drills 0.004” (0.10 mm) diameter range up to 20 or more times the diameter. Deep hole drilling typically requires different operating procedures. Typically RPM’s should be reduced the deeper the micro drill enters the material. To insure best results and minimize drill wreckage, we recommend using a multiple step operation. Micro drills of same diameter, but in different head lengths should be used for this purpose. Shorter head length micro drill should start the hole, creating so called pilot hole in the material. Second step would involve of using longer head length micro drill of same diameter to reach middle of desired hole depth. For final operation longer head length micro drill of same diameter would complete the desired hole depth and exit the material.
For Drilling thicker materials, we recommend coolant nozzles running coolant from multiple directions, as well as drilling submerged in coolant. This will insure maximum amount of coolant and lubrication reaching your drilling zone. Apply more pressure and reduce speed the deeper you penetrate into your material. Lift drill up, after every 50 to 100 microns of depth the micro drill enters into your material, letting the drill cool and coolant reach deeper into your hole. Carefully examine the diamond tip condition, making sure it still has diamond coating and tip attached, and is not overheated.
RECOMMENDED DRESSING PROCESS
Dressing procedures are established by end user and based on experience and the application concerned. There is not one common method that applies to all applications.
Dressing stick to dress the blade should be same or similar diamond grit/mesh size as the diamond micro drill being dressed. When drilling ultra hard and dense materials such as silicon nitride, it is a good idea to implement a secondary dressing process. Dressing the micro drill before starting to drill the material. Doing so will re-sharpen the diamond particles, so they are working at their maximum level of efficiency from the very beginning. This can be accomplished by taking five passes through the dressing stick, so that that the dressing stick covers the diamond section. Make sure coolant is turned on and working during this process.
When and how often should I dress my diamond micro drill?
There are no specific recommendations or guidelines on when or how often diamond micro drill should be dressed. The micro drilling machine operator should use their best judgment in determining when and how to dress the micro being used. A good rule of thum to remember: when you notice drilling rate/speed is significantly slower than when the drill was first used is a good sign the diamond micro drill you are using needs to be dressed. Eventually all diamond drills will need to be dressed, regardless of the material being drilled. The amount of dressing a diamond micro will require will depend on the material hardness, density, porosity being cut, as well as material diameter and shape/geometry. Dressing will re-sharpen and re-expose the diamond crystals/particles in the blade bond matrix, as well as unload the drill from material debris covering the diamond section surface. When cutting very soft and gummy materials such the diamond micro drill will have to be dressed more frequently than when cutting ceramics and other ultra had and brittle materials.
At same time when drilling thicker materials where the diamond micro drill head length is taken almost to its maximum drilling capacity. For example drilling 500 microns deep into material with 100 micron diamond drill diameter. The diamond micro drill should be dressed continuously during its operation. Dong so will help prevent “build up” edge on the micro drills head tipe and keep it from binding up.
The more abrasive the material shorter drill life. Abrasive materials remove and wear away diamond particles faster
Faster the RPM’s longer the drill life
For every material requires different pecking cycle, pressure of coolant, and coolant flow.
PECKING CYCLE
Recommended feed rate is .010” inches per minute. You should determine how many pecking cycles will be needed for your material per minute.
10 cycles per minute
lower the rpm’s the more cycles should be used.
For example if rpm’s are 80,000 than you should use 12 cycles. If rpm’s is 250,000 RPM you should have 6 cycles to drill .010” thickness of material.
The smaller diameter the drill, higher number of pecking cycles should be used.
Run out should be less than 25 microns. Drilling equipment run out should be correlated to diameter of the drill. For example drilling 75 micron drill (75 x 0.05%) run out should be no more than 0.4 micron.
Coolant pressure should be 150 PSI or more. Coolant pressure should not affect diamond micro drill head.
STARTING TO DRILL
Starting to drill (first entry) where point of contact is made between micro drill and material is a very important first step of the micro drilling process. Correct entrance into materiall being drilled will pave the way and influence peformance of the overall micro drilling process. For best results we recommend that top layer of material provide adequate flatness and a smooth surface for the drill bit to make contact with, allowing the micro drill to enter the material as straight as possible. The material should be hard, in order to prevent entry burrs, which can be pushed back into the hole creating subsequent problems later on in the process. It also needs to have a consistent thickness and composition to ensure consistency in hole wall quality.
for production operations the front and rear layer of material should not increase drill wear, as this can impact hole wall quality, as well as the number of holes a drill bit can produce. In addition, reducing the number of holes the micro drilling is able to drill before dressing (for diamond and cbn micro drills) or resharpening for carbide drills. The entry and backer materials should minimize drill temperature to reduce smearing and drill bit wear, and the materials selected should be designed to not deposit back into the hole.
For some very sensitive micro drilling applications where burring and surface finish quality is critical (within few microns). It may be a good idea to utilize additional material substrate to place on front and back of material. There are a number of different backup and entry materials available such as borosilicate, soda lime glass substrates, and ceramic substrates such as Al203. Which backing material to use will depend on the properties of material being drilled and your overall objectives. Doing so can help solve some of the problematic issues. For example micro cracks and stress introduced when drilling very difficult to drill materials such as very hard and dense ceramic wafers/substrates.
PROPER MICRO DRILLING HANDLING
Many problems associated with the diamond or carbide micro drills can be attributed to poor handling techniques. This is specially true for very small size micro drills below 150 microns in diameter. Micro drills in many cases are handled several times before drilling. Attention to detail and great caution and care should be taken by the user when handling these tools. As the smallest error can fracture or bend the very small drilling tip. A great deal of effort has been taken by micro drill manufacturers to properly package these tool to properly store and a prevent damage while in transit.
MICRO DRILL RUN OUT
Run out is the greatest contributor to micro drill breakage and accuracy problems. While runout can be tolerated to some extent when drilling larger holes, small hole drilling is extremely sensitive to runout. Axial runout causes overheating, poor hole quality, breakage, and short drill life. Radial runout, or “whipping”, causes breakage both in and out of the material, as well as drill wander when drilling high aspect holes. A big help in the drastic reduction of spindle run out has been the elimination of collars on the drill bit.
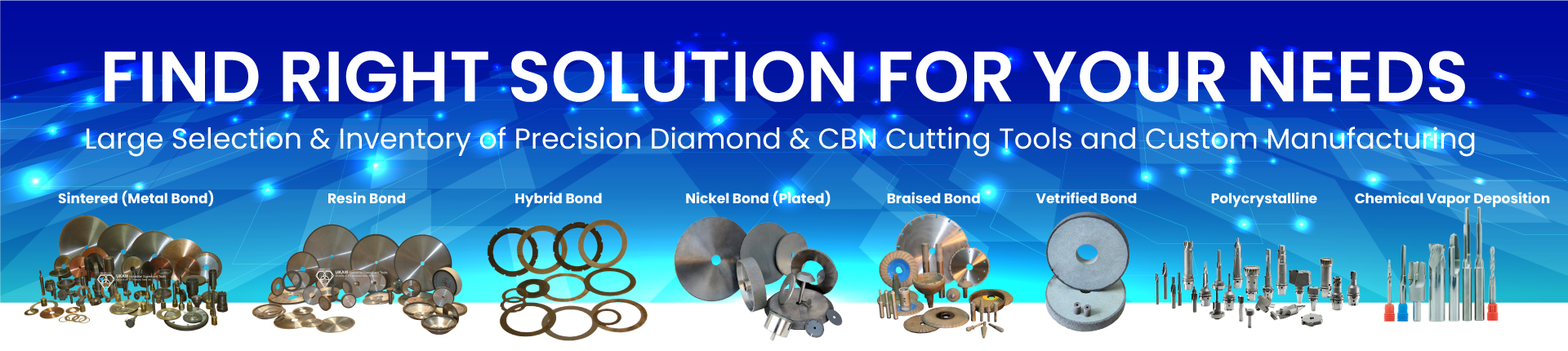
ARE YOU USING RIGHT DIAMOND CORE DRILLS & TOOLS
FOR YOUR APPLICATION?
LET US
HELP YOU
HAVING ISSUES WITH
YOUR CURRENT DIAMOND CORE DRILLS & TOOLS?
Knowledge Center
Select right Diamond Drill for your application
How to Properly Use Precision Diamond Drills
Diamond Drills Guide
Diamond Tools Guide – Selecting Right Drills & Tools for your application
Optimizing your Diamond Drilling Operation
Micro Drilling Guide
Selecting Right Drilling Equipment for your Application. What you features & functionality you should look for?
Diamond Core Drill & Drill Trouble Shooting Guide
Understanding & Calculating Return on Investment for Diamond Core Drills & Other Tools
Understanding Tradeoffs – Searching for Perfect Diamond Drill & Tool
Why Use Diamond Drills?
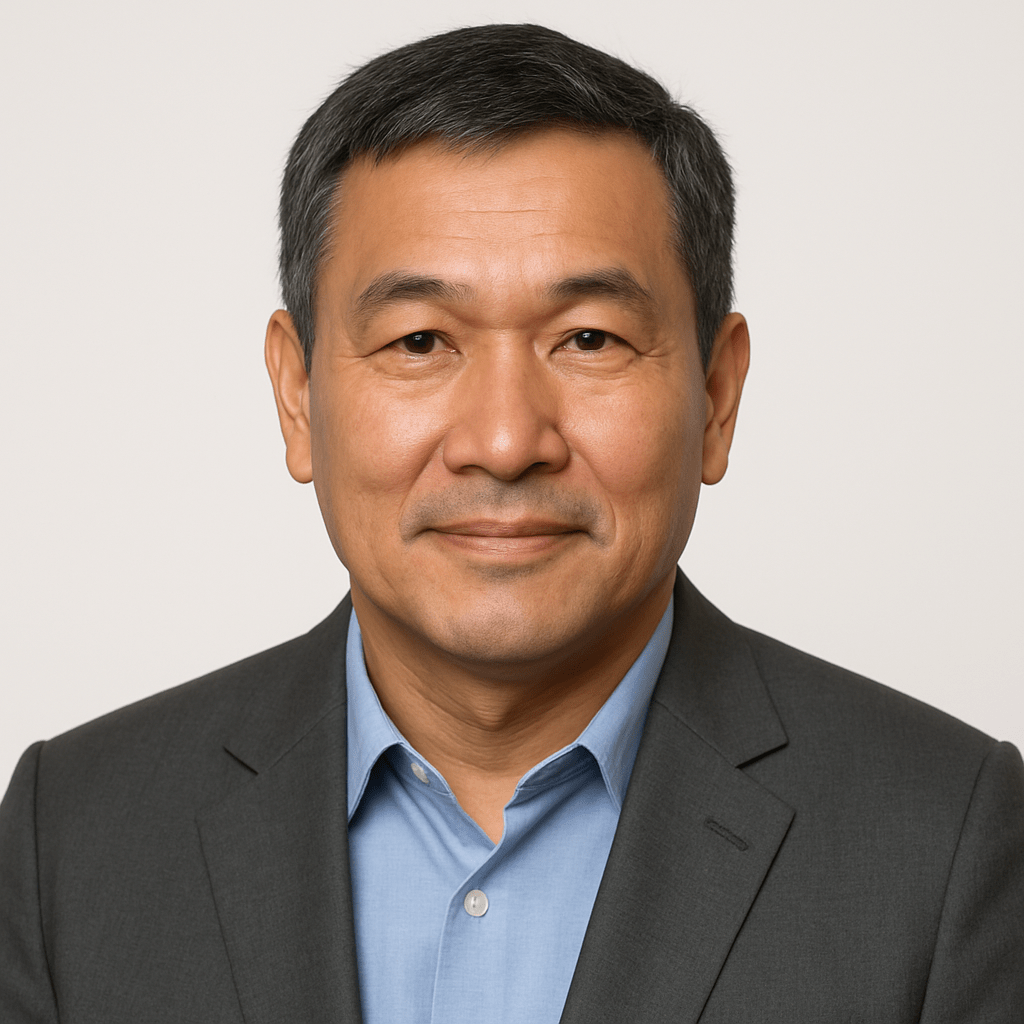
Ayan Sadyk is a materials scientist and process engineer with over two decades of experience in the industrial diamond tooling sector. His expertise lies in integrating ultra-thin diamond blades, CBN wheels, and advanced cutting systems into precision manufacturing workflows for applications in optics, semiconductors, and technical ceramics.
With a background in materials behavior and surface integrity, Mr. Sadyk brings a data-driven, application-specific approach to cutting and grinding process development. He has worked closely with manufacturers and R&D facilities across Eastern Europe, North America, and the Middle East, helping optimize tool life, surface finish, and process stability.
As an author, he focuses on bridging materials science with tooling innovation—writing on topics such as blade wear mechanisms, thermal effects in hard material sectioning, and adaptive process design.