-
0 items in quote
No products in the Quote Basket.
Silicon Carbide Paper
SMART CUT® Silicon Carbide Abrasive Paper is meticulously designed for preparing metallographic specimens, incorporating superior silicon carbide grains embedded in a resilient, waterproof backing for both dry and wet grinding. This versatile paper transitions smoothly from coarse cutting to fine polishing, ensuring that specimens are precisely prepared for microscopic analysis.
DESCRIPTION
SPECIFICATIONS
FREQUENTLY ASKED QUESTIONS
INDUSTRIES USED IN
ACCESSORIES
USAGE RECOMMENDATION
DESCRIPTION
SMART CUT® abrasive paper features micro-graded silicon carbide that accelerates the cutting process while minimizing heat build-up, preserving the metallurgical integrity of the specimen. The even distribution of the grains delivers a consistent and controlled scratch pattern, crucial for achieving an excellent surface finish.
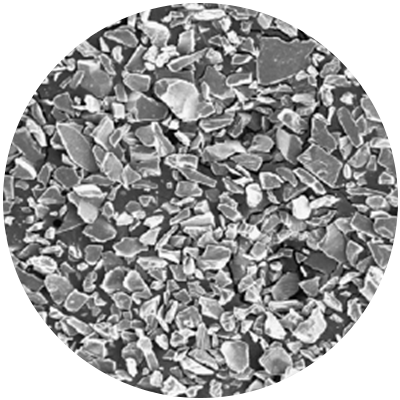
The construction of the paper includes a waterproof resin bond that enhances its durability and prevents disintegration in wet environments, ensuring prolonged usability and consistent performance under various conditions. The flexible C-weight paper backing is specifically designed to effectively manage contoured surfaces, making it ideal for complex sample shapes without compromising the abrasive surface’s integrity.
SMART CUT® Silicon Carbide Abrasive Paper is available in various formats including discs, sheets, and rolls. These are designed to meet diverse tooling and user preferences and are compatible with industry standards. With its extended lifespan and ability to produce consistent results, SMART CUT® abrasive paper offers a cost-effective solution for laboratories that prioritize high reproducibility.
SPECIFICATIONS
- Formats Available: Discs (other formats such as sheets and rolls are also available)
- Diameters Available: 8 inches (200mm), 10 inches (250mm), 12 inches (300mm) – other diameter upon request
Inside Diameter: no hole (custom inside diameter available upon request) - Grit Sizes (ANSI): 60, 120, 180, 240, 320
- Grit Sizes (FEPA): P60, P120, P180, P280, P400
- Micron Estimates: 268 microns to 35 microns
- Customization: Custom specifications, additional sizes, hole diameters, and grit sizes available on request
- Packaging Options: Available in packages of 100 pcs
FREQUENTLY ASKED QUESTIONS
Silicon carbide paper is a type of abrasive paper that is primarily used in metallography for the surface preparation of metals and alloys. Due to its high hardness and brittleness, silicon carbide is an ideal abrasive for cutting and polishing metals. It helps to produce a smooth, flat surface necessary for microscopic examination of the metal’s microstructure.
Silicon carbide papers are available in a range of grit sizes, from coarse (around 60-120 grit) to fine (up to 4000 grit). Coarser grits are typically used for the initial stages of sample preparation to remove significant material or surface roughness. Finer grits are used for subsequent polishing stages to refine the surface, resulting in minimal scratches and more precise metallurgical analysis.
Selecting the right grit size of silicon carbide paper depends on the hardness and initial condition of the sample. Start with a coarser grit for harder materials or those with significant surface imperfections. Gradually move to finer grits as the surface becomes smoother. This stepwise refinement helps in achieving a mirror-like finish necessary for detailed microscopic analysis.
SMART CUT® silicon carbide paper includes unique features such as a water-resistant backing and a non-clogging formulation that enhances performance and usability in both wet and dry conditions. These features are specifically designed to meet the demanding needs of modern metallurgical labs. SMART CUT® silicon carbide grinding paper provide same or higher level of performance to well known brands, at more affordable cost. We invite you to test and compare. We can cross reference almost any competitor part number of specification.
SMART CUT® silicon carbide paper is engineered with a proprietary blend of abrasive grains that offers superior durability and cutting efficiency. SMART CUT® papers feature an advanced bonding technology that ensures the grains stay in place longer, providing a consistent scratch pattern and prolonged usage life, which is critical for high-throughput laboratories and industrial environments.
Yes, silicon carbide paper can be used with both manual and automatic polishing machines. When used with automatic equipment, it is important to ensure that the paper is securely fixed and that the machine settings (such as speed and pressure) are appropriately adjusted to avoid tearing the paper or damaging the sample.
The lifespan of silicon carbide paper depends on the material being polished and the amount of pressure applied during preparation. It should be replaced when it no longer effectively removes material from the sample or when it becomes clogged with debris, which can impair the polishing process and affect the quality of the surface finish.
Using a lubricant such as water, oil, or specialized polishing fluids can help prevent the sample from overheating, reduce the wear on the abrasive surface, and facilitate the removal of debris. This results in a better finish and prolongs the life of the silicon carbide paper.
Safety is paramount when using abrasive papers. Always wear protective gear, including gloves and eye protection, to guard against particles and debris. Ensure that the work area is well-ventilated, especially if dry polishing, to avoid inhaling dust. Additionally, check that the sample is securely mounted and that the paper is properly affixed to avoid slippage during the polishing process.
Silicon carbide paper should be used and disposed of responsibly to minimize environmental impact. Used abrasive papers can contribute to landfill waste. Whenever possible, opt for recyclable or partially recycled materials to reduce waste. Also, consider the impact of lubricants used during polishing; biodegradable lubricants are preferable for reducing environmental harm.
Silicon carbide is harder and sharper than aluminum oxide, making it more suitable for processing harder materials such as metals and hard alloys. Its sharpness provides a faster cutting action and generally produces a finer finish than aluminum oxide. However, aluminum oxide is more durable and is preferable for softer metals or materials that require a more delicate approach.
Yes, silicon carbide paper is versatile and can be used for both wet and dry polishing. Wet polishing is recommended to reduce dust, minimize heat buildup on the sample surface, and extend the life of the abrasive paper. Dry polishing may be suitable for quick jobs or when using equipment that does not support wet polishing.
To achieve uniform preparation:
- Apply consistent pressure throughout the polishing process.
- Use a figure-eight or circular motion to avoid creating grooves or patterns in the sample.
- Ensure each step progresses to a finer grit to gradually eliminate scratches from the previous stage.
- Frequently clean the sample and the paper to remove any accumulated debris.
The speed and pressure applied during polishing can significantly impact the effectiveness of silicon carbide paper. High speeds can generate excessive heat, leading to sample damage. High pressure can cause rapid wear of the paper and uneven sample surface. It’s crucial to find a balance that achieves efficient material removal without damaging the sample or the abrasive paper.
Common mistakes include:
- Using too coarse a grit for the final stages, which can leave deep scratches.
- Insufficient cleaning between grit changes, leading to contamination and suboptimal finishes.
- Applying uneven pressure, resulting in an uneven surface.
- Using worn-out paper, which can increase polishing time and reduce the quality of the finish.
Many international standards and guidelines, such as those from ASTM and ISO, provide detailed recommendations on the proper use of abrasives in metallography. These standards often specify the type of abrasive, grit size, polishing motion, pressure, speed, and lubrication to achieve reliable and reproducible results.
Silicon carbide paper comes with different types of backing materials, such as paper, cloth, or polyester film. Paper backings are flexible and suitable for irregular surfaces but are less durable. Cloth backings offer greater durability and tear resistance, making them ideal for high-pressure applications. Polyester film backings provide the best uniformity and surface finish, especially beneficial for precision applications requiring minimal surface imperfections.
Reusing silicon carbide paper depends on the condition of the abrasive surface after initial use. If the grit is not worn out and the paper is not clogged with debris, it can be used for another sample. However, for optimal results and to avoid cross-contamination, it is recommended to use fresh abrasive for critical or precision applications.
Silicon carbide paper should be stored in a cool, dry environment to prevent moisture absorption and warping of the backing material. Proper storage ensures the abrasive maintains its effectiveness and is protected from environmental factors that could degrade its quality.
A systematic progression through increasing grit sizes is crucial for effective sample preparation. Start with a coarse grit to remove larger imperfections and material quickly. Progress through medium to fine grits, each step refining the surface by removing scratches from the previous grit size. Typically, jumping more than one grit size can leave residual scratches that are difficult to remove in later stages.
For final polishing stages, silicon carbide paper may be substituted with other finer abrasives, such as diamond pastes or alumina suspensions, especially when a highly reflective surface is required. Silicon carbide paper is typically used up to very fine grits but may not achieve the ultra-fine finish provided by these other abrasives.
When using silicon carbide paper, especially in dry polishing:
- Always wear respiratory protection to avoid inhaling abrasive dust.
- Use eye protection to guard against flying particles.
- Ensure adequate ventilation in the workspace.
- Handle the abrasive paper carefully to avoid cuts from the sharp edges.
Consider both the initial cost and the operational cost (including usage life and the need for replacements). Higher quality or specialized abrasive papers may cost more upfront but could offer better performance and longer life, reducing the overall cost per sample prepared.
Disposal methods for used silicon carbide paper should comply with local environmental regulations. Consider recycling if the abrasive paper is free of hazardous materials. Otherwise, follow standard industrial waste disposal practices to minimize environmental impact.
The particle shape of silicon carbide in abrasive papers can significantly impact its cutting efficiency. Silicon carbide particles are generally angular in shape, which helps in creating a more aggressive cutting action compared to rounder grains. This angular nature makes silicon carbide ideal for initial material removal and rough polishing phases, where rapid stock removal is necessary.
While primarily used for metals and alloys, silicon carbide paper is also effective on a variety of non-metal materials such as ceramics, glass, and mineral samples. Its hardness makes it suitable for these materials, providing efficient material removal and fine surface finishes necessary for detailed examination.
When using silicon carbide paper with wet polishing techniques, managing the slurry (a mixture of abrasive particles and liquid) is crucial. Ensure that the slurry is evenly distributed across the surface to maintain effective abrasion. Regularly clean the sample and work surface to prevent the slurry from drying out, which can cause scratching and damage to the sample surface.
High-grade silicon carbide paper should exhibit uniform grain distribution, strong bonding of the abrasive grains to the backing material, and consistent cutting performance. The backing should be sturdy yet flexible enough to conform to various sample shapes without tearing. High-quality silicon carbide paper also resists clogging, maintains its abrasive properties throughout its use, and produces consistent finishes.
The orientation of silicon carbide grains on the paper can affect the abrasive efficiency. Ideally, the grains should be randomly oriented to maximize the cutting points and reduce the likelihood of grooving or pattern formation on the sample surface. This random orientation helps ensure a more uniform material removal and a smoother final surface.
Silicon carbide paper used in metallography may adhere to standards set by organizations such as the American Society for Testing and Materials (ASTM) or the International Organization for Standardization (ISO). These standards can specify parameters like grit size, backing material, and abrasive density, ensuring consistency and reliability in metallographic preparations.
Before adopting a specific brand or type of silicon carbide paper for large-scale use, conduct preliminary tests on sample materials to evaluate its performance. Factors to assess include the rate of material removal, surface finish quality, grain shedding, and paper durability. Comparison tests against known standards or previously used abrasives can provide a benchmark for performance.
The thickness of the backing material impacts the flexibility and durability of the abrasive paper. Thicker backings offer greater durability and are less likely to tear during use, making them ideal for heavy-duty applications. Conversely, thinner backings provide greater flexibility, which is beneficial for polishing intricate or curved surfaces without creasing or tearing the paper.
Yes, silicon carbide paper can be custom-sized or modified to meet specific application needs. Yes we offer cutting services to create custom dimensions or shapes of abrasive paper. Additionally, holes or patterns can be added to the paper to accommodate specific polishing machines or to improve slurry flow during wet polishing.
Best practices for transitioning between different grit sizes involve using a gradual progression to avoid deep scratches that are difficult to remove. After using a coarser grit, the surface should be thoroughly inspected and cleaned before moving to a finer grit. This ensures that any remaining coarse abrasive particles do not scratch the surface during subsequent polishing steps.
Temperature can significantly affect the performance of silicon carbide paper. High temperatures can soften the bonding agent, leading to premature grain shedding and reduced abrasive life. It is important to use appropriate lubrication or cooling methods to manage the temperature and preserve the integrity of the abrasive paper during intensive polishing sessions.
If silicon carbide paper is not performing as expected, consider the following troubleshooting tips:
- Check if the paper is suited for the material being polished. Some materials require specific types of abrasives.
- Inspect the paper for uniformity in grain distribution. Inconsistent grain size can lead to uneven abrasion.
- Ensure that the paper is properly attached to the polishing tool to avoid slipping or creasing.
- Evaluate the polishing parameters, such as speed and pressure, to ensure they are optimal for the type of abrasive and the material.
- Replace the paper if it shows signs of clogging, as clogged abrasives can become ineffective and cause damage to the sample.
The performance of silicon carbide paper can be objectively measured by evaluating several key parameters:
- Material Removal Rate (MRR): This measures the amount of material removed per unit of time, providing a quantifiable measure of the abrasive’s efficiency.
- Surface Finish Quality: Using profilometers or similar instruments to measure the surface roughness after polishing provides insights into the smoothness achieved.
- Abrasive Lifespan: Tracking how long a piece of abrasive paper remains effective before needing replacement helps determine its durability.
- Consistency: Assessing the uniformity of the finish across multiple uses and batches of paper can indicate quality control in manufacturing.
While silicon carbide is a popular choice for many applications due to its hardness and cost-effectiveness, alternatives like diamond, aluminum oxide, and cerium oxide offer specific advantages:
- Diamond: Provides superior hardness and longevity, ideal for very hard materials.
- Aluminum Oxide: Less aggressive than silicon carbide, making it suitable for softer or more ductile materials.
- Cerium Oxide: Excellent for chemical mechanical polishing where both mechanical action and chemical reactions are desired for achieving ultra-smooth surfaces.
Proper handling of silicon carbide paper involves several safety precautions to protect users:
- Dust Management: Always use dust extraction or wear a suitable respirator to prevent inhalation of fine particles.
- Protective Equipment: Wear gloves and eye protection to safeguard against accidental cuts or particles entering the eyes.
- Proper Disposal: Dispose of used silicon carbide paper and accumulated debris according to local regulations, particularly if contaminated with hazardous materials.
Water quality can significantly impact the effectiveness of silicon carbide paper in wet polishing scenarios. Hard water can lead to the buildup of mineral deposits on both the sample and the abrasive, which may reduce the cutting efficiency and potentially scratch the sample. Using deionized or distilled water can prevent these issues, ensuring consistent abrasive performance and prolonging the life of the silicon carbide paper.
For large quantities of silicon carbide paper, proper storage is crucial to maintain its effectiveness. Store the paper in a cool, dry place away from direct sunlight to prevent degradation of the bonding agents and the backing material. Additionally, keeping the paper flat or properly rolled (without sharp bends or creases) will ensure that it remains in good condition for use, preventing curling or other deformities that could impact performance.
Automation in the use of silicon carbide paper, particularly in industrial and research settings, can lead to greater consistency and reproducibility in sample preparation. Automated polishing machines can precisely control speed, pressure, and movement patterns, which are often challenging to replicate manually. This not only ensures uniform application of the abrasive across the sample but also significantly reduces the potential for human error, enhances throughput, and can lower long-term operational costs.
Silicon carbide paper is suitable for precision applications, especially in the initial stages of material removal and coarse polishing. However, its limitations become apparent as the need for an ultra-fine finish increases. In such cases, transitioning to micro-grit abrasives or other types of polishing compounds (like diamond paste or alumina suspension) might be necessary to achieve the desired surface smoothness required for high-precision analyses.
The particle size distribution (PSD) of the grit in silicon carbide paper is critical for its performance. A narrow PSD ensures that the abrasive particles are of uniform size, which leads to a more consistent scratch pattern and a smoother finish. Conversely, a broad PSD can result in a mixed scratch depth, which might be undesirable for high-precision polishing but beneficial for rapid material removal in earlier stages.
The flexibility of the backing material used in silicon carbide paper plays a crucial role in its effectiveness. Flexible backings, such as paper or cloth, allow the abrasive to conform to the SMART CUT®s of complex or irregularly shaped samples, ensuring even contact and consistent abrasion. Rigid backings like polyester or mylar are better suited for flat surfaces where uniform material removal is needed. The choice of backing depends on the specific requirements of the sample preparation process.
Optimizing the use of silicon carbide paper in a cost-effective manner involves several strategies:
- Maximize Use: Employing both sides of the abrasive paper if possible, or using segmented patches to fully utilize the material before disposal.
- Proper Maintenance: Cleaning the abrasive surface regularly to prevent clogging and extend its usability.
- Bulk Purchasing: Acquiring silicon carbide paper in bulk from suppliers can reduce costs, especially for high-volume laboratories and industrial settings.
- Recycling Programs: Participating in recycling programs can reduce waste and potentially lower costs associated with waste disposal.
The life cycle of silicon carbide paper generally compares favorably with other abrasives, especially when used appropriately for its intended materials and conditions. Silicon carbide is harder and sharper than many other abrasives like aluminum oxide, which allows it to maintain its cutting ability longer. However, its brittleness can lead to quicker wear in some applications. Life cycle considerations should include not only the durability of the abrasive but also the quality of finish it provides over time.
INDUSTRIES USED IN
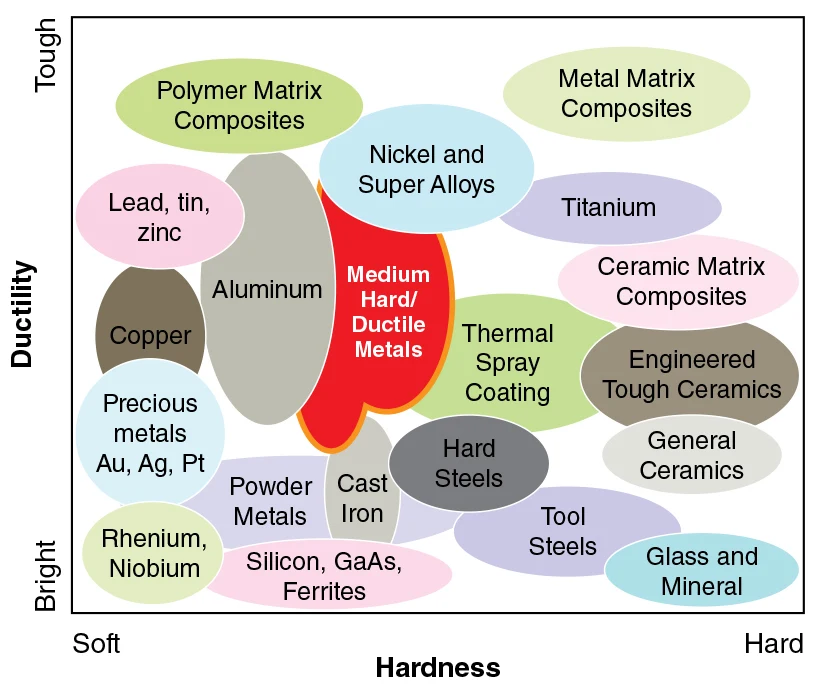

INDUSTRIES USED IN:
- Advanced Ceramics
- Composites
- Glass
- Geology
- Quartz
- Materials Research
- Medical Devices
- Metallography
- Photonics / Optics
- Semiconductor
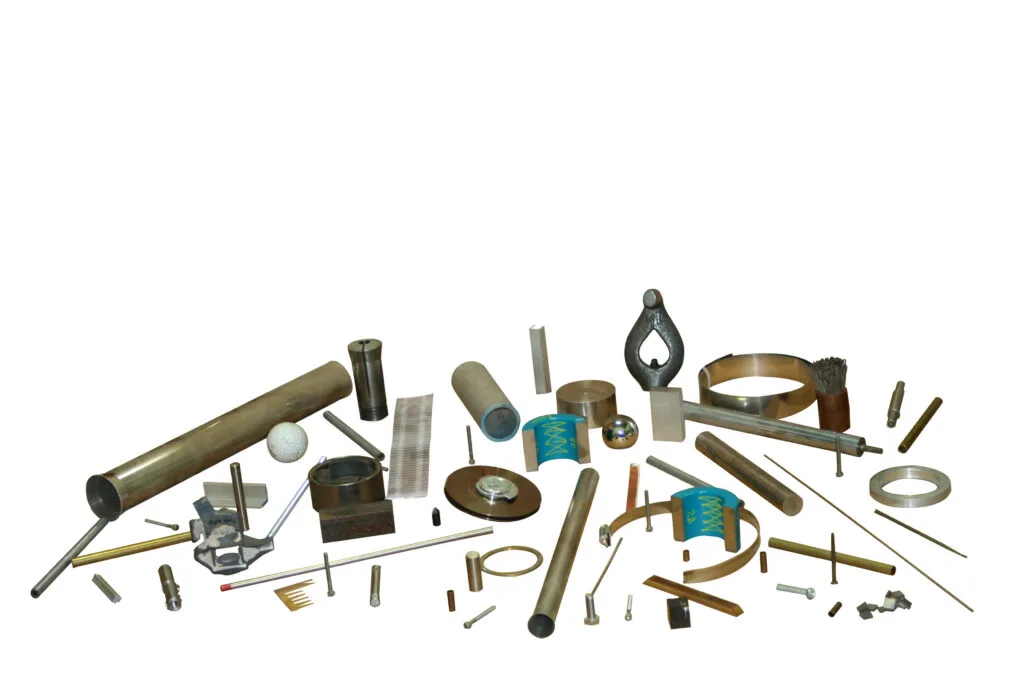
Ferrous & Non-Ferrous Metals:
- Plain Carbon Steels
- Electronic Packages
- Stainless Steels Plastics
- Tool Steels Fasteners
- Aluminum Refractories
- Copper Base Alloys Integrated Circuits
- Magnesium Thermal Spray Coatings
- Titanium Metal Matrix Composites
- Biomedical Wafers
- Petrographic
- PCB.s Ceramics
ACCESSORIES
Tab Content
USAGE RECOMMENDATION
Silicon Carbide Paper Selection & Usage Guide
Metallographic / Sample Preparation Process
1. Select the Right Silicon Carbide Paper
Grit Size Determination
Selecting the appropriate grit size of silicon carbide paper is essential for achieving desired results in sample preparation. The choice of grit size should be based on the material hardness, the amount of material to be removed, and the desired final finish. For harder materials or when a significant amount of material needs to be removed, start with coarser grits such as 80-120 grit. This will allow effective material removal without damaging the sample. As the surface becomes smoother, switch to finer grits to refine the surface incrementally up to ultra-fine grits of 1000-4000 for applications requiring a high polish. Always progress through grits gradually, ensuring each step completely removes the scratches from the previous one.
Backing Type
The backing material impacts the flexibility, durability, and usability of silicon carbide paper. Paper backings are best suited for general use and contour polishing where flexibility is needed to conform to various sample shapes. They are typically lighter and less expensive but may wear out quicker under heavy use. Cloth backings are ideal for flat and high-pressure applications, offering greater durability and tear resistance, making them more suitable for prolonged use or for tough materials. For precision applications where minimal thickness variation is crucial, such as in semiconductor or optical materials, polyester backings are the superior choice due to their exceptional durability and uniformity.
Compatibility
Ensuring that the silicon carbide paper is compatible with your polishing equipment is crucial for its effective use. Determine whether the paper is designed for manual hand-polishing or machine-operated polishers, as this will affect the type of paper, adhesive, and grit choice. Check the polishing equipment’s manufacturer recommendations for abrasive papers to ensure optimal performance. Consider the type of adhesive needed; some papers come with pressure-sensitive adhesives for easy application and removal, ideal for automatic polishers requiring quick changes between grits. Others may need a more permanent adhesive for extended use. Also, ensure that the size and shape of the silicon carbide paper are compatible with your equipment to prevent poor attachment, uneven wear, and potential damage.
2. Prepare to Set up
Environment Setup
Setting up the right environment is crucial for the successful use of silicon carbide paper in polishing applications. The area where the polishing or grinding is to take place must be kept clean and free from contaminants. This is especially important when working with high-purity materials or in applications that demand a high degree of precision. Any dust, debris, or residual material from previous operations could impact the abrasive effectiveness of the silicon carbide paper and potentially contaminate the sample, leading to inaccurate results. Ensuring a controlled environment also helps maintain the integrity of both the abrasive paper and the material being processed, which is vital for achieving consistent and reliable outcomes.
Equipment Check
Before beginning the polishing process, a thorough check of all equipment is necessary. This includes ensuring that all devices are not only clean but also fully functional and properly calibrated. This step is vital for both manual and, more critically, for automated systems where precision and repeatability depend on the equipment operating within specified parameters. Proper calibration ensures that the equipment will function as expected, providing consistent pressure, speed, and motion, which are essential for achieving the desired surface finish. Additionally, verifying that the equipment is clean helps prevent any cross-contamination between different materials or grits of silicon carbide paper, which can otherwise alter the surface properties of the sample being prepared.
3. Mounting and Installation
Proper Adhesion
Achieving proper adhesion of the silicon carbide paper to the platen or holder is critical for effective polishing or grinding. The paper must be securely attached to avoid slipping during use, which can affect the uniformity of material removal and potentially result in suboptimal finishing or damage to the sample. To facilitate this, it is essential to use adhesives that are specifically designed for abrasive papers. These adhesives should provide a strong bond to keep the paper in place during the polishing process but also allow for easy removal and replacement of the paper without leaving residues that could contaminate the platen or the new abrasive sheet. Depending on the system, this may involve using spray adhesives, pressure-sensitive adhesive (PSA) backings, or magnetic backing systems that align with the specific requirements of the polishing equipment and materials.
Flatness
Ensuring that the silicon carbide paper is perfectly flat on the mounting surface is another crucial step. Any deviations from flatness, such as wrinkles, folds, or air bubbles under the paper, can lead to uneven contact with the sample. This unevenness can cause inconsistent material removal rates, scratch patterns that are difficult to polish out, or even physical damage to the delicate samples. To achieve optimal flatness, the paper should be carefully laid on the platen, starting from one edge and gradually smoothing it out towards the opposite edge to avoid trapping air. For larger sheets or more rigid backings, using a roller or a similar tool might help in applying even pressure and achieving perfect adhesion across the entire surface.
4. Polishing Process
Initial Set-Up
The initial set-up in the polishing process is crucial for ensuring effective and efficient material removal. Begin by selecting the appropriate grit size of the silicon carbide paper based on the condition of the sample’s surface. For samples with significant roughness or imperfections, it’s advisable to start with a coarser grit. This approach helps quickly reduce high spots and smooth out rough areas without excessive wear on finer grits, which are not designed for heavy material removal. As the surface becomes smoother, transition through progressively finer grits to refine the surface to the desired finish.
Water or Coolant Application
In wet polishing, the application of water or a suitable coolant is essential to maintain the quality of both the sample and the abrasive. Evenly distributing a coolant across the surface of the silicon carbide paper helps in several ways: it reduces heat generation during polishing, which can alter the physical properties of the sample; it prevents premature dulling of the abrasive grains; and it helps remove swarf and debris, which can cause additional scratches and surface defects. The type of coolant may vary depending on the material being polished and environmental or safety considerations.
Pressure and Speed
Adjusting the pressure and speed during the polishing process is critical to achieving optimal results. The amount of pressure applied should be enough to facilitate effective abrasion but not so high that it causes excessive wear or damage to the silicon carbide paper and the sample. Similarly, the speed of the polishing tool should be set to a level that allows for efficient material removal without generating excessive heat. High speeds, combined with too much pressure, can lead to thermal damage to both the sample and the abrasive paper. Each material may require different settings, which should be determined based on experimental results or established guidelines.
Polishing Motion
The motion used during polishing affects the uniformity of the material removal and the final finish of the sample. Consistent and controlled motions, such as circular or figure-eight patterns, are recommended as they ensure that all areas of the sample are evenly abraded. This uniformity is crucial for preventing localized over-polishing or under-polishing, which can lead to artifacts in the sample analysis. The specific polishing motion may need to be adjusted depending on the shape of the sample and the type of material to account for any unique physical properties or desired outcomes.
5. Progression and Transition
Grit Progression
Proper grit progression is essential for achieving a smooth and defect-free surface on the sample being polished. Start with a coarser grit to effectively handle large imperfections or significant roughness. This initial stage is about removing the major surface irregularities and preparing the sample for finer finishing. Once the initial leveling is achieved, move to medium grits to begin smoothing the surface. Each subsequent grit should be finer than the last, with each step designed to remove the scratches left by the previous one. This gradual progression ensures that by the time you reach the finest grits, the surface is nearly free of visible marks and is prepared for final finishing or detailed analysis. Skipping grits can result in inefficient polishing, as finer grits are not designed to remove deep scratches left by a much coarser grit efficiently. This approach not only wastes time but can also lead to residual scratches that are difficult, if not impossible, to remove later, compromising the quality of the sample’s finish.
Cleaning Between Stages
Cleaning between each stage of grit progression is critical to maintaining the integrity of the sample’s surface. Each change in grit can potentially introduce cross-contamination if the sample and work area are not properly cleaned, leading to the embedding of coarse abrasive particles on a finer polishing stage. Such contamination can cause unexpected scratches, adversely affecting the final finish and potentially skewing analysis results. To prevent this, thoroughly clean the sample and the work area after using each grit. Use a soft brush and a stream of clean water or an appropriate cleaning fluid to remove all particles from the surface of the sample. Additionally, wipe down the equipment and change or clean the water or coolant used in wet polishing to ensure it is free of suspended abrasive particles from the previous stages. This thorough cleaning process helps ensure that each polishing stage effectively refines the surface without the interference of remnants from previous steps.
6. Post-Polishing Care
Inspection
The inspection phase is a critical component of the post-polishing process. Once the final polishing stage is completed, a thorough examination of the sample under appropriate lighting or using a microscope is essential. This inspection should focus on ensuring that the surface of the sample meets all specified criteria for smoothness and is free from any defects that could impact subsequent analyses or applications. Look for uniformity in the finish and the absence of residual scratches that could indicate inadequate polishing or contamination during earlier stages. If any imperfections are detected, it may be necessary to revisit earlier polishing steps or adjust the polishing parameters to achieve the desired finish.
Cleaning
Proper cleaning after polishing is crucial not only for preserving the integrity of the sample but also for maintaining the longevity and performance of the polishing equipment. Residues from polishing compounds and silicon carbide particles can adhere to both the sample and equipment, potentially causing cross-contamination in future uses or damaging sensitive components of the equipment.
To effectively remove these residues, use a soft, lint-free cloth or a suitable cleaning agent that does not react with the sample material. For the equipment, ensure all surfaces that came into contact with the silicon carbide paper and the sample are thoroughly cleaned. Use compressed air, solvents, or specialized cleaning solutions designed for laboratory equipment to ensure no abrasive particles are left behind. Additionally, regularly check and maintain the cleaning tools themselves, as these can also accumulate residues that might lead to contamination.
7. Maintenance and Storage
Abrasive Care
Proper care of silicon carbide paper is crucial for extending its usability and maintaining its effectiveness. After use, if the paper is intended for reuse, it should be cleaned gently to remove any accumulated debris and residues. This can be done using a soft brush or a clean, dry cloth to brush away particles without damaging the abrasive surface. For more thorough cleaning, a mild solvent or water may be used, depending on the type of backing and adhesive. Once cleaned, the paper should be allowed to dry completely before storage.
In terms of storage, silicon carbide paper should be kept either flat or gently rolled. Avoid folding the paper, as this can create creases that compromise its flatness and lead to uneven polishing results in future uses. If rolling the paper for storage, use a wide diameter roll to prevent kinking and ensure the paper remains smooth.
Storage Conditions
The environment in which silicon carbide paper is stored can significantly affect its longevity and performance. To preserve the adhesive and abrasive properties of the paper, store it in a cool, dry place. Exposure to high humidity can cause the backing to warp or the adhesive to weaken, leading to detachment of the abrasive grains. Similarly, high temperatures can soften the adhesive, potentially causing it to become tacky or to degrade prematurely.
It’s also advisable to keep the paper away from direct sunlight. UV light can degrade some adhesives and backing materials, reducing the overall lifespan of the abrasive paper. Storing the paper in an environment-controlled room or cabinet is ideal to prevent such damage and ensure the paper maintains its effectiveness for as long as possible.
9. Disposal
Proper disposal of used silicon carbide paper is essential for minimizing its environmental impact. Users must adhere to local environmental regulations specific to their area when disposing of used abrasive materials. These regulations often categorize waste into different types, such as hazardous or non-hazardous, and dictate specific disposal methods and designated facilities for each category.
Before considering disposal, explore any available recycling options. Some components of silicon carbide paper, particularly the backing material, may be recyclable depending on their composition. Local waste management services can provide information on whether they offer recycling programs for abrasive materials and the requirements for participation. Recycling used abrasives can significantly reduce waste and contribute to resource conservation.
Additionally, users should seek ways to minimize the environmental impact of their activities. This can be achieved by extending the life of silicon carbide paper through proper usage and maintenance, thereby reducing the frequency of its replacement. Choosing abrasive products that feature recyclable or biodegradable components can also help. When purchasing new abrasives, opting for products manufactured through environmentally friendly practices can further support
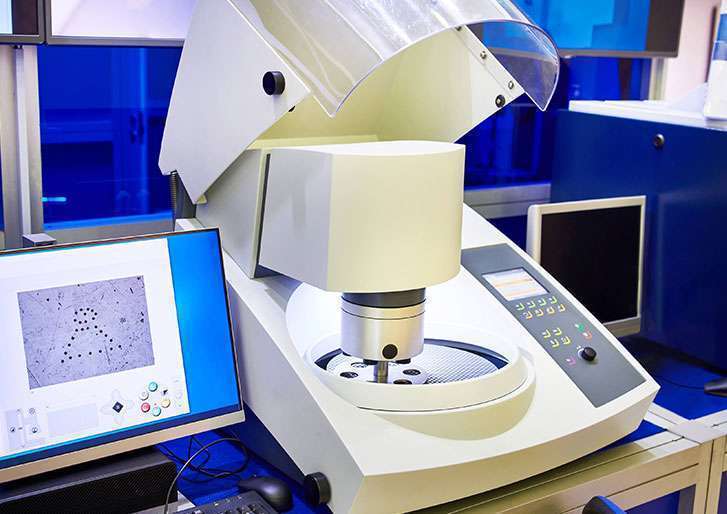
SMART CUT® Silicon Carbide Abrasive Paper is available in various formats including discs, sheets, and rolls. These are designed to meet diverse tooling and user preferences and are compatible with industry standards. With its extended lifespan and ability to produce consistent results, SMART CUT® abrasive paper offers a cost-effective solution for laboratories that prioritize high reproducibility
Ideal for both academic and industrial applications, SMART CUT® Silicon Carbide Abrasive Paper ensures that each metallographic analysis begins with a well-prepared sample, setting the stage for accurate and successful microscopic evaluations. SMART CUT® Silicon Carbide is available in both plain and pressure-sensitive adhesive (PSA) backing. Please note that custom specifications and additional sizes, hole diameters, and grit sizes are available upon request. The listed grit sizes adhere to USA standards, with a range from 60 to 1200 (European FEPA size P60 to P4000). These are available in common diameters of 8 inches (200mm), 10 inches (250mm), and 12 inches (300mm) as detailed in our specifications. Compare to BUEHLER, STRUERS, LECO & Others. Why pay more?
Advantages:
- High Level of Compatibility: Can be used on all grinding and polishing machines such as BUEHLER, STRUERS, LECO & many others
- Fast Material Removal: They offer quicker stock removal due to the softer bond.
- Consistency: Maintains uniformity in scratch pattern, crucial for reliable and repeatable results.
- Durability: The robust backing material resists tearing and shredding, adding to the product’s longevity and cost-effectiveness.
- Premium Silicon Carbide: Utilizes superior quality, micro-graded silicon carbide that provides faster cutting action and reduces heat build-up, which is critical for maintaining the metallurgical integrity of the specimen.
- Waterproof Bonding: The waterproof resin bond not only enhances the durability of the paper but also prevents disintegration in wet applications, ensuring extended usability and consistent performance.
- Flexible Backing: The flexible C-weight paper backing accommodates contoured surfaces without compromising the integrity of the abrasive surface, making it ideal for complex sample shapes.
- Pressure Sensitive Adhesive (PSA) Options: Available with or without PSA backing, offering ease of use and quick changes between grits, significantly reducing preparation time in successive grinding stages.
- Cost-Effective: Long lifespan and enhanced durability reduce the need for frequent replacements, offering greater value over time.
- Uniform Results: The precision engineering behind the grain distribution ensures that each piece of paper delivers consistent performance, crucial for laboratories where reproducibility is paramount.
Diameter & Type |
Diameter & Type |
---|---|
12in (300mm) - PSA Back |
ANSI |
60 |
120 |
180 |
240 |
320 |
FEPA |
P60 |
P120 |
P180 |
P280 |
P400 |
Micron (est.) |
268 |
120 |
78 |
52 |
35 |
Table of Comparison
Silicon Carbide Backing
Comparison table including a column for Tri-tab PSA-backed abrasive discs, which highlights their distinct features relative to plain-backed, regular PSA-backed, and foil or polyester plastic-backed discs:
Feature/Backing Type |
Plain-Backed (Non-Adhesive) |
PSA (Pressure Sensitive Adhesive) |
Foil or Polyester Plastic Backing |
Tri-tab PSA |
---|---|---|---|---|
Adhesion Method |
Requires mechanical fastening |
Self-adhesive, sticks directly |
Typically self-adhesive |
Self-adhesive with easy-tab removal |
Ease of Use |
Less convenient for quick changes |
Very convenient for quick changes |
Very convenient for quick changes |
Enhanced convenience with easy tabs |
Flexibility |
More flexible, good for contours |
Less flexible than plain-backed |
Least flexible, very durable |
Less flexible than plain-backed |
Durability |
Moderate durability |
High durability |
Highest durability |
High durability |
Common Applications |
Hand sanding, delicate surfaces |
Automated machines, quick swaps |
High-stress environments, precision tasks |
Quick change environments, automated machines |
Surface Suitability |
Suitable for varied surfaces |
Best for flat surfaces |
Best for hard, flat surfaces |
Best for flat surfaces |
Cost |
Generally less expensive |
More expensive due to adhesive |
Most expensive due to material |
Slightly more expensive than regular PSA due to tabs |
Removability/Reusability |
Can be reused with new fastening |
Single use, as adhesive may weaken |
Single use, as adhesive may weaken |
Easier to remove, single use |
Environmental Considerations |
Easier to recycle |
Least easy to recycle |
Less easy to recycle |
Less easy to recycle |
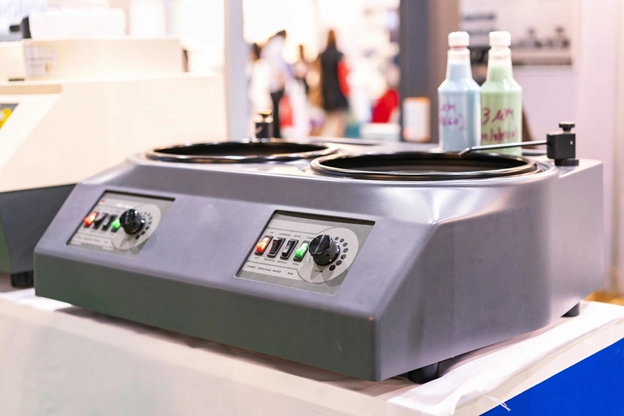
How to choose the right backing for Silicon Carbide Grinding Paper
Plain-backed abrasive papers are generally the most affordable option for grinding and polishing tasks. However, they necessitate the use of either double-sided adhesive or a paper-holding ring for attachment. One significant drawback of using a paper-holding ring is that it restricts the mounted specimen from extending over the edge of the grinding paper. This limitation often results in uneven wear of the abrasive surface, leading to over-grinding of the mount away from the sample. Such uneven material removal can produce a crescent-shaped artifact on the edge of the specimen, commonly referred to as “mooning” or MRD (Material Removal Differential). This artifact can significantly impact the analysis and integrity of the specimen’s edges.
PSA-backed or adhesive-backed papers are removal grinding papers and represent a more costly alternative to plain-backed and foil-backed papers. Their design, which allows for secure and uniform adhesion, greatly simplifies usage and effectively mitigates issues associated with “mooning” and MRD. These papers facilitate consistent grinding across both the center and edges of the papers, ensuring more uniform material removal and reducing the likelihood of edge artifacts.
Foil-backed or polyester-backed grinding papers combine ease of use with economic advantages. They typically employ a receiver adhesive disk that securely holds the paper in place. This disk can be washed and reused, thereby extending the life of the abrasive system. While these papers are more cost-effective than their PSA-backed counterparts, they still provide a reliable attachment that helps avoid uneven wear and the resultant problems seen with plain-backed papers. Additionally, their robust backing material adds a layer of durability, making them suitable for more intensive or longer grinding sessions.
Comparison Table for 8" Diameter
SMART CUT® Silicon Carbide Discs-Plain Backing to Buehler, Struers, & Lco
Grit Size |
Our Item Number |
Buehler Item No |
Struers Item No |
LECO Item No |
---|---|---|---|---|
60 grit |
30-08-0060 |
PAPZO-60 |
810-217-300 |
|
80 grit |
PAPZO-80 |
|||
120 grit |
30-08-0120 |
PAPZO-120 |
810-219-300 |
|
240 grit |
30-08-0240 |
810-223-300 |
||
400 grit |
30-08-0400 |
810-227-300 |
||
600 grit |
6053002 |
30-08-0600 |
810-229-300 |
|
800 grit |
6053004 |
30-08-0800 |
4040-0010 |
810-035-100 |
1000 grit |
6053006 |
30-08-1000 |
4040-0011 |
|
1200 grit |
6053008 |
30-08-1200 |
4040-0012 |
810-036-100 |
Comparison Table for 10" Diameter
Silicon Carbide Discs-Plain Backing to Buehler, Struers, & Lco
Grit Size |
Our Item Number |
Buehler Item No |
Struers Item No |
LECO Item No |
---|---|---|---|---|
60 grit |
30-10-0060 |
PAPZI-60 |
812-374-300 |
|
120 grit |
30-10-0120 |
PAPZI-120 |
812-375-300 |
|
240 grit |
30-10-0240 |
812-377-300 |
||
400 grit |
30-10-0400 |
812-379-300 |
||
600 grit |
6055002 |
30-10-0600 |
812-380-300 |
|
800 grit |
6055004 |
30-10-0800 |
4040-0071 |
812-217-200 |
1000 grit |
6055006 |
30-10-1000 |
4040-0072 |
|
1200 grit |
6055008 |
30-10-1200 |
4040-0073 |
812-219-200 |
Comparison Table for 12" Diameter
Silicon Carbide Discs-Plain Backing to Buehler, Struers, & Lco
Grit Size |
Our Item Number |
Buehler Item No |
Struers Item No |
LECO Item No |
---|---|---|---|---|
60 grit |
30-12-0060 |
PAPZU-600 |
810-291-300 |
|
120 grit |
30-12-0120 |
PAPZE-120 |
810-292-300 |
|
240 grit |
30-12-0240 |
810-294-300 |
||
400 grit |
30-12-0400 |
810-296-300 |
||
600 grit |
6057002 |
30-12-0600 |
810-297-300 |
|
800 grit |
6057004 |
30-12-0800 |
4040-0034 |
|
1000 grit |
6057006 |
30-12-1000 |
4040-0035 |
|
1200 grit |
6057008 |
30-12-1200 |
4040-0036 |
Comparison Table for 8" Diameter
Silicon Carbide Discs-PSA Adhesive Backing
Grit Size |
Our Item Number |
Buehler Item No |
Struers Item No |
LECO Item No |
---|---|---|---|---|
60 grit |
6052001 |
30-08-0060 |
PAPZO-60 |
810-259-300 |
80 grit |
PAPZO-80 |
|||
120 grit |
6052003 |
30-08-0120 |
PAPZO-120 |
810-261-300 |
240 grit |
6052006 |
30-08-0240 |
PAPZO-240 |
810-265-300 |
400 grit |
6052010 |
30-08-0400 |
810-269-300 |
|
600 grit |
30-08-0600 |
810-034-500 |
||
800 grit |
30-08-0800 |
810-033-100 |
||
1000 grit |
30-08-1000 |
|||
1200 grit |
30-08-1200 |
810-034-100 |
Comparison Table for 10" Diameter
Silicon Carbide Discs-PSA Adhesive Backing
Grit Size |
Our Item Number |
Buehler Item No |
Struers Item No |
LECO Item No |
---|---|---|---|---|
60 grit |
6054001 |
30-10-0060 |
PAPZI-60 |
812-367-300 |
80 grit |
PAPZI-80 |
|||
120 grit |
6054003 |
30-10-0120 |
PAPZI-120 |
812-368-300 |
240 grit |
6054006 |
30-10-0240 |
812-370-300 |
|
400 grit |
6054010 |
30-10-0400 |
812-372-300 |
|
600 grit |
30-10-0600 |
812-373-300 |
||
800 grit |
30-10-0800 |
|||
1000 grit |
30-10-1000 |
|||
1200 grit |
30-10-1200 |
Comparison Table for 12" Diameter
Silicon Carbide Discs-PSA Adhesive Backing
Grit Size |
Our Item Number |
Buehler Item No |
Struers Item No |
LECO Item No |
---|---|---|---|---|
60 grit |
6056001 |
30-12-0060 |
PAPZU-600 |
810-245-300 |
120 grit |
6056003 |
30-12-0120 |
PAPZE-120 |
810-247-300 |
240 grit |
6056006 |
30-12-0240 |
PAPZE-240 |
810-251-300 |
400 grit |
6056010 |
30-12-0400 |
810-255-300 |
|
600 grit |
6057002 |
30-12-0600 |
810-257-300 |
|
800 grit |
6057004 |
30-12-0800 |
||
1000 grit |
6057006 |
30-12-1000 |
||
1200 grit |
6057008 |
30-12-1200 |
SMART CUT® Premium Silicon Carbide Grinding Discs PSA Back, (Pressure Sensitive Adhesive)
8" (203mm)– Package of 100 pcs
Showing 1 – 10 of 10 results Showing all 10 results Showing the single result No results found
Sort by
Filters Sort results
Reset Apply
Image | Item No: | Description | Unit | Price | Quantity | Add to cart |
---|---|---|---|---|---|---|
SMART CUT® Premium SiC Grinding Discs, PSA back, 260 microns… | pkg/100 | $129.00 | Max: Min: 1 Step: 1 | |||
SMART CUT® Premium SiC Grinding Discs, PSA back, 200 microns… | pkg/100 | $0.00 | Max: Min: 1 Step: 1 | |||
SMART CUT® Premium SiC Grinding Discs, PSA back, 125 microns… | pkg/100 | $99.00 | Max: Min: 1 Step: 1 | |||
SMART CUT® Premium SiC Grinding Discs, PSA back, 80 microns… | pkg/100 | $99.00 | Max: Min: 1 Step: 1 | |||
SMART CUT® Premium SiC Grinding Discs, PSA back, 52 microns… | pkg/100 | $99.00 | Max: Min: 1 Step: 1 | |||
SMART CUT® Premium SiC Grinding Discs, PSA back, 40 microns… | pkg/100 | $99.00 | Max: Min: 1 Step: 1 | |||
SMART CUT® Premium SiC Grinding Discs, PSA back, 30 microns, 400… | pkg/100 | $99.00 | Max: Min: 1 Step: 1 | |||
SMART CUT® Premium SiC Grinding Discs, PSA back, 15 microns… | pkg/100 | $99.00 | Max: Min: 1 Step: 1 | |||
SMART CUT® Premium SiC Grinding Discs, PSA back, 10 microns… | pkg/100 | $129.00 | Max: Min: 1 Step: 1 | |||
SMART CUT® Premium SiC Grinding Discs, PSA back, 5 microns… | pkg/100 | $129.00 | Max: Min: 1 Step: 1 |
SMART CUT® Premium Silicon Carbide Grinding Discs Plain Back
8" (203mm)– Package of 100 pcs
Showing 1 – 10 of 10 results Showing all 10 results Showing the single result No results found
Sort by
Filters Sort results
Reset Apply
Image | Item No: | Description | Unit | Price | Quantity | Add to cart |
---|---|---|---|---|---|---|
SMART CUT® Premium SiC Grinding Discs, Plain back, 260 microns… | pkg/100 | $99.00 | Max: Min: 1 Step: 1 | |||
SMART CUT® Premium SiC Grinding Discs, Plain back, 125 microns… | pkg/100 | $61.00 | Max: Min: 1 Step: 1 | |||
SMART CUT® Premium SiC Grinding Discs, Plain back, 40 microns… | pkg/100 | $61.00 | Max: Min: 1 Step: 1 | |||
SMART CUT® Premium SiC Grinding Discs, Plain back, 5 microns… | pkg/100 | $99.00 | Max: Min: 1 Step: 1 | |||
SMART CUT® Premium SiC Grinding Discs, Plain back, 200 microns… | pkg/100 | $99.00 | Max: Min: 1 Step: 1 | |||
SMART CUT® Premium SiC Grinding Discs, Plain back, 80 microns… | pkg/100 | $61.00 | Max: Min: 1 Step: 1 | |||
SMART CUT® Premium SiC Grinding Discs, Plain back, 52 microns… | pkg/100 | $61.00 | Max: Min: 1 Step: 1 | |||
SMART CUT® Premium SiC Grinding Discs, Plain back, 30 microns… | pkg/100 | $61.00 | Max: Min: 1 Step: 1 | |||
SMART CUT® Premium SiC Grinding Discs, Plain back, 15 microns… | pkg/100 | $61.00 | Max: Min: 1 Step: 1 | |||
SMART CUT® Premium SiC Grinding Discs, Plain back, 10 microns… | pkg/100 | $99.00 | Max: Min: 1 Step: 1 |
SMART CUT® Premium Silicon Carbide Grinding Discs PSA Back
10" (254mm) – Package of 100 pcs
Showing 1 – 10 of 10 results Showing all 10 results Showing the single result No results found
Sort by
Filters Sort results
Reset Apply
Image | Item No: | Description | Unit | Price | Quantity | Add to cart |
---|---|---|---|---|---|---|
SMART CUT® Premium SiC Grinding Discs, PSA back, 200 microns… | pkg/100 | $180.00 | Max: Min: 1 Step: 1 | |||
SMART CUT® Premium SiC Grinding Discs, PSA back, 80 microns… | pkg/100 | $135.00 | Max: Min: 1 Step: 1 | |||
SMART CUT® Premium SiC Grinding Discs, PSA back, 40 microns… | pkg/100 | $135.00 | Max: Min: 1 Step: 1 | |||
SMART CUT® Premium SiC Grinding Discs, PSA back, 15 microns… | pkg/100 | $135.00 | Max: Min: 1 Step: 1 | |||
SMART CUT® Premium SiC Grinding Discs, PSA back, 260 microns… | pkg/100 | $180.00 | Max: Min: 1 Step: 1 | |||
SMART CUT® Premium SiC Grinding Discs, PSA back, 125 microns… | pkg/100 | $140.00 | Max: Min: 1 Step: 1 | |||
SMART CUT® Premium SiC Grinding Discs, PSA back, 52 microns… | pkg/100 | $135.00 | Max: Min: 1 Step: 1 | |||
SMART CUT® Premium SiC Grinding Discs, PSA back, 30 microns… | pkg/100 | $135.00 | Max: Min: 1 Step: 1 | |||
SMART CUT® Premium SiC Grinding Discs, PSA back, 10 microns… | pkg/100 | $180.00 | Max: Min: 1 Step: 1 | |||
SMART CUT® Premium SiC Grinding Discs, PSA back, 5 microns… | pkg/100 | $180.00 | Max: Min: 1 Step: 1 |
SMART CUT® Premium Silicon Carbide Grinding Discs Plain Back
10" (254mm) – Package of 100 pcs
Showing 1 – 10 of 10 results Showing all 10 results Showing the single result No results found
Sort by
Filters Sort results
Reset Apply
Image | Item No: | Description | Unit | Price | Quantity | Add to cart |
---|---|---|---|---|---|---|
SMART CUT® Premium SiC Grinding Discs, Plain back, 260 microns… | pkg/100 | $130.00 | Max: Min: 1 Step: 1 | |||
SMART CUT® Premium SiC Grinding Discs, Plain back, 125 microns… | pkg/100 | $110.00 | Max: Min: 1 Step: 1 | |||
SMART CUT® Premium SiC Grinding Discs, Plain back, 40 microns… | pkg/100 | $100.00 | Max: Min: 1 Step: 1 | |||
SMART CUT® Premium SiC Grinding Discs, Plain back, 5 microns… | pkg/100 | $139.00 | Max: Min: 1 Step: 1 | |||
SMART CUT® Premium SiC Grinding Discs, Plain back, 200 microns… | pkg/100 | $110.00 | Max: Min: 1 Step: 1 | |||
SMART CUT® Premium SiC Grinding Discs, Plain back, 80 microns… | pkg/100 | $100.00 | Max: Min: 1 Step: 1 | |||
SMART CUT® Premium SiC Grinding Discs, Plain back, 52 microns… | pkg/100 | $100.00 | Max: Min: 1 Step: 1 | |||
SMART CUT® Premium SiC Grinding Discs, Plain back, 30 microns… | pkg/100 | $100.00 | Max: Min: 1 Step: 1 | |||
SMART CUT® Premium SiC Grinding Discs, Plain back, 15 microns… | pkg/100 | $100.00 | Max: Min: 1 Step: 1 | |||
SMART CUT® Premium SiC Grinding Discs, Plain back, 10 microns… | pkg/100 | $139.00 | Max: Min: 1 Step: 1 |
SMART CUT® Premium Silicon Carbide Grinding Discs PSA Back
12" (305mm) – Package of 100 pcs
Showing 1 – 10 of 10 results Showing all 10 results Showing the single result No results found
Sort by
Filters Sort results
Reset Apply
Image | Item No: | Description | Unit | Price | Quantity | Add to cart |
---|---|---|---|---|---|---|
SMART CUT® Premium SiC Grinding Discs, PSA back, 200 microns… | pkg/100 | $230.00 | Max: Min: 1 Step: 1 | |||
SMART CUT® Premium SiC Grinding Discs, PSA back, 80 microns… | pkg/100 | $195.00 | Max: Min: 1 Step: 1 | |||
SMART CUT® Premium SiC Grinding Discs, PSA back, 40 microns… | pkg/100 | $185.00 | Max: Min: 1 Step: 1 | |||
SMART CUT® Premium SiC Grinding Discs, PSA back, 15 microns… | pkg/100 | $185.00 | Max: Min: 1 Step: 1 | |||
SMART CUT® Premium SiC Grinding Discs, PSA back, 260 microns… | pkg/100 | $230.00 | Max: Min: 1 Step: 1 | |||
SMART CUT® Premium SiC Grinding Discs, PSA back, 125 microns… | pkg/100 | $205.00 | Max: Min: 1 Step: 1 | |||
SMART CUT® Premium SiC Grinding Discs, PSA back, 52 microns… | pkg/100 | $185.00 | Max: Min: 1 Step: 1 | |||
SMART CUT® Premium SiC Grinding Discs, PSA back, 30 microns… | pkg/100 | $185.00 | Max: Min: 1 Step: 1 | |||
SMART CUT® Premium SiC Grinding Discs, PSA back, 10 microns… | pkg/100 | $230.00 | Max: Min: 1 Step: 1 | |||
SMART CUT® Premium SiC Grinding Discs, PSA back, 5 microns… | pkg/100 | $230.00 | Max: Min: 1 Step: 1 |
SMART CUT® Premium Silicon Carbide Grinding Discs Plain Back
12" (305mm) – Package of 100 pcs
Showing 1 – 10 of 10 results Showing all 10 results Showing the single result No results found
Sort by
Filters Sort results
Reset Apply
Image | Item No: | Description | Unit | Price | Quantity | Add to cart |
---|---|---|---|---|---|---|
SMART CUT® Premium SiC Grinding Discs, Plain back, 260 microns… | pkg/100 | $160.00 | Max: Min: 1 Step: 1 | |||
SMART CUT® Premium SiC Grinding Discs, Plain back, 125 microns… | pkg/100 | $130.00 | Max: Min: 1 Step: 1 | |||
SMART CUT® Premium SiC Grinding Discs, Plain back, 40 microns… | pkg/100 | $120.00 | Max: Min: 1 Step: 1 | |||
SMART CUT® Premium SiC Grinding Discs, Plain back, 5 microns… | pkg/100 | $160.00 | Max: Min: 1 Step: 1 | |||
SMART CUT® Premium SiC Grinding Discs, Plain back, 200 microns… | pkg/100 | $160.00 | Max: Min: 1 Step: 1 | |||
SMART CUT® Premium SiC Grinding Discs, Plain back, 80 microns… | pkg/100 | $120.00 | Max: Min: 1 Step: 1 | |||
SMART CUT® Premium SiC Grinding Discs, Plain back, 52 microns… | pkg/100 | $120.00 | Max: Min: 1 Step: 1 | |||
SMART CUT® Premium SiC Grinding Discs, Plain back, 30 microns… | pkg/100 | $120.00 | Max: Min: 1 Step: 1 | |||
SMART CUT® Premium SiC Grinding Discs, Plain back, 15 microns… | pkg/100 | $120.00 | Max: Min: 1 Step: 1 | |||
SMART CUT® Premium SiC Grinding Discs, Plain back, 10 microns… | pkg/100 | $160.00 | Max: Min: 1 Step: 1 |
Premium Silicon Carbide Grinding Discs PSA Back, 8" (203mm)
(pressure sensitive adhesive) – package of 25 pcs
Showing 1 – -1 of 12 results Showing all 12 results Showing the single result No results found
Sort by Price low to high
Filters Sort results
Reset Apply
Image | PROD# | Description | UNIT | Quantity | Get Quote |
---|---|---|---|---|---|
Premium SiC Grinding Discs, PSA back, 260 microns, 60 grit… | pkg/25 | Max: Min: 1 Step: 1 | |||
Premium SiC Grinding Discs, PLAIN back, 260 microns, 60 grit… | pkg/25 | Max: Min: 1 Step: 1 | |||
Premium SiC Grinding Discs, PSA back, 200 microns, 80 grit… | pkg/25 | Max: Min: 1 Step: 1 | |||
Premium SiC Grinding Discs, PLAIN back, 200 microns, 80 grit… | pkg/25 | Max: Min: 1 Step: 1 | |||
Premium SiC Grinding Discs, PSA back, 125 microns, 120 grit… | pkg/25 | Max: Min: 1 Step: 1 | |||
Premium SiC Grinding Discs, PSA back, 80 microns, 180 grit… | pkg/25 | Max: Min: 1 Step: 1 | |||
Premium SiC Grinding Discs, PSA back, 52 microns, 240 grit… | pkg/25 | Max: Min: 1 Step: 1 | |||
Premium SiC Grinding Discs, PSA back, 40 microns, 320 grit… | pkg/25 | Max: Min: 1 Step: 1 | |||
Premium SiC Grinding Discs, PSA back, 30 microns, 400 grit… | pkg/25 | Max: Min: 1 Step: 1 | |||
Premium SiC Grinding Discs, PSA back, 15 microns, 600 grit… | pkg/25 | Max: Min: 1 Step: 1 | |||
Premium SiC Grinding Discs, PSA back, 10 microns, 800 grit… | pkg/25 | Max: Min: 1 Step: 1 | |||
Premium SiC Grinding Discs, PSA back, 5 microns, 1200 grit… | pkg/25 | Max: Min: 1 Step: 1 |
Premium Silicon Carbide Grinding Discs PSA Back, 8" (203mm)
(pressure sensitive adhesive) – package of 100 pcs
Showing 1 – -1 of 10 results Showing all 10 results Showing the single result No results found
Sort by Price low to high
Filters Sort results
Reset Apply
Image | PRODUCT | Description | UNIT | Quantity | Get Quote |
---|---|---|---|---|---|
Premium SiC Grinding Discs, PSA back, 260 microns, 60 grit… | pkg/25 | Max: Min: 1 Step: 1 | |||
Premium SiC Grinding Discs, PSA back, 200 microns, 80 grit… | pkg/25 | Max: Min: 1 Step: 1 | |||
Premium SiC Grinding Discs, PSA back, 125 microns, 120 grit… | pkg/25 | Max: Min: 1 Step: 1 | |||
Premium SiC Grinding Discs, PSA back, 80 microns, 180 grit… | pkg/25 | Max: Min: 1 Step: 1 | |||
Premium SiC Grinding Discs, PSA back, 52 microns, 240 grit… | pkg/25 | Max: Min: 1 Step: 1 | |||
Premium SiC Grinding Discs, PSA back, 30 microns, 400 grit… | pkg/25 | Max: Min: 1 Step: 1 | |||
Premium SiC Grinding Discs, PSA back, 30 microns, 400 grit… | pkg/25 | Max: Min: 1 Step: 1 | |||
Premium SiC Grinding Discs, PSA back, 15 microns, 600 grit… | pkg/25 | Max: Min: 1 Step: 1 | |||
Premium SiC Grinding Discs, PSA back, 10 microns, 800 grit… | pkg/25 | Max: Min: 1 Step: 1 | |||
Premium SiC Grinding Discs, PSA back, 5 microns, 1200 grit… | pkg/25 | Max: Min: 1 Step: 1 |
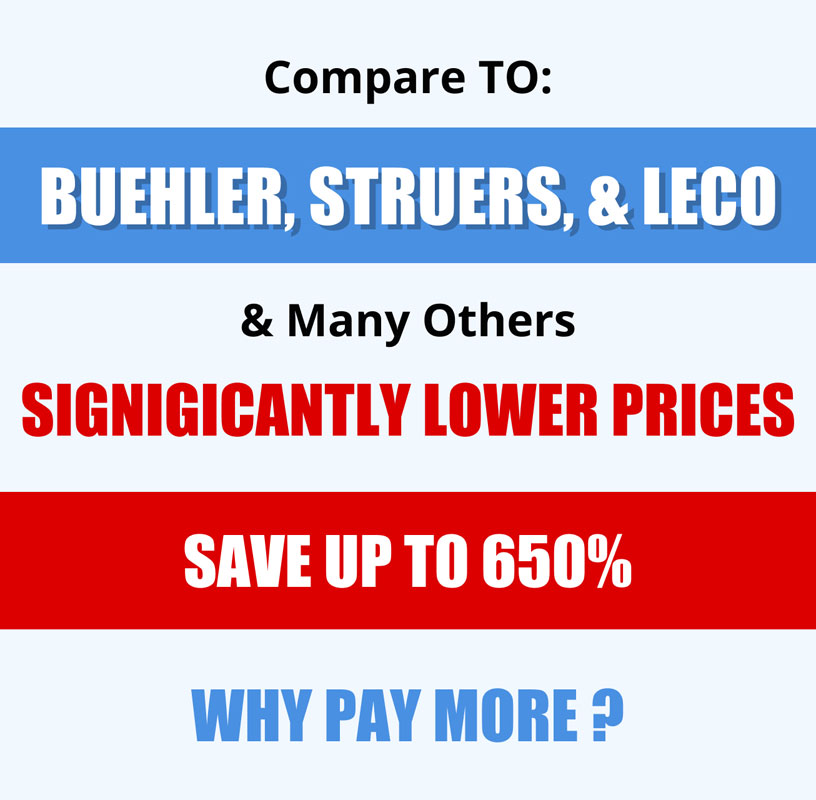
Why Choose SMART CUT® Silicon Carbide Paper?
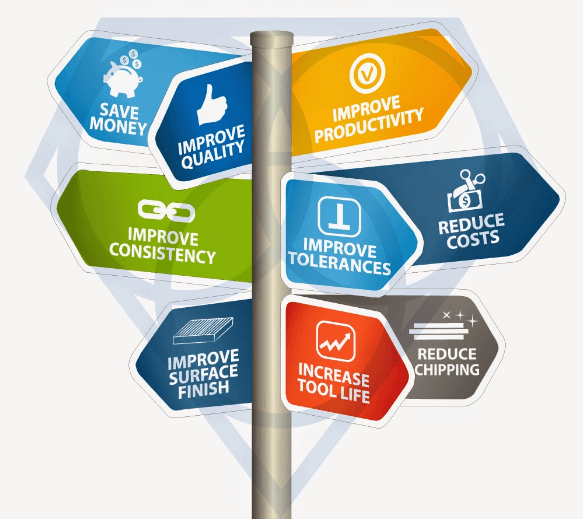
- Unmatched Selection For Many Applications
- Unmatched Technical Support & Expertise
- Superior Quality & Consistency
- Super Technology & innovation
- Immediate Worldwide Delivery
- American Based Manufacturer
-
Custom
Manufacturing - Better Value manufacturer Direct Price
Related Products
Metal Bond Diamond Discs
Metal Bond Diamond Discs, have diamond particles held firmly in place on a rigid backing by electroplated erosion resisting nickel for maximum bond strength and heat dissipation. A hard nickel alloy is used to rigidly bond a layer of sharp, blocky diamond to a steel backing. The sharp diamond particles cut cleanly with no edge rounding. Diamond Laps / Metal Bond Diamond Grinding Discs radically reduce the time required for material lapping/grinding process. Metal bond diamond grinding discs are available with either magnetic or PSA backing.
Resin Bond Diamond Discs
Resin Bond Discs are designed removal of material/sample scratches, chips. high spots, & as well as pre-polishing on a larger variety of materials. Using a propriety technique, a high concentration of premium diamond is loaded onto each disc to provide an extremely aggressive grinding rate yet leaves an exceptionally smooth surface finish. Each disc is color coded to easily determine the diamond size of the disc. These resin bond diamond discs are guaranteed to out-perform many cloth polishing discs using loose conventional abrasive or diamond compound/slurry finishing systems. Depending on the application and process these discs on average will last for 100-200 parts/samples & maintain consistent level of performance. These are perfect for hard materials such as metals, ceramics, refractories, cement, geological rocks, glass, optics, composites, and many other materials 35 and up Rockwell C scale of hardness. All discs come with a 3M pressure-sensitive adhesive backing that bonds to backing plates, or with magnetic backing to attach to steel plates. Must be used with coolant. Not recommended for heavy stock material removal
Diamond Suspensions
UKAM Industrial Superhard Tools offers a wide range of water-based and oil-based diamond suspensions, tailored to the requirements of specific applications. Our ready-to-use diamond suspensions combine micron diamond sizes graded at the highest level of precision with chemical formulations engineered to offer excellent material removal rate and surface quality. Diamond suspensions are used in various industries for lapping and polishing of hard materials.
Recently Viewed Products
ARE YOU USING RIGHT SILICON CARBIDE PAPER
FOR YOUR APPLICATION?
LET US
HELP YOU
HAVING ISSUES WITH
YOUR CURRENT SILICON CARBIDE PAPER?
Knowledge Center
02
Jun
Diamond vs CBN (cubic boron nitride) Tools
Cubic Boron Nitride (CBN) is a synthetic material that is renowned for its exceptional hardness and high thermal stability. It is composed of boron and nitrogen atoms arranged in a crystal lattice structure, similar to...
02
Jun
Discover the Right Diamond Powder for Your Application: Choosing Between Monocrystalline and Polycrystalline Diamonds
Which to use for your application?
Diamond shape plays a significant role in the effectiveness of polishing solutions, affecting both the polishing rate and the quality of the final finish. Understanding the differences between monocrystalline and...
02
Jun
Comparing Two Different Cutting Methods (Low Speed Saw vs. Wire Saw)
Share this Article with Friend or Colleague
For metallography, sample preparation, materials research and working with large variety of materials, selecting the optimal cutting technology is crucial for achieving high-quality results across various materials and applications....
11
Jun
Selecting the Right Diamond Suspension for your Application – Monocrystalline or Polycrystalline?
Choosing the correct diamond suspension, whether monocrystalline or polycrystalline, significantly impacts the quality and efficiency of the polishing and material removal processes. Understanding the properties and applications of both types of suspensions can help you...
17
Jun
Improve Sample Quality & Optimize your Polishing Operating for Metallography & Sample Preparation
Polishing is important step in metallography & sample preparation for revealing the true microstructure of materials, including grain boundaries, phases, and inclusions, which provide insights into material properties and history. This guide is designed to...
26
Jun
Optimize your Grinding Operation for Metallography & Sample Preparation
Share this Article with Friend or Colleague
Grinding is a fundamental mechanical process in metallography that involves removing material from a specimen using hard, abrasive particles. This process is essential for preparing specimens for microscopic...
08
Jul
Low Speed Saw Case Studies
Share this Article with Friend or Colleague
Introduction
In the realm of precision cutting, the SMART CUT® 6005 Low Speed Diamond Saw stands out for its capability to handle a variety of materials with high accuracy. To...
11
Sep
What is the difference between Lapping, Grinding, & Polishing
Some of the major differences include the type and diamond mesh size of diamond discs used, type and size of abrasives used and their holding method. Other factors include RPM’s (speed) used and pressure applied...
30
Jan
Selecting Right Silicon Carbide Paper / Discs for Metallography / Sample Preparation
Selecting the right silicon carbide paper for metallographic sample preparation is important for achieving accurate and reliable results in material analysis. The grinding and polishing process plays a fundamental role in preparing specimens for microscopic...
30
Jan
Upgrading Metallography Grinding with Silicon Carbide Paper
This guide covers the best practices for using silicon carbide paper in metallography. It includes tips on proper grit progression, optimizing pressure and speed settings, preventing common issues, and extending the life of the abrasive....
- Unmatched Selection For Many Applications
- Superior Quality & Consistency
- Immediate Worldwide Delivery
- Technical Support & Expertise
- American Based Manufacturer
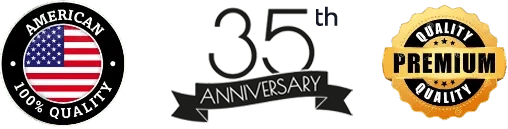

- Different Product
- Different Technology
- Different Company
- Expect MORE from your tools
Let Us HELP You!
Subscribe To Our Newsletter
Signup for email offers, updates, and more
Contact Us
- 25205 & 25201 Avenue Tibbits Valencia CA 91355 USA
-
Phone : (661) 257-2288
FAX : (661) 257 -3833 - lel@ukam.com
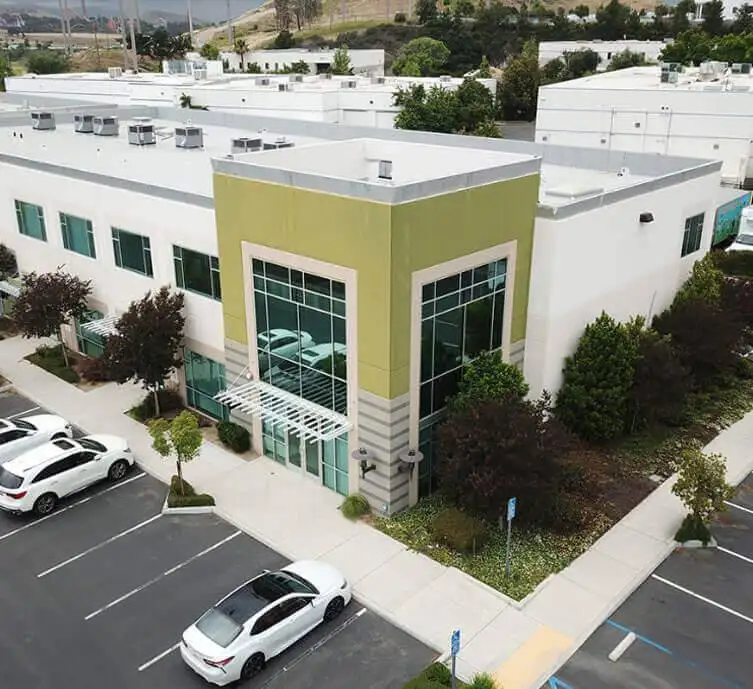
UKAM Industrial Superhard Tools is a U.S. High Technology, Specialty Diamond Tool & Equipment manufacturer. We specialize in producing ultra thin & high precision cutting blades and precision cutting machines diamond drills, diamond micro tools, standard & custom advanced industrial diamond tools and consumables.
- 25205 & 25201 Avenue Tibbits Valencia CA 91355 USA
-
Phone : (661) 257-2288
FAX : (661) 257 -3833 - lel@ukam.com
- 25205 & 25201 Avenue Tibbits Valencia CA 91355 USA
-
Phone : (661) 257-2288
FAX : (661) 257 -3833 - lel@ukam.com
DIAMOND TOOLS BY BOND
EQUIPMENT
KNOWLEDGE CENTER
OUR PRODUCTS
COMPANY
CUSTOMER SERVICE
Shipping Methods


Safe & Secure Payments

© Copyright 1990-2025. UKAM Industrial Superhard Tools – Terms of Use