-
0 items in quote
No products in the Quote Basket.
Metal Bond Diamond Discs
Metal Bond Diamond Discs, have diamond particles held firmly in place on a rigid backing by electroplated erosion resisting nickel for maximum bond strength and heat dissipation. A hard nickel alloy is used to rigidly bond a layer of sharp, blocky diamond to a steel backing. The sharp diamond particles cut cleanly with no edge rounding. Diamond Laps / Metal Bond Diamond Grinding Discs radically reduce the time required for material lapping/grinding process. Metal bond diamond grinding discs are available with either magnetic or PSA backing.
DESCRIPTION
SPECIFICATIONS
FREQUENTLY ASKED QUESTIONS
INDUSTRIES USED IN
ACCESSORIES
USAGE RECOMMENDATION
DESCRIPTION
Metal Bond Diamond Discs, have diamond particles held firmly in place on a rigid backing by electroplated erosion resisting nickel for maximum bond strength and heat dissipation. A hard nickel alloy is used to rigidly bond a layer of sharp, blocky diamond to a steel backing. The sharp diamond particles cut cleanly with no edge rounding. Diamond Laps / Metal Bond Diamond Grinding Discs radically reduce the time required for material lapping/grinding process. Metal bond diamond grinding discs are available with either magnetic or PSA backing.
SPECIFICATIONS
Outisde Diameter: 8″ (200mm), 10″ (250mm), 12″ (300mm)
Thickness: .090″ (2.28mm) to 0.104mm (2.65mm)
Inside Diameter: None (fully impregnated)
Composition: Steel with diamond plated coating, using galvanic method
Diamond Size: 250 to 6 microns
Bond Type: Nickel Bond
Backing: PSA Adhesive, Magnetic
Pressure: 1 to 30 PSI
RPM’s Range: 50 to 5,500
Equipment Used On: Laboratory Grinding & Polishing Machines
FREQUENTLY ASKED QUESTIONS
Metal bond diamond discs are abrasive tools used for grinding and polishing materials. They consist of diamond particles bonded to a metal substrate and are known for their durability and ability to maintain shape.
Selection depends on the material you are processing, the desired surface finish, and the specific requirements of your grinding or polishing machine. Consider the grit size, the hardness of the bond, and whether a PSA or magnetic backing is more suitable for your setup.
PSA (Pressure Sensitive Adhesive) backing allows for the disc to be easily attached and removed from a platen. Magnetic backing uses magnetic force for attachment, offering quick changeover and firm holding during operation.
Yes, metal bond diamond discs are versatile and can be used on a wide range of materials, including metals, ceramics, glass, and composites. The key is to match the disc properties to the material being processed.
RPM recommendations vary based on the material and the disc being used. Harder materials generally require lower RPMs, while softer materials can be processed at higher RPMs. Always start at the lower end of the recommended range and adjust as needed.
Start with low pressure and increase gradually as needed. The amount of pressure depends on the material hardness, the disc’s diamond concentration, and the desired removal rate. Excessive pressure can cause premature wear and sample damage.
Coolant is crucial for preventing overheating, reducing friction, and removing swarf. Water is commonly used, but for certain applications, specific coolants with additives may be necessary. The coolant should be compatible with both the sample and the machine.
Metal bond diamond discs, regardless of the brand, serve the same basic function in grinding and polishing applications for materials research and sample preparation. However, there can be differences performance, and specific features offered by different brands such as Buehler and Struers. Buehler and Struers each have their proprietary methods for bonding the diamond grit to the disc, which can affect the wear rate and how the disc performs over time. From our tests and client feed back our discs are compatible to use on their machines and many others and offer same or similar level of performance at much more attractive price point.
Keep the disc clean, free of debris, and check for wear regularly. Use a suitable dressing stick to expose new diamond particles when necessary. Store discs in a clean, dry place when not in use.
Yes, always wear appropriate personal protective equipment (PPE), ensure that the disc is securely attached to the platen, and follow all machine safety guidelines. Handle coolants responsibly and be aware of any chemical hazards.
Metal bond diamond discs can be reused multiple times until the diamond layer is worn down. The lifespan of the disc depends on the usage conditions, including the pressure, speed, and type of material being processed.
Discs should be disposed of in accordance with local regulations. Some components may be recyclable, so consult with your supplier or local waste management services for guidance.
For support, contact the supplier or manufacturer of the disc. They can provide you with detailed information and assistance tailored to your specific product and application.
The grit size is selected based on the desired surface finish and the stage of the preparation process. Coarser grits are used for initial grinding to quickly remove material, while finer grits are used for polishing to achieve a smooth surface. The material of the sample and the specifics of the research requirement will guide the grit selection.
Metal bond diamond discs offer greater durability, longer life, and superior heat dissipation compared to resin bond discs. They are better suited for heavy grinding where precision and longevity are crucial.
While metal bond diamond discs are versatile, using the same disc for different materials might not be optimal. Material residues can become embedded in the disc, leading to cross-contamination and compromised results. It’s best to use dedicated discs for different material types, especially when purity is a concern.
If the disc is not cutting as expected, it may be glazed or loaded with material. Use a dressing stick to redress the surface, exposing new diamond particles. Also, verify that the machine settings such as speed and pressure are correctly adjusted for your material.
To extend the life of your diamond disc, use the correct RPM, pressure, and coolant for your specific application. Avoid excessive pressures that can cause premature wear and ensure the disc is cleaned and stored properly after use.
Yes, breaking in a new diamond disc can help ensure consistent performance and longevity. This usually involves running the disc at a low pressure with sufficient coolant to expose the initial layer of diamond particles.
The disc should be replaced when you notice a significant drop in performance, such as reduced cutting ability, or when the diamond layer is visibly worn down to the bonding matrix.
Many manufacturers offer custom solutions, allowing you to specify the size, shape, diamond grit size, and concentration to fit your specific needs and equipment.
Magnetic backings provide a strong hold and allow for quick and easy disc changes, which can be advantageous in high-throughput environments. PSA backings are also secure but might require more effort to switch between discs and can leave adhesive residue.
If the material is sensitive to water, alternative coolants or dry grinding techniques may be required. Consult with the disc manufacturer for options suitable for water-sensitive applications.
Performance can be affected by the machine’s capabilities, the operator’s skill, the sample material, the type of coolant used, and environmental factors such as temperature and humidity.
High humidity can affect the adhesive on PSA-backed discs, while extreme temperatures can impact the bond strength and the viscosity of coolants, affecting grinding and polishing efficacy.
They can often be used on various machines as long as the backing is compatible and the machine can accommodate the size and weight of the metal bond discs. However, check with the machine’s manufacturer to ensure compatibility.
To achieve the best surface finish, ensure that you progress through the grit sizes in sequential order without skipping steps. Each successive grit size should effectively remove the scratches from the previous step. Proper lubrication and machine speed, coupled with consistent, light pressure, will contribute to a superior finish.
Single-layer metal bond discs have a single layer of diamond particles that are bonded to the surface, whereas multi-layer discs have multiple layers of diamonds that become exposed as the disc wears down, providing a longer-lasting solution. The choice between the two depends on the specific application and longevity requirements.
Extreme temperatures can affect the thermal expansion of the metal disc and the sample, which may lead to changes in tension and, consequently, variations in performance. It’s essential to maintain a stable temperature, especially when working with precision parts.
Yes, metal bond diamond discs are suitable for both manual and automated systems. Ensure that the discs are compatible with your equipment and that you follow the manufacturer’s guidelines for the best results.
Diamond disc loading can be mitigated by using ample coolant to flush away debris, periodic dressing of the disc surface to clear embedded particles, and adjusting the pressure and speed to prevent material from clogging the disc.
Store metal bond diamond discs in a cool, dry place away from direct sunlight and extremes of temperature. Ensure that magnetic-backed discs are stored with a protective cover to prevent the magnetic surface from collecting metal debris.
Wear can be measured by visually inspecting the disc for diamond grit exposure and checking the disc profile for uniformity. Some laboratories may use precise measurement tools to gauge disc thickness and compare it against the disc’s original specifications.
Always adhere to safety guidelines, which include wearing appropriate PPE such as eye protection, gloves, and hearing protection. Ensure that the machine guards are in place and that the disc is securely attached to the machine. Never exceed the maximum recommended speed for the disc.
Minor damage or glazing can often be repaired through proper dressing. However, significant damage to the bonding matrix or diamond layer usually means the disc needs to be replaced.
Grinding and polishing can generate airborne particles that may be hazardous if inhaled. Always use appropriate dust extraction systems and consider wearing a respirator in addition to other PPE. Regularly clean the work area to minimize the accumulation of dust.
Develop standard operating procedures (SOPs) for the use of diamond discs that include specific guidelines for machine settings, pressure, speed, and coolant flow. Train all operators to follow these SOPs closely and implement regular quality checks to monitor results.
The concentration of diamond affects the aggressiveness and longevity of the disc. Higher concentrations can provide a faster material removal rate and longer disc life, while lower concentrations might be better for finer, more controlled material removal.
When transitioning, take into account that metal bond diamond discs will behave differently in terms of cutting action and lifespan. Adjust your processes gradually and document any changes in outcomes to fine-tune your approach for optimal results.
Yes, when transitioning from coarser to finer grits, you typically need to reduce the pressure to prevent overloading the finer disc. Finer grits are often used for lighter, more precise finishing work.
Ensure the disc is properly secured before beginning your work. With PSA backing, apply even pressure to avoid air bubbles, which can compromise adhesion. With magnetic backing, clean both the disc and the platen to ensure a strong magnetic bond.
Diamond discs can be recycled in many cases, as the diamond can be reclaimed and the metal substrate recycled. Always check with the manufacturer or local waste management services for recycling or disposal guidelines.
Surface contaminants can reduce the effectiveness of the cutting action by clogging the abrasive surface of the disc. It’s crucial to keep both the workpiece and the disc clean to maintain performance.
What are the best practices for documenting the usage of diamond discs for quality control purposes?
Record the usage time, material type, speeds, pressures, and any noticeable wear or performance changes of the disc. This information can help predict the lifespan of the disc and assist in maintaining consistent results.
Softer bonds are usually better for harder materials because they wear away more quickly, which continuously exposes fresh diamond. Harder bonds are suitable for softer materials as they hold the diamonds longer and resist wear.
Dry grinding requires careful monitoring as it can lead to overheating of the workpiece and the disc. Use intermittent grinding techniques, such as short passes with cooling intervals, to prevent heat buildup.
Yes, they can be used on both ferrous and non-ferrous materials. However, care must be taken when switching between material types to avoid cross-contamination.
Use uniform, light pressure, and avoid excessive heat buildup. Following proper grinding and polishing sequences with the appropriate disc types also helps prevent sample deformation.
While sufficient coolant is necessary, excessive use can lead to a slurry that might impede the grinding process, reduce the effectiveness of the diamond cutting action, and cause small samples to be washed away from the holder.
Diamond pull-out can happen if the bond is too weak or if the disc is used under extreme conditions. Ensure you are using the disc within the recommended parameters and that the bond hardness is appropriate for the material being processed.
Vibration can lead to uneven wear and a suboptimal finish on the workpiece. Ensure the equipment is well-maintained and that the disc is correctly balanced and mounted.
For precision applications, maintaining consistent process control is vital. This includes careful monitoring of speeds, pressures, and coolant flow, as well as frequent inspections of the disc for wear and damage.
Maintain flatness by using a low to moderate, consistent force and ensure the sample is evenly supported. Utilize a specimen holder if available and make regular checks for flatness during the process, adjusting your technique as necessary.
Yes, cleaning the disc after each use prevents cross-contamination and maintains the disc’s cutting efficiency. Use a soft brush and a mild detergent or a specially designed cleaner to remove any debris, then rinse with water if the disc material allows, and dry it thoroughly.
Uneven wear can be corrected with a dressing stick or by conditioning the disc on a flattening plate. Regularly check the disc surface for wear patterns and address them early to prolong disc life and maintain performance.
Continuous surface discs provide smoother finishes and are typically used for fine grinding or polishing, while interrupted surface discs are used for rapid material removal and where heat dissipation is critical.
The orientation can affect the material removal rate and the surface finish. For anisotropic materials, the direction of grinding and polishing should be considered to prevent preferential material removal.
Verify that the disc is correctly and securely attached to the platen, check the machine for any defects, ensure there are no loose parts, and confirm that the coolant supply is functioning properly.
For conductive materials, there’s usually no effect, but when processing semiconductors or electronic materials, one must consider the potential for static buildup and ensure proper grounding and static dissipation methods are in place.
Some discs can be reconditioned by relapping the diamond surface or by reapplying a new layer of diamond. Check with the manufacturer for refurbishing services.
Downforce is typically calculated based on the machine settings, taking into account the area of the disc and the applied pressure. Review your equipment’s manual for specific instructions on how to calculate and adjust the force.
An incorrect pH level can cause premature wear of the metal bond or even corrosion. It’s important to use a coolant with a pH level recommended by the disc and equipment manufacturer.
A well-graded particle size distribution often leads to more consistent cutting action and can help with the longevity of the disc, whereas a narrow distribution might be used for specific finishing requirements.
When transitioning, ensure that the previous abrasive’s scratches are completely removed by the new abrasive. Clean the sample thoroughly to prevent cross-contamination, and adjust machine settings according to the type of disc being used.
Signs that a disc may be nearing the end of its life include a significant drop in cutting or grinding efficiency, visible wear on the disc surface, or the exposure of the disc’s core material. Consistently poor surface finishes on samples can also be an indicator.
If contamination is an issue, it might be necessary to switch to a disc with a different metal bond that doesn’t react with the material being worked on, or use a different type of abrasive disc entirely.
Metal bond diamond discs can be used with specialized equipment, including ultrasonic or vibration-assisted machines, but always consult the machine’s manufacturer to ensure compatibility. These machines may require discs with specific properties for optimal performance.
Oxidation can be a concern for metal bonds at high temperatures, which can be caused by high-speed friction. Use appropriate coolant and operating speeds to manage temperature and prevent oxidation.
Edge rounding can be mitigated by using proper sample support and ensuring the disc does not overhang the sample’s edges. Adjusting the machine’s settings to a lower speed and less pressure around the edges may also help.
Very soft materials require a gentle approach with fine grit and low pressure to avoid embedding, while very hard materials might need coarser grits and more pressure to be effective. In both cases, the bond hardness and diamond concentration must be appropriate for the material.
Depending on the degree of wear, a disc might be repurposed for pre-grinding or coarse grinding applications where precision is less critical.
Maintaining parallelism is crucial for uniform material removal and to avoid sample tilting or uneven wear of the disc. Use precision mounting and regularly check and calibrate your machine to maintain parallelism.
Since metal bond diamond discs contain industrial diamonds and potentially other metals, they may be classified as special waste. Always check with local environmental regulations for proper disposal or recycling methods.
The grit profile affects how the diamond interacts with the material. Blocky grits may provide a more robust cutting action, while elongated or sharper grits might be used for finer finishes but may wear down more quickly.
Improper use can be indicated by premature wear of the disc, excessive heat generation, discoloration of the material being processed, or unusual vibration during operation.
Some discs may require a break-in period where they are used at lower speeds and pressures to condition the diamond surface. Refer to the manufacturer’s instructions for specifics.
Metal bond diamond discs can be used for precision shaping if the machine and the disc specifications are suitable for such tasks. Precision shaping requires control over factors such as depth of cut, feed rates, and the disc’s grit size.
Minimize sub-surface damage by using the correct sequence of grit sizes, ensuring adequate coolant flow, and avoiding excessive pressure. Gradual progression from coarser to finer grits helps prevent deep scratches that can lead to sub-surface damage.
Store metal bond diamond discs in a dry, cool place away from direct sunlight and extreme temperatures. Keep them flat to avoid warping and separate from other discs to prevent contamination or damage to the abrasive surface.
Sintered metal bond diamond discs generally offer a longer life and are suitable for heavy-duty material removal. Electroplated discs usually have a single layer of diamond and are chosen for precise grinding applications where disc profile is critical.
Higher diamond concentrations provide a greater number of cutting points, which can lead to a higher material removal rate and potentially a longer disc life. Lower concentrations might be used for finer finishes or where less aggressive material removal is desired.
For heat-sensitive materials, it’s important to use lower pressures, slower speeds, and a copious amount of coolant to prevent thermal damage. Intermittent grinding with cooling periods can also help manage the temperature.
Manual grinding requires a more careful and controlled approach, with consistent hand pressure and movement. Automatic machines can provide consistent results but should be closely monitored to ensure the settings remain within the recommended range for the disc and material.
Improper mounting can lead to disc slippage, uneven wear, or sample damage. Ensure PSA-backed discs are applied evenly without bubbles, and for magnetic-backed discs, the platen surface should be clean to ensure strong adhesion.
Can I interchange metal bond diamond discs designed for one manufacturer’s equipment with another’s?
While many discs are designed to be interchangeable, it is essential to check compatibility. Differences in platen design, magnetic strength, and other factors can impact the performance and safety of the disc.
Slurry should be removed between steps when changing materials to prevent cross-contamination. Use a dedicated rinse or cleaning station, and consider using a filtration system to manage and recycle the slurry if appropriate.
Check for disc wear, ensure the equipment is functioning properly, verify that the disc is mounted correctly, and inspect for any contamination on the disc or workpiece. Also, review the material removal rates and ensure they align with the disc’s specifications.
Common mistakes include using the wrong grit size, applying excessive pressure, using an incorrect speed, and neglecting the need for proper coolant flow. Additionally, improper mounting can lead to disc slippage or sample damage.
Metal bond discs are more durable with a metal matrix, suited for hard materials and high-pressure applications. Resin bond discs are more flexible, better for polishing, and offer a finer finish but wear down quicker.
Yes, but metal bond discs are optimal for harder materials, while resin bond discs are better for softer or more delicate materials.
Choose metal bond discs for heavy grinding due to their durability and ability to withstand high pressure.
Not typically; they are more prone to heat damage and might require lower speeds, especially if a high-quality surface finish is needed.
Metal bond discs generally last longer than resin bond discs, which may need to be replaced more frequently.
Yes, metal bond discs tend to be more expensive initially but may be more cost-effective over time due to their longevity. Resin bond discs are cheaper but might incur higher costs due to more frequent replacement.
Resin bond discs usually provide a better surface finish and are preferred for final polishing steps.
Yes, both can be used with coolant, which is recommended to improve performance and lifespan.
Diamond discs are embedded with diamond particles, which are the hardest known materials, offering superior grinding efficiency and longevity over other abrasives like silicon carbide or aluminum oxide.
Yes, diamond discs typically outlast other abrasive discs because diamonds maintain their cutting ability longer, leading to less frequent changes and downtime.
Diamond discs can provide an exceptionally fine finish, especially in resin bond form, but the ultimate finish quality also depends on the abrasive grit size and the material being worked on.
Generally, yes. The superior hardness of diamonds allows for quicker material removal, which can speed up the grinding and polishing process.
Diamond discs are versatile and can be used on a wide range of materials, but their cost-effectiveness is higher when used on hard, dense materials that other abrasives might struggle with.
Diamond discs tend to be more expensive initially compared to standard abrasives; however, their longevity and efficiency often lead to lower costs over time.
Not necessarily. The choice depends on specific application needs, including the material to be processed, desired outcome, equipment capabilities, and cost considerations.
Diamond and CBN are close in terms of hardness and performance. However, diamond is unsuitable for use with steel and ferrous metals due to carbon solubility in these materials, where CBN is the preferred abrasive.
Conventional abrasives may be preferred for softer materials, initial rough cutting, or where cost constraints make diamond discs less viable.
Diamond discs are harder and last longer than ceramic abrasives. However, ceramics can be a cost-effective alternative for softer materials or applications where the extreme hardness of diamond is not required.
Avoid using diamond discs with ferrous materials, as carbon from the diamond can dissolve in iron, leading to reduced disc life and possible material contamination.
Often, yes. While the upfront cost is higher for diamond discs, their longevity and efficiency can reduce long-term operational costs.
Safety concerns are generally similar, but always ensure proper handling and adherence to safety guidelines as diamond discs can remove material very quickly.
Other abrasives like silicon carbide or aluminum oxide can be used for precision work, but diamond abrasives often provide greater precision with less effort and time, especially for very hard materials.
Diamond discs often require compatible equipment capable of providing the appropriate speeds, feeds, and coolant flow to optimize their performance and lifespan.
Diamond discs typically require less frequent changes and maintenance, which can save on labor and reduce machine downtime.
The longer lifespan of diamond discs means fewer disc changes and potentially less waste. However, the production impact varies, so consider the manufacturer’s practices for both types of abrasives.
Diamond discs are extremely versatile for a wide range of hard materials. However, other abrasives may be preferred for specific applications, like working with softer materials or when a specific type of finish is required.
Diamond discs should be stored carefully to avoid contamination and damage to the diamond surface. Other abrasives may not require as careful handling, but all abrasives should be stored in a dry, stable environment to maintain their effectiveness.
The process can be more complex due to the need for precise operating conditions to maximize the disc’s life and performance, while other abrasives may offer more flexibility in terms of operating conditions.
Diamond discs often require less aggressive surface preparation since they can effectively grind and polish without needing a roughened surface to begin with. Other abrasives may need a more pronounced texture to achieve efficient material removal.
Diamond discs are not recommended for use on steel and other ferrous materials due to the risk of carbon contamination and reduced effectiveness. In such cases, CBN or other abrasives are more suitable.
Yes, you can switch between different types of discs if the equipment is compatible, but you should always recalibrate and adjust the settings to suit the abrasives you’re using.
Accordion Content
Diamond discs are standard in industries where high precision and efficiency are required, such as in semiconductor, advanced ceramics, and aerospace material processing.
INDUSTRIES USED IN
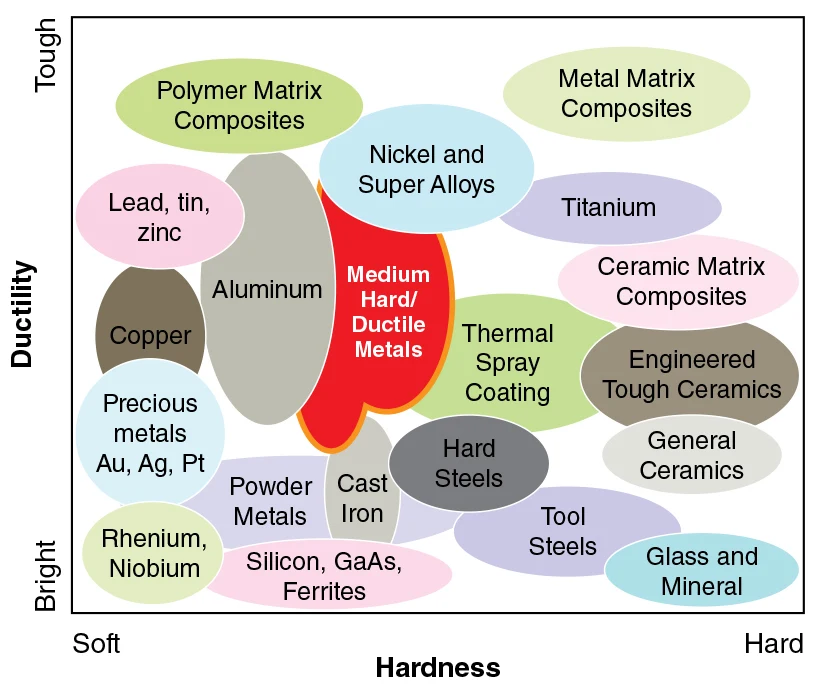

INDUSTRIES USED IN:
- Advanced Ceramics
- Composites
- Glass
- Geology
- Quartz
- Materials Research
- Medical Devices
- Metallography
- Photonics / Optics
- Semiconductor
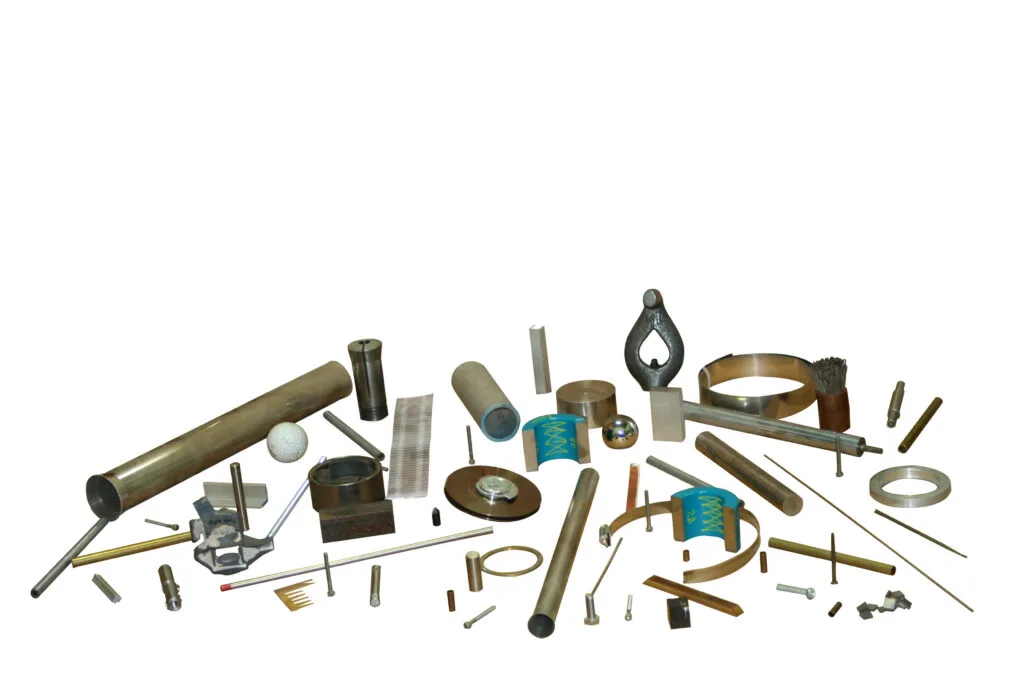
Ferrous & Non-Ferrous Metals:
- Plain Carbon Steels
- Electronic Packages
- Stainless Steels Plastics
- Tool Steels Fasteners
- Aluminum Refractories
- Copper Base Alloys Integrated Circuits
- Magnesium Thermal Spray Coatings
- Titanium Metal Matrix Composites
- Biomedical Wafers
- Petrographic
- PCB.s Ceramics
ACCESSORIES
Showing 1 – -1 of 16 results Showing all 16 results Showing the single result No results found
Sort by Name A – Z
Filters Sort results
Reset Apply
Image | Item No. | Description | Price | Quantity | Add to cart |
---|---|---|---|---|---|
Color: 5/8″-11″ thread. Fits into drill press chuck. Shank adapter threads into 5/8″-11″ female thread of diamond drill. Can be used with any other tool with 5/8″-11″ thread. | $26.72 | Max: Min: 1 Step: 1 | |||
Color: 5/8″-11″ thread. Fits into drill press chuck. Shank adapter threads into 5/8″-11″ female thread of diamond drill. Can be used with any other tool with 5/8″-11″ thread. | $22.46 | Max: Min: 1 Step: 1 | |||
1 Gallon Blue SMART CUT® General Materials Formula Synthetic Water Soluble Coolant | $99.81 | Max: Min: 1 Step: 1 | |||
1 Quart Blue SMART CUT® General Materials Formula Synthetic Water Soluble Coolant | $34.81 | Max: Min: 1 Step: 1 | |||
5 Gallons Blue SMART CUT® General Materials Formula Synthetic Water Soluble Coolant | $317.41 | Max: Min: 1 Step: 1 | |||
55 Gallons Blue SMART CUT® General Materials Formula Synthetic Water Soluble Coolant | $1,745.00 | Max: Min: 1 Step: 1 | |||
1/2″ x 1/2″ x 6.0″ White Recommended for coarser grits found in segment wheels, core drills, or Blanchard grinding. Excellent performance on 120 grit tools. | $8.65 | Max: Min: 1 Step: 1 | |||
1.0″ x 1.0″ x 6.0″ White Recommended for coarser grits found in segment wheels, core drills, or Blanchard grinding. Excellent performance on 120 grit tools. | $15.99 | Max: Min: 1 Step: 1 | |||
1/2″ x 1/2″ x 6.0″ White For use on diamond tools 150 to 220 Grit Size. | $8.65 | Max: Min: 1 Step: 1 | |||
1.0″ x 1.0″ x 6.0″ Black Recommended for use in Diamond Tools 150 Grit Size (mesh size) or finer. | $15.39 | Max: Min: 1 Step: 1 | |||
2.0″ x 2.0″ x 6.0″ Black Recommended for use in Diamond Tools 150 Grit Size (mesh size) or finer. | $39.47 | Max: Min: 1 Step: 1 | |||
1.0″ x 1.0″ x 6.0″ Black Recommended for coarser grits found in segment wheels, core drills, or Blanchard grinding. Excellent performance on 120 grit tools. | $15.99 | Max: Min: 1 Step: 1 | |||
2.0″ x 2.0″ x 6.0″ Black Recommended for coarser grits found in segment wheels, core drills, or Blanchard grinding. Excellent performance on 120 grit tools. | $39.47 | Max: Min: 1 Step: 1 | |||
$154.87 | Max: Min: 1 Step: 1 | ||||
$154.87 | Max: Min: 1 Step: 1 | ||||
$235.00 | Max: Min: 1 Step: 1 |
USAGE RECOMMENDATION
Metal Bond Diamond Disc Usage Recommendations
Metal bond diamond discs are commonly used in sample preparation and materials research for grinding and polishing hard materials such as ceramics, metals, and glass. The two main types of backing for these discs are Pressure-Sensitive Adhesive (PSA) and magnetic. Below are some usage recommendations for both types of backings:
General Recommendations
- 1. Equipment Compatibility Ensure the grinding and polishing machines are compatible with metal bond diamond discs. Check the manufacturer’s specifications for compatibility.
- 2. Disc Selection Select the appropriate grit size of the metal bond diamond disc according to the material and desired finish. Lower grit sizes are for coarse grinding, and higher grit sizes are for fine grinding and polishing.
- 3. Speed and Pressure Adjust the rotational speed and applied pressure according to the disc manufacturer’s recommendations and material being worked on. Excessive speed or pressure can lead to sample overheating, disc wear, or sample damage.
- 4. Coolant Use Use an appropriate coolant to prevent overheating of the material and the disc. This also helps in removing swarf and prolonging the disc’s life.
- 5. Wear Personal Protective Equipment (PPE) Always wear safety glasses, gloves, and other appropriate PPE when operating grinding and polishing machines.
- 6. Disc StorageStore discs in a clean, dry, and cool place to preserve the adhesive and magnetic properties.
PSA Backing Usage Recommendations
- 1. Surface Preparation The platen on the grinding/polishing machine should be clean and free of debris before applying a PSA backed disc to ensure proper adhesion.
- 2. Application Apply the PSA backed disc evenly to the platen to avoid air bubbles, which can cause uneven grinding or polishing.
- 3. Removal Remove the disc carefully to avoid tearing. If the adhesive residue remains on the platen, clean it off to ensure proper adhesion of the next disc.
- 4. Reusability PSA discs are generally single-use; once removed, they may not adhere properly if re-applied.
Magnetic Backing Usage Recommendations
- 1. Compatibility Ensure that the grinding/polishing machine platen is suitable for magnetic discs, i.e., it should be made of a ferromagnetic material to secure the disc in place.
- 2. Application Place the magnetic disc on the platen carefully, ensuring it is properly aligned and flat to avoid any wobble during grinding or polishing.
- 3. Removal Magnetic discs can be easily removed by hand. There is no adhesive to worry about, making switching between grits faster and cleaner.
- 4. Reusability Magnetic discs can be reused multiple times as long as they remain in good condition. Inspect the disc for wear or damage before each use.
For Both Types
- 1. Cleaning Clean the disc after each use to remove any contaminants that could affect future grinding and polishing processes.
- 2. Inspection Regularly inspect the discs for any signs of wear, damage, or degradation. Replace them if they show significant wear or damage.
- 3. Documentation Keep a log of disc usage, including the material worked on, to help predict disc life and plan for replacements.
- 4. Disposal Follow proper disposal procedures for used discs, especially when working with materials that could be hazardous or require special handling.
During Use
- Monitoring Continuously monitor the process for changes in noise, vibration, and disc performance which could indicate issues.
- Progressive Steps When moving from coarser to finer grits, ensure complete removal of scratches from the previous step before proceeding.
- Edge Work: Be cautious when working near the edges of the sample to prevent chipping, especially on brittle materials.
- Wear Patterns: Monitor wear patterns on the discs to identify any issues with machine alignment or balance.
- Usage Log: Keep a detailed usage log with dates, material types, and any operator observations to predict disc lifespan and schedule maintenance or replacement.
- Dressing Tools: Use dressing tools regularly to maintain the condition of the diamond disc surface, especially for magnetic discs, as they are reused more frequently.
- Platen Condition: Regularly check and maintain the flatness and condition of the machine platen, as this can directly affect the performance of the disc.
Monitoring and Adjustment
- Sample Monitoring: Monitor the sample regularly for signs of overheating, such as discoloration or warping.
- Disc Condition: Check the condition of the disc frequently, looking for glazing or clogging, which may require cleaning, dressing, or replacement.
- Process Documentation: Document the parameters used for each material and adjust based on the quality of the outcome to build a knowledge base for your specific applications.
- Real-Time Monitoring: Use real-time monitoring of force, vibration, and acoustic emissions to actively control the grinding/polishing process, making adjustments on-the-fly as necessary.
- Process Simulation: Use simulations to predict the outcomes of different RPMs, pressures, and coolant flows before actual material processing to minimize trial and error.
Post-Use
- Cleaning of Machine: After disc removal, clean the machine’s platen to prevent contamination or damage to the next disc applied.
- Disc Maintenance: After use, clean the disc with a soft brush and appropriate cleaner to remove any remaining particles and coolant that could cause corrosion or clogging.
RPM’s
Usage recommendations for RPM (rotational speed), pressure, and coolant when using metal bond diamond discs in grinding and polishing machines can be quite specific and are often determined by a combination of the machine’s capabilities, the type of material being worked on, and the desired outcome. However, there are some general guidelines you can follow:
RPM (Rotational Speed)
- General Rule: As a general rule, harder materials require slower RPMs, while softer materials can be processed at higher RPMs.
- Fine Polishing: When performing fine polishing, lower speeds are typically recommended to prevent overheating and to provide better control over the finish.
- Initial Grinding: For initial grinding stages, moderate to high speeds can be used to remove material quickly.
- Machine Specifications: Always adhere to the machine manufacturer’s recommended speed settings for different disc diameters and materials.
- Stepwise Refinement: Use a stepwise approach where you start at higher RPMs for rough grinding and reduce speed as you move to finer grits and polishing stages.
- Surface Speed vs. RPM: Remember that the surface speed (often measured in meters per second or feet per minute) is more relevant than RPM. As disc size increases, RPM should decrease to maintain the same surface speed.
- Variable Speed Processing: Use variable speed processing where the machine modulates the RPM based on the stage of grinding or polishing, which may be controlled by programmable logic controllers (PLCs) for precision work.
Specific Recommendations
Here are some starting points for various materials, but these should be adjusted based on actual experience, observations, and manufacturer’s instructions:
- Ceramics: Low to moderate RPM (around 150-300 RPM for coarse grinding), with moderate pressure and ample coolant to prevent cracking.
- Metals: Moderate RPM (about 300-600 RPM for coarse grinding), with variable pressure depending on the hardness of the metal, and significant coolant flow to prevent heat build-up.
- Glass: Low RPM (around 150-300 RPM), with light to moderate pressure, and steady coolant flow to prevent thermal shock and cracking.
Pressure
- Consistent Application: Ensure that pressure is applied consistently and evenly across the sample to prevent uneven wear and potential sample deformation.
- Machine Limitations: Be aware of the limitations of your machine—applying too much pressure can overload the motor and reduce its lifespan.
- Feedback Loops: Utilize machines with feedback loops that adjust pressure automatically in response to the resistance encountered during grinding or polishing.
- Pulsed-Pressure Technique: Experiment with pulsed-pressure techniques, where pressure is cyclically applied and released, to potentially enhance material removal rates and minimize subsurface damage.
Coolant
- Type of Coolant: Water is often used as a coolant, but in some cases, a specific grinding/polishing coolant may be required for better performance or to prevent sample contamination.
- Flow Rate: Ensure an adequate flow rate that is sufficient to cool the disc and the sample, and to remove debris from the cutting/grinding surface.
- Coolant Direction: Direct the coolant flow so that it optimally bathes the area of contact between the disc and the sample.
- Coolant Maintenance: Maintain coolant cleanliness to avoid contamination of the sample or the disc, and change out coolant according to the manufacturer’s recommendations.
- Temperature Control: Ensure the coolant is at a consistent temperature to provide stable working conditions for both the sample and the disc.
- Relevance of Purity: Use deionized or distilled water if purity is a concern, particularly for final polishing stages or when preparing samples for sensitive analytical techniques.
- Distribution: Check the distribution of coolant across the disc surface; it should cover the entire working area evenly.
- Coolant Composition: Investigate and utilize additives in the coolant that can enhance performance, such as rust inhibitors for ferrous materials or surfactants to improve debris removal.
- Coolant Path: Customize the path and nozzles for coolant delivery to ensure it optimally targets the area of contact, especially for complex sample geometries.
About Metal Bond Diamond Discs
Only the highest quality diamonds and raw material is used in manufacturing process. The highest quality standards and consistency are maintained using sophisticated measurement and inspection equipment. Please inquire, we will be happy to accommodate your specific needs. Whatever your application or objectives, UKAM Industrial Superhard Tools can help you get there faster.
Features:
- Firm Bonding: Diamond particles are electroplated onto a rigid steel backing with erosion-resisting nickel for maximum bond strength and heat dissipation.
- Sharp, Blocky Diamonds: Utilizes sharp, blocky diamond particles that maintain clean cuts with no edge rounding.
- Reduced Processing Time: Radically reduces the time needed for material lapping and grinding processes.
- No Deformation: Ensures no deformation during use, maintaining precision and consistency.
- Scratch-Free Performance: Prevents the introduction of scratches on the work material.
- No Pull-Outs: Diamond particles remain firmly in place, eliminating the risk of pull-outs.
- No Foreign Elements: Prevents the introduction of foreign materials into the cutting or grinding process.
- No Smearing: Cuts cleanly without smearing the material.
- Long Tool Life: Provides extended tool life for high-performance use.
- Thermal Stability: Does not cause thermal damage to the workpiece, ensuring precision.
- Available with Two Backing Types: Choose between PSA adhesive backing or magnetic backing.
- Diamond Size Range: Available with diamond sizes from 250 microns to 6 microns.
- Pressure Range: Can be used within a pressure range of 1 to 30 PSI.
- RPM Range: Recommended RPM range of 50 to 5,500.
- Thickness Range: Available in thicknesses from 0.090" (2.28mm) to 0.104" (2.65mm).
- Outside Diameter Options: Available in 8" (200mm), 10" (250mm), and 12" (300mm).
- Laboratory Use: Primarily used with laboratory grinding and polishing machines.
- Nickel Bond: Uses a nickel bond for a robust and consistent bond strength.
- Fully Impregnated: Features a fully impregnated design with no inside diameter.
8" OD Metal Bond Diamond Discs - PSA backing
Showing 1 – -1 of 8 results Showing all 8 results Showing the single result No results found
Sort by Name A - Z
Filters Sort results
Reset Apply
UKAM NO(MAGNETIC BACKING) | IMAGE | MICRON SIZE | MESH SIZE | BUEHLER NO. | STRUERS NO. | LECO NO. | PRICE | Quantity | Add to cart |
---|---|---|---|---|---|---|---|---|---|
6040060 | 250 | 60 | 4080-0025 | $225.00 3pcs: $213.75 ea $202.50 ea $180.00 ea | Max: Min: 1 Step: 1 | ||||
6040061 | 160 | 100 | 40-4948 40-4949 | $218.00 3pcs: $207.10 ea $196.20 ea $174.40 ea | Max: Min: 1 Step: 1 | ||||
6040062 | 125 | 120 | 15-6199 | 4080-0030 | $212.00 3pcs: $201.40 ea $190.80 ea $169.60 ea | Max: Min: 1 Step: 1 | |||
6040063 | 70 | 240 | 15-6170 40-4958 40-4959 | 811-508 | $205.00 3pcs: $194.75 ea $184.50 ea $164.00 ea | Max: Min: 1 Step: 1 | |||
6040064 | 45 | 325 | 15-6145 40-4968 40-4969 | 4080-0027 4080-0069 | 811-510 | $198.00 3pcs: $188.10 ea $178.20 ea $ 158.40 ea | Max: Min: 1 Step: 1 | ||
6040065 | 30 | 600 | 40-4978 40-4979 | $192.81 3pcs: $183.17 ea $173.53 ea $154.25 ea | Max: Min: 1 Step: 1 | ||||
6040066 | 15 | 1200 | 15-6115 40-4988 40-4989 | 080-0028 | 811-511 | $192.81 3pcs: $183.17 ea $173.53 ea $154.25 ea | Max: Min: 1 Step: 1 | ||
6040067 | 9 | 1800 | 15-6109 | 811-512 | $192.81 3pcs: $183.17 ea $173.53 ea $154.25 ea | Max: Min: 1 Step: 1 |
8" OD Metal Bond Diamond Discs - Magnetic Backing
Showing 1 – -1 of 9 results Showing all 9 results Showing the single result No results found
Sort by
Filters Sort results
Reset Apply
UKAM NO (MAGNETIC BACKING) | Image | MICRON SIZE | MESH SIZE | BUEHLER NO. | STRUERS NO. | LECO NO. | Price | Quantity | Add to cart |
---|---|---|---|---|---|---|---|---|---|
6040069 | 250 | 60 | 4080-0025 | $237.00 3pcs: $225.15 ea $213.30 ea $189.60 ea | Max: Min: 1 Step: 1 | ||||
6040070 | 160 | 100 | 40-4948 ⋅ 40-4949 | $230.00 3pcs: $218.50 ea $207.00 ea $184.00 ea | Max: Min: 1 Step: 1 | ||||
6040071 | 125 | 120 | 15-6199 | 4080-0030 | $224.00 3pcs: $212.80 ea $201.60 ea $179.20 ea | Max: Min: 1 Step: 1 | |||
6040072 | 70 | 240 | 15-6170 ⋅ 40-4958 ⋅ 40-4959 | 811-508 | $217.00 3pcs: $206.15 ea $195.30 ea $173.60 ea | Max: Min: 1 Step: 1 | |||
6040073 | 45 | 325 | 15-6145 ⋅ 40-4968 ⋅ 40-4969 | 4080-0027 4080-0069 | 811-510 | $210.00 3pcs: $199.50 ea $189.00 ea $168.00 ea | Max: Min: 1 Step: 1 | ||
6040074 | 30 | 600 | 40-4978 ⋅ 40-4979 | $204.00 3pcs: $193.80 ea $183.60 ea $163.20 ea | Max: Min: 1 Step: 1 | ||||
6040075 | 15 | 1200 | 15-6115 ⋅ 40-4988 ⋅ 40-4989 | 080-0028 | 811-511 | $204.00 3pcs: $193.80 ea $183.60 ea $163.20 ea | Max: Min: 1 Step: 1 | ||
6040076 | 9 | 1800 | 15-6109 | 811-512 | $204.00 3pcs: $193.80 ea $183.60 ea $163.20 ea | Max: Min: 1 Step: 1 | |||
6040077 | 6 | 3000 | 15-6106 | $204.00 3pcs: $193.80 ea $183.60 ea $163.20 ea | Max: Min: 1 Step: 1 |
10" OD Metal Bond Diamond Discs - PSA Backing
Showing 1 – 9 of 9 results Showing all 9 results Showing the single result No results found
Sort by
Filters Sort results
Reset Apply
UKAM NO(MAGNETIC BACKING) | IMAGE | MICRON SIZE | MESH SIZE | BUEHLER NO. | STRUERS NO. | LECO NO. | Price | Quantity | Add to cart |
---|---|---|---|---|---|---|---|---|---|
6040078 | 250 | 60 | 4080-0033 | $240.00 3pcs: $228.00 ea $216.00 ea $192.00 ea | Max: Min: 1 Step: 1 | ||||
6040079 | 160 | 100 | 4080-0034 | $230.00 3pcs: $218.50 ea $207.00 ea $184.00 ea | Max: Min: 1 Step: 1 | ||||
6040080 | 125 | 120 | 15-8199 | $225.00 3pcs: $213.75 ea $202.50 ea $180.00 ea | Max: Min: 1 Step: 1 | ||||
6040081 | 70 | 240 | 15-8170 | $215.00 3pcs: $204.25 ea $193.50 ea $172.00 ea | Max: Min: 1 Step: 1 | ||||
6040082 | 45 | 325 | 51-8145 | 4080-35 | $215.00 3pcs: $204.25 ea $193.50 ea $172.00 ea | Max: Min: 1 Step: 1 | |||
6040083 | 30 | 600 | $215.00 3pcs: $204.25 ea $193.50 ea $172.00 ea | Max: Min: 1 Step: 1 | |||||
6040084 | 15 | 1200 | 15-8115 | 4080-36 | $215.00 3pcs: $204.25 ea $193.50 ea $172.00 ea | Max: Min: 1 Step: 1 | |||
6040085 | 9 | 1800 | 15-8109 | $215.00 3pcs: $204.25 ea $193.50 ea $172.00 ea | Max: Min: 1 Step: 1 | ||||
6040086 | 6 | 3000 | 15-8106 | $215.00 3pcs: $204.25 ea $193.50 ea $172.00 ea | Max: Min: 1 Step: 1 |
10" OD Metal Bond Diamond Discs - Magnetic Backing
Filters Sort results
Reset Apply
UKAM NO(MAGNETIC BACKING) | Image | MICRON SIZE | MESH SIZE | BUEHLER NO. | STRUERS NO. | LECO NO. | PRICE | QUANTITY | Add To Cart |
---|---|---|---|---|---|---|---|---|---|
6040087 | 250 | 60 | 4080-0033 | $255.00 3pcs: $242.25 ea $229.50 ea $203.33 ea | Max: Min: 1 Step: 1 | ||||
6040088 | 160 | 100 | 4080-0034 | $245.00 3pcs: $232.75 ea $220.50 ea $196.00 ea | Max: Min: 1 Step: 1 | ||||
6040089 | 125 | 120 | 15-8199 | $240.00 3pcs: $228.00 ea $216.00 ea $192.00 ea | Max: Min: 1 Step: 1 | ||||
6040090 | 70 | 240 | 15-8170 | $230.00 3pcs: $218.50 ea $207.00 ea $184.00 ea | Max: Min: 1 Step: 1 | ||||
6040091 | 45 | 325 | 51-8145 | 4080-35 | $230.00 3pcs: $218.50 ea $207.00 ea $184.00 ea | Max: Min: 1 Step: 1 | |||
6040092 | 30 | 600 | $230.00 3pcs: $218.50 ea $207.00 ea $184.00 ea | Max: Min: 1 Step: 1 | |||||
6040093 | 15 | 1200 | 15-8115 | 4080-36 | $230.00 3pcs: $218.50 ea $207.00 ea $184.00 ea | Max: Min: 1 Step: 1 | |||
6040094 | 9 | 1800 | 15-8109 | $230.00 3pcs: $218.50 ea $207.00 ea $184.00 ea | Max: Min: 1 Step: 1 | ||||
6040095 | 6 | 3000 | 15-8106 | $230.00 3pcs: $218.50 ea $207.00 ea $184.00 ea | Max: Min: 1 Step: 1 |
12" OD Metal Bond Diamond Discs - PSA Backing
Filters Sort results
Reset Apply
UKAM NO (MAGNETIC BACKING) | IMAGE | MICRON SIZE | MESH SIZE | BUEHLER NO. | STRUERS NO. | LECO NO. | PRICE | QUANTITY | ADD TO CART |
---|---|---|---|---|---|---|---|---|---|
6080060 | 250 | 60 | 4080-0037 | 811-516 | $255.00 3pcs: $242.25 ea $229.50 ea $203.33 ea | Max: Min: 1 Step: 1 | |||
6080061 | 160 | 100 | $240.00 3pcs: $228.00 ea $216.00 ea $192.00 ea | Max: Min: 1 Step: 1 | |||||
6080062 | 125 | 120 | 15-6299 | 4080-0038 | 811-517 | $230.00 3pcs: $218.50 ea $207.00 ea $184.00 ea | Max: Min: 1 Step: 1 | ||
6080063 | 70 | 240 | 15-6270 | 811-518 | $225.00 3pcs: $213.75 ea $202.50 ea $180.00 ea | Max: Min: 1 Step: 1 | |||
6080064 | 45 | 325 | 15-6245 | 4080-0039 | $225.00 3pcs: $213.75 ea $202.50 ea $180.00 ea | Max: Min: 1 Step: 1 | |||
6080065 | 30 | 600 | 811-519 | $225.00 3pcs: $213.75 ea $202.50 ea $180.00 ea | Max: Min: 1 Step: 1 | ||||
6080066 | 15 | 1200 | 15-6215 | 4080-0040 | 811-520 | $225.00 3pcs: $213.75 ea $202.50 ea $180.00 ea | Max: Min: 1 Step: 1 | ||
6080067 | 9 | 1800 | 15-6209 | 811-521 | $225.00 3pcs: $213.75 ea $202.50 ea $180.00 ea | Max: Min: 1 Step: 1 | |||
6080068 | 6 | 3000 | 15-6206 | $225.00 3pcs: $213.75 ea $202.50 ea $180.00 ea | Max: Min: 1 Step: 1 |
12" OD Metal Bond Diamond Discs - Magnetic Backing
Showing 1 – -1 of 9 results Showing all 9 results Showing the single result No results found
Sort by
Filters Sort results
Reset Apply
UKAM NO(MAGNETIC BACKING) | Image | MICRON SIZE | MESH SIZE | BUEHLER NO. | STRUERS NO. | LECO NO. | Price | Quantity | Add to cart |
---|---|---|---|---|---|---|---|---|---|
6080069 | 250 | 60 | 4080-0037 | 811-516 | $270.00 3pcs: $256.50 ea $243.00 ea $216.00 ea | Max: Min: 1 Step: 1 | |||
6080070 | 160 | 100 | $255.00 3pcs: $242.25 ea $229.50 ea $203.33 ea | Max: Min: 1 Step: 1 | |||||
6080071 | 125 | 120 | 15-6299 | 4080-0038 | 811-517 | $245.00 3pcs: $232.75 ea $220.50 ea $196.00 ea | Max: Min: 1 Step: 1 | ||
6080072 | 70 | 240 | 15-6270 | 811-518 | $240.00 3pcs: $228.00 ea $216.00 ea $192.00 ea | Max: Min: 1 Step: 1 | |||
6080073 | 45 | 325 | 15-6245 | 4080-0039 | $240.00 3pcs: $228.00 ea $216.00 ea $192.00 ea | Max: Min: 1 Step: 1 | |||
6080074 | 30 | 600 | 811-519 | $240.00 3pcs: $228.00 ea $216.00 ea $192.00 ea | Max: Min: 1 Step: 1 | ||||
6080075 | 15 | 1200 | 15-6215 | 4080-0040 | 811-520 | $240.00 3pcs: $228.00 ea $216.00 ea $192.00 ea | Max: Min: 1 Step: 1 | ||
6080076 | 9 | 1800 | 15-6209 | 811-521 | $240.00 3pcs: $228.00 ea $216.00 ea $192.00 ea | Max: Min: 1 Step: 1 | |||
6080077 | 6 | 3000 | 15-6206 | $240.00 3pcs: $228.00 ea $216.00 ea $192.00 ea | Max: Min: 1 Step: 1 |
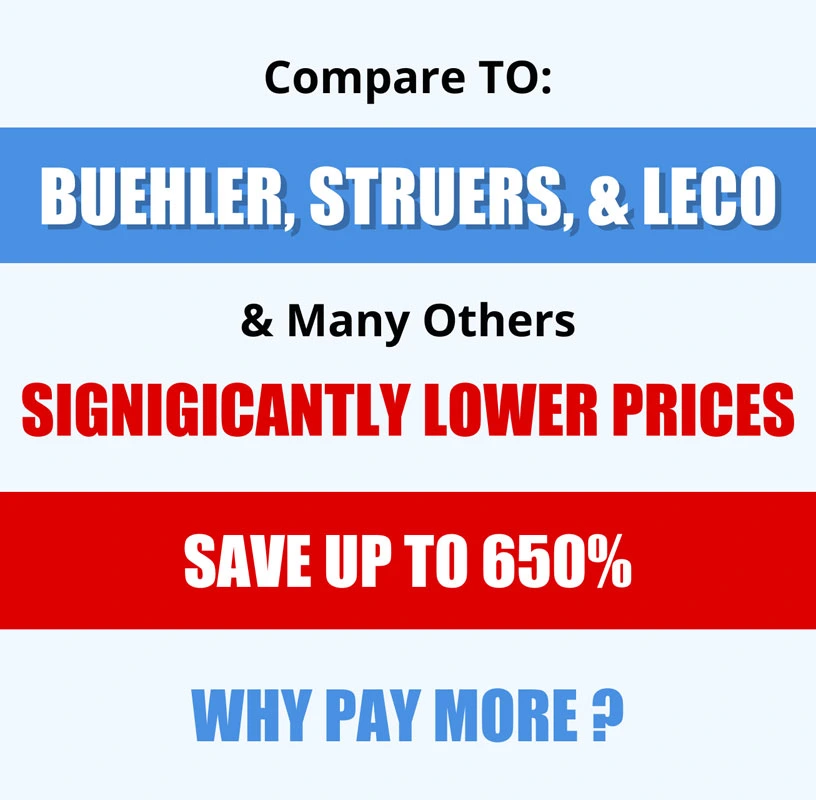
Why Choose Us?
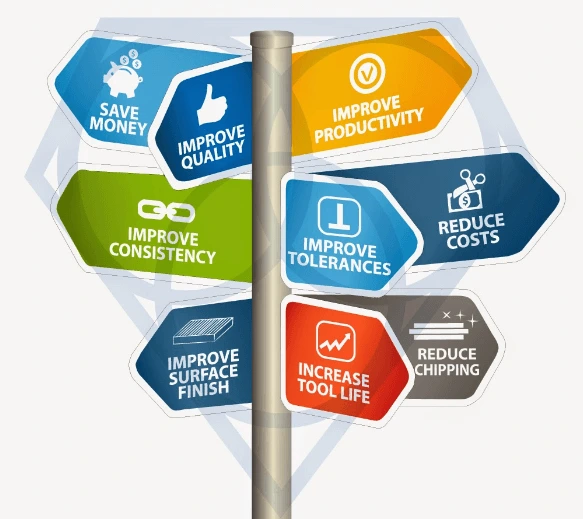
- Unmatched Selection For Many Applications
- Unmatched Technical Support & Expertise
- Superior Quality & Consistency
- Super Technology & innovation
- Immediate Worldwide Delivery
- American Based Manufacturer
-
Custom
Manufacturing - Better Value manufacturer Direct Price
Related Products
Resin Bond Diamond Discs
Resin Bond Discs are designed removal of material/sample scratches, chips. high spots, & as well as pre-polishing on a larger variety of materials. Using a propriety technique, a high concentration of premium diamond is loaded onto each disc to provide an extremely aggressive grinding rate yet leaves an exceptionally smooth surface finish. Each disc is color coded to easily determine the diamond size of the disc. These resin bond diamond discs are guaranteed to out-perform many cloth polishing discs using loose conventional abrasive or diamond compound/slurry finishing systems. Depending on the application and process these discs on average will last for 100-200 parts/samples & maintain consistent level of performance. These are perfect for hard materials such as metals, ceramics, refractories, cement, geological rocks, glass, optics, composites, and many other materials 35 and up Rockwell C scale of hardness. All discs come with a 3M pressure-sensitive adhesive backing that bonds to backing plates, or with magnetic backing to attach to steel plates. Must be used with coolant. Not recommended for heavy stock material removal
Silicon Carbide Paper
SMART CUT® Silicon Carbide Abrasive Paper is meticulously designed for preparing metallographic specimens, incorporating superior silicon carbide grains embedded in a resilient, waterproof backing for both dry and wet grinding. This versatile paper transitions smoothly from coarse cutting to fine polishing, ensuring that specimens are precisely prepared for microscopic analysis.
Diamond Suspensions
UKAM Industrial Superhard Tools offers a wide range of water-based and oil-based diamond suspensions, tailored to the requirements of specific applications. Our ready-to-use diamond suspensions combine micron diamond sizes graded at the highest level of precision with chemical formulations engineered to offer excellent material removal rate and surface quality. Diamond suspensions are used in various industries for lapping and polishing of hard materials.
Recently Viewed Products
ARE YOU USING RIGHT Diamond Discs
FOR YOUR APPLICATION?
LET US
HELP YOU
HAVING ISSUES WITH
YOUR CURRENT Diamond Discs?
Knowledge Center
02
Jun
Diamond vs CBN (cubic boron nitride) Tools
Cubic Boron Nitride (CBN) is a synthetic material that is renowned for its exceptional hardness and high thermal stability. It is composed of boron and nitrogen atoms arranged in a crystal lattice structure, similar to...
02
Jun
Discover the Right Diamond Powder for Your Application: Choosing Between Monocrystalline and Polycrystalline Diamonds
Which to use for your application?
Diamond shape plays a significant role in the effectiveness of polishing solutions, affecting both the polishing rate and the quality of the final finish. Understanding the differences between monocrystalline and...
02
Jun
Comparing Two Different Cutting Methods (Low Speed Saw vs. Wire Saw)
Share this Article with Friend or Colleague
For metallography, sample preparation, materials research and working with large variety of materials, selecting the optimal cutting technology is crucial for achieving high-quality results across various materials and applications....
11
Jun
Selecting the Right Diamond Suspension for your Application – Monocrystalline or Polycrystalline?
Choosing the correct diamond suspension, whether monocrystalline or polycrystalline, significantly impacts the quality and efficiency of the polishing and material removal processes. Understanding the properties and applications of both types of suspensions can help you...
17
Jun
Improve Sample Quality & Optimize your Polishing Operating for Metallography & Sample Preparation
Polishing is important step in metallography & sample preparation for revealing the true microstructure of materials, including grain boundaries, phases, and inclusions, which provide insights into material properties and history. This guide is designed to...
26
Jun
Optimize your Grinding Operation for Metallography & Sample Preparation
Share this Article with Friend or Colleague
Grinding is a fundamental mechanical process in metallography that involves removing material from a specimen using hard, abrasive particles. This process is essential for preparing specimens for microscopic...
08
Jul
Low Speed Saw Case Studies
Share this Article with Friend or Colleague
Introduction
In the realm of precision cutting, the SMART CUT® 6005 Low Speed Diamond Saw stands out for its capability to handle a variety of materials with high...
11
Sep
What is the difference between Lapping, Grinding, & Polishing
Some of the major differences include the type and diamond mesh size of diamond discs used, type and size of abrasives used and their holding method. Other factors include RPM’s (speed) used and pressure applied...
30
Jan
Select the Right Silicon Carbide Paper Discs for Metallography Sample Preparation
Selecting the right silicon carbide paper for metallographic sample preparation is important for achieving accurate and reliable results in material analysis. The grinding and polishing process plays a fundamental role in preparing specimens for microscopic...
30
Jan
Upgrading Metallography Grinding with Silicon Carbide Paper
This guide covers the best practices for using silicon carbide paper in metallography. It includes tips on proper grit progression, optimizing pressure and speed settings, preventing common issues, and extending the life of the abrasive....
- Unmatched Selection For Many Applications
- Superior Quality & Consistency
- Immediate Worldwide Delivery
- Technical Support & Expertise
- American Based Manufacturer
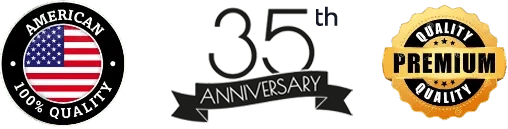

- Different Product
- Different Technology
- Different Company
- Expect MORE from your tools
Let Us HELP You!
Subscribe To Our Newsletter
Signup for email offers, updates, and more
Contact Us
- 25205 & 25201 Avenue Tibbits Valencia CA 91355 USA
-
Phone : (661) 257-2288
FAX : (661) 257 -3833 - lel@ukam.com
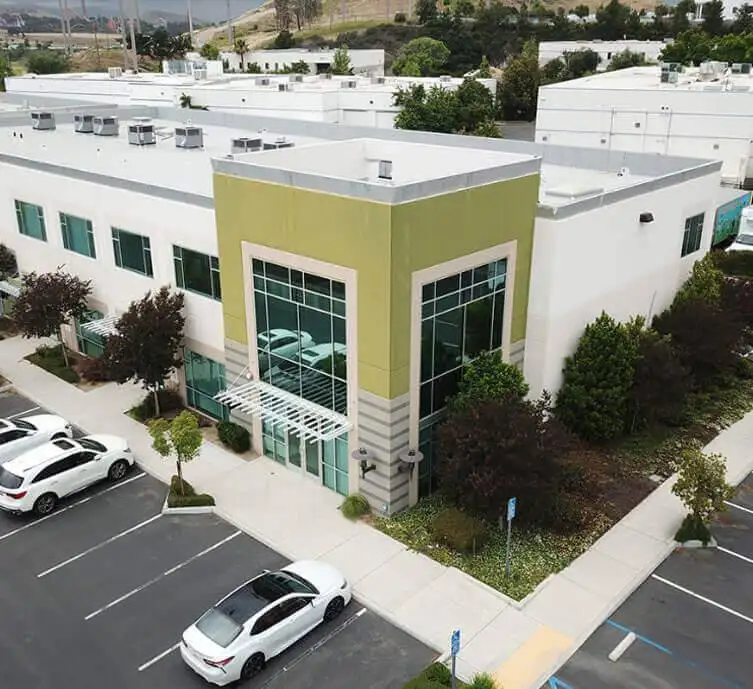
UKAM Industrial Superhard Tools is a U.S. High Technology, Specialty Diamond Tool & Equipment manufacturer. We specialize in producing ultra thin, high precision cutting blades, precision cutting machines diamond drills, diamond micro tools, standard & custom advanced industrial diamond tools and consumables.
- 25205 & 25201 Avenue Tibbits Valencia CA 91355 USA
-
Phone : (661) 257-2288
FAX : (661) 257 -3833 - lel@ukam.com
- 25205 & 25201 Avenue Tibbits Valencia CA 91355 USA
-
Phone : (661) 257-2288
FAX : (661) 257 -3833 - lel@ukam.com
DIAMOND TOOLS BY BOND
EQUIPMENT
KNOWLEDGE CENTER
OUR PRODUCTS
COMPANY
CUSTOMER SERVICE
Shipping Methods


Safe & Secure Payments

© Copyright 1990-2025. UKAM Industrial Superhard Tools – Terms of Use