-
0 items in quote
No products in the Quote Basket.
Diamond Foils
Diamond powders are fully sprayed on the surface of copper foil, this features in longer tool life.
- The diamond foils can be cut to any shape & size easily, and stick on to your own tools, thus a llowing for a whole range of tailored tools.
- Aggressive cutting action and wide range of grit sizes produce fast cutting or polishing on hard steels of any hardness、 tungsten carbides、stones、glass and hard ceramics...etc.
- Other application of diamond foils is to stick on parts of machine to increase the wear resistant and avoid the sliding.
Description
Specifications
Frequently Asked Questions
Industries Used In
Accessories
Recommendations
Description
Tab Content
Specifications
Cutting and Polishing : The foils are suitable for aggressive cutting and polishing actions. They work effectively on hard steels of any hardness, tungsten carbides, stones, glass, and hard ceramics, among others.
Wear Resistance: Another application is to stick these foils on parts of machines to increase wear resistance and prevent sliding.
10 x 100mm: Available in grit sizes #120 to #1800 (Item numbers DF1012 to DF1180).
50 x 100mm: Available in grit sizes #120 to #1800 (Item numbers DF2012 to DF2180)
100 x 100mm: Available in grit sizes #120 to #1800 (Item numbers DF3012 to DF3180).
200 x 200mm: Available in grit sizes #120 to #1800 (Item numbers DF4012 to DF4180).
Frequently Asked Questions
Diamond Foils are specialized cutting and polishing tools made by coating copper foil with diamond powders. These foils are designed for use in various industrial and crafting applications, offering enhanced durability and adaptability. The surface of these foils is fully sprayed with diamond powders, significantly increasing the durability and lifespan of tools. This makes them more resistant to wear and tear, especially in high-wear environments. Yes, they can be easily cut into any shape and size, allowing users to tailor them for specific applications. This adaptability ensures a wide range of customized tools can be created to meet different requirements. Diamond Foils are effective on a variety of hard materials, including hard steels, tungsten carbides, stones, glass, and hard ceramics. Their aggressive cutting action and varying grit sizes make them versatile for different hardness levels and textures. They come in a wide range of grit sizes, accommodating everything from fast cutting to fine polishing needs. This range ensures that users can select the appropriate grit size for their specific material and desired finish. Yes, aside from cutting and polishing, they can be used to increase wear resistance and prevent sliding in machine parts. This application helps in enhancing the longevity and efficiency of machinery. Yes, they are designed for easy application. They can be cut to size and shape as needed and can be stuck onto tools or machine parts without requiring specialized equipment. Diamond Foils are beneficial for professionals in industries like metalworking, glassworking, stoneworking, and ceramics, as well as for hobbyists and craftsmen who require precision cutting and polishing. By increasing the wear resistance and reducing the sliding of machine parts, Diamond Foils contribute to safer working conditions, particularly in industries where machinery is extensively used. Diamond Foils offer superior durability and efficiency compared to many traditional tools. Their diamond powder coating provides a harder and more abrasive surface, which is effective on very hard materials and offers a longer lifespan. Yes, to an extent. While they are designed for durability, the longevity of the foils depends on the usage intensity, material hardness, and proper maintenance. Regular cleaning and proper storage can extend their usability. As with any cutting or polishing tool, it’s important to use Diamond Foils with proper safety gear, including gloves and eye protection. Ensure the foils are securely attached to tools or machines to prevent accidents. Diamond Foils, being reusable and durable, can be considered more environmentally friendly than disposable alternatives. Their long life reduces the need for frequent replacements, thus minimizing waste. While they are primarily designed for hard materials, they can be used on softer materials with caution. It’s important to choose the appropriate grit size and apply gentle pressure to avoid damaging the material. The choice of grit size depends on the material and the desired finish. Lower grit sizes are more abrasive and suitable for rough cutting, while higher grit sizes are better for fine polishing. Testing on a small area first can help determine the best grit size. The technique may vary based on the application, but generally, it involves applying steady pressure and moving the foil in consistent strokes or motions. It’s essential to avoid applying too much pressure, which could damage the tool or the material. After use, clean the foils to remove any debris. Store them flat or in a way that prevents bending or creasing. Keeping them in a dry environment will prevent corrosion of the copper foil. Absolutely. Their ease of use and adaptability make them ideal for various DIY projects, especially those involving hard materials that require precise cutting or fine polishing. yes, we offer custom orders where you can specify the dimensions, grit size, and other features tailored to your specific needs. Contact us for free quote and recommendation : The unique aspect of Diamond Foils is their flexibility and customizability. They can be easily shaped and applied to various tools and surfaces, unlike many rigid diamond-coated tools. This flexibility allows for more specialized and tailored applications. Considering their durability and versatility, Diamond Foils can be highly cost-effective. Their long lifespan reduces the need for frequent replacements, and their adaptability can reduce the need for multiple specialized tools. Yes, they are well-suited for precision engineering applications. Their ability to cut and polish with high accuracy makes them ideal for tasks requiring meticulous attention to detail. While Diamond Foils are versatile, they are best suited for hard materials. Using them on very soft or elastic materials might not be effective and could potentially damage the foil or the material. Their fast cutting and polishing capabilities, combined with their durability, significantly boost efficiency. They reduce the time and effort needed for hard material processing, which can be crucial in industrial settings. Absolutely. Artists and crafters who work with hard materials like glass, ceramics, or hard stones find Diamond Foils useful for shaping, detailing, and finishing their work. Over time and with use, the effectiveness of the diamond coating may gradually diminish. Regular cleaning and proper use can help maintain their performance for a longer period. They should be stored in a clean, dry place to prevent corrosion or damage. Avoiding exposure to extreme temperatures and moisture will also help prolong their life. Yes, they can be used with certain types of automated machinery, especially those designed for cutting, grinding, or polishing. It’s important to ensure that the machinery is compatible with the foils and that proper mounting techniques are used. While Diamond Foils are generally resistant to temperature and humidity changes, extreme conditions can affect their adhesive quality and cutting efficiency. It’s advisable to use and store them in environments with moderate temperature and humidity. Their high abrasive quality and availability in various grit sizes allow for precise material removal and surface finishing, which is crucial in applications requiring high precision. Generally, they are not designed to be resharpened or refurbished. Once the diamond coating wears down, the foil usually needs to be replaced. Used Diamond Foils should be disposed of responsibly due to the metal and diamond content. Recycling or proper waste disposal methods should be followed according to local regulations. The choice depends on the material you’re working with and the desired outcome. Consider the hardness of the material and the type of finish you need. Contact our technical support for assistance Diamond Foils generally have good resistance to many chemicals due to the nature of the diamond coating and copper base. However, exposure to harsh chemicals should be avoided to maintain their integrity. The thickness can impact flexibility and the amount of pressure that can be applied. Thicker foils might offer more durability but less flexibility, while thinner ones may be more suitable for detailed work. Yes, they can be used in aerospace applications, especially for precision machining and finishing of hard materials commonly used in aerospace components. They should be gently cleaned with a soft brush and mild detergent if necessary. Avoid using harsh abrasives that could damage the diamond coating. Proper mounting depends on the tool or machine. Ensure the foil is flat and securely adhered, and follow any specific instructions provided by the manufacturer for mounting. Unused Diamond Foils should be stored in a dry, cool place away from direct sunlight. They should also be kept flat or in a manner that prevents bending or creasing. Yes, they can be a valuable tool for educational purposes, especially in courses related to materials science, engineering, and manufacturing. Their use can provide practical experience in machining and finishing hard materials. Absolutely. Their precision and range of grit sizes make them ideal for cutting, shaping, and polishing various gemstones, a common requirement in the jewelry industry. When using on curved surfaces, it’s important to choose a foil thickness that allows flexibility. Applying even pressure and using a suitable technique for the curvature will yield the best results. Yes, their precision and ability to handle hard materials make them suitable for certain applications in semiconductor manufacturing, such as material shaping and surface finishing. The optimal speed depends on the material and the specific application. Generally, a moderate speed that allows control and precision without generating excessive heat is recommended. While laser cutting offers high precision, Diamond Foils provide a more tactile approach, which can be preferable for certain applications. They are highly efficient for manual or machine-assisted cutting and polishing tasks. Yes, they can be used to refurbish or sharpen old tools, especially if the tool’s material is compatible with the abrasive nature of the diamond coating. Diamond Foils are versatile tools used for grinding and polishing across a wide range of materials. They excel in precision grinding, contouring, surface finishing, and mirror polishing. Diamond Foils offer exceptional material removal capabilities. They can swiftly remove burrs, rough edges, and unwanted protrusions from various surfaces. Yes, Diamond Foils are excellent for precision grinding. Their abrasive nature and the ability to choose the right grit size allow for tight tolerances and exact measurements. Absolutely. Diamond Foils are highly effective in shaping and contouring materials, making them ideal for creating intricate designs or smoothing irregular surfaces. They are valuable for sharpening cutting tools like blades and drill bits. The abrasive surface quickly restores a sharp edge, extending the life of tools. Before painting, coating, or bonding, surfaces often require preparation. Diamond Foils can roughen or smoothen surfaces as needed, ensuring proper adhesion and finishing. Diamond Foils excel at achieving high-quality surface finishes by removing fine scratches, imperfections, and blemishes, leaving a smooth and polished surface. Yes, Diamond Foils with fine grit sizes are employed for mirror polishing, creating glossy, reflective surfaces on materials like metal, glass, or ceramics. Jewelry makers and gemstone enthusiasts use Diamond Foils for polishing gemstones and precious metals, enhancing their luster and brilliance. Diamond Foils are invaluable for glassworkers and ceramic artisans, helping to achieve smooth and clear finishes on glass and ceramics. Yes, they are used to restore the luster of old or damaged surfaces, such as antique furniture, metal sculptures, or valuable items. Diamond Foils are effective for polishing the edges of various materials, providing both aesthetic and functional benefits. Consider selecting the appropriate grit size and technique to achieve the desired result. Starting with coarser grits for material removal and progressing to finer grits for polishing is common practice. Additionally, using the right pressure and lubricants can optimize performance and extend the lifespan of Diamond Foils. Yes, Diamond Foils are versatile and can be used on a wide range of materials, including hard steels, tungsten carbides, stones, glass, ceramics, and more. The grit size determines the level of abrasiveness. Lower grit sizes are coarser and ideal for material removal, while higher grit sizes are finer and suitable for achieving smoother, polished surfaces. The choice of grit size depends on the material and the desired finish. Coarser grits (lower numbers) are used for rough grinding, while finer grits (higher numbers) are used for polishing. It’s essential to test on a small area to determine the best grit size. Yes, Diamond Foils are well-suited for precision engineering applications. Their ability to remove material with high accuracy makes them ideal for tasks requiring meticulous attention to detail. To optimize performance, ensure that the foils are securely mounted on tools or machines. Use appropriate pressure and movements for the specific application, and consider using lubricants or coolants to reduce heat generation and enhance efficiency. Yes, Diamond Foils can be used manually or with machine assistance. They are adaptable to various tool setups and can be employed based on the specific requirements of the task. While Diamond Foils can be used in damp conditions, their effectiveness and adhesion might vary in wet environments. It’s advisable to consult the manufacturer for specific wet application guidelines. After use, clean the Diamond Foils gently to remove debris. Store them flat or in a way that prevents bending or creasing. Keeping them in a dry environment will prevent corrosion of the copper foil. It’s important to use Diamond Foils with proper safety gear, including gloves and eye protection. Ensure that the foils are securely attached to tools or machines to prevent accidents. Additionally, follow standard safety guidelines for grinding and polishing. When using Diamond Foils on softer materials, choose the appropriate grit size and apply gentle pressure to avoid damaging the material. It’s important to exercise caution to prevent excessive material removal. The primary difference lies in the abrasive material. Diamond Foils feature a diamond powder coating, making them exceptionally hard, while abrasive paper uses abrasive grains like aluminum oxide or silicon carbide. Diamond Foils are much harder due to the diamond coating, making them highly effective for grinding and polishing even the hardest materials. Abrasive paper is generally less hard. Diamond Foils offer higher precision and control, especially in precision engineering and applications with tight tolerances, thanks to their abrasive nature and grit size options. Yes, both are versatile, but Diamond Foils are particularly suited for precision tasks like tool sharpening and lapidary work, while abrasive paper is used in woodworking, metalworking, and general sanding. Diamond Foils typically have a longer lifespan, especially when used on hard materials. They are less likely to wear out quickly. Diamond Foils excel at producing fine and smooth surface finishes, often superior to abrasive paper, making them ideal for high-quality finishes. Diamond Foils are used in precision industries such as aerospace, jewelry making, semiconductor manufacturing, and optics, where high precision and quality finishes are essential. Abrasive paper is widely used in woodworking, metal fabrication, automotive bodywork, and general sanding and polishing tasks. Diamond Foils can be used on soft materials, but it’s important to choose the appropriate grit size and apply gentle pressure to prevent excessive material removal. They may perform exceptionally well on softer materials due to their precision. Diamond Foils are generally more expensive than abrasive paper due to the use of diamonds as the abrasive material. However, their longevity and performance often justify the investment for specialized applications. Diamond Foils can be used on curved or irregular surfaces, provided the foil thickness allows flexibility, and the technique adapts to the curvature. Abrasive paper can also conform to curved surfaces, but it might not be as precise as Diamond Foils. Both Diamond Foils and abrasive paper can be used with a variety of machinery and tools, depending on the application. However, the choice of machinery or tools should consider the specific abrasive material and task requirements. Diamond Foils can handle damp conditions, but their performance may vary in wet environments. Abrasive paper is available in wet and dry variants, making it more suitable for wet applications. Both can be used for heavy material removal, but Diamond Foils, especially those with coarser grit sizes, may excel in such applications due to their hardness and cutting power. Diamond Foils consist of a thin copper foil with a diamond powder coating, providing a rigid and flat abrasive surface. Diamond Cloth, on the other hand, is a flexible fabric-like material embedded with diamond abrasive particles. Diamond Cloth is more flexible and can conform to curved or irregular surfaces, while Diamond Foils are relatively rigid due to their copper foil base. Diamond Foils are commonly used for precision grinding, polishing, and finishing tasks where a flat, rigid abrasive surface is required. They find applications in industries like aerospace and electronics. Diamond Foils offer high precision and control, making them ideal for tasks requiring tight tolerances and exact measurements. Diamond Cloth provides good control but may not achieve the same level of precision due to its flexibility. Diamond Foils typically have a longer lifespan, especially when used on hard materials, as they are less likely to wear out quickly. The lifespan of Diamond Cloth may vary depending on the backing material and application. Diamond Foils excel at producing fine and smooth surface finishes, often superior to Diamond Cloth. Diamond Cloth can produce good surface finishes but may not reach the same level of quality. Diamond Foils are preferred in industries requiring precision and high-quality finishing, such as aerospace and optics. Diamond Cloth is versatile and suitable for general-purpose and specialized applications. Diamond grit size refers to the size of the individual abrasive particles (diamonds in Diamond Foil and other minerals in abrasive paper) used for grinding and polishing. It determines the coarseness or fineness of the abrasive material. Both Diamond Foil and abrasive paper offer a wide range of grit sizes, from coarse to fine. The available grit sizes are similar for both products, allowing users to choose the appropriate level of abrasiveness. The grit size numbering system is the same for both Diamond Foil and abrasive paper. Lower grit numbers indicate coarser grit sizes, suitable for heavy material removal, while higher numbers represent finer grit sizes used for surface finishing and polishing. Coarser grit sizes (lower numbers) in both Diamond Foil and abrasive paper are used for aggressive material removal, such as shaping, grinding, and initial stock removal in various applications. Finer grit sizes (higher numbers) are employed for precision grinding, achieving smoother surface finishes, and polishing tasks. They are ideal for applications where a high-quality finish is required. No, both Diamond Foil and abrasive paper use the same grit size numbering system, ensuring consistency in selecting the appropriate grit size regardless of the abrasive material. Yes, users can select from a range of grit sizes in both Diamond Foil and abrasive paper, allowing them to tailor the abrasive material to the material removal and finishing needs of their specific tasks. The choice of grit size directly affects the speed of material removal. Coarser grits (lower numbers) remove material more quickly but may leave a rough surface. Finer grits (higher numbers) remove material more slowly but provide smoother finishes. Coarser grit sizes are commonly used in heavy-duty industries like metal fabrication for rapid stock removal and shaping. They are also used in woodworking for initial sanding of rough surfaces. Finer grit sizes are preferred in applications where a smooth and polished finish is essential, such as in jewelry making, optics, and precision engineering. They are also used in automotive and aerospace industries for surface refinement. Yes, users often progress from coarser to finer grit sizes during a multi-step grinding or polishing process. This approach allows for efficient material removal followed by surface refinement Grit size standards are generally consistent across brands, but variations may exist. It’s advisable to refer to the manufacturer’s specifications and guidelines for precise grit size information. The choice of grit size depends on factors such as material hardness, desired finish, and the amount of material removal required. Manufacturers often provide recommendations for grit selection based on different applications. Diamond Foil is specialized for precision tasks with high control and is ideal for fine finishes. In contrast, diamond discs with metal bond are suited for heavy material removal, while resin bond discs offer versatility for general grinding and polishing across various industries. Diamond Foil is available in a range of grit sizes, from coarse to fine. Coarser grits are used for material removal, while finer grits are for achieving smooth and polished finishes. Diamond Foil is relatively rigid and specialized for precision tasks, while Diamond Film is highly flexible and versatile for various applications. Diamond Film is often used for surface refinement, sharpening, and microfabrication. When selecting the right grit size for Diamond Foil, consider factors such as the material you’re working on, your surface finish requirements, material removal rate, and the level of precision needed. Experimentation and testing can help determine the optimal grit size. Diamond Foil may have a higher initial cost due to the diamond material. However, its longer lifespan, especially on hard materials, can make it cost-effective for precision applications. The cost also depends on the specific project and requirements. Diamond Foil can be used for wet grinding, but its effectiveness may vary depending on the specific product and application. It’s important to consult the manufacturer’s guidelines for wet grinding recommendations. Diamond Foil is commonly used in industries such as aerospace, jewelry making, and optics. It is utilized for tasks like shaping intricate components, polishing jewelry, and achieving high-quality optical surfaces. Diamond Foil generally has a longer lifespan, especially when used on hard materials, compared to resin bond diamond discs, which may require more frequent replacement. Proper maintenance is essential to maximize the lifespan of both products. When disposing of used Diamond Foil and waste materials, it’s important to follow local environmental regulations. Some Diamond Foil products may contain recyclable components, so proper disposal is crucial. Diamond Foil offers several advantages over traditional abrasive materials like sandpaper. It has a longer lifespan, especially on hard materials, leading to reduced replacement frequency. Additionally, Diamond Foil provides high precision and control, making it ideal for tasks that require fine finishes and shaping of intricate components. Yes, Diamond Foil can be used for heavy material removal tasks, especially when using coarser grits. It is versatile and can handle a wide range of material removal requirements, from heavy stock removal to precision finishing. Diamond Foil is known for its ability to achieve excellent surface finishes. It can provide smooth and polished surfaces, making it suitable for applications where surface quality is critical, such as optics and jewelry making. Safety precautions should always be taken when using Diamond Foil. Wear appropriate personal protective equipment (PPE) such as safety glasses, gloves, and, if needed, a dust mask, especially when dry grinding to minimize exposure to dust particles. When wet grinding, follow safety guidelines for handling coolants and lubricants. Some Diamond Foil products can be customized or cut into specific shapes and sizes. If customization is necessary for your application, inquire if this service is available from the manufacturer. Lubrication or coolant is used in wet grinding applications with Diamond Foil to keep the workpiece and Diamond Foil cool, minimize dust, and extend the life of the abrasive. Its usage depends on the specific application and manufacturer recommendations. While Diamond Foil may have a higher initial cost due to the diamond material, its longer lifespan, especially on hard materials, can make it cost-effective in the long run, especially for precision applications. The cost comparison depends on the specific project and requirements. Yes, there are specialty Diamond Foil products designed for unique applications. For example, some products may have an electroplated coating for electrochemical grinding, or hybrid Diamond Foils may be tailored to specific material requirements. Consult with manufacturers for specialized options. When working on edges or corners of workpieces, Diamond Foil should be used with care to avoid excessive pressure that could cause uneven wear or damage. Proper technique and control are essential for achieving desired results in these areas. Yes, Diamond Foil is well-suited for microfabrication and precision work due to its high precision and control. It can shape and finish intricate components with accuracy, making it valuable in industries like optics and electronics.
Certainly! Here are examples of grit sizes and their typical applications:
• Coarse Grit (e.g., 40-80): Used for rapid material removal, shaping, and grinding. Suitable for removing stock from rough surfaces.
• Medium Grit (e.g., 120-240): Ideal for general grinding, smoothing surfaces, and preparing for finer grits.
• Fine Grit (e.g., 320-600): Used for achieving smooth surface finishes and minor material removal
• Very Fine Grit (e.g., 800-1500+): Suited for fine polishing, achieving high-quality finishes, and removing minor imperfections.
Are there specific industries or applications where coarser grit sizes are favored over finer grits?
Industries Used In
Tab Content
Accessories
Recommendations
A tool or equipment to hold and apply the Diamond Foil (e.g., a flat surface, polishing machine, or hand tool).
Lubricant or coolant (optional, for wet grinding).
Inspect the Diamond Foil for any damage or defects before use. Do not use damaged Diamond Foil.
If wet grinding, make sure to use the appropriate coolant or lubricant to keep the Diamond Foil and workpiece cool and to minimize dust.
For machine-based applications, follow the machine’s instructions for mounting the Diamond Foil.
If wet grinding, apply a suitable coolant or lubricant to the workpiece and Diamond Foil surface to keep them cool and minimize dust. Follow manufacturer recommendations for coolant usage.
Gradually progress from coarser to finer grits to achieve the desired finish. Each grit size will refine the surface further.
Start Light: Begin with light pressure. When starting a grinding or polishing task, it’s a good practice to apply minimal pressure to ensure that you have control over the process and to prevent uneven wear of the Diamond Foil.
Progress Gradually: If you are not achieving the desired material removal or surface finish, you can gradually increase the pressure. Increase it in small increments to avoid overloading the Diamond Foil.
Grit Size Matters: Coarser grits (lower numbers) require less pressure for material removal, while finer grits (higher numbers) may benefit from slightly more pressure to achieve desired results.
Material Hardness: Consider the hardness of the material you are working on. Hard materials may require more pressure for effective grinding, while softer materials may require less.
Maintain Control: Always prioritize control and precision. Excessive pressure can lead to uneven wear, overheating, or damage to the workpiece. Maintain a steady and controlled motion.
Experiment and Test: Conduct tests on sample pieces or scrap material to determine the optimal pressure for your specific application. Experimentation and testing can help you find the right balance.
Consult Manufacturer Guidelines: Consult the manufacturer’s guidelines and recommendations for pressure settings specific to the Diamond Foil product you are using. They may provide valuable insights.
Monitor Wear: Periodically check the condition of the Diamond Foil during the grinding or polishing process. If you notice uneven wear or degradation, adjust the pressure or replace the Diamond Foil as needed.
Coolant Delivery System: Ensure you have a proper coolant delivery system in place. This can include a nozzle or sprayer that delivers a controlled stream of coolant to the workpiece and Diamond Foil.
Coolant Flow Rate: Adjust the flow rate of the coolant to provide adequate coverage of the workpiece and Diamond Foil. The flow rate should be sufficient to keep the grinding area wet throughout the process.
Positioning the Nozzle: Position the coolant nozzle or sprayer so that it directs the coolant to the point where the Diamond Foil contacts the workpiece. This ensures effective cooling and lubrication.
Monitor Coolant Temperature: Check the temperature of the coolant regularly. Coolant that becomes too hot can be less effective. If necessary, use a system to maintain the coolant at an appropriate temperature.
Safety Precautions: When using coolant, be aware of safety precautions. Ensure that the work area is safe from electrical hazards, and take precautions to prevent slipping on wet surfaces.
Clean Work Area: After completing the grinding or polishing task, clean the work area and remove any coolant residues. Proper cleanup helps maintain a safe and organized workspace.
Dispose of Coolant Properly: Dispose of used coolant in accordance with local environmental regulations. Some coolants may be recyclable, so consider recycling options if available.
Manufacturer Recommendations: Follow the manufacturer’s recommendations for coolant usage specific to the Diamond Foil product you are using. Different Diamond Foil products may have varying requirements.
Experiment and Adjust: As with other parameters in the grinding and polishing process, be prepared to experiment and adjust the coolant settings to achieve the best results for your specific application.
Equipment Speed Settings: Diamond Foil can be used with various types of equipment, including rotary tools, grinders, and polishing machines. The speed at which you should use Diamond Foil often depends on the capabilities of your equipment. Check the manufacturer’s recommendations for the recommended speed settings for your specific Diamond Foil product.
Material Hardness: The hardness of the material being worked on can influence the speed at which Diamond Foil should be used. Softer materials may require lower speeds, while harder materials may benefit from higher speeds to achieve efficient material removal.
Grit Size: Consider the grit size of the Diamond Foil. Coarser grits are typically used for heavy material removal and may require lower speeds to prevent overheating. Finer grits may be used at higher speeds for polishing and finishing.
Surface Finish: If you are aiming for a high-quality surface finish, particularly in applications like optics or jewelry making, slower speeds with finer grit Diamond Foil may be preferred to achieve precision and control.
Operator Skill: The skill and experience of the operator play a significant role in determining the appropriate speed. Experienced operators tend to have better control over the equipment and can adjust the speed as needed to achieve desired results.
Trial and Error: It’s often necessary to conduct trials and experiments with different speed settings to determine the optimal speed for your specific task. Start with a lower speed and gradually increase it while monitoring the results.
Store the Diamond Foil in a dry and clean environment, away from direct sunlight and moisture.
Exercise caution when handling used Diamond Foil, as it may still contain abrasive particles.
Keep bystanders away from the work area to prevent accidents or exposure to dust and debris.
Dimensions |
Diamond Grit Size & Item Number |
||||||||
---|---|---|---|---|---|---|---|---|---|
#120 |
#150 |
#200 |
#300 |
#400 |
#600 |
#800 |
#1200 |
#1800 |
|
10 x 100mm 50 x 100mm 100 x 100mm 200 x 200mm |
DF1012 DF2012 DF3012 DF4012 |
DF1015 DF2015 DF3015 DF4015 |
DF1020 DF2020 DF3020 DF4020 |
DF1030 DF2030 DF3030 DF4030 |
DF1040 DF2040 DF3040 DF4040 |
DF1060 DF2060 DF3060 DF4060 |
DF1080 DF2080 DF3080 DF4080 |
DF1120 DF2120 DF3120 DF4120 |
DF1180 DF2180 DF3180 DF4180 |
Advantages:
Enhanced Tool Life :
The full spraying of diamond powders on the copper foil surface significantly extends the lifespan of the tools. This durability is especially beneficial in high-wear environments.
Customizability :
These foils can be easily cut into any shape and size, making them versatile for a wide range of applications. This adaptability allows users to create custom tools tailored to specific needs.
Aggressive Cutting Action :
Diamond Foils are effective for fast cutting or polishing, thanks to their aggressive cutting action. This makes them suitable for working with various hard materials.
Wide Range of Grit Sizes :
The availability of a broad spectrum of grit sizes enables these foils to be used for a variety of applications, from rough cutting to fine polishing.
Versatility in Materials :
They are effective on a diverse array of hard materials, including hard steels of any hardness, tungsten carbides, stones, glass, and hard ceramics. This versatility makes them useful in various industrial and crafting contexts.
Wear Resistance :
Another application of Diamond Foils is their use in enhancing the wear resistance of machine parts. This helps in reducing wear and tear, thus prolonging the machine parts' lifespan.
Table Comparing Diamond Foil, Abrasive Paper, And Diamond Cloth Based On Various Characteristics:
Characteristic |
Diamond Foil |
Abrasive Paper |
Diamond Cloth |
---|---|---|---|
Abrasive Material |
Diamond powder coating on copper foil |
Aluminum oxide, silicon carbide or other minerals |
Diamond abrasive particles embedded in a flexible backing (e.g., cloth, paper, polyester) |
Form and Structure |
thin, rigid copper foil with a diamond coating |
Flexible sheets, rolls, or belts made of abrasive grains bonded to a backing |
Flexible sheets, rolls, or belts with diamond abrasive particles embedded in a backing material |
Flexibility |
Relatively rigid |
Flexible |
Highly flexible |
Applications |
Precision grinding, polishing, and finishing |
General grinding, sanding, and polishing in various industries |
Versatile for grinding, polishing, lapping, and honing on a wide range of surfaces |
Precision and Control |
High precision and control |
Good control |
Good control, may be slightly less precise due to flexibility |
Longevity |
Longer lifespan, especially on hard materials |
May require more frequent replacement, especially when used on hard materials |
Lifespan varies based on backing material and application |
Surface Finish |
Excellent for achieving fine and smooth finishes |
Capable of producing good surface finishes |
Capable of achieving good surface finishes, may not be as fine as Diamond Foil |
Versatility |
Suited for precision tasks and high-quality finishes |
Versatile for general-purpose grinding and polishing |
Versatile for a wide range of applications due to flexibility |
Specialized vs. General |
Specialized for precision applications |
General-purpose and specialized applications |
Versatile for various applications |
Wet Applications |
May vary in effectiveness, consult manufacturer guidelines |
Available in wet and dry variants |
Wet applications available for some products |
Heavy Material Removal |
Coarser grits can handle heavy material removal |
Coarser grits suitable for heavy stock removal |
Coarser grits can handle heavy material removal |
Typical Grit Sizes |
Coarse to fine, suitable for precision |
Coarse to fine, suitable for various tasks |
Coarse to fine, suitable for a wide range of applications |
Specific Industries |
Aerospace, jewelry making, optics |
Woodworking, metalworking, automotive, various industries |
Wide range, including lapidary, optics, and surface refinement |
Cost |
Generally higher due to diamond material |
Varies based on abrasive material, often more affordable |
Varies based on backing material and brand |
Abrasive |
Diamond powder |
Aluminum oxide, silicon |
Diamond abrasive particles |
Material |
coating on copper foil |
carbide, or other minerals |
embedded in a flexible backing (e.g., cloth, paper, polyester) |
Form and Structure |
Thin, rigid copper foil with a diamond coating |
Flexible sheets, rolls, or belts made of abrasive grains bonded to a backing |
Flexible sheets, rolls, or belts with diamond abrasive particles embedded in a backing material |
Flexibility |
Relatively rigid |
Flexible |
Highly flexible |
Applications |
Precision grinding, polishing, and finishing |
General grinding, sanding, and polishing in various industries |
Versatile for grinding, polishing, lapping, and honing on a wide range of surfaces |
Precision and Control |
High precision and control |
Good control |
Good control, may be slightly less precise due to flexibility |
Longevity |
Longer lifespan, especially on hard materials |
May require more frequent replacement, especially when used on hard materials |
Lifespan varies based on backing material and application |
Surface Finish |
Excellent for achieving fine and smooth finishes |
Capable of producing good surface finishes |
Capable of achieving good surface finishes, may not be as fine as Diamond Foil |
Versatility |
Suited for precision tasks and high-quality finishes |
Versatile for general-purpose grinding and polishing |
Versatile for a wide range of applications due to flexibility |
Specialized vs. General |
Specialized for precision applications |
General-purpose and specialized applications |
Versatile for various applications |
Wet Applications |
May vary in effectiveness, consult manufacturer guidelines |
Available in wet and dry variants |
Wet applications available for some products |
Heavy Material Removal |
Coarser grits can handle heavy material removal |
Coarse grits suitable for heavy stock removal |
Coarser grits can handle heavy material removal |
Typical Grit Sizes |
Coarse to fine, suitable for precision |
Coarse to fine, suitable for various tasks |
Coarse to fine, suitable for a wide range of applications |
Specific Industries |
Aerospace, jewelry making, optics |
Woodworking, metalworking, automotive, various industries |
Wide range, including lapidary, optics, and surface refinement |
Cost |
Generally higher due to diamond material |
Varies based on abrasive material, often more affordable |
Varies based on backing material and brand |
Characteristic
Diamond Foil
Abrasive Paper
Diamond Cloth
Abrasive Material
Diamond powder coating on copper foil
Aluminum oxide, silicon carbide or other minerals
Diamond abrasive particles embedded in a flexible backing (e.g., cloth, paper, polyester)
Form and Structure
thin, rigid copper foil with a diamond coating
Flexible sheets, rolls, or belts made of abrasive grains bonded to a backing
Flexible sheets, rolls, or belts with diamond abrasive particles embedded in a backing material
Flexibility
Relatively rigid
Flexible
Highly flexible
Applications
Precision grinding, polishing, and finishing
General grinding, sanding, and polishing in various industries
Versatile for grinding, polishing, lapping, and honing on a wide range of surfaces
Precision and Control
High precision and control
Good control
Good control, may be slightly less precise due to flexibility
Longevity
Longer lifespan, especially on hard materials
May require more frequent replacement, especially when used on hard materials
Lifespan varies based on backing material and application
Surface Finish
Excellent for achieving fine and smooth finishes
Capable of producing good surface finishes
Capable of achieving good surface finishes, may not be as fine as Diamond Foil
Versatility
Suited for precision tasks and high-quality finishes
Versatile for general-purpose grinding and polishing
Versatile for a wide range of applications due to flexibility
Specialized vs. General
Specialized for precision applications
General-purpose and specialized applications
Versatile for various applications
Wet Applications
May vary in effectiveness, consult manufacturer guidelines
Available in wet and dry variants
Wet applications available for some products
Heavy Material Removal
Coarser grits can handle heavy material removal
Coarser grits suitable for heavy stock removal
Coarser grits can handle heavy material removal
Typical Grit Sizes
Coarse to fine, suitable for precision
Coarse to fine, suitable for various tasks
Coarse to fine, suitable for a wide range of applications
Specific Industries
Aerospace, jewelry making, optics
Woodworking, metalworking, automotive, various industries
Wide range, including lapidary, optics, and surface refinement
Cost
Generally higher due to diamond material
Varies based on abrasive material, often more affordable
Varies based on backing material and brand
Abrasive
Diamond powder
Aluminum oxide, silicon
Diamond abrasive particles
Material
coating on copper foil
carbide, or other minerals
embedded in a flexible backing (e.g., cloth, paper, polyester)
Form and Structure
Thin, rigid copper foil with a diamond coating
Flexible sheets, rolls, or belts made of abrasive grains bonded to a backing
Flexible sheets, rolls, or belts with diamond abrasive particles embedded in a backing material
Flexibility
Relatively rigid
Flexible
Highly flexible
Applications
Precision grinding, polishing, and finishing
General grinding, sanding, and polishing in various industries
Versatile for grinding, polishing, lapping, and honing on a wide range of surfaces
Precision and Control
High precision and control
Good control
Good control, may be slightly less precise due to flexibility
Longevity
Longer lifespan, especially on hard materials
May require more frequent replacement, especially when used on hard materials
Lifespan varies based on backing material and application
Surface Finish
Excellent for achieving fine and smooth finishes
Capable of producing good surface finishes
Capable of achieving good surface finishes, may not be as fine as Diamond Foil
Versatility
Suited for precision tasks and high-quality finishes
Versatile for general-purpose grinding and polishing
Versatile for a wide range of applications due to flexibility
Specialized vs. General
Specialized for precision applications
General-purpose and specialized applications
Versatile for various applications
Wet Applications
May vary in effectiveness, consult manufacturer guidelines
Available in wet and dry variants
Wet applications available for some products
Heavy Material Removal
Coarser grits can handle heavy material removal
Coarse grits suitable for heavy stock removal
Coarser grits can handle heavy material removal
Typical Grit Sizes
Coarse to fine, suitable for precision
Coarse to fine, suitable for various tasks
Coarse to fine, suitable for a wide range of applications
Specific Industries
Aerospace, jewelry making, optics
Woodworking, metalworking, automotive, various industries
Wide range, including lapidary, optics, and surface refinement
Cost
Generally higher due to diamond material
Varies based on abrasive material, often more affordable
Varies based on backing material and brand
Different Technology
SMART CUT® technology
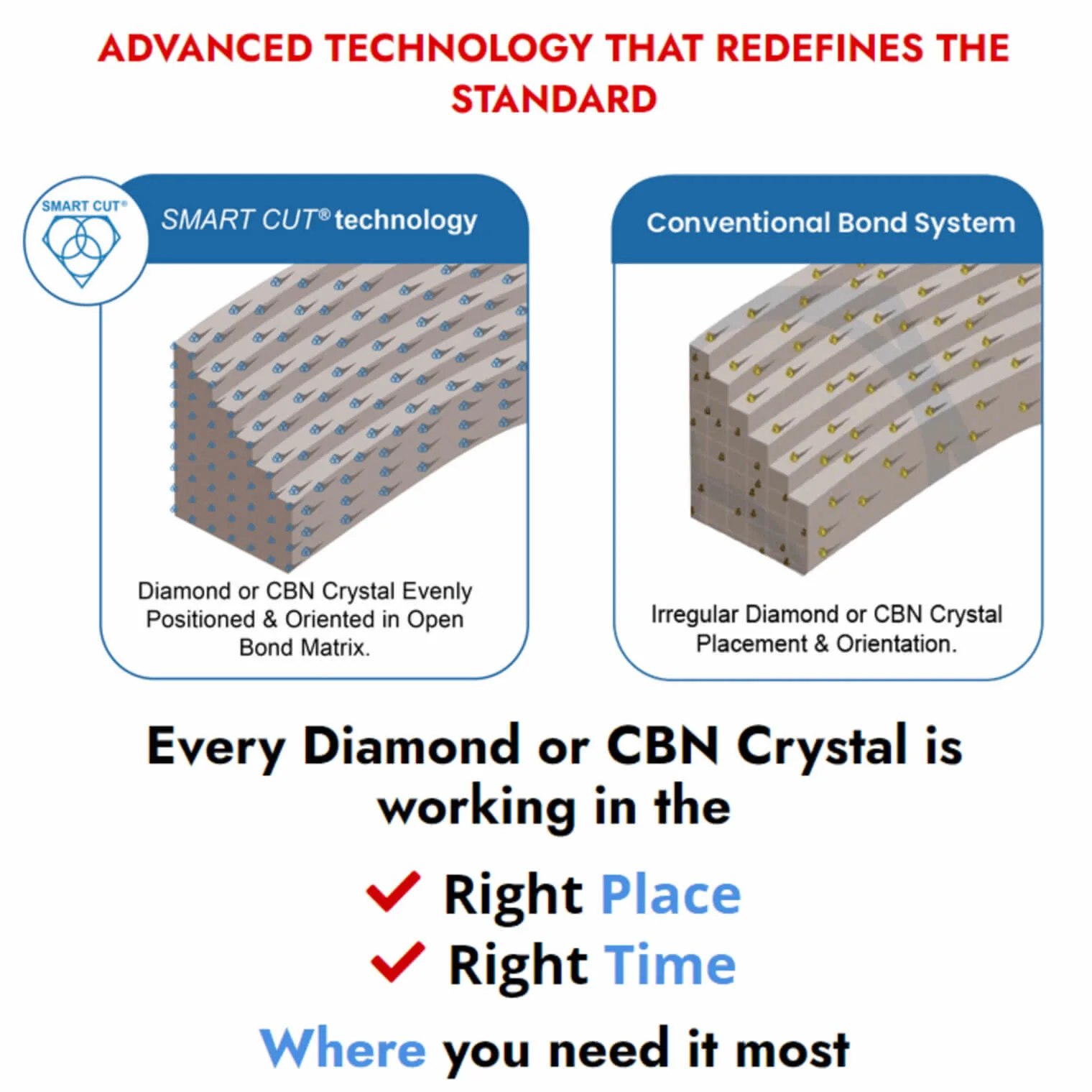
How SMART CUT ® Bond Works?
Step 1
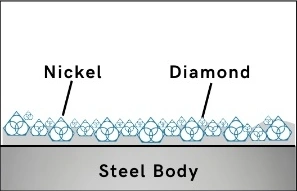
Sharpest And Finest Quality Diamonds
The sharpest and finest quality diamonds or CBN crystals that go into a SMART CUT® Diamond Bond, immediately penetrate into the material, grinding and polishing as they cut.
The newly exposed diamonds don’t effect diamonds already working on the material. Unlike many other diamond bonds, diamonds in a SMART CUT® Bond remains sharp and grow sharper with each cut, prolonging product life and consistent performance.
Step 2
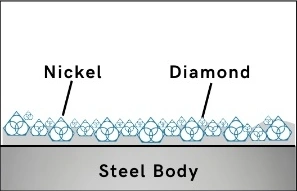
Diamonds or CBN Crystals
Diamonds or CBN Crystals are activated only at the exposed layer. As Bond Matrix layer begin to wear out, diamonds in a new Bond Matrix layer are immediately activated, substituting the already used up diamond layer. The SMART CUT® Diamond Hybrid Bond makes sure every diamond is in the right place and at the right time, working where you need it most.
Step 3
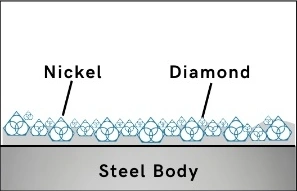
Advanced Formulated Open Diamond Bond Design
This advanced formulated open diamond bond design insures minimal chipping, fast cut, constant speed of cut, minimal cutting noise, and most important of all, consistent performance.
About Nickel Bond (Electroplated) Tools
Electroplated (nickel bond) diamond products usually have a single layer of diamonds, held by a tough durable nickel alloy. Nickel is frequently used as a base for plating diamond. Because of its excellent strength, toughness and flexibility during the plating process. Electroplated diamond products are able to retain their original shape and dimensions thought their working life. Unlike sintered (meal bond) or resin bond diamond products, where diamond particles are buried in bond and held together by metal or resin binder deep inside.
Electroplating allows diamond particles to protrude from the bond matrix, providing a free, faster cutting action with minimum heat generation.
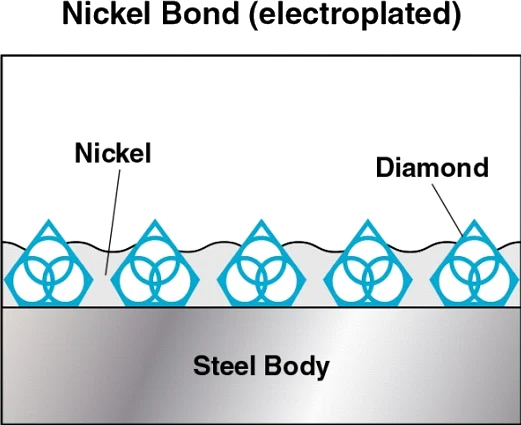
Faster
Cutting Action
Diamond & CBN tools made utilizing SMART CUT® technology are much more aggressive than your conventional tools. They can cut faster, while still leaving behind a smooth finish free of material deformation.
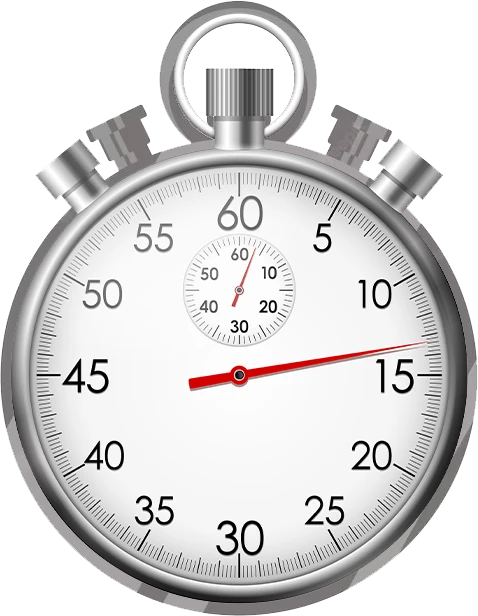
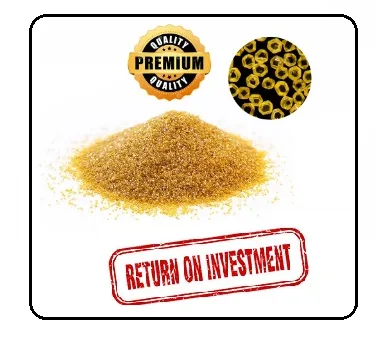
Manufactured Using
The Highest Quality Raw Materials
Only the highest quality synthetic diamonds and raw materials are used in the manufacturing process. The highest quality standards and product consistency is maintained, using sophisticated inspection and measurement equipment.
Best
Performance & Value on the Market
SMART CUT Multi Layered Electroplated Diamond Drills are the best investment you can make! Although they may cost more than electroplated (nickel bond), Diamond Drills. They will more than pay for themselves in terms of overall performance and provide best Return on Investment.
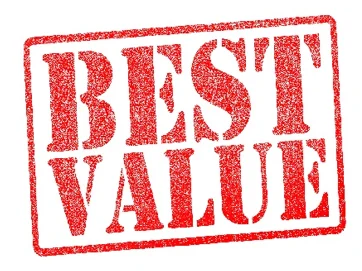
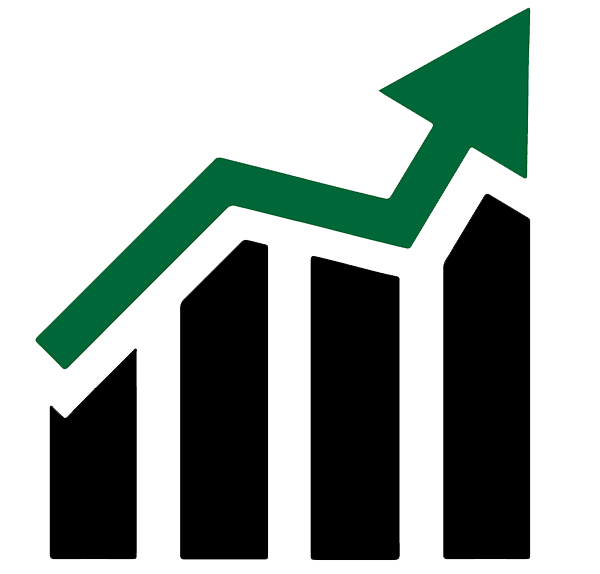
Longer
Life
In most cases tools manufactured utilizing SMART CUT® technology, will outlast other conventional material (sintered), resin, and nickel bonded diamond & CBN tools. SMART CUT® diamond & CBN tools are more sturdy than tools manufactured with conventional technologies. They are capable to retain their form and bond configuration all the way through the tools life.
More
Consistent Performance
SMART CUT® Series Resin Bond, CBN Blades have hundreds of diamond layers impregnated inside the resin matrix. Unlike Many Other Blade Types, they wear evenly, and are known for their consistency. You will get consistent cutting speed, and overall consistent performance, with minimum amount of dressing even on the hardest to cut materials

Why Work With Us?
Comprehensive Source Of Information On Dicing Blades
We understand that your success depends on select the right dicing blade, and optimizing your dicing parameters to best fit your applications/needs. The more you understand about what we can do for you, the better our partnership will be. On our website you will find the Most Comprehensive Source of Information on Everything you wanted to know about diamond dicing blades & industrial diamond tools.
Large Inventory & Custom Manufacturing
Largest Inventory of Precision & Ultra Thin Diamond Dicing Blades in the U.S. Available in different sizes, thickness, arbor sizes, diamond concentrations, diamond mesh sizes, and bond hardness's.
Experience Makes All The Difference
"ONE OF THE MOST EXPERIENCED COMPANIES IN THE INDUSTRY"
Over the years we have enjoyed working with all types if clients, regardless of size. Proprietary dicing blade chemistry, precision manufacturing methods, modern quality control methods, allow us to control and regulate the dozens of variables that affect blade life, quality of cut, surface finish. Reducing and often eliminating additional steps often required after cutting.
Umatched Technical Support
We Are a Partner In Your Success
Developing close ties with our customers is the foundation of our business. At the core of
our company is a team of world class engineers, knowledgeable customer service personnel here to serve you. Whether is designing or manufacturing a special solution. We will go out of our way to optimizing your process to ultimate level of efficiency.
Advanced
Technology
American Manufacturer As one of the few remaining independent U.S.Diamond Tool & machine builders. We have the experience & tradition to help you remain at frontier of technology Our experience has been further enhanced by acquiring assets and processes from some of the oldest American tool manufacturers, along with their decades of experience and R& D. This has positioned us as one of the most experienced companies in the industry.
Superior Quality &
Consistency
Our unique bond formulations, tool designs, stringent requirements, and utilization of exceptionally high-quality diamonds and raw materials ensure top-notch products that adhere to strict ISO 9000 standards.
Our proprietary technology allow us to control and regulate the dozens of variable that affect toolife, quality, & consistency
Expect More From Your Tools
ARE YOU USING RIGHT diamond foil
FOR YOUR APPLICATION?
LET US
HELP YOU
HAVING ISSUES WITH
YOUR CURRENT diamond foil?
Knowledge Center
02
Jun
Diamond vs CBN (cubic boron nitride) Tools
Cubic Boron Nitride (CBN) is a synthetic material that is renowned for its exceptional hardness and high thermal stability. It is composed of boron and nitrogen atoms arranged in a crystal lattice structure, similar to...
02
Jun
Discover the Right Diamond Powder for Your Application: Choosing Between Monocrystalline and Polycrystalline Diamonds
Which to use for your application?
Diamond shape plays a significant role in the effectiveness of polishing solutions, affecting both the polishing rate and the quality of the final finish. Understanding the differences between monocrystalline and...
02
Jun
Comparing Two Different Cutting Methods (Low Speed Saw vs. Wire Saw)
Share this Article with Friend or Colleague
For metallography, sample preparation, materials research and working with large variety of materials, selecting the optimal cutting technology is crucial for achieving high-quality results across various materials and applications....
11
Jun
Selecting the Right Diamond Suspension for your Application – Monocrystalline or Polycrystalline?
Choosing the correct diamond suspension, whether monocrystalline or polycrystalline, significantly impacts the quality and efficiency of the polishing and material removal processes. Understanding the properties and applications of both types of suspensions can help you...
17
Jun
Improve Sample Quality & Optimize your Polishing Operating for Metallography & Sample Preparation
Polishing is important step in metallography & sample preparation for revealing the true microstructure of materials, including grain boundaries, phases, and inclusions, which provide insights into material properties and history. This guide is designed to...
26
Jun
Optimize your Grinding Operation for Metallography & Sample Preparation
Share this Article with Friend or Colleague
Grinding is a fundamental mechanical process in metallography that involves removing material from a specimen using hard, abrasive particles. This process is essential for preparing specimens for microscopic...
08
Jul
Low Speed Saw Case Studies
Share this Article with Friend or Colleague
Introduction
In the realm of precision cutting, the SMART CUT® 6005 Low Speed Diamond Saw stands out for its capability to handle a variety of materials with high...
11
Sep
What is the difference between Lapping, Grinding, & Polishing
Some of the major differences include the type and diamond mesh size of diamond discs used, type and size of abrasives used and their holding method. Other factors include RPM’s (speed) used and pressure applied...
30
Jan
Select the Right Silicon Carbide Paper Discs for Metallography Sample Preparation
Selecting the right silicon carbide paper for metallographic sample preparation is important for achieving accurate and reliable results in material analysis. The grinding and polishing process plays a fundamental role in preparing specimens for microscopic...
30
Jan
Upgrading Metallography Grinding with Silicon Carbide Paper
This guide covers the best practices for using silicon carbide paper in metallography. It includes tips on proper grit progression, optimizing pressure and speed settings, preventing common issues, and extending the life of the abrasive....
- Unmatched Selection For Many Applications
- Superior Quality & Consistency
- Immediate Worldwide Delivery
- Technical Support & Expertise
- American Based Manufacturer
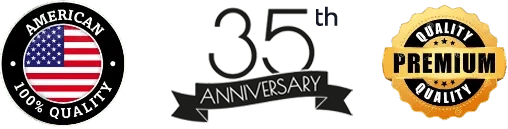

- Different Product
- Different Technology
- Different Company
- Expect MORE from your tools
Let Us HELP You!
Subscribe To Our Newsletter
Signup for email offers, updates, and more
Contact Us
- 25205 & 25201 Avenue Tibbits Valencia CA 91355 USA
-
Phone : (661) 257-2288
FAX : (661) 257 -3833 - lel@ukam.com
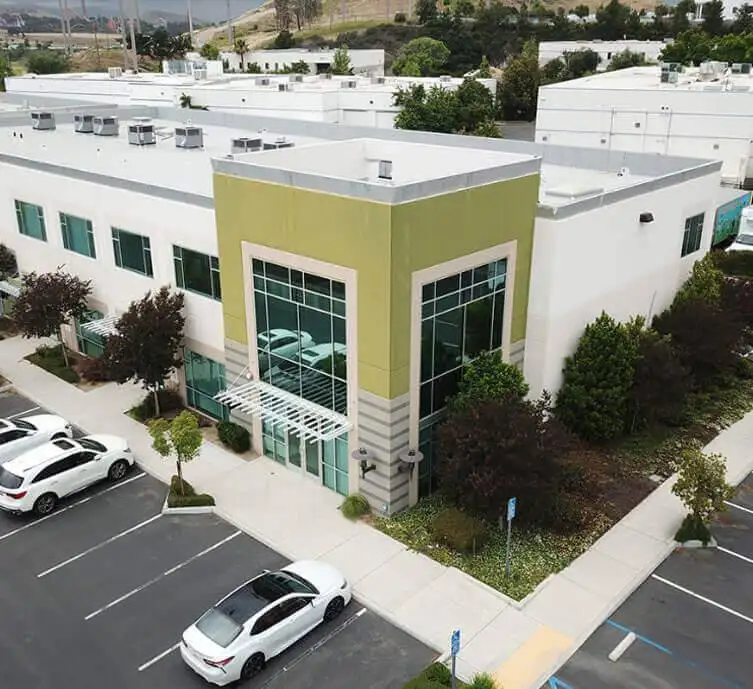
UKAM Industrial Superhard Tools is a U.S. High Technology, Specialty Diamond Tool & Equipment manufacturer. We specialize in producing ultra thin, high precision cutting blades, precision cutting machines diamond drills, diamond micro tools, standard & custom advanced industrial diamond tools and consumables.
- 25205 & 25201 Avenue Tibbits Valencia CA 91355 USA
-
Phone : (661) 257-2288
FAX : (661) 257 -3833 - lel@ukam.com
- 25205 & 25201 Avenue Tibbits Valencia CA 91355 USA
-
Phone : (661) 257-2288
FAX : (661) 257 -3833 - lel@ukam.com
DIAMOND TOOLS BY BOND
EQUIPMENT
KNOWLEDGE CENTER
OUR PRODUCTS
COMPANY
CUSTOMER SERVICE
Shipping Methods


Safe & Secure Payments

© Copyright 1990-2025. UKAM Industrial Superhard Tools – Terms of Use