-
0 items in quote
No products in the Quote Basket.
Smart Cut Carbide Micro Drills
SMART CUT Carbide drills are made by combining tungsten particles with carbon and cobalt under high pressure and heat. This could be likened to a concrete post made up of sand and using cement as a binder. A carbide drill does not get dull because of wear like a steel drill does. It gets dull because the cobalt gets warm and it cannot hold the tungsten particles on the very fine cutting edges. Tungsten is a very hard metal and does not in itself experience much wear.

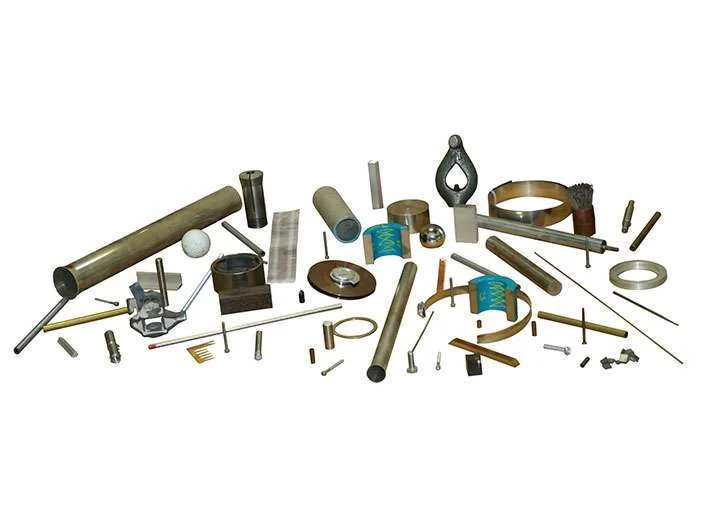
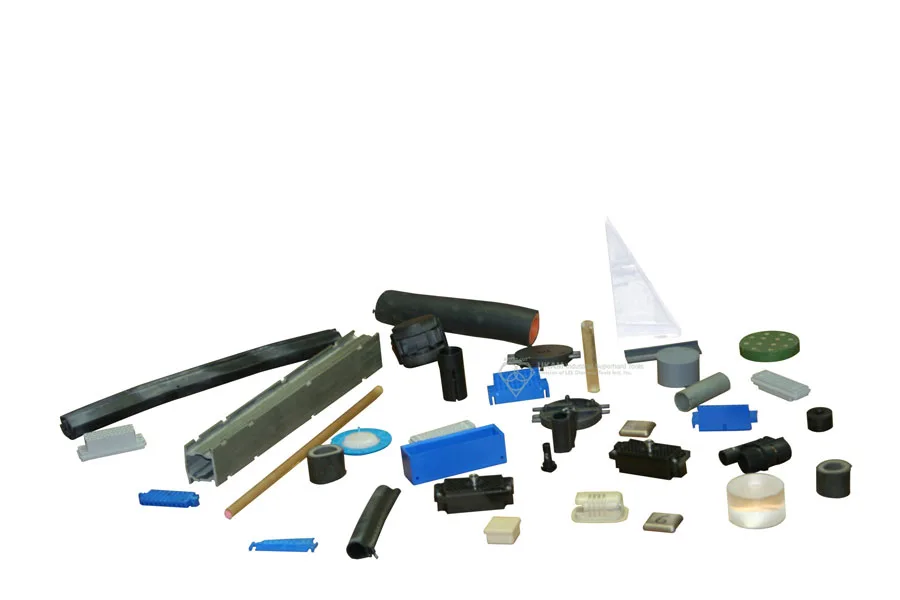
Application
- Low carbon steel
- High carbon steel
- Stainless steels
- Nickel alloys
- Cast iron
- Aluminum
- Copper – brass alloys
- Plastics
Specifications
Diameter tolerance is (+0/-0.0002") Call for specific diameters
- Material: Carbide
- Overall Length: 1.50"
- Shank Diameter: .125"
Two Flute - Four Facet Point
Item No. |
Outside Diameter |
Flute Length |
Specification |
---|---|---|---|
CBMD1 |
0.0015" |
.020” |
DRILL N/R.020"FL 90PT |
CBMD2 |
0.0020" |
.015” |
DRILL 015FL 90PT (50) |
CBMD3 |
0.0020" |
.020” |
DRILL 020FL 90PT (50) |
CBMD4 |
0.0020" |
.045’ |
DRILL 045FL 90PT (50) |
CBMD5 |
0.0021" |
.032” |
DRILL 032FL 90PT (50) |
CBMD6 |
0.0022" |
.015” |
DRILL N/S .015"FL 90PT |
CBMD7 |
0.0022" |
.020” |
DRILL N/R .020"FL 90PT |
CBMD8 |
0.0022" |
.020” |
DRILL 020FL 90PT (50) |
CBMD9 |
0.0022" |
.025” |
DRILL N/R .025"FL 90PT |
CBMD10 |
0.0022" |
.025” |
DRILL 025FL 90PT (50) |
CBMD11 |
0.0022" |
.045” |
DRILL 045FL 90PT (50) |
CBMD12 |
0.0025" |
.017” |
DRILL .017"FL 90PT N/S |
CBMD13 |
0.0025" |
.017” |
DRILL 017FL 90PT |
CBMD14 |
0.0025" |
.030” |
DRILL N/S .030"FL 90PT |
CBMD15 |
0.0026" |
.020” |
DRILL 020FL 130PT |
CBMD16 |
0.0029" |
.035” |
DRILL .035"FL 118PT |
CBMD17 |
0.0029" |
.035” |
DRILL .035"FL 90PT |
CBMD18 |
0.0031" |
.015” |
DRILL N/S .015"FL 90PT |
Advantages
-
High Precision: Allows for the creation of highly accurate and consistent micro-sized holes.
-
Customizability: Available in various sizes and with optional specialized coatings to suit specific application needs.
-
Innovative Design: Features unique flute designs for improved chip removal and coolant flow, reducing heat buildup.
-
Versatility: Compatible with a wide range of drilling machines, including CNC systems and high-speed drilling stations.
-
Reduced Tool Wear: Advanced geometries and materials reduce the frequency of tool replacements, lowering operational costs.
-
High-Speed Performance: Capable of operating at high speeds without compromising precision or tool integrity.
-
Minimized Drill Breakage: Robust construction significantly reduces the risk of breakage, even under intense operational conditions.
-
Optimal Chip Evacuation: Efficient chip evacuation maintains clean cutting areas, improving the overall drilling process and outcome.
-
Precision Cooling: Optimized coolant paths ensure effective heat dissipation, crucial for maintaining the longevity and performance of both the drill and the workpiece.
-
Low Maintenance: Designed for easy maintenance and cleaning, which is essential for maintaining performance in high-throughput environments.
About Carbide Micro Drills
SMART CUT® Carbide Micro Drills, precision-engineered for optimal performance in demanding drilling applications. Produced from high-grade carbide, renowned for its exceptional hardness and resistance to wear. This ensures that SMART CUT® Carbide Micro Drills not only last longer but also perform consistently under rigorous conditions.
SMART CUT® Carbide Micro Drills are available in a variety of sizes, starting from micro-scale diameters, which are perfect for industries that require tight tolerances and superior finishes. These drills are especially useful in fields such as electronics, medical device manufacturing, and precision engineering, where minute and precise holes are crucial.
SMART CUT® Carbide Micro Drills are available with a variety of point geometries, each suited to different materials and drilling techniques. From standard twist drills to specialized tip geometries designed to minimize entry and exit burrs, each drill is a product of extensive research and development.
The drills can be customized to meet specific requirements, offering flexibility in length, diameter, and even specialized coatings. These coatings, which include options like Titanium Nitride and Diamond-like Carbon, further enhance the drill's performance by reducing friction and increasing efficiency when cutting through hard or abrasive materials.
SMART CUT® Carbide Micro Drills are compatible with a range of precision drilling machines, including CNC equipment and high-speed drilling stations. This versatility ensures that they can be integrated seamlessly into any production line, enhancing existing setups with minimal adjustment.
What are coatings?
Coatings are thin layers of materials applied to the surfaces of cutting tools, such as carbide micro drills, using techniques like Chemical Vapor Deposition (CVD) or Physical Vapor Deposition (PVD). These coatings, which are usually just a few microns thick, serve to enhance the performance, durability, and functionality of the tools.
Why use coatings?
One of the main advantages of applying coatings to carbide micro drills is the significant increase in hardness and wear resistance they provide. Coatings like Titanium Nitride (TiN), Titanium Carbonitride (TiCN), and Diamond-like Carbon (DLC) enhance the surface hardness of the drills, making them more resistant to wear and abrasion. This allows the tools to last longer, maintain their sharpness, and require less frequent replacement, thus reducing downtime and the costs associated with tool changes.
Additionally, some coatings such as Titanium Aluminum Nitride (TiAlN) can withstand high temperatures, which is crucial for high-speed drilling operations that generate significant heat. These coatings act as thermal barriers, protecting the carbide substrate from the heat that could lead to softening or structural failure, and allowing for faster drilling speeds and prolonged tool life.
Coatings also improve lubricity and reduce friction. For example, DLC coatings have low friction coefficients, which minimize the amount of heat generated due to friction and prevent material from sticking to the drill. This reduces galling and welding of the work material to the drill, leading to smoother operations, finer finishes, and more precise holes.
Furthermore, coatings like Chromium Nitride (CrN) and nickel-based options provide excellent resistance to oxidation and corrosion. This is particularly important when drilling materials that are corrosive or when working in corrosive environments, thereby extending tool life and maintaining performance integrity.
Improved cutting efficiency is another benefit of using coatings. By reducing the energy and force required for cutting, some coatings enable more efficient material removal. This leads to better overall machining performance, including higher speeds, lower power consumption, and reduced wear on both the tool and the machine.
Coatings Available – Table of Comparison
Coating Type |
Hardness (HV) |
Heat Resistance (°C) |
Key Properties |
Typical Applications |
Materials Used On |
Features of Coating |
---|---|---|---|---|---|---|
Diamond-like Carbon (DLC) |
2000 - 5000 |
Up to 400 |
Low friction, high hardness |
Precision tools, automotive parts |
Steel, alloys, ceramics |
Reduces adhesive wear, minimal friction, enhances durability |
Titanium Nitride (TiN) |
1800 - 2300 |
Up to 500 |
Reduces wear, thermal stability |
General machining, cutting tools |
Steel, titanium, aluminum |
Increases surface hardness, extends tool life |
Titanium Aluminum Nitride (TiAlN) |
2800 - 3500 |
Up to 800 |
High hardness, thermal resistance |
High-speed and high-temperature applications |
High-alloy steels, titanium |
Excellent for high-temperature applications, resists oxidation |
Titanium Carbonitride (TiCN) |
3000 - 4000 |
Up to 400 |
Higher toughness, abrasive wear resistance |
Hard material cutting, milling tools |
Steel, hard metals |
Greater hardness than TiN, superior wear resistance |
Chromium Nitride (CrN) |
1600 - 2000 |
Up to 700 |
Corrosion resistance, hardness |
Corrosive environments, food processing |
Stainless steel, aluminum |
Good toughness, excellent against corrosion and oxidation |
Nickel-based Coatings |
400 - 700 |
Variable |
Corrosion and wear resistance |
Marine, oil and gas, chemical processing |
Copper, brass, marine metals |
Enhances bonding, protects against harsh environments |
Ceramic Coatings |
2500 - 4500 |
Over 1000 |
Chemical stability, heat resistance |
Aerospace, high-performance cutting |
Composites, hard superalloys |
High thermal barrier, reduces thermal stresses |
CVD Diamond Coating |
8000 - 10000 |
Up to 600 |
Extreme hardness, wear resistance |
Abrasive material cutting, advanced machining |
Graphite, ceramics, metals |
Superior abrasion resistance, suitable for very hard materials |
Recommended RPM’s for SMART CUT® Carbide Micro Drills
Recommended RMP’s based on material type, hardness, drill diameter, cutting speed (Vc), and chip load per tooth:
Material Type |
Hardness |
Drill Diameter (mm) |
Cutting Speed (Vc) m/min |
Chip Load Per Tooth (Microns) |
---|---|---|---|---|
Low Carbon Steel, Magnetic Soft Steel, Leaded Steels |
≤ 120 |
Ø < 1.0 |
50 |
80 |
Ø < 1.5 |
30 |
45 |
||
Ø < 2.0 |
35 |
52 |
||
Ø < 2.5 |
40 |
60 |
||
Ø < 3.0 |
46 |
68 |
||
Plain Carbon Steel Low, Medium Carbon |
< 250 |
Ø < 1.0 |
25 |
60 |
Ø < 1.5 |
25 |
40 |
||
Ø < 2.0 |
29 |
46 |
||
Ø < 2.5 |
33 |
53 |
||
Ø < 3.0 |
38 |
61 |
||
Structural Steel, Case Carburizing Steel |
< 200 |
Ø < 1.0 |
25 |
60 |
Ø < 1.5 |
25 |
40 |
||
Ø < 2.0 |
29 |
46 |
||
Ø < 2.5 |
33 |
53 |
||
Ø < 3.0 |
38 |
61 |
||
Alloyed Steel, Medium Carbon, Tool Steel, Wrought |
< 250 |
Ø < 1.0 |
20 |
50 |
Ø < 1.5 |
12 |
35 |
||
Ø < 2.0 |
14 |
40 |
||
Ø < 2.5 |
16 |
46 |
||
Ø < 3.0 |
18 |
53 |
||
Alloyed Steel, Hardened and Tempered Steel, Tool Steel |
> 250 ≤ 350 |
Ø < 1.0 |
15 |
35 |
Ø < 1.5 |
10 |
25 |
||
Ø < 2.0 |
12 |
29 |
||
Ø < 2.5 |
13 |
33 |
||
Ø < 3.0 |
15 |
38 |
||
Stainless Steel (Ferritic + Austenitic, Ferritic, Martensitic) |
< 300 |
Ø < 1.0 |
23 |
53 |
Ø < 1.5 |
5 |
25 |
||
Ø < 2.0 |
6 |
29 |
||
Ø < 2.5 |
7 |
33 |
||
Ø < 3.0 |
8 |
38 |
||
Nickel Alloys (Nickel, Unalloyed, Nickel Alloys Nimonic 75, Monel 400) |
< 150 |
Ø < 1.0 |
15 |
40 |
Ø < 1.5 |
10 |
15 |
||
Ø < 2.0 |
12 |
17 |
||
Ø < 2.5 |
13 |
20 |
||
Ø < 3.0 |
15 |
23 |
||
Titanium (Titanium Alloy, Cast) |
< 270 |
Ø < 1.0 |
25 |
56 |
Ø < 1.5 |
7 |
25 |
||
Ø < 2.0 |
8 |
29 |
||
Ø < 2.5 |
9 |
33 |
||
Ø < 3.0 |
11 |
38 |
||
Cast Iron (Soft Gray Cast, Ferritic) |
< 150 |
Ø < 1.0 |
30 |
80 |
Ø < 1.5 |
20 |
50 |
||
Ø < 2.0 |
23 |
58 |
||
Ø < 2.5 |
26 |
66 |
||
Ø < 3.0 |
30 |
76 |
||
Aluminum (Al Alloys, Si>5%) |
- |
Ø < 1.0 |
200 |
350 |
Ø < 1.5 |
150 |
300 |
||
Ø < 2.0 |
100 |
200 |
||
Ø < 2.5 |
45 |
60 |
||
Ø < 3.0 |
52 |
69 |
||
Copper - Brass Alloys (Copper Alloys, Wrought) |
- |
Ø < 1.0 |
100 |
225 |
Ø < 1.5 |
25 |
40 |
||
Ø < 2.0 |
29 |
46 |
||
Ø < 2.5 |
33 |
53 |
||
Ø < 3.0 |
38 |
61 |
Related Products
SMART CUT® 005DME MCDU
SMART CUT® 005DME diamond micro drills are produced using electroplated (nickel bond) galvanic plating process. These tools can be used for drilling and machining large variety of materials such as Precision Optics, Silicon Carbide, Boron Nitride, Boron Carbide, Alumina Ceramics, Silicon, Sapphire & Yag, Glass, Quartz, & Pyrex Tubing & Many Other Applications.
Small diameter below .020” (0.5mm) are made using diamond plating (galvanic) method, where the diamond crystals are deposited evening on the tip evenly over time. The steel body using is usually high speed steel ranging in hardness from 40 to 50 Rockwell scale C. Precision tolerances are maintain on diameter.
SMART CUT® Diamond & CBN Micro Drills, Sintered (Metal Bond)
PCD (Polycrystalline) Micro Drills
Diamond Micro Drills
SMART CUT® PCD (Polycrystalline Diamond Micro Drills) are available starting 0.4mm diameter with various head length and shank diameters in 3mm and 3.2mm Micro PCD drills are used in the semiconductor industry for monocrystalline applications such as cleaning and inspection jigs.CVD Micro Drills
Micro Drills
SMART CUT® CVD diamond micro drills are used for drilling micro holes in large variety of hard and brittle materials such as sapphire, high density ceramics, micro-circuit substrates, glass, silicon, various wafers, substrates, tubes etc We offer large variety of standard stock & custom micro drills from 0.05mm diameter to 6mm. with 3mm and 3.2mm shanks, and various heald lengths from 0.5mm and up, and flute specifications.SMART CUT® 010DME (SMCDU)
SMART CUT® 010DME diamond micro drills are produced using electroplated (nickel bond) galvanic plating process. These tools can be used for drilling and machining large variety of materials such as Precision Optics, Silicon Carbide, Boron Nitride, Boron Carbide, Alumina Ceramics, Silicon, Sapphire & Yag, Glass, Quartz, & Pyrex Tubing & Many Other Applications.
Small diameter below .020” (0.5mm) are made using diamond plating (galvanic) method, where the diamond crystals are deposited evening on the tip evenly over time.
The steel body using is usually high speed steel ranging in hardness from 40 to 50 Rockwell scale C. Precision tolerances are maintain on diameter. Diamond sizes used range form 6 microns to 120 microns. Head length made in proportion to diameter of the tool. Usually it cannot exceed 15 times the diameter of the tool. Diamond grit size used in in proportion to diameter of the drill tip and can range form 3 to 70 microns. shank size is usually 1/8” (3.2mm) or .040” (1mm).
SMART CUT® Micro & Miniature Diamond Core Drills
SMART CUT® Micro & Miniature Core Drills
Recently Viewed Products
ARE YOU USING RIGHT DIAMOND CORE DRILLS & TOOLS
FOR YOUR APPLICATION?
LET US
HELP YOU
HAVING ISSUES WITH
YOUR CURRENT DIAMOND CORE DRILLS & TOOLS?
Knowledge Center
02
Jun
How to Properly Use Precision Diamond Drills
Step by step guide on how to properly use and care for your diamond drills. Selecting the right diamond drill/diamond drill bit parameters, often involves a trial and error process. Many which can be avoided...
02
Jun
Diamond Drills Guide
Diamond are used across large variety of industries and applications. This guide explores the wide range of diamond drill types, including hollow core drills designed for removing a cylindrical core, non-core formation drills that grind...
02
Jun
Diamond Tools Guide – Selecting Right Drills & Tools for your application
These tools are used for many different industries grinding and shaping material into different forms, expanding exiting inside diameters, grinding, finishing and polishing existing material. Grinding different angles and radius, creating cavities of various forms,...
02
Jun
Optimizing your Diamond Drilling Operation
There are numerous factors that influence the performance of diamond drills. Understanding these factors helps users select the appropriate diamond drill specifications for their specific applications, optimizing drilling operations to achieve maximum efficiency....
02
Jun
Micro Drilling Guide
Share this Article with Friend or Colleague
In order for you to get the most out of your diamond micro drill or carbide / high speed steel micro drill, we strongly urge you to read...
02
Jun
Selecting Right Drilling Equipment for your Application. What you features & functionality you should look for?
Share this Article with Friend or Colleague
There are hundreds or even thousands of different drilling equipment options. Selecting the right equipment for a specific application involves carefully considering several variables and attributes of the...
03
May
Diamond Core Drill & Drill Trouble Shooting Guide
Learn the most common problems most people have in using diamond drills. How to resolve them and avoid them in first place
https://ukam.com/wp-content/uploads/2024/07/diamond-drill-troublehsooting-guide.mp4
Troubleshooting Drilling Problems
Having issues with your diamond drilling operation? This Illustrated Guide...
09
Sep
Understanding & Calculating Return on Investment for Diamond Core Drills & Other Tools
The term "ROI" (Return On Investment) is widely used across industries, often interpreted differently depending on the context. However, few truly understand what ROI represents and its specific implications, particularly in the context of diamond...
09
Sep
Understanding Tradeoffs – Searching for Perfect Diamond Drill & Tool
Choosing the right diamond drill or tool can significantly impact efficiency, cost, and quality. However, this is not a simple and clear-cut process. Selecting the optimal drill or tool involves navigating a complex landscape of...
19
Sep
Why Use Diamond Drills?
Diamond, known as the hardest material on Earth, enables diamond drills and tools to grind away material at a micro (nano) scale. This extreme hardness allows diamond tools to effectively work on materials with a...
- Unmatched Selection For Many Applications
- Superior Quality & Consistency
- Immediate Worldwide Delivery
- Technical Support & Expertise
- American Based Manufacturer
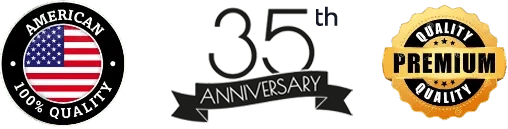

- Different Product
- Different Technology
- Different Company
- Expect MORE from your tools
Let Us HELP You!
Subscribe To Our Newsletter
Signup for email offers, updates, and more
Contact Us
- 25205 & 25201 Avenue Tibbits Valencia CA 91355 USA
-
Phone : (661) 257-2288
FAX : (661) 257 -3833 - lel@ukam.com
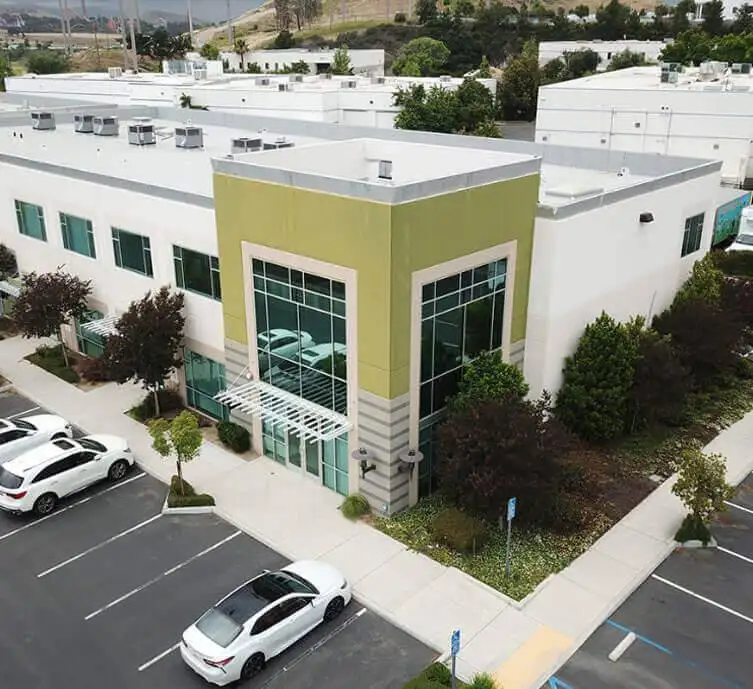
UKAM Industrial Superhard Tools is a U.S. High Technology, Specialty Diamond Tool & Equipment manufacturer. We specialize in producing ultra thin, high precision cutting blades, precision cutting machines diamond drills, diamond micro tools, standard & custom advanced industrial diamond tools and consumables.
- 25205 & 25201 Avenue Tibbits Valencia CA 91355 USA
-
Phone : (661) 257-2288
FAX : (661) 257 -3833 - lel@ukam.com
- 25205 & 25201 Avenue Tibbits Valencia CA 91355 USA
-
Phone : (661) 257-2288
FAX : (661) 257 -3833 - lel@ukam.com
DIAMOND TOOLS BY BOND
EQUIPMENT
KNOWLEDGE CENTER
OUR PRODUCTS
COMPANY
CUSTOMER SERVICE
Shipping Methods


Safe & Secure Payments

© Copyright 1990-2025. UKAM Industrial Superhard Tools – Terms of Use