Table of Contents
ToggleIntroduction
In the realm of precision cutting, the SMART CUT® 6005 Low Speed Diamond Saw stands out for its capability to handle a variety of materials with high accuracy. To better understand its performance and optimize its usage, a detailed study was conducted using sapphire material. This study aims to provide valuable insights into the operational parameters of the saw, such as wheel diameter, load, wheel speed, and arm position, and their effects on cutting time. The findings will be incorporated into user manuals to enhance consumer knowledge and usage efficiency.
Experimental Setup
The SMART CUT® 6005 saw was subjected to a series of tests to evaluate how different parameters influence its cutting performance. Each test focused on a specific variable, providing a comprehensive overview of the saw's capabilities and limitations.
Cutting Time vs. Wheel Speed
The first test examined the relationship between wheel speed and cutting time. A 25 mm sapphire rod sample was cut using a 5” diamond wheel at varying speeds. For each speed setting on the dial (ranging from 1 to 10), three cuts were made, and the cutting times were recorded and averaged.
Results and Analysis
The results, illustrated in Graph 1, indicate that increasing wheel speed significantly reduces cutting time. However, this reduction is not linear; the decrease in cutting time levels off at higher speeds. This suggests that while higher speeds enhance efficiency, there is a threshold beyond which the benefits diminish.
Graph 1: Cutting Times as a Function of Wheel Speed
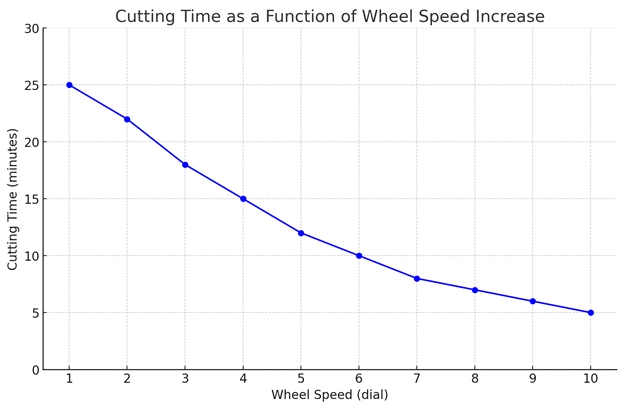
The graph shows a rapid decrease in cutting time at lower speeds, which stabilizes at higher speeds. This trend is expected to hold true for other hard materials, given the motor speed characteristics rather than the material composition.
Cutting Time vs. Wheel Diameter
The second set of experiments explored the effect of wheel diameter on cutting time. Using 4”, 5”, and 6” diamond wheels, the sapphire rod was cut, and the cutting times were measured.
Results and Analysis
Larger wheel diameters were found to decrease cutting times due to the increased contact area and more efficient cutting action. This finding underscores the importance of selecting the appropriate wheel diameter for optimal performance.
Cutting Time vs. Applied Load
To assess the impact of load on cutting time, varying loads were applied to the saw arm while cutting the sapphire rod with a 5” diamond wheel. Three cuts were made at each load setting, and the cutting times were averaged.
Results and Analysis
As depicted in Graph 2, there is a direct correlation between applied load and cutting time. Increasing the load generally reduces cutting time up to a point. However, excessive load can lead to potential damage and reduced efficiency, particularly with soft, ductile materials like copper.
Graph 2: Cutting Time as a Function of Applied Load
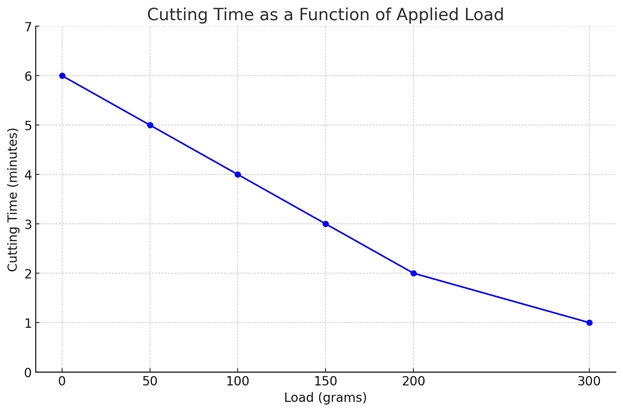
The graph illustrates that while higher loads enhance cutting speed, they must be carefully managed to avoid wheel clogging and damage.
Cutting Time vs. Arm Position
The final test investigated the influence of arm position on cutting time. The SMART CUT® 6005 allows for adjustment to four different positions, optimizing the specimen's location relative to various diameter cutting wheels.
Results and Analysis
Three cuts were made at each arm position with different wheel diameters (4”, 5”, and 6”). The averaged cutting times were plotted in Graph 3.
Graph 3: Cutting Time as a Function of Arm Position for Varying Diameter Wheels
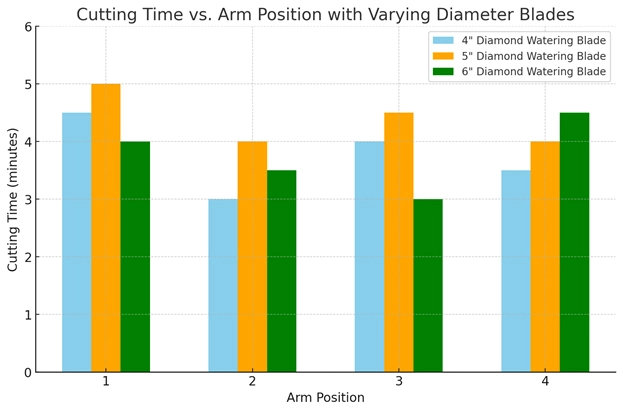
The data indicates no significant relationship between arm position and cutting time. Therefore, arm position adjustments should be primarily used for positioning the sample when changing wheel diameters or optimizing specimen placement.
Conclusion
The study provides critical insights into the operational parameters of the SMART CUT® 6005 Low Speed Diamond Saw. Key findings include:
-
1. Wheel Speed: Increasing wheel speed reduces cutting time, but the benefits level off at higher speeds.
-
2. Wheel Diameter: Larger diameters result in shorter cutting times due to increased contact area.
-
3. Applied Load: Higher loads decrease cutting time, but excessive load can cause wheel damage and inefficiency.
-
4. Arm Position: No significant impact on cutting time, but essential for sample positioning.
Case Studies of Sectioning Aluminum, Brass, and Quartz rods 12mm diameter Using SMART CUT® 6005 Low Speed Diamond Saw
The diamond wafering blades underwent testing under conditions comparable to those used in a previous evaluation, where the particle sizes of the diamond wafering blades varied. This experiment involved three different materials: Aluminum, Brass, and Quartz. The objective was to ascertain the cutting durations for each of the five types of diamond wafering blades.
For this experiment, a SMART CUT® 6005 Low Speed Diamond Saw was employed. Each type of diamond wafering blade was utilized to cut the specified materials. The materials were prepared as 12-millimeter diameter rods to ensure uniformity throughout the testing process. Initially, the specimens were affixed to a graphite plate, which in turn was secured onto an aluminum mounting block. This assembly was then positioned in the Cross mount vice of the SMART CUT® 6005. Specimens were mounted using low melting point wax with a melting point of 100 degrees Celsius. The following diamond wafering blades were tested:
Diamond wafering blades:
-
1. 4-inch diameter; 0.012-inch thickness; Fine diamond wafering blade; low concentration. (Series 10LCU)
-
2. 4-inch diameter; 0.012-inch thickness; Medium diamond wafering blade; low concentration. (Series 15LCU)
-
3. 4-inch diameter; 0.012-inch thickness; Coarse diamond wafering blade; high concentration. (Series 20HCU)
-
4. 4-inch diameter; 0.012-inch thickness; diamond wafering blade; coarse, high concentration. (Series 30HCU)
-
5. 4-inch diameter; 0.012-inch thickness; Diamond wafering blade; medium, high concentration. (Series 15HCU)
Each diamond wafering blade was utilized to perform three cuts on each type of material, resulting in a total of nine cuts per wheel. The diamond wafering blades were conditioned with a silicon carbide dressing stick immediately before each cut. The following cutting parameters were consistently applied throughout the experiment:
Cutting Parameters:
-
Load: 90 grams
-
Blade Dressing: Conducted prior to each cut
-
Wheel Speed: Maximum setting on the dial
-
Coolant: SMART CUT water-soluble coolant
-
Coolant Density: 30:1 ratio
The duration of each cut was meticulously timed, recorded, and the average time per cut for each sample was calculated and subsequently illustrated in a graphical format.
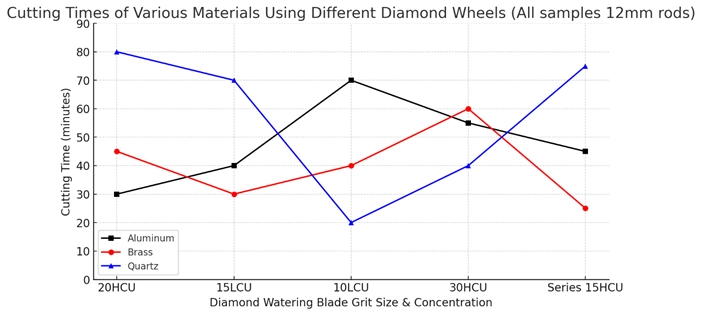
Based on the graph showing the cutting times of various materials using different diamond wafering blades, several insights and patterns can be deduced:
1. Material Response to Grit Size & Concentration
-
Aluminum: The cutting time for aluminum shows a trend where the finest grit size (10LCU) results in the longest cutting time, with times decreasing significantly with coarser grits (20HCU and 15LCU). However, the finest grit size does not always result in the longest cutting times, as seen with the 30HCU and Series 15HCU, where cutting times drop and then increase again.
-
Brass: For brass, the trend is less consistent, where medium grit sizes (15LCU) appear to facilitate faster cutting compared to finer (10LCU) and coarser (20HCU) grits. Interestingly, brass responds better to the specific composition of the 30HCU wheel, showing a reduced cutting time.
-
Quartz: Quartz displays a clear preference for coarser grit sizes, with the 20HCU resulting in the fastest cutting time. The fine grit size (10LCU) is significantly less efficient, resulting in the longest cutting times. This suggests that coarser grit sizes might be more effective at cutting harder materials like quartz.
2. Impact of Wheel Concentration
-
The concentration and composition of the diamond grit in the wheels (30HCU and Series 15HCU) show varied effects on different materials. For example, aluminum and quartz show an increase in cutting time with the Series 15HCU compared to 30HCU, indicating that the specifics of diamond concentration can significantly impact performance.
3. Optimal Wheel Selection
-
Choosing the right diamond wafering blade for a specific material is crucial to optimizing cutting time and efficiency. For instance, while coarse wheels generally perform better for harder materials (as seen with quartz), the specific grit size and concentration can lead to different outcomes.
-
For softer materials like aluminum, a medium to coarse grit (but not the coarsest or finest) seems to provide a good balance between cutting speed and possibly quality of cut.
4. General Observations
-
Each material has a unique response curve to different diamond wafering blade types, underscoring the importance of selecting the correct wheel based on both the material being cut and the desired outcomes (e.g., speed vs. surface finish).
-
The variability in cutting times across different diamond wafering blades also highlights the potential trade-offs between cutting speed and other factors such as the surface quality and life expectancy of the cutting blade.
Overall, the data from the graph suggests that there is no "one-size-fits-all" approach when selecting diamond wafering blades for cutting various materials. Each combination of material type, diamond grit size, and concentration needs to be carefully considered to achieve optimal cutting performance.
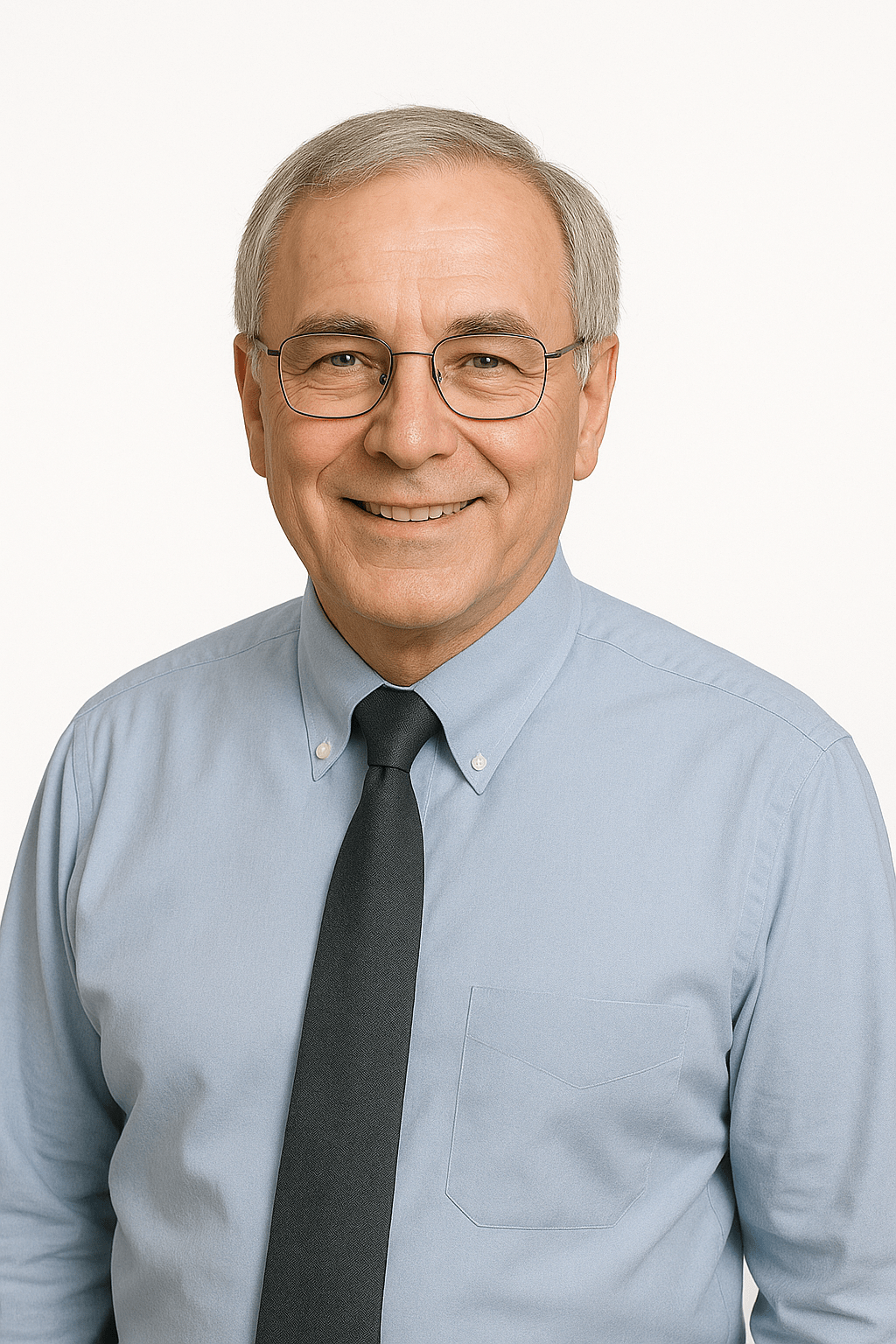
Alexander Schneider is a senior applications engineer and leading authority in the industrial diamond tooling industry, with over 35 years of hands-on experience in the development, application, and optimization of ultra-thin and high-precision diamond blades, diamond core drills, and diamond and CBN grinding wheels. His work spans a wide range of advanced materials including ceramics, glass, composites, semiconductors, and high-performance metals.
Throughout his career, he has collaborated with leading R&D institutions, national laboratories, and high-tech manufacturing companies across Europe, North America, and Asia, providing technical expertise and tailored solutions for demanding cutting and surface preparation applications.
Mr. Schneider has played a pivotal role in advancing precision cutting, sectioning, dicing, and grinding technologies used in research, production, and failure analysis. He is widely respected for his ability to optimize tool design and cutting parameters to meet exacting industry standards—balancing factors such as cut quality, blade life, material integrity, and process consistency.
As an author, Mr. Schneider is known for delivering practical, application-focused insights that translate complex technical challenges into clear, actionable strategies. His articles and technical guides serve as trusted resources for engineers, researchers, and manufacturers seeking to improve precision, reduce process variability, and enhance tool performance in critical applications.
ARE YOU USING SEMICONDUCTOR TOOLS
FOR YOUR APPLICATION?
LET US
HELP YOU
HAVING ISSUES WITH
YOUR CURRENT SEMICONDUCTOR TOOLS?
Knowledge Center
Selecting the Right Diamond Band Saw blade for your Application
Diamond Band Saw Blades Usage Recommendations & Best Practices
Diamond Wire vs band saw blades and circular blades
The Comprehensive Guide to the Processes of Silicon Wafers Production
Manufacturing Processes for Silicon Semiconductors From Ingot to Integrated Circuit
Evaluating & Comparing Diamond Blades
How to Improve & Optimize Your Diamond Sawing Operation
Troubleshooting Diamond Sawing Problems
Silicon Fabrication Guide
Diamond Wire Advantages & Application
Why use diamond
How to Selecting Right Diamond Tools for your application
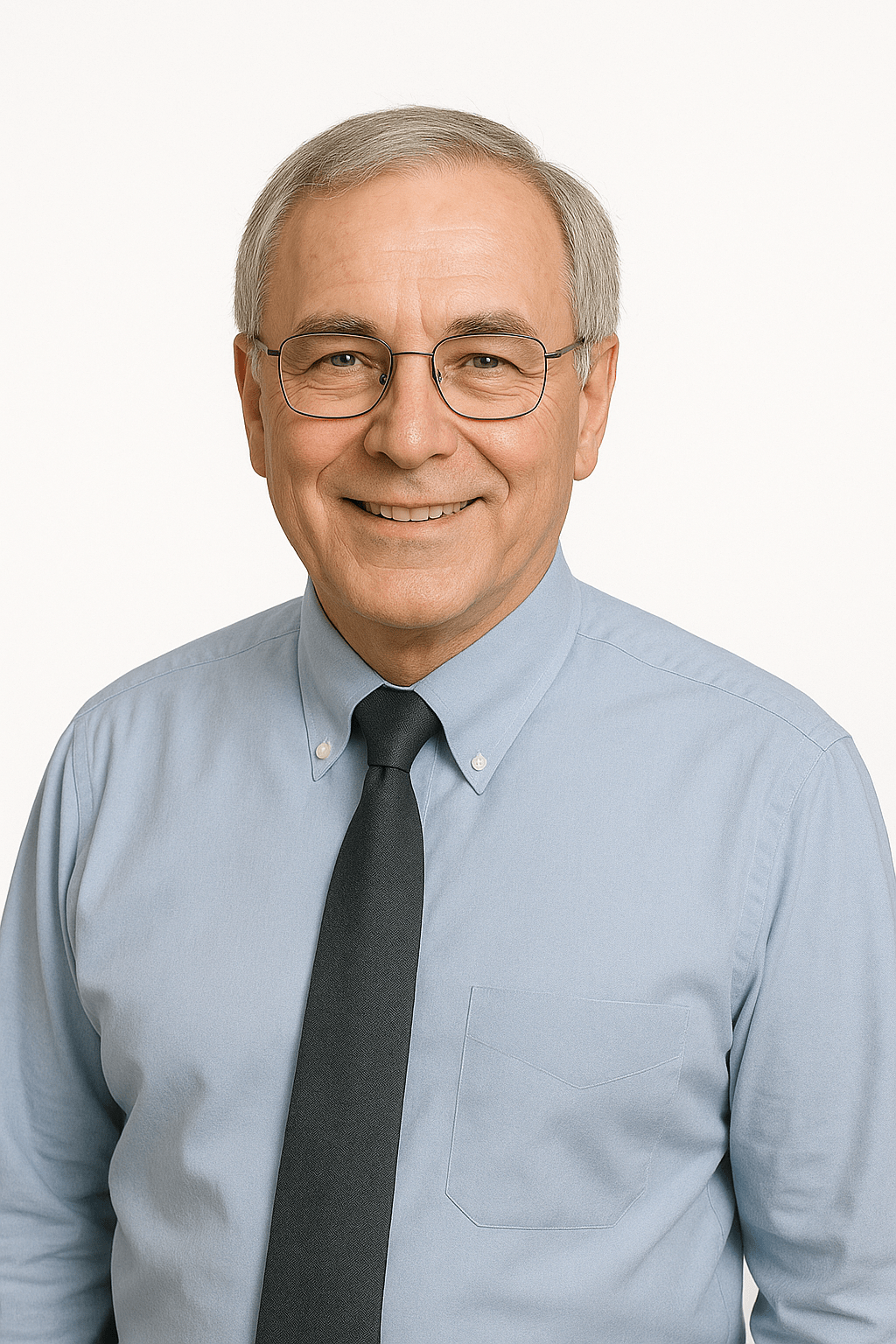
Alexander Schneider is a senior applications engineer and leading authority in the industrial diamond tooling industry, with over 35 years of hands-on experience in the development, application, and optimization of ultra-thin and high-precision diamond blades, diamond core drills, and diamond and CBN grinding wheels. His work spans a wide range of advanced materials including ceramics, glass, composites, semiconductors, and high-performance metals.
Throughout his career, he has collaborated with leading R&D institutions, national laboratories, and high-tech manufacturing companies across Europe, North America, and Asia, providing technical expertise and tailored solutions for demanding cutting and surface preparation applications.
Mr. Schneider has played a pivotal role in advancing precision cutting, sectioning, dicing, and grinding technologies used in research, production, and failure analysis. He is widely respected for his ability to optimize tool design and cutting parameters to meet exacting industry standards—balancing factors such as cut quality, blade life, material integrity, and process consistency.
As an author, Mr. Schneider is known for delivering practical, application-focused insights that translate complex technical challenges into clear, actionable strategies. His articles and technical guides serve as trusted resources for engineers, researchers, and manufacturers seeking to improve precision, reduce process variability, and enhance tool performance in critical applications.