Drilling composite materials, such as Carbon Fiber Reinforced Polymer (CFRP), Glass Fiber Reinforced Polymer (GFRP), Kevlar, and hybrid laminates, presents unique challenges due to their abrasive nature, heterogeneous structure, and susceptibility to issues like delamination, fiber breakout, and material fraying. These advanced materials are increasingly used in industries such as aerospace, automotive, and construction because of their exceptional strength-to-weight ratio, durability, and performance under demanding conditions. However, their distinct properties make them significantly more difficult to machine than traditional materials like metals or plastics.
Share this Article with Friend or Colleague
Selecting the right diamond drills and tools for composite materials is important to achieving clean, precise holes while maintaining the structural integrity of the material and maximizing tool longevity. When choosing a tool for drilling composites, several factors must be carefully evaluated to ensure optimal performance and efficiency, including the specific type of composite, the workpiece thickness, the hole diameter, and the required surface finish. Each of these factors influences not only the quality of the final product but also the wear resistance and life span of the tool.
In this article, we will explore the key considerations for selecting diamond drills and tools for drilling composites. By understanding the unique challenges posed by these materials and the advanced technologies behind diamond tools, you can optimize your drilling processes, reduce tool wear, and ensure high-quality results in composite machining operations.
About Composite Materials
A composite material typically consists of strong, rigid fibers embedded in a weaker, more flexible matrix. The goal is often to create a material that combines high strength and stiffness with low density. In commercial applications, the most common composites use glass or carbon fibers within matrices made from thermosetting polymers like epoxy or polyester resins. Sometimes, thermoplastic polymers are preferred because they can be remolded after initial production.
There are also other types of composites, where the matrix is made of metal or ceramic. These are mostly still in the development phase, facing challenges such as high manufacturing costs. In these cases, fibers (or sometimes particles) are added to improve properties like creep resistance, wear resistance, fracture toughness, and thermal stability. The focus of this discussion is on the basic mechanics of stiffness and strength, which apply broadly to all types of composites but are particularly relevant to fiber-reinforced polymers.
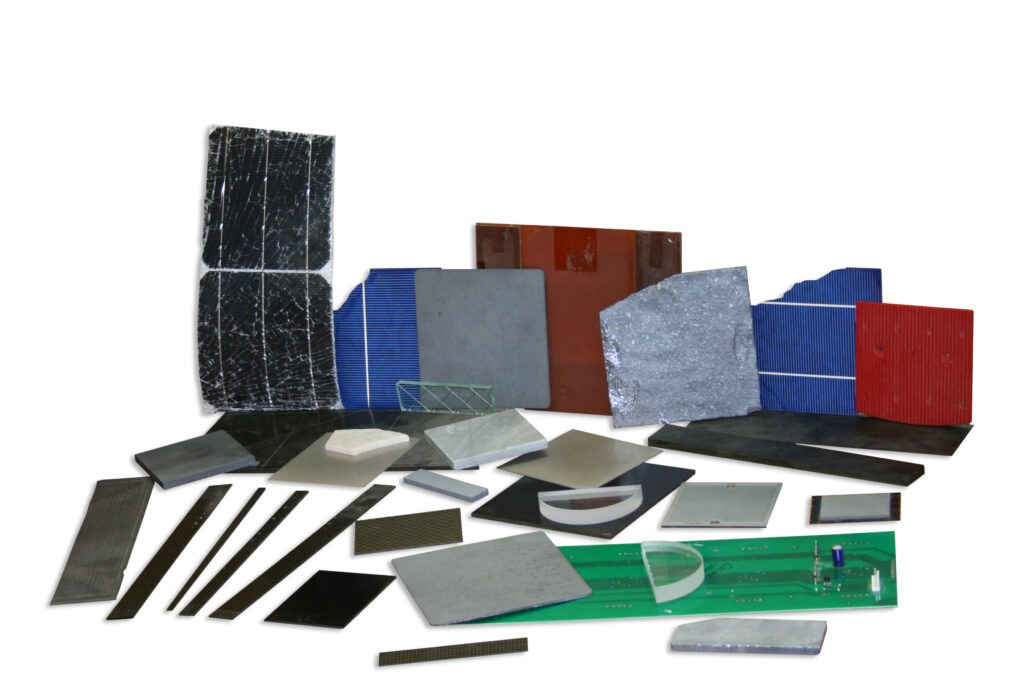
Selecting the right diamond drills and tools for composite materials is important to achieving clean, precise holes while maintaining the structural integrity of the material and maximizing tool longevity. When choosing a tool for drilling composites, several factors must be carefully evaluated to ensure optimal performance and efficiency, including the specific type of composite, the workpiece thickness, the hole diameter, and the required surface finish. Each of these factors influences not only the quality of the final product but also the wear resistance and life span of the tool.
In this article, we will explore the key considerations for selecting diamond drills and tools for drilling composites. By understanding the unique challenges posed by these materials and the advanced technologies behind diamond tools, you can optimize your drilling processes, reduce tool wear, and ensure high-quality results in composite machining operations.
Challenges of Working with Composite Materials
Composites encompass a wide variety of material compositions, generally categorized into metal-matrix composites (MMC), polymer-matrix composites (PMC), and ceramic-matrix composites (CMC). The diversity of these materials, along with their varying hardness and grinding/polishing characteristics, makes it difficult to generalize drilling and relate techniques.
Composites are engineered materials consisting of fillers embedded in a matrix. Common fillers include ceramic or graphite particles, as well as carbon or ceramic fibers, which are encased in a polymer, metal, or ceramic matrix. The broad range of mechanical and chemical properties in composite materials makes them particularly challenging to work with. For example, metal-matrix composites (MMCs), such as silicon carbide ceramic particles within an aluminum matrix, are especially difficult to drill and machine due to the combination of hard, brittle ceramic particles and a soft, ductile metal matrix.
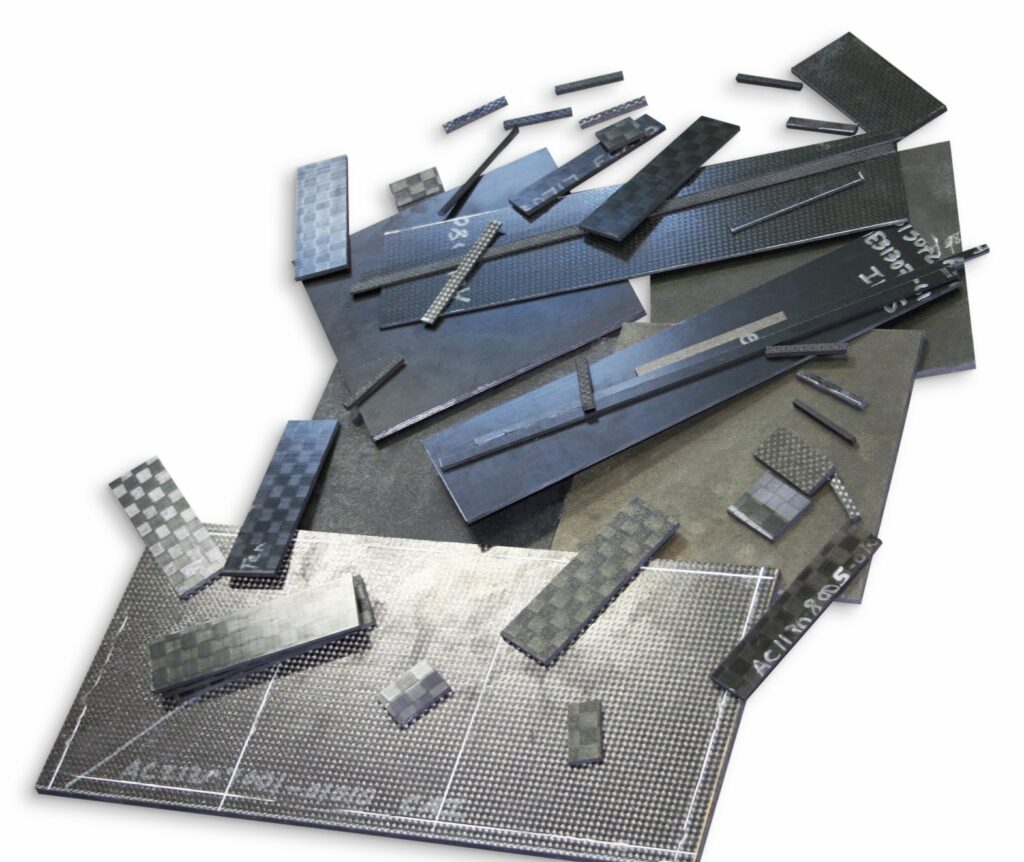
Key Variables to Consider When Selecting Diamond Drills & Tools for Drilling Composites
When selecting the appropriate drill for composite materials, several factors must be carefully considered to ensure optimal performance, efficiency, and the longevity of the tool. Composite materials, such as carbon fiber-reinforced polymers (CFRP), fiberglass, and Kevlar, are increasingly used in industries like aerospace, automotive, and construction due to their lightweight and high-strength properties. However, these same properties, along with their heterogeneous structure, make them significantly more challenging to machine than traditional materials like metals or plastics.
First, the hardness and abrasiveness of the composite material are crucial in drill selection. Composites often contain highly abrasive fibers, such as carbon or ceramic, embedded in a matrix that may be softer or more ductile, like a polymer or metal. These variations make the material more difficult to drill without causing rapid wear to the cutting tool. For example, diamond-coated or carbide tools are often preferred because of their ability to withstand the abrasive nature of composites, significantly extending tool life compared to conventional high-speed steel (HSS) drills. The wrong drill can lead to tool degradation, material distortion, and ultimately an inefficient drilling process.
Another critical factor is the precision and quality of the hole being drilled. Composites are prone to specific failure modes like delamination, fiber pull-out, and matrix cracking, especially when drilled improperly. The choice of drill geometry is important in minimizing these issues. Drills with specially designed point angles, cutting edges, and multi-faceted geometries reduce the mechanical stresses on the composite, resulting in clean, precise holes with minimal damage to the surrounding material. Additionally, tools designed with coolant channels or coated with lubricating layers can further reduce friction, helping to avoid heat buildup and protect the material’s integrity. In applications like aerospace or advanced automotive manufacturing, maintaining tight tolerances and high surface quality is essential for both structural performance and aesthetic considerations.
Speed and feed rate optimization is another major consideration. Drilling composites generates significant friction, leading to rapid heat buildup, which can compromise both the drill and the workpiece. Excessive heat can cause thermal degradation of the matrix material, particularly in polymer-based composites, leading to weakening or warping of the part. It can also increase tool wear and reduce cutting efficiency. For this reason, composites typically require lower cutting speeds and feed rates compared to metals. Additionally, the use of coolant or air jets to dissipate heat and remove debris is often necessary, especially with finer drills or when working with thick or layered composite structures.
The drilling environment and setup must also be factored in. Depending on the complexity of the composite structure and its layering, drill selection may vary for handheld drills versus CNC machines. For precision drilling in critical areas, controlled environments using automated systems ensure better consistency and reduce operator error, while handheld tools may be more suitable for larger, less sensitive areas.
Tool wear monitoring is also important, as composite materials can dull even the hardest drills faster than expected. In high-volume production settings, automated systems may include wear detection and tool-changing mechanisms to maintain efficiency and prevent defective holes. Regular inspection and replacement of drills are essential to maintaining consistent quality, as worn-out tools can lead to poor hole finishes, rough edges, and increased fiber damage.
Moreover, drill coatings and finishes play a role in enhancing performance. Diamond coatings, in particular, are often applied to drills used in composite machining because they provide a hard, wear-resistant surface that minimizes tool degradation. This is especially important for longer production runs where the consistency of the tool’s cutting ability can directly impact the quality of the product.
When drilling composite materials, various drill types offer distinct advantages based on the specific application and the material being worked on. Solid carbide drills are known for their high precision and wear resistance, making them ideal for tough composites and metals. These drills offer excellent cutting speed and are widely used in high-speed drilling operations in aerospace, automotive, and manufacturing industries, particularly for hard composites where tool longevity is crucial.
Understanding Different Diamond Bond Types Used For Machining Composites
Different drilling technologies are designed to tackle the unique challenges of machining composites like carbon fiber, fiberglass, and other advanced materials. Sintered (metal bond) diamond drills provide exceptional durability for abrasive composites, while electroplated diamond drills offer faster cutting speeds for softer materials. Brazed bond diamond drills excel in high-temperature applications, and Chemical Vapor Deposition (CVD) diamond drills are ideal for high-precision operations. Polycrystalline Diamond (PCD) drills, with their extreme hardness, are suited for heavy-duty applications, while solid carbide and coated carbide drills balance speed and wear resistance for softer composites.
Sintered (Metal Bond) Diamond Drills
Sintered diamond core drills are one of the most durable options for drilling composites, particularly in highly abrasive materials like carbon fiber or fiberglass. These drills are designed with multiple layers of diamond grit, making them long-lasting and self-sharpening. As the outer layer of diamonds wears away, new diamonds are exposed, ensuring that the drill remains effective for extended periods of use. Sintered drills excel in abrasive composites where tool wear is a significant concern. However, they tend to be slower in cutting speed compared to other types and come with a higher initial cost, making them more suitable for applications where durability is paramount, such as prolonged or high-volume drilling operations.
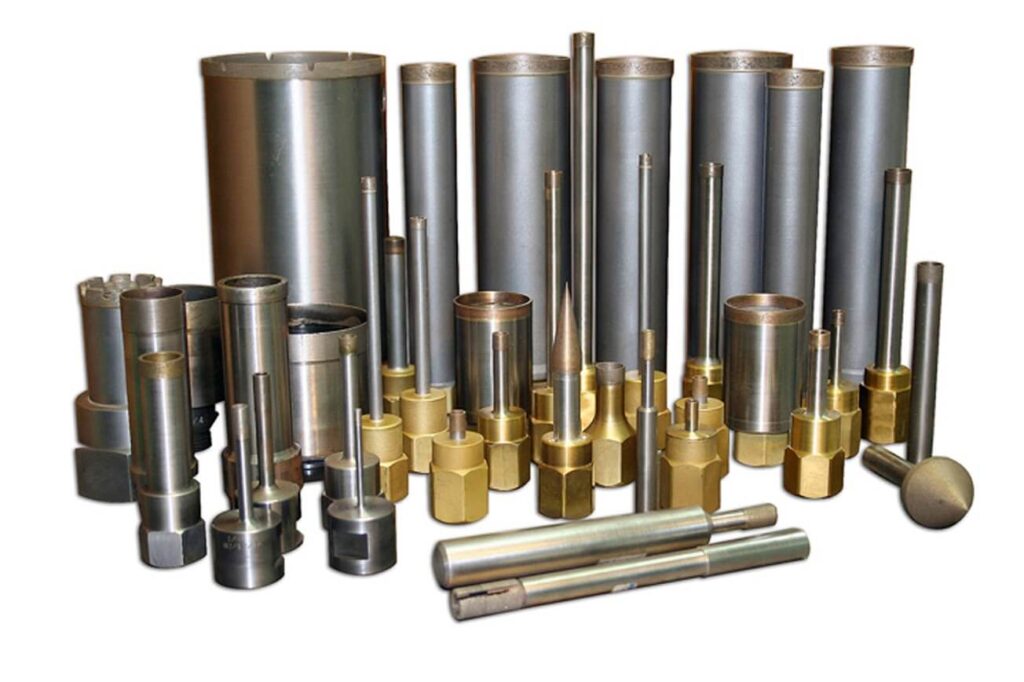
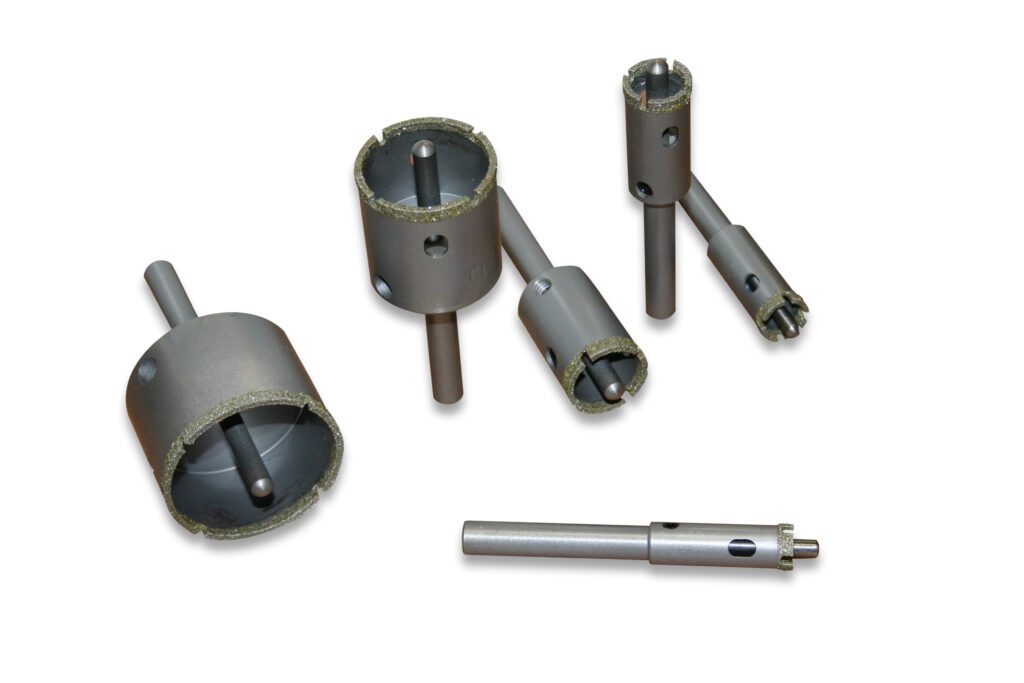
Electroplated Diamond Drills
Electroplated diamond drills are characterized by a single layer of diamond grit bonded to the surface using an electroplating process. These drills are typically less expensive than sintered drills and offer faster cutting speeds, which makes them ideal for precision drilling in softer composite materials like plastics, glass, or light-duty ceramics. However, because they feature only a single diamond layer, electroplated drills wear out faster and are less durable than sintered or brazed drills. They are best suited for short-term applications where high precision is needed but wear resistance is less critical.
Brazed Bond Diamond Drills
Brazed diamond core drills are known for their strong bond and ability to handle high temperatures, making them well-suited for drilling medium to hard composites. The brazing process involves securing diamond grit to the tool using a high-temperature metal bonding method, resulting in a durable tool that performs well in higher-temperature applications. Brazed drills are often used in industries such as aerospace, automotive, and construction, where composite materials like carbon fiber-reinforced polymers or medium-hard composites are common. While they offer a good balance between durability and cutting speed, they are generally less long-lasting than sintered drills.
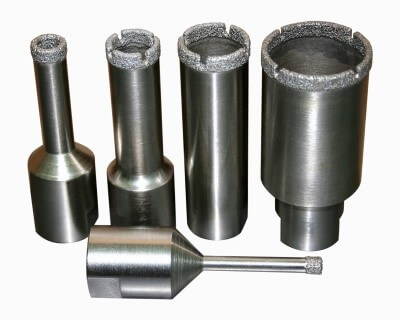
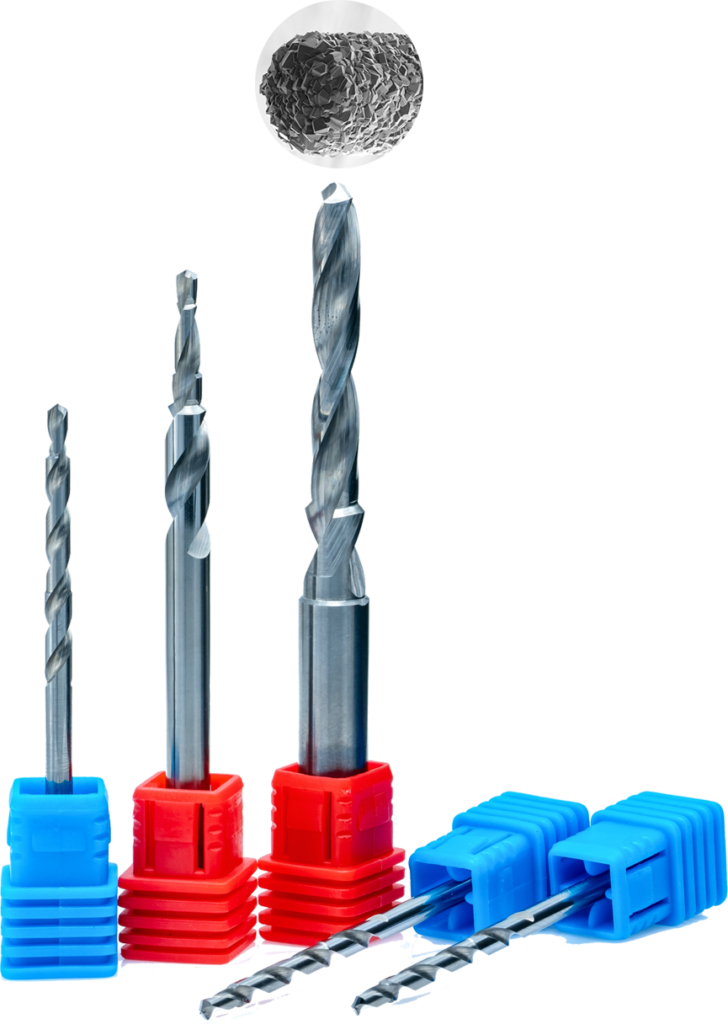
CVD diamond drills
CVD Diamond Drills are made by depositing a thin, uniform layer of synthetic diamond onto the tool via a chemical vapor deposition process. This type of drill offers excellent wear resistance and is highly effective in drilling advanced composites that require precision and low friction. CVD diamond drills are particularly well-suited for high-temperature applications and delicate composites found in industries such as aerospace and medical device manufacturing. However, their high production cost limits their use to applications where precision and material integrity are critical.
Polycrystalline Diamond (PCD) Drills
PCD diamond drills are made from polycrystalline diamond segments sintered onto a carbide substrate. These drills are extremely hard and durable, making them ideal for drilling highly abrasive materials such as carbon fiber-reinforced polymers, glass fiber-reinforced polymers (GFRP), and metal matrix composites. PCD drills have a very long lifespan and are well-suited for high-volume, heavy-duty applications where composite materials are consistently machined. Despite their superior durability, PCD drills are brittle and can chip under extreme conditions. Additionally, they come with a high initial cost, making them more suitable for large-scale operations that require extended tool life.
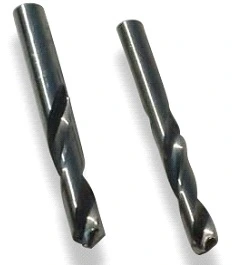
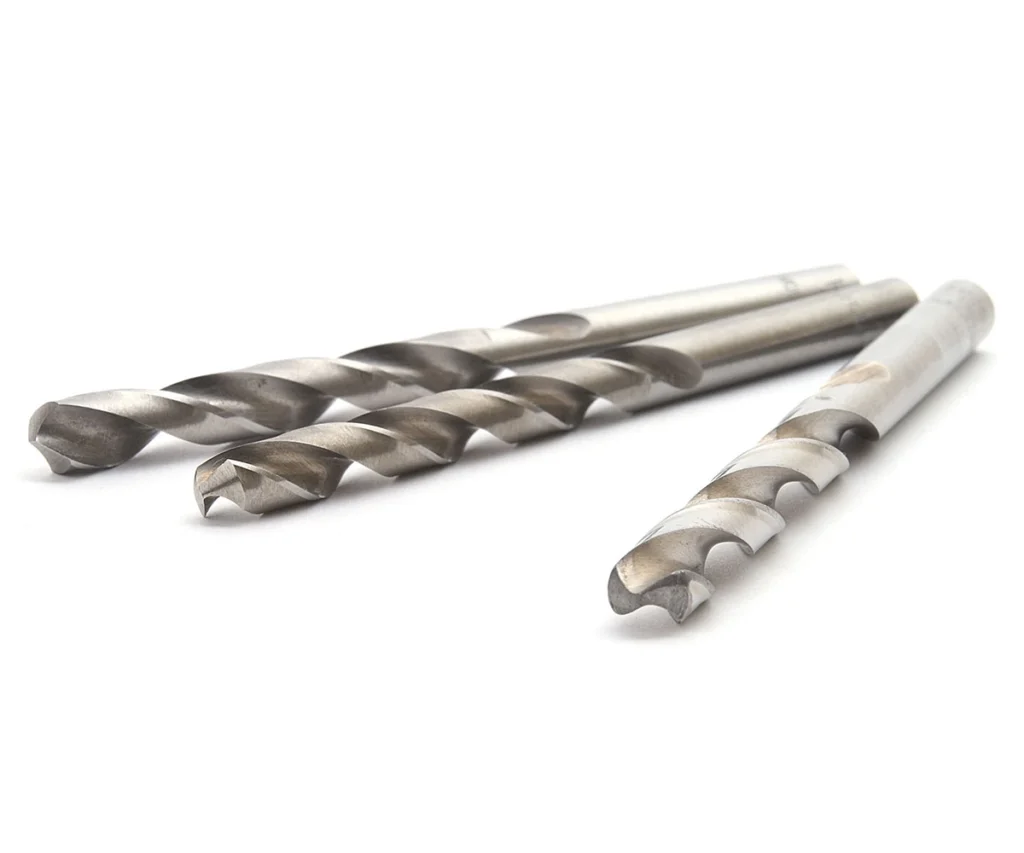
Solid Carbide Drills
Solid carbide drills are a common choice for drilling composite materials and metals where high-speed drilling and precision are required. Although carbide is not as hard as diamond, it provides excellent wear resistance and high cutting speeds, making it suitable for softer composites and soft metals. Solid carbide drills are often used in the aerospace, automotive, and manufacturing industries, where they can effectively handle high-speed drilling without excessive tool wear. However, they wear more quickly in abrasive composites compared to diamond-coated tools, making them better suited for softer materials.
Coated Carbide Drills - Coated carbide drills are an enhanced version of solid carbide drills, featuring an additional layer of diamond or another wear-resistant coating. This coating improves the drill's ability to handle harder composites and extend its lifespan.
These drills offer a good balance between cutting speed and durability, making them useful for a wide range of composite materials. However, once the coating wears off, the performance of the drill decreases significantly, making them less effective for highly abrasive composites in the long term.
Comparison of Diamond Drill Types for Composite Applications
Characteristic / Factor |
Sintered (Metal Bond) |
Electroplated |
Brazed Bond |
CVD (Chemical Vapor Deposition) |
PCD (Polycrystalline Diamond) |
Solid Carbide |
Coated Carbide |
---|---|---|---|---|---|---|---|
Advantages |
- Long-lasting due to multiple diamond layers |
- Fast cutting |
- Strong bond |
- Uniform diamond coating |
- Extremely hard and durable |
- High cutting precision |
- Improved wear resistance |
Disadvantages |
- Higher initial cost |
- Short lifespan |
- Less durable than sintered |
- Expensive to produce |
- High initial cost |
- Wears quickly with abrasive composites |
- Coating wears off over time |
Typical Applications |
- High-abrasive composites |
- Softer composites |
- Medium to hard composites |
- Advanced composites in aerospace |
- High-abrasive materials |
- Soft metals and softer composites |
- Softer composites |
Lifespan |
Long |
Short to Medium |
Medium to Long |
Long |
Very Long |
Medium |
Medium to Short |
Cost |
High |
Medium |
Medium to High |
Very High |
Very High |
Medium |
Medium to High |
When to Use |
- When durability and handling of abrasive materials is needed |
- For precision jobs on soft materials |
- For projects requiring moderate durability and temperature resistance |
- When high precision and durability are required in sensitive composites |
- For high-volume, abrasive material drilling |
- High-speed applications in soft composites |
- For harder composites where a balance of speed and durability is needed |
Material Compatibility |
- Carbon fiber |
- Glass |
- Carbon fiber |
- Carbon fiber |
- Carbon fiber |
- Softer composites |
- Mixed composites |
Heat Resistance |
High |
Low |
Medium |
High |
Very High |
Medium |
Medium |
Best for Composite Layers |
Multi-layered composites |
Thin or soft composites |
Multi-layer composites |
High-precision, multi-layer composites |
High-abrasive layered composites |
Single-layer composites |
Soft-layered composites |
Cut Quality |
Excellent for abrasive materials; minimal chipping |
Good, but faster wear can reduce quality |
Good, durable cuts |
Excellent cut quality, especially on high-precision materials |
Superior, clean cuts in abrasive composites |
Good for softer materials |
Good, but coating wear may affect quality over time |
Chipping and Delamination Control |
Excellent for controlling delamination and fiber pull-out |
Moderate; best for softer composites |
Good for moderate to hard composites |
Excellent, minimal delamination |
Superior, especially for fiber-reinforced composites |
Moderate control |
Good control for softer materials |
Debris Removal & Clogging Prevention |
Very effective; self-sharpening helps reduce clogging |
Moderate, requires frequent chip clearing |
Good, effective at preventing clogging |
Excellent due to smooth, uniform cutting action |
Excellent, especially with deep holes |
Moderate; may need frequent clearing |
Moderate; good for composites that generate less debris |
Ease of Sharpening or Maintenance |
Naturally exposes new diamonds; low maintenance |
Requires frequent replacement or re-coating |
Easier to maintain, but replacement may be necessary |
Not easily re-sharpened; replacement may be costly |
Hard to sharpen; long-lasting but difficult to maintain |
Easily re-sharpened |
Needs re-coating when worn |
Speed of Drilling (Efficiency) |
Moderate drilling speed, optimized for durability |
Fast cutting but wears quickly |
Moderate to fast, depending on material |
Moderate but highly efficient with precise materials |
Moderate to slow, but highly efficient in tough materials |
Fast cutting speed |
Moderate to fast |
Vibration and Stability |
Very stable, designed for high-stress applications |
Moderate stability, best for light-duty tasks |
Stable and good for medium to hard composites |
Very stable for high-precision tasks |
Extremely stable; ideal for precision cutting |
Moderate stability |
Stable in soft materials, prone to vibration when worn |
Environmental Considerations (Wet/Dry Drilling) |
Best used with coolant; handles heat well |
Suitable for dry drilling, but frequent cooling needed |
Works well with or without coolant; good heat resistance |
Requires coolant for high-temp applications |
Handles both wet and dry conditions; prefers coolant |
Performs well dry, needs care in heat management |
Performs well dry but benefits from cooling |
Tool Flexibility (Multiple Material Types) |
Highly versatile; can be used on various hard materials |
Best for soft to medium composites and materials |
Versatile; handles medium to hard materials well |
Mostly for high-precision and advanced composites |
Best for abrasive composites and reinforced materials |
Good for softer composites, some metals |
Good for a range of materials but best for soft composites |
Diamond Drill Types & Configurations
Different types and configurations of diamond drills are designed to tackle the unique challenges posed by these materials, such as delamination, fiber pull-out, and excessive wear on the tool. From sintered and electroplated drills to PCD and CVD-coated options, each type offers distinct advantages based on the application and material. Here we will explore a large range of tools—including twist drills, hole saws, countersinks, and more—each suited for different applications and drilling requirements in composite materials.
Comparison of Drill Types for Composite Applications
Drill Type |
Description |
Advantages |
Applications |
---|---|---|---|
Solid Carbide Drills |
High-precision drills made from carbide, suitable for tough composites and metals |
- High cutting speed and precision |
- High-speed drilling in aerospace, automotive, manufacturing |
Twist Drills |
Most common drill bit with helical flute design for chip removal, made from carbide or diamond-coated |
- Effective chip evacuation |
- General-purpose drilling in composites, soft metals, and ceramics |
Hole Saws |
Circular saw blades mounted on a drill, often diamond-coated for tough materials |
- Capable of drilling large holes |
- Large diameter holes in automotive, construction, and composites |
Countersink Drills |
Drills designed to create countersunk holes where fasteners sit flush with the surface |
- Flush fit for fasteners |
- Aerospace, automotive, and precision manufacturing |
Step Drills |
Conical drills that create holes of various diameters without bit changes |
- Multiple hole sizes with one bit |
- Electrical, plumbing, fabrication |
Trepanning Drills |
Specialized drills for cutting large circular holes without drilling through the center |
- Preserves core material |
- Aerospace, research, and composite sample preparation |
Forstner Drills |
Drills for flat-bottomed holes with smooth edges, typically carbide-tipped or diamond-coated |
- Clean, flat-bottomed holes |
- Composite panel assembly |
Auger Drills |
Drills with a helical structure for deep holes and efficient chip removal |
- Effective for deep holes |
- Electrical and construction |
Features of Different Drill Bits for Composite Applications
Characteristic |
Solid Carbide Drills |
Twist Drills |
Hole Saws |
Countersink Drills |
Step Drills |
Trepanning Drills |
Forstner Drills |
Auger Drills |
---|---|---|---|---|---|---|---|---|
Cut Quality |
High |
Moderate |
High |
High |
Moderate |
High |
High |
Moderate |
Chipping & Delamination Prevention |
Excellent for small holes |
Moderate |
Excellent |
Good |
Good |
Excellent |
Excellent |
Moderate |
Debris Removal (Chip Evacuation) |
Moderate |
High |
Moderate |
Moderate |
Moderate |
Moderate |
Low |
High |
Vibration & Stability |
Very stable |
Moderate |
Stable |
Very stable |
Moderate |
Very stable |
Stable |
Stable |
Heat Management |
Moderate |
Moderate |
High |
Good |
Good |
High |
Low |
High |
Cost |
Medium |
Low |
High |
Medium |
Medium |
High |
Medium |
Medium |
Lifespan |
Long |
Short |
Long |
Medium |
Medium |
Long |
Medium |
Medium |
Ease of Sharpening or Maintenance |
Requires sharpening periodically |
Easy to replace |
Moderate |
Moderate |
Easy |
Hard to sharpen |
Moderate |
Easy |
Speed of Drilling |
Fast |
Fast |
Moderate |
Moderate |
Fast |
Moderate |
Slow |
Moderate |
Material Flexibility |
High versatility |
High versatility |
Moderate |
Moderate |
High |
Low |
Low |
Moderate |
Best for Wet or Dry Drilling |
Dry, with some cooling |
Dry |
Wet |
Wet |
Dry |
Wet |
Dry |
Dry |
Diamond & Carbide Twist Drills
Diamond and Carbide Twist Drills are widely used for drilling composite materials due to their helical flute design, which facilitates efficient chip evacuation. This design is particularly beneficial when working with composites, as it helps maintain clean cuts and prevents issues like delamination, fiber pull-out, or overheating of the material. Made from carbide or coated with diamond, these drills perform well across a variety of materials, including composites, metals, ceramics, and advanced polymers. The diamond coating provides enhanced wear resistance and superior heat dissipation, which is especially important for cutting high-performance composites like carbon fiber-reinforced plastics (CFRP) and glass-reinforced plastics (GRP).
In composite drilling, the main challenges include maintaining the material’s integrity, minimizing damage to fibers, and achieving precise hole edges.
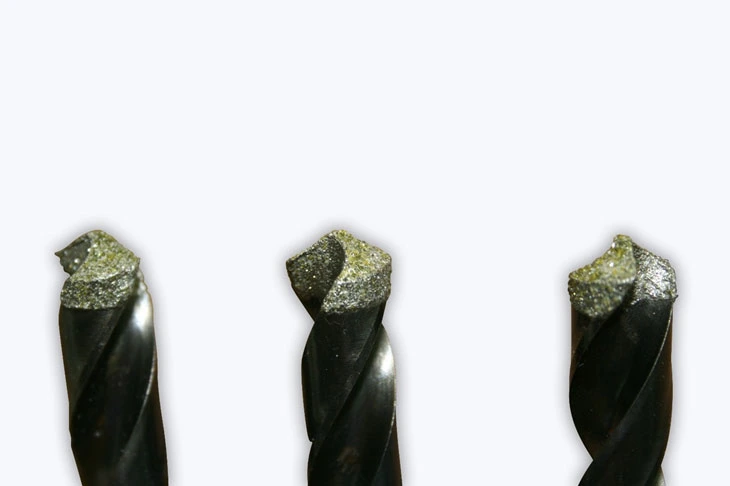
Standard drill bits may cause fraying, chipping, or splintering, but diamond and carbide twist drills are designed to mitigate these issues. The sharp cutting edge of diamond-coated drills ensures cleaner, more precise holes, even in tough materials. Carbide twist drills are well-suited for high-speed drilling, providing the strength needed to handle the abrasiveness of composites while maintaining stability under stress. Diamond-coated drills enhance this performance further by extending tool life and improving cutting efficiency, particularly in dry drilling conditions.
The precision and accuracy offered by diamond and carbide twist drills are essential in industries like aerospace, automotive, and marine manufacturing, where composite materials are widely used. These drills produce clean, precise holes with minimal entry and exit burrs, which are crucial for maintaining tight tolerances in high-performance structures. By reducing the risk of delamination and applying consistent cutting pressure, they ensure the quality of the drilled holes, which is important for fastening and assembly.
Another advantage of these drills is their durability. Diamond-coated twist drills, in particular, have a longer tool life, reducing the need for frequent tool changes and increasing productivity in manufacturing environments. Their helical flute design also improves chip evacuation, reducing frictional heat buildup that can lead to material damage. For high-speed drilling, carbide twist drills are a reliable option, as they can withstand the high temperatures generated during the process.
When selecting diamond twist drills for drilling composite materials, several factors, including diamond grit size, drill diameter, drilling depth, and flute configurations, play a critical role in determining the tool's effectiveness. Below is an overview of the typical specifications:
Diamond Grit Sizes
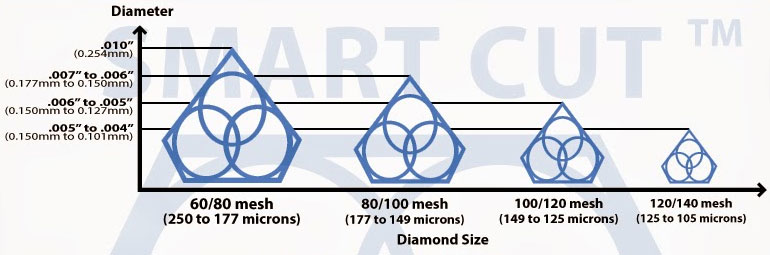
The diamond grit size used in diamond twist drills can vary depending on the material being drilled and the desired finish. Common diamond grit sizes for drilling composites are:
-
Coarse (40-80 mesh): Used for fast material removal in less delicate composites where surface finish is not a primary concern.
-
Medium (100-200 mesh): Often the most commonly used grit size for general-purpose composite drilling, offering a balance between material removal rate and surface finish.
-
Fine (240-400 mesh): Utilized when a smooth surface finish and precision are required, particularly in high-performance composites like carbon fiber-reinforced plastics (CFRP) or glass-reinforced plastics (GRP).
Available Diameters
Diamond twist drills come in a wide range of diameters to accommodate various applications. Some typical diameters used for drilling composites include:
-
Micro & Minatare diameters (0.1 mm to 3 mm): These smaller diameters are used for precise drilling in applications like printed circuit boards (PCBs) or small composite components where fine holes are necessary.
-
Standard diameters (3 mm to 12 mm): These sizes are commonly used for general-purpose drilling in medium-sized composite materials, such as aerospace panels, automotive parts, or sports equipment.
-
Larger diameters (12 mm and above): Larger drills are used for creating bigger holes in thicker or more robust composites, typically in industrial or construction applications.

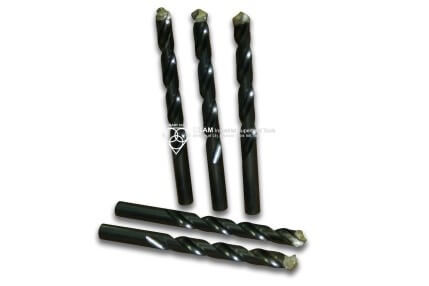
Typical Drilling Depths
The depth of the hole that can be drilled using diamond twist drills depends on the length of the drill bit. The typical drilling depths can be categorized as:
-
Shallow drilling (up to 10 mm): Ideal for thin composite materials, such as sheets or panels, where precision and minimal material damage are important.
-
Medium-depth drilling (10 mm to 50 mm): Common in general-purpose applications where the material has moderate thickness, such as in automotive or aerospace components.
-
Deep drilling (50 mm and above): Required for thicker composite structures, often in construction or heavy-duty applications. In these cases, care must be taken to avoid overheating and excessive wear on the drill bit.
Angle or Flute Configurations
Flute design and the angle of the cutting edges are crucial in optimizing the performance of diamond twist drills in composite materials:
-
Helical flute angle: Typically, a moderate to high helix angle (20° to 40°) is preferred. A steeper helix helps in more efficient chip evacuation, reducing the risk of clogging or heat buildup. This is especially important when drilling fibrous composites, which tend to generate a large amount of dust and chips.
-
Point angle: The point angle of the drill bit typically ranges from 90° to 130°. A sharper point angle (closer to 90°) is better for drilling delicate or thin composite materials, as it reduces the pressure on the material and minimizes the risk of delamination or chipping. For thicker composites, a larger point angle (closer to 130°) provides more stability and strength.
-
Flute configuration: Diamond twist drills may have either single or multi-flute designs, depending on the specific application. Single flutes are often used for delicate materials where maximum chip evacuation is required, while multi-flutes are used for more aggressive drilling where higher material removal rates are needed.
CVD Twist Drills
Chemical Vapor Deposition (CVD) twist drills feature a thin, uniform layer of synthetic diamond deposited onto the carbide substrate of the drill bit. The CVD diamond layer provides an ultra-hard cutting edge, enhancing the drill’s ability to handle abrasive materials without excessive wear.
-
Material: CVD diamond is applied as a coating over a carbide drill bit. The diamond layer is typically only a few micrometers thick but offers significant hardness and abrasion resistance.
-
Diamond Layer: The CVD diamond is pure and uniform, providing consistent performance and reducing the risk of delamination or uneven wear on the cutting edge.
-
Grit Size: The CVD diamond grit size is typically very fine, offering smooth cutting and high surface finish quality, particularly in applications where precision is crucial.
-
Diameter Range: CVD-coated drills are available in a wide range of diameters, from micro sizes (0.1 mm) for intricate drilling to larger sizes (up to 12 mm or more) for industrial applications.
-
Helix Angle: The helix angle is typically moderate (20° to 30°), ensuring efficient chip removal while maintaining the strength of the cutting edge.
-
Point Angle: Typically, CVD twist drills have point angles between 90° and 130°, which can be optimized for the specific material being drilled.
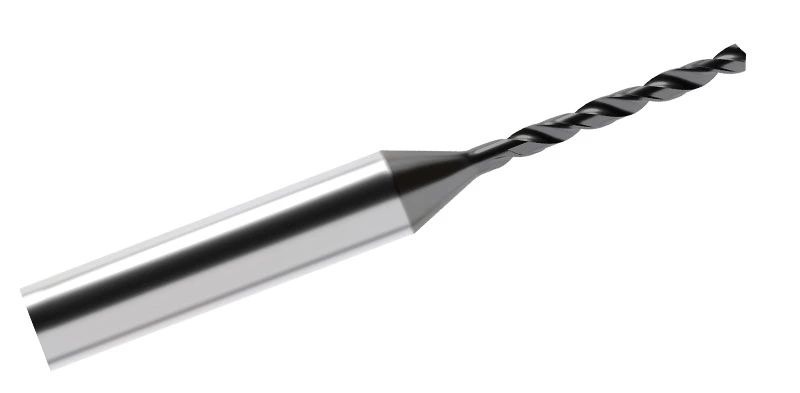
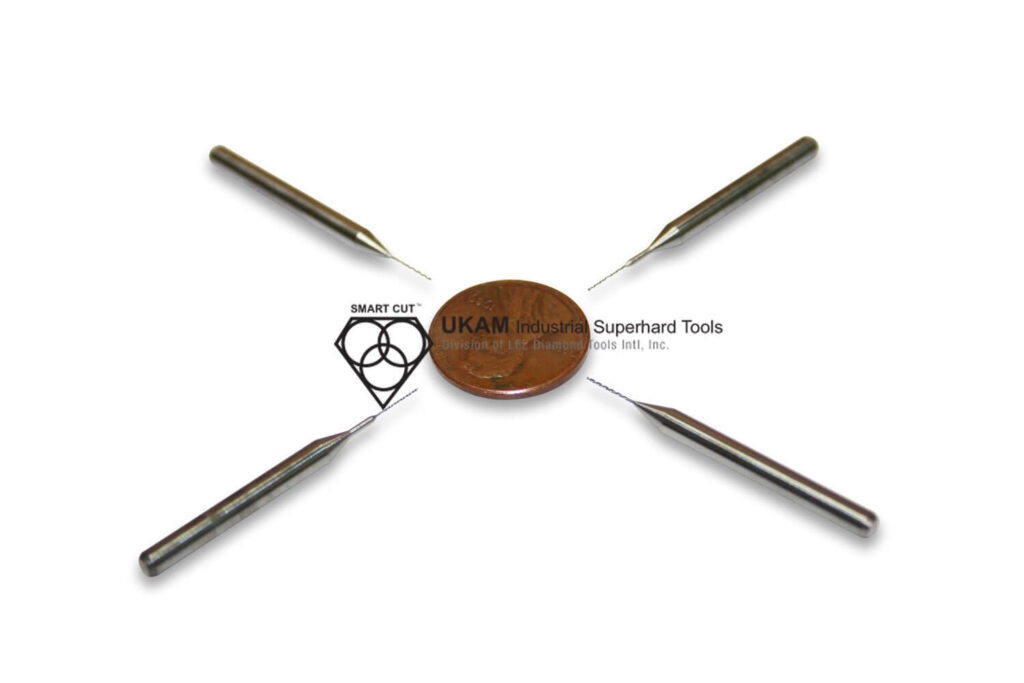
CVD twist drills are commonly used in industries that require precision drilling in abrasive and hard-to-cut materials:
-
Aerospace: Used to drill carbon fiber-reinforced plastics (CFRP), glass-reinforced plastics (GRP), and titanium alloys. CVD drills provide superior wear resistance and prevent delamination in high-performance composite structures.
-
Automotive: Ideal for drilling composite body panels and high-strength alloys used in lightweight vehicles. CVD twist drills ensure clean, precise cuts while minimizing tool wear.
-
Electronics: Used in the drilling of printed circuit boards (PCBs) and other composite substrates. The fine diamond coating on CVD drills provides exceptional accuracy and reduces the likelihood of micro-cracks or defects in sensitive materials.
-
Medical Devices: CVD drills are used in applications requiring high precision, such as drilling ceramics or composite materials for prosthetics and implants.
PCD Twist Drills
Polycrystalline Diamond (PCD) twist drills are made by sintering diamond particles together under high pressure and temperature, forming an extremely hard and wear-resistant cutting surface. Unlike CVD, which is a thin diamond coating, PCD involves bonding a solid layer of diamond to the drill bit, typically at the cutting edges, making it even more durable.
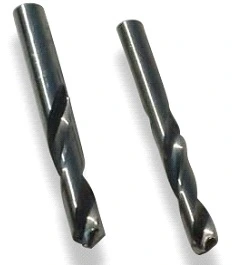
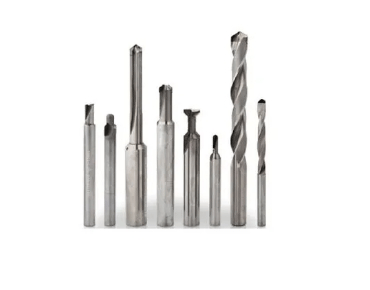
-
Material: PCD consists of diamond particles fused onto a carbide substrate, creating a thick, robust layer of diamond on the cutting edge.
-
Thickness: The PCD layer is typically thicker than CVD coatings, providing even greater wear resistance and longer tool life.
-
Grit Size: PCD drill bits usually feature a coarser grit compared to CVD, allowing for more aggressive cutting in tough materials.
-
Diameter Range: PCD drills come in a wide range of sizes, often starting from around 3 mm for industrial applications and extending up to larger diameters for cutting thicker materials.
-
Helix Angle: The helix angle on PCD drills is designed to optimize chip removal while ensuring durability, typically in the range of 15° to 25°.
-
Point Angle: Point angles for PCD twist drills can vary from 90° to 140°, depending on the specific application. A larger point angle is often used for drilling harder composites and metals.
PCD twist drills are known for their exceptional durability and are widely used in industries that require long tool life and superior performance in abrasive materials:
-
Aerospace: PCD twist drills are frequently used in drilling composite materials, such as CFRP and GRP, as well as aluminum and titanium alloys. The robust nature of PCD allows for drilling multiple holes without frequent tool changes, increasing efficiency in high-volume aerospace manufacturing.
-
Automotive: These drills are used in the manufacturing of lightweight, high-strength vehicle components made from composite materials, aluminum, and carbon fiber. PCD drills provide precise cuts and reduce tool wear when drilling into abrasive composite structures.
-
Construction: PCD twist drills are often employed in drilling glass-reinforced concrete and other composite building materials that are highly abrasive. The durability of PCD makes it ideal for large-scale construction projects where long tool life is critical.
-
Construction: PCD twist drills are often employed in drilling glass-reinforced concrete and other composite building materials that are highly abrasive. The durability of PCD makes it ideal for large-scale construction projects where long tool life is critical.
Comparing Diamond, Carbide, CVD & PCD Twist Drills
Electroplated diamond, carbide, CVD (Chemical Vapor Deposition), and PCD (Polycrystalline Diamond) twist drills each serve different purposes and offer varying levels of performance, depending on the material being drilled and the application's demands.
Electroplated diamond twist drills are designed for drilling abrasive materials such as composites, ceramics, glass, and stone. These drills feature a single layer of diamond grit bonded to the drill bit through electroplating, providing a sharp, abrasive edge that efficiently cuts through hard surfaces. However, because the diamond layer is only a single coating, these drills tend to have a shorter lifespan compared to CVD or PCD drills, as the grit wears off relatively quickly during extended use. They are highly effective for precision drilling in brittle materials, delivering smooth finishes and minimizing damage. Electroplated diamond drills often require coolants to prevent overheating and prolong tool life, making them suitable for aerospace, medical devices, and precision manufacturing industries.
Carbide twist drills, on the other hand, are made from tungsten carbide, a material known for its durability and heat resistance. These drills are commonly used for metals, composites, and other materials. While carbide drills perform well in general-purpose drilling applications, they may wear out faster when used on highly abrasive materials. Carbide drills can be brittle and are prone to chipping under heavy loads or when drilling particularly hard materials. However, they are cost-effective, capable of operating at high speeds, and often used in aerospace, automotive, and general manufacturing sectors.
CVD twist drills have a thin, uniform diamond coating applied over a carbide substrate. This synthetic diamond layer offers enhanced hardness and wear resistance, making these drills ideal for high-precision drilling in composite materials, ceramics, and certain metals. The CVD diamond layer, though thinner than PCD, provides superior cutting precision and extended tool life compared to carbide drills. CVD twist drills also deliver smoother finishes and reduce the risk of delamination or chipping when working with composite materials. While they are more durable than carbide, CVD drills still wear faster in highly abrasive conditions. These drills are commonly used in aerospace, electronics, and automotive applications.
PCD twist drills, made from polycrystalline diamond, offer the highest durability and longest tool life among the four types. PCD consists of sintered diamond particles fused onto a carbide substrate, resulting in a thicker and more robust diamond layer than that found on CVD-coated drills. PCD drills are designed for heavy-duty, continuous use in abrasive materials such as composites, ceramics, and metals. They excel in applications that demand long-lasting tool performance and precise cuts, even under the most challenging conditions. However, PCD drills are more expensive and can be difficult to resharpen. Their durability and ability to maintain precision make them ideal for industries like aerospace, automotive, construction, and oil and gas, where high abrasion resistance is necessary.
Drill Type |
Best for |
Strengths |
Limitations |
Applications |
---|---|---|---|---|
Electroplated Diamond |
Abrasive composites and ceramics |
High initial sharpness, smooth cutting in brittle materials |
Shorter tool life, single-layer diamond grit |
Aerospace, medical devices, precision composites, glass, ceramics |
Carbide |
Metals, composites, and general-purpose |
Cost-effective, high-speed drilling, good for metals |
Wears faster in abrasives, brittle under heavy loads |
Automotive, aerospace, general manufacturing |
CVD Diamond |
Composites and high-precision drilling |
Wear-resistant, precision drilling, smooth finishes |
Thinner diamond layer, moderate tool life |
Aerospace, electronics, high-performance composites, ceramics |
PCD |
Tough, abrasive composites and ceramics |
Exceptional durability, long tool life, superior cutting |
Higher cost, difficult to resharpen |
Aerospace, automotive, oil & gas, construction, drilling high-abrasion composites |
Diamond & Carbide Hole Saws
Diamond hole saws are used for applications requiring large holes, are the preferred option. These drills, often diamond-coated, are capable of drilling large diameter holes with minimal delamination and smooth, chip-free results. Hole saws are typically used in automotive, construction, and other industries that work with large composite materials.
Diamond hole saws for drilling composite materials come in various configurations to tackle the unique challenges posed by composites, such as delamination, uneven tool wear, and material chipping. Standard diamond hole saws, which feature continuous or segmented diamond rims, are commonly used for drilling softer or less abrasive composites. These can be customized with different diamond grit sizes depending on the material.
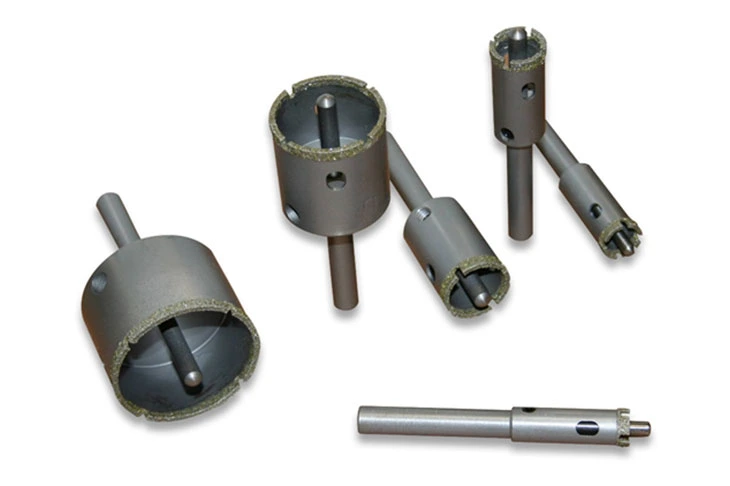

Continuous Diamond Rims
Diamond hole saws with continuous rims have an uninterrupted cutting surface, where the diamond abrasive is uniformly distributed along the entire edge of the saw. This design provides smoother and more consistent cutting performance, especially beneficial when working with delicate or brittle composites. The continuous rim minimizes the risk of material delamination, chipping, and fiber pull-out, which are common issues in cutting composite materials with uneven or aggressive tools.
Because continuous rim hole saws generate a more uniform cutting force, they are ideal for applications where a high-quality, precision finish is required, such as in aerospace or high-performance automotive components.
Additionally, the continuous edge helps in reducing vibrations during the cutting process, resulting in a quieter operation and less mechanical stress on both the material and the tool itself. These saws also tend to be more efficient at cutting thinner composites, offering a fine cut with less risk of material damage.
Segmented Diamond Rims
On the other hand, diamond hole saws with segmented rims feature gaps between the diamond segments along the rim of the saw. These gaps allow for improved cooling and better debris removal during the cutting process. When cutting thicker composite materials or working in high-speed operations, segmented rims can help prevent heat buildup, which can lead to material degradation or tool wear. The segmented design also allows for more aggressive cutting, which can be useful for faster material removal when precision is less of a concern, or when cutting larger holes in thicker composites.
Segmented rims are often used in applications where a higher feed rate is necessary, or when dealing with composite materials that generate a significant amount of dust or resin build-up during cutting. The gaps between the segments allow for better airflow and coolant penetration, helping to keep the cutting surface cooler and reducing the risk of overheating, which can compromise both the tool and the material.
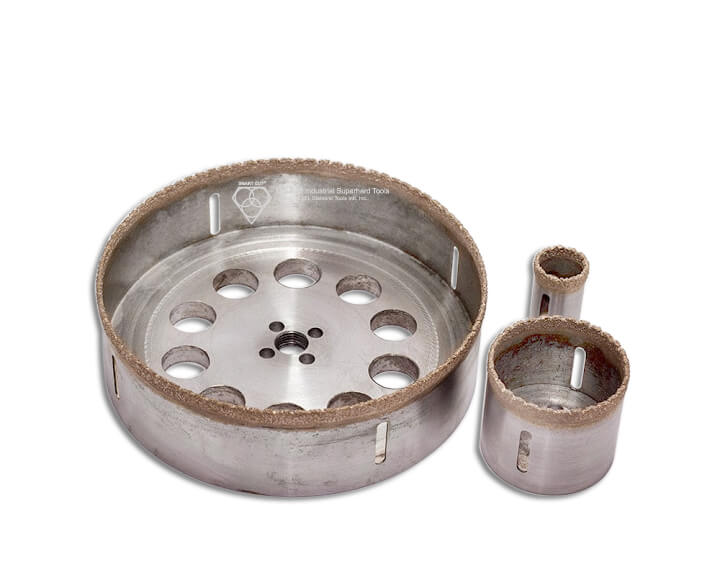
Choosing Between Continuous and Segmented Diamond Rims

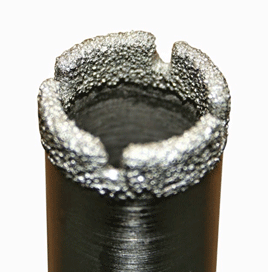
The choice between continuous and segmented diamond rims largely depends on the material being cut, the required surface finish, and the specific operational needs. For delicate, thin, or high-value composite materials where the quality of the cut is important, a continuous rim is often the preferred choice due to its ability to produce clean, precise edges with minimal damage. In contrast, for thicker, more robust composites or in situations where speed and efficiency are prioritized over cut quality, a segmented rim can offer faster material removal and better cooling performance.
At the same time, continuous rims are more suited for materials that require a wet-cutting process, as the uniform edge allows for even distribution of the coolant, keeping the material from overheating. Segmented rim or slotted diamond hole saws, while effective for wet-cutting, are also highly effective in dry-cutting operations due to their enhanced airflow and debris removal capabilities.
In industries like aerospace, automotive, and marine manufacturing, where precision and surface finish are critical, continuous diamond rim hole saws are often used to drill holes in carbon fiber composites or fiberglass panels, ensuring a clean cut with minimal post-processing. On the other hand, segmented diamond rims are favored in construction or heavy manufacturing environments, where thicker composite materials like glass-reinforced concrete or laminated composites are frequently drilled, and speed and efficiency are more critical than fine surface finish.
Diamond Hole Saws With Pilot
In certain applications, diamond hole saws are fitted with pilot bits to ensure more accurate guidance during the drilling process. This added precision is particularly beneficial when working with delicate or high-performance materials like carbon fiber or fiber-reinforced plastics, where tool drift or misalignment can lead to costly damage or flawed cuts. The pilot bit helps maintain stability and alignment, reducing the likelihood of deviations that could compromise the material's structural integrity or lead to surface imperfections.
Pilot bits can either be stationary or removable, depending on the design and specific needs of the operation. They can be manufactured from various types of metals, such as steel, aluminum, or tungsten, each chosen for its specific properties like durability, heat resistance, or wear resistance.
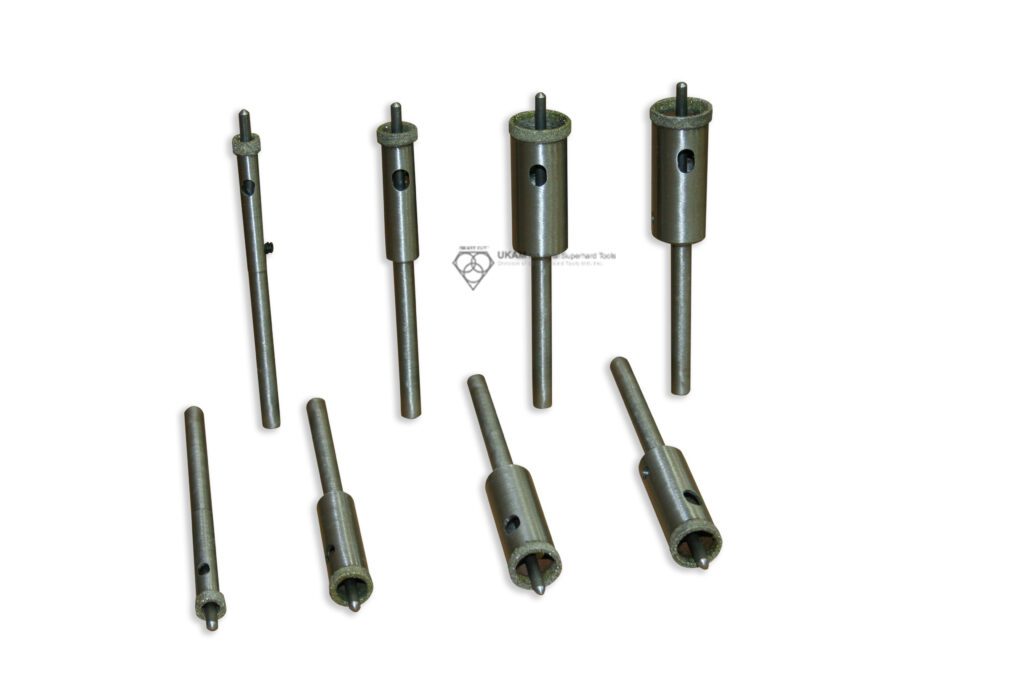
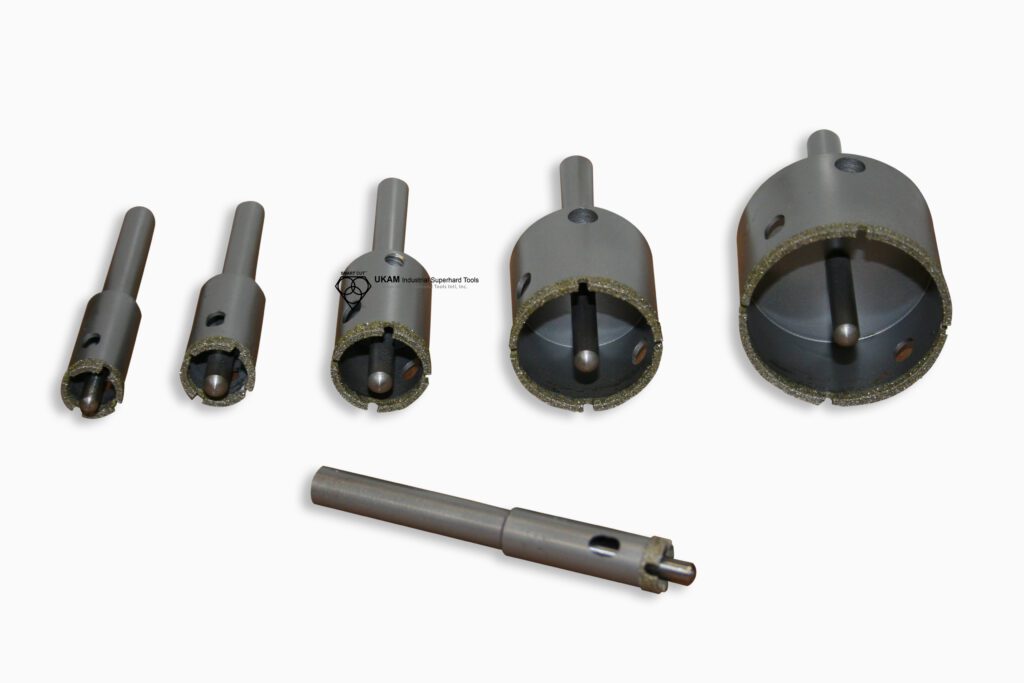
Depending on the application, the pilot bit may be uncoated for standard operations, or it can be coated with diamond or carbide to enhance cutting performance, extend tool life, and improve precision in more challenging materials. Diamond-coated pilots are particularly useful in abrasive materials, while carbide coatings offer added toughness for harder substrates.
Additionally, the pilot bit not only assists in guiding the hole saw but can also help in the initial penetration phase, particularly in materials that are prone to cracking or splintering. This dual role of alignment and penetration makes pilot bits an essential component for improving the overall efficiency, accuracy, and longevity of diamond hole saw drilling operations.
Diamond Hole Saw Wall / Kerf Thickness
When using diamond hole saws for composite materials, the kerf thickness—the width of material removed during cutting—is crucial for achieving precision, minimizing damage, and optimizing performance. In composite materials like carbon fiber-reinforced plastics (CFRP) and glass-reinforced plastics (GRP), the right kerf thickness helps prevent delamination, chipping, and fiber pull-out.
Typically, diamond-coated hole saws for composites have a kerf thickness between 1.0 mm to 2.5 mm. Thinner kerfs (around 1.0 mm to 1.5 mm) are ideal for delicate, thin composites, offering better precision and smoother edges. Moderate to thicker kerfs (up to 2.5 mm) are used for more robust composite materials, balancing cutting efficiency and tool durability. However, thicker kerfs may increase stress on the material and should be used carefully to avoid damaging the composite.
Selecting the right kerf thickness depends on the material’s properties, the required precision, and the desired balance between tool life and cutting performance. Thinner kerfs provide cleaner cuts, while thicker kerfs allow for faster, more aggressive drilling in tougher composites.
Diamond Hole Saw Types & Configurations
Diamond hole saws come in a variety of configurations tailored to specific drilling applications There are also specific configurations available to enhance performance, such as adjustable depth stops for controlling the depth of the hole, anti-vibration designs to protect fragile composite materials, and diamond-impregnated edges for cutting through composites with variable densities or abrasiveness
Vacuum-brazed diamond hole saws, which bond diamond particles directly to the surface through vacuum-brazing technology, offer high durability and enhanced performance when drilling abrasive materials such as ceramic-matrix composites or carbon fiber composites. The exposed diamond surface helps to prevent clogging and improve cooling.
For composites requiring cooler cutting conditions, some diamond hole saws feature segmented teeth, which allow for better heat dissipation and chip removal, minimizing the risk of overheating and material damage. These are especially useful for drilling thicker or layered composites. Thin-wall diamond hole saws are another option, designed to create more precise cuts with minimal material waste, making them ideal for high-performance applications in aerospace and other industries.
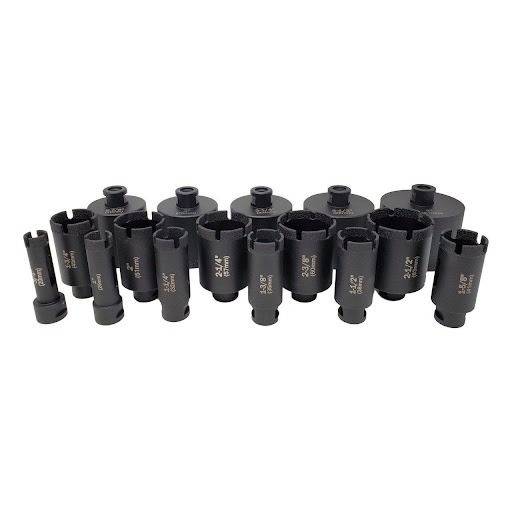
Electroplated diamond hole saws use electroplating technology to bond diamond particles, resulting in a sharp, aggressive cutting edge. These are well-suited for drilling softer polymer-matrix composites, providing quick and clean cuts. Additionally, some diamond hole saws come with integrated coolant holes, which facilitate coolant flow during drilling. This helps to reduce heat build-up, prolonging tool life and improving the overall quality of the drilled hole, particularly in heat-sensitive composites.
diamond hole saws with tapered walls - Another option is diamond hole saws with tapered walls, designed to reduce friction and prevent material binding, especially during deep-hole drilling in thick composite structures. For composites with multiple layers of different materials, multi-layer diamond hole saws are designed to handle the varying densities and hardness levels, such as sandwich composites found in marine or aerospace applications.
One type is designed for drilling or coring when both the material and the drill are mechanically secured, featuring a Core Easy Release System that allows for the effortless removal of the core, enhancing overall efficiency in both production and maintenance.
Diamond Hole Saw with rear core ejector system - Another configuration for diamond hole saws is optimized for high-volume production and utilizes a rear core ejector system. In this setup, the core is expelled by centrifugal force, which eliminates the need for manual core removal and streamlines the drilling process, making it ideal for continuous, high-speed operations. This helps to prevent the accumulation of debris inside the saw and improve efficiency, especially in high-production settings.
For situations where the drilling location has already been pre-determined with a pilot hole, there is a diamond hole saw type that is designed to accommodate this setup, with the standard pilot hole diameter being 1/4". This configuration ensures precise alignment and accurate hole placement, making it highly effective for precision work.
There is also a diamond hole saw specifically engineered to be used alongside a drill bushing. This version has a drill bushing journal that is 1/16" larger than the hole diameter, allowing for smooth operation and reducing wear on both the drill and the material. The drill bushing ensures proper alignment during drilling, especially in more delicate or critical applications.
Finally, another variant is particularly suited for use with water-fed rotary unions (water swivel adopters), offering superior performance when drilling with a through-center water-cooling system. This configuration allows for effective cooling and debris removal during drilling, which is essential when working with tough or abrasive materials, extending the life of both the tool and the workpiece.
Each of these diamond hole saw configurations is designed to meet the demands of specific drilling applications, from high-precision pilot hole drilling to high-speed, high-volume production, ensuring efficiency, accuracy, and minimal tool wear.
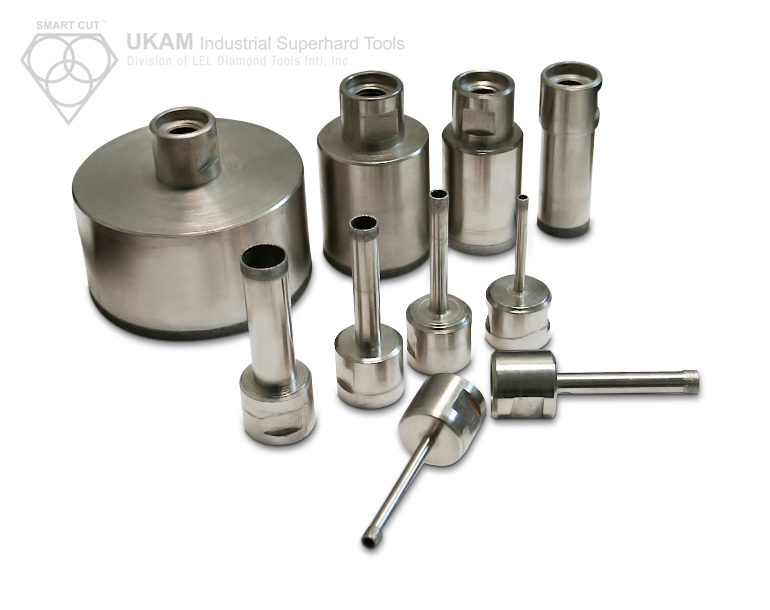
Diamond Grit Sizes for Diamond Hole Saws & Drills
Diamond hole saws come in a range of diamond grit sizes, from 35 to 120 mesh, to accommodate different drilling applications and material characteristics.
The selection of diamond grit size for drilling depends largely on the material being drilled, the desired drilling speed, and the surface finish requirements. Coarser grits are best for fast, aggressive cutting in dry conditions, while finer grits, used with coolant, are ideal for applications requiring precision and a smooth finish.
Coarse Diamond Grits (35 to 50 mesh)
Coarser diamond grit sizes, typically in the 35 to 50 mesh range, are most suitable for situations where coolant is not used. These coarse grits provide a more aggressive cutting action, enabling faster material removal and reducing friction. This is particularly important in dry drilling environments where there is a risk of overheating. Coarser grit sizes are ideal for drilling hard materials like concrete, stone, or some metal-matrix composites, where speed is more important than achieving a fine surface finish.
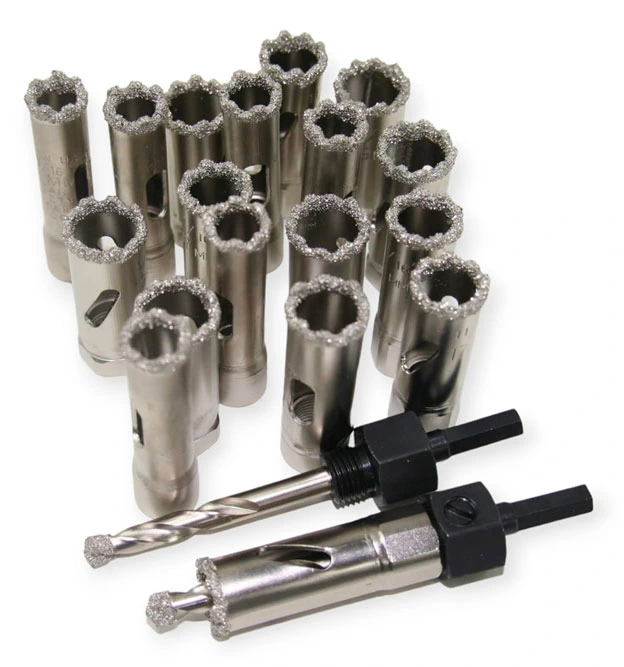

Medium Diamond Grits (50 to 80 mesh)
For more balanced drilling needs, medium diamond grit sizes, generally between 50 to 80 mesh, offer a compromise between cutting speed and surface finish quality. These grits are more versatile and are commonly used in conjunction with coolant to manage heat and debris during the drilling process. Coolant improves tool performance and extends the tool’s lifespan by reducing friction and preventing overheating. Medium grit sizes are suitable for drilling composites, ceramics, and metals where a moderate level of precision is required, making them well-suited for general-purpose applications.
Fine Diamond Grits (80 to 120 mesh)
Finer diamond grit sizes, ranging from 80 to 120 mesh, are preferred in situations where high precision and a smooth surface finish are needed. These fine grits are more delicate and tend to wear faster when used without coolant, so the use of a coolant is crucial in maintaining their effective drilling capability Coolant helps manage friction and heat, which is particularly important when drilling brittle materials like ceramics, glass, or carbon fiber composites. Fine grit hole saws are often used in high-precision industries such as aerospace, optics, and electronics, where surface integrity and accuracy are critical.
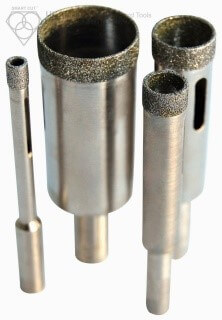
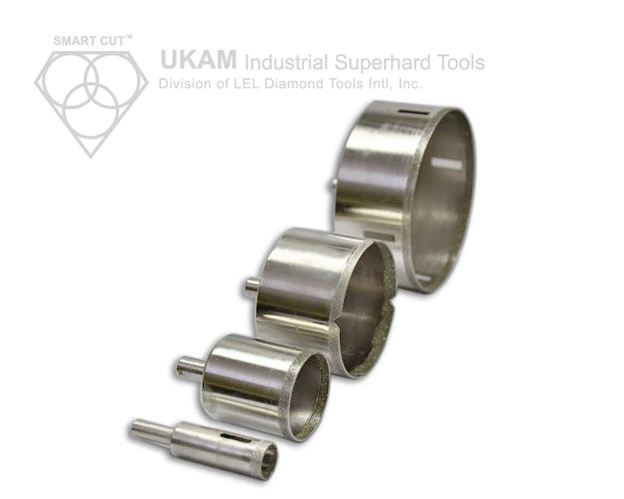
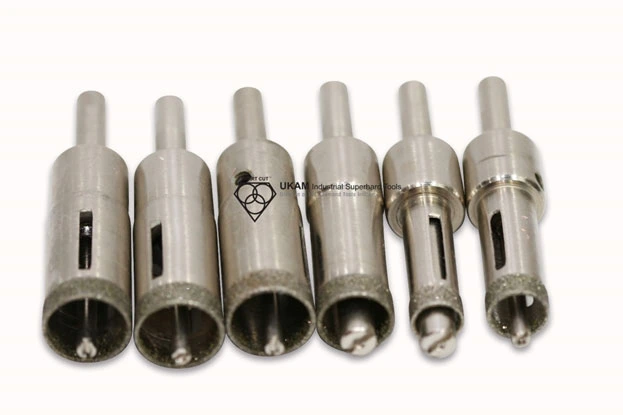
Diamond Countersink drills
Diamond countersinks are essential tools for creating precise, flush countersunk holes in composite materials, commonly used in aerospace, automotive, and precision manufacturing. Their diamond coating offers exceptional wear resistance, ensuring long-lasting sharpness and cutting efficiency even in tough materials like carbon fiber and glass fiber composites. These tools minimize risks of delamination, fiber pull-out, and surface damage, producing clean, burr-free holes. Diamond countersinks are ideal for applications requiring smooth, flush fastener installation, maintaining structural integrity and surface quality. Their durability and precision make them ideal for high-performance, high-volume production environments.
Diamond countersinks and counterbores are essential tools for working with composite materials, offering precision, durability, and adaptability to a range of composite drilling needs. These tools come in several specialized configurations to handle specific tasks such as countersinking, counterboring, and drilling through challenging materials like Kevlar, carbon fiber, and other composite structures. Below is a detailed explanation of each type and its application in working with composites.
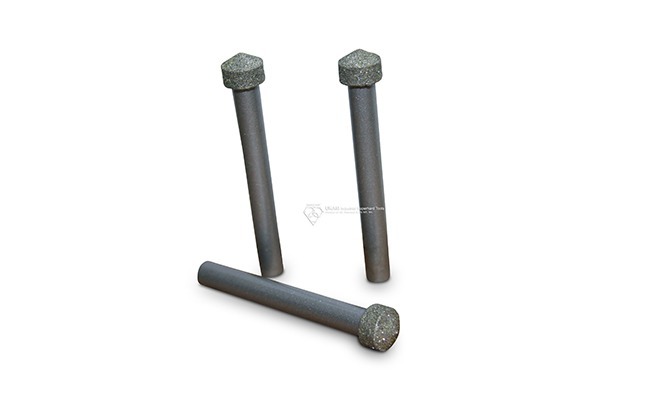
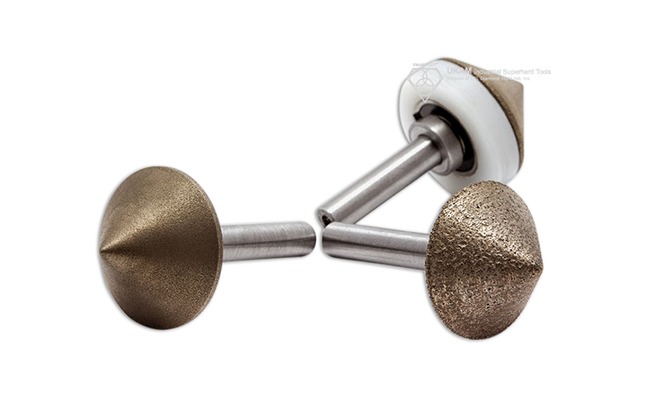
Countersinks for Composites
Diamond countersinks are designed to create beveled edges in composite materials, such as Graphite Epoxy, Carbon Fiber, Boron Fiber, and Fiberglass. These allowing fasteners to sit flush with the surface. This is especially critical in industries such as aerospace, automotive, and marine, where both structural integrity and smooth finishes are vital. The key components of countersinks include the outside diameter (O.D.), the included angle (typically between 90 and 120 degrees, depending on the fastener type), and the body length, which can be short, medium, or long, depending on the application and the reach required.
For drilling composite materials like carbon fiber, fiberglass, or polymer matrix composites, countersinks must provide precise, clean edges without causing delamination or chipping. Diamond-coated countersinks are particularly effective in handling the varying hardness and structure of composites, ensuring long tool life and smooth finishes.
There are different body lengths to suit specific needs:
-
Short bodies (1/2") are useful for tight spaces and applications requiring minimal reach.
-
Medium bodies (3/4") are the most common and offer a balance between reach and control.
-
Long bodies (up to 1-1/2") are ideal for deep countersinking or areas with difficult access.
Countersinks are also available with different shank types, such as cylindrical or threaded (1/4"-28 or 3/8"-24). Cylindrical shanks are common for general-purpose countersinking, while threaded shanks are often used in more precise operations requiring micro-stops to control depth.
These tools are engineered to be used in conventional micro-stop cage units, making them adaptable to standard machining environments. The diamond countersinks feature a electroplated (nickel bond) diamond coating with a diamond mesh size of 60 grit. Our standard stock diamond countersinks are manufactured with a 100-degree angle, the most commonly used angle for fastener installation in composite materials. However, we also offer customization options for different angles and diameters to accommodate specific customer needs. For applications that require non-standard dimensions or special geometries, custom countersinks can be designed and manufactured to meet unique requirements.
In addition to diamond countersinks, we offer a range of other specialized countersinks, including those made from Polycrystalline Diamond (PCD) and solid carbide. PCD countersinks are known for their extreme hardness and wear resistance, making them ideal for machining composites and other abrasive materials. Solid carbide countersinks, on the other hand, are highly versatile and are available in a wide variety of geometric styles. Each style is specifically tailored to handle different material types, ensuring optimal cutting performance.
For example, when countersinking Kevlar—a notoriously challenging material due to its tendency to fray—a countersink with a specially designed flute geometry is essential to create a clean, fuzz-free edge. Without this special design, Kevlar fibers can snag and fray during the machining process, compromising the quality of the cut and the performance of the fastener. Our Kevlar-specific countersinks ensure smooth, clean cuts, maintaining the integrity of the material.
Other styles of countersinks are available for materials such as aluminum, titanium, carbon graphite, and other composite materials. Each material presents unique challenges during the countersinking process, and our specialized countersinks are designed to overcome these challenges. For instance, countersinks for aluminum require a design that minimizes heat generation to avoid material deformation, while those used for titanium must account for the material's high strength and resistance to cutting.
All of our countersinks are manufactured with a standard thread design, allowing them to be easily operated in a conventional micro-stop cage unit. This ensures compatibility with most industry-standard tools and equipment, making our countersinks a convenient and flexible solution for a variety of applications. Additionally, our countersinks are made with an integral pilot design, which enhances stability during cutting and ensures consistent countersink depth and positioning. This feature is particularly important in high-precision applications where even minor variations in depth can affect the performance of the fastener and the overall structure.
Our solid carbide countersinks stand out for their exceptional cutting edge quality. These tools feature super-finished cutting edges, which allow them to maintain their original sharpness much longer than conventional countersinks. The wear resistance of solid carbide countersinks makes them an ideal choice for high-volume production environments where tool longevity and performance consistency are critical. Whether used in manual operations or CNC-controlled systems, these tools deliver reliable performance, reducing the need for frequent tool changes and increasing overall machining efficiency.
Counterbores for Composites
Diamond counterbores are used to enlarge or create flat-bottomed holes, typically to house fasteners like bolts, ensuring they sit flush with or below the surface. In composites, this process is especially challenging because of the different layers and materials involved, which may react differently to drilling pressure and heat. Diamond-coated counterbores provide the necessary durability and precision to handle tough, layered composites without causing damage like fiber pull-out or delamination.
The diameter of the counterbore is an important factor, typically customized to the specific fastener or component being used. These tools are designed with a cylindrical shank for standard use, or a medium body for more specific applications, allowing for flexibility depending on the material and the required finish.
Counterbores are particularly important in high-strength composite applications where fasteners need to be flush or recessed, such as in aircraft fuselages or racing car bodies. The diamond coating ensures that the composite fibers remain intact while cutting through tough materials like carbon fiber and polymer matrices.
Counter Bore-Sink Combination Tools
A counter bore-sink combination tool merges the functions of a counterbore and countersink, allowing for both processes to be completed in one step. This is highly efficient when working with composites, especially in environments where time and precision are critical, such as in aerospace and automotive manufacturing.
These tools are designed with an outer diameter for the counterbore section and a transition diameter that moves to the countersink portion. This allows the user to drill and countersink in a single pass, reducing the need for multiple tool changes and increasing overall efficiency. The included angle in the countersink section is typically around 90 degrees, which is common for many fastener heads.
Counter bore-sink tools are particularly valuable when working with composite materials that combine different layers, such as honeycomb structures or sandwich panels. The diamond edges ensure clean cuts through all layers, preventing chipping or material damage while delivering smooth, precise results.
Single Polycrystalline Blade Countersinks for Kevlar
Kevlar, a highly durable and abrasive composite material, requires specialized tools for drilling and countersinking. Single polycrystal diamond blade countersinks are specifically designed for use with Kevlar, offering a sharp, wear-resistant cutting edge capable of handling the toughness of Kevlar fibers without causing fraying, delamination, or material weakening.
Kevlar is widely used in the defense, aerospace, and automotive industries due to its lightweight yet extremely strong properties. However, its fibrous nature makes it difficult to machine without causing defects. Polycrystalline diamond (PCD) countersinks are engineered to cut smoothly through Kevlar, producing clean, precise countersinks that maintain the structural integrity of the material.
These countersinks are often used in conjunction with a micro-stop to control depth, ensuring consistent results across multiple applications. The tool’s long-lasting polycrystal blade ensures durability, even in high-production environments.
Polycrystalline Diamond Spade Drills for Kevlar
Spade drills are another important tool for working with Kevlar and other hard composites. These drills are designed with a polycrystalline diamond cutting edge that can handle the extreme abrasiveness of Kevlar. Due to the toughness of the fibers, traditional drilling tools tend to wear down quickly, making diamond spade drills essential for precision and durability.
The spade drill is ideal for creating holes in Kevlar without causing fraying, delamination, or overheating, which are common issues when drilling composites. These drills are typically not used for freehand drilling but rather in controlled, stationary setups to ensure accuracy and to prevent tool wear.
Spade drills are commonly used in aerospace and defense applications, where Kevlar components require high-precision drilling. These tools are available in various diameters and depths, tailored to the specific needs of each application.
Polycrystalline Diamond Two-Blade Routers for Kevlar
Routers equipped with polycrystal diamond blades are also designed for Kevlar and other challenging composite materials. The two-blade configuration allows for efficient material removal while maintaining the integrity of the fibers. Kevlar’s abrasive nature requires tools that can handle high wear, and the polycrystalline diamond ensures a long-lasting, sharp edge that resists dulling.
These routers are often used for shaping and cutting Kevlar components in high-performance applications, such as racing cars and aircraft. They are available in various diameters and cut widths, with options for larger cuts using additional blades. These tools allow for precise control over the material, producing clean edges and smooth finishes without damaging the composite structure.
Table of comparison for different types and configurations of diamond countersink drills and related tools used for composites
Tool Type |
Key Features |
Ideal Applications |
Advantages |
Challenges |
---|---|---|---|---|
Diamond Countersink Drills |
- Diamond coating for wear resistance and clean, burr-free cuts |
Aerospace, automotive, marine for creating precise, flush countersunk holes |
- Long tool life |
- Higher initial cost compared to traditional countersinks |
Counterbores for Composites |
- Designed to enlarge holes or create flat-bottomed holes for fasteners |
High-strength composite applications, aircraft fuselages, racing car bodies |
- Excellent precision |
- Requires customization based on fastener type |
Counter Bore-Sink Combination Tools |
- Combines countersinking and counterboring |
Aerospace, automotive, and marine manufacturing |
- Efficiency in performing multiple operations |
- Specialized tool with higher complexity |
Single Polycrystalline Blade Countersinks for Kevlar |
- PCD cutting edge designed for Kevlar |
Aerospace, defense, automotive industries for Kevlar components |
- Extremely durable |
- More expensive and brittle than carbide tools |
Polycrystalline Diamond Spade Drills for Kevlar |
- PCD edge designed for high-abrasion Kevlar |
Aerospace, defense applications requiring precision drilling of Kevlar |
- Ideal for tough fibers |
- Not suitable for freehand drilling |
Polycrystalline Diamond Two-Blade Routers |
- Two-blade design for efficient material removal |
High-performance applications in aerospace and automotive, especially with Kevlar |
- Long-lasting sharpness |
- More expensive, specialized equipment required |
Solid Carbide Countersinks |
- Durable, with super-finished cutting edges |
High-volume production environments, precision manufacturing for various composites |
- Retains sharpness longer |
- Wears faster in abrasive composites than diamond tools |
CVD Diamond Countersinks |
- Thin, uniform layer of synthetic diamond deposited via Chemical Vapor Deposition (CVD) |
High-precision applications in aerospace, medical, and high-tech manufacturing where delicate composites are used |
- High precision |
- Higher cost than traditional countersinks |
Diamond Routers
Diamond routers are essential for shaping, trimming, and cutting composite materials like CFRP and GFRP. Their industrial-grade diamond coatings provide durability and sharpness, ensuring long-lasting performance even on tough, abrasive materials. Commonly used for edge finishing, slotting, and grooving, these routers excel in creating smooth, burr-free cuts in aerospace and automotive composites. They also maintain precision when shaping complex geometries or trimming laminates without causing delamination.
There are several common designs for diamond routers, each tailored to specific machining operations. The most frequently used types include straight routers, ball nose routers, and tapered routers.
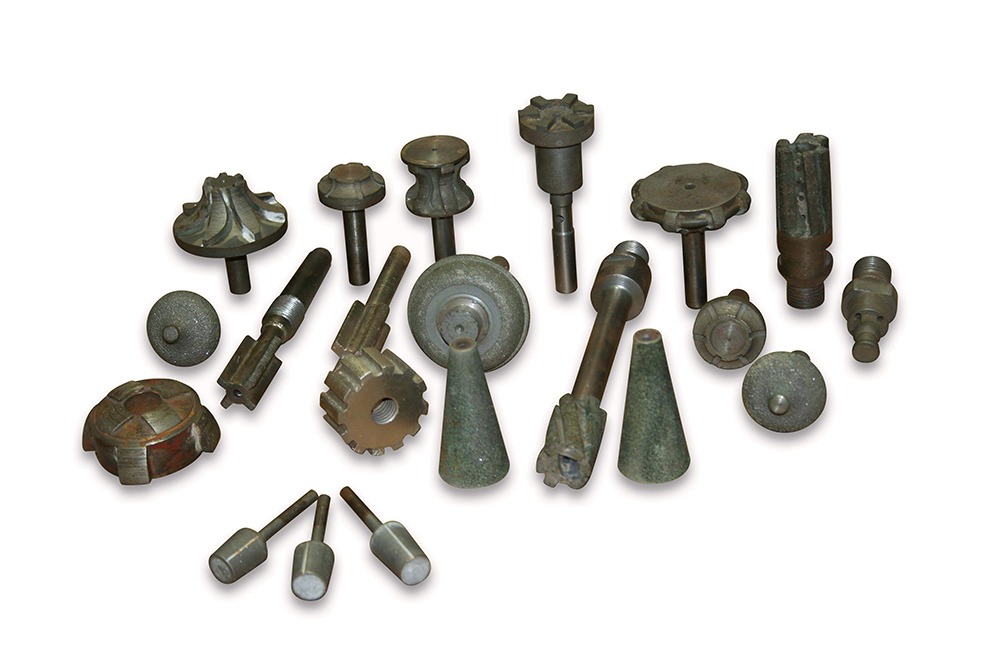
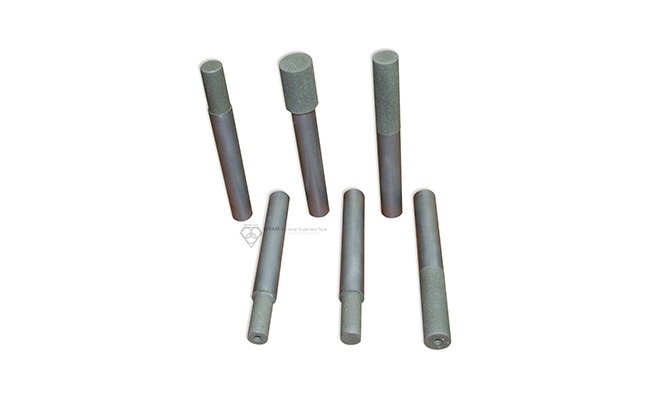
Straight routers
Straight routers are particularly useful for trimming, edge finishing, and general cutting tasks, where precision and clean edges are critical. Straight routers are essential tools for composite machining, particularly for trimming, edge finishing, and general cutting tasks that require precision and clean cuts. These tools are versatile and widely used in industries like aerospace, automotive, and construction, where composite materials such as carbon fiber, fiberglass, and advanced polymers are commonly used.
Straight routers come in two main configurations: fluted and non-fluted.
Fluted straight routers
Fluted straight routers are equipped with helical flutes that help remove chips and debris during cutting. These flutes allow for more efficient material removal, which reduces friction and heat generation, making them ideal for high-speed cutting tasks.
The fluted design also contributes to smoother cuts and prevents material buildup, which is especially important when working with abrasive composites.
The number of flutes can vary depending on the application, with two-flute or four-flute designs being common. More flutes generally result in a finer finish but may reduce chip clearance.
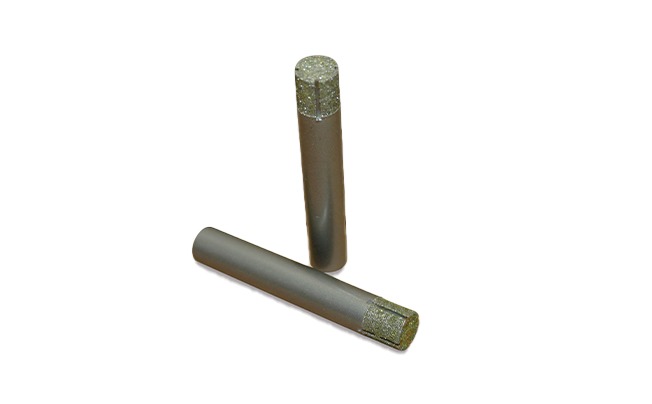
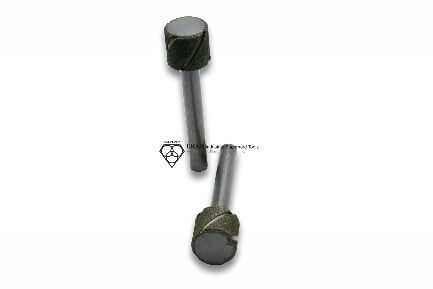
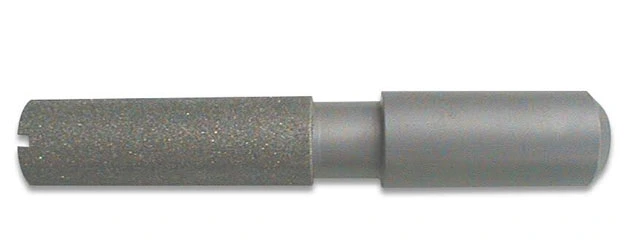
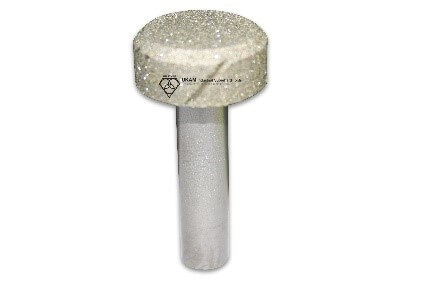
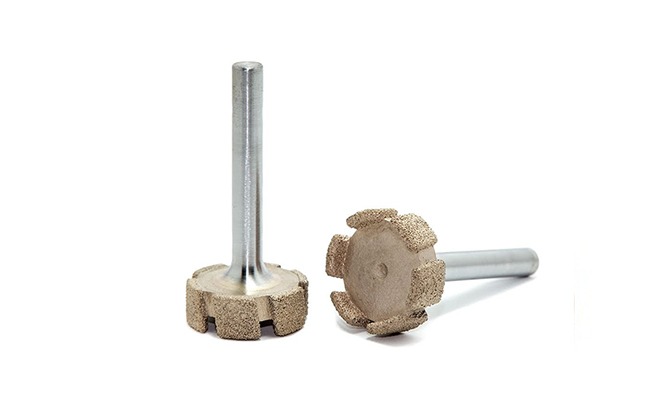
Non-fluted straight routers
on the other hand, have smooth cutting surfaces without flutes. These routers are used in applications where maximum control and minimal material removal are needed. They excel in tasks requiring detailed trimming or edge finishing, where surface quality is critical but chip evacuation is less of a concern. Non-fluted straight routers are often chosen for delicate operations, particularly in thin composite materials where precision is a priority.
The selection between fluted and non-fluted straight routers depends on the material type, the nature of the cut, and the required finish quality. Fluted routers are better suited for heavier material removal and continuous operations, while non-fluted routers are ideal for more controlled, precision work. Both configurations are available in a variety of sizes, angles, and cutting depths.
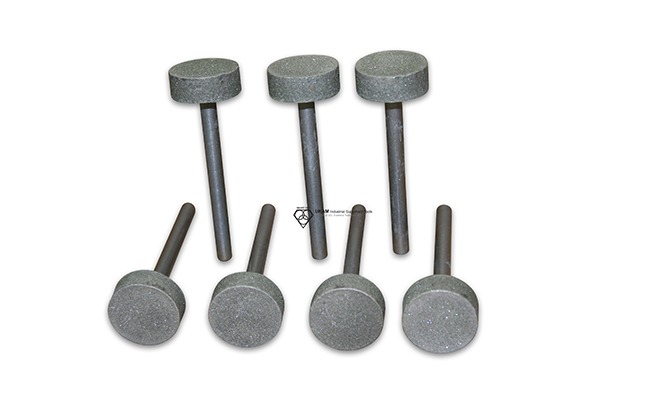
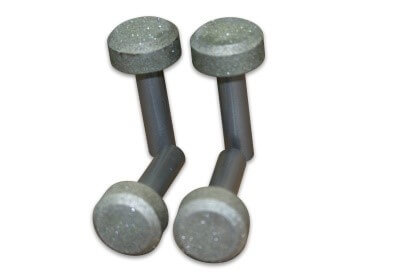
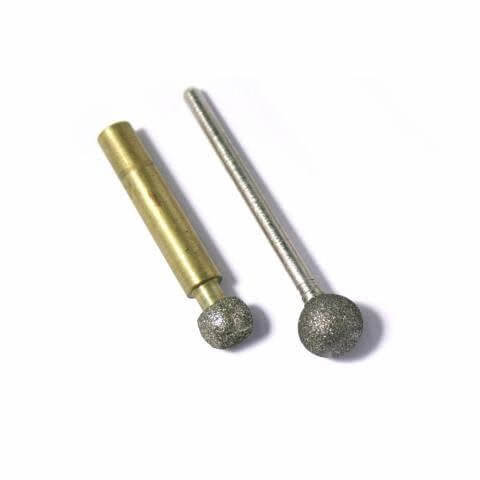
Ball Nose Routers
with their rounded tip, are excellent for machining 3D contours and curved surfaces, which are often required in the aerospace and automotive sectors.
Tapered Router
with its conical shape, is highly effective for grooving, slotting, and beveling, especially in situations where narrow spaces must be reached or angled cuts must be made in composite panels.
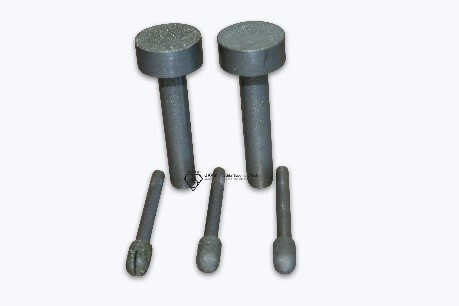
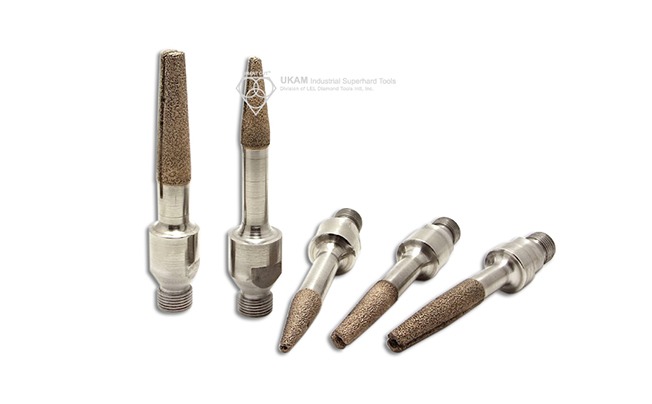
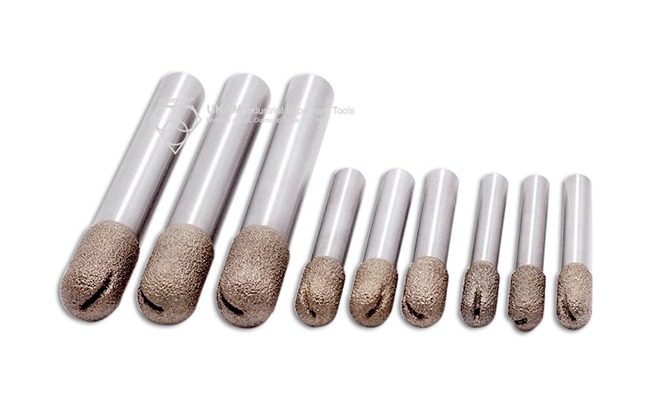
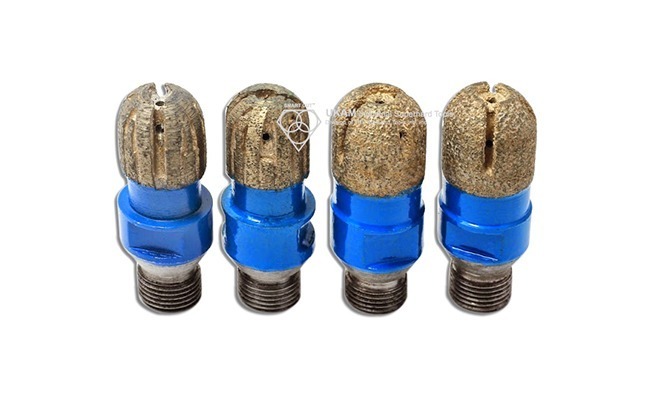
The diamond coating on these routers plays a central role in their effectiveness. This coating is applied either through sintering or electroplating, two processes that provide different benefits. Sintered routers, where diamond particles are fused into the tool body using heat, are highly durable and offer excellent wear resistance, making them suitable for demanding, high-precision applications. Electroplated routers, on the other hand, have a single layer of diamond bonded to the tool surface via a nickel matrix. These routers provide sharper cutting edges, which are critical for applications requiring fine details, though they may not last as long as sintered alternatives.
In terms of specifications, diamond routers are available in a variety of diameters, typically ranging from 3 mm to 25 mm. The choice of diameter depends on the nature of the cut and the size of the area to be machined. Larger diameters are used when bulk material needs to be removed, while smaller diameters are preferred for intricate work or in tight spaces. Length is another important consideration, with standard lengths ranging from 30 mm to 150 mm, depending on the depth of cut required. Longer routers are suited for deep cuts or for accessing narrow cavities in composite structures, while shorter lengths provide greater control for precision work. The shank diameter, typically available in 6 mm, 8 mm, or 12 mm sizes, is another key specification, as it must ensure a secure fit in the router collet to minimize vibration and maximize stability during operation.
Cutting edge length, or CEL, can range from 5 mm to 50 mm depending on the application. Shorter cutting edges are often used for controlled, precise trimming, while longer edges are required for deeper cuts and extended surface contact. The grit size of the diamond coating is also a significant factor in tool performance, as it determines the quality of the surface finish and the rate of material removal.
Grit sizes typically range from 40 to 1200 mesh.
-
Coarse Grit (40–150 mesh): Ideal for rough cutting and bulk material removal. This is particularly useful when machining large composite parts or when speed is more important than surface finish.
-
Medium Grit (150–600 mesh): Provides a balance between cutting speed and surface finish. Medium-grit routers are commonly used for general-purpose trimming and edge finishing in composite materials.
-
Fine Grit (600–1200 mesh): Used for applications requiring smooth, high-quality surface finishes. Fine-grit diamond routers are ideal for delicate work, such as finishing aerospace components or trimming thin composite laminates.
Another important consideration when selecting a diamond router is whether it is compatible with coolant
-
Wet Cutting: Many diamond routers are designed for use with water-based or oil-based coolants. Wet cutting reduces heat buildup, which can cause resin smearing or fiber burning in composites like CFRP and GFRP.
-
Dry Cutting: Some diamond routers are optimized for dry cutting, particularly when used in automated environments where coolant use may not be practical. These routers typically feature specialized coatings or geometries that minimize heat buildup even at high speeds.
The design of diamond routers also includes features such as chip breakers, which help break up composite chips during cutting, preventing clogging and improving overall efficiency. This feature is especially useful when machining thick or highly abrasive composite materials. Additionally, the router’s flute design plays a role in material removal and cutting control. Helical flutes are more efficient for material evacuation during slotting or grooving, while straight flutes provide greater control for trimming and edge finishing.
PCD (Polycrystalline) Diamond Routers
PCD (Polycrystalline Diamond) routers are high-performance tools designed for cutting abrasive materials such as composites, aluminum, and hard plastics. Due to their extreme hardness, they provide excellent wear resistance and maintain sharp cutting edges for extended periods. These routers are widely used in industries like aerospace, automotive, and marine, where precision and material integrity are critical.
PCD routers produce clean, burr-free cuts, which minimizes issues like delamination and fiber pull-out, making them ideal for machining composites like CFRP and GFRP. Common configurations include straight routers for general cutting, ball nose routers for 3D contouring, and compression routers to reduce fraying in multi-layer composites.
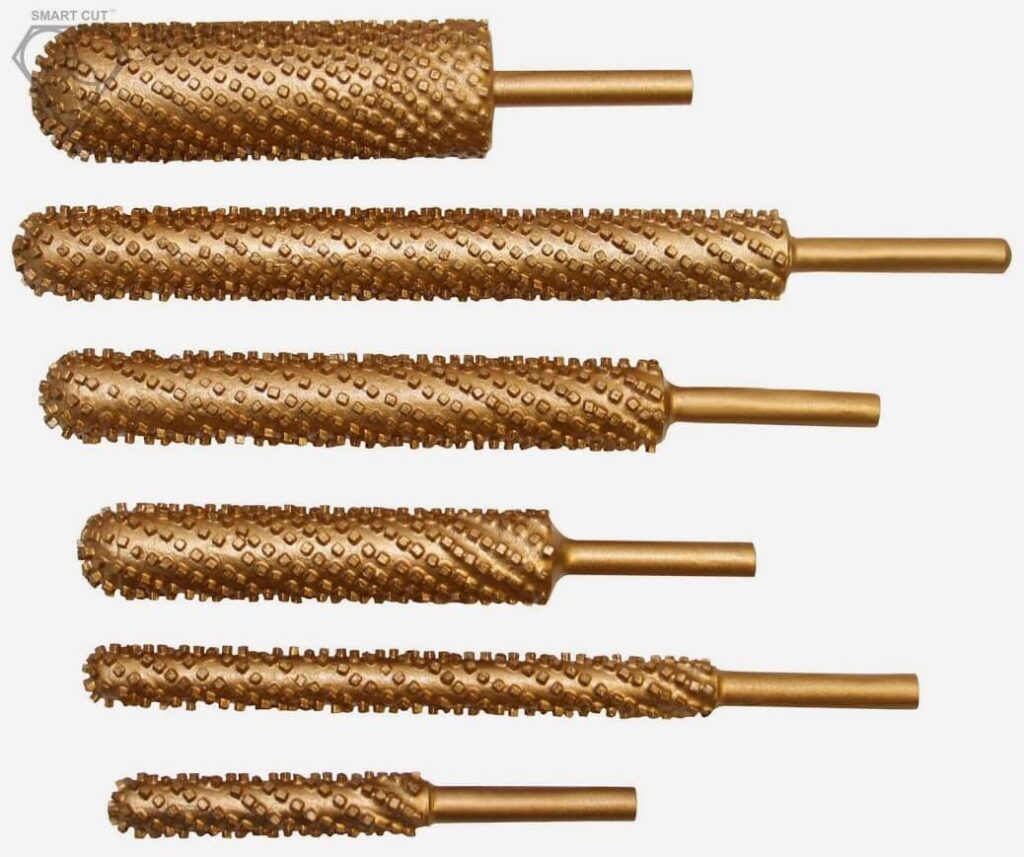
While PCD routers are more expensive than carbide alternatives, their longer lifespan and ability to withstand heat and abrasion make them cost-effective in high-production environments. However, they can be brittle and challenging to resharpen, limiting their use in irregular or high-impact conditions.
Step drills are unique in that they can create holes of varying diameters without needing to switch drill bits. Their conical design makes them suitable for materials with varying thicknesses, and they are commonly used in electrical, plumbing, and fabrication industries where drilling into composites of different thicknesses is required.
trepanning drills - For applications where it is essential to preserve the core material, are ideal. These specialized drills are used to cut large circular holes without drilling through the center, making them perfect for sample preparation or in aerospace and research industries where minimal material disruption is needed.
Forstner drills, typically carbide-tipped or diamond-coated, are used for creating clean, flat-bottomed holes with smooth edges. They are particularly useful in applications where reducing chipping or delamination is critical, such as composite panel assembly and aesthetic applications that require precise finishes.
auger drills, which feature a helical structure, are highly effective for drilling deep holes. These drills provide continuous chip removal and generate minimal heat, making them suitable for electrical and construction industries, particularly when drilling deep holes in soft composites. Each of these drill types plays a crucial role in the efficient and effective drilling of composite materials, ensuring precision and minimizing damage to the workpiece.
Diamond-coated end mills
are highly effective for machining composite materials due to their durability, heat resistance, and ability to handle deep cutting operations. These tools come in various diameters, typically ranging from 1 mm to 25 mm, which allows them to perform well in both intricate and large-scale applications. For smaller, detailed work, end mills with diameters of 1–5 mm are commonly used, while larger diameters are reserved for removing large amounts of material in thicker composite parts.
End mills feature a range of flute configurations, with 2-flute designs preferred for effective chip evacuation in softer composites, and 3 or 4-flute designs used in higher feed rate applications where a smoother finish is required.
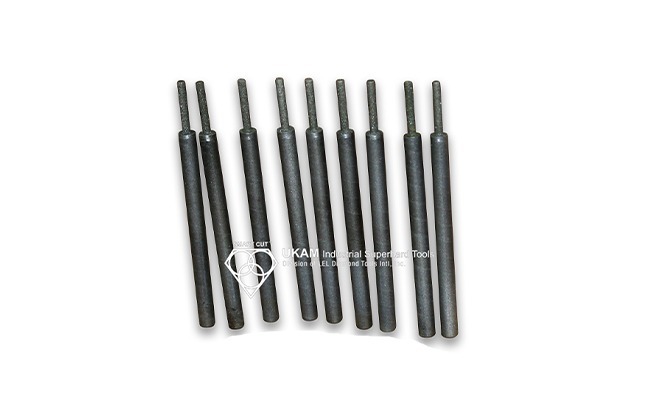
The cutting depth can vary greatly, from shallow cutting lengths of 5 mm to deep cuts over 100 mm, making these tools suitable for diverse applications in composite panels and thick, layered structures.
The helix angle plays an important role in tool performance, typically ranging from 30° to 45°. Higher helix angles improve chip removal, which is particularly useful when working with layered composites that produce a large volume of chips. Additionally, shank types like straight and tapered are available to meet different machining requirements. Tapered shanks offer increased rigidity, especially during deep cutting, reducing tool deflection and chatter.
Diamond-coated end mills come in several configurations, including ball nose, square, and roughing designs. Ball nose end mills are ideal for 3D contouring and sculpting, making them a top choice for aerospace and automotive components with complex shapes. Square end mills are used for precise cutting of flat surfaces, grooves, and pockets, while roughing end mills are designed for high-speed, aggressive material removal. Long reach end mills, with their extended shank and cutting length, are used in applications requiring access to deep cavities or complex internal geometries in composites.
Diamond-coated end mills can also feature variable helix designs, which reduce vibration and improve surface finish, particularly when machining high-strength composites like Kevlar. Chipbreaker designs enhance chip management by breaking large composite chips, thereby reducing friction and heat. Single-flute designs, offering maximum space for chip evacuation, are ideal for high-speed machining of softer composite materials.
Diamond-coated rotary points (Diamond Counter Shape Tools)
are versatile tools used in composite manufacturing for shaping, deburring, and finishing tasks. Their use is particularly effective in working with materials like Carbon Fiber Reinforced Polymer (CFRP), Glass Fiber Reinforced Polymer (GFRP), and Kevlar. These materials are known for being tough and abrasive, which makes diamond coating on the points essential for achieving clean, smooth finishes without tearing or chipping.
The cutting diameters of these points vary widely, ranging from small sizes suited for fine detailing to larger diameters that are more appropriate for substantial material removal. The shank diameter is another critical specification, commonly available in 3 mm, 6 mm, and 8 mm sizes, ensuring stability and compatibility with a range of tools.
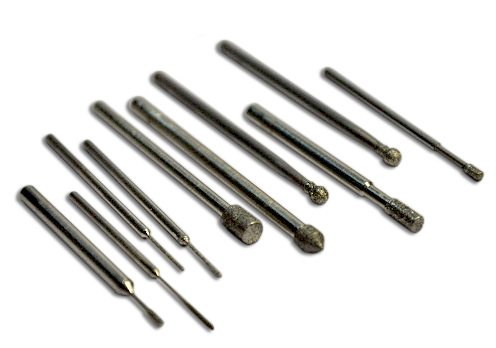
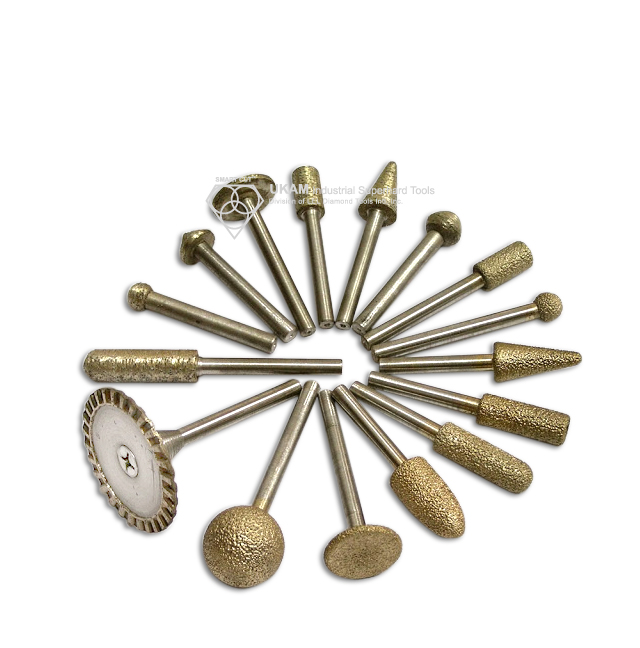
Coating thickness can vary as well, typically ranging from 5 to 15 microns, with thicker coatings offering greater wear resistance, particularly when working on abrasive materials. The grit size of the diamond coating also impacts the results; coarser grits are better suited for rapid material removal, while finer grits provide smoother finishes, particularly when dealing with delicate edges or surfaces.
Diamond-coated rotary points come in various configurations, each designed to meet specific application needs. Cylindrical points are ideal for trimming straight edges and smoothing flat surfaces, while ball-shaped points excel at shaping complex contours and curves. Cone-shaped points work best for accessing narrow or angled edges, and tree-shaped points are useful for rounding off corners in composite structures. Flame-shaped points are particularly well-suited for finishing curved or intricate surfaces, providing smooth, rounded edges. Tapered points allow for precise machining in confined areas, especially when creating beveled surfaces on thick composites.
These points are widely used in applications requiring precision and high-quality finishes, such as aerospace, automotive, and marine manufacturing. They are essential for deburring, edge shaping, surface finishing, and even more specialized tasks like slotting and grooving in composite materials. Their diamond coating not only extends tool life but also minimizes heat generation and ensures smooth results, reducing the risk of delamination or fiber pull-out in the process.