1 |
Excessive Drill Wear
Signs: Rapid reduction in Diamond Drills diameter; visible wear on the cutting edges
|
- Incorrect feed rate or speed;
- Inadequate coolant;
- Material hardness
- Inappropriate drill specification
- Inappropriate wall thickness of diameter and dimensions of material
- Bond Hardness too Soft
- Incorrect RPM’s or Feed Rate
- Using Incorrect Coolant
- Coolant Not affectively used
- Not Dressing the Drill
- Poor Equipment Maintenance
|
- Reduced cutting efficiency;
- Increased drill time
- Process Inconsistency & Inefficiency
|
- Adjust feed rate and speed;
- Ensure adequate coolant flow;
- Use a drill suited for the material’s hardness
- Optimize Drill Specification
- Optimize Type of Coolant Used and How It Reaches Drilling Zone
- Optimize Drill RPM’s & Fee Rate
- Check the Condition of your Drilling Equipment
- Make sure the diamond drill is being dressed properly
|
2 |
Diamond Drills Breakage
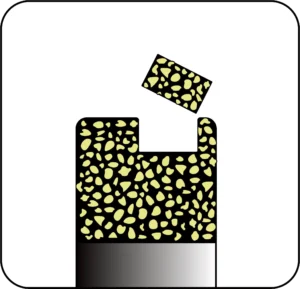
Signs: Sudden snapping or fracturing of the diamond drill; visible cracks or chips on the diamond drill
|
- Excessive pressure
- Misalignment; Material defects
|
- Sudden halt in drilling
- Potential damage to workpiece
|
- Apply correct pressure;
- Ensure proper alignment;
- Inspect material for defects before drilling
|
3 |
Poor Surface Finish
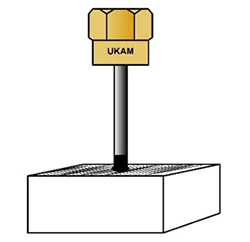
Signs: Rough or uneven hole finish; excessive burring around the hole entrance or exit
|
- Inadequate coolant;
- Worn Diamond Drill
- Incorrect feed rate or speed
|
- Rough hole surface
- Potential need for post-processing
|
- Ensure proper coolant flow;
- Replace or sharpen diamond drill;
- Adjust feed rate and speed
|
4 |
Diamond Drill or Material Overheating
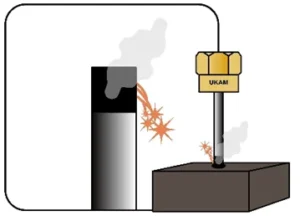
Signs: Excessive heat generation; discoloration of the Diamond Drills or material; smoke or burning smell
|
- Insufficient coolant;
- High feed rate or speed;
- Prolonged drilling without breaks
- Incorrect Coolant or Mix Ratio Used
- Inadequate Amount of Coolant Reaching Drilling zone
- Incorrect Diamond Drill Specification
|
- Premature wear of the drill;
- Potential thermal damage to the material
- Possible Chipping
- Possible Material Micro Cracking
- Possible Material Deformation
- Change in Material Properties
|
- Optimize Coolant:
- Align the coolant nozzles
- Increase coolant flow
- Use specialized water soluble coolant
- Adjust feed rate and speed
- Allow intermittent breaks during drilling
- Try using diamond drill more optimized for the application
|
5 |
Core Ejection Issues
Signs: Difficulty in removing the core from the material; the core sticks or breaks during ejection
|
- Inadequate core breaker;
- Incorrect drill design;
- Material adhesion
|
- Difficulty in removing the core;
- Potential damage to the core or hole
|
- Use an adequate core breaker;
- Choose the correct drill design;
- Apply release agents if necessary
|
6 |
Diamond Drills Wonders
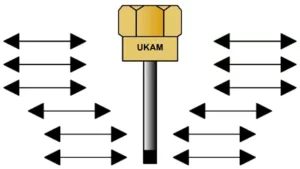
Signs: Diamond Drill deviates from the intended path; uneven hole diameter; off-center hole entrance or exit
|
- Misalignment;
- Uneven surface;
- Inadequate drill rigidity
|
- Inaccurate hole location;
- Potential damage to workpiece
|
- Ensure proper alignment;
- Flatten surface before drilling;
- Use a more rigid drill setup
|
7 |
Material Cracking
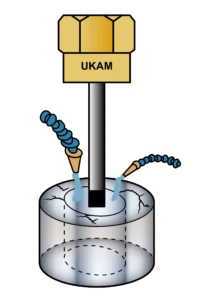
Signs: Visible cracks in the material around the hole; chipping or flaking of the material surface
|
- Excessive pressure;
- Thermal shock;
- Material flaws
|
- Cracks in the material;
- Compromised structural integrity
|
- Reduce pressure;
- Ensure proper coolant temperature;
- Inspect and pre-treat material if necessary
|
8 |
Diamond Drills Glazing
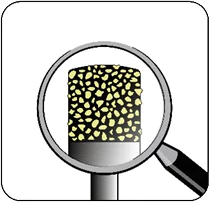
Signs: Smooth, shiny surface on the Diamond Drills edges; reduced cutting debris; increased force required to drill
|
- Inadequate coolant;
- Too low feed rate;
- Material abrasiveness
|
- Reduced cutting ability;
- Increased friction and heat
|
- Increase coolant flow;
- Adjust feed rate;
- Use a drill suited for abrasive materials
|
9 |
Inconsistent Hole Size
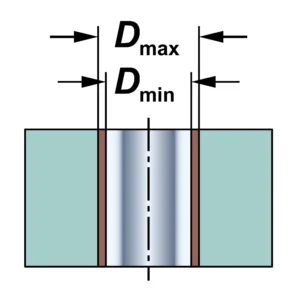
Signs: Hole diameter varies from top to bottom or between multiple holes; holes not consistent with Diamond Drills size
|
- Drill wear;
- Misalignment;
- Material heterogeneity
|
- Holes not meeting tolerance;
- Potential rework or scrap
|
- Monitor and replace Diamond Drills as needed;
- Ensure proper alignment;
- Adjust process for material variance
|
10 |
Inaccurate Hole Tolerances
Sings: Holes are consistently larger or smaller than the specified diameter. Measurement of the hole diameter shows deviation from the design specifications.
|
- Diamond wear or damage
- Inaccurate Diamond Drill size
- Misalignment or instability during drilling.
- Excessive Run Out
- Inaccurate Tolerances
- Runout on Collet or Chuck
- Incorrect Material Mount
- Incorrect Drilling Equipment
- Incorrection Drill Specification
- Not Maintaining the Drill
- Incorrect Drilling Technique runout
|
- Compromised precision in hole dimensions;
- Potential for part rejection or rework.
|
- Regularly inspect and replace worn or damaged diamond drills
- Verify diamond drill size before use.
- Ensure drill and workpiece stability and alignment.
|
11 |
Noise and Vibration
Signs: Unusual sounds during operation; excessive shaking or movement of the drill or workpiece
|
- Misalignment;
- Loose components;
- Inadequate mounting
|
- Unpleasant working conditions;
- Potential inaccuracies in drilling
|
- Check and correct alignment;
- Tighten all components;
- Ensure proper mounting and support
|
12 |
Drill Jamming
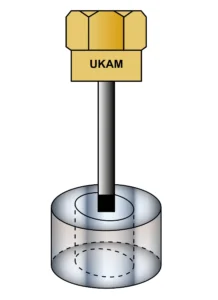
Signs: Diamond Drills gets stuck in the material; difficulty in advancing or retracting the drill
|
- Material swarf build-up;
- Inadequate lubrication;
- Diamond Drills misalignment
|
- Interrupted drilling process;
- Potential for Diamond Drills breakage
|
- Clean Diamond Drills regularly;
- Ensure proper lubrication;
- Check and correct Diamond Drills alignment
|
13 |
Sound Fluctuation
Signs: Irregular or intermittent cutting sounds; changes in drilling noise patterns
|
- Diamond Drills wear;
- Loose components;
- Inconsistent material density
|
- Inconsistent drilling performance;
- Potential for inaccuracies
|
- Inspect and replace worn diamond drills;
- Tighten loose components;
- Adjust drilling parameters for material
|
14 |
Diamond Drill Overloading
Signs: Excessive power consumption or increased load on the drilling machine
|
- Dull diamond drill; Inadequate coolant;
- Material hardness
|
- Increased operational costs;
- Potential overheating of machine
|
- Sharpen or replace diamond drill;
- Ensure adequate coolant flow;
- Use a drill suited for the material’s hardness
|
15 |
Slow/ Inefficient Drilling
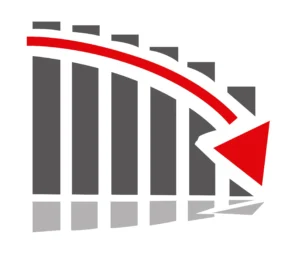
Signs: Slow drilling progress; increased time to penetrate material
|
- Blunt drill edges
- Inadequate drilling speed
- Hard or abrasive material
- Incorrect Drill Specification
- Coolant not adequately reaching the drilling zone
- Incorrect feed rates
- Material core (plug) is stuck inside core drill
- Poor Equipment Maintenance
- Operator Oversight
|
- Prolonged drilling time;
- Increased wear on diamond drill
- Higher Process Cost
- Loss of Productivity
|
- Dress the diamond drill
- Adjust drilling speed;
- Select a more suitable Diamond Drills for the material
- Use Larger (coarser) Diamond
- Use Softer Bond Matrix
- Optimize rpm’s and fee rate
- Try higher RPM’s
|
16 |
Diamond Drill Overheating
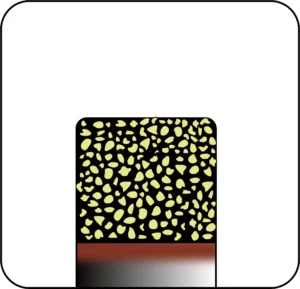
Signs: Discoloration or burn marks on the material around the hole
|
- Excessive friction; Inadequate coolant;
- Too high drilling speed
|
- Aesthetic damage to material;
- Potential structural damage
|
- Reduce drilling speed; Increase coolant flow;
- Adjust drilling parameters
|
17 |
Diamond Drill Instability
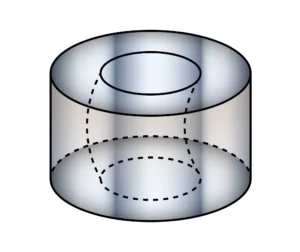
Signs: Chattering or bouncing of the diamond drill
|
- Unstable drill setup;
- Worn drill bearings or spindle; Misalignment
|
- Poor hole quality;
- Potential damage to Diamond Drills or material
|
- Stabilize drill setup;
- Replace worn components; Ensure proper alignment
|
18 |
Debris Accumulation
Swarf or debris accumulation around the Diamond Drills or in the hole
|
- Inadequate chip removal;
- Insufficient coolant flow; Incorrect drill design
|
- Blocked drilling path;
- Potential for Diamond Drills overheating
|
- Improve chip removal; Increase coolant flow;
- Use a drill with appropriate chip removal design
|
19 |
Trouble Starting Hole
Signs: Difficulty in starting the hole; Diamond Drills skidding or slipping on the material surface
|
- Inadequate surface preparation;
- Diamond Drills not sharp enough; Incorrect angle of entry
|
- Inaccurate hole initiation;
- Potential for surface damage
|
- Prepare surface properly;
- Sharpen or replace diamond drill; Ensure correct angle of entry
|
20 |
Drill Vibrating
Signs: Excessive tool vibration or machine movement
|
- Imbalanced diamond drill;
- Loose machine components; Uneven work surface
|
- Reduced drilling accuracy;
- Increased wear on machine and diamond drill
|
- Balance diamond drill;
- Tighten loose components; Ensure work surface is even and stable
|
21 |
Drilling Heat Buildup
Signs: Unusual or excessive heat in the drill chuck or spindle
|
- Overworked drill motor;
- Inadequate lubrication; Excessive drilling speed
|
- Potential damage to drill or machine;
- Reduced lifespan of components
|
- Allow motor to cool periodically;
- Ensure proper lubrication; Adjust drilling speed
|
22 |
Decline in Drilling Performance
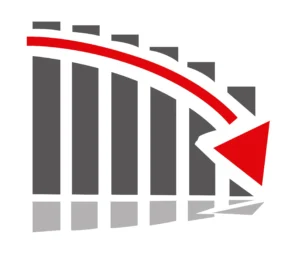
Signs: Reduced cutting speed despite constant machine settings
|
- Diamond Drills wear;
- Hardening of the material;
- Inadequate coolant
|
- Increased drilling time;
- Potential for overheating
|
- Inspect and replace the diamond drill;
- Adjust coolant flow;
- Review material specifications
|
23 |
Short Drill Life
Signs: Frequent need for Diamond Drills replacement
|
- Excessive wear rate;
- Unsuitable Diamond Drills material;
- Incorrect drilling parameters
|
- Increased operational costs;
- Downtime for replacements
|
- Choose appropriate Diamond Drills material;
- Optimize drilling parameters;
- Regularly inspect diamond drills
|
24 |
Diamond Drill Jammed
Signs: Diamond Drills becomes lodged or jammed in the hole
|
- Swarf build-up;
- Inadequate hole clearance;
- Material deformation
|
- Interrupted drilling process;
- Potential for Diamond Drills damage
|
- Ensure adequate hole clearance;
- Use appropriate Diamond Drills design;
- Regularly clear swarf
|
25 |
Drill Life Inconsistency
Signs: Inconsistent Diamond Drills life across similar operations
|
- Variable material properties;
- Inconsistent machine calibration;
- Fluctuating operating conditions
|
- Unpredictable maintenance schedule;
- Variable drilling performance
|
- Standardize material selection; Calibrate machines regularly;
- Monitor and stabilize operating conditions
|
26 |
Excessive Drilling Noise
Excessive noise from the drilling machine
|
- Worn or damaged machine components; Misalignment;
- Unbalanced load
|
- Unpleasant working environment;
- Potential for machine damage
|
- Inspect and replace damaged components;
- Align and balance machine;
- Distribute load evenly
|
27 |
Drill Angle Instability
Difficulty in maintaining the desired drilling angle
|
- Unstable machine setup; Worn machine components;
- Inadequate operator training
|
- Inaccurate hole angle;
- Compromised hole integrity
|
- Stabilize machine setup;
- Replace worn components; Provide adequate training
|
28 |
Diamond Drill Deflection
Increased occurrence of Diamond Drills deflection
|
- Inadequate drill rigidity; Uneven material density;
- Incorrect Diamond Drills design
|
- Inaccurate hole dimensions;
- Potential for off-center drilling
|
- Use a more rigid drill setup;
- Assess material density;
- Choose the correct Diamond Drills design
|
29 |
Diamond Drill Tube Wear
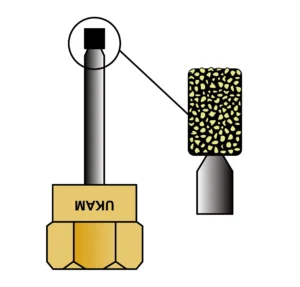
Visible wear or damage on the drill sides/body
|
- Abrasive material;
- Inadequate coolant;
- High feed rate or speed
|
- Reduced Diamond Drills effectiveness;
- Increased heat generation
|
- Use diamond drills designed for abrasive materials;
- Ensure proper coolant flow; Adjust feed rate and speed
|
30 |
Feed Rate Issues
Difficulty in controlling Diamond Drills feed rate
|
- Inconsistent material density;
- Worn machine components;
- Inadequate operator control
|
- Inconsistent drilling performance;
- Potential for material damage
|
- Assess material density;
- Maintain machine components; Train operators adequately
|
31 |
Material Bottom Side Deformation
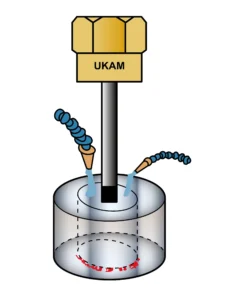
Excessive burring or material deformation at the hole exit
|
- Too high feed rate;
- Inadequate support for the material;
- Dull diamond drill
|
- Poor hole quality;
- Additional finishing required
|
- Adjust feed rate;
- Provide adequate material support;
- Sharpen or replace the diamond drill
|
32 |
Diamond Drills Wondering
Diamond Drills “walking” or drifting at the start of drilling
|
- Uneven starting surface;
- Diamond Drills not perpendicular to material;
- Inadequate clamping
|
- Inaccurate hole start;
- Potential for material damage
|
- Flatten starting surface;
- Ensure Diamond Drills is perpendicular; Secure material properly
|
33 |
Excessive Wear on One Drill Side
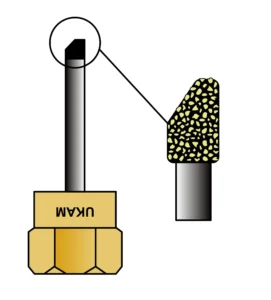
Signs: Excessive wear on one side of the diamond drill
|
- Misalignment;
- Uneven material hardness;
- Improper Diamond Drills rotation
|
- Asymmetrical Diamond Drills wear;
- Reduced Diamond Drills life
|
- Check and correct alignment;
- Assess material properties;
- Ensure proper Diamond Drills rotation
|
34 |
Diamond Drill Overheating
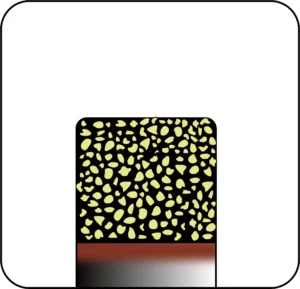
Changes in Diamond Drills coloration (e.g., bluing, yellowing)
|
- Overheating due to high friction;
- Inadequate coolant supply
- Excessive drilling speed
- Diamond Crystal too Fine for the application
- Bond Matrix is too High
- Inappropriate Drill Specification
|
- Potential loss of Diamond Drills hardness;
- Reduced cutting efficiency
- Material Deformation
- Material Burring, chipping, cracking
- Diamond section breakage or cracking
- Drill stops drilling
|
- Optimize drilling speed;
- Increase coolant flow;
- Monitor Diamond Drills temperature
- Increase RPM’s
- Make sure the RPM’s are recommended for the application
- Use dressing stick to dress the drill
- Consider using diamond drill more optimized for the application
|
35 |
Drilling Depth Issues
Signs: Difficulty in achieving the required hole depth
|
- Inadequate Diamond Drills length;
- Material hardening at deeper levels;
- Diamond Drills deflection
|
- Incomplete drilling;
- Inaccurate hole depth
|
- Use the correct length diamond drill;
- Adjust drilling parameters for depth;
- Ensure drill rigidity
|
36 |
Drilling Torque Variations
Fluctuations in drilling torque or resistance
|
- Inconsistent material composition;
- Worn diamond drill; Clutch or gearbox issues
|
- Inconsistent drilling performance;
- Potential for stalling or jamming
|
- Assess material consistency;
- Replace worn diamond drills; Service clutch or gearbox
|
37 |
Material Discoloration
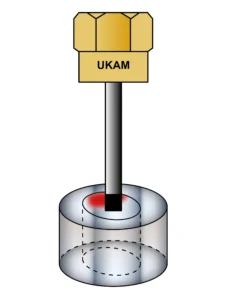
Material discoloration around the hole
|
- Excessive heat generation; Chemical reaction with coolant;
- Material sensitivity
|
- Aesthetic or structural material damage;
- Potential weakening of material
|
- Adjust drilling parameters;
- Check and replace coolant;
- Assess material sensitivity
|
38 |
Chip Removal Issues
Signs: Increased difficulty in chip removal
|
- Inadequate flute design; High material ductility;
- Insufficient coolant pressure
|
- Clogged diamond drill;
- Reduced drilling efficiency;
- Potential overheating
|
- Optimize flute design;
- Adjust drilling parameters for ductile materials;
- Increase coolant pressure
|
39 |
Diamond Drills Stalling
Diamond Drills fails to cut or progress through the material
|
- Diamond Drills wear or damage;
- Material hardness exceeds Diamond Drills capacity;
- Incorrect Diamond Drills type
|
- Stalled drilling process;
- Potential for Diamond Drills damage
|
- Inspect and replace diamond drill;
- Use a Diamond Drills suited for the material hardness;
- Ensure correct Diamond Drills type
|
40 |
Diamond Section Glazed Over
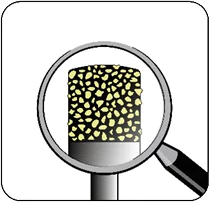
Signs: Unusual or rapid Diamond Drills dulling
|
- Abrasive material;
- Inadequate coolant;
- Incorrect drilling parameters
- Diamond Crystals too Friable
- Bond Matrix too High
- Drilling speed is too High or low
- Incorrect drilling speed
- Incorrect drill specification
|
- Frequent Diamond Drills replacement;
- Increased operational costs
- Diamond drill slows down
- Diamond drill stops drilling altogether
- Diamond Drill Overheats
- Possible Material Deformation
- Material Burring, Chipping, & cracking
- Possible Diamond Section Breakage
|
- Select diamond drills designed for abrasive materials;
- Optimize coolant flow;
- Adjust drilling parameters
|
41 |
Diamond Drill Suddenly Stops
Sudden increase in drilling noise or vibration
|
- Diamond Drills or machine component failure;
- Material fracture;
- Loose fixtures
|
- Potential for immediate halt in drilling;
- Safety hazard
|
- Stop drilling immediately;
- Inspect Diamond Drills and machine;
- Secure all fixtures
|
42 |
Uneven Wear on Diamond Section
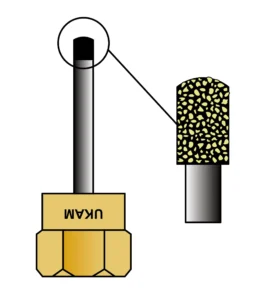
Uneven wear on the drills diamond section surface
|
- Uneven material hardness;
- Diamond Drills not level with material;
- Inconsistent feed pressure
|
- Uneven drilling;
- Reduced Diamond Drills life
|
- Assess material for uniformity;
- Level Diamond Drills with material;
- Apply consistent feed pressure
|
43 |
Diamond Drills “pulls” into the material unexpectedly
|
- Too aggressive feed rate;
- Diamond Drills design not suited for material;
- Inadequate clamping of material
|
- Loss of control over drilling;
- Potential for over-drilling or material damage
|
- Adjust feed rate;
- Select appropriate Diamond Drills design;
- Ensure material is clamped securely
|
44 |
Difficulty in Starting Hole
Difficulty in hole start or Diamond Drills skating on material surface
|
- Lack of pilot hole or starting point;
- Hard or slippery material surface;
- Worn Diamond Drills tip
|
- Inaccurate hole placement;
- Increased time for hole initiation
|
- Create a pilot hole or use a center punch;
- Assess and prepare material surface;
- Replace or sharpen Diamond Drills tip
|
45 |
Drill Mounting Overheating
Excessive accumulation of heat in the Diamond Drills shank
|
- High friction in the chuck;
- Over-tightening of the diamond drill;
- Inadequate lubrication in chuck area
|
- Potential for Diamond Drills or chuck damage;
- Reduced Diamond Drills life
|
- Adjust chuck tightness;
- Ensure proper lubrication;
- Monitor and manage friction levels
|
46 |
Wall Smoothness Variability
Inconsistent hole wall smoothness
|
- Fluctuating feed rate; Diamond Drills vibration;
- Material inhomogeneity
|
- Variable hole quality;
- Potential need for post-processing
|
- Stabilize feed rate;
- Minimize Diamond Drills vibration;
- Assess material for consistency
|
47 |
Edge Sharpness Loss
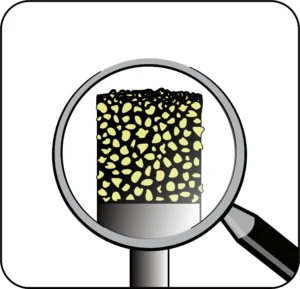
Diamond Drills unable to retain cutting edge sharpness
|
- Material abrasiveness; Inadequate cooling;
- Incorrect Diamond Drills material
|
- Frequent Diamond Drills re-sharpening or replacement;
- Increased downtime
|
- Use diamond drills designed for abrasive materials;
- Optimize cooling; Select appropriate Diamond Drills material
|
48 |
Sharp Decline in Drill Performance
Sudden decrease in drilling performance
|
- Takes lot longer to drill
- Decrease in drilling speed & feed rate
- Sudden material hardness change;
- Diamond Drills reaching end of life
|
- Slowed drilling progress;
- Potential for Diamond Drills failure
|
- Clean flutes regularly; Assess material for consistency;
- Monitor Diamond Drills life and replace as needed
|
49 |
Diamond Drills Bending
Diamond Drills bending or flexing during operation
|
- Excessive length to diameter ratio;
- Inadequate support for diamond drill; High lateral pressure
|
- Diamond Drills deflection;
- Inaccurate hole dimensions
|
- Use diamond drills with appropriate length to diameter ratio;
- Ensure Diamond Drills is adequately supported;
- Minimize lateral pressure
|
50 |
Shank or Drill Mount Fracture
Premature shank wear or failure
|
- Excessive chuck pressure;
- Misalignment in chuck;
- Repeated high-torque scenarios
|
- Reduced Diamond Drills life;
- Potential for Diamond Drills s lippage or breakage
|
- Adjust chuck pressure;
- Ensure proper alignment in chuck;
- Monitor and manage torque levels
|
51 |
Loss of Concentricity
Diamond Drills loses concentricity
|
- Worn spindle or bearings;
- Improper Diamond Drills installation;
- Material side forces
|
- Hole diameter inconsistency;
- Reduced drill accuracy
|
- Service or replace spindle/bearings;
- Ensure proper Diamond Drills installation;
- Stabilize material during drilling
|
52 |
Increased Diamond Drills side play
|
- Worn chuck jaws;
- Overuse or wear of Diamond Drills shank;
- Misalignment in drill setup
|
- Reduced precision;
- Potential for hole deviation
|
- Replace or adjust chuck jaws;
- Replace worn diamond drills;
- Ensure proper alignment in setup
|
53 |
Intermittent Drilling Action
Diamond Drills exhibits intermittent cutting action
|
- Intermittent material hardness;
- Fluctuating feed rate;
- Diamond Drills vibration
|
- Inconsistent hole quality;
- Potential for material damage
|
- Assess material for consistency;
- Stabilize feed rate; Minimize Diamond Drills vibration
|
54 |
Excessive coolant consumption
Excessive coolant consumption
|
- Coolant leaks;
- Inefficient coolant delivery system;
- High evaporation rate
|
- Increased operational costs;
- Potential for inadequate cooling
|
- Check for and repair leaks;
- Optimize coolant delivery system;
- Assess coolant type and application
|
55 |
Coolant Foaming
Coolant foaming or discoloration
|
- Contamination;
- Chemical reaction with materials;
- Incorrect coolant mixture
|
- Reduced cooling efficiency;
- Potential for material or tool corrosion
|
- Identify and remove contaminants;
- Assess material compatibility;
- Check and adjust coolant mixture
|
56 |
Diamond Drills exhibits premature wear patterns
|
- Material abrasiveness;
- Inadequate coolant;
- Incorrect drilling parameters
|
- Reduced Diamond Drills life;
- Increased replacement frequency
|
- Select diamond drills for abrasive materials;
- Optimize coolant flow;
- Adjust drilling parameters
|
57 |
Poor Drill Alignment
Difficulty in maintaining Diamond Drills alignment during deep hole drilling
|
- Diamond Drills deflection;
- Inadequate machine rigidity;
- Misalignment in setup
|
- Hole deviation at depth;
- Reduced hole accuracy
|
- Use drill guides or bushings;
- Ensure machine rigidity;
- Check and correct alignment
|
58 |
Material fuses to the diamond drill
|
- Excessive heat generation;
- Material ductility;
- Inadequate coolant or feed rate
|
- Stalled drilling process;
- Potential for material waste
|
- Optimize feed rate;
- Use suitable coolant;
- Select appropriate Diamond Drills material
|
59 |
Oversized Holes
Diamond Drills produces oversized holes
|
- Diamond Drills wear;
- Material thermal expansion;
- Diamond Drills wobble
|
- Hole size inconsistency;
- Reduced dimensional accuracy
|
- Replace worn diamond drills;
- Control material temperature;
- Check and correct Diamond Drills mounting
|
60 |
undersized holes
Diamond Drills produces undersized holes
|
- Incorrect Diamond Drills sizing;
- Material compression;
- Inadequate cutting pressure
|
- Hole size inconsistency;
- Potential for rework or scrap
|
- Verify Diamond Drills size;
- Assess material properties;
- Adjust cutting pressure
|
61 |
Drill Mounting Deformation
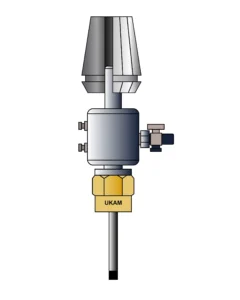
Diamond Drills shank wear or deformation
|
- Excessive chuck pressure;
- Misalignment in chuck;
- Repeated high-torque scenarios
|
- Reduced Diamond Drills life;
- Potential for Diamond Drills slippage or breakage
|
- Adjust chuck pressure; Ensure proper alignment in chuck;
- Monitor and manage torque levels
|
62 |
Inconsistent drilling speed
Inconsistent drilling speed despite constant settings
|
- Variable voltage supply; Worn or damaged motor;
- Mechanical issues in drill feed mechanism
|
- Inconsistent drilling performance;
- Potential for reduced precision
|
- Check and stabilize power supply;
- Service or replace motor;
- Inspect and repair feed mechanism
|
63 |
Excessive Dust Generation
Excessive dust or debris generation during drilling
|
- Inadequate dust extraction;
- High material brittleness;
- Incorrect Diamond Drills type
|
- Poor visibility and working conditions;
- Potential health hazards
|
- Improve dust extraction system;
- Adjust drilling parameters;
- Select appropriate Diamond Drills type
|
64 |
Difficulty Removing Diamond Drill from Material
Diamond Drills fails to disengage properly from the material |
- Material adhesion; Vacuum effect in the hole;
- Mechanical issues with drill retraction
|
- Difficulty in Diamond Drills removal;
- Potential for Diamond Drills or material damage
|
- Apply release agents;
- Ensure proper hole ventilation;
- Inspect and repair retraction mechanism
|
65 |
Unusual wear or damage on non-cutting parts of the diamond drill
|
- Contact with debris or workpiece;
- Handling or storage issues;
- Accidental collisions
|
- Reduced Diamond Drills life;
- Potential for inaccuracies in drilling
|
- Protect Diamond Drills during non-use;
- Ensure proper handling and storage;
- Avoid collisions
|
66 |
frequent recalibration Required
Diamond Drills requires frequent recalibration or adjustment
|
- Inconsistent material hardness;
- Thermal expansion of drill or material;
- Wear and tear of drill components
|
- Increased downtime for recalibration;
- Potential for reduced accuracy
|
- Assess material consistency;
- Monitor temperature effects;
- Regularly inspect and maintain drill components
|
67 |
Difficulty in achieving straight hole walls
|
- Diamond Drills deflection; Inadequate machine stability;
- Uneven material density
|
- Hole wall irregularities;
- Reduced hole quality
|
- Use more rigid drill setup;
- Enhance machine stability;
- Assess and accommodate material density
|
68 |
Rough Surface at Entrance or Exit
Diamond Drills produces a rough hole entrance or exit
|
- Inadequate Diamond Crystal Sharpness & Exposure;
- High feed rate
- Material chipping or flaking
- Diamond Crystal too Coarse or Fine
- Drilling Speed too High or Low
- Insufficient Coolant reaching the drilling zone
- Incorrect diamond drill application
|
- Poor hole quality
- Potential for additional finishing processes
- Process Inconsistency
- Loss of Productivity
- Higher Cost
- Scrap Parts
|
- Dress the Diamond Drill
- Adjust feed rate
- Optimize drilling parameters for material
- User Finer diamond grit size
- Optimize Diamond Concentration
- Use Softer Bond Matrix
- Use Different Bond Type
- Make Sure Coolant is reaching drilling zone
- Make sure the material is supported and does not move
|
69 |
Material Delamination
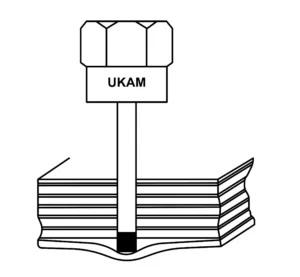
Material layers separate or delaminate during drilling
|
- High drilling pressure;
- Inadequate support for layered materials;
- Diamond Drills not suited for layered materials
|
- Layer separation;
- Compromised material integrity
|
- Reduce drilling pressure; Provide adequate support;
- Use diamond drills designed for layered materials
|
70 |
Tapered Hole
Diamond Drills produces a tapered hole
|
- Diamond Drills not perpendicular to material;
- Worn or damaged diamond drill;
- Inconsistent material density
|
- Hole dimension inconsistencies;
- Reduced hole quality
|
- Ensure Diamond Drills is perpendicular;
- Replace worn or damaged diamond drills;
- Assess material density
|
71 |
Bell Mouthed Hole
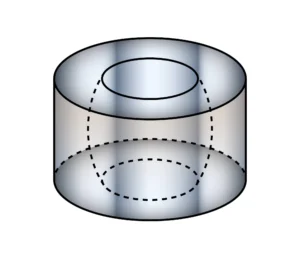
Diamond Drills produces a bell-mouthed hole
|
- Excessive Diamond Drills wear at the tip; Inadequate support for material;
- Diamond Drills wobbling
|
- Hole diameter inconsistency;
- Compromised hole geometry
|
- Replace or sharpen diamond drill;
- Ensure material is adequately supported;
- Stabilize Diamond Drills to prevent wobble
|
72 |
Difficulty Maintaining Consistent Hole Depth
Difficulty in maintaining consistent hole depth
|
- Inconsistent feed rate;
- Fluctuating Diamond Drills pressure;
- Material compressibility
|
- Variable hole depth;
- Potential for incomplete drilling
|
- Stabilize feed rate; Apply consistent pressure;
- Account for material compressibility
|
73 |
Holes with Rough Interior Surface
Diamond Drills produces a hole with a rough interior surface
|
- Blunt diamond drill;
- High feed rate;
- Abrasive material
|
- Poor hole interior finish;
- Potential for additional processing
|
- Sharpen or replace diamond drill;
- Adjust feed rate;
- Use diamond drills suitable for abrasive materials
|
74 |
Material Burning
Material burns or smokes during drilling
|
- Excessive friction; Inadequate coolant;
- Too high drilling speed
|
- Potential thermal damage to material;
- Safety hazard
|
- Reduce drilling speed; Increase coolant flow;
- Monitor and adjust drilling parameters
|
75 |
Irregular Shape Holes
Diamond Drills produces a hole with an irregular shape
|
- Diamond Drills deflection;
- Material inhomogeneity;
- Inadequate clamping of material
|
- Compromised hole geometry;
- Reduced precision
|
- Minimize Diamond Drills deflection;
- Assess material uniformity;
- Ensure material is clamped securely
|
76 |
Excessive Wear on Drills Body
Excessive tool wear on the diamond drill’s non-cutting areas
|
- Contact with workpiece during retraction;
- Abrasive debris in the work area;
- Inadequate tool storage
|
- Reduced tool life;
- Potential for tool failure
|
- Avoid contact with workpiece during retraction;
- Keep work area clean; Store tools properly
|
77 |
hole with a conical entrance
Diamond Drills produces a hole with a conical entrance
|
- Diamond Drills not entering material straight;
- Inadequate material surface preparation;
- Diamond Drills tip wear
|
- Inaccurate hole entrance geometry;
- Potential for rework
|
- Ensure straight Diamond Drills entry;
- Prepare material surface properly;
- Inspect and maintain Diamond Drills tip
|
78 |
Drill Stuck Inside Chuck or Collet
Difficulty in Diamond Drills removal after drilling
|
- Material contraction or warping;
- Vacuum effect in the hole;
- Diamond Drill expansion due to heat
|
- Stuck diamond drill;
- Potential for tool or material damage
|
- Allow material and Diamond Drills to cool;
- Ensure proper hole ventilation;
- Apply release agents if necessary
|
79 |
Hole with a stepped profile
Diamond Drills produces a hole with a stepped profile
|
- Diamond Drills retraction and re-entry;
- Material hardness variation;
- Inconsistent feed rate
|
- Stepped hole profile;
- Compromised hole integrity
|
- Avoid unnecessary Diamond Drills retraction;
- Assess material for hardness variation;
- Stabilize feed rate
|
80 |
Shank Corrosion
Diamond Drills shank shows signs of corrosion or rust
|
- Exposure to corrosive substances;
- Inadequate tool maintenance;
- High humidity storage conditions
|
- Reduced tool life;
- Potential for tool failure
|
- Avoid exposure to corrosive substances;
- Maintain tools properly;
- Store in low humidity conditions
|
81 |
Chipping at Hole Exit
Diamond Drills produces a hole with a rough or chipped exit
|
- Sudden material exit support loss;
- High exit feed rate;
- Brittle material
|
- Poor hole exit quality;
- Potential for material damage
|
- Support material at exit point;
- Reduce feed rate at hole exit;
- Adjust drilling parameters for material
|
82 |
Diamond Drill Uneven Exposure
Diamond Drills shows uneven diamond exposure
|
- Uneven wear;
- Inconsistent diamond distribution;
- Material abrasiveness
|
- Inconsistent cutting performance;
- Reduced Diamond Drills life
|
- Ensure even Diamond Drills wear;
- Select diamond drills with consistent diamond distribution
- Adjust for material abrasiveness
|
83 |
Over Exposed Diamond Crystals
Signs: Diamond protrude from bond material within minimal support its bond matrix. Visible amount of diamond pullout
|
- Inadequate bond matrix hardness
- Excessive wear rate of the bond matrix
- Improper bond matrix composition for the material being drilled.
|
- Increased risk of diamond loss;
- Reduced diamond drill life and efficiency.
|
- Select a diamond drill with a bond matrix of appropriate hardness for the material
- Optimize drilling parameters to reduce wear rate of the bond matrix
- Ensure the bond matrix composition is suitable for the material and drilling conditions.
|
84 |
Excessive Premature Diamond Loss
Signs: Diamond section shows signs of high amount of lost diamond crystal from the bond matrix
|
- Excessive drilling pressure.
- Impact with very hard or abrasive materials.
- Inadequate bond hardness relative to the material being drilled.
|
- Reduced cutting efficiency;
- Increased wear and tear on the diamond drill.
|
- Adjust drilling pressure to appropriate levels.
- Assess and match the diamond drill specifications with the material hardness.
- Select a diamond drill with a bond hardness that is appropriate for the material.
|
85 |
Crushed Diamond Crystals
Signs: Diamond crystals in bond show signs of high amount of fracture
|
- Excessive drilling pressure
- Impact with very hard or abrasive materials
- Inadequate bond hardness relative to the material being drilled.
|
- Reduced cutting efficiency
- Increased wear and tear on the diamond drill
|
- Adjust drilling pressure to appropriate levels
- Assess and match the diamond drill specifications with the material hardness
- Select a diamond drill with a bond hardness that is appropriate for the material.
|
86 |
Diamond Crystal Premature Loss of Sharp Point
Signs: Diamond crystals premature glazing (loss of sharp point) and poor exposure from bond matrix
|
- Premature diamond wear
- Inappropriate drilling parameters for the material
- Insufficient diamond protrusion from the bond.
|
- Slower drilling process;
- Increased wear on the diamond drill and machinery.
|
- Monitor and adjust for diamond wear
- Tailor drilling parameters to the specific material
- Check and ensure adequate diamond protrusion for effective cutting
|
87 |
Diamond Drill Stops Drilling
Diamond Drills experiences sudden loss of cutting ability
|
- Diamond grit pull-out;
- Bond material failure;
- Impact or excessive load
|
- Immediate halt in drilling progress;
- Potential for Diamond Drills damage
|
- Inspect Diamond Drills for damage;
- Select diamond drills with appropriate bond material;
- Avoid excessive loads
|
88 |
Wider Hole on entrance & exit
Diamond Drills produces a hole with a double-diameter profile
|
- Diamond Drills size change during operation;
- Material layer hardness change; Diamond Drills slippage
|
- Hole dimension inconsistency;
- Compromised hole integrity
|
- Ensure consistent Diamond Drills size;
- Assess material layers for hardness
- Secure Diamond Drills properly
|
89
|
Diamond Drills Loss of Profile
Diamond Drills shows signs of abnormal flattening or rounding
|
- Excessive pressure;
- Soft bond material for given material;
- High temperature during drilling
|
- Reduced cutting efficiency;
- Premature Diamond Drills wear
|
- Adjust drilling pressure;
- Select bond material suited for the material;
- Manage drilling temperature
|
90
|
Excessive Drilling Noise
Diamond Drills produces excessive noise during retraction
|
- Material snagging on diamond drill;
- Inadequate retraction speed;
- Diamond Drills misalignment
|
- Unpleasant noise;
- Potential for Diamond Drills or material damage
|
- Ensure smooth Diamond Drills path;
- Adjust retraction speed;
- Align Diamond Drills properly
|
91
|
Diamond Drill Slipping
Diamond Drills experiences intermittent engagement with the material
|
- Diamond Drills bouncing;
- Inconsistent material surface;
- Worn Diamond Drills bearings or spindle
|
- Inconsistent drilling;
- Potential for hole defects
|
- Stabilize Diamond Drills engagement;
- Flatten material surface;
- Service or replace bearings or spindle
|
92 |
Tapered Hole
Diamond Drills produces a hole with a tapered exit
|
- Diamond Drills withdrawal angle;
- Inadequate support at hole exit;
- Material deformation
|
- Hole exit dimension inconsistency;
- Reduced hole quality
|
- Control Diamond Drills withdrawal angle;
- Support material at hole exit;
- Account for material deformation
|
93
|
Diamond Section Coming Off
Diamond Drills shows signs of solder failure or diamond section coming off
|
- Excessive heat;
- Mechanical shock;
- Improper Diamond Drills use
|
- Potential for segment detachment;
- Compromised drilling performance
|
- Manage heat generation;
- Avoid mechanical shocks;
- Use Diamond Drills as intended
|
94 |
Hole Waviness
Diamond Drills produces a hole with an irregular or wavy profile
|
- Diamond Drills vibration;
- Inconsistent feed rate;
- Material inhomogeneity
|
- Hole profile irregularity;
- Compromised hole quality
|
- Minimize Diamond Drills vibration;
- Stabilize feed rate;
- Assess material for consistency
|
94
|
Material Burring
Signs: Raised edges or small fragments of material at the hole entrance or exit
|
- Dull or damaged diamond drill edges.
- Excessive feed rate or pressure.
- Inadequate support for the material at the drilling point.
- Diamond drill vibration or instability.
- Material properties such as ductility or softness.
- Inadequate or improper use of coolant.
|
- Compromised hole quality;
- Potential for additional finishing work or material damage.
- Reduced quality of hole finish; Potential for increased post-processing work.
|
- Inspect and replace or sharpen diamond drills as necessary.
- Adjust feed rate and pressure to appropriate levels.
- Provide stable support for the material during drilling.
- Stabilize the drill setup to minimize vibration.
- Select diamond drills and drilling parameters suitable for the material’s properties.
- Optimize coolant flow and type to enhance cutting conditions.
|
95 |
Material Scratches
Sings: Visible scratches or grooves on the surface of the material around the drilled hole
|
- Foreign particles between the diamond drill and material.
- Diamond drill misalignment or wobbling.
- Rough handling or improper storage of the diamond drill causing edge damage.
|
- Aesthetic damage to the material;
- Potential for reduced structural integrity.
|
- Ensure a clean working environment and clean material surface.
- Check and correct diamond drill alignment.
- Handle and store diamond drills properly to prevent damage.
|
96 |
Material Smearing
Signs: Material residue adhering to the sides of the drilled hole
|
- Excessive heat generation during drilling.
- Inadequate or improper use of coolant.
- Soft or ductile material that tends to smear.
|
- Compromised hole quality;
- Potential for inaccurate hole dimensions and increased finishing work.
|
- Optimize drilling parameters to manage heat.
- Ensure proper coolant flow and application.
- Select diamond drills and drilling parameters suitable for the material’s properties.
|
97 |
Material Pull Out
Sings: Material fragments or chunks dislodged from the hole walls
|
- Abrupt or excessive pressure at the start of drilling.
- Diamond drill not properly aligned or secured.
- Surface irregularities or material brittleness.
|
- Compromised surface finish and structural integrity of the hole entrance;
- Potential for material waste or rework.
|
- Gradually apply pressure and start drilling at a reduced speed.
- Ensure diamond drill alignment and secure clamping.
- Inspect material surface and prepare adequately before drilling.
|
98 |
Top Sided Chipping
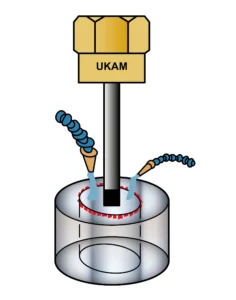
Sings: Uneven or rough edges around the hole entrance
|
- Abrupt or excessive pressure at the start of drilling.
- Diamond drill not properly aligned or secured.
- Surface irregularities or material brittleness.
- Diamond drill vibration or instability.
- Inadequate material support at the drilling point.
- Incorrect or worn diamond drill for the material type.
|
- Compromised surface finish and structural integrity of the hole entrance;
- Potential for material waste or rework.
- Reduced quality of hole entrance;
- Potential for additional processing or finishing work.
|
- Gradually apply pressure and start drilling at a reduced speed.
- Ensure diamond drill alignment and secure clamping.
- Inspect material surface and prepare adequately before drilling.
- Stabilize the drill setup to minimize vibration.
- Provide stable support for the material at the drilling point.
- Select and use the correct, sharp diamond drill for the material.
|
99 |
Bottom Side Chipping
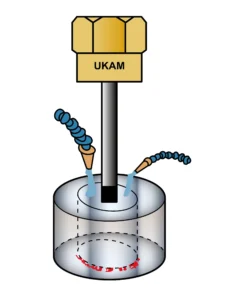
Sings: Chipping or flaking on the exit side of the drilled hole
|
- Sudden release of pressure as the diamond drill exits the material.
- Lack of supporting material or backing plate at the exit point.
- Excessive feed rate or pressure as the diamond drill completes the hole.
- Diamond drill vibration or wobbling.
- Material brittleness or susceptibility to chipping.
- Inadequate or improper use of coolant.
|
- Compromised finish and integrity of the hole exit;
- Potential for material waste or rework.
- Reduced quality of hole finish;
- Potential for additional processing or finishing work.
|
- Gradually reduce pressure and feed rate before the diamond drill exits the material.
- Use a backing plate or support material to provide stability at the exit point.
- Monitor and adjust drilling parameters as the diamond drill nears the exit side.
- Stabilize the drill setup to minimize vibration.
- Select diamond drills and drilling parameters suitable for the material’s properties.
- Optimize coolant flow and type to enhance cutting conditions.
|
100 |
Excessive Backside Chipping
Chipping or flaking on the exit side of the drilled hole
|
- Sudden release of pressure as the diamond drill exits the material.
- Lack of supporting material or backing plate at the exit point.
- Excessive feed rate or pressure as the diamond drill completes the hole.
|
- Compromised finish and integrity of the hole exit;
- Potential for material waste or rework.
|
- Gradually reduce pressure and feed rate before the diamond drill exits the material.
- Use a backing plate or support material to provide stability at the exit point.
- Monitor and adjust drilling parameters as the diamond drill nears the exit side.
|
101 |
Consistently Spaced Chipping
Signs: Chipping or flaking observed predominantly on one side of the drilled hole
|
- Regular imperfections or inclusions in the material.
- Cyclic loading or vibration during drilling.
- Periodic engagement of damaged or irregular diamond drill segments.
|
- Compromised hole integrity and finish;
- Potential for reduced structural strength of the hole.
|
- Assess material quality and plan drilling to avoid imperfections.
- Stabilize the drilling process to minimize vibration.
- Inspect the diamond drill for damage and ensure uniform segment distribution.
|
102 |
One Sided Chipping
Sings: Chipping or flaking observed predominantly on one side of the drilled hole
|
- Diamond drill misalignment or tilt.
- Uneven material support or surface.
- Inconsistent pressure or side loading during drilling.
|
- Compromised hole integrity and aesthetics;
- Potential for material waste or rework.
|
- Ensure proper diamond drill alignment and machine calibration.
- Provide even and stable support for the material.
- Apply consistent and straight drilling pressure.
|
103 |
Diamond Drill Gummed Up
|
- Accumulation of cutting debris in the diamond segments.
- Inadequate or improper use of coolant.
- Drilling soft, gummy materials that clog the diamond drill.
|
- Slower drilling process;
- Increased effort and time required for drilling.
|
- Clean the diamond drill regularly to remove debris.
- Ensure proper coolant flow and application.
- Use diamond drills designed for specific materials to reduce clogging.
|
104 |
Nick of Diamond Section Chipped Out
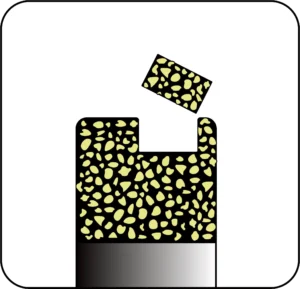
visible nick or missing segment in the diamond section |
- Impact with hard inclusions or foreign objects.
- Excessive force or pressure.
- Diamond drill fatigue or overuse.
|
- Reduced cutting efficiency;
- Potential for uneven drilling or further diamond drill damage.
|
- Inspect material for hardness and inclusions before drilling.
- Apply appropriate force and pressure.
- Regularly inspect diamond drills for wear and replace as necessary.
|
105 |
Crack in Diamond Section
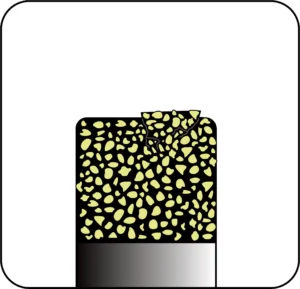
Sings: Visible cracks in the diamond section of the diamond drill
|
- Mechanical stress or impact.
- Thermal shock due to rapid temperature changes.
- Material defects or inclusions in the diamond section.
|
- Reduced structural integrity of the diamond drill;
- Potential for diamond section failure.
|
- Avoid excessive force or pressure during drilling.
- Manage temperature changes and ensure proper coolant use.
- Inspect diamond drills for material quality and avoid using bits with visible defects
|
106 |
Drill Tube Fractured From Collet
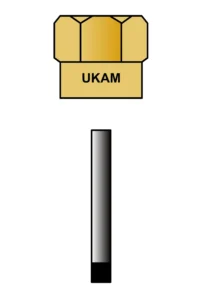
Fracture or separation at the brazed joint between the drill tube and brass collet
|
- Inadequate brazing process or material.
- Excessive mechanical stress or torque.
- Thermal stress due to extreme temperature changes.
|
- Loss of drill stability;
- Immediate halt in drilling;
- Potential for damage to the workpiece or drilling equipment.
|
- Ensure high-quality brazing with appropriate materials and techniques.
- Apply torque within the specified limits.
- Avoid rapid temperature changes during drilling operations.
|
107 |
Difficulty in screwing or unscrewing Drill
Difficulty in screwing or unscrewing the diamond drill from the machinery
|
- Deformation or damage to the collet thread
- Material build-up or galling in the threads
- Cross-threading or misalignment during attachment.
|
- Increased setup time;
- Potential for thread damage or inability to properly secure the drill tube.
|
- Inspect and repair any damaged threads
- Clean and maintain the threads to prevent material build-up.
- Ensure proper alignment and careful handling when attaching or detaching the drill tube.
|