-
0 items in quote
No products in the Quote Basket.
SMART CUT® Series 310M Lapidary Blades
Diamond Lapidary Blades
SMART CUT® Series 310M
Sintered (Metal Bond) Blades New Generation & Technology
SMART CUT® series 310M precision sintered (metal bonded) diamond lapidary blades provide unmatched performance for cutting Precious & Semi Precious Stones and also used in art glass applications (cutting flat soda lime and borosilicate glass). Designed for Professionals & Users who understand and appreciate quality.
Manufactured utilizing SMART CUT® technology, these blades will give you the BEST RESTURN ON INVESTMENT & LOWEST COST OF OWNERSHIP. Giving you consistent results you can count on everyday. They will last longer & cut faster than ordinary notched, plated, and other sintered (metal bond) lapidary blades. SMART CUT® series 310M blades are designed to work on virtually any material you can find. You can cut very hard materials up to hardness of sapphire than switch to cutting very soft materials and the blade will maintain the same consistent performance.
DESCRIPTION
SPECIFICATIONS
FREQUENTLY ASKED QUESTIONS
APPLICATION
ACCESSORIES
USAGE RECOMMENDATION
DESCRIPTION
SMART CUT® series 310M blades are real time and material savers. Proper use of the series 310M blades has been proven to actually minimizes and almost eliminate your after cutting work. With SMART CUT® series 310M blades you can do many operations. The blade grinds and polishes the material as it cuts. You don’t have to spend time on other steps such as polishing the material after cutting. THINNEST Sintered (metal bond) Diamond Blades commercially available for lapidary (precious & semi precious stone) application! The Diamond Thickness (TH) specified is actual thickness of diamond section, not core thickness. If you are cutting valuable materials or just want to have thinner kerf blade there is no substitute for these blades.
Special arbors can be machined same day. Stock arbors can be bushed to smaller sizes. Please specify at time of order.
SPECIFICATIONS
Bond Type: Sintered (Metal bond)
Edge Type: Continuous Rim
Application: Lapidary, Glass
Diamond Grit Size: 80/100 mesh and 100/120 mesh depending on diameter and kerf thickness
Diamond Type: Synthetic
Diamond depth: 5mm, 7mm, & 10mm
Blade Outside Diameters: 4″ (101.6mm) to 16″ (400mm)
Kerf Thickness: .014″ (0.35mm) to .070″ (1.77mm)
Inside Diameter: 5/8”, ½”, ¾”, 1”
Saws Used On:
+ Trim Saws
+ Slab Saws
+ Tile Saws Saws
+ Gang Saws
FREQUENTLY ASKED QUESTIONS
kerf thickness is proportional to diameter of the blade. Thinnest that we can produce is .004″ (0.10mm) in 3″ (75mm) OD. Larger blade diameters such as 4” OD the thinnest kerf thickness is .006” (0.15mm). When we talk about blade thickness we mean actual diamond (kerf thickness) not thickness of the steel core. Which will always be thinner then the diamond section.
0.5mm (12.7mm) is usually the smallest diameter. we can make any increment up to 48”. Minimum order can range from 1 pc, 3 pcs and 20 pcs depending on blade specification
48” this would be segmented (largest continuous rim we can make is 20” (500mm)
we can make any arbor size needed usually same day for a small fee
80/100 mesh (180/150 micron)
yes we can make any thickness you require, please specify. There may a minimum order quantity which can range from 3 pcs to 20 pcs depending on blade specification
Maximum diameter of material can be cut depends on blade diameter, see chart below
There is no specific way to determine specific life of the blades as there are many variables involved. The lifespan of the blade swill depend on lot of different factors such as: Material Hardness, Density, Cutting Depth, Material Shape/Geometry, RPM’s, Feed Rate, Coolant Used, Equipment Type/Condition, Material Holding Method, Operator Experience
tolerance depends on diameter of the blade. For very thin blades usually the tolerance on thickness is + .001”. for thicker kerf thickness blades tolerance on thickness can be + .002”
how fast will they cut?
Cutting speed will depend on material diameter and material properties (hardness, density, shape) and
we recommend flange size at least 1/3 diameter of the blade. The optimal flange size (blade exposure) depends on blade diameter and kerf thickness.
These can be used on lapidary trim and slab saws. As well as tile and other similar cutting machines that can provide the recommended rpm’s range and coolant supply to the cutting zone.
we recommend using water soluable coolant or mineral oil specially if cutting very hard materials. Coolant provides lubrication and reduceds amount of heat generated while cutting. Plain water is not able to provide sufficient lubrication and coolant the blade fast enough. However plain water can be used if needed just the blade may require more dressing and cutting efficiency will not be as affective and life usually shorter
We recommend using 100 grit dressing stick. Alumina oxide or silicon carbide, soft can be used for this purpose.
Depends on materials being cut, dimensions of material rpm’s and coolant used and how effective coolant is reaching the cutting zone. With optimal performance there would be minimal dressing.
no, these must be used with coolant
these blades will outperform all sintered (metal bond) lapidary blades on the market. Please note these are designed specifically for lapidary applications. For other applications we have in stock and produce other blade specifications with different diamond grit sizes, concentrations, bond types, and tolerances
these blades are designed for cutting large variety of ultra hard to soft materials ranging from sapphire and down to glass. We offer many other blade specifications for ultra hard materials such as advanced ceramics, optical glass, composites, glass/quartz tubing etc. Very hard and very brittle materials require finer diamond grit sizes, higher diamond concentrations, different types of diamond, bond composition and bond hardness for optimal performance.
Wheel stiffeners provide stability, rigidity and additional support to your Blade which help prevent the blade from “walking” & loosing its flatness. Diameter of the wheel stiffeners used should minimize the blade exposure & allow to cut material thickness that needed with highest amount of accuracy. Wheel stiffeners may be used without your existing flanges
while there is no specific rule to determine the diameter of the wheel stiffener to be used they should be sufficient enough to minimize the blade exposure. For very thin kerf blades, wheel stiffeners should be 2/3rd the outside Diameter of the Diamond Blade. For thicker and larger blades 1/3 rd the diameter of the blade is sufficient
yes we offer excellent quantity discounts
Yes we can, this is our business
Faster, freer cutting speed, less dressing and longer blade life
The rpm’s are based on diameter of the blade, material type, hardness, thickness. The smaller diameter the blade the faster the rpm’s. The larger the blade diameter the lower the rpm’s
Make sure to use coolant, have coolant sufficiently reaching the cutting zone, use recommended rpm’s, dress the blade when needed, and do not force the blade
You have to feel the blade grind away the material, its something that comes with experience
Concrete, brick/block, and any other abrasive material such as sand stone
tile blades usually have very coarse diamond – such as 40/50 mesh, very low diamond concentration and low to medium diamond quality. They are more cobalt base. Most tile blades are thicker kerf between .050” to .070” kerf thickness. They are designed for cutting softer materials. For cutting hard lapidary materials they would take very long time to go through same amount of material, constantly requiring dressing. If they will cut at all.
For majority lapidary applications the surface finish is very smooth, that secondary finishing operations are not required
Its pretty simple. Just push the material into the rotating blade. You will feel the diamond cut through at its own pace
They cut faster, freer, and last longer
Possibly, we have some distributors in different countries
We can ship to almost any country that is not restricted by the US government. We can use almost any shipping method such as US air mail, dhl, ups, fed ex, ups and others
APPLICATION
Designed for cutting a large variety of precious & semi precious stones, gem stones, colored stones, lapidary materials, rocks, glass and similar materials from up to 9.0 on mohes scale fast & easy.
ACCESSORIES
Showing 1 – -1 of 16 results Showing all 16 results Showing the single result No results found
Sort by Name A – Z
Filters Sort results
Reset Apply
Item No:SMARTC2G Price: $99.81 |
Item No:SMARTC1G Price: $34.81 |
Item No:SMARTC4A Price: $317.41 |
Item No:SMARTC7A Price: $1,745.00 |
Item No:UKAMDRST13 Price: $8.65 |
Showing 1 – -1 of 6 results Showing all 6 results Showing the single result No results found
Sort by Price low to high
Filters Sort results
Reset Apply
Item No:8030012 Diameter: 30mm Inside Diameter: 1/2″ Flanges for Accessories Description: Additional Information ARE YOU USING RIGHT TOOLS FOR YOUR APPLICATION? LET US HELP YOU CONTACT US HAVING ISSUES WITH YOUR Price $70.00 |
Item No:8030015 Diameter: 30mm Inside Diameter: 5/8″ Flanges for Accessories Description: Additional Information ARE YOU USING RIGHT TOOLS FOR YOUR APPLICATION? LET US HELP YOU CONTACT US HAVING ISSUES WITH YOUR Price $70.00 |
Item No:8030013 Diameter: 40mm Inside Diameter: 1/2″ Flanges for Accessories Description: Additional Information ARE YOU USING RIGHT TOOLS FOR YOUR APPLICATION? LET US HELP YOU CONTACT US HAVING ISSUES WITH YOUR Price $75.00 |
Item No:8030016 Diameter: 40mm Inside Diameter: 5/8″ Flanges for Accessories Description: Additional Information ARE YOU USING RIGHT TOOLS FOR YOUR APPLICATION? LET US HELP YOU CONTACT US HAVING ISSUES WITH YOUR Price $75.00 |
Item No:8030014 Diameter: 45mm Inside Diameter: 1/2″ Flanges for Accessories Description: Additional Information ARE YOU USING RIGHT TOOLS FOR YOUR APPLICATION? LET US HELP YOU CONTACT US HAVING ISSUES WITH YOUR Price $80.00 |
Item No:8030017 Diameter: 45mm Inside Diameter: 5/8″ Flanges for Accessories Description: Additional Information ARE YOU USING RIGHT TOOLS FOR YOUR APPLICATION? LET US HELP YOU CONTACT US HAVING ISSUES WITH YOUR Price $80.00 |
USAGE RECOMMENDATION
02
Jun
How to Improve & Optimize Your Diamond Sawing Operation
There are numerous variables that affect the performance of diamond and CBN cutting blades. Understanding these variables will help end users select the right diamond blade specifications for their applications and optimize their…
02
Jun
Evaluating & Comparing Diamond Blades
Share this Article with Friend or Colleague
Proper testing procedures and methodologies must be set up and used to obtain accurate as well as repeatable testing results. This article will discuss several simple procedures which…
08
Apr
Mastering the Art of Lapidary cutting
Mastering the Art of Lapidary, Gemstone, Cabochon, & Slab Cutting: A Comprehensive Guide to Slab and Trim Sawing Techniques
The process of transforming rough lapidary rocks & gemstones into beautiful, polished pieces is both an art…
10
Apr
What Makes a Great Diamond Lapidary Blade
Cutting is a foundational step in the lapidary process, and the choice of diamond Lapidary blade significantly influences subsequent stages. While the market offers a plethora of blades for lapidary work, their performance and quality…
10
Apr
Signs of a High Quality Diamond Lapidary Blade
Getting the best results when using lapidary blades is not only skill but also about using the right blade for the application. When we talk about a good blade for lapidary application, we are really…
12
Apr
How to Properly Use Diamond Lapidary Blades
Share this Article with Friend or Colleague
(Guide on getting the most from your blade)
Welcome to the User Guide on How to Properly Use Diamond Lapidary Blades. This guide is designed to provide detailed insights and…
Safety Precautions:
- 1. Personal Protective Equipment (PPE): Always wear appropriate safety gear, including safety shoes, snug-fitting attire, safety goggles, hearing and head protection, and proper respiratory equipment.
- 2. Machine Safety: Always use the blade guards provided with your machine. Do not remove or tamper with any safety devices – they are there for your safety.
Blade Storage:
- 1. When not in use, store the sintered metal bond diamond lapidary blade in a dry and clean environment. Avoid exposure to extreme temperatures, moisture, or direct sunlight.
- 2. Use protective covers or blade guards to prevent accidental damage during storage.
- 3. Keep the blade out of reach of children and unauthorized users.
Before Installation:
- 1. Inspect Machine Shaft: Examine the shaft of your machine for any looseness that might suggest worn bearings. Check for any wear on the shaft itself. Ensure the blade fits securely onto the shaft.
- 2. Examine the Blade:Before mounting, visually inspect the blade for any cracks or signs of damage. Remember, a damaged or improperly mounted blade can be hazardous.
- 3. Check the blade’s rotation direction and ensure it is properly mounted on the saw machine according to the manufacturer’s instructions.
- 4. Make sure the blade is securely fastened to the arbor and that the arbor nut is tightened properly.
Installation:
- 1. Flange Size: Always use a pair of matching flanges, roughly 1/3 the diameter of the blade. Ensure flanges are clean and free of rust or dirt. After tightening the flange nut, the blade should rotate true and even.
- 2. Alignment: For slabbing, ensure accurate carriage alignment to prevent the blade from bending.
- 3. Blade Tracking: Ensure that the blade tracks properly on the saw arbor. Misalignment can lead to uneven wear and reduced blade life. Periodically check and adjust the blade’s alignment as needed.
- 4. Blade Balance: Imbalanced blades can cause vibrations and lead to uneven cuts or equipment wear. To maintain blade balance, periodically check for any accumulated material on the blade body and clean it off.
- 5. Use Proper Size Flanges A pair of the same size flanges with proper relief should be approximately 1/3″ the diameter of the blade. Flanges must be free of rust and dirt. Your blade should turn perfectly rue after flange nut is tightened. Carriage alignment must be accurate for slabbing to prevent bending of the blade.
- 6. Rotate the blade according to Rotation Direction Make sure that arrow on the blade points in the same direction as shaft rotation
- 7. Make Sure Material is Properly Secured Ensure that the material you intend to cut is securely clamped or held in place to prevent it from moving during cutting.
Material Preparation
- 1. Before cutting, inspect the material you intend to work on. Ensure it is free from loose or abrasive particles that could damage the blade or create uneven cuts.
- 2. For large or irregularly shaped materials, consider pre-shaping or trimming them with other tools before using the lapidary blade. This can reduce the stress on the blade and improve cutting precision.
USE RECOMMENDED RPM’S
Blade Diameter Recommended RPM Blade Diameter Recommended RPM 4″ (100mm) 4,000 16″ (400mm) 1,000 5″ (125mm) 3,438 18″ (450mm) 1,000 6″ (150mm) 2,675 20″ (500mm) 900 8″ (200mm) 2,000 22″ (550mm) 825 10″ (250mm) 1,600 24″ (600mm) 700 12″ (300mm) 1,325 30″ (762mm) 550 14″ (350mm) 1,140 36″ (914mm) 500
Best performance and life will result when the blades are operated in the range of 3150 to 500 surface feet per minute. Optimum performance and life will be obtained at the 5000 s.f.m. For your convenience we present the following chart of optimum RPM of shaft for each blade size.
- Adjust the cutting speed and water flow rate according to the material being cut. Softer materials may require slower speeds and less water, while harder materials may require higher speeds and more water.
- When cutting brittle materials like certain types of glass or very hard stones, use a slower blade speed to reduce the chances of cracking or chipping.
- For materials with varying hardness, consider adjusting the blade speed or using a slower feed rate when transitioning from softer to harder areas. This helps maintain a more even cutting surface.
Coolants
- 1. Never run a diamond blade dry. Severe damage will result Coolants do 3 things. They cool your blade and material being cut, clean out the cut being made of abrasive particles, and provide lubrication to keep the cutting edge clean. SMART CUT diamond blades are designed to give you a straight cut in plain water. However, significantly better performance and longer life may be obtained by using water soluble coolant such as SMART CUT coolant or SMART CUT mineral OIL
- 2. Regularly check the water or coolant supply system of your lapidary saw machine. Ensure that the water or coolant flow is consistent and that nozzles are clean and free from blockages.
- 3. Use clean, clear water or coolant in the cooling system to prevent mineral buildup that can clog nozzles and reduce cooling efficiency.
- 4. Periodically inspect and clean the water or coolant reservoir and filter to maintain the quality of the cooling water.
Feed Rates
- 1. Never force a diamond blade Feed material slowly into blade so that the blade doesn’t lead off. Excessive pressure can cause your blade to bend or dish. The rate of feed should never be so great that the blade slows down. Avoid cutting with excessive lateral pressure, which can cause blade warping or damage. Keep the blade’s cutting edge perpendicular to the material being cut.
- 2. Keep an eye on the blade during operation and listen for any unusual sounds. If you notice any vibrations, strange noises, or decreased cutting performance, stop immediately and inspect the blade for damage.
- 3. When cutting materials with embedded crystals like geodes, proceed slowly and carefully to avoid damaging the blade or the crystals.
- 4. Use a continuous and steady feed rate when cutting to maintain a smooth and uniform surface. Avoid rapid or jerky movements, which can lead to uneven cuts.
Blade Dressing
Any diamond blade may occasionally require dressing of the edge to remove surplus metal or glazing to expose new diamond particles. You can dress by making a few cuts in an old 220 grit grinding wheel or a dressing stick made specifically for this purpose. Use coolant with this procedure. The SMART CUT diamond bond is designed to minimize this procedure. By using enough coolant and following the suggested procedures, you can’t rest assured this will require the minimal amount of time as compared to most blades.
Continuously Monitor the Cutting Operation
- Never place your hands or fingers right Next to the Cutting Edge
- Never continue to cut with a damaged blade,one that is dished, bent, flutters, or is not running rue. Continued use will damage the diamonds, pull the matrix out, excessively wear your blade, or cause an accident. If your blade has a tendency to pull to one side, making uneven cuts, reverse the blade. If you still have the same problem, the problem could be the vise alignment If, after reversing, the blade cuts to the opposite side, die blade is bent or dished. If this is the case, the blade must be repaired before further use.
- Most frequent source for blade damage is attempting to cut too large a rock. Maximum material/rock size should be no more than 3/8” of blade diameter.
Blade Cleaning:
- 1. After each use, clean the bladethoroughly to remove any residue, such as mineral buildup or adhesive from previous cuts. Soak the blade in a cleaning solution recommended by the manufacturer, and then use a soft brush to scrub away any stubborn debris.
- 2. Rinse the blade with clean water to ensure all cleaning agents are removed. Pat the blade dry with a clean cloth before storing it.
- 3. Do Not Leave the blade on the arbor or in coolant for long period of time.
Used Coolant Disposal
Disposing of coolant used in lapidary work, such as water or water-based cutting fluids, should be done in an environmentally responsible manner. Follow these steps to properly dispose of coolant after cutting lapidary materials:
1. Containment and Collection:
- Collect the used coolant in a designated container, such as a plastic bucket or drum. Ensure that the container is clean and free from contaminants.
- If there are any solid particles or sediment in the coolant, allow them to settle at the bottom of the container. You can use a settling tank or let the container sit undisturbed for a period to facilitate this process.
2. Separation of Solids:
- After settling, carefully decant or siphon the clear coolant from the container, leaving the settled solids behind. These solids may contain abrasive debris and should not be disposed of down the drain.
3. Recycling or Reuse:
- If the coolant is still in good condition and free from contamination, consider reusing it for further lapidary work. Filter the coolant to remove any remaining suspended particles before reuse
- Some lapidary workshops use a recirculating system that continually filters and treats the coolant for extended use.
3. Recycling or Reuse:
- If the coolant is still in good condition and free from contamination, consider reusing it for further lapidary work. Filter the coolant to remove any remaining suspended particles before reuse
- Some lapidary workshops use a recirculating system that continually filters and treats the coolant for extended use.
4. Dispose of Solids:
- The solids separated from the coolant should be handled as hazardous waste due to potential contamination with abrasive particles and minerals. Check local regulations and guidelines for disposing of hazardous waste in your area.
- In some cases, lapidary workshops collect and dispose of abrasive solids through waste disposal services that specialize in handling hazardous materials.
5. Proper Disposal of Used Coolant:
- The clear, separated coolant can often be disposed of down the drain, especially if it is primarily water-based and does not contain harmful chemicals. However, it’s essential to comply with local, state, and federal regulations regarding wastewater disposal.
- Check with your local municipal or environmental agency for specific guidelines on disposing of used coolant. Some areas may require proper treatment or recycling of wastewater.
6. Neutralization and pH Adjustment:
- If your lapidary work involves the use of acidic or alkaline cutting fluids, it may be necessary to neutralize the coolant before disposal. Neutralization ensures that the pH level of the wastewater is within acceptable limits.
- Consult with a chemical expert or follow recommended guidelines for neutralizing and adjusting the pH of the coolant.
7. Professional Services:
- For lapidary workshops with large volumes of used coolant or those dealing with complex coolant mixtures, consider hiring professional waste management services that specialize in hazardous waste disposal.
Blade Troubleshooting:
- 1. If you encounter excessive chipping or blade wear, it may be due to a mismatch between the blade and the material being cut. Consider using a blade specifically designed for the material’s hardness and composition.
- 2. If the blade starts to wander or deviate from the desired cutting path, it may indicate a misalignment issue. Check the blade’s mounting and alignment, and make necessary adjustments to ensure it runs true.
- 3. Should the blade develop a wobble or vibrations during operation, stop immediately, and inspect for damage or wear. A wobbling blade can be dangerous and should not be used until the issue is resolved.
- 4. In the event of a blade jam or binding, switch off the saw immediately to prevent damage to both the blade and the equipment. Carefully remove the material causing the jam and inspect the blade for any damage before resuming cutting.
Consult our Illustrated Diamond Blade Trouble Shooting Guide which shows all the possible issues people experience when using blades and how to fix and prevent them
Blade Replacement:
- 1. Replace your sintered metal bond diamond lapidary blade when it shows signs of significant wear or damage, such as reduced cutting efficiency, loss of diamond edge, warping/cutting not straight or visible cracks.
- 2. When replacing a blade, follow the saw manufacturer’s instructions for removal and installation. Ensure that the new blade is compatible with your cutting machine.
Features
- More Precision
- Minimal Dressing
- More Universal
- Heat Resistant
- Easier to Use
- Save Material
- No Oil Required Water Cooled
- Real Time & Material Savers
- Best Performance & Value For Your Money
Benefits
- Chip Free Cutting
- Cuts Faster
- Lasts Longer
- More Aggressive
- Smoother Finish
- Straight Cut
- Superior Quality
- Superior Consistency
- Reduce Time Spent On Secondary Steps (Such Polishing & Grinding)
Application
Designed for cutting a large variety of precious & semi precious stones, gem stones, colored stones, lapidary materials, rocks, glass and similar materials from up to 9.0 on mohes scale fast & easy.

- AGATE
- AMETHYST
- AZURILE
- RUBIE
- GEMSTONES
- TOURMALINE
- OPAL
- EMERALD
- RHODONITE
- GARNET
- QUARTZ
- SODA LIME & BOROSILICATE GLASS
- AMETRINE
- PETRIFIED WOOD
- ZIRCONIA
- TURQUOISE
- TOPAZ
- TSAVORITE
- ONYX
- LAPIS LAZULI
- ROUGH GEM STONE
- TANZANITE
- JADE
- METEORITES
Showing 1 – -1 of 9 results Showing all 9 results Showing the single result No results found
Sort by Name A - Z
Filters Sort results
Reset Apply
Item No:23-4675W Diameter OD: 6" (152.4mm) Diamond Thickness TH: .032" (0. 8mm) Diamond Height: .276" (7mm) Arbor ID: 5/8-1/2" B Internet Price (1pc): $64.00$70.00 3 pcs (each): $51.00 Price $64.00$70.00 |
Item No:23-4679W Diameter OD: 8" (203.2mm) Diamond Thickness TH: .032" (0. 8mm) Diamond Height: .276" (7mm) Arbor ID: 5/8-1/2" B Internet Price (1pc): $61.00$80.00 3 pcs (each): Price $61.00$80.00 |
Item No:23-4713W Diameter OD: 10" (254mm) Diamond Thickness TH: .060" (1.52mm) Diamond Height: .314"(10mm) Arbor ID: 5/8" Internet Price (1pc): $94.50$114.00 3 pcs (each): $84.00 Price $94.50$114.00 |
Item No:23-4716AW Diameter OD: 12" (300mm) Diamond Thickness TH: .085" (2.16mm) Diamond Height: .394" (10mm) Arbor ID: 1" B to 3/4" Internet Price (1pc): $178.00$198.00 3 pcs (each): $165.00 Price $178.00$198.00 |
Item No:23-4716W Diameter OD: 12" (300mm) Diamond Thickness TH: .0512" (1.3mm) Diamond Height: .394" (10mm) Arbor ID: 1" B to 3/4" Internet Price (1pc): $198.00$225.00 3 pcs (each): $180.00 Price $198.00$225.00 |
Item No:23-4717AW Diameter OD: 14" (350mm) Diamond Thickness TH: .085" (2.16mm) Diamond Height: .394" (10mm) Arbor ID: 1" B to 3/4" Internet Price (1pc): $210.00$235.00 3 pcs (each): $190.00 Price $210.00$235.00 |
Item No:23-4717W Diameter OD: 14" (350mm) Diamond Thickness TH: .0512" (1.3mm) Diamond Height: .394" (10mm) Arbor ID: 1" B to 3/4" Internet Price (1pc): $225.00$250.00 3 pcs (each): $205.00 Price $225.00$250.00 |
Item No:23-4718W Diameter OD: 16" (400mm) Diamond Thickness TH: .0512"(1.0mm) Diamond Height: .394" (10mm) Arbor ID: 1" B to 3/4" Internet Price (1pc): $265.00$285.00 3 pcs (each): $215.00 Price $265.00$285.00 |
Item No:23-4728AW Diameter OD: 16" (400mm) Diamond Thickness TH: .085" (2.16mm) Diamond Height: .394" (10mm) Arbor ID: 1" B to 3/4" Internet Price (1pc): $234.00$255.00 3 pcs (each): $215.00 Price $234.00$255.00 |
Why Work With Us?
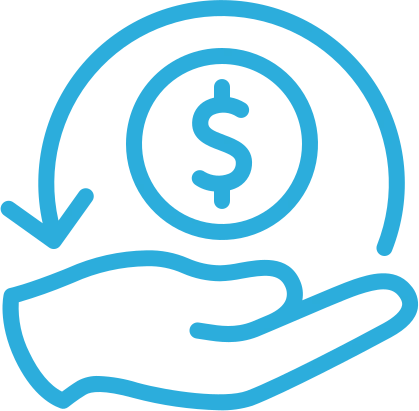
Best Return
on Investment
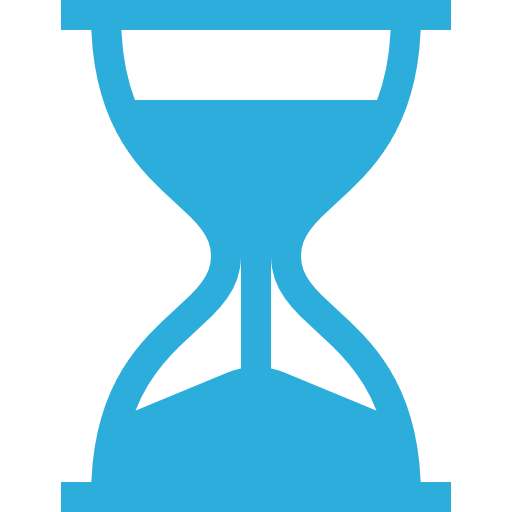
Attractive Cost of
Ownership
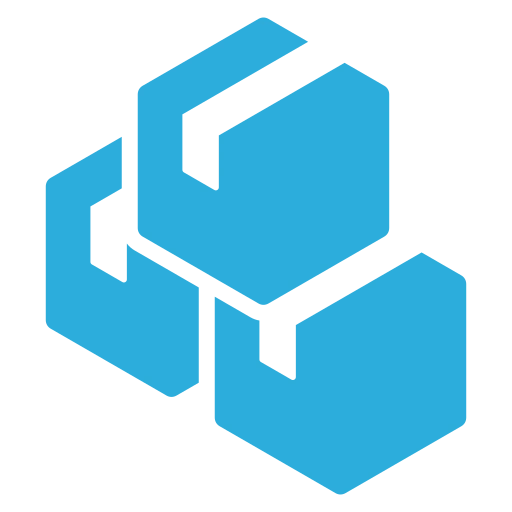
Thousands of Diamond & CBN Blades in stock
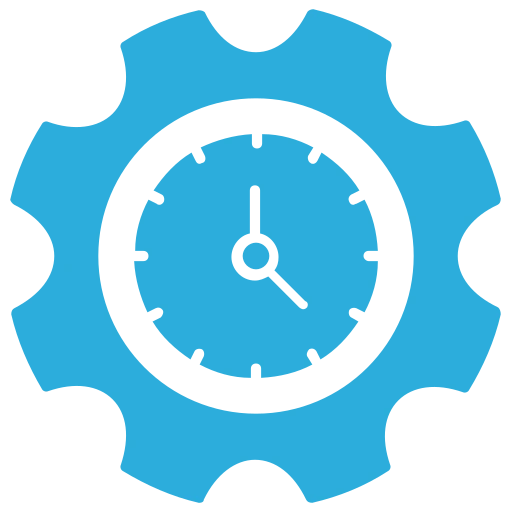
Custom Manufacturer with Fast Lead times
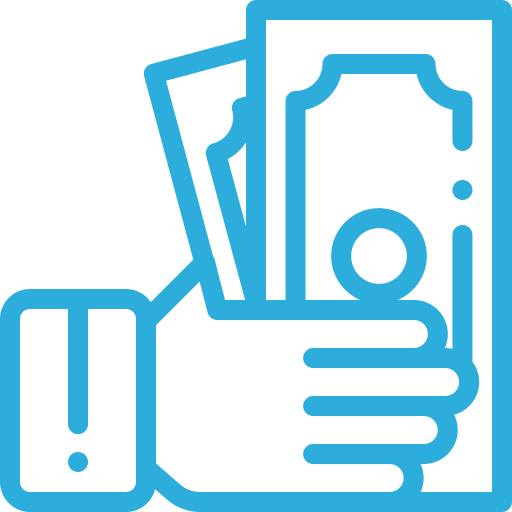
Unmatched
Prices in North America
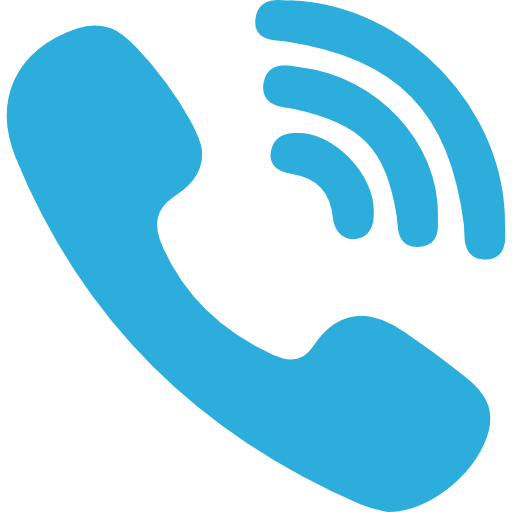
Unmatched Experience & Technical Support
Its what you cant see that makes all the Difference
SMART CUT® technology
How SMART CUT® Bond Works?
Step 1
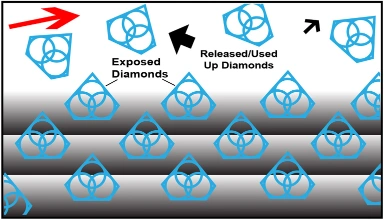
Sharpest And Finest Quality Diamonds
The newly exposed diamonds don’t effect diamonds already working on the material. Unlike many other diamond bonds, diamonds in a SMART CUT® Bond remains sharp and grow sharper with each cut, prolonging product life and consistent performance.
Step 2
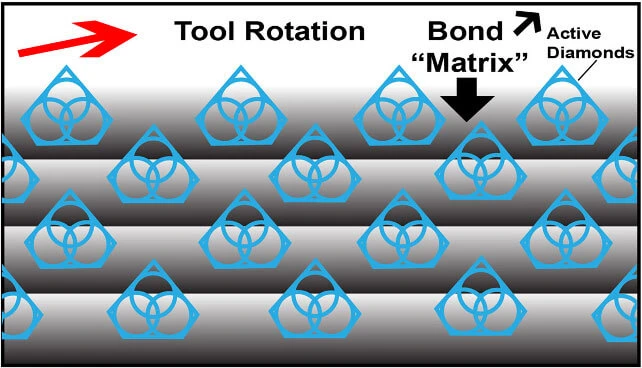
Diamonds or CBN Crystals
Diamonds or CBN Crystals are activated only at the exposed layer. As Bond Matrix layer begin to wear out, diamonds in a new Bond Matrix layer are immediately activated, substituting the already used up diamond layer. The SMART CUT® Diamond Hybrid Bond makes sure every diamond is in the right place and at the right time, working where you need it most.
Step 3
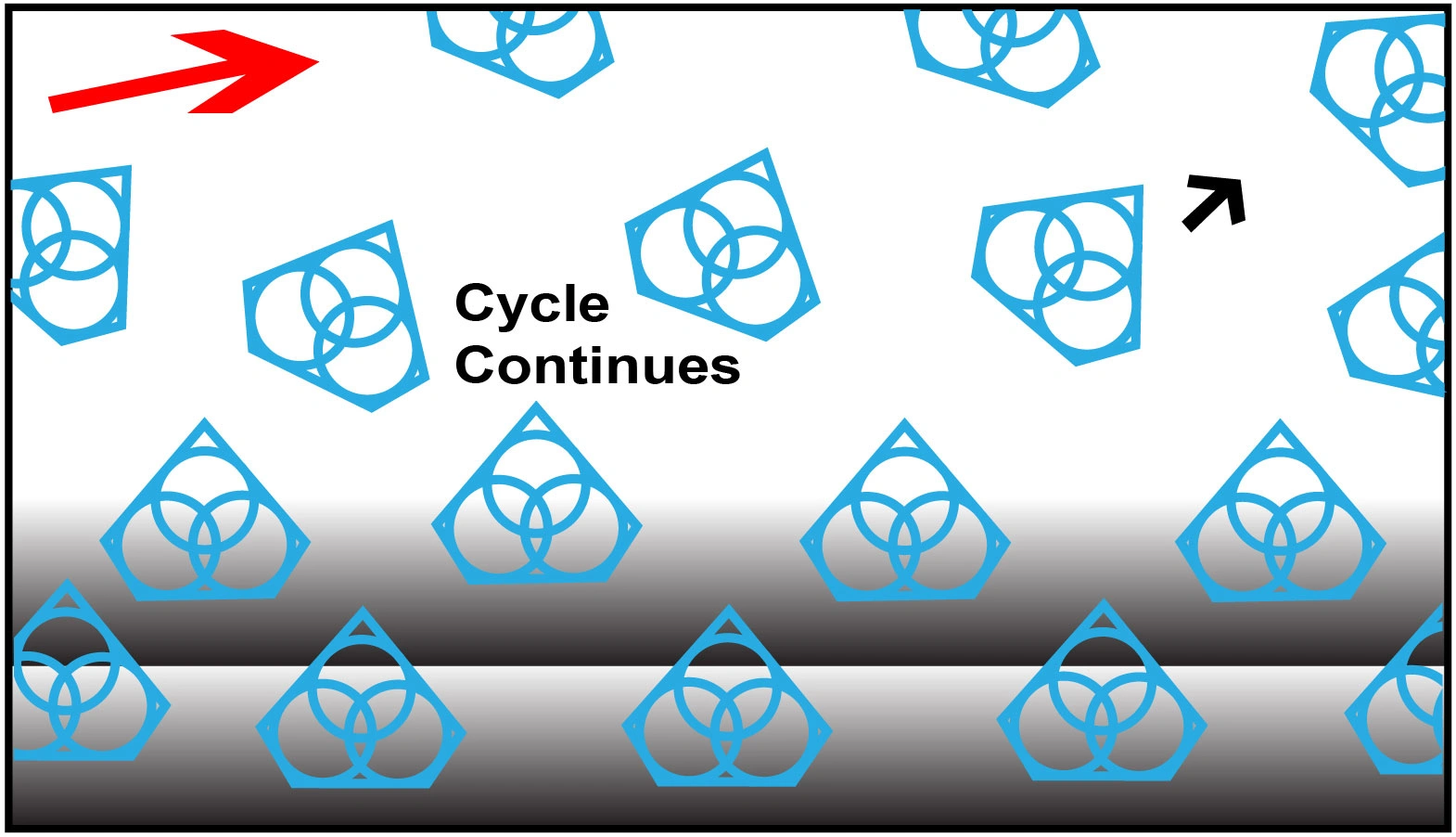
Advanced Formulated Open Diamond Bond Design
This advanced formulated open diamond bond design insures minimal chipping, fast cut, constant speed of cut, minimal cutting noise, and most important of all, consistent performance.

Quality & Experience Consistent Results
UKAM Industrial Superhard Tools is one of the companies behind the original THIN KERF Sintered (metal bond) diamond blades & drills for lapidary application. Producing blades sold under "private label" for a number of well known equipment manufacturers.
Our proprietary diamond tool chemistry, precision manufacturing methods, modern quality control methods, allow us to control and regulate the dozens of variables that affect diamond tool life, quality of cut, and consistent performance. Discover why some of the Leading Fortune 500 companies, Industry, Military, Jewelry manufacturers, to Professional Lapidary Hobbyists around the world prefer SMART CUT® diamond tools.
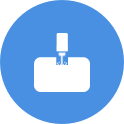
Cut The Hardest Materials Cut Hardest Materials Fast & Easy
SMART CUT® series 310M blades are designed to work on virtually any material you can find. You can cut very hard materials up to hardness of sapphire than switch to cutting very soft materials and the blade will maintain the same consistent performance.


Save Money Blade Life Is 80% To 40% Longer
Blade life is 80% to 40% longer compared to other conventional sintered blades.

SAVE TIME No Grinding & Polishing Required
SMART CUT® series 310M blades are real time and material savers. Proper use of the series 310M blades has been proven to actually minimizes and almost eliminate your after cutting work. With SMART CUT® series 310M blades you can do many operations. The blade grinds and polishes the material as it cuts. You don't have to spend time on other steps such as polishing the material after cutting.

Save Material Thinnest Kerf Thickness
THINNEST Sintered (metal bond) Diamond Blades commercially available for lapidary (precious & semi precious stone) application! The Diamond Thickness (TH) specified is actual thickness of diamond section, not core thickness. If you are cutting valuable materials or just want to have thinner kerf blade there is no substitute for these blades.
Why waste Valuable Time, Money, & Material?
Don't struggle with inferior lapidary blades - DEMAND THE BEST!!!





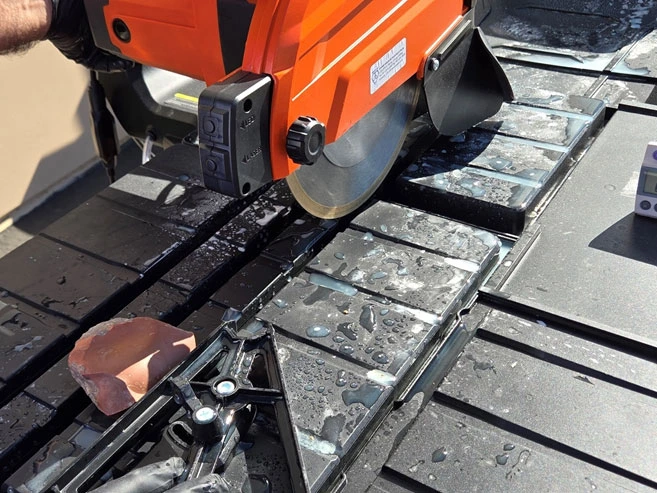
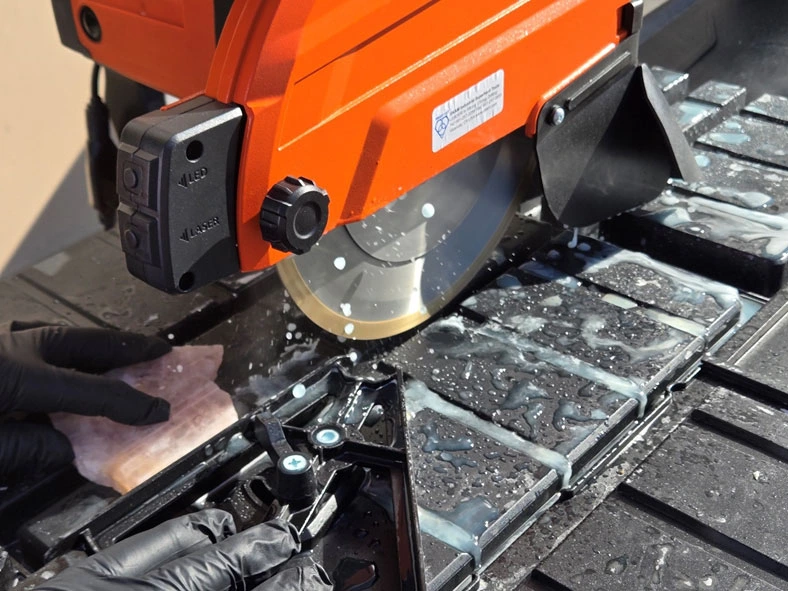
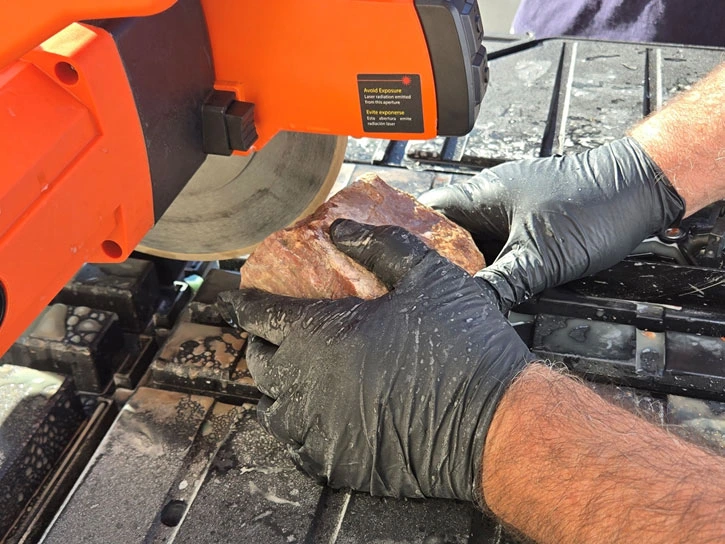
SMART CUT® Difference
How SMART CUT® Lapidary Blades are Different in comparison to other lapidary blades.
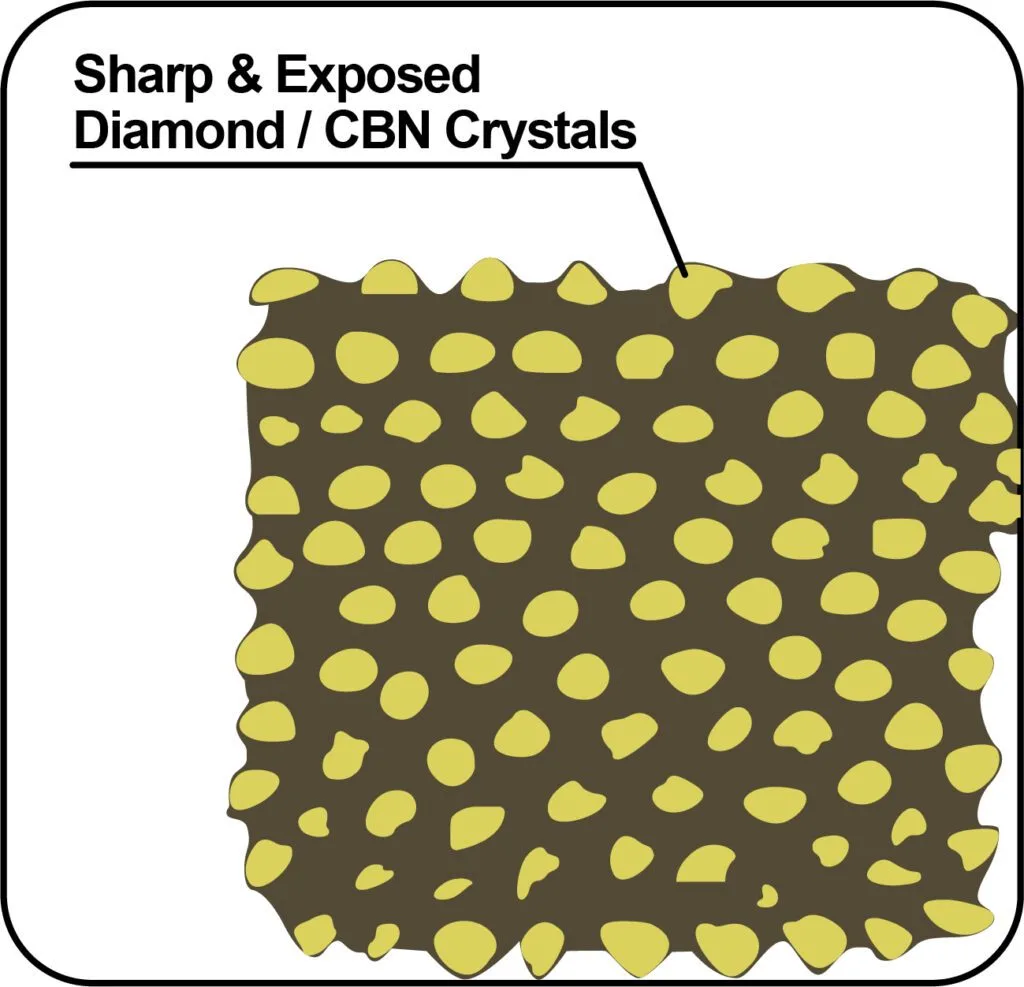
No
Glazing
Diamond & CBN lapidary blades with SMART CUT® technology require minimum dressing, the bond renews itself.
Faster
Cutting Action
Diamond lapidary blades made utilizing SMART CUT® technology are much more aggressive than your conventional lapidary blades. They can cut faster, while still leaving behind a smooth finish free of material deformation.
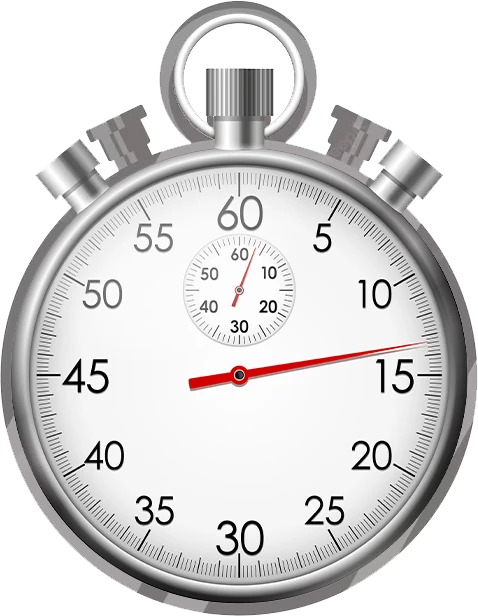
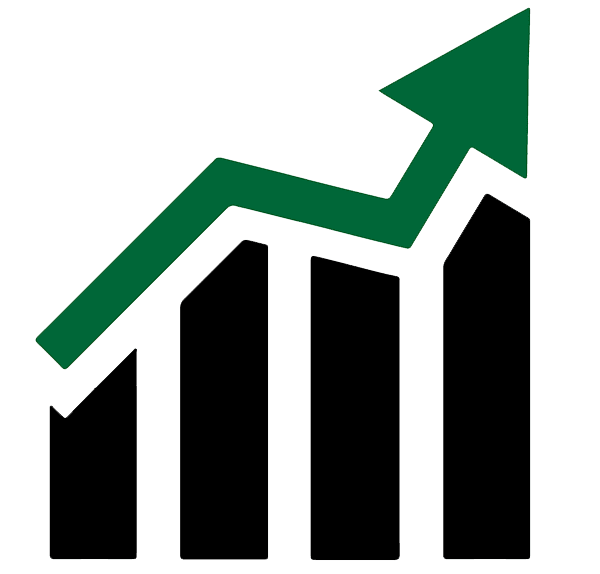
Longer
Life
In most cases lapidary blades manufactured utilizing SMART CUT® technology, will outlast other conventional lapidary blades. SMART CUT® lapidary blades are more sturdy than tools manufactured with conventional technologies. They are capable to retain their form and bond configuration all the way through the tools life.
More
Consistent Performance
SMART CUT® Series 310M Sintered (Metal Bond) Diamond Lapidary Blades have hundreds of diamond layers impregnated inside the metal matrix. Unlike Many Other Blade Types, they wear evenly, and are known for their consistency. You will get consistent cutting speed, and overall consistent performance, with minimum amount of dressing even on the hardest to cut materials

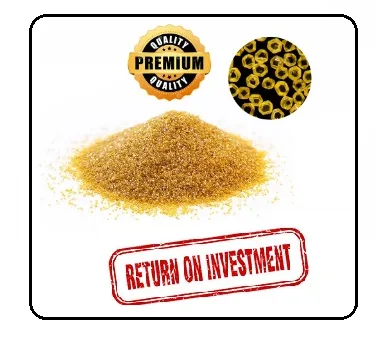
Manufactured Using
The Highest Quality Raw Materials
Only the highest quality synthetic diamonds and raw materials are used in the manufacturing process. The highest quality standards and product consistency is maintained, using sophisticated inspection and measurement equipment.
Best
Performance & Value on the Market
SMART CUT® Series 310M Sintered (metal bond) Lapidary blades are the best investment you can make! Although they may cost more than other sintered (metal bond), electroplated (nickel bond), hot or cold rolled or some notched lapidary blades. Designed for users that understand and appreciate quality. They will more than pay for themselves in terms of overall performance and provide best Return on Investment.
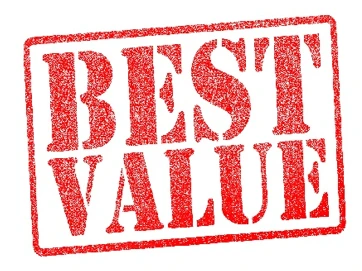
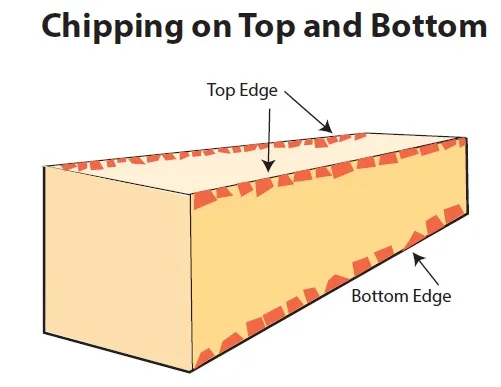
Minimize
Chipping & Improve Surface Finish
SMART CUT® Series 310M Lapidary Blades open bond design have diamonds oriented and evenly distributed in a bond matrix. Providing faster, freer cutting action with minimum heat generation. This translates in improved surface finish and minimum chipping.
310M Lapidary Blades
Manufactured utilizing SMART CUT® technology, these blades will give you the BEST PERFORMANCE & VALUE

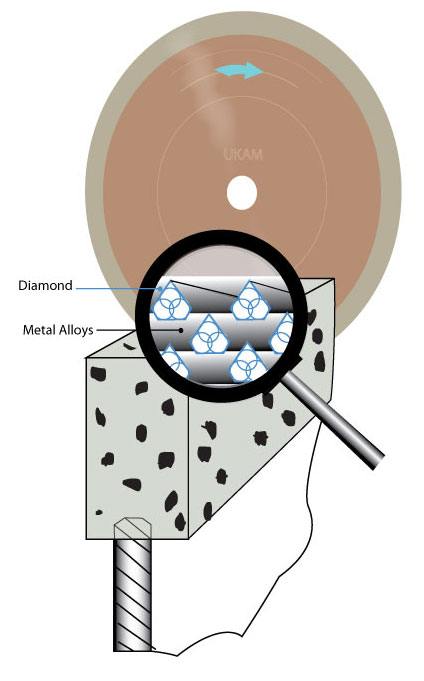
Diamond-Depth


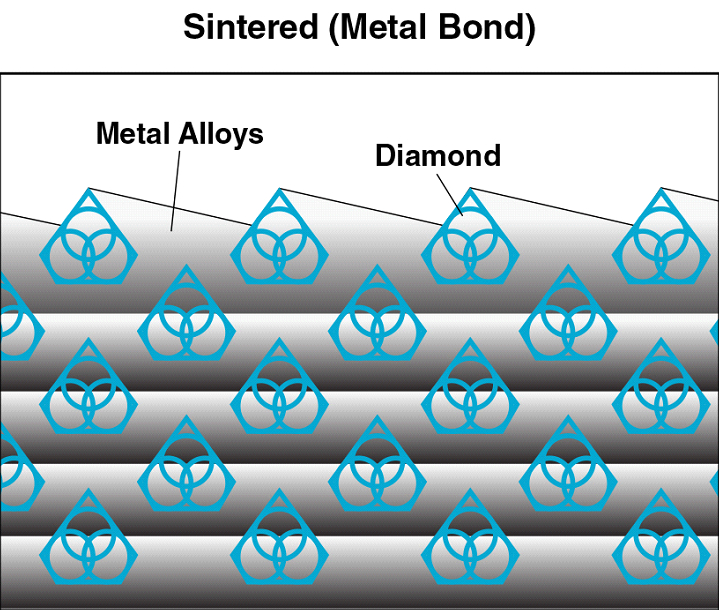

High Quality Diamond
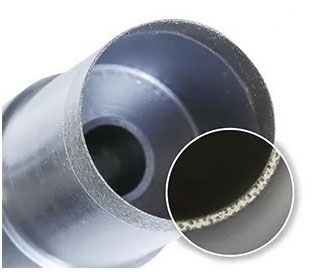
Precision Steel Core
Inside Diameter
Compare SMART CUT® Series 310M blades to other Sintered (Metal Bond) lapidary blades on the market
Any other blade have 5mm diamond depth/height. This has remained industry standard for many decades. While this is sufficient for most people. The return on investment (ROI) can be lot higher
What is diamond depth and why its important?
Diamond depth (height) indicates the height of diamond section/layer extends from the steel core. The higher the diamond depth, the longer the blade life (in most cases). Diamond height will vary depending on the blade diameter and thickness. In the past there was direct correlation between diamond depth and blade price. The higher the diamond height, the higher the blade price. Today advanced in industrial diamond powder and blade manufacturing technology has significantly reduced the cost of industrial diamond to the point that its only a small part of the overall manufacturing cost equation.

Diamond depth (height) indicates the height of diamond section/layer extends from the steel core. The higher the diamond depth, the longer the blade life (in most cases). Diamond height will vary depending on the blade diameter and thickness. In the past there was direct correlation between diamond depth and blade price. The higher the diamond height, the higher the blade price. Today advanced in industrial diamond powder and blade manufacturing technology has significantly reduced the cost of industrial diamond to the point that its only a small part of the overall manufacturing cost equation.7mm to 10mm in on order to provide longest life and best value/RPI possible for your blade investment.
SMART CUT® Series 310M blades will outlast almost all other lapidary blades on the market today by 40% to 80%.

The longer life can be attributed not only the higher diamond depth, but to higher diamond quality used. Advanced diamond distribution an orientation techniques, and proprietary bond chemistry. Combined with our competitive prices you re sure to obtain the best value and return on investment possible
Why Sintered (Metal Bond) Diamond Lapidary Blades With SMART CUT® technology Offer The Best Value & Performance For Your Money?
ABOUT SINTERED (METAL BOND)
Sintered (Metal bonded) diamond blades are “impregnated” with diamonds. Diamonds sintered and multiple (hundreds) layers of diamonds impregnated inside the metal matrix. Electroplated and other types of diamond blades for lapidary application have only one layer of diamond that stays on the surface. Diamonds in a sintered (metal bond) diamond blade are furnaces sintered in a matrix made of iron, cobalt, nickel, bronze, copper, tungsten, alloys of these powders or other metals in various combinations. The compacted materials are then hot pressed or sintered to full density. Heating rate, applied pressure, sintering temperature and holding time, are all controlled according to the matrix composition. This means that selected diamonds are mixed and sintered with specific metal alloys to achieve the best cutting performance possible on any materials such as sapphire, agate, emerald, ruby, opal, petrified wood, glass, and etc.
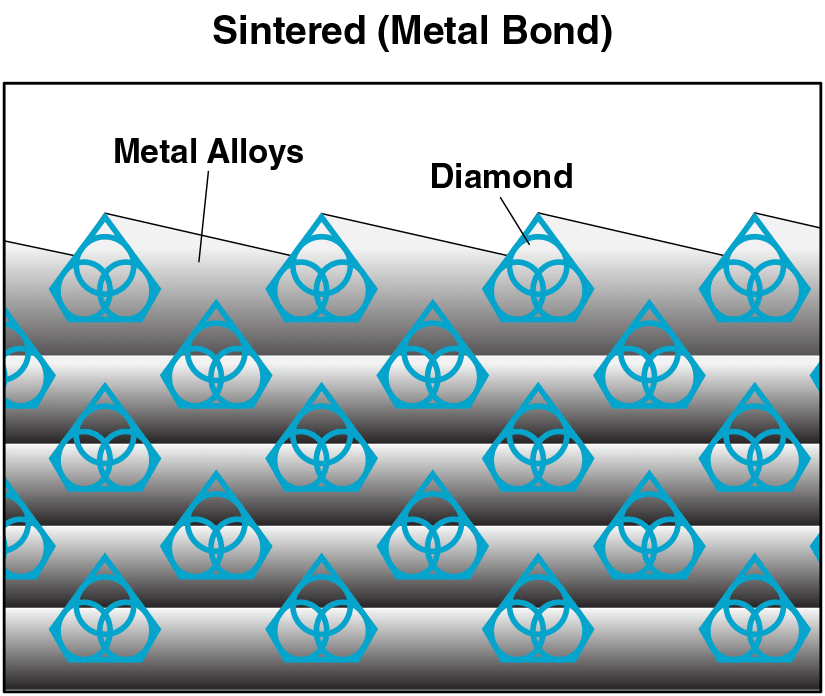
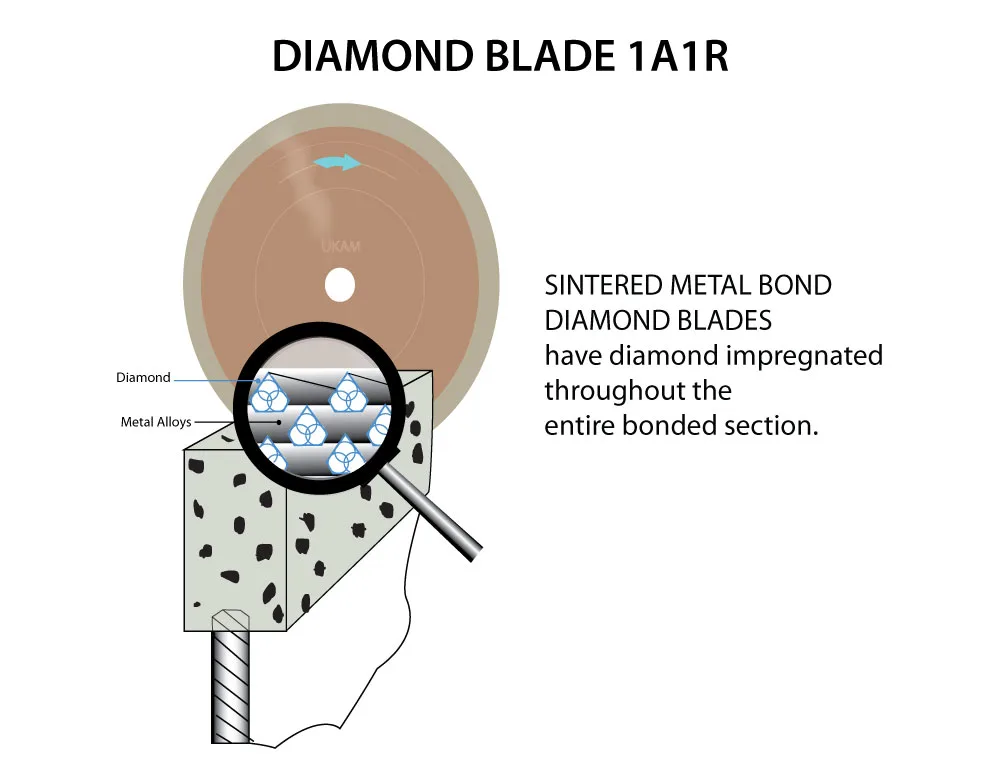
The metal bond surrounding the diamonds must wear away to continuously keep re-exposing the diamonds for the diamond tool to continue cutting.
Sintered (metal bonded) diamond tools are recommended for cutting hard materials from 45 to 75 on Rockwell Scale (5 to 9.5 on mohs scale of hardness). It is more wear resistant and holds diamond well in place, usually producing the highest yield/cutting & best price per cut ratio.
They will last longer & cut faster than ordinary notched, plated, and other sintered (metal bond) lapidary blades.
They wear evenly, and are known for their long life & consistency. Sintered (metal bonded) diamond blades are the latest technology available in Diamond Blades. And represent the BEST VALUE & PERFORMANCE PER CUT.
They will last longer & cut faster than ordinary notched, plated, and other sintered (metal bond) lapidary blades.
Compare SMART CUT® Series 310M SINTERED (Metal bond) DIAMOND LAPIDARY BLADES To Other Bond Types
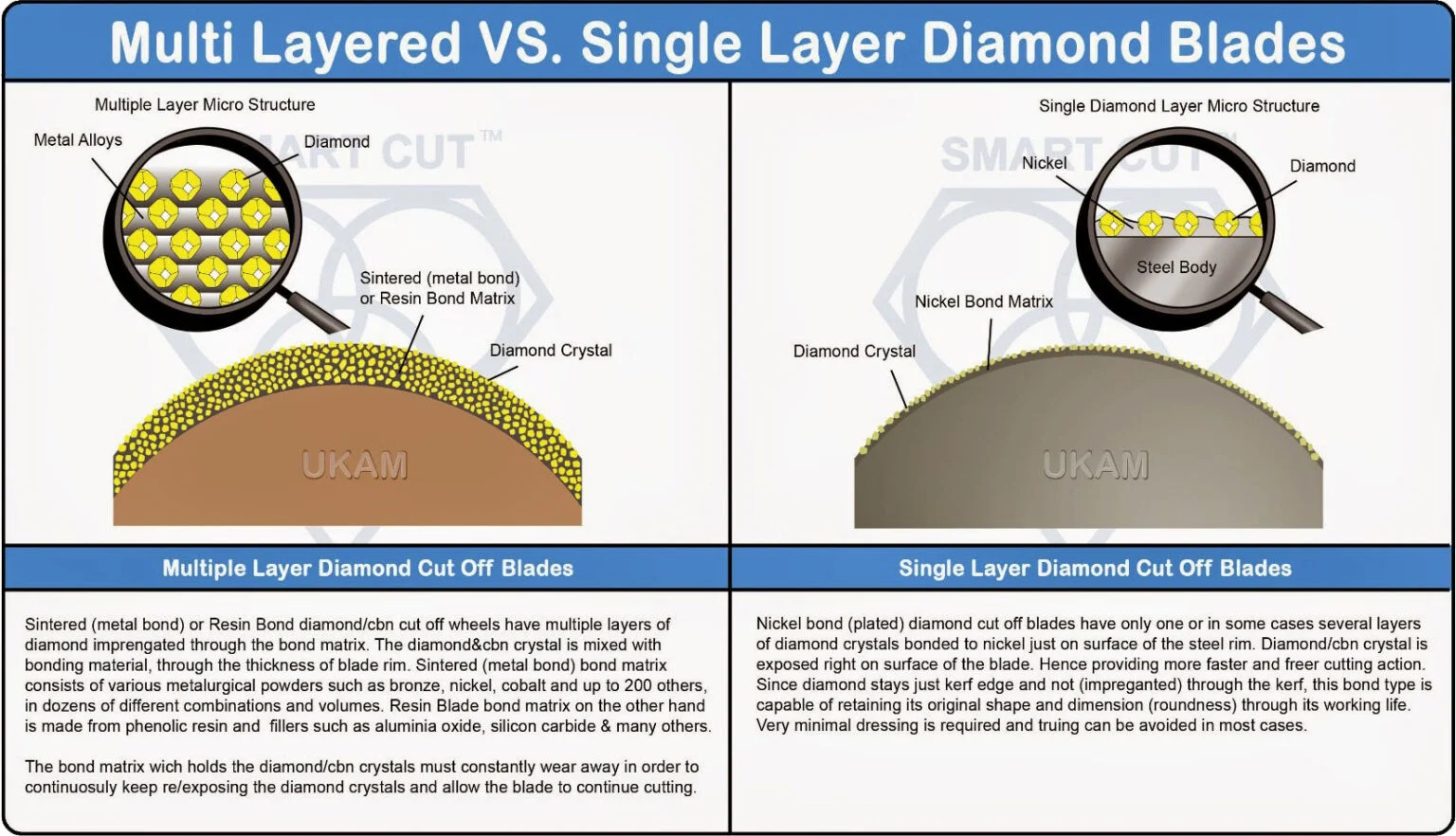
Sintered (Metal Bonded) Lapidary Blades
- Hundreds layers of diamond
- Stands up well under aggressive conditions
- Super smooth finish
- Longest lasting blade
- Very Universal (work on ultra hard to soft materials)
- Most cost effective
Electroplated, notched, hot or colled rolled blades, Lapidary Blades
- Single layer of diamond
- Cannot be dressed (in most cases)
- Least Expensive
- Shortest Blade Life
- Cannot be used for a number of (ultra hard) materials
Sintered (metal bonded) lapidary blades are the best investment you can make! Although they may cost more than electroplated (nickel bond), hot or colled rolled or some notched lapidary blades, sintered (metal bond) blades will more than pay for themselves in terms of:
Longer Life
Other Bond type blades may cost less, and at first glance may seem like the most cost effective alternative. However, they will cost you more in the long run. Depending on material and application, sintered (metal bonded) blades may last as much as 50 to 100 other diamond lapidary blade types put together. You can’t get more life out of any other blade !!! Instead of constantly putting blades on and off the saw, you will save money by using one blade. This means cost per cut, sintered (metal bond) blades are the best choice
More Consistent performance & Faster Cutting Speed
Other Blade Types have only one layer of diamond coated on metal core. Diamonds sit only on the surface. When this diamond portion is peeled off, the blade will slow down, cut on the side (not cut straight) or stop working (cutting) altogether. While other blade types may provide acceptable level of performance softer lapidary materials such as topaz, turquoise, amethyst, and etc. They will immediately burn out on harder materials such as agates, petrified wood, sapphire and etc. Metal bonded blades are sintered and impregnated inside the metal matrix. Multiple (hundreds) layers of diamonds are impregnated inside the metal matrix. Unlike Blade Types, metal bond blades wear evenly, and are known for their consistency. You will get consistent cutting speed, and overall consistent performance from sintered (metal bonded) blades.
Diamond Lapidary Blade Table of Comparison
Features |
SMART CUT Series 310M |
Conventional Sintered (Metal Bond) Lapidary Blades |
Conventional Sintered (metal bond) Non Lapidary Blades |
Electroplated Lapidary Blades |
Notched Lapidary Blades |
---|---|---|---|---|---|
Blade Picture |
|
|
|
|
|
Diamond Section Close Up |
|
|
|
|
|
Bond Type |
Sintered (Metal bond) Multiple Layers of diamonds embedded in a very soft metal matrix |
Sintered (Metal bond) Multiple Layers of diamonds embedded in a medium soft metal matrix |
Sintered (Metal bond) Multiple Layers of diamonds embedded in a medium to hard metal matrix |
Electroplated (Nickel Bond) Single Layer of Diamonds in Nickel Matrix |
Notched Rim Serrated or notched edge filled with diamond |
Kerf Thickness |
Thin to Thick |
Thin to Thick |
Thick |
Very Thin To Medium |
Very Thin To Medium |
Diamond Grit Size |
Medium / Coarse |
Medium / Coarse |
Very Coarse |
Medium |
Medium |
Diamond Quality |
Very High |
Medium |
Low |
Low |
Very Low |
Diamond Depth |
25 to 200 con |
5mm |
10 to 5mm |
Diamond coating on surface |
|
Tolerances on kerf thickness |
±0.05mm to ±0.1mm |
±0.05mm to ±0.1mm |
±0.2mm to ±0.5mm |
±0.1mm |
±0.1mm to ± 0.2mm |
SMART CUT technology (diamond orientation) |
Yes |
NO |
NO |
NO |
NO |
Side Run Out |
0.015mm |
0.03mm |
0.05mm |
Good |
Good |
Cut Quality |
Yes |
Good |
Poor |
Good |
Satisfactory |
Cutting Speed |
Excellent/ Very Fast |
Good (Moderate to Fast) |
Poor (Slow) |
Excellent (very fast) in begging |
Good |
Life Span |
Excellent |
Good |
Poor |
Poor |
Very Poor |
Frequency of Dressing |
Minimum |
Medium |
Very Frequent |
Minimum |
Minimum |
Heat Generation |
Minimum |
Medium |
High |
Minimum |
Minimum |
Capability to cut ultra hard materials |
Excellent |
Very Good |
Poor |
Good |
Satisfactory |
Cost |
Higher |
Medium |
Low |
Medium/Low |
Very Low |
Capability to Alter Inside Diameter/arbor size |
Yes |
Yes |
No |
No |
No |
STORY BEHIND
SMART CUT® Series 310M Lapidary Blades
In redesigning and updating our original sintered (metal bond) lapidary thin kerf blade, we wanted to give our customers something more, something better than anyone could give them, something they always wanted and could not get before.
We did some serious research. We talked to the experts. Serious users, both professional gem cutters, lapidaries, and rockhounds. People like yourself.
The people who use diamond blades everyday, every chance they get. The people who complain and professionals who know what to look for in a diamond blade to get the job done right. We wanted to know what and why they liked about the diamond blades they used. What they don’t like, what they want, and what they weren’t getting.
So with this in mind, in 1994 we spend over 4 years in research and development making our popular sintered (metal bond) thin kerf blades even more superior. Following the suggestions of customers like you, we took the best features and advantages the sintered (metal bond) thin kerf blades had to offer to create next generation of the SMART CUT series 310M blade.

Diamond Lapidary Blade
Diamond Lapidary Blade Table of Comparison
Are you using the right blade for your application?
many Clients wast valueable time & money by using incorrect blades for their application.
Learn what variables you should consider when chosing your next lapidary blade
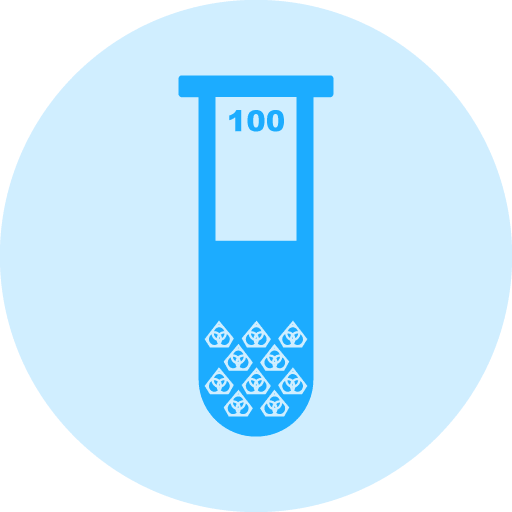
Diamond Concentration :
Diamond Concentration is still a factor in determining the life and cutting speed of your Diamond Lapidary Blade. Higher diamond concentration is recommended and usually used for cutting softer and more abrasive types of materials. However, the trade off is slower cutting speed. Low diamond concentration is recommended and widely used for cutting harder materials
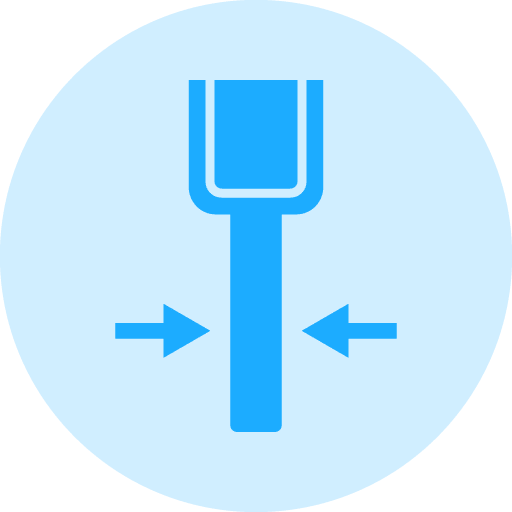
Blade Thickness :
Lapidary blade thickness typically ranges from .014” (0.35mm) to .085” (2.0mm). Thinner and thicker wafering blade are available, frequently from stock upon request. Kef thickness typically increases with blade diameter (in proportion to diameter of the blade). Kerf is the amount of material removed from the material due to the thickness of blade passing though the material. Blade thickness is important for users requiring most minimal amount of material loss cutting specially when cutting very valuable materials such as gemstones or meteorites There are large variety of factors that will contribute to optimal blade thickness for your material/application Including your desired cutting speed, feed rate, material diameter, thickness, hardness, density, and shape. As well as skill & experience of the operator. Thicker blades are more stiff and can whistand higher/feed rates. Another advantage of thicker kerf blades is they are more forgiving to operator error and abuse. Thicker kerf blade are recommended for use in environment where large number of individuals will be sharing and using same equipment. Perfect for less experienced and novice saw operators, such as students and beginning users.
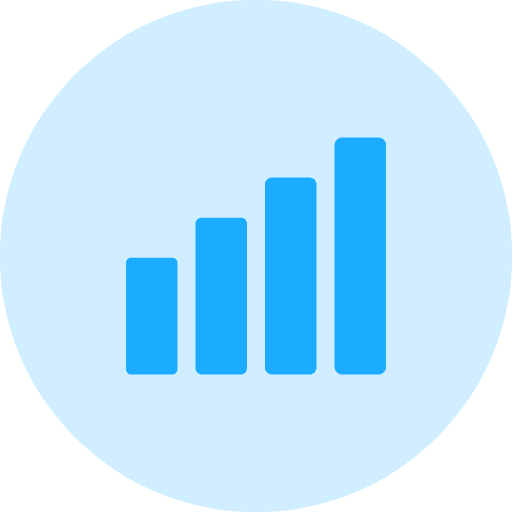
Feed Rates :
Feed rate is amount of force applied to the blade to go through material being cut. This will typically vary depending on blade diameter, kerf thickness & material being cut. Generally, harder materials are cut at higher feed rates and speeds (such a precious and semi precious stones) and more softer and brittle materials are cut at lower loads and speeds (such as glass, quartz). The Speeds/RPM’s you are using, shape/geometry of the material, and how the specimen is being clamped/hold in place will affect the load that can be used for your application.
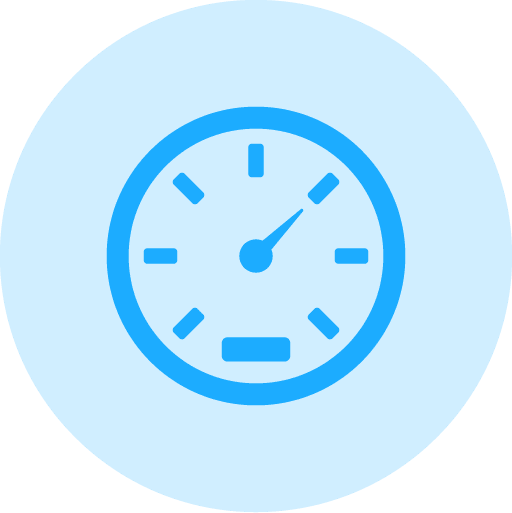
Blade Speeds/RPM’s :
Most lapidary blades are used between 4,000 to 1,000 RPM’s Typically harder and more denser materials such as Sapphire, are cut at higher RPM’s/speeds Where more brittle materials such as as glass are cutting at lower RPM’s. Most rim saws RPM’s are typically limited from 1,000 to 4,000 RPM’s. Slabbing saws 500 to 1000 rpm’s. And trim saws from 3,000 to 6,000 rpm’s.
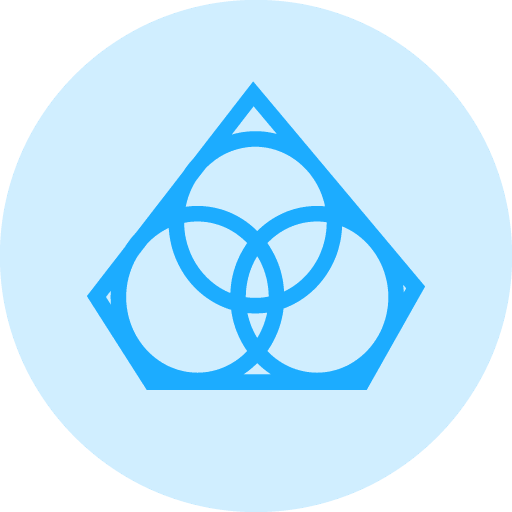
Diamond Particle/Grit size :
Diamond Mesh Size plays a major role in determining your cutting speed, cut quality/surface finish, level of chipping you will obtain. Diamond Mesh size does have considerable effect on cutting speed. Coarse Diamonds are larger than finer diamonds and will cut faster. However, the tradeoff is increase in chipping and surface finish. If you are cutting fragile, more delicate materials then we have available from stock finer mesh size diamond blades. If you need to cut as fast as possible and surface finish is not a concern we also offer much coarser cutting blades for this application.
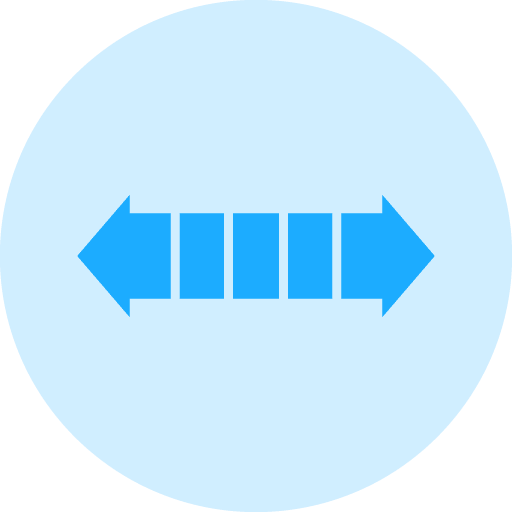
Bond Hardness :
Ability of the bond matrix to hold diamonds. As the hardness of the bond is increased, its diamond retention capabilities increase as well. However the trade off is slower cutting speed. Life of the diamond blade is usually increased with hardness of its bond matrix. Bonds are designated on their scale of hardness from Soft, Medium, and Hard. There are dozens of variations and classification schemes based on bond degree of hardness or softness. Using diamond blades with optimum bond hardness for your application is important to successful precision diamond sawing operation. Bond matrix that is too soft for the material being cut will release diamond particles faster than needed, resulting in faster wear and shorter diamond blade life. On other hand bond matrix that is too hard will result in much slower cutting speeds and require constant dressing to expose the next diamond layer. As rule of thumb, harder materials such as sapphire generally require a softer bond. Whereas softer and more brittle materials require a harder bond.

Blade Outside Diameter :
Typically lapidary blade diameters range form 4” (100mm) to 8” (200mm) for trimming and 10” (254mm) and up are usually used for slabbing. The diameter should be selected based on material diameter and thickness being cut. Smaller diameter blades are thinner than the larger diameter blades and are more prone to bending and warping. Although large diameter blades are thicker, they are typically used for cutting larger and pieces of material at higher loads and speeds than smaller blades Blade Inside Diameter - Most trim saws and tile saws has 5/8” arbor these are for blades 4” to 10” OD. Larger cutting machines such as 12” to 18” OD usually have 1” arbor. We can provide bushings to smaller arbor. We can also expand the current arbor size to anything you want same day.
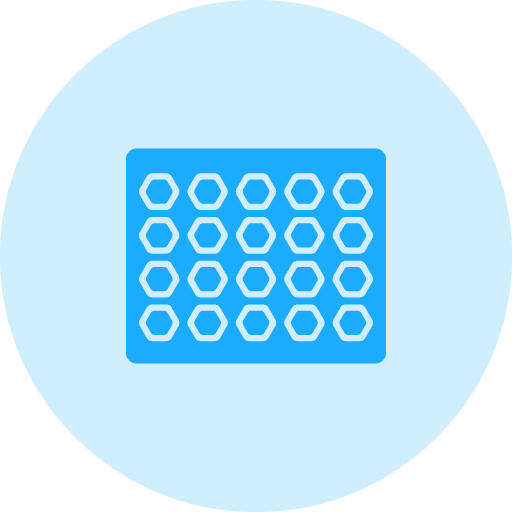
Bond Type :
Metal bonding offers long life and durability, and is the best bond type to use for lapidary applications.
Why Work With Us?
Comprehensive Source of Information on Diamond Lapidary Blades
We understand that your success depends on select the right diamond lapidary blade, and optimizing your parameters to best fit your applications/needs.
The more you understand about what we can do for you, the better our partnership will be.
On our website you will find the Most Comprehensive Source of Information on Everything you wanted to know about diamond & CBN blades & industrial diamond tools.
Large Inventory & Custom Manufacturing
Largest Inventory of Diamond Lapidary Blades in the U.S Available in different diameters, wall thicknesses, angles, radiuses, drill depths, mounting types, bond types, diamond mesh sizes, concentrations, bond hardness, tolerances. Custom Manufacturing to fit your particular requirements is available with short lead times and no minimum order quantities.
Experience makes all the Difference
"ONE OF THE MOST EXPERIENCED COMPANIES IN THE INDUSTRY"
Over the years we have enjoyed working with all types if clients, regardless of size. Proprietary lapidary blade chemistry, precision manufacturing methods, modern quality control methods, allow us to control and regulate the dozens of variables that affect lapidary blade life, quality of cut, surface finish. Reducing and often eliminating additional steps often required after cutting.
Umatched Technical Support
We Are a Partner In Your Success
Developing close ties with our customers is the foundation of our business. At the core of our company is a team of world class engineers, knowledgeable customer service personnel here to serve you. Whether is designing or manufacturing a special solution. We will go out of our way to optimizing your process to ultimate level of efficiency.
Advanced Technology
American Manufacturer As one of the few remaining independent U.S.Diamond Tool & machine builders. We have the experience & tradition to help you remain at frontier of technology Our experience has been further enhanced by acquiring assets and processes from some of the oldest American tool manufacturers, along with their decades of experience and R& D. This has positioned us as one of the most experienced companies in the industry.
Superior Quality &
Consistency
Our unique bond formulations, tool designs, stringent requirements, and utilization of exceptionally high-quality diamonds and raw materials ensure top-notch products that adhere to strict ISO 9000 standards.
Our proprietary technology allow us to control and regulate the dozens of variable that affect toolife, quality, & consistency
Expect More From Your Tools
Related Products
SMART CUT® 330MS segmented lapidary blade
SMART CUTTM Series - 330MS Wide Slot Segment Design - Diamond Depth (Height): 8mm SMART CUT Series 330MS Wide spacing between segments. Designed for fast and more aggressive cutting, where chipping and very smooth cut loss is not essential. And loss of material is not critical. Perfect for medium to hard lapidary materials, and less experienced blade users.
SMART CUT® 325M Continuous Slabbing Blade
SMART CUT® Series - 325M Continuous Rim - Diamond Depth (Height): 8mm
The SMART CUT® Series 330MS Continuous Rim, Sintered (Metal Bond) blade is an excellent choice for manufacturing, and R & D organizations, and professionals who need precise and clean cuts with very little chipping. This blade is specially designed to work with delicate materials like natural stone, semi-precious stone, glass, ceramics and other ultra hard and brittle materials.SMART CUT® Series – 405M
SMART CUT Series 300M
SMART CUT® 320MS
Narrow Slot Segment Design - Diamond Depth (Height): 5mm - 16" to 36" Diameter
SMART CUT® Series slabbing sintered (metal bond) diamond cut off blades, are Segmented Design with (narrow spacing between the segments). Designed for smooth cutting of ultra hard materials. Such as soft rocks & minerals, advanced ceramics, glass, composites, and some metals. Perfect for users who wish to minimizes loss of valuable material. This is a popular slabbing blade used among geological laboratories. Most widely used blade for cutting precious & semi precious stones / rocks. SMART CUT® Series slabbing sintered (metal bond) diamond cut off blades, are Segmented Design with (narrow spacing between the segments). Designed for smooth cutting of ultra hard materials. Such as soft rocks & minerals, advanced ceramics, glass, composites, and some metals. Perfect for users who wish to minimizes loss of valuable material. This is a popular slabbing blade used among geological laboratories. Most widely used blade for cutting precious & semi precious stones / rocks.SMART CUT® Series 305M
Sintered (Metal Bond) Blades New Generation & Technology
SMART CUT® Series 305M Heavy Duty blades provide unmatched performance on a very wide variety of ultra hard to soft materials.
Designed for Industry, R & D & other users who understand and appreciate quality. They are used and preferred world wide by some of the leading Fortune 500 companies, Military Contractors, Space & Science Organizations, & many other professional users.
SMART CUT® SERIES 301M
SMART CUT® SERIES 301M lapidary blades have undergone significant enhancements to elevate their performance and durability. Engineered with an increased diamond concentration and a reinforced steel core enriched with higher carbon content, these blades exhibit improved tension memory. This structural enhancement ensures that the blades maintain their integrity and alignment during rigorous cutting operations, thereby extending their lifespan and reliability.
The incorporation of a solid diamond sintered kerf in the design not only enhances the cutting capability but also optimizes coolant flow across the blade. This feature is pivotal in maintaining the blade’s temperature, reducing wear, and facilitating smoother cuts. The enhanced design ensures superior performance, particularly when cutting challenging materials such as agate, petrified wood, or jade, where precision and smoothness are critical.
SMART CUT® SERIES 315M Diamond Lapidary Blades
SMART CUT® SERIES 315M Sintered (Metal bond) diamond lapidary blades are specially designed to efficiently cut a wide range of hard lapidary materials using high-speed, water-cooled tile and brick saws, ensuring minimal chipping and maximizing performance. These blades are capable of delivering precise, straight cuts in dense rocks such as quartz, agate, geodes, petrified wood, jasper, as well as granite, marble, and porcelain tiles when used with your lapidary saw. The precision and reliability of SMART CUT® SERIES 315M blades make them indispensable tools for both professional and amateur lapidaries.
Recently Viewed Products
ARE YOU USING RIGHT LAPIDARY BLADES
FOR YOUR APPLICATION?
LET US
HELP YOU
HAVING ISSUES WITH
YOUR CURRENT LAPIDARY BLADES?
Knowledge Center
12
Apr
How to Properly Use Diamond Lapidary Blades
Share this Article with Friend or Colleague
(Guide on getting the most from your blade)
Welcome to the User Guide on How to Properly Use Diamond Lapidary Blades. This guide is designed to provide detailed insights and...
10
Apr
Signs of a High Quality Diamond Lapidary Blade
Getting the best results when using lapidary blades is not only skill but also about using the right blade for the application. When we talk about a good blade for lapidary application, we are really...
10
Apr
What Makes a Great Diamond Lapidary Blade
Cutting is a foundational step in the lapidary process, and the choice of diamond Lapidary blade significantly influences subsequent stages. While the market offers a plethora of blades for lapidary work, their performance and quality...
08
Apr
Mastering the Art of Lapidary cutting
Mastering the Art of Lapidary, Gemstone, Cabochon, & Slab Cutting: A Comprehensive Guide to Slab and Trim Sawing Techniques
The process of transforming rough lapidary rocks & gemstones into beautiful, polished pieces is both an art...
02
Jun
Evaluating & Comparing Diamond Blades
Share this Article with Friend or Colleague
Proper testing procedures and methodologies must be set up and used to obtain accurate as well as repeatable testing results. This article will discuss several simple procedures which...
02
Jun
How to Improve & Optimize Your Diamond Sawing Operation
There are numerous variables that affect the performance of diamond and CBN cutting blades. Understanding these variables will help end users select the right diamond blade specifications for their applications and optimize their...
02
Jun
Troubleshooting Diamond Sawing Problems
Having issues with your diamond cutting operation? This Illustrated Guide can help. Learn the most common problems most people have in using diamond cutting blades. How to resolve them and avoid them in...
02
Jun
How to properly use Diamond Tools
UKAM Industrial Superhard Tools manufactures precision diamond tools for a large variety of applications, materials, and industries.
Share this Article with Friend or Colleague
Metal Bonded Diamond Tools are “impregnated” with diamonds. This means that selected...
02
Jun
How to Selecting Right Diamond Tools for your application
Selecting the appropriate Diamond & CBN Tool specification is a crucial aspect of achieving your objectives. Opting for the ideal specification not only yields optimal results but also ensures the best return on investment. Conversely,...
- Unmatched Selection For Many Applications
- Superior Quality & Consistency
- Immediate Worldwide Delivery
- Technical Support & Expertise
- American Based Manufacturer
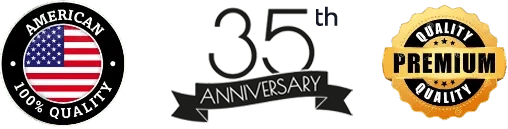

- Different Product
- Different Technology
- Different Company
- Expect MORE from your tools
Let Us HELP You!
Subscribe To Our Newsletter
Signup for email offers, updates, and more
Contact Us
- 25205 & 25201 Avenue Tibbits Valencia CA 91355 USA
-
Phone : (661) 257-2288
FAX : (661) 257 -3833 - lel@ukam.com
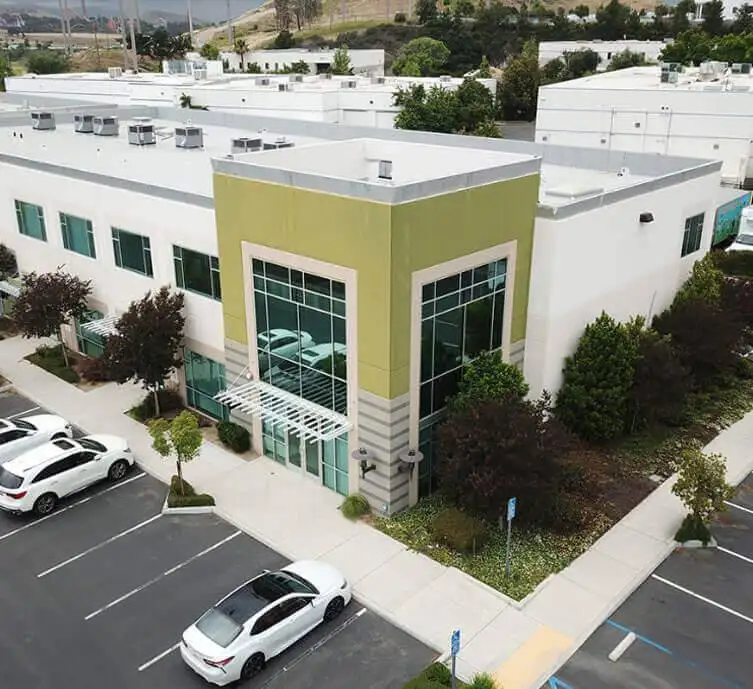
UKAM Industrial Superhard Tools is a U.S. High Technology, Specialty Diamond Tool & Equipment manufacturer. We specialize in producing ultra thin, high precision cutting blades, precision cutting machines diamond drills, diamond micro tools, standard & custom advanced industrial diamond tools and consumables.
- 25205 & 25201 Avenue Tibbits Valencia CA 91355 USA
-
Phone : (661) 257-2288
FAX : (661) 257 -3833 - lel@ukam.com
- 25205 & 25201 Avenue Tibbits Valencia CA 91355 USA
-
Phone : (661) 257-2288
FAX : (661) 257 -3833 - lel@ukam.com
DIAMOND TOOLS BY BOND
EQUIPMENT
KNOWLEDGE CENTER
OUR PRODUCTS
COMPANY
CUSTOMER SERVICE
Shipping Methods


Safe & Secure Payments

© Copyright 1990-2025. UKAM Industrial Superhard Tools – Terms of Use