-
0 items in quote
No products in the Quote Basket.
SMART CUT® SIMPLE PRECISION GRINDING / POLISHING HEAD
CONTROLLED AUTOMATED REMOVAL OF MATERIAL TO YOUR DESIRED PARAMETERS
SMART CUT® Simple Precision Grinding/Polishing Head is a cutting-edge solution designed for precision grinding and polishing, offering full control over material removal while maintaining consistency in flatness and pressure. With this innovative tool, operators can easily adjust the grinding/polishing pressure and specify the exact amount of material to be removed, ensuring tailored results for each application. Once set, the head will automatically apply the pre-determined pressure and stop once the desired amount of material has been removed, allowing for seamless, hands-off operation.
This versatile tool is especially effective for high-precision cross-sectioning and sample preparation, making it an invaluable asset for industries focused on failure analysis, yield analysis, quality control, research and development, and materials science.
DESCRIPTION
SPECIFICATIONS
FEATURES
ADVANTAGES
INDUSTRIES USED IN
FAQ
OPERATING MANUALS
DESCRIPTION
The SMART CUT® Simple Precision Grinding/Polishing Head ensures uniform material removal, delivering consistent results even for the most delicate and hard-to-handle materials.
How It Works:
- Set Parameters: The operator uses a thickness gauge or caliper to determine the amount of material to be removed and sets the desired pressure.
- Adjust the Stop: Once the parameters are set, the adjusted stop is placed to mark the desired material removal point.
- Automated Operation: The grinding/polishing head applies the set pressure and continues until the predetermined amount of material has been removed, automatically stopping once the objective is met.
SPECIFICATIONS
- Large variety of samples can be uniformly ground and polished
- can work with unencapsulated samples
- operator can pre-set exact amount of material to be removed
- operator can adjust the amount of pressure to be applied in real time, without stopping the operation
- Very easy to use with no operator training required
FEATURES
- Automated Control: The operator can set the desired pressure and material removal amount with precision, and the head will automatically stop once the objective is met.
- Consistent Pressure Application: Ensures uniform grinding and polishing, essential for high-precision materials like semiconductors, ceramics, composites, and metals.
- Versatile Compatibility: Works with both 8″ and 12″ machines, providing flexibility across various platforms and setups.
- Precision Measurement: Use a thickness gauge or caliper to determine the exact amount of material to be removed, with adjustable stops ensuring accuracy.
- Reliable Results: Perfect for critical applications such as failure analysis, R&D, and quality control, where consistent and precise results are a must.
ADVANTAGES
- Efficiency: Automated pressure control and material removal make the process more efficient, reducing the need for manual adjustments and oversight.
- Ease of Use: Operators can quickly and accurately set parameters, making the head easy to operate even in fast-paced environments.
- Consistency: Uniform material removal is guaranteed, helping to eliminate variation between samples and ensuring reliable results.
- Time-Saving: The tool’s automatic stop feature saves time by stopping once the set goal has been achieved, allowing operators to focus on other tasks.
INDUSTRIES USED IN
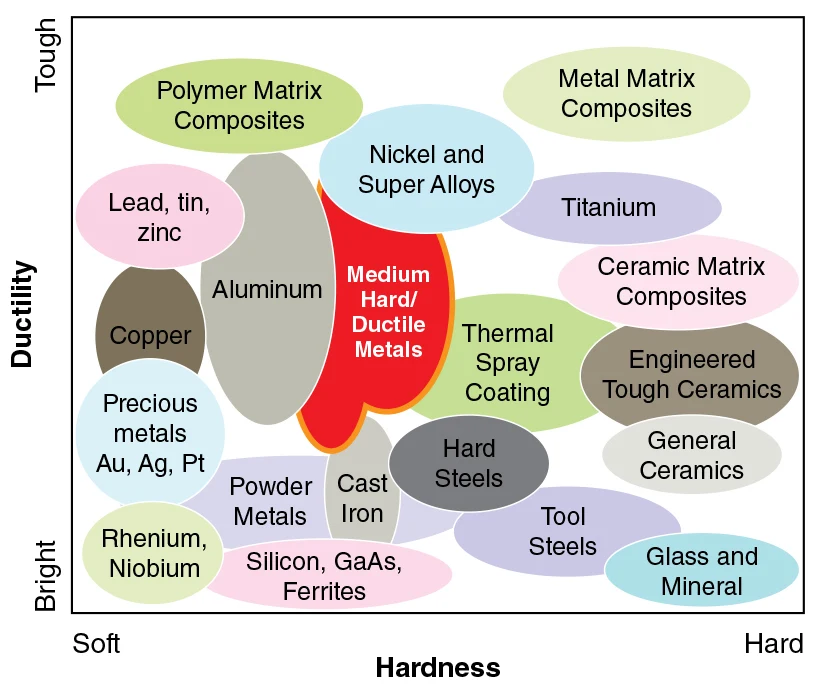

INDUSTRIES USED IN:
- Advanced Ceramics
- Composites
- Glass
- Geology
- Quartz
- Materials Research
- Medical Devices
- Metallography
- Photonics / Optics
- Semiconductor
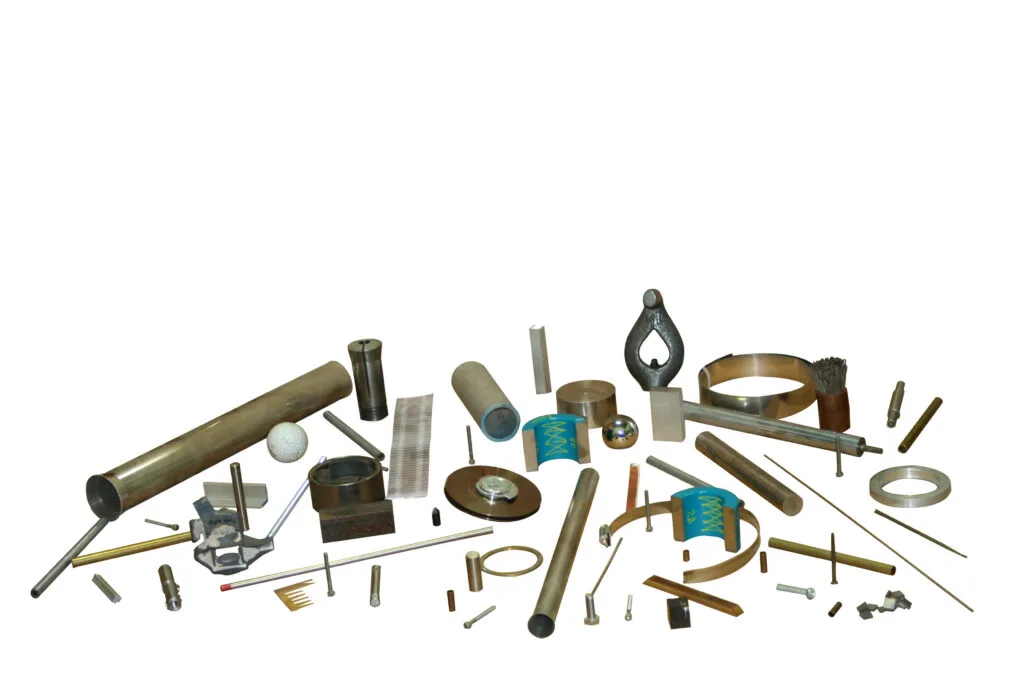
Ferrous & Non-Ferrous Metals:
- Plain Carbon Steels
- Electronic Packages
- Stainless Steels Plastics
- Tool Steels Fasteners
- Aluminum Refractories
- Copper Base Alloys Integrated Circuits
- Magnesium Thermal Spray Coatings
- Titanium Metal Matrix Composites
- Biomedical Wafers
- Petrographic
- PCB.s Ceramics
FAQ
The SMART CUT® Simple Precision Grinding/Polishing Head is capable of handling a wide variety of materials, including metals, ceramics, composites, advanced ceramics, semiconductors, and other hard materials. It’s perfect for use in applications such as failure analysis, yield testing, and research and development.
Setting the pressure and material removal amount is simple. You can use a thickness gauge or caliper to measure the desired material removal, then adjust the stop to the appropriate position. The operator then sets the pressure using the machine’s control panel, and the head will automatically apply that pressure during operation.
Yes, the SMART CUT® Simple Precision Grinding/Polishing Head is compatible with both 8″ and 12″ machines, offering flexibility for a variety of setups and applications.
The maximum material thickness depends on the material being processed, but the grinding/polishing head can handle substantial material removal with precision. It is designed to deliver controlled, uniform results regardless of the material thickness.
Once the operator has set the desired material removal and pressure parameters, the SMART CUT® head will automatically stop once the pre-set material has been removed. This feature ensures accuracy and eliminates the need for constant monitoring during the process.
While the SMART CUT® Simple Precision Grinding/Polishing Head is designed for high-precision applications, it can also handle moderate-to-high throughput environments where consistent and repeatable results are essential. However, for extreme production runs, additional automation or equipment may be required.
This tool is ideal for precision grinding and polishing, making it beneficial in various applications such as failure analysis, yield analysis, quality control, research and development, metallography, and sample preparation. It is commonly used in industries such as electronics, materials science, and semiconductors.
The SMART CUT® Simple Precision Grinding/Polishing Head stands out for its precise, automated material removal, adjustable pressure control, and ability to handle a wide range of materials. Its automatic stop feature ensures that the process stops once the set parameters have been met, reducing the need for operator intervention.
The head is designed for ease of maintenance, with simple cleaning procedures and minimal wear parts. Regular checks and calibrations are recommended to ensure consistent performance. Refer to the operating manual for specific maintenance and troubleshooting instructions.
Can the SMART CUT® Simple Precision Grinding/Polishing Head be used for both grinding and polishing?
Yes, the SMART CUT® head is versatile and can be used for both grinding and polishing applications. This flexibility makes it suitable for various stages of material processing, ensuring high-quality, finished results.
The optimal operating environment is a clean, well-ventilated space with minimal vibrations. Proper setup and calibration are essential to achieve the best results. It’s important to ensure that the machine it is connected to is compatible and operating within the manufacturer’s specified parameters.
The material removal can be adjusted based on the sample size using a thickness gauge or caliper. Once the desired material removal amount is determined, the stop is adjusted accordingly to ensure the tool grinds or polishes to the correct depth.
Yes, the SMART CUT® Simple Precision Grinding/Polishing Head is versatile and can be used for both small and large sample sizes. It is equipped with adjustable settings to ensure accurate and controlled material removal regardless of the sample size, making it ideal for both high-precision research and large-scale production environments.
Absolutely. The SMART CUT® head is specifically designed for precision cross-sectioning, providing consistent results in applications such as failure analysis, quality control, and research & development. Its precise material removal capabilities ensure uniformity and accuracy during cross-sectioning of delicate and hard-to-handle materials.
The SMART CUT® head offers highly precise material removal, with controllable pressure and pre-set material thickness settings. The precision of the tool makes it perfect for applications that require extremely tight tolerances, such as microelectronics, advanced ceramics, and materials testing. The automated stop feature ensures that the exact material removal is achieved, reducing operator error.
Yes, the SMART CUT® Simple Precision Grinding/Polishing Head can be used with a variety of abrasive materials, including diamond, silicon carbide, and aluminum oxide. The type of abrasive material used will depend on the specific application and the material being processed, ensuring optimal grinding or polishing results.
For optimal results, it is important to carefully calibrate the pressure settings and material removal parameters based on the sample and desired outcome. Regular maintenance and proper cleaning of the grinding/polishing head will also help ensure consistency and extend the tool’s lifespan. It’s also essential to ensure that the machine the head is connected to is properly set up to handle the load and speed required.
The SMART CUT® Simple Precision Grinding/Polishing Head is built for long-lasting performance and durability. Its lifespan will depend on the frequency of use, the materials being processed, and the maintenance practices followed. Regular care and periodic checks will help prolong its life and maintain high precision over time.
The automatic stop feature ensures that the SMART CUT® head stops once the set material removal has been achieved, eliminating the potential for over-grinding or under-grinding. This reduces the need for continuous supervision and allows the operator to focus on other tasks, while also ensuring that the desired result is consistently achieved.
While the SMART CUT® head is excellent for both grinding and polishing, it can be used exclusively for polishing if required. By adjusting the pressure settings and material removal parameters, the tool can be fine-tuned for polishing applications, delivering a high-quality finish on a wide variety of materials.
The SMART CUT® head is highly customizable in terms of pressure settings, material removal rates, and sample handling. Custom configurations can be discussed with SMART CUT® directly to meet specific needs. Additionally, various accessories, such as sample holders or adjustable stops, may be available depending on the application.
Advisable to have a basic understanding of grinding and polishing techniques.
The SMART CUT® head is designed for minimal maintenance. Regular checks for wear and tear on parts such as the grinding surfaces and adjustment mechanisms are recommended. Keeping the tool clean and lubricating moving parts as necessary will help ensure smooth operation and longevity. Specific maintenance instructions are included in the user manual.
Yes, the SMART CUT® head can be integrated into automated systems for high-throughput applications. The automatic material removal and stop features are ideal for use in automated setups, allowing the grinding/polishing process to be streamlined and performed with minimal human intervention, increasing productivity and consistency in production environments.
OPERATING MANUALS
Tab Content
Industries and Applications:
- Materials Research and Development: Ideal for high-precision applications in materials science, such as grinding and polishing advanced ceramics, semiconductors, and composites.
- Quality Control and Assurance: Essential for inspecting and testing material properties, offering reliable results for precision measurement and testing.
- Failure Analysis and Yield Testing: Widely used in failure analysis for precise cross-sectioning of samples to identify causes of failure in electronic components, materials, and mechanical parts.
- Metallography and Sample Preparation: Excellent for preparing metal, alloy, and composite samples for metallographic analysis.
samples are placed into rings provided) pressure is controllable. can be used for 8′ and 12″ machine).
Set how much material you wish to remove, by using thickness gage or caliper. place adjusted stop. The polishing head will continue to grind material until it reaches adjusted stop.
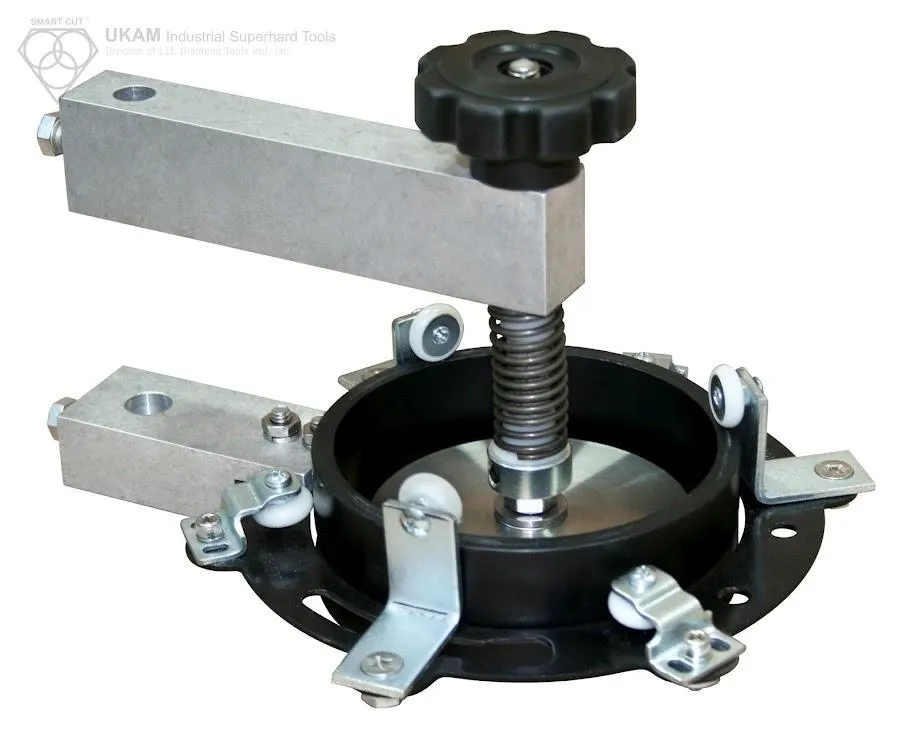
Why Choose Us?
Optimize your application to ultimate level of efficiency
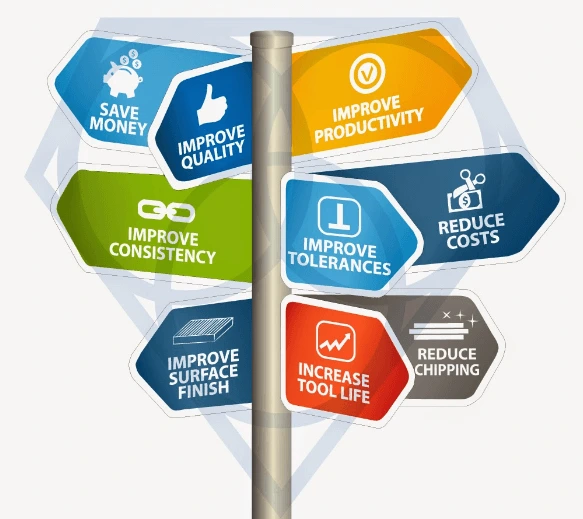
- Unmatched Selection For Many Applications
- Unmatched Technical Support & Expertise
- Superior Quality & Consistency
- Super Technology & innovation
- Immediate Worldwide Delivery
- American Based Manufacturer
-
Custom
Manufacturing - Better Value manufacturer Direct Price
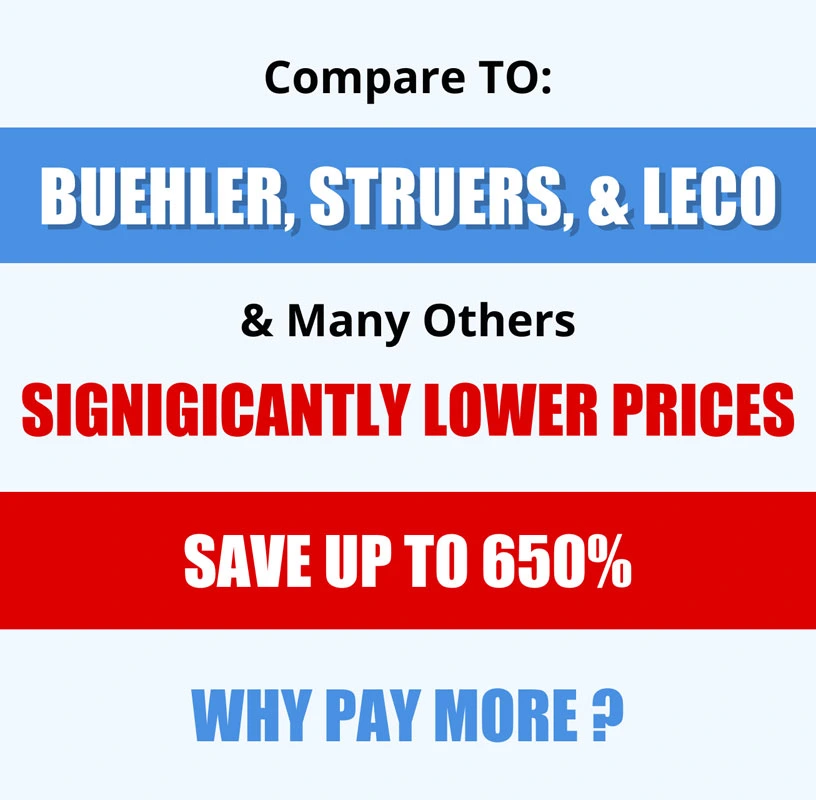
Why Work With Us?
Comprehensive Source of Information on Diamond & CBN Blades
The more you understand about what we can do for you, the better our partnership will be. On our website you will find the Most Comprehensive Source of Information on Everything you wanted to know about diamond dicing blades & industrial diamond tools.
Large Inventory & Custom Manufacturing
Largest Inventory of Precision & Ultra Thin Diamond Dicing Blades in the U.S. Available in different sizes, thickness, arbor sizes, diamond concentrations, diamond mesh sizes, and bond hardness's.
Experience makes all the Difference
"ONE OF THE MOST EXPERIENCED COMPANIES IN THE INDUSTRY"
Over the years we have enjoyed working with all types if clients, regardless of size. Proprietary dicing blade chemistry, precision manufacturing methods, modern quality control methods, allow us to control and regulate the dozens of variables that affect blade life, quality of cut, surface finish. Reducing and often eliminating additional steps often required after cutting.
Umatched Technical Support
We Are a Partner In Your Success
Developing close ties with our customers is the foundation of our business. At the core of
our company is a team of world class engineers, knowledgeable customer service personnel here to serve you. Whether is designing or manufacturing a special solution. We will go out of our way to optimizing your process to ultimate level of efficiency.
Advanced
Technology
American Manufacturer As one of the few remaining independent U.S.Diamond Tool & machine builders. We have the experience & tradition to help you remain at frontier of technology Our experience has been further enhanced by acquiring assets and processes from some of the oldest American tool manufacturers, along with their decades of experience and R& D. This has positioned us as one of the most experienced companies in the industry.
Superior Quality &
Consistency
Our unique bond formulations, tool designs, stringent requirements, and utilization of exceptionally high-quality diamonds and raw materials ensure top-notch products that adhere to strict ISO 9000 standards.
Our proprietary technology allow us to control and regulate the dozens of variable that affect toolife, quality, & consistency
Expect More From Your Tools
Related Products
SMART CUT® 6055 Precision Automatic Diamond Cut-Off Saw
SMART CUT® 6045 Sectioning Saw
SMART CUT® SM Polishing and Grinding Head
SMART CUT® AMF Water Soluble Coolant
Advanced Materials Formula
Super Premium water soluble synthetic coolant & Lubricant for Diamond Slicing, Dicing, Drilling, and Grinding & Machining of Ceramics, Glass, Optics, Quartz, Silicon, and Other Hard & Brittle Materials
SMART CUT® Water Soluble Coolant – Advanced Materials Formula is a high-performance, fully synthetic, aqueous-based coolant specifically engineered for precision machining in the most demanding applications. Designed to excel in the cutting and grinding of advanced materials such as ceramics, composites, optics and ultra-hard, brittle materials. This premium coolant/lubricant optimizes removal rates while delivering superior surface finishes.Recently Viewed Products
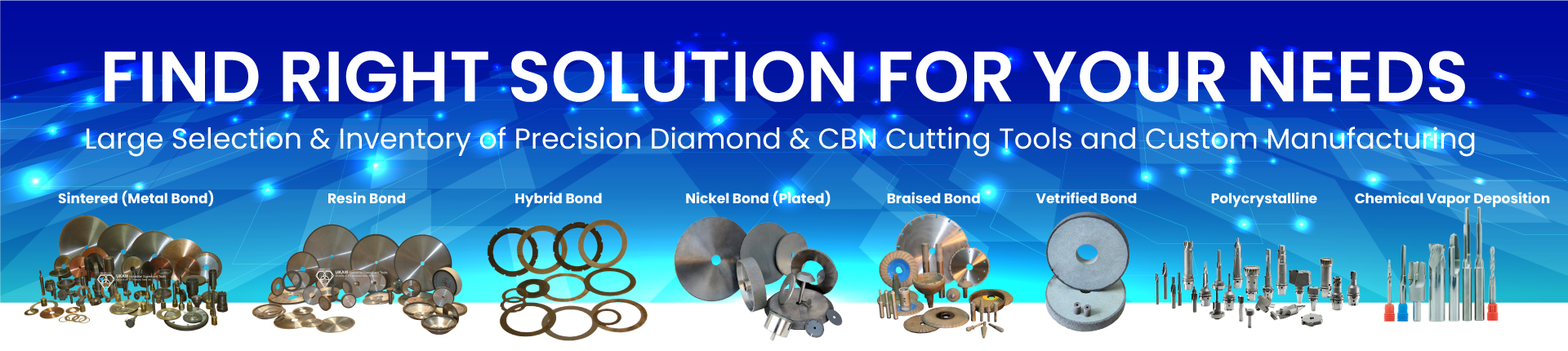
ARE YOU USING RIGHT CONSUMABLES?
FOR YOUR APPLICATION?
LET US
HELP YOU
HAVING ISSUES WITH
YOUR CURRENT METALLOGRAPHIC CONSUMABLES?
Knowledge Center
02
Jun
How to properly use Diamond Tools
UKAM Industrial Superhard Tools manufactures precision diamond tools for a large variety of applications, materials, and industries.
Share this Article with Friend or Colleague
Metal Bonded Diamond Tools are “impregnated” with diamonds. This means that selected...
02
Jun
Why use diamond
Diamond is the hardest material known to man kind. When used on diamond/tools, diamond grinds away material on micro (nano) level. Due to its hardness Diamond will work all types of materials from...
02
Jun
Diamond vs CBN (cubic boron nitride) Tools
Cubic Boron Nitride (CBN) is a synthetic material that is renowned for its exceptional hardness and high thermal stability. It is composed of boron and nitrogen atoms arranged in a crystal lattice structure, similar to...
02
Jun
Discover the Right Diamond Powder for Your Application: Choosing Between Monocrystalline and Polycrystalline Diamonds
Which to use for your application?
Diamond shape plays a significant role in the effectiveness of polishing solutions, affecting both the polishing rate and the quality of the final finish. Understanding the differences between monocrystalline and...
02
Jun
What is Diamond Mesh Size and how to select best one for your application
Diamond grit size can be defined as the size of the diamond particles used in the bond matrix. The larger the diamond particles (grit size) the faster the tool will cut.
Share this Article with Friend or...
02
Jun
What is Diamond Concentration and which to use for your application
Diamond concentration is measured based on the volume of diamond within a section of the tool. It is typically defined as Concentration 100, which equates to 4.4 carats per cubic centimeter of the diamond layer...
11
Jun
Selecting the Right Diamond Suspension for your Application – Monocrystalline or Polycrystalline?
Choosing the correct diamond suspension, whether monocrystalline or polycrystalline, significantly impacts the quality and efficiency of the polishing and material removal processes. Understanding the properties and applications of both types of suspensions can help you...
17
Jun
Improve Sample Quality & Optimize your Polishing Operating for Metallography & Sample Preparation
Polishing is important step in metallography & sample preparation for revealing the true microstructure of materials, including grain boundaries, phases, and inclusions, which provide insights into material properties and history. This guide is designed to...
26
Jun
Optimize your Grinding Operation for Metallography & Sample Preparation
Share this Article with Friend or Colleague
Grinding is a fundamental mechanical process in metallography that involves removing material from a specimen using hard, abrasive particles. This process is essential for preparing specimens for microscopic...
11
Sep
What is the difference between Lapping, Grinding, & Polishing
Some of the major differences include the type and diamond mesh size of diamond discs used, type and size of abrasives used and their holding method. Other factors include RPM’s (speed) used and pressure applied...
29
Jan
Guide to Selecting the Right SMART CUT® Metallographic / Metallurgical Polishing Cloth & Pads for Your Application
Understand Types of Polishing Cloths/Pads
A. Non-Woven Synthetic Cloths
B. Woven Cloths
C. Composite Pads
D. Specialty Cloths/Pads
E. Foam and Felt Pads
Comparison table of various types of polishing cloths and pads used in metallography, highlighting their properties, optimal uses,...
30
Jan
Select the Right Silicon Carbide Paper Discs for Metallography Sample Preparation
Selecting the right silicon carbide paper for metallographic sample preparation is important for achieving accurate and reliable results in material analysis. The grinding and polishing process plays a fundamental role in preparing specimens for microscopic...
30
Jan
Upgrading Metallography Grinding with Silicon Carbide Paper
This guide covers the best practices for using silicon carbide paper in metallography. It includes tips on proper grit progression, optimizing pressure and speed settings, preventing common issues, and extending the life of the abrasive....
- Unmatched Selection For Many Applications
- Superior Quality & Consistency
- Immediate Worldwide Delivery
- Technical Support & Expertise
- American Based Manufacturer
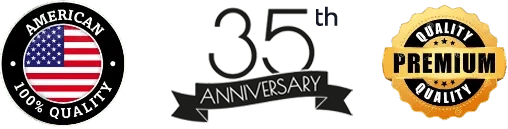

- Different Product
- Different Technology
- Different Company
- Expect MORE from your tools
Let Us HELP You!
Subscribe To Our Newsletter
Signup for email offers, updates, and more
Contact Us
- 25205 & 25201 Avenue Tibbits Valencia CA 91355 USA
-
Phone : (661) 257-2288
FAX : (661) 257 -3833 - lel@ukam.com
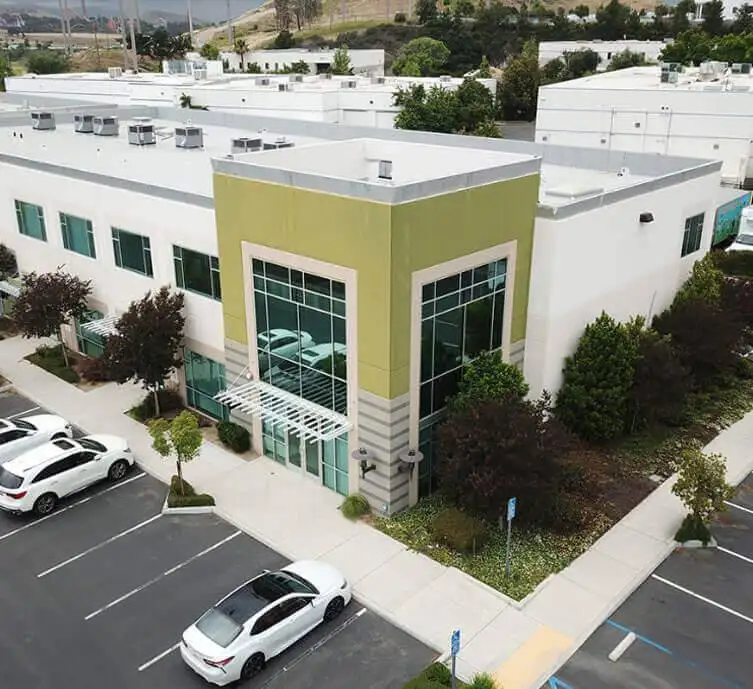
UKAM Industrial Superhard Tools is a U.S. High Technology, Specialty Diamond Tool & Equipment manufacturer. We specialize in producing ultra thin, high precision cutting blades, precision cutting machines diamond drills, diamond micro tools, standard & custom advanced industrial diamond tools and consumables.
- 25205 & 25201 Avenue Tibbits Valencia CA 91355 USA
-
Phone : (661) 257-2288
FAX : (661) 257 -3833 - lel@ukam.com
- 25205 & 25201 Avenue Tibbits Valencia CA 91355 USA
-
Phone : (661) 257-2288
FAX : (661) 257 -3833 - lel@ukam.com
DIAMOND TOOLS BY BOND
EQUIPMENT
KNOWLEDGE CENTER
OUR PRODUCTS
COMPANY
CUSTOMER SERVICE
Shipping Methods


Safe & Secure Payments

© Copyright 1990-2025. UKAM Industrial Superhard Tools – Terms of Use