-
0 items in quote
No products in the Quote Basket.
DIAMOND CUP WHEELS For Sample Preparation
SMART CUT® Diamond Cup Wheels are designed for use with Struers, Buehler, and other thin section cutting and grinding machines. These wheels are ideal for grinding and thinning a wide range of materials, from geological minerals to microelectronic packages. Available in diameters ranging from 100mm to 203mm, SMART CUT® Diamond Cup Wheels offer flexibility to meet a variety of sample preparation needs. They come in both sintered (metal bond) and resin bond options, with diamond grit size ranges to suit different materials and applications. Custom specifications can be created to fit any machine, with fast lead times and no minimum order quantity.
SMART CUT® Diamond Cup Wheels are produced using high-quality diamond abrasives engineered for durability and long-lasting performance. This ensures consistent, reliable results with each use, reducing the need for frequent replacements and saving both time and money. They offer exceptional precision, making them ideal for applications such as geological thin section preparation, metallurgical sample preparation, and more.
DESCRIPTION
SPECIFICATIONS
FREQUENTLY ASKED QUESTIONS
INDUSTRIES USED IN
ACCESSORIES
USAGE RECOMMENDATION
DESCRIPTION
These wheels are specifically designed to seamlessly integrate with Struers, Buehler, and other thin section machines, ensuring compatibility with your existing equipment. They are versatile, capable of handling both hard and soft materials, including rocks, minerals, ceramics, and more, making them a valuable tool in your laboratory.
The user-friendly design of SMART CUT® Diamond Cup Wheels makes them easy to install and operate, ensuring excellent results whether you’re a novice or an experienced operator. With their reliable performance and reduced need for frequent replacements, these wheels offer a cost-effective solution for your sample preparation needs.
By choosing SMART CUT® products, you can save up to 650% compared to competitors such as Buehler, Struers, LECO, and others.
SPECIFICATIONS
- Diameter range: 100mm to 203mm
- Bond types: Sintered (metal bond) and Resin bond
- Custom specifications available
- Lead time: stock to 3 to 4 weeks
- Compatibility: Struers, Buehler, and other thin section machines
- Material types: Suitable for hard and soft materials
- Application: Geological minerals, microelectronic packages, etc.
Diamond Grit Sizes: 35 µm, 40 µm, 70 µm, 91 µm, custom diamond sizes available
- Inside Diameter: Typically 12.7mm (1/2″), but custom sizes can be made to fit specific machines.
- Diamond Depth: Varies based on the application, but typically ranges from 5mm to 10mm for standard models.
- Pin Holes: Custom pin holes can be incorporated based on machine compatibility, with placement and size tailored to fit specific equipment.
FREQUENTLY ASKED QUESTIONS
SMART CUT Diamond Cup Wheels are primarily used for sample preparation in materials science, geology, and metallurgy. They are designed to grind and polish samples to achieve precise and uniform surfaces for analysis.
Yes, these cup wheels are designed to be compatible with Struers, Buehler, and other Thin Section Machines commonly used in sample preparation applications. They are crafted to seamlessly integrate with your existing equipment.
SMART CUT Diamond Cup Wheels are versatile and can be used on a wide range of materials, including rocks, minerals, ceramics, metals, and more. They are suitable for both hard and soft materials, making them a versatile choice for various applications.
These cup wheels are built with exceptional durability in mind. They are designed to withstand the demands of rigorous sample preparation tasks, reducing the need for frequent replacements and saving you time and money.
Yes, precision is a key feature of SMART CUT Diamond Cup Wheels. They are engineered to deliver precise and uniform grinding results, ensuring that your samples meet the highest standards of accuracy.
Absolutely. These cup wheels are designed with a user-friendly approach, making installation and operation straightforward. Both novice and experienced operators can use them with ease.
By investing in SMART CUT Diamond Cup Wheels, you can expect consistent and reliable sample preparation results, reduced replacement costs, and improved efficiency. They are a cost-effective solution that enhances the quality of your research and analysis.
Yes, we offer a range of grit sizes to suit your specific sample preparation needs. You can choose the appropriate grit size depending on the material and finish requirements of your samples.
Proper maintenance is essential for extending the life of your SMART CUT Diamond Cup Wheels. We recommend regularly cleaning them with a suitable cleaning solution and ensuring that they are dry and free of debris before and after each use. Follow the manufacturer’s guidelines for specific cleaning and maintenance instructions.
SMART CUT Diamond Cup Wheels can be used for both wet and dry grinding, depending on your application requirements. Wet grinding is often preferred for heat-sensitive materials, while dry grinding may be suitable for others. Always consider the material and safety precautions when choosing your grinding method.
To maintain the quality and performance of your cup wheels, it’s advisable to store them in a dry and climate-controlled environment, away from direct sunlight and extreme temperatures. Ensure they are stored in a way that prevents any damage or deformation.
Customization options may be available depending on your specific needs. Contact our sales or customer support team to discuss any custom requirements you have, and we will do our best to accommodate your requests.
The lifespan of these cup wheels can vary depending on factors such as usage frequency, material type, and maintenance practices. However, with proper care and maintenance, you can expect them to have a relatively long service life, providing consistent performance over time.
Yes, these cup wheels are versatile and can be used for both rough grinding and fine polishing. They offer flexibility in achieving the desired surface finish for your samples, whether you need to remove material quickly or achieve a mirror-like polish.
While these cup wheels themselves do not have built-in safety features, it’s essential to follow safety protocols when using them. Ensure that your equipment and workspace are properly maintained, and always use appropriate safety measures to prevent accidents.
SMART CUT Diamond Cup Wheels are designed to provide precise control, making them suitable for delicate or fragile samples. However, it’s crucial to adjust grinding parameters carefully and use proper technique to minimize the risk of sample damage.
SMART CUT Diamond Cup Wheels can be used in controlled environments like cleanrooms, provided that you take appropriate precautions to prevent contamination. Ensure that all equipment and materials used in the cleanroom meet the required cleanliness standards.
Yes, SMART CUT Diamond Cup Wheels can be adapted for use in automated sample preparation systems or robotic setups. Custom mounting and automation solutions can be discussed to meet your specific automation needs.
The recommended RPM may vary depending on the machine and application. It is essential to consult the manufacturer’s guidelines for your specific Thin Section Machine or equipment to determine the appropriate RPM settings for optimal performance.
While these cup wheels are designed with precision and accuracy in mind, they are typically used in laboratory or controlled settings. Their performance may be affected by field conditions, and their primary application is in sample preparation for research and analysis.
The choice of grit size depends on the material you are working with and the desired finish. Smaller grit sizes (e.g., 80-120) are suitable for coarse grinding and removing material quickly, while larger grit sizes (e.g., 220-400) are better for finer polishing and achieving smoother surfaces. Consider your sample’s characteristics and the analysis requirements when selecting the grit size. For your reference we have made cross reference to most BUEHLER & STRUERS part numbers to make the selection process for you easier.
SMART CUT Diamond Cup Wheels can be used for both wet and dry grinding, but it’s a good practice to have separate cup wheels for each type of preparation. This helps prevent cross-contamination and ensures consistent results for both wet and dry applications.
While it is possible to reprofile or reshape cup wheels in some cases, it is a specialized task that requires expertise and the right equipment. This can be done by us for a fee if needed. It’s generally recommended to replace cup wheels when they become worn or damaged to ensure the highest level of performance and safety.
SMART CUT Diamond Cup Wheels are versatile and can be adapted for non-standard sample shapes or sizes. Custom tooling or adaptors can often be used to accommodate unique sample geometries or sizes. Contact our technical support team to discuss your specific requirements.
SMART CUT Diamond Cup Wheels are manufactured to high-quality standards, but specific safety certifications may vary depending on your location and application. It’s advisable to ensure that your laboratory or facility follows safety regulations and guidelines relevant to your industry and region when using these cup wheels.
its possible to reuse the steel body and braise new diamond section on it. However its often not financially feasible as it could be more work to refurbish your existing cup wheel then to produce a new one.
While these cup wheels can operate at room temperature, prolonged use at high speeds may generate heat. It’s advisable to monitor the operating temperature and, if necessary, use a cooling system to prevent overheating and maintain consistent performance.
It’s essential to clean the cup wheels thoroughly between dry and wet sample preparation to avoid cross-contamination. Using separate cup wheels for each type of preparation or ensuring thorough cleaning and drying between applications is recommended.
Yes, SMART CUT Diamond Cup Wheels can be integrated with automated sample loading and unloading systems to enhance productivity and efficiency in your sample preparation process. Customized solutions and adaptors can be discussed to facilitate automation.
Maintaining the condition of SMART CUT Diamond Cup Wheels may involve occasional dressing or truing to restore their cutting efficiency. Consult the product documentation or contact our technical support team for guidance on the recommended dressing methods and frequency.
SMART CUT Diamond Cup Wheels can be used for preparing samples for electron microscopy and other high-resolution imaging techniques. Their precision and ability to achieve fine surface finishes make them suitable for applications where sample quality is critical.
Disposing of worn-out or damaged cup wheels should be done in accordance with local regulations and environmental guidelines. Check with your local waste management authorities for proper disposal methods or recycling options for diamond abrasive tools.
When working with samples containing embedded or fragile components, it’s crucial to adjust grinding parameters and techniques to minimize the risk of damage. SMART CUT Diamond Cup Wheels provide precision control, allowing you to work with care around sensitive components.
SMART CUT Diamond Cup Wheels are available in various sizes to accommodate different sample sizes and equipment specifications. Contact our sales team to inquire about the available size options and select the ones that best suit your needs.
Depending on your requirements, we may offer accessories and supplementary products that complement the use of SMART CUT Diamond Cup Wheels. Contact our sales team to explore the available options, including coolant systems, safety gear, and more.
While these cup wheels are designed primarily for sample preparation, they can be used for routine maintenance of machinery or equipment surfaces in some cases. Their versatility makes them suitable for various precision grinding tasks.
To reduce vibration and noise during operation, ensure that your equipment is properly maintained and securely mounted. Using appropriate mounting hardware and ensuring the cup wheels are balanced can also help minimize vibrations and noise.
SMART CUT Diamond Cup Wheels do not have a specific shelf life, but proper storage is essential to maintain their performance. Store them in a dry, climate-controlled environment, away from direct sunlight and extreme temperatures, to ensure their longevity and quality.
SMART CUT Diamond Cup Wheels can be used for a range of sample thicknesses, but there may be limitations depending on the specific cup wheel size and equipment setup. Ensure that the cup wheel size and equipment are suitable for the sample thickness you intend to work with.
It’s time to replace a worn-out cup wheel when you notice a decline in grinding performance, reduced efficiency, or a deterioration in the quality of the prepared sample surfaces. Regularly inspect the cup wheel for signs of wear and replace it as needed to maintain consistent results.
Can SMART CUT Diamond Cup Wheels be used for both manual and automated sample preparation processes?
Yes, these cup wheels are versatile and can be used for both manual and automated sample preparation processes. Whether you prefer a hands-on approach or automation, SMART CUT Diamond Cup Wheels can accommodate your needs.
SMART CUT Diamond Cup Wheels can be used for research and industrial applications involving composites and advanced materials. Their versatility and precision make them suitable for a wide range of materials used in various industries.
Yes, SMART CUT Diamond Cup Wheels are designed to provide consistent and repeatable results, ensuring that your sample preparation is reliable and meets the highest standards of accuracy and quality.
Proper alignment and mounting are crucial for optimal performance. Follow the manufacturer’s guidelines and instructions provided with your equipment to ensure that SMART CUT Diamond Cup Wheels are correctly aligned and securely mounted before use.
When working with hazardous materials, it’s essential to follow all safety protocols and guidelines established in your laboratory or facility. SMART CUT Diamond Cup Wheels themselves do not pose additional hazards, but the materials you are grinding may require specific safety precautions. Consult with your laboratory’s safety experts for guidance.
Yes, SMART CUT Diamond Cup Wheels can be used for delicate geological samples, including fossils and thin mineral sections. Their precision control allows for gentle material removal when working with fragile specimens.
Handling and disposing of coolant or abrasive slurry should be done in accordance with local environmental regulations. Proper containment, recycling, or disposal methods should be followed to minimize the environmental impact.
Yes, these cup wheels can be adapted for specialized applications like semiconductor wafer thinning and precision optics preparation. Customized solutions and tooling may be necessary, and we can work with you to meet these specific requirements.
SMART CUT Diamond Cup Wheels are versatile and can be used for samples with irregular shapes or challenging geometries. Their precision control and adaptability make them suitable for a wide range of sample configurations.
SMART CUT Diamond Cup Wheels can be used in controlled atmosphere or glovebox environments, provided that your equipment and workspace are properly adapted for such conditions. Ensure that all safety and containment measures are in place as needed.
SMART CUT Diamond Cup Wheels are generally resistant to many chemicals, but their performance may be affected by extremely harsh or corrosive chemical environments. It’s important to consider the specific chemicals involved in your application and consult with our technical support team for guidance on chemical compatibility.
Yes, we can provide guidance on optimal grinding parameters to help you achieve the best results with SMART CUT Diamond Cup Wheels. Factors such as material type, sample size, and desired surface finish can influence the selection of grinding parameters, and our technical support team can assist you in making informed choices.
SMART CUT Diamond Cup Wheels can be used for applications requiring high surface flatness and parallelism, including semiconductor wafer manufacturing. Their precision control and quality abrasives make them suitable for achieving the required surface characteristics.
SMART CUT Diamond Cup Wheels can be used for applications involving high-temperature materials, but their maximum temperature tolerance may vary depending on the specific cup wheel type. Contact our technical support team to determine the temperature limits for safe operation.
When working with samples containing embedded electronics or delicate microstructures, it’s essential to use precision and care to minimize the risk of damage. SMART CUT Diamond Cup Wheels can be used for such applications, but careful handling and adjustment of grinding parameters are necessary to protect embedded components.
We recommend using water-based coolants or lubricants for wet grinding with SMART CUT Diamond Cup Wheels. These coolants help dissipate heat, reduce friction, and improve the efficiency and quality of the grinding process. Ensure that the coolant is compatible with the materials you are working with and follow safety guidelines for handling coolants in your laboratory or facility.
The recommended RPM settings for SMART CUT Diamond Cup Wheels can vary depending on the cup wheel size, equipment, and application. It is crucial to consult the manufacturer’s guidelines for your specific Thin Section Machine or equipment to determine the appropriate RPM settings for optimal performance. Generally, a lower RPM may be suitable for finer grinding and polishing, while a higher RPM may be used for rough grinding.
Maintaining the condition of SMART CUT Diamond Cup Wheels may involve occasional dressing to restore their cutting efficiency. We recommend using a diamond dressing tool or a dressing stick designed for the purpose. Follow our guidelines for dressing, and ensure that the cup wheel is properly trued and conditioned before use. Dressing frequency may vary depending on usage and the specific cup wheel condition.
The recommended feed rates when using SMART CUT Diamond Cup Wheels depend on factors such as material type, cup wheel size, and desired surface finish. It’s important to start with a slower feed rate and gradually increase it while monitoring the quality of the sample surface. A slower feed rate is often preferred for achieving precise and controlled results, while faster feed rates may be suitable for rough grinding. Adjust the feed rate based on the specific requirements of your sample preparation task and the feedback you observe during the process.
We generally recommend using water-based coolants or lubricants with SMART CUT Diamond Cup Wheels for wet grinding. Oil-based coolants may not be as effective in dissipating heat and could potentially lead to less desirable results. It’s essential to consider the specific requirements of your application and consult with our technical support team for guidance if you are considering alternative coolants.
The maximum RPM that SMART CUT Diamond Cup Wheels can handle safely depends on various factors, including cup wheel size, material type, and equipment specifications. Always adhere to the manufacturer’s guidelines and recommendations for your specific Thin Section Machine or equipment to ensure safe operation. Exceeding the recommended RPM can lead to safety hazards and reduced cup wheel lifespan.
The frequency of dressing SMART CUT Diamond Cup Wheels can vary based on usage and cup wheel condition. In general, it is advisable to dress the cup wheel when you notice a decline in cutting efficiency, decreased surface quality, or uneven wear. Regular inspection and maintenance can help you determine the appropriate dressing intervals for your specific sample preparation tasks.
The recommended feed rates for SMART CUT Diamond Cup Wheels can vary depending on the material type and cup wheel size. Generally, lower feed rates are preferred for achieving precision when working with materials like ceramics and minerals. For metals or more robust materials, you may use slightly higher feed rates for efficient material removal. Always start with a slower feed rate and adjust it based on the material’s response and the desired finish. Reference material-specific guidelines if available, and consult with our technical support team for assistance in optimizing feed rates for your specific applications.
Yes, deionized or distilled water is suitable for use as a coolant with SMART CUT Diamond Cup Wheels. These types of water have low mineral content, reducing the risk of mineral deposits on your samples. Deionized or distilled water is commonly used for wet grinding to achieve high-quality results and maintain the integrity of your samples.
When switching between wet and dry grinding with SMART CUT Diamond Cup Wheels, it’s important to ensure that the cup wheel is properly dressed and conditioned for the specific grinding mode. Dry grinding may require a different dressing approach compared to wet grinding. Follow the dressing recommendations for each mode, and thoroughly clean and dry the cup wheel before transitioning to the other method to avoid cross-contamination.
Yes, you can use an automated dressing system with SMART CUT Diamond Cup Wheels to improve efficiency and consistency in the dressing process. Automated dressing systems can be customized to suit your specific equipment and requirements. Consult with our technical support team to explore the possibility of integrating an automated dressing solution into your sample preparation setup.
The recommended dressing parameters, including dressing speed and depth, can vary depending on the cup wheel type and material. Specific dressing parameters are typically provided by the manufacturer and can be found in the product documentation. Ensure that you follow these parameters for safe and effective dressing of your SMART CUT Diamond Cup Wheels.
SMART CUT Diamond Cup Wheels can handle higher feed rates for faster material removal; however, it’s important to strike a balance between speed and sample quality. While higher feed rates may expedite the process, they can lead to reduced precision and potentially lower surface quality. It’s advisable to adjust the feed rate within the recommended range for your specific application to achieve both efficiency and desired results.
Dressing SMART CUT Diamond Cup Wheels for applications involving advanced materials like composites or semiconductors may require special attention to prevent contamination and ensure precision. Consider using dedicated dressing tools and equipment to maintain the cup wheels’ integrity and quality. Additionally, take care to prevent cross-contamination when transitioning between different materials in sample preparation.
Over-dressing SMART CUT Diamond Cup Wheels can lead to the removal of too much abrasive material, reducing the cup wheel’s lifespan and effectiveness. Excessive dressing may result in a loss of the desired cup wheel profile and negatively impact the quality of the prepared samples. It’s essential to follow recommended dressing intervals and parameters to avoid over-dressing and maintain consistent performance.
When transitioning between different grit sizes of SMART CUT Diamond Cup Wheels in a multi-step sample preparation process, it’s important to ensure that the cup wheel is dressed to the appropriate profile for each step. Follow the dressing recommendations for each grit size to maintain the cup wheel’s efficiency and produce high-quality results at each stage of the process. Proper dressing helps optimize the performance of the cup wheels throughout the sample preparation workflow.
Yes, you can use a coolant recycling system with SMART CUT Diamond Cup Wheels. A coolant recycling system helps conserve water resources and reduces waste by continuously filtering and reusing the coolant. The benefits include cost savings, environmental sustainability, and maintaining consistent coolant quality during extended sample preparation sessions. Consult with our technical support team to explore the compatibility and advantages of incorporating a coolant recycling system into your setup.
When dressing SMART CUT Diamond Cup Wheels, it’s essential to wear appropriate personal protective equipment (PPE), which may include safety glasses, gloves, and a dust mask or respirator, depending on the dressing method and materials used. Additionally, ensure that the dressing process is carried out in a well-ventilated area, and follow safety protocols outlined in your laboratory or facility’s safety guidelines to prevent accidents and protect your health.
Depending on your specific requirements, there may be specialized dressing tools or accessories available for SMART CUT Diamond Cup Wheels. These tools can help optimize the dressing process and improve its efficiency. Contact our sales or technical support team to explore the availability of dressing-related accessories and tools that can enhance your sample preparation workflow.
Yes, SMART CUT Diamond Cup Wheels can be dressed to customize cup wheel profiles for specific sample preparation needs. The dressing process can be tailored to achieve desired profiles and shapes, allowing you to optimize the cup wheel’s performance for your unique applications. Consult with our technical support team for guidance on customizing cup wheel profiles to meet your specific requirements.
When dressing SMART CUT Diamond Cup Wheels for precision optics preparation or similar high-precision applications, attention to detail is crucial. Ensure that the dressing process is performed with precision and care to achieve the desired cup wheel profile and maintain consistency in the grinding and polishing stages. Use specialized dressing tools and follow recommended parameters to optimize performance for high-precision tasks.
The time to replace a dressing tool or dressing stick used with SMART CUT Diamond Cup Wheels is typically determined by wear and effectiveness. If you notice signs of wear, reduced dressing efficiency, or decreased quality in the dressing process, it may be time to replace the dressing tool. Regular inspection and maintenance of dressing tools are essential to ensure consistent and reliable dressing performance.
INDUSTRIES USED IN
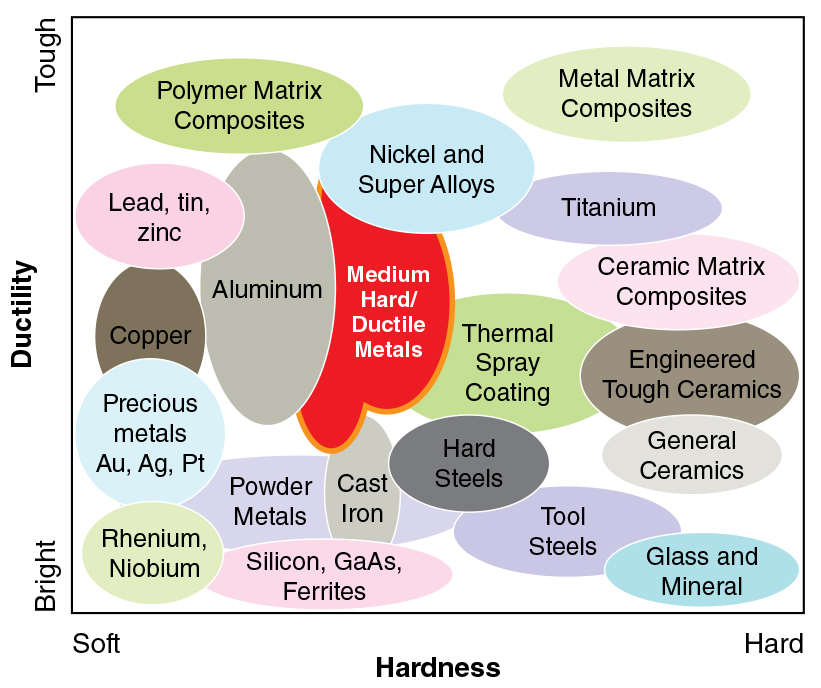
INDUSTRIES USED IN:
- Advanced Ceramics
- Composites
- Glass
- Geology
- Quartz
- Materials Research
- Medical Devices
- Metallography
- Photonics / Optics
- Semiconductor
FERROUS & NON-FERROUS METALS:
- Plain Carbon Steels
- Electronic Packages
- stainless Steels Plastics
- Tool Steels Fasteners
- Aluminum Refractories
- Copper Base Alloys Integrated Circuits
- Magnesium Thermal Spray Coatings
- Titanium Metal Matrix Composites
- Biomedical Wafers
- Petrographic
ACCESSORIES
Showing 1 – -1 of 13 results Showing all 13 results Showing the single result No results found
Sort by Price low to high
Filters Sort results
Reset Apply
Image | Name | COMPATIBILITY WITH DRILL SERIES | Price | Quantity | Add to cart |
---|---|---|---|---|---|
Recommended for use in Diamond Tools 150 Grit Size (mesh… | $15.39 | Max: Min: 1 Step: 1 | |||
Recommended for coarser grits found in segment wheels, core drills… | $15.99 | Max: Min: 1 Step: 1 | |||
5/8″-11″ thread. Fits into drill press chuck. Shank adapter threads… | $22.46 | Max: Min: 1 Step: 1 | |||
5/8″-11″ thread. Fits into drill press chuck. Shank adapter threads… | $26.72 | Max: Min: 1 Step: 1 | |||
SMART CUT® General Materials Formula Synthetic Water Soluble Coolant | $34.81 | Max: Min: 1 Step: 1 | |||
Recommended for use in Diamond Tools 150 Grit Size (mesh… | $39.47 | Max: Min: 1 Step: 1 | |||
Recommended for coarser grits found in segment wheels, core drills… | $39.47 | Max: Min: 1 Step: 1 | |||
SMART CUT® General Materials Formula Synthetic Water Soluble Coolant | $99.81 | Max: Min: 1 Step: 1 | |||
105DE, 135DB, 115DM, 125DM, 130DMN, 140DM (up to 1-5/8″ OD) | $154.87 | Max: Min: 1 Step: 1 | |||
105DE, 135DB, 115DM, 125DM, 130DMN, 140DM (up to 1-5/8″ OD) | $154.87 | Max: Min: 1 Step: 1 | |||
105DE, 135DB, 115DM, 125DM, 130DMN, 140DM (up to 1-5/8″ OD) | $235.00 | Max: Min: 1 Step: 1 | |||
SMART CUT® General Materials Formula Synthetic Water Soluble Coolant | $317.41 | Max: Min: 1 Step: 1 | |||
SMART CUT® General Materials Formula Synthetic Water Soluble Coolant | $1,745.00 | Max: Min: 1 Step: 1 |
USAGE RECOMMENDATION
Usage Recommendations for SMART CUT Diamond Cup Wheels for Sample Preparation:
Select the Appropriate Grit Size
Choose the grit size of the SMART CUT Diamond Cup Wheel based on your sample material and the desired finish. Smaller grit sizes (e.g., 80-120) are suitable for rough grinding, while larger grit sizes (e.g., 220-400) are ideal for finer polishing.
Confirm Compatibility
Ensure that the SMART CUT Diamond Cup Wheel is compatible with your Thin Section Machine or equipment. Consult the manufacturer’s guidelines for recommended cup wheel specifications and RPM settings. Verify that the SMART CUT Diamond Cup Wheel is compatible with the specific material you are preparing. Different materials may require adjustments in grinding parameters and coolant selection.
Mount Securely
Properly mount and secure the cup wheel on your equipment according to the manufacturer’s instructions. Ensure that it is aligned correctly for safe and effective operation.
- When preparing samples, use proper fixturing or clamping techniques to securely hold the material in place. This minimizes vibrations and ensures uniform material removal, especially for irregularly shaped samples.
- Choose the appropriate sample holder or mounting method based on your sample’s size, shape, and material properties.
- Use proper fixturing or clamping techniques to secure your sample during grinding. This minimizes vibrations and ensures uniform material removal, especially when working with irregularly shaped samples.
- Depending on the sample size, shape, and material properties, choose the appropriate material holding technique. Proper material holding minimizes sample movement and vibration during grinding.
Use Coolants for Wet Grinding
For wet grinding applications, use water-based coolants or lubricants to enhance cooling, reduce friction, and improve grinding efficiency. Deionized or distilled water is often recommended.
For wet grinding applications, it is recommended to use water-based coolants or lubricants. Deionized or distilled water is often preferred for its low mineral content Water-based coolants help dissipate heat, reduce friction, and improve grinding efficiency. They also aid in maintaining consistent sample quality.
Consistent Coolant Flow
Ensure a consistent and adequate flow of coolant over the SMART CUT Diamond Cup Wheel during the grinding process. Proper coolant flow helps maintain temperature control and prevents overheating.
Coolant Concentration Control
Regularly monitor and maintain the concentration of the coolant solution. Ensure that the coolant concentration remains within the recommended range for efficient cooling and lubrication. If using water-based coolants, regularly monitor and maintain the concentration of the coolant solution. Ensure that the concentration remains within the recommended range for optimal cooling and lubrication.
Monitor RPM Settings
Set the rotations per minute (RPM) of your equipment to the recommended level for the specific SMART CUT Diamond Cup Wheel size and application. Avoid exceeding the maximum RPM to ensure safety.
- The recommended RPM for SMART CUT Diamond Cup Wheels can vary depending on the cup wheel size, material type, and equipment specifications.
- Refer to the manufacturer’s guidelines for your specific Thin Section Machine or equipment to determine the appropriate RPM settings for optimal performance.
- Avoid exceeding the maximum RPM recommended for the cup wheel to ensure safe and effective grinding.
- Adjust your RPMs and feed rates based on the hardness of the material you are working with. Softer materials may require different settings than harder ones to achieve optimal results.
Adjust Feed Rate
Begin with a slower feed rate and gradually increase it while observing the quality of the sample surface. Adjust the feed rate based on material response and desired results.
- The recommended feed rates when using SMART CUT Diamond Cup Wheels can vary depending on the material type, cup wheel size, and desired surface finish.
- Start with a slower feed rate and gradually increase it while observing the quality of the sample surface. Adjust the feed rate based on the material’s response and the desired finish.
- Consult manufacturer guidelines and specific material recommendations for optimal feed rates in your application.
- Adjust the feed rate and grit size to achieve the desired material removal rate. Balance the need for efficiency with the requirement for maintaining sample quality.
- Adjust the feed rates and grit sizes to optimize the material removal rate. Balancing the material removal rate with the desired finish is crucial for efficient sample preparation.
Dress Cup Wheels Regularly
Maintain the condition of the cup wheel by dressing it regularly. Follow the manufacturer’s recommendations for dressing intervals and parameters, ensuring the cup wheel is properly trued and conditioned.
Dressing Frequency
Dress the SMART CUT Diamond Cup Wheel regularly to maintain its cutting efficiency. The frequency of dressing may vary depending on usage and the cup wheel’s condition, but regular inspection is essential.
Dressing Parameters
Follow the manufacturer’s guidelines for dressing parameters, including dressing speed and depth. Proper dressing ensures that the cup wheel maintains its effectiveness and shape. Maintain and replace dressing tools or sticks as needed. A well-maintained dressing tool is essential for maintaining the cup wheel’s effectiveness during the dressing process.
Flanges
- Use appropriate flanges to securely mount the SMART CUT Diamond Cup Wheel on your equipment. Ensure that the flanges are compatible with the cup wheel size and type.
- Follow the manufacturer’s instructions for correct alignment and mounting to prevent equipment vibration and ensure safe operation.
- Periodically inspect and maintain the flanges used to mount the SMART CUT Diamond Cup Wheel. Ensure that they are in good condition and securely attached to prevent any issues during operation.
Prevent Cross-Contamination: If switching between wet and dry grinding, clean and dry the cup wheel thoroughly to prevent cross-contamination between different sample preparation methods.
Customize Dressing for Profiles: Customize the dressing process to achieve specific cup wheel profiles that meet your sample preparation needs, especially for applications requiring unique shapes or profiles.
Safety Measures: Prioritize safety during the entire process. Wear appropriate personal protective equipment (PPE) such as safety glasses, gloves, and respiratory protection as needed. Follow safety guidelines and protocols established in your laboratory or facility.
Quality Control: Regularly inspect the cup wheel for signs of wear and replace it when you notice reduced grinding efficiency or a decline in sample quality.
Material Handling: When preparing samples with embedded components or delicate features, exercise caution and precise control to minimize the risk of damage to these elements. Adjust grinding parameters to protect sensitive components.
Work Area Ventilation: Ensure proper ventilation in the workspace to dissipate any airborne dust or particles generated during the sample preparation process. A well-ventilated area enhances safety and air quality.
Contaminant Control: Regularly clean the sample preparation equipment, including the SMART CUT Diamond Cup Wheel, to prevent contamination between different sample batches and maintain consistent results.
Quality Inspection: Implement a quality control process to inspect and verify the quality of the prepared samples. Use microscopy or other analytical techniques to assess the sample’s surface finish and ensure it meets your requirements.
Record Keeping: Maintain detailed records of the sample preparation process, including grit sizes, RPM settings, feed rates, and any deviations from standard procedures. This documentation can aid in troubleshooting and process optimization.
Regular Maintenance: Perform routine maintenance on your equipment, including the Thin Section Machine and cup wheel, to ensure they remain in optimal working condition. Address any equipment issues promptly to minimize downtime.
Material Hardness Assessment: Consider the hardness of the material you are preparing and adjust the grinding parameters accordingly. Harder materials may require slower feed rates and finer grit sizes to achieve optimal results.
Documentation of Grinding Parameters: Document and log the specific grinding parameters used for each sample. This record-keeping helps maintain consistency in your sample preparation process and facilitates repeatability.
Sample Labeling: Clearly label each sample to track its origin, preparation date, and relevant details. This labeling system aids in sample identification and traceability.
Sample Cleaning: After grinding, thoroughly clean and rinse the prepared samples to remove any residual abrasive particles and contaminants. Proper cleaning ensures the accuracy of subsequent analyses or examinations.
Calibration Checks: Periodically calibrate your equipment, including the Thin Section Machine and any associated measurement devices, to maintain accuracy and consistency in your sample preparation and analysis.
Quality Inspection Interval: Implement a regular quality inspection interval to assess the surface finish and sample quality. Frequent inspections help identify any deviations from the desired results.
Trouble Shooting Guide
DIAMOND CUP WHEELS For Struers Machines
Used on Accutom-50 and Discoplan-TS machines
Showing 1 – -1 of 4 results Showing all 4 results Showing the single result No results found
Sort by Price low to high
Filters Sort results
Reset Apply
Image | UKAM ITEM # | STRUERS ITEM NO | OUTSIDE DIAMETER | INSIDE DIAMETER | DESCRIPTION | DIAMOND GRIT SIZE | Price | Quantity | Add to cart |
---|---|---|---|---|---|---|---|---|---|
4080-0082 | 100mm (4") | 12.7mm (1/2") | Diamond, Metal bond (sintered) for hard, brittle materials. Used on Struers Accutom-50 | 91 um | $698.00 | Max: Min: 1 Step: 1 | |||
4080-0083 | 100mm (4") | 12.7mm (1/2") | Diamond, Resin Bond for hard, ductile materials. Used on Struers Accutom-50 | 40 um | $698.00 | Max: Min: 1 Step: 1 | |||
4080-0013 | 150mm (6.0") | 31.75mm (1.25") | Diamond, Metal bond (sintered) for hard, brittle materials. Used on Struers Discoplan-TS | 70 um | $892.00 | Max: Min: 1 Step: 1 | |||
4080-0014 | 150mm (6.0") | 31.75mm (1.25") | Diamond, Resin Bond for hard, ductile materials. Used on Struers Discoplan-TS | 35 um | $892.00 | Max: Min: 1 Step: 1 |
6401501,6401502,6401503,6401504,
DIAMOND CUP WHEELS For Buehler Machines

Showing 1 – -1 of 1 results Showing all 1 results Showing the single result No results found
Sort by Price low to high
Filters Sort results
Reset Apply
Image | UKAM ITEM # | BUEHLER ITEM NO | OUTSIDE DIAMETER | DESCRIPTION | DIAMOND GRIT SIZE | Price | Quantity | Add to cart |
---|---|---|---|---|---|---|---|---|
40-4508 | 8" (254mm) | Diamond, Metal bond (sintered) for hard, brittle materials. Used on Buehler Petro Thin | 70 um | $898.00 | Max: Min: 1 Step: 1 |
Adventages
- Premium Diamond Abrasives: Our SMART CUT Diamond Cup Wheels are equipped with high-quality diamond abrasives that are engineered for long-lasting performance. This ensures consistent, reliable results with each use.
- Exceptional Durability: Built to withstand the demands of rigorous sample preparation, these cup wheels are constructed with durability in mind. They are designed to last, reducing the need for frequent replacements and saving you time and money.
- Precision Grinding: Achieve precise and uniform sample surfaces with ease. The SMART CUT Diamond Cup Wheels deliver exceptional grinding accuracy, making them ideal for various applications, including geological thin section preparation, metallurgical sample preparation, and more.
- Compatibility: These cup wheels are specifically designed to fit Struers, Buehler, and other Thin Section Machines, ensuring a seamless integration into your existing equipment setup. You can trust that they will perform flawlessly with your machinery.
- Versatile Application: Whether you're working with rocks, minerals, ceramics, or other materials, these cup wheels are versatile enough to handle a wide range of sample types. They are suitable for both hard and soft materials, making them a valuable tool in your lab.
- User-Friendly Design: The SMART CUT Diamond Cup Wheels are easy to install and use, allowing you to streamline your sample preparation process. Their user-friendly design ensures that both novice and experienced operators can achieve excellent results.
- Cost-Effective Solution: By reducing the need for frequent replacements and delivering consistent results, our SMART CUT Diamond Cup Wheels offer a cost-effective solution for your sample preparation needs.
Compare to BUEHLER, STRUERS, LECO & MANY OTHERS
SAVE UP TO 650%



How SMART CUT® Bond Works?
Step 1
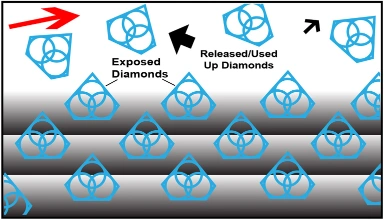
Sharpest And Finest Quality Diamonds
The newly exposed diamonds don’t effect diamonds already working on the material. Unlike many other diamond bonds, diamonds in a SMART CUT® Bond remains sharp and grow sharper with each cut, prolonging product life and consistent performance.
Step 2
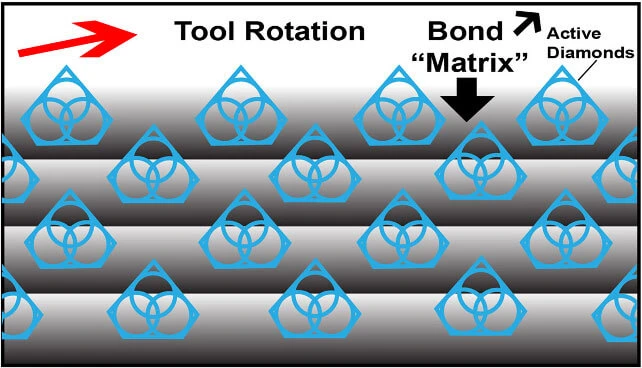
Diamonds or CBN Crystals
Diamonds or CBN Crystals are activated only at the exposed layer. As Bond Matrix layer begin to wear out, diamonds in a new Bond Matrix layer are immediately activated, substituting the already used up diamond layer. The SMART CUT® Diamond Hybrid Bond makes sure every diamond is in the right place and at the right time, working where you need it most.
Step 3
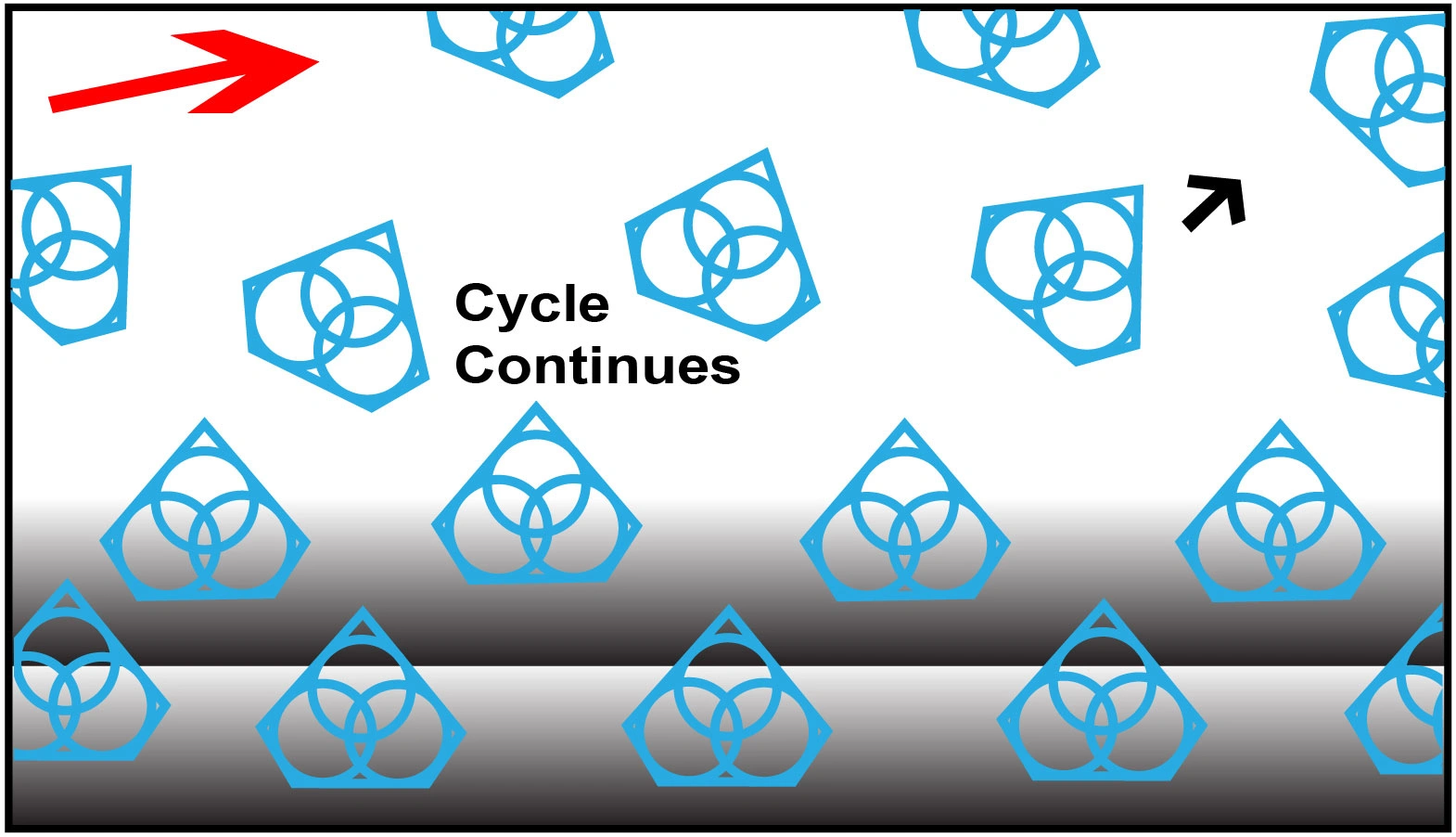
Advanced Formulated Open Diamond Bond Design
This advanced formulated open diamond bond design insures minimal chipping, fast cut, constant speed of cut, minimal cutting noise, and most important of all, consistent performance.
Better Cut Quality & Less Material Deformation
Diamond & CBN tools with SMART CUT® technology make any work much faster & easier, Thousands of sharp and high quality diamond or CBN particles oriented and evenly distributed on both matrix, allow most jobs to be completed by applying little or only moderate amount of pressure even on the most toughest and challenging materials. Freeing the user from constantly having to dress and renew the diamond layer
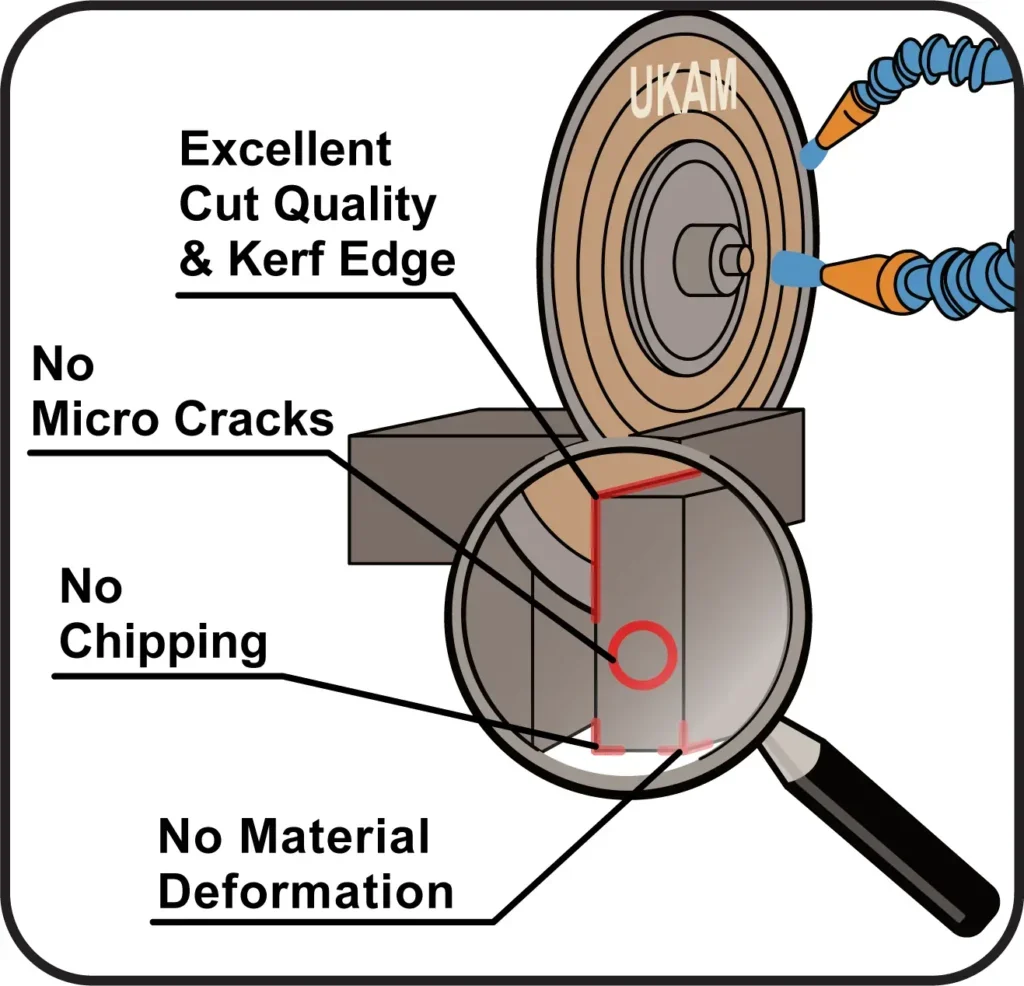
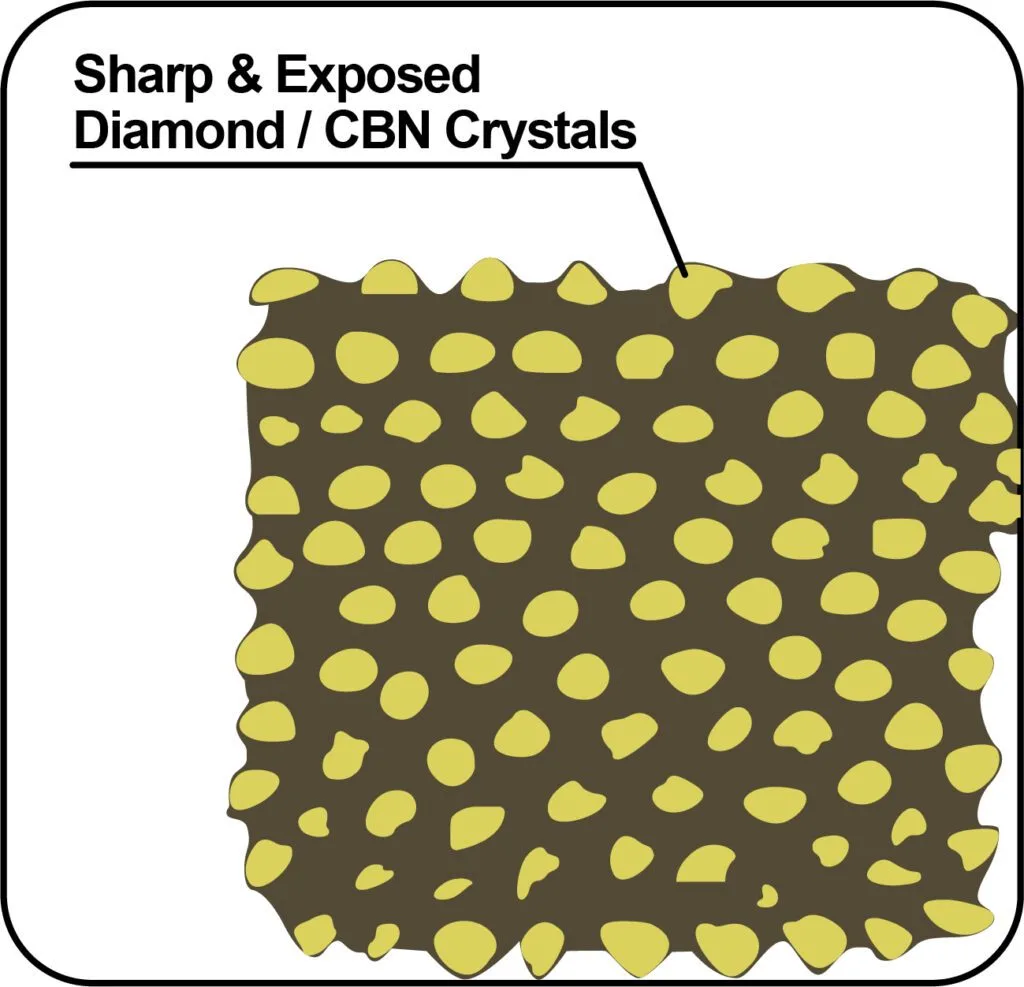
No Glazing
Diamond & CBN tools with SMART CUT® technology require minimum dressing, the bond renews itself.
Faster Drilling Action
Diamond & CBN tools made utilizing SMART CUT® technology are much more aggressive than your conventional tools. They can cut faster, while still leaving behind a smooth finish free of material deformation.
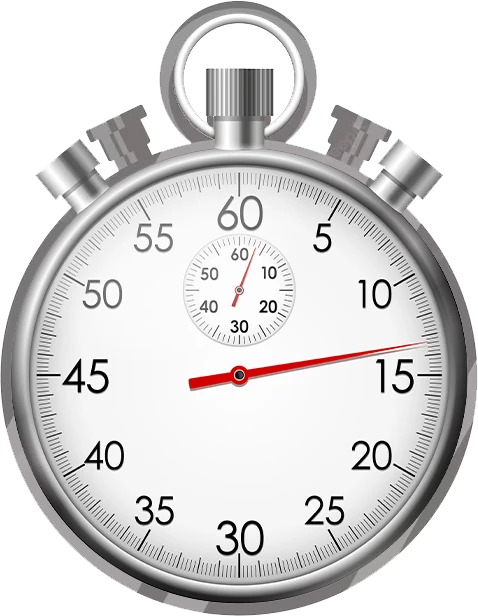
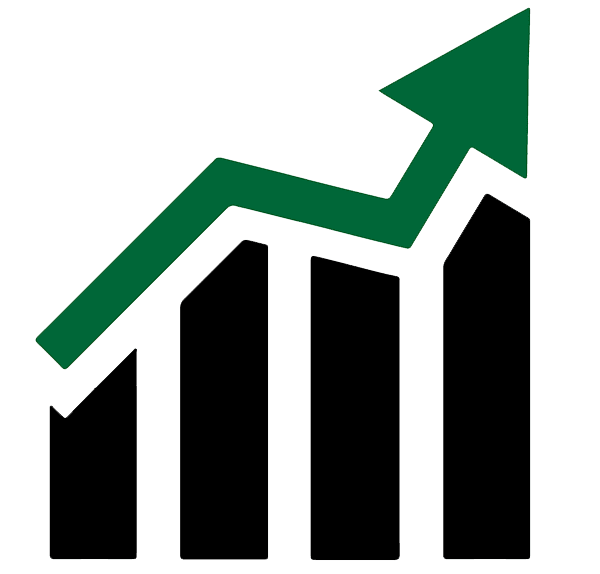
Longer Life
In most cases tools manufactured utilizing SMART CUT® technology, will outlast other conventional material (sintered), resin, and nickel bonded diamond & CBN tools. SMART CUT® diamond & CBN tools are more sturdy than tools manufactured with conventional technologies. They are capable to retain their form and bond configuration all the way through the tools life.
More Consistent Performance
Diamond & CBN Wheels are produced using only the highest quality raw materials are used in manufacturing process. Utilizing world class quality control, inspection, and measurement equipment. Highly Experienced Engineers constantly monitor and control all material input & output at all stages of manufacturing process. Insuring product consistency for use in demanding & sensitive applications SMART CUT® DIAMOND & CBN wear evenly, and are known for their consistency. You will get consistent cutting speed, and overall consistent performance, with minimum amount of dressing.
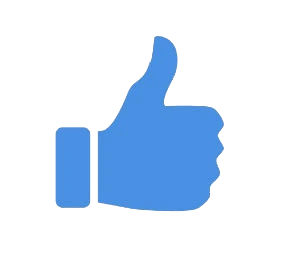
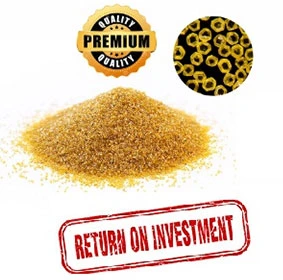
Manufactured Using The Highest Quality Raw Materials
Only the highest quality synthetic diamonds and raw materials are used in the manufacturing process. The highest quality standards and product consistency is maintained, using sophisticated inspection and measurement equipment.
Best Performance & Value on the Market
SMART CUT® Diamond & CBN Wheels are the best investment you can make! Although we may not always be the lowest cost solution provider. Our Diamond & CBN wheels can provide the best ROI. Designed for users that understand and appreciate quality. They will more than pay for themselves in terms of overall performance and provide best Return on Investment.
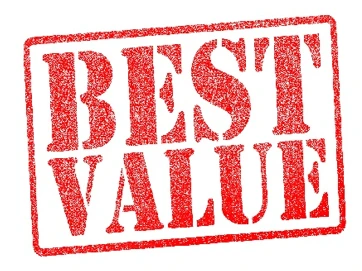
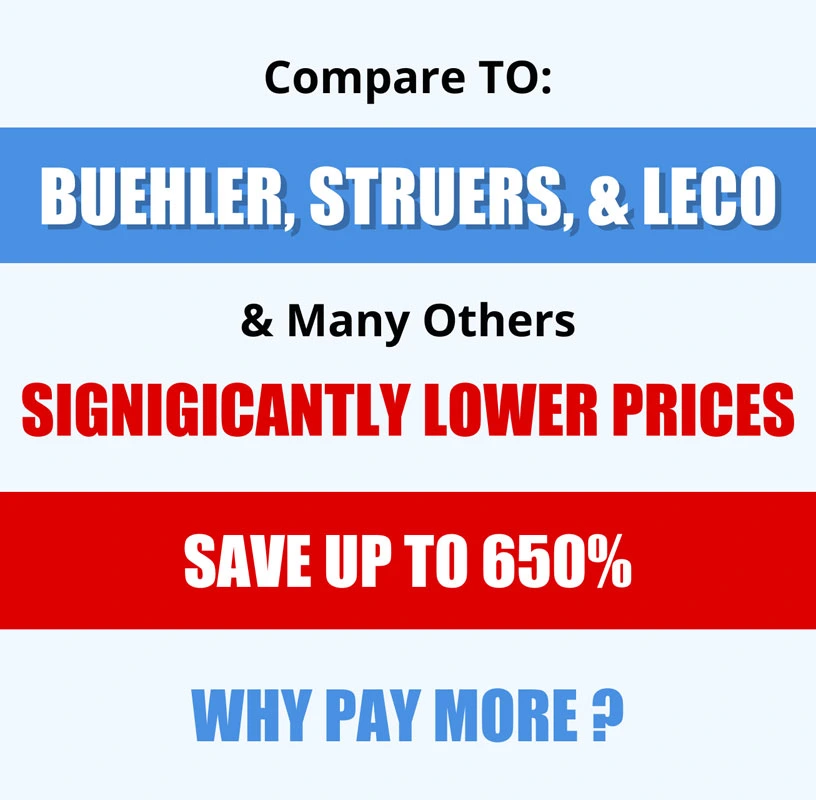
Why Choose Us?
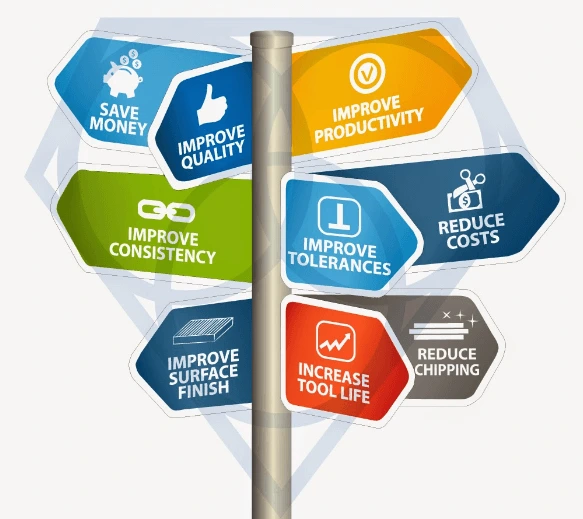
- Unmatched Selection For Many Applications
- Unmatched Technical Support & Expertise
- Superior Quality & Consistency
- Super Technology & innovation
- Immediate Worldwide Delivery
- American Based Manufacturer
-
Custom
Manufacturing - Better Value manufacturer Direct Price
Why Work With Us?
Read More
We produce diamond consumables for some of the leading world OEM manufacturers. We offer Manufacturers Direct Prices
We have the largest variety of diamond & cbn wafering blades available in stock. As well as large inventory of diamond & abrasive consumables. We also custom manufacture diamond and cbn tools, consumables and machines to better fit customer specific needs. Just about any tools & consumables can be designed and manufactured per client drawing or specificrtion
WE ARE A PARTNER IN YOUR SUCCESS
Our proprietory diamond chemistory , precision , manufacturing metods , quality control methods allow us to control and regulate the dozens of variables to that affect consumable life , quality , and consistency.
The more you understand about what we can do for you the better our partnership will be. Here you will find most comprehensive source of information and optimizing and improving your cutting , drilling , grinding and polishing on the web. find everything you ever wanted to know about diamond tools.
AMERICAN MANUFACTURER
"ONE OF THE MOST EXPERIENCED COMPANIES IN THE INDUSTRY"
Save Money Save up to 650%
COMPARE TO: BUEHLER , STRUERS , LECO & MANY OTHERS
Large Inventory & Custom Manufacturing
Umatched Technical Support
Developing close ties with our customers is the foundation of our business. At the core of
our company is a team of world class engineers, knowledgeable customer service personnel here to serve you. Whether is designing or manufacturing a special solution. We will go out of our way to optimizing your process to ultimate level of efficiency
Superior Quality & Consistency
EXPECT MORE FROM YOUR TOOLS
Comprehensive Source Of Information For Sample Preparation
Advanced Technology
As one of the few remaining independent U.S.Diamond Tool & machine builders. We have the experience & tradition to help you remain at frontier of technology Our experience has been further enhanced by acquiring assets and processes from some of the oldest American tool
manufacturers, along with their decades of experience and R& D. This has positioned us as one of the most experienced companies in the industry .Depend on us to bring you technology of tomorrow today.
Experience Makes All The Differences
Over the years we have worked with some of the leading Fortune 500 companies , thousands of universities , government and private research labs , and small organisations. We have made thousands of custom tools , built custom machines , work-holding fixtures , etc for hundreds of applications. Many of our staff members have been working in their respective fields for over 50 years and have gained a wealth of knowledge over the years
Let Us Help You
Related Products
SMART CUT® 2010 Table Top Petrographic Precision Cutting Machine
SMART CUT® 6070 GEO TRIM SAW
SMART CUT® 2005 GEO
Petrographic Diamond Blades
SMART CUT® DIAMOND WAFERING BLADES SINTERED (METAL BOND)
$0.00
Recently Viewed Products
ARE YOU USING RIGHT TOOLS
FOR YOUR APPLICATION?
LET US
HELP YOU
HAVING ISSUES WITH
YOUR CURRENT TOOLS?
Knowledge Center
02
Jun
How to properly use Diamond Tools
UKAM Industrial Superhard Tools manufactures precision diamond tools for a large variety of applications, materials, and industries.
Share this Article with Friend or Colleague
Metal Bonded Diamond Tools are “impregnated” with diamonds. This means that selected...
02
Jun
Why use diamond
Diamond is the hardest material known to man kind. When used on diamond/tools, diamond grinds away material on micro (nano) level. Due to its hardness Diamond will work all types of materials from...
02
Jun
Diamond vs CBN (cubic boron nitride) Tools
Cubic Boron Nitride (CBN) is a synthetic material that is renowned for its exceptional hardness and high thermal stability. It is composed of boron and nitrogen atoms arranged in a crystal lattice structure, similar to...
02
Jun
What is Diamond Mesh Size and how to select best one for your application
Diamond grit size can be defined as the size of the diamond particles used in the bond matrix. The larger the diamond particles (grit size) the faster the tool will cut.
Share this Article with Friend or...
02
Jun
What is Diamond Concentration and which to use for your application
Diamond concentration is measured based on the volume of diamond within a section of the tool. It is typically defined as Concentration 100, which equates to 4.4 carats per cubic centimeter of the diamond layer...
02
Jun
Diamond Tool Coolants Why, How, When & Where to Use
Coolant is one of the most overlooked variables in the overall diamond or cbn tool machining process. Effective and proper use of coolant and recalculating coolant system will pay off in terms of improved surface...
18
Jul
Get to Know the Diamond Tool Bond Types and Which to use for your application
The indication of this premature loss of diamond is deep pocket left behind. The presence of many pockets means the diamond is wasted without being used. Each diamond must protrude high to cut fast with...
17
May
Choosing The Correct Diamond Bond Type
Selecting the appropriate diamond bond type for specific applications is crucial for several reasons. Diamond bond type directly affects the tool's performance, efficiency, and longevity. Different bond types determine how well a tool can withstand...
- Unmatched Selection For Many Applications
- Superior Quality & Consistency
- Immediate Worldwide Delivery
- Technical Support & Expertise
- American Based Manufacturer
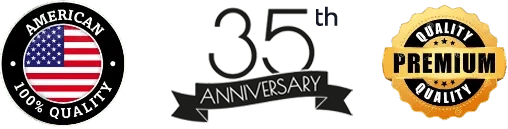

- Different Product
- Different Technology
- Different Company
- Expect MORE from your tools
Let Us HELP You!
Subscribe To Our Newsletter
Signup for email offers, updates, and more
Contact Us
- 25205 & 25201 Avenue Tibbits Valencia CA 91355 USA
-
Phone : (661) 257-2288
FAX : (661) 257 -3833 - lel@ukam.com
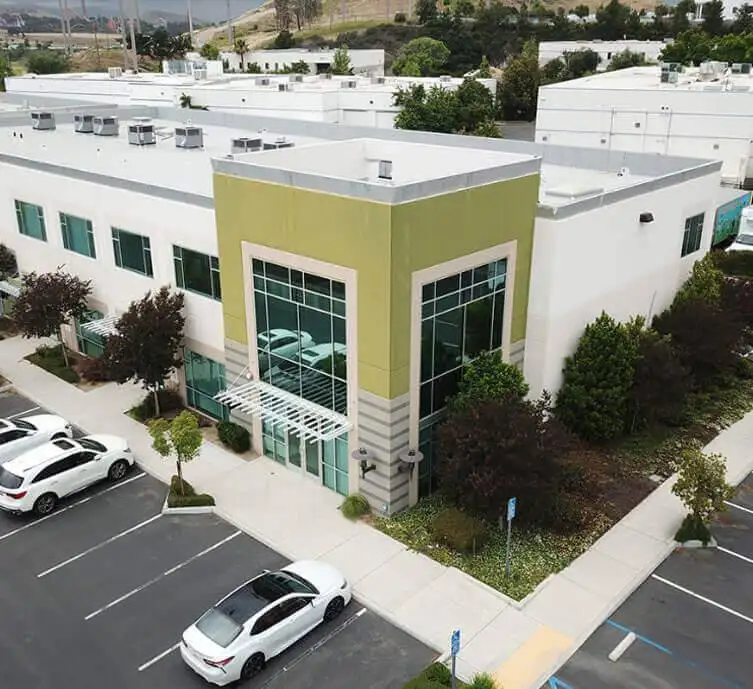
UKAM Industrial Superhard Tools is a U.S. High Technology, Specialty Diamond Tool & Equipment manufacturer. We specialize in producing ultra thin, high precision cutting blades, precision cutting machines diamond drills, diamond micro tools, standard & custom advanced industrial diamond tools and consumables.
- 25205 & 25201 Avenue Tibbits Valencia CA 91355 USA
-
Phone : (661) 257-2288
FAX : (661) 257 -3833 - lel@ukam.com
- 25205 & 25201 Avenue Tibbits Valencia CA 91355 USA
-
Phone : (661) 257-2288
FAX : (661) 257 -3833 - lel@ukam.com
DIAMOND TOOLS BY BOND
EQUIPMENT
KNOWLEDGE CENTER
OUR PRODUCTS
COMPANY
CUSTOMER SERVICE
Shipping Methods


Safe & Secure Payments

© Copyright 1990-2025. UKAM Industrial Superhard Tools – Terms of Use