-
0 items in quote
No products in the Quote Basket.
CBN, Resin Bond Cut Off Blades
SMART CUT® Series 600 RCBN
SMART CUT® Series 600 RCBN CBN, Cut Off blades are designed for cutting of extremely hard ferrous metals (HV 500 – 1400) used on large variety of high speed & abrasive cut off saws.
Resin bond CBN Cut Off Blades offer superior cut quality than any type diamond wafering blade available. Recommended for applications where cut quality and surface finish is very important. Compared to their sintered (metal bond) wafering blade counterparts. Resin Bond CBN Cut Off Blades offer far superior cut quality than the finest size metal bond (sintered) bade. Recommended for cutting Tool Steels, Heat-sensitive Materials, Hard Alloys, Soft Ferrous Alloys, Titanium Alloys where low heat generation or improved surface finish is desired. Most commonly used at higher speeds.
DESCRIPTION
SPECIFICATIONS
FREQUENTLY ASKED QUESTIONS
INDUSTRIES USED IN
ACCESSORIES
USAGE RECOMMENDATION
DESCRIPTION
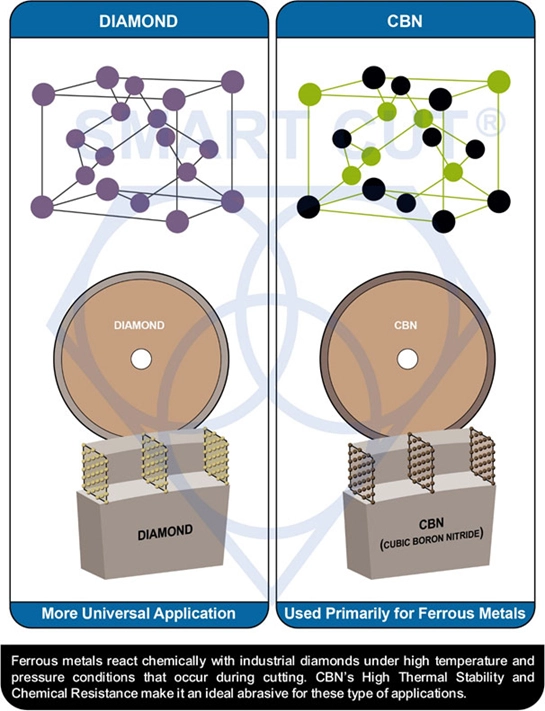
The resin bond diamond cut off blades / cut off wheels excel in delivering superior cut quality compared to other diamond cutting blade, making them ideal for applications where cut quality and surface finish is highly important. They are designed to operate at higher speeds to minimize heat generation and improve surface finishes.
SMART CUT® resin bond diamond wheels are engineered to maximize blade life while maintaining your desired cut quality and speed. These blades offer numerous advantages, including unmatched cut quality that often eliminates the need for secondary finishing operations. They feature a faster and freer cutting speed, generate less heat, and apply minimal stress to the material.
Manufactured using phenolic resin as the binder and diamond abrasive as the cutting medium, these blades incorporate ceramic and other advanced components as fillers. SMART CUT® Resin Bond Bond Diamond Cut off Blades & Wheels are produced using an advanced molding process and can be customized various geometries, diamond sizes, concentrations, and bond hardness to fit your particular objectives.
SMART CUT® CBN, Resin Bond Cut off Blades offer Best Return on Investment & Lowest Cost of Ownership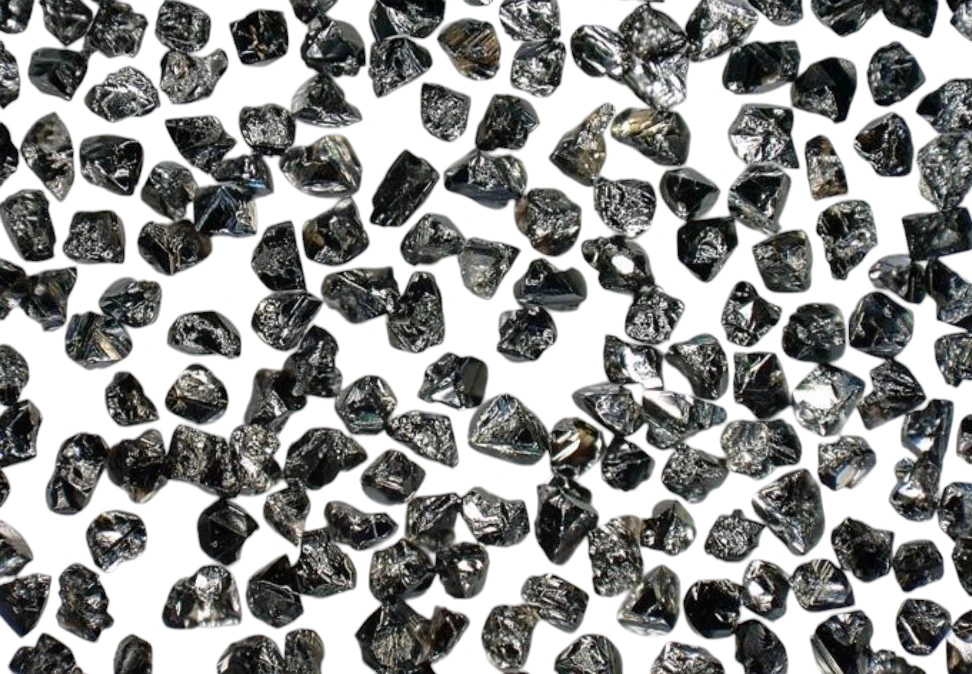
Advantages:
- Softer Bond: The resin bond is comparatively softer than metal bonds, allowing for a smoother cutting experience.
- Fast Material Removal: They offer quicker stock removal due to the softer bond.
- Better Surface Finish: Resin bond blades generally provide a superior surface finish on the material being cut.
- Less Heat Production: Resin bonds produce less heat during the cutting process, reducing the risk of thermal damage.
- Self-Sharpening: As the resin wears away, new sharp CBN particles are exposed, providing a consistent cut.
SPECIFICATIONS
Tab Content
FREQUENTLY ASKED QUESTIONS
It’s a type of cutting blade that utilizes Cubic Boron Nitride (CBN) as the abrasive material held together with a resin bond. CBN is known for its hardness, second only to diamond, making these blades ideal for cutting hard materials.
Resin bond CBN cut-off blades are optimal for cutting hardened steels, superalloys, ceramics, and other hard materials. They are especially preferred for ferrous metals since CBN does not react with them, unlike diamond.
Resin bonds offer a controlled wear rate and are more forgiving under conditions where excessive heat or loading might occur. They also produce less heat during cutting, ensuring minimal thermal damage to the workpiece.
No. Resin bond CBN blades require less frequent dressing compared to many other abrasive wheels. This increases operational efficiency and reduces downtime.
Yes, they are designed to absorb more stress than rigid bonds, making them less prone to breakage and increasing the safety of operations.
While the initial investment may be higher than traditional abrasive wheels, their efficiency, longevity, and reduced need for replacement often lead to a lower cost per cut, offering better value over time.
Yes, resin bond CBN cut-off blades are versatile and can be used on various machines, including high-speed grinders.
These blades typically produce superior surface finishes, which can often reduce or eliminate the need for subsequent finishing processes.
Due to their durability and resistance to wear, resin bond CBN cut-off blades generally have a longer lifespan than many other abrasive blades. The exact frequency of replacement will depend on usage and the materials being cut.
Yes, but the specific application and cutting conditions might dictate the preferred method. Wet cutting can help in cooling and dust management, while dry cutting might be more convenient for certain setups.
While both are superabrasives, CBN is preferable for cutting ferrous metals since diamond can react with and wear quickly against these materials. CBN is also slightly less hard than diamond but is more than adequate for most hard materials.
Keep them clean after each use and store them in a cool, dry place. Avoid dropping or exposing them to extreme temperature changes to maintain blade integrity.
Like all tools, performance might diminish with extensive use. However, with proper care and occasional dressing, these blades can offer consistent performance for a long time.
Yes, these blades can be designed with varying degrees of hardness or softness depending on the specific application. Consult the manufacturer or distributor for the most suitable grade for your needs.
The longevity and efficiency of these blades can reduce the frequency of replacements, which can be more environmentally friendly. However, like all industrial tools, it’s essential to dispose of used blades properly.
Yes, with proper dressing tools and techniques, you can restore the blade’s cutting edge. However, always ensure that you’re using appropriate methods to avoid damaging the blade.
While resin bond CBN blades are designed to handle regular cutting tasks efficiently, they can be damaged by severe impacts. It’s essential to handle and use them with care.
Resin bond CBN blades produce less heat compared to other cutting tools. However, for prolonged cutting, especially in dense materials, using cutting fluids or periodic breaks can help manage heat.
Typically, CBN blades can achieve faster cutting speeds and maintain those speeds consistently, given the hardness and durability of the material.
A resin bond typically consists of a synthetic or natural resin, fillers, and other additives. The specific formulation can vary based on the manufacturer’s design and the blade’s intended application.
Prolonged exposure to high humidity can impact the bond, especially if it’s stored in such conditions for an extended period. Similarly, drastic temperature changes can cause thermal stress. It’s best to store these blades in a controlled environment.
Yes, these blades are compatible with many CNC machines, provided they fit the machine’s specifications and operational speeds.
Always wear appropriate safety gear, like goggles and gloves. Ensure the blade is securely fixed, and the equipment is free from defects. Maintain a safe distance, and ensure bystanders are adequately protected.
CBN boasts impressive durability, especially when cutting ferrous metals. While diamond might offer slightly higher wear resistance in some applications, CBN often outlasts other abrasives when cutting ferrous materials.
The optimal speed varies depending on the blade’s diameter, kerf thickness and material type and shape.
yes we manufacture almost any blade specification. Standard lead time is 4 to 5 weeks
Some components of the blade can be recycled. However, the recycling process might differ from regular metals due to the presence of CBN and resin. Check with local recycling facilities or the blade manufacturer for guidance.
Absolutely. Harder and more abrasive materials can wear down the blade faster than softer ones. It’s essential to match the blade’s specifications with the material to ensure optimal lifespan.
Thicker blades tend to be more robust and can handle heavier cutting loads, but they might remove more material and generate more heat. Conversely, thinner blades provide finer cuts but might be more susceptible to deflection or breakage under heavy loads.
While primarily designed for machine-based operations, some blades might be suitable for manual applications. Ensure you select the right blade type and adhere to safety guidelines when using them manually.
Look for decreased cutting performance, increased cutting resistance, visible physical damage, or if the blade has been excessively dressed and thinned out.
Wet cutting uses coolant or water, which can extend blade life, reduce dust, and manage heat. Dry cutting, on the other hand, doesn’t use any coolant, making it more straightforward but potentially resulting in more heat and wear.
Larger diameter blades can cut deeper and often have longer lifespans due to the increased amount of abrasive material. However, they might require more powerful machines and might not be as agile as smaller diameter blades.
When stored properly — in a cool, dry place away from direct sunlight and extreme temperatures — these blades can have a shelf life of several years without significant degradation.
A common misconception is that they’re suitable for cutting any material because of CBN’s hardness. However, they’re specifically designed for particular hard materials and might not perform as well with softer or extremely abrasive materials.
Yes, manufacturers can use various resins, such as phenolic, polyimide, or epoxy, depending on the desired blade properties. The type of resin can influence the blade’s heat resistance, flexibility, and cutting performance.
The grit size determines the finish and speed of the cut. Coarser grits remove material faster but might produce a rougher finish. Finer grits, on the other hand, produce smoother finishes but might cut more slowly.
Yes, lubricants or coolants can be used to minimize heat generation and prevent material from sticking to the blade. Ensure the lubricant is compatible with both the blade and the material being cut.
While all cutting operations produce some noise, resin bond CBN blades, when used correctly and in good condition, shouldn’t generate excessive noise. However, always use appropriate hearing protection during operation.
Regularly inspect the blade for wear or damage, ensure proper blade alignment, use appropriate cutting speeds, and apply coolants or lubricants when suitable.
The hardness of CBN makes it capable of handling materials with variations in hardness. However, unexpected inclusions or irregularities might affect the cut or cause premature wear on the blade.
Absolutely. Due to their hard-wearing nature and the fine finishes they can produce, resin bond CBN blades are often used in precision cutting applications.
While resin bond CBN blades manage heat relatively well, prolonged cutting without proper heat management (like using coolants) might lead to warping or other heat-related issues.
While new abrasive materials are continually being developed, CBN remains one of the top superabrasives, especially for cutting ferrous materials. However, it’s essential to stay updated on industry advancements and select the blade most suited for the job.
Mild detergents or specialized cleaning solutions for superabrasive tools can be used. However, avoid using harsh chemicals that might degrade the resin bond or the CBN.
While they might have a higher upfront cost compared to traditional abrasive blades due to the presence of CBN, their longevity and cutting efficiency can offer better value over the long run.
As long as the machine meets the operational specifications (like RPM) of the blade, and the blade fits securely, it can be used. However, always ensure the machine is in good working condition.
Prolonged UV exposure can degrade many types of resins. It’s advisable to store the blades away from direct sunlight or UV sources.
A higher concentration of CBN typically results in a more aggressive cut and longer blade life. However, it might also increase the cost of the blade.
Visible chipping, inconsistent cutting performance, or a blade that wears down too quickly might indicate a compromised resin bond.
Resin bond CBN blades are designed to handle the heat generated during cutting. Still, using them within recommended operational guidelines and employing coolants can help manage thermal expansion.
Depending on the machine and the specific application, multiple blades can sometimes be set up in tandem for specific cutting operations. Always consult the machinery’s manual and the blade manufacturer for recommendations.
Sort by Price low to high
INDUSTRIES USED IN
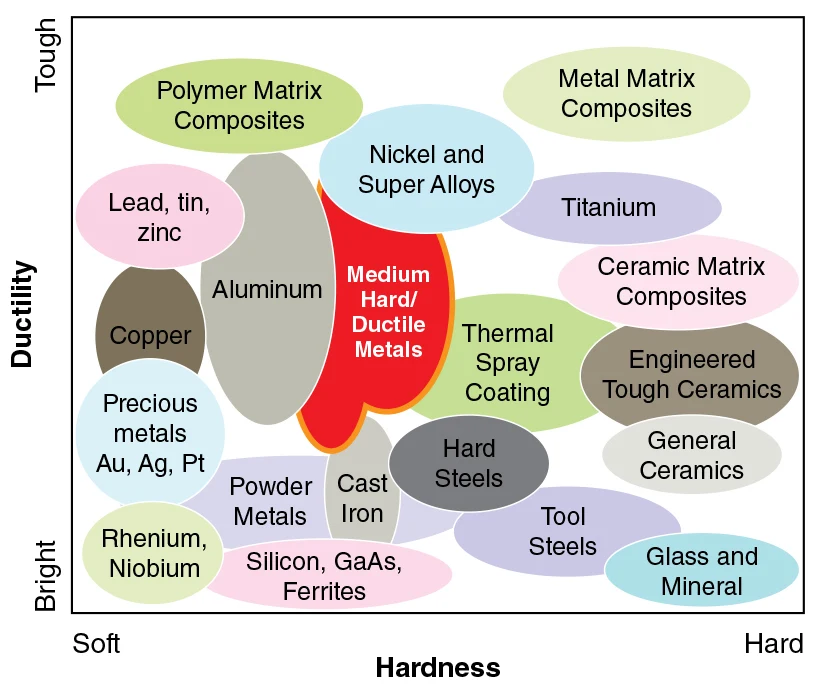

INDUSTRIES USED IN:
- Advanced Ceramics
- Composites
- Glass
- Geology
- Quartz
- Materials Research
- Medical Devices
- Metallography
- Photonics / Optics
- Semiconductor
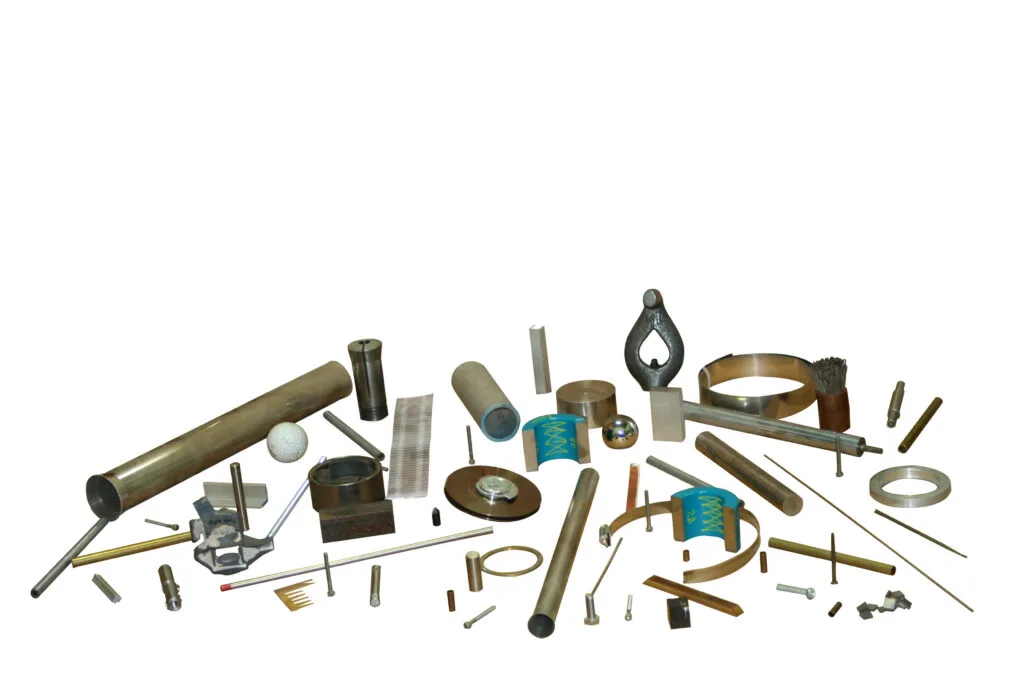
Ferrous & Non-Ferrous Metals:
- Plain Carbon Steels
- Electronic Packages
- Stainless Steels Plastics
- Tool Steels Fasteners
- Aluminum Refractories
- Copper Base Alloys Integrated Circuits
- Magnesium Thermal Spray Coatings
- Titanium Metal Matrix Composites
- Biomedical Wafers
- Petrographic
- PCB.s Ceramics
ACCESSORIES
Showing 1 – -1 of 16 results Showing all 16 results Showing the single result No results found
Sort by Name A – Z
Filters Sort results
Reset Apply
Image | Item No. | Description | Price | Quantity | Add to cart |
---|---|---|---|---|---|
Color: 5/8″-11″ thread. Fits into drill press chuck. Shank adapter threads into 5/8″-11″ female thread of diamond drill. Can be used with any other tool with 5/8″-11″ thread. | $26.72 | Max: Min: 1 Step: 1 | |||
Color: 5/8″-11″ thread. Fits into drill press chuck. Shank adapter threads into 5/8″-11″ female thread of diamond drill. Can be used with any other tool with 5/8″-11″ thread. | $22.46 | Max: Min: 1 Step: 1 | |||
1 Gallon Blue SMART CUT® General Materials Formula Synthetic Water Soluble Coolant | $99.81 | Max: Min: 1 Step: 1 | |||
1 Quart Blue SMART CUT® General Materials Formula Synthetic Water Soluble Coolant | $34.81 | Max: Min: 1 Step: 1 | |||
5 Gallons Blue SMART CUT® General Materials Formula Synthetic Water Soluble Coolant | $317.41 | Max: Min: 1 Step: 1 | |||
55 Gallons Blue SMART CUT® General Materials Formula Synthetic Water Soluble Coolant | $1,745.00 | Max: Min: 1 Step: 1 | |||
1/2″ x 1/2″ x 6.0″ White Recommended for coarser grits found in segment wheels, core drills, or Blanchard grinding. Excellent performance on 120 grit tools. | $8.65 | Max: Min: 1 Step: 1 | |||
1.0″ x 1.0″ x 6.0″ White Recommended for coarser grits found in segment wheels, core drills, or Blanchard grinding. Excellent performance on 120 grit tools. | $15.99 | Max: Min: 1 Step: 1 | |||
1/2″ x 1/2″ x 6.0″ White For use on diamond tools 150 to 220 Grit Size. | $8.65 | Max: Min: 1 Step: 1 | |||
1.0″ x 1.0″ x 6.0″ Black Recommended for use in Diamond Tools 150 Grit Size (mesh size) or finer. | $15.39 | Max: Min: 1 Step: 1 | |||
2.0″ x 2.0″ x 6.0″ Black Recommended for use in Diamond Tools 150 Grit Size (mesh size) or finer. | $39.47 | Max: Min: 1 Step: 1 | |||
1.0″ x 1.0″ x 6.0″ Black Recommended for coarser grits found in segment wheels, core drills, or Blanchard grinding. Excellent performance on 120 grit tools. | $15.99 | Max: Min: 1 Step: 1 | |||
2.0″ x 2.0″ x 6.0″ Black Recommended for coarser grits found in segment wheels, core drills, or Blanchard grinding. Excellent performance on 120 grit tools. | $39.47 | Max: Min: 1 Step: 1 | |||
$154.87 | Max: Min: 1 Step: 1 | ||||
$154.87 | Max: Min: 1 Step: 1 | ||||
$235.00 | Max: Min: 1 Step: 1 |
USAGE RECOMMENDATION
Tab Content
Showing 1 – -1 of 12 results Showing all 12 results Showing the single result No results found
Sort by Price low to high
Filters Sort results
Reset Apply
Image | Item No | Outside Diameter | Kerf Thickness | Arbor Size / Inside Diameter | Price | Quantity | Add to cart |
---|---|---|---|---|---|---|---|
8" (200mm) | .035” (0.89mm) | 32mm | $0.00 | Max: Min: 1 Step: 1 | |||
8" (200mm) | .045” (1.14mm) | 1.25” | $225.00 2 pcs - $220.00 ea ⋅ 3 pcs - $215.00 ea | Max: Min: 1 Step: 1 | |||
8" (200mm) | .045” (1.14mm) | 32mm | $225.00 2 pcs - $220.00 ea ⋅ 3 pcs - $215.00 ea | Max: Min: 1 Step: 1 | |||
8" (200mm) | .035” (0.89mm) | 1.25” | $235.00 2 pcs - $230.00 ea ⋅ 3 pcs - $225.00 ea | Max: Min: 1 Step: 1 | |||
10” (254mm) | .060” (1.52mm) | 1.25” | $245.00 2 pcs - $240.00 ea ⋅ 3 pcs - $235.00 ea | Max: Min: 1 Step: 1 | |||
10” (254mm) | .060” (1.52mm) | 32mm | $245.00 2 pcs - $240.00 ea ⋅ 3 pcs - $235.00 ea | Max: Min: 1 Step: 1 | |||
12" (300mm) | .065” (1.65mm) | 1.25” | $285.00 2 pcs - $280.00 ea ⋅ 3 pcs - $275.00 ea | Max: Min: 1 Step: 1 | |||
12" (300mm) | .065” (1.65mm) | 32mm | $285.00 2 pcs - $280.00 ea ⋅ 3 pcs - $275.00 ea | Max: Min: 1 Step: 1 | |||
14” (350mm) | .065” (1.65mm) | 1.25” | $305.00 2 pcs - $300.00 ea ⋅ 3 pcs - $295.00 ea | Max: Min: 1 Step: 1 | |||
14” (350mm) | .065” (1.65mm) | 32mm | $305.00 2 pcs - $300.00 ea ⋅ 3 pcs - $295.00 ea | Max: Min: 1 Step: 1 | |||
16” (400mm) | .095” (2.43mm) | 1.25” | $575.00 2 pcs - $300.00 ea ⋅ 3 pcs - $295.00 ea | Max: Min: 1 Step: 1 | |||
16” (400mm) | .095” (2.43mm) | 32mm | $575.00 2 pcs - $300.00 ea ⋅ 3 pcs - $295.00 ea | Max: Min: 1 Step: 1 |
Materials recommended for cutting with CBN:
- Alloy steels (45-68 RC)
- Carbon tool steels (45-68 RC)
- Die steel (45-68 RC)
- High speed steel (45-68 RC)
- Chilled cast iron
- Ni Hard
- Forged steel
- Meehanite iron
- Moly chrome steel rolls
- Inconel 600
- Rene
- Incoloy
- Monel
- Stellite
- Colmonoy
- Waspoloy
- Tool Steels
- Alloy Steels
- Hardening Steels
- Stainless Steels
- Bearing Steels
- Heat-Resistant Alloys
- Super Heat-Resistant Alloys
- Sintered Metals
- Ferrous Metals (Ferrous and other)
- Copper Alloys
- Hard Ferrous (steel) parts over 45 Rockwell C
- Iron
- Cobalt Alloys
- Nickel Superalloys
- Lead Alloys
About Resin Bond CBN Tools
Resin Bond is the softest of all the bonds, frequently used in applications that require a smooth surface. This type of wafering blades is used on majority of ultra hard and tough metals. Resin bond wafering blades allow the bond matrix to wear faster, and allow for diamond particles/crystals to break out of their matrix faster, so that new sharp diamond particles become exposed. This self sharpening characteristic of resin bond wafering blades, based on faster bond wear out is what make this blade an excellent choice for large variety of ferrous metals.
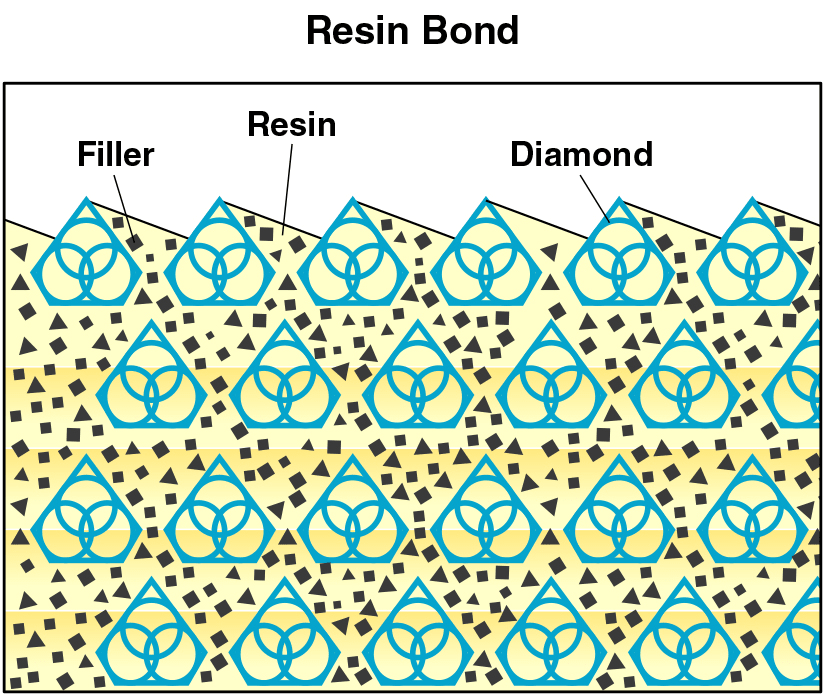
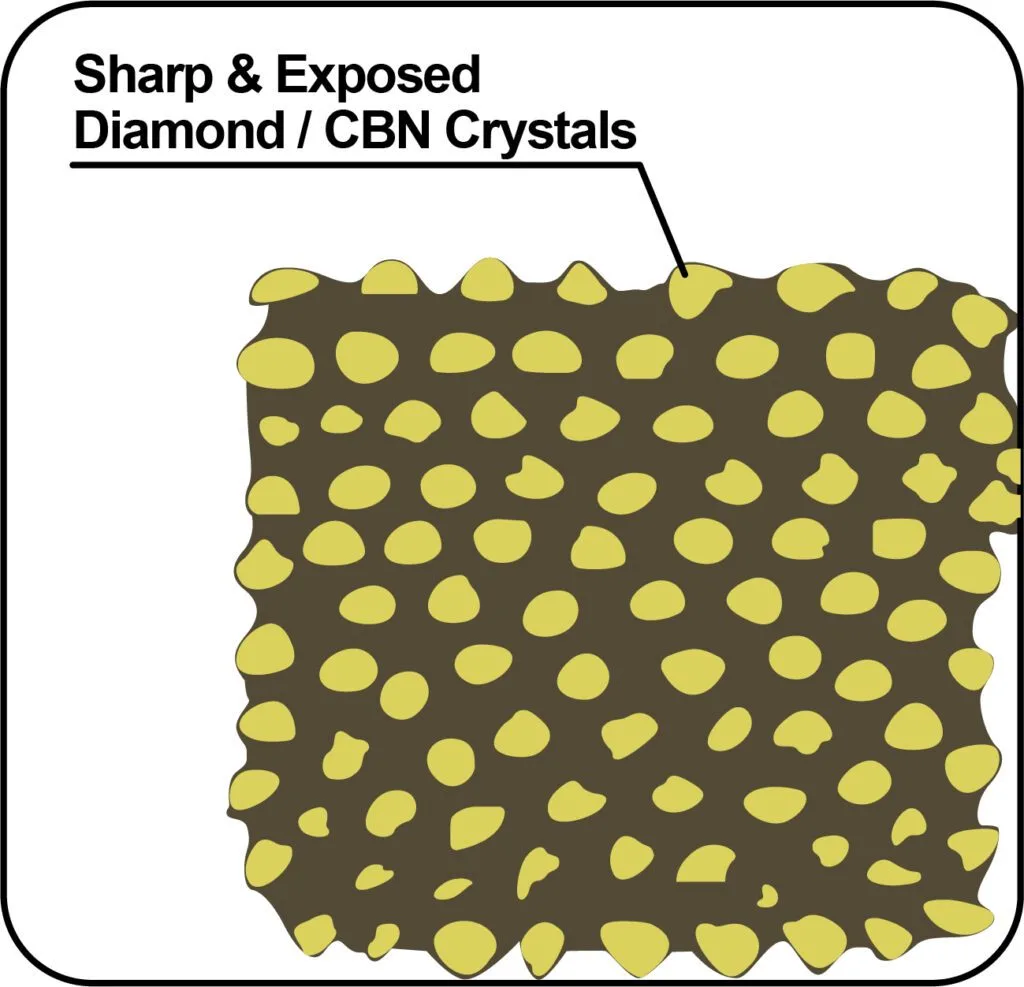
No Glazing
Diamond & CBN tools with SMART CUT® technology require minimum dressing, the bond renews itself.
Faster Cutting Action
Diamond & CBN tools made utilizing SMART CUT® technology are much more aggressive than your conventional tools. They can cut faster, while still leaving behind a smooth finish free of material deformation.
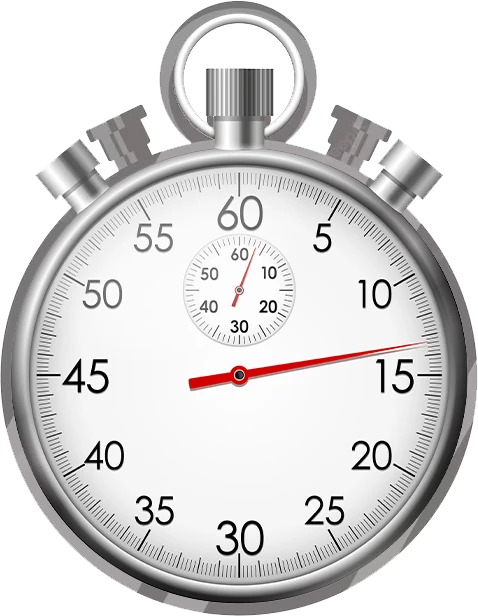
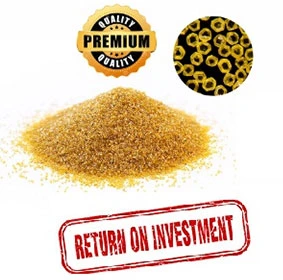
Manufactured Using The Highest Quality Raw Materials
Only the highest quality synthetic diamonds and raw materials are used in the manufacturing process. The highest quality standards and product consistency is maintained, using sophisticated inspection and measurement equipment.
Best Performance & Value on the Market
SMART CUT® Resin Bond, CBN Blades are the best investment you can make! While the initial investment in CBN blades may be higher than traditional abrasive wheels, their long lifespan and efficiency often result in a lower cost per cut. This can provide to significant savings in time and money.
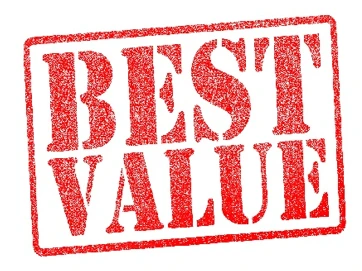
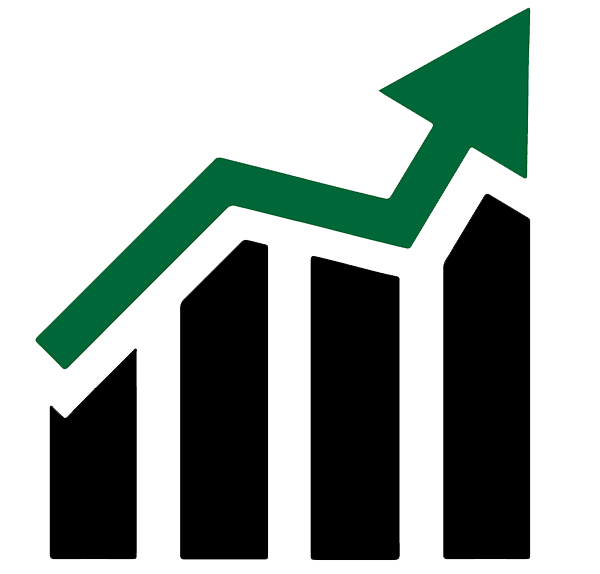
Longer Life
In most cases tools manufactured utilizing SMART CUT® technology, will outlast other conventional material (sintered), resin, and nickel bonded diamond & CBN tools. SMART CUT® diamond & CBN tools are more sturdy than tools manufactured with conventional technologies. They are capable to retain their form and bond configuration all the way through the tools life.
More Consistent Performance
SMART CUT® Series Resin Bond, CBN Blades have hundreds of diamond layers impregnated inside the resin matrix. Unlike Many Other Blade Types, they wear evenly, and are known for their consistency. You will get consistent cutting speed, and overall consistent performance, with minimum amount of dressing even on the hardest to cut materials.
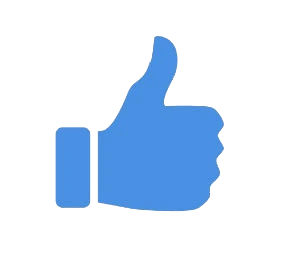
How SMART CUT® Resin Bond Works?
The sharpest and finest quality diamonds or CBN crystals that go into a SMART CUT® Resin Bond Diamond & CBN Dicing Blades, immediately penetrate into the material, grinding and polishing as they cut.
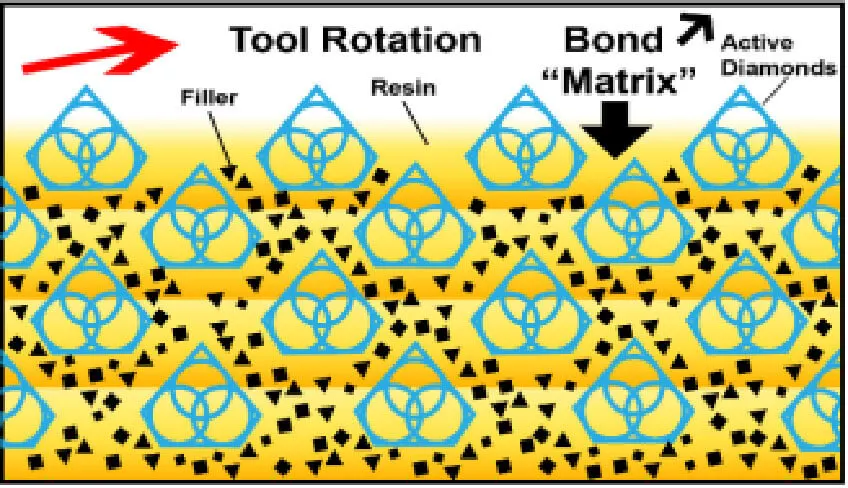
Diamonds or CB Crystals are activated only at the exposed layer. As Bond Matrix layer begin to wear out, diamonds in a new Bond Matrix layer are immediately activated, substituting the already used up diamond layer. The SMART CUT® Bond Diamond Bond makes sure every diamond is in the right place. and at the right time, working where you need it most.
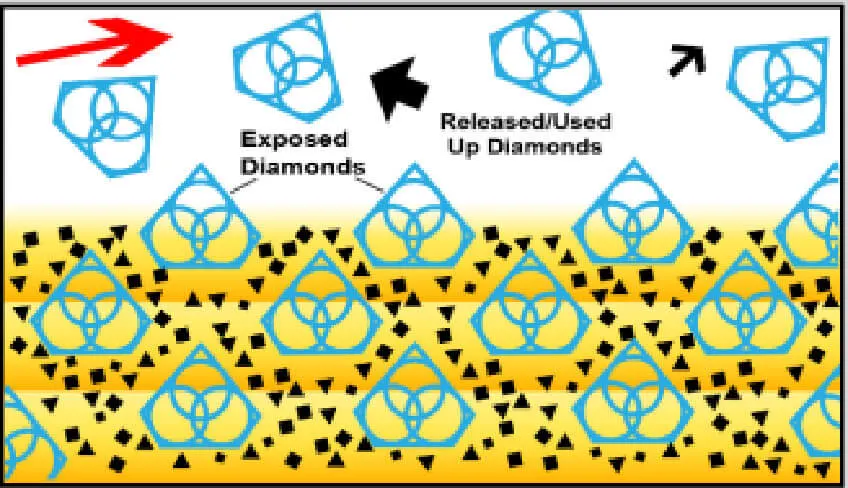
The newly exposed diamonds don't effect diamonds already working on the material. Unlike many other diamond bonds, diamonds in a SMART CUT® remains sharp and grow sharper with each cut, prolonging product life and consistent performance.
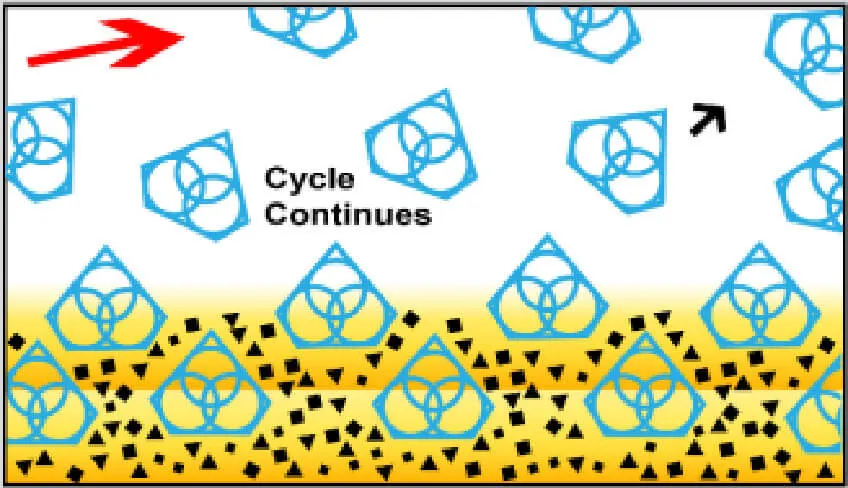
This advanced formulated open diamond bond design insures minimal chipping, fast cut, constant speed of cut, minimal cutting noise, and most important of all, consistent performance.
Diamond Cut Off Wheel Blade
Selection Variables
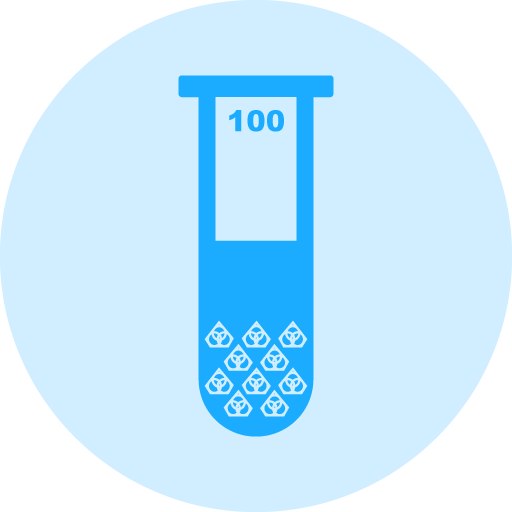
Diamond Concentration
Diamond Concentration – Diamond Concentration is still a factor in determining the life and cutting speed of your Diamond Cut off Wheels / Blades.
High diamond concentration helps enhance the longevity of the blade by distributing the cutting workload across more diamonds, reducing wear on individual diamonds and extending the blade's overall life. This setup results in a smoother finish since more cutting points engage with the material simultaneously, which is crucial for materials requiring a high-quality finish like optical materials or precision ceramics.
With more diamonds embedded in the resin matrix, these blades maintain their cutting capability longer, ensuring consistent performance throughout their lifespan. This is vital for applications needing uniform cuts in serial production or where precise dimensional tolerances are critical. Although resin bonds inherently generate less heat, the increased number of cutting points with high diamond concentration disperses the friction-generated heat more evenly, further reducing the risk of thermal damage to sensitive materials.
Low concentration resin bond diamond cut off blades and wheels provide several advantages, especially suited for cutting hard and brittle materials like ceramics, glass, or sapphire. With fewer diamonds embedded in the resin matrix, each diamond can exert more force on the material, enhancing precision and minimizing material deformation. This setup also reduces the risk of removing too much material too quickly, which is vital in applications requiring high precision and minimal kerf.
The increased spacing between the diamonds allows for better chip formation and removal, preventing the accumulation of debris that can affect cutting quality and increase the risk of blade overheating. Additionally, fewer diamonds mean less friction during cutting, which results in decreased heat generation. This is crucial when working with materials sensitive to thermal damage, such as those that might warp or undergo microstructural changes.
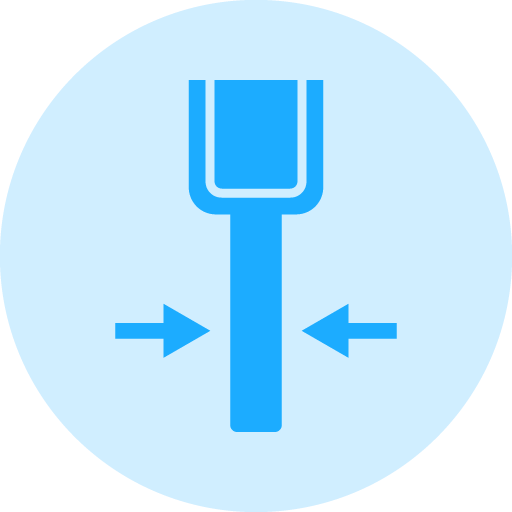
Blade Thickness
For resin bond diamond cut off blades and wheels, blade thickness plays a critical role in determining the amount of material removed during the cutting process, which is referred to as the kerf. The kerf size increases in proportion to the blade diameter, and it represents the width of the material that is removed as the blade passes through the sample. Choosing the correct blade thickness is essential for minimizing material loss, while insuring blade stability and cut quality.
For applications demanding high precision, thinner and smaller diameter blades are preferable. Blades ranging from 3 inches to 6 inches (75mm to 150mm) in diameter with a thickness of 0.015 inches to .020” thickness (0.4mm to 0.5mm) are typically best suited for these purposes. The optimal blade thickness for a particular material or application depends on various factors, including the cutting equipment used on, desired cutting speed, load or feed rate, material diameter, thickness, hardness, density, and shape, as well as the skill and experience of the operator.
Thicker resin bond diamond cut off blades offer increased stiffness and can withstand higher loads and feed rates. Another advantage of a thicker kerf is that it is more forgiving to operator error and misuse. This makes thicker kerf blades particularly recommended for environments where equipment is shared among a large number of individuals, They are ideal for less experienced or novice saw operators, providing a safer and more forgiving use-case scenario.
.
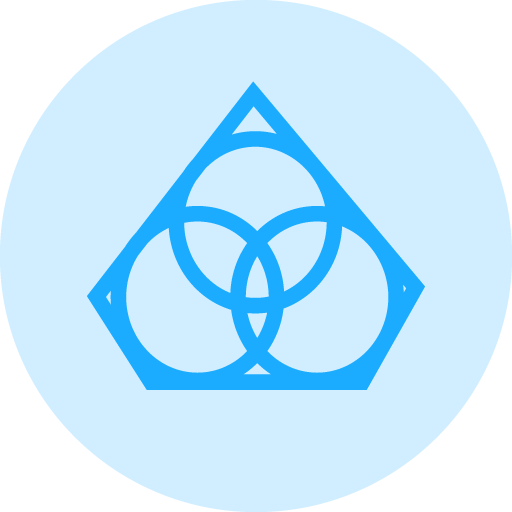
Diamond Particle/Grit size
The diamond particle or grit size in resin bond diamond cut off wheels plays a an important role in how they perform across various cutting parameters such as cutting speed, surface finish, & blade life. Larger, coarser diamond particles allow the wheel to cut through material more quickly, improving time efficiency and increase blade life. However, this comes with a trade-off as coarser diamonds can increase microstructural damage to the material due to their aggressive cutting action.
On the other hand, finer diamond grits contribute to a superior surface finish and higher quality cut. These smaller particles make less aggressive cuts, and produce better surface finish with minimal to no chipping on edges of material. Additionally, finer diamonds ideal for cutting fragile or delicate materials where maintaining the material's integrity is essential.
Choosing the right diamond grit size is key for optimizing the cutting process with resin bond diamond cut off wheels. For delicate or brittle materials, finer diamond grits are preferable to minimize chipping and microstructural damage while ensuring a high-quality surface finish. In scenarios where cutting speed is a priority and the material can tolerate more aggressive cutting, coarser diamond grits might be more suitable.
Coarse Diamond Grit Size, ranging from 60 to 100 mesh, are typically for cutting large variety of hard materials such as tungsten carbide, metals, and some ultra hard ceramics such as boron nitride and silicon carbide.
Medium Diamond Grit Sizes, As grit sizes become slightly finer, in the 120 to 200 mesh range labeled as medium, these are more commonly used for most resin bond diamond cut off blade / wheel applications such as cutting most types of glass, ceramics, optical glass, and other ultra hard and brittle materials
Fine grit size, which span from 229 to 320 mesh, designed for providing smoothest surface finish and minimal amount of chipping possible. These sizes are usually used for cutting quartz, Pyrex, fragile crystals and other fragile materials
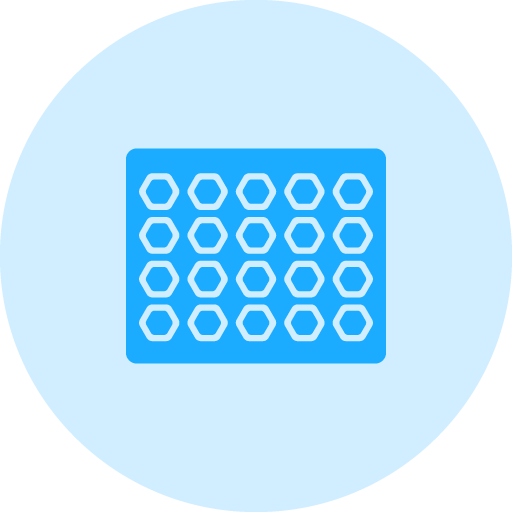
Bond Type
Resin bond diamond cut off blades are renowned for their exceptional cut quality, surpassing that of any other type of diamond blade available. They are specifically recommended for applications where the quality of the cut and the surface finish are paramount. This superior performance is particularly evident when compared to sintered (metal bond) blades, which, while durable, do not typically match the precision and smoothness provided by resin bond blades.
Resin bond blades use a composite material in which diamond particles are embedded in a resin matrix. This configuration allows for a smoother interaction with the material being cut, resulting in cleaner cuts with minimal chipping and superior surface finishes. The flexibility of the resin bond also enables a finer control over the cutting process, which is crucial in applications requiring high precision, such as in the fabrication of intricate components in the electronics and aerospace industries.
Furthermore, the unique properties of resin bond blades allow them to deliver excellent performance on a wide range of materials, including hard, brittle substances like glass, ceramics, and semiconductor materials.
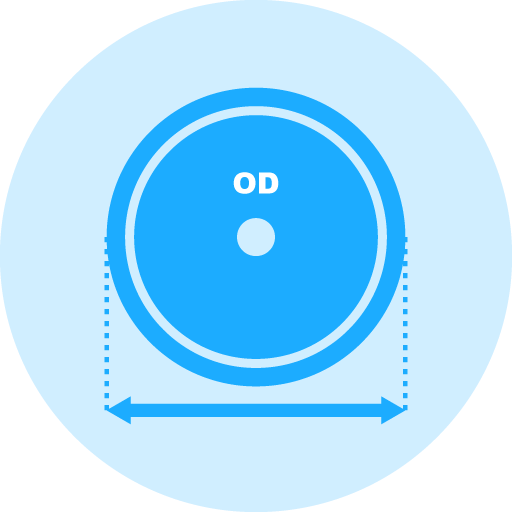
Blade Outside Diameter
These diameters are carefully chosen based on the specific needs of the application, the properties of the material being cut, and the capabilities of the cutting machine. Resin diamond cut off blades & cutoff wheels, which are available in sizes ranging from 1 inch to 20 inches in diameter, offer varied capabilities based on their size. The diameter of the blade should be chosen with consideration to the diameter and thickness of the material being cut. Smaller diameter blades, which tend to be thinner, are more susceptible to bending and warping during use. On the other hand, larger diameter blades, being thicker, provide greater stability and are typically employed for cutting larger and heavier materials. These larger blades can handle higher loads and speeds, making them suitable for more demanding cutting tasks.
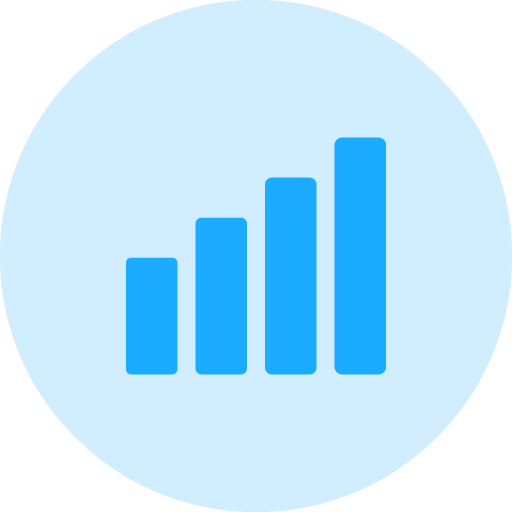
Feed Rates
Feed rates for resin bond diamond cut off blades in tile saws and precision cutting saws are critical to the cutting performance and quality of the final cut, and these rates must be adjusted to achieve desired objectives
For harder materials such as ceramics and metals, a faster feed rate may be necessary to efficiently cut through the material. This requires careful handling to ensure the blade does not overheat or wear prematurely. On the other hand, brittle materials like silicon, often used in precision applications, benefit from a slower feed rate to prevent chipping or cracking.
The optimal feed rate is also influenced by the speeds or RPMs at which the blade operates. Higher speeds can allow for quicker cuts but might increase the risk of damage to sensitive materials. Additionally, the geometry and size of the material, along with how securely it is held in place, are important considerations. Proper clamping of the material minimizes movement and vibration, enhancing the blade's effectiveness and the quality of the cut. Adjusting the feed rate manually requires a careful balance of these factors
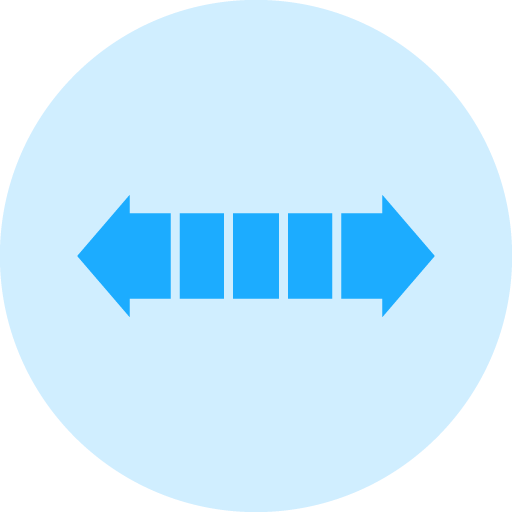
Bond Hardness
In resin bond diamond cut off blades, the hardness of the bond matrix significantly influences its ability to retain diamond particles and impacts the overall performance of the blade. As the bond hardness increases, the retention of diamonds improves, which can enhance the blade's durability but may result in a slower cutting speed. Blades with harder bond matrices generally exhibit a longer lifespan due to this increased retention.
Resin bond diamond cut off blades are classified according to their bond hardness, with designations ranging from Soft, Medium, to Hard, and numerous variations within these categories based on the degree of hardness or softness.
Selecting a blade with the optimum bond hardness is critical for achieving efficient and precise diamond sawing operations. A bond matrix that is too soft for the material being cut tends to release diamond particles prematurely, leading to rapid wear and a reduced lifespan of the blade. Conversely, a bond matrix that is too hard can significantly slow down the cutting process and necessitate frequent dressing to expose new layers of diamond.
For cutting harder materials like sapphire and alumina, softer bonds are typically preferred because they allow for easier diamond exposure and faster cutting, essential for maintaining efficiency without damaging the blade. For softer and more brittle materials, harder bonds are advantageous as they ensure better diamond retention, reducing the frequency of blade replacements and maintaining consistent performance.
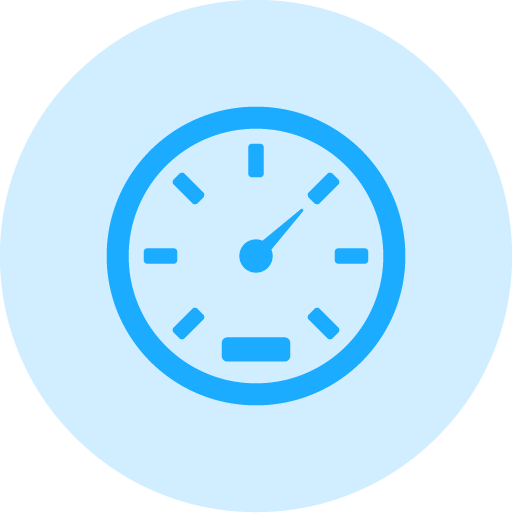
Blade Speeds/RPM’s
Resin bond diamond cut off wheels are usually used at higher speeds then sintered (metal bond) Resin bond diamond blades are usually used on manual saws such as tile saws and precision cut off saws, it’s essential to select the right RPM range to ensure optimal cutting performance and to maintain the integrity of the material. Tile saws and other lower-powered manual saws typically operate at RPMs up to 5,000, which is suitable for cutting large variety of materials such as glass.
In contrast, precision manual and automatic cut off saws, which handle a wider variety of materials and more complex cutting tasks, can accommodate a broader RPM spectrum. These saws might operate at speeds up to 100 to 6,000 RPMs.. The higher speeds enable efficient cutting of dense materials, whereas lower speeds are preferable for brittle materials such as advanced ceramics.Adjusting the blade speed according to the material properties, from the hardness to the brittleness, is critical.
Diamond Wafering Blade
Selection Variables
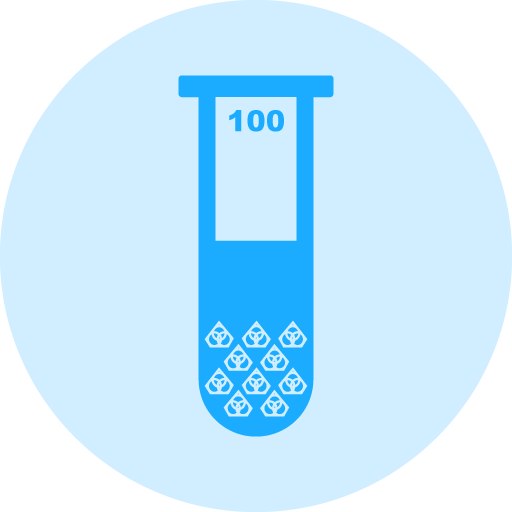
Diamond Concentration
Diamond Concentration – Diamond Concentration is still a factor in determining the life and cutting speed of your Diamond Sectioning/Wafering Blade. Higher diamond concentration is recommended and usually used for cutting softer and more abrasive types of materials. However, the trade off is significantly slower cutting speed. Low diamond concentration is recommended and widely used for cutting ultra hard and brittle materials.
Low Diamond Concentration - typically low concentration wafering blades should be for cutting ultra hard and brittle materials such as ceramics and glass. In Low Concentration Wafering Blades, diamond works by fracture process. Pressure on each diamond crystal/particle is higher which provides enough stress to chip off small flakes in the cut.
High Diamond Concentration - High concentration diamond wafering blades are recommended for cutting metals, plastics and polymers. In this application, materials cut by a plowing mechanism. In this applications diamond plough through the material, work hardened strips of materials become brittle and break off. The greater number of diamond by volume, the quicker the cutting action will be. Increasing the number of diamond s also lowers the per unit force. For metals where it is possible to induce deep deformation layers, a lower per unit force is desirable to reduce the deformation during the cut.
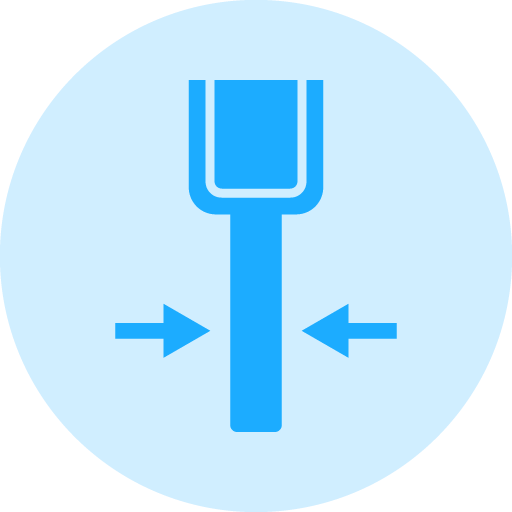
Blade Thickness
Wafering blade thickness typically ranges from .006” to .040” (1mm). Thinner and thicker wafering blade are available, frequently from stock upon request. Kef thickness typically increases with blade diameter (in proportion to diameter of the blade). Kerf is the amount of material removed from the material/sample due to the thickness of blade passing though the material/sample. Blade thickness is important for users requiring most minimal amount of material loss during sectioning
For example if the user requires precision position of the cutting plane relative to the detail on the sample (IC circuit for example), a thinner and smaller diameter blade would be best for this application. Blades ranging from 3” to 5” (75mm to 125mm) in diameter and thickness .006” to .015” (0.2mm to 0.4mm) would be bet suited for this purpose. There are large variety of factors that will contribute to optimal blade thickness for your material/application Including your desired cutting speed, load/feed rate, material diameter, thickness, hardness, density, and shape. As well as skill & experience of the operator. Thicker wafering blades are more stiff and can whistand higher loads/feed rates. Another advantage of thicker kerf blades is they are more forgiving to operator error and abuse. Thicker kerf blade are recommended for use in environment where large number of individuals will be sharing and using same equipment. Perfect for less experienced and novice saw operators, such as in University laboratory.
.
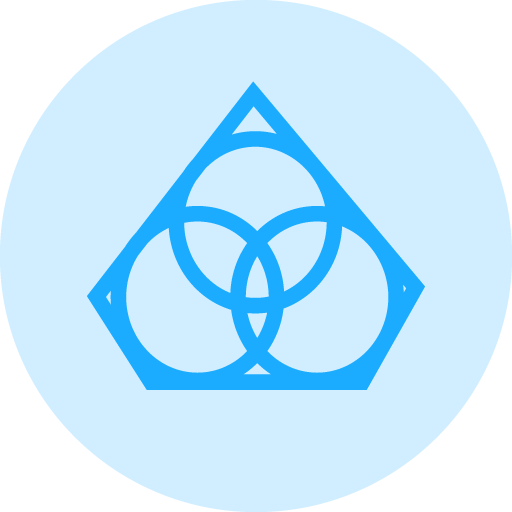
Diamond Particle/Grit size
Diamond Mesh Size plays a major role in determining your cutting speed, cut quality/surface finish, level of chipping you will obtain, and material microstructure damage you will obtain. Diamond Mesh size does have considerable effect on cutting speed. Coarse Diamonds are larger than finer diamonds and will cut faster. However, the tradeoff is increase in material micro damage. If you are cutting fragile, more delicate materials then finer mesh size diamond wafering blades are recommended.
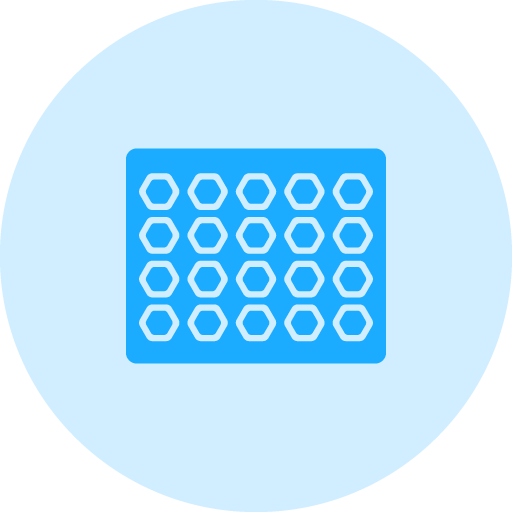
Bond Type
Metal bonding offers long life and durability, while resin bonding creates less heat, provides better surface finish and is well suited for cutting hard, delicate or brittle materials.
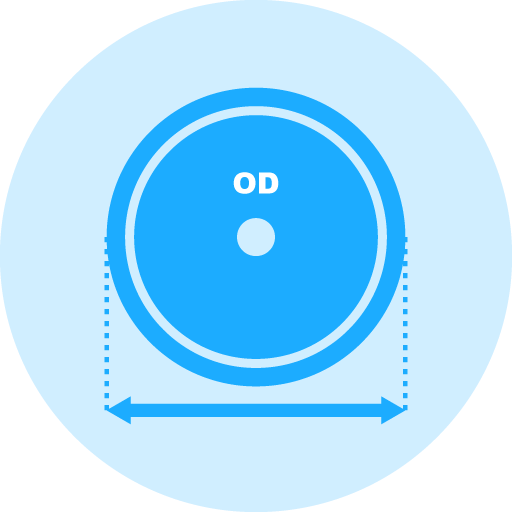
Blade Outside Diameter
typically wafering blade diameters range form 3” (75mm) to 8” (200mm). Wafering blade diameter should be selected based on material diameter and thickness being cut. Smaller diameter wafering blades are thinner than the larger diameter blades and are more prone to bending and warping. Although large diameter blades are thicker, they are typically used for cutting larger and heavier samples at higher loads and speeds than smaller blades
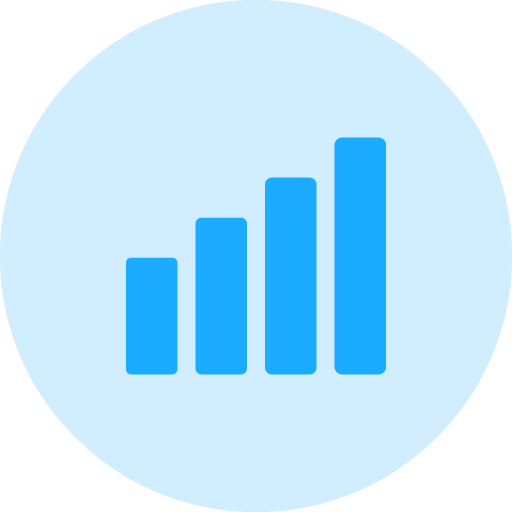
Feed Rates
load/feed rate applied to wafering blades typically vary from 10-1000 grams. Generally, harder specimens are cut at higher loads and speeds (e.g. ceramics and minerals) and more brittle specimens are cut at lower loads and speeds (e.g. electronic silicon substrates). The Speeds/RPM’s you are using, shape/geometry of the specimen, and how the specimen is being clamped/hold in place will affect the load that can be used for your application.
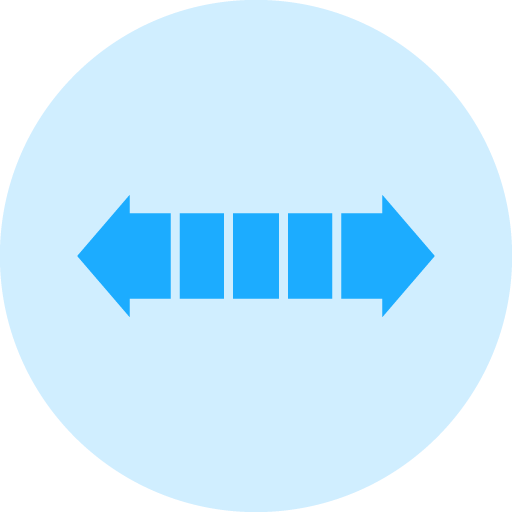
Bond Hardness
Ability of the bond matrix to hold diamonds. As the hardness of the bond is increased, its diamond retention capabilities increase as well. However the trade off is slower cutting speed. Life of the diamond blade is usually increased with hardness of its bond matrix. Bonds are designated on their scale of hardness from Soft, Medium, and Hard. There are dozens of variations and classification schemes based on bond degree of hardness or softness.
Using diamond blades with optimum bond hardness for your application is important to successful precision diamond sawing operation. Bond matrix that is too soft for the material being cut will release diamond particles faster than needed, resulting in faster wear and shorter diamond blade life. On other hand bond matrix that is too hard will result in much slower cutting speeds and require constant dressing to expose the next diamond layer. As rule of thumb, harder materials such as sapphire and alumina generally require a softer bond. Whereas softer and more brittle materials require a harder bond.
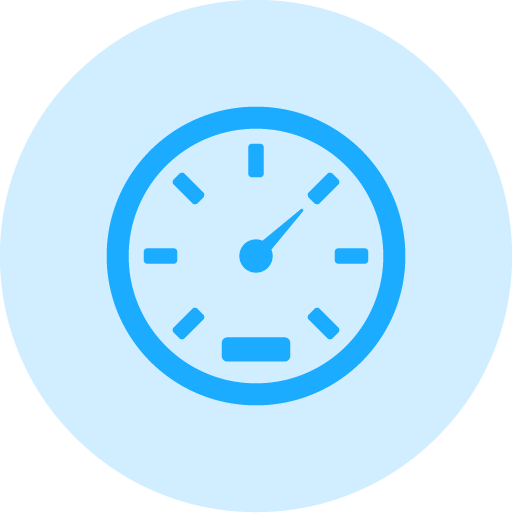
Blade Speeds/RPM’s
Most wafering blades are used between 50 to 6,000 RPM’s Typically harder and more denser materials such as Silicon Carbide, are cut at higher RPM’s/speeds Where more brittle materials such as silicon wafers and gallium arsenide are cutting at lower RPM’s. Low Speed saws RPM’s are typically limited from 0 to 600 RPM’s. Where high speed saws offer much large variety of cutting speeds from 0 to 6,000 RPM’s.
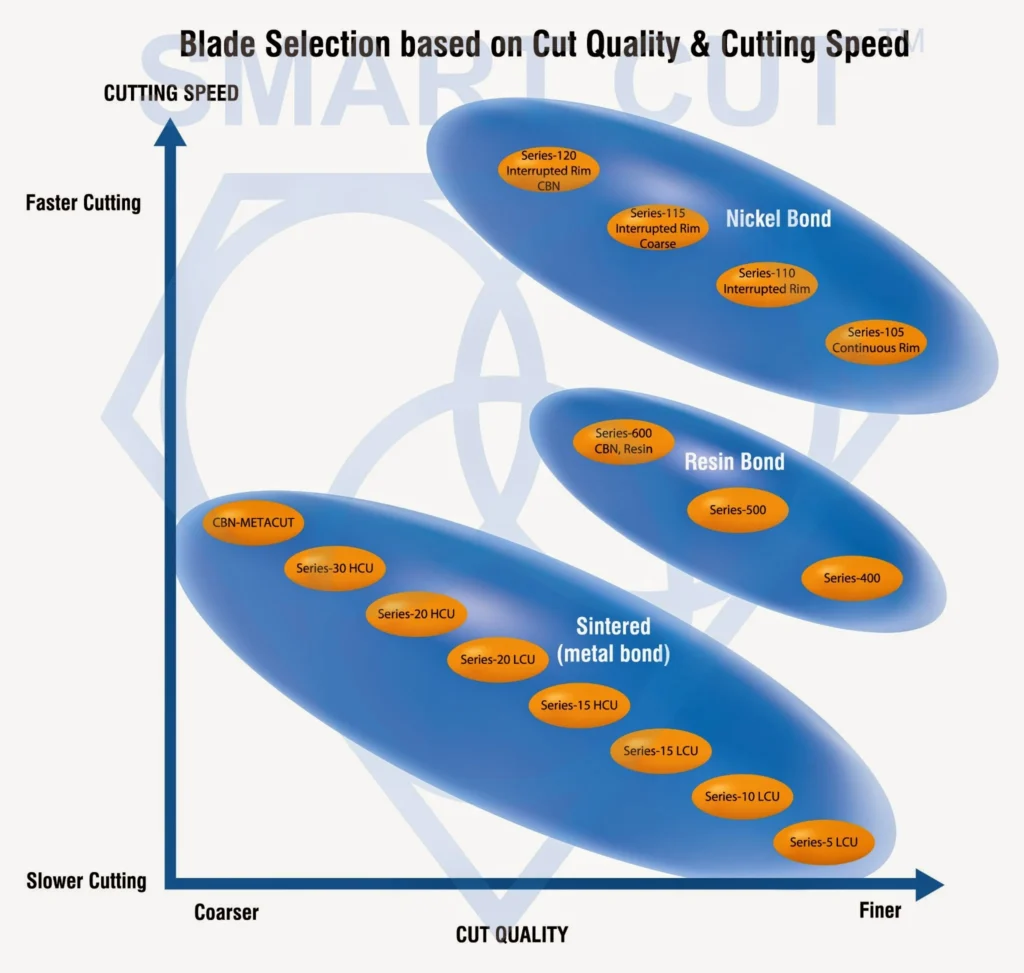
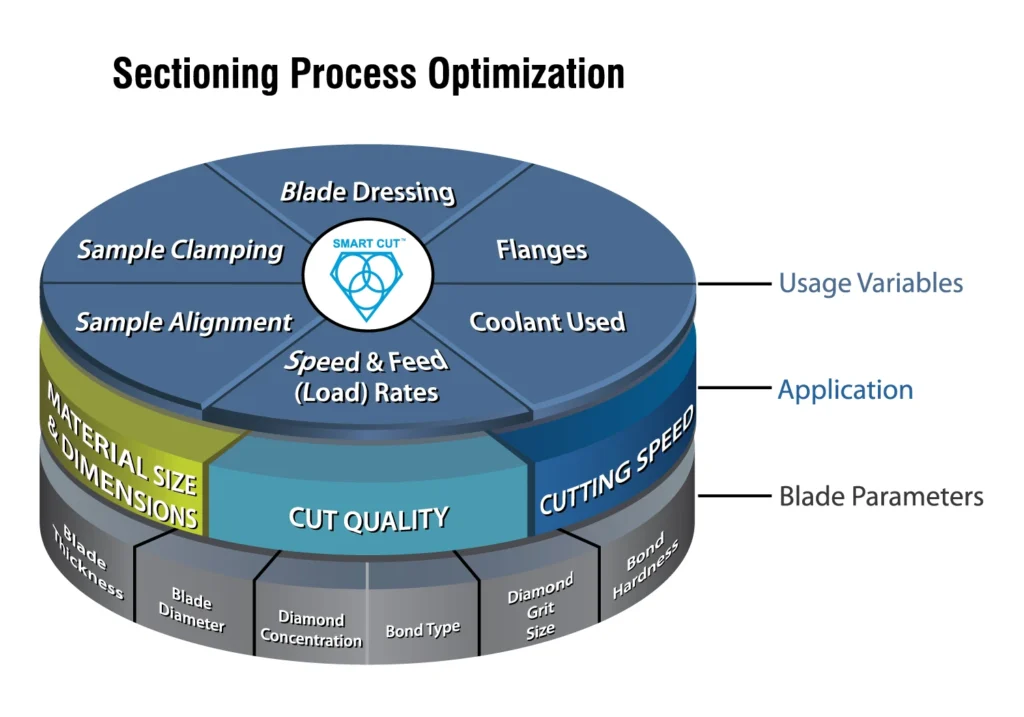
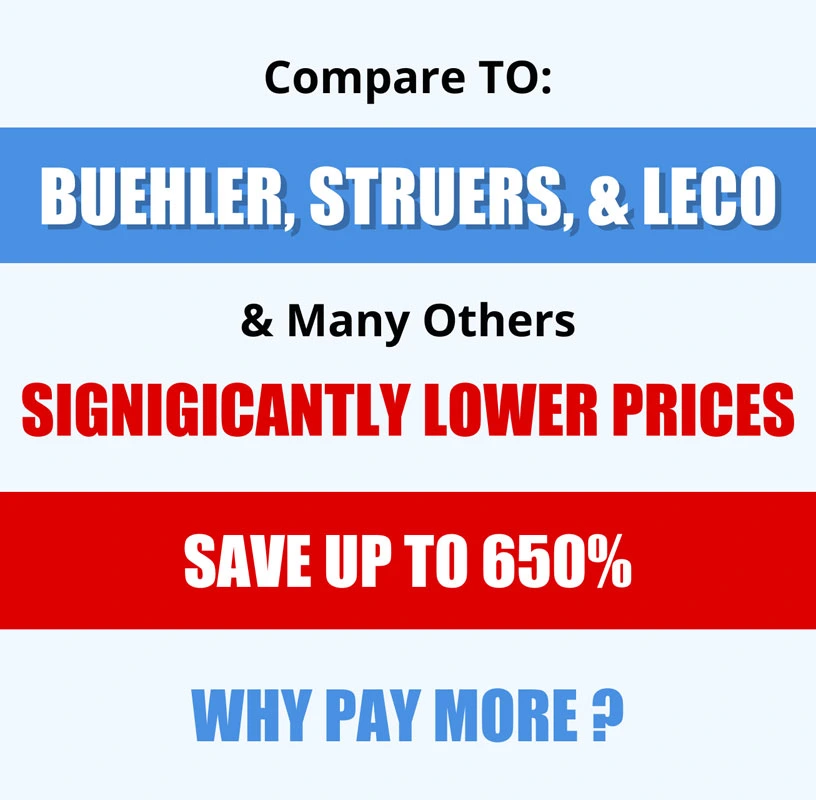
Why Work With Us?
Read More
We produce diamond consumables for some of the leading world OEM manufacturers. We offer Manufacturers Direct Prices
We have the largest variety of diamond & cbn wafering blades available in stock. As well as large inventory of diamond & abrasive consumables. We also custom manufacture diamond and cbn tools, consumables and machines to better fit customer specific needs. Just about any tools & consumables can be designed and manufactured per client drawing or specificrtion
WE ARE A PARTNER IN YOUR SUCCESS
Our proprietory diamond chemistory , precision , manufacturing metods , quality control methods allow us to control and regulate the dozens of variables to that affect consumable life , quality , and consistency.
The more you understand about what we can do for you the better our partnership will be. Here you will find most comprehensive source of information and optimizing and improving your cutting , drilling , grinding and polishing on the web. find everything you ever wanted to know about diamond tools.
AMERICAN MANUFACTURER
"ONE OF THE MOST EXPERIENCED COMPANIES IN THE INDUSTRY"
Save Money Save up to 650%
COMPARE TO: BUEHLER , STRUERS , LECO & MANY OTHERS
Large Inventory & Custom Manufacturing
Umatched Technical Support
Developing close ties with our customers is the foundation of our business. At the core of
our company is a team of world class engineers, knowledgeable customer service personnel here to serve you. Whether is designing or manufacturing a special solution. We will go out of our way to optimizing your process to ultimate level of efficiency
Superior Quality & Consistency
EXPECT MORE FROM YOUR TOOLS
Comprehensive Source Of Information For Sample Preparation
Advanced Technology
As one of the few remaining independent U.S.Diamond Tool & machine builders. We have the experience & tradition to help you remain at frontier of technology Our experience has been further enhanced by acquiring assets and processes from some of the oldest American tool
manufacturers, along with their decades of experience and R& D. This has positioned us as one of the most experienced companies in the industry .Depend on us to bring you technology of tomorrow today.
Experience Makes All The Differences
Over the years we have worked with some of the leading Fortune 500 companies , thousands of universities , government and private research labs , and small organisations. We have made thousands of custom tools , built custom machines , work-holding fixtures , etc for hundreds of applications. Many of our staff members have been working in their respective fields for over 50 years and have gained a wealth of knowledge over the years
Let Us Help You
Related Products
SMART CUT® CBN WAFERING BLADES SINTERED (METAL BOND)
SMART CUT® Series 3000R Resin Bond, Diamond Cut Off Blade
Resin Bond Diamond Cut off blades (Fine Size Diamond) for use on manual tile saws
SMART CUT® Series 3000R are the highest quality & most commonly used Resin Bond Diamond Cut off Blades / Cut Off Wheels available today. Finer Diamond Grit Size, and Slightly Higher Diamond Content then the SMART CUT Series 2000R blades. They are used for cutting very thin wall tubing, more fragile material, that need best surface finish possible to achieve. Cutting speed would be slower then the 2000R series. These blades cut more slowly due to their finer grit size, which provides less aggressive material removal. They are better suited for precision tasks where cut quality is prioritized over speed. The finer grit results in a much smoother surface finish with minimal chipping, making them ideal when a high-quality, clean cut is needed, especially for delicate materials The resin bond diamond cut off blades / cut off wheels excel in delivering superior cut quality compared to other diamond cutting blade, making them ideal for applications where cut quality and surface finish is highly important. They are designed to operate at higher speeds to minimize heat generation and improve surface finishes.SMART CUT® Series 400 Wafering Blade, Resin Bond
Resin Bond Diamond Wafering Blades for use on Precision & Laboratory type Cut off Saws
SMART CUT® Series 400 are Designed for Precision, Chip Free cutting of wide variety of materials These are very thin kerf blades and are very delicate. Must be used on high precision specialized laboratory cutting saws (not tile saws, trim saws, etc) The diamond section can be easily broken if the material moves while cutting, blade is dropped, material is feed to fast into the blade, material is not fed consistently straight into the blade (shifts position) etc. Diamond Size is Medium providing faster cutting speed, while still providing surface quality unmatched by 95% of other blades.SMART CUT 105N Diamond, Nickel Bond Wafering Blades INTERRUPTED RIM
SMART CUT™ Series 105N more freer cutting & aggressive than continuous rim nickel bond wafering blades. Best Suited for cutting larger variety of micro-electronics packages, pcb boards, plastics, composites, soft and precious metals, fish and human bones, graphite, GRP, FR4. Core steel with memory. Always snaps back to its original shape no matter how much bent.
Standard arbor size inside diameter is ½” (12.7mm) (* we can modify arbor size of any blade to anything you want same day for a small additional fee, if needed)
SMART CUT® Series 100N Wafering Blade, Nickel Bond
NICKEL BOND, DIAMOND CONTINUOUS RIM
SMART CUT® Series 100N will provide finer cut quality than interrupted rim nickel bond wafering blades. Best suited for cutting soft and fragile crystals, silicon wafers & substrates, fiberglass, glass fibers. made with stainless steel core Standard arbor size inside diameter is ½” (12.7mm) (* we can modify arbor size of any blade to anything you want same day for a small additional fee, if needed) Nickel Bond Diamond Cut off blades Blades usually have a single layer of diamonds, held by a tough durable nickel alloy. diamond particles to protrude from the bond matrix, providing a free, faster cutting action with minimum heat generation.Diamond, Nickel Bond Cut Off Blades for Laboratory & Other Saws
SMART CUT® Fully Sintered (Metal Bond) Diamond & CBN, Wafering Blades
SMART CUT® Fully Sintered (Metal Bond) diamond wafering blades are fully sintered from OD to ID of the blade. Meaning they have diamonds completely impregnated through the blade. Unlike standard diamond & cbn wafering blades with steel core and diamond section. Instead of having a steel core and small diamond bond edge (usually 1/8"/3.2mm). The diamond edge is all the way through the blade, from its Outside Diameter to Inside Diameter of the blade. You can use until the entire Outside Diameter of the blade is consumed.
Recently Viewed Products
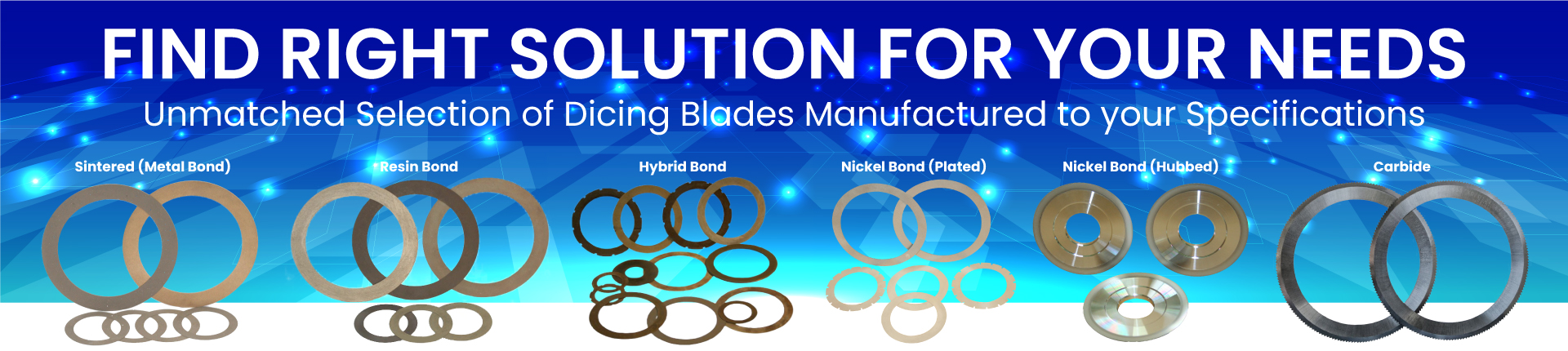
ARE YOU USING RIGHT DIAMOND & CBN BLADES
FOR YOUR APPLICATION?
LET US
HELP YOU
HAVING ISSUES WITH
YOUR CURRENT DIAMOND & CBN BLADES?
Knowledge Center
02
Jun
How to Properly Use Precision Diamond & CBN Blades
The diamond blade itself is only a small factor in your cutting operation. Successful diamond sawing is both an art & science. Requiring proper use and understanding of the right: RPM's, Coolants, Equipment, Dressing Devices, Accessories...
02
Jun
Precision & Ultra Thin Diamond Blade Guide
Diamond and CBN blades are available in an extensive array of varieties, each differing in bond types, manufacturing methods, and design specifics. Ultra Thin & High Precision Diamond Blades are particularly versatile, applicable...
02
Jun
How to Improve & Optimize Your Diamond Sawing Operation
There are numerous variables that affect the performance of diamond and CBN cutting blades. Understanding these variables will help end users select the right diamond blade specifications for their applications and optimize their...
02
Jun
Evaluating & Comparing Diamond Blades
Share this Article with Friend or Colleague
Proper testing procedures and methodologies must be set up and used to obtain accurate as well as repeatable testing results. This article will discuss several simple procedures which...
31
Jul
Top 5 Diamond & CBN Cutting Blade Performance Metrics
Share this Article with Friend or Colleague
When evaluating diamond and cubic boron nitride (CBN) cutting blades, it's crucial to consider key performance metrics and criteria. Different applications have varying goals, making it...
01
Aug
Diamond & CBN Cutting Blade Performance Metrics that you Should Know
Share this Article with Friend or Colleague
When evaluating diamond and cubic boron nitride (CBN) cutting blades, it's crucial to consider key performance metrics and criteria. Different applications have varying goals, making it important to...
02
Aug
Total Cost of Ownership & Why its Important
Share this Article with Friend or Colleague
Diamond and CBN cutting blades are available in a myriad of specifications, with virtually limitless options. The industry is saturated with numerous manufacturers, each professing to offer the...
05
Aug
Understanding Tradeoffs- Searching for Perfect Diamond & CBN Blade
Share this Article with Friend or Colleague
Choosing the right blade diamond or cbn blade can significantly impact efficiency, cost, and quality. However, this is not simple and clear cut process. Selecting the optimal blade...
- Unmatched Selection For Many Applications
- Superior Quality & Consistency
- Immediate Worldwide Delivery
- Technical Support & Expertise
- American Based Manufacturer
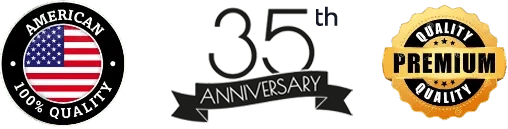

- Different Product
- Different Technology
- Different Company
- Expect MORE from your tools
Let Us HELP You!
Subscribe To Our Newsletter
Signup for email offers, updates, and more
Contact Us
- 25205 & 25201 Avenue Tibbits Valencia CA 91355 USA
-
Phone : (661) 257-2288
FAX : (661) 257 -3833 - lel@ukam.com
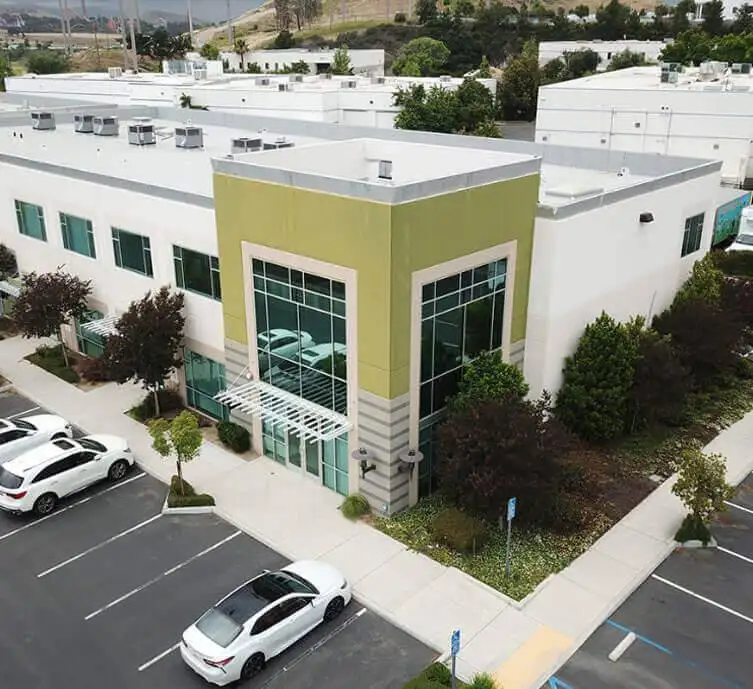
UKAM Industrial Superhard Tools is a U.S. High Technology, Specialty Diamond Tool & Equipment manufacturer. We specialize in producing ultra thin, high precision cutting blades, precision cutting machines diamond drills, diamond micro tools, standard & custom advanced industrial diamond tools and consumables.
- 25205 & 25201 Avenue Tibbits Valencia CA 91355 USA
-
Phone : (661) 257-2288
FAX : (661) 257 -3833 - lel@ukam.com
- 25205 & 25201 Avenue Tibbits Valencia CA 91355 USA
-
Phone : (661) 257-2288
FAX : (661) 257 -3833 - lel@ukam.com
DIAMOND TOOLS BY BOND
EQUIPMENT
KNOWLEDGE CENTER
OUR PRODUCTS
COMPANY
CUSTOMER SERVICE
Shipping Methods


Safe & Secure Payments

© Copyright 1990-2025. UKAM Industrial Superhard Tools – Terms of Use