Table of Contents
TogglePolishing is important step in metallography & sample preparation for revealing the true microstructure of materials, including grain boundaries, phases, and inclusions, which provide insights into material properties and history. This guide is designed to cover everything you wanted to know about polishing.
Why is polishing important?
Polishing is a crucial step in metallography, essential for revealing the true microstructure of materials, including grain boundaries, phases, and inclusions. This process provides critical insights into material properties and history, aiding in various scientific and industrial applications.
What is the goal of polishing?
The primary goal of polishing is to achieve a smooth, reflective surface by removing scratches and deformations introduced during grinding. A scratch-free surface ensures uniform light interaction, enhancing the clarity and contrast of microstructural features under microscopic examination. Accurate representation of microstructures is vital; proper polishing techniques prevent artifacts like scratches, smearing, and overpolishing, which can distort observations.
Enhanced microscopy relies on well-polished samples. For optical microscopy, a uniform reflective surface improves the visibility of fine details, while for electron microscopy, particularly SEM, a polished surface is essential for high-resolution images and techniques like EBSD. Polishing in metallography extends to various industrial applications beyond academic research.
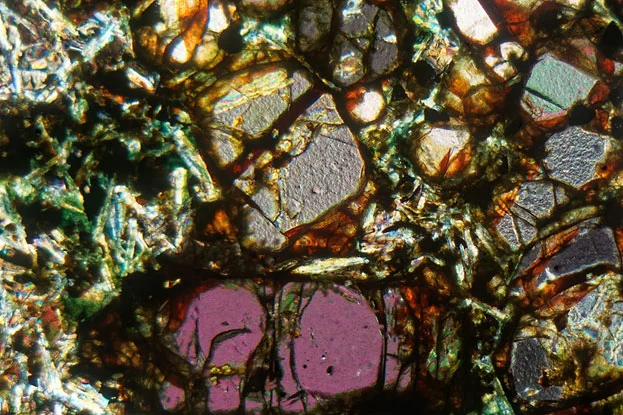
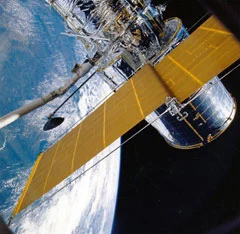
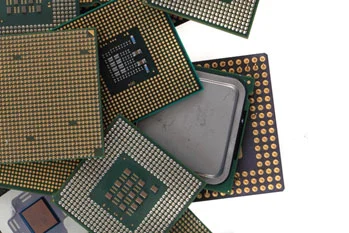
In materials science, polishing aids in developing materials with desirable properties, such as high strength and durability. In metallurgy, it evaluates processing effects on metal microstructures and assists in quality control by detecting defects.
In industries such as aerospace, automotive, and electronics, polished samples ensure materials meet stringent specifications and standards. Polishing helps identify manufacturing defects, ensuring consistent and reliable production processes. During failure analysis, polished samples enable forensic engineers to determine root causes and develop prevention strategies.
Polishing also plays a crucial role in the study and application of advanced ceramics and composite materials. By revealing the microstructure, polishing helps optimize these materials for high-performance applications, such as thermal barriers and biomedical implants. In nanotechnology, polishing prepares samples for high-resolution analysis, facilitating the development of materials with novel properties for electronics, medicine, and energy storage.
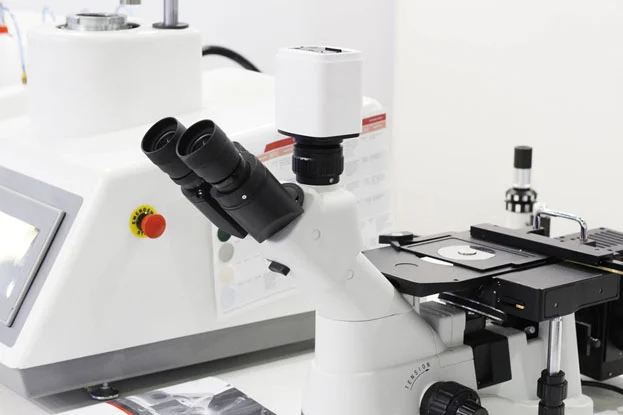
Typical Polishing Process
Laboratories vary significantly in their polishing procedures, often influenced by outdated methods or advice from sales representatives. Some labs may use up to five polishing steps, believing this will produce better quality surfaces. However, excessive polishing can lead to issues such as rounded edges, relief of harder constituents, and removal or relief of non-metallic inclusions. On the other hand, laboratories using only two or three polishing steps may achieve superior surface quality by minimizing overpolished conditions and focusing on the effectiveness of each step.
The polishing process typically involves covering a wheel with a suitable cloth, applying an appropriate polishing media and lubricant, and polishing until all traces of the prior surface finish are removed. Traditional polishing steps include coarse polishing with 6 or 3µm diamond abrasives and fine polishing with 1µm diamond on appropriate cloths. Proper polishing avoids issues like disturbed metal structures, pitting, dragging out inclusions, comet tailing, staining, and relief differences, ultimately producing a deformation-free surface necessary for accurate microstructural analysis.
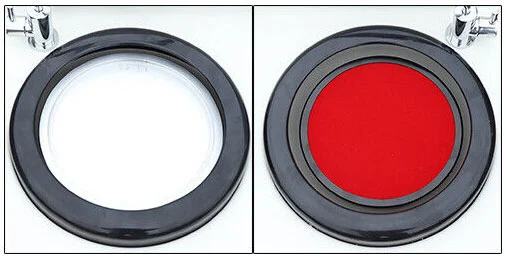
Principles of Polishing
Polishing in metallography is defined as the process of creating a flat, smooth, and scratch-free surface on a material sample. This process is vital for preparing samples for microscopic examination, where the true microstructure of the material can be observed and analyzed.
The primary objective of polishing is to achieve a flat, scratch-free surface. During the initial grinding stages, coarse abrasives remove material and eliminate larger imperfections. However, this process leaves behind scratches and deformations. Polishing aims to remove these scratches, gradually refining the surface with progressively finer abrasives until a mirror-like finish is obtained. This smooth, reflective surface is crucial for microscopic examination, as it ensures that the light interacts uniformly with the material, enhancing the visibility of microstructural features.
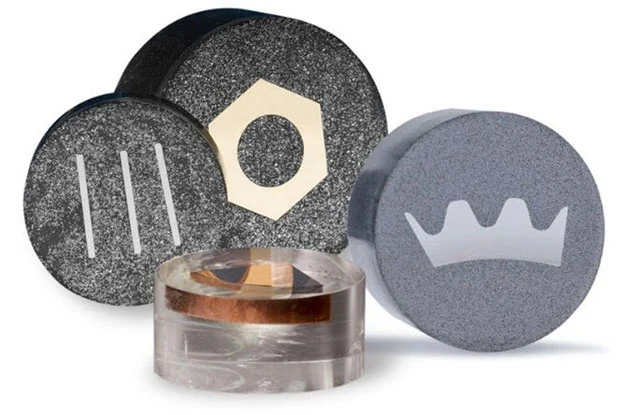
Another key objective of polishing is to prepare samples for microscopic examination. A well-polished sample is essential for both optical and electron microscopy. In optical microscopy, a smooth, scratch-free surface improves the clarity and contrast of the observed microstructures, allowing for accurate identification and analysis of features such as grain boundaries, phases, and inclusions. In electron microscopy, particularly in scanning electron microscopy (SEM), a polished surface is necessary to obtain high-resolution images and perform advanced analytical techniques such as electron backscatter diffraction (EBSD).
Additionally, achieving a polished surface free of artifacts is critical. Artifacts such as scratches, pull-outs, and smearing can obscure or distort the true microstructure, leading to inaccurate interpretations. Proper polishing techniques prevent these artifacts, ensuring that the observed microstructure accurately represents the material's inherent properties and characteristics.
Stages of Polishing
Polishing in metallography involves a series of systematic stages designed to transform a rough, uneven sample surface into a smooth, reflective one that is ideal for microscopic examination. The stages include coarse grinding, fine grinding, polishing, and final polishing. Each stage plays a crucial role in progressively refining the sample surface to reveal its true microstructure.
Coarse Grinding - Coarse grinding is the initial stage of the polishing process. The primary goal here is to remove any large irregularities, such as surface damage, deformations, or significant material variations from the sample. This stage uses coarse abrasives, typically silicon carbide or alumina, mounted on a rotating grinding wheel or disc. The coarse grit (ranging from 60 to 240 grit) ensures rapid material removal, flattening the sample surface while introducing uniform scratches. Coarse grinding sets the foundation for subsequent stages by creating a relatively even surface, essential for effective fine grinding and polishing.
Fine Grinding - Following coarse grinding, fine grinding further refines the sample surface. This stage uses progressively finer abrasives, generally ranging from 320 to 1200 grit, to remove the deeper scratches left by the coarse grinding stage. The goal of fine grinding is to eliminate any residual deformation and create a smooth, flat surface with minimal scratches. Fine grinding is crucial because it prepares the sample for the polishing stages, ensuring that any remaining scratches are shallow and easily removable. The transition from coarse to fine grinding must be carefully managed to avoid introducing new artifacts or damaging the sample surface.
Polishing - Polishing is the stage where the sample surface is further refined to achieve a smooth, reflective finish. This stage typically involves the use of polishing cloths combined with fine abrasives such as alumina, diamond, or silica suspensions. The abrasives are much finer than those used in the grinding stages, often in the range of 3 to 1 micron. Polishing removes the fine scratches left by the grinding stages, producing a surface that is smooth and suitable for microscopic examination. The choice of polishing cloth and abrasive depends on the material being polished and the desired surface quality. Proper polishing techniques ensure that the sample surface is free from artifacts, enhancing the visibility of microstructural features.
Final Polishing - The final polishing stage is the last step in the polishing process, aimed at achieving the highest possible surface quality. This stage often uses extremely fine abrasives, such as colloidal silica, which can be as fine as 0.05 microns. The final polishing cloth is also chosen for its ability to produce a high-quality finish without introducing new scratches or artifacts. The objective of final polishing is to produce a mirror-like surface that is entirely free of scratches, deformation, and contamination. This pristine surface is crucial for high-resolution microscopic examination, allowing for detailed and accurate analysis of the material's microstructure.
Polishing Machines
Polishing machines are essential tools in the metallographic preparation process, providing the means to achieve the smooth, reflective surfaces required for accurate microscopic examination. These machines vary in complexity and automation, offering different levels of control and efficiency to suit various needs and applications.
Types of Machines
Manual Polishing Machines
Manual polishing machines are the most basic type, requiring the operator to manually control the polishing process. These machines typically consist of a rotating wheel or disc on which the polishing cloth and abrasives are applied. The operator manually applies the sample to the polishing surface, adjusting pressure and movement as needed.
Manual machines are cost-effective and offer high control over the process, making them suitable for small-scale operations or research laboratories where customization and hands-on control are preferred.
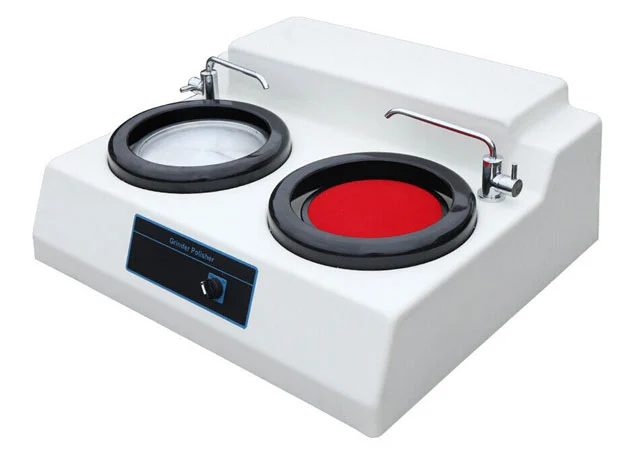
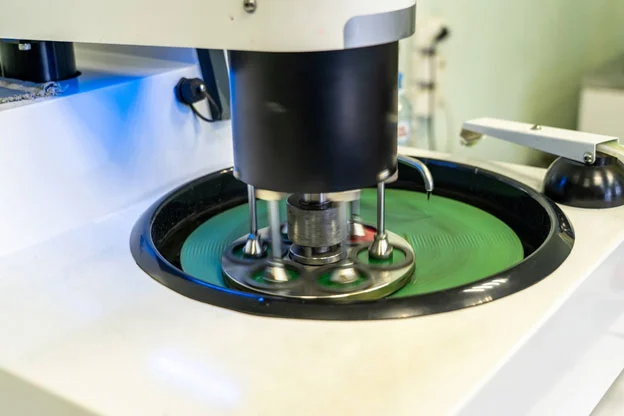
Semi-Automatic Polishing Machines
Semi-automatic polishing machines provide a balance between manual control and automation. These machines allow for some automated functions, such as rotation speed and time settings, while still requiring manual intervention for tasks like changing polishing cloths and applying abrasives. They often include features like programmable settings, which enable repeatable processes and consistent results.
Semi-automatic machines are ideal for laboratories that need to process multiple samples with consistent quality but still require some level of manual control and flexibility.
Automatic Polishing Machines
Automatic polishing machines offer the highest level of automation, performing most of the polishing process without manual intervention. These machines can automatically change polishing stages, apply abrasives, and control pressure and movement. They are equipped with advanced features such as programmable sequences, automatic sample loading and unloading, and digital controls for precise parameter adjustments.
Automatic machines are designed for high-throughput environments where consistency, efficiency, and minimal operator involvement are critical, such as in large industrial laboratories or production facilities.
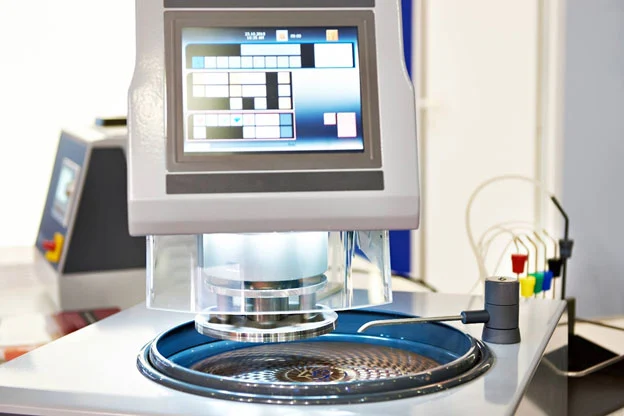
Key Features and Selection Criteria
When selecting a polishing machine, several key features and criteria should be considered to ensure the machine meets the specific needs of the application:
Automation Level - The degree of automation required depends on the volume of samples and the need for consistency. Manual machines are suitable for low-volume, high-control scenarios, while automatic machines are best for high-throughput, repetitive tasks.
Programmability - Machines with programmable settings allow for the creation of repeatable processes, ensuring consistent results across multiple samples. This feature is particularly valuable in environments where standardized procedures are essential.
Sample Size and Number - The size and number of samples to be polished simultaneously can influence the choice of machine. Some machines are designed to handle multiple samples at once, improving efficiency for high-volume applications.
Flexibility and Versatility - The ability to use different polishing cloths, abrasives, and accessories is important for handling a variety of materials and polishing requirements. Machines that offer versatility are more adaptable to different tasks and sample types.
Ease of Use and Maintenance - User-friendly interfaces, easy access to components, and straightforward maintenance procedures enhance the overall usability of the machine. Features such as touch-screen controls and automated maintenance alerts can significantly improve the user experience.
Quality and Durability- The build quality and durability of the machine are critical for long-term performance and reliability. Investing in a high-quality machine from a reputable manufacturer can ensure consistent results and reduce downtime due to maintenance or repairs.
Cost and Budget - Budget constraints are always a consideration. While manual machines are more cost-effective, semi-automatic and automatic machines offer higher efficiency and consistency, potentially justifying the higher initial investment through long-term savings and improved productivity.
Types of Discs and Cloths for Different Materials
Polishing discs and cloths come in various types, each designed to handle specific materials and achieve particular finishes. The most common types include:
Metal Bond and Resin Bond Diamond Discs: These are used primarily for the initial grinding stages. Metal bond diamond discs, often embedded with coarse abrasives, are ideal for hard materials such as metals and ceramics. Resin Bond diamond discs are slightly less aggressive and are used for softer materials or to refine the surface after initial grinding.
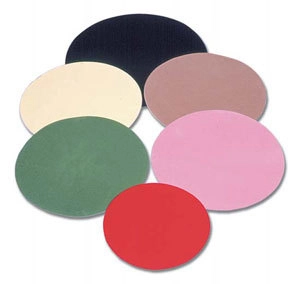
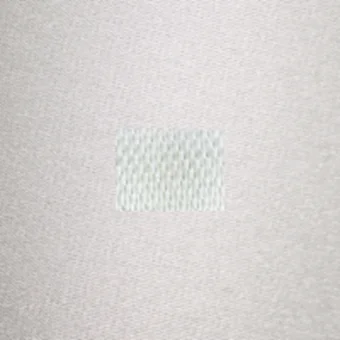
Textile-Based Cloths:
These cloths, made from materials like canvas, felt, or silk, are commonly used in the intermediate and final polishing stages. The texture and durability of textile-based cloths make them suitable for polishing metals and alloys, providing a good balance between material removal and surface finish.
Synthetic Cloths:
Made from materials such as polyester or polyurethane, synthetic cloths are designed for specific polishing needs. For instance, low-nap cloths are used for fine polishing of hard metals, while high-nap cloths are better for softer materials or for achieving a high-gloss finish.
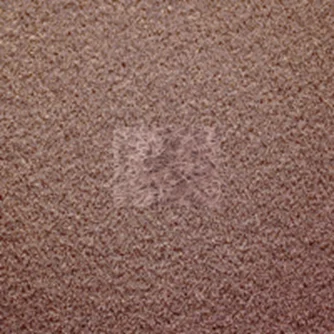
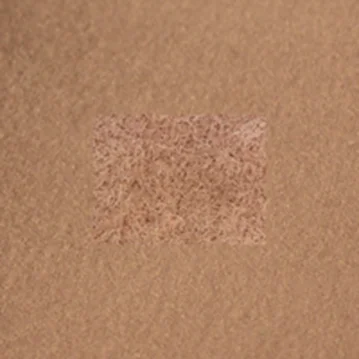
NAP and Non-NAP Cloths:
NAP cloths have a textured surface that is effective in holding fine polishing abrasives, making them suitable for final polishing stages where a high-quality finish is required. Non-NAP cloths have a smooth surface and are used in intermediate polishing stages to remove minor scratches and prepare the surface for final polishing.
Selection Based on Sample Material and Desired Finish
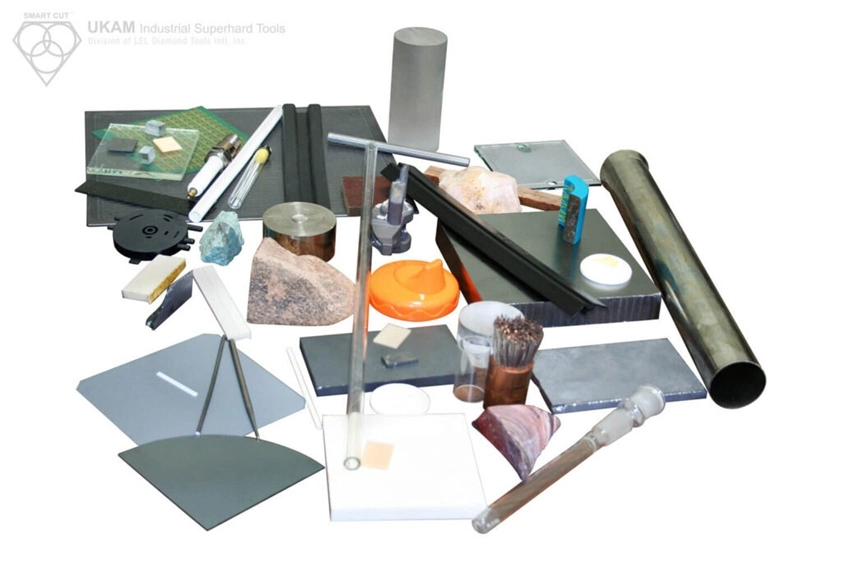
The choice of polishing discs and cloths depends largely on the sample material and the desired finish. Selecting the right combination ensures efficient material removal and the achievement of a smooth, artifact-free surface.
Hard Metals and Alloys: For hard metals such as steel or titanium, metal bond or resin bonded discs are used in the initial grinding stages to quickly remove material and flatten the surface. Subsequent stages utilize synthetic or textile-based cloths with progressively finer abrasives. For the final polishing, NAP cloths with diamond or colloidal silica suspensions are preferred to achieve a mirror-like finish.
Soft Metals: When working with softer metals like aluminum or copper, resin bonded discs or fine-grit silicon carbide papers are used for grinding to avoid excessive scratching. Polishing is then carried out using synthetic or textile-based cloths, with low-nap cloths being preferred for intermediate stages and high-nap cloths for the final finish.
Ceramics and Hard Materials:
Ceramics require aggressive initial grinding with metal bond or resin bonded discs. For polishing, synthetic cloths are generally used, as they provide the necessary durability and effectiveness. The final polishing often involves NAP cloths with diamond suspensions to achieve a high-quality finish without introducing new artifacts.
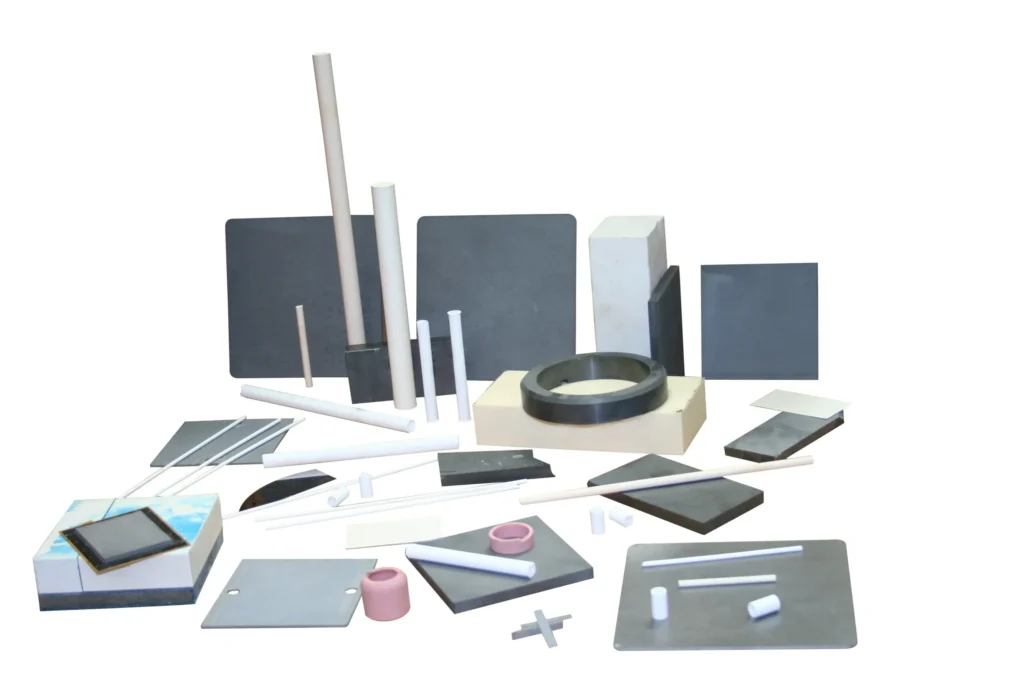
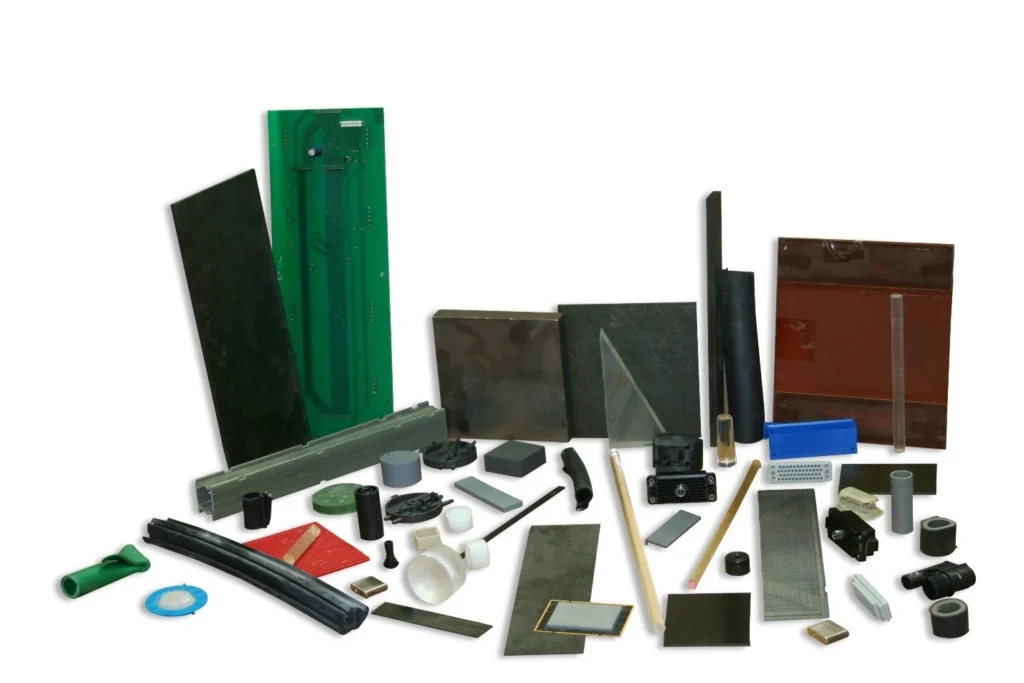
Composite Materials:
The heterogeneous nature of composites requires careful selection of polishing media. Initial grinding can be done with resin bonded discs, followed by polishing with textile or synthetic polishing cloths. The final polishing stage should use NAP cloths with fine abrasives to ensure that both the matrix and the reinforcement phases are evenly polished.
Advanced Materials:
For materials like advanced ceramics or superalloys, a combination of synthetic polishing cloths and specialized abrasives is often necessary. Intermediate stages may use non-NAP cloths to refine the surface, while final stages use high-nap or NAP cloths with ultra-fine abrasives to achieve the desired finish.
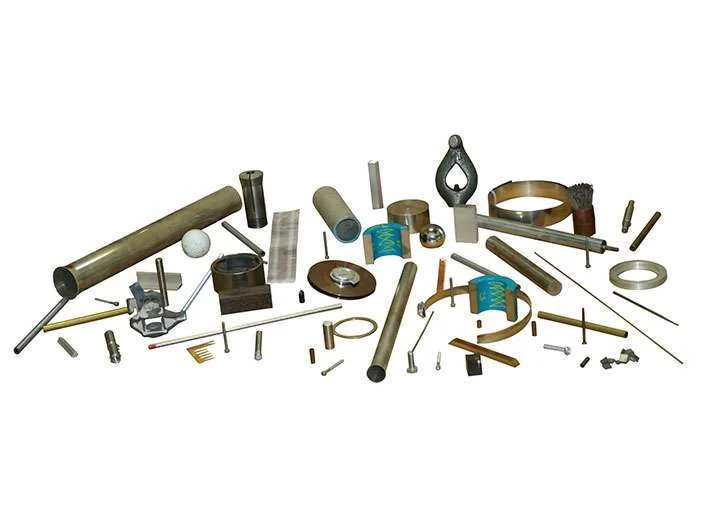
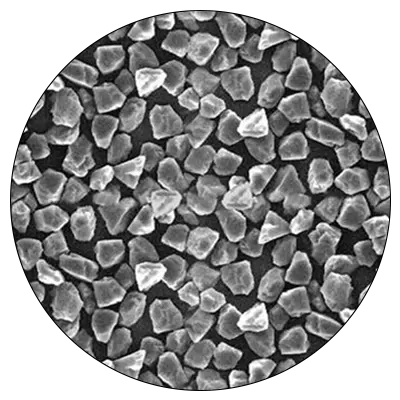
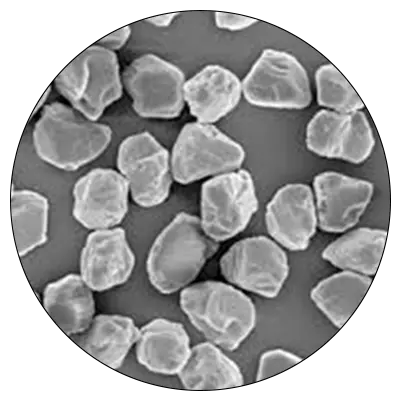
Abrasive Media
Abrasive media are the key components used in the grinding and polishing stages of metallographic sample preparation. They play a critical role in progressively refining the surface of a sample to achieve a smooth, scratch-free finish. The choice of abrasive media depends on the material being processed and the specific requirements of each stage in the polishing process. The most commonly used abrasives include silicon carbide, alumina, and diamond, each offering unique properties suited to different applications.
Types of Abrasives
Silicon Carbide (SiC)
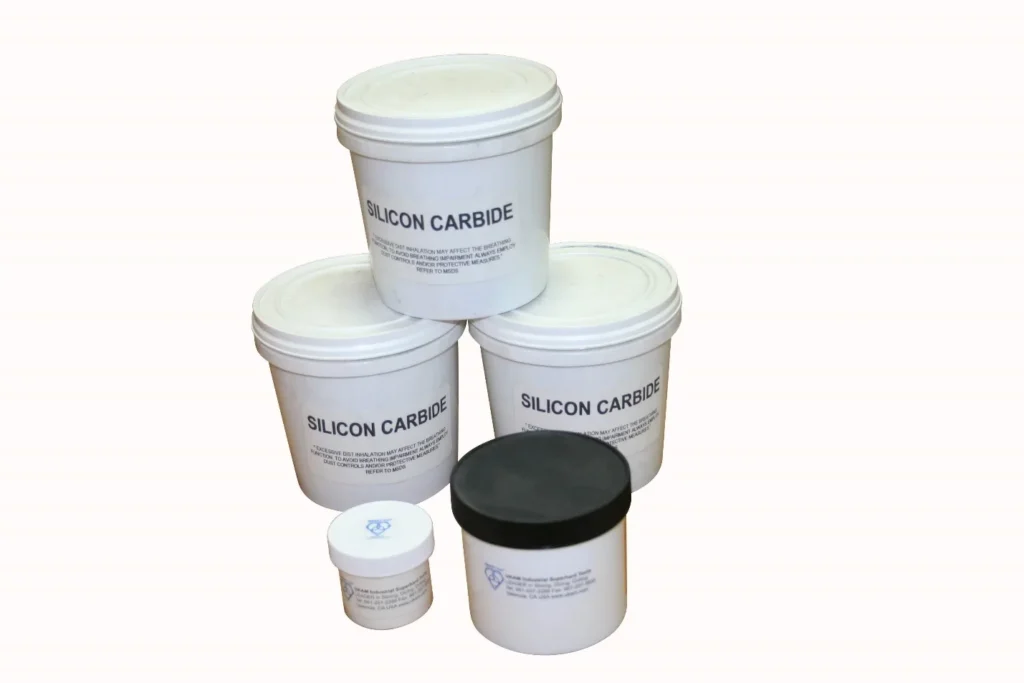
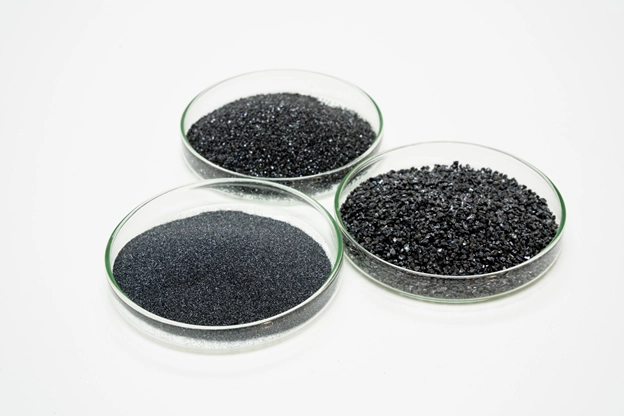
Silicon carbide is a widely used abrasive due to its hardness and relatively low cost. It is typically used in the initial grinding stages. Available in various grit sizes, from coarse to fine, SiC is effective in quickly removing material and flattening the sample surface. It is suitable for a wide range of materials, including metals, ceramics, and composites.
Alumina (Aluminum Oxide)
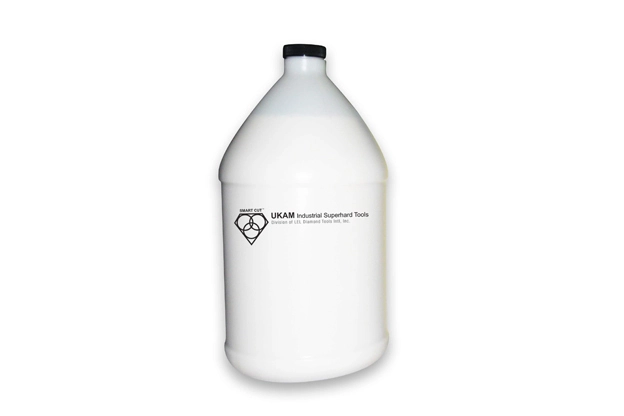
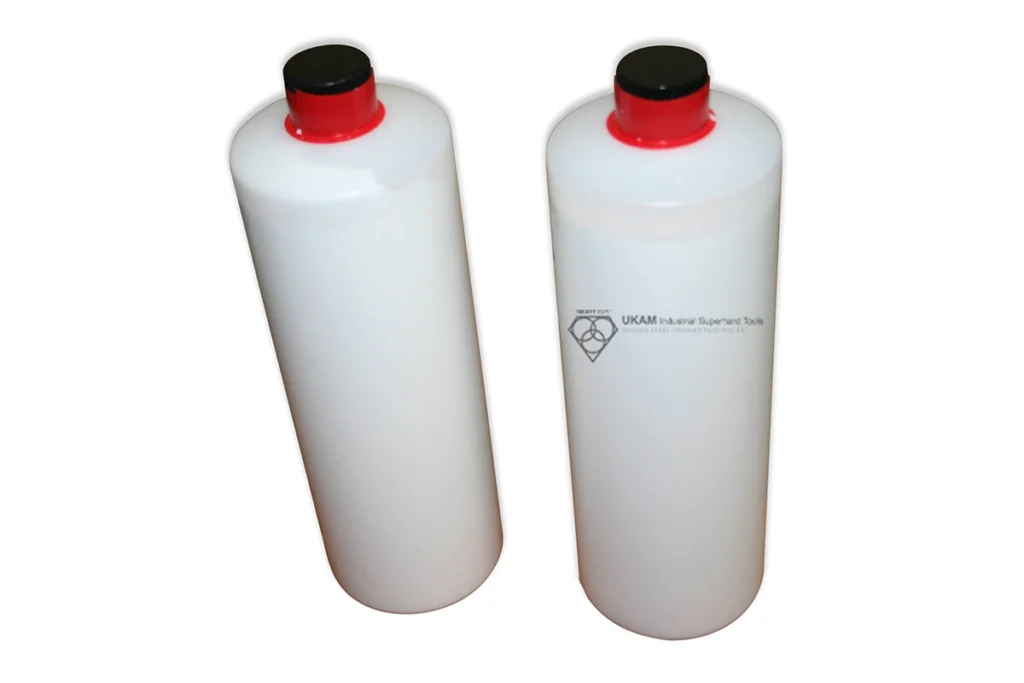
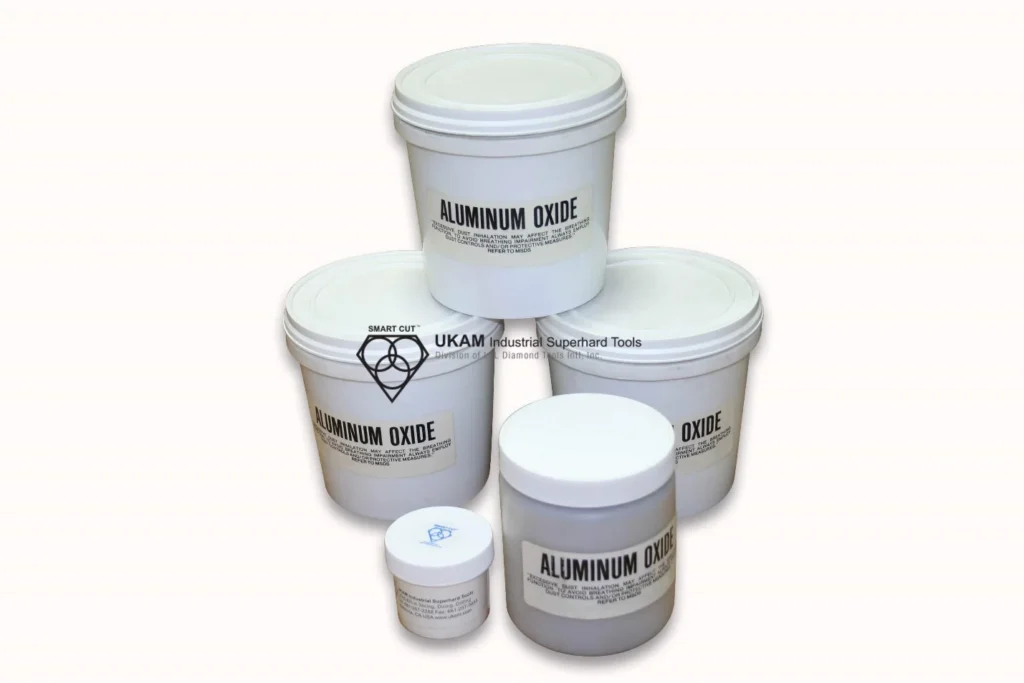
Alumina is a versatile abrasive known for its hardness and durability. It is used in both grinding and polishing stages. It comes in different forms, such as powders and suspensions, and can be used on various polishing cloths. Alumina is particularly effective for polishing softer metals and alloys, providing a good balance between material removal and surface finish.
Diamond
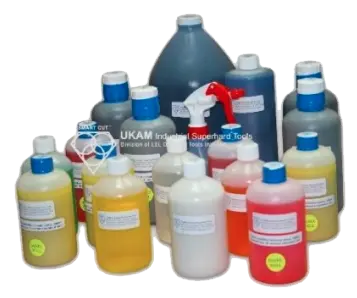
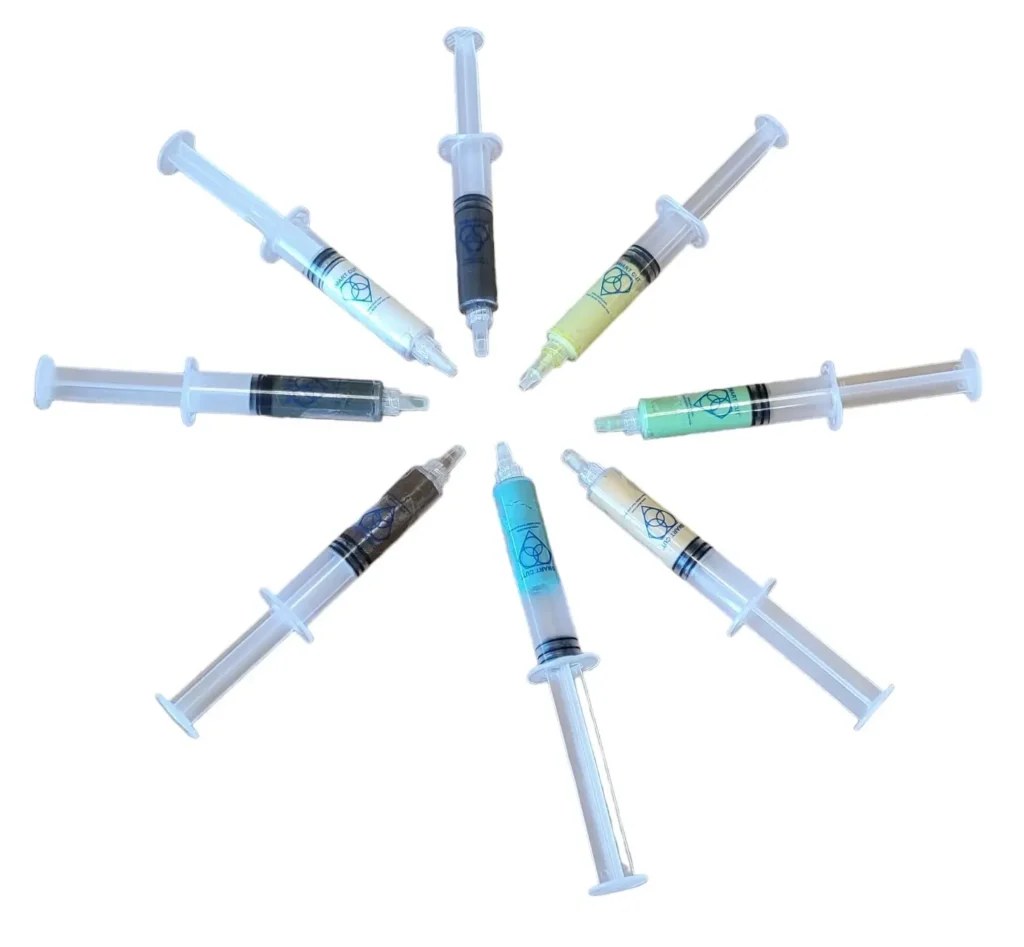
Diamond abrasives are the hardest and most effective media for polishing hard materials. They are used in the later stages of polishing where a fine finish is required. Available as sprays, compounds/pastes, or suspensions, diamond abrasives offer superior cutting action and can produce a high-quality, scratch-free surface. They are ideal for polishing hard metals, ceramics, and advanced materials where precision and high-quality finish are essential.
Colloidal Silica - Colloidal silica is a fine abrasive used in the final polishing stages. It consists of silica particles suspended in a liquid, typically providing a very fine, uniform finish. It is particularly effective for polishing to a mirror-like surface, removing the final layer of fine scratches and achieving a high degree of surface smoothness. Colloidal silica is often used for polishing metals and ceramics where an exceptionally fine finish is required.
Comparison of Types of Abrasives
Abrasive Type |
Description |
Applications |
Forms Available |
Advantages |
Typical Uses |
---|---|---|---|---|---|
Silicon Carbide (SiC) |
A widely used abrasive known for its hardness and low cost. It is effective in quickly removing material and flattening surfaces. |
Initial grinding stages |
Various grit sizes (coarse to fine) |
Quick material removal, effective on a wide range of materials (metals, ceramics, composites) |
Coarse grinding of metals, ceramics, and composites |
Alumina (Aluminum Oxide) |
A versatile abrasive with high hardness and durability, used in both grinding and polishing stages. |
Grinding and polishing of softer metals and alloys |
Powders, suspensions |
Hard and durable, good balance between material removal and surface finish |
Polishing softer metals and alloys, intermediate stages |
Diamond |
The hardest abrasive, providing superior cutting action and high-quality finishes. |
Later stages of polishing, requiring a fine finish |
Sprays, pastes, suspensions |
Superior cutting action, produces scratch-free surfaces, ideal for hard materials |
Polishing hard metals, ceramics, and advanced materials |
Colloidal Silica |
A fine abrasive with silica particles suspended in a liquid, used in final polishing stages. |
Final polishing, achieving a mirror-like surface |
Liquid suspension |
Provides very fine, uniform finish, excellent for removing final fine scratches |
Final polishing of metals and ceramics for a smooth, reflective finish |
Choosing the Right Abrasive for Each Stage of Polishing
Coarse Grinding
In the coarse grinding stage, the primary goal is to remove significant material quickly and flatten the sample surface. Silicon carbide is typically used due to its hardness and cost-effectiveness. Coarse grit sizes, such as 60 to 240 grit, are selected to achieve rapid material removal and prepare the sample for finer grinding stages.
Fine Grinding
Fine grinding aims to refine the surface created by coarse grinding, removing deeper scratches and preparing the sample for polishing. Both silicon carbide and alumina abrasives are used in this stage. Finer grit sizes, ranging from 320 to 1200 grit, are employed to gradually reduce the size of surface scratches and achieve a smoother finish.
Intermediate Polishing
Intermediate polishing involves the use of finer abrasives to further smooth the sample surface and remove any remaining scratches from the grinding stages. Diamond abrasives are often introduced at this stage for hard materials. Alumina and diamond abrasives in micron sizes (e.g., 3 to 1 micron) are used to achieve a finer surface finish, preparing the sample for final polishing.
Final Polishing
The final polishing stage is crucial for achieving a mirror-like, scratch-free surface. The finest abrasives, such as diamond and colloidal silica, are used to remove the last traces of surface imperfections. Diamond pastes or suspensions, often in sizes below 1 micron, are applied using high-nap or NAP cloths to produce a high-quality finish. Colloidal silica is typically used for the ultimate polishing step, especially for samples requiring an exceptionally smooth and reflective surface.
Mechanical Polishing
Mechanical polishing is a critical step in the metallographic preparation process, involving the systematic removal of material to produce a smooth, reflective surface. This process can be performed manually or using automated systems, each with distinct advantages and limitations.
Manual "Hand" Polishing
Manual polishing involves the operator directly controlling the sample against the polishing surface. This method provides high control over the polishing process, making it suitable for small-scale operations or when specific, delicate adjustments are required. The equipment used typically includes a rotating wheel or disc with various polishing cloths and abrasives. The operator adjusts pressure and movement as needed, using different cloths and abrasives sequentially, starting with coarser materials for initial stages and progressing to finer abrasives for final polishing. While manual polishing offers flexibility and control, it is labor-intensive and can lead to variability in results due to differences in operator technique and fatigue.
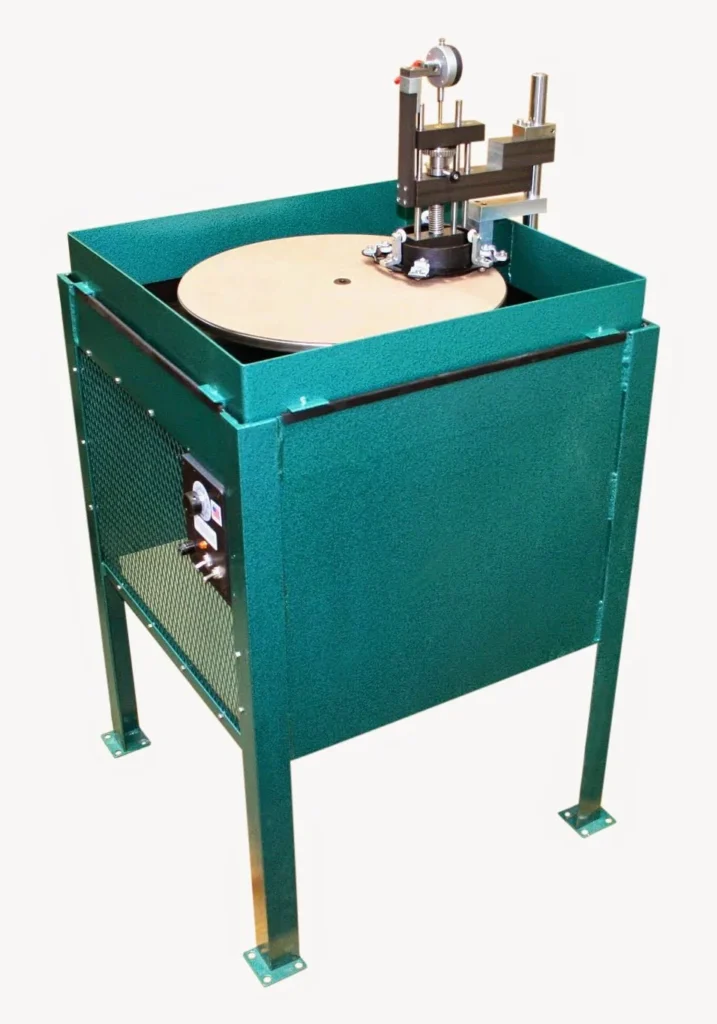
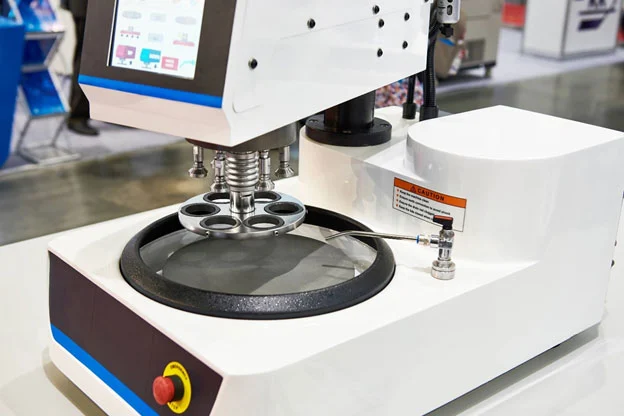
Automated Polishing
Automated polishing systems provide consistent and efficient polishing by automating most of the process. These systems are ideal for high-throughput environments where uniformity and repeatability are critical. Automated polishing machines can handle multiple samples simultaneously, with programmable settings for rotation speed, pressure, and polishing time. Advanced systems may include features like automatic abrasive application, sample loading/unloading, and process monitoring to ensure consistent results. Automated polishing offers high efficiency and consistency, reducing operator involvement and variability. However, the initial cost of automated systems can be high, and they may require more maintenance and technical expertise to operate effectively.
Feature |
Manual Polishing |
Automated Polishing |
---|---|---|
Control |
High control by operator |
Programmed, less manual control |
Flexibility |
High, suitable for delicate adjustments |
Limited to pre-programmed settings |
Labor Intensity |
Labor-intensive, operator-dependent |
Low, minimal operator involvement |
Consistency |
Variable, dependent on operator skill |
High, consistent results |
Throughput |
Low, suitable for small-scale operations |
High, ideal for large-scale operations
|
Initial Cost |
Low |
High |
Maintenance |
Simple, less technical expertise required |
More complex, requires technical expertise |
Efficiency |
Lower, time-consuming |
High, efficient for multiple samples |
Suitability |
Best for small-scale or customized tasks |
Best for high-volume, repetitive tasks |
Polishing Procedures - Coarse Grinding
Objectives and Methods: Coarse grinding is the initial step in the polishing process, primarily aimed at rapidly removing material to create a flat, uniform surface on the specimen. This step is crucial for eliminating surface irregularities and achieving a consistent plane, which is essential for the subsequent grinding and polishing stages. By effectively leveling the surface, coarse grinding helps in reducing the amount of material that needs to be removed in later stages, thus saving time and effort.
Selecting the Right Grit Size: The selection of the appropriate grit size for coarse grinding is determined by the hardness of the material and the extent of material removal required. For hard materials, coarser grits in the range of 60-240 are recommended, as they can efficiently cut through the material and remove larger amounts of material quickly. Softer materials, on the other hand, require finer grits in the range of 320-600 to avoid excessive removal and damage. Using the correct grit size ensures that the grinding process is efficient and that the surface is adequately prepared for finer grinding stages.
Recommended Procedures and Tips: To achieve the best results during coarse grinding, it is advisable to start with the coarsest grit that can effectively remove any damage or irregularities from the sectioning process. This initial step is critical as it sets the foundation for the entire polishing process. Throughout coarse grinding, it is important to use water or an appropriate lubricant. This helps to minimize the generation of heat and the buildup of debris, which can cause damage to the specimen and the grinding equipment. Applying consistent pressure is also essential to ensure that the sample is evenly ground across its entire surface. Uneven pressure can lead to irregular grinding patterns, making it more difficult to achieve a uniform plane. Regularly rotating the sample during grinding can help in achieving a more consistent surface finish and preventing the formation of deep scratches or grooves.
Polishing Procedure - Fine Grinding
Transition from Coarse to Fine Grinding: Transitioning from coarse to fine grinding is crucial in specimen preparation. After coarse grinding has leveled the specimen and removed major imperfections, fine grinding refines the surface further, eliminating the scratches left by coarse abrasives. This step is essential for preparing the specimen for polishing, ensuring the surface is smooth enough for detailed microstructural clarity. The primary goal during this phase is to use progressively finer grit sizes, reducing scratch depth and size, making them easier to remove in polishing.
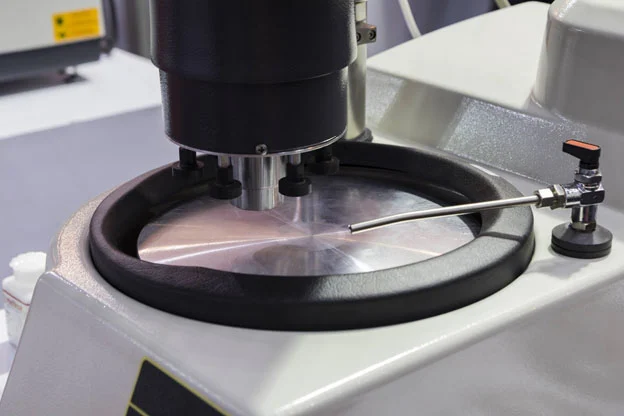
Importance of Sequential Grit Sizes: Using sequentially finer grit sizes during fine grinding is vital. It helps gradually refine the surface, with each successive step removing the scratches left by the previous grit size. This approach prevents new, deep scratches that could complicate polishing. Typically, fine grinding involves grit sizes ranging from 400 to 1200, depending on the material and desired surface quality. Carefully selecting and using appropriate grit sizes in sequence results in a progressively smoother surface, essential for achieving a high-quality polish. Skipping grit sizes or using inappropriate grits can lead to uneven surfaces and residual scratches that are difficult to remove later.
Techniques to Avoid Damage and Maintain Sample Integrity: Maintaining sample integrity and avoiding damage during fine grinding requires careful technique and attention to detail:
-
Steady, Gentle Pressure: Apply consistent, light pressure throughout the grinding process. Excessive pressure can deform the specimen and introduce new surface defects, counterproductive to achieving a smooth finish.
-
Use of Clean Water or Lubricant: Use clean water or appropriate lubricant to cool the specimen and grinding surface, minimizing heat generation and preventing thermal damage. This also helps in removing debris that could scratch the specimen.
-
Regular Rotation of Specimen: Regularly rotate the specimen during grinding to ensure uniform wear and prevent grooves or patterns that could affect subsequent polishing stages.
-
Clean Equipment and Abrasives: Keep grinding equipment and abrasives clean to avoid contamination. Contaminants can scratch the specimen surface and compromise the fine grinding quality.
-
Monitor Grinding Time: Carefully monitor grinding time to avoid overgrinding or undergrinding. Overgrinding can cause excessive material removal and damage, while undergrinding might leave deep scratches that are hard to polish out. Balancing grinding time ensures the surface is adequately prepared without compromising structural integrity.
Polishing Procedure – Intermediate Polishing
Intermediate Polishing Steps: Intermediate polishing bridges the gap between fine grinding and final polishing. It uses finer abrasives (3µm to 1µm) to remove residual scratches and deformations from fine grinding. The goal is to create a surface free from visible imperfections, ready for final polishing. Each step progressively reduces scratch depth and smooths the surface. Consistency and patience are crucial, as rushing can leave scratches that are difficult to remove later.
Choosing Appropriate Polishing Cloths and Suspensions: Choosing the right polishing cloths and suspensions is vital for successful intermediate and final polishing. The choice depends on the material and desired surface finish. Low-nap or medium-nap cloths are commonly used for intermediate polishing, as they hold abrasive particles while maintaining consistent contact with the surface.
Polishing suspensions like diamond, alumina, or colloidal silica are selected based on their abrasive properties and material compatibility. Diamond suspensions are favored for their hardness and efficiency, while alumina suspensions suit softer materials or less aggressive needs. Colloidal silica is often reserved for final polishing to achieve a high-quality, scratch-free finish. Regular application of the suspension ensures a steady supply of abrasive particles, preventing drying out and surface damage.
Techniques for Achieving a Mirror-Like Finish: Achieving a mirror-like finish requires careful attention to detail and proper techniques:
-
Gradual Transition in Abrasive Sizes: Ensure smooth transitions between abrasive sizes. Clean the specimen and cloth thoroughly after each step to remove residual particles that could cause scratches in the next step.
-
Consistent and Light Pressure: Apply consistent, light pressure to avoid new scratches or deformation. Excessive pressure can cause abrasive particles to dig into the surface, creating unwanted marks.
-
Proper Use of Lubricants: Use appropriate lubricants to keep the surface cool and reduce friction. This maintains a smooth polishing action and prevents heat damage. Regularly check and replenish the lubricant for continuous, effective polishing.
-
Rotating and Changing Directions: Periodically rotate the specimen and change polishing directions. This helps uniformly polish the surface and avoid directional scratches. Each step should leave the surface smoother than the previous one, with finer scratch patterns.
-
Inspection and Adjustment: Regularly inspect the specimen under a microscope to monitor progress. If scratches or imperfections are found, adjust the technique or repeat the previous step to ensure they are removed before proceeding.
-
Cleanliness and Contamination Control: Maintain a clean environment to prevent contamination. Contaminants on the cloth or surface can introduce new scratches, undermining the polishing process. Use clean tools and materials at each stage to ensure a pristine surface finish.
Polishing Procedures - Final Polishing
The final polishing stage is crucial for achieving a flawless, mirror-like surface. It removes the last traces of scratches and deformation from previous steps, revealing the true microstructure of the specimen. The goal is to produce a surface free of artifacts that can interfere with microscopic examination. Techniques involve applying light, consistent pressure and using fine abrasives to gently smooth the surface. Automated polishing machines ensure uniformity and precision, but manual polishing can also be effective with careful attention.
Using Colloidal Silica or Other Final Polishing Agents: Colloidal silica is a popular choice for final polishing due to its fine particles (~0.05µm) that produce exceptionally smooth surfaces. The colloidal solution evenly distributes the particles across the polishing cloth and specimen. To maintain effectiveness, keep the polishing cloth moist but not overly saturated. Alumina suspensions are another option, chosen based on material properties. Both types of suspensions should be used with appropriate cloths and lubricants for the best results.
Ensuring an Artifact-Free Surface: Achieving an artifact-free surface is essential. Here are key practices:
-
Consistent Pressure and Speed: Apply light, consistent pressure and maintain uniform speed to avoid new scratches.
-
Regular Cleaning: Clean the specimen and polishing cloth between steps to remove abrasive particles and contaminants.
-
Proper Lubrication: Use the right amount of lubricant to keep the cloth and specimen cool and reduce friction.
-
Inspection and Monitoring: Regularly inspect the specimen under a microscope. Adjust techniques or repeat steps if artifacts are detected.
-
Avoiding Overpolishing: Balance sufficient polishing to remove imperfections with avoiding excessive polishing that could damage the specimen.
-
Using High-Quality Materials: Select high-quality polishing cloths and suspensions appropriate for the material to reduce the risk of defects.
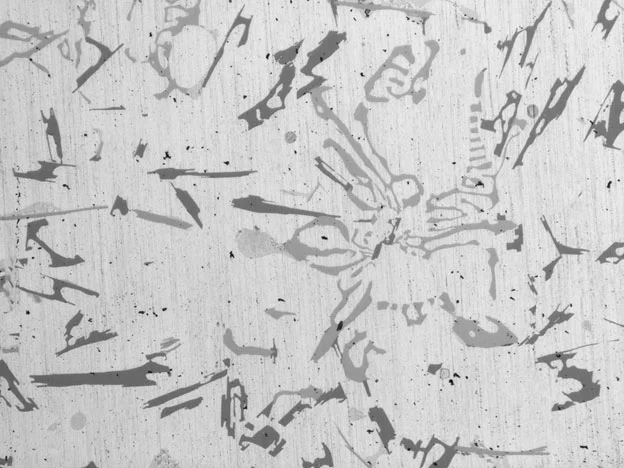
Comparison of Polishing Procedures
Polishing Stage |
Objective/Method |
Grit Size Selection |
Recommended Procedures and Tips |
---|---|---|---|
Coarse Grinding |
Rapidly remove material to create a flat, uniform surface. Essential for eliminating irregularities and achieving a consistent plane for subsequent stages. |
Hard materials: 60-240 grit. Softer materials: 320-600 grit. Choose appropriate grit based on material hardness and required material removal. |
Start with the coarsest grit to remove sectioning damage. Use water or lubricant to minimize heat and debris. Apply consistent pressure to ensure even grinding. Rotate the sample regularly to achieve a consistent surface and prevent deep scratches. |
Fine Grinding |
Further refine the surface, removing scratches left by coarse grinding. Prepare the surface for polishing to achieve detailed microstructural clarity. |
Sequentially use finer grit sizes: 400-1200, depending on material and desired surface quality. Ensure each step removes scratches from the previous grit size. |
Apply steady, gentle pressure to avoid deforming the specimen. Use clean water or lubricant to cool the specimen and remove debris. Rotate the specimen regularly for uniform wear. Keep grinding equipment clean to avoid contamination. Monitor grinding time to balance adequate preparation with avoiding damage. |
Intermediate Polishing |
Bridge the gap between fine grinding and final polishing. Use finer abrasives (3µm to 1µm) to remove residual scratches and deformations. |
Select polishing cloths and suspensions based on material and desired finish. Low-nap or medium-nap cloths commonly used. Diamond, alumina, or colloidal silica suspensions based on abrasive properties. |
Gradual transition in abrasive sizes. Clean specimen and cloth after each step. Apply consistent, light pressure to avoid new scratches. Use appropriate lubricants to keep the surface cool and reduce friction. Rotate specimen and change polishing directions to avoid directional scratches. Regularly inspect the specimen under a microscope. Maintain a clean environment to prevent contamination. |
Final Polishing |
Achieve a flawless, mirror-like surface. Remove the last traces of scratches and deformation, revealing the true microstructure of the specimen. |
Use fine abrasives such as colloidal silica (~0.05µm) or alumina suspensions based on material properties. |
Apply light, consistent pressure and maintain uniform speed to avoid new scratches. Keep the polishing cloth moist, not overly saturated, to ensure effective polishing. Clean specimen and cloth between steps to remove contaminants. Regularly inspect under a microscope. Avoid overpolishing to prevent damage. Use high-quality polishing cloths and suspensions appropriate for the material to minimize defects. |
Key Polishing Variables for metallography & sample preparation
Surface - Surfaces for grinding and polishing are selected based on the equipment, sample material, and preparation needs. Different surfaces include grinding stones, polishing paper, disks, and cloths. These surfaces vary in abrasive bond type, abrasive type, hardness, resilience, surface pattern, and fiber projections.
Grain Size (Grit/Grain Size) - Always start preparation with the smallest possible grain size to avoid excessive specimen damage. For subsequent steps, use the largest practical intervals between grain sizes to minimize preparation time.
Abrasive - The removal rate in grinding and polishing depends on the abrasive used. Diamonds, with a hardness of about 8,000 HV, can cut through all materials and phases. Polycrystalline diamonds, with many small cutting edges, provide high material removal and shallow scratch depth.
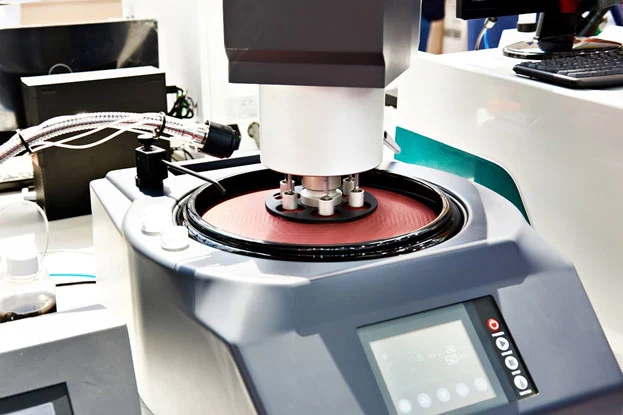
Silicon carbide (SiC), at about 2,500 HV, is commonly used for grinding non-ferrous metals, while aluminum oxide (about 2,000 HV) is mainly for ferrous metals. Colloidal silica is used for a scratch-free finish in oxide polishing steps. The abrasive should generally be 2.5 to 3 times harder than the material being prepared. Avoid softer abrasives to prevent preparation artifacts. The amount of abrasive needed depends on the surface and the specimen's hardness. Hard specimens and low-resilience cloths require more abrasive.
Lubricant - Lubricants combine lubricating and cooling properties and are chosen based on the material and preparation stage. Types include thin lubricants for high cooling and low lubrication, special lubricants for soft and ductile materials, and alcohol or water-based lubricants. Soft materials need more lubricant to avoid damage but less abrasive, while hard materials require less lubricant and more abrasive. The polishing cloth should be moist, not wet. Excess lubricant can reduce material removal by forming a thick layer between the specimen and the disk. Two-in-one diamond suspensions include balanced lubrication and cooling liquids for optimal preparation.
Rotational Speed - For primary grinding, high disk speed ensures fast material removal. For fine grinding, diamond polishing, and oxide polishing, use speeds of 150 rpm for both disks and specimen holders, turning in the same direction. High speeds with loose abrasives require more abrasive and lubricant as the suspension can be thrown from the disk.
Force - Force, measured in Newtons, should be adjusted based on the specimen size and number. For standard preparation, force is standardized for six 30 mm diameter specimens in a holder, with the specimen area about 50% of the mount. Smaller specimens or fewer specimens in a holder require reduced force to avoid damage, while larger specimens need slightly increased force or extended preparation time. Higher forces can increase temperature and risk thermal damage.
Time - Preparation time, measured in minutes, should be as short as possible to avoid artifacts like relief or edge rounding. Adjust time based on specimen size: extend time for larger specimens, keep time constant but reduce force for smaller specimens.
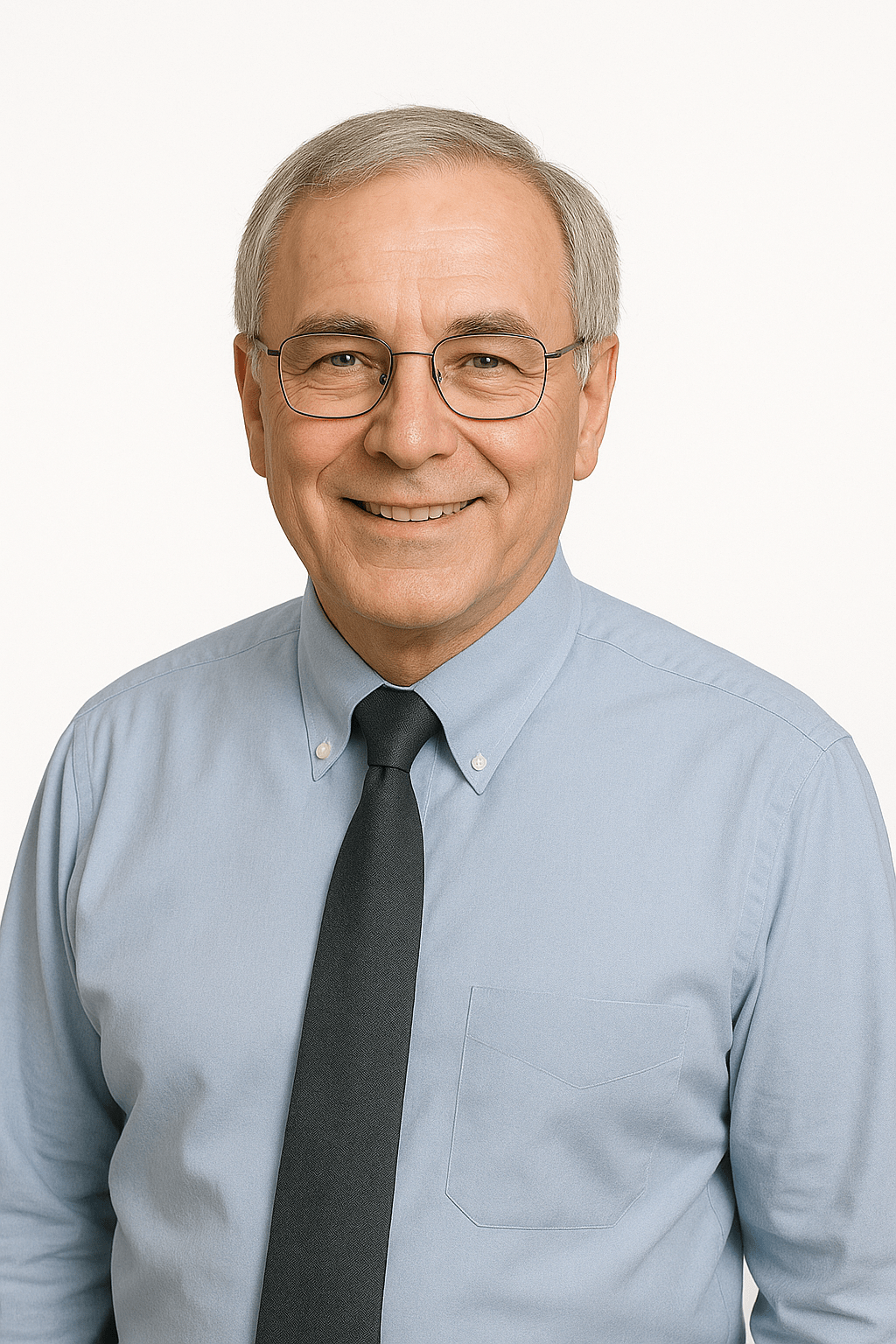
Alexander Schneider is a senior applications engineer and leading authority in the industrial diamond tooling industry, with over 35 years of hands-on experience in the development, application, and optimization of ultra-thin and high-precision diamond blades, diamond core drills, and diamond and CBN grinding wheels. His work spans a wide range of advanced materials including ceramics, glass, composites, semiconductors, and high-performance metals.
Throughout his career, he has collaborated with leading R&D institutions, national laboratories, and high-tech manufacturing companies across Europe, North America, and Asia, providing technical expertise and tailored solutions for demanding cutting and surface preparation applications.
Mr. Schneider has played a pivotal role in advancing precision cutting, sectioning, dicing, and grinding technologies used in research, production, and failure analysis. He is widely respected for his ability to optimize tool design and cutting parameters to meet exacting industry standards—balancing factors such as cut quality, blade life, material integrity, and process consistency.
As an author, Mr. Schneider is known for delivering practical, application-focused insights that translate complex technical challenges into clear, actionable strategies. His articles and technical guides serve as trusted resources for engineers, researchers, and manufacturers seeking to improve precision, reduce process variability, and enhance tool performance in critical applications.
ARE YOU USING SEMICONDUCTOR TOOLS
FOR YOUR APPLICATION?
LET US
HELP YOU
HAVING ISSUES WITH
YOUR CURRENT SEMICONDUCTOR TOOLS?
Knowledge Center
Selecting the Right Diamond Band Saw blade for your Application
Diamond Band Saw Blades Usage Recommendations & Best Practices
Diamond Wire vs band saw blades and circular blades
The Comprehensive Guide to the Processes of Silicon Wafers Production
Manufacturing Processes for Silicon Semiconductors From Ingot to Integrated Circuit
Evaluating & Comparing Diamond Blades
How to Improve & Optimize Your Diamond Sawing Operation
Troubleshooting Diamond Sawing Problems
Silicon Fabrication Guide
Diamond Wire Advantages & Application
Why use diamond
How to Selecting Right Diamond Tools for your application
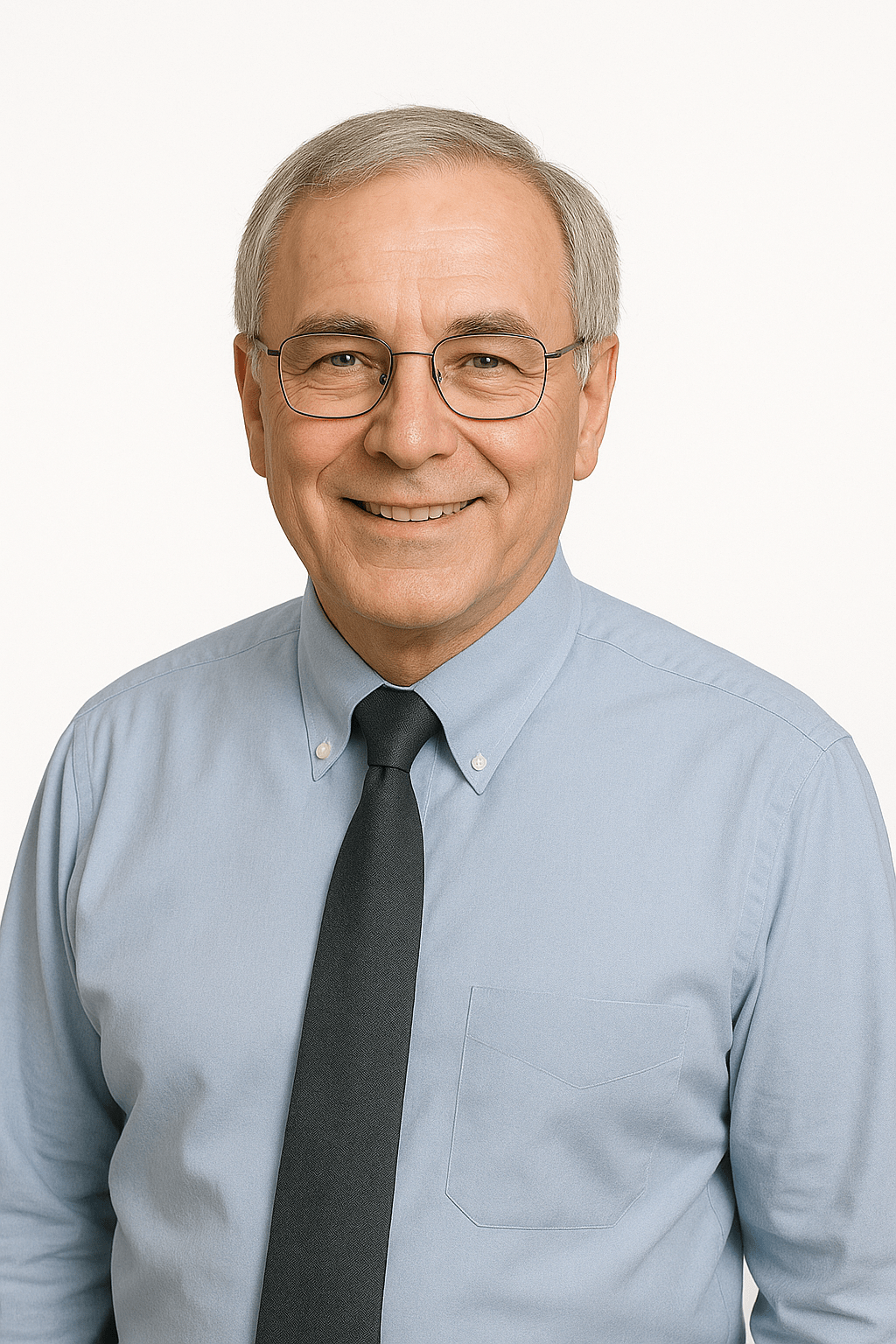
Alexander Schneider is a senior applications engineer and leading authority in the industrial diamond tooling industry, with over 35 years of hands-on experience in the development, application, and optimization of ultra-thin and high-precision diamond blades, diamond core drills, and diamond and CBN grinding wheels. His work spans a wide range of advanced materials including ceramics, glass, composites, semiconductors, and high-performance metals.
Throughout his career, he has collaborated with leading R&D institutions, national laboratories, and high-tech manufacturing companies across Europe, North America, and Asia, providing technical expertise and tailored solutions for demanding cutting and surface preparation applications.
Mr. Schneider has played a pivotal role in advancing precision cutting, sectioning, dicing, and grinding technologies used in research, production, and failure analysis. He is widely respected for his ability to optimize tool design and cutting parameters to meet exacting industry standards—balancing factors such as cut quality, blade life, material integrity, and process consistency.
As an author, Mr. Schneider is known for delivering practical, application-focused insights that translate complex technical challenges into clear, actionable strategies. His articles and technical guides serve as trusted resources for engineers, researchers, and manufacturers seeking to improve precision, reduce process variability, and enhance tool performance in critical applications.