Electroplated (Nickel Bond)
Electroplated (Nickel Bond)
Diamond & CBN Tools
UKAM Industrial Superhard Tools manufactures Precision Electroplated Diamond Products from 0.5 microns to 20 grit (diamond mesh size) in Synthetic, Natural Diamond or CBN (cubic boron nitride). For a large variety of applications, materials, and industries.
We have a stock program that includes most popular electroplated specifications for various industries and custom manufacture based on your requirements.

Electroplated (Nickel Bond)
Diamond & CBN Tools
UKAM Industrial Superhard Tools manufactures Precision Electroplated Diamond Products from 0.5 microns to 20 grit (diamond mesh size) in Synthetic, Natural Diamond or CBN (cubic boron nitride). For a large variety of applications, materials, and industries.
We have a stock program that includes most popular electroplated specifications for various industries and custom manufacture based on your requirements.
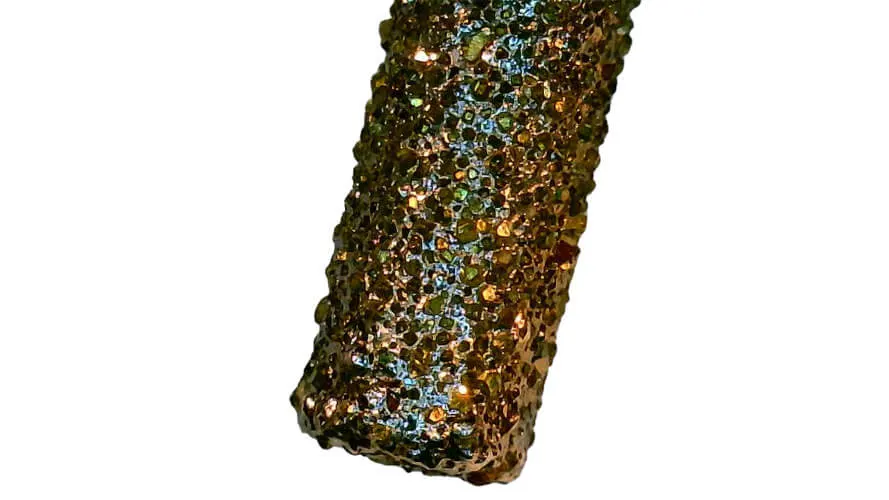
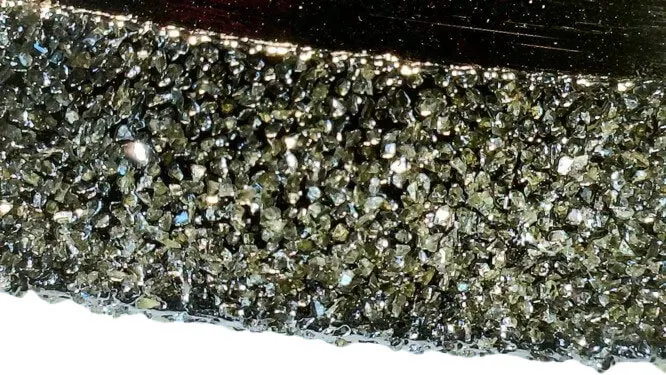
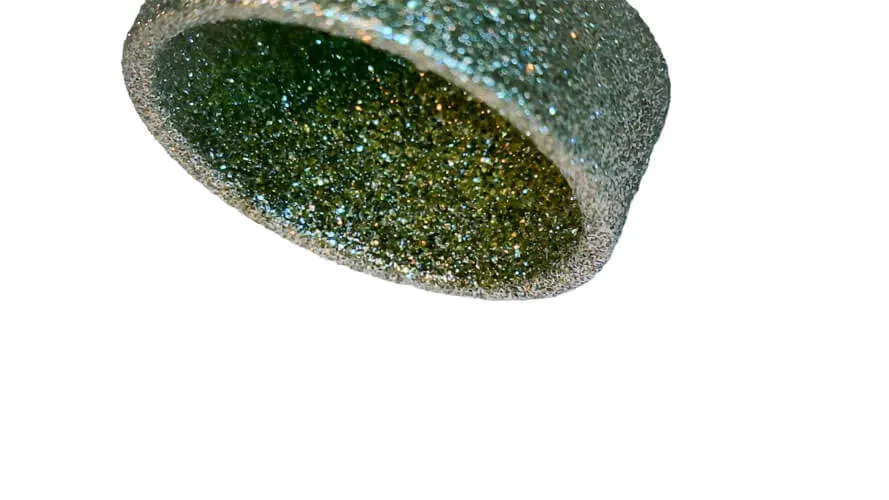
Tools can produce just about any type or shape of electroplated tools, from print supplied by you, or we will plate a blank your provide

Advantages of Electroplated Diamond Tools:
- Free Cutting Action - better removal rates and less thermal damage to the part
- Good Form Holding Characteristics - -hold simple and intricate forms for the entire life of the tool or wheel, from first grind to last.
- Maximum Abrasive Particle Exposure
- High Stock/Material Removal Rates - Lower long term cost with the potential reduction or elimination of time associated with set-up, dressing and tool changes.
- Reusable - striped & replated with potential savings of 25% over new electroplated products.
About Nickel Bond
(Electroplated) Tools
Electroplated (nickel bond) diamond products usually have a single layer of diamonds, held by a tough durable nickel alloy. Nickel is frequently used as a base for plating diamond. Because of its excellent strength, toughness and flexibility during the plating process. Electroplated diamond products are able to retain their original shape and dimensions thought their working life. Unlike sintered (meal bond) or resin bond diamond products, where diamond particles are buried in bond and held together by metal or resin binder deep inside.
Electroplating allows diamond particles to protrude from the bond matrix, providing a free, faster cutting action with minimum heat generation.
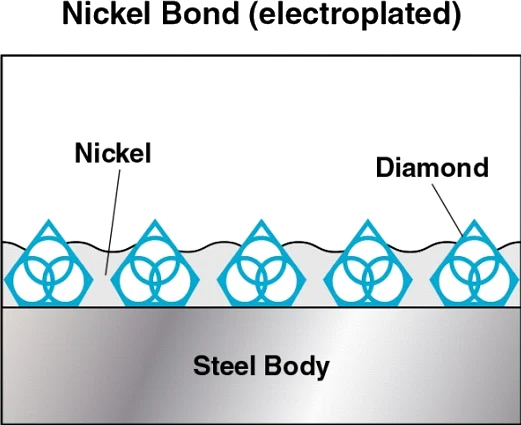
Electroplated Diamond Products Manufactured by UKAM Industrial are Multi Layered. They have 3 layers of diamonds, not just 1 layer of diamonds like conventional electroplated diamond tools.
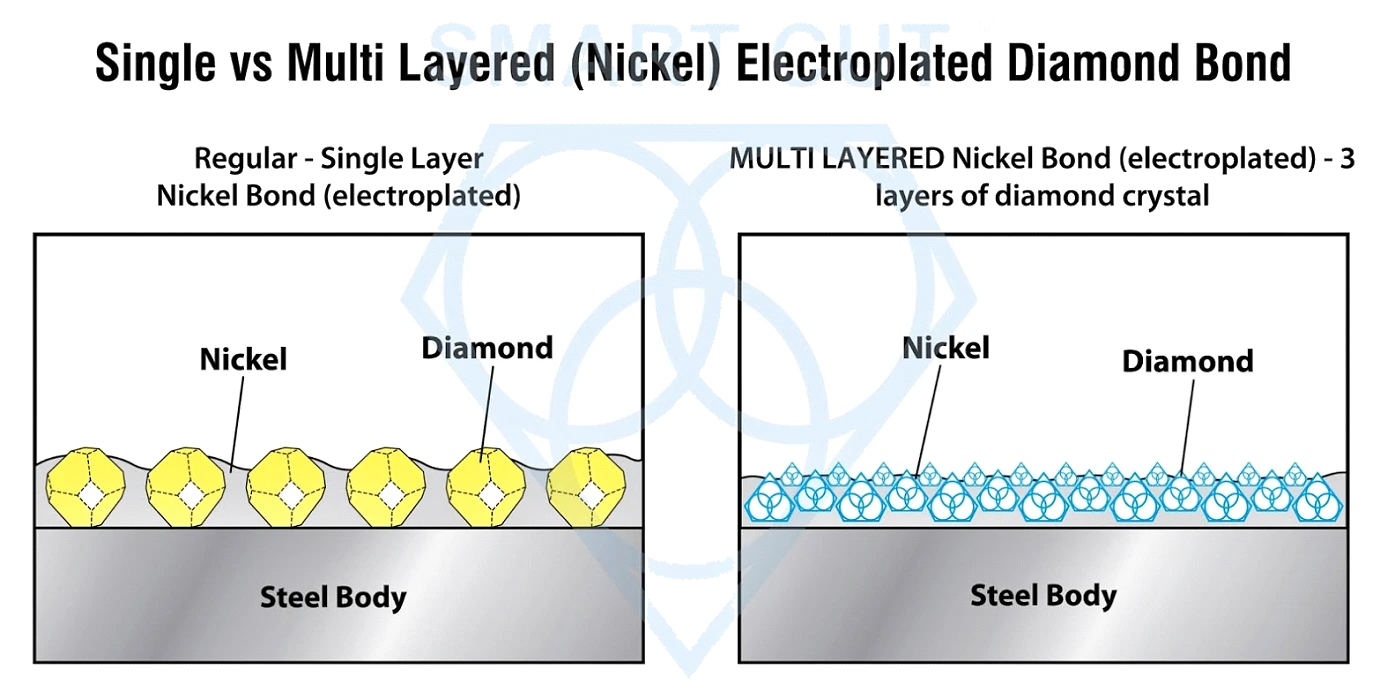
How SMART CUT® Bond Works?
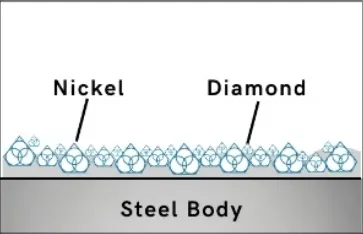
Sharpest And Finest Quality Diamonds
Diamonds or CBN Crystals are activated only at the exposed layer. As Bond Matrix layer begin to wear out, diamonds in a new Bond Matrix layer are immediately activated, substituting the already used up diamond layer. The SMART CUT® Bond Diamond Bond makes sure every diamond is in the right place. and at the right time, working where you need it most.
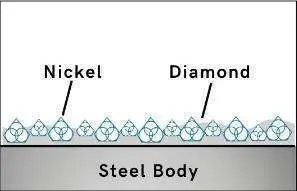
Diamonds or CBN Crystals
The newly exposed diamonds don’t effect diamonds already working on the material. Unlike many other diamond bonds, diamonds in a SMART CUT® remains sharp and grow sharper with each cut, prolonging product life and consistent performance.
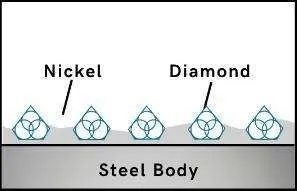
Advanced Formulated Open Diamond Bond Design
This advanced formulated open diamond bond design insures minimal chipping, fast
cut, constant speed of cut, minimal cutting noise, and most important of all, consistent performance.
Multi Layered
Electroplated Diamond & CBN Coatings
They have several layers of diamonds, held by a tough durable nickel alloy. Providing high diamond concentration, better diamond crystal retention and maximum diamond particle (grit) exposure/protrusion ratio. This provides freer, faster cutting action with minimum heat generation. Advantages of this type of technology include: longer tool life, more uniformity in performance, less stress to material being worked on, minimum material deformation, and better preservation of true material micro structure. This is specially important for more delicate, sensitive applications such as: glass, crystals, silicon wafers, carbon composites, sapphire, etc.
Electroplating is the only bond that allows different diamond crystal protrusion/exposure through use of different coating thicknesses. Usually the exposure ratio is based on the application (materials to be cut) The final specification depends primarily on the machining task and the associated necessary chip clearance space. For high-speed grinding the coating thickness should be about 30 to 40% of the grit particle diameter, when grinding or cutting glass fibre-reinforced plastics 30 to 50%, when machining ceramic material and cemented carbide 60 to 70%, and when machining stone up to 100%.

Electroplated diamond tools can provide cost saving in custom tooling, where the used up tool and be stripped and re-plated with new diamond crystal (provided that its not damaged). Lifespan of this bond family is much shorter then others, as there is only a single layer of diamond coating bonded to nickel. Just about any shape can be plated with almost any size diamond (superabrasive). Electroplating can also provide production cost savings because the part's finish shape can be easily produced by the plated tool.
UKAM Industrial Superhard Tools can produce just about any type or shape of electroplated tools, from print supplied by you, or we will plate a blank your provide
High Quality & Consistency
Electroplated (Nickel Bond) Tools
Our standard stock program and custom electroplated diamond tools are produced in a clean environment. Steel bodies are machined to very high precision tolerances from hardened steel on newest CNC machines. Only the highest quality raw materials are used in manufacturing process. Utilizing world class quality control, inspection, and measurement equipment. Highly Experienced Engineers and chemists constantly monitor and control all material input & output at all stages of manufacturing process. Insuring product consistency for use in demanding & sensitive applications
We have experience in working in fields challenging fields such: Nano Technology, MEMS, Materials Research, and etc. In last 25 years over 9 million plated tools/parts have been produced. Customers include some of the Leading Fortune 500 companies, Universities, Military, Space Flight Organizations, Laboratories, Advanced Material Fabricating Facilities to small machine shops.
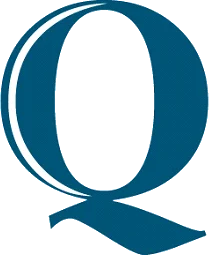
How Diamond Plating (Coating) is Done
- Electroplated diamond tools are produced using a galvanic process, where diamond is deposited to steel body in chemical solution by time. The base which is typically nickel (copper, chromium, and some other metals can also be used depending on the application) is connected to anode, while the steel body to be plated is attached to the anode. The steel body to be plated needs to be conductive in order for the current to pass through it. Before a part is plated, depending on its composition (type of steel), form, and finish it may undergo cleaning and treatment in electrolyte baths. Sometimes very thin layer of metal coating is done as well. This prepares the surface of the part/tool for optimum retention and insures uniformity of diamond coating (minimizing pours and inclusions). Faces of the part/tool that should not be plated are masked utilizing self adhesive tapes, plastic jigs, lacquers, and other methods. The part/tool is then attached to specialized steel holder that is conductive and then dipped into tank filled with chemical solution filled with diamond. The rectifier has been programmed to provide the right amount of current for predetermined amount of time. The part/tool is connected electrically and the plating process begins. Coating thickness is based on time.
- A container is filled with a solution of a salt of the metal that is to form the coating. For example, if Nickel is to form the coating, the solution will consist of nickel sulfate (a salt of nickel) mixed with water. This solution is called the electrolytic bath. The part/tool to be plated (coated with diamond) is immersed in the bath. A metal bar, composed either of the metal that is to form the coating or of a metal that is not affected by the electrolytic bath, is also immersed in the bath. The entire apparatus is called an electrolytic cell.
- The object to be coated is connected to the negative terminal of an electric battery or other source of direct current, and becomes the cathode (the electrode through which negative charge enters an electrical device). The metal bar is connected to the positive terminal of the electric power source and becomes the anode (the electrode through which negative charge leaves).
- When electric power is applied, electrolysis of the electrolytic bath occurs. The bath gives up its metal content to the surface of the cathode. This coating forms an alloy with the metal of the cathode, and adheres to the cathode after the cathode has been removed from the bath. As the electroplating process continues, the metal salts in the bath are used up. If the anode is a bar of the coating metal, the bar dissolves in the bath at the same rate that the bath gives up its metal to the cathode. If the anode is made of another metal, salts of the coating metal must be added to the bath as metal becomes deposited on the cathode.
- The longer the process continues, the greater the thickness of the coating on the cathode.

How Electroplating Works
Our standard stock program and custom electroplated diamond tools are produced in a clean environment. Steel bodies are machined to very high precision tolerances from hardened steel on newest CNC machines. Only the highest quality raw materials are used in manufacturing process. Utilizing world class quality control, inspection, and measurement equipment. Highly Experienced Engineers and chemists constantly monitor and control all material input & output at all stages of manufacturing process. Insuring product consistency for use in demanding & sensitive applications
We have experience in working in fields challenging fields such: Nano Technology, MEMS, Materials Research, and etc. In last 25 years over 9 million plated tools/parts have been produced. Customers include some of the Leading Fortune 500 companies, Universities, Military, Space Flight Organizations, Laboratories, Advanced Material Fabricating Facilities to small machine shops.

DIAMOND PLATING
Variables
- dimensions of the steel body to be plated
- size and type of diamond crystal
- Metal Powder Used to Hold the diamond crystals
- Current Size
- Time
EXAMPLE OF
DIAMOND & CBN TOOLS















































































































Examples of
Electroplated Diamond Tools
CUSTOM ELECTROPLATED
Diamond Tools
We pride ourselves in working with some of the leading glass, composite, semiconductor, stone, and optics manufacturers.
In addition to manufacturing standard electroplated diamond products, UKAM Industrial Superhard Tools can electroplate diamonds on just about any material or substrate per customer drawing and specifications. Our stripping System allows a tool blank to be Stripped & Replated as many as 100 times over before loosing .0000001" of the surface.
Applications / Materials Used On
Typical Electroplated Diamond Tool
- Fiberglass
- Graphite
- Refractory
- Green Carbide
- Silicon
- Alumina
- Beryllium Oxide
- Brake Linings
- Cerments
- Polyesters
- Asbestos
- Micarta
- Carbide
- Stone
- Glass Bonded Mica
- Barium Titanate
- Epoxy
- Optical Materials
- Optical Materials
- Ceramics
- Refrasil
- Ferrites
- Marble
- Silicone
- Transmission Bands
- Taped Graphite
- Composites
- Carbon
- Pure Glass
- Astralite
- Quartz
- Porcelain
- Onyx
- Clutch Linings
- Glass Laminated
- AND MANY OTHERS
Electroplated Diamond Tools
Frequently used in following
- Aircraft
- Circuit Board
- Missle
- Diving Board
- Marble
- Boast
- Automotive
- Casket
- Pool Slide
- Glass
- Aerospace
- Construction
- Paneling
- Swimming Pool
- Composites
- Yacht
- Pure Glass
- Tank (Water & Acid)
- Form Grinding
- AND MANY OTHERS
Diamond
mainly used on any nonferrous materials, such as: carbides, ceramics, glass, fiberglass, reinforced plastics etc., and CBN is for use on ferrous materials, tool and diesteels, high alloy steels and nickel rich alloys.
CBN (cubic boron nitride)
mainly used on tool and die steels, high alloy steels, and nickel rich alloys.
Diamond Definition
Diamond Mesh Size
Thickness of Diamond Coating
Recommended Application
Size of each particle A
Size of each particle B
Saw Grit
40/60
0.036"
Sawing
0.016"
0.002"
Super Course
60/80
0.023"
Roughing (Heavy Stock Removal)
0.010"
0.0015"
Large Course
80/100
0.0186"
Medium Roughing (General Grinding)
0.008"
0.0013"
Course
100/120
0.0174"
Semi Roughing (Semifinish Grinding)
0.0075"
0.0012"
Medium
140/170
0.012"
Rough Finishing (Finish Grinding)
0.005"
0.001"
Fine
0.008"
0.012"
Finishing
0.003"
0.001"
Extra Fine
270/325
0.0064"
Fine finishing
0.0025"
0.0007"
Super Fine
325/400
0.005"
Extra finishing
0.002"
0.0005"
45 Microns*
400/500
0.0034"
Super finishing
0.0015"
0.0002"
30 Microns*
500/600
0.003"
Polishing
0.0013"
0.0002"
15 Microns*
800/1200
0.0022"
Polishing
0.0001"
0.0002"
9 Microns* 8/10 6/12
1,800
0.0007"
Polishing
0.00035"
0.00008"
6 Microns* 4/8
3,000
0.00048"
Fine polishing
0.00024"
0.00008"
3 Microns*
8,000
0.00032"
Extra polishing
0.00016"
0.0000075"
* Not recommended for removing more than .000001" per pass.
Surface Finish Requirement
Due to the aggressive nature of diamond and CBN electroplated products, "super fine" finishes can be difficult to achieve. The following will help you select the appropriate grit size to achieve your required finish:
GRIT SIZE
30/40
40/50
60/80
80/100
100/120
120/140
140/170
170/200
200/230
230/270
270/325
45 Micron (400)
30 Micron (600)
15 Micron (1200)
APPROXIMATE RMS
200-250+
150-200
125-150
90+125
64-90
48-64
32-48
24-32
20-24
16-20
14-16
13-14
12
12
*When converting from conventional aluminum oxide or silicon carbide wheels to electroplated products, double the conventional grit size to find the equivalent
electroplated grit size. For example: a 60 grit Aluminum Oxide would equal 120 grit electroplated.
Diamond Particle Size Chart
Due to the aggressive nature of diamond and CBN electroplated products, "super fine" finishes can be difficult to achieve. The following will help you select the appropriate grit size to achieve your required finish:
DIAMOND GRIT SIZE
30/40
40/50
60/80
80/100
100/120
120/140
140/170
170/200
200/230
230/270
270/325
325/400
45 Micron (400)
30 Micron (600)
15 Micron (1200)
LAYER THICKNESS
0.022"
0.018
0.010
0.007
0.0065
0.006
0.005
0.0045
0.004
0.0035
0.003
0.0025
0.002
0.0015
0.001
STANDARD TOLERANCE +/-
0.010"
0.006
0.004
0.003
0.003
0.002
0.002
0.002
0.002
0.001
0.001
0.001
0.001
0.001
0.001
Total tool tolerance for electroplated diamond tools is determined by sum of backing material tolerance and respective profile tolerance.
Specific tolerances are available on many tools upon request.
ELECTROPLATED DIAMOND
TOOLS SHAPE & ACCURACY
Electroplated diamond products are an excellent choice for applications requiring repeating specific shapes or close tolerances or both. Its important for the End User / Customer to be familiar with the specific tolerances and sizes of the abrasive particles to insure the manufacturing feasibility of the electroplated diamond wheel or tool.
Guide For Machining Blanks With Radius
For example, the female radius in the steel blank must be larger than the finished diamond plated size and so naturally a male radius must be smaller. Just how much larger or smaller the radius must be depends on the diamond grit (mesh) size selected. Based on the required grit size and the specifications on the form we can determine the manufacturing feasibility of your electroplated diamond tool.
- Female radius on the steel blank must be larger than the finished size required
- Example: If a 0.250" female radius is needed with 100/120 Grit.- How much larger than the finished radius should the tool radius be? 100/120=0.0075", therefore 0.250" + 0.0075=0.2575
- Male radius on the steel blank must be smaller than the finished size required
- Example: If a 0.250" male radius is needed with 100/120 Grit.- How much smaller than the finished radius should the tool radius be? 100/120=0.0075", therefore 0.250" - 0.0075=0.2425
Recommended Steel Blank Materials
Blank material hardness should be about 50 to 60 on Rockwell scale of hardness. Diamonds usually provide best adhesion to materials with high carbon content. High speed steels such as 4130, 4140 usually used for most blanks to be electroplated with diamonds. Steel used should have no lead content.

TYPICAL SPEEDS & FEEDS for
Ectroplated Diamond Tools
Once you have determined the appropriate diamond mesh (grit size) for your application, it’s important to know if you have the speeds necessary to have your diamond tools operate to its ultimate potential. This is particularly important with CBN which requires high speeds and pressure to perform successfully.
- Diamond: 5,000 to 6,000 SFPM (Surface Feet Per Minute)
- CBN: 6,500 to 12,000 SFPM
- SFPM: Wheel Speed in RPM's X Wheel Diameter in Inches X .262
TYPICAL SPEEDS & FEEDS for
Ectroplated Diamond Tools
Diamond (Synthetic or Natural)
Electroplated diamond tools can be used dry, however, the life & performance of the tool will be significantly superior when used with coolant. Frequent coolants used with diamond electroplated tools include plain water or Synthetic Water Soluble Coolants, such as SMART CUT coolant. Synthetic water soluble coolants are recommended and will promote superior tools performance, life, and consistency.
CBN (Cubic Boron Nitride / Borazon)
Straight oil coolants are frequently used with CBN (cubic boron nitride) diamond tools. Recently due to rising health and environmental issues associated with straight oil coolants, most companies are are using new synthetic water soluble oil coolants, such as SMART CUT coolant. Many companies today are achieving success with these water based oil coolants when working with CBN tools. Please remember that life of electroplated diamond tools will be lower with used dry or with water based coolants.
Electroplated (Nickel Bond) Diamond & CBN Tools
Capabilities & Specifications
- Diameters Available: 0.025mm to 762mm
- thicknesses available: .0005" (12 microns) to any thickness in .0005” (5micron) increments
- arbor sizes available (inside diameters): any arbor size. Standard are 1/8”, ¼”, 3/8”, ½”, 5/8”, ¾”, 1”, 1.25”, 40mm, 2.75”, 3.5”. For most wheels we can alter the arbor size to anything you need, almost same day and can also produce any arbor size. Wheels mounted on straight shank & mandrel available
- diamond type: synthetic diamond, synthetic coated diamond & cbn (cubic boron nitride)
- diamond depth (diamond height): 1.58mm to 20mm and fully impregnated with diamond (from OD to ID)
- Edge Type: Continuous Rim and Slotted
- Core Available: Steel, Stainless Steel, Bronze, Steel with Memory, High carbon steel, tungsten carbide, fully impregnated with diamond
- Edge Shape: 1A1R, 1A1, 1E1, 1M1, 1N1, 1V1, 1A8, 1E8, 1zm8, 1N8, 1V8 1A1, 14U1, 6A2, 6A2 SP, 9A3, 12A2-45, 11V9-70, 12S2-45SS, 12V5-45 (other kerf angles & radiuses can be produced upon request)
- Bond Hardness: Super Soft, Soft, Medium, Hard
- Tolerances Available: ODT tolerances +.050/.000 Arbor Hole Tolerance+.001/-.000 Rim Thickness +.002/-.001 Core Thickness: +.001/-.001
- diamond grit sizes: 35 mesh to 1 micron
- diamond concentration: low, medium & high (from 10 con to 150 con)
Contact Us for FREE Quote & Recommendation
Why Work With Us?
Comprehensive Source of Information on Diamond & CBN Blades
The more you understand about what we can do for you, the better our partnership will be. On our website you will find the Most Comprehensive Source of Information on Everything you wanted to know about diamond dicing blades & industrial diamond tools.
Large Inventory & Custom Manufacturing
Largest Inventory of Precision & Ultra Thin Diamond Dicing Blades in the U.S. Available in different sizes, thickness, arbor sizes, diamond concentrations, diamond mesh sizes, and bond hardness's.
Experience makes all the Difference
"ONE OF THE MOST EXPERIENCED COMPANIES IN THE INDUSTRY"
Over the years we have enjoyed working with all types if clients, regardless of size. Proprietary dicing blade chemistry, precision manufacturing methods, modern quality control methods, allow us to control and regulate the dozens of variables that affect blade life, quality of cut, surface finish. Reducing and often eliminating additional steps often required after cutting.
Umatched Technical Support
We Are a Partner In Your Success
Developing close ties with our customers is the foundation of our business. At the core of
our company is a team of world class engineers, knowledgeable customer service personnel here to serve you. Whether is designing or manufacturing a special solution. We will go out of our way to optimizing your process to ultimate level of efficiency.
Advanced Technology
American Manufacturer As one of the few remaining independent U.S.Diamond Tool & machine builders. We have the experience & tradition to help you remain at frontier of technology Our experience has been further enhanced by acquiring assets and processes from some of the oldest American tool manufacturers, along with their decades of experience and R& D. This has positioned us as one of the most experienced companies in the industry.
Superior Quality &
Consistency
Our unique bond formulations, tool designs, stringent requirements, and utilization of exceptionally high-quality diamonds and raw materials ensure top-notch products that adhere to strict ISO 9000 standards.
Our proprietary technology allow us to control and regulate the dozens of variable that affect toolife, quality, & consistency
Expect More From Your Tools
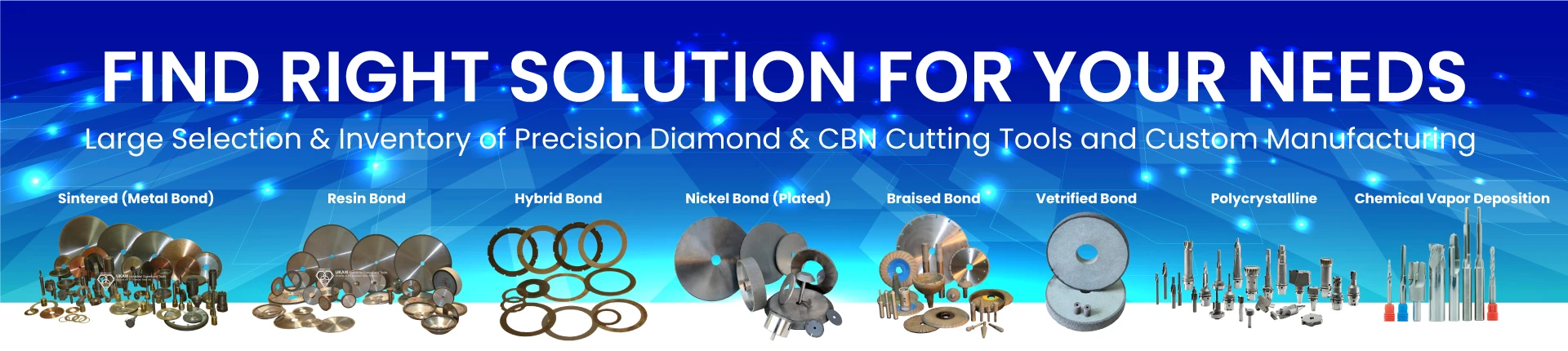