Table of Contents
ToggleThis article provides important guidelines for optimizing the dicing process in semiconductor packaging, focusing on package singulation for various technologies such as BGA, QFN, LED, CMOS, and wafer substrates. It covers key variables such as the recommended blade types, coolant options, RPMs, feed rates, and mounting methods to ensure high-quality results and efficient throughput. By exploring specific material requirements and common concerns, this guide offers valuable insights into selecting the ideal dicing parameters for each application.
Share this Article with Friend or Colleague
DICING SOLUTIONS FOR PACKAGE SINGULATION
BGA (Ball-Grid Array)
Common Materials: FR4 and epoxy mold compound
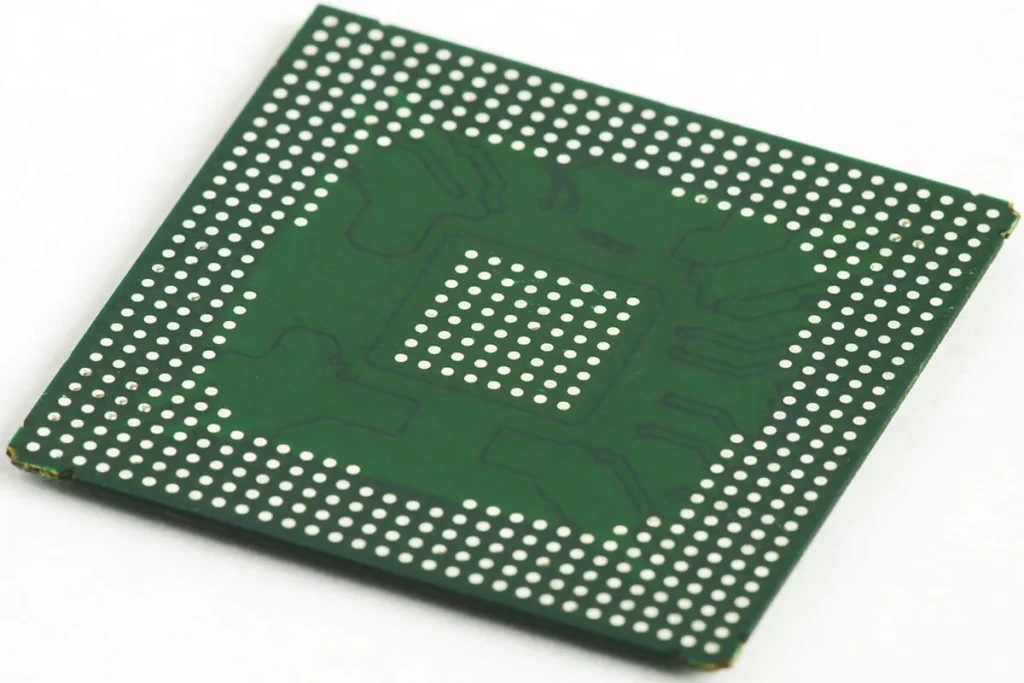
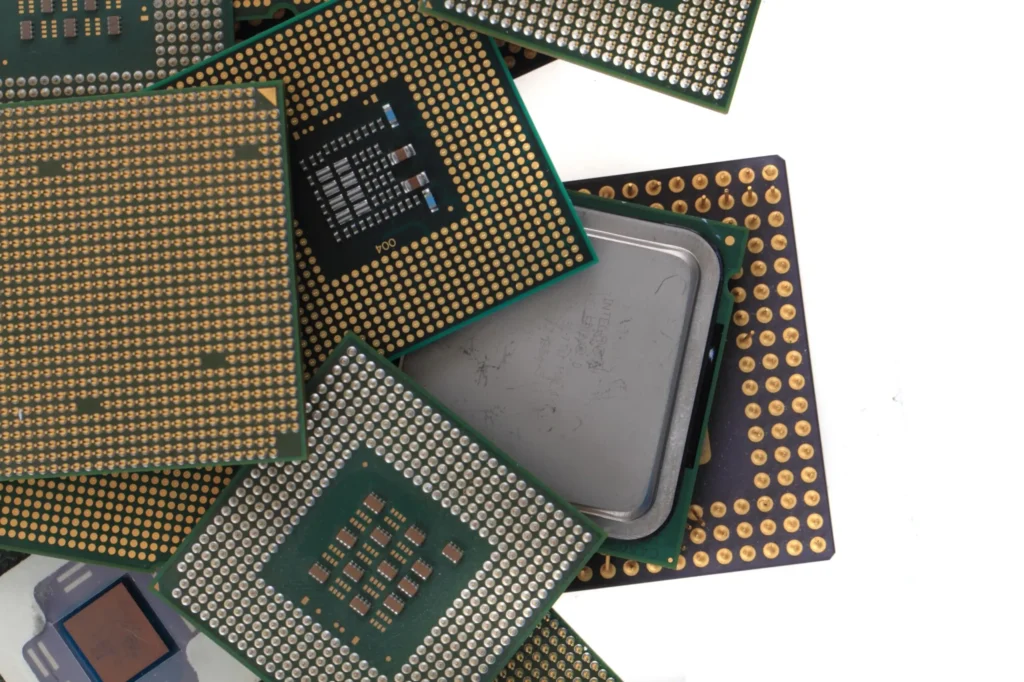
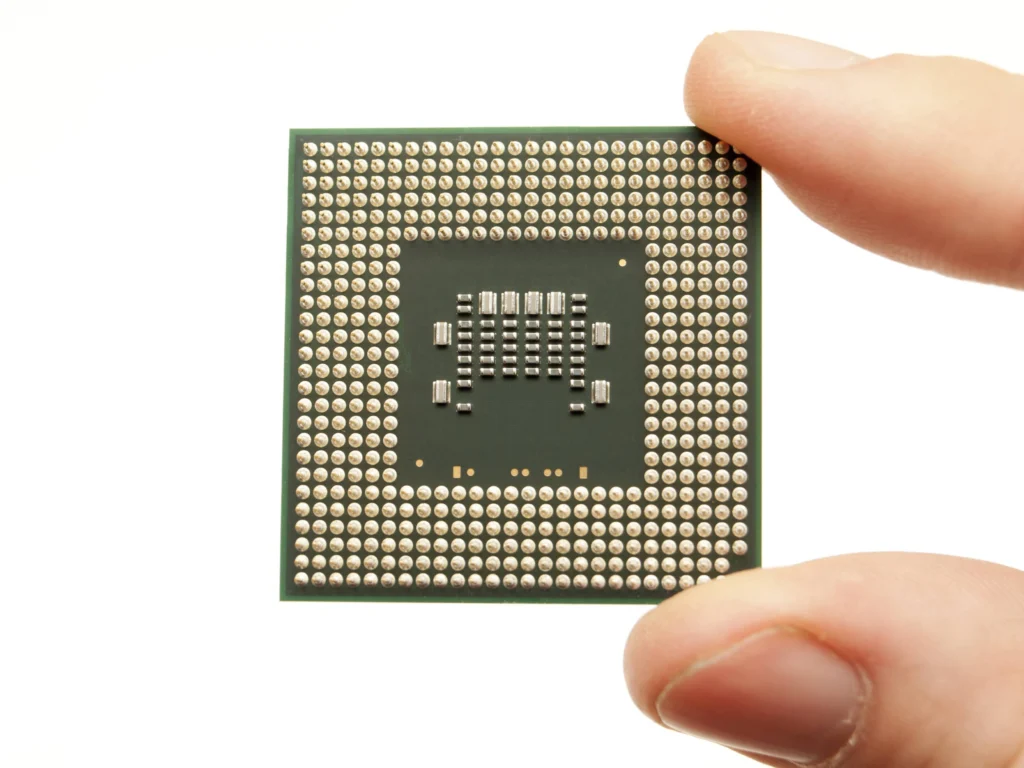
Variations:
- LFBGA (Low-Profile Fine-Pitch)
- TFBGA (Thin & Fine-Pitch)
- W-BGA (Window-Type)
- FC-BGA (Flip Chip)
- VFBGA (Very Fine-Pitch)
- POP (Package-on-Package)
- SIP (System-in-Package)
- SD (Secure Digital)
- Micro SD Card
- CBGA (Ceramic)
- PBGA (Plastic)
- UFBG (Ultra-Fine)
- MBGA (Micro)
Typical Concerns:
- Cut quality
- chipping
- burrs
- slivers
- protrusions
- race shorts
- Blade life
Dicing Blade Recommendation:
- SMART CUT HYBRID BOND or sintered (metal bond) series
- Diamond size: 30 – 55 microns
- Blade Thickness: .008” – .014”
Dicing Process Recommendations:
- Feed rate: 50-250 mm/sec
- Spindle speed: 20-40 krpm depending on blade O.D.
- Multi panel mounting on UV tape
- Minimal dressing so as not to create a large radius on the blade edge
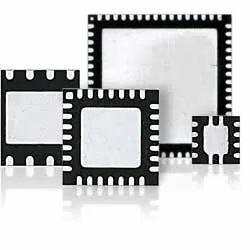
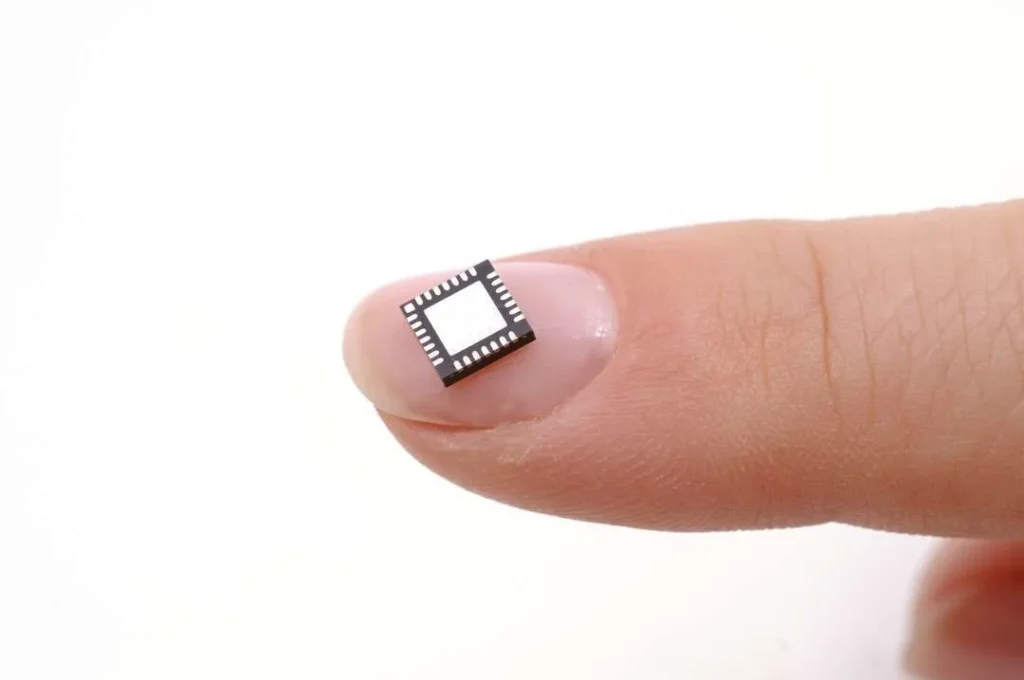
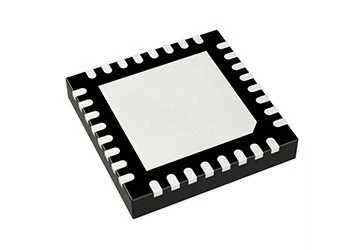
Variations:
- HVQFN (Heatsink Very-Thin)
- MLF (Micro Lead Frame)
- FUSION QUADR
- (VQFP: Very Thin Quad Flat Package)
- HQFN (High Power)
Typical Concerns:
- Chipping
- Burrs
- Lead smearing
- Melting
Dicing Blade Recommendation:
- SMART CUT HYBRID BOND or sintered (metal bond) series
- Diamond grit size: 45 – 88 microns
- Thickness: .008” – .020”
Dicing Process Recommendations:
- Feed rate: Half Etched substrates 30-75 mm/sec, Full Copper substrates 15-30 mm/sec
- Spindle speed: 22-35 krpm depending on blade O.D.
- Multi panel mounting on UV tape
- Override process over one substrate to reach final feed rate
LED (Light-Emitting Diode)
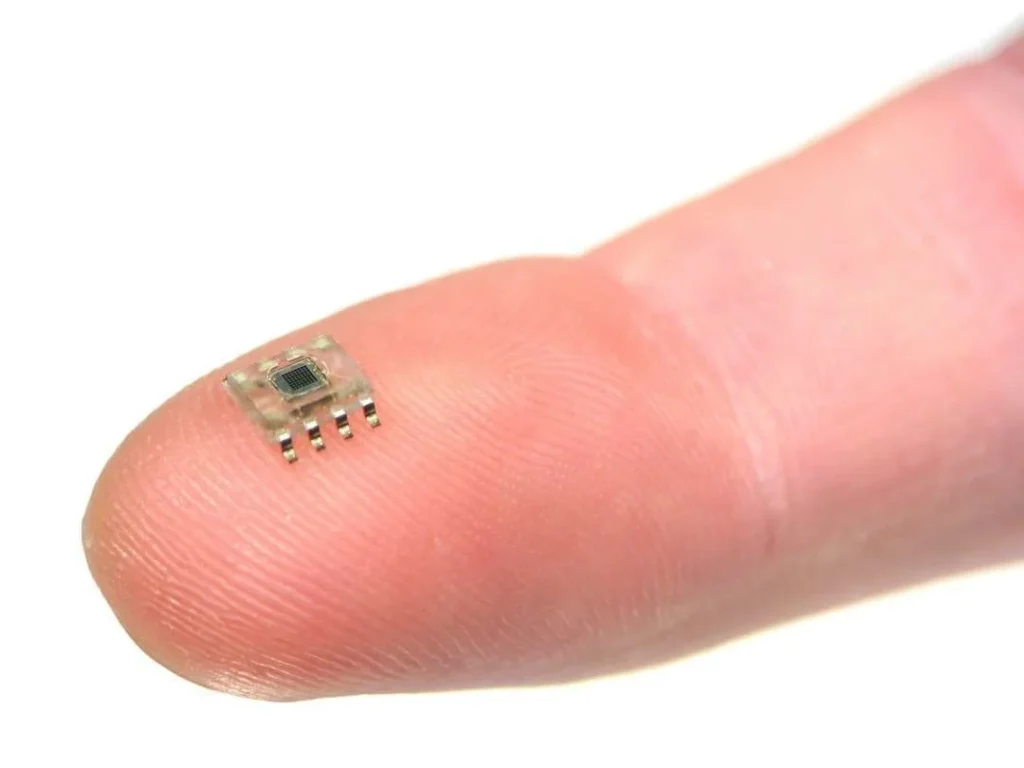
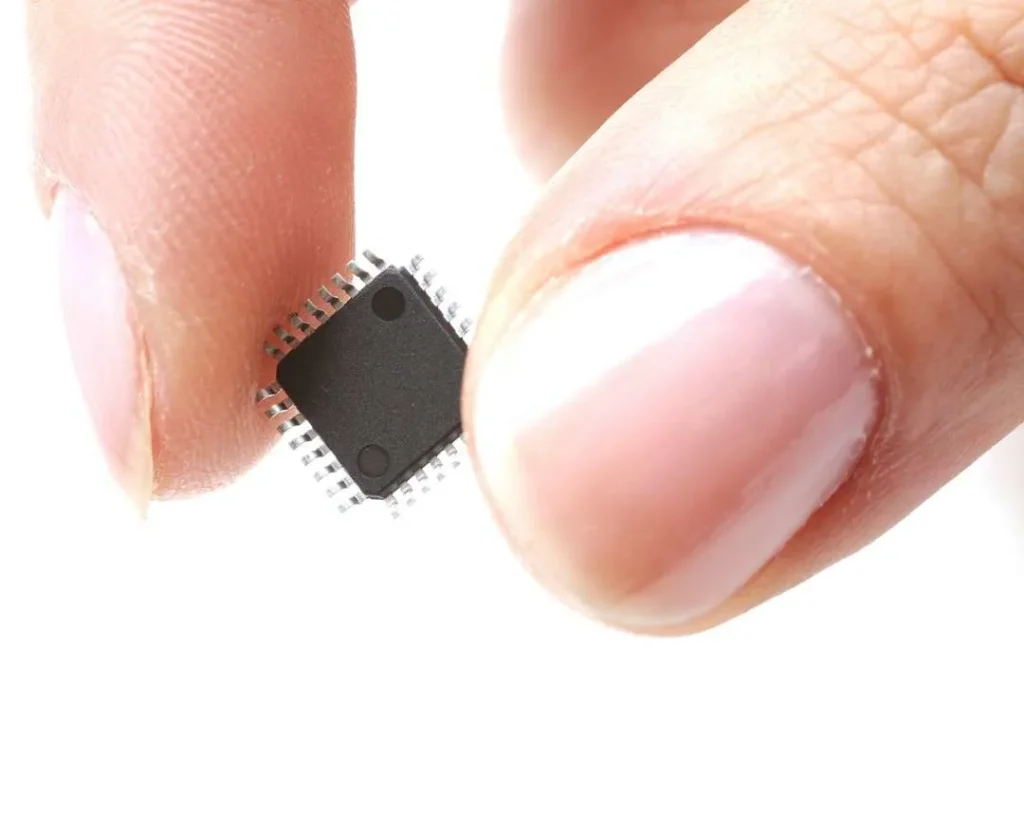
Variations:
Chip LED, High Power LED.
Typical Concerns:
- Copper burrs
- End of blade life due to limited exposure
- Throughput (maximize UPH)
Dicing Blade Recommendation:
- SMART CUT HYBRID BOND or Nickel Bond series
- Diamond size: 10,13 & 17 microns
- Thickness: .003” – .008”
Dicing Process Recommendations:
- Feed rate: 80-150 mm/sec
- Spindle speed: 25-30 krpm
- Multi panel mounting on UV tape
CMOS (Complementary Metal-Oxide Semiconductor)
Common Materials - Borosilicate Glass, HTCC (High Temperature Co-fired Ceramics).
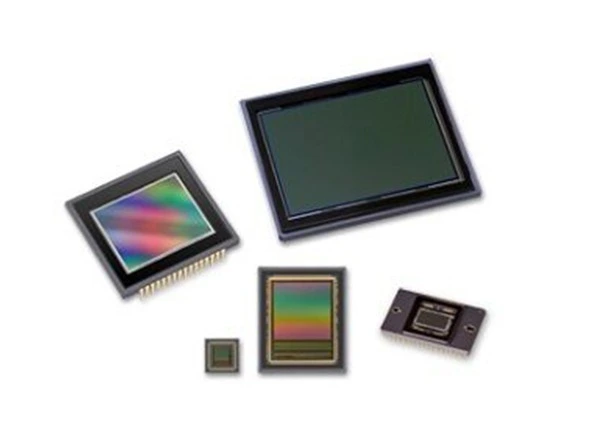
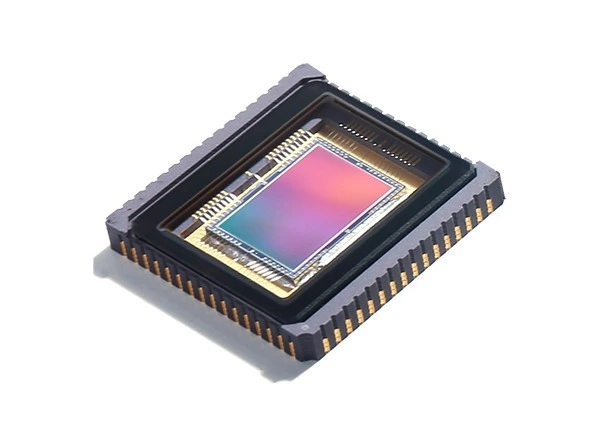
Variations:
CIS (CMOS Image Sensor) Glass Lid, CIS (CMOS Image Sensor) Substrate.
Typical Concerns:
- Chip Damage and Breakage
- Cutting Precision and Kerf Control
- Heat Dissipation
- Surface Quality
- Blade Life & Consistency
Dicing Blade Recommendation:
- Bond Type: Resin Bond, Sintered (Metal Bond), Hybrid Bond, Nickel bond
- Diamond Size: 2 to 30 microns
- Kerf Thickness:10 to 30 microns
Dicing Process Recommendations:
- Feed rate: 80-150 mm/sec
- Spindle speed: 25-30 krpm
- Multi panel mounting on UV tape
DWDM (Dense Wavelength Division Mulitplexing) Filters
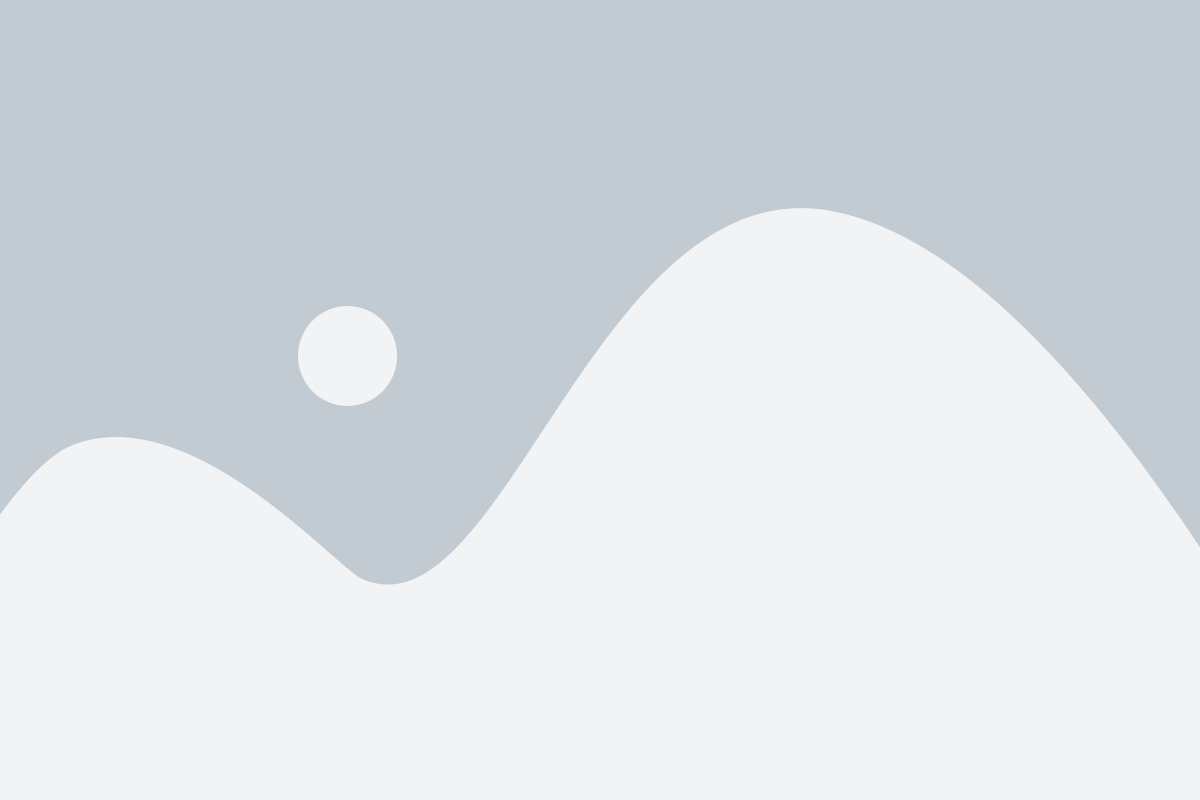
Variations:
SAW (Surface Acoustic Wave) Filter devices, Beam Splitters, Passive Components
Typical Concerns:
- Top-side and back-side chipping
- Cut perpendicularity
- Kerf side surface finish
Dicing Blade Recommendation:
- SMART CUT series Resin, HYBRID, & Sintered (metal bond) blades
- Diamond size: 30 – 45 microns (resin) and 7 – 15 microns (sintered)
- Thickness: .006″ – .012”
Dicing Process Recommendations:
- Feed rate: 4 – 20 mm/sec
- Spindle speed: 20 – 30 krpm (2″) 10 – 15 krpm (4″)
- SMART CUT® XP Dicing Coolant Lubricant Surfacant may reduce chipping and improve surface finish
HDD (Hard Disk Drive)
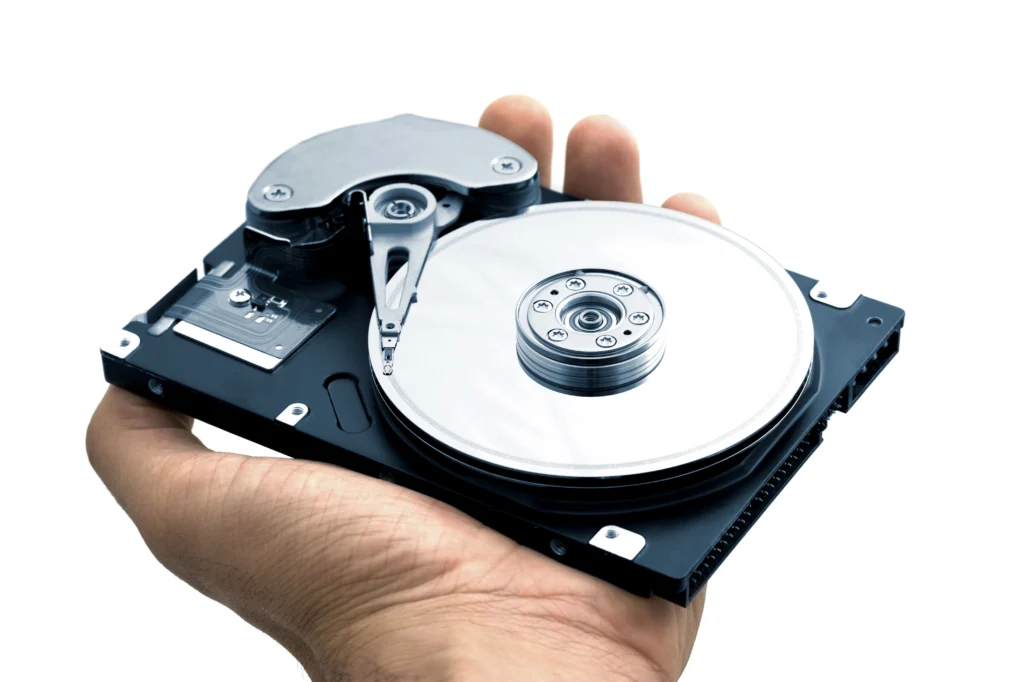
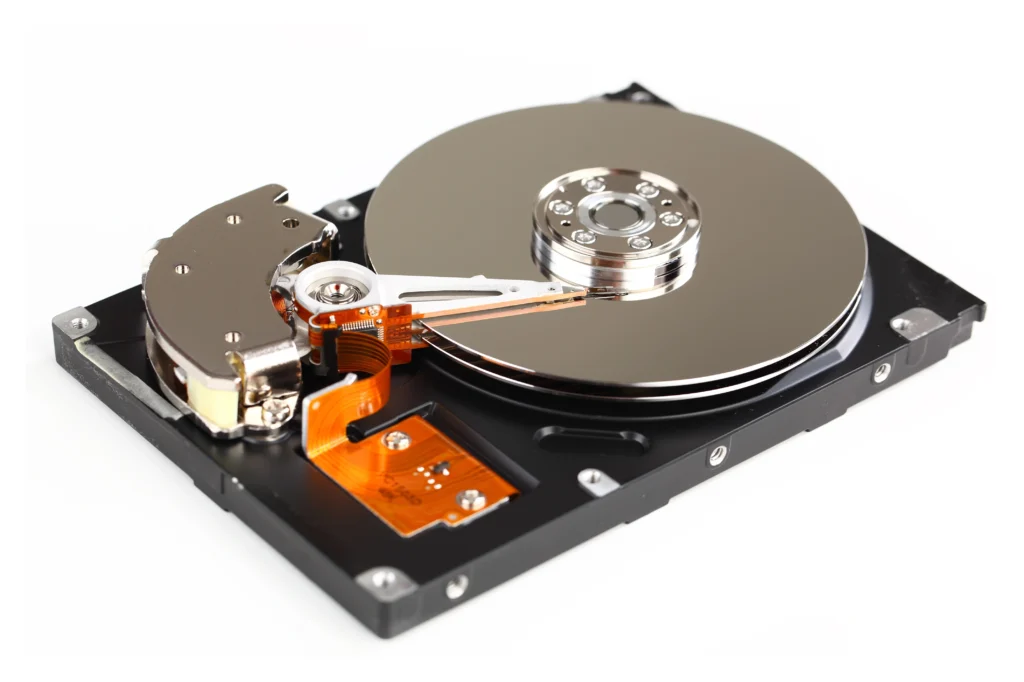
Typical Concerns:
- High Mechanical (internal) stress
- burrs
- large kerf width
- lack of accuracy
Dicing Blade Recommendation:
- Bond Type: Resin Bond, Sintered (Metal Bond)
- Diamond Size: 1 to 25 microns
- Kerf Thickness: 15 to 100 microns
Dicing Process Recommendations:
- Feed Rates: 1 mm/s to 5 mm/s
- RPM’s: 15,000 RPM to 30,000 RPM
- Mounting Type: Vacuum chucks or magnetic chucks
- Coolant Used: Water-soluble coolants
Semiconductor Wafer
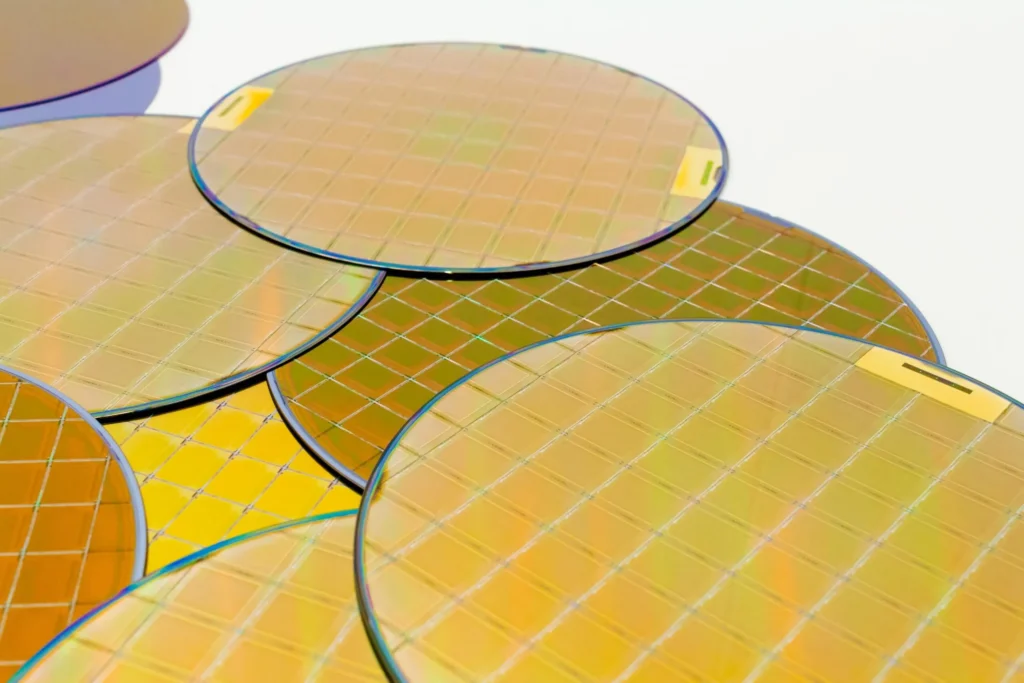
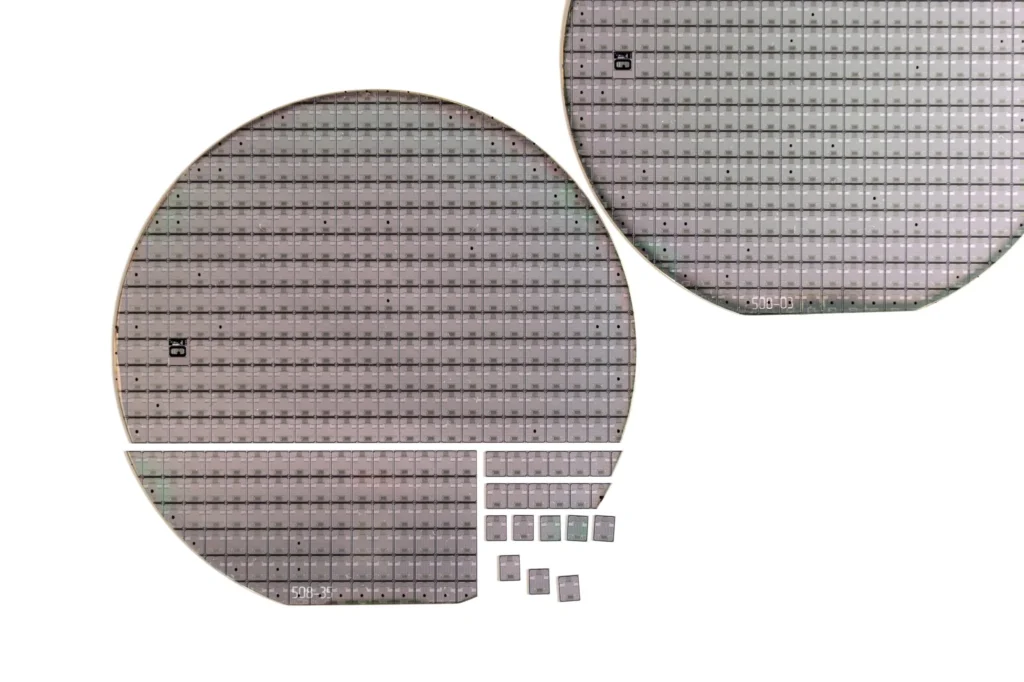
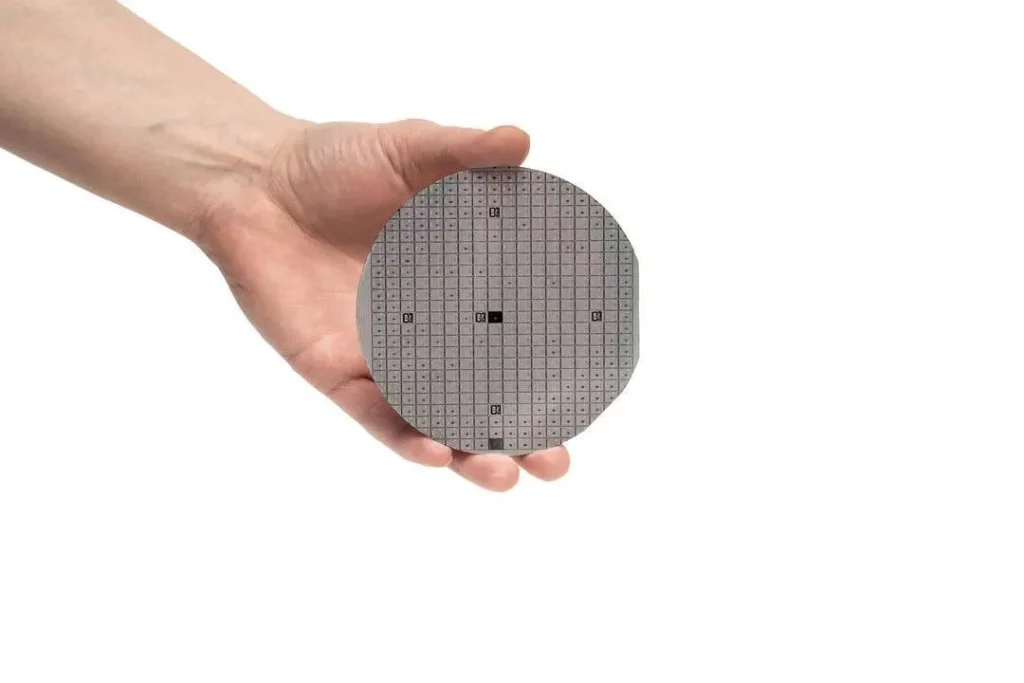
Typical Concerns:
- Feed Rates: 1 mm/s to 5 mm/s
- RPM’s: 15,000 RPM to 30,000 RPM
- Mounting Type: Vacuum chucks or magnetic chucks
- Coolant Used: Water-soluble coolants
Dicing Blade Recommendation:
- SMART CUT Nickel Bond or HYBRID series
- Diamond size: 4 – 6 microns
- Thickness: .0008” – .0016”
Dicing Process Recommendations:
- Feed rate: 25 – 75 mm/sec
- Spindle speed: 30 – 50 krpm
- Mounting: Blue or UV tape
- Cooling type: DI water with and without additives
- Carbon dioxide bubbler is optional
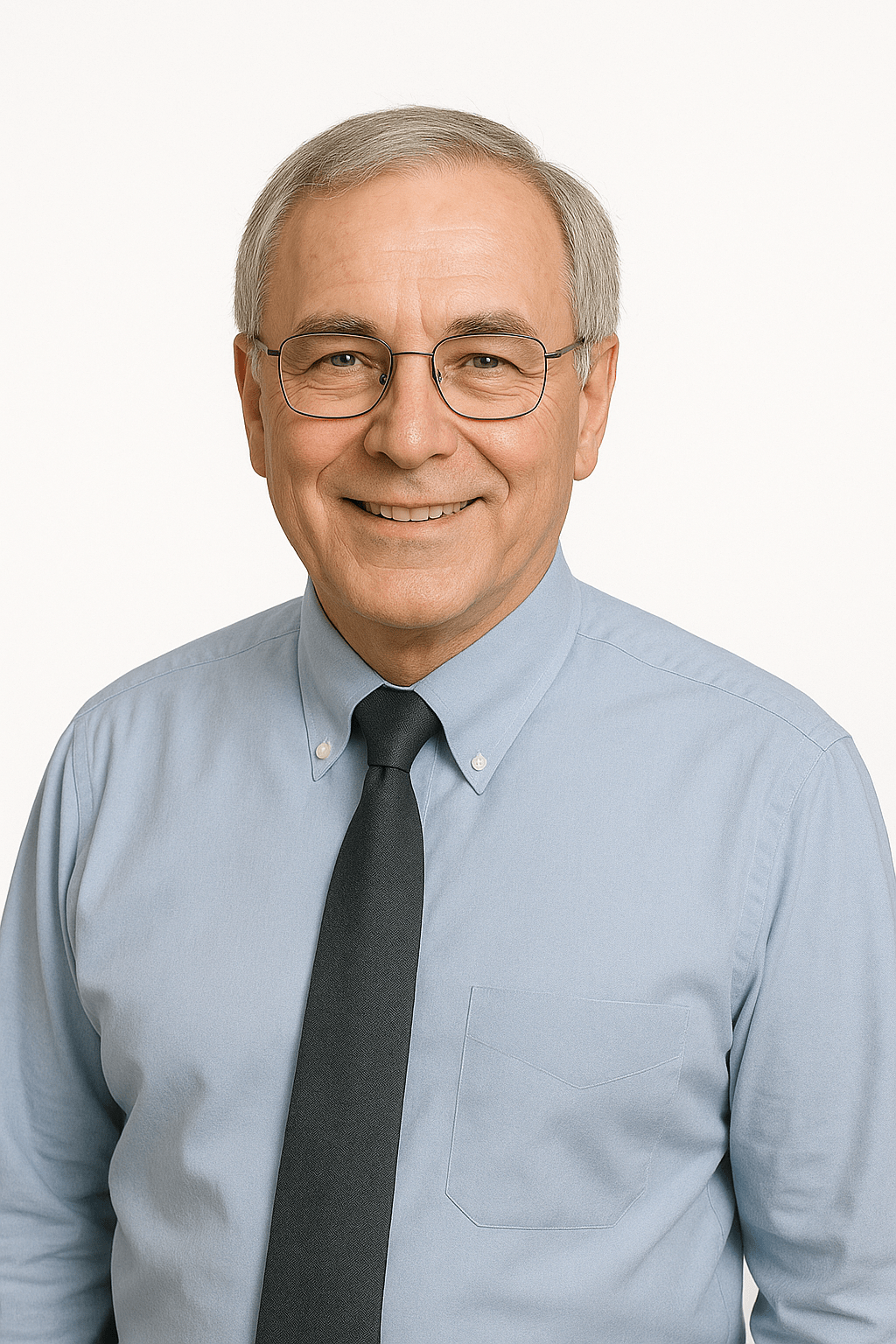
Alexander Schneider is a senior applications engineer and leading authority in the industrial diamond tooling industry, with over 35 years of hands-on experience in the development, application, and optimization of ultra-thin and high-precision diamond blades, diamond core drills, and diamond and CBN grinding wheels. His work spans a wide range of advanced materials including ceramics, glass, composites, semiconductors, and high-performance metals.
Throughout his career, he has collaborated with leading R&D institutions, national laboratories, and high-tech manufacturing companies across Europe, North America, and Asia, providing technical expertise and tailored solutions for demanding cutting and surface preparation applications.
Mr. Schneider has played a pivotal role in advancing precision cutting, sectioning, dicing, and grinding technologies used in research, production, and failure analysis. He is widely respected for his ability to optimize tool design and cutting parameters to meet exacting industry standards—balancing factors such as cut quality, blade life, material integrity, and process consistency.
As an author, Mr. Schneider is known for delivering practical, application-focused insights that translate complex technical challenges into clear, actionable strategies. His articles and technical guides serve as trusted resources for engineers, researchers, and manufacturers seeking to improve precision, reduce process variability, and enhance tool performance in critical applications.
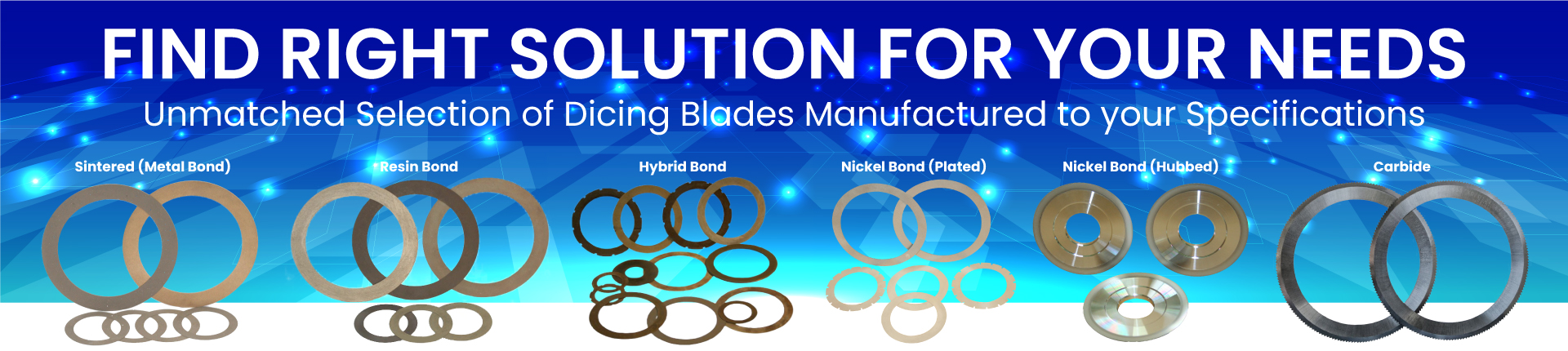
ARE YOU USING RIGHT DICING BLADES
FOR YOUR APPLICATION?
LET US
HELP YOU
HAVING ISSUES WITH
YOUR CURRENT DICING BLADES?
Knowledge Center
Select right Diamond Dicing Blade for your application
Dicing Blade Operations Recommendations
Optimizing Dicing Blade Performance
Trouble Shooting Dicing Problems
Application Recommendations
Dicing Blade Case Studies
Optimizing QFN Package Dicing Process Using SMART CUT® Dicing Blades
Selecting the Right Wafer Dicing Saw Practical Guide
How to Selecting Right Diamond Tools for your application
How to properly use Diamond Tools
Why use diamond
What is Diamond Mesh Size and how to select best one for your application
What is Diamond Concentration and which to use for your application
Diamond Tool Coolants Why, How, When & Where to Use
Diamond vs CBN (cubic boron nitride) Tools
Choosing The Correct Diamond Bond Type
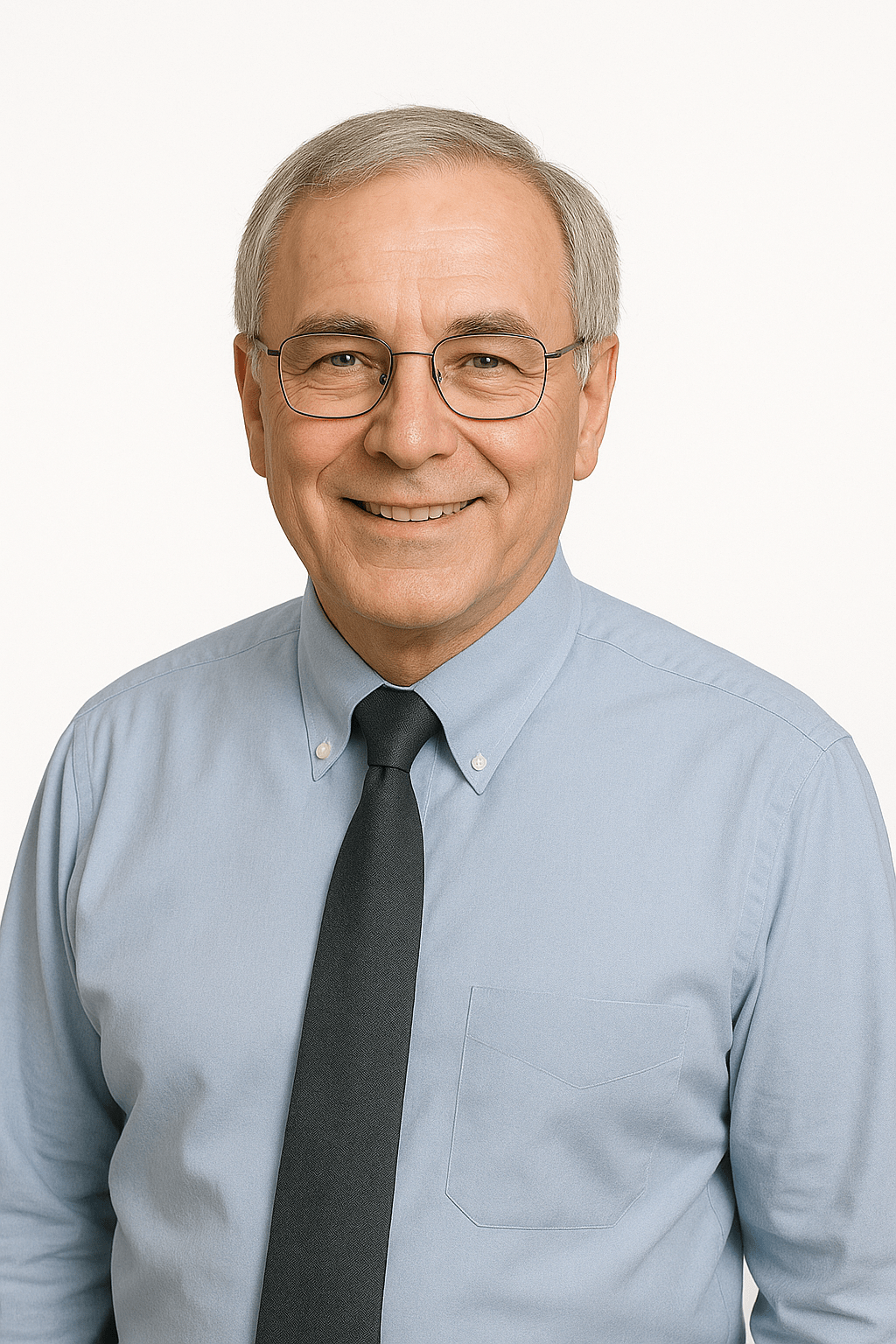
Alexander Schneider is a senior applications engineer and leading authority in the industrial diamond tooling industry, with over 35 years of hands-on experience in the development, application, and optimization of ultra-thin and high-precision diamond blades, diamond core drills, and diamond and CBN grinding wheels. His work spans a wide range of advanced materials including ceramics, glass, composites, semiconductors, and high-performance metals.
Throughout his career, he has collaborated with leading R&D institutions, national laboratories, and high-tech manufacturing companies across Europe, North America, and Asia, providing technical expertise and tailored solutions for demanding cutting and surface preparation applications.
Mr. Schneider has played a pivotal role in advancing precision cutting, sectioning, dicing, and grinding technologies used in research, production, and failure analysis. He is widely respected for his ability to optimize tool design and cutting parameters to meet exacting industry standards—balancing factors such as cut quality, blade life, material integrity, and process consistency.
As an author, Mr. Schneider is known for delivering practical, application-focused insights that translate complex technical challenges into clear, actionable strategies. His articles and technical guides serve as trusted resources for engineers, researchers, and manufacturers seeking to improve precision, reduce process variability, and enhance tool performance in critical applications.