Table of Contents
ToggleWhen evaluating Diamond & CBN wafering blades, especially for metallography and sample preparation, it is critical to consider a set of key evaluation criteria and performance metrics. These factors help determine the effectiveness of a blade and can significantly influence the quality of the results in sample analysis. Here are the primary criteria and performance metrics that differentiate one blade from another, making one a better solution than another:
Key Performance Metrics for Diamond & CBN Wafering Blades
-
Cutting Speed: How quickly a blade can complete a cut without sacrificing quality. Faster speeds can increase throughput but must not compromise the integrity of the sample.
-
Surface Finish: The quality of the surface after cutting is crucial. A finer finish reduces the need for subsequent grinding and polishing, thereby saving time and preserving the material's characteristics. Minimizing chipping and other forms of cut-induced damage is crucial for maintaining the structural integrity of the sample.
-
Wafering Blade Life: This refers to how long a blade can maintain its cutting effectiveness before it needs to be replaced. A longer blade life reduces downtime and the cost of consumables.
-
Consistency: The ability of the blade to consistently produce quality cuts throughout its life span. Inconsistency can lead to wasted material and unreliable results.
-
Required Force: A blade that requires less force to cut through materials is preferable as it minimizes potential sample damage and operator fatigue.
-
Heat Dissipation: Effective heat management prevents sample damage and preserves the blade’s life. Blades that dissipate heat efficiently perform better in demanding conditions.
-
Material Compatibility: A blade's ability to handle different types of materials effectively without degradation is essential, especially when working with a variety of samples.
-
Wear Resistance: Resistance to wear and tear defines how well a blade holds up under regular use, impacting its longevity and reliability.
-
Vibration: Lower vibration levels indicate a more stable cut, enhancing the precision and quality of the sample.
-
Amount of Material Deformation: It’s essential to minimize deformation during cutting to ensure that the true microstructure of the material is preserved for accurate analysis.
-
Secondary Grinding and Polishing Steps Required: Blades that produce cleaner cuts reduce the need for extensive secondary processing, thereby enhancing overall efficiency and sample quality.
-
Thermal Stability: Assesses the blade's ability to maintain its properties and performance at varying temperatures. Blades with high thermal stability perform consistently across a range of operational conditions, which is crucial when working with thermally sensitive materials.
-
Wafering Blade Flexibility: Evaluates the blade's ability to flex without breaking, particularly when making intricate cuts or when operating under variable loads. This is important for ensuring the blade's reliability in complex cutting scenarios.
-
Recovery Time: The time it takes for a blade to return to optimal performance after dressing or any form of maintenance. Faster recovery can significantly reduce downtime.
-
Edge Durability: Measures how long the cutting edge remains effective before it dulls. Durable edges reduce the frequency of blade replacements and maintenance.
-
Startup Performance: Assesses how quickly and effectively a blade reaches its optimal cutting performance from startup. This can be crucial in production environments where time and quick setup are valued.
-
Cost per Cut: Considers the total cost of using the blade divided by the number of cuts it can make before it is deemed ineffective. This metric helps in assessing the economic efficiency of the blade over its lifespan.
-
Impact Resistance: Evaluates the blade's ability to withstand sudden stresses or impacts without cracking or chipping. This is particularly relevant for cutting hard, brittle materials.
-
Profile Retention: Measures how well a blade maintains its original profile and cutting characteristics over its lifespan. High profile retention reduces the need for frequent adjustments and recalibrations.
-
Blade Stiffness:, A measurement of the rigidity of the blade. Stiffer blades are less prone to wobbling and can provide more precise cuts, especially important in high-precision applications.
Cutting Speed
The cutting speed of a diamond wafering blade is a fundamental performance metric that significantly influences the efficiency, productivity, and cost-effectiveness of sectioning large variety samples for metallography, sample preparation, materials science, and precision manufacturing. Cutting speed refers to how fast, effectively and consistently the diamond or cbn wafering blade moves through the material, generally measured in surface feet per minute (SFM) or meters per minute (MPM).
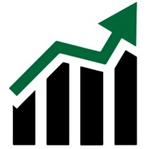
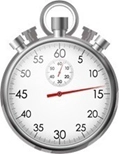
This metric impacts several critical aspects of the sectioning cutting process. Another explanation for cutting speed is measuring amount of material the blade is able to cut within certain amount of time without needing to dress the blade.
A notable feature of exceptional wafering blades is their ability to maintain high cutting speeds without bogging down, ensuring efficient and fast and freer cutting speed. With minimal amount of material stress, deformation, and secondary sample preparation steps such as grinding and polishing.
Efficiency and Productivity
Higher cutting speeds can dramatically decrease amount of time it takes to section a sample, allowing the operator to section more samples in a shorter amount of times. However, it's essential to balance speed with the cut quality, surface finish, amount of material deformation and secondary steps that can be required after sectioning.
Heat Generation and Surface Finish
The speed at which the blade cuts also affects the amount of heat generated during the process. Excessive heat can damage both the blade and the material, altering material properties or leading to unwanted thermal expansion. Furthermore, the cutting speed can influence the smoothness of the cut surface; optimal speeds help minimize imperfections, reducing the need for additional finishing processes.
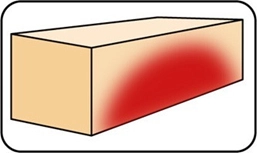
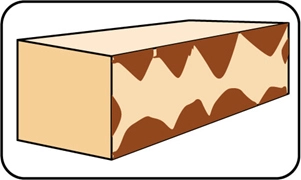
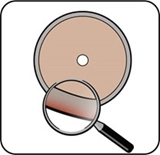
Blade Wear and Durability
While high speeds may seem beneficial for productivity, they can also accelerate the wear and tear on a blade, shortening its usable life. This necessitates a careful consideration of speed to balance efficiency with longevity.
Optimize Cutting Speed
Optimizing cutting speed involves considering the sample / material’s hardness and thickness, which can dictate the need for slower speeds to ensure precision and unnecessary damage and deformation. Additionally, the blade's specifications, such as its diameter and bond type, kerf thickness, diamond size, concentration, bond hardness, etc can influence the ideal speed.
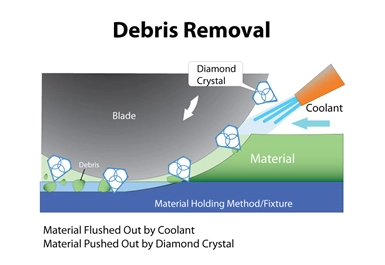
Surface Finish (Cut Quality & Chipping Level)
Cut quality and the level of chipping are crucial for determining the performance of diamond wafering blades, especially in fields like materials science, electronics, and precision engineering where the accuracy of the cut can significantly affect the usability and analysis of a sample. High-quality cuts are characterized by their cleanliness and the minimal finishing required post-cutting, whereas chipping involves small fragments of the material breaking away during the cutting process, compromising the integrity and dimensions of the sample.
Cut quality refers to the smoothness and precision of the cut surfaces, which should be free from irregularities and deformations. High-quality cuts are typically characterized by their cleanliness and the minimal finishing required post-cutting.
Chipping, on the other hand, involves small fragments of the material breaking away during the cutting process, which can significantly compromise the integrity and dimensions of the sample.
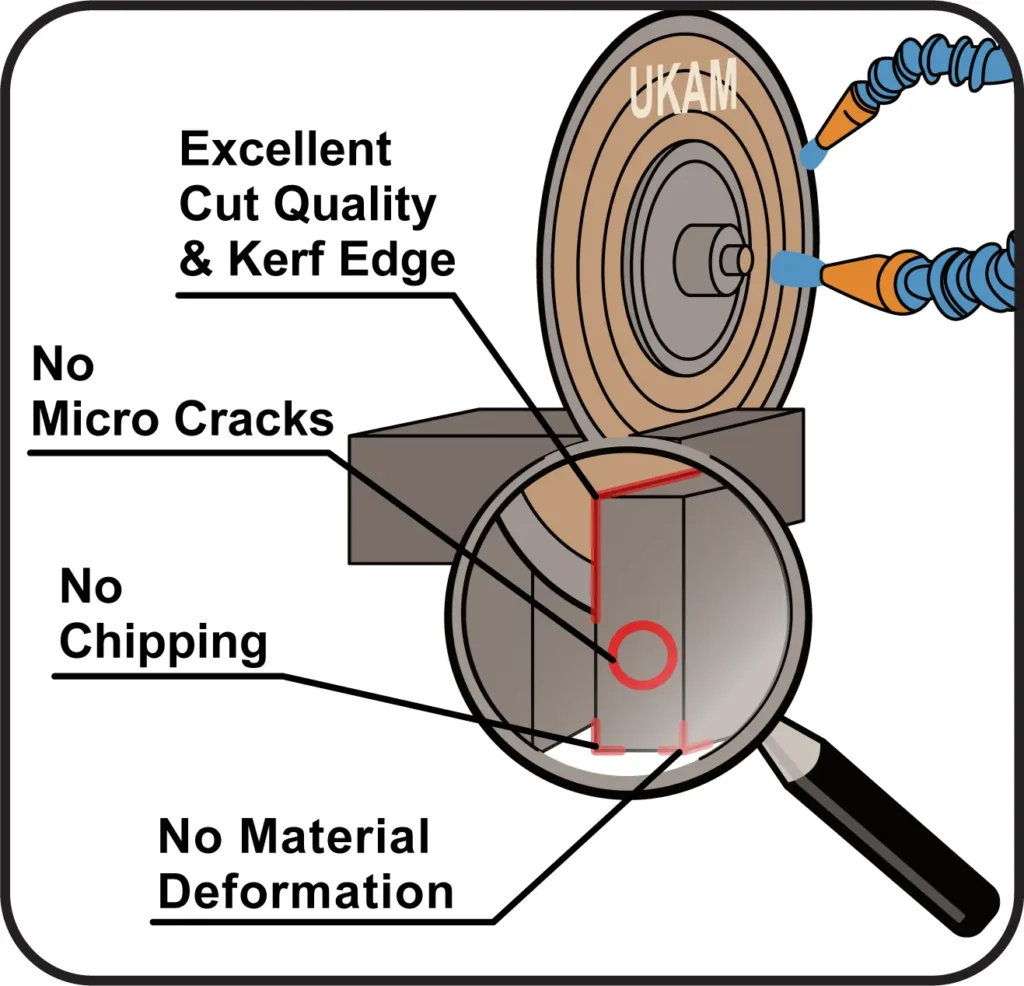
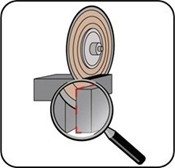
Wafering blades with exposed diamond crystals are less likely to cause chipping and usually produce better cut quality and minimum chipping. Regular maintenance and dressing of the blade ensure it remains sharp and effective. The type of diamond and diamond size used, its concentration, and the bond hardness are also significant, with finer diamond sizes providing higher cut quality with minimal chipping.
The speed at which the blade cuts through the material impacts chipping and overall cut quality. Cutting too fast may lead to increased chipping, while too slow can cause unwanted friction and potential burn marks on the material. Different materials react differently; hard, brittle materials are more prone to chipping and require wafering blades designed for such challenges.
Proper cooling and lubrication reduce thermal stress on the material and the wafering blade, minimizing the thermal expansion that could lead to chipping and cracks. Coolants help in removing debris from the cut, maintaining a clear path for the blade and improving cut quality.
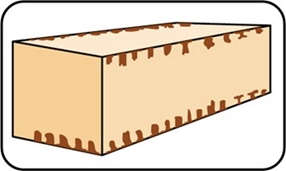
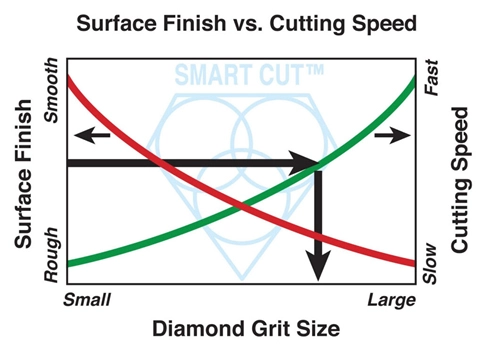
Wafering Blade Life
Blade life, in the context of diamond wafering blades, refers to the duration a blade can maintain its cutting effectiveness before it requires replacement. This metric is vital because it directly affects operational efficiency, cost of consumables, and overall productivity. A longer wafering blade life means fewer blade replacements, reducing downtime and minimizing costs associated with purchasing new wafering blades and related maintenance.
Several factors influence blade life, including high quality raw materials (such as what type of diamond and quality of diamond), diamond grit size, diamond concentration, diamond bond type (such as sintered, resin bond, nickel bond), the blade's design (such as what type of steel core or fully impregnated with diamond), diamond depth/height, bond composition and bond hardness and the conditions under which it is used (rpm’s, feed rates, coolant types, type of cutting machine, etc). Lastly matching the right wafering blade for the material / sample being sectioned and the cutting equipment and settings it will be used on will determine the life of wafering blade.
High quality wafering blades made from high quality materials, using higher diamond depth, higher diamond concentration, using consistent high technology manufacturing methods and quality control methods tend to have longer lifespans because they resist wear and tear more effectively. The design of the blade, including the kerf thickness and type of bond matrix, also contributes to its longevity.
Raw Materials Quality
The type and quality of raw materials used in the wafering blades manufacturing process are critical for its longevity. Higher Quality diamonds offer greater durability and cutting efficiency, with synthetic diamonds being preferred for their consistency, hardness and resistance to wear. The quality of these diamonds directly affects the blade's performance and lifespan. Beyond the diamonds themselves, the steel core's properties, composition, and manufacturing process are crucial factors that influence the blade's performance, longevity, and reliability. The steel core is the backbone of a diamond wafering blade. It provides structural support and ensures the blade's stability during cutting. The steel core's properties, including its hardness, flexibility, and resistance to wear and heat, significantly affect the blade's overall quality.
Diamond Grit Size
Diamond grit size refers to the size of the diamond particles embedded in the blade. Smaller grit sizes can lead to smoother cuts but might wear out faster, while larger grit sizes are more durable but may not cut as cleanly. Choosing the right grit size is a balance between precision and longevity, depending on the application.
Diamond Concentration
Diamond concentration indicates the density of diamonds in the blade. Higher concentrations generally offer greater cutting power and longer blade life because they provide more cutting edges. However, the ideal concentration depends on the application, with softer materials requiring lower concentrations and harder materials benefiting from higher concentrations.
Diamond Bond Type
The bond type that holds the diamond particles in place plays a significant role in blade life. Sintered bonds are typically more durable and suitable for heavy-duty applications. Resin bonds offer flexibility and are used in applications where smoother cuts are needed, but they might not last as long as sintered bonds. Nickel bonds are common in electroplated blades, providing a strong attachment for diamonds but with a potentially shorter lifespan compared to sintered bonds.
Blade Design
The design of the blade, including the type of steel core and whether it's fully impregnated with diamonds, influences its lifespan. Blades with thicker cores or reinforced designs tend to be more durable and resistant to warping or bending. A fully impregnated diamond blade, where diamonds are embedded throughout the blade, can last longer due to the continuous exposure of fresh diamonds as the blade wears down.
Diamond Depth/Height
The depth or height of the diamond section indicates how much diamond material is available for cutting. Greater diamond depth typically leads to longer blade life because there's more material to work with before the blade becomes ineffective. A deeper diamond section can also mean less frequent maintenance and fewer replacements.
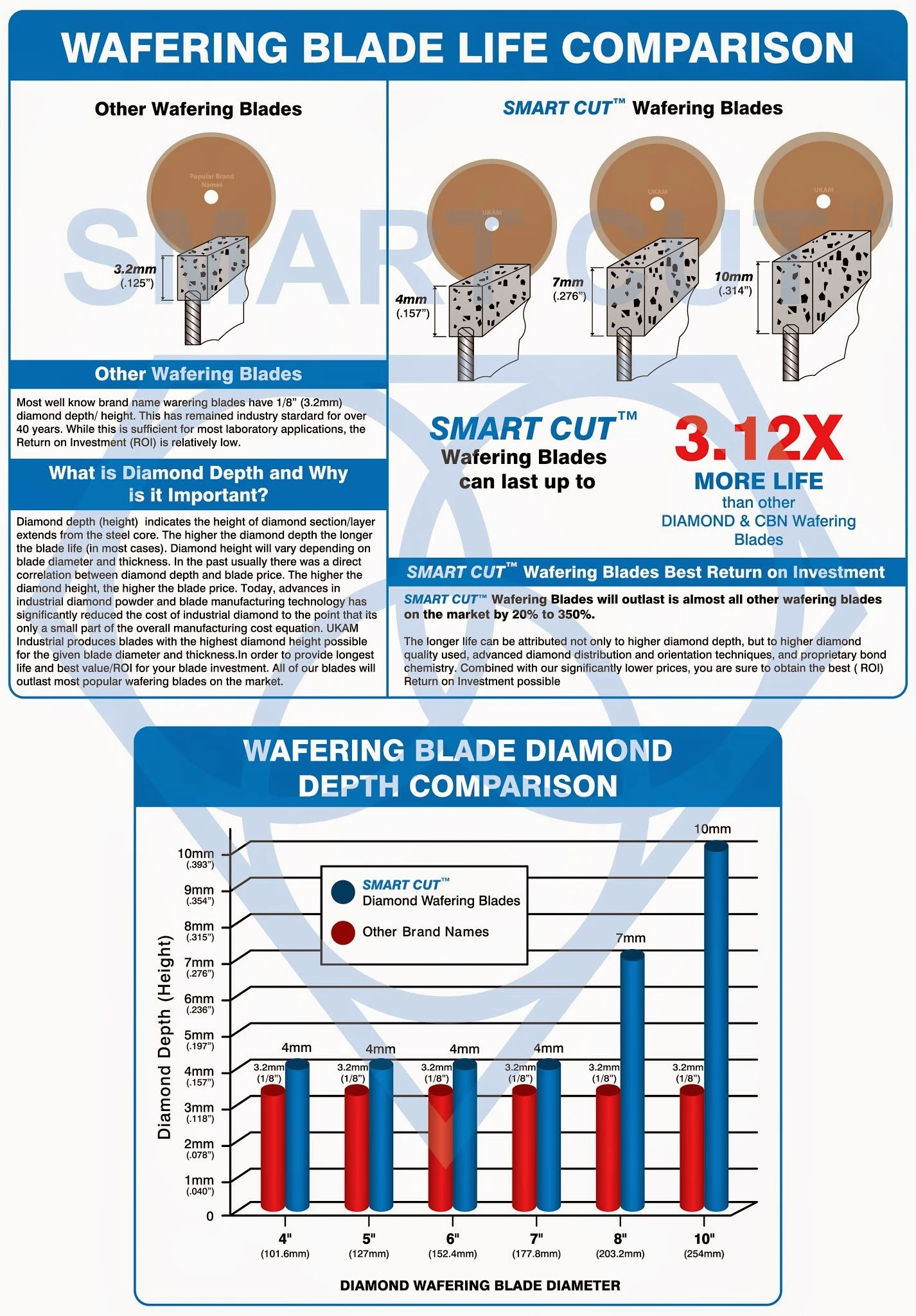
Bond Composition and Hardness
The bond composition and hardness determine how well the blade withstands wear and tear. A harder bond generally offers more durability but might require more force to cut through materials. A softer bond exposes new diamonds more quickly, which can be beneficial for softer materials, but might wear out faster.
Diamond Distribution and Orientation
The uniformity of diamond distribution within the bond matrix determines how consistently a blade performs. A well-distributed arrangement ensures that the cutting edge has a consistent number of diamond particles across its surface, leading to smoother cuts and more even wear. Uneven distribution can cause some areas of the blade to wear out faster, resulting in inconsistent cuts and reduced lifespan.
Orientation plays a role in how diamonds are positioned within the bond matrix. Proper orientation, where the diamond particles are aligned in a way that maximizes their cutting edges, enhances cutting efficiency and extends blade life. Blades with diamonds that are randomly or improperly oriented might require more force to cut, leading to faster wear.
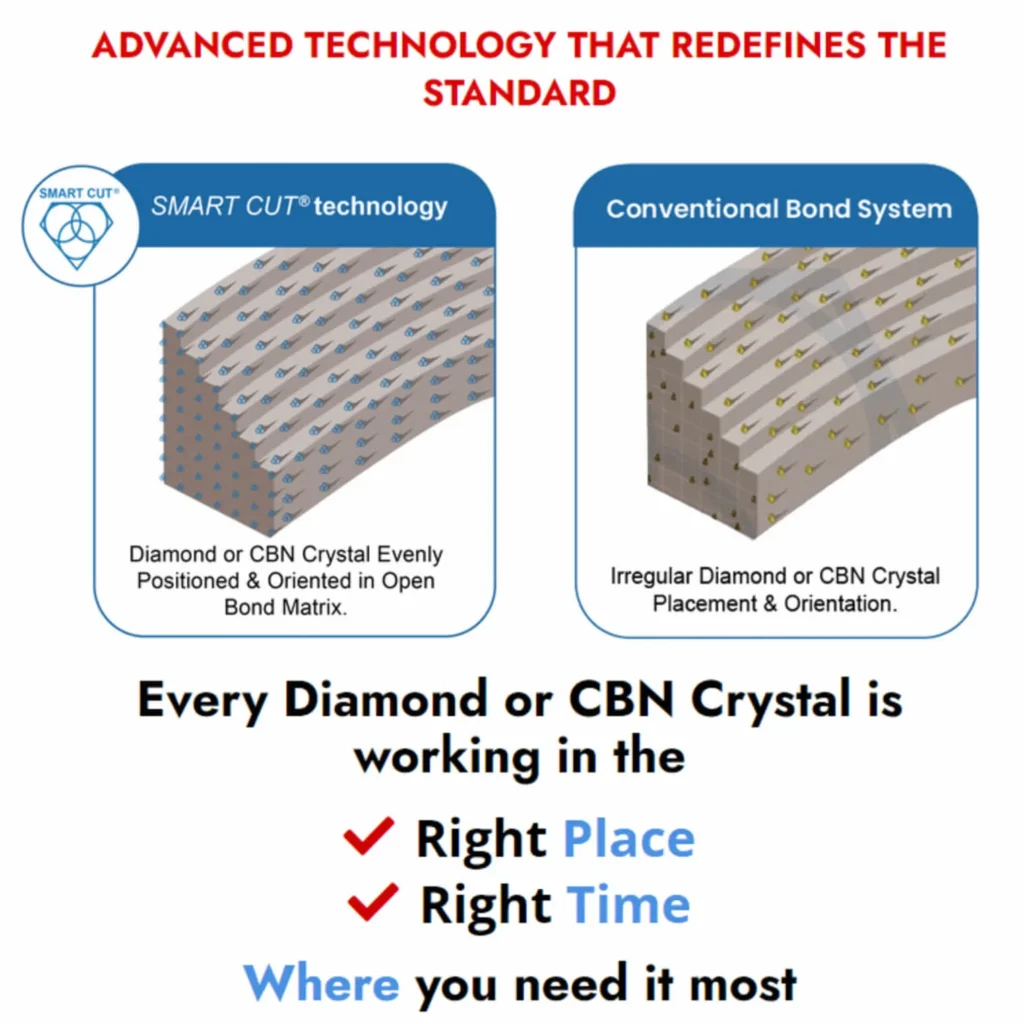
Conditions of Use
The conditions under which the blade is used, such as RPMs, feed rates, coolant types, and the type of cutting machine, also impact blade life. Operating a blade at the correct RPMs and feed rates reduces stress and wear. Proper coolant types and flow ensure effective cooling, preventing overheating. The type of cutting machine and its settings must align with the blade's specifications to avoid unnecessary stress and wear.
Matching the Blade to the Material and Equipment
Selecting the right wafering blade for the material being sectioned and ensuring it is compatible with the cutting equipment are crucial for blade life. Using an incompatible blade can lead to rapid wear and reduced lifespan. The correct blade for the specific application and cutting equipment ensures efficient and effective cutting, extending the blade's life.
Caring for Blades
To extend blade life, proper maintenance is essential. Regular dressing to expose the the diamond crystals inside the bond matrix, and cleaning help keep the blade in optimal condition, ensuring it can continue to cut effectively without excessive wear. Adequate cooling and lubrication during sectioning are also critical for maintaining blade life, as they help prevent overheating and reduce friction, which can accelerate wear.
Operational practices
Operational practices play a significant role in determining blade life. Operating the blade at the recommended speed and applying appropriate pressure can significantly extend its lifespan. Excessive speed or force can cause premature wear, leading to shorter blade life. In contrast, gentle and consistent cutting techniques help the blade maintain its effectiveness over a longer period.
Blade life has a direct impact on operational costs. Longer blade life reduces the frequency of blade replacements, lowering the cost of consumables. This, in turn, contributes to a more cost-effective cutting process. Fewer blade replacements also mean less downtime, leading to greater productivity and improved workflow.
Furthermore, a longer blade life contributes to overall safety. A blade that maintains its effectiveness is less likely to break or cause accidents during operation. It also ensures more consistent cut quality, reducing the need for re-cuts or additional processing, which can be time-consuming and costly.
Consistency
Consistency in a diamond wafering blade refers to its ability to produce quality cuts reliably throughout its lifespan. Inconsistent blades can lead to uneven cuts, chipping, or other defects, increasing process cost and compromising results.
A consistent wafering blade maintains its cutting efficiency over time, offering stable performance across various materials and applications. Factors contributing to consistency include the blade's design and construction, the quality of its materials, and the manufacturing techniques used. High-quality blades with a robust bond matrix and uniform diamond distribution are more likely to deliver consistent results. Proper operational conditions, such as correct cutting speed and pressure, also play a role in maintaining consistency.
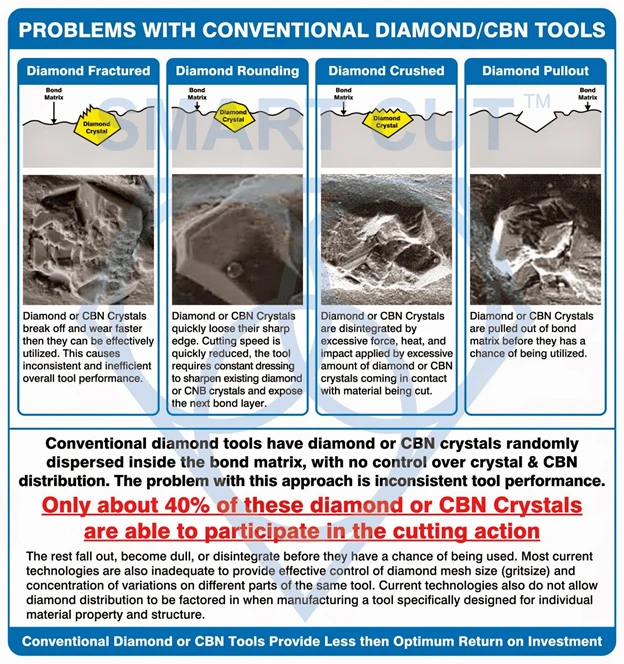
To measure consistency in diamond wafering blades for metallography and sample preparation, you need to assess how reliably a blade produces uniform cuts over time. This involves examining the quality of the cuts for smoothness, straightness, and minimal chipping or rough edges. Consistent blades maintain these qualities throughout their lifespan, even with extended use.
Another indicator of consistency is the wafering blades performance across various samples or materials. For example, a consistent wafering blade should deliver similar results, whether cutting different types of metals or varying thicknesses. Monitoring how quickly a blade wears down can also reveal its consistency; a blade that maintains its shape and diamond crystal exposure is more consistent, while rapid or uneven wear suggests inconsistency.
The frequency of adjustments and maintenance can signal inconsistency. Blades that require frequent dressing, re-sharpening, or recalibration are often less consistent. Operator feedback is also helpful; experienced operators can detect changes in performance, like increased vibration or wobbly cuts, which may indicate inconsistency.
Using consistency testing tools, such as those that measure cut straightness and surface roughness, can provide more precise data on a wafering blades performance. By combining these observations, you can determine if a blade is consistently delivering high-quality and repeatable results, which is crucial for reliable and accurate sample preparation. A consistent wafering blade leads to fewer operational disruptions, reduced waste, and ultimately, more efficient and cost-effective sectioning processes.
Required Force
The required force for operating a diamond wafering blade is a crucial performance metric that significantly influences both the quality of the cut and the overall user experience. A blade that requires less force to section samples offers several benefits:
Minimized Sample Damage: High force during cutting can cause cracks, fractures, or other structural deformations in delicate materials.
This is especially important in fields like metallography or materials science, where maintaining the integrity of the sample is essential for accurate testing and analysis.
Reduced Operator Fatigue: Blades that glide through materials more easily reduce physical strain on the operator. This is particularly beneficial during long periods of use or when precise cuts are required, helping to maintain high levels of concentration and reducing the risk of errors due to fatigue. This not only enhances safety but also boosts productivity.
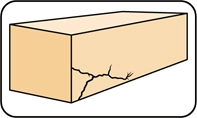
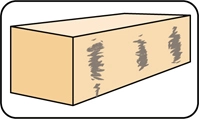
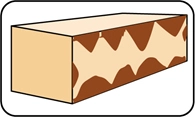
Enhanced Blade Longevity and Equipment Health: Operating with less force extends the life of the blade and the cutting machinery. It reduces wear and tear, leading to fewer maintenance issues, lower replacement costs, and less downtime for repairs. Additionally, a lower cutting force decreases the chances of the blade overheating, which can degrade its cutting efficiency and lifespan.
Improved Cut Quality: Blades that require less force typically produce cleaner cuts with smoother edges. This reduces the need for secondary finishing processes and ensures that cuts are more accurate and consistent. In precision applications, where minor imperfections can cause significant issues, the ability to make clean cuts is invaluable.
Achieving a lower required force involves selecting the right blade and maintaining optimal cutting conditions:
-
Blade Design and Materials: Choosing a blade with the appropriate design and diamond grit for the specific material type can significantly reduce the necessary cutting force.
-
Blade Sharpness and Maintenance: Regular maintenance and dressing of the blade to keep it sharp decrease the force needed for cutting. A dull blade requires more force, increasing material stress and operator effort.
-
Cutting Speed and Techniques: Optimizing the speed and feed rate of the blade can influence the force required, minimizing force while maximizing efficiency.
-
Use of Coolants and Lubricants: Applying suitable coolants or lubricants reduces resistance during cutting, decreasing the force needed. These substances keep the blade cool and reduce friction, facilitating smoother cuts.
Heat Dissipation
Effective heat management and dissipation is crucial when using diamond wafering blades, as it significantly impacts the integrity of the sample being cut and the longevity of the diamond or cbn wafering blade. Wafering Blades that efficiently dissipate heat are key to maintaining optimal performance, especially in demanding conditions where extended use can lead to significant heat buildup.
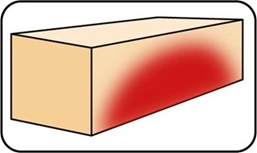
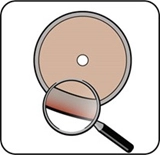
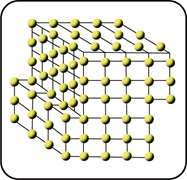
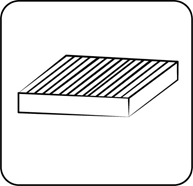
As the wafering blade is sectioning the sample, the friction generated can lead to significant heat buildup. Without proper management, this heat can compromise the wafering blade's structural integrity and cutting efficiency. A wafering blade that effectively dissipates heat maintains its cool even under intense operation, safeguarding against potential warping or degradation of the diamond cutting edge
Heat generated during the cutting process can alter the material properties of the sample, such as inducing thermal expansion or changing its microstructure.
This is particularly problematic in fields like material science or metallurgy, where even minor thermal alterations can skew test results or misinterpret analyses. Additionally, excessive heat can wear down the diamond cutting edges faster, reducing the blade's effectiveness and lifespan. It can also weaken the bond matrix that holds the diamonds, leading to premature diamond loss and uneven wear.
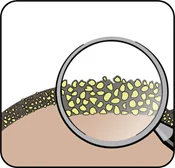
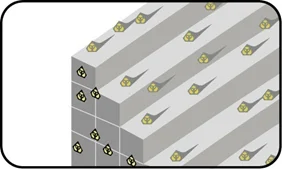
The use of coolants is also pivotal in managing heat during cutting. Water-based coolants are commonly used for their excellent heat absorption properties, helping reduce the temperature of both the blade and the material. Oil-based coolants are preferred when water could cause rusting or other issues, and they also lubricate the cutting area, reducing friction and heat generation. Synthetic coolants offer the benefits of cooling and lubrication while minimizing bacterial growth.
Proper cutting technique further influences heat dissipation. Operating the blade at the correct speed for the material and blade type minimizes friction and heat buildup. Adjusting the feed rate to avoid forcing the blade through the material can also prevent excessive heat.
Material Compatibility
Material compatibility is a crucial performance metric for diamond wafering blades, particularly in settings where various materials need precise and careful cutting. This metric reflects a wafering blade's ability to handle different types of materials without suffering degradation in performance or structural integrity. It affects not only the efficiency and versatility of cutting operations but also the quality of the results.
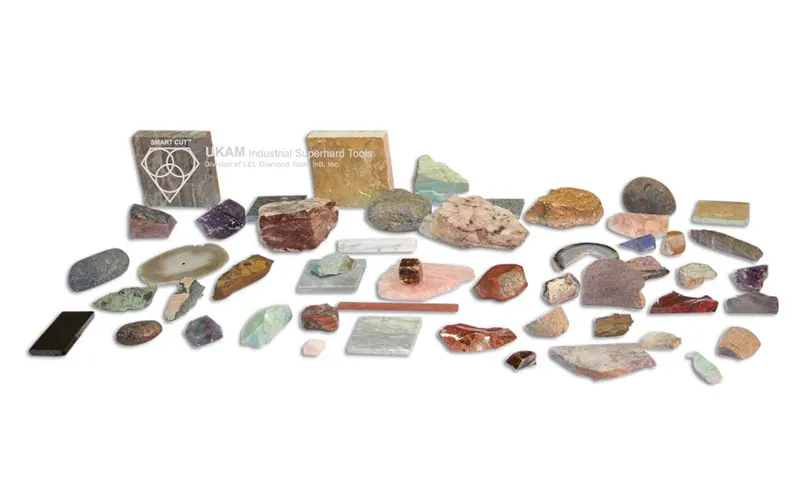
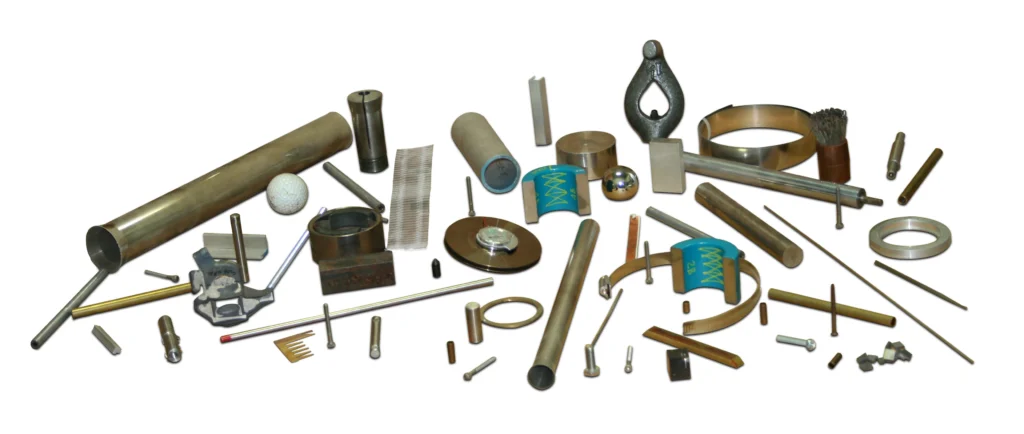
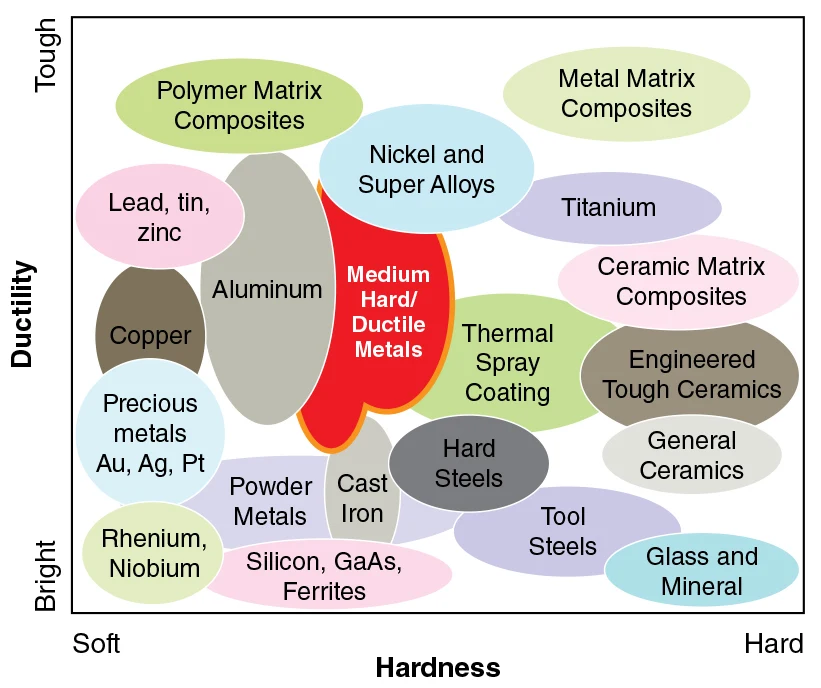
Material compatibility involves the wafering blade's capacity to maintain its cutting performance when used on a range of sample types, from metals and ceramics to composites and minerals. Wafering Blades must be chosen based on their design to match the material being cut to prevent rapid wear and tear, potential damage to the material, or inefficient cutting.
The ability of a wafering blade to seamlessly transition between different material types without the need for constant adjustments or blade changes is a testament is one of the most important performance metrics.
Several factors influence a wafering blades compatibility with different materials. The composition and design of the blade, including the type and quality of the diamond size and the bonding matrix, are critical.
For example, a hard bond matrix is better suited for cutting softer materials to prevent premature diamond shedding, while a softer bond is preferred for harder materials to allow regular exposure of fresh, sharp diamond edges.
The size of the diamond particles also affects the wafering cutting ability. Coarser diamond sizes might cut faster but can be unsuitable for materials requiring a smooth finish, whereas finer diamond size are better for achieving better cut quality and less material deformation but may cut more slowly. Additionally, the thickness of the blade and its edge configuration—bond type (such as sintered, resin bond, nickel bond, etc)—play roles in determining the suitability of a wafering blade for specific materials.
Often, finding the best wafering blade for a specific material involves some trial and error, allowing operators to assess how different blades perform with various materials in terms of speed, finish, and blade longevity.
Using the correct diamond or cbn wafering blade for a material not only enhances cutting efficiency, reducing the time required to section samples and minimizing energy consumption, but also ensures an excellent cut quality and minimum material deformation. This reduces the need for additional preparation process such as grinding and polishing, lowering overall processing time and costs. When a wafering blade is matched correctly with the material, it wears uniformly and lasts longer, reducing the frequency of blade replacements and associated costs.
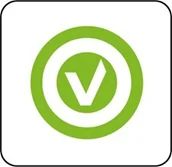
Wear Resistance
Wear resistance is a critical attribute of diamond wafering blades, as it significantly impacts the wafering blades longevity, reliability, cost, and overall effectiveness in sectioning operation. A blade's resistance to wear and tear indicates how well it can maintain its cutting performance over time, even under conditions of regular use.
The wear resistance of a diamond wafering blade is not just about the blade's ability to last a long time; it also ensures that the quality of cuts remains high throughout the blade's life. Optimized diamond wafering blades are distinguished by their ability to retain their cutting edge and diameter over extended periods, demonstrating resilience against the wear and tear. Additionally, enhanced wear resistance translates into lower overall costs by reducing the frequency of blade replacements and minimizing downtime due to maintenance.
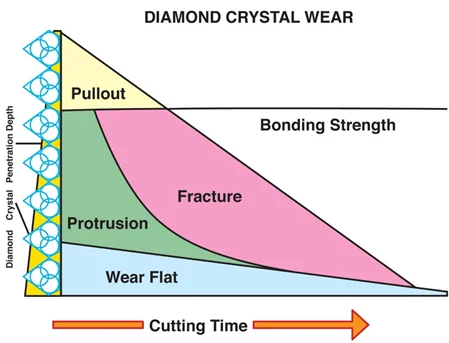
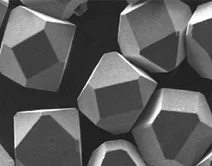
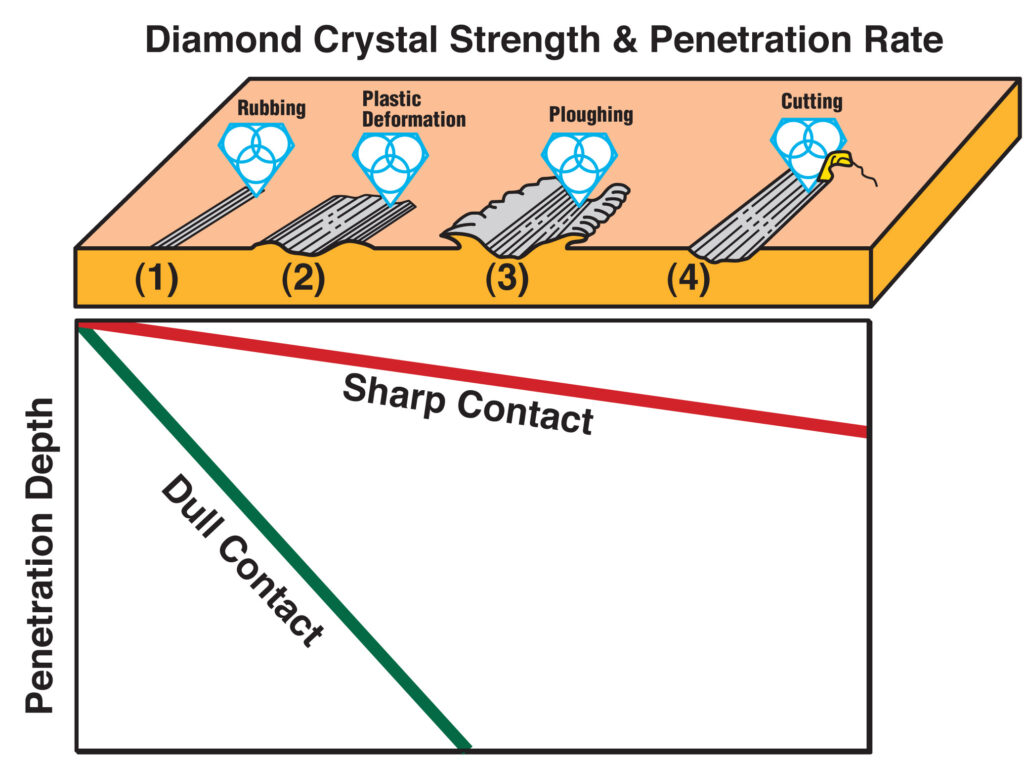
The wear resistance of a blade is influenced by several factors, including the quality of the materials used in its construction, the technology employed in the manufacturing process, and the specific design of the blade itself.
Material Quality: The type and quality of the diamond grit used in the blade affect its wear resistance. Higher-grade diamonds and a stronger bonding matrix can significantly enhance a blade's durability, allowing it to maintain its cutting efficiency longer, even under strenuous conditions.
Manufacturing Technology: Advanced manufacturing technology that can help control the wafering blade bond hardness and amount and frequency of wear. Proper diamond crystal distribution and orientation inside the bond matrix, helps insure that each diamond crystal is working in the right place and right time where its needed most. This uniformity helps prevent premature wear and tear and allows for more consistent performance.
Operational Factors: How the wafering blade is used also affects its wear resistance. Proper operation, including maintaining the correct cutting speed and feed rate, using adequate cooling and lubrication, and avoiding excessive force, helps preserve the blade's condition and extend its lifespan. Regular maintenance, such as checking for alignment and ensuring the blade is kept clean and sharp, also plays a vital role in preventing excessive wear.
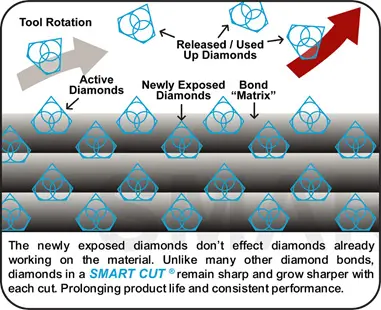
Vibration
Vibration is a critical factor in the performance of diamond wafering blades, with lower vibration levels indicating a more stable and precise cutting process. The presence of vibration during cutting can lead to several issues that impact both the cutting process and the longevity of the blade and equipment.
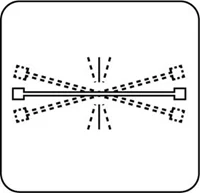
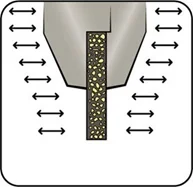
The Impact of Vibration on Sectioning Process
Vibration can also result in incorrect installation of the blade or proper placement of the sample inside the chuck holding the sample. In addition, vibration can cause increased wear and tear on the blade, reducing its lifespan, and can lead to premature failure of sectioning saw.
Causes of Vibration in Diamond Wafering Blades
Several factors can lead to vibration during sample preparation:
-
Blade Imbalance: An imbalanced blade, due to manufacturing defects, uneven wear, or improper installation, can create wobbling during rotation, causing vibration on both low-speed and high-speed sectioning saws.
-
Improper Installation: If the blade is not correctly aligned or secured to the saw, it can lead to increased vibration during operation.
-
Excessive Cutting Force: Applying too much pressure during cutting, especially at high speeds, can cause the blade to vibrate.
-
Inadequate Cooling: Heat buildup without proper cooling can cause the blade to warp or distort, leading to vibration.
-
Machine Issues: Problems with the motor, bearings, or other components of the sectioning saw can transfer vibration to the blade, affecting the quality of the cut.
Material Deformation
Reducing material deformation during sectioning is important in order to preserve the true microstructure of a sample, which is essential for applications such metallography, sample preparation, materials science, and electronics. Deformation can lead to inaccuracies in analysis and compromise the reliability of test results. It can manifest as warping, bending, or even microfractures, significantly impacting the quality of the final analysis.
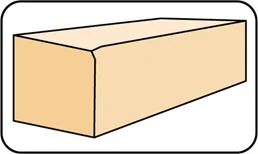
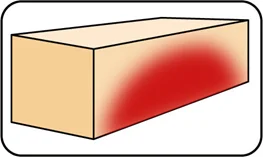
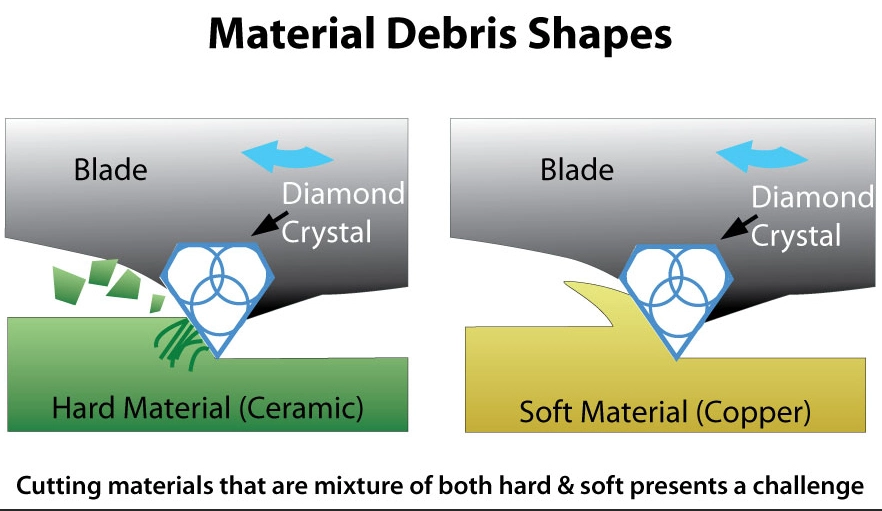
Vibration during sectioning can also lead to deformation, especially for thin or delicate samples, as it causes them to flex or shift. An inappropriate blade can contribute to this problem, particularly if it has an incorrect bond strength or diamond grit size, which increases stress on the material. The cutting speed, if too fast or too slow, can lead to overheating or excessive force, both of which contribute to deformation.
Material deformation often results from excessive cutting force, which can cause softer or ductile materials to bend or stretch. Heat buildup is another common cause, especially when there's insufficient cooling during cutting. This heat can lead to thermal expansion, altering the sample's microstructure and potentially melting some materials.
To minimize material deformation, it's essential to select the right diamond wafering blade for the material type and cutting requirements. This involves choosing the right diamond grit size, concentration, bond type, bond hardness, and blade design to ensure a clean cut with minimal stress on the sample. The correct cutting speed and pressure are equally important, as operating within the recommended speed range helps avoid overheating and excessive force and secondary processes such as grinding and polishing.
Proper cooling and lubrication are also crucial. Using coolants and lubricants reduces friction during cutting and dissipates heat, preventing heat-induced deformation and reducing wear on the blade. Controlling vibration contributes to a more stable cutting process, which decreases the risk of material deformation. This can be achieved through proper blade installation, alignment, and the use of anti-vibration features. Regular maintenance of the cutting equipment also plays a role, as it reduces the likelihood of machine-related issues causing deformation.
Secondary Finishing Operations: Grinding & Polishing
The need for secondary grinding and polishing in sample preparation significantly affects the efficiency of laboratory processes and the quality of final samples. Diamond wafering blades that produce clean, precise cuts help minimize these additional steps, resulting in a smoother workflow and higher-quality outcomes.
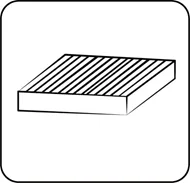
Better Surface Finish is important because this reduce the time and cost associated with secondary processing. Achieving accurate cuts with minimal roughness or chipping means that there’s less need for extensive grinding and polishing, allowing samples to be processed more quickly. This is particularly important in high-throughput laboratories, where time and resources are at a premium.
Moreover, cleaner cuts help preserve the structural integrity of the sample, ensuring that the microstructure remains intact for accurate analysis.
Excessive grinding and polishing can alter a sample's properties, leading to potential errors in metallographic studies, materials science research, and other analytical applications.
By minimizing additional processing, there's a lower risk of changing the sample's characteristics.
Several factors contribute to the need for secondary processing. If a diamond crystals are not exposed sufficiently or they wear out quickly,
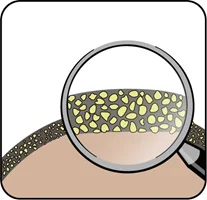
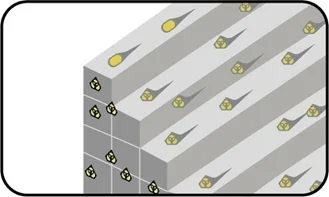
it may create rough surface that will require more grinding and polishing. Similarly, sectioning at the wrong speed or with improper technique can result in uneven edges or chipping, leading to additional work to correct these flaws.
Vibration during cutting can cause jagged cuts, while heat buildup from inadequate cooling can leave burn marks or other thermal damage—all of which require further processing. The material's characteristics also play a role; some materials are more prone to chipping or rough cuts due to their hardness or brittleness.
To reduce the need for secondary grinding and polishing, several strategies can be employed. Using high-quality wafering blades designed for the material/sample being sectioned, utilizing with high quality diamond crystals that are more evenly distributed and oriented inside the bond matrix. Operating the blade at the correct speed and applying appropriate pressure can lead to better cut quality, as can maintaining proper cooling and lubrication to avoid heat-related damage.
Keeping the diamond exposed through regular dressing is also important, as wafering blades with glazed bond are more likely to produce a rougher finish. Employing precision cutting techniques, such as gradual pressure and stability during cutting, reduces the risk of chipping and uneven edges.
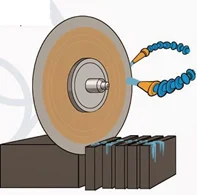
Thermal Stability
Thermal stability is a crucial aspect of diamond wafering blades, particularly when cutting generates heat or when working with thermally sensitive materials. Blades with high thermal stability maintain their properties and performance despite temperature fluctuations, ensuring reliable and consistent cutting results. If a wafering blade lacks thermal stability, it can warp, distort, or degrade under high temperatures, leading to inaccurate cuts, reduced blade life, and safety risks.
Material composition plays a key role in thermal stability. Wafering Blades made from high-quality materials with durable bond matrices are better at resisting heat-related damage.
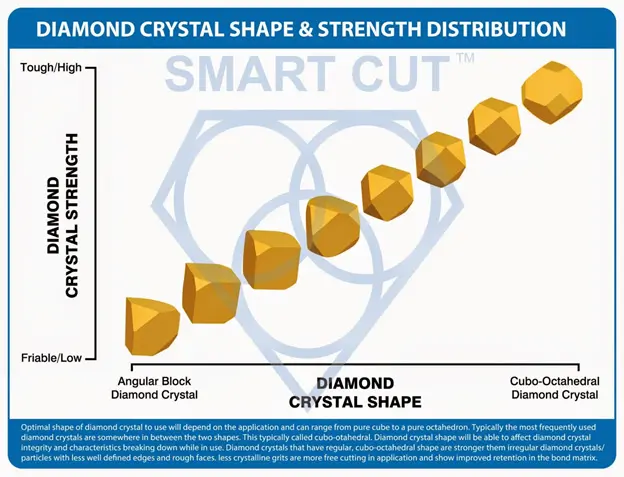
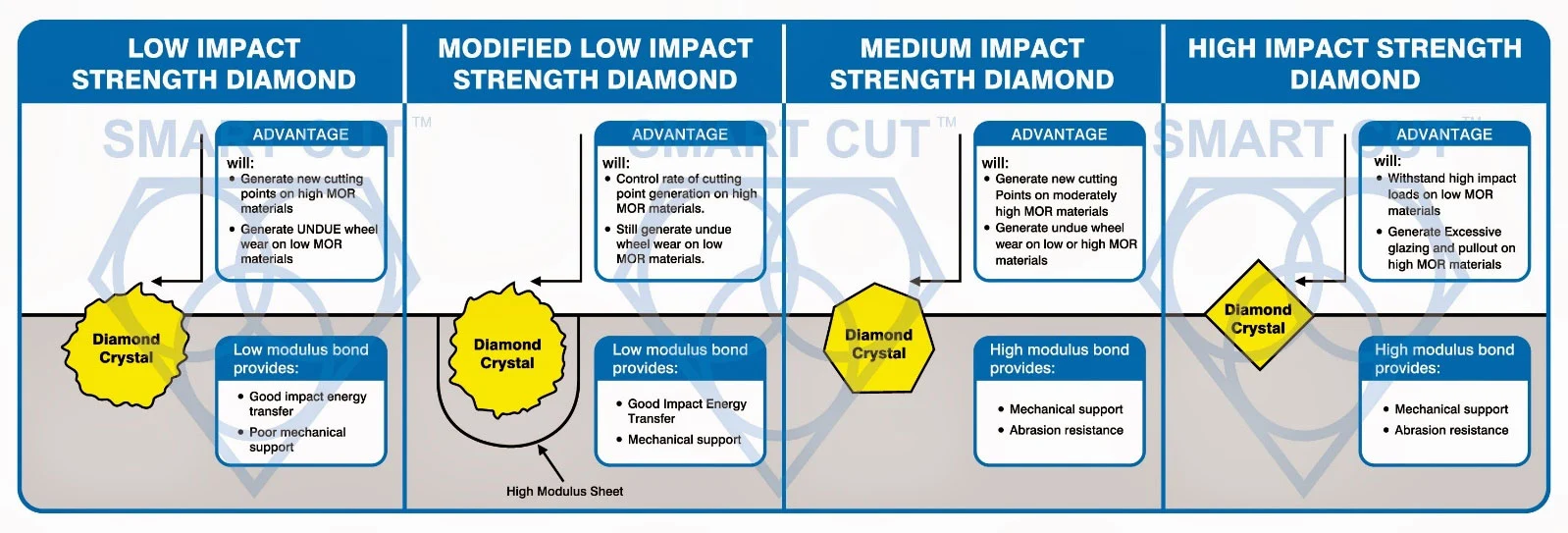
The bond matrix, which holds the diamond particles in place, must withstand elevated temperatures without breaking down. Wafering Blade design also contributes to thermal stability—thicker blades tend to resist warping. Advanced manufacturing techniques such as right sintering temperatures, process, and bond formulation composition can improve stability by creating strong bonds and uniform distribution of diamond particles.
Lubrication reduces friction, which can also lower heat generation during cutting. Optimized cutting parameters are crucial—operating the blade at the recommended speed and applying appropriate pressure can prevent overheating, while cutting too quickly or with too much force can lead to excessive heat buildup.
Maintaining thermal stability requires proper cooling and lubrication. Using water-based or oil-based coolants helps keep the blade and the material cool, preventing heat-induced damage.
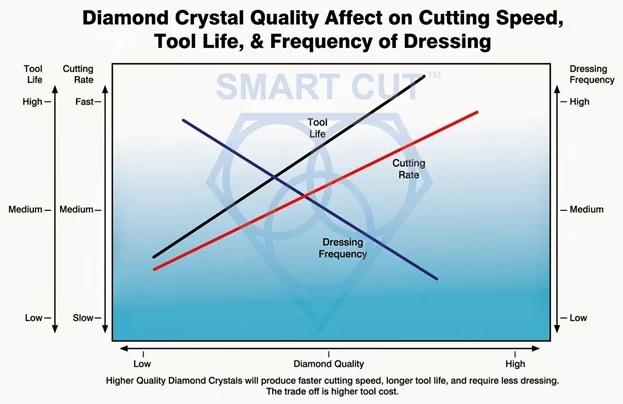
Regular maintenance and monitoring help ensure consistent performance. Checking the blade's condition, including its alignment and diamond exposure, and watching for signs of thermal instability like discoloration or warping, allows for early intervention before major issues occur.
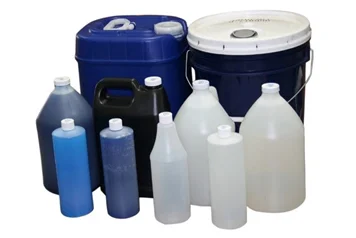
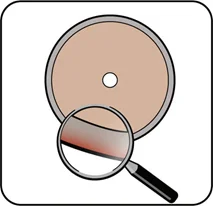
Wafering Blades with high thermal stability provide consistent results even in high-heat environments, essential for working with thermally sensitive materials where any change in temperature can affect the sample's microstructure.
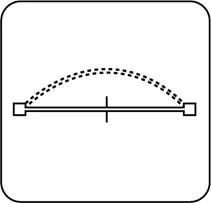
Wafering Blade Flexibility
Wafering Blade flexibility is an essential characteristic of diamond wafering blades, particularly in situations where intricate cuts are required or when operating under variable loads. A flexible blade can adapt to different cutting conditions, allowing for precision and reliability in complex scenarios. This adaptability is crucial in applications where a rigid blade might break or cause unexpected outcomes due to its inability to withstand variable stresses.
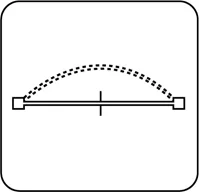
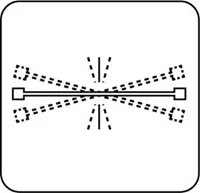
A flexible blade is one that can bend or flex slightly without breaking or loosing its tension/flatness, providing a level of resilience that allows it to navigate complex cuts and withstand sudden changes in pressure or load. This flexibility can be crucial when making intricate cuts, such as those required in electronics, where precision and accuracy are paramount. A flexible blade can accommodate tight corners and fine details, reducing the risk of chipping or breaking the sample.
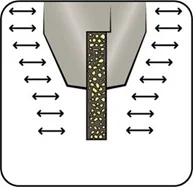
Blade flexibility also plays a role in reducing vibration. When a blade can flex, it is less likely to transmit vibrations to the material, resulting in smoother cuts and better overall stability. This is particularly important when working with delicate or brittle materials, where excessive vibration can cause damage or deformation.
The level of blade flexibility is influenced by several factors, including the wafering blades material composition, thickness, and design. Blades made from high-quality metals or alloys with some inherent flexibility are more capable of bending without breaking. Thinner blades generally offer more flexibility, allowing them to adapt to varying loads and intricate cutting patterns.
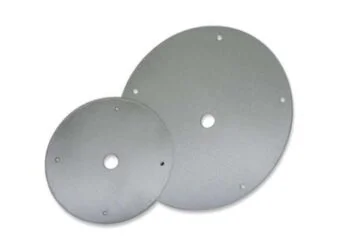
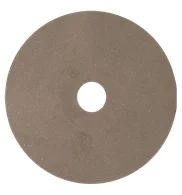
The design of the blade, including the type of steel core used will also highly influence flexibility, with some blades allowing for greater movement without compromising stability. Such as Nickel Bond Wafering Baldes that are made using memory steel. This type of Core steel allows the blade to flex as much as needed. The blade will always snaps back to its original shape no matter how much bent. Fully sintered (metal bond) impregnated blades allow for minimal flexibility, as blade is fully impregnated with diamond from OD to ID of the blade all the way through. There is no steel core or relief between the steel core and the diamond section.
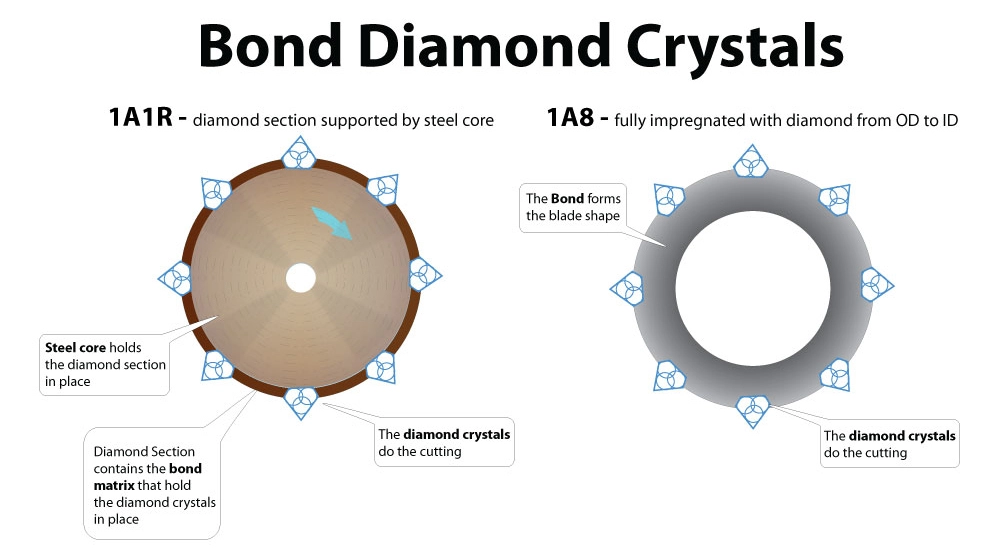
Operating conditions can also impact blade flexibility. When making intricate cuts or working under variable loads, maintaining a controlled cutting speed and applying consistent pressure is crucial. A flexible blade can better withstand sudden changes in speed or force, reducing the likelihood of breakage or unintended deviations in the cut.
Another benefit of blade flexibility is its contribution to blade longevity. A flexible blade is less likely to crack or snap under stress, extending its lifespan and reducing the frequency of blade replacements.
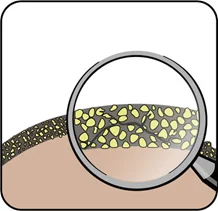
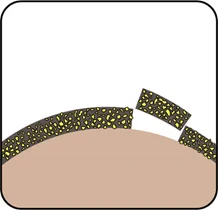
This flexibility can also help prevent damage to the cutting equipment, as a more flexible blade is less likely to cause excessive wear on the machine's components.
To optimize blade flexibility, it's essential to choose the right wafering blade for the specific application and cutting conditions. This involves considering the blade's material composition, thickness, and design features that promote flexibility. Regular maintenance, including checking for signs of wear or stress, helps ensure that the blade retains its flexibility over time.
Wafering Blade Recovery Time
Recovery time is the period it takes for a diamond wafering blade to regain its optimal performance after maintenance, such as dressing. A shorter recovery time is beneficial in high-throughput environments where downtime can be costly.
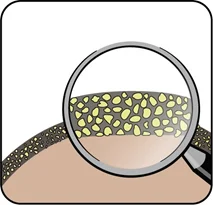
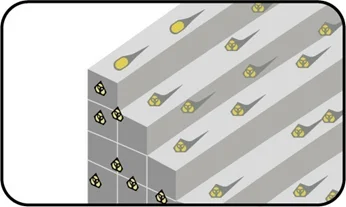
After a blade undergoes maintenance, it might take time to return to peak efficiency. The quicker this transition, the faster operations can resume, leading to increased productivity.
Dressing or sharpening a blade involves removing a worn or glazed layer to expose fresh diamond particles. This process temporarily halts operations, and recovery time is influenced by how quickly the blade regains its cutting efficiency.
Faster recovery means less disruption to workflow, allowing for greater throughput and better use of resources.
Wafering Blade quality and design play a significant role in recovery time. Wafering Blades made from high-quality materials, such as higher quality blocky and strong diamond crystals with they right bond matrix composition and hardness tend to recover more quickly because they retain their structure during maintenance.
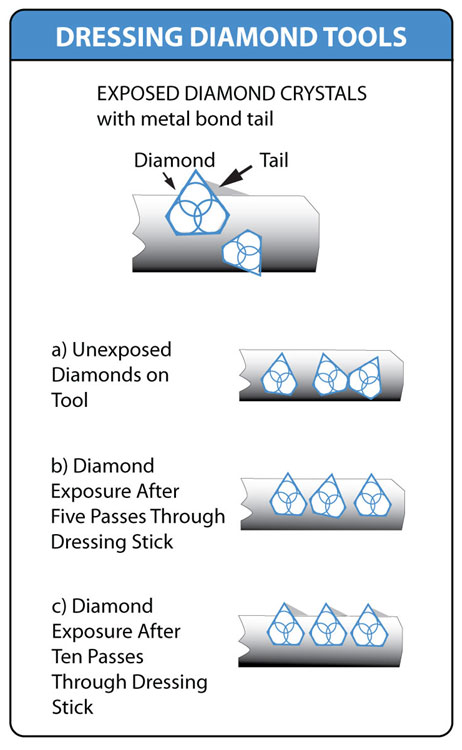
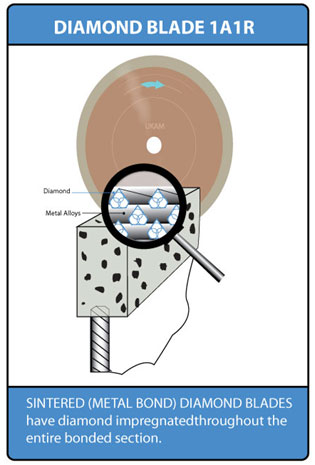
The method used to dress or sharpen the blade also affects recovery time. Efficient techniques that expose fresh diamond particles without causing excessive wear contribute to a shorter recovery period.
The structure of the blade, including its thickness and diamond section, can influence recovery time. Thicker blades might require more time to dress, while thinner blades can recover faster due to their lighter structure. Bond Type is another very important aspect of how frequently a blade needs to be dressing. Some bond types such as resin bond wafering blades are more self dressing and nickel bond require little to no dressing as the diamond crystals are more exposed on the surface of the core still body, instead of being impregnated inside and metal binder. Operator expertise is another factor—experienced operators can perform maintenance tasks more efficiently, reducing the time required for recovery.
Faster recovery times are advantageous because they allow for quicker resumption of cutting operations. This leads to reduced downtime and lower maintenance costs, as the blade needs less frequent or extensive dressing. It also contributes to blade longevity, since over-dressing can shorten the blade's lifespan.
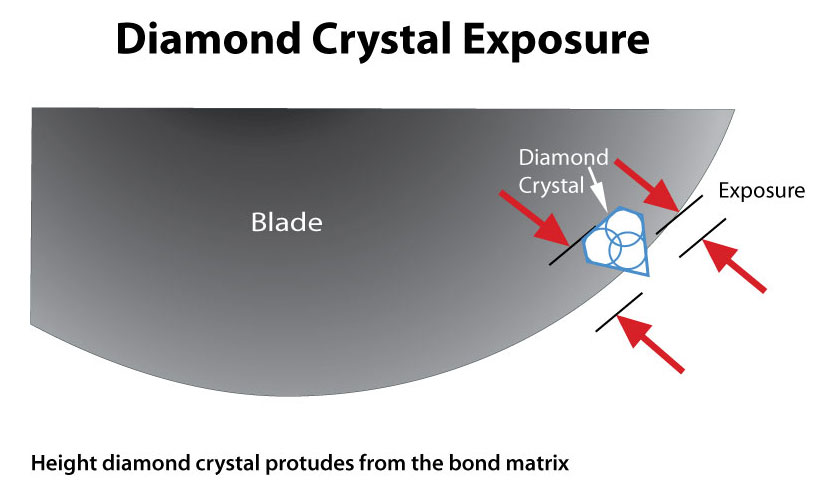
Wafering Blade Edge Quality
Edge durability is a key aspect of diamond wafering blade performance. It measures how long the cutting edge remains effective before the diamond crystals inside the bond matrix lose their sharp edges, impacting the frequency of blade replacements and maintenance. A blade with high edge durability maintains its sharpness and cutting efficiency over time, even with frequent use. This is especially important in high-throughput environments where downtime for blade maintenance or replacement can be costly.
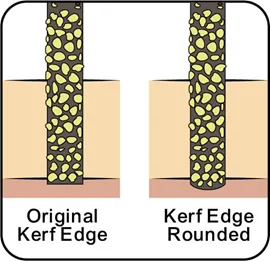
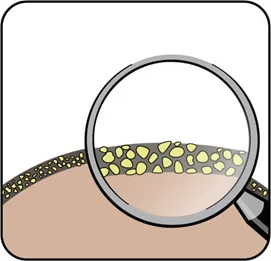
A durable diamond section edge and exposed diamond crystals inside ensures consistent cut quality. As wafering blades glazes over, they can create rough cuts, chipping, and increased heat due to higher friction, which affects the material and the cutting process. A blade with a durable edge continues to deliver clean, accurate cuts without frequent re-sharpening or replacement, which reduces operational costs and improves overall efficiency.
Several factors contribute to edge durability. The quality of the diamond crystals is crucial, with higher-grade diamonds offering greater resistance to wear.
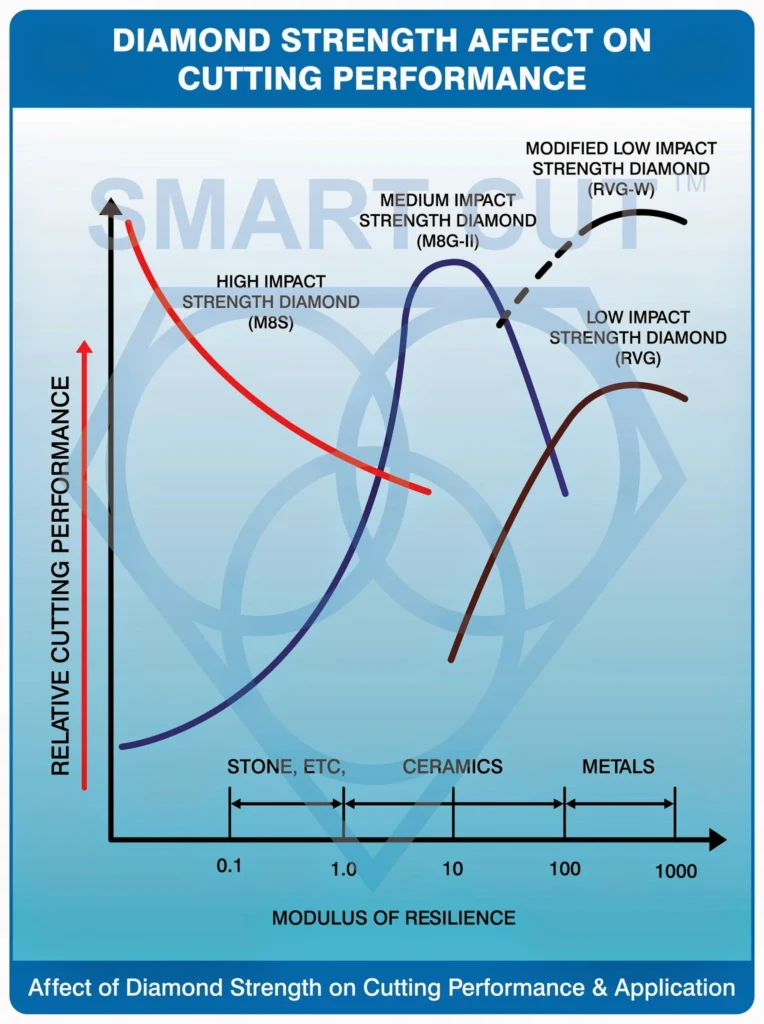
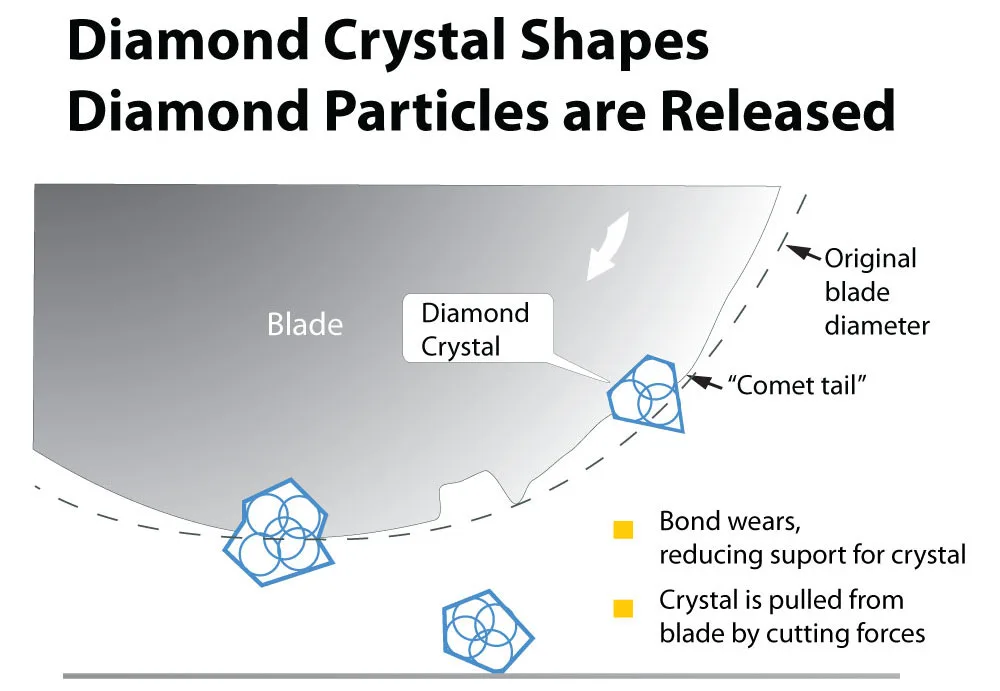
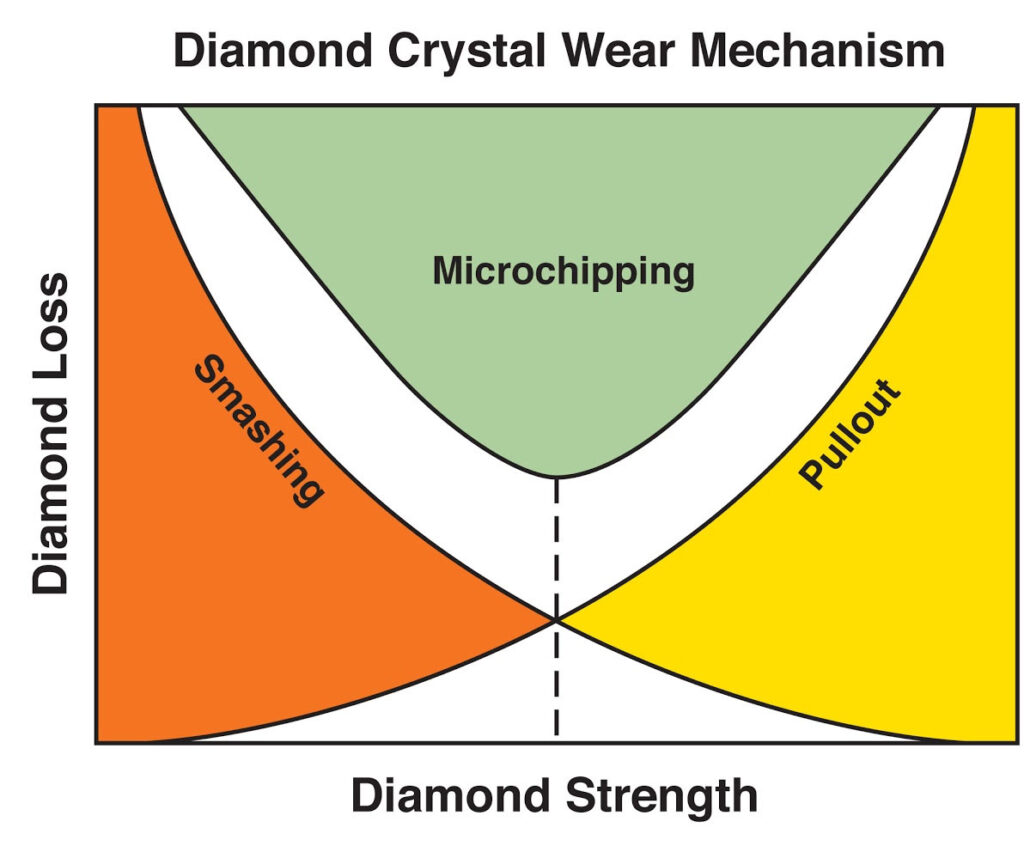
The bond matrix, which holds the diamonds in place, must be strong enough to keep them secure under high stress.
Blade design also matters, with thicker blades providing more support for the cutting edge, and nickel bond wafering blades with interrupted coating edge helping to dissipate heat, reducing wear.
Operational conditions affect edge durability as well. Proper use of the blade, including maintaining the correct cutting speed and applying appropriate pressure, can extend the edge's lifespan. Incorrect operation, such as using excessive force, can lead to faster dulling of the blade. Adequate cooling and lubrication are also vital, as they prevent heat-related damage and reduce friction during cutting.
A Wafering blade with high edge durability reduces downtime and maintenance costs. It also contributes to blade longevity, as durable edges are less likely to degrade quickly. This is particularly beneficial in production environments where consistent operation is key. By maintaining a durable edge, the need for additional finishing processes due to poor cuts is minimized, leading to more reliable and precise results.
Improving edge durability involves selecting high-quality blades with strong bond matrices, ensuring proper cooling and lubrication, and optimizing cutting parameters.
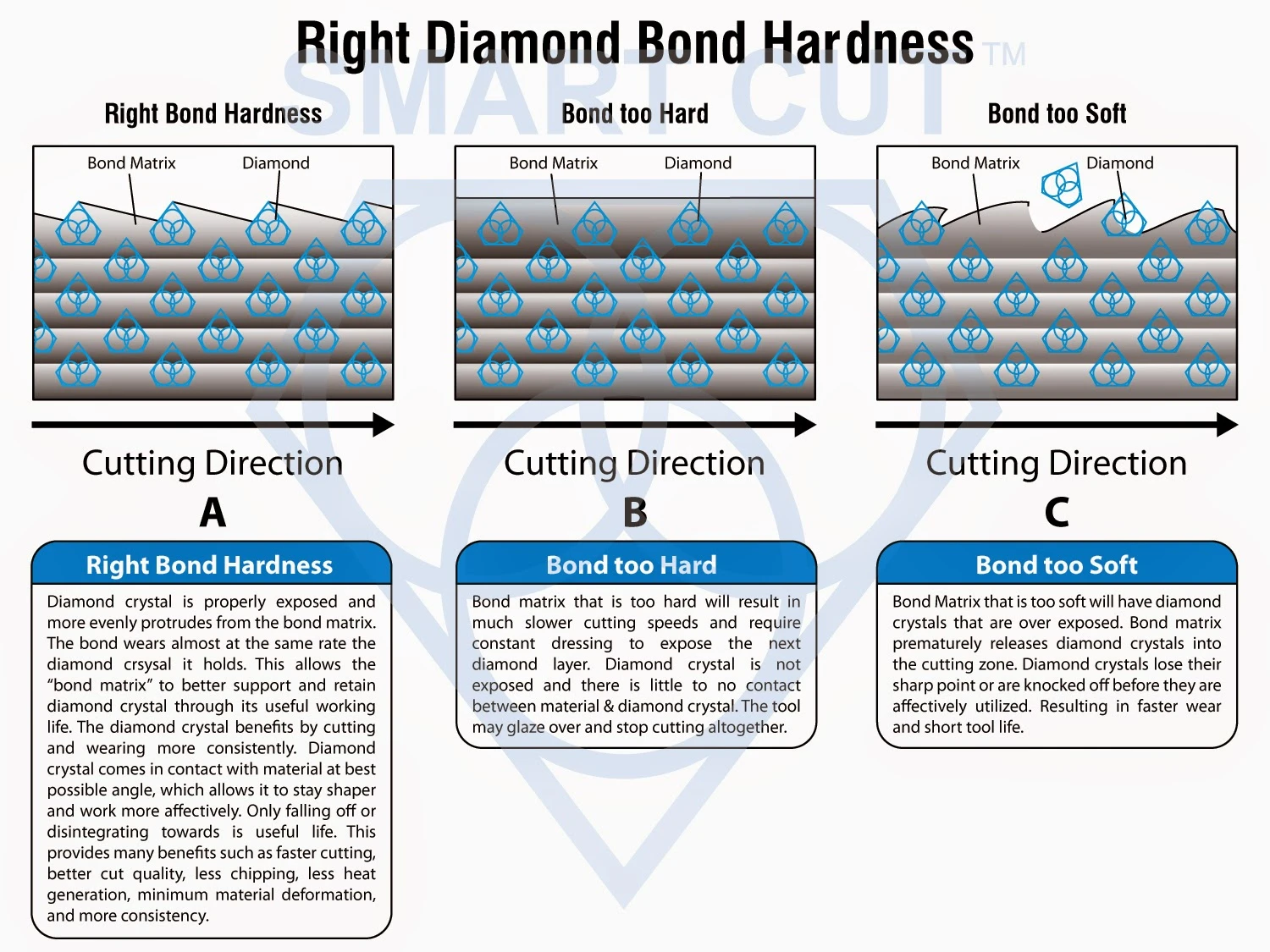
Regular maintenance, such as routine inspection and dressing, helps keep the blade's edge sharp. These practices ensure that the cutting edge remains effective for longer periods, reducing the frequency of blade replacements and contributing to a more efficient and cost-effective cutting process. Find out more about bond hardness>>>
Cost Per Cut (cost per sample)
Cost per cut is a significant metric for assessing the economic efficiency of diamond wafering blades. It represents the total cost of using the wafering blade, from purchase to replacement, divided by the number of cuts or samples that can be sectioned before it is deemed ineffective. This metric is valuable because it provides a clear measure of the wafering blades value over its lifespan, allowing for informed decisions when selecting blades for specific applications or budgets.
This metric considers not just the blade's purchase price and maintenance but also operational costs like labor and overhead. A key aspect to consider in cost per cut is the time it takes to section through a sample, as this can significantly influence labor costs, which are often a major part of overhead.
To calculate cost per cut, you must consider several factors. The initial purchase price of the wafering blade is the most obvious cost, but other expenses can contribute to the total cost. These might include maintenance, dressing, sharpening, and eventual replacement. Additionally, operational costs such as energy consumption and the use of coolants or lubricants also play a role. The more efficient a blade is in terms of maintenance and operational requirements, the lower the cost per cut or sample sectioned.
A lower cost per cut is ideal, indicating that the blade offers good value by providing a high number of quality cuts before it becomes ineffective. This is particularly important in high-volume cutting operations, where the total number of cuts can be significant, and the cumulative costs can quickly add up. A wafering blade with a low cost per cut allows companies to maintain profitability and stay within budget while achieving high-quality results.
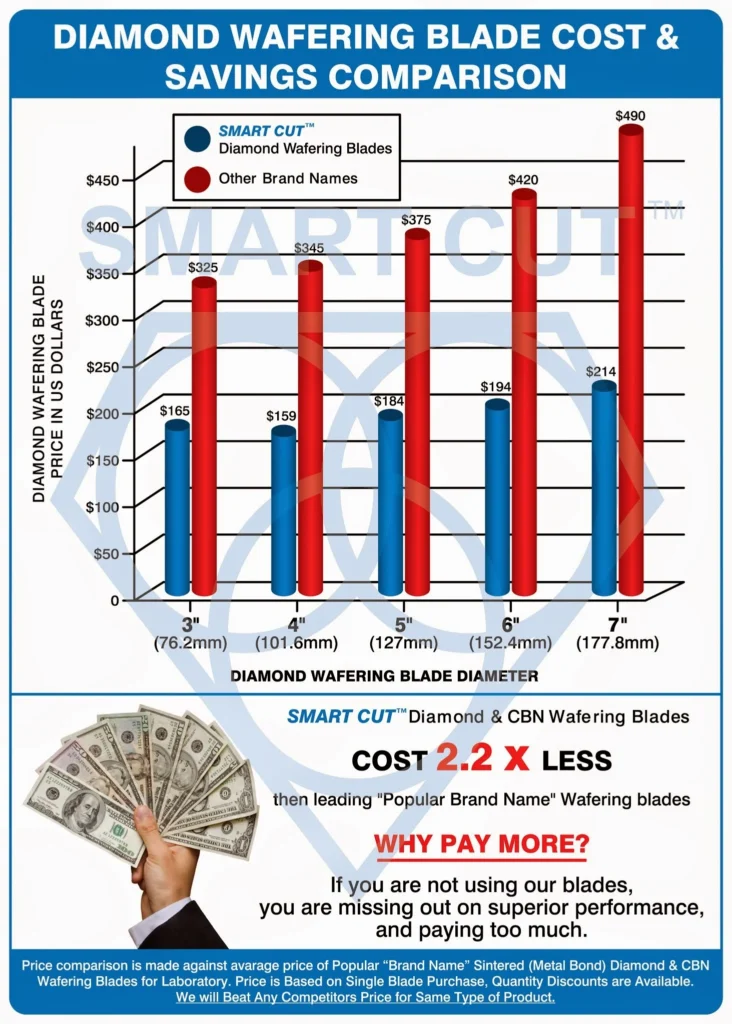
Diamond Depth / Height
The diamond depth, also known as the height of the diamond section of a wafering blade, plays a crucial role in determining the lifespan and overall performance of the blade. This measurement indicates the thickness or height of the diamond-embedded section along the blade's edge. A deeper diamond section generally suggests a longer-lasting blade, while a shallower section might indicate a shorter lifespan.
Here's how diamond depth influences the lifespan of a wafering blade:
A greater diamond depth means more embedded diamond material, which contributes to the blade's durability and lifespan. Since diamond is the primary cutting agent in the blade, having more diamond material allows for a longer period of effective cutting before the blade wears out. As the blade is used, the diamond section gradually erodes due to friction and wear, exposing new diamonds for continued cutting action. With a deeper diamond section, the blade can sustain more cuts and last longer before it becomes ineffective.
Several factors influence cost per cut:
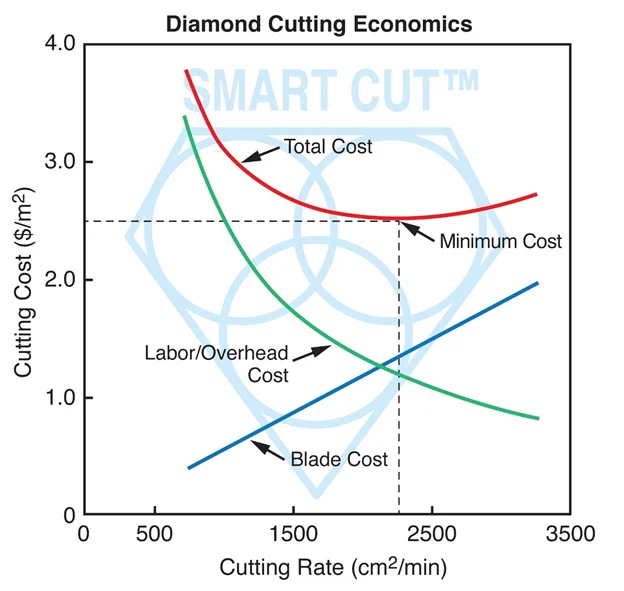
-
Blade Quality and Durability: High-quality wafering blades with durable bond matrix tend to have a lower cost per cut because they last longer and require less frequent replacement. A blade that maintains its cutting performance over a longer period is more economically efficient.
-
Maintenance Requirements: Blades that require less frequent dressing or maintenance contribute to a lower cost per cut. Excessive maintenance can increase operational downtime and add to the overall cost of using the blade.
-
Operational Efficiency: Blades that operate efficiently, requiring less energy and coolant, help reduce the overall cost of each cut. Efficient blades also tend to produce cleaner cuts, reducing the need for additional processing, which further contributes to cost savings.
-
Consistent Performance: Blades that perform consistently over their lifespan offer better value because they provide a predictable number of cuts without a significant decline in quality. This consistency reduces the likelihood of material waste due to poor cuts or the need for re-cutting.
-
Labor and Overhead Costs: Labor is a significant expense in many operations. A blade that sections through samples quickly can reduce labor costs by allowing operators to complete more tasks in less time. Similarly, overhead costs, such as energy consumption and equipment wear, are influenced by the speed and efficiency of the blade. Faster cuts reduce energy use and equipment stress, contributing to a lower cost per cut.
Impact Resistance
Impact resistance refers to a diamond wafering blade's ability to endure sudden stresses or impacts without cracking or chipping. This characteristic is crucial, particularly when cutting hard, brittle materials, where unexpected shocks or uneven pressure could cause significant damage to the blade. A wafering blade with high impact resistance maintains its structural integrity even in challenging conditions, ensuring greater safety, durability, and reliability during cutting operations.
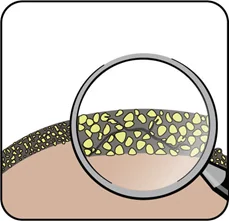
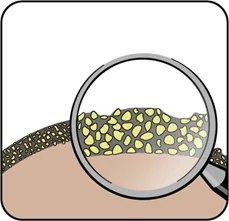
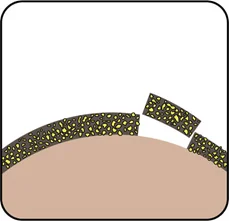
When dealing with hard or brittle materials like ceramics, glass, or certain metals, there is a higher risk of sudden stress due to changes in cutting angles, unexpected obstructions, or high pressure. A wafering blade with low impact resistance might crack or chip under these conditions, leading to operational disruptions, increased costs, and potential safety risks for operators.
In contrast, a wafering blade designed with high impact resistance can absorb these stresses, providing a more stable and reliable cutting experience.
Several factors contribute to a wafering blades impact resistance. The composition of the blade, particularly the quality of the metal or alloy used in the core, is vital. High-quality metals with flexibility and toughness are better at resisting impacts. The strength of the bond matrix holding the diamond particles in place also matters. A robust bond is less likely to break or fracture when subjected to sudden stress, helping maintain the blade's integrity. The blade's design and structure play a role, with thicker blades or those with specific segment configurations providing more support to withstand stress.
To ensure high impact resistance, it's essential to select blades made from durable materials that are known for their toughness and flexibility. Regular maintenance and inspection can identify potential issues early on, reducing the risk of cracks or chipping. Proper cutting techniques, such as avoiding excessive force or sudden changes in direction, help minimize the risk of impact-related stress on the blade. Additionally, ensuring the cutting machine is set to the correct speed and pressure for the material can prevent undue stress.
Profile Retention
Profile retention in diamond wafering blades refers to the ability of a blade to maintain its original shape, structure, and cutting characteristics over time. This metric is crucial because it directly impacts the blade's performance, consistency, and the quality of cuts it produces. A wafering blade with high profile retention remains stable throughout its lifespan, reducing the need for frequent adjustments, recalibrations, and ultimately extending its usability.
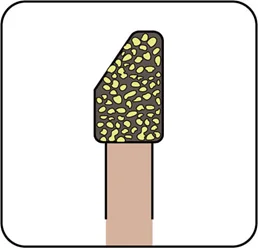
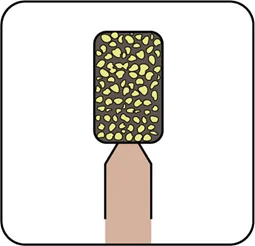
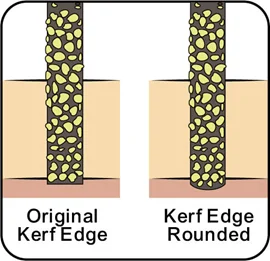
Wafering Blades with low profile retention tend to lose their shape or experience distortions as they wear down. This can lead to various issues, such as uneven cuts, increased vibration, and a higher risk of chipping or cracking. These problems not only affect the quality of the cuts but can also increase maintenance costs and lead to more frequent blade replacements. Additionally, wafering blades that do not retain their profile may require constant adjustments, disrupting workflow and reducing overall efficiency.
Profile retention is particularly important in precision applications where accurate and consistent cuts are critical. In fields like metallography, materials science, and sample preparation, even minor deviations from the desired blade profile can lead to significant errors in sample preparation or analysis. High profile retention ensures that the blade's cutting edge remains stable, providing consistent results over a longer period.
Blade Stiffness
Blade stiffness refers to the rigidity of a diamond wafering blade and is an essential metric for evaluating wafering blades performance, especially precision applications such as sample preparation. Where even slight deviations can compromise the quality of the cut and lead to errors or require additional time in subsequent steps during the sample preparation process. A stiffer blade is less prone to wobbling or bending during operation, allowing for more precise and accurate cuts.
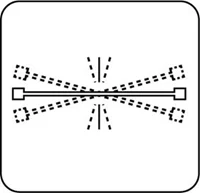
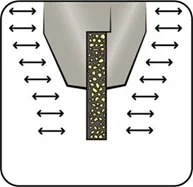
Stiffness is crucial for maintaining stability during cutting. A blade that is too flexible may wobble, leading to uneven cuts, increased vibration, and a higher risk of chipping or cracking.
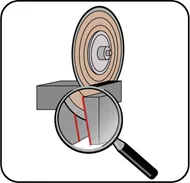
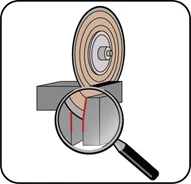
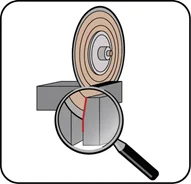
This wobbling can also cause the blade to deviate from its intended path, resulting in inconsistent cuts and potentially damaging the material being cut. Stiffer blades, on the other hand, provide greater control and precision, ensuring that cuts are straight and consistent throughout the operation.
Several factors contribute to blade stiffness:
-
Blade Material and Composition: The type of metal or alloy steel core or diamond bond matrix used in the blade's construction affects its stiffness. High-quality, high hardness and rigid materials are less likely to bend or flex during cutting, contributing to greater stability.
-
Blade Thickness: Thicker kerf blades tend to be stiffer, offering more resistance to bending. This added rigidity can be beneficial in high-precision applications where consistent cuts are required.
-
Blade Design: The design and structure, core type and bond type of the blade also influence its stiffness. Certain designs, like nickel bond blades with stainless steel cores or cores made from memory steel, or fully sintered (metal bond) blades offer additional rigidity, reducing the chances of wobbling during operation.
-
Minimize Blade Exposure By Supporting the Blade: Use Flanges to provide additional support and stability to the blade. They help maintain the blade's tension, prevent warping, maintain flatness, avoid blade wreckage, minimize slanting cuts, and protect the material being cut from damage. Flange Diameter should be in proportion to the wafering blades diameter and kerf thickness.
Stiff blades are particularly valuable in applications where precision is critical. For example, in metallography, where samples must be prepared with exacting accuracy, a stiff blade ensures that cuts are straight and free from distortion. This precision is crucial for obtaining reliable results from microscopic examinations or other analytical techniques.
To achieve optimal blade stiffness, consider the following practices:
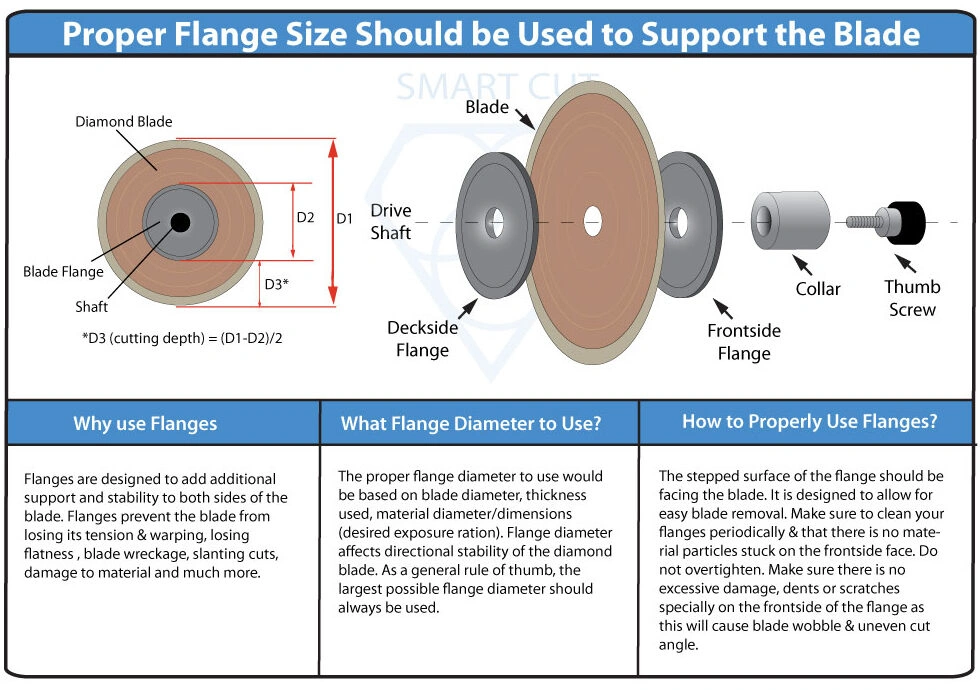
-
Select Blades with Rigid Materials: Choose blades made from high-quality metals or alloys known for their rigidity. These materials provide a solid foundation for maintaining stiffness.
-
Use Thicker Blades for Stability: In applications where precision is critical, using a thicker blade can offer greater stiffness and stability, reducing the risk of wobbling.
-
Optimize Cutting Parameters: Operating the blade within the recommended speed range and applying appropriate pressure helps maintain stiffness. Excessive force or speed can cause the blade to bend or wobble, affecting cut quality.
-
Regular Maintenance and Inspection: Regularly check the blade for signs of wear, warping, or other issues that could affect stiffness. Check flanges to make sure there is no material swarf particles stuck on its face. Proper maintenance helps ensure that the blade retains its rigidity throughout its lifespan.
-
Use proper diameter flanges for the blade diameter and kerf thickness: The proper flange diameter should be based on the blade diameter, thickness of the material used, and the desired exposure ratio. Flange diameter influences directional stability and overall blade safety. The general rule is to use the largest possible flange diameter that still supports the blade.
-
Use Wheel Stiffeners to with Existing Flanges to minimize blade exposure: Wheel stiffeners provide additional stability, rigidity, and support to your diamond blades. They help prevent the blade from "walking" (shifting during cutting) and maintain its flatness. The diameter of the wheel stiffeners should be chosen to minimize blade exposure while allowing enough flexibility to cut varying material thicknesses with precision. Wheel stiffeners can be used with or without existing flanges.
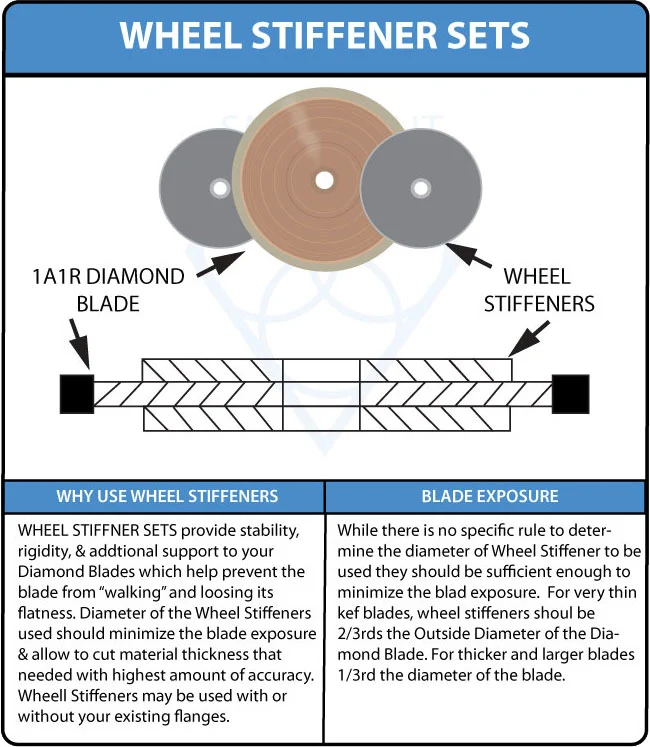
Stiff blades offer several benefits. They provide more precise cuts, reducing the need for re-cuts or additional finishing processes. Stiffer blades also contribute to greater safety, as they are less likely to wobble or break during operation, reducing the risk of accidents. Additionally, stiff blades tend to have a longer lifespan, as they are more resistant to wear and tear.Top of Form
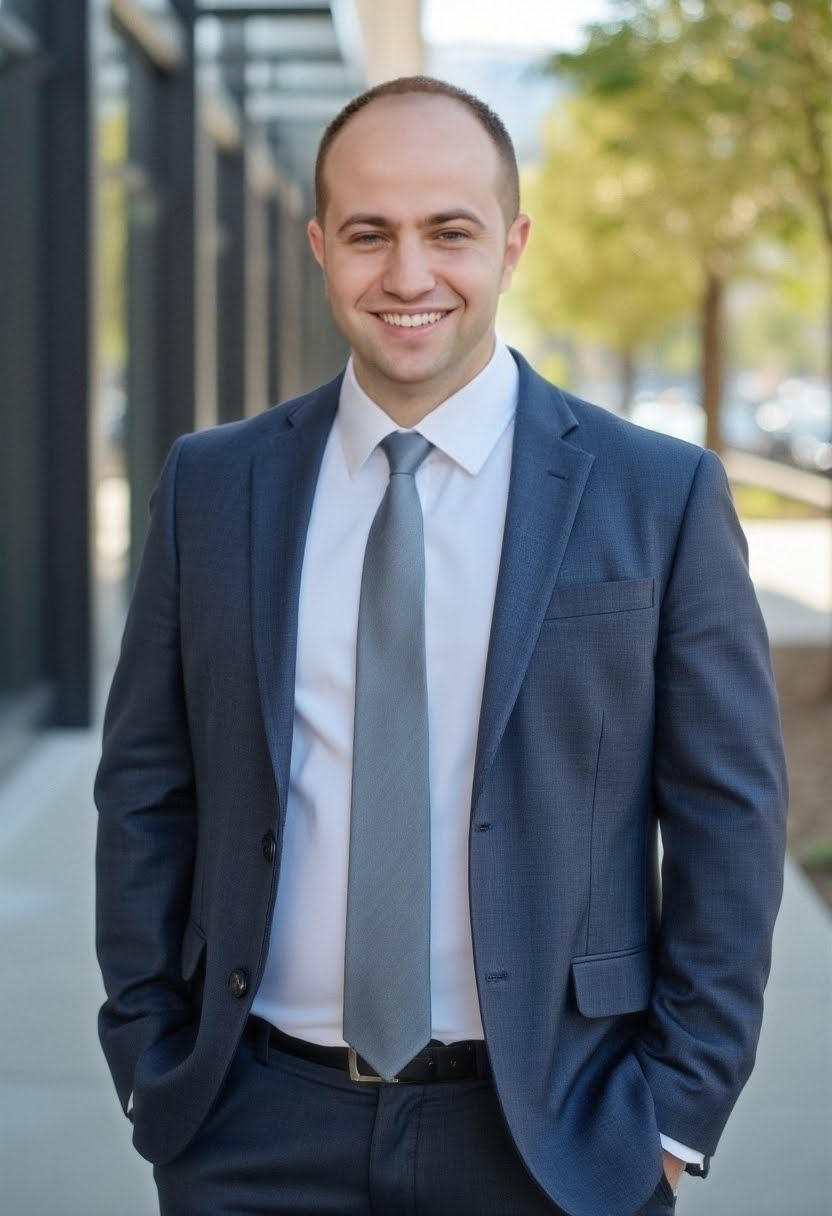
Brian is an experienced professional in the field of precision cutting tools, with over 27 years of experience in technical support. Over the years, he has helped engineers, manufacturers, researchers, and contractors find the right solutions for working with advanced and hard-to-cut materials. He’s passionate about bridging technical knowledge with real-world applications to improve efficiency and accuracy.
As an author, Brian Farberov writes extensively on diamond tool design, application engineering, return on investment strategies, and process optimization, combining technical depth with a strong understanding of customer needs and market dynamics.

ARE YOU USING RIGHT WAFERING BLADES
FOR YOUR APPLICATION?
LET US
HELP YOU
HAVING ISSUES WITH
YOUR CURRENT WAFERING BLADES?
Knowledge Center
Selecting Right Wafering Blade for your application
Wafering Blade Usage Recommendations
Wafering Blade Case Studies
Understanding & Comparing Diamond & CBN Wafering Blades
Diamond & CBN Wafering Blade Guide
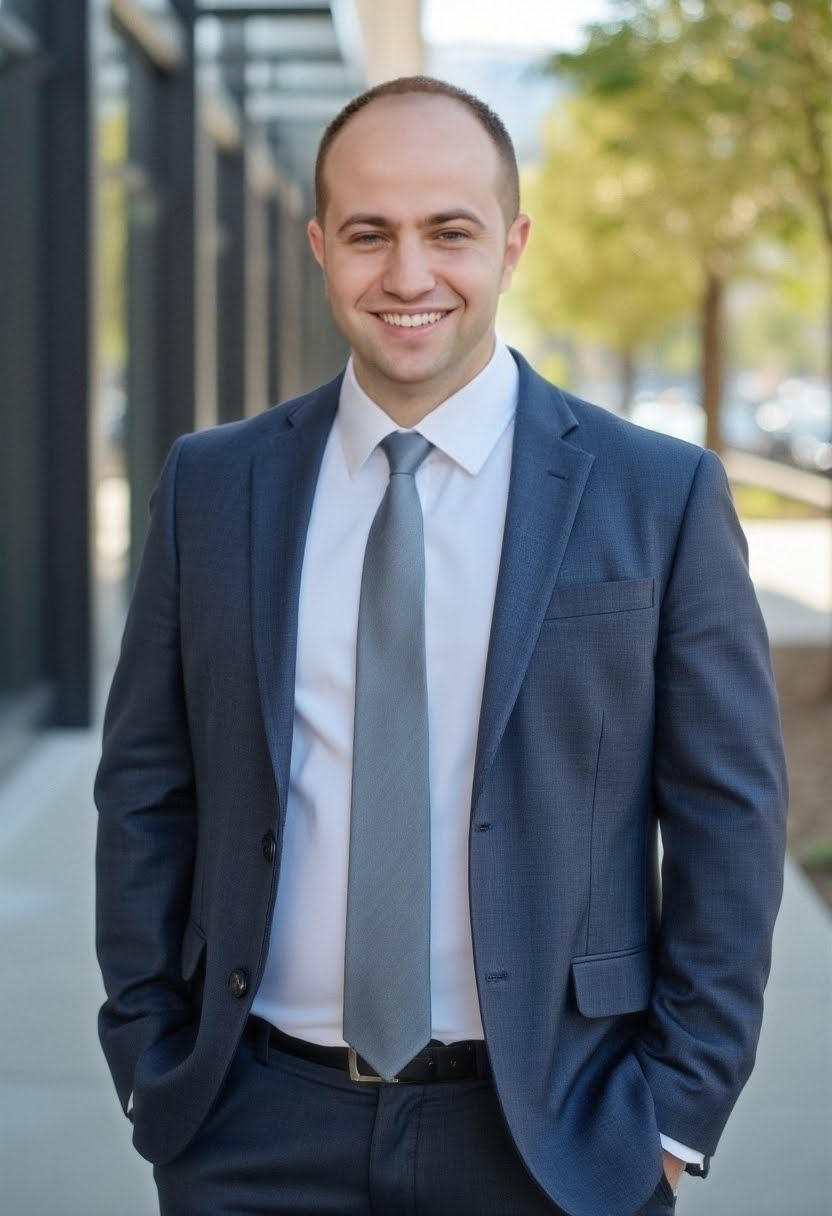
Brian is an experienced professional in the field of precision cutting tools, with over 27 years of experience in technical support. Over the years, he has helped engineers, manufacturers, researchers, and contractors find the right solutions for working with advanced and hard-to-cut materials. He’s passionate about bridging technical knowledge with real-world applications to improve efficiency and accuracy.
As an author, Brian Farberov writes extensively on diamond tool design, application engineering, return on investment strategies, and process optimization, combining technical depth with a strong understanding of customer needs and market dynamics.