Table of Contents
ToggleFor metallography, sample preparation, materials research and working with large variety of materials, selecting the optimal cutting technology is crucial for achieving high-quality results across various materials and applications. This article delves into a comparative analysis of two prominent cutting methods: the Low Speed Saw and the Wire Saw. Each method offers unique advantages and challenges, making them suitable for different types of materials and precision requirements.
By conducting our tests with each saw operating at the same revolutions per minute (RPMs) and loads, we aim to provide an unbiased comparison of their cutting efficiency, surface finish, material integrity, and overall usability.
This analysis will serve as a guide for engineers, researchers, and professionals in the fields of microelectronics, semiconductors, advanced ceramics, and materials sciences. By exploring the strengths and limitations of each cutting method, we can better understand their applicability and effectiveness in various industrial settings, ultimately guiding users to make informed decisions based on their specific cutting needs.
Cutting Glass Optical Ferrules Using
SMART CUT® 6005 Low Speed Saw and SMART CUT® 6012 Wire Saw
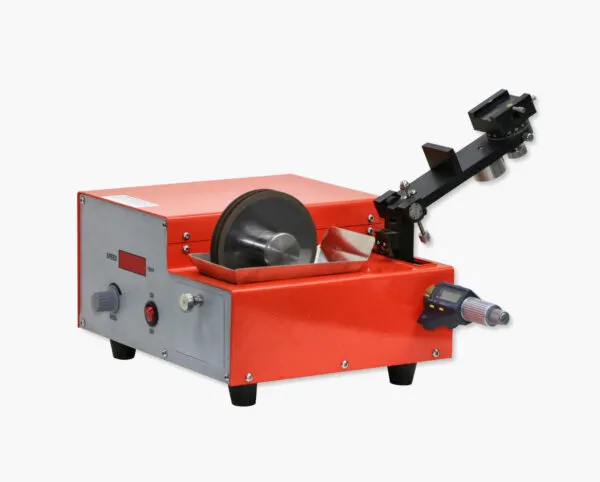
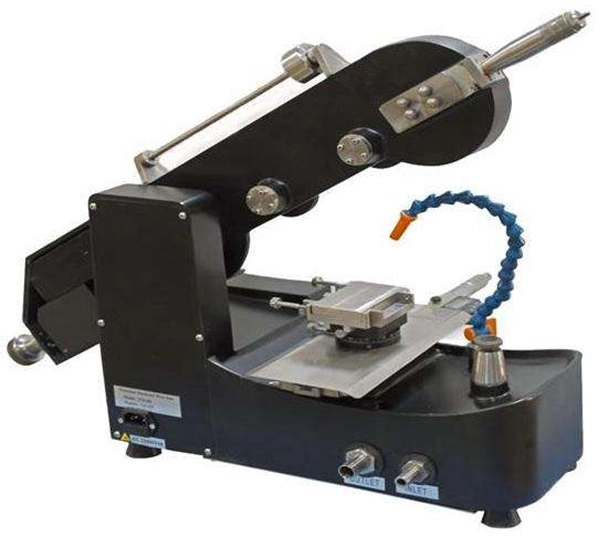
1.0: Purpose
The primary goal of this study is to precisely cut quartz optical ferrules near the bond interface, ensuring minimal surface chipping and structural fractures. Achieving controlled, precise cuts with maximum parallelism is crucial when processing sensitive optical components. This experiment compares two cutting methodologies to determine the most effective approach for achieving the highest quality cuts.
2.0: Experiments and Procedure
In this series of controlled tests, different cutting wheels and saw setups are evaluated for their effectiveness on quartz optical ferrules. The performance of each method is assessed in terms of surface finish, edge retention, and overall cut integrity.
Experimental Setup and Cutting Techniques
The experiment is conducted under real-world conditions with equipment calibrated to high standards to ensure consistent results. Two primary cutting techniques are evaluated:
-
Low-Speed Saw Cutting: This method uses various types of diamond wafering blades, known for precision and minimal material loss.
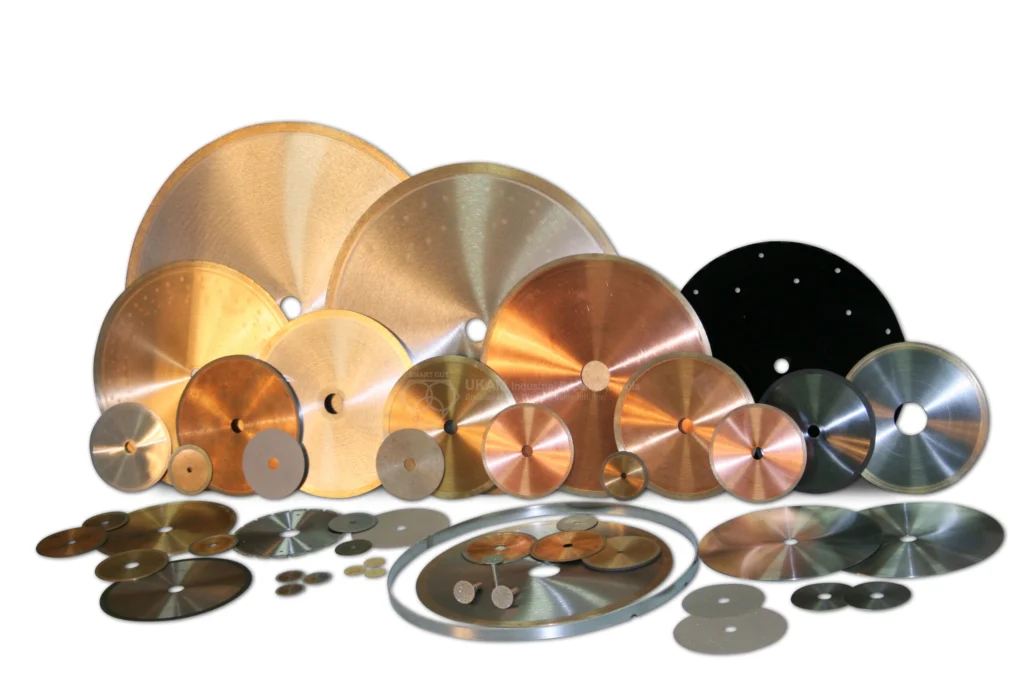
-
Wire Saw Cutting: This technique utilizes a wire embedded with abrasive particles, suitable for intricate cuts that require minimal mechanical stress on the material.
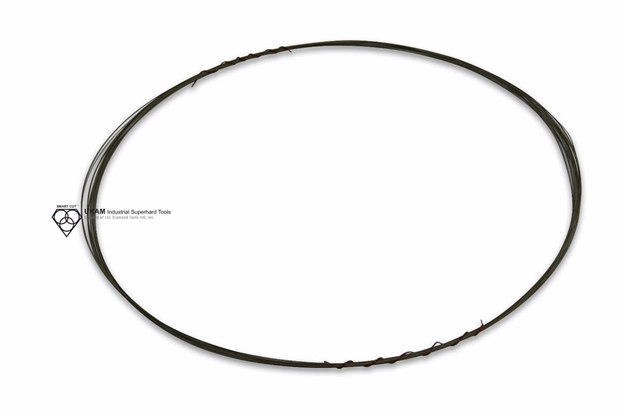
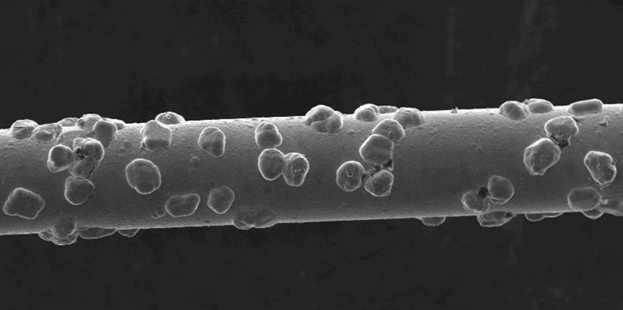
Material Preparation and Cutting Parameters
Quartz optical ferrules are securely mounted to prevent movement during cutting, with the mounting technique standardized across all tests. Specific parameters such as load, speed, and abrasive material type (e.g., diamond, SiC) are controlled based on preliminary trials to optimize cutting conditions.
Data Collection and Analysis
After each cutting session, specimens are examined for:
-
Surface Finish: Checked visually and through microscopy for any sub-surface damages or irregularities.
-
Edge Retention: Measured for sharpness and integrity, noting any deviations or chipping.
-
Cut Quality: Assessed for overall cleanliness, kerf width, and material loss.
High-resolution images and detailed notes document each test. These are analyzed to compare the effectiveness of each cutting method.
Illustration of the Process
Below is a detailed diagram (Figure 1) showing the geometry of the optical ferrule and the specific cuts made during the experiments. This helps in understanding how each cutting technique impacts the material.
Figure 1: Illustration of Optical Ferrule Geometry and Cutting Process
Through this structured and detailed experimental approach, the study aims to identify the most effective cutting technique that combines precision, efficiency, and minimal material damage, thus enhancing the processing of optical ferrules in industrial applications.
SMART CUT® 6005 Low Speed Saw
In our experiments with the SMART CUT® 6005 Low Speed Saw, we tested a variety of cutting wheels to understand their effects on the quality of cuts made on quartz optical ferrules:
-
1. SiC Abrasive Wheel (4"): Known for its robust cutting capabilities.
-
2. Diamond Wheel, Fine Diamond Size, Low Concentration (10LCU): Designed for precise cuts with minimal kerf and excellent surface finish.
-
3. Diamond Wheel, Medium Diamond Size, High Concentration (15HCU): Balances cut quality with durability, suitable for moderate to tough materials.
-
4. Diamond Wheel, Coarse Diamond Size, High Concentration (20HCU): Best for rapid material removal with less emphasis on surface finish.
Each wheel performed two cuts on specimens securely mounted to a graphite block using low melting point wax, which also shielded the top surface of the specimens to minimize chipping at the initial contact point. The consistent cutting parameters were:
-
Load: 120 grams
-
Wheel Speed: 350 rpm
SMART CUT® 6012 Wire Saw Cuts
Similarly, the SMART CUT® 6012 Wire Saw utilized different slurry types and grit sizes to evaluate their influence on the cut quality:
-
1. Al2O3 Slurry (22-micron Abrasive Size): Offers a standard cutting experience with moderate surface quality.
-
2. Silicon Carbide (SiC) Slurry (14-micron Abrasive Size): Provides a slightly smoother cut due to the finer abrasive size.
-
3. Boron Carbide (BC) Slurry (22-micron Particle Size): Tough and aggressive, suitable for more robust cutting applications.
-
4. Diamond Slurry (15-micron Particle Size): Delivers the finest cuts with superior surface finish and minimal damage.
Each type of slurry was applied to two cuts on identically mounted ferrule specimens, ensuring uniform handling and protection. The cutting conditions maintained were:
-
Load: 120 grams
-
Wire: 0.010" stainless steel
-
Speed: 350 rpm
-
Slurry: Automatically applied
3.0: Results
Following the cutting operations, post-cut evaluations focused on three key aspects: surface finish, edge retention, and overall cutting quality. Our findings indicate varying levels of performance across different cutting media and techniques. For instance, diamond wheels and slurries typically yielded higher quality finishes and better edge retention compared to other abrasives, which is critical in applications requiring precision and minimal post-processing.
Analysis of Cutting Techniques
-
Low-Speed Saw Cuts: Demonstrated excellent control over cut quality with fine and medium diamond wheels, suggesting their use in applications requiring high precision and minimal surface damage.
-
Wire Saw Cuts: Showed variability based on slurry type, with diamond slurry outperforming others in terms of achieving a high-quality finish and maintaining material integrity.
Cutting Instrument |
Cutting Media Description |
Result Observations |
---|---|---|
SiC abrasive cutting wheel |
Good surface finish, minimal chipping at ferrule edges |
|
Diamond wheel: coarse diamond |
Fair surface finish, no significant edge chipping |
|
Diamond wheel: medium diamond |
Good surface finish, minimal edge chipping |
|
Diamond wheel: fine diamond |
Excellent surface finish, no edge chipping |
|
Al2O3 slurry |
Fair surface finish, no edge chipping |
|
SiC slurry |
Poor surface finish, noticeable smearing |
|
BC slurry |
Poor surface finish, pronounced smearing |
|
Diamond slurry |
Fair surface finish, slight smearing |
Conclusions
Although the SMART CUT® 6012 Wire Saw cuts produced less crisp surfaces compared to the SMART CUT® 6005 Low Speed Saw, both methods yielded satisfactory outcomes in terms of cutting time, accuracy, and kerf loss. Each method demonstrates potential suitability for this application, pending further optimization based on specific project requirements.
1. Cutting Wheel Efficiency
-
Diamond Wheels: The use of diamond wheels with varying grit sizes demonstrates a clear impact on the quality of cuts. Fine diamond wheels (10LCU) provide excellent surface finishes with minimal chipping, indicating a high suitability for precision applications where surface integrity is paramount.
-
SiC Abrasive Wheel: Offers good performance, but may not achieve the superior finish provided by finer diamond grits, suggesting its use in less critical applications where a slightly lower surface quality is acceptable.
2. Slurry-Based Wire Saw Cutting:
-
Diamond Slurry (15 micron): Shows better outcomes in terms of surface finish and minimal chipping compared to other slurries, reinforcing diamond's superiority in precision cutting applications.
-
Al2O3 and SiC Slurries: Provide satisfactory to poor finishes with varying degrees of chipping. These might be chosen for less delicate operations or where cost considerations override the need for a perfect finish.
-
Boron Carbide (BC) Slurry: Tends to perform less well, possibly due to its particulate properties affecting the smoothness of the cut, suggesting its use might be more situational depending on the specific material properties of the specimen.
3. Load and Speed Parameters:
-
The uniform load (120 grams) and speed (350 rpm) across tests simplify the comparison of cutting media effects, isolating the medium itself as the primary variable affecting outcomes.
-
These conditions seem adequate for both saws, as they allow for consistent application and evaluation of different cutting media, though adjustments might be necessary depending on specific material sensitivities or cutting requirements.
Recommendations for Optimization
-
Material-Specific Tailoring: Further refinements in wheel and slurry selection should consider the specific material properties of the specimens being cut. For optical ferrules, where precision is critical, finer diamond grits and optimized slurry formulations could enhance outcomes.
-
Parameter Adjustments: Experimenting with varying loads and speeds could further optimize the cutting process, potentially reducing defects like chipping and improving overall efficiency.
-
Further Testing: Continued testing with a broader range of materials and more granular adjustments to cutting parameters could help in developing a more comprehensive understanding of the best practices for each type of cutting tool and material.
In summary, the choice between using a low-speed saw with diamond wheels and a wire saw with various slurries should be guided by the specific requirements of the cutting application, balancing factors like cost, cut quality, and the physical properties of the material being processed. Fine diamond wheels and diamond slurries are generally preferred for high-precision, high-quality cuts in sensitive optical materials.
Comparative Analysis of Kerf Loss and Other Variables Between Diamond Wheels and Diamond Wire
In the precision cutting industry, understanding the implications of kerf loss is critical. Kerf loss refers to the amount of material lost during the cutting or sectioning process, which is pivotal for determining the final dimensions and the quality of the specimen's edges and surfaces. This article will explore the findings from recent experiments that examine kerf loss and edge damage on silicon material, focusing on differences between cutting methods involving diamond wheels and diamond wires, as well as the impact of blade thickness and abrasive particle size.
Kerf Loss Analysis
Kerf loss traditionally suggests that more material would be lost with larger abrasive sizes and thicker cutting blades. However, experimental data challenges this intuition, showing no clear correlation between blade size, abrasive size, and kerf loss.
Diamond Wheel Cutting: For diamond wheels, variations in wheel thickness showed surprisingly little impact on kerf loss, with differences among three tested diamond wheels being less than 5µm. Additionally, the kerf loss relative to the actual blade width was minimal, at about 58µm, translating to approximately 29µm per side of the wheel. This data suggests that changes in diamond particle size do not significantly affect the kerf loss, which aligns with the observations that there is no strong relationship between these factors.
Diamond Wire Cutting: Similar to diamond wheels, larger diameters of diamond wires were expected to result in greater kerf loss. Yet, the differences observed were minimal (only 17µm difference between wire diameters), indicating no significant relationship between wire diameter and kerf loss. Notably, overall kerf loss from diamond wire cutting was substantially higher, around 350µm, which approximates the diameter of the wire used, suggesting other factors may influence kerf loss more than wire diameter or particle size.
Plain Wire with Abrasive Slurry: Using abrasive slurry with plain wire showed a different pattern, with kerf loss showing little to no dependence on the abrasive particle size or wire diameter. Even with varying abrasive sizes, kerf loss remained consistent, with only about 10µm difference between sizes, and minimal impact from wire diameter, with losses as low as 5µm to 19µm for different diameters.
Edge Chipping Analysis
Edge chipping is another significant factor, especially in applications requiring high precision, such as sample preparation for electron microscopy. The extent of edge chipping can dictate how much material needs to be left during cutting to accommodate subsequent processing stages like lapping and polishing.
Diamond wheel methods generally induced more chipping than wire blade methods, likely due to the interaction between the diamond particles and the material being cut. Interestingly, the thinner diamond wheels demonstrated reduced chipping, akin to the results seen with wire blade methods. Conversely, using abrasive slurry with plain wire resulted in the smoothest cuts, indicating this method might be preferable when minimal chipping is essential.
Consumable Item |
Thickness |
Diamond Size |
Concentration |
Kerf Loss (um) |
Edge Chip Min (um) |
Edge Chip Max (um) |
---|---|---|---|---|---|---|
Diamond wafering blade series 20LCU |
0.012 |
coarse |
Low |
360 |
20 |
240 |
Diamond wafering blade series 10LCU |
0.012 |
fine |
high |
360 |
10 |
340 |
Diamond wafering blade series 10LCU |
0.006 |
fine |
high |
210 |
<10 |
100 |
Diamond wire |
0.015 |
-- |
-- |
730 |
<=10 |
160 |
Diamond wire |
0.010 |
-- |
-- |
620 |
<10 |
240 |
Wire |
0.015 |
8um |
BC |
400 |
<5 |
105 |
Wire |
0.010 |
8um |
BC |
260 |
<5 |
135 |
Wire |
0.005 |
8um |
BC |
130 |
0 |
55 |
Cutting performance data for different consumable items. Showing Kerf Loss, Edge Chip Min, and Edge Chip Max measurements for each item
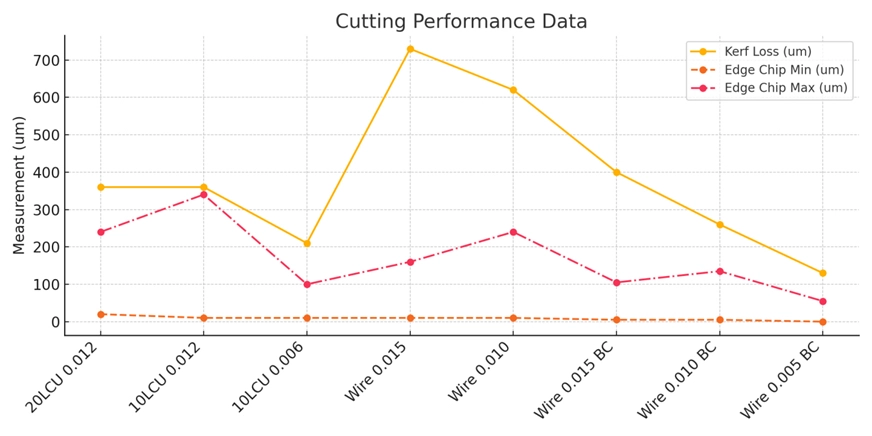
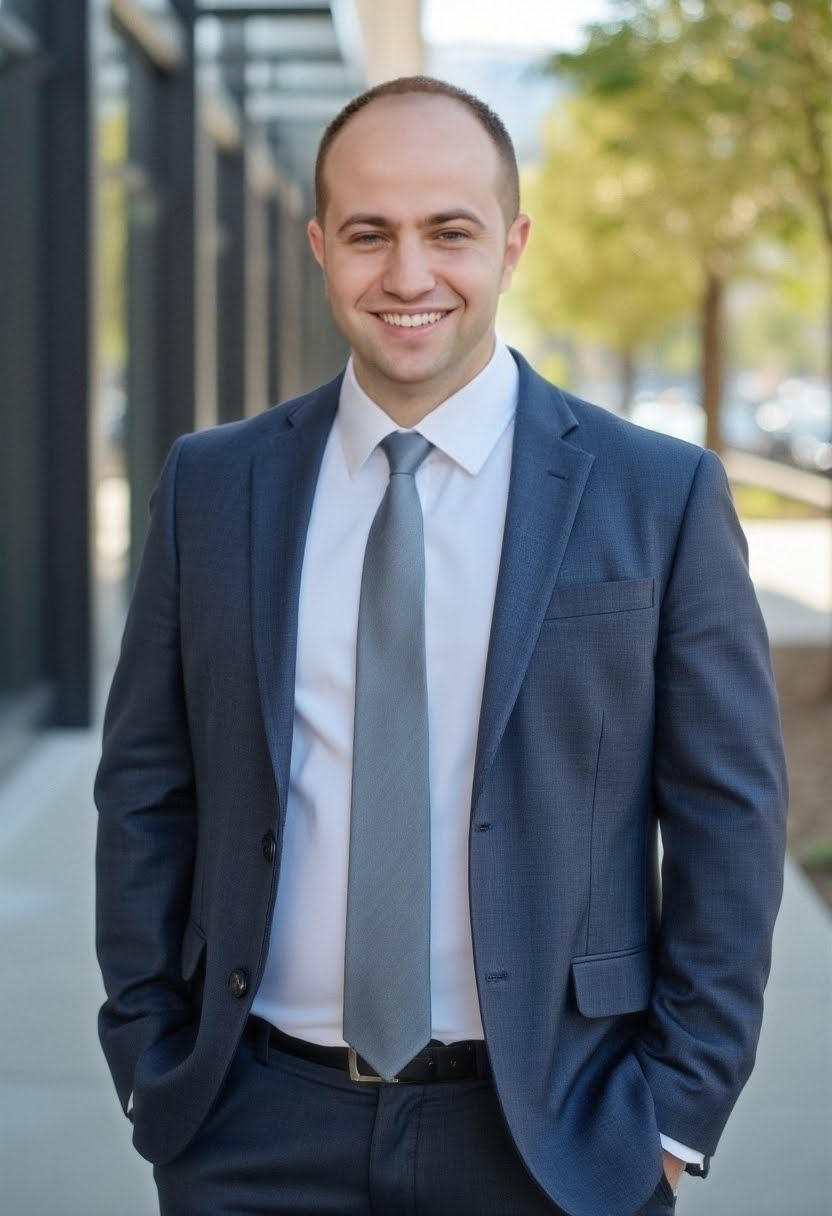
Brian is an experienced professional in the field of precision cutting tools, with over 27 years of experience in technical support. Over the years, he has helped engineers, manufacturers, researchers, and contractors find the right solutions for working with advanced and hard-to-cut materials. He’s passionate about bridging technical knowledge with real-world applications to improve efficiency and accuracy.
As an author, Brian Farberov writes extensively on diamond tool design, application engineering, return on investment strategies, and process optimization, combining technical depth with a strong understanding of customer needs and market dynamics.
ARE YOU USING RIGHT TOOLS
FOR YOUR APPLICATION?
LET US
HELP YOU
HAVING ISSUES WITH
YOUR CURRENT TOOLS?
Knowledge Center
How to Selecting Right Diamond Tools for your application
How to properly use Diamond Tools
Why use diamond
Diamond vs CBN (cubic boron nitride) Tools
What is Diamond Mesh Size and how to select best one for your application
What is Diamond Concentration and which to use for your application
Diamond Tool Coolants Why, How, When & Where to Use
Choosing The Correct Diamond Bond Type
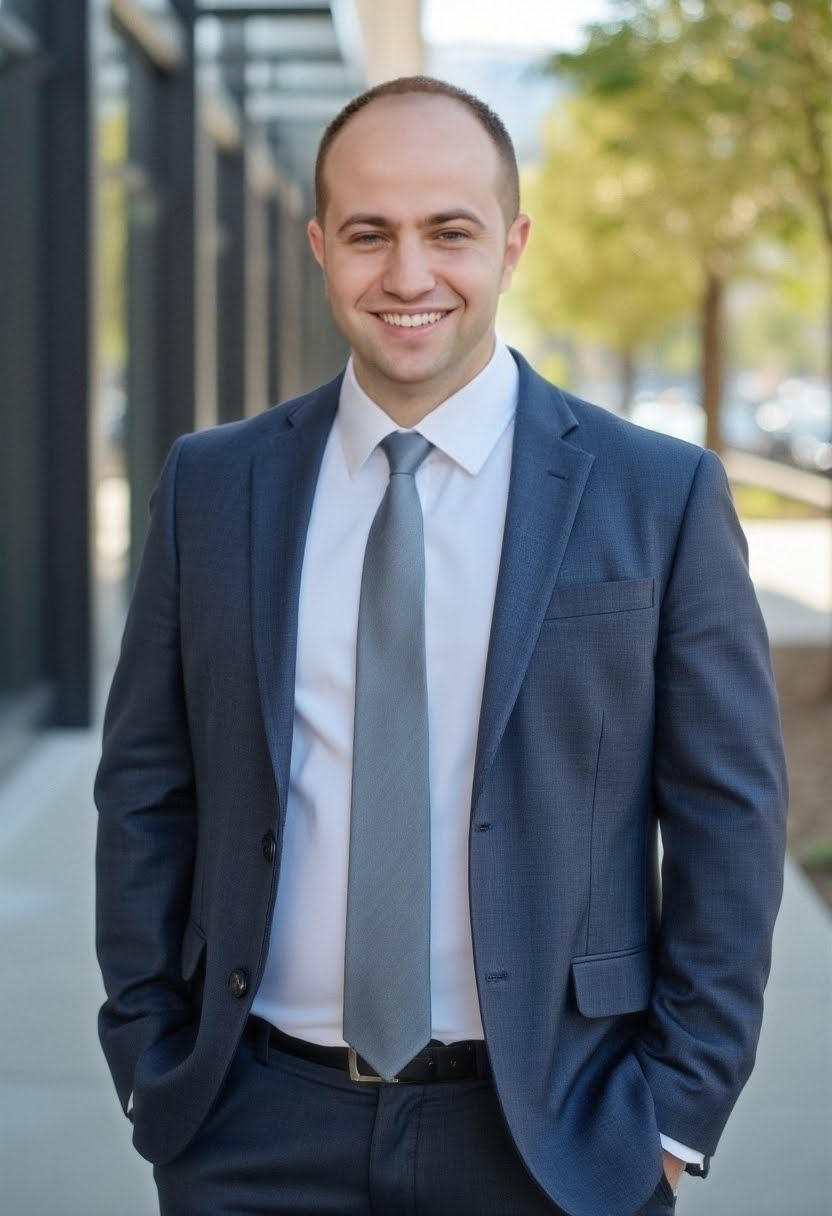
Brian is an experienced professional in the field of precision cutting tools, with over 27 years of experience in technical support. Over the years, he has helped engineers, manufacturers, researchers, and contractors find the right solutions for working with advanced and hard-to-cut materials. He’s passionate about bridging technical knowledge with real-world applications to improve efficiency and accuracy.
As an author, Brian Farberov writes extensively on diamond tool design, application engineering, return on investment strategies, and process optimization, combining technical depth with a strong understanding of customer needs and market dynamics.