-
0 items in quote
No products in the Quote Basket.
SMART CUT® LP - Grinding/Polishing Machine (METAL BOND)
SMART CUT® LP is most affordable, entry level Laboratory Variable Speed Polishing, Grinding, Lapping Machine. Designed for Mechanical Sample Preparation.
SMART CUT® LP is Perfect for coarse & fine grinding and polishing of large variety of materials. Including: Ultra Hard & Brittle, Metals, Ceramics, Refractories, Cement, and Petrographic thin sections. As well as full range of optical materials, such as: Bk7, Fused Silica, Zeroder, Quartz, Soda Lime Glass, Yag, Sapphire, and Many Others. Its Variable Speed allows the operator the flexibility to move from high speed rough grinding to low speed final polishing. It’s molded plastic housing will never rust. Capable of withstanding more exploitation, requires less maintenance, and much easier to use that Fully Automatic Polishing, Lapping, & Grinding Equipment.
DESCRIPTION
SPECIFICATIONS
ADVANTAGES
INDUSTRIES USED IN
FAQ
OPERATING MANUALS
ACCESSORIES
DESCRIPTION
Preferred by thousands of Universities, Government Research Laboratories, Commercial Laboratories & Advanced Material fabrication facilities.
Theses machines comes with EVERYTHING YOU NEED to go from rough surface to final polish. The consumables package included for 4 diamond discs and one felt polishing disc with diamond compound. All of this available unbeatable price, makes this a must have for every user who needs to grind and polish variety of samples fast and easy.
Compare to Brand Name Grinding / Polishing Machines for Sample Preparation & Materials Research. Perfect for Manufacturing and R & D facilities on a Budget. What you will save on cost of Consumables will more than pay for SMART CUT® LP in short period of time.
SPECIFICATIONS
- Everything you need to go from rough finish to final polish
- Can be used for almost any Application
- Variable Speed from 500 to 3,000 RPM
- Very Easy to Use
- Runs Quietly and Cleanly
- Can withstand more exploitation & requires less maintenance
- Most Affordable Entry Level Solutions Available Today
- Perfect for Manufacturing and R & D organizations on a Budget
ADVANTAGES
Tab Content
INDUSTRIES USED IN
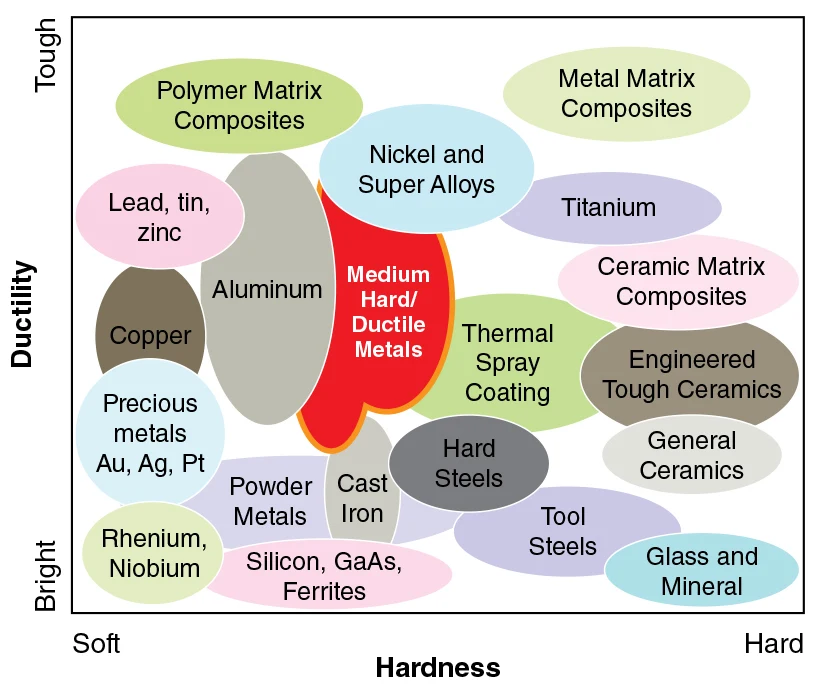

INDUSTRIES USED IN:
- Advanced Ceramics
- Composites
- Glass
- Geology
- Quartz
- Materials Research
- Medical Devices
- Metallography
- Photonics / Optics
- Semiconductor
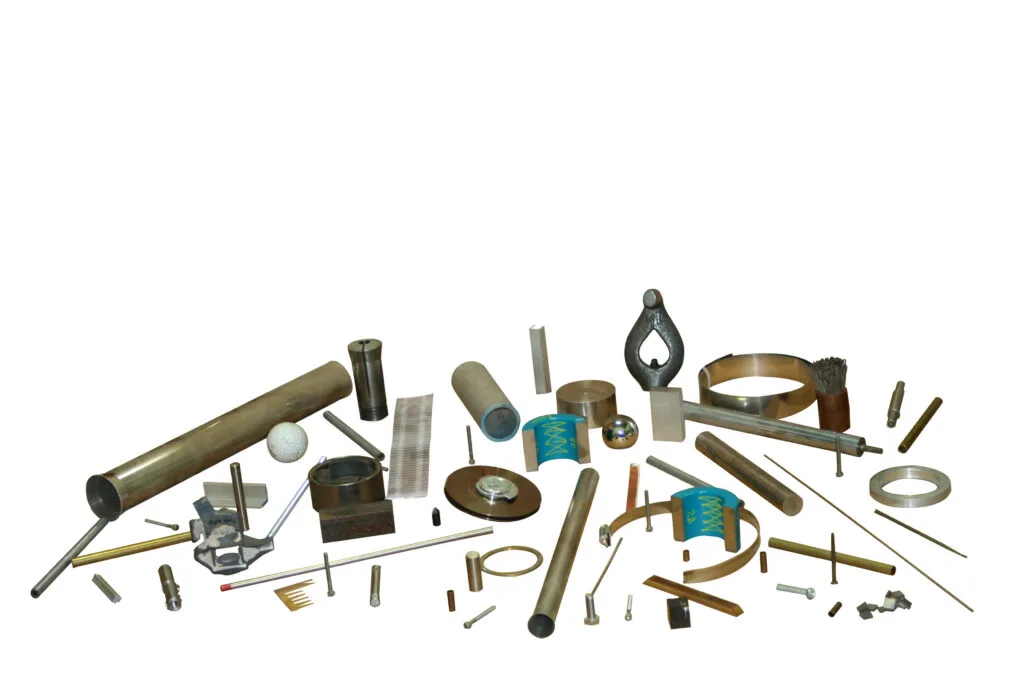
Ferrous & Non-Ferrous Metals:
- Plain Carbon Steels
- Electronic Packages
- Stainless Steels Plastics
- Tool Steels Fasteners
- Aluminum Refractories
- Copper Base Alloys Integrated Circuits
- Magnesium Thermal Spray Coatings
- Titanium Metal Matrix Composites
- Biomedical Wafers
- Petrographic
- PCB.s Ceramics
FAQ
Tab Content
OPERATING MANUALS
What We Do
we manufacture custom tools to fit your specific requirements and specifications. We have the capability to manufacture over 30,000+ different types of custom diamond & cbn tools and consumables to better fit your particular material, application, specifications, and requirements
Why Custom Tools?
Not all requirements are the same. We manufacture tools to fit your particular equipment, tolerances, surface finish, life span, and overall see the difference tools optimized for your application can make?
How We Work
We will work with you to determine your needs, and develop the right bond formulation, concentration, and grit sizes. Our tools are designed and specially selected to provide maximum possible tool life, for your desired cut quality and speed.
Custom Tool Manufacturing Process
The following process describes custom tool manufacturing process form initial first inquiry to final delivery.

DISCOVERY
We discuss your specific requirement in detail to determine the best solution for your needs.

RECOMMEND SOLUTION
We provide you with recommend options for your application based on your requirements along with quotation and lead time.

PREPAIRE TO IMPLEMENT
When you are ready to order, we send you confirmation of the tool specification always in writting. Your order is placed in que to be produced within the quoted lead time.

IMPLEMENT & DELIVER
The finished products go through quality control process and also inspected for conformance to specification agreed upon. The order is packaged and shipped to you using your requested shipping method. Certificate of conformance or any other documentation can be provided upon request.

SERVICE &
SUPPORT
We follow up with you to receive feedback on the tool performance. We also provide usage recommendatios and technical support if needed.
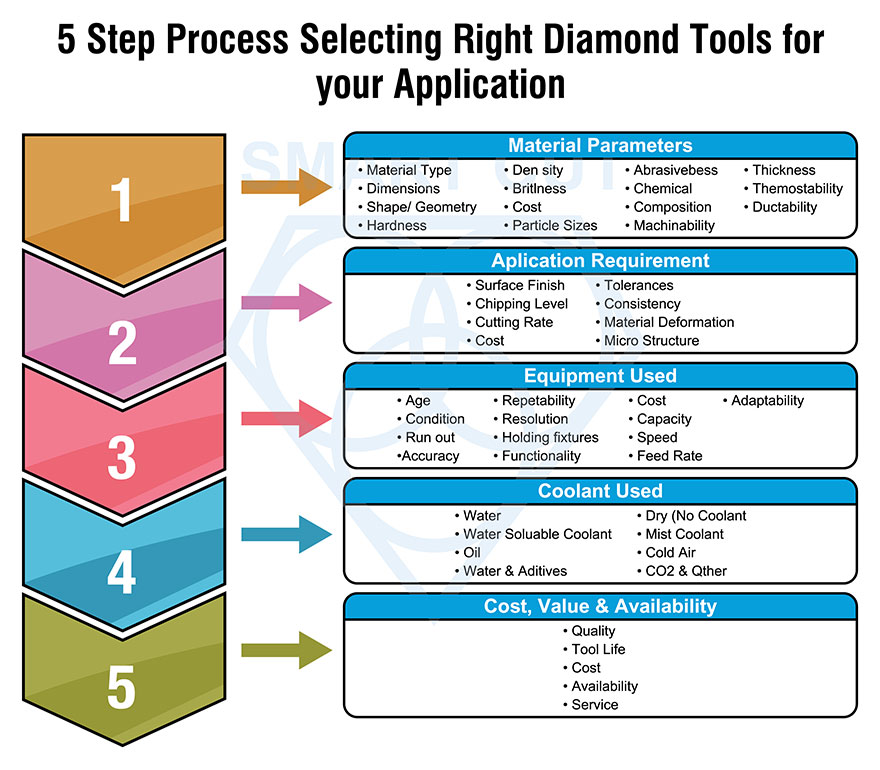
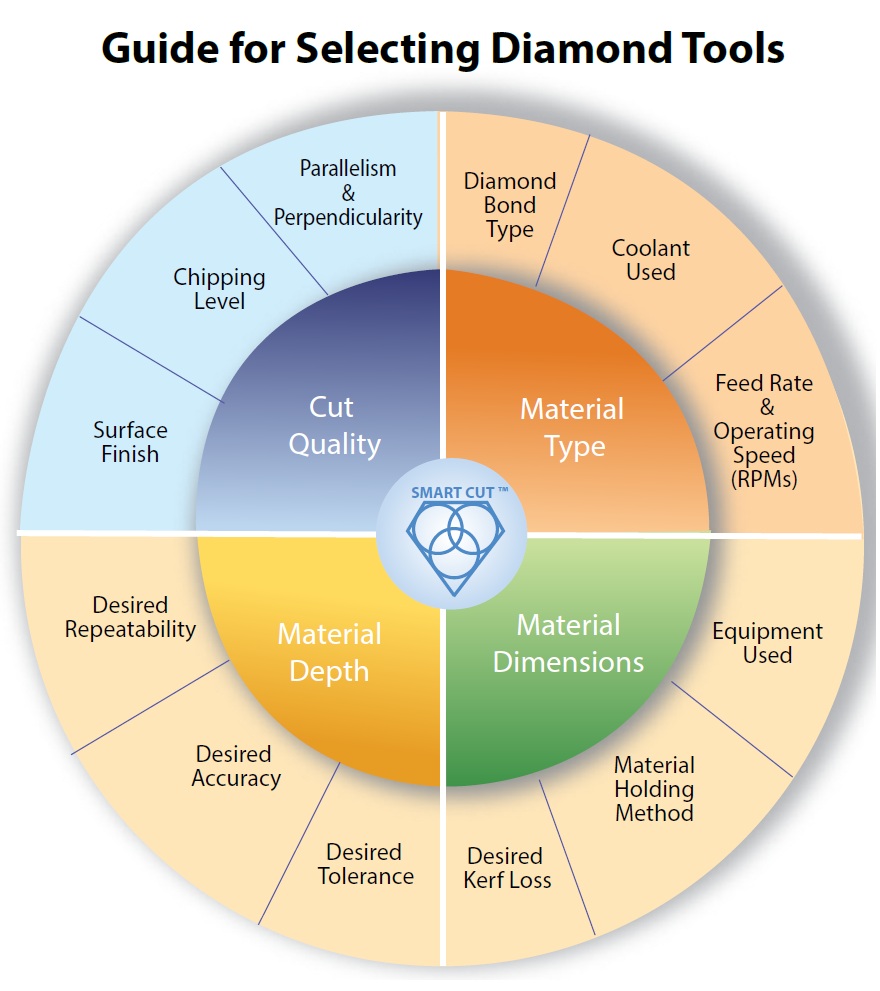
Custom Diamond and CBN wheel FAQ
To place an order, you can contact our customer service team via phone, email, or our website. You will need to provide specific details about your grinding application, including material to be ground, required wheel dimensions, and desired grit size.
Yes, we are happy to help. We will send you a question are asking many questions about your requirements, how the tool will be used and the usage environment. This information is very important for helping us understand your unique specifications and requirements. The more information you can provide the more accurate recommendation and solutions we can provide.
Usually there is no minimum order for custom tools, with few acceptations. We encourage you to try small quantity to make sure you are happy with the tool performance first. As additional fine tuning and improvements can be made based on your feedback.
Lead time varies depending on tool specification and current schedule. Usually the lead time range can be from 1 to 5 weeks. expedited lead time of 1 to 2 weeks is usually available at additional cost if needed
Prices are based on tool specification, tolerances, quantity and lead time. Our prices are pretty competitive for world market. We regularly export our products to dozens of different countries across all continents. Usually custom products in small quantity the pricing is usually higher then standard of the shelf products which are mass produced in large quantities.
We can provide hand sketch if needed. if you need drawing we can create in solid works or auto cad for a small fee which may be reimbursable upon receipt of order
Over many decades we have made and sold thousands of different types of unique and one of a kind tools for almost every application. we maintain records of bond formulations and specifications used over many years we have also acquired the “know how” of several other US tool manufacturers that have produced custom tools over many decades, some going far back as to 1960’s. we also have our own R & D research program and we regularly work with different research originations and outside consultants. Most of the time we produce the right tool formulation first time, but sometimes we can make additional improvements second and third time around. Our goal is to make you happy
We ask lot of detailed question about tool specification and your usage process. Sometimes it may be worthwhile for you to send us your used tool so we can inspect it.
Yes we can provide basic recommendations and recommended usage information. If you need specific hands on approach such as “process development” this can be done on case by case based for a fee. If we are not able to help we can often recommend independent outside consultant or organization that can assist.
For a custom wheel order, you should provide the following information:
• Type of wheel (Diamond or CBN)
• Wheel dimensions (diameter, thickness, and arbor hole size)
• Grit size
• Material to be ground
• Grinding machine details
• Desired surface finish
Yes, you can request a specific bond type based on your grinding application. Common bond types include resin, vitrified, metal, and electroplated.
The lead time for custom wheels varies depending on the complexity of the wheel and our current production schedule. Typical leads times range from 4 to 5 weeks. Expedited lead time of 1 to 2 weeks is also available at additional cost if needed. Our customer service team will provide an estimated delivery date when you place your order.
Due to the custom nature of these wheels, they are typically non-returnable. However, if the wheel does not meet the specified requirements or is defective, we will work with you to resolve the issue.
Yes, you can order a sample wheel to test on your application before placing a bulk order. We highly encourage that you test the wheel for your particular application in your environment. Please contact our customer service team for more information.
Yes, we offer discounts for bulk orders. Please contact our sales team for more information.
Proper care and maintenance are essential to ensure the longevity and performance of your wheel. You should regularly clean the wheel, check for any damage, and use it at the recommended speed. Additionally, it’s important to use the correct coolant and dressing tools.
Yes, we can customize the wheel profile to meet your specific requirements. Please provide detailed drawings or specifications of the profile you need when placing your order.
Diamond wheels are suitable for grinding non-ferrous and non-metallic materials such as glass, ceramics, and tungsten carbide. CBN wheels are ideal for grinding ferrous materials such as steel, cast iron, and nickel-based alloys.
Yes, we have a team of experienced engineers and technicians who can provide technical support and advice for your specific grinding application.
Yes, you can request specific tolerances for your custom wheel. Please provide the required tolerances when placing your order, and we will do our best to meet your specifications.
Once your order has been placed, you will receive an order confirmation with a tracking number. You can use this number to track the status of your order on our website or contact our customer service team for updates.
We will do our best to accommodate any changes to your order, but please note that changes may not be possible once the production process has started.
We accept various payment methods, including credit card, PayPal, and bank transfer. Please contact our sales team for more information.
Cancellations are handled on a case-by-case basis. If the production process has not started, we may be able to cancel your order. However, once production has begun, cancellations are generally not accepted.
A balanced wheel is essential for optimal performance and safety. If you notice any vibrations or irregularities during operation, your wheel may be out of balance. Please contact our technical support team for assistance with balancing your wheel.
Yes, we offer a warranty on our custom wheels. The length and terms of the warranty will depend on the specific wheel and application. Please contact our sales team for more information.
The grit size should be selected based on the material to be ground and the desired surface finish. A coarser grit is generally used for rapid material removal, while a finer grit is used for a smoother finish. Our technical support team can help you choose the right grit size for your application.
Yes, we can manufacture custom wheels to fit specific brands and models of grinding machines. Please provide the make and model of your machine when placing your order.
Yes, we ship custom wheels internationally. Please contact our sales team for more information on shipping options and costs.
Resin bonds are flexible and suitable for grinding materials that are prone to heat damage. Vitrified bonds are rigid and offer high precision grinding. Metal bonds are durable and suitable for grinding hard materials. Electroplated bonds have a single layer of abrasive and are used for precision grinding.
A custom wheel may be necessary if your application requires specific dimensions, grit sizes, bond types, or shapes that are not available in standard wheels. Our technical support team can help you determine if a custom wheel is necessary for your application.
Diamond is the hardest known material and is suitable for grinding non-ferrous and non-metallic materials. CBN is the second-hardest known material and is suitable for grinding ferrous materials.
Yes, you can request a specific concentration of Diamond or CBN in your custom wheel. The concentration will affect the wheel’s performance and life.
Please refer to local regulations and guidelines for disposing of grinding wheels. In general, worn-out wheels should be treated as industrial waste and disposed of accordingly.
Yes, we can manufacture custom wheels with specific colors or logos. Please provide your requirements when placing your order.
Yes, we can manufacture a custom wheel with different abrasive grains to suit specific grinding applications.
Regularly clean your custom wheel to remove any accumulated grit, dust, and swarf. Avoid exposing the wheel to moisture to prevent corrosion or damage to the bond. Store the wheel in a dry and cool place away from direct sunlight.
Always wear safety goggles, gloves, and other appropriate personal protective equipment when using any grinding wheel. Follow the manufacturer’s guidelines and safety instructions for your specific grinding machine.
The performance of a custom wheel can be measured in terms of material removal rate, wheel wear rate, surface finish quality, and overall efficiency.
The wheel speed will depend on the specific grinding application, material to be ground, and the wheel’s dimensions. Our technical support team can help you determine the optimal wheel speed for your application.
Yes, you can specify the hardness level for your custom wheel, which will affect its grinding performance.
Our custom wheels comply with industry standards and regulations, including ANSI, ISO, and OSHA. Specific certifications may vary depending on the wheel and application.
Yes, you can request a custom wheel with specific porosity to achieve desired grinding performance and coolant flow.
You can conduct a trial run with the custom wheel on your grinding machine, following all safety guidelines. Observe the wheel’s performance in terms of material removal rate, surface finish quality, and overall efficiency. Our technical support team can assist you in evaluating the wheel’s performance.
Factors that affect the life of a custom wheel include the type of material being ground, the grit size, bond type, wheel speed, and coolant usage.
Yes, you can specify whether the custom wheel is intended for wet or dry grinding, and we will manufacture the wheel accordingly.
The bond type should be selected based on the material to be ground, desired surface finish, and grinding machine characteristics. Our technical support team can help you choose the right bond type for your application.
The minimum order quantity for a custom wheel depends on the specific requirements and dimensions of the wheel. For most wheels there is no minimum order quantities. Please contact our sales team for more information.
Yes, you can request a quote for a custom wheel through our website by providing the specific requirements and dimensions for your wheel.
Yes, you can specify the face width or thickness for your custom wheel, and we will manufacture the wheel accordingly.
The wheel bond plays a crucial role in holding the abrasive grains together. The bond type affects the wheel’s wear rate, grinding performance, and the finish quality of the workpiece.
Yes, we can manufacture custom wheels with specific profile shapes to meet your unique grinding needs. Please provide a detailed drawing or specifications of the profile shape when placing your order.
If you’re not satisfied with the performance of your custom wheel, please contact our customer service team immediately. We will work with you to address any issues and find a suitable solution.
The abrasive concentration in a wheel is typically measured as a percentage of the volume of abrasive grains to the total volume of the wheel. A higher concentration means more abrasive grains and typically results in a longer wheel life and better performance.
The wheel’s hardness affects its ability to resist wear and maintain its shape during grinding. A harder wheel typically lasts longer but may produce a rougher surface finish.
Yes, we can manufacture custom wheels with specific arbor hole sizes to fit your grinding machine.
Yes, we can manufacture custom wheels with specific grinding face geometries to meet your unique requirements. Please provide detailed drawings or specifications when placing your order.
Factors to consider when choosing the grit size include the material to be ground, desired surface finish, and grinding operation type. A finer grit is typically used for finishing operations, while a coarser grit is used for roughing operations.
The wheel shape affects how the abrasive grains interact with the workpiece, influencing the grinding performance and resulting surface finish.
Yes, we can manufacture custom wheels designed specifically for grinding materials such as glass or ceramics.
Wheel balance is critical for achieving optimal grinding performance and preventing vibration and machine wear.
Yes, you can specify the bond hardness for your custom wheel, which will affect its grinding performance.
The wheel diameter affects the peripheral speed of the wheel, which in turn influences the grinding performance and resulting surface finish.
The type of abrasive grain (e.g., Diamond, CBN, aluminum oxide) affects the wheel’s hardness, sharpness, and heat resistance, which in turn influences the grinding performance.
Yes, we can manufacture custom wheels with specific profiles for gear grinding applications. Please provide detailed specifications or drawings when placing your order.
Factors to consider when choosing the bond type include the material to be ground, grinding operation type, wheel speed, and desired surface finish.
Wheel speed affects the material removal rate, heat generation, and resulting surface finish of the workpiece.
Yes, we can manufacture custom wheels with specific porosity levels to meet specific grinding requirements.
ACCESSORIES
Showing 1 – 8 of 8 results Showing all 8 results Showing the single result No results found
Sort by Price low to high
Filters Sort results
Reset Apply
Image | Item No | Shipping Weight | Dimension | Description | Price | Quantity | Add to cart |
---|---|---|---|---|---|---|---|
6″ OD Replacement Consumables package No backing plates | $169.00$190.00 | Max: Min: 1 Step: 1 | |||||
6″ OD Replacement Consumables package No backing plates | $225.00$254.00 | Max: Min: 1 Step: 1 | |||||
6″ OD Replacement Consumables package with backing plates | $289.00$325.00 | Max: Min: 1 Step: 1 | |||||
8″ OD Replacement Consumables package with backing plates | $350.00$394.50 | Max: Min: 1 Step: 1 | |||||
15 lbs | 12″ | 6″ SMART CUT® LP grinder/polisher NO consumables package | $589.00$698.50 | Max: Min: 1 Step: 1 | |||
17 lbs | 14″ | 8″ SMART CUT® LP grinder/polisher NO consumables package | $698.00$798.50 | Max: Min: 1 Step: 1 | |||
17 lbs | 12″ | 6″ SMART CUT® LP grinder/polisher with consumables package | $789.50$889.50 | Max: Min: 1 Step: 1 | |||
19 lbs | 14″ | 8″ SMART CUT® LP grinder/polisher with consumables package | $889.50$989.50 | Max: Min: 1 Step: 1 |
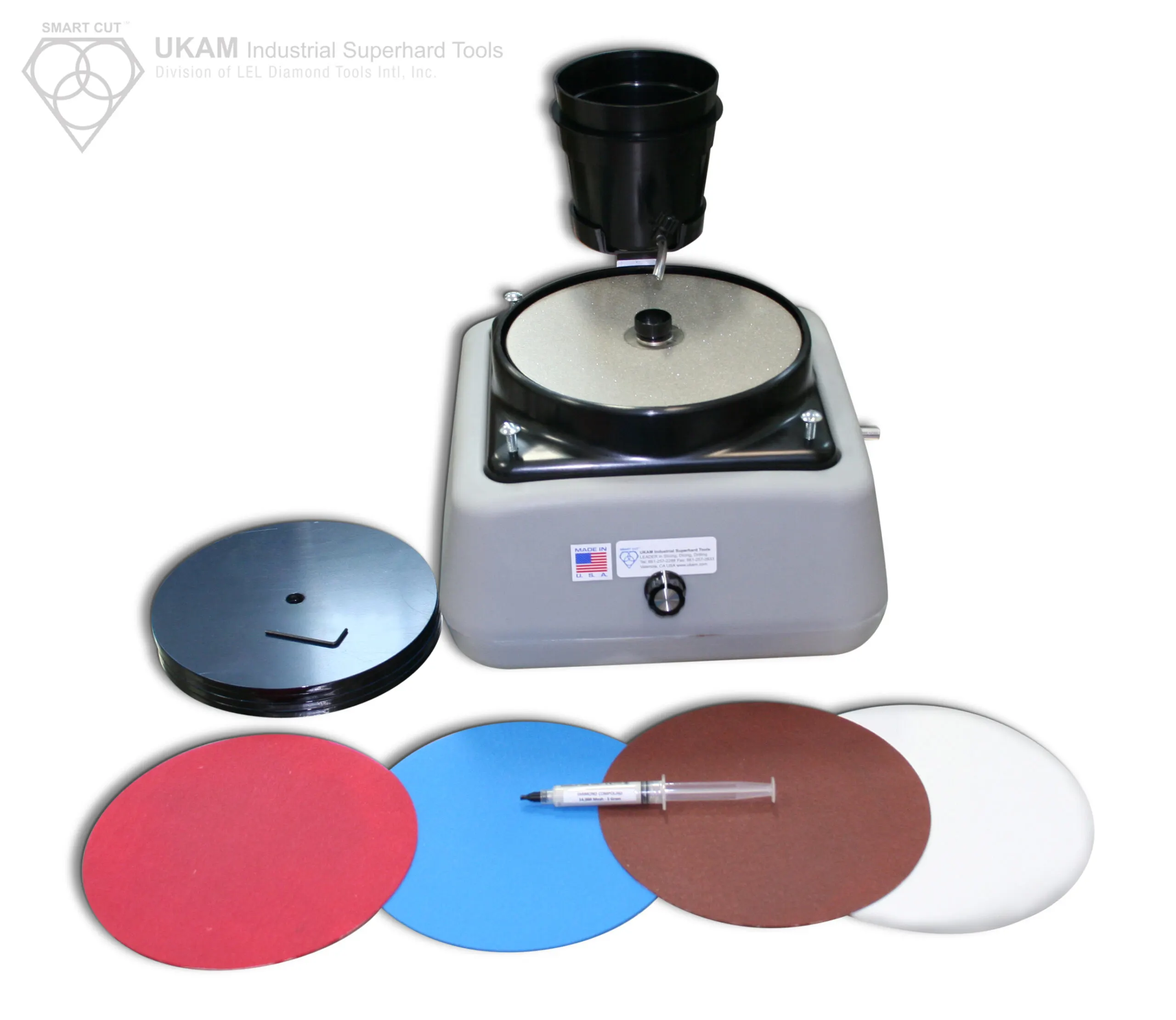
CONSUMABLES PACKAGE INCLUDED
Consumables package that comes with the machine is designed to take the user from Rough Finish to final polish. Consisting All “Fixed Abrasive” Diamond Discs. (1) one metal bond disc 180 mesh (81 microns) to grind surface of material flat. And (3) three resin bond diamond discs: 325 mesh/45 microns (brown color), 600 mesh/30 microns (red color), 1,200 mesh/12 microns (blue color) to smooth and polish the material (removing all the scratches in imperfections). And (1) one felt polishing disc to be used with diamond or any other type of abrasive media in order to achieve final desired finish or polish. And 4 units of disc backing plates. Each Resin bond and Felt Polishing Disc has PSA backing and is attached to backing plate provided.
TYPICAL PROCESS FROM ROUGH GRINDING TO FINAL POLISH
Steps outline below can be skipped or substituted depending on users needs.
Step 1: Rough Grinding: Metal Bond Diamond Disc, hydraulically pressed to a backing plate 180 mesh (81 microns)
Step 2: Pre-Polishing: Resin Bond Diamond Disc 325 mesh/45 microns (brown color)
Step 3: Pre-Polishing: Resin Bond Diamond Disc 600 mesh/30 microns (red color)
Step 4: Pre-Polishing: Resin Bond Diamond Disc 1,200 mesh/12 microns (blue color)
Step 5: Synthetic Felt Polishing Disc (white color): use with abrasive (such as cerium Oxide) or diamond (5 gram of syringe of diamond paste) to give you optical polish. This will achieve final desired finish
VARIABLE SPEED
Variable speed from 500 to 3,000 RPM. The SMART CUT® LP has a large range of speeds to accommodate a wide variety of materials and applications. Operator can adjust the RPM as needed. High RPM setting is recommended for grinding and lower RPM setting is recommended for final polishing.
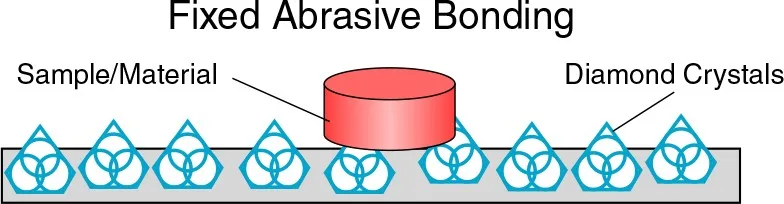
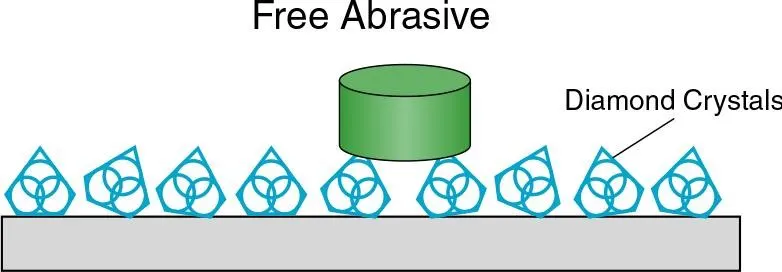
CAN BE USED WITH BOTH FIXED (ABRASIVE) DIAMOND DISCS & FELT DISCS WITH LOOSE ABRASIVE
These machines can use both Fixed (abrasive) Diamond Discs & Felt discs with loose abrasive (diamond powder, diamond paste, diamond slurry, and all abrasive powders). Allowing you to select the most optimum and economic option for you application. Fixed Abrasive diamond discs (have diamond impeded on the surface of the disc (metal bond) or diamond impregnated inside the disc (resin bond).
Advantages of using “Fixed Abrasive” System includes: consistent application of diamond through the entire machine steel plate. Life in number of parts that can be processed (significantly lower consumables cost, and in much shorter time it would take to achieve same results with loose abrasives.
No used up diamond slurry or abrasive having to recycle or clean, makes this much cleaner and greener option that is friendly to the environment.
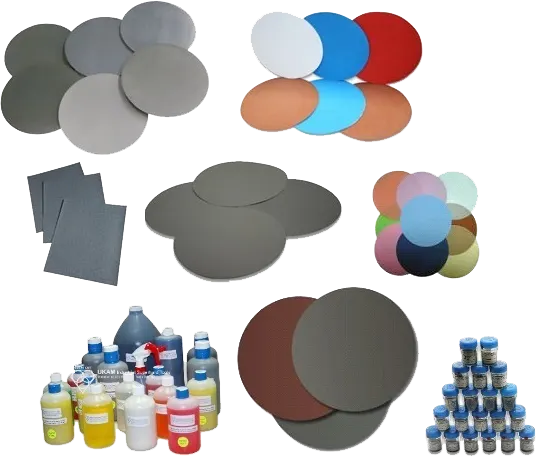
Diamond
Grinding & Polishing Consumables
- Abrasive Belts
- Abrasive Powders
- Abrasive Suspensions
- Abrasive Pastes
- Polishing Pads
- Diamond Suspensions
- Diamond Paste
- Diamond Cup Powders
- Abrasives Discs
- Abrasive Rolls/Strips
- Diamond Belts
- Diamond film
- Grinding/Polishing Machines
- Diamond grinding/polishing strips/foils
Why Choose Us?
Optimize your application to ultimate level of efficiency
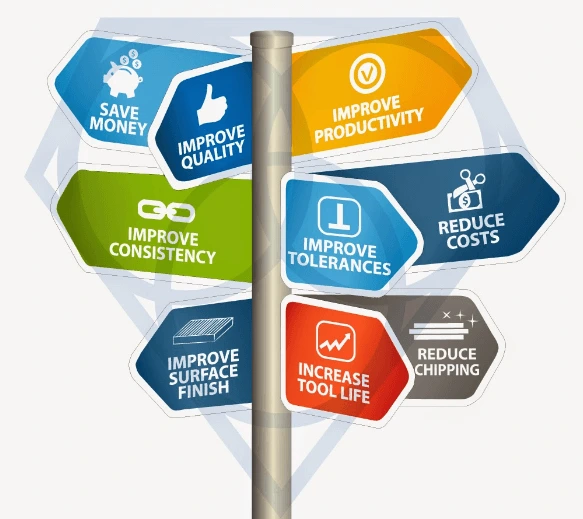
- Unmatched Selection For Many Applications
- Unmatched Technical Support & Expertise
- Superior Quality & Consistency
- Super Technology & innovation
- Immediate Worldwide Delivery
- American Based Manufacturer
-
Custom
Manufacturing - Better Value manufacturer Direct Price
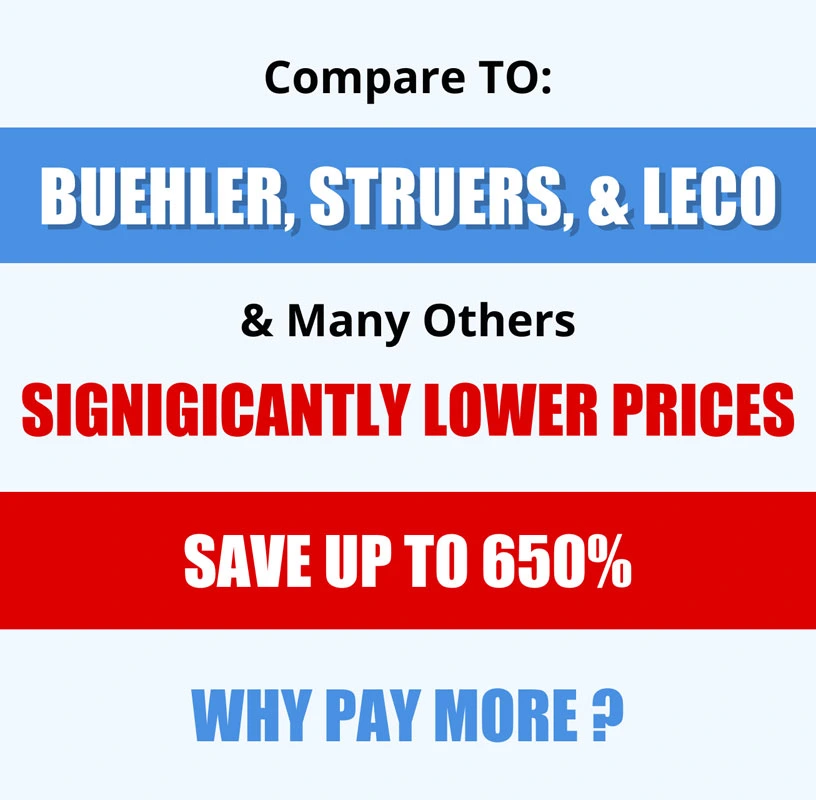
Why Work With Us?
Read More
We produce diamond consumables for some of the leading world OEM manufacturers. We offer Manufacturers Direct Prices
We have the largest variety of diamond & cbn wafering blades available in stock. As well as large inventory of diamond & abrasive consumables. We also custom manufacture diamond and cbn tools, consumables and machines to better fit customer specific needs. Just about any tools & consumables can be designed and manufactured per client drawing or specificrtion
WE ARE A PARTNER IN YOUR SUCCESS
Our proprietory diamond chemistory , precision , manufacturing metods , quality control methods allow us to control and regulate the dozens of variables to that affect consumable life , quality , and consistency.
The more you understand about what we can do for you the better our partnership will be. Here you will find most comprehensive source of information and optimizing and improving your cutting , drilling , grinding and polishing on the web. find everything you ever wanted to know about diamond tools.
AMERICAN MANUFACTURER
"ONE OF THE MOST EXPERIENCED COMPANIES IN THE INDUSTRY"
Save Money Save up to 650%
COMPARE TO: BUEHLER , STRUERS , LECO & MANY OTHERS
Large Inventory & Custom Manufacturing
Umatched Technical Support
Developing close ties with our customers is the foundation of our business. At the core of
our company is a team of world class engineers, knowledgeable customer service personnel here to serve you. Whether is designing or manufacturing a special solution. We will go out of our way to optimizing your process to ultimate level of efficiency
Superior Quality & Consistency
EXPECT MORE FROM YOUR TOOLS
Comprehensive Source Of Information For Sample Preparation
Advanced Technology
As one of the few remaining independent U.S.Diamond Tool & machine builders. We have the experience & tradition to help you remain at frontier of technology Our experience has been further enhanced by acquiring assets and processes from some of the oldest American tool
manufacturers, along with their decades of experience and R& D. This has positioned us as one of the most experienced companies in the industry .Depend on us to bring you technology of tomorrow today.
Experience Makes All The Differences
Over the years we have worked with some of the leading Fortune 500 companies , thousands of universities , government and private research labs , and small organisations. We have made thousands of custom tools , built custom machines , work-holding fixtures , etc for hundreds of applications. Many of our staff members have been working in their respective fields for over 50 years and have gained a wealth of knowledge over the years
Let Us Help You
Related Products
SMART CUT® MP-A Manual Grinder / Polishing Machine
SMART CUT® NP Dual Manual Grinder / Polisher
SMART CUT® NP Single Wheel Metallographic Grinder and Polisher
SMART CUT® LG Manual Metallurgical Grinder/Polisher with Single Wheel
SMART CUT® LP – 12” (300MM)
Recently Viewed Products
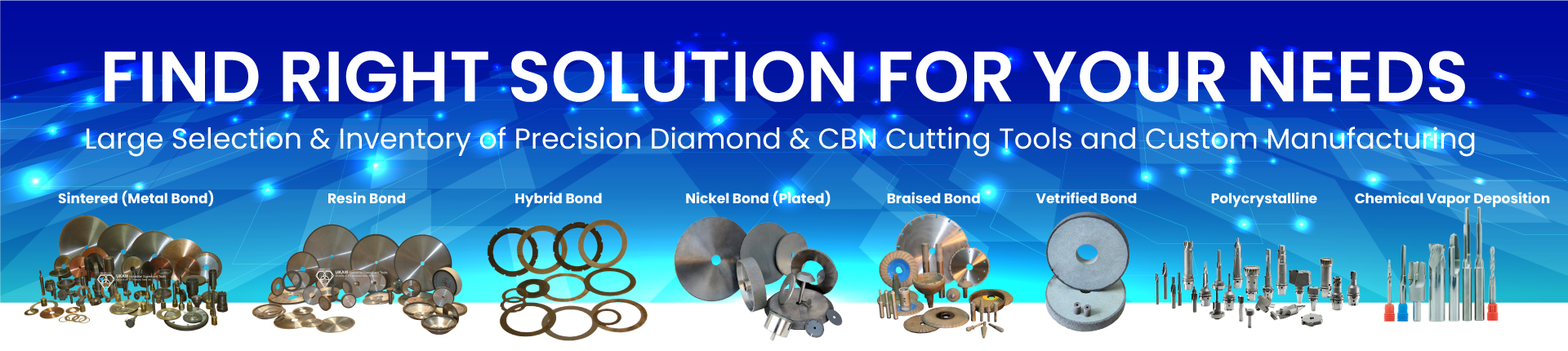
ARE YOU USING RIGHT CONSUMABLES?
FOR YOUR APPLICATION?
LET US
HELP YOU
HAVING ISSUES WITH
YOUR CURRENT METALLOGRAPHIC CONSUMABLES?
Knowledge Center
02
Jun
How to properly use Diamond Tools
UKAM Industrial Superhard Tools manufactures precision diamond tools for a large variety of applications, materials, and industries.
Share this Article with Friend or Colleague
Metal Bonded Diamond Tools are “impregnated” with diamonds. This means that selected diamonds...
02
Jun
Why use diamond
Diamond is the hardest material known to man kind. When used on diamond/tools, diamond grinds away material on micro (nano) level. Due to its hardness Diamond will work all types of materials from...
02
Jun
Diamond vs CBN (cubic boron nitride) Tools
Cubic Boron Nitride (CBN) is a synthetic material that is renowned for its exceptional hardness and high thermal stability. It is composed of boron and nitrogen atoms arranged in a crystal lattice structure, similar to...
02
Jun
Discover the Right Diamond Powder for Your Application: Choosing Between Monocrystalline and Polycrystalline Diamonds
Which to use for your application?
Diamond shape plays a significant role in the effectiveness of polishing solutions, affecting both the polishing rate and the quality of the final finish. Understanding the differences between monocrystalline and...
02
Jun
What is Diamond Mesh Size and how to select best one for your application
Diamond grit size can be defined as the size of the diamond particles used in the bond matrix. The larger the diamond particles (grit size) the faster the tool will cut.
Share this Article with Friend or...
02
Jun
What is Diamond Concentration and which to use for your application
Diamond concentration is measured based on the volume of diamond within a section of the tool. It is typically defined as Concentration 100, which equates to 4.4 carats per cubic centimeter of the diamond layer...
11
Jun
Selecting the Right Diamond Suspension for your Application – Monocrystalline or Polycrystalline?
Choosing the correct diamond suspension, whether monocrystalline or polycrystalline, significantly impacts the quality and efficiency of the polishing and material removal processes. Understanding the properties and applications of both types of suspensions can help you...
17
Jun
Improve Sample Quality & Optimize your Polishing Operating for Metallography & Sample Preparation
Polishing is important step in metallography & sample preparation for revealing the true microstructure of materials, including grain boundaries, phases, and inclusions, which provide insights into material properties and history. This guide is designed to...
26
Jun
Optimize your Grinding Operation for Metallography & Sample Preparation
Share this Article with Friend or Colleague
Grinding is a fundamental mechanical process in metallography that involves removing material from a specimen using hard, abrasive particles. This process is essential for preparing specimens for microscopic...
11
Sep
What is the difference between Lapping, Grinding, & Polishing
Some of the major differences include the type and diamond mesh size of diamond discs used, type and size of abrasives used and their holding method. Other factors include RPM’s (speed) used and pressure applied...
29
Jan
Guide to Selecting the Right SMART CUT® Metallographic / Metallurgical Polishing Cloth & Pads for Your Application
Proper selection of SMART CUT® Metallographic / Metallurgical Polishing Cloths and Pads is important to achieving best results in metallography and sample preparation. These products are specially designed for precision, durability, and compatibility with various...
30
Jan
Selecting Right Silicon Carbide Paper / Discs for Metallography / Sample Preparation
Selecting the right silicon carbide paper for metallographic sample preparation is important for achieving accurate and reliable results in material analysis. The grinding and polishing process plays a fundamental role in preparing specimens for microscopic...
30
Jan
Upgrading Metallography Grinding with Silicon Carbide Paper
This guide covers the best practices for using silicon carbide paper in metallography. It includes tips on proper grit progression, optimizing pressure and speed settings, preventing common issues, and extending the life of the abrasive....
- Unmatched Selection For Many Applications
- Superior Quality & Consistency
- Immediate Worldwide Delivery
- Technical Support & Expertise
- American Based Manufacturer
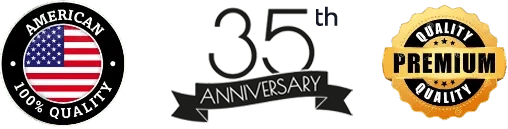

- Different Product
- Different Technology
- Different Company
- Expect MORE from your tools
Let Us HELP You!
Subscribe To Our Newsletter
Signup for email offers, updates, and more
Contact Us
- 25205 & 25201 Avenue Tibbits Valencia CA 91355 USA
-
Phone : (661) 257-2288
FAX : (661) 257 -3833 - lel@ukam.com
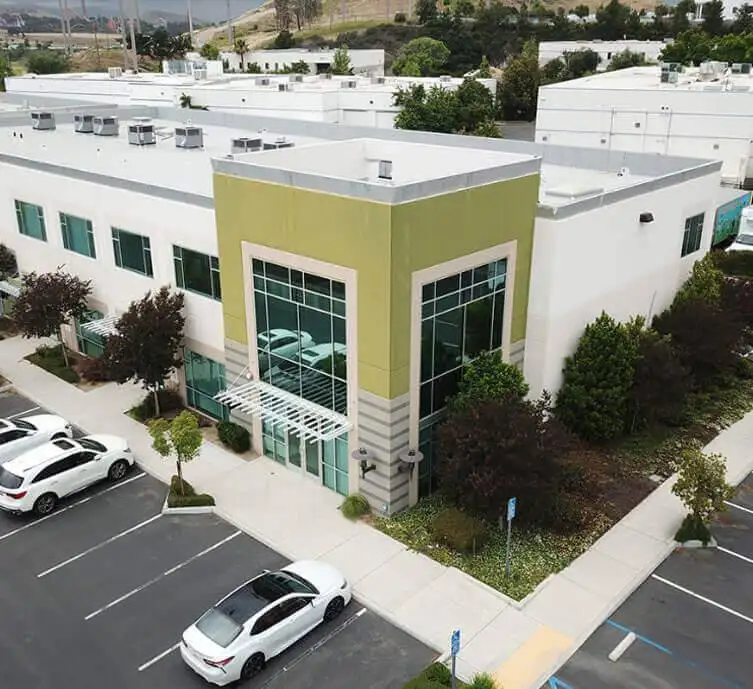
UKAM Industrial Superhard Tools is a U.S. High Technology, Specialty Diamond Tool & Equipment manufacturer. We specialize in producing ultra thin & high precision cutting blades and precision cutting machines diamond drills, diamond micro tools, standard & custom advanced industrial diamond tools and consumables.
- 25205 & 25201 Avenue Tibbits Valencia CA 91355 USA
-
Phone : (661) 257-2288
FAX : (661) 257 -3833 - lel@ukam.com
- 25205 & 25201 Avenue Tibbits Valencia CA 91355 USA
-
Phone : (661) 257-2288
FAX : (661) 257 -3833 - lel@ukam.com
DIAMOND TOOLS BY BOND
EQUIPMENT
KNOWLEDGE CENTER
OUR PRODUCTS
COMPANY
CUSTOMER SERVICE
Shipping Methods


Safe & Secure Payments

© Copyright 1990-2025. UKAM Industrial Superhard Tools – Terms of Use