-
0 items in quote
No products in the Quote Basket.
DESCRIPTION
SPECIFICATIONS
INDUSTRIES USED IN
FAQ
ACCESSORIES
USAGE RECOMENDATION
DESCRIPTION
- Superior Quality Diamonds: Each carving point is embedded with high-grade, finely milled diamonds, ensuring exceptional durability and sharpness. This means you can work on even the hardest materials with ease, without worrying about wear and tear.
- Braised Bond Technology: Our advanced braising technique securely bonds the diamonds to the metal base, providing a stronger hold than traditional methods. This results in a longer lifespan for the carving point and consistent performance throughout its use.
- Precision Design: The carving points are meticulously crafted to provide the utmost precision. Whether you’re working on intricate jewelry designs, detailed woodwork, or delicate stone carving, these tools offer the control and accuracy you need.
- Versatile Application: Ideal for a wide range of materials, including granite, marble, glass, wood, and metals. Whether you’re a professional jeweler, woodworker, or hobbyist, these diamond carving points will elevate your work.
- Variety of Shapes and Sizes: The set includes a diverse range of shapes and sizes, allowing you to choose the perfect tool for every detail of your project. From fine lines to deep grooves, you’ll have the right tool at your fingertips.
- Easy to Use: Designed to fit most standard rotary tools, these carving points are easy to install and use, making them accessible for both professionals and beginners.
- Safe and Reliable: Engineered with safety in mind, the robust construction reduces the risk of breakage, ensuring a safe working environment.
SPECIFICATIONS
- Material: High-grade diamond particles, metal base
- Bonding Technique: Advanced braising
- Shapes & Sizes: Various, to suit all types of detailed work
- Compatibility: Fits most standard rotary tools
- Application: Suitable for granite, marble, glass, wood, and metals
- Advanced vacuum brazing technology;
- Ideal for detailed carving and grinding;
- Last substantially longer than electroplated bits;
- 6mm Shank fits standard DREMEL tools;
- Material: Engineered Stones, Granite, Marble;
- Dry or Wet use.
INDUSTRIES USED IN
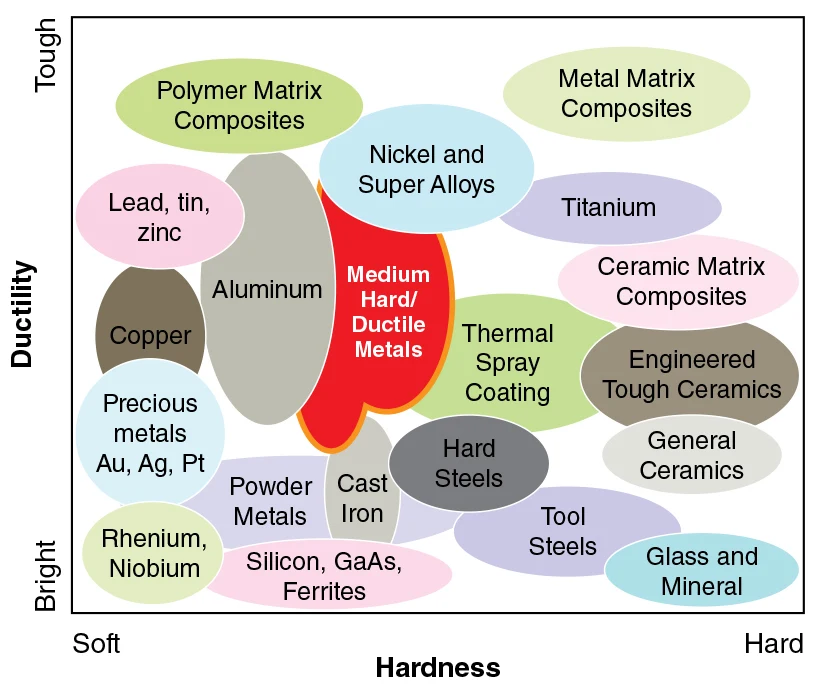

INDUSTRIES USED IN:
- Advanced Ceramics
- Composites
- Glass
- Geology
- Quartz
- Materials Research
- Medical Devices
- Metallography
- Photonics / Optics
- Semiconductor
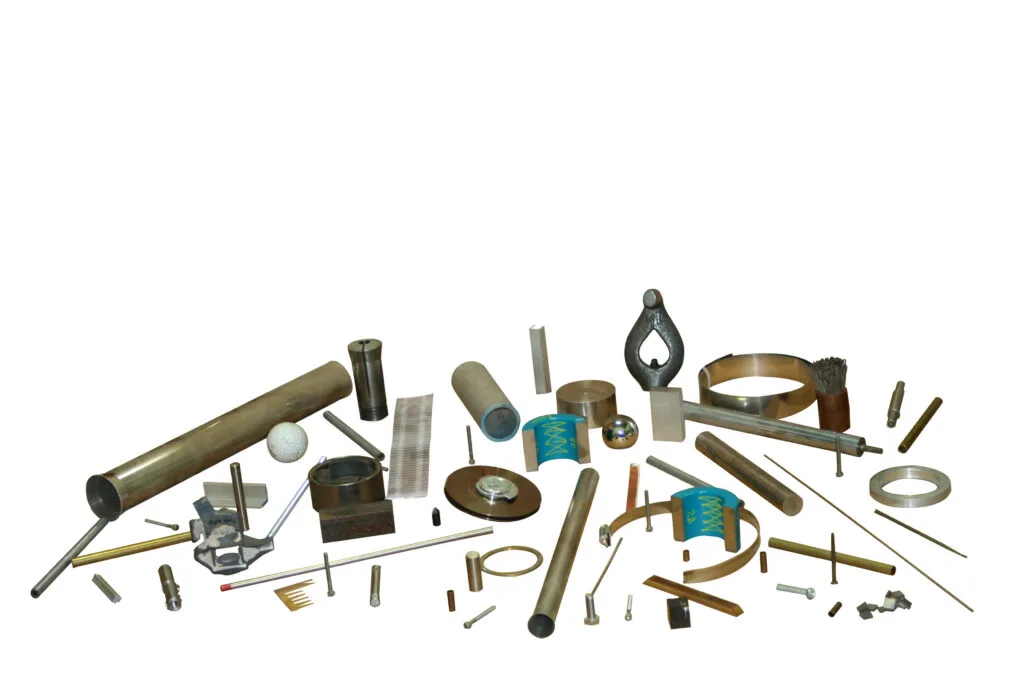
Ferrous & Non-Ferrous Metals:
- Plain Carbon Steels
- Electronic Packages
- Stainless Steels Plastics
- Tool Steels Fasteners
- Aluminum Refractories
- Copper Base Alloys Integrated Circuits
- Magnesium Thermal Spray Coatings
- Titanium Metal Matrix Composites
- Biomedical Wafers
- Petrographic
- PCB.s Ceramics
FAQ
ACCESSORIES
Showing 1 – -1 of 16 results Showing all 16 results Showing the single result No results found
Sort by Name A – Z
Filters Sort results
Reset Apply
Image | Item No. | Description | Price | Quantity | Add to cart |
---|---|---|---|---|---|
Color: 5/8″-11″ thread. Fits into drill press chuck. Shank adapter threads into 5/8″-11″ female thread of diamond drill. Can be used with any other tool with 5/8″-11″ thread. | $26.72 | Max: Min: 1 Step: 1 | |||
Color: 5/8″-11″ thread. Fits into drill press chuck. Shank adapter threads into 5/8″-11″ female thread of diamond drill. Can be used with any other tool with 5/8″-11″ thread. | $22.46 | Max: Min: 1 Step: 1 | |||
1 Gallon Blue SMART CUT® General Materials Formula Synthetic Water Soluble Coolant | $99.81 | Max: Min: 1 Step: 1 | |||
1 Quart Blue SMART CUT® General Materials Formula Synthetic Water Soluble Coolant | $34.81 | Max: Min: 1 Step: 1 | |||
5 Gallons Blue SMART CUT® General Materials Formula Synthetic Water Soluble Coolant | $317.41 | Max: Min: 1 Step: 1 | |||
55 Gallons Blue SMART CUT® General Materials Formula Synthetic Water Soluble Coolant | $1,745.00 | Max: Min: 1 Step: 1 | |||
1/2″ x 1/2″ x 6.0″ White Recommended for coarser grits found in segment wheels, core drills, or Blanchard grinding. Excellent performance on 120 grit tools. | $8.65 | Max: Min: 1 Step: 1 | |||
1.0″ x 1.0″ x 6.0″ White Recommended for coarser grits found in segment wheels, core drills, or Blanchard grinding. Excellent performance on 120 grit tools. | $15.99 | Max: Min: 1 Step: 1 | |||
1/2″ x 1/2″ x 6.0″ White For use on diamond tools 150 to 220 Grit Size. | $8.65 | Max: Min: 1 Step: 1 | |||
1.0″ x 1.0″ x 6.0″ Black Recommended for use in Diamond Tools 150 Grit Size (mesh size) or finer. | $15.39 | Max: Min: 1 Step: 1 | |||
2.0″ x 2.0″ x 6.0″ Black Recommended for use in Diamond Tools 150 Grit Size (mesh size) or finer. | $39.47 | Max: Min: 1 Step: 1 | |||
1.0″ x 1.0″ x 6.0″ Black Recommended for coarser grits found in segment wheels, core drills, or Blanchard grinding. Excellent performance on 120 grit tools. | $15.99 | Max: Min: 1 Step: 1 | |||
2.0″ x 2.0″ x 6.0″ Black Recommended for coarser grits found in segment wheels, core drills, or Blanchard grinding. Excellent performance on 120 grit tools. | $39.47 | Max: Min: 1 Step: 1 | |||
$154.87 | Max: Min: 1 Step: 1 | ||||
$154.87 | Max: Min: 1 Step: 1 | ||||
$235.00 | Max: Min: 1 Step: 1 |
USAGE RECOMENDATION
Step 1: Preparation:
- Gather all necessary materials and ensure you have the correct carving point for your project.
- Wear appropriate safety gear including goggles, gloves, and a dust mask if needed.
Step 2: Set-Up:
- Ensure your rotary tool is turned off and unplugged.
- Attach the carving point to the rotary tool according to the tool’s instructions.
- Securely fasten the carving point in the collet or chuck of the rotary tool.
- Plug in and turn on your rotary tool.
Step 3: Testing:
- Test the carving point on a scrap piece of material to ensure it is properly attached and working correctly.
- Adjust the speed of your rotary tool according to the material you are working with.
Step 4: Engraving or Sculpting:
- Hold the rotary tool like a pen, with a firm but comfortable grip.
- Gently touch the carving point to the material, starting at one end of your design.
- Move the carving point along the material, following your design or pattern.
- Use steady and controlled movements, letting the tool do the work.
- Work in small sections, periodically checking your progress.
Step 5: Finishing:
- Once you have completed your design, turn off and unplug the rotary tool.
- Carefully remove the carving point from the tool.
- Clean the carving point with water and a soft brush, and dry thoroughly before storing.
- Store the carving point in its original packaging or a protective case.
Step 6: Maintenance:
- Regularly clean and inspect your carving points for any signs of wear or damage.
- Replace any carving points that become dull or damaged.
Step 7: Post-Project Cleaning and Storage:
- After using the carving points, it is important to clean them thoroughly to remove any debris or residue.
- Use a soft brush and water to gently clean the carving points. Avoid using any harsh chemicals or abrasive materials as this can damage the electroplated diamond coating.
- Dry the carving points completely before storing them to prevent rust or corrosion.
- Store the carving points in a dry and cool place, away from direct sunlight or extreme temperatures.
- If possible, store the carving points in their original packaging or a protective case to prevent them from getting damaged.
Step 8: Regular Maintenance:
- Regularly inspect your carving points for any signs of wear or damage. If you notice any issues, replace the carving point immediately to avoid any accidents or injuries.
- If the carving point becomes dull over time, consider having it sharpened by a professional to extend its lifespan.
Step 9: Safety Precautions:
- Always use the carving points in a well-ventilated area to avoid inhaling any dust or debris.
- If you are working on a project that produces a lot of dust, consider using a dust collector or vacuum to keep the area clean.
- Be aware of your surroundings and keep any loose clothing or hair away from the rotary tool while it is in operation.
Step 10: Creativity and Experimentation:
- Once you are comfortable with the basic operation of the carving points, don’t be afraid to experiment and get creative with your projects.
- Try different techniques and patterns to achieve unique and intricate designs.
- Share your work with others and learn from fellow crafters to continuously improve and expand your skills.
Step 11: Advanced Techniques:
- As you gain more experience, you can start experimenting with advanced techniques such as layering and cross-hatching to add depth and texture to your projects.
- Practice on scrap materials first before applying these techniques to your final project.
Step 12: Combining Materials:
- Try using the carving points on different materials such as glass, ceramics, or even gemstones to create unique and personalized pieces.
- Experiment with combining different materials in one project to add contrast and interest.
Using the Right RPM’s for your Application
The optimal RPM (revolutions per minute) for using electroplated diamond carving points depends on several factors, including the material being carved, the size and shape of the carving point, and the specific project requirements. However, here are some general guidelines to consider:
1.Soft Materials (e.g., wood, plastic):
- Use a lower RPM, typically between 5,000 to 15,000 RPM, to prevent overheating and minimize the risk of damaging the material.
2.Hard Materials (e.g., glass, stone, metal):
- Use a higher RPM, typically between 10,000 to 30,000 RPM, to effectively cut through the material and achieve a smooth finish.
3.Intricate or Detailed Work:
- Use a lower RPM to have more control and precision when working on intricate or detailed designs.
4. General Carving and Shaping:
- Use a moderate RPM that provides a balance between cutting efficiency and control.
It is important to always start with a lower RPM and gradually increase it until you find the optimal speed for your specific project. Additionally, always refer to the manufacturer’s guidelines and recommendations for using electroplated diamond carving points, as they may provide specific RPM ranges for their products.
Recommended Coolant & Application
When using electroplated diamond carving points, introducing a coolant can help reduce heat, minimize dust, and potentially extend the life of the carving points. Water is typically used as a coolant for this type of application. Here’s how to use and introduce coolant:
Coolant to Use:
- Use clean water as a coolant. It is the most common and safest option for cooling and lubricating the carving points during operation.
How to Introduce Coolant:
Dipping Method:
- Dip the carving point in water before starting the carving or engraving process.
- Periodically withdraw the carving point and dip it back in water to keep it cool.
Spray Bottle Method:
- Fill a spray bottle with clean water.
- Spray the water onto the material being carved to keep the carving point cool during operation.
Sponge Method:
- Soak a sponge in water and place it near your working area.
- Periodically touch the carving point to the wet sponge to cool it down.
Additional Tips:
- Ensure that your rotary tool is compatible with the use of coolant and that it is protected from water to avoid any electrical hazards.
- If you’re working on an electrical device or material that may be damaged by water, be extra cautious to prevent water from coming into contact with electrical components.
- Always follow the manufacturer’s guidelines and recommendations for using coolant with electroplated diamond carving points.
Recommended Feed Rates
The feed rate and pressure to apply when using electroplated diamond carving points depend on several factors, including the material being carved, the hardness of the diamond, the size and shape of the carving point, and the specific project requirements. However, here are some general guidelines to consider:
Feed Rate:
- The feed rate should be adjusted based on the material being carved. For softer materials like wood or plastic, a slower feed rate is usually sufficient. For harder materials like stone or glass, a moderate to faster feed rate may be needed.
- It’s important to allow the tool and carving point to do the work, rather than forcing the tool through the material.
Pressure to Apply:
- Apply light to moderate pressure when using the carving points. Too much pressure can cause the carving point to wear down quickly, damage the material, or even break the point.
- It’s important to maintain a consistent pressure to achieve a smooth and even carving or engraving.
Additional Tips:
- Always start with a light pressure and adjust as needed based on the material and desired outcome.
- Pay attention to the feedback from the tool and material. If you notice any unusual sounds or resistance, adjust the feed rate or pressure accordingly.
- Be patient and take your time, especially when working on intricate or detailed designs.
Remember that practice and experience are key to finding the optimal feed rate and pressure for your specific projects. It may take some trial and error to find the right balance, but with time and practice, you will develop a feel for what works best.
Selecting Right Diamond Carving Point Shape for your Application
The shape of the electroplated diamond carving point to use depends on the specific project requirements and the desired outcome. Here are some general guidelines to consider:
Cylinder or Diamond Bullet Shapes:
- Ideal for carving, shaping, and hollowing out areas.
- Great for working on flat and curved surfaces.
Diamond Bullet or Spherical Shapes:
- Suitable for creating rounded details, concave cuts, and hollowing out areas.
- Perfect for carving curved lines and patterns.
Pointed or Needle Shapes:
- Excellent for fine detailing, engraving, and precision work.
- Ideal for creating intricate patterns and designs.
Wheel or Disc Shapes:
- Suitable for cutting, shaping, and grinding flat surfaces.
- Great for creating straight lines and edges.
Tapered Shapes:
- Ideal for carving and shaping in tight or hard-to-reach areas.
- Perfect for creating angles and bevels.
Flame Shapes:
- Flame shapes are versatile and can be used for both detailed work and larger carvings.
- They are suitable for carving, shaping, and finishing work.
Oval Shapes:
- Oval shapes are perfect for smooth contouring and shaping.
- They are great for creating rounded edges and smooth finishes.
Inverted Diamond Bullet Shapes:
- Inverted Diamond Bullet shapes are ideal for creating v-cuts and angled details.
- They can be used for precision work in tight corners and intricate designs.
Parallel Shapes:
- Parallel shapes are great for carving flat and even surfaces.
- They are often used for leveling and smoothing out areas.
Custom Shapes:
- Custom-shaped carving points are available for specific applications and unique project requirements.
- These may include shapes designed for specific materials, patterns, or artistic effects.
Rounded Cylinder Shapes:
- Rounded cylinder shapes are ideal for creating soft curves and contours.
- They can be used for both carving and smoothing out rough areas.
Tapered Cylinder Shapes:
- Tapered cylinder shapes provide precision and control for carving intricate details.
- They are great for working in tight spaces and creating defined edges.
Elliptical Shapes:
- Elliptical shapes are perfect for creating smooth, flowing lines and curves.
- They can be used for both carving and finishing work.
Square or Rectangular Shapes:
- Square or rectangular shapes are ideal for creating straight lines and sharp angles.
- They can be used for carving, shaping, and edging.
Specialty Shapes:
- Specialty shapes are designed for specific applications, such as carving lettering or creating specific patterns.
- They may include unique shapes that are not typically found in standard sets.
When choosing the shape of the electroplated diamond carving point, consider the following:
- Material: Different shapes may work better on certain materials.
- Detail Level: Finer details may require smaller, more pointed shapes, while larger areas may benefit from broader shapes.
- Comfort and Control: Choose a shape that feels comfortable in your hand and gives you the best control over the carving process.
- Versatility: Some shapes are more versatile and can be used for various tasks, while others are more specialized.
- Experimentation: Don’t be afraid to experiment with different shapes to find the one that works best for your project.
- Mixing and Matching: Sometimes, a combination of shapes may be necessary to achieve the desired result.
- Learning from Others: Watch tutorials or ask experienced carvers for advice on which shapes work best for specific applications.
It’s important to consider the size and shape of the area you are working on, as well as the level of detail required for the project. For larger areas and rough shaping, choose a larger, more robust carving point. For fine detailing and precision work, opt for a smaller, more pointed carving point.
Experimenting with different shapes and sizes will help you find the perfect carving point for your needs and preferences. As you gain experience, you will develop a sense of which shapes work best for different applications and materials.
Equipment Diamond Carving Points are Used On:
Electroplated diamond carving points are typically used with a rotary tool or a die grinder. Here are the details:
Rotary Tool:
- A rotary tool is a handheld, motor-driven device that rotates a variety of attachments at high speeds.
- Rotary tools are versatile and can be used for a wide range of applications, including carving, engraving, polishing, grinding, and more.
- They are available in both corded and cordless versions, with cordless versions providing more mobility and flexibility.
- Popular brands include Dremel, Foredom, Proxxon, and Black & Decker.
Die Grinder:
- A die grinder is a more powerful, industrial-grade version of a rotary tool.
- It is typically used for heavy-duty applications, such as grinding, cutting, and polishing metals and other hard materials.
- Die grinders are available in both electric and pneumatic (air-powered) versions.
- They are generally more robust and durable than rotary tools and can handle more demanding tasks.
When choosing a rotary tool or die grinder for your electroplated diamond carving points, consider the following:
- Power Source: Consider whether a corded or cordless tool is more suitable for your needs.
- Speed Range: Look for a tool that offers a range of speeds, as this will give you more control over the carving process.
- Collet Size: Ensure that the tool has a collet size that is compatible with the shank size of your carving points.
- Ergonomics: Choose a tool that feels comfortable in your hand and allows for precise control.
- Brand and Model: Consider the brand and model of the tool, as this can affect the availability of accessories and replacement parts.
Using the right equipment will enhance your carving experience and allow you to achieve the best possible results with your electroplated diamond carving points.
Using the Right Collet or Chuck to hold the diamond carving points on your machine
For electroplated diamond carving points, using a collet chuck is typically recommended. A collet chuck provides a secure and precise method for holding the carving point, allowing for better control and accuracy during the carving or engraving process. Here are the main differences and benefits of each:
Collet Chuck:
- Provides a secure and precise hold on the carving point.
- Minimizes vibration and wobble, resulting in smoother and more accurate carving or engraving.
- Allows for easy and quick tool changes.
- Suitable for smaller diameter shanks, which are common with diamond carving points.
Check or Chuck:
- Typically used for holding larger diameter tools or accessories.
- May not provide as precise or secure a hold on smaller diameter carving points.
- May require additional accessories or adapters to hold smaller diameter shanks.
In conclusion, for electroplated diamond carving points, which often have smaller diameter shanks, a collet chuck is preferred due to its ability to securely and precisely hold the carving point, resulting in better control, accuracy, and overall performance during the carving or engraving process.
Using the Right Diamond Grit Size for your Application
The diamond grit size to use depends on the specific application and the material you are working with. Here are some general guidelines:
Coarse Grit (30-60 grit):
- Ideal for heavy material removal, shaping, and grinding.
- Suitable for working with harder materials like stone, glass, and metal.
Medium Grit (70-120 grit):
- Suitable for general-purpose carving and shaping.
- Works well on a variety of materials including wood, stone, and glass.
Fine Grit (150-300 grit):
- Perfect for finishing, polishing, and detailed work.
- Suitable for all types of materials including wood, stone, glass, and metal.
Extra Fine Grit (above 300 grit):
- Ideal for final polishing and achieving a smooth, mirror-like finish.
- Suitable for all types of materials including wood, stone, glass, and metal.
It is always best to start with a coarser grit to remove excess material and shape the piece, then progressively move to finer grits to achieve the desired smoothness and finish. Also, remember to follow the manufacturer’s recommendations and guidelines for the specific electroplated diamond carving points you are using.
Selecting Right Bond Type to use for your Diamond Carving Points
When selecting the right bond type for your application, it’s essential to consider the material you will be working with, the desired outcome, and the specific requirements of your project. Here are some general guidelines on how to choose between sintered (metal bond), plated, brazed bond, and resin bond:
Sintered (Metal Bond):
- Best suited for hard materials like stone, glass, and ceramics.
- Durable and long-lasting, making it ideal for heavy-duty applications.
- Provides a slower cutting speed but offers a longer tool life.
Plated:
- Suitable for a wide range of materials including stone, glass, and ceramics.
- Ideal for detailed work and precision carving.
- Provides a faster cutting speed but may wear out more quickly than sintered bonds.
Brazed Bond:
- Suitable for hard materials like stone, glass, and ceramics.
- Offers a good balance between cutting speed and tool life.
- Ideal for both heavy-duty applications and detailed work.
- Offers very fast cutting speed and aggressive and free grinding.
- Can by used dry (without coolant) in some applications
Resin Bond:
- Best suited for softer materials like marble, limestone, and composite materials.
- Ideal for polishing and achieving a smooth finish.
- Provides a faster cutting speed but may wear out quickly on harder materials.
- Consider the hardness of the material you will be working with. Harder materials typically require a stronger bond type, while softer materials may be better suited to a softer bond.
- Consider the level of precision and detail required for your project. Detailed work may require a finer bond type, while heavy-duty applications may benefit from a stronger bond.
Selecting Right Diameter to use for your application
When selecting the right tool diameter of the head or tip of an electroplated diamond carving point, consider the following factors:
Material Thickness:
- For thicker materials, a larger diameter may be more suitable as it can handle more material removal.
- For thinner or more delicate materials, a smaller diameter can provide more precision and control.
Detail Level:
- For intricate and detailed work, choose a smaller diameter tip that allows for precision and intricate control.
- For rough shaping or larger carvings, a larger diameter tip may be more appropriate.
Size of the Work Area:
- For large areas, a larger diameter tip can cover more surface area and speed up the process.
- For smaller or confined spaces, a smaller diameter tip will provide better access and control.
Desired Outcome:
- Consider the final outcome you want to achieve. If you’re looking for a smooth and polished finish, a smaller diameter may be more suitable. If you’re looking to remove a lot of material quickly, a larger diameter may be more appropriate.
Compatibility with Your Tool:
- Make sure the diameter of the head or tip is compatible with your rotary tool or die grinder. Check the collet size and ensure it can accommodate the diameter of the carving point.
User Experience and Skill Level:
- For beginners or those less experienced, starting with a medium-sized diameter might be more manageable and allow for better control.
- As you gain more experience, you can then experiment with different diameters to find what works best for your specific needs.
Type of Carving or Engraving:
- For deep carving or engraving, a larger diameter might be more appropriate to remove more material.
- For surface detailing or light engraving, a smaller diameter will provide more precision.
Tool RPM and Feed Rate:
- Consider the recommended RPM and feed rate for the specific diameter of the tool. Different diameters may perform optimally at different speeds and feed rates.
Cost and Availability:
- Take into account the cost and availability of the specific diameter you are considering. Some diameters may be more readily available than others.
Personal Preference:
- Ultimately, personal preference plays a role in selecting the right diameter. Through trial and error, you may find that you prefer working with a specific diameter based on your individual carving or engraving style.
When selecting the right tool diameter, it’s crucial to find a balance between the requirements of the material, the level of detail, and your personal preference and experience. It may take some experimentation to find the diameter that works best for you, but the effort will be worth it in the end when you achieve the desired results for your project.
Showing 1 – 9 of 9 results Showing all 9 results Showing the single result No results found
Sort by Price low to high
Filters Sort results
Reset Apply
Image | Item No | DESCRIPTION | Diamond Grit Size | Shank Diameter | Price | Quantity | Add to cart |
---|---|---|---|---|---|---|---|
Flat end cylinder braised bond diamond carving point | 40/50 mesh | 6mm | $26.41 | Max: Min: 1 Step: 1 | |||
Cone braised bond diamond carving point | 40/50 mesh | 6mm | $26.41 | Max: Min: 1 Step: 1 | |||
40/50 mesh | 6mm | $37.10 | Max: Min: 1 Step: 1 | ||||
Round cylinder braised bond diamond carving point | 40/50 mesh | 6mm | $37.10 | Max: Min: 1 Step: 1 | |||
Flat end cylinder braised bond diamond carving point | 40/50 mesh | 6mm | $39.70 | Max: Min: 1 Step: 1 | |||
Flat end cylinder braised bond diamond carving point | 40/50 mesh | 6mm | $39.70 | Max: Min: 1 Step: 1 | |||
Bullet shape braised bond diamond carving point | 40/50 mesh | 6mm | $54.90 | Max: Min: 1 Step: 1 | |||
Ball Shape braised diamond carving point | 40/50 mesh | 6mm | $58.70 | Max: Min: 1 Step: 1 | |||
Disc braised bond diamond carving point | 40/50 mesh | 6mm | $76.90 | Max: Min: 1 Step: 1 |
How SMART CUT® Bond Works?
Step 1
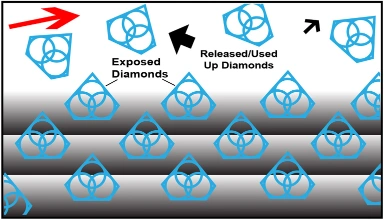
Sharpest And Finest Quality Diamonds
The newly exposed diamonds don’t effect diamonds already working on the material. Unlike many other diamond bonds, diamonds in a SMART CUT® Bond remains sharp and grow sharper with each cut, prolonging product life and consistent performance.
Step 2
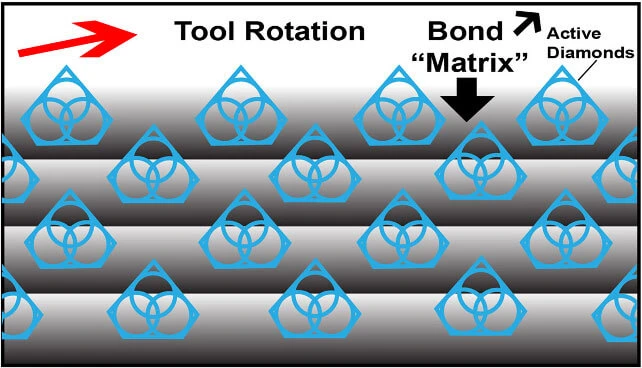
Diamonds or CBN Crystals
Diamonds or CBN Crystals are activated only at the exposed layer. As Bond Matrix layer begin to wear out, diamonds in a new Bond Matrix layer are immediately activated, substituting the already used up diamond layer. The SMART CUT® Diamond Hybrid Bond makes sure every diamond is in the right place and at the right time, working where you need it most.
Step 3
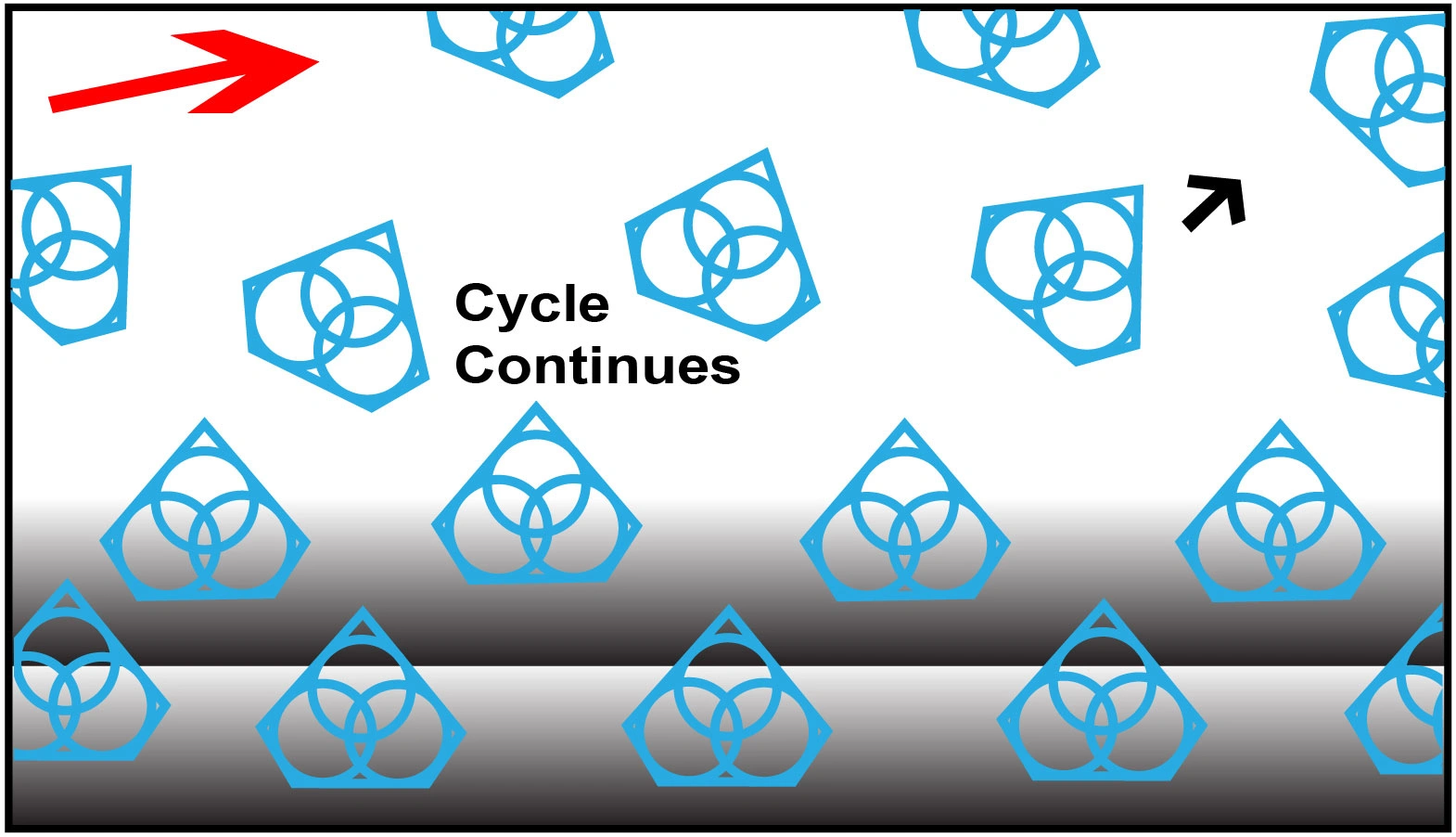
Advanced Formulated Open Diamond Bond Design
This advanced formulated open diamond bond design insures minimal chipping, fast cut, constant speed of cut, minimal cutting noise, and most important of all, consistent performance.
About Brazed Bond
Brazed Diamond Tools are produced using and process that creates a fusion between the diamonds and the metal bond. While they may appear similar to electroplated (nickel bond) diamond tools. They are produced utilizing completely different process. Brazed Bond Diamond Tools are produced inside vacuum oven at a high temperature, single layer of diamond crystal bonded to steel body with very high diamond exposure. Not only does it promote high diamond exposure, but it also eliminates the loss of diamond particles through pull-out. The diamond section will not strip or peel from the steel body. This translates into multiple benefits, including: aggressive tools that last longer, cut faster, run cooler and load less, providing increased productivity and part consistency.
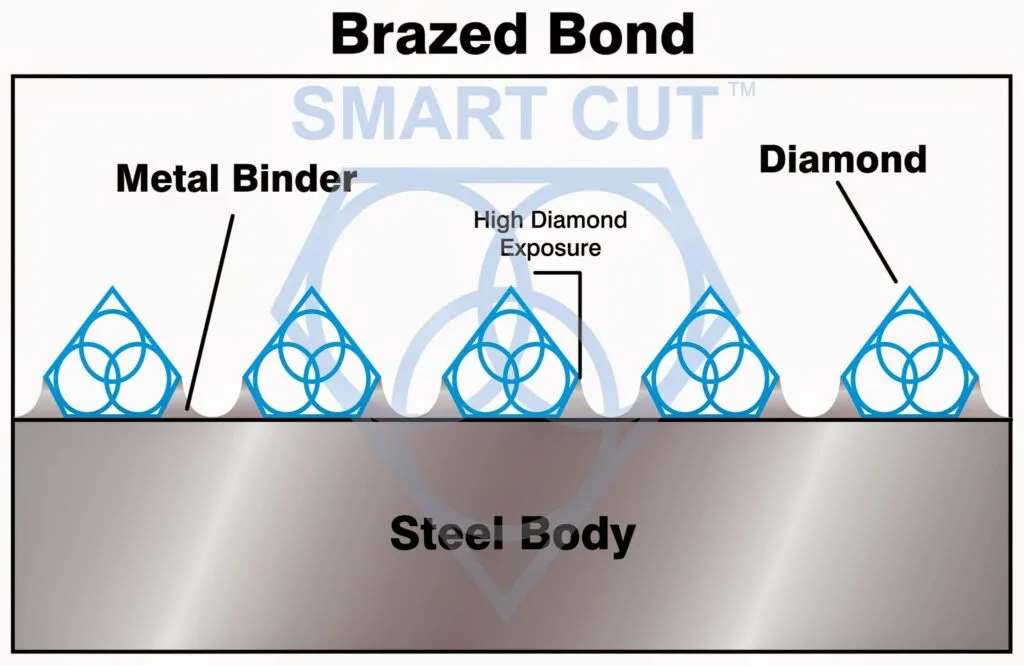
SMART CUT® Difference
How SMART CUT® Diamond Craving Points are Different in comparison to other Craving Points.
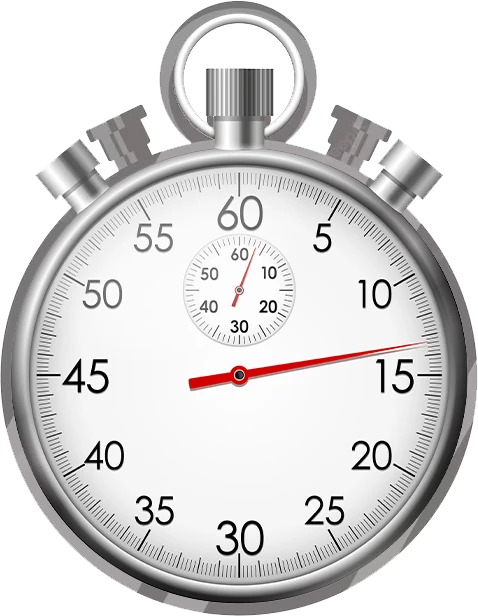
Faster & Freer Action
Craving points made utilizing SMART CUT technology are much more aggressive than your conventional Tools. They can cut faster, while still leaving behind a smooth finish free of material deformation.
Longer Life
In most cases tools manufactured utilizing SMART CUT technology, will outlast other conventional nickel bonded diamond CBN drills. SMART CUT diamond CBN tools are more sturdy than tools manufactured with conventional technologies. They are capable to retain their form and bond configuration all the way through the tools life.
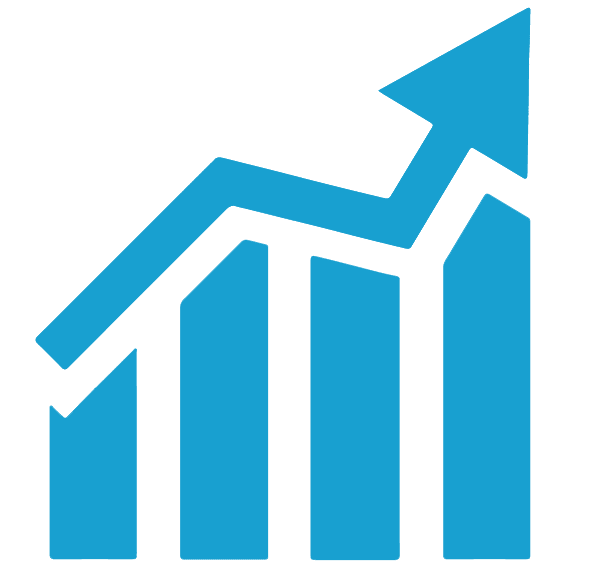
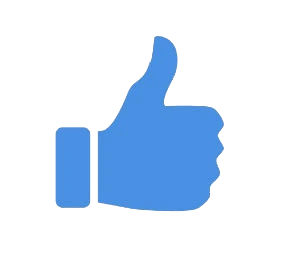
More Consistent Performance
SMART CUT Multi Layered Electroplated diamond cutting blade three diamond layers impregnated inside the bond matrix. Unlike Many Other blade Types, they wear evenly, and are known for their consistency. You will get consistent cutting speed, and overall consistent performance, with minimum amount of dressing even on the hardest to cut materials
Manufactured Using The Highest Quality Raw Materials
Only the highest quality synthetic diamonds and raw materials are used in the manufacturing process. The highest quality standards and product consistency is maintained, using sophisticated inspection and measurement equipment.
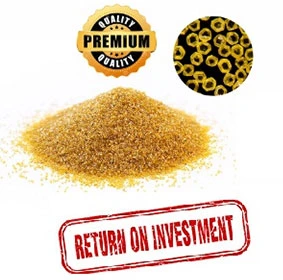
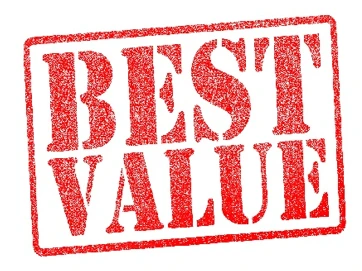
Best Performance & Value on the Market
SMART CUT Multi Layered Electroplated Diamond Drills are the best investment you can make! Although they may cost more than electroplated (nickel bond), Diamond Drills. They will more than pay for themselves in terms of overall performance and provide best Return on Investment.
Why Choose Us?
Optimize Your Application To Ultimate Level Of Efficiency
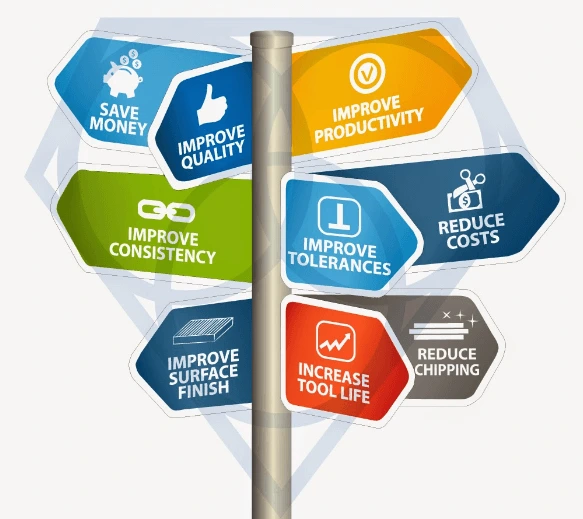
- Unmatched Selection For Many Applications
- Unmatched Technical Support & Expertise
- Superior Quality & Consistency
- Super Technology & innovation
- Immediate Worldwide Delivery
- American Based Manufacturer
-
Custom
Manufacturing - Better Value manufacturer Direct Price
DIAMOND CARVING POINT
Selection Variables
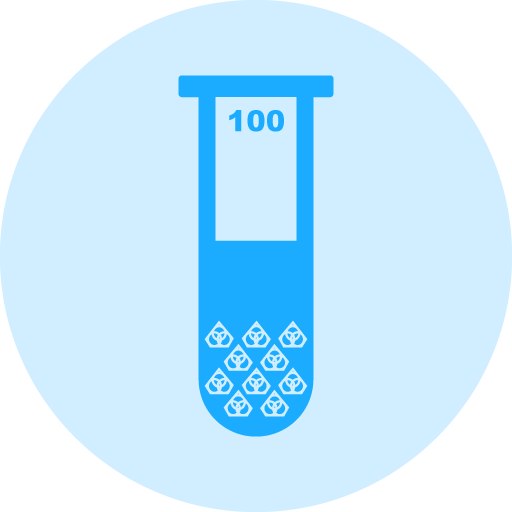
Diamond Concentration
Diamond concentration is a critical parameter in determining the performance characteristics—particularly the cutting efficiency, surface finish, tool life, and heat generation—of sintered metal bond diamond carving points. This refers to the volume of diamond abrasive content embedded within the metal bond matrix, typically expressed as a percentage or relative index. The optimal concentration varies depending on the material being worked, the shape and profile of the carving point, the RPM, feed pressure, and the intricacy of the carving application.
Low Diamond Concentration
Sintered diamond carving points with lower diamond concentration are ideally suited for ultra-hard, dense, and brittle materials such as advanced ceramics, quartz, sapphire, zirconia, and specialty glass. In these applications, material removal occurs primarily through a fracture mechanism—individual diamond particles create localized stress fields that exceed the material’s fracture toughness, chipping away micro-fragments from the surface.
In low-concentration formulations, the diamond particles are spaced farther apart, resulting in higher localized pressure on each diamond particle. This intensified point pressure enhances the ability of each diamond to initiate cracks in hard, brittle materials. While such tools may wear faster than their high-concentration counterparts, they are highly effective in applications where precision, control, and minimized subsurface damage are required.
High Diamond Concentration
Conversely, high diamond concentration sintered carving points are preferred for softer, more ductile, and abrasive materials, such as composites, polymer matrix materials, copper alloys, aluminum, and certain metals. In these scenarios, cutting is governed by a plowing and abrasion mechanism. The higher diamond content allows for more contact points, distributing cutting forces more evenly across the tool surface, reducing unit pressure on each individual diamond.
This results in faster material removal rates, enhanced durability of the tool, and reduced risk of tool glazing. Additionally, for materials prone to plastic deformation or smearing, higher diamond density minimizes the tendency to induce heat-affected zones or deformation layers by reducing the force per diamond contact point.
However, it is important to note that increasing diamond concentration also results in a reduced self-sharpening ability of the carving point. As the tool wears, embedded diamonds may remain in the bond structure longer than necessary unless properly dressed, which can temporarily degrade performance. Therefore, frequent dressing or re-exposing of fresh diamond is recommended, especially when working with intricate or high-precision geometries.
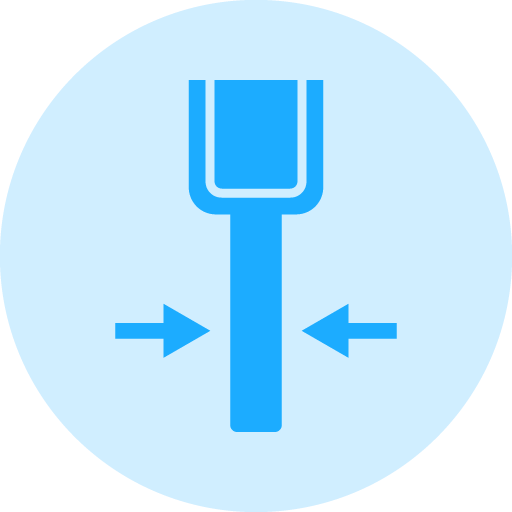
Tool Thickness and Kerf Width
In the context of sintered metal bond diamond carving points, tool thickness—which includes both the diameter of the working tip and the body or shank thickness—directly influences the kerf width, cutting performance, material loss, and overall stability of the tool during operation. While these carving tools do not resemble wafering blades in geometry, the same principles of material removal, rigidity, and control over dimensional accuracy apply.
The kerf, or the width of material removed during carving, is determined by the effective width of the diamond-impregnated portion of the tool, which may range from as small as 0.3 mm to over 3.0 mm, depending on the tool design and intended application. In precision micro-carving or engraving tasks—particularly on intricate parts, fine details, or microelectronic components—minimal kerf width is essential to preserve dimensional integrity and reduce material waste.
Thin Carving Points (Small Tip Diameter / Narrow Kerf)
Tools with very fine diamond tips (e.g., <1.0 mm in diameter) are typically used in applications requiring high precision, minimal material loss, and delicate feature carving, such as microchannels, fine lettering, or detailed relief patterns in ceramics, sapphire, glass, or other hard brittle materials. These tools are essential when the cutting path must be tightly controlled in relation to surface features—similar to aligning a cutting plane precisely on an IC circuit trace.
However, the trade-off with thinner carving points is that they tend to be less rigid, making them more susceptible to deflection, vibration, and breakage under aggressive loads or feed rates. As such, they are best operated at moderate RPMs with light, controlled feed pressure, particularly by skilled technicians or robotic systems designed for micro-fabrication.
Thicker Carving Points (Larger Tip Diameter / Wider Kerf)
Larger diameter or thicker-bodied carving tools provide significantly greater rigidity and durability, making them well-suited for rough carving, deburring, shaping, and edge profiling of larger or denser materials. These tools can withstand higher loads and feed pressures, and are more tolerant of operator variability or inadvertent misuse, making them ideal for educational labs, shared equipment environments, or general-purpose material shaping.
Thicker carving points are also less prone to chatter or flex, especially when used on harder, vibration-sensitive materials or where longer tool extensions are necessary. While they result in wider kerf widths and greater material removal per pass, they offer improved control and reduce the risk of tool failure or part damage in less experienced hands.
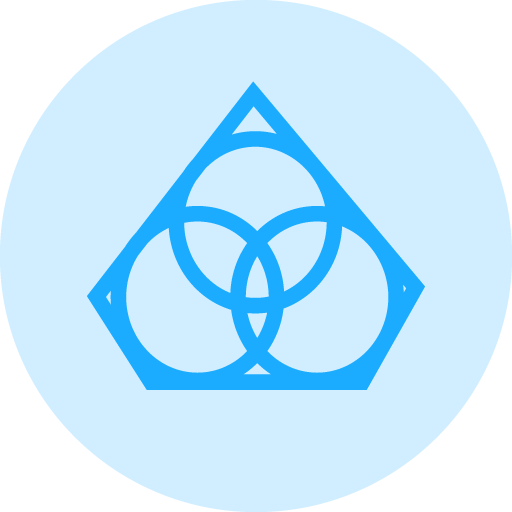
Diamond Grit / Mesh Size
The diamond grit size (also referred to as mesh size) embedded within sintered metal bond diamond carving points has a significant influence on cutting speed, surface finish quality, material removal rate, chipping level, and the extent of subsurface damage. Selecting the appropriate grit size is crucial to achieving the desired balance between aggressiveness of cut and fineness of finish, especially when working on hard, brittle, or intricate surfaces.
Coarse Diamond Grit (Lower Mesh Size)
Sintered carving points containing coarse diamond particles—typically in the 35/50 to 60/80 mesh range—are ideal for applications requiring fast stock removal, such as rough shaping, contour grinding, or bulk material removal on hard ceramics, engineered stone, glass composites, and certain metals.
Larger diamond crystals penetrate deeper into the material and provide more aggressive cutting action, leading to faster carving speeds and higher productivity. However, this comes at the cost of increased chipping, rougher surface finish, and greater subsurface microstructural damage, especially in delicate or brittle materials. These tools are best suited for early stages of shaping where surface finish is not a critical concern.
Fine Diamond Grit (Higher Mesh Size)
For fine detailing, finishing passes, and precision surface work, carving points utilizing fine diamond grit—such as 120/140 mesh or finer (180/200, 220/240, 325/400)—are strongly recommended. These finer particles remove material via a more gradual, refined abrasion mechanism, producing minimal edge chipping, lower thermal/mechanical stress, and smoother surface finishes.
Fine mesh carving points are essential for applications involving intricate patterns, high-tolerance parts, fragile structures, or materials sensitive to cracking, such as sapphire, quartz, and zirconia. While they offer slower material removal rates compared to coarser grits, they greatly reduce the risk of damaging the part or compromising dimensional accuracy.
Balancing Grit Size with Application Needs
Ultimately, the ideal diamond mesh size should be chosen based on the material characteristics, stage of the carving process, machine RPM/load, and the desired finish. In many advanced applications, a multi-step process is used—starting with coarser grit carving points for rough shaping, followed by finer grit tools for detailing and polishing—to optimize both efficiency and quality.
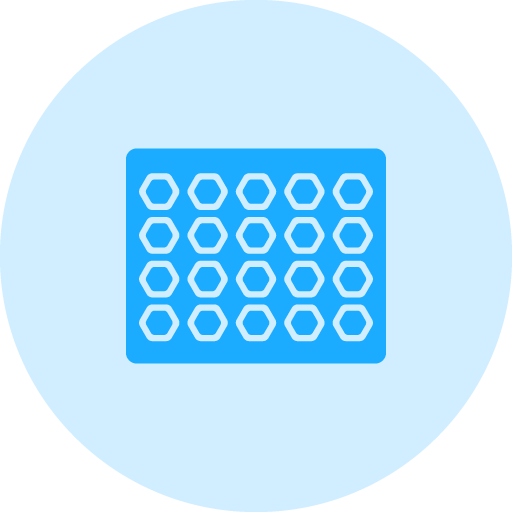
Bond Type
The bond type used in a diamond carving point plays a central role in determining its cutting characteristics, life span, surface finish quality, resistance to heat, and overall suitability for a specific material or application. In diamond carving points, the most common bond types include sintered metal bond, resin bond, electroplated (nickel bond), and brazed bond. Each of these offers distinct advantages and trade-offs depending on the hardness of the workpiece, complexity of the carving, and operational parameters such as feed rate, spindle speed, and cooling.
Sintered metal bond diamond carving points are manufactured by sintering a blend of metal powders with diamond crystals under high pressure and temperature, creating a dense, durable structure. These carving tools are engineered for longevity and are ideal for use on extremely hard, abrasive materials such as alumina, zirconia, silicon carbide, and technical ceramics. Their primary advantage lies in their extended tool life and ability to maintain performance under high loads and continuous-duty operations. However, they tend to generate more heat and require higher cutting forces compared to other bond types. Because the diamond particles are embedded throughout the body of the tool, sintered tools can be dressed periodically to expose new layers of diamond, making them especially valuable for long-term use in industrial environments.
Resin bond diamond carving points, by contrast, are made by mixing diamond abrasives with a polymer-based resin, typically phenolic or polyurethane. These tools produce a smoother, more forgiving cut and are ideal for applications that require a delicate touch, particularly on brittle, heat-sensitive materials such as glass, quartz, sapphire, and other crystals. Resin bonds offer excellent surface finish and produce significantly less heat during carving operations. They are often the bond of choice for applications where chipping, microfracturing, or thermal stress must be avoided. The trade-off is that resin bond carving points wear faster than sintered tools and are generally less suitable for heavy-duty or high-load operations.
Electroplated diamond carving points, also referred to as nickel-bonded tools, consist of a single exposed layer of diamond particles attached to the surface of the tool using an electroplating process. These tools offer extremely aggressive, sharp cutting action and are ideal for rapid material removal, shaping, and profiling. They are particularly effective in soft-to-medium-hard materials and are widely used in applications where intricate detail and fast results are required. Electroplated tools do not require dressing, as the diamonds are fully exposed from the beginning of the tool’s life. However, they have a much shorter life expectancy, as there is no diamond layer beneath the plated surface. Once the diamond layer is worn, the tool must be replaced.
Brazed bond diamond carving points represent a more recent advancement and provide an excellent balance between durability and aggressiveness. In brazed tools, diamond particles are fused directly to the surface of the tool body using a high-temperature brazing alloy, typically silver-based. This creates a strong mechanical bond that allows a higher exposure of each diamond crystal compared to electroplating. As a result, brazed carving points offer faster cutting speeds, better debris clearance, and improved heat dissipation. They are especially well suited for hard-to-machine materials such as composites, carbon fiber, ceramics, and natural stone. The diamonds are strongly retained yet highly exposed, providing aggressive cutting performance while still maintaining reasonable tool life. Brazed tools do not have embedded diamonds throughout the body like sintered tools, so once the surface diamonds wear out, the tool cannot be dressed or renewed.
Selecting the optimal bond type for diamond carving points requires consideration of material hardness, fragility, thermal sensitivity, part geometry, and production volume. Sintered bond is preferred for high-load industrial use and longevity on abrasive materials. Resin bond excels in fine finishing and delicate work where surface integrity is critical. Electroplated tools are unmatched in detail carving and fast, light-duty operations, while brazed bond carving points offer a high-performance solution for applications demanding both speed and durability. Matching the correct bond type to the application ensures better results, reduced tool wear, improved part quality, and maximum return on investment.
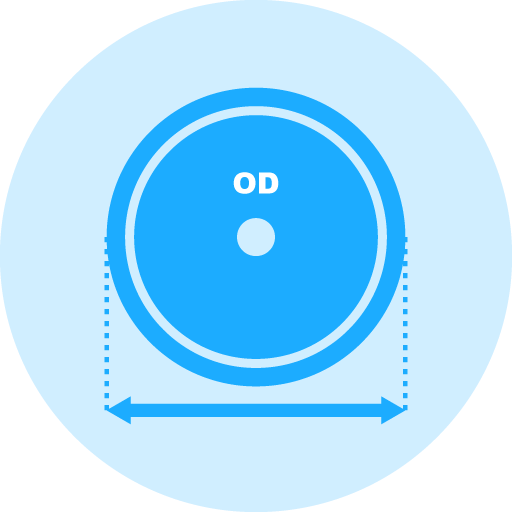
Tool Head Diameter
The outside diameter or head size of sintered metal bond diamond carving points plays a significant role in determining their rigidity, stability, cutting depth, access to tight areas, and overall performance. While carving points do not follow the same standard diameter sizes as wafering blades, the principles of tool head dimension selection remain just as important—particularly in high-precision or deep-carving applications.
Smaller Diameter Carving Points
Diamond carving tools with smaller head diameters, typically ranging from 0.5 mm to 5 mm, are ideal for fine detail work, tight corners, internal radii, engraving, and micro-shaping operations. Their compact profile allows precise access to intricate geometries and confined spaces on parts made of ceramics, composites, or hard crystals.
However, smaller diameter tools are generally more flexible and prone to deflection, particularly under high lateral loads or aggressive feed rates. This can lead to dimensional inaccuracy, increased tool chatter, or uneven surface finishes, especially on denser or more rigid materials. As such, they are best used at lower RPMs and feed pressures, with careful operator control to maintain precision and tool life.
Larger Diameter Carving Points
Conversely, sintered carving points with larger tool head diameters—ranging from 6 mm to 25 mm or more, depending on the application—offer increased rigidity, deeper cutting capability, and improved heat dissipation. These tools are typically employed in bulk material removal, contouring of larger surfaces, and rough shaping operations on materials such as ceramic matrix composites, stone, or technical glasses.
The added mass and structural stiffness of larger diameter carving heads allow them to withstand higher cutting forces and rotational speeds, making them more suitable for high-load, high-volume production scenarios. However, due to their larger contact area and greater cutting surface, they may generate more heat and friction, necessitating the use of appropriate coolants or lubrication.
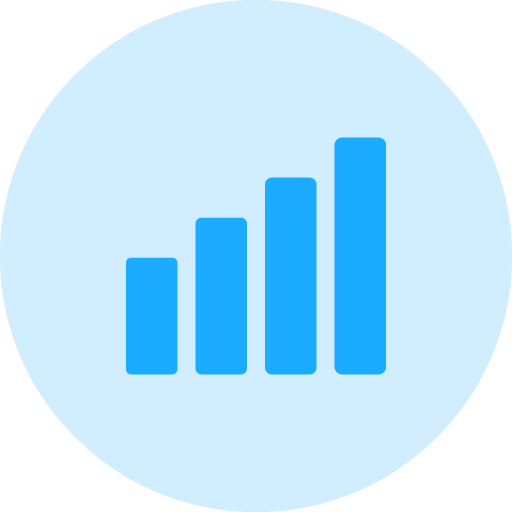
Feed Rate
In the use of sintered metal bond diamond carving points, the applied feed rate and load are critical variables that directly affect cutting efficiency, surface finish, tool life, and the risk of part damage. Unlike wafering blades, carving tools rely on operator-controlled or programmed pressure, often in combination with RPM, coolant flow, and tool geometry to manage the contact force between the tool and the workpiece.
Harder, denser materials such as ceramics, quartz, and engineered stone generally tolerate higher feed rates and contact pressure, especially when using coarser grit tools and proper coolant. These materials resist deformation, allowing more aggressive cutting without risk of excessive chipping—provided the tool is rigid and well-cooled.
Brittle, delicate, or layered materials—such as fused silica, silicon substrates, or brittle glasses—require lower feed pressures and slower engagement speeds to avoid microfracturing and subsurface damage. In these cases, finer grit tools and gentle pressure are essential, often paired with continuous coolant to minimize thermal and mechanical stress.
Several factors influence the ideal feed rate for diamond carving points, including:
Spindle speed: Higher RPM generally allows lighter feed pressure while maintaining effective material removal.
Tool diameter and shape: Smaller tools require lighter pressure to avoid breakage or deflection.
Workpiece geometry: Complex shapes and sharp edges demand reduced feed force to maintain control.
Fixturing: Rigid, vibration-free clamping ensures stable tool engagement and accurate cuts.
Coolant use: Essential to prevent overheating and maintain cutting efficiency at any feed rate.
Improper feed pressure can result in glazing (if too light) or premature bond wear and tool failure (if too heavy). The best results are achieved when feed rate and load are matched to the material, tool type, and operational conditions. Skilled users rely on visual, tactile, and acoustic feedback; in automated systems, these values should be carefully programmed and optimized per application.
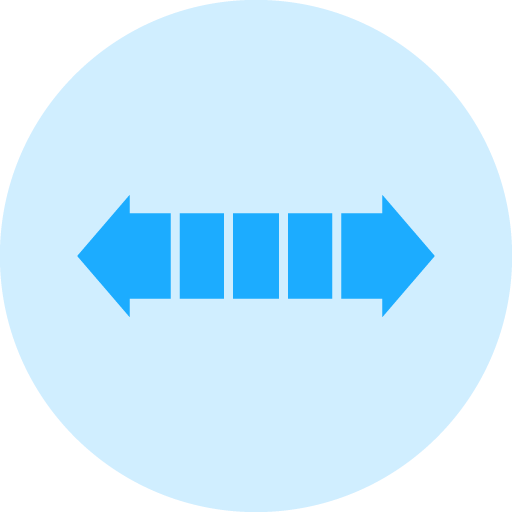
Bond Hardness
Bond hardness refers to the ability of the metal bond matrix to retain diamond particles during operation. It is one of the most critical factors influencing the cutting performance, tool longevity, and frequency of dressing for sintered metal bond diamond carving points. The selection of an appropriate bond hardness is essential to ensure efficient material removal, preserve tool life, and maintain consistent performance throughout the carving process.
As the hardness of the bond increases, the metal matrix becomes more resistant to wear and is able to hold the diamond particles more securely for longer periods. This typically results in extended tool life, particularly in applications where aggressive material contact and long carving durations are required. However, the trade-off is a slower cutting rate and a reduced self-sharpening effect, as the hard bond does not release dull or worn diamond particles as readily. This can lead to glazing—where the surface of the tool becomes smooth and less effective—necessitating frequent dressing to restore cutting performance.
Conversely, a softer bond matrix allows for faster exposure of new, sharp diamond particles as the worn crystals are released more readily during use. This promotes faster material removal rates and consistent cutting action, especially beneficial when working on extremely hard and dense materials such as sapphire, alumina, zirconia, or certain technical ceramics. However, if the bond is too soft for the specific material or application, it may prematurely release diamonds, leading to rapid tool wear and reduced carving point life.
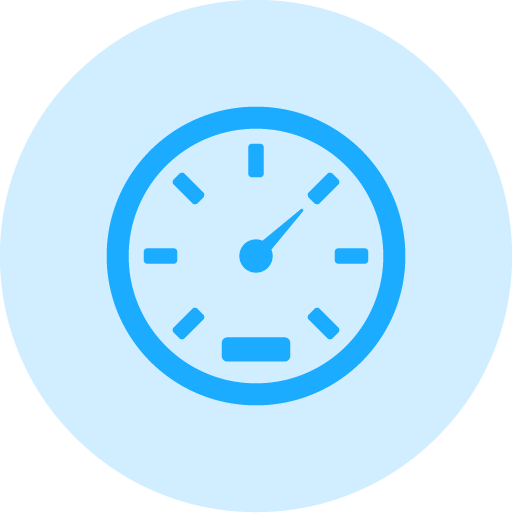
Carving Point RPM’s / Speed
The rotational speed (RPM) at which sintered metal bond diamond carving points are operated plays a central role in determining cutting performance, surface quality, tool life, and thermal load. Proper RPM selection is essential to balance material removal rate with precision, particularly when working on ultra-hard, brittle, or heat-sensitive materials.
Diamond carving points are typically used across a broad speed range, from 500 RPM to over 35,000 RPM, depending on the tool diameter, grit size, material being processed, and the capabilities of the spindle or handpiece. Harder and denser materials, such as sapphire, silicon carbide, and alumina, generally benefit from higher RPMs, as increased speed enhances cutting efficiency and reduces the force required per contact point. However, sufficient coolant must be used to manage the increased heat generation.
By contrast, brittle and fragile materials—such as silicon wafers, fused silica, gallium arsenide, or certain crystals—require lower rotational speeds to minimize thermal cracking, chipping, and subsurface damage. For these applications, fine grit carving points operated at moderate to low RPMs provide better control and preserve material integrity.
Equipment limitations also play a role in defining RPM ranges. Low-speed rotary tools or micromotor systems typically operate between 0 and 5,000 RPM, suitable for precision work and fine detailing. High-speed spindles, CNC machines, or air turbines may offer speeds from 5,000 to 35,000 RPM or higher, enabling faster material removal for suitable applications.
Optimal RPM depends on the material hardness, brittleness, tool diameter, grit size, coolant use, and operator control. Excessively low RPMs may cause glazing or inefficient cutting, while too high a speed can result in tool overheating, accelerated wear, or damage to delicate substrates. Therefore, establishing a recommended RPM range for each application and tool type is key to achieving consistent and reliable results.
Why Work With Us?
Read More
We produce diamond consumables for some of the leading world OEM manufacturers. We offer Manufacturers Direct Prices
We have the largest variety of diamond & cbn wafering blades available in stock. As well as large inventory of diamond & abrasive consumables. We also custom manufacture diamond and cbn tools, consumables and machines to better fit customer specific needs. Just about any tools & consumables can be designed and manufactured per client drawing or specificrtion
WE ARE A PARTNER IN YOUR SUCCESS
Our proprietory diamond chemistory , precision , manufacturing metods , quality control methods allow us to control and regulate the dozens of variables to that affect consumable life , quality , and consistency.
The more you understand about what we can do for you the better our partnership will be. Here you will find most comprehensive source of information and optimizing and improving your cutting , drilling , grinding and polishing on the web. find everything you ever wanted to know about diamond tools.
AMERICAN MANUFACTURER
"ONE OF THE MOST EXPERIENCED COMPANIES IN THE INDUSTRY"
Save Money Save up to 650%
COMPARE TO: BUEHLER , STRUERS , LECO & MANY OTHERS
Large Inventory & Custom Manufacturing
Umatched Technical Support
Developing close ties with our customers is the foundation of our business. At the core of
our company is a team of world class engineers, knowledgeable customer service personnel here to serve you. Whether is designing or manufacturing a special solution. We will go out of our way to optimizing your process to ultimate level of efficiency
Superior Quality & Consistency
EXPECT MORE FROM YOUR TOOLS
Comprehensive Source Of Information For Sample Preparation
Advanced Technology
As one of the few remaining independent U.S.Diamond Tool & machine builders. We have the experience & tradition to help you remain at frontier of technology Our experience has been further enhanced by acquiring assets and processes from some of the oldest American tool
manufacturers, along with their decades of experience and R& D. This has positioned us as one of the most experienced companies in the industry .Depend on us to bring you technology of tomorrow today.
Experience Makes All The Differences
Over the years we have worked with some of the leading Fortune 500 companies , thousands of universities , government and private research labs , and small organisations. We have made thousands of custom tools , built custom machines , work-holding fixtures , etc for hundreds of applications. Many of our staff members have been working in their respective fields for over 50 years and have gained a wealth of knowledge over the years
Let Us Help You
Related Products
Sintered (Metal Bond) Diamond Carving Points
Recently Viewed Products

ARE YOU USING RIGHT TOOLS
FOR YOUR APPLICATION?
LET US
HELP YOU
HAVING ISSUES WITH
YOUR CURRENT TOOLS?
Knowledge Center
02
Jun
How to properly use Diamond Tools
UKAM Industrial Superhard Tools manufactures precision diamond tools for a large variety of applications, materials, and industries.
Share this Article with Friend or Colleague
Metal Bonded Diamond Tools are “impregnated” with diamonds. This means that selected...
02
Jun
Why use diamond
Diamond is the hardest material known to man kind. When used on diamond/tools, diamond grinds away material on micro (nano) level. Due to its hardness Diamond will work all types of materials from...
02
Jun
Selecting Right Wafering Blade for your application
Cross Sectioning is the first and most important step in the sample preparation process. Getting the best results involves obtaining a smooth surface finish, minimum chipping, material deformation, without sacrificing cutting speed. Today, most laboratories, work with dozens...
02
Jun
Wafering Blade Usage Recommendations
The wafering/sectioning blade itself is only a small factor in your sectioning operation. Successful wafering/sectioning operation is both an art & science. Requiring proper use and understanding of selecting the right diamond wafering/sectioning...
02
Jun
Wafering Blade Case Studies
Step by step guide on how to properly use and care for your diamond drills. Selecting the right diamond drill/diamond drill bit parameters, often involves a trial and error process. Many which can be avoided...
22
Apr
Diamond & CBN Wafering Blade Performance Metrics
When evaluating Diamond & CBN wafering blades, especially for metallography and sample preparation, it is critical to consider a set of key evaluation criteria and performance metrics. These factors help determine the effectiveness of a...
24
Apr
Understanding & Comparing Diamond & CBN Wafering Blades
Share this Article with Friend or Colleague
Diamond wafering blades are designed for sectioning a large variety of materials and sample types. In order to identify the best diamond wafering blade for your specific material/application,...
25
Apr
Diamond & CBN Wafering Blade Guide
Share this Article with Friend or Colleague
All you need to know about wafering blades (understanding variables & specifications)
This guide is designed to help you navigate the various variables and possibilities associated with diamond wafering...
09
Oct
How to Properly Use Diamond Carving Points
Diamond carving points are essential tools for anyone working with hard materials like glass, stone, and metals. These tools help with detailed tasks like engraving and finishing, providing good control and helping you work efficiently....
- Unmatched Selection For Many Applications
- Superior Quality & Consistency
- Immediate Worldwide Delivery
- Technical Support & Expertise
- American Based Manufacturer
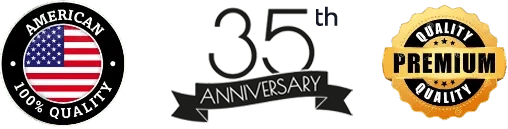

- Different Product
- Different Technology
- Different Company
- Expect MORE from your tools
Let Us HELP You!
Subscribe To Our Newsletter
Signup for email offers, updates, and more
Contact Us
- 25205 & 25201 Avenue Tibbits Valencia CA 91355 USA
-
Phone : (661) 257-2288
FAX : (661) 257 -3833 - lel@ukam.com
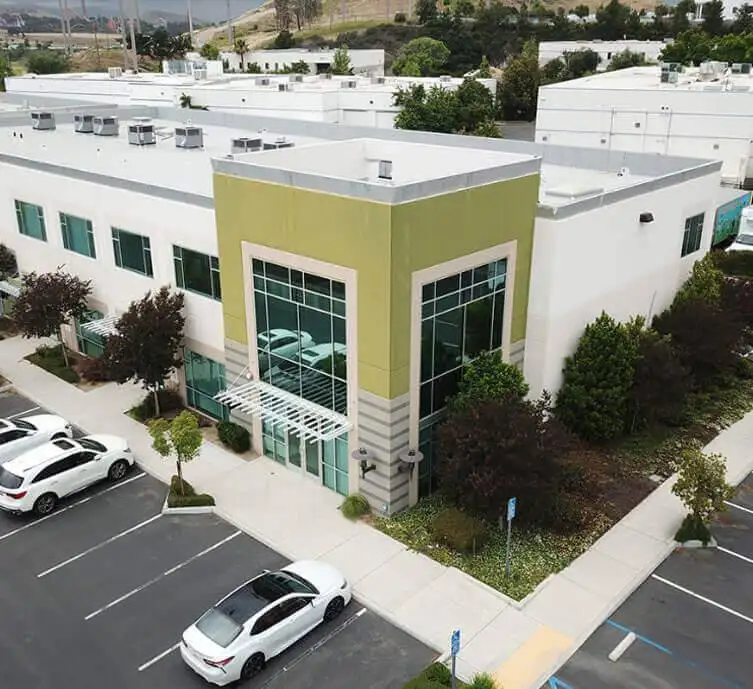
UKAM Industrial Superhard Tools is a U.S. High Technology, Specialty Diamond Tool & Equipment manufacturer. We specialize in producing ultra thin, high precision cutting blades, precision cutting machines diamond drills, diamond micro tools, standard & custom advanced industrial diamond tools and consumables.
- 25205 & 25201 Avenue Tibbits Valencia CA 91355 USA
-
Phone : (661) 257-2288
FAX : (661) 257 -3833 - lel@ukam.com
- 25205 & 25201 Avenue Tibbits Valencia CA 91355 USA
-
Phone : (661) 257-2288
FAX : (661) 257 -3833 - lel@ukam.com
DIAMOND TOOLS BY BOND
EQUIPMENT
KNOWLEDGE CENTER
OUR PRODUCTS
COMPANY
CUSTOMER SERVICE
Shipping Methods


Safe & Secure Payments

© Copyright 1990-2025. UKAM Industrial Superhard Tools – Terms of Use