-
0 items in quote
No products in the Quote Basket.
SMART CUT® Abrasive Cut Off Blades
For Metallography & Sample Preparation
SMART CUT® Resin Bond Abrasive Cut Off Blades specifically designed for metallography and sample preparation are meticulously engineered with aluminum oxide or silicon carbide particles embedded in a phenolic binder. These blades are specifically formulated to achieve the optimal surface finish required for metallographic preparations. Available in diameters ranging from 250mm to 400mm, and inside diameters of 1.25” and 32mm. These abrasive cut-off wheels are tailored for precision in metallography and sample preparation. They provide sharp, clean cuts with minimal material deformation, making them perfect for a wide range of materials in both laboratory and industrial settings.
DESCRIPTION
SPECIFICATION
FREQUENTLY ASKED QUESTIONS
INDUSTRIES USED IN
ACCESSORIES
USAGE RECOMMENDATION
DESCRIPTION
Designed to operate optimally with coolant, SMART CUT® abrasive wheels set the standard for quality in cutting metallurgical specimens. They efficiently produce cross-sections that typically require little to no additional treatment prior to metallographic analysis, ensuring that the structure and metallurgical properties of the specimens remain intact.
Select from an extensive range of dozens specialized blades, each tailored for specific applications. Our silicon carbide wheels are expertly formulated for cutting non-ferrous and non-metallic materials, while the aluminum oxide wheels are crafted for ferrous materials. Coarser grits provide efficient cutting of heavier sections, reducing heat generation and increasing speed. Conversely, finer grits yield superior surfaces and minimize burning on delicate materials. Soft wheels are designed to degrade more quickly, constantly exposing fresh cutting surfaces—this makes them ideal for slicing through hard materials. In contrast, hard wheels degrade more slowly, offering extended wear and are best suited for softer materials.
SPECIFICATION
Tab Content
FREQUENTLY ASKED QUESTIONS
SMART CUT® Abrasive Cut-Off Blades are engineered for precise and efficient cutting of a wide variety ferrous and non ferrous metallurgical samples as well as other materials including advanced ceramics, composites, optics, metals, and other hard materials. These blades are ideal for applications requiring ultra-thin, high-precision cuts. They are designed to deliver high-quality cuts with minimal chipping and optimal surface finish.
SMART CUT® Abrasive Cut-Off Blades come in a variety of sizes to accommodate different precision and metallurgical abrasive cutting saws. The sizes range from small diameter blades for precision cutting to larger blades for heavy-duty applications.
Choosing the right blade depends on several factors such as the type of material, material thickness, desired cut quality, and specific application requirements. We provide a selection guide chart based on the material type and hardness. You can also contact our technical support team for recommendation.
SMART CUT® Abrasive Cut-Off Blades are compatible with a variety of metallurgical and metallographic cutting machines. However, it is crucial to ensure that the machine is capable of operating at the recommended RPM, and horse power and coolant and that it supports the blade’s specifications for optimal performance and safety.
The lifespan of the blade depends on the material being cut, the cutting conditions, coolant, rpm’s, feed rates and how well the blade is maintained. The performance is on par with leading abrasive metallurgical/metallographic blade suppliers such as BUEHLER, STRUERS, LECO & many others. With proper usage and maintenance, these blades offer extended life and consistent cutting performance.
To maintain optimal performance, it is essential to regularly inspect the blades for wear and damage, clean them properly, and store them in a dry, safe environment. Using the correct cutting parameters and avoiding excessive force will also help extend the blade’s life.
Yes, UKAM Industrial Superhard Tools offers technical support to assist with any issues or questions regarding blade performance, selection, and optimization. Our team of experienced engineers is available to provide guidance and solutions tailored to your application.
The recommended RPM varies depending on the blade size and material being cut. Detailed guidelines are provided with each blade to ensure optimal performance and safety. It is important to follow these recommendations to prevent damage to the blade and ensure precise cuts.
Yes, these blades are designed for both wet and dry cutting applications. However, wet cutting is generally preferred as it helps to reduce heat generation, minimize dust, and prolong blade life.
When using SMART CUT® Abrasive Cut-Off Blades, it is essential to:
- Wear appropriate personal protective equipment (PPE) such as safety glasses, gloves, and a dust mask.
- Ensure the cutting machine is properly guarded and in good working condition.
- Follow the recommended operating parameters and guidelines.
- Avoid excessive force and ensure the workpiece is securely clamped.
Signs that it may be time to replace the blade include:
- Decreased cutting performance and speed
- Visible wear or damage to the blade
- Increased chipping or poor surface finish on the cut material
- Excessive vibration or noise during cutting
Yes, UKAM Industrial Superhard Tools offers custom sizes and specifications to meet specific customer requirements. Contact our sales team to discuss your unique needs and obtain a custom solution.
Proper mounting and alignment are crucial for optimal blade performance and safety. Follow these steps:
- Ensure the machine is turned off and unplugged.
- Clean the mounting flange and spindle to remove any debris.
- Mount the blade securely, ensuring it is properly seated and aligned.
- Tighten the flange nut to the manufacturer’s recommended torque specification.
- Perform a test run to check for proper alignment and smooth operation.
SMART CUT® Abrasive Cut-Off Blades are designed with advanced materials and manufacturing techniques to provide superior precision, longer life, and better cut quality compared to traditional cutting blades. They are particularly effective for sectioning a full range of metallurgical / metallographic samples and hard and brittle materials with minimal chipping & minimum material deformation.
Yes, SMART CUT® Abrasive Cut-Off Blades are suitable for use in automated metallurgical & metallographic cutting systems. Ensure that the system is compatible with the blade specifications and operating parameters for seamless integration and optimal performance.
To achieve the best performance and longevity:
- Use the recommended RPM and cutting parameters.
- Opt for wet cutting whenever possible.
- Regularly clean and inspect the blade.
- Avoid using excessive force during cutting.
- Store the blade in a dry and safe environment.
- Follow our maintenance and usage guidelines.
Yes, using the appropriate coolant is important for improving the performance and life of the blade. We provides specific coolant recommendations tailored to different materials and applications to ensure optimal cutting conditions and blade longevity. Our SMART CUT water soluble coolant is excellent solution to be used with these blades.
These blades are engineered with advanced bonding and abrasive technologies that allow for smoother, more precise cuts. The design ensures minimal chipping, making them ideal for applications requiring high-quality surface finishes.
Typical applications include:
- Semiconductor wafer slicing
- Metallurgical sample preparation
- Cutting advanced ceramics and composites
- Precision cutting in the optics industry
- Fine cutting of hard metals and alloys
- Research and development projects requiring precise material sectioning
Yes, these blades are versatile and suitable for cutting both small and large pieces of material. It is important to select the appropriate blade size and type based on the material dimensions and specific cutting requirements.
Proper handling and storage are essential to prevent damage:
- Handle blades with care, avoiding any impacts or drops.
- Store blades in a dry, cool environment away from direct sunlight and moisture.
- Keep blades in their original packaging or protective sleeves until ready for use.
- Avoid stacking blades directly on top of each other without protective layers in between.
To optimize the cutting process:
- Use the recommended RPM and feed rates.
- Ensure the workpiece is securely clamped and stable.
- Maintain a consistent coolant flow during wet cutting.
- Regularly inspect and dress the blade to maintain sharpness.
- Avoid excessive cutting force and allow the blade to do the work.
Yes, these blades are designed to handle multi-material cutting tasks effectively. However, it is essential to ensure that the blade selected is suitable for all materials involved in the cutting process and that the machine settings are adjusted accordingly for each material type.
Excessive wear or premature blade failure can be caused by several factors such as incorrect operating parameters, improper material selection, or inadequate cooling. If you experience these issues, review the cutting conditions, ensure you are using the recommended RPM and feed rates, and verify the compatibility of the blade with the material. For persistent problems, contact UKAM Industrial Superhard Tools’ technical support for expert advice and troubleshooting.
To clean the blades after use:
- Disconnect the blade from the machine.
- Use a soft brush or cloth to remove any debris or material build-up.
- For stubborn residues, use a mild cleaning solution compatible with the blade material.
- Rinse thoroughly with water and dry completely before storage.
SMART CUT® Abrasive Cut-Off Blades are distinguished by their advanced bonding technology, superior abrasive quality, and precision engineering. These attributes ensure high performance, longer blade life, and exceptional cutting accuracy, making them a preferred choice for demanding applications.
To ensure consistent cut quality:
- Regularly inspect the blade for wear and damage.
- Maintain optimal cutting parameters as recommended.
- Use appropriate coolant for wet cutting.
- Ensure the workpiece is securely clamped and stable.
- Regularly dress the blade to keep it sharp.
Yes, SMART CUT® Abrasive Cut-Off Blades are designed for high-speed cutting applications. It is essential to ensure that the cutting machine can safely operate at the required high speeds and that the blade is rated for those speeds to prevent any safety hazards or performance issues.
Blade thickness directly impacts cutting performance. Thinner blades generally provide more precise cuts with less material loss and reduced chipping, while thicker blades offer greater durability and stability for cutting harder or thicker materials. Selecting the right blade thickness depends on the specific application and material properties.
To avoid compromising the blade’s performance and safety, store them in a dry, cool environment away from direct sunlight, moisture, and extreme temperatures. Avoid placing heavy objects on top of stored blades to prevent warping or damage.
These blades are designed to minimize noise and vibration, providing a smoother and quieter cutting experience. Proper installation, correct machine settings, and the use of recommended flanges also contribute to reducing noise and vibration.
Yes, SMART CUT® Abrasive Cut-Off Blades are highly suitable for precision sectioning in metallographic applications. They provide clean, precise cuts with minimal deformation, making them ideal for preparing samples for microscopic analysis and other metallographic procedures.
To ensure the blade remains balanced:
- Install the blade correctly and securely on the machine.
- Use recommended flanges for proper alignment.
- Regularly inspect the blade for wear and replace it if it becomes unbalanced.
- Maintain consistent cutting parameters to avoid excessive stress on the blade.
These blades contribute to environmental benefits by providing precise cuts with minimal material waste. Their long life and efficiency reduce the frequency of blade replacements, thereby decreasing overall waste generation. Additionally, using proper coolant can minimize dust and particulate emissions during cutting.
While both types of blades offer high precision and performance, the choice between SMART CUT® Abrasive Cut-Off Blades and diamond blades depends on the specific material and application. Abrasive blades are often preferred for ferrous and non ferrous metallurgical samples that require a smooth, clean cut with minimum material deformation. They cutting speed is usually much faster and freer. Also the cost is much lower then diamond and cbn cut off blades/wheels. Diamond & CBN cut off wheels/blades provide better performance on more harder metals and other ultra hard and brittle materials.
Best practices for achieving maximum blade life include:
- Following recommended cutting parameters (RPM, feed rate, coolant usage).
- Regularly inspecting and maintaining the blade and cutting equipment.
- Avoiding excessive force and allowing the blade to do the cutting.
- Properly storing the blade when not in use to prevent damage.
Yes, SMART CUT® Abrasive Cut-Off Blades can be used for both rough cutting and finishing operations. However, the specific blade type and configuration should be chosen based on the desired cut quality and the nature of the material being cut.Yes, SMART CUT® Abrasive Cut-Off Blades can be used for both rough cutting and finishing operations. However, the specific blade type and configuration should be chosen based on the desired cut quality and the nature of the material being cut.
To achieve an optimal surface finish, use the following practices:
- Select the appropriate blade for your specific material.
- Ensure the blade is sharp and in good condition.
- Utilize the recommended cutting parameters, including RPM and feed rate.
- Employ proper cooling techniques, such as wet cutting, to reduce heat and minimize surface damage.
- Securely clamp the workpiece to prevent movement during cutting.
UKAM Industrial Superhard Tools offers a range of dressing sticks and other tools specifically designed for maintaining the sharpness and performance of their abrasive cut-off blades. Regular dressing helps to expose fresh abrasive particles, ensuring consistent cutting performance.
Cutting speed significantly impacts the blade’s performance. Higher speeds can improve cutting efficiency and reduce cycle times, but they may also increase heat generation and wear. Lower speeds can enhance precision and reduce chipping. It is crucial to balance speed with other cutting parameters for optimal results.
Yes, SMART CUT® Abrasive Cut-Off Blades can be used for plunge cutting. It is important to ensure that the machine and blade are properly aligned and that the material is securely clamped. Using the correct plunge speed and technique will help achieve clean and precise cuts.
SMART CUT® Abrasive Cut-Off Blades are designed to handle a range of material hardness levels. Selecting the appropriate blade type and specification for the material hardness ensures optimal performance. Harder materials may require blades with more robust bonding and abrasives, while softer materials may benefit from finer grit sizes.
To minimize heat generation:
- Use wet cutting techniques with the recommended coolant.
- Operate the blade at the optimal RPM and feed rate.
- Ensure the workpiece is securely clamped to prevent movement.
- Avoid excessive force and allow the blade to cut naturally.
SMART CUT® Abrasive Cut-Off Blades are designed to provide superior performance and longer life, offering better cost-effectiveness over time compared to other blades. Their precision and efficiency can reduce material waste and the need for frequent replacements, leading to overall cost savings and best return on investment
Yes, these blades can be used in manual cutting operations, provided that the cutting equipment supports the blade specifications and the operator follows recommended safety and operating guidelines to ensure precise and safe cuts.
Ensure safety by:
- Wearing appropriate personal protective equipment (PPE) such as safety glasses, gloves, and hearing protection.
- Following the manufacturer’s recommended operating parameters.
- Properly securing the workpiece and ensuring the cutting machine is in good working condition.
- Regularly inspecting the blade for wear and damage and replacing it as needed.
SMART CUT® Abrasive Cut-Off Blades are designed to provide superior cut quality, with minimal chipping and a smooth surface finish. Compared to other brands like Buehler, Struers, LECO, ATM, and Allied, SMART CUT® blades offer competitive or superior performance, particularly in applications requiring minimum material deformation, minimum chipping, and excellent cut quality, long life, and consistent performance.
INDUSTRIES USED IN
Tab Content
ACCESSORIES
Tab Content
USAGE RECOMMENDATION
Tab Content


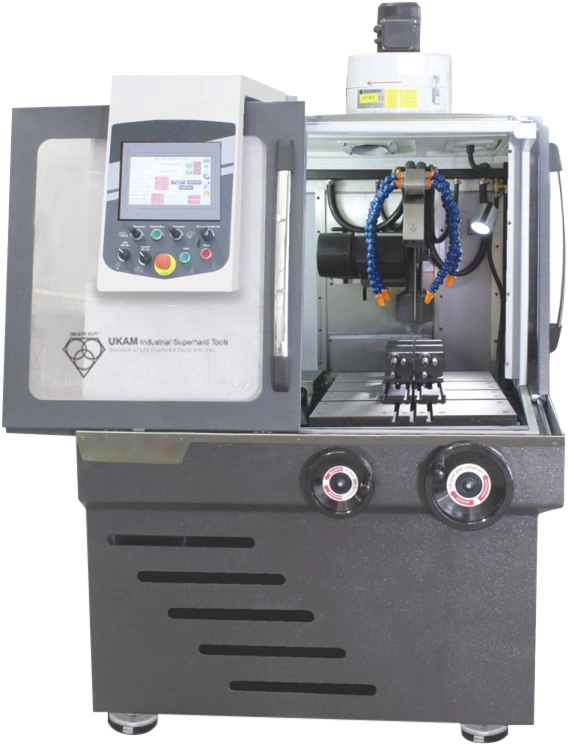
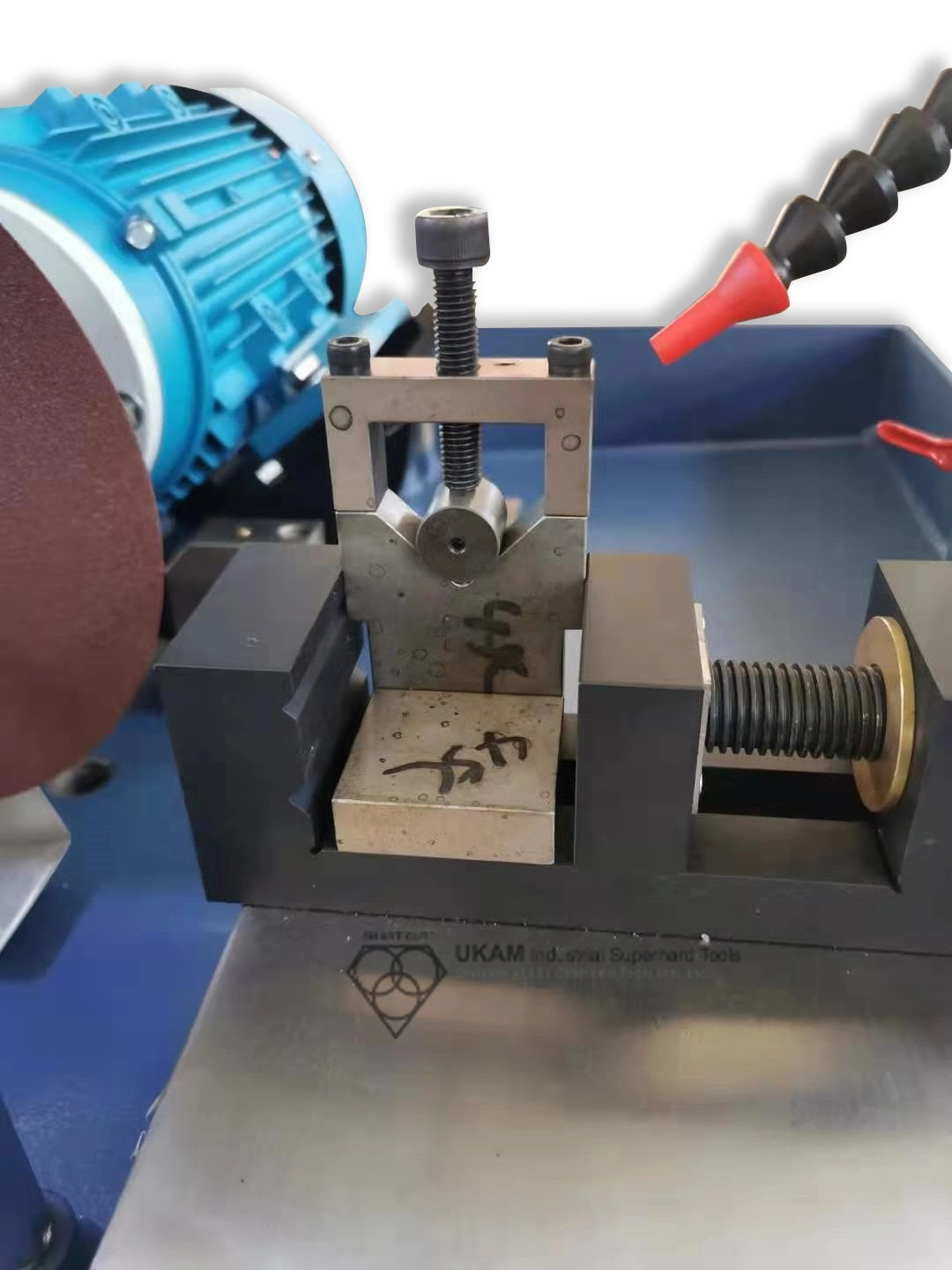
Advantages
- Precision Cutting: Our wheels are manufactured with premium abrasive grains bonded with advanced resins to ensure sharp, clean cuts that reduce material deformation and loss.
- Superior Durability: Constructed for longevity, these wheels offer excellent wear resistance, enabling longer operational life and reducing the need for frequent replacements.
- Optimized Formulations: Each wheel is formulated to cater to specific material hardness and composition, ensuring optimal cutting performance and efficiency.
- Smooth Operation: Designed to operate at lower temperatures to prevent thermal damage and to maintain the integrity of the sample’s microstructure.
- Enhanced Productivity: Fast cutting speeds and exceptional durability lead to increased throughput and lower downtime.
- Reduced Cost: Durable construction and efficient material removal lower the total cost of operations by extending the life of the wheels and reducing material waste.
- Consistent Results: Uniform quality and performance of the wheels ensure reproducible results critical for analytical consistency in testing and research.
Application
- Metallography: Perfect for cutting a wide range of metallurgical samples, from soft aluminum to hardened steels, with precision and ease.
- Sample Preparation: Provides clean and precise cuts required for preparing specimens for microscopy and analysis, minimizing the need for subsequent surface grinding or polishing.
- Quality Control: Essential for facilities requiring consistent and reliable sample preparation for quality assurance and testing procedures.
SMART CUT® Resin Bond
Abrasive Cut Off Blades – Sold in package of 10 pcs
Showing 1 – 17 of 17 results Showing all 17 results Showing the single result No results found
Sort by
Filters Sort results
Reset Apply
Image | Details |
---|---|
$0.00 Max: Min: 1 Step: 1 Add to cart | |
$0.00 Max: Min: 1 Step: 1 Add to cart | |
$0.00 Max: Min: 1 Step: 1 Add to cart | |
$0.00 Max: Min: 1 Step: 1 Add to cart | |
$0.00 Max: Min: 1 Step: 1 Add to cart | |
$0.00 Max: Min: 1 Step: 1 Add to cart | |
$0.00 Max: Min: 1 Step: 1 Add to cart | |
$0.00 Max: Min: 1 Step: 1 Add to cart | |
SMART CUT® Rubber Bond
Abrasive Cut Off Blades
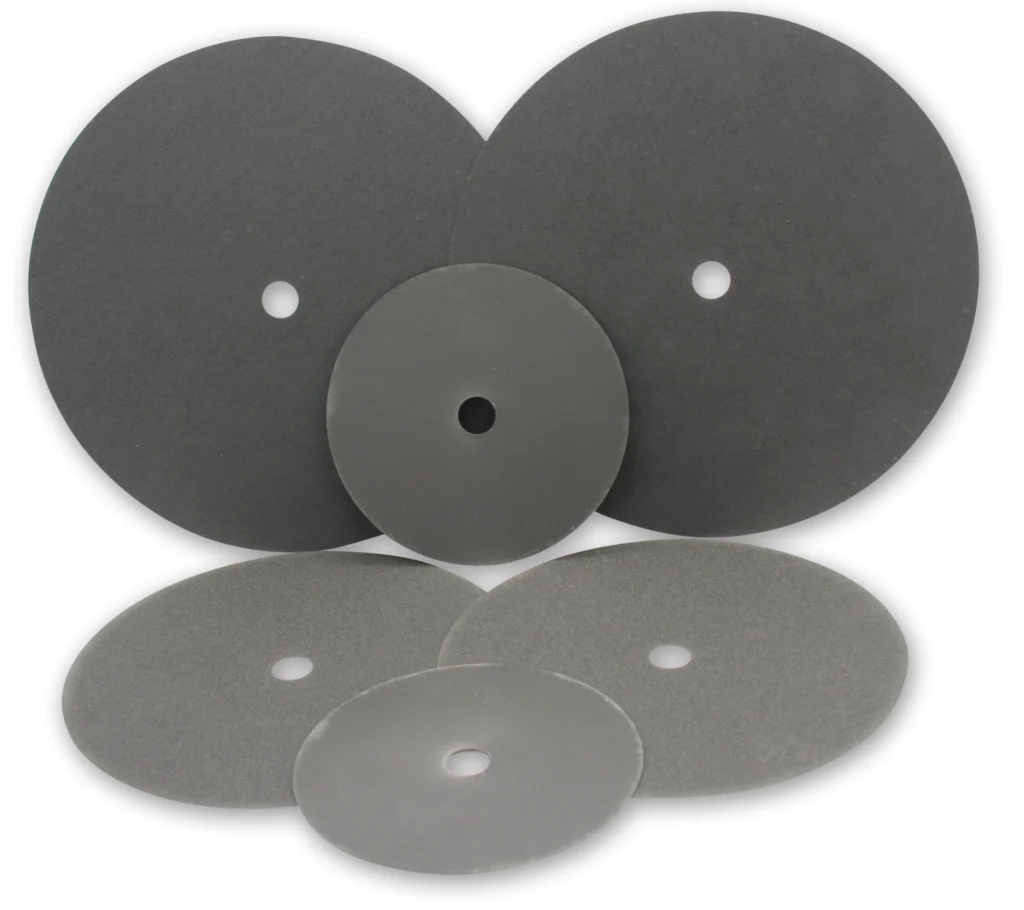
SMART CUT® Rubber Bond Abrasive Cut-Off Blades are expertly designed for metallography and sample preparation, blending advanced rubber bonding technology with high-grade abrasive materials. These blades are exceptionally well-suited for processing a range of materials, from ferrous and non-ferrous metals to delicate and brittle materials that demand meticulous handling to preserve their structural integrity.
Featuring an innovative rubber bond, these SMART CUT® Rubber Bond Abrasive Cut-Off Blades significantly enhance flexibility and shock absorption, which substantially reduces both vibration and noise during operation. This contributes to smoother operations and extends the blade's lifespan by minimizing the risks of cracks or breaks under stress. The cutting performance of the rubber bond is distinguished by its ability to make clean, precise cuts with minimal heat generation, thereby maintaining the unaltered metallurgical properties of the sample for precise analysis.
Crafted from sheets of natural rubber using the traditional calendered method, SMART CUT® Rubber Bond Abrasive Cut-Off Blades blades possess a unique composition that renders them ideal for high-quality, cool, burn-free sectioning on metallographic samples. We offer sample wheels tailored to meet your specific sectioning applications for evaluation.
Custom specifications are available upon request, often requiring only small order quantities and featuring very fast lead times. We offer sample wheels tailored to meet your specific sectioning applications for evaluation.
Why pay more for brand names like Buehler, Struers, Leco, and others when you can get comparable quality and performance at a more competitive price?
Advantages
- Enhanced Durability: Rubber bonding enhances flexibility and shock absorption, reducing vibrations and extending lifespan.
- Precise, Cool Cuts: Minimal heat generation during cutting preserves the sample's integrity for accurate analysis.
- Protection for Delicate Materials: The blade's shock absorption minimizes the risk of damage to brittle materials.
- Burn-Free Sectioning: High-quality, burn-free cuts are ideal for precise metallographic examinations.
- Tailored Solutions: Customizable blades are available to optimize performance for specific applications.
- Cost Efficiency: Durable construction reduces replacement frequency, lowering operational costs.
- Reduced Blade Swarf: The rubber bond limits the amount of metal swarf or debris produced during cutting, keeping the work area cleaner and reducing contamination risks.
- Improved Safety: The reduced vibration and smoother operation lower the risk of accidental blade breakage or mishandling, enhancing operator safety.
- Environmental Resistance: Rubber bonded blades are more resistant to various environmental factors like humidity and temperature changes, which can affect the performance of other types of blades.
- Versatility in Application: These blades are capable of handling a diverse range of materials beyond metals, such as plastics and ceramics, making them versatile tools in various industrial applications.
- Lower Maintenance Requirements: The durability and resistance to wear and tear mean these blades require less frequent maintenance, saving time and resources for users.
- Enhanced Control: The flexibility of the rubber bond provides better control over the cutting process, allowing for more precise and deliberate cuts, which is crucial in settings requiring high precision.
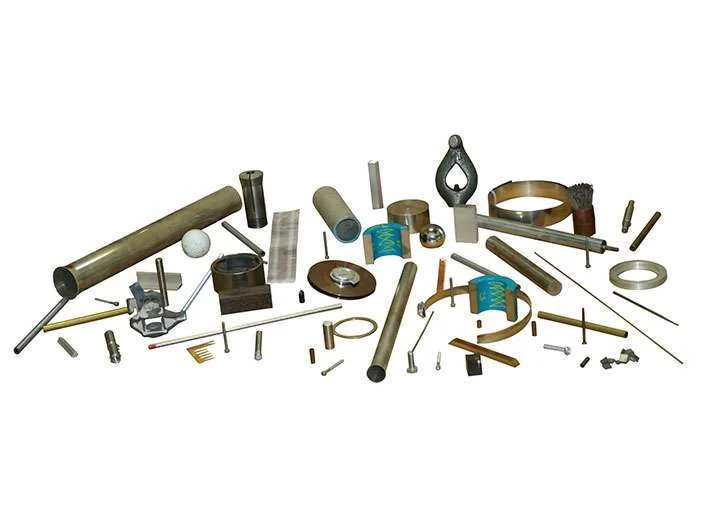


SMART CUT® Rubber Bond
Abrasive Cut Off Blades – Sold in Package of 10 pcs
Showing 1 – 17 of 17 results Showing all 17 results Showing the single result No results found
Sort by
Filters Sort results
Reset Apply
Image | Details |
---|---|
$0.00 Max: Min: 1 Step: 1 Add to cart | |
$0.00 Max: Min: 1 Step: 1 Add to cart | |
$0.00 Max: Min: 1 Step: 1 Add to cart | |
$0.00 Max: Min: 1 Step: 1 Add to cart | |
$0.00 Max: Min: 1 Step: 1 Add to cart | |
$0.00 Max: Min: 1 Step: 1 Add to cart | |
$0.00 Max: Min: 1 Step: 1 Add to cart | |
$0.00 Max: Min: 1 Step: 1 Add to cart | |
$0.00 Max: Min: 1 Step: 1 Add to cart |
Table of Comparison for SMART CUT®
Abrasive Cut Off Blades
Attribute |
Resin Bond (Aluminum Oxide) |
Resin Bond (Silicon Carbide) |
Rubber Bond (Aluminum Oxide) |
Rubber Bond (Silicon Carbide) |
---|---|---|---|---|
|
|
|
||
Abrasive Material |
Aluminum Oxide |
Silicon Carbide |
Aluminum Oxide |
Silicon Carbide |
Bond Type |
Resin (phenolic, epoxy) |
Resin (phenolic, epoxy) |
Rubber (natural or synthetic) |
Rubber (natural or synthetic) |
Cutting Speed |
High |
High |
Moderate |
Moderate |
Flexibility |
Low |
Low |
High |
High |
Heat Resistance |
Moderate |
Moderate |
High |
High |
Water Resistance |
Low |
Low |
High |
High |
Durability |
High |
High |
Moderate |
Moderate |
Material Compatibility |
Hard, brittle materials |
Very hard materials |
Softer, more sensitive materials |
Softer, more sensitive materials |
Cut Quality |
Smooth, minimal deformation |
Smooth, minimal deformation |
Very smooth, minimal chipping |
Very smooth, minimal chipping |
Application |
Dry cutting |
Dry cutting |
Wet or dry cutting |
Wet or dry cutting |
Cost |
Low to Moderate |
Low to Moderate |
Moderate to high |
Moderate to high |
Maintenance |
Low |
Low |
Moderate |
Moderate |
Noise Level |
Higher |
Higher |
Lower |
Lower |
Thermal Stability |
Good |
Good |
Excellent |
Excellent |
Impact Resistance |
Low |
Low |
Moderate |
Moderate |
Cutting Precision |
High |
High |
Moderate |
Moderate |
Suitability for Delicate Materials |
Poor |
Poor |
Excellent |
Excellent |
Wear Rate |
Moderate |
Moderate |
High |
High |
Vibration Damping |
Low |
Low |
High |
High |
Environmental Suitability |
Best in controlled environments |
Best in controlled environments |
Versatile in various settings |
Versatile in various settings |
Ease of Use |
Easy for skilled operators |
User-friendly for all levels |
User-friendly for all levels |
User-friendly for all levels |
Recommended Application for SMART CUT®
Abrasive Cut Off Blades
Recommended abrasive cut-off wheel types with various metal hardness categories, using either resin or rubber bonds with aluminum oxide or silicon carbide:
Metal Type and Hardness |
Recommended Wheel Type |
Abrasive Material |
Bond Type |
Reason for Recommendation |
---|---|---|---|---|
Ferrous Metals <15 HRC (Soft Material) |
Resin Bond Cut-Off Wheel |
Aluminum Oxide |
Resin |
Aluminum oxide provides efficient cutting for soft ferrous metals; resin bond offers durability. |
Ferrous Metals 30-50 HRC (Medium Soft Material) |
Resin Bond Cut-Off Wheel |
Aluminum Oxide |
Resin |
Balances cutting efficiency and durability for medium soft metals. |
Ferrous Metals 50-58 HRC (Medium Hard Material) |
Resin Bond Cut-Off Wheel |
Silicon Carbide |
Resin |
Silicon carbide ensures sharp and durable cutting for medium hard metals. |
Ferrous Metals 60-70 HRC (Hard Material) |
Resin Bond Cut-Off Wheel |
Silicon Carbide |
Resin |
Best for hard materials, maintaining sharpness and durability under extreme conditions. |
Ferrous Metals >70 HRC (Very Hard Material) |
Resin Bond Cut-Off Wheel |
Silicon Carbide |
Resin |
Silicon carbide's extreme hardness and sharpness handle the toughest cutting jobs. |
Non-Ferrous Metals (Cast Iron, Bronze, Copper, Aluminum) |
Rubber Bond Cut-Off Wheel |
Aluminum Oxide |
Rubber |
Aluminum oxide's versatility and the rubber bond's flexibility suit softer non-ferrous metals, reducing heat and chipping. |
Non-Ferrous Metals (Titanium) |
Rubber Bond Cut-Off Wheel |
Silicon Carbide |
Rubber |
Silicon carbide's sharpness and rubber's thermal resistance are ideal for tough, lightweight metals like titanium. |
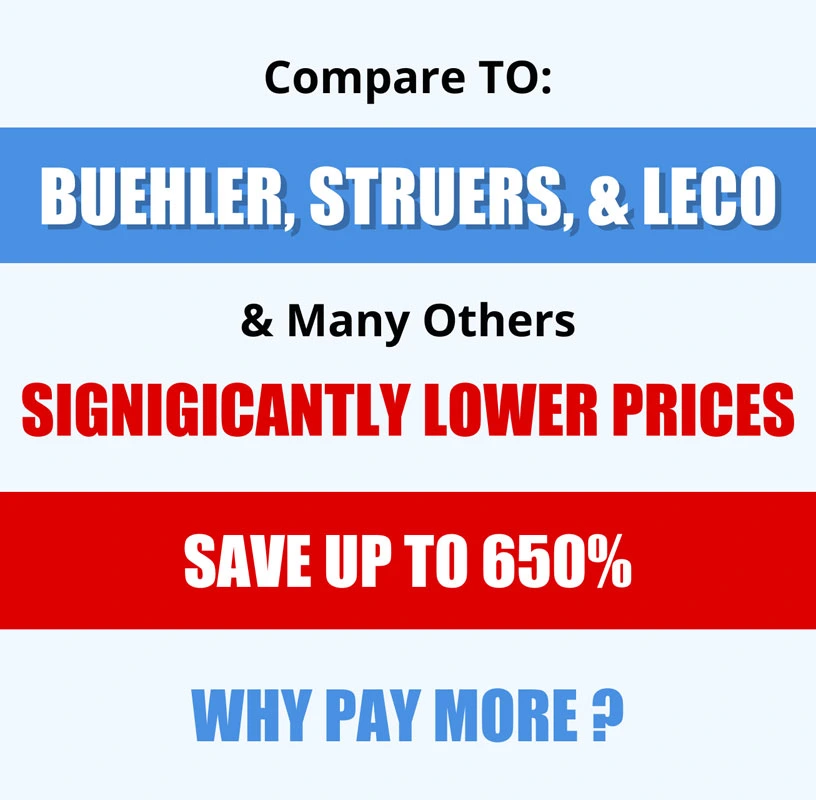
Why Choose Us?
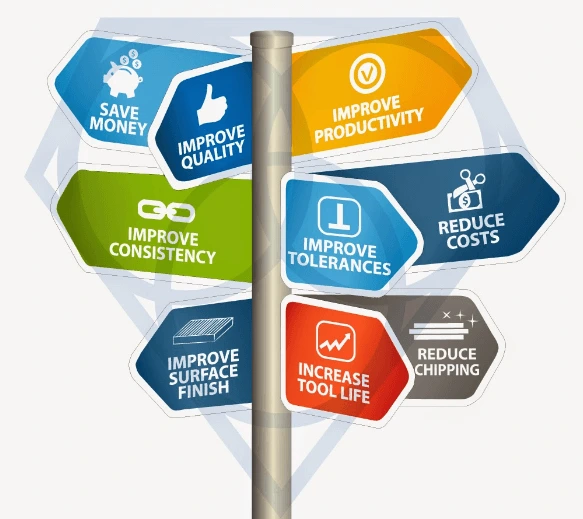
- Unmatched Selection For Many Applications
- Unmatched Technical Support & Expertise
- Superior Quality & Consistency
- Super Technology & innovation
- Immediate Worldwide Delivery
- American Based Manufacturer
-
Custom
Manufacturing - Better Value manufacturer Direct Price
Why Work With Us?
Read More
We produce diamond consumables for some of the leading world OEM manufacturers. We offer Manufacturers Direct Prices
We have the largest variety of diamond & cbn wafering blades available in stock. As well as large inventory of diamond & abrasive consumables. We also custom manufacture diamond and cbn tools, consumables and machines to better fit customer specific needs. Just about any tools & consumables can be designed and manufactured per client drawing or specificrtion
WE ARE A PARTNER IN YOUR SUCCESS
Our proprietory diamond chemistory , precision , manufacturing metods , quality control methods allow us to control and regulate the dozens of variables to that affect consumable life , quality , and consistency.
The more you understand about what we can do for you the better our partnership will be. Here you will find most comprehensive source of information and optimizing and improving your cutting , drilling , grinding and polishing on the web. find everything you ever wanted to know about diamond tools.
AMERICAN MANUFACTURER
"ONE OF THE MOST EXPERIENCED COMPANIES IN THE INDUSTRY"
Save Money Save up to 650%
COMPARE TO: BUEHLER , STRUERS , LECO & MANY OTHERS
Large Inventory & Custom Manufacturing
Umatched Technical Support
Developing close ties with our customers is the foundation of our business. At the core of
our company is a team of world class engineers, knowledgeable customer service personnel here to serve you. Whether is designing or manufacturing a special solution. We will go out of our way to optimizing your process to ultimate level of efficiency
Superior Quality & Consistency
EXPECT MORE FROM YOUR TOOLS
Comprehensive Source Of Information For Sample Preparation
Advanced Technology
As one of the few remaining independent U.S.Diamond Tool & machine builders. We have the experience & tradition to help you remain at frontier of technology Our experience has been further enhanced by acquiring assets and processes from some of the oldest American tool
manufacturers, along with their decades of experience and R& D. This has positioned us as one of the most experienced companies in the industry .Depend on us to bring you technology of tomorrow today.
Experience Makes All The Differences
Over the years we have worked with some of the leading Fortune 500 companies , thousands of universities , government and private research labs , and small organisations. We have made thousands of custom tools , built custom machines , work-holding fixtures , etc for hundreds of applications. Many of our staff members have been working in their respective fields for over 50 years and have gained a wealth of knowledge over the years
Let Us Help You
ARE YOU USING ABRASIVE CUT OFF BLADES
FOR YOUR APPLICATION?
LET US
HELP YOU
HAVING ISSUES WITH
YOUR CURRENT ABRASIVE CUT OFF BLADES?
Knowledge Center
02
Jun
How to Properly Use Precision Diamond & CBN Blades
The diamond blade itself is only a small factor in your cutting operation. Successful diamond sawing is both an art & science. Requiring proper use and understanding of the right: RPM's, Coolants, Equipment, Dressing Devices, Accessories...
02
Jun
Precision & Ultra Thin Diamond Blade Guide
Diamond and CBN blades are available in an extensive array of varieties, each differing in bond types, manufacturing methods, and design specifics. Ultra Thin & High Precision Diamond Blades are particularly versatile, applicable...
02
Jun
Troubleshooting Diamond Sawing Problems
Having issues with your diamond cutting operation? This Illustrated Guide can help. Learn the most common problems most people have in using diamond cutting blades. How to resolve them and avoid them in...
02
Jun
How to Improve & Optimize Your Diamond Sawing Operation
There are numerous variables that affect the performance of diamond and CBN cutting blades. Understanding these variables will help end users select the right diamond blade specifications for their applications and optimize their...
02
Jun
Evaluating & Comparing Diamond Blades
Share this Article with Friend or Colleague
Proper testing procedures and methodologies must be set up and used to obtain accurate as well as repeatable testing results. This article will discuss several simple procedures which...
02
Jun
Selecting Right Wafering Blade for your application
Cross Sectioning is the first and most important step in the sample preparation process. Getting the best results involves obtaining a smooth surface finish, minimum chipping, material deformation, without sacrificing cutting speed. Today, most laboratories, work with dozens...
02
Jun
Wafering Blade Usage Recommendations
The wafering/sectioning blade itself is only a small factor in your sectioning operation. Successful wafering/sectioning operation is both an art & science. Requiring proper use and understanding of selecting the right diamond wafering/sectioning...
02
Jun
Wafering Blade Case Studies
Step by step guide on how to properly use and care for your diamond drills. Selecting the right diamond drill/diamond drill bit parameters, often involves a trial and error process. Many which can be avoided...
22
Apr
Diamond & CBN Wafering Blade Performance Metrics
When evaluating Diamond & CBN wafering blades, especially for metallography and sample preparation, it is critical to consider a set of key evaluation criteria and performance metrics. These factors help determine the effectiveness of a...
24
Apr
Understanding & Comparing Diamond & CBN Wafering Blades
Share this Article with Friend or Colleague
Diamond wafering blades are designed for sectioning a large variety of materials and sample types. In order to identify the best diamond wafering blade for your specific material/application,...
25
Apr
Diamond & CBN Wafering Blade Guide
Share this Article with Friend or Colleague
All you need to know about wafering blades (understanding variables & specifications)
This guide is designed to help you navigate the various variables and possibilities associated with diamond wafering...
31
Jul
Top 5 Diamond & CBN Cutting Blade Performance Metrics
Share this Article with Friend or Colleague
When evaluating diamond and cubic boron nitride (CBN) cutting blades, it's crucial to consider key performance metrics and criteria. Different applications have varying goals, making it...
01
Aug
Diamond & CBN Cutting Blade Performance Metrics that you Should Know
Share this Article with Friend or Colleague
When evaluating diamond and cubic boron nitride (CBN) cutting blades, it's crucial to consider key performance metrics and criteria. Different applications have varying goals, making it important to...
02
Aug
Total Cost of Ownership & Why its Important
Share this Article with Friend or Colleague
Diamond and CBN cutting blades are available in a myriad of specifications, with virtually limitless options. The industry is saturated with numerous manufacturers, each professing to offer the...
05
Aug
Understanding Tradeoffs- Searching for Perfect Diamond & CBN Blade
Share this Article with Friend or Colleague
Choosing the right blade diamond or cbn blade can significantly impact efficiency, cost, and quality. However, this is not simple and clear cut process. Selecting the optimal blade...
19
Aug
Understanding & Calculating Return on Investment for Diamond & CBN Blades
The term "ROI" (Return On Investment) is frequently mentioned across various industries, often with different interpretations depending on the context. However, few take the time to thoroughly understand what ROI truly represents and its specific...
- Unmatched Selection For Many Applications
- Superior Quality & Consistency
- Immediate Worldwide Delivery
- Technical Support & Expertise
- American Based Manufacturer
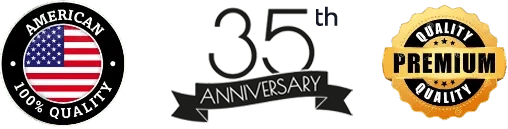

- Different Product
- Different Technology
- Different Company
- Expect MORE from your tools
Let Us HELP You!
Subscribe To Our Newsletter
Signup for email offers, updates, and more
Contact Us
- 25205 & 25201 Avenue Tibbits Valencia CA 91355 USA
-
Phone : (661) 257-2288
FAX : (661) 257 -3833 - lel@ukam.com
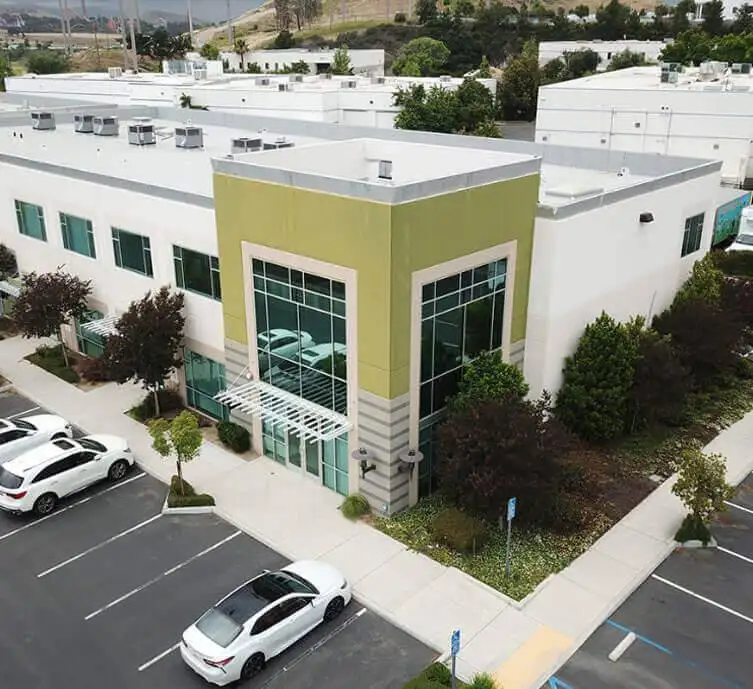
UKAM Industrial Superhard Tools is a U.S. High Technology, Specialty Diamond Tool & Equipment manufacturer. We specialize in producing ultra thin, high precision cutting blades, precision cutting machines diamond drills, diamond micro tools, standard & custom advanced industrial diamond tools and consumables.
- 25205 & 25201 Avenue Tibbits Valencia CA 91355 USA
-
Phone : (661) 257-2288
FAX : (661) 257 -3833 - lel@ukam.com
- 25205 & 25201 Avenue Tibbits Valencia CA 91355 USA
-
Phone : (661) 257-2288
FAX : (661) 257 -3833 - lel@ukam.com
DIAMOND TOOLS BY BOND
EQUIPMENT
KNOWLEDGE CENTER
OUR PRODUCTS
COMPANY
CUSTOMER SERVICE
Shipping Methods


Safe & Secure Payments

© Copyright 1990-2025. UKAM Industrial Superhard Tools – Terms of Use