-
0 items in quote
No products in the Quote Basket.
SMART CUT® 015DSE Miniature (Mini) Multi-Layered Electroplated Solid Diamond Drills
SMART CUT® 015DSE Miniature (Mini) Multi-Layered Electroplated Solid Diamond Drills are precision-engineered and manufactured in the USA and Europe, ensuring superior quality, consistency, and performance compared to standard electroplated drills commonly produced in Asia. Designed for precision drilling across a wide range of materials, including ceramic, tile, advanced ceramics, glass, quartz, optical materials, composites, natural and synthetic stone, as well as semi-precious and precious stones, these drills deliver exceptional accuracy, extended lifespan, and superior cutting performance.
Unlike inexpensive electroplated miniature diamond solid drills from Asia, which are typically produced using just piano wire. These suffer from short lifespan due to low-quality diamond grit, thin or uneven plating, and poor adhesion, the SMART CUT® 015DSE series is engineered for longevity and precision. Many lower-cost alternatives exhibit premature wear, inconsistent drilling performance, uneven grit distribution, excessive runout, and poor dimensional accuracy due to weak structural integrity and inferior base materials.
DESCRIPTION
SPECIFICATIONS
FREQUENTLY ASKED QUESTIONS
INDUSTRIES USED IN
ACCESSORIES
USAGE RECOMMENDATION
DESCRIPTION
Overheating is a common issue in these drills due to poor coolant flow and inefficient heat dissipation, leading to chipping, material damage, and unreliable drilling results. Additionally, many cheap imports lack custom sizing options and suffer from contamination issues, including low-purity nickel plating and machining residues, further degrading performance. Users also face inconsistent batch quality, lack of technical support, and no performance guarantees, making them a high-risk investment despite their lower initial cost.
In contrast, SMART CUT® 015DSE Mini Multi-Layered Electroplated Solid Diamond Drills feature a flat cylindrical shape with a transition angle, ensuring greater stability, support, and drilling accuracy. The head length and drill depth are proportionate to the diameter, optimizing performance for each drill size. The multi-layered nickel bond diamond coating provides superior diamond adhesion within the bond matrix, significantly extending tool life compared to standard electroplated miniature drills. With higher consistency, better surface finish, and enhanced structural integrity, these drills offer a drastically improved drilling experience.
The shank size varies depending on the drill diameter, incorporating a transition angle where the shank is larger than the head length, which provides increased accuracy, superior stability, and better load-bearing capacity. This design allows SMART CUT® drills to withstand more pressure and force than typical music wire-plated drills, making them significantly more durable and effective.
Ideal for drilling precious and semi-precious stones, beads, glass, crystals, ultra-hard and brittle ceramics, composites, hard metals, and many other difficult materials, these drills perform exceptionally well on Foredom, Dremel machines, high-speed air spindles, and other equipment operating at 9,000+ RPM. They significantly outlast all other electroplated drills available on the market today, making them the most cost-effective and high-performance solution for precision drilling applications.
For specialized applications, custom manufacturing is available, allowing for adjustments to diamond coating height, drill angles, and radius to fit specific requirements. The standard stock configuration features a flat-end cylindrical design, but modifications can be made as needed.
Engineered for professionals who demand exceptional performance, accuracy, and longevity, the SMART CUT® 015DSE Mini Multi-Layered Electroplated Diamond Drills provide a smoother surface finish, faster drilling speeds, greater tool durability, and unmatched reliability. Each package contains six drills, ensuring a reliable and long-lasting solution for high-precision drilling needs.
SPECIFICATIONS
Bond Type: Nickel Bond (Plated) Multi Layered
Edge Type: Flat End Cylinder
Diamond Grit Size: Medium Fine
Transition Angle Sold in Pack of 6 units
Shank Diameter is slightly smaller than diameter of diamond drill tip
Drilling Depth (mm): 1.25″ (31.75mm)
Recommended Operating Speed: 7,000-10,000
Maximum Operating Speed: 30,000.
Always drill with a coolant and use submerged-pressure sensitive feed.
Recommended Coolant: water, for ultra hard materials best results will be achieved with mineral oil or synthetic water soluble coolant.
FREQUENTLY ASKED QUESTIONS
SMART CUT Series 015DSE drills are most commonly used for drilling small holes in various materials, including jewelry-making materials like stones, glass, and other hard substances.
SMART CUT Series 015DSE drills have multiple layers of diamond coating, which enhances diamond adhesion and results in longer lifespan, improved consistency, and better surface finish compared to standard electroplated miniature drills.
These drills have a flat-bottom cylinder shape with a transition angle. They are available in various sizes, ranging from 0.75mm to 2.5mm in diameter.
The recommended operating speed for SMART CUT Series 015DSE drills is between 7,000 and 10,000 RPM (revolutions per minute), with a maximum operating speed of 30,000 RPM.
These drills are versatile and can be used to drill smooth and clean holes in a wide variety of materials, including ceramic, glass, quartz, optical materials, composites, natural and synthetic stones, and many others.
For most applications, water is a recommended coolant. However, for ultra-hard materials, better results can be achieved with mineral oil or synthetic water-soluble coolant.
Yes, these drills can be used with various equipment, including high-speed drill presses, mounted handpiece drills (e.g., Foredom and Dremel), and high-speed air spindles.
Yes, custom manufacturing for SMART CUT Series 015DSE drills is available. The height of the diamond coating and other specifications can be adjusted to fit specific requirements.
Yes, quantity discounts may be available for bulk purchases. Please inquire with our sales department.
Yes, there is an option to purchase a mixed package of assorted sizes, including 2.5mm, 2.2mm, 2.0mm, 1.5mm, 1.2mm, and 1mm drills in a single package.
Yes, other drill sizes and drilling depths can be produces upon request. Please inquire with our sales department.
Yes, these drills are commonly used in jewelry-making for precision drilling of small holes in stones, glass, and other jewelry materials.
SMART CUT Series 015DSE drills are designed to have a longer lifespan and better performance compared to standard music wire plated drills, thanks to their multi-layered diamond coating and enhanced diamond adhesion, heat tread steel body and transition angle for maximum stability
The head length of SMART CUT Series 015DSE drills is 15.00mm (.591″), and the drill depth is 45.00mm (1.772″). These dimensions are proportionate to the diameter of the drill and are designed to provide accurate drilling and support.
Yes, these small plated miniature drills can withstand more pressure and force compared to typical music wire plated drills due to their transition angle design and enhanced diamond adhesion.
Yes, SMART CUT Series 015DSE drills are suitable for drilling through hard metals, ceramics, and various other materials thanks to their high diamond concentration and multi-layered diamond coating.
It is recommended to use submerged-pressure-sensitive feed when drilling with SMART CUT Series 015DSE drills to ensure smooth and precise drilling.
Yes, these drills have a flat-end cylinder shape, making them suitable for drilling holes with flat bottom cylinders.
Operators should always drill with a coolant and follow safety guidelines when using SMART CUT Series 015DSE drills to ensure safe and efficient drilling.
Are these drills suitable for drilling holes in natural and synthetic stones used in jewelry-making?
Yes, SMART CUT Series 015DSE drills are suitable for drilling holes in both natural and synthetic stones commonly used in jewelry-making.
Yes, these drills are designed for consistent performance, providing smooth drilling and high-quality results.
Yes, SMART CUT Series 015DSE drills are effective for precision drilling in glass and quartz materials, producing clean and precise holes.
While these drills are versatile, it’s essential to consider the specific requirements of your material. Extremely hard or abrasive materials may require sintered (metal bond) drills
Yes, these drills are commonly used in professional jewelry-making workshops for precision drilling tasks.
Yes, these drills can handle materials with varying hardness within the same project by adjusting the drilling parameters as needed.
Diamond drills are designed to be used with coolant, they can be used without coolant in some cases when drilling more shallow holes, this would require frequent dressing.
Absolutely, these drills are suitable for drilling holes in advanced ceramics and optical materials, providing accurate and smooth results.
To select the correct drill size for your project, consider the desired hole diameter and the material you’ll be drilling. You can consult the drill’s specifications and guidelines for guidance.
Yes, these drills are compatible with high-speed air spindles and similar equipment, making them versatile for various applications.
To extend the lifespan of these drills, it’s essential to use the recommended operating speeds, coolants, and feed methods. Regularly inspect the drill for wear and replace it as needed.
When not in use, it’s advisable to store these drills in a dry and cool place, away from direct sunlight and extreme temperatures, to prevent any potential damage or degradation.
Yes, the angle and radius of these drills can be customized if needed, allowing for tailored drilling solutions based on specific project requirements.
Yes, these drills can effectively create holes in composite materials, delivering precise results.
When changing or replacing drills during a project, ensure that the equipment is turned off and follow safety procedures to prevent accidents or injuries.
Yes, SMART CUT Series 015DSE drills are suitable for creating holes in ceramic, tile, and related materials.
Yes, custom manufacturing for these drills is available, allowing you to request specific specifications to meet your unique drilling needs.
These drills are commonly used in various industries, including jewelry-making, ceramics, optics, and more, making them versatile for a wide range of applications.
Yes, these drills are designed for fast and consistent drilling performance, ensuring efficient and reliable results in your projects.
Yes, these drills are suitable for drilling holes in ultra-hard and brittle materials, thanks to their multi-layered diamond coating and superior design.
Yes, you can typically order these drills in larger quantities to meet the demands of industrial applications. Quantity discounts are available
While water is acceptable for many applications, for ultra-hard materials, mineral oil or synthetic water-soluble coolant is advised for optimal results.
Yes, these drills are ideal for creating precise holes in both natural and synthetic stones, making them suitable for jewelry-making and similar tasks.
Yes, these drills are effective for drilling holes in semi-precious and precious stones commonly used in jewelry-making.
Yes, SMART CUT Series 015DSE drills are suitable for creating holes in both natural and synthetic crystals, providing precision and quality results.
These drills are suitable for both personal and industrial use. They are commonly used in jewelry-making as well as various industrial applications.
To achieve a smooth surface finish, it’s essential to use the recommended operating speed and feed method and ensure that the drill is in good condition without excessive wear.
Can these drills be used for drilling holes in both soft and hard materials within the same project?
Yes, these drills can be used for drilling holes in materials with varying hardness within the same project by adjusting the drilling parameters accordingly.
While specific guidelines for drilling speed can depend on the material, the recommended operating speed for these drills is typically between 7,000 and 10,000 RPM.
Yes, these drills are compatible with mounted handpiece drills, including popular brands like Foredom and Dremel, making them versatile for various applications.
The choice of mineral oil or synthetic water-soluble coolant for ultra-hard materials may vary based on the specific material and drilling conditions. It’s advisable to consult with the manufacturer or supplier for recommendations.
Operators should follow standard safety precautions when using high-speed equipment with these drills, including wearing appropriate safety gear and ensuring proper ventilation.
Yes, you can typically purchase replacement drills individually if you need to replace a single drill rather than buying a full set.
SMART CUT Series 015DSE drills are known for their superior performance and durability, especially when drilling hard and brittle materials, thanks to their multi-layered diamond coating, heat tread steel body and transition angle.
Yes, these drills are well-suited for precision drilling in the field of gemology and gemstone cutting, where accuracy and quality are essential.
SMART CUT Series 015DSE drills are designed to be compatible with various drilling equipment, and compatibility issues are typically minimal. For most drilling equipment such as Dremel or foredom you can purchase a universal chuck which will allow you to use any size shank. This is easier then trying to use different collet for every different drill shank diameter.
Yes, these drills are suitable for drilling holes in ceramic tiles, making them useful for tile-related projects.
Yes, these drills are suitable for drilling holes in hard jewelry-making materials like sapphires and rubies, thanks to their high diamond concentration and durability.
Absolutely, these drills are well-suited for precision drilling in the field of lapidary work and stone cutting, where precision and control are vital.
Yes, these drills can be used in laboratory settings for research and testing purposes, especially when precise drilling is required.
Yes, SMART CUT Series 015DSE drills can be used for creating holes in optical materials that require stringent quality standards, ensuring precision and quality.
These drills may come with manufacturer-specific guidelines for optimal use. It’s advisable to review and follow these guidelines for the best results.
While these drills are primarily designed for drilling holes, they may also be used for engraving or etching surfaces with the appropriate techniques and equipment.
Yes, SMART CUT Series 015DSE drills are suitable for drilling holes in composite materials commonly used in aerospace and engineering applications.
Yes, you may be able to purchase these drills directly from the manufacturer’s website or through authorized distributors.
To maintain the quality of these drills, store them in a dry and cool environment, away from direct sunlight and extreme temperatures. You can use the same jewel package the drills come packaged in for storage.
Yes, the angle and radius of these drills can be customized to create holes with specific angles if needed.
Yes, these drills can be used with both manual and automated drilling equipment, providing flexibility in your drilling processes.
Yes, these drills are commonly used for creating holes in both natural and synthetic gemstones in the jewelry production industry.
To maintain sharpness and effectiveness, it’s important to follow the recommended operating speeds, coolants, and feed methods, as well as regularly inspecting the drill for wear.
Yes, these drills can be used for creating holes in high-precision optical components commonly used in scientific instruments, ensuring accuracy and quality.
While the sizes mentioned in the product description are available, you can inquire with the manufacturer for larger sizes or specialized applications to meet your needs.
Some manufacturers or suppliers may provide instructional videos or tutorials on their websites to assist users in using these drills effectively. You can check their resources for guidance.
Yes, these drills are suitable for creating holes in various engineered materials used in manufacturing processes, offering precision and consistent performance.
Some manufacturers may offer sample or trial orders for testing purposes. It’s a good idea to inquire with the manufacturer or supplier about such options.
Manufacturers typically provide technical specifications and data sheets for their products. You can request these documents for reference and detailed information about the drills.
When using these drills in combination with jewelry-making techniques like wire wrapping or metalwork, ensure that you have the appropriate tools and techniques to incorporate the drilled holes into your designs.
Yes, SMART CUT Series 015DSE drills are suitable for creating holes in synthetic materials like acrylic or resin, making them versatile for craft and art projects.
While water is a commonly recommended coolant, compatibility issues with specific coolants can vary.
Yes, these drills can be used for drilling holes in ceramic or porcelain tiles, making them useful for home improvement and renovation projects.
SMART CUT Series 015DSE drills are primarily designed for non-medical applications. For dental precision drilling, it’s advisable to use drills specifically designed and approved for dental procedures.
While these drills are highly versatile, extremely hard or abrasive materials may pose challenges, and specialized tools may be required for optimal results.
Yes, these drills can be used for creating holes in materials with irregular or curved surfaces with the appropriate techniques and equipment.
Wearing appropriate safety gear, including protective eyewear and gloves, is recommended when handling these drills to ensure safe usage.
Yes, these drills are suitable for creating holes in composite materials used in the marine industry, making them valuable for boat construction and repairs.
Yes, these drills can be used for precision drilling in the field of watchmaking and horology, where accuracy and fine craftsmanship are essential.
Yes, these drills are suitable for creating holes in materials used in electronics manufacturing, including PCBs, for precise and controlled drilling.
INDUSTRIES USED IN
Composites
Gem Stones
Sapphire
Silicon
Glass Materials
Lapidary
Stone
Advanced Ceramics
Photonics
ACCESSORIES
Showing 1 – -1 of 16 results Showing all 16 results Showing the single result No results found
Sort by Name A – Z
Filters Sort results
Reset Apply
Image | Item No. | Description | Price | Quantity | Add to cart |
---|---|---|---|---|---|
Color: 5/8″-11″ thread. Fits into drill press chuck. Shank adapter threads into 5/8″-11″ female thread of diamond drill. Can be used with any other tool with 5/8″-11″ thread. | $26.72 | Max: Min: 1 Step: 1 | |||
Color: 5/8″-11″ thread. Fits into drill press chuck. Shank adapter threads into 5/8″-11″ female thread of diamond drill. Can be used with any other tool with 5/8″-11″ thread. | $22.46 | Max: Min: 1 Step: 1 | |||
1 Gallon Blue SMART CUT® General Materials Formula Synthetic Water Soluble Coolant | $99.81 | Max: Min: 1 Step: 1 | |||
1 Quart Blue SMART CUT® General Materials Formula Synthetic Water Soluble Coolant | $34.81 | Max: Min: 1 Step: 1 | |||
5 Gallons Blue SMART CUT® General Materials Formula Synthetic Water Soluble Coolant | $317.41 | Max: Min: 1 Step: 1 | |||
55 Gallons Blue SMART CUT® General Materials Formula Synthetic Water Soluble Coolant | $1,745.00 | Max: Min: 1 Step: 1 | |||
1/2″ x 1/2″ x 6.0″ White Recommended for coarser grits found in segment wheels, core drills, or Blanchard grinding. Excellent performance on 120 grit tools. | $8.65 | Max: Min: 1 Step: 1 | |||
1.0″ x 1.0″ x 6.0″ White Recommended for coarser grits found in segment wheels, core drills, or Blanchard grinding. Excellent performance on 120 grit tools. | $15.99 | Max: Min: 1 Step: 1 | |||
1/2″ x 1/2″ x 6.0″ White For use on diamond tools 150 to 220 Grit Size. | $8.65 | Max: Min: 1 Step: 1 | |||
1.0″ x 1.0″ x 6.0″ Black Recommended for use in Diamond Tools 150 Grit Size (mesh size) or finer. | $15.39 | Max: Min: 1 Step: 1 | |||
2.0″ x 2.0″ x 6.0″ Black Recommended for use in Diamond Tools 150 Grit Size (mesh size) or finer. | $39.47 | Max: Min: 1 Step: 1 | |||
1.0″ x 1.0″ x 6.0″ Black Recommended for coarser grits found in segment wheels, core drills, or Blanchard grinding. Excellent performance on 120 grit tools. | $15.99 | Max: Min: 1 Step: 1 | |||
2.0″ x 2.0″ x 6.0″ Black Recommended for coarser grits found in segment wheels, core drills, or Blanchard grinding. Excellent performance on 120 grit tools. | $39.47 | Max: Min: 1 Step: 1 | |||
$154.87 | Max: Min: 1 Step: 1 | ||||
$154.87 | Max: Min: 1 Step: 1 | ||||
$235.00 | Max: Min: 1 Step: 1 |
USAGE RECOMMENDATION
02
Jun
How to Properly Use Precision Diamond Drills
Step by step guide on how to properly use and care for your diamond drills. Selecting the right diamond drill/diamond drill bit parameters, often involves a trial and error process. Many which can be avoided…
02
Jun
Diamond Drills Guide
Diamond are used across large variety of industries and applications. This guide explores the wide range of diamond drill types, including hollow core drills designed for removing a cylindrical core, non-core formation drills that grind…
02
Jun
Diamond Tools Guide – Selecting Right Drills & Tools for your application
These tools are used for many different industries grinding and shaping material into different forms, expanding exiting inside diameters, grinding, finishing and polishing existing material. Grinding different angles and radius, creating cavities of various forms,…
02
Jun
Optimizing your Diamond Drilling Operation
There are numerous factors that influence the performance of diamond drills. Understanding these factors helps users select the appropriate diamond drill specifications for their specific applications, optimizing drilling operations to achieve maximum efficiency….
02
Jun
Micro Drilling Guide
Share this Article with Friend or Colleague
In order for you to get the most out of your diamond micro drill or carbide / high speed steel micro drill, we strongly urge you to read…
03
May
Diamond Core Drill & Drill Trouble Shooting Guide
Learn the most common problems most people have in using diamond drills. How to resolve them and avoid them in first place
Troubleshooting Drilling Problems
Having issues with your diamond drilling operation? This Illustrated Guide…
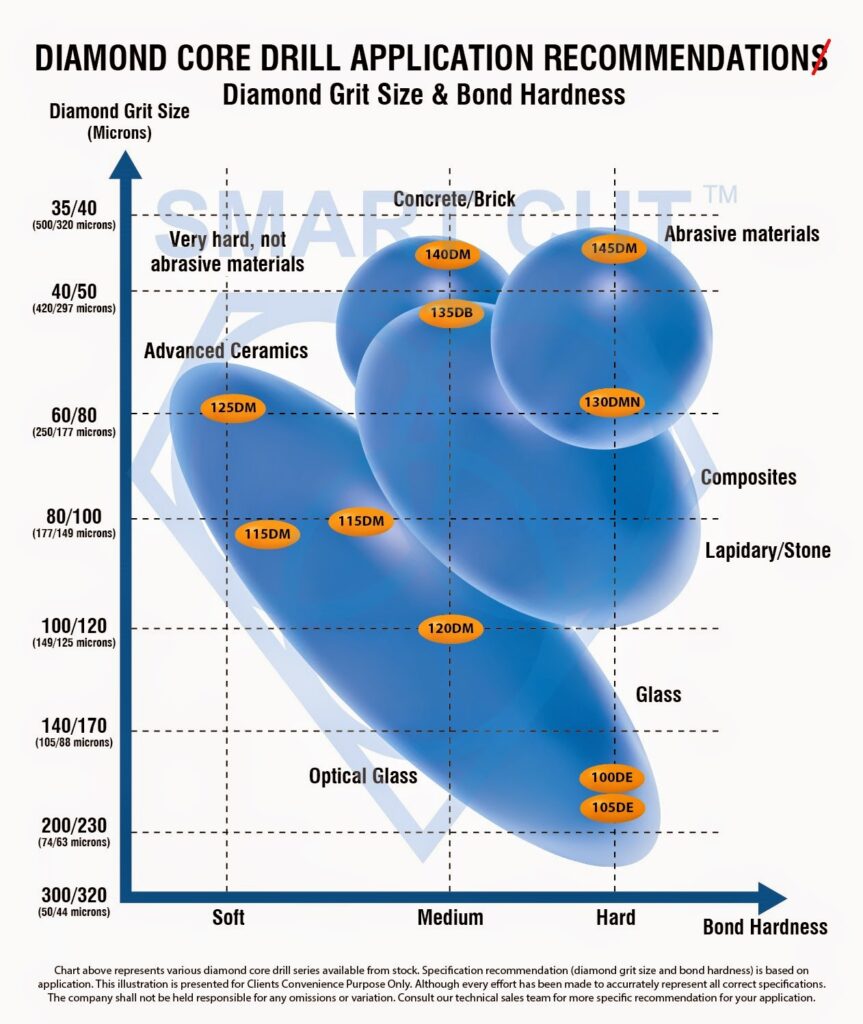
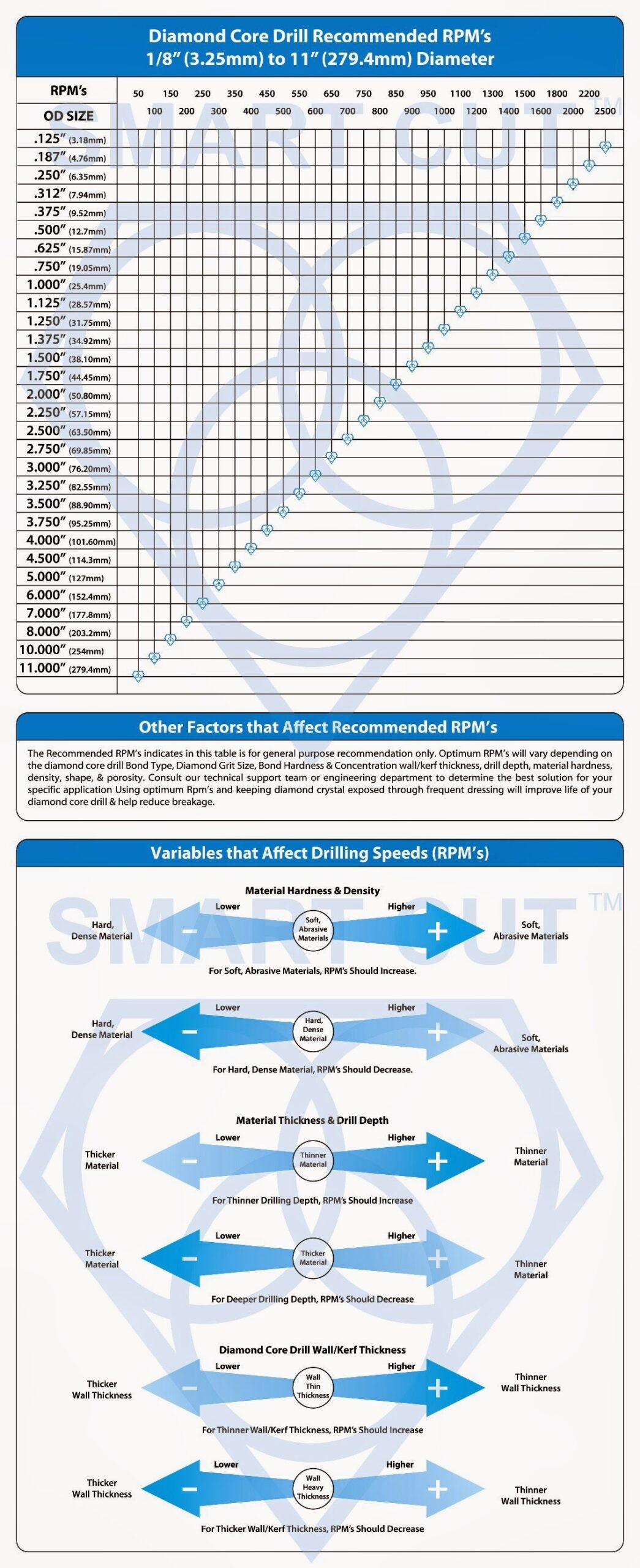
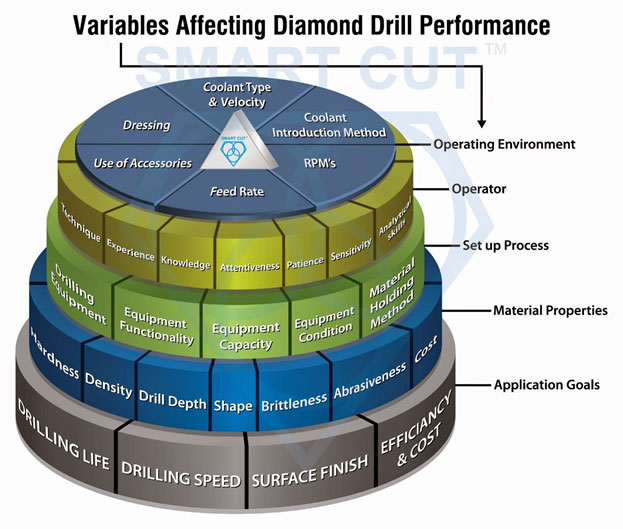
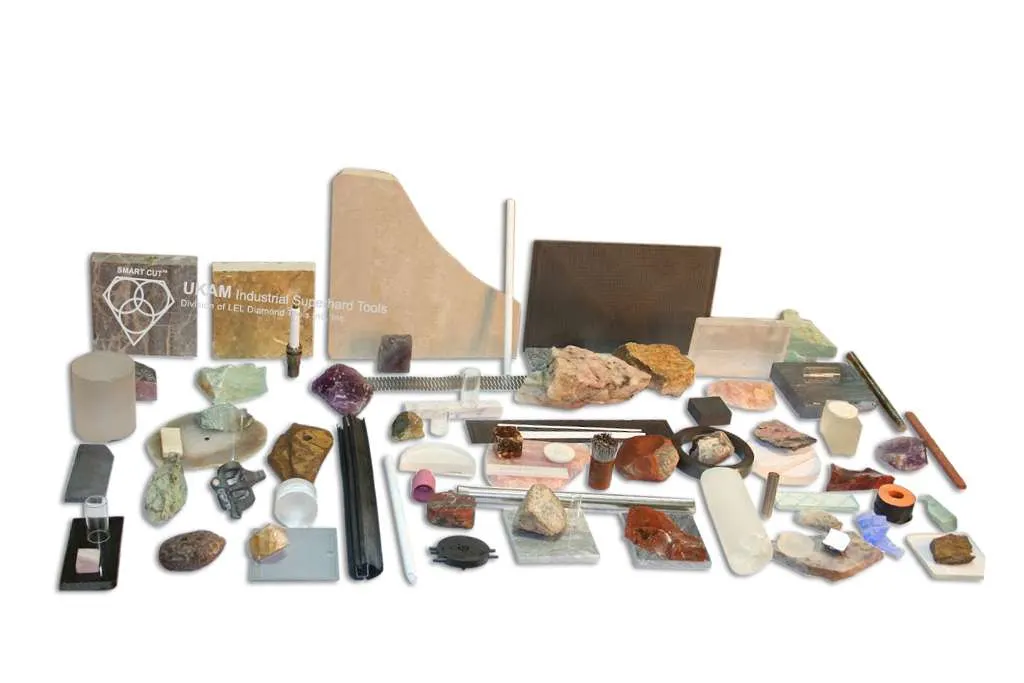
Application (Materials Used on)
- ceramic, tile & related materials
- advanced ceramics
- glass & quartz
- optical materials
- composites
- natural & synthetic stone
- semi-precious & precious stone
- many other materials
Equipment Used on:
- High Speed Drill Press
- Mounted Hand Piece Drill (such as: Foredom & Dremel),
- High Speed Air Spindles
Features
- Multi Layered Nickel Bond Diamond Coating
- Flat End Cylinder
- Precision Hardened & Heat Tread steel body
- Transition Angle for Better Stability
- Medium Fine Diamond Size
- Better Tolerances then Comparable Drills
- Custom Manufacturing Possible
Advantages
- Superior Design that is Easier to Use
- Smooth Surface Finish Quality
- Fast Drilling & Consistent Performance
- Superior Quality & Consistency
- More Accurate Drilling
- Better Diamond Adhesion
- Longer Life Span
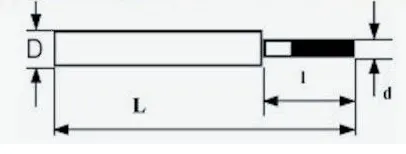
SMART CUT® 015DSE Sold in Package of 6 pcs
All drills are packaged in clear jewel box
Price: $25.99 for package of 6 drills
SMART CUT® 015DSE
Sold in Package of 6 pcs
Price: $25.99 for package of 6 drills
Showing 1 – -1 of 7 results Showing all 7 results Showing the single result No results found
Sort by
Filters Sort results
Reset Apply
Image | Item No. | Diameter | Price (package of 6 pcs) | Quantity | Add to cart |
---|---|---|---|---|---|
0.75mm (.0295") | $25.99 | Max: Min: 1 Step: 1 | |||
1.0mm (.0393") | $25.99 | Max: Min: 1 Step: 1 | |||
1.2mm (.0472") | $25.99 | Max: Min: 1 Step: 1 | |||
1.5mm (.059") | $25.99 | Max: Min: 1 Step: 1 | |||
2.0mm (.080") | $25.99 | Max: Min: 1 Step: 1 | |||
2.2mm (.0866") | $25.99 | Max: Min: 1 Step: 1 | |||
2.5mm (.0984") | $25.99 | Max: Min: 1 Step: 1 |
Other more exact drill sizes & drilling depths are available upon request. Quantity Discounts are available.
Drilling smooth and clean holes in a wide variety of
Advantages
- Superior Design that is Easier to Use
- Smooth Surface Finish Quality
- Fast Drilling & Consistent Performance
- Superior Quality & Consistency
- More Accurate Drilling
- Better Diamond Adhesion
- Longer Life Span
Features
- Multi Layered Nickel Bond Diamond Coating
- Flat End Cylinder
- Precision Hardened & Heat Tread steel body
- Transition Angle for Better Stability
- Medium Fine Diamond Size
- Better Tolerances then Comparable Drills
- Custom Manufacturing Possible
Equipment Used on:
- High Speed Drill Press
- Mounted Hand Piece Drill (such as: Foredom & Dremel),
- High Speed Air Spindles
Application (Materials Used on)
- ceramic, tile & related materials
- advanced ceramics
- glass & quartz
- optical materials
- composites
- natural & synthetic stone
- semi-precious & precious stone
- many other materials
Head length and drill depth depends and is in proportion on diameter of the drill. Plated drills have The shank size varies depending on diameter of the drill. Our multi layered electroplated solid drills have a transition angle where the shank is larger then the head length. This provides more accurate drilling, and support. Hence these small plated miniature drills can withstand more pressure and force then typical music wire plated drills. Most popular type of diamond drills for drilling small holes for jewelry (stone, glass, & many other materials). Available from stock from 0.75mm to 2.5mm
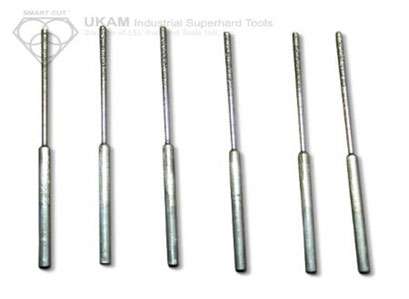

Multi Layered Electroplated solid drills are flat cylinder shape with transition angle. Head length and drill depth depends and is in proportion on diameter of the drill. Plated drills have multiple layers of diamond coating which provides best diamond adhesion in the bond matrix. This provides longer life span, compared to standard and comparable electroplated miniature drills. Higher level of consistency and better surface finish. The shank size varies depending on diameter of the drill. Our multi layered electroplated solid drills have a transition angle where the shank is larger then the head length. This provides more accurate drilling, and support. Hence these small plated miniature drills can withstand more pressure and force then typical music wire plated drills.
Typical applications include drilling precious and semi precious stones, beads, glass, crystals, ultra hard and brittle ceramic, composites, hard metals, and many other. Used on: Foredoom, Dremel Machines, High Speed Air Spindles, & other equipment running at 9,000+ RPM. Custom Manufacturing for Multi Layered Electroplated solid drills is available. The Height of diamond coating can be adjusted to fit your particular requirements. Standard configuration of standard stock diamond the miniature diamond drills is flat end cylinder but the angle and radius can also be customized if needed.
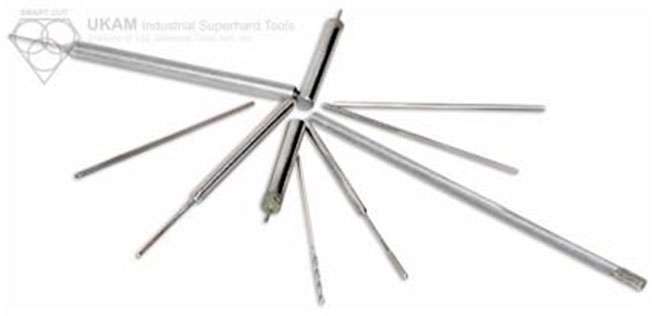
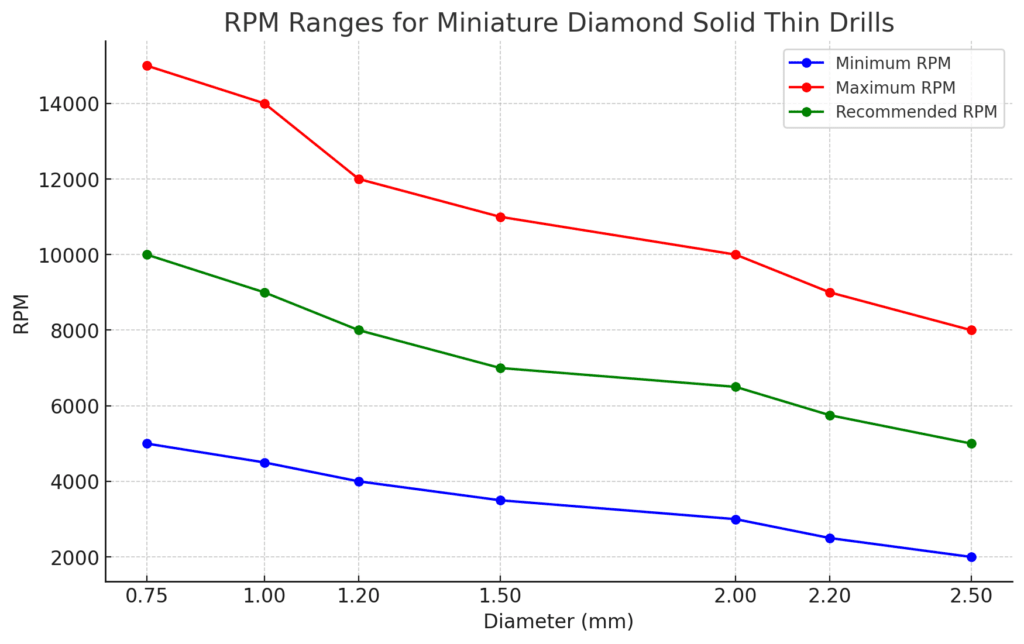
Recommended RPM’s: The RPM values provided in this table serve as general guidelines for typical drilling applications. However, the optimal RPM settings will vary based on several factors including the desired cut quality, drill depth, material hardness, density, shape, and porosity. Please see our Guide on How to Properly Use Diamond Drills. To ensure the highest level of performance and safety, we advise consulting with our technical support team. They can assist in tailoring these parameters to your specific application, ensuring that you use the optimal RPM and appropriate coolant type. Properly adjusting these factors can significantly enhance the lifespan of your diamond drills and minimize the risk of tool breakage.
Recommended Feed Rate: starting at lower feed rates and gradually increasing to find the optimal drilling ratio is crucial for precision drilling. It is important to continuously clear the drill of grinding debris to prevent clogging and overheating.
Plunge feeding is generally not recommended due to the increased risk of material damage and tool wear. Instead, we advocate for the use of a peck feed cycle. This technique involves withdrawing the drill periodically to clear debris, which helps in maintaining the integrity of both the drill and the workpiece. This method not only helps develop a better "feel" for the material and the process but also improves the overall drilling efficiency by reducing stress on the tool and preventing overheating.
SMART CUT® 015DSE Miniature (Mini) Multi-Layered Electroplated Solid Diamond Drills vs. Standard Mini Drills
Feature |
SMART CUT® 015DSE |
Conventional Diamond Drills |
---|---|---|
|
||
Diamond Grit Type |
Precision-graded, High Quality synthetic diamond |
Medium to Low Grade diamond |
Diamond Grit Quality |
High-quality, consistent hardness and toughness |
Inconsistent quality, variable toughness |
Diamond Grit Size Consistency |
Tightly controlled for uniform performance |
Large variations in grit size |
Diamond Distribution Uniformity |
Evenly distributed for consistent cutting |
Unevenly distributed, causing irregular cutting |
Diamond Exposure & Retention |
Strong retention, long-lasting exposure |
Weak retention, diamonds wear out quickly |
Bond Type |
Multi-layered nickel bond |
Single-layer nickel bond |
Diamond Layer Thickness |
Thick, uniform multi-layered coating |
Thin and inconsistent coating |
Diamond Wear Rate |
Slow wear rate, long-lasting performance |
Fast wear rate, short lifespan |
Diamond Cutting Efficiency |
High cutting efficiency, smooth operation |
Lower efficiency, requires more pressure |
Heat Resistance of Diamond Section |
Excellent heat resistance, reduced thermal damage |
Poor heat resistance, prone to overheating |
Impact Resistance of Diamond Section |
Superior impact resistance, minimal fracture risk |
Brittle, high risk of fractures |
Ability to Cut Hard & Brittle Materials |
Cuts ultra-hard materials with precision |
Struggles with ultra-hard and brittle materials |
Resistance to Diamond Pullout |
High resistance to diamond pullout |
High risk of diamond pullout |
Diamond Coating Integrity Over Time |
Remains intact even after multiple uses |
Degrades quickly, reducing effectiveness |
Sharpness Retention During Drilling |
Sharp cutting edges retained over long usage |
Edges dull quickly, requiring frequent replacement |
Surface Finish Quality After Drilling |
Consistently smooth and precise surface finish |
Rough and inconsistent surface finish |
Diamond Depth & Coating Height |
Optimized diamond depth for extended use |
Shallow diamond depth, wears out fast |
Diamond Orientation for Cutting |
Engineered for maximum cutting performance |
Random orientation, reducing effectiveness |
Number of Diamond Layers |
Multiple layers for increased longevity |
Single-layer coating, short lifespan |
RECOMMENDED APPLICATIONS
For Electroplated Diamond Drills
Electroplated diamond drills usually have a single layer of diamonds, held by a tough durable nickel alloy. Providing high diamond concentration and maximum diamond particle (grit) exposure/protrusion ratio. This provides freer, faster drilling action with minimum heat generation. Electroplated Diamond Drills provide excellent performance on softer materials ranging from 6 to 1 on mohs scale of hardness. While electroplated diamond drills, specifically manufactured by UKAM Industrial, will still work on harder materials (up to 9 on mohs scale). Diamond drill life will be (very short) significantly reduced. Diamonds stay on the surface of the drill allowing for fast material removal. Perfect for softer, more ductile, and gummable materials.
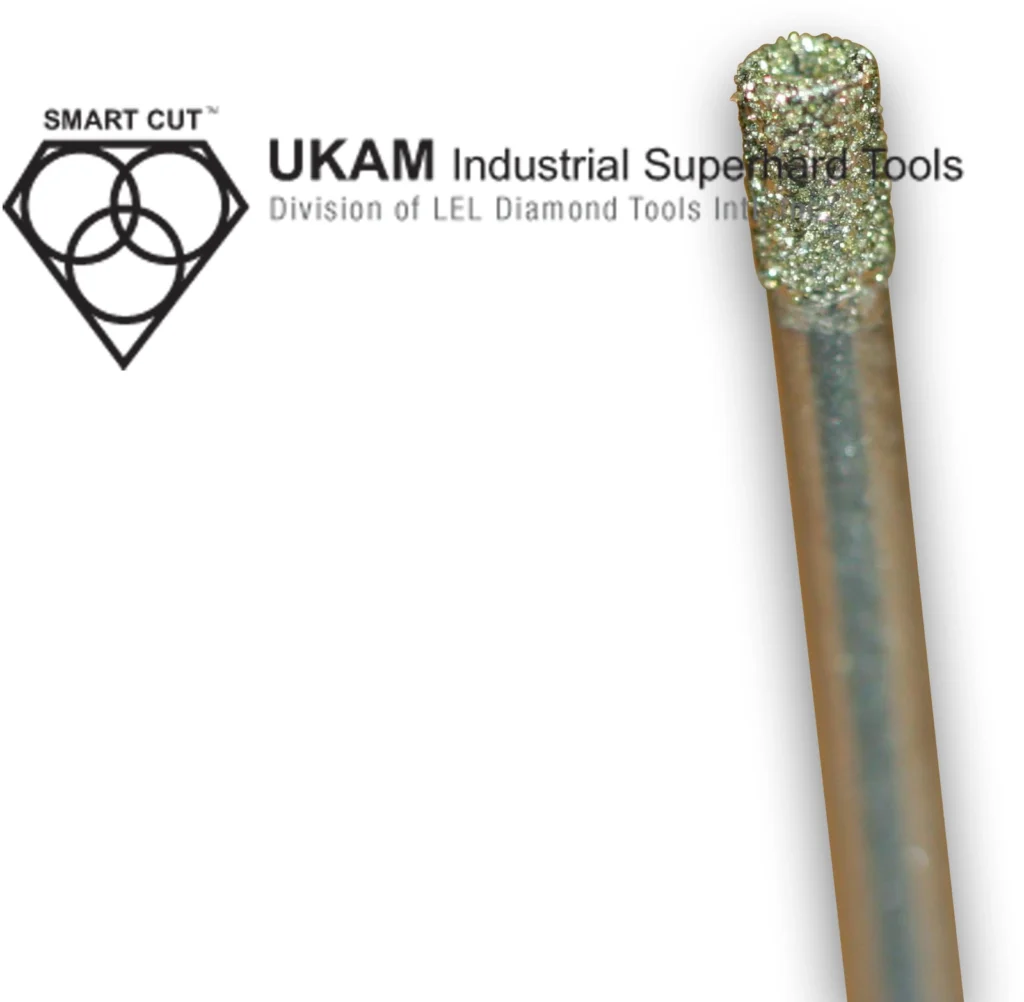
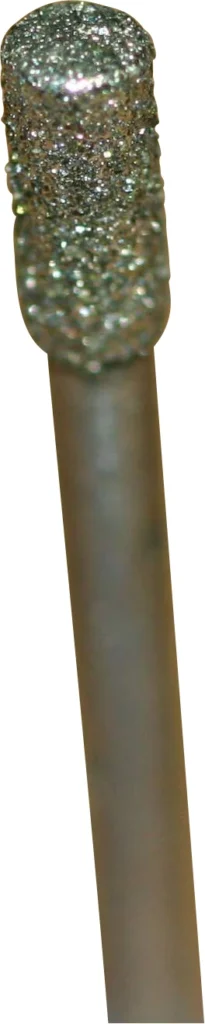
Not recommended for drilling very abrasive materials such as sandstone and concrete (they will wear out on these materials almost immediately). Electroplated Diamond Drills last less than metal bond drills and are the least expensive diamond drills available. They provide very smooth surface finish quality & less thermal damage to the part being drilled.
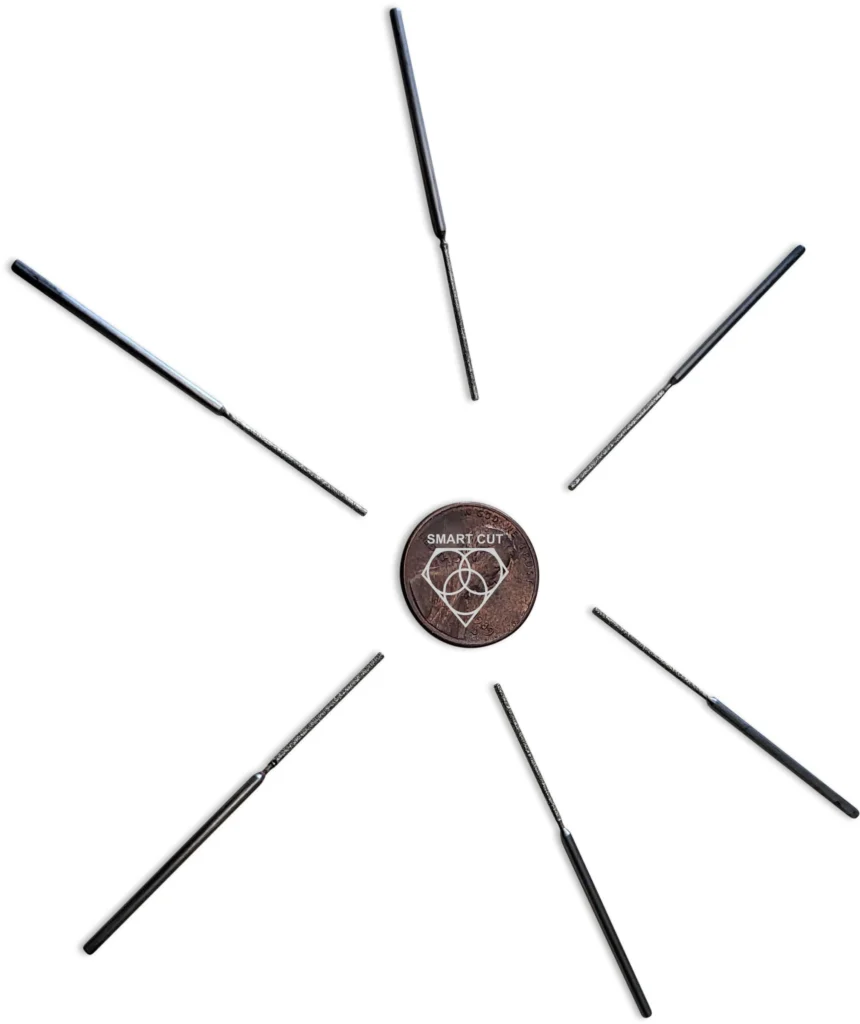
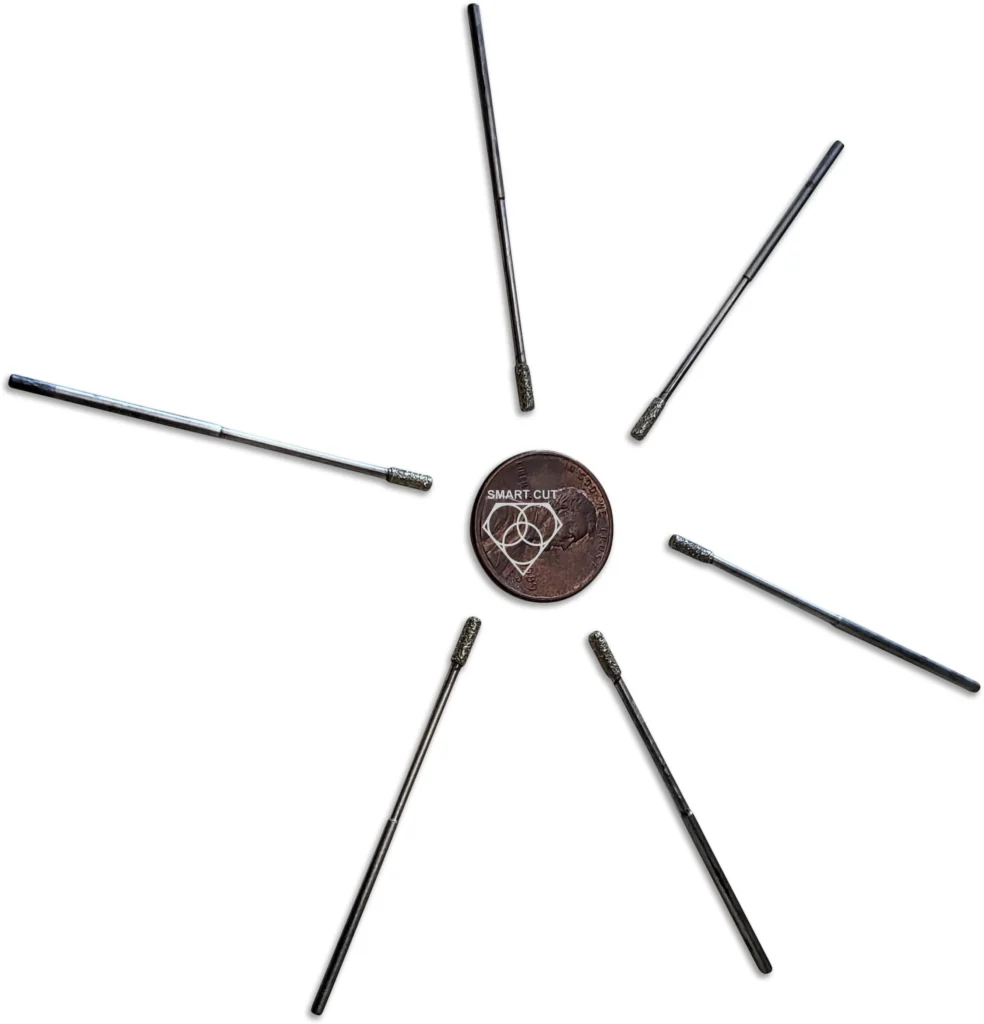
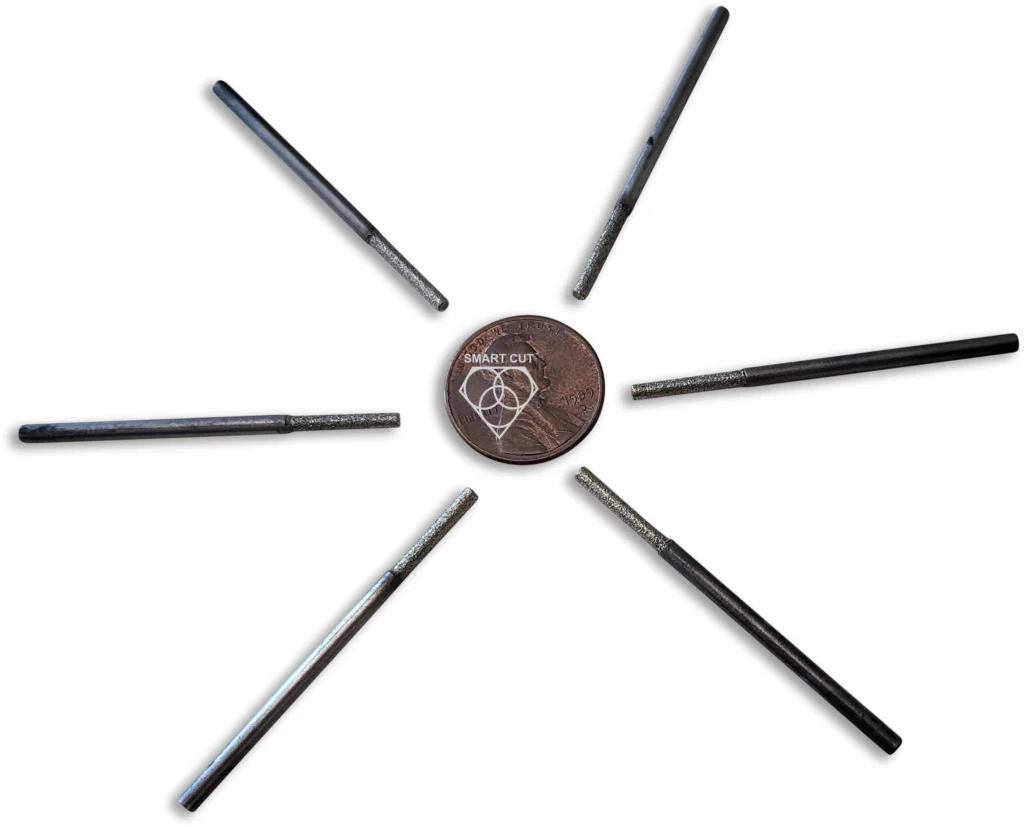
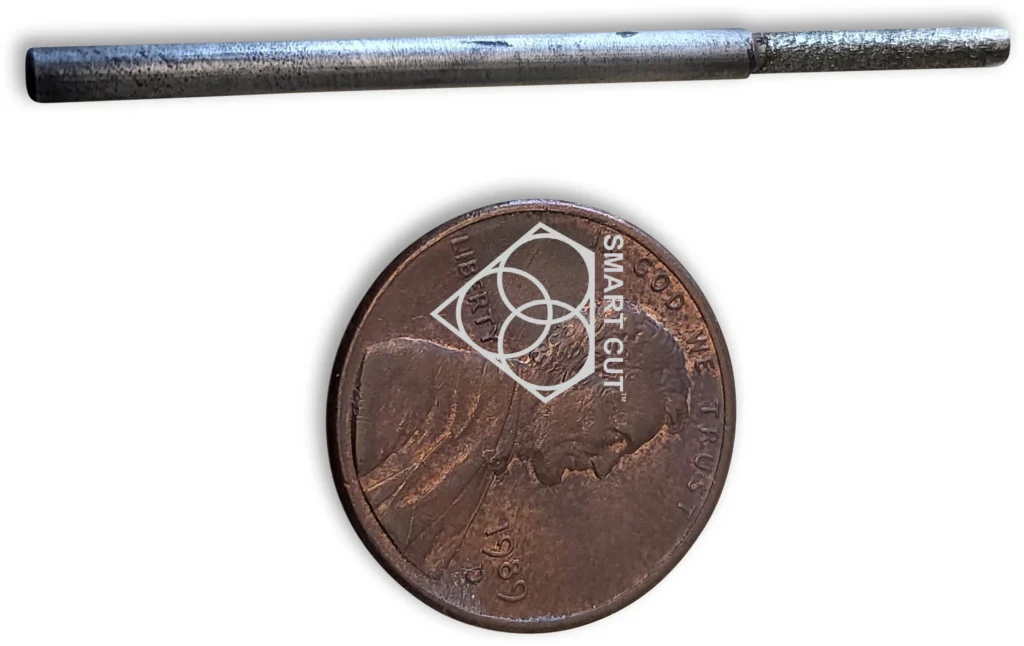
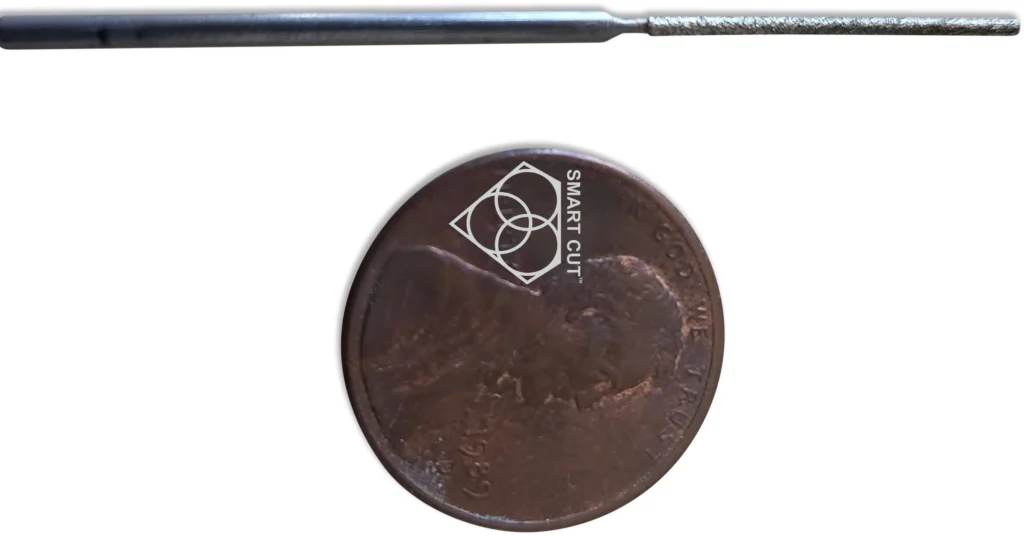
Electroplated diamond drills are frequently used in glass and composite industries (as well as some photonics / optics) applications. Electroplated Diamond Drills are designed for small & occasional use. They are widely used by beginning diamond drill users (novices) in numerous hobby/craft applications. Such as drilling beads, clock faces, and etc. (not recommended for professional or serious industrial use).
They are also usually more forgiving to operator/user drilling mistakes than most other types of diamond drills/bits. Electroplated core drills are just about the only type of diamond drill that may be used dry (without coolant) in a few applications if needed. Best performance and results will be achieved when drilling less than 1/4" (6.35mm) into material. Performance/Life in many harder materials will decline when drilling thicker materials.
SMART CUT® Difference
How SMART CUT® Mini Multi Layered Electroplated Diamond Drills are Different in comparison to other Mini Electroplated Diamond Drills.
Faster Drilling Action
Diamond drills made utilizing SMART CUT® technology are much more aggressive than your conventional drills. They can drill faster, while still leaving behind a smooth finish free of material deformation.
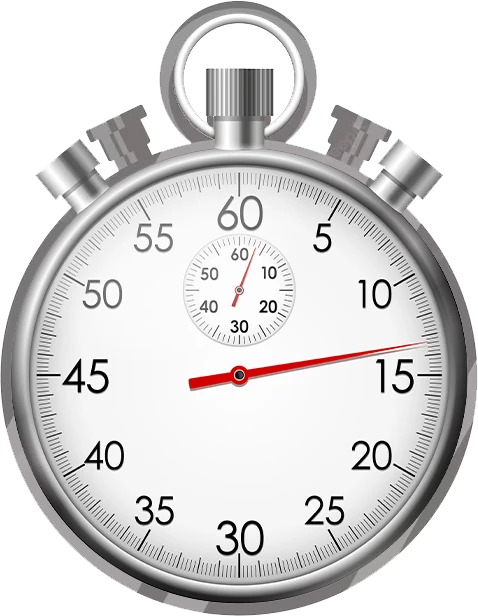
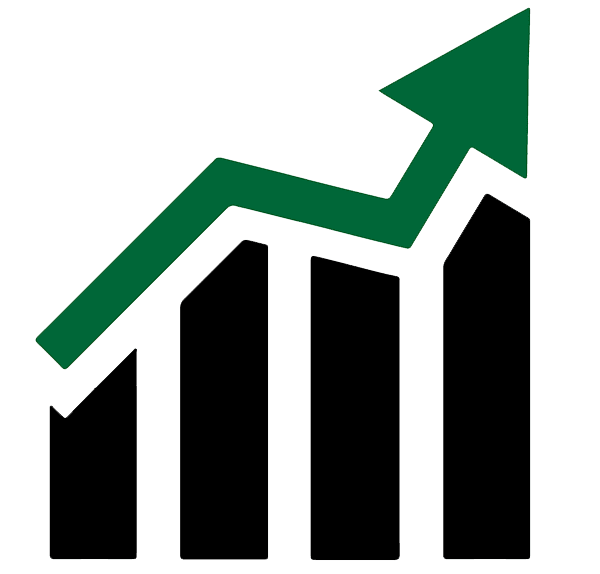
Longer Life
In most cases tools manufactured utilizing SMART CUT® technology, will outlast other conventional nickel bonded diamond & CBN drills. SMART CUT® diamond & CBN tools are more sturdy than tools manufactured with conventional technologies. They are capable to retain their form and bond configuration all the way through the tools life.
More Consistent Performance
SMART CUT Multi Layered Electroplated Diamond Drills have three diamond layers impregnated inside the bond matrix. Unlike Many Other drill Types, they wear evenly, and are known for their consistency. You will get consistent cutting speed, and overall consistent performance, with minimum amount of dressing even on the hardest to cut materials
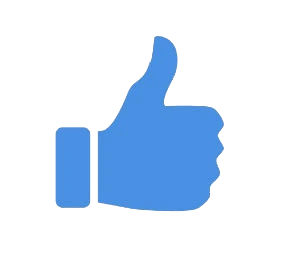
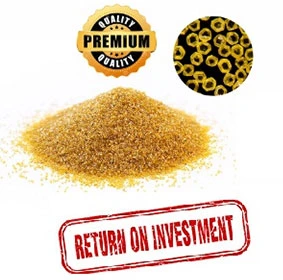
Manufactured Using The Highest Quality Raw Materials
Only the highest quality synthetic diamonds and raw materials are used in the manufacturing process. The highest quality standards and product consistency is maintained, using sophisticated inspection and measurement equipment.
Best Performance & Value on the Market
SMART CUT® Multi Layered Electroplated Diamond Drills are the best investment you can make! Although they may cost more than electroplated (nickel bond), Diamond Drills. They will more than pay for themselves in terms of overall performance and provide best Return on Investment.
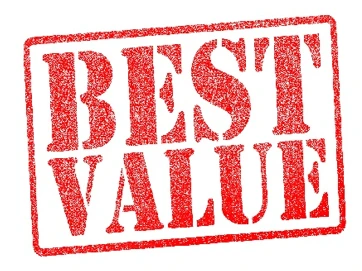
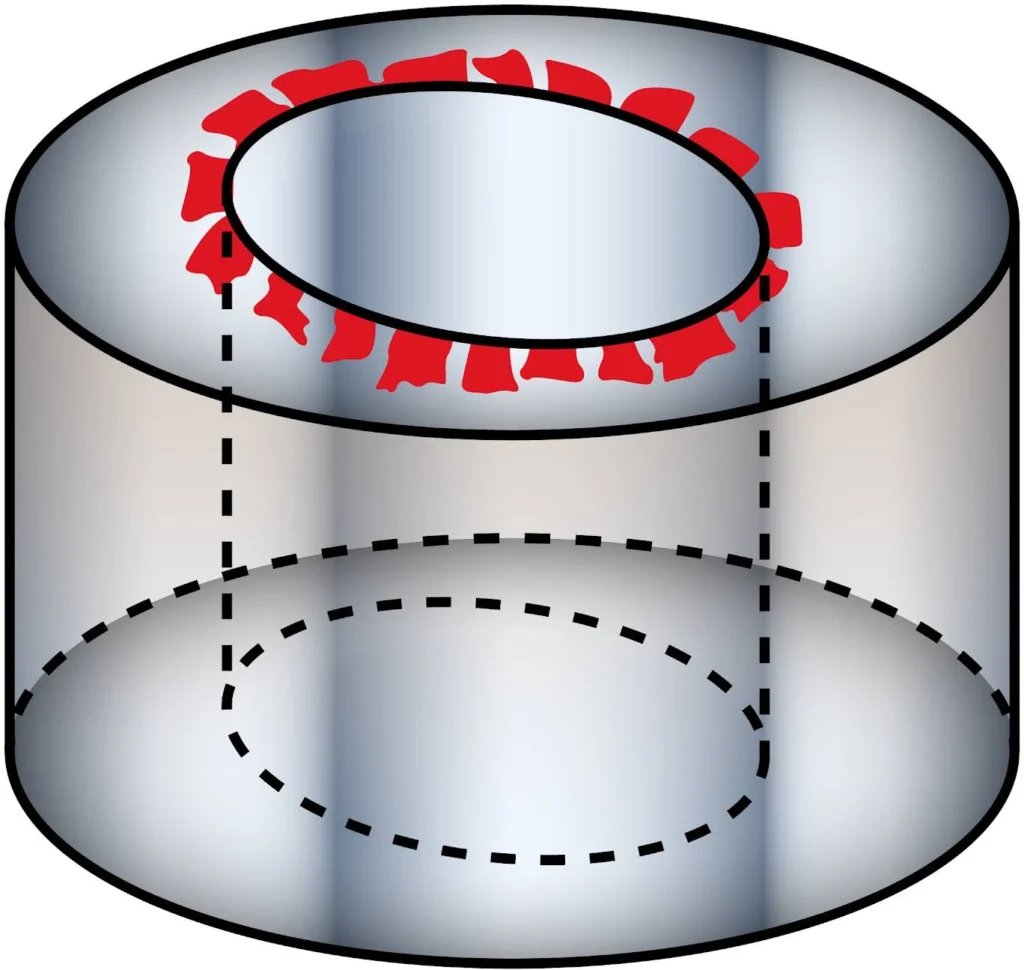
Minimize Chipping & Improve Surface Finish
SMART CUT Multi Layered Electroplated Diamond Drills have diamonds oriented and evenly distributed in a bond matrix. Providing faster, freer cutting action with minimum heat generation. This translates in improved surface finish and minimum chipping.
About Nickel Bond (Electroplated) Tools
Electroplated (Nickel Bond) diamond products usually have a single layer of diamonds, held by a tough durable nickel alloy. Nickel is frequently used as a base for plating diamond. Because of its excellent strength, toughness and flexibility during the plating process. Electroplated diamond products are able to retain their original shape and dimensions thought their working life. Unlike sintered (meal bond) or resin bond diamond products, where diamond particles are buried in bond and held together by metal or resin binder deep inside. Electroplating allows diamond particles to protrude from the bond matrix, providing a free, faster cutting action with minimum heat generation.
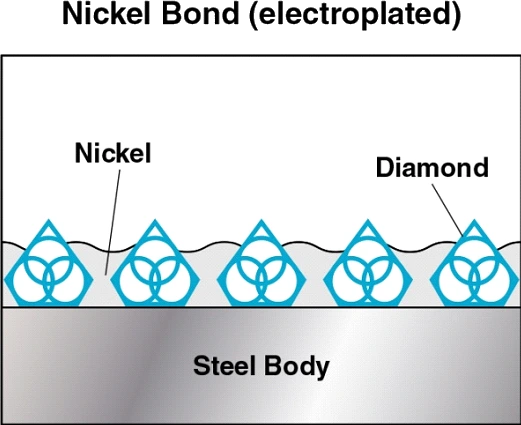
Electroplated Diamond Products Manufactured by UKAM Industrial are Multi Layered. They have 3 layers of diamonds, not just 1 layer of diamonds like conventional electroplated diamond tools.
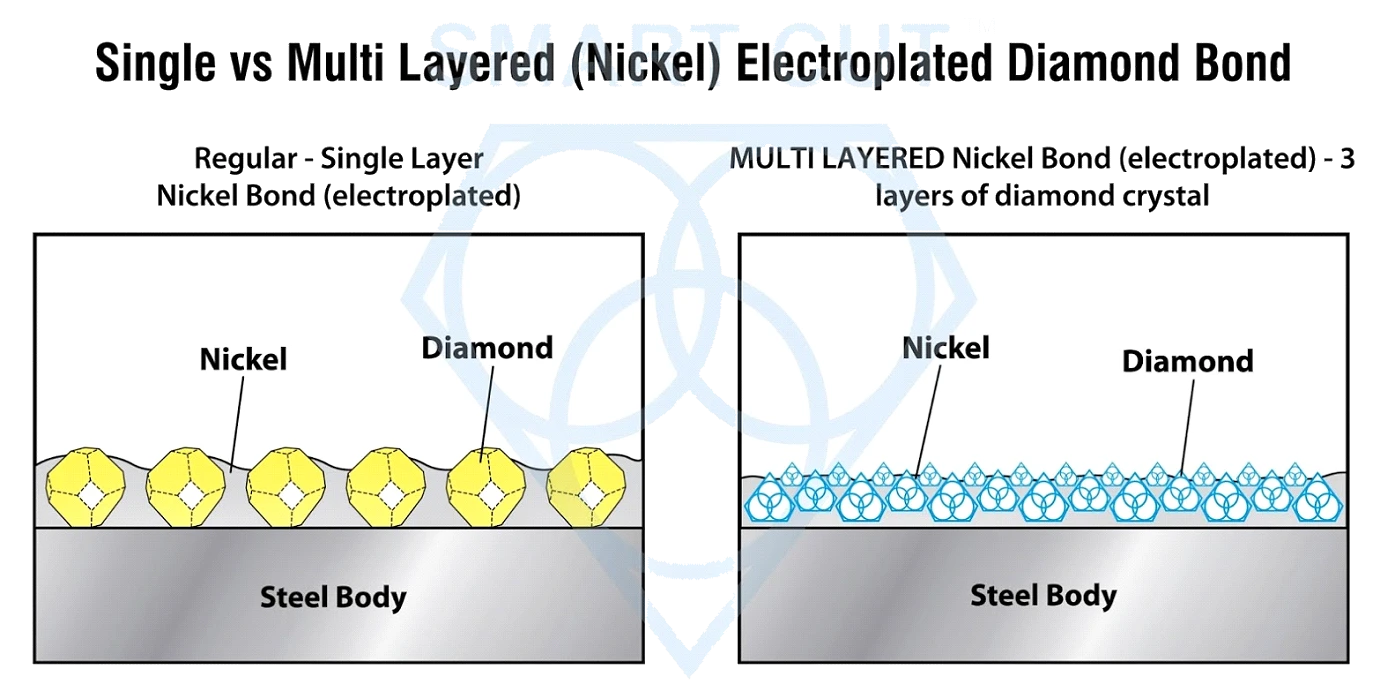
Its what you cant see that makes all the Difference
How SMART CUT® Bond Works?
The sharpest and finest quality diamonds or CBN crystals that go into a SMART CUT® Diamond Bond, immediately penetrate into the material, grinding and polishing as they cut.
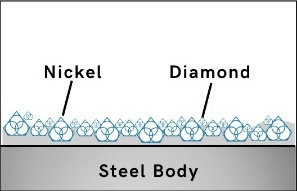
Diamonds or CB Crystals are activated only at the exposed layer. As Bond Matrix layer begin to wear out, diamonds in a new Bond Matrix layer are immediately activated, substituting the already used up diamond layer. The SMART CUT® Bond Diamond Bond makes sure every diamond is in the right place. and at the right time, working where you need it most.
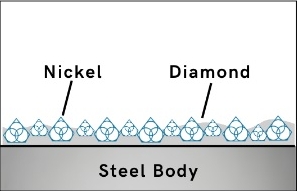
The newly exposed diamonds don't effect diamonds already working on the material. Unlike many other diamond bonds, diamonds in a SMART CUT® remains sharp and grow sharper with each cut, prolonging product life and consistent performance.
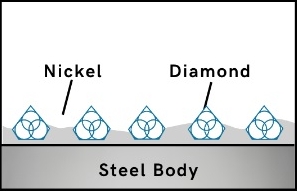
This advanced formulated open diamond bond design insures minimal chipping, fast cut, constant speed of cut, minimal cutting noise, and most important of all, consistent performance.
How SMART CUT ® Bond Works?
Step 1
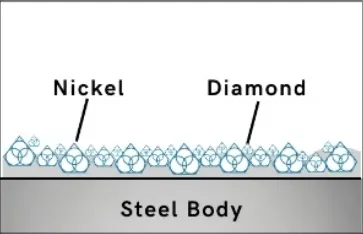
Sharpest And Finest Quality Diamonds
Diamonds or CBN Crystals are activated only at the exposed layer. As Bond Matrix layer begin to wear out, diamonds in a new Bond Matrix layer are immediately activated, substituting the already used up diamond layer. The SMART CUT® Bond Diamond Bond makes sure every diamond is in the right place. and at the right time, working where you need it most.
Step 2
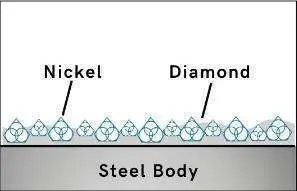
Diamonds or CBN Crystals
The newly exposed diamonds don’t effect diamonds already working on the material. Unlike many other diamond bonds, diamonds in a SMART CUT® remains sharp and grow sharper with each cut, prolonging product life and consistent performance.
Step 3
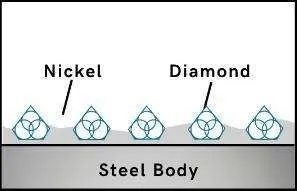
Advanced Formulated Open Diamond Bond Design
This advanced formulated open diamond bond design insures minimal chipping, fast
cut, constant speed of cut, minimal cutting noise, and most important of all, consistent performance.
Related Products
SMART CUT® 030DSM
METAL BOND (SINTERED) DIAMOND SOLID DRILLS
SMART CUT 030DSM, Metal Bond (Sintered) Diamond Solid Drills have hundreds of layers of diamond impregnated inside the metal matrix. Will last significantly longer than electroplated diamond solid drills. Recommended for drilling Ultra Hard Materials (harder than 8 on mohes scale or 60 on Rockwell Scale. Available in stock from 0.8mm to 6mm diameter. Sintered (Metal Bond) diamond solid miniature/thin drills – have hundreds of layers of diamond impregnated inside metal matrix. These miniature drills will last significantly longer than electroplated diamond solid drills. Recommended for drilling Ultra Hard Materials (harder than 8 on mohes scale or 60 on Rockwell Scale and clients that need very long life span. Varying with application and material, an average electroplated diamond sold drill drill will last you 10 to 15 holes. Metal Bond (Sintered) Diamond Solid Drill may last as much as 120+ holes (when used properly).SMART CUT® 025DTE
MINATURE TWISTED ELECTROPLATED DIAMOND SOLID DRILLS
SMART CUT® 025DTE Miniature Twisted Electroplated Diamond Solid Drills are high-performance precision tools designed for micro-drilling and reaming applications in a wide variety of materials. These drills are especially well-suited for drilling pearls, where material sensitivity and surface integrity are critical. Their twisted flute design promotes faster material removal and improved chip evacuation, enabling significantly higher drilling speeds compared to standard diamond drills. This advanced geometry also contributes to smoother hole finishes and reduced risk of cracking or chipping, making them ideal for delicate materials such as natural and cultured pearls, beads, ceramics, glass, composites, shells, and even certain metals and hardened materials in niche applications. The electroplated diamond layer is applied directly onto a solid steel shank, exposing sharp diamond particles that enhance cutting efficiency and tool longevity.SMART CUT® 020DHE
MINATURE ELECTROPLATED DIAMOND HOLLO CORE DRILLS
SMART CUT® 020DHE Electroplated miniature hollow core drills are precision-engineered tools designed for drilling small, holes in a wide range of materials. These drills consist of a steel tube with a diamond coating applied to the tip, ensuring superior cutting ability even in the hardest and most brittle materials. Available from stock in diameters ranging from 1 mm to 3.5 mm OD. SMART CUT® 020DHE hollow core plays an important role in enhancing stability, particularly in deep drilling applications. This feature allows for precise control, ensuring the drill remains aligned throughout the process. It also minimizes deflection and bending, common issues when using solid drills for small-diameter, deep holes. As a result, users can achieve more accurate and clean-cut drilling with reduced risks of damage to both the tool and the material.Recently Viewed Products
ARE YOU USING RIGHT DIAMOND CORE DRILLS & TOOLS
FOR YOUR APPLICATION?
LET US
HELP YOU
HAVING ISSUES WITH
YOUR CURRENT DIAMOND CORE DRILLS & TOOLS?
Knowledge Center
02
Jun
Select right Diamond Drill for your application
Learn important diamond drill methodology. understand diamond drill specifications and their differences Selecting the right Diamond Drills/Bits for your application is key to obtaining desired diamond drilling results. Using the Right Diamond Drill will...
02
Jun
How to Properly Use Precision Diamond Drills
Step by step guide on how to properly use and care for your diamond drills. Selecting the right diamond drill/diamond drill bit parameters, often involves a trial and error process. Many which can be avoided...
02
Jun
Diamond Drills Guide
Diamond are used across large variety of industries and applications. This guide explores the wide range of diamond drill types, including hollow core drills designed for removing a cylindrical core, non-core formation drills that grind...
02
Jun
Diamond Tools Guide – Selecting Right Drills & Tools for your application
These tools are used for many different industries grinding and shaping material into different forms, expanding exiting inside diameters, grinding, finishing and polishing existing material. Grinding different angles and radius, creating cavities of various forms,...
02
Jun
Optimizing your Diamond Drilling Operation
There are numerous factors that influence the performance of diamond drills. Understanding these factors helps users select the appropriate diamond drill specifications for their specific applications, optimizing drilling operations to achieve maximum efficiency....
02
Jun
Micro Drilling Guide
Share this Article with Friend or Colleague
In order for you to get the most out of your diamond micro drill or carbide / high speed steel micro drill, we strongly urge you to read...
02
Jun
Selecting Right Drilling Equipment for your Application. What you features & functionality you should look for?
Share this Article with Friend or Colleague
There are hundreds or even thousands of different drilling equipment options. Selecting the right equipment for a specific application involves carefully considering several variables and attributes of the...
03
May
Diamond Core Drill & Drill Trouble Shooting Guide
Learn the most common problems most people have in using diamond drills. How to resolve them and avoid them in first place
https://ukam.com/wp-content/uploads/2024/07/diamond-drill-troublehsooting-guide.mp4
Troubleshooting Drilling Problems
Having issues with your diamond drilling operation? This Illustrated Guide...
09
Sep
Understanding & Calculating Return on Investment for Diamond Core Drills & Other Tools
The term "ROI" (Return On Investment) is widely used across industries, often interpreted differently depending on the context. However, few truly understand what ROI represents and its specific implications, particularly in the context of diamond...
09
Sep
Understanding Tradeoffs – Searching for Perfect Diamond Drill & Tool
Choosing the right diamond drill or tool can significantly impact efficiency, cost, and quality. However, this is not a simple and clear-cut process. Selecting the optimal drill or tool involves navigating a complex landscape of...
19
Sep
Why Use Diamond Drills?
Diamond, known as the hardest material on Earth, enables diamond drills and tools to grind away material at a micro (nano) scale. This extreme hardness allows diamond tools to effectively work on materials with a...
- Unmatched Selection For Many Applications
- Superior Quality & Consistency
- Immediate Worldwide Delivery
- Technical Support & Expertise
- American Based Manufacturer
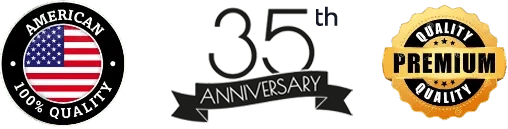

- Different Product
- Different Technology
- Different Company
- Expect MORE from your tools
Let Us HELP You!
Subscribe To Our Newsletter
Signup for email offers, updates, and more
Contact Us
- 25205 & 25201 Avenue Tibbits Valencia CA 91355 USA
-
Phone : (661) 257-2288
FAX : (661) 257 -3833 - lel@ukam.com
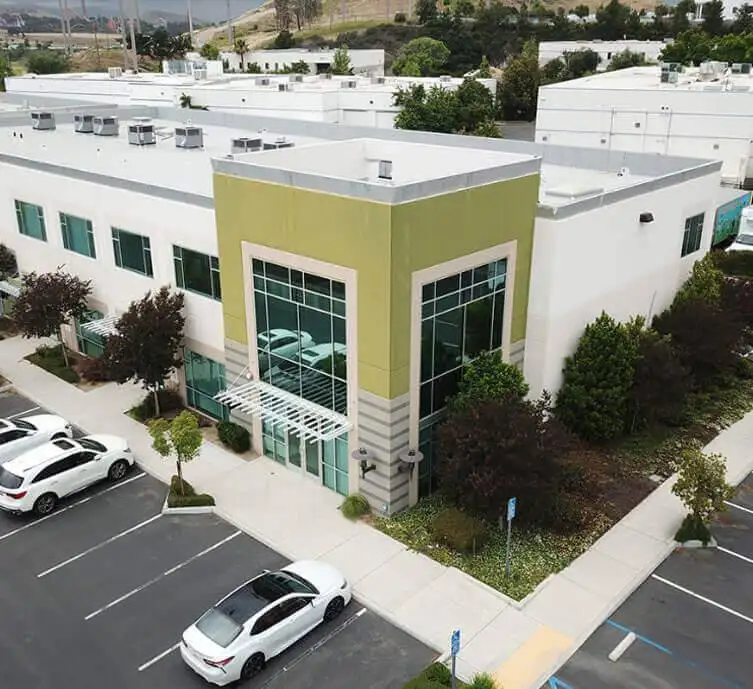
UKAM Industrial Superhard Tools is a U.S. High Technology, Specialty Diamond Tool & Equipment manufacturer. We specialize in producing ultra thin, high precision cutting blades, precision cutting machines diamond drills, diamond micro tools, standard & custom advanced industrial diamond tools and consumables.
- 25205 & 25201 Avenue Tibbits Valencia CA 91355 USA
-
Phone : (661) 257-2288
FAX : (661) 257 -3833 - lel@ukam.com
- 25205 & 25201 Avenue Tibbits Valencia CA 91355 USA
-
Phone : (661) 257-2288
FAX : (661) 257 -3833 - lel@ukam.com
DIAMOND TOOLS BY BOND
EQUIPMENT
KNOWLEDGE CENTER
OUR PRODUCTS
COMPANY
CUSTOMER SERVICE
Shipping Methods


Safe & Secure Payments

© Copyright 1990-2025. UKAM Industrial Superhard Tools – Terms of Use