Table of Contents
ToggleGrinding is a fundamental mechanical process in metallography that involves removing material from a specimen using hard, abrasive particles. This process is essential for preparing specimens for microscopic examination as it establishes a smooth and uniform surface by eliminating deformations, scratches, and other imperfections from earlier stages such as sectioning.
Key Aspects and Techniques of Grinding
-
Material Removal Rate: This rate is influenced by the grit size of the abrasive, the speed of the grinding equipment, and the pressure applied. Using larger grits and higher speeds can accelerate material removal but may also increase the risk of new deformations. The goal is to find a balance that allows effective removal without damaging the specimen.
-
Surface Integrity: Achieving a flat, damage-free surface is crucial for accurate microscopic analysis. The selection of abrasives, grinding parameters, and equipment plays a significant role in maintaining this integrity.
-
Heat Management: Managing heat generation is critical during grinding. Excessive heat can alter the material properties of the specimen and potentially lead to inaccurate interpretations of its microstructure.
What is Grinding - Steps and Abrasives
In the process of grinding metallographic specimens, it's essential to begin with the coarsest abrasive that will effectively flatten the surface and mitigate the effects of sectioning. Typically, a grit size ranging from 180 to 240 is suitable for surfaces that have been cut by abrasive wheels. For surfaces that have undergone more rough treatments, such as those cut by hacksaws, a grit size between 120 and 180 is recommended.
As the grinding process progresses, it is important to transition to progressively finer abrasives. This usually involves moving from 220 or 240 grit up to 600 grit. This gradual transition is crucial as it helps to minimize surface damage while still allowing for effective material removal. Maintaining the integrity of the specimen’s surface is vital for accurate further analysis and preparation.
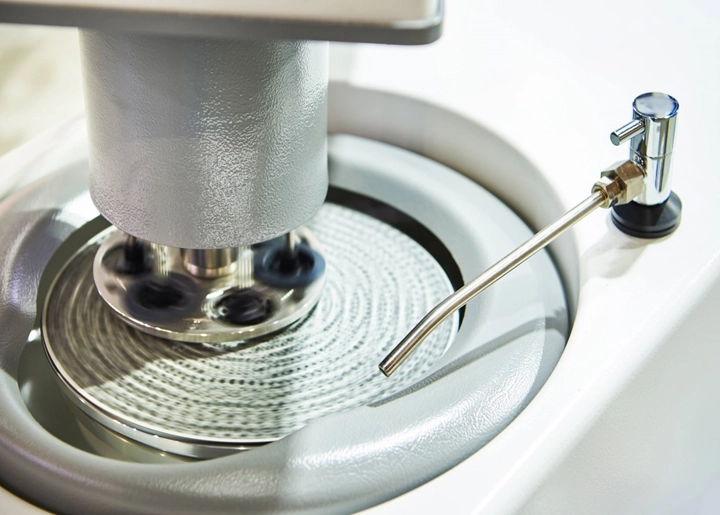
Grinding should ideally be conducted under wet conditions whenever possible. This practice helps keep the specimen cool, minimizing the heat effects that can alter material properties and prevents the abrasive from clogging with metal particles, which can compromise the grinding effectiveness and potentially damage the specimen.
Each step in the grinding process is designed to remove the surface damage inflicted by the previous one. While using finer abrasives tends to reduce the damage, it also decreases the material removal rate. Therefore, finding the right balance of abrasive size is critical, particularly considering the hardness of the material being processed.
In automated grinding setups, the initial step often involves planar grinding. This critical phase aims to remove any damage from sectioning and level all specimens to a uniform plane, which is essential for consistent results in subsequent processes. For this purpose, abrasives such as silicon carbide and alumina are commonly used. However, for very hard materials, the application of metal-bonded or resin-bonded diamond disks may be more appropriate. These disks, which feature uniformly distributed diamond particles, are available in a range of grit sizes from about 70 to 9 micrometers and are highly effective in achieving the desired surface quality.
An innovative alternative to traditional SiC papers for planar grinding involves using a stainless steel woven mesh cloth that is charged with a coarse diamond slurry. This method is particularly effective for achieving flat and uniform planar surfaces, leveraging the cutting power of diamond particles to efficiently prepare the specimen for further analysis and treatment. This approach not only enhances the grinding process but also contributes to the overall preparation quality of the metallographic specimens.
Alternatives and Innovations
After establishing planar surfaces, there are several single-step alternatives to finer SiC papers that can simplify the process. These include using platens, thick woven polyester cloths, silk, or rigid grinding disks with an intermediate diamond grit size of 9 to 3 micrometers. These methods allow continued effective grinding without the need for progressively finer grit papers.
This streamlined approach not only maintains the integrity of the specimen for accurate microscopic examination but also enhances the efficiency and effectiveness of the metallographic preparation process.
Step-by-Step Guide on the Grinding Process for Metallographic Samples
Grinding is an essential phase in the preparation of metallographic samples, crucial for achieving a perfectly flat and damage-free surface necessary for microscopic examination. Here is a detailed, sequential guide to the grinding process:
Specimen Mounting: Before grinding, it's imperative to securely mount the specimen. Typically, this involves embedding the specimen in a mounting resin, which stabilizes it and protects delicate edges during grinding. The choice between conductive and non-conductive resins depends on the material’s nature and the requirements of the analysis. The mounting medium should not stress or thermally damage the specimen.
Initial Grinding: The process begins with using a coarse abrasive, such as grit 120-180, aimed at removing major surface deformations and imperfections. This step is critical for leveling the specimen and preparing it for further refinement. It’s important to apply uniform pressure and keep the specimen cool to prevent the introduction of thermal or mechanical stresses.
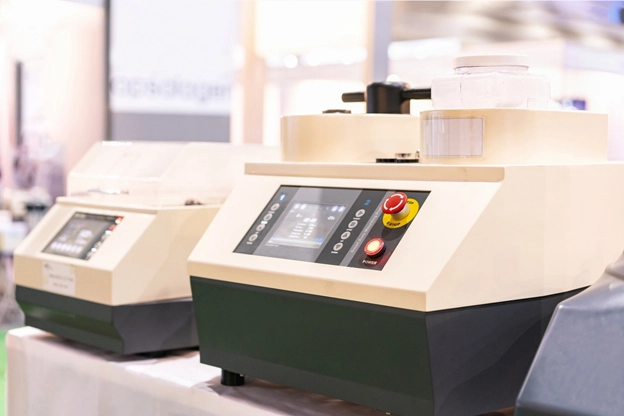
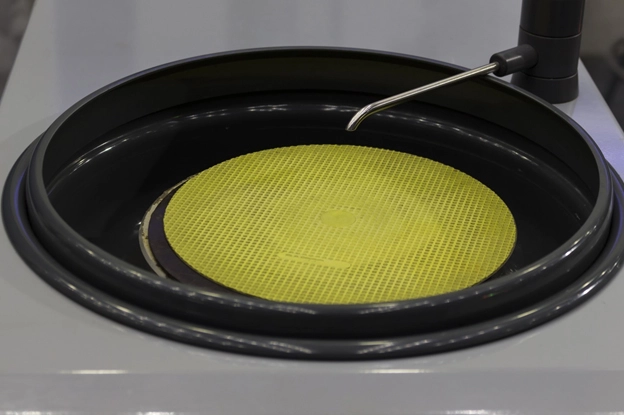
Intermediate Grinding: After leveling the specimen, the next step involves switching to a medium-grit abrasive, approximately grit 240-320. This stage focuses on smoothing the surface further and eliminating the deeper scratches left by the coarser abrasive. Continuous monitoring of the specimen’s surface during this phase ensures consistent material removal and prevents over-grinding.
Fine Grinding: The third phase transitions to using fine-grit abrasives, such as grit 400-600, to prepare the surface for polishing by achieving a finer finish. This stage is vital for minimizing surface damage and scratches, crucial for the precise microscopic analysis that follows. Gradually moving to finer grits ensures that each previous scratch pattern is effectively removed.
Cleaning: Between each grinding stage, thorough cleaning of the specimen and the grinding equipment is crucial. This can be done using clean, flowing water, possibly with a mild detergent, followed by a rinse with distilled water, and drying with clean, soft cloths or air blowing. This step is essential to prevent contamination and ensures that no residual abrasive particles are left that could scratch the specimen in subsequent finer grinding or polishing steps.
Inspection: After the fine grinding step, a meticulous inspection of the specimen is necessary using a microscope or magnifying glass. This is to verify that the surface is free of any residual scratches or imperfections and to ensure uniformity and smoothness. These qualities indicate a properly prepared surface that will not distort the microscopic examinations to come.
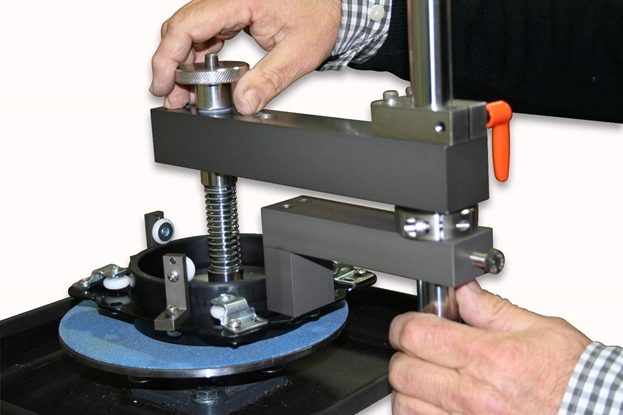
Differentiation between Grinding and Polishing
While both grinding and polishing are abrasive processes used in the preparation of specimens, they serve different purposes and are characterized by distinct differences:
-
Purpose: Grinding is primarily used to remove large amounts of material and to produce a flat surface. Polishing, on the other hand, is used to produce a mirror-like, smooth finish and is critical for enhancing the clarity and contrast of the microstructure under examination.
-
Abrasive Size: Grinding uses coarser abrasives to remove material efficiently, whereas polishing uses finer abrasives to minimize surface scratches and improve finish.
-
Equipment and Consumables: Polishing often requires different equipment and consumables, such as polishing cloths, finer abrasive particles (often in a slurry), and lower speeds to prevent damage to the specimen’s surface.
Table of Comparison for Grinding vs Polishing
Aspect |
Grinding |
Polishing |
---|---|---|
Purpose |
Used to remove large amounts of material and produce a flat surface. |
Used to produce a mirror-like, smooth finish and enhance clarity and contrast of the microstructure. |
Abrasive Size |
Coarser abrasives for efficient material removal. |
Finer abrasives to minimize surface scratches and improve finish. |
Equipment and Consumables |
Standard grinding equipment, such as grinding wheels and discs. |
Requires specialized equipment like polishing cloths, finer abrasive particles (often in slurry form), and typically lower speeds to prevent surface damage. |
Grinding Media
The abrasives typically used for metallographic specimen preparation include silicon carbide (SiC), aluminum oxide (Al2O3), emery (Al2O3 - Fe3O4), composite ceramics, and diamond. Among these, emery paper has fallen out of favor in modern metallography due to its relatively low efficiency in cutting. Silicon carbide is widely preferred and is commonly available as waterproof paper. Although less prevalent, aluminum oxide papers often provide a higher cutting rate than silicon carbide, especially for certain metals.
These grinding abrasives are adhered to backings made of paper, polymer, or cloth, which are available in different weights. They come in various forms such as sheets, discs, and belts to suit different applications. There is also some use of standard grinding wheels, where abrasives are embedded within a bonding material.
Additionally, these abrasives can be used in powder form. This involves charging the grinding surfaces with the abrasives mixed into a premade slurry or suspension. It's worth noting that finer SiC papers can cause embedding issues when grinding softer metals like lead (Pb), tin (Sn), cadmium (Cd), and bismuth (Bi). Embedding problems also occur with diamond abrasives, particularly when grinding soft metals and aluminum, especially when using slurries on napless cloths.
Types of Abrasives Used in Grinding
Silicon Carbide (SiC)
Silicon Carbide is a synthetic abrasive created through a high-temperature reaction between silica and carbon. It features a hexagonal-rhombohedral crystal structure and possesses a hardness of approximately 2500 HV. SiC is particularly valued in cutting and grinding operations for its hardness and the sharpness of its edges. It is available in a variety of grit sizes, ranging from the very coarse 60 grit to the very fine 1200 grit. This is a popular choice for grinding softer materials, as it is harder than aluminum oxide but more brittle, which makes it effective for rapid material removal under controlled conditions.
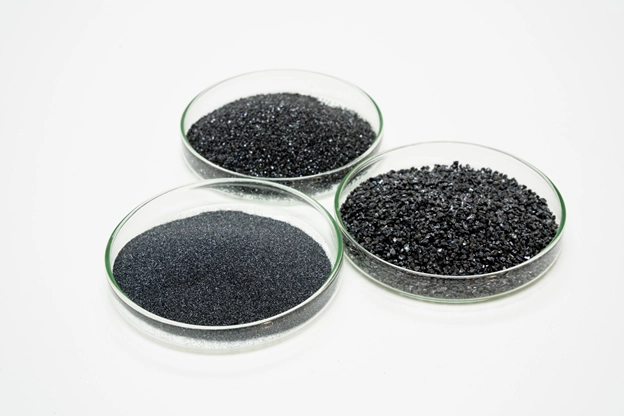
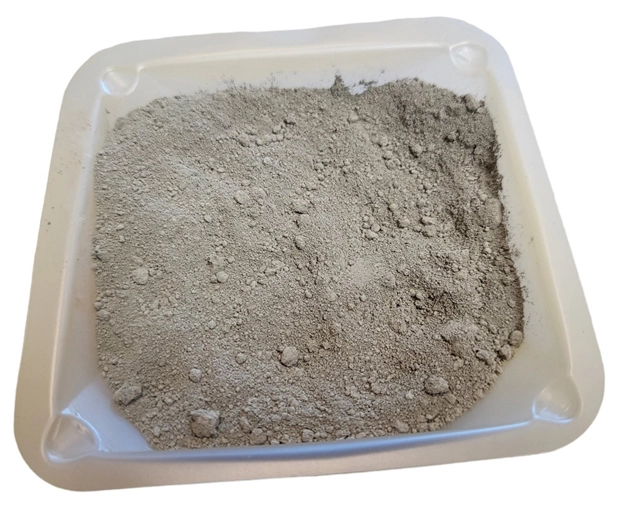
Alumina
Alumina, derived from naturally occurring bauxite, is available in two phases: the softer gamma phase (Mohs hardness of 8) and the harder alpha phase (Mohs hardness of 9, 2000 HV). Alumina abrasives are primarily used as a final polishing abrasive due to their finer grit and smoothing capabilities. Often used for ferrous alloys, aluminum oxide is a durable and cost-effective abrasive, suitable for a wide range of materials.
Diamond
Diamond, the hardest material known (Mohs hardness of 10, 8000 HV), is available in both natural and synthetic forms. It has a cubic crystal structure. For metallographic applications, synthetic polycrystalline diamond is recommended, particularly for rough polishing tasks due to its exceptional hardness and durability. Noted for its unrivaled hardness and durability, diamond abrasives are ideal for grinding very hard materials. Diamond grinding wheels are known for maintaining a sharp cutting edge and achieving high material removal rates.
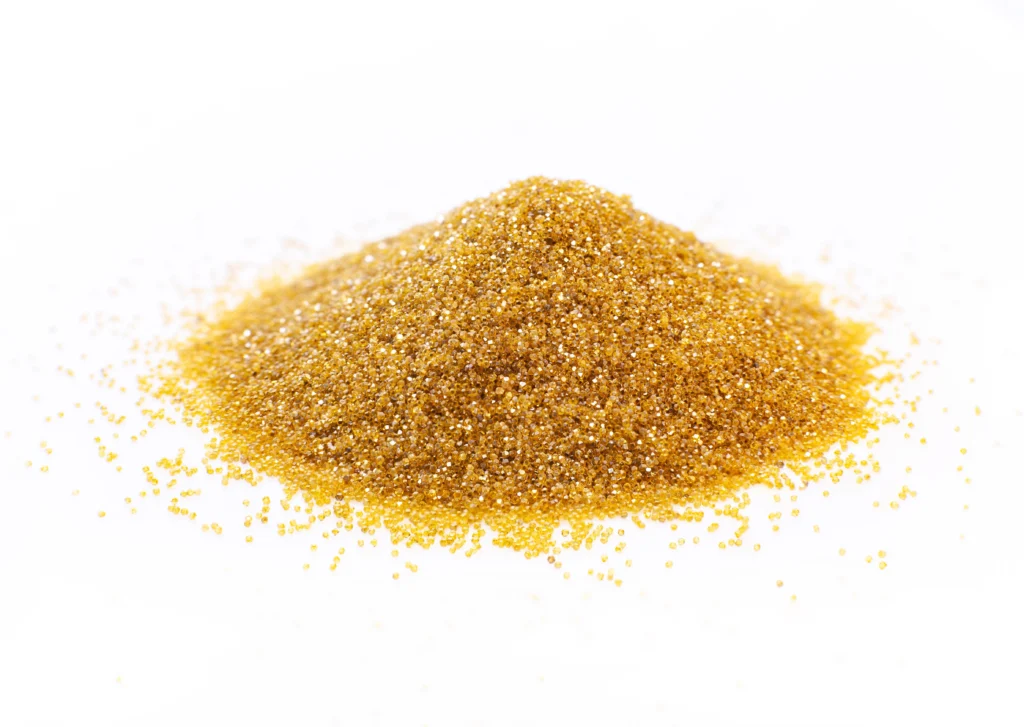
Zirconia
Zircon, or zirconium silicate, is a less common abrasive utilized for coarse grinding. It is a very tough material, which allows it to last longer in the grinding process. However, it is not as hard or sharp as other abrasives, necessitating higher pressures to be effective. Zirconia abrasives are typically available in 60 or 120 grit sizes, which are most effective for metallographic grinding.
Table of Comparison – Abrasive Types
Abrasives |
Chemical Composition |
Crystal Structure |
Hardness |
Grit Sizes |
Common Applications |
Advantages |
---|---|---|---|---|---|---|
Silicon Carbide (SiC) |
Silicon and carbon |
Hexagonal-rhombohedral |
2500 HV |
60 to 1200 grit |
Grinding softer materials |
Very hard and sharp, excellent for rapid material removal under controlled conditions. |
Alumina (Aluminum Oxide) |
Derived from bauxite |
Gamma phase (softer), Alpha phase (harder) |
Gamma: Mohs 8, Alpha: Mohs 9, 2000 HV |
Finer grits, commonly used for final polishing |
Primarily used for ferrous alloys |
Durable, cost-effective, suitable for a wide range of materials. |
Diamond |
Carbon |
Cubic |
8000 HV |
Varied, typically used for rough polishing |
Grinding very hard materials like ceramics and metals |
Unrivaled in hardness and durability, maintains sharp cutting edge, high material removal rates. |
Zirconia (Zirconium Silicate) |
Zirconium silicate |
Not specified |
Less than SiC and diamond but very tough |
Typically 60 or 120 grit |
Coarse grinding of metallographic specimens |
Very tough, lasts longer in the grinding process, effective at higher pressures. |
Recommendations for Selecting the Right Abrasive Media
Selecting the right grinding media involves several critical factors:
-
Grit Size: The grit size determines the finish and material removal rate. Coarse grits remove material faster but leave rougher surfaces, while finer grits produce a smoother finish but are slower.
-
Bonding Material: The bonding material holds the abrasive particles together. Options include vitrified (ceramic), resin, rubber, and metal bonds. Vitrified bonds are common for precision grinding; resin bonds are used for fast stock removal; rubber and metal bonds are chosen for specific applications requiring high durability.
-
Compatibility with Material: The abrasive material must be harder than the material being ground. For example, diamond is necessary for grinding ceramics, while softer materials like aluminum can be ground with silicon carbide or aluminum oxide.
Lifespan and Maintenance of Grinding Consumables
The lifespan of grinding wheels and discs depends on several factors:
-
Usage Frequency: Regular use can decrease the lifespan due to wear, but proper maintenance can extend it.
-
Material Hardness: Harder materials wear down abrasives faster than softer materials.
-
Maintenance Practices: Regular dressing (reshaping and restoring the grinding surface) of wheels can extend their useful life by exposing fresh abrasive particles and removing clogged material.
-
Storage Conditions: Proper storage in a controlled environment free from humidity and temperature fluctuations preserves the integrity of grinding consumables.
Grinding Equipment Automation
In metallography, the grinding process employs specialized equipment designed to handle the unique requirements of preparing metallographic samples:
Manual Grinding Machines:
These are the simplest form of grinding machines where the operation involves manual control over the grinding process. They are suitable for low-volume laboratories where precise control by a skilled technician is feasible.
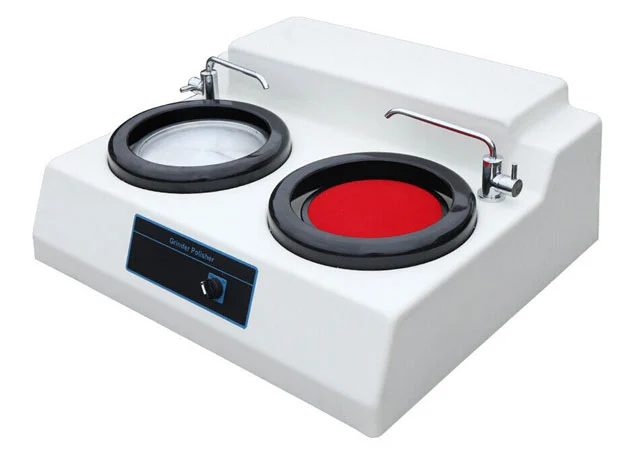
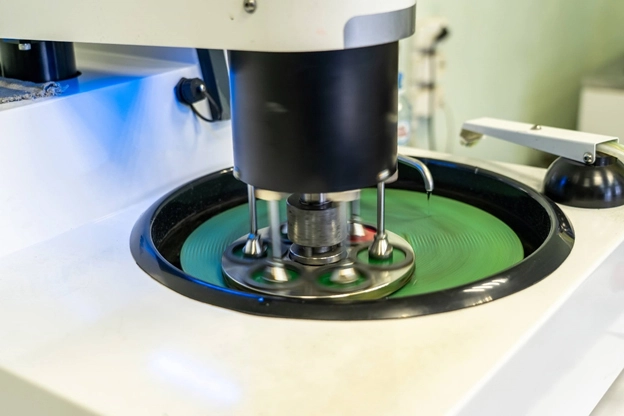
Semi-Automatic Grinding Machines:
These machines reduce the manual labor involved by automating certain aspects of the grinding process, such as the pressure applied and the sample movement. Operators still need to set up and monitor the grinding process, making these machines a good balance between automation and control.
Fully Automatic Grinding Machines:
These are advanced systems designed to handle high throughput and repeatable processes with minimal human intervention. They are equipped with features that control all aspects of grinding, from sample placement to final surface finish, and are ideal for high-volume, high-precision operations.
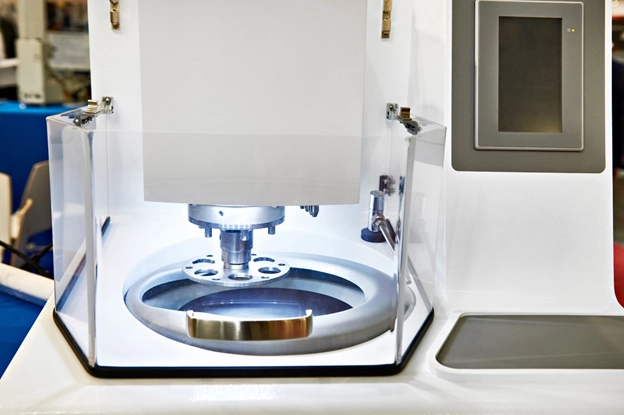
Grinding Equipment Types
Roll Grinding Machine
This machine utilizes stationary grinding papers supplied in strips or rolls. The specimen is manually rubbed against the grinding paper from top to bottom, and the process can be performed either dry or wet. The use of water helps to cool the specimen surface and facilitate the removal of grinding debris, enhancing the effectiveness of the grinding process and maintaining the integrity of the specimen. Roll grinders are particularly common in educational settings where simplicity and instructional clarity are valued, although they are less frequently used in industrial applications where automated grinding machines are more prevalent.
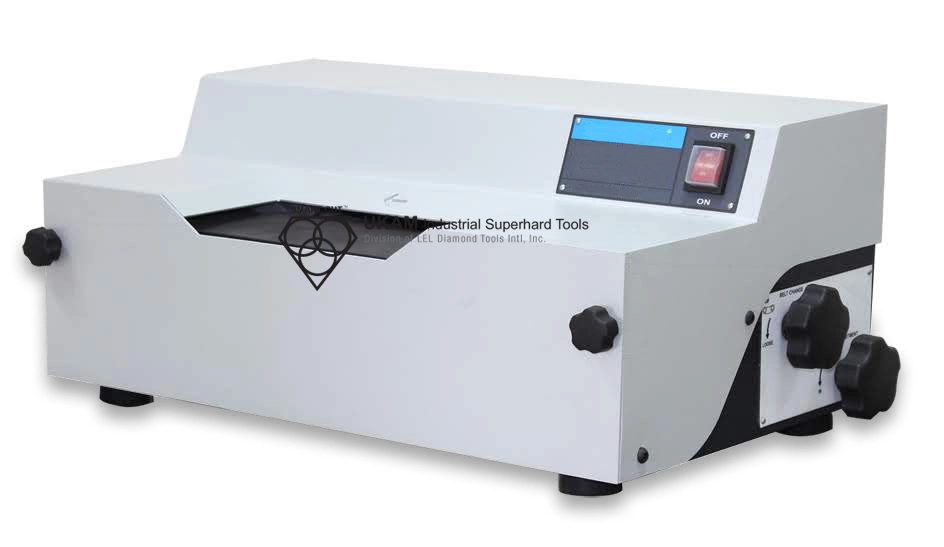
Belt Grinders
Belt grinders, a staple in most laboratories, are utilized for a variety of purposes. These grinders operate with coarse abrasive papers ranging from 60 to 240 grit and are primarily employed for deburring after sectioning, rounding off edges that do not require preservation for analysis, flattening cut surfaces in preparation for macro-etching, or eliminating damage from sectioning. Manual grinding tasks are also performed using these machines. Another option available for these tasks is the high-speed disc grinder, which is similarly equipped to handle rough surfaces and preparatory grinding.
Lapping Machine
Lapping is a precision surface finishing process where abrasive particles move freely on the surface of a carrier disc. During this process, the disc is periodically charged with small amounts of a hard abrasive, such as diamond or silicon carbide. The materials commonly used for lapping disks include cast iron and plastic, which are among the most prevalent.
Lapping generally results in a flatter specimen surface compared to grinding, though it does not remove metal in the same aggressive manner as grinding. In lapping, some carrier plates—often called laps—are specifically treated with diamond slurries. At the beginning of the lapping process, the diamond particles roll across the lap's surface, similar to other grinding processes. However, these particles soon become embedded into the lap and begin to cut into the surface, thereby producing microchips. This mechanism helps in achieving the desired surface flatness and smoothness.
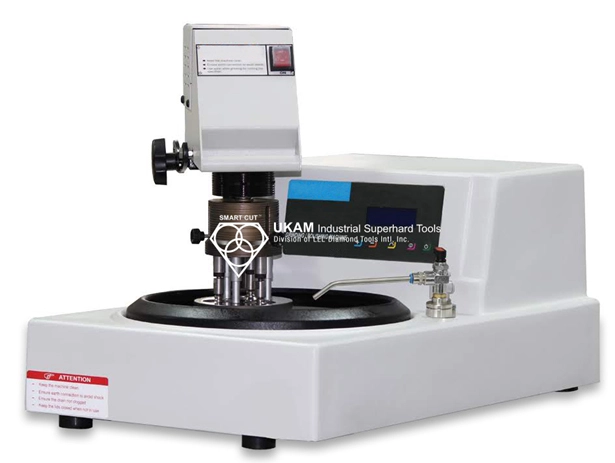
Guide on Selecting Optimal Grinding Machine
An ideal grinding machine in metallography should not only effectively prepare specimens but also provide features that ensure precision, flexibility, and reliability throughout the grinding process. Here are some detailed attributes that define an exemplary grinding machine:
Stability and Vibration Resistance: The structural integrity of the grinding machine is paramount. A well-designed machine should have a heavy-duty, vibration-resistant base and frame. This stability is critical as it prevents any undue vibrations during the grinding process, which could otherwise introduce new deformations or artifacts into the specimen. These anomalies can lead to incorrect interpretations of the material's microstructure, potentially compromising the scientific accuracy of the analysis.
Speed Control: Different grinding tasks require varying speeds to achieve the best results. The ideal grinding machine offers adjustable speed settings that can be tailored to the hardness of the material being processed and the specific requirements of the preparation procedure. This versatility is crucial for preventing damage to the specimen due to excessive speed and for optimizing the material removal rates to achieve the desired surface quality.
Sample Size Accommodation: The capability to handle diverse sample sizes and shapes is another essential feature. Metallographic specimens can range widely—from tiny electronic components to large industrial parts. A versatile grinding machine should have adjustable fixtures and supports that can securely hold various sample sizes. This adaptability ensures that regardless of the specimen size, the machine can provide consistent and effective grinding without compromising the quality or accuracy of the preparation.
Cooling System: Overheating during grinding can alter the microstructural properties of the specimen. An ideal machine incorporates a cooling system that continually bathes the grinding area with a coolant (typically water or a specialized cooling fluid). This system helps to dissipate heat effectively, preserving the true microstructure of the material and preventing thermal damage.
Dust and Debris Management: Effective removal of grinding debris and dust is essential for maintaining a clean working environment and for protecting the machine's components. An ideal grinding machine includes a dust extraction system that vacuums up particulates as they are generated, keeping the area clean and reducing the risk of contamination between specimens.
User Safety and Ergonomics: Safety features such as emergency stops, protective shields, and ergonomic design should be integral to the machine. These features protect the operator from accidents and reduce fatigue during prolonged use, ensuring that the grinding process is not only effective but also safe.
Ease of Maintenance: Regular maintenance is vital for the longevity and performance of any mechanical equipment. An ideal grinding machine is designed with easy-access components that simplify routine maintenance tasks such as changing grinding wheels or cleaning. This ease of maintenance not only prolongs the machine's operational life but also ensures that it remains reliable and efficient over time.
Parameters Influencing Grinding
The quality and efficiency of grinding in metallography can be greatly affected by various operational parameters. Understanding the influence of speed, load, coolant use, and techniques for uniform material removal is essential to optimize the grinding process and prevent specimen damage. Below, we explore these aspects in detail.
Influence of Speed (RPM) on Grinding Outcomes
Speed, measured in revolutions per minute (RPM), is a critical parameter in grinding:
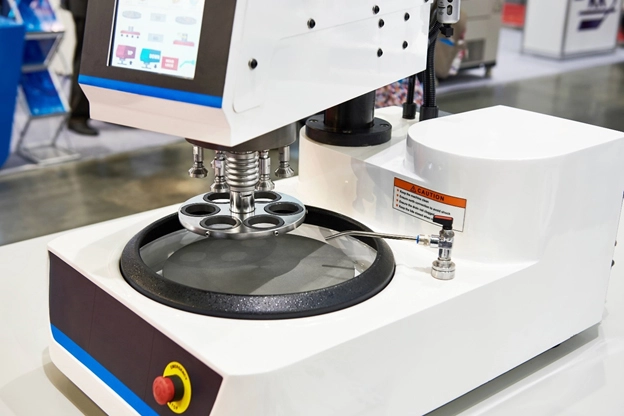
-
Material Removal Rate: Higher speeds generally increase the material removal rate, as the abrasive makes contact with the specimen more frequently. However, this must be balanced with the heat generation that occurs at higher speeds.
-
Heat Generation: Excessive speed can generate significant heat, which might alter the microstructure of the material or induce thermal damage, such as burns or cracks.
-
Surface Finish: Optimal speeds are required to achieve the desired surface finish. Too high a speed might leave deeper scratches or grooves, while too low a speed might result in inadequate material removal.
The selection of speed depends on the material's hardness, the type of abrasive used, and the desired finish. It's advisable to consult guidelines specific to the material and grinding media for the best results.
Grinding Pressure and Its Effects on Specimen Preparation
Grinding and polishing pressure, determined by the force applied to the specimen and its mounting material, is a critical aspect of metallographic preparation. Measured in pounds or Newtons, this pressure is defined as the force per unit area (psi, N/m², or Pa). When working with specimens significantly harder than the mounting compound, it is crucial to consider the force in relation to the specimen's surface area. Increasing the grinding or polishing pressure on larger, hard specimens can boost stock removal rates. However, it's important to note that higher pressures may also escalate both surface and subsurface damage.
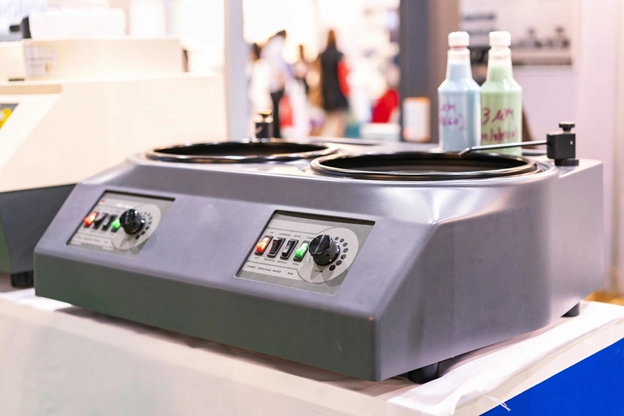
Using silicon carbide (SiC) grinding papers, for example, demonstrates that increasing the grinding pressure can be advantageous as the abrasive grains become dull, maintaining the cutting rate and extending the paper's usability. Additionally, higher pressures generate more frictional heat, which can be beneficial in the chemical mechanical polishing (CMP) of ceramics, minerals, and composites. For delicate specimens like nodular cast iron, higher pressures, when combined with lower relative velocities, can aid in preserving inclusions and secondary phases.
Effects of Load (Pressure) on the Specimen During Grinding
The load or pressure applied during grinding is pivotal and has multiple effects:
-
Uniform Material Removal: Proper pressure is necessary to ensure that the abrasive particles effectively engage with the material. Excessive pressure, however, can lead to rapid abrasive wear and heighten the risk of damaging the specimen.
-
Specimen Integrity: Too much pressure can deform or fracture the specimen, particularly if it is brittle or thin, such as ceramics or thin metal sections. Managing this balance is critical to maintain the integrity of the material being processed.
-
Abrasive Wear: Optimal pressure not only ensures efficient abrasive wear but also extends the life of the grinding media by promoting even wear patterns.
Importance of Coolant in Grinding Processes
Coolant plays a multi-faceted role in grinding:
-
Temperature Control: It helps to dissipate heat generated during grinding, preventing thermal damage to the specimen and the degradation of the abrasive media.
-
Removal of Swarf: Coolant helps in flushing away the swarf (the debris created during grinding), which can improve the grinding efficiency and prevent clogging of the abrasive surface.
-
Reducing Friction and Wear: By lubricating the interface between the specimen and the abrasive, coolants reduce friction and wear, contributing to longer abrasive life and smoother surface finishes.

Selecting the right type of coolant and maintaining the correct flow rate are essential for maximizing these benefits.
Relative Velocity
Modern grinding and polishing machines typically feature specimens mounted on a disk holder, which are then processed on a disk platen surface. This setup allows for a variable velocity distribution based on the relative speeds of the head and base. Achieving better flatness and reduced surface damage can often be accomplished by matching the head and base speeds while ensuring both rotate in the same direction. This synchronization minimizes velocity distribution across the sample as it rotates.
Grinding Direction
The orientation of the specimen during the grinding process can significantly impact the preparation results, especially for specimens with coatings. Generally, for materials with brittle coatings, the grinding direction should ensure that the brittle component is in compression. This means that the abrasive movement should be from the coating into the substrate. Conversely, for brittle substrates with ductile coatings, the abrasive should move from the brittle substrate into the ductile coating. This approach helps to maintain the integrity of the coating and substrate during the grinding and polishing process.
Parameter |
Effects on Grinding Outcomes |
Optimization Strategies |
---|---|---|
Speed (RPM) |
- Higher speeds increase material removal rates but can also generate excessive heat, risking thermal damage. - Speed influences the surface finish, with too high speeds causing deeper scratches, and too low speeds leading to inadequate material removal. |
- Select optimal speeds based on material hardness, abrasive type, and desired finish. - Consult specific guidelines for material and abrasive. |
Pressure (Load) |
- Proper pressure ensures effective material engagement and uniform removal. - Excessive pressure can cause rapid abrasive wear and damage the specimen. - High pressure can deform or fracture delicate specimens. |
- Adjust pressure based on specimen hardness and size to balance material removal with minimal damage. |
Coolant Use |
- Controls temperature, preventing thermal damage. - Facilitates swarf removal, enhancing grinding efficiency. - Reduces friction and wear, extending abrasive life. |
- Use appropriate coolants for the material and maintain proper flow rates to maximize benefits. |
Relative Velocity |
- Affects the uniformity of material removal and surface flatness. - Inconsistent velocity can lead to uneven grinding and surface damage. |
- Synchronize speeds of the head and base to minimize velocity distribution and improve flatness. |
Grinding Direction |
- Critical for specimens with coatings or varying material properties. - Incorrect grinding direction can compromise the integrity of coatings or layered materials. |
- Align grinding direction to support the mechanical integrity of the material layers or coatings, ensuring proper compression and support. |
Trouble Shooting Grinding Issues
For Metallography & Sample Preparation
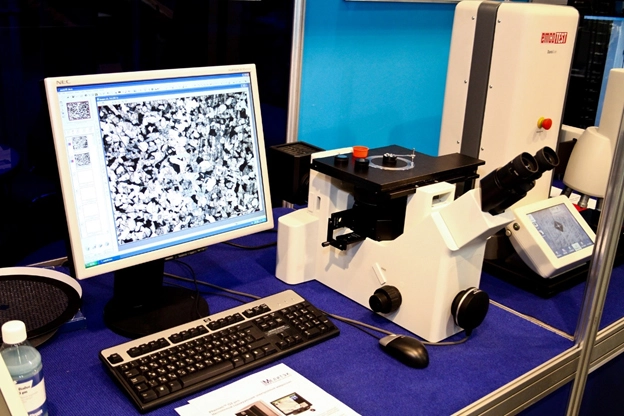
Issue |
Cause |
Resolution |
---|---|---|
Uneven Surface |
Inconsistent pressure, use of worn or improper abrasives, or an unbalanced machine. |
Ensure even pressure distribution, replace worn abrasives, and check machine balance and alignment. |
Excessive Heat |
High grinding speed, excessive pressure, or insufficient cooling. |
Adjust speed and pressure to recommended settings, enhance cooling with adequate fluid flow. |
Surface Contamination |
Cross-contamination from previous grinding steps, or using dirty or clogged abrasives. |
Clean the specimen and equipment thoroughly between steps; use fresh abrasives and clean fluids. |
Deep Scratches |
Using too coarse an abrasive for the initial grinding or not properly progressing to finer grits. |
Start with a properly graded coarse abrasive and gradually transition to finer abrasives. |
Specimen Deformation |
Too much force applied or soft mounting materials. |
Reduce the applied force and use appropriate mounting materials that provide better support during grinding. |
Abrasive Wear |
Using abrasives beyond their effective lifespan, or improper abrasive for the material. |
Regularly replace abrasives and ensure the abrasive type is suitable for the specimen’s material. |
Incomplete Material Removal |
Insufficient grinding, skipping grit sequences, or uneven application of abrasives. |
Ensure complete and uniform grinding at each grit level before progressing; do not skip intermediate grits. |
Glazing of Abrasive Papers |
Using low-quality abrasives or abrasives not suitable for the material type. |
Use high-quality abrasives appropriate for the specific material and ensure regular replacement. |
Swirl Marks |
Inconsistent movement during grinding or inadequate equipment maintenance. |
Use consistent, systematic grinding patterns and regularly maintain equipment to ensure optimal functioning. |
Vibration Marks |
Loose fixtures or worn machinery parts. |
Tighten all fixtures and replace or repair worn parts to stabilize the grinding process. |
Loss of Detail |
Over-grinding, especially on soft materials or materials with multiple hardness phases. |
Carefully monitor the grinding process, particularly with soft or complex materials, to prevent excessive material loss. |
Material Pullout |
Aggressive grinding on brittle materials or materials with heterogeneous hardness. |
Adjust the grinding parameters to be gentler, using finer grits and less pressure, especially on brittle materials. |
Edge Rounding |
Improper support for specimen edges or excessive pressure. |
Ensure the specimen is adequately supported and adjust the pressure to minimize deformation, particularly around the edges. |
Loading of Abrasive Papers |
Accumulation of ground material on the abrasive surface, especially with soft materials. |
Use anti-loading discs or clean the abrasive surface frequently to prevent build-up and ensure effective grinding. |
Burn Marks |
Excessive friction and heat during grinding. |
Reduce the grinding speed and improve cooling measures to prevent overheating of the specimen surface. |
Chattering |
Loose or worn parts in the grinding machine or an unbalanced grinding wheel. |
Tighten or replace loose components and balance the grinding wheel to reduce vibration and improve surface finish. |
Premature Abrasive Wear |
High pressure or using the abrasive beyond its capacity. |
Adjust grinding pressure to optimal levels and replace abrasives at appropriate intervals to avoid premature wear. |
Differential Grinding |
Variance in hardness within the specimen leading to uneven material removal. |
Use a gradual grinding approach with multiple grit sizes to accommodate different hardness levels within the same specimen. |
Corrosion During Grinding |
Use of inappropriate coolant or exposure to corrosive environments during grinding. |
Use coolants that provide adequate lubrication and protection against corrosion, and ensure the work area is free from corrosive agents. |
Residual Stress Formation |
Aggressive grinding techniques or inadequate cooling. |
Optimize grinding parameters to be less aggressive and enhance cooling techniques to minimize stress formation in the material. |
Contamination from Abrasives |
Transfer of material from the abrasive media to the specimen surface. |
Use high-purity abrasives and clean both specimen and tools regularly to prevent cross-material contamination. |
Inefficient Material Removal |
Inadequate selection of abrasive grit for the material type or worn abrasives. |
Select the appropriate abrasive grit size for the material and ensure timely replacement of worn abrasives. |
Rapid Abrasive Wear |
Using abrasives that are too soft or inappropriate for the material hardness. |
Select abrasives that match the hardness of the specimen material to ensure efficient grinding and prolong abrasive life. |
Differential Grinding |
Variation in material hardness within the same specimen leading to uneven material removal. |
Use a gradual, controlled grinding approach with constant monitoring to manage different material phases within a specimen. |
Surface Smearing |
Excessive speed or pressure causing the material to deform rather than be removed. |
Reduce speed and pressure, ensuring the abrasive action cuts the material instead of deforming it. |
Formation of Relief |
Inconsistent grinding that creates uneven topography on the surface. |
Maintain consistent grinding practices and regularly inspect the surface to ensure evenness. |
Contamination from Fixtures |
Metallic transfer from clamps or holders to the specimen surface. |
Use clean, non-reactive fixtures and regularly clean all contact surfaces to prevent cross-contamination. |
Overheating |
Continuous grinding without adequate cooling, leading to thermal damage. |
Implement intermittent grinding with frequent cooling periods to prevent heat accumulation. |
Poor Initial Cut |
Beginning the grinding process with a cut that is too shallow or uneven. |
Ensure the initial cut is level and appropriate for the material, setting a proper foundation for subsequent grinding. |
Incomplete Grinding |
Missed areas or insufficient grinding leading to incomplete preparation. |
Employ systematic grinding patterns to cover all surface areas uniformly. |
Mechanical Artifacts |
Artifacts introduced by grinding, such as twinning or phase transformations in sensitive materials. |
Optimize grinding parameters and select materials-specific abrasives to minimize mechanical impact on sensitive specimens. |
Noise and Vibration |
Poor machine maintenance or imbalance in the grinding setup. |
Regularly maintain and calibrate machinery to ensure smooth operation and reduce noise and vibration. |
Non-uniform Particle Distribution |
Uneven distribution of abrasive particles on grinding discs leading to inconsistent grinding. |
Regularly check and replace grinding discs to ensure even distribution of abrasive particles for consistent grinding results. |
Compromised Edge Preservation |
Insufficient support during grinding, leading to edge rounding or loss of fine details. |
Use appropriate mounting techniques and supportive backings to preserve edges and fine structural details of specimens. |
Abrasive Decoupling |
Abrasive particles detaching from the grinding disc due to excessive force or poor adhesive bonds. |
Ensure high-quality abrasives are used and maintain optimal grinding pressures to prevent abrasive detachment. |
Fluid Contamination |
Use of contaminated or inappropriate fluids which can lead to surface defects. |
Use high-quality, clean, and appropriate grinding fluids; regularly change fluids to avoid contamination. |
Specimen Swarf Build-up |
Accumulation of grinding debris on the specimen or within the machine leading to surface scratches. |
Implement frequent cleaning of both specimen and machine throughout the grinding process to prevent debris build-up. |
Abrasive Grit Imbedding |
Grit particles embedding into the specimen surface during grinding, causing surface damage. |
Select appropriate abrasive materials and avoid excessive pressures that can cause grit to embed into softer materials. |
Insufficient Cooling |
Inadequate cooling leading to changes in material properties or thermal damage. |
Ensure effective and continuous cooling during grinding to prevent overheating and maintain material integrity. |
Grinding Path Inconsistency |
Irregular or changing grinding paths that lead to non-uniform surface texture. |
Standardize grinding motions and paths to achieve a consistent surface finish across the entire specimen. |
Operator Error |
Inconsistent results due to variability in operator technique or understanding. |
Standardize training and procedures to minimize human error and ensure consistent technique across all operations. |
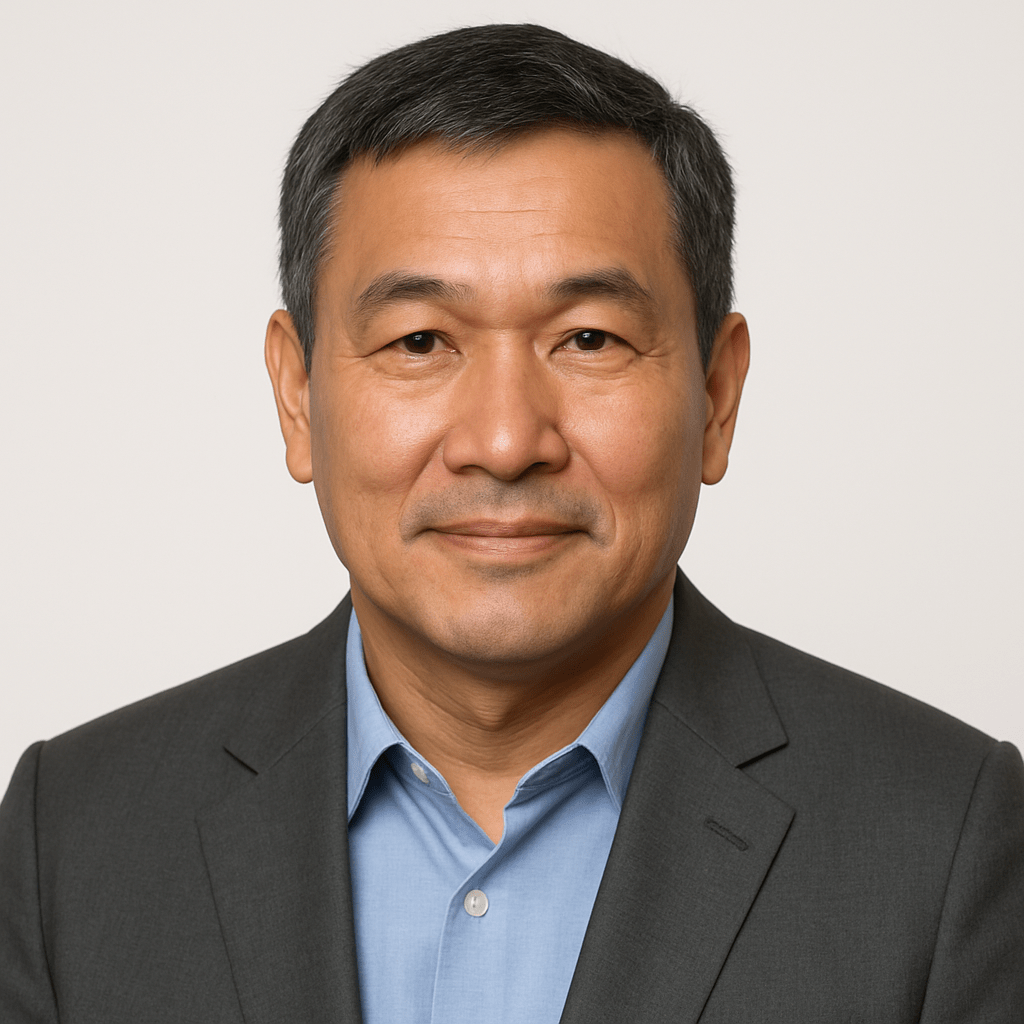
Ayan Sadyk is a materials scientist and process engineer with over two decades of experience in the industrial diamond tooling sector. His expertise lies in integrating ultra-thin diamond blades, CBN wheels, and advanced cutting systems into precision manufacturing workflows for applications in optics, semiconductors, and technical ceramics.
With a background in materials behavior and surface integrity, Mr. Sadyk brings a data-driven, application-specific approach to cutting and grinding process development. He has worked closely with manufacturers and R&D facilities across Eastern Europe, North America, and the Middle East, helping optimize tool life, surface finish, and process stability.
As an author, he focuses on bridging materials science with tooling innovation—writing on topics such as blade wear mechanisms, thermal effects in hard material sectioning, and adaptive process design.
ARE YOU USING SEMICONDUCTOR TOOLS
FOR YOUR APPLICATION?
LET US
HELP YOU
HAVING ISSUES WITH
YOUR CURRENT SEMICONDUCTOR TOOLS?
Knowledge Center
Selecting the Right Diamond Band Saw blade for your Application
Diamond Band Saw Blades Usage Recommendations & Best Practices
Diamond Wire vs band saw blades and circular blades
The Comprehensive Guide to the Processes of Silicon Wafers Production
Manufacturing Processes for Silicon Semiconductors From Ingot to Integrated Circuit
Evaluating & Comparing Diamond Blades
How to Improve & Optimize Your Diamond Sawing Operation
Troubleshooting Diamond Sawing Problems
Silicon Fabrication Guide
Diamond Wire Advantages & Application
Why use diamond
How to Selecting Right Diamond Tools for your application
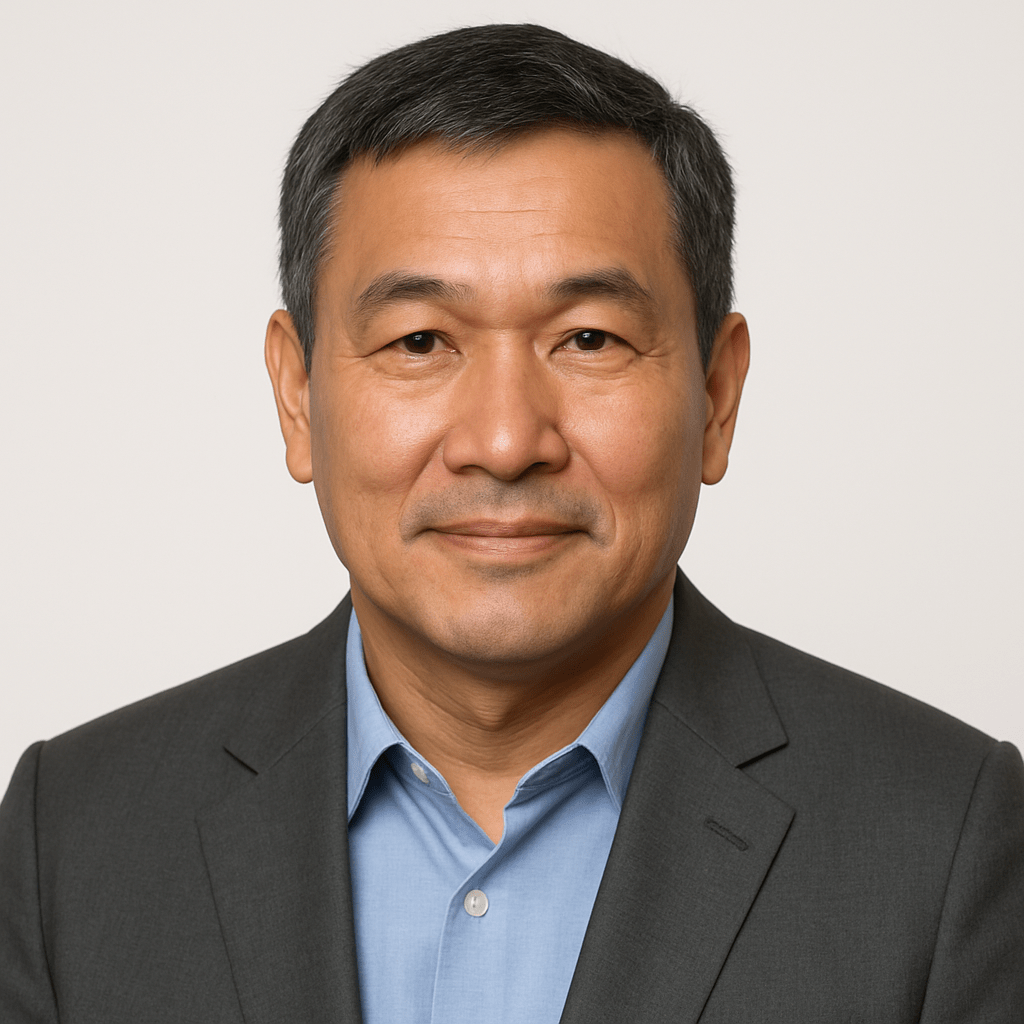
Ayan Sadyk is a materials scientist and process engineer with over two decades of experience in the industrial diamond tooling sector. His expertise lies in integrating ultra-thin diamond blades, CBN wheels, and advanced cutting systems into precision manufacturing workflows for applications in optics, semiconductors, and technical ceramics.
With a background in materials behavior and surface integrity, Mr. Sadyk brings a data-driven, application-specific approach to cutting and grinding process development. He has worked closely with manufacturers and R&D facilities across Eastern Europe, North America, and the Middle East, helping optimize tool life, surface finish, and process stability.
As an author, he focuses on bridging materials science with tooling innovation—writing on topics such as blade wear mechanisms, thermal effects in hard material sectioning, and adaptive process design.