Table of Contents
Toggle(Guide on getting the most from your blade)
Welcome to the User Guide on How to Properly Use Diamond Lapidary Blades. This guide is designed to provide detailed insights and essential practices for operating diamond lapidary blades efficiently and safely. Whether you are a professional lapidary or beginning rockhound involved cutting hard lapidary materials, understanding how to correctly handle and maintain your diamond lapidary blades is important.
Diamond lapidary blades are highly specialized diamond blades designed for cutting through some of the toughest materials usually from 4 to 9 on mohs scale of hardness ranging from soft as glass to ultra hard gemstones. Their effectiveness depends not only on the quality of the blade itself but significantly on the knowledge and practices of the operator. Misuse or neglect can lead to suboptimal performance, shortened blade lifespan, and even safety hazards.
In this guide, we will cover everything from the initial installation of a new blade to maintenance routines that will extend its operational life. We will also explore key aspects such as the importance of using the correct blade for specific materials, understanding and adjusting cutting speeds, and the proper ways to clean, store, and eventually replace your blade.
Our goal is to empower you with knowledge and best practices that ensure your diamond lapidary blades perform at their best, ensuring quality, precision, consistency and maximizing your return on investment. Let’s dive into how you can achieve the highest level of performance and safety with your diamond lapidary blades.
SAFETY PRECAUTIONS
It is essential to maintain a clean and organized workspace, free from clutter and potential hazards. All cutting materials and tools should be securely stored when not in use, and the floor should be kept clear of debris and liquids to prevent slips, trips, or falls. Good housekeeping practices play a crucial role in reducing the risk of accidents and ensuring easy access during emergencies.
Electrical safety is another priority. Regularly check power cords, plugs, and electrical outlets for any signs of damage or wear. Secure all electrical connections, and ensure that machines are properly grounded. Extension cords should not be used as a permanent power solution since they can present a fire hazard and may not provide sufficient power for heavy machinery. Adhering to the manufacturer’s electrical requirements is vital to avoid overloading circuits.
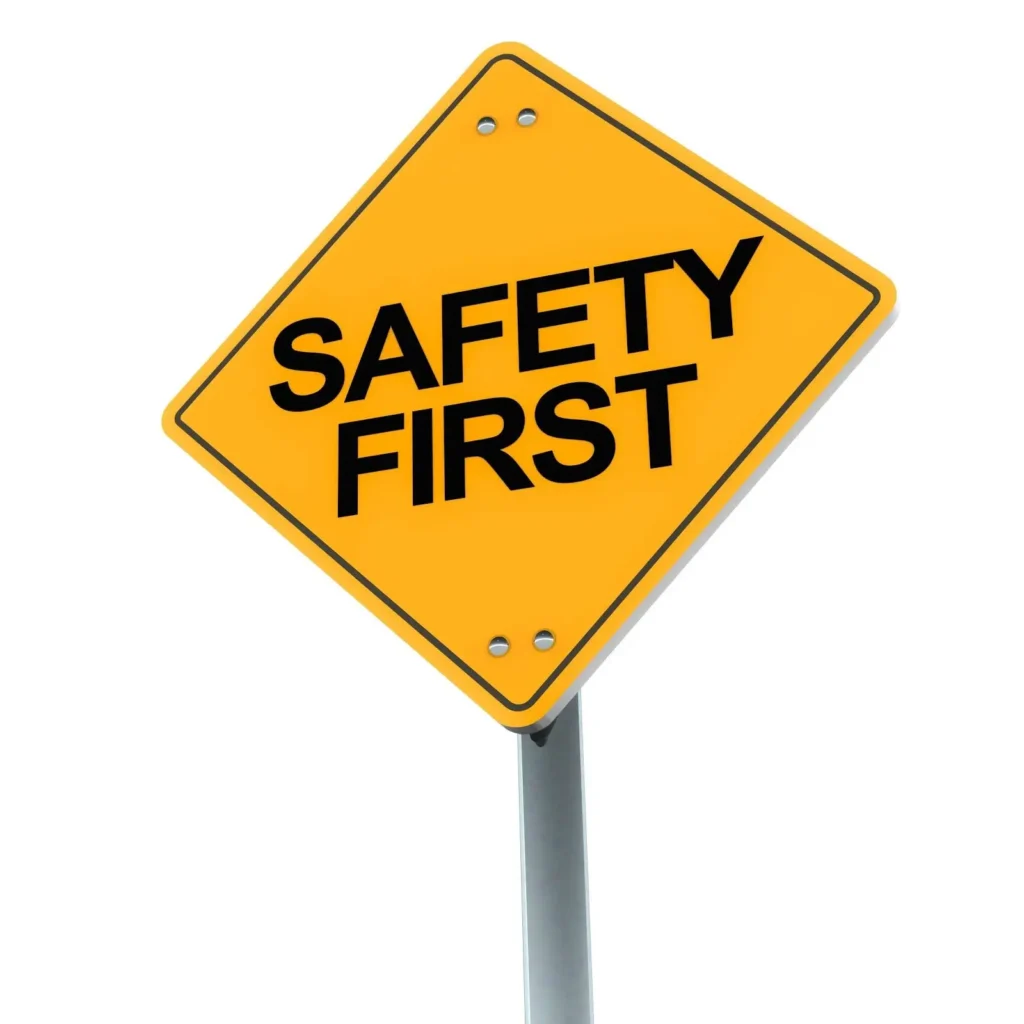
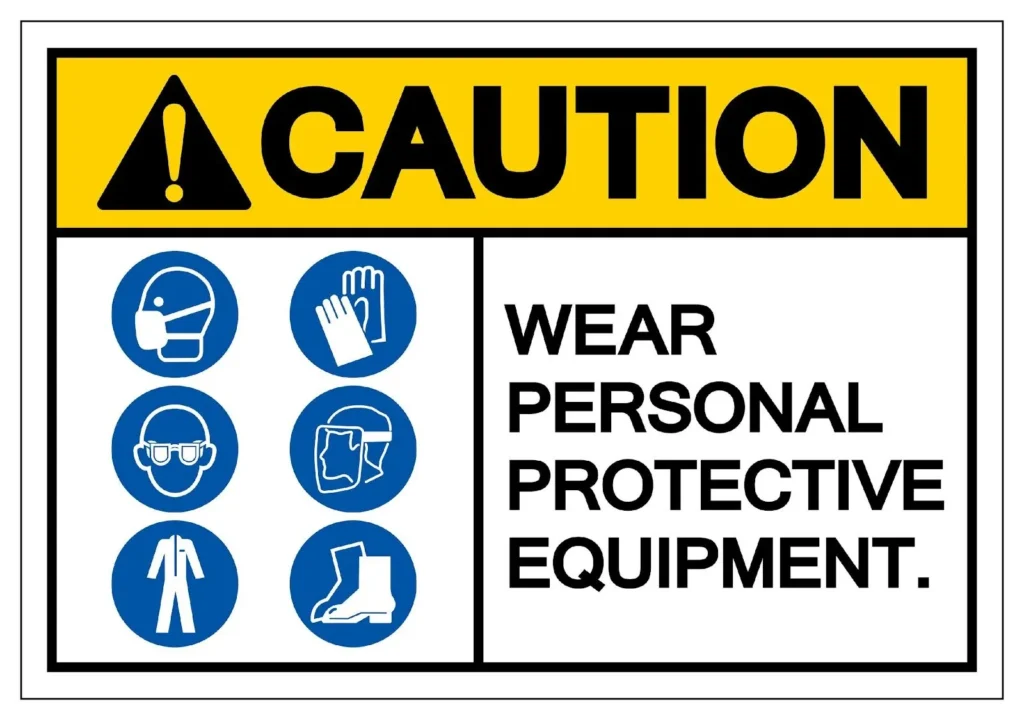
Using appropriate coolant systems and dust extraction methods is important for minimizing exposure to harmful particles and vapors produced during cutting. These systems must be checked and maintained regularly to ensure they are functioning effectively. Proper coolant and dust control management not only improves workplace safety but also enhances cut quality and prolongs the life of the blade. Fire safety measures include keeping fire extinguishers easily accessible and ensuring they are suitable for potential fire types, such as electrical or chemical fires that could occur in a cutting environment. It is essential to regularly train staff on how to use fire extinguishers correctly and familiarize them with fire procedures, including knowledge of exit locations and assembly points.
Understanding the machine’s emergency stop features is critical. All users should be well-versed in these features, and regular drills or briefings should be conducted to practice emergency stop procedures, helping to save lives and prevent damage in case of malfunctions or accidents.
A well-stocked first aid kit should be kept readily available in the cutting area, with all staff members informed of its location. Basic first aid training is important, especially for treating common injuries like cuts and abrasions that can occur when handling cutting tools. A clear response protocol should be established for more serious injuries, including whom to contact and how to access medical assistance swiftly.
Respecting the limitations of cutting equipment and diamond lapidary blades is fundamental to safe operations. Machines should not be pushed beyond their designed capacity, as this can lead to equipment failure and increased accident risks. The materials being cut must be compatible with the blade and machine specifications to avoid hazardous situations.
Continuous education and updates on safe practices, new safety equipment, and any changes in regulations are necessary for all operators. Fostering a safety-conscious culture where workers are encouraged to report hazards and suggest improvements promotes proactive accident prevention. Regular safety meetings help maintain safety as a priority in the workplace, creating a safer environment for all personnel involved in operations with diamond lapidary blades.

PROPERLY STORING YOUR BLADES
Here’s how you can extend the life and maintain the quality of your blades through proper storage. If possible, keep them in a climate-controlled environment with stable temperature and humidity levels. Extreme temperature fluctuations can cause materials to expand or contract, potentially leading to micro-cracks or stress in the diamond blade. High humidity can cause rust to form on metal parts of the blade or core, which compromises structural integrity. To mitigate these risks, using a dehumidifier or air conditioner in storage areas is beneficial.
Blades should be stored vertically in racks that prevent them from touching each other or lying flat on surfaces that could warp them over time. Contact with hard surfaces or other blades can lead to scratches or chips on the diamond edge. Storage racks designed specifically for blades maximize space and minimize the risk of accidental damage during handling. If vertical storage is not possible, lay the blades flat on a cushioned surface, ensuring they are separated by a soft material to prevent movement and rubbing against each other.
To prevent rust on the metal components of the blade, apply a light coat of rust inhibitor, especially in environments prone to moisture. Ensure that the rust inhibitor used is compatible with the blade and does not interfere with its performance. Before using a blade treated with rust inhibitor, clean it according to the manufacturer’s instructions to ensure that no residue remains, which could affect cutting capability.
Even while in storage, blades should undergo periodic inspections to check for signs of wear, damage, or environmental impact. This practice helps identify potential issues early before they develop into more serious problems. Look for any corrosion, debris buildup, or physical damage. Early detection and maintenance can prolong the life of the blade and ensure it is ready for use when needed.
Maintain documentation of each blade's usage history, maintenance, and storage location. Labeling blades by type, size, and any relevant performance notes helps streamline selection for specific jobs and tracks their condition over time. Proper organization allows for effective blade rotation, ensuring all blades are used equally and properly maintained.
For long-term storage, consider using protective coatings or wraps designed for metal tools. These products help shield blades from environmental factors and prevent accidental damage during handling. Ensure that any protective materials used are compatible with both the diamond and metal components of the blade and can be easily removed without leaving any residues.

BEFORE INSTALLING YOUR NEW BLADE

Before installing your diamond lapidary blade, a thorough pre-installation check is crucial to ensure operator safety and the optimal performance of your equipment. Begin by examining the machine's shaft, which is essential for a stable and accurate cutting process. Look for any looseness or play in the shaft that may indicate worn bearings, as this can affect both the precision of your cuts and the overall health of your machine. Additionally, check the shaft for wear, tear, or deformations, as an uneven surface can lead to improper blade alignment, uneven cuts, or blade damage. Ensure that the blade can be mounted securely on the shaft, with no gaps or movement, to provide a stable base for precise cutting.
Inspect the blade thoroughly before installation, checking for any cracks, chips, or other signs of damage on its edge and surface. Even minor imperfections can cause significant issues during operation, potentially leading to hazardous blade failures. A damaged or improperly mounted blade not only poses risks to the operator but can also compromise the quality of the workpiece. Confirm that the blade is in optimal condition before installation to maintain a safe working environment and achieve the best cutting results.
Each blade is designed for a specific rotation direction, which is typically indicated by an arrow on the blade. Make sure this direction matches the rotation of the saw machine, as mounting the blade incorrectly can reduce cutting efficiency. Carefully verify the manufacturer's instructions and the blade’s markings to confirm correct orientation, ensuring the blade functions as designed.
Once the blade’s orientation is confirmed, mount it onto the arbor, ensuring it sits flush and even. Properly secure the blade by tightening the arbor nut to the manufacturer’s specified torque. A loose blade can lead to vibration, inaccurate cuts, and potential safety hazards. However, avoid overtightening, as this can damage both the blade and the machine. A securely mounted blade guarantees stable, vibration-free operation, resulting in precise cuts and a safer working environment.


Proceeding with the pre-installation checks, ensure the machine’s moving parts, particularly around the shaft and arbor, have proper lubrication. Insufficient lubrication can cause increased friction, leading to wear and tear that might affect both blade performance and machine lifespan. Well-lubricated components facilitate smoother operation and help dissipate the heat generated during cutting.
Check the alignment of all machine components that interact with the blade, including guides, beds, and clamps. Misaligned parts can result in inaccurate cuts, increased blade wear, and potentially dangerous kickbacks. Use precision tools to verify that all components are aligned according to machine specifications, which is especially important for machines that have been in long-term use or have recently undergone maintenance.
Ensure that the machine's power supply is stable and matches the required specifications for both the machine and blade. Power supply fluctuations can cause inconsistent blade speeds, affecting cut quality and potentially damaging the blade. If your machine uses coolant pumps or auxiliary systems, verify that they are also functioning correctly and ready for use when cutting begins.
Plan ahead for calibration and initial testing after installation. Have materials prepared for test cuts, allocate time for any necessary adjustments, and gather the tools required to streamline the process. Calibration and testing are vital to confirm that the machine and blade are correctly set up and ready for precise lapidary work.
Lastly, check that all necessary safety gear is available and in good condition. This includes eye protection, gloves, ear protection, and any other personal protective equipment recommended for your machine and materials. Additionally, review emergency stop procedures and confirm that all machine safety features are functional and easily accessible. Creating a safe working environment is paramount, protecting the operator, equipment, and materials during processing.
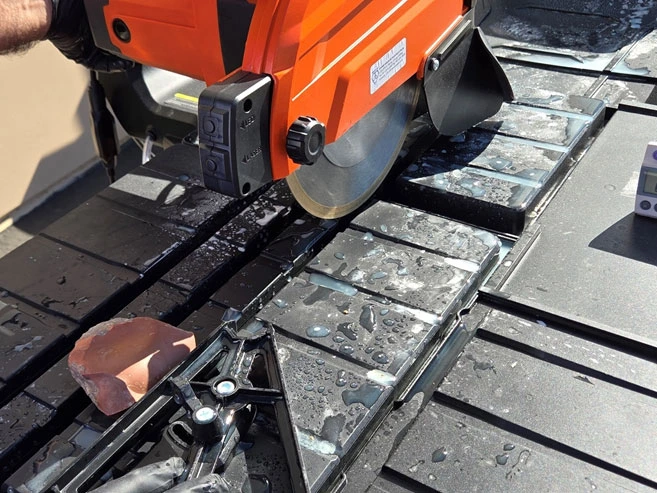
INSTALLING YOUR DIAMOND LAPIDARY BLADE
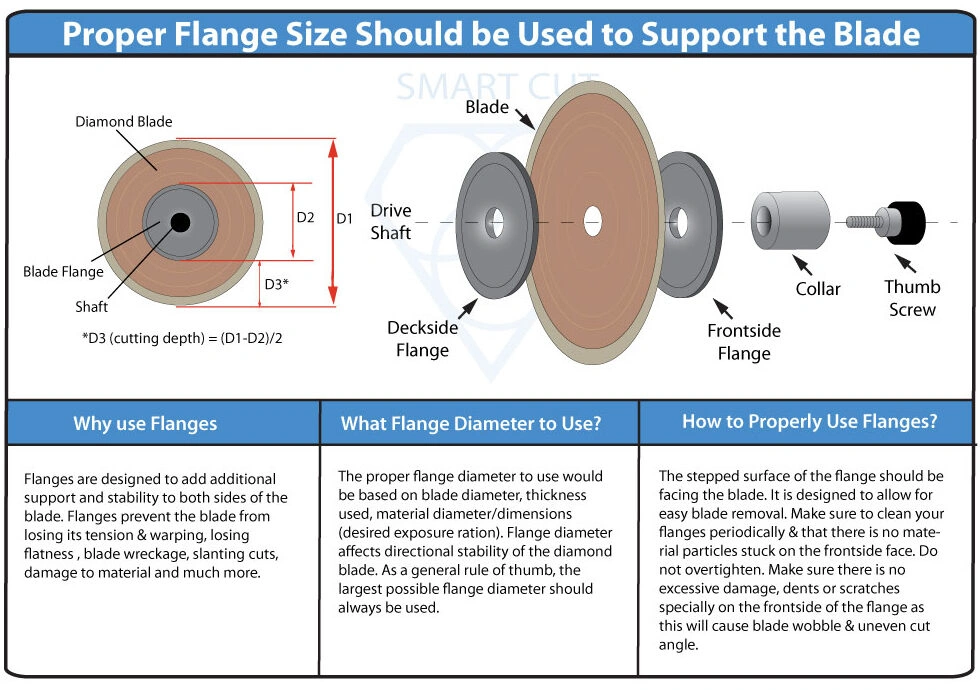
Begin the installation of your diamond lapidary blade by examining it for any damage or imperfections that could lead to operational failures. Ensure the blade fits securely on the machine's arbor, avoiding a loose fit that could cause wobbling or slipping. Use matching flanges that are approximately 1/3 the diameter of the blade; these should be clean, flat, and free from rust or distortions to prevent blade wobble and ensure accurate cuts. Secure the blade using a torque wrench to apply the manufacturer’s recommended torque, then manually check to ensure that the blade is firmly attached and rotates smoothly without any wobble.
Before initial use, it is crucial to check the alignment of the blade, especially for tasks like slabbing, to prevent the blade from bending or veering off course. Regularly verify the blade's tracking on the saw arbor to prevent uneven wear. Inspect for and remove any debris or buildup on the blade to avoid vibrations and inaccuracies.

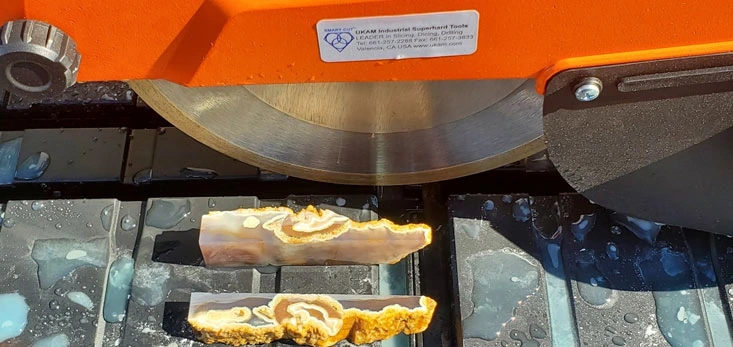
Perform a few test cuts on scrap material to assess the installation quality. This step helps identify any unresolved issues, allowing for adjustments before proceeding with primary cutting tasks. Monitor the coolant flow closely during these test cuts to confirm effective delivery to the blade and material.
To maintain optimal performance, regularly check the blade alignment and the integrity of flanges. Proper installation and regular calibration of the cutting equipment are essential to ensure precise, efficient cuts and to extend the operational life of the blade. Keeping a detailed log of installation processes can assist in troubleshooting and refining future installations.
The iterative process of testing, adjusting, and refining the setup based on feedback from initial cuts establishes a foundation for high-quality, safe, and efficient cutting operations. This approach ensures that the blade, machine, and operator work in concert, optimizing cutting conditions and enhancing the longevity of the diamond lapidary blades.
MATERIAL PREPARATION
Before cutting, thoroughly clean the material to remove dust, dirt, or any residue that may affect cutting accuracy or damage the blade. Use a brush or mild cleaning solution for general cleaning, and for stubborn residues, apply specialized agents that are safe for the material. Always rinse and dry the material before proceeding.
To ensure precision, use a non-permanent marker to draw clear cutting lines on the material. These markings serve as a guide and help avoid mistakes that can waste material or harm the blade. Make sure they are accurate and visible throughout the cutting process. Depending on the cutting type saw used, securely fasten the cleaned and marked material in place using clamps or a vise to prevent movement during cutting. Stability is essential for achieving precise cuts and avoiding blade kickback or material chipping.
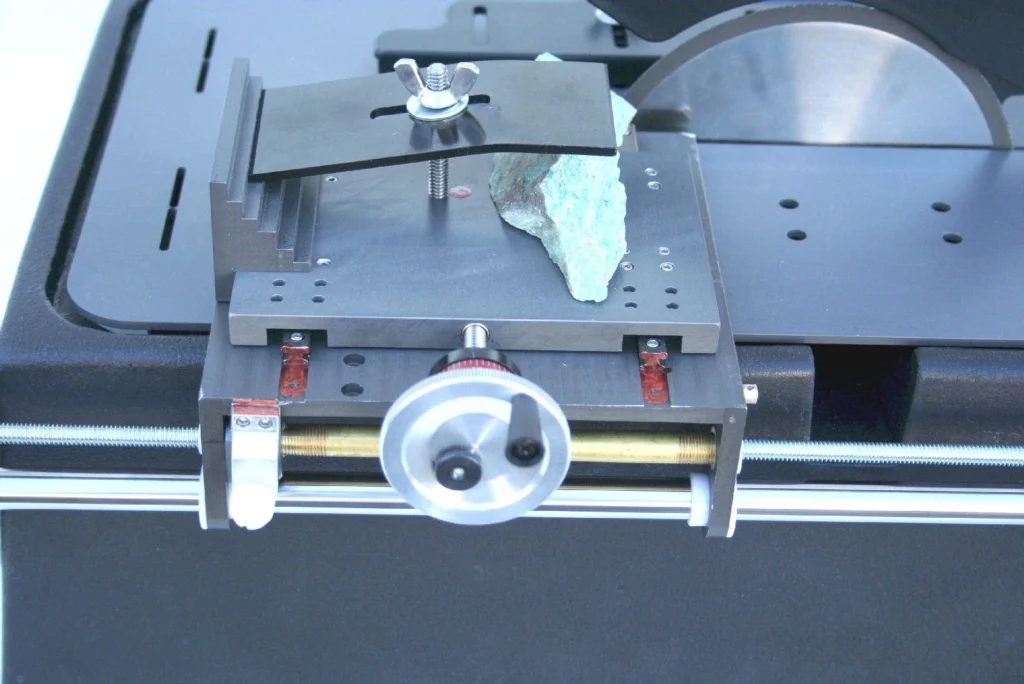
Check for internal stresses in the material, especially in stones or composites, which can lead to breakage during cutting. If possible, perform a stress test or consult an expert to identify these issues. Understanding the material's properties helps in selecting the right blade and technique.

If working with materials sensitive to temperature changes, allow them to acclimate to the workshop environment before cutting. Sudden temperature shifts can cause certain materials to crack or warp, compromising the cut quality. Understanding the material’s hardness, brittleness, and other properties is crucial. This knowledge aids in choosing the correct blade and cutting speed. Improper settings can lead to inefficient cuts, blade damage, or destruction of the material.
For projects with multiple cuts, plan the sequence carefully to reduce material waste and avoid stressing the blade. A strategic cutting order helps maintain the material's structural integrity and prevents breakage. When working with large or heavy pieces, use support systems to hold both the main material and any offcuts securely. This prevents shifting and accidents, resulting in cleaner cuts.
USE RECOMMENDED RPM’S
The revolutions per minute (RPM) recommended for each blade diameter are determined to ensure a balance between cutting efficiency and blade wear. By adhering to these guidelines, operators can not only enhance performance but also improve safety during cutting operations.
By selecting the appropriate RPM and adjusting operational parameters like water flow and feed rate, the efficiency and lifespan of diamond lapidary blades can be maximized. Furthermore, by fine-tuning RPMs according to blade size, material characteristics, and cutting conditions, operators are able to achieve precise cuts while enhancing both safety and blade longevity.
The optimal RPMs for diamond lapidary blades are shaped by a combination of factors that determine the most effective and safe cutting speeds. These include the blade's diameter, kerf thickness, diamond grit size, the type of cutting machine used, the machine's horsepower, and the type of diamond section edge. More about RPM’s >>>


Typically, smaller diameter blades require higher RPMs as they need to maintain a faster linear speed for effective cutting. For example, a 4-inch blade might operate effectively between 5,000 to 6,000 RPM, whereas a 10-inch blade might be better suited to speeds around 3,000 to 3,500 RPM. The kerf thickness of the blade also influences RPM requirements; thinner kerf blades generally need higher RPMs because they remove less material per cut, which allows them to cut faster without overburdening the blade.
The horsepower of the cutting machine is a crucial factor as well; more powerful machines can sustain higher RPMs, providing the necessary torque to maintain consistent cutting speeds through more challenging materials. Different types of cutting machines, such as tile saws, lapidary saws, and general-purpose saws, may have specific RPM recommendations based on their design and intended function.
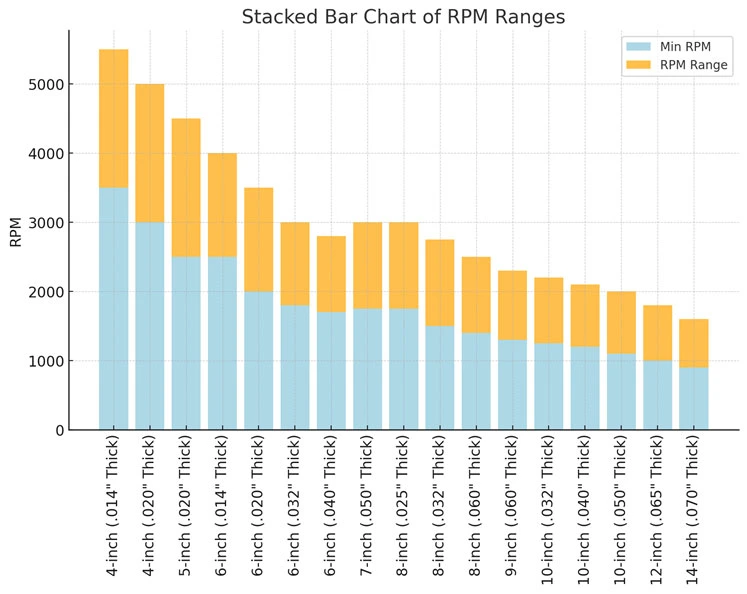
The blade's diamond section edge type also impacts the suitable RPM.
Continuous rim blades - run at moderate to high RPMs for smooth, chip-free cuts, with slower speeds for harder materials and higher RPMs for softer ones. Unlike segmented, notched, or slotted blades, which can run at higher RPMs due to better cooling, continuous rim blades need careful speed control to prevent overheating, as they lack gaps for heat dissipation. Proper coolant is crucial at all speeds to maintain blade life and cut quality.


Segmented rims, designed for faster cutting on hard materials, They can operate at higher rpms. Excellent for high speed saws. The segments allow better air cooling and debris removal, making them suitable for tougher materials while maintaining efficient cutting.
Notched / Turbo rims, combine the cutting speed of segmented blades with the smoother finish of continuous rims, are used at medium RPMs. This balance allows for effective debris removal and cooling while still providing a smoother cut than fully segmented blades. The medium RPM range optimizes both speed and precision, making these blades versatile for various materials.


Blades with slotted or gulleted edges, Blades with slotted or gulleted edges, designed for improved cooling and debris removal, typically operate at medium RPMs. While they provide better cooling than continuous rim blades, they generally run at slightly lower RPMs than segmented blades, offering a balance between cutting speed and maintaining blade temperature.
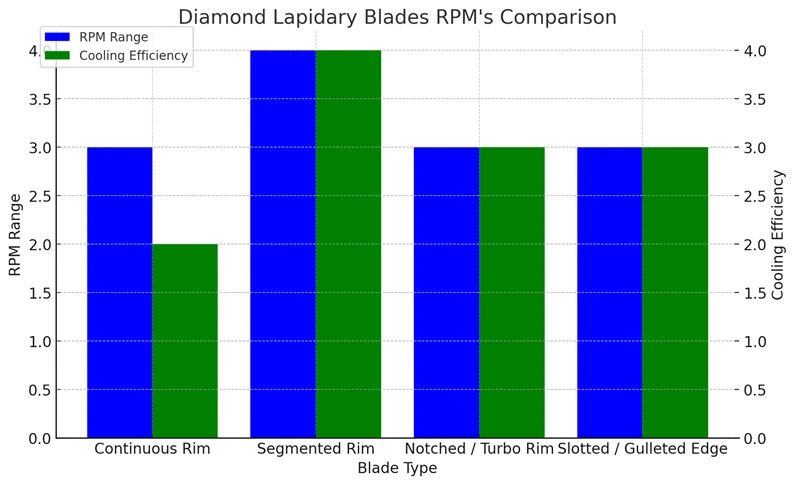
Feature |
Continuous Rim |
Segmented Rim |
Notched / Turbo Rim |
Slotted / Gulleted Edge |
---|---|---|---|---|
RPM Range |
Moderate to High |
High |
Medium |
Medium |
Cut Quality |
Smooth, chip-free cuts; slower for hard materials, faster for softer ones. |
Faster cutting on hard materials; suitable for high-speed saws. |
Balance of speed and smoother finish; versatile for various materials. |
Enhanced cooling and debris removal; balance between speed and temperature. |
Cooling Efficiency |
Lower (requires proper coolant and speed control to prevent overheating). |
High (better air cooling due to segments). |
Moderate (effective cooling with smoother cuts). |
Moderate (better cooling than continuous rim but less than segmented). |
Best Use |
Precision cutting; delicate materials requiring smooth finish. |
Hard materials; faster, high-speed cutting. |
Mixed-use; materials needing balance of speed and smoothness. |
Applications needing improved cooling and efficient debris removal. |
The characteristics of the material being cut, such as type, size, shape, hardness, and density, also play a significant role in determining the optimal RPM settings. Harder materials generally require lower RPMs to minimize the risk of overheating both the blade and the material, while softer materials may be handled at higher RPMs. Adjusting RPMs to match the specific material characteristics is critical for maintaining blade longevity and ensuring a high-quality cut.

Effective cooling and lubrication, usually achieved through proper coolant flow, are essential, particularly at higher RPMs to prevent overheating of the blade and material. Conducting trial cuts on scrap material is advisable to fine-tune the RPM settings for new or unfamiliar materials, ensuring each cutting operation is performed under the best possible conditions. This comprehensive approach to selecting RPMs, by taking into account all relevant factors including the specifics of the blade and material characteristics, guarantees optimal performance and safety.
Surface feet per minute (SFPM) is a crucial measure for optimal blade performance, indicating how fast the cutting edge moves across the material. Staying within the recommended SFPM range is essential to ensure the blade cuts effectively without overheating or becoming overloaded, which can result in premature wear or failure.
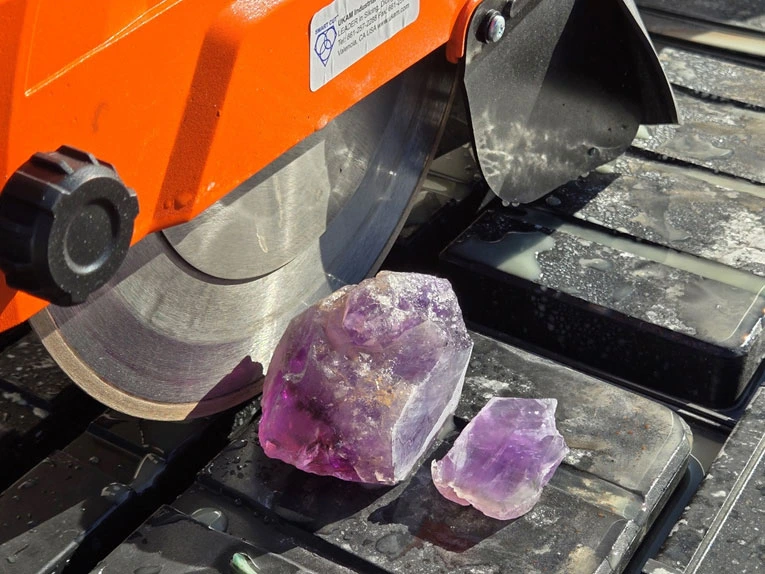
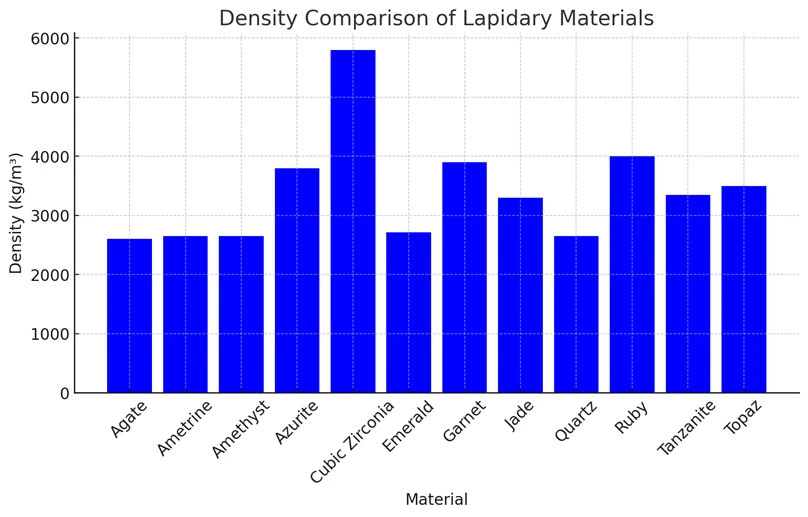
The density and composition of the material being cut play a significant role in determining the cutting speed. Harder, denser materials generally require lower RPMs to prevent blade overheating and material damage, while softer materials can be cut at higher speeds. It is advisable to start at the lower end of the recommended speed range for a new material and adjust based on performance and cut quality. Coolant flow is critical for cooling the blade and removing debris from the cutting area. This not only prolongs the life of the blade but also prevents overheating, which can damage both the blade and material. The amount of coolant required depends on the blade speed and material type, with harder materials and higher speeds needing more coolant for effective cooling.


When working with brittle materials, blade speed must be carefully managed. Cutting too quickly can lead to chipping or cracking. Lower speeds reduce the impact on the material's surface, minimizing damage. A gentle approach, gradually increasing speed, can help find the optimal rate for clean cuts without material loss. For materials with varying hardness, a uniform blade speed may not be effective. Different densities within the material can lead to uneven cuts or blade damage if not managed properly. Adjusting the speed as you move through different zones of hardness helps maintain smooth and consistent cutting performance.
Regularly monitor the blade for signs of wear, such as changes in cutting performance, noise, and vibration. If you find that cutting requires more effort or there is visible wear on the blade’s edge, adjustments to speed or coolant flow may be needed. If you're uncertain about the appropriate speed for a new or unusual material, consulting with experts can save time and prevent costly errors. Their experience and knowledge can provide guidance for optimal cutting.
Be prepared to make adjustments to the RPM as you work, based on feedback from the cutting process. If the blade begins to struggle or heat builds up excessively, lowering the speed or increasing coolant flow may be necessary. Conversely, if the blade is not engaging effectively or the cut seems too slow, a slight speed increase may improve performance. As a blade wears down and its diameter decreases, adjustments in RPM within the recommended range can help maintain optimal performance. Increasing the speed compensates for the reduced surface speed, keeping the cutting process efficient.
When starting a cut, especially with larger or denser materials, consider using a soft start technique. Gradually increasing the blade speed from a lower RPM reduces initial shock and wear on the blade, extending its life and lowering the risk of material damage. The capabilities of your equipment are essential for maintaining accurate and consistent RPMs and coolant flow rates.
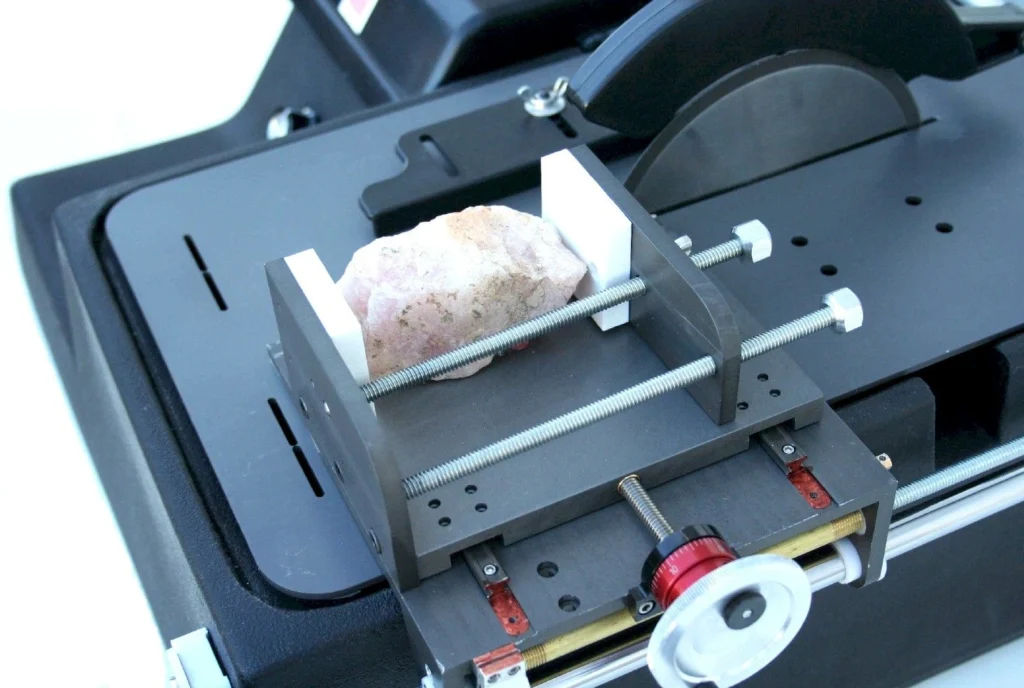
Advanced equipment with features like variable speed controls and automatic coolant adjustments allows for better control over the cutting process and real-time adaptation to changing conditions.
It is important to avoid operating the blade at speeds higher than recommended. Over-speeding significantly increases the risk of blade damage, equipment wear, and personal injury. High speeds can cause the blade to overheat, leading to warping, cracking, or even disintegration. Always operate within the manufacturer’s specified RPM range for a safe and effective cutting experience.
The type of material being cut also impacts optimal RPM. Synthetic materials or lapidary materials of varying composition may require different speeds compared to natural stones or tiles, due to variations in abrasiveness and heat sensitivity. Performing trial cuts on scrap pieces of the same material can help identify the best speed settings before making final cuts. Safety checks should be a regular part of your process to ensure all components, especially those related to speed control and blade stability, are functioning correctly. Inspect the blade arbor, drive belts, and motor performance to prevent unexpected speed changes during operation, ensuring both safety and consistent cutting performance.
RECOMMENDED SPEEDS BASED ON BLADE DIAMETER
Recommended rpm’s based on blade diameter, which you can adjust based on more specific blade characteristics or manufacturer recommendations:
Blade Diameter (inches) |
Recommended RPM’s |
---|---|
4 |
5,000 - 6,000 |
6 |
4,000 - 4,500 |
8 |
3,500 - 4,000 |
10 |
3,000 - 3,500 |
12 |
2,500 - 3,000 |
14 |
2,200 - 2,700 |
16 |
1,950 - 2,500 |
18 |
1,750 - 2,250 |
20 |
1,550 - 2,000 |
24 |
1,300 - 1,750 |
These ranges are set to optimize cutting performance and blade life, while also considering safety. Smaller blades require higher RPMs to achieve the necessary cutting speed, while larger blades need to rotate more slowly to maintain control and precision. Remember, these are general guidelines and specific blades, especially those with special coatings or designs, may have different recommendations.
Material |
Density (kg/m³) |
Knoop Hardness (kg/mm²) |
Mohs Hardness |
Recommended Cutting Speed |
Recommended Feed Rate |
What to Look Out For |
---|---|---|---|---|---|---|
Agate |
2600 |
800 |
6.5-7 |
Moderate |
Low to moderate |
Watch for chipping; ensure the blade is sharp and cooling fluids are used to prevent overheating. |
Ametrine |
2650 |
1050 |
7 |
Moderate |
Gentle |
Maintain color integrity by ensuring even cuts and avoid overheating to preserve distinct zones. |
Amethyst |
2650 |
750 |
7 |
Moderate |
Gentle |
Prevent thermal shock and overheating which can lead to fracturing in this heat-sensitive gem. |
Azurite |
3800 |
N/A |
3.5-4 |
High |
Moderate |
Use a finer blade and high speeds to minimize pressure and avoid crushing the soft structure. |
Cubic Zirconia |
5800 |
1200-1400 |
8.5 |
Low |
Slow |
Requires diamond-coated tools; monitor for overheating due to extreme hardness. |
Emerald |
2710 |
1350 |
7.5-8 |
Low |
Very slow |
Carefully manage feed to prevent stress on inclusions, which could lead to internal cracks or fractures. |
Garnet |
3900 |
1300 |
6.5-7.5 |
Variable depending on type |
Variable depending on type |
Adjust speed and feed based on specific garnet type; hardness varies significantly. |
Jade |
3300 |
1200 |
6-7 |
Low |
Slow |
Tough material requires slow, steady feeds to prevent cracking or fracturing along the cut. |
Quartz |
2650 |
1200 |
7 |
Moderate |
Moderate |
Hardness and abrasiveness can dull blades quickly; use sufficient cooling. |
Lapis Lazuli |
2500-2800 |
N/A |
5-5.5 |
High |
Moderate |
Softness makes it prone to scratching; gentle handling required during cutting. |
Meteorites |
Varies |
N/A |
Varies |
Variable |
Variable |
Metal content requires careful attention to speed and feed to avoid overheating and structural damage. |
Opal |
2100-2500 |
700 |
5.5-6.5 |
Low |
Very gentle |
Fragile nature requires extra care to prevent cracking; ensure the blade is well-lubricated and clean. |
Onyx |
2500-2700 |
100-200 |
6-7 |
Moderate |
Moderate |
Brittle characteristics can lead to chipping; smooth and steady cuts are necessary. |
Petrified Wood |
2200-2400 |
N/A |
7-8 |
Moderate |
Moderate |
Varying hardness within pieces; use a versatile blade and adjust feed rate as necessary. |
Rhodonite |
3400-3600 |
N/A |
5.5-6.5 |
High |
Moderate |
Can show cleavage easily; ensure precise and controlled cutting to maintain material integrity. |
Ruby |
4000 |
1800 |
9 |
Low |
Slow |
Extreme hardness requires diamond tools; closely monitor for signs of blade wear and overheating. |
Tanzanite |
3350 |
700 |
6.5-7 |
Low |
Gentle |
Sensitive to thermal shock; avoid rapid temperature changes and use a gentle feed to prevent fracturing. |
Topaz |
3500 |
1350 |
8 |
Moderate |
Careful |
Cleavage planes require careful handling to avoid splitting; ensure cuts are well-planned and precise. |
Tourmaline |
3000-3300 |
1000-1100 |
7-7.5 |
Moderate |
Moderate |
Color variations may affect hardness; monitor and adjust feed rate accordingly to prevent cracking. |
Tsavorite |
3700 |
1600-1800 |
7-7.5 |
Moderate |
Moderate |
Similar to garnet with inclusions that require careful cutting; ensure blade is consistently sharp. |
Turquoise |
N/A |
5-6 |
High |
Gentle |
Porous nature makes it sensitive; avoid excessive pressure and use high speeds for clean cuts. |
COOLANTS
Proper coolant application is essential for maintaining diamond blade performance, reducing heat buildup, and ensuring the longevity of both the blade and the material being cut. The effective use of coolant helps in optimizing cutting efficiency and reducing wear on the blade, leading to longer service life and higher-quality cuts.
The Role of Coolant in Blade Performance The primary functions of coolant in cutting operations are to cool the blade, reduce friction, and flush away debris and swarf from the cutting area. Applying coolant evenly to both sides of the blade is vital. When the blade is cooled effectively, it prevents overheating that could lead to blade warping or deterioration of the diamond segments. Overheating is a common cause of blade damage and can result in lower quality cuts or even blade failure. Consistent coolant flow also reduces friction, allowing for smoother and more efficient cutting, especially on tough or delicate materials.
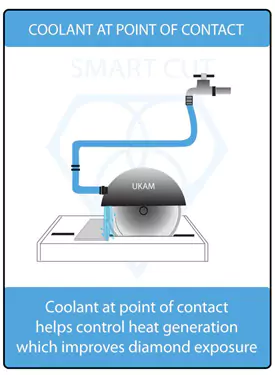

Optimal Coolant Spray Angles For maximum effectiveness, the coolant should be sprayed onto the blade at a downward angle between 30 to 45 degrees. This approach ensures that the coolant reaches the side surfaces of the blade as well as the cutting edge. The periphery of the blade, where the diamond edge meets the material, requires focused cooling and lubrication. Angled coolant spray helps to cover these critical areas, ensuring that heat is dissipated evenly and debris is removed effectively.
For cutting lapidary materials, selecting the right coolant is essential for quality cuts and for preserving both the diamond lapidary blade and the material being worked on. When choosing a coolant, consider factors such as the hardness of the material, the desired type of cut, and environmental or health considerations. Opting for coolants that are non-toxic, biodegradable, and non-staining is important in settings where health and cleanliness are priorities. Understanding the distinct properties and benefits of various coolants can significantly improve lapidary operations, enhancing efficiency, ensuring optimal results, and prolonging equipment lifespan.


Water is the most economical and accessible coolant, often used for cutting softer stones with a hardness of less than 6.0 on the Mohs scale. It is safe for both the user and the environment, effectively reducing heat and removing debris during cutting. However, water lacks lubricating properties and is not as effective in heat removal as other coolants.
Water-soluble oils provide improved lubrication and cooling compared to plain water. These oils often include rust inhibitors to protect both the saw and blade, making them versatile for a variety of materials and cutting conditions. The concentration of these coolants can be adjusted to achieve the desired balance of lubrication and cooling efficiency.
Synthetic coolants are popular for their non-staining properties, especially when cutting precious and semi-precious materials. They offer excellent rust and corrosion protection and degrade more slowly than oil-based coolants, which extends their lifespan. Many synthetics are also biodegradable, which addresses environmental disposal concerns. SMART CUT water-soluble coolant is an excellent choice for lapidary applications.
Semi-synthetic coolants strike a balance between oil-based and synthetic options. They provide good lubrication, improved cooling, and rust protection, usually at a lower cost than fully synthetic coolants. Their versatility makes them suitable for studios with mixed-use applications, accommodating a range of materials and cutting speeds.
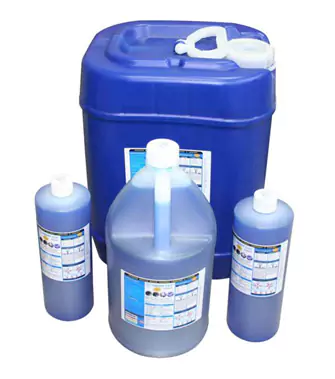
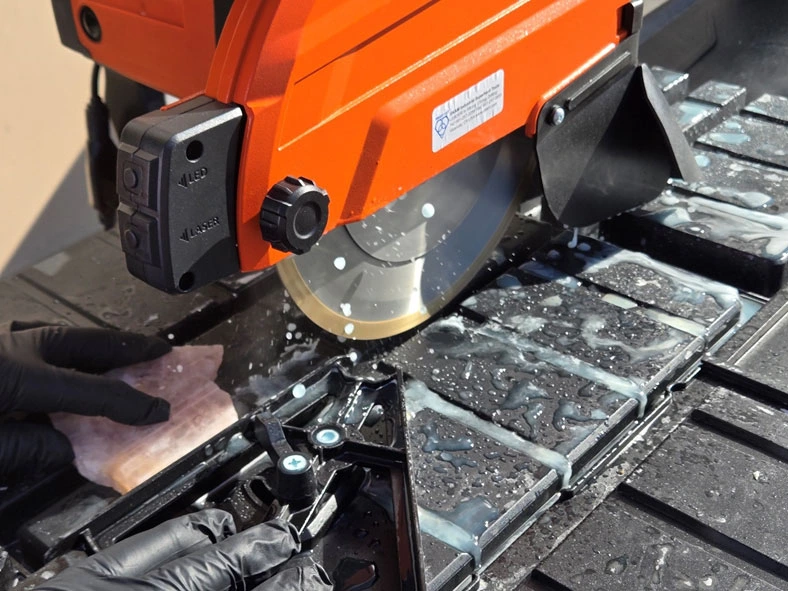
Adjusting coolant flow based on material type is key. Harder materials tend to generate more heat and require increased coolant flow for effective dissipation. Softer materials, on the other hand, might need less coolant. Observing the cutting process and making appropriate adjustments to coolant flow ensures the ideal balance between cooling and lubrication.
Coolant temperature plays a significant role in cutting performance. During prolonged sessions or in warm environments, the coolant can heat up, reducing its effectiveness. Monitoring coolant temperature with a gauge, taking breaks to let it cool, or adding ice packs to the reservoir are practical ways to manage temperature.
While water is commonly used due to availability and cost-effectiveness, adding specific additives can enhance its performance. These additives prevent rust, reduce foam, and increase lubrication. Always follow the manufacturer’s recommendations when selecting additives to ensure they are compatible with both the blade and the material.
Eco-friendly and safe coolants are preferable for minimizing environmental impact and workplace hazards. Choosing biodegradable, non-toxic coolants that are safe to handle helps maintain a healthier work environment and reduces contamination during disposal.
Proper coolant disposal is vital for environmental compliance. After its useful life, coolants should be disposed of according to local regulations, especially if they contain additives requiring special handling as hazardous waste. A proper system for collecting and disposing of used coolant prevents environmental damage and meets regulatory requirements. Develop an emergency response plan for coolant spills to ensure quick action that prevents slips, falls, and equipment damage. Absorbent materials and spill kits should be kept nearby, and staff should be trained on immediate response procedures to enhance workplace safety.
Regularly review and upgrade the coolant system to improve efficiency and safety. Modern systems often offer better filtration, precise flow control, and automated temperature management, contributing to more effective cooling and lubrication during cutting operations. Operators should be trained in the proper use, maintenance, and disposal of coolants. Understanding the role of coolants, recognizing inadequate cooling, and adjusting coolant flow are critical skills for maximizing blade performance and longevity.
Implementing visual methods to monitor coolant flow at the point of contact between blade and material, such as using safe-colored dyes, can help operators see how effectively coolant reaches the cutting zone. This allows for accurate adjustments and enhances cutting and blade life. Conduct regular audits of the coolant system to evaluate its efficiency. This includes reviewing flow rate, temperature control, filtration, and the condition of hoses, pumps, and nozzles. Addressing any issues uncovered in audits can improve cutting performance and safety significantly.


For operations with high coolant use, recycling systems are a beneficial investment. These systems filter and recondition the coolant for reuse, lowering waste and costs while maintaining consistent coolant quality for optimal cooling and lubrication. If foam forms in the coolant, which can occur in certain water additives or high-flow systems, adding anti-foaming agents can help. Foam can obstruct coolant delivery and reduce cooling capacity. The selected anti-foaming agents should be compatible with the coolant and materials being cut.
Automated monitoring systems in advanced setups can track coolant flow rates, temperature, and composition, adjusting these parameters in real time for optimal cutting conditions. Automation removes guesswork and allows operators to focus more on the cutting process. Seasonal temperature variations affect coolant strategies. In warmer months, increasing coolant flow or enhancing cooling measures is necessary, while in colder conditions, steps must be taken to prevent coolant from freezing or becoming too viscous for circulation.
Consider operator comfort and safety when selecting coolants. Products that produce minimal mist or cause less skin irritation contribute to a safer working environment. Providing protective gear designed specifically for coolant use can prevent skin and respiratory exposure. Establishing a feedback loop with operators can be invaluable for continuous improvement. Their insights into coolant use and cutting performance help optimize strategies, extend blade life, and improve cut quality over time.
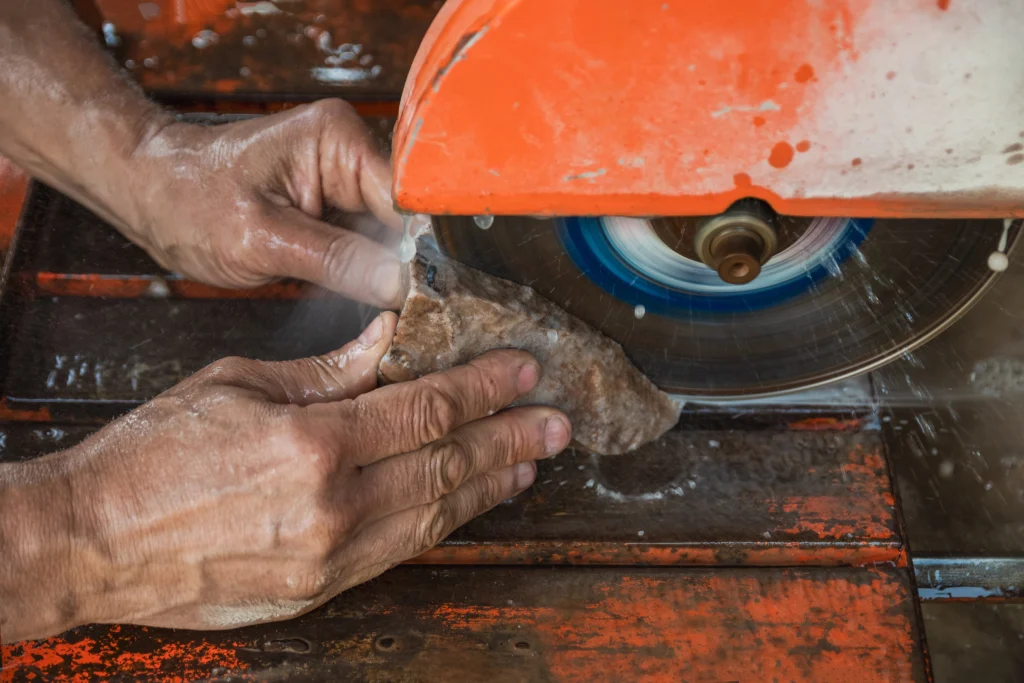
FEED RATES
To optimize cutting efficiency and prevent damage, adjusting the feed rate according to the hardness of the material is essential. Harder materials require a slower feed rate to allow effective cutting without overheating or overloading the blade, while softer materials can be cut more quickly—provided that the speed increase does not compromise cut quality or blade integrity.
Ensuring adequate support for the material near the cutting zone is very important. Unsupported or poorly supported materials can cause the blade to bind or pinch, which can affect the feed rate and potentially damage both the material and the blade. Proper support minimizes unnecessary stress on the blade and allows for a more controlled feed rate.

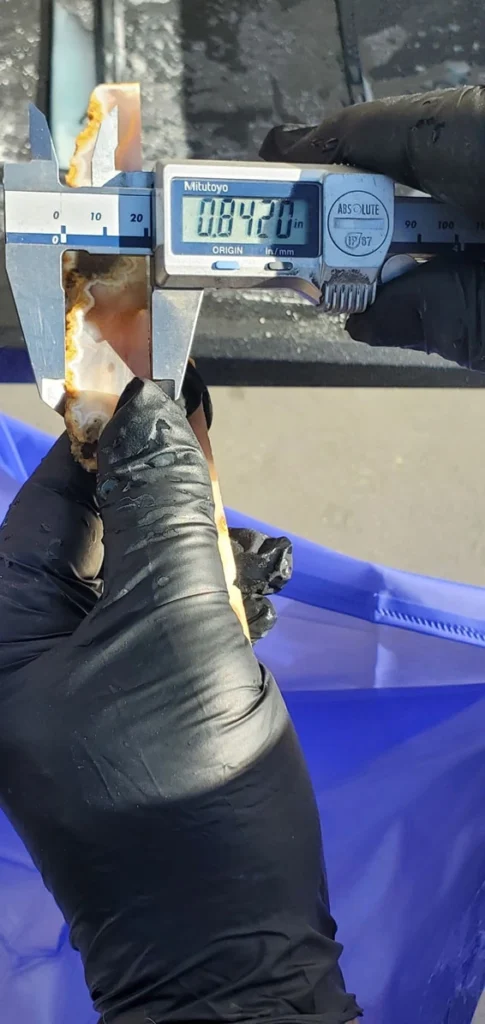
For materials with varying densities or embedded objects, using variable feed rates can improve cutting efficiency and blade life. Start with a slower feed rate when encountering harder sections or inclusions, then increase speed in softer areas. This approach requires attentiveness but can yield better results and extend blade longevity.
If using more sophisticated computer-controlled cutting machines often feature feed rate indicators or controls to help maintain the optimal speed for introducing materials to the blade. These features are particularly useful for less experienced operators or those working with unfamiliar materials, as they provide guidance on achieving the correct feed rate.
Blade temperature must be monitored continuously during cutting to prevent overheating, which can cause premature wear or blade failure. If the blade overheats, reduce the feed rate, increase coolant flow, or pause cutting to allow the blade to cool down. The material’s thickness also influences the appropriate feed rate;
thicker materials generally necessitate a slower feed rate to ensure the blade can cut through without strain. Adjusting the feed rate to match the thickness helps maintain control over the cut and prevents blade damage.

Aim for a consistent, fluid motion when feeding the material. Avoid sudden stops and starts, as they can cause chipping or breakage along the material’s edges. A steady feed rate is key to achieving a smooth finish and preserving blade sharpness. Regularly check the blade alignment to ensure optimal cutting performance. Misalignment can affect the feed rate and lead to irregular cuts or blade damage, so regular adjustments are essential for maintaining consistent feed rates. Create a feedback loop with operators to refine feed rate practices based on real-world experiences. Their insights can lead to adjustments that enhance cutting efficiency, improve safety, and extend the blade’s lifespan. As a diamond lapidary blade wears, its performance changes, often requiring adjustments in the feed rate to maintain optimal cutting efficiency. Regularly assess the condition of blades and make necessary feed rate changes to ensure consistent cutting quality throughout their lifespan.
It is also important to ensure that debris and cut material are efficiently ejected from the cutting area.
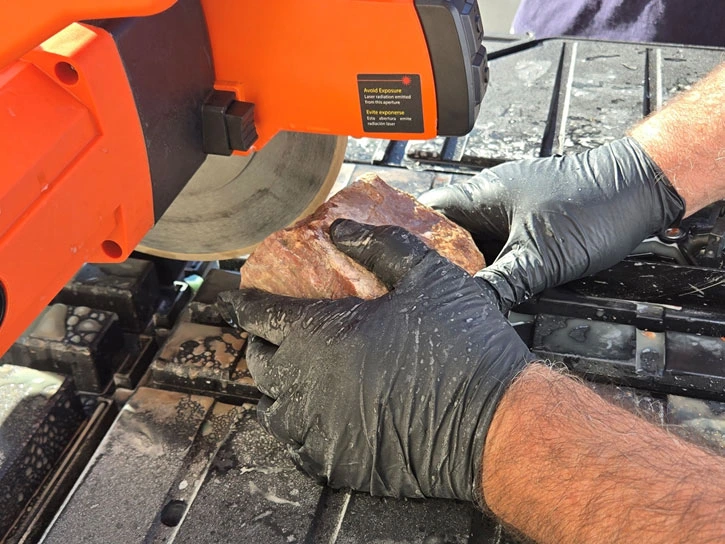

Accumulation of material can hinder the blade’s progress, requiring feed rate adjustments. Keeping the cutting zone clear not only improves efficiency but also reduces the risk of blade jamming or damage. The blade's thickness plays a role in determining the feed rate. Thicker blades can handle more aggressive feed rates due to increased strength and stability, while thinner blades require a more cautious approach to prevent deflection or breakage. Matching the feed rate to the blade’s characteristics optimizes performance and prolongs its life.
Operator skill and experience are critical in effectively managing feed rates. Experienced operators can intuitively judge optimal rates based on the sound of the cut, the feel of the material feed, and the cut surface's appearance. Training operators to develop these skills can significantly enhance cutting performance. Documenting effective feed rate methods for different materials and blades can help improve performance. Keeping a record of successful practices will help in replicating good cuts, refining techniques, and training new operators, as well as troubleshooting cutting issues.
Regularly review and adjust feed rate processes as cutting conditions, blade conditions, and material characteristics change over time. Continuous improvements in feed rate management can enhance performance, efficiency, and safety. Use cooling breaks during long or demanding cuts can prevent overheating and material damage. These breaks allow the blade to cool, the material to stabilize, and the operator to assess the process, making necessary adjustments for the remainder of the cut.
BLADE DRESSING
To ensure the longevity and effectiveness of your diamond blades while maintaining a safe and efficient cutting operation, it's essential to adopt a meticulous approach to blade dressing and operational monitoring.
Starting with blade dressing, it’s not just a routine task but a critical maintenance step that directly impacts blade performance and lifespan. Regular assessment of the blade's condition helps determine the optimal frequency for dressing, which varies depending on the materials you're cutting and the intensity of the blade's usage. For blades subjected to heavy use or abrasive materials, more frequent dressing might be necessary to maintain cutting efficiency.
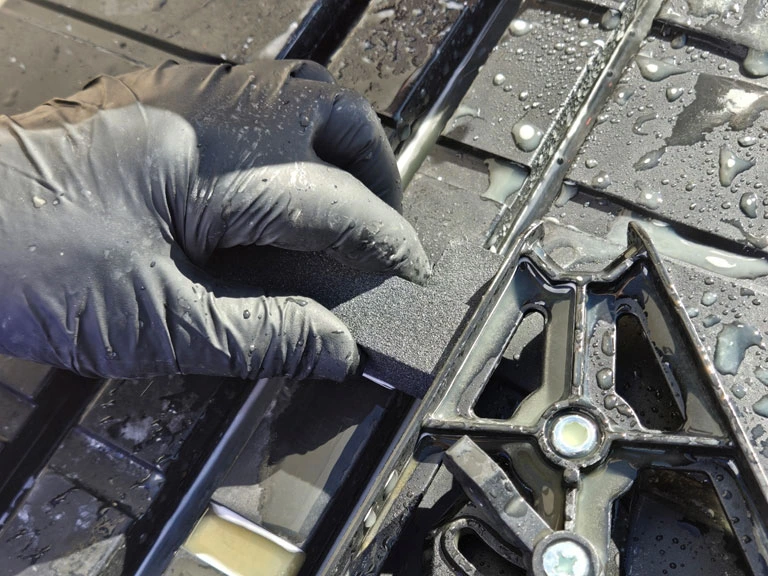

When dressing your blade, consider the materials used for this process. Traditional methods involve a 220 grit grinding wheel or dressing sticks >>>, but for harder diamond blades, using silicon carbide or diamond dressing blocks can be more effective. These materials are adept at removing the glaze from the blade and exposing new diamond particles without removing excessive material from the blade itself. This delicate balance ensures the blade is rejuvenated for optimal cutting without significantly reducing its thickness or lifespan.
The technique employed during the dressing process is crucial. The goal is to apply gentle, consistent pressure to expose new diamond particles, enhancing the blade's cutting ability. This requires a careful approach to avoid aggressive dressing, which could prematurely wear down the blade. Furthermore, the use of coolants during dressing is vital. Coolants help prevent overheating and minimize thermal shock to the diamond section/edge, contributing to a safer and more effective dressing process. More about Dressing>>>

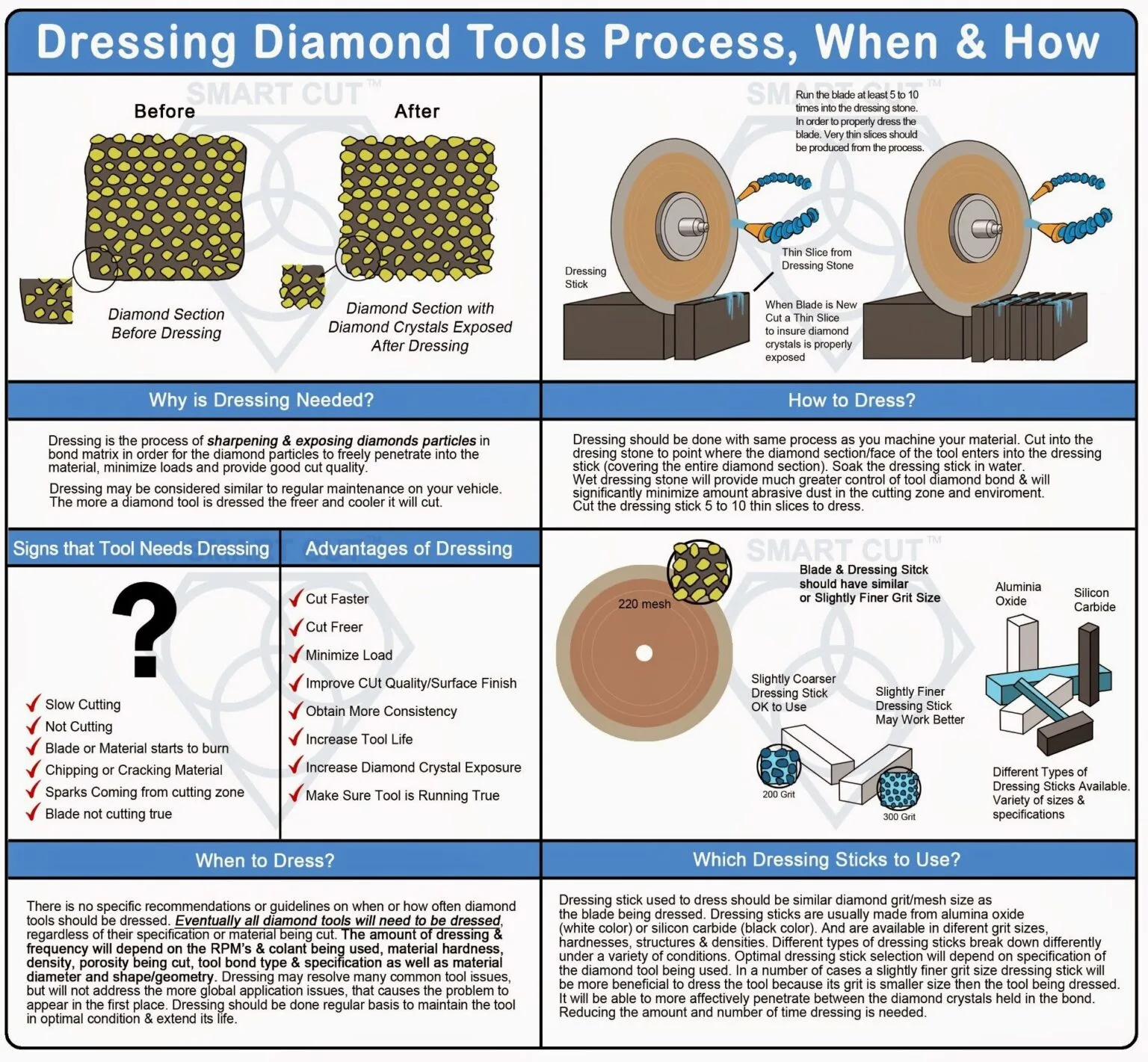
Monitoring the cutting operation in real-time is equally important. Before initiating a cut, a thorough inspection of the blade for any signs of wear or damage is essential. Look for cracks, missing chips from diamond section, or any signs of bending. Early detection of these issues can prevent further damage and ensure the blade operates at peak performance.
For operations equipped with the technology, real-time blade monitoring systems offer an advanced way to keep tabs on blade performance. These systems can detect increased vibration or changes in cutting forces, alerting operators to potential issues before they escalate. Such immediate feedback allows for quick adjustments, enhancing both safety and efficiency.
Blade alignment within the machine also requires regular attention. Ensuring the blade is correctly aligned guarantees that it cuts straight and true, preventing uneven wear and maintaining the quality of the cut. This is particularly crucial after replacing or dressing a blade, as even minor misalignments can impact cutting performance.
The size of the material being cut should adhere to the guideline of not exceeding 3/8” of the blade diameter to avoid blade damage. For larger materials, using a smaller blade for pre-cutting or employing alternative methods to reduce the material to a manageable size can prevent undue stress on the blade.
Adhering to safety protocols is non-negotiable. When dressing diamond lapidary, operators must keep their hands and fingers away from the cutting edge to prevent injuries. For smaller or irregularly shaped materials, using appropriate tools to feed the material into the blade ensures safety while maintaining control over the cut.
CLEANING BLADES AFTER USE
To maintain the optimal performance of diamond blades, an effective cleaning regimen is essential. Proper cleaning can enhance performance and extend the blade's life. It's important to select a cleaning solution specifically designed for diamond blades. Some solutions are more effective at dissolving certain types of residue, such as concrete dust, metal particles, or lapidary materials. Always ensure that the solution is compatible with your blade’s material to prevent damage during cleaning.
The frequency of cleaning depends on the type of material being cut. Sticky or abrasive materials may necessitate more frequent cleanings to prevent buildup, which can impair cutting performance. Establish a cleaning schedule based on the materials you typically work with and adhere to it consistently. Cleaning is also an ideal time to inspect the blade for wear or damage, such as chips, missing segments, or warping. Early detection of these issues helps prevent blade failure and maintains cut quality. For blades with stubborn residue buildup, consider using an ultrasonic cleaner.

Ultrasonic cleaning effectively removes tough debris without abrasive scrubbing that could damage the blade. This method is especially beneficial for blades used in precision cutting, where maintaining blade integrity is crucial.
Avoid using harsh chemicals or solvents that can corrode the metal parts of the blade or degrade the bonding material securing the diamonds. Stick to manufacturer-recommended solutions or mild, neutral pH cleaners to prevent unintentional damage. After rinsing, thoroughly dry the blade to prevent rust. Moisture left on the steel core or segments can lead to corrosion. Use a clean, dry cloth to wipe down the blade, and consider using compressed air to remove water from hard-to-reach areas.
Once cleaned and dried, store the blade in a dry, dust-free environment to prevent contamination. Ideally, hang the blade on a wall-mounted rack to allow air circulation around it, reducing moisture accumulation and the risk of rust. Keep records of all blade maintenance, including cleaning, to track performance over time. These records will help identify when a blade is nearing the end of its useful life and needs replacement, ensuring that you always work with tools in optimal condition.
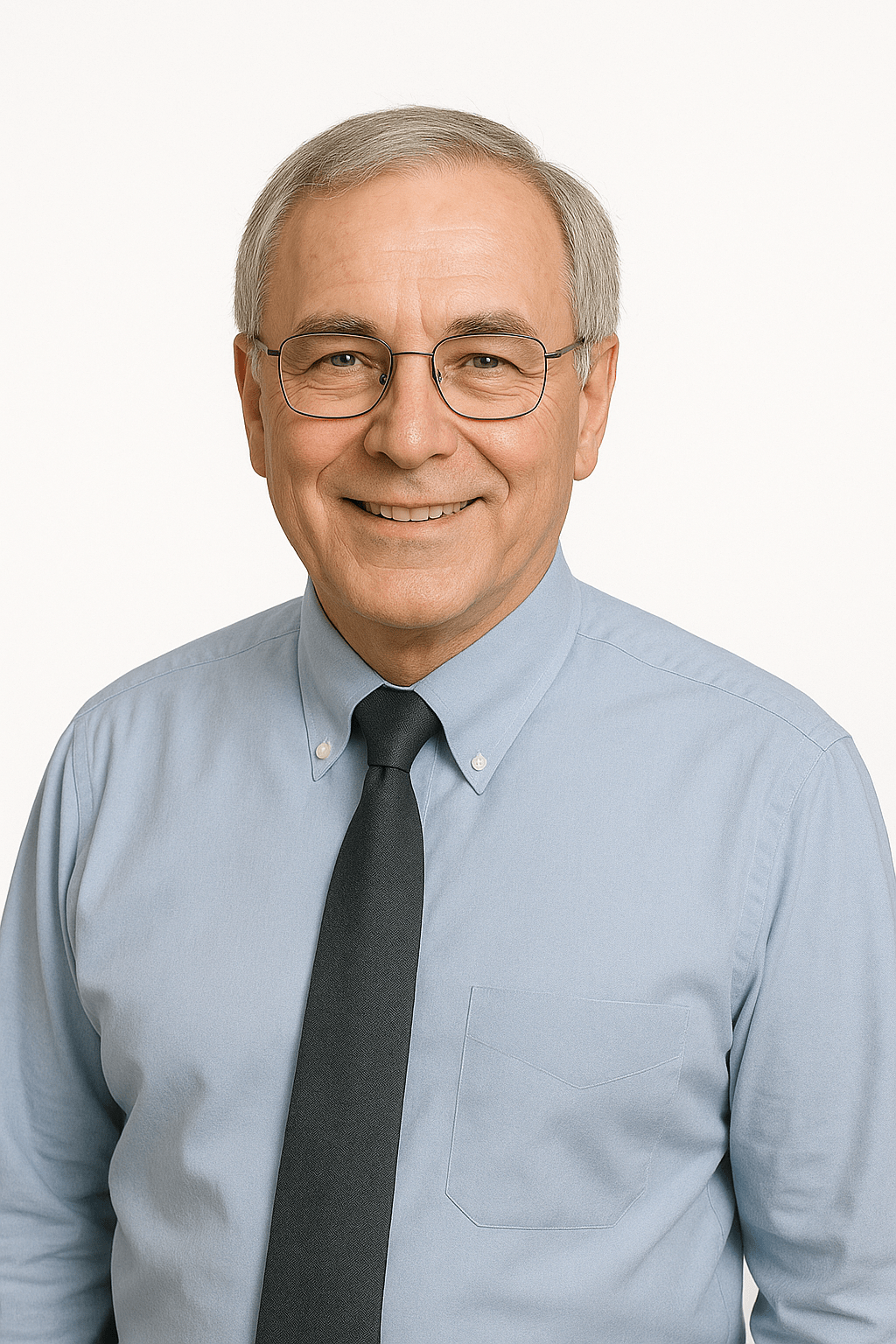
Alexander Schneider is a senior applications engineer and leading authority in the industrial diamond tooling industry, with over 35 years of hands-on experience in the development, application, and optimization of ultra-thin and high-precision diamond blades, diamond core drills, and diamond and CBN grinding wheels. His work spans a wide range of advanced materials including ceramics, glass, composites, semiconductors, and high-performance metals.
Throughout his career, he has collaborated with leading R&D institutions, national laboratories, and high-tech manufacturing companies across Europe, North America, and Asia, providing technical expertise and tailored solutions for demanding cutting and surface preparation applications.
Mr. Schneider has played a pivotal role in advancing precision cutting, sectioning, dicing, and grinding technologies used in research, production, and failure analysis. He is widely respected for his ability to optimize tool design and cutting parameters to meet exacting industry standards—balancing factors such as cut quality, blade life, material integrity, and process consistency.
As an author, Mr. Schneider is known for delivering practical, application-focused insights that translate complex technical challenges into clear, actionable strategies. His articles and technical guides serve as trusted resources for engineers, researchers, and manufacturers seeking to improve precision, reduce process variability, and enhance tool performance in critical applications.
ARE YOU USING RIGHT LAPIDARY BLADES
FOR YOUR APPLICATION?
LET US
HELP YOU
HAVING ISSUES WITH
YOUR CURRENT LAPIDARY BLADES?
Knowledge Center
How to Properly Use Diamond Lapidary Blades
Signs of a High Quality Diamond Lapidary Blade
What Makes a Great Diamond Lapidary Blade
Mastering the Art of Lapidary cutting
Evaluating & Comparing Diamond Blades
How to Improve & Optimize Your Diamond Sawing Operation
Troubleshooting Diamond Sawing Problems
How to properly use Diamond Tools
How to Selecting Right Diamond Tools for your application
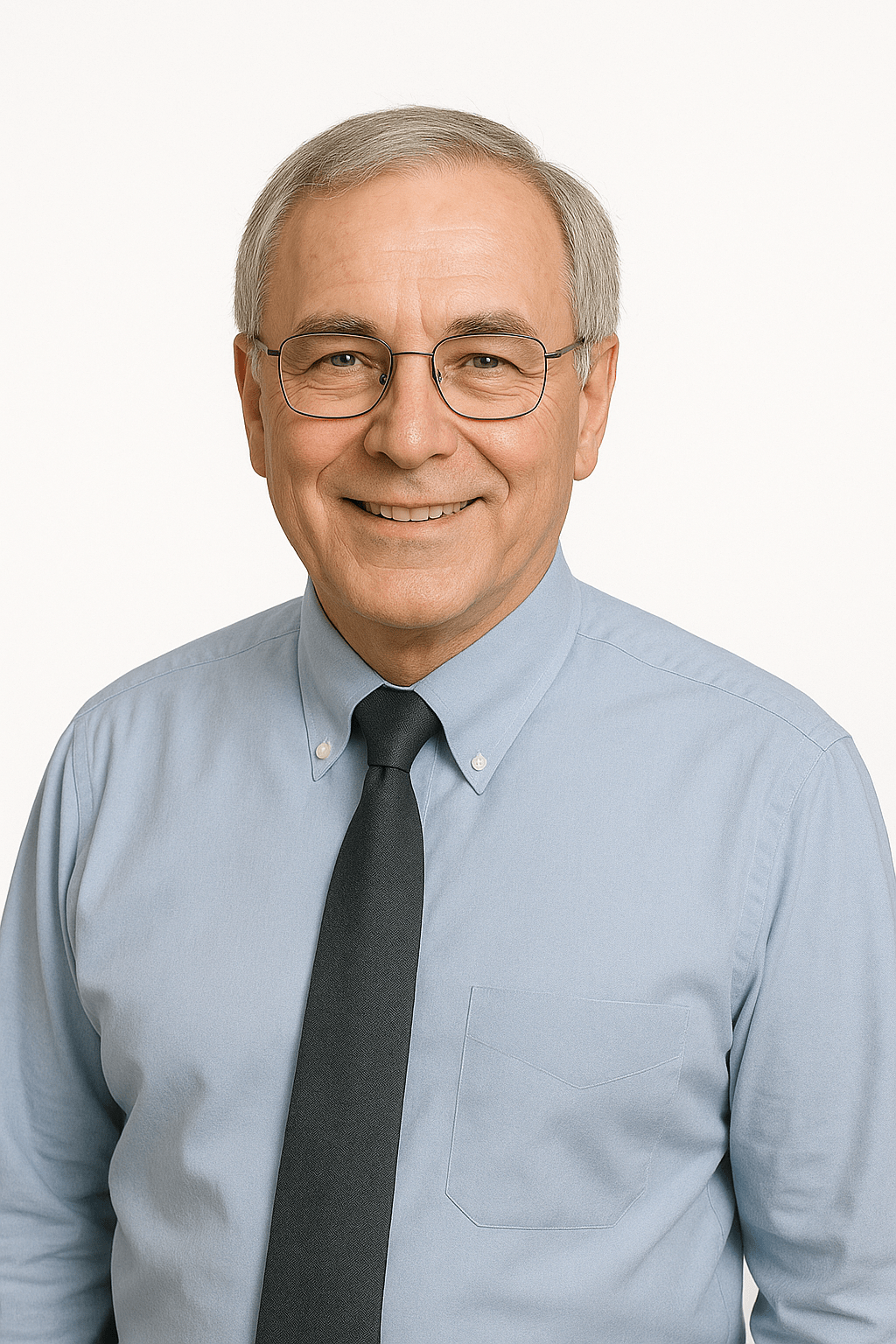
Alexander Schneider is a senior applications engineer and leading authority in the industrial diamond tooling industry, with over 35 years of hands-on experience in the development, application, and optimization of ultra-thin and high-precision diamond blades, diamond core drills, and diamond and CBN grinding wheels. His work spans a wide range of advanced materials including ceramics, glass, composites, semiconductors, and high-performance metals.
Throughout his career, he has collaborated with leading R&D institutions, national laboratories, and high-tech manufacturing companies across Europe, North America, and Asia, providing technical expertise and tailored solutions for demanding cutting and surface preparation applications.
Mr. Schneider has played a pivotal role in advancing precision cutting, sectioning, dicing, and grinding technologies used in research, production, and failure analysis. He is widely respected for his ability to optimize tool design and cutting parameters to meet exacting industry standards—balancing factors such as cut quality, blade life, material integrity, and process consistency.
As an author, Mr. Schneider is known for delivering practical, application-focused insights that translate complex technical challenges into clear, actionable strategies. His articles and technical guides serve as trusted resources for engineers, researchers, and manufacturers seeking to improve precision, reduce process variability, and enhance tool performance in critical applications.