Table of Contents
ToggleCubic Boron Nitride (CBN) is a synthetic material that is renowned for its exceptional hardness and high thermal stability. It is composed of boron and nitrogen atoms arranged in a crystal lattice structure, similar to diamond. CBN is the second hardest material known after diamond and exhibits similar properties to diamond in terms of wear resistance and thermal conductivity.
Share this Article with Friend or Colleague
CBN is primarily used in industrial applications, particularly for machining ferrous materials such as hardened steels, cast iron, and superalloys. Its hardness and thermal stability make it highly effective in high-speed machining operations, where it can withstand the heat and pressures generated during cutting and grinding processes. CBN tools, such as inserts, grinding wheels, and drills, are engineered to deliver superior performance, extended tool life, and high precision in demanding machining applications.
The exceptional properties of CBN have made it a valuable material in various industries, including automotive, aerospace, and manufacturing. Its ability to machine hardened materials with precision and efficiency has revolutionized the productivity and quality of metalworking CBN continues to be a subject of ongoing research and development to further enhance its properties and expand its applications in the field of cutting and abrasive tools. operations.
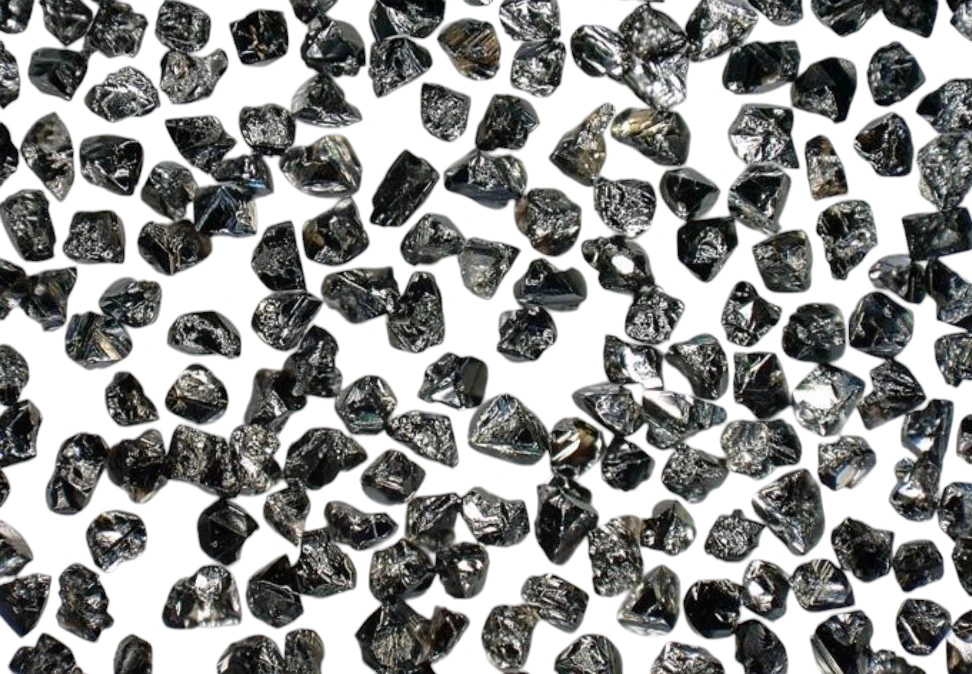
CBN is recommended for working with metals, specially iron and steel. Since carbon in steel reacts with carbon in diamond, quickly dulling the diamond crystal and slowing the material removal. CBN tools provide significantly reduced cutting times for tough, gummy materials, such as lead and titanium. However, CBN are not recommended for ceramics and other non metallic materials. CBN will provide optimal performance on difficult to cut materials. These CBN tools will significantly reduce your cutting time on ferrous materials compared to diamond tools.
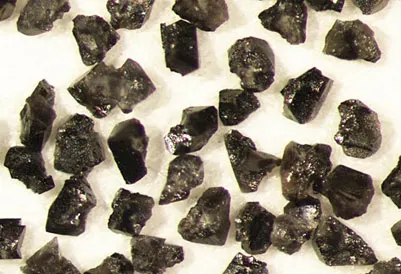
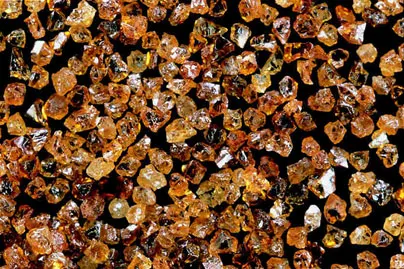
Application Comparison Diamond vs CBN (cubic boron nitride) Tools
In the realm of abrasive machining, understanding the interaction between tool materials and workpiece materials is crucial for optimizing performance and tool life. One significant interaction is the chemical reaction between industrial diamond tools and ferrous metals under high temperature and pressure conditions, commonly encountered during cutting processes. This section delves into the details of this reaction and its implications.
The Nature of Diamond and Its Use in Cutting Tools
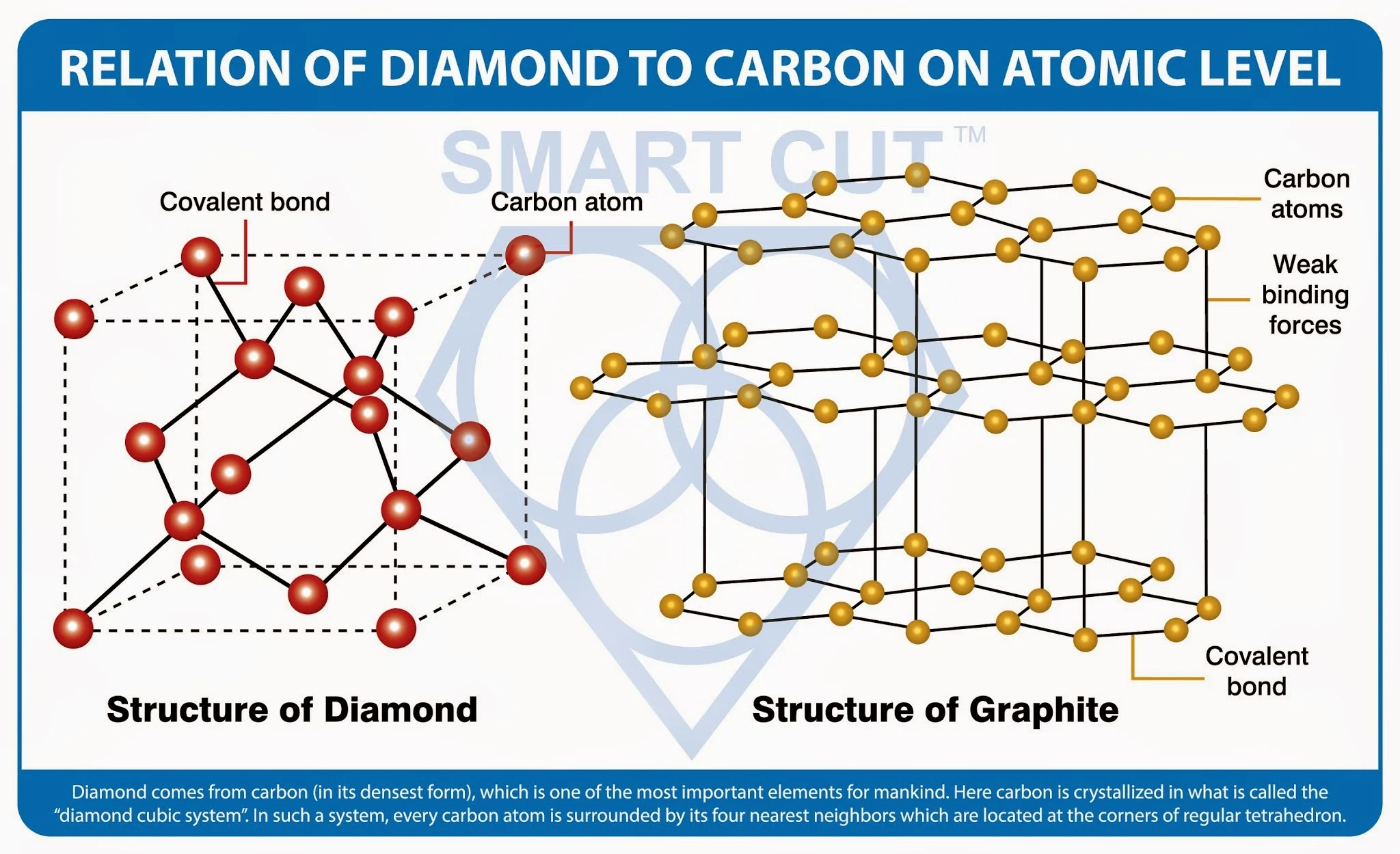
Industrial diamond is renowned for its exceptional hardness, making it an ideal material for cutting and grinding applications. Diamonds, both natural and synthetic, are widely used in tools designed to cut, grind, or shape a variety of materials. However, despite their unparalleled hardness, diamonds are composed of carbon, which is susceptible to chemical reactions under certain conditions.
Interaction with Ferrous Metals
Ferrous metals, such as steel, cast iron, and other alloys containing iron, are prevalent in many industrial applications. When diamond tools are used to cut or grind ferrous metals, the high temperatures and pressures generated during these processes can lead to a chemical reaction between the carbon in the diamonds and the iron in the ferrous metals.
The Chemical Reaction
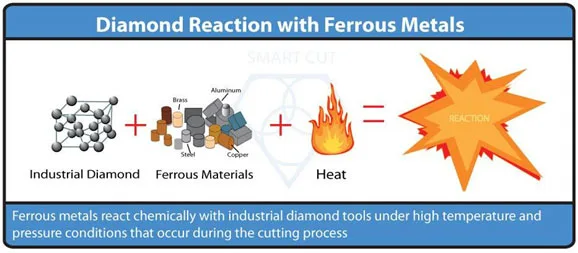
The illustration provided encapsulates this reaction:
-
1. Industrial Diamond: Represented by a molecular structure, diamonds consist of carbon atoms arranged in a crystal lattice.
-
2. Ferrous Materials: Shown with images of metals like brass, steel, copper, and aluminum, these materials contain iron, which is the reactive component.
-
3. Heat: Depicted by a flame icon, high temperatures are inherent in cutting and grinding operations.
-
4. Reaction: Illustrated by an explosion icon, this signifies the chemical interaction that occurs.
When the diamond comes into contact with ferrous materials at elevated temperatures, a reaction takes place. The carbon atoms in the diamond react with the iron atoms in the ferrous metal, leading to the formation of iron carbide. This reaction is undesirable as it degrades the diamond, reducing its effectiveness and leading to accelerated wear and tool failure.
Implications for Tool Performance
The chemical reaction between diamonds and ferrous metals has several implications:
-
Tool Wear: The formation of iron carbide results in the loss of diamond material, which significantly reduces the tool's lifespan.
-
Cutting Efficiency: As the diamond degrades, the cutting efficiency diminishes, leading to slower machining processes and inferior surface finishes.
-
Cost Considerations: Frequent replacement of diamond tools due to rapid wear increases operational costs and downtime.
Materials recommended for cutting with CBN:
-
Alloy steels (45-68 RC)
-
Carbon tool steels (45-68 RC)
-
Die steel (45-68 RC)
-
High speed steel (45-68 RC)
-
Chilled cast iron
-
Ni Hard
-
Forged steel
-
Meehanite iron
-
Moly chrome steel rolls
-
Inconel 600
-
Rene
-
Incoloy
-
Monel
-
Stellite
-
Colmonoy
-
Waspoloy
-
Tool Steels
-
Alloy Steels
-
Hardening Steels
-
Stainless Steels
-
Bearing Steels
-
Heat-Resistant Alloys
-
Super Heat-Resistant Alloys
-
Sintered Metals
-
Ferrous Metals (Ferrous and other)
-
Copper Alloys
-
Hard Ferrous (steel) parts over 45 Rockwell C
-
Iron
-
Cobalt Alloys
-
Nickel Superalloys
-
Lead Alloys
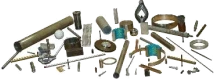
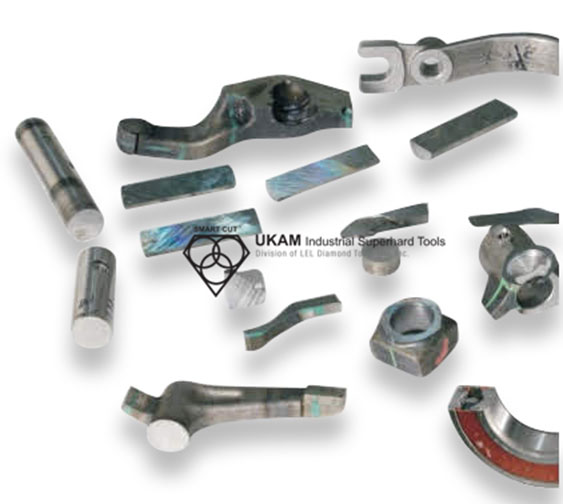
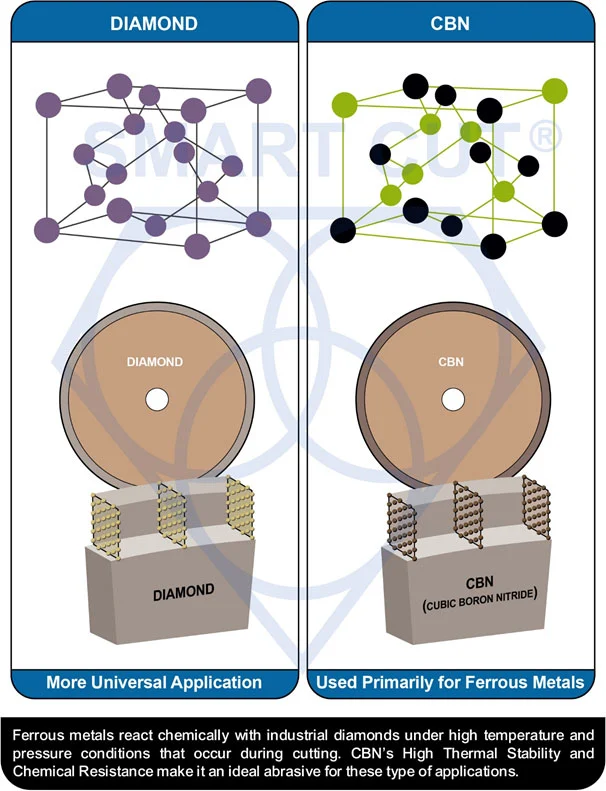
Properties of CBN
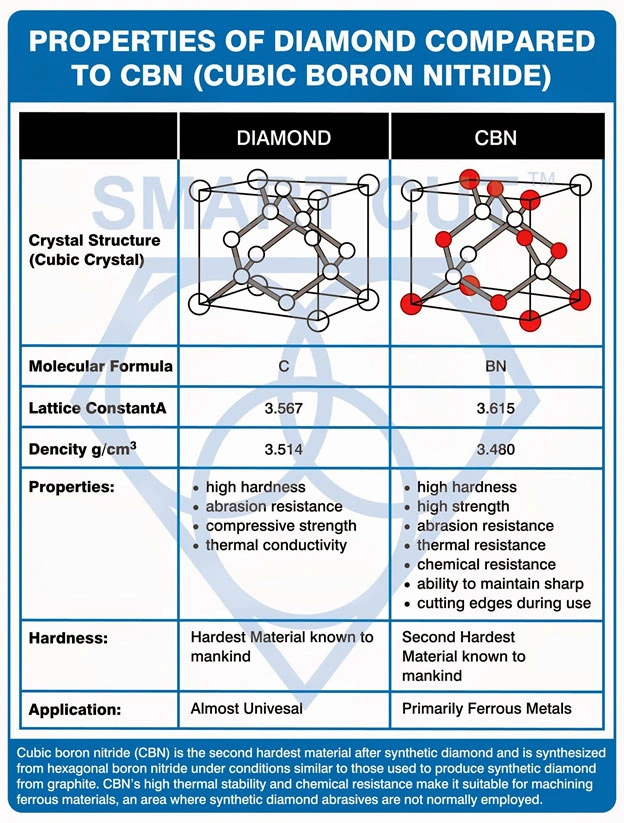
Exceptional Hardness: CBN's hardness is second only to diamond, making it incredibly effective for cutting and grinding hard materials. This hardness ensures that CBN tools can maintain their cutting edge and resist wear over prolonged periods, resulting in consistent performance and reduced tool changes.
High Thermal Stability: CBN can withstand temperatures exceeding 1,832°F (1,000°C) without losing its structural integrity. This thermal stability is particularly advantageous in high-speed machining operations where significant heat is generated. The ability to remain stable at high temperatures prevents thermal degradation of the tool, ensuring long-lasting performance and precision.
Wear Resistance: The wear resistance of CBN is comparable to that of diamond, allowing it to maintain sharp cutting edges even when machining tough materials. This property significantly extends the tool life, reducing the frequency of replacements and contributing to overall cost savings in manufacturing processes.
Thermal Conductivity: CBN exhibits high thermal conductivity, which helps in dissipating heat away from the cutting zone. This efficient heat management reduces the risk of thermal damage to the workpiece and prolongs the tool's lifespan by preventing overheating.
Comparison Chart: Diamond vs. Cubic Boron Nitride (CBN)
Aspect |
Diamond |
Cubic Boron Nitride (CBN) |
---|---|---|
Hardness |
Extremely hard (10 on the Mohs scale) |
Second hardest material after diamond (9 on the Mohs scale) |
Abrasive Performance |
Exceptionally high |
High |
Heat Resistance |
Excellent |
Excellent |
Chemical Stability |
Highly chemically stable |
Highly chemically stable |
Applications |
Widely used in various cutting, grinding, and drilling applications |
Primarily used for machining ferrous materials |
Cutting Speed |
Suitable for high-speed cutting operations |
Suitable for high-speed cutting operations |
Material Compatibility |
Effective for a wide range of materials, including both non-ferrous and ferrous metals |
Primarily used for machining ferrous metals |
Cost |
Expensive |
Relatively expensive |
Thermal Conductivity |
High |
High |
Fracture Toughness |
Lower compared to CBN |
Higher compared to diamond |
Surface Finish |
Can provide a smoother surface finish in some applications |
Can provide a smoother surface finish in some applications |
Availability |
Abundantly available as natural and synthetic diamonds |
Available, but less common than diamond |
Wear Resistance |
Exceptional |
Exceptional |
Electrical Conductivity |
Non-conductive |
Non-conductive |
Uses in Industrial Applications |
Cutting tools, grinding wheels, wire drawing dies, saw blades, and more |
Machining of hardened steels, high-speed steels, and other ferrous materials |
Tool Life |
Generally longer tool life compared to CBN |
Tool life depends on the application and material being machined |
Chemical Inertness |
Chemically inert, suitable for applications where chemical reactions are a concern |
Chemically inert, suitable for applications where chemical reactions are a concern |
Precision Machining |
Suitable for applications requiring high precision and tight tolerances |
Suitable for applications requiring high precision and tight tolerances |
Brittle Materials Machining |
Can be used to machine brittle materials such as glass and certain ceramics |
Not recommended for machining brittle materials |
Cutting Tool Availability |
Wide range of cutting tools available, including inserts, blades, and drills |
Cutting tools available, but less common than diamond |
Usage in Specific Industries |
Widely used in aerospace, automotive, electronics, and gemstone industries |
Commonly used in the automotive, aerospace, and manufacturing industries |
Environmental Impact |
Diamond mining can have significant environmental concerns |
CBN production has a relatively lower environmental impact compared to diamond mining |
Performance Comparison CBN vs. Diamond & Other Abrasives
Hardness Comparison
This chart compares the hardness of CBN to other common abrasives. Hardness is a crucial factor in determining the abrasive's ability to cut hard materials.
Abrasive |
Hardness (GPa) |
---|---|
Aluminum Oxide |
21 |
Silicon Carbide |
25 |
CBN |
48 |
Diamond |
100 |
The hardness of an abrasive material is a crucial factor in determining its ability to cut hard materials. The following chart compares the hardness of Cubic Boron Nitride (CBN) to other common abrasives, highlighting CBN's superior hardness, which makes it an excellent choice for demanding applications.
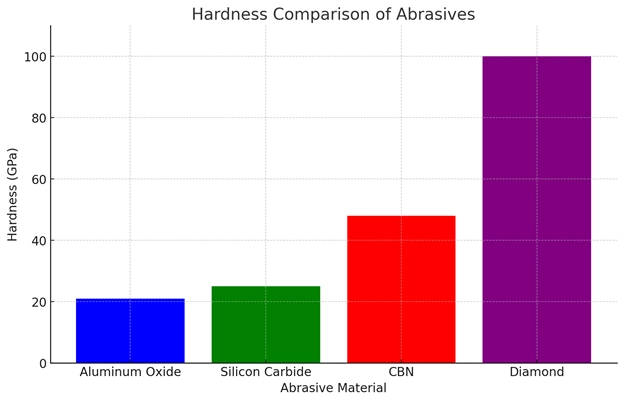
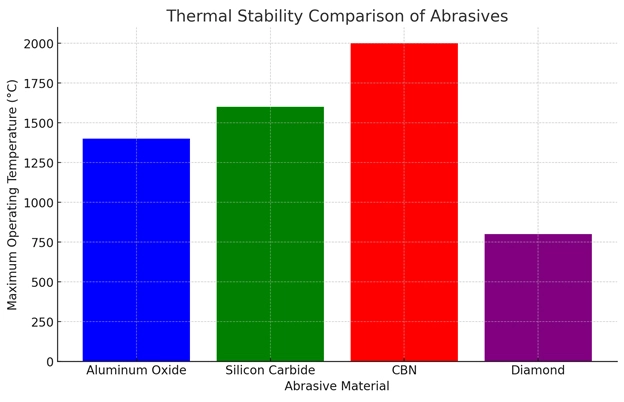
Thermal Stability
This chart illustrates the thermal stability of CBN compared to other abrasives. Thermal stability is essential for maintaining performance under high-temperature conditions.
Abrasive |
Maximum Operating Temperature (°C) |
---|---|
Aluminum Oxide |
1,400 |
Silicon Carbide |
1,600 |
CBN |
2,000 |
Diamond |
800 |
CBN has a significantly higher maximum operating temperature compared to aluminum oxide and silicon carbide, showcasing its superior thermal stability. Diamond, while harder than CBN, has a much lower thermal tolerance, making CBN more suitable for high-temperature grinding applications.
Wear Resistance
This chart shows the relative wear resistance of different abrasives. Wear resistance impacts the tool life and frequency of replacements.
Abrasive |
Maximum Operating Temperature |
---|---|
Aluminum Oxide |
1 |
Silicon Carbide |
1.5 |
CBN |
4 |
Diamond |
5 |
CBN has significantly higher wear resistance than aluminum oxide and silicon carbide, and is just slightly less wear-resistant than diamond. This property of CBN ensures longer tool life and reduces the frequency of tool replacements, making it highly effective for demanding applications.
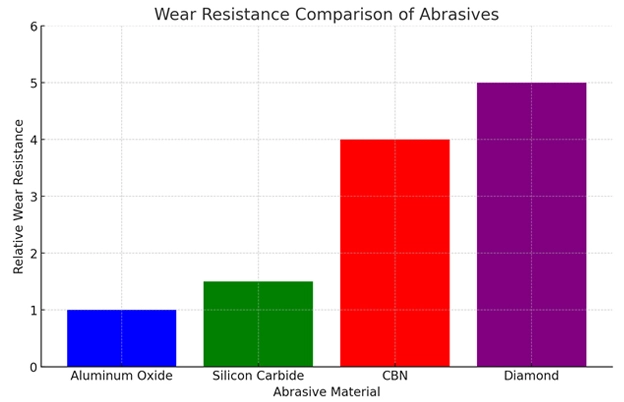
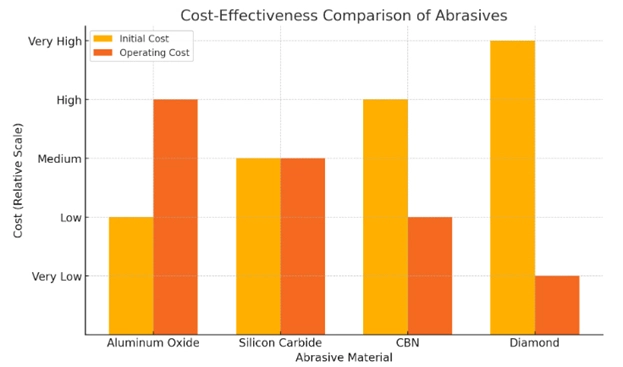
Cost-Effectiveness
This chart provides a cost-effectiveness comparison, taking into account the initial cost and the total operating cost over time.
Abrasive |
Initial Cost |
Operating Cost over Time |
---|---|---|
Aluminum Oxide |
Low |
High |
Silicon Carbide |
Medium |
Medium |
CBN |
High |
Low |
Diamond |
Very High |
Very Low |
CBN, while having a high initial cost, shows a low operating cost over time, making it very cost-effective in the long run. Diamond, despite its very high initial cost, also shows a very low operating cost, further enhancing its cost-effectiveness. In contrast, aluminum oxide, though inexpensive initially, incurs higher operating costs over time.
Grinding Efficiency
This chart compares the grinding efficiency of different abrasives, which is measured by the material removal rate.
Abrasive |
Material Removal Rate (g/min) |
---|---|
Aluminum Oxide |
50 |
Silicon Carbide |
70 |
CBN |
120 |
Diamond |
150 |
CBN significantly outperforms aluminum oxide and silicon carbide, and closely follows diamond, the hardest known material. This chart clearly demonstrates CBN's superior efficiency in grinding applications, making it a highly effective choice for high-speed and precision machining tasks.
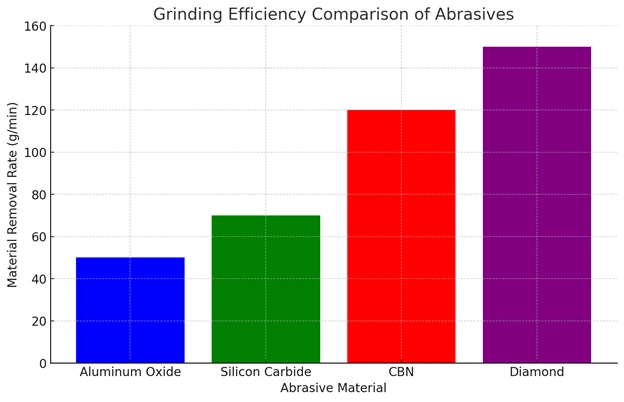
Applications of CBN
CBN is primarily used in industrial applications for machining ferrous materials such as hardened steels, cast iron, and superalloys. Its unique combination of hardness and thermal stability makes it highly effective in high-speed machining operations, where it can withstand the heat and pressures generated during cutting and grinding processes.
High-Speed Machining: In high-speed machining, CBN tools excel due to their ability to endure extreme conditions without significant wear. This makes them ideal for operations involving hardened steels and superalloys, where maintaining tight tolerances and achieving high surface quality are critical. The superior wear resistance and thermal stability of CBN tools ensure that they can perform consistently at high speeds, enhancing productivity and precision.
Grinding Operations: CBN grinding wheels are widely used for precision grinding of ferrous materials. Their hardness allows them to grind efficiently without frequent wheel changes, while their thermal conductivity helps manage the heat generated during the grinding process. This results in high-quality surface finishes and accurate geometries, reducing the need for secondary finishing operations.
Tooling for Hard Materials: CBN is used to manufacture various cutting tools, including inserts, drills, and milling cutters, specifically designed for machining hard materials. These tools offer extended life and superior performance compared to conventional tools, making them indispensable in industries that require high precision and efficiency, such as aerospace, automotive, and tool making.
Applications of CBN in Abrasive Tools
Grinding Tools
CBN grinding tools, such as wheels, segments, discs, and belts, are widely used in industries like metalworking, tool and die making, and bearing manufacturing. These tools offer several advantages over conventional abrasives, including longer tool life, higher precision, and greater efficiency.
The high hardness and thermal stability of CBN grinding tools allow them to maintain their cutting edges longer, reducing the frequency of tool changes and improving overall productivity. Additionally, CBN tools can operate at higher speeds and feed rates, resulting in faster material removal and improved surface finishes.
Cutting Tools
CBN cutting tools, including saws, blades, inserts, and end mills, are essential for machining hardened steels, cast irons, superalloys, and composites. These tools provide numerous benefits in cutting applications, such as reduced wear, high precision, and consistent performance.
The exceptional hardness of CBN cutting tools allows them to maintain sharp edges for longer periods, reducing tool wear and the need for frequent replacements. This leads to more consistent machining results and improved dimensional accuracy of the finished products.
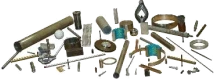
Other Applications
Beyond grinding and cutting, CBN finds applications in honing, polishing, and drilling. CBN honing stones and sticks are used for precision honing operations, while CBN polishing films, pads, and slurry are employed in achieving superior surface finishes. Additionally, CBN micro drills and core drills are used in advanced manufacturing processes, including microelectronics and additive manufacturing.
Key Benefits of CBN Tools

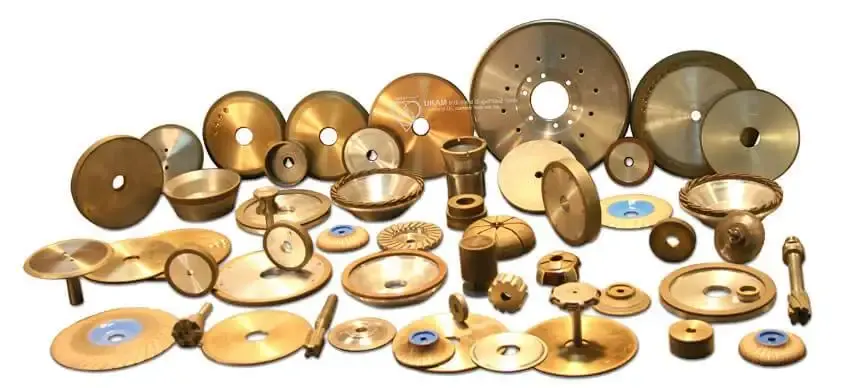
Enhanced Performance
One of the primary benefits of CBN tools is their enhanced performance compared to conventional abrasive tools. CBN tools offer increased tool life and durability, resulting in fewer tool changes and reduced downtime, which leads to significant cost savings over time despite the higher initial investment. Moreover, CBN tools enable higher cutting speeds and feed rates, leading to faster machining times and increased productivity, which is particularly valuable in high-volume production environments where efficiency is critical. Conventional grinding wheels tend to break down quickly, leading to high frictional heat and reduced material removal rates as the grains dull. This degradation can compromise part accuracy and geometry, requiring frequent wheel changes and adjustments. In contrast, CBN wheels maintain their sharp cutting edges for extended periods, providing sustained cutting capacity. This prolonged efficiency reduces the frequency of wheel changes and minimizes downtime, further contributing to higher productivity.
Quality of Work
CBN tools are known for delivering superior surface finishes and reduced thermal damage to workpieces. The excellent thermal conductivity of CBN helps dissipate heat more effectively, minimizing the risk of thermal damage and preserving the integrity of the workpiece. This is especially important in applications where precision and surface quality are paramount.
Cost Efficiency
Although CBN tools and wheels generally come with a higher initial cost compared to traditional abrasive tools, their long-term cost benefits are substantial. The extended tool life and reduced need for frequent replacements result in lower overall tooling costs, while the longer lifespan and sustained performance of CBN wheels lead to overall cost savings. Additionally, the increased efficiency and productivity achieved with CBN tools contribute to cost savings in labor and machine maintenance. The reduced frequency of wheel changes, lower downtime, and improved grinding efficiency contribute to lower operational costs. Furthermore, the high-quality finishes and precise geometries achieved with CBN wheels can reduce the need for secondary finishing operations, further enhancing cost-effectiveness.
Superior Hardness and Toughness of CBN Tools & Wheels
CBN (Cubic Boron Nitride) wheels exhibit superior hardness and toughness, making them exceptionally effective for grinding applications involving hard ferrous metals. CBN wheels are more than twice as hard as conventional abrasives like aluminum oxide and silicon carbide. This remarkable hardness allows them to efficiently grind materials such as high-speed steels, tool steels, and other hardened alloys.
Hardness
The superior hardness of CBN wheels enables them to maintain their cutting edge much longer than traditional abrasives. This extended cutting edge retention leads to consistent material removal rates and high-quality surface finishes, reducing the need for frequent wheel changes and adjustments. The exceptional hardness of CBN crystals also ensures that they can penetrate and grind the hardest materials without excessive wear, contributing to prolonged tool life and reduced overall grinding costs.
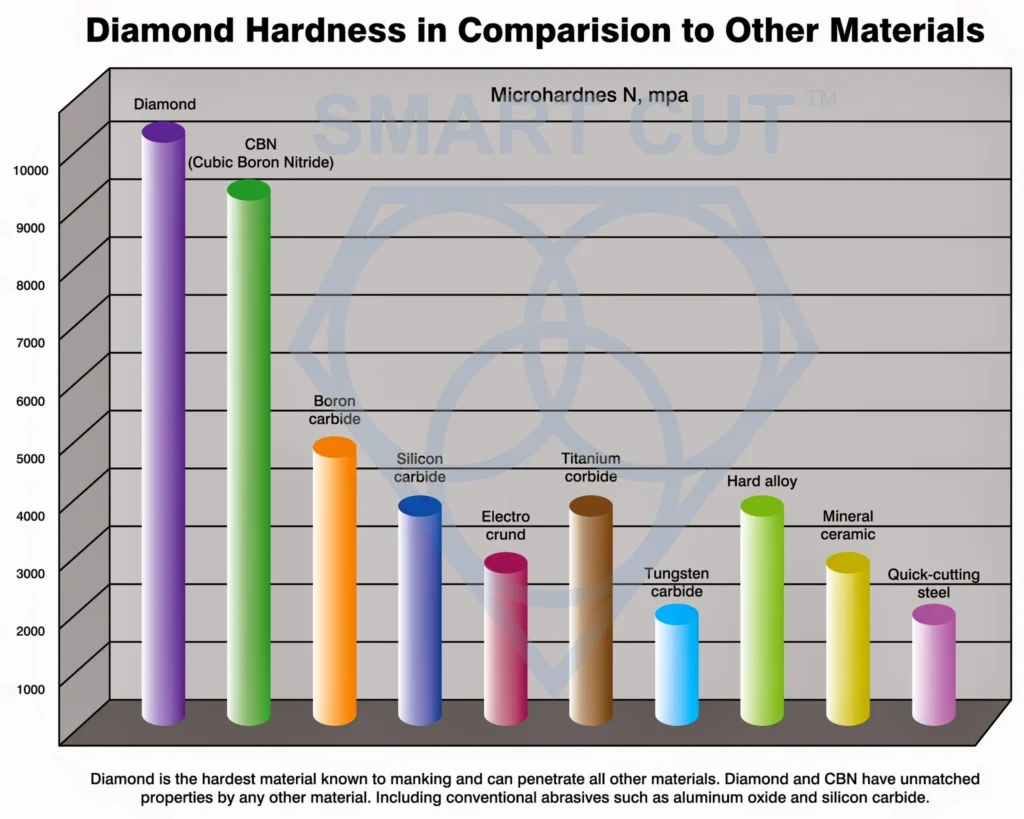
Toughness
However, hardness alone is not sufficient for efficient grinding; the abrasive must also be tough enough to withstand the high machining pressures and heat generated during the grinding process. CBN crystals possess the necessary toughness to endure these harsh conditions. Their ability to resist fracturing and maintain structural integrity under high stress ensures that the grinding process remains stable and efficient.
Combined Benefits
The combination of superior hardness and toughness in CBN wheels provides several key advantages:
-
1. Enhanced Performance: CBN wheels offer sustained cutting capacity and maintain sharp cutting edges for extended periods, resulting in consistent performance throughout their lifespan.
-
2. Prolonged Wheel Life: The durability of CBN wheels means they wear out much slower than traditional abrasives, leading to fewer replacements and lower maintenance costs.
-
3. Reduced Downtime: The extended life and consistent performance of CBN wheels reduce the frequency of wheel changes and adjustments, minimizing downtime and increasing productivity.
-
4. Improved Grinding Efficiency: CBN wheels can operate at higher cutting speeds and feed rates, significantly enhancing machining efficiency and reducing overall production times.
-
5. High-Quality Finishes: The superior cutting action of CBN wheels results in finer surface finishes and more precise geometries, reducing the need for secondary finishing operations.
High Thermal Conductivity of CBN Wheels
CBN (Cubic Boron Nitride) wheels are renowned for their high thermal conductivity, a critical attribute in managing the heat generated during grinding processes. This superior thermal conductivity plays a pivotal role in ensuring the quality and integrity of the workpiece by effectively dissipating heat, thereby preventing a range of thermal-related issues.
Excessive heat generated during grinding can lead to several detrimental effects on both the grinding wheel and the workpiece, including uncontrolled thermal expansion, surface burns, and metallurgical damage. High temperatures can cause materials to expand unevenly, leading to dimensional inaccuracies and distortion of the workpiece. Elevated temperatures can cause surface burns on the workpiece, affecting its aesthetic and structural properties. Prolonged exposure to high temperatures can alter the metallurgical properties of the workpiece, potentially compromising its strength, hardness, and durability.
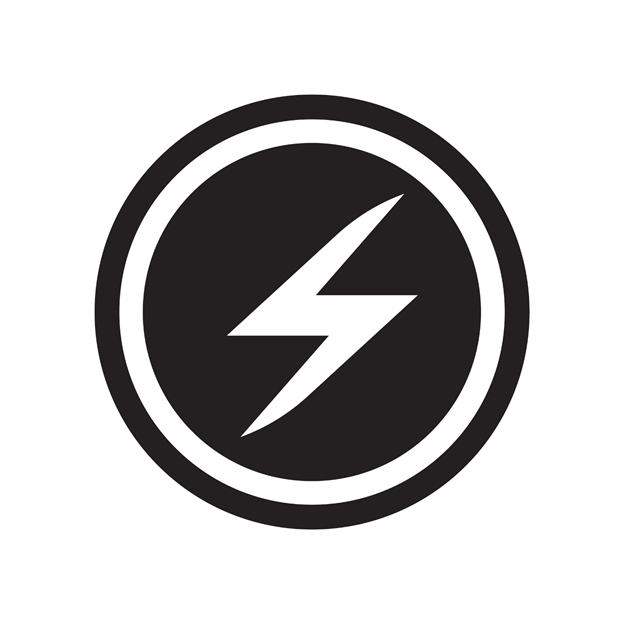
The high thermal conductivity of CBN abrasives helps dissipate heat more effectively than conventional abrasives, such as aluminum oxide and silicon carbide. By rapidly transferring heat away from the grinding zone, CBN wheels prevent excessive heat buildup, maintaining a cooler grinding environment. This effective heat management reduces the risk of thermal damage to the workpiece, ensuring that its metallurgical properties remain intact and avoiding issues such as warping or surface burns. Maintaining lower temperatures allows for more aggressive grinding parameters (higher cutting speeds and feed rates) without compromising the quality of the workpiece, thus enhancing overall grinding performance and efficiency.
The high thermal conductivity of CBN wheels is particularly beneficial in high-speed and high-feed grinding applications, where heat generation is significantly higher. By preventing thermal expansion and distortion, CBN wheels help maintain the dimensional accuracy and integrity of the workpiece, which is crucial in precision grinding applications. Lower operating temperatures reduce wear and tear on the grinding wheel, extending its service life and reducing the frequency of wheel replacements. Effective heat management ensures consistent surface finishes and prevents the formation of thermal cracks or burns, resulting in higher-quality end products. Additionally, the high thermal conductivity of CBN wheels can reduce the reliance on external coolants, leading to cost savings and a more environmentally friendly grinding process.
In practical applications, the high thermal conductivity of CBN wheels proves indispensable across various industries, including aerospace, automotive, and tool manufacturing, where precision and quality are paramount. For instance, grinding high-temperature alloys and hardened steels used in turbine blades and other critical components benefit from the superior heat management of CBN wheels. High-speed grinding of hardened gear components in the automotive industry requires effective thermal control to maintain tight tolerances and surface integrity. Precision grinding of cutting tools, dies, and molds in tool manufacturing relies on CBN wheels to achieve fine surface finishes and exacting geometries without thermal damage.
Reduced Wheel Glazing with CBN Wheels
Wheel glazing is a common issue in grinding operations, occurring when the abrasive grains on a grinding wheel become dull, and the bond material fails to break down and expose new sharp grains. This results in a smooth, glass-like surface on the wheel, significantly reducing its cutting ability and overall efficiency. CBN (Cubic Boron Nitride) wheels are engineered to mitigate this problem effectively due to their superior properties.
Mechanism of Wheel Glazing
In traditional abrasive wheels, glazing happens when the abrasive particles wear down, and the bond material does not release these dull grains to reveal new, sharp ones. This leads to a polished surface on the wheel, which cannot effectively cut the workpiece, resulting in decreased material removal rates and poor surface finishes. The glazed wheel generates more heat and friction, further degrading the grinding process and potentially damaging the workpiece.
Advantages of CBN Wheels in Reducing Glazing
CBN wheels possess several characteristics that make them less prone to glazing compared to conventional abrasive wheels. The high thermal conductivity of CBN wheels plays a crucial role in preventing wheel glazing. By efficiently dissipating heat away from the grinding zone, CBN wheels maintain a cooler operating temperature. This thermal management reduces the likelihood of the bond material softening and failing to release worn grains, thus preventing the formation of a glazed surface. The exceptional hardness and wear resistance of CBN crystals also contribute to reduced glazing. CBN abrasives maintain their sharpness for longer periods, meaning they continue to cut efficiently without significant dulling. This prolonged sharpness ensures that the wheel remains effective throughout its service life, reducing the need for frequent dressing and minimizing downtime.
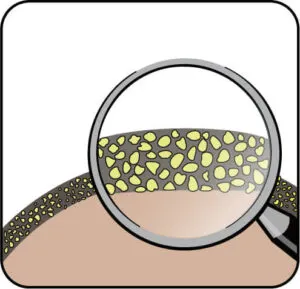
Consistent Grinding Performance
The reduced propensity for glazing in CBN wheels translates to consistent grinding performance. With a lower risk of developing a glazed surface, CBN wheels can maintain their cutting ability, providing uniform material removal rates and high-quality surface finishes. This consistency is particularly valuable in precision grinding applications, where maintaining tight tolerances and achieving superior surface quality is essential.
Extended Wheel Life
By minimizing wheel glazing, CBN wheels offer an extended service life. The reduced need for frequent dressing not only prolongs the life of the wheel but also reduces maintenance efforts and costs. This longevity, combined with the wheels' ability to maintain high performance, results in a more cost-effective grinding solution over time.
Enhanced Productivity
The ability of CBN wheels to resist glazing enhances overall productivity in grinding operations. With fewer interruptions for dressing and maintenance, machine uptime is maximized, leading to higher production rates. The consistent performance of CBN wheels ensures that grinding processes can run more smoothly and efficiently, contributing to improved output quality and operational efficiency.
Thermal and Chemical Stability of CBN Whee
CBN (Cubic Boron Nitride) abrasives are highly valued for their exceptional thermal and chemical stability, which significantly enhances their performance in grinding operations. These properties ensure that CBN wheels can withstand extreme conditions while maintaining their integrity, leading to superior grinding efficiency and precision.
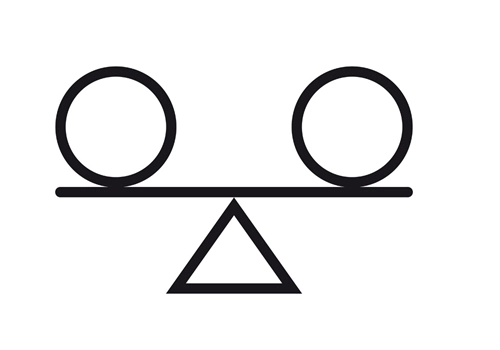
High-Temperature Stability
CBN abrasives are thermally stable at temperatures exceeding 1,832°F (1,000°C), which is much higher than typical grinding temperatures. This remarkable thermal stability allows CBN wheels to maintain their structural integrity and cutting performance even under extreme heat conditions generated during high-speed grinding. The high-temperature stability of CBN wheels offers several critical benefits:
-
Reduced Wheel Wear: CBN wheels experience less thermal degradation compared to conventional abrasive wheels. This reduction in thermal wear ensures that the wheel maintains its form and cutting efficiency over longer periods, resulting in extended tool life.
-
Consistent Performance: The ability to withstand high temperatures without losing effectiveness ensures that CBN wheels provide consistent grinding performance. This consistency is crucial for maintaining high-quality surface finishes and precise geometries on the workpiece.
-
Enhanced Productivity: With reduced wear and prolonged effectiveness, CBN wheels require fewer replacements and less frequent dressing, leading to increased machine uptime and higher productivity.
Chemical Stability
In addition to their thermal stability, CBN abrasives exhibit excellent chemical stability, particularly when grinding ferrous metals. Unlike conventional abrasives, CBN does not chemically react with iron-based materials. This chemical inertness offers several advantages:
-
Preventing Adverse Reactions: The absence of chemical reactions between CBN and ferrous metals ensures that the grinding process remains stable and predictable. This stability prevents issues such as material smearing or undesirable changes in the workpiece's metallurgical properties.
-
Maintaining Workpiece Integrity: The chemical stability of CBN ensures that the workpiece retains its integrity throughout the grinding process. This is particularly important when working with high-strength alloys and hardened steels, where maintaining precise tolerances and surface quality is critical.
Benefits in Prolonged Grinding Operations
The combined thermal and chemical stability of CBN wheels makes them particularly well-suited for prolonged grinding operations. In applications where continuous grinding is required, such as in high-volume production environments, the ability of CBN wheels to withstand extreme conditions without significant wear or chemical degradation is invaluable. This reliability translates to:
-
Precision and Accuracy: The stable performance of CBN wheels ensures that workpieces are ground to precise dimensions and tolerances, maintaining high accuracy throughout the production run.
-
Quality Surface Finishes: CBN wheels consistently produce high-quality surface finishes, reducing the need for secondary finishing operations and enhancing overall product quality.
-
Operational Efficiency: With fewer interruptions for wheel changes and maintenance, grinding operations can run more smoothly and efficiently, leading to cost savings and increased throughput.
Precision and Accuracy with CBN Wheels
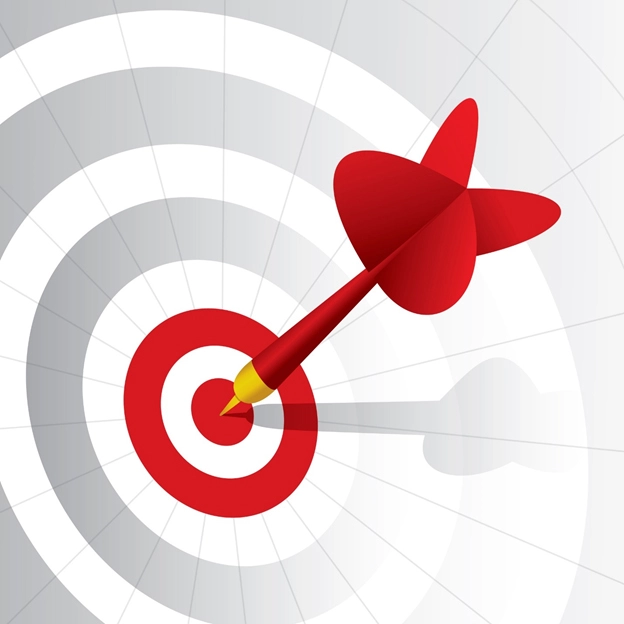
CBN (Cubic Boron Nitride) wheels are renowned for their ability to deliver exceptional precision and accuracy in grinding operations. This is due to their prolonged cutting efficiency and stability, which ensure consistent performance over time. The following sections detail how these properties contribute to enhanced precision and accuracy, making CBN wheels indispensable in high-precision industries.
Prolonged Cutting Efficiency
The cutting efficiency of CBN wheels is significantly superior to that of conventional abrasive wheels. CBN abrasives maintain their sharpness and cutting ability for extended periods, which is crucial for achieving consistent material removal rates. This prolonged cutting efficiency means that the grinding process remains stable and predictable, leading to higher precision in part dimensions and surface finishes. The reduced need for frequent wheel changes and adjustments further contributes to maintaining tight tolerances throughout the grinding operation.
Stability in Performance
CBN wheels are designed to withstand high temperatures and pressures without significant degradation. This stability ensures that the wheels perform consistently, even during prolonged grinding sessions. The ability to maintain a consistent grinding profile is essential for achieving precise geometries and surface finishes on the workpiece. Unlike conventional abrasives, which may wear unevenly and require frequent dressing, CBN wheels retain their form and cutting properties, providing reliable performance and reducing the risk of dimensional inaccuracies.
Tighter Tolerances
The consistent performance of CBN wheels allows for tighter tolerances in grinding operations. This is particularly important in industries where precision is critical, such as aerospace, automotive, and tool-making. For example, in aerospace manufacturing, components such as turbine blades and engine parts must be produced to exacting standards to ensure safety and performance. CBN wheels enable the production of these components with high precision, reducing the need for rework and enhancing overall quality.
Superior Surface Finishes
CBN wheels provide excellent surface finishes due to their consistent cutting action and minimal wear. The sharpness of CBN abrasives ensures that the material is removed cleanly and smoothly, resulting in finer surface finishes. This is particularly beneficial in applications where surface quality is crucial, such as in the production of precision tools and molds. The high-quality finishes achieved with CBN wheels often eliminate the need for secondary finishing operations, saving time and reducing overall production costs.
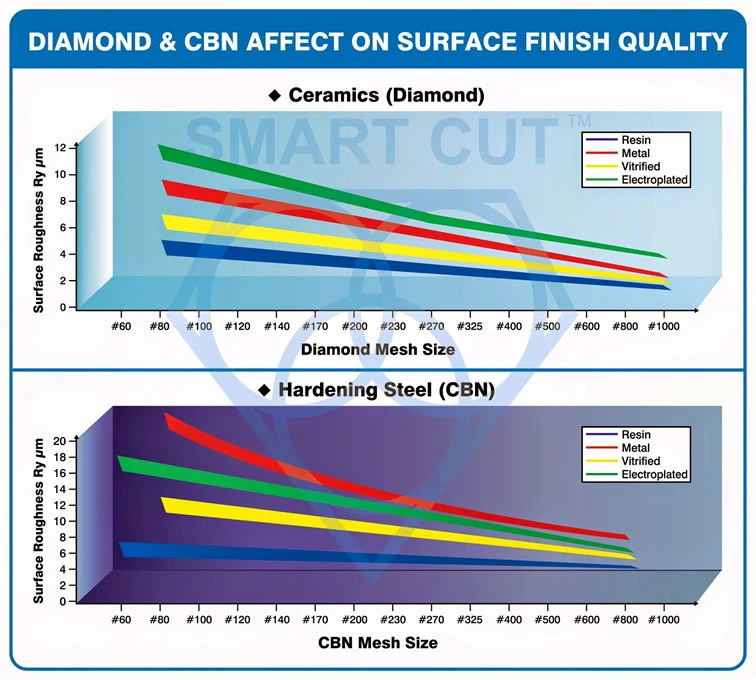
Enhanced Control Over Grinding Parameters
The stability and efficiency of CBN wheels provide greater control over grinding parameters such as speed, feed rate, and depth of cut. This enhanced control allows operators to fine-tune the grinding process to achieve the desired outcomes with minimal variability. As a result, CBN wheels contribute to improved process consistency and repeatability, which are essential for maintaining high precision in batch production and mass manufacturing.
Cost-Effectiveness of CBN Wheels
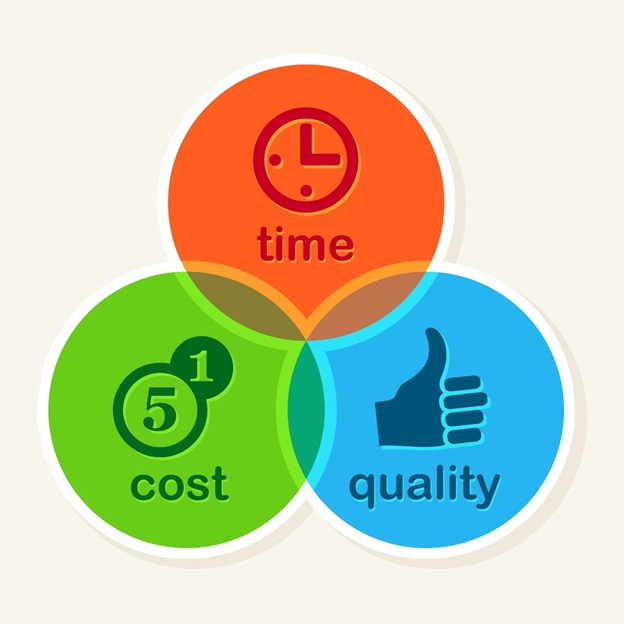
While the initial cost of CBN (Cubic Boron Nitride) wheels may be higher compared to conventional abrasive wheels, their long-term cost-effectiveness is unmatched due to several key factors. These factors contribute to significant overall savings in grinding operations, making CBN wheels a wise investment for industries that require high precision and efficiency.
Longer Lifespan
One of the most significant cost-saving aspects of CBN wheels is their extended lifespan. CBN abrasives are incredibly durable and wear-resistant, maintaining their cutting efficiency far longer than traditional abrasive wheels. This prolonged life means fewer replacements are needed, which directly translates to lower costs for new wheels. The reduced frequency of wheel changes also minimizes the time and labor associated with these replacements, further contributing to cost savings.
Sustained Performance
CBN wheels provide sustained performance throughout their service life. Unlike conventional wheels that can quickly lose their cutting ability and require frequent dressing, CBN wheels maintain a consistent grinding profile. This reliability ensures that grinding operations remain efficient, reducing variability and maintaining high-quality output. The consistency in performance means that less time is spent on adjustments and maintenance, which enhances overall productivity and reduces operational costs.
Reduced Downtime
Downtime in manufacturing operations can be costly, both in terms of lost production time and labor costs. CBN wheels help minimize downtime by reducing the need for frequent wheel changes and maintenance. Their durability and consistent performance mean that machines can run longer without interruption, leading to higher production rates and better utilization of resources. This reduction in downtime is a crucial factor in the cost-effectiveness of CBN wheels.
Improved Grinding Efficiency
CBN wheels enhance grinding efficiency by allowing for higher cutting speeds and feed rates. This increased efficiency means that more material can be removed in a shorter amount of time, speeding up the overall grinding process. The ability to grind faster without sacrificing quality results in higher throughput and lower per-unit production costs. Additionally, the improved efficiency reduces energy consumption, further contributing to cost savings.
High-Quality Finishes and Precise Geometries
The superior cutting action of CBN wheels results in high-quality surface finishes and precise geometries on the workpieces. Achieving these results with conventional abrasive wheels often requires additional finishing operations, such as polishing or secondary grinding, to meet the desired specifications. By delivering excellent finishes and accuracy in the initial grinding process, CBN wheels reduce or eliminate the need for these secondary operations, saving both time and money.
Lower Operational Costs
The combined benefits of longer lifespan, sustained performance, reduced downtime, and improved grinding efficiency lead to significantly lower operational costs. These savings are particularly noticeable in high-volume production environments where the cost of consumables and machine downtime can have a substantial impact on the bottom line. The initial investment in CBN wheels is quickly offset by the reduction in ongoing expenses, making them a cost-effective choice in the long run.
Applications Benefiting from Cost-Effectiveness
Industries that demand high precision, such as aerospace, automotive, and tool-making, stand to benefit the most from the cost-effectiveness of CBN wheels. In aerospace manufacturing, the production of complex components requires tight tolerances and superior surface finishes, which CBN wheels can provide consistently and efficiently. The automotive industry benefits from the durability and efficiency of CBN wheels in the production of gears, bearings, and other high-precision parts, leading to lower production costs and improved quality. Tool and die makers also appreciate the cost savings from reduced wheel changes and high-quality output, which streamline their manufacturing processes and enhance profitability.
Case Studies for CBN Tools
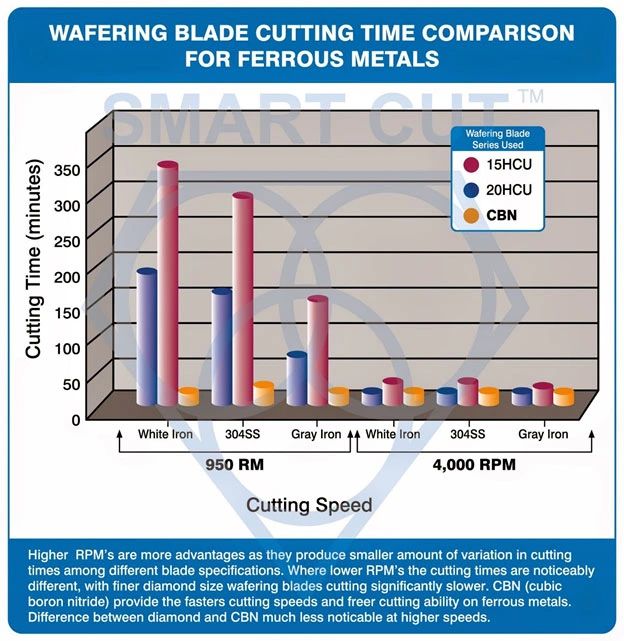
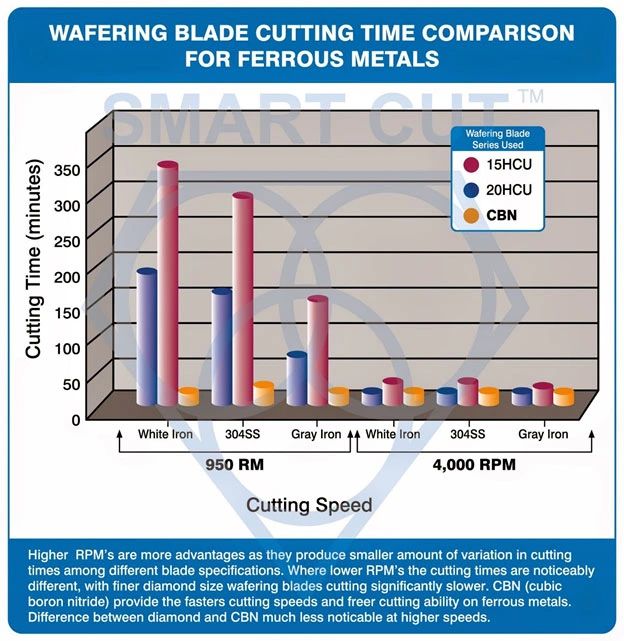
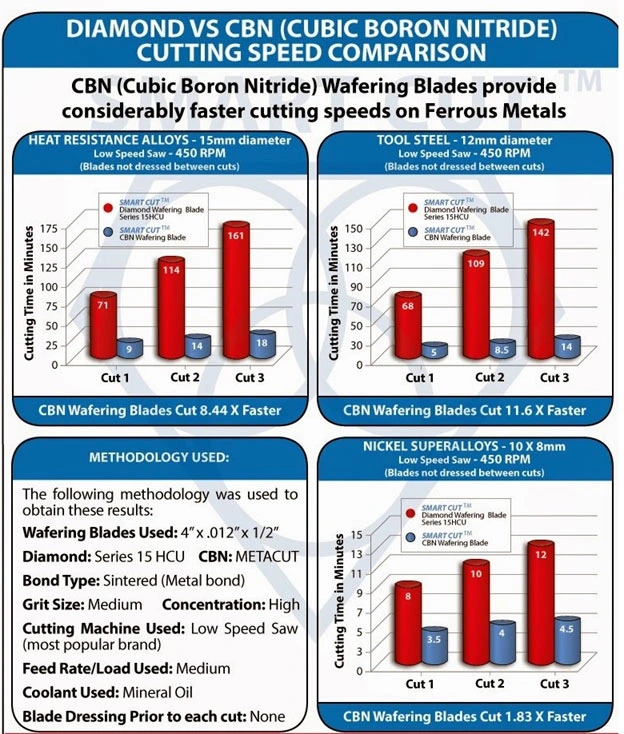
performance of CBN versus diamond and conventional abrasives (such as aluminum oxide and silicon carbide) for various materials, applications, and tools. This comparison highlights differences in tool life, material removal rates, surface finish quality, and cost-effectiveness across different scenarios.
Comparative Case Studies of Tool Performance (Diamond, CBN, & Conventional Abrasives)
Material/Application |
Tool Type |
Abrasive Type |
Tool Life |
Material Removal Rate |
Surface Finish Quality |
Cost-Effectiveness |
---|---|---|---|---|---|---|
Hardened Steel |
Grinding Wheel |
CBN |
Excellent |
High |
High |
High |
Diamond |
Very Good |
Very High |
Very High |
Moderate |
||
Conventional |
Poor |
Low |
Moderate |
Low |
||
Tool Steel |
End Mill |
CBN |
Very Good |
Moderate |
High |
Moderate |
Diamond |
Poor |
Low |
Low |
Low |
||
Conventional |
Good |
Moderate |
Moderate |
Moderate |
||
High-Speed Steel |
Drill Bit |
CBN |
Excellent |
High |
High |
High |
Diamond |
Good |
Moderate |
Moderate |
Low |
||
Conventional |
Poor |
Low |
Low |
Very Low |
||
Cast Iron |
Turning Tool |
CBN |
Excellent |
High |
High |
High |
Diamond |
Good |
Moderate |
Moderate |
Moderate |
||
Conventional |
Moderate |
Low |
Low |
Low |
||
Superalloys (e.g., Inconel) |
Milling Cutter |
CBN |
Excellent | High | Very High |
Moderate |
Diamond |
Moderate |
Moderate |
Moderate |
Low |
||
Conventional |
Poor |
Low |
Poor |
Very Low |
||
Composites |
Saw Blade |
CBN |
Very Good |
High |
High |
Moderate |
Diamond |
Excellent |
Very High |
Very High |
High |
||
Conventional |
Moderate |
Moderate |
Moderate |
Low |
1. CBN vs. Diamond
-
CBN is particularly effective for ferrous materials where diamond could potentially suffer from chemical wear due to carbon affinity with the workpiece.
-
Diamond excels in non-metallic materials and some composites due to its unrivaled hardness and material removal capabilities, but its performance can diminish in ferrous applications.
2. CBN vs. Conventional Abrasives:
-
CBN offers significantly better performance than conventional abrasives across nearly all metrics for hard and tough materials like hardened steel and superalloys. It demonstrates excellent tool life and high-quality finishes.
-
Conventional abrasives typically have shorter tool life and offer lower quality finishes, which limits their use in precision and high-performance applications.
3. Application-Specific Considerations:
-
For applications involving hard ferrous materials, CBN often presents the best balance between cost and performance, providing long tool life and high efficiency.
-
For non-ferrous materials and specific composites, diamond might be preferred due to its superior surface finish and material removal rate, despite the higher cost.
-
Conventional abrasives remain a cost-effective solution for less demanding applications or where initial tool cost is a major concern.
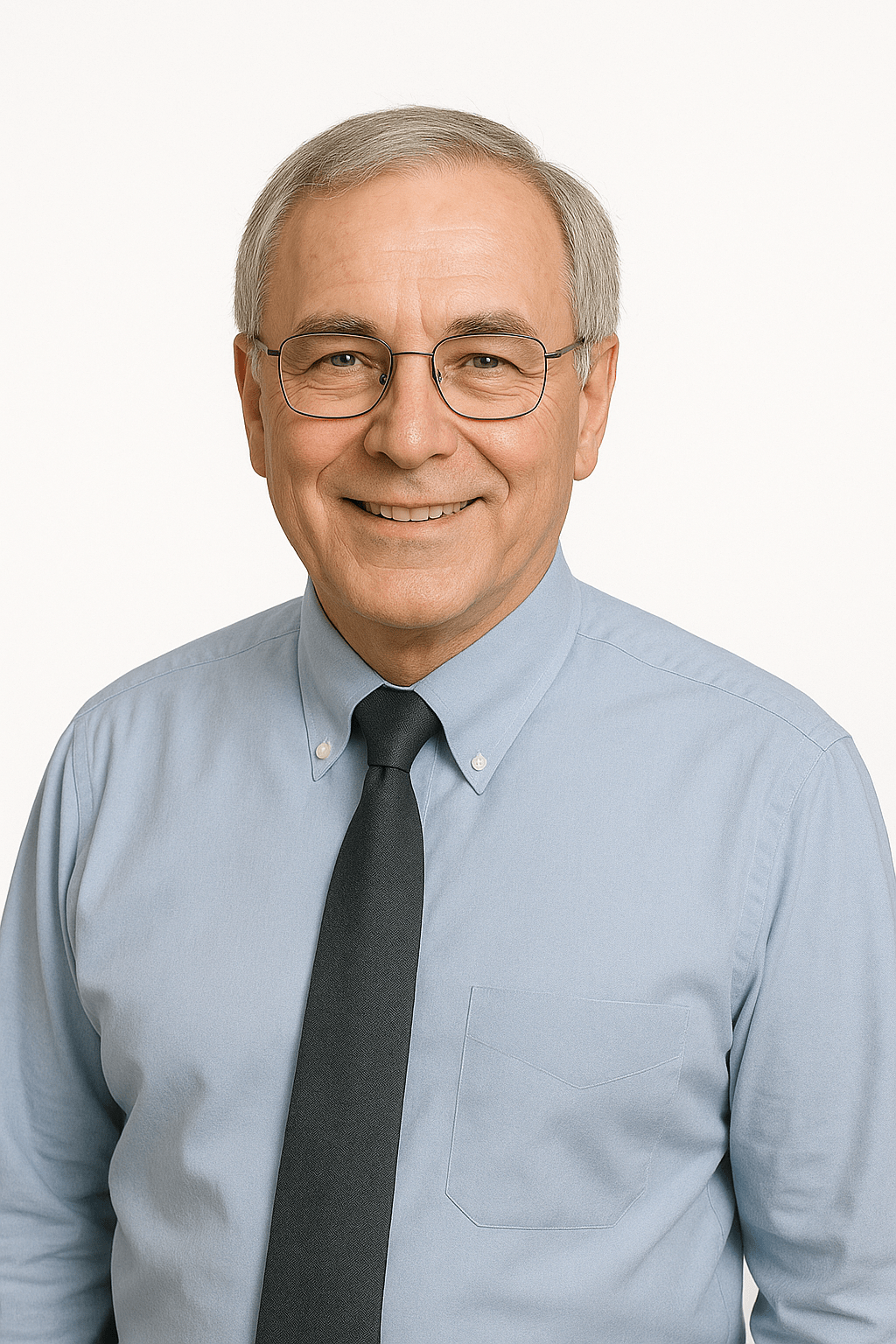
Alexander Schneider is a senior applications engineer and leading authority in the industrial diamond tooling industry, with over 35 years of hands-on experience in the development, application, and optimization of ultra-thin and high-precision diamond blades, diamond core drills, and diamond and CBN grinding wheels. His work spans a wide range of advanced materials including ceramics, glass, composites, semiconductors, and high-performance metals.
Throughout his career, he has collaborated with leading R&D institutions, national laboratories, and high-tech manufacturing companies across Europe, North America, and Asia, providing technical expertise and tailored solutions for demanding cutting and surface preparation applications.
Mr. Schneider has played a pivotal role in advancing precision cutting, sectioning, dicing, and grinding technologies used in research, production, and failure analysis. He is widely respected for his ability to optimize tool design and cutting parameters to meet exacting industry standards—balancing factors such as cut quality, blade life, material integrity, and process consistency.
As an author, Mr. Schneider is known for delivering practical, application-focused insights that translate complex technical challenges into clear, actionable strategies. His articles and technical guides serve as trusted resources for engineers, researchers, and manufacturers seeking to improve precision, reduce process variability, and enhance tool performance in critical applications.
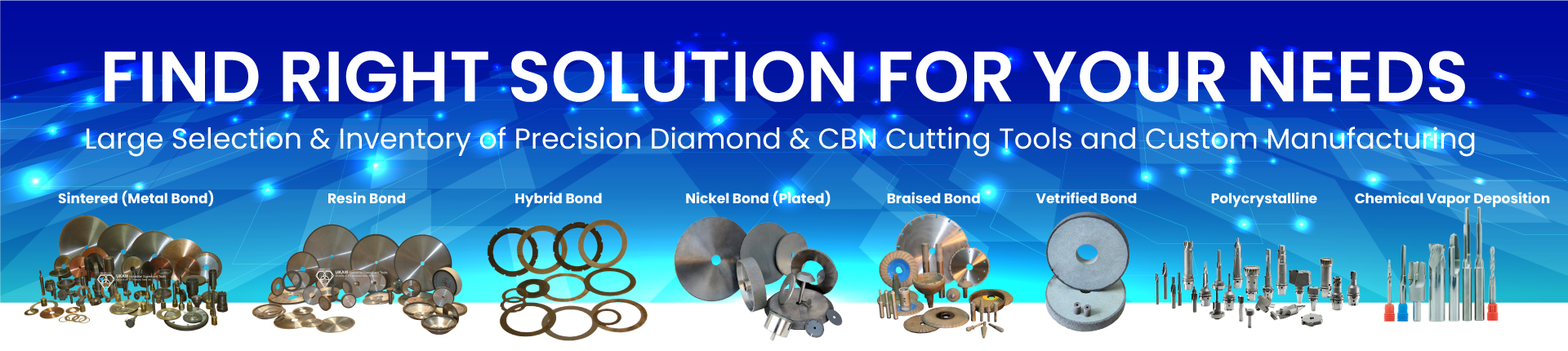
ARE YOU USING RIGHT TOOLS
FOR YOUR APPLICATION?
LET US
HELP YOU
HAVING ISSUES WITH
YOUR CURRENT TOOLS?
Knowledge Center
How to Selecting Right Diamond Tools for your application
How to properly use Diamond Tools
Why use diamond
Diamond vs CBN (cubic boron nitride) Tools
What is Diamond Mesh Size and how to select best one for your application
What is Diamond Concentration and which to use for your application
Diamond Tool Coolants Why, How, When & Where to Use
Choosing The Correct Diamond Bond Type
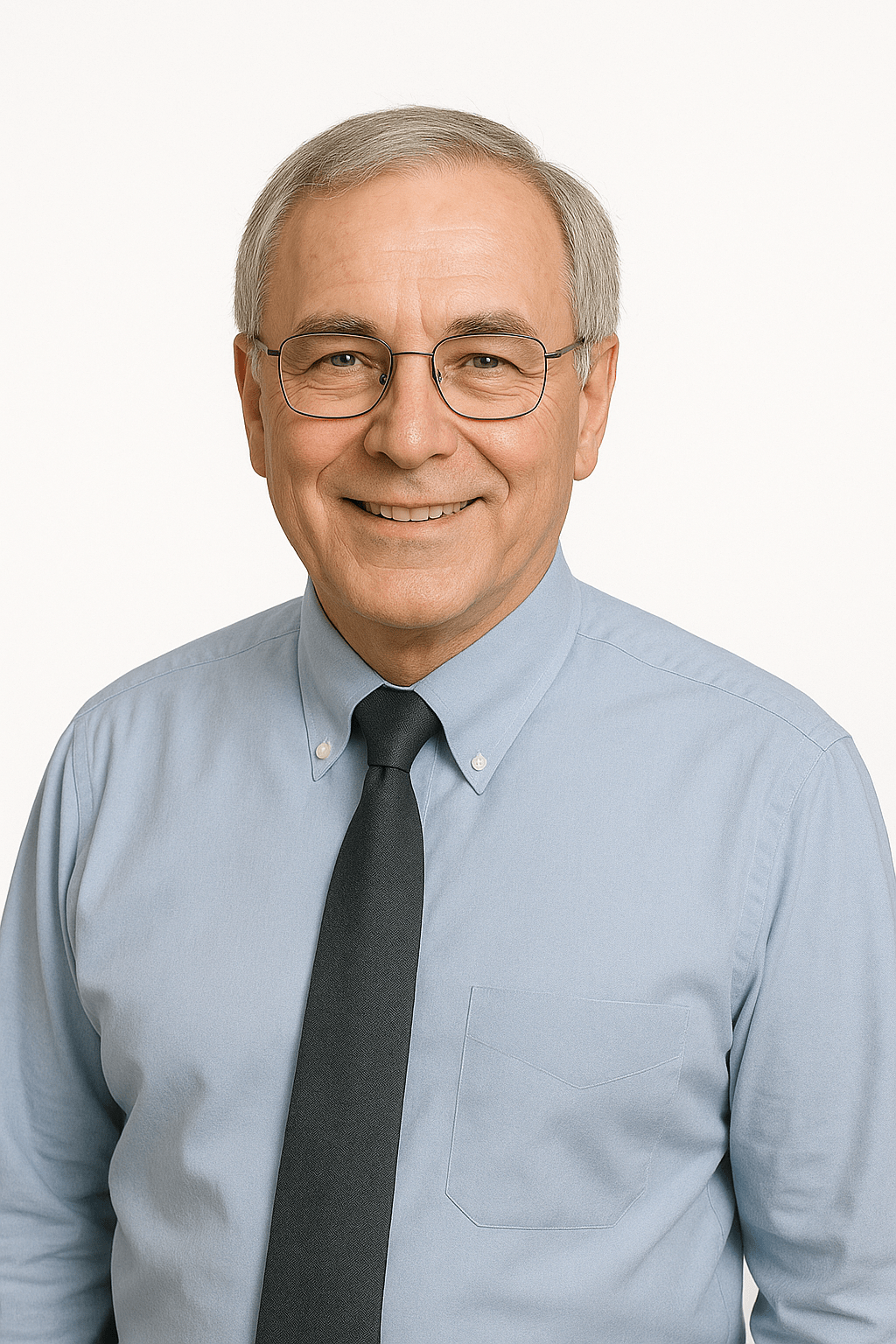
Alexander Schneider is a senior applications engineer and leading authority in the industrial diamond tooling industry, with over 35 years of hands-on experience in the development, application, and optimization of ultra-thin and high-precision diamond blades, diamond core drills, and diamond and CBN grinding wheels. His work spans a wide range of advanced materials including ceramics, glass, composites, semiconductors, and high-performance metals.
Throughout his career, he has collaborated with leading R&D institutions, national laboratories, and high-tech manufacturing companies across Europe, North America, and Asia, providing technical expertise and tailored solutions for demanding cutting and surface preparation applications.
Mr. Schneider has played a pivotal role in advancing precision cutting, sectioning, dicing, and grinding technologies used in research, production, and failure analysis. He is widely respected for his ability to optimize tool design and cutting parameters to meet exacting industry standards—balancing factors such as cut quality, blade life, material integrity, and process consistency.
As an author, Mr. Schneider is known for delivering practical, application-focused insights that translate complex technical challenges into clear, actionable strategies. His articles and technical guides serve as trusted resources for engineers, researchers, and manufacturers seeking to improve precision, reduce process variability, and enhance tool performance in critical applications.