Table of Contents
ToggleSurface finish is typically measured in terms of roughness or smoothness. It influences the appearance, functionality, and performance of a product. A well-controlled surface finish can enhance the product’s aesthetics, reduce friction, improve corrosion resistance, and facilitate better bonding between surfaces.
Achieving Optimal Surface Finish, Surface roughness, Surface Texture, Surface Flatness with Diamond & CBN Tools
When it comes to manufacturing and machining, the quality of a surface is more than just a matter of aesthetics; it's crucial for ensuring the functionality and longevity of a product. Surface characteristics such as finish, roughness, texture, and flatness each play distinct roles in how a part will fit, perform, and last over time. This guide delves into these four key surface characteristics, exploring their definitions, how they differ from each other, and why they are important. Whether it’s the smooth feel of a polished metal, the flatness required for a perfect seal, or the detailed texture that affects material interaction, understanding these aspects helps in achieving the desired performance and quality in manufactured products.
By considering factors such as specifications of diamond or cbn tooling used, machining parameters, material properties, and environmental conditions, you can achieve the desired objective whether its surface quality, surface roughness, surface texture, or surface flatness.
When selecting diamond tools, engineers, researchers, contractors and hobbyists should consider the specific requirements of their applications, including the desired surface finish, material properties, and operational conditions. By doing so, they can ensure that their products meet the highest standards of quality and performance while promoting sustainability and reducing environmental impact.
Understanding Surface Finish, Surface roughness, Surface Texture, Surface Flatness
Characteristic |
Description |
Measurement |
Impact/Importance |
---|---|---|---|
Surface Roughness |
Refers to the fine microscopic irregularities on the surface, including peaks, valleys, and grooves. |
Measured using instruments like profilometers (contact and non-contact) and atomic force microscopy. |
Affects friction, wear, lubrication retention, and adhesion. Critical for precision engineering where contact surfaces interact closely. |
Surface Finish |
Encompasses all aspects of a surface's final form, including roughness, waviness, lay, and visible flaws like scratches. |
Measured through both visual inspection and technical instruments like profilometers. |
Influences both the tactile feel and visual aesthetics of a product. Important for consumer-facing products and in applications requiring specific functional interactions between surfaces. |
Surface Texture |
The composite feel and appearance of a surface, including all irregularities and patterns. |
Evaluated with tactile instruments and advanced imaging techniques like laser scanning. |
Determines the material’s interaction with the environment and other materials; affects aesthetics, functional performance, and coating adherence. |
Surface Flatness |
Measures how closely a surface conforms to a perfectly flat plane. |
Measured using precision tools such as dial indicators, CMMs, and laser leveling systems. |
Essential for ensuring proper assembly, uniform stress distribution, and operational functionality in parts that must fit perfectly together. |
Key Differences:
-
Surface Roughness is mainly about the tiny, often microscopic details that directly affect the mechanical performance of a part.
-
Surface Finish is broader, considering the overall quality and incorporating both tactile and visual aspects, making it significant for both functionality and consumer perception.
-
Surface Texture is a comprehensive look at the surface's structural quality, affecting both functional aspects like fluid retention and aesthetic qualities.
-
Surface Flatness focuses solely on the geometric accuracy of the surface plane, crucial for assembly accuracy and structural integrity.
Here's a breakdown of which variables apply to Surface Finish, Surface Roughness, Surface Texture, and Surface Flatness:
Variables Impacting Surface Characteristics:
Variable |
Surface Finish |
Surface Roughness |
Surface Texture |
Surface Flatness |
---|---|---|---|---|
Diamond Grit Size |
![]() |
![]() |
![]() |
|
Diamond Bond Type |
![]() |
![]() |
![]() |
|
Diamond Concentration |
![]() |
![]() |
![]() |
|
Diamond Bond Hardness |
![]() |
![]() |
![]() |
|
Wheel Speed |
![]() |
![]() |
![]() |
|
Feed Rate |
![]() |
![]() |
![]() |
|
Coolant Flow |
![]() |
![]() |
![]() |
|
Tool Wear |
![]() |
![]() |
![]() |
|
Environmental Temperature |
|
|
|
|
Environmental Humidity |
![]() |
![]() |
![]() |
![]() |
Cleanliness |
![]() |
![]() |
![]() |
|
Tool Geometry |
![]() |
![]() |
![]() |
|
Cutting Depth |
![]() |
![]() |
![]() |
|
Material Hardness |
![]() |
![]() |
![]() |
|
Vibration Control |
![]() |
![]() |
![]() |
![]() |
Operator Skill |
![]() |
![]() |
![]() |
|
Lubrication Type |
![]() |
![]() |
![]() |
|
Pressure Applied |
![]() |
![]() |
![]() |
![]() |
Backing Material |
![]() |
![]() |
||
Overlap Factor |
![]() |
![]() |
![]() |
Key Insights:
-
Surface Finish: Almost all variables impact surface finish as it encompasses overall quality, including roughness, texture, and other visual or tactile features.
-
Surface Roughness: Specifically affected by most variables, as roughness is a primary component of the overall surface finish and directly influenced by tool characteristics and operating conditions.
-
Surface Texture: Influenced by similar variables as roughness and finish, because texture is about the feel and appearance, which depend on detailed surface properties.
-
Surface Flatness: Though many variables impact flatness, it is less influenced by factors like grit size or bond type and more by overall machine setup, environmental conditions, and application of force.
Surface roughness and surface finish
Surface roughness and surface finish are terms that are often tossed around when talking about how smooth or textured a material's surface is after it has been manufactured. Though people sometimes use these terms as if they mean the same thing, they actually describe different aspects of the surface's characteristics.
Surface Roughness
Think of surface roughness as the tiny, almost microscopic bumps and dips on a surface. These small features, which include peaks, valleys, and grooves, can be felt if you drag your fingernail lightly across the surface. Roughness is really important in fields where tiny details matter, like in machine parts where one piece has to slide smoothly over another. To measure these tiny features, tools like profilometers (which can touch the surface or not) or even atomic force microscopes (which can see extremely small details) are used. The level of roughness can affect things like how much friction there is between moving parts, how quickly parts might wear out, or how well parts stick together.
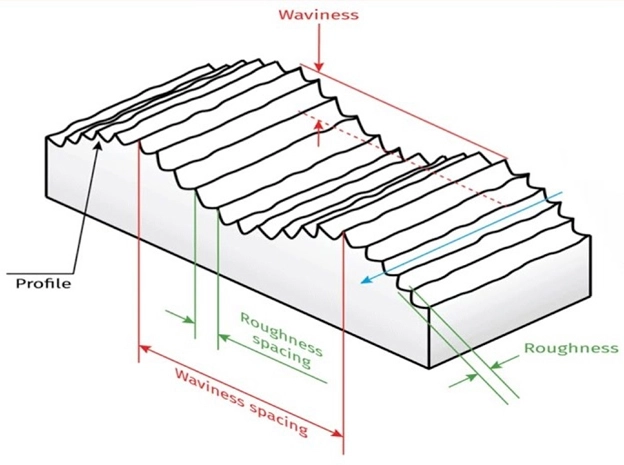
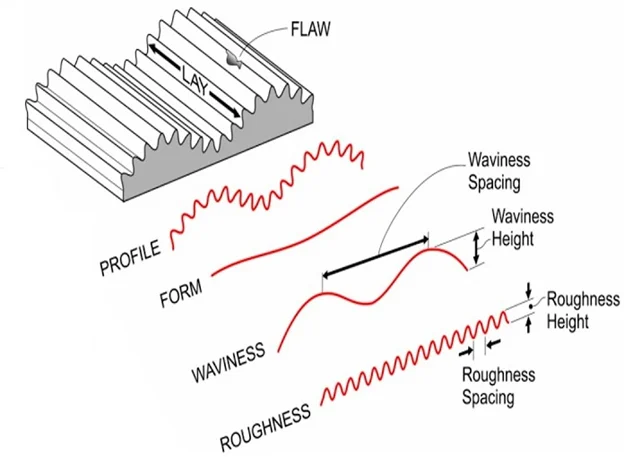
Surface Finish
Surface finish, on the other hand, includes not just the tiny details like roughness but also bigger, more visible patterns that might be seen or felt on a surface. This can be things like waviness (larger, more spread out ups and downs on the surface), lay (the direction of the finishing marks), and any visible flaws like scratches or pits. Checking the surface finish isn't just about feeling for bumps or looking at it under a microscope; it also involves looking at the surface with your eyes to see if it's shiny, dull, or scratched. The appearance and feel of a surface are especially important for products that people handle directly, like consumer electronics or decorative items, because they influence a person’s perception of quality.
Distinguishing Between Surface Roughness and Surface Finish
The key difference lies in the scale and scope of what they measure. Surface roughness is all about the tiny, microscopic details, and you need special equipment to measure it accurately. Surface finish, however, considers everything from the smallest scratch to the overall texture and look of a surface. It’s measured both by looking at the detailed roughness and by simply examining the surface visually.
Surface texture and surface flatness
Surface texture and surface flatness are two more terms that describe aspects of a material's surface characteristics, each focusing on different qualities that affect the functionality and aesthetics of the product. Understanding these terms helps in producing parts that meet specific requirements for a wide range of applications.
Surface Texture
Surface texture refers to the overall tactile quality of a surface, which includes the composite of irregularities such as roughness, waviness, and any other structural imperfections present on a surface. It’s essentially an umbrella term that encompasses various features on a surface, including the finer details captured by surface roughness measurements and the larger, more visible patterns discussed under surface finish. Surface texture can be evaluated using several methods, from tactile instruments like profilometers that physically touch the surface, to optical methods like laser scanners that don’t make contact. The texture of a surface affects how it interacts with the environment and other materials, influencing factors like lubrication retention, coating adhesion, and the surface's aesthetic appeal.

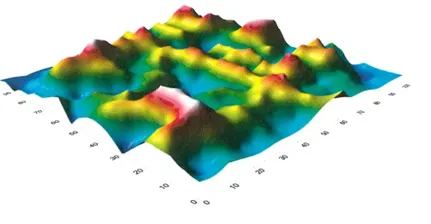
Surface Flatness
Surface flatness, on the other hand, is a measure of how closely a surface adheres to a perfect plane. Unlike surface texture, which can involve a variety of patterns and imperfections, flatness is specifically about the evenness of the entire surface. When measuring flatness, you're checking for any deviations from a perfectly flat plane across the entire surface of the part. This is crucial in applications where a surface must mate perfectly with another, such as in gaskets, seals, and machine bases. Poor flatness can lead to issues like improper assembly, uneven stress distribution, and operational malfunction. Surface flatness is usually measured with precision tools such as dial indicators, coordinate measuring machines (CMMs), or laser leveling systems that can detect even minuscule deviations from flatness.
Key Differences and Considerations
While surface texture focuses on the micro to macroscopic irregularities on a surface, surface flatness is concerned with the overall planarity of the surface. Surface texture can affect things like the material’s frictional characteristics and visual appeal, while flatness is more about ensuring that parts fit together correctly without gaps or uneven stress points.
In practice, both surface texture and flatness are critical to the performance and quality of manufactured parts. Engineers and designers must specify acceptable levels for both characteristics to ensure that parts function as intended in their final application. Each characteristic must be measured and controlled with appropriate tools and techniques
to meet these specifications, supporting the overall functionality and aesthetic requirements of the product.
Which of these is more important? - Surface Finish, Surface roughness, Surface Texture, Surface Flatness
The importance of the variables surface finish, roughness, texture, and flatness can vary significantly depending on the specific application and the functional requirements of the manufactured parts. Here’s a general guideline on their relative importance, although the exact order can change based on the context:
1. Surface Roughness
-
Why It's Often Most Important: Surface roughness is frequently considered the most critical because it directly influences the mechanical interaction between surfaces, such as friction, wear resistance, and lubrication retention. In industries like automotive, aerospace, and precision engineering, where components must interact with high precision and minimal friction, roughness is a key quality attribute.
2. Surface Flatness
-
High Importance in Certain Applications: Flatness is crucial in applications where parts must fit together perfectly to function correctly. This includes gasket interfaces, machine bases, and assembly interfaces in semiconductor manufacturing. Poor flatness can lead to assembly issues, uneven stress distributions, and operational inefficiencies.
3. Surface Finish
-
Aesthetic and Functional Roles: Surface finish is broadly important because it encompasses roughness and other aspects like waviness and flaws. It affects both the tactile and visual quality of parts and can be critical for consumer-facing products where aesthetic appeal is important. Surface finish also plays a role in protective coatings adherence, which is vital for corrosion resistance.
4. Surface Texture
-
Specialized Importance: Texture includes the patterns and features on a surface that can affect material behavior with respect to light, adhesion, fluid dynamics, and more. Its importance rises in specialized applications, such as optical devices where light reflection must be controlled, or in fluid dynamics where the surface texture influences flow behavior.
Understanding Surface Texture
Surface texture encompasses several key elements that define the quality and smoothness of a machined surface. The three primary characteristics are waviness, lay, and roughness.
-
Waviness: Refers to broader irregularities caused by deflection, machine vibrations, or warping. It can be minimized by rigidly securing the tool and workpiece to avoid movement during machining.
-
Lay: Indicates the direction of the predominant surface pattern, often resulting from feed marks.
-
Roughness: Consists of finely spaced irregularities or deviations on the surface. It is influenced by tool shape, feed rate, and machining conditions. Roughness is often measured using parameters like Ra (Roughness Average) and Rmax (maximum peak-to-valley height).
Measurement Techniques for Surface Texture
Several methods are used to measure and evaluate surface texture and geometry:
1. Electronic Measurement:
-
Averaging Instruments: Use a stylus to measure the surface profile and provide numerical values like Ra.
-
Profiling Instruments: Offer detailed surface profiles and are used for research and development applications.
2. Optical Measurement:
-
Microscopic Inspection: Visual examination under a microscope to assess texture and geometry.
-
Interferometry: A non-contact method providing high-resolution measurements.
3. Visual or Tactual Measurement:
-
Visual Comparators: Use reference specimens for visual comparison.
-
Tactual (Fingernail Test): Tactile assessment using a fingernail to gauge surface roughness.
Diamond Tool, Material, & Machining Variables & How they Affect Surface Finish, Surface roughness, Surface Texture, Surface Flatness
Variable |
Influence on Surface Finish |
Influence on Surface Roughness |
Influence on Surface Texture |
Influence on Surface Flatness |
---|---|---|---|---|
Diamond Grit Size |
Finer grits lead to a glossier, more aesthetically pleasing finish. |
Finer grits minimize the depth of surface indentations, lowering roughness metrics. |
Smoother texture with finer grits due to reduced abrasiveness. |
Minimal impact, but uniform grit size can aid in consistent grinding. |
Diamond Bond Type |
Softer bonds provide a smoother finish by allowing the diamond particles to release easily. |
Harder bonds retain diamonds longer, potentially increasing surface irregularities. |
The flexibility of the bond affects how pronounced the textural features are. |
Harder bonds keep the wheel shape better, improving flatness control. |
Diamond Concentration |
High concentration levels even out the finish by distributing the cutting load. |
A dense distribution of diamonds ensures more uniform micro-cuts, reducing peak roughness. |
High concentration prevents gaps in the texture, leading to a more uniform appearance. |
Consistent diamond presence aids in maintaining a level grind. |
Diamond Bond Hardness |
Harder bonds may keep particles longer, potentially compromising the finish over time. |
Harder bonds may not conform to the surface as well, increasing roughness. |
Bond hardness affects the resilience of the texture against deformation. |
Harder bonds reduce wheel wear, aiding in sustained flatness during long runs. |
Wheel Speed |
Higher wheel speeds can polish the surface more effectively, enhancing the finish. |
Increased speeds can reduce the impact of each diamond, lowering roughness. |
High speeds may smooth out textural features, making them less noticeable. |
Too high speeds may lead to uneven material removal affecting flatness. |
Feed Rate |
Slower feed rates allow more thorough cuts, improving finish quality. |
A slower rate provides diamonds more time to cut cleanly, decreasing roughness. |
Controlled feed rates ensure consistent pattern imprints in the texture. |
Careful feed management prevents overcutting, crucial for maintaining flatness. |
Coolant Flow |
Proper coolant reduces thermal strains on the surface, enhancing the finish. |
Coolants wash away debris that can cause extra abrasion, thus reducing roughness. |
Coolants help maintain the integrity of the surface texture by preventing overheating. |
Coolants preserve flatness by preventing warping from heat build-up. |
Tool Wear |
As tools wear, the finish can degrade due to less effective cutting edges. |
Worn tools often leave a rougher surface due to uneven and less precise cuts. |
Worn tools may create an inconsistent texture due to variable cutting depths. |
Worn tools might not remove material uniformly, compromising flatness. |
Environmental Temperature |
Extreme temperatures can alter the material properties, affecting the finish. |
Temperature swings can expand or contract materials, altering roughness levels. |
Thermal changes may warp textures, especially in thermally sensitive materials. |
Temperature variations can cause materials to warp, impacting flatness. |
Environmental Humidity |
Humidity can affect surface contaminants, impacting the quality of the finish. |
Moist conditions may cause materials to swell slightly, influencing roughness. |
Humidity can alter the way materials react under machining, affecting texture. |
Moisture changes in the environment can lead to material distortion, affecting flatness. |
Cleanliness |
Dirt or debris on the surface or tool can mar the finish during machining. |
Particles can embed into the material, increasing surface roughness. |
Contaminants can disrupt the intended texture, creating an uneven surface. |
Dust and debris can cause uneven machining or settling, impacting flatness. |
Tool Geometry |
Properly shaped tools enhance finish by matching the material and cutting needs. |
Incorrect tool geometry increases roughness by not aligning with the workpiece. |
Tool shape directly designs the texture pattern and depth on the surface. |
Precise tool geometry ensures even material removal, crucial for flatness. |
Cutting Depth |
Shallow cutting depths can enhance the finish by minimizing surface trauma. |
Deeper cuts increase roughness by creating larger valleys and peaks. |
Cutting depth determines the depth of textural features imprinted on the surface. |
Uneven cutting depths can create a wavy surface, detrimental to flatness. |
Material Hardness |
Matches to material hardness optimize finish by preventing excessive abrasion. |
Harder materials may resist tooling, resulting in higher roughness. |
Material hardness can define the clarity and form of the created texture. |
Appropriate hardness matching is necessary to maintain consistent flatness. |
Vibration Control |
Reducing vibrations improves the finish by eliminating chatter marks. |
Vibrations can introduce artifacts that raise roughness metrics. |
Steady operation without vibration helps produce a consistent texture. |
Vibrations during machining can lead to an uneven surface, affecting flatness. |
Backing Material |
A stable backing improves finish by supporting consistent grinding pressure. |
Firm backing materials reduce roughness by preventing flex during grinding. |
The backing's stability influences texture uniformity. |
Stiff backing materials help maintain the grinder's shape, promoting flatness. |
Overlap Factor |
Increased overlap can polish out imperfections, enhancing the final finish. |
More overlap reduces visible roughness by smoothing transition areas. |
Overlapping grinding passes help unify the texture appearance. |
Proper overlap in passes ensures even grinding, crucial for flatness. |
Pressure Applied |
Optimal pressure improves the finish by ensuring efficient but gentle material removal. |
Excessive pressure can gouge the surface, increasing roughness. |
Pressure settings influence the depth and form of textural elements. |
Even and appropriate pressure application is essential to preserve flatness. |
Understanding the impact of different variables of diamond wheels on surface characteristics like finish, roughness, texture, and flatness is key to optimizing the machining process. Let’s explore how each variable influences these different surface properties:
Diamond & CBN Wheel / Tool Grit Size
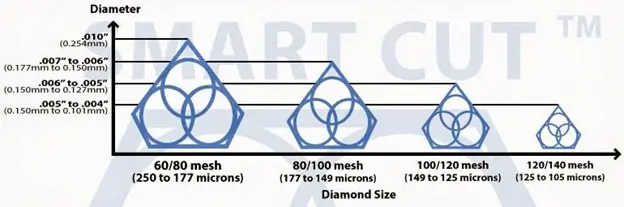
-
Impact on Surface Finish: Smaller grit sizes create finer finishes with minimal scratches and fewer visible marks, leading to an aesthetically pleasing surface. Larger grit sizes can leave noticeable scratches, affecting visual quality.
-
Impact on Surface Roughness: Directly correlates with the fineness of the grit. Finer grits reduce the peak-to-valley height on the surface, resulting in lower roughness values. Coarser grits increase these heights, creating a rougher feel.
-
Impact on Surface Texture: The texture can be smoother with finer grits as they create less pronounced textural deviations. Coarser grits provide a more textured feel due to larger particle sizes.
-
Impact on Surface Flatness: Generally, grit size has a lesser direct impact on flatness compared to other factors. However, uniform grit size can contribute to more consistent material removal, aiding in maintaining flatness during grinding operations.
Diamond & CBN Wheel Bond Type
-
Impact on Surface Finish: Resin bonds, being softer, allow for a finer finish as the diamond particles can dislodge easily, minimizing scratches. Vitrified and metal bonds, being harder, can maintain a rougher finish due to less frequent dislodging of abrasives.
-
Impact on Surface Roughness: Softer bonds like resin tend to produce lower roughness levels because of their flexibility in conforming to surface contours. Harder bonds like metal and vitrified might not conform as well, leading to higher roughness levels.
-
Impact on Surface Texture: Resin bonds can enhance a smooth texture, while vitrified and metal bonds may contribute to a more aggressive texture due to their rigid nature.
-
Impact on Surface Flatness: Harder bonds such as vitrified and metal maintain better flatness control during grinding due to their structural integrity and less wear, ensuring more uniform surface removal.
Diamond & CBN Wheel/Tool Concentration
-
Impact on Surface Finish: Higher diamond concentrations lead to a smoother finish as more cutting edges engage with the material, creating a finer grind. Lower concentrations may result in a rougher finish due to less even cutting.
-
Impact on Surface Roughness: High concentration levels help maintain consistent roughness by providing more uniform cutting action. Lower concentrations can lead to variable roughness levels as the tool wears.
-
Impact on Surface Texture: Increased concentration enhances the texture uniformity by maintaining consistent cutting action across the surface.
-
Impact on Surface Flatness: Higher concentrations can better maintain flatness, especially in harder materials, by ensuring consistent cutting without gouging or uneven material removal.
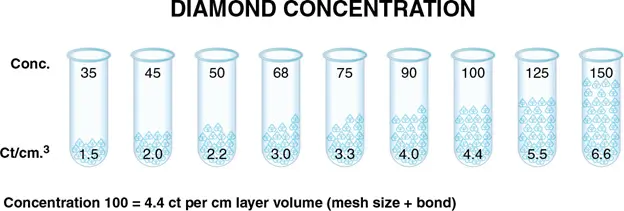
Diamond & CBN Wheel Speed and Feed Rate
-
Impact on Surface Finish: Higher speeds can produce a smoother finish if combined with correct feed rates to prevent heat build-up. Too slow speeds might not effectively cut, leading to a poor finish.
-
Impact on Surface Roughness: Appropriate speeds and controlled feed rates lead to lower roughness by minimizing chipping and tearing of the material surface.
-
Impact on Surface Texture: Consistent and optimal speeds and feed rates contribute to a uniform texture by avoiding irregular tool marks and scratches.
-
Impact on Surface Flatness: Maintaining steady and appropriate speeds and feed rates ensures even material removal, critical for achieving and maintaining flatness during machining.
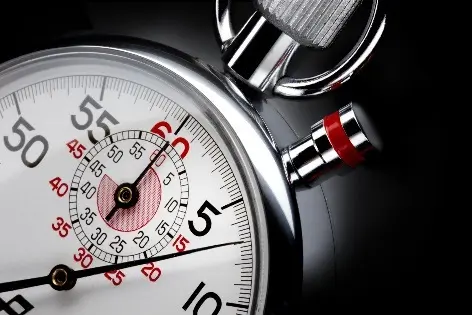
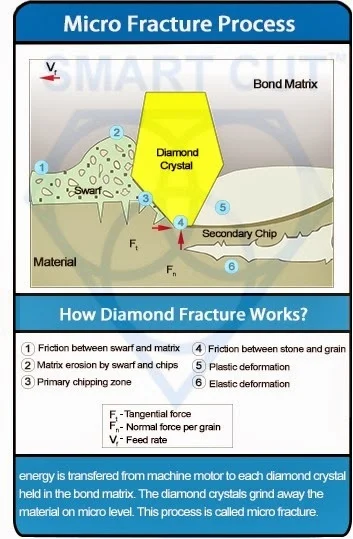
Diamond & CBN Wheel/Tool Wear
-
Impact on Surface Finish: As diamond tools wear, their cutting efficiency decreases, leading to a deterioration in surface finish. Fresh, sharp tools maintain a high-quality finish, while worn tools can leave behind a rough and uneven surface.
-
Impact on Surface Roughness: Tool wear directly increases surface roughness. A new tool maintains minimal roughness, but as the edges dull, the roughness values tend to rise due to uneven cutting and increased friction.
-
Impact on Surface Texture: Worn tools may produce an inconsistent texture characterized by unintended patterns or irregularities, as the worn diamonds do not cut as cleanly.
-
Impact on Surface Flatness: Maintaining tool sharpness is crucial for flatness, especially on large surface areas. Dull tools can lead to uneven material removal, affecting the overall flatness of the workpiece.
-
Multi-Pass Machining: Taking multiple shallow cuts instead of a single deep cut can result in a smoother surface finish by reducing tool stress and heat buildup. This technique is especially useful for achieving fine finishes.
-
Controlled Feed Rates: Consistent and steady feed rates help maintain a uniform surface finish, reducing the risk of irregular patterns or tool chatter.
-
Cross-Hatch Patterns: In some cases, machining with cross-hatch patterns can enhance lubrication and reduce friction, contributing to smoother finishes.
Coolant Use
-
Impact on Surface Finish: Proper use of coolants keeps the cutting area cool and removes swarf efficiently, leading to a superior surface finish. Inadequate coolant flow can cause thermal damage to the surface, manifesting as burns or cracks.
-
Impact on Surface Roughness: Coolants lubricate the cutting process, reducing roughness by minimizing tool wear and preventing metal welding to the surface.
-
Impact on Surface Texture: Adequate coolant prevents texture alterations caused by overheating. Overheating can alter the material properties, leading to a textured surface that feels rougher or has scaling.
-
Impact on Surface Flatness: Consistent coolant flow ensures even temperature distribution during machining, critical for maintaining flatness, especially in materials susceptible to thermal distortion.
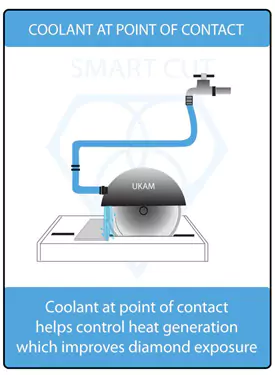
Environmental Conditions
-
Impact on Surface Finish: Environmental factors such as temperature and humidity can affect how materials and tools behave during machining, impacting the finish. Controlled environments are crucial for achieving high precision finishes.
-
Impact on Surface Roughness: Fluctuations in temperature and humidity can cause materials to expand or contract slightly, affecting roughness measurements. Stable conditions help maintain consistent roughness.
-
Impact on Surface Texture: Environmental stability ensures that the material's characteristics do not change unpredictably during machining, which could otherwise alter the intended texture.
-
Impact on Surface Flatness: Temperature and humidity variations can warp or distort materials, especially over large surfaces, making it difficult to maintain flatness.
Vibration Control
-
Impact on Surface Finish: Minimizing vibrations during machining is crucial for achieving a good surface finish. Vibrations can cause irregular tool paths and surface marks.
-
Impact on Surface Roughness: Vibrations typically increase the roughness by creating a wavy or bumpy surface as the tool fails to make smooth, consistent contact with the material.
-
Impact on Surface Texture: Control over vibrations ensures the texture remains consistent with the intended design specifications, without additional patterns caused by unintended tool movements.
-
Impact on Surface Flatness: Vibration can lead to non-uniform material removal, significantly affecting the flatness of precision components.
Backing Material
-
Impact on Surface Finish: The type of backing material used with diamond abrasives can affect the surface finish. A rigid backing can maintain a consistent finish by providing stable support for the abrasive, while a flexible backing might allow for minor deviations that affect the finish quality.
-
Impact on Surface Roughness: Rigid backings ensure uniform pressure distribution, leading to a more consistent roughness. In contrast, flexible backings may result in variable roughness due to uneven pressure application.
-
Impact on Surface Texture: The stability offered by rigid backings aids in achieving the desired texture without distortion. Flexible backings may introduce variability in texture, especially when dealing with complex or detailed surfaces.
-
Impact on Surface Flatness: Maintaining surface flatness is easier with rigid backings as they resist bending and warping during the grinding process, essential for large surface areas or thin materials.
Overlap Factor in Grinding
-
Impact on Surface Finish: The overlap of grinding passes affects the final surface finish. Higher overlap can smooth out potential marks or scratches from previous passes, enhancing the finish.
-
Impact on Surface Roughness: Increased overlap typically reduces roughness by providing a more uniform grind across the surface, minimizing peaks and valleys.
-
Impact on Surface Texture: Consistent overlap helps maintain a uniform texture by evenly distributing the abrasive action over the surface.
-
Impact on Surface Flatness: Adequate overlap helps prevent gouges and dips, which are crucial for maintaining flatness, especially when precision is required.
Pressure Applied
-
Impact on Surface Finish: The amount of pressure applied during grinding affects the surface finish. Too much pressure can cause damage and deteriorate the finish, while too little might not adequately perform the intended grinding.
-
Impact on Surface Roughness: Optimal pressure results in a smoother roughness profile by ensuring that the tool is effectively engaging with the material. Excessive pressure might increase roughness by causing deeper cuts and potential material deformation.
-
Impact on Surface Texture: Controlled pressure helps achieve the desired texture by allowing the diamond tool to perform as designed without altering material properties through excessive force.
-
Impact on Surface Flatness: Consistent and appropriate pressure is key to maintaining flatness, as varying pressures can lead to an uneven surface where some areas might be over or under-processed.
Diamond & CBN Wheel / Tool Variables that Affect Surface Finish
Surface finish is influenced by a variety of factors, including tooling, machining parameters, material properties, environmental conditions, and external factors. Here's a detailed examination of the primary factors:
Variable |
Increase Effect on Surface Finish |
Decrease Effect on Surface Finish |
---|---|---|
Diamond Grit Size |
Larger grit results in a coarser, rougher finish. |
Larger grit results in a coarser, rougher finish. |
Diamond Bond Type |
Softer bond may wear faster but provides a smoother finish. |
Harder bond results in a rougher but more durable wheel. |
Diamond Concentration |
Higher concentration provides more cutting points, leading to a more consistent finish. |
Lower concentration wears faster, potentially leading to uneven finishes. |
Diamond Bond Hardness |
Harder bonds are more durable but may produce a rougher surface finish. |
Softer bonds wear faster, resulting in a smoother but less durable surface. |
Wheel Speed |
Higher speeds can provide smoother finishes but may risk overheating. |
Lower speeds tend to produce rougher finishes but with increased control. |
Feed Rate |
Lower feed rates result in smoother finishes by reducing the force on the tool. |
Higher feed rates can accelerate work but may result in rougher finishes. |
Coolant Flow |
Adequate coolant flow improves finish by reducing heat and friction. |
Inadequate coolant flow can cause heat build-up and worse finishes. |
Tool Wear |
Fresh, less worn tools provide a smoother finish. |
Increased wear leads to deteriorating finish quality. |
Environmental Temperature |
Stable, controlled temperatures help maintain consistent finishes. |
Fluctuating temperatures can cause material expansion/contraction, affecting finish. |
Environmental Humidity |
Controlled humidity prevents material and tool corrosion, maintaining finish quality. |
High humidity can cause rust and degradation, worsening the finish. |
Cleanliness |
Clean environments reduce contamination and improve finish. |
Dust and debris can embed in surfaces, worsening finish quality. |
Tool Geometry |
Optimized tool angles and shapes provide smoother finishes. |
Improper tool geometry can increase roughness and tool wear. |
Cutting Depth |
Shallower cuts can produce smoother finishes by reducing tool stress. |
Deeper cuts may result in rougher finishes due to increased tool stress. |
Material Hardness |
Matching the tool to material hardness ensures smoother finishes. |
Mismatched tool and material hardness can result in poor finishes and increased wear. |
Vibration Control |
Increased machine stability and vibration damping lead to smoother finishes. |
Poor vibration control can cause irregular finishes and tool wear. |
Operator Skill |
Skilled operation can achieve higher precision and smoother finishes. |
Lack of experience or skill can result in inconsistent and poor finishes. |
Lubrication Type |
Proper lubrication type can reduce surface damage and improve finish. |
Unsuitable or poor-quality lubricants can lead to increased wear and rough finishes. |
Pressure Applied |
Consistent and optimal pressure ensures uniform material removal and smoother finishes. |
Excessive or uneven pressure can lead to gouges and rough finishes. |
Tooling Factors
-
Tool Material and Sharpness: Diamond tools are known for their precision and hardness, contributing to superior surface finishes.
-
Tool Geometry: The shape and configuration of the cutting edge affect the surface finish.
-
Tool Vibration: Excessive vibration can lead to surface irregularities. Proper tool balancing is crucial.
Machining Parameters
-
Cutting Speed and Feed Rate: Higher cutting speeds with lower feed rates typically produce finer surface finishes.
-
Depth of Cut: Deeper cuts may lead to rougher surfaces. Shallow cuts often yield smoother results.
-
Cooling and Lubrication: Coolants and lubricants reduce friction and heat, improving surface finish and tool life.
Material Factors
-
Material Hardness and Composition: Harder materials require more durable tools and can lead to rougher surfaces if not properly machined.
-
Material Coatings: Coatings can affect surface finish by creating additional layers.
-
Material Imperfections: Defects like inclusions or voids can cause surface irregularities.
Environmental and External Factors
-
Machine Stability: Instability in the machine can cause misalignment and vibrations.
-
Environmental Conditions: Temperature and humidity can affect material behavior and surface finish.
-
Operator Skill: Experienced operators generally produce better results.
Secondary Operations
-
Post-Machining Processes: Polishing, deburring, or grinding can improve surface finish but must be done correctly to avoid new defects.
-
Heat Treatment: Can affect the surface structure and introduce stresses that impact surface finish.
Several variables and specifications associated with diamond wheels and tools can significantly affect the resulting surface finish during machining. Understanding these variables and their correlations with surface finish is essential for selecting the appropriate tool and achieving consistent quality.
Diamond Wheel Grit Size
Grit size refers to the size of the abrasive particles in the diamond wheel or tool. It plays a crucial role in determining the surface finish:
-
Finer Grits: These result in smoother surface finishes due to smaller abrasive particles. Finer grits are ideal for applications requiring high precision and low roughness, such as polishing and fine grinding.
-
Coarser Grits: These are typically used for rapid material removal and rough grinding. Coarser grits can produce a rougher surface finish due to larger abrasive particles and deeper cutting action.
Correlation with Surface Finish
A finer grit size correlates with a smoother surface finish, as it creates smaller scratches and less pronounced surface irregularities. Coarser grits result in a rougher surface due to their larger cutting edges.
Diamond Wheel Bond Type
The bond type describes the material that holds the abrasive particles together in a diamond wheel. It influences the tool's wear resistance and flexibility, affecting surface finish:
-
Resin Bonds:These bonds offer flexibility and are known for providing a smooth surface finish. Resin-bonded wheels are often used for fine grinding and polishing applications.
-
Vitrified Bonds: These bonds offer rigidity and durability, allowing for higher grinding forces. Vitrified wheels are commonly used for precision grinding and can produce fine surface finishes with the right grit size.
-
Metal Bonds: These are known for their durability and are often used for coarse grinding or high-impact applications. Metal-bonded wheels can result in a rougher surface finish due to their stiffness.
Correlation with Surface Finish
Resin bonds are generally associated with smoother surface finishes due to their flexibility, while vitrified bonds offer a balance between rigidity and smoothness. Metal bonds, being more rigid, are typically used for rougher applications and can produce coarser finishes.
Diamond Wheel Concentration
Concentration refers to the amount of abrasive material in the diamond wheel. It affects the wheel's cutting ability and wear resistance:
-
High Concentration: This provides more cutting edges and greater durability, leading to a more consistent surface finish over time.
-
Low Concentration: This can lead to faster wear and a less consistent surface finish due to fewer abrasive particles.
Correlation with Surface Finish
A higher concentration of abrasive material correlates with a more consistent surface finish due to the increased number of cutting edges. Lower concentration can result in more variability in the surface finish as the tool wears down faster.
Diamond Wheel Shape and Geometry
The shape and geometry of the diamond wheel or tool influence its cutting characteristics and surface contact area:
-
Flat Wheels: These are used for surface grinding and can produce a smooth finish due to their large contact area.
-
Cup Wheels: Often used for grinding edges or contours, these can create different surface patterns depending on the angle and pressure applied.
-
Profiled Wheels: These have specific shapes for grinding unique profiles and can produce specialized surface textures.
Correlation with Surface Finish
Flat wheels tend to produce smoother finishes due to their consistent contact with the surface, while cup wheels and profiled wheels can create varying patterns depending on how they are used. The geometry of the tool affects the resulting surface texture and can influence the level of roughness.
Diamond Wheel Speed and Feed Rate
The speed at which the diamond wheel operates and the rate at which the material is fed into the wheel also impact the surface finish:
-
High Speed: This can produce a smoother finish as it may reduce the likelihood of tool loading and uneven cuts.
-
Low Speed: This might lead to rougher surfaces due to slower cutting action and increased heat buildup.
-
Controlled Feed Rate: A consistent and controlled feed rate contributes to a uniform surface finish.
Correlation with Surface Finish
Higher wheel speeds generally correlate with smoother finishes, as the faster cutting action reduces tool loading. A controlled feed rate helps maintain consistency and prevents irregularities in the surface finish.
Tool Wear and Its Impact on Surface Finish
Tool wear is an inevitable part of machining, and its rate can significantly affect the surface finish. Diamond tools, despite their exceptional hardness, will eventually experience wear over time. The key is to manage tool wear to ensure consistent surface quality.
-
Gradual Wear: As diamond tools wear down gradually, the cutting edges become less sharp, potentially leading to a rougher surface finish. Regular tool maintenance and dressing are essential to maintain cutting efficiency.
-
Unexpected Tool Wear: If a tool wears unexpectedly or unevenly, it can cause inconsistent surface finishes, with increased roughness or irregular patterns. Monitoring tool condition and implementing predictive maintenance can help prevent such issues.
Correlation with Surface Finish
Properly managing tool wear correlates with smoother and more consistent surface finishes. Regular dressing of grinding wheels helps maintain sharp cutting edges, contributing to better surface quality. Unexpected or uneven wear can lead to rougher finishes and may require additional polishing or reworking to meet quality standards.
Coolant Application and Surface Finish
The use of coolants and lubricants is critical in controlling heat and friction during machining. Proper application of coolants can greatly impact the surface finish quality.
-
Adequate Coolant Flow: Ensures that the cutting area stays cool, reducing the risk of heat-related damage to the surface and prolonging tool life.
-
Inadequate Coolant Flow: Can lead to overheating, causing warping, burns, or surface discoloration, which negatively affects surface finish.
Correlation with Surface Finish
Adequate coolant application correlates with smoother surface finishes by minimizing heat buildup and reducing friction. This contributes to a more stable machining process and extends tool life. Inadequate coolant flow, however, can lead to rougher surfaces due to heat damage and increased tool wear.
Machining Techniques and Surface Finish
Different machining techniques can affect the surface finish, with each approach offering unique outcomes based on the tool's interaction with the material.
-
Multi-Pass Machining: Taking multiple shallow cuts instead of a single deep cut can result in a smoother surface finish by reducing tool stress and heat buildup. This technique is especially useful for achieving fine finishes.
-
Controlled Feed Rates: Consistent and steady feed rates help maintain a uniform surface finish, reducing the risk of irregular patterns or tool chatter.
-
Cross-Hatch Patterns: In some cases, machining with cross-hatch patterns can enhance lubrication and reduce friction, contributing to smoother finishes.
Correlation with Surface Finish
Multi-pass machining and controlled feed rates are associated with smoother surface finishes due to their focus on stability and reduced tool stress. Techniques like cross-hatching can further improve surface quality by promoting even lubrication and reducing wear. Conversely, rapid or inconsistent feed rates may lead to rougher surfaces and increased tool wear.
The Role of Diamond Tools in Achieving Optimal Surface Finish
Diamond tools, such as grinding wheels, slicing and cut-off blades, and diamond drills, are highly regarded for their precision, durability, and ability to machine a wide range of materials. Here's how diamond tools contribute to achieving optimal surface finish:
Diamond Grinding Wheels
Diamond grinding wheels are used extensively in machining hard materials. They are designed with diamond particles embedded in a bonding matrix, offering high hardness and abrasion resistance. These wheels create smooth, uniform surfaces by removing material with precision. Applications like aerospace and automotive require close tolerances and fine surface finishes, making diamond wheels ideal.
Diamond Slicing and Cut-Off Blades
Diamond slicing and cut-off blades are used to cut through materials with minimal chipping and roughness. These blades are crucial in industries that require precision cutting, such as electronics, medical devices, and optics. The smooth edges achieved by these blades reduce the need for additional finishing operations, saving time and cost.
Diamond Drills for Precision Machining
Diamond drills, including thin-wall core drills and micro drills, are used for creating precise holes in various materials. These tools are indispensable in industries like construction, jewelry, and electronics. The high precision of diamond drills ensures that holes are created with minimal surface irregularities, crucial for applications requiring tight tolerances and smooth finishes.
What is Surface Roughness
Surface roughness is a critical component of surface finish, encompassing various characteristics that define the texture and quality of a machined surface. Understanding these concepts helps engineers and machinists maintain consistent and high-quality surface finishes.
Roughness refers to the texture on the surface caused by machining processes, characterized by small irregularities and deviations. Basically, these are small bumps and dips you can feel or see on a surface that's been shaped by tools. Imagine running your finger across a finely carved wooden table; the tiny imperfections you feel are similar to what roughness measures in machined surfaces. This roughness depends on factors like the shape of the cutting tool, how fast the tool moves, and the conditions under which the machining takes place.
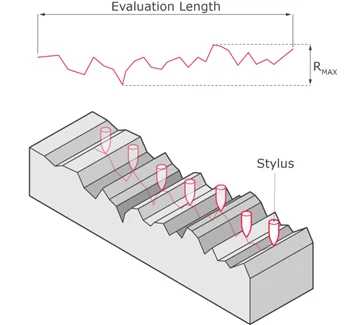
How to Measure Surface Roughness
The two most common roughness measurements are Ra (Roughness Average) and RMS (Root Mean Square).
Ra (Roughness Average)
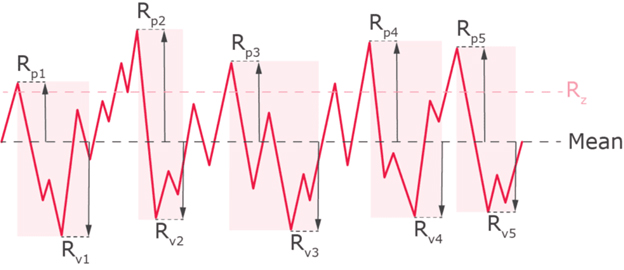
This is like the average height of all the bumps and dips found over a certain area of the surface. It gives a general idea of how smooth or rough the surface feels. This calculated as the arithmetic average of the absolute values of the roughness profile deviations over a given length. Ra is the most common measure of surface roughness because it is simple to understand and correlates well with perceived surface texture.
RMS (Root Mean Square)
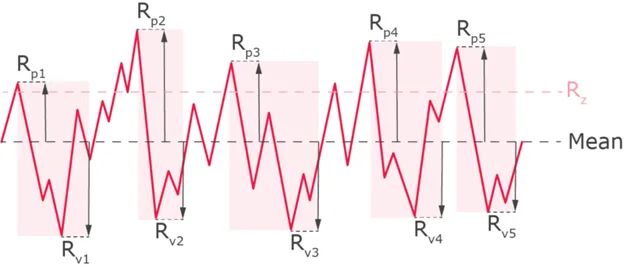
This measures the height from the highest peak to the deepest dip within a specific length of the surface. It tells us about the biggest single imperfection found. This the square root of the average of squared deviations from the mean centerline. RMS values are typically about 11% higher than Ra, providing an alternative perspective on surface texture. This measurement provides a slightly different perspective by giving more weight to higher peaks and deeper valleys.
An easy way to think about Ra and Rmax is by picturing a mountain range: Ra would be the average height of all peaks and valleys, while Rmax would be the height of the tallest mountain to the deepest nearby valley.
A simple relationship between Ra and Rmax, especially when the surface irregularities are shaped like triangles, is that Ra is about one-quarter of Rmax. This means that if you know the height of the tallest peak to the deepest valley, the average roughness is roughly one-fourth of that measurement.
Additional Surface Roughness Measurement Parameters:
-
Roughness Height represents the vertical distance from a reference line to the peaks of the surface irregularities. This measurement is typically given in millimeters, microns, or microinches.
-
Roughness Width indicates the horizontal distance between successive peaks or ridges, providing insights into the predominant roughness pattern.
-
Lay describes the direction of the predominant pattern on the surface, often related to the machining process.
-
Waviness refers to larger-scale surface variations, typically caused by tool deflection or machine vibrations.
-
Waviness Height is the vertical distance between peaks and valleys within the surface profile.
Common Challenges in Achieving Surface Finish
Despite the advancements in diamond tool technology, certain challenges persist in achieving and maintaining high-quality surface finishes. Here are some common issues and potential solutions:
Tool Wear and Maintenance
Diamond tools are known for their durability, but they can wear over time. Worn tools can lead to roughness, burrs, or other surface defects. Regular monitoring and proper maintenance are crucial to ensure consistent surface finishes.
-
Tool Dressing and Conditioning: Some diamond tools, especially grinding wheels, require dressing to maintain their cutting performance. Proper dressing ensures consistent results and extends tool life.
-
Tool Replacement: Identifying when a tool has reached the end of its useful life is important to prevent surface defects caused by excessive wear.
Machine Stability and Calibration
Machine stability is critical for achieving high-quality surface finishes. Instability can lead to misalignment, vibrations, and other issues that degrade the surface quality.
-
Regular Calibration: Machines should be calibrated regularly to ensure proper alignment and functioning within specified tolerances.
-
Process Variability: Consistency in machine settings and environmental conditions is crucial for maintaining stable surface finishes.
Secondary Operations and Heat Treatment
Secondary operations, such as polishing, deburring, or grinding, can improve surface finish, but they must be done correctly to avoid introducing new defects.
-
Post-Machining Processes: Properly executed secondary operations can enhance surface quality. However, improper techniques can cause new surface irregularities.
-
Heat Treatment: This process can affect the surface structure and introduce stresses that impact surface finish. Careful control of heat treatment parameters is essential for maintaining a high-quality surface.
Impact of Surface Finish on Product Performance
Surface finish significantly affects a product's performance, durability, and reliability. A smooth surface can reduce friction, leading to improved efficiency and reduced wear. This is particularly important in components subject to high stress, where rough surfaces can cause premature failure or reduced lifespan.
Reducing Friction and Wear
In applications where parts move against each other, a smooth surface finish helps reduce friction and wear. This contributes to the longevity of components like bearings, gears, and shafts. Diamond tools, known for their precision, can create surfaces that promote consistent lubrication, reducing friction and extending the life of moving parts.
Ensuring Proper Fit and Assembly
Surface finish also influences how well components fit together. In precision engineering, tight tolerances and smooth surfaces are crucial for proper assembly. Diamond tools enable manufacturers to achieve the required precision, ensuring that parts align correctly and function as intended.
Impact on Aesthetics and Customer Perception
The aesthetic quality of a product can also be affected by surface finish. A smooth, polished surface often indicates high-quality craftsmanship and can enhance the overall appearance of a product. This is especially relevant in industries where visual appeal is important, such as automotive and consumer electronics.
Industry Standards and Regulations
Different industries have specific standards and regulations regarding surface finish. Compliance with these standards is crucial for product quality and safety. Understanding these requirements ensures that manufacturers meet industry-specific specifications for performance and reliability.
Common Industry Standards
-
ISO Standards: The International Organization for Standardization (ISO) provides guidelines for surface finish measurement and quality control.
-
ANSI Standards: The American National Standards Institute (ANSI) also has standards for surface finish, outlining acceptable tolerances and measurement techniques.
-
Industry-Specific Regulations: Certain industries, like aerospace and medical devices, have stringent requirements for surface finish to ensure safety and performance.
Importance of Compliance
Compliance with industry standards is essential for gaining customer trust and ensuring product safety. Manufacturers must stay up-to-date with the latest regulations and implement quality control measures to meet these requirements.
Advanced Techniques for Achieving Optimal Surface Finish
To achieve a high-quality surface finish, manufacturers often employ advanced techniques that leverage cutting-edge technology and precise engineering practices. These techniques enhance the precision of diamond tools and contribute to consistent and repeatable results.
Adaptive Machining Strategies
Adaptive machining involves real-time adjustments based on sensor feedback, allowing for consistent control over machining parameters. This technique can help compensate for tool wear, material variations, and environmental changes, leading to improved surface finish.
Multi-Pass Machining
Multi-pass machining involves making several shallow cuts instead of a single deep cut, which reduces stress on the tool and minimizes surface defects. This technique is especially useful in precision applications where maintaining a consistent surface finish is critical.
Cross-Hatch Patterning
Creating a cross-hatch pattern during machining can enhance lubrication and reduce friction. This technique involves changing the direction of cuts, leading to a consistent surface texture that promotes even lubrication and reduces wear.
Use of Coolants and Lubricants
Coolants and lubricants play a vital role in improving surface finish by reducing friction and heat. Proper application of coolants helps prevent tool damage and surface defects caused by excessive heat, leading to smoother results and longer tool life.
Best Practices for Maintaining High-Quality Surface Finish
Maintaining a high-quality surface finish requires a combination of best practices, including regular tool maintenance, consistent machine calibration, and effective quality control measures. The following best practices can help ensure optimal results.
Regular Tool Maintenance
Regularly inspecting and maintaining diamond tools is crucial for achieving consistent surface finishes. This includes monitoring tool wear, dressing grinding wheels, and replacing tools when they reach the end of their useful life.
Consistent Machine Calibration
Machine calibration ensures that tools are aligned and function within specified tolerances. Regular calibration helps prevent misalignment and vibrations, which can lead to surface defects.
Implementation of Quality Control Measures
Quality control measures, such as profilometry and visual inspection, help ensure that surface finishes meet the required standards. These measures can identify surface defects early, allowing for corrective action before parts are completed.
Proper Training and Operator Skill Development
Operator skill and experience significantly impact surface finish quality. Providing proper training and promoting skill development can lead to better results and reduce the risk of human error during machining.
Impact of Surface Finish on Product Reliability
Surface finish has a direct impact on product reliability and longevity. A high-quality surface finish reduces friction, wear, and the risk of defects, contributing to improved product performance. This section explores how surface finish influences product reliability.
Reducing Friction and Wear
A smooth surface reduces friction between moving parts, leading to longer-lasting components. This is particularly important in high-stress applications where excessive wear can lead to premature failure.
Preventing Stress Concentrations and Fatigue
Surface finish plays a role in preventing stress concentrations, which can lead to fatigue cracks. Diamond tools can create smooth surfaces with minimal irregularities, reducing the risk of stress-related defects.
Ensuring Proper Functionality
Proper surface finish ensures that components fit together as intended and function correctly. This is crucial in precision applications where tight tolerances and accurate assembly are essential.
Methods Used for Measuring Surface Finish
Surface finish is a critical aspect of machining and manufacturing, indicating the texture and quality of a surface. Various measurement techniques are used to quantify surface roughness, providing valuable data for quality control and industry compliance. Here are the key methods for measuring surface finish, along with their advantages and limitations.
Electronic Measurement
Electronic measurement uses instruments that quantify surface texture electronically, offering precise and repeatable data on surface roughness. These instruments fall into two main categories:
-
Averaging (Tracer-Type) Instruments: These devices employ a stylus that moves across the surface to be measured, with the vertical motion electronically amplified to create a surface profile. This profile can be recorded as a numerical roughness value, often expressed as the arithmetic average (AA). Averaging instruments are widely used for routine surface finish measurements due to their reliability and ease of use.
-
Profiling (Displacement-Type) Instruments: Similar to averaging instruments, profiling equipment uses a stylus to measure the surface, but it provides more detailed surface profiles. Profiling is typically employed in research and development applications where detailed surface characteristics are required. Due to the complexity of these instruments, they require skilled operators and are less common in routine industrial settings.
Optical Measurement
Optical measurement techniques rely on light and optical principles to assess surface texture, offering a non-contact approach. These methods vary in complexity, from basic microscopic inspection to advanced techniques like interferometry:
-
Microscopic Inspection: This simple optical method involves examining the surface under a microscope, allowing operators to visually inspect texture and geometry. It is commonly used for quick assessments or when electronic instruments are unavailable.
-
Interferometry and Other Optical Techniques: These advanced optical methods, such as interferometry, provide high-resolution surface measurements. They analyze interference patterns created by light reflections to determine surface topography. Optical methods have the advantage of being non-contact, reducing the risk of damage to the surface. This makes them ideal for applications where contact methods might affect surface integrity.
Visual and Tactual Measurement
Visual and tactual methods are the most straightforward ways to evaluate surface finish. Although less accurate than electronic or optical methods, they are useful for quick assessments or when resources are limited:
-
Visual Comparators: Visual comparators consist of precision reference specimens with various replicated surfaces of different roughness values. Operators can use a magnifier to visually compare the workpiece surface against these reference specimens.
-
Tactual (Fingernail Test): This tactile method involves drawing a fingernail across the workpiece at right angles to the tool marks. The tactile feedback provides an indication of the surface's roughness. If the workpiece and the reference specimen have similar roughness, the tactile response will be comparable. This method is particularly useful in field applications or for quick checks during production.
Each measurement method has its unique advantages and limitations. Electronic measurement provides high accuracy and is suitable for quantitative assessments. Optical measurement offers non-contact evaluation with high resolution, while visual and tactual methods, though less precise, are useful for quick assessments. The choice of method depends on the required accuracy, available resources, and specific application needs. By selecting the appropriate measurement techniques, manufacturers can ensure consistent surface finish quality, meeting industry standards and customer expectations.
Measuring Surface Flatness
When we talk about measuring surface flatness, we're essentially looking at how smooth and even a surface is. This is important because in many areas, like manufacturing or construction, precision matters a lot. Imagine trying to build something with pieces that don't fit together because the surface isn't flat — it wouldn't work too well!
Here are some ways we can measure surface flatness:
1. Visual Inspection:
-
This is like just looking at the surface and seeing if it looks flat or if there are any obvious bumps or gaps. It's the simplest method and can give you a general idea, but it might not catch smaller imperfections.
2. Using Tools:
-
We can use tools like rulers, straight edges, or special thin metal strips called feeler gauges. These tools help us see if there are any gaps between the surface and the straight edge, which tells us if it's flat or not.
3. Optical Methods:
-
There are advanced methods that use special cameras or lasers to take detailed pictures of the surface. These pictures help us see even tiny bumps or dips that we might not notice with our eyes.
4. Coordinate Measuring Machines (CMM):
-
These are like high-tech measuring devices that have a moving arm. The arm touches the surface at different points and records data. Then, with the help of computers, we can see if the surface is flat or not based on that data.
5. Digital Levels:
-
Digital levels are like smart rulers. They give us precise measurements and tell us exactly how flat the surface is. They're easy to use and can be handy for quick checks.
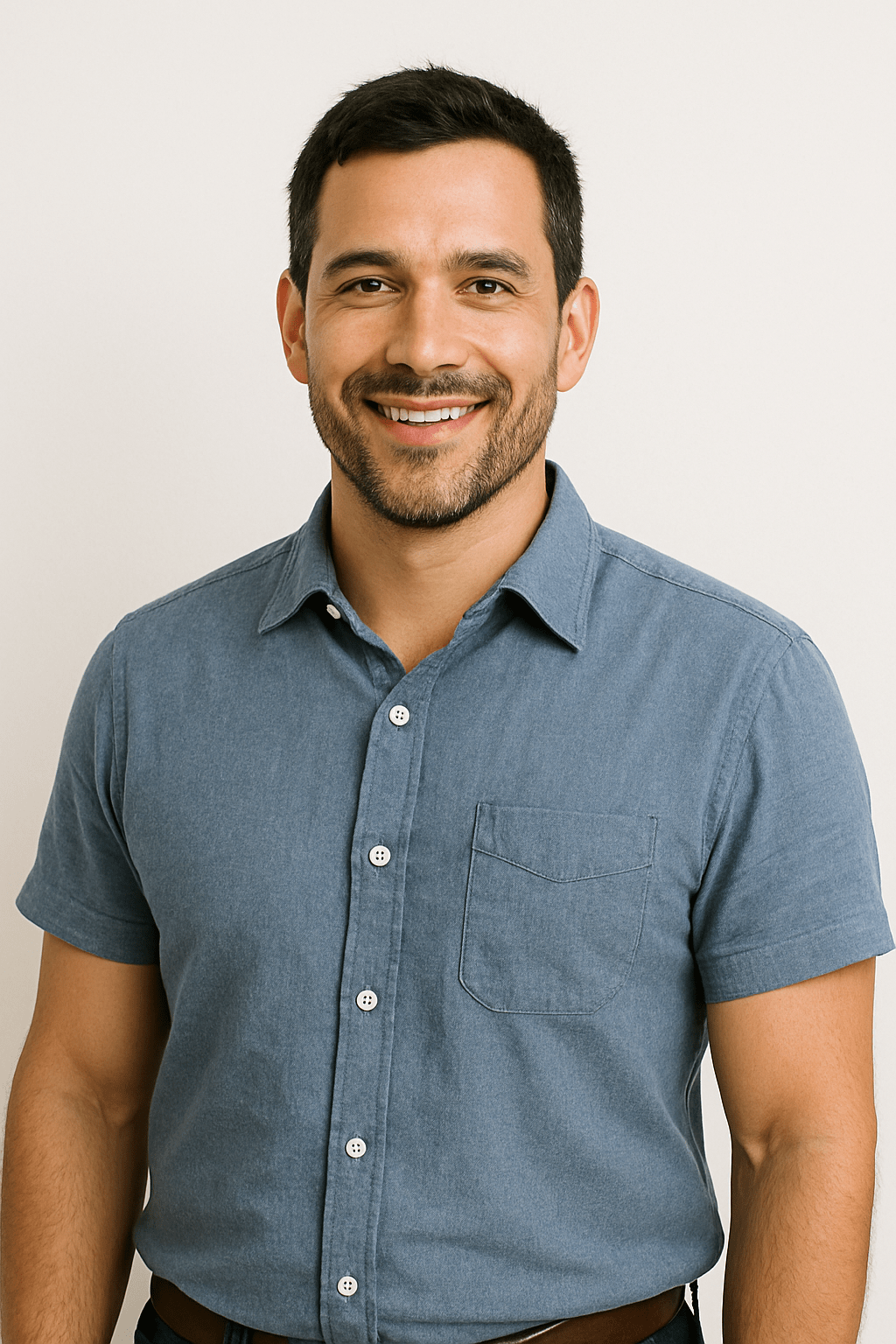
Carlos Sanchez is a senior technical specialist and field applications trainer with more than 17 years of experience in the use and optimization of industrial diamond tools, including ultra-thin diamond blades, core drills, and CBN grinding wheels. With a foundation in industrial engineering and technical operations, Mr. Sanchez has worked extensively with manufacturers and laboratories around the world, providing hands-on support and practical training for a wide range of cutting, grinding, and sample preparation applications.
Fluent in both English and Spanish, Carlos is known for his ability to translate complex tooling concepts into clear, actionable procedures for engineers, technicians, and production staff. His approach emphasizes real-world process improvement, tool longevity, and operator education—ensuring clients get the most out of their diamond tooling investments.
As an author, Mr. Sanchez shares field-tested insights on tool performance optimization, defect prevention, training methodologies, and troubleshooting common cutting issues.
ARE YOU USING RIGHT TOOLS
FOR YOUR APPLICATION?
LET US
HELP YOU
HAVING ISSUES WITH
YOUR CURRENT TOOLS?
Knowledge Center
How to Selecting Right Diamond Tools for your application
How to properly use Diamond Tools
Why use diamond
Diamond vs CBN (cubic boron nitride) Tools
What is Diamond Mesh Size and how to select best one for your application
What is Diamond Concentration and which to use for your application
Diamond Tool Coolants Why, How, When & Where to Use
Choosing The Correct Diamond Bond Type
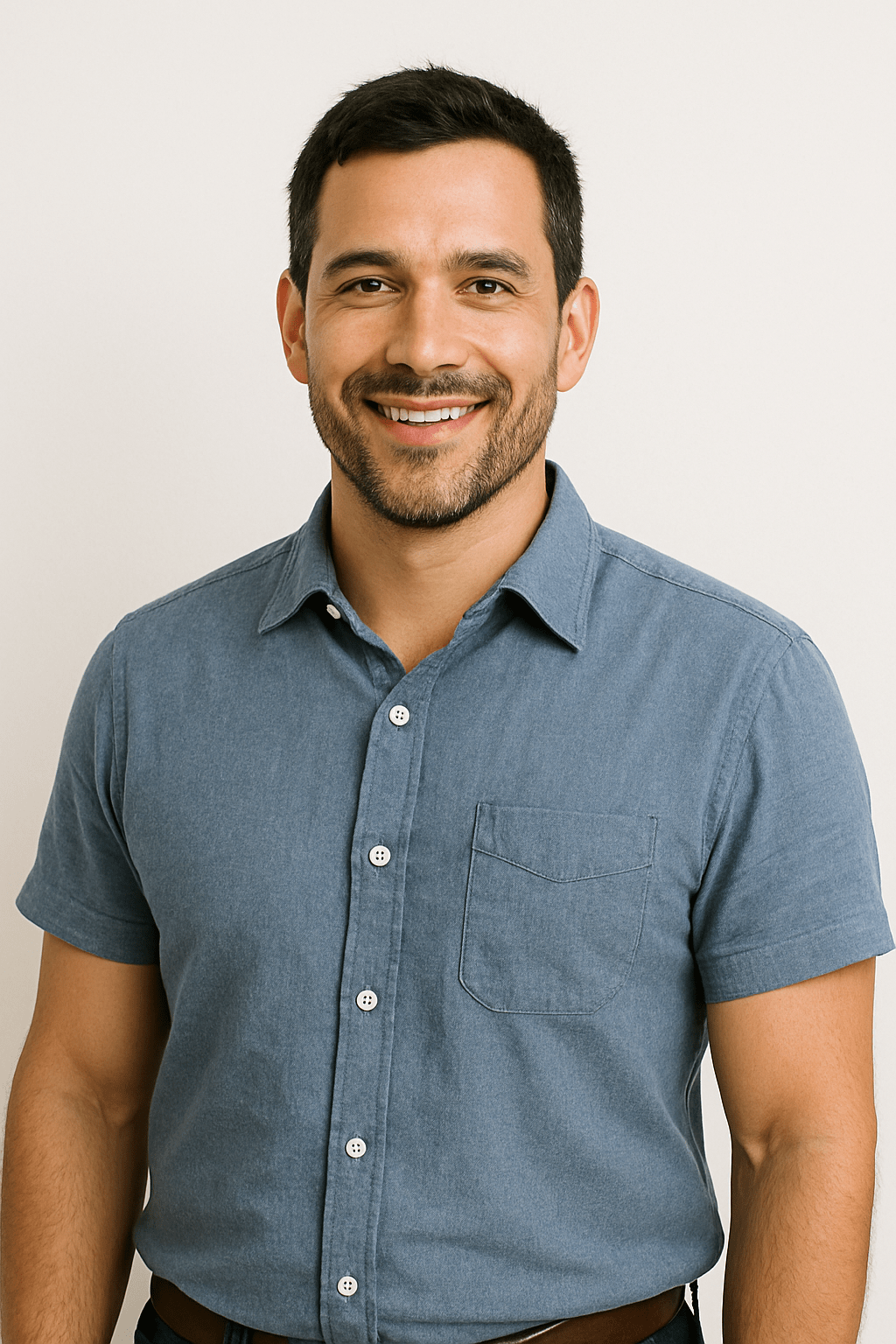
Carlos Sanchez is a senior technical specialist and field applications trainer with more than 17 years of experience in the use and optimization of industrial diamond tools, including ultra-thin diamond blades, core drills, and CBN grinding wheels. With a foundation in industrial engineering and technical operations, Mr. Sanchez has worked extensively with manufacturers and laboratories around the world, providing hands-on support and practical training for a wide range of cutting, grinding, and sample preparation applications.
Fluent in both English and Spanish, Carlos is known for his ability to translate complex tooling concepts into clear, actionable procedures for engineers, technicians, and production staff. His approach emphasizes real-world process improvement, tool longevity, and operator education—ensuring clients get the most out of their diamond tooling investments.
As an author, Mr. Sanchez shares field-tested insights on tool performance optimization, defect prevention, training methodologies, and troubleshooting common cutting issues.