Table of Contents
ToggleWhen evaluating diamond and cubic boron nitride (CBN) cutting blades, it's crucial to consider key performance metrics and criteria. Different applications have varying goals, making it important to understand these factors to determine a blade's effectiveness and impact on result quality. There are many metrics that are important in optimizing your cutting operation to ultimate level of efficiency. In a previous article we discussed the main top 5 Key metrics include surface finish, blade life, cost, and consistency.
Here we will discuss the other 14 important diamond & cbn blade performance metrics. Each metric provides critical insights into their efficiency, durability, and overall effectiveness in different operational conditions.
Understanding these metrics is important for professionals seeking to optimize cutting processes, enhance product quality, and minimize operational costs. Each performance metric not only defines the operational excellence of these blades but also guides users in selecting the right diamond or cbn blade for the right application, Through this exploration, we aim to equip users with the knowledge to make informed decisions about their diamond & cbn blades to optimize their process to ultimate level of efficiency.
Metric |
Description |
Implications |
Operational Impact and Interdependencies |
---|---|---|---|
Required Force |
A blade that requires less force to cut through materials minimizes potential sample damage and operator fatigue. |
Enhances operator comfort and reduces material wastage. |
Lower force reduces wear on equipment and extends blade life, leading to cost savings in blade replacement and machine maintenance. |
Heat Dissipation |
Effective heat management improves cut quality and increases the blade's life. Blades that dissipate heat efficiently perform better under demanding conditions. |
Prevents thermal damage to both blade and work material, maintaining their structural integrity. |
Efficient heat management ensures consistent performance and extends the operational life of the blade under high-load conditions. |
Material Compatibility |
A blade's ability to handle different types of materials effectively without degradation is essential. |
Determines the versatility and applicability of a blade across various materials, essential in multi-material cutting environments. |
Correct blade selection reduces the need for multiple blade changes and minimizes downtime, enhancing workflow efficiency. |
Wear Resistance |
Resistance to wear and tear defines how well a blade holds up under regular use, impacting its longevity and reliability. |
Increases the operational lifespan of the blade, reducing the frequency of replacements. |
Directly influences maintenance schedules and operational costs; higher wear resistance leads to longer intervals between blade replacements. |
Vibration |
Lower vibration levels indicate a more stable cut, improving cut quality and consistency. |
Enhances the precision and quality of cuts, important in applications requiring high detail and finish. |
Reduces mechanical stress on equipment and operator, leading to better safety and longer machinery life. |
Amount of Material Deformation |
Minimizing deformation during cutting is crucial to preserve the true microstructure of the material and ensure material/part reliability. |
Critical for maintaining the integrity of materials in precision applications like semiconductor and aerospace component manufacturing. |
Affects the accuracy of the final product and the need for post-processing, impacting production timelines and costs. |
Secondary Grinding and Polishing |
Blades that produce cleaner cuts reduce the need for secondary finishing operations. |
Improves overall process efficiency and reduces labor and material costs associated with post-processing. |
Enhances throughput and reduces time to market by streamlining production processes. |
Thermal Stability |
Assesses the blade's ability to maintain its properties and performance at varying temperatures. Blades with high thermal stability perform consistently in varied conditions. |
Essential for maintaining cutting efficiency in environments with fluctuating or high temperatures. |
Critical for operations involving thermally sensitive materials, preventing damage due to heat build-up. |
Blade Flexibility |
Evaluates the blade's ability to flex without breaking, particularly important when making intricate cuts or operating under variable loads. |
Prevents blade failure in complex or detailed cutting scenarios, ensuring reliability and reducing blade waste. |
Impacts the choice of blade for specific applications, particularly in industries requiring intricate cutting patterns like electronics or jewelry making. |
Recovery Time |
The time it takes for a blade to return to optimal performance after dressing or maintenance. Faster recovery reduces downtime. |
Directly impacts production efficiency, with shorter recovery times leading to higher uptime. |
Minimizes operational interruptions, enhancing productivity and reducing costs associated with downtime. |
Edge Durability |
Measures how long the cutting edge remains effective before it dulls. Durable edges reduce the frequency of blade replacements and maintenance. |
Leads to consistent performance over a longer period, reducing the need for frequent recalibrations or adjustments. |
Enhances the blade's value proposition by extending its useful life and reducing the total cost of ownership. |
Impact Resistance |
Evaluates the blade's ability to withstand sudden stresses or impacts without cracking or chipping. Particularly relevant for cutting hard, brittle materials. |
Ensures blade integrity and reliability in harsh or unpredictable cutting environments. |
Essential for maintaining operational safety and reducing blade failure, which can lead to costly material damage or accidents. |
Profile Retention |
Measures how well a blade maintains its original profile and cutting characteristics over its lifespan. High profile retention reduces the need for frequent adjustments. |
Key for applications requiring precision over prolonged periods, reducing recalibration efforts and maintaining consistent cutting quality. |
Impacts equipment efficiency and the quality of outputs, directly influencing customer satisfaction and repeat business in precision-critical industries. |
Blade Stiffness |
A measurement of the rigidity of the blade. Stiffer blades are less prone to wobbling and provide more precise cuts, crucial in high-precision applications. |
Improves cutting accuracy and reduces potential for errors in sensitive cutting operations. |
Affects blade selection criteria based on the precision requirement of the application, influencing overall project outcomes in sectors like microelectronics and medical device manufacturing. |
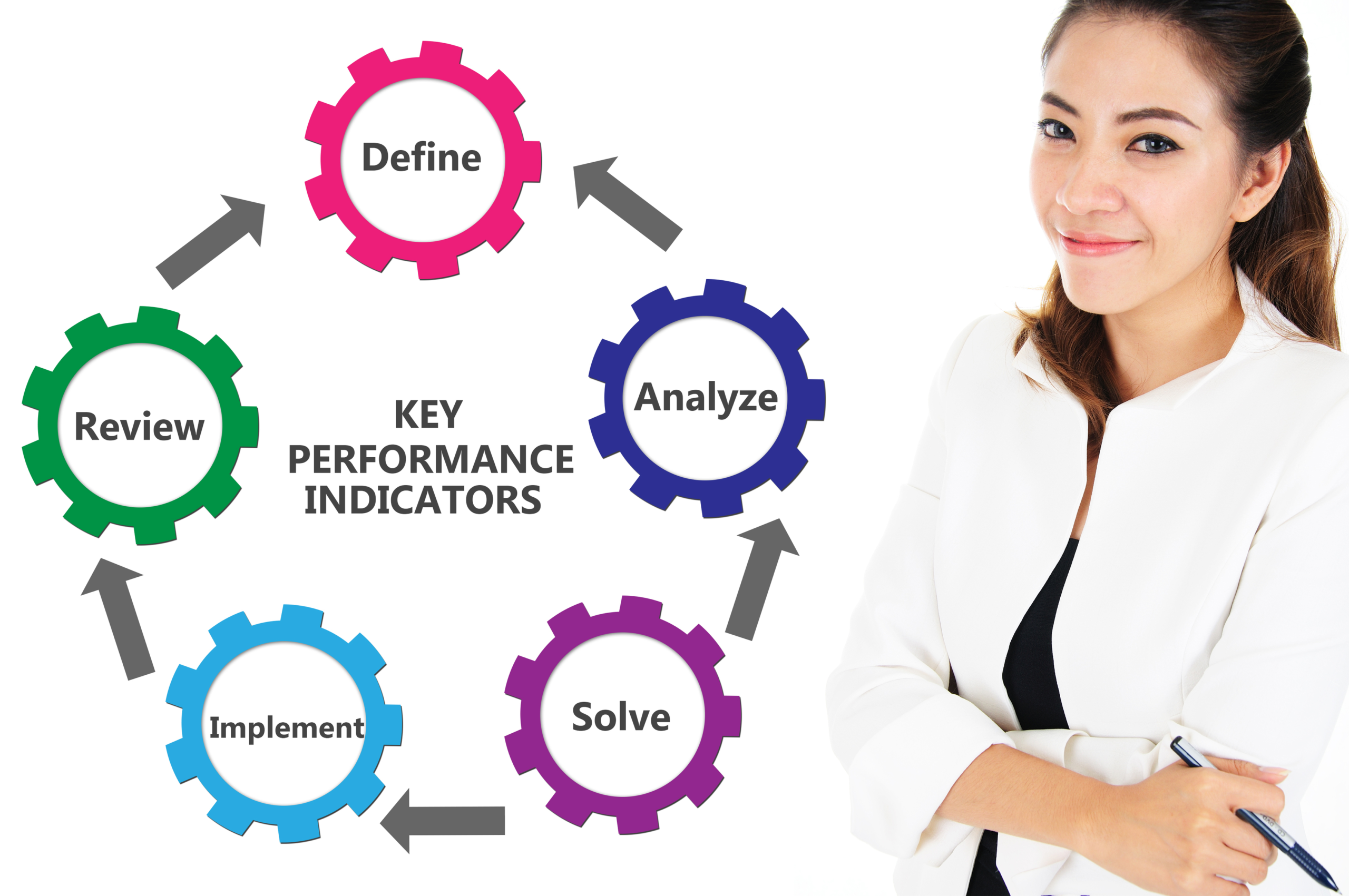
Required Cutting Force
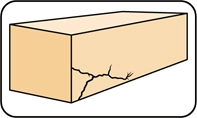
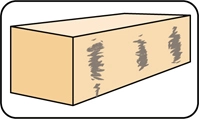
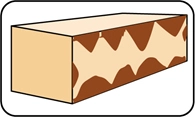
The required force for operating a diamond or cbn blade is a crucial performance metric that significantly influences both the quality of the cut and the overall user experience. A blade that requires less force is highly desirable due to several key benefits that it offers, including minimizing heat generation, enhancing cut quality and surface finish, reducing material damage and deformation, saving time, and lessening operator fatigue.
Minimizing Heat Generation - One of the foremost benefits of a blade that requires less force to cut through materials is the reduction in heat generation. Excessive force during cutting leads to increased friction, which in turn raises the temperature at the cutting interface. High temperatures can adversely affect both the blade and the material being cut. For the blade, excessive heat can cause premature wear and reduce its lifespan. For the material, high temperatures can result in thermal damage, altering its properties and potentially leading to undesirable outcomes such as warping or melting. By using a blade that cuts efficiently with minimal force, heat generation is significantly reduced, preserving the integrity of both the blade and the material.
Improving Cut Quality and Surface Finish - The quality of the cut and surface finish are is important for many applications. A blade that requires less force to cut through materials can achieve cleaner, more precise cuts, with less or no chipping. Excellent cut quality and minimum chipping is critical for many applications such as microelectronics, advanced ceramics, and optics, where even the slightest imperfection can compromise the functionality of the final product. Lower cutting forces result in smoother surfaces, reducing the need for additional finishing processes and thereby streamlining production.
Enhanced Blade Longevity and Equipment Health: Operating with less force extends the life of the blade and the cutting machinery. It reduces wear and tear, leading to fewer maintenance issues, lower replacement costs, and less downtime for repairs. Additionally, a lower cutting force decreases the chances of the blade overheating, which can degrade its cutting efficiency and lifespan.
Minimizing Material Damage and Deformation - When a blade exerts excessive force during cutting, it can cause significant damage and deformation to the material. This is particularly problematic when working with brittle or delicate materials such as advanced ceramics, composites, fragile crystals, and many ther materials. Minimizing the required cutting force helps in preserving the structural integrity of the material, ensuring that it remains intact and free from cracks, chips, or other forms of damage. This is essential for maintaining the performance characteristics of the material in its intended application.
Saving Time and Enhancing Efficiency - Efficiency is a critical factor in any cutting operation. Blades that cut through materials with less force enable faster cutting speeds without compromising the quality of the cut. This translates into time savings and increased throughput, which are vital for maintaining competitive advantage in manufacturing and production environments. By optimizing the cutting process, businesses can achieve higher productivity and reduce operational costs.
Reducing Operator Fatigue - The physical demands placed on operators during cutting operations can be significant, especially when dealing with hard or dense materials. A blade that requires less force to cut through materials reduces the physical strain on operators, minimizing fatigue and the risk of repetitive strain injuries. This not only enhances the well-being of the workforce but also improves overall operational safety and productivity.
How to Measure Diamond & CBN Cutting Force
Dynamometers - Dynamometers are widely used to measure cutting forces in machining and cutting operations. These devices can measure both static and dynamic forces, providing real-time data on the forces acting on the blade during the cutting process. The key advantages of using dynamometers include high precision and the ability to capture force variations throughout the cut.
⦁ Rotary Dynamometers: These are mounted on rotating spindles and measure forces in multiple directions (axial, radial, and tangential). They are particularly useful for high-speed cutting operations.
⦁ Stationary Dynamometers: These are fixed to the machine structure and measure forces directly as the material is fed into the blade. They are typically used for lower-speed, more controlled cutting operations.
Load Cells - Load cells are transducers that convert force into an electrical signal, which can then be measured and recorded. In cutting applications, load cells can be integrated into the cutting setup to continuously monitor the force exerted by the blade on the material. They offer high accuracy and are suitable for a wide range of force measurement applications.
⦁ Single-axis Load Cells: Measure force in one direction, ideal for straightforward cutting operations.
⦁ Multi-axis Load Cells: Measure forces in multiple directions simultaneously, providing a comprehensive understanding of the cutting dynamics.
Force Sensors and Strain Gauges - Force sensors and strain gauges are often used in combination to measure the forces during cutting. Strain gauges, attached to the blade or tool holder, detect minute deformations caused by cutting forces. These deformations are converted into electrical signals, which can be analyzed to determine the cutting force.
⦁ Force Sensors: Directly measure the force applied and are typically more robust and easier to integrate into cutting machines.
⦁ Strain Gauges: Provide highly sensitive measurements and can detect small force variations, making them suitable for precise cutting applications.
How to Measure Heat Dissipation
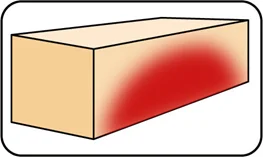
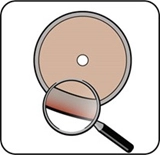
Thermocouples and Infrared Thermography - Thermocouples and infrared thermography are widely used to measure temperature changes in cutting processes. These methods provide detailed information on heat generation and dissipation, helping to assess the thermal performance of the blades.
⦁ Thermocouples: These are sensors that measure temperature by producing a voltage based on the temperature difference between two junctions. Thermocouples can be attached to the blade or the workpiece to monitor temperature changes during cutting.
⦁ Infrared Thermography: This technique involves using an infrared camera to capture thermal images of the cutting process. It provides a non-contact method to measure temperature distribution across the blade and the material being cut.
Calorimetric Methods - Calorimetric methods involve measuring the heat produced during cutting and assessing how effectively it is dissipated. This can be done by capturing the heat in a fluid medium and measuring the temperature change in the medium.
⦁ Flow Calorimetry: In this method, a coolant flows over the blade and workpiece, absorbing the heat generated during cutting. By measuring the temperature rise of the coolant, the amount of heat dissipated can be calculated.
⦁ Differential Scanning Calorimetry (DSC): DSC measures the difference in the amount of heat required to increase the temperature of the sample and reference. It helps in understanding the thermal properties of the blade material and its efficiency in heat dissipation.
Thermal Conductivity Measurement - The thermal conductivity of the blade material is a key factor in its ability to dissipate heat. Measuring the thermal conductivity provides insights into the blade’s heat dissipation efficiency.
⦁ Laser Flash Analysis: This technique involves heating the surface of a sample with a short laser pulse and measuring the time it takes for the heat to propagate through the material. The thermal diffusivity and conductivity can then be calculated.
⦁ Hot Wire Method: In this method, a wire embedded in the blade material is heated, and the temperature change over time is measured. The thermal conductivity is determined based on the rate of temperature rise.
Measuring Material Compatibility in Diamond and CBN Cut-Off Blades
Material compatibility is a critical factor in the performance of diamond and cubic boron nitride (CBN) cut-off blades. The ability of a blade to handle different types of materials effectively without degradation determines its versatility and longevity, particularly when working with a variety of material types and shapes. This section outlines the primary techniques and methods used to measure material compatibility, providing valuable insights into the performance and durability of cutting blades across diverse materials and geometries.
Wear Rate Analysis
Measuring the wear rate of a blade when cutting different materials provides direct insight into its compatibility. The wear rate indicates how quickly the blade degrades, which reflects its ability to handle various materials without significant wear.
⦁ Gravimetric Method: This involves measuring the weight of the blade before and after a cutting operation. The difference in weight indicates the amount of material worn away, providing a measure of the wear rate.
⦁ Optical Microscopy: Microscopic examination of the blade edge before and after cutting can reveal wear patterns and the extent of degradation. This method helps in identifying specific areas of the blade that are more susceptible to wear.
Cutting Efficiency Tests
Cutting efficiency tests measure the performance of the blade in terms of cutting speed, feed rate, and the quality of the cut. These tests help in assessing how well the blade handles different materials and shapes.
⦁ Cutting Speed and Feed Rate: By measuring the speed and feed rate at which the blade can cut through different materials and shapes, one can determine the blade’s efficiency and compatibility with those materials.
⦁ Surface Finish Analysis: The quality of the cut surface, including roughness and the presence of any defects, provides an indication of the blade’s effectiveness in cutting different materials and shapes.
Blade Life Testing
Blade life testing involves evaluating the longevity of the blade when used on various materials. This method provides a comprehensive understanding of the blade’s durability and material compatibility.
⦁ Cyclic Cutting Tests: Repeatedly cutting through different materials and shapes and measuring the number of cycles the blade can endure before failure provides a direct measure of its lifespan.
⦁ Endurance Testing: Continuous cutting operations on different materials until the blade reaches the end of its usable life help in understanding its wear resistance and overall durability.
Material Interaction Studies
Analyzing the interaction between the blade material and the workpiece material can reveal compatibility issues. Chemical and physical interactions can affect blade performance and longevity.
⦁ Chemical Analysis: Studying any chemical reactions between the blade material and the workpiece material, such as corrosion or bonding, helps in understanding potential compatibility issues.
⦁ Mechanical Testing: Assessing the mechanical impact of cutting different materials on the blade, such as chipping, cracking, or deformation, provides insights into its robustness and compatibility.
Measuring Wear Resistance in Diamond and CBN Cut-Off Blades
Wear resistance is a fundamental characteristic that determines the longevity and reliability of diamond and cubic boron nitride (CBN) cut-off blades. It defines how well a blade holds up under regular use, directly impacting its performance, maintenance frequency, and overall cost-effectiveness. This section outlines the primary techniques and methods used to measure wear resistance, providing valuable insights into the durability and resilience of cutting blades in various applications.
⦁ Gravimetric Method: This involves measuring the weight of the blade before and after a specified number of cutting operations. The difference in weight indicates the material loss due to wear, providing a measure of the wear rate.
⦁ Optical Microscopy: Microscopic examination of the blade edge before and after cutting can reveal wear patterns, the extent of wear, and specific areas of the blade that are more susceptible to wear.
Hardness Testing
The hardness of the blade material is a key factor in its wear resistance. Hardness tests measure the resistance of the blade material to deformation and scratching.
⦁ Vickers Hardness Test: This test involves pressing a diamond indenter into the blade material and measuring the size of the indentation. The hardness value is calculated based on the indentation size.
⦁ Rockwell Hardness Test: This test measures the depth of penetration of an indenter under a large load compared to the penetration made by a preload. It provides a direct measure of the material's hardness.
Abrasive Wear Testing
Abrasive wear testing evaluates the blade’s resistance to wear caused by abrasive materials. This method simulates real-world cutting conditions where abrasive particles contribute to blade wear.
⦁ Pin-on-Disk Test: A pin made of the blade material is pressed against a rotating disk covered with abrasive material. The wear is measured by the loss of material from the pin.
⦁ Abrasive Jet Testing: An abrasive-laden jet is directed at the blade material, and the rate of material removal is measured. This test helps in understanding how the blade material responds to abrasive conditions.
Fatigue Testing
Fatigue testing measures the blade’s ability to withstand cyclic loading conditions without failing. It provides insights into the blade’s long-term durability and resistance to wear under repeated use.
⦁ Rotary Fatigue Test: The blade is subjected to repeated rotational stresses, simulating the cyclic loading conditions encountered during cutting operations. The number of cycles to failure is recorded to assess the blade's fatigue resistance.
⦁ Bending Fatigue Test: The blade is repeatedly bent to induce cyclic stresses, and the number of cycles to failure is measured. This test helps in evaluating the blade's resistance to fatigue-induced wear.
Measuring Vibration in Diamond and CBN Cut-Off Blades
Vibration is a critical factor affecting the precision and quality of cuts made by diamond and cubic boron nitride (CBN) cut-off blades. Lower vibration levels indicate a more stable cutting process, resulting in enhanced precision and better quality of the material. This section outlines the primary techniques and methods used to measure vibration, providing valuable insights into the stability and performance of cutting blades in various applications.
To measure and calculate vibration in diamond and CBN cut-off blades, a variety of advanced techniques and tools are employed to ensure precision and stability in cutting operations. Vibration is a critical factor affecting the precision and quality of cuts. Lower vibration levels indicate a more stable cutting process, resulting in enhanced precision and better sample quality.
Accelerometers are widely used to measure vibrations in cutting operations. These devices detect and measure acceleration forces in multiple directions, providing detailed information about vibration levels during the cutting process. Single-axis accelerometers measure vibration in one direction and are useful for basic vibration analysis, while tri-axis accelerometers measure vibrations in three directions (x, y, and z axes), offering a comprehensive understanding of the vibration dynamics. These are particularly useful for detailed vibration analysis in complex cutting operations.
Laser vibrometers provide a non-contact method of measuring vibrations, using laser beams to detect the motion of the blade or workpiece surface with high precision and accuracy. Single-point laser vibrometers measure vibration at a single point on the blade or workpiece, ideal for focused vibration analysis, while scanning laser vibrometers measure vibrations over a surface area by scanning multiple points, useful for obtaining a detailed vibration profile of the blade and workpiece.
Displacement sensors measure the relative movement between the blade and the workpiece during cutting, providing information on the amplitude and frequency of vibrations. Capacitive displacement sensors measure the displacement between the sensor and the target surface with high precision, suitable for measuring small vibrations. Inductive displacement sensors measure displacement using electromagnetic induction, robust and suitable for harsh cutting environments.
Acoustic emission sensors detect the high-frequency waves generated by blade vibration during cutting, providing information on the onset and intensity of vibrations. Surface acoustic emission sensors attach to the blade or workpiece surface to measure emitted acoustic waves, while waveguide acoustic emission sensors use waveguides to transmit acoustic waves from the cutting area to the sensor, allowing for measurements in difficult-to-access areas.
To measure and calculate vibration, start by attaching the appropriate sensors to the blade, workpiece, or both. Ensure proper calibration of all sensors to guarantee accurate measurements. Perform cutting operations under controlled conditions and collect vibration data from the sensors, focusing on key metrics such as amplitude, frequency, and direction of vibrations. Analyze the collected data to identify patterns and levels of vibration, using software tools to process the sensor data, filter noise, and identify peaks in vibration intensity.
Conduct a frequency analysis to determine the dominant frequencies of the vibrations, helping to understand the sources of vibration and their impact on cutting performance. Measure the amplitude of the vibrations to assess their magnitude, as high amplitudes may indicate instability and potential issues with the cutting process. Correlate the vibration data with the quality of cuts produced, analyzing how different levels of vibration affect parameters like surface finish, accuracy, and material deformation.
Amount of Material Deformation
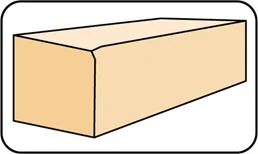
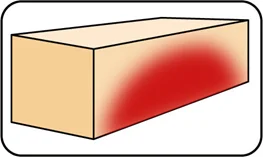
When cutting materials, particularly in fields such as metallurgy, semiconductor manufacturing, and advanced materials research, minimizing deformation is paramount. Deformation during the cutting process can alter the material's true microstructure, leading to inaccurate analysis and compromised results. High-quality diamond and CBN blades play a crucial role in ensuring minimal material deformation. Here’s a detailed explanation of this benefit, along with additional operational benefits.
Minimizing Material Deformation
Preservation of Microstructure: High-quality diamond and CBN blades are engineered to make clean, precise cuts with minimal force. This precision is critical for preserving the true microstructure of the material. When the microstructure is maintained, the material's intrinsic properties and characteristics are accurately represented, which is essential for analysis and further processing.
Reduced Thermal Impact: High-quality blades are designed to generate less heat during cutting. Excessive heat can cause thermal deformation, altering the material’s microstructure and potentially leading to phase changes or other thermal effects. By minimizing heat generation, these blades help preserve the material’s original properties.
Smooth Cutting Action: The superior sharpness and construction of high-quality blades ensure a smooth cutting action, reducing the mechanical stress exerted on the material. Lower mechanical stress translates to less deformation, maintaining the integrity of the cut surfaces and edges.
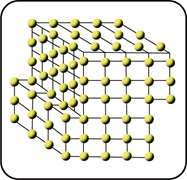
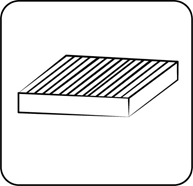
Enhanced Surface Quality: Minimizing deformation also improves the surface quality of the cut material. A high-quality surface finish reduces the need for additional polishing or surface treatments, which can introduce further deformation or contamination.
Improved Analytical Accuracy: For applications in research and quality control, the ability to preserve the material’s true microstructure is crucial. Accurate representation of the microstructure ensures reliable analytical results, leading to better decision-making and more effective process control.
Increased Reliability in Results: Consistent, deformation-free cuts lead to more reliable and reproducible results. This consistency is essential for comparative studies, quality assurance, and process optimization.
Reduced Post-Processing: Minimizing deformation reduces the need for extensive post-processing steps, such as grinding, polishing, or etching. This not only saves time and labor but also maintains the material’s integrity throughout the preparation process.
Enhanced Efficiency: With less deformation and reduced need for secondary processing, the overall efficiency of the cutting and analysis process is improved. This efficiency translates to faster turnaround times and increased throughput in laboratory and production settings.
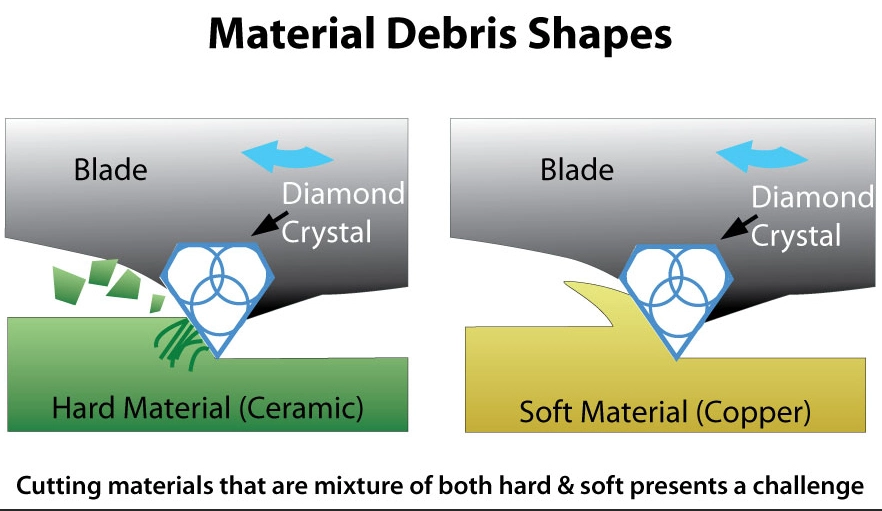
Vibration during cutting can also lead to deformation, especially for thin or delicate materials, as it causes them to flex or shift. An inappropriate blade can contribute to this problem, particularly if it has an incorrect bond strength or diamond grit size, which increases stress on the material. The cutting speed, if too fast or too slow, can lead to overheating or excessive force, both of which contribute to deformation.
Material deformation often results from excessive cutting force, which can cause softer or ductile materials to bend or stretch. Heat buildup is another common cause, especially when there's insufficient cooling during cutting. This heat can lead to thermal expansion, altering the sample's microstructure and potentially melting some materials.
To minimize material deformation, it's essential to select the right diamond blade for the material type and cutting requirements. This involves choosing the right diamond grit size, concentration, bond type, bond hardness, and blade design to ensure a clean cut with minimal stress on the material being cut. The correct cutting speed and pressure are equally important, as operating within the recommended speed range helps avoid overheating and excessive force and secondary processes such as grinding and polishing.
Proper cooling and lubrication are also crucial. Using coolants and lubricants reduces friction during cutting and dissipates heat, preventing heat-induced deformation and reducing wear on the blade. Controlling vibration contributes to a more stable cutting process, which decreases the risk of material deformation. This can be achieved through proper blade installation, alignment, and the use of anti-vibration features. Regular maintenance of the cutting equipment also plays a role, as it reduces the likelihood of machine-related issues causing deformation.
How to Measure Material Deformation
To measure the metric of material deformation when using diamond and CBN blades, start by documenting the material's original microstructure and properties before cutting. Use tools such as scanning electron microscopes (SEM), optical microscopes, or other imaging techniques to capture detailed images and measurements of the material's structure and surface.
Next, perform controlled cutting tests using high-quality diamond or CBN blades under consistent conditions. Select a standardized material representative of typical use cases, and maintain uniform cutting parameters such as speed, feed rate, depth of cut, and coolant application.
After cutting, conduct a detailed examination of the cut material to assess the extent of deformation. Compare the post-cutting microstructure with the baseline measurements using the same imaging tools. Look for changes such as micro-cracks, phase changes, thermal deformations, or any other alterations to the material's intrinsic properties.
Quantify the deformation by evaluating changes in dimensions, surface roughness, and microstructural alterations. Use profilometers to measure surface roughness and any deviations from the original surface quality. Quantify the changes in the microstructure by analyzing the images captured before and after cutting.
Monitor and record the cutting forces and temperatures during the cutting process. Use force sensors and thermocouples to measure the mechanical stress and heat generated during cutting. Correlate these measurements with the extent of material deformation observed.
Examine the necessity for secondary processes such as grinding and polishing to achieve the desired surface finish. Document the amount of material removed during these processes and compare it to the initial cuts to evaluate the effectiveness of the blades in minimizing deformation.
Perform statistical analysis on the collected data to identify trends and correlations between cutting parameters, blade quality, and material deformation. Use this analysis to refine cutting techniques and blade selection to further minimize deformation.
For a practical example, start with an initial setup by documenting the original microstructure of a sample material using SEM. Use a high-quality diamond blade to cut the sample under consistent conditions. Re-examine the cut sample with SEM to identify any changes or deformations. Measure surface roughness and dimensional changes using profilometers. Record cutting forces and temperatures to understand their impact on deformation. Assess the amount of material removed during any necessary grinding or polishing. Finally, use statistical methods to correlate cutting parameters with material deformation.
Example of Calculation for Deformation Reduction Benefits
⦁ Improved Analytical Accuracy: $10,000 (from reduced errors and more reliable data)
⦁ Increased Reliability in Results: $8,000 (from consistent, reproducible outcomes)
⦁ Reduced Post-Processing Costs: $5,000 (savings in labor and materials)
⦁ Enhanced Efficiency: $7,000 (savings from faster processes and increased throughput)
Total Benefits from Minimizing Deformation:
Total Deformation Reduction Benefits=$10,000+$8,000+$5,000+$7,000=$30,000
Secondary Grinding and Polishing Steps Required:
the performance of high-quality diamond and cubic boron nitride (CBN) blades in producing cleaner cuts significantly reduces the need for extensive secondary grinding and polishing. This advantage directly enhances overall operational efficiency, material quality, and surface finish. Here is an in-depth exploration of these benefits.
Cleaner Initial Cuts: High-quality blades are designed to make precise and clean cuts, which result in smoother surfaces with minimal rough edges. This reduces the need for extensive grinding and polishing to achieve the desired surface finish. The reduction in roughness means fewer post-processing steps are necessary, saving both time and resources.
Enhanced Surface Finish: The superior cutting ability of high-quality blades ensures a fine surface finish right from the initial cut. Achieving a better surface finish at the cutting stage minimizes the amount of polishing needed to reach the final desired quality. This is especially crucial in industries where surface finish is critical, such as optics, aerospace, and semiconductor manufacturing.
Minimized Material Removal: Cleaner cuts lead to less material needing to be removed during secondary processing. This not only preserves more of the original material but also speeds up the polishing process. Less material removal means faster polishing times and reduced wear on polishing equipment.
Reduced Risk of Contamination: With fewer grinding and polishing steps, there is a reduced risk of introducing contaminants to the material surface. This is essential for maintaining the purity and integrity of the material, particularly in high-precision applications where surface contamination can affect performance and reliability.
Increased Efficiency: By minimizing the need for secondary grinding and polishing, high-quality blades streamline the production process. This efficiency translates to faster turnaround times and higher throughput, allowing manufacturers to meet production targets more effectively and respond quickly to market demands.
Cost Savings: Reducing secondary processing steps leads to significant cost savings. There is less expenditure on consumables such as grinding wheels, polishing pads, and abrasive compounds. Labor costs are also reduced as less time is spent on manual finishing processes. These savings contribute to a lower total cost of ownership and higher overall profitability.
Enhanced Material Quality: When secondary processing is minimized, the material quality is better preserved. Excessive grinding and polishing can sometimes introduce micro-cracks, distortions, or other imperfections. By reducing these steps, the material maintains its integrity, leading to higher-quality finished products that meet stringent industry standards.
Improved Consistency and Repeatability: Cleaner cuts lead to more consistent and repeatable results. This is critical for industries that rely on precision and uniformity, such as medical device manufacturing and electronics. Consistency in the cutting process reduces variability in the final products, ensuring that each item meets the required specifications.
Reduced Equipment Wear: Minimizing secondary grinding and polishing reduces wear and tear on the equipment used for these processes. This extends the lifespan of grinding and polishing machinery, leading to lower maintenance costs and fewer replacements. The reduced mechanical stress on the equipment also means less downtime and higher overall operational efficiency.
Environmental Benefits: Fewer grinding and polishing steps result in lower consumption of abrasive materials and less waste generation. This reduction in waste contributes to more sustainable manufacturing practices and aligns with growing environmental regulations and standards.
How to Measure secondary grinding and polishing steps
To measure the metric of secondary grinding and polishing steps required, follow a systematic approach that involves both quantitative and qualitative assessments. Begin by conducting a baseline analysis using a standardized material and process with high-quality diamond and cubic boron nitride (CBN) blades. Document the initial surface finish, roughness, and overall quality of cuts made by the blades without any secondary processing. This initial data serves as a reference point for evaluating the need for additional grinding and polishing.
Next, perform controlled cutting tests where the blades are used to cut the standardized material under consistent conditions. After each cut, measure the surface finish and roughness using tools such as profilometers or surface roughness testers. Document the quality of the cut surfaces to determine the extent of secondary processing required to achieve the desired finish.
Proceed by implementing the necessary secondary grinding and polishing steps to bring the material to the required finish. Record the time and resources spent on these additional steps, including the usage of grinding wheels, polishing pads, abrasive compounds, and labor. Quantify the amount of material removed during these processes to assess the efficiency and preservation of the original material.
Analyze the data by comparing the initial cuts surface quality to the final desired finish achieved after secondary processing. Calculate the reduction in secondary processing steps and time when using high-quality blades versus standard blades. This analysis should include the measurement of reduced material removal, improved surface finish, and minimized risk of contamination.
Additionally, evaluate the operational benefits such as increased efficiency, cost savings, enhanced material quality, improved consistency and repeatability, reduced equipment wear, and environmental benefits. Use statistical methods to correlate the reduction in secondary grinding and polishing steps with overall production efficiency and cost-effectiveness.
How to Calculate Secondary Processing Reduction Benefits
⦁ Increased Efficiency: $20,000 (from faster turnaround times and higher throughput)
⦁ Cost Savings on Consumables: $12,000 (from reduced use of grinding wheels, polishing pads, and abrasives)
⦁ Enhanced Material Quality: $15,000 (from improved product quality and reduced defects)
⦁ Improved Consistency and Repeatability: $10,000 (from reduced variability and higher precision)
⦁ Reduced Equipment Wear: $8,000 (from extended equipment lifespan)
⦁ Environmental Benefits: $5,000 (from reduced waste and compliance with environmental standards)
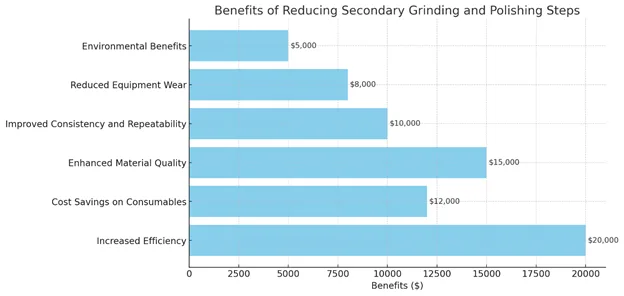
Total Benefits from Reducing Secondary Processing:
Total Secondary Processing Reduction Benefits=$20,000 + $12,000 + $15,000 + $10,000 + $8,000 + $5,000 = $70,000
Comprehensive ROI Calculation
When incorporating these secondary processing reduction benefits into the overall ROI calculation, the comprehensive financial impact becomes even more apparent. Using the previous comprehensive annual benefits:
⦁ Previous Comprehensive Annual Benefits: $241,000
Total Annual Benefits Including Secondary Processing Reduction: Total Annual Benefits=$241,000+$70,000=$311,000
Using the same initial investment of $10,300:
Net Returns: Net Returns=$311,000−$10,300=$300,700\
ROI Calculation: ROI(%)=($300,700$10,300)×100≈2919.42%
Thermal Stability: Assessing Performance Across Varying Temperatures
Thermal stability is a crucial characteristic for diamond and cubic boron nitride (CBN) blades, especially when working with thermally sensitive materials. High thermal stability ensures that the blades maintain their properties and performance across a wide range of operational conditions. This consistency is vital for maintaining precision and quality in cutting processes. Here’s an in-depth exploration of the benefits associated with high thermal stability, along with additional operational benefits.
Consistent Performance: Blades with high thermal stability maintain their cutting efficiency and sharpness even at elevated temperatures. This consistency is essential for ensuring uniform cutting quality and preventing performance degradation due to thermal effects.
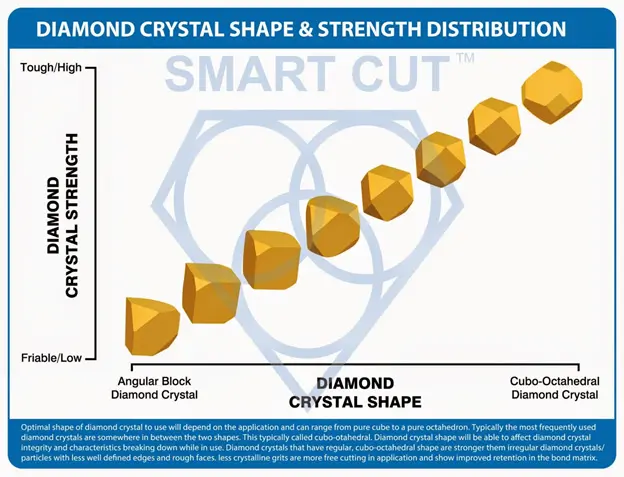
Consistent Performance: Blades with high thermal stability maintain their cutting efficiency and sharpness even at elevated temperatures. This consistency is essential for ensuring uniform cutting quality and preventing performance degradation due to thermal effects.
Protection of Material Properties: When cutting thermally sensitive materials, it is crucial to prevent heat-induced damage. High thermal stability in blades minimizes the risk of thermal deformation, micro-cracks, or changes in the material's microstructure. This preservation of material properties is vital for applications requiring high precision and reliability.
Reduced Thermal Expansion: High-quality blades with excellent thermal stability exhibit minimal thermal expansion. This stability ensures that the blade dimensions remain constant, preventing inaccuracies and maintaining cutting precision.
Enhanced Blade Life: Blades that perform well under varying temperatures experience less wear and tear. Reduced thermal stress contributes to a longer blade lifespan, decreasing the frequency of replacements and lowering overall costs.
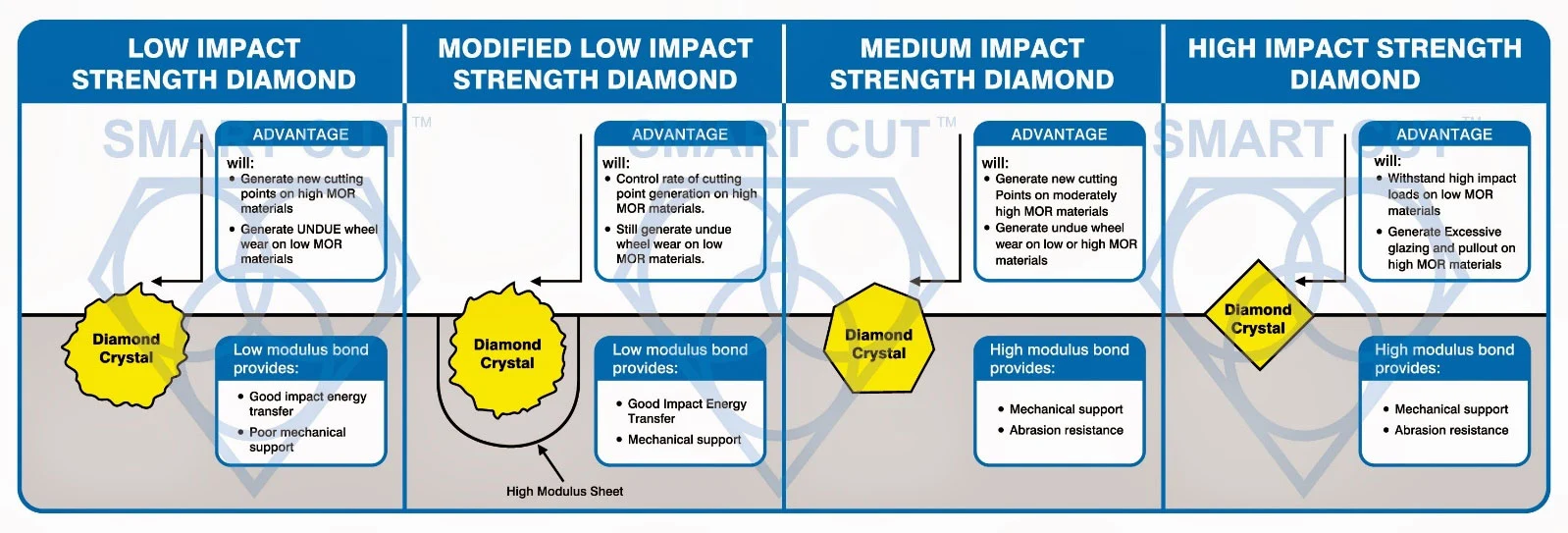
Improved Cutting Precision: Consistent blade performance across temperature variations ensures that cuts are precise and accurate. This precision reduces the need for rework and enhances the overall quality of the finished product.
Increased Versatility: Blades with high thermal stability are suitable for a broader range of applications and materials. This versatility allows use of same blade across different processes, simplifying inventory management and reducing the need for multiple blade types.
Enhanced Safety: Stable thermal performance reduces the likelihood of blade failure or breakage, which can pose safety risks. Reliable blade operation contributes to a safer working environment for operators.
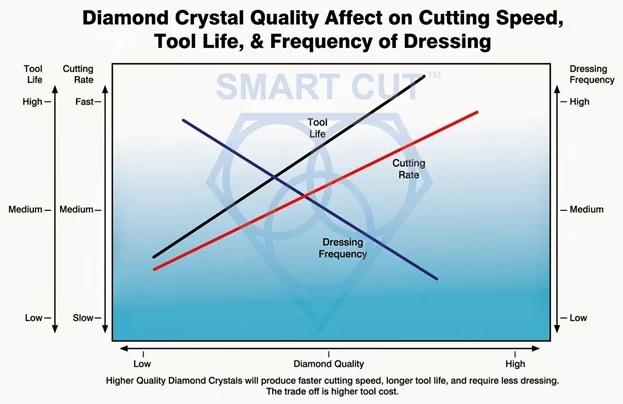
Reduced Downtime: High thermal stability means fewer blade changes and less downtime due to thermal-related performance issues. This continuity boosts productivity and allows for more efficient use of manufacturing resources.
Cost Savings: The extended lifespan and consistent performance of thermally stable blades lead to significant cost savings. Reduced need for replacements, minimized rework, and lower maintenance costs all contribute to a more economical operation.
How to Measure for Thermal Stability
Measuring and evaluating the thermal stability of diamond and cubic boron nitride (CBN) blades involves a detailed assessment of how well these blades maintain their properties and performance under varying temperature conditions. The process begins with measuring the rate at which the blade material conducts heat, known as thermal conductivity, using techniques like laser flash analysis (LFA) or transient plane source (TPS). High thermal conductivity indicates better heat dissipation, reducing the risk of thermal damage.
Next, the thermal expansion coefficient is measured to determine the change in blade dimensions as a function of temperature. This is typically done using a dilatometer. A low thermal expansion coefficient means the blade will maintain its dimensions and precision at different temperatures. Additionally, a thermal stability index is assessed by evaluating the blade's performance over a range of temperatures using differential scanning calorimetry (DSC) or thermogravimetric analysis (TGA). This helps in identifying changes in physical and chemical properties at elevated temperatures.
Wear resistance at high temperatures is tested under operational conditions to measure wear rates, often using high-temperature tribometers or in-situ wear testing apparatus. Lower wear rates at high temperatures indicate better thermal stability. Cutting efficiency and quality are also crucial metrics, assessed by performing cutting tests at various temperatures and measuring cutting forces, edge quality, and surface finish. Consistent cutting performance and high-quality results across temperature variations are indicative of good thermal stability.
Microstructural analysis is another important aspect, where the microstructure of the blade material is analyzed before and after exposure to high temperatures using scanning electron microscopy (SEM) or transmission electron microscopy (TEM). This analysis helps identify signs of degradation, such as grain growth or phase transformations, which can indicate thermal instability. Residual stress measurement, conducted using X-ray diffraction (XRD) or Raman spectroscopy, further aids in evaluating the thermal stability by assessing the residual stresses in the blade material induced by thermal cycling. Low residual stresses after thermal cycling suggest good thermal stability.
The comprehensive evaluation process starts with pre-test preparations, including calibrating all measurement instruments and preparing blade samples to ensure they are free from defects. Baseline measurements of initial thermal conductivity, thermal expansion, microstructure, and other parameters are recorded. The blade samples are then exposed to a series of thermal cycles, simulating operational conditions across a relevant temperature range. Performance testing involves conducting cutting operations at various temperatures and measuring cutting efficiency, wear rates, and quality, ensuring that performance metrics are consistent across different temperature conditions.
Post-test analysis includes microstructural examination to identify changes due to thermal exposure and measuring any residual stresses induced by thermal cycling. The data from pre- and post-test measurements are compared to evaluate any significant deviations that indicate thermal instability. All measurements, test conditions, and results are documented in a detailed report, which includes a thorough analysis of the data and recommendations based on the findings. These recommendations may involve adjustments in blade design or material selection to enhance thermal stability.
How To Calculation for Thermal Stability Benefits
⦁ Improved Cutting Precision: $10,000 (from reduced rework and enhanced product quality)
⦁ Increased Versatility: $8,000 (savings from using fewer blade types)
⦁ Enhanced Safety: $5,000 (from reduced accidents and downtime)
⦁ Reduced Downtime: $12,000 (from fewer blade changes and thermal-related issues)
⦁ Cost Savings: $15,000 (from extended blade life and consistent performance)
Total Benefits from High Thermal Stability: Total Thermal Stability Benefits=$10,000+$8,000+$5,000+$12,000+$15,000=$50,000
Comprehensive ROI Calculation
When incorporating these thermal stability benefits into the overall ROI calculation, the comprehensive financial impact becomes even more apparent. Using the previous comprehensive annual benefits:
⦁ Previous Comprehensive Annual Benefits: $311,000
Total Annual Benefits Including Thermal Stability: Total Annual Benefits=$311,000+$50,000=$361,000
Using the same initial investment of $10,300:
Net Returns: Net Returns=$361,000−$10,300=$350,700
ROI Calculation: ROI(%)=($350,700$10,300)×100≈3406.80%
Diamond & CBN Cut-Off Blade Flexibility
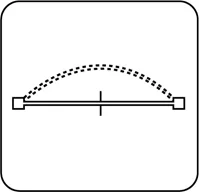
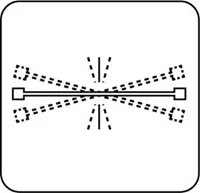
A flexible blade is one that can bend or flex slightly without breaking or loosing its tension/flatness, providing a level of resilience that allows it to navigate complex cuts and withstand sudden changes in pressure or load. This flexibility can be crucial when making intricate cuts, such as those required in electronics, where precision and accuracy are paramount. A flexible blade can accommodate tight corners and fine details, reducing the risk of chipping or breaking the sample.
Here is an in-depth exploration of the benefits associated with blade flexibility, along with additional operational benefits.
Enhanced Reliability: Blades with high flexibility can handle complex cutting tasks without breaking or cracking. This reliability is crucial for maintaining consistent performance in demanding applications where precision and accuracy are paramount.
Ability to Make Intricate Cuts: Flexible blades can perform intricate cuts with ease, adapting to curves and angles without losing integrity. This capability is essential for industries requiring detailed work, such as jewelry making, medical device manufacturing, and custom fabrication.
Adaptation to Variable Loads: High flexibility allows the blade to absorb and adapt to variable loads during cutting. This adaptability reduces the risk of blade failure and ensures a smoother cutting process, even when dealing with materials of varying hardness or density.
Reduced Risk of Breakage: Flexible blades are less prone to breaking under stress, which enhances safety and reduces the need for frequent replacements. This durability translates to lower operational costs and less downtime.
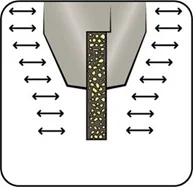
Improved Cutting Precision: Blades that can flex without breaking maintain their sharpness and cutting edge, resulting in precise and accurate cuts. This precision reduces the need for rework and enhances the overall quality of the finished product.
Increased Versatility: Flexible blades are suitable for a wide range of cutting applications, from straight cuts to intricate patterns. This versatility allows manufacturers to use a single blade type across multiple processes, simplifying inventory management and reducing costs.
Enhanced Safety: Blades that flex rather than break under stress contribute to a safer working environment. The reduced risk of blade failure minimizes the chance of accidents and injuries, ensuring operator safety.
Reduced Downtime: The durability and reliability of flexible blades mean fewer blade changes and less downtime due to breakages. This continuity boosts productivity and allows for more efficient use of manufacturing resources.
Cost Savings: The extended lifespan and consistent performance of flexible blades lead to significant cost savings. Reduced need for replacements, minimized rework, and lower maintenance costs all contribute to a more economical operation.
The level of blade flexibility is influenced by several factors, including the wafering blades material composition, thickness, and design. Diamond & CBN Blades made from high-quality metals or alloys with some inherent flexibility are more capable of bending without breaking. Thinner blades generally offer more flexibility, allowing them to adapt to varying loads and intricate cutting patterns.
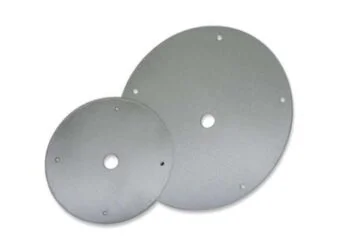
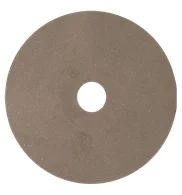
The design of the blade, including the type of steel core used will also highly influence flexibility, with some blades allowing for greater movement without compromising stability. Such as Nickel Bond diamond & cbn blades that are made using memory steel. This type of Core steel allows the blade to flex as much as needed. The blade will always snaps back to its original shape no matter how much bent. Fully sintered (metal bond) impregnated blades allow for minimal flexibility, as blade is fully impregnated with diamond from OD to ID of the blade all the way through. There is no steel core or relief between the steel core and the diamond section.
How to Measure & Evaluate Diamond & CBN Cut-Off Blade Flexibility
Flexural testing measures a blade's ability to bend without breaking, providing a direct assessment of its flexibility. In a three-point bending test, the blade is placed on two supports, and a load is applied at the center. The deflection of the blade under the load is measured to determine its flexibility. A four-point bending test is similar but uses two loading points to distribute the load more evenly, offering a more detailed assessment of the blade’s flexibility.
Dynamic Mechanical Analysis (DMA) measures the mechanical properties of the blade material as it is deformed under periodic stress, providing insights into its flexibility and damping characteristics. The storage modulus indicates the stored energy in the blade and reflects its stiffness. The loss modulus represents the energy dissipated as heat, related to the blade’s damping capacity. Tan delta, the ratio of loss modulus to storage modulus, indicates the material’s ability to dissipate energy.
Tensile testing measures the blade's response to tension, providing information on its elasticity and flexibility. The stress-strain curve, a graph plotting the stress applied to the blade against the strain (deformation) experienced, helps determine the elastic limit, yield point, and ultimate tensile strength.
Vibration analysis measures the blade's response to vibrational loads, providing insights into its flexibility and stability under dynamic conditions. Natural frequency measurement determines the natural frequencies of the blade, which are influenced by its flexibility. Lower natural frequencies indicate higher flexibility. Mode shape analysis identifies the deformation patterns of the blade under vibrational loads, helping to understand its flexural behavior.
Finite Element Analysis (FEA) is a computational method used to simulate and analyze the flexibility of the blade under various conditions. FEA models the blade's behavior under bending and torsional loads, predicting its deflection and stress distribution. It also helps in optimizing the blade’s design to enhance its flexibility while maintaining stability.
Diamond & CBN Blade Recovery Time: Minimizing Downtime for Optimal Performance
Recovery time refers to the duration it takes for a blade to return to its optimal performance after undergoing dressing or any form of maintenance. Faster recovery times are crucial for minimizing downtime, thereby enhancing productivity and efficiency in manufacturing operations. Here’s an in-depth exploration of the benefits associated with faster recovery times, along with additional operational benefits.
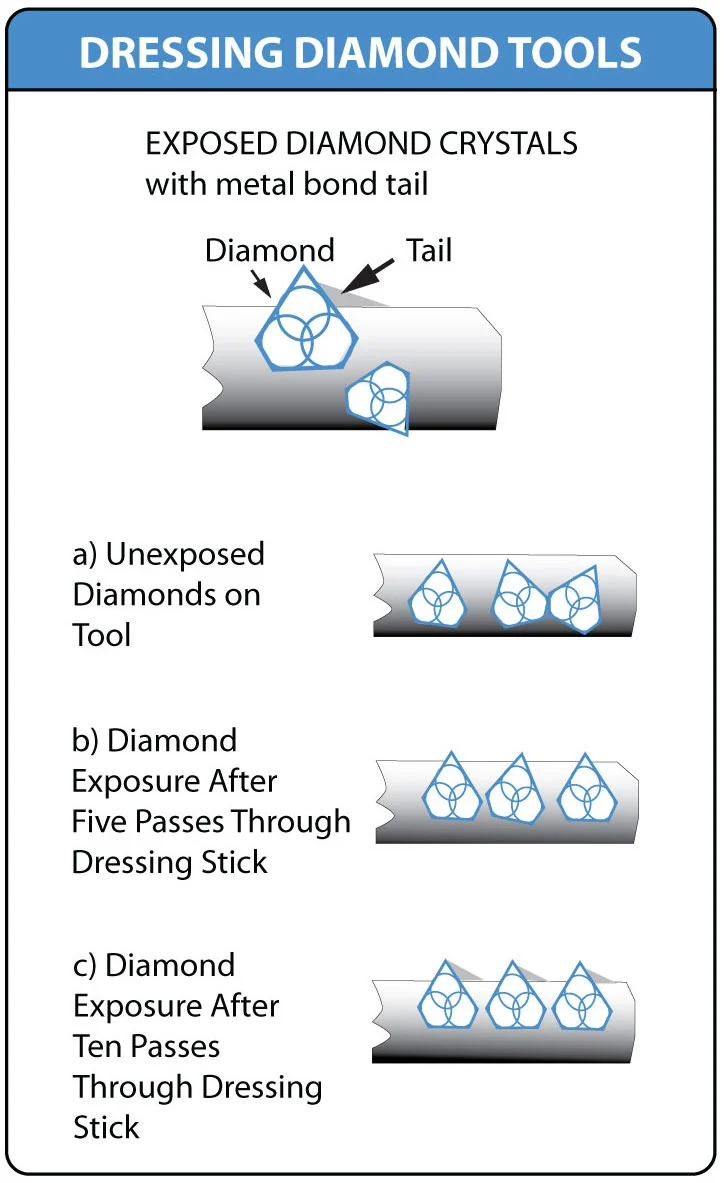
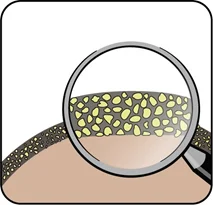
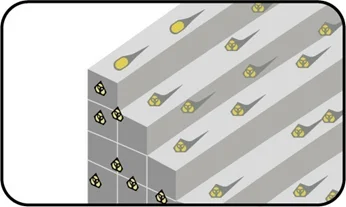
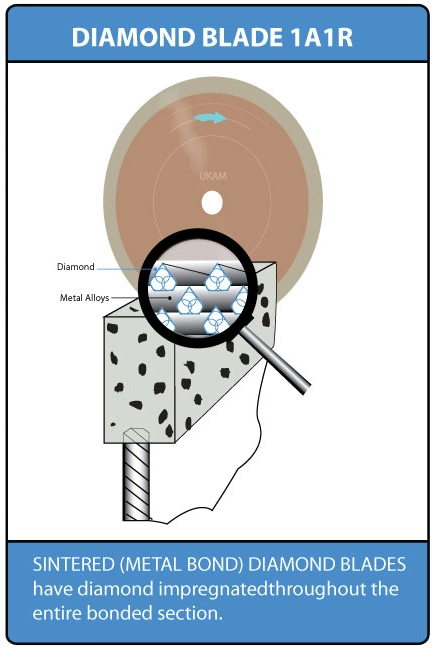
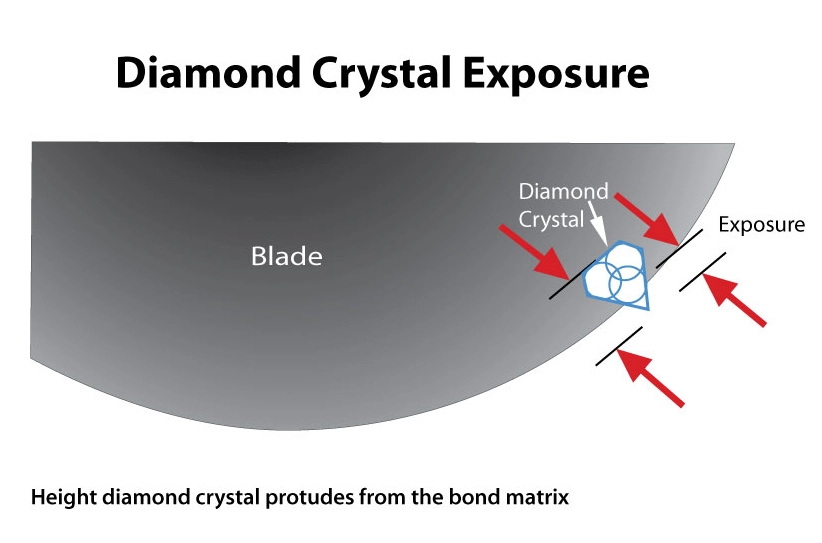
Benefits of Faster Recovery Time
Minimized Downtime: Blades that recover quickly from maintenance or dressing are back in operation sooner, reducing the overall downtime of the cutting process. This increased uptime allows for more continuous production and higher throughput.
Enhanced Productivity: Faster recovery times mean that operators can spend less time waiting for blades to be ready for use. This improved productivity allows for more efficient use of labor and resources, ultimately increasing output.
Consistent Cutting Quality: Quick recovery ensures that blades return to their optimal sharpness and performance levels rapidly. This consistency in cutting quality reduces the likelihood of defects and rework, maintaining high standards in the final product.
Improved Scheduling Flexibility: With faster recovery times, maintenance schedules can be more flexible and less disruptive to production. This flexibility allows for maintenance to be performed as needed without significantly impacting the overall production schedule.
Increased Equipment Longevity: Efficient maintenance and quick recovery times reduce the stress on cutting equipment. This reduction in stress can extend the lifespan of both the blades and the machinery, leading to lower long-term capital expenditures.
Cost Savings: Minimized downtime and enhanced productivity translate into significant cost savings. Reduced labor costs, fewer delays, and optimized use of materials contribute to a more cost-effective operation.
Enhanced Safety: Quick recovery times reduce the duration that maintenance personnel are exposed to potential hazards associated with blade maintenance. This reduction in exposure enhances workplace safety and reduces the risk of accidents.
Better Resource Utilization: Efficient blade recovery allows for better utilization of resources, including human resources and machinery. This optimized utilization ensures that all elements of the production process are working at peak efficiency.
Competitive Advantage: Operations with minimal downtime and high productivity levels gain a competitive edge in the market. The ability to meet production targets reliably and efficiently positions a company favorably against its competitors.
How to Measure Diamond & CBN Blade Recovery Time
Measuring the recovery time of diamond and CBN blades involves tracking the duration it takes for a blade to return to its optimal performance after undergoing dressing or maintenance. Start by conducting a baseline performance test on the blade to document its cutting efficiency, sharpness, and quality of cuts under controlled conditions. After this initial test, perform the necessary maintenance or dressing on the blade. Immediately after the maintenance, record the blade's performance again to assess its initial post-maintenance efficiency. Continue to monitor the blade's performance at regular intervals, noting the time it takes for the blade to regain its optimal sharpness and cutting quality. The recovery time is determined by the duration from the completion of maintenance to the point where the blade consistently meets the pre-maintenance performance levels. This process may involve cutting standardized materials under consistent conditions to ensure that performance metrics are comparable. Statistical analysis of the collected data will provide insights into the blade's recovery efficiency, which can be correlated with operational productivity and downtime minimization.
Example Calculation for Recovery Time Benefits
⦁ Minimized Downtime: $15,000 (from increased uptime and continuous production)
⦁ Enhanced Productivity: $10,000 (from efficient use of labor and resources)
⦁ Consistent Cutting Quality: $8,000 (from reduced defects and rework)
⦁ Improved Scheduling Flexibility: $5,000 (from less disruptive maintenance schedules)
⦁ Cost Savings: $12,000 (from overall reduced operational costs)
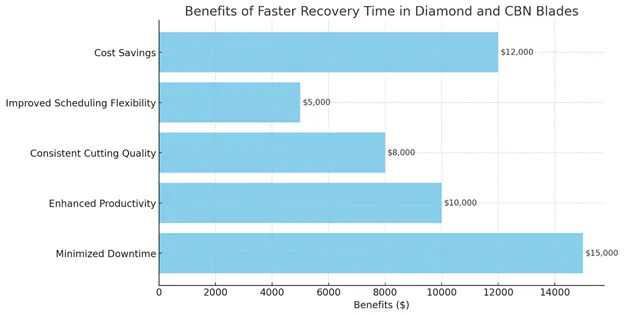
Total Benefits from Faster Recovery Time: Total Recovery Time Benefits=$15,000+$10,000+$8,000+$5,000+$12,000=$50,000
Comprehensive ROI Calculation
When incorporating these recovery time benefits into the overall ROI calculation, the comprehensive financial impact becomes even more apparent. Using the previous comprehensive annual benefits:
⦁ Previous Comprehensive Annual Benefits: $411,000
Total Annual Benefits Including Recovery Time: Total Annual Benefits=$411,000+$50,000=$461,000
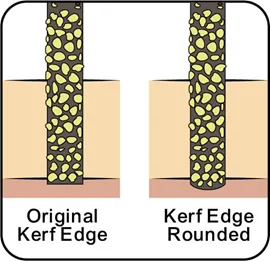
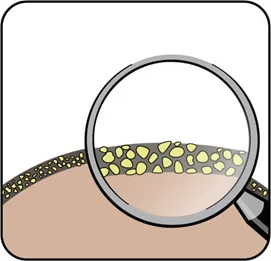
Edge durability is a critical measure of diamond and cubic boron nitride (CBN) blade performance. It indicates how long the cutting edge remains effective before the diamond crystals within the bond matrix lose their sharpness. High edge durability impacts the frequency of blade replacements and maintenance, as well as how consistently the blade can retain its edge profile, shape, and geometry. Here’s an in-depth exploration of the benefits associated with edge durability, along with additional operational benefits.
Extended Blade Life: High edge durability ensures that blades maintain their sharpness for longer periods, reducing the need for frequent replacements. This extended lifespan translates to lower costs for purchasing new blades and less frequent maintenance interventions.
Consistent Cutting Performance: Blades with high edge durability provide consistent cutting quality over time. This reliability reduces the likelihood of defects and rework, ensuring that finished products meet quality standards. Consistent edge retention also means the blade retains its profile, shape, and geometry, contributing to precision cutting.
Reduced Downtime: Durable blades require less frequent changes, leading to reduced downtime for maintenance and blade replacements. This increased uptime allows for more continuous production and higher throughput, boosting overall productivity.
Enhanced Material Utilization: Blades that maintain their sharpness create cleaner cuts with less material waste. This efficiency maximizes the yield from each piece of material, which is particularly important when working with expensive or scarce materials.
Cost Savings: Extended blade life and reduced maintenance frequency result in significant cost savings. These savings are derived from lower expenditure on replacement blades, reduced labor costs for maintenance, and minimized downtime costs.
Improved Safety: Durable blades reduce the frequency of maintenance and replacements, lowering the risk of accidents associated with these tasks. Consistent blade performance also reduces the likelihood of blade-related failures during cutting operations, enhancing overall workplace safety.
Increased Efficiency: The reliability and longevity of durable blades streamline the cutting process, making it more efficient. This efficiency allows for better resource allocation and optimized production schedules.
Environmental Benefits: Longer-lasting blades contribute to sustainability by reducing waste from frequent blade replacements. This reduction in waste supports environmental goals and compliance with regulatory standards.
How to Measure Diamond & CBN Edge Durability
Measuring edge durability in diamond and CBN blades involves a systematic approach that starts with establishing a baseline measurement through initial inspections. Precise measurement tools such as micrometers, calipers, and profile projectors are used to document the blade's edge geometry, thickness, and overall dimensions. Standardized sharpness testing methods, like edge stability tests or controlled material cutting tests, evaluate the initial sharpness.
Controlled cutting tests are then conducted using a standardized material under consistent conditions, ensuring any performance changes are due to wear and not varying factors. Periodic inspections are performed at regular intervals, based on the number of cuts, time of use, or material processed, to assess changes in the blade’s profile. The same measurement tools and sharpness testing methods are used to compare the current profile with the original, documenting any wear or deviations.
Detailed images of the edge are captured using microscopes or high-magnification imaging tools to analyze signs of wear. Performance metrics such as surface finish, cut accuracy, and defect presence are evaluated over time, determining the blade’s lifespan by recording the total number of cuts or material volume processed before replacement or reconditioning is needed. Data analysis identifies trends in blade wear and performance degradation, using statistical methods to correlate edge durability with cutting performance and blade life. This comprehensive approach ensures an accurate assessment of a blade’s edge durability, crucial for optimizing performance and reducing maintenance.
Example Calculation for Edge Durability Benefits
⦁ Extended Blade Life: $20,000 (from fewer replacements and extended usage)
⦁ Consistent Cutting Performance: $12,000 (from reduced defects and rework)
⦁ Reduced Downtime: $15,000 (from less frequent blade changes)
⦁ Enhanced Material Utilization: $10,000 (from reduced material waste)
⦁ Cost Savings: $8,000 (from overall reduced operational costs)
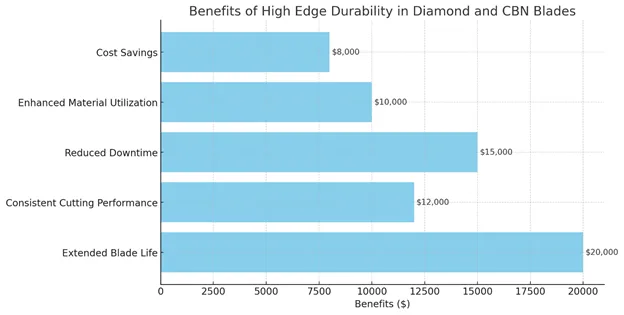
Total Benefits from High Edge Durability: Total Edge Durability Benefits=$20,000+$12,000+$15,000+$10,000+$8,000=$65,000
Comprehensive ROI
Calculation
When incorporating these edge durability benefits into the overall ROI calculation, the comprehensive financial impact becomes even more apparent. Using the previous comprehensive annual benefits:
⦁ Previous Comprehensive Annual Benefits: $461,000
Total Annual Benefits Including Edge Durability: Total Annual Benefits=$461,000+$65,000=$526,000
Using the same initial investment of $10,300:
Net Returns:
Net Returns = $526,000 - $10,300 = $515,700
ROI Calculation:
ROI(%) = ($515,700 / $10,300) x 100 ≈ 5008.74%
Profile Retention: Maintaining Cutting Characteristics Over Blade Lifespan
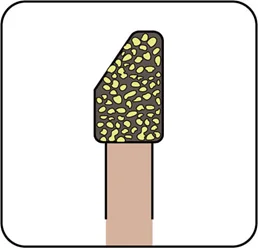
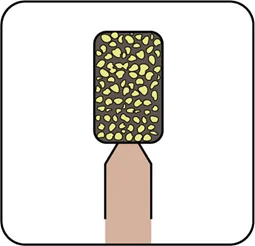
Profile retention refers to a blade's ability to maintain its original profile and cutting characteristics throughout its lifespan. High profile retention is essential for ensuring consistent performance and reducing the need for frequent adjustments and recalibrations.
Blades with high profile retention maintain their cutting characteristics over time, ensuring consistent cutting quality. This consistency reduces the likelihood of defects and rework, leading to higher-quality finished products. High profile retention minimizes the need for frequent adjustments and recalibrations, saving time and labor costs, and allowing for more efficient production processes. Blades that retain their profile longer require fewer replacements, translating to lower costs for purchasing new blades and less frequent maintenance interventions. Maintaining the original profile of the blade ensures precise cuts, which is crucial for applications requiring tight tolerances and detailed work, such as in the aerospace, medical, and electronics industries.
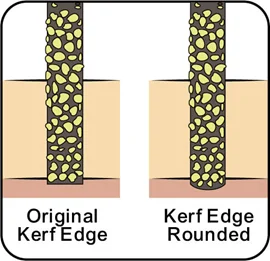
With less time spent on adjustments and recalibrations, production processes become more efficient. This efficiency allows for better resource allocation and optimized production schedules. Reduced maintenance and blade replacement frequency result in significant cost savings. These savings are derived from lower expenditure on replacement blades, reduced labor costs for maintenance, and minimized downtime costs. High profile retention reduces the frequency of maintenance and adjustments, lowering the risk of accidents associated with these tasks. Consistent blade performance also reduces the likelihood of blade-related failures during cutting operations, enhancing overall workplace safety. Longer-lasting blades contribute to sustainability by reducing waste from frequent blade replacements, supporting environmental goals and compliance with regulatory standards.
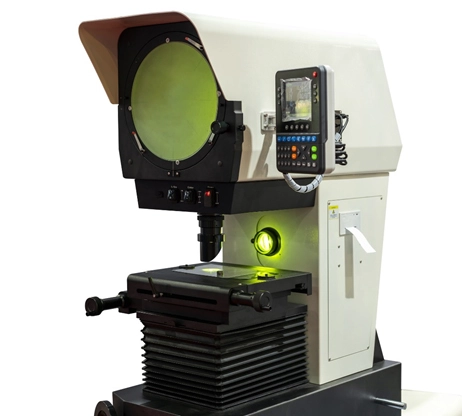
Measuring and Testing Profile Retention in Diamond and CBN Blades
Profile retention, which refers to a blade's ability to maintain its original profile and cutting characteristics throughout its lifespan, is a crucial metric for assessing blade performance. To measure and test this metric accurately and reliably, follow these steps and methods.
Start by conducting an initial inspection to establish a baseline measurement. Before using the blade, inspect and record its original profile using precise measurement tools such as micrometers, calipers, and profile projectors. Document the blade's edge geometry, thickness, and overall dimensions. Evaluate the initial sharpness of the blade using standardized sharpness testing methods, such as edge stability tests or controlled material cutting tests.
Next, conduct controlled cutting tests using a standardized material that represents a typical use case for the blade.
Define and maintain consistent cutting conditions, including speed, feed rate, depth of cut, and coolant use, to ensure that any changes in blade performance are due to wear and not varying conditions.
Conduct periodic inspections at regular intervals during the blade’s use. These intervals can be based on the number of cuts, time of use, or amount of material processed. Use the same measurement tools as in the baseline measurement to assess changes in the blade’s profile. Compare the current profile with the original to identify any deviations or wear. Re-evaluate the sharpness of the blade at each interval using the same sharpness testing methods and document the decrease in sharpness over time.
Analyze the wear by examining the blade’s cutting edge for signs of wear, such as rounding, chipping, or deformation. Use microscopes or high-magnification imaging tools to capture detailed images of the edge. Analyze how the blade’s profile changes over time and look for any significant deviations from the original profile that could impact cutting performance.
Evaluate performance metrics such as cut quality by assessing the quality of the cuts made by the blade over time. Measure surface finish, cut accuracy, and the presence of any defects. Determine the blade’s lifespan by recording the total number of cuts or the total volume of material processed before the blade requires replacement or reconditioning.
Analyze the collected data to identify trends in blade wear and performance degradation. Use statistical methods to correlate profile changes with cutting performance and blade life. Compare the performance of different blades under the same testing conditions to evaluate their profile retention capabilities.
To ensure precise measurements and testing, use measurement tools such as micrometers and calipers for precise measurement of blade dimensions and edge geometry, profile projectors for detailed inspection of the blade’s profile, and microscopes for high-magnification imaging of the blade’s cutting edge. Utilize testing equipment like sharpness testing devices for standardized testing of blade sharpness and cutting machines for performing controlled cutting tests under consistent conditions. Data analysis software, including statistical software for analyzing wear data and performance metrics and imaging software for capturing and analyzing images of the blade’s edge and profile, can assist in this process.
For a practical example, start with an initial setup by measuring the initial profile of a new diamond blade using a profile projector and recording the blade’s sharpness using a standardized sharpness testing device. Conduct the tests by using the blade to cut a standardized material, such as aluminum or silicon, under controlled conditions. Inspect the blade after every 100 cuts, recording any changes in profile and sharpness. After 1,000 cuts, compare the final profile with the initial profile. Document the degree of wear and any impact on cutting performance, such as increased force required or reduced cut quality. Compile the data into a report, highlighting how well the blade maintained its profile and cutting characteristics over time, and use this information to assess the blade’s overall performance and durability.
Performance Metrics for Material Compatibility in Diamond Blades and CBN Wheels
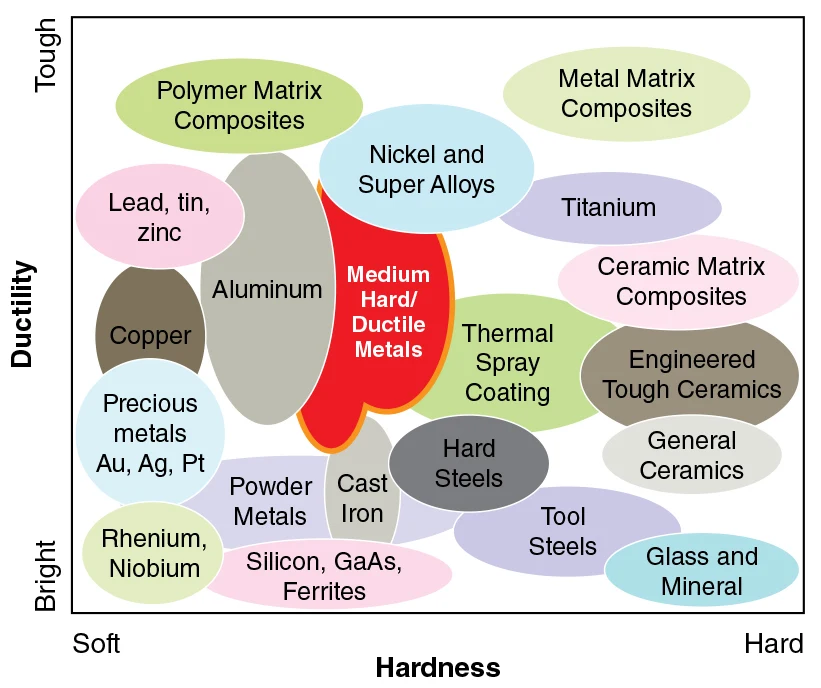
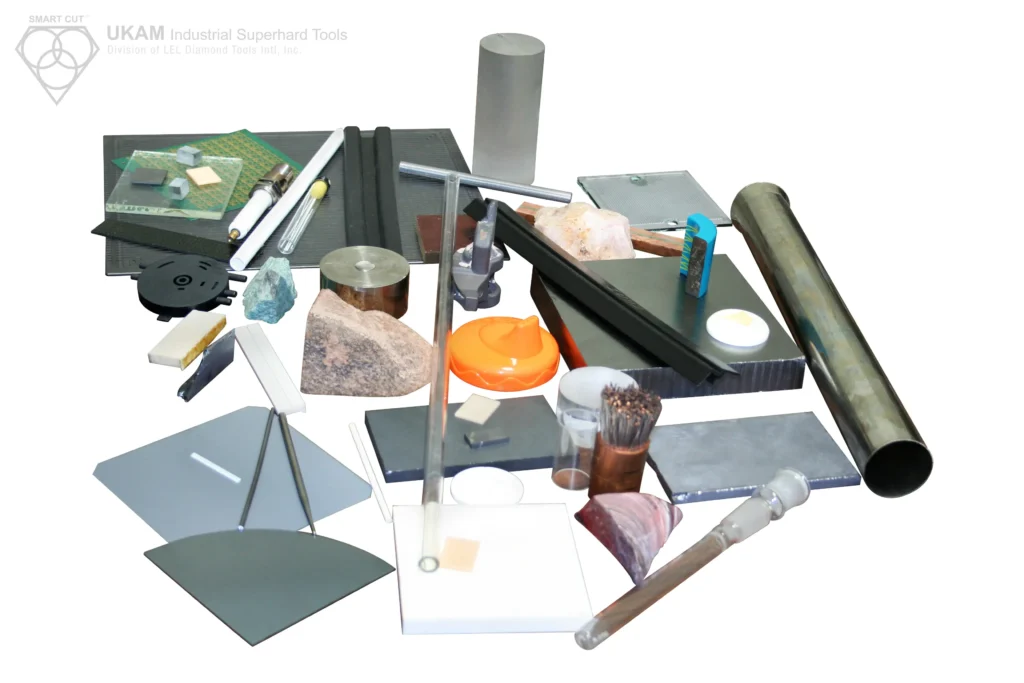
Material compatibility is a key performance metric for diamond blades and CBN (Cubic Boron Nitride) wheels, especially important when these tools are used with a variety of materials. Ensuring that a blade or wheel can handle different types of materials effectively without degradation requires attention to several critical factors.
The hardness and abrasiveness of the material being cut influence the choice between diamond blades and CBN wheels. Diamond blades are optimal for harder, non-metallic materials such as concrete, stone, glass, and ceramic due to the hardness of the diamond, which allows it to cut through these materials effectively. In contrast, CBN cutting wheels/blades are better suited for hard ferrous metals, including high-speed steel and tool steel, due to their toughness.
Thermal stability is another crucial factor. Diamonds can degrade in high-temperature applications, particularly when cutting materials that generate significant heat during cutting. They are not suitable for cutting steel and other ferrous metals as the carbon in the diamond may dissolve into the iron. CBN wheels, however, exhibit excellent thermal stability up to around 1,000°C, making them highly effective for grinding high-temperature alloys and hardened ferrous materials.
Chemical stability also plays a significant role. While diamond blades are chemically inert with most non-metals, they can suffer from graphitization or oxidation in certain environments, especially at higher temperatures. CBN wheels are resistant to chemical wear from ferrous materials, making them suitable for cutting and grinding applications involving iron-containing metals.
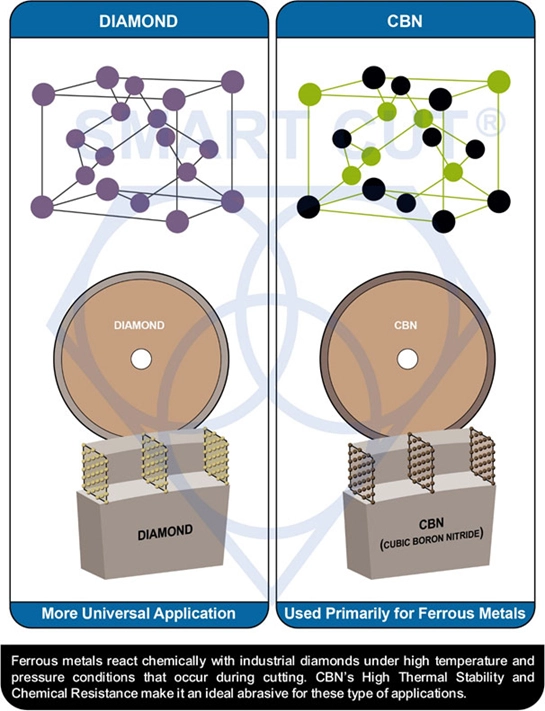
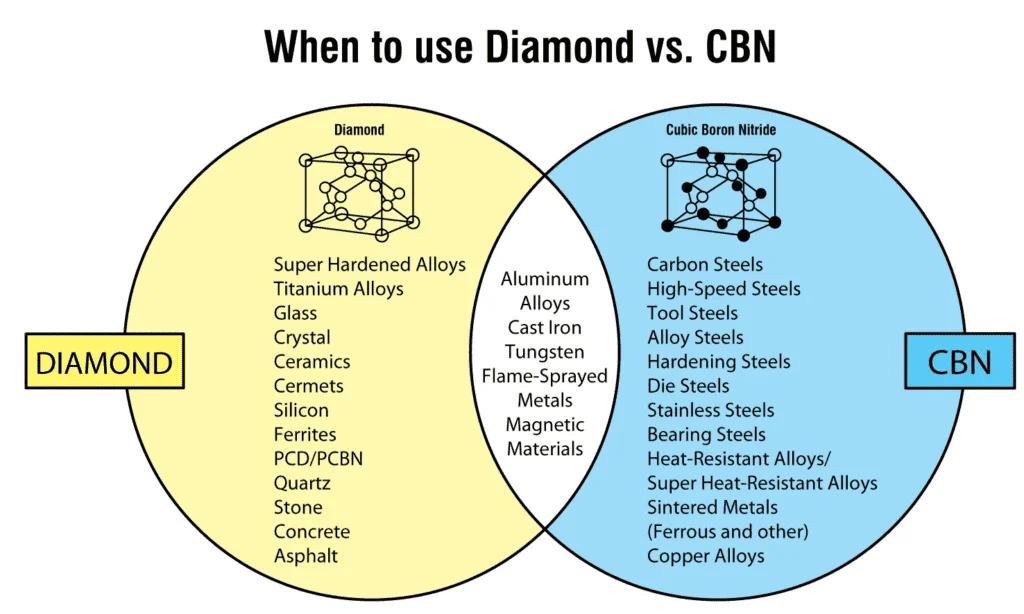
Wear resistance is crucial for both diamond blades and CBN wheels. Diamond blades exhibit high wear resistance when used on compatible materials, ensuring a longer life and consistent performance. Similarly, CBN wheels are also highly wear-resistant, especially against the abrasive effects of ferrous metals, which leads to prolonged operational life.
Edge retention is essential for maintaining precision in cutting and grinding operations. Diamond blades maintain a sharp cutting edge due to the hardness of the diamonds, crucial for precision cutting of hard and brittle materials. The hardness of CBN ensures excellent edge retention necessary for maintaining precision in grinding operations.
Finally, impact resistance is an important consideration. Diamond blades typically have lower impact resistance, which can lead to segment loss or blade failure when used improperly. CBN wheels generally offer better impact resistance, suitable for rougher grinding applications where mechanical stresses are higher.
How To Measure & test Material Compatibility
To measure and assess material compatibility of diamond and CBN cut-off blades, start by selecting a range of materials that the blades are expected to cut. These materials should represent the typical use cases and include a variety of hardness levels, compositions, and structures.
Begin by preparing samples of each material. Ensure that the samples are of uniform size and shape to facilitate consistent testing. Use the diamond or CBN blades to cut these samples under controlled conditions, maintaining uniform cutting parameters such as speed, feed rate, depth of cut, and coolant application.
During the cutting process, monitor and record the blade's performance metrics, including cutting force, cutting speed, surface finish, and the presence of any defects or irregularities in the cuts. Use tools such as profilometers to measure the surface roughness and optical microscopes to examine the quality of the cut edges.
After cutting each material, inspect the blade for signs of wear and degradation. Document any changes in the blade's edge, such as rounding, chipping, or loss of sharpness. Use high-magnification imaging tools like scanning electron microscopes (SEM) to capture detailed images of the blade's edge before and after cutting each material.
Analyze the collected data to evaluate the blade's performance with each material. Compare the cutting efficiency, surface quality, and blade wear for different materials to identify patterns and correlations. This analysis helps in understanding how well the blade handles different materials and its overall durability and compatibility.
To quantify material compatibility, calculate metrics such as the rate of blade wear, cutting efficiency, and surface finish quality for each material. Perform statistical analysis to determine the significance of the differences observed and identify any outliers or anomalies.
Additionally, consider conducting long-term durability tests by repeatedly cutting each material to simulate extended use. Monitor the blade's performance over time and document how it degrades with prolonged exposure to different materials. This long-term testing provides insights into the blade's lifespan and reliability.
Compile the findings into a comprehensive report, highlighting the blade's compatibility with various materials. Include detailed data on cutting performance, surface quality, blade wear, and any observed degradation. Provide recommendations for optimizing blade usage with different materials, such as adjusting cutting parameters or selecting specific blades for particular materials.
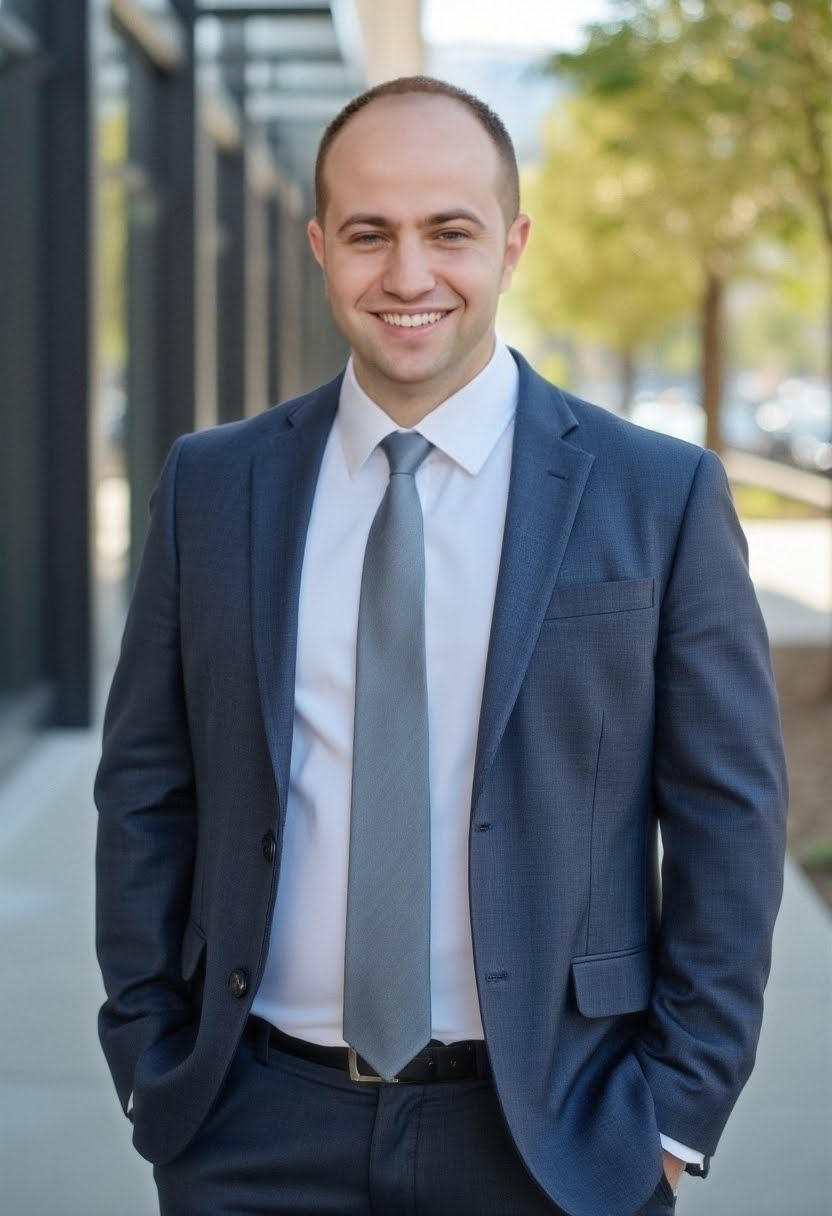
Brian is an experienced professional in the field of precision cutting tools, with over 27 years of experience in technical support. Over the years, he has helped engineers, manufacturers, researchers, and contractors find the right solutions for working with advanced and hard-to-cut materials. He’s passionate about bridging technical knowledge with real-world applications to improve efficiency and accuracy.
As an author, Brian Farberov writes extensively on diamond tool design, application engineering, return on investment strategies, and process optimization, combining technical depth with a strong understanding of customer needs and market dynamics.
ARE YOU USING RIGHT DIAMOND & CBN BLADES
FOR YOUR APPLICATION?
LET US
HELP YOU
HAVING ISSUES WITH
YOUR CURRENT DIAMOND & CBN BLADES?
Knowledge Center
Select right Diamond Blade for your application
How to Properly Use Precision Diamond & CBN Blades
Precision & Ultra Thin Diamond Blade Guide
How to Improve & Optimize Your Diamond Sawing Operation
Evaluating & Comparing Diamond Blades
Top 5 Diamond & CBN Cutting Blade Performance Metrics
Total Cost of Ownership & Why its Important
Understanding Tradeoffs- Searching for Perfect Diamond & CBN Blade
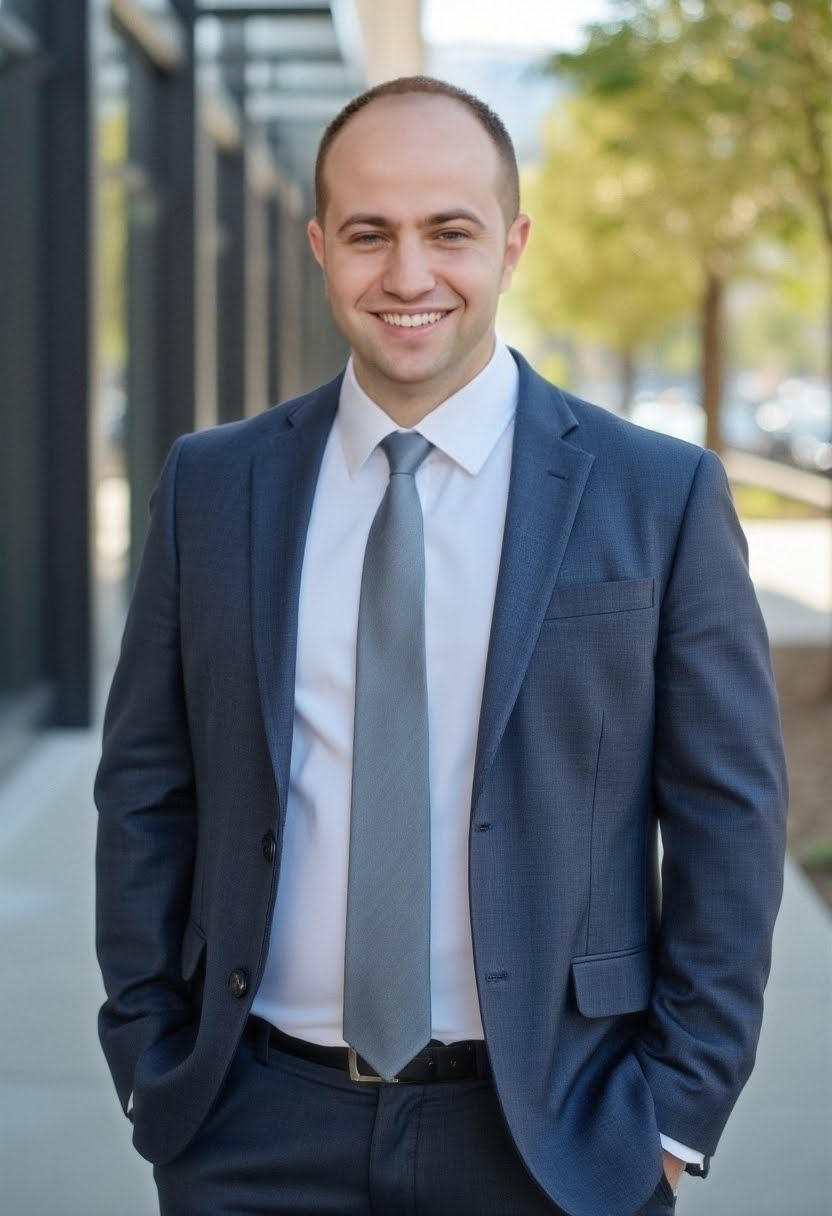
Brian is an experienced professional in the field of precision cutting tools, with over 27 years of experience in technical support. Over the years, he has helped engineers, manufacturers, researchers, and contractors find the right solutions for working with advanced and hard-to-cut materials. He’s passionate about bridging technical knowledge with real-world applications to improve efficiency and accuracy.
As an author, Brian Farberov writes extensively on diamond tool design, application engineering, return on investment strategies, and process optimization, combining technical depth with a strong understanding of customer needs and market dynamics.