Table of Contents
ToggleDiamond, known as the hardest material on Earth, enables diamond drills and tools to grind away material at a micro (nano) scale. This extreme hardness allows diamond tools to effectively work on materials with a hardness of 40 on the Rockwell scale and above, including some that defy machining by conventional abrasives like carbide and high-speed steel.
Share this Article with Friend or Colleague
One of the key advantages of using diamond in tooling is its superior material removal capability. Diamond drills can achieve precise and minute material removal, which is unattainable with softer abrasives. Additionally, diamond's durability ensures longer tool life and fewer replacements, a critical benefit in continuous production environments where downtime can be costly.
Diamond drills generate less heat during operation compared to other abrasives. This reduced heat generation helps minimize thermal damage to both the workpiece and the tools themselves, preserving the integrity and properties of high-precision parts.
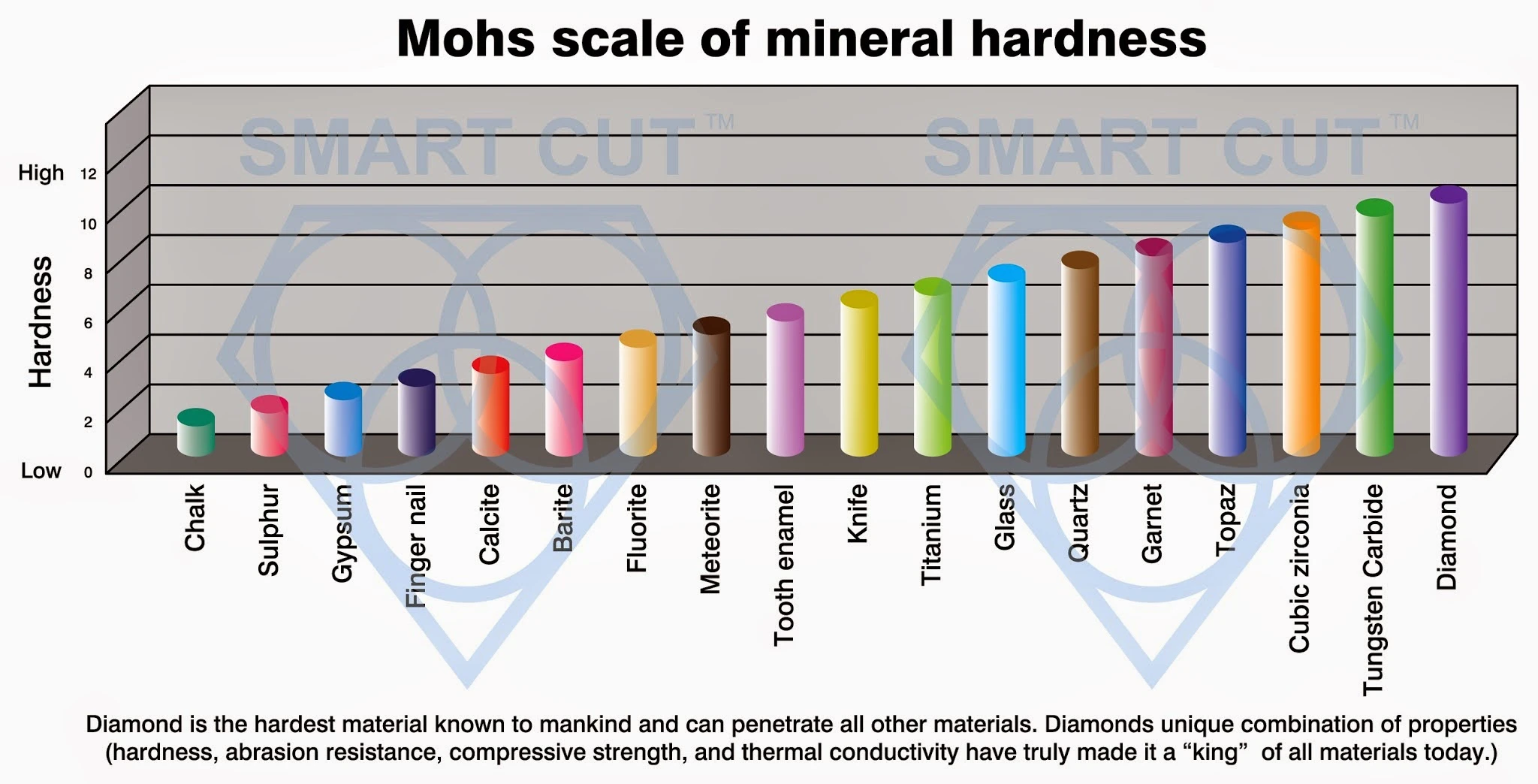
Table of comparison between diamond and carbide drills
Aspect |
Diamond Drills |
Carbide Drills |
---|---|---|
Durability |
Very high durability, lasts 10-30 times longer than HSS and 2-5 times longer than carbide drills. |
Good durability, but less than diamond drills. Prone to breakage under extreme conditions. |
Cost |
Generally more expensive upfront but cost-effective over time due to longer lifespan. |
Less expensive upfront, but frequent replacements increase long-term costs. |
Material Suitability |
Excellently suited for very hard, abrasive materials like ceramics, glass, and composites. |
Best for softer, non-abrasive materials such as wood and softer metals like aluminum. |
Heat Management |
Excellent thermal conductivity helps minimize heat buildup, preserving tool and workpiece integrity. |
Generates more heat, which can lead to faster wear and damage unless managed with coolants. |
Cutting Speed |
Can maintain high cutting speeds in hard materials due to superior hardness. |
High cutting speeds in softer materials but may struggle with harder or more abrasive surfaces. |
Finish Quality |
Produces smoother finishes and reduces chipping in hard, brittle materials. |
Can provide clean cuts but may cause chipping in harder, more brittle materials. |
Versatility |
Ideal for specialized applications requiring precision in hard-to-machine materials. |
More versatile across common materials and general applications. |
Maintenance |
Lower frequency of replacement due to wear resistance, but can be harder to sharpen. |
Requires regular sharpening and replacement, but generally easier to maintain. |
Life Span
Diamond drills offer a significantly longer lifespan compared to other types of drills such as carbide, high-speed steel, and cobalt, particularly when drilling hard and abrasive materials. Typically, diamond drills can last 10 to 30 times longer than high-speed steel (HSS) drills and 2 to 5 times longer than carbide drills. Their ability to produce smoother finishes and reduce chipping in hard, brittle materials like glass, ceramics, stone, and composites is due to their method of grinding away material on a micro scale, as opposed to other drills that cut with a sharp edge, resulting in a superior finish.
Longer drill life translates into fewer tool changes and less downtime. This is particularly important in high-volume production settings where the cost of stopping machines to replace a worn drill can quickly accumulate. The longer life of diamond drills not only reduces the frequency of these disruptions but also diminishes the overall cost of tooling over time.
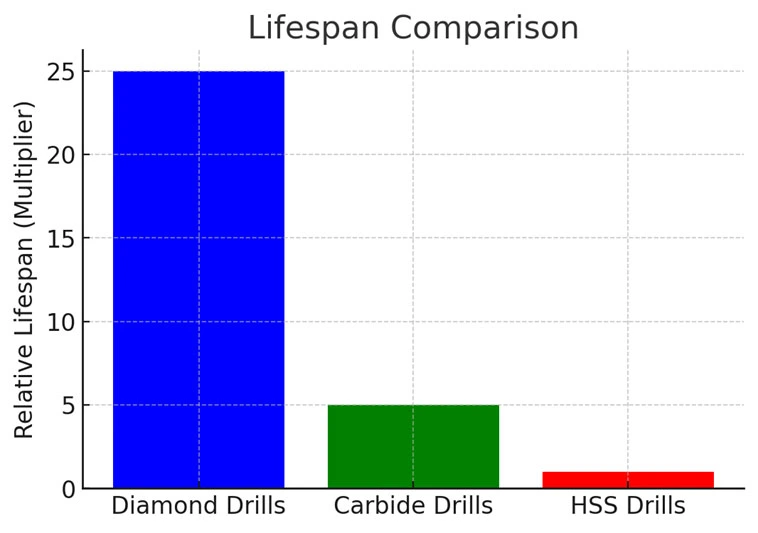
Additionally, the ability of diamond to maintain a sharp cutting edge for extended periods means that it can continue to perform at an optimal level far longer than HSS or carbide drills. This sustained performance is important in applications requiring consistent precision and quality, where even minor variations in drill wear can affect the outcome of the machining process.
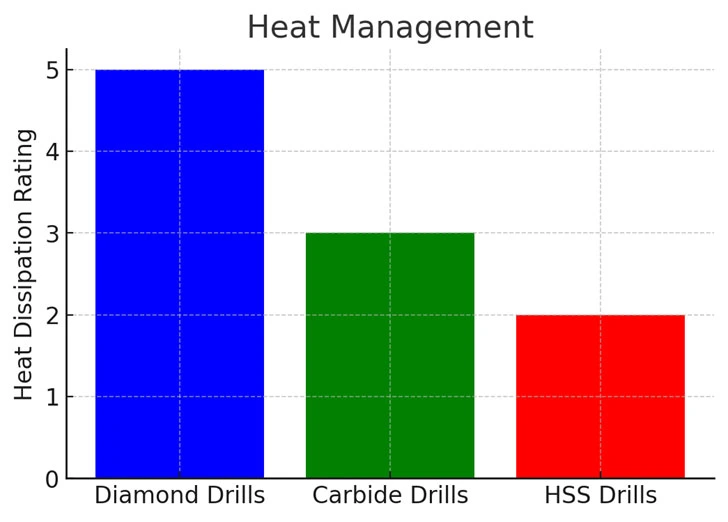
Heat Management
Additionally, diamond drills excel in heat management thanks to their excellent thermal conductivity, which aids in effective heat dissipation. This reduces the risk of overheating, a frequent cause of damage to both the drill and the material being worked on. Furthermore, the hardness of the diamond particles and their heat dissipation properties allow diamond drills to operate faster than other types of drills.
The ability to manage heat effectively is crucial because overheating is one of the primary reasons for drill failure and can also lead to damage in the materials being drilled. When drills overheat, they can lose their tempering, leading to a loss in hardness and, consequently, effectiveness. This can also cause thermal damage to the workpiece, such as cracks and deformities, especially in materials sensitive to high temperatures.
Diamond’s superior thermal conductivity means that heat generated at the drilling interface—where the drill contacts the material—is quickly conducted away from both the diamond particles and the material. This rapid heat dissipation helps to maintain a cooler drilling environment, reducing the likelihood of damaging the workpiece due to excessive heat. It also preserves the sharpness and cutting ability of the diamond, ensuring that the drill continues to operate effectively over a longer period.
Furthermore, the inherent hardness of diamond particles, combined with their excellent heat dissipation properties, enables diamond drills to operate at higher speeds than other types of drills without the same risk of overheating. This ability to maintain higher operational speeds without compromising on safety or efficiency is a distinct advantage in high-demand settings, allowing for faster completion of tasks without sacrificing quality.
Cost Comparison
Regarding cost, the price of diamond drills and bits varies based on numerous specifications including the drill's diameter, bond type, diamond type, concentration, radius/angle, tolerances, mounting type, and quantity. Contrary to common misconceptions, diamond drills are not always more expensive than other types of drills such as carbide; they are often comparably priced or even less expensive.
When considering the costs associated with diamond drills compared to other types of drills such as carbide or cobalt, it's crucial to take into account a variety of specifications that can influence both the upfront price and overall cost-effectiveness. Factors such as the drill's diameter, bond type, diamond type, concentration, radius/angle, tolerances, mounting type, and the quantity purchased all play significant roles in determining cost. Contrary to the common perception that diamond drills are invariably more expensive, they can actually be competitively priced or even more affordable than their counterparts depending on these variables.
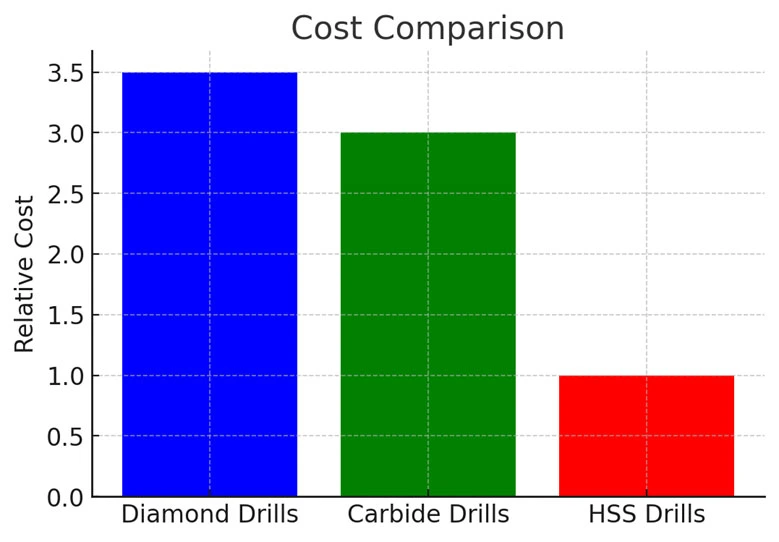
The cost variability in diamond drills stems largely from their design and manufacturing specifics. For example, drills that utilize specialized diamond types or those with a higher concentration of diamonds might carry a higher initial cost but also tend to offer better performance and longer durability. This can lead to cost savings over time due to less frequent need for replacements. Additionally, the choice of bond—such as sintered, or electroplated—also impacts both the drill's performance and its cost, with each type offering different benefits suited to varying durability needs and applications.
While carbide or cobalt drills are often less expensive and sufficient for standard applications, especially in metal drilling, diamond drills, especially those made using PCD (polycrystalline diamond) or through chemical vapor deposition techniques, prove to be more cost-effective for more challenging tasks. This includes drilling abrasive or very hard materials where their superior durability and performance justify the higher initial price.
The long-term cost-effectiveness of diamond drills is highlighted by their longevity and the reduced frequency of replacement or re-sharpening. PCD drills, for instance, are highly durable and ideal for cutting non-ferrous materials like aluminum and copper, as well as non-metallic materials such as wood, ceramics, rubber, and plastic. Their wear resistance significantly lowers maintenance costs and minimizes downtime in production settings, factors that contribute to overall savings.
However, in applications where precision and the quality of the finish are critical, diamond drills excel by producing cleaner cuts and minimizing material damage. This high level of performance can reduce waste and enhance product quality, contributing to cost reductions in the manufacturing process that, while not directly linked to the price of the drill, affect the total cost of operations.
In essence, when making purchasing decisions, it's important for businesses to consider not just the initial cost of diamond drills but also the total cost of ownership. This includes looking at aspects like durability, maintenance needs, and the potential for operational efficiencies and reduced waste, which can make diamond drills a more economical option in the long run despite a possibly higher upfront investment.
Surface Finish
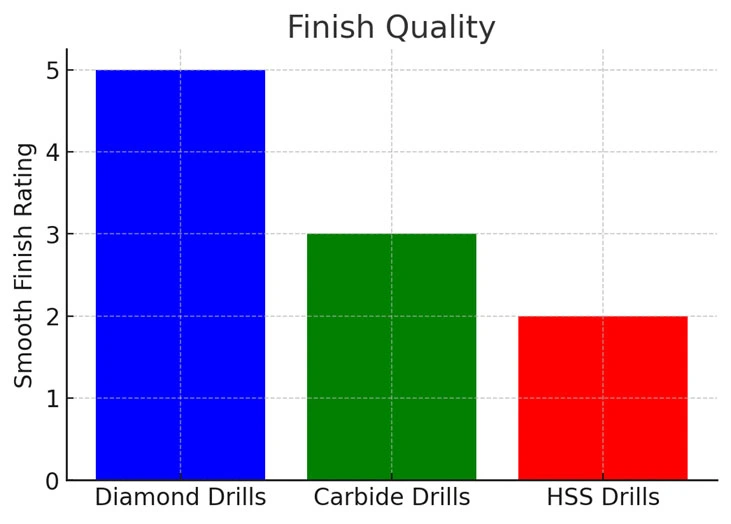
Material Versatility
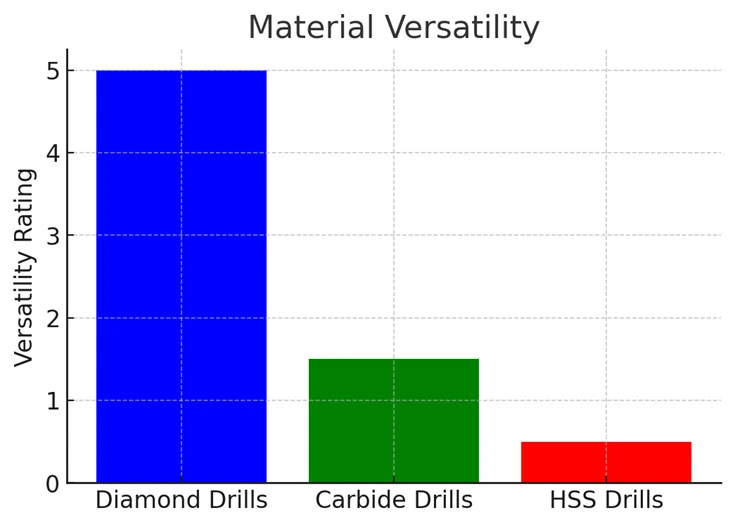
Diamond drills are known for their efficiency in handling extremely hard materials such as stone, ceramics, glass, composites, and many other ultra hard and brittle materials, which are often challenging for traditional drills. This capability makes them indispensable in industries like ceramics, stone, glass, composites, natural and semi precious stone, optics, construction, and engineering, where durability, excellent surface finish, and accuracy is important.
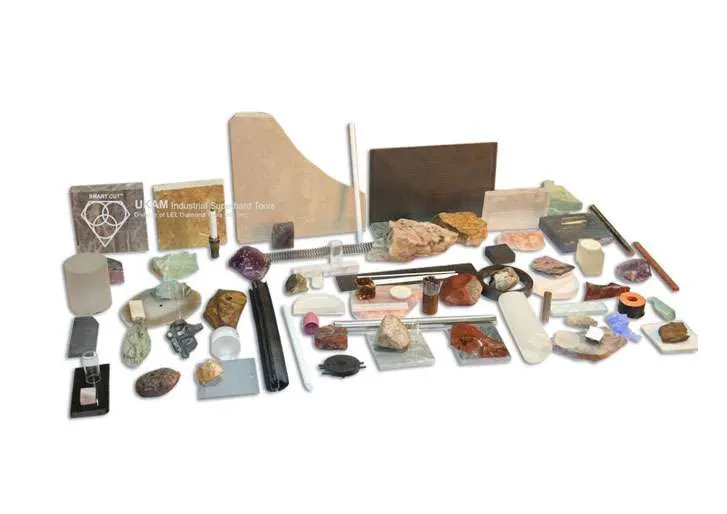
While specific materials and applications require properly optimized diamond drill specifications, diamond remains the most universally applicable material for drills, often allowing a single specification to be used across a range of materials and applications. For drilling metals and related materials, while carbide or cobalt drills might be more suitable for softer metals, specific diamond drill types like those made with chemical vapor deposition and PCD (polycrystalline diamond) are also effective. PCD drills, primarily used for non-ferrous materials such as aluminum and copper, as well as non-metallic materials like wood, ceramics, rubber, and plastic, offer excellent wear resistance which extends their life without the need for frequent replacement or re-sharpening.
Cutting Speed
When comparing the cutting speeds of diamond and carbide drills, it's crucial to consider the type of material being drilled, as this significantly affects the performance of each drill type. Diamond drills, known for their unmatched hardness, maintain a sharp cutting edge longer than carbide, allowing them to operate at higher speeds, especially in very hard, abrasive materials such as ceramics, hardened glass, and certain stones. This capability enables them to cut through these materials with less force, focusing more energy on the cutting motion itself, thereby enhancing speed and efficiency.
Carbide drills, while not as hard as diamond, are highly effective in softer materials, particularly metals like steel and aluminum. In these materials, carbide drills can achieve high cutting speeds due to their ability to handle the metal's toughness without significant wear. This resistance to wear allows carbide drills to maintain consistent performance over time, which is crucial for projects requiring extensive drilling in metals.
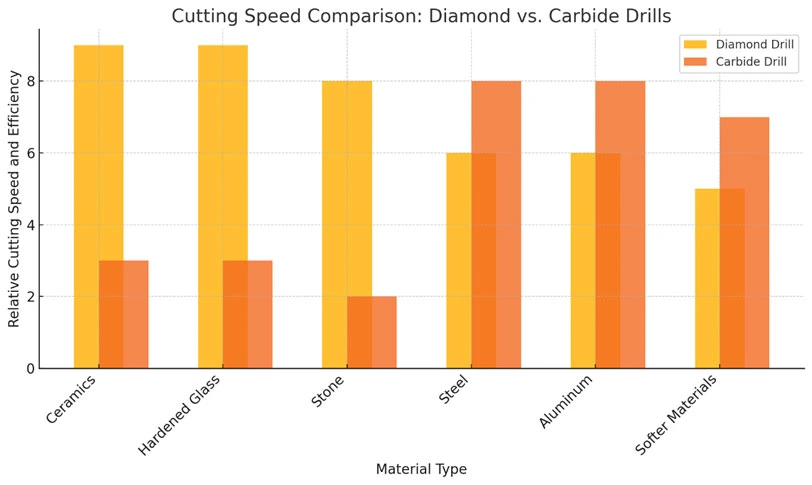
However, carbide drills can generate significant heat at high speeds, which may necessitate the use of coolants to manage temperature and prevent damage to both the drill bit and the workpiece. This factor can sometimes limit the effective cutting speed of carbide drills in more demanding applications.
In contrast, diamond drills excel in situations that challenge other drills, such as in cutting extremely hard materials where carbide drills would quickly wear out. The superior hardness of diamond allows these drills to sustain high cutting rates without degradation, making them ideal for specialized applications requiring precision and efficiency.
How Diamond Drills Work
Diamond drills operate through a grinding mechanism rather than cutting. Embedded with industrial-grade diamonds, these drills do not cut but rather grind away the material as they rotate. This unique method is achieved by the diamonds set on the surface of the drill bit. As the bit spins, the diamonds abrade the material to create a hole.
Diamond drills are either made from natural or synthetic diamond particles held inside various bond types, such as sintered (metal), electroplated, or braised bonds, which determine how the diamonds are held and how quickly they are exposed and released. This variety allows customization based on the material being drilled and the desired finish quality, speed, and longevity of the drill itself.
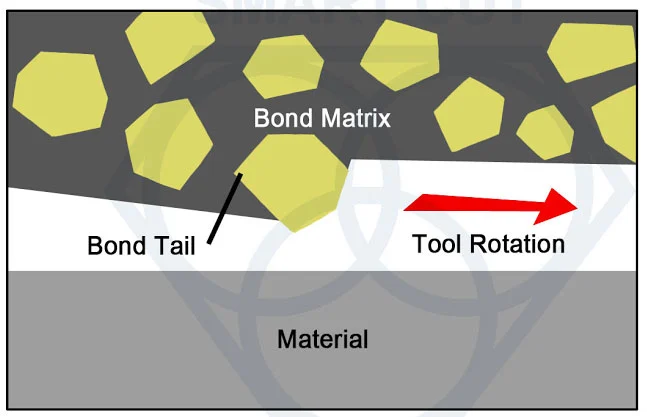
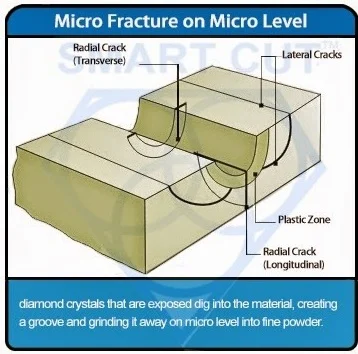
Diamond drills also reduce heat generation during the drilling process due to the natural thermal conductivity of diamonds. This feature minimizes the risk of overheating and damage to both the drill bit and the material, enhancing safety and extending the lifespan of the tool. However, diamond drills are not suitable for drilling metals because the carbon in the diamond can react with the metal, which reduces the tool's lifespan.
The design of the diamond drill can vary significantly based on its application. The tip can be hollow, as seen in core drills, or solid for non-core formations, with specific angles or radii tailored to the task. In diamond core drilling, the bulk of the drilling effort is exerted by the diamonds located along the sides of the diamond section. These peripheral diamonds grind away the material to form the hole, while diamonds at the bottom help maintain a flat bottom within the drilled area, ensuring precision and control in the depth and shape of the hole.
Diamond Core drills, for example, feature a hollow tip to facilitate the extraction of a core sample, essential in applications such as geological explorations or when precise cylindrical samples from materials are necessary for further analysis. This allows for the core to be retrieved intact, preserving the structure and composition necessary for accurate testing and analysis.
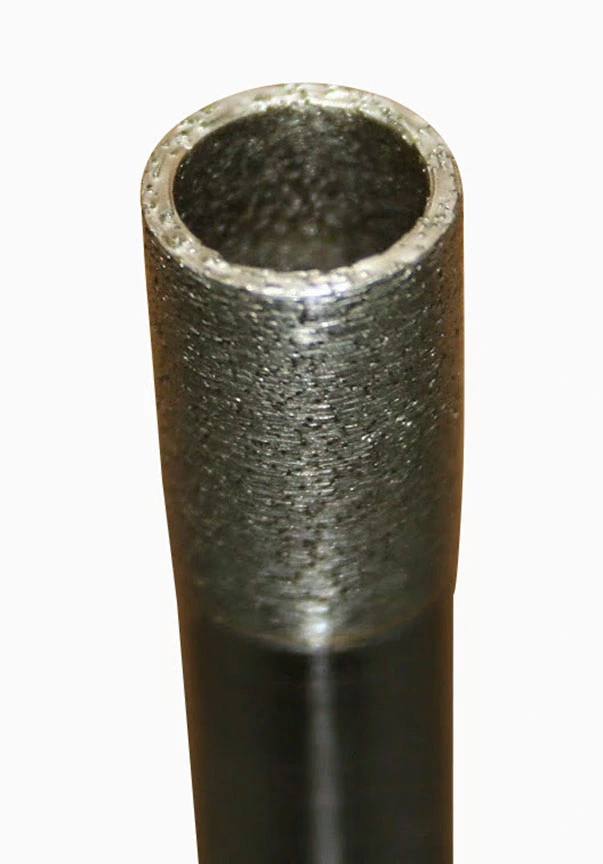
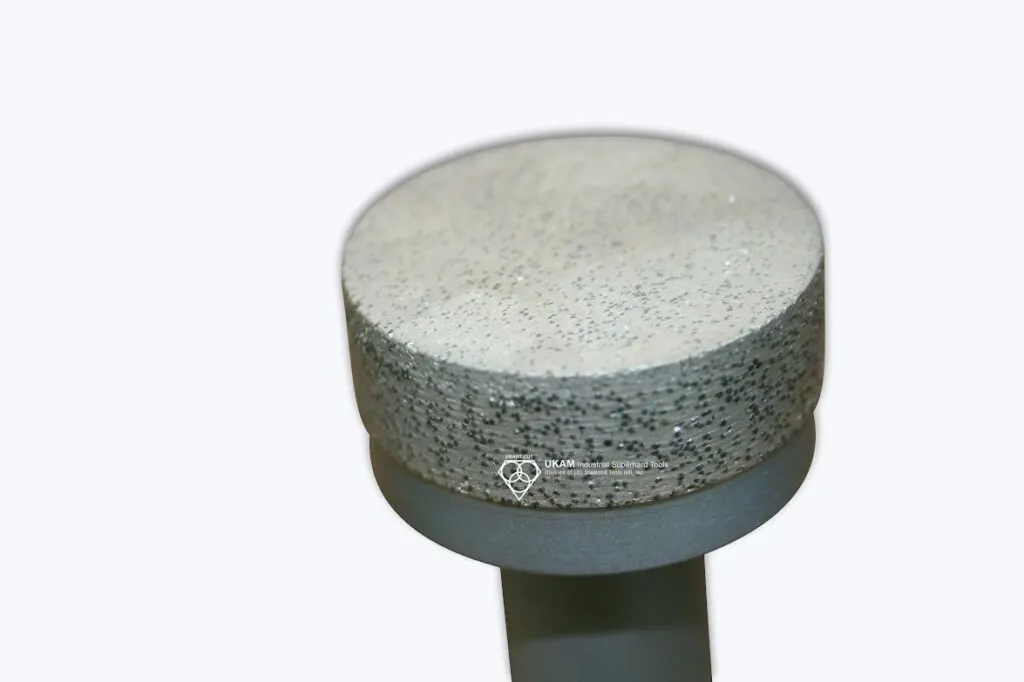
For tasks where no core is needed, diamond drills with solid tips are used. These are typically employed in construction and manufacturing to create holes for fixtures or to provide relief holes in dense materials. The solid tip is robust and suitable for drilling through tough materials, providing a straightforward solution for creating through-holes.
Diamonds placed at the bottom of the drill bit are pivotal in maintaining a flat bottom within the drilled area. This design feature is crucial for applications that demand precise depth control and a flat base within the hole, such as in precision manufacturing where components must be mounted accurately, or in installations where fixture stability is paramount.
The edge geometry of diamond drills is meticulously designed to maximize their effectiveness across various demanding applications, particularly when working with hard, abrasive materials like ceramics, glass, and composites. The precise angles and radii at the tip of these drills play a crucial role in determining how the tool interacts with the material it cuts, influencing several key performance metrics.
A sharper angle at the tip can significantly improve penetration rates in harder materials, allowing for quicker and more efficient drilling. This sharper tip reduces the amount of force needed to begin drilling, speeding up the process while also minimizing wear on the tool itself. This is especially beneficial in industrial settings where time efficiency translates directly into cost savings.
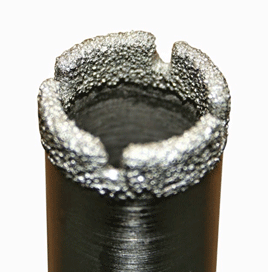
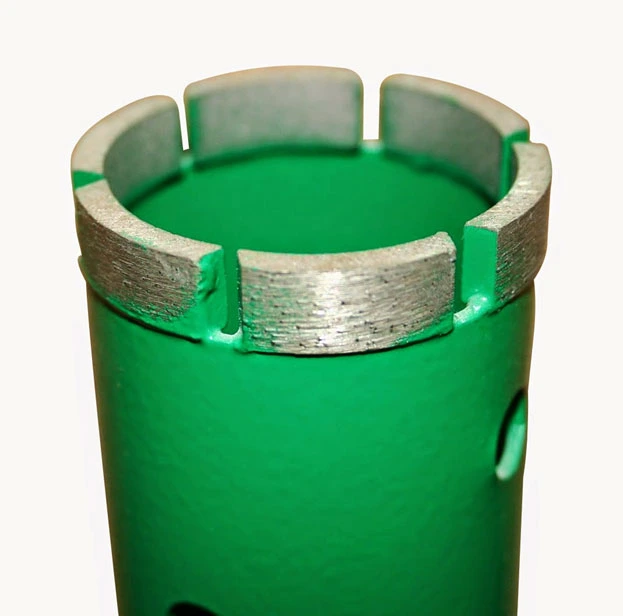
Furthermore, the design of the edge also optimizes material removal rates. By refining the edge geometry, the drill can remove material more effectively and quickly, which is a significant advantage in environments where production speed is critical. The wear rate of the drill is also influenced by its edge design. Properly configured edges help distribute the mechanical and thermal stresses encountered during drilling more evenly, extending the lifespan of the drill significantly by preventing premature wear and failure.
The quality of the holes produced is critically impacted by the edge geometry as well. Precise angles and sharp radii ensure that the drill cuts cleanly through the material, minimizing chipping and cracking at the entry and exit points of the drill. This precision is crucial in fields like electronic component fabrication or aerospace, where high accuracy is essential.
Additionally, with the correct edge geometry, the force required to penetrate materials, especially harder ones, is greatly reduced. This reduction in necessary force not only makes the drilling process faster but also more energy-efficient. Lower energy consumption during drilling not only helps reduce operational costs but also minimizes the environmental impact of manufacturing processes.
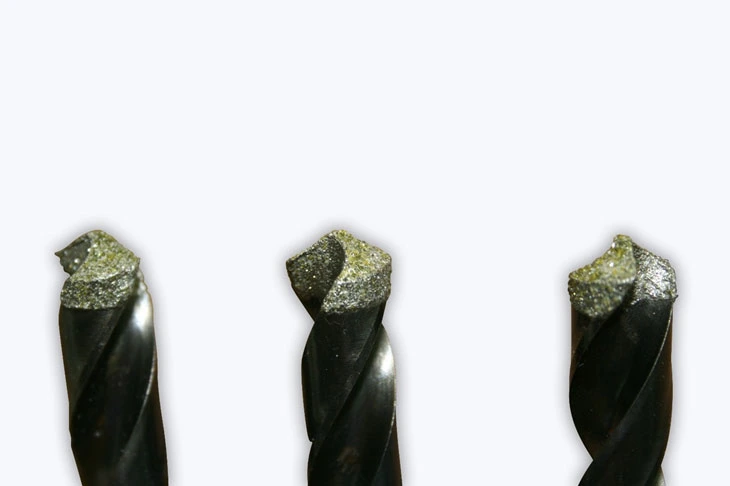
How Carbide Drills Work
Carbide drills operate by cutting or chipping away at the material. Carbide, recognized for its extreme hardness second only to diamond, is typically tipped or brazed onto the cutting edges of the drill bit. These drills are designed with a solid tip that penetrates into the material, efficiently cutting through it to create chips or fragments.
Carbide drills consist of carbide particles, typically tungsten carbide, bonded with a metal, usually cobalt. They're harder than steel but softer than diamond. These drills are often coated with materials like Titanium Nitride (TiN), Titanium Carbonitride (TiCN), Titanium Aluminum Nitride (Tialn), Aluminum Titanium Nitride (Altin), Zirconium Nitride (Zrn), Chromium Nitride (Crn), and others to enhance their life, hardness, and heat resistance.
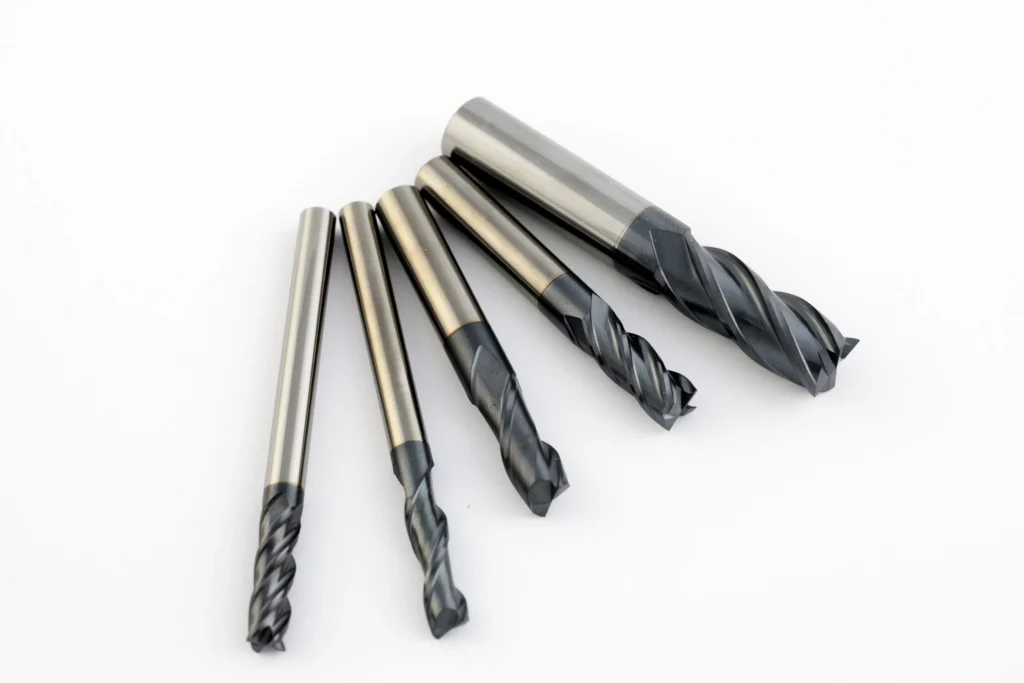
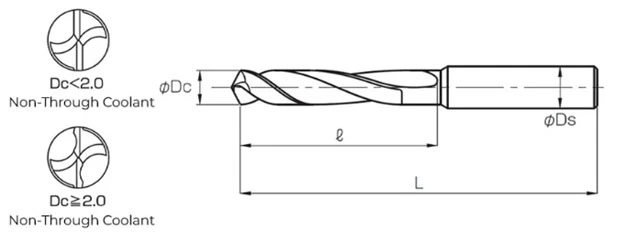
Carbide drills are ideal for drilling metals, plastics, and other tough materials and can maintain their sharpness longer than high-speed steel (HSS) bits and operate at higher speeds. However, they are brittle and prone to chipping if mishandled or used on unstable equipment. Despite their higher cost compared to traditional steel bits, their extended life and superior performance often justify the investment.
The geometry of carbide drills can vary widely depending on their intended use. Types include twist drills, spade drills, and other specialized forms tailored to specific industrial or commercial applications. The primary cutting edges at the tip of the drill shear off the material, while secondary cutting edges along the flutes facilitate the evacuation of chips from the drill hole. This dual-action allows for efficient cutting and removal of material, ensuring clean holes and maintaining the integrity of the drill bit.
Drill design significantly influences functionality and efficiency, with various features tailored to optimize performance for different materials and applications. The angle at the tip of the drill, known as the point angle, determines the drill's aggressiveness. A 118-degree angle is typically ideal for softer materials like wood or plastic, providing a good balance between sharpness and durability, while a 135-degree angle is more suited for harder materials like metals, offering greater stability and preventing the drill from wandering.
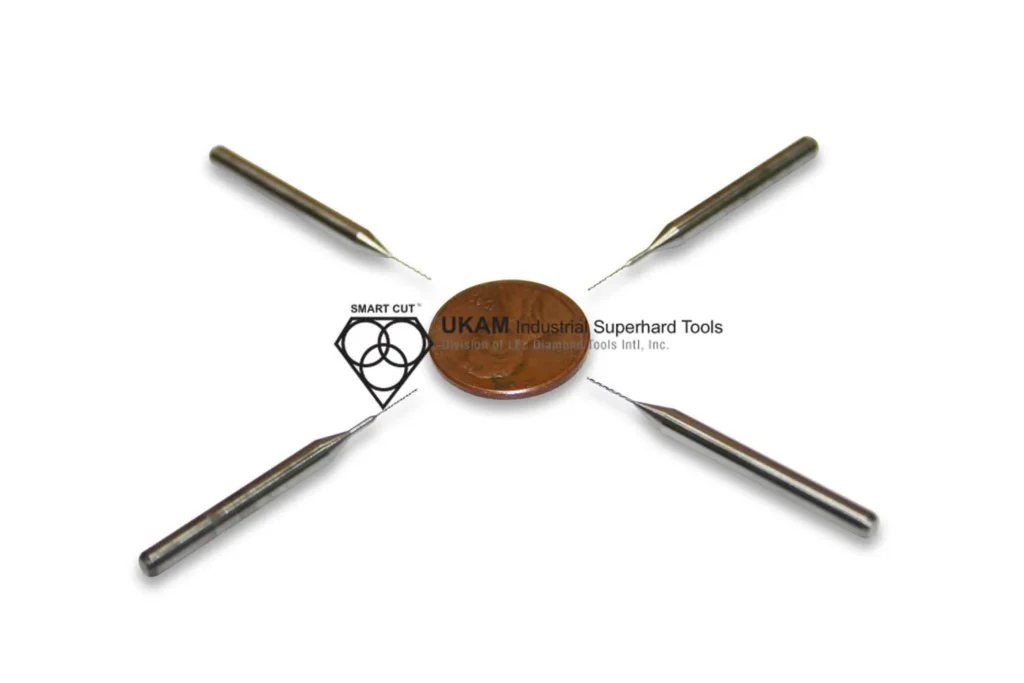
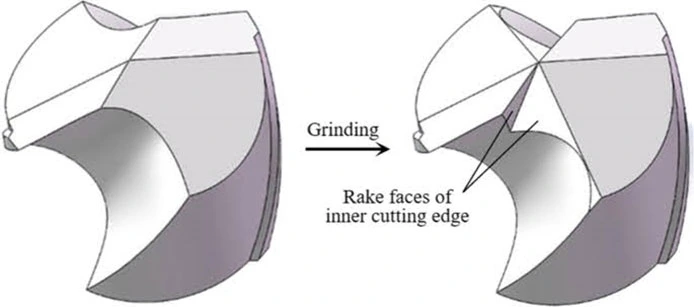
The flutes, or grooves along the side of the drill bit, play multiple roles, including chip removal, cooling, and affecting the drill's strength and flexibility. Wider flutes can remove more material and improve cooling but may make the drill more prone to breaking. They are essential for keeping the hole clear of debris and allowing coolant to reach the cutting surface, which helps manage heat and maintain the integrity of both the drill bit and the material.
The helix angle of the flutes also impacts performance. Low helix angles, around 15 to 30 degrees, are used for harder materials like stainless steel and provide more support to the cutting edge, reducing load and heat per tooth. Higher helix angles, above 30 degrees, are better for softer materials like aluminum or plastic, facilitating smoother and faster chip removal.
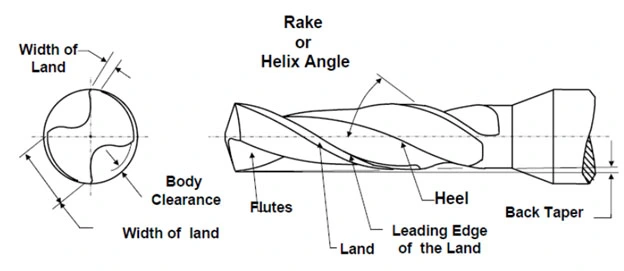
How Cobal Drills Work
Cobalt drills are essentially high-speed steel drills with a certain percentage of cobalt (usually 5-8%) added to improve heat and wear resistance. They are especially effective for drilling tough metals like stainless steel that generate a lot of heat during drilling. These drills maintain their hardness at high temperatures, making them well-suited for such applications. While more expensive than standard HSS drills, cobalt drills are usually less costly than carbide drills and are valued primarily for their heat resistance.
Comparing Diamond, Carbide, & Cobalt Drills
While carbide of drills are valuable for different applications, diamond drills provide superior performance on very hard or abrasive materials where traditional cutting actions are ineffective. Conversely, carbide drills are preferable for applications requiring sharp, clean cuts and where material removal is straightforward. Each type of drill offers distinct benefits, making them suitable for specific tasks within diverse operational contexts.
In terms of cost efficiency, diamond drills, though expensive, are cost-effective for drilling hard, abrasive materials due to their durability. Carbide drills, while pricier than HSS drills, offer better performance and longevity for metal drilling. Cobalt drills find a balance in cost and are particularly effective for high-temperature applications.
Both carbide and cobalt drills handle heat well, with cobalt drills specifically designed to withstand the high temperatures encountered when drilling hard metals. This prevents them from losing their temper and becoming dull. Regarding hardness and wear, diamond stands out as the hardest material, making diamond drills the optimal choice for very hard materials. Carbide offers significant hardness and wear resistance, suitable for a variety of tough materials.
Diamond Drill Bond Types
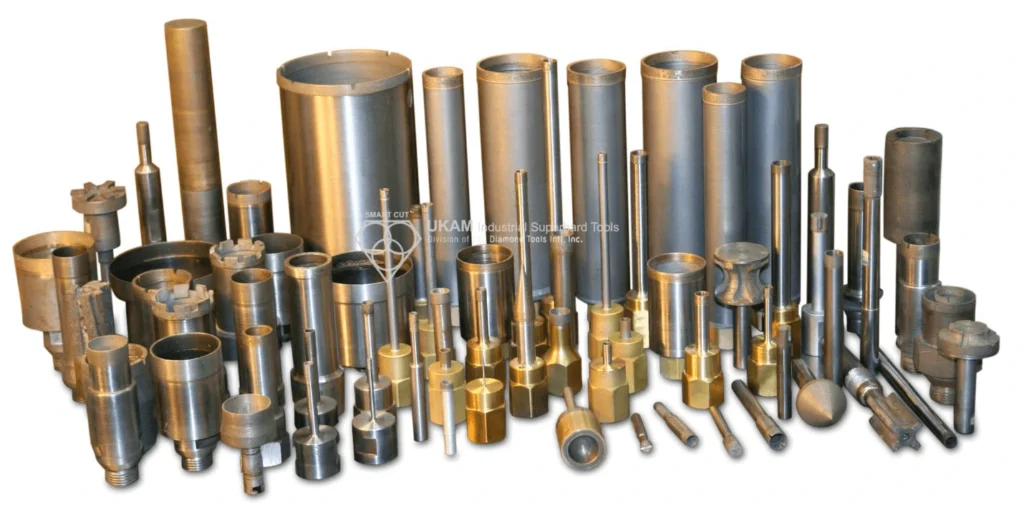
Diamond drills are essential tools in industries requiring precise cutting and drilling of hard materials. The type of diamond drill used depends on factors like application, material type, and tool longevity. Below is a summary of the different types of diamond drills, their features, and applications.
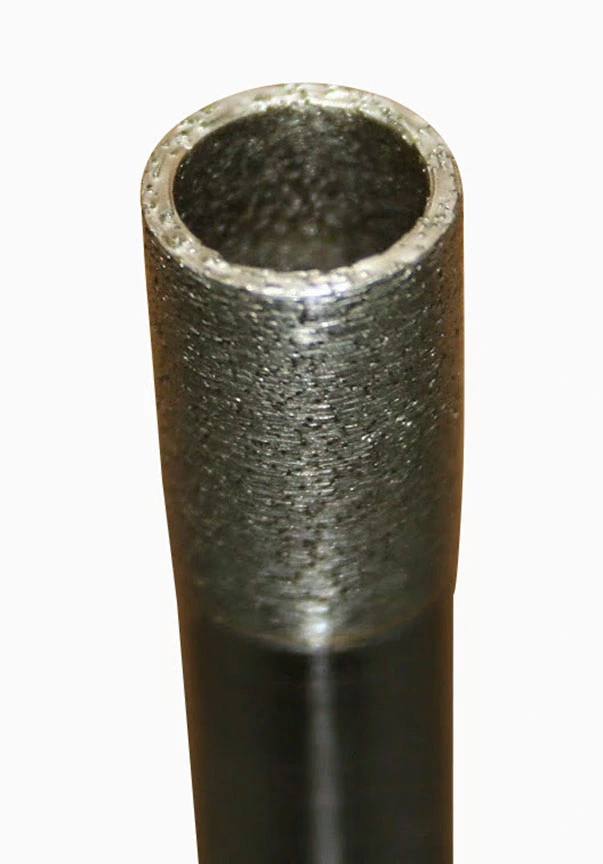
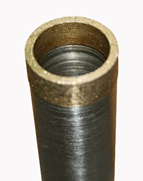
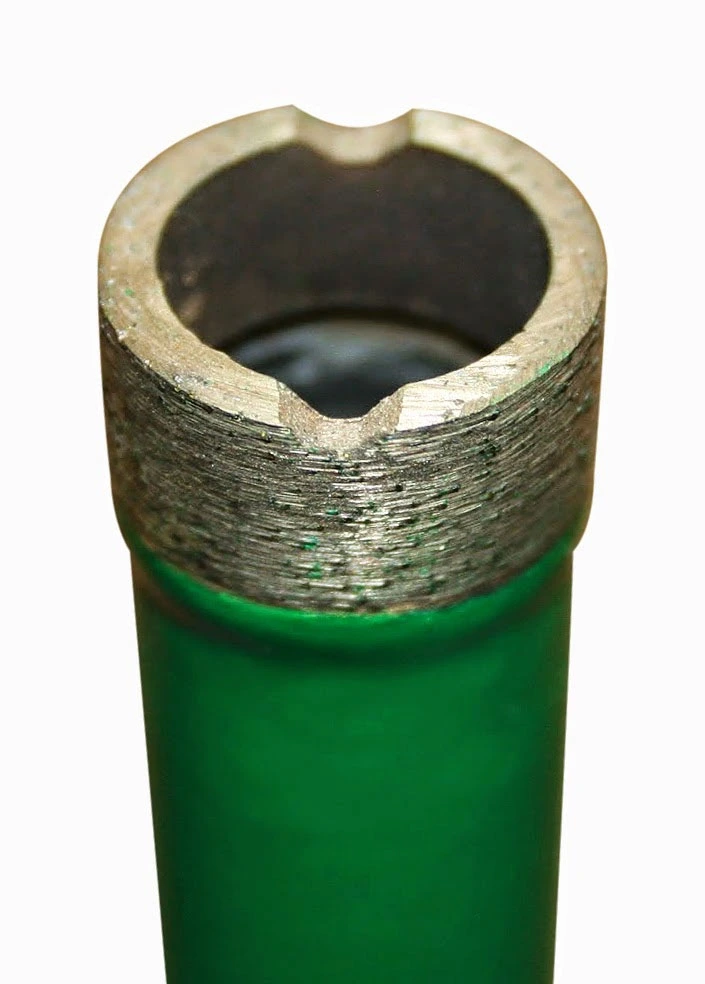
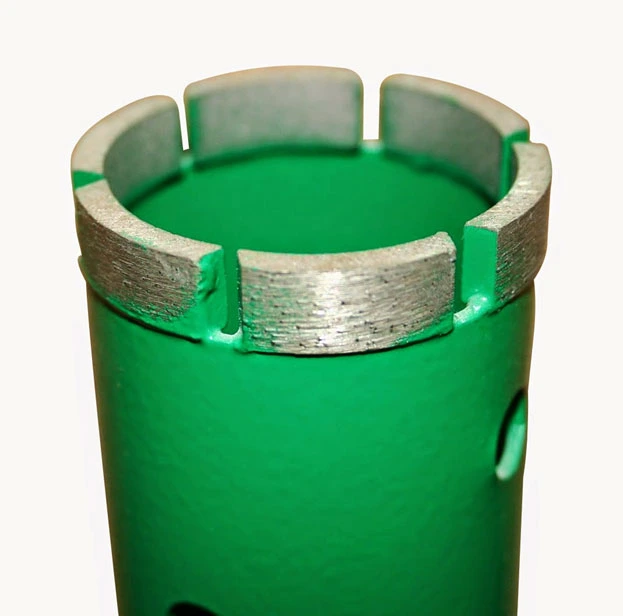
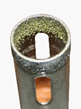
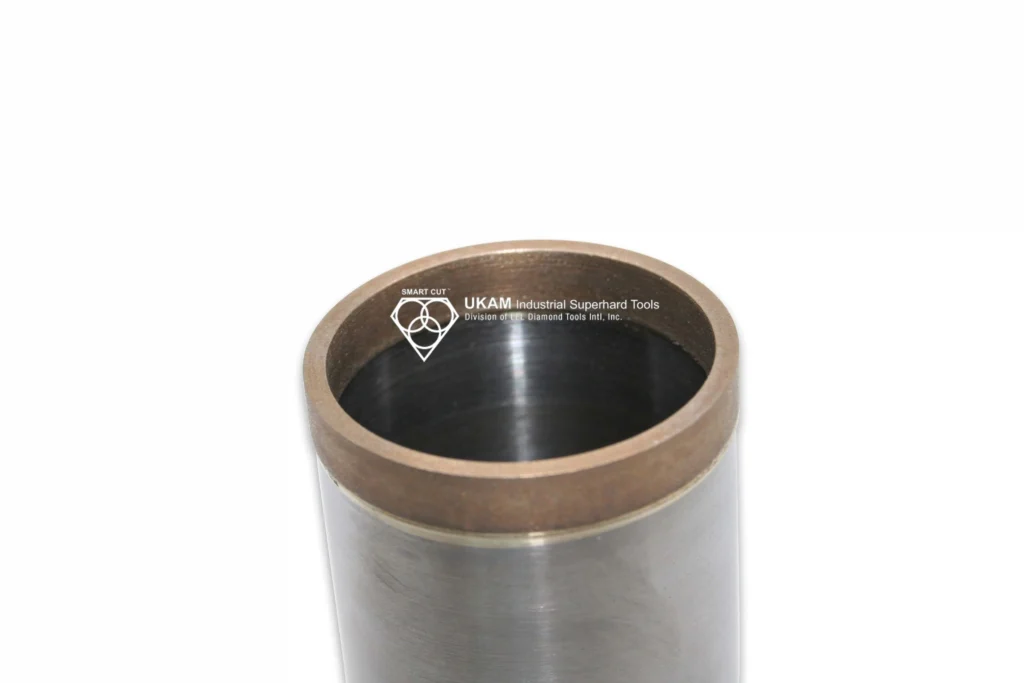
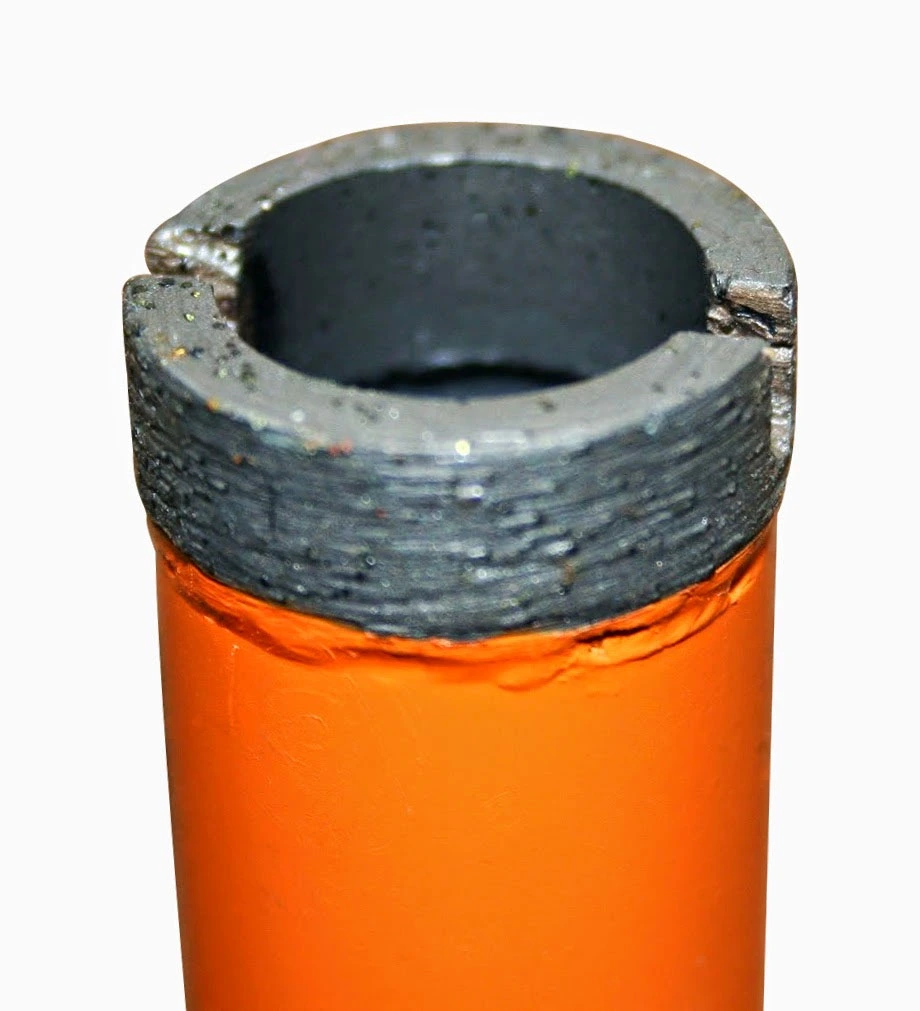
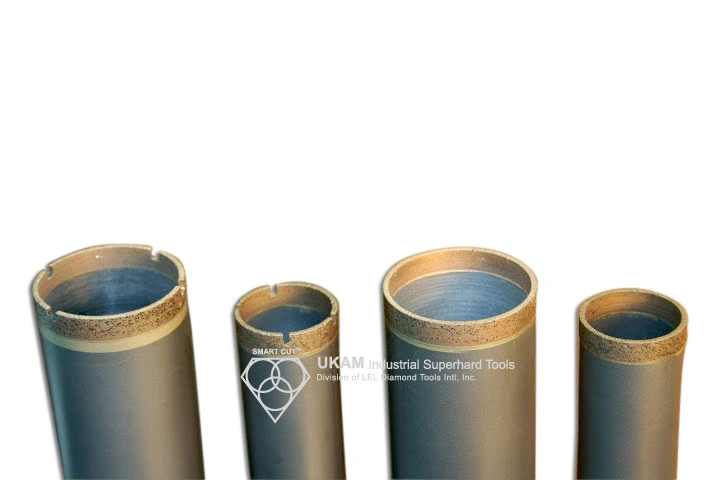
Sintered diamond drills, also known as metal bond drills, are made by bonding diamond particles with a powdered metal matrix, such as bronze or tungsten carbide, which is sintered to create a durable structure. The metal bond ensures that new diamond particles are constantly exposed as the tool wears, making these drills highly durable and precise. They are ideal for drilling through hard, dense materials like ceramics, glass, and granite, and are commonly used in industries requiring long-lasting tools, such as optics and semiconductors.
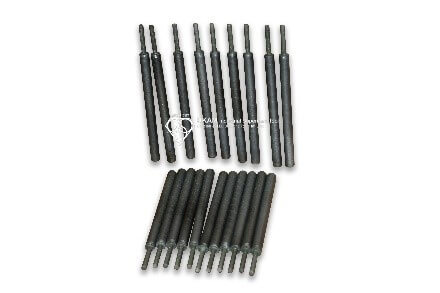
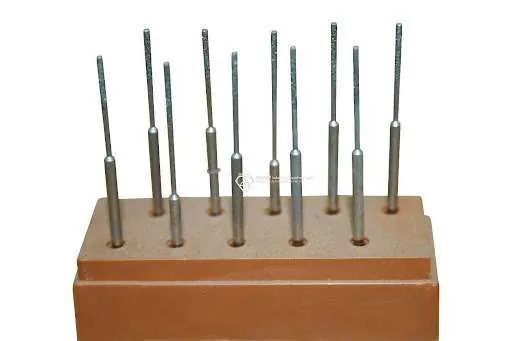
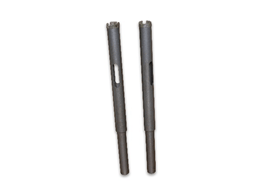
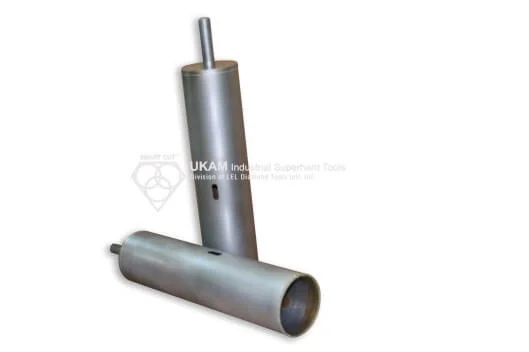
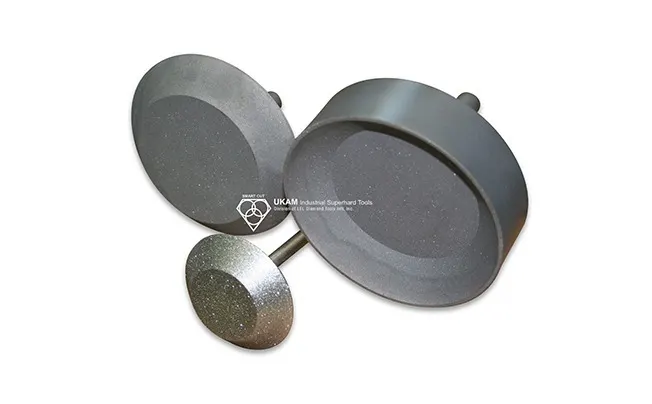
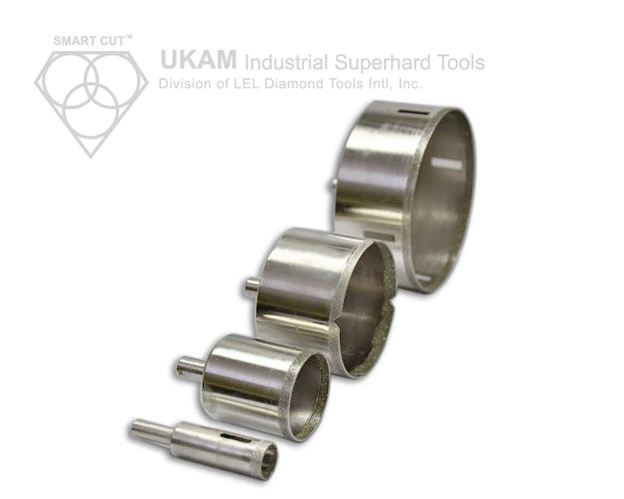
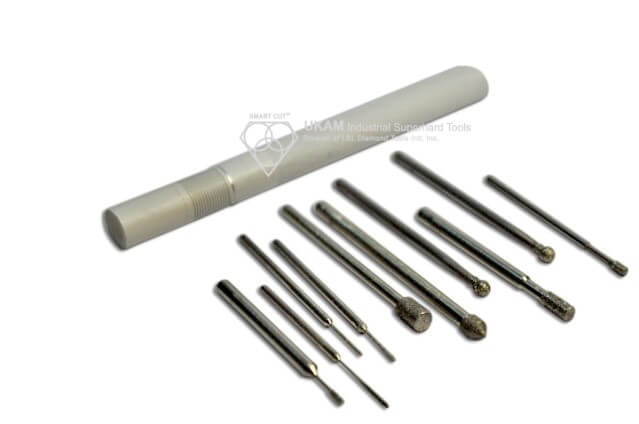
Electroplated diamond drills consist of a single layer of diamond particles bonded to a metal shank via electroplating, typically using nickel. They offer high cutting speeds and aggressive material removal due to the exposed diamond layer. These drills are cost-effective for shorter production runs and are suitable for applications involving softer materials, such as composites, plastics, and softer ceramics, where quick, shallow drilling is required.
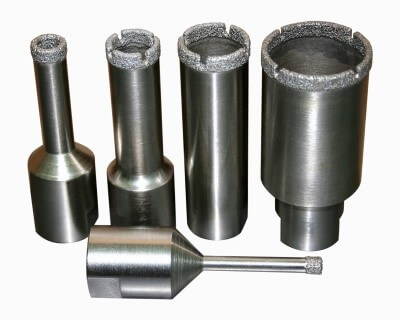
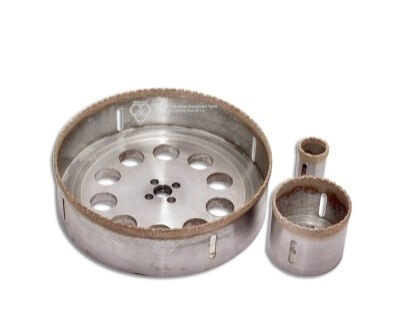
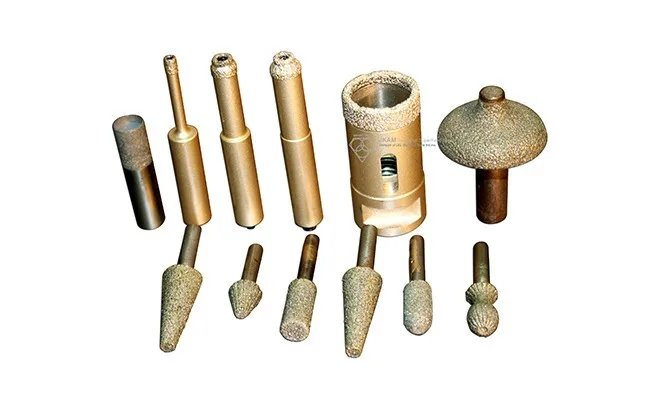
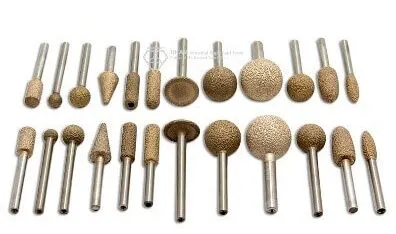
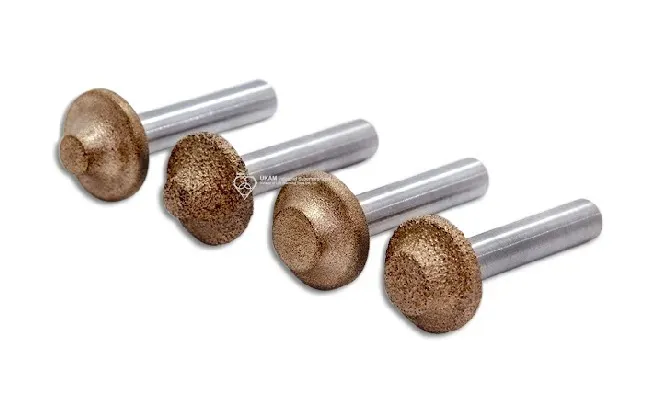
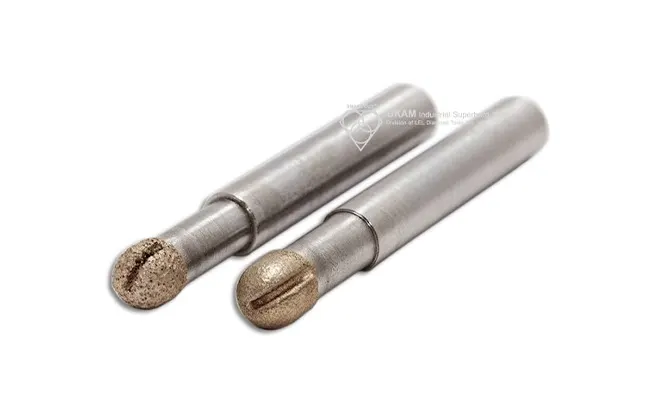
Brazed diamond drills use a brazing process to solder diamond particles directly onto a steel shank. This design exposes a high concentration of diamonds, allowing for efficient and aggressive cutting. They work well in wet and dry conditions and are suitable for drilling hard natural stones, concrete, and ceramics. They are widely used in construction and fabrication, offering a balance between cutting speed and tool life.
Polycrystalline Diamond (PCD) drills are constructed by fusing diamond grit into polycrystalline segments, which are then bonded to a carbide shank. Known for their exceptional wear resistance and thermal stability, PCD drills are highly durable and best suited for drilling non-metallic materials like composites, aluminum alloys, and ceramics. Their reliability and long tool life make them ideal for applications demanding consistent precision, such as in the automotive and aerospace industries.
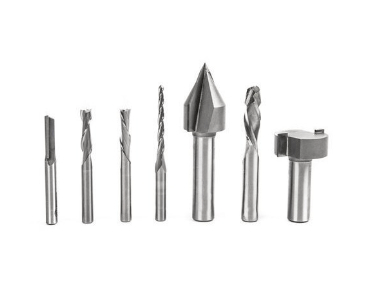
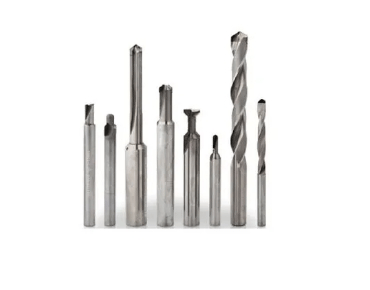
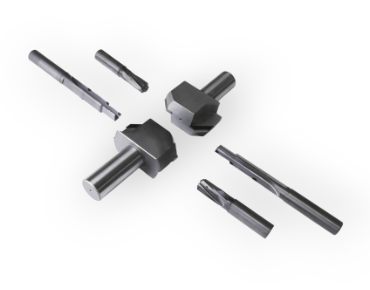
PCD tools are widely used for machining a variety of materials, including aluminum and its alloys, copper, wood, wood-based fibers, aluminum oxide, reinforced floorboards, wear-resistant plastics, Bakelite, graphite, stone, tungsten carbide, epoxy resins, fiberglass composites, carbon-phenolic, hard rubber, unfired ceramics, and plastics. This versatility allows PCD tools to effectively reduce production costs and extend tool life across many applications like sawing, routing, drilling, and profiling.
In contrast, Polycrystalline Cubic Boron Nitride (PCBN) cutting tools are designed for materials that are more challenging to machine, such as hardened steel, tool steel, mold steel, bearing steel, chilled and high-chromium cast iron, nickel-based superalloys, gray cast iron, zinc alloys, and sintered tungsten carbide. Find Out More about PCD Diamond & CBN Tools >>>
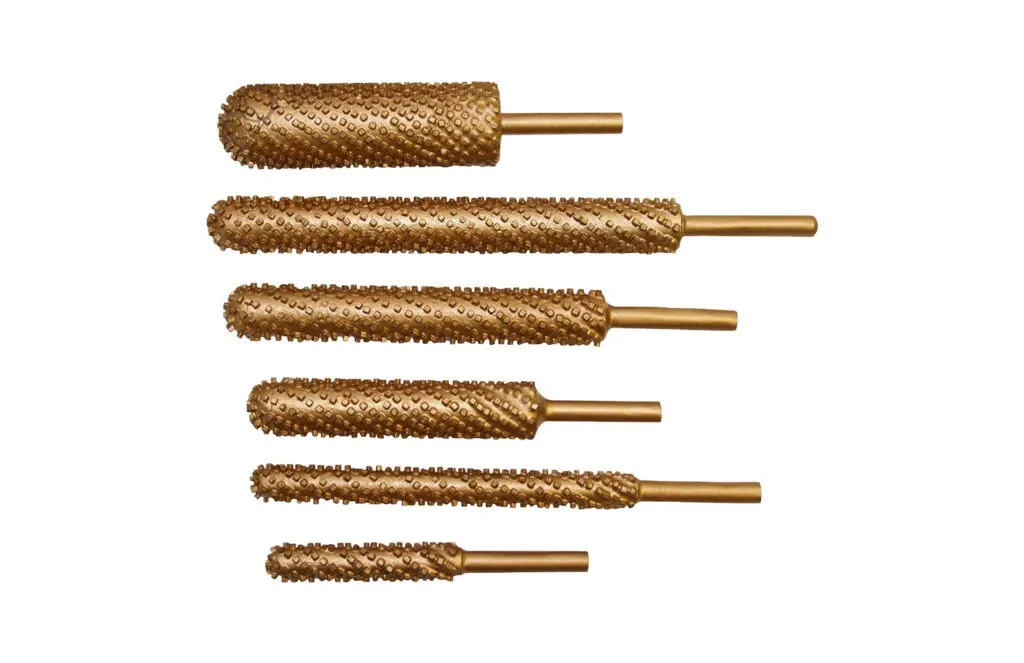
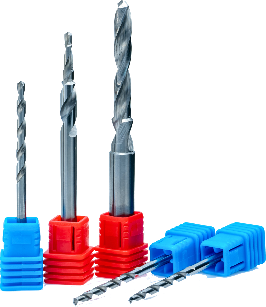
Chemical Vapor Deposition (CVD) diamond drills are produced by depositing pure diamond films onto a carbide substrate. This coating offers high hardness, thermal conductivity, and reduced friction, making CVD drills suitable for precise drilling in advanced materials like silicon, quartz, and delicate ceramics. They are particularly popular in the electronics, optics, and medical device industries for their ability to achieve high-quality surface finishes.
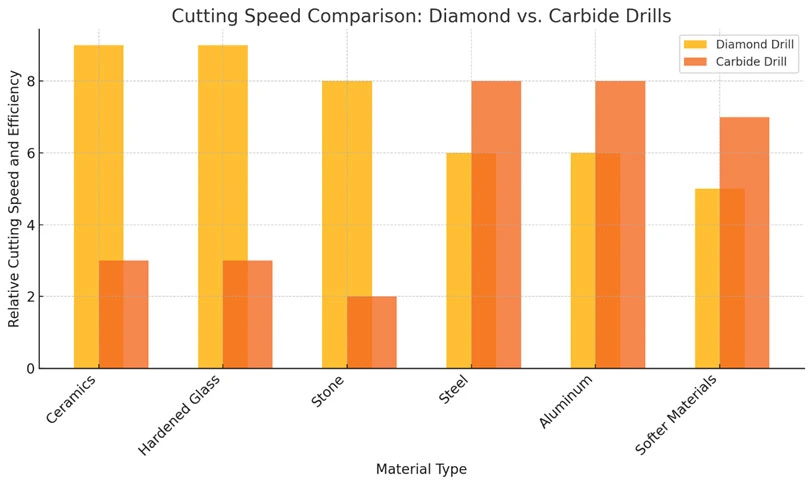
Comparison table - overview of the different drill types:
Aspect / Property |
Diamond Drills |
PCD Drills |
CVD Diamond Drills |
Carbide Drills |
Cobalt Drills |
HSS Drills |
Ceramic Drills |
---|---|---|---|---|---|---|---|
Hardness |
Extremely Hard |
Extremely Hard |
Extremely Hard |
Very Hard |
Harder than HSS |
Standard |
Very Hard |
Material Composition |
Synthetic Diamonds |
Diamonds on Tungsten Carbide |
Diamond Coated |
Tungsten Carbide |
HSS with 5-8% Cobalt |
High-Speed Steel |
Ceramic-based materials |
Heat Resistance |
High |
Very High |
High |
High |
Very High |
Moderate |
Very High |
Cost |
High |
Very Expensive |
High |
High to Medium |
Medium to Low |
Very Low |
Expensive |
Recommended Application |
Hard, abrasive, brittle materials |
Non-ferrous metals, composites |
Hard, abrasive materials |
Metals, tough materials |
Hard metals (heat generating) |
General purpose (softer materials) |
Aerospace, automotive |
Wear Resistance |
Very High |
Superior |
Very High |
High |
High |
Moderate |
High |
Brittleness |
High (Brittle) |
Brittle |
Moderate |
High (Brittle) |
Moderate |
Low |
Brittle |
Lifespan |
Long |
Very Long |
Long |
Long |
Longer than HSS |
Shortest |
Long but can chip |
Thermal Reactivity |
Reactive with Iron |
Stable |
Stable |
Stable |
Stable |
Stable |
Stable |
Coolant Requirement |
Often Required |
Often Required |
Sometimes Required |
Sometimes Required |
Depends on Application |
Often Not Required |
Often Not Required |
Toughness |
Moderate |
High |
High |
High |
High |
Moderate |
High |
Chip Resistance |
Low |
High |
High |
Moderate |
High |
Low |
Moderate |
Cutting Speed |
Fast |
Fastest |
Fast |
Very Fast |
Fast |
Moderate |
Moderate |
Coating Options |
None |
Various |
Various |
Various |
Limited |
Various |
Limited |
Flexibility |
Low |
Low |
Moderate |
Moderate |
High |
High |
Low |
Precision |
Very High |
Very High |
Very High |
High |
Moderate |
Low |
High |
Surface Finish Quality |
Excellent |
Excellent |
Excellent |
Good |
Good |
Moderate |
Good |
Environmental Suitability |
Suitable for dry and wet conditions |
Suitable for dry conditions |
Suitable for dry conditions |
Suitable for wet conditions |
Suitable for wet conditions |
Suitable for dry conditions |
Suitable for wet conditions |
Impact Resistance |
Low |
Moderate |
Moderate |
Moderate |
High |
High |
Low |
Maintenance Requirements |
High |
Moderate |
Moderate |
Low |
Low |
Low |
Moderate |
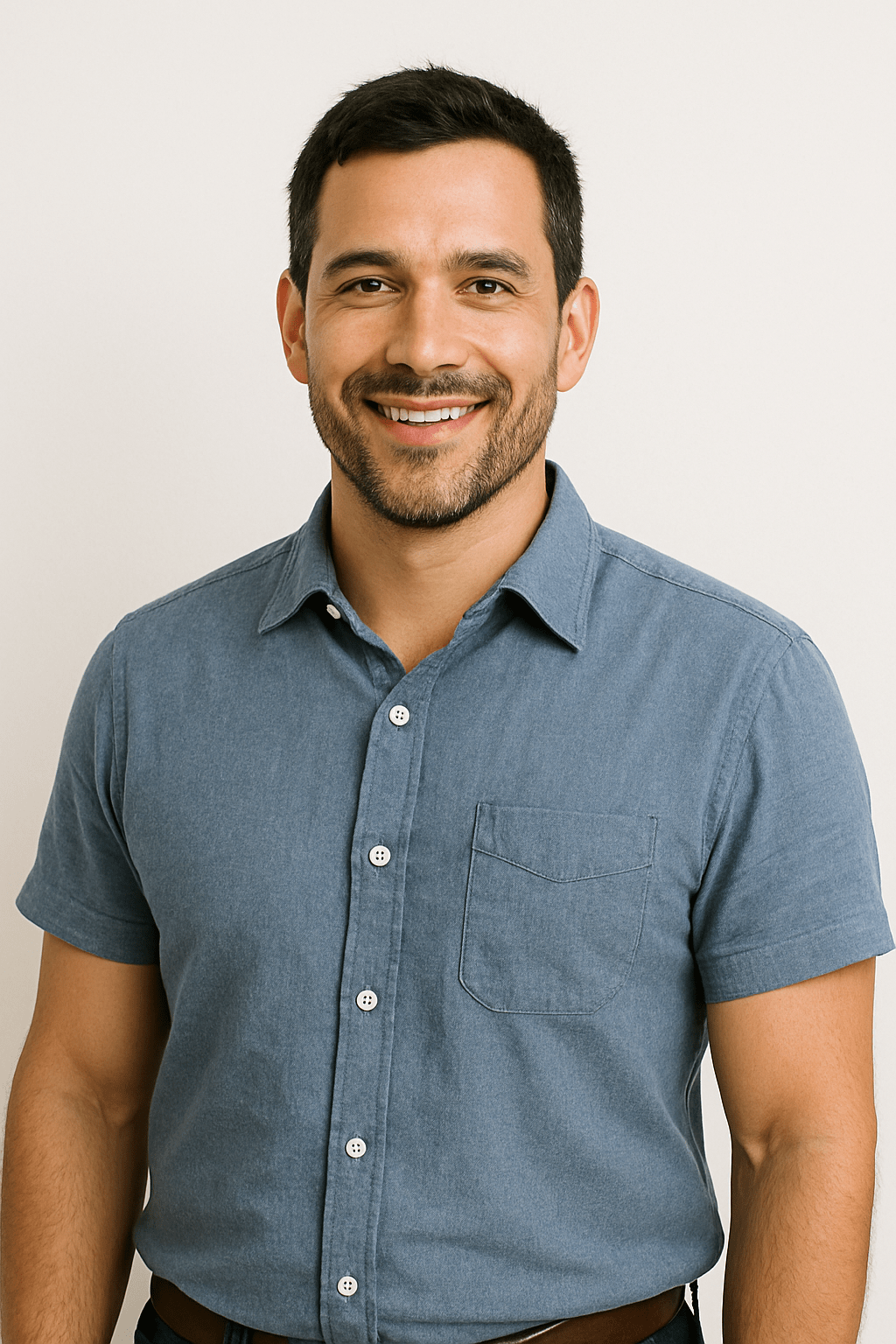
Carlos Sanchez is a senior technical specialist and field applications trainer with more than 17 years of experience in the use and optimization of industrial diamond tools, including ultra-thin diamond blades, core drills, and CBN grinding wheels. With a foundation in industrial engineering and technical operations, Mr. Sanchez has worked extensively with manufacturers and laboratories around the world, providing hands-on support and practical training for a wide range of cutting, grinding, and sample preparation applications.
Fluent in both English and Spanish, Carlos is known for his ability to translate complex tooling concepts into clear, actionable procedures for engineers, technicians, and production staff. His approach emphasizes real-world process improvement, tool longevity, and operator education—ensuring clients get the most out of their diamond tooling investments.
As an author, Mr. Sanchez shares field-tested insights on tool performance optimization, defect prevention, training methodologies, and troubleshooting common cutting issues.
ARE YOU USING RIGHT DIAMOND CORE DRILLS & TOOLS
FOR YOUR APPLICATION?
LET US
HELP YOU
HAVING ISSUES WITH
YOUR CURRENT DIAMOND CORE DRILLS & TOOLS?
Knowledge Center
Select right Diamond Drill for your application
How to Properly Use Precision Diamond Drills
Diamond Drills Guide
Diamond Tools Guide – Selecting Right Drills & Tools for your application
Optimizing your Diamond Drilling Operation
Micro Drilling Guide
Selecting Right Drilling Equipment for your Application. What you features & functionality you should look for?
Diamond Core Drill & Drill Trouble Shooting Guide
Understanding & Calculating Return on Investment for Diamond Core Drills & Other Tools
Understanding Tradeoffs – Searching for Perfect Diamond Drill & Tool
Why Use Diamond Drills?
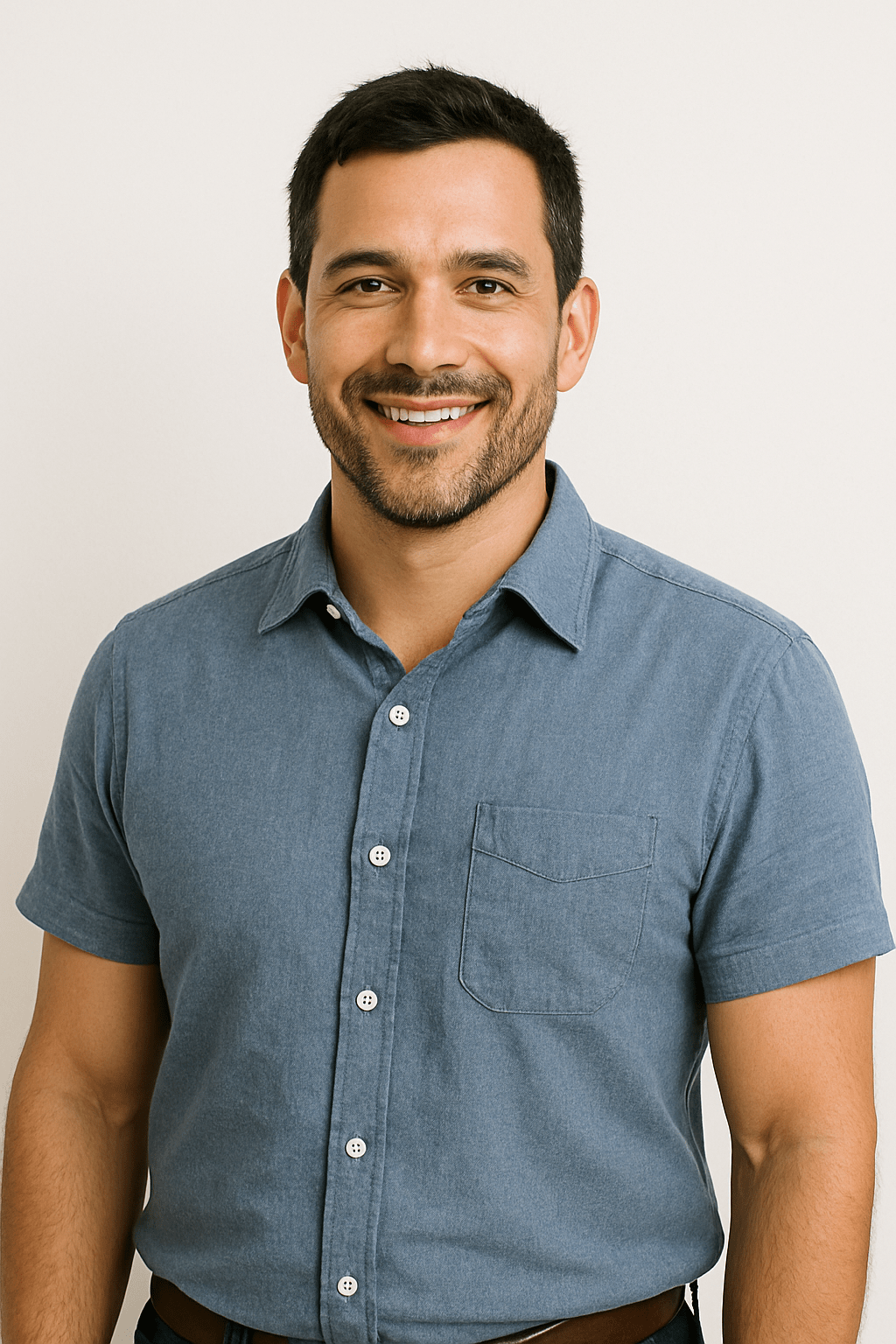
Carlos Sanchez is a senior technical specialist and field applications trainer with more than 17 years of experience in the use and optimization of industrial diamond tools, including ultra-thin diamond blades, core drills, and CBN grinding wheels. With a foundation in industrial engineering and technical operations, Mr. Sanchez has worked extensively with manufacturers and laboratories around the world, providing hands-on support and practical training for a wide range of cutting, grinding, and sample preparation applications.
Fluent in both English and Spanish, Carlos is known for his ability to translate complex tooling concepts into clear, actionable procedures for engineers, technicians, and production staff. His approach emphasizes real-world process improvement, tool longevity, and operator education—ensuring clients get the most out of their diamond tooling investments.
As an author, Mr. Sanchez shares field-tested insights on tool performance optimization, defect prevention, training methodologies, and troubleshooting common cutting issues.