Table of Contents
ToggleShare this Article with Friend or Colleague
Choosing the right blade diamond or cbn blade can significantly impact efficiency, cost, and quality. However, this is not simple and clear cut process. Selecting the optimal blade involves navigating a complex landscape of trade-offs, where factors such as cutting speed, surface finish, blade longevity, and cost must be carefully balanced. This article explores the critical performance trade-offs associated with diamond and CBN blades, providing insights to help you make informed decisions that align with your specific cutting requirements and operational goals. Understanding these trade-offs is essential for optimizing your processes, enhancing productivity, and achieving superior results in your cutting applications.
Table Showing Interrelationship & Tradeoffs
Variables Compared |
Importance |
Interrelationships and Trade-offs |
---|---|---|
Cutting Speed vs. Surface Finish |
Cutting speed affects how quickly a blade cuts through material but can impact the quality of finish. |
Higher speeds can decrease surface quality due to increased heat and vibration, requiring a balance to achieve optimal results. |
Quality / Longevity vs. Price |
Higher quality and longer-lasting blades cost more but provide better long-term value. |
Investing in high-quality blades reduces long-term costs by decreasing replacement frequency and improving performance. |
Cutting Speed vs. Life |
Higher cutting speeds can reduce blade life due to increased wear and tear. |
A balance must be found between speed and blade durability to optimize both productivity and cost-effectiveness. |
Surface Finish vs. Blade Price |
The price of the blade can influence the achievable surface finish. |
Higher-priced blades often yield a finer finish due to better materials and technology, but at an increased cost. |
Cutting Speed vs. Blade Price |
Faster cutting speeds may require more expensive blades capable of handling higher stresses. |
Blades designed for high speeds typically cost more due to advanced materials and engineering, impacting overall budget. |
Surface Finish vs. Blade Life |
The pursuit of an excellent surface finish can affect how long a blade lasts. |
Blades that offer finer finishes may wear out quicker, especially if not matched properly with the material and cutting parameters. |
Quality & Blade Life vs. Price |
The better the quality and the longer the life expectancy of a blade, the higher the price. |
Investing in higher-quality blades that last longer can be cost-effective over time, despite a higher initial price. |
Feed Rate vs. Blade Life |
The speed at which material is fed to the blade impacts how quickly the blade wears out. |
Higher feed rates generally increase blade wear, reducing lifespan, while lower rates extend life but may reduce efficiency. |
Feed Rate vs. Cutting Speed |
Feed rate and cutting speed together determine the cutting efficiency and blade stress. |
Optimal synchronization of feed rate and cutting speed is essential to maximize efficiency and minimize blade wear. |
Cutting Speed vs. Surface Finish
When selecting diamond and cubic boron nitride (CBN) blades for cutting applications, understanding the relationship between cutting speed and surface finish is essential. This balance directly influences the quality of the cut, diamond &cbn blade longevity, and overall efficiency of the cutting process. While high-speed cutting is often associated with increased productivity, it does not always guarantee the best surface finish. Here, we delve into the intricacies of how cutting speed affects surface finish and the factors that must be considered to achieve optimal results.
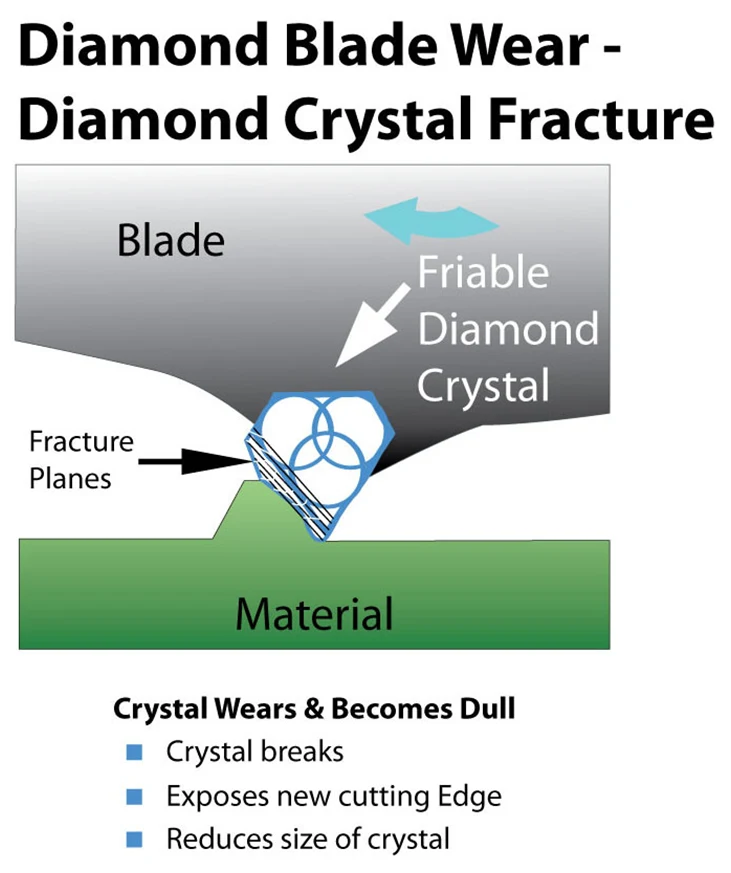
High-speed cutting offers several advantages, such as increased productivity by allowing faster material removal, reduced cutting forces, and improved chip evacuation. However, these benefits come with significant challenges. One of the primary challenges is the generation of excessive heat. This heat can adversely affect the surface integrity of the material, leading to thermal damage, micro-cracks, and undesirable changes in the material’s properties. Additionally, high speeds can cause vibrations and chatter, resulting in a rougher surface finish. This is particularly critical in applications requiring precision and smooth surfaces, such as in the optics, ceramics, composites, and semiconductor industries. Moreover, elevated temperatures can accelerate the blade diamond or cbn section wear, reducing the lifespan of the blade and increasing the frequency of blade changes, which can offset the productivity gains.
To optimize cutting speed for a superior surface finish, several factors need to be considered. The properties of the material being cut, including its thermal conductivity, hardness, and toughness, play a significant role in determining the optimal cutting speed. For instance, materials with low thermal conductivity are more susceptible to thermal damage at high speeds. The thickness of the material also affects the cutting speed; thicker materials may require slower speeds to ensure heat dissipation and maintain surface integrity.
The composition and bond matrixof diamond and CBN blades also affect their performance at various speeds. Blades with a softer bond matrix may wear faster at high speeds, compromising the surface finish. Additionally, the design of the blade, including the diamond or cbn grit size and concentration, influences the cutting dynamics. Finer grit sizes can provide better surface finishes but may require slower speeds to avoid rapid wear.
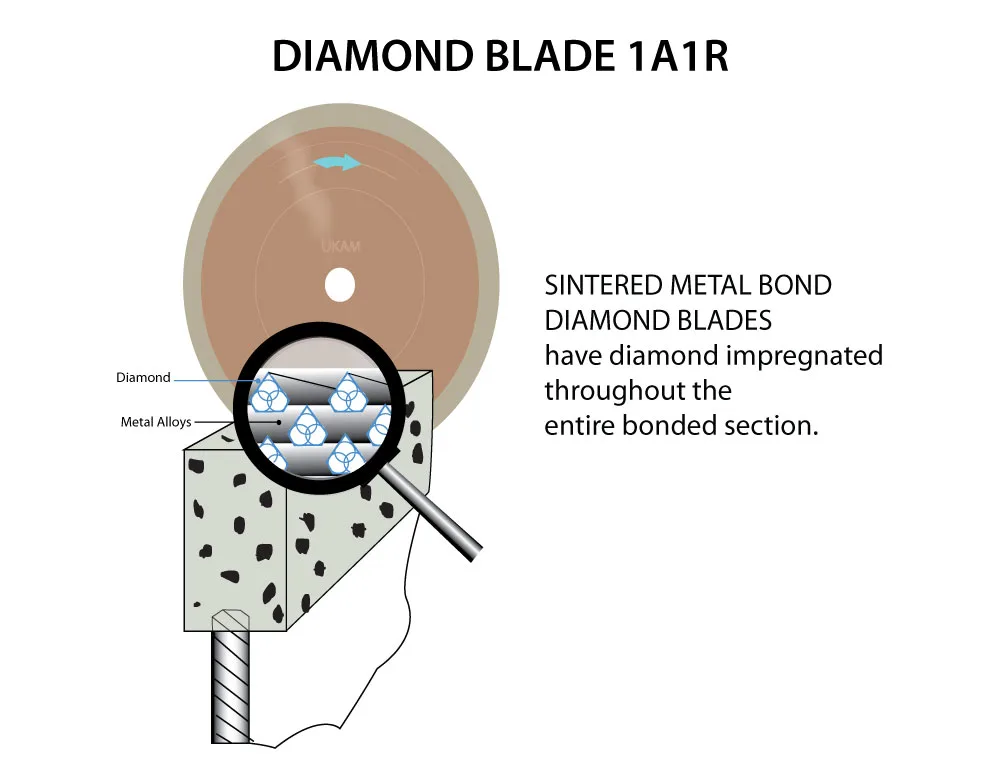
Diamond & CBN Grit Size
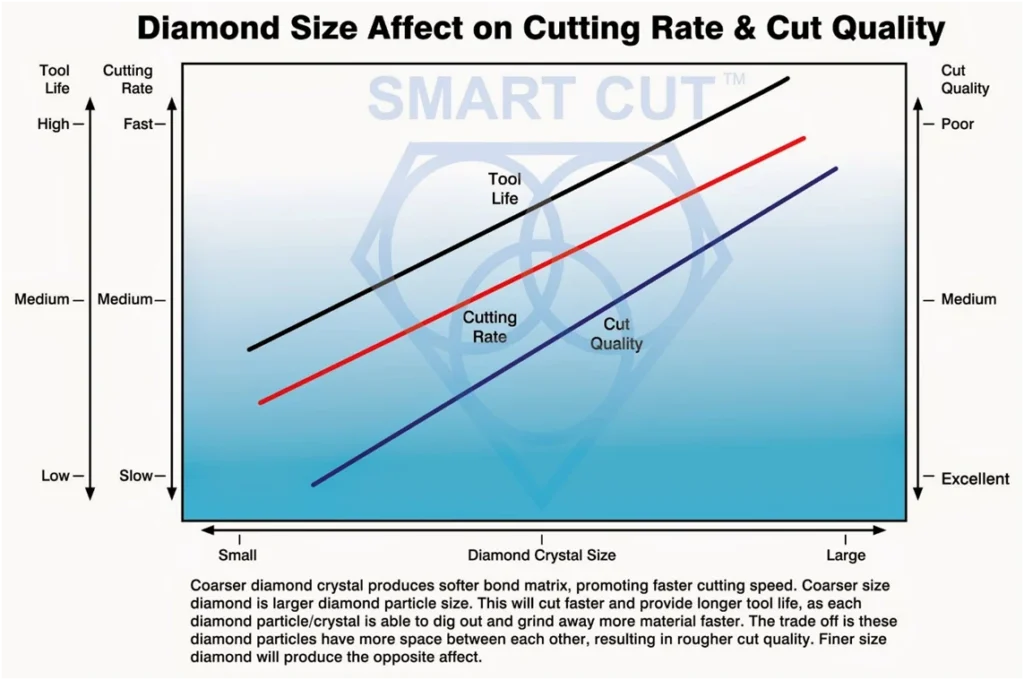
The illustration above shows how diamond or cbn grit size influences performance of diamond or cbn cutting blades in terms of tool life, cutting rate, and cut quality. As the diamond crystal size increases, so does the cutting blade life. Larger diamond particles are typically set in a softer bond matrix, which facilitates their longevity by allowing worn diamonds to be easily replaced. This feature is especially valuable in prolonged cutting tasks or when dealing with very hard materials where frequent blade replacement would be impractical.
Simultaneously, the cutting rate is improved with the use of larger diamond or cbn particles. These coarser diamonds or cbn particles remove more material per pass because of their larger cutting surfaces, thus boosting productivity. However, achieving a balance between cutting speed and the nature of the material, along with the desired finish, is crucial to prevent excessive wear or damage.
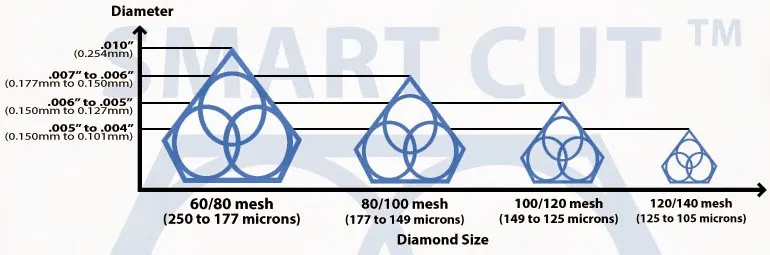
Conversely, the quality of the cut declines as the size of the diamond or cbn crystals increases. While larger diamonds or cbn particles expedite the cutting process, they also create a rougher finish due to the larger gaps between the diamonds or cbn particles, resulting in a less smooth cut surface. This aspect is particularly significant when a high-quality, fine finish is required.
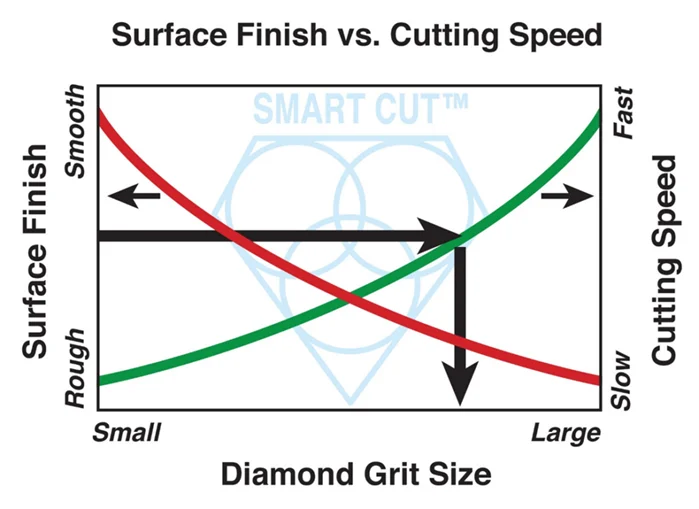
The red line in the chart shows that as the diamond grit size increases, the cutting speed decreases. This is because larger diamond particles cut more aggressively, but the overall speed is reduced due to the increased effort required to push larger particles through the material.
Conversely, the green line illustrates that a smaller diamond grit size leads to a smoother surface finish. Smaller particles create less disturbance in the material as they pass through, leading to finer cuts. This results in a smoother finish on the material being cut.
This chart is essential for understanding the trade-offs between cutting speed and surface finish when selecting a diamond or CBN blade. If the priority is to achieve a fine, smooth finish, a blade with a smaller grit size would be preferable, even though it may cut more slowly. On the other hand, if speed is more critical and a rougher finish is acceptable, a blade with a larger grit size would be more suitable. This information helps users choose the right blade based on their specific needs, balancing efficiency with quality of the final product.
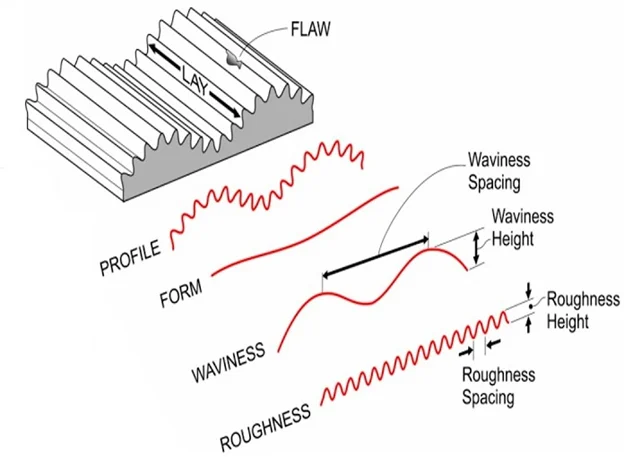

Diamond & CBN Concentration
When the concentration of diamond or cbn particles in a diamond or cbn cutting blade is increased, the cutting blade life becomes longer. This happens because a higher diamond or cbn concentration means there are more abrasive particles embedded within a tougher bond matrix, which improves the durability of the diamond or cbn cut off blade matrix
As more diamond or cbn particles are packed into the blade bond matrix, the cutting rate actually decreases. This is because densely packed diamonds or cbn particles hinder the blades ability to remove material quickly; they don't cut as aggressively due to less space between each diamond or cbn particles.
However, an increased diamond or cbn concentration improves the cut quality. With more diamond or cbn particles, the cutting blade interacts with the material more finely and uniformly, resulting in smoother and more precise cuts. This is beneficial for tasks requiring high accuracy and fine finishes.
Additionally, diamond &cbncutting blades with a higher diamond or cbn concentration require less frequent dressing—the process of cleaning and reshaping the tool to maintain its effectiveness. This reduced need for dressing arises because the blade cutting edge maintains its optimal shape for a longer period, thanks to the robust structure provided by the densely packed diamond or cbn particles.
In the diagram, as the diamond concentration in a blade decreases, the cutting speed increases, as illustrated by the red line. This implies that blades with a lower concentration of diamonds can achieve faster cutting speeds. This is likely because there are fewer diamond particles to create friction and resistance, allowing the blade to move through the material more quickly.
On the other hand, the green line shows that the cutting ratio improves with higher diamond concentration. The cutting ratio here refers to the efficiency of the blade in terms of the amount of material removed relative to the wear on the blade itself. A higher diamond concentration means that the workload is distributed among more diamonds, reducing the wear on individual particles and enhancing the overall efficiency and longevity of the blade.
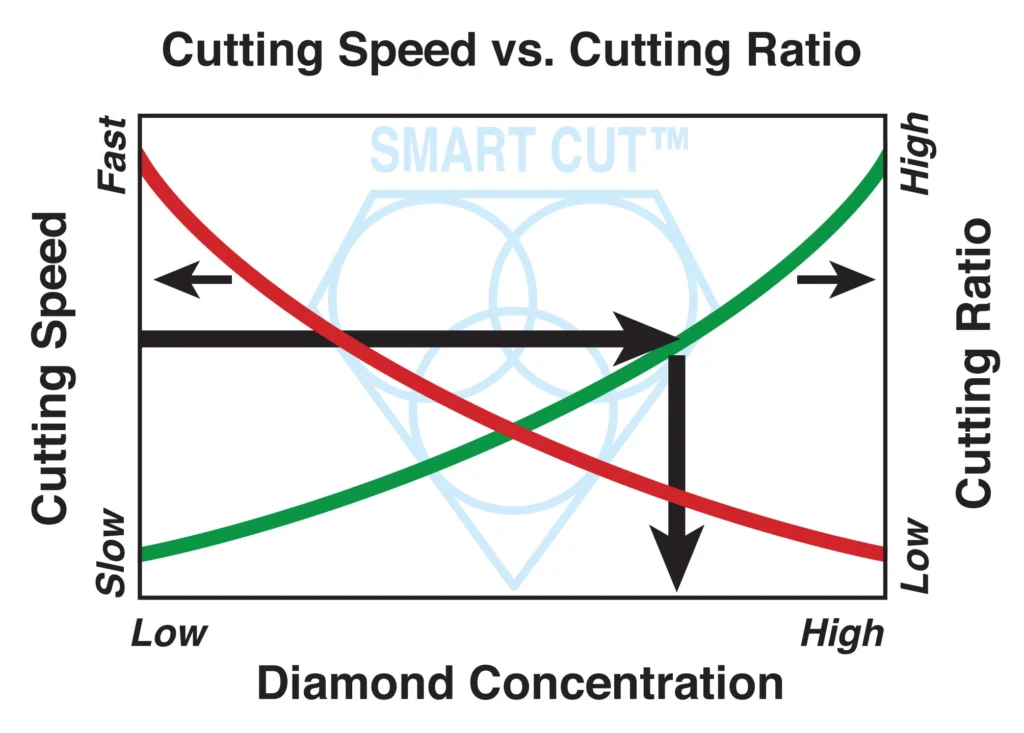
This chart is crucial for users who need to select the right type of diamond or CBN blade for specific applications. If the priority is to maximize cutting speed, choosing a blade with a lower diamond concentration might be beneficial, especially for quick, rough cuts. Conversely, for operations where blade longevity and material removal efficiency are more critical, a blade with a higher diamond concentration would be more appropriate. Understanding these dynamics helps in making informed decisions to balance cutting speed and efficiency based on the specific needs of the cutting task.
Cooling and lubrication are critical in mitigating the heat generated during high-speed cutting. The use of coolants helps maintain lower temperatures, protecting the surface finish and extending tool life. Adequate lubrication reduces friction and assists in chip removal, contributing to a smoother surface finish.
The feed rate must be carefully controlled in conjunction with cutting speed. A higher feed rate at high speeds can exacerbate surface roughness, while a lower feed rate can help achieve a better finish. Similarly, shallow cuts at high speeds can minimize heat build-up and maintain surface quality, whereas deeper cuts may necessitate slower speeds to prevent thermal damage.
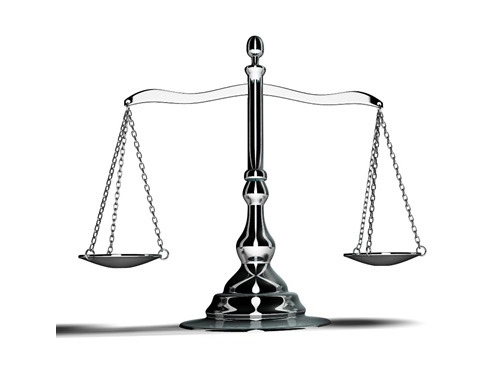
A balanced approach to cutting speed, considering the material, blade characteristics, and cooling/lubrication strategies, is crucial. Often, a moderate cutting speed, optimized for the specific application, provides the best compromise between productivity and surface finish. Regular testing and calibration of cutting parameters are essential. Adjustments based on real-time feedback and surface finish inspections can help in fine-tuning the process for optimal results. Employing advanced cutting technologies, such as adaptive control systems that automatically adjust cutting speeds based on real-time data, can enhance both efficiency and surface finish quality.
Quality & Blade Life vs. Price
Higher-quality diamond and cubic boron nitride (CBN) cutting blades generally come at a higher price, but the investment in premium quality blades can often be justified through their numerous advantages. The foremost benefit of using high-quality blades lies in their ability to produce superior results consistently. These blades are manufactured with advanced materials and precise engineering, ensuring butter cut quality, minimum to no chipping and higher level of accuracy and repetability. This level of performance is more crucial in industries such as semiconductor manufacturing, optics, and advanced ceramics, where even minor imperfections can lead to significant issues.
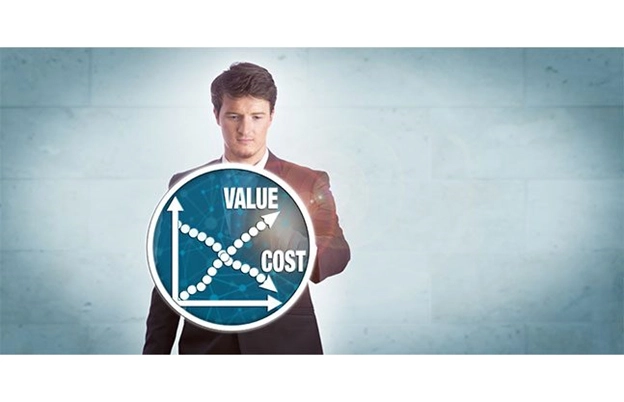
Also, high-quality diamond &cbn blades contribute to reduced waste. Lower-quality blades tend to wear out quickly, leading to frequent replacements and higher material wastage due to inconsistent cuts and defects. In contrast, premium blades maintain their cutting edge for extended periods, resulting in consistent performance and minimizing material loss. This reduction in waste not only conserves valuable materials but also translates into substantial cost savings over time, as fewer blades need to be replaced.
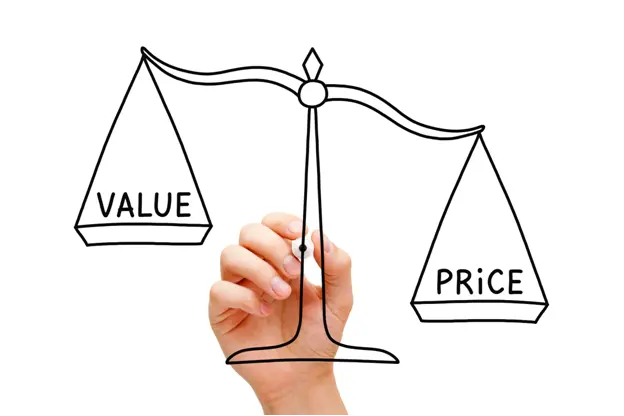
Additionally, the use of high-quality cutting blades can significantly decrease the need for secondary finishing processes. Inferior blades often leave rough surfaces, burrs, or other imperfections that require additional finishing steps, such as grinding, polishing, or deburring. These secondary processes add time and labor costs to the production cycle. High Quality diamond and CBN blades produce smoother finishes from the outset, reducing the need for these extra steps and streamlining the production process. This enhancement in efficiency further justifies the investment in high quality diamond &cbn blades.
Another factor to consider is the extended blade life of high quality diamond &cbn cutting blades. Although the initial cost may be higher, the longevity of these blades can offset the initial investment. High-quality blades are designed to endure rigorous use and maintain their performance over a longer duration, reducing the frequency of tool changes and associated downtime. This durability translates into higher productivity and lower operational costs over time. The consistent performance of these blades also ensures that production schedules are not disrupted by unexpected diamond &cbn blade failures or the need for frequent adjustments.
Reliability and consistency are additional advantages of high-quality cutting blades. Premium tools undergo stringent quality control measures during manufacturing, ensuring that each blade meets exacting standards. This reliability results in predictable and repeatable performance, which is critical for maintaining tight tolerances and achieving high-quality outputs. In industries where precision and reliability are essential, the cost of using inferior tools can far outweigh the savings on initial purchase prices.
When evaluating the cost of diamond &cbn cutting blades / wheels, it is essential to consider the total cost of ownership rather than just the initial purchase price. The total cost of ownership includes the price of the tool, its lifespan, performance consistency, maintenance requirements, and the impact on overall production efficiency. High-quality diamond &cbn blades, despite being more expensive upfront, often prove to be more cost-effective over their lifespan due to their superior performance and durability. This comprehensive approach to cost evaluation provides a more accurate picture of the true value of high quality diamond &cbn blades .
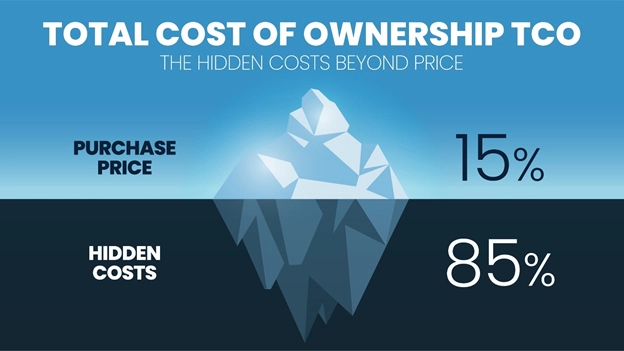
Cutting Speed vs. Blade Life
Higher cutting speeds in the use of diamond and cubic boron nitride (CBN) cutting blades can lead to increased productivity, but this advantage often comes with trade-offs, particularly regarding the life span of the diamond &cbn blades. The relationship between cutting speed and diamond &cbn blade life is a critical factor that must be carefully managed to optimize both efficiency and cost-effectiveness in manufacturing processes.
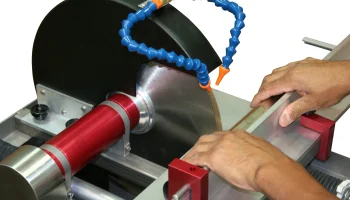
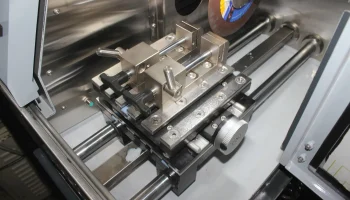
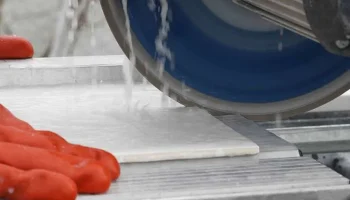
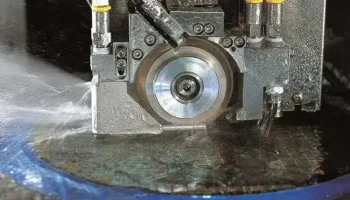
Operating at higher cutting speeds allows for faster material removal, which can significantly enhance production rates. This increased efficiency can be especially beneficial in high-volume manufacturing settings where time savings directly translate into greater throughput and reduced operational costs. Additionally, high-speed cutting can improve chip evacuation, reducing the likelihood of clogging and helping to maintain a cleaner cutting environment.
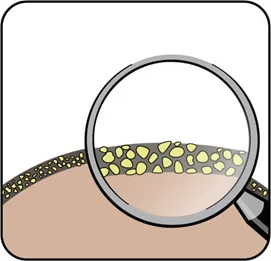
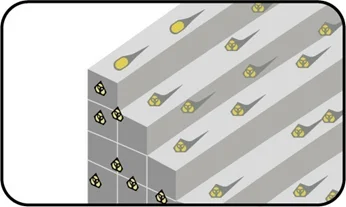
However, the primary downside of higher cutting speeds is the accelerated wear and tear on the diamond &cbn cutting blades. The increased friction and heat generated at higher speeds can lead to rapid degradation of the blade's cutting edge. This wear can manifest in various forms, including micro-fractures, chipping, and general dulling of the blade, all of which reduce the tool's effective life span. As a result, blades used at high speeds often require more frequent replacement, which can negate the initial productivity gains by increasing the cost and downtime associated with tool changes.
Heat management becomes a crucial aspect when operating at high speeds. Excessive heat can not only damage the cutting blade but also adversely affect the material being cut, potentially leading to thermal damage, surface cracks, and other imperfections. Effective use of coolants and lubricants is essential to mitigate these effects, helping to dissipate heat and reduce friction. However, even with optimal cooling strategies, the inherent increase in wear at higher speeds cannot be entirely eliminated.
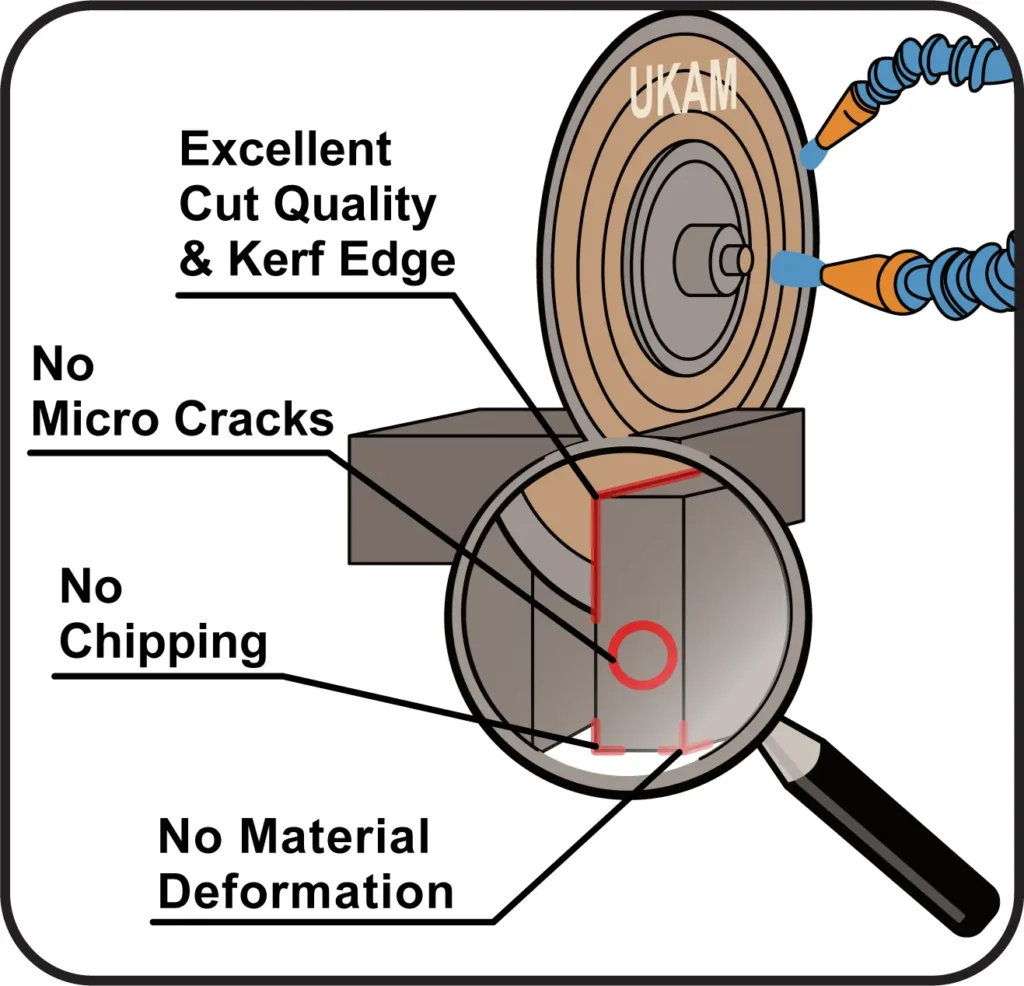
Also, higher cutting speeds can impact the consistency and quality of the cut. The increased thermal and mechanical stresses can lead to variations in cut dimensions, surface finish, and overall part quality. These inconsistencies can be particularly problematic in industries that require high precision, such as aerospace, medical device manufacturing, and advanced electronics.
To balance cutting speed and diamond &cbn cutting blade life effectively, it is essential to consider the specific requirements of the application, including the material properties, desired cut quality, and volume of use. In many cases, a moderate cutting speed may offer the best compromise, providing a balance between productivity and tool longevity. By optimizing cutting parameters, you can achieve a sustainable approach that maximizes efficiency without incurring excessive diamond &cbn blade wear and replacement costs.
Regular monitoring and adjustment of cutting conditions are also vital. By continuously assessing diamond &cbn blade wear and performance, adjustments can be made to cutting speeds, feed rates, and cooling strategies to maintain optimal conditions. Implementing predictive maintenance and tool management systems can further enhance this process, allowing for timely interventions before significant wear-related issues arise.
Surface Finish Vs. Blade Price
The relationship between price and surface finish when selecting diamond and CBN blades is intricate, involving considerations of initial cost versus the quality of results obtained. This interrelationship reflects a fundamental economic trade-off: higher-priced blades typically offer better surface finishes but at an increased cost, while lower-priced options may often compromise finish quality but are more budget-friendly.
Higher-priced diamond and CBN blades often boast superior manufacturing quality, incorporating finer, more uniform grit sizes, better diamond distribution, higher concentrations of premium diamond or CBN particles.As well as specialized and proprietary bond formulations that often take decades to develop and improve. These features are crucial for achieving a finer surface finish, essential in precision-dependent industries. The precision in manufacturing these blades ensures that the cuts are consistent and clean, with minimal surface irregularities and defects.
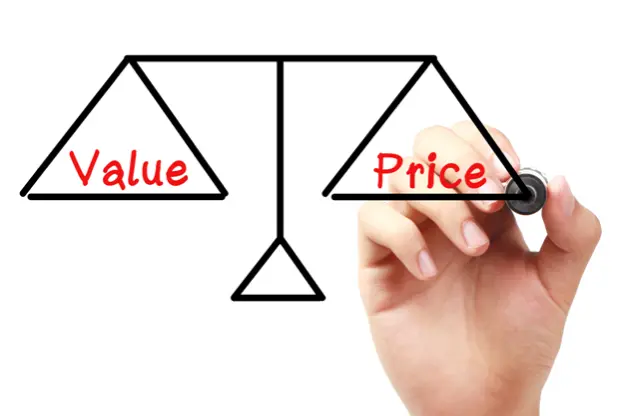
Furthermore, these blades might utilize advanced bond materials and technologies that enhance the cutting characteristics, allowing for smoother finishes that reduce or even eliminate the need for secondary finishing processes. However, the increased cost of these high-quality blades is not merely a reflection of better materials or manufacturing techniques; it also embodies the research and development efforts to optimize blade performance across various materials and cutting conditions. This investment in quality can lead to significant cost savings over time, as the need for rework or additional finishing steps is minimized. At the same time, the consistency and reliability of higher-priced blades can translate into less downtime due to blade changes or maintenance, further justifying the initial higher expenditure.
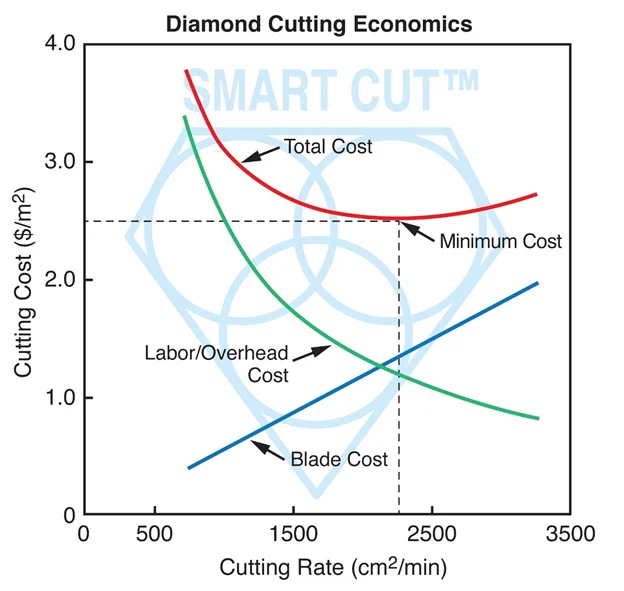
On the other hand, opting for lower-priced blades can be economically attractive, especially for operations where the highest levels of precision and finish are not critical. These blades are typically made with coarser grit, lower diamond or CBN concentrations, or less durable bond materials. Such as most tile blades or do it your self blades, while they are adequate for many standard cutting tasks, the finish they produce may be rougher, potentially necessitating additional finishing steps post-cutting. This need for further processing can inadvertently increase the total cost of operation, both in terms of time and material usage.
Moreover, the use of cheaper blades often leads to increased blade turnover rates. The less expensive materials and simpler manufacturing processes can result in blades that wear out faster, particularly when used on hard or abrasive materials. This frequent need for replacement not only adds direct costs in terms of blade purchases but also indirect costs such as machine downtime and labor for blade changes.
Deciding between higher-priced, high-quality blades and more economical options involves a careful analysis of the specific cutting requirements and the ultimate goals of the project. For applications where surface finish is paramount, the higher initial cost of premium blades can be a worthwhile investment, offering long-term benefits in terms of reduced secondary processing and lower total cost of ownership. In contrast, for less critical applications or when budget constraints are tighter, lower-priced blades might represent a more pragmatic choice, provided that the potential for increased downstream processing is factored into the overall cost assessment.
Cutting Speed vs. Blade Price
The relationship between cutting speed and blade price in the selection of diamond and CBN blades involves a complex balance, where operational efficiency must be weighed against cost effectiveness. This dynamic is characterized by the need for diamond &cbnblades that can withstand the rigors of high-speed cutting, which typically demands advanced engineering and premium materials. These high-performance blades are designed to endure the increased heat and friction associated with faster speeds, ensuring longevity and sustained performance. Consequently, these blades are priced higher due to the superior quality of materials, complex manufacturing processes, and the technology used to optimize their durability and efficiency.
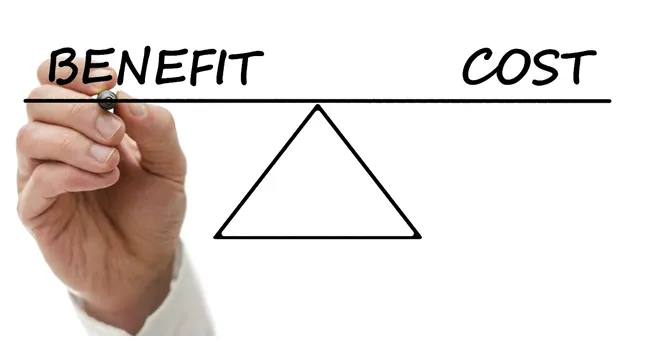
On the other hand, operating at higher speeds with less expensive (economy) blades often leads to rapid wear and degradation, limiting their practicality to lower-speed applications. Diamond or CBN Blades that are lower in price are generally made with less expensive materials and simpler manufacturing techniques, making them suitable for conditions where the cutting demands are not as severe. This makes them a more cost-effective option when high-speed cutting is not critical for productivity or when the material being cut is less challenging in terms of hardness and abrasiveness.
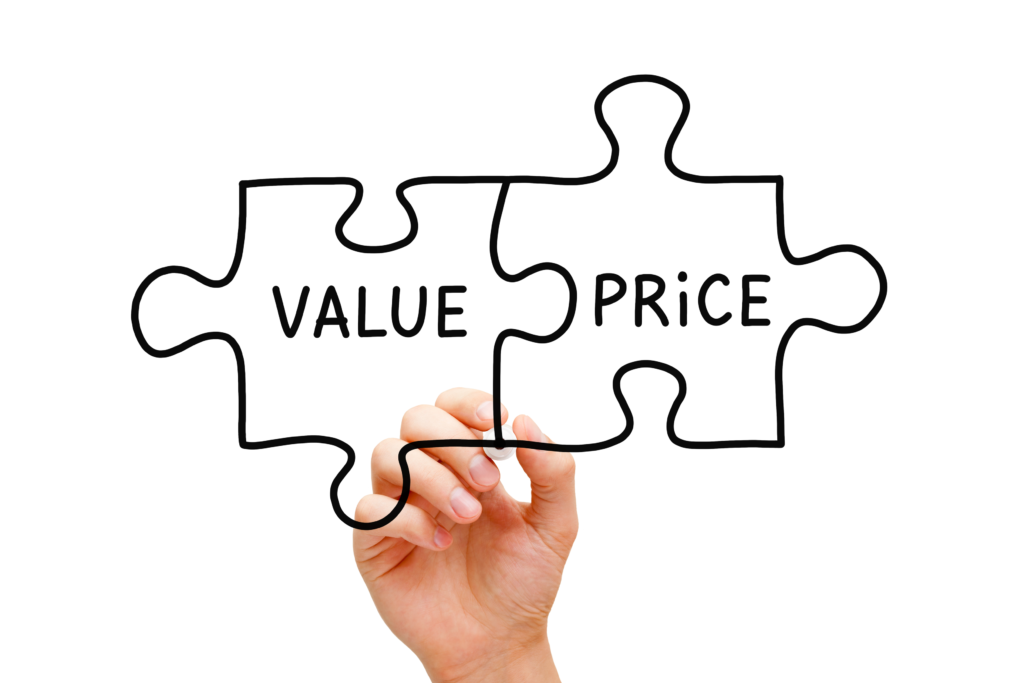
Choosing between higher speed with more expensive blades versus lower speed with more economical blades requires a strategic evaluation of production demands, material properties, and overall cost implications. The urgency and volume of production may necessitate high speeds, advocating for a higher initial investment in more costly blades. However, the choice also depends on the type of material being cut; harder or more abrasive materials may require the resilience of higher-priced blades to maintain efficiency and cut quality at increased speeds.
A thorough cost-benefit analysis is crucial in this decision-making process. The analysis should consider the long-term savings that can be achieved through increased productivity against the higher upfront costs of premium blades. This includes not only the price of the blades but also the frequency of replacements and potential downtime for blade changes.
Feed Rate vs. Blade Life
The relationship between feed rate and blade life is a crucial consideration in the context of cutting operations using diamond and CBN blades. Feed rate, which is the speed at which material is fed towards the blade, significantly impacts both the quality of the cut and the longevity of the blade itself.
When materials are fed into the blade at higher rates, the blade experiences increased stress and higher impact forces. This heightened activity can accelerate wear and potentially lead to faster degradation of the blade's cutting edges. Additionally, high feed rates tend to generate more heat and can cause frequent instances of chipping or breakage of the material, especially if the blade or setup isn't equipped to handle such speeds.
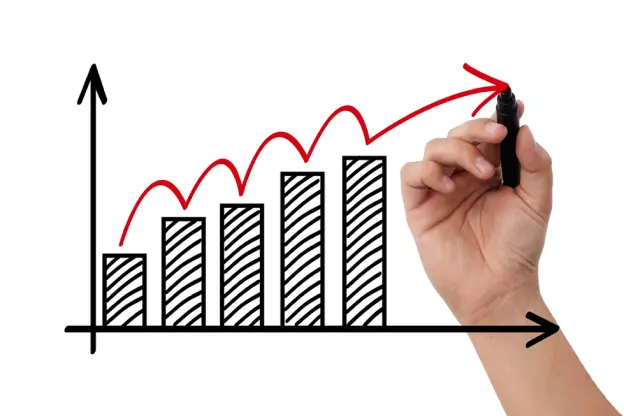
Conversely, operating at lower feed rates puts less stress on the blade, which can beneficially extend its operational life. This gentler cutting process minimizes heat generation and reduces the likelihood of blade overload, thus preserving the integrity of the cutting edge. However, if the feed rate is too low, it can lead to underutilization of the blade's capabilities, reducing operational efficiency and potentially increasing the time and cost per cut.
Finding the right balance in feed rate is essential for maximizing blade life while maintaining efficiency. It involves a careful analysis of the blade's capabilities, the properties of the material being cut, and the specific demands of the cutting application. For example, harder materials might necessitate slower feed rates to minimize wear on the blade, while softer materials might be processed faster without significantly impacting blade life.
Feed Rate vs. Cutting Speed
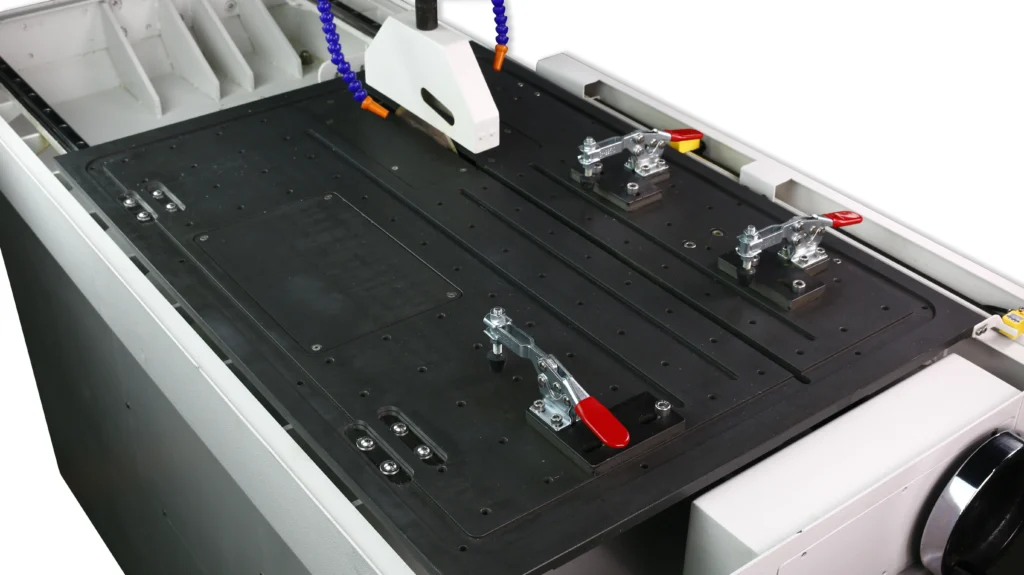
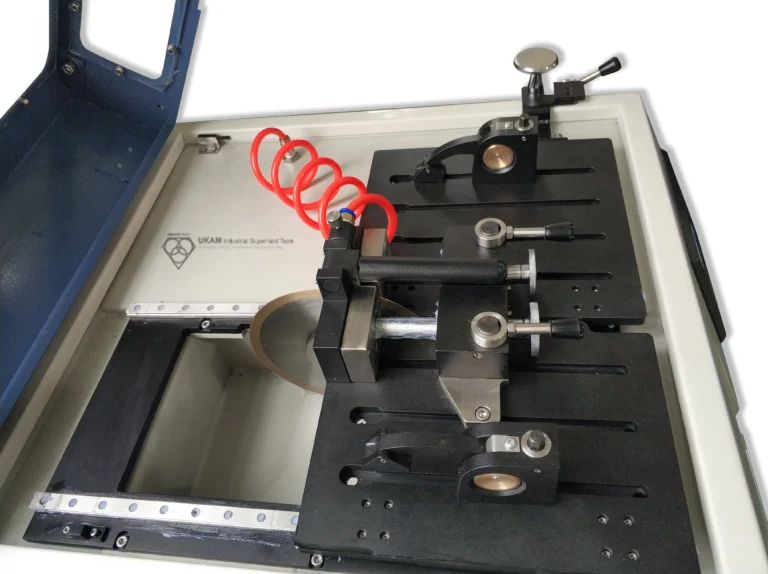
The relationship between feed rate and cutting speed is pivotal in optimizing the performance of cutting operations, particularly when using advanced tools like diamond and CBN blades. Both feed rate and cutting speed need to be carefully balanced to achieve optimal cutting efficiency, quality, and tool life.
Feed rate—the speed at which the workpiece is fed into the blade—directly influences the amount of material removed per pass and the stress exerted on both the blade and the material. Higher feed rates generally increase the rate of material removal, but they also put greater stress on the blade, potentially leading to quicker wear and deterioration of the tool. Moreover, pushing the blade harder into the material can result in undesirable effects such as increased heat generation, greater mechanical stress, and potential for chipping or cracking the workpiece, especially in brittle materials.
Cutting speed, on the other hand, refers to the speed at which the blade itself moves through the material. Higher cutting speeds can lead to more efficient cutting by reducing the time taken per cut, enhancing productivity. However, just like with high feed rates, increased cutting speeds can elevate temperatures at the cutting zone, which might affect the material's integrity and the blade’s lifespan due to thermal and mechanical stresses.
Balancing these two parameters is critical. If the feed rate is too high relative to the cutting speed, the blade might be subjected to excessive load, leading to premature wear or failure. Conversely, if the cutting speed is too high for a given feed rate, the blade may not effectively remove material, possibly glazing over or burning the material rather than cutting cleanly through it. This imbalance can also lead to suboptimal cuts, with issues in surface finish and dimensional accuracy.
Achieving the right combination of feed rate and cutting speed depends largely on the material being cut, the type of blade used, and the desired outcome of the cut. Softer materials may allow for higher feed rates and cutting speeds without as much wear on the blade, whereas harder materials might require more moderate speeds to avoid blade damage and achieve a quality finish.
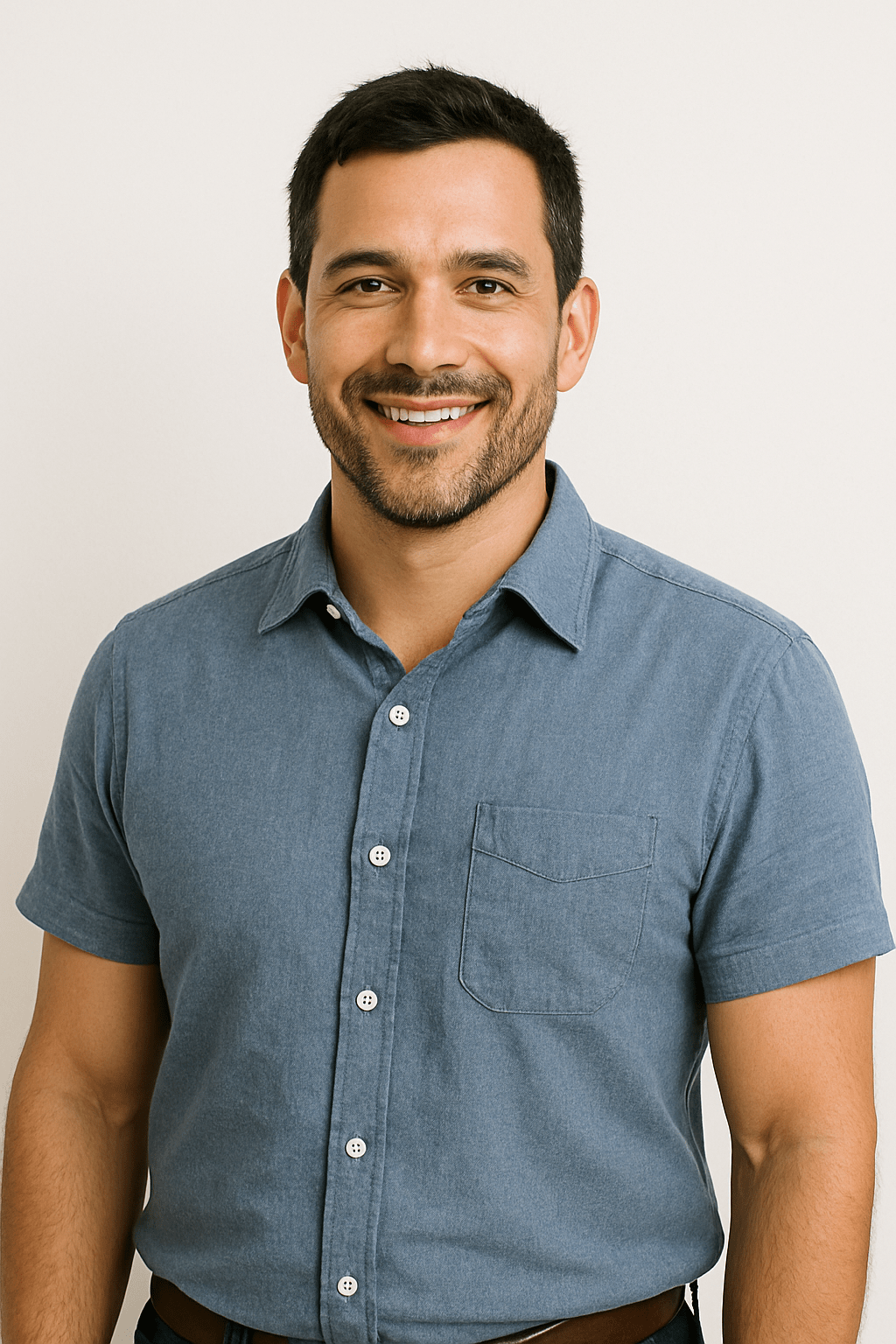
Carlos Sanchez is a senior technical specialist and field applications trainer with more than 17 years of experience in the use and optimization of industrial diamond tools, including ultra-thin diamond blades, core drills, and CBN grinding wheels. With a foundation in industrial engineering and technical operations, Mr. Sanchez has worked extensively with manufacturers and laboratories around the world, providing hands-on support and practical training for a wide range of cutting, grinding, and sample preparation applications.
Fluent in both English and Spanish, Carlos is known for his ability to translate complex tooling concepts into clear, actionable procedures for engineers, technicians, and production staff. His approach emphasizes real-world process improvement, tool longevity, and operator education—ensuring clients get the most out of their diamond tooling investments.
As an author, Mr. Sanchez shares field-tested insights on tool performance optimization, defect prevention, training methodologies, and troubleshooting common cutting issues.
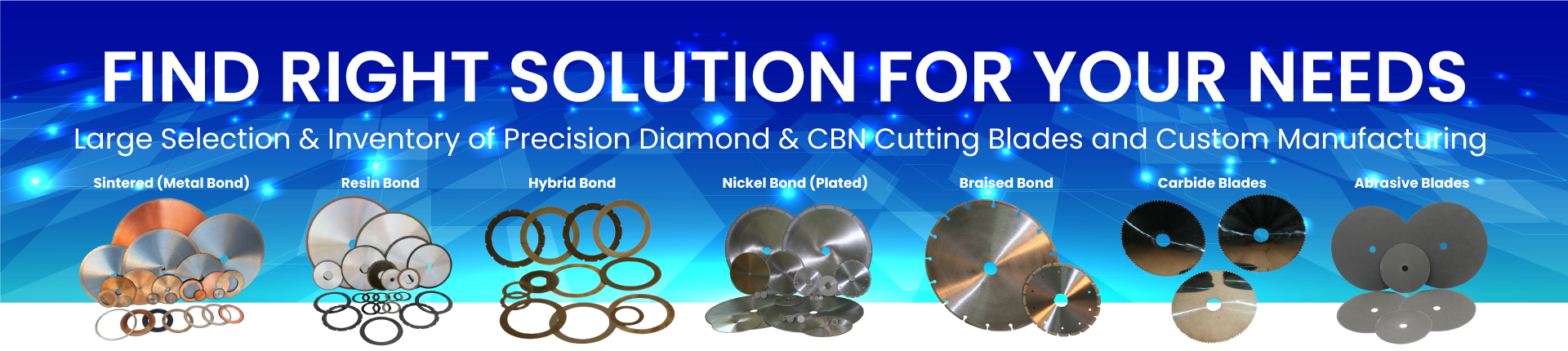
Knowledge Center
Select right Diamond Blade for your application
How to Properly Use Precision Diamond & CBN Blades
Precision & Ultra Thin Diamond Blade Guide
How to Improve & Optimize Your Diamond Sawing Operation
Evaluating & Comparing Diamond Blades
Top 5 Diamond & CBN Cutting Blade Performance Metrics
Diamond & CBN Cutting Blade Performance Metrics that you Should Know
Total Cost of Ownership & Why its Important
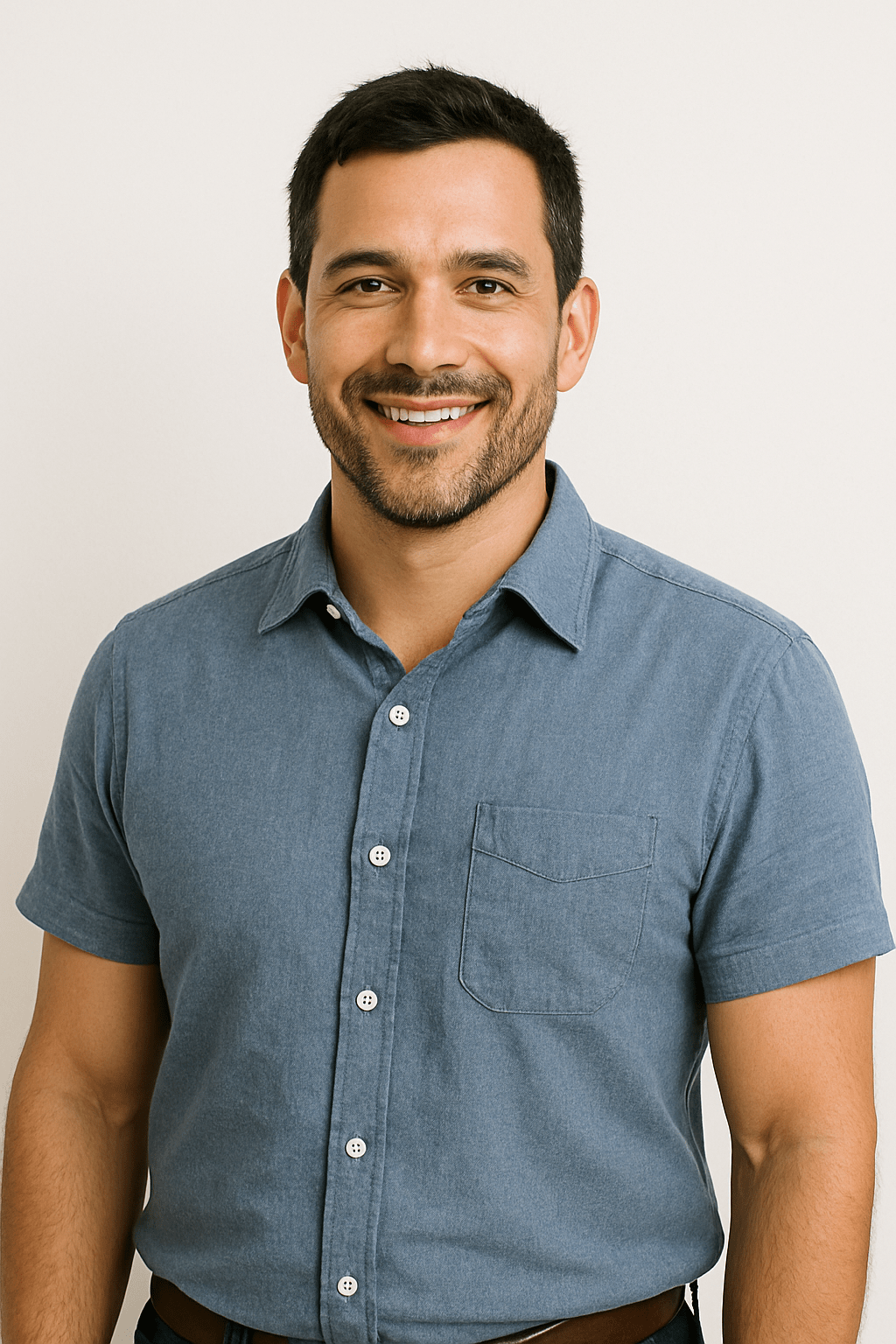
Carlos Sanchez is a senior technical specialist and field applications trainer with more than 17 years of experience in the use and optimization of industrial diamond tools, including ultra-thin diamond blades, core drills, and CBN grinding wheels. With a foundation in industrial engineering and technical operations, Mr. Sanchez has worked extensively with manufacturers and laboratories around the world, providing hands-on support and practical training for a wide range of cutting, grinding, and sample preparation applications.
Fluent in both English and Spanish, Carlos is known for his ability to translate complex tooling concepts into clear, actionable procedures for engineers, technicians, and production staff. His approach emphasizes real-world process improvement, tool longevity, and operator education—ensuring clients get the most out of their diamond tooling investments.
As an author, Mr. Sanchez shares field-tested insights on tool performance optimization, defect prevention, training methodologies, and troubleshooting common cutting issues.