Table of Contents
ToggleDiamond wafering blades are designed for sectioning a large variety of materials and sample types. In order to identify the best diamond wafering blade for your specific material/application, we have implemented a grading system that spans diamond mesh/particle sizes from 5 (the finest) to 30 (the coarsest). This scale helps users select the appropriate blade for their specific sectioning requirements. A blade designated as number 10, for instance, will feature larger diamond particles than one rated at No. 5; however, the increase in particle size is not directly proportional, meaning they are not simply twice as large. Furthermore, we have provided cross-references to Buehler, Struers, and Leco part numbers, allowing you to easily find the equivalent diamond or CBN wafering blade for your needs.
The choice of diamond or cbn particle size is important because it directly influences the amount of deformation during the sectioning operation. Typically, the smaller the diamond particles or crystals, the lesser the deformation observed in the cut section. This is particularly beneficial when amount of material deformation is important and the integrity of the section must be maintained. Smaller diamond particles ensure a smoother cut with finer surface finish and no to minimum chipping, making them ideal for delicate or precision-sensitive samples / materials.
There is an optimal blade series for every application. Optimal Blade series is point where:
BEST CUT QUALITY, LEAST AMOUNT OF MATERIAL DEFORMATION, AND FASTEST CUTTING RATE MEET TOGETHER
There is a trade off between the three variables. Optimum Performance is typically somewhere in the middle
Smaller Wafering Blade Series
will produce much finer finish, however at cost of much slower cutting speed. Too fine blade series can do more harm then good as the diamond crystals will be too small to dig out the amount of material necessary and as result glaze over. Causing more material deformation and poor overall performance.
Larger Wafering Blade Series
will cut much faster but provide rougher finish and more material deformation. Requiring additional time spent of secondary steps such as grinding and polishing.
Nevertheless, the optimal particle size also depends on the characteristics of the material being sectioned. Some materials, such as those that are particularly hard or abrasive, necessitate the use of larger diamond particles. Using finer diamond particles in such cases would not only be uneconomical but could also result in excessive wafering blade wear, heat generation and undesirable material deformation. Larger particles are more effective at reducing the cutting load per diamond crystal, thereby minimizing premature wear and enhancing the blade's lifespan.
However when selecting the right diamond particle size for your application, you should also consider the speed and quality of the cut. Larger diamond or cbn particles might accelerate the sectioning process, especially in less delicate applications, thereby offering a balance between efficiency and cost. However, for very delicate and sensitive applications where minimal surface damage and excellent cut quality are required, finer particles are preferable despite their potentially slower cutting speeds.
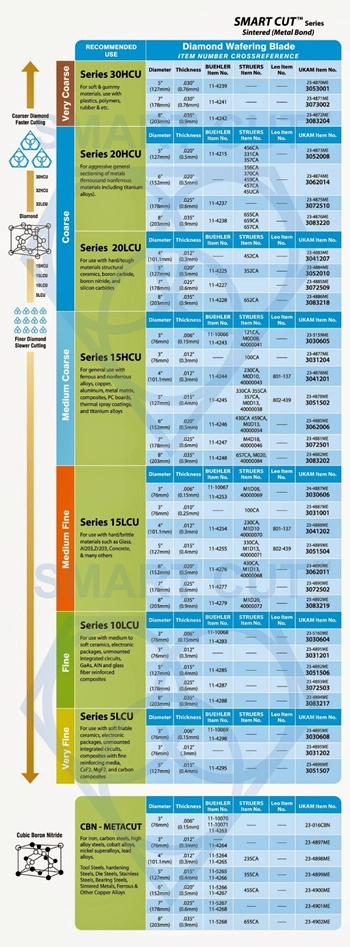
Series 30HCU
High Concentration/Very Coarse for Soft & Gummy Materials
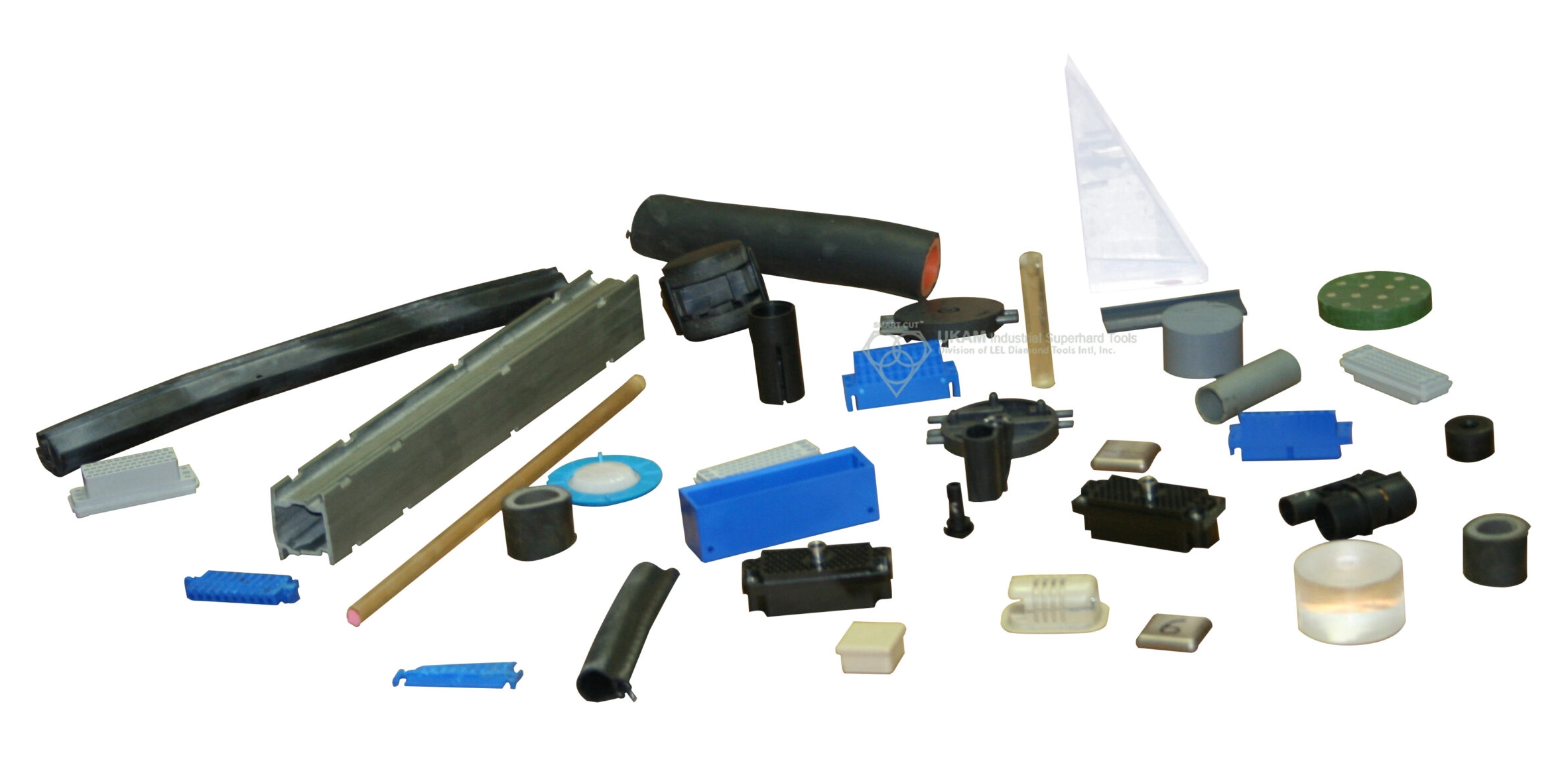
Series 30HCU diamond wafering blades are tailored for cutting soft and gummy materials, including plastics, polymers, rubber, and similar substances. The high concentration of larger diamond particles enhances the blade's efficiency in cutting materials that might clog or gum other types of blades. It's designed to reduce blade loading and improve swarf removal, ensuring cleaner cuts and longer blade life.
The high concentration of larger diamond particles is a key feature of the Series 30HCU. This design ensures that the cutting edge remains sharp and efficient, capable of penetrating soft materials without the excessive force that typically causes deformation or displacement of the material. The larger diamonds act as robust cutting points that slice through the material, minimizing the amount of material that adheres to the blade itself.
Example of Application:
-
Plastics: This includes a broad range of plastics from thermoplastics like polyethylene and polypropylene to thermosetting plastics such as phenolic resins and epoxies. Plastics that are particularly soft or have a low melting point are ideal candidates for this blade series.
-
Polymers: Similar to plastics but often referring to materials used in more specialized applications, such as polytetrafluoroethylene (PTFE), polyvinyl chloride (PVC), and other similar materials used in both consumer products and industrial applications.
-
Rubber: All types of natural and synthetic rubber, including silicone rubber, neoprene, nitrile rubber, and butyl rubber. These materials require precise cuts to maintain the integrity of the material structure.
-
Elastomers: Materials that exhibit elastic properties similar to those of rubbers, used in various industrial sealing and cushioning applications.
-
Foam: Both open-cell and closed-cell foams, which might be used in automotive, aerospace, or consumer goods for insulation, padding, or structural support.
-
Composite materials: Specifically, those that include a polymer matrix combined with various fibers like glass or carbon. While some composites are very tough and require different blade types, those with a softer matrix are suitable for the Series 30HCU.
-
Fiberglass: Especially in forms where the fiberglass is embedded in a resin that is relatively soft and can be cut without damaging the glass fibers.
-
Resins and adhesives: Various types of resins that are uncured or partially cured can be cut using these blades, as well as adhesives that might need to be sectioned for quality control or analysis.
-
Synthetic gels: Various types of hydrogels and other soft, gel-like materials often used in medical devices and consumer products.
-
Tissue samples: In biomedical or research contexts where soft tissue samples need to be sectioned without significant deformation.
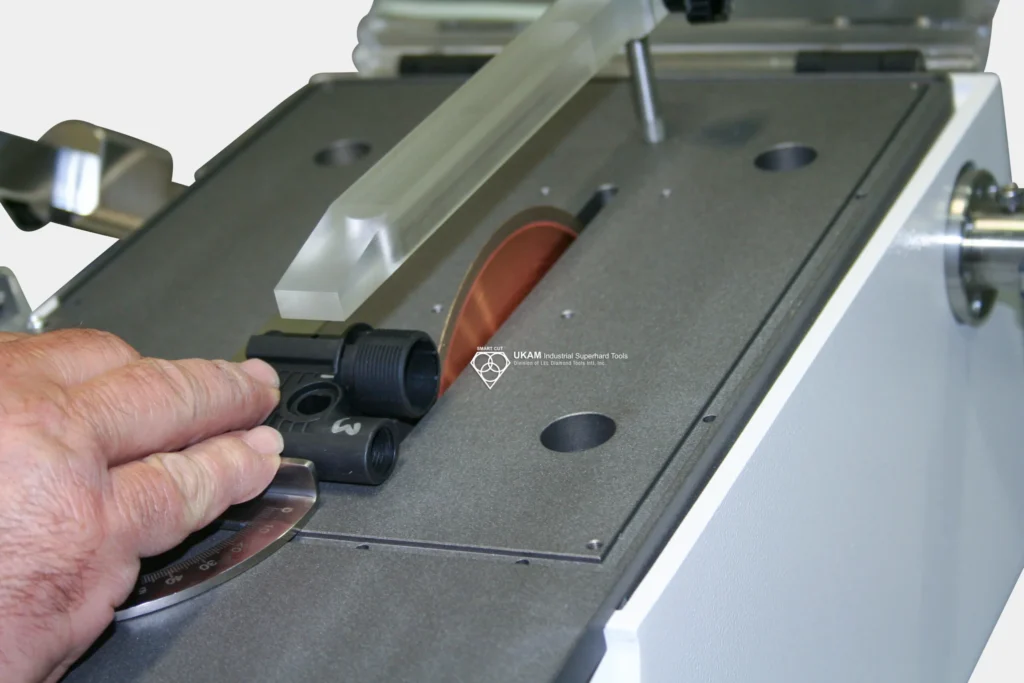
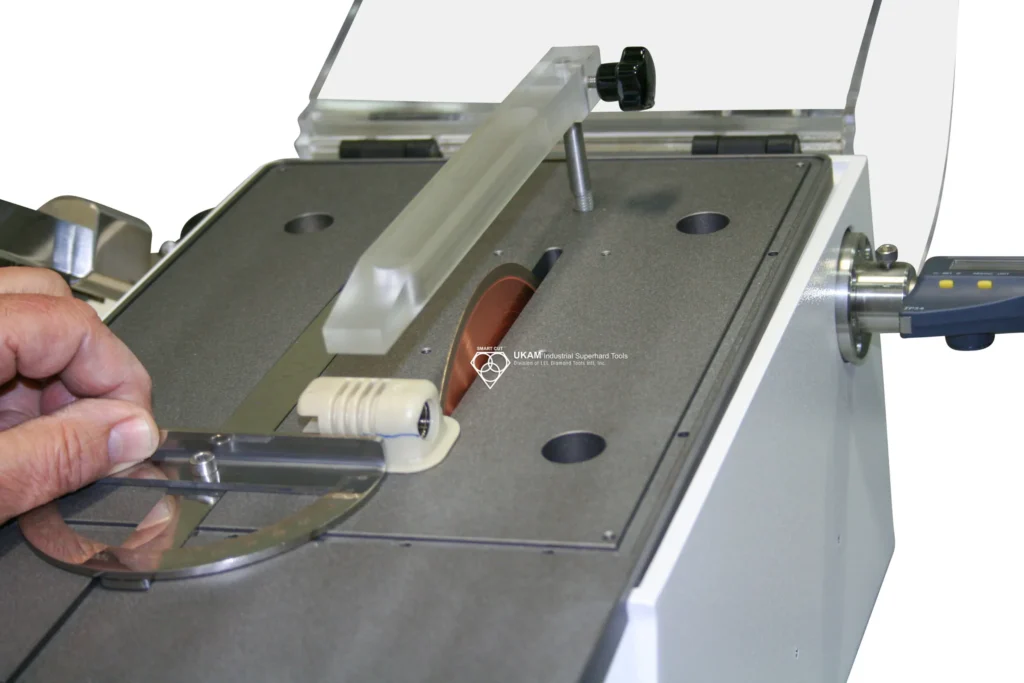
Medium to High Speed Laboratory Saw - Recommended Settings
RPM, feed rate, coolant type, and additional considerations for sectioning these materials for metallography and sample preparation on a laboratory precision cutting saw with a 6" diameter blade:
Material |
Recommended RPM |
Feed Rate (in/min) |
Coolant Type |
Additional Considerations |
---|---|---|---|---|
Plastics (Polyethylene, Polypropylene) |
1500 - 2000 |
0.7 - 1 |
Water-based coolants |
Avoid overheating; gentle pressure to avoid deformation. |
Thermosetting Plastics (Phenolic Resins, Epoxies) |
1500 - 2000 |
0.5 - 0.7 |
Water-based coolants |
Maintain consistent pressure; prone to cracking. |
Polymers (PTFE, PVC) |
1500 - 2000 |
0.7 - 1 |
Water-based coolants |
Prone to deformation; use consistent feed rate. |
Rubber (Natural, Synthetic) |
1500 - 2000 |
0.7 - 1 |
Water-based coolants |
High flexibility; maintain low pressure. |
Elastomers |
1500 - 2000 |
0.7 - 1 |
Water-based coolants |
Consistent feed rate to avoid tearing. |
Foam (Open-cell, Closed-cell) |
1500 - 2000 |
0.5 - 0.7 |
Water-based coolants |
Use gentle pressure; prone to deformation. |
Composite Materials (Soft Matrix) |
1500 - 2000 |
0.7 - 1 |
Water-based coolants |
Maintain steady pressure; avoid excessive feed rate. |
Fiberglass (Soft Resin Matrix) |
1500 - 2000 |
0.5 - 0.7 |
Water-based coolants |
Prone to fraying; maintain a consistent feed rate. |
Resins and Adhesives (Uncured, Partially Cured) |
1500 - 2000 |
0.5 - 0.7 |
Water-based coolants |
Use low pressure to avoid adhesive buildup. |
Synthetic Gels |
1500 - 2000 |
0.5 - 0.7 |
Water-based coolants |
Consistent pressure; avoid gel spillage. |
Tissue Samples (Biomedical, Research) |
1500 - 2000 |
0.5 - 0.7 |
Water-based coolants |
Use low pressure; maintain consistent feed rate. |
Low Speed Laboratory Saw - Recommended Settings
Example of Recommended RPM’s & Feed Rates, Recommend Coolant Type and Additional Considerations. This information is for reference purposes only Information was reference sectioning 1/4” (6.4mm) diameter sample using Low Speed Saw
Material |
Recommended RPM |
Feed Rate (mm/s) |
Coolant Type |
Additional Considerations |
---|---|---|---|---|
Plastics (Polyethylene, Polypropylene) |
300-600 |
0.2-0.5 |
Water-based or None |
Use higher RPMs for softer plastics; avoid melting the material |
Thermosetting Plastics (Phenolic Resins, Epoxies) |
200-400 |
0.1-0.3 |
Water-based |
Careful heat management to prevent curing during cut |
Polymers (PTFE, PVC) |
300-700 |
0.3-0.6 |
Water-based or None |
Adjust feed rate to minimize heat generation and deformation |
Rubber (Natural, Synthetic) |
200-500 |
0.2-0.4 |
Water-based |
Slow speed for thick sections to avoid tearing |
Elastomers |
250-550 |
0.2-0.5 |
Water-based or None |
Maintain consistent feed to ensure clean cuts |
Foam (Open-cell, Closed-cell) |
400-800 |
0.3-0.6 |
None |
Higher RPMs may be used due to material softness |
Composite Materials (Soft Matrix) |
200-400 |
0.1-0.3 |
Water-based |
Support the material well to prevent tearing and delamination |
Fiberglass (Soft Resin Matrix) |
300-600 |
0.2-0.4 |
Water-based |
Use gentle pressure to cut through resin without fraying fibers |
Resins and Adhesives (Uncured, Partially Cured) |
200-500 |
0.1-0.25 |
Water-based |
Prevent material from sticking to blade and clogging |
Synthetic Gels |
250-550 |
0.3-0.6 |
Water-based or None |
Avoid compression and deformation during cutting |
Tissue Samples (Biomedical, Research) |
300-600 |
0.2-0.4 |
Water-based |
Delicate handling to preserve tissue integrity |
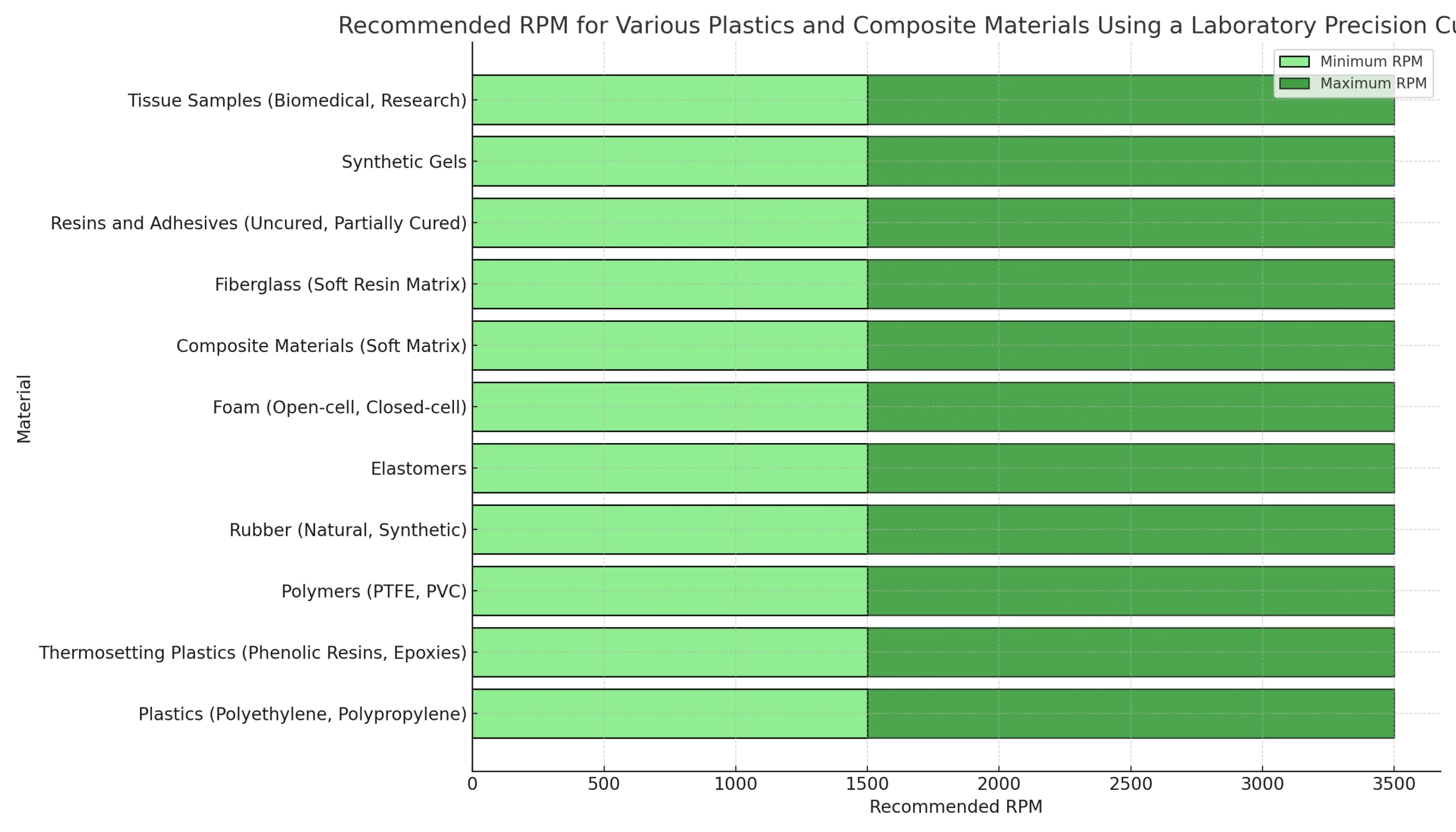
Series 20HCU
High Concentration/Coarse for Aggressive General Sectioning
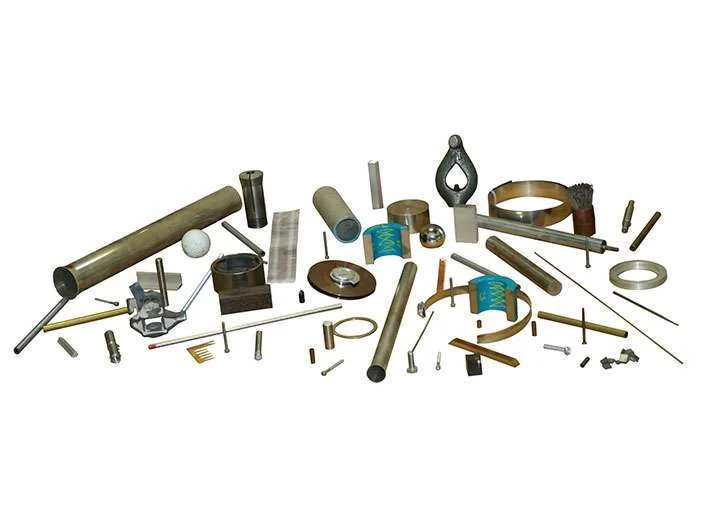
The Series 20HCU diamond wafering blades are meticulously designed to handle aggressive sectioning demands of both ferrous and nonferrous metals, including high-performance materials like titanium alloys. These blades are ideal for applications where precision and efficiency are required under challenging conditions.
High Diamond Concentration
The hallmark of the Series 20HCU is its high diamond concentration, which significantly enhances cutting capability. This design feature ensures that each cut is performed with maximum efficiency, reducing the time needed for each sectioning task without compromising the integrity of the material. The dense distribution of diamonds on the blade surface allows for more aggressive cutting actions, suitable for harder materials that would otherwise wear down lesser blades quickly.
Example of Application:
-
Steel: Including but not limited to carbon steel, stainless steel, tool steel, and high-speed steel. These materials are common in machine parts, tools, and structural components.
-
Titanium Alloys: Such as Ti-6Al-4V, commonly used in aerospace, medical implants, and other high-performance engineering applications due to their excellent strength-to-weight ratio and corrosion resistance.
-
Aluminum Alloys: Including those used in automotive and aerospace applications, like 2024, 7075, and other series, known for their lightweight and strong properties.
-
Copper Alloys: This includes bronze, brass, and other copper-based metals widely used in electrical, thermal, and architectural applications.
-
Nickel Alloys: Such as Inconel and Monel, which are used for their ability to withstand extreme environments, making them ideal for the chemical and aerospace industries.
-
Superalloys: Used primarily in jet engines and turbines due to their ability to perform at high temperatures and stresses.
-
Precious Metals: Such as silver, gold, and platinum, often used in specialized electronics and decorative applications.
-
Magnesium Alloys: Known for being extremely lightweight, these are used in automotive and aerospace applications where weight reduction is crucial.
-
Zinc Alloys: Often used in die casting processes for the automotive, consumer goods, and hardware industries.
-
Lead and Its Alloys: Commonly used in batteries, radiation shielding, and construction materials.
-
Tungsten and Its Alloys: Known for their high melting points and densities, used in military, mining, and aerospace applications.
-
Chromium Alloys: Used in stainless steel to enhance corrosion resistance and in superalloys to improve high-temperature strength.
-
Molybdenum Alloys: Employed in aircraft parts, electrical contacts, industrial motors, and filaments.
-
Cobalt Alloys: Such as those used in high-strength alloys for turbine blades and orthopedic implants.
-
Beryllium Alloys: Often used in aerospace applications for their high stiffness, light weight, and dimensional stability across a wide temperature range.
-
Metal Matrix Composites (MMCs): Combining metals with different properties, such as aluminum with ceramic particles, used in high-performance applications like racing cars and aerospace.
-
Hardened Metals: Metals that have been treated to increase their hardness, making them more durable and wear-resistant for tools and machining parts.
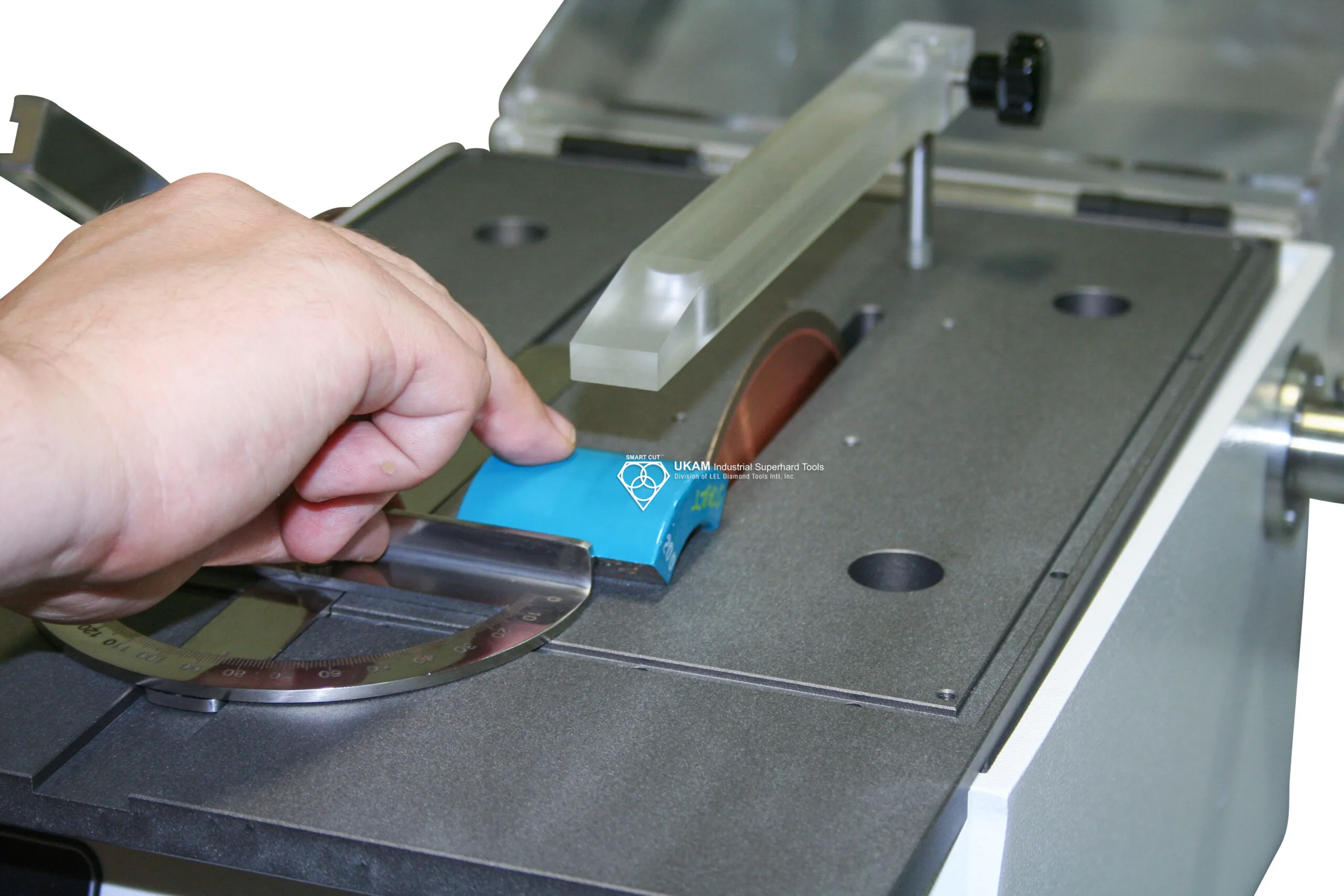
Medium to High Speed Laboratory Saw - ecommended Settings
RPM, feed rate, coolant type, and additional considerations for sectioning these materials for metallography and sample preparation on a laboratory precision cutting saw with a 6" diameter blade:
Material |
Recommended RPM |
Feed Rate (in/min) |
Coolant Type |
Additional Considerations |
---|---|---|---|---|
Steel (Carbon, Stainless, Tool, High-Speed) |
1800 - 2200 |
0.5 - 0.7 |
Water-based coolants |
Use consistent pressure; high-speed steels require diamond blades. |
Titanium Alloys (e.g., Ti-6Al-4V) |
1500 - 2000 |
0.7 - 1 |
Water-based coolants |
Hard material; maintain consistent feed rate. |
Aluminum Alloys (2024, 7075) |
1500 - 2000 |
0.7 - 1 |
Water-based coolants |
Avoid blade clogging; maintain consistent pressure. |
Copper Alloys (Bronze, Brass) |
1500 - 2000 |
0.5 - 0.7 |
Water-based coolants |
Use low pressure; copper can deform with high pressure. |
Nickel Alloys (Inconel, Monel) |
1800 - 2200 |
0.5 - 0.7 |
Water-based coolants |
Use diamond blades; maintain consistent pressure. |
Superalloys |
1800 - 2200 |
0.5 - 0.7 |
Water-based coolants |
Hard and abrasive; maintain consistent feed rate. |
Precious Metals (Silver, Gold, Platinum) |
1500 - 2000 |
0.5 - 0.7 |
Water-based coolants |
Maintain low pressure; avoid blade deformation. |
Magnesium Alloys |
1500 - 2000 |
0.5 - 0.7 |
Water-based coolants |
Extremely reactive; use slow feed rate. |
Zinc Alloys |
1500 - 2000 |
0.5 - 0.7 |
Water-based coolants |
Gentle pressure; zinc is prone to deformation. |
Lead and Its Alloys |
1500 - 2000 |
0.5 - 0.7 |
Water-based coolants |
Maintain low pressure; prone to deformation. |
Tungsten and Its Alloys |
2000 - 2500 |
0.3 - 0.5 |
Water-based coolants |
High-density material; maintain low pressure. |
Chromium Alloys |
1800 - 2200 |
0.5 - 0.7 |
Water-based coolants |
Consistent feed rate; avoid blade wear. |
Molybdenum Alloys |
1800 - 2200 |
0.5 - 0.7 |
Water-based coolants |
Maintain constant pressure; prone to cracking. |
Cobalt Alloys |
1800 - 2200 |
0.5 - 0.7 |
Water-based coolants |
Hard material; use diamond blades. |
Beryllium Alloys |
1800 - 2200 |
0.5 - 0.7 |
Water-based coolants |
Use gentle pressure; beryllium is brittle. |
Metal Matrix Composites (MMCs) |
1800 - 2200 |
0.5 - 0.7 |
Water-based coolants |
Consistent pressure; maintain a steady feed rate. |
Hardened Metals |
2000 - 2500 |
0.3 - 0.5 |
Water-based coolants |
Hard material; use diamond blades. |
Steel (Carbon, Stainless, Tool, High-Speed) |
1800 - 2200 |
0.5 - 0.7 |
Water-based coolants |
Avoid overheating; use consistent feed rate. |
Titanium Alloys (e.g., Ti-6Al-4V) |
1500 - 2000 |
0.7 - 1 |
Water-based coolants |
High strength; avoid blade wear. |
Aluminum Alloys (2024, 7075) |
1500 - 2000 |
0.7 - 1 |
Water-based coolants |
Avoid blade clogging; maintain consistent pressure. |
Copper Alloys (Bronze, Brass) |
1500 - 2000 |
0.5 - 0.7 |
Water-based coolants |
Maintain low pressure; avoid deformation. |
Nickel Alloys (Inconel, Monel) |
1800 - 2200 |
0.5 - 0.7 |
Water-based coolants |
Consistent feed rate; use diamond blades. |
Superalloys |
1800 - 2200 |
0.5 - 0.7 |
Water-based coolants |
Hard and abrasive; maintain steady pressure. |
Precious Metals (Silver, Gold, Platinum) |
1500 - 2000 |
0.5 - 0.7 |
Content |
Use gentle pressure; avoid blade wear. |
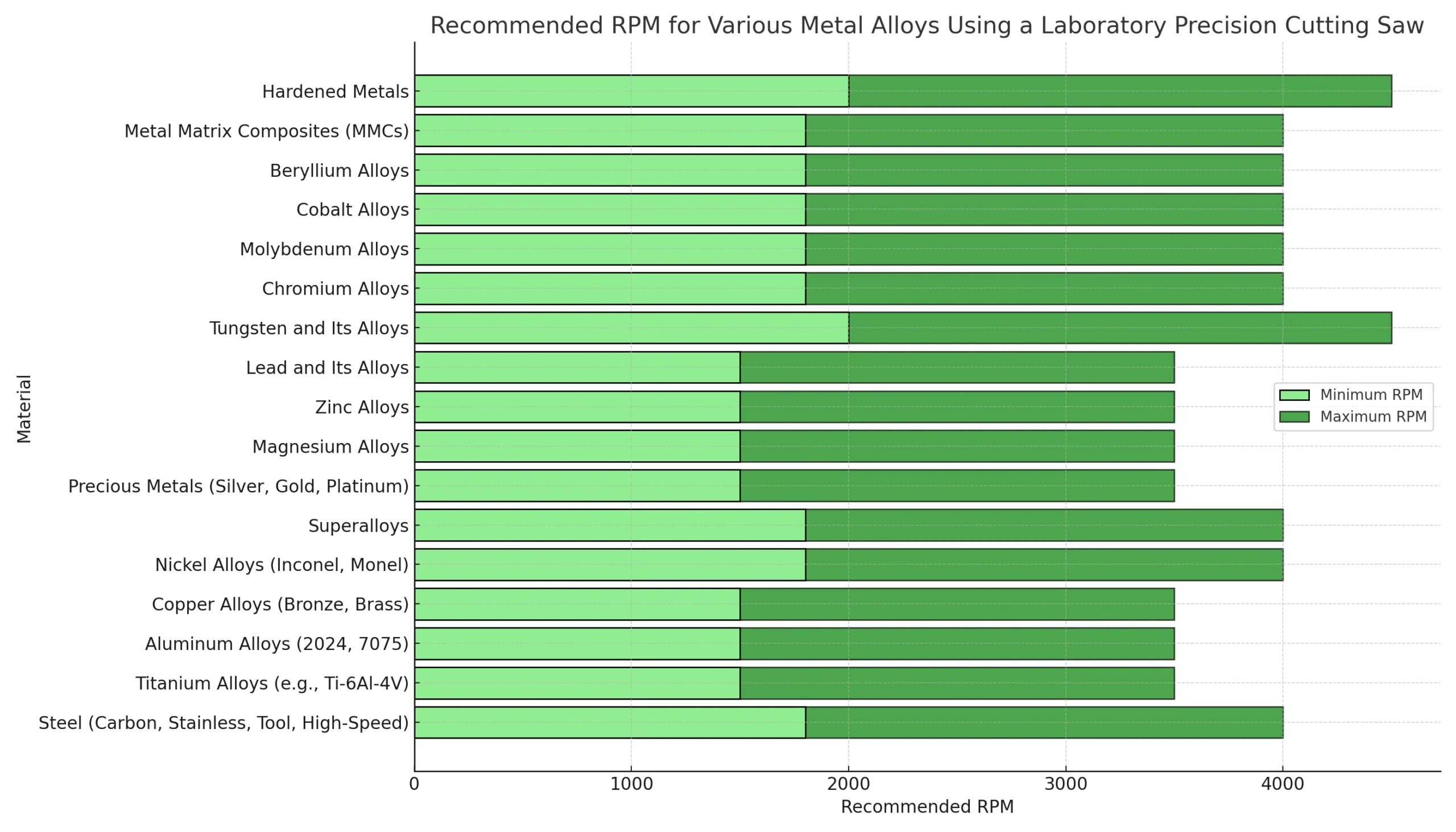
Low Speed Laboratory Saw - Recommended Settings
Example of Recommended RPM’s & Feed Rates, Recommend Coolant Type and Additional Considerations. This information is for reference purposes only Information was reference sectioning 1/4” (6.4mm) diameter sample using Low Speed Saw
Material Category |
Recommended RPM |
Feed Rate (mm/s) |
Coolant Type |
Additional Considerations |
---|---|---|---|---|
Steel (Carbon, Stainless, Tool, High-Speed) |
200-500 |
0.2-0.5 |
Water-based or Oil-based |
Match coolant type to material properties and cutting conditions |
Titanium Alloys (e.g., Ti-6Al-4V) |
150-350 |
0.1-0.3 |
Water-based |
Use gentle feeds to prevent work hardening and stress |
Aluminum Alloys (2024, 7075) |
400-800 |
0.3-0.6 |
Water-based |
Higher RPMs suitable for softer, nonferrous metals |
Copper Alloys (Bronze, Brass) |
300-600 |
0.2-0.4 |
Water-based |
Prevent burring with appropriate feed rates |
Nickel Alloys (Inconel, Monel) |
200-400 |
0.1-0.3 |
Water-based |
Adjust RPM based on specific alloy hardness |
Superalloys |
150-300 |
0.1-0.25 |
Water-based |
Manage heat buildup due to high-temperature resistance |
Precious Metals (Silver, Gold, Platinum) |
300-700 |
0.2-0.5 |
Water-based |
Use higher RPMs cautiously to maintain material integrity |
Magnesium Alloys |
500-1000 |
0.3-0.6 |
Water-based |
Light and fast cuts to prevent material ignition |
Zinc Alloys |
400-800 |
0.3-0.5 |
Water-based |
Careful handling to avoid cracking and warping |
Lead and Its Alloys |
200-400 |
0.2-0.4 |
Water-based |
Low speed and feed to prevent deformation |
Tungsten and Its Alloys |
100-300 |
0.1-0.25 |
Water-based |
Very low speeds due to extreme hardness and density |
Chromium Alloys |
200-400 |
0.1-0.3 |
Water-based |
Adjust for hardness and corrosion resistance |
Molybdenum Alloys |
300-600 |
0.2-0.4 |
Water-based |
Manage feeds to prevent cracking due to brittleness |
Cobalt Alloys |
150-350 |
0.1-0.3 |
Water-based |
High toughness requires careful speed management |
Beryllium Alloys |
100-300 |
0.1-0.25 |
Water-based |
Handle with care due to toxicity and high stiffness |
Metal Matrix Composites (MMCs) |
250-500 |
Content |
Water-based |
Support during cutting to prevent delamination |
Hardened Metals |
150-300 |
0.1-0.2 |
Water-based |
Very low feed rates to cope with increased hardness |
Series 15HCU
High Concentration for Metals and Alloys
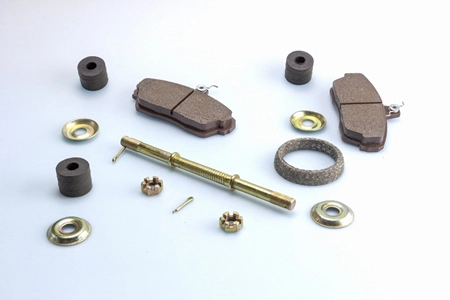
Series 15HCU diamond wafering blades are designed for general use across a wide range of metals and alloys such as copper, aluminum, metal matrix composites, and titanium alloys. It's particularly effective for materials that require a delicate approach but still need a certain level of aggressiveness to achieve clean cuts.
Example of Application:
-
Ferrous Alloys: These include various types of steel and iron where precision is critical, such as tool steels, stainless steels, and cast irons used in everything from construction to intricate mechanical components.
-
Nonferrous Alloys: This encompasses a wide range of metals that do not contain iron, primarily focused on metals like aluminum and titanium alloys, which are prized in aerospace and automotive sectors for their strength-to-weight ratio.
-
Copper: Integral to electrical components due to its excellent conductivity, copper requires precise sectioning to ensure optimal performance in electrical applications and heat exchangers.
-
Aluminum: Used across a broad spectrum of industries, aluminum alloys require precise cuts for applications in transportation, packaging, and structural applications.
-
Metal Matrix Composites (MMCs): Combining the ductility of metal with the strength of ceramic or other fibers, MMCs are used in automotive brake rotors and aerospace components. The SERIES 15HCU blades provide the clean, sharp cuts needed for these composite materials without delaminating or damaging the matrix.
-
PC Boards: Precision is paramount when sectioning printed circuit boards for electronics. The SERIES 15HCU ensures clean cuts that do not fray or damage the delicate circuits and components mounted on these boards.
-
Thermal Spray Coatings: Often used to enhance the surface properties of materials, such as wear and corrosion resistance, precise cutting is necessary to maintain the integrity of the coatings during inspection and quality control processes.
-
Titanium Alloys: Particularly in biomedical applications and aerospace engineering, where the non-reactive nature of titanium is essential, the SERIES 15HCU provides the necessary precision to cut without inducing stress or altering the material properties.
-
Aluminum Alloys: Especially those used in precision components where a clean cut is essential to maintain material integrity.
-
Brass and Bronze: Common in musical instruments, decorative items, and fittings where precision and aesthetic are critical.
-
Copper: Widely used in electrical wiring and plumbing that requires clean and non-deformed cuts for reliable installations.
-
Titanium Alloys: Utilized in medical devices and implants where every cut impacts the integrity and functionality of the final product.
-
Nickel Silver (German Silver): Often used in ornamental work and in places where corrosion resistance and appearance are important.
-
Low Carbon Steel: Used in construction and manufacturing, where precise cuts can reduce material waste and improve joint quality.
-
Super Duplex Stainless Steel: Used in chemical processing and marine environments, where precision cuts are crucial for maintaining material properties.
-
Zirconium Alloys: In nuclear reactors, where exact specifications are necessary for safety and functionality.
-
Soft Magnetic Alloys: Such as those used in transformer cores and motors, where precise dimensions are critical to ensuring performance.
-
Tin Alloys: Used in specialty applications like bearings and fusible alloys, requiring precision in the melting point adjustments.
-
Soft Precious Metals (e.g., Gold, Silver): Specifically for applications requiring delicate handling to preserve the purity and properties of the material.
-
Phosphor Bronze: Commonly used in electrical and electronic applications for its spring qualities, necessitating clean and accurate cuts.
-
Lead Frame Alloys: Used in the semiconductor industry, where exact cuts are crucial for component reliability.
-
Amorphous Metals: Used in thin ribbons for transformers and various electronic applications, where precision is key.
-
Pewter: Often used in decorative household items and jewelry, where fine detail and smooth finishes are desired.
-
Babbitt Metal: Used in bearings that require exact tolerances for optimal performance and longevity.
-
Cadmium Copper: Primarily used in areas where high conductivity and durability are required, such as overhead conductors.
-
High Conductivity Copper: Especially in electronic and thermal applications where precise cuts ensure optimal performance.
-
Low Alloy Steels: Commonly used in the automotive industry for parts that require precise dimensions to ensure functional integrity.
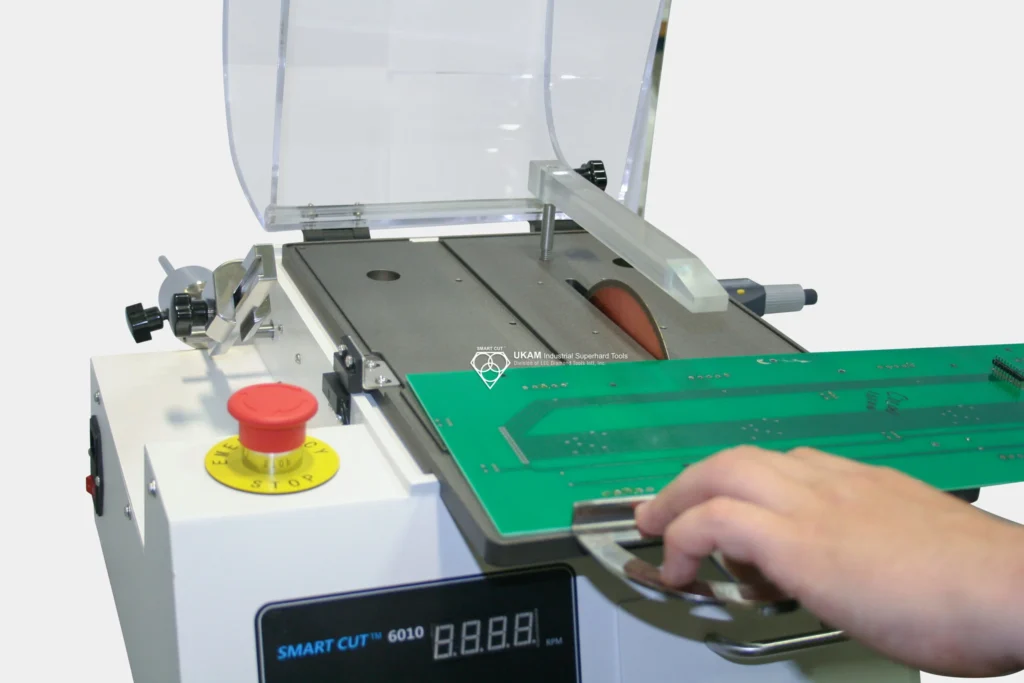
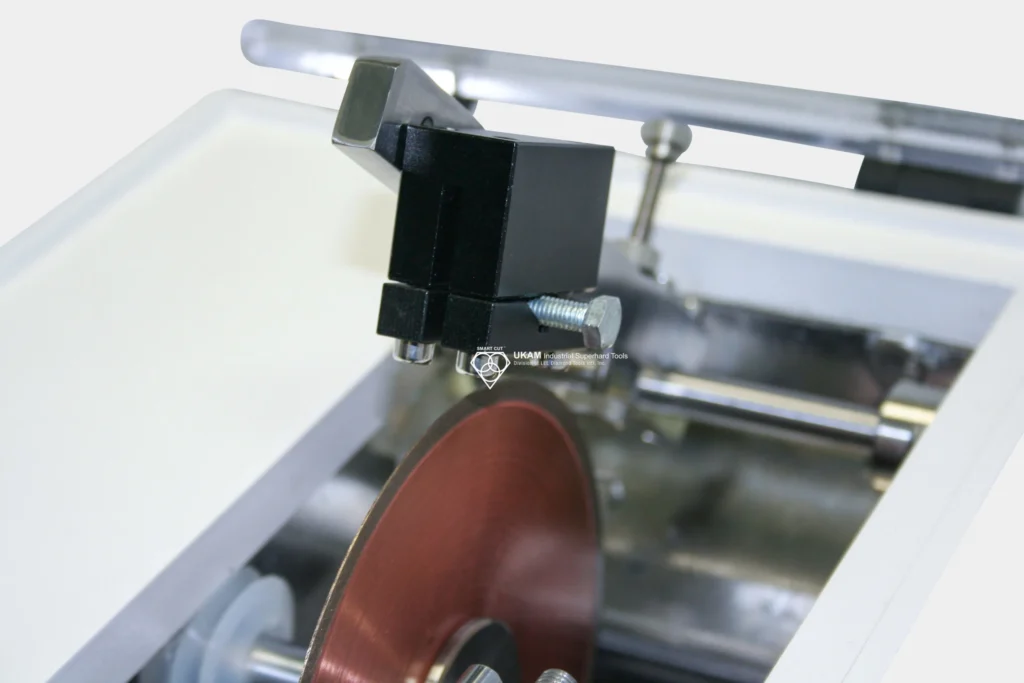
Medium to High Speed Laboratory Saw - Recommended Settings
RPM, feed rate, coolant type, and additional considerations for sectioning these materials for metallography and sample preparation on a laboratory precision cutting saw with a 6" diameter blade:
Material |
Recommended RPM |
Feed Rate (in/min) |
Coolant Type |
Additional Considerations |
---|---|---|---|---|
Ferrous Alloys (Tool Steels, Stainless Steels, Cast Irons) |
1800 - 2200 |
0.5 - 1 |
Water-based coolants |
Maintain steady pressure; use diamond blades for hard steels. |
Nonferrous Alloys (Aluminum, Titanium) |
1500 - 2000 |
0.7 - 1 |
Water-based coolants |
Use low pressure; prevent blade clogging with aluminum. |
Copper |
1500 - 2000 |
0.5 - 0.7 |
Water-based coolants |
Maintain consistent pressure; prevent material deformation. |
Aluminum Alloys |
1500 - 2000 |
0.7 - 1 |
Water-based coolants |
Avoid high feed rates to prevent blade damage. |
Metal Matrix Composites (MMCs) |
1800 - 2200 |
0.5 - 0.7 |
Water-based coolants |
Hard and abrasive; use diamond blades. |
PC Boards |
1500 - 2000 |
0.5 - 0.7 |
Water-based coolants |
Maintain steady feed rate to prevent fraying. |
Thermal Spray Coatings |
1500 - 2000 |
0.5 - 0.7 |
Water-based coolants |
Use gentle pressure; maintain consistent feed rate. |
Titanium Alloys |
1500 - 2000 |
0.7 - 1 |
Water-based coolants |
Hard material; consistent feed rate to avoid blade wear. |
Brass and Bronze |
1500 - 2000 |
0.5 - 0.7 |
Water-based coolants |
Maintain low pressure; brass can deform with high pressure. |
Nickel Silver (German Silver) |
1500 - 2000 |
0.5 - 0.7 |
Water-based coolants |
Use gentle pressure; prone to deformation. |
Low Carbon Steel |
1800 - 2200 |
0.5 - 0.7 |
Water-based coolants |
Avoid overheating; use consistent feed rate. |
Super Duplex Stainless Steel |
1800 - 2200 |
0.5 - 0.7 |
Water-based coolants |
High corrosion resistance; use diamond blades. |
Zirconium Alloys |
1500 - 2000 |
0.5 - 0.7 |
Water-based coolants |
High strength; consistent feed rate to avoid blade wear. |
Soft Magnetic Alloys |
1500 - 2000 |
0.5 - 0.7 |
Water-based coolants |
Consistent feed rate to avoid damage to magnetic properties. |
Tin Alloys |
1500 - 2000 |
0.5 - 0.7 |
Water-based coolants |
Maintain low pressure to prevent blade damage. |
Soft Precious Metals (Gold, Silver) |
1500 - 2000 |
0.5 - 0.7 |
Water-based coolants |
Gentle pressure; avoid blade deformation. |
Phosphor Bronze |
1500 - 2000 |
0.5 - 0.7 |
Water-based coolants |
Prone to deformation; use consistent feed rate. |
Lead Frame Alloys |
1500 - 2000 |
0.5 - 0.7 |
Water-based coolants |
Avoid excessive force; prone to breakage. |
Amorphous Metals |
1800 - 2200 |
0.5 - 0.7 |
Water-based coolants |
Consistent feed rate; high RPM to avoid blade wear. |
Pewter |
1500 - 2000 |
0.5 - 0.7 |
Water-based coolants |
Gentle pressure; prone to deformation. |
Babbitt Metal |
1500 - 2000 |
0.5 - 0.7 |
Water-based coolants |
Consistent feed rate; avoid excessive pressure. |
Cadmium Copper |
1500 - 2000 |
0.5 - 0.7 |
Water-based coolants |
Use gentle pressure; prone to deformation. |
High Conductivity Copper |
1500 - 2000 |
0.5 - 0.7 |
Water-based coolants |
Consistent feed rate; avoid overheating. |
Low Alloy Steels |
1800 - 2200 |
0.5 - 0.7 |
Water-based coolants |
Hard material; use diamond blades. |
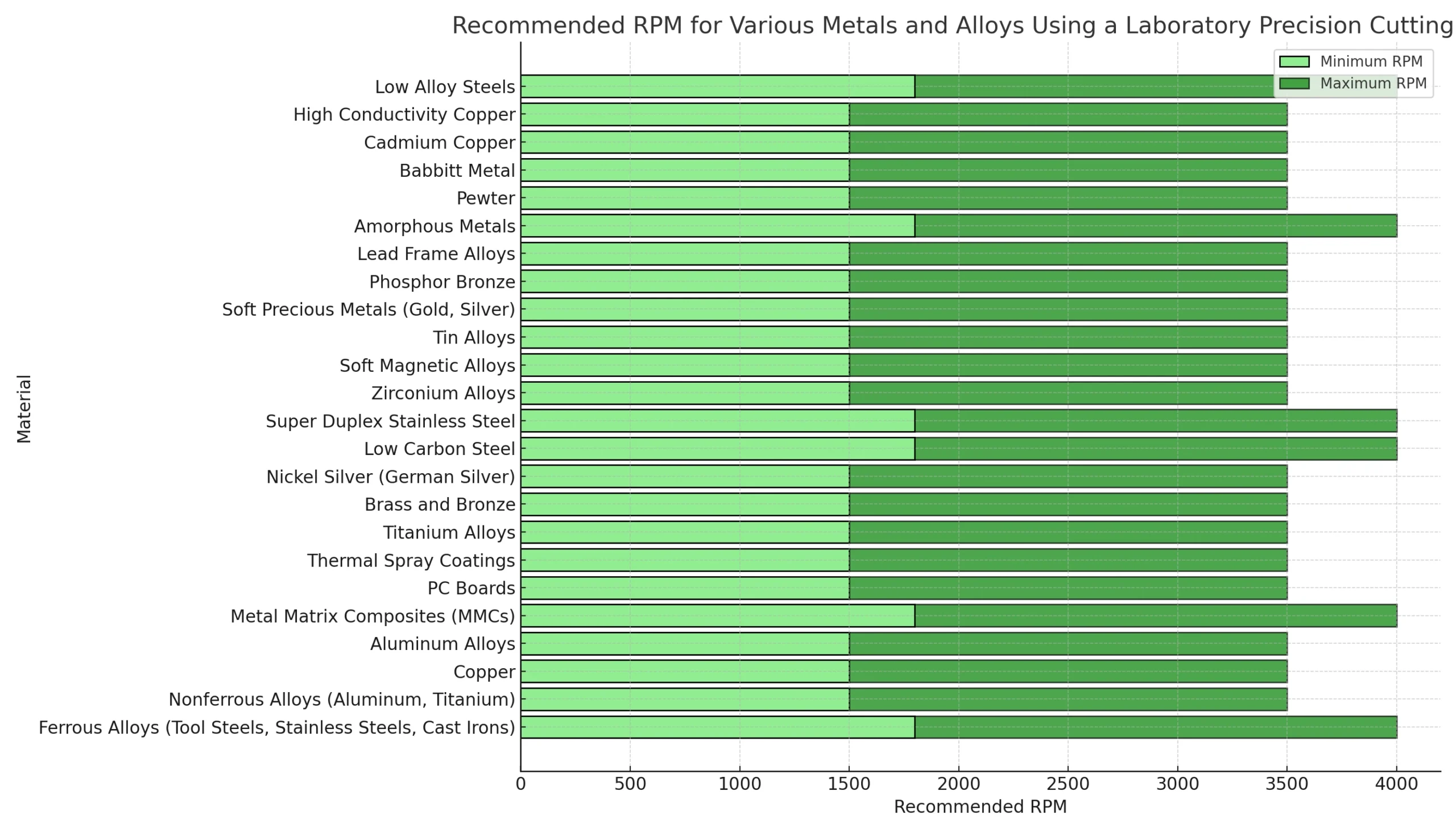
Low Speed Laboratory Saw - Recommended Settings
Example of Recommended RPM’s & Feed Rates, Recommend Coolant Type and Additional Considerations. This information is for reference purposes only Information was reference sectioning 1/4” (6.4mm) diameter sample using Low Speed Saw
Material Category |
Recommended RPM |
Feed Rate (mm/s) |
Coolant Type |
Additional Considerations |
---|---|---|---|---|
Ferrous Alloys (Tool Steels, Stainless Steels, Cast Irons) |
200-400 |
0.1-0.3 |
Water-based or Oil-based |
Use higher feed rates for softer ferrous alloys |
Nonferrous Alloys (Aluminum, Titanium) |
400-800 |
0.2-0.5 |
Water-based |
Higher RPMs may be used for softer nonferrous alloys |
Copper |
300-600 |
0.2-0.4 |
Water-based |
Gentle approach to prevent burring and deformation |
Aluminum Alloys |
500-1000 |
0.3-0.6 |
Water-based |
Adjust feed rate according to alloy hardness and thickness |
Metal Matrix Composites (MMCs) |
250-500 |
0.1-0.3 |
Water-based |
Use a steady feed to avoid delamination |
PC Boards |
300-600 |
0.1-0.25 |
Water-based |
Ensure clean cuts to avoid damaging circuits |
Thermal Spray Coatings |
200-400 |
0.1-0.2 |
Water-based |
Precise cuts to maintain coating integrity |
Titanium Alloys |
200-500 |
0.1-0.3 |
Water-based |
Low feed rates to prevent work hardening |
Brass and Bronze |
500-1000 |
0.2-0.5 |
Water-based |
Care to maintain aesthetic quality of the cut surface |
Nickel Silver (German Silver) |
300-700 |
0.2-0.4 |
Water-based |
Adjust according to material hardness |
Low Carbon Steel |
300-700 |
0.2-0.4 |
Water-based or Oil-based |
Suitable for construction and manufacturing cuts |
Super Duplex Stainless Steel |
200-400 |
0.1-0.25 |
Water-based or Oil-based |
Prevent corrosion with appropriate coolant |
Zirconium Alloys |
200-500 |
0.1-0.3 |
Water-based |
Handle with care due to their use in critical applications |
Soft Magnetic Alloys |
300-600 |
0.2-0.4 |
Water-based |
Precision is critical for performance |
Tin Alloys |
400-800 |
0.3-0.6 |
Water-based |
Delicate handling to maintain properties |
Soft Precious Metals (Gold, Silver) |
300-700 |
0.2-0.5 |
Water-based |
Gentle cutting to preserve material purity |
Phosphor Bronze |
400-800 |
0.2-0.5 |
Water-based |
Ensure clean and precise cuts for spring applications |
Lead Frame Alloys |
300-600 |
0.1-0.25 |
Water-based |
Critical for maintaining component dimensions in semiconductors |
Amorphous Metals |
300-700 |
0.2-0.4 |
Water-based |
Consistency and precision are key for thin materials |
Pewter |
500-1000 |
0.3-0.6 |
Water-based |
Maintain smooth finishes in decorative applications |
Babbitt Metal |
300-700 |
0.2-0.5 |
Water-based |
Ensure even cuts to prevent bearing failures |
Cadmium Copper |
300-600 |
0.2-0.4 |
Water-based |
High conductivity and durability require precise cuts |
High Conductivity Copper |
300-600 |
0.2-0.4 |
Water-based |
Precision essential for electronic and thermal applications |
Low Alloy Steels |
300-700 |
0.2-0.4 |
Water-based or Oil-based |
Critical for automotive parts requiring exact dimensions |
Series 20LCU
Low Concentration for Hard and Tough Materials
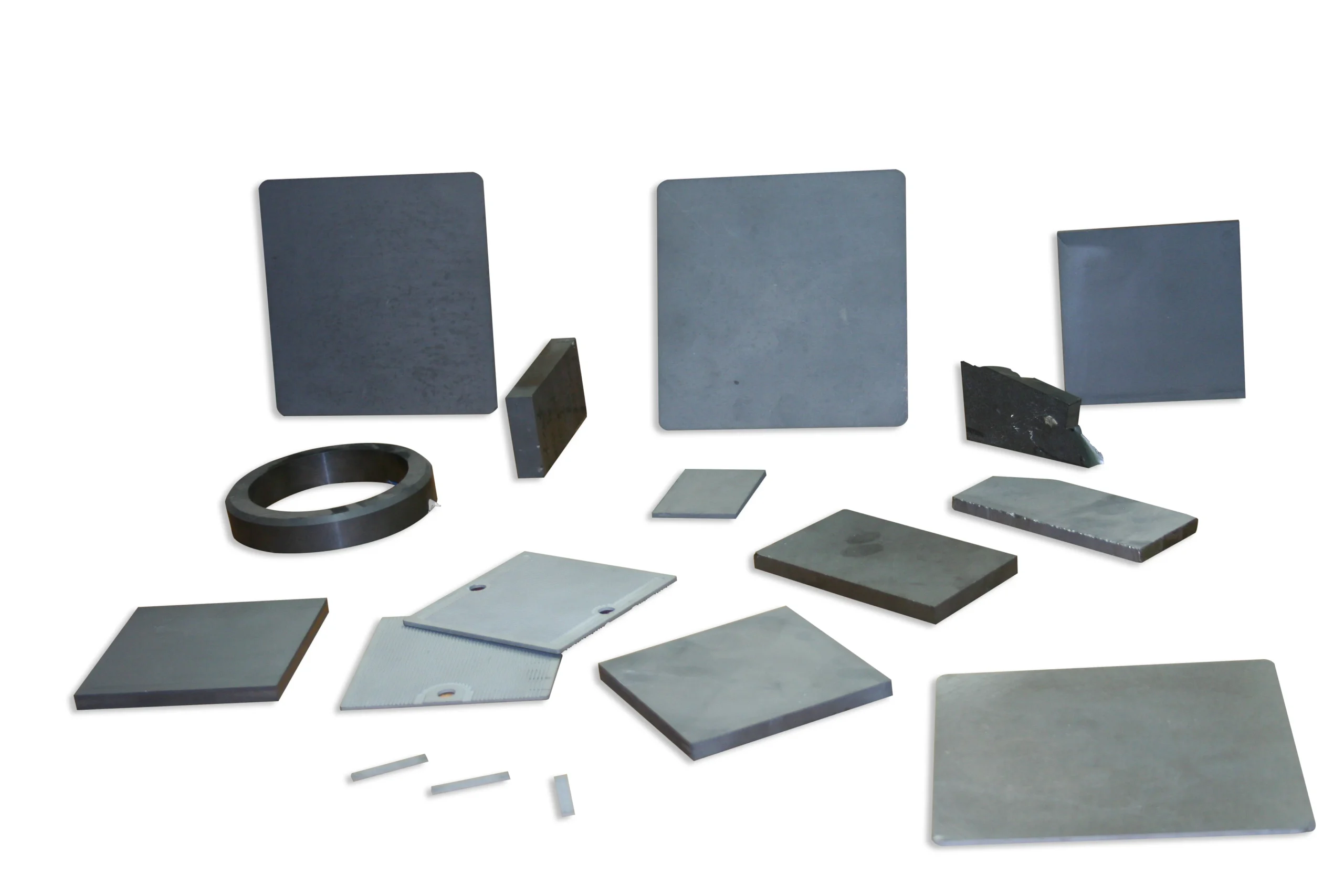
Series 20LCU diamond wafering blades are designed for cutting extremely hard or tough materials, such as structural ceramics, boron carbide, boron nitride, and silicon carbides. The lower diamond concentration helps minimize potential damage to brittle materials, providing a balance between durability and precision.
Example of Application:
-
Silicon Carbide (SiC): Used in semiconductors, high-temperature turbines, and abrasive applications due to its high hardness and thermal resistance.
-
Boron Carbide (B4C): One of the hardest materials, used in body armor, abrasives, and high-pressure applications due to its exceptional hardness and lightweight properties.
-
Boron Nitride: Especially useful in high-temperature equipment due to its thermal and chemical stability.
-
Sapphire (Aluminum Oxide - Al2O3): Used in optical applications, watch crystals, and semiconductor substrates for its hardness and optical transparency.
-
Tungsten Carbide: Common in cutting tools, mining machinery, and wear-resistant applications because of its extreme hardness and resistance to abrasion.
-
Ceramic Matrix Composites (CMCs): Utilized in aerospace, automotive, and energy sectors for their high-temperature stability and strength.
-
Zirconium Dioxide (Zirconia): Used in dental and medical applications for its durability and biocompatibility.
-
Advanced Technical Ceramics: Such as silicon nitride, used in engine components, bearings, and metal forming tools for their hardness and wear resistance.
-
Alumina (Aluminum Oxide): A common ceramic material used in substrates and insulators in electronics for its electrical insulation properties and mechanical strength.
-
Ceramic Coatings: Applied to metals to enhance surface properties like wear resistance and thermal barrier capabilities.
-
Glass Ceramics: Employed in optical materials and cooktops due to their ability to withstand sudden changes in temperature.
-
Composite Armor: Involving layers of ceramics and other materials designed to provide protection against high-velocity projectiles.
-
Ceramic Bearings: Used in applications requiring high stiffness, high wear resistance, and stability under varying temperatures.
-
Porous Ceramics: Used for filtration and bioapplications, requiring precise cutting to maintain pore structure and functionality.
-
High-Performance Refractories: Used in high-temperature industrial processes, needing precise dimensioning for optimal performance.
-
Ceramic Insulators: Critical in electrical applications for their ability to withstand high voltages and temperatures.
-
Ceramic Cutting Tools: For machining metals at high speeds, where standard metal tools would wear out quickly.
-
Ceramic Guides and Fixtures: In textile machinery where high wear resistance and precision are required.
-
Diamond Compounds: For applications requiring the grinding and polishing of other high-hardness materials.
-
Piezoceramics: Used in sensors and actuators, requiring precise cuts to function correctly at specific frequencies.
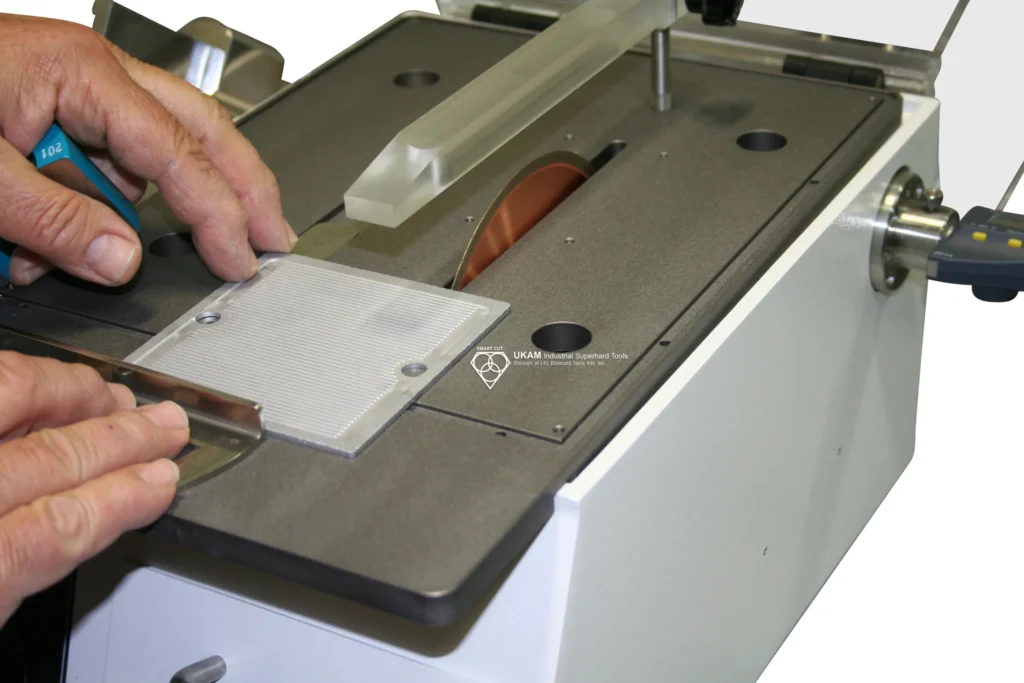
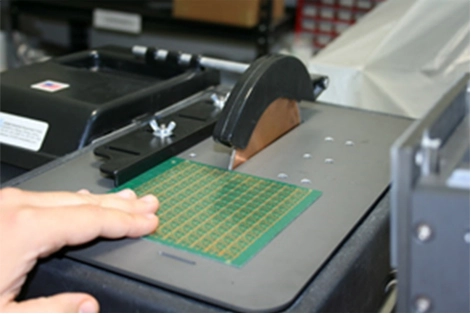
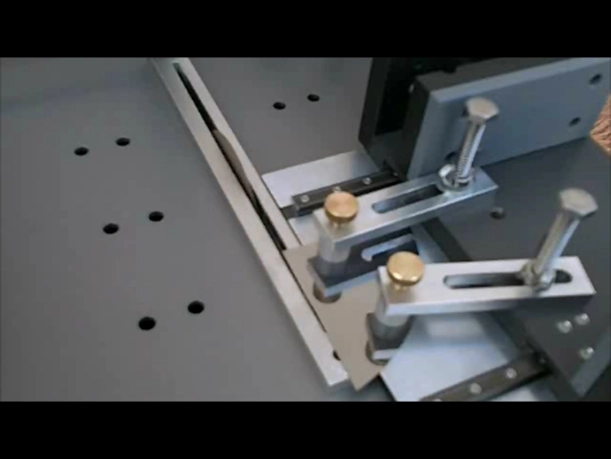
Medium to High Speed Laboratory Saw - Recommended Settings
recommended RPM, feed rate, coolant type, and additional considerations for sectioning these materials for metallography and sample preparation when sectioning 1/2" diameter material on a laboratory precision cutting saw using a 6" diameter blade:
Material |
Recommended RPM |
Feed Rate (in/min) |
Coolant Type |
Additional Considerations |
---|---|---|---|---|
Silicon Carbide (SiC) |
2000 - 2500 |
0.3 - 0.5 |
Water-based coolants |
Extremely abrasive; use low pressure to prevent blade wear. |
Boron Carbide (B4C) |
2000 - 2500 |
0.3 - 0.5 |
Water-based coolants |
High hardness; consistent feed rate to avoid chipping. |
Boron Nitride |
1800 - 2200 |
0.3 - 0.5 |
Water-based coolants |
Ensure smooth blade movement to avoid cracking. |
Sapphire (Al2O3) |
2000 - 2500 |
0.3 - 0.5 |
Water-based coolants |
Very brittle; use diamond blades. |
Tungsten Carbide |
2000 - 2500 |
0.3 - 0.5 |
Water-based coolants |
Hard metal; maintain consistent pressure. |
Ceramic Matrix Composites (CMCs) |
1800 - 2200 |
0.3 - 0.5 |
Water-based coolants |
Use diamond blades; material can fray. |
Zirconium Dioxide (Zirconia) |
1800 - 2200 |
0.3 - 0.5 |
Water-based coolants |
Maintain steady feed rate; very hard and dense. |
Advanced Technical Ceramics |
1800 - 2200 |
0.3 - 0.5 |
Water-based coolants |
Use diamond blades; consistent feed rate. |
Alumina (Aluminum Oxide) |
2000 - 2500 |
0.3 - 0.5 |
Water-based coolants |
Very hard; maintain steady feed rate. |
Ceramic Coatings |
1800 - 2200 |
0.3 - 0.5 |
Water-based coolants |
Use consistent feed rate to avoid chipping. |
Glass Ceramics |
1500 - 2000 |
0.3 - 0.5 |
Water-based coolants |
Maintain steady pressure to avoid cracking. |
Composite Armor |
1800 - 2200 |
0.3 - 0.5 |
Water-based coolants |
Consistent feed rate; avoid excessive force. |
Ceramic Bearings |
1800 - 2200 |
0.3 - 0.5 |
Water-based coolants |
Use gentle pressure to prevent bearing damage. |
Porous Ceramics |
1500 - 2000 |
0.3 - 0.5 |
Water-based coolants |
Prone to breakage; maintain constant feed rate. |
High-Performance Refractories |
2000 - 2500 |
0.3 - 0.5 |
Water-based coolants |
Hard and heat-resistant; use diamond blades. |
Ceramic Insulators |
1500 - 2000 |
0.3 - 0.5 |
Water-based coolants |
Fragile; use low pressure to avoid breakage. |
Ceramic Cutting Tools |
1800 - 2200 |
0.3 - 0.5 |
Water-based coolants |
Very hard; consistent feed rate. |
Ceramic Guides and Fixtures |
1800 - 2200 |
0.3 - 0.5 |
Water-based coolants |
Use consistent pressure; prone to breakage. |
Diamond Compounds |
2000 - 2500 |
0.3 - 0.5 |
Water-based coolants |
Maintain low pressure; diamond blades needed. |
Piezoceramics |
1800 - 2200 |
0.3 - 0.5 |
Water-based coolants |
Consistent feed rate; prone to cracking. |
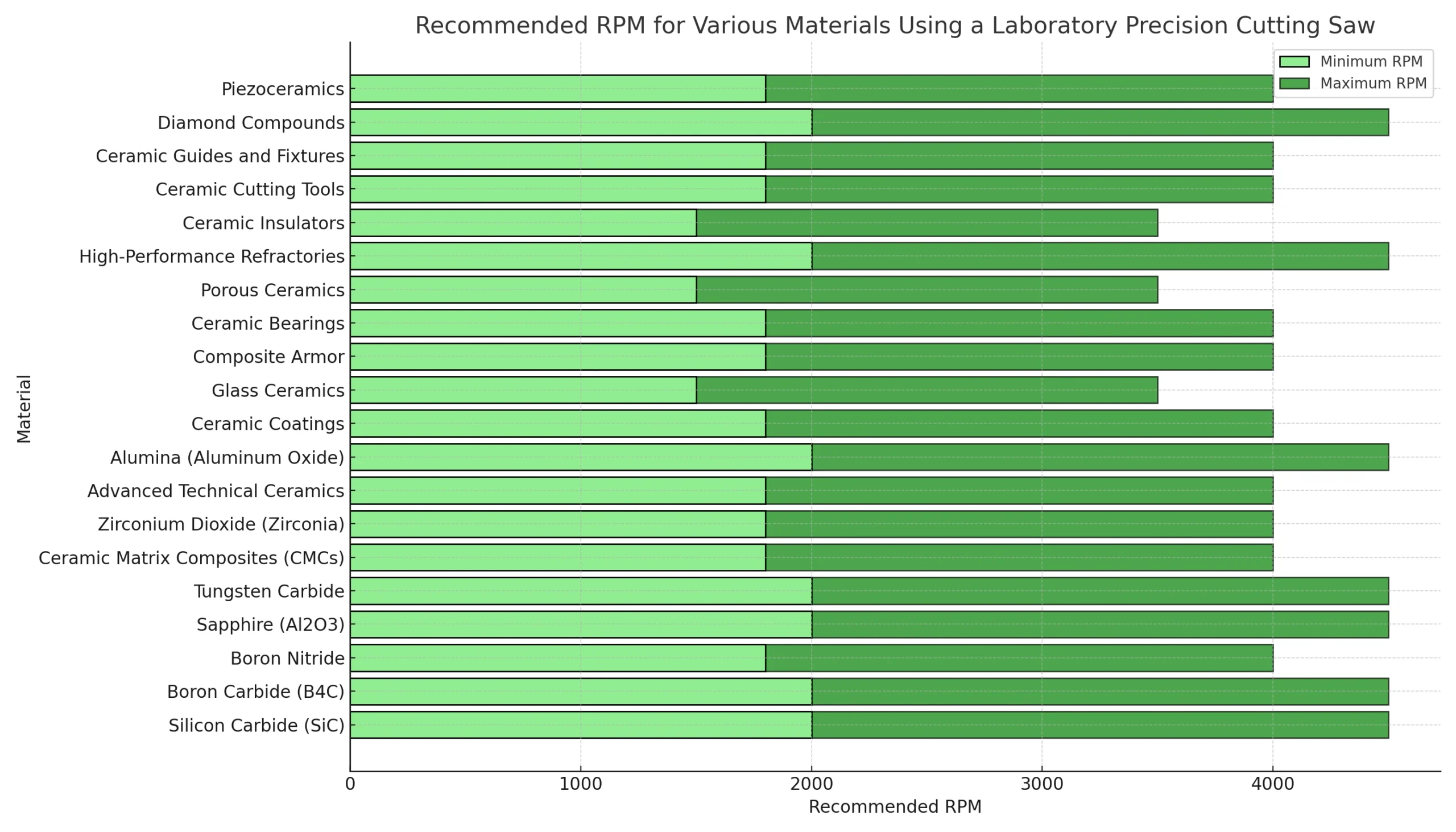
Low Speed Laboratory Saw - Recommended Settings
Below is a detailed table providing recommended RPMs, feed rates, coolant types, and additional considerations for cutting a 1/4" diameter sample/material using Series 20LCU diamond wafering blades, which are designed for hard and tough materials:
Material Category |
Recommended RPM |
Feed Rate (mm/s) |
Coolant Type |
Additional Considerations |
---|---|---|---|---|
Silicon Carbide (SiC) |
150-300 |
0.1-0.2 |
Water-based |
Use gentle pressure to avoid sub-surface damage |
Boron Carbide (B4C) |
100-200 |
0.05-0.1 |
Water-based |
Extremely brittle; requires very careful handling |
Boron Nitride |
150-300 |
0.1-0.2 |
Water-based |
Maintain steady feed to prevent thermal shock |
Sapphire (Al2O3) |
100-250 |
0.1-0.2 |
Water-based |
Very hard material; slow cutting speed recommended |
Tungsten Carbide |
200-400 |
0.1-0.2 |
Water-based |
High abrasion resistance; requires robust blade performance |
Ceramic Matrix Composites (CMCs) |
150-300 |
0.1-0.25 |
Water-based |
Support material to avoid delamination |
Zirconium Dioxide (Zirconia) |
150-300 |
0.1-0.2 |
Water-based |
High fracture toughness; careful handling needed |
Advanced Technical Ceramics |
150-300 |
0.1-0.2 |
Water-based |
Includes materials like silicon nitride; precise control needed |
Alumina (Aluminum Oxide) |
150-300 |
0.1-0.25 |
Water-based |
Electrical insulator properties require precise cuts |
Ceramic Coatings |
100-250 |
0.1-0.2 |
Water-based |
Precision required to evaluate coating thickness |
Glass Ceramics |
100-200 |
0.1-0.2 |
Water-based |
Handle gently to avoid thermal stress and chipping |
Composite Armor |
150-300 |
0.1-0.25 |
Water-based |
Composite layers require uniform cutting force |
Ceramic Bearings |
150-300 |
0.1-0.2 |
Water-based |
High precision needed for bearing functionality |
Porous Ceramics |
150-300 |
0.1-0.25 |
Water-based |
Gentle cutting to maintain pore structure |
High-Performance Refractories |
100-250 |
0.1-0.2 |
Water-based |
Requires stable cutting to maintain structure |
Ceramic Insulators |
150-300 |
0.1-0.2 |
Water-based |
High voltage applications demand precise cuts |
Ceramic Cutting Tools |
200-400 |
0.1-0.2 |
Water-based |
Hard materials require slow and steady cutting |
Ceramic Guides and Fixtures |
150-300 |
0.1-0.25 |
Water-based |
Precision essential for textile machinery applications |
Diamond Compounds |
200-400 |
0.1-0.2 |
Water-based |
Grinding and polishing require consistent feed rates |
Piezoceramics |
150-300 |
0.1-0.2 |
Water-based |
Accuracy critical for functional performance |
Series 15LCU
Low Concentration for Hard and Brittle Materials
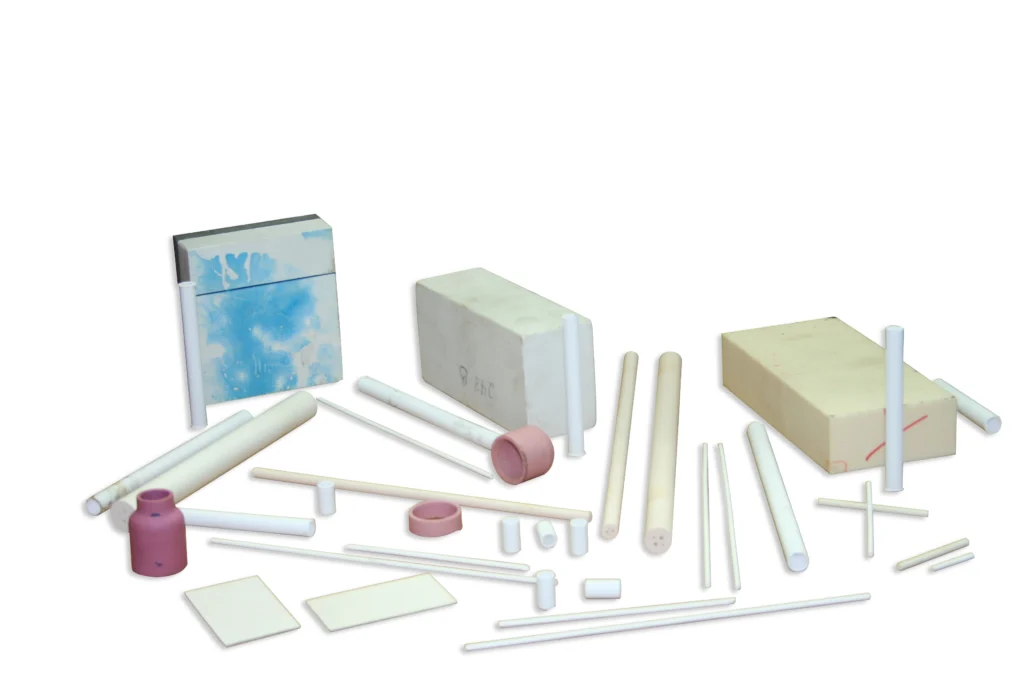

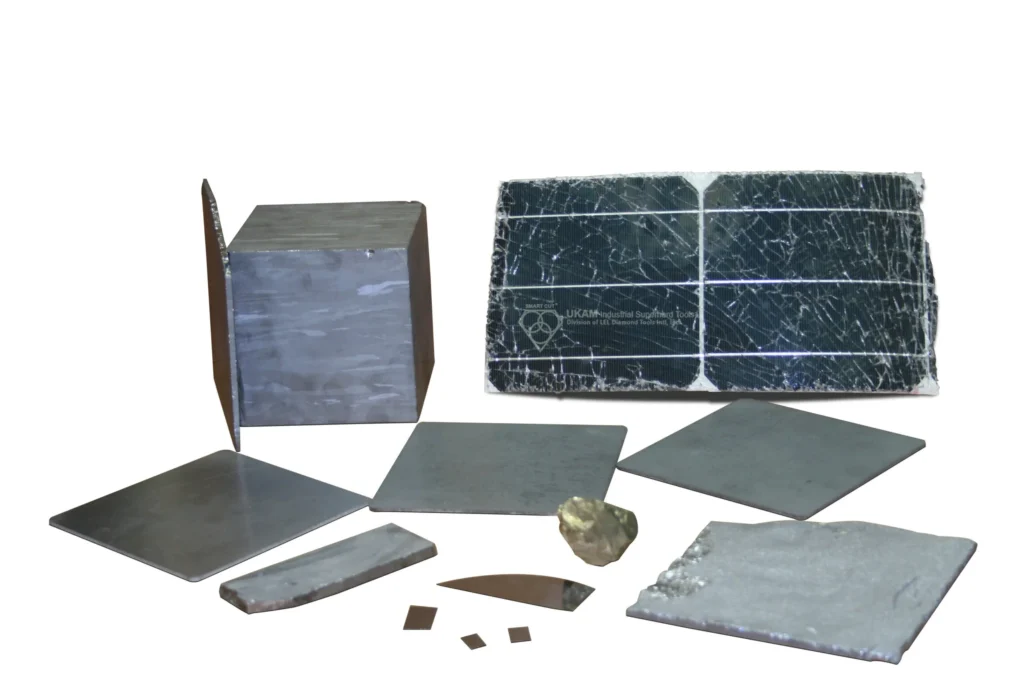
Series 15LCU Diamond Wafering Blades are designed for sectioning hard and brittle materials like glass, alumina (Al203), zirconia (Zr203), and concrete, these blades ensure minimal chip and thermal damage, which is crucial for maintaining the integrity of such materials during sectioning.
Example of Application:
-
Glass: Including optical glass, tempered glass, and other specialized glass types used in construction, automotive, and technology applications, where a clean cut is essential to maintain optical properties.
-
Alumina (Al2O3): Widely used in ceramic substrates, electrical insulators, and abrasion-resistant products. Its hardness and brittleness require precise cutting techniques to prevent chipping.
-
Zirconia (ZrO2): Employed in dental ceramics and other bio-ceramics, known for its high fracture toughness and chemical resistance, necessitating careful handling during sectioning.
-
Concrete: Especially fiber-reinforced and high-performance concrete, which are tougher and more brittle than standard concrete and are used in specialized structural applications.
-
Quartz and Fused Silica: Used in optical applications and semiconductor manufacturing, requiring extremely precise cuts to ensure the integrity of the material’s structure and properties.
-
Silicon: Essential for semiconductor industry, where precise and clean cuts are necessary for wafer production and processing.
-
Sapphire: Used in high-durability windows, watch crystals, and semiconductor substrates, demanding a blade that can deliver precision without inducing structural damage.
-
Ceramic Matrix Composites (CMCs): Including those reinforced with silicon carbide or carbon fibers, used in aerospace and automotive sectors for their high temperature and wear resistance.
-
Brittle Polymers: Such as certain grades of polycarbonate and Plexiglas, which require careful handling to prevent cracking during cutting.
-
Porcelain: Used in electrical insulators and ceramic components, where a clean and precise cut can prevent material waste and ensure functional integrity.
-
Advanced Technical Ceramics: Such as boron nitride and silicon nitride, used in high-performance applications in the electronics and aerospace industries.
-
Marble and Granite: Natural stones that are prone to chipping if not cut with precision, used in architecture and sculpture.
-
Porous Ceramics: Used in filtration systems and biomedical applications, where the integrity of the pores must not be compromised during sectioning.
-
Pyrolytic Graphite: Known for its thermal and electrical properties, used in semiconductor and thermal management applications.
-
Fiberglass: Often used in composite materials for automotive and aerospace industries, requiring a blade that minimizes damage to the fibers.
-
Basalt Fiber: Used in construction and textile applications, where precision cutting is essential to maintain the material’s tensile strength.
-
Ceramic Coatings: Applied to metal substrates to improve their thermal, wear, and corrosion resistance; precise cutting is crucial for quality control and performance assessment.
-
Electroceramics: Such as piezoelectric and ferroelectric materials, which are sensitive to thermal and mechanical stresses during cutting.
-
Diamond-like Carbon (DLC): Coatings used in tribological applications; sectioning requires a blade that does not induce sub-surface damage.
-
Hardened Glass Ceramics: Such as those used in cooktops and lab equipment, where a clean, precise cut is crucial for functionality and safety.
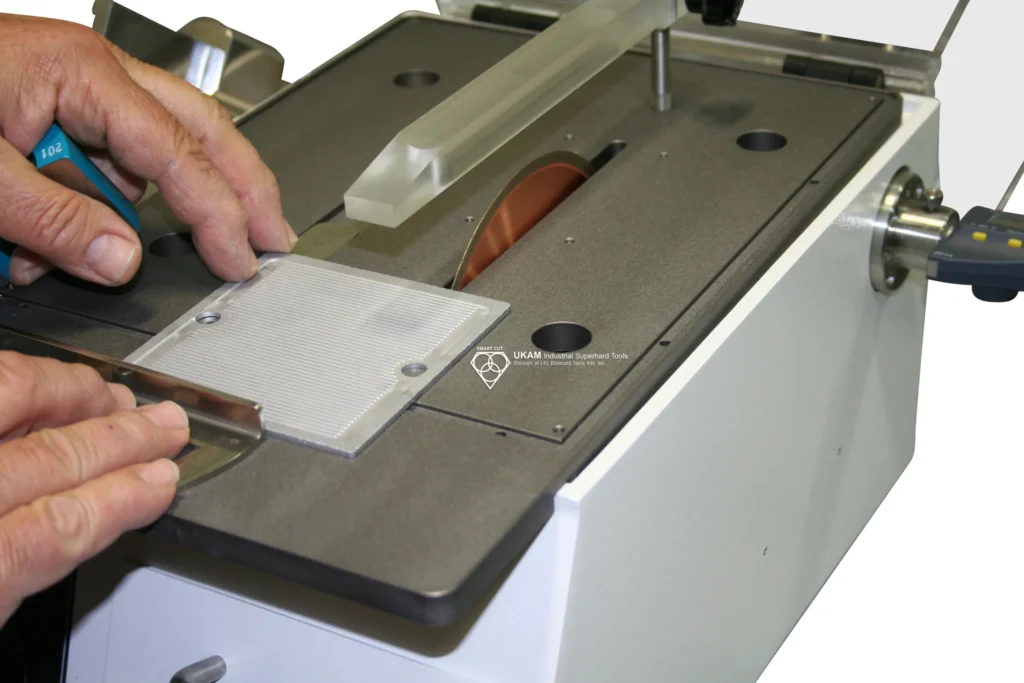
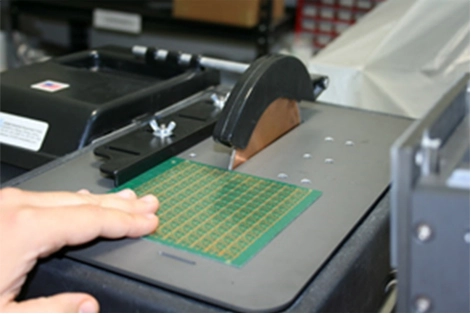
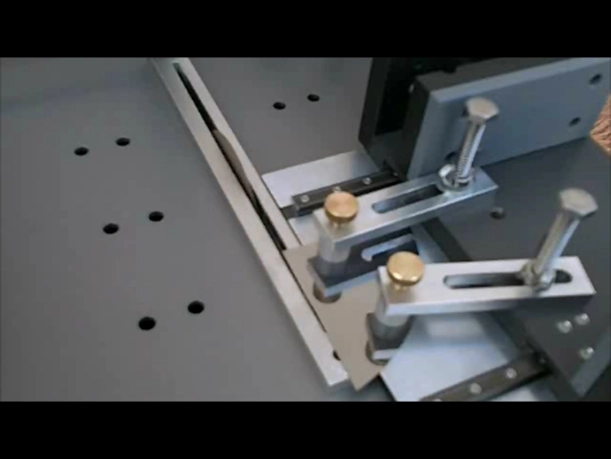
Medium to High Speed Laboratory Saw - Recommended Settings
recommended RPM, feed rate, coolant type, and additional considerations for sectioning 1/2" diameter samples of various materials on a laboratory precision cutting saw using a 6" diameter blade:
Material |
Recommended RPM |
Feed Rate (in/min) |
Coolant Type |
Additional Considerations |
---|---|---|---|---|
Glass (Optical, Tempered) |
1500 - 2000 |
0.5 - 1 |
Water-based coolants |
Use constant and gentle pressure to avoid chipping. |
Alumina (Al2O3) |
2000 - 2500 |
0.3 - 0.5 |
Water-based coolants |
Very hard material; use a diamond blade to ensure smooth cuts. |
Zirconia (ZrO2) |
1800 - 2200 |
0.3 - 0.5 |
Water-based coolants |
Maintain consistent feed rate to prevent blade overheating. |
Concrete |
1000 - 1500 |
0.7 - 1 |
Water-based coolants |
Coarse and dense; use a high-feed rate to prevent blade wear. |
Quartz and Fused Silica |
1500 - 2000 |
0.5 - 0.7 |
Water-based coolants |
Maintain steady pressure to avoid blade vibration. |
Silicon |
2000 - 2500 |
0.5 - 0.7 |
Water-based coolants |
Use low pressure and high RPM to prevent microcracks. |
Sapphire |
2000 - 2500 |
0.3 - 0.5 |
Water-based coolants |
Very brittle; maintain constant feed rate. |
Ceramic Matrix Composites (CMCs) |
1800 - 2200 |
0.5 - 0.7 |
Water-based coolants |
Material can fray; ensure blade is sharp. |
Brittle Polymers (Polycarbonate, Plexiglas) |
1500 - 2000 |
0.5 - 1 |
Water or alcohol-based |
Gentle pressure to avoid deformation. |
Porcelain |
1500 - 2000 |
0.3 - 0.5 |
Water-based coolants |
Maintain consistent pressure to avoid cracks. |
Advanced Technical Ceramics (Silicon Nitride, Boron Nitride) |
1800 - 2200 |
0.3 - 0.5 |
Water-based coolants |
Use diamond blades; consistent feed rate. |
Marble and Granite |
1000 - 1500 |
0.5 - 0.7 |
Water-based coolants |
Maintain slow feed rate; higher force required for dense stone. |
Porous Ceramics |
1500 - 2000 |
0.3 - 0.5 |
Water-based coolants |
Use gentle pressure to avoid breakage. |
Pyrolytic Graphite |
1800 - 2200 |
0.3 - 0.5 |
Water-based coolants |
Delicate; maintain constant pressure. |
Fiberglass |
1500 - 2000 |
0.5 - 0.7 |
Water-based coolants |
Use high-feed rate; material is prone to fraying. |
Basalt Fiber |
1800 - 2200 |
0.5 - 0.7 |
Water-based coolants |
Maintain steady feed rate; prone to fraying. |
Ceramic Coatings |
1800 - 2200 |
0.3 - 0.5 |
Water-based coolants |
Use diamond blades; consistent feed rate. |
Electroceramics |
1500 - 2000 |
0.3 - 0.5 |
Water-based coolants |
Very brittle; use gentle pressure. |
Diamond-like Carbon (DLC) |
1800 - 2200 |
0.3 - 0.5 |
Water-based coolants |
Use high RPM to avoid blade wear; maintain steady pressure. |
Hardened Glass Ceramics |
1500 - 2000 |
0.5 - 0.7 |
Water-based coolants |
Consistent feed rate to avoid chipping. |
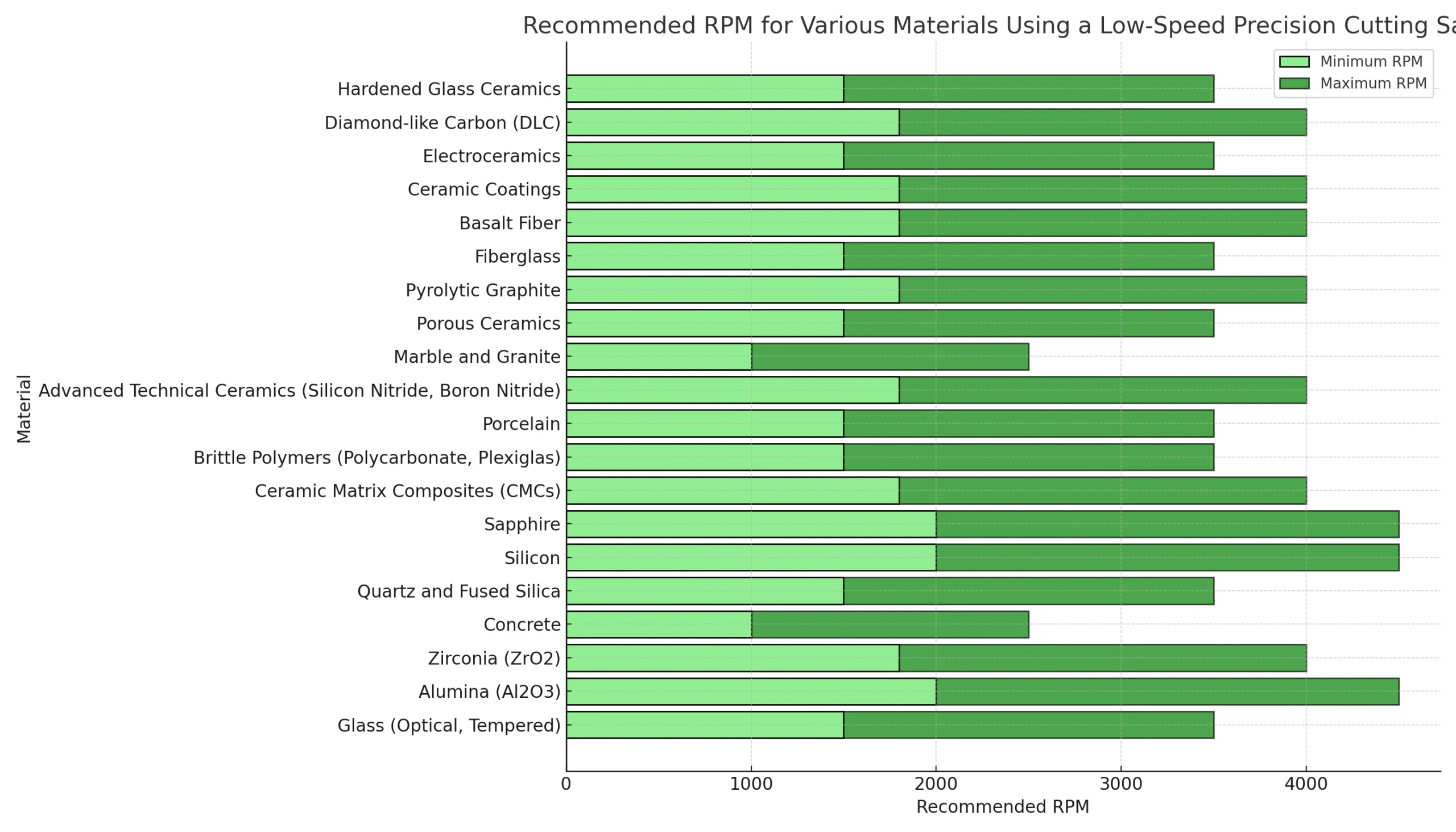
Low Speed Laboratory Saw - Recommended Settings
Example of Recommended RPM’s & Feed Rates, Recommend Coolant Type and Additional Considerations. This information is for reference purposes only Information was reference sectioning 1/4” (6.4mm) diameter sample using Low Speed Saw
Material Category |
Recommended RPM |
Feed Rate (mm/s) |
Coolant Type |
Additional Considerations |
---|---|---|---|---|
Glass (Optical, Tempered) |
100-200 |
0.1-0.2 |
Water-based |
Support material to prevent flex and chipping |
Alumina (Al2O3) |
150-300 |
0.15-0.25 |
Water-based |
Use gentle pressure to minimize chipping |
Zirconia (ZrO2) |
150-300 |
0.15-0.25 |
Water-based |
Careful handling to maintain fracture toughness |
Concrete |
100-250 |
0.2-0.4 |
Water-based |
Adequate cooling to prevent aggregate fracturing |
Quartz and Fused Silica |
150-300 |
0.1-0.2 |
Water-based |
Extremely gentle cuts to preserve optical properties |
Silicon |
200-400 |
0.2-0.3 |
Water-based |
Clean, controlled cuts to maintain wafer integrity |
Sapphire |
100-250 |
0.1-0.25 |
Water-based |
Very gentle approach to avoid structural damage |
Ceramic Matrix Composites (CMCs) |
150-300 |
0.15-0.3 |
Water-based |
Support material during cutting to avoid delamination |
Brittle Polymers (Polycarbonate, Plexiglas) |
200-400 |
0.2-0.4 |
Water-based |
Avoid excessive pressure to prevent cracking |
Porcelain |
150-300 |
0.15-0.25 |
Water-based |
Precise, steady cuts to avoid waste and ensure integrity |
Advanced Technical Ceramics (Silicon Nitride, Boron Nitride) |
150-300 |
0.1-0.25 |
Water-based |
Handle with care to preserve material properties |
Marble and Granite |
100-200 |
0.1-0.2 |
Water-based |
Use a stable platform and adequate water flow |
Porous Ceramics |
150-300 |
0.15-0.25 |
Water-based |
Gentle cutting to maintain pore structure |
Pyrolytic Graphite |
200-400 |
0.2-0.3 |
Water-based |
Consistent feed to avoid thermal shock |
Fiberglass |
150-300 |
0.2-0.4 |
Water-based |
Minimize damage to fibers by reducing pressure |
Basalt Fiber |
150-300 |
0.15-0.3 |
Water-based |
Controlled cuts to maintain fiber integrity |
Ceramic Coatings |
100-250 |
0.1-0.25 |
Water-based |
Precise control to assess coating uniformity |
Electroceramics |
200-400 |
0.1-0.2 |
Water-based |
Care to prevent cracking under thermal stress |
Diamond-like Carbon (DLC) |
200-400 |
0.2-0.3 |
Water-based |
Ensure clean cuts to maintain coating integrity |
Hardened Glass Ceramics |
100-200 |
0.1-0.2 |
Water-based |
Extra care to prevent chipping and preserve functionality |
Series 10LCU
Low Concentration for Medium to Soft Ceramics, Electronic Packages, Composite Materials
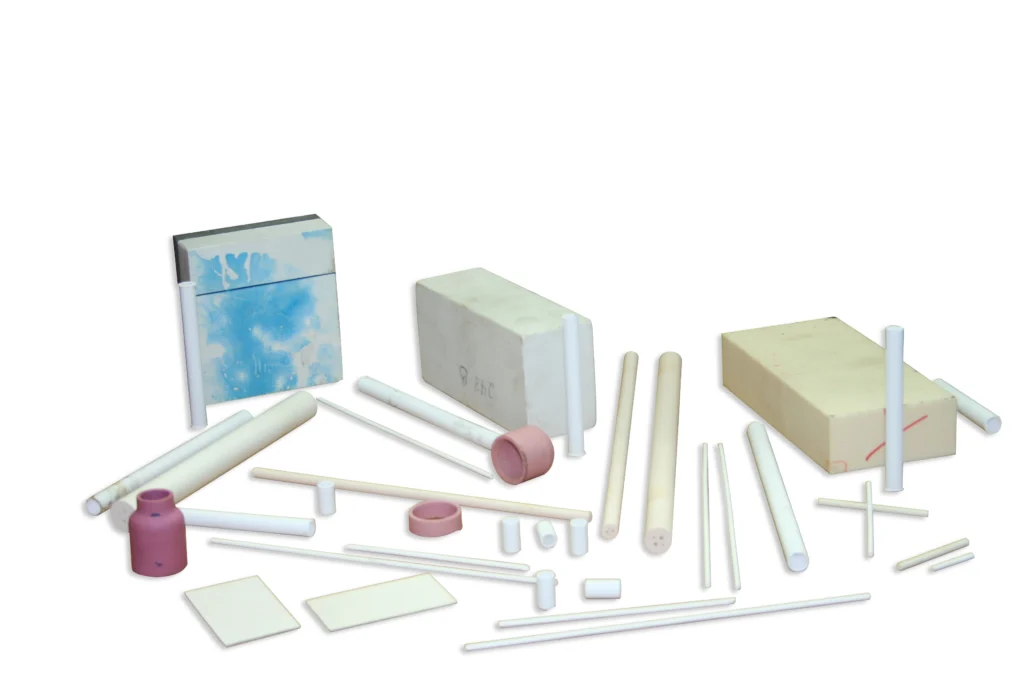

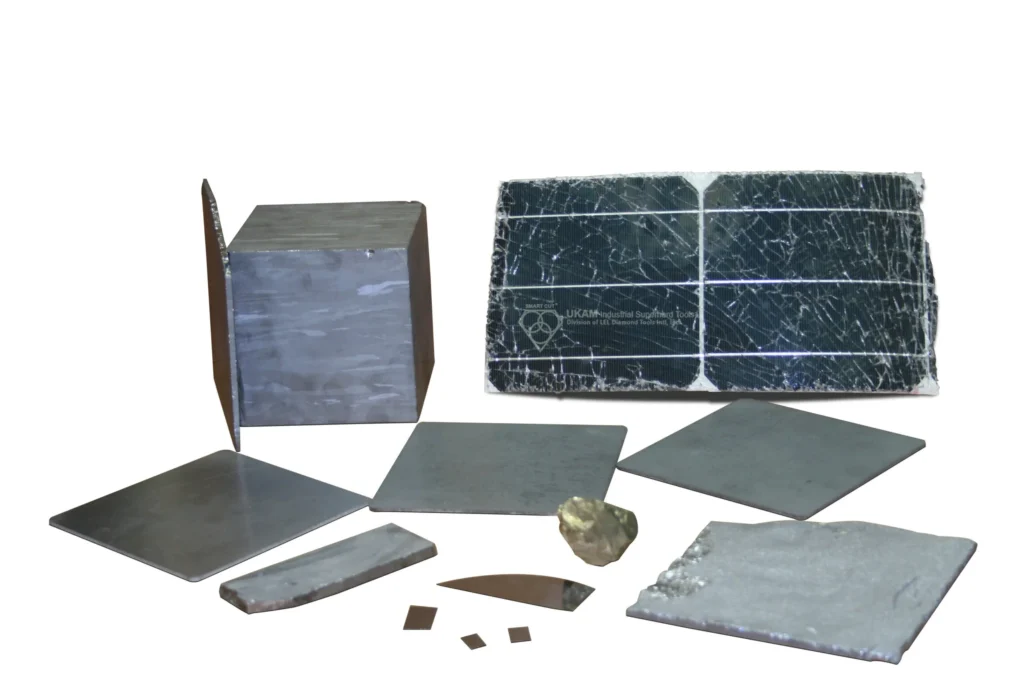
Series 10LCU diamond wafering blades are Ideal for medium to soft ceramics, electronic packages, and composite materials like GaAs and AIN, this series supports precision cutting of delicate materials where excessive force can cause structural damage. The blades in this series are engineered to deliver high precision cuts with minimal material loss.
Example of Application:
-
Medium to Soft Ceramics: Including materials like earthenware and other porous ceramics that require delicate handling during the cutting process to avoid chipping or cracking.
-
Electronic Packages: Such as multilayer ceramic capacitors (MLCCs), semiconductor packages, and other component enclosures that require precise dimensions for proper electronic function.
-
Gallium Arsenide (GaAs): Used in semiconductor devices like integrated circuits (ICs) and solar cells, where precision cuts are crucial for maintaining the electronic properties of the material.
-
Aluminum Nitride (AlN): Known for its high thermal conductivity and electrical insulating properties, used in electronic substrates and heat-sinks.
-
Composite Materials: Including fiberglass, carbon fiber composites, and polymer matrix composites that are used in aerospace, automotive, and sporting goods.
-
Piezoelectric Materials: Such as PZT (lead zirconate titanate) used in sensors and actuators, requiring precise dimensional control to function effectively.
-
Soft Polymers and Polymer Blends: Used in a variety of applications from medical devices to consumer electronics, where a smooth cut can prevent damage to the material’s structure.
-
Fiber-Reinforced Plastics (FRP): Especially those used in light structural applications, where the integrity of the fibers must be maintained during cutting.
-
Printed Circuit Boards (PCBs): For cutting intricate shapes and designs in PCBs without damaging the circuits and electronic components.
-
Low-Fired Ceramics: Used in decorative pottery and sculptures, where a gentle cut can preserve the artistic details and quality of the work.
-
Bio-ceramics:uch as those used in dental and bone substitutes, where precision is necessary for the implants to match the biological environment accurately.
-
Graphene and Other 2D Materials: For cutting ultra-thin materials that are sensitive to mechanical stress and can benefit from the minimal force exerted by the low concentration blades.
-
Organic Semiconductors: Used in flexible electronic devices, requiring careful handling to maintain their electronic properties during the manufacturing process.
-
Thermoelectric Materials: Such as bismuth telluride, which are used in power generation and cooling applications and need precise shaping to function efficiently.
-
Optoelectronic Components: Including light-emitting diodes (LEDs) and laser diodes that require clean cuts to ensure proper light transmission and function.
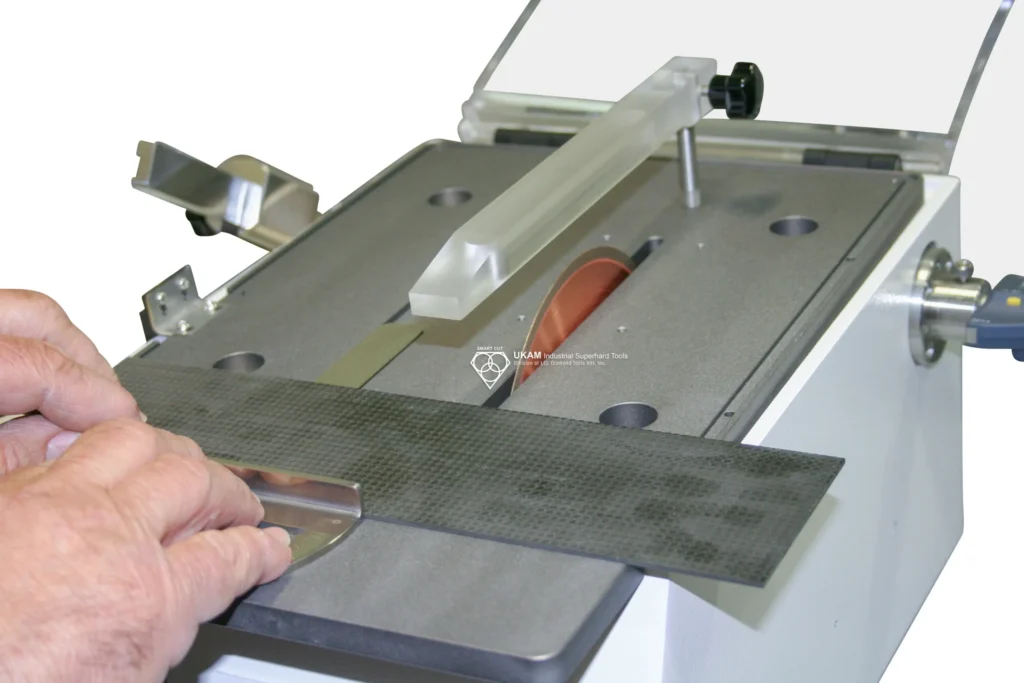
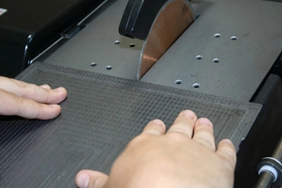
Medium to High Speed Laboratory Saw - Recommended Settings
recommended RPM, feed rate, coolant type, and additional considerations for sectioning various material categories for metallography and sample preparation on a laboratory precision cutting saw with a 6-inch diameter blade. The provided data applies to 1/2-inch diameter material.
Material Category |
Recommended RPM |
Feed Rate (mm/s) |
Coolant Type |
Additional Considerations |
---|---|---|---|---|
Medium to Soft Ceramics |
1,200 - 1,500 |
0.5 - 1.5 |
Water-based coolants |
Maintain a constant flow to avoid overheating. Ensure blade alignment to prevent chipping. |
Electronic Packages |
1,200 - 1,400 |
0.5 - 1.5 |
Water-based coolants |
Avoid excessive pressure on the blade to prevent delamination. |
Gallium Arsenide (GaAs) |
1,200 - 1,400 |
0.5 - 1.0 |
Alcohol-based coolants |
Handle with care due to brittleness. Use a stable fixture to avoid vibration. |
Aluminum Nitride (AlN) |
1,300 - 1,500 |
0.7 - 1.5 |
Water-based coolants |
Ensure blade sharpness to reduce chipping. Consider using a dressing stick to maintain blade integrity. |
Composite Materials |
1,100 - 1,300 |
0.3 - 1.0 |
Water-based coolants |
Variability in structure requires careful handling. Avoid using excessive force. |
Piezoelectric Materials |
1,200 - 1,400 |
0.3 - 0.7 |
Alcohol-based coolants |
Requires careful handling due to sensitivity to pressure. Avoid blade overheating. |
Soft Polymers and Polymer Blends |
1,000 - 1,200 |
0.2 - 0.6 |
Water-based coolants |
Avoid blade overheating due to lower melting points. Use slower RPM to prevent deformation. |
Fiber-Reinforced Plastics (FRP) |
1,100 - 1,300 |
0.3 - 1.0 |
Water-based coolants |
Ensure proper cutting pressure to avoid fiber delamination. |
Printed Circuit Boards (PCBs) |
1,200 - 1,400 |
0.5 - 1.5 |
Water-based coolants |
Avoid overheating to prevent damage to components. Ensure proper blade selection to avoid chipping. |
Low-Fired Ceramics |
1,200 - 1,500 |
0.5 - 1.0 |
Water-based coolants |
Control the pressure to avoid fracture. Ensure blade sharpness to reduce chipping. |
Bio-ceramics |
1,300 - 1,500 |
0.5 - 1.5 |
Water-based coolants |
Keep a consistent flow of coolant to avoid overheating. Consider additional blade alignment checks. |
Graphene and Other 2D Materials |
1,000 - 1,200 |
0.2 - 0.5 |
Alcohol-based coolants |
Handle with care due to extreme thinness. Minimize vibration during cutting. |
Organic Semiconductors |
1,200 - 1,400 |
0.5 - 1.0 |
Water-based coolants |
Maintain a consistent flow of coolant to avoid overheating. Consider slower RPM to avoid chipping. |
Thermoelectric Materials |
1,100 - 1,300 |
0.3 - 1.0 |
Alcohol-based coolants |
Use a consistent feed rate to avoid cracking. Maintain proper blade sharpness for optimal cutting. |
Optoelectronic Components |
1,200 - 1,400 |
0.5 - 1.0 |
Alcohol-based coolants |
Use stable fixtures to reduce vibration. Minimize pressure on the blade to avoid delamination. |
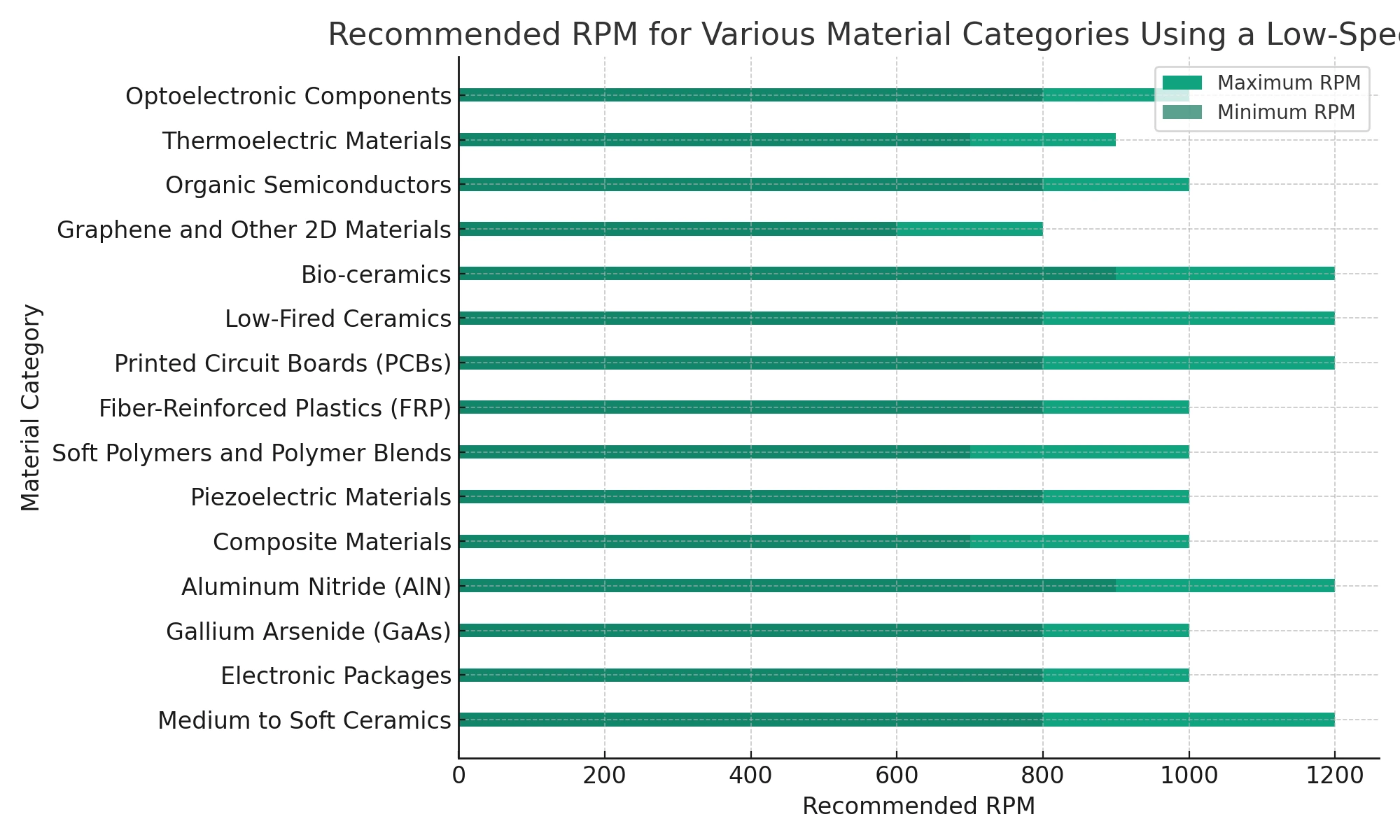
Low Speed Laboratory Saw - Recommended Settings
Example of Recommended RPM’s & Feed Rates, Recommend Coolant Type and Additional Considerations. This information is for reference purposes only Information was reference sectioning 1/4” (6.4mm) diameter sample using Low Speed Saw
Material Category |
Recommended RPM |
Feed Rate (mm/s) |
Coolant Type |
Additional Considerations |
---|---|---|---|---|
Medium to Soft Ceramics |
200-400 |
0.3-0.5 |
Water-based |
Gentle approach to avoid chipping; continuous coolant flow |
Electronic Packages |
250-500 |
0.2-0.4 |
Water with additives |
Minimize thermal impact; precise dimension control |
Gallium Arsenide (GaAs) |
300-600 |
0.2-0.5 |
Water-based |
Avoid thermal damage; ensure clean cuts for device integrity |
Aluminum Nitride (AlN) |
300-600 |
0.2-0.5 |
Water-based |
High thermal conductivity requires effective cooling |
Composite Materials |
400-800 |
0.3-0.6 |
Water-based |
Support structure to prevent delamination |
Piezoelectric Materials |
300-500 |
0.2-0.4 |
Water with additives |
Prevent cracking; maintain material properties |
Soft Polymers and Polymer Blends |
350-700 |
0.3-0.5 |
Water-based |
Gentle cuts to prevent structural damage |
Fiber-Reinforced Plastics (FRP) |
350-700 |
0.3-0.5 |
Water-based |
Support material during cutting to maintain fiber integrity |
Printed Circuit Boards (PCBs) |
200-400 |
0.2-0.4 |
Water with additives |
Prevent delamination and damage to circuits |
Low-Fired Ceramics |
200-400 |
0.3-0.5 |
Water-based |
Gentle approach to preserve artistic details |
Bio-ceramics |
250-500 |
0.2-0.4 |
Water with additives |
Precise cuts essential for medical application accuracy |
Graphene and Other 2D Materials |
300-600 |
0.2-0.4 |
Water-based |
Minimize mechanical stress during cutting |
Organic Semiconductors |
300-500 |
0.2-0.4 |
Water-based |
Maintain cleanliness and prevent contamination |
Thermoelectric Materials |
250-500 |
0.3-0.5 |
Water-based |
Ensure dimensional accuracy for functional efficiency |
Optoelectronic Components |
300-600 |
0.2-0.4 |
Water with additives |
Avoid damage to light paths; clean cuts required |
CBN (Cubic Boron Nitride) Wafering Blades Series: METACUT (High Concentration)
iron, carbon steels, high alloy steels, cobalt alloys, nickel super alloys, and lead alloys
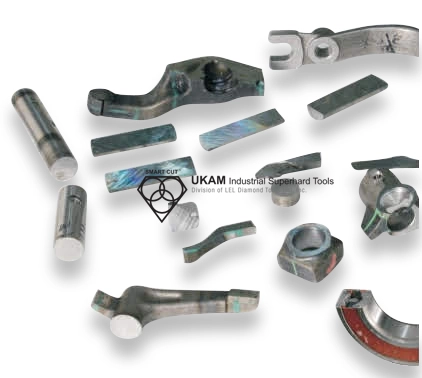
CBN Wafering Blades are designed for sectioning iron, carbon steels, high alloy steels, cobalt alloys, nickel super alloys, and lead alloys. CBN is recommended for cutting had metals, specially iron and steel. Since carbon in steel reacts with carbon in diamond, quickly dulling the diamond crystal and slowing the material removal. CBN blades provide significantly reduced cutting times for tough, gummy materials, such as lead and titanium.
Example of Application:
Iron
-
Known For: Base material for steel, magnetic properties, high strength, and malleability.
-
Applications: Used in structural steel manufacturing, automotive parts, machinery, and general industrial applications.
Carbon Steels
-
Known For: Combination of iron and carbon, offering a wide range of properties based on carbon content, such as toughness and ductility.
-
Applications: Construction materials, automotive components, machinery parts, and general-purpose engineering.
High Alloy Steels
-
Known For: Steels with additional alloying elements for improved strength, durability, and resistance to corrosion or heat.
-
Applications: Aerospace parts, high-performance machinery, and automotive components subjected to high stress.
Cobalt Alloys
-
Known For: High resistance to heat and wear, magnetic properties, and good corrosion resistance.
-
Applications: Aerospace components, medical devices like implants, and high-wear parts due to their robustness.
Nickel Super Alloys
-
Known For: Excellent heat resistance and corrosion resistance, commonly used in high-temperature environments.
-
Applications: Aerospace turbines, power generation components, and high-temperature applications in industrial machinery.
Lead Alloys
-
Known For: High density, malleability, and corrosion resistance.
-
Applications: Electronics (batteries), radiation shielding, and specialty casting due to its flexibility and unique properties.
Cast Iron
-
Known For: Strong, brittle, and resistant to wear; often used where durability is required.
-
Applications: Automotive engine blocks, machinery components, and heavy industrial equipment due to its toughness.
Tool Steels
-
Known For: High hardness, wear resistance, and heat resistance; often used for making tools and dies.
-
Applications: Cutting tools, dies, and molds in manufacturing due to their durability and resistance to deformation.
Stainless Steels
-
Known For: Corrosion resistance, strength, and durability; contains chromium to prevent rusting.
-
Applications: Food processing equipment, medical instruments, and architectural elements due to its resistance to corrosion and aesthetic appeal.
Titanium Alloys
-
Known For: High strength-to-weight ratio, corrosion resistance, and biocompatibility.
-
Applications: Aerospace components, medical implants, and high-performance engineering where weight is a concern.
Powdered Metals
-
Known For: Tailored properties, flexibility in manufacturing, and uniformity.
-
Applications: Precision-engineered components, automotive parts, and specialty manufacturing due to their customizable characteristics.
High-speed Steels
-
Known For: Resistance to heat, hardness, and wear resistance, suitable for high-speed applications..
-
Applications: Cutting tools, drill bits, and machinery components where high temperatures are common during use.
Bronze
-
Known For: Corrosion resistance, durability, and ease of casting; an alloy of copper and tin.
-
Applications: Bearings, bushings, and marine components due to its resilience and resistance to rust.
Copper Alloys
-
Known For: High conductivity, malleability, and resistance to corrosion.
-
Applications: Electrical components, plumbing, and heat exchangers due to its conductivity and flexibility.
Medium to High Speed Laboratory Saw - Recommended Settings
Material |
Recommended RPM |
Feed Rate (mm/min) |
Coolant Type |
Additional Considerations |
---|---|---|---|---|
Iron |
800 - 1200 |
10 - 20 |
Water-based coolant |
Moderate pressure and ensure steady feed |
Carbon Steels |
800 - 1200 |
10 - 20 |
Water-based coolant |
Steady feed, use lower RPM for softer steels |
High Alloy Steels |
1000 - 1500 |
5 - 15 |
Water-based coolant |
Ensure proper cooling to prevent overheating |
Cobalt Alloys |
800 - 1200 |
5 - 15 |
Water-based coolant |
Low feed rate, avoid excessive heat |
Nickel Super Alloys |
800 - 1000 |
5 - 10 |
Water-based coolant |
Maintain a low feed rate to prevent blade wear |
Lead Alloys |
800 - 1200 |
15 - 25 |
Water-based coolant |
Gentle pressure, avoid contamination |
Cast Iron |
800 - 1200 |
10 - 20 |
Water-based coolant |
Steady feed, moderate pressure |
Tool Steels |
1000 - 1500 |
5 - 15 |
Water-based coolant |
Low feed rate, ensure cooling |
Stainless Steels |
1000 - 1500 |
10 - 20 |
Water-based coolant |
Consistent feed, use moderate pressure |
Titanium Alloys |
1000 - 1500 |
5 - 15 |
Water-based coolant |
Slow feed rate, ensure proper cooling |
Powdered Metals |
800 - 1000 |
5 - 10 |
Water-based coolant |
Low feed rate, avoid blade binding |
High-speed Steels |
1000 - 1500 |
5 - 15 |
Water-based coolant |
Avoid overheating, moderate pressure |
Bronze |
800 - 1200 |
10 - 20 |
Water-based coolant |
Steady feed, avoid blade deflection |
Copper Alloys |
800 - 1200 |
10 - 20 |
Water-based coolant |
Avoid blade deflection, steady feed |
Composite Materials |
1000 - 1500 |
10 - 20 |
Water-based coolant |
Use slower RPM for delicate composites |
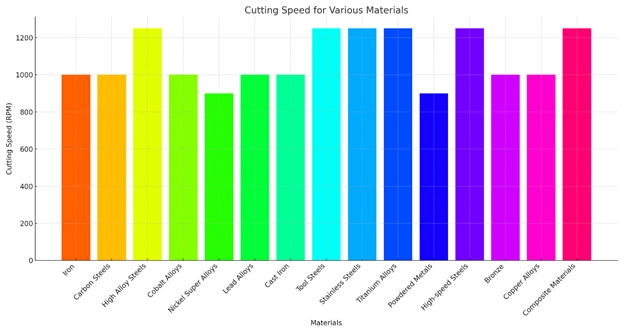
Low Speed Laboratory Saw - Recommended Settings
RPM, feed rate, coolant type, and additional considerations for sectioning these materials for metallography and sample preparation on a laboratory precision cutting saw with a 4" diameter blade for 1/4" diameter material, focusing on lower RPM ranges for low-speed saws:
Material |
Recommended RPM |
Feed Rate (in/min) |
Coolant Type |
Additional Considerations |
---|---|---|---|---|
Iron |
500 - 800 |
0.3 - 0.5 |
Water-based coolants |
Consistent pressure; avoid high feed rate to prevent overheating. |
Carbon Steels |
500 - 800 |
0.3 - 0.5 |
Water-based coolants |
Maintain steady pressure; avoid excessive heat buildup. |
High Alloy Steels |
500 - 800 |
0.3 - 0.5 |
Water-based coolants |
Use diamond blades; consistent feed rate. |
Cobalt Alloys |
500 - 800 |
0.3 - 0.5 |
Water-based coolants |
High hardness; maintain consistent pressure. |
Nickel Super Alloys |
500 - 800 |
0.3 - 0.5 |
Water-based coolants |
Consistent feed rate; avoid high pressure to prevent blade damage. |
Lead Alloys |
500 - 800 |
0.3 - 0.5 |
Water-based coolants |
Maintain low pressure; lead is prone to deformation. |
Cast Iron |
500 - 800 |
0.3 - 0.5 |
Water-based coolants |
Consistent pressure; avoid high feed rates. |
Tool Steels |
500 - 800 |
0.3 - 0.5 |
Water-based coolants |
Use low pressure to avoid blade wear. |
Stainless Steels |
500 - 800 |
0.3 - 0.5 |
Water-based coolants |
Consistent pressure; use diamond blades for hard steels. |
Titanium Alloys |
500 - 800 |
0.3 - 0.5 |
Water-based coolants |
Hard material; maintain consistent feed rate. |
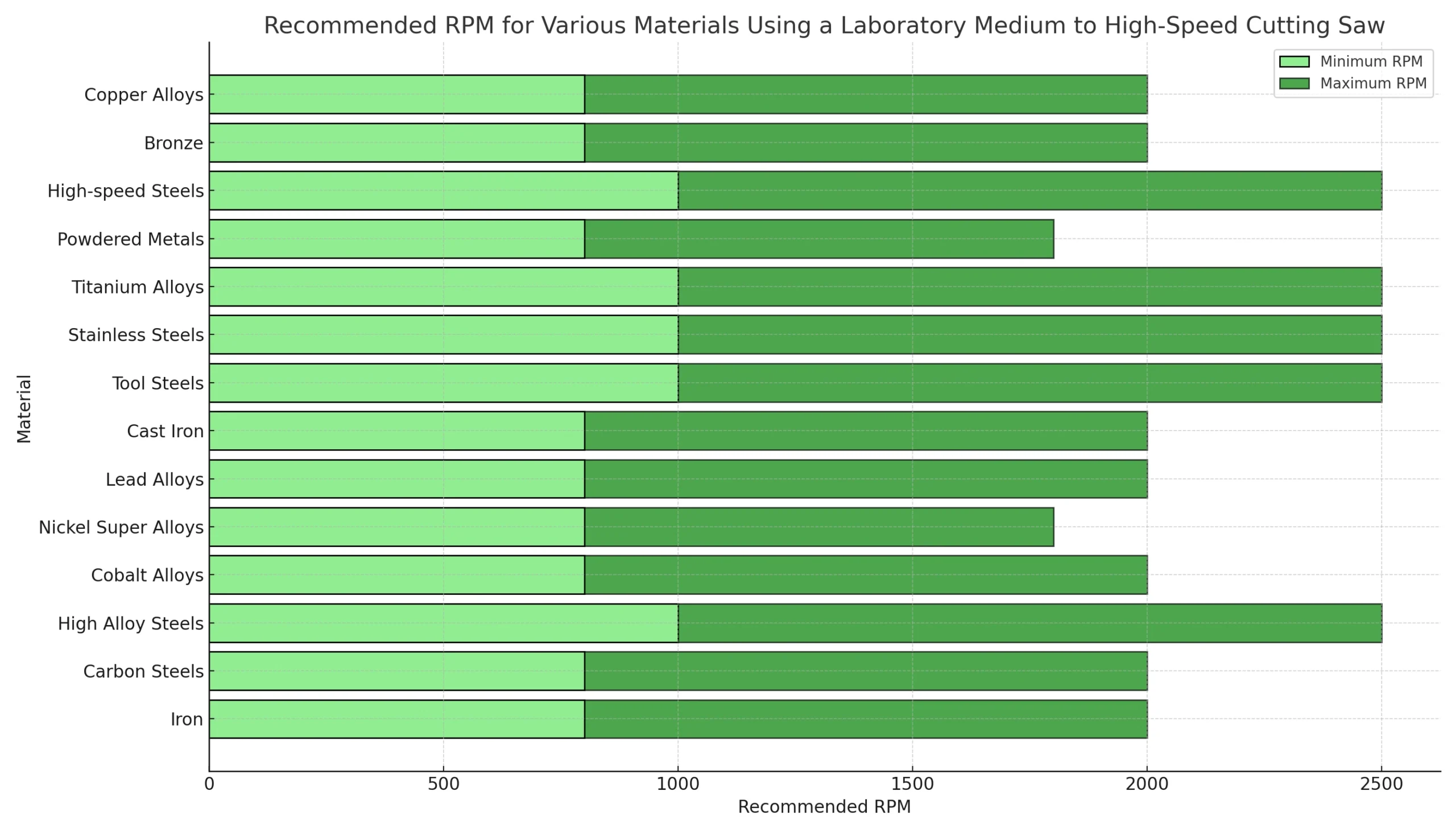
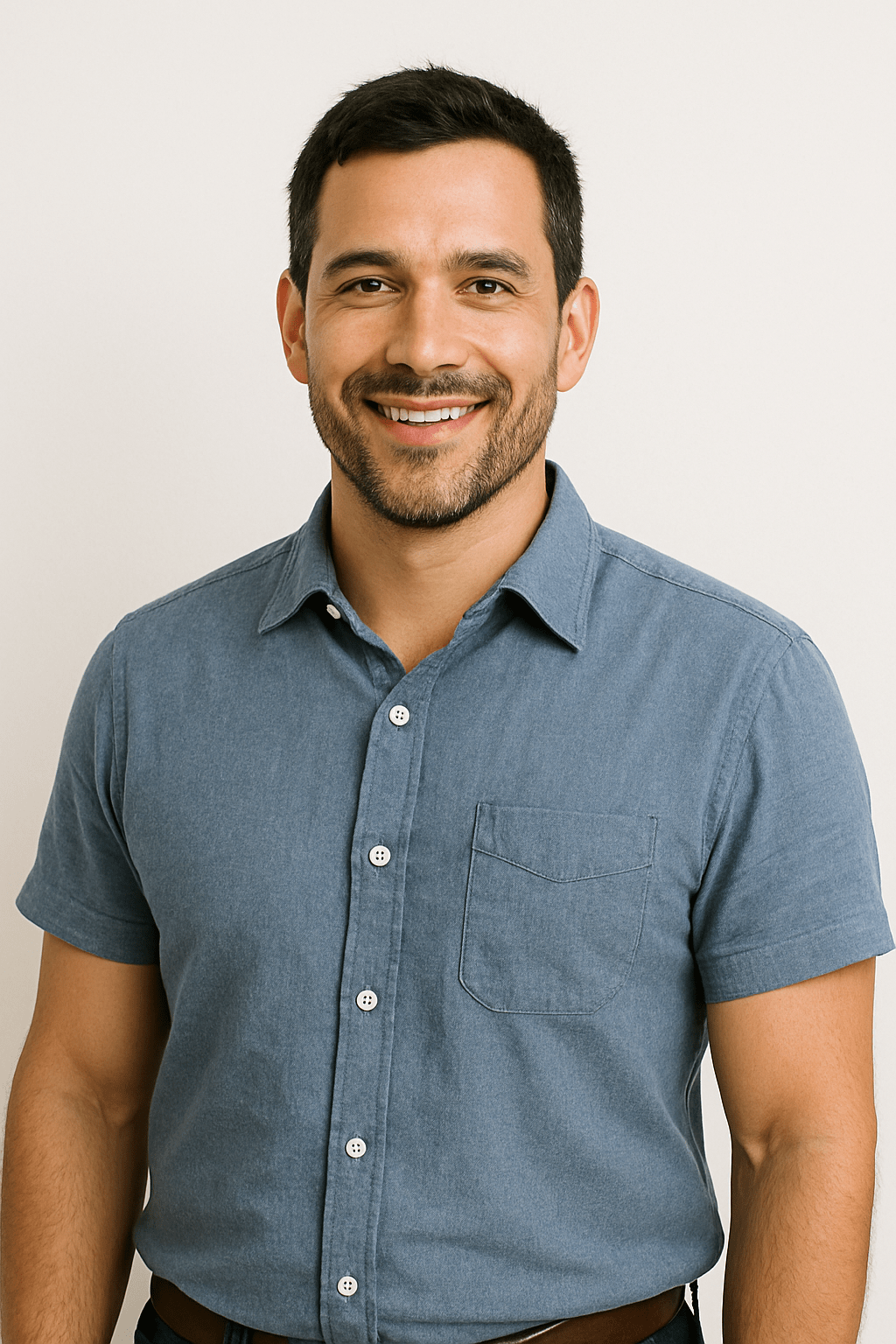
Carlos Sanchez is a senior technical specialist and field applications trainer with more than 17 years of experience in the use and optimization of industrial diamond tools, including ultra-thin diamond blades, core drills, and CBN grinding wheels. With a foundation in industrial engineering and technical operations, Mr. Sanchez has worked extensively with manufacturers and laboratories around the world, providing hands-on support and practical training for a wide range of cutting, grinding, and sample preparation applications.
Fluent in both English and Spanish, Carlos is known for his ability to translate complex tooling concepts into clear, actionable procedures for engineers, technicians, and production staff. His approach emphasizes real-world process improvement, tool longevity, and operator education—ensuring clients get the most out of their diamond tooling investments.
As an author, Mr. Sanchez shares field-tested insights on tool performance optimization, defect prevention, training methodologies, and troubleshooting common cutting issues.

ARE YOU USING RIGHT WAFERING BLADES
FOR YOUR APPLICATION?
LET US
HELP YOU
HAVING ISSUES WITH
YOUR CURRENT WAFERING BLADES?
Knowledge Center
Selecting Right Wafering Blade for your application
Wafering Blade Usage Recommendations
Wafering Blade Case Studies
Diamond & CBN Wafering Blade Performance Metrics
Diamond & CBN Wafering Blade Guide
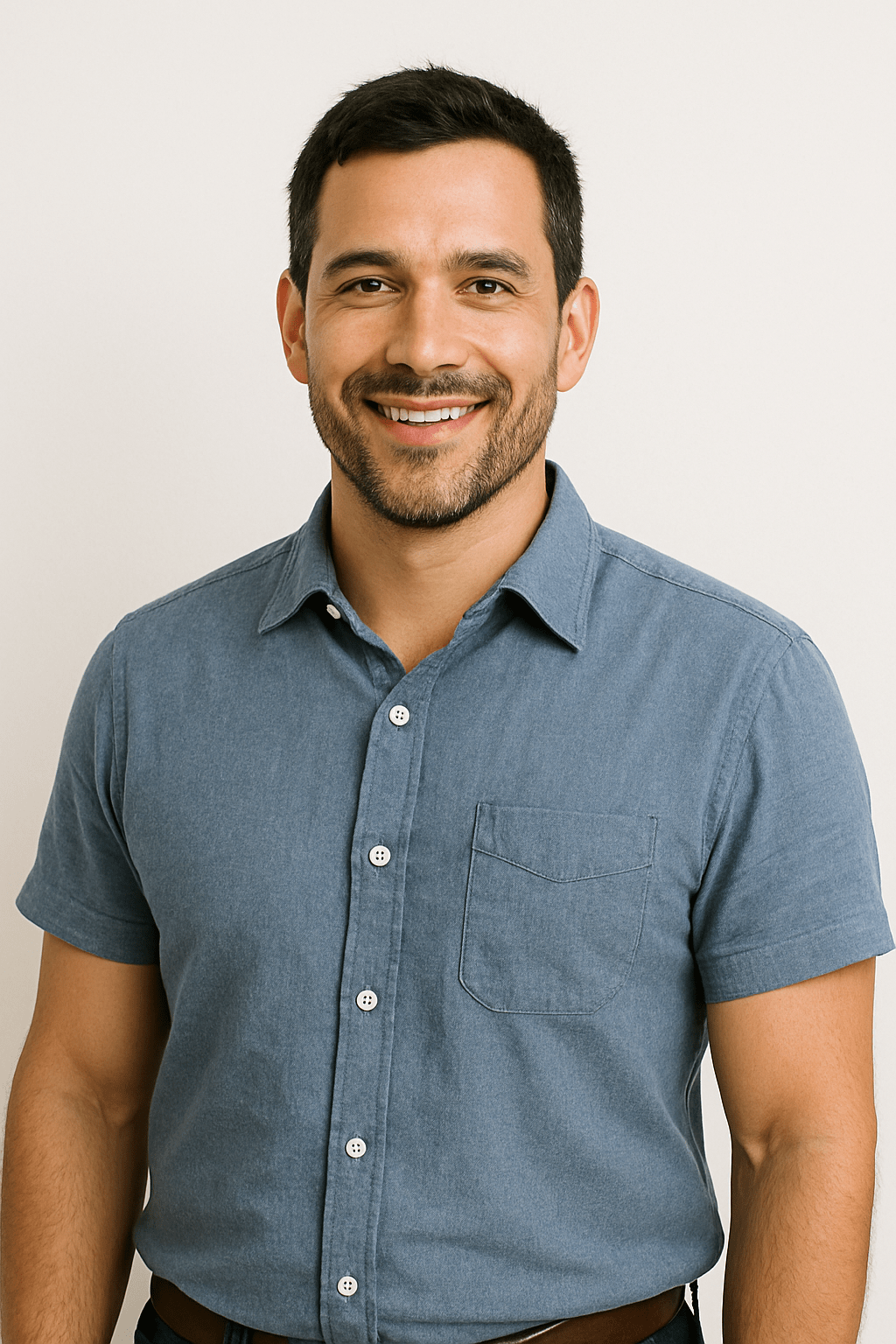
Carlos Sanchez is a senior technical specialist and field applications trainer with more than 17 years of experience in the use and optimization of industrial diamond tools, including ultra-thin diamond blades, core drills, and CBN grinding wheels. With a foundation in industrial engineering and technical operations, Mr. Sanchez has worked extensively with manufacturers and laboratories around the world, providing hands-on support and practical training for a wide range of cutting, grinding, and sample preparation applications.
Fluent in both English and Spanish, Carlos is known for his ability to translate complex tooling concepts into clear, actionable procedures for engineers, technicians, and production staff. His approach emphasizes real-world process improvement, tool longevity, and operator education—ensuring clients get the most out of their diamond tooling investments.
As an author, Mr. Sanchez shares field-tested insights on tool performance optimization, defect prevention, training methodologies, and troubleshooting common cutting issues.