-
0 items in quote
No products in the Quote Basket.
SMART CUT® 455M
Diamond Cut Off Blade for Glass, Optical Glass, & Ceramic
Introducing the SMART CUT® 455M Series Precision Glass Cutting Blade - Your Ultimate Solution for Flawless, Chip-Free Cuts!
Are you tired of the frustration that comes with chipping, rough surface finish and uneven cuts when working with fine glass materials? Look no further than the SMART CUT® 455M, a cutting-edge blade engineered specifically for precision glass cutting where minimizing chipping and excellent surface finish is important. Many vendors offer diamond blades for cutting glass, but very few deliver the right bond composition/formulation and performance needed for effective, chip-free cuts.
The SMART CUT® 455M Blade stands as a testament to our many decades of experience in developing high-precision tools for the optical glass, and materials sciences industry. This expertise has allowed us to create a unique bond formulation that maximizes cutting efficiency and durability.
Description
Specifications
Frequently Asked Questions
Industries Used In
Accessories
Recommendations
Description
Designed for both high performance and longevity, the 455M Blade offers exceptional cutting quality across a wide range of hard and brittle materials. Whether you’re in the semiconductor, ceramics, or precision optics industries, this blade is engineered to exceed your expectations, providing you with superior results in every application.
Produced with high diamond concentration of high quality and fine diamond grit size, evenly spaced diamonds and an optimized bond formulation, and radius on diamond edge to minimize chipping. This is essential for achieving clean, chip-free cuts with a superior surface finish.
The high diamond concentration ensures that the blade remains effective and durable over long periods, providing consistent cutting performance without requiring frequent re-dressing. This is especially beneficial when cutting glass, where a consistent cutting action is necessary to avoid inconsistent edges and unwanted surface imperfections. Additionally, cutting with high diamond concentration and fine grit minimizes the need for frequent blade changes, maximizing tool longevity and offering a cost-effective solution for high-volume glass cutting operations.
The fine diamond grit size helps to reduce the cutting force and distribute the cutting action more evenly, which results in less chipping and a better surface finish, reducing the force applied during cutting and minimizing the risk of chipping. The fine grits help the blade create even, controlled cuts, which is important when working with brittle materials like glass. This results in cleaner edges and improved surface finish, reducing the need for secondary finishing / post-cutting operations and ensuring a high-quality final product.
In glass cutting applications, minimizing chipping and improving the surface finish is not just important for the quality of the product but also for the overall efficiency of the process. With minimal chipping, there is less material waste, and less time is spent on secondary finishing, reducing overall labor cost and time.
For the best results, pair it with our SMART CUT® water-soluble coolant, which enhances the surface finish and reduces heat generation during cutting, ensuring a clean and consistent cut with every pass.
Please note that if you are working with tubing, our SMART CUT® series 2000 Resin Bond Blades are a better solution for that specific application, as they offer optimized cutting performance for such materials.
A standout feature of the SMART CUT® 455M Blade is the advanced design of its diamond cutting radius. The radius on each diamond edge has been specifically engineered to minimize chipping, especially when exiting the cut. This is crucial for ensuring clean and smooth cuts without compromising the edge quality of the material. Unlike traditional cutting methods, where the blade often leaves chips or fractures at the exit point, the SMART CUT® 455M Blade’s precision-radius design allows the diamonds to gradually disengage from the material, reducing the likelihood of edge chipping during the critical moment when the blade exits the cut.
This feature is especially valuable when cutting glass, & fragile or brittle materials, such as optical glass or advanced ceramics, where even minor chips or cracks can affect the material’s integrity and the final product’s quality. By focusing on the cutting radius and reducing the stress at the exit point, the SMART CUT® 455M Blade ensures superior edge retention, improved cut quality, and extended blade life.
SMART CUT® 455M Blade utilizes the SMART CUT® technology to provide fine, evenly spaced diamonds for consistent and precise cuts. Our enhanced bonding technology ensures that the diamonds stay securely in place, even during heavy cutting, providing longer blade life. The careful consideration of the diamond radius further reinforces the cutting capabilities of this blade.
Special arbors can be machined same day. Stock arbors can be bushed to smaller sizes. Please specify at time of order. Custom specifications can be produced with fast lead times & minimum / no order quantities.
Specifications
- Outside Diameters: 4″ (100MM) TO 14″ (350MM)
- Kerf Thickness: .060″ (1.5mm) to .080″ (2.0mm)
-
Inside Diameter: 5/8″ (15.75mm) to 1.0″ (25.4mm)
*we can machine inside diameter to almost anything you want usually same day - Diamond depth/height: 8mm
- Diamond size: 180 mesh
- Diamond Concentration: high
- Diamond Edge: radius at edge
- Application: Larger Range of Glass, Optical Glass, & Some Ceramic Materials
- Equipment Used On: Tile Saws, Masonry Saws, Precision Saws, almost any saw type
- Recommended Coolant: SMART CUT water soluble coolant, water possible (not recommended for optical results)
- Maximum RPM’s: 15,000 to 3,500 depending on blade diameter
Frequently Asked Questions
The SMART CUT Diamond Cut Off Blade comes in outside diameters ranging from 4 inches (100mm) to 14 inches (350mm).
The kerf thickness of the blade can vary from .060 inches (1.5mm) to .080 inches (2.0mm), depending on the specific size.
The inside diameter options range from 5/8 inches (15.75mm) to 1.0 inch (25.4mm). Custom machining of the inside diameter to meet specific requirements is also offered, usually with same-day service.
The diamond depth/height is 8mm, and the diamond size is 180 mesh.
The blade features a high diamond concentration, ensuring efficient cutting and long blade life.
Yes, the blade is designed with a radius at the edge, which helps reduce friction and chipping during cutting.
The SMART CUT Diamond Cut Off Blade is suitable for a larger range of glass, optical glass, and some ceramic materials.
This blade is compatible with various types of cutting equipment, including tile saws, masonry saws, precision saws, and almost any saw type.
It is recommended to use SMART CUT water-soluble coolant with this blade. While water is possible, it’s not recommended for achieving optical-quality results.
The maximum RPM (Revolutions Per Minute) range for this blade varies depending on the blade diameter. It can range from 15,000 to 3,500 RPM, with the specific range corresponding to the blade diameter. Please refer to the product documentation for precise RPM guidelines.
Yes, this blade is suitable for cutting both straight and curved shapes in glass, optical glass, and some ceramic materials. Its design minimizes chipping, making it versatile for precision cutting.
This blade is typically used for wet cutting applications. It is recommended to use SMART CUT water-soluble coolant or water for optimal results. Dry cutting is generally not recommended, especially for achieving high-quality cuts.
It’s crucial to adhere to the recommended RPM range for the specific blade diameter you are using. Exceeding the maximum RPM can be dangerous and may result in blade failure. Always follow the manufacturer’s guidelines for safe operation.
While the SMART CUT Diamond Cut Off Blade is designed for a range of glass and ceramic materials, it can be used for cutting extremely hard materials such as sapphire, however the cutting rate would be slow and dressing frequent. Resin bond blade would be better solution for this application. Consult our technical support for blade recommendations for cutting such materials.
Proper care and maintenance of the blade, such as regular cleaning and ensuring it remains properly lubricated with coolant, can help prolong its lifespan and maintain cutting quality. Follow the manufacturer’s maintenance recommendations.
Yes, always follow safety guidelines when using cutting equipment and blades. Wear appropriate personal protective equipment, including safety glasses, hearing protection, and gloves. Ensure that the cutting area is well-ventilated, and follow all safety instructions provided by the equipment manufacturer.
The SMART CUT Diamond Cut Off Blade is suitable for various scales of cutting projects, including industrial applications. However, for larger projects, consider blade longevity and ensure proper cooling and lubrication for consistent performance.
The SMART CUT Diamond Cut Off Blade is engineered for precision cutting with minimized chipping and excellent surface finish. Its high diamond concentration, fine diamond particles, and unique bond formulation contribute to longer blade life and superior performance, making it a preferred choice for many applications.
Yes, this blade is designed to minimize chipping, making it suitable for cutting delicate and thin glass materials. However, it’s important to follow proper cutting techniques and use the recommended RPM range and coolant for optimal results.
Yes, the SMART CUT Diamond Cut Off Blade can be used for cutting large glass sheets or panels. Its versatility and ability to deliver smooth, chip-free cuts make it a viable choice for architectural glass cutting.
While the SMART CUT Diamond Cut Off Blade is suitable for various glass applications, including tubing, SMART CUT series Resin Bond Blades may be a better solution for cutting tubing. However if very fine “fire polish” type of finish for you is not necessary, then our sintered (metal bond) SMART CUT 455M blade would be excellent solution for your needs.
When changing or installing the blade, ensure that the cutting machine is powered off and unplugged. Follow instructions for safe blade installation, including securing the blade properly and using any recommended safety tools or procedures.
the blade can be dressed to bring it back to life. Dressing should be done on regular basis to keep the diamond particles sharp and wear away metal layer exposing the diamond particles. As long as there is diamond left on the blade it can typically still be used if you expose the diamond crystals.
The lifespan of the blade can vary depending on factors such as the type of material being cut, the RPM used, and the cutting conditions. However, the high-quality diamond particles and bond formulation are designed to provide a longer blade life compared to standard blades.
Yes, the SMART CUT Diamond Cut Off Blade is suitable for cutting some ceramic materials. It is recommended for applications where minimizing chipping and achieving a smooth surface finish are essential. Usually these blade can be used for cutting softer ceramics such as pzt, zirconia, crystals and many others. For Ultra hard ceramics such as boron nitride, silicon carbide, and alumina our resin bond series blades would be a better solution
To extend the blade’s life, it’s important to keep it clean, use the recommended coolant, dressing on periodic bases, and follow proper cutting techniques. Regularly inspect the blade for wear and replace it when necessary.
The primary applications for the SMART CUT Diamond Cut Off Blade are glass, optical glass, and some ceramic materials. While it may be suitable for other materials, it is best used for its intended applications. For cutting different materials, consider using specialized blades designed for those materials. We can produce any blade specification in very short amount of time if needed
While this blade is typically used for wet cutting applications, it is not recommended for dry cutting, especially if you aim for optimal results. Wet cutting with the recommended coolant or water helps dissipate heat and reduce dust, enhancing cutting efficiency and blade life.
The SMART CUT Diamond Cut Off Blade is versatile and can be used by both professionals and hobbyists. Its precision cutting capabilities and minimized chipping make it valuable for a wide range of applications across various industries.
When not in use, it’s advisable to store the blade in a dry and clean environment to prevent any potential corrosion. Keeping the blade clean and free from debris is essential for maintaining its performance. Regularly inspect the blade for any signs of wear or damage.
This blade is compatible with a variety of cutting equipment, its more designed for stationary saws, but can be used on handheld and portable tools if they have right rpm’s range and allow continuous flow of coolant. Its adaptability allows for flexibility in different cutting setups.
When changing the blade on a cutting machine, ensure that the machine is powered off and unplugged. Follow instructions for safe blade removal and installation, and use any recommended safety tools or procedures.
When handling coolants, follow our safety guidelines and recommendations provided with the coolant product. Use appropriate personal protective equipment and ensure proper ventilation in the workspace.
Yes, the SMART CUT Diamond Cut Off Blade is well-suited for precision cuts in glass and ceramics used in electronics manufacturing. Its ability to deliver chip-free cuts and excellent surface finish is valuable for such applications.
Like most cutting blades, the noise level during cutting operations can vary depending on the equipment and material being cut. It’s advisable to wear hearing protection when operating cutting equipment to reduce exposure to noise.
The SMART CUT Diamond Cut Off Blade is designed to minimize chipping, making it suitable for cutting delicate materials. However, for materials with fragile coatings, it’s important to exercise caution and use appropriate cutting techniques to minimize the risk of surface damage. Our resin bond series blades may be a better solution for these applications.
Yes, the SMART CUT Diamond Cut Off Blade is suitable for cutting decorative and intricate patterns in glass art projects. Its ability to deliver chip-free cuts and smooth surface finishes makes it ideal for artistic and precision work.
While basic knowledge of using cutting equipment is important, no special training or skills are typically required to operate this blade. Following guidelines for usage and safety is essential for effective and safe operation.
Disposal of used blades should be done in accordance with local regulations and environmental guidelines. Depending on the composition of the blade, recycling options may be available for the metal components. Ensure that any diamond dust or residue is disposed of safely to minimize environmental impact.
Yes, the SMART CUT Diamond Cut Off Blade can be used for precision cutting of glass and ceramic components in the automotive industry. Its ability to provide clean cuts and minimal chipping is valuable for manufacturing automotive glass and ceramics.
When storing the blade for extended periods, it’s advisable to protect it from moisture and environmental contaminants. Applying a rust inhibitor or coating to the blade can help prevent corrosion during storage.
The SMART CUT Diamond Cut Off Blade can be used for cutting glass with varying thicknesses. However, when cutting materials with significant variations in thickness, adjustments to cutting speed and technique may be necessary to achieve consistent results.
Yes, this blade can be used for cutting specialized glass materials used in the medical and laboratory industries. Its precision and minimized chipping are valuable for producing clean cuts in laboratory glassware and medical components. For thin wall tubing resin bond series blades may be better solution.
The recommended feed rate or cutting speed can vary based on the blade size, material, and specific cutting conditions. Consult our tech support for the most suitable feed rate and cutting speed for your application.
Yes, this blade can be used for cutting circular glass or ceramic pieces with precision. Its radius edge design helps achieve smoother and more precise circular cuts.
The blade itself is the primary component. Any additional accessories or attachments for specific cutting applications would need to be acquired separately. We recommend using with our These additional FAQs provide further information about the versatility, suitability, and specific applications of the SMART CUT Diamond Cut Off Blade, as well as considerations for storage and disposal. Always refer to the manufacturer’s recommendations and guidelines for the best results when using the blade.
Yes, the SMART CUT Diamond Cut Off Blade is suitable for cutting glass or ceramics with intricate designs and tight tolerances. Its precision and minimal chipping make it an excellent choice for such applications.
This blade is compatible with a wide range of cutting equipment, including CNC machines, as well as manual cutting machines. Its adaptability allows for both automated and manual cutting processes.
While this blade is primarily designed for straight cuts, it can be used for beveling or edging glass and ceramic pieces with the appropriate technique. However, for more specialized beveling applications, dedicated tools may be recommended.
After use, it’s important to clean the blade thoroughly to remove any debris or residue. Using a brush or cleaning solution specifically designed for diamond blades can help maintain performance. Regular maintenance, such as inspections and coolant replacement, is also essential.
While this blade is designed for glass and ceramic materials, cutting laminated glass with embedded metal or wire may result in premature wear of the blade. Specialized blades may be more suitable for such applications.
This blade is primarily designed for cutting rather than engraving or etching. For engraving or etching work on glass or ceramics, dedicated engraving tools or methods are typically employed.
When handling the coolant, follow the manufacturer’s safety data sheets (SDS) and recommendations. It’s important to use appropriate personal protective equipment and dispose of used coolant in accordance with local environmental regulations.
Can this blade be used for cutting glass or ceramic materials with embedded additives or impurities?
The ability to cut glass or ceramics with embedded additives or impurities depends on the specific composition and hardness of the material. It’s advisable to perform a test cut or consult with our tech support for guidance on cutting such materials.
While this blade can cut glass, cutting glass bottles or containers for recycling may not be its primary intended use.
Yes, this blade can be used for cutting glass or ceramic tiles for tiling projects, both for interior and exterior applications. Its precision cutting and minimized chipping make it suitable for tile cutting.
While the SMART CUT Diamond Cut Off Blade can provide precision cuts, its use in cleanroom environments may depend on specific cleanliness requirements. Consult with your facility’s cleanliness guidelines and the blade manufacturer for compatibility.
This blade is primarily designed for straight cuts, but with skilled operation, it can be used for cutting glass or ceramics with complex shapes. For highly specialized shapes, consider dedicated tools or methods.
While there may not be a fixed maintenance schedule, regular blade inspections, cleaning, dressing, and coolant replacement are advisable to ensure consistent performance. Blade maintenance frequency can depend on usage intensity and the materials being cut.
The SMART CUT Diamond Cut Off Blade can be used for cutting mirrored glass or glass with reflective coatings. However, our resin bond blades would be much better solution for this application.
While the blade is suitable for many glass and ceramic materials, cutting heat-treated or
Yes, there are recommended cutting speeds and feed rates based on the material being cut and the specific blade size.
This blade can be used for cutting sensitive coatings or fragile surfaces, but extra care should be taken to avoid damage. Adjusting cutting parameters and techniques may be necessary to minimize the risk of coating or surface damage. Consider also using our resin bond blades for this applciation
Yes, the SMART CUT Diamond Cut Off Blade is suitable for cutting architectural glass used in windows, doors, and glass partitions. Its precision and minimized chipping are valuable for such applications.
Yes, the SMART CUT Diamond Cut Off Blade is suitable for cutting stained glass for art and decorative projects. Its precision cutting capabilities help achieve clean and precise cuts in stained glass.
Absolutely, this blade can be used for cutting ceramic tiles with intricate patterns or designs for mosaic projects. Its precision and minimized chipping make it a valuable tool for mosaic artists.
While this blade can cut glass and ceramics, materials with embedded fibers or reinforcement may require specialized cutting tools. Consult with the manufacturer or supplier for recommendations for such materials.
The disposal of used coolant should follow local environmental regulations and guidelines. Many coolants can be treated and recycled. Contact local authorities or waste management facilities for proper disposal procedures.
The disposal of used coolant should follow local environmental regulations and guidelines. Many coolants can be treated and recycled. Contact local authorities or waste management facilities for proper disposal procedures.
Can this blade be used for cutting glass or ceramics at an angle or bevel for specific applications?
While the blade is primarily designed for straight cuts, it can be used for cutting at angles or creating beveled edges with the right technique and equipment.
Always prioritize safety when cutting glass or ceramics. Use appropriate personal protective equipment (PPE), including safety glasses, hearing protection, and gloves. Ensure proper ventilation in the workspace to reduce exposure to dust and coolant.
Yes, this blade can be used for cutting glass or ceramics with unusual shapes or sizes, including circular or irregular pieces. Its precision and minimized chipping can help achieve accurate cuts.
It’s recommended to follow the recommendations provided ensure safe and effective cutting. These blades should have arrow to show rotation direction
Yes, this blade can be used for cutting glass or ceramics with varying levels of hardness or fragility within the same project. However, it’s important to adjust cutting parameters and techniques accordingly to accommodate the differences in material properties.
This blade is designed for precision cutting, so textured or uneven surfaces may require extra care and attention during cutting. It’s advisable to stabilize the material as needed to achieve clean cuts.
When cutting thick glass or ceramics, it’s important to use appropriate cutting techniques, adjust cutting parameters, and ensure that the equipment is well-suited for the thickness. Follow safety guidelines and wear necessary protective gear.
While the SMART CUT Diamond Cut Off Blade excels at surface cutting, cutting internal complex patterns or structures may be challenging. For such applications, consider specialized tools or methods.
Submerging the material in water or other appropriate cutting fluids is a common practice when using diamond blades for cutting glass or ceramics. It helps dissipate heat and reduce dust. Ensure the equipment is designed for wet cutting.
Spare parts and accessories, such as bushings or flanges, are often available for maintaining and replacing components of the blade. Consult with your machine manufacturer or supplier for specific replacement parts and compatibility. We also offer flanges and wheel stiffeners to fit most popular cutting equipment.
The suitability for cutting intricate patterns or inlays involving multiple materials can vary depending on the specific materials and their compatibility with the blade.
Industries Used In
Tab Content
Accessories
Showing 1 – -1 of 13 results Showing all 13 results Showing the single result No results found
Sort by Price low to high
Filters Sort results
Reset Apply
Image | Name | COMPATIBILITY WITH DRILL SERIES | Price | Quantity | Add to cart |
---|---|---|---|---|---|
Recommended for use in Diamond Tools 150 Grit Size (mesh… | $15.39 | Max: Min: 1 Step: 1 | |||
Recommended for coarser grits found in segment wheels, core drills… | $15.99 | Max: Min: 1 Step: 1 | |||
5/8″-11″ thread. Fits into drill press chuck. Shank adapter threads… | $22.46 | Max: Min: 1 Step: 1 | |||
5/8″-11″ thread. Fits into drill press chuck. Shank adapter threads… | $26.72 | Max: Min: 1 Step: 1 | |||
SMART CUT® General Materials Formula Synthetic Water Soluble Coolant | $34.81 | Max: Min: 1 Step: 1 | |||
Recommended for use in Diamond Tools 150 Grit Size (mesh… | $39.47 | Max: Min: 1 Step: 1 | |||
Recommended for coarser grits found in segment wheels, core drills… | $39.47 | Max: Min: 1 Step: 1 | |||
SMART CUT® General Materials Formula Synthetic Water Soluble Coolant | $99.81 | Max: Min: 1 Step: 1 | |||
105DE, 135DB, 115DM, 125DM, 130DMN, 140DM (up to 1-5/8″ OD) | $154.87 | Max: Min: 1 Step: 1 | |||
105DE, 135DB, 115DM, 125DM, 130DMN, 140DM (up to 1-5/8″ OD) | $154.87 | Max: Min: 1 Step: 1 | |||
105DE, 135DB, 115DM, 125DM, 130DMN, 140DM (up to 1-5/8″ OD) | $235.00 | Max: Min: 1 Step: 1 | |||
SMART CUT® General Materials Formula Synthetic Water Soluble Coolant | $317.41 | Max: Min: 1 Step: 1 | |||
SMART CUT® General Materials Formula Synthetic Water Soluble Coolant | $1,745.00 | Max: Min: 1 Step: 1 |
Recommendations
02
Jun
How to Properly Use Precision Diamond & CBN Blades
The diamond blade itself is only a small factor in your cutting operation. Successful diamond sawing is both an art & science. Requiring proper use and understanding of the right: RPM’s, Coolants, Equipment, Dressing Devices, Accessories…
02
Jun
Precision & Ultra Thin Diamond Blade Guide
Diamond and CBN blades are available in an extensive array of varieties, each differing in bond types, manufacturing methods, and design specifics. Ultra Thin & High Precision Diamond Blades are particularly versatile, applicable…
02
Jun
Troubleshooting Diamond Sawing Problems
Having issues with your diamond cutting operation? This Illustrated Guide can help. Learn the most common problems most people have in using diamond cutting blades. How to resolve them and avoid them in…
02
Jun
How to Improve & Optimize Your Diamond Sawing Operation
There are numerous variables that affect the performance of diamond and CBN cutting blades. Understanding these variables will help end users select the right diamond blade specifications for their applications and optimize their…
02
Jun
Evaluating & Comparing Diamond Blades
Share this Article with Friend or Colleague
Proper testing procedures and methodologies must be set up and used to obtain accurate as well as repeatable testing results. This article will discuss several simple procedures which…
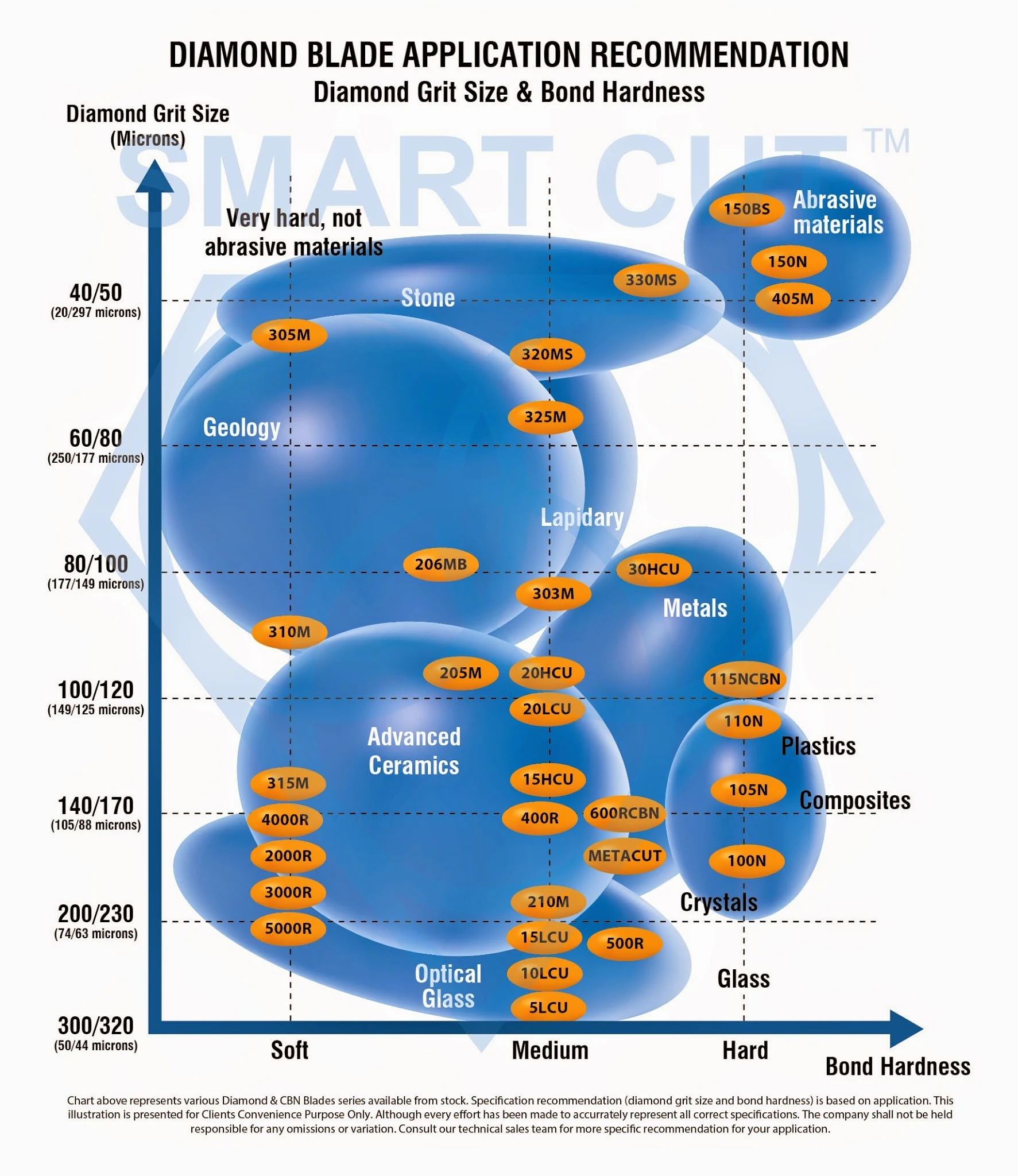
Filters Sort results
Reset Apply
Image | New Item No: | Diameter | Kerf Thickness | Arbor Size (Inside Diameter) | Price | Quantity | Add to Cart |
---|---|---|---|---|---|---|---|
4" | .060” (1.52mm) | 5/8” (15.87mm) | $90.47 | Max: Min: 1 Step: 1 | |||
5" | .060” (1.52mm) | 5/8” (15.87mm) | $102.53 | Max: Min: 1 Step: 1 | |||
6" | .060” (1.52mm) | 5/8” (15.87mm) | $117.64 | Max: Min: 1 Step: 1 | |||
7" | .060” (1.52mm) | 5/8” (15.87mm) | $128.43 | Max: Min: 1 Step: 1 | |||
8" | .060” (1.52mm) | 5/8” (15.87mm) | $155.32 | Max: Min: 1 Step: 1 | |||
10" | .060” (1.52mm) | 5/8” (15.87mm) | $172.90 | Max: Min: 1 Step: 1 | |||
12” | .080” (2.0mm) | 1.0” (25.4mm) | $235.80 | Max: Min: 1 Step: 1 | |||
14” | .080” (2.0mm) | 1.0” (25.4mm) | $275.10 | Max: Min: 1 Step: 1 |
Why Work With Us?
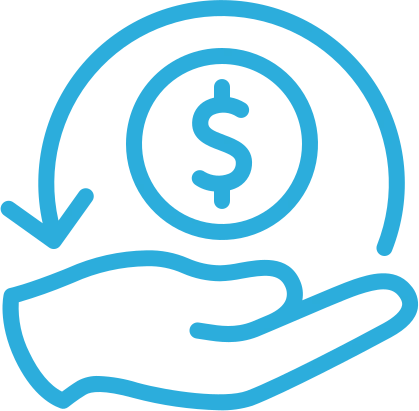
Best Return
on Investment
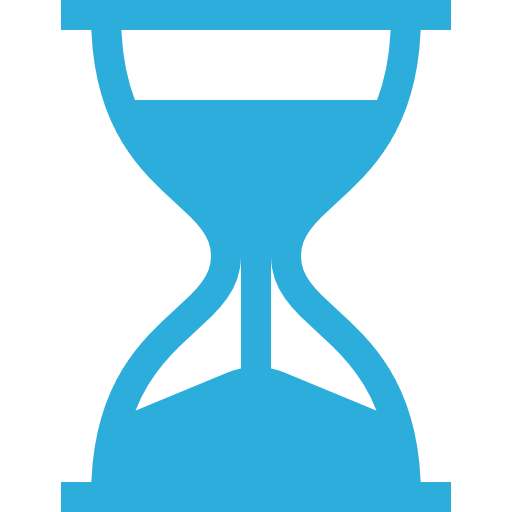
Attractive Cost of
Ownership
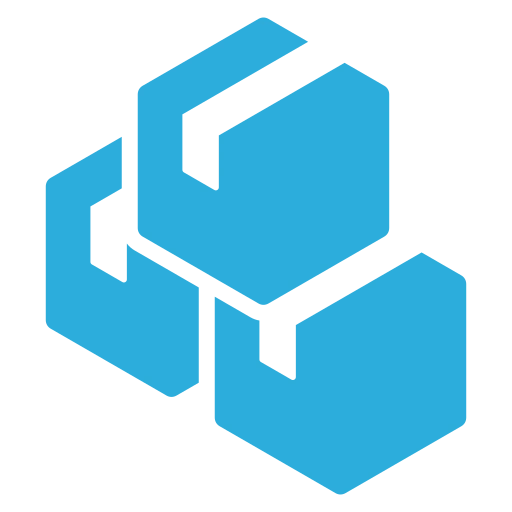
Thousands of Diamond & CBN Blades in stock
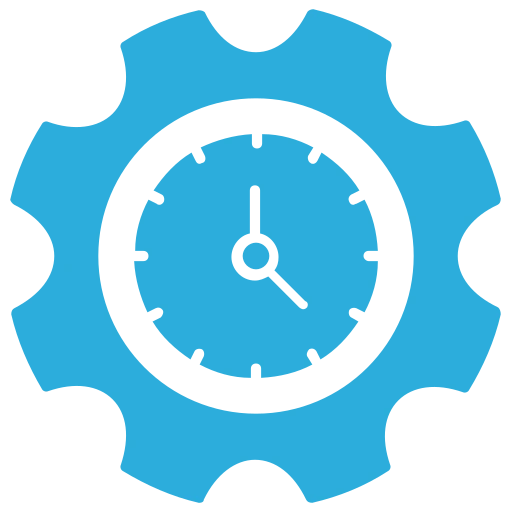
Custom Manufacturer with Fast Lead times
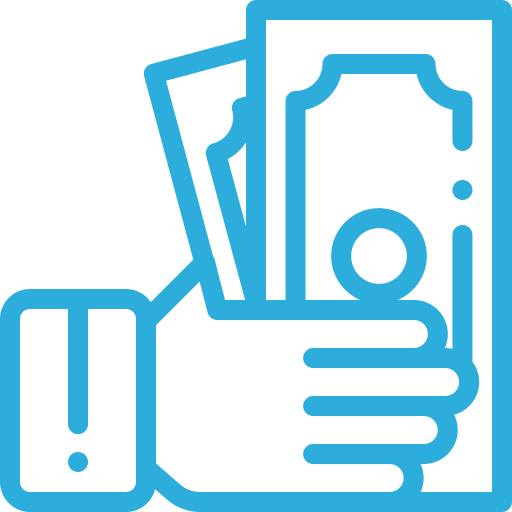
Unmatched
Prices in North America
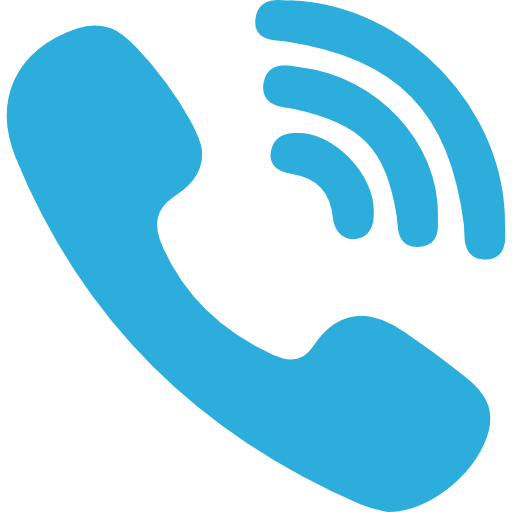
Unmatched Experience & Technical Support
Features:
- Unique Bond Formulation: SMART CUT 455M series is your solution when it comes to delivering straight, true, and chip-free cuts, even in the most delicate glass materials.
- Radius on Diamond Edge – this helps reduce amount of force and friction when entering and exiting front and back side of material and minimum stress and material pullout
- High Diamond Concentration & Fine Diamond Particles – our sintered (metal bond) blade has high diamond concentration of high quality fine diamond particles held in sintered (metal bond) bond matrix. This combination will provide long blade life
- Exceptional Versatility: This blade is designed to excel across a wide range of glass and ceramic types, where minimum chipping and smooth surface finish is required
- Fits on Almost Any Cutting Machine: we can machine the Inside Diameter (arbor size of these blades) to almost any you want or bush to any arbor size usually same day. We can also machine custom bushings.
- Whether you’re working on intricate glass art projects, cutting precise pieces for the electronics industry, or handling specialized glass materials, SMART CUT 455M series blade is the blade that will improve your cutting of these glass and ceramic materials. Say goodbye to the frustration of chipping and imprecise cuts and say hello to perfection with every slice.
Advantages:
- Chip Free Cutting
- Smooth Surace Finish
- Minimum Material Deformation
- Long Life
- High Degree of Consistency
- Excellent Performance
About Sintered (Metal Bond)
Sintered (metal bonded) diamond tools have multiple layers of diamonds impregnated inside the metal matrix. Diamonds are furnaces sintered in a matrix made of iron, cobalt, nickel, bronze, copper, tungsten, alloys of these powders or other metals in various combinations. Metal bonded diamond tools are “impregnated” with diamonds. This means that selected diamonds are mixed and sintered with specific metal alloys to achieve the best cutting performance possible on any materials such as sapphire, advanced ceramics, optics, glass, granite, tile and etc. The metal bond surrounding the diamonds must wear away to continuously keep re-exposing the diamonds for the diamond tool to continue cutting. Sintered (metal bonded) diamond tools are recommended for machining hard materials from 45 to 75 on rockwell scale (5 to 9.5 on mohe’s scale of hardness).
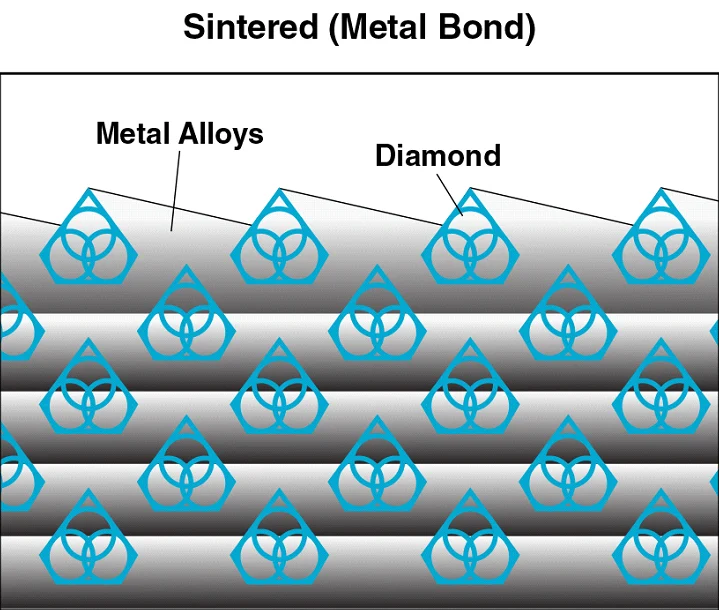
How SMART CUT® Bond Works?
Step 1
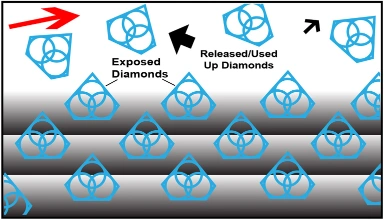
Sharpest And Finest Quality Diamonds
The newly exposed diamonds don’t effect diamonds already working on the material. Unlike many other diamond bonds, diamonds in a SMART CUT® Bond remains sharp and grow sharper with each cut, prolonging product life and consistent performance.
Step 2
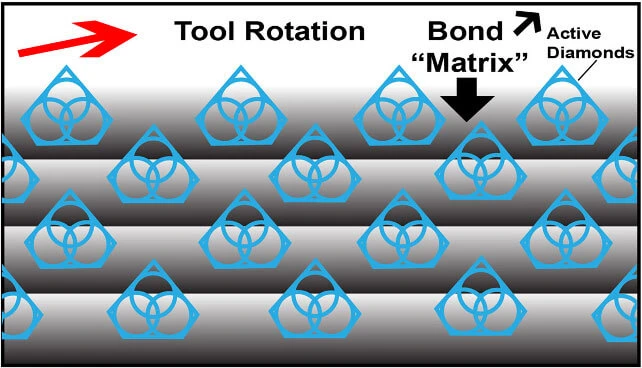
Diamonds or CBN Crystals
Diamonds or CBN Crystals are activated only at the exposed layer. As Bond Matrix layer begin to wear out, diamonds in a new Bond Matrix layer are immediately activated, substituting the already used up diamond layer. The SMART CUT® Diamond Hybrid Bond makes sure every diamond is in the right place and at the right time, working where you need it most.
Step 3
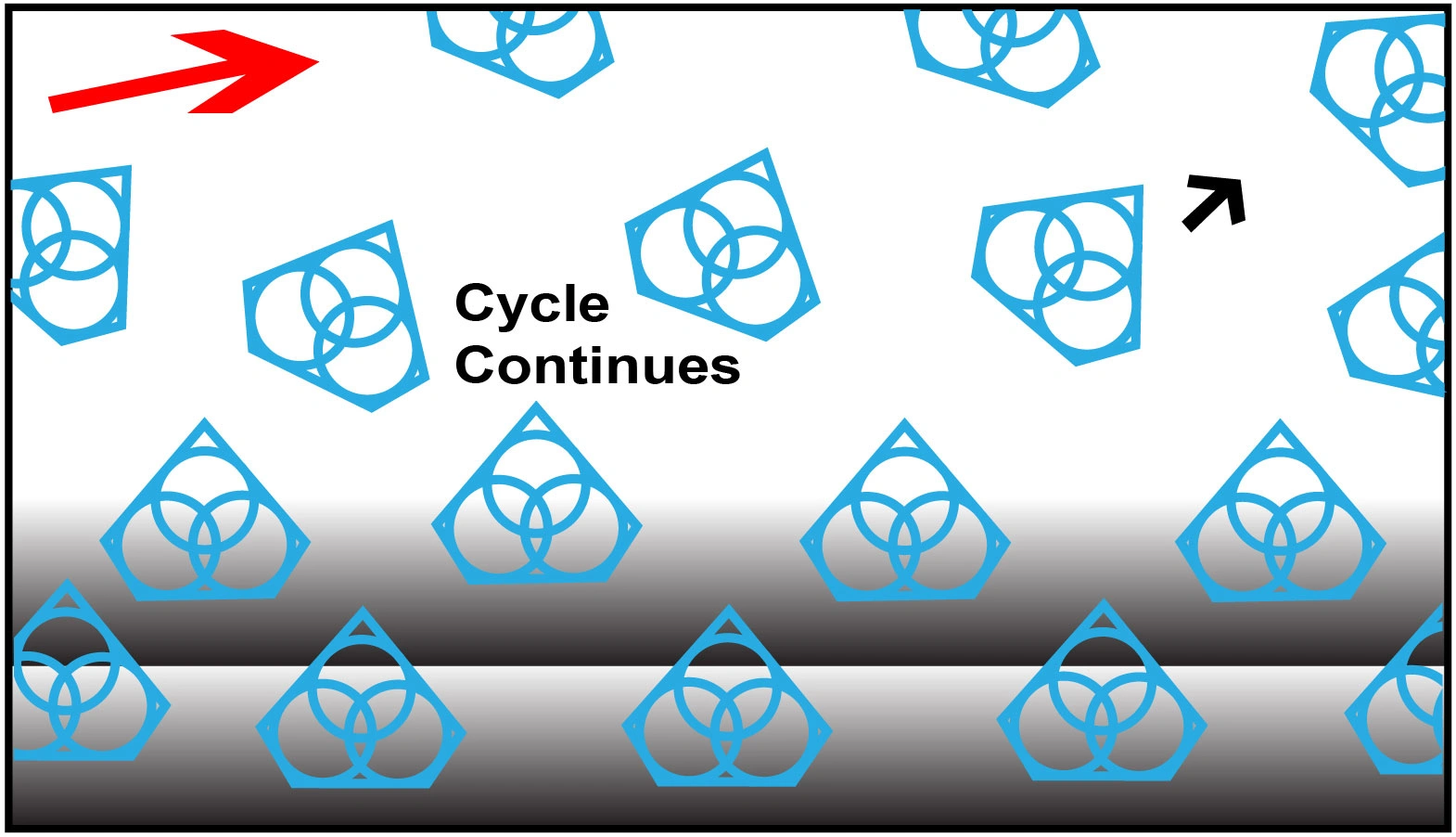
Advanced Formulated Open Diamond Bond Design
This advanced formulated open diamond bond design insures minimal chipping, fast cut, constant speed of cut, minimal cutting noise, and most important of all, consistent performance.
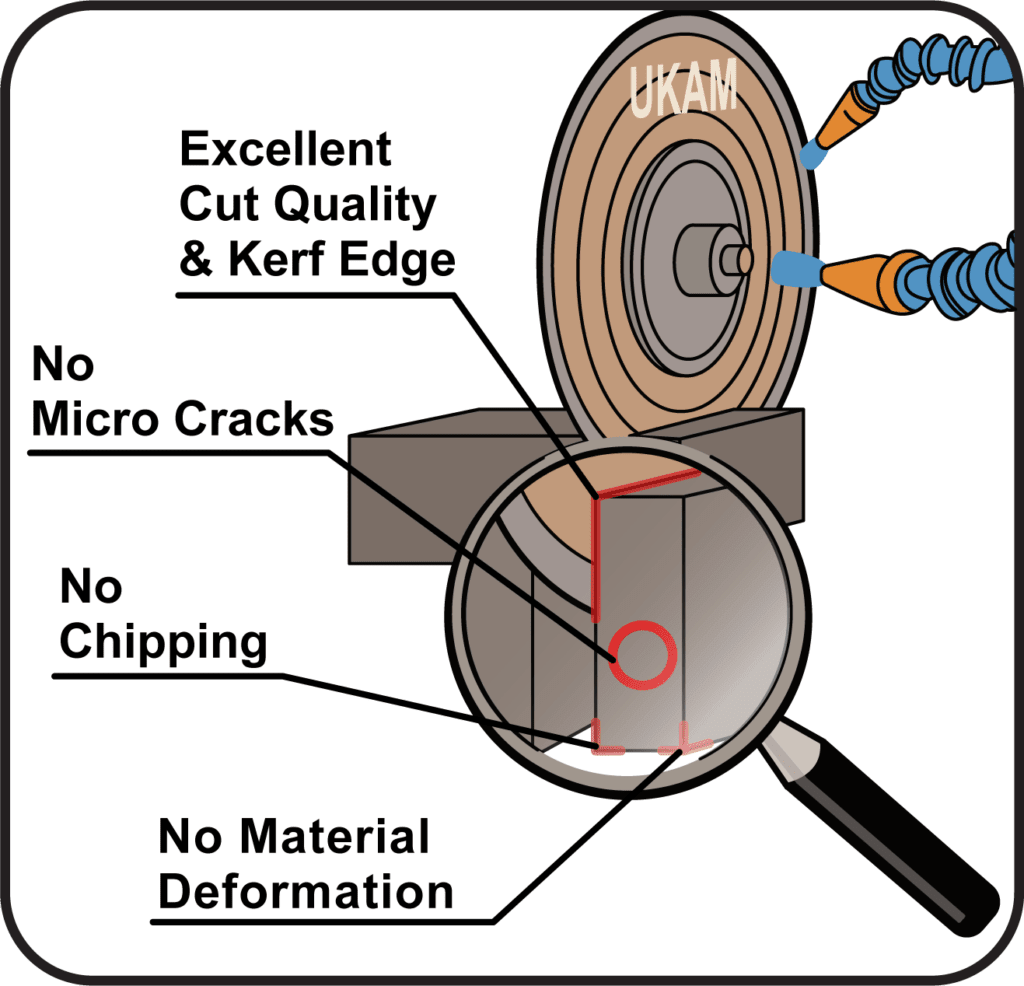
Better Cut Quality
& Less Material Deformation
Diamond Blades with SMART CUT® technology make any work much faster & easier, Thousands of sharp and high quality diamond particles oriented and evenly distributed on both matrix, allow cutting action to be completed by applying little or only moderate amount of pressure even on the most toughest and challenging materials. Freeing the user from constantly having to dress and renew the diamond layer.
No
Glazing
Diamond & CBN Blades with SMART CUT® technology require minimum dressing, the bond renews itself. The innovative bond formulation allows these blades to maintain faster and freer cutting speed, and efficiency without glazing, ensuring consistent performance and long blade life
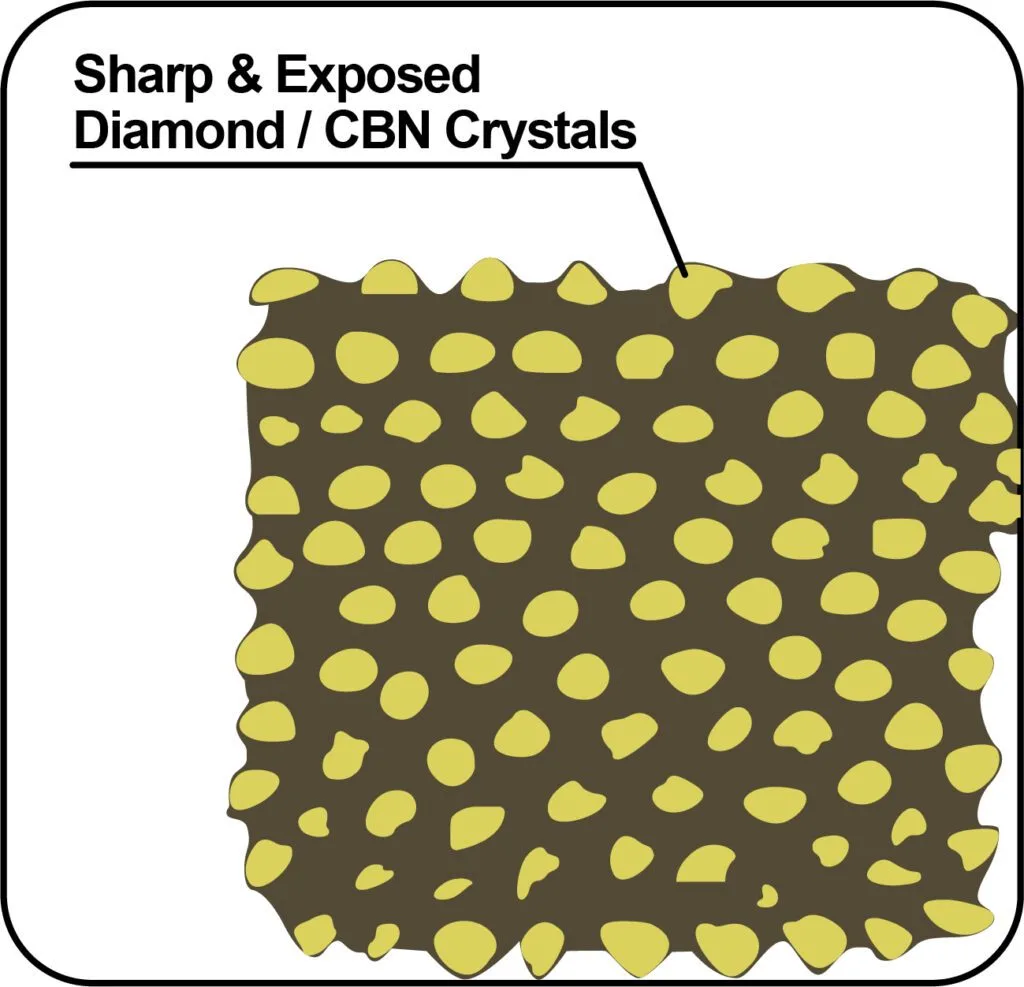
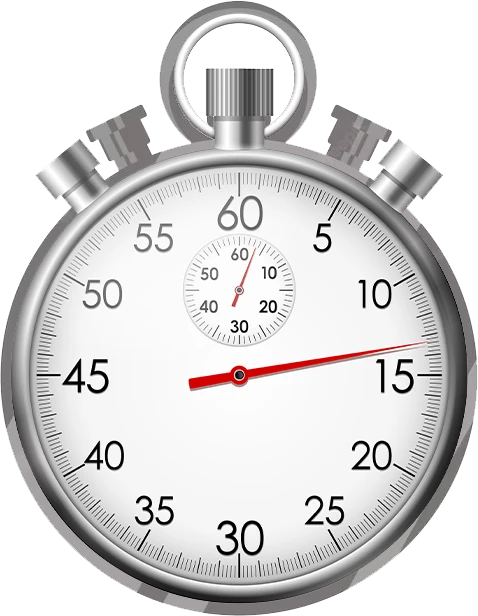
Faster
Cutting Action
SMART CUT® series 455MS blades made utilizing SMART CUT® technology are much more aggressive then conventionally blades. They can cut faster, while still leaving behind a smooth surface finish.
Longer
Life
SMART CUT® blades will outlast almost all other blades on the market today. The longer life can be attributed not only the higher diamond depth, but to higher diamond quality used. Advanced diamond distribution an orientation techniques, and proprietary bond chemistry. Combined with our competitive prices you re sure to obtain the best value and return on investment possible.
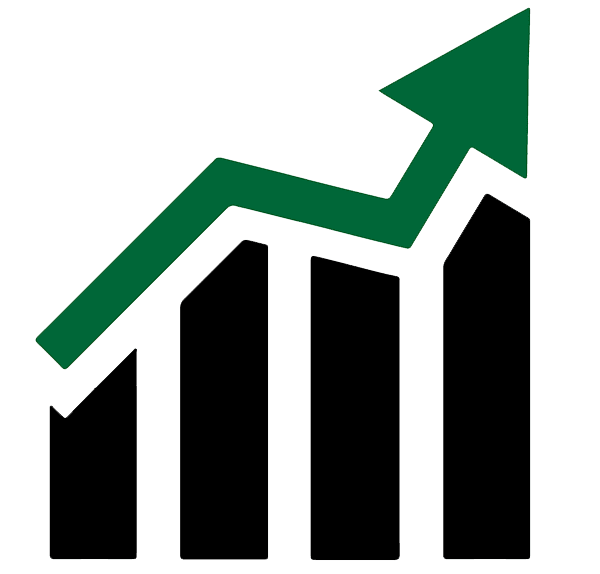

More
Consistent Performance
SMART CUT® Series Diamond Blades have hundreds of diamond layers impregnated inside the metal matrix. Unlike Many Other Blade Types, they wear evenly, and are known for their consistency. You will get consistent cutting speed, and overall consistent performance, with minimum amount of dressing even on the hardest to cut materials
Best
Performance & Value on the Market
SMART CUT® Series Sintered (metal bond) blades are the best investment you can make! Although they may cost more than other sintered (metal bond), blades. Designed for users that understand and appreciate quality. They will more than pay for themselves in terms of overall performance and provide best Return on Investment.
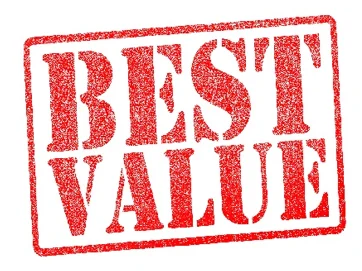
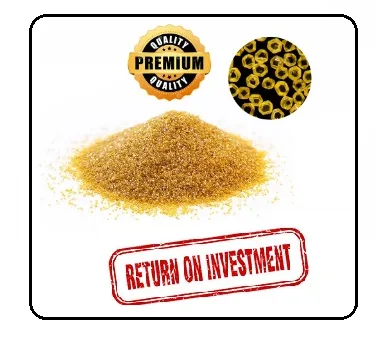
Manufactured Using
The Highest Quality Raw Materials
Only the highest quality synthetic diamonds and raw materials are used in the manufacturing process. The highest quality standards and product consistency is maintained, using sophisticated inspection and measurement equipment.
Diamond Cut Off Blade Selection Variables
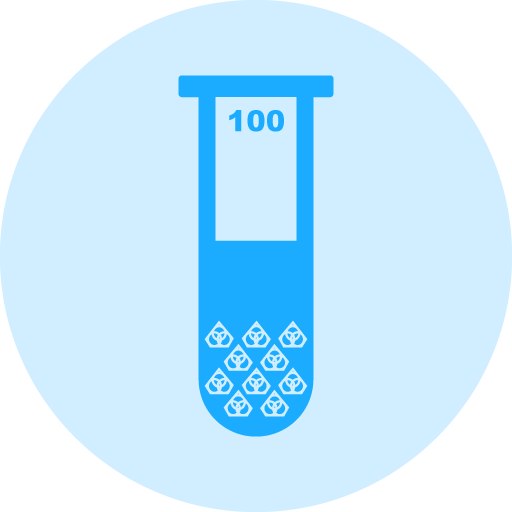
Diamond Concentration:
Diamond concentration significantly influences the performance of blades for cutting various types of glass and ceramics. Understanding the optimal concentration for specific materials ensures superior cut quality, longer blade life, and precision.
Low Diamond Concentration – SMART CUT® Glass Blades with low diamond concentration are designed for cutting more common glass types such as Soda Lime Glass, Borocilicate Glass, Art Glass, and Flat Glass. These materials are typically flat and non-hollow. The low concentration of diamonds ensures the blade operates at lower pressure on each diamond, which is ideal for cutting through softer glass materials without excessive chipping or cracking. While the cutting speed is slightly slower, these blades provide cleaner cuts for flat glass, reducing the risk of surface damage, making them perfect for tasks that require smooth, controlled cutting.
High Diamond Concentration – High diamond concentration blades are recommended for cutting more challenging materials like Glass Tubing, Fused Silica/Fused Quartz, Optical Glass, and PZT Ceramics. The higher concentration of diamonds results in a stronger cutting edge, which offers superior cutting speed and longer blade life. These blades are ideal for tougher glass and ceramics, where a more robust blade is necessary to achieve precision cuts and prevent excessive wear. The dense diamond concentration provides efficient material removal and clean cuts, particularly in hollow or complex glass shapes.
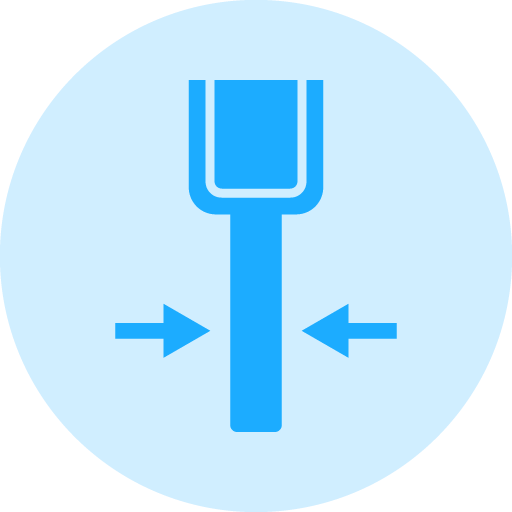
Blade Thickness:
The SMART CUT® 455M Precision Glass Cutting Blade is specifically designed to provide flawless, chip-free cuts for a wide range of glass and ceramic materials. This blade is available in thicknesses of 0.060" (1.52mm) for most sizes, with the larger sizes offering a 0.080" (2.0mm) thickness for enhanced durability. The blade thickness is crucial for achieving the desired balance between precision, durability, and cutting efficiency.
Standard Thickness (0.060" / 1.52mm) – This thickness is ideal for cutting Soda Lime Glass, Stained Glass, Art Glass, Ceramic Glass, Quartz Glass, Float Glass, and Optical Glass. It allows for precision cuts with minimal material loss and is perfect for achieving smooth, chip-free edges on flat glass. The 0.060" thickness is optimal for high-precision applications, providing a balance between cutting speed and cut quality.
Thicker Thickness (0.080" / 2.0mm) – Available in the 12" and 14" sizes, this thickness is recommended for more demanding applications where increased durability and higher cutting stability are needed, such as cutting Glass Tubing, Fused Silica, and PZT Ceramics.
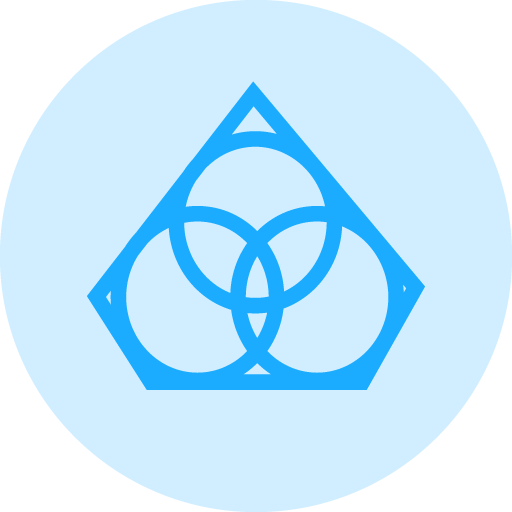
Diamond Particle/Grit Size:
The SMART CUT® 455M Glass Blade utilizes fine diamond particles carefully selected to provide superior cutting performance, especially when working with delicate glass and ceramic materials. The diamond grit size significantly influences the cutting speed, cut quality, and the level of chipping and material microstructure damage during the cutting process.
Fine Diamond Grit Size – The SMART CUT® 455M blade is equipped with fine, evenly spaced diamonds, which ensures smooth and precise cuts with minimal chipping, particularly when cutting fragile glass materials such as Soda Lime Glass, Art Glass, Optical Glass, and Ceramic Glass. The fine grit size contributes to a high-quality surface finish and reduces the risk of damaging the material’s microstructure, making it ideal for high-precision applications where cut quality is paramount.
The trade-off with using finer diamond grit is a slower cutting speed compared to coarser grits, but this is necessary when working with delicate materials that require clean, controlled cuts. Coarse diamonds, while cutting faster, tend to increase material micro-damage and cause more chipping. The fine diamond grit used in the SMART CUT® 455M blade provides the perfect balance, offering excellent surface finishes and minimized chipping, even for the most sensitive glass and ceramic materials.
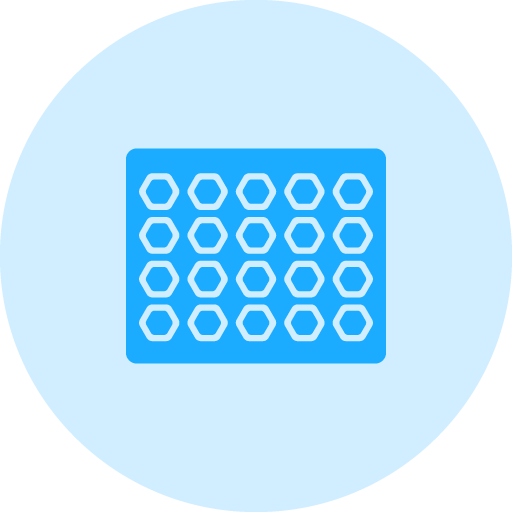
Bond Type:
The SMART CUT® 455M Glass Blade features a metal bond, providing exceptional durability, long blade life, and consistent performance for a wide range of glass and ceramic materials.
Metal Bond – The metal bond in the SMART CUT® 455M ensures superior diamond retention, making it ideal for cutting tougher, denser materials such as Tempered Glass, Fused Silica, Quartz Glass, and Ceramic Glass. The metal bond offers enhanced stability and high cutting speeds while maintaining rigidity throughout the cutting process. This bond type is perfect for applications requiring consistent performance and long-lasting durability, especially in high-volume cutting operations or tougher glass materials.
Resin Bond – Resin bond blades are better suited for cutting hollow materials like glass tubing, irregularly shaped hollow materials, or when working with glass types requiring tight tolerances for edge chipping and surface finish. Resin bonds create less heat during cutting and are designed to minimize chipping and produce a smoother surface finish, which is especially important in precision cutting applications such as optical glass or delicate glass assemblies.
However, it is important to note that resin bond blades are more fragile than metal bond blades and are prone to breakage under higher pressures or in non-experienced hands. Because of their fragility, they are not recommended for novice users or environments where the blade may be subjected to excessive pressure or impact. Resin bond blades are ideal for specialized, high-precision tasks where superior surface finish and minimal edge chipping are critical, such as in cutting hollow glass tubes, thin-walled materials, and complex, irregular shapes.
In contrast, metal bond blades provide a more forgiving and durable solution for general glass cutting needs, offering better resilience to operator error and wear over time.
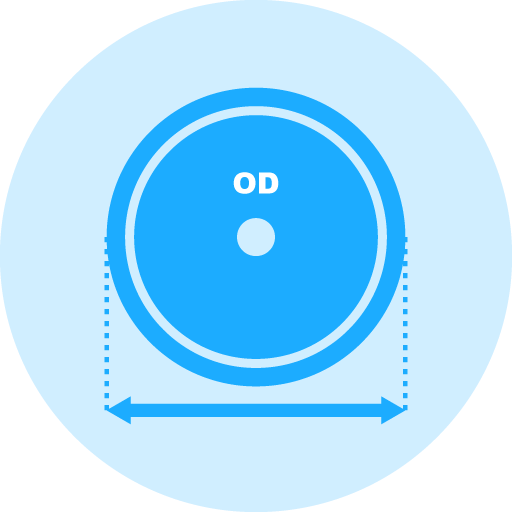
Blade Outside Diameter:
The SMART CUT® 455M Glass Blade is available in diameters ranging from 4” (100mm) to 14” (350mm), allowing you to select the ideal size based on the glass material's dimensions and thickness.
Smaller Diameter Blades (4” to 8”) – These blades are suitable for cutting smaller pieces of glass such as Soda Lime Glass, Art Glass, and Stained Glass. The smaller diameter blades are thinner, which makes them more flexible and ideal for cutting thinner glass materials. However, they are more prone to bending or warping under higher loads. Smaller blades are typically used for more detailed cuts at lower feed rates and speeds.
Larger Diameter Blades (10” to 14”) – Larger diameter blades offer enhanced rigidity and are more suited for cutting thicker glass materials or when higher feed rates and speeds are required. They provide greater stability during operation and are typically used for heavier, denser glass materials such as Tempered Glass, Fused Silica, and Quartz Glass. The added thickness in larger blades also reduces the risk of flexing, ensuring precise and efficient cuts at higher loads.
Selecting the correct outside diameter for your glass cutting application ensures optimal performance, stability, and efficiency. The SMART CUT® 455M Glass Blade provides versatile options to meet the cutting demands of both small and large glass materials.
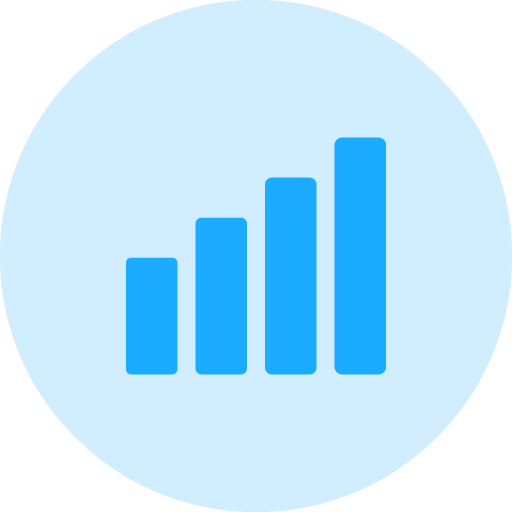
Feed Rates
Feed rates for resin bond diamond cut off blades in tile saws and precision cutting saws are critical to the cutting performance and quality of the final cut, and these rates must be adjusted to achieve desired objectives
For harder materials such as ceramics and metals, a faster feed rate may be necessary to efficiently cut through the material. This requires careful handling to ensure the blade does not overheat or wear prematurely. On the other hand, brittle materials like silicon, often used in precision applications, benefit from a slower feed rate to prevent chipping or cracking.
The optimal feed rate is also influenced by the speeds or RPMs at which the blade operates. Higher speeds can allow for quicker cuts but might increase the risk of damage to sensitive materials. Additionally, the geometry and size of the material, along with how securely it is held in place, are important considerations. Proper clamping of the material minimizes movement and vibration, enhancing the blade's effectiveness and the quality of the cut. Adjusting the feed rate manually requires a careful balance of these factors
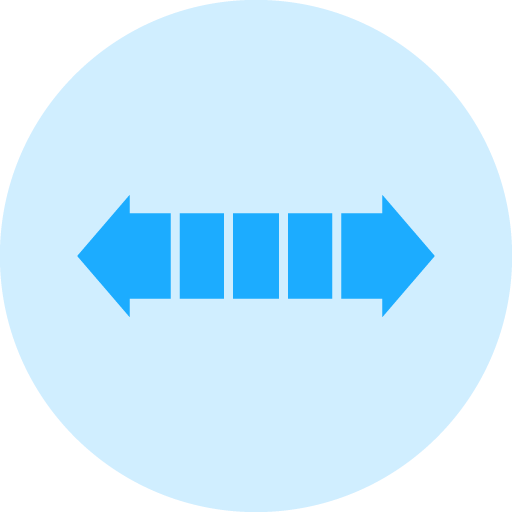
Bond Hardness:
The SMART CUT® 455M Glass Blade is designed with a medium bond hardness, optimized to provide excellent diamond retention while ensuring efficient cutting performance across a wide range of glass and ceramic materials. The bond matrix is formulated to balance durability with cutting speed, offering a longer blade life without sacrificing cut quality.
Medium Bond Hardness – The SMART CUT® 455M blade’s medium bond hardness ensures that diamond particles are retained at the optimal rate for consistent cutting performance. This bond hardness is ideal for cutting glass materials such as Soda Lime Glass, Stained Glass, Ceramic Glass, Optical Glass, Quartz Glass, and Fused Silica. The medium bond retains diamonds securely during the cutting process, which increases the life of the blade while maintaining a fast and smooth cutting action.
A bond matrix that is too soft could cause premature diamond release, resulting in faster wear and shorter blade life, while a bond matrix that is too hard would slow down the cutting process, requiring frequent dressing to expose fresh diamonds. The SMART CUT® 455M’s medium bond hardness strikes the perfect balance, offering efficient cutting without compromising the blade’s longevity.
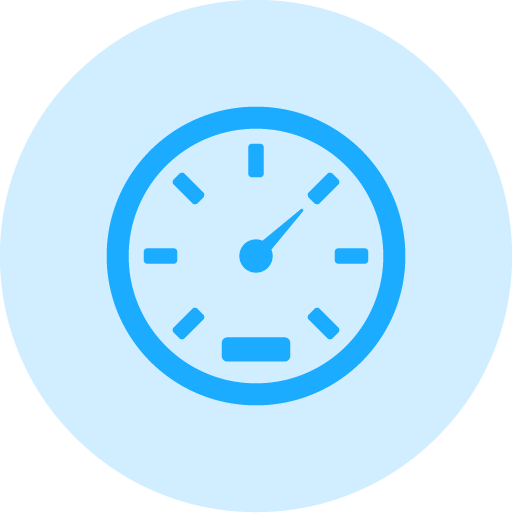
Blade Speeds/RPMs:
The SMART CUT® 455M Glass Blade is designed to operate across a realistic RPM range for optimal performance when cutting different glass materials. The actual RPM range typically depends on the specific material being cut and the cutting machine used.
For Softer Glass Materials – Softer materials like Soda Lime Glass, Art Glass, Stained Glass, and Ceramic Glass are best cut at higher RPMs, generally in the range of 2,000 to 3,500 RPM. The higher RPMs help improve cutting speed, reduce the buildup of heat, and allow for smoother finishes, while minimizing chipping for these more fragile materials.
For Harder Glass Materials – Harder glass materials, such as Optical Glass, Fused Silica, and Quartz Glass, should be cut at lower RPMs to prevent excessive heat generation and reduce the risk of cracking. The recommended RPM range for these materials is 1,000 to 2,500 RPM. Cutting at slower speeds offers better control, ensuring precise and clean cuts while protecting the integrity of the material.
Diamond Wafering Blade
Selection Variables
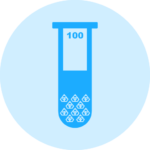
Diamond Concentration :
Diamond Concentration is still a factor in determining the life and cutting speed of your Diamond Sectioning/Wafering Blade. Higher diamond concentration is recommended and usually used for cutting softer and more abrasive types of materials. However, the trade off is significantly slower cutting speed. Low diamond concentration is recommended and widely used for cutting ultra hard and brittle materials.
Low Diamond Concentration - Typically low concentration wafering blades should be for cutting ultra hard and brittle materials such as ceramics and glass. In Low Concentration Wafering Blades, diamond works by fracture process. Pressure on each diamond crystal/particle is higher which provides enough stress to chip off small flakes in the cut.
High Diamond Concentration - High concentration diamond wafering blades are recommended for cutting metals, plastics and polymers. In this application, materials cut by a plowing mechanism. In this applications diamond plough through the material, work hardened strips of materials become brittle and break off. The greater number of diamond by volume, the quicker the cutting action will be. Increasing the number of diamond s also lowers the per unit force. For metals where it is possible to induce deep deformation layers, a lower per unit force is desirable to reduce the deformation during the cut.
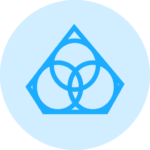
Diamond Particle/Grit size -
Diamond Mesh Size plays a major role in determining your cutting speed, cut quality/surface finish, level of chipping you will obtain, and material microstructure damage you will obtain. Diamond Mesh size does have considerable effect on cutting speed. Coarse Diamonds are larger than finer diamonds and will cut faster. However, the tradeoff is increase in material micro damage. If you are cutting fragile, more delicate materials then finer mesh size diamond wafering blades are recommended.
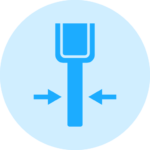
Blade Thickness :
Wafering blade thickness typically ranges from .006” to .040” (1mm). Thinner and thicker wafering blade are available, frequently from stock upon request. Kef thickness typically increases with blade diameter (in proportion to diameter of the blade). Kerf is the amount of material removed from the material/sample due to the thickness of blade passing though the material/sample. Blade thickness is important for users requiring most minimal amount of material loss during sectioning. For example if the user requires precision position of the cutting plane relative to the detail on the sample (IC circuit for example), a thinner and smaller diameter blade would be best for this application. Blades ranging from 3” to 5” (75mm to 125mm) in diameter and thickness .006” to .015” (0.2mm to 0.4mm) would be bet suited for this purpose. There are large variety of factors that will contribute to optimal blade thickness for your material/application Including your desired cutting speed, load/feed rate, material diameter, thickness, hardness, density, and shape. As well as skill & experience of the operator. Thicker wafering blades are more stiff and can whistand higher loads/feed rates. Another advantage of thicker kerf blades is they are more forgiving to operator error and abuse. Thicker kerf blade are recommended for use in environment where large number of individuals will be sharing and using same equipment. Perfect for less experienced and novice saw operators, such as in University laboratory.
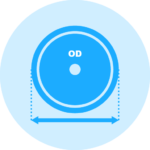
Blade Outside Diameter :
Typically wafering blade diameters range form 3” (75mm) to 8” (200mm). Wafering blade diameter should be selected based on material diameter and thickness being cut. Smaller diameter wafering blades are thinner than the larger diameter blades and are more prone to bending and warping. Although large diameter blades are thicker, they are typically used for cutting larger and heavier samples at higher loads and speeds than smaller blades.
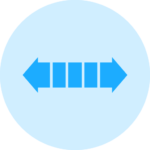
Bond Hardness :
Ability of the bond matrix to hold diamonds. As the hardness of the bond is increased, its diamond retention capabilities increase as well. However the trade off is slower cutting speed. Life of the diamond blade is usually increased with hardness of its bond matrix. Bonds are designated on their scale of hardness from Soft, Medium, and Hard. There are dozens of variations and classification schemes based on bond degree of hardness or softness. Using diamond blades with optimum bond hardness for your application is important to successful precision diamond sawing operation. Bond matrix that is too soft for the material being cut will release diamond particles faster than needed, resulting in faster wear and shorter diamond blade life. On other hand bond matrix that is too hard will result in much slower cutting speeds and require constant dressing to expose the next diamond layer. As rule of thumb, harder materials such as sapphire and alumina generally require a softer bond. Whereas softer and more brittle materials require a harder bond.
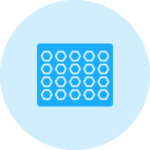
Bond Type :
Metal bonding offers long life and durability, while resin bonding creates less heat, provides better surface finish and is well suited for cutting hard, delicate or brittle materials.
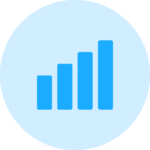
Feed Rates :
Load/Feed Rate applied to wafering blades typically vary from 10-1000 grams. Generally, harder specimens are cut at higher loads and speeds (e.g. ceramics and minerals) and more brittle specimens are cut at lower loads and speeds (e.g. electronic silicon substrates). The Speeds/RPM’s you are using, shape/geometry of the specimen, and how the specimen is being clamped/hold in place will affect the load that can be used for your application.

Blade Speeds/RPM’s :
Most wafering blades are used between 50 to 6,000 RPM’s Typically harder and more denser materials such as Silicon Carbide, are cut at higher RPM’s/speeds Where more brittle materials such as silicon wafers and gallium arsenide are cutting at lower RPM’s. Low Speed saws RPM’s are typically limited from 0 to 600 RPM’s. Where high speed saws offer much large variety of cutting speeds from 0 to 6,000 RPM’s.
Why Choose Us?
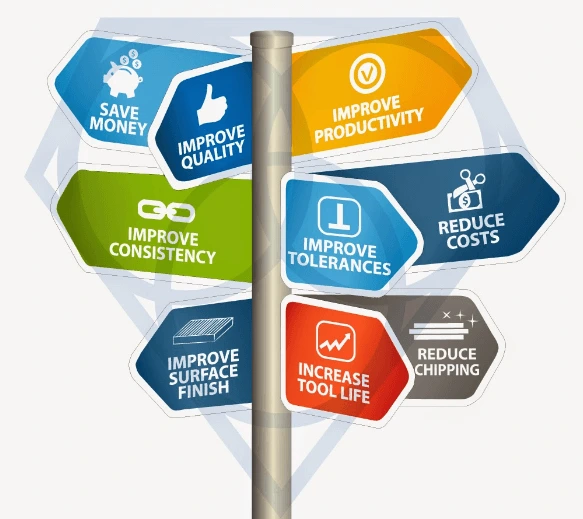
- Unmatched Selection For Many Applications
- Unmatched Technical Support & Expertise
- Superior Quality & Consistency
- Super Technology & innovation
- Immediate Worldwide Delivery
- American Based Manufacturer
-
Custom
Manufacturing - Better Value manufacturer Direct Price
Related Products
SMART CUT® Precision Diamond Blades (Universal Application)
$0.00
SMART CUT® Series 3000R Resin Bond, Diamond Cut Off Blade
Resin Bond Diamond Cut off blades (Fine Size Diamond) for use on manual tile saws
SMART CUT® Series 3000R are the highest quality & most commonly used Resin Bond Diamond Cut off Blades / Cut Off Wheels available today. Finer Diamond Grit Size, and Slightly Higher Diamond Content then the SMART CUT Series 2000R blades. They are used for cutting very thin wall tubing, more fragile material, that need best surface finish possible to achieve. Cutting speed would be slower then the 2000R series. These blades cut more slowly due to their finer grit size, which provides less aggressive material removal. They are better suited for precision tasks where cut quality is prioritized over speed. The finer grit results in a much smoother surface finish with minimal chipping, making them ideal when a high-quality, clean cut is needed, especially for delicate materials The resin bond diamond cut off blades / cut off wheels excel in delivering superior cut quality compared to other diamond cutting blade, making them ideal for applications where cut quality and surface finish is highly important. They are designed to operate at higher speeds to minimize heat generation and improve surface finishes.SMART CUT™ Series 2000
SMART CUT® Series 2000 are the highest quality & most commonly used Resin Bond Diamond Cut off Blades / Cut Off Wheels available today. Designed specifically for cutting a wide array of materials such as soda lime and borosilicate glass tubing, along with ultra hard and brittle materials such as ceramic tubing materials like Al203, silicon carbide, sapphire, and tungsten carbide, & exotic metals. These blades also handle metals and alloys with ease. While they can be used dry, employing coolant is advised to achieve the best results.
The resin bond diamond cut off blades / cut off wheels excel in delivering superior cut quality compared to other diamond cutting blade, making them ideal for applications where cut quality and surface finish is highly important. They are designed to operate at higher speeds to minimize heat generation and improve surface finishes.
SMART CUT® resin bond diamond wheels are engineered to maximize blade life while maintaining your desired cut quality and speed. These blades offer numerous advantages, including unmatched cut quality that often eliminates the need for secondary finishing operations. They feature a faster and freer cutting speed, generate less heat, and apply minimal stress to the material.
Recently Viewed Products
ARE YOU USING RIGHT DIAMOND & CBN BLADES
FOR YOUR APPLICATION?
LET US
HELP YOU
HAVING ISSUES WITH
YOUR CURRENT DIAMOND & CBN BLADES?
Knowledge Center
02
Jun
Select right Diamond Blade for your application
Selecting the right parameters for your Precision & Ultra Thin Diamond Blade can be a very time consuming, trial & error frustrating process. The guide below has been designed to help you better understand...
02
Jun
How to Properly Use Precision Diamond & CBN Blades
The diamond blade itself is only a small factor in your cutting operation. Successful diamond sawing is both an art & science. Requiring proper use and understanding of the right: RPM's, Coolants, Equipment, Dressing Devices, Accessories...
02
Jun
Precision & Ultra Thin Diamond Blade Guide
Diamond and CBN blades are available in an extensive array of varieties, each differing in bond types, manufacturing methods, and design specifics. Ultra Thin & High Precision Diamond Blades are particularly versatile, applicable...
02
Jun
How to Improve & Optimize Your Diamond Sawing Operation
There are numerous variables that affect the performance of diamond and CBN cutting blades. Understanding these variables will help end users select the right diamond blade specifications for their applications and optimize their...
02
Jun
Evaluating & Comparing Diamond Blades
Share this Article with Friend or Colleague
Proper testing procedures and methodologies must be set up and used to obtain accurate as well as repeatable testing results. This article will discuss several simple procedures which...
31
Jul
Top 5 Diamond & CBN Cutting Blade Performance Metrics
Share this Article with Friend or Colleague
When evaluating diamond and cubic boron nitride (CBN) cutting blades, it's crucial to consider key performance metrics and criteria. Different applications have varying goals, making it...
01
Aug
Diamond & CBN Cutting Blade Performance Metrics that you Should Know
Share this Article with Friend or Colleague
When evaluating diamond and cubic boron nitride (CBN) cutting blades, it's crucial to consider key performance metrics and criteria. Different applications have varying goals, making it important to...
02
Aug
Total Cost of Ownership & Why its Important
Share this Article with Friend or Colleague
Diamond and CBN cutting blades are available in a myriad of specifications, with virtually limitless options. The industry is saturated with numerous manufacturers, each professing to offer the...
05
Aug
Understanding Tradeoffs- Searching for Perfect Diamond & CBN Blade
Share this Article with Friend or Colleague
Choosing the right blade diamond or cbn blade can significantly impact efficiency, cost, and quality. However, this is not simple and clear cut process. Selecting the optimal blade...
- Unmatched Selection For Many Applications
- Superior Quality & Consistency
- Immediate Worldwide Delivery
- Technical Support & Expertise
- American Based Manufacturer
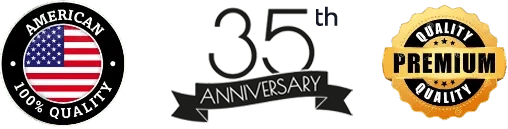

- Different Product
- Different Technology
- Different Company
- Expect MORE from your tools
Let Us HELP You!
Subscribe To Our Newsletter
Signup for email offers, updates, and more
Contact Us
- 25205 & 25201 Avenue Tibbits Valencia CA 91355 USA
-
Phone : (661) 257-2288
FAX : (661) 257 -3833 - lel@ukam.com
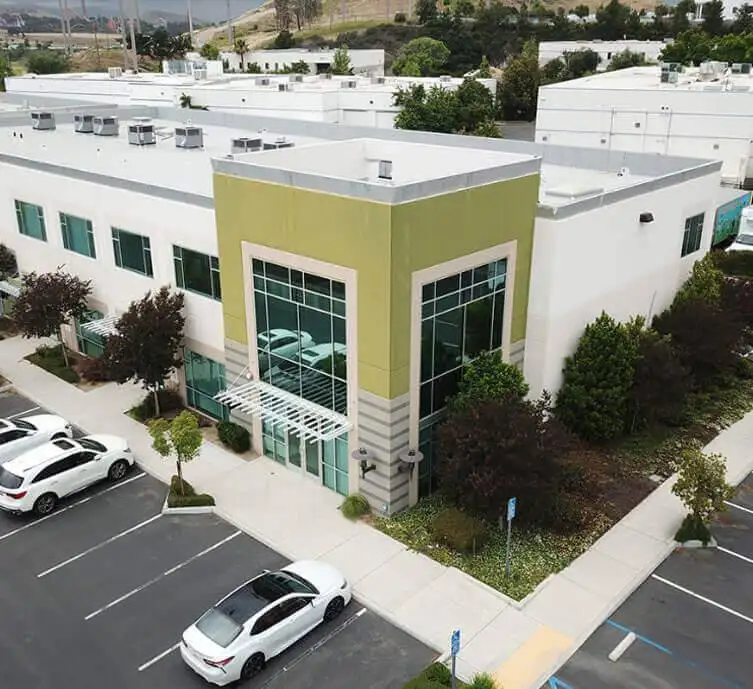
UKAM Industrial Superhard Tools is a U.S. High Technology, Specialty Diamond Tool & Equipment manufacturer. We specialize in producing ultra thin, high precision cutting blades, precision cutting machines diamond drills, diamond micro tools, standard & custom advanced industrial diamond tools and consumables.
- 25205 & 25201 Avenue Tibbits Valencia CA 91355 USA
-
Phone : (661) 257-2288
FAX : (661) 257 -3833 - lel@ukam.com
- 25205 & 25201 Avenue Tibbits Valencia CA 91355 USA
-
Phone : (661) 257-2288
FAX : (661) 257 -3833 - lel@ukam.com
DIAMOND TOOLS BY BOND
EQUIPMENT
KNOWLEDGE CENTER
OUR PRODUCTS
COMPANY
CUSTOMER SERVICE
Shipping Methods


Safe & Secure Payments

© Copyright 1990-2025. UKAM Industrial Superhard Tools – Terms of Use