-
0 items in quote
No products in the Quote Basket.
SMART CUT® Diamond Bottoming / Non-Coring (no core formation) Diamond Drills with 5/8-11” Female Thread
SMART CUT® series high precision tolerance and accuracy non core formation sintered (metal bond) diamond drills. Each Diamond Core Drill steel body is machined from a single piece of steel on high precision CNC machine. This provides Very Precision Tolerances, Accuracy, & Consistency. Diamond Height (depth) of 10mm, insure that these drills provide highest possible diamond drill life in industry
DESCRIPTION
SPECIFICATIONS
ADVANTAGES
INDUSTRIES USED IN
FAQ
ACCESSORIES
USAGE RECOMMENDATION
DESCRIPTION
SPECIFICATIONS
standard drilling depth: 1.5″ with 5/8-11″ female thread. We can produce any diameter, drilling depth, and any mounting type such as 5/8-11″, 3/4-16″, 5/8-18″, 1-14″, 1/2″ gas, jacobs, matthews, or any straight shank per customer specification. Wide variety of bond hardness’s, diamond mesh sizes and concentrations are available to accommodate different material requirements. We will work with you to determine your needs, and recommend the right solution for your specific material/application. Lead time is typically 10 to 14 work days. Expedited service/lead time is available upon request. REQUEST QUOTE TODAY!
ADVANTAGES
- Very Precision Tolerances
- Highest Possible Life in Industry
- Unique Design (made from single piece of steel)
- Unmatched Consistency
- Many Available from stock or Produced to your Specifications Affordable Prices
INDUSTRIES USED IN
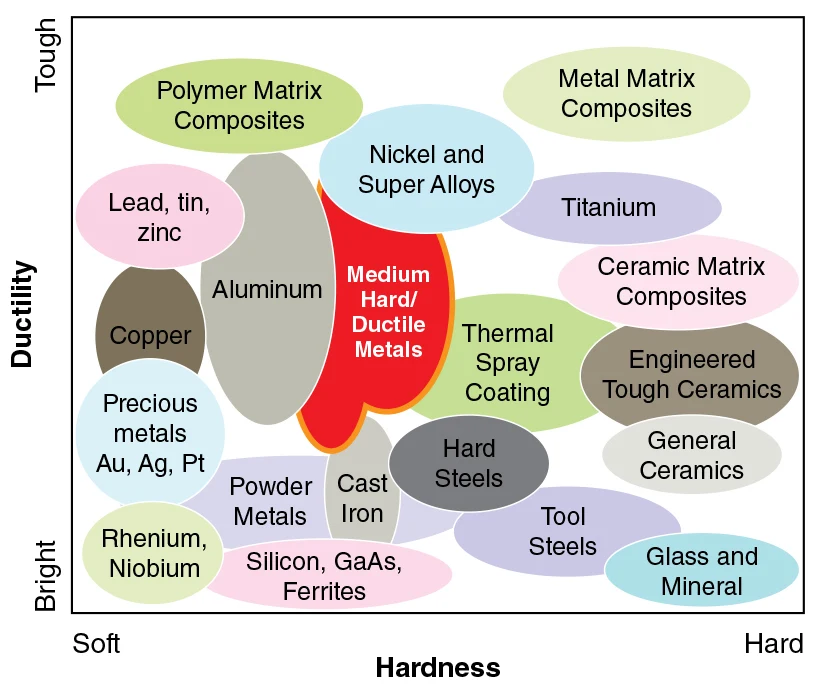

INDUSTRIES USED IN:
- Advanced Ceramics
- Composites
- Glass
- Geology
- Quartz
- Materials Research
- Medical Devices
- Metallography
- Photonics / Optics
- Semiconductor
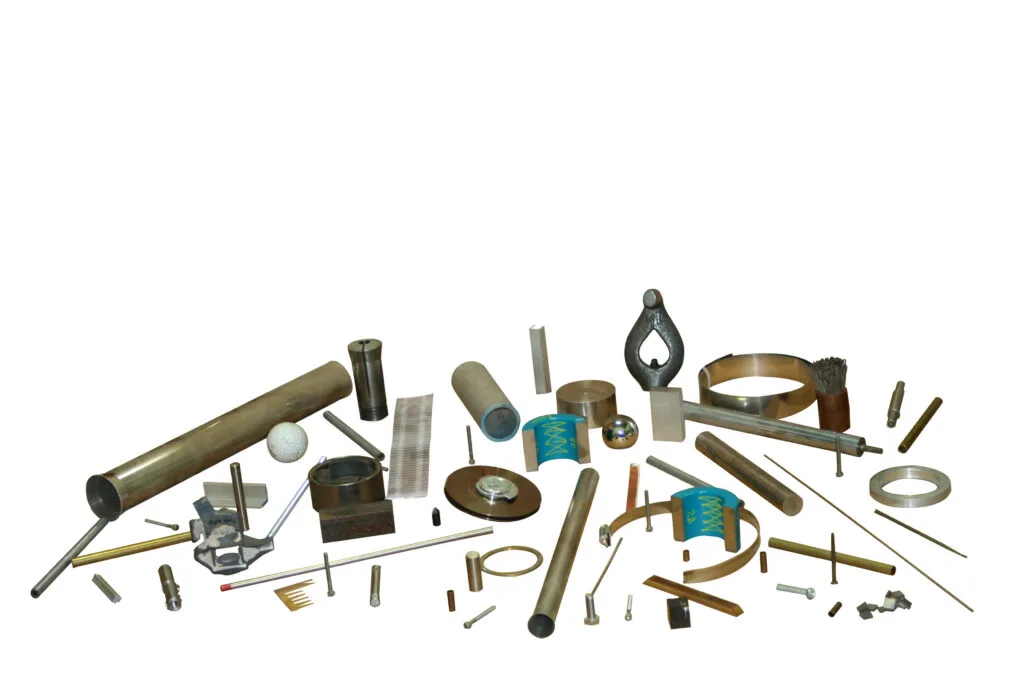
Ferrous & Non-Ferrous Metals:
- Plain Carbon Steels
- Electronic Packages
- Stainless Steels Plastics
- Tool Steels Fasteners
- Aluminum Refractories
- Copper Base Alloys Integrated Circuits
- Magnesium Thermal Spray Coatings
- Titanium Metal Matrix Composites
- Biomedical Wafers
- Petrographic
- PCB.s Ceramics
FAQ
The 120DE SMART CUT Series Thin Wall Diamond Core Drill is a high-performance drilling tool designed for precision drilling in hard materials. It utilizes sintered (metal bond) diamond technology to provide exceptional durability and efficiency.
These diamond core drills are versatile and can be used on a wide range of materials, including but not limited to composites, glass, concrete, sandstone/flagstone, natural stone, optical materials, precious and semiprecious stones, advanced/technical ceramics, ultra-hard and brittle materials, and many others. They are suitable for both industrial and hobbyist applications.
These core drills are available in diameters ranging from ¾” (19.05mm) to 4.75” (120.65mm).
They feature a 5/8-11″ female thread for easy attachment to drilling equipment.
The drilling depth is 2.25″ (75mm).
The overall length of these core drills is 2.5”.
- Diamond Depth (Height): .314” (8.0mm)
- Diamond Size: 60/80 mesh
- Diamond Edge: Continuous rim with 4 slots
Yes, these core drills must be used with coolant, which can include water, mineral oil, and water-soluble coolant, to ensure optimal performance and extend their lifespan.
Yes, these core drills are compatible with most popular drilling equipment, making them suitable for a wide range of applications and industries.
To maximize the lifespan of these core drills, it is essential to use them with coolant as recommended. Additionally, proper maintenance and following the manufacturer’s guidelines for usage will contribute to their longevity.
Yes, these core drills are suitable for both professional contractors and serious hobby enthusiasts or craftsmen. They are versatile and can be used in various applications.
Yes, these core drills are specifically designed to handle ultra-hard materials that might pose challenges to other types of drills. They excel in drilling such materials efficiently.
The tolerance on the outside diameter of these core drills is .0085″ (0.21mm), ensuring precise and consistent hole sizes.
Yes, these core drills are suitable for drilling materials ranging from 8.5 to 4.5 on Mohs scale, making them versatile for a wide range of applications, from hard ceramics to glass.
When using these core drills, it’s essential to follow safety guidelines, including wearing appropriate personal protective equipment (PPE), using coolant as recommended, and ensuring proper machine setup and operation to minimize risks associated with drilling.
Sintered (metal bond) diamond core drills are known for their long life and consistency, but eventually, they may wear out. They can be re-tipped, however its not usually worthwhile as it would cost more then a new drill.
While the use of coolant helps reduce dust generation, drilling may still produce some dust. It’s essential to use proper dust extraction equipment and follow safety guidelines to minimize dust exposure.
These core drills are primarily designed for wet drilling applications, as they are recommended to be used with coolant. Dry drilling without coolant may lead to reduced performance and increased wear on the drill.
Maintenance requirements typically include keeping the core drills clean and well-lubricated, checking for any signs of wear or damage, dressing and follow our usage recommendations
In addition to using coolant, you may need accessories such as a suitable drillingmachine, or guide for precise drilling.
These core drills can be used for both horizontal and vertical drilling applications, offering versatility in various drilling orientations.
Yes, these core drills are suitable for a wide range of projects, from professional industrial applications to DIY or home improvement projects.
To maintain their performance and longevity, it’s recommended to store these core drills in a clean, dry, and cool environment, preferably in their original packaging or protective cases.
The expected lifespan can vary depending on factors such as material hardness, usage frequency, and maintenance practices. However, sintered (metal bond) diamond core drills are known for their durability and long life compared to other drilling methods.
While these core drills are primarily designed for creating round holes, they can be used as a starting point for creating larger or differently shaped holes with additional tools or machining processes.
When handling coolant, it’s essential to follow safety guidelines and use appropriate personal protective equipment (PPE) to prevent skin and eye contact. Ensure proper containment and disposal of used coolant according to local regulations.
Core drills can produce noise during operation, and it’s advisable to use hearing protection when working with them. Additionally, working in a controlled and insulated environment can help reduce noise levels.
These core drills are primarily designed for wet drilling applications using coolant. While dry cutting may be possible, it is generally recommended to use them with the recommended coolant for optimal performance and longevity.
ACCESSORIES
Showing 1 – -1 of 13 results Showing all 13 results Showing the single result No results found
Sort by Price low to high
Filters Sort results
Reset Apply
Image | Name | COMPATIBILITY WITH DRILL SERIES | Price | Quantity | Add to cart |
---|---|---|---|---|---|
Recommended for use in Diamond Tools 150 Grit Size (mesh… | $15.39 | Max: Min: 1 Step: 1 | |||
Recommended for coarser grits found in segment wheels, core drills… | $15.99 | Max: Min: 1 Step: 1 | |||
5/8″-11″ thread. Fits into drill press chuck. Shank adapter threads… | $22.46 | Max: Min: 1 Step: 1 | |||
5/8″-11″ thread. Fits into drill press chuck. Shank adapter threads… | $26.72 | Max: Min: 1 Step: 1 | |||
SMART CUT® General Materials Formula Synthetic Water Soluble Coolant | $34.81 | Max: Min: 1 Step: 1 | |||
Recommended for use in Diamond Tools 150 Grit Size (mesh… | $39.47 | Max: Min: 1 Step: 1 | |||
Recommended for coarser grits found in segment wheels, core drills… | $39.47 | Max: Min: 1 Step: 1 | |||
SMART CUT® General Materials Formula Synthetic Water Soluble Coolant | $99.81 | Max: Min: 1 Step: 1 | |||
105DE, 135DB, 115DM, 125DM, 130DMN, 140DM (up to 1-5/8″ OD) | $154.87 | Max: Min: 1 Step: 1 | |||
105DE, 135DB, 115DM, 125DM, 130DMN, 140DM (up to 1-5/8″ OD) | $154.87 | Max: Min: 1 Step: 1 | |||
105DE, 135DB, 115DM, 125DM, 130DMN, 140DM (up to 1-5/8″ OD) | $235.00 | Max: Min: 1 Step: 1 | |||
SMART CUT® General Materials Formula Synthetic Water Soluble Coolant | $317.41 | Max: Min: 1 Step: 1 | |||
SMART CUT® General Materials Formula Synthetic Water Soluble Coolant | $1,745.00 | Max: Min: 1 Step: 1 |
USAGE RECOMMENDATION
02
Jun
How to Properly Use Precision Diamond Drills
Step by step guide on how to properly use and care for your diamond drills. Selecting the right diamond drill/diamond drill bit parameters, often involves a trial and error process. Many which can be avoided…
02
Jun
Diamond Drills Guide
Diamond are used across large variety of industries and applications. This guide explores the wide range of diamond drill types, including hollow core drills designed for removing a cylindrical core, non-core formation drills that grind…
02
Jun
Diamond Tools Guide – Selecting Right Drills & Tools for your application
These tools are used for many different industries grinding and shaping material into different forms, expanding exiting inside diameters, grinding, finishing and polishing existing material. Grinding different angles and radius, creating cavities of various forms,…
02
Jun
Optimizing your Diamond Drilling Operation
There are numerous factors that influence the performance of diamond drills. Understanding these factors helps users select the appropriate diamond drill specifications for their specific applications, optimizing drilling operations to achieve maximum efficiency….
02
Jun
Micro Drilling Guide
Share this Article with Friend or Colleague
In order for you to get the most out of your diamond micro drill or carbide / high speed steel micro drill, we strongly urge you to read…
03
May
Diamond Core Drill & Drill Trouble Shooting Guide
Learn the most common problems most people have in using diamond drills. How to resolve them and avoid them in first place
Troubleshooting Drilling Problems
Having issues with your diamond drilling operation? This Illustrated Guide…
What are Diamond Bottoming Drills/Tools?
Diamond Bottoming Drills, also known as Flat Bottom Tip Drills, Bottoming Drills, Disintegrating Diamond Core Drills, or Diamond Offset Style Core Drills, utilize a sintered (metal bond) to offer unparalleled precision in drilling. These specialized tools are essential for creating blind holes in hard materials ranging from sapphire and quartz to slate, without leaving a core behind.
Designed for creating flat-bottomed holes or features in a variety of ultra-hard and brittle materials. Unlike standard drills that produce conical or pointed holes, bottoming drills have a flat cutting surface at the tip, allowing for the creation of clean, even bottoms in drilled holes. This design makes them ideal for applications where a precise, flat-bottom finish is required, such as in countersinking flat surfaces, milling pockets, or producing specific hole geometries in advanced materials.
Showing 1 – -1 of 75 results Showing all 75 results Showing the single result No results found
Sort by Price low to high
Filters Sort results
Reset Apply
Image | SKU | Outside Diameter | Diamond Height | Drilling Depth | Get Quote |
---|---|---|---|---|---|
3mm (.118") | 7mm (.276") | 1.5" (38.1mm) | |||
3.2mm (.125") | 7mm (.276") | 1.5" (38.1mm) | |||
3.5mm (.138") | 7mm (.276") | 1.5" (38.1mm) | |||
4mm (.157") | 7mm (.276") | 1.5" (38.1mm) | |||
4.5mm (.177") | 7mm (.276") | 1.5" (38.1mm) | |||
4.7mm (.187") | 7mm (.276") | 1.5" (38.1mm) | |||
5mm (.197") | 7mm (.276") | 1.5" (38.1mm) | |||
5.5mm (.216") | 7mm (.276") | 1.5" (38.1mm) | |||
6mm (.236") | 8mm (.314) | 1.5" (38.1mm) | |||
6.4mm (.250") | 10mm (.393) | 1.5" (38.1mm) | |||
7mm (.276") | 10mm (.393) | 1.5" (38.1mm) | |||
7.5mm (.295") | 10mm (.393) | 1.5" (38.1mm) | |||
8mm (.314") | 10mm (.393) | 1.5" (38.1mm) | |||
8.5mm (.334") | 10mm (.393) | 1.5" (38.1mm) | |||
9mm (.354") | 10mm (.393) | 1.5" (38.1mm) | |||
9.5mm (.374") | 10mm (.393) | 1.5" (38.1mm) | |||
10mm (.393") | 10mm (.393) | 1.5" (38.1mm) | |||
10.5mm (.413") | 10mm (.393) | 1.5" (38.1mm) | |||
11mm (.433") | 10mm (.393) | 1.5" (38.1mm) | |||
11.5mm (.452") | 10mm (.393) | 1.5" (38.1mm) | |||
12mm (.472") | 10mm (.393) | 1.5" (38.1mm) | |||
12.7mm (.500") | 10mm (.393) | 1.5" (38.1mm) | |||
13mm (.512") | 10mm (.393) | 1.5" (38.1mm) | |||
13.5mm (.531") | 10mm (.393) | 1.5" (38.1mm) | |||
14mm (.551") | 10mm (.393) | 1.5" (38.1mm) | |||
14.5mm (.570") | 10mm (.393) | 1.5" (38.1mm) | |||
15mm (.590") | 10mm (.393) | 1.5" (38.1mm) | |||
15.5mm (.610") | 10mm (.393) | 1.5" (38.1mm) | |||
16mm (.630") | 10mm (.393) | 1.5" (38.1mm) | |||
16.5mm (.650") | 10mm (.393) | 1.5" (38.1mm) | |||
17mm (.670") | 10mm (.393) | 1.5" (38.1mm) | |||
17.5mm (.689") | 10mm (.393) | 1.5" (38.1mm) | |||
18mm (.709") | 10mm (.393) | 1.5" (38.1mm) | |||
18.5mm (.728") | 10mm (.393) | 1.5" (38.1mm) | |||
19mm (.748") | 10mm (.393) | 1.5" (38.1mm) | |||
19.5mm (.767") | 10mm (.393) | 1.5" (38.1mm) | |||
20mm (.787") | 10mm (.393) | 1.5" (38.1mm) | |||
20.5mm (.807") | 10mm (.393) | 1.5" (38.1mm) | |||
21mm (.826") | 10mm (.393) | 1.5" (38.1mm) | |||
21.5mm (.846") | 10mm (.393) | 1.5" (38.1mm) | |||
22mm (.826") | 10mm (.393) | 1.5" (38.1mm) | |||
22.5mm (.885") | 10mm (.393) | 1.5" (38.1mm) | |||
23mm (.905") | 10mm (.393) | 1.5" (38.1mm) | |||
23.5mm (.925") | 10mm (.393) | 1.5" (38.1mm) | |||
24mm (.944") | 10mm (.393) | 1.5" (38.1mm) | |||
24.5mm (.964") | 10mm (.393) | 1.5" (38.1mm) | |||
25mm (.984") | 10mm (.393) | 1.5" (38.1mm) | |||
25.4mm (1.0") | 10mm (.393) | 1.5" (38.1mm) | |||
26mm (1.023") | 10mm (.393) | 1.5" (38.1mm) | |||
26.5mm (1.043") | 10mm (.393) | 1.5" (38.1mm) | |||
27mm (1.062") | 10mm (.393) | 1.5" (38.1mm) | |||
27.5mm (1.082") | 10mm (.393) | 1.5" (38.1mm) | |||
28mm (1.102") | 10mm (.393) | 1.5" (38.1mm) | |||
28.5mm (1.122") | 10mm (.393) | 1.5" (38.1mm) | |||
29.0mm (1.141") | 10mm (.393) | 1.5" (38.1mm) | |||
29.5mm (1.161") | 10mm (.393) | 1.5" (38.1mm) | |||
30mm (1.181") | 10mm (.393) | 1.5" (38.1mm) | |||
30.5mm (1.200") | 10mm (.393) | 1.5" (38.1mm) | |||
31mm (1.220") | 10mm (.393) | 1.5" (38.1mm) | |||
31.5mm (1.240") | 10mm (.393) | 1.5" (38.1mm) | |||
32mm (1.259") | 10mm (.393) | 1.5" (38.1mm) | |||
32.5mm (1.279") | 10mm (.393) | 1.5" (38.1mm) | |||
33mm (1.299") | 10mm (.393) | 1.5" (38.1mm) | |||
33.5mm (1.318") | 10mm (.393) | 1.5" (38.1mm) | |||
34mm (1.338") | 10mm (.393) | 1.5" (38.1mm) | |||
34.5mm (1.358") | 10mm (.393) | 1.5" (38.1mm) | |||
35mm (1.337") | 10mm (.393) | 1.5" (38.1mm) | |||
36mm (1.417") | 10mm (.393) | 1.5" (38.1mm) | |||
36.5mm (1.437") | 10mm (.393) | 1.5" (38.1mm) | |||
37mm (1.456") | 10mm (.393) | 1.5" (38.1mm) | |||
37.5mm (1.476") | 10mm (.393) | 1.5" (38.1mm) | |||
38mm (1.496") | 10mm (.393) | 1.5" (38.1mm) | |||
38.1mm (1.50") | 10mm (.393) | 1.5" (38.1mm) | |||
38.5mm (1.515") | 10mm (.393) | 1.5" (38.1mm) | |||
39mm (1.535") | 10mm (.393) | 1.5" (38.1mm) |
1070101,1070102,1070103,1070104,1070105,1070106,1070107,1070108,1070109,10701010,10701011,10701012,10701013,10701014,10701015,10701016,10701017,10701018,10701019,10701020,10701021,10701022,10701023,10701024,10701025,10701026,10701027,10701028,10701029,10701030,10701031,10701032,10701033,10701034,10701035,10701036,10701037,10701038,10701039,10701040,10701041,10701042,10701043,10701044,10701045,10701046,10701047,10701048,10701049,10701050,10701051,1070152,1070153,1070154,1070155,1070156,1070157,1070157-1,1070159,10701560,10701561,10701562,10701563,10701564,10701565,10701566,10701567,10701569,10701570,10701571,10701572,10701573,10701574,10701575,10701576,
How Diamond Bottoming Drills/Tools Work?
These drills uniquely function both as a drill and a grinding disc, allowing them to not only create holes but also to grind the bottom and interior sides of these holes to a flat and smooth finish. This dual functionality is especially critical for drilling blind holes larger than 3/8" OD (outside diameter), which is a task beyond the capabilities of most standard drills.
Designed to deliver coolant directly through the center via a slot on the side of the diamond section or through a specifically designed hole, these drills ensure continuous lubrication and cooling during operations. This feature helps in maintaining the integrity of both the drill and the material being worked on, minimizing heat-induced damage and wear.
The grinding mechanism of these drills ensures high-quality surface finishes within the drilled holes, reducing the necessity for further finishing processes. This efficiency not only saves time but also enhances the overall quality of the workpiece.
Advantages
-
Efficient Material Removal: Allows for quick removal of material without core retention.
-
Enhanced Precision: Ideal for creating flat-bottom holes and precise endpoints.
-
Versatile Applications: Suitable for various industries including electronics and engineering.
-
Reduced Waste: Minimizes material wastage, crucial when working with valuable substrates.
-
Adaptable to Various Materials: Effective on a wide range of materials from metals to ceramics.
If you are only drilling partially through a material, using a hollow diamond core drill might not be the best option. This type of drill can trap the core—the cylinder of material removed during drilling—inside the hollow drill bit if you don’t drill all the way through. Removing a trapped core can be difficult and may even damage the drill bit.
In these cases, a non-core formation diamond drill (solid drill) is usually a better choice for several reasons. Firstly, it grinds away the entire volume of the hole without producing a cylindrical core, so there's no worry about material getting trapped inside the drill. Secondly, a solid drill offers more precise control over the depth of drilling, particularly when used with a drill press or other machinery equipped with depth stops or measurements. Lastly, solid drills tend to produce a smoother finish in the hole, which is beneficial if the partial hole will be visible or used in a precision application.
However, if there's a specific need to extract a partial core from a material, a hollow core drill would be used, but it would require a method for core removal from the bit afterward. This scenario is less common but does occur in some research and specialized material analysis applications.
Diamond Bottoming/Non Core Formation
Custom Manufacturing Capabilities
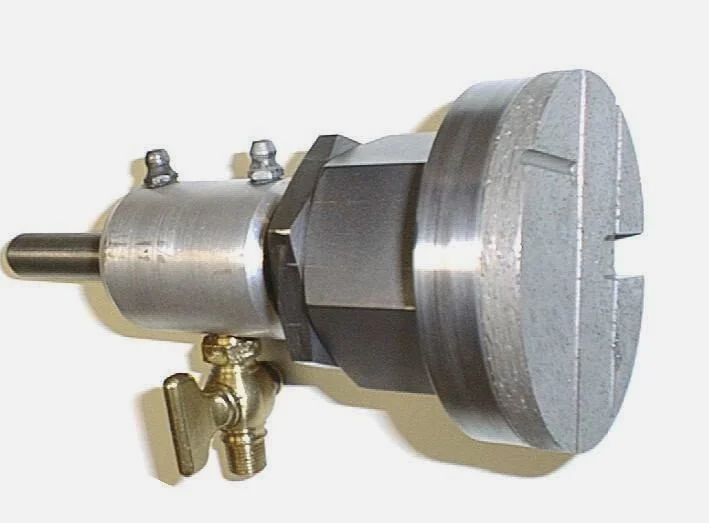





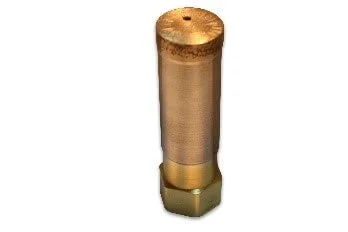
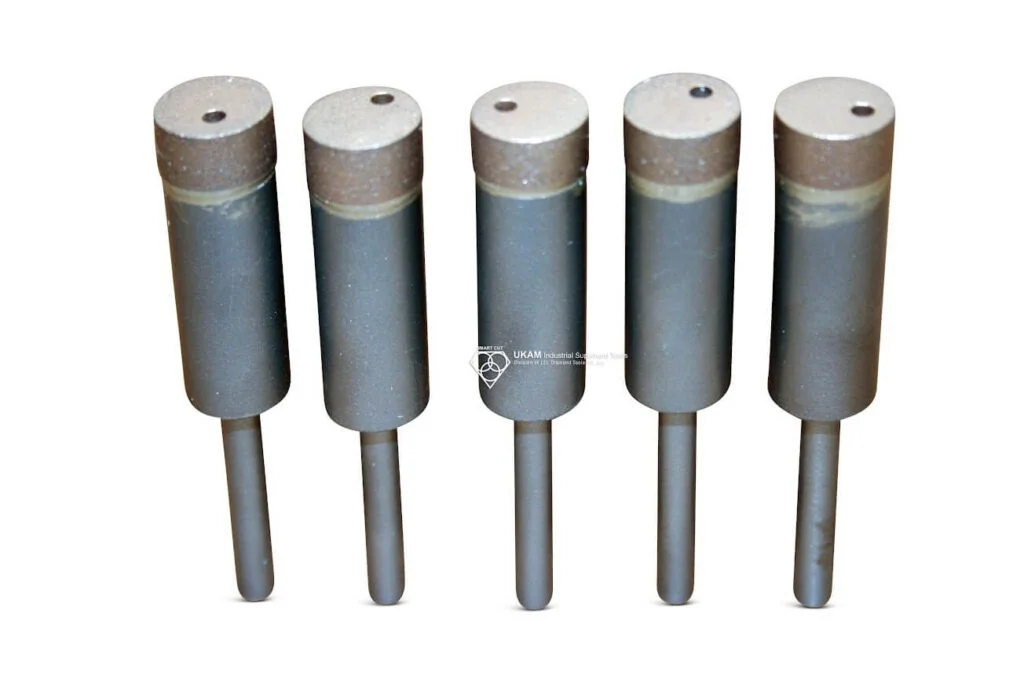
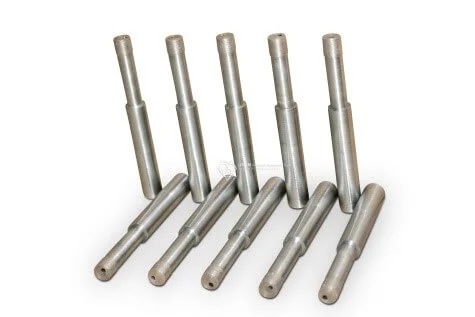

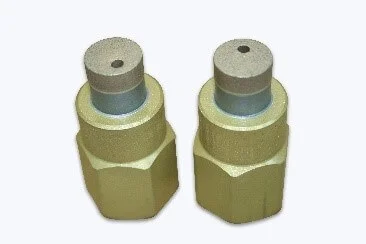


In addition to the standard SMART CUT series Diamond Bottoming/Non Core Formation typically available from stock. We can produce large variety of custom Diamond Bottoming/Non Core Formation and tools per your specification or drawing
- Almost any diameter
- Head geometry (anygle/radius)
- Diamond Section Slotts or Channels
- Custom drill lengths
- Custom shank diameters & Mounting Types
- Almost any diamond or cbn size in proportion to diameter of the tool
Diamond & Core Drill
Selection Variables
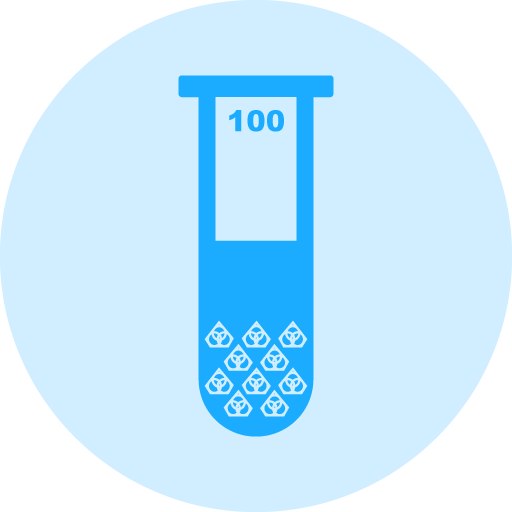
Diamond Concentration
Diamond concentration plays a critical role in determining the life and cutting speed of diamond core drills. Higher concentration offers longer tool life and faster cutting speeds, while lower concentration is typically used for softer materials that require a smoother finish.

Drilling Speed/RPMs
Diamond core drills generally operate at RPMs between 500 and 3,000, depending on the material being drilled. Softer materials allow for higher RPMs, while harder materials require slower speeds for improved cutting efficiency and to avoid damaging the tool or material. Always adjust RPM according to the specific characteristics of the material and drill size.
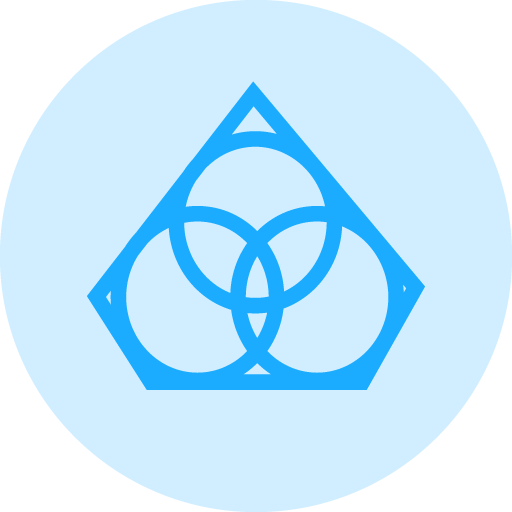
Diamond Particle/Grit size
The diamond grit size is crucial in determining the cutting speed, surface finish, and precision of diamond core drills. Finer grits provide a smoother surface finish, but may cut more slowly, while coarser grits offer faster cutting speeds but can leave a rougher surface. The choice of grit size depends on the material being drilled and the desired outcome.
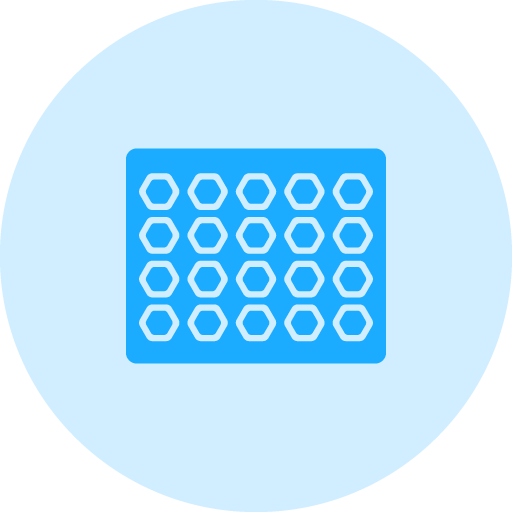
Bond Type
The bond type used in diamond core drills influences the drill’s life, durability, and heat resistance. Common bond types for diamond core drills include: Sintered (Metal Bond): Provides a longer tool life and high resistance to wear and heat, making it ideal for drilling hard and abrasive materials. Electroplated: Offers a good combination of speed and precision, typically used for softer materials or applications where a smoother surface finish is needed. Braised Bond: Ideal for applications requiring higher strength, these bonds are used for tougher materials and applications where durability is key. PCD (Polycrystalline Diamond): Used for ultra-hard materials, PCD bond drills offer excellent wear resistance and are ideal for materials like ceramics and composite materials. <:>CVD (Chemical Vapor Deposition) Diamond: Offers exceptional cutting performance, often used in extremely hard materials like high-performance ceramics and advance.
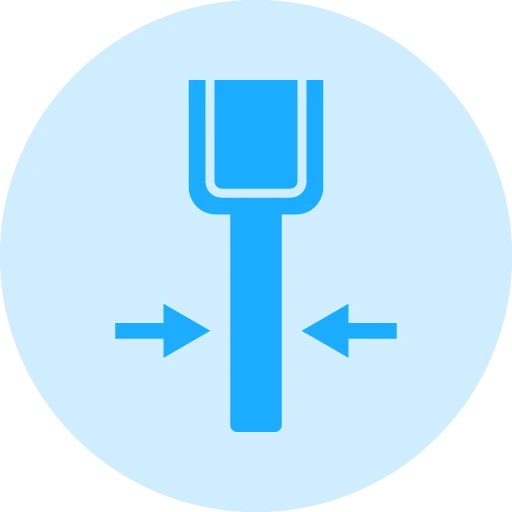
Kerf (Wall) Thickness
The kerf, or wall thickness, of diamond core drills is a key variable in determining the overall performance of the drill. Standard core drills typically feature a kerf thickness ranging from 0.5mm to 3.0mm, with thicker kerfs providing longer tool life and greater stability during drilling. Thinner kerfs allow for faster cutting but may wear out quicker and require more frequent maintenance. The selection of kerf thickness depends on the material being drilled and the precision required.
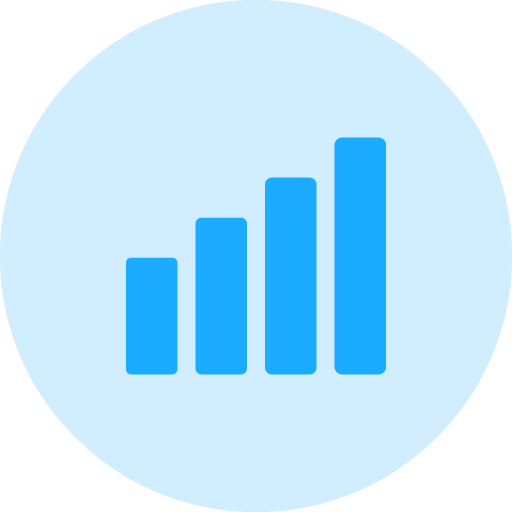
Feed Rates
The load/feed rate applied to diamond core drills significantly impacts their performance and lifespan. For tougher materials, feed rates typically range between 5-50 mm/min, while softer materials may allow for higher feed rates. Proper feed rate adjustment ensures optimal tool life and drilling speed, while preventing overheating or excessive wear.
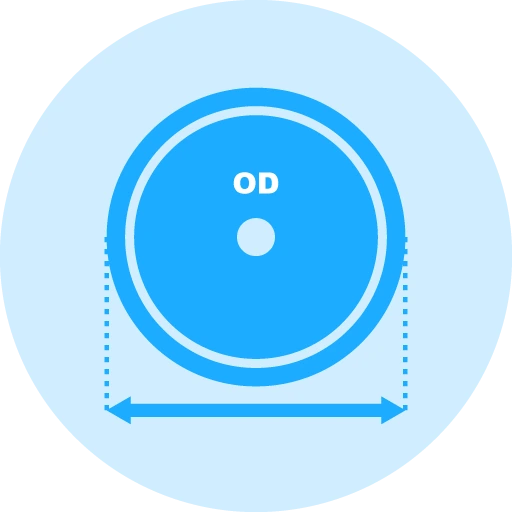
Core Drill Diameter
The diameter of the diamond core drill is directly related to the size of the hole you wish to create. Core drills typically range from small diameters (e.g., 3mm) up to large diameters (e.g., 200mm or more). Larger core drills offer greater drilling capacity, while smaller ones provide more precision for fine hole making.
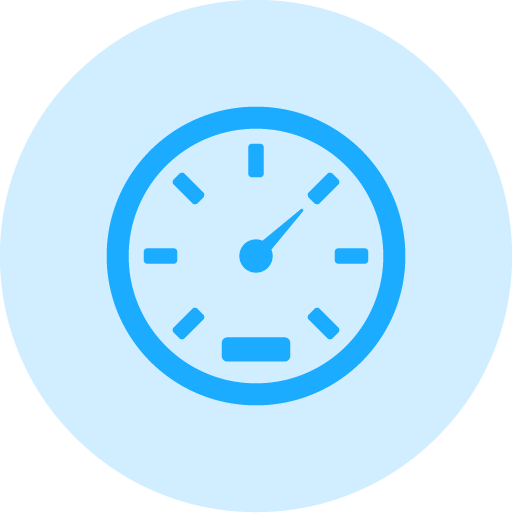
Drilling depth
The depth of a diamond drill bit, often referred to as drilling depth, working length, or drilling length, is the maximum depth to which the drill can penetrate the workpiece. Drilling depth in diamond core drills depends on the material, drill size, and equipment. Softer materials allow for deeper holes with faster cutting, while harder materials require slower speeds and lower feed rates to prevent overheating. Larger drill diameters may reduce depth due to more material removal per rotation, often requiring multiple passes. Drilling equipment, including motor power and cooling systems, also plays a key role; more powerful motors and efficient cooling allow for deeper drilling.
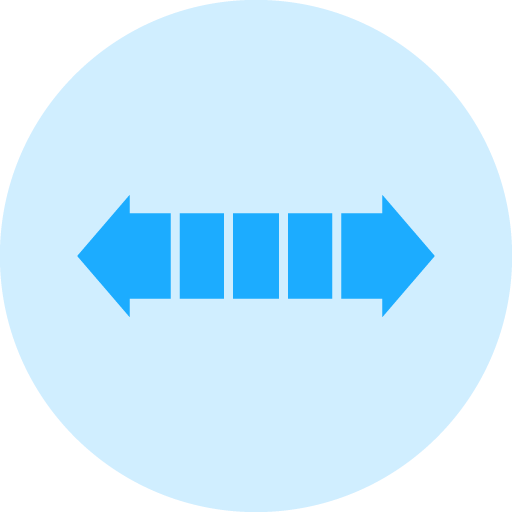
Bond Hardness
For diamond core drills, the bond hardness plays a crucial role in the performance and longevity of the drill. The bond matrix's ability to retain diamonds directly impacts the drilling efficiency and the tool's lifespan. As the hardness of the bond increases, the retention of diamonds improves, but the trade-off is typically a slower cutting speed. A harder bond matrix provides greater tool life but may lead to reduced cutting efficiency.
There are generally three categories for bond hardness in diamond core drills: Soft, Medium, and Hard. The bond's hardness is selected based on the material being drilled. For example, harder materials such as ceramics or hard metals often require a softer bond to allow the diamonds to be released at a controlled rate, preventing excessive wear and improving cutting performance. Conversely, softer and more brittle materials like concrete or certain composites benefit from a harder bond, which maintains the diamond's retention and extends the drill's lifespan, though it may slow the cutting process.
Using the right bond hardness for the material you're drilling is key to optimizing both cutting speed and tool life. A bond that is too soft will cause diamonds to be released too quickly, resulting in faster wear and a shorter drill life. On the other hand, a bond that is too hard may cause the drill to cut slower and require more frequent dressing to expose new diamonds.
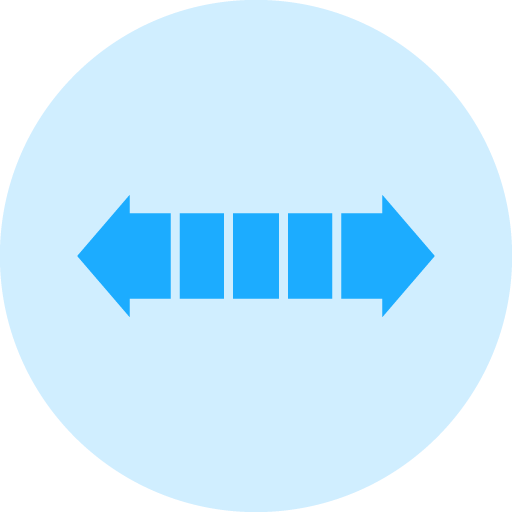
Mounting Type
The mounting type of a diamond core drill refers to how the drill is secured to the drilling machine or equipment. The mounting type plays a significant role in stability, precision, and overall drilling performance. Here are the typical mounting types for diamond core drills:
Unmounted diamond core drills:
Unmounted diamond core drills are specialized tools designed for precision drilling without being pre-mounted to any specific holding mechanism such as a male, female, or straight shank. These drills comprise a steel tube paired with a diamond-embedded segment, offering flexibility in setup and application.
Shaft Mounting:
In this type, the diamond core drill is mounted directly onto a shaft or spindle of the drilling machine. The shaft typically has a locking mechanism (like a set screw or collar) to securely hold the drill in place. This mounting method ensures a stable connection and allows for precise drilling. Shaft mounting is commonly used in machines where the drill operates at high speeds and requires excellent stability.
Threaded Mounting:
Some diamond core drills feature a threaded arbor or core bit holder, allowing the drill to be screwed directly onto the machine's spindle. This method is commonly found in portable core drilling systems or for specific applications like wet drilling, where easy removal and installation are essential.
Choosing the right mounting type for your diamond core drill depends on factors such as the size of the drill, the type of drilling machine, and the specific application requirements. Proper mounting ensures optimal performance, stability, and safety during the drilling process.
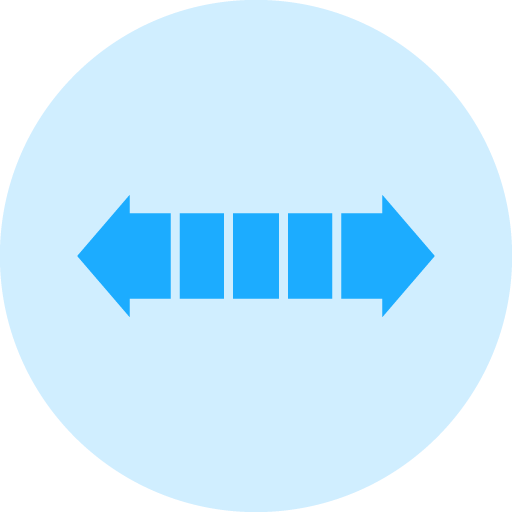
Tolerances on Outside or Inside Diameter
The tolerance range for the outside diameter of diamond core drills varies depending on several factors including the drill's diameter, wall thickness, bond type, and the intended application. These tolerances are crucial as they determine the drill's suitability for precision tasks and influence how the drill interacts with the material it cuts.
For small diamond core drills with diameters less than 10mm, the diameter tolerance typically ranges from ±0.02 to ±0.05 mm. This tight tolerance is necessary for applications that require high accuracy, such as in electronics or medical device manufacturing, where small, precise holes are crucial.
Medium-sized drills, ranging from 10mm to 50mm in diameter, usually have a tolerance of ±0.05 to ±0.15 mm. These are commonly used in mechanical applications and construction where slightly larger variances are acceptable.
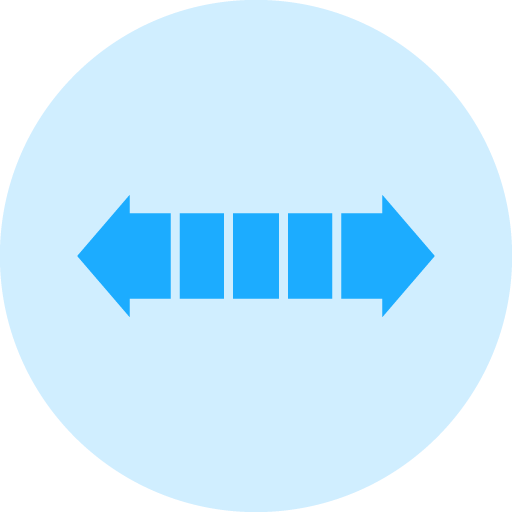
Run Out
Runout is a critical specification for diamond drills as it directly impacts the quality of the holes drilled and the longevity of the tool itself. The term "runout" refers to the degree to which a tool or workpiece deviates from perfect rotation along its central axis. High runout can lead to uneven wear on the tool, compromised hole quality, and increased heat generation, which are particularly detrimental when drilling hard, brittle materials such as glass, ceramics, and certain stones where precision is critical.
Standard and Precision Diamond Drills - Standard diamond drills typically exhibit runout ranging from 0.0005 inches (0.013mm) to 0.002 inches (0.05mm), which is acceptable for general-purpose drilling where absolute precision is not necessary. However, "standard" runout may vary based on the drill's manufacturer and specific applications. Precision diamond drills, manufactured to higher standards with stricter tolerances, usually have runout less than 0.0002 inches (0.005mm), with ultra-precision drills potentially having even tighter runout specifications.

ARE YOU USING RIGHT DIAMOND CORE DRILLS & TOOLS
FOR YOUR APPLICATION?
LET US
HELP YOU
HAVING ISSUES WITH
YOUR CURRENT DIAMOND CORE DRILLS & TOOLS?
Knowledge Center
02
Jun
Select right Diamond Drill for your application
Learn important diamond drill methodology. understand diamond drill specifications and their differences Selecting the right Diamond Drills/Bits for your application is key to obtaining desired diamond drilling results. Using the Right Diamond Drill will...
02
Jun
How to Properly Use Precision Diamond Drills
Step by step guide on how to properly use and care for your diamond drills. Selecting the right diamond drill/diamond drill bit parameters, often involves a trial and error process. Many which can be avoided...
02
Jun
Diamond Drills Guide
Diamond are used across large variety of industries and applications. This guide explores the wide range of diamond drill types, including hollow core drills designed for removing a cylindrical core, non-core formation drills that grind...
02
Jun
Diamond Tools Guide – Selecting Right Drills & Tools for your application
These tools are used for many different industries grinding and shaping material into different forms, expanding exiting inside diameters, grinding, finishing and polishing existing material. Grinding different angles and radius, creating cavities of various forms,...
02
Jun
Optimizing your Diamond Drilling Operation
There are numerous factors that influence the performance of diamond drills. Understanding these factors helps users select the appropriate diamond drill specifications for their specific applications, optimizing drilling operations to achieve maximum efficiency....
02
Jun
Micro Drilling Guide
Share this Article with Friend or Colleague
In order for you to get the most out of your diamond micro drill or carbide / high speed steel micro drill, we strongly urge you to read...
02
Jun
Selecting Right Drilling Equipment for your Application. What you features & functionality you should look for?
Share this Article with Friend or Colleague
There are hundreds or even thousands of different drilling equipment options. Selecting the right equipment for a specific application involves carefully considering several variables and attributes of the...
03
May
Diamond Core Drill & Drill Trouble Shooting Guide
Learn the most common problems most people have in using diamond drills. How to resolve them and avoid them in first place
https://ukam.com/wp-content/uploads/2024/07/diamond-drill-troublehsooting-guide.mp4
Troubleshooting Drilling Problems
Having issues with your diamond drilling operation? This Illustrated Guide...
09
Sep
Understanding & Calculating Return on Investment for Diamond Core Drills & Other Tools
The term "ROI" (Return On Investment) is widely used across industries, often interpreted differently depending on the context. However, few truly understand what ROI represents and its specific implications, particularly in the context of diamond...
09
Sep
Understanding Tradeoffs – Searching for Perfect Diamond Drill & Tool
Choosing the right diamond drill or tool can significantly impact efficiency, cost, and quality. However, this is not a simple and clear-cut process. Selecting the optimal drill or tool involves navigating a complex landscape of...
19
Sep
Why Use Diamond Drills?
Diamond, known as the hardest material on Earth, enables diamond drills and tools to grind away material at a micro (nano) scale. This extreme hardness allows diamond tools to effectively work on materials with a...
- Unmatched Selection For Many Applications
- Superior Quality & Consistency
- Immediate Worldwide Delivery
- Technical Support & Expertise
- American Based Manufacturer
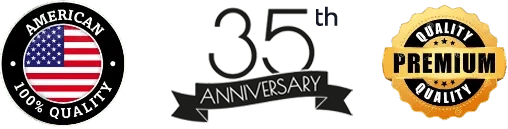

- Different Product
- Different Technology
- Different Company
- Expect MORE from your tools
Let Us HELP You!
Subscribe To Our Newsletter
Signup for email offers, updates, and more
Contact Us
- 25205 & 25201 Avenue Tibbits Valencia CA 91355 USA
-
Phone : (661) 257-2288
FAX : (661) 257 -3833 - lel@ukam.com
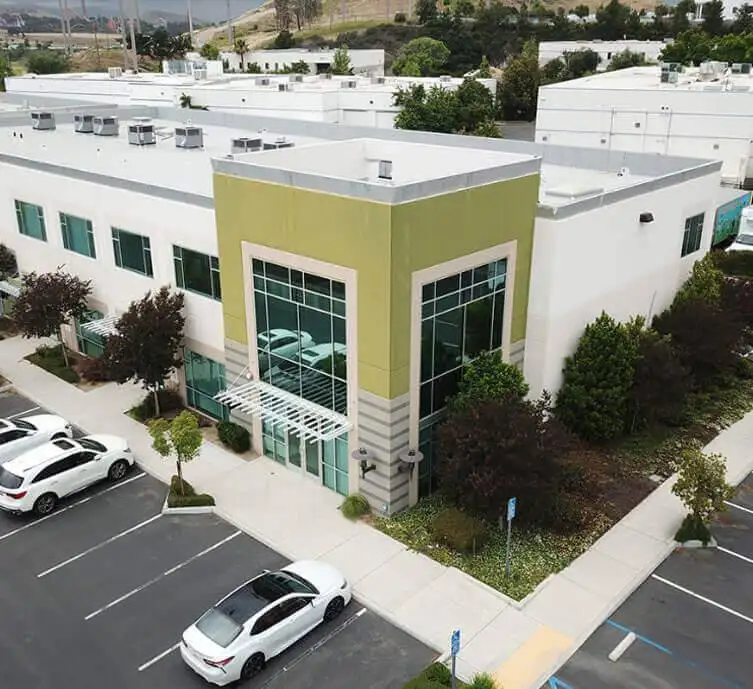
UKAM Industrial Superhard Tools is a U.S. High Technology, Specialty Diamond Tool & Equipment manufacturer. We specialize in producing ultra thin, high precision cutting blades, precision cutting machines diamond drills, diamond micro tools, standard & custom advanced industrial diamond tools and consumables.
- 25205 & 25201 Avenue Tibbits Valencia CA 91355 USA
-
Phone : (661) 257-2288
FAX : (661) 257 -3833 - lel@ukam.com
- 25205 & 25201 Avenue Tibbits Valencia CA 91355 USA
-
Phone : (661) 257-2288
FAX : (661) 257 -3833 - lel@ukam.com
DIAMOND TOOLS BY BOND
EQUIPMENT
KNOWLEDGE CENTER
OUR PRODUCTS
COMPANY
CUSTOMER SERVICE
Shipping Methods


Safe & Secure Payments

© Copyright 1990-2025. UKAM Industrial Superhard Tools – Terms of Use