-
0 items in quote
No products in the Quote Basket.
SMART CUT® 205M
Diamond, Sintered (Metal Bond) Cut Off Blades for Advanced Ceramics & Ultra Hard/Dense Materials
SMART CUT® 205M Diamond Sintered Metal Bond Cut Off Blades are meticulously engineered for ultra hard and brittle materials. These blades offer unmatched accuracy, fast cutting speed, precision and durability, making them an essential for large variety advanced ceramics, composites, optics, and many other materials.
Description
Specifications
Frequently Asked Questions
Industries Used In
Accessories
Recommendations
Description
SMART CUT® 205M blades feature a high concentration of premium-quality diamonds impregnated inside of soft bond metal bond matrix. This design ensures a smooth, swift cutting action, prolonged blade life, and minimal amount stress to material being cut.
Ultra Hard Materials such as sapphire, silicon carbide, boron nitride, alumina oxide, yag and other similar materials are very hard to cut and not many blades are able to provide the right combination of cutting speed, surface finish and life. This is why SMART CUT® 205M Blades stand out from the rest.
Specifications
- Outside Diameters: 10″ (254mm) to 16” (400mm)
- Blade Kerf Thickness: .060” (1.52mm) to .082” (2.08mm)
- Inside Diameter: 1.25”, 32mm
- Diamond Depth: 10mm
- Diamond Concentration: High
- Diamond Grit Size: Medium
- Application: Ultra Hard & Brittle Materials
- Bond Hardness: Soft
- Bond Type: Sintered (Metal Bond)
- Binder Type: Bronze, Cobalt
- Diamond Type: Synthetic
- Core Type: Steel
Frequently Asked Questions
SMART CUT 205M Diamond Sintered Metal Bond Cut Off Blades are precision-engineered cutting tools designed specifically for ultra-hard and brittle materials. They are used to cut advanced ceramics, composites, optics, and other similarly challenging materials with high accuracy, speed, precision, and durability.
SMART CUT 205M Blades feature a high concentration of premium-quality diamonds embedded within a soft bond metal matrix. This unique design ensures a smooth and swift cutting action, extends the blade’s lifespan, and minimizes stress on the material being cut. These blades are exceptional at cutting ultra-hard materials like sapphire, silicon carbide, boron nitride, alumina oxide, and more, offering an excellent combination of cutting speed, surface finish, and longevity.
SMART CUT 205M Blades are ideal for a wide range of applications involving ultra-hard and dense materials, including but not limited to:
- Cutting advanced ceramics
- Trimming composites
- Precision cutting of optics
- Processing hard and brittle materials
Yes, the arbor size (inside diameter) of SMART CUT 205M Blades can be customized to meet your specific requirements. We offer the flexibility to change the arbor size to anything you need on the same day.
SMART CUT 205M Diamond Sintered Metal Bond Cut Off Blades are designed to cut a wide range of ultra-hard and dense materials, including, but not limited to:
- Sapphire
- Silicon carbide
- Boron nitride
- Alumina oxide
- YAG (Yttrium Aluminum Garnet)
- Advanced ceramics
- Composites
- Glass
- Quartz
- Single crystals
These blades excel in providing precise cuts on materials that are notoriously difficult to machine with conventional cutting tools.
Yes, SMART CUT 205M Blades can be used for wet cutting applications. SMART CUT water soluble coolant and other suitable coolants/lubricants can be employed to reduce heat generation, minimize dust, and extend the blade’s lifespan during cutting. Wet cutting also helps maintain the integrity of the material being processed.
The lifespan of SMART CUT 205M Blades can vary depending on factors such as the material being cut, the cutting conditions, and the operator’s expertise. However, these blades are known for their extended lifespan compared to many other cutting tools. Proper maintenance, such as keeping the blades clean and well-lubricated, can contribute to maximizing their longevity.
Yes, safety is paramount when using any cutting tools. Some safety precautions to consider when using SMART CUT 205M Blades include:
- Wearing appropriate personal protective equipment (PPE), such as safety glasses, gloves, and a dust mask.
- Ensuring the workspace is well-ventilated to minimize exposure to dust and fumes.
- Following the manufacturer’s guidelines for blade installation and usage.
- Avoiding excessive pressure or overloading during cutting, which can lead to blade damage or breakage.
- Keeping hands and body parts clear of the cutting path and the blade.
- Using proper machine guards and safety features on cutting equipment.
Always prioritize safety to prevent accidents and ensure a successful cutting operation.
SMART CUT 205M Blades are versatile and can be used with various types of cutting machinery, including precision saws, CNC machines, and other equipment designed for cutting hard materials. It’s important to ensure that the blade’s arbor size is compatible with the machinery you plan to use.
SMART CUT 205M Blades are designed to have a long lifespan, but they are typically not re-sharpened or reconditioned. Once the diamonds in the blade matrix wear down, it’s more cost-effective to replace the blade with a new one to maintain cutting performance.
To maintain the integrity of SMART CUT 205M Blades when not in use, it is advisable to store them in a dry and clean environment. Properly secure the blades to prevent damage, and store them away from direct sunlight or extreme temperature variations. It’s also a good practice to keep the blades in their original packaging to protect them from dust and contaminants.
While SMART CUT 205M Blades are designed to minimize dust generation compared to some other cutting methods, they may still produce some dust when cutting certain materials. To reduce dust, consider using a wet cutting technique with water or a suitable coolant. Additionally, wearing appropriate personal protective equipment, such as a dust mask, is recommended to minimize exposure to airborne particles.
SMART CUT 205M Blades are precision-engineered for accuracy, but cutting extremely thin materials can be challenging due to the risk of breakage or material deformation. It’s important to carefully consider the thickness and fragility of the material in question and adjust cutting parameters accordingly. In some cases, specialized techniques may be required for cutting very thin materials effectively.
SMART CUT 205M Blades can be used for both wet and dry cutting applications. The choice between wet and dry cutting depends on the material being cut and your specific cutting requirements. Wet cutting with water or a suitable coolant is often preferred to reduce heat, control dust, and prolong blade life. However, dry cutting may be suitable for some applications where using a coolant is not practical or desirable.
Changing the arbor size of SMART CUT 205M Blades should be done with care and following proper safety procedures. If you plan to change the arbor size yourself, consult the manufacturer’s instructions for guidance. It’s important to ensure that the new arbor size is securely and correctly fitted to prevent accidents during use.
Yes, SMART CUT 205M Blades are suitable for both manual and automated cutting processes. They can be used with precision saws and CNC machines, making them versatile tools that can accommodate various cutting setups and workflows.
To maintain the performance and longevity of SMART CUT 205M Blades during use, it is advisable to:
- Keep the blade clean by regularly removing debris and residue.
- Ensure proper lubrication or coolant flow to minimize heat generation.
- Monitor the blade for signs of wear or damage and replace it as needed.
- Follow the manufacturer’s guidelines for maintenance and safety.
- Use the appropriate cutting parameters for your specific application to prevent excessive wear.
Regular inspection and maintenance will help maximize the lifespan and cutting efficiency of the blades.
Yes, SMART CUT 205M Blades can be used for both straight cuts and intricate shapes, making them suitable for a wide range of cutting applications. Their precision and accuracy allow for versatility in cutting various shapes and sizes within the capabilities of the blade diameter.
SMART CUT 205M Blades are typically self-sharpening during use due to the diamond impregnation within the metal bond matrix. This means they usually do not require dressing or conditioning during regular use. However, if you notice a decline in cutting performance or blade wear, consult the manufacturer or distributor for guidance on whether dressing or conditioning is necessary.
Yes, SMART CUT 205M Blades are versatile and suitable for both laboratory research and industrial applications. They are commonly used in materials science research, aerospace, precision machining, and other industries that require cutting of ultra-hard and brittle materials.
If you have specific questions about using these blades in your laboratory or industrial setting, please feel free to reach out to our technical support team for further assistance.
Disposal of SMART CUT 205M Blades should be done in accordance with local regulations and environmental guidelines. Because these blades may contain diamond abrasive materials, it’s important to dispose of them responsibly. Contact your local waste disposal authority for guidance on proper disposal methods for diamond abrasive tools.
While SMART CUT 205M Blades are versatile and can be used for dry cutting, it’s important to consider the specific material and cutting conditions. Dry cutting at high speeds may generate more heat, which could potentially reduce blade life and affect the quality of the cut. It’s advisable to consult the manufacturer’s guidelines and perform test cuts to determine the suitability of dry cutting at high speeds for your application.
Yes, SMART CUT 205M Blades can be used for both rough cutting and finishing operations. Their ability to provide a smooth and precise cut makes them suitable for finishing applications where a high-quality surface finish is required. Additionally, they can handle rough cutting tasks efficiently.
SMART CUT 205M Blades are designed to be compatible with a wide range of cutting machines and equipment. They have a standard arbor size (1.25″ or 32mm inside diameter), which fits many common cutting equipment. However, it’s essential to ensure that the blade’s arbor size matches the equipment you intend to use.
Yes, SMART CUT 205M Blades can be used to cut materials of varying thicknesses. Their precision and versatility allow for cutting thin materials as well as thicker ones, provided that the equipment and cutting parameters are adjusted accordingly to accommodate the specific material thickness.
SMART CUT 205M Blades are designed to minimize chipping and micro-cracking in the cut material, especially when used with the appropriate cutting parameters and techniques. However, the extent of chipping or micro-cracking may still depend on the material being cut, its inherent properties, and the specific cutting conditions. It’s advisable to perform test cuts and optimize cutting parameters to achieve the best results for your application.
SMART CUT 205M Blades are capable of cutting transparent materials with minimal optical distortion, provided that they are used correctly and with the appropriate cutting parameters. However, the level of distortion may still vary depending on the material’s refractive index and the quality of the cutting process. It’s recommended to take precautions and conduct test cuts to ensure the desired optical quality is maintained.
Yes, SMART CUT 205M Blades are suitable for cutting large and thick pieces of ultra-hard materials. Their range of available diameters, combined with their ability to handle high cutting speeds, makes them effective for cutting through large and thick sections of materials like sapphire, silicon carbide, and more.
The recommended procedure for mounting SMART CUT 205M Blades onto cutting equipment may vary depending on the specific equipment and manufacturer’s instructions. However, in general, it involves securely attaching the blade to the machine’s arbor or spindle, ensuring proper alignment and tightening to prevent blade wobble. Always follow the equipment manufacturer’s guidelines and safety precautions when mounting the blade.
SMART CUT 205M Blades are well-suited for cutting brittle materials like glass and certain ceramics. Their design, which minimizes stress on the material being cut, can help reduce the risk of cracking. However, it’s essential to optimize cutting parameters, such as speed, feed rate, and lubrication, to minimize the chance of material damage. Test cuts are often recommended to determine the best parameters for specific brittle materials.
Yes, SMART CUT 205M Blades are versatile and can be used for both straight-line cuts and curved cuts with a high degree of precision. Their ability to maintain accuracy and provide smooth cutting action allows for intricate shapes and precise contours to be achieved in addition to straight cuts.
During extended cutting operations, it’s essential to periodically clean SMART CUT 205M Blades to remove debris and maintain optimal cutting performance. This can be done by stopping the machine, allowing the blade to cool, and then carefully cleaning it with a suitable cleaning brush or tool. Proper lubrication or coolant maintenance is also crucial to prevent overheating. Regularly inspect the blade for signs of wear and replace it if necessary to ensure consistent cutting quality.
In laboratory settings or cleanroom environments, it’s essential to maintain a clean and controlled workspace. Specific safety precautions may include:
- Ensuring that the cutting equipment and surroundings are clean and free from contaminants.
- Using appropriate personal protective equipment (PPE) to prevent contamination and ensure operator safety.
- Following cleanroom protocols for equipment usage and maintenance.
- Minimizing dust and particulate generation through proper dust extraction or containment systems.
Always adhere to the cleanliness and safety standards of the specific laboratory or cleanroom environment where you intend to use SMART CUT 205M Blades.
SMART CUT 205M Blades can be used for cutting materials with varying hardness within the same application. Their versatility and ability to cut through a wide range of ultra-hard and brittle materials make them suitable for applications where different materials need to be processed in sequence. However, it’s important to adjust cutting parameters as needed to accommodate the varying hardness of materials and ensure consistent cutting performance.
When cutting highly abrasive materials, such as composites with abrasive fillers, it’s important to be aware that the abrasive nature of the material can impact blade wear. Consider the following:
- Monitor blade wear more closely and be prepared to replace the blade as needed.
- Use appropriate cutting parameters to optimize cutting efficiency while minimizing wear.
- Consider using a wet cutting technique with a suitable coolant to reduce heat and abrasive wear.
Properly maintaining and inspecting the blade during and after cutting abrasive materials will help ensure its longevity and performance.
SMART CUT 205M Blades can be used for cutting materials sensitive to temperature changes, but it’s important to manage heat generation during cutting to avoid potential damage. Using a wet cutting technique with water or a suitable coolant can help dissipate heat and maintain temperature stability. Additionally, optimizing cutting parameters to minimize heat generation is crucial when working with thermally sensitive materials.
SMART CUT 205M Blades are versatile and can be used for both production and research purposes. They are commonly used in research and development applications to investigate and process ultra-hard and brittle materials. However, they are equally suitable for production applications where precision cutting and high-quality results are required.
Handling SMART CUT 205M Blades safely is crucial to prevent accidents and ensure operator safety. Some recommended safety precautions include:
- Wear appropriate personal protective equipment (PPE), including safety glasses, gloves, and a dust mask.
- Handle blades with care and avoid dropping or mishandling them.
- When not in use, store blades in a safe and secure location to prevent damage.
- Follow manufacturer guidelines for blade installation and removal.
- Dispose of used blades properly, following local regulations and guidelines for diamond abrasive tools.
Always prioritize safety when handling SMART CUT 205M Blades.
SMART CUT 205M Blades are primarily designed for cutting ultra-hard and brittle materials. While they can be used for cutting materials with high thermal conductivity, it’s important to consider the specific cutting conditions and parameters to manage heat generation effectively. Using appropriate cooling methods and adjusting cutting parameters may be necessary to ensure the integrity of the cut and minimize blade wear.
Yes, SMART CUT 205M Blades can be used for both wet and dry cutting of materials with varying hardness. The choice between wet and dry cutting depends on the specific material, the desired cut quality, and other factors. Wet cutting with water or a suitable coolant is often preferred to control heat, reduce dust, and extend blade life. Dry cutting may be suitable for certain applications, but it’s essential to adjust cutting parameters accordingly.
When cutting materials that are prone to chemical reactions with water or coolants, it’s important to choose an appropriate coolant that will not react with the material being cut. Some materials, such as certain metals or chemicals, may require specialized cutting techniques or dry cutting to avoid chemical reactions. Always consider the compatibility of the material and the coolant to ensure safe and effective cutting.
SMART CUT 205M Blades can be used for cutting materials with impurities or contaminants, but it’s important to be aware that these impurities can affect blade wear and cutting performance. Depending on the nature of the impurities, they may lead to increased blade wear or other challenges during cutting. It’s advisable to monitor blade wear more closely and consider appropriate cleaning methods to maintain cutting efficiency when working with impure materials.
SMART CUT 205M Blades can be used for cutting composite materials with multiple layers of different hardness or composition. Their precision and versatility make them suitable for such applications. However, it’s important to optimize cutting parameters and take into account the variations in hardness and composition to achieve clean and accurate cuts through each layer.
SMART CUT 205M Blades can be used for cutting sensitive materials, but it’s crucial to take precautions to minimize mechanical stress. This may involve adjusting cutting parameters, such as speed and feed rate, to reduce the impact of mechanical stress during cutting. Additionally, using a wet cutting technique with a suitable coolant can help dissipate heat and minimize stress on the material. Careful handling and proper machine setup are also essential to prevent damage to delicate components or substrates.
SMART CUT 205M Blades can be used for cutting abrasive materials, but it’s important to be prepared for potential rapid blade wear. Abrasive materials can accelerate the wear of cutting tools, including diamond blades. Monitoring the blade’s condition closely during cutting and having replacement blades on hand may be necessary to maintain cutting efficiency.
SMART CUT 205M Blades can be used for cutting composite materials with embedded reinforcements like carbon fibers or metal fibers. However, the presence of these reinforcements can affect blade wear and cutting performance. It’s important to consider the nature and distribution of the reinforcements and optimize cutting parameters accordingly. Test cuts may be necessary to determine the most effective cutting approach.
Yes, SMART CUT 205M Blades can be used for cutting materials with layered structures, such as laminates or semiconductor wafers. Their precision and ability to maintain a smooth cutting action make them suitable for applications where clean, accurate cuts through layered materials are required. Properly optimizing cutting parameters is important for achieving high-quality results.
SMART CUT 205M Blades can be used for cutting highly reflective materials, but precautions should be taken to minimize potential reflections or glare. Proper lighting and safety measures should be in place to ensure the safety of the operator. Additionally, using appropriate coolant or lubrication can help manage heat generation and maintain cutting performance when working with reflective materials.
Yes, SMART CUT 205M Blades are well-suited for cutting highly brittle materials like ceramics and glass. Their design minimizes stress on the material, reducing the risk of fracturing during cutting. However, it’s important to optimize cutting parameters, such as feed rate and speed, to prevent excessive pressure on the material and ensure clean cuts.
Yes, SMART CUT 205M Blades are compatible with automated cutting systems, including CNC machines. Their precision and durability make them suitable for high-precision and repeatable cutting tasks. These blades can be used in conjunction with automated systems to achieve consistent and accurate results in various applications.
SMART CUT 205M Blades are suitable for cutting materials with stringent surface finish requirements, such as optical components or semiconductor wafers. Their ability to provide smooth and precise cuts makes them well-suited for applications where a high-quality surface finish is essential. Properly optimizing cutting parameters and using appropriate coolants or lubrication is important to achieve the desired surface finish.
Yes, SMART CUT 205M Blades can be used for cutting materials with complex geometries, including multi-faceted gemstones and intricate semiconductor packages. Their versatility allows for precise cuts and intricate shapes to be achieved. When cutting materials with complex geometries, it’s important to plan the cutting path and optimize cutting parameters to ensure accuracy.
SMART CUT 205M Blades can be used for cutting materials that require minimal post-processing. Their ability to provide clean and precise cuts reduces the need for extensive post-cutting finishing work. However, the extent of post-processing required may still depend on the specific material and application. It’s advisable to assess the finished cut and make any necessary adjustments to meet the desired specifications.
SMART CUT 205M Blades are compatible with a range of cutting speeds, allowing for adjustments based on material characteristics and cutting requirements. The ability to vary cutting speed makes these blades versatile and adaptable to different materials and cutting conditions. It’s important to consult the manufacturer’s guidelines and perform test cuts to determine the optimal cutting speed for your specific application.
SMART CUT 205M Blades can be used for cutting materials with high thermal expansion coefficients, but it’s important to consider potential thermal effects during cutting. High thermal expansion materials can expand and contract during the cutting process, affecting the precision of the cut. Using appropriate cooling methods and optimizing cutting parameters can help mitigate the impact of thermal expansion and maintain cutting accuracy.
SMART CUT 205M Blades can be used for cutting materials with stringent flatness requirements, such as precision optics or semiconductor wafers. Their precision and ability to provide smooth, accurate cuts contribute to achieving the desired flatness. Properly optimizing cutting parameters and ensuring the equipment is well-maintained are important factors in meeting flatness specifications.
Yes, SMART CUT 205M Blades can be used for cutting materials with complex layer structures, including multilayer ceramics and advanced electronic components. Their versatility allows for precise cuts through different layers, provided that the cutting parameters are adjusted to accommodate variations in material properties and layer composition.
When cutting materials that are highly sensitive to vibration, it’s important to minimize vibrations during the cutting process. SMART CUT 205M Blades are designed to provide smooth and precise cuts, but vibrations can still occur, especially at high cutting speeds. Using stable cutting equipment, ensuring proper blade installation, and reducing cutting forces by optimizing parameters can help minimize vibrations and protect sensitive devices or instruments.
SMART CUT 205M Blades are engineered to minimize edge chipping when cutting brittle materials like glass or ceramics. Their design reduces stress on the material, helping to reduce the risk of edge chipping. However, it’s essential to optimize cutting parameters and handle the material carefully to further minimize the potential for edge chipping.
SMART CUT 205M Blades can be used for cutting materials that are highly porous, but it’s important to be aware that the porous nature of the material can affect blade wear and cutting performance. Porous materials may require adjustments to cutting parameters and may generate more dust or debris during cutting. Properly maintaining and inspecting the blade during and after cutting is essential when working with porous materials.
SMART CUT 205M Blades can be used for cutting materials with stringent dimensional tolerances, such as critical aerospace components or medical devices. Their precision and ability to provide accurate cuts make them suitable for applications where precise dimensions are crucial. Properly optimizing cutting parameters and carefully monitoring the cutting process are essential for meeting dimensional tolerances.
SMART CUT 205M Blades are primarily designed for cutting non-metallic and ultra-hard materials. While they can be used for some non-ferrous materials, they may not be suitable for highly magnetic materials. Highly magnetic materials may require specialized cutting tools designed to handle magnetic properties without affecting the cutting process. Consider alternative cutting methods or tools for such materials.
SMART CUT 205M Blades are compatible with a wide range of cutting machines, including precision saws, CNC machines, and other cutting equipment designed for diamond blade use. These blades can be integrated into various cutting setups to suit your specific application.
The recommended RPMs for SMART CUT 205M Blades can vary depending on the blade diameter and the specific material being cut. In general, a range of 1,000 to 4,000 RPM is commonly used as a starting point. However, it’s crucial to consult the our guidelines and perform test cuts to determine the optimal RPMs for your specific application.
When using SMART CUT 205M Blades, it is recommended to use coolants to dissipate heat generated during cutting. Water-based coolants or specialized cutting fluids are commonly used. Coolants help reduce friction, control heat, and minimize the risk of thermal damage to both the material being cut and the blade. They also help in reducing dust and extending blade life.
When using SMART CUT 205M Blades, you can expect a high-quality surface finish. These blades are designed to provide smooth and precise cuts, which contribute to achieving a fine surface finish. The exact finish can vary based on the material being cut and the cutting parameters, but they are generally capable of meeting stringent surface finish requirements.
SMART CUT 205M Blades are engineered to minimize chipping during cutting, especially in brittle materials like ceramics and glass. When used with appropriate cutting parameters and techniques, you can expect minimal to no visible chipping. However, the level of chipping may still depend on the material’s properties and the care taken during the cutting process. Proper optimization and testing can help achieve the desired results.
Please note that the specific RPM, coolant, feed rate, surface finish, and chipping levels may vary depending on the material being cut and the equipment used. Always refer to the manufacturer’s guidelines and perform test cuts to fine-tune these parameters for your unique application.
Yes, optimizing cutting parameters is essential for achieving the best results when using SMART CUT 205M Blades on different materials. Here are some general guidelines:
- RPM: Consult our guidelines and perform test cuts to determine the optimal RPM for each material. Harder materials may require lower RPMs, while softer materials may tolerate higher RPMs.
- Coolant Type: Choose the appropriate coolant based on the material’s compatibility and your application. Water-based coolants are commonly used, but specialized cutting fluids may be required for specific materials.
- Feed Rate: Start with the manufacturer-recommended feed rates and adjust them based on the material’s hardness. Slower feed rates are generally preferred for harder materials to optimize cutting quality.
SMART CUT 205M Blades can be used for dry cutting applications, but there are important considerations:
- Dry cutting may generate more heat, so monitor blade temperature and material integrity closely.
- Use a suitable dust extraction system to control dust and protect operator health.
- Optimize cutting parameters to reduce heat generation and minimize the risk of thermal damage to the material.
- Consider the material’s specific requirements and consult the manufacturer’s guidelines for dry cutting recommendations.
Achieving the desired surface finish and minimizing chipping involves fine-tuning cutting parameters:
- To improve surface finish, consider reducing the feed rate for a smoother cut.
- To minimize chipping, optimize the feed rate and ensure proper coolant flow to reduce heat and stress on the material.
- Experiment with different combinations of parameters and perform test cuts to find the optimal settings for your specific material and application.
SMART CUT 205M Blades can be used for materials with varying hardness within the same application. To adjust cutting parameters:
- Determine the hardness differences among materials.
- Start with parameters suitable for the hardest material.
- Adjust the feed rate and coolant flow to minimize heat and stress on softer materials.
- Perform test cuts on each material to ensure the best cutting parameters for all hardness levels.
When cutting materials with complex layer structures:
- Adjust cutting parameters based on the properties of each layer.
- Optimize the feed rate and coolant flow for consistent cuts through different layers.
- Perform test cuts to ensure clean cuts and maintain the integrity of all layers.
- Pay attention to any variations in hardness, composition, or density within the layered structure.
When cutting vibration-sensitive materials:
- Choose stable and well-maintained cutting equipment to minimize vibrations.
- Optimize feed rates to reduce cutting forces and vibration.
- Ensure precise blade installation and alignment to minimize vibrations during cutting.
- Monitor the cutting process closely to protect sensitive devices or instruments from potential damage.
When cutting highly porous materials:
- Adjust feed rates to accommodate variations in material density and porosity.
- Ensure proper coolant flow to control heat and prevent thermal damage.
- Be prepared for increased dust or debris generation and use dust extraction systems if necessary.
- Perform test cuts to determine the best combination of parameters for clean and efficient cutting of porous materials.
To meet stringent flatness requirements:
- Maintain precise alignment and stability of the cutting equipment.
- Optimize feed rates and ensure consistent coolant flow to minimize surface irregularities.
- Monitor surface quality during cutting and adjust parameters as needed.
- Perform post-cut inspections to verify flatness and make any necessary adjustments.
SMART CUT 205M Blades are primarily designed for non-metallic and ultra-hard materials. They may not be suitable for highly magnetic materials. For cutting highly magnetic materials, consider alternative cutting tools designed to handle magnetic properties without affecting the cutting process. Magnetic materials often require specialized cutting techniques and tools.
When cutting highly reflective materials:
- Use appropriate lighting and safety measures to minimize reflections and glare.
- Optimize feed rates and coolant flow to control heat and maintain cutting performance.
- Be prepared for variations in material properties and monitor the cutting process closely.
Consider using anti-reflective coatings or specialized techniques to reduce reflections during cutting.
SMART CUT 205M Blades can be used for temperature-sensitive materials, but temperature control is crucial:
- Utilize proper coolant flow to dissipate heat and maintain temperature stability.
- Adjust feed rates to minimize heat generation during cutting.
- Monitor material temperature and take precautions to prevent thermal damage.
- Perform test cuts to optimize cutting parameters for temperature-sensitive materials.
Optimizing cutting parameters is essential to achieve the best results when working with various materials and applications. Always consider the specific characteristics and requirements of the material being cut, and be prepared to perform test cuts to fine-tune parameters accordingly.
Achieving precise dimensional tolerances requires careful optimization of cutting parameters:
- Maintain stable equipment and ensure precise blade installation to minimize variations.
- Adjust feed rates and coolant flow to control heat and achieve the desired dimensions.
- Monitor cutting accuracy throughout the process and make necessary adjustments as needed.
- Perform post-cut inspections to verify dimensional tolerances and make any final adjustments.
SMART CUT 205M Blades can be used for materials with high thermal expansion coefficients, but consider these factors:
- Use appropriate coolant to control heat and minimize thermal expansion effects.
- Adjust feed rates and cutting speeds to reduce the impact of thermal expansion.
- Monitor material movement during cutting and make real-time adjustments as needed.
- Perform test cuts to find the optimal parameters for materials with high thermal expansion coefficients.
SMART CUT 205M Blades can help minimize post-processing requirements:
- Optimize feed rates and coolant flow to achieve clean and precise cuts.
- Monitor surface quality during cutting to minimize the need for additional finishing.
- Perform post-cut inspections to assess the quality of the cut and reduce post-processing steps as needed.
- Fine-tune cutting parameters to achieve the desired level of finish directly from the cutting process.
SMART CUT 205M Blades can be used for both wet and dry cutting:
- For wet cutting, use water-based coolants or cutting fluids to control heat and debris.
- For dry cutting, adjust parameters to reduce heat and dust generation.
- Be prepared to switch between wet and dry cutting techniques based on material characteristics and desired results.
- Regularly clean the blade and equipment when switching between cutting methods.
For materials reactive with water or coolants:
- Choose a coolant that is compatible with the material.
- Use minimal coolant or opt for dry cutting if possible.
- Monitor the cutting process closely and be prepared for potential reactions.
- Ensure proper ventilation and safety measures when working with reactive materials.
Blade dressing is essential for maintaining the performance of SMART CUT 205M Blades. The frequency of dressing depends on several factors, including the material being cut, cutting parameters, and blade wear. Here’s more information:
Blade dressing is the process of exposing new diamond abrasive particles on the blade’s cutting edge. Over time, diamond blades can wear, leading to reduced cutting efficiency and quality. Dressing helps restore the blade’s sharpness and cutting effectiveness.
Several indicators suggest it’s time to dress the blade:
- Reduced cutting speed or efficiency.
- Poor surface finish.
- Increased cutting noise or vibration.
- Visible signs of wear on the blade’s cutting edge.
- Uneven or chipped cuts.
Several factors influence how often you should dress SMART CUT 205M Blades:
- Material hardness: Harder materials may cause faster blade wear.
- Cutting parameters: Higher speeds or feed rates can accelerate wear.
- Material impurities: Materials with abrasive contaminants may wear the blade more quickly.
Blade quality: Blade quality and initial sharpness affect wear rates.
Blade dressing can be done using a dressing stick or dressing tool designed for diamond blades. The process typically involves running the dressing tool against the rotating blade to expose new diamond abrasive particles. Follow the manufacturer’s guidelines for dressing procedures and use appropriate safety equipment.
When dressing the blades, take these precautions:
- Wear appropriate personal protective equipment, including safety glasses and gloves.
- Ensure the dressing tool is compatible with the blade’s specifications.
- Follow manufacturer instructions for the dressing process.
- Use the proper technique to prevent over-dressing or damage to the blade.
SMART CUT 205M Blades can be dressed multiple times to extend their lifespan. However, there are limitations to how many times a blade can be dressed, as excessive dressing can reduce blade life. The number of dressings a blade can withstand depends on factors like blade quality and initial sharpness.
Dressing SMART CUT 205M Blades can be done in-house if you have the necessary equipment and follow manufacturer guidelines. However, if you’re unsure or inexperienced, it’s advisable to consult a professional or the blade manufacturer for guidance to ensure proper dressing and blade maintenance.
The dressing process can vary based on the material being cut and the application. Consult the blade manufacturer’s guidelines for specific recommendations on dressing SMART CUT 205M Blades for different materials or applications. Tailoring the dressing process to the material and application can help maximize blade performance.
Regular blade dressing is essential for maintaining the cutting effectiveness and longevity of SMART CUT 205M Blades. By monitoring wear indicators and following proper dressing procedures, you can ensure consistent cutting performance and quality results.
Neglecting to dress SMART CUT 205M Blades regularly can lead to several undesirable consequences:
- Reduced cutting efficiency and slower cutting speeds.
- Lower quality surface finish with increased roughness.
- Increased heat generation, potentially causing thermal damage to the material.
- Increased risk of blade wear and damage, shortening the blade’s lifespan.
- Inaccurate cuts, which can impact the dimensional accuracy of the workpiece.
Over-dressing SMART CUT 205M Blades can have adverse effects, including excessive diamond particle removal and reduced blade life. To avoid over-dressing, follow these guidelines:
- Use a dressing tool designed for diamond blades.
- Dress the blade according to the manufacturer’s recommendations.
- Avoid excessive pressure or prolonged dressing, which can remove too many abrasive particles.
- Regularly inspect the blade to assess the need for dressing without overdoing it.
The frequency of dressing SMART CUT 205M Blades is highly dependent on the specific application, material, and cutting parameters. While there’s no one-size-fits-all rule, a good practice is to monitor the blade’s performance regularly. When you observe signs of reduced cutting efficiency, poor surface finish, or other wear indicators, consider dressing the blade. Keep records of blade performance to establish a maintenance schedule tailored to your specific needs.
Blade dressing can be integrated into routine blade maintenance. Performing regular inspections and dressing when needed can help prevent excessive wear and maintain consistent cutting performance. Incorporating blade dressing into your maintenance schedule can contribute to longer blade life and better cutting results.
Advanced techniques and tools for dressing SMART CUT 205M Blades can enhance the dressing process and extend blade life. These may include:
- Using specialized dressing sticks or tools designed for specific blade types.
- Employing automated or computer-controlled dressing systems for precision.
- Implementing laser-dressing techniques for fine-tuning the blade edge.
Consulting with blade manufacturers for customized dressing solutions based on your application needs.
SMART CUT 205M Blades can be re-dressed to restore some of their original sharpness and cutting effectiveness. However, there is a limit to how much they can be restored, as the diamond abrasive particles wear down over time. Blade quality, initial sharpness, and the number of previous dressings can influence how effectively a blade can be restored. Eventually, when the diamond particles are too worn, the blade may need replacement.
When dressing SMART CUT 205M Blades for highly abrasive materials:
- Be prepared for more frequent dressing due to accelerated wear.
- Use dressing tools designed for diamond blades to maintain blade integrity.
- Monitor blade condition closely and perform intermediate dressings as needed.
- Adjust cutting parameters to minimize heat and maintain cutting efficiency.
Blade dressing can be performed on-site if you have the necessary equipment and expertise. However, if you’re uncertain or prefer professional handling, you can send blades to specialized services for dressing and maintenance. These services often have specialized tools and experience to ensure effective blade dressing and prolong blade life.
Industries Used In
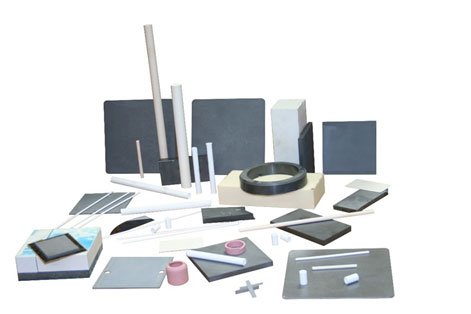
Advanced Ceramic Materials
- Alumina
- Silicon Carbide
- Beryllia
- Boron Carbide
- Boron Nitride
- Refractories
- Ceramic To Metal Seals
- Technical Ceramics
- Semiconductor Materials
- Sapphire
- Silica Fused
- Zirconia
- Carbon
- Porcelain
- Many Others
Accessories
Showing 1 – -1 of 13 results Showing all 13 results Showing the single result No results found
Sort by Price low to high
Filters Sort results
Reset Apply
Image | Name | COMPATIBILITY WITH DRILL SERIES | Price | Quantity | Add to cart |
---|---|---|---|---|---|
Recommended for use in Diamond Tools 150 Grit Size (mesh… | $15.39 | Max: Min: 1 Step: 1 | |||
Recommended for coarser grits found in segment wheels, core drills… | $15.99 | Max: Min: 1 Step: 1 | |||
5/8″-11″ thread. Fits into drill press chuck. Shank adapter threads… | $22.46 | Max: Min: 1 Step: 1 | |||
5/8″-11″ thread. Fits into drill press chuck. Shank adapter threads… | $26.72 | Max: Min: 1 Step: 1 | |||
SMART CUT® General Materials Formula Synthetic Water Soluble Coolant | $34.81 | Max: Min: 1 Step: 1 | |||
Recommended for use in Diamond Tools 150 Grit Size (mesh… | $39.47 | Max: Min: 1 Step: 1 | |||
Recommended for coarser grits found in segment wheels, core drills… | $39.47 | Max: Min: 1 Step: 1 | |||
SMART CUT® General Materials Formula Synthetic Water Soluble Coolant | $99.81 | Max: Min: 1 Step: 1 | |||
105DE, 135DB, 115DM, 125DM, 130DMN, 140DM (up to 1-5/8″ OD) | $154.87 | Max: Min: 1 Step: 1 | |||
105DE, 135DB, 115DM, 125DM, 130DMN, 140DM (up to 1-5/8″ OD) | $154.87 | Max: Min: 1 Step: 1 | |||
105DE, 135DB, 115DM, 125DM, 130DMN, 140DM (up to 1-5/8″ OD) | $235.00 | Max: Min: 1 Step: 1 | |||
SMART CUT® General Materials Formula Synthetic Water Soluble Coolant | $317.41 | Max: Min: 1 Step: 1 | |||
SMART CUT® General Materials Formula Synthetic Water Soluble Coolant | $1,745.00 | Max: Min: 1 Step: 1 |
Recommendations
02
Jun
How to Properly Use Precision Diamond & CBN Blades
The diamond blade itself is only a small factor in your cutting operation. Successful diamond sawing is both an art & science. Requiring proper use and understanding of the right: RPM’s, Coolants, Equipment, Dressing Devices, Accessories…
02
Jun
Precision & Ultra Thin Diamond Blade Guide
Diamond and CBN blades are available in an extensive array of varieties, each differing in bond types, manufacturing methods, and design specifics. Ultra Thin & High Precision Diamond Blades are particularly versatile, applicable…
02
Jun
Troubleshooting Diamond Sawing Problems
Having issues with your diamond cutting operation? This Illustrated Guide can help. Learn the most common problems most people have in using diamond cutting blades. How to resolve them and avoid them in…
02
Jun
How to Improve & Optimize Your Diamond Sawing Operation
There are numerous variables that affect the performance of diamond and CBN cutting blades. Understanding these variables will help end users select the right diamond blade specifications for their applications and optimize their…
02
Jun
Evaluating & Comparing Diamond Blades
Share this Article with Friend or Colleague
Proper testing procedures and methodologies must be set up and used to obtain accurate as well as repeatable testing results. This article will discuss several simple procedures which…
31
Jul
Top 5 Diamond & CBN Cutting Blade Performance Metrics
Share this Article with Friend or Colleague
When evaluating diamond and cubic boron nitride (CBN) cutting blades, it’s crucial to consider key performance metrics and criteria. Different applications have varying goals, making it…
01
Aug
Diamond & CBN Cutting Blade Performance Metrics that you Should Know
Share this Article with Friend or Colleague
When evaluating diamond and cubic boron nitride (CBN) cutting blades, it’s crucial to consider key performance metrics and criteria. Different applications have varying goals, making it important to…
02
Aug
Total Cost of Ownership & Why its Important
Share this Article with Friend or Colleague
Diamond and CBN cutting blades are available in a myriad of specifications, with virtually limitless options. The industry is saturated with numerous manufacturers, each professing to offer the…
05
Aug
Understanding Tradeoffs- Searching for Perfect Diamond & CBN Blade
Share this Article with Friend or Colleague
Choosing the right blade diamond or cbn blade can significantly impact efficiency, cost, and quality. However, this is not simple and clear cut process. Selecting the optimal blade…
19
Aug
Understanding & Calculating Return on Investment for Diamond & CBN Blades
The term “ROI” (Return On Investment) is frequently mentioned across various industries, often with different interpretations depending on the context. However, few take the time to thoroughly understand what ROI truly represents and its specific…
10
Oct
Everything You Wanted to Know About Cutting Glass with Diamond Blades
Cutting glass is a delicate process that requires the right set up, technique and process to avoid cracks, chips, or fractures. The inherent brittleness and hardness of glass make it challenging to work…
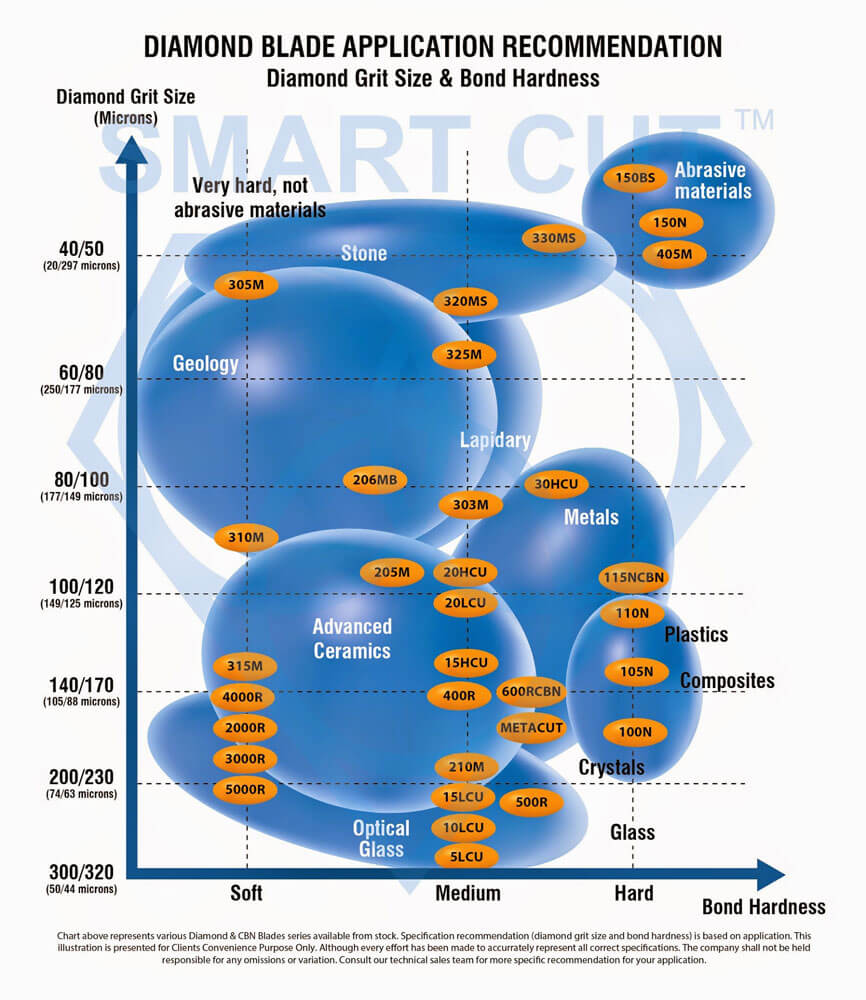
3106008, 3128206, 3148202, 3168201
Filters Sort results
Reset Apply
Image | New Item No: | Outside Diameter | Kerf Thickness | Arbor Size / Inside Diameter | Price | Quantity | Add To Cart |
---|---|---|---|---|---|---|---|
10” | .060" | 1.25” 32mm | $190.00 | Max: Min: 1 Step: 1 | |||
12" | .082" | 1.25” 32mm | $275.00 | Max: Min: 1 Step: 1 | |||
14" | .082" | 1.25” 32mm | $295.00 | Max: Min: 1 Step: 1 | |||
16" | .082" | 1.25” 32mm | $325.00 | Max: Min: 1 Step: 1 |
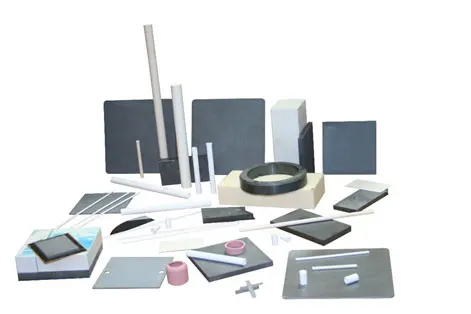
Advanced Ceramic Materials
- Alumina
- Silicon Carbide
- Beryllia
- Boron Carbide
- Boron Nitride
- Refractories
- Ceramic To Metal Seals
- Technical Ceramics
- Semiconductor Materials
- Sapphire
- Silica Fused
- Zirconia
- Carbon
- Porcelain
- Many Others
About Sintered (Metal Bond)
Sintered (metal bonded) diamond tools have multiple layers of diamonds impregnated inside the metal matrix. Diamonds are furnaces sintered in a matrix made of iron, cobalt, nickel, bronze, copper, tungsten, alloys of these powders or other metals in various combinations. Metal bonded diamond tools are “impregnated” with diamonds. This means that selected diamonds are mixed and sintered with specific metal alloys to achieve the best cutting performance possible on any materials such as sapphire, advanced ceramics, optics, glass, granite, tile and etc. The metal bond surrounding the diamonds must wear away to continuously keep re-exposing the diamonds for the diamond tool to continue cutting. Sintered (metal bonded) diamond tools are recommended for machining hard materials from 45 to 75 on rockwell scale (5 to 9.5 on mohe’s scale of hardness).
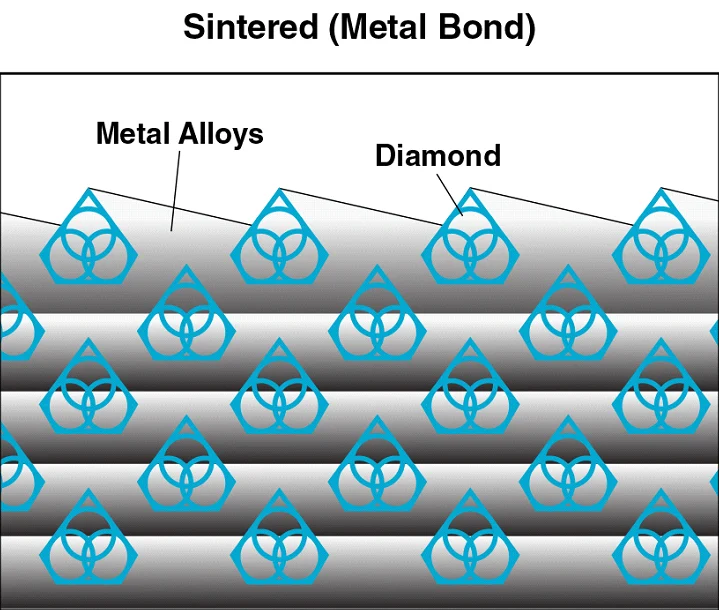
How SMART CUT® Bond Works?
Step 1
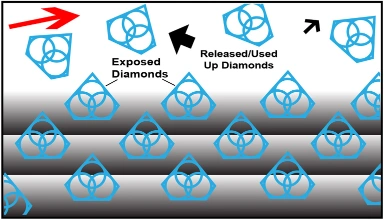
Sharpest And Finest Quality Diamonds
The newly exposed diamonds don’t effect diamonds already working on the material. Unlike many other diamond bonds, diamonds in a SMART CUT® Bond remains sharp and grow sharper with each cut, prolonging product life and consistent performance.
Step 2
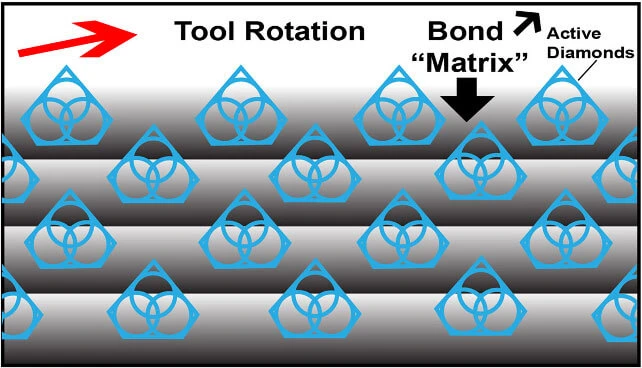
Diamonds or CBN Crystals
Diamonds or CBN Crystals are activated only at the exposed layer. As Bond Matrix layer begin to wear out, diamonds in a new Bond Matrix layer are immediately activated, substituting the already used up diamond layer. The SMART CUT® Diamond Hybrid Bond makes sure every diamond is in the right place and at the right time, working where you need it most.
Step 3
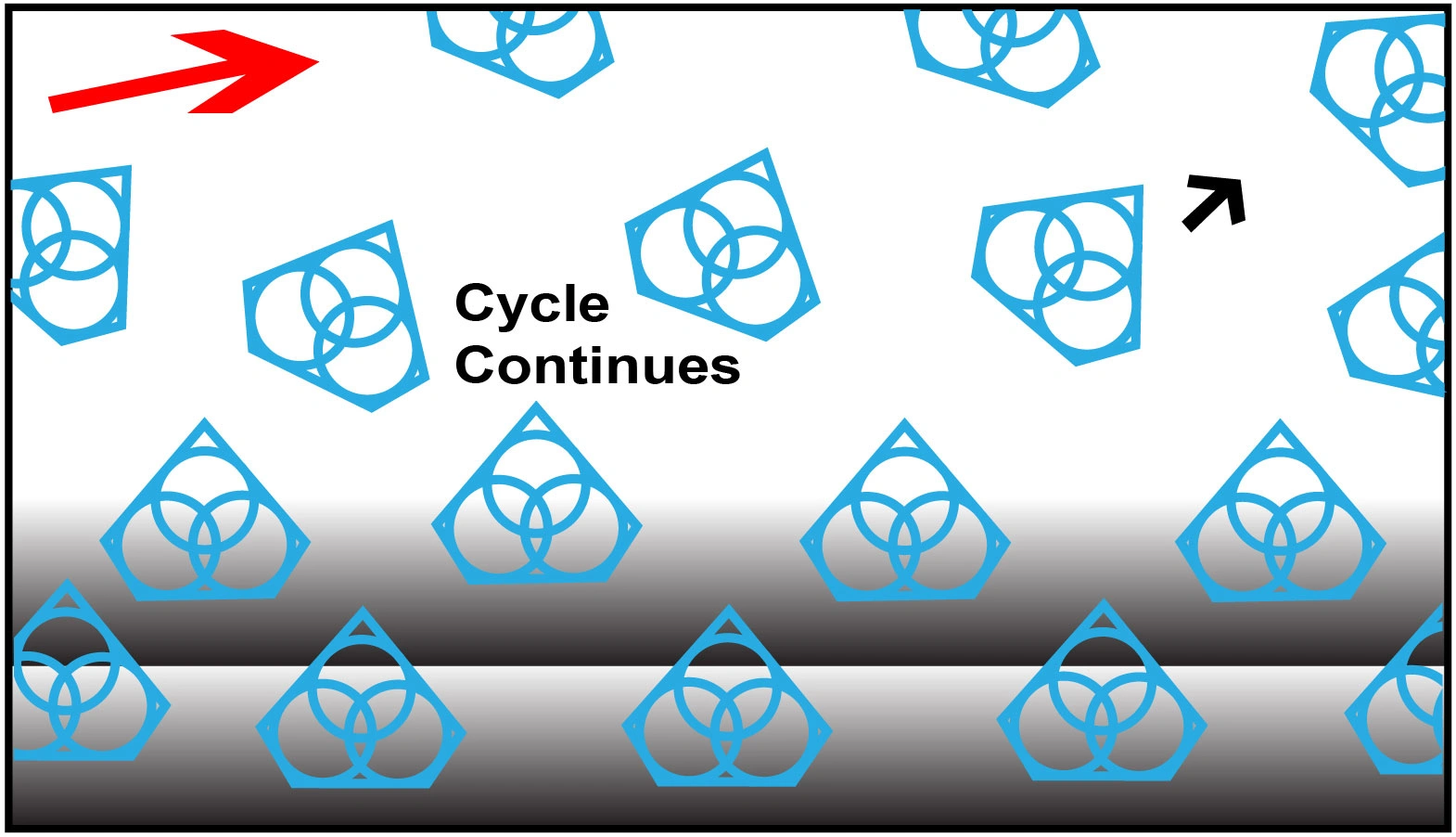
Advanced Formulated Open Diamond Bond Design
This advanced formulated open diamond bond design insures minimal chipping, fast cut, constant speed of cut, minimal cutting noise, and most important of all, consistent performance.
No
Glazing
Diamond & CBN blades with SMART CUT® technology require minimum dressing, the bond renews itself.
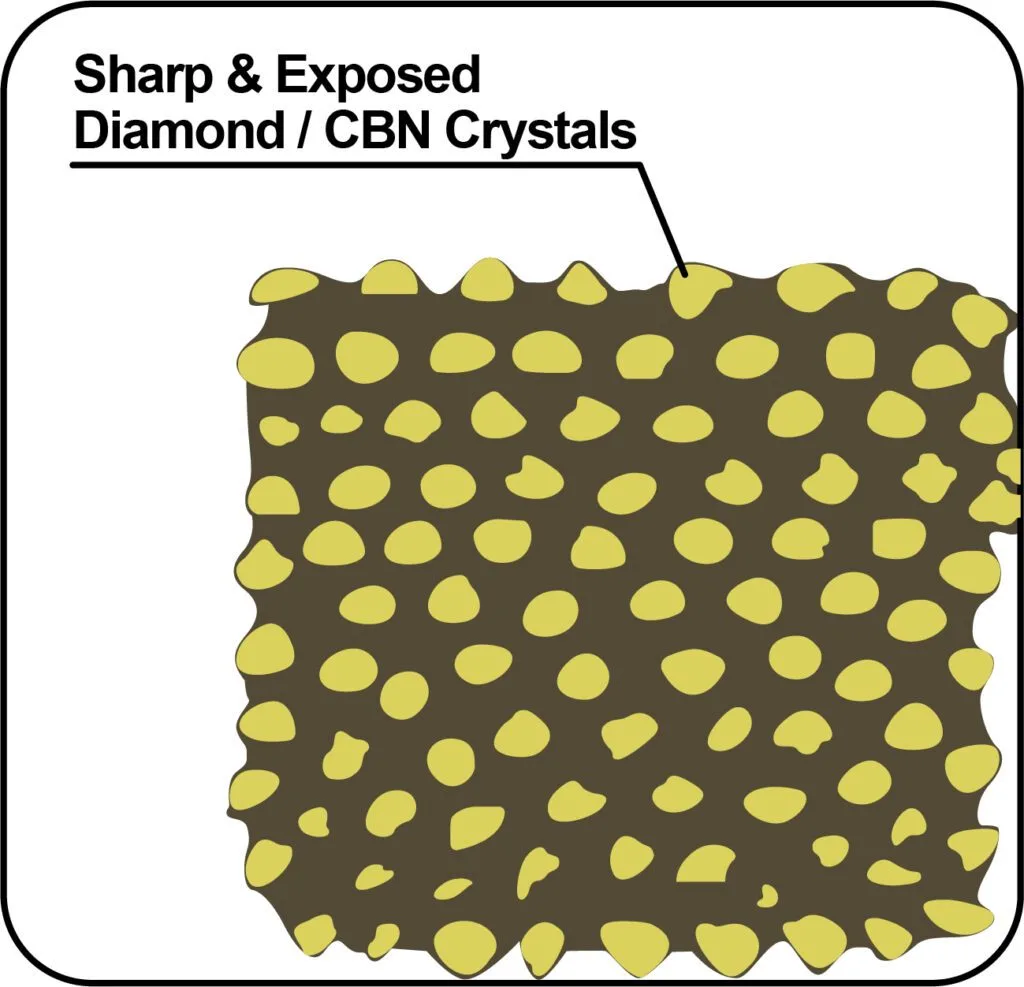
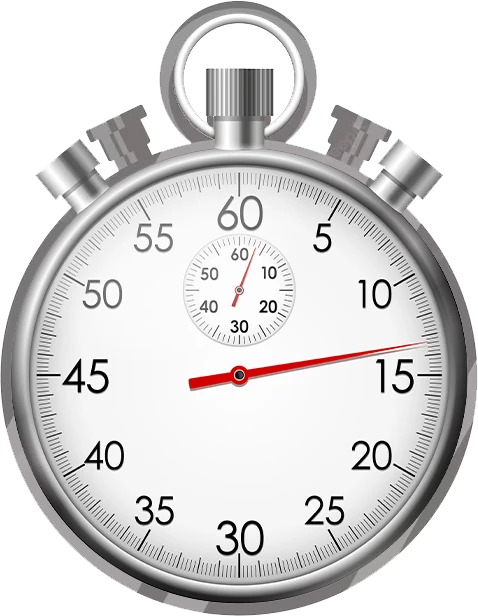
Faster
Cutting Action
SMART CUT® blades made utilizing SMART CUT® technology are much more aggressive then conventionally blades. They can cut faster, while still leaving behind a smooth surface finish.
Best
Performance & Value on the Market
SMART CUT® Series Sintered (metal bond) blades are the best investment you can make! Although they may cost more than other sintered (metal bond), blades. Designed for users that understand and appreciate quality. They will more than pay for themselves in terms of overall performance and provide best Return on Investment.
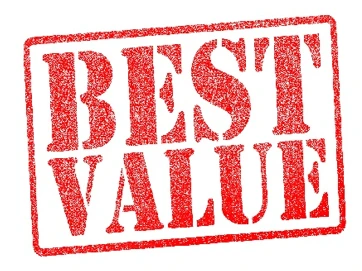
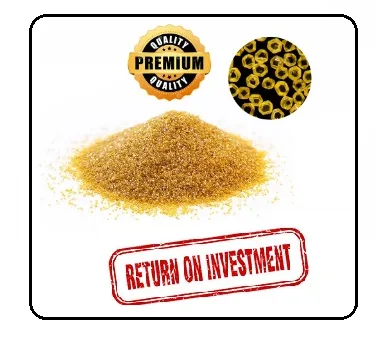
Manufactured Using
The Highest Quality Raw Materials
Only the highest quality synthetic diamonds and raw materials are used in the manufacturing process. The highest quality standards and product consistency is maintained, using sophisticated inspection and measurement equipment.
Diamond Cut Off Wheel Blade
Selection Variables
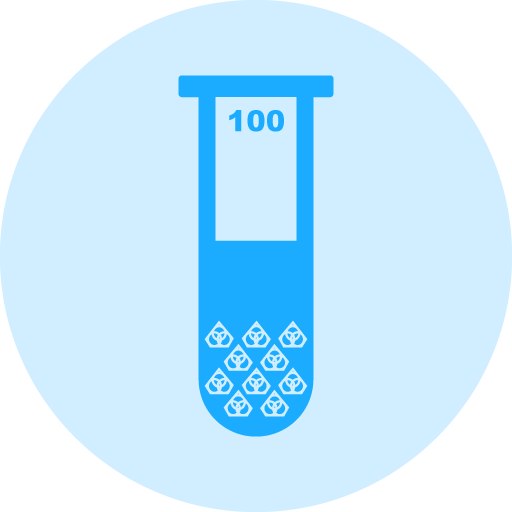
Diamond Concentration
Diamond Concentration – Diamond Concentration is still a factor in determining the life and cutting speed of your Diamond Cut off Wheels / Blades.
High diamond concentration helps enhance the longevity of the blade by distributing the cutting workload across more diamonds, reducing wear on individual diamonds and extending the blade's overall life. This setup results in a smoother finish since more cutting points engage with the material simultaneously, which is crucial for materials requiring a high-quality finish like optical materials or precision ceramics.
With more diamonds embedded in the resin matrix, these blades maintain their cutting capability longer, ensuring consistent performance throughout their lifespan. This is vital for applications needing uniform cuts in serial production or where precise dimensional tolerances are critical. Although resin bonds inherently generate less heat, the increased number of cutting points with high diamond concentration disperses the friction-generated heat more evenly, further reducing the risk of thermal damage to sensitive materials.
Low concentration resin bond diamond cut off blades and wheels provide several advantages, especially suited for cutting hard and brittle materials like ceramics, glass, or sapphire. With fewer diamonds embedded in the resin matrix, each diamond can exert more force on the material, enhancing precision and minimizing material deformation. This setup also reduces the risk of removing too much material too quickly, which is vital in applications requiring high precision and minimal kerf.
The increased spacing between the diamonds allows for better chip formation and removal, preventing the accumulation of debris that can affect cutting quality and increase the risk of blade overheating. Additionally, fewer diamonds mean less friction during cutting, which results in decreased heat generation. This is crucial when working with materials sensitive to thermal damage, such as those that might warp or undergo microstructural changes.
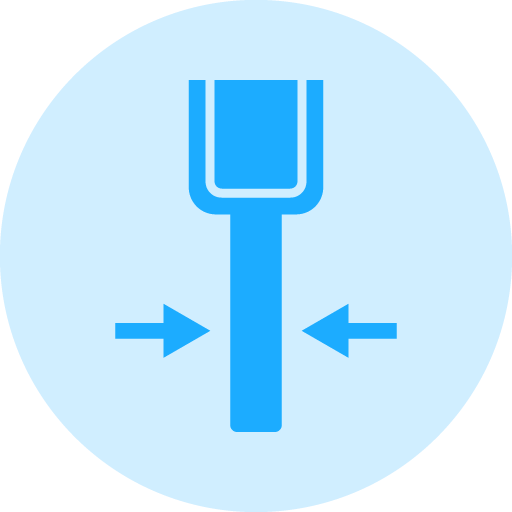
Blade Thickness
For resin bond diamond cut off blades and wheels, blade thickness plays a critical role in determining the amount of material removed during the cutting process, which is referred to as the kerf. The kerf size increases in proportion to the blade diameter, and it represents the width of the material that is removed as the blade passes through the sample. Choosing the correct blade thickness is essential for minimizing material loss, while insuring blade stability and cut quality.
For applications demanding high precision, thinner and smaller diameter blades are preferable. Blades ranging from 3 inches to 6 inches (75mm to 150mm) in diameter with a thickness of 0.015 inches to .020” thickness (0.4mm to 0.5mm) are typically best suited for these purposes. The optimal blade thickness for a particular material or application depends on various factors, including the cutting equipment used on, desired cutting speed, load or feed rate, material diameter, thickness, hardness, density, and shape, as well as the skill and experience of the operator.
Thicker resin bond diamond cut off blades offer increased stiffness and can withstand higher loads and feed rates. Another advantage of a thicker kerf is that it is more forgiving to operator error and misuse. This makes thicker kerf blades particularly recommended for environments where equipment is shared among a large number of individuals, They are ideal for less experienced or novice saw operators, providing a safer and more forgiving use-case scenario.
.
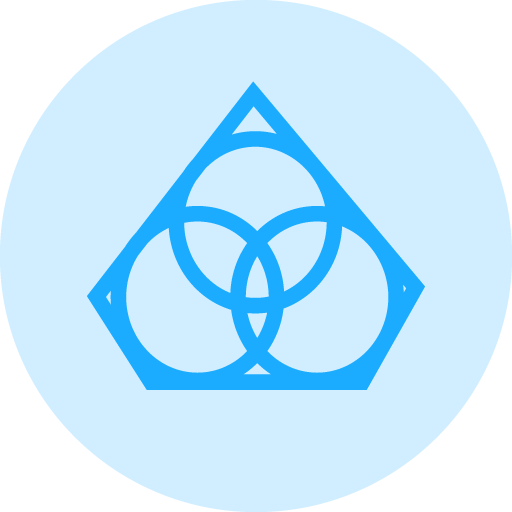
Diamond Particle/Grit size
The diamond particle or grit size in resin bond diamond cut off wheels plays a an important role in how they perform across various cutting parameters such as cutting speed, surface finish, & blade life. Larger, coarser diamond particles allow the wheel to cut through material more quickly, improving time efficiency and increase blade life. However, this comes with a trade-off as coarser diamonds can increase microstructural damage to the material due to their aggressive cutting action.
On the other hand, finer diamond grits contribute to a superior surface finish and higher quality cut. These smaller particles make less aggressive cuts, and produce better surface finish with minimal to no chipping on edges of material. Additionally, finer diamonds ideal for cutting fragile or delicate materials where maintaining the material's integrity is essential.
Choosing the right diamond grit size is key for optimizing the cutting process with resin bond diamond cut off wheels. For delicate or brittle materials, finer diamond grits are preferable to minimize chipping and microstructural damage while ensuring a high-quality surface finish. In scenarios where cutting speed is a priority and the material can tolerate more aggressive cutting, coarser diamond grits might be more suitable.
Coarse Diamond Grit Size, ranging from 60 to 100 mesh, are typically for cutting large variety of hard materials such as tungsten carbide, metals, and some ultra hard ceramics such as boron nitride and silicon carbide.
Medium Diamond Grit Sizes, As grit sizes become slightly finer, in the 120 to 200 mesh range labeled as medium, these are more commonly used for most resin bond diamond cut off blade / wheel applications such as cutting most types of glass, ceramics, optical glass, and other ultra hard and brittle materials
Fine grit size, which span from 229 to 320 mesh, designed for providing smoothest surface finish and minimal amount of chipping possible. These sizes are usually used for cutting quartz, Pyrex, fragile crystals and other fragile materials
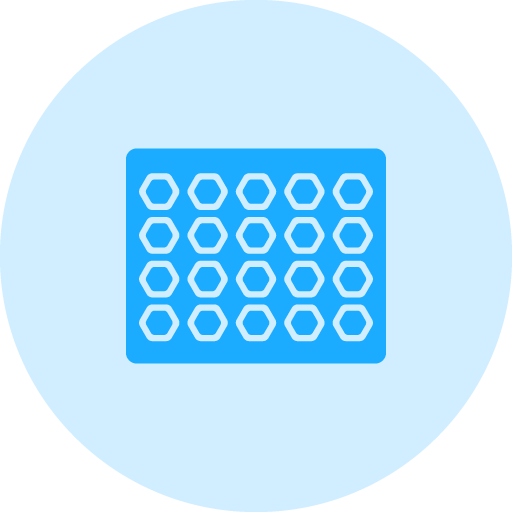
Bond Type
Resin bond diamond cut off blades are renowned for their exceptional cut quality, surpassing that of any other type of diamond blade available. They are specifically recommended for applications where the quality of the cut and the surface finish are paramount. This superior performance is particularly evident when compared to sintered (metal bond) blades, which, while durable, do not typically match the precision and smoothness provided by resin bond blades.
Resin bond blades use a composite material in which diamond particles are embedded in a resin matrix. This configuration allows for a smoother interaction with the material being cut, resulting in cleaner cuts with minimal chipping and superior surface finishes. The flexibility of the resin bond also enables a finer control over the cutting process, which is crucial in applications requiring high precision, such as in the fabrication of intricate components in the electronics and aerospace industries.
Furthermore, the unique properties of resin bond blades allow them to deliver excellent performance on a wide range of materials, including hard, brittle substances like glass, ceramics, and semiconductor materials.
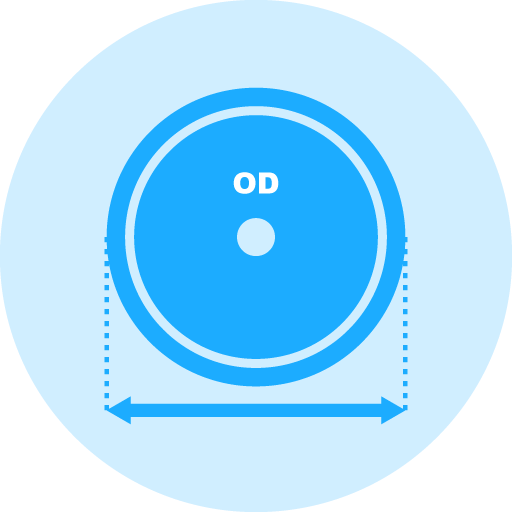
Blade Outside Diameter
These diameters are carefully chosen based on the specific needs of the application, the properties of the material being cut, and the capabilities of the cutting machine. Resin diamond cut off blades & cutoff wheels, which are available in sizes ranging from 1 inch to 20 inches in diameter, offer varied capabilities based on their size. The diameter of the blade should be chosen with consideration to the diameter and thickness of the material being cut. Smaller diameter blades, which tend to be thinner, are more susceptible to bending and warping during use. On the other hand, larger diameter blades, being thicker, provide greater stability and are typically employed for cutting larger and heavier materials. These larger blades can handle higher loads and speeds, making them suitable for more demanding cutting tasks.
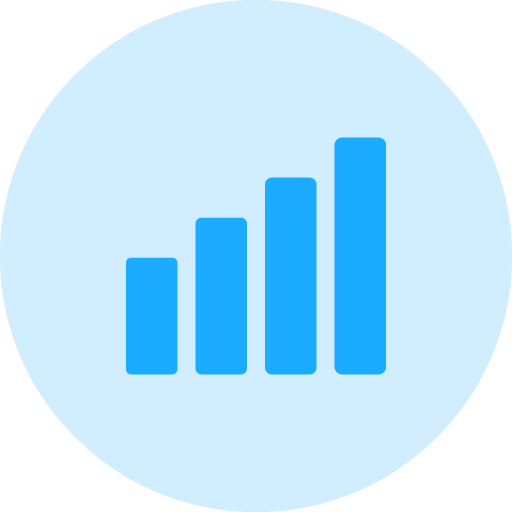
Feed Rates
Feed rates for resin bond diamond cut off blades in tile saws and precision cutting saws are critical to the cutting performance and quality of the final cut, and these rates must be adjusted to achieve desired objectives
For harder materials such as ceramics and metals, a faster feed rate may be necessary to efficiently cut through the material. This requires careful handling to ensure the blade does not overheat or wear prematurely. On the other hand, brittle materials like silicon, often used in precision applications, benefit from a slower feed rate to prevent chipping or cracking.
The optimal feed rate is also influenced by the speeds or RPMs at which the blade operates. Higher speeds can allow for quicker cuts but might increase the risk of damage to sensitive materials. Additionally, the geometry and size of the material, along with how securely it is held in place, are important considerations. Proper clamping of the material minimizes movement and vibration, enhancing the blade's effectiveness and the quality of the cut. Adjusting the feed rate manually requires a careful balance of these factors
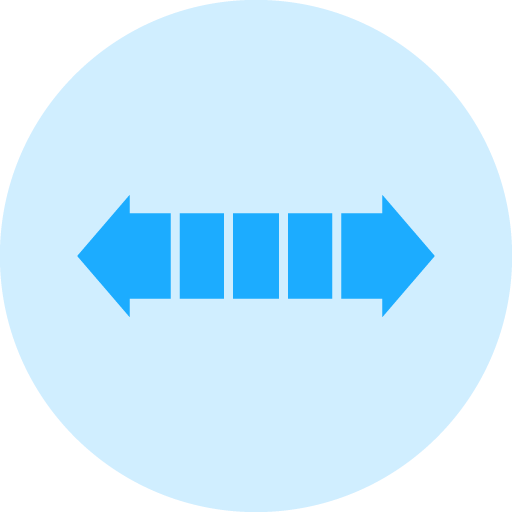
Bond Hardness
In resin bond diamond cut off blades, the hardness of the bond matrix significantly influences its ability to retain diamond particles and impacts the overall performance of the blade. As the bond hardness increases, the retention of diamonds improves, which can enhance the blade's durability but may result in a slower cutting speed. Blades with harder bond matrices generally exhibit a longer lifespan due to this increased retention.
Resin bond diamond cut off blades are classified according to their bond hardness, with designations ranging from Soft, Medium, to Hard, and numerous variations within these categories based on the degree of hardness or softness.
Selecting a blade with the optimum bond hardness is critical for achieving efficient and precise diamond sawing operations. A bond matrix that is too soft for the material being cut tends to release diamond particles prematurely, leading to rapid wear and a reduced lifespan of the blade. Conversely, a bond matrix that is too hard can significantly slow down the cutting process and necessitate frequent dressing to expose new layers of diamond.
For cutting harder materials like sapphire and alumina, softer bonds are typically preferred because they allow for easier diamond exposure and faster cutting, essential for maintaining efficiency without damaging the blade. For softer and more brittle materials, harder bonds are advantageous as they ensure better diamond retention, reducing the frequency of blade replacements and maintaining consistent performance.
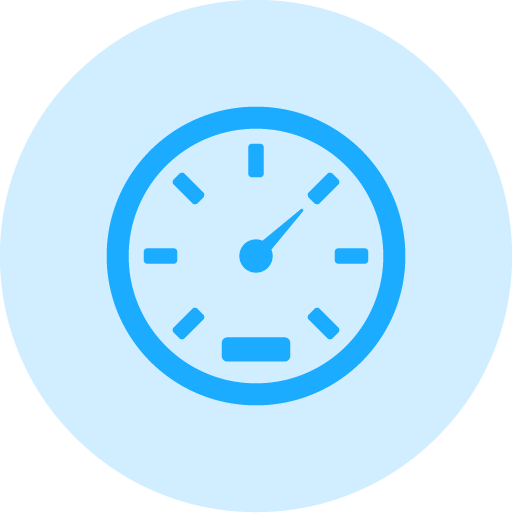
Blade Speeds/RPM’s
Resin bond diamond cut off wheels are usually used at higher speeds then sintered (metal bond) Resin bond diamond blades are usually used on manual saws such as tile saws and precision cut off saws, it’s essential to select the right RPM range to ensure optimal cutting performance and to maintain the integrity of the material. Tile saws and other lower-powered manual saws typically operate at RPMs up to 5,000, which is suitable for cutting large variety of materials such as glass.
In contrast, precision manual and automatic cut off saws, which handle a wider variety of materials and more complex cutting tasks, can accommodate a broader RPM spectrum. These saws might operate at speeds up to 100 to 6,000 RPMs.. The higher speeds enable efficient cutting of dense materials, whereas lower speeds are preferable for brittle materials such as advanced ceramics.Adjusting the blade speed according to the material properties, from the hardness to the brittleness, is critical.
Diamond Wafering Blade
Selection Variables
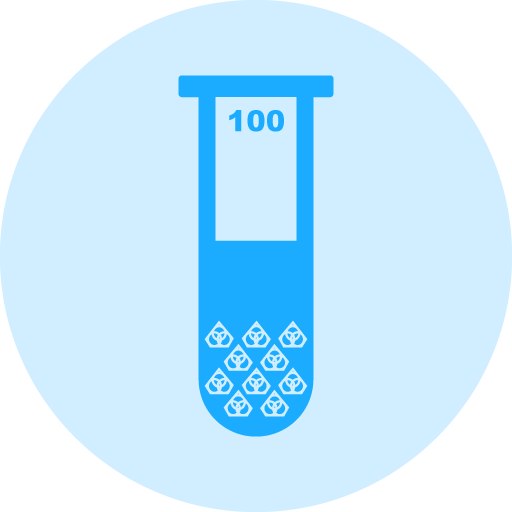
Diamond Concentration :
Diamond Concentration is still a factor in determining the life and cutting speed of your Diamond Sectioning/Wafering Blade. Higher diamond concentration is recommended and usually used for cutting softer and more abrasive types of materials. However, the trade off is significantly slower cutting speed. Low diamond concentration is recommended and widely used for cutting ultra hard and brittle materials.
Low Diamond Concentration - Typically low concentration wafering blades should be for cutting ultra hard and brittle materials such as ceramics and glass. In Low Concentration Wafering Blades, diamond works by fracture process. Pressure on each diamond crystal/particle is higher which provides enough stress to chip off small flakes in the cut.
High Diamond Concentration - High concentration diamond wafering blades are recommended for cutting metals, plastics and polymers. In this application, materials cut by a plowing mechanism. In this applications diamond plough through the material, work hardened strips of materials become brittle and break off. The greater number of diamond by volume, the quicker the cutting action will be. Increasing the number of diamond s also lowers the per unit force. For metals where it is possible to induce deep deformation layers, a lower per unit force is desirable to reduce the deformation during the cut.
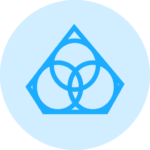
Diamond Particle/Grit size -
Diamond Mesh Size plays a major role in determining your cutting speed, cut quality/surface finish, level of chipping you will obtain, and material microstructure damage you will obtain. Diamond Mesh size does have considerable effect on cutting speed. Coarse Diamonds are larger than finer diamonds and will cut faster. However, the tradeoff is increase in material micro damage. If you are cutting fragile, more delicate materials then finer mesh size diamond wafering blades are recommended.
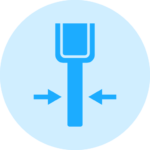
Blade Thickness :
Wafering blade thickness typically ranges from .006” to .040” (1mm). Thinner and thicker wafering blade are available, frequently from stock upon request. Kef thickness typically increases with blade diameter (in proportion to diameter of the blade). Kerf is the amount of material removed from the material/sample due to the thickness of blade passing though the material/sample. Blade thickness is important for users requiring most minimal amount of material loss during sectioning. For example if the user requires precision position of the cutting plane relative to the detail on the sample (IC circuit for example), a thinner and smaller diameter blade would be best for this application. Blades ranging from 3” to 5” (75mm to 125mm) in diameter and thickness .006” to .015” (0.2mm to 0.4mm) would be bet suited for this purpose. There are large variety of factors that will contribute to optimal blade thickness for your material/application Including your desired cutting speed, load/feed rate, material diameter, thickness, hardness, density, and shape. As well as skill & experience of the operator. Thicker wafering blades are more stiff and can whistand higher loads/feed rates. Another advantage of thicker kerf blades is they are more forgiving to operator error and abuse. Thicker kerf blade are recommended for use in environment where large number of individuals will be sharing and using same equipment. Perfect for less experienced and novice saw operators, such as in University laboratory.
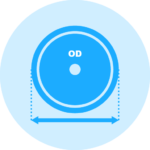
Blade Outside Diameter :
Typically wafering blade diameters range form 3” (75mm) to 8” (200mm). Wafering blade diameter should be selected based on material diameter and thickness being cut. Smaller diameter wafering blades are thinner than the larger diameter blades and are more prone to bending and warping. Although large diameter blades are thicker, they are typically used for cutting larger and heavier samples at higher loads and speeds than smaller blades.
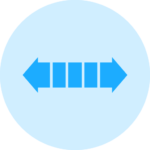
Bond Hardness :
Ability of the bond matrix to hold diamonds. As the hardness of the bond is increased, its diamond retention capabilities increase as well. However the trade off is slower cutting speed. Life of the diamond blade is usually increased with hardness of its bond matrix. Bonds are designated on their scale of hardness from Soft, Medium, and Hard. There are dozens of variations and classification schemes based on bond degree of hardness or softness. Using diamond blades with optimum bond hardness for your application is important to successful precision diamond sawing operation. Bond matrix that is too soft for the material being cut will release diamond particles faster than needed, resulting in faster wear and shorter diamond blade life. On other hand bond matrix that is too hard will result in much slower cutting speeds and require constant dressing to expose the next diamond layer. As rule of thumb, harder materials such as sapphire and alumina generally require a softer bond. Whereas softer and more brittle materials require a harder bond.
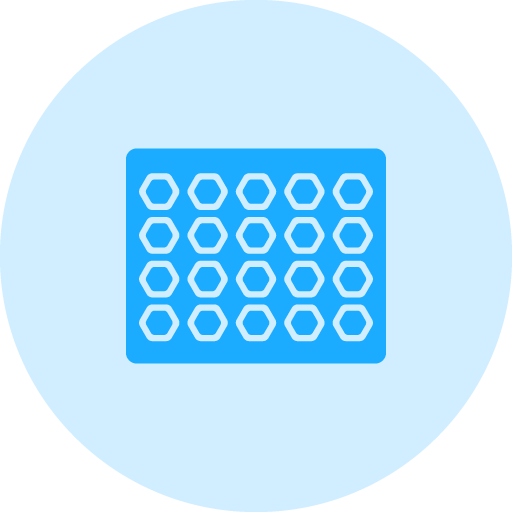
Bond Type :
Metal bonding offers long life and durability, while resin bonding creates less heat, provides better surface finish and is well suited for cutting hard, delicate or brittle materials.
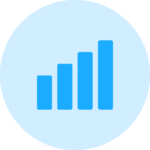
Feed Rates :
Load/Feed Rate applied to wafering blades typically vary from 10-1000 grams. Generally, harder specimens are cut at higher loads and speeds (e.g. ceramics and minerals) and more brittle specimens are cut at lower loads and speeds (e.g. electronic silicon substrates). The Speeds/RPM’s you are using, shape/geometry of the specimen, and how the specimen is being clamped/hold in place will affect the load that can be used for your application.

Blade Speeds/RPM’s :
Most wafering blades are used between 50 to 6,000 RPM’s Typically harder and more denser materials such as Silicon Carbide, are cut at higher RPM’s/speeds Where more brittle materials such as silicon wafers and gallium arsenide are cutting at lower RPM’s. Low Speed saws RPM’s are typically limited from 0 to 600 RPM’s. Where high speed saws offer much large variety of cutting speeds from 0 to 6,000 RPM’s.
Why Choose Us?
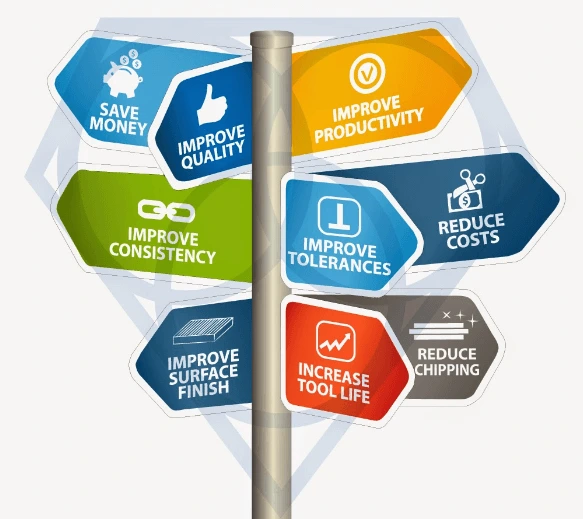
- Unmatched Selection For Many Applications
- Unmatched Technical Support & Expertise
- Superior Quality & Consistency
- Super Technology & innovation
- Immediate Worldwide Delivery
- American Based Manufacturer
-
Custom
Manufacturing - Better Value manufacturer Direct Price
Related Products
Petrographic Diamond Blades
Abrasive Polishing Powders
Grinding & Polishing Powders Aluminum Oxide, & Silicon Carbide Powdered Abrasives
UKAM Industrial Superhard Tools offers a wide range of precision abrasives for grinding and polishing large variety of samples. Including petrographic specimens other metals, alloys, electronic devices, semiconductors, ceramics, ferrous metals and many others. Abrasive Powders are available in the following quantities: 1 lb, 5 lb, 10 lb containers Grit Sizes: 120 grit to 8 micronsDiamond, Nickel Bond Cut Off Blades for Laboratory & Other Saws
SMART CUT® Fully Sintered (Metal Bond) Diamond & CBN, Wafering Blades
SMART CUT® Fully Sintered (Metal Bond) diamond wafering blades are fully sintered from OD to ID of the blade. Meaning they have diamonds completely impregnated through the blade. Unlike standard diamond & cbn wafering blades with steel core and diamond section. Instead of having a steel core and small diamond bond edge (usually 1/8"/3.2mm). The diamond edge is all the way through the blade, from its Outside Diameter to Inside Diameter of the blade. You can use until the entire Outside Diameter of the blade is consumed.
Recently Viewed Products
Recently Viewed Products
ARE YOU USING RIGHT DIAMOND & CBN BLADES
FOR YOUR APPLICATION?
LET US
HELP YOU
HAVING ISSUES WITH
YOUR CURRENT DIAMOND & CBN BLADES?
Knowledge Center
02
Jun
Select right Diamond Blade for your application
Selecting the right parameters for your Precision & Ultra Thin Diamond Blade can be a very time consuming, trial & error frustrating process. The guide below has been designed to help you better understand...
02
Jun
How to Properly Use Precision Diamond & CBN Blades
The diamond blade itself is only a small factor in your cutting operation. Successful diamond sawing is both an art & science. Requiring proper use and understanding of the right: RPM's, Coolants, Equipment, Dressing Devices, Accessories...
02
Jun
Precision & Ultra Thin Diamond Blade Guide
Diamond and CBN blades are available in an extensive array of varieties, each differing in bond types, manufacturing methods, and design specifics. Ultra Thin & High Precision Diamond Blades are particularly versatile, applicable...
02
Jun
How to Improve & Optimize Your Diamond Sawing Operation
There are numerous variables that affect the performance of diamond and CBN cutting blades. Understanding these variables will help end users select the right diamond blade specifications for their applications and optimize their...
02
Jun
Evaluating & Comparing Diamond Blades
Share this Article with Friend or Colleague
Proper testing procedures and methodologies must be set up and used to obtain accurate as well as repeatable testing results. This article will discuss several simple procedures which...
31
Jul
Top 5 Diamond & CBN Cutting Blade Performance Metrics
Share this Article with Friend or Colleague
When evaluating diamond and cubic boron nitride (CBN) cutting blades, it's crucial to consider key performance metrics and criteria. Different applications have varying goals, making it...
01
Aug
Diamond & CBN Cutting Blade Performance Metrics that you Should Know
Share this Article with Friend or Colleague
When evaluating diamond and cubic boron nitride (CBN) cutting blades, it's crucial to consider key performance metrics and criteria. Different applications have varying goals, making it important to...
02
Aug
Total Cost of Ownership & Why its Important
Share this Article with Friend or Colleague
Diamond and CBN cutting blades are available in a myriad of specifications, with virtually limitless options. The industry is saturated with numerous manufacturers, each professing to offer the...
05
Aug
Understanding Tradeoffs- Searching for Perfect Diamond & CBN Blade
Share this Article with Friend or Colleague
Choosing the right blade diamond or cbn blade can significantly impact efficiency, cost, and quality. However, this is not simple and clear cut process. Selecting the optimal blade...
- Unmatched Selection For Many Applications
- Superior Quality & Consistency
- Immediate Worldwide Delivery
- Technical Support & Expertise
- American Based Manufacturer
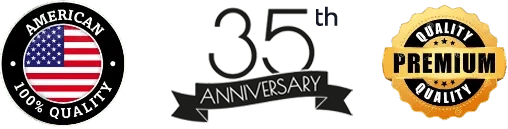

- Different Product
- Different Technology
- Different Company
- Expect MORE from your tools
Let Us HELP You!
Subscribe To Our Newsletter
Signup for email offers, updates, and more
Contact Us
- 25205 & 25201 Avenue Tibbits Valencia CA 91355 USA
-
Phone : (661) 257-2288
FAX : (661) 257 -3833 - lel@ukam.com
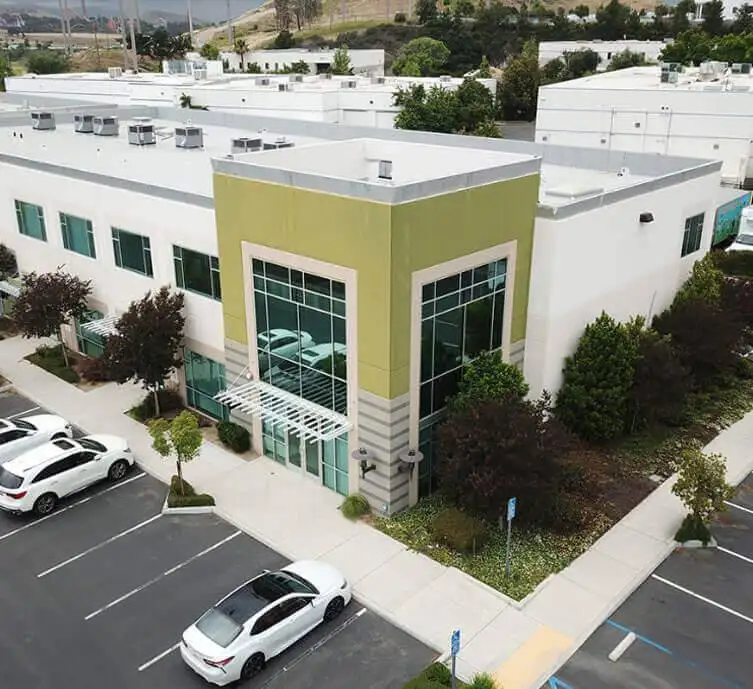
UKAM Industrial Superhard Tools is a U.S. High Technology, Specialty Diamond Tool & Equipment manufacturer. We specialize in producing ultra thin, high precision cutting blades, precision cutting machines diamond drills, diamond micro tools, standard & custom advanced industrial diamond tools and consumables.
- 25205 & 25201 Avenue Tibbits Valencia CA 91355 USA
-
Phone : (661) 257-2288
FAX : (661) 257 -3833 - lel@ukam.com
- 25205 & 25201 Avenue Tibbits Valencia CA 91355 USA
-
Phone : (661) 257-2288
FAX : (661) 257 -3833 - lel@ukam.com
DIAMOND TOOLS BY BOND
EQUIPMENT
KNOWLEDGE CENTER
OUR PRODUCTS
COMPANY
CUSTOMER SERVICE
Shipping Methods


Safe & Secure Payments

© Copyright 1990-2025. UKAM Industrial Superhard Tools – Terms of Use